
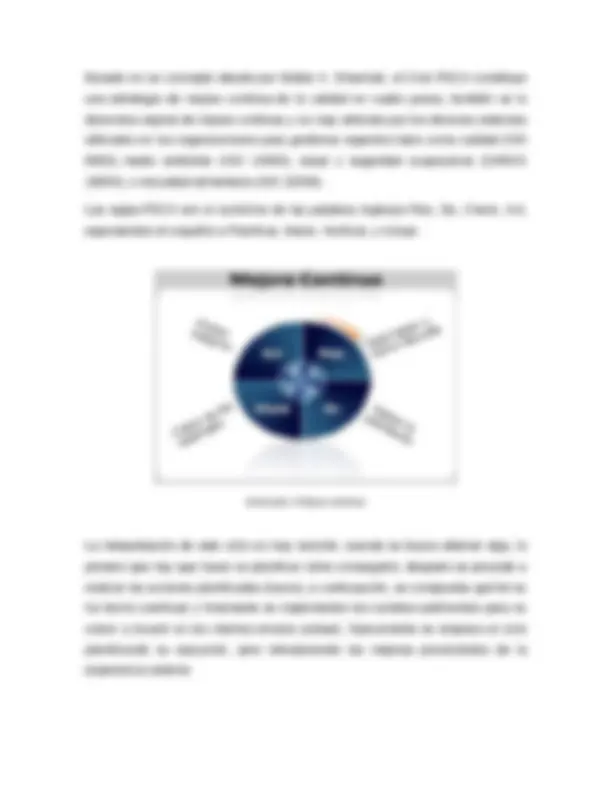
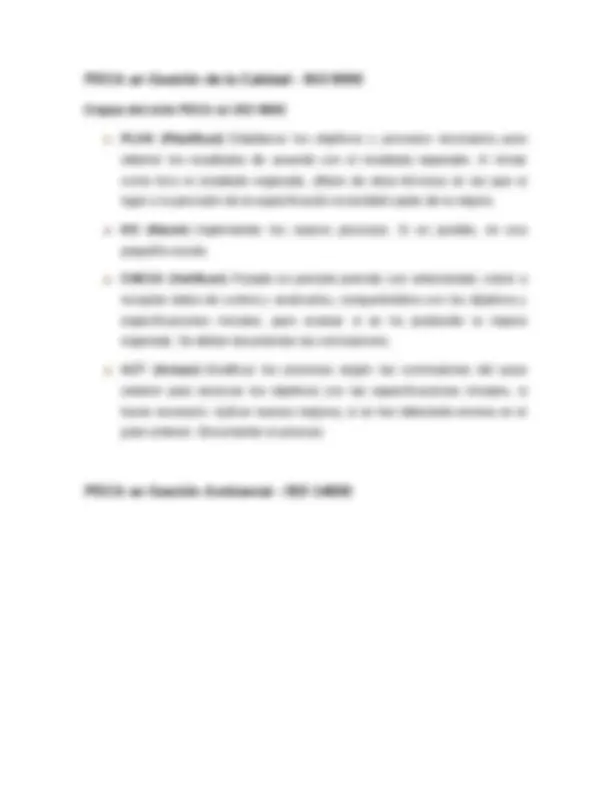
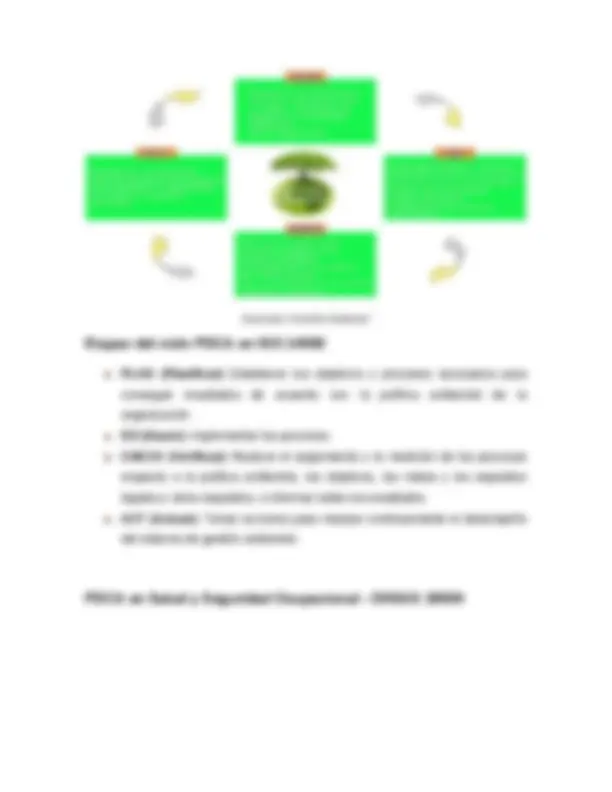
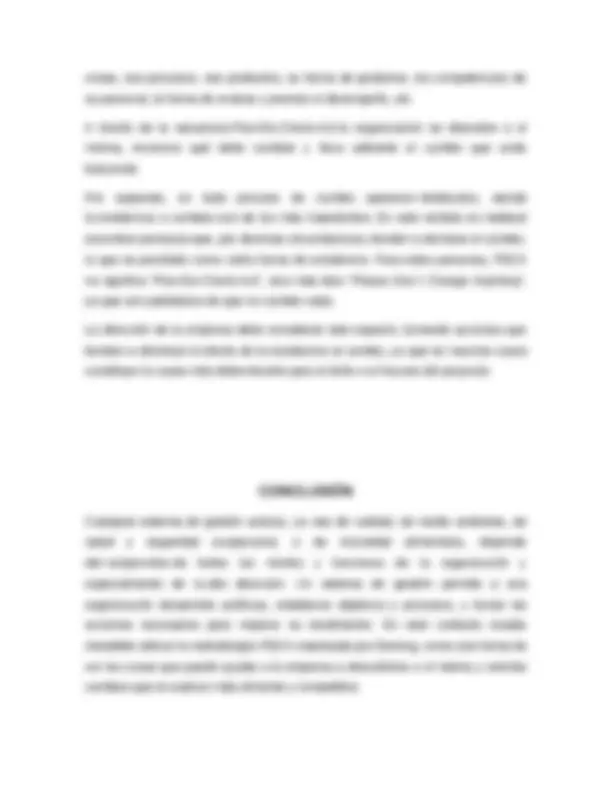
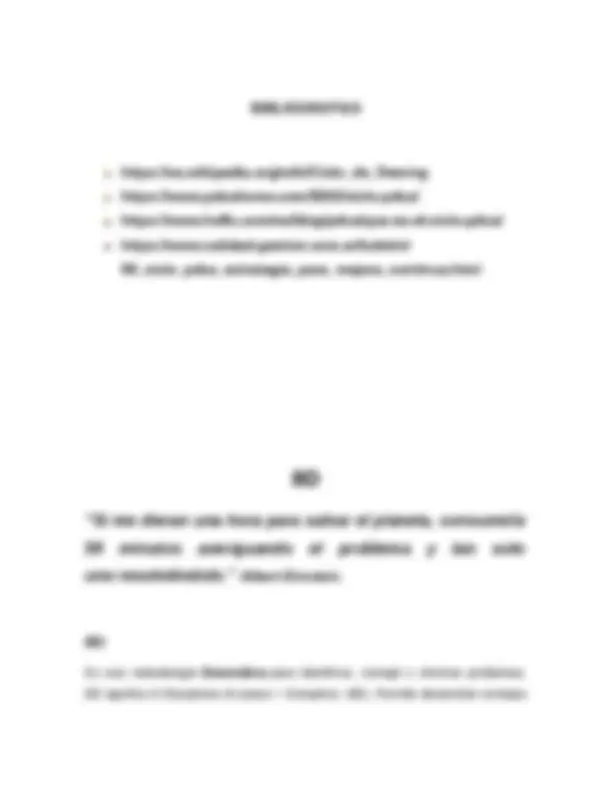
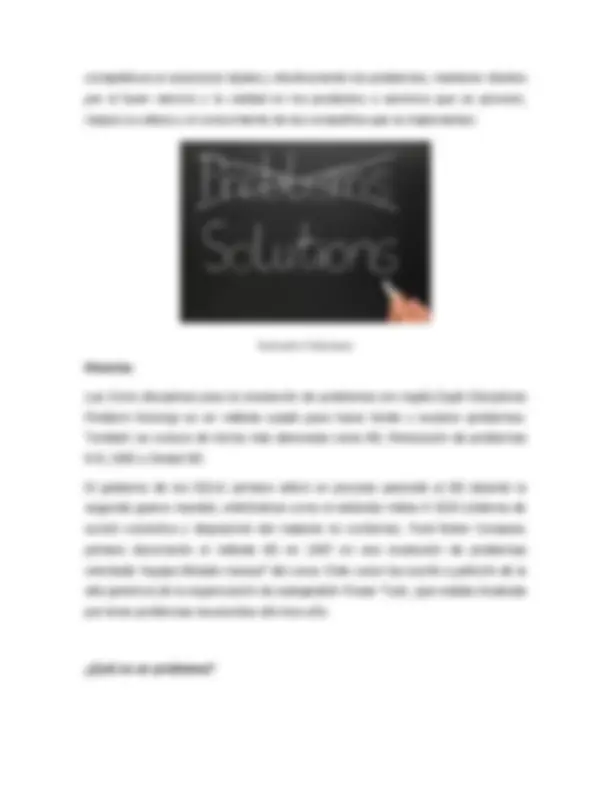
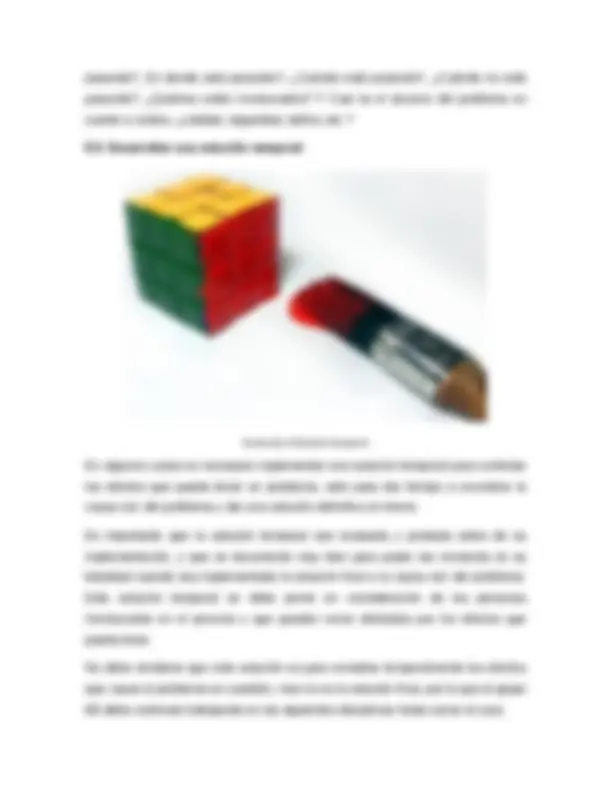
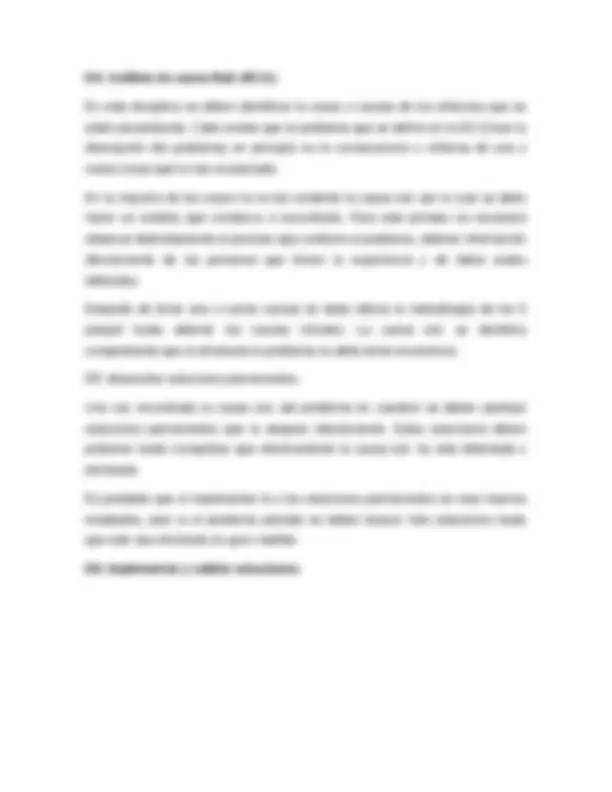
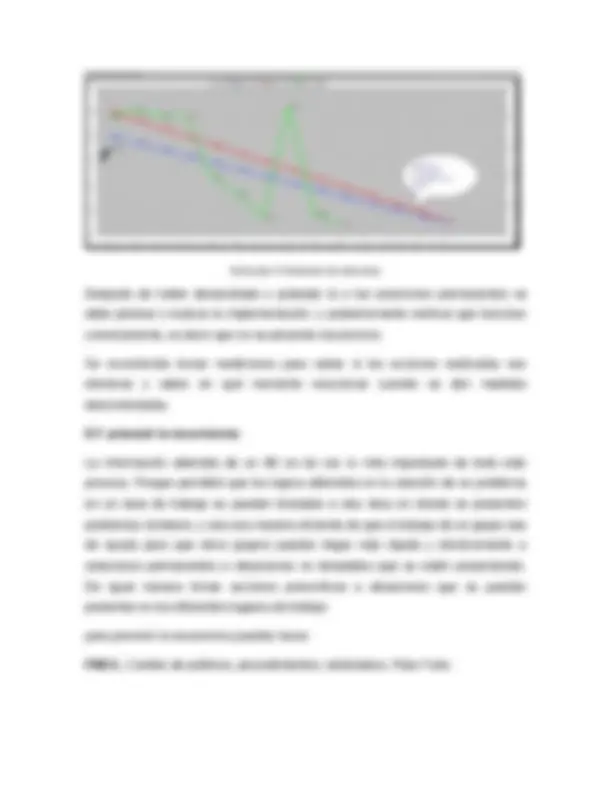
Prepara tus exámenes y mejora tus resultados gracias a la gran cantidad de recursos disponibles en Docsity
Gana puntos ayudando a otros estudiantes o consíguelos activando un Plan Premium
Prepara tus exámenes
Prepara tus exámenes y mejora tus resultados gracias a la gran cantidad de recursos disponibles en Docsity
Prepara tus exámenes con los documentos que comparten otros estudiantes como tú en Docsity
Los mejores documentos en venta realizados por estudiantes que han terminado sus estudios
Estudia con lecciones y exámenes resueltos basados en los programas académicos de las mejores universidades
Responde a preguntas de exámenes reales y pon a prueba tu preparación
Consigue puntos base para descargar
Gana puntos ayudando a otros estudiantes o consíguelos activando un Plan Premium
Comunidad
Pide ayuda a la comunidad y resuelve tus dudas de estudio
Descubre las mejores universidades de tu país según los usuarios de Docsity
Ebooks gratuitos
Descarga nuestras guías gratuitas sobre técnicas de estudio, métodos para controlar la ansiedad y consejos para la tesis preparadas por los tutores de Docsity
El rozamiento entre 2 órganos es función de su dureza y sobre todo de su estado superficial. Durante la fricción, el contacto no se produce en toda el área, sino sólo entre las irregularidades de las superficies que interfieren entre sí; en dichos puntos se crean presiones específicas muy elevadas que, al mismo tiempo que aumentan la temperatura, provocan la fusión de los puntos de contacto y determinan el encolado Parcial de las piezas.
Tipo: Apuntes
1 / 17
Esta página no es visible en la vista previa
¡No te pierdas las partes importantes!
PDCA
El éxito de cualquier método que actualmente utilizan las organizaciones para gestionar aspectos tales como calidad (ISO 9000), medio ambiente (ISO 14000), salud y seguridad ocupacional (OHSAS 18000), o inocuidad alimentaria (ISO 22000) , depende del compromiso de todos los niveles, especialmente de la alta dirección, y permite desarrollar políticas, establecer objetivos y procesos, y tomar las acciones necesarias para mejorar su rendimiento. En este contexto resulta ineludible utilizar la metodología PDCA impulsada por Deming, como una forma de ver las cosas que puede ayudar a la empresa a descubrirse a sí misma y orientar cambios que la vuelvan más eficiente y competitiva.
El Ciclo PDCA también es conocido como "Círculo de Deming", ya que fue el Dr. Williams Edwards Deming uno de los primeros que utilizó este esquema lógico en la mejora de la calidad y le dio un fuerte impulso. Ilustración 1 PDCA
Etapas del ciclo PDCA en ISO 9000 : PLAN (Planificar): Establecer los objetivos y procesos necesarios para obtener los resultados de acuerdo con el resultado esperado. Al tomar como foco el resultado esperado, difiere de otras técnicas en las que el logro o la precisión de la especificación es también parte de la mejora. DO (Hacer): Implementar los nuevos procesos. Si es posible, en una pequeña escala. CHECK (Verificar): Pasado un período previsto con anterioridad, volver a recopilar datos de control y analizarlos, comparándolos con los objetivos y especificaciones iniciales, para evaluar si se ha producido la mejora esperada. Se deben documentar las conclusiones. ACT (Actuar): Modificar los procesos según las conclusiones del paso anterior para alcanzar los objetivos con las especificaciones iniciales, si fuese necesario. Aplicar nuevas mejoras, si se han detectado errores en el paso anterior. Documentar el proceso.
Ilustración 3 Gestión Ambiental
PLAN (Planificar): Establecer los objetivos y procesos necesarios para conseguir resultados de acuerdo con la política ambiental de la organización. DO (Hacer): Implementar los procesos. CHECK (Verificar): Realizar el seguimiento y la medición de los procesos respecto a la política ambiental, los objetivos, las metas y los requisitos legales y otros requisitos, e informar sobre los resultados. ACT (Actuar): Tomar acciones para mejorar continuamente el desempeño del sistema de gestión ambiental.
conformidades, acciones correctivas y preventivas, control de riesgos, auditorías internas. ACT (Actuar): Tomar acciones para mejorar continuamente el desempeño del sistema de gestión SySO. Revisión por la Dirección.
Etapas del ciclo PDCA en ISO 22000 PLAN (Planificar): Planificación de productos inocuos, análisis de peligros, validación de medidas de control, establecimiento de Plan HACCP, establecimiento de PPR operacionales. DO (Hacer): Implementar los procesos. Asignación de recursos y responsabilidades, formación y toma de conciencia, comunicación y participación, control de documentos, control operativo. CHECK (Verificar): Realizar el seguimiento y la medición de los procesos respecto a la política de Inocuidad, los objetivos, las metas y los requisitos legales y otros requisitos, e informar sobre los resultados. Medición y seguimiento, evaluación del cumplimiento, investigación de incidentes, no conformidades, acciones correctivas y preventivas, control de peligros, auditorías internas. ACT (Actuar): Tomar acciones para mejorar continuamente el desempeño del sistema de Inocuidad. Revisión por la Dirección.
El Mejoramiento Continuo es una decisión de la dirección de la empresa, que la convierte en una forma de administrar y predica con el ejemplo permanentemente. La estrategia que plantea el Ciclo PDCA implica que toda empresa necesita un cambio que la haga apta para sobrevivir, cuestionándose la forma de hacer las
cosas, sus procesos, sus productos, su forma de gestionar, las competencias de su personal, la forma de evaluar y premiar el desempeño, etc. A través de la secuencia Plan-Do-Check-Act la organización se descubre a sí misma, reconoce qué debe cambiar y lleva adelante el cambio que anda buscando. Por supuesto, en todo proceso de cambio aparecen obstáculos, siendo la resistencia a cambiar uno de los más importantes. En este sentido es habitual encontrar personas que, por diversas circunstancias, tienden a demorar el cambio, lo que es percibido como cierta forma de resistencia. Para estas personas, PDCA no significa “Plan-Do-Check-Act”, sino más bien “Please Don´t Change Anything” , ya que son partidarios de que no cambie nada. La dirección de la empresa debe considerar este aspecto, tomando acciones que tiendan a disminuir el efecto de la resistencia al cambio, ya que en muchos casos constituye la causa más determinante para el éxito o el fracaso del proyecto.
Cualquier sistema de gestión exitoso, ya sea de calidad, de medio ambiente, de salud y seguridad ocupacional, o de inocuidad alimentaria, depende del compromiso de todos los niveles y funciones de la organización y especialmente de la alta dirección. Un sistema de gestión permite a una organización desarrollar políticas, establecer objetivos y procesos, y tomar las acciones necesarias para mejorar su rendimiento. En este contexto resulta ineludible utilizar la metodología PDCA impulsada por Deming, como una forma de ver las cosas que puede ayudar a la empresa a descubrirse a sí misma y orientar cambios que la vuelvan más eficiente y competitiva.
competitivas al solucionar rápida y efectivamente los problemas, mantiene clientes por el buen servicio y la calidad en los productos o servicios que se proveen, mejora la cultura y el conocimiento de las compañías que la implementan. Ilustración 5 Soluciones Historia: Las Ocho disciplinas para la resolución de problemas (en inglés Eight Disciplines Problem Solving) es un método usado para hacer frente y resolver problemas. También se conoce de forma más abreviada como 8D, Resolución de problemas 8-D, G8D o Global 8D. El gobierno de los EEUU primero utilizó un proceso parecido al 8D durante la segunda guerra mundial, refiriéndose como el estándar militar # 1520 (sistema de acción correctiva y disposición del material no conforme). Ford Motor Company primero documento el método 8D en 1987 en una resolución de problemas orientada “equipo titulado manual” del curso. Este curso fue escrito a petición de la alta gerencia de la organización de autogestión Power Train, que estaba frustrada por tener problemas recurrentes año tras año. ¿Qué es un problema?
Es la diferencia existente entre una situación deseada (estándar) y una situación actual (Real). Un problema suele ser un asunto del que se espera una rápida y efectiva solución, generalmente lo que vemos de los problemas son los síntomas, la metodológica permite encontrar la causa raíz para darle el debido tratamiento. las 8 disciplinas son: D1: ESTABLECER UN GRUPO PARA SOLUCIÓN DEL PROBLEMA D2: CREAR LA DESCRIPCIÓN DEL PROBLEMA D3: DESARROLLAR UNA SOLUCIÓN TEMPORAL D4: ANÁLISIS DE CAUSA RAÍZ D5: DESARROLLAR SOLUCIONES PERMANENTES D6: IMPLEMENTAR Y VALIDAR SOLUCIONES D7: PREVENIR LA RECURRENCIA D8: CERRAR EL PROBLEMA Y RECONOCER CONTRIBUCIONES D1: Establecer un grupo para la solución del problema: Ilustración 6 Grupo
pasando?, En donde está pasando?, ¿Cuándo está pasando?, ¿Cuándo no está pasando?, ¿Quiénes están involucrados? Y Cual es el alcance del problema en cuanto a costos, ¿calidad, seguridad, daños, etc.? D3: Desarrollar una solución temporal Ilustración 8 Solución temporal En algunos casos es necesario implementar una solución temporal para controlar los efectos que pueda tener un problema, esto para dar tiempo a encontrar la causa raíz del problema y dar una solución definitiva al mismo. Es importante que la solución temporal sea evaluada y probada antes de su implementación, y que se documente muy bien para poder ser removida en su totalidad cuando sea implementada la solución final a la causa raíz del problema. Esta solución temporal se debe poner en consideración de las personas involucradas en el proceso y que puedan verse afectadas por los efectos que pueda tener. No debe olvidarse que esta solución es para remediar temporalmente los efectos que cause el problema en cuestión, mas no es la solución final, por lo que el grupo 8D debe continuar trabajando en las siguientes disciplinas hasta cerrar el caso.
D4: Análisis de causa Raíz (RCA): En esta disciplina se deben identificar la causa o causas de los síntomas que se están presentando. Cabe anotar que el problema que se define en la D2 (Crear la descripción del problema) en principio es la consecuencia o síntoma de una o varias cosas que lo han ocasionado. En la mayoría de los casos no es tan evidente la causa raíz por lo cual se debe hacer un análisis que conduzca a encontrarla. Para esto primero es necesario observar detenidamente el proceso que contiene el problema, obtener información directamente de las personas que tienen la experiencia y de datos reales obtenidos. Después de tener una o varias causas se debe utilizar la metodología de los 5 porqué hasta obtener las causas iniciales. La causa raíz se identifica comprobando que al eliminarla el problema no debe tener recurrencia. D5: desarrollar soluciones permanentes. Una vez encontrada la causa raíz del problema en cuestión se deben plantear soluciones permanentes que la ataquen directamente. Estas soluciones deben probarse hasta comprobar que efectivamente la causa raíz ha sido detectada y eliminada. Es probable que al implementar la o las soluciones permanentes se vean buenos resultados, pero si el problema persiste se deben buscar más soluciones hasta que este sea eliminado en gran medida. D6: Implementar y validar soluciones:
1)Revisando el historial de problema 2) Identificar las políticas y prácticas que permitieron que este problema ocurriera 3) Desarrolle un plan de acciones de prevención Es importante en este punto del 8D realizar auditorías para asegurarse de que la solución implementada está funcionando de acuerdo a lo esperado. D8: cerrar el problema y reconocer contribuciones: Una vez un problema ha sido auditado y se ha determinado que su solución es efectiva debe ser cerrado oficialmente. En este punto se debe remover la solución temporal que se dio en el paso D3, a menos de que se considere parte de la solución permanente. Para finalizar el proceso el grupo debe preguntarse que estuvo bien y que no, revisar las responsabilidades de los miembros y el líder del grupo, las expectativas de los stakeholders, si los procedimientos pueden ser aplicados en algún otro lugar, si se encontraron problemas adicionales, que se aprendió y si finalmente se resolvió el problema. Es importante reconocer la contribución de cada uno de los miembros del equipo, ya que toda la organización se beneficia por las actividades que contribuyen al mejoramiento continuo.
El método Análisis de problemas y toma de decisiones puede incrementar la efectividad de cualquier organización que siga los sencillos pasos, este método nos brinda grandes beneficios como lo son: Es una propuesta eficaz para encontrar una causa raíz, las acciones correctivas apropiadas para eliminarla, y poner en acción a ejecución correctiva permanente. Ayuda a explorar el sistema de control que permitió que ocurra el problema. El punto de escape se estudia con el fin de mejorar la capacidad del
sistema de control para detectar prematuramente la falta o su causa si ocurre otra vez. El circuito de prevención explora los sistemas que permitieron que se de la situación en la cual se activó por primera vez la falla y su mecanismo causal.
https://www.ipeaformacion.com/resolucion-de-problemas/la- metodologia-8d-las-ocho-disciplinas/ https://www.pdcahome.com/las-8d/#:~:text=El%20uso%20de%20las %208D,para%20as%C3%AD%20implantar%20soluciones%20eficaces. https://leansolutions.co/conceptos-lean/lean-manufacturing/8d-ocho- disciplinas/ https://www.nueva-iso-9001-2015.com/2020/06/metodologia-de-las-8d- para-la-resolucion-de-problemas-la-conoces/