
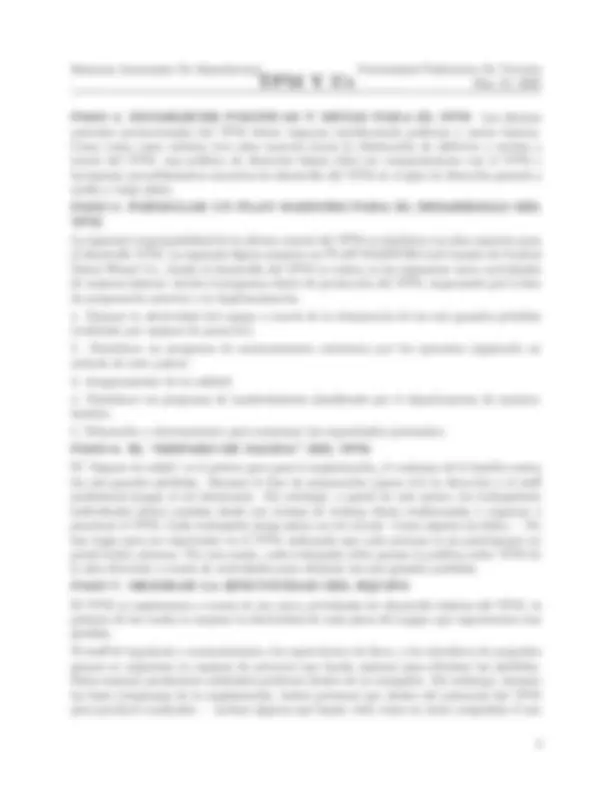


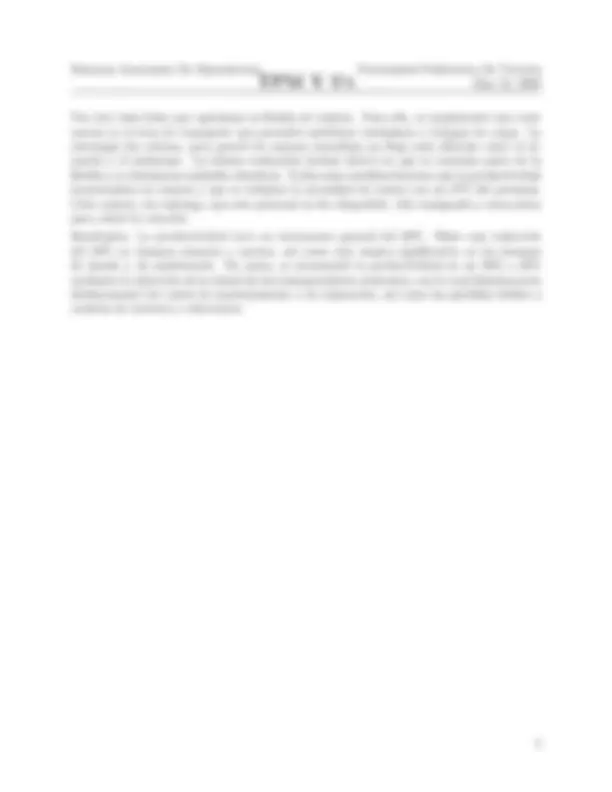
Prepara tus exámenes y mejora tus resultados gracias a la gran cantidad de recursos disponibles en Docsity
Gana puntos ayudando a otros estudiantes o consíguelos activando un Plan Premium
Prepara tus exámenes
Prepara tus exámenes y mejora tus resultados gracias a la gran cantidad de recursos disponibles en Docsity
Prepara tus exámenes con los documentos que comparten otros estudiantes como tú en Docsity
Los mejores documentos en venta realizados por estudiantes que han terminado sus estudios
Estudia con lecciones y exámenes resueltos basados en los programas académicos de las mejores universidades
Responde a preguntas de exámenes reales y pon a prueba tu preparación
Consigue puntos base para descargar
Gana puntos ayudando a otros estudiantes o consíguelos activando un Plan Premium
Comunidad
Pide ayuda a la comunidad y resuelve tus dudas de estudio
Descubre las mejores universidades de tu país según los usuarios de Docsity
Ebooks gratuitos
Descarga nuestras guías gratuitas sobre técnicas de estudio, métodos para controlar la ansiedad y consejos para la tesis preparadas por los tutores de Docsity
mantenimiento productivo total muy bueno
Tipo: Resúmenes
1 / 8
Esta página no es visible en la vista previa
¡No te pierdas las partes importantes!
May 12, 2020
Alumno: Mario Alberto Altamirano Lugo Matricula: 1730148
El Mantenimiento Productivo Total o por sus siglas en ingl´es tambi´en conocido como TPM, es un enfoque sistem´atico para comprender la funci´on de los equipos, la relaci´on del equipo con la calidad del producto y la causa probable y la frecuencia de fallo de los componentes. Previene los defectos y aver´ıas de calidad, elimina la necesidad de ajustes, y hace el trabajo m´as f´acil y m´as seguro para los operadores de los equipos. No cabe duda que existen muchas ventajas y/o beneficio por usar esta filosof´ıa de trabajo, en este ´articulo enlistaremos algunos.
¿Qu´e benficios trae TPM a una empresa?
Ventajas:
Beneficios del equipo:
May 12, 2020
12 Pasos para Implementar el TPM
PASO 1: ANUNCIO DE LA ALTA DIRECCION DE LA DECISION DE IN- TRODUCIR EL TPM
El primer paso en el desarrollo TPM es hacer un anuncio oficial de la decisi´on de implantar el TPM. La alta direcci´on debe informar a sus empleados de su decisi´on e infudir entusiasmo por el proyecto. Esto puede cumplirse a trav´es de una presentaci´on formal que introduce el concepto, metas, y beneficios esperados del TPM, y tambi´en incluye propuestas personales de la alta direcci´on a los empleados sobre las razones que fundamentan la decisi´on de implantar el TPM. Esto puede seguirse con informaci´on impresa en boletines internos.
Es esencial en este punto que la alta direcci´on tenga un fuerte compromiso con el TPM y en- tienda lo que entra˜na el compromiso. Como se ha mencionado anteriormente, la preparaci´on para la implantaci´on significa crear un entorno favorable para un cambio efectivo. Durante este per´ıodo (como en la fase de dise˜no de un producto), debe crearse un fundamento fuerte de forma que las posteriores modificaciones (como los cambios de dise˜no que pueden resultar en retrasos de entregas) no sean necesarias.
PASO 2: LANZAMIENTO DE CAMPA ˜NA EDUCACIONAL
El segundo paso en el programa de desarrollo TPM es el entrenamiento y promoci´on en el mismo, lo que debe empezar tan pronto como sea posible despu´es de introducir el programa.
El objetivo de la educaci´on es, no solamente explicar el TPM, sino tambi´en elevar la moral y romper la resistencia al cambio -en este caso, el cambio al TPM.
La resistencia frente al TPM puede adoptar diferentes formas: algunos trabajadores pueden preferir la divisi´on de tareas m´as convencional (los operarios manejan el equipo, mientras los trabajadores de mantenimiento lo reparan). Los trabajadores de la l´ınea de producci´on a menudo temen que el TPM incrementar´a la carga de trabajo, mientras el personal de mantenimiento es esc´eptico sobre la capacidad de los operarios de l´ınea para practicar el PM. Adicionalmente, los que est´an practicando el PM con buenos resultados pueden dudar de que el TPM provea beneficios a˜nadidos.
PASO 3: CREAR ORGANIZACIONES PARA PROMOVER EL TPM
Una vez que se ha completado la educaci´on introductoria al nivel de personal de direcci´on (de jefes de secci´on hacia arriba), puede empezar la creaci´on de un sistema promocional del TPM.
La estructura promocional TPM se basa en una matriz organizacional, conformada por grupos horizontales tales como comit´es y grupos de proyecto en cada nivel de la organizaci´on vertical de direcci´on. Es extremadamente importante para el ´exito y desarrollo general del TPM. Como se ilustra en la figura 12, los grupos se organizan por rangos, por ejemplo, el comit´e promocional del TPM, los comit´es promocionales de f´abrica y departamento, y los c´ırculos PM al nivel del suelo de la f´abrica. Es cr´ıtica la integraci´on arriba-abajo, desde las metas orientadas por la direcci´on con los movimientos desde abajo, y las actividades de los peque˜nos grupos en la f´abrica.
May 12, 2020
del TPM incrementa la productividad y calidad, reduce los costes, mejora los resultados, y crea un entorno favorable de trabajo.
PASO 8: ESTABLECER UN PROGRAMA DE MANTENIMIENTO AUTONOMO PARA LOS OPERARIOS
La segunda de las cinco actividades de desarrollo del TPM, el mantenimiento aut´onomo, es el paso octavo del programa de desarrollo. Debe atacarse justo despu´es del —disparo de salida.
El mantenimiento aut´onomo por los operarios es una caracter´ıstica ´unica del TPM; su organi- zaci´on es central para la promoci´on del TPM dentro de la compa˜n´ıa. Cuanto mas antigua es una compa˜n´ıa, mas dificultoso es implantar el mantenimiento aut´onomo, porque los operarios y el personal de mantenimiento encuentran penoso apartarse del concepto: —Yo opero-tu reparas‖. Los operarios est´an acostumbrados a dedicarse a tiempo completo a la producci´on, y el personal de mantenimiento espera asumir la plena responsabilidad del mismo.
Paso 9: ESTABLECER UN PROGRAMA DE MANTENIMIENTO PARA EL DEPARTAMENTO DE MANTENIMIENTO
El noveno paso en el programa de desarrollo es tambi´en una de las cinco actividades b´asicas TPM -un programa de mantenimiento peri´odico para el departamento de mantenimiento.
Como hemos mencionado anteriormente, el mantenimiento programado realizado por el departamento de mantenimiento, debe coordinarse con las actividades de mantenimiento aut´onomo del departamento de operaciones, de forma que los departamentos puedan fun- cionar como las ruedas de un coche.
PASO 10: CONDUCIR ENTRENAMIENTO PARA MEJORAR CAPACIDADES DE OPERACI ´ON Y MANTENIMIENTO
La mejora de. las capacidades de operaci´on y mantenimiento es la cuarta actividad de desarrollo del TPM y el d´ecimo paso del programa de desarrollo del TPM.
En Jap´on, las grandes corporaciones del acero y la electr´onica proveen a sus empleados con entrenamiento t´ecnico en centros bien equipados, pero otras compa˜n´ıas japonesas infra estiman el valor del entrenamiento, especialmente el entrenamiento en t´ecnicas de manten- imiento. La educaci´on y el entrenamiento son inversiones en personal que rinden m´ultiples beneficios. Una compa˜n´ıa que implante el TPM debe invertir en entrenamiento que permita a los empleados gestionar apropiadamente el equipo. En adici´on al entrenamiento en t´ecnicas de mantenimiento, los operarios deben afinar tambi´en sus capacidades en operaci´on.
PASO 11: DESARROLLO TEMPRANO DE UN PROGRAMA DE GESTION DE EQUIPOS
La ´ultima categor´ıa de las actividades de desarrollo del TPM es la gesti´on temprana (o antic- ipada) del equipo. Cuando se instala el nuevo equipo, a menudo aparecen problemas durante las operaciones de test, y arranque, aunque durante el dise˜no, la fabricaci´on, y la instalaci´on toda parece marchar normalmente. Puede que los ingenieros de mantenimiento e ingenier´ıa tengan que hacer muchas mejoras antes de que comience la operaci´on normal. Incluso en- tonces, se necesitan reparaciones en el per´ıodo inicial, inspecci´on, ajuste, y lubricaci´on y
May 12, 2020
limpieza iniciales para evitar el deterioro, y las aver´ıas son a menudo tan dif´ıciles de reparar que los ingenieros de supervisi´on se desmoralizan completamente. Como resultado, pueden pasarse por alto la inspecci´on, lubricaci´on, y limpieza, lo que necesariamente prolonga las paradas del equipo incluso para las aver´ıas menores.
PASO 12: IMPLANTACION PLENA DEL TPM Y CONTEMPLAR METAS MAS ELEVADAS
El paso final en el programa de desarrollo del TPM es perfeccionar la implantaci´on del TPM y fijar metas futuras a´un m´as elevadas. Durante este per´ıodo de estabilizaci´on cada uno trabaja continuamente para mejorar los resultados TPM, de forma que puede esperarse que dure alg´un tiempo.
Figure 1: Los 8 pilares del TPM.
May 12, 2020
Beneficios
La metodolog´ıa 5S nos indica y ayuda a deshacernos de los materiales innecesarios, a que todo se encuentre ordenado e identificado, a eliminar las fuentes de suciedad y a arreglar los desperfectos, a que todos los elementos se aprecien a simple vista sin necesidad de largas b´usquedas y a que todo esto se mantenga y mejore constantemente.
El tiempo dedicado a operaciones de b´usqueda, almacenamientos, comunicaciones y desplaza- mientos puede reducirse significativamente gracias a las 5S.
Hay un gran potencial de mejora, puesto que el objetivo final de las 5S es reducir el tiempo de ejecuci´on de las tareas y mejorar la seguridad en el trabajo.
Las 5S no son zafarranchos de limpieza ante la visita del Consejo de Administraci´on. Es una t´ecnica de gesti´on utilizada para la creaci´on y el mantenimiento sistem´atico de la limpieza y el orden de las ´areas de trabajo. Se trata de una herramienta muy importante si pretendemos optimizar los procesos de una organizaci´on. 5S es un m´etodo cuyo principio es: “Un sitio para cada cosa y cada cosa en su sitio”.
Y todo est´a orientado a una ´unica cuesti´on: reducir el tiempo de ejecuci´on de los trabajos reduciendo el despilfarro, la accidentabilidad, es decir, aumentar la pro- ductividad y la seguridad.
Ejemplo De Implementacion de TPM y 5´s
Uno de los principales retos fue en convencer al cliente de que la metodolog´ıa Lean de Mejora Continua tambi´en funciona para la industria alimenticia, a pesar de que s´olo al final de su l´ınea de empaque se utilizaba un proceso discreto (pues los paquetes de galletas se guardan manualmente en sus cajas).
”Recomendamos llevar a cabo tres eventos Kaizen con el fin de lograr una nueva organizaci´on de todas las l´ıneas de empaque” comenta Jos´e Medell´ın.
Soluci´on: A trav´es de una serie de eventos Kaizen se obtuvo una nueva organizaci´on de la l´ınea de empaque. La implementaci´on del TPM (Mantenimiento Productivo Total), repercuti´o en un uso m´as eficiente de las m´aquinas. Tambi´en se llev´o a cabo la optimizaci´on del inventario, lo cual gener´o mayor flujo del mismo. El primer evento Kaizen implic´o la optimizaci´on del inventario para generar un mayor flujo, atendiendo as´ı el ´area de oportunidad m´as clara dentro de la empresa. El objetivo principal fue reducir las demoras de distribuci´on por tiempo muerto de las m´aquinas. La soluci´on implementada consisti´o en seguir la estrategia de TPM (Mantenimiento Productivo Total), gracias a la cual se logr´o dar un uso m´as eficiente a las m´aquinas. No obstante, todav´ıa era necesario reducir los defectos de calidad. Esta meta se logr´o a trav´es de lo que conocemos como An´alisis de Soluciones de Problemas de Calidad.
Despu´es se identific´o otro reto importante en la l´ınea de empaque, que es un ´area discreta. Despu´es de realizar un an´alisis fue posible eliminar algunos pasos de este proceso, reduciendo las l´ıneas de empaque y acerc´andolas m´as al almac´en. De esta manera se volvi´o mucho m´as eficiente el movimiento del personal y del producto.
May 12, 2020
Por otro lado hubo que optimizar la flotilla de trailers. Para ello, se implement´o una eval- uaci´on en el ´area de transporte que permiti´o establecer est´andares y tiempos de carga. La estrategia fue exitosa, pues gener´o de manera inmediata un flujo m´as eficiente entre el al- mac´en y el embarque. La misma evaluaci´on incluso deriv´o en que se renovara parte de la flotilla y se eliminaran unidades obsoletas. Todas estas medidas hicieron que la productividad incrementara en esencia y que se redujera la necesidad de contar con un 27% del personal. Cabe aclarar, sin embargo, que este personal no fue despedido: s´olo reasignado a otras ´areas para cubrir la rotaci´on.
Resultados: La productividad tuvo un incremento general del 30%. Hubo una reducci´on del 40% en tiempos muertos y merma, as´ı como una mejora significativa en los tiempos de lavado y de sanitizaci´on. En suma, se increment´o la productividad en un 30% o 40% mediante la reducci´on de la mitad de los transportadores existentes, con lo cual disminuyeron dr´asticamente los costos de mantenimiento y de reparaci´on, as´ı como las p´erdidas debido a cambios de motores y refacciones.