
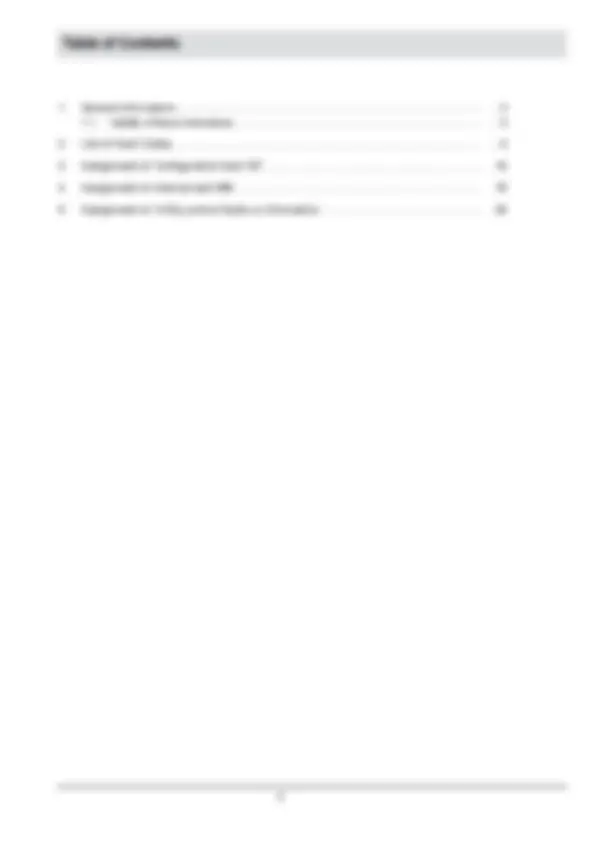
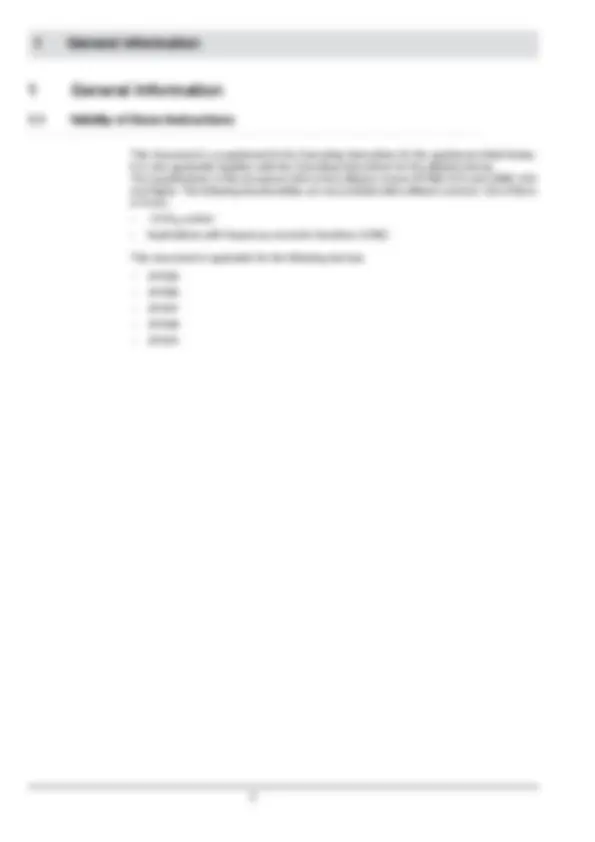
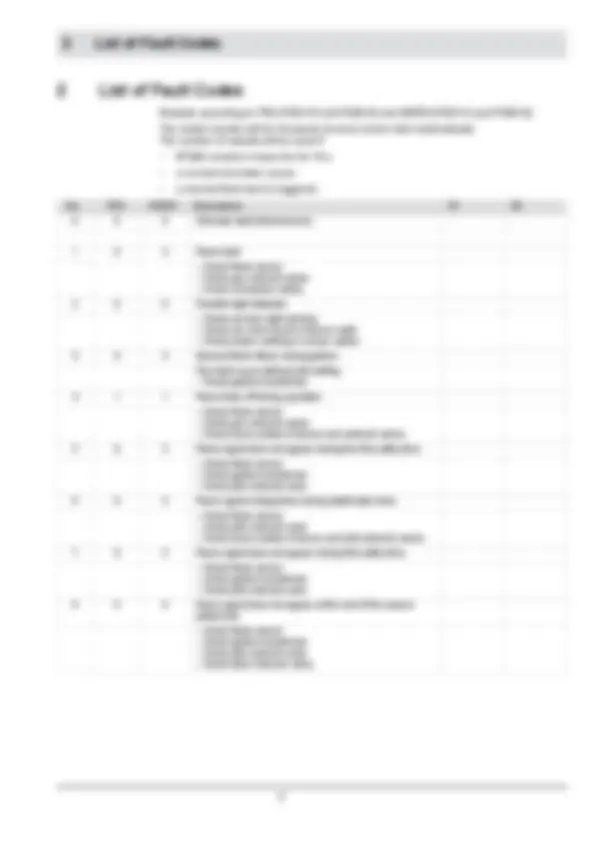
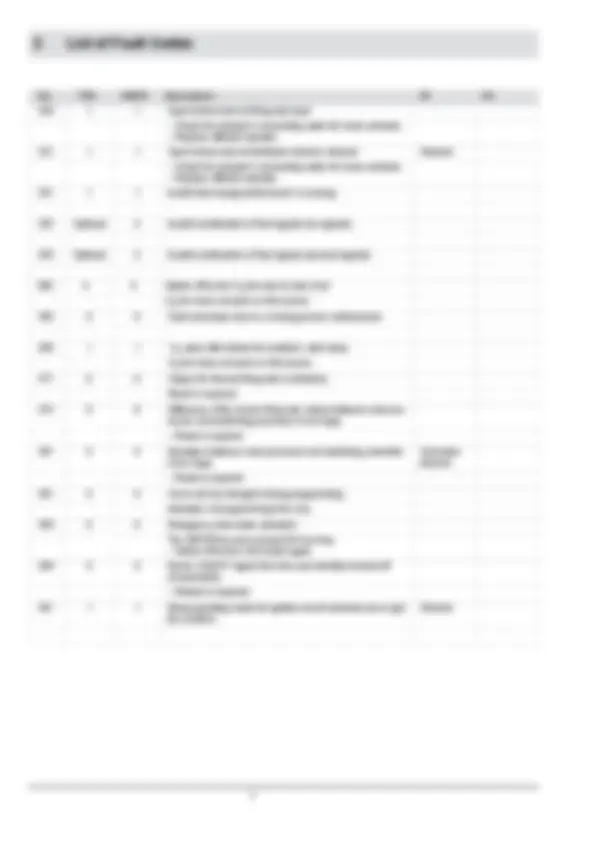
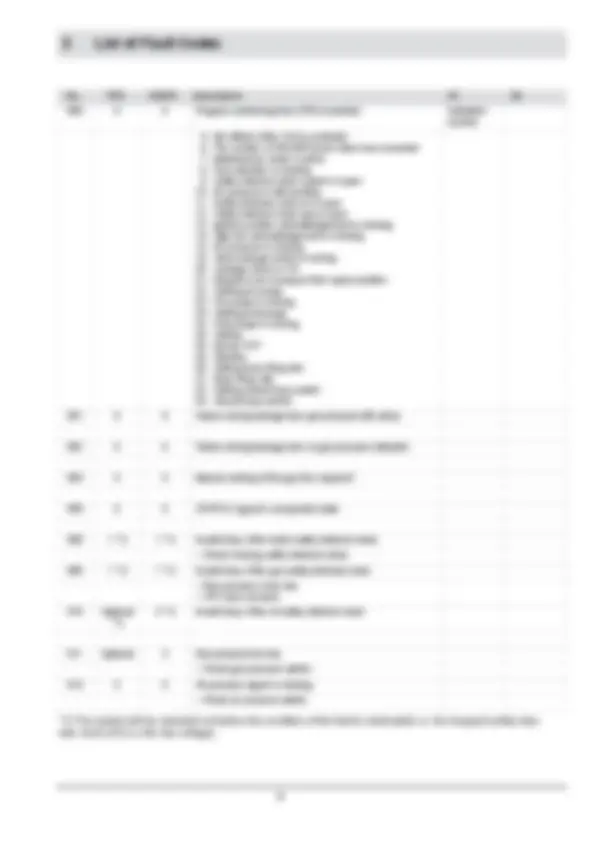
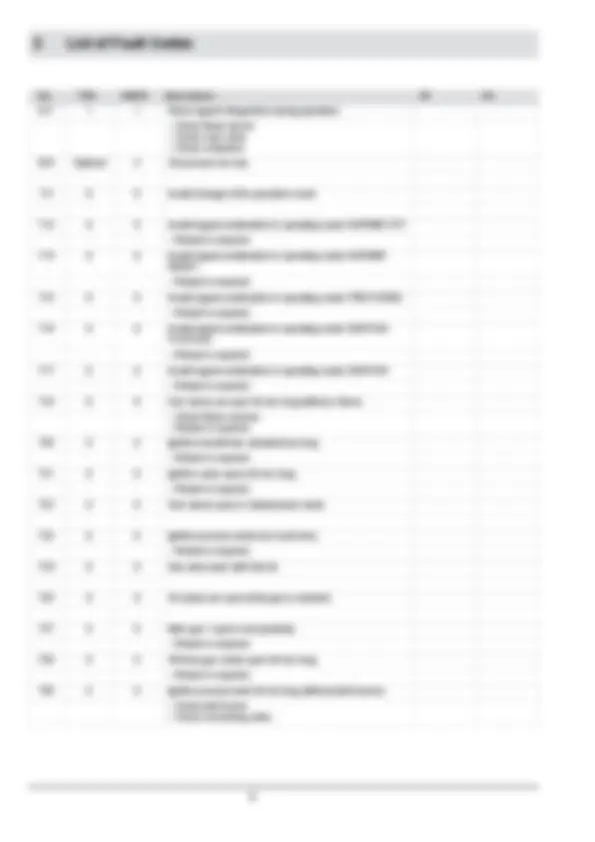
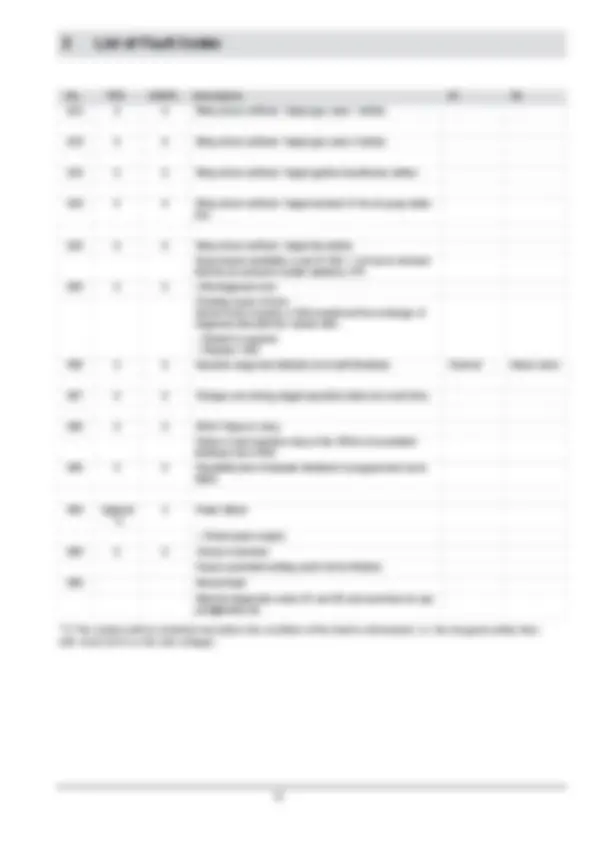
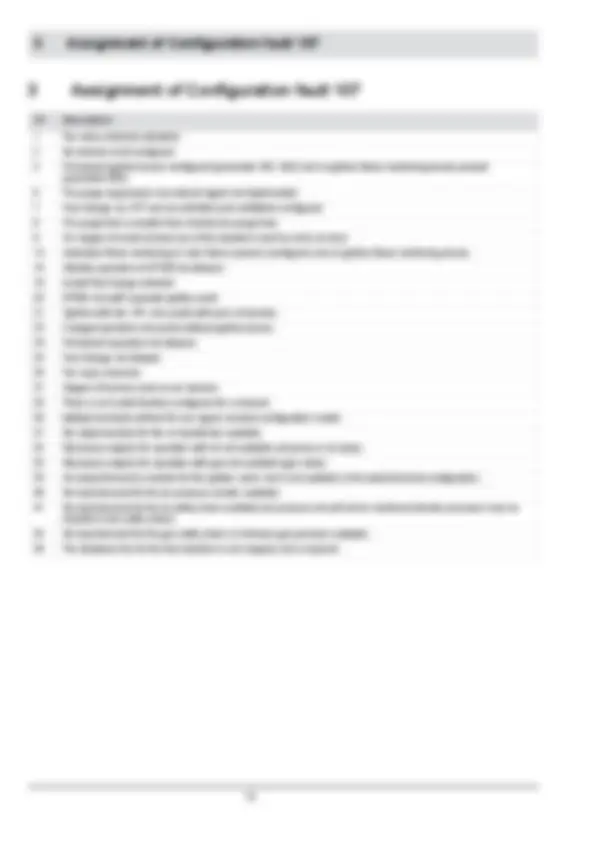
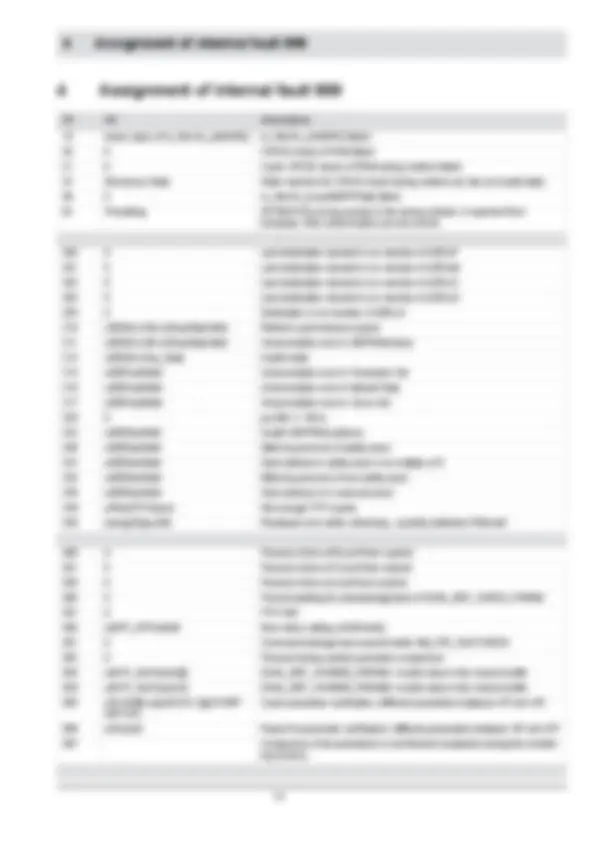
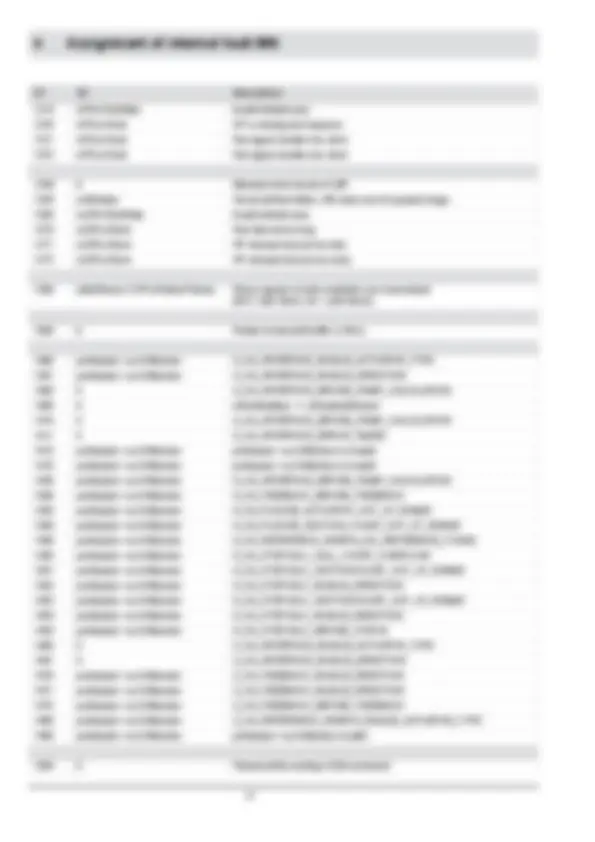
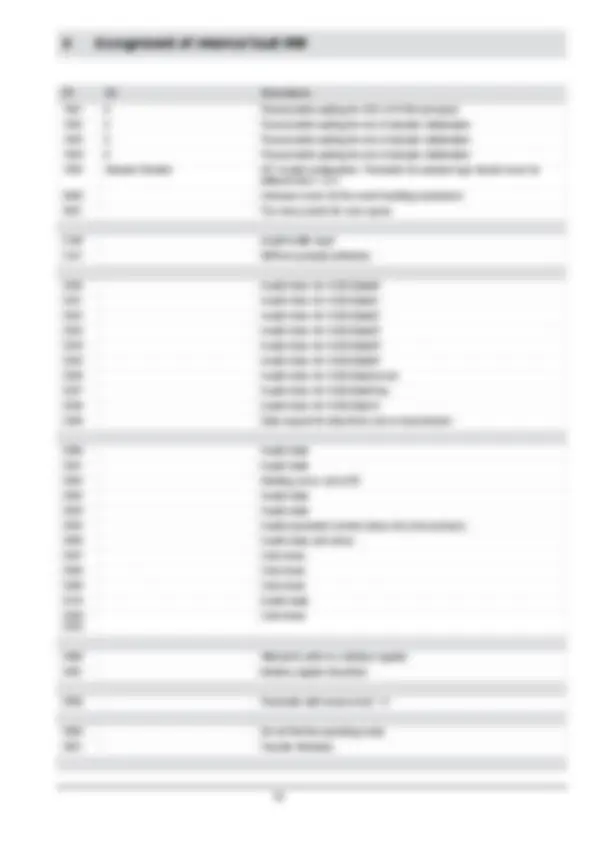
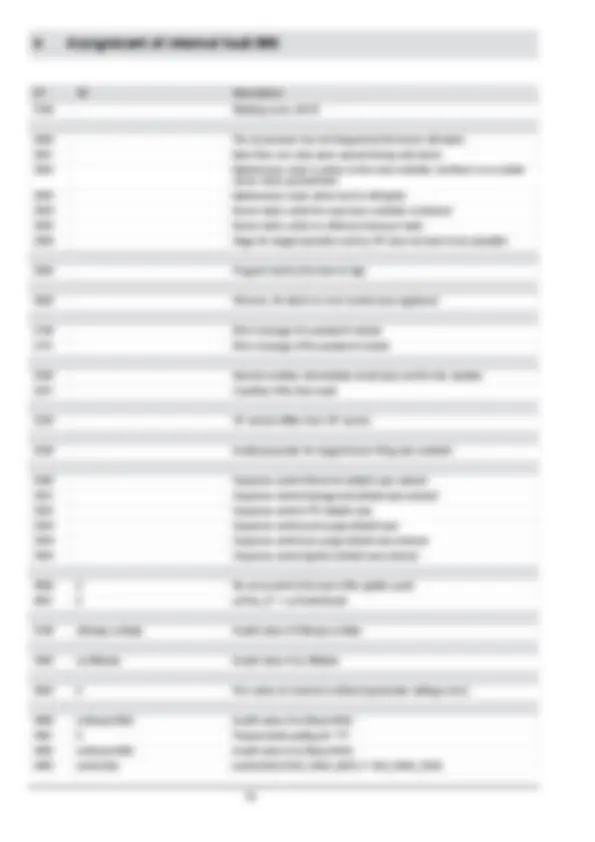
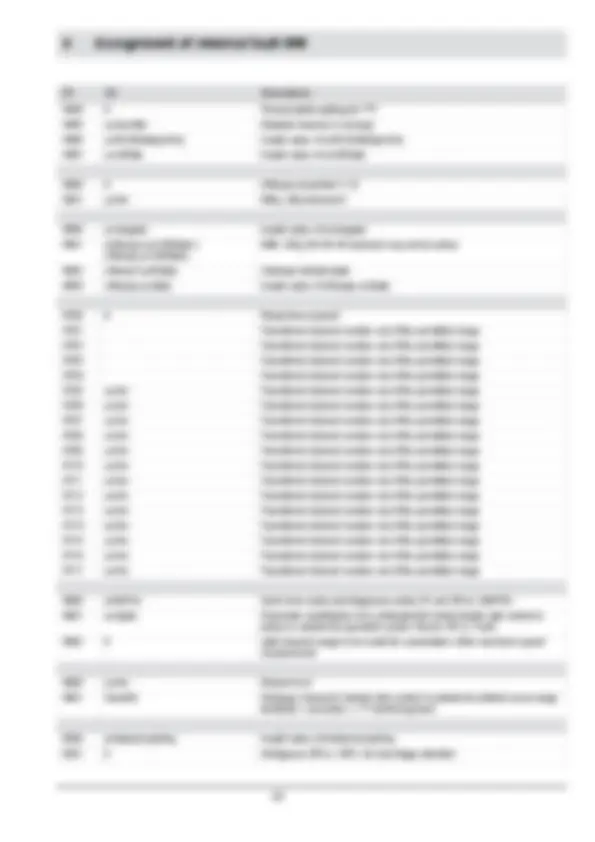
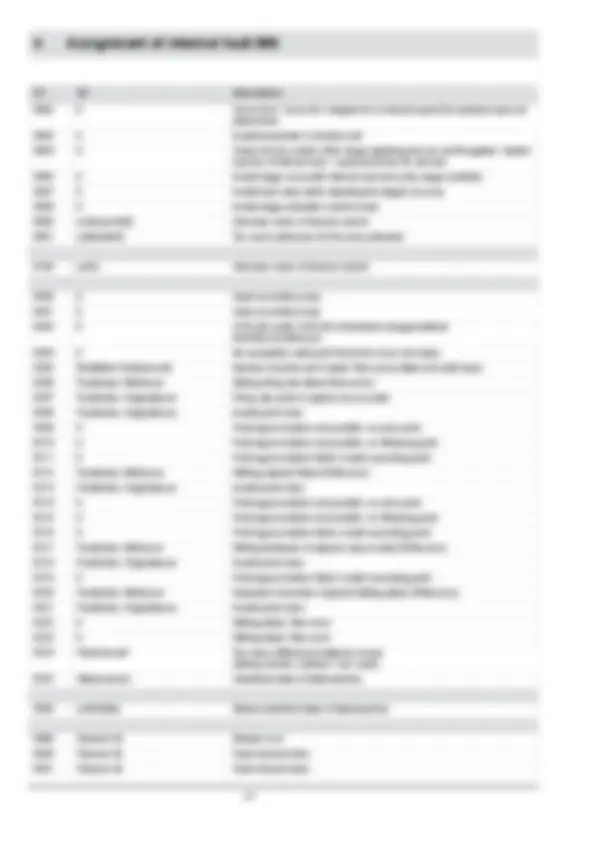
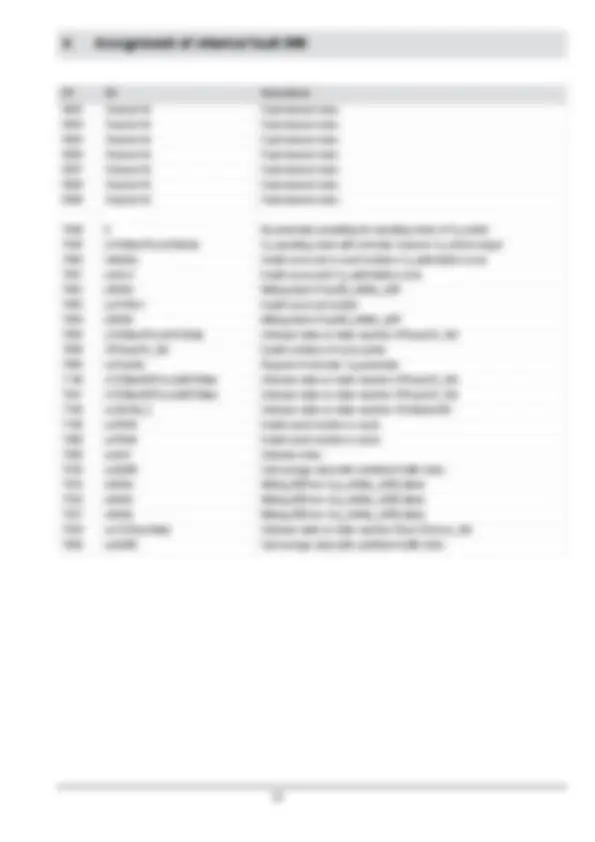
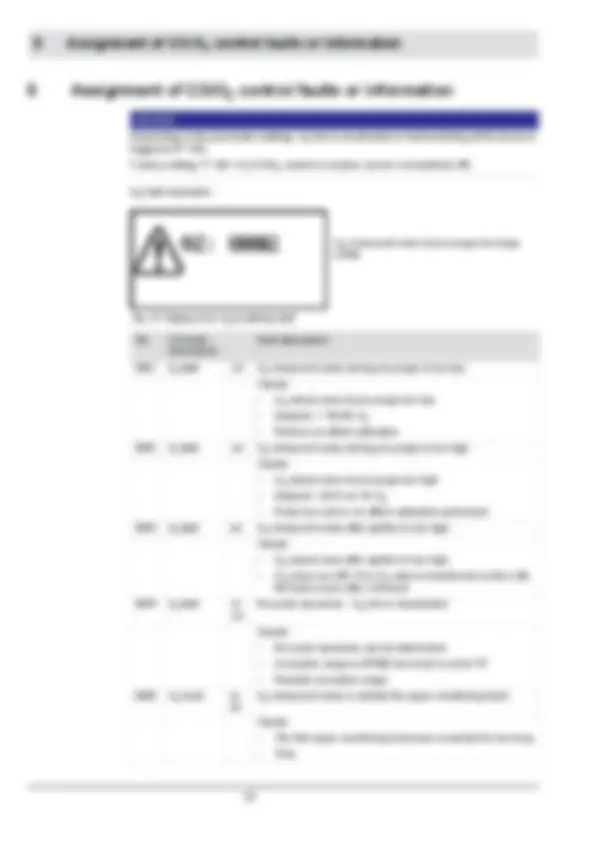
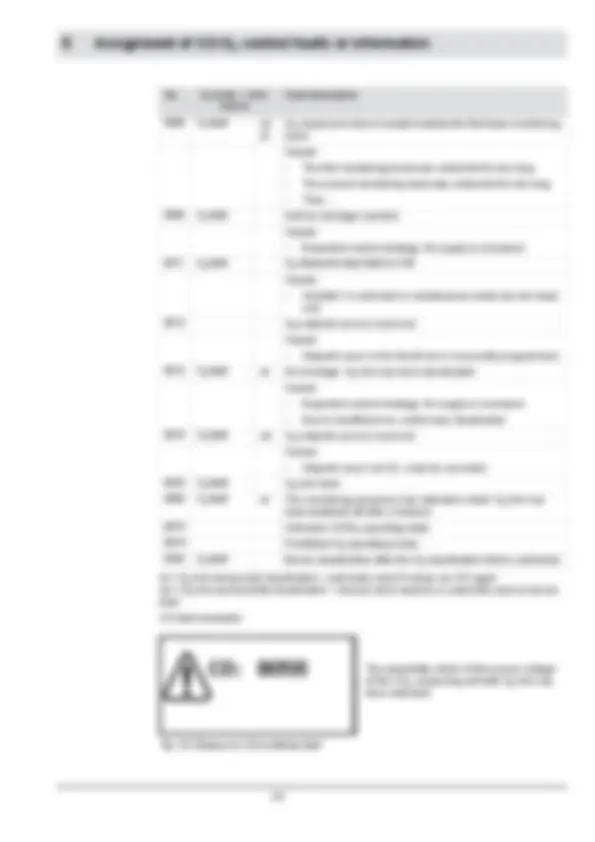
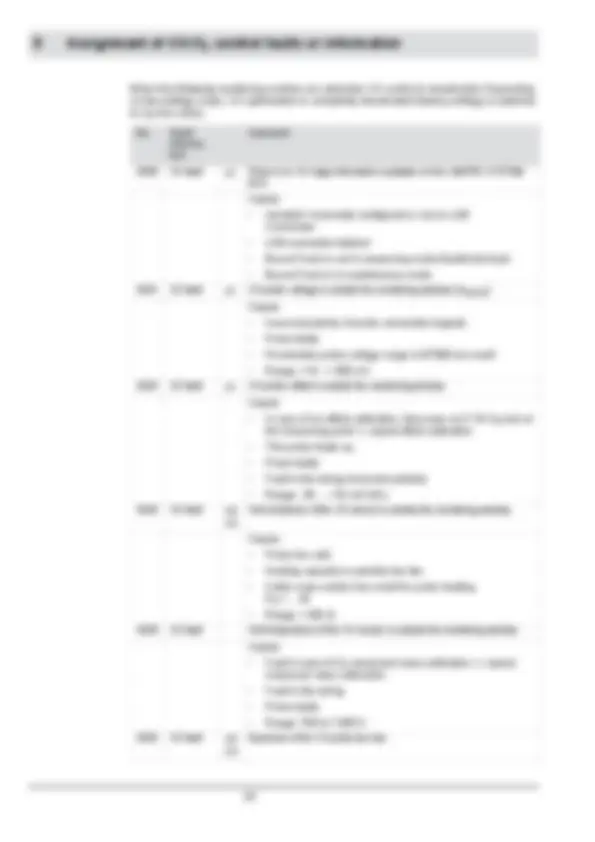
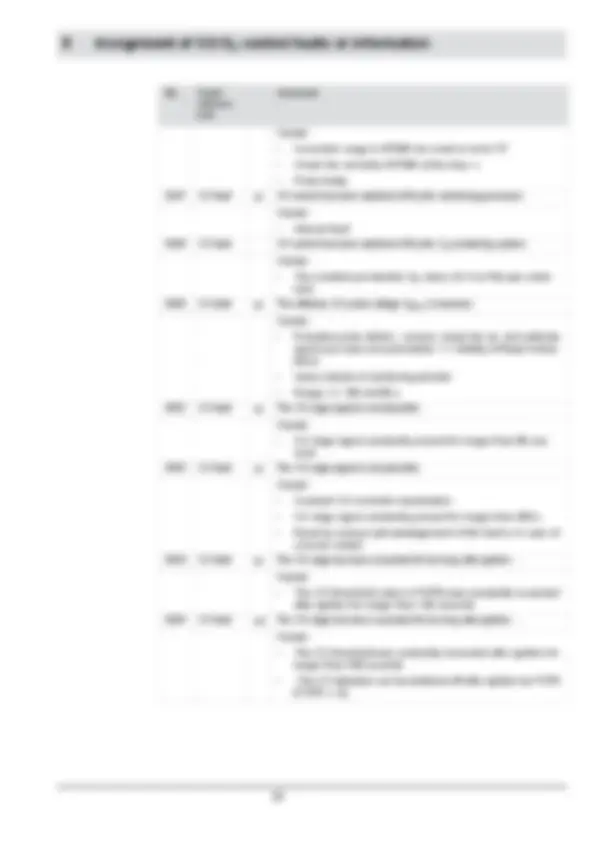
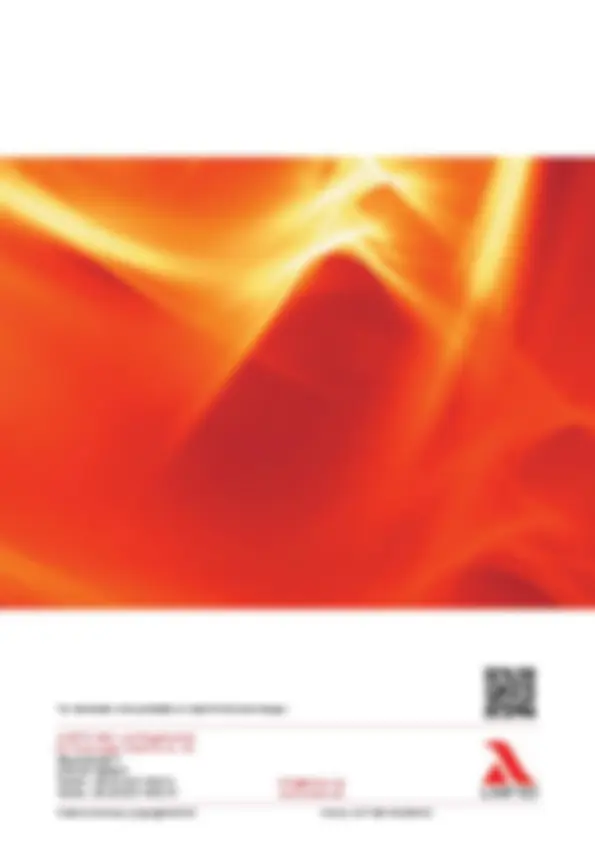
Prepara tus exámenes y mejora tus resultados gracias a la gran cantidad de recursos disponibles en Docsity
Gana puntos ayudando a otros estudiantes o consíguelos activando un Plan Premium
Prepara tus exámenes
Prepara tus exámenes y mejora tus resultados gracias a la gran cantidad de recursos disponibles en Docsity
Prepara tus exámenes con los documentos que comparten otros estudiantes como tú en Docsity
Los mejores documentos en venta realizados por estudiantes que han terminado sus estudios
Estudia con lecciones y exámenes resueltos basados en los programas académicos de las mejores universidades
Responde a preguntas de exámenes reales y pon a prueba tu preparación
Consigue puntos base para descargar
Gana puntos ayudando a otros estudiantes o consíguelos activando un Plan Premium
Comunidad
Pide ayuda a la comunidad y resuelve tus dudas de estudio
Descubre las mejores universidades de tu país según los usuarios de Docsity
Ebooks gratuitos
Descarga nuestras guías gratuitas sobre técnicas de estudio, métodos para controlar la ansiedad y consejos para la tesis preparadas por los tutores de Docsity
Error Code Description for LAMTEC BT3XX Burner Controllers
Tipo: Resúmenes
1 / 28
Esta página no es visible en la vista previa
¡No te pierdas las partes importantes!
1 General Information
1.1 Validity of these Instructions
2 List of Fault Codes
1 0 3 Flame fault
No. TRD EN676 Description D1 D 201 1 1 First monitoring band fall short for too long: channel Channel
211 0 0 Second monitoring band exceeded for too long: channel Channel
3 Fuel/air ratio control is blocked: channel Channel
3 Actuator returns invalid position (difference to target position too large)
Channel
3 Actuator feedback remains constantly for too long, even when actuator has moved.
Channel
281 1 1 Feedback signal of at least 1 actuator is incorrect channel To identify the actuator’s direction of rotation two pulse form signals, offset 90 degrees, are returned by the actuator. If fault 281 occurs, these signals are not identified correctly. Cause of error:
Channel
Actuators are mixed up while reconnecting. The test for rec- ognising this fault is described in the manual of the BT300 – print no. DLT1201. At least one actuator does not reach it’s test position:
No. TRD EN676 Description D1 D 320 1 1 Open broken wire at firing rate input
352 Optional 3 Invalid combination of fuel signals (no signals)
353 Optional 3 Invalid combination of fuel signals (several signals)
360 0 0 Switch off by the O 2 trim due to lack of air O 2 trim does not work on this burner. 362 0 0 Fault shut-down due to a missing burner maintenance
363 1 1 O 2 value falls below the smallest, valid value. O 2 trim does not work on this burner. 371 0 0 Output for internal firing rate is defective. Reset is required. 372 0 0 Difference of the burner firing rate values between main pro- cessor and watchdog processor is too large.
Correction channel
Channel
No. TRD EN676 Description D1 D 617 1 1 Flame signal extinguishes during operation.
711 0 0 Invalid change of the operation mode
713 0 0 Invalid signal combination in operating mode BURNER OFF
723 0 0 Ignition process needs too much time.
725 0 0 Oil valves are open while gas is selected.
727 0 0 Main gas 1 opens unexpectedly.
No. TRD EN676 Description D1 D 730 0 0 Maintenance mode without pilot burner
731 0 0 Ignition valve opens without pilot burner.
740 0 0 Leakage test: Main gas valve 1 leaky.
741 0 0 Leakage test: Main gas valve 1 opens for too long.
742 0 0 Leakage test: Main gas valve 2 leaky.
743 0 0 Flame monitoring: Flame burns for too long after shutdown.
759 0 0 BT300 leaves SETTING mode automatically after 24 hours.
763 0 0 Different curve selection on main processor and watchdog processor
764 1 1 CO-controller - internal curve set failure Curve set
800 0 0 Parameter defective. Parameter No.
801 0 0 Channel control mode is inconsistent between main proces- sor and watchdog processor.
Channel
Fatal error, an automatic restart is not possible. 802 1 1 Integration of a channel into the fuel/air ratio control needs too much time.
Channel
Only one automatic restart is possible. 803 0 0 Channel is out of 1st monitoring band for too long. Channel
No. TRD EN676 Description D1 D 923 0 0 Relay driver self-test: Output gas valve 1 defect.
924 0 0 Relay driver self-test: Output gas valve 2 defect.
925 0 0 Relay driver self-test: Output ignition transformer defect.
928 0 0 Relay driver self-test: Output terminal 41 for oil pump defec- tive.
929 0 0 Relay driver self-test: Output fan defect. If permanent ventilation is set (P 330 = 1) it has to checked that the air pressure monitor switches OFF. 985 0 0 VSM diagnosis error Possible cause of error: BurnerTronic expects a VSM module but the exchange of diagnosis data with the module fails.
987 0 0 Change-over during staged operation takes too much time.
988 0 0 DFM: Failure in relay Failure in fuel selection relay in the DFM or inconsistent feedback from DFM. 989 0 0 Plausibility test of actuator feedback in programmed curve failed.
990 Optional *1)
3 Power failure
3 Assignment of Configuration fault 107
D1 Description 1 Too many channels activated. 2 No channel at all configured. 3 Permanent ignition burner configured (parameter 302, 303), but no ignition flame monitoring device present (parameter 800). 6 Pre-purge suppression via external signal not implemented. 7 Fuel change via OFF and an unlimited post ventilation configured. 8 Pre-purge time is smaller than minimal pre-purge time. 9 For stages oil mode at least one of the actuators must be set to air duct. 13 Australian flame monitoring (2 main flame scanner) configured, but no ignition flame monitoring device. 18 Standby operation at BT300 not allowed. 19 Invalid fuel change selected. 20 BT300 only with separate ignition point. 21 ’Ignition with fan ON’, only useful with pure oil devices. 23 3-staged operation only works without ignition burner. 24 Permanent operation not allowed. 25 Fuel change not allowed. 26 Too many channels. 27 Staged oil burners need an air channel. 28 There is an invalid function configured for a channel. 30 Multiple terminals defined for one signal, terminal configuration invalid. 31 No output terminal for fan or transformer available. 32 Necessary outputs for operation with oil not available (oil pump or oil valve). 33 Necessary outputs for operation with gas not available (gas valve). 34 An output terminal is needed for the ignition valve, but is not available in the actual terminal configuration. 40 No input terminal for the air pressure monitor available. 41 No input terminal for the oil safety chain available (oil pressure min will not be monitored directly, because it can be included in the safety chain). 42 No input terminal for the gas safety chain or minimum gas pressure available. 43 The feedback line for the fuel selection is not mapped, but is required.
410 sIO.sIn.ulInputsN Detected positive half-wave on terminal input! 411 input status received from UP Different input status between controllers 412 0 The readback input of the fuel selection relay contacts in the dual fuel is invalid. DFM probably defect. 420 uil 0 1 2 3 4 5 6 7 8
Input status of digital input on HP and UP is inconsistent (>20ms) Terminal X.10.2 = burner ON Terminal X.10.1 = fault release Terminal X.9.2 = firing rate + Help: Adjust firing-rate controller more precisely Terminal X.9.1 = firing rate - Help: Adjust firing-rate controller more precisely Terminal X.8 = air pressure Terminal X.7 = safety chain boiler Terminal X.6 = safety chain boiler Terminal X.5 = oil pressure Terminal X21 = UV input/input contact flame scanner Help: Use QRA2m up to software version 3.1 and adjust the flame scanner in a way that a UV current higher than 250 A can be measured. With soft- ware version 3.3 and higher set new UV settings in P 800. 430 ucPin2Test Pin short circuit test detected an error! Currently tested, pin not configured as output or is stuck at 1 431 ucPin2Test Pin short circuit test detected an error! Short-circuit between pins, pull-up of input stage defective or pin sticks externally at 0 440 0 sIO.sIn.uiTestSignalTimeout expired 450 0 Main power relay (K2) does not switch correctly to off when out of power. 451 ucRelay
0 1 2 3 4 5 6 7 8
Relay does not switch correctly, if main relays K1 and K2 are switched on. Relay PWR Relay oil pump Relay fan Relay V Relay V Relay V Relay ignition transformer Relay alarm Relay DFM 452 uiFaultParam
0 1 2 3 4 5 6 7 8
Relay does not switch correctly, if main relays K1 and K2 are switched on. Relay PWR Relay oil pump Relay bowler Relay V Relay V Relay V Relay ignition transformer Relay alarm Relay DFM 460 uiFaultParam Error in power supply of the relay or failure in read back of relay coil of K1 or K2. Parameter 2: Bit 0: error state of K Bit 1: error state of K
D1 D2 Description
461 uiFaultParam Read back status of relay K1 or K2 differs from desired switching status, relay probably defect. Parameter 2: Bit 0: nominal state of K Bit 1: nominal state of K Bit 8: read back of K Bit 9: read back of K
500 0 Timeout while waiting for end of write cycle 501 0 SLA+W has been transmitted; NO ACK has been received 502 0 SLA+R has been transmitted; NO ACK has been received 503 0 Data byte has been transmitted; NO ACK has been received 504 0 BUS error due to an illegal START or STOP condition 505 0 Arbitration lost in SLA+R/W or Data bytes 510 ulI2CStat Unknown/invalid state!
600 sSRCtrl.uiOffset Correction of defective triple in Safety RAM structure failed 610 (ulong32)pucDst Invalid destination address 620 (ulong32)puiDst Invalid destination address 630 (ulong32)pulDst Invalid destination address
700 0 CPU self-test failed 701 sSelftest.sMngr.eState State-event-machine failed with AC_ERR 710 sSelftest.sWD.eErrorState Watchdog self-test failed 711 sSelftest.sWD.eState Invalid default case 720 Selftest.sVM.ucTest2Perform Invalid default case 721 Selftest.sVM.eErrorState Supply voltage monitor self-test failed 722 Selftest.sVM.eState Invalid default case 730 sSelftest.sRR.eErrorState Relay release circuit self-test failed 731 sSelftest.sRR.eState Invalid default case 740 sSelftest.sRPW.eErrorState Relay PWR release circuit self-test failed 741 sSelftest.sRPW.eState Invalid default case 750 0: USR-Stack, 1: IRQ-Stack Stack overflow detected 751 0 Stack address is NULL-Pointer 752 0 Stack address is NULL-Pointer
800 sWDog.ulReleasePtrn1 Trigger release patterns are invalid! 810 eFeedIndex Invalid Feed Index 820 eTriggerCtrl Invalid Trigger Mode 830 0 No valid watchdog trigger received (frequency or operation cycle invalid).
900 uiErrorCode Fault from LPC_API error handler 920 0 Invalid entry in iStoerResRam 930 uiMaskedFaultCode uiMaskedFaultCode out of range!
1200 0 Flame signal doesn't disappear during self-test.
D1 D2 Description
1501 0 Timeout while waiting for ACK of ICOM command 1502 0 Timeout while waiting for end of actuator initialisation 1503 0 Timeout while waiting for end of actuator initialisation 1504 0 Timeout while waiting for end of actuator initialisation 1505 Actuator Number HP: Invalid configuration. Parameter for actuator type should never be different from 1 or 2. 2000 Unknown event, for the event handling mechanism 2001 Too many events for even queue
2100 Invalid buffer input 2101 EEProm probably defective
2200 Invalid Index for SQBLData 2201 Invalid Index for SQBLData 2202 Invalid Index for SQBLData 2203 Invalid Index for SQBLData 2204 Invalid Index for SQBLData 2205 Invalid Index for SQBLData 2206 Invalid Index for SQBLDataKurven 2207 Invalid Index for SQBLDataPara 2208 Invalid Index for SQBLData 2209 Data request for data block, but no transmission.
2300 Invalid state 2301 Invalid state 2302 Deleting curve, end of EI 2303 Invalid state 2304 Invalid state 2305 Invalid parameter number (does not exist anymore). 2306 Invalid state cold check 2307 Cold check 2308 Cold check 2309 Cold check 2310 Invalid state 2350 - 2354
Cold check
2400 Attempt to write to a Modbus register 2401 Modbus register described
2500 Parameter with access level > 4
2600 Do not find the operating mode 2601 Transfer forbidden
D1 D2 Description
2700 Deleting curve, left EI
2800 The air pressure has not dropped but the burner still starts. 2801 More than one valve were opened during cold check. 2802 Maintenance mode is active on the main controller, but there is no mainte- nance mode parametrised. 2803 Maintenance mode active but it is still ignite. 2804 Burner starts, while the supervisor controller is blocked. 2805 Burner starts, while no reference test was made. 2806 Stage for staged operation sent by HP does not seem to be plausible.
2900 Program load by the timer to high
3000 All errors, for which no error number was registered
3100 Error message of a password module 3101 Error message of the password module
3200 Internal overflow, intermediate result does not fit in the variable. 3201 Overflow of the final result
3230 UP version differs from HP version
3250 Invalid parameter for staged burner-firing rate controller
3300 Sequence control BrennUm default case entered 3301 Sequence control leakage test default case entered 3302 Sequence control FAT default case 3303 Sequence control post purge default case 3304 Sequence control pre purge default case entered 3305 Sequence control ignition default case entered
4000 0 No curve point to the load of the ignition point. 4001 0 ucPIdx_R >= ucPunktAnzahl
4100 sRampe.ucState Invalid value of sRampe.ucState
4200 ucVBMode Invalid value of ucVBMode
4302 0 If no active air channel is defined (parameter settings error).
4400 ucSteuerArtEx Invalid value of ucSteuerArtEx 4401 0 Timeout while waiting for ??? 4402 ucSteuerArtEx Invalid value of ucSteuerArtEx 4403 ucKanStat (ucKanStat & Def_VKM2_MSK) != Def_VKM2_DVAL
D1 D2 Description