
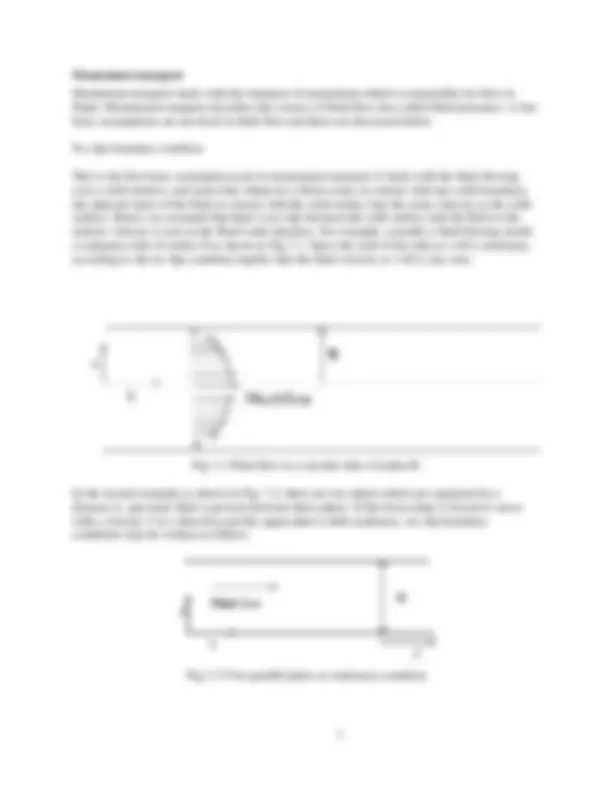
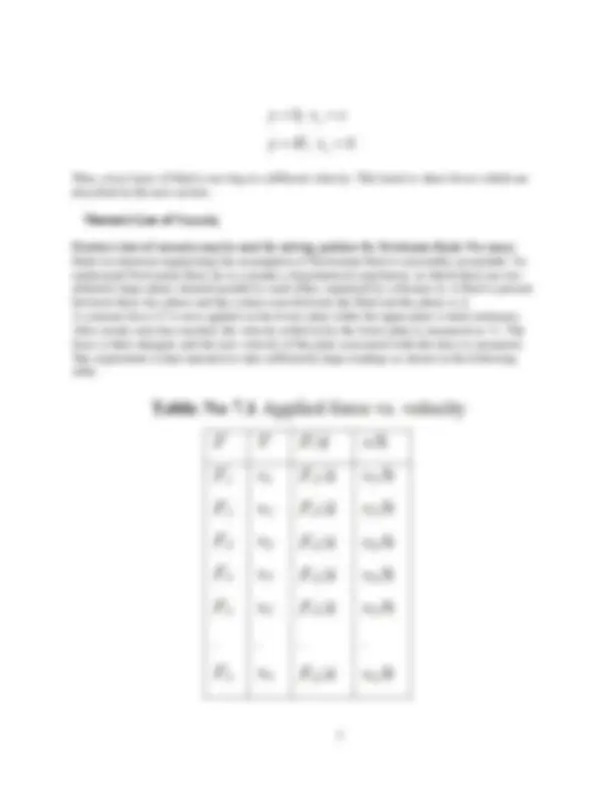
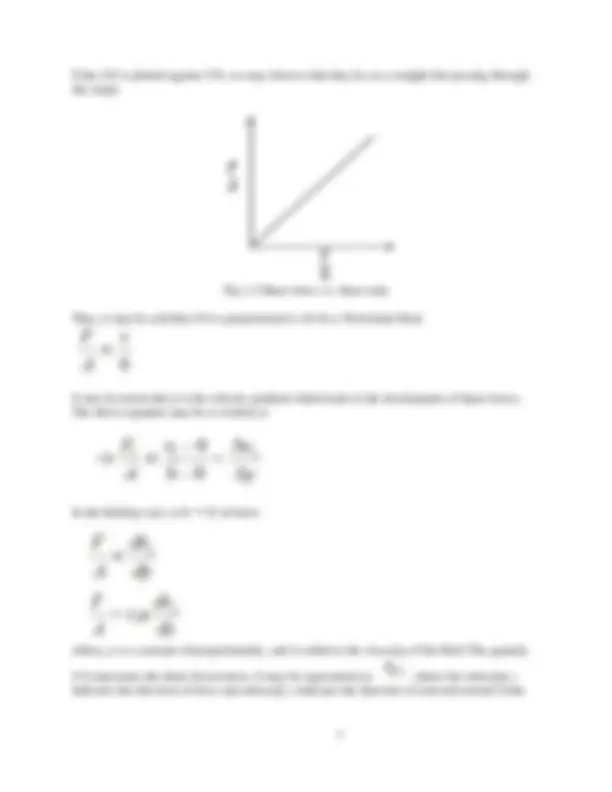
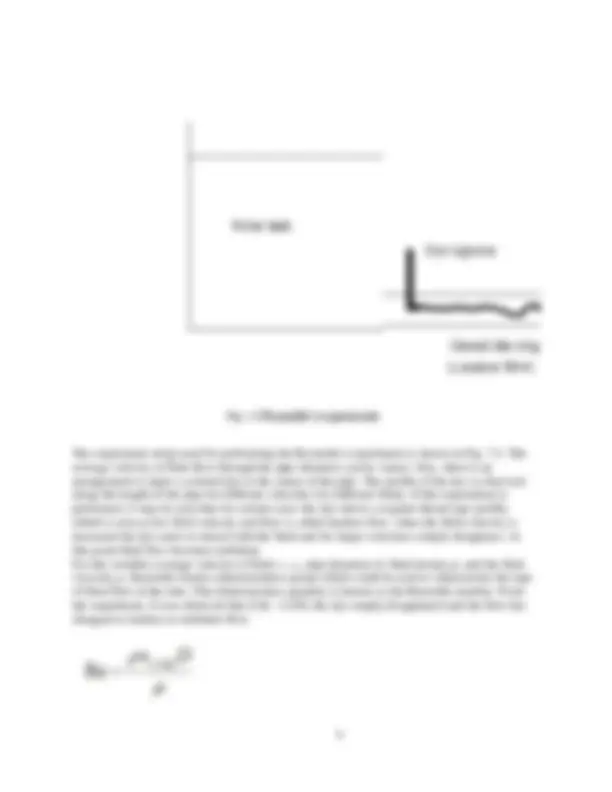
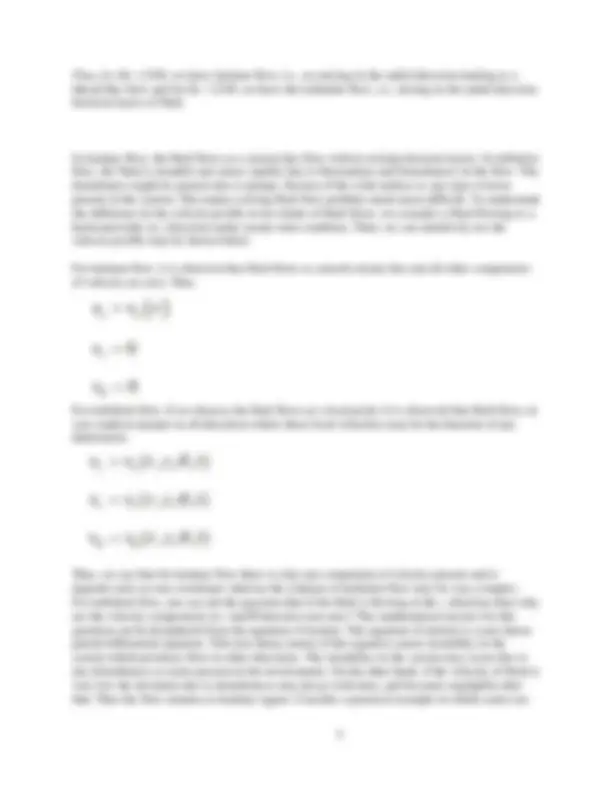
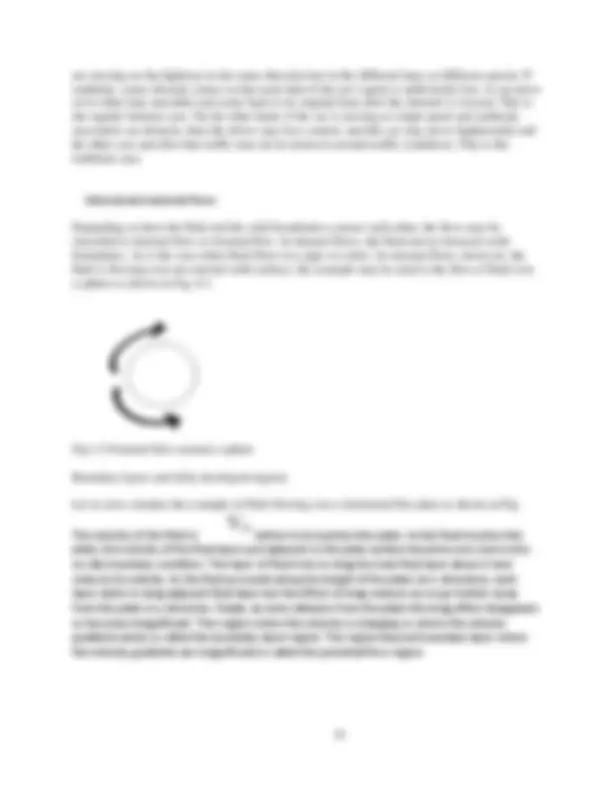
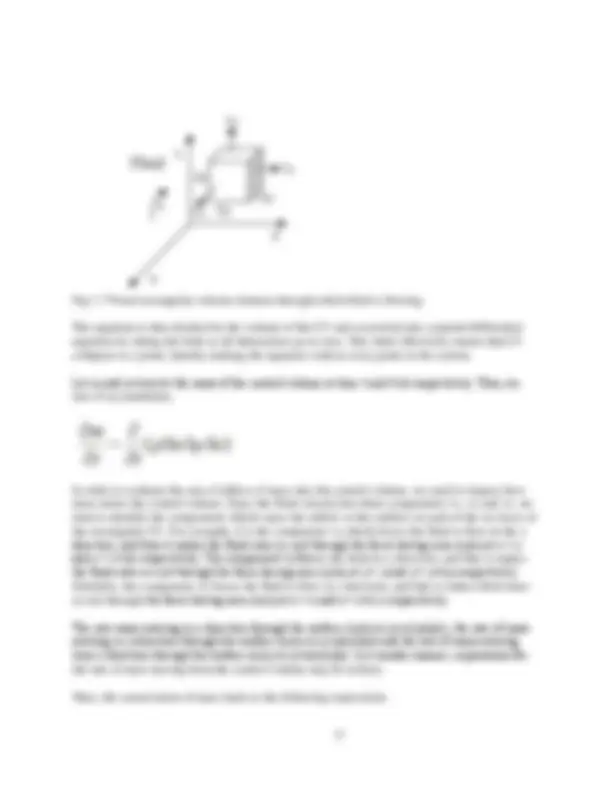
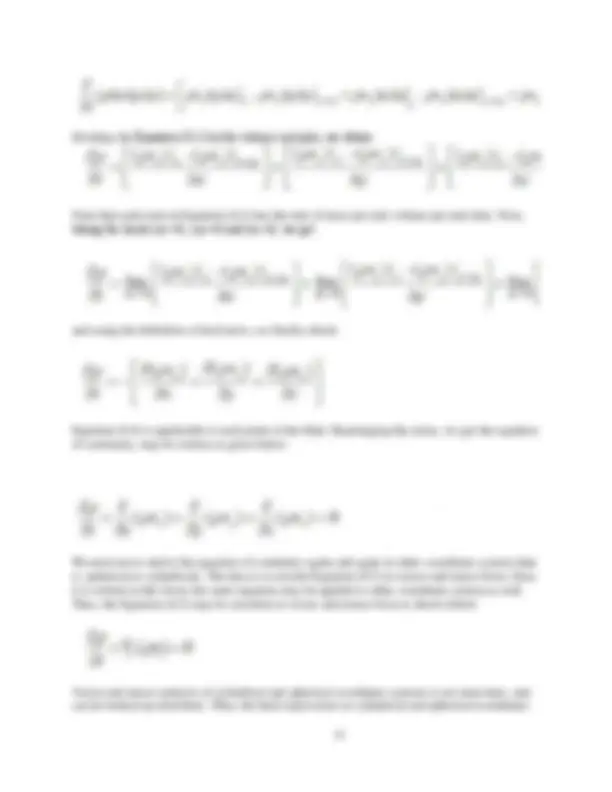
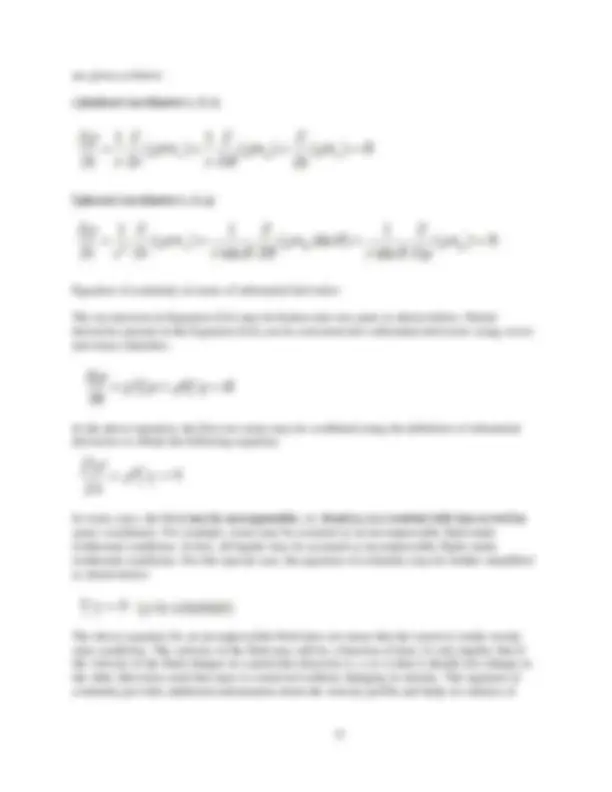
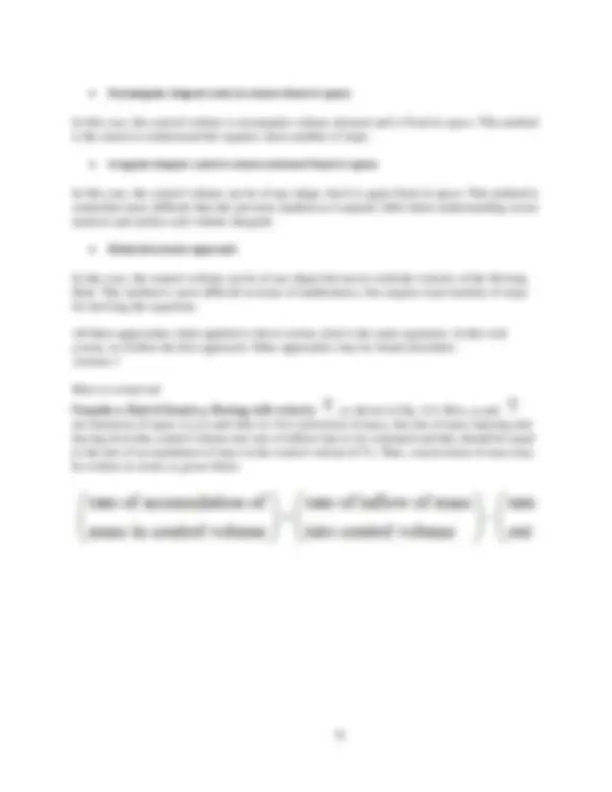
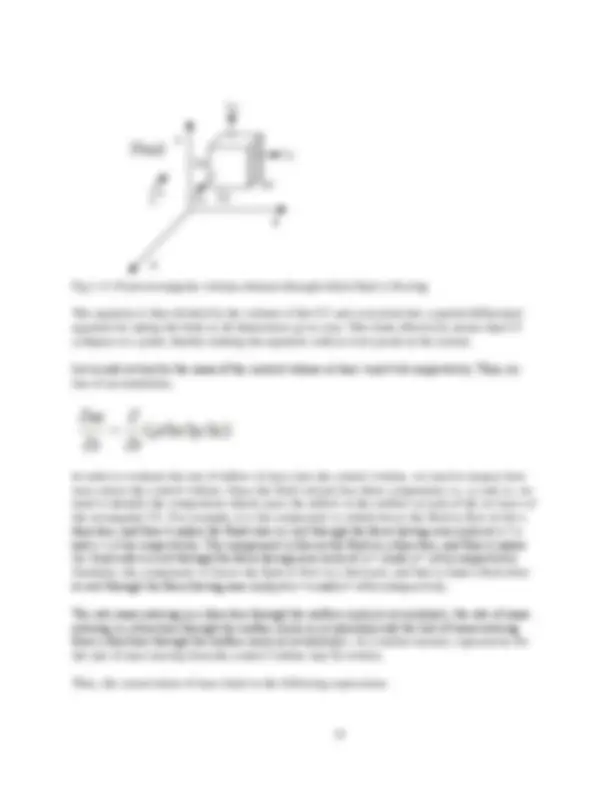
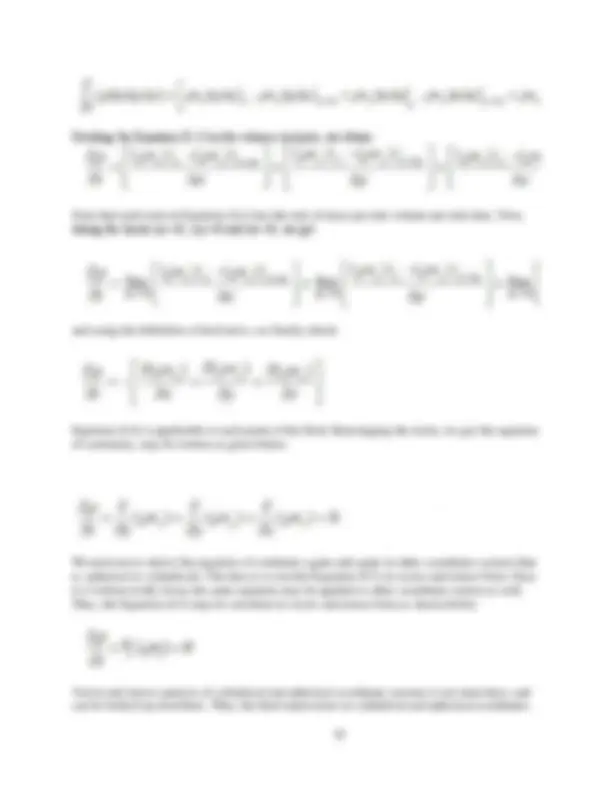
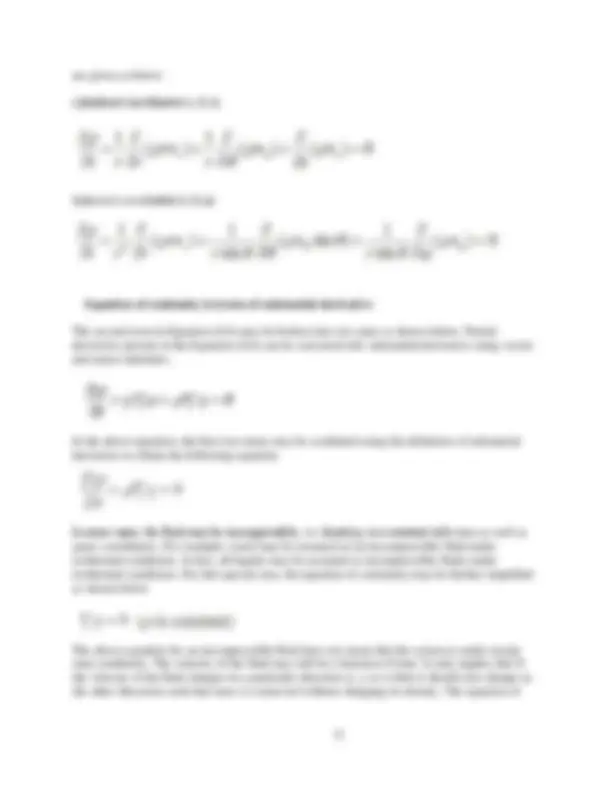
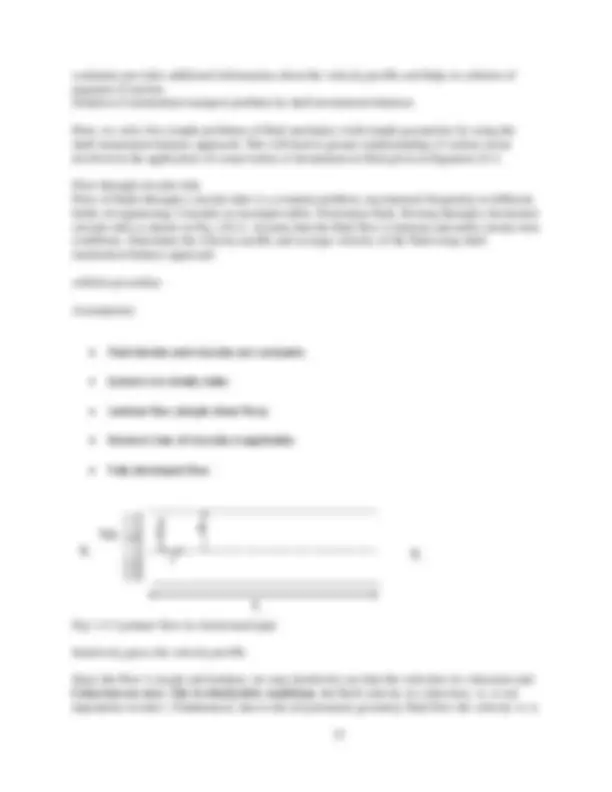
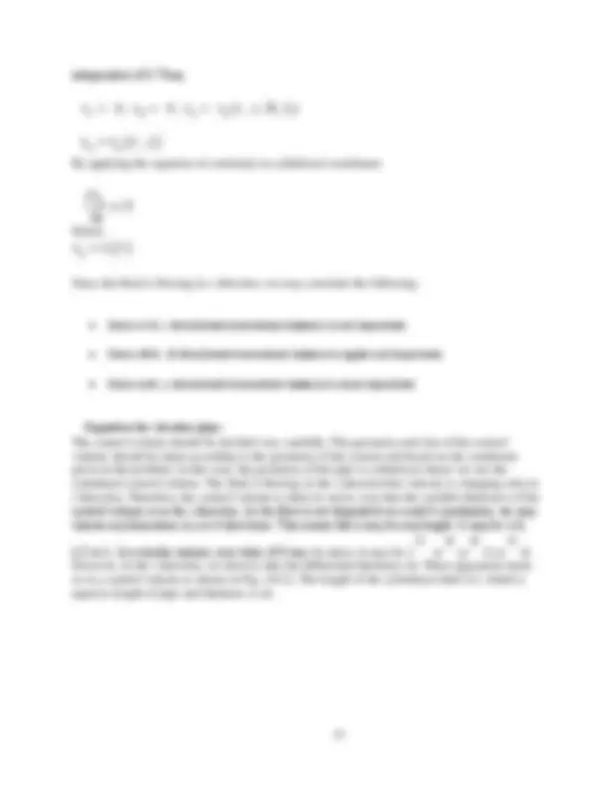
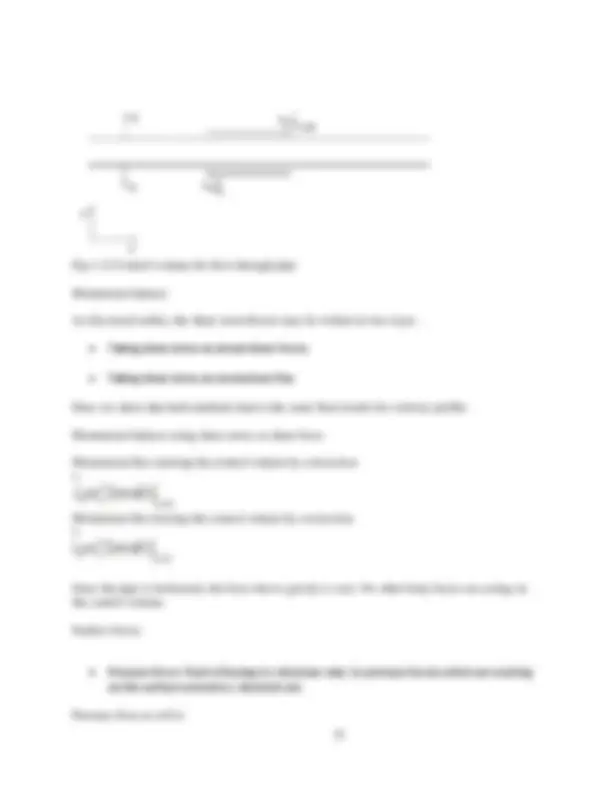
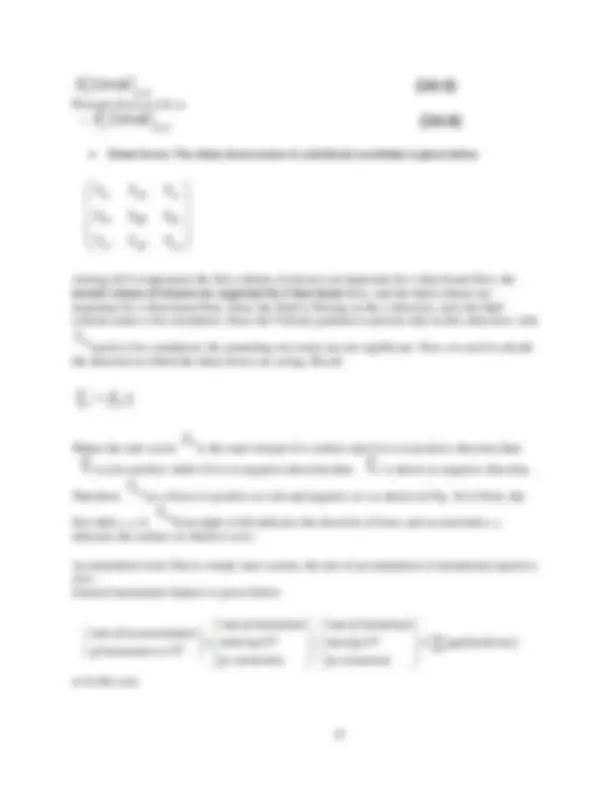
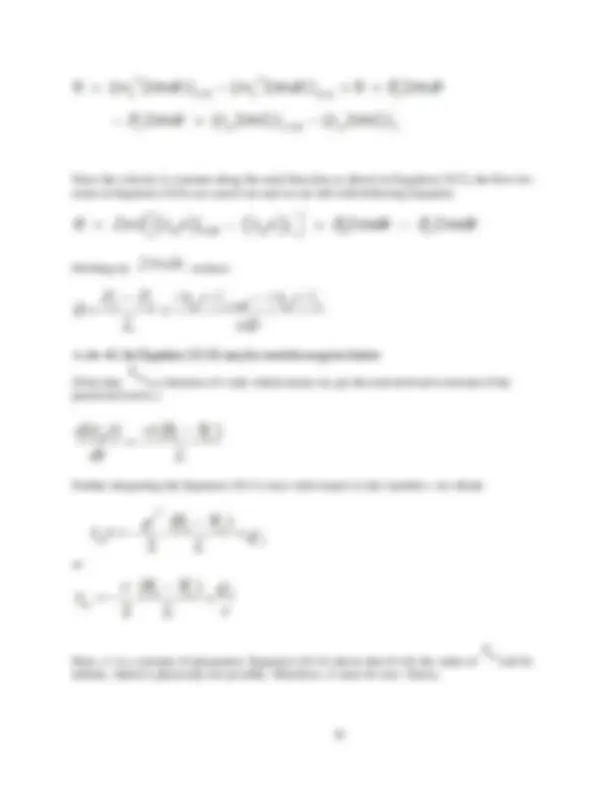
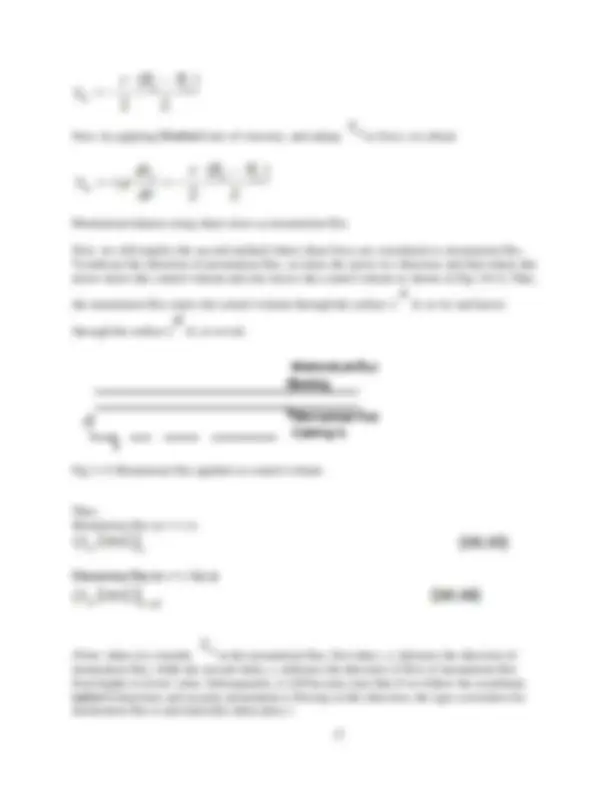
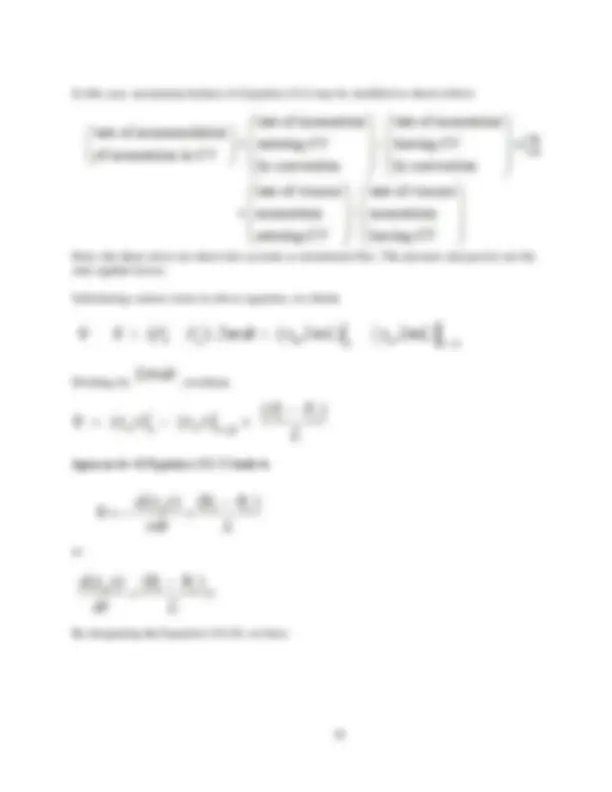
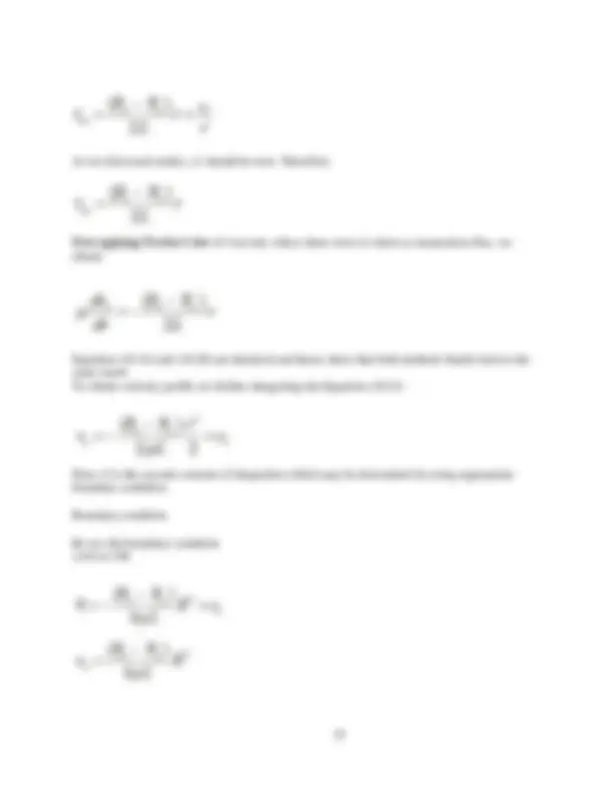
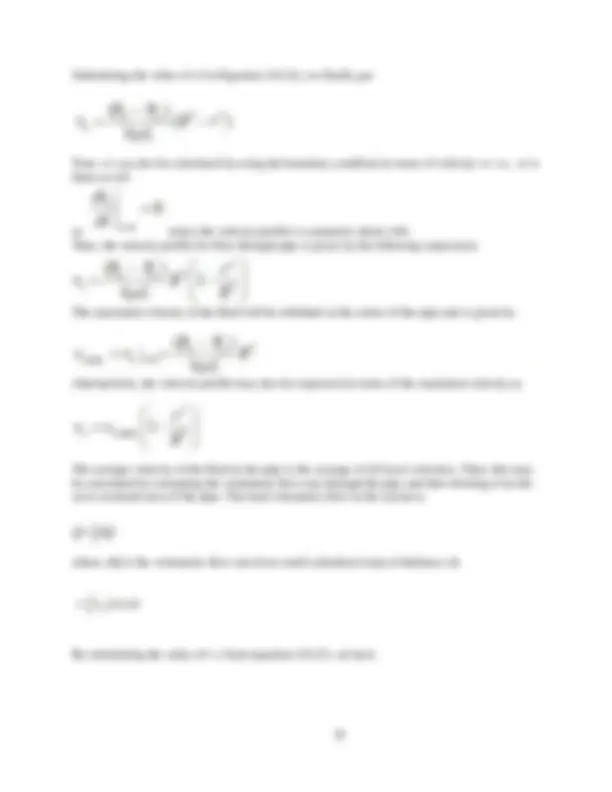
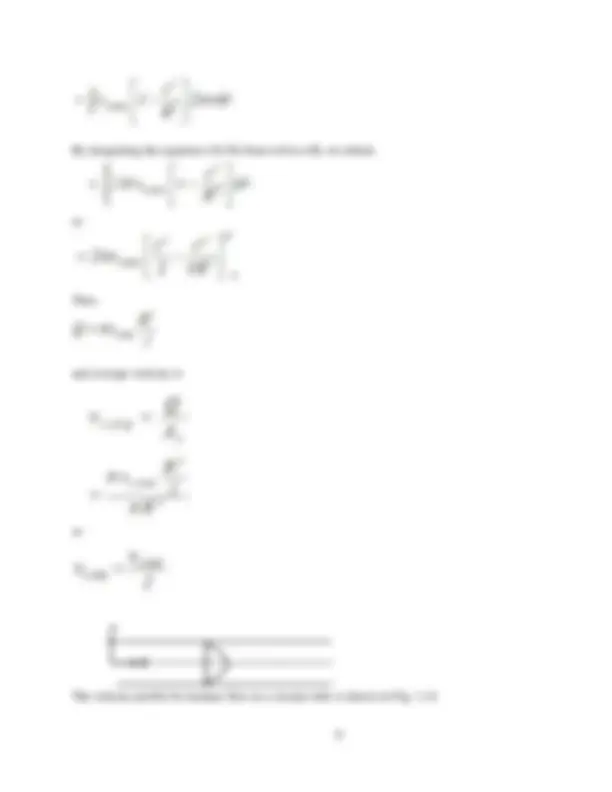
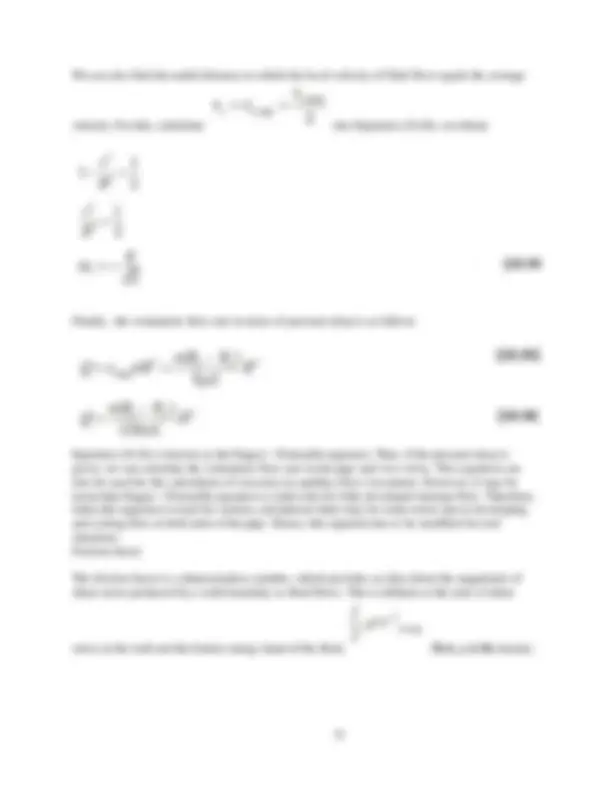
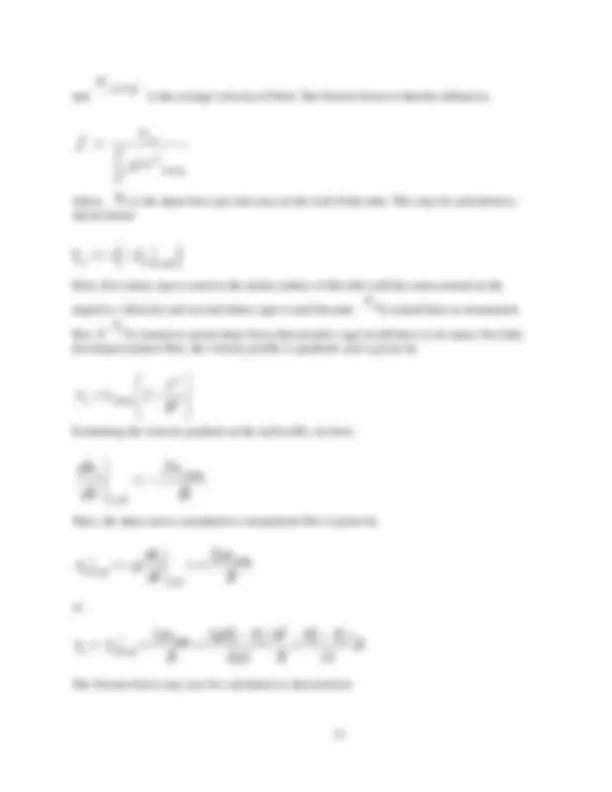
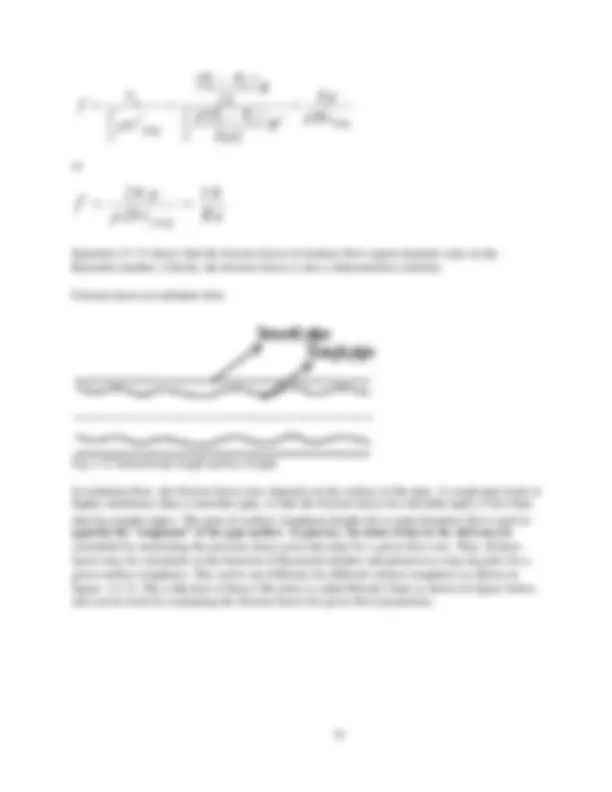
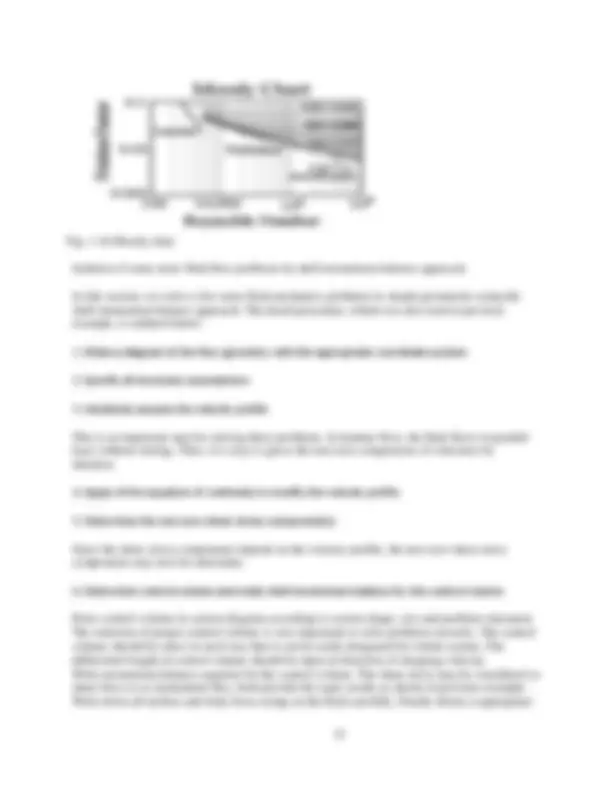
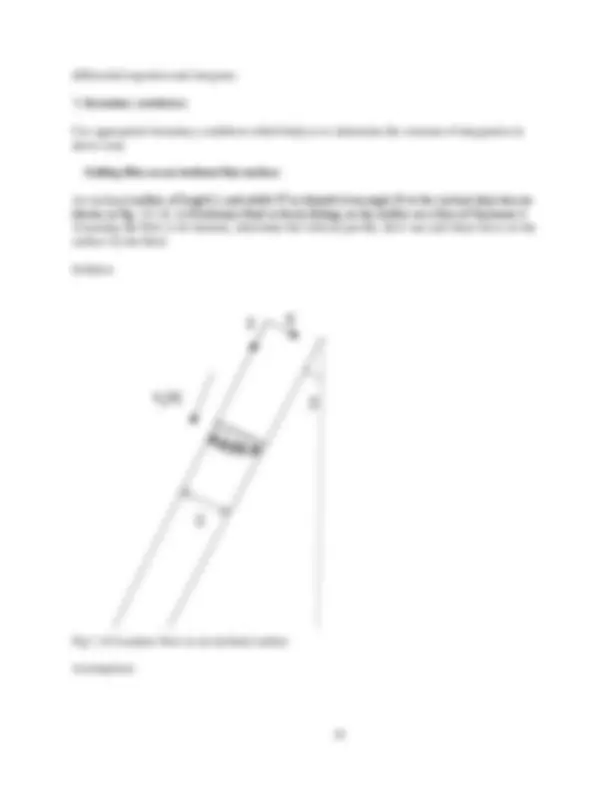
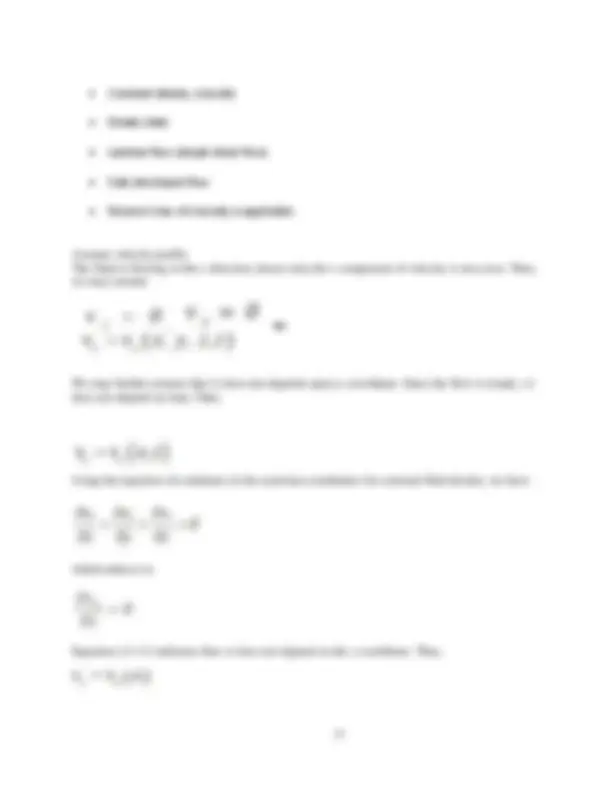
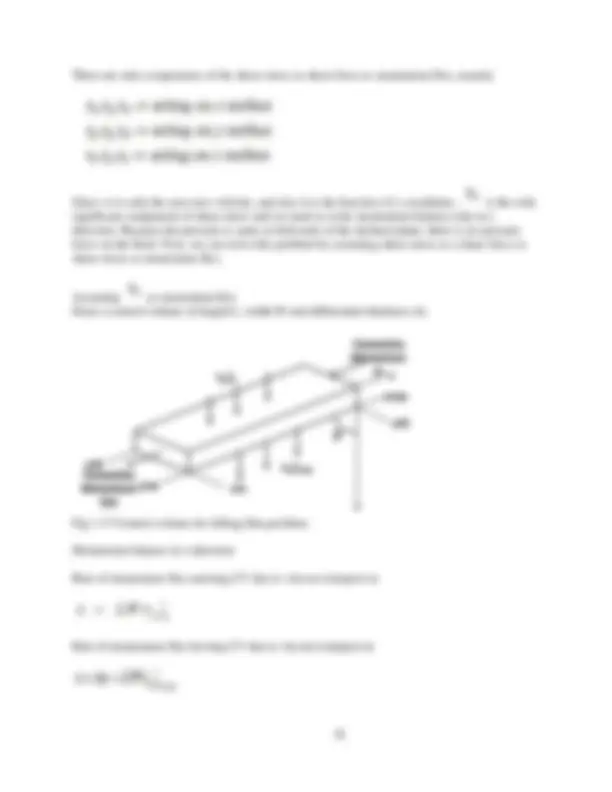
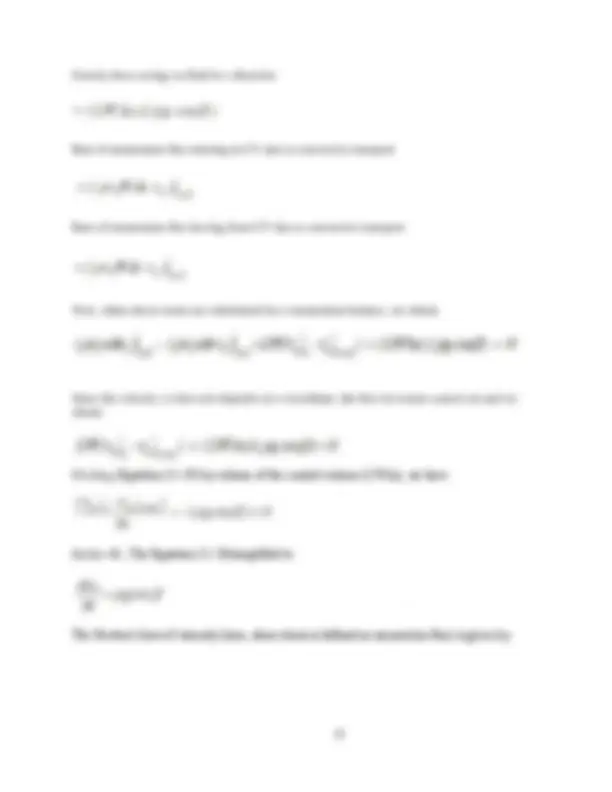
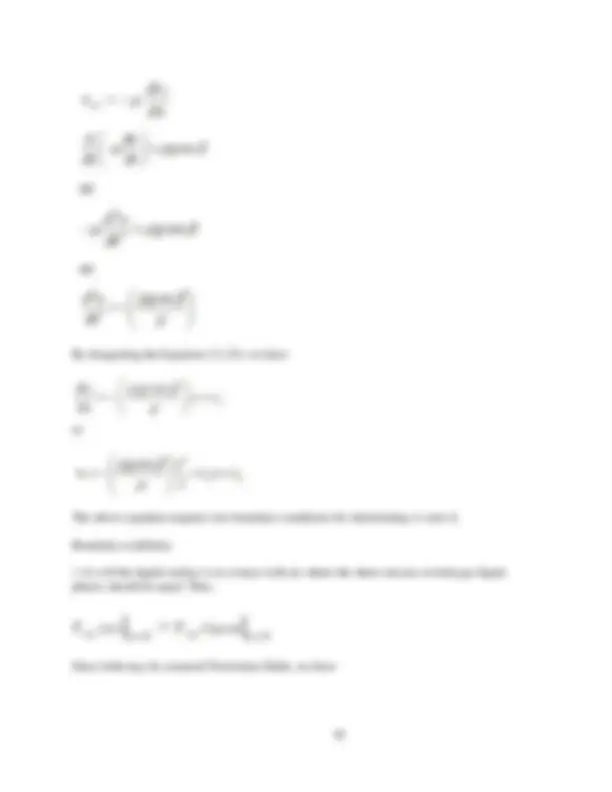
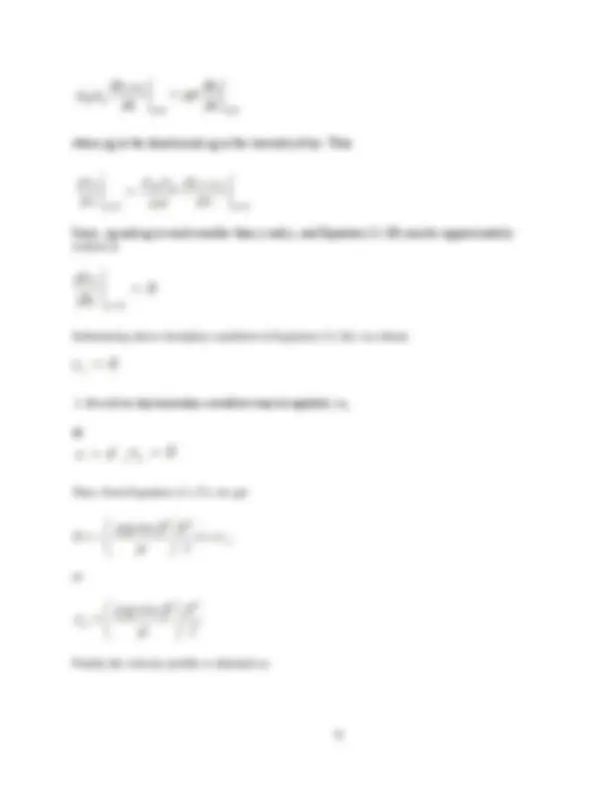
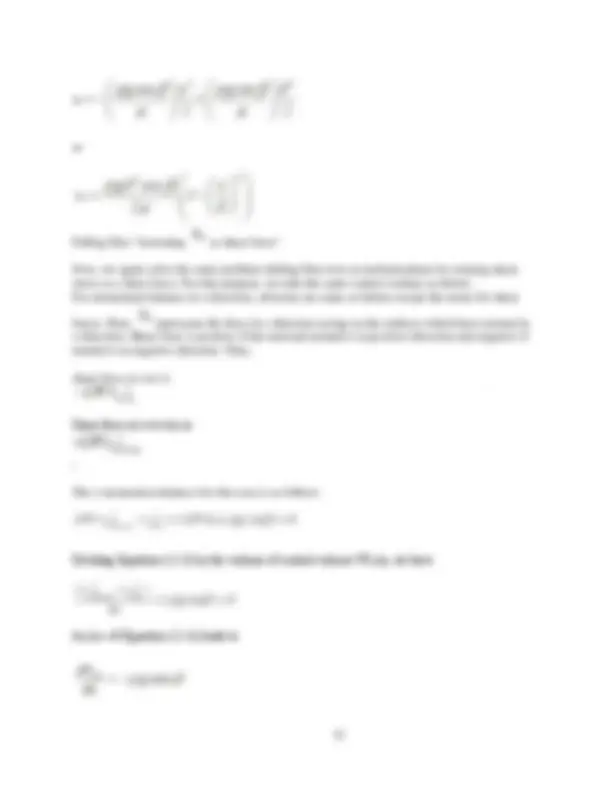
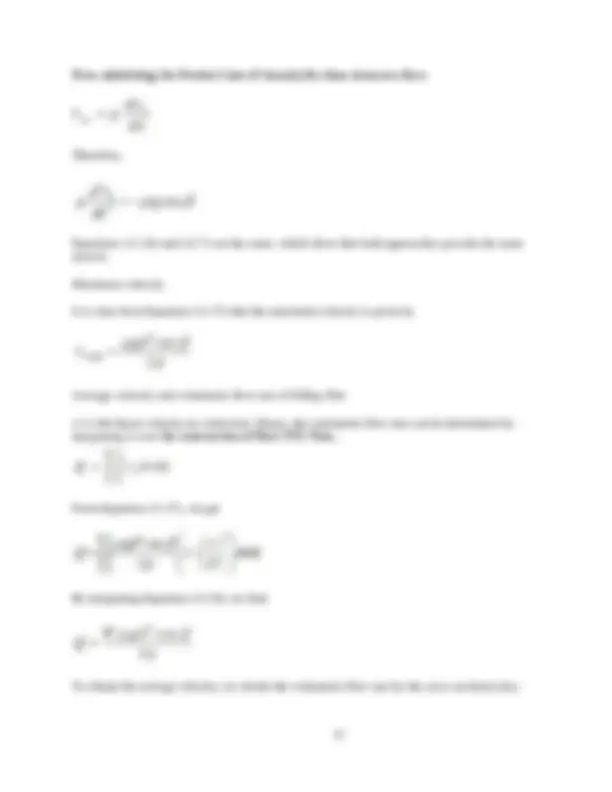
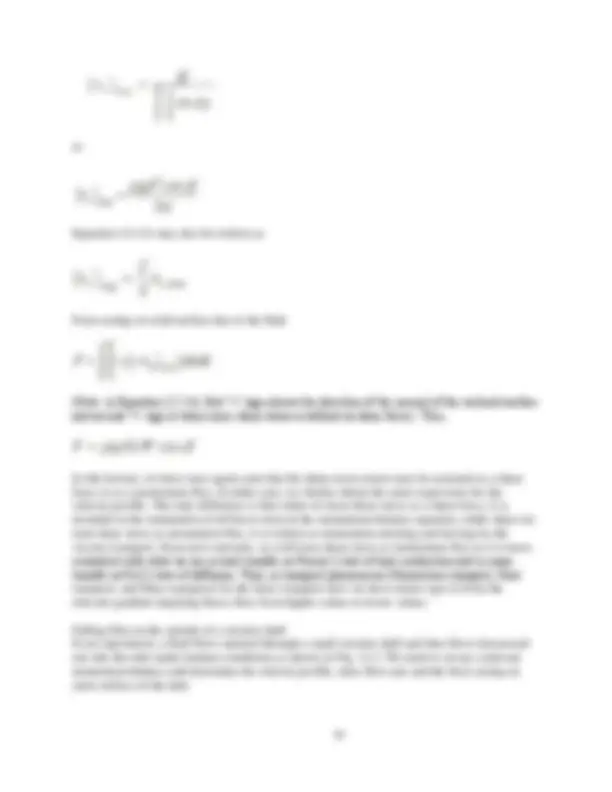
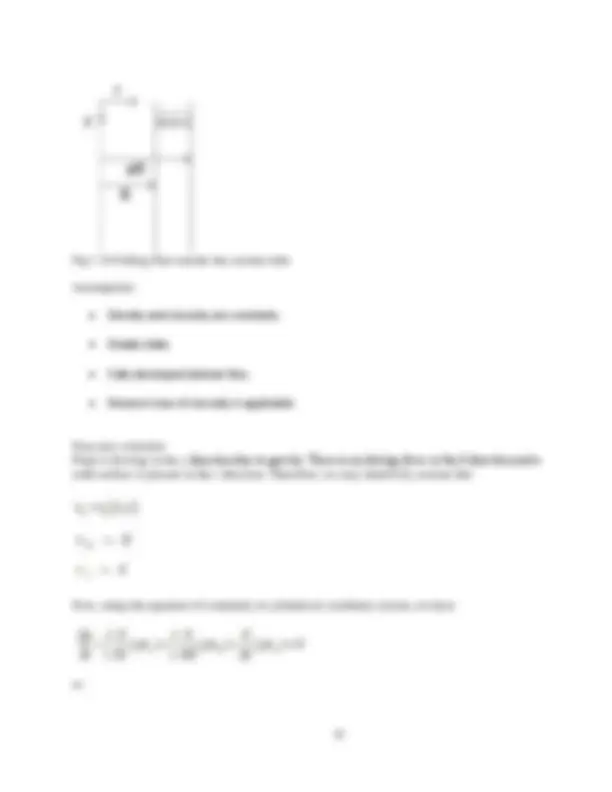
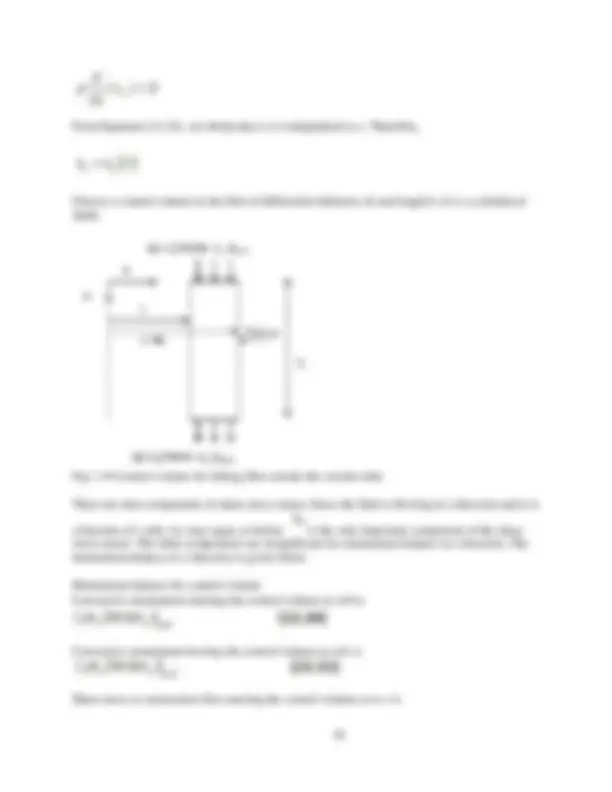
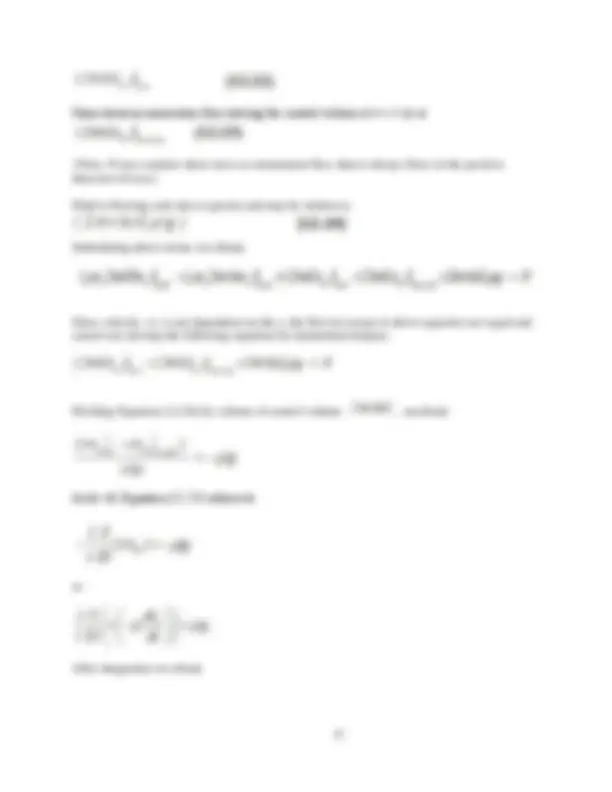
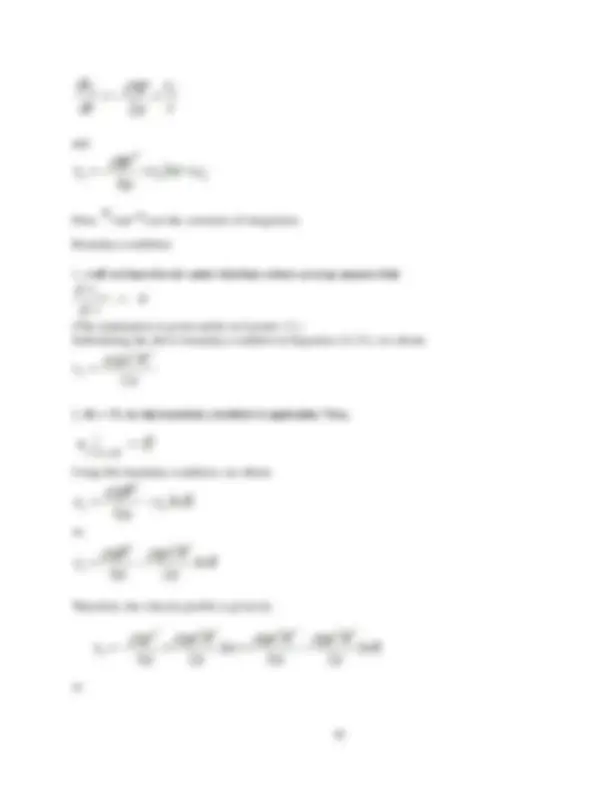
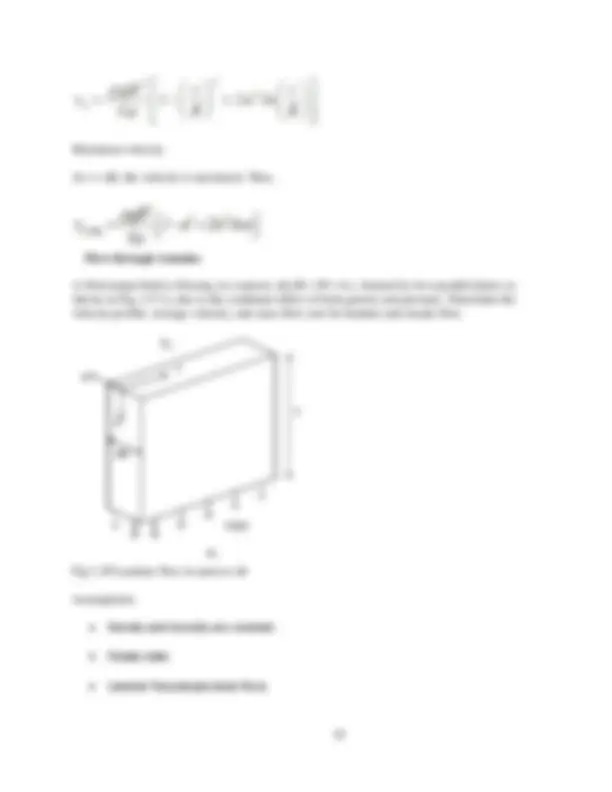
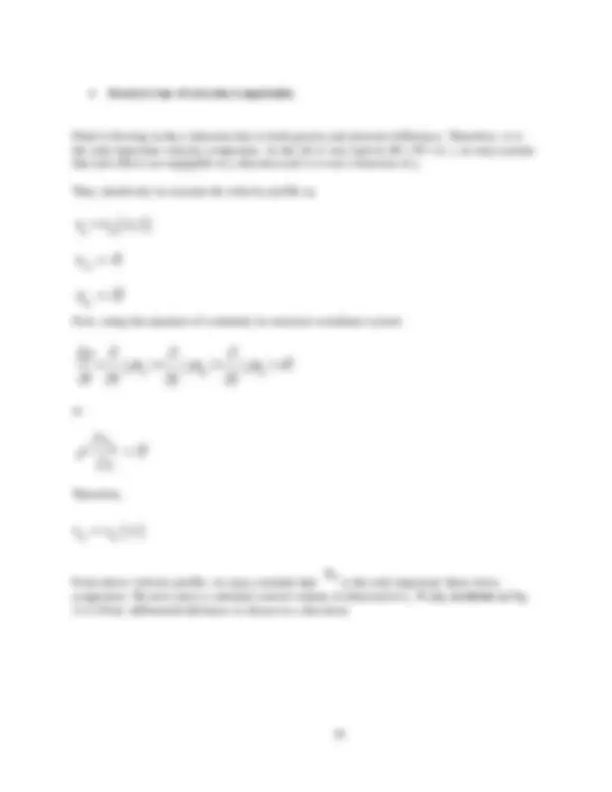
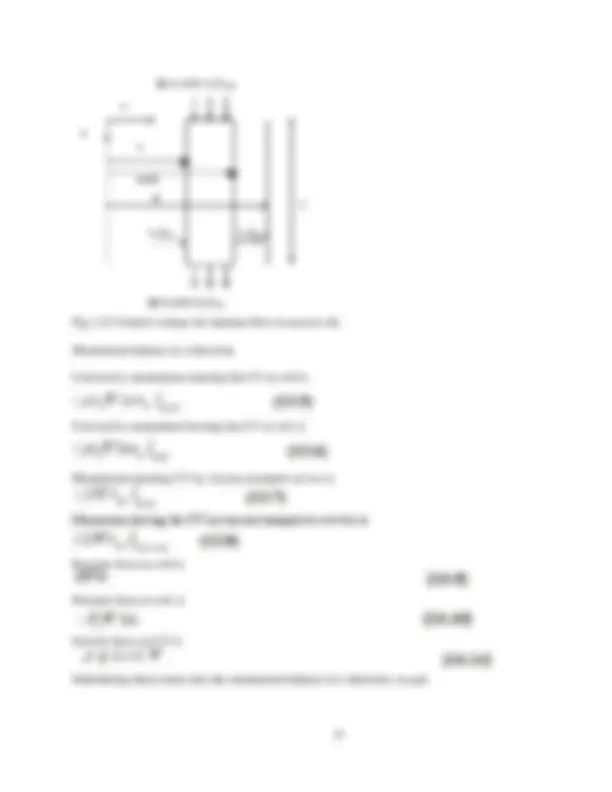
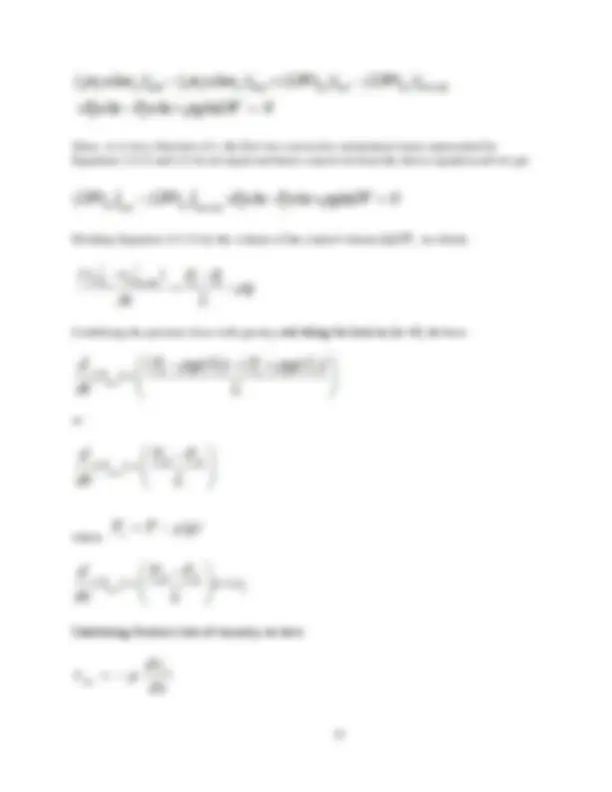
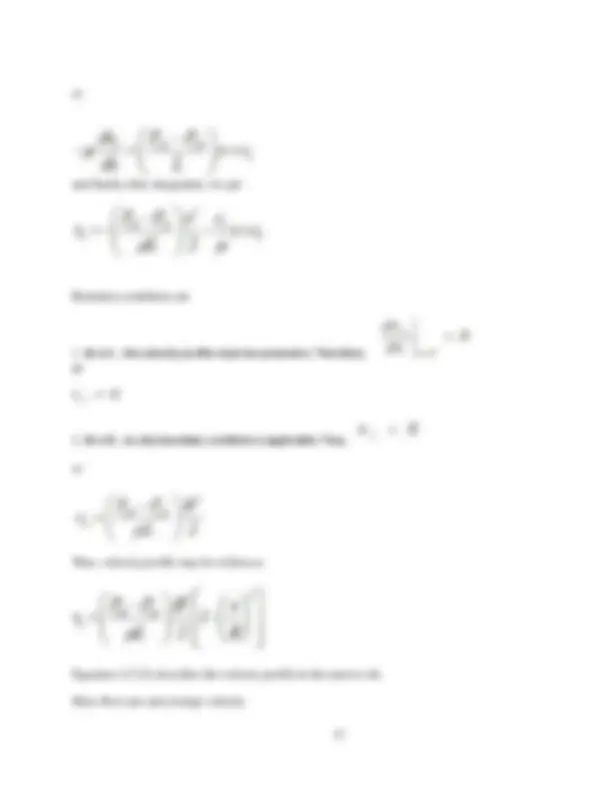
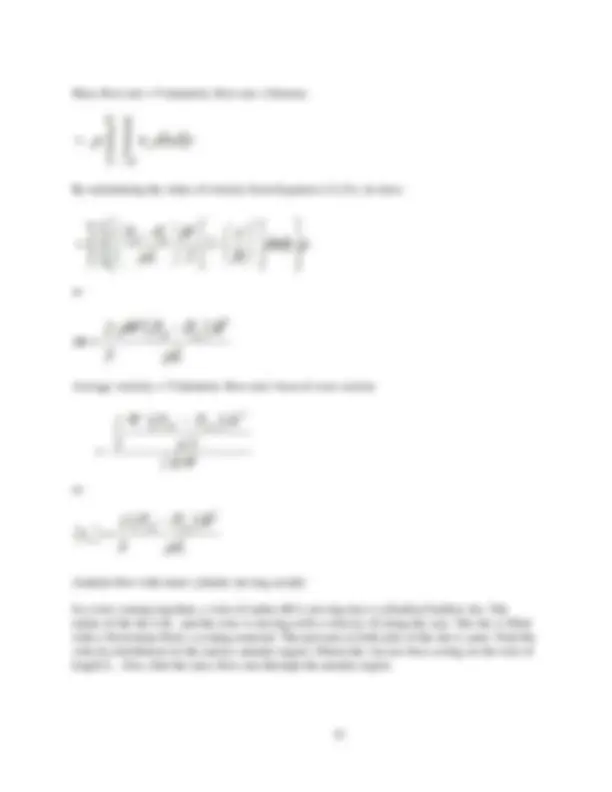
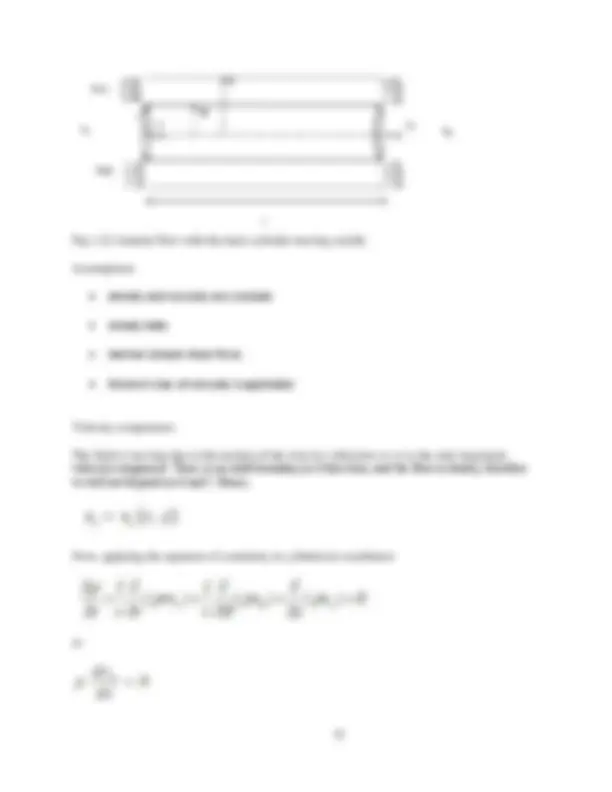
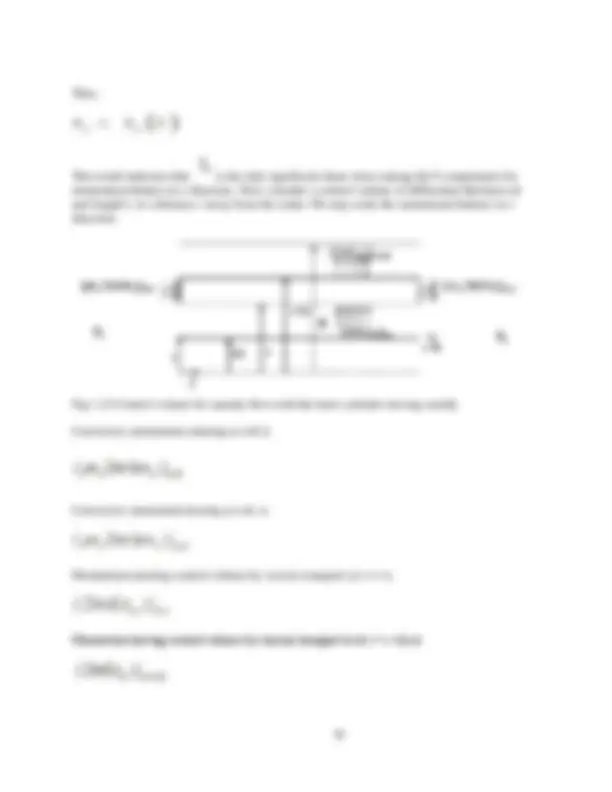
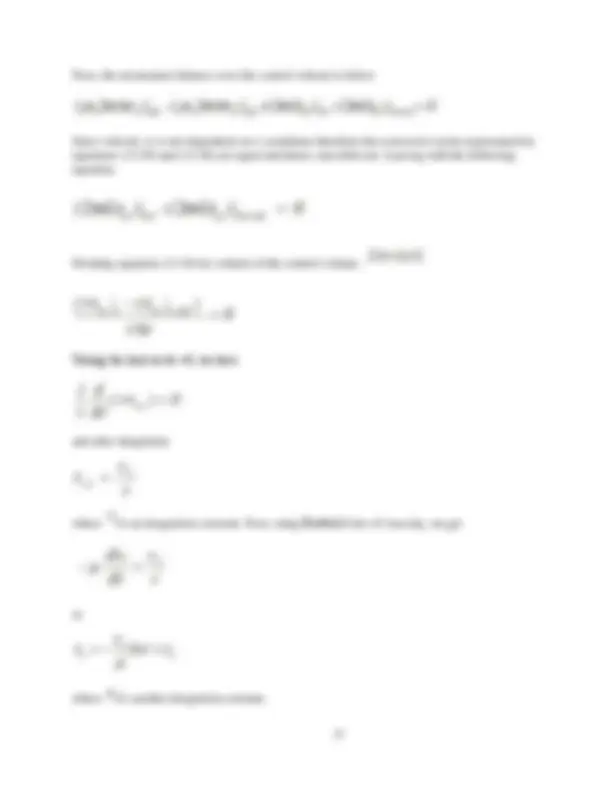
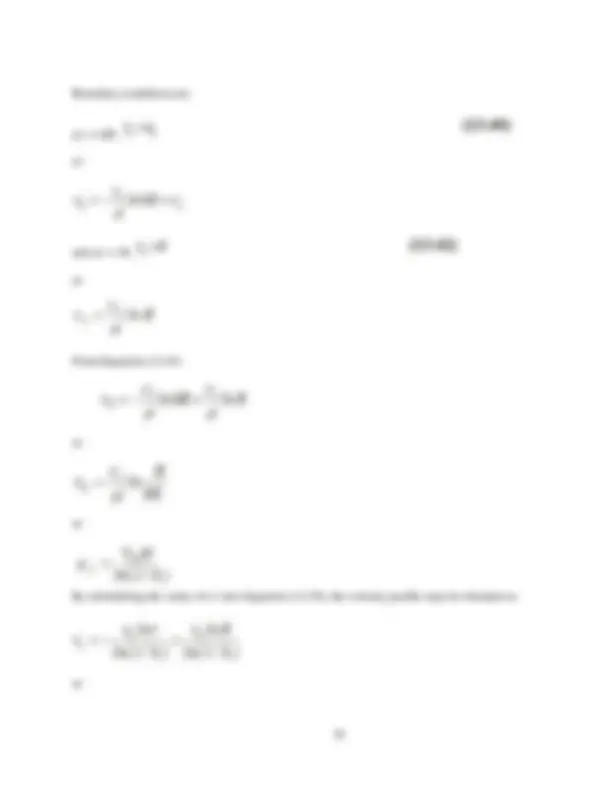
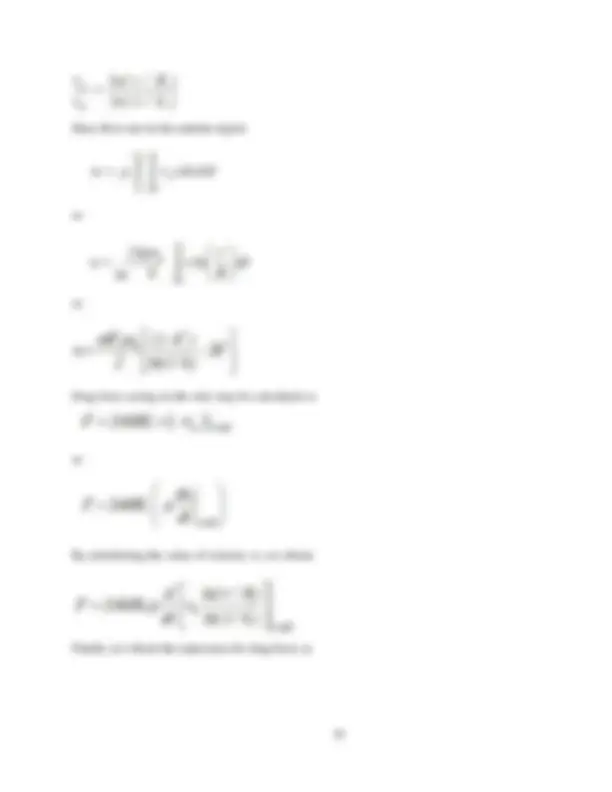
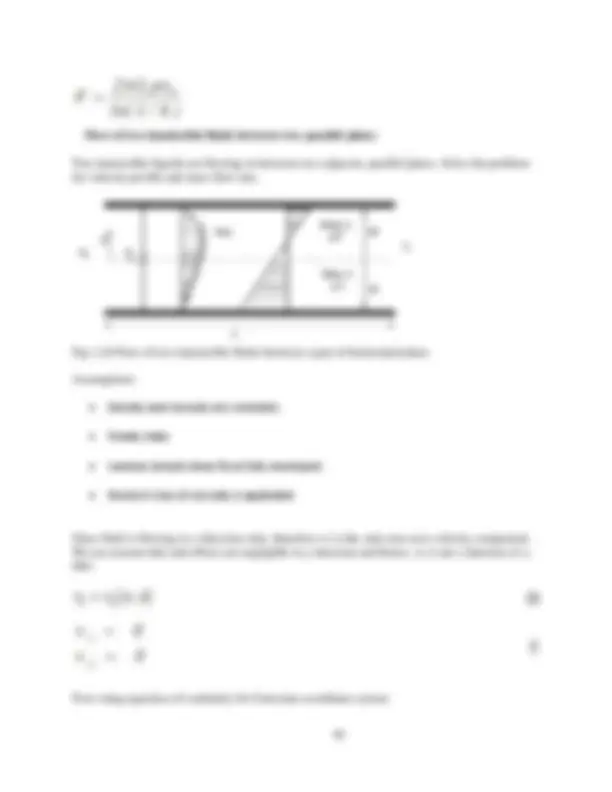
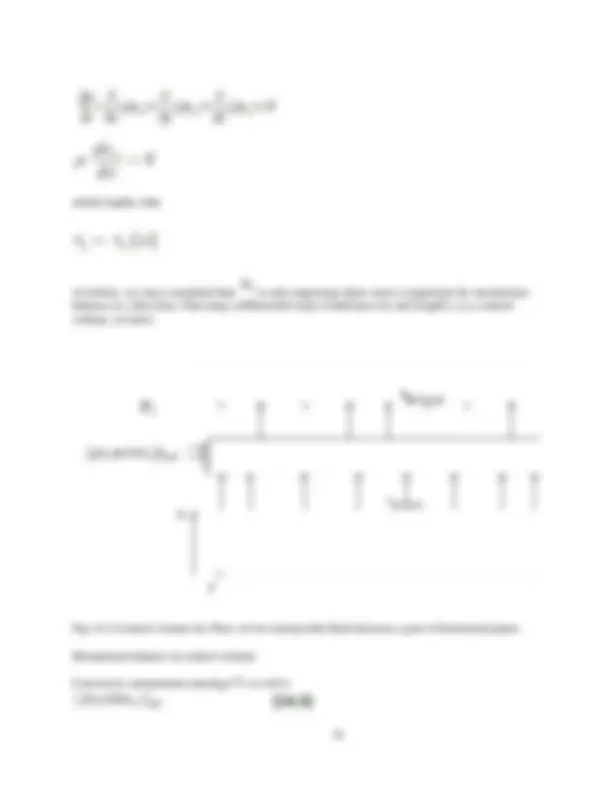
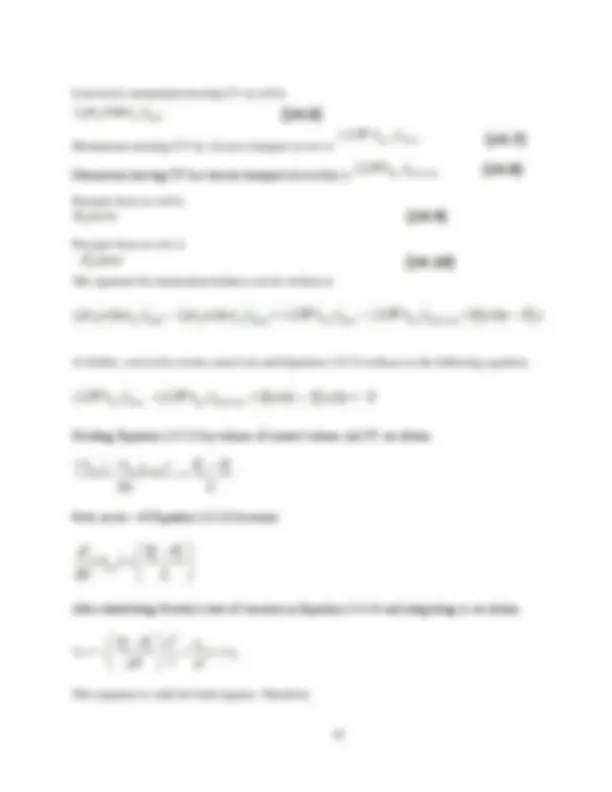
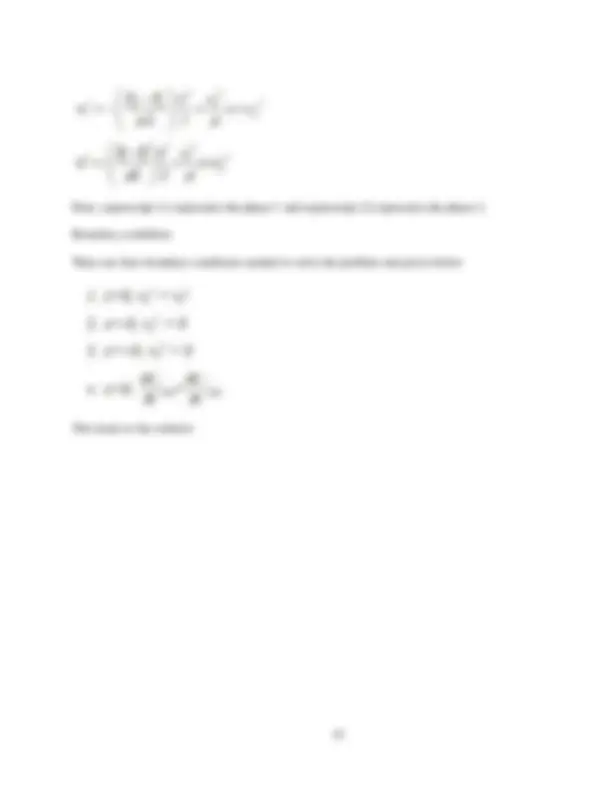
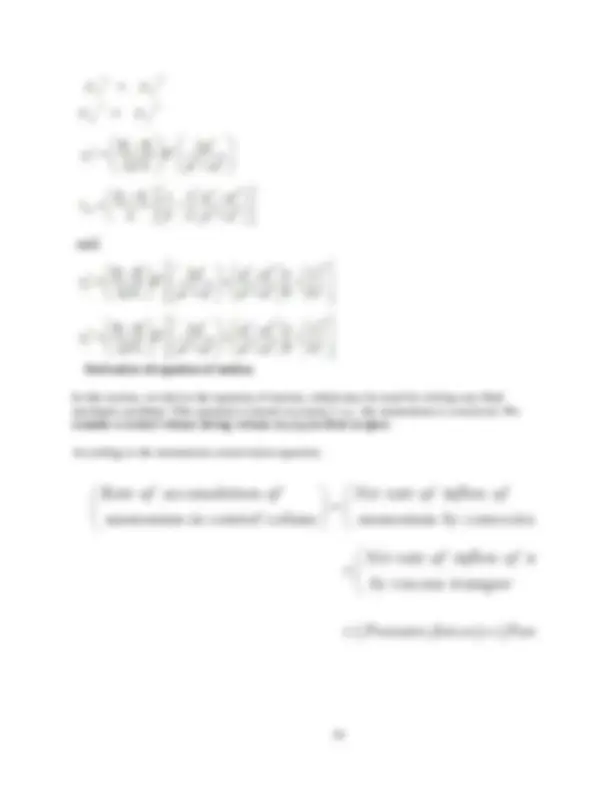
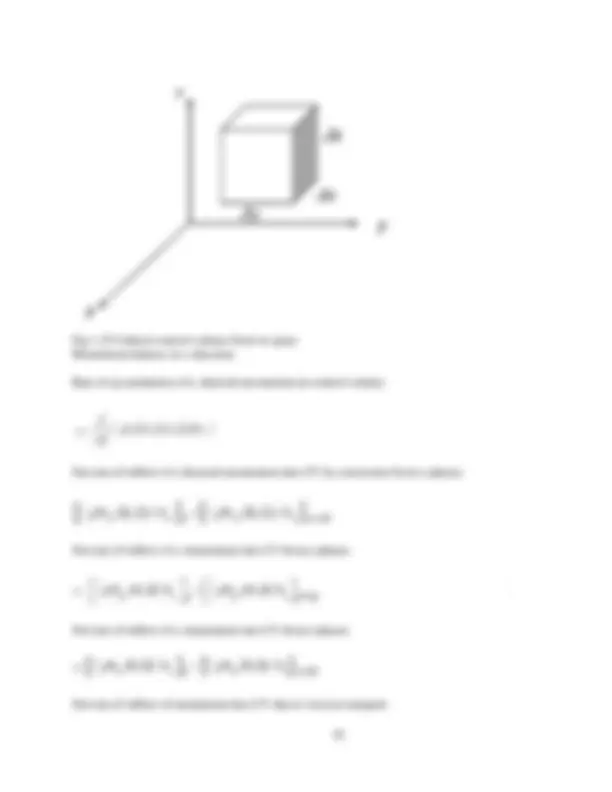
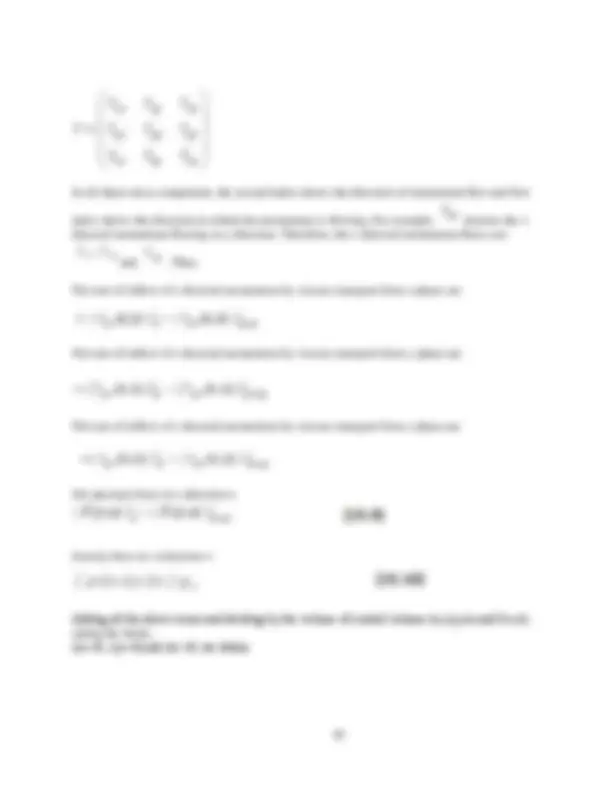
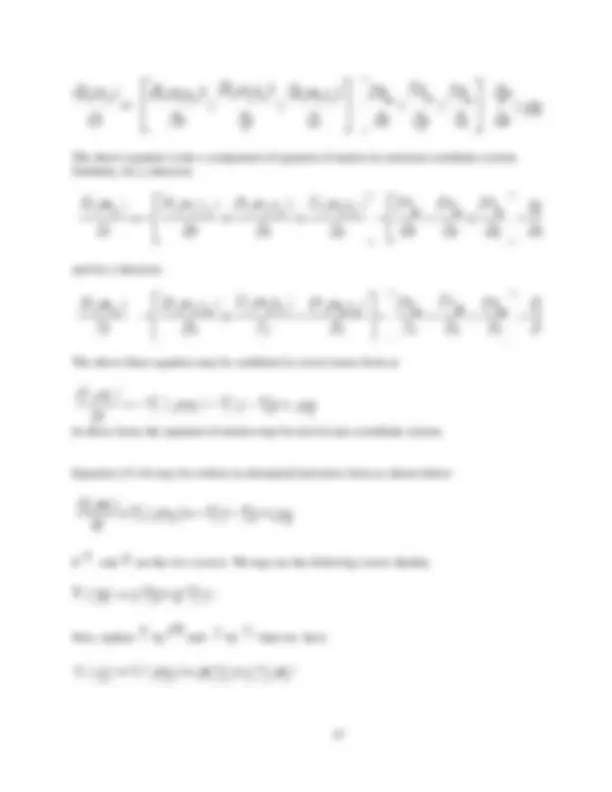
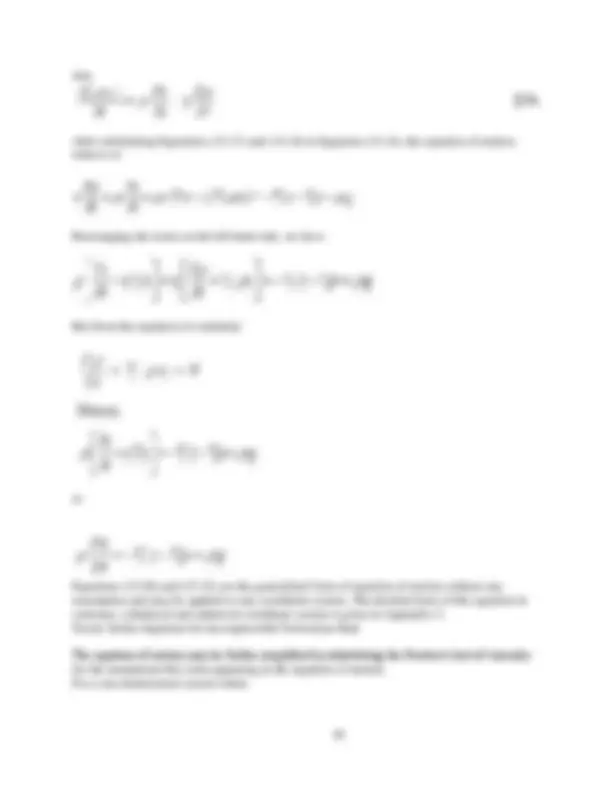
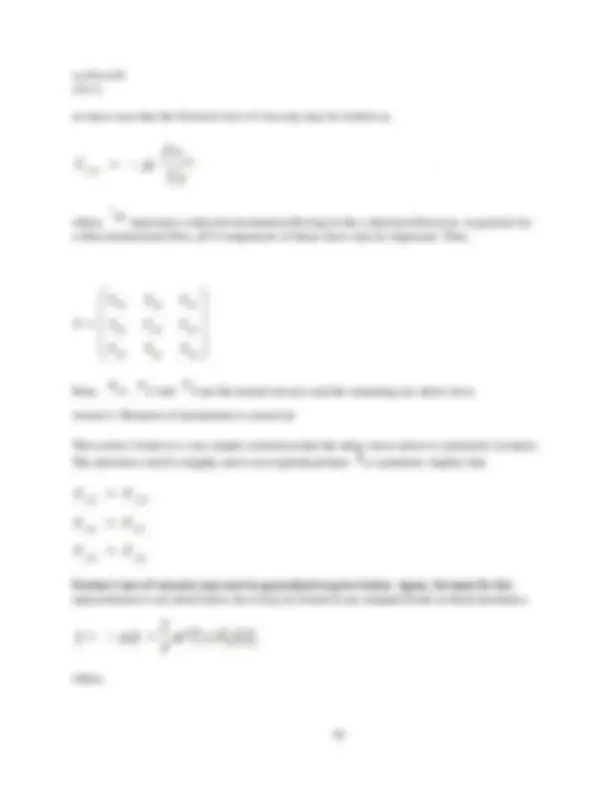
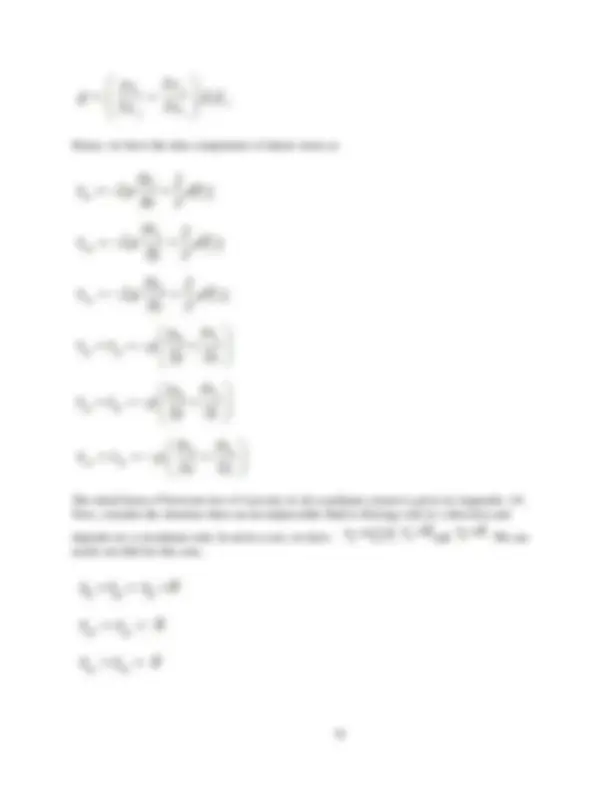
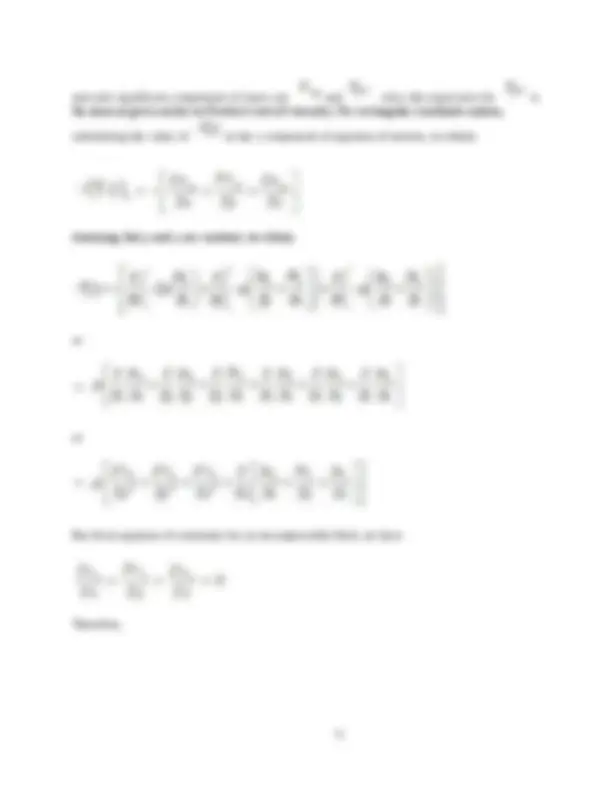
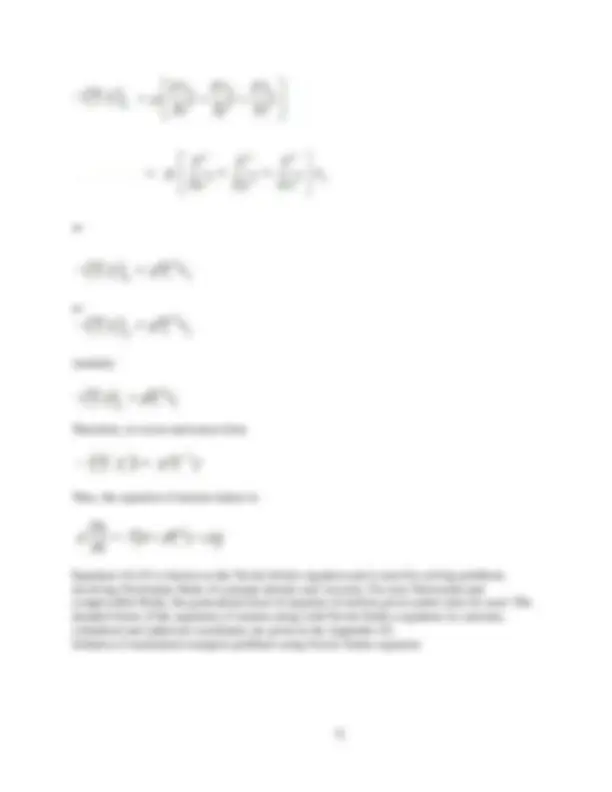
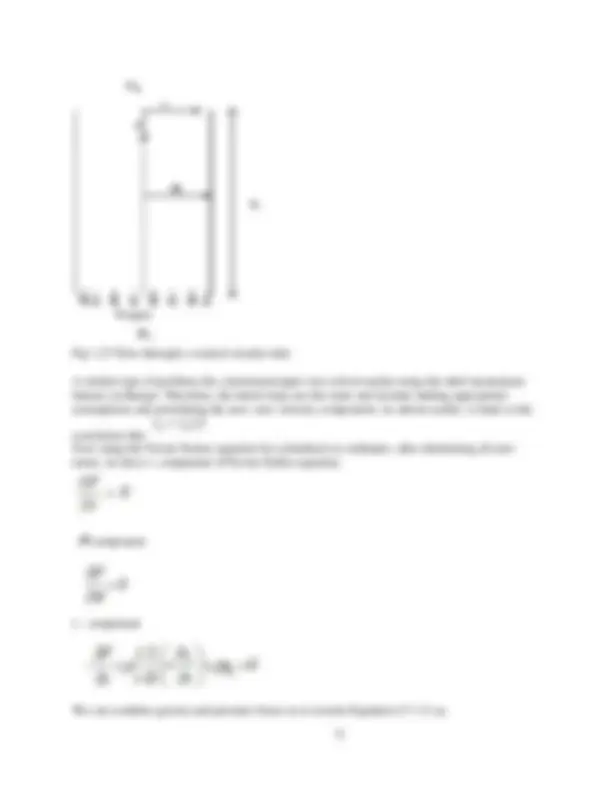
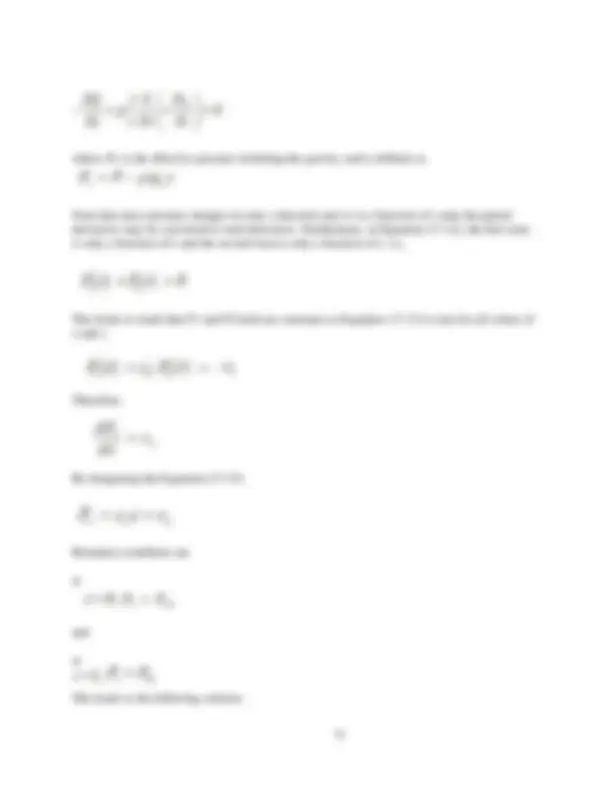
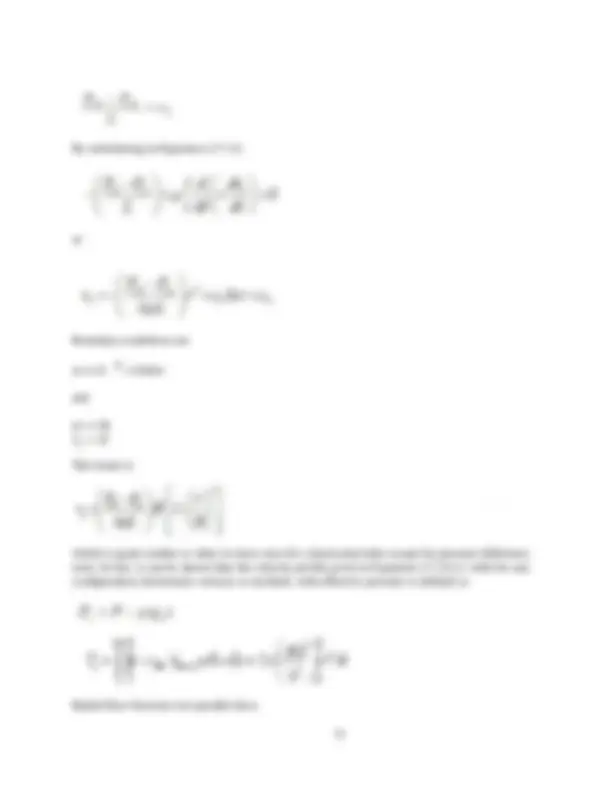
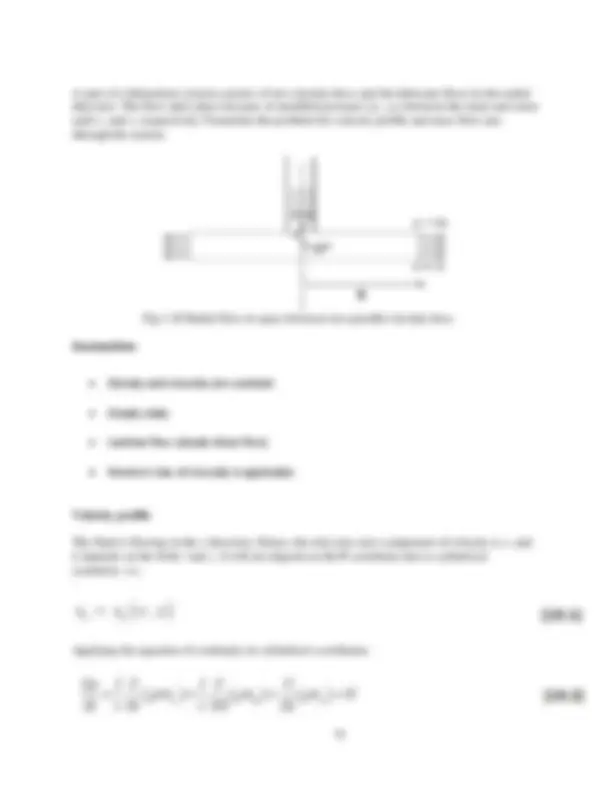
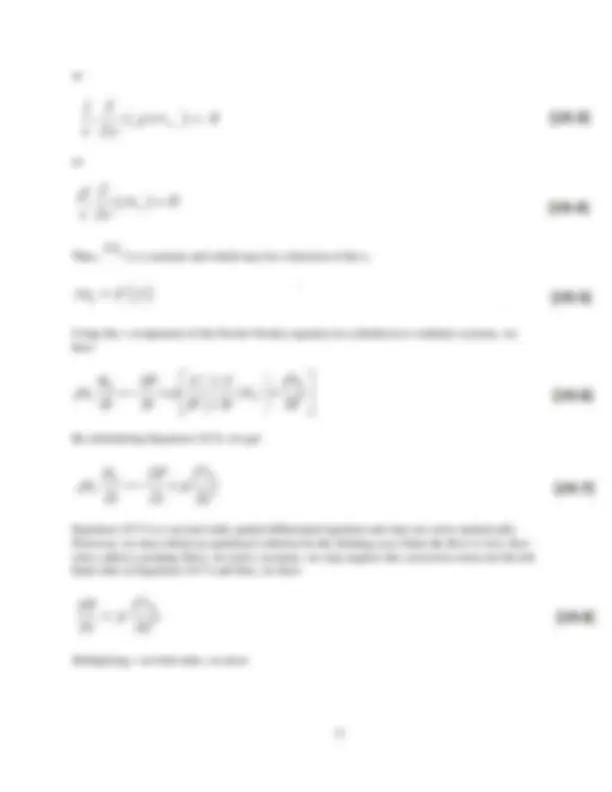
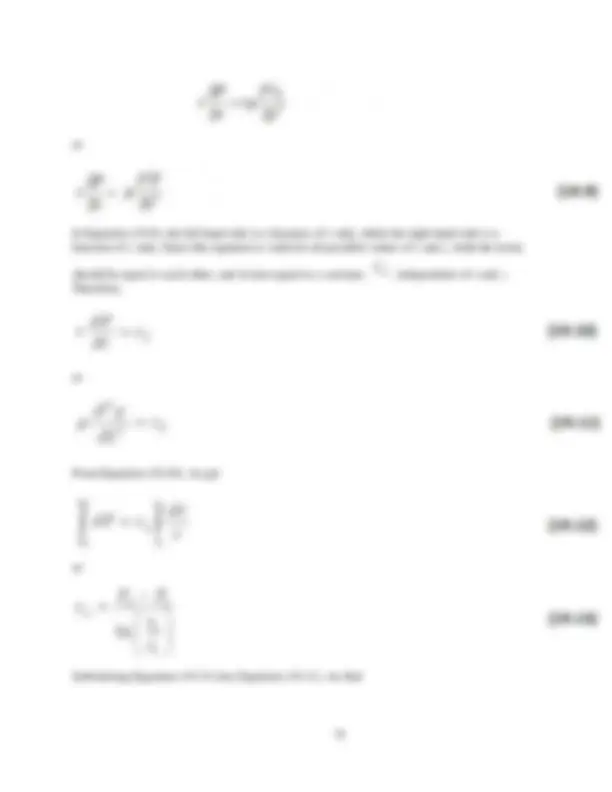
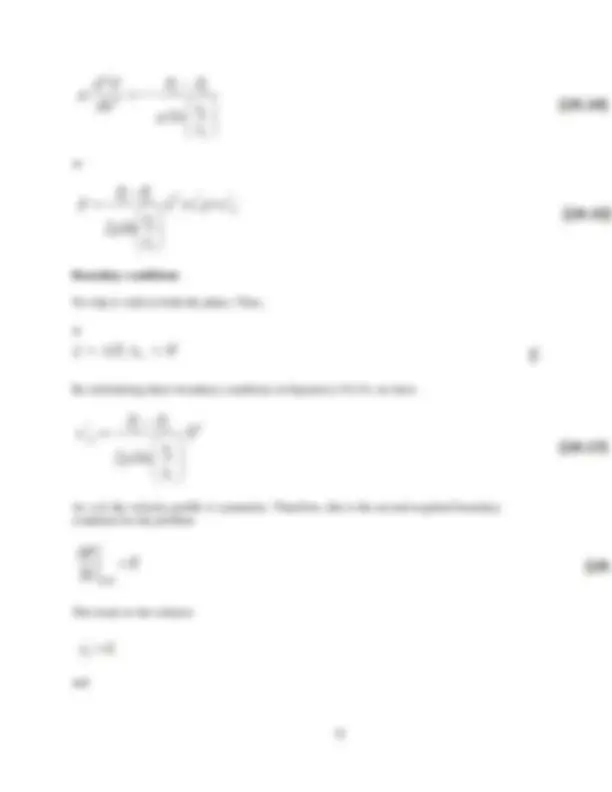
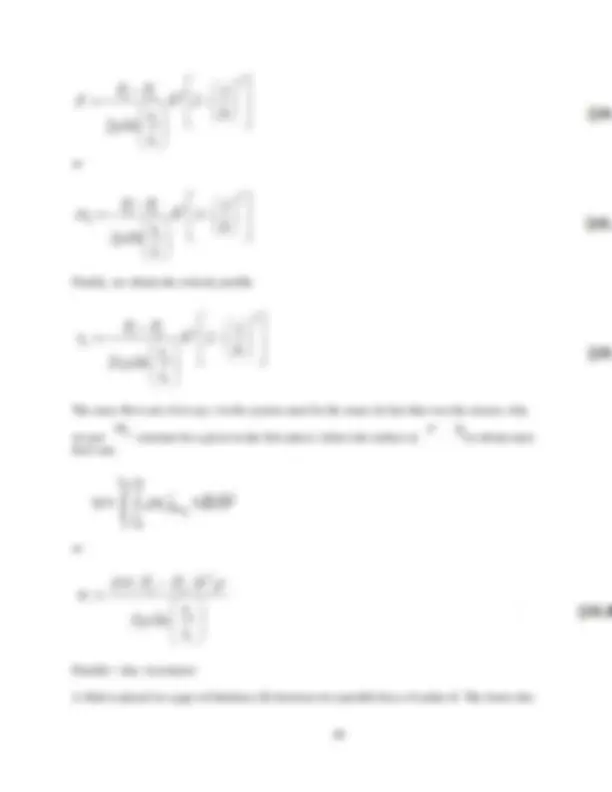
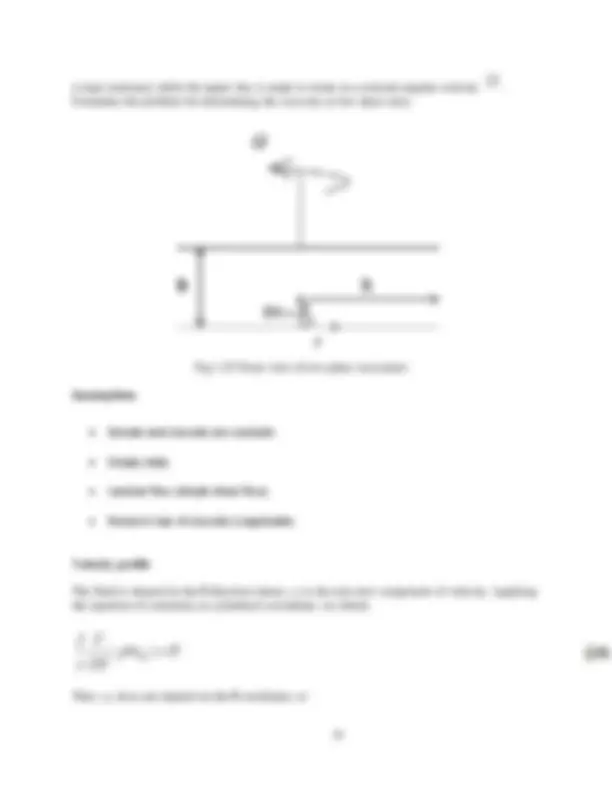
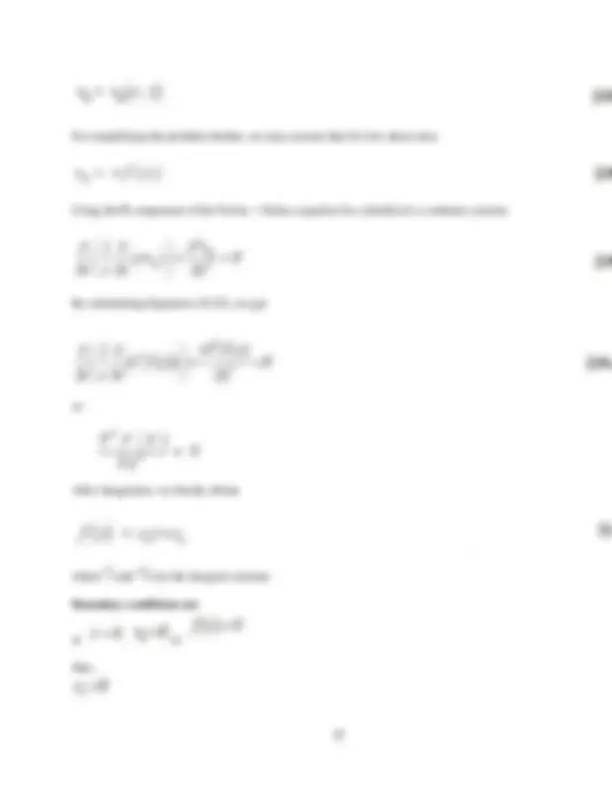
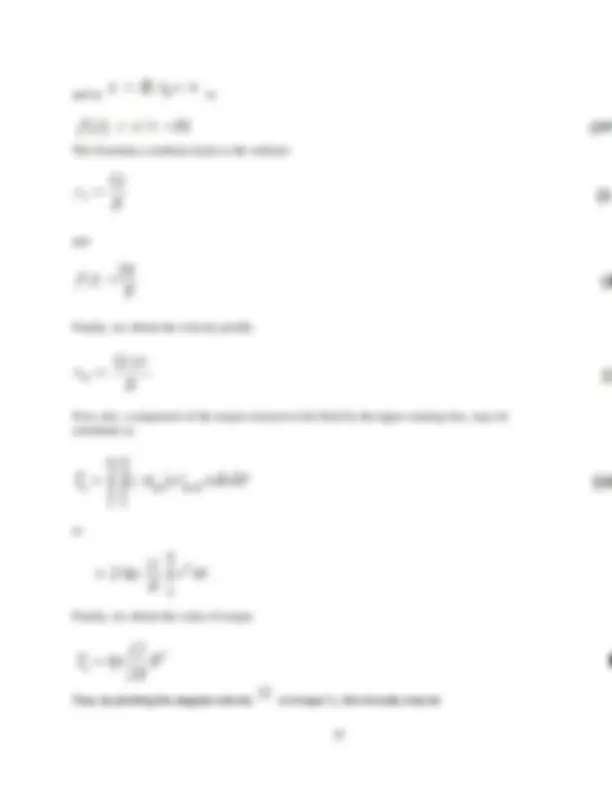
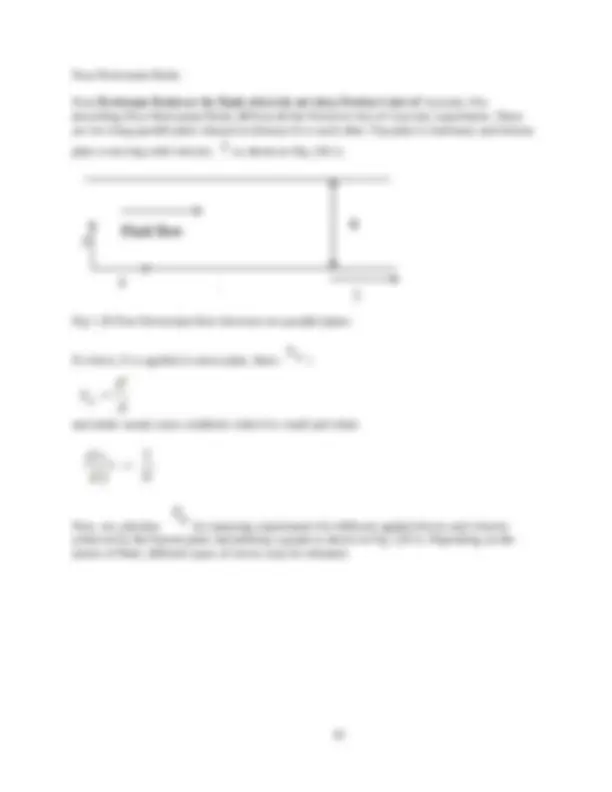
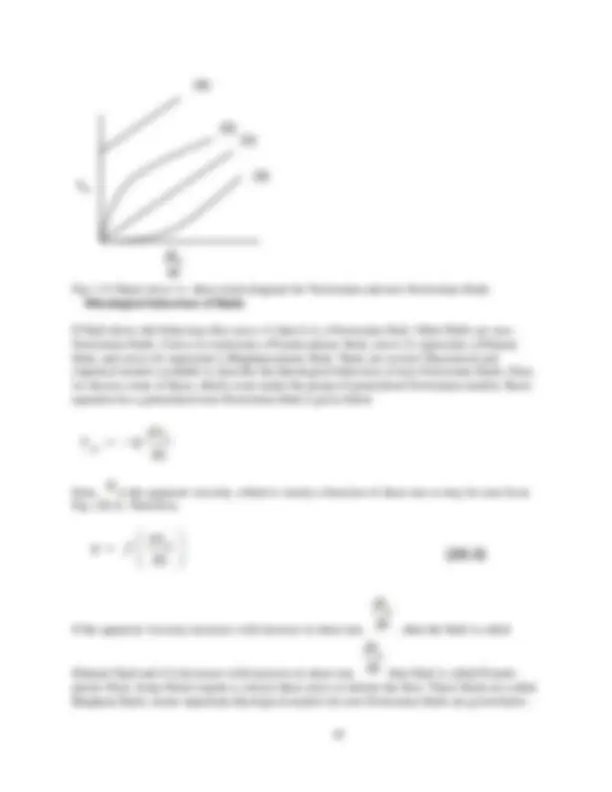
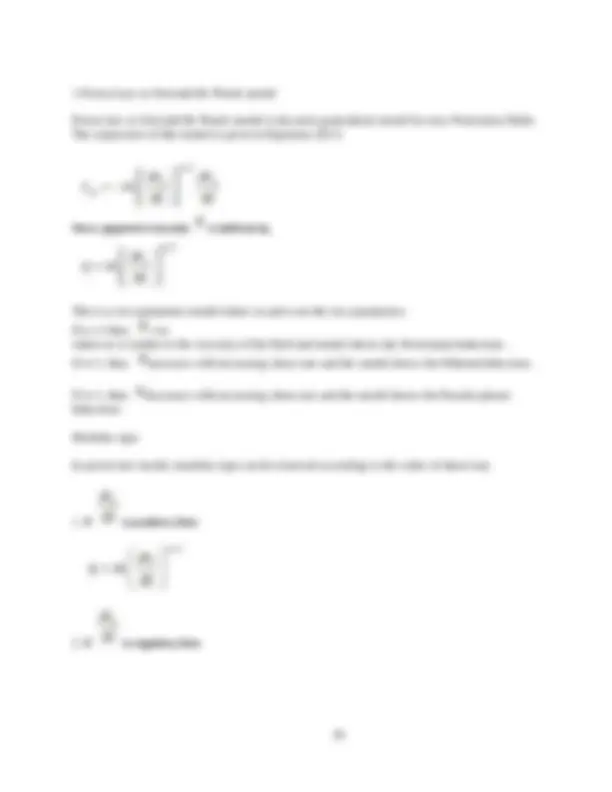
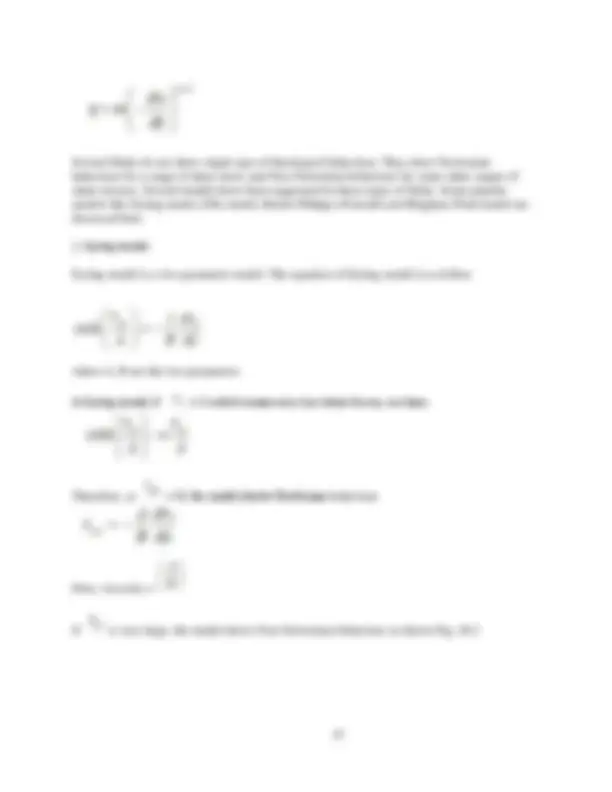
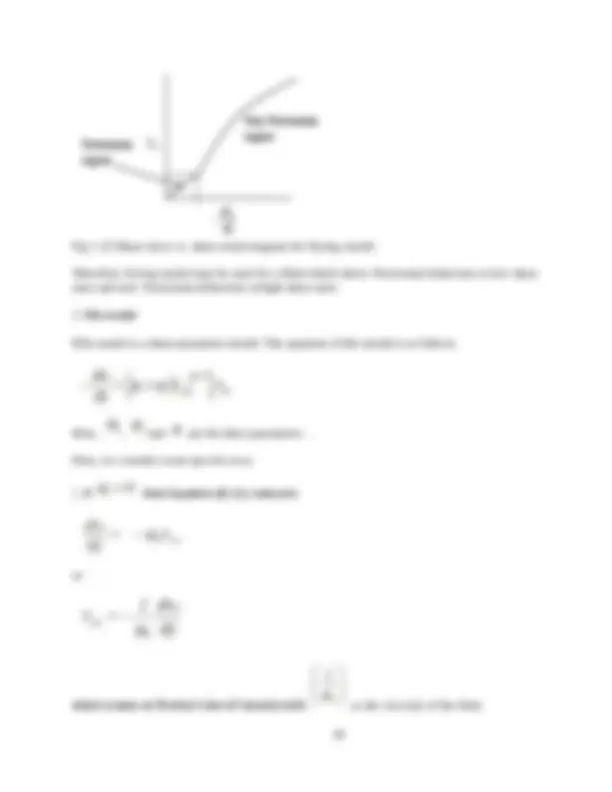
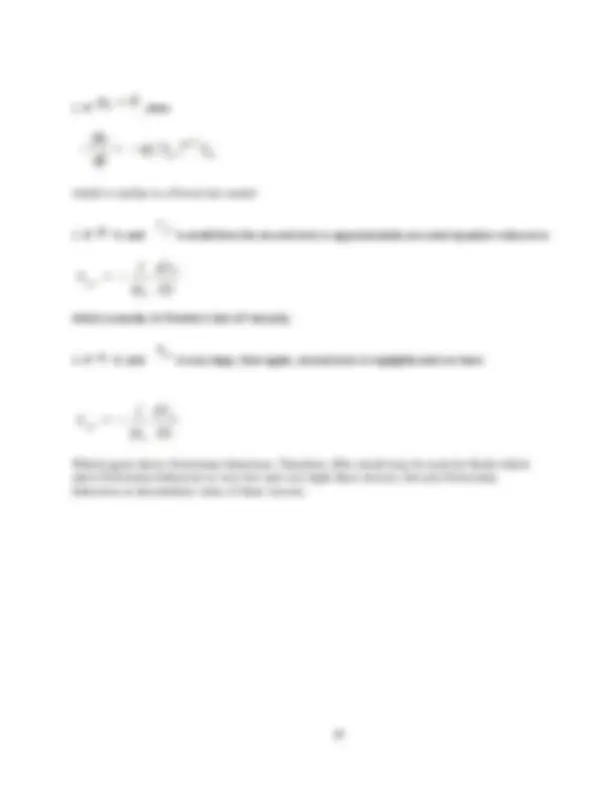
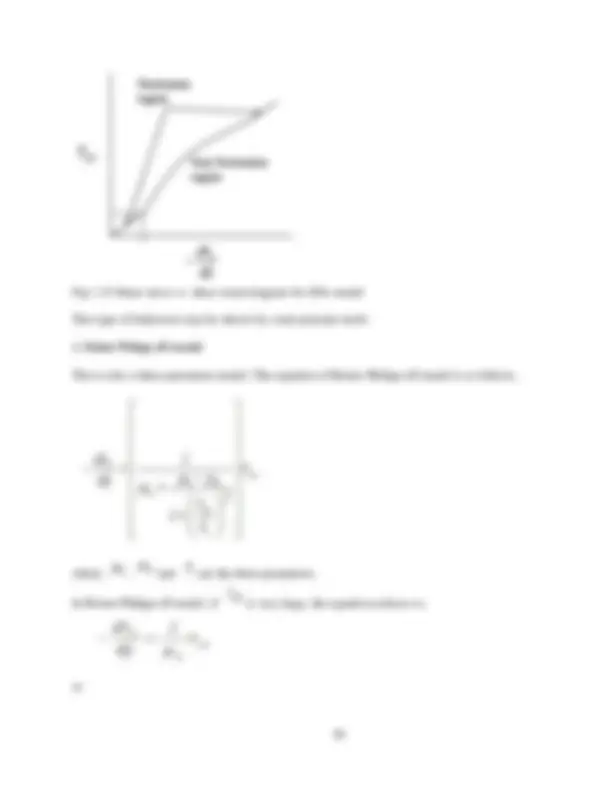
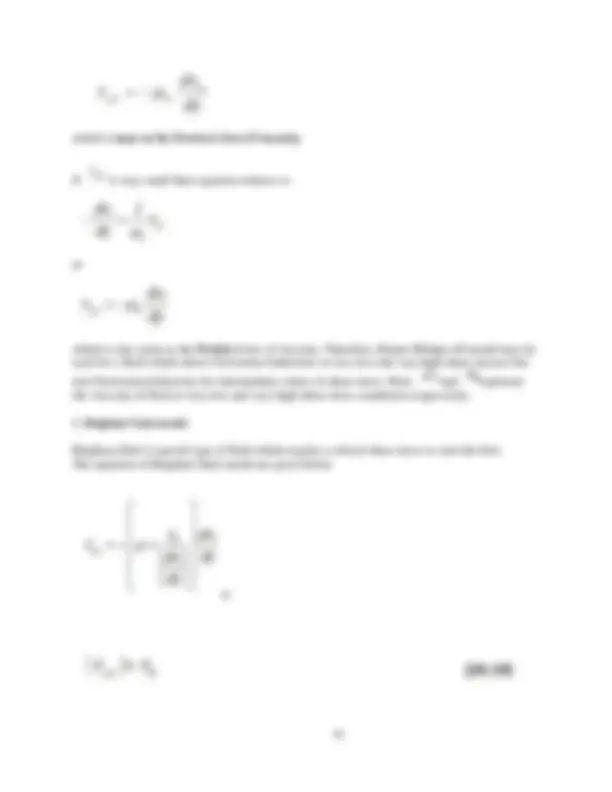
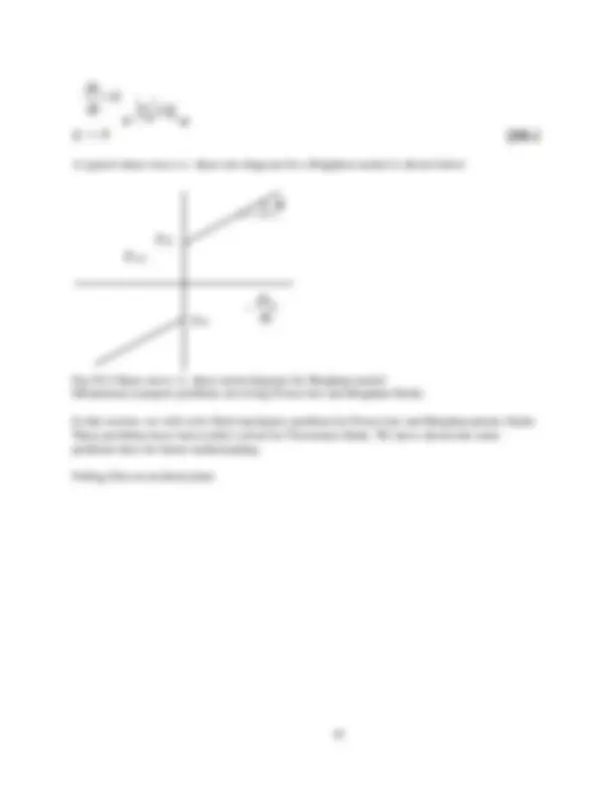
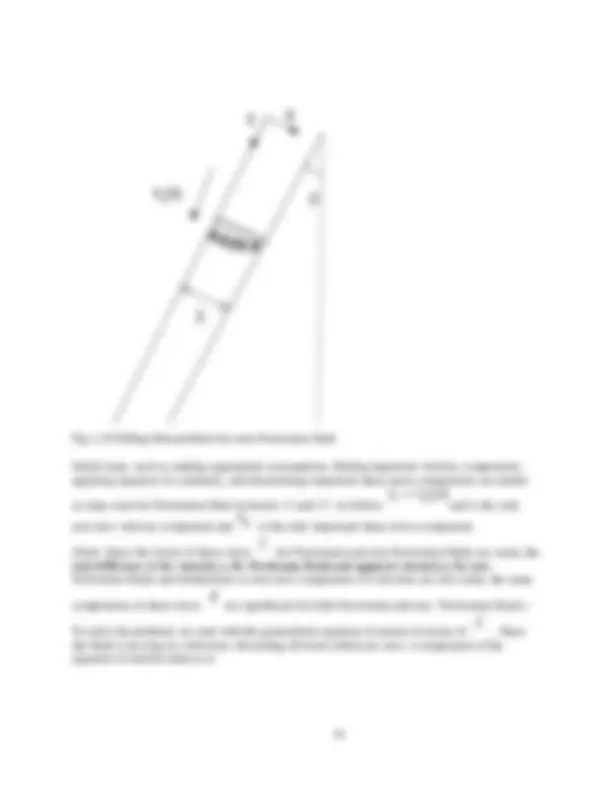
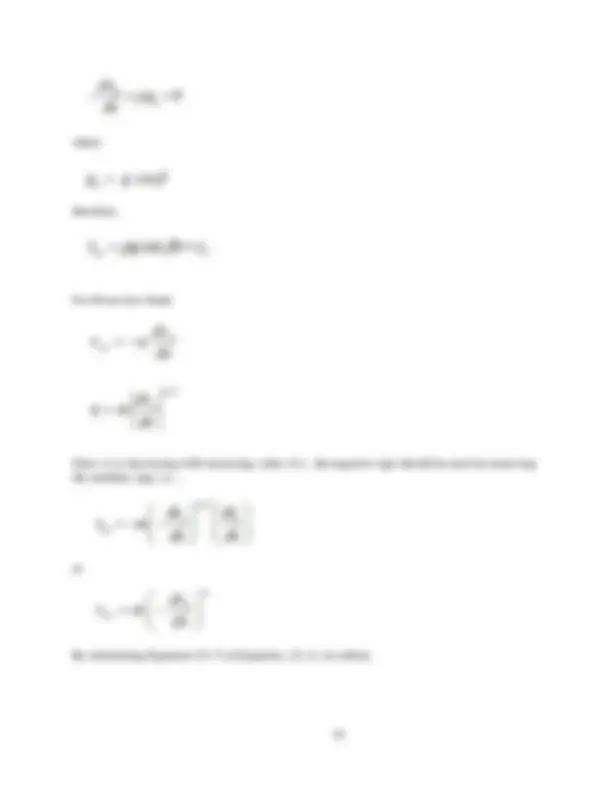
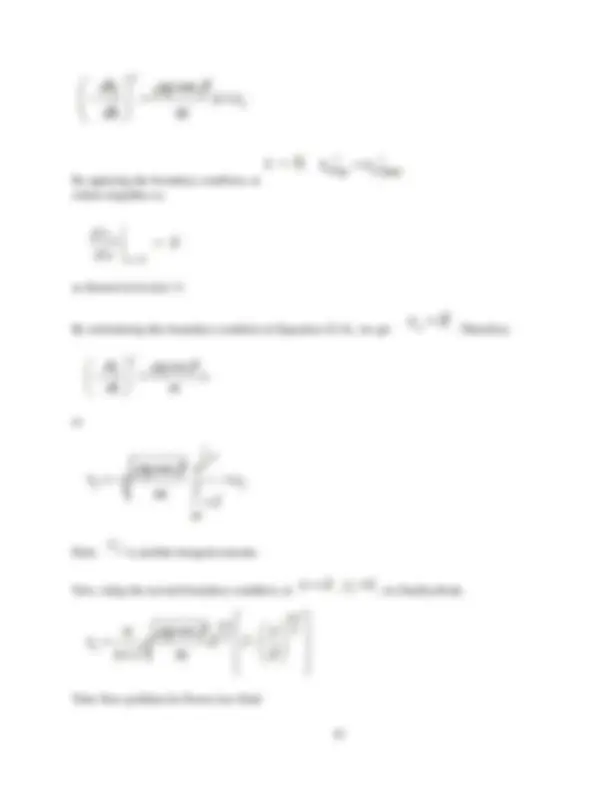

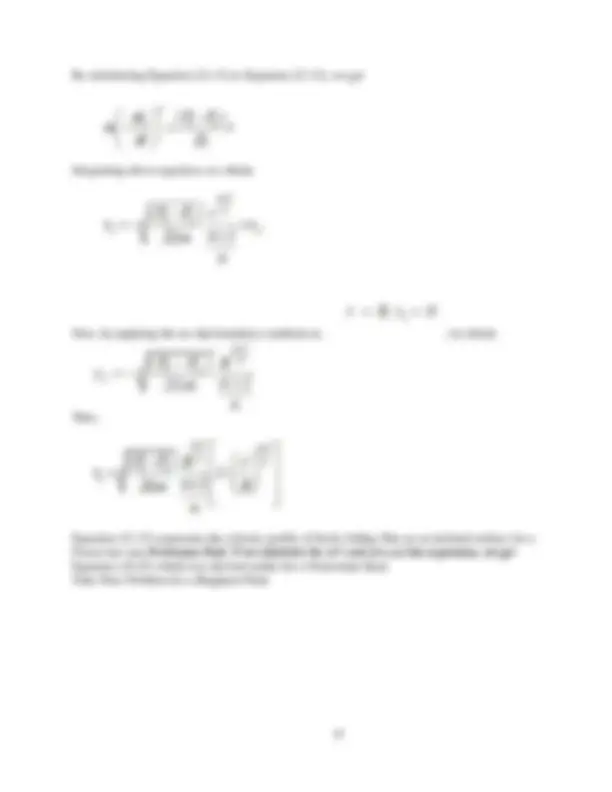

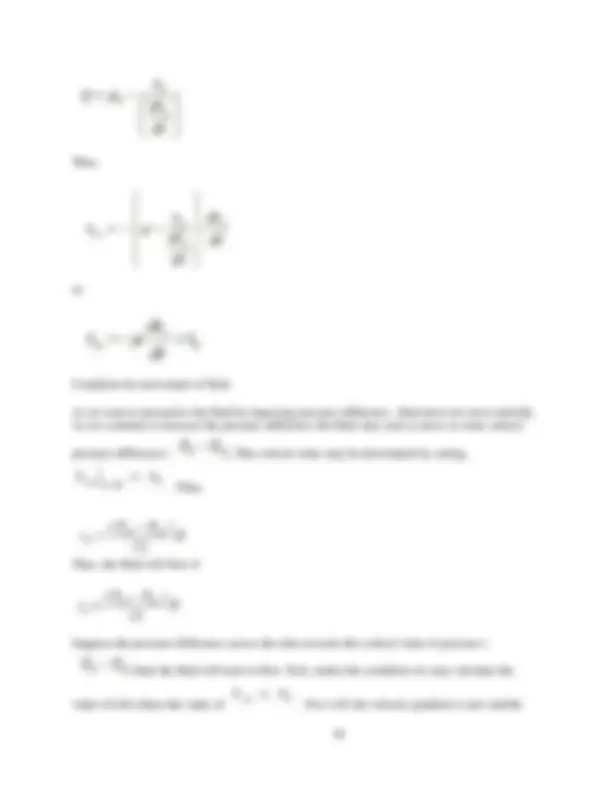
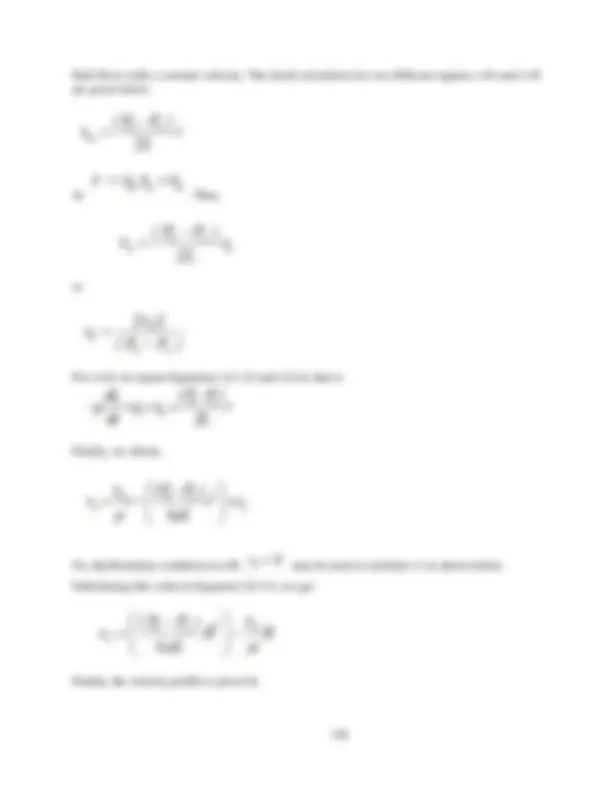
Study with the several resources on Docsity
Earn points by helping other students or get them with a premium plan
Prepare for your exams
Study with the several resources on Docsity
Earn points to download
Earn points by helping other students or get them with a premium plan
Community
Ask the community for help and clear up your study doubts
Discover the best universities in your country according to Docsity users
Free resources
Download our free guides on studying techniques, anxiety management strategies, and thesis advice from Docsity tutors
This pdf contains a wide variety of information about Transport Phenomena which is the most important part of students pursuing chemical engineering.
Typology: Study notes
1 / 265
This page cannot be seen from the preview
Don't miss anything!
Transport Phenomena is the subject which deals with the movement of different physical quantities in any chemical or mechanical process and describes the basic principles and laws of transport. It also describes the relations and similarities among different types of transport that may occur in any system. Transport in a chemical or mechanical process can be classified into three types:
Thus, every layer of fluid is moving at a different velocity. This leads to shear forces which are described in the next section. Newton’s Law of Viscosity Newton’s law of viscosity may be used for solving problem for Newtonian fluids. For many fluids in chemical engineering the assumption of Newtonian fluid is reasonably acceptable. To understand Newtonian fluid, let us consider a hypothetical experiment, in which there are two infinitely large plates situated parallel to each other, separated by a distance h. A fluid is present between these two plates and the contact area between the fluid and the plates is A. A constant force F1 is now applied on the lower plate while the upper plate is held stationary. After steady state has reached, the velocity achieved by the lower plate is measured as V 1. The force is then changed, and the new velocity of the plate associated with this force is measured. The experiment is then repeated to take sufficiently large readings as shown in the following table.
If the F/A is plotted against V/h , we may observe that they lie on a straight line passing through the origin. Fig 1.3 Shear stress vs. shear stain Thus, it may be said that F/A is proportional to v/h for a Newtonian fluid. It may be noted that it is the velocity gradient which leads to the development of shear forces. The above equation may be re-written as In the limiting case, as h → 0 , we have where, μ is a constant of proportionality, and is called as the viscosity of the fluid. The quantity F/A represents the shear forces/stress. It may be represented as , where the subscript x indicates the direction of force and subscript y indicates the direction of outward normal of the
The SI unit of viscosity is kg/m.s or Pa.s. In CGS unit is g/cm.s and is commonly known as poise ( P ). where 1 P = 0.1 kg/m.s. The unit poise is also used with the prefix centi- , which refers to one-hundredth of a poise, i.e. 1 cP = 0.01 P. The viscosity of air at 25 oC is 0.018 cP, water at 25 oC is 1 cP and for many polymer melts it may range from 1000 to 100,000 cP , thus showing a long range of viscosity. Laminar and turbulent flow Fluid flow can broadly be categorized into two kinds: laminar and turbulent. In laminar flow, the fluid layers do not inter-mix, and flow separately. This is the flow encountered when a tap is just opened and water is allowed to flow very slowly. As the flow increases, it becomes much more irregular and the different fluid layers start mixing with each other leading to turbulent flow. Osborne Reynolds tried to distinguish between the two kinds of flow using an ingenious experiment and known as the Reynolds’s experiment. The basic idea behind this experiment is described below. Reynolds’s experiment
Fig 1.4 Reynolds’s experiments The experiment setup used for performing the Reynolds's experiment is shown in Fig. 7.5. The average velocity of fluid flow through the pipe diameter can be varied. Also, there is an arrangement to inject a colored dye at the center of the pipe. The profile of the dye is observed along the length of the pipe for different velocities for different fluids. If this experiment is performed, it may be seen that for certain cases the dye shows a regular thread type profile, which is seen at low fluid velocity and flow is called laminar flow. when the fluid velocity is increased the dye starts to mixed with the fluid and for larger velocities simply disappears. At this point fluid flow becomes turbulent. For the variables average velocity of fluid vz avg , pipe diameter D , fluid density ρ , and the fluid viscosity μ , Reynolds found a dimensionless group which could be used to characterize the type of fluid flow in the tube. This dimensionless quantity is known as the Reynolds number. From the experiment, It was observed that if Re >2100 , the dye simply disappeared and the flow has changed to laminar to turbulent flow.
are moving on the highway in the same direction but in the different lanes at different speeds. If suddenly, some obstacle comes on the road, then if the car's speed is sufficiently low, it can move on to other lane smoothly and come back to its original lane after the obstacle is crossed. This is the regular laminar case. On the other hand, if the car is moving at a high speed and suddenly encounters an obstacle, then the driver may lose control, and this car may move haphazardly and hit other cars and after that traffic may never return to normal traffic conditions. This is the turbulent case. Internal and external flows Depending on how the fluid and the solid boundaries contact each other, the flow may be classified as internal flow or external flow. In internal flows, the fluid moves between solid boundaries. As is the case when fluid flows in a pipe or a duct. In external flows, however, the fluid is flowing over an external solid surface, the example may be sited is the flow of fluid over a sphere as shown in Fig. 8.1. Fig 1.5 External flow around a sphere Boundary layers and fully developed regions Let us now consider the example of fluid flowing over a horizontal flat plate as shown in Fig. The velocity of the fluid is before it encounters the plate. As the fluid touches the plate, the velocity of the fluid layer just adjacent to the plate surface becomes zero due to the no slip boundary condition. This layer of fluid tries to drag the next fluid layer above it and reduces its velocity. As the fluid proceeds along the length of the plate (in x-direction), each layer starts to drag adjacent fluid layer but the effect of drag reduces as we go further away from the plate in y-direction. Finally, at some distance from the plate this drag effect disappears or becomes insignificant. This region where the velocity is changing or where the velocity gradients exists, is called the boundary layer region. The region beyond boundary layer where the velocity gradients are insignificant is called the potential flow region.
Fig 1.6 External flow over a flat plate As depicted in Fig. 8.2, the boundary layer keeps growing along the x-direction, and may be referred to as the developing flow region. In internal flows (e.g. fluid flow through a pipe), the boundary layers finally merge after flow over a distance as shown in Fig. 8.3 below. Fig 8.3 Developing flow and fully developed flow region The region after the point at which the layers merge is called the fully developed flow region and before this it is called the developing flow region. In fact, fully developed flow is another important assumption which is taken for finding solution for varity of fluid flow problem. In the fully developed flow region (as shown in Figure 8.3), the velocity vz is a function of r direction only. However, the developing flow region, velocity vz is also changing in the z direction. Main axioms of transport phenomena The basic equations of transport phenomena are derived based on following five axioms. Mass is conserved, which leads to the equation of continuity. Momentum is conserved, which leads to the equation of motion. Moment of momentum is conserved leads to an important result that the 2nd order stress tensor is symmetric.
Fig 1.7 Fixed rectangular volume element through which fluid is flowing The equation is then divided by the volume of the CV and converted into a partial differential equation by taking the limit as all dimensions go to zero. This limit effectively means that CV collapses to a point, thereby making the equation valid at every point in the system. Let m and m+Δm be the mass of the control volume at time t and t+Δt respectively. Then, the rate of accumulation, In order to evaluate the rate of inflow of mass into the control volume, we need to inspect how mass enters the control volume. Since the fluid velocity has three components vx, vy and vz, we need to identify the components which cause the inflow or the outflow at each of the six faces of the rectangular CV. For example, it is the component vx which forces the fluid to flow in the x direction, and thus it makes the fluid enter or exit through the faces having area ΔyΔz at x = x and x = x+Δx respectively. The component vy forces the fluid in y direction, and thus it makes the fluid enter or exit through the faces having area ΔxΔz at y = y and y = y+Δy respectively. Similarly, the component vz forces the fluid to flow in z direction, and thus it makes fluid enter or exit through the faces having area ΔxΔy at z = z and z = z+Δ z respectively. The rate mass entering in x direction through the surface ΔyΔz is (ρvxΔyΔz|x), the rate of mass entering in y direction through the surface ΔxΔz is (ρvyΔxΔz|y) and the rate of mass entering from z direction through the surface ΔxΔy is (ρvzΔxΔy|z). In a similar manner, expressions for the rate of mass leaving from the control volume may be written. Thus, the conservation of mass leads to the following expressions
Dividing the Equation (8.1) by the volume ΔxΔyΔz, we obtain Note that each term in Equation (8.2) has the unit of mass per unit volume per unit time. Now, taking the limits Δx→0, Δy→0 and Δz→0, we get and using the definition of derivative, we finally obtain Equation (8.4) is applicable to each point of the fluid. Rearranging the terms, we get the equation of continuity, may be written as given below. We need not to derive the equation of continuity again and again in other coordinate system (that is, spherical or cylindrical). The idea is to rewrite Equation (8.5) in vector and tensor form. Once it is written in this form, the same equation may be applied to other coordinate system as well. Thus, the Equation (8.5) may be rewritten in vector and tensor form as shown below. Vector and tensor analysis of cylindrical and spherical coordinate systems is not done here, and can be looked up elsewhere. Thus, the final expressions in cylindrical and spherical coordinates
Internal and external flows Depending on how the fluid and the solid boundaries contact each other, the flow may be classified as internal flow or external flow. In internal flows, the fluid moves between solid boundaries. As is the case when fluid flows in a pipe or a duct. In external flows, however, the fluid is flowing over an external solid surface, the example may be sited is the flow of fluid over a sphere as shown in Fig. 8.1. Fig 1.8 External flow around a sphere Boundary layers and fully developed regions Let us now consider the example of fluid flowing over a horizontal flat plate as shown in Fig. The velocity of the fluid is before it encounters the plate. As the fluid touches the plate, the velocity of the fluid layer just adjacent to the plate surface becomes zero due to the no slip boundary condition. This layer of fluid tries to drag the next fluid layer above it and reduces its velocity. As the fluid proceeds along the length of the plate (in x-direction), each layer starts to drag adjacent fluid layer but the effect of drag reduces as we go further away from the plate in y-direction. Finally, at some distance from the plate this drag effect disappears or becomes insignificant. This region where the velocity is changing or where the velocity gradients exists, is called the boundary layer region. The region beyond boundary layer where the velocity gradients are insignificant is called the potential flow region. Fig 1.9 External flow over a flat plate
As depicted in Fig. 8.2, the boundary layer keeps growing along the x-direction, and may be referred to as the developing flow region. In internal flows (e.g. fluid flow through a pipe), the boundary layers finally merge after flow over a distance as shown in Fig. 8.3 below. Fig 1.10 Developing flow and fully developed flow region The region after the point at which the layers merge is called the fully developed flow region and before this it is called the developing flow region. In fact, fully developed flow is another important assumption which is taken for finding solution for varity of fluid flow problem. In the fully developed flow region (as shown in Figure 8.3), the velocity vz is a function of r direction only. However, the developing flow region, velocity vz is also changing in the z direction. Main axioms of transport phenomena The basic equations of transport phenomena are derived based on following five axioms. Mass is conserved, which leads to the equation of continuity. Momentum is conserved, which leads to the equation of motion. Moment of momentum is conserved leads to an important result that the 2nd order stress tensor is symmetric. Energy is conserved, which leads to equation of thermal energy. Mass of component i in a multi-component system is conserved, which leads to the convective diffusion equation. The solution of equations, resulting from axiom 2, 4 and 5 leads to the solution of velocity, temperature and concentration profiles. Ones these profiles are known, all other important information needed can be determined. We first take the axiom - 1. Other axioms will be taken up one by one letter on. There are three types of control volumes (CV) which may be chosen for deriving the equations based these axioms.
Fig 1.11 Fixed rectangular volume element through which fluid is flowing The equation is then divided by the volume of the CV and converted into a partial differential equation by taking the limit as all dimensions go to zero. This limit effectively means that CV collapses to a point, thereby making the equation valid at every point in the system. Let m and m+Δm be the mass of the control volume at time t and t+Δt respectively. Then, the rate of accumulation, In order to evaluate the rate of inflow of mass into the control volume, we need to inspect how mass enters the control volume. Since the fluid velocity has three components vx, vy and vz, we need to identify the components which cause the inflow or the outflow at each of the six faces of the rectangular CV. For example, it is the component vx which forces the fluid to flow in the x direction, and thus it makes the fluid enter or exit through the faces having area ΔyΔz at x = x and x = x+Δx respectively. The component vy forces the fluid in y direction, and thus it makes the fluid enter or exit through the faces having area ΔxΔz at y = y and y = y+Δy respectively. Similarly, the component vz forces the fluid to flow in z direction, and thus it makes fluid enter or exit through the faces having area ΔxΔy at z = z and z = z+Δ z respectively. The rate mass entering in x direction through the surface ΔyΔz is (ρvxΔyΔz|x), the rate of mass entering in y direction through the surface ΔxΔz is (ρvyΔxΔz|y) and the rate of mass entering from z direction through the surface ΔxΔy is (ρvzΔxΔy|z). In a similar manner, expressions for the rate of mass leaving from the control volume may be written. Thus, the conservation of mass leads to the following expressions
Dividing the Equation (8.1) by the volume ΔxΔyΔz, we obtain Note that each term in Equation (8.2) has the unit of mass per unit volume per unit time. Now, taking the limits Δx→0, Δy→0 and Δz→0, we get and using the definition of derivative, we finally obtain Equation (8.4) is applicable to each point of the fluid. Rearranging the terms, we get the equation of continuity, may be written as given below. We need not to derive the equation of continuity again and again in other coordinate system (that is, spherical or cylindrical). The idea is to rewrite Equation (8.5) in vector and tensor form. Once it is written in this form, the same equation may be applied to other coordinate system as well. Thus, the Equation (8.5) may be rewritten in vector and tensor form as shown below. Vector and tensor analysis of cylindrical and spherical coordinate systems is not done here, and can be looked up elsewhere. Thus, the final expressions in cylindrical and spherical coordinates