
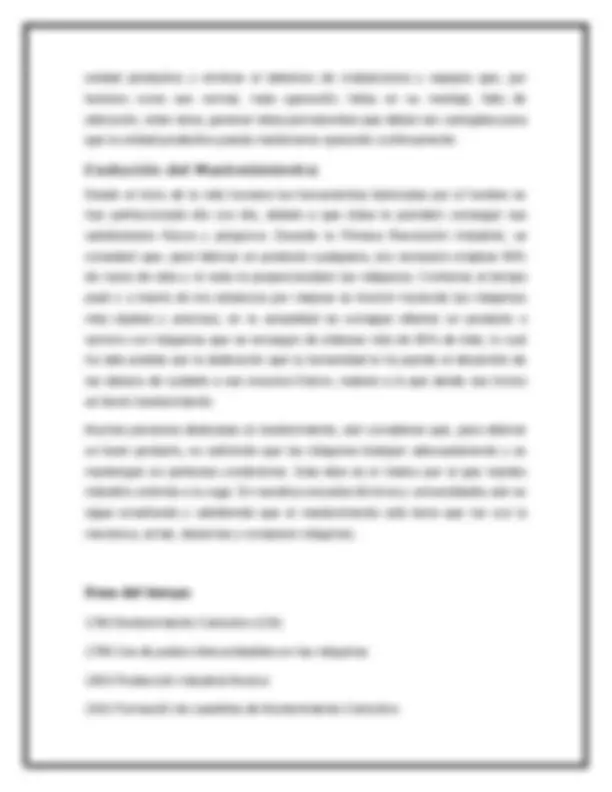
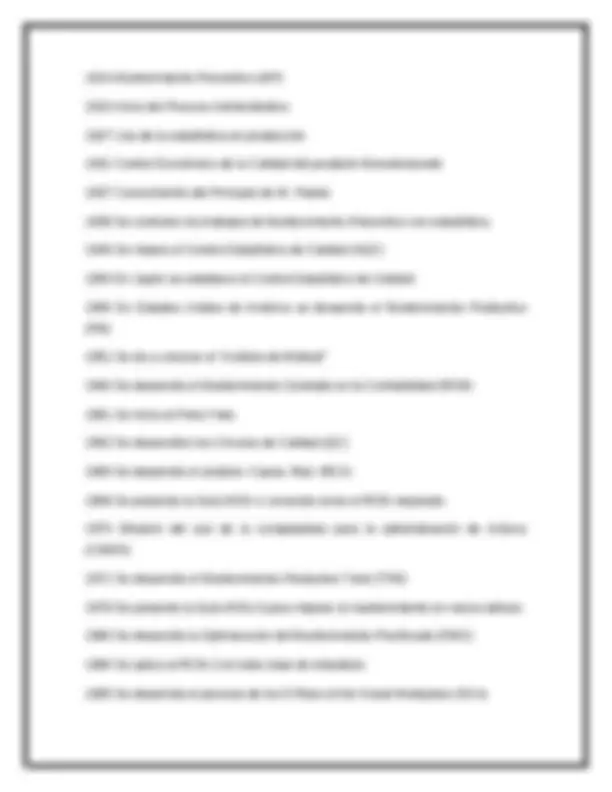
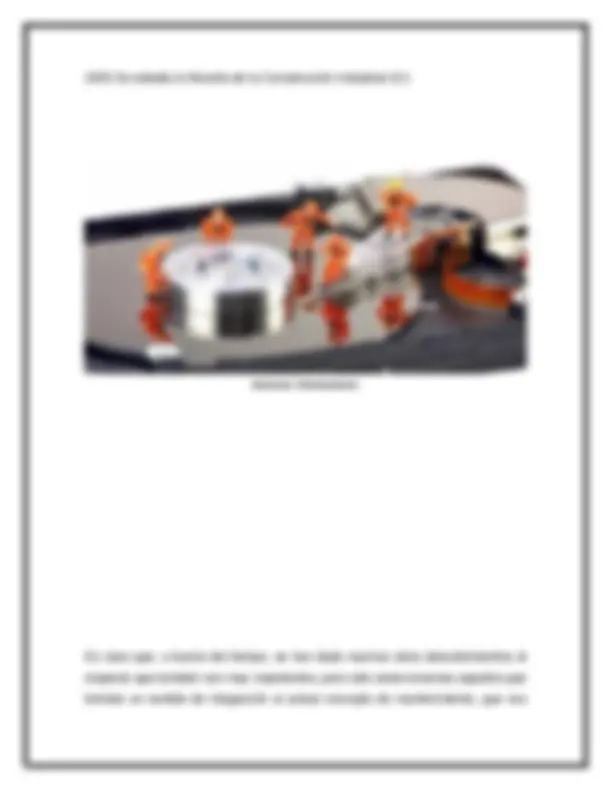
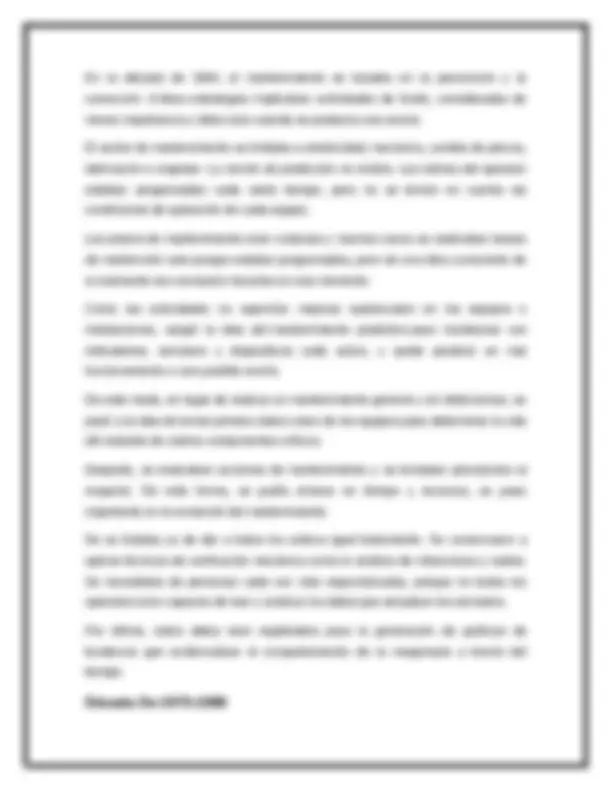
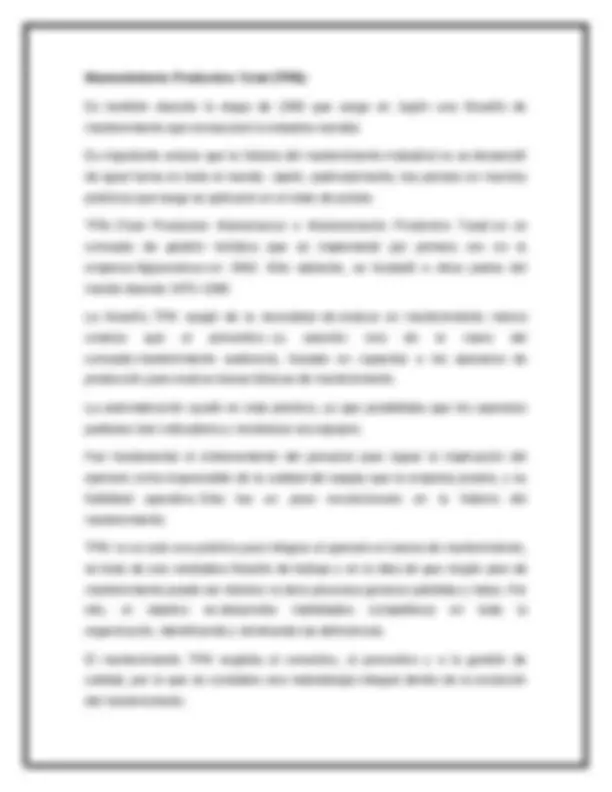
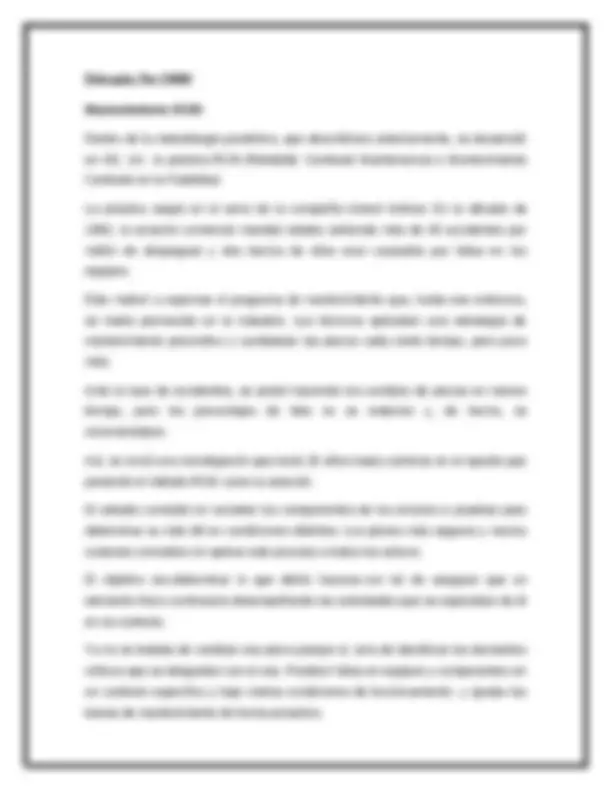

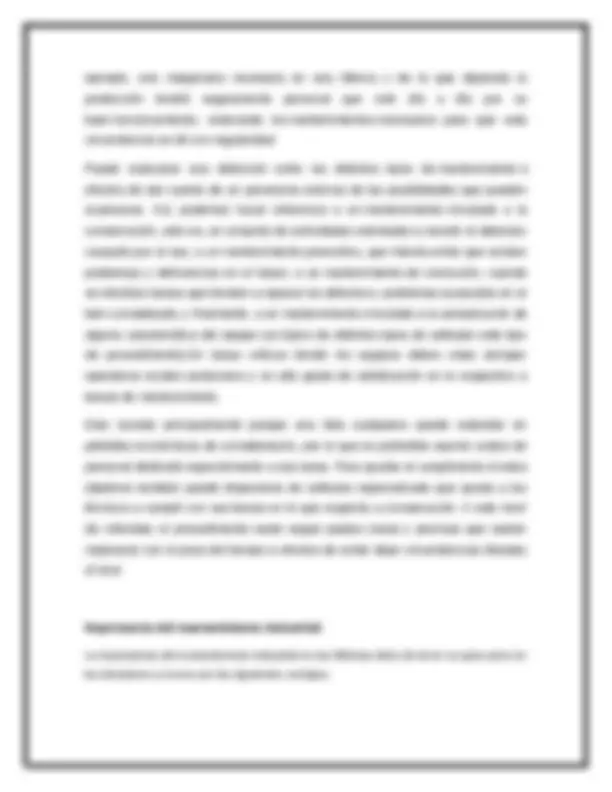
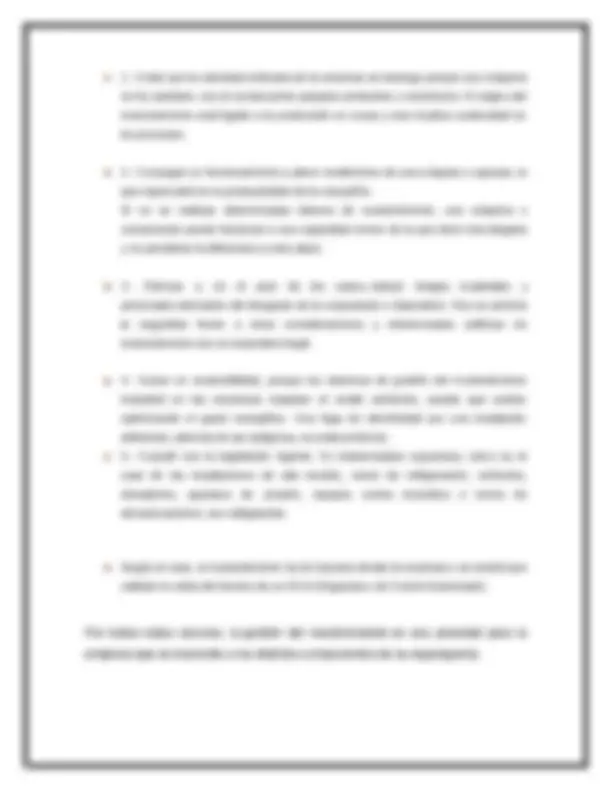
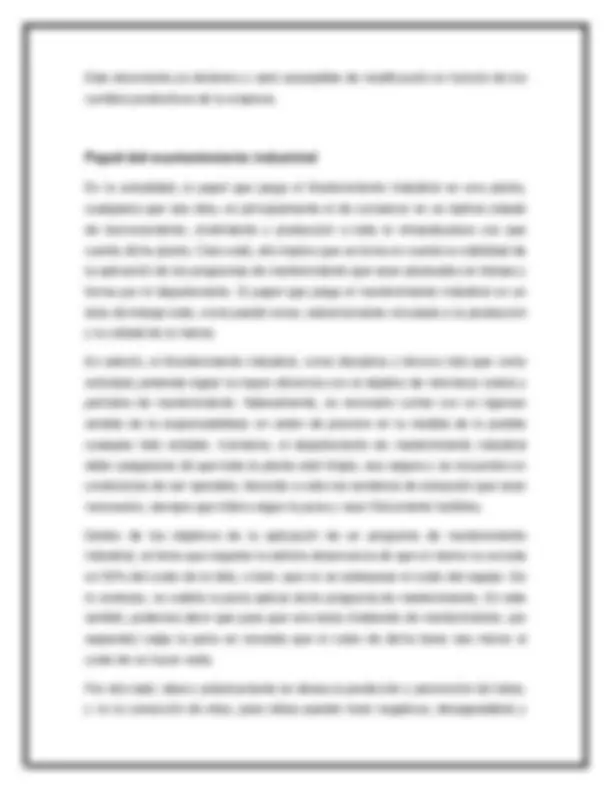
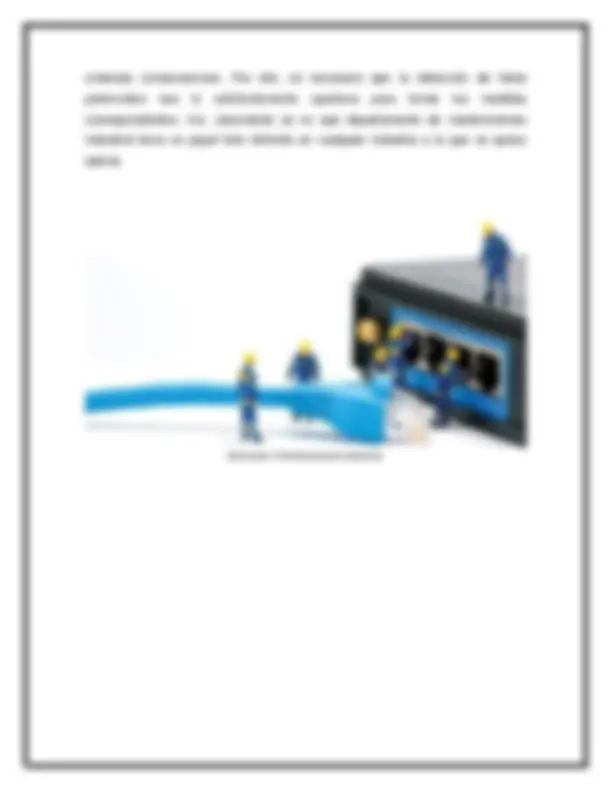
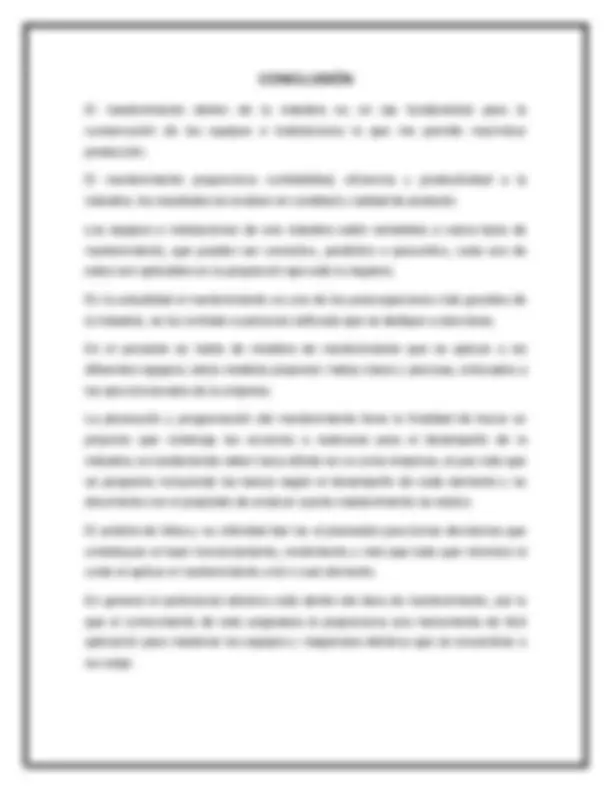
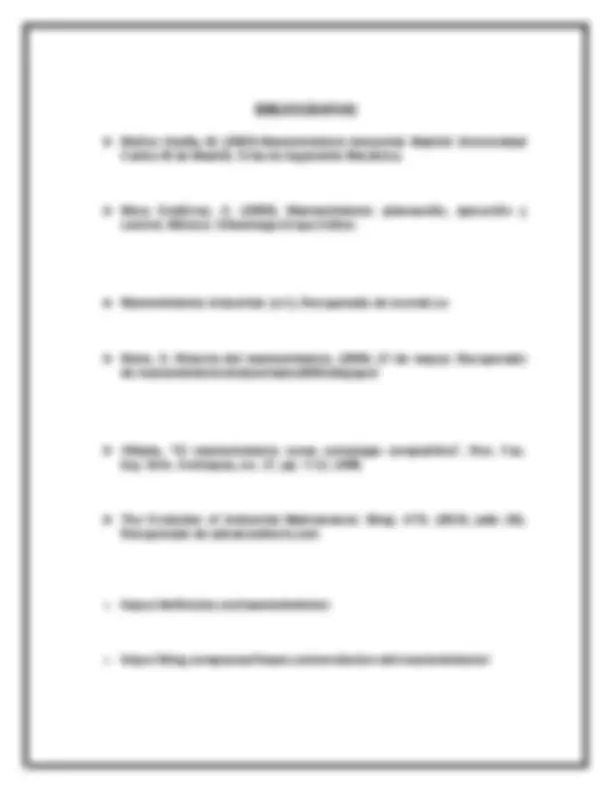
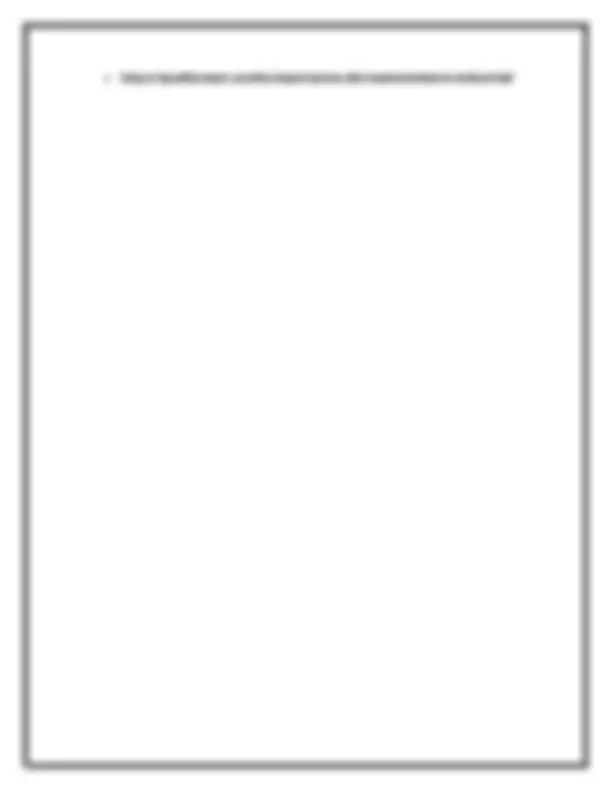
Prepara tus exámenes y mejora tus resultados gracias a la gran cantidad de recursos disponibles en Docsity
Gana puntos ayudando a otros estudiantes o consíguelos activando un Plan Premium
Prepara tus exámenes
Prepara tus exámenes y mejora tus resultados gracias a la gran cantidad de recursos disponibles en Docsity
Prepara tus exámenes con los documentos que comparten otros estudiantes como tú en Docsity
Los mejores documentos en venta realizados por estudiantes que han terminado sus estudios
Estudia con lecciones y exámenes resueltos basados en los programas académicos de las mejores universidades
Responde a preguntas de exámenes reales y pon a prueba tu preparación
Consigue puntos base para descargar
Gana puntos ayudando a otros estudiantes o consíguelos activando un Plan Premium
Comunidad
Pide ayuda a la comunidad y resuelve tus dudas de estudio
Descubre las mejores universidades de tu país según los usuarios de Docsity
Ebooks gratuitos
Descarga nuestras guías gratuitas sobre técnicas de estudio, métodos para controlar la ansiedad y consejos para la tesis preparadas por los tutores de Docsity
El rozamiento entre 2 órganos es función de su dureza y sobre todo de su estado superficial. Durante la fricción, el contacto no se produce en toda el área, sino sólo entre las irregularidades de las superficies que interfieren entre sí; en dichos puntos se crean presiones específicas muy elevadas que, al mismo tiempo que aumentan la temperatura, provocan la fusión de los puntos de contacto y determinan el encolado Parcial de las piezas.
Tipo: Apuntes
1 / 22
Esta página no es visible en la vista previa
¡No te pierdas las partes importantes!
Desde el principio de la humanidad, hasta finales del siglo XVII, las funciones de preservación y mantenimiento no tuvieron un gran desarrollo debido a la menor importancia que tenía la máquina con respecto a la mano de obra, ya que hasta 1880 el 90% del trabajo lo realizaba el hombre y la máquina solo hacía el 10%. La conservación que se proporcionaba a los recursos de las empresas era solo mantenimiento correctivo (las máquinas solo se reparaban en caso de paro o falla importante). Con la 1ª guerra mundial, en 1914, las máquinas trabajaron a toda su capacidad y sin interrupciones, por este motivo la máquina tuvo cada vez mayor importancia. Así nació el concepto de mantenimiento preventivo que a pesar de ser oneroso (caro), era necesario. A partir de 1950 gracias a los estudios de fiabilidad se determinó que a una máquina en servicio siempre la integraban 2 factores: la máquina y el servicio que esta proporciona. De aquí surge la idea de preservar, o sea, cuidar que Introducción a la conservación industrial este dentro de los parámetros de calidad deseada. De esto se desprende el siguiente principio: “el servicio se mantiene y el recurso se preserva” por esto se hicieron estudios cada vez más profundos sobre fiabilidad y mantenibilidad. Así nació la “ingeniería de conservación” (preservación y mantenimiento). La idea del mantenimiento se trata de la reducción del tiempo que el equipo permanece en reparación, de la tendencia a la eliminación de los almacenes de refacciones, de la planeación e implementación de programas de mantenimiento que permitan a la empresa mantener la producción de las plantas en sus máximos valores. En la actualidad se puede definir como las actividades que se encargan de mantener y controlar el correcto y permanente funcionamiento de toda la
1914 Mantenimiento Preventivo (MP) 1916 Inicio del Proceso Administrativo 1927 Uso de la estadística en producción 1931 Control Económico de la Calidad del producto Manufacturado 1937 Conocimiento del Principio de W. Pareto 1939 Se controlan los trabajos de Mantenimiento Preventivo con estadística. 1946 Se mejora el Control Estadístico de Calidad (SQC) 1950 En Japón se establece el Control Estadístico de Calidad 1950 En Estados Unidos de América se desarrolla el Mantenimiento Productivo (PM) 1951 Se da a conocer el “Análisis de Weibull” 1960 Se desarrolla el Mantenimiento Centrado en la Confiabilidad (RCM) 1961 Se inicia el Poka-Yoke 1962 Se desarrollan los Círculos de Calidad (QC) 1965 Se desarrolla el análisis- Causa- Raíz (RCA) 1968 Se presenta la Guía MSG-1 conocida como el RCM mejorado. 1970 Difusión del uso de la computadora para la administración de Activos (CMMS) 1971 Se desarrolla el Mantenimiento Productivo Total (TPM) 1978 Se presenta la Guía MSG-3 para mejorar el mantenimiento en naves aéreas. 1980 Se desarrolla la Optimización del Mantenimiento Planificado (PMO) 1980 Se aplica el RCM-2 en toda clase de industrias 1995 Se desarrolla el proceso de los 5 Pilars of the Visual Workplace (5S’s)
2005 Se estudia la filosofía de la Conservación Industrial (IC) Es claro que, a través del tiempo, se han dado muchos otros descubrimientos al respecto que también son muy importantes, pero sólo seleccionamos aquellos que brindan un sentido de integración al actual concepto de mantenimiento, que nos Ilustración 1 Mantenimiento
La producción a gran escala y el formato de línea de producción había intensificado el trabajo de las máquinas y el rendimiento dependía cada vez más de su buen funcionamiento. La idea de competitividad, reducción de costos y productividad aportada inicialmente por la industria automotriz había elevado la importancia de los activos, algo decisivo en la evolución del mantenimiento. La falla de un elemento en la cadena productiva significaba una demora inaceptable que podía acarrear pérdidas masivas a una empresa. Esto se terminó de potenciar durante la Segunda Guerra Mundial. La maquinaria pasó a ser el elemento clave para la producción de herramientas, armas, equipos y vehículos militares. Así, comenzaron los primeros programas organizados de mantenimiento preventivo. Esta etapa en la historia del mantenimiento se enfoca en preservar la vida útil de los equipos, particularmente de los activos militares, cuyo mantenimiento correctivo significaba que no podían operarse durante las reparaciones. Era necesario evitar la falla temprana minimizando impactos y costos, y así disponer durante el mayor tiempo posible de los aviones, barcos y tanques para ir a la batalla. Los planes de mantenimiento preventivo consistían en: Realizar inspecciones rutinarias. Detección y monitoreo sistemático de fallas. Cambio de algunos componentes en atención al número de horas de funcionamiento.
Mantenimiento Predictivo:
En la década de 1960, el mantenimiento se basaba en la prevención y la corrección. Ambas estrategias implicaban actividades de fondo, consideradas de menor importancia y útiles solo cuando se producía una avería. El sector de mantenimiento se limitaba a electricidad, mecánica, cambio de piezas, lubricación o engrase. La noción de predicción no existía. Las rutinas del operario estaban programadas cada cierto tiempo, pero no se tenían en cuenta las condiciones de operación de cada equipo. Los planes de mantenimiento eran costosos y muchas veces se realizaban tareas de mantención solo porque estaban programadas, pero sin una idea consciente de si realmente era necesario hacerlas en ese momento. Como las actividades no suponían mejoras sustanciales en los equipos o instalaciones, surgió la idea del mantenimiento predictivo para monitorear con indicadores, sensores y dispositivos cada activo, y poder predecir un mal funcionamiento o una posible avería. De este modo, en lugar de realizar un mantenimiento general y sin distinciones, se pasó a la idea de tomar primero datos clave de los equipos para determinar la vida útil restante de ciertos componentes críticos. Después, se realizaban acciones de mantenimiento y se tomaban previsiones al respecto. De esta forma, se podía ahorrar en tiempo y recursos, un paso importante en la evolución del mantenimiento. No se trataba ya de dar a todos los activos igual tratamiento. Se comenzaron a aplicar técnicas de verificación mecánica como el análisis de vibraciones y ruidos. Se necesitaba de personas cada vez más especializadas, porque no todos los operarios eran capaces de leer y analizar los datos que arrojaban los sensores. Por último, estos datos eran registrados para la generación de gráficos de tendencia que evidenciaban el comportamiento de la maquinaria a través del tiempo.
Mantenimiento RCM: Dentro de la metodología predictiva, que describimos anteriormente, se desarrolló en EE. UU. la práctica RCM (Reliability Centered Maintenance) o Mantenimiento Centrado en la Fiabilidad. La práctica surgió en el seno de la compañía United Airlines. En la década de 1960, la aviación comercial mundial estaba sufriendo más de 60 accidentes por millón de despegues y dos tercios de ellos eran causados por fallas en los equipos. Esto motivó a repensar el programa de mantenimiento que, hasta ese entonces, se había promovido en la industria. Los técnicos aplicaban una estrategia de mantenimiento preventivo y cambiaban las piezas cada cierto tiempo, pero poco más. Ante la tasa de accidentes, se probó haciendo los cambios de piezas en menos tiempo, pero los porcentajes de falla no se reducían y, de hecho, se incrementaban. Así, se inició una investigación que tomó 20 años hasta culminar en el reporte que presentó el método RCM como la solución. El estudio consistió en someter los componentes de los aviones a pruebas para determinar su vida útil en condiciones distintas. Los planes más seguros y menos costosos consistían en aplicar este proceso a todos los activos. El objetivo era determinar lo que debía hacerse con tal de asegurar que un elemento físico continuaría desempeñando las actividades que se esperaban de él en su contexto. Ya no se trataba de cambiar una pieza porque sí, sino de identificar los elementos críticos que se desgastan con el uso. Predecir fallas en equipos y componentes en un contexto específico y bajo ciertas condiciones de funcionamiento y ajustar las tareas de mantenimiento de forma proactiva.
Actualidad: Importancia De La Tecnología En El Mantenimiento Industrial En un contexto de globalización, la evolución de equipos y técnicas es cada vez más dinámica. Entre 1980 y 2000, el mundo industrial cambió de muchas formas, pero la revolución informática impactó especialmente en la producción, la calidad, el flujo de trabajo, etc. Desde entonces hasta la actualidad, todas las compañías han tenido que adaptarse a las nuevas tecnologías. El mantenimiento industrial tuvo que modernizarse. Hoy, un Software de Mantenimiento es imprescindible para gestionar activos industriales. Poder administrar los equipos de forma ordenada y detallada genera una mejor productividad y permite a las empresas encontrar su lugar en el mercado y poder competir. La complejidad de los equipos y sus componentes informáticos intrínsecos hacen necesaria la incorporación de herramientas que permitan leer datos (sensores) y gestionarlos. De otra forma, es casi imposible llevar un control y monitoreo sobre activos tan complejos. Los Software de Mantenimiento te permitirán: Gestionar los procesos de mantenimiento en tu negocio. Asignar tareas. Realizar monitoreos y diagnósticos de fallas. Identificar las prácticas óptimas. Mejorar el desempeño a futuro. Controlar el cumplimiento de tareas asignadas.
Permite la elaboración adecuada del presupuesto, ajustada a las necesidades de la empresa.
Definición de Mantenimiento: Se denomina mantenimiento al procedimiento mediante el cual un determinado bien recibe tratamientos a efectos de que el paso del tiempo, el uso o el cambio de circunstancias exteriores no lo afecte. Existe gran multitud de campos en los que el término puede ser aplicado, ya sea tanto para bienes físicos como virtuales. Así, es posible referirse al mantenimiento de una casa, de una obra de arte, de un vehículo, de un programa o conjunto de programas, de un sistema, etc. El mantenimiento suele ser llevado a cabo por especialistas en la materia. El mantenimiento es especialmente importante en los bienes requeridos para la producción de viene y servicios. Así, todos aquellos elementos necesarios como parte de un proceso de producción económica serán testeados con regularidad para llegar a una conclusión en lo que respecta a su mantenimiento. Así, por Ilustración 2 Mantenimiento Preventivo
ejemplo, una maquinaria necesaria en una fábrica y de la que dependa la producción tendrá seguramente personal que vele día a día por su buen funcionamiento, realizando los mantenimientos necesarios para que esta circunstancia se dé con regularidad. Puede realizarse una distinción entre los distintos tipos de mantenimiento a efectos de dar cuenta de un panorama extenso de las posibilidades que pueden acarrearse. Así, podemos hacer referencia a un mantenimiento vinculado a la conservación, esto es, un conjunto de actividades orientadas a revertir el deterioro causado por el uso; a un mantenimiento preventivo, que intenta evitar que existan problemas y deficiencias en el futuro; a un mantenimiento de corrección, cuando se efectúan tareas que tienden a reparar los defectos y problemas acaecidos en el bien considerado; y finalmente, a un mantenimiento vinculado a la actualización de alguna característica del equipo (es típico de distintos tipos de software este tipo de procedimiento).En áreas críticas donde los equipos deben estar siempre operativos existen protocolos y un alto grado de sofisticación en lo respectivo a tareas de mantenimiento. Esto sucede principalmente porque una falla cualquiera puede redundar en pérdidas económicas de consideración, por lo que es preferible asumir costos de personal dedicado especialmente a esa tarea. Para ayudar al cumplimento d estos objetivos también puede disponerse de software especializado que ayuda a los técnicos a cumplir con sus tareas en lo que respecta a conservación. A este nivel de criticidad, el procedimiento suele seguir pautas claras y precisas que suelen mejorarse con el paso del tiempo a efectos de evitar dejar circunstancias libradas al azar. Importancia del mantenimiento industrial: La importancia del mantenimiento industrial en las fábricas debe de tener un gran peso en las decisiones a tomar por las siguientes ventajas:
Composición de una correcta gestión del mantenimiento: La gestión del mantenimiento industrial parte de dos premisas fundamentales que se clasifican en este orden: la seguridad y la criticidad. 1.- La seguridad se refiere a la necesidad de evitar daños materiales o personales debido a la falta de mantenimiento de una maquinaria o dispositivo. Por este motivo, hay determinados equipos en los que el mantenimiento es obligatorio y tienen que monitorizarse y apuntar el seguimiento en un libro de registro. En algunos casos el mantenimiento puede ejecutarse por el personal de la compañía, pero en otros, será un organismo autorizado por la Administración quien lo realice. 2.- La criticidad se refiere al perjuicio de la avería de una máquina o dispositivo en relación con la instalación en la que está ubicado. Esta medida es cuantitativa y cualitativa, porque sirve para saber si una avería inutiliza toda la instalación, parte, o tendrá un impacto marginal. Ilustración 3 importancia del mantenimiento industrial
Conocer la criticidad de cada aparato o instalación es fundamental para realizar una gestión profesional y responsable. En un equipo, una rotura de la correa de transmisión supone un alto nivel de criticidad, mientras que la avería en un piloto luminoso representa una baja criticidad. Una adecuada gestión del mantenimiento tendrá que considerar los equipos y los recursos humanos. 1.- En los equipos, hay que realizar un inventario de los componentes disponibles, empezando por sus tipos y siguiendo por su relación con el proceso productivo de la compañía. Posteriormente, hay que observar si los equipos son seguros o no, el nivel de criticidad, la tipología de cada maquinaria, antigüedad y las características de la instalación. 2.- Con respecto a la gestión de los recursos humanos, se debe elaborar un organigrama donde se especifique el número de empleados y queden definidas las funciones de cada miembro, así como las relaciones jerárquicas. También hay que incluir la ratio entre supervisores y subalternos, así como los programas de formación del personal. Por otra parte, es imprescindible contar en las tareas especializadas con personal que cumpla los estándares de la ISO, puesto que en algunos casos las autoridades lo requerirán. Posteriormente, se diseñará un plan de mantenimiento adaptado a las necesidades de cada compañía. Este documento señala las acciones que hay que realizar en las instalaciones, bienes de equipo u otros aparatos en un determinado periodo de tiempo con el fin de alargar su vida útil.
costosas consecuencias. Por ello, es necesario que la detección de fallas potenciales sea lo suficientemente oportuna para tomar las medidas correspondientes. Así, claramente se ve que departamento de mantenimiento industrial tiene un papel bien definido en cualquier industria a la que se quiera aplicar. Ilustración 4 Mantenimiento Industrial
El mantenimiento dentro de la industria es un eje fundamental para la conservación de los equipos e instalaciones lo que me permite maximizar producción. El mantenimiento proporciona confiabilidad, eficiencia y productividad a la industria, los resultados se evalúan en cantidad y calidad de producto. Los equipos e instalaciones de una industria están sometidos a varios tipos de mantenimiento, que pueden ser correctivo, predictivo o preventivo, cada uno de estos son aplicables en la proporción que este lo requiera. En la actualidad el mantenimiento es una de las preocupaciones más grandes de la industria, se ha confiado a personal calificado que se dedique a esta tarea. En el presente se habla de modelos de mantenimiento que se aplican a los diferentes equipos; estos modelos proponen metas claras y precisas, enfocados a los ejes funcionales de la empresa. La planeación y programación del mantenimiento tiene la finalidad de trazar un proyecto que contenga las acciones a realizarse para el desempeño de la industria; es fundamental saber hacia dónde se va como empresa, es por esto que se programa incluyendo las tareas según el desempeño de cada elemento y se documenta con el propósito de analizar cuanto mantenimiento se realiza. El análisis de fallas y su criticidad dan luz al planeador para tomar decisiones que contribuyan al buen funcionamiento, rendimiento y más que todo que minimice el costo al aplicar el mantenimiento a tal o cual elemento. En general el profesional eléctrico está dentro del área de mantenimiento, por lo que el conocimiento de esta asignatura le proporciona una herramienta de fácil aplicación para mantener los equipos y maquinaria eléctrica que se encuentran a su cargo.