
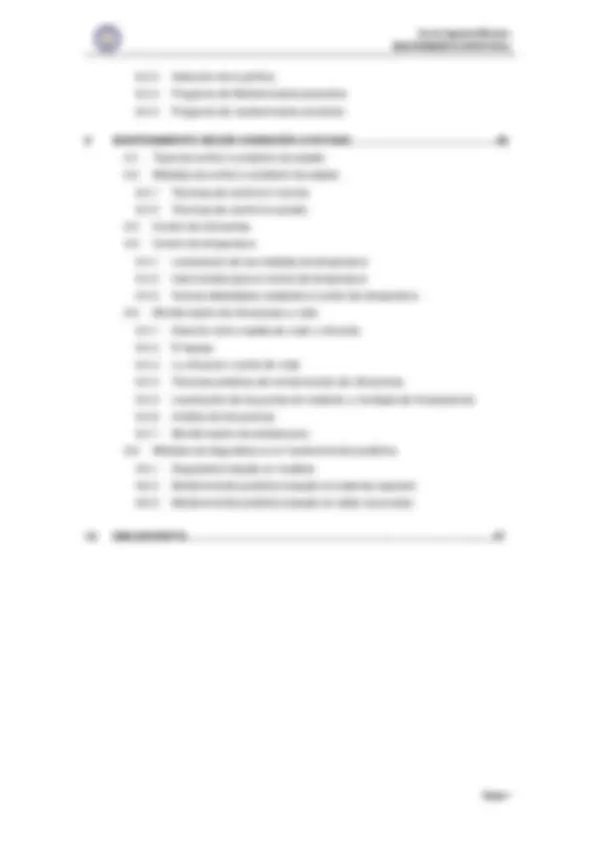
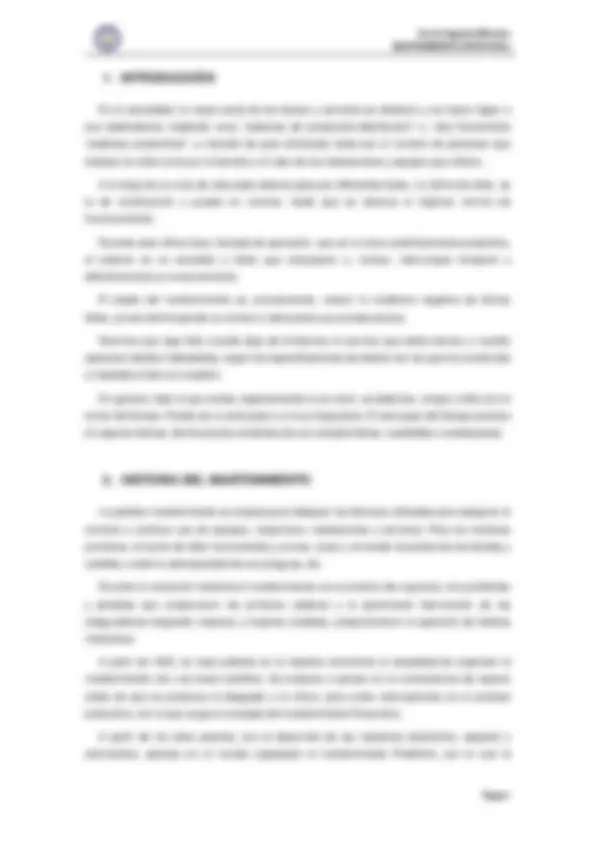
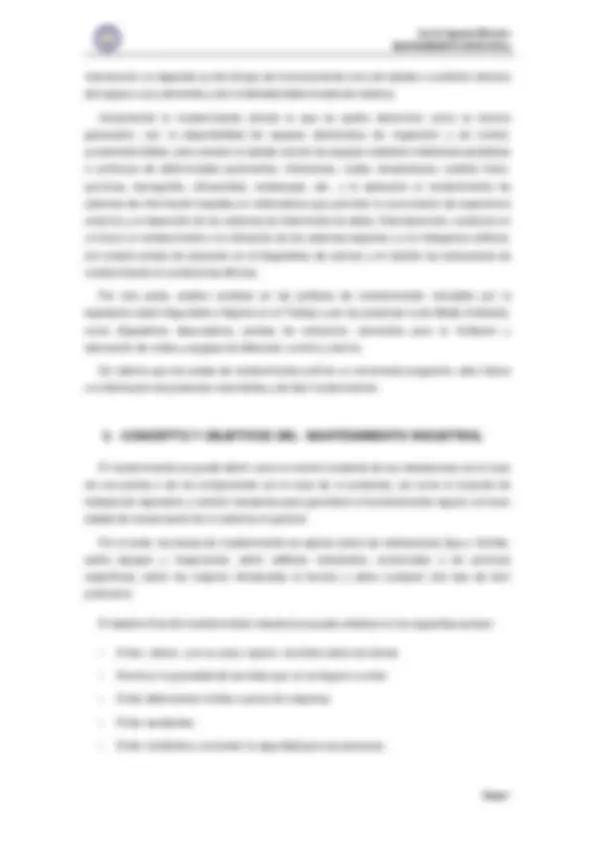
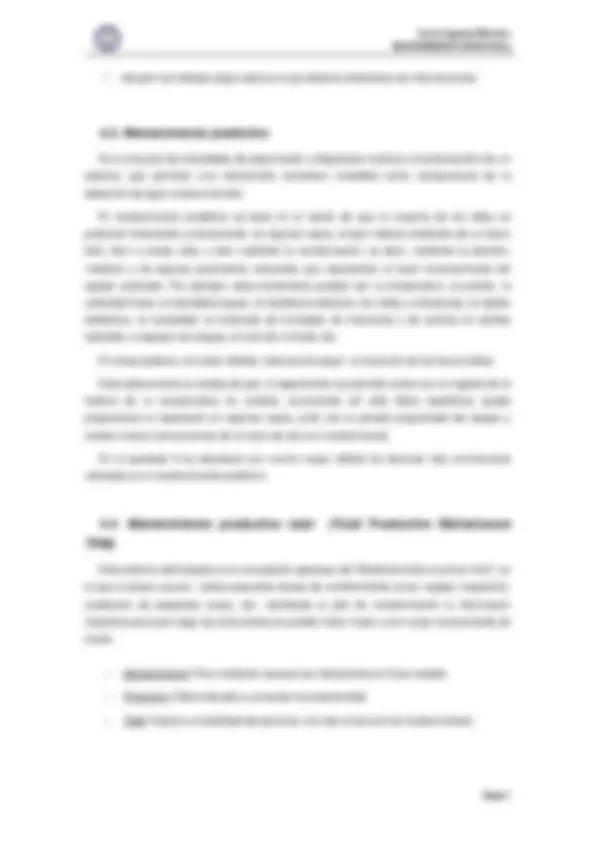
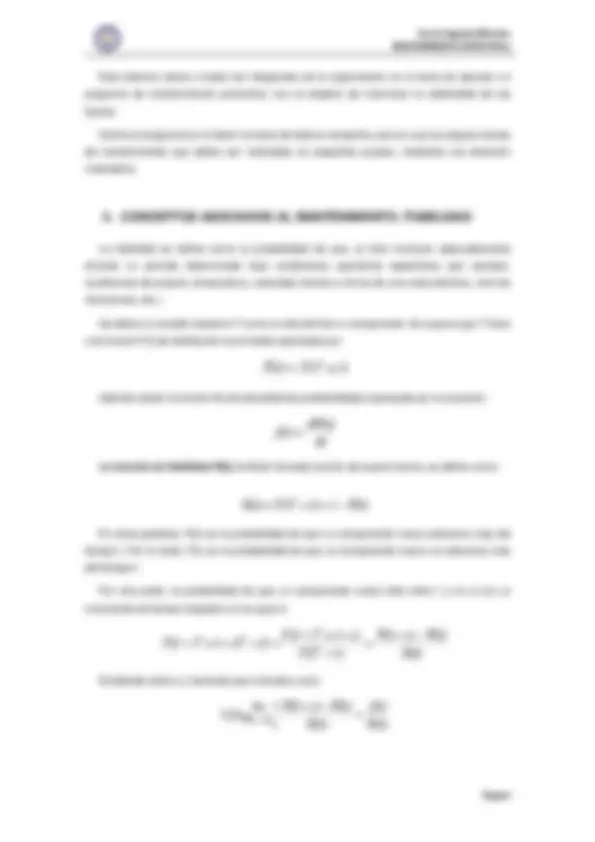
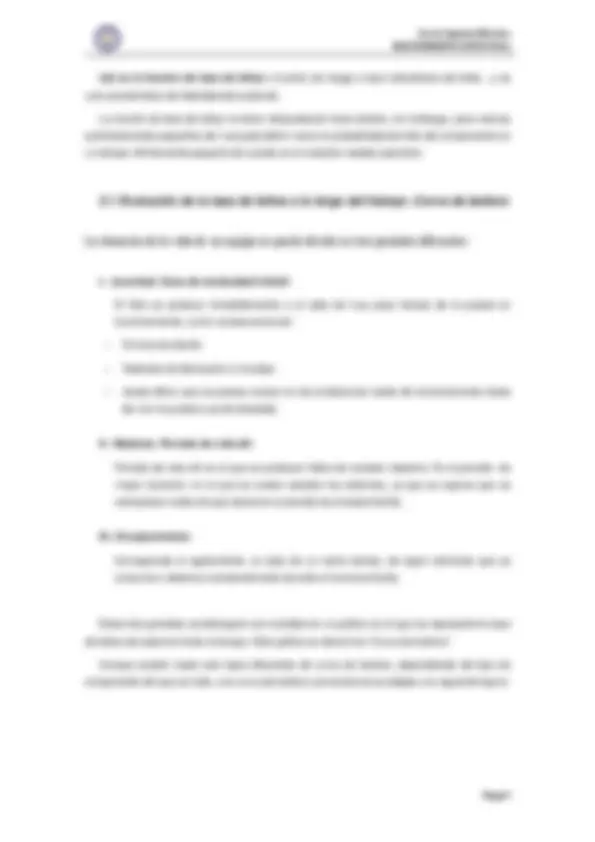
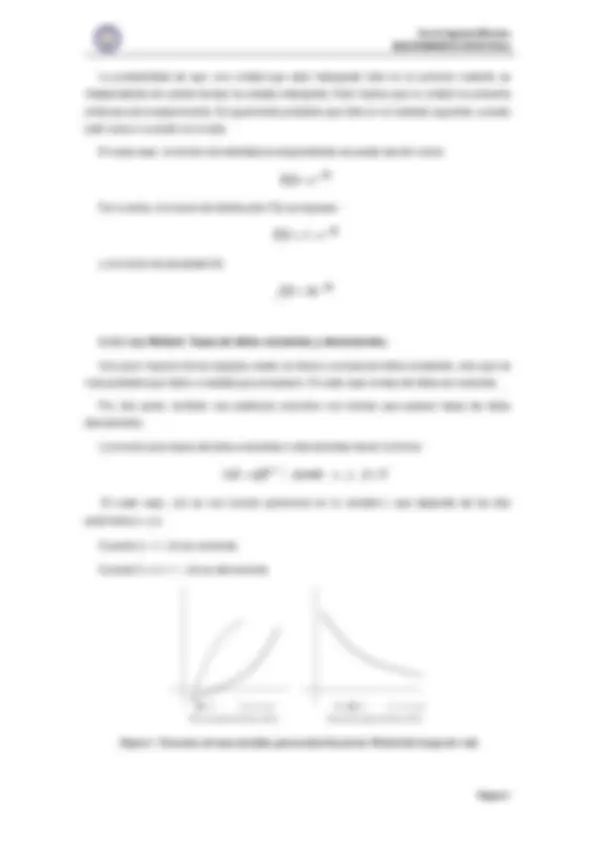
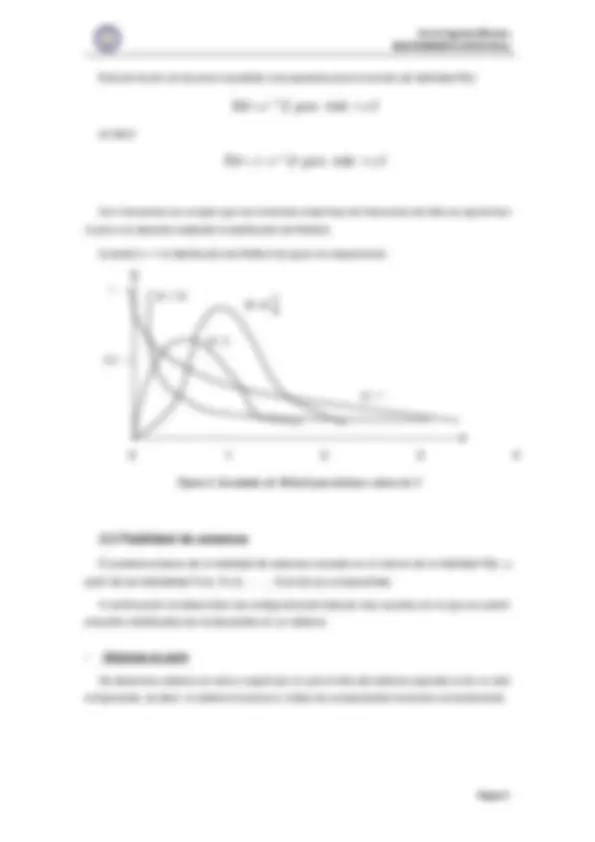

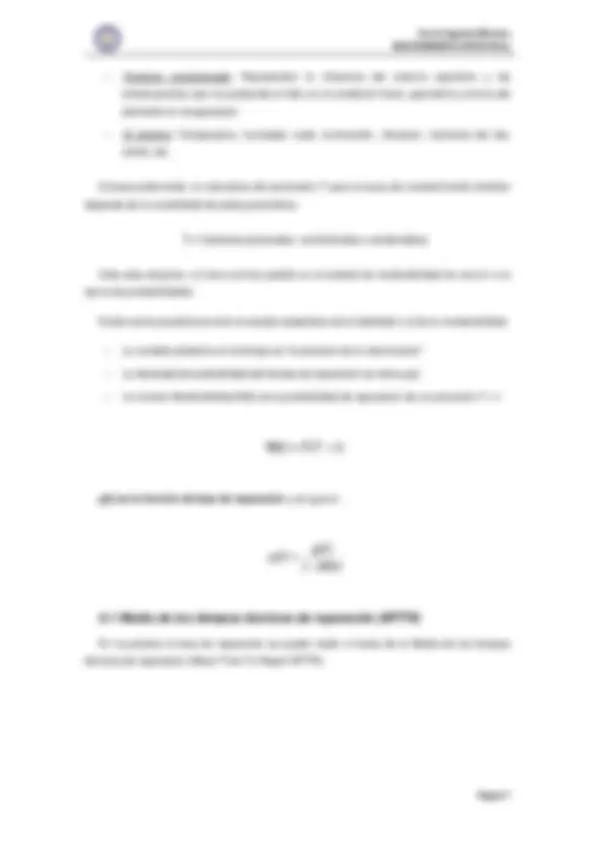
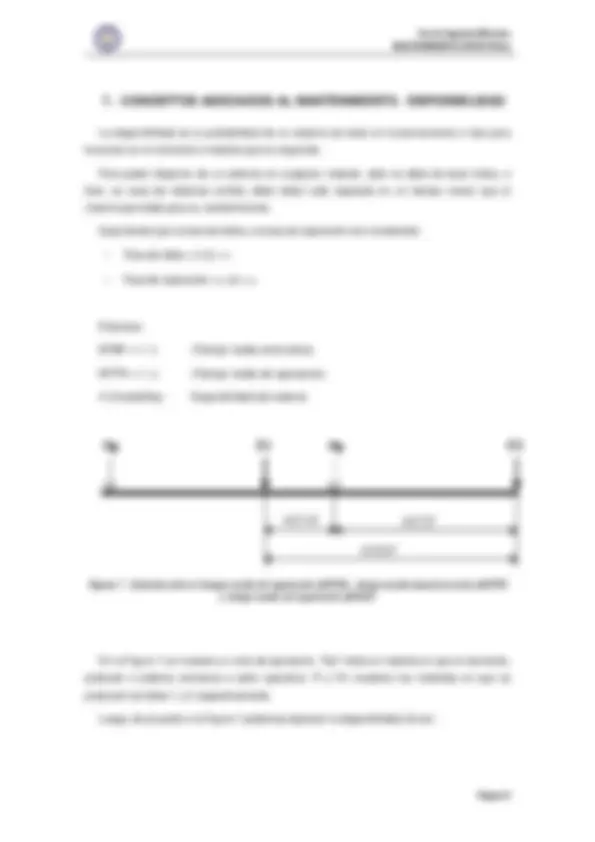
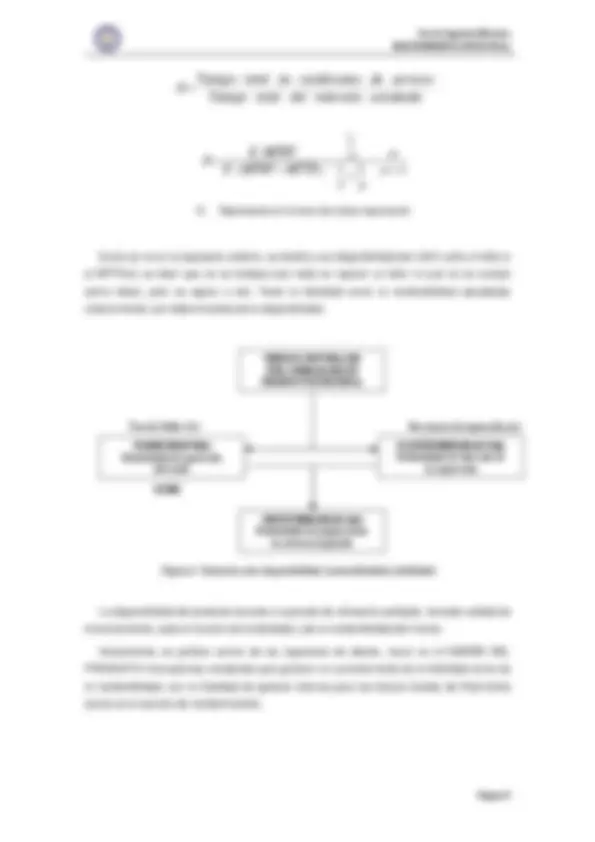
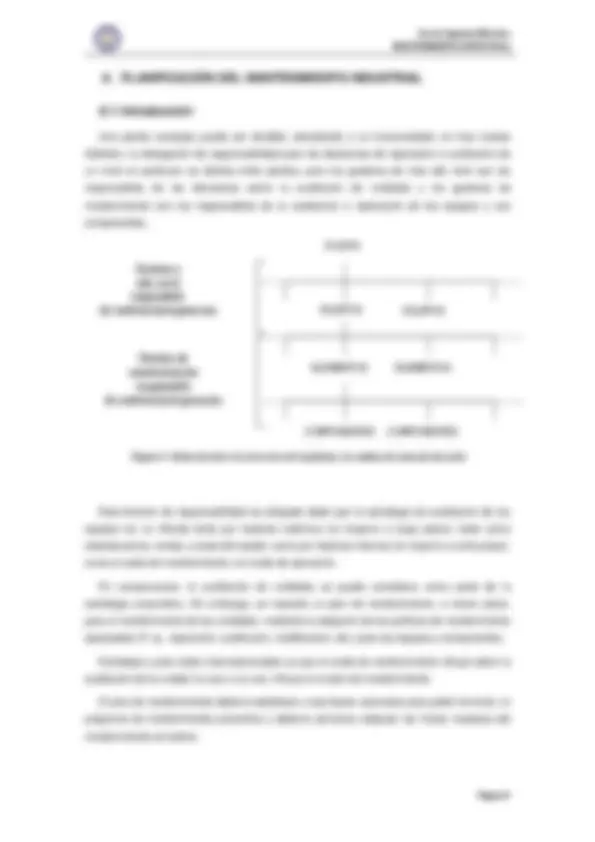
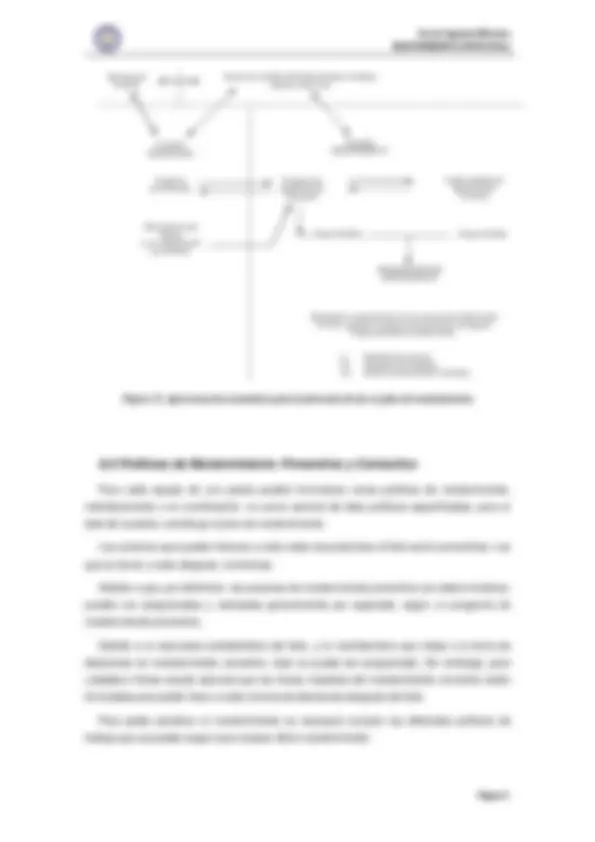
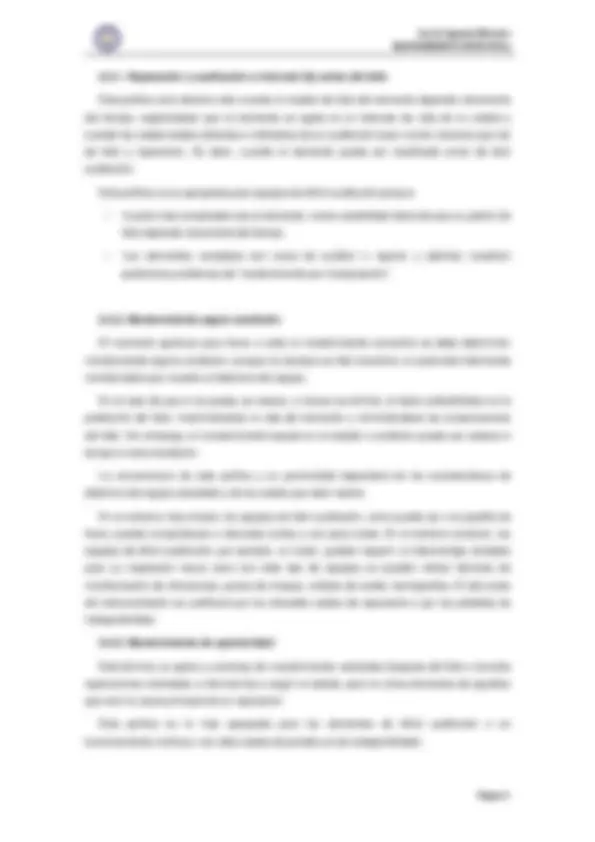
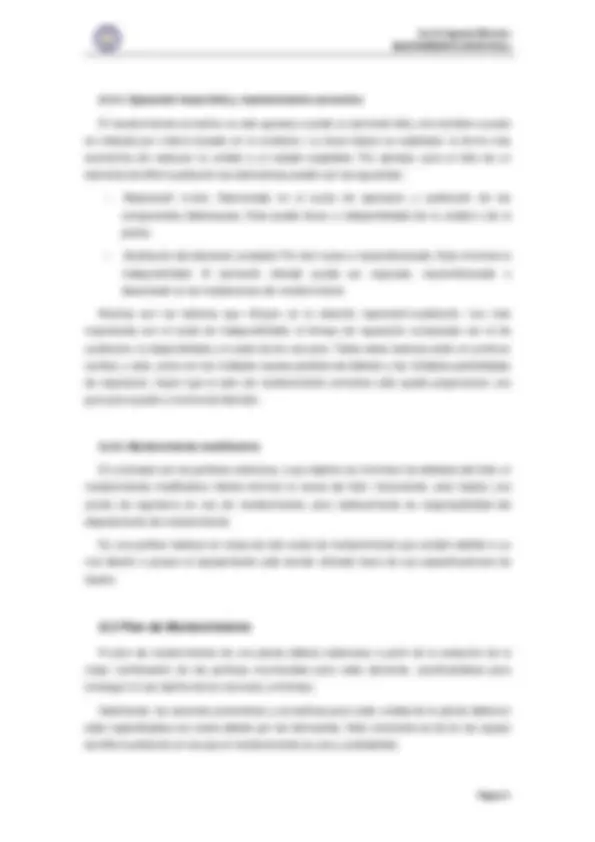
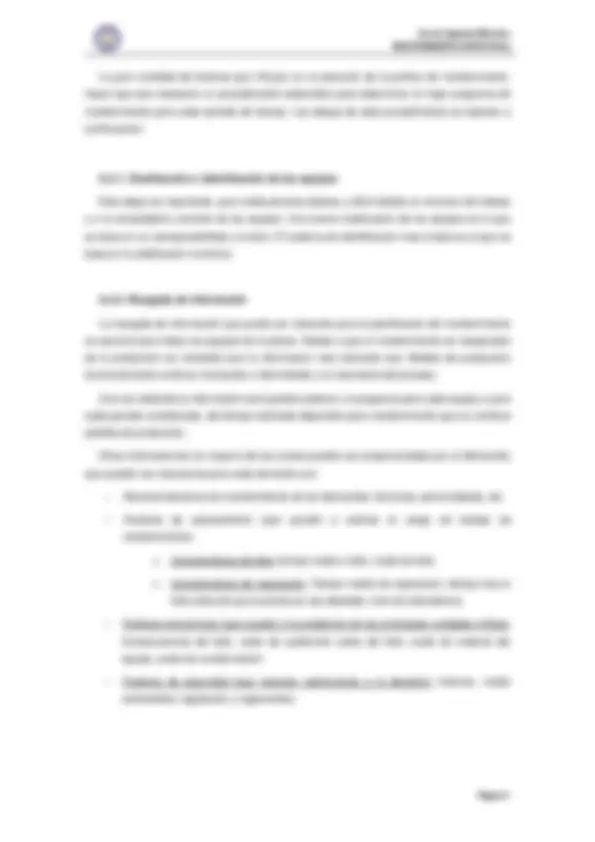

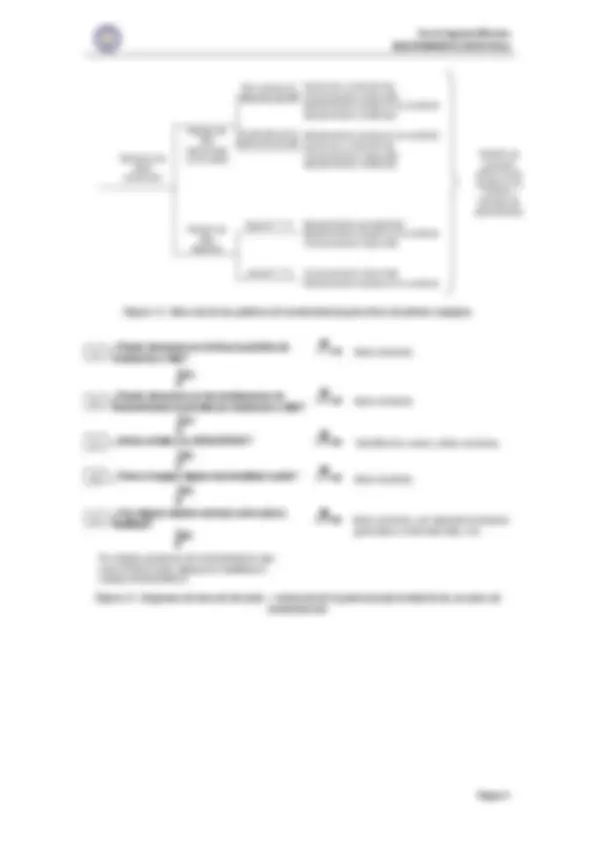
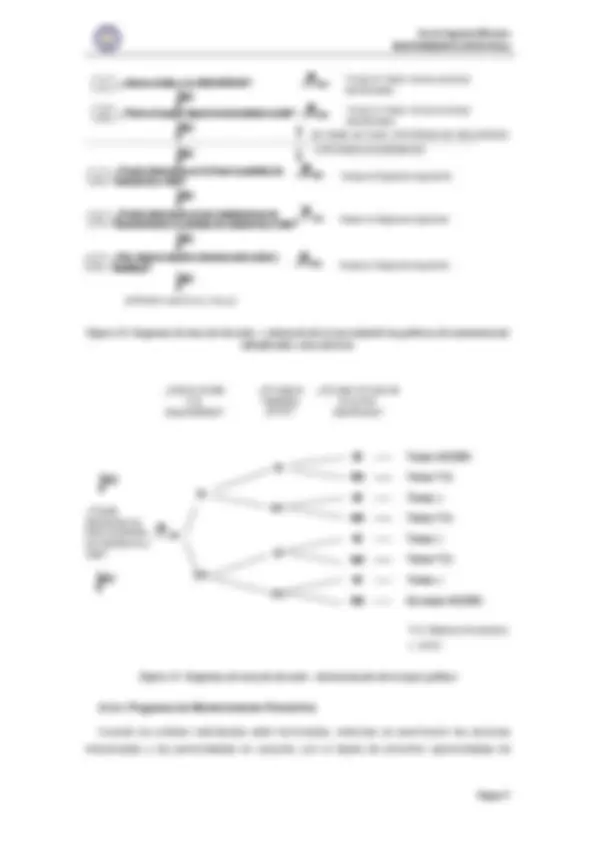
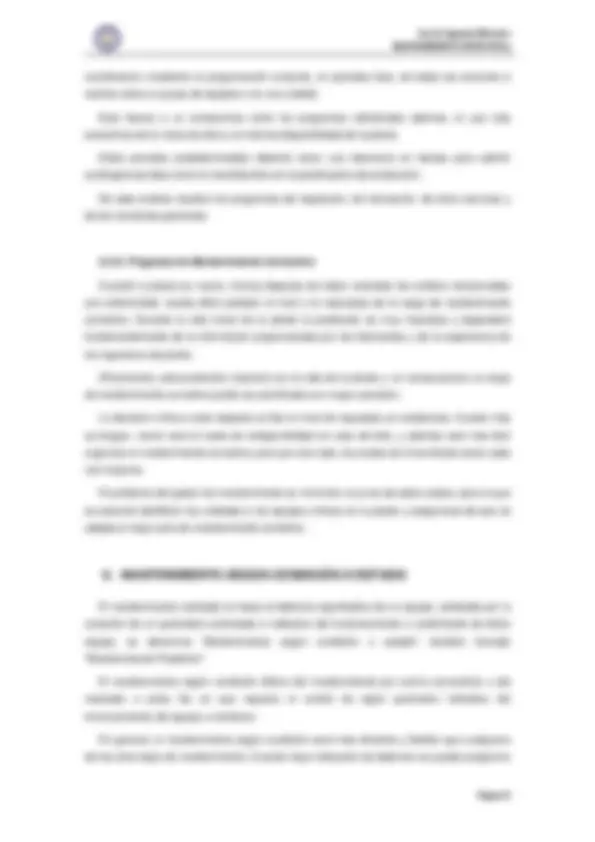
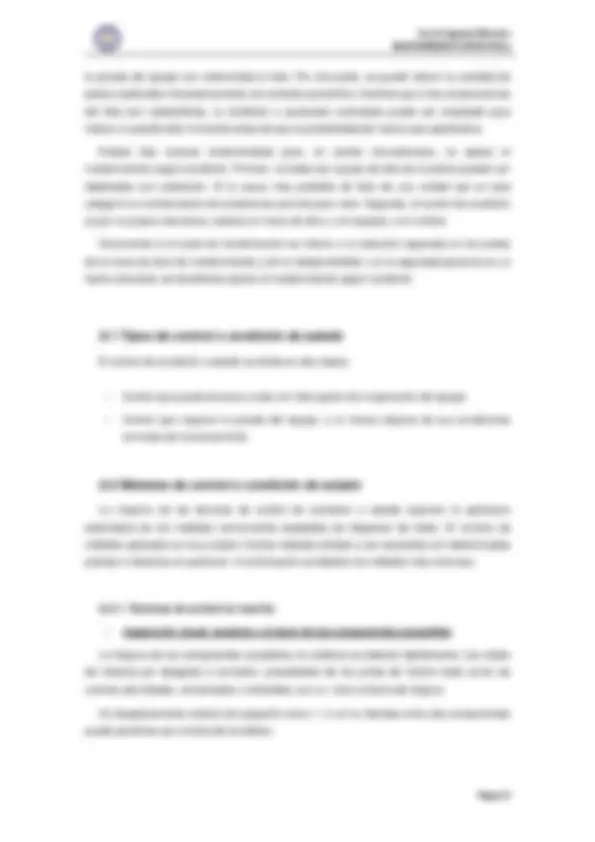
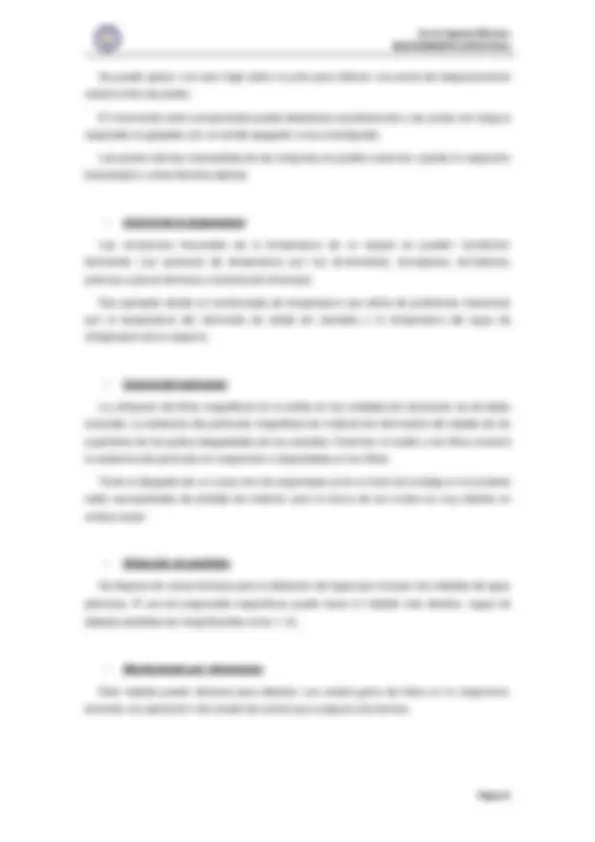
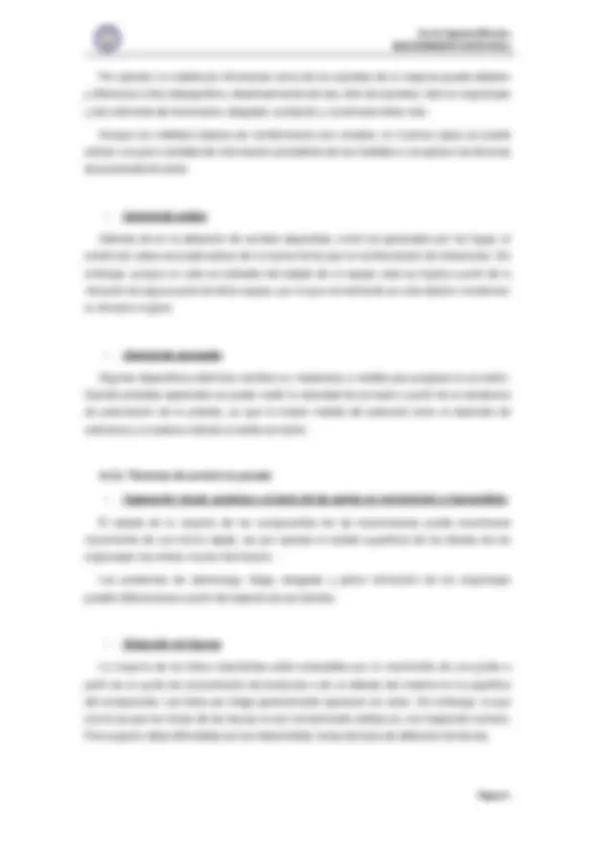
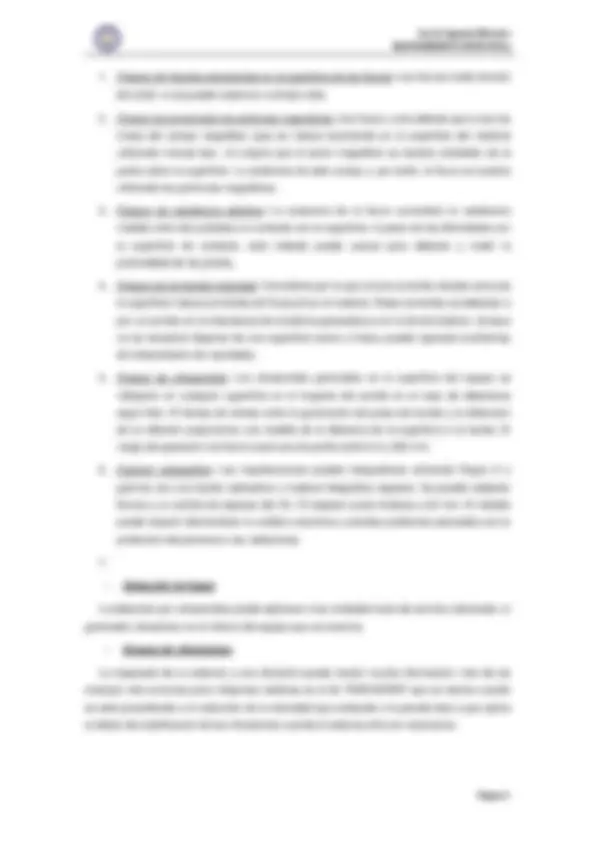
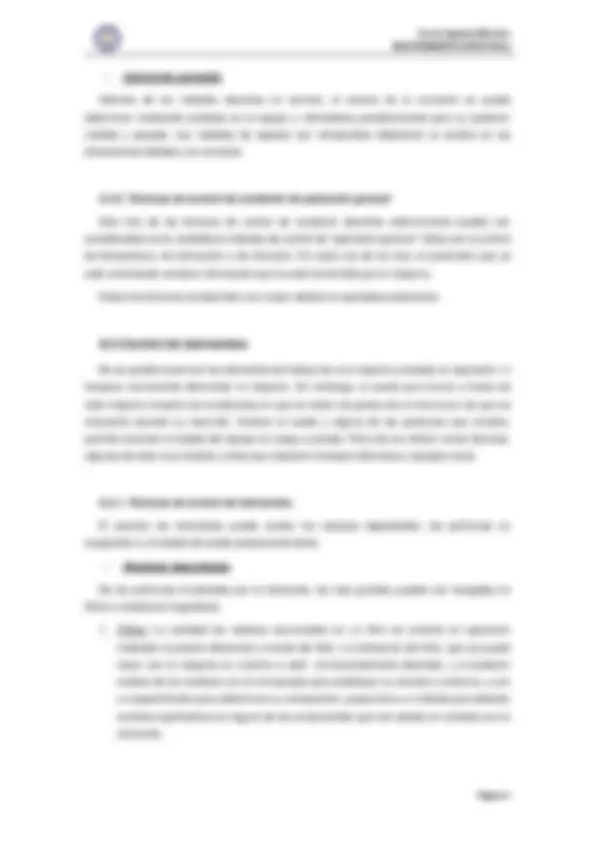
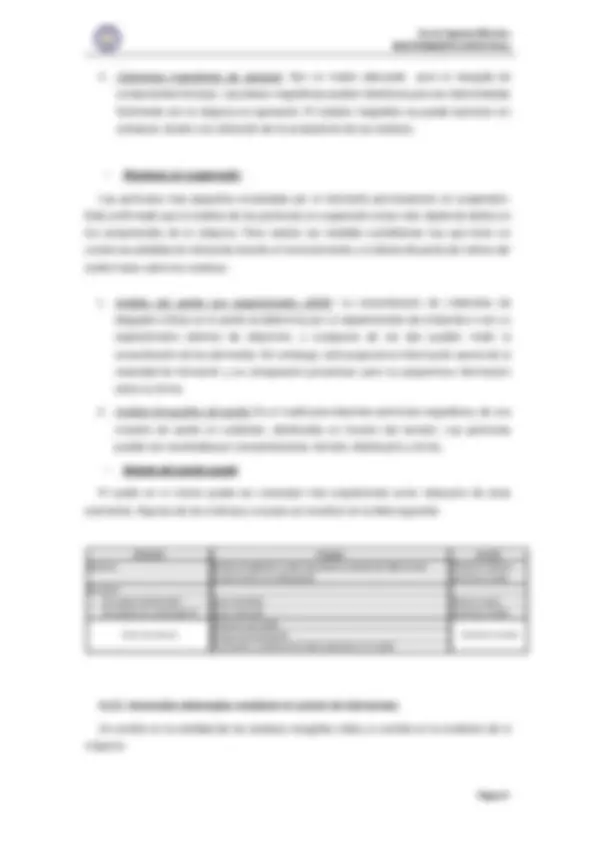
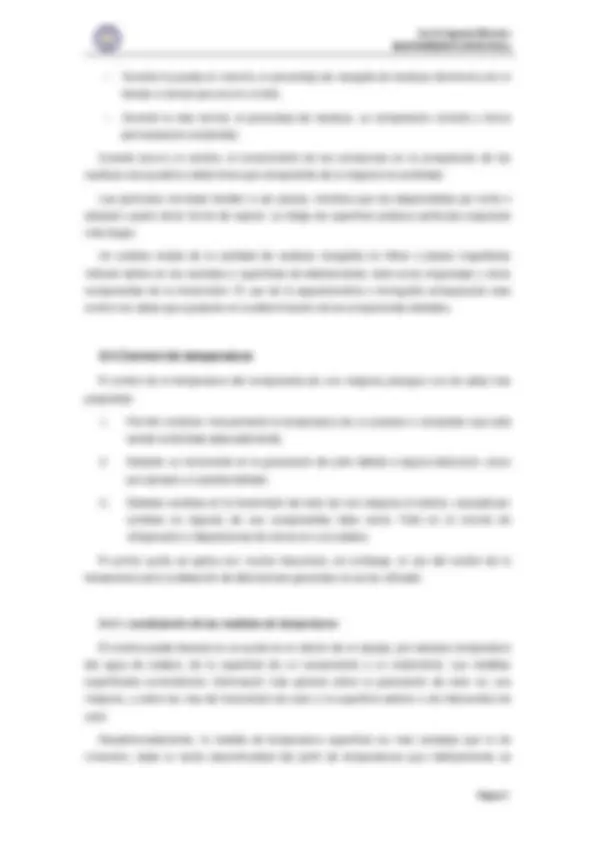
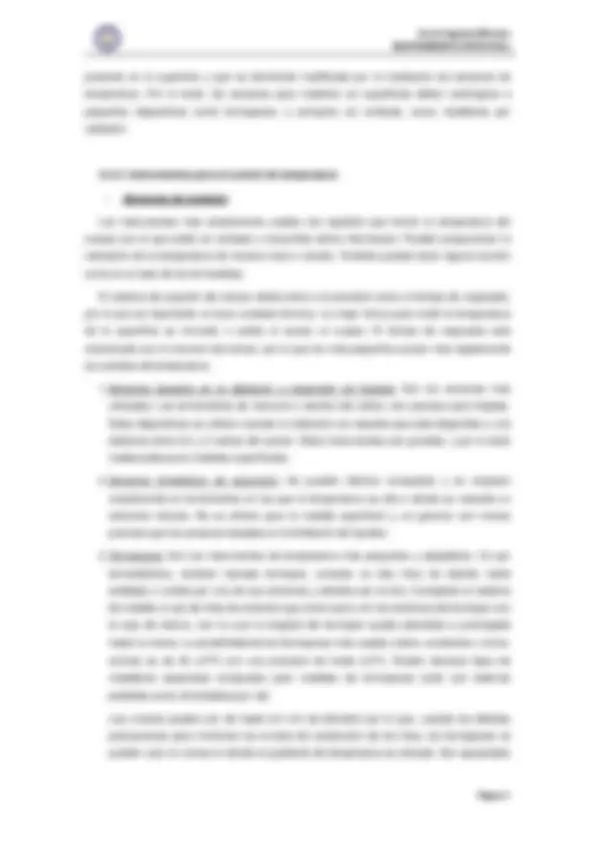
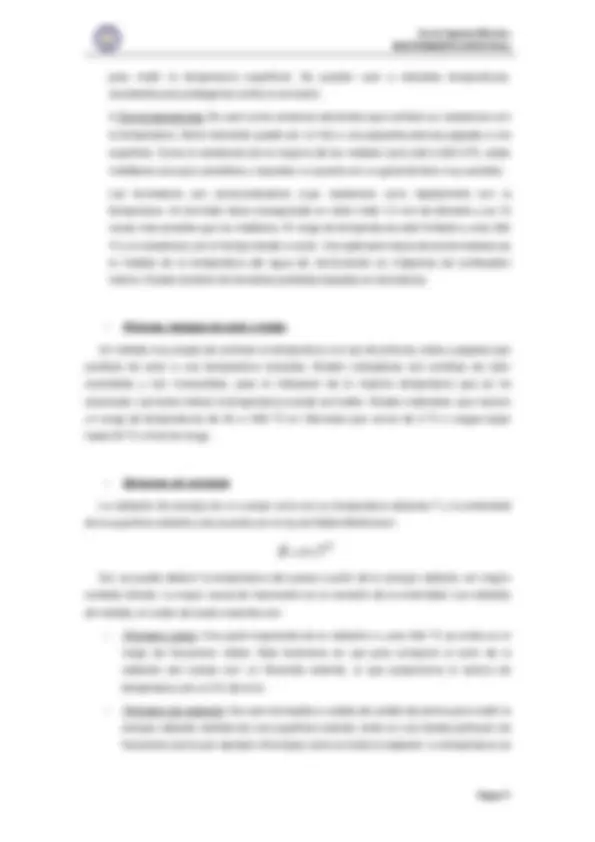
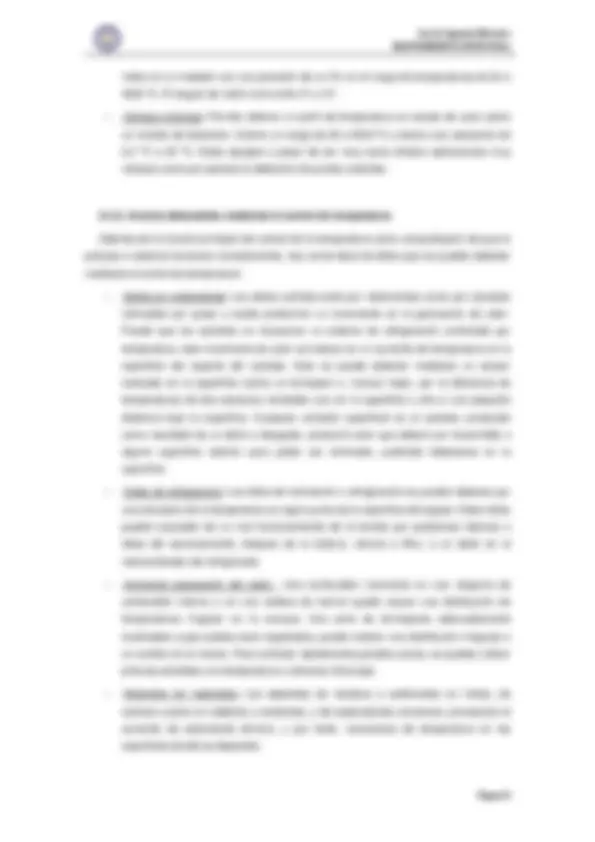
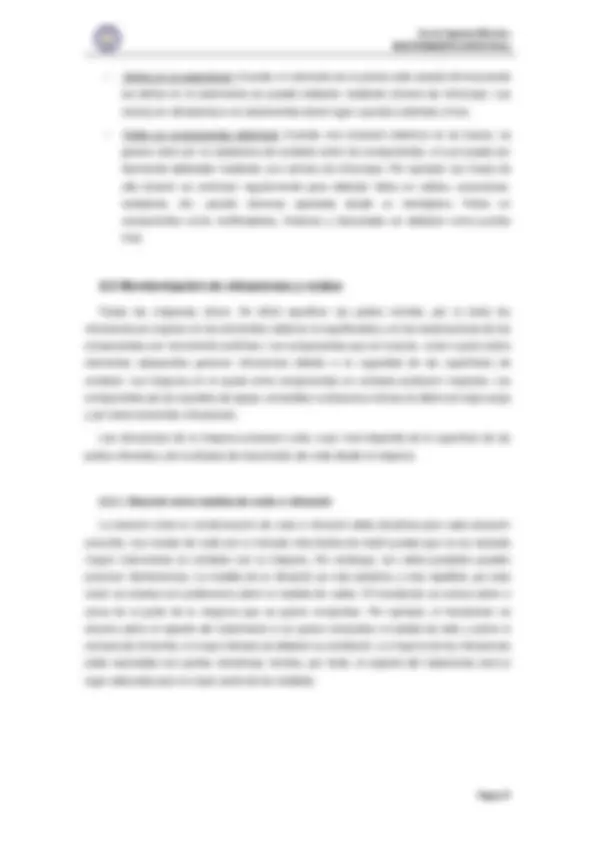
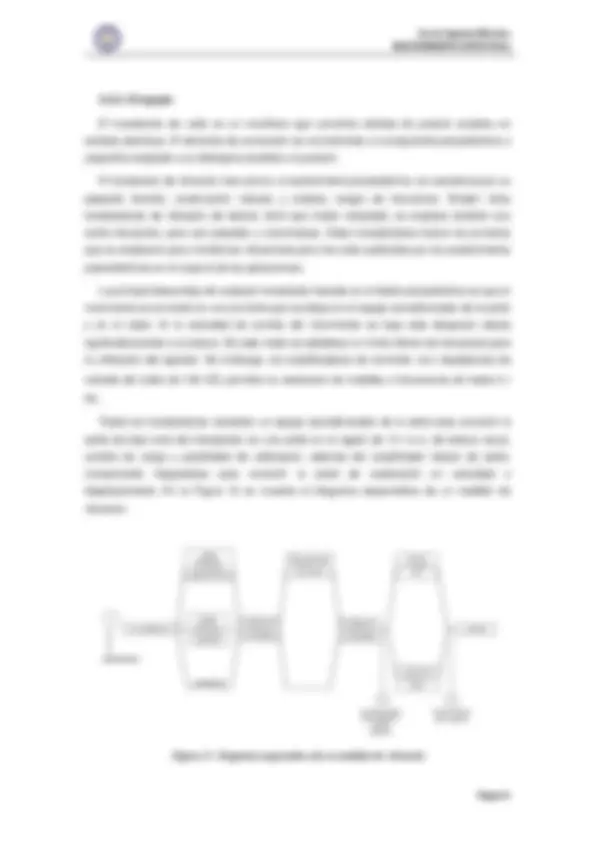
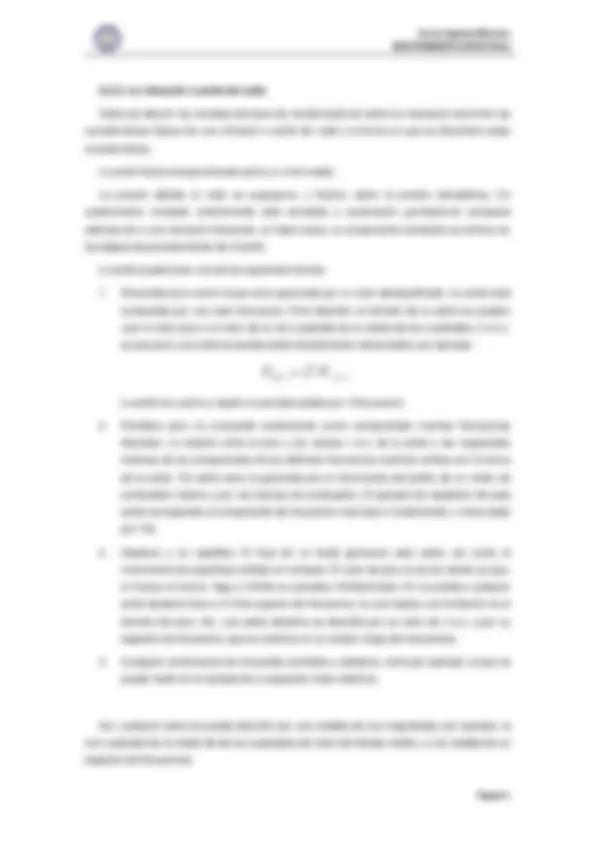
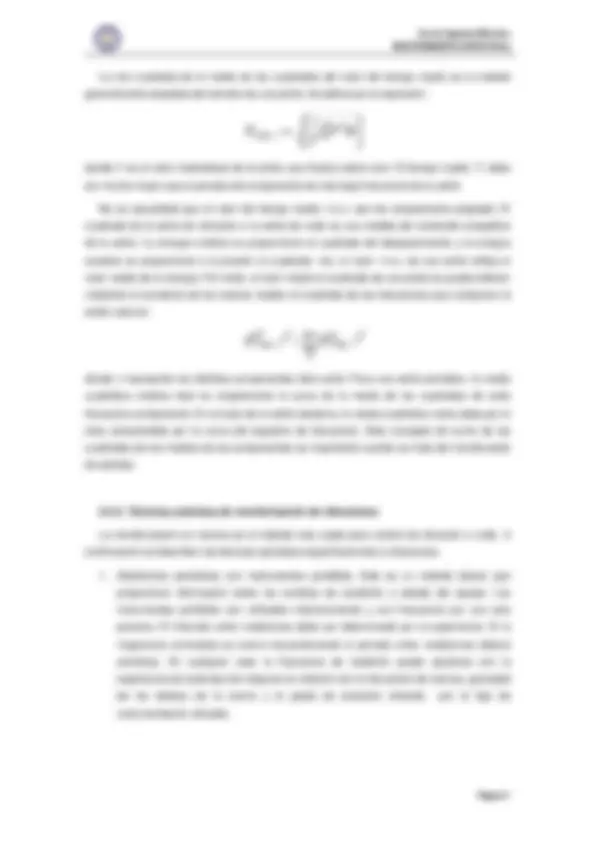
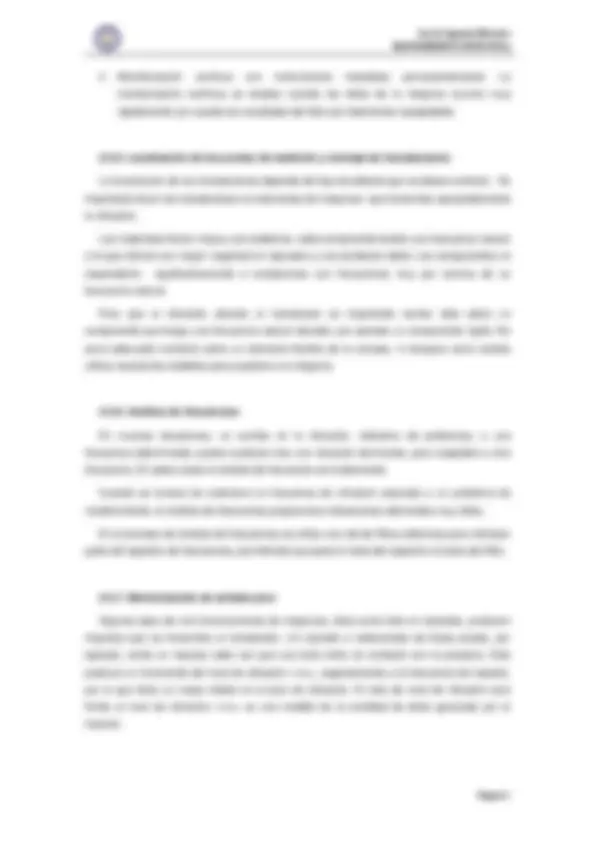
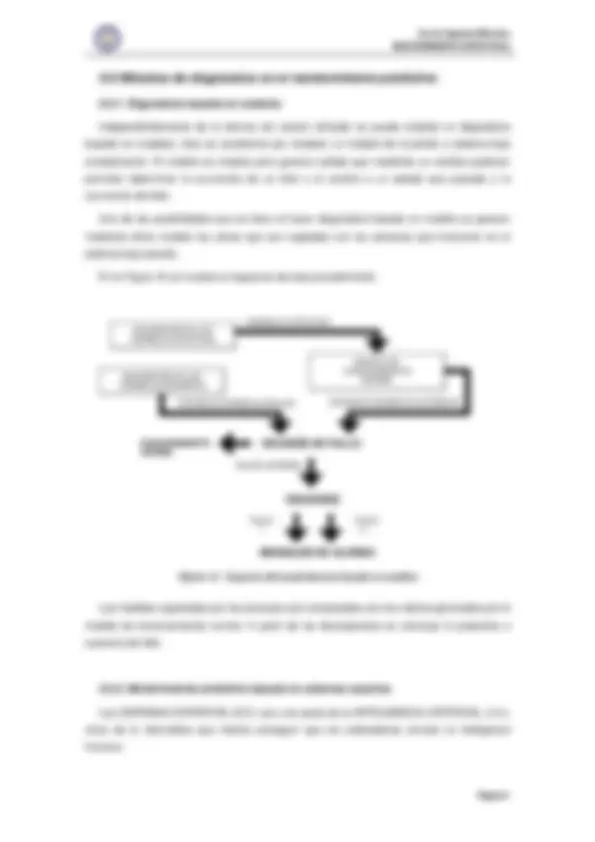
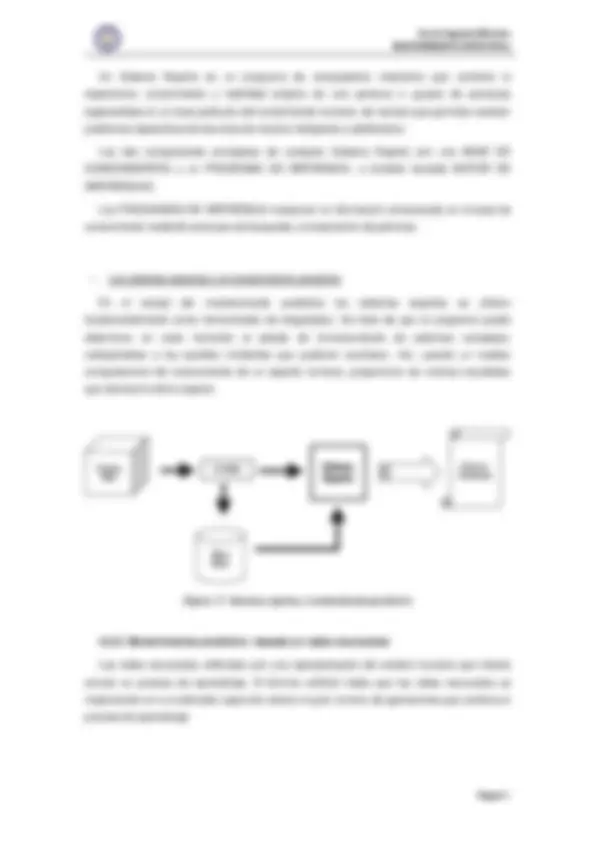
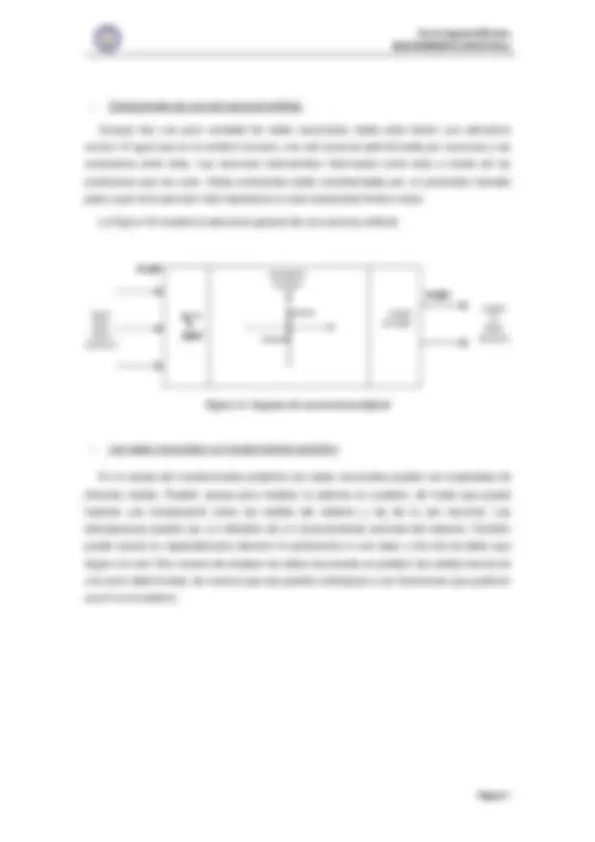
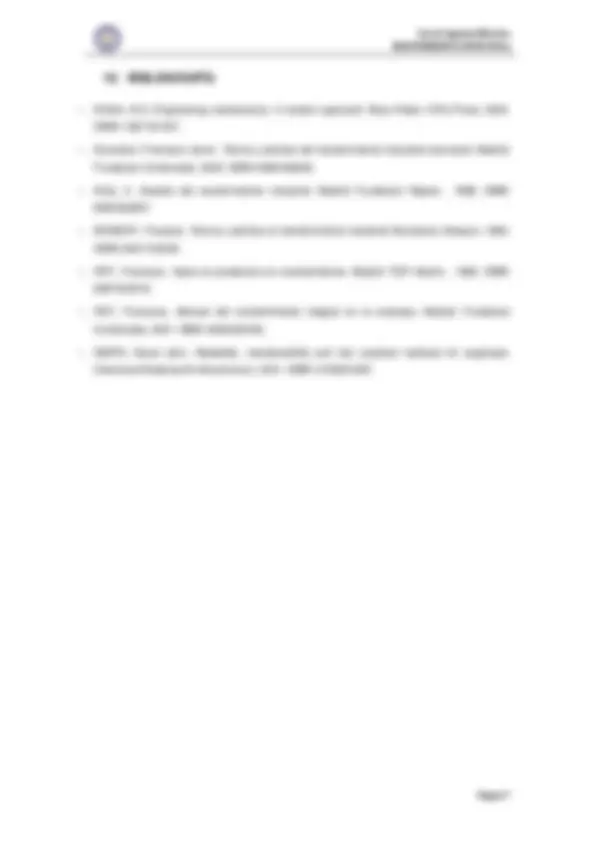
Prepara tus exámenes y mejora tus resultados gracias a la gran cantidad de recursos disponibles en Docsity
Gana puntos ayudando a otros estudiantes o consíguelos activando un Plan Premium
Prepara tus exámenes
Prepara tus exámenes y mejora tus resultados gracias a la gran cantidad de recursos disponibles en Docsity
Prepara tus exámenes con los documentos que comparten otros estudiantes como tú en Docsity
Los mejores documentos en venta realizados por estudiantes que han terminado sus estudios
Estudia con lecciones y exámenes resueltos basados en los programas académicos de las mejores universidades
Responde a preguntas de exámenes reales y pon a prueba tu preparación
Consigue puntos base para descargar
Gana puntos ayudando a otros estudiantes o consíguelos activando un Plan Premium
Comunidad
Pide ayuda a la comunidad y resuelve tus dudas de estudio
Descubre las mejores universidades de tu país según los usuarios de Docsity
Ebooks gratuitos
Descarga nuestras guías gratuitas sobre técnicas de estudio, métodos para controlar la ansiedad y consejos para la tesis preparadas por los tutores de Docsity
Libro de mantenimiento historia
Tipo: Monografías, Ensayos
1 / 48
Esta página no es visible en la vista previa
¡No te pierdas las partes importantes!
MANTENIMIENTO INDUSTRIAL
4.1 Mantenimiento correctivo 4.2 Mantenimiento preventivo 4.3 Mantenimiento predictivo 4.4 Mantenimiento productivo total (Total Productive Maintenance TPM) 5 CONCEPTOS ASOCIADOS AL MANTENIMIENTO. FIABILIDAD………………………... 5.1 Evolución de la tasa de fallos a lo largo del tiempo. Curva de bañera 5.2 Tiempo medio entre fallos (MTBF). 5.3 Tiempo medio hasta la avería (MTTF) 5.4 Modelos matemáticos de distribución de probabilidad de fallos 5.4.1 Ley exponencial de fallos. Tasa de fallos constante 5.4.2 Ley de Weibull. Tasa de fallos crecientes y decrecientes 5.5 Fiabilidad de sistemas 6 CONCEPTOS ASOCIADOS AL MANTENIMIENTO. MANTENIBILIDAD………...….…. 6.1 Media de los tiempos técnicos de reparación 7 CONCEPTOS ASOCIADOS AL MANTENIMIENTO. DISPONIBILIDAD………………... 8 PLANIFICACIÓN DEL MANTENIMIENTO INDUSTRIAL…………………………………. 8.1 Introducción 8.2 Políticas de Mantenimiento: Preventivo y Correctivo 8.2.1 Reparación o sustitución a intervalo fijo antes del fallo 8.2.2 Mantenimiento según condición 8.2.3 Mantenimiento de oportunidad 8.2.4 Operación hasta fallo y mantenimiento correctivo 8.2.5 Mantenimiento modificativo 8.2.6 Operación hasta fallo y mantenimiento correctivo 8.3 Plan de Mantenimiento 8.3.1 Clasificación e identificación de equipos 8.3.2 Recogida de información
MANTENIMIENTO INDUSTRIAL
En la actualidad, la mayor parte de los bienes y servicios se obtienen y se hacen llegar a sus destinatarios mediante unos “sistemas de producción-distribución” o, más brevemente “ sistemas productivos ”, a menudo de gran dimensión tanto por el número de personas que trabajan en ellos como por el tamaño y el valor de las instalaciones y equipos que utilizan. A lo largo de su ciclo de vida cada sistema pasa por diferentes fases. La última de ellas es la de construcción y puesta en marcha, hasta que se alcanza el régimen normal de funcionamiento. Durante esta última fase, llamada de operación, que es la única auténticamente productiva, el sistema se ve sometido a fallos que entorpecen o, incluso, interrumpen temporal o definitivamente su funcionamiento. El objeto del mantenimiento es, precisamente, reducir la incidencia negativa de dichos fallos, ya sea disminuyendo su número o atenuando sus consecuencias. Decimos que algo falla cuando deja de brindarnos el servicio que debía darnos o cuando aparecen efectos indeseables, según las especificaciones de diseño con las que fue construido o instalado el bien en cuestión. En general, todo lo que existe, especialmente si es móvil, se deteriora, rompe o falla con el correr del tiempo. Puede ser a corto plazo o a muy largo plazo. El solo paso del tiempo provoca en algunos bienes, disminuciones evidentes de sus características, cualidades o prestaciones.
La palabra mantenimiento se emplea para designar las técnicas utilizadas para asegurar el correcto y continuo uso de equipos, maquinaria, instalaciones y servicios. Para los hombres primitivos, el hecho de afilar herramientas y armas, coser y remendar las pieles de las tiendas y vestidos, cuidar la estanqueidad de sus piraguas, etc. Durante la revolución industrial el mantenimiento era correctivo (de urgencia), los accidentes y pérdidas que ocasionaron las primeras calderas y la apremiante intervención de las aseguradoras exigiendo mayores y mejores cuidados, proporcionaron la aparición de talleres mecánicos. A partir de 1925, se hace patente en la industria americana la necesidad de organizar el mantenimiento con una base científica. Se empieza a pensar en la conveniencia de reparar antes de que se produzca el desgaste o la rotura, para evitar interrupciones en el proceso productivo, con lo que surge el concepto del mantenimiento Preventivo. A partir de los años sesenta, con el desarrollo de las industrias electrónica, espacial y aeronáutica, aparece en el mundo anglosajón el mantenimiento Predictivo, por el cual la
MANTENIMIENTO INDUSTRIAL intervención no depende ya del tiempo de funcionamiento sino del estado o condición efectiva del equipo o sus elementos y de la fiabilidad determinada del sistema. Actualmente el mantenimiento afronta lo que se podría denominar como su tercera generación, con la disponibilidad de equipos electrónicos de inspección y de control, sumamente fiables, para conocer el estado real de los equipos mediante mediciones periódicas o continuas de determinados parámetros: vibraciones, ruidos, temperaturas, análisis físico- químicos, tecnografía, ultrasonidos, endoscopia, etc., y la aplicación al mantenimiento de sistemas de información basados en ordenadores que permiten la acumulación de experiencia empírica y el desarrollo de los sistemas de tratamiento de datos. Este desarrollo, conducirá en un futuro al mantenimiento a la utilización de los sistemas expertos y a la inteligencia artificial, con amplio campo de actuación en el diagnóstico de avenas y en facilitar las actuaciones de mantenimiento en condiciones difíciles. Por otra parte, existen cambios en las políticas de mantenimiento marcados por la legislación sobre Seguridad e Higiene en el Trabajo y por las presiones la de Medio Ambiente, como dispositivos depuradores, plantas de extracción, elementos para la limitación y atenuación de ruidos y equipos de detección, control y alarma. Se vaticina que los costes de mantenimiento sufrirán un incremento progresivo, esto induce a la fabricación de productos más fiables y de fácil mantenimiento.
El mantenimiento se puede definir como el control constante de las instalaciones (en el caso de una planta) o de los componentes (en el caso de un producto), así como el conjunto de trabajos de reparación y revisión necesarios para garantizar el funcionamiento regular y el buen estado de conservación de un sistema en general. Por lo tanto, las tareas de mantenimiento se aplican sobre las instalaciones fijas y móviles, sobre equipos y maquinarias, sobre edificios industriales, comerciales o de servicios específicos, sobre las mejoras introducidas al terreno y sobre cualquier otro tipo de bien productivo. El objetivo final del mantenimiento industrial se puede sintetizar en los siguientes puntos:
MANTENIMIENTO INDUSTRIAL Asimismo, fallos no detectadas a tiempo, ocurridos en partes cuyo cambio hubiera resultado de escaso coste, pueden causar daños importantes en otros elementos o piezas conexos que se encontraban en buen estado de uso y conservación. Otro inconveniente de este sistema, es que se debe disponer de un capital importante invertido en piezas de repuesto.
Es el conjunto de actividades programadas de antemano, tales como inspecciones regulares, pruebas, reparaciones, etc., encaminadas a reducir la frecuencia y el impacto de los fallos de un sistema. Las desventajas que presenta este sistema son:
MANTENIMIENTO INDUSTRIAL
Es el conjunto de actividades de seguimiento y diagnóstico continuo (monitorización) de un sistema, que permiten una intervención correctora inmediata como consecuencia de la detección de algún síntoma de fallo. El mantenimiento predictivo se basa en el hecho de que la mayoría de los fallos se producen lentamente y previamente, en algunos casos, arrojan indicios evidentes de un futuro fallo, bien a simple vista, o bien mediante la monitorización, es decir, mediante la elección, medición y de algunos parámetros relevantes que representen el buen funcionamiento del equipo analizado. Por ejemplo, estos parámetros pueden ser: la temperatura, la presión, la velocidad lineal, la velocidad angular, la resistencia eléctrica, los ruidos y vibraciones, la rigidez dieléctrica, la viscosidad, el contenido de humedad, de impurezas y de cenizas en aceites aislantes, el espesor de chapas, el nivel de un fluido, etc. En otras palabras, con este método, tratamos de seguir la evolución de los futuros fallos. Este sistema tiene la ventaja de que el seguimiento nos permite contar con un registro de la historia de la característica en análisis, sumamente útil ante fallos repetitivos; puede programarse la reparación en algunos casos, junto con la parada programada del equipo y existen menos intervenciones de la mano de obra en mantenimiento. En el apartado 9 se abordarán con mucho mayor detalle las técnicas más comúnmente utilizadas en el mantenimiento predictivo.
Este sistema está basado en la concepción japonesa del "Mantenimiento al primer nivel", en la que el propio usuario realiza pequeñas tareas de mantenimiento como: reglaje, inspección, sustitución de pequeñas cosas, etc., facilitando al jefe de mantenimiento la información necesaria para que luego las otras tareas se puedan hacer mejor y con mayor conocimiento de causa.
MANTENIMIENTO INDUSTRIAL λλλλ (t) es la función de tasa de fallos o función de riesgo o tasa instantánea de fallos , y es una característica de fiabilidad del producto. La función de tasa de fallas no tiene interpretación física directa, sin embargo, para valores suficientemente pequeños de t se pude definir como la probabilidad de fallo del componente en un tiempo infinitamente pequeño dt cuando en el instante t estaba operativo.
I.- Juventud. Zona de mortandad infantil. El fallo se produce inmediatamente o al cabo de muy poco tiempo de la puesta en funcionamiento, como consecuencia de:
MANTENIMIENTO INDUSTRIAL Figura 1. Curva de “bañera” En una curva de la bañera de tipo convencional se aprecian las tres zonas descritas anteriormente: I.Zona de mortandad infantil : Las averías van disminuyendo con el tiempo, hasta tomar un valor constante y llegar a la vida -útil. En esta zona fallan los componentes con defectos de fabricación, por lo que la tasa de averías disminuye con el tiempo. Los fabricantes, para evitar esta zona, someten a sus componentes a un "quemado" inicial ("burn-in" en inglés), desechando los componentes defectuosos. Este quemado inicial se realiza sometiendo a los componentes a determinadas condiciones extremas, que aceleran los mecanismos de fallo. Los componentes que pasan este periodo son los que nos venden los fabricantes, ya en la zona de vida útil. II.Zona de vida útil, con tasa de fallos aproximadamente constante. Es la zona de mayor duración, en la que se suelen estudiar los sistemas, ya que se supone que se reemplazan antes de que alcancen la zona de envejecimiento. iii. Zona de envejecimiento: La que la tasa de averías vuelve a crecer, debido a que los componentes fallan por degradación de sus características por el transcurso de tiempo. Aún con reparaciones y mantenimiento, las tasas de fallos aumentan, hasta que resulta demasiado costoso el mantenimiento. Fallos iniciales
Fallos relativos a tension-resistencia Fallos por desgaste (envejecimiento) Estructural Mecánica T A S A D E F A L L O Tiempo
MANTENIMIENTO INDUSTRIAL La probabilidad de que una unidad que está trabajando falle en el próximo instante es independiente de cuánto tiempo ha estado trabajando. Esto implica que la unidad no presenta síntomas de envejecimiento. Es igualmente probable que falle en el instante siguiente, cuando está nueva o cuando no lo está. En este caso, la función de fiabilidad correspondiente se puede escribir como: λ t
−
Por lo tanto, la función de distribución F(t) se expresa:
y la función de densidad f(t):
5.4.2. Ley Weibull. Tasas de fallos crecientes y decrecientes. Una gran mayoría de los equipos reales no tienen una tasa de fallos constante, sino que es más probable que fallen a medida que envejecen. En este caso la tasa de fallos es creciente. Por otra parte, también nos podemos encontrar con bienes que posean tasas de fallos decrecientes. La función para tasas de fallos crecientes o decrecientes tienen la forma:
En este caso, λ(t) es una función polinomial en la variable t, que depende de los dos parámetros α y β. Cuando β > 1, λ(t) es creciente. Cuando 0 < β < 1 , λ(t) es decreciente β > 1 t Tasa creciente de Fallos (TCF) 0 < β < 1 t Tasa decreciente de Fallos (TCF) Figura 2. Funciones de tasas de fallos para la distribución de Weibull del tiempo de vida
MANTENIMIENTO INDUSTRIAL Esta forma de λ(t) da como resultado una expresión para la función de fiabilidad R(t):
α t
− es decir:
Con frecuencia se cumple que las funciones empíricas de frecuencia de fallo se aproximan mucho a la descrita mediante la distribución de Weibull. Cuando β = 1 la distribución de Weibull es igual a la exponencial.
1 β = 1/ β = 2 (^1) _ 2 β = 2 (^1) _ 2 β = 2 β = 1
El problema básico de la fiabilidad de sistemas consiste en el cálculo de la fiabilidad R(t), a partir de las fiabilidades R 1 (t), R 2 (t),.... , Rn(t) de sus componentes. A continuación se desarrollan las configuraciones básicas más usuales con la que se suelen encontrar distribuidos los componentes en un sistema:
MANTENIMIENTO INDUSTRIAL Freno de servicio Freno de emergencia Una de las ruedas Rueda de repuesto Fallo del automóvil Fallo del automóvil Figura 5. Ejemplo de sistema en paralelo. Fallo en el automóvil La característica inherente al modelo paralelo se llama redundancia : Es decir existe más de un componente para desempeñar una función dada. La redundancia puede ser de dos clases:
MANTENIMIENTO INDUSTRIAL C 1 C 2
Figura 6. Ejemplo de un sistema redundante en espera La fiabilidad de un sistema en reserva formado por dos componentes (el operacional y el de reserva) como se muestra en la Figura 6 es la probabilidad de que la unidad operacional funcione correctamente durante el tiempo t, o bien de que habiendo fallado en el tiempo t 1 , la unidad en reserva no falle al entrar en funcionamiento y continúe operando con éxito hasta que haya transcurrido el tiempo que hay entre t 1 y t. De ese modo la fiabilidad R(t) del sistema será: R(t) = R 1 (t) + F(t 1 ) · R 2 (t-t 1 ) Donde: R 1 (t): Fiabilidad de la unidad operacional en el tiempo t. F (t 1 ): Probabilidad de fallo de la unidad operacional en el tiempo t 1. R 2 (t - t 1 ): Probabilidad de fallo de la unidad de reserva en el tiempo t - t 1
La mantenibilidad es una característica inherente a un elemento, asociada a su capacidad de ser recuperado para el servicio cuando se realiza la tarea de mantenimiento necesaria según se especifica. Así, la mantenibilidad podría ser expresada cuantitativamente, mediante el tiempo T empleado en realizar la tarea de mantenimiento especificada en el elemento que se considera, con los recursos de apoyo especificados. Intervienen en la ejecución de estas tareas tres factores:
MANTENIMIENTO INDUSTRIAL
La disponibilidad es la probabilidad de un sistema de estar en funcionamiento o listo para funcionar en el momento o instante que es requerido. Para poder disponer de un sistema en cualquier instante, éste no debe de tener fallos, o bien, en caso de haberlos sufrido, debe haber sido reparado en un tiempo menor que el máximo permitido para su mantenimiento. Suponiendo que la tasa de fallos y la tasa de reparación son constantes:
MANTENIMIENTO INDUSTRIAL Tiempo total del intervalo estudiado Tiempo total en condiciones de servicio A = ( )
λ μ μ λ λ μ
K: Representa el número de ciclos-reparación. Como se ve en la expresión anterior, se tendría una disponibilidad del 100% ante un fallo si el MTTR=0, es decir que no se tardase casi nada en reparar un fallo, lo cual no se cumple (sería ideal), pero se aspira a ello. Tanto la fiabilidad como la mantenibilidad estudiadas anteriormente, son determinantes de la disponibilidad. DISPONIBILIDAD A(t) Probabilidad de proporcionar un servicio requerido TIEMPO DE VIDA DE UNA UNIDAD DE UN PRODUCTO/SISTEMA FIABILIDAD R(t) Probabilidad de operación adecuada MANTENIBILIDAD M(t) Probabilidad de duración de La reparación Tasa de Fallos λ(t) Frecuencia de reparación μ(t) MTBF Figura 8. Relación entre disponibilidad, mantenibilidad y fiabilidad La disponibilidad del producto durante un periodo de utilización prefijado, llamada calidad de funcionamiento, está en función de la fiabilidad y de la mantenibilidad del mismo. Actualmente, es política común de los ingenieros de diseño, incluir en el DISEÑO DEL PRODUCTO innovaciones constantes que generen un aumento tanto de la fiabilidad como de la mantenibilidad, con la finalidad de generar ahorros para los futuros Costes de Post-Venta (como en el servicio de mantenimiento).