
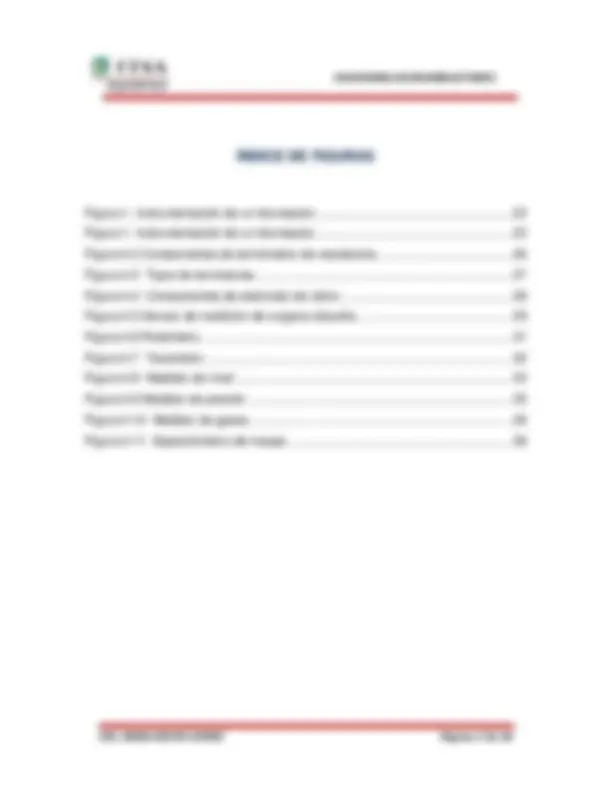
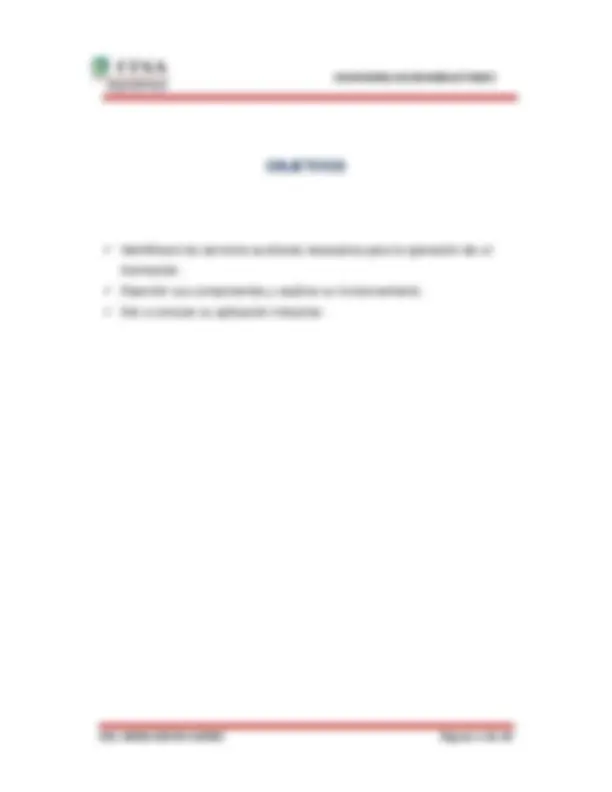
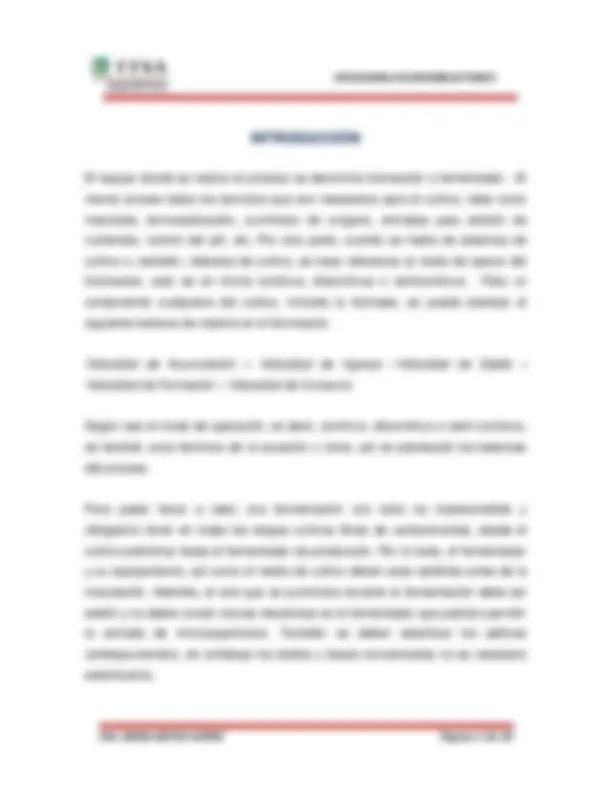
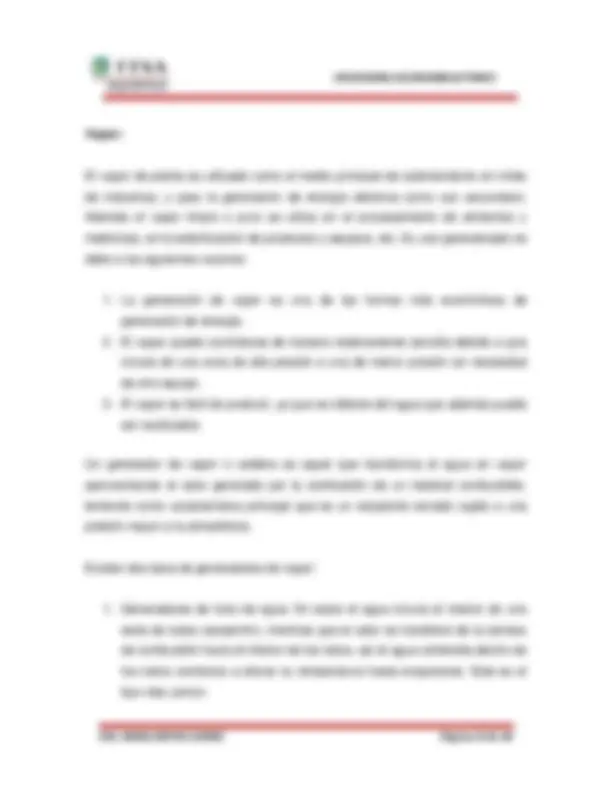
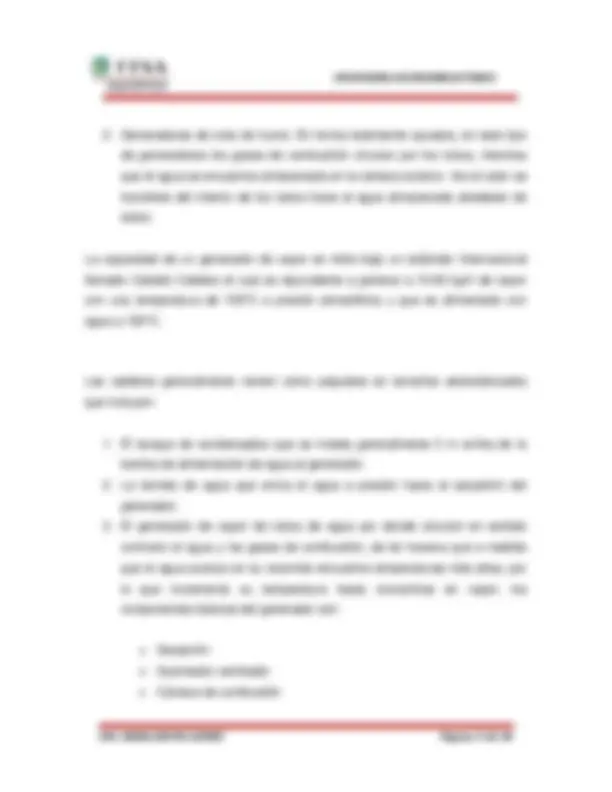
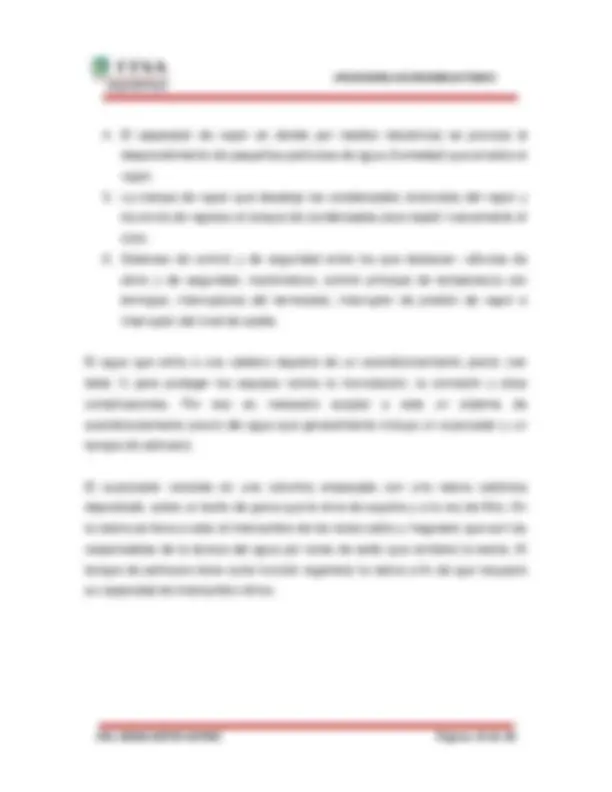
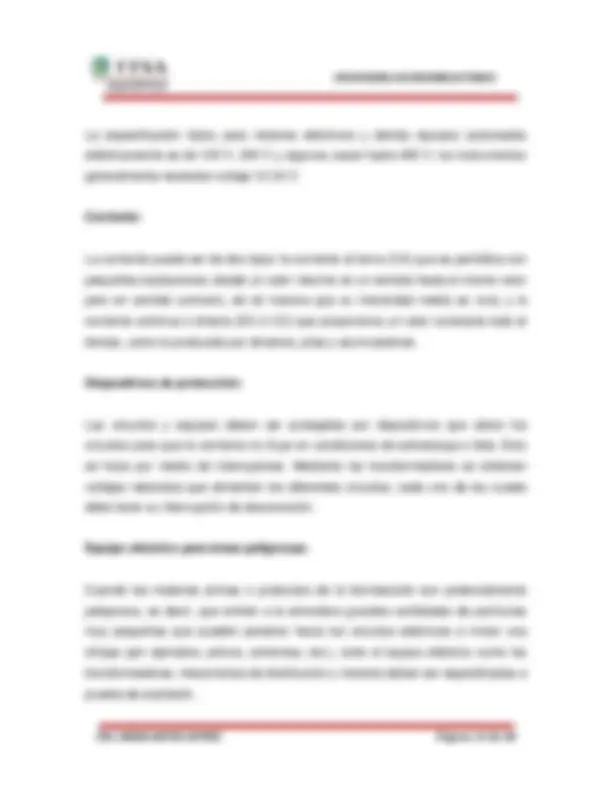
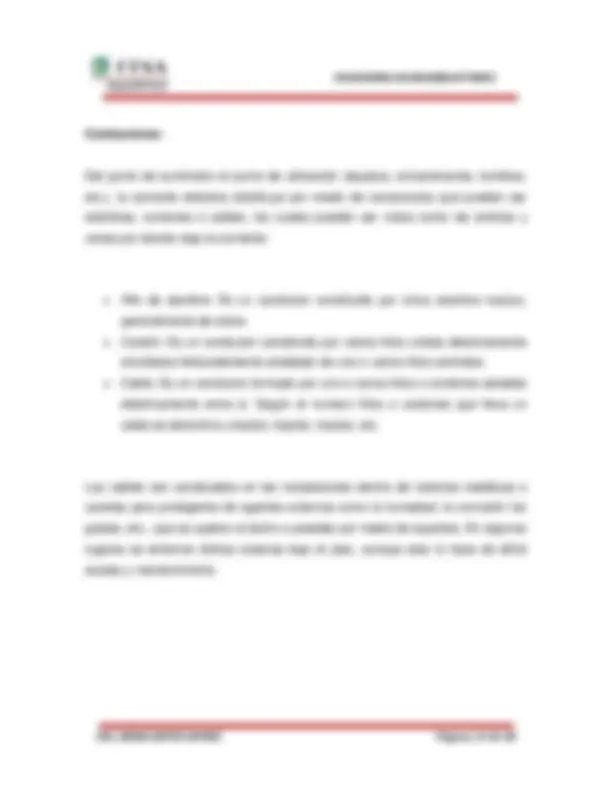
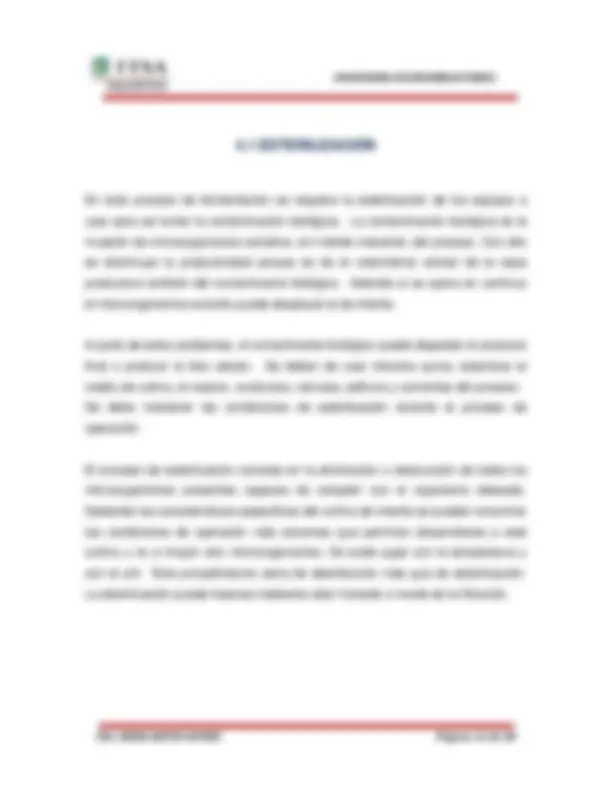
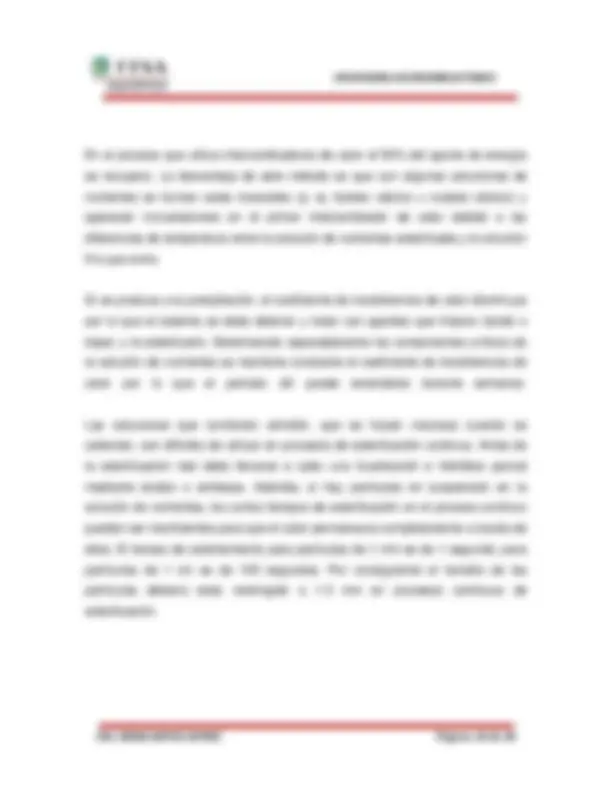
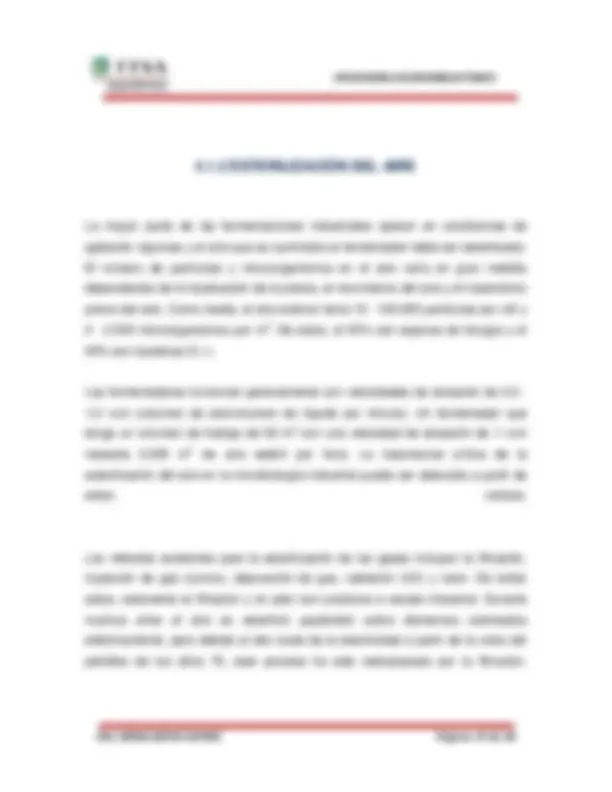
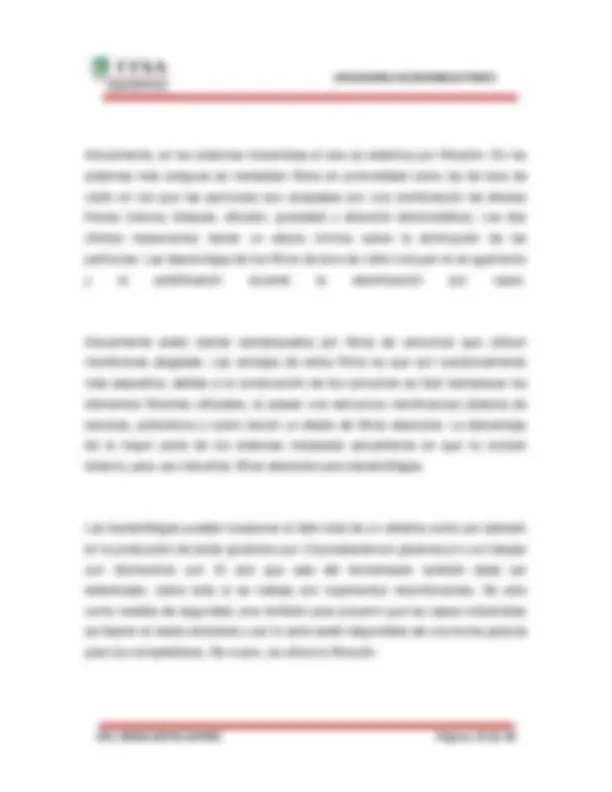
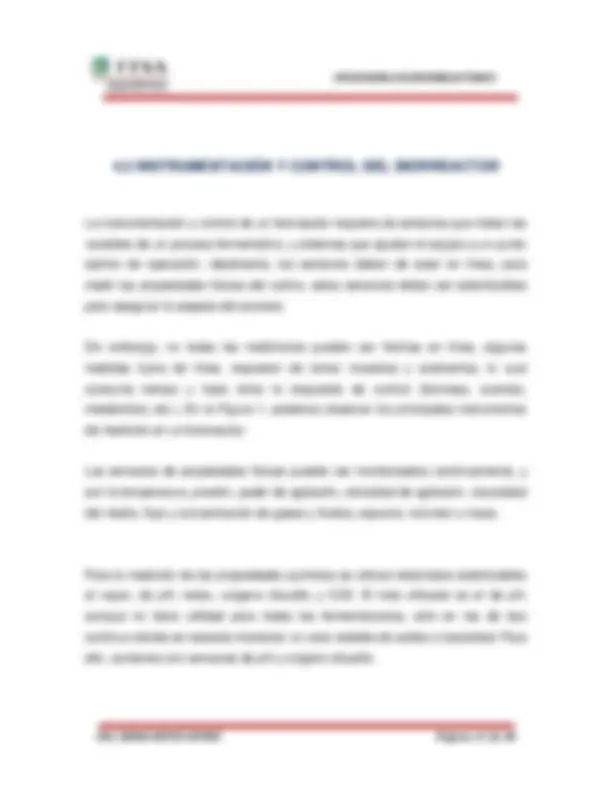
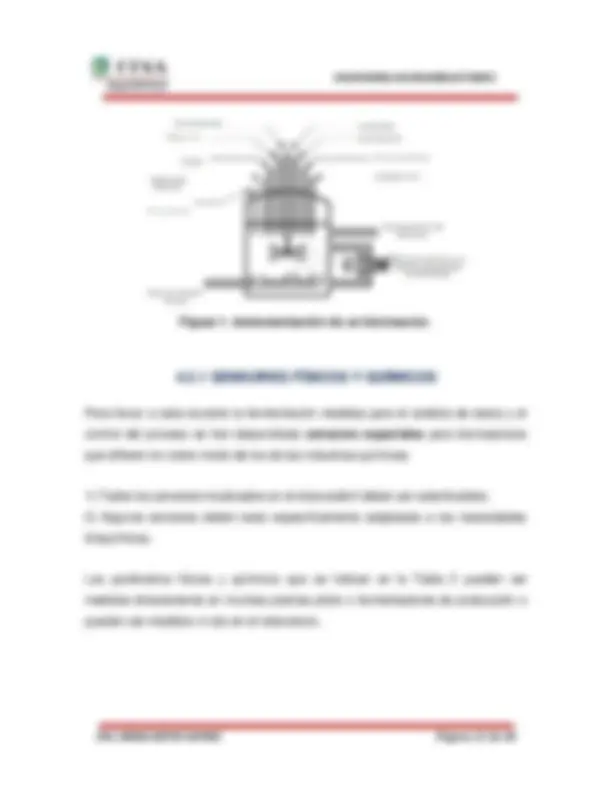
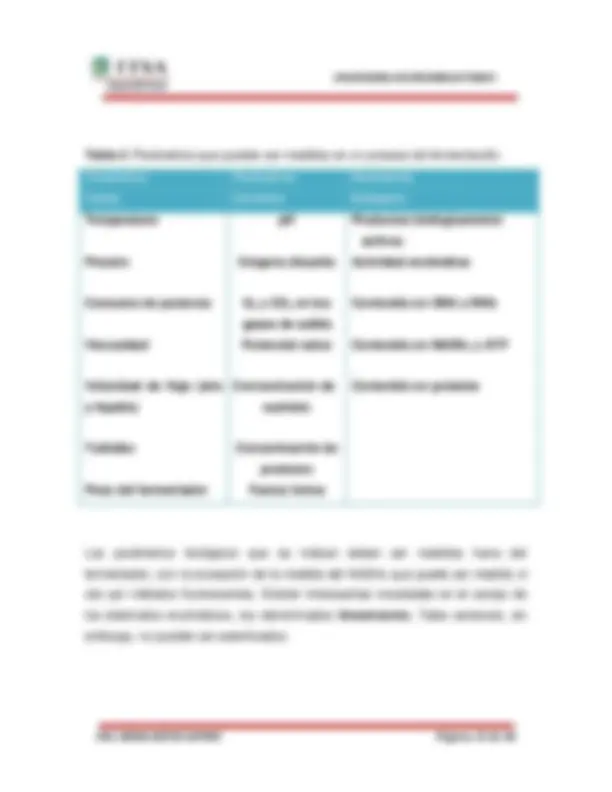
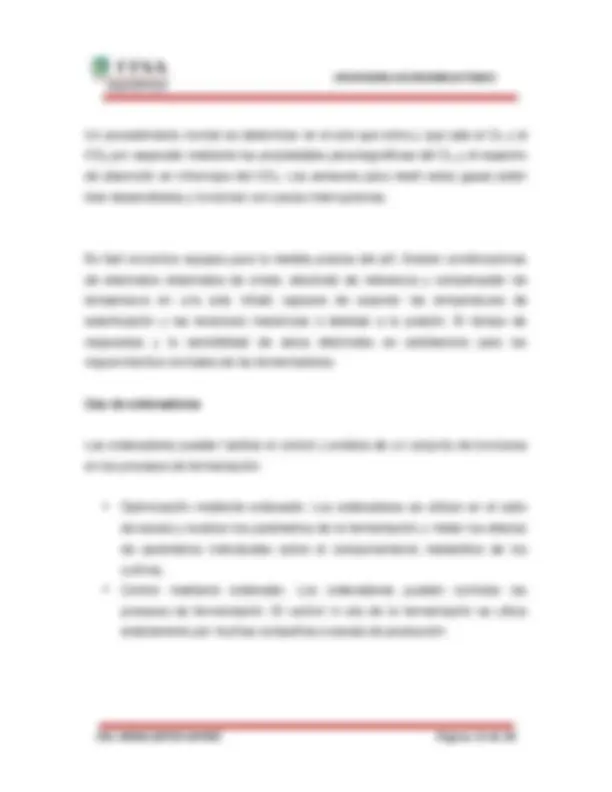
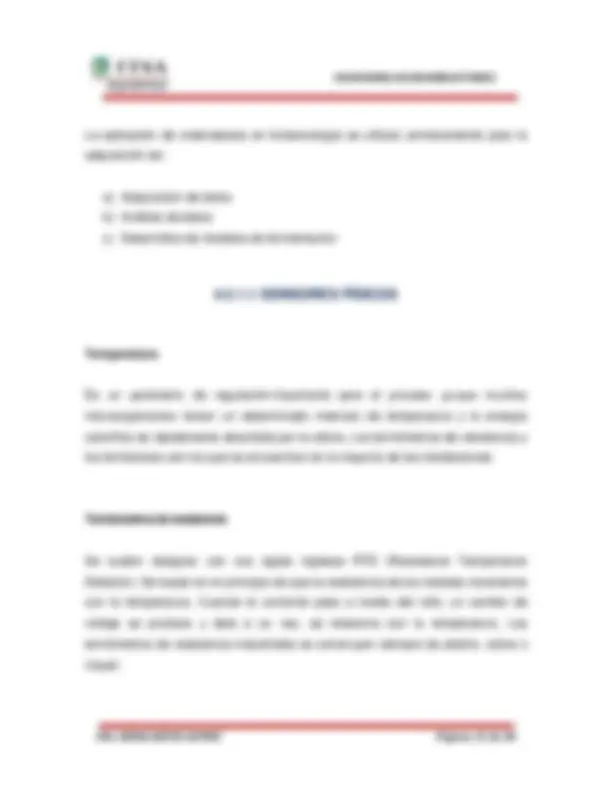
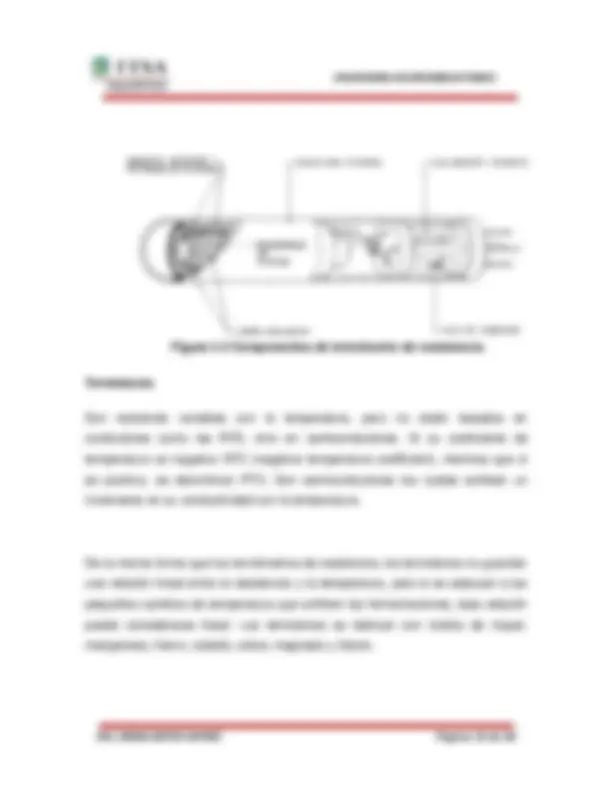
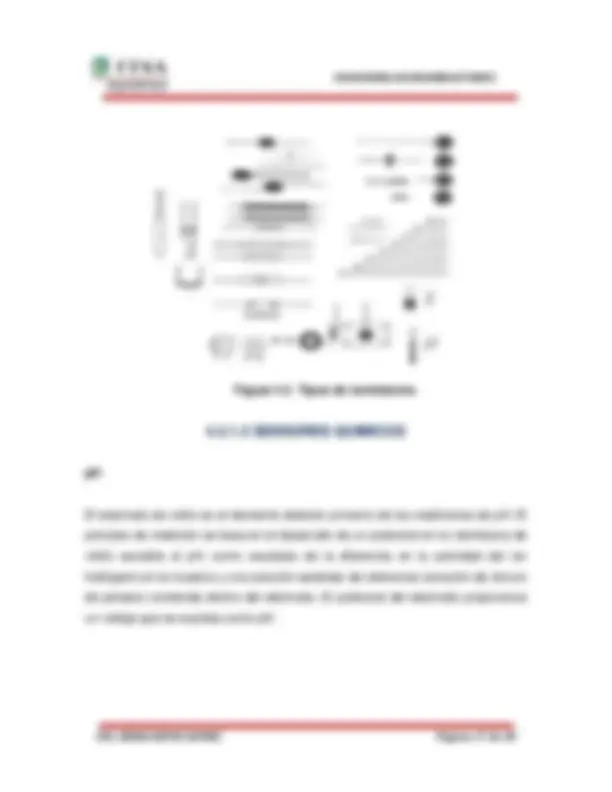
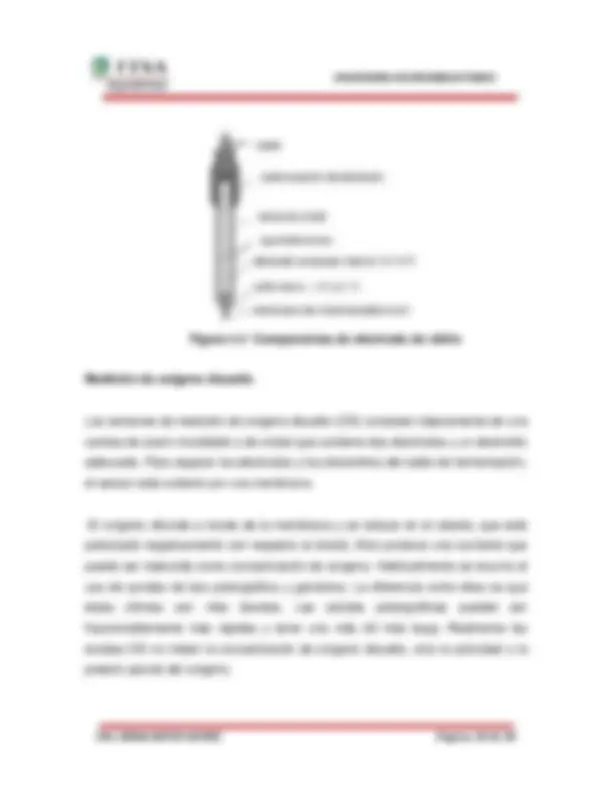
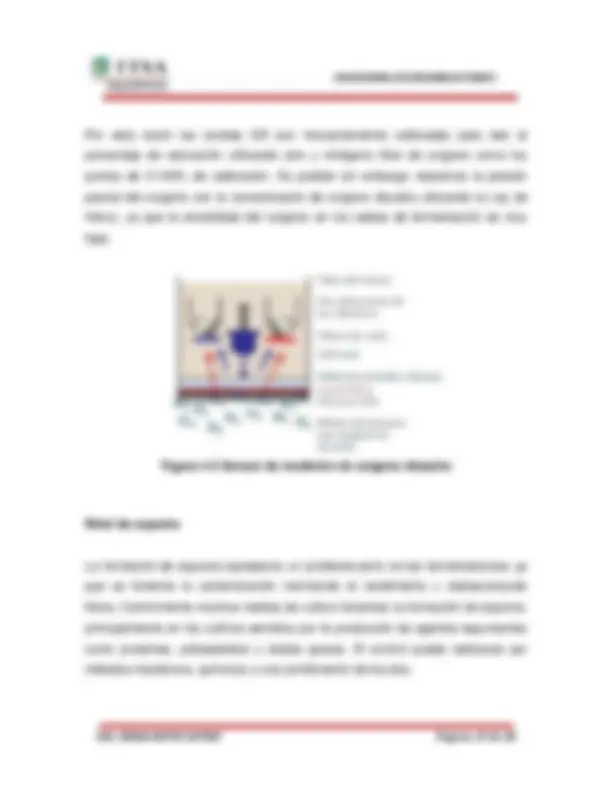
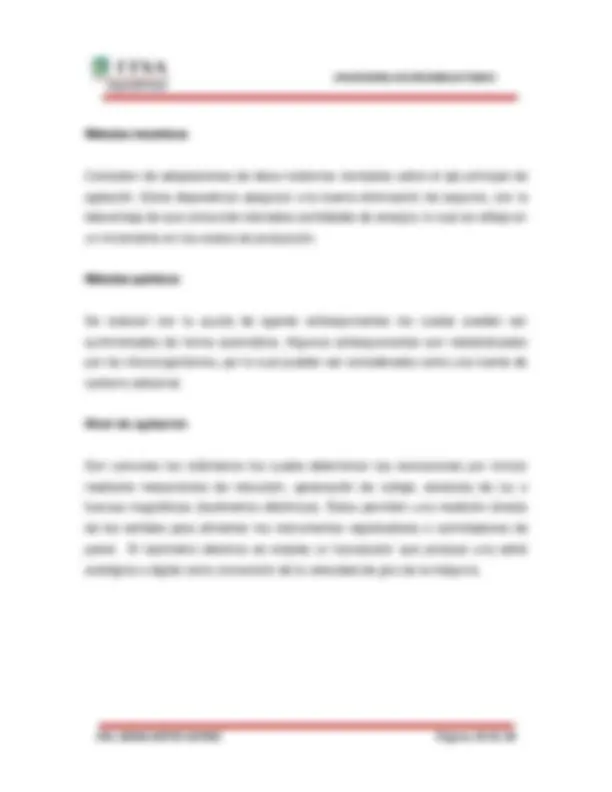
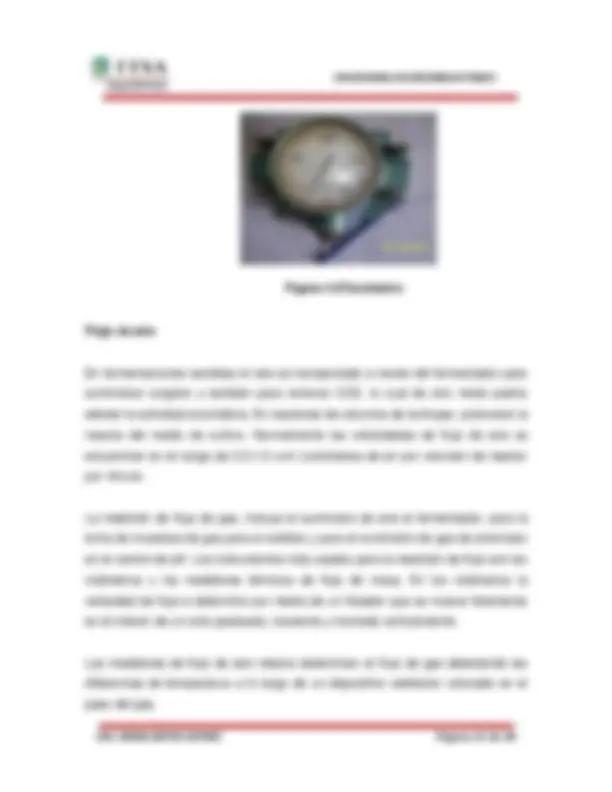
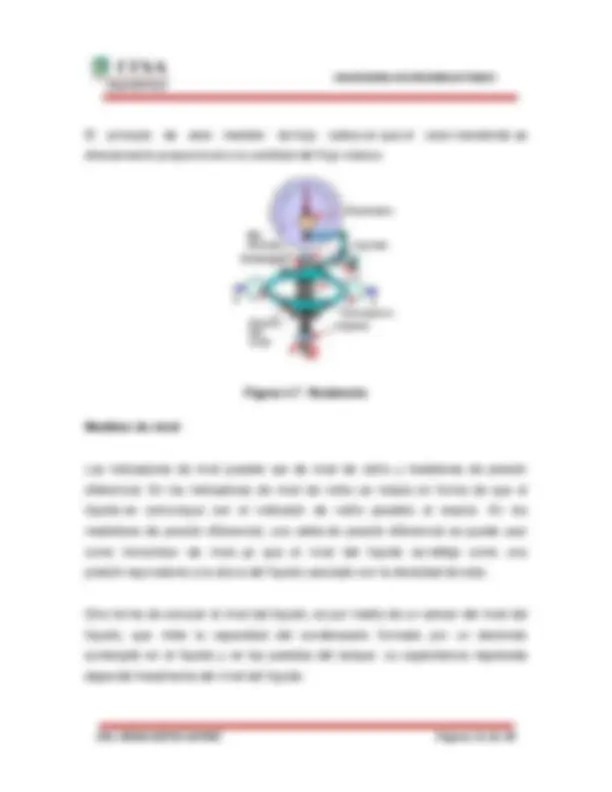
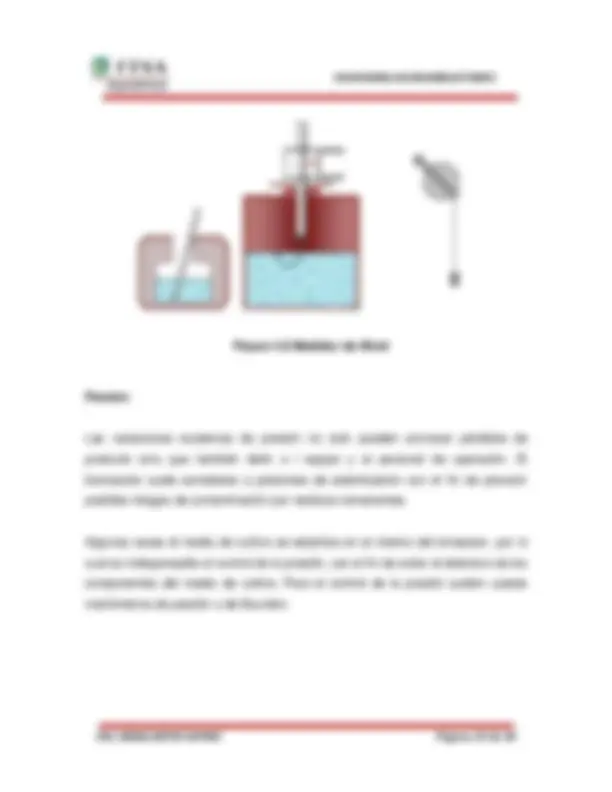
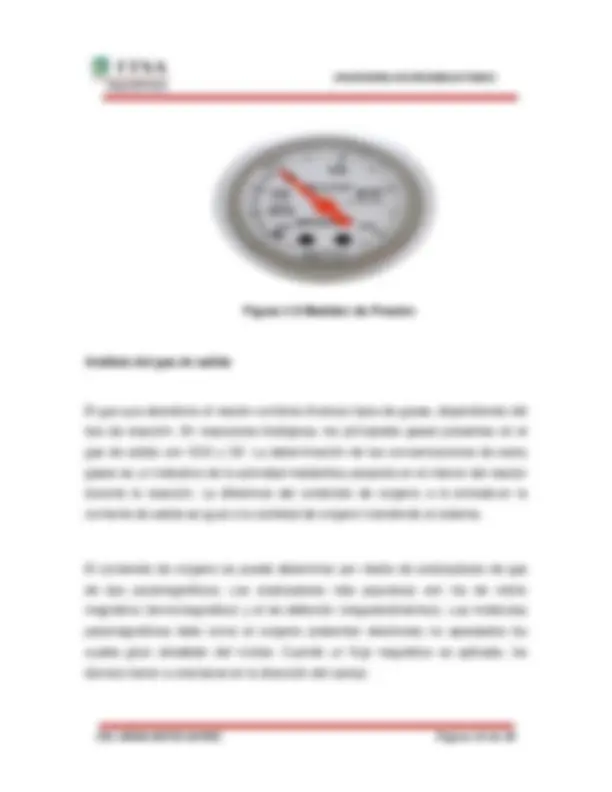
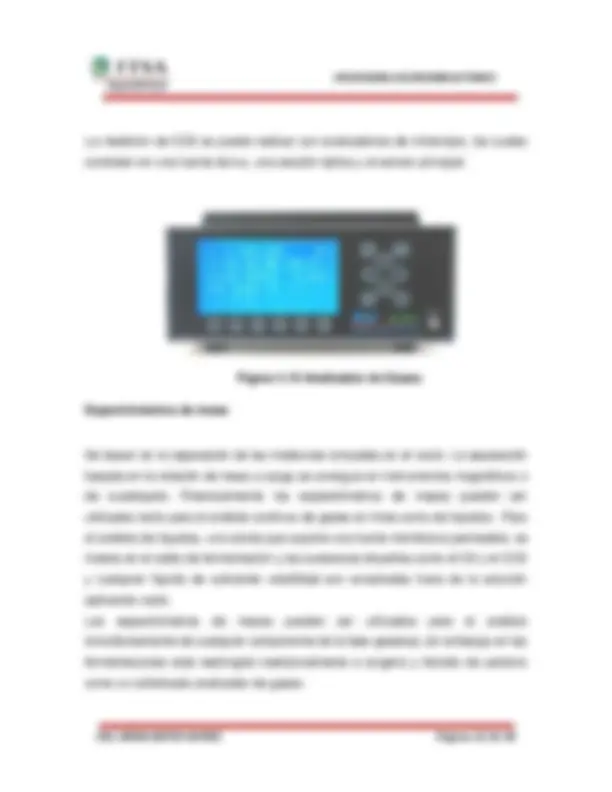
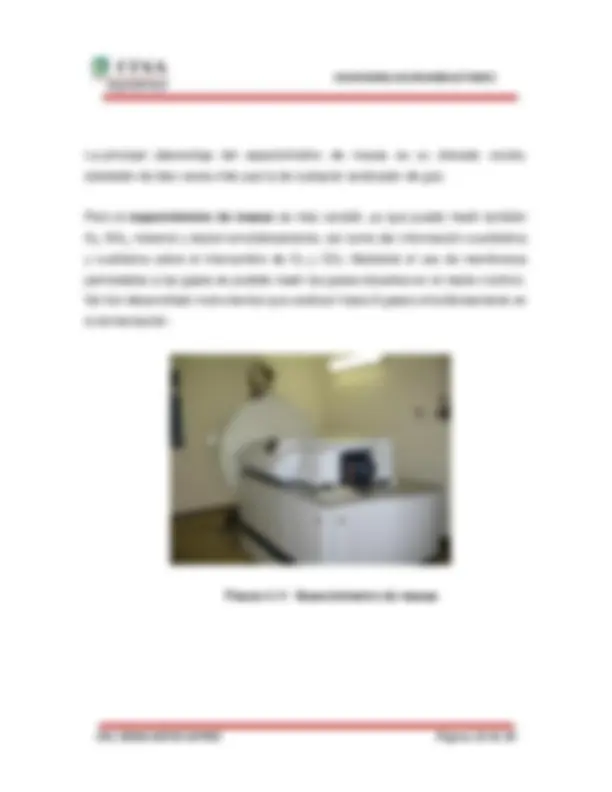
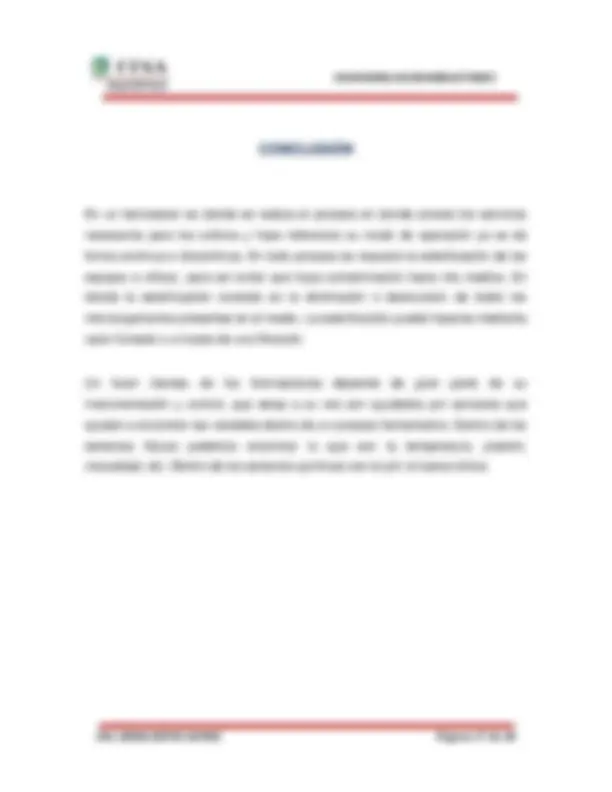
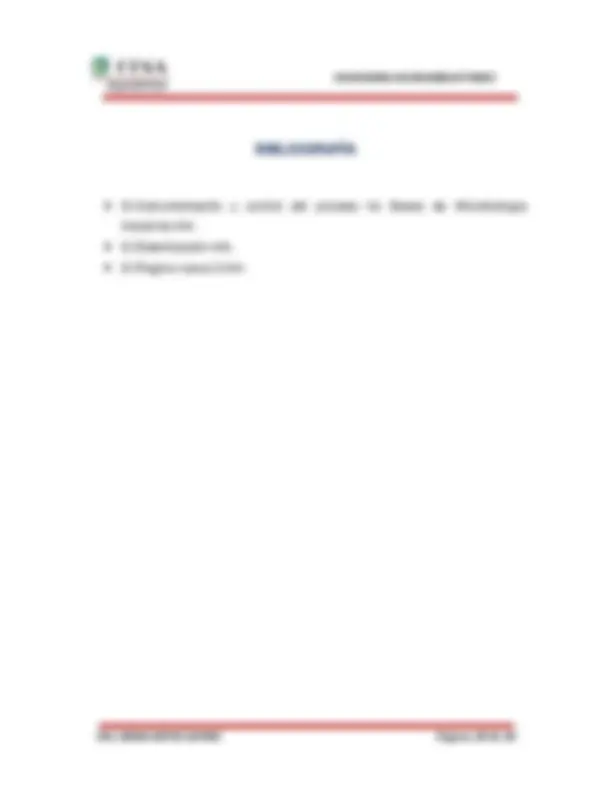
Prepara tus exámenes y mejora tus resultados gracias a la gran cantidad de recursos disponibles en Docsity
Gana puntos ayudando a otros estudiantes o consíguelos activando un Plan Premium
Prepara tus exámenes
Prepara tus exámenes y mejora tus resultados gracias a la gran cantidad de recursos disponibles en Docsity
Prepara tus exámenes con los documentos que comparten otros estudiantes como tú en Docsity
Los mejores documentos en venta realizados por estudiantes que han terminado sus estudios
Estudia con lecciones y exámenes resueltos basados en los programas académicos de las mejores universidades
Responde a preguntas de exámenes reales y pon a prueba tu preparación
Consigue puntos base para descargar
Gana puntos ayudando a otros estudiantes o consíguelos activando un Plan Premium
Comunidad
Pide ayuda a la comunidad y resuelve tus dudas de estudio
Descubre las mejores universidades de tu país según los usuarios de Docsity
Ebooks gratuitos
Descarga nuestras guías gratuitas sobre técnicas de estudio, métodos para controlar la ansiedad y consejos para la tesis preparadas por los tutores de Docsity
todo sobre biorreactores, partes, funciones, tipos.
Tipo: Apuntes
1 / 38
Esta página no es visible en la vista previa
¡No te pierdas las partes importantes!
En oferta
Identificara los servicios auxiliares necesarios para la operación de un biorreactor. Describir sus componentes y explicar su funcionamiento. Dar a conocer su aplicación industrial.
El equipo donde se realiza el proceso se denomina biorreactor o fermentador. El mismo provee todos los servicios que son necesarios para el cultivo, tales como mezclado, termostatización, suministro de oxígeno, entradas para adición de nutrientes, control del pH, etc. Por otra parte, cuando se habla de sistemas de cultivo o, también, métodos de cultivo, se hace referencia al modo de operar del biorreactor, esto es en forma continua, discontinua o semicontinua. Para un componente cualquiera del cultivo, incluida la biomasa, se puede plantear el siguiente balance de materia en el biorreactor.
Velocidad de Acumulación = Velocidad de Ingreso – Velocidad de Salida + Velocidad de Formación – Velocidad de Consumo
Según sea el modo de operación, es decir, continuo, discontinuo o semi-continuo, se tendrán unos términos de la ecuación u otros, así se plantearán los balances del proceso.
Para poder llevar a cabo una fermentación con éxito es imprescindible y obligatorio tener en todas las etapas cultivos libres de contaminantes, desde el cultivo preliminar hasta el fermentador de producción. Por lo tanto, el fermentador y su equipamiento, así como el medio de cultivo deben estar estériles antes de la inoculación. Además, el aire que se suministra durante la fermentación debe ser estéril y no deben existir roturas mecánicas en el fermentador que podrían permitir la entrada de microorganismos. También se deben esterilizar los aditivos (antiespumantes), sin embargo los ácidos y bases concentrados no es necesario esterilizarlos.
Los servicios auxiliares necesarios en la operación de un biorreactor incluyen aire comprimido, diversos gases comprimidos (nitrógeno, oxígeno, etc.), agua de enfriamiento (agua helada y agua de torre), agua para servicios varios, vapor de planta y energía eléctrica.
Aire:
El aire tiene varios usos en un biorreactor, entre ellos por orden de importancia:
La elección de aire a utilizar del uso que se haga de él. El aire debe ser seco y libre de aceite. Además, cuando se requiera que el proceso o producto no se afecte por la introducción de microorganismos ajenos, contenidos en la corriente de aire, será necesario que este sea estéril.
Vapor:
El vapor de planta es utilizado como el medio principal de calentamiento en miles de industrias, y para la generación de energía eléctrica como uso secundario. Además el vapor limpio o puro se utiliza en el procesamiento de alimentos y medicinas, en la esterilización de productos y equipos, etc. Su uso generalizado se debe a las siguientes razones:
Un generador de vapor o caldera es aquel que transforma el agua en vapor aprovechando el calor generado por la combustión de un material combustible, teniendo como característica principal que es un recipiente cerrado sujeto a una presión mayor a la atmosférica.
Existen dos tipos de generadores de vapor:
El agua que entra a una caldera requiere de un acondicionamiento previo (ver tabla 1) para proteger los equipos contra la incrustación, la corrosión y otras complicaciones. Por eso es necesario acoplar a este un sistema de acondicionamiento previo del agua que generalmente incluye un suavizador y un tanque de salmuera
El suavizador consiste en una columna empacada con una resina catiónica depositada sobre un lecho de grava que le sirve de soporte y a la vez de filtro. En la resina se lleva a cabo el intercambio de los iones calcio y magnesio que son los responsables de la dureza del agua por iones de sodio que contiene la resina. El tanque de salmuera tiene como función regenerar la resina a fin de que recupere su capacidad de intercambio iónico.
El sistema de distribución de vapor se realiza por medio de tuberías, generalmente de acero al carbón de cédula 40, cuidando que las velocidades y caídas de presión estén comprendidas en los intervalos recomendados para el dimensionamiento de las mismas. El vapor puro requerirá de tuberías de acero inoxidable con acabado sanitario.
En adición al sistema de distribución de vapor deberán preverse los sistemas de manejo de condensados, ya que estos pueden realizarse con un importante ahorro en el acondicionamiento del agua de alimentación a la caldera y en la energía requerida para el calentamiento de la misma hasta el punto de ebullición.
Agua de enfriamiento:
El agua como servicio auxiliar se utiliza como fluido de enfriamiento para el control de la temperatura del caldo de fermentación en los biorreactores. Esta agua, a diferencia del agua de proceso, nunca entra en contacto con las materias primas o productos de la biorreacción, ni con las superficies en contacto con estos, sino que circula a través de las chaquetas o serpentines según el diseño del biorreactor.
La especificación típica para motores eléctricos y demás equipos accionados eléctricamente es de 120 V, 240 V y algunos casos hasta 480 V, los instrumentos generalmente necesitan voltaje 12-24 V.
Corriente:
La corriente puede ser de dos tipos: la corriente al terna (CA) que es periódica con pequeñas oscilaciones, desde un valor máximo en un sentido hasta el mismo valor pero en sentido contrario, de tal manera que su intensidad media es nula; y la corriente continua o directa (DC ó CC) que proporciona un valor constante todo el tiempo, como la producida por dinamos, pilas y acumuladores.
Dispositivos de protección:
Los circuitos y equipos deben ser protegidos por dispositivos que abran los circuitos para que la corriente no fluya en condiciones de sobrecarga o falla. Esto se hace por medio de interruptores. Mediante los transformadores se obtienen voltajes reducidos que alimentan los diferentes circuitos, cada uno de los cuales debe tener su interrupción de desconexión.
Equipo eléctrico para áreas peligrosas:
Cuando las materias primas o productos de la biorreacción son potencialmente peligrosos, es decir, que emiten a la atmosfera grandes cantidades de partículas muy pequeñas que pueden penetrar hacia los circuitos eléctricos e iniciar una chispa (por ejemplos; polvos, solventes, etc.), tanto el equipo eléctrico como los transformadores, mecanismos de distribución y motores deben ser especificados a prueba de explosión.
Conductores:
Del punto de suministro al punto de utilización (equipos, comprensores, bombas, etc.), la corriente eléctrica distribuye por medio de conductores que pueden ser alambres, cordones o cables, los cuales pueden ser vistos como las arterias y venas por donde viaja la corriente:
o Hilo de alambre: Es un conductor constituido por único alambre macizo, generalmente de cobre. o Cordón: Es un conductor constituido por varios hilos unidos eléctricamente enrollados helicoidalmente alrededor de uno o varios hilos centrales. o Cable: Es un conductor formado por uno o varios hilos o cordones aislados eléctricamente entre si. Según el numero hilos o cordones que lleva un cable se denomina unipolar, bipolar, tripolar, etc.
Los cables son canalizados en las instalaciones dentro de tuberías metálicas o canales para protegerlos de agentes externos como la humedad, la corrosión los golpes, etc., que se sujetan al techo o paredes por medio de soportes. En algunos lugares se entierran dichas tuberías bajo el piso, aunque esto lo hace de difícil acceso y mantenimiento.
El medio nutritivo que se prepara inicialmente contiene una variedad de células vegetativas diferentes y de esporas que proceden de los constituyentes del medio, del agua y del recipiente. Estos microorganismos deben ser eliminados por un procedimiento adecuado antes de la inoculación. Existen un conjunto de procedimientos para la esterilización, pero en la práctica, para instalaciones a gran escala, el calor es el principal mecanismo utilizado.
Un conjunto de factores influyen en el éxito de la esterilización por calor: el número y tipo de microorganismos presentes, la composición del medio de cultivo, el valor del pH y el tamaño de las partículas en suspensión. Las células vegetativas son eliminadas rápidamente a temperaturas relativamente bajas, pero para la destrucción de las esporas se necesitan temperaturas de 121°C.
La esterilización por filtración se utiliza frecuentemente para todos los componentes de la solución de nutrientes que son sensibles al calor y que serían por tanto desnaturalizados durante el proceso de esterilización por vapor utilizado normalmente en fermentación industrial. Las vitaminas, los antibióticos o los componentes de la sangre son ejemplos de compuestos lábiles al calor que deben ser esterilizados por filtración.
La esterilización continua se lleva a cabo normalmente en 30-120 segundos a 140° C. El calentamiento del medio de cultivo para la esterilización continua puede ser llevado a cabo mediante inyección de vapor o mediante intercambiadores de calor. La esterilización con inyección de vapor se hace inyectando vapor en la solución de nutrientes. La temperatura se eleva rápidamente a 140° C y se mantiene durante 30-120 segundos.
Debido a la formación de condensados la solución nutritiva se diluye; para corregir esto la solución caliente se bombea a través de una válvula de expansión a un vaporizador y el condensado se retira mediante bombas de vacío de forma que la solución esterilizada de nutrientes tiene la misma concentración después del proceso de enfriamiento que antes. La desventaja de este proceso es la sensibilidad que presenta a cambios en la viscosidad del medio y a variaciones en la presión.
En el proceso continuo que utiliza intercambiadores de calor, la solución de nutrientes, en el primer intercambiador de calor, se precalienta a 90-120° C durante 20-30 segundos por la solución nutritiva previamente esterilizada que sale. Luego, en el segundo intercambiador de calor, se calienta indirectamente con vapor a 140° C. Esta temperatura se mantiene durante 30-120 segundos en una tubería de mantenimiento antes de que sea colocada en el primer intercambiador mediante enfriamiento preliminar y posteriormente en un tercer cambiador para refrigeración a la temperatura del fermentador. La fase de enfriamiento es sólo de 20-30 segundos.
La mayor parte de las fermentaciones industriales operan en condiciones de agitación vigorosa y el aire que se suministra al fermentador debe ser esterilizado. El número de partículas y microorganismos en el aire varía en gran medida dependiendo de la localización de la planta, el movimiento del aire y el tratamiento previo del aire. Como media, el aire exterior tiene 10 - 100.000 partículas por m3 y 5 - 2.000 microorganismos por m^3. De estos, el 50% son esporas de hongos y el 40% son bacterias G (-).
Los fermentadores funcionan generalmente con velocidades de aireación de 0,5 - 1,0 vvm (volumen de aire/volumen de líquido por minuto). Un fermentador que tenga un volumen de trabajo de 50 m^3 con una velocidad de aireación de 1 vvm necesita 3.000 m^3 de aire estéril por hora. La importancia crítica de la esterilización del aire en la microbiología industrial puede ser deducida a partir de estos valores.
Los métodos existentes para la esterilización de los gases incluyen la filtración, inyección de gas (ozono), depuración de gas, radiación (UV) y calor. De todos estos, solamente la filtración y el calor son prácticos a escala industrial. Durante muchos años el aire se esterilizó pasándolo sobre elementos calentados eléctricamente, pero debido al alto coste de la electricidad a partir de la crisis del petróleo de los años 70, este proceso ha sido reemplazado por la filtración.
Actualmente, en los sistemas industriales el aire se esteriliza por filtración. En los sistemas más antiguos se instalaban filtros en profundidad como los de lana de vidrio en los que las partículas son atrapadas por una combinación de efectos físicos (inercia, bloqueo, difusión, gravedad y atracción electrostática). Los dos últimos mecanismos tienen un efecto mínimo sobre la eliminación de las partículas. Las desventajas de los filtros de lana de vidrio incluyen el arrugamiento y la solidificación durante la esterilización por vapor.
Actualmente están siendo reemplazados por filtros de cartuchos que utilizan membranas plegadas. Las ventajas de estos filtros es que son sustancialmente más pequeños, debido a la construcción de los cartuchos es fácil reemplazar los elementos filtrantes utilizados, al poseer una estructura membranosa (ésteres de celulosa, polisulfona o nylon) tienen un efecto de filtros absolutos. La desventaja de la mayor parte de los sistemas instalados actualmente es que no existen todavía, para uso industrial, filtros absolutos para bacteriófagos.
Los bacteriófagos pueden ocasionar el fallo total de un sistema como por ejemplo en la producción de ácido glutámico por Corynebacterium glutamicum o al trabajar con Escherichia coli. El aire que sale del fermentador también debe ser esterilizado, sobre todo si se trabaja con organismos recombinantes. No sólo como medida de seguridad, sino también para prevenir que las cepas industriales se liberen al medio ambiente y por lo tanto estén disponibles de una forma gratuita para los competidores. De nuevo, se utiliza la filtración.