
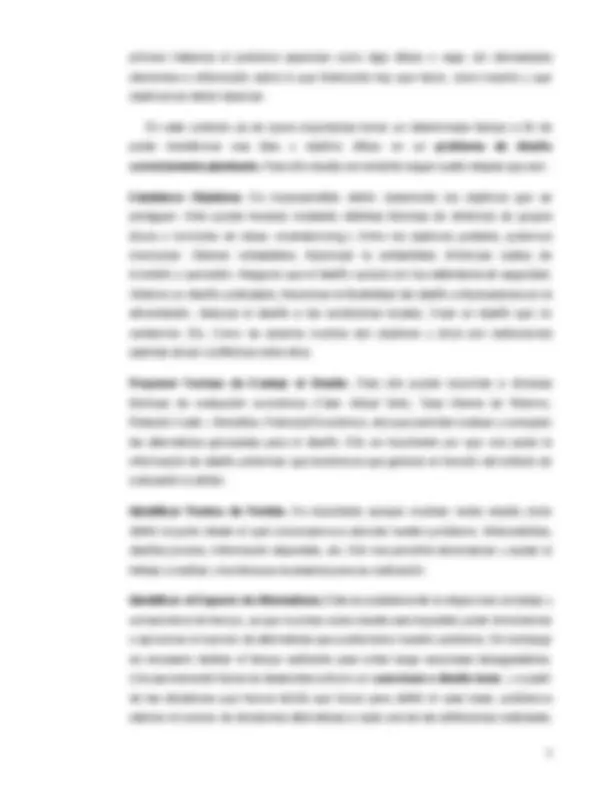

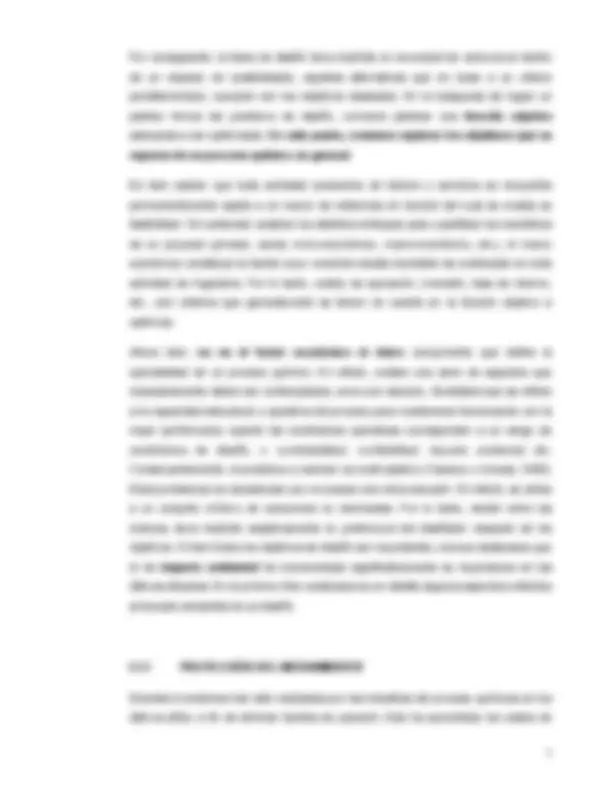
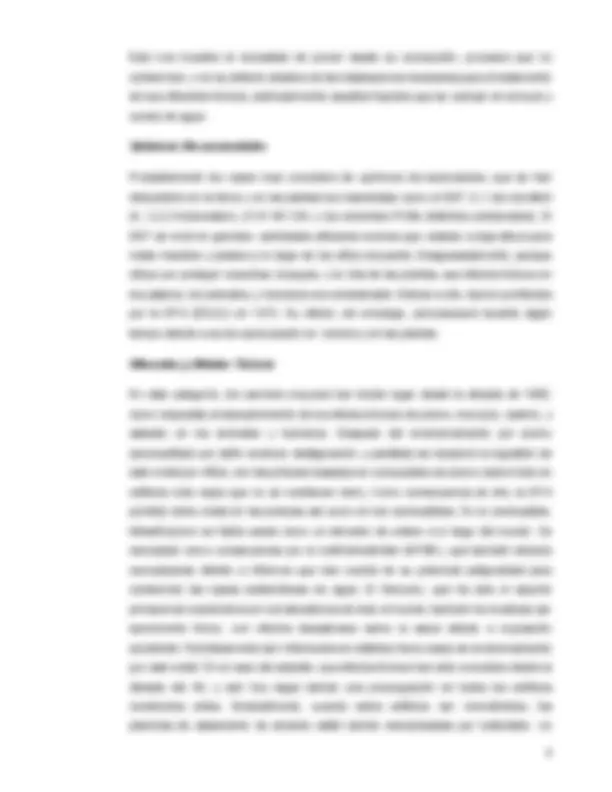
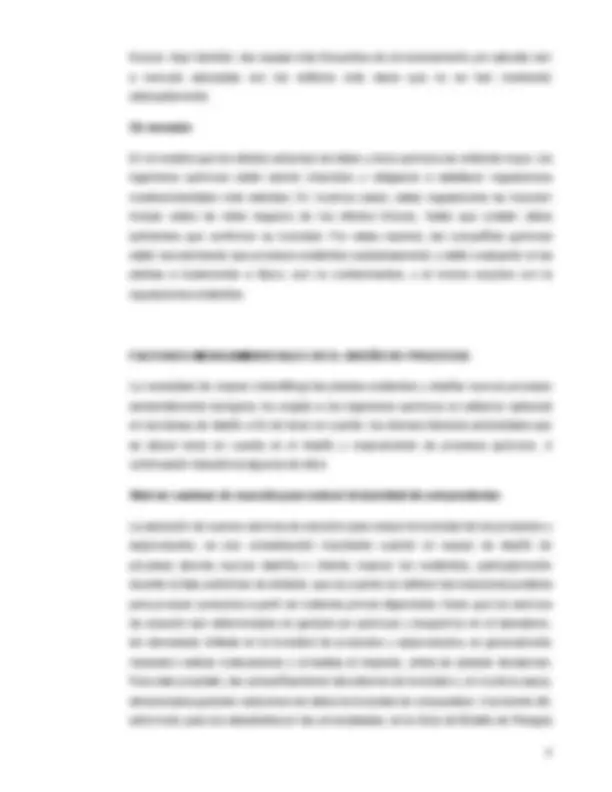
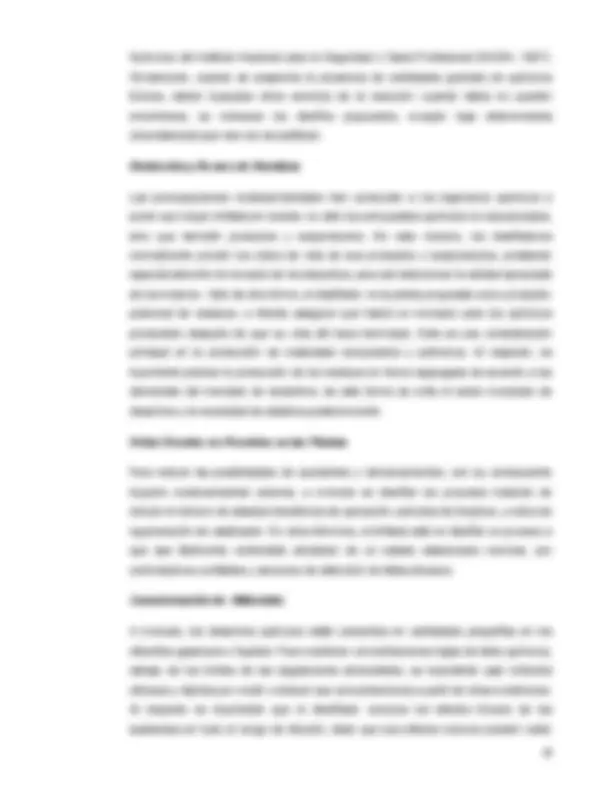
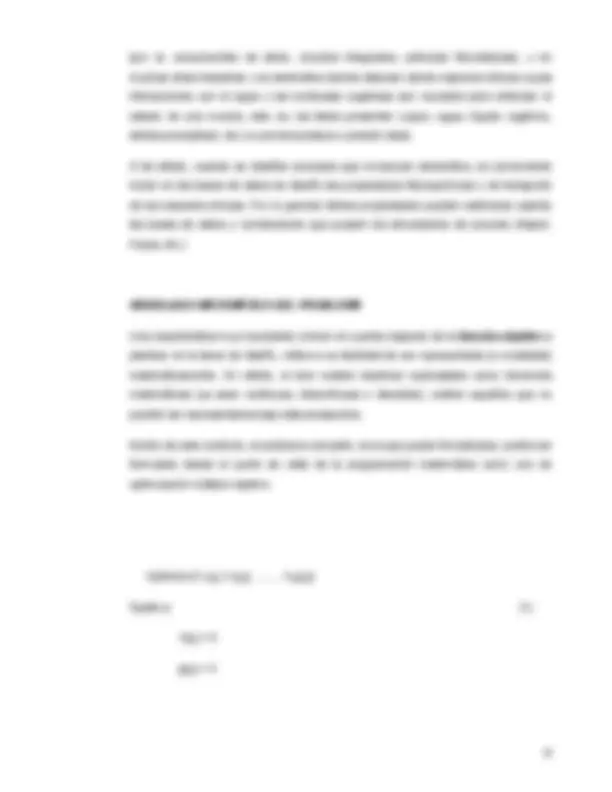
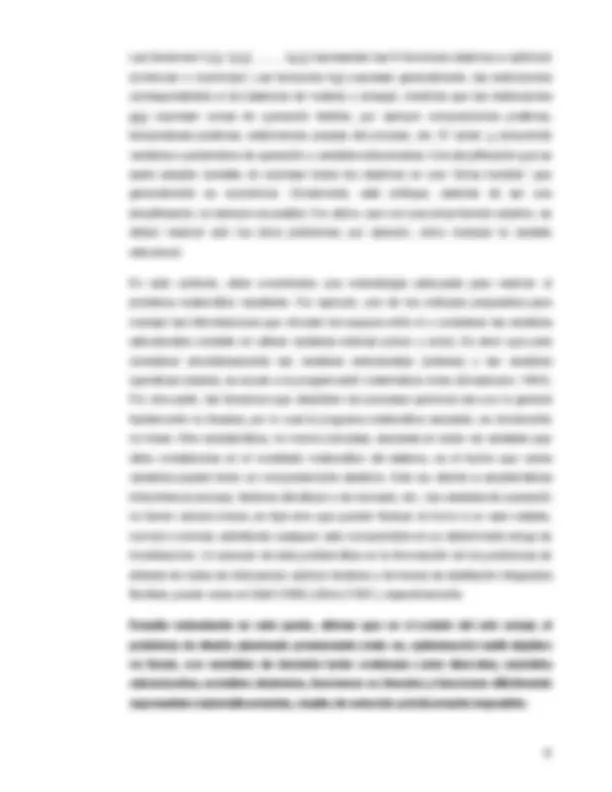
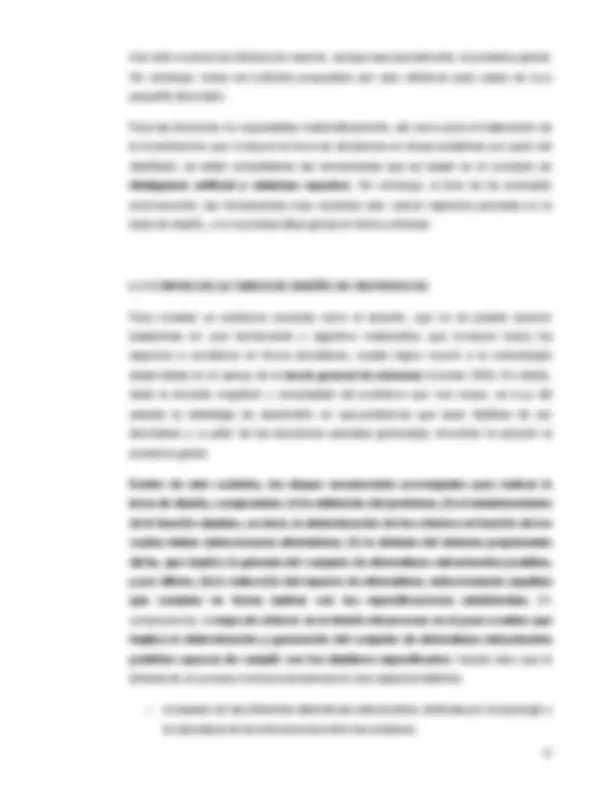
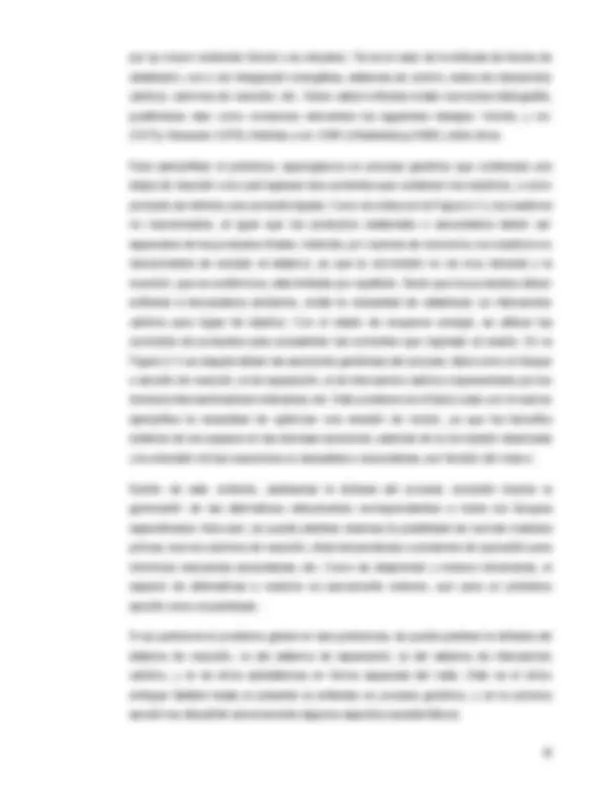
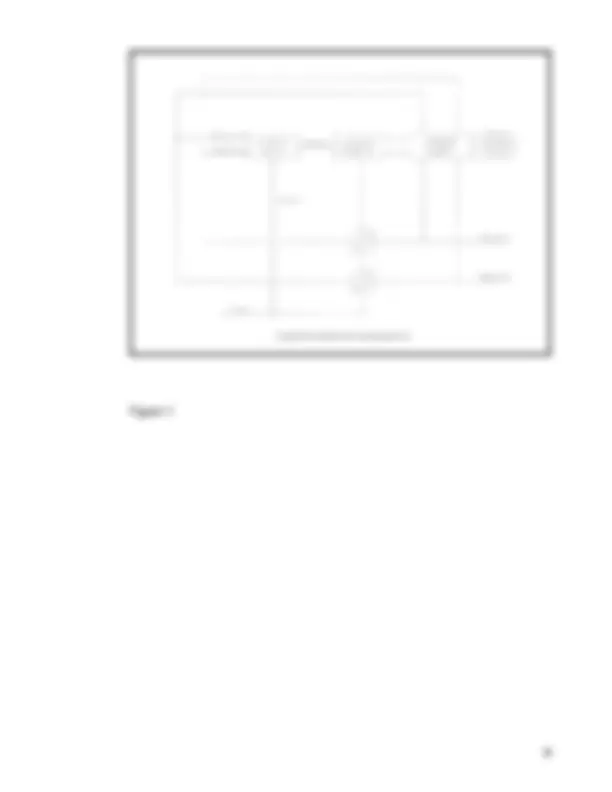
Prepara tus exámenes y mejora tus resultados gracias a la gran cantidad de recursos disponibles en Docsity
Gana puntos ayudando a otros estudiantes o consíguelos activando un Plan Premium
Prepara tus exámenes
Prepara tus exámenes y mejora tus resultados gracias a la gran cantidad de recursos disponibles en Docsity
Prepara tus exámenes con los documentos que comparten otros estudiantes como tú en Docsity
Los mejores documentos en venta realizados por estudiantes que han terminado sus estudios
Estudia con lecciones y exámenes resueltos basados en los programas académicos de las mejores universidades
Responde a preguntas de exámenes reales y pon a prueba tu preparación
Consigue puntos base para descargar
Gana puntos ayudando a otros estudiantes o consíguelos activando un Plan Premium
Comunidad
Pide ayuda a la comunidad y resuelve tus dudas de estudio
Descubre las mejores universidades de tu país según los usuarios de Docsity
Ebooks gratuitos
Descarga nuestras guías gratuitas sobre técnicas de estudio, métodos para controlar la ansiedad y consejos para la tesis preparadas por los tutores de Docsity
DOCUMENTO APTO PARA SABER COMO DISEÑAR PLANTAS
Tipo: Apuntes
1 / 19
Esta página no es visible en la vista previa
¡No te pierdas las partes importantes!
Existen en la actualidad distintos tipos de modelos y diferentes herramientas informáticas para implementarlos. Así, para el diseño de equipos específicos o bien para la resolución de balances de materia y energía, por lo general, es suficiente aplicar procedimientos analíticos o numéricos apropiados para la resolución de sistemas de ecuaciones, ya sean algebraicas o diferenciales. Sin embargo, también sabemos que, cuando el problema es crear un proceso o diagrama de flujo para obtener ciertos productos a partir de determinadas materias primas (diseño del proceso), el conocimiento y el tipo de modelos a utilizar, son sustancialmente distintos. Ello se debe a que en esta tarea se deben tomar decisiones y se debe seleccionar una alternativa entre cientos de ellas.
Todo este cúmulo de conocimientos sobre modelado matemático, sistemas de representación basados en la teoría de sistemas, administración y gestión de datos, razonamiento simbólico, métodos numéricos, y avances en el campo informático; ha generado en las últimas décadas una nueva disciplina dentro de la Ingeniería Química y particularmente dentro de lo que tradicionalmente conocíamos como Ingeniería de Procesos ( Conjunto de actividades dedicadas al: Diseño, Control y Operación de Procesos).
En un principio denominada Diseño de Procesos Asistido por Computadora ya que su aplicación solo abordaba los cálculos básicos de procesos, actualmente ha evolucionado su aplicación a la mayoría de las actividades dentro de la Ingeniería de Proceso. Surge así la hoy denominada Ingeniería de Sistemas de Procesos ó Process System Engineering que puede definirse como “El conjunto de conocimientos en la Ingeniería Química que aborda el modelado y desarrollo sistemático de herramientas y métodos de solución para Síntesis, Análisis y Evaluación del: Diseño de Procesos, Control de Procesos y Operación de Procesos”.
El objetivo de esta unidad es introducir al lector en los principales conceptos de la metodología de diseño de un proceso, desde la generación de su diagrama de flujo (flow-sheet) y estructura. Esto es importante, ya que no resulta apropiado simular a optimizar un proceso si paralelamente no nos cuestionamos acerca de la génesis del mismo o de las reglas que permiten en una forma sistemática, crear y evaluar diferentes alternativas para el diseño, de forma de poder decidir entre ellas de una manera adecuada.
La síntesis de procesos es una de las tareas más complejas y exigentes confrontada por el ingeniero químico. Desde un punto de vista pragmático, el uso de técnicas de síntesis de procesos se introdujo lentamente como consecuencia de las condiciones cambiantes en la producción industrial y el surgimiento de tremendos avances productivos y tecnológicos. En este punto, conviene aclarar que la mayoría de los procesos químicos en uso en la actualidad surgieron hace mucho tiempo, cuando no existían métodos sistemáticos para la generación de las estructuras óptimas de los mismos (camino de reacción, redes de intercambio, sistemas integrados, trenes de separación, etc.). Resulta lógico pensar, por lo tanto, que estas innovaciones se fueron dando parcialmente, paso a paso, con el transcurso del tiempo. Desde este punto de vista, resulta ilustrativo el análisis de la evolución de las tecnologías utilizadas en los distintos procesos químicos (Rotstein y Stephanopoulos, 1979). En efecto, dado que en todo proceso químico existe la transformación fisicoquímica de materias primas en los productos deseados, se puede calcular el trabajo mínimo asociado (calculado termodinámicamente como un proceso ideal o reversible). Por lo tanto, se dispone de al menos un elemento de comparación, punto de referencia ideal u objetivo a alcanzar. Dicha magnitud sirve para comparar el consumo real de cualquier alternativa con respecto al trabajo mínimo. En este contexto, es interesante observar la evolución de diferentes procesos pertenecientes a diversos campos (no sólo a la industria química) que, mediante la incorporación de nuevos métodos y tecnología en el diseño, han avanzado hacia alternativas más interesantes y próximas a la óptima.
Planteo Correcto de un Problema de Diseño de Proceso
Teniendo en cuenta que el diseño de un nuevo proceso o el mejoramiento de uno existente generalmente comienza a partir de una decisión tomada por una entidad (Empresa, Gobierno, Consultora, Oficina de Ingeniería de Proceso, etc) cuyo nivel de conocimiento tecnológico es por lo general escaso o simplemente nulo, y generalmente esta fundado en ideas fuerza de tipo económico o social, resulta esperable que en una
Así podremos tener una idea aproximada de nuestro espacio de soluciones. Esta es una de las razones que justifican el desarrollo de un caso base
Resulta complejo plantear en función de un esquema formal, la actividad de diseño en la Ingenieria de Procesos. En primer lugar y en forma simplificada, se podría afirmar que un proceso químico esta vinculado al tratamiento de materiales, mediante transformaciones fisicoquímicas y/o biológicas, o procesos de separación física. En forma genérica, se denomina proceso a la unidad o sistema estructural de transformación por medio del cual los materiales que ingresan se transforman en los productos deseados. Esta unidad o sistema estructural esta compuesto por módulos (equipos a operaciones unitarias), encargados de realizar tareas especificas (separación, calentamiento, reacción química, etc). Los equipos están conectados entre sí por medio de las corrientes que los vinculan, con el objeto de satisfacer la(s) tarea(s) especificada(s) de la mejor manera posible. Para utilizar un lenguaje común, se adopta un simbolismo esquemático que permite visualizar la topología (esquema estructural del proceso), que constituye el diagrama de flujo flowsheet.
Sin embargo, este poco puede aportar a menos que se especifiquen condiciones de operación (temperaturas, presiones, etc.) y las propiedades asociadas a las corrientes. Existen, por lo tanto, dos grandes grupos de variables que deben ser diferenciadas. En este contexto, llamamos variables estructurales a aquellas que están íntimamente ligadas a la estructura del flowsheet, es decir, que especifican la presencia de los distintos equipos y su diagrama de interconexiones. Por otro lado, están las variables de operación que representan condiciones operativas (temperatura, caudal, presión, etc.), y ciertas características funcionales de los equipos, como ser áreas, numero de etapas, etc., por lo general identificadas como parámetros de diseño.
De hecho, existen numerosas variantes para el armado del diagrama de flujo de un proceso determinado, como así también, numerosas posibilidades para la asignación ó especificación de las variables de operación y parámetros de equipo. El diseñador deberá optar por algún conjunto de ellas, de manera tal de optimizar la estructura resultante en función de los distintos aspectos funcionales a considerar en la operación de plantas químicas. Nótese que cualitativamente, este problema no es distinto al que enfrenta un arquitecto al diseñar un edificio para ciertos fines, o un ingeniero eléctrico al diseñar un circuito para determinado objetivo.
Por consiguiente, la tarea de diseño lleva implícita la necesidad de seleccionar dentro de un espacio de posibilidades, aquellas alternativas que en base a un criterio predeterminado, cumplan con los objetivos deseados. En la búsqueda de lograr un planteo formal del problema de diseño, conviene plantear una función objetivo adecuada a ser optimizada. En este punto, conviene explorar los objetivos que se esperan de un proceso químico en general.
Es bien sabido que toda actividad productiva de bienes o servicios se encuentra permanentemente sujeta a un marco de referencia en función del cual se evalúa su factibilidad. Sin pretender analizar los distintos enfoques para cuantificar los beneficios de un proyecto (privado, social, micro-económico, macro-económico, etc.), el marco económico constituye la fuente cuyo veredicto resulta inevitable de contemplar en toda actividad de Ingenieria. Por lo tanto, costos de operación, inversión, tasa de retorno, etc., son criterios que generalmente se tienen en cuenta en la función objetivo a optimizar.
Ahora bien, no es el factor económico el único componente que define la operabilidad de un proceso químico. En efecto, existen una serie de aspectos que necesariamente deben ser contemplados, como por ejemplo, flexibilidad que se refiere a la capacidad estructural y operativa del proceso para mantenerse funcionando con la mejor performance cuando las condiciones operativas corresponden a un rango de condiciones de diseño, o controlabilidad, confiabilidad, impacto ambiental, etc. Consecuentemente, el problema a resolver es multi-objetivo (Takama y Umeda, 1980). Estos problemas se caracterizan por no poseer una única solución. En efecto, se arriba a un conjunto mínimo de soluciones no dominadas. Por lo tanto, decidir entre las mismas, lleva implícito subjetivamente la preferencia del diseñador respecto de los objetivos. Si bien todos los objetivos de diseño son importantes, merece destacarse que el de impacto ambiental ha incrementado significativamente su importancia en las últimas décadas. En el próximo ítem analizaremos en detalle algunos aspectos referidos al impacto ambiental de un diseño:
Grandes inversiones han sido realizadas por las industrias del proceso químicas en los últimos años, a fin de eliminar fuentes de polución. Esto ha aumentado los costos de
considerables de SO 2 , óxidos de nitrógeno (NOx), CO, CO 2 , hollín, ceniza, e hidrocarburos no-quemados. Éstos, a su vez, producen muchos problemas medioambientales, incluyendo la lluvia ácida (principalmente concentrada en H 2 SO 4 ), humo y nieblas (concentrados en NOx), la acumulación del llamado gas de invernadero (CO 2 ), compuestos tóxicos volátiles (por ejemplo, formaldehído, fenol), y gases orgánicos (ej., CO), qué reacciona con NOx, sobre todo en los días calientes de verano, alterando el nivel de O 3. A medida que los impactos adversos de contaminantes en los animales, vida de la planta, y humanos van descubriéndose por científicos e ingenieros, se buscan los métodos para reducir significativamente sus niveles. En algunos casos, esto se realiza por alguno de los diversos métodos, como separar las fuentes (por ejemplo, compuestos de azufre) de hidrocarburos o combustibles; ajustando los procesos de combustión (ej., reduciendo la temperatura y tiempo de residencia de la llama para producir menos NOx); separando hollín, ceniza, y los compuestos nocivos de los gases efluentes; reaccionando los gases efluentes en los convertidores catalíticos; o a través del uso de algas para consumir (a través de la fotosíntesis) las grandes cantidades de CO 2 en gases efluentes (una técnica recientemente propuesta y actualmente en estudio). Como regla del arte (heurístico), debe notarse que el costo de limpiar los productos de la combustión es aproximadamente un orden de magnitud menos del costo de eliminar contaminantes del combustible. Este es un heurístico importante, sobre todo cuando diseñamos procesos que son consumidores intensivos de energía, y requieren cantidades grandes de combustible.
Manejo de Residuos Tóxicos
En las industrias químicas y plantas nucleares de potencia, se producen cantidades grandes de residuos tóxicos anualmente, principalmente en corrientes de agua residuales o de desecho, que en 1988 sumaron el 97% del total de residuos producidos. Mientras una porción pequeña se incinera (en el orden del 3% en los 80s), el volumen principal, se deposita sobre o debajo de la tierra, con una variedad de métodos introducidos durante el último siglo. Desde la década de los 1960s, muchos de los sitios de entierro han puesto en peligro la salud de las personas que residen en los alrededores, y mas grave aun, han contaminado las napas freáticas y sistemas de suministro de agua de grandes regiones y hasta de países en su totalidad. Un ejemplo de ello es la contaminación producida por la industria de materiales electrónicos en los arroyos y napas del Silicon Valley en California EEUU.
Esto nos muestra la necesidad de prever desde su concepción, procesos que no contaminen, o en su defecto dotarlos de las instalaciones necesarias para el tratamiento de sus efluentes tóxicos, particularmente aquellos líquidos que se vuelcan en arroyos y cursos de agua..
Químicos Bio-acumulados
Probablemente los casos mas conocidos de químicos bio-acumulados, que se han descubierto en la tierra y en las plantas los insecticidas como el DDT (1,1 bis clorofenil (4- 2,2,2 tricloroetano; (C16 H9 Cl5) y los solventes PCBs (bifenilos policlorados). El DDT se roció en grandes cantidades utilizando aviones que volaban a baja altura para matar insectos y pestes a lo largo de los años cincuenta. Desgraciadamente, aunque eficaz por proteger cosechas, bosques, y la vida de las plantas, sus efectos tóxicos en los pájaros, los animales, y humanos era considerable. Debido a ello, fueron prohibidos por la EPA (EEUU) en 1972. Su efecto, sin embargo, permanecerá durante algún tiempo debido a su bio-acumulación en la tierra y en las plantas.
Minerales y Metales Tóxicos
En esta categoría, los cambios mayores han tenido lugar desde la década de 1960, como respuesta al descubrimiento de los efectos tóxicos de plomo, mercurio, cadmio, y asbesto en los animales y humanos. Después del envenenamiento por plomo (acompañado por daño cerebral, desfiguración, y parálisis) se relacionó la ingestión de este metal por niños, con las pinturas basadas en compuestos de plomo (sobre todo en edificios más viejos que no se mantienen bien), Como consecuencia de ello, la EPA prohibió dicho metal en las pinturas así como en los combustibles. En el combustible, tetraetil-plomo se había usado como un elevador de octano a lo largo del mundo. Se reemplazó como consecuencia por el metil-terbutil-éter (MTBE), que también debería reemplazarse debido a informes que dan cuenta de su potencial peligrosidad para contaminar las napas subterráneas de agua. El Mercurio, que ha sido el soporte principal de manómetros en los laboratorios de todo el mundo, también ha mostrado ser sumamente tóxico. con efectos desastrosos sobre la salud debido a exposición accidental. Periódicamente son informados en distintos foros casos de envenenamiento por este metal. En el caso del asbesto, sus efectos tóxicos han sido conocidos desde la década del 40, y aún hoy sigue siendo una preocupación en todos los edificios construidos antes. Gradualmente, cuando estos edificios van renovándose, las planchas de aislamiento de amianto están siendo reemplazadas por materiales no
Químicos del Instituto Nacional para la Seguridad y Salud Profesional (NIOSH, 1987). Obviamente, cuando se sospecha la presencia de cantidades grandes de químicos tóxicos, deben buscarse otros caminos de la reacción; cuando éstos no pueden encontrarse, se rechazan los diseños propuestos, excepto bajo determinadas circunstancias que rara vez se justifican.
Reducción y Re-uso de Residuos
Las preocupaciones medioambientales han conducido a los ingenieros químicos a poner aun mayor énfasis en reciclar, no sólo los compuestos químicos no reaccionados, sino que también productos y subproductos. De esta manera, los diseñadores normalmente prevén los ciclos de vida de sus productos y subproductos, prestando especial atención al mercado de los desechos, para así seleccionar la calidad apropiada de los mismos. Visto de otra forma, el diseñador ve la planta propuesta como productor potencial de residuos, e intenta asegurar que habrá un mercado para los químicos producidos después de que su vida útil haya terminado. Esta es una consideración principal en la producción de materiales compuestos y polímeros. Al respecto, es importante planear la producción de los residuos en forma segregada de acuerdo a las demandas del mercado de desechos, de esta forma se evita el sobre mezclado de desechos y la necesidad de aislarlos posteriormente.
Evitar Eventos no Previstos en las Plantas
Para reducir las posibilidades de accidentes y derramamientos, con su consecuente impacto medioambiental adverso, a menudo se diseñan los procesos tratando de reducir el número de estados transitorios de operación, periodos de limpieza, y ciclos de regeneración de catalizador. En otros términos, el énfasis está en diseñar un proceso a que sea fácilmente controlable alrededor de un estado estacionario nominal, con controladores confiables y sensores de detección de fallas eficaces.
Caracterización de Materiales
A menudo, los desechos químicos están presentes en cantidades pequeñas en los efluentes gaseosos o líquidos. Para mantener concentraciones bajas de tales químicos, debajo de los límites de las regulaciones ambientales, es importante usar métodos eficaces y rápidos por medir o deducir sus concentraciones a partir de otras mediciones. Al respecto es importante que el diseñador conozca los efectos tóxicos de las sustancias en todo el rango de dilución, dado que sus efectos nocivos pueden variar
significativamente con la dilución. Otra consideración importante es tratar de diseñar plantas que usen materias primas desecho de otras planta. Cuando ello es posible, es vital conocer las características y concentraciones de las materias primas - desechos disponibles.
Objetivos de Diseño, Restricciones, y Optimización
Normalmente los objetivos ambientales no son bien definidos, debido a que los objetivos económicos del diseño generalmente involucran alguna medida de rentabilidad, y la polución por lo general es difícil de cuantificar en términos económicos. Como consecuencia de ello, el diseñador a menudo formula funciones objetivos mixtas o multi-objetivos que intentan expresar las mejoras ambientales en términos financieros. En otros casos, el diseñador puede conformarse con la optimización de una función objetivo económica, sujeta a los límites en las concentraciones de solutos contaminantes en las corrientes de desechos. Es importante evaluar si las restricciones son estrictas (no permiten ser violadas) o flexibles (capaces de ser violadas bajo circunstancias excepcionales). Debe ponerse el énfasis en la formulación de cada restricción y hasta que punto deben ser respetadas.
Regulaciones
Como hemos mencionado previamente, algunas regulaciones ambientales pueden tratarse como restricciones a ser satisfechas durante la operación del proceso que esta siendo diseñado. Normalmente cuando se desarrolla un modelo matemático del proceso bajo diseño, el diseñador debe constatar que las condiciones de operación que esta fijando satisfacen las restricciones mencionadas. Por otra parte, una vez definida la función objetivo deben ajustarse las variables de diseño a fin de obtener valores máximos o mínimos de la función objetivo, mientras se satisfacen las restricciones. Otras regulaciones, sin embargo, son más difíciles de cuantificar. Éstos generalmente involucran las expectativas del público y la posible repercusión negativa debido a que perciben a la planta como una fuente de polución. De igual forma, suelen existir también regulaciones referidas a la posible localización de las plantas químicas en zonas alejadas de los centros urbanos, y que muchas veces ocasionan serios trastornos a las empresas. Para evitar esto por lo general las empresas ponen fuerte énfasis en cumplir estrictamente con las regulaciones ambientales y mantienen muy buenos registros de seguridad, a fin de ganar la confianza de la comunidad.
(por ej. componentes de silicio, circuitos integrados, películas fotovoltaicas), y en muchas otras industrias. Los electrolitos fuertes disocian dando especies iónicas cuyas interacciones con el agua y las moléculas orgánicas son cruciales para entender el estado de una mezcla, esto es, las fases presentan (vapor, agua, líquido orgánico, sólidos precipitado, etc.) a una temperatura y presión dada.
A tal efecto, cuando se diseñan procesos que involucran electrolitos, es conveniente incluir en las bases de datos de diseño las propiedades fisicoquímicas y de transporte de las especies iónicas. Por lo general dichas propiedades pueden estimarse usando las bases de datos y correlaciones que poseen los simuladores de proceso (Aspen, Hysys, etc.)
Una característica muy importante a tener en cuenta respecto de la función objetivo a plantear en la tarea de diseño, refiere a su facilidad de ser representada (o modelada) matemáticamente. En efecto, si bien existen objetivos expresables como funciones matemáticas (ya sean continuas, discontinuas o discretas), existen aquellos que no pueden ser representados bajo esta perspectiva.
Dentro de este contexto, el problema completo, si es que puede formalizarse, podría ser formulado desde el punto de vista de la programación matemática como uno de optimización múltiple objetivo.
Optimice {f 1 (x), f 2 (x), ....... , f (^) N (x)}
Sujeto a: (1)
h(x) = 0
g(x) > 0
Las funciones f 1 (x), f 2 (x), ....... , fN (x) representan las N funciones objetivos a optimizar (minimizar o maximizar). Las funciones h(x) expresan generalmente, las restricciones correspondientes a los balances de materia y energía, mientras que las restricciones g(x) expresan zonas de operación factible, por ejemplo composiciones positivas, temperaturas positivas, restricciones propias del proceso, etc. El vector x comprende variables o parámetros de operación y variables estructurales. Una simplificación que se suele adoptar consiste en expresar todos los objetivos en una "única medida", que generalmente es económica. Obviamente, este enfoque, además de ser una simplificación, no siempre es posible. Por ultimo, aun con una única función objetivo, se deben resolver aún los otros problemas, por ejemplo, cómo manejar la variable estructural.
En este contexto, debe encontrarse una metodología adecuada para resolver el problema matemático resultante. Por ejemplo, uno de los métodos propuestos para manejar las interrelaciones que vinculan los equipos entre sí y considerar las variables estructurales consiste en utilizar variables enteras (ceros y unos). Es decir que para considerar simultáneamente las variables estructurales (enteras) y las variables operativas (reales), se acude a la programación matemática mixta (Grossmann, 1985). Por otra parte, las funciones que describen los procesos químicos son por lo general fuertemente no lineales, por lo cual el programa matemático asociado, es obviamente no lineal. Otra característica, no menos compleja, asociada al vector de variables que debe considerarse en el modelado matemático del sistema, es el hecho que varias variables pueden tener un comportamiento aleatorio. Esto es, debido a características inherentes al proceso, factores climáticos o de mercado, etc., las variables de operación no tienen valores únicos y/o fijos sino que pueden fluctuar en torno a un valor estable, normal o nominal, admitiendo cualquier valor comprendido en un determinado rango de incertidumbre. Un ejemplo de esta problemática en la formulación de los problemas de síntesis de redes de intercambio calórico flexibles y de trenes de destilación integrados flexibles, puede verse en Galli (1990) y Benz (1991), respectivamente.
Resulta redundante en este punto, afirmar que en el estado del arte actual, el problema de diseño planteado previamente (esto es, optimización multi-objetivo no lineal, con variables de decisión tanto continuas como discretas, variables estructurales, variables aleatorias, funciones no lineales y funciones difícilmente expresables matemáticamente), resulta de solución prácticamente imposible.
♦ el espacio de los diseños alternativos para cada una de las unidades de operación que componen el sistema.
En contraste con la etapa de síntesis, la etapa de análisis o simulación implica la investigación de las características de cada alternativa generada, por ejemplo, mediante la evaluación de las variables de salida, conociendo las características del sistema y las variables de entrada. Por lo general se utilizan reglas heurísticas con las cuales es posible reducir el numero de estructuras generadas en la etapa de síntesis. La tarea de optimización se plantea generalmente en la etapa de análisis, y permite seleccionar el mejor sistema entre las alternativas posibles. Por lo general, la optimización del sistema en el primer espacio de decisiones se formula como un problema de programación entera mientras la optimización en el segundo espacio resulta en un problema de programación continua, no-lineal. La naturaleza mixta entero-real del problema de optimización, su no-linealidad y su alta dimensionalidad, crea un problema matemático difícilmente superable.
En forma esquemática podemos representar el proceso como una Caja Negra y definir el concepto de Síntesis y Análisis ó Simulación:
PROCESO ¿?
Entradas Conocidas Salidas Conocidas o Deseadas
SINTESIS
PROCESO CONOCIDO
Entradas Conocidas Salidas Desconocidas
ANALISIS
Dentro de este contexto, se comprende que el núcleo central de la tarea de diseño en la Ingenieria de procesos, de acuerdo a la visión de la descomposición del problema global en sub-problemas o etapas independientes, esta constituido por el lazo iterativo SÍNTESIS ANÁLISIS EVALUACIÓN - OPTIMIZACIÓN. Consecuentemente, no resulta extraño desde una perspectiva histórica, la aparición cronológica de procedimientos o algoritmos para implementarlas, en general como instrumentos independientes. No obstante, aun hoy (y en el futuro a mediano plazo), el alcance de las herramientas o metodologías de implementación masiva propuestas resulta parcial. En efecto, no existe posibilidad practica de implementar una herramienta efectiva o algoritmo de calculo, o procedimiento secuencial, que contemple simultáneamente todas las etapas y variables que deben necesariamente ser tenidas en cuenta. Esto podrá revertirse en un futuro, pero dada la complejidad del problema, todavía habrá de dedicarse mucho esfuerzo de investigación al respecto y muy probablemente deberá esperarse bastante tiempo para lograrlo.
Debido a la elevada dimensión de los problemas asociados a la tarea de diseño, su elevado índice combinatorio y la gran cantidad de información que debe manejarse, la única herramienta viable para tal fin resultan ser los métodos computacionales.
La etapa de análisis o simulación fue la primera en desarrollarse y manifestarse bajo esta óptica. En efecto, en la década del 70 comienza a consolidarse una línea de investigación que abarca los métodos computacionales en la Ingenieria química; en particular la simulación de procesos por computadora o process flowsheeting, como una parte de una actividad mas general, la actividad del diseño de procesos asistido por computadora (Computer Aided Design CAD). En forma similar, con respecto a la etapa de síntesis, los conceptos utilizados para la construcción de algoritmos se nutren de los mas variados campos del conocimiento. Programación mixta, álgebra booleana, termodinámica, computación, sistemas expertos, etc., son algunos de los basamentos conceptuales que dieron sustento teórico a los diversos algoritmos propuestos para la generación de estructuras y la selección de la óptima.
Complementando la idea expuesta mas arriba, además de no existir una herramienta computacional (programa o algoritmo) capaz de resolver el problema del ciclo completo de actividades en la tarea de diseño, debido a la gran variedad de alternativas que deben contemplarse, tampoco existe algoritmo efectivo para la síntesis de procesos genéricos completos. A medida que se simplifica (particiona) el problema, es decir, se adoptan subsistemas del complejo a diseñar, los algoritmos propuestos se caracterizan