
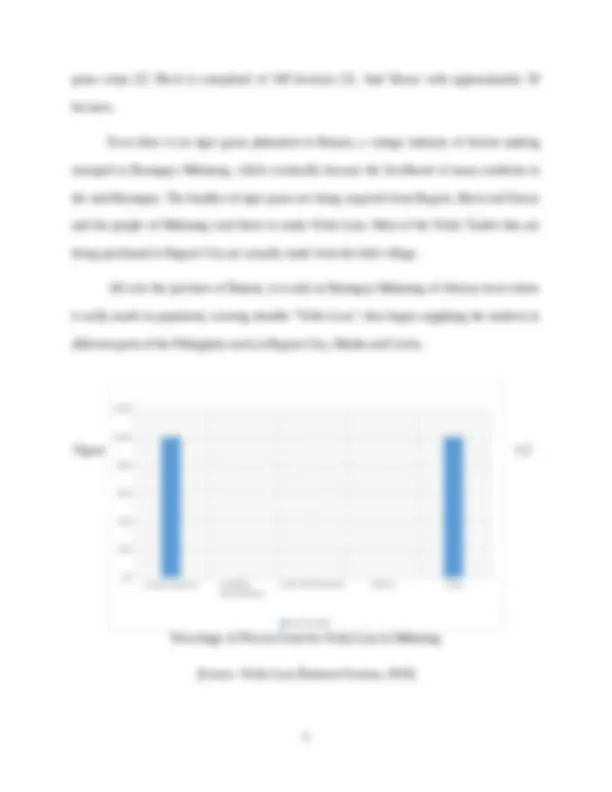
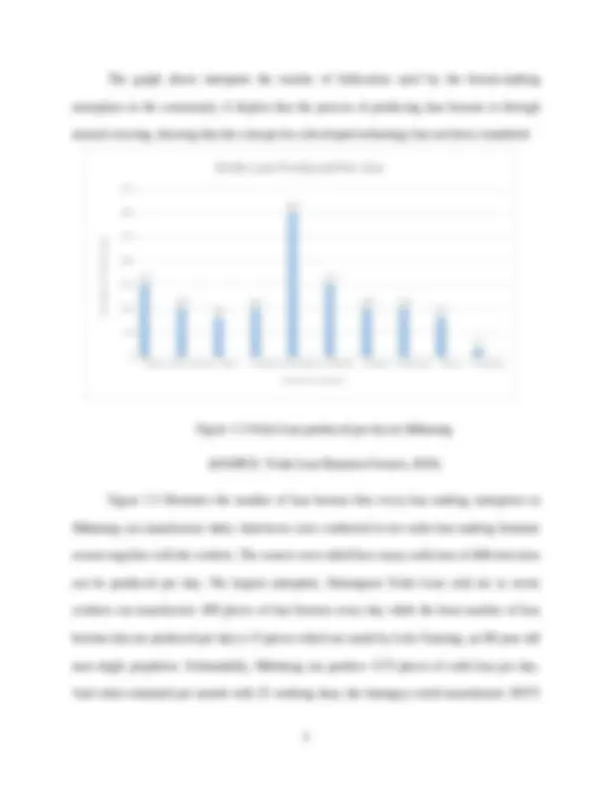
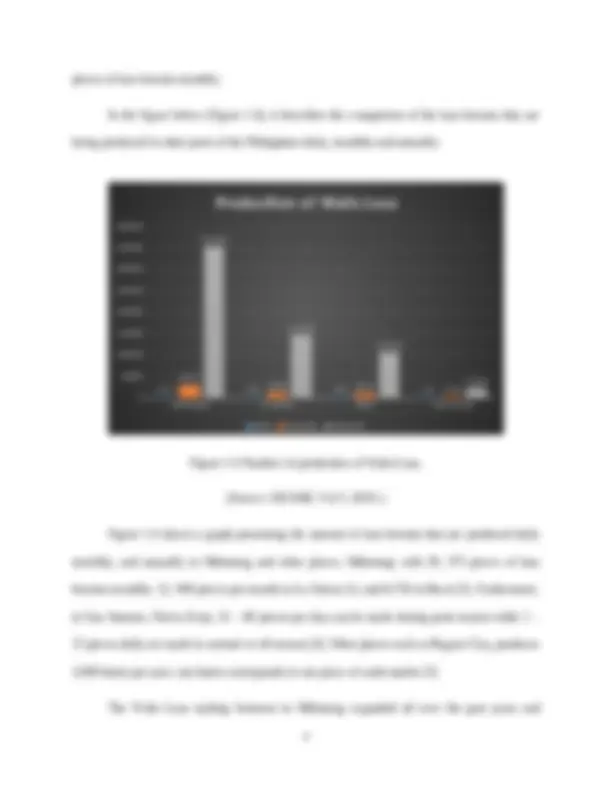
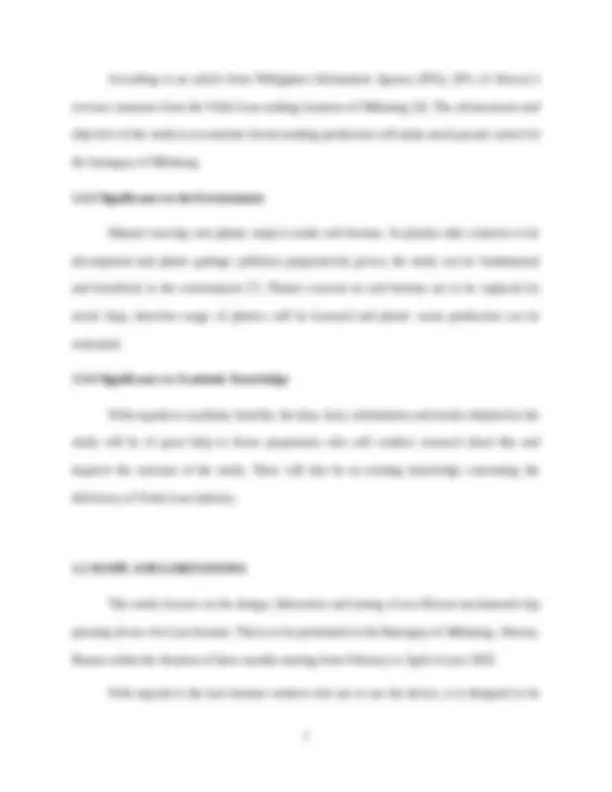
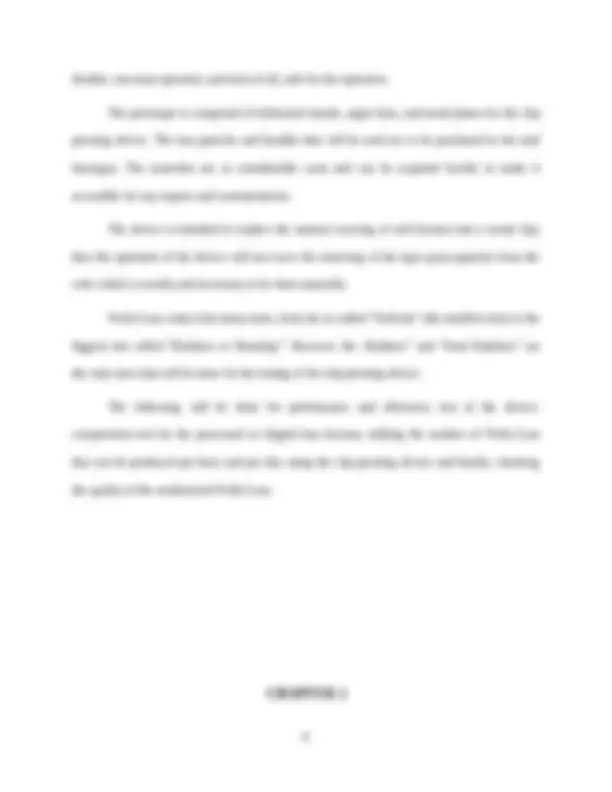
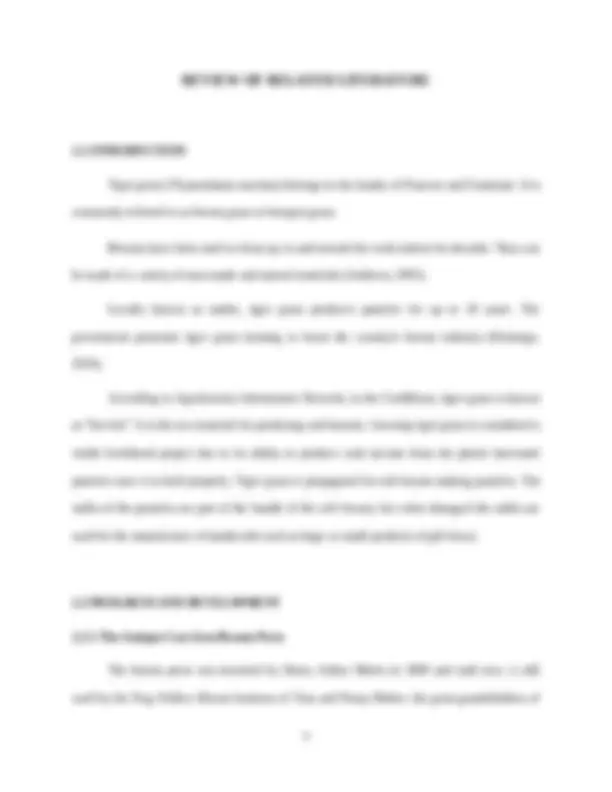
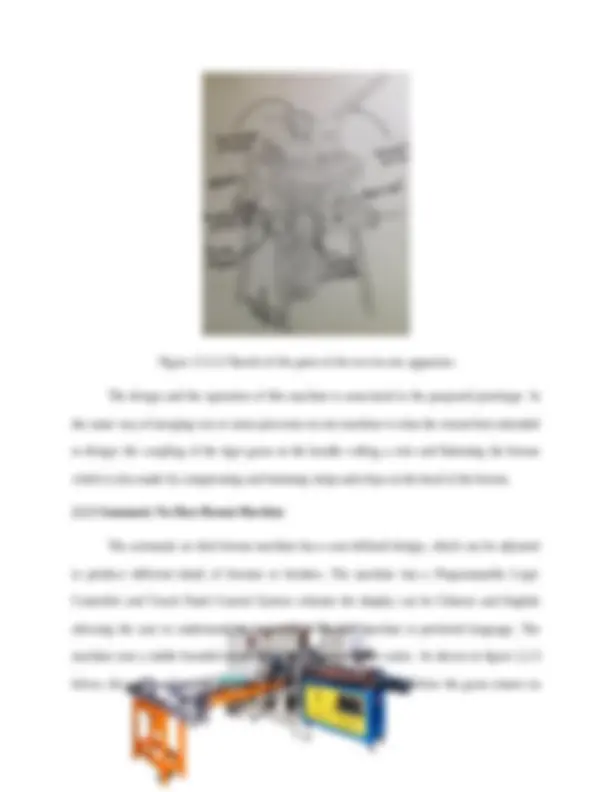
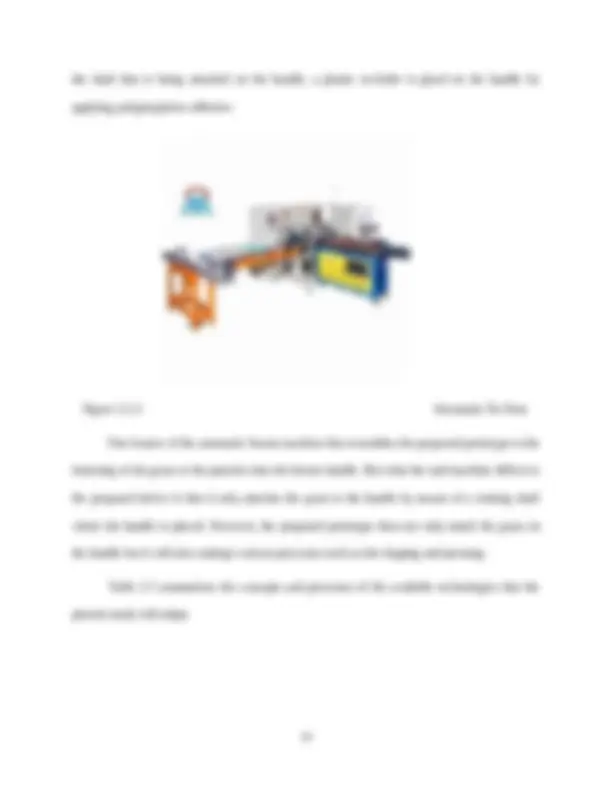
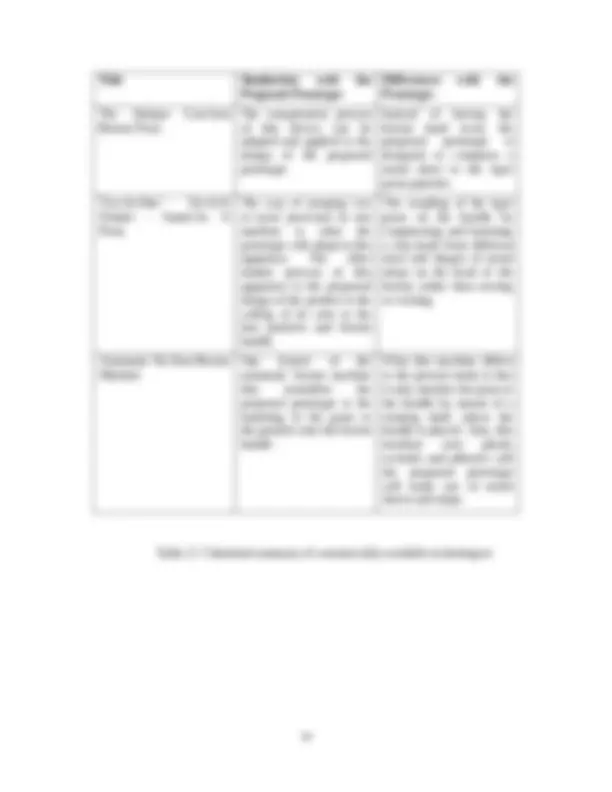
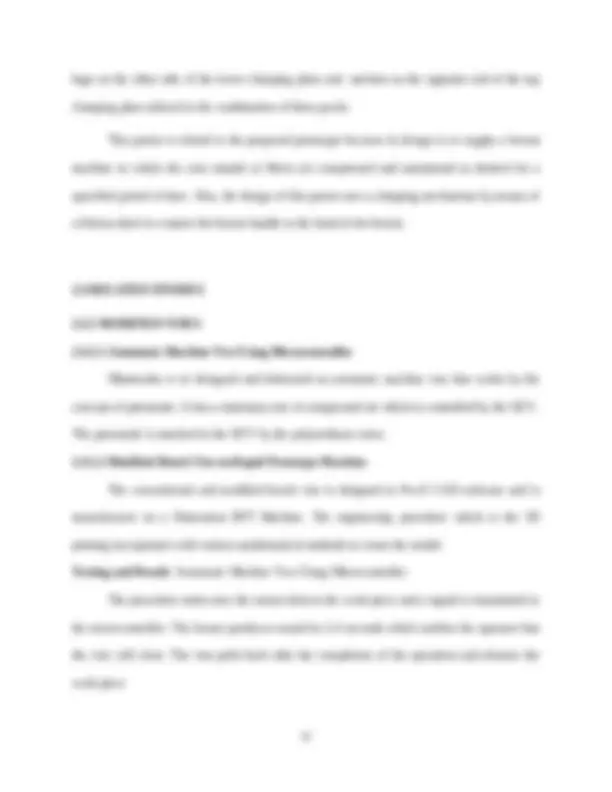
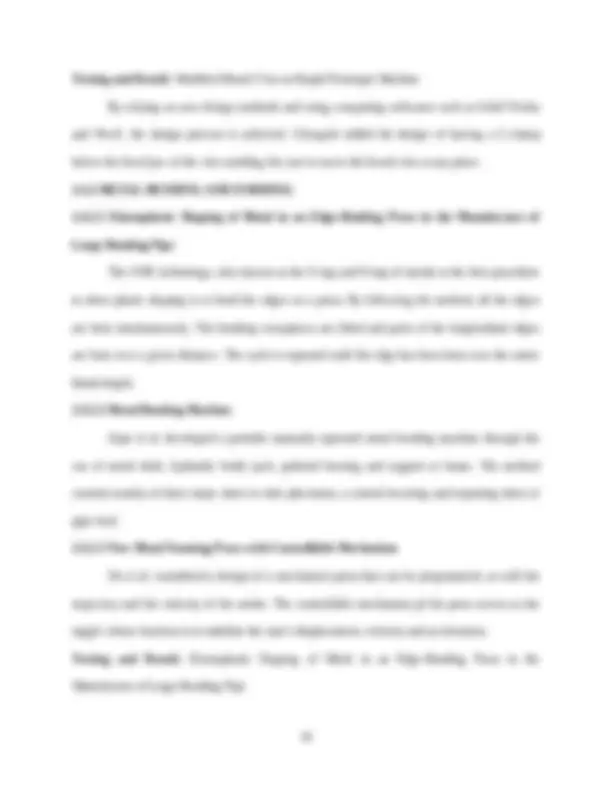
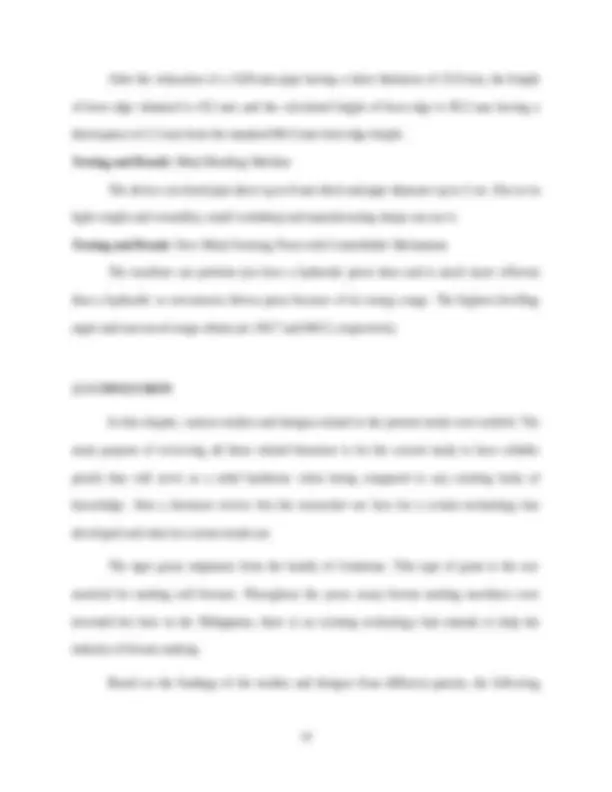
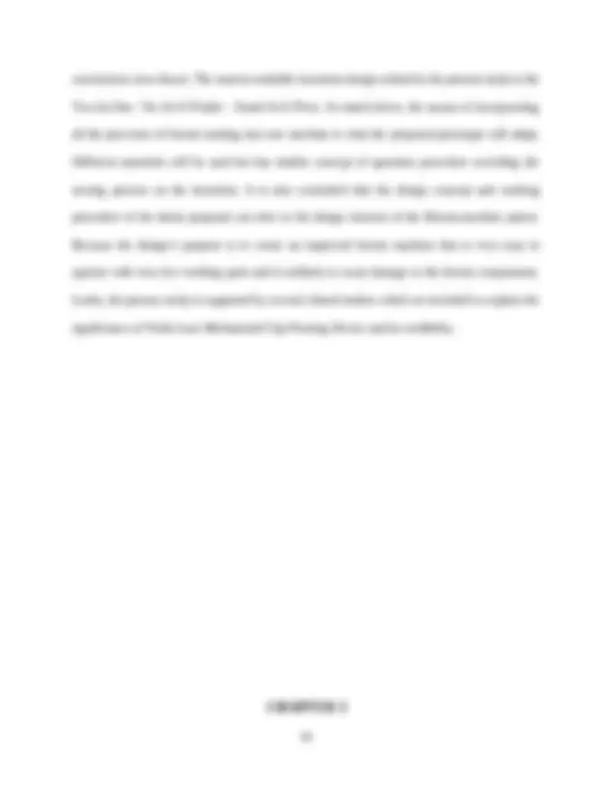
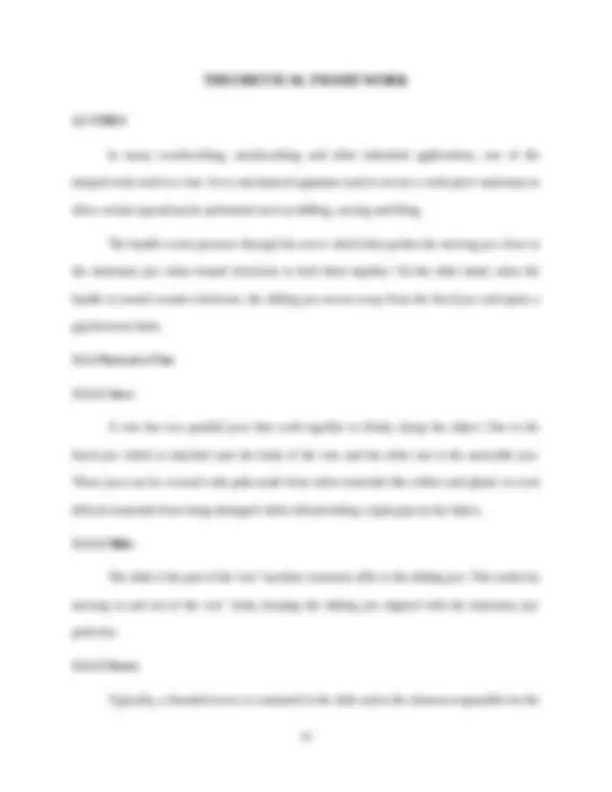
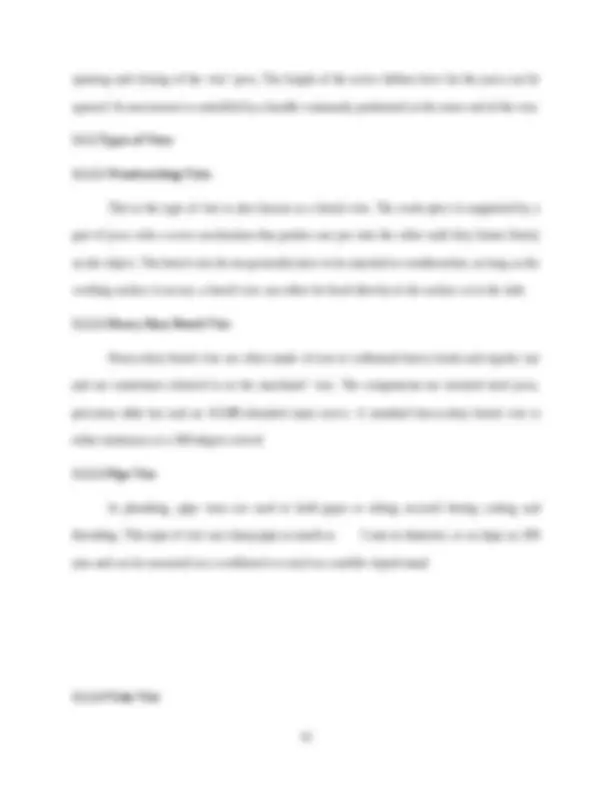
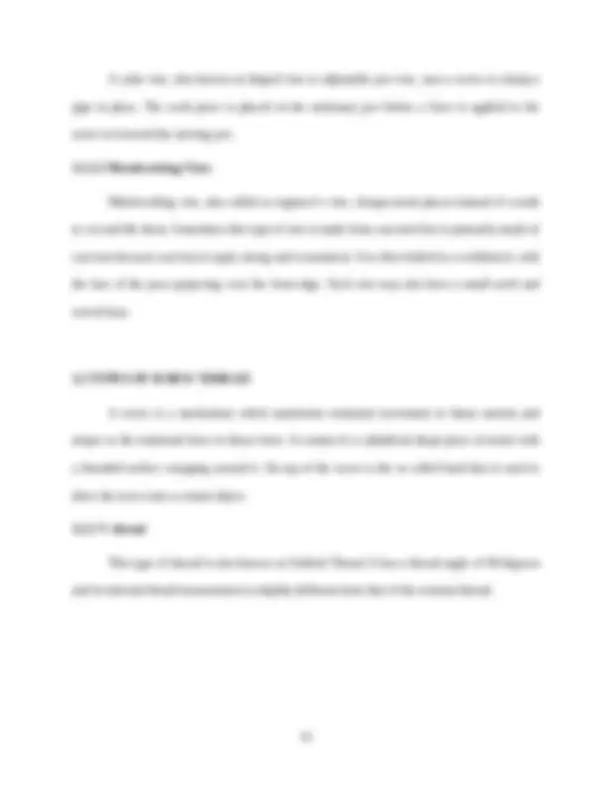
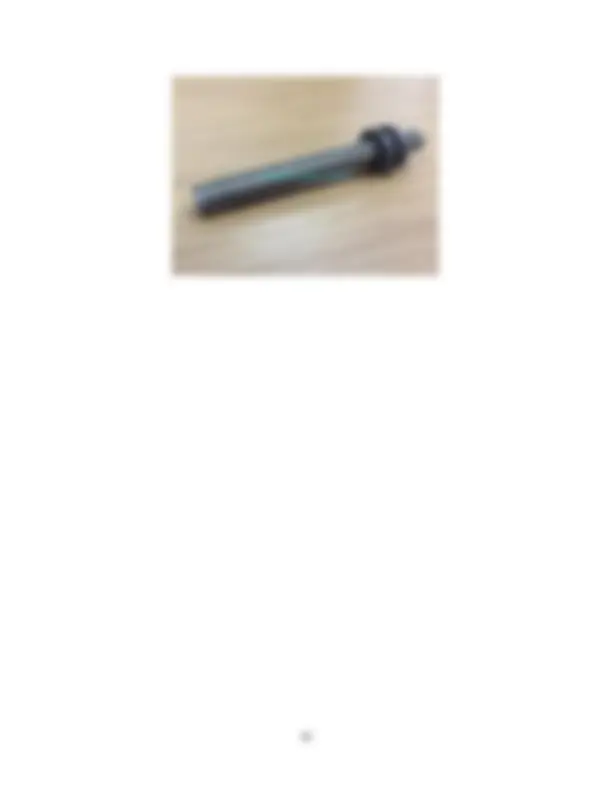
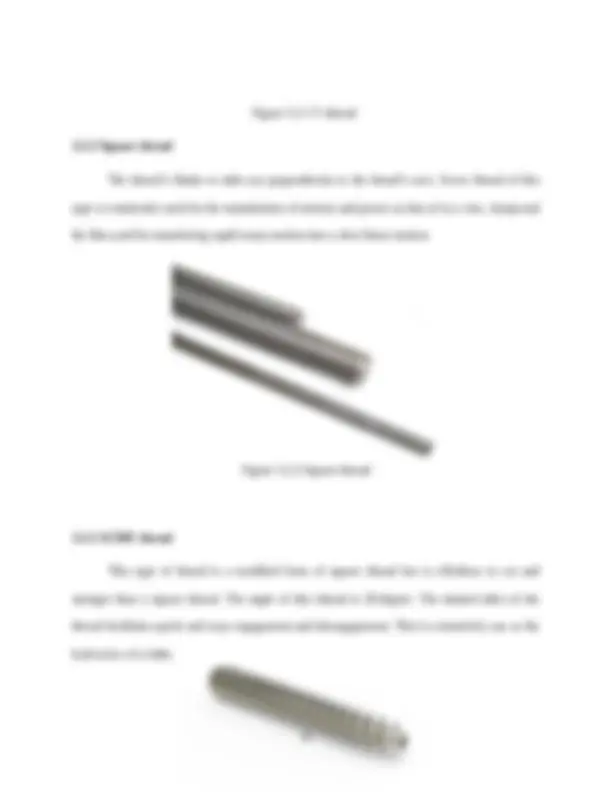
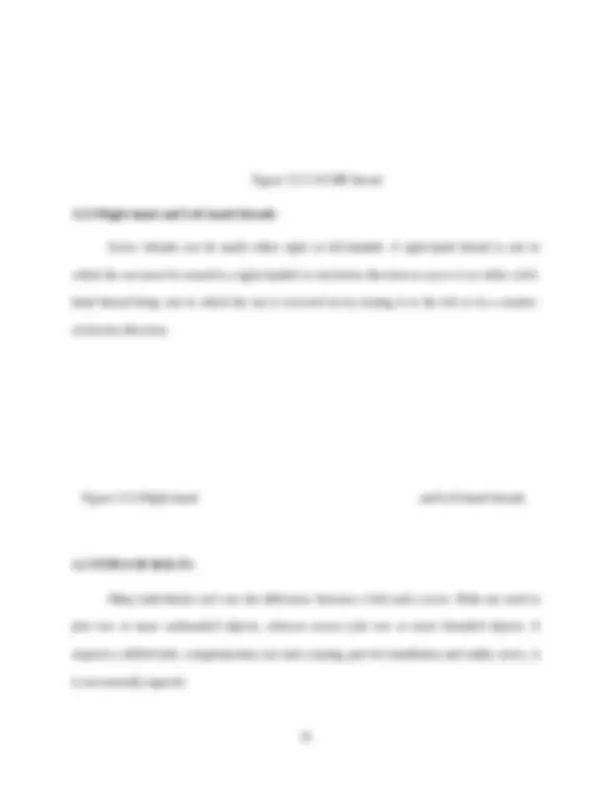
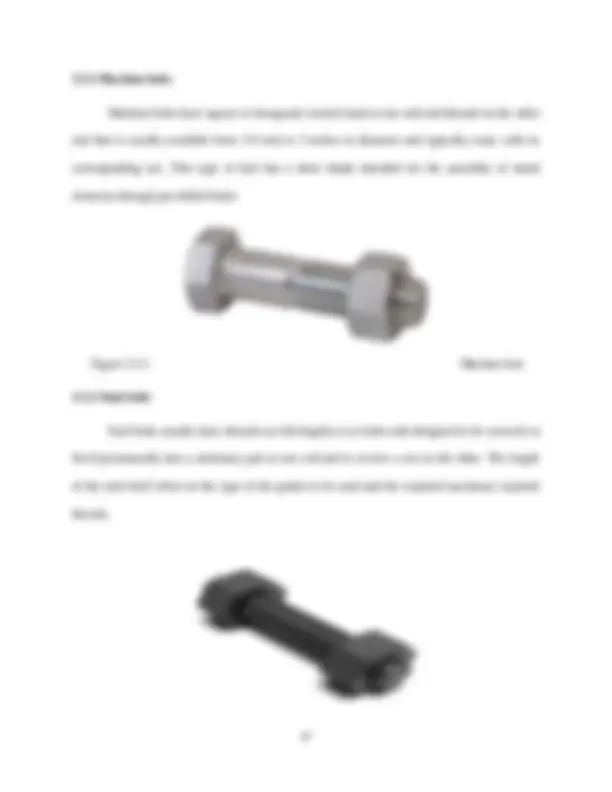
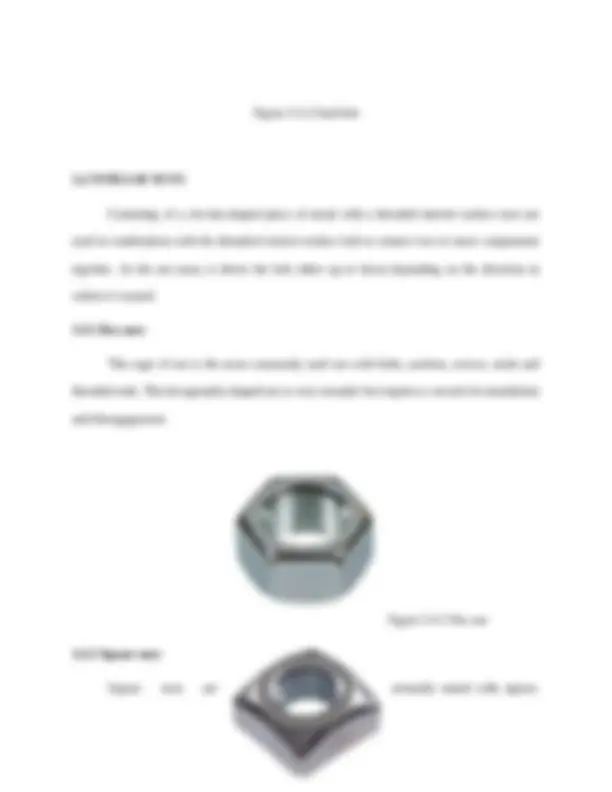
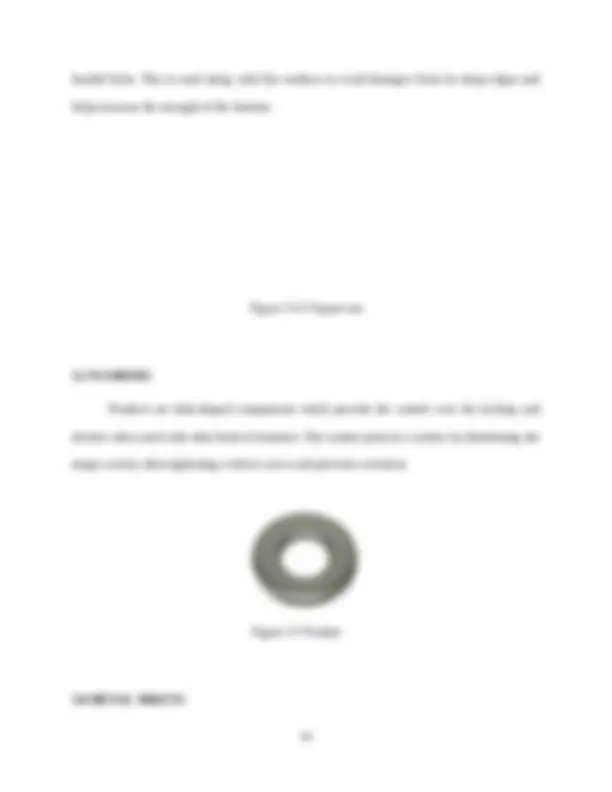
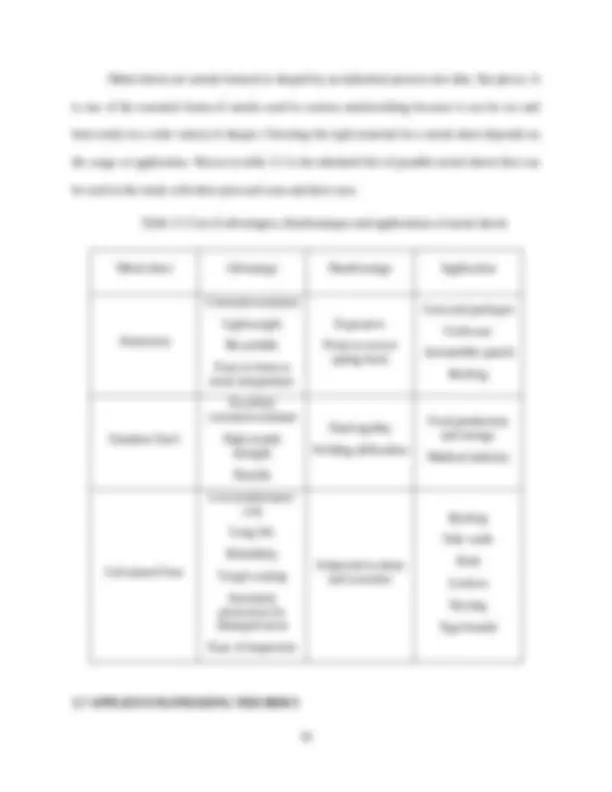
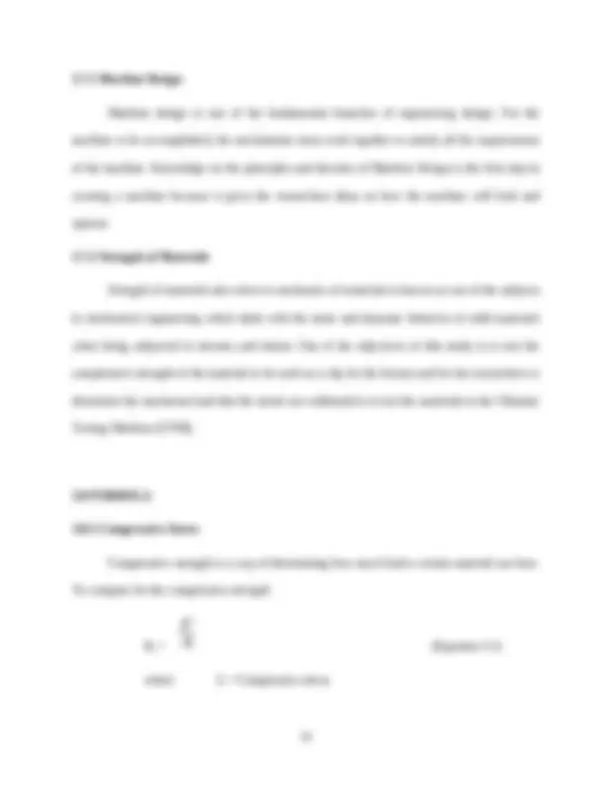
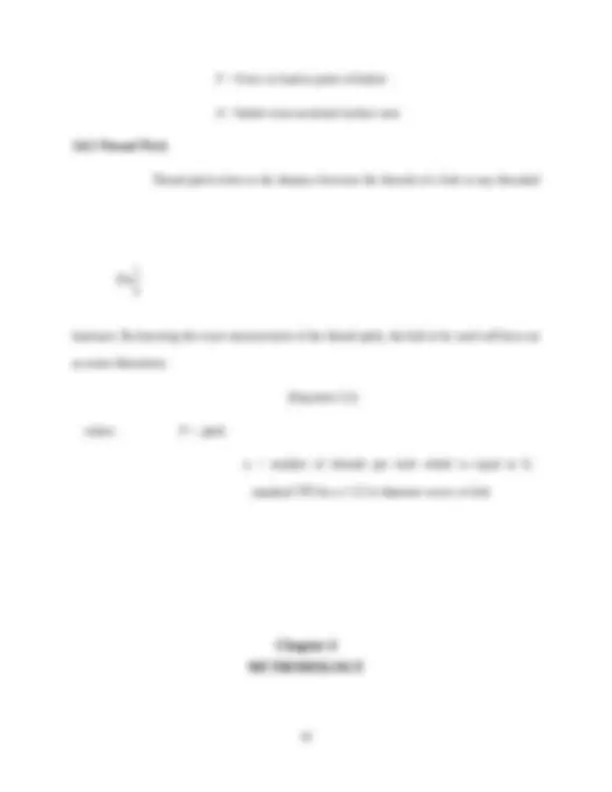
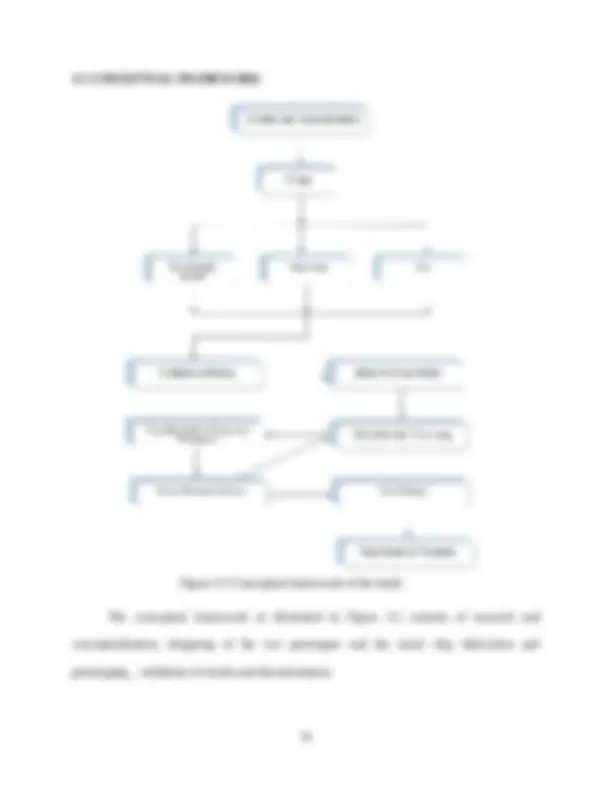
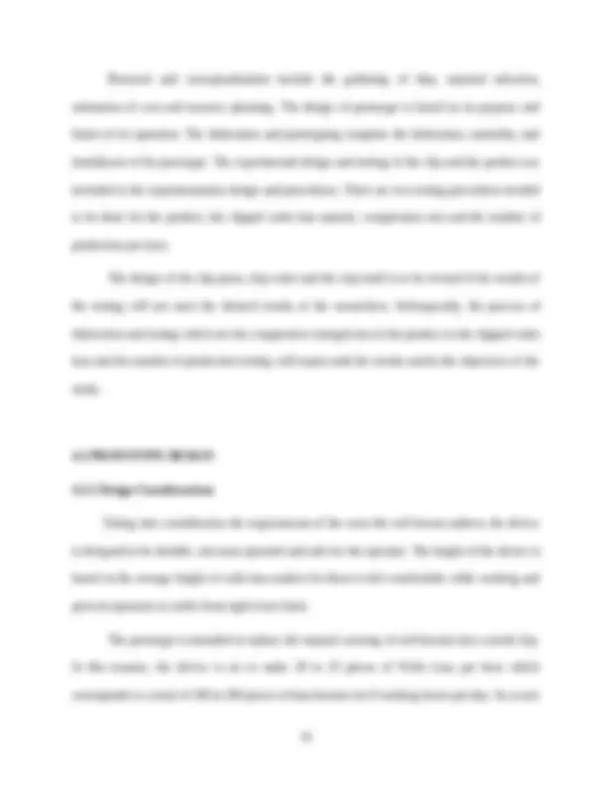
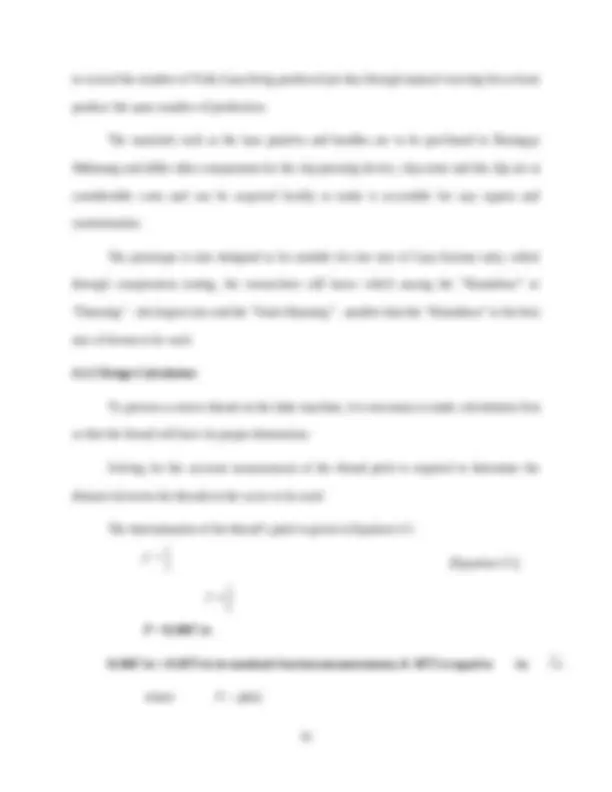
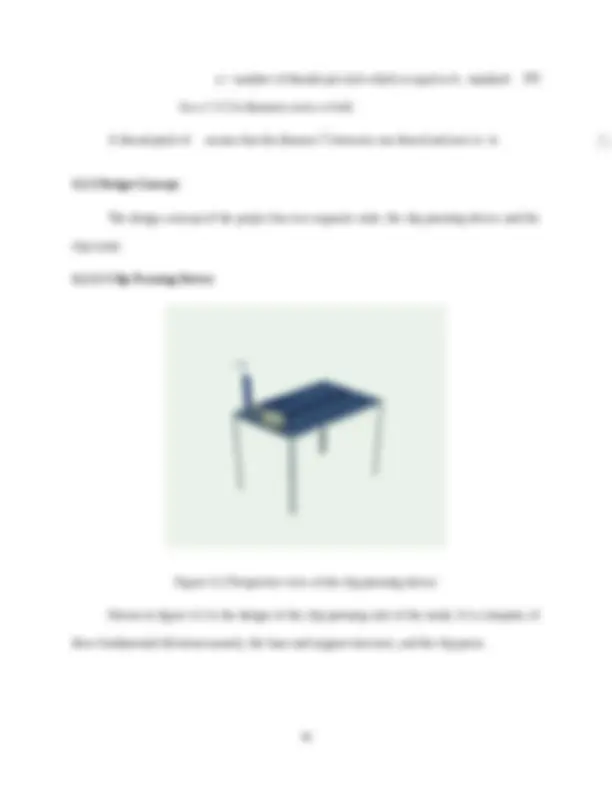
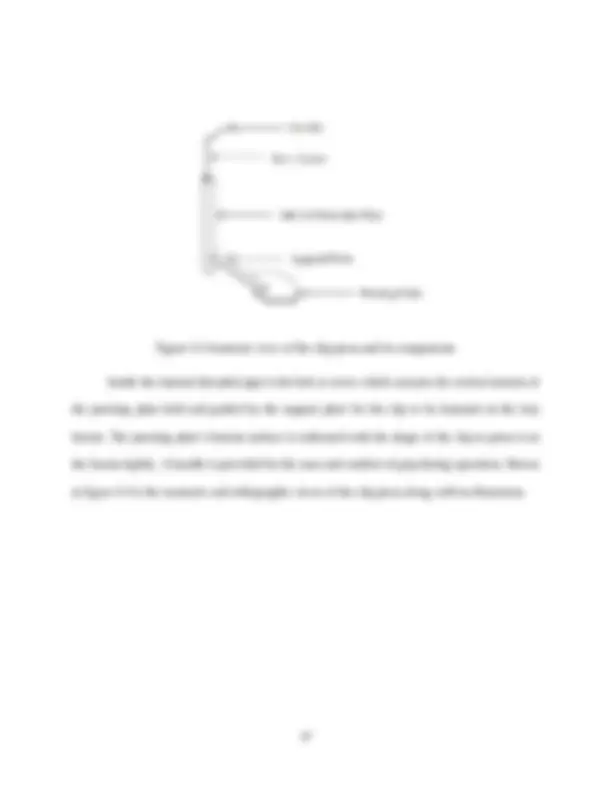
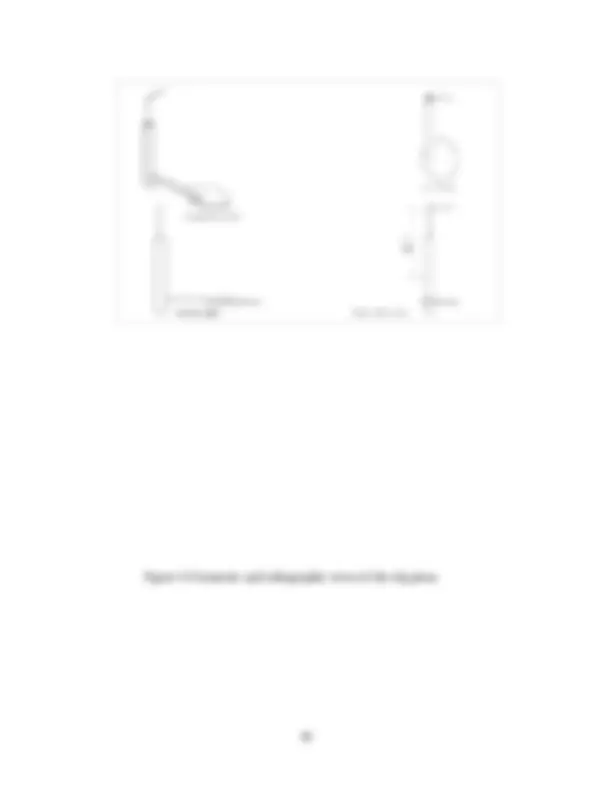
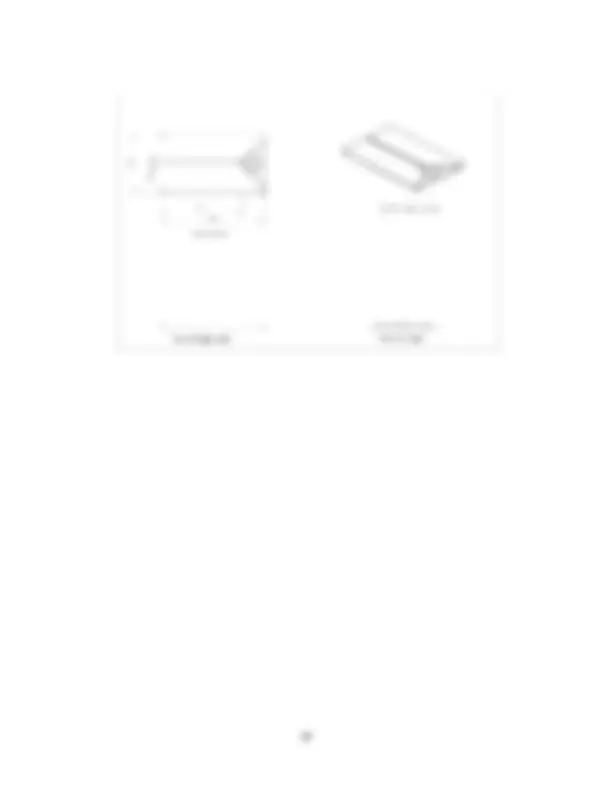

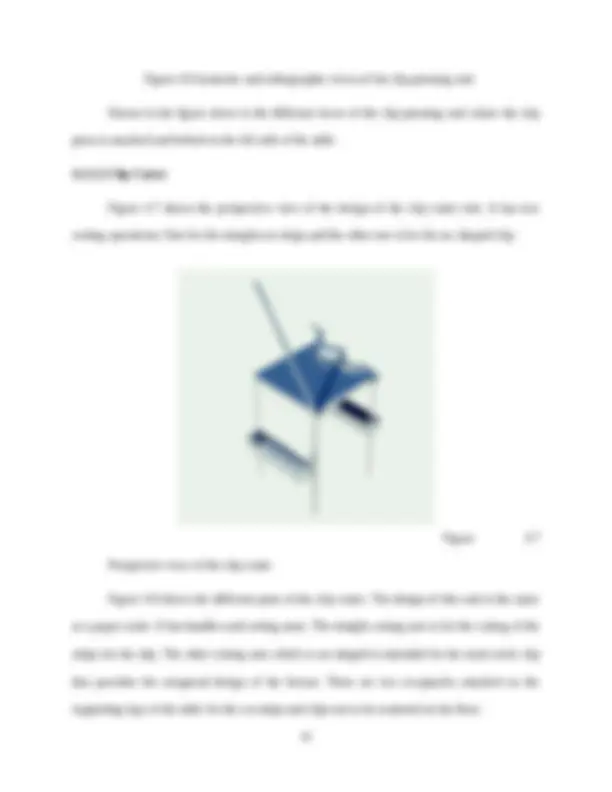
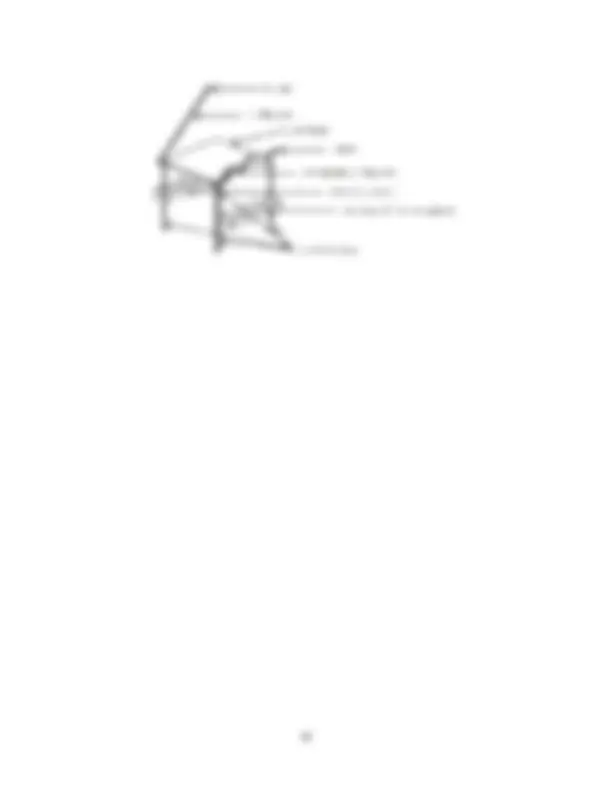
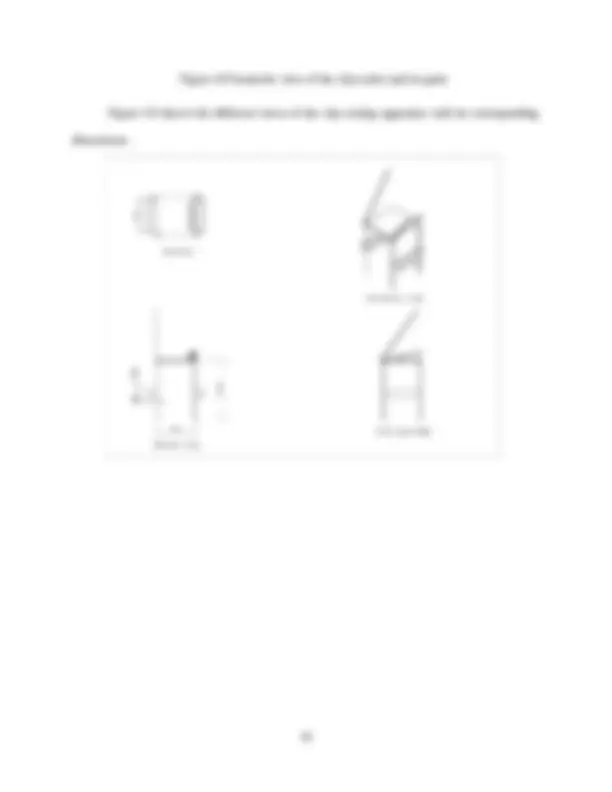
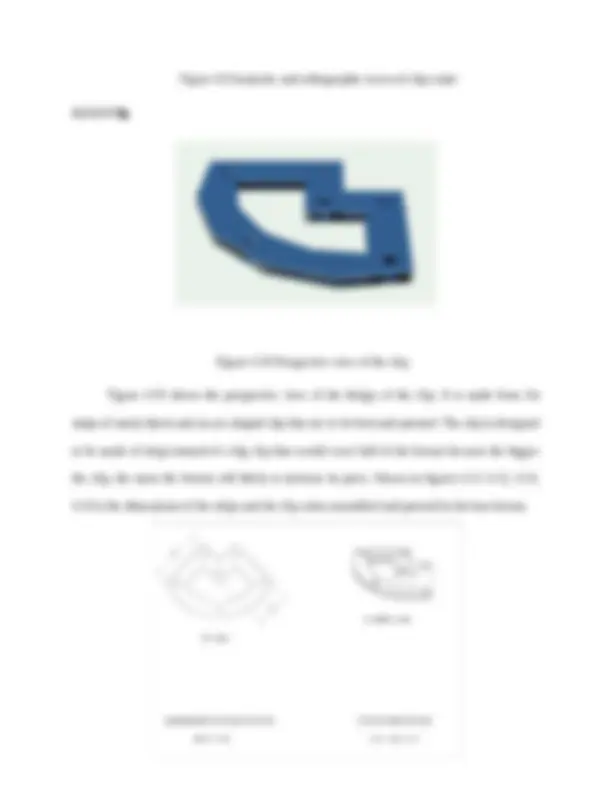
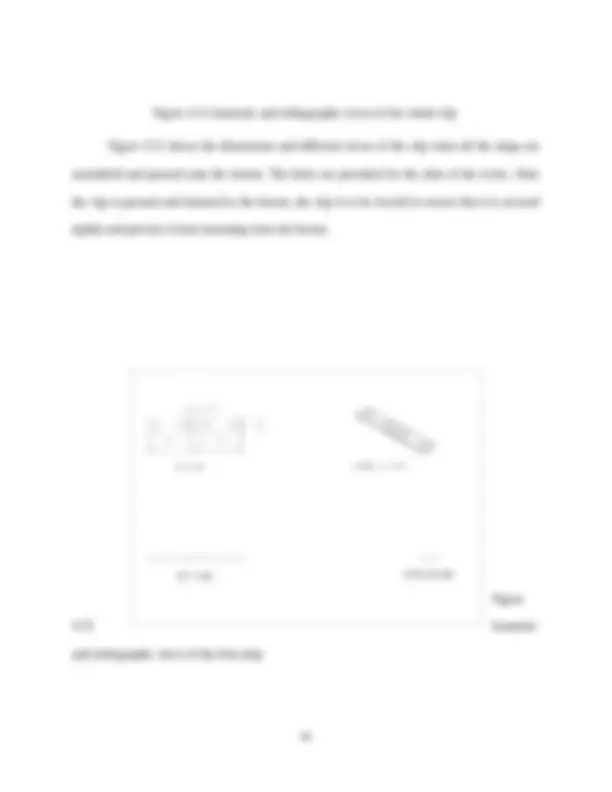
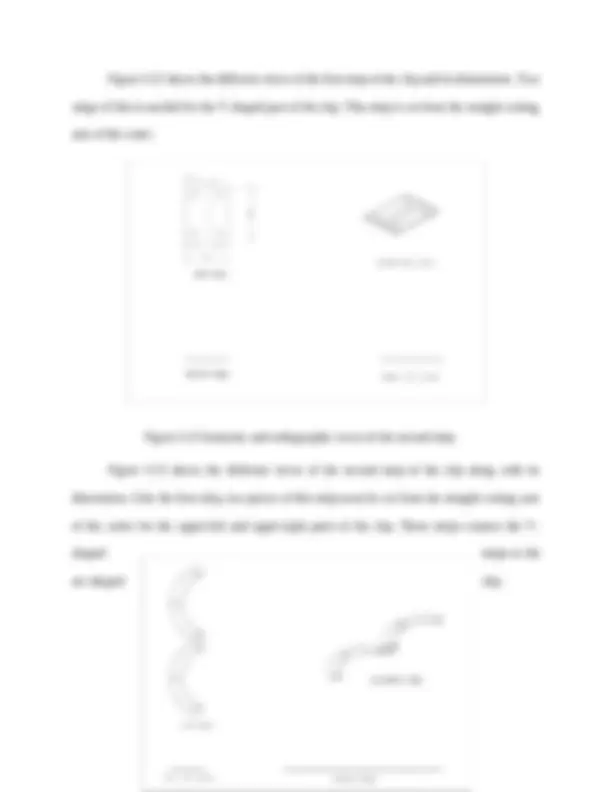
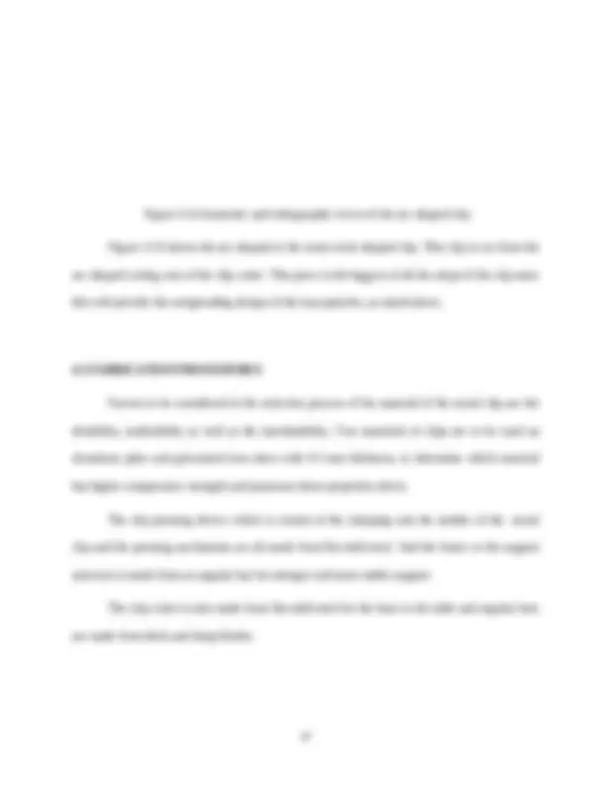
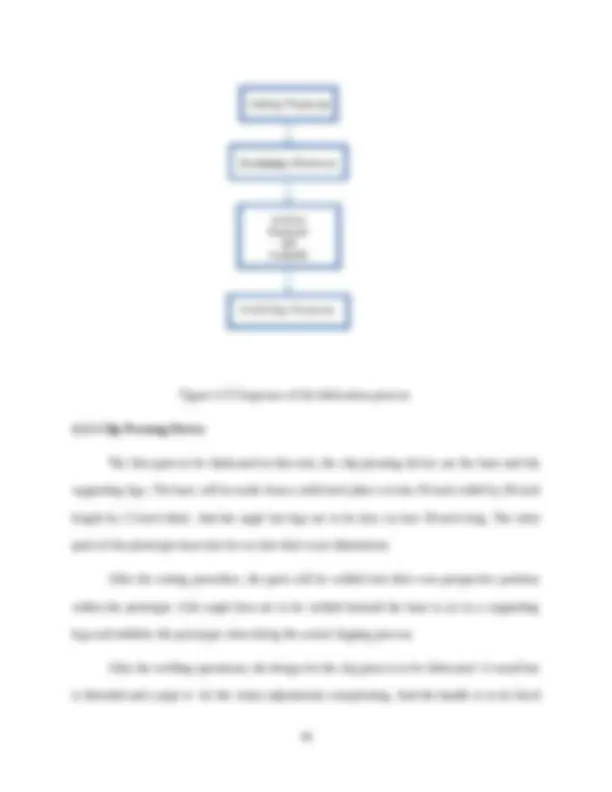
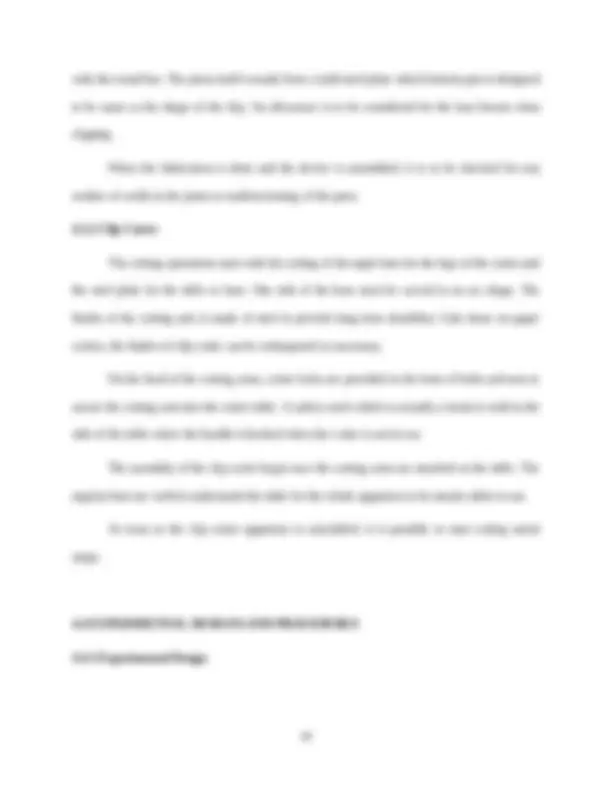
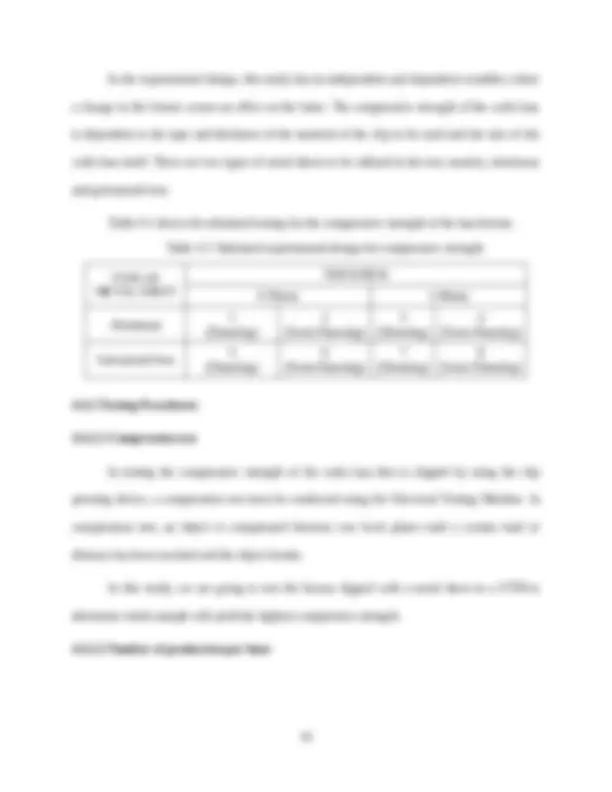
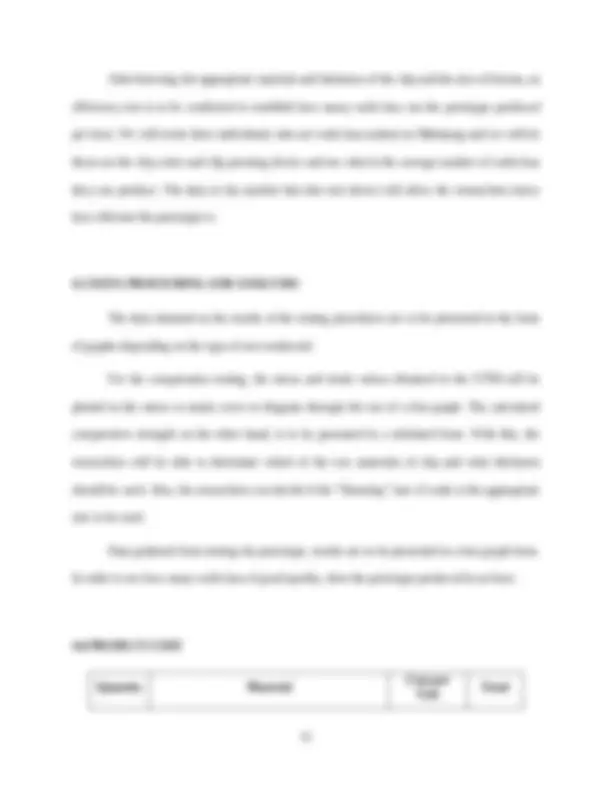
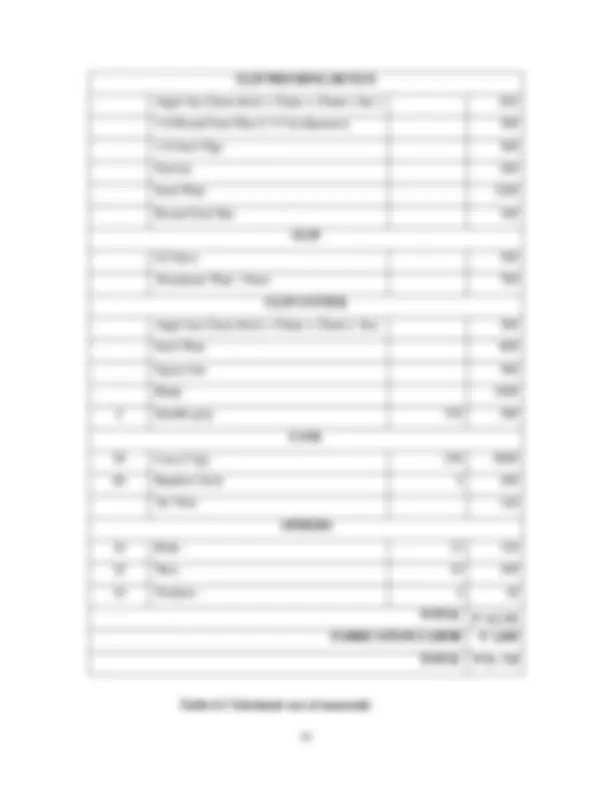
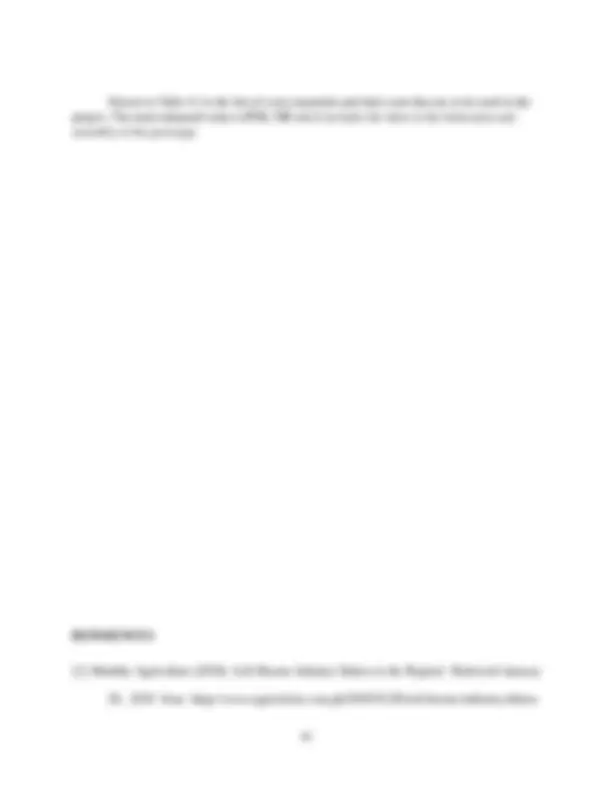
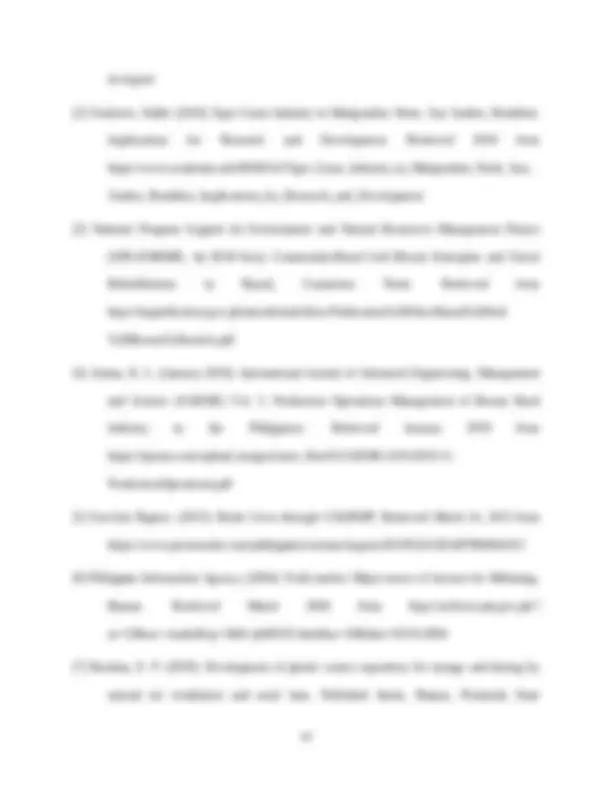
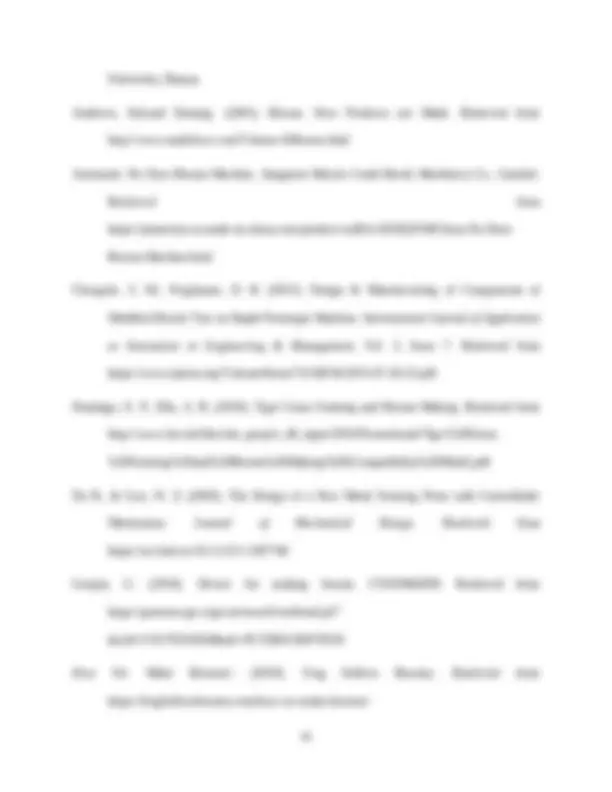
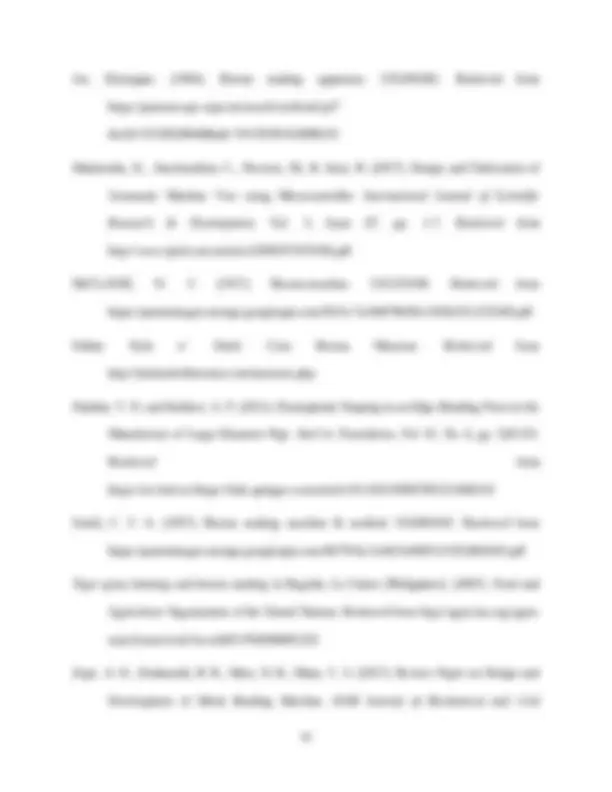
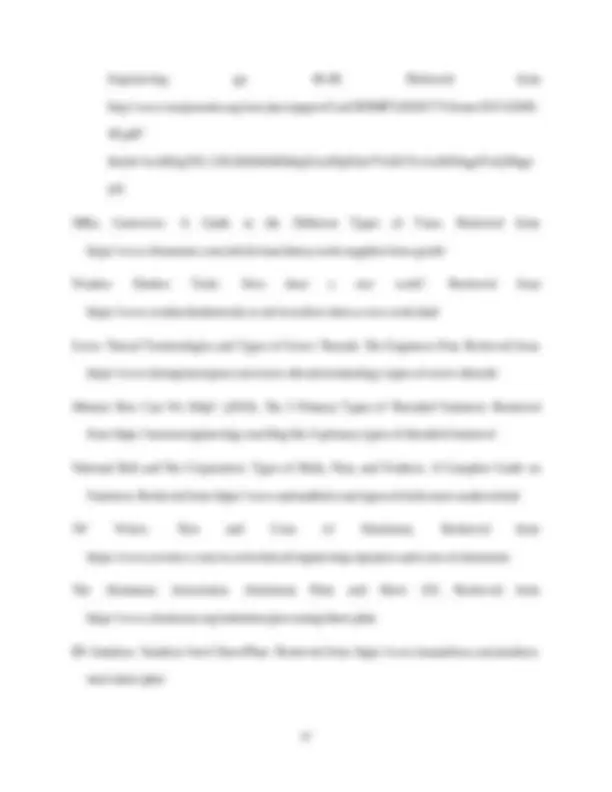
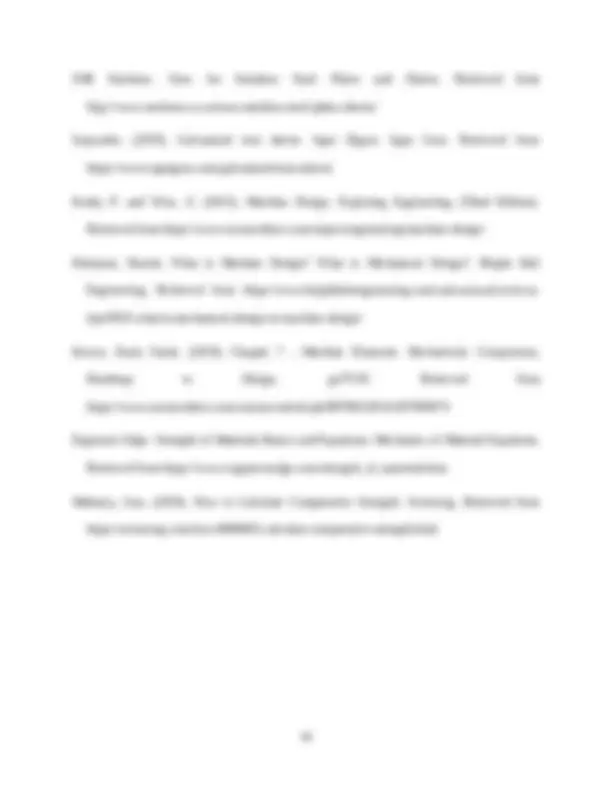
Study with the several resources on Docsity
Earn points by helping other students or get them with a premium plan
Prepare for your exams
Study with the several resources on Docsity
Earn points to download
Earn points by helping other students or get them with a premium plan
Community
Ask the community for help and clear up your study doubts
Discover the best universities in your country according to Docsity users
Free resources
Download our free guides on studying techniques, anxiety management strategies, and thesis advice from Docsity tutors
This thesis is a big help to the broom workers to speed up the production in the manufacture so as to also reduce the time consuming and fatigue of the worker, because in the manual there are many processes that go through before finishing a broom, in our thesis we have put it together on one device so that more products can be made.
Typology: Thesis
1 / 59
This page cannot be seen from the preview
Don't miss anything!
Department of Mechanical Engineering College of Engineering and Architecture BATAAN PENINSULA STATE UNIVERSITY
In partial fulfillment of the requirements for the degree of BACHELOR OF SCIENCE IN MECHANICAL ENGINEERING for the course MEPS-523 ME PROJECT STUDY 1 ALLIAH JHERRYL D. DELA CRUZ REJEAM C. CABRITIT JOHN PAULO B. CUNTAPAY MICHICO M. DELA ROSA EDRIC JAMES B. LETADA LOUIE JAY S. TIMBANG November 2019
Walis Lasa is popularly known as “Walis Tambo”. A variety of broom which is made from Tiger grass (Thysanolaena maxima), a type of grass where it is commonly propagated in Benguet Province, Ilocos Region, Romblon, Bicol Region, Davao, Nueva Ecija and Pampanga. Figure 1.1 Percentage of plantation of tiger grass crops in the Philippines (Source: “Soft Broom Industry Shines In The Region!” Monthly Agriculture 2018) Figure 1.1 shows a graph interpretation of provinces where tiger grass are breed. La Union has the highest percentage which corresponds to its existing 687 hectares of tiger grass plantations [1]. The second largest plantation is located in Romblon with 300-hectare of tiger 44% 30% 11% 10% 5%
La Union Romblon Bicol Davao Other parts in the Philippines
The graph above interprets the routine of fabrication used by the broom-making enterprises in the community. It depicts that the process of producing lasa brooms is through manual weaving, showing that the concept for a developed technology has not been considered. Figure 1.3 Walis Lasa produced per day in Mabatang (SOURCE: Walis Lasa Business Owners, 2019) Figure 1.3 illustrates the number of lasa brooms that every lasa making enterprises in Mabatang can manufacture daily. Interviews were conducted to ten walis lasa making business owners together with the workers. The owners were asked how many walis lasa of different sizes can be produced per day. The largest enterprise, Dominguez Walis Lasa with six to seven workers can manufacture 300 pieces of lasa brooms every day while the least number of lasa brooms that are produced per day is 15 pieces which are made by Lolo Francing, an 80-year old man single proprietor. Substantially, Mabatang can produce 1175 pieces of walis lasa per day. And when estimated per month with 25 working days, the barangay could manufacture 29375 Tancio De Guzman Datu Canuto Dominguez Cabritit Canare Manrique Berco Francing 0 50 100 150 200 250 300 350 150 100 80 100 300 150 100 100 80 15
Business Owners Number of Walis Lasa
pieces of lasa brooms monthly. In the figure below (Figure 1.4), it describes the comparison of the lasa brooms that are being produced in other parts of the Philippines daily, monthly and annually. Figure 1.4 Number of production of Walis Lasa. (Source: IJEAMS, Vol 5, 2019; ) Figure 1.4 shows a graph presenting the amount of lasa brooms that are produced daily monthly, and annually in Mabatang and other places. Mabatang with 29, 375 pieces of lasa brooms monthly. 12, 000 pieces per month in La Union [1], and 8,750 in Bicol [3]. Furthermore, in San Antonio, Nueva Ecija, 31 – 60 pieces per day can be made during peak season while 1 – 15 pieces daily are made in normal or off-season [4]. Other places such as Baguio City, produces 2,000 kimis per year, one kimis corresponds to one piece of walis tambo [5]. The Walis Lasa making business in Mabatang expanded all over the past years and Mabatang La Union Bicol Nueva Ecija 0 50000 100000 150000 200000 250000 300000 350000 400000 (^1175 500 350 ) 29375 (^12000 8750 ) 352500 144000 105000 21000
Daily Monthly Annually
According to an article from Philippines Information Agency (PIA), 20% of Abucay’s revenue emanates from the Walis Lasa making business of Mabatang [6]. The advancement and objective of the study to accumulate broom making production will attain much greater assets for the barangay of Mabatang. 1.4.3 Significance to the Environment Manual weaving uses plastic strips to make soft brooms. As plastics take centuries to be decomposed and plastic garbage pollution progressively grows, the study can be fundamental and beneficial to the environment [7]. Plastics weaved on soft brooms are to be replaced by metal clips, therefore usage of plastics will be lessened and plastic waste production can be restrained. 1.4.4 Significance to Academic Knowledge With regards to academic benefits, the data, facts, information and results obtained in the study will be of great help to future proponents who will conduct research about this and improve the outcome of the study. There will also be an existing knowledge concerning the deficiency of Walis Lasa industry. 1.5 SCOPE AND LIMITATIONS This study focuses on the design, fabrication and testing of an efficient mechanized clip pressing device for Lasa brooms. This is to be performed in the Barangay of Mabatang, Abucay, Bataan within the duration of three months starting from February to April of year 2020. With regards to the lasa brooms workers who are to use the device, it is designed to be
Tiger grass (Thysanolaena maxima) belongs to the family of Poaceae and Graminae. It is commonly referred to as broom grass or bouquet grass. Brooms have been used to clean up, in and around the work station for decades. They can be made of a variety of man-made and natural materials (Andrews, 2001). Locally known as tambo, tiger grass produces panicles for up to 10 years. The government promotes tiger grass farming to boost the country's broom industry (Domingo, 2010). According to Agroforestry Information Network, in the Cordilleras, tiger grass is known as “boi-boi”. It is the raw material for producing soft brooms. Growing tiger grass is considered a viable livelihood project due to its ability to produce cash income from the plant's harvested panicles once it is bred properly. Tiger grass is propagated for soft broom making panicles. The stalks of the panicles are part of the handle of the soft broom, but when damaged the stalks are used for the manufacture of handicrafts such as large or small products of gift boxes. 2.2 PROGRESS AND DEVELOPMENT 2.2.1 The Antique Cast Iron Broom Press The broom press was invented by Henry Arthur Morris in 1890 and until now, it still used by the Frog Hollow Broom business of Tom and Penny Bieber, the great-grandchildren of
Morris. The press grips the broom corn firmly whereas being hand sewn by the broom maker as shown in figure 2.2.1 below. Figure 2.2.1 The Antique Cast-Iron Broom Press invented by Morris The device is made from wood and metal. It has a metal lever that is connected to the pair of metal jaws whose function is to compress and flatten the broom. After the broom is pressed, the hand sewing takes place by using long needles and sewing sleeves to thrust the needles and twine through the flattened broom. The compression process of this device can be adapted and applied to the design of the proposed prototype. But instead of having the broom hand sewn, the proposed prototype is designed to compress a metal sheet to the tiger grass panicles and attached the upper end or the head of the panicles to the handle by coiling a wire. 2.2.2 Two-In-One / Sit-At-It Winder - Stand-At-It Press
Figure 2.2.2.2 Sketch of the parts of the two-in-one apparatus The design and the operation of this machine is associated to the proposed prototype. In the same way of merging two or more processes in one machine is what the researchers intended to design: the coupling of the tiger grass on the handle coiling a wire and flattening the broom which is also made by compressing and fastening strips and clips on the head of the broom. 2.2.3 Automatic No Dust Broom Machine The automatic no dust broom machine has a user-defined design, which can be adjusted to produce different kinds of brooms or brushes. The machine has a Programmable Logic Controller and Touch Panel Control System wherein the display can be Chinese and English allowing the user to understand the operation of the said machine to preferred language. The machine uses a stable branded motor that produces much lower noise. As shown in figure 2.2. below, the said machine can stick and trim brooms simultaneously. Before the grass rotates on
the shaft that is being attached on the handle, a plastic excluder is glued on the handle by applying polypropylene adhesive. Figure 2.2.3 Automatic No Dust One feature of the automatic broom machine that resembles the proposed prototype is the fastening of the grass or the panicles into the broom handle. But what the said machine differs to the proposed device is that it only attaches the grass to the handle by means of a rotating shaft where the handle is placed. However, the proposed prototype does not only attach the grass on the handle but it will also undergo various processes such as the clipping and pressing. Table 2.1 summarizes the concepts and processes of the available technologies that the present study will adapt.
Figure 2.3. Broom Making Apparatus In figure 2.3.1, the system consists of a base plate designed to be mounted flat on the supporting surface. The base plate is connected to an upward opening U-shaped holder and has a narrowed U-shaped bottom. This patent resembles the proposed prototype in a way that it compresses the end branches of the broom. But what it differs on the present study is that it has a lever arm that being rotated so the broom is squeezed between the U-shaped surface and the forming surface. While in the proposed prototype the broom is to pressed by a metal plate with a circular handle on top and not a lever arm. Figure 2.3.2 Device for making
broom In figure 2.3.2, the device for making broom is compose of (1) operating table, ( 2 ) linear actuator, ( 21 ) sleeve, ( 22 ) pointed rod, ( 23 ) slider, ( 24 ) hydraulic cylinder, ( 3 ) locker, ( 31 ) bottom bearing parts, ( 33 ) trigger, ( 34 ) metal ring, ( 4 ) driving device, ( 41 ) motor, ( 4 2) hydraulic pump,( 43 ) hydraulic distributor, ( 5 ) baffle, ( 6 ) ring maker. The similarity of this patent to the present is study is the metal ring that securely fastened the broom head and the broom bar together after the broom bar is inserted in the broom head, which avoids loosening of the broom head and the broom bar during manual processing. Also, they have the same objective of saving time and labor and being well handled. The broom is long-lived and of good quality. In figure 2.3.3 as shown above, a broom device consisting of a couple of key clamping bars, ties between the clamping bars, a set of clamping plates placed between the clamping bars,
Testing and Result: Modified Bench Vise on Rapid Prototype Machine By relying on new design methods and using computing softwares such as Solid Works and Pro-E, the design process is achieved. Chougule added the design of having a C-clamp below the fixed jaw of the vise enabling the user to move the bench vise at any place. 2.4.2 METAL BENDING AND FORMING 2.4.2.1 Elastoplastic Shaping of Metal in an Edge-Bending Press in the Manufacture of Large Bending Pipe The UOE technology, also known as the U-ing and O-ing of metals is the first procedure in sheet plastic shaping is to bend the edges on a press. By following the method, all the edges are bent simultaneously. The bending crosspieces are lifted and parts of the longitudinal edges are bent over a given distance. The cycle is repeated until the edge has been bent over the entire blank length. 2.4.2.2 Metal Bending Machine Zope et al. developed a portable manually operated metal bending machine through the use of metal shaft, hydraulic bottle jack, pedestal bearing and support or frame. The method consists mainly of three steps: sheet or tube placement, a central lowering and repeating sheet or pipe feed. 2.4.2.3 New Metal Forming Press with Controllable Mechanism Du et al. considered a design of a mechanical press that can be programmed, as well the trajectory and the velocity of the stroke. The controllable mechanism pf the press serves as the toggle whose function is to stabilize the ram’s displacement, velocity and acceleration. Testing and Result: Elastoplastic Shaping of Metal in an Edge-Bending Press in the Manufacture of Large Bending Pipe
After the relaxation of a 1420-mm pipe having a sheet thickness of 25.8 mm, the length of bent edge obtained is 412 mm and the calculated height of bent edge is 90.2 mm having a discrepancy of 2.5 mm from the standard 88±5 mm bent edge height. Testing and Result: Metal Bending Machine The device can bend pipe sheet up to 8 mm thick and pipe diameter up to 2 cm. Due to its light weight and versatility, small workshop and manufacturing shops can use it. Testing and Result: New Metal Forming Press with Controllable Mechanism The machine can perform just how a hydraulic press does and is much more efficient than a hydraulic or servomotor driven press because of its energy usage. The highest dwelling angle and ram travel range obtain are 450.7 and 664.5, respectively. 2.5 CONCLUSION In this chapter, various studies and designs related to the present study were tackled. The main purpose of reviewing all these related literature is for the current study to have reliable proofs that will serve as a solid backbone when being compared to any existing body of knowledge. Also a literature review lets the researcher see how far a certain technology has developed and what its current trends are. The tiger grass originates from the family of Graminae. This type of grass is the raw material for making soft brooms. Throughout the years, many broom making machines were invented but here in the Philippines, there is no existing technology that intends to help the industry of broom making. Based on the findings of the studies and designs from different patents, the following