
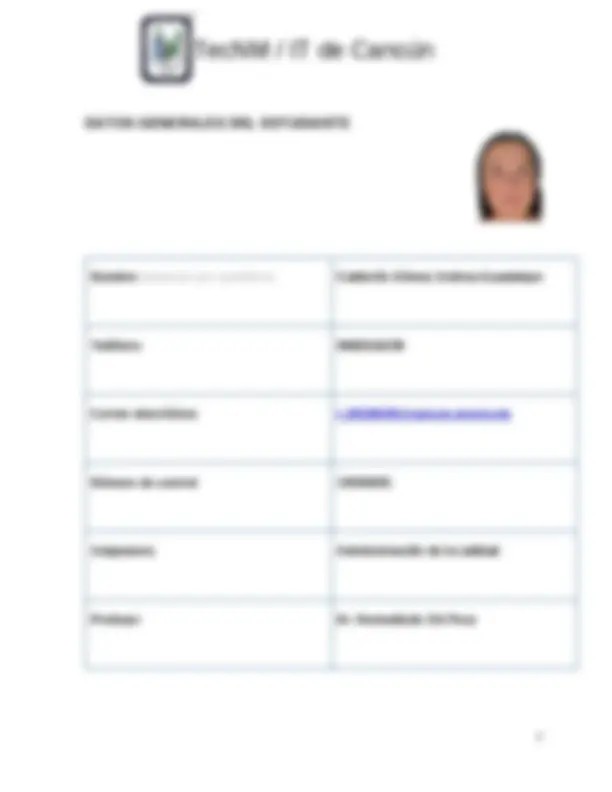
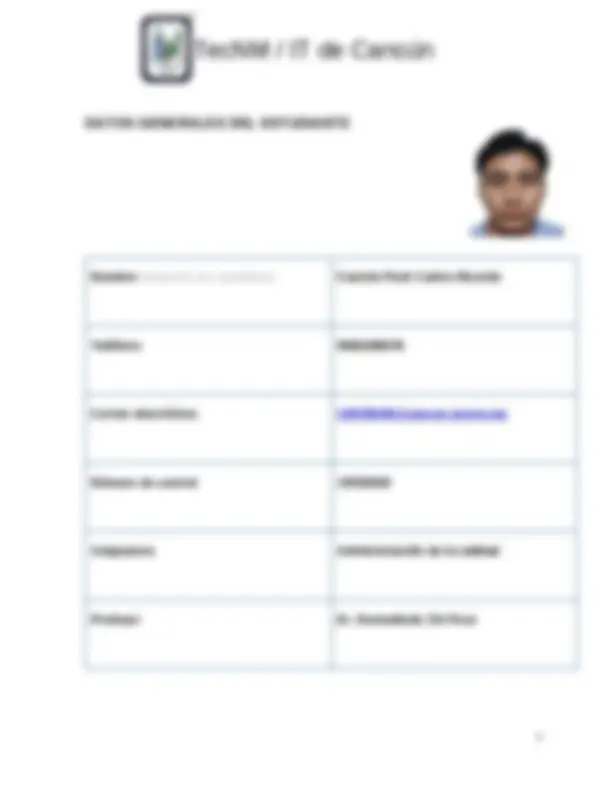
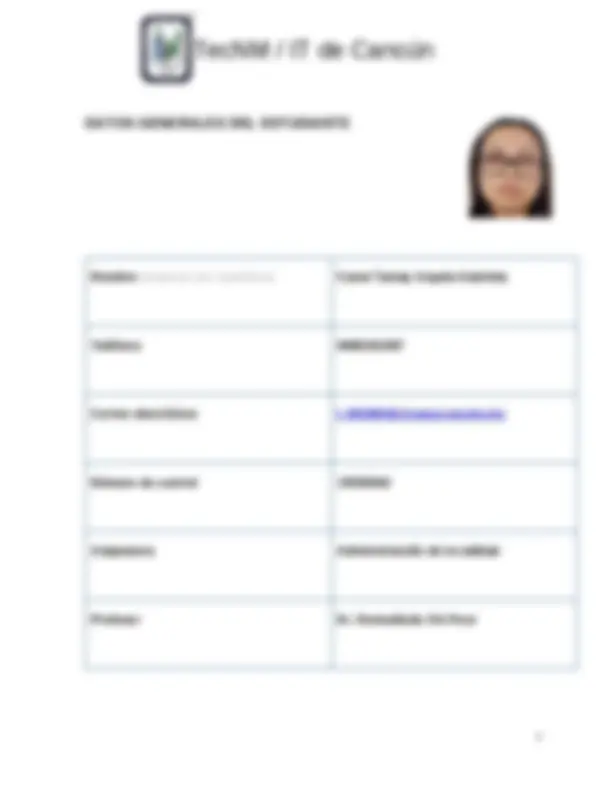
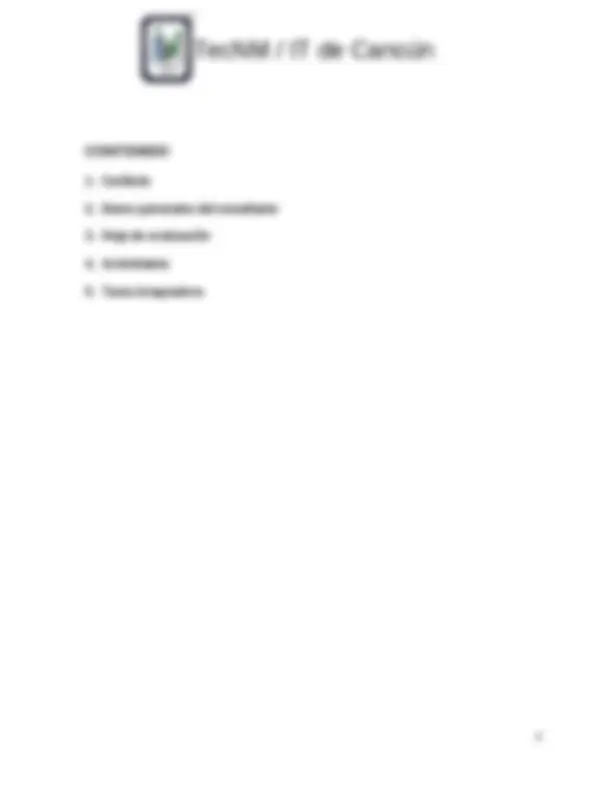
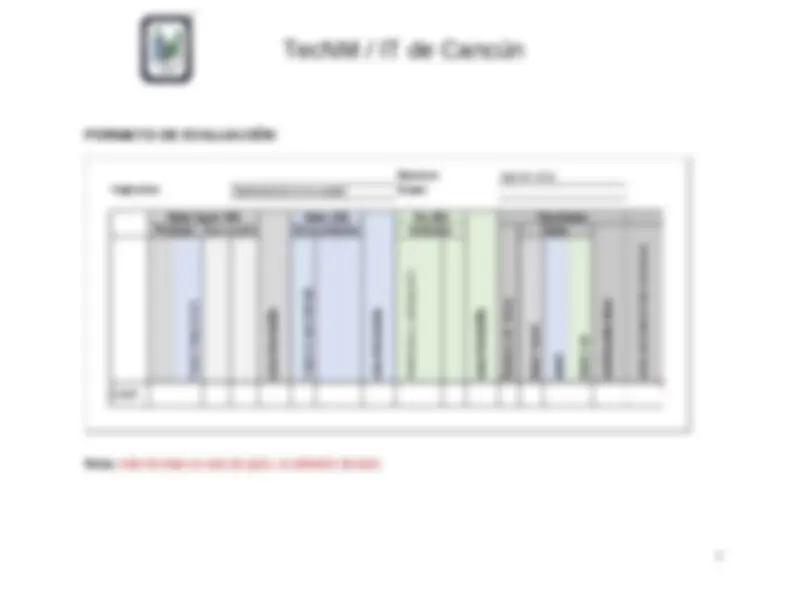
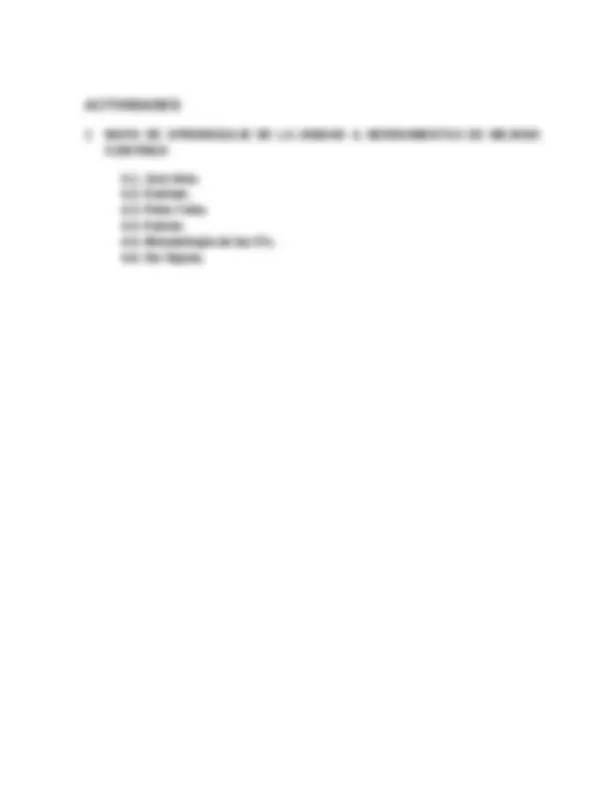
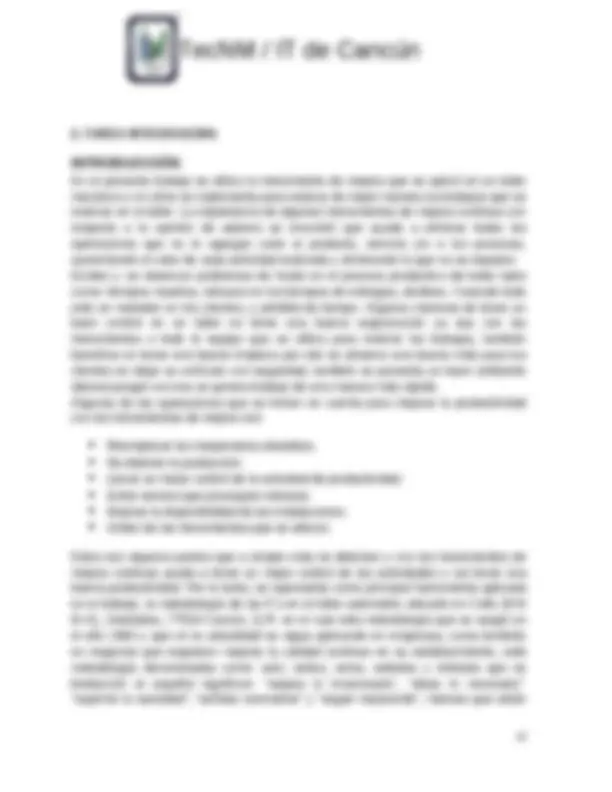
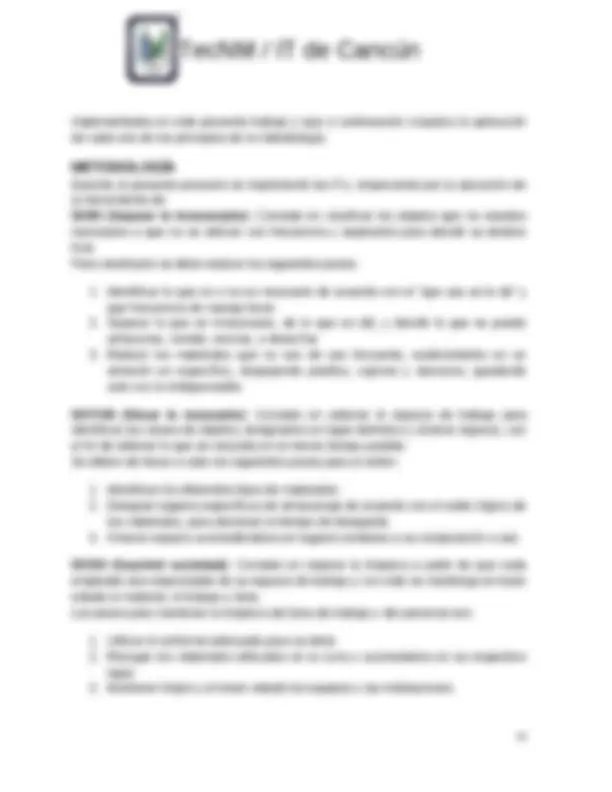
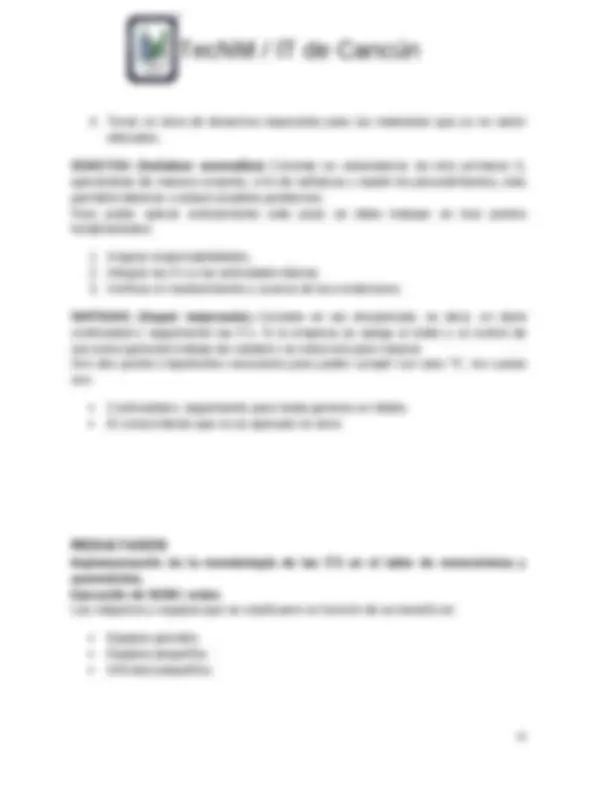
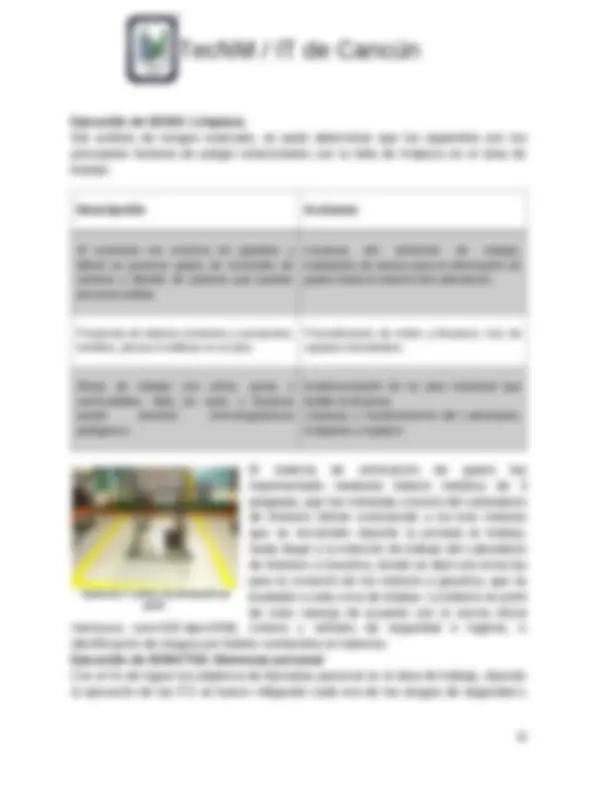
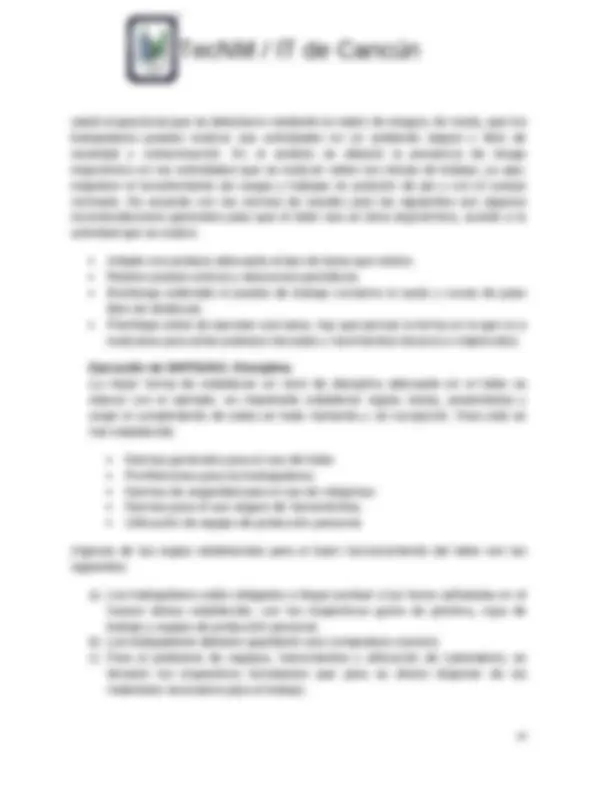
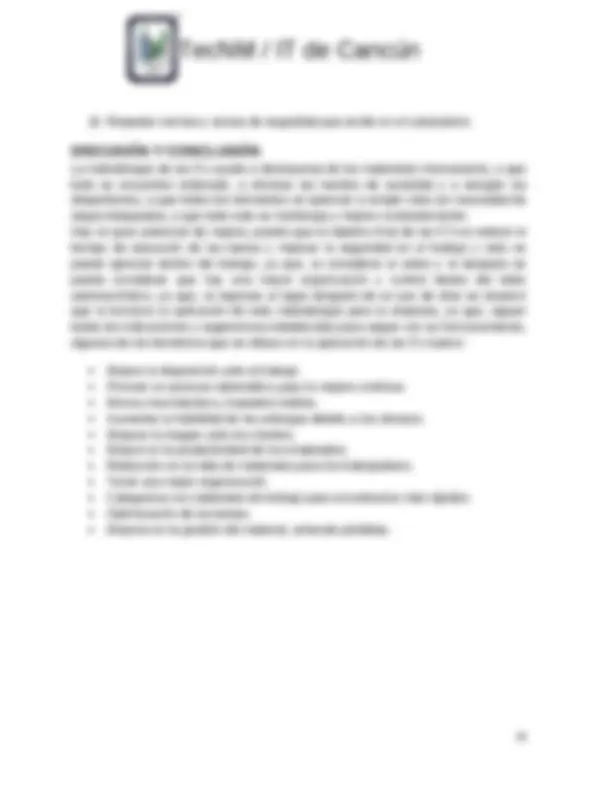
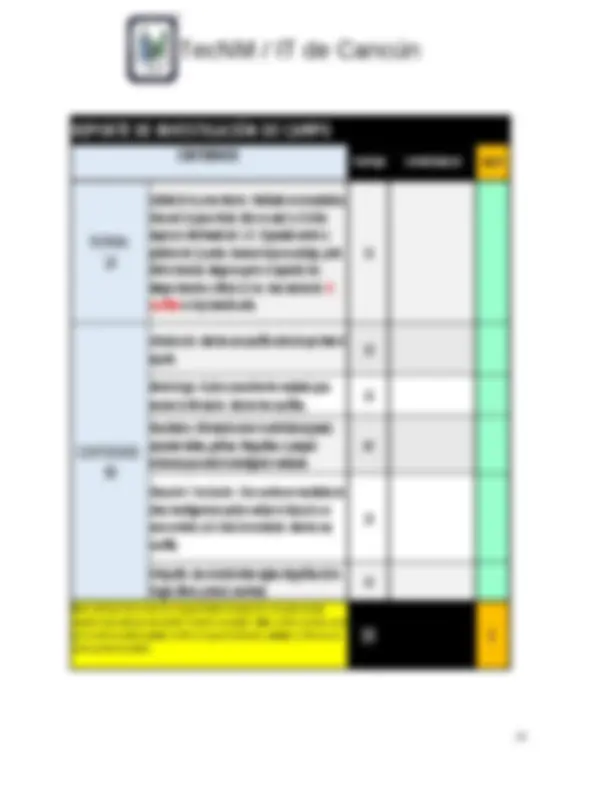
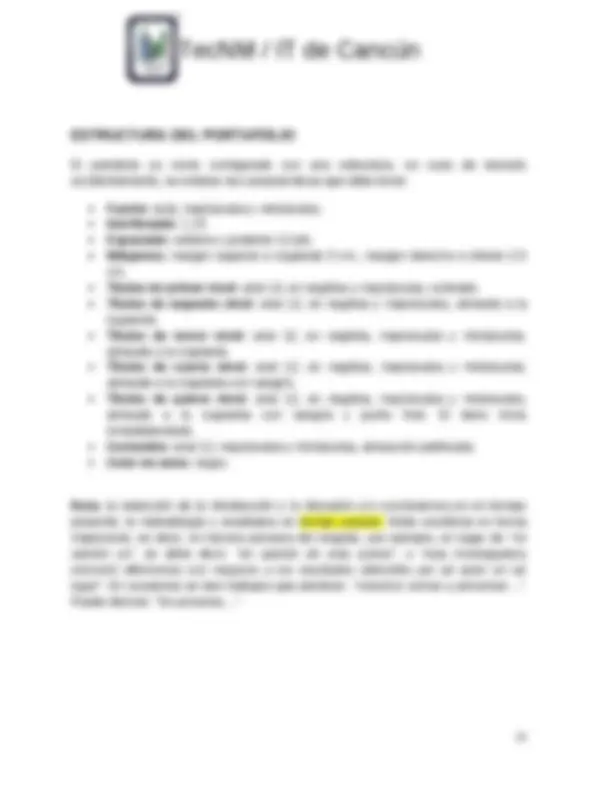
Prepara tus exámenes y mejora tus resultados gracias a la gran cantidad de recursos disponibles en Docsity
Gana puntos ayudando a otros estudiantes o consíguelos activando un Plan Premium
Prepara tus exámenes
Prepara tus exámenes y mejora tus resultados gracias a la gran cantidad de recursos disponibles en Docsity
Prepara tus exámenes con los documentos que comparten otros estudiantes como tú en Docsity
Los mejores documentos en venta realizados por estudiantes que han terminado sus estudios
Estudia con lecciones y exámenes resueltos basados en los programas académicos de las mejores universidades
Responde a preguntas de exámenes reales y pon a prueba tu preparación
Consigue puntos base para descargar
Gana puntos ayudando a otros estudiantes o consíguelos activando un Plan Premium
Comunidad
Pide ayuda a la comunidad y resuelve tus dudas de estudio
Descubre las mejores universidades de tu país según los usuarios de Docsity
Ebooks gratuitos
Descarga nuestras guías gratuitas sobre técnicas de estudio, métodos para controlar la ansiedad y consejos para la tesis preparadas por los tutores de Docsity
Un portafolio de evidencias sobre la aplicación de la metodología de las 5's en un taller mecánico. Se describe cómo se implementó cada uno de los principios de esta metodología (seiri, seiton, seiso, seiketsu y shitsuke) para mejorar la organización, limpieza y seguridad del taller. Se analizan los beneficios obtenidos, como la mejora en la disposición ante el trabajo, la categorización de los materiales para encontrarlos más rápido, y el mantenimiento del orden y la limpieza. El documento incluye formatos de evaluación, reportes de investigación de campo y una estructura detallada del portafolio de evidencias. Es un recurso valioso para estudiantes y profesionales interesados en la gestión de la calidad y la mejora continua en entornos industriales y de servicios.
Tipo: Tesis
1 / 22
Esta página no es visible en la vista previa
¡No te pierdas las partes importantes!
Arias Pérez María Guadalupe Calderón Gómez Andrea Guadalupe Canche Pech Carlos Ricardo Canul Tamay Angela Gabriela Castillo Santiago Daniela Guadalupe Cauich Pérez Patricia Marian GRUPO: LAD1001-B NÚMERO DE EQUIPO: 5 Cancún, Quintana Roo Agosto - diciembre 2022
Nombre (empezar por apellidos) Arias Pérez María Guadalupe Teléfono 9984764018 Correo electrónico L19530026@cancun.tecnm.mx Número de control 19530026 Asignatura Administración de la calidad Profesor Dr. Hermelindo Chi Poot
Nombre (empezar por apellidos) Canche Pech Carlos Ricardo Teléfono 9983499076 Correo electrónico l19530040@cancun.tecnm.mx Número de control 19530040 Asignatura Administración de la calidad Profesor Dr. Hermelindo Chi Poot
Nombre (empezar por apellidos) Canul Tamay Angela Gabriela Teléfono 9985351907 Correo electrónico L19530042@canun.tecnm.mx Número de control 19530042 Asignatura Administración de la calidad Profesor Dr. Hermelindo Chi Poot
Nombre (empezar por apellidos) Cauich Pérez Patricia Marian Teléfono 9982215666 Correo electrónico L19530046@cancun.tecnm.mx Número de control 19530046 Asignatura Administración de la calidad Profesor Dr. Hermelindo Chi Poot Pegar fotografía. Solo del rostro
**1. Carátula
4.1. Just time. 4.2. Kanban. 4.3. Poka Yoke. 4.4. Kaizen. 4.5. Metodología de las 9’s. 4.6. Six Sigma.
4.4 KAIZEN ¿Qué es? ¿Para qué sirve? Características ¿Cómo se usa? Método enfocado en la mejora continua de toda la empresa y de sus componentes. De manera a Alcanzar potencias occidentales. Ayuda a obtener mayor productividad. Conduce la calidad mejorada. Trabajo en equipo. Cambios inmediatos. Duración corta.Objetivo claro. Sentido de organización.
En el presente trabajo se utiliza la herramienta de mejora que se aplicó en un taller mecánico y el cómo se implementa para realizar de mejor manera los trabajos que se realizan en el taller. La importancia de algunas herramientas de mejora continua con respecto a la opinión de autores se encontró que ayuda a eliminar todas las operaciones que no le agregan valor al producto, servicio y/o a los procesos, aumentando el valor de cada actividad realizada y eliminando lo que no se requiere. Existen y se observan problemas de fondo en el proceso productivo del taller tales como: tiempos muertos, retrasos en los tiempos de entregas, etcétera. Creando todo esto un malestar en los clientes, y pérdida de tiempo. Algunas maneras de tener un buen control en un taller es tener una buena organización ya sea con las herramientas o todo el equipo que se utiliza para realizar los trabajos, también beneficia en tener una buena limpieza por ello se observa una buena vista para los clientes en dejar su vehículo con seguridad, también se presenta un buen ambiente laboral porqué con eso se genera trabajo de una manera más rápida. Algunas de las operaciones que se toman en cuenta para mejorar la productividad con las herramientas de mejora son:
Estos son algunos puntos que a simple vista se detectan y con las herramientas de mejora continua ayuda a tener un mejor control de las actividades y así tener una buena productividad. Por lo tanto, se representa como principal herramienta aplicada en el trabajo, la metodología de las 5´s en el taller automotriz ubicado en Calle 26-B M-41, Arboledas, 77534 Cancún, Q.R. en el cual esta metodología que se surgió en el año 1960 y que en la actualidad se sigue aplicando en empresas, como también en negocios que requieren mejorar la calidad continua en su establecimiento, está metodología denominadas como: seiri, seiton, seiso, seiketsu y shitsuke que se traducción al español significan: “separa lo innecesario”, “situar lo necesario”. “suprimir la suciedad”, “señalar anomalías” y “seguir mejorando”, mismas que están
implementados en este presente trabajo y que a continuación visualiza la aplicación de cada uno de los principios de la metodología.
Durante el presente proyecto se implementó las 5´s, empezando por la ejecución de la herramienta de: SEIRI (Separar lo innecesario): Consiste en clasificar los objetos que no resultan necesarios o que no se utilizan con frecuencia y separarlos para decidir su destino final. Para clasificarlo se debe realizar los siguientes pasos:
Una vez clasificado se tomaron todos los materiales designados como innecesarios y utilizando el criterio general para clasificación y evaluación de elementos se procedió a separar los componentes defectuosos, los que no se utilizan, los obsoletos y los funcionales. Se estableció una disposición final para los mismos, de estos, algunos se separaron, la mayoría fueron reubicados y otros fueron desechados definitivamente. En cuanto a las herramientas estas fueron clasificadas como: a) Herramientas para medir y comprobar. b) Herramientas de sujeción. c) Herramientas para cortar. d) Herramientas de golpear. e) Herramientas para atornillar. f) Equipos para lubricar. g) Caja de herramientas. Ejecución de SEITON: organización Se designó el espacio físico definitivo para cada una de las áreas del taller de motocicletas y automóviles, maquinaria, dinamómetro y bodega de herramientas. Se tomó en consideración mantener un orden lógico, la frecuencia de utilización, el tamaño y movilidad de los equipos, la necesidad de disponer de mesas de trabajo, la señalización de áreas de trabajo y pasillos de circulación. Se organizó dos áreas de almacenamiento de productos pequeños en estanterías, uno para repuestos de motores diésel y otro para los de gasolina. Para productos de tamaño mediano se determinó un área fija en el piso cercana al área de trabajo, que permita el acceso de la grúa manual para su transporte. A los motores de gasolina considerados como equipos grandes con bases móviles, se designó un área en la que se puedan almacenar todos motores que se emplean continuamente. Al lado del área de almacenamiento se asignó un área para la realizar trabajos. Al dinamómetro se le asignó un área cercana a la puerta de acceso, que facilite la ubicación de vehículos. El Laboratorio de Inyección se ubicó en un área cerrada que protege a los equipos; a cada máquina se le ha asignado un área fija, debido al tamaño y la necesidad de instalaciones eléctricas. Ilustración 1 : zona de almacenamiento.
La bodega de herramientas se mantendrá en un área cerrada que garantice la seguridad física de las mismas. Las herramientas de lubricación, cajas de herramientas, aceites, grasas, solventes, pintura y otros productos se organizan en estanterías. Toda área industrial debe estar apropiadamente señalizada para reducir los riesgos de atrapamiento, quemaduras, golpes y enfermedades, profesionales asociados al movimiento mecánico de las máquinas, al ambiente de trabajo, a desplazamientos de los operadores en sus puestos de trabajo y a la movilización de personas y maquinaria a través de los pasillos. Con este fin se utilizan señales complementarias de riesgo permanente, estas sirven para señalizar lugares donde no se utilicen formas geométricas normalizadas y que suponen un riesgo permanente de choque, caída, etcétera. Respecto a los pasillos para circulación de personas, se designaron a lo largo de todo el Laboratorio y servirán para la circulación de personas a través de las áreas, también como rutas de evacuación con dos puertas de salida. Toda la señalización horizontal se ha pintado con líneas continuas de 10 centímetros de ancho, con pintura amarilla de alto tráfico. La señalética vertical comprende todos los letreros que se colocaron en las paredes del taller. Se instalaron letreros cuyos símbolos, formas y colores se sujetan a las disposiciones de la norma oficial mexicana nom-003-segob-2011, señales y avisos para protección civil. -colores, formas y símbolos a utilizar y en su defecto se utilizaron aquellos con un significado relevante para el taller. Se ha implementado la señalética de forma que el riesgo que indica sea fácilmente advertido o identificado por los trabajadores. Existen cuatro tipos: Señales de obligación. Señales de prevención o advertencia. Señales de información. Señales de equipo contra incendios. A continuación, se muestran las siguientes señales que se deben utilizar en el taller: 17 Ilustración 2 : letreros de seguridad.
salud ocupacional que se detectaron mediante la matriz de riesgos, de modo, que los trabajadores puedan realizar sus actividades en un ambiente seguro y libre de suciedad y contaminación. En el análisis se detectó la presencia de riesgo ergonómico en las actividades que se realizan sobre las mesas de trabajo, ya que, requieren el levantamiento de cargas y trabajar en posición de pie y con el cuerpo inclinado. De acuerdo con las normas de nuestro país las siguientes son algunas recomendaciones generales para que el taller sea un área ergonómica, acorde a la actividad que se realiza: Adopte una postura adecuada al tipo de tarea que realice. Realice pausas activas y descansos periódicos. Mantenga ordenado el puesto de trabajo conserve el suelo y zonas de paso libre de obstáculo. Planifique antes de ejecutar una tarea, hay que pensar la forma en la que va a realizarse para evitar posturas forzadas y movimientos bruscos o imprevistos. Ejecución de SHITSUKE: Disciplina La mejor forma de establecer un nivel de disciplina adecuado en el taller es educar con el ejemplo, es importante establecer reglas claras, presentarlas y exigir el cumplimiento de estas en todo momento y sin excepción. Para esto se han establecido: Normas generales para el uso del taller. Prohibiciones para los trabajadores. Normas de seguridad para el uso de máquinas. Normas para el uso seguro de herramientas. Utilización de equipo de protección personal. Algunas de las reglas establecidas para el buen funcionamiento del taller son las siguientes: a) Los trabajadores están obligados a llegar puntual a las horas señaladas en el horario labora establecido, con las respectivas guías de práctica, ropa de trabajo y equipo de protección personal. b) Los trabajadores deberán guardarán una compostura correcta. c) Para el préstamo de equipos, herramientas y utilización de Laboratorio, se llenarán los respectivos formularios que para su efecto disponer de los materiales necesarios para el trabajo.
d) Respetar normas y avisos de seguridad que existe en el Laboratorio.
La metodología de las 5´s ayudo a deshacerse de los materiales innecesarios, a que todo se encuentre ordenado, a eliminar las fuentes de suciedad y a arreglar los desperfectos, a que todos los elementos se aprecien a simple vista sin necesidad de largas búsquedas, a que todo esto se mantenga y mejore constantemente. Hay un gran potencial de mejora, puesto que el objetivo final de las 5´S es reducir el tiempo de ejecución de las tareas y mejorar la seguridad en el trabajo y esto se puede apreciar dentro del trabajo, ya que, al considerar el antes y el después se puede considerar que hay una mayor organización y control dentro del taller automovilístico, ya que, al regresar al lugar después de un par de días se observó que si funciono la aplicación de esta metodología para la empresa, ya que, siguen todas las indicaciones y sugerencias establecidas para seguir con su funcionamiento, algunos de los beneficios que se obtuvo en la aplicación de las 5´s fueron: Mejora la disposición ante el trabajo. Proveer un proceso sistemático para la mejora continua. Menos movimientos y traslados inútiles. Aumentar la fiabilidad de las entregas debido a los retrasos. Mejorar la imagen ante los clientes. Mejora en la productividad de los empleados. Reducción en la falta de materiales para los trabajadores. Tener una mejor organización. Categorizar los materiales de trabajo para encontrarlos más rápidos. Optimización de las tareas. Mejoras en la gestión del material, evitando pérdidas.