
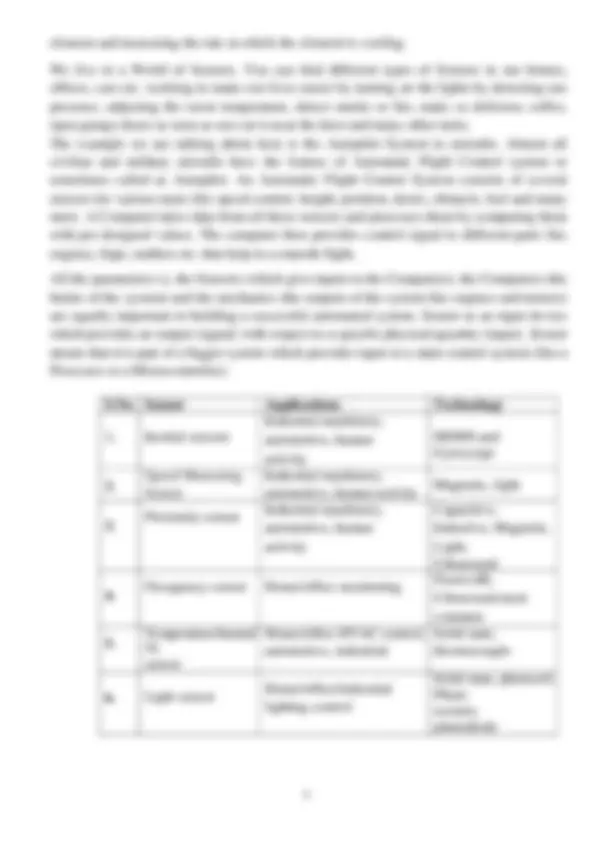
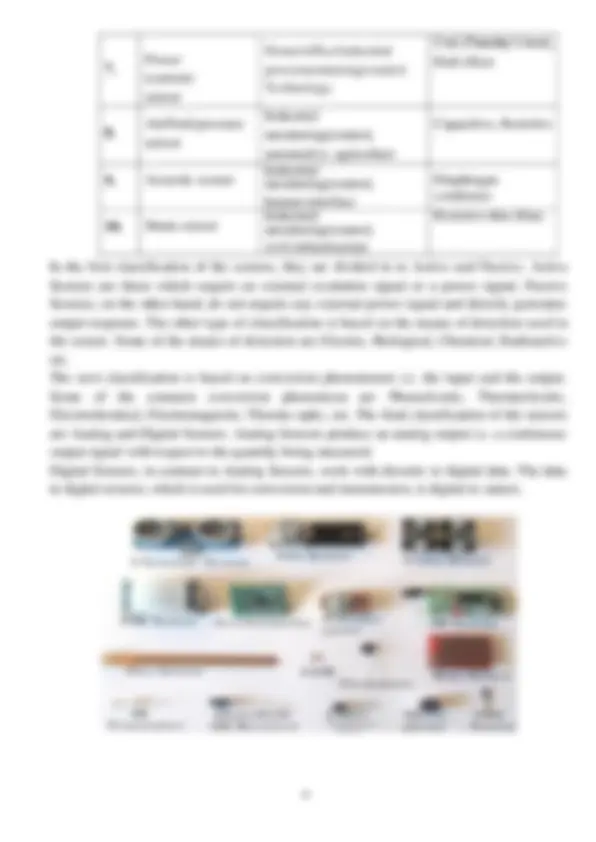
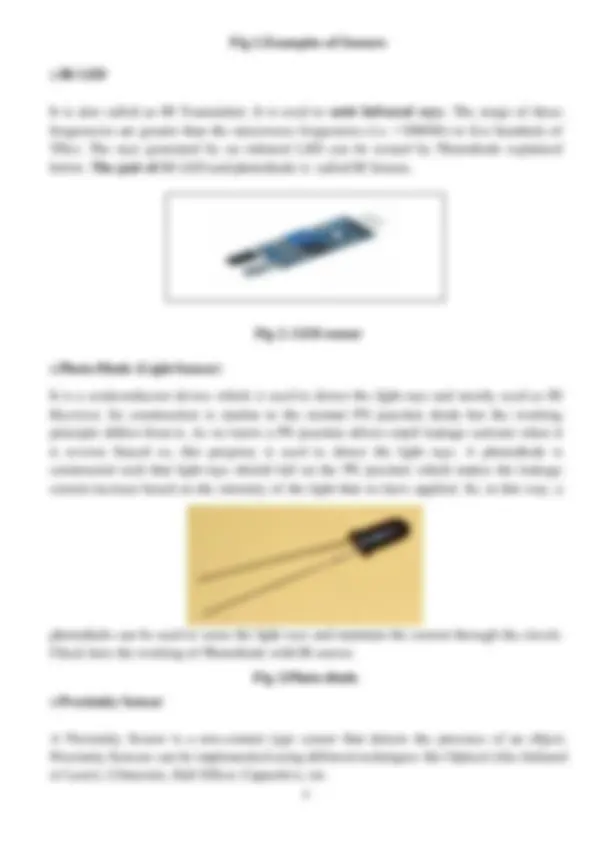
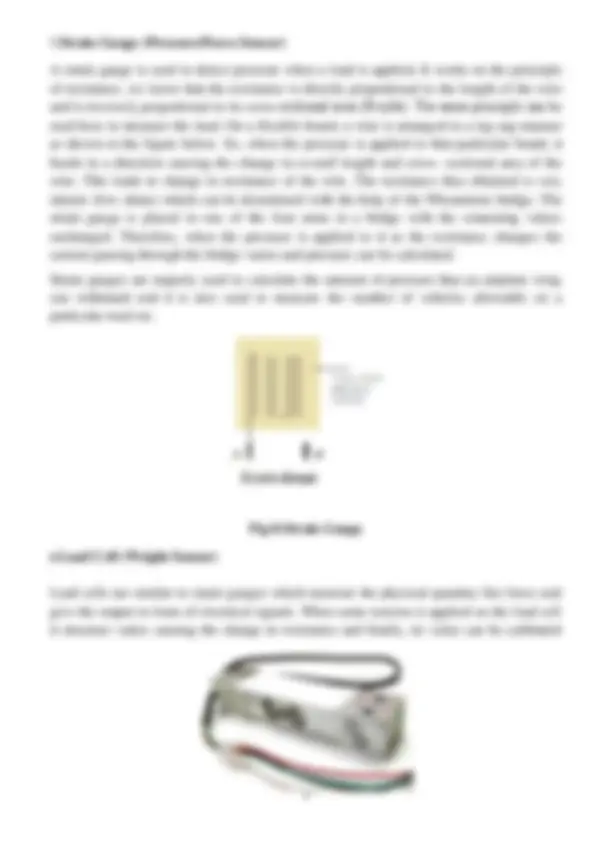
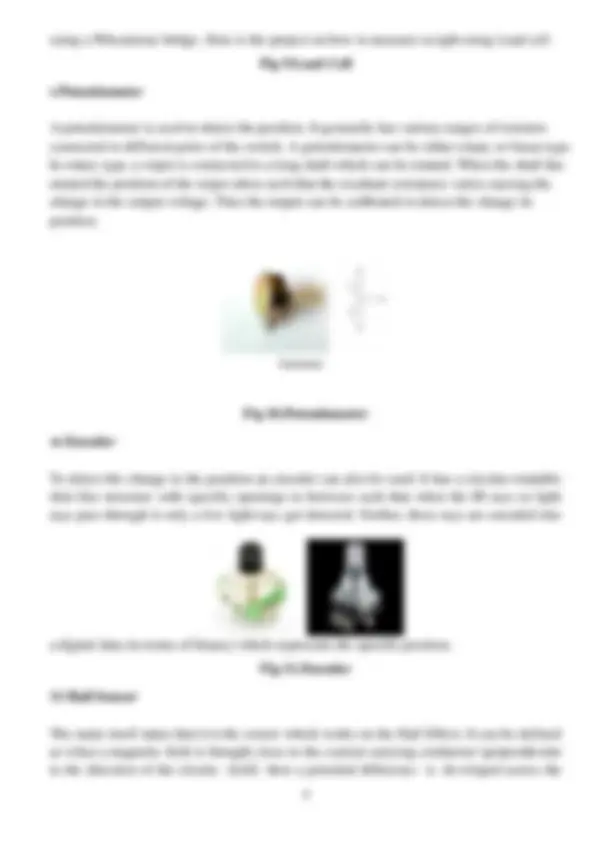
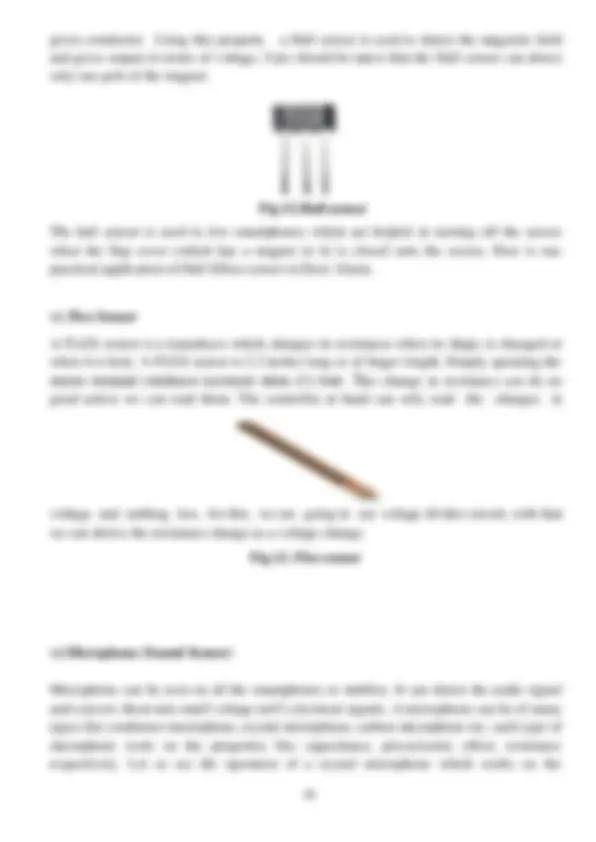
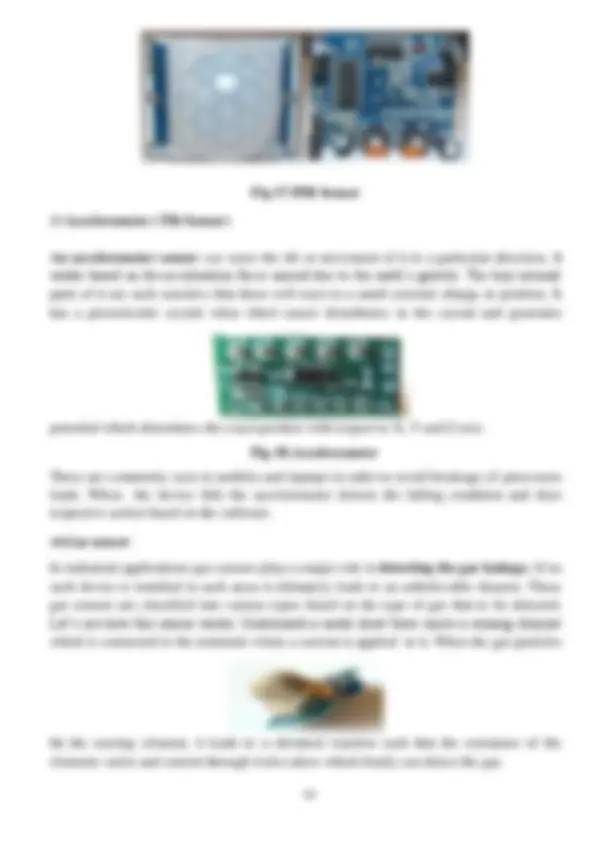
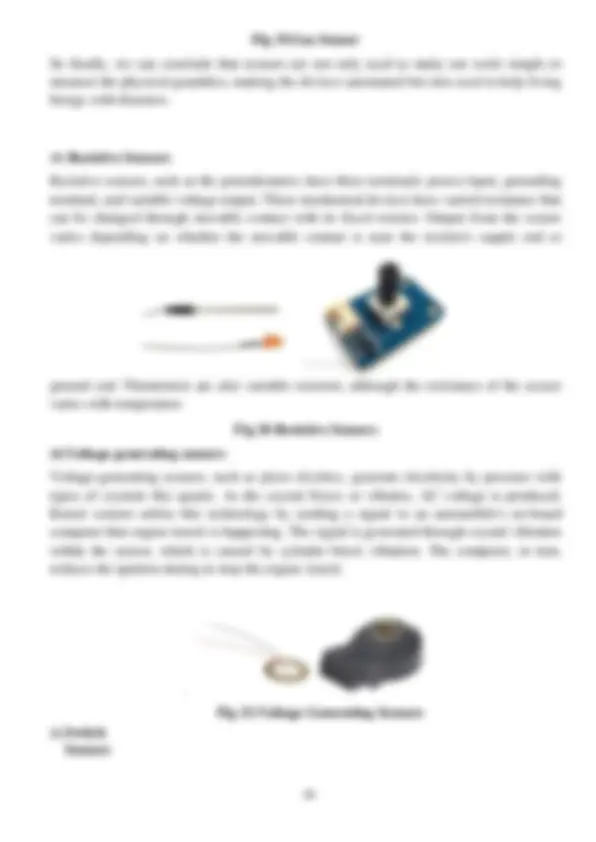
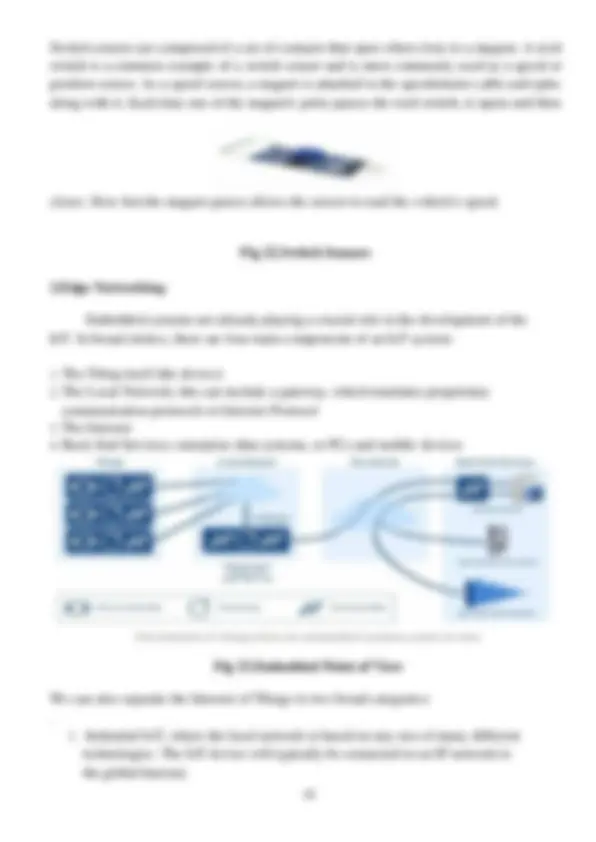
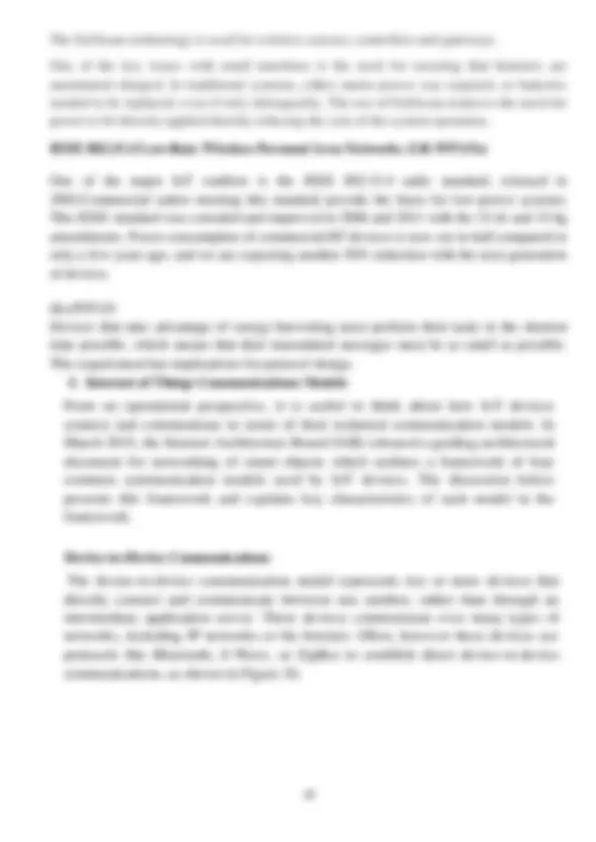
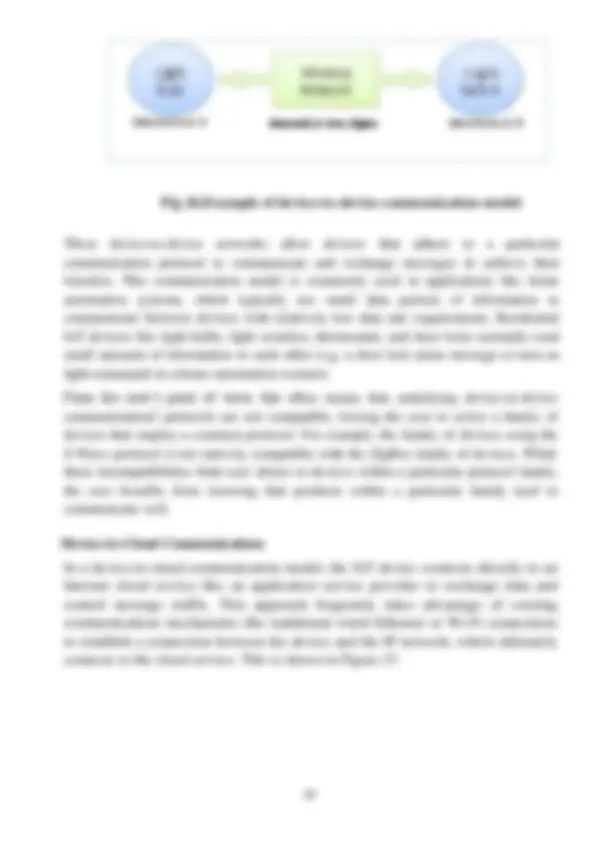
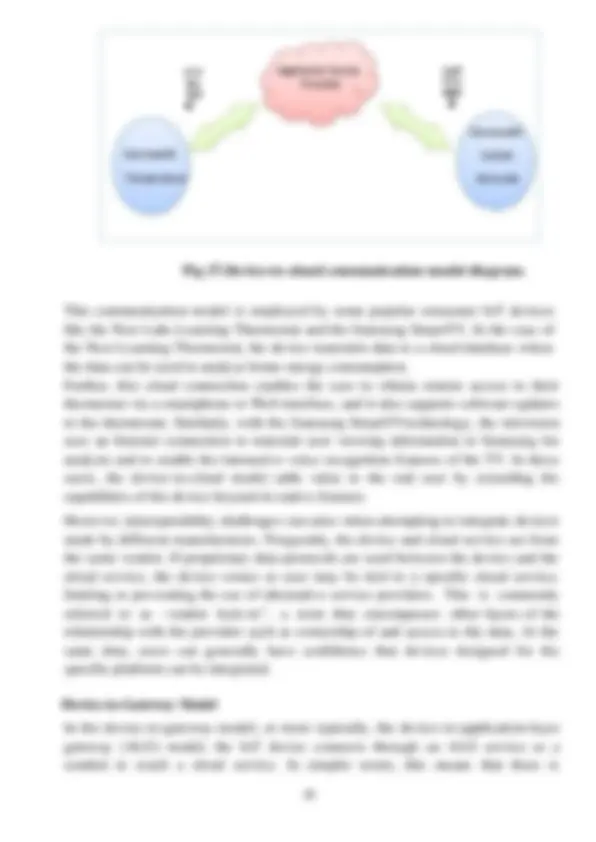
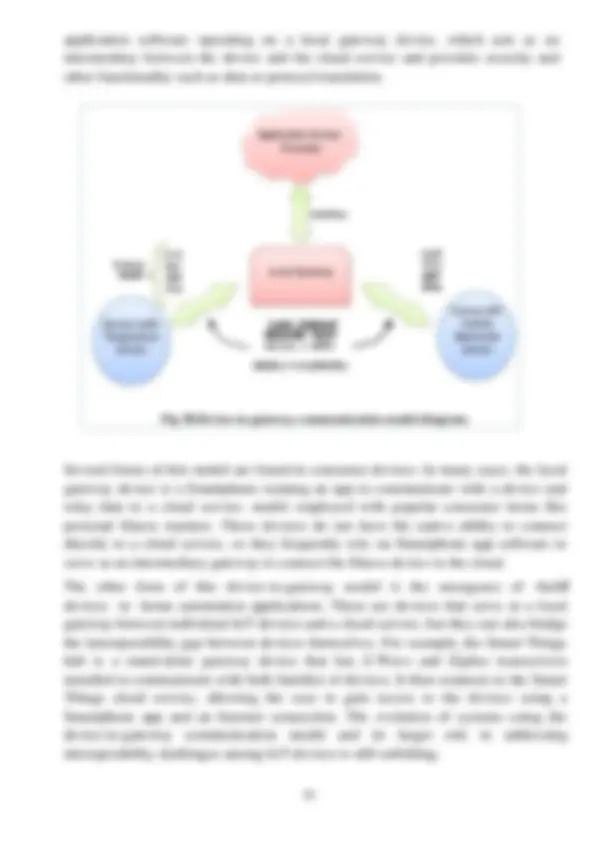
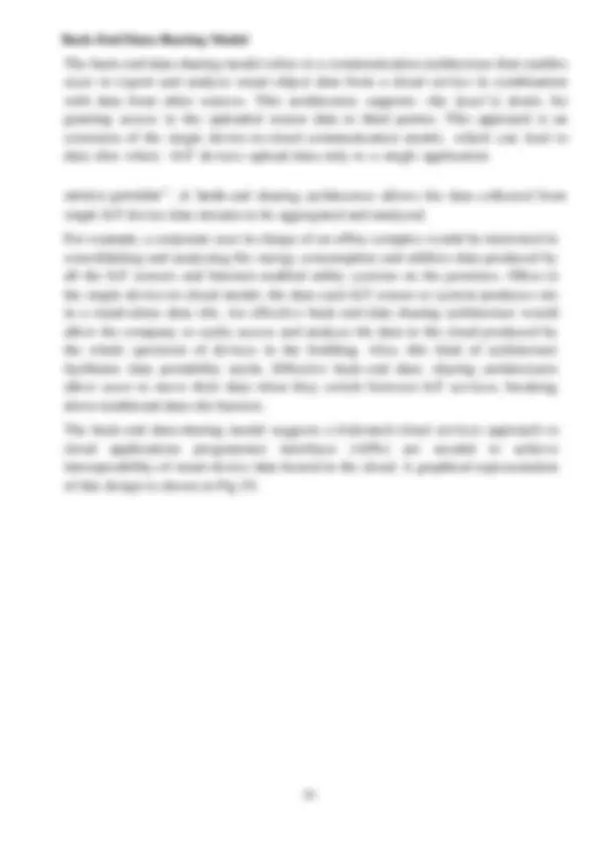
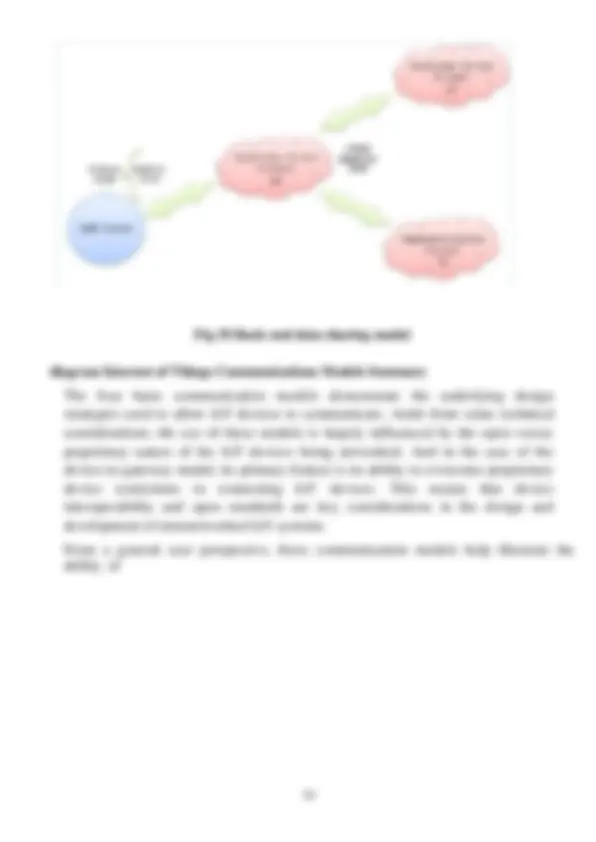
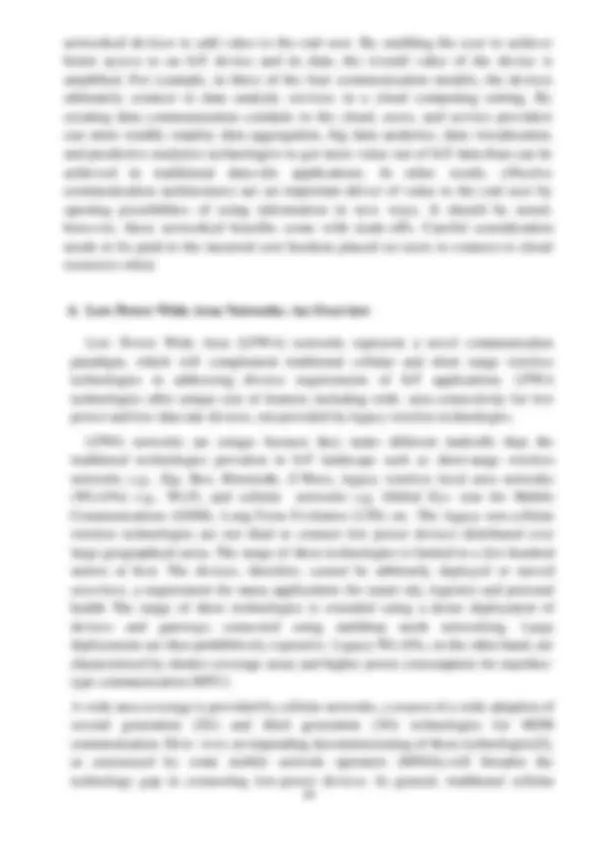
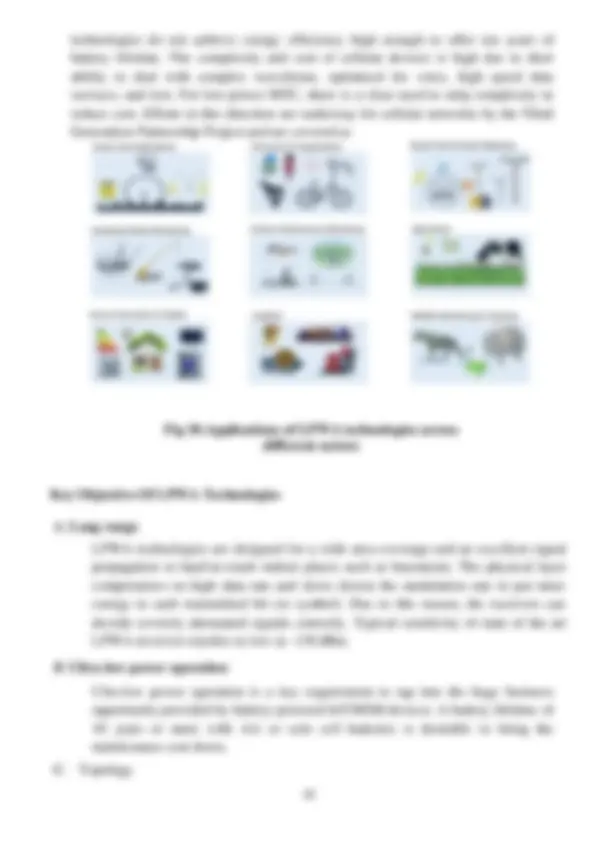
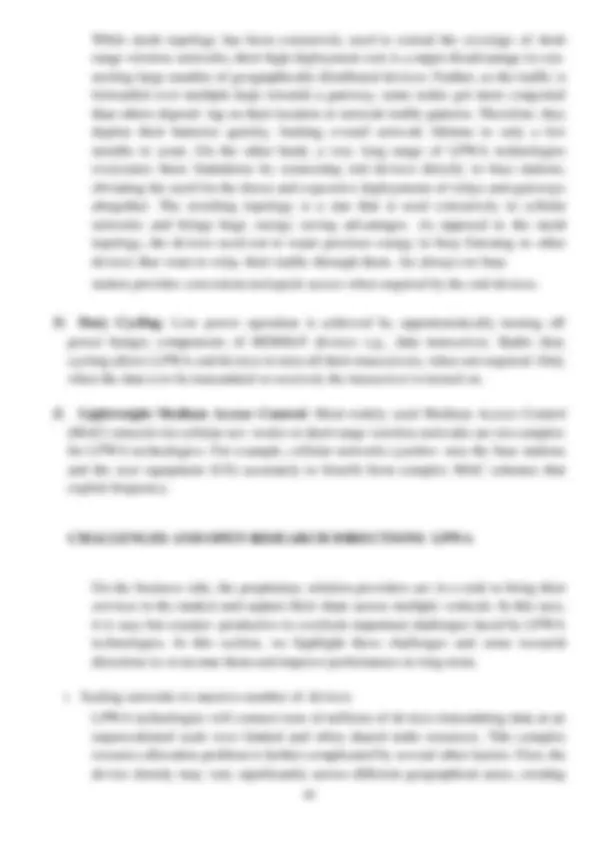
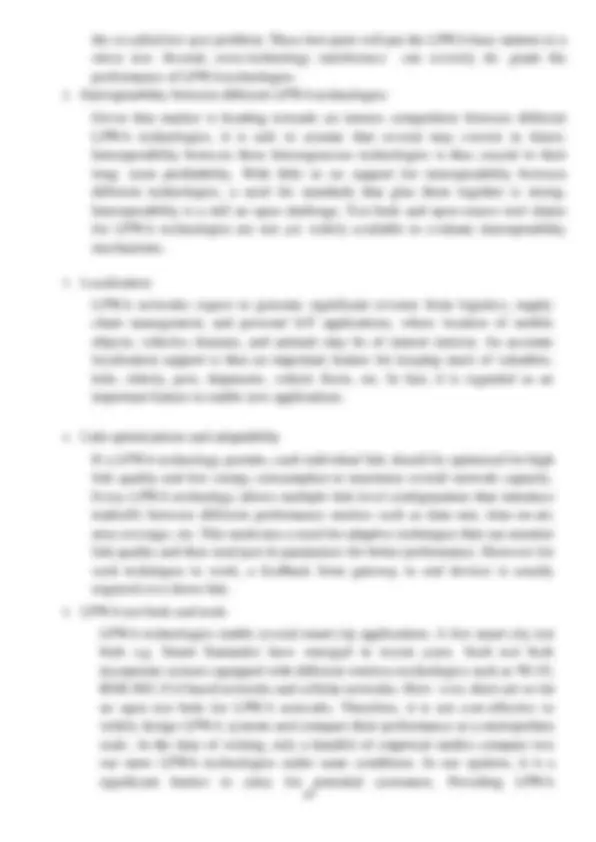
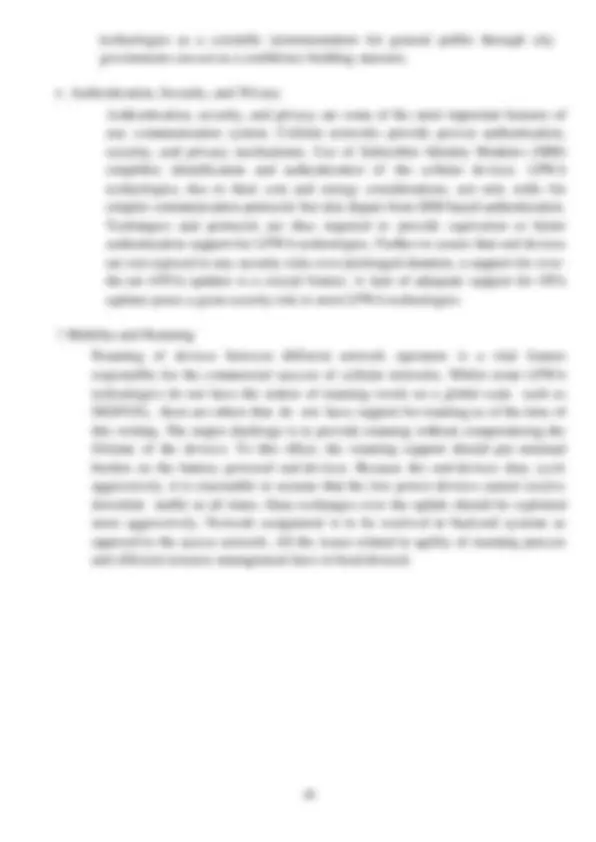
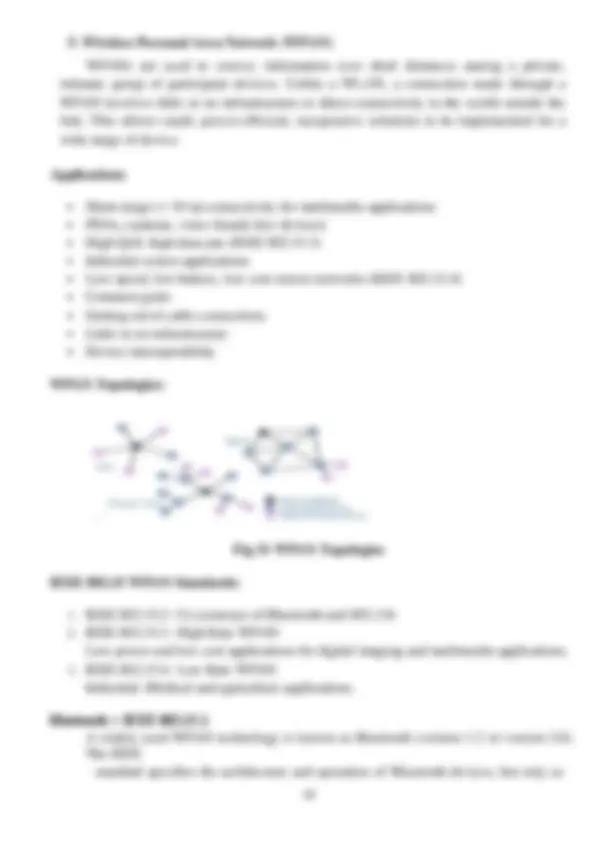
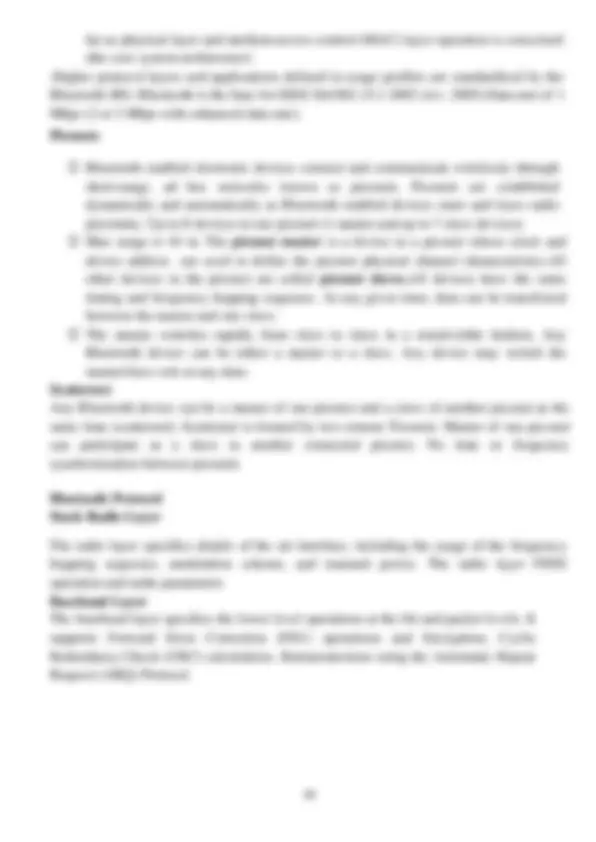
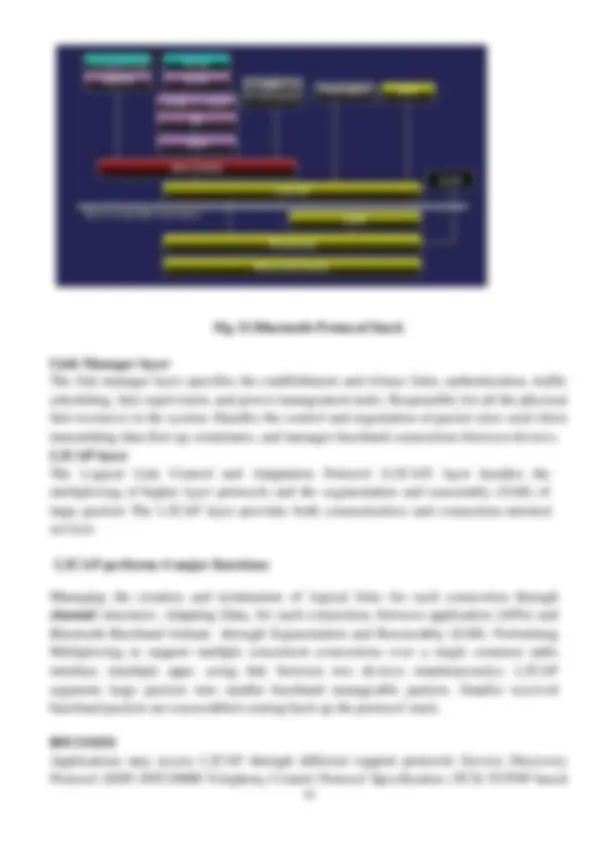
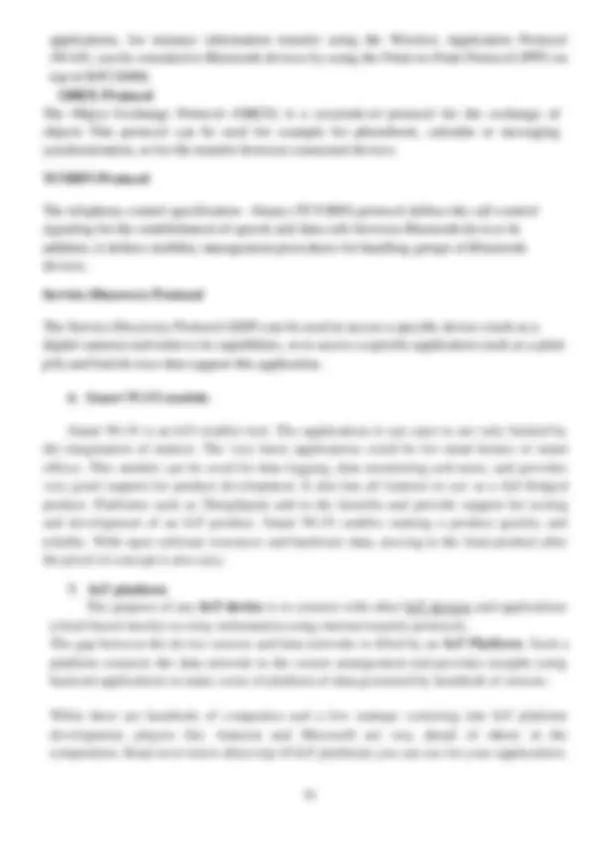
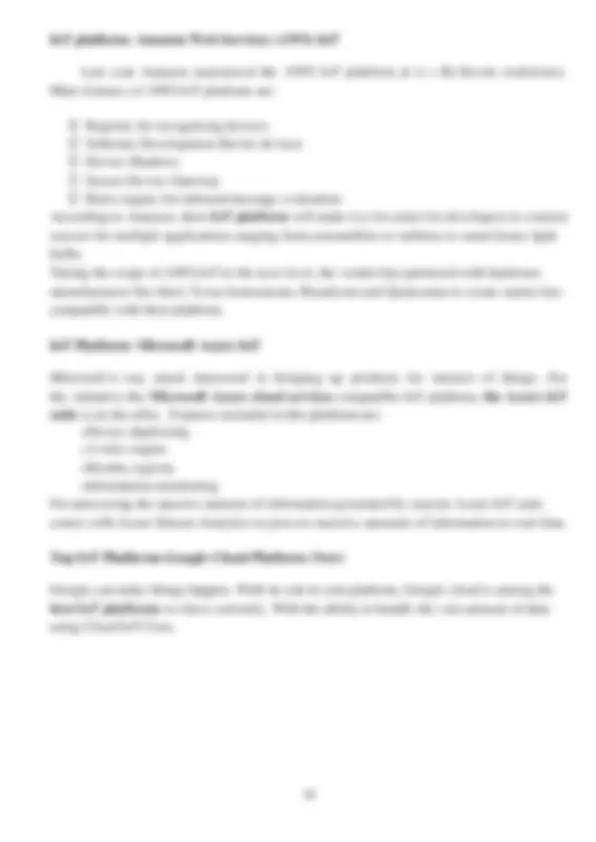
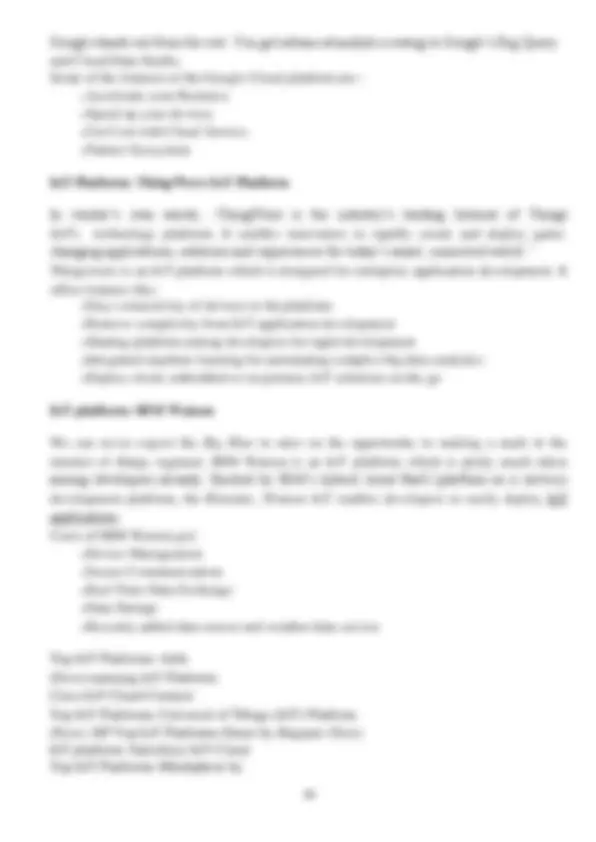
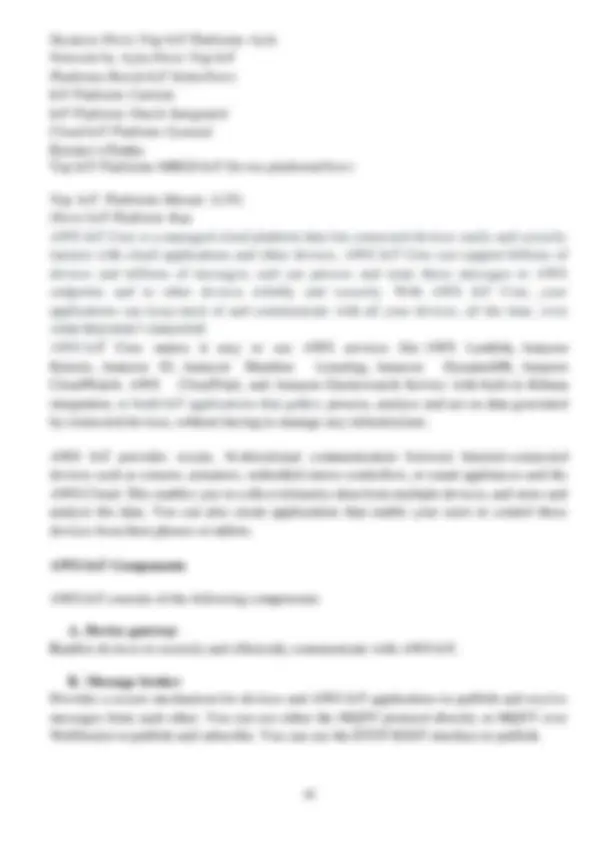
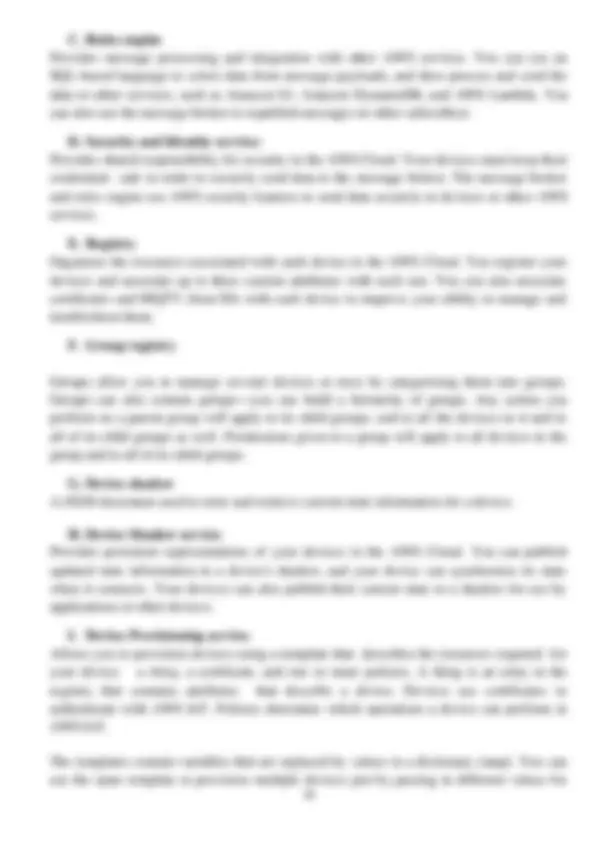
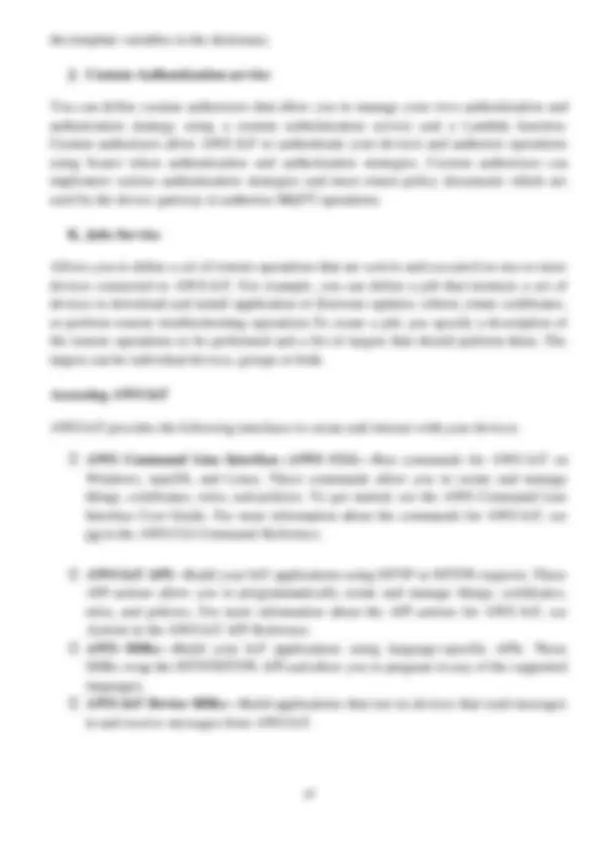
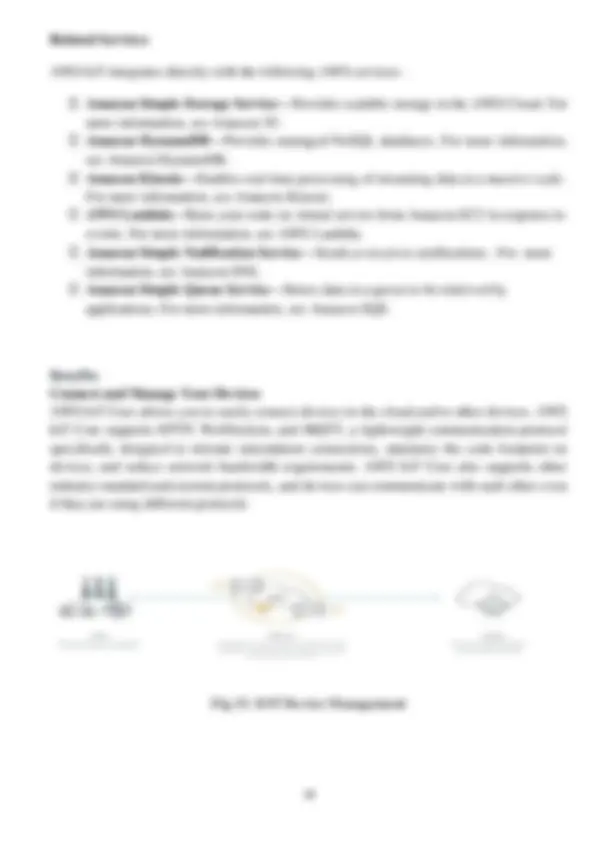
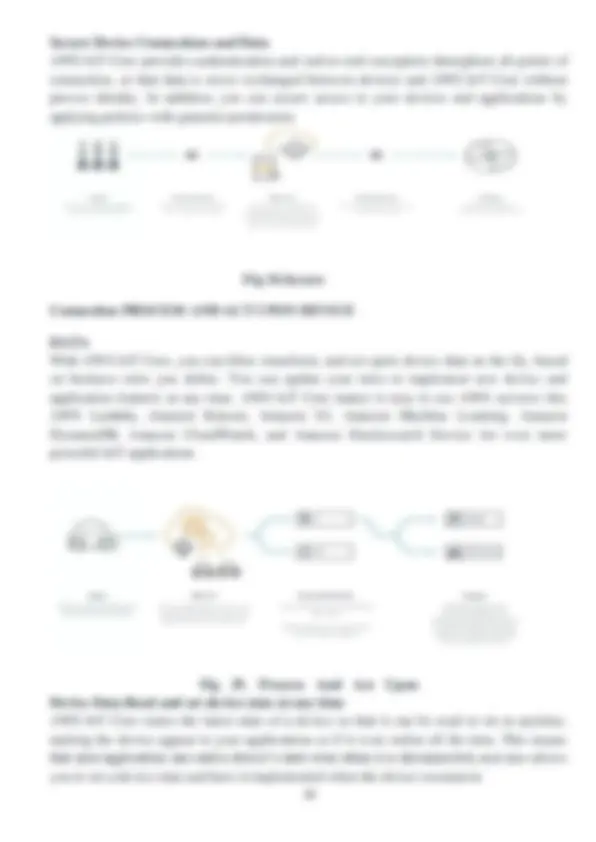
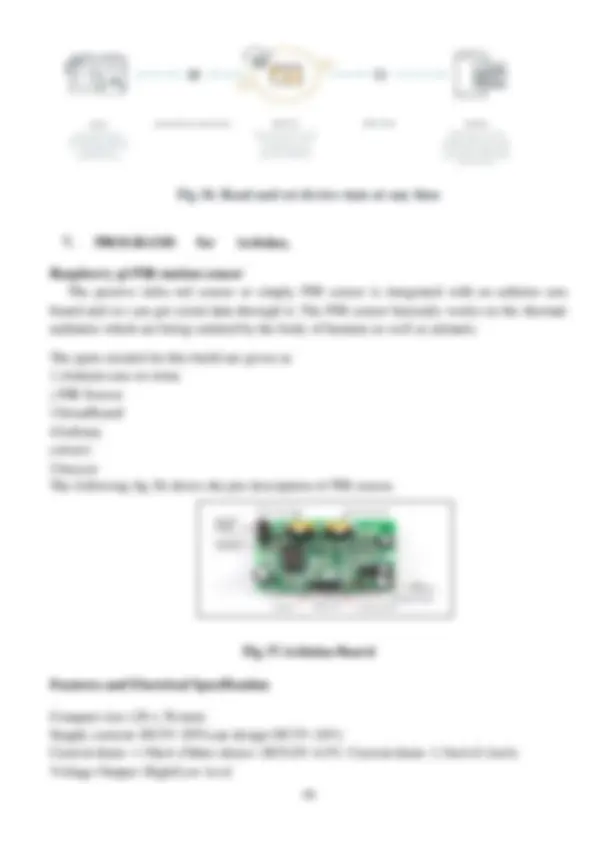
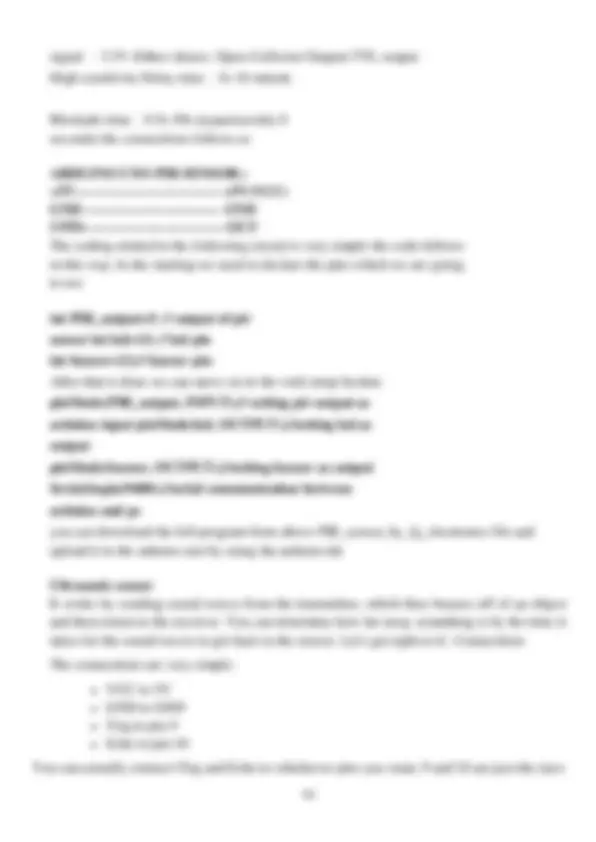
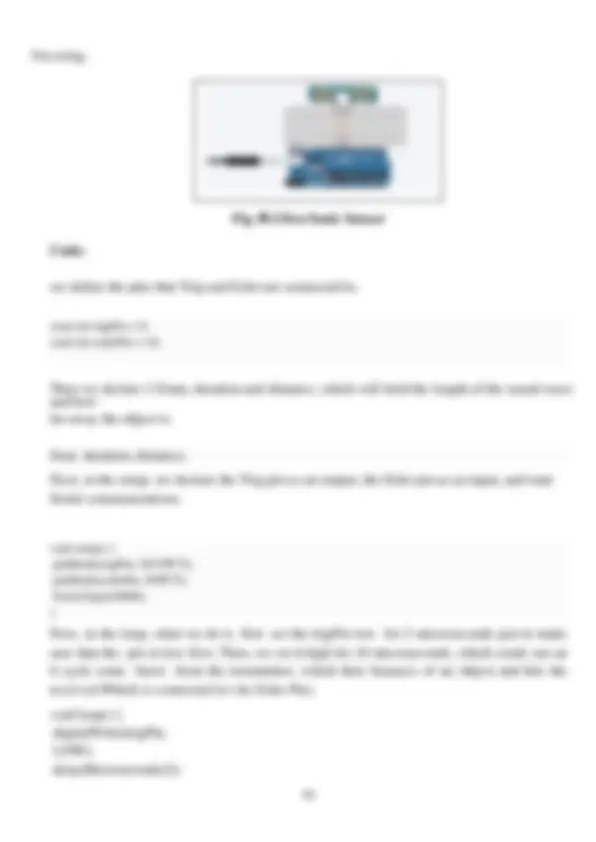
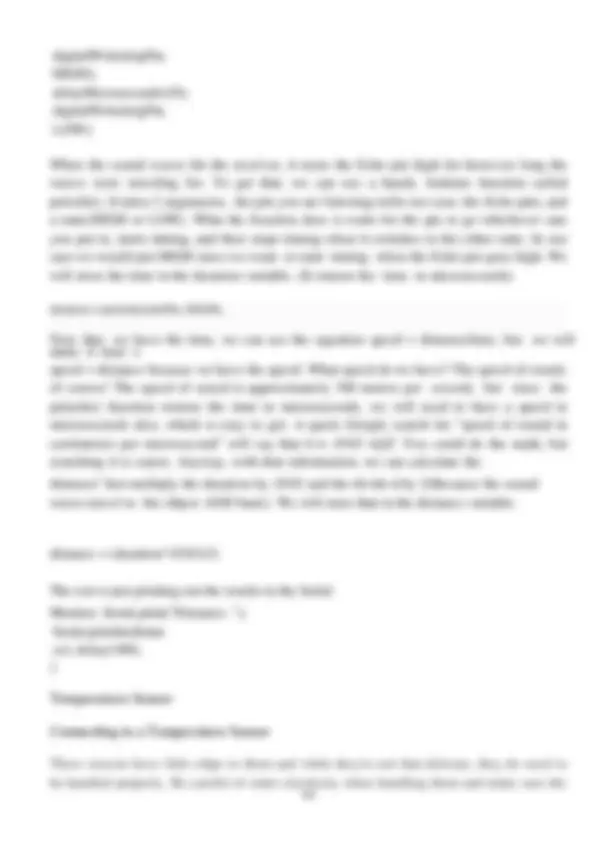
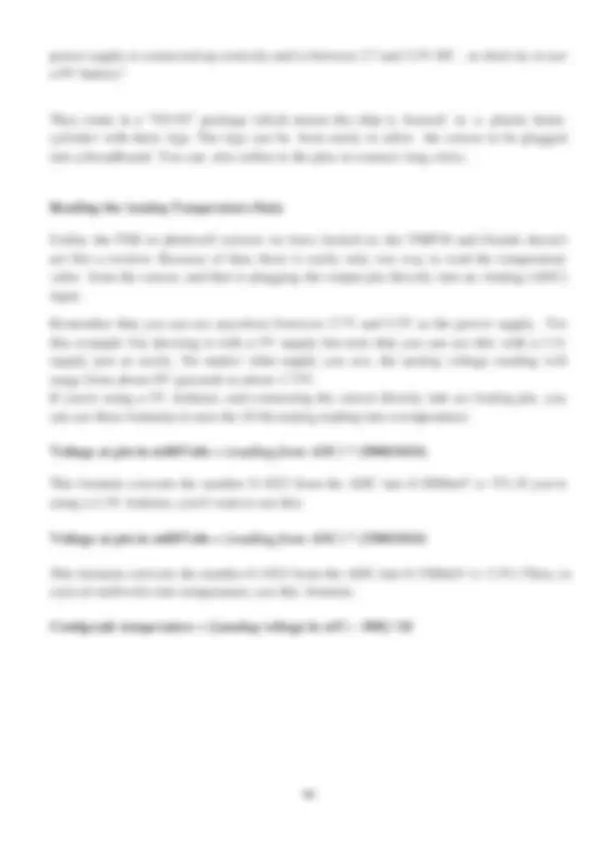
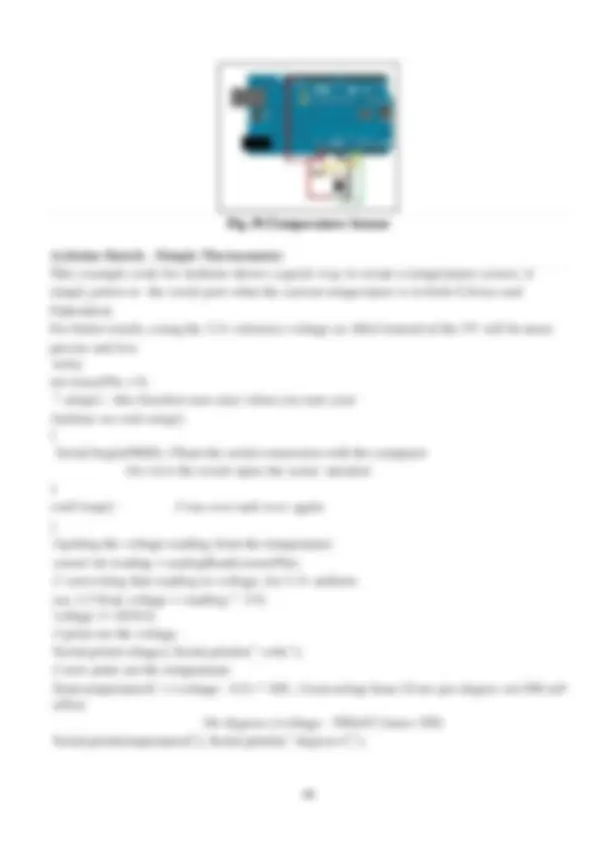

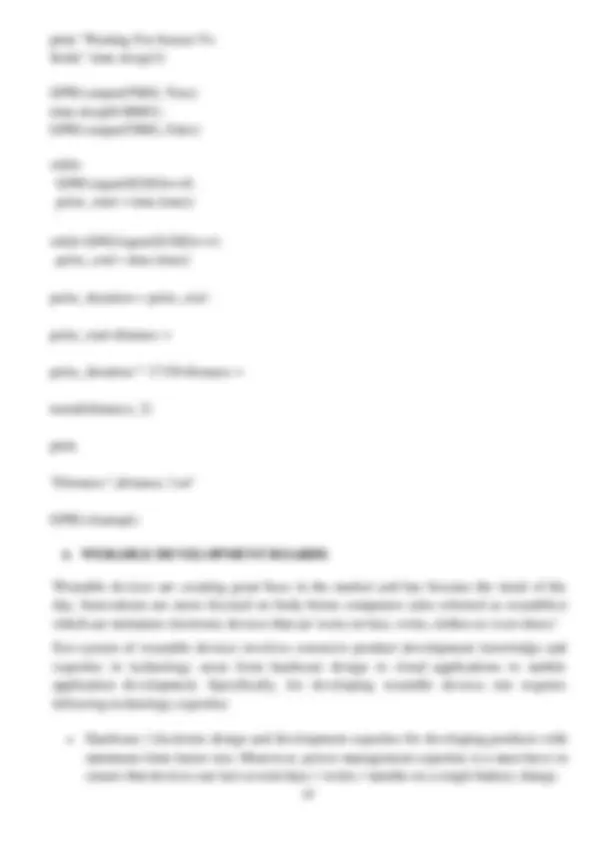
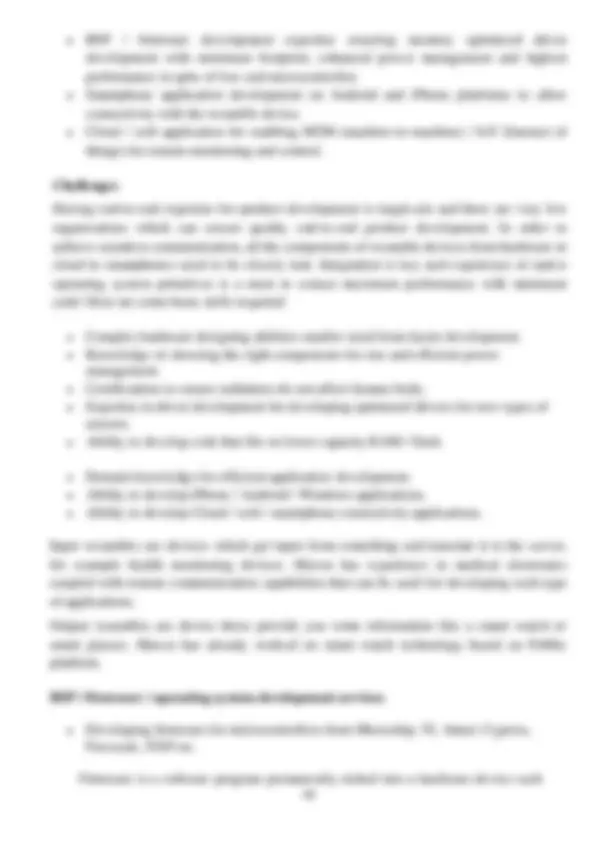
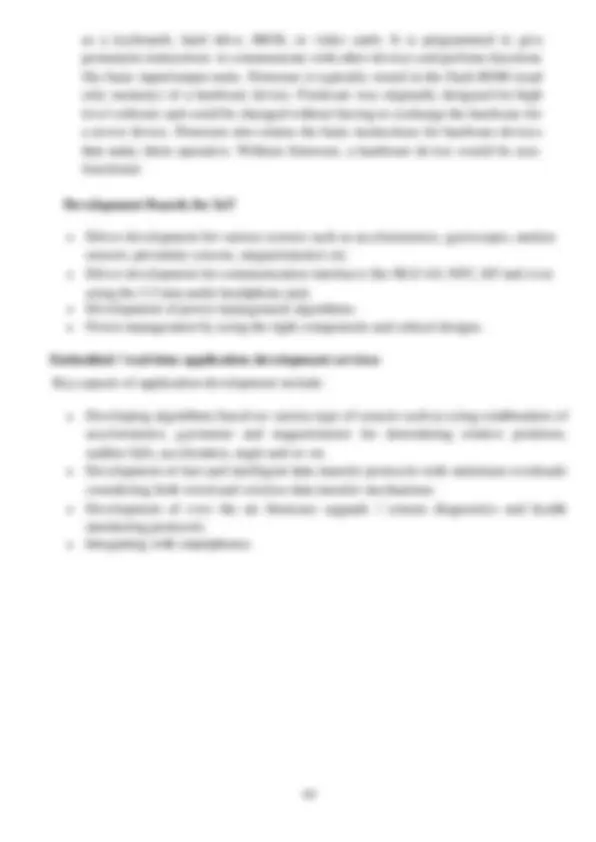
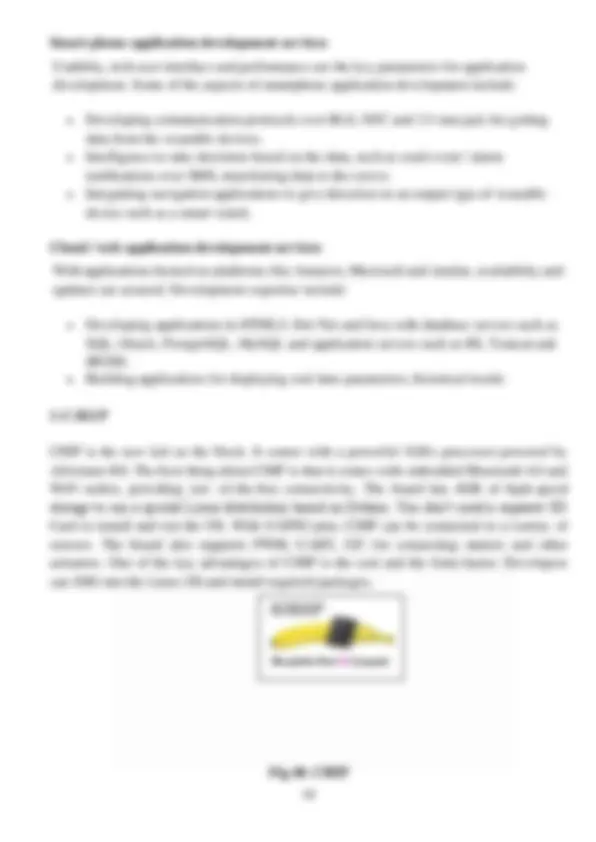
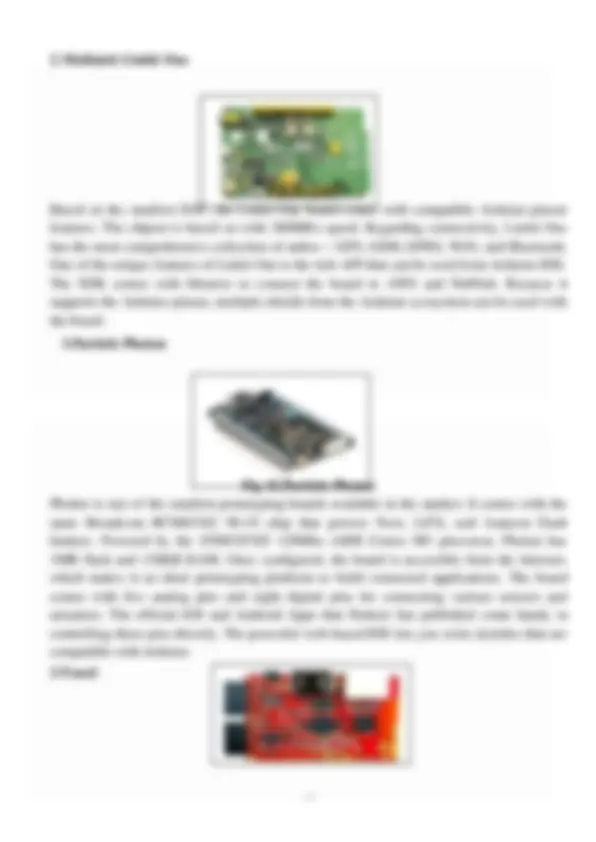
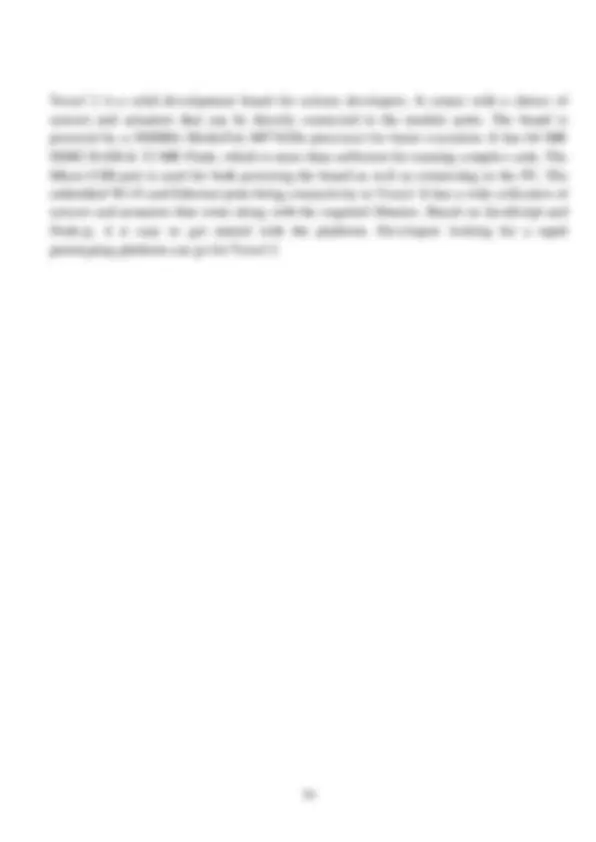
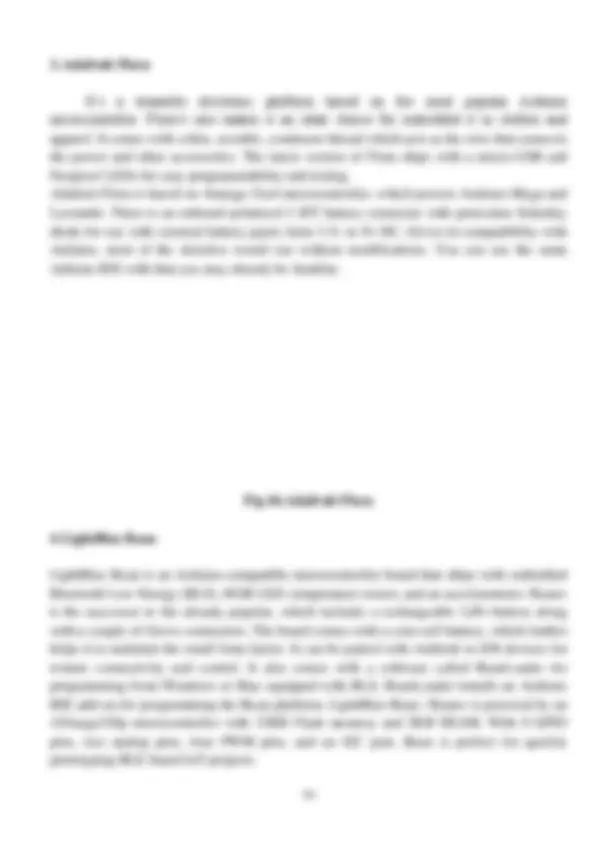
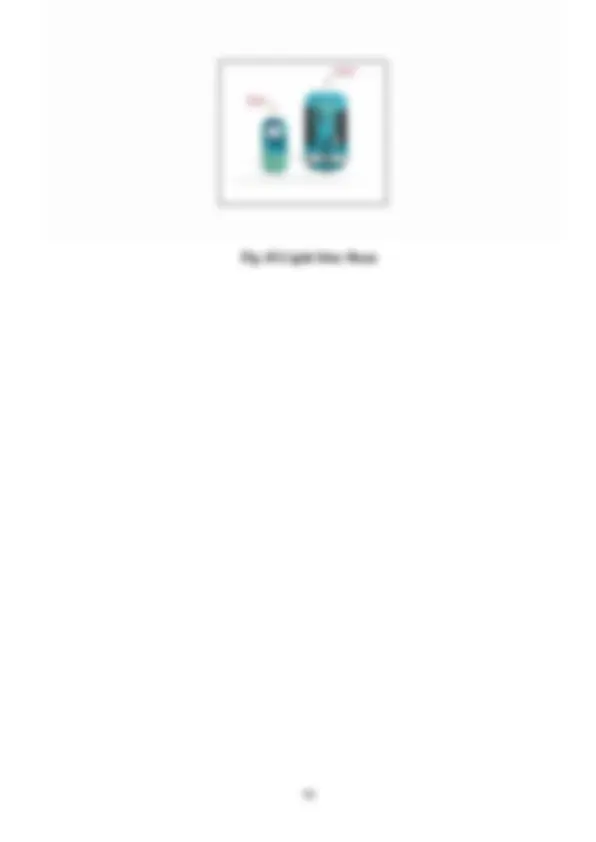
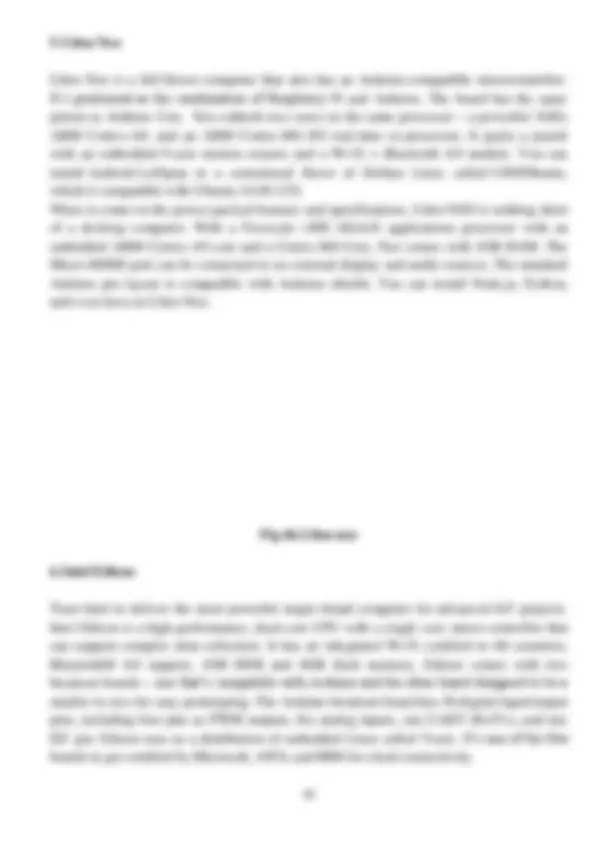
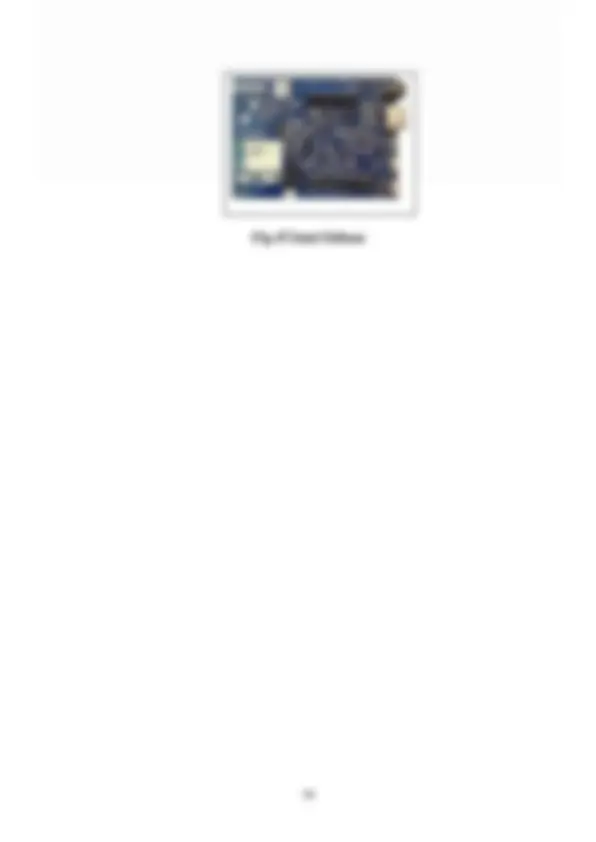
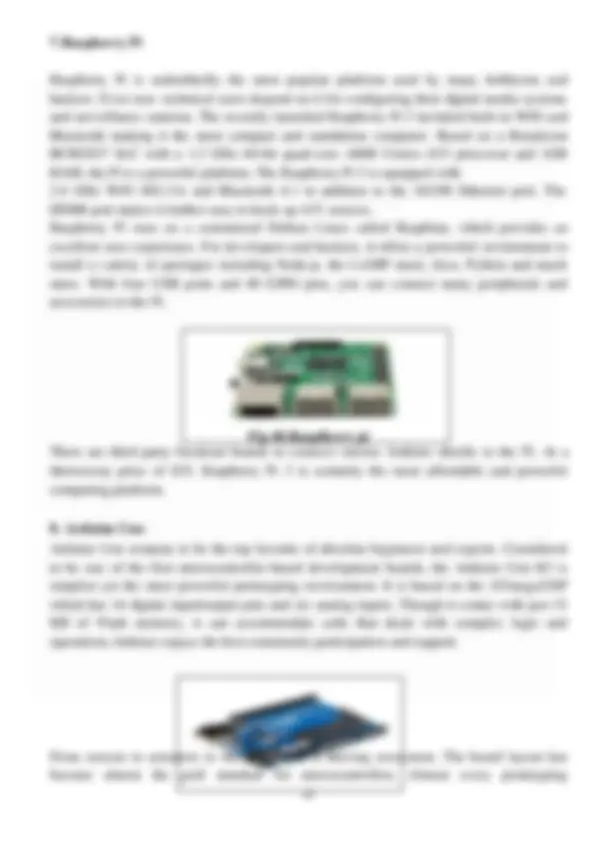
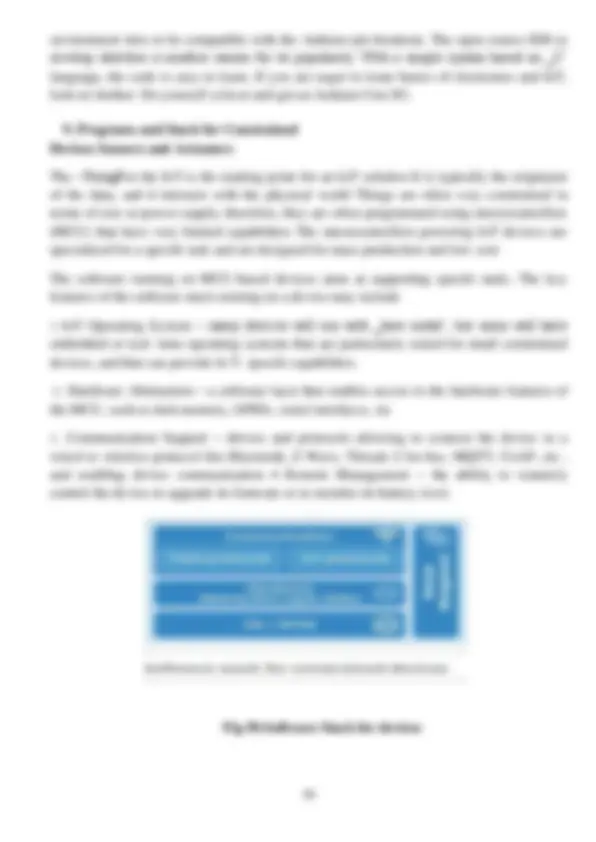
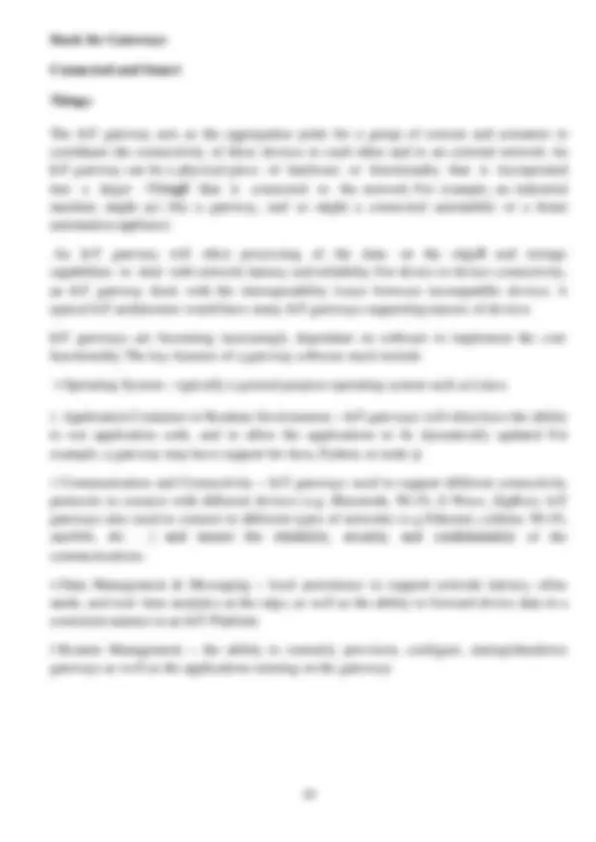
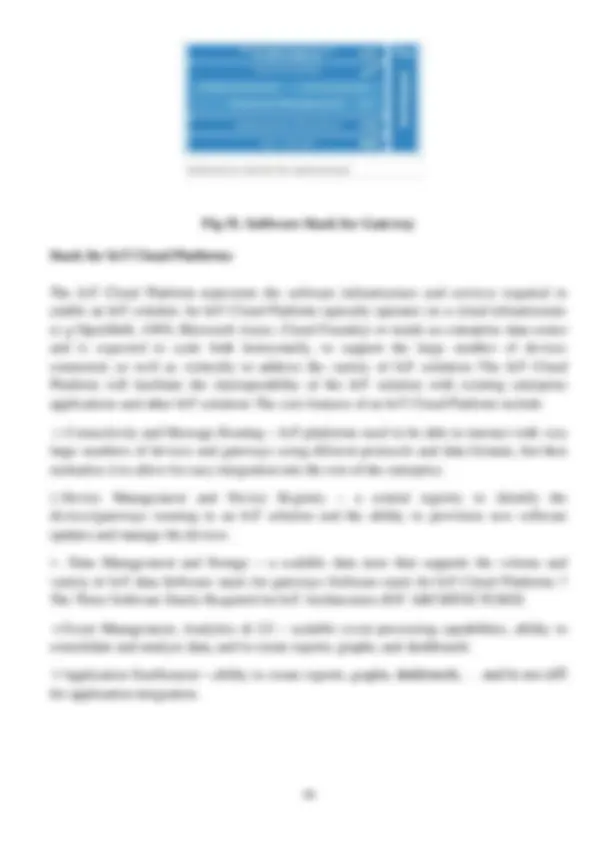
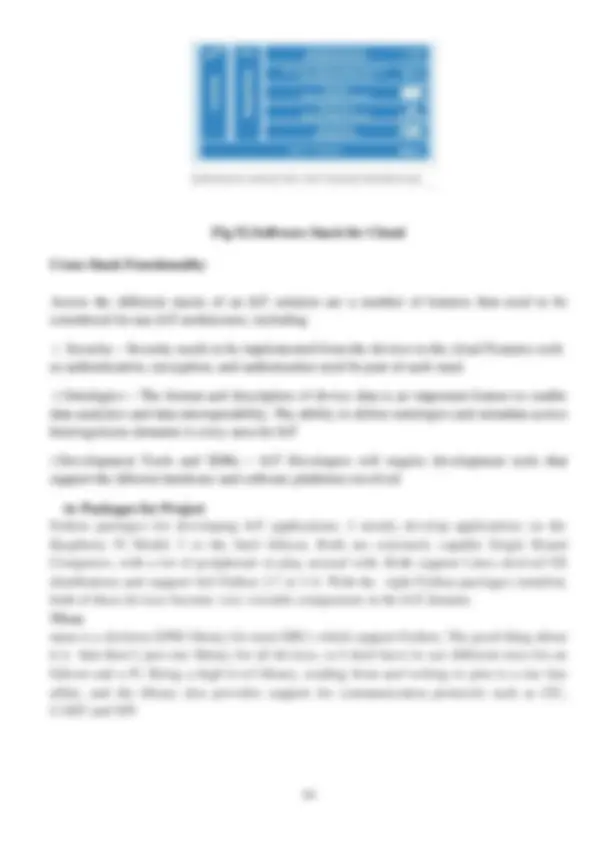
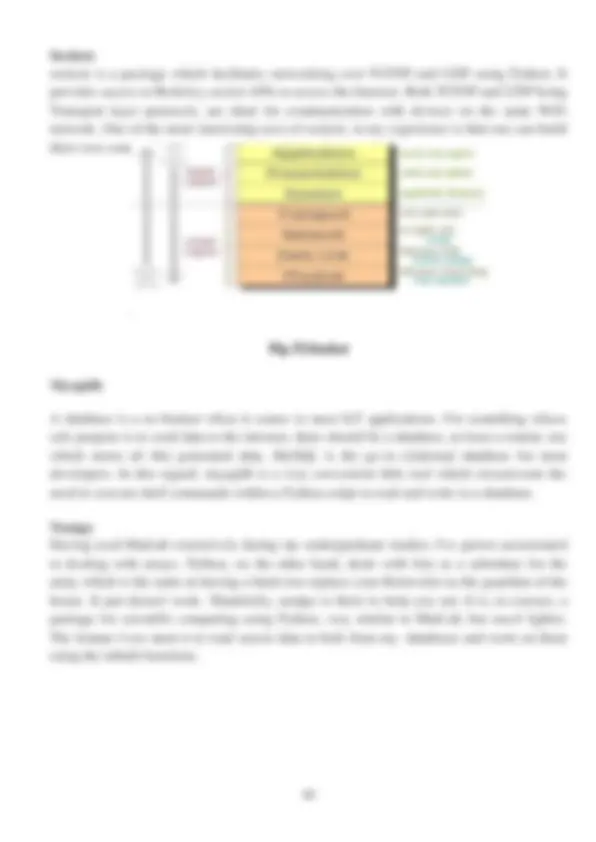
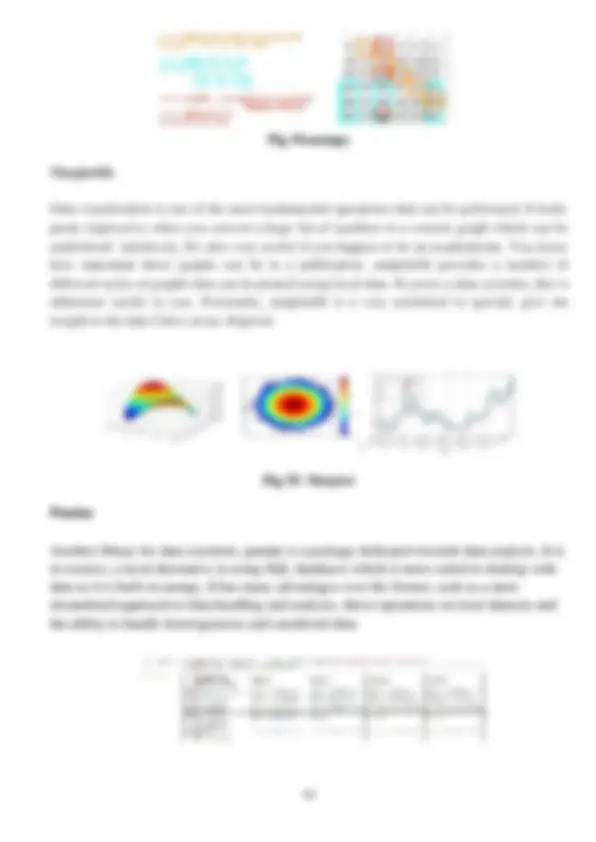
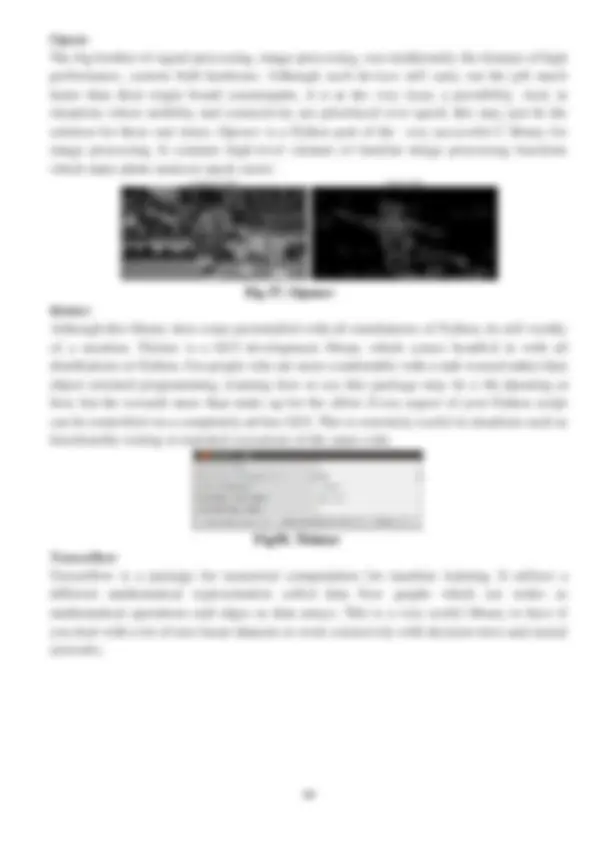
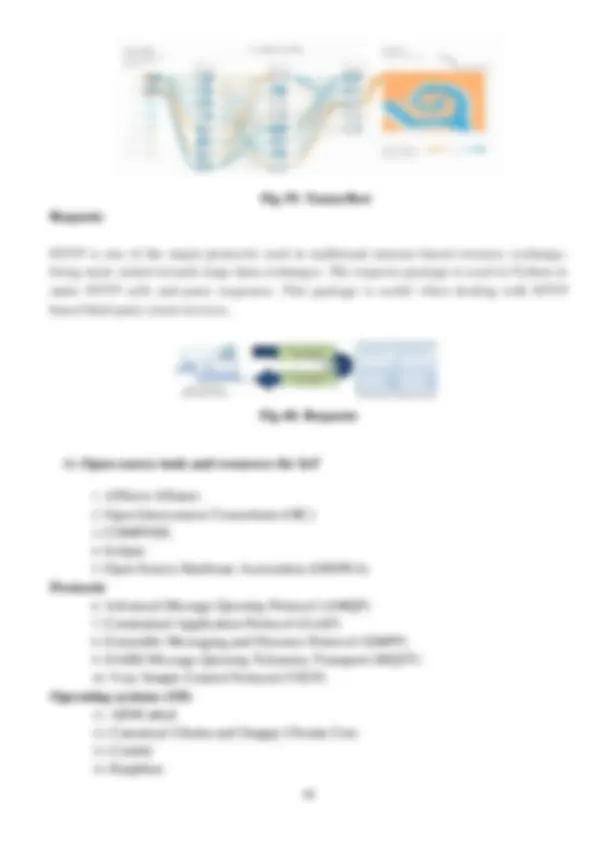
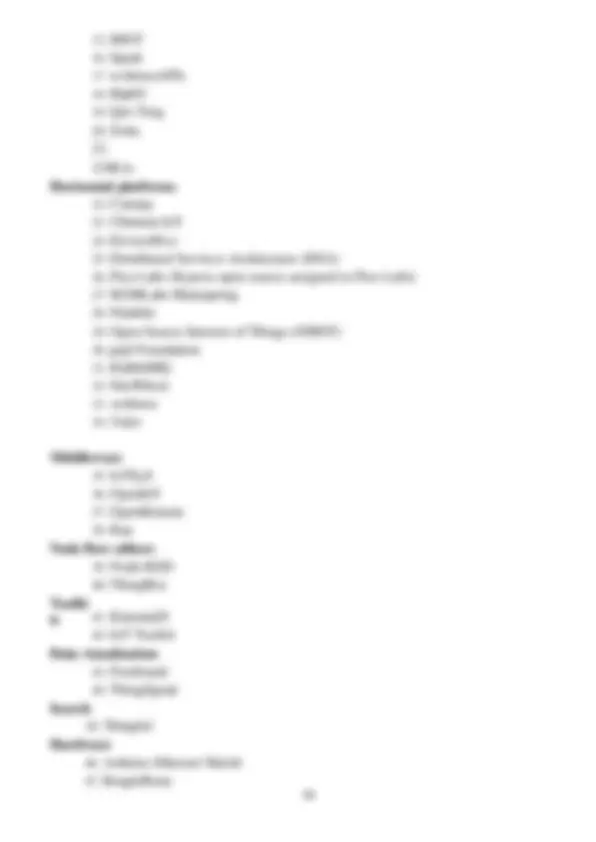
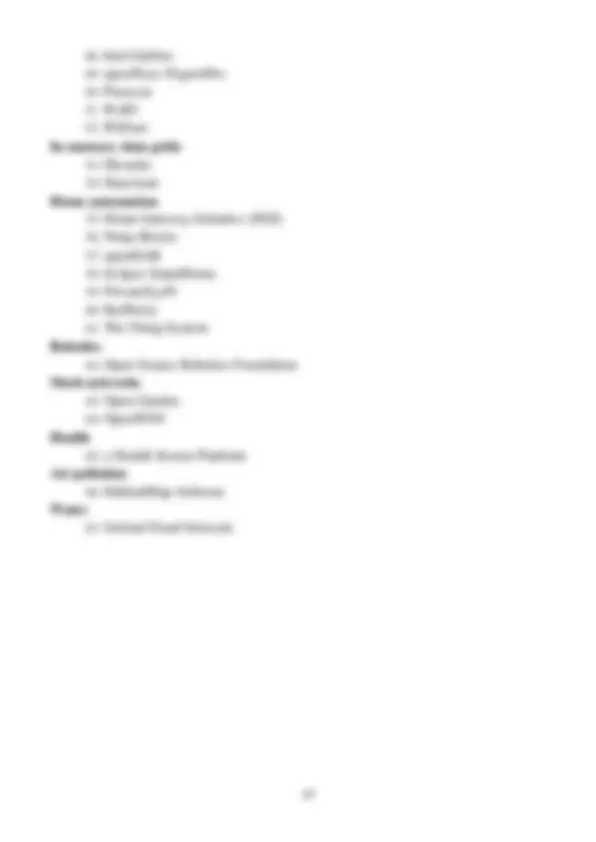
Study with the several resources on Docsity
Earn points by helping other students or get them with a premium plan
Prepare for your exams
Study with the several resources on Docsity
Earn points to download
Earn points by helping other students or get them with a premium plan
Community
Ask the community for help and clear up your study doubts
Discover the best universities in your country according to Docsity users
Free resources
Download our free guides on studying techniques, anxiety management strategies, and thesis advice from Docsity tutors
An overview of Internet of Things (IoT) communication models, focusing on device-to-device and device-to-gateway communications. It also introduces various IoT platforms and their components. Students and professionals interested in IoT development can benefit from this document as study notes, summaries, or cheat sheets.
Typology: Summaries
1 / 67
This page cannot be seen from the preview
Don't miss anything!
Application Sensors & Actuators - Edge Networking (WSN) – Gateways - IoT Communication Model – WPAN & LPWA, IoT platform for available applications, Hardware Devices: Arduino, Raspberry pi and Smartwifi, etc, Wearable Development Boards, Softwares, Programs and Stacks available for building IoT applications, Installation of various packages necessary for project and list of tools.
1.SENSORS AND ACTUATORS
A transducer is any physical device that converts one form of energy into another. So, in the case of a sensor, the transducer converts some physical phenomenon into an electrical impulse that can then be interpreted to determine a reading. A microphone is a sensor that takes vibration energy (sound waves), and converts it to electrical energy in a useful way for other components in the system to correlate back to the original sound.
Another type of transducer that we will encounter in many IoT systems is an actuator. In simple terms, an actuator operates in the reverse direction of a sensor. It takes an electrical input and turns it into physical action. For instance, an electric motor, a hydraulic system, and a pneumatic system are all different types of actuators.
Examples of actuators
Digital micromirror device Electric motor Electroactive polymer Hydraulic cylinder Piezoelectric actuator Pneumatic actuator Screw jack Servomechanism Solenoid Stepper motor
In typical IoT systems, a sensor may collect information and route to a control center where a decision is made and a corresponding command is sent back to an actuator in response to that sensed input. There are many different types of sensors. Flow sensors, temperature sensors, voltage sensors, humidity sensors, and the list goes on. In addition, there are multiple ways to measure the same thing. For instance, airflow might be measured by using a small propeller like the one you would see on a weather station. Alternatively, as in a vehicle measuring the air through the engine, airflow is measured by heating a small
Power (current) sensor
Home/office/industrial powermonitoring/control Technology
Coil (Faraday‘s law), Hall effect
Air/fluid pressure sensor
Industrial monitoring/control, automotive, agriculture
Capacitive, Resistive
9. Acoustic sensor^
Industrial monitoring/control, human interface
Diaphragm condenser
10. Strain sensor
Industrial monitoring/control, civil infrastructure
Resistive thin films
In the first classification of the sensors, they are divided in to Active and Passive. Active Sensors are those which require an external excitation signal or a power signal. Passive Sensors, on the other hand, do not require any external power signal and directly generates output response. The other type of classification is based on the means of detection used in the sensor. Some of the means of detection are Electric, Biological, Chemical, Radioactive etc. The next classification is based on conversion phenomenon i.e. the input and the output. Some of the common conversion phenomena are Photoelectric, Thermoelectric, Electrochemical, Electromagnetic, Thermo-optic, etc. The final classification of the sensors are Analog and Digital Sensors. Analog Sensors produce an analog output i.e. a continuous output signal with respect to the quantity being measured. Digital Sensors, in contrast to Analog Sensors, work with discrete or digital data. The data in digital sensors, which is used for conversion and transmission, is digital in nature.
Fig 1.Examples of Sensors
1. IR LED
It is also called as IR Transmitter. It is used to emit Infrared rays. The range of these frequencies are greater than the microwave frequencies (i.e. >300GHz to few hundreds of THz). The rays generated by an infrared LED can be sensed by Photodiode explained below. The pair of IR LED and photodiode is called IR Sensor.
Fig 2. LED sensor
2. Photo Diode (Light Sensor)
It is a semiconductor device which is used to detect the light rays and mostly used as IR Receiver. Its construction is similar to the normal PN junction diode but the working principle differs from it. As we know a PN junction allows small leakage currents when it is reverse biased so, this property is used to detect the light rays. A photodiode is constructed such that light rays should fall on the PN junction which makes the leakage current increase based on the intensity of the light that we have applied. So, in this way, a
photodiode can be used to sense the light rays and maintain the current through the circuit. Check here the working of Photodiode with IR sensor.
Fig 3.Photo diode
3. Proximity Sensor
A Proximity Sensor is a non-contact type sensor that detects the presence of an object. Proximity Sensors can be implemented using different techniques like Optical (like Infrared or Laser), Ultrasonic, Hall Effect, Capacitive, etc.
temperature coefficient that means when the temperature increases the resistance decreases. So, the thermistor‘s resistance can be varied with the rise in temperature which causes more current flow through it. This change in current flow can be used to determine the amount of change in temperature. An application for thermistor is, it is used to detect the rise in temperature and control the leakage current in a transistor circuit which helps in maintaining its stability. Here is one simple application for Thermistor to control the DC fan automatically.
Fig 6.Thermistor
6. Thermocouple (Temperature Sensor)
Another component that can detect the variation in temperature is a thermocouple. In its construction, two different metals are joined together to form a junction. Its main principle is when the junction of two different metals are heated or exposed to high temperatures a potential across their terminals varies. So, the varying potential can be further used to measure the amount of change in temperature.
Fig 7.Thermo couple
7. Strain Gauge (Pressure/Force Sensor)
A strain gauge is used to detect pressure when a load is applied. It works on the principle of resistance, we know that the resistance is directly proportional to the length of the wire and is inversely proportional to its cross-sectional area (R=ρl/a). The same principle can be used here to measure the load. On a flexible board, a wire is arranged in a zig-zag manner as shown in the figure below. So, when the pressure is applied to that particular board, it bends in a direction causing the change in overall length and cross- sectional area of the wire. This leads to change in resistance of the wire. The resistance thus obtained is very minute (few ohms) which can be determined with the help of the Wheatstone bridge. The strain gauge is placed in one of the four arms in a bridge with the remaining values unchanged. Therefore, when the pressure is applied to it as the resistance changes the current passing through the bridge varies and pressure can be calculated.
Strain gauges are majorly used to calculate the amount of pressure that an airplane wing can withstand and it is also used to measure the number of vehicles allowable on a particular road etc.
Fig 8.Strain Guage
8. Load Cell (Weight Sensor)
Load cells are similar to strain gauges which measure the physical quantity like force and give the output in form of electrical signals. When some tension is applied on the load cell it structure varies causing the change in resistance and finally, its value can be calibrated
given conductor. Using this property a Hall sensor is used to detect the magnetic field and gives output in terms of voltage. Care should be taken that the Hall sensor can detect only one pole of the magnet.
Fig 12.Hall sensor
The hall sensor is used in few smartphones which are helpful in turning off the screen when the flap cover (which has a magnet in it) is closed onto the screen. Here is one practical application of Hall Effect sensor in Door Alarm.
12. Flex Sensor
A FLEX sensor is a transducer which changes its resistance when its shape is changed or when it is bent_._ A FLEX sensor is 2.2 inches long or of finger length. Simply speaking the sensor terminal resistance increases when it‘s bent. This change in resistance can do no good unless we can read them. The controller at hand can only read the changes in
voltage and nothing less, for this, we are going to use voltage divider circuit, with that we can derive the resistance change as a voltage change.
Fig 13. Flex sensor
13.Microphone (Sound Sensor)
Microphone can be seen on all the smartphones or mobiles. It can detect the audio signal and convert them into small voltage (mV) electrical signals. A microphone can be of many types like condenser microphone, crystal microphone, carbon microphone etc. each type of microphone work on the properties like capacitance, piezoelectric effect, resistance respectively. Let us see the operation of a crystal microphone which works on the
piezoelectric effect. A bimorph crystal is used which under pressure or vibrations produces proportional alternating voltage. A diaphragm is connected to the crystal through a drive pin such that when the sound signal hits the diaphragm it moves to and fro, this movement changes the position of the drive pin which causes vibrations in the crystal thus an alternating voltage is generated with respect to the applied sound signal. The obtained voltage is fed to an amplifier in order to increase the overall strength of the signal.
Fig 14.Microphone
14.Ultrasonic sensor
Ultrasonic means nothing but the range of the frequencies. Its range is greater than audible range (>20 kHz) so even it is switched on we can‘t sense these sound signals. Only specific speakers and receivers can sense those ultrasonic waves. This ultrasonic sensor is used to calculate the distance between the ultrasonic transmitter and the target and also used to measure the velocity of the target.
Ultrasonic sensor HC-SR04 can be used to measure distance in the range of 2cm-400cm with an accuracy of 3mm. Let‘s see how this module works. The HCSR04 module generates a sound vibration in ultrasonic range when we make the ‗Trigger‘ pin high for about 10us which will send an 8 cycle sonic burst at the speed of sound and after striking the object, it will be received by the Echo pin. Depending on the time taken by sound vibration to get back, it provides the appropriate pulse output. We can calculate the distance of the object based on the time taken by the ultrasonic wave to return back to the sensor.
Fig 15.Utrasonic sensor
Fig 17.PIR Sensor
17.Accelerometer (Tilt Sensor)
An accelerometer sensor can sense the tilt or movement of it in a particular direction. It works based on the acceleration force caused due to the earth‘s gravity. The tiny internal parts of it are such sensitive that those will react to a small external change in position. It has a piezoelectric crystal when tilted causes disturbance in the crystal and generates
potential which determines the exact position with respect to X, Y and Z axis.
Fig 18.Accelerometer
These are commonly seen in mobiles and laptops in order to avoid breakage of processors leads. When the device falls the accelerometer detects the falling condition and does respective action based on the software.
18.Gas sensor
In industrial applications gas sensors plays a major role in detecting the gas leakage. If no such device is installed in such areas it ultimately leads to an unbelievable disaster. These gas sensors are classified into various types based on the type of gas that to be detected. Let‘s see how this sensor works. Underneath a metal sheet there exists a sensing element which is connected to the terminals where a current is applied to it. When the gas particles
hit the sensing element, it leads to a chemical reaction such that the resistance of the elements varies and current through it also alters which finally can detect the gas.
Fig 19.Gas Sensor
So finally, we can conclude that sensors are not only used to make our work simple to measure the physical quantities, making the devices automated but also used to help living beings with disasters.
19. Resistive Sensors
Resistive sensors, such as the potentiometer, have three terminals: power input, grounding terminal, and variable voltage output. These mechanical devices have varied resistance that can be changed through movable contact with its fixed resistor. Output from the sensor varies depending on whether the movable contact is near the resistor's supple end or
ground end. Thermistors are also variable resistors, although the resistance of the sensor varies with temperature
Fig 20 Resistive Sensors
20.Voltage generating sensors
Voltage-generating sensors, such as piezo electrics, generate electricity by pressure with types of crystals like quartz. As the crystal flexes or vibrates, AC voltage is produced. Knock sensors utilize this technology by sending a signal to an automobile's on-board computer that engine knock is happening. The signal is generated through crystal vibration within the sensor, which is caused by cylinder block vibration. The computer, in turn, reduces the ignition timing to stop the engine knock.
21.Switch Sensors
Fig 21.Voltage Generating Sensors
So to better understand how to build IoT devices, you first need to figure out how they will communicate with the rest of the world.
Local Network Your choice of communication technology directly affects your device‘s hardware requirements and costs. Which networking technology is the best choice? IoT devices are deployed in so many different ways — in clothing, houses, buildings, campuses, factories, and even in your body — that no single networking technology can fit all bills.
Let‘s take a factory as a typical case for an IoT system. A factory would need a large number of connected sensors and actuators scattered over a wide area, and a wireless technology would be the best fit.
Fig 24.Wireless Sensor Network Architecture
A wireless sensor network (WSN) is a collection of distributed sensors that monitor physical or environmental conditions, such as temperature, sound, and pressure. Data from each sensor passes through the network node-to-node. WSN Nodes WSN nodes are low cost devices, so they can be deployed in high volume. They also operate at low power so that they can run on battery, or even use energy harvesting. A WSN node is an embedded system that typically performs a single function (such as measuring temperature or pressure, or turning on a light or a motor). Energy harvesting is a new technology that derives energy from external sources (for example, solar power, thermal energy, wind energy, electromagnetic radiation, kinetic energy, and more). The energy is captured and stored for use by small, low-power wireless autonomous devices, like the nodes on a WSN.
Fig 25.Edge Nodes
WSN Edge Nodes
A WSN edge node is a WSN node that includes Internet Protocol connectivity. It acts as a gateway between the WSN and the IP network. It can also perform local processing, provide local storage, and can have a user interface.
Fig 25.WSN Edge
WSN Technologies
The battle over the preferred networking protocol is far from over. There are multiple candidates. Wi-Fi The first obvious networking technology candidate for an IoT device is Wi-Fi, because it is so ubiquitous. Certainly, Wi-Fi can be a good solution for many applications. Almost every house that has an Internet connection has a Wi-Fi router. However, Wi-Fi needs a fair amount of power. There are myriad devices that can‘t afford that level of power: battery operated devices, for example, or sensors positioned in locations that are difficult to power from the grid.
New application protocols and data formats that enable autonomous operation For example, EnOceanhas patented an energy-harvesting wireless technology to meet the power consumption challenge. EnOcean‘s wireless transmitters work in the frequencies of 868 MHz for Europe and 315 MHz for North America. The transmission range is up to 30 meters in buildings and up to 300 meters outdoors.
EnOcean wireless technology uses a combination of energy harvesting and very low power wireless communications to enable virtually indefinite communications to be maintained without the need for recharging.
Manufacturer A Bluetooth,Z+Wave,ZigBee Manufacturer B
Fig 26.Example of device-to-device communication model
These device-to-device networks allow devices that adhere to a particular communication protocol to communicate and exchange messages to achieve their function. This communication model is commonly used in applications like home automation systems, which typically use small data packets of information to communicate between devices with relatively low data rate requirements. Residential IoT devices like light bulbs, light switches, thermostats, and door locks normally send small amounts of information to each other (e.g. a door lock status message or turn on light command) in a home automation scenario. From the user‘s point of view, this often means that underlying device-to-device communication2 protocols are not compatible, forcing the user to select a family of devices that employ a common protocol. For example, the family of devices using the Z-Wave protocol is not natively compatible with the ZigBee family of devices. While these incompatibilities limit user choice to devices within a particular protocol family, the user benefits from knowing that products within a particular family tend to communicate well.
Device-to-Cloud Communications
In a device-to-cloud communication model, the IoT device connects directly to an Internet cloud service like an application service provider to exchange data and control message traffic. This approach frequently takes advantage of existing communications mechanisms like traditional wired Ethernet or Wi-Fi connections to establish a connection between the device and the IP network, which ultimately connects to the cloud service. This is shown in Figure 27.
Fig 27.Device-to-cloud communication model diagram.
This communication model is employed by some popular consumer IoT devices like the Nest Labs Learning Thermostat and the Samsung SmartTV. In the case of the Nest Learning Thermostat, the device transmits data to a cloud database where the data can be used to analyze home energy consumption. Further, this cloud connection enables the user to obtain remote access to their thermostat via a smartphone or Web interface, and it also supports software updates to the thermostat. Similarly, with the Samsung SmartTVtechnology, the television uses an Internet connection to transmit user viewing information to Samsung for analysis and to enable the interactive voice recognition features of the TV. In these cases, the device-to-cloud model adds value to the end user by extending the capabilities of the device beyond its native features. However, interoperability challenges can arise when attempting to integrate devices made by different manufacturers. Frequently, the device and cloud service are from the same vendor. If proprietary data protocols are used between the device and the cloud service, the device owner or user may be tied to a specific cloud service, limiting or preventing the use of alternative service providers. This is commonly referred to as ―vendor lock-in‘‘, a term that encompasses other facets of the relationship with the provider such as ownership of and access to the data. At the same time, users can generally have confidence that devices designed for the specific platform can be integrated.
Device-to-Gateway Model
In the device-to-gateway model, or more typically, the device-to-application-layer gateway (ALG) model, the IoT device connects through an ALG service as a conduit to reach a cloud service. In simpler terms, this means that there is
Temperature Monoxide
Device with Devicewith Carbon
CoAP DTLS UDP IP
Application Service Provider
HTTP TLS TCP IP