
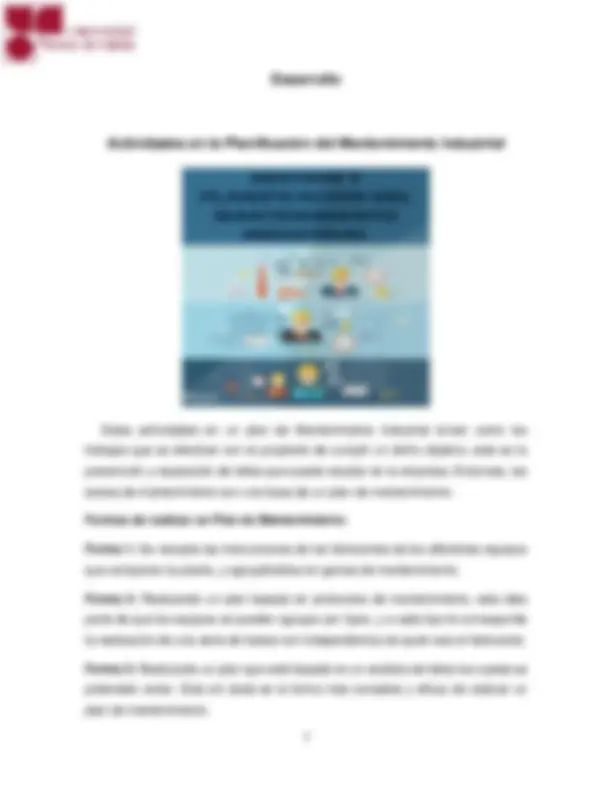
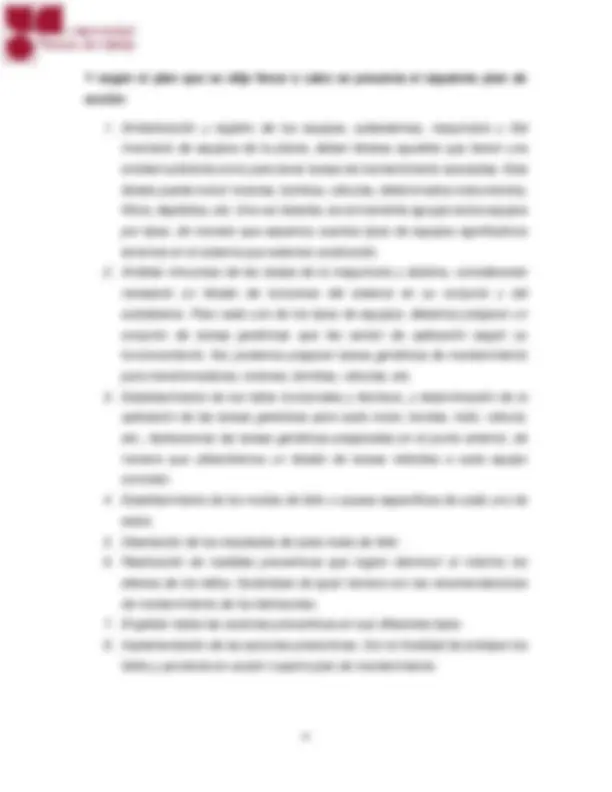
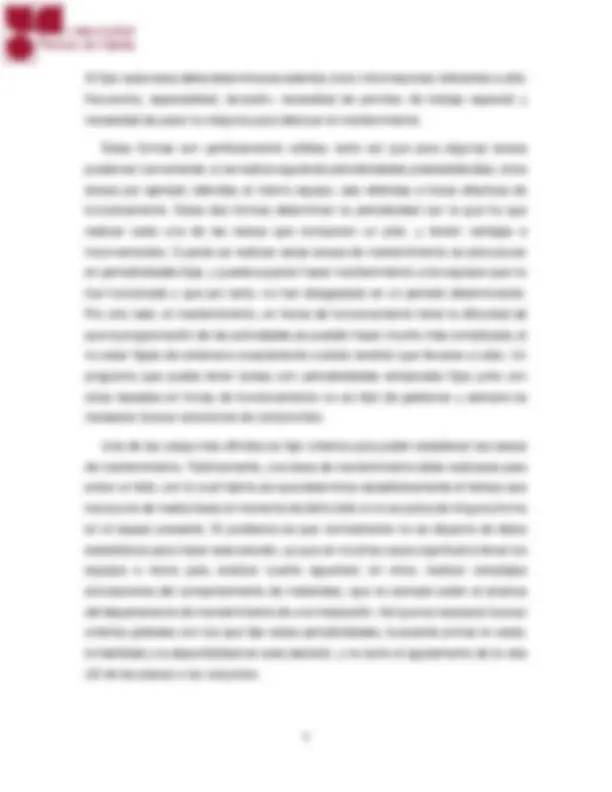
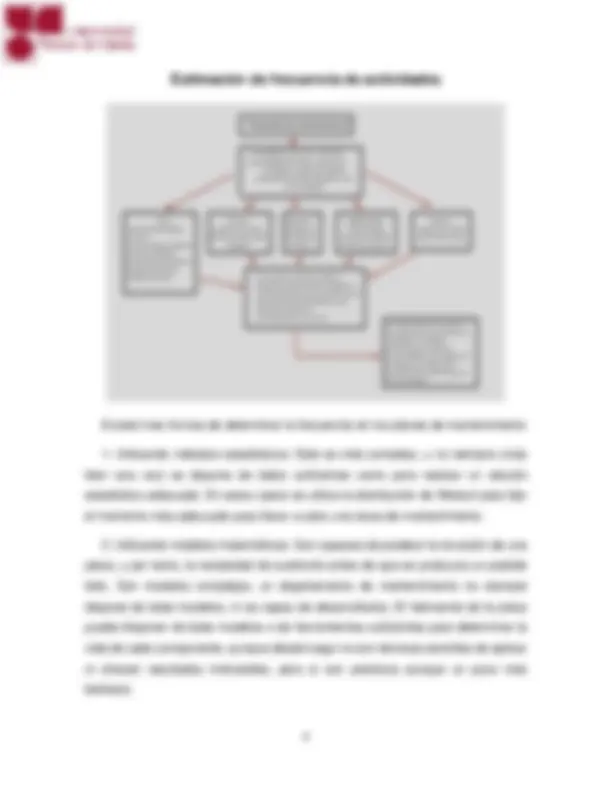
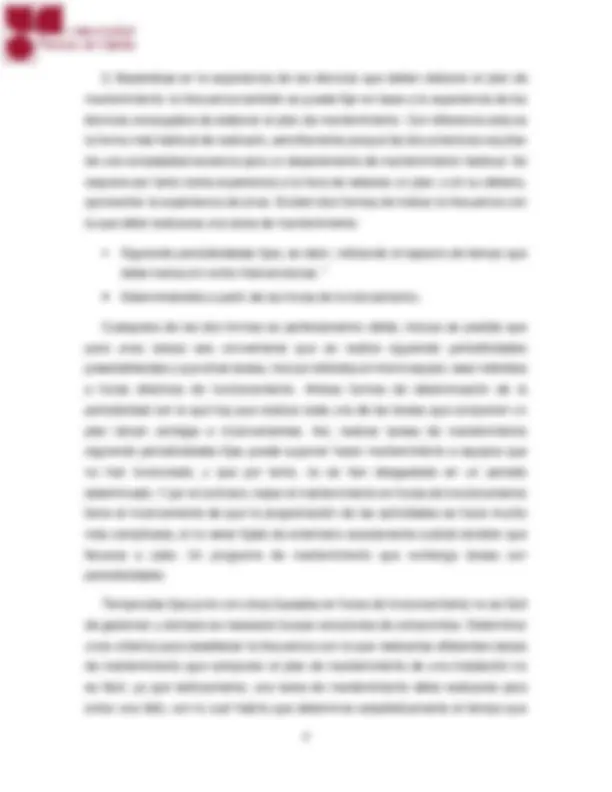
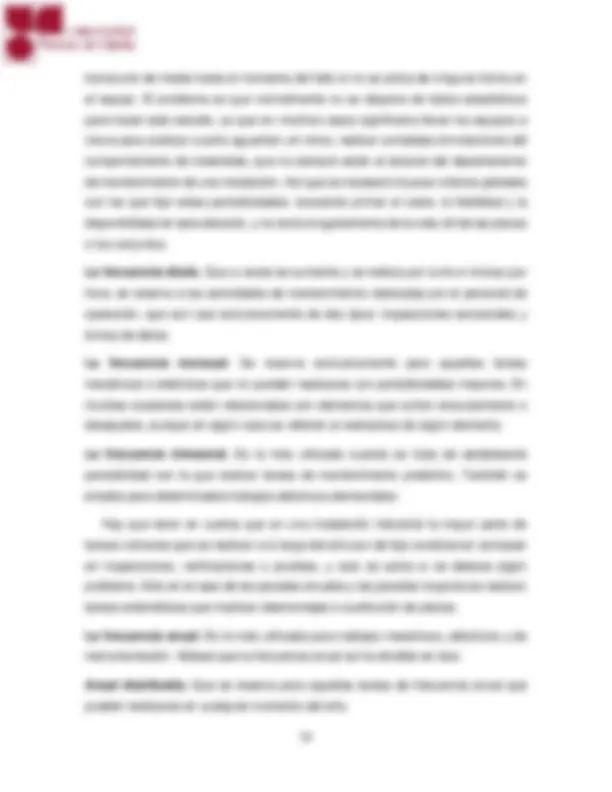
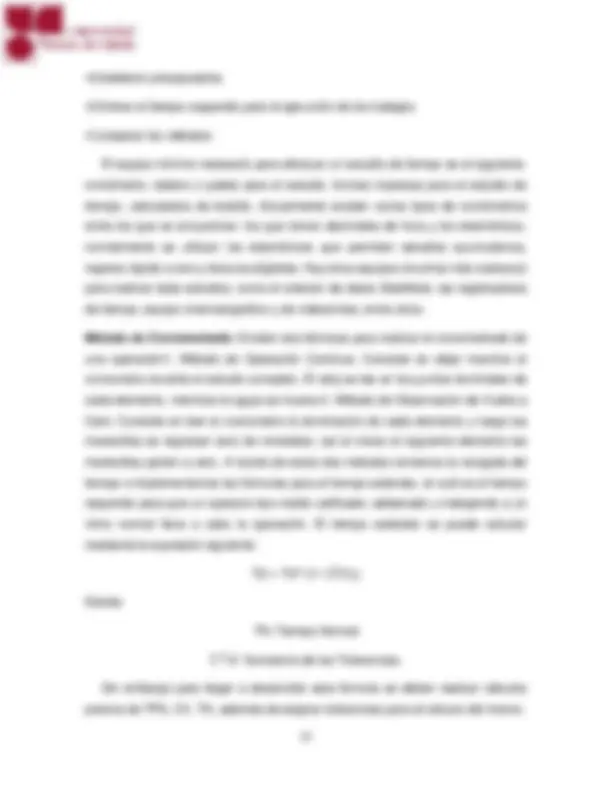
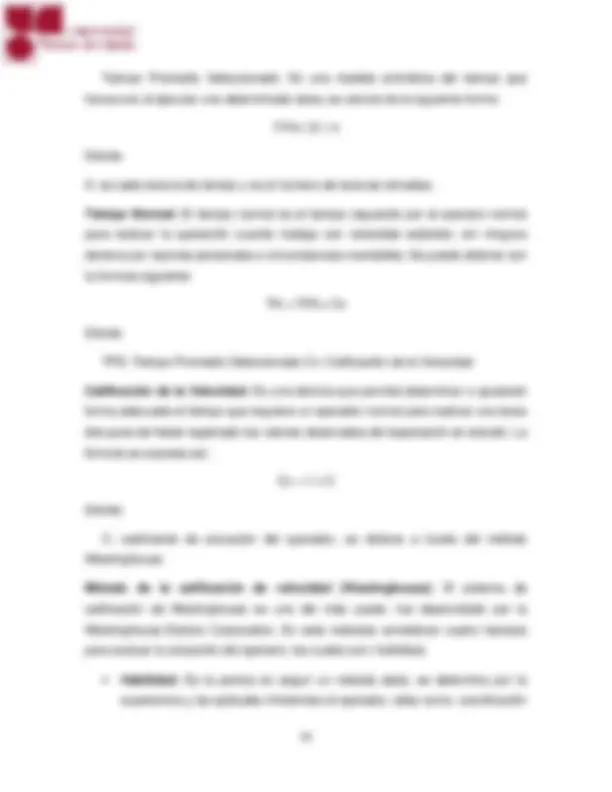
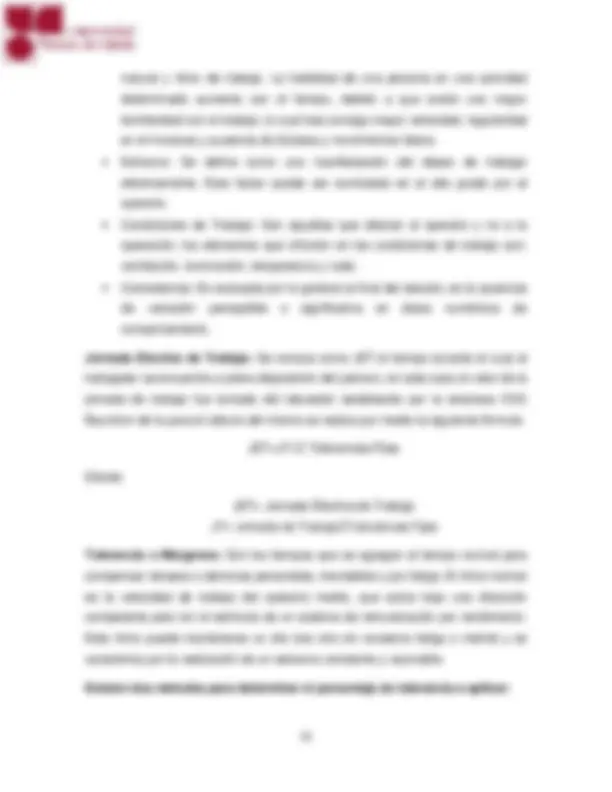
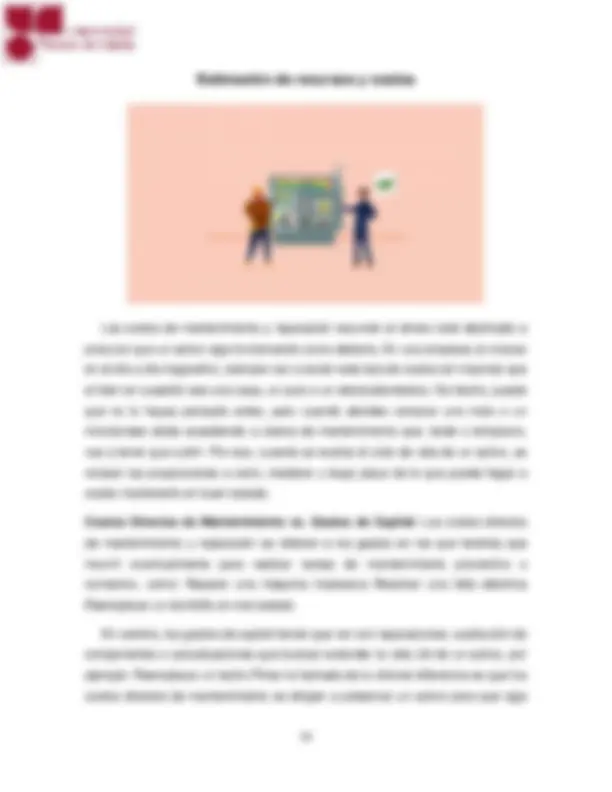
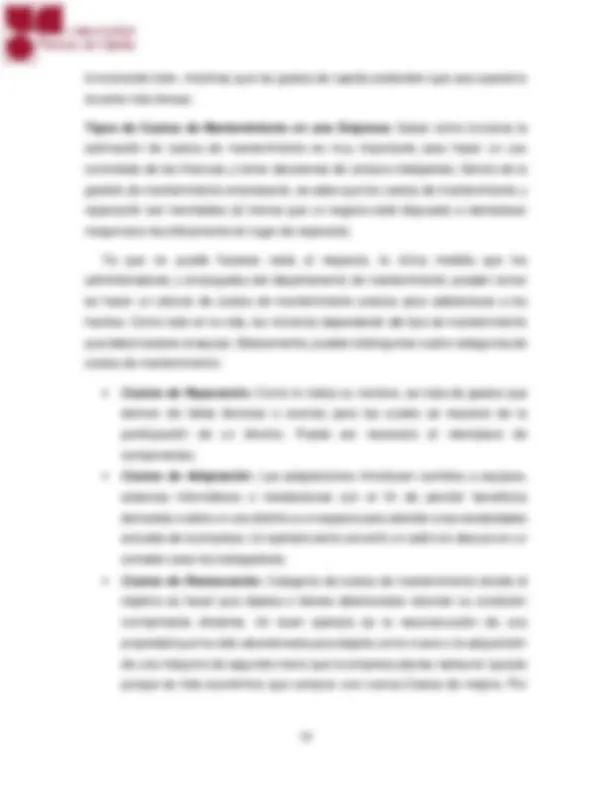
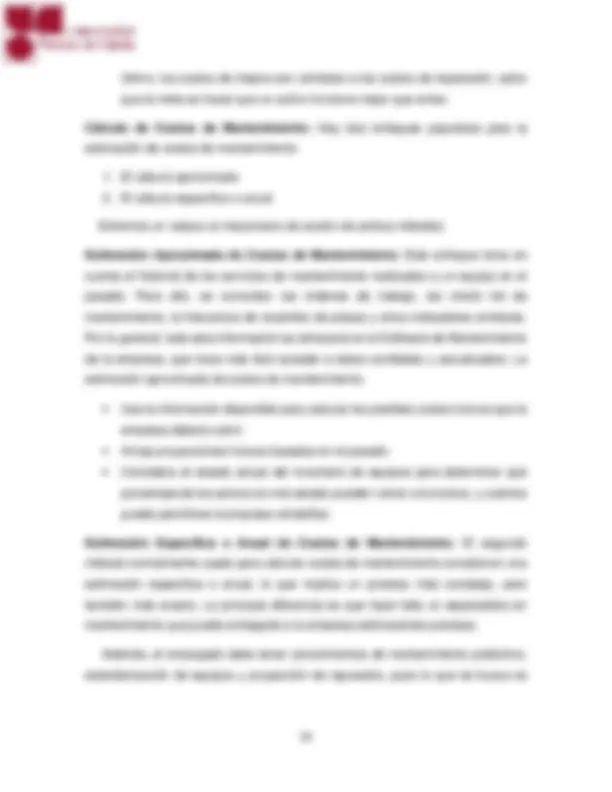
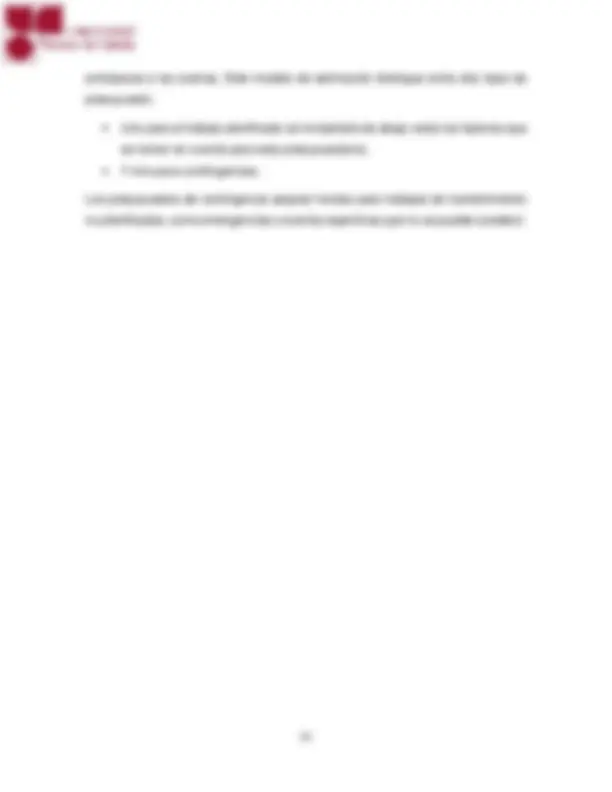
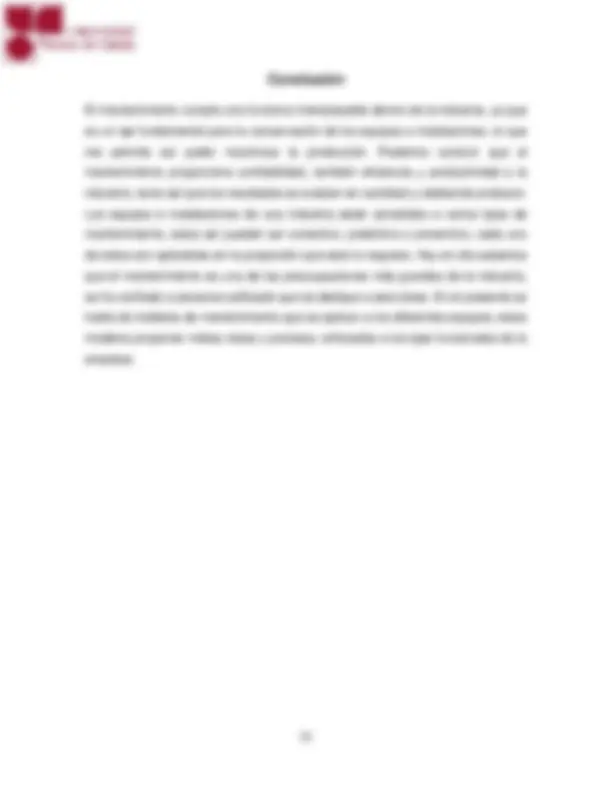
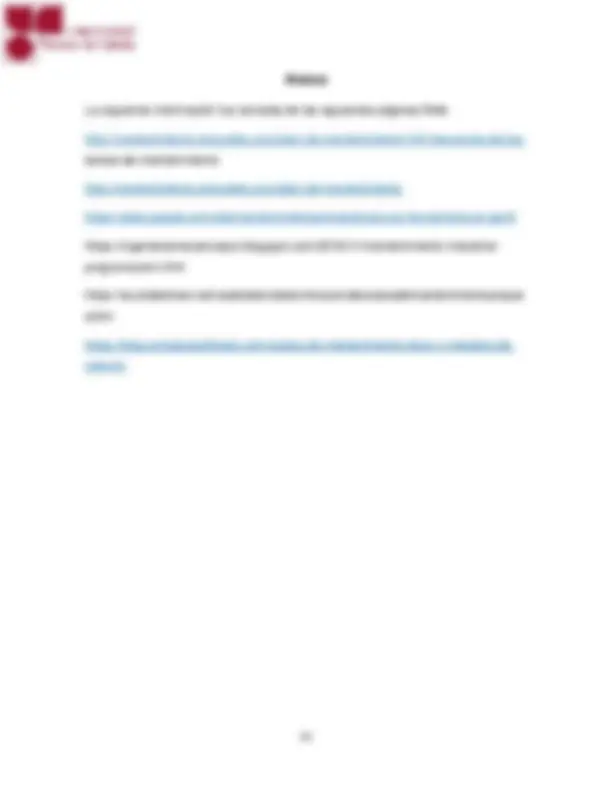
Prepara tus exámenes y mejora tus resultados gracias a la gran cantidad de recursos disponibles en Docsity
Gana puntos ayudando a otros estudiantes o consíguelos activando un Plan Premium
Prepara tus exámenes
Prepara tus exámenes y mejora tus resultados gracias a la gran cantidad de recursos disponibles en Docsity
Prepara tus exámenes con los documentos que comparten otros estudiantes como tú en Docsity
Los mejores documentos en venta realizados por estudiantes que han terminado sus estudios
Estudia con lecciones y exámenes resueltos basados en los programas académicos de las mejores universidades
Responde a preguntas de exámenes reales y pon a prueba tu preparación
Consigue puntos base para descargar
Gana puntos ayudando a otros estudiantes o consíguelos activando un Plan Premium
Comunidad
Pide ayuda a la comunidad y resuelve tus dudas de estudio
Descubre las mejores universidades de tu país según los usuarios de Docsity
Ebooks gratuitos
Descarga nuestras guías gratuitas sobre técnicas de estudio, métodos para controlar la ansiedad y consejos para la tesis preparadas por los tutores de Docsity
Si vas a descargar, por favor, valora el trabajo para seguir subiendo contenido.
Tipo: Apuntes
1 / 23
Esta página no es visible en la vista previa
¡No te pierdas las partes importantes!
República bolivariana de Venezuela Ministerio del poder popular para la educación superior Universidad Alonso de Ojeda Vicerrectorado académico – Facultad de ingeniería industrial Catedra: Mantenimiento Industrial Profesor: ING. Emilio Barreto Realizado por: Damián Nava C.I: 26.522. Ciudad Ojeda, 2021
Sabemos que el mantenimiento industrial es uno de los ejes fundamentales dentro de la industria, tanto así que este se encuentra cuantificado en la cantidad y calidad de la producción; El mismo que ha estado sujeto a diferentes cambios al paso del tiempo; en la actualidad el mantenimiento se ve como una inversión que ayuda a mejorar y mantener la calidad en la producción. “Si no sabéis a donde vais, probablemente acabaréis en otra parte" Lawrence J. Peter. Actualmente el mantenimiento busca aumentar y confiabilidad la producción; aparece el mantenimiento preventivo, el mantenimiento predictivo, el mantenimiento proactivo, la gestión de mantenimiento asistido por computador y el mantenimiento basado en la confiabilidad. El presente trabajo es un análisis del mantenimiento dentro de la industria; esta publicado con el afán de ser una herramienta que proporcione conocimientos generales para planear y programar las actividades que se realiza en los diferentes elementos eléctricos y mecánicos dentro de la industria, y tener una visión clara de hacia donde se quiere llevar a la empresa interventora.
Y según el plan que se elija llevar a cabo se presenta el siguiente plan de acción:
1. Simbolización y registro de los equipos, subsistemas, maquinaria y Del inventario de equipos de la planta, deben listarse aquellos que tienen una entidad suficiente como para tener tareas de mantenimiento asociadas. Este listado puede incluir motores, bombas, válvulas, determinados instrumentos, filtros, depósitos, etc. Una vez listados, es conveniente agrupar estos equipos por tipos, de manera que sepamos cuantos tipos de equipos significativos _tenemos en el sistema que estemos analizando.
Al fijar cada tarea debe determinarse además cinco informaciones referentes a ella: frecuencia, especialidad, duración, necesidad de permiso de trabajo especial y necesidad de parar la máquina para efectuar el mantenimiento. Estas formas son perfectamente validas; tanto así que para algunas tareas puede ser conveniente, si se realice siguiendo periodicidades preestablecidas, otras tareas por ejemplo referidas al mismo equipo, sea referidas a horas efectivas de funcionamiento. Estas dos formas determinan la periodicidad con la que ha que realizar cada una de las tareas que componen un plan, y tienen ventajas e inconvenientes. Cuando se realizan estas tareas de mantenimiento se estructuran en periodicidades fijas, y puede suponer hacer mantenimiento a los equipos que no han funcionado y que por tanto, no han desgastado en un periodo determinando. Por otro lado, el mantenimiento, en horas de funcionamiento tiene la dificultad de que la programación de las actividades se pueden hacer mucho más complicada, al no estar fijado de antemano exactamente cuándo tendrán que llevarse a cabo. Un programa que pueda tener tareas con periodicidades temporales fijas junto con otras basadas en horas de funcionamiento no es fácil de gestionar y siempre es necesario buscar soluciones de compromiso. Una de las cosas más difíciles es fijar criterios para poder establecer las tareas de mantenimiento. Teóricamente, una tarea de mantenimiento debe realizarse para evitar un fallo, con lo cual habría así que determinar estadísticamente el tiempo que transcurre de media hasta el momento de dicho fallo si no se actúa de ninguna forma en el equipo presente. El problema es que normalmente no se dispone de datos estadísticos para hacer este estudio, ya que en muchos casos significaría llevar los equipos a rotura para analizar cuanto aguantan; en otros, realizar complejas simulaciones del comportamiento de materiales, que no siempre están al alcance del departamento de mantenimiento de una instalación. Así que es necesario buscar criterios globales con los que fijar estas periodicidades, buscando primar el coste, la fiabilidad y la disponibilidad en esta decisión, y no tanto el agotamiento de la vida útil de las piezas o los conjuntos.
Obra civil. No es habitual que el personal de plantilla realice este tipo de trabajos, por lo que para facilitar su programación, realización y control puede ser conveniente crear una categoría específica. Duración: La estimación de la duración de las tareas es una información complementaria del plan de mantenimiento. Siempre se realiza de forma aproximada, y se asume que esta estimación lleva implícito un error por exceso o por defecto. Permiso de trabajo: Determinadas tareas requieren de un permiso especial para llevarlas a cabo. Así, las tareas de corte y soldadura, las que requieren la entrada en espacios confinados, las que suponen un riesgo eléctrico, etc. Requieren normalmente de un permiso de trabajo especial. Resulta útil que en el plan de mantenimiento esté contenida esta información, de manera que estén diferenciados aquellos trabajos que requieren de un permiso, de aquellos que se realizan simplemente con una orden de trabajo.
Existen tres formas de determinar la frecuencia en los planes de mantenimiento
transcurre de media hasta el momento del fallo si no se actúa de ninguna forma en el equipo. El problema es que normalmente no se dispone de datos estadísticos para hacer este estudio, ya que en muchos casos significaría llevar los equipos a rotura para analizar cuanto aguantan; en otros, realizar complejas simulaciones del comportamiento de materiales, que no siempre están al alcance del departamento de mantenimiento de una instalación. Así que es necesario buscar criterios globales con los que fijar estas periodicidades, buscando primar el coste, la fiabilidad y la disponibilidad en esta decisión, y no tanto el agotamiento de la vida útil de las piezas o los conjuntos. La frecuencia diaria. Que a veces se aumenta y se realiza por turno e incluso por hora, se reserva a las actividades de mantenimiento realizadas por el personal de operación, que son casi exclusivamente de dos tipos: inspecciones sensoriales y tomas de datos. La frecuencia mensual. Se reserva exclusivamente para aquellas tareas mecánicas o eléctricas que no pueden realizarse con periodicidades mayores. En muchas ocasiones están relacionadas con elementos que sufren ensuciamiento o desajustes, aunque en algún caso se refieren al reemplazo de algún elemento. La frecuencia trimestral. Es la más utilizada cuando se trata de establecerla periodicidad con la que realizar tareas de mantenimiento predictivo. También se emplea para determinados trabajos eléctricos elementales. Hay que tener en cuenta que en una instalación industrial la mayor parte de tareas rutinarias que se realizan a lo largo del año son de tipo condicional: se basan en inspecciones, verificaciones o pruebas, y solo se actúa si se detecta algún problema. Solo en el caso de las paradas anuales y las paradas mayores se realizan tareas sistemáticas que implican desmontajes o sustitución de piezas. La frecuencia anual. Es la más utilizada para trabajos mecánicos, eléctricos y de instrumentación. Nótese que la frecuencia anual se ha dividido en dos: Anual distribuida. Que se reserva para aquellas tareas de frecuencia anual que pueden realizarse en cualquier momento del año.
Anual en parada. que se reserva para aquellas tareas de frecuencia anual que debe ser realizadas exclusivamente coincidiendo con la parada anual que muchas instalaciones organizan, y que supone la base del mantenimiento en muchos casos. Esta distinción facilita que las tareas anuales a realizar en parada puedan ser más fácilmente externalizarles, mientras que las tareas anuales distribuidas pueden ser realizadas perfectamente por el personal habitual. La periodicidad bienal. Se reserva casi en exclusiva para la calibración de instrumentación y para la verificación de lazos de control. Las periodicidades trianual, cuatrienal, etc., se reservan para la realización de tareas de mantenimiento legal. Un problema habitual a la hora de fijar la frecuencia con la que realizar determinadas tareas es que algunas de ellas pueden estar referidas a horas de funcionamiento, en vez de a espacios de tiempo naturales. Algunos fabricantes de equipos prefieren referirse a horas de funcionamiento, lo cual parece muy lógico: si un equipo no se ha utilizado, no parece necesario realizar mantenimiento en él. No es fácil mezclar tareas que deben realizarse con frecuencias naturales fijas con tareas que se realizan por horas de funcionamiento, con periodos variables entre ellas. Hay muchas formas de abordar el problema, entre las que están las siguientes:
•Establecer presupuestos. •Eliminar el tiempo requerido para la ejecución de los trabajos. •Comparar los métodos El equipo mínimo necesario para efectuar un estudio de tiempo es el siguiente: cronómetro, tablero o paleta para el estudio, formas impresas para el estudio de tiempo, calculadora de bolsillo. Actualmente existen varios tipos de cronómetros entre los que se encuentran: los que toman decimales de hora y los electrónicos, normalmente se utilizan los electrónicos que permiten estudios acumulativos, regreso rápido a cero y lecturas digitales. Hay otros equipos (muchos más costosos) para realizar tales estudios, como el colector de datos DateMyte, las registradores de tiempo, equipo cinematográfico y de videocintas, entre otros. Método de Cronometrado: Existen dos técnicas para realizar el cronometrado de una operación1. Método de Operación Continua. Consiste en dejar marchar el cronometro durante el estudio completo. El reloj se lee en los puntos terminales de cada elemento, mientras la aguja se mueve.2. Método de Observación de Vuelta a Cero: Consiste en leer el cronometro la terminación de cada elemento y luego las manecillas se regresan cero de inmediato; así al iniciar el siguiente elemento las manecillas parten a cero. A través de estos dos métodos tomamos la recogida del tiempo e implementamos las fórmulas para el tiempo estándar, el cuál es el tiempo requerido para que un operario tipo medio calificado, adiestrado y trabajando a un ritmo normal lleve a cabo la operación. El tiempo estándar se puede calcular mediante la expresión siguiente: TE = TN* (1+ ΣTOL) Dónde: TN: Tiempo Normal Σ Tol: Sumatoria de las Tolerancias. Sin embargo para llegar a desarrollar esta fórmula se deben realizar cálculos previos de TPS, CV, TN, además de asignar tolerancias para el cálculo del mismo.
Tiempo Promedio Seleccionado: Es una medida aritmética del tiempo que transcurre al ejecutar una determinada tarea; se calcula de la siguiente forma: TPS= ΣX / n Dónde: X: es cada lectura de tiempo y es el número de lecturas tomadas. Tiempo Normal: El tiempo normal es el tiempo requerido por el operario normal para realizar la operación cuando trabaja con velocidad estándar, sin ninguna demora por razones personales o circunstancias inevitables. Se puede obtener con la formula siguiente: TN = TPS x Cv Dónde: TPS: Tiempo Promedio Seleccionado Cv: Calificación de la Velocidad Calificación de la Velocidad: Es una técnica que permite determinar o ajustaren forma adecuada el tiempo que requiere un operador normal para realizar una tarea des pues de haber registrado los valores observados de laoperación en estudio. La fórmula se expresa así: Cv = 1 ± C Dónde: C: coeficiente de actuación del operador, se obtiene a través del método Westinghouse. Método de la calificación de velocidad (Westinghouse): El sistema de calificación de Westinghouse es uno del más usado, fue desarrollado por la Westinghouse Electric Corporation. En este métodos consideran cuatro factores para evaluar la actuación del operario, las cuales son: habilidad,
Uno es el Estudio de Producción, el cual requiere que un observador estudiado o quizás tres operaciones durante un periodo largo de tiempo. El observador registra la duración y la razón de cada intervalo de tiempo perdido y luego de establecer una muestra representativa determina el porcentaje de tolerancia aplicable para cada característica. La segunda técnica para establecer tolerancia es mediante el muestreo del trabajo. Este método consiste en realizar un gran número de observaciones en forma aleatoria, por lo cual se requiere solo los servicios a tiempo parcial o al menos intermitente del observado. En este método no se usa cronometro, el observador solamente camina a través del área de trabajo bajo estudio en momentos previamente establecidos y hace una breve anotación de lo que cada operario está haciendo. El número de demoras dividido por el número total de observaciones será igual al porcentaje de tolerancia requerido. Número de Ciclos a Registrarse: El número de ciclos que deben observarse para obtener un tiempo medio representativo de una operación determinada depende de las siguientes normas: •El número de ciclos varía en función de las variaciones de los tiempos de los elementos de la tarea •El número de ciclos dependerá del grado de exactitud de se desee. •En un trabajo que dure varios años y en el que intervengan varios operarios, es conveniente obtener tiempos exactos. •Si el trabajo se efectúa solo espontáneamente con la intervención de un solo operario, no será necesario una exactitud muy rigurosa. •El estudio debe hacerse por un número de ciclos que permita observar varias veces los elementos pocos frecuentes. •Cuando trabaje más un operario en la misma tarea será mejor hacer un estudio breve (algunos 10 ciclos) de varios operarios espontáneamente, con preferencia a hacer un estudio largo a un solo operario.
El estudio deberá continuar durante el número de ciclos que el analista considere necesarios para obtener una visión representativa del proceso. Existen varios métodos que permiten determinar el número de observaciones a realizar para obtener una muestra representativa en el cálculo del tiempo estándar. El método utilizado en el desarrollo de este estudio, es el que aplica la compañía General Electric, el cual determina el número de observaciones necesarias, dependiendo de la duración del ciclo. Tiempo de ciclo (min) Observaciones a realizar (N) 0,10 200 0.25 100 0.50 60 0.75 40 1.00 30 2.00 20 4.00 – 5.00 15 5.00 – 10.00 10 10.00 – 20.00 8 20.00 – 40.00 5 Más de 40.00 3
funcionando bien, mientras que los gastos de capital pretenden que sea operativo durante más tiempo. Tipos de Costos de Mantenimiento en una Empresa: Saber cómo funciona la estimación de costos de mantenimiento es muy importante para hacer un uso controlado de las finanzas y tomar decisiones de compra inteligentes. Dentro de la gestión de mantenimiento empresarial, se sabe que los costos de mantenimiento y reparación son inevitables (al menos que un negocio esté dispuesto a reemplazar maquinaria neuróticamente en lugar de repararla). Ya que no puede hacerse nada al respecto, la única medida que los administradores y encargados del departamento de mantenimiento pueden tomar es hacer un cálculo de costos de mantenimiento preciso para adelantarse a los hechos. Como todo en la vida, los números dependerán del tipo de mantenimiento que deba hacerse al equipo. Básicamente, pueden distinguirse cuatro categorías de costos de mantenimiento:
último, los costos de mejora son similares a los costos de reparación, salvo que la meta es hacer que un activo funcione mejor que antes. Cálculo de Costos de Mantenimiento: Hay dos enfoques populares para la estimación de costos de mantenimiento: