
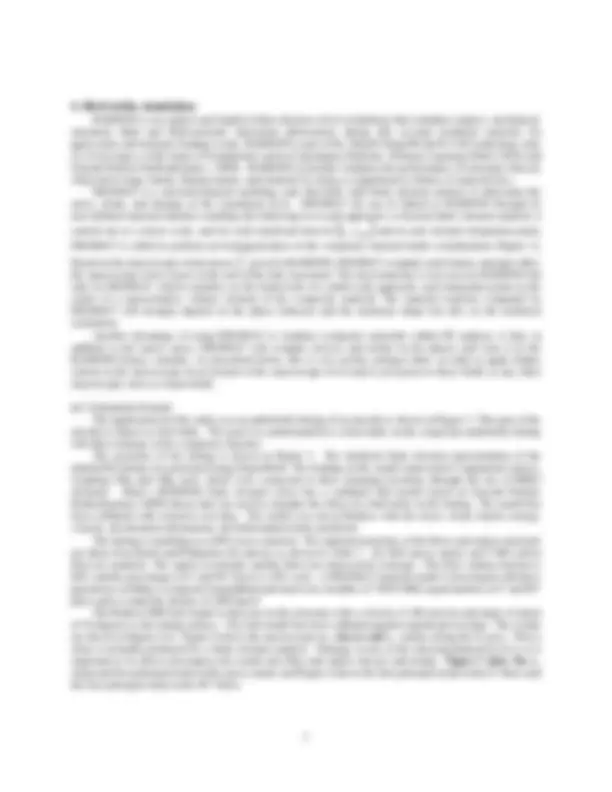
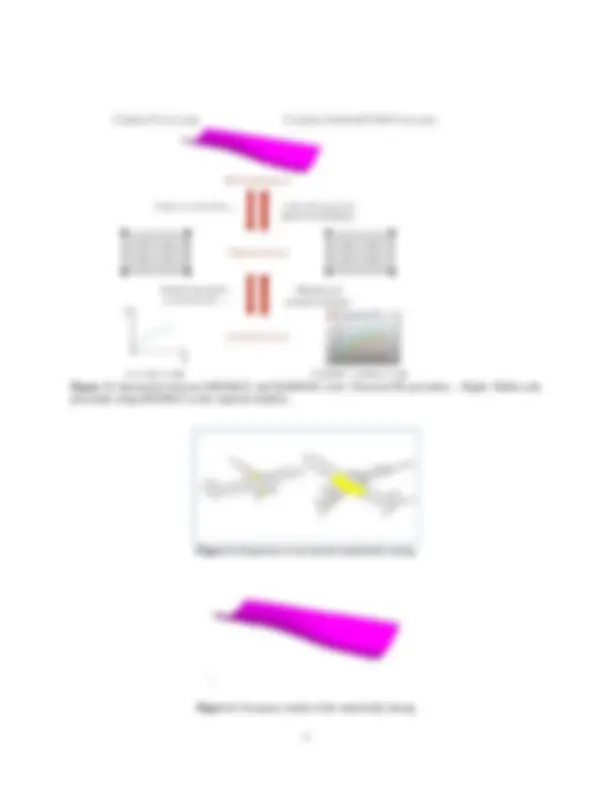
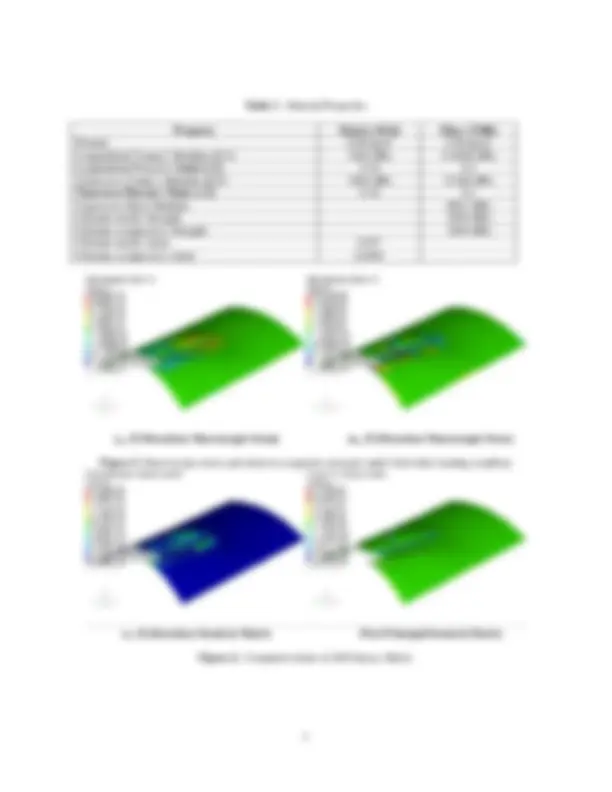
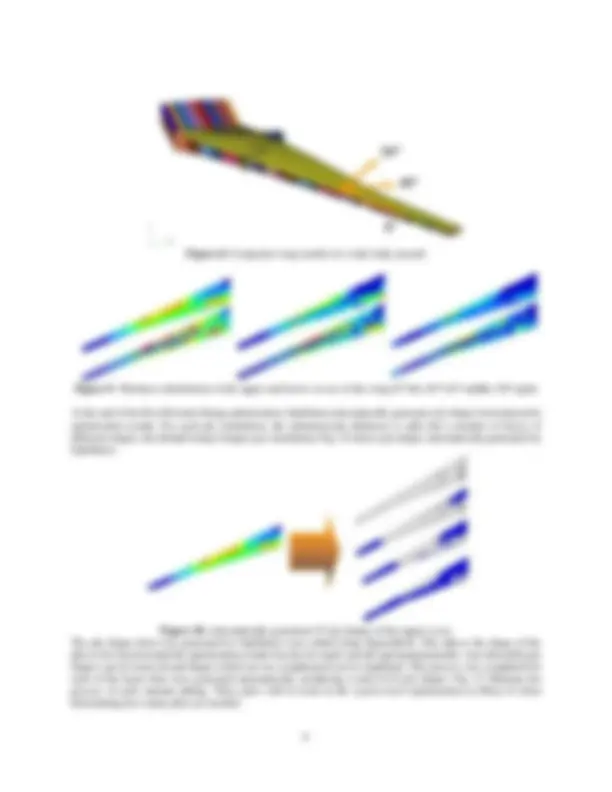
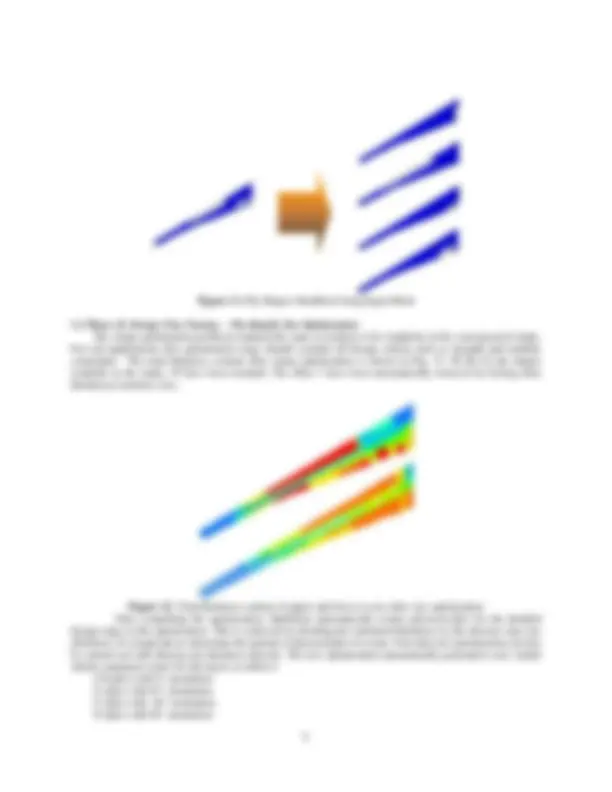
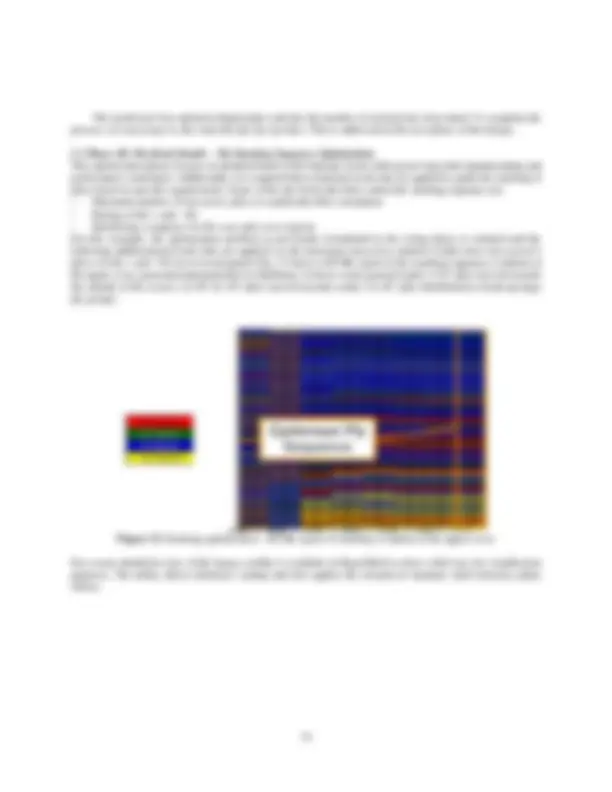
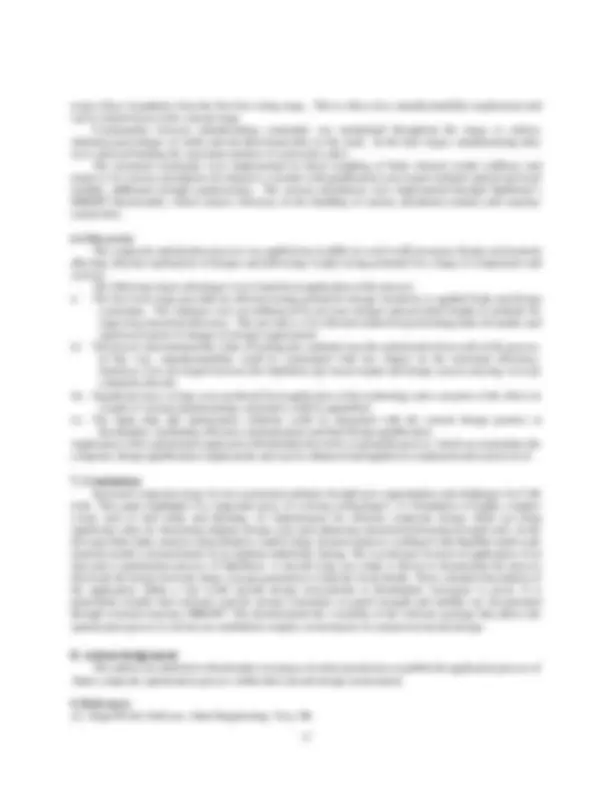
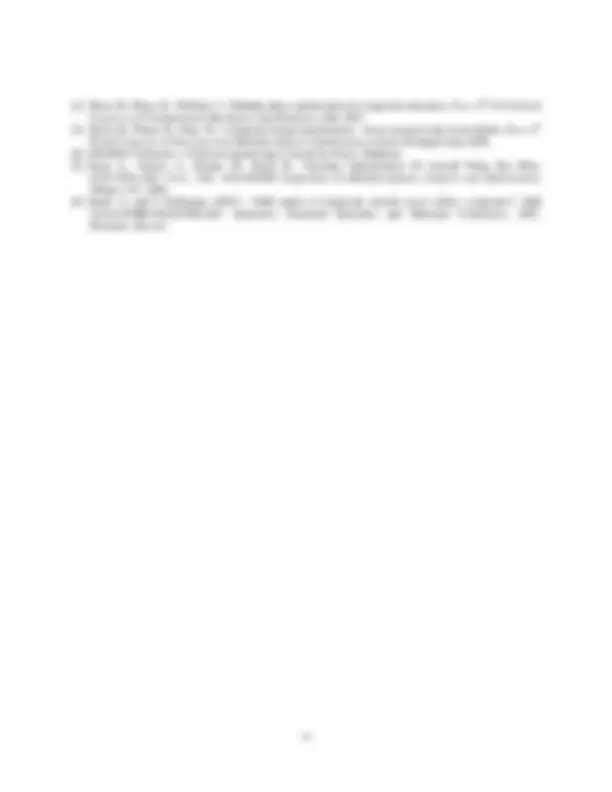
Prepara tus exámenes y mejora tus resultados gracias a la gran cantidad de recursos disponibles en Docsity
Gana puntos ayudando a otros estudiantes o consíguelos activando un Plan Premium
Prepara tus exámenes
Prepara tus exámenes y mejora tus resultados gracias a la gran cantidad de recursos disponibles en Docsity
Prepara tus exámenes con los documentos que comparten otros estudiantes como tú en Docsity
Los mejores documentos en venta realizados por estudiantes que han terminado sus estudios
Estudia con lecciones y exámenes resueltos basados en los programas académicos de las mejores universidades
Responde a preguntas de exámenes reales y pon a prueba tu preparación
Consigue puntos base para descargar
Gana puntos ayudando a otros estudiantes o consíguelos activando un Plan Premium
Comunidad
Pide ayuda a la comunidad y resuelve tus dudas de estudio
Descubre las mejores universidades de tu país según los usuarios de Docsity
Ebooks gratuitos
Descarga nuestras guías gratuitas sobre técnicas de estudio, métodos para controlar la ansiedad y consejos para la tesis preparadas por los tutores de Docsity
altair optistruct analysis of structures and topology optimization, implicit, finite elements
Tipo: Guías, Proyectos, Investigaciones
1 / 14
Esta página no es visible en la vista previa
¡No te pierdas las partes importantes!
Ming Zhou, Sam Patten, Martin Kemp, Robert Yancey, Erwan Mestres, Jean-Baptiste Mouillet
Altair Engineering, zhou@altair.com
Usage of fiber reinforced composite material entered an new era when leading aircraft OEMs took an unprecedented step to design and manufacture essentially full composite airframe for commercial airliners. Composite structures offer unmatched design potential as the laminate material properties can be tailored almost continuously throughout the structure. However, this increased design freedom also brings new challenges for the design process and software. Moreover, as a relatively new material, composite behaviors are more complex and less fully understood by design engineers. Therefore, reliable simulation for highly complex events like bird strike and ditching can play an important role in shortening the product design cycle. This paper showcases two area of CAE tools for composite applications. On advanced simulation, bird strike simulation with Altair Radioss [1] is demonstrated on an aircraft underbelly fairing. On design optimization, an airplane wing structure is designed using an innovative composite optimization process implemented in Altair OptiStruct [1-3]. OptiStruct has seen increasing adoption among aerospace OEMs, as demonstrated in the Bombardier application process described in this paper.
Computational tools have become an indispensible part of engineering tool set in today's product development environment. CAE software traditionally emphasize simulation of physical behavior of products in various operating conditions. In recent years, design optimization has become increasingly popular, largely driven by maturing software capabilities. This is a quite natural trend as optimization methods can help shortening the cycle of design improvements based on simulation results. In particular, concept generation through topology or Free-Size optimization brought game changing effect by inverting the order of CAD and CAE in the design process, bringing detailed performance consideration into the initial concept design stage. It has been shown that optimization technology can have significant impact on design innovation. For example, applying OptiStruct Airbus achieved over 40% weight reduction on a group of A380 leading edge ribs [5]. Similar successes have been demonstrated in all major industries including aerospace, automotive, heavy equipments, electronics, shipbuilding etc. This paper focuses on two aspects of advanced CAE tools for aerospace applications : (1) simulation of complex events such as bird strike using explicit finite element analysis; and (2) design optimization of composite structures. Composites behave far differently under impact than metals since they are made up of primarily brittle materials. Whereas metals deform and yield, composites tend to fracture. In many cases, the damage from impact occurs beneath the surface making damage difficult to detect visually. Composite damage mechanisms are also varied and can include delamination, fiber breakage, matrix failure or a combination of all of these. Damage progression is difficult to measure, even in laboratory settings, since the damage occurs internally and can progress very fast. Computational modeling of damage mechanisms in composites can yield significant information that can improve the design and performance of these materials. Models can predict damage progression, even at very small time scales, they can differentiate between different failure modes, and can handle the many variables involved in characterizing a composite structure. With an accurate damage model, many different design parameters can be analyzed, such as laminate lay-up, fiber volume fraction, and different combinations of fiber and matrix materials. With this ability, the best materials and designs can be chosen for specific structural applications. This paper presents an accurate simulation technique coupling the non linear explicit finite element simulation software RADIOSS [1] for modeling the impact of the bird on the structure
(impacted elements, impact forces, far field behavior) and DIGIMAT [4] for modeling the behavior of the composite material in the impact zone. The same software tools can also be applied to simulate ditching of an airplane in emergency water landing. The second part of the paper showcases application of an innovative composite design optimization technology implemented in OptiStruct [1]. Structural optimization has seen accelerated deployment throughout all industries in the past decade, largely due to the recognition that tremendous efficiency gain can be achieved at concept design stage through topology optimization. For metal structure, a two phase design process has become well established, where at Phase-I topology optimization is applied to generalize design concept, while design details are further optimized using sizing and shape optimization at Phase-II. For composite structure, the added design freedom prompts a modification of the process leading from concept to design details. While different forms of composite materials exist, the predominant usage is composite laminate where thin plies of various orientations are stacked together to form a shell structure. In recent years, the authors have developed a Three-Phase optimization process for composite laminate design optimization [2-3]. The target of the first phase is the material distribution in terms of orientation and thickness. This is achieved through free-size optimization where thickness of each 'super-ply' of a unique fiber direction is allowed to change freely throughout the structure. As a result thickness contour of each fiber orientation is obtained. A discrete interpretation of the thickness contour results in concept design of ply shapes and thicknesses. Then in Phase-II the interpreted ply-based structural model is further optimization under all design constraints with discrete design variables representing the number of plies of each ply patch. During Phase-III, ply stacking optimization is performed to refine the design according to detailed manufacturing constraints. It should be emphasized that manufacturing constraints are considered throughout all three optimization phases. For example, one important design/manufacturing requirement of aerospace OEMs is that no plies of same orientation is allowed to be stacked continuously for more than 3 or 4 plies. Such requirement would translate into percentage requirement during Phase-I and II so that a balanced distribution of fiber orientation is achieved to allow feasible stacking during Phase-III. The Three-Phase optimization process is illustrated in Fig. 1. This optimization process is implemented in the commercial software Altair OptiStruct. Another unique modeling technique developed in conjunction with the optimization process is a ply-based FEA model where PLY entities are defined as sets of elements [1]. Then ply layup is specified by a STACK definition. This modeling approach follows the design and manufacturing language known as Ply-Book. It provides a more intuitive interface between design and analysis, and makes design optimization more transparent. The software package OptiStruct has found quick adoption by OEMs producing aircraft, racing car and yacht made of advanced composites. Among these applications large to medium size airliners are of particular importance due to their enormous economic scale. In this paper a case study of a composite wing of a wide body long range aircraft is presented, followed by a description of the application process at Bombardier.
Figure 1. Illustration of composite optimization phases
Laminate Stacking?
Phase 3
Rule based
ply shuffling
0 45
(^45) - (^00) (^45) - (^9090) -45 45 (^00) -45 45
Automation
Patch Interpretation
Ply Tailoring?
Free Sizing!
Phase 1
Number of Plies?
Ply Bundle Sizing!
Phase 2
Discrete Ply Thickness
Automation Optimized Stacking Sequence!
Figure 2: Interaction between DIGIMAT and RADIOSS. Left: Classical FE procedure – Right: Multi-scale procedure using DIGIMAT as the material modeler.
Figure 3. Depiction of an aircraft underbelly fairing
Figure 4. Geometry model of the underbelly fairing
Table 1. Material Properties
Property Matrix (M18) Fiber (T300) Density 1160 kg/m^3 1760 kg/m^3 Longitudinal Young’s Modulus (E11) 3500 MPa 233000 MPa Longitudinal Poisson’s Ratio (ν11) 0.38 0. Transverse Young’s Modulus (E22) 3500 MPa 23100 MPa Transverse Poisson’s Ratio (ν22) 0.38 0. Transverse Shear Modulus 8963 MPa Ultimate tensile Strength 1990 MPa Ultimate compressive Strength 1990 MPa Ultimate tensile strain 0. Ultimate compressive strain 0.
ε 11 (X-Direction) Macroscopic Strain σ 11 (X-Direction) Macroscopic Stress
Figure 5. Macroscopic stress and strain in composite structure under bird strike loading condition
ε 11 (X-direction) Strain in Matrix First Principal Strain in Matrix
Figure 6. Computed strains in M18 Epoxy Matrix
Figure 7. Failure indicators in Carbon fibers, in Epoxy matrix phase and at macroscopic level.
The Three-Phase composite design process is demonstrated through the design of composite wing covers of a wide body aircraft shown in Fig. 8. Ten load cases of key significance are considered. In this simplified concept proof exercise only constraints on wing tip displacement and rotation are considered, with upper bounds not exceeding those of a baseline aluminum wing under each load case. Only carbon fiber composite top and bottom covers are optimized. Ply orientations available are 0, +45/-45, 90 plies, with leading edge as reference.
5.1 Phase-I: Concept Design - Free-Size Optimization Manufacturing Constraints considered include:
Figure 8. Composite wing model of a wide body aircraft
Figure 9. Thickness distribution of the upper and lower covers of the wing (0º left; 45º/-45º middle; 90º right)
At the end of the Free Element Sizing optimization, OptiStruct automatically generates ply shapes based upon the optimization results. For each ply orientation, the optimized ply thickness is split into a number of layers of different shapes, the default being 4 shapes per orientation. Fig. 10 shows ply shapes automatically generated by OptiStruct.
Figure 10. Automatically generated 0º ply shapes of the upper cover The ply shapes that were generated by OptiStruct were edited using HyperMesh. This allows the shape of the plies to be based around the optimization results but also be made smooth and manufacturable. Any infeasible ply shapes can be removed and shapes which are too complicated can be simplified. This process was completed for each of the layers that were generated automatically, producing a total of 62 ply shapes. Fig. 11 illustrate the process of such manual editing. These plies will be used in the system level optimization at Phase II when determining how many plies are needed.
The model now has optimum shaped plies and also the number of each ply has been tuned. To complete the process, it is necessary to also meet the ply lay-up rules. This is addressed in the next phase of the design.
5.3 Phase III: Ply-Book Details – Ply Stacking Sequence Optimization This optimization phase focuses on detailed finish of the final ply-book while preserving both manufacturing and performance constraints. Additionally, it is required that certain ply book rules be applied to guide the stacking of plies based on specific requirements. Some of the ply book rules that control the stacking sequence are:
Figure 13. Stacking optimization - HTML report of stacking evolution of the upper cover
For a more detailed review of the layup, a utility is available in HyperMesh to show solid view for visualization purposes. The utility allows thickness scaling and also applies the element & laminate shell reference plane offsets.
Figure 14. Bottom Wing Cover Solid Visualization of Plies (Thickness x5) The solid visualization makes it possible to see: (1) How the plies transition / overlap across different zones; (2) Thickness drop off; (3) Manufacturing sequence (ply book). Also when using a solid visualization in conjunction with the cross sectioning tools in HyperView, it is possible to perform a detailed investigation into the layup throughout the length & width of the covers. Another benefit would be for generating an inner mould surface for the laminates.
5.4 Conclusions Through this study, the Three-Phase optimization process has successfully demonstrated its capacity for maximizing utilization of the potential of composite material, while significantly shortening the design process. As a simplified concept proof study detailed strength and buckling criteria necessary for design phases II and III are ignored. However, these constraints can be efficiently addressed in the optimization process, as shown in a Bombardier application discussed in the next section.
This section outlines application of the Altair Composite Optimization technology to composite component design at Bombardier. As part of Bombardier’s ongoing technology development initiatives, application of the process was explored at single and multiple component levels. A description of the process and method of application inside a dynamic aerospace design environment is described. Methods for incorporating structural and manufacturing constraints are introduced. The interfaces developed between design and stressing groups are also summarized, which underpin the successful application of the technology in an environment where design requirements can frequently change.
6.1 Integration of Altair’s Composite Design Process Integration of Altair’s composite optimization process with the design process and all of the necessary interfaces is shown schematically in Fig. 15. The main additions to the process are interfaces accommodating inputs and outputs to and from the design team. Notably, custom responses and constraints are needed to align the optimization with strength, stiffness and stability qualification requirements. Export of the optimization solution is also required in a number of different formats including: CAD format laminate descriptions, qualification report summaries and additional finite element formats.
respect these boundaries from the first free sizing stage. This is often a key manufacturability requirement and can be locked down at the concept stage. Commonality between manufacturing constraints was maintained throughout the stages to enforce minimum percentages of cloths and uni-directional plies in the stack. In the later stages, manufacturing rules were enforced limiting the maximum number of consecutive plies. The structural constraints were implemented by direct sampling of finite element results (stiffness and strain) or by custom calculations developed to correlate with qualification assessment methods (global and local stability, additional strength requirements). The custom calculations were implemented through OptiStruct’s DRESP3 functionality, which ensures efficiency in the handling of custom calculation routines and response sensitivities.
6.4 Discussion The composite optimization process was applied successfully in a real world aerospace design environment allowing efficient exploration of designs and delivering weight saving potential for a range of components and systems. The following major advantages were found from application of the process: i) The free-form stage provided an efficient testing ground for design sensitivity to applied loads and design constraints. The solutions were not influenced by previous designs and provided insight of methods for improving structural efficiency. This provides a very efficient method for performing trade off studies and rapid assessment of changes in design requirements. ii) The process demonstrated the value of locking ply continuity into the optimization from early in the process. In this way, manufacturability could be constrained with less impact on the structural efficiency. Interfaces were developed between the OptiStruct ply based output and design system carrying over ply continuity directly. iii) Significant mass savings were predicted from application of the technology and a measure of the effect on weight of varying manufacturing constraints could be quantified. iv) The input data and optimization solutions could be integrated with the current design practice at Bombardier, facilitating efficient communication and final design qualification. Application of the optimization approach at Bombardier has led to a repeatable process, which accommodates the composite design qualification requirements and can be enhanced and applied at component and system level.
Increased composite usage for new generation airliners brought new opportunities and challenges for CAE tools. This paper highlights two important areas of evolving technologies: (1) Simulation of highly complex events such as bird strike and ditching; (2) Optimization for efficient composite design. Both can bring significant value for shortening airplane design cycle and enhancing structural performance/weight ratio. In the first part Bird strike analysis using Radioss explicit finite element analysis combined with DigiMat multi-scale material model is demonstrated on an airplane underbelly fairing. The second part focused on application of an innovative optimization process of OptiStruct. A aircraft wing case study is shown to demonstrate the process that leads the design from ply shape concept generation to final ply-book details. Then a detailed description of the application within a real world aircraft design environment at Bombardier Aerospace is given. It is particularly notable that customer specific design constraints on panel strength and stability are incorporated through external responses DRESP3. This demonstrated the versatility of the software package that allows the optimization process to fit into an established complex environment of commercial aircraft design.
The authors are indebted to Bombardier Aerospace for their permission to publish the application process of Altair composite optimization process within their aircraft design environment.
9. References [1] HyperWorks Software, Altair Engineering, Troy, MI.
[2] Zhou, M., Fluey, R., Willmet, T.: Multiple phase optimization of composite structures. Proc. 9 th^ US National Congress of Computational Mechanics , San Francisco, July 2007. [3] Zhou, M., Fluery, R., Dias, W.: Composite design optimization – from concept to ply-book details. Proc. 8 th World Congress of Structural and Multidisciplinary Optimization , Lisbon, Portugal, June 2009. [4] DIGIMAT Software, e-Xstream engineering, Louvain-la-Neuve, Belgium. [5] Krog, L., Tucker, A., Kempt, M., Boyd, R., Topology Optimization Of Aircraft Wing Box Ribs, AIAA-2004-4481, Proc. 10th AIAA/ISSMO Symposium on Multidisciplinary Analysis and Optimization , Albany, NY, 2004. [6] Kueh, A. and S. Pellegrino (2007). “ABD matrix of single-ply triaxial weave fabric composites”. 48th AIAA/ASME/ASCE/AHS/ASC Structures, Structural Dynamics and Materials Conference, 2007, Honolulu, Hawaii.