
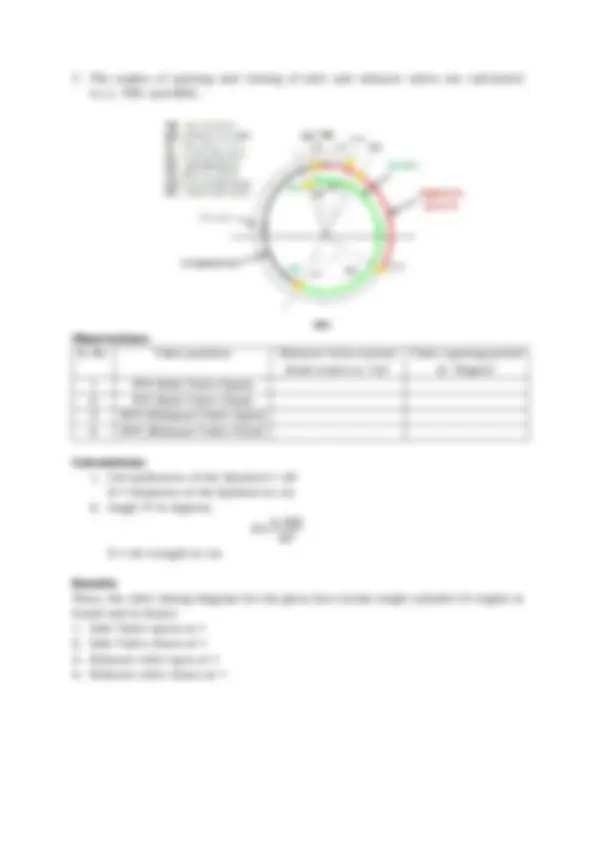
Study with the several resources on Docsity
Earn points by helping other students or get them with a premium plan
Prepare for your exams
Study with the several resources on Docsity
Earn points to download
Earn points by helping other students or get them with a premium plan
Community
Ask the community for help and clear up your study doubts
Discover the best universities in your country according to Docsity users
Free resources
Download our free guides on studying techniques, anxiety management strategies, and thesis advice from Docsity tutors
This is valve timing diagram which
Typology: Schemes and Mind Maps
1 / 2
This page cannot be seen from the preview
Don't miss anything!
Objective: To draw the actual valve timing diagram of a four-stroke single-cylinder CI engine. Apparatus required: Measuring tape, Sectional four-stroke single-cylinder CI engine test rig Theory: In a four-stroke CI engine, the thermodynamic cycle of operations is completed in two revolutions of the crankshaft or four strokes of the piston. During the four strokes, there are five events to be completed, viz., suction, compression, combustion, expansion and exhaust. The suction stroke starts when the piston is at TDC and about to move downwards. The inlet valve is open at this time and the exhaust valve is closed. Due to the suction created by the motion of the piston towards the BDC, the air is drawn into the cylinder. When the piston reaches the BDC the suction stroke ends and the inlet valve closes. The air taken into the cylinder during the suction stroke is compressed by the return stroke of the piston. During this stroke, both inlet and exhaust valves are in a closed position. The air is now compressed to the clearance volume. At the end of the compression stroke, a metered quantity of fuel (diesel) is injected into the hot compressed air in fine sprays by the fuel injector and it starts burning. During the burning process, the chemical energy of the fuel is converted into heat energy. The high pressure of the burnt gases forces the piston towards the BDC. Both the valves are in a closed position. Of the four strokes only during this stroke, power is produced. Both pressure and temperature decrease during expansion. At the end of the expansion stroke, the exhaust valve opens and the inlet valve remains closed. The pressure falls to atmospheric level as a part of the burnt gases escape. The piston starts moving from BDC to TDC and sweeps the burnt gases out from the cylinder. The exhaust valve closes when the piston reaches TDC. Procedure:
S = Arc Length in cm Results: Thus, the valve timing diagram for the given four-stroke single-cylinder CI engine is found and is drawn