
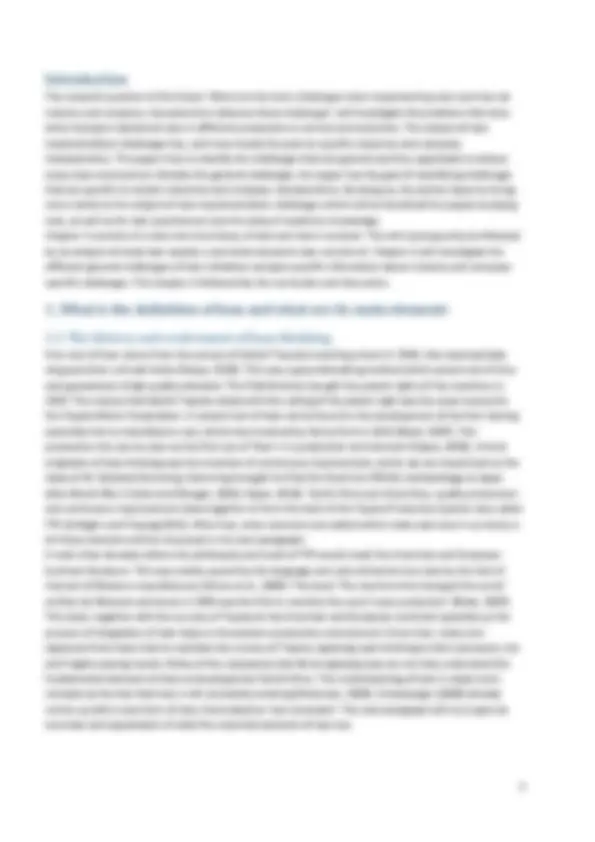
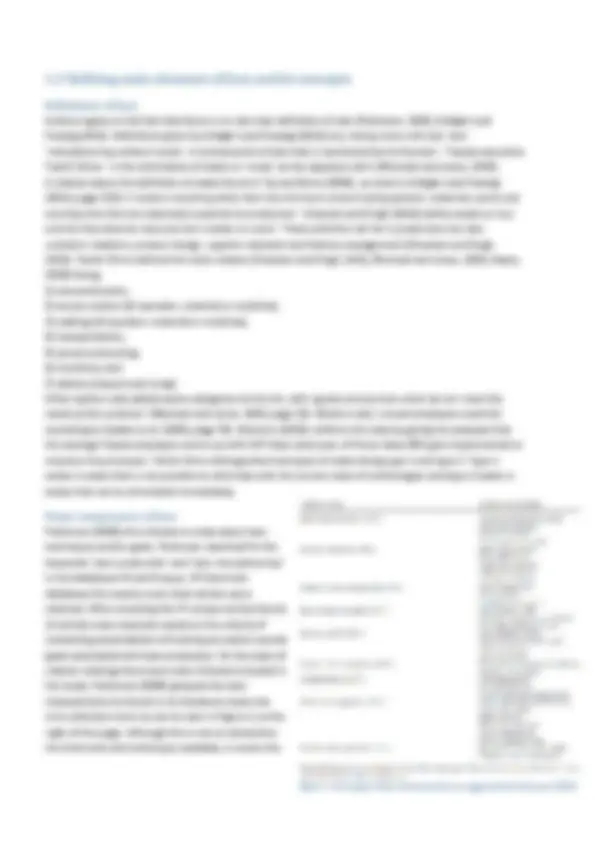
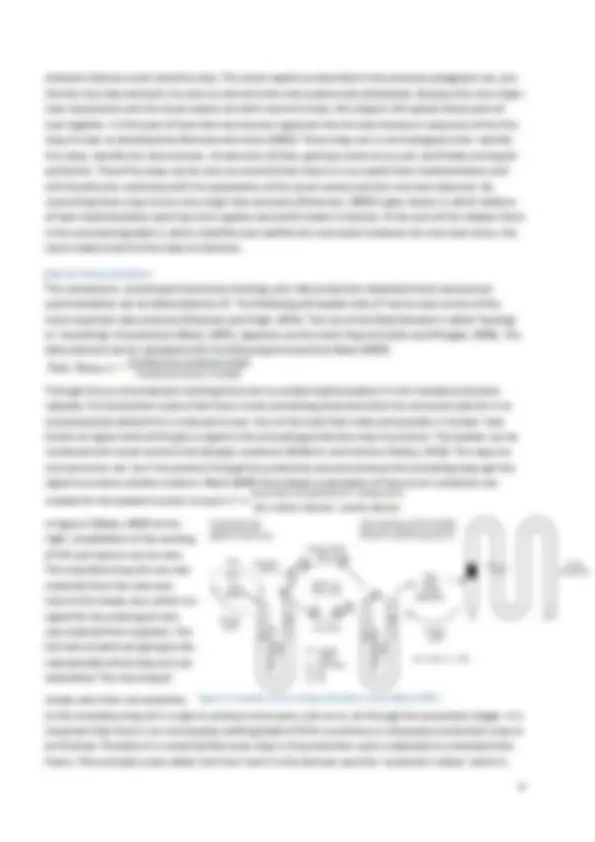
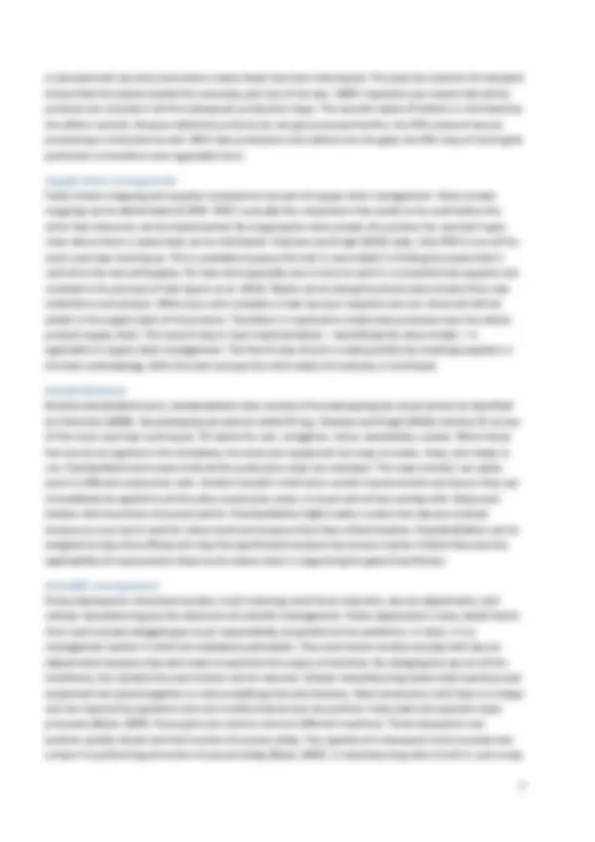
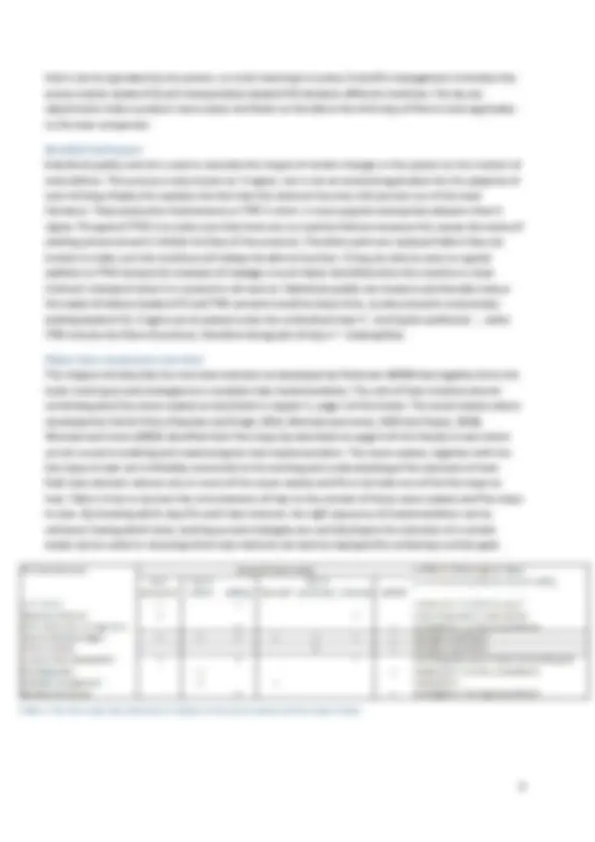
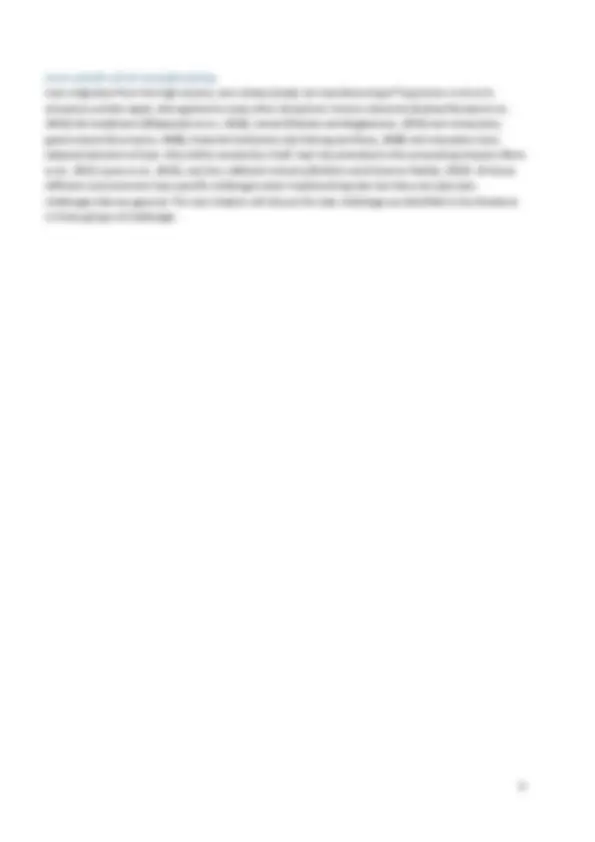
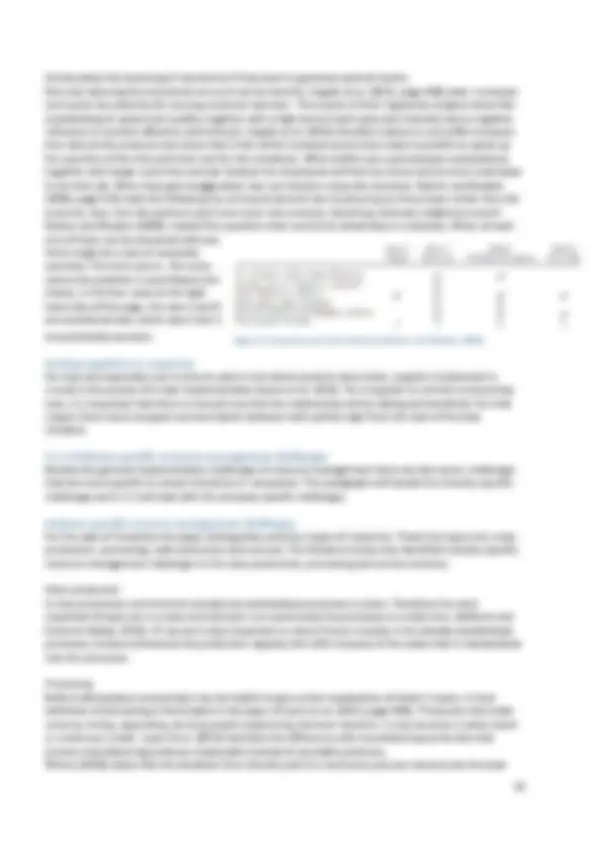
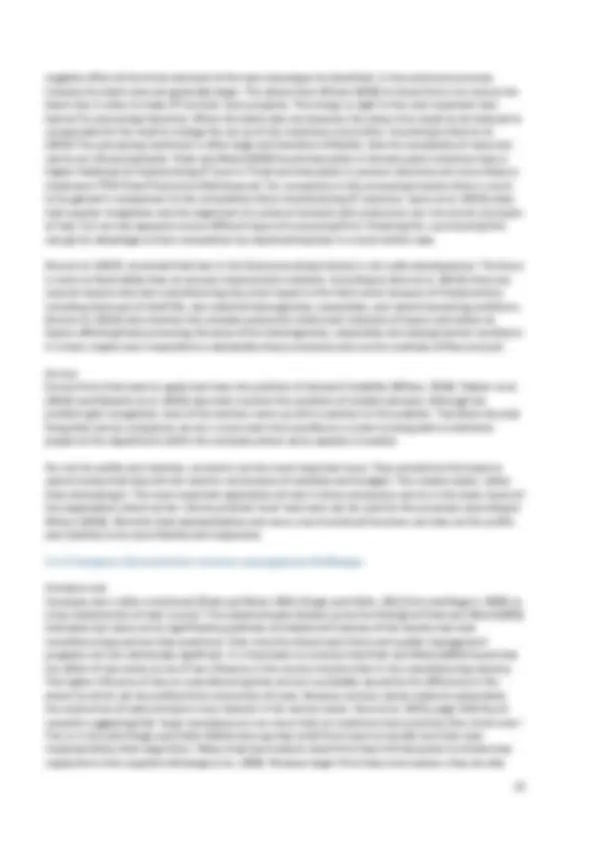
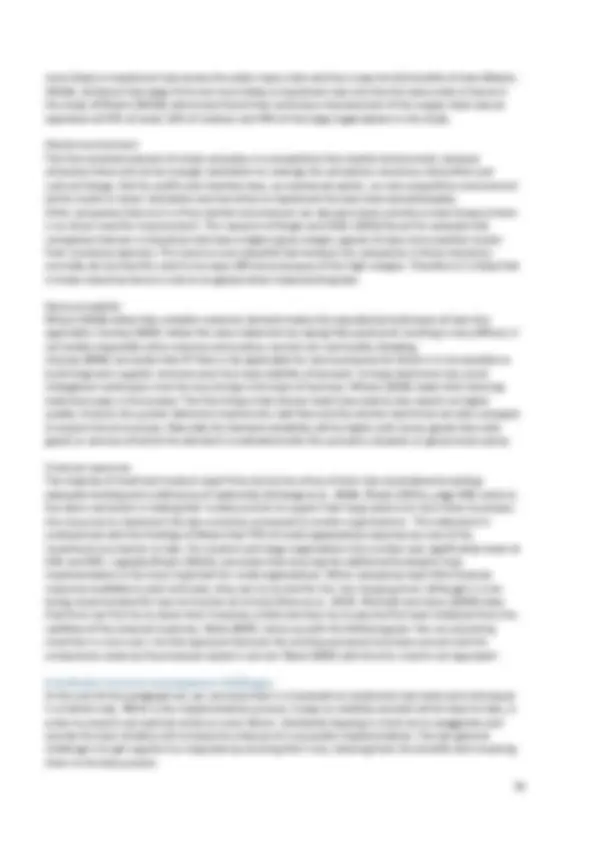
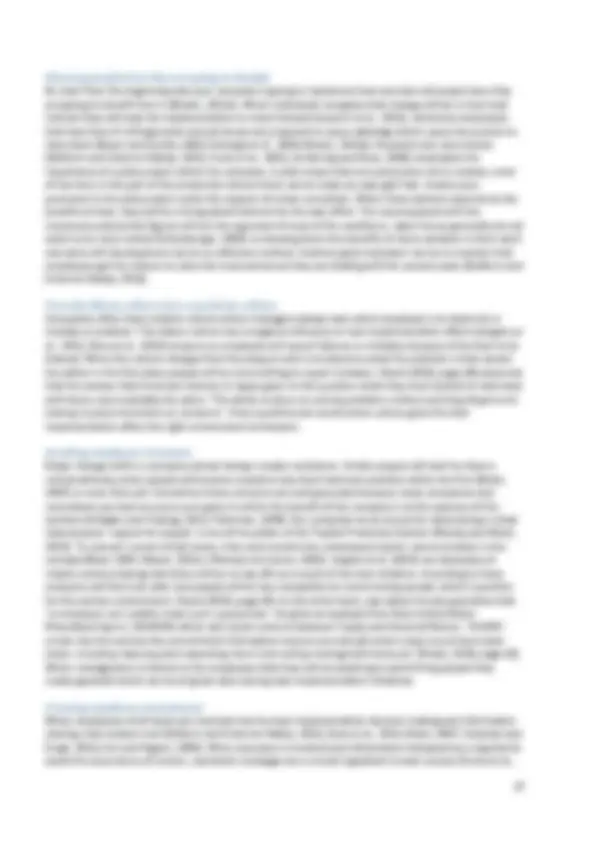
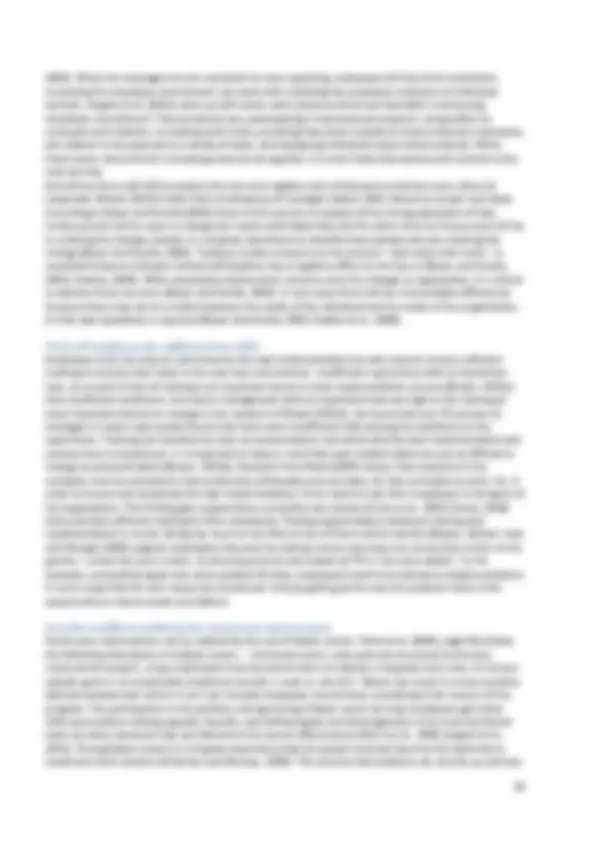
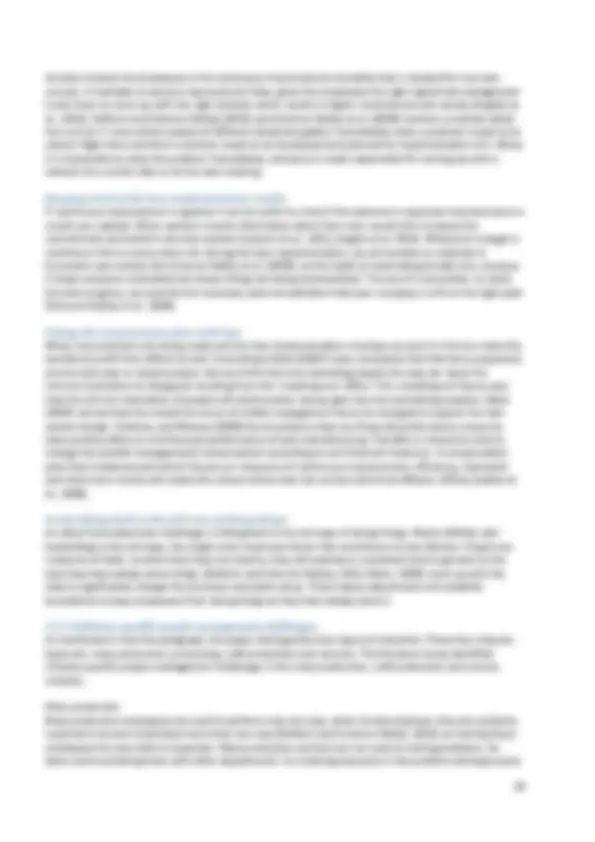
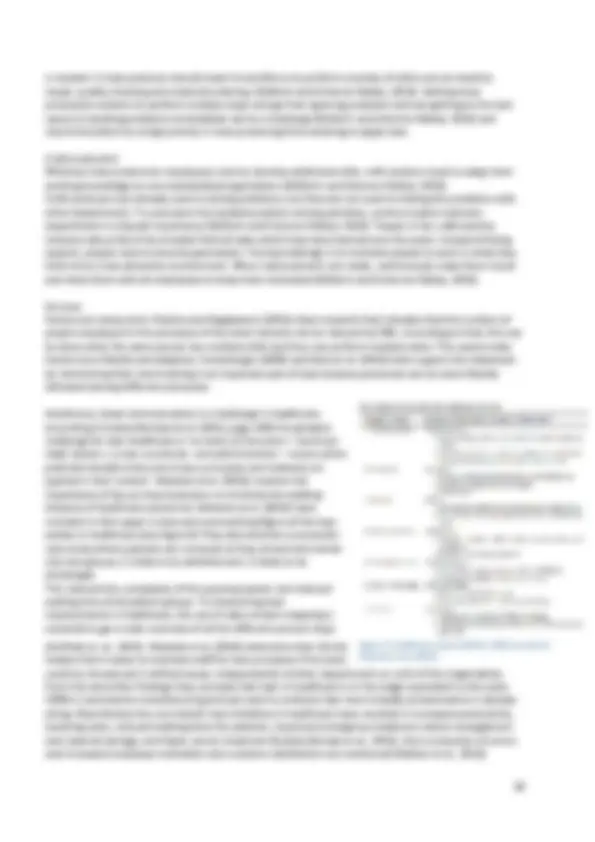
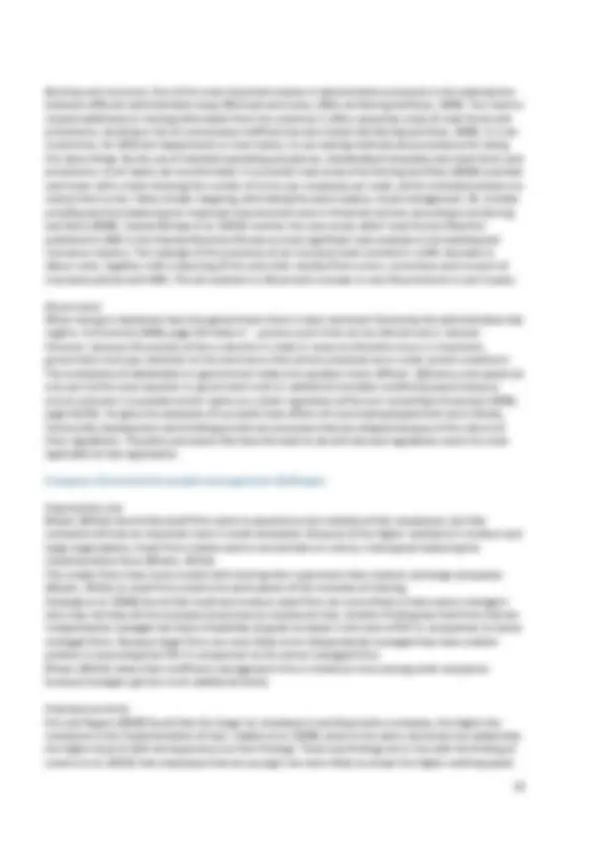
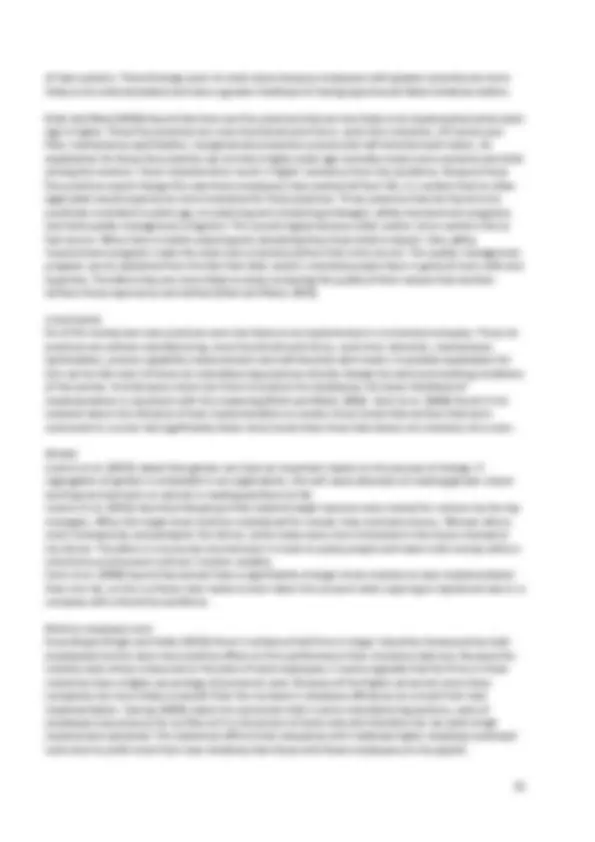
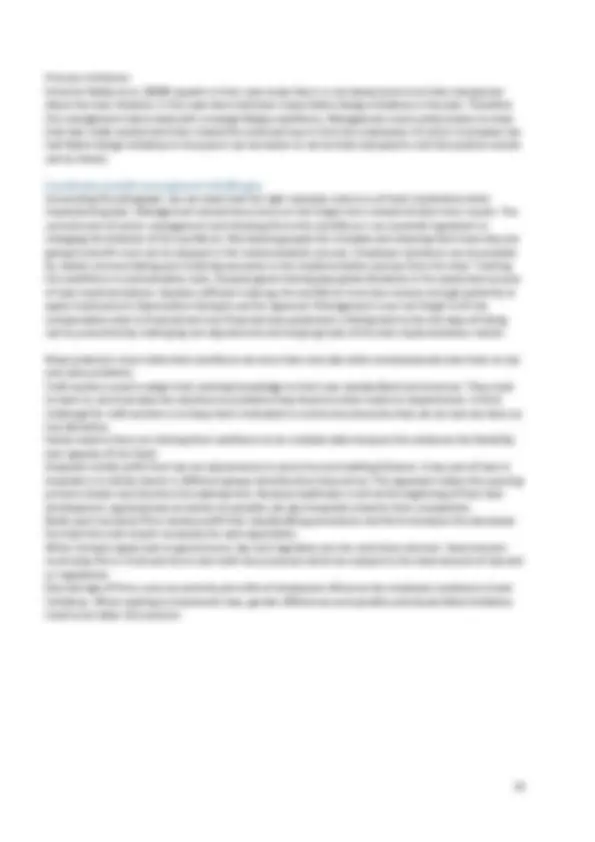
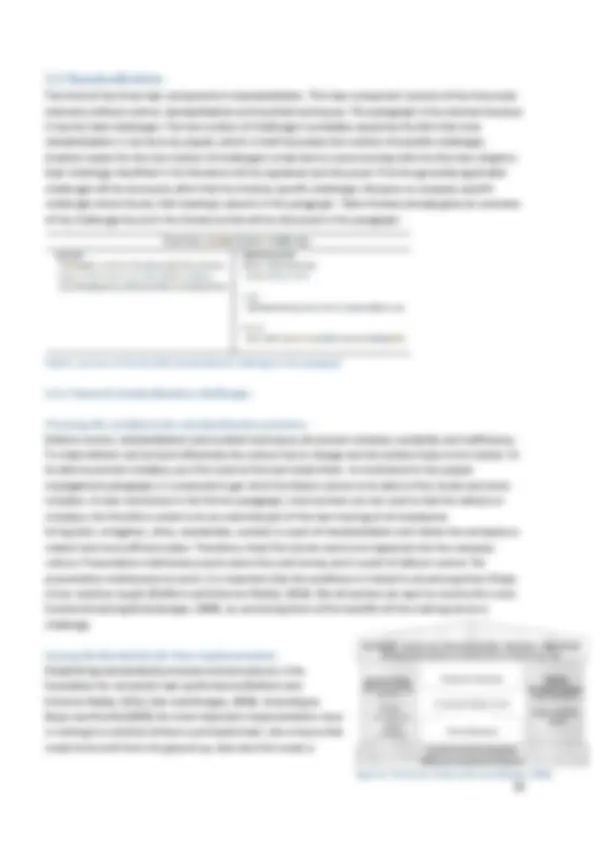
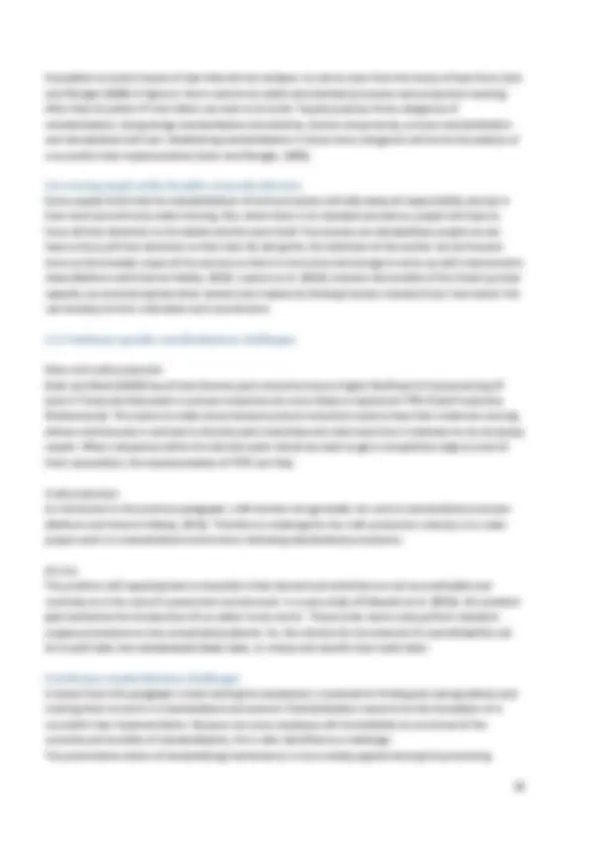
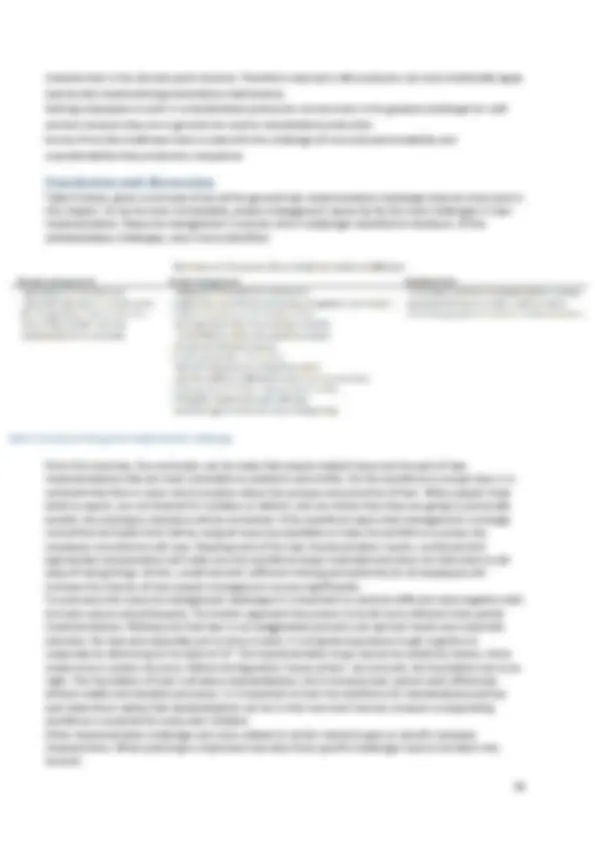
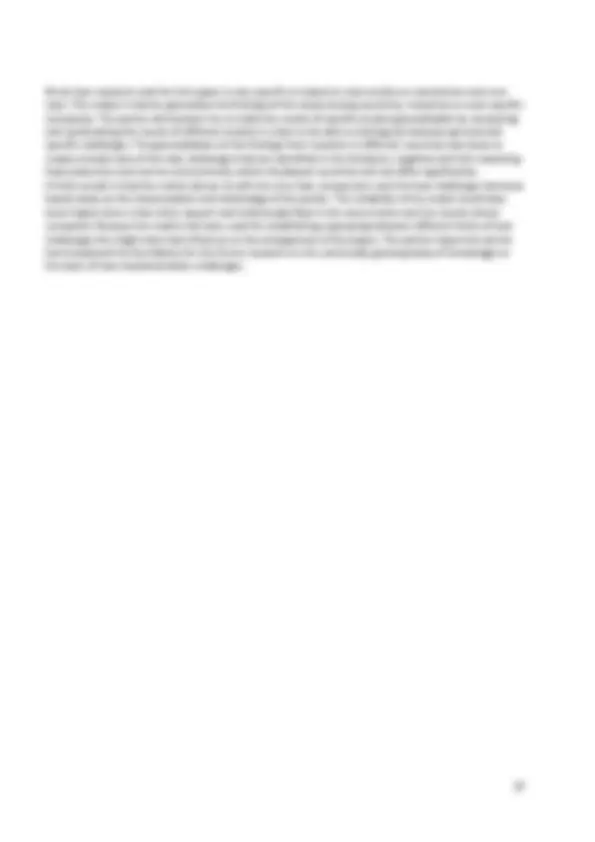
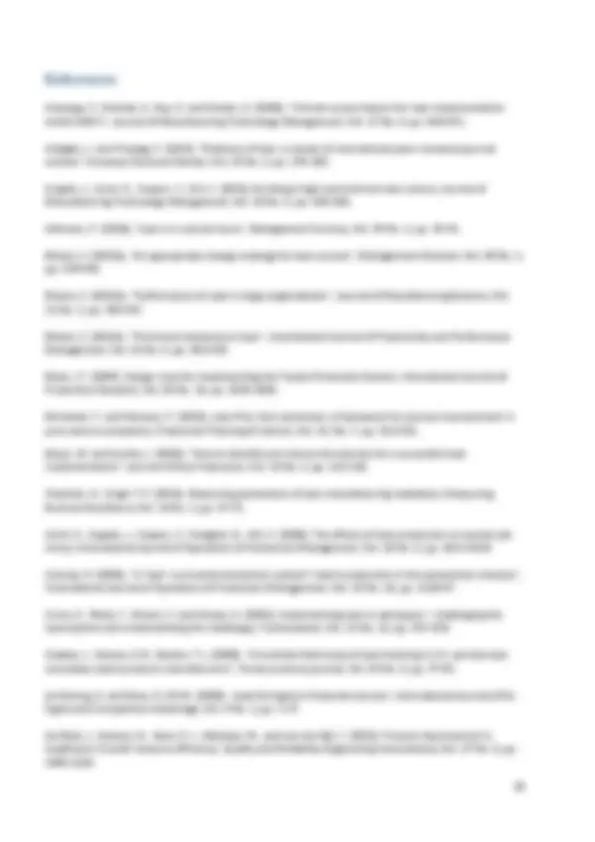
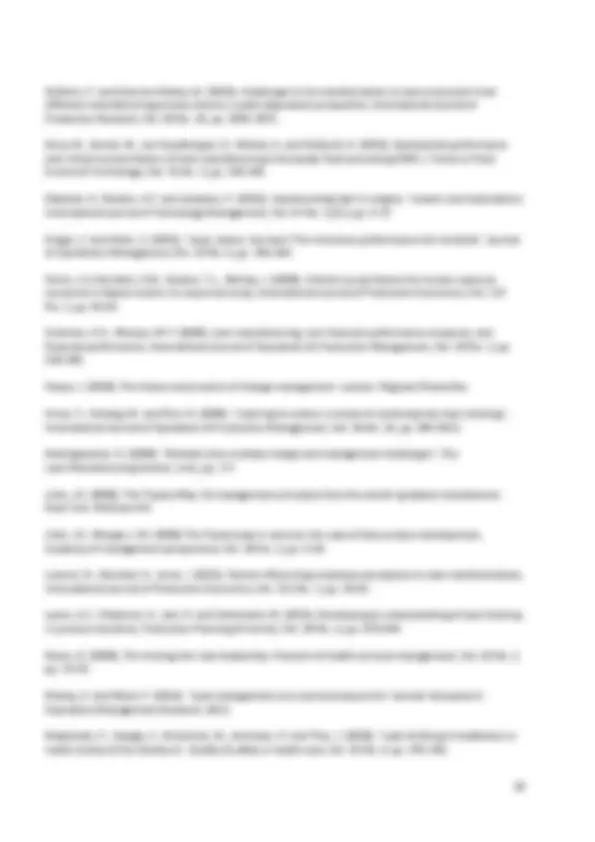
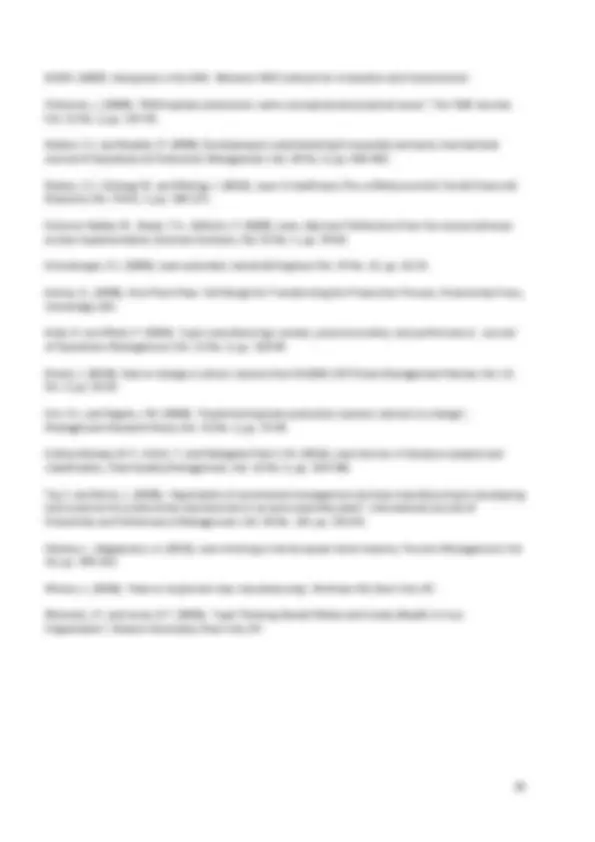
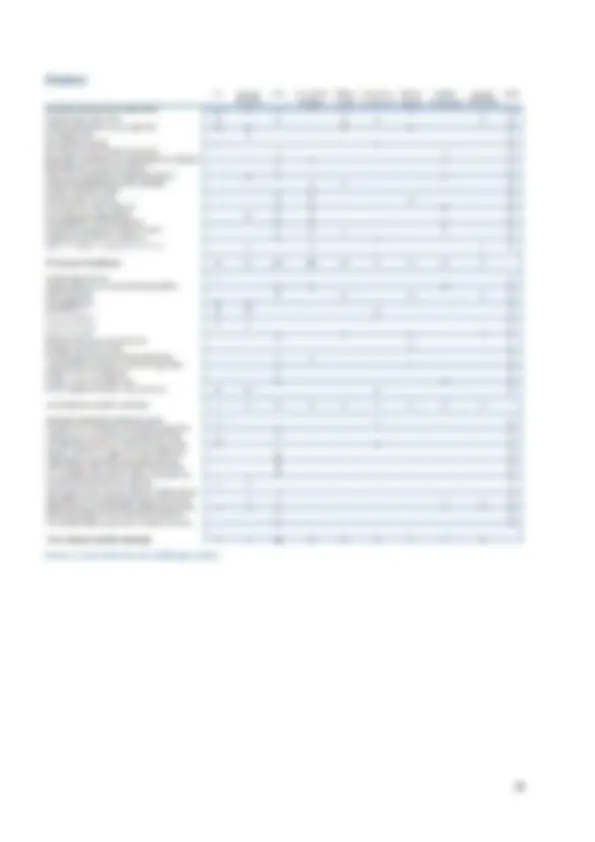
Study with the several resources on Docsity
Earn points by helping other students or get them with a premium plan
Prepare for your exams
Study with the several resources on Docsity
Earn points to download
Earn points by helping other students or get them with a premium plan
Community
Ask the community for help and clear up your study doubts
Discover the best universities in your country according to Docsity users
Free resources
Download our free guides on studying techniques, anxiety management strategies, and thesis advice from Docsity tutors
An in-depth analysis of the challenges faced when implementing lean thinking in various industries, including manufacturing, service industries, and production. language and cultural barriers, lack of interest from Western manufacturers, financial constraints, and the importance of management commitment and employee involvement. It also discusses the benefits of lean implementation in healthcare, education, and other sectors.
What you will learn
Typology: Lecture notes
1 / 32
This page cannot be seen from the preview
Don't miss anything!
28 th^ November 2013, Wageningen
1.2 Defining main elements of lean and its concepts
Definitions of lean
Authors agree on the fact that there is no real clear definition of lean (Pettersen, 2009; Arlbjørn and
Freytag 2013). Definitions given by Arlbjørn and Freytag (2013) are; ‘ doing more with less’ and
‘ manufacturing without waste’. A central point of lean that is mentioned by his founder – Toyota executive
Taiichi Ohno – is the elimination of waste or ‘ muda’ as the Japanese call it (Womack and Jones, 2003).
A citation about the definition of waste found in Taj and Berro (2006), as cited in Arlbjørn and Freytag
(2013; page 183) is ‘ waste is anything other than the minimum amount of equipment, materials, parts and
working time that are absolutely essential to production’. Chauhan and Singh (2012) define waste as ‘ any
activity that absorbs resources but creates no value ’. Those activities can be in production but also
customer relations, product design, supplier networks and factory management (Chauhan and Singh,
2012). Taiichi Ohno defined the seven wastes (Chauhan and Singh, 2012; Womack and Jones, 2003; Hayes,
being;
overproduction;
excess motion (of operator, material or machine);
waiting (of operator, material or machine);
transportation;
excess processing;
inventory; and
defects (rework and scrap)
Other authors also added waste categories to this list, with ‘ goods and services which do not meet the
needs of the customer ’ (Womack and Jones, 2003; page 15). Waste is also ‘ unused employee creativity ’
according to Czabke et al. (2008; page 78). Atkinson (2010) confirms this idea by giving the example that
the average Toyota employee comes up with 187 ideas each year, of these ideas 98% gets implemented to
improve the processes. Taiichi Ohno distinguished two types of waste being type 1 and type 2. Type 1
waste is waste that is not possible to eliminate with the current state of technologies and type 2 waste is
waste that can be eliminated immediately.
Major components of lean
Pettersen (2009) did a literature study about lean
techniques and/or goals. Pettersen searched for the
keywords ‘ Lean production ’ and ‘ lean manufacturing ’
in the databases ISI and Scopus. Of those two
databases the twenty most cited articles were
selected. After screening the 37 unique articles found,
12 articles were selected, based on the criteria of
containing presentations of techniques and/or overall
goals associated with lean production. On the basis of
citation rankings there were also 13 books included in
the study. Pettersen (2009) grouped the lean
characteristics he found in his literature study into
nine collective terms as can be seen in figure 1, at the
right of this page. Although this is not an exhaustive
list of all tools and techniques available, it covers the
Figure 1; Grouping of lean characteristics as suggested by Pettersen (2009)
elements that are most central to lean. The seven wastes as described in the previous paragraph can, just
like the nine lean elements, be seen as central to the lean practice and philosophy. Because the nine major
lean components and the seven wastes are both central to lean, this chapter will explain those parts of
lean together. A third part of lean that has become ingrained into the lean literature comprises of the five
steps to lean as developed by Womack and Jones (2003). These steps are in chronological order: identify
the value, identify the value stream, introduction of flow, getting customers to pull, and finally striving for
perfection. These five steps can be seen as essential lean steps to a successful lean implementation and
will therefore be combined with the explanation of the seven wastes and the nine lean elements. By
connecting those steps to the nine major lean elements (Pettersen, 2009) it gets clearer in which stadium
of lean implementation each lean term applies and which waste it reduces. At the end of this chapter there
is the summarizing table 1, which simplifies and clarifies the connection between the nine lean terms, the
seven wastes and the five steps to leanness.
Just-in-time practices
This component, consisting of production leveling, pull, takt production (standard time) and process
synchronization can be abbreviated as JIT. The following will explain why JIT can be seen as one of the
most important lean practices (Chauhan and Singh, 2012). The use of the Daily Demand is called ‘leveling’
or ‘smoothing’ of production (Black, 2007), Japanese use the word Heijunka (Liker and Morgan, 2006). The
daily demand can be calculated with the following formula from Black (2007):
Through the use of production leveling there are no sudden big fluctuations in the needed production
capacity. Pull production means that there is only something produced when the consumer asks for it so
overproduction (waste # 1) is reduced to zero. One of the tools that make pull possible is ‘ kanban’ also
known as signal cards which give a signal to the preceding production step to produce. The kanban can be
combined with visual controls like (empty) containers (Deflorin and Scherrer-Rathje, 2012). This way the
end consumer can ‘ pull’ the product through the production process because the preceding steps get the
signal to produce another product. Black (2007) formulated a calculation of how much containers are
needed for the kanban function to work:
In figure 2 (Black, 2007) at the
right, visualization of the working
of this pull system can be seen.
The manufacturing cell uses raw
materials from the carts and
returns the empty cars, which is a
signal for the ordering of new
raw material from suppliers. The
full carts of parts are going to the
subassembly where they are sub
assembled. The returning of
empty carts from sub assembly
to the manufacturing cell is a sign to produce more parts, and so on, all through the production stages. It is
important that there is no unnecessary waiting (waste # 3) for a previous or subsequent production step to
be finished. Therefore it is essential that every step in the production cycle is adjusted to a standard time
frame. This principle is also called ‘ takt time’ and it is the German word for ‘conductor’s baton’ which is
Figure 2; Example of the working of kanban system (Black, 2007)
Human relationship management
The three characteristics of this collective term are, team organization, cross training and employee
involvement. Team organisation means that the workforce is organized in small teams, who are most of
the time heterogeneous in expertise and are responsible for a part of the production process. This team
can be responsible for a certain product or ‘ product family ’. Because the team members have different
expertise and backgrounds they can approach the waste from different angles. The element of cross
training means that employees are trained to do a variety of tasks. Task can include handling different
machinery, doing quality checks (see waste # 7), or minor machine repairs (Deflorin and Scherrer-Rathje,
2012). This way, personnel can more easily replace people that are absent or help where extra capacity is
needed so waiting time (waste # 3) is minimized. A cross trained workforce does not only make the
company more flexible and responsive but also makes the jobs of the people themselves more interesting.
Employee involvement is one of the essential elements of a lean implementation effort. When employees
feel involved they are more susceptible to changing their behavior. Therefore all employees usually are
involved in the decision making around lean in the company. Communication of the lean results involves
the people and keeps them motivated. Waste number three (waiting) is lowered by being able to use
employees where they are most needed at the moment. The seventh waste (defects) gets prevented by
employees being trained to do quality checks. Because the workforce is cross-trained the third step of flow
gets cultivated. Employees are trained to locate and eliminate waste, this element belongs in step five of
Womack and Jones (2003), being striving for perfection.
Improvement strategies
Improvement strategies consists of improvement circles, continuous improvement, and root cause
analysis. Improvement circles are teams that are multidisciplinary and therefore have a broader view of all
the processes and can therefore locate waste in a broader scope. Continuous improvement can be traced
back to the plan-do-check-act methodology of W. Edwards Demming, which now has the name Total
Quality Management or TQM in short (Womack and Jones, 2003). The term TQM is an accumulation of
failure prevention and quality checking tools. Kaizen events can also be seen as continuous improvement
processes. In a Kaizen event certain specific improvement goals are tried to be made with the use of teams
that are focusing on a certain element of waste (Farris et al., 2009). Root cause analysis is also known as
the 5 why’s because this is the lean tool that is used to get to the root of a cause by asking why five times.
The idea behind this theory is that when there is a problem, you need to ask ‘why’ five times to come to
the root cause of the problem. Step five of lean – striving for perfection – applies here. The improvement
strategies are used to eliminate all the seven types of waste.
Defects control
The four elements are, autonomation, failure prevention (poka yoke), 100% inspection, and line stop
(andon). To make sure there are no defective products produced, there are visual and sometimes
electronic controls embedded in every process step. This autonomation concept is called Jidoka (Womack
and Jones, 2003). This way a defect can be detected immediately instead of at the end when the product is
finished. Whenever personnel (or a machine) sees a defect or when something else is going wrong the line
stop ‘ andon’ cord or button is used to stop the machine, or it can automatically stop itself (Liker and
Morgan, 2006). Then a quality manager will speed to the location of the problem that is located by a light
or a sound (Liker and Morgan, 2006). A promise from the management of NUMMI cited by Shook (2010;
page 66) is ‘ Whenever you have a problem completing your standardized work, your team leader will come
to your aid within your job cycle ’. Failure prevention is also called poka yoke in Japanese. Where Jidoka is
more about finding problems, poka yoke is there to prevent them from happening. An example can be that
a conveyer belt can only move when a laser beam has been interrupted. This way the machine for example
knows that the worker picked the necessary part out of the box. 100% inspection just means that all the
products are checked in all the subsequent production steps. The seventh waste of defects is minimized by
the defect controls. Because defective products do not get processed further, the fifth waste of excess
processing is minimized as well. With lean production zero defects are the goal, the fifth step of striving for
perfection is therefore most applicable here.
Supply chain management
Value stream mapping and supplier involvement are part of supply chain management. Value stream
mapping can be abbreviated as VSM. VSM is actually the component that needs to be used before the
other lean elements can be implemented. By mapping the value stream of a product (or service) it gets
clear where there is waste that can be eliminated. Chauhan and Singh (2012) state, that VSM is one of the
most used lean techniques. This is probably because this tool is very helpful in finding the waste that is
central to the lean philosophy. For lean and especially Just-in-time to work it is essential that suppliers are
involved in the process of lean (Lyons et al. 2013). Waste can be along the whole value stream from raw
material to end product. When your own company is lean but your suppliers are not, there will still be
waste in the supply chain of the product. Therefore it is optimal to create lean processes over the whole
product supply chain. The second step in lean implementation – identifying the value stream – is
applicable in supply chain management. The fourth step of pull is made possible by involving suppliers in
the lean methodology. With this lean concept the sixth waste of inventory is minimized.
Standardization
Besides standardized work, standardization also consists of housekeeping and visual control as identified
by Pettersen (2009). Housekeeping can also be called 5S’ing. Chauhan and Singh (2012) mention 5S as one
of the most used lean techniques. 5S stands for sort, straighten, shine, standardize, sustain. When those
five words are applied in the workplace, the tools and equipment are easy to locate, clean, and ready to
use. Standardized work means that all the production steps are standard. This way a worker can easily
work in different production cells. Another benefit is that when certain improvements are found, they can
immediately be applied to all the other production areas. A visual control has overlap with Jidoka and
kanban who have been discussed earlier. Standardization fights waste number two (excess motion)
because no one has to look for where tools are because they have a fixed location. Standardization can be
assigned to step three (flow) and step five (perfection) because less excess motion inhibits flow and the
applicability of improvement ideas to the whole chain is supporting the goal of perfection.
Scientific management
Policy deployment, time/work studies, multi manning, work force reduction, lay out adjustments, and
cellular manufacturing are the elements of scientific management. Policy deployment is also called Hoshin
Kanri and includes delegating as much responsibility as possible to the workforce. In short, it is a
management system in which all employees participate. Time and motion studies overlap with lay out
adjustments because they both want to optimize the output of activities. By changing the lay out of the
machinery, the needed time and motion can be reduced. Cellular manufacturing means that machines and
equipment are placed together to reduce walking time and distance. Most production cells have a U-shape
and are manned by operators who are multifunctional and can perform many tasks and operate many
processes (Black, 2007). Decouplers are used to connect different machines. Those decouplers can
perform quality checks and the function of process delay. The capacity of a decoupler never exceeds two
unless it is performing a function of process delay (Black, 2007). A manufacturing cells is built in such a way
Lean outside of car manufacturing
Lean originates from the high volume, low variety (mass) car manufacturing of Toyota but is since its
discovery outside Japan, also applied to many other disciplines. Service industries (Suárez-Barraza et al.,
governments (Scorscone, 2008), financial institutions (de Koning and Does, 2008) and education have
adopted elements of lean. Also within production itself, lean has extended to the processing industry (Dora
et al., 2013; Lyons et al., 2013), and the craftwork industry (Deflorin and Scherrer-Rathje, 2012). All these
different environments have specific challenges when implementing lean but there are also lean
challenges that are general. The next chapter will discuss the lean challenges as identified in the literature
in three groups of challenges.
2. Lean implementation challenges
This chapter will describe the challenges that are faced when trying to implement lean thinking. The
challenges are mainly formulated from the perspective of the lean stereotype by Wilson (2010). These
stereotype elements consist of being a manufacturing firm, producing discrete parts and having stable
product demand. Many challenges are also applicable outside the roam of this lean stereotype. Eroglu and
Hofer (2011) found in their research that some industries, because of the particular product, or the
conditions of manufacturing, demand, or supply may not be suitable to lean operations. Shah and Ward
(2003) on the other hand state that lean practices are prevalent in all industries. This chapter will try to
bring nuance to these two opposing statements.
The nine elements from chapter 1 can be divided into three broad groups, being resource related, people
related and variability related. On the basis of the implementation challenges found in the literature study,
a matrix of the nine lean elements and the found lean challenges has been made. This matrix (see annex 1)
allowed for the identification of lean components that more or less share the same challenges. The lean
components arising from the matrix were identical to the classification that could be made on the basis of
the underlying goals. This finding did cause the classification of challenges into three groups. These three
groups are ‘resources management’, ‘people management’ and ‘standardization’.
The ‘resources management’ group consists of JIT, resource reduction and supply chain management
because these lean components have the reduction of the needed resources as a central goal. The second
group named ‘people management’ is formed by HRM, improvement strategies and scientific
management, because most of the challenges in these lean elements are caused by or at least involve
people. Defects control, standardization and bundled techniques are forming the core of the
‘standardization’ group because these three groups all want to lower the variability by standardizing
processes. For structuring the paragraphs of this chapter, these three lean element groupings are used to
discuss the lean challenges found in the literature. Some challenges might have a slight overlap between
two or three of the groupings. In that case the author has tried to fit the challenge under one of the three
components that has the highest relevance.
2.1 Resource management The first of the three lean components is resource management. This lean component consists of the three lean elements; just in time practices, resource reduction and supply chain management. Each challenge as identified in the literature will be explained and discussed. First the generally applicable challenges will be discussed, after that the industry specific and company specific challenges will be identified. The table below already summarizes the content of this paragraph for an overview of the challenges identified.
Table 2; Overview of the identified resource management challenges
blindly adopt the lowering of inventories if they want to generate optimal results. Not only lowering the inventories to much can be harmful. Angelis et al. (2011; page 580) state ‘ increased work pace has potential for causing excessive leanness’. The results of their regression analysis show that emphasizing on speed over quality; together with a high level of work pace and intensity have a negative influence on workers affective commitment. Angelis et al. (2011) therefore advise to use buffers because this reduces the pressure and stress that is felt, while increased cycle times make it possible to speed up for a portion of the time and then rest for the remainder. When buffers are used between workstations, together with longer cycle time and job rotation the employees will feel less stress and be more motivated to do their job. When lean gets exaggerated, lean can become corporate anorexia. Radnor and Boaden (2004; page 431) state the following ‘ by striving to become lean by focusing on the process rather than the outcome, they miss the optimum point and move into anorexia, becoming relatively ineffective overall ’. Radnor and Boaden (2004) created five questions that need to be asked about a company. When at least one of them can be answered with yes, there might be a case of corporate anorexia. The more yes’es , the more severe the problem is according to this theory. In the four cases at the right hand side of this page, the case 1 and 4 are considered lean, while case 2 and 3
are potentially anorexic.
Getting suppliers to cooperate For lean and especially Just-in-time to work in the whole product value chain, supplier involvement is crucial in the process of a lean implementation (Lyons et al. 2013). For a supplier to commit to becoming lean, it is important that there is mutual trust that the relationship will be lasting and beneficial. For that reason there has to be good communication between both parties right from the start of the lean initiative.
2.1.2 Industry specific resource management challenges Besides the general implementation challenges of resource management there are also some, challenges that are more specific to certain industries or companies. This paragraph will handle the industry specific challenges and 2.1.3 will deal with the company specific challenges.
Industry specific resource management challenges For the sake of simplicity this paper distinguishes only four types of industries. These four types are, mass production, processing, craft production and services. The literature study only identified industry specific resource management challenges in the mass production, processing and service industry.
Mass production A mass production environment already has standardized processes in place. Therefore the most important thing to do in a mass environment is to synchronize the processes to a takt time. (Deflorin and Scherrer-Rathje, 2012). Of course it stays important to check if there is waste in the already standardized processes, because otherwise the production capacity will suffer because of the waste that is standardized into the processes.
Processing Before talking about processing it can be helpful to give a short explanation of what it means. A clear definition of processing is formulated in the paper of Lyons et al. (2013; page 480); ‘ Production that adds value by mixing, separating, forming and/or performing chemical reactions. It may be done in either batch or continuous mode ’. Lyons et al. (2013) describes the difference with manufacturing as the fact that process manufacturing produces measurable instead of countable produces. Wilson (2010) states that the deviation from discrete parts to continuous process industry has the least
Figure 4; Corporate anorexia indicators (Radnor and Boaden, 2004)
negative effect of the three elements of the lean stereotype he identified. In the continuous process industry the batch sizes are generally larger. The advice from Wilson (2010) to those firms is to reduce the batch size in order to make JIT function more properly. This brings us right to the next important lean barrier for processing industries. When the batch sizes are lowered, the setup time needs to be lowered to compensate for the need to change the set up of the machinery more often. According to Dora et al. (2013) The processing machinery is often large and therefore inflexible. Also the complexity of resources can be an influencing factor. Shah and Ward (2003) found that plants in discrete parts industries have a higher likelihood of implementing JIT (Just In Time) and that plants in process industries are more likely to implement TPM (Total Productive Maintenance). For companies in the processing industry there is much to be gained in comparison to the competition when implementing JIT practices. Lyons et al. (2013) state that supplier integration and the alignment of customer demand with production are ‘structural’ principles of lean, but are less apparent across different types of processing firms. Knowing this, a processing firm can get an advantage to their competition by implementing lean in a more holistic way.
Dora et al. (2013) concluded that lean in the food processing industry is not really developed yet. The focus is more on food safety than on process improvement methods. According to Dora et al. (2013) there are several reasons why lean manufacturing has a low impact to the food sector because of characteristics including shortness of shelf-life, raw material heterogeneity, seasonality, and varied harvesting conditions. Dora et al. (2013) also mention the complex production chains and networks of buyers and sellers as factors affecting food processing. Because of the heterogeneity, seasonality and varying harvest conditions it is hard, maybe even impossible to standardize these processes and use the methods of flow and pull.
Service Service firms that want to apply lean have the problem of demand instability (Wilson, 2010). Radnor et al. (2012) and Edwards et al. (2012) also both mention this problem of instable demand. Although the problem gets recognized, none of the authors come up with a solution to this problem. Therefore the only thing that service companies can do is cross-train their workforce in order to being able to distribute people to the department within the company where extra capacity is needed.
For not for profits and charities, survival is not the most important issue. They sometimes find ways to spend money that they did not need to use because of subsidies and budgets. This creates waste, rather than eliminating it. The most important application of lean in these companies can be in the lower levels of the organisation where at the ‘service provider level’ lean tools can be used for the processes according to Wilson (2010). We think that standardization and more cross functional functions can help not for profits and charities to be more flexible and responsive.
2.1.3 Company characteristic resource management challenges
Company size Company size is often mentioned (Shah and Ward, 2003; Eroglu and Hofer ,2011; Sim and Rogers, 2009) as a key characteristic of lean success. This statement gets backed up by the findings of Shah and Ward (2003) that plant size seems to be significantly positively correlated with twenty of the twenty-two lean manufacturing practices they examined. Only cross-functional work force and quality management programs are not statistically significant. It is important to mention that Shah and Ward (2003) found that the effect of size seems to be of less influence in the service industry than in the manufacturing industry. The higher influence of size on manufacturing than service is probably caused by the difference in the extent to which can be profited from economies of scale. Because services cannot easily be automated, the economies of scale principle is less relevant in the service sector. Dora et al. (2013; page 161) found research suggesting that ‘ large manufacturers are more likely to implement lean practices than small ones ’. This is in line with Eroglu and Hofer (2011) who say that small firms seem to benefit less from lean implementation than large firms. Many small and medium sized firms have limited power to dictate lean supply form their suppliers (Achanga et al., 2006). Because larger firms have more power, they are also
Table 3; overview of the identified people management challenges in this paragraph
Mass producers need to focus on the synchronization of the processes to takt time because standardized processes are already in place. Processing firms have more points of attention. They need to try to lower batch sizes, while at same time reducing their set-up time. By implementing JIT and trying to integrate suppliers, processing firms can stand out from their competition and create a competitive edge. Service firms need to cross-train their employees in order to being able to try to compensate for the instability of demand in the service sector. The size of a company has strong influence on the likelihood of a successful lean implementation. Larger firms in general have more (financial) resources available and have more negotiating power towards suppliers. Therefore large companies can more easily and holistically implement lean. A lack of a market free environment or demand stability lowers the chances of success for firms with lean aspirations.
2.2 People management The second of the three lean components is people management. This lean component consists of the three lean elements; human resource management, improvement strategies and scientific management. This paragraph is by far the one with the greatest number of challenges. The great number of challenges is probably caused by the fact that it is hard to change a culture and because people have their own will and personal agenda. Farris et al. (2009) state that the relationship between the degree of human resource implementation and lean manufacturing success has been reported in several studies. Losonci et al. (2011, p. 31) phrase the sentence: ‘ We know very little about the causes of implementation problems, but the evidence seems to suggest that human resource issues often are their root ’. Each challenge as identified in the literature will be explained and discussed. First the generally applicable challenges will be discussed, after that the industry specific and company specific challenges will be identified. Just like in the previous paragraph, the table below summarizes the content of this paragraph for an overview of the challenges identified in the literature.
2.2.1 General people management challenges
Getting rid of the short term philosophy To make a chance of real and lasting lean success, the company philosophy often needs to change. Company executives need to realize that there are no quick fixes to getting lean. This is emphasized by Scherrer-Rathje et al. (2009) who call implementing lean ‘ a daunting task’. So, the idea of the existence of a lean template that is ready to use for implementation is incorrect. No two companies are exactly the same; therefore do not try to find a universal implementation manual and do not try to precisely copy the methods of others companies that already successfully implemented lean. Firms that want to become lean need to be aware of the fact that a lean transformation is not a one-time effort but a never ending pursuit
(Deflorin and Scherrer-Rathje, 2012; Scherrer-Rathje et al., 2009; Mann, 2009; Bhasin, 2012c). Because not all the lean results are financial, there is a need for looking at both financial and non-financial results (Black, 2007). Fullerton and Wempe (2009; page 229) confirm this by stating ‘ lean manufacturing practices are effective when accompanied by the complementary use of performance measures that provide informative and motivating information in world-class manufacturing environments ’. Like with almost all habitual changes, results will almost never be visual immediately, therefore management needs to get rid of the ‘ make the month mentality ’ and be patient for the real lasting results to appear (Chauhan and Singh, 2012; Wilson, 2010; Bhasin, 2012c). Womack and Jones (2003) state that it takes at least five years for a company to become truly lean. This statement is in line with the experience of Koenigsaecker (2000). Koenigsaecker classifies the first two years as ‘ disharmony and anti-change’ , the third year as stabilized change and ‘b uilding the long-term foundation ’. Beyond year three, the results start to add up and change becomes the norm and the workforce starts to have ‘ pride in lean accomplishments’. Conti et al. (2006) did research on the effects of lean implementation on employee stress levels. They found that stress first starts to rise when the level of implementation gets higher, but that there is an inflexion point at which the stress levels starts to decline again. The morale of this information is to have an implementation horizon of at least five years, to give the stress and discomfort of change the opportunity to develop into a feeling of positivity and triumph.
Establishing, maintaining and showing management commitment Maybe even the most important guideline every lean aspiring company should follow is to let senior management show their commitment and involvement to the lean initiative (Scherrer-Rathje et al., 2009; Dora et al., 2013; Angelis et al., 2011; Black, 2007; Chauhan and Singh, 2012; Boyer and Sovilla, 2003; Achanga et al., 2006; Sim and Rogers, 2009). Management can show their commitment through providing sufficient resources to the lean journey. This commitment can be in the form of time, money and active involvement. Bhasin (2012c) found that more than half of the 68 surveyed organisations feel that the added responsibilities of lean, cause a struggle with the time needed to implement lean. So, besides active involvement and money, senior management must also provide middle management and line-workers with the necessary workload relief to avoid a shortage of available time to spend on implementation issues. Being able to pay for the development of skill and expertise is found to be one of the most important success factors (Dora et al., 2013; Angelis et al., 2011; Shook, 2010). So, sufficient financial resources have to be made available to cover the cost of training, external consultants and other related costs.
The active involvement of management in lean activities must not be undervalued. Successful case studies like Losonci et al., (2011) mention CEO’s or senior managers to walk around the shop floor and participate in improvement activities. Mann (2009) advises executives to spend one hour, every week or two, to spend on ‘ gemba walking ’ (gemba means ‘where the work is done’). According to Mann (2009) the first six months to a year of gemba walking can best be done together with a lean teacher or consultant.
Establishing clarity, purpose and priorities Management must not only try to show their commitment to lean. According to Wilson (2010) and Achanga et al. (2006), lacking an implementation plan is an important reason for lean implementation failures. So, an important task of (senior) management, is to come up with a lean implementation plan with clarity and purpose (Wilson, 2010; Bhasin, 2012c; Hines et al., 2004). Also having a clear prioritization in the plan is important because it is better to work on a specified project than wanting to do it all at once (Bhasin, 2012a; Womack and Jones, 2003). The successful case study of Crute et al. (2003) emphasizes the importance of clear and specific goal setting. When goals are too vague, cannot be measured or are not able to be traced back to lean initiatives, the motivation among the workforce will decrease fast.
2003). When the messages are not consistent or even opposing, employees will lose their motivation. Increasing the employee commitment can assist with subsiding the employee resistance of individual workers. Angelis et al. (2011) came up with seven work practices which are favorable in enhancing employee commitment. Those practices are; participating in improvement projects, using buffers to uncouple work stations, increasing cycle times, providing help when needed to meet production standards, job rotation to be exposed to a variety of tasks, and displaying individual output when practical. When these seven commitment increasing practices are applied, it is more likely that workers will commit to the lean journey. Sometimes there will still be people who are very negative and critical and sometimes even refuse to cooperate. Bhasin (2012c) state that a small group of managers (about 10%) refuses to accept new ideas. According to Boyer and Sovilla (2003) three to five percent of people will be strong advocates of lean, ninety percent will be open to change but needs solid leadership and the other three to five percent will be in resisting the change needed. It is of great importance to identify those people who are resisting the change (Boyer and Sovilla, 2003). Trying to involve everyone to the process – also those who resist – is essential because missing or limited participation has a negative effect on the buy-in (Boyer and Sovilla, 2003; Cooney, 2002). When employees express their concerns over the changes or approaches, it is critical to address those concerns (Boyer and Sovilla, 2003). In rare cases there will be irreconcilable differences because there may not be a match between the needs of the individual and the needs of the organisation. In that case separation is required (Boyer and Sovilla, 2003; Czabke et al., 2008).
Train all employees for sufficient lean skills Employees must not only be committed to the lean implementation but also need to receive sufficient training to execute their tasks in the new lean environment. Insufficient supervisory skills to implement lean, as a result of lack of training is an important barrier to lean implementation success (Bhasin, 2012c). Also insufficient workforce- and senior management skills to implement lean are high on the ranking of most important barriers to change in the research of Bhasin (2012c). He found that over 75 percent of managers in seven case studies found that there were insufficient skills among the workforce or the supervisors. Training can therefore be seen as a preventative cost which aids the lean implementation and reduces time to implement. It is important to keep in mind that work related habits are just as difficult to change as personal habits (Bhasin, 2012a). Research from Black (2007) shows, that everyone in the company must be educated in lean production philosophy and concepts, for lean principles to work. So, in order to ensure and accelerate the lean implementation, firms need to train their employees in all layers of the organisation. This finding gets supported by successful case studies (Crute et al., 2003; Shook, 2010) that provided sufficient training for their employees. Finding a good balance between training and implementation is crucial. Doing too much or too little of one of them will be harmful (Bhasin, 2012c). Liker and Morgan (2006; page 6) emphasize that point by stating ‘ serious learning only comes from action at the gemba – where the work is done. So drawing pictures and models of TPS is not value added ’. To, for example, successfully apply root cause analysis (5 why), employees need to be trained to analyze problems in such a way that the root causes are discovered. Only by getting at the root of a problem there is the opportunity to reduce waste and defects.
Give the workforce authority for continuous improvement Continuous improvement can be realized by the use of Kaizen events. Farris et al. (2009; page 42) phrase the following description of a Kaizen event; ‘…the Kaizen event, a focused and structured continuous improvement project, using a dedicated cross-functional team to address a targeted work area, to achieve specific goals in an accelerated timeframe (usually 1 week or shorter). ’ Kaizen can result in a more positive attitude towards lean which in turn can increase employee commitment, providing to the success of the program. The participation in the problem solving during a Kaizen event can help employees get better skills and problem solving capacity. Specific, well defined goals and heterogeneity in the cross-functional team are other elements that can determine the events effectiveness (Farris et al., 2009; Angelis et al., 2011). During Kaizen events it is of great importance that the people involved have the full authority to implement their solution (Fullerton and Wempe, 2009). This ensures that problems do not pile up and also
directly involves the employees in the continuous improvement mentality that is needed for true lean success. A mandate to execute improvement ideas, gives the employees the right signal that management trusts them to come up with the right solution which results in higher commitment and morale (Angelis et al., 2011). Deflorin and Scherrer-Rathje (2012) and Scherrer-Rathje et al. (2009) mention a method called the ‘ just do it ’ room where people of different disciplines gather immediately when a problem needs to be solved. Right there and then a solution needs to be developed and planned for implementation of it. When it is impossible to solve the problem immediately, someone is made responsible for coming up with a solution at a curtain date or at the next meeting.
Keeping track of the lean implementation results If continuous improvement is applied, it can be useful to check if the planned or expected improvements in results are realized. When workers receive information about their own results this increases the commitment and belief in the lean systems (Losonci et al., 2011; Angelis et al. 2011). Whenever a target is reached or there is some other win during the lean implementation, do not hesitate to celebrate it. Successful case studies like Scherrer-Rathje et al. (2009) use this habit of celebrating (small) wins, because it keeps everyone motivated and shows things are being accomplished. The use of a consultant, to check the lean progress, can provide the necessary external validation that your company is still on the right path (Scherrer-Rathje et al., 2009).
Fitting the compensation plan with lean When improvements are being made and the lean implementation is being a success it is time to make the workforce profit from efforts as well. According to Black (2007) many companies feel that bonus payments are the best way to reward people. But we think that only rewarding people this way can cause the intrinsic motivation to disappear resulting from the ‘crowding out’ effect. This crowding out theory says that the intrinsic motivation of people will decline when money gets into the motivating equation. Black (2007) notices that the reward structure of middle management has to be changed to support the lean system design. Fullerton and Wempe (2009) found evidence that non-financial performance measures have positive effect on the financial performance of lean manufacturing. Therefore it should be wise to change the (middle management) reward system according to non-financial measures. A compensation plan that is balanced and which focuses on measures of continuous improvement, efficiency, teamwork and short-term results will create the culture where lean can survive and thrive (Bhasin, 2012a; Czabke et al., 2008).
Avoid sliding back to the old ways of doing things An often formulated lean challenge is sliding back to the old ways of doing things. Bhasin (2012c) calls backsliding to the old ways, the single most important factor that contributes to lean failures. People are creatures of habit, so when they have the chance, they will wanted or unwanted tend to go back to the way they have always done things. (Deflorin and Scherrer-Rathje, 2012; Mann, 2009) come up with the idea to significantly change the processes and plant setup. These layout adjustments will establish boundaries to keep employees from doing things as they have always done it.
2.2.2 Industry specific people management challenges As mentioned in the first paragraph, this paper distinguishes four types of industries. These four industry types are, mass production, processing, craft production and services. The literature study identified industry specific people management challenges in the mass production, craft production and service industry.
Mass production Mass production employees are used to perform only one step, when introducing lean, they are suddenly required to do and understand more than one step (Deflorin and Scherrer-Rathje, 2012) so training these employees the new skills is important. Mass production workers are not used to solving problems, let alone communicating them with other departments. So involving everyone in the problem-solving process