
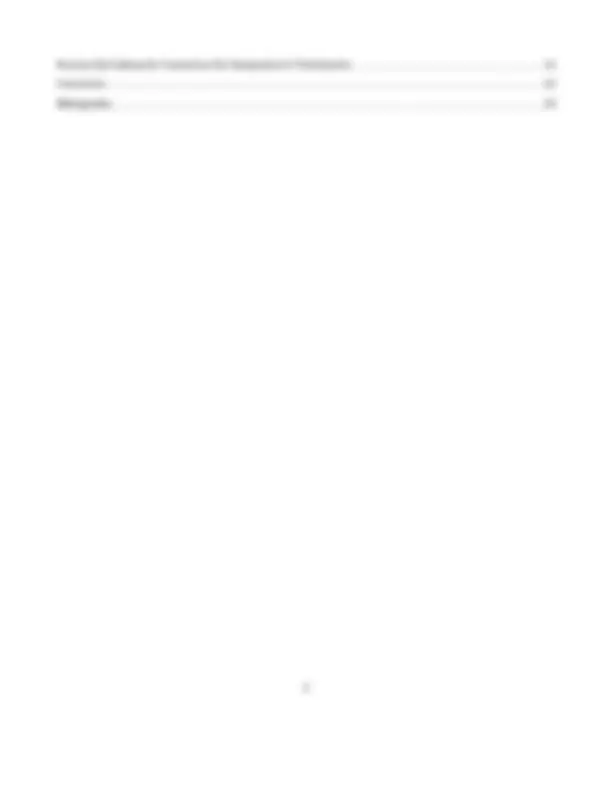
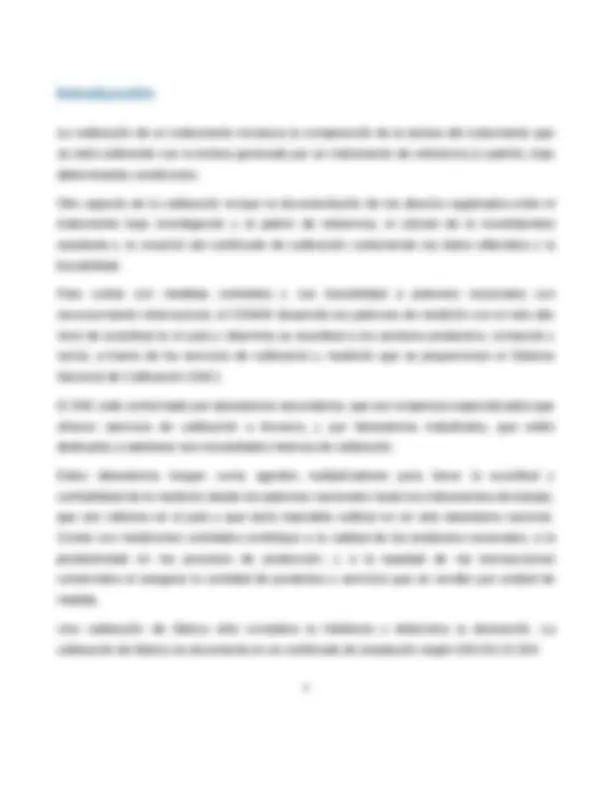
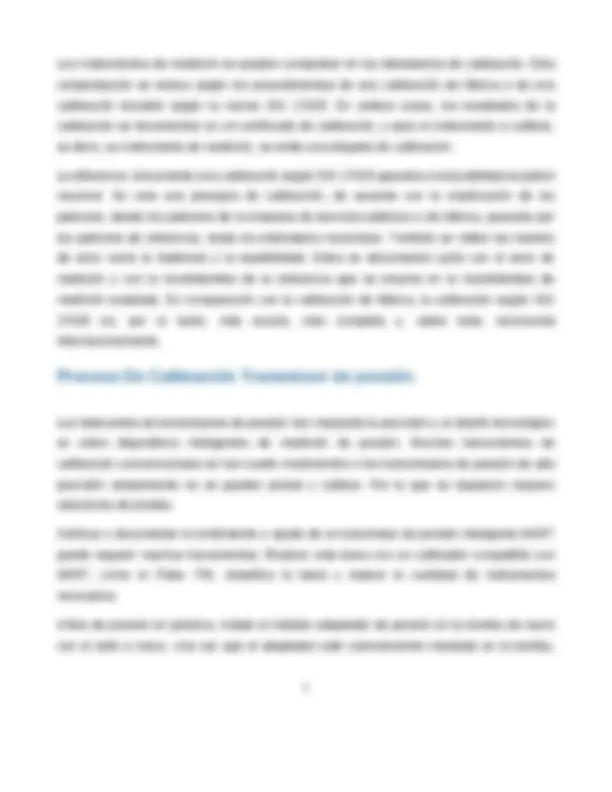
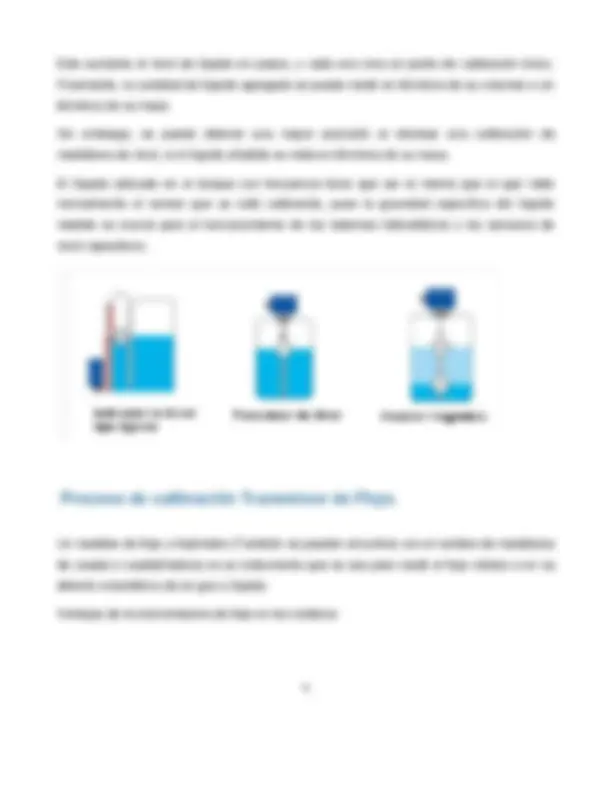
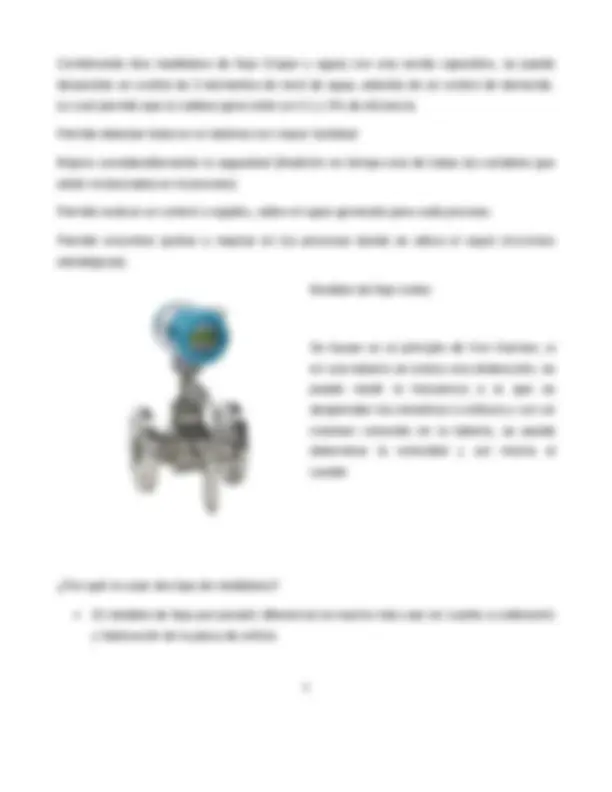
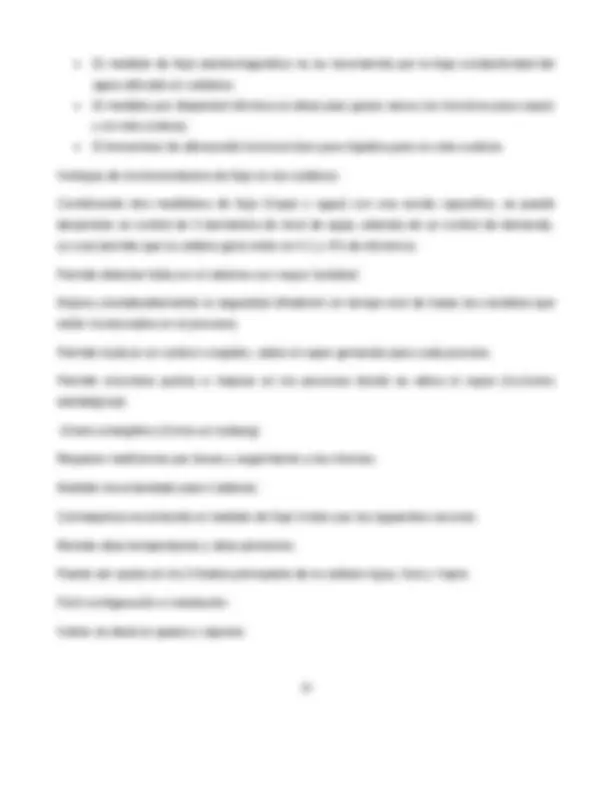
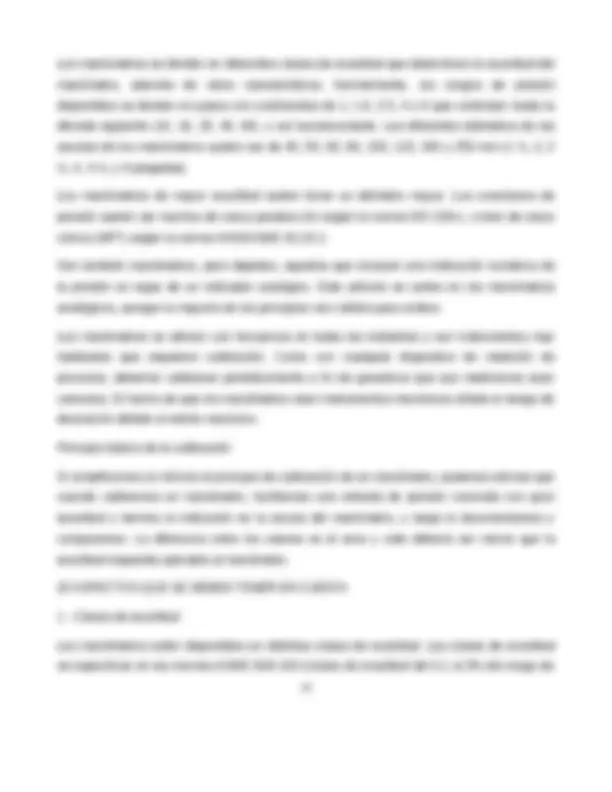
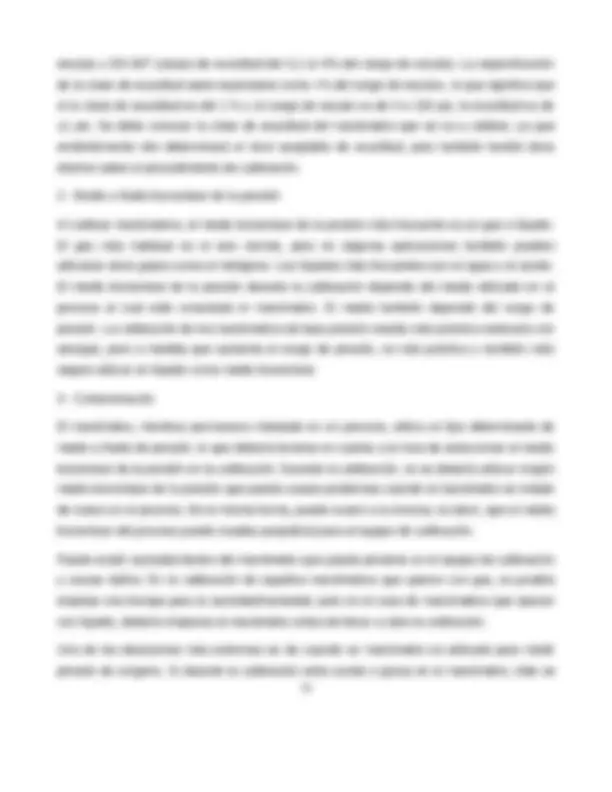
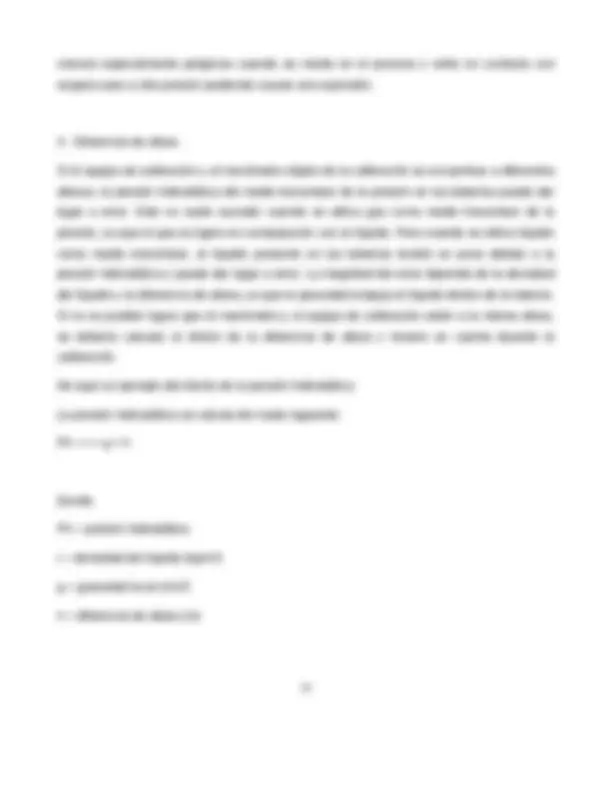
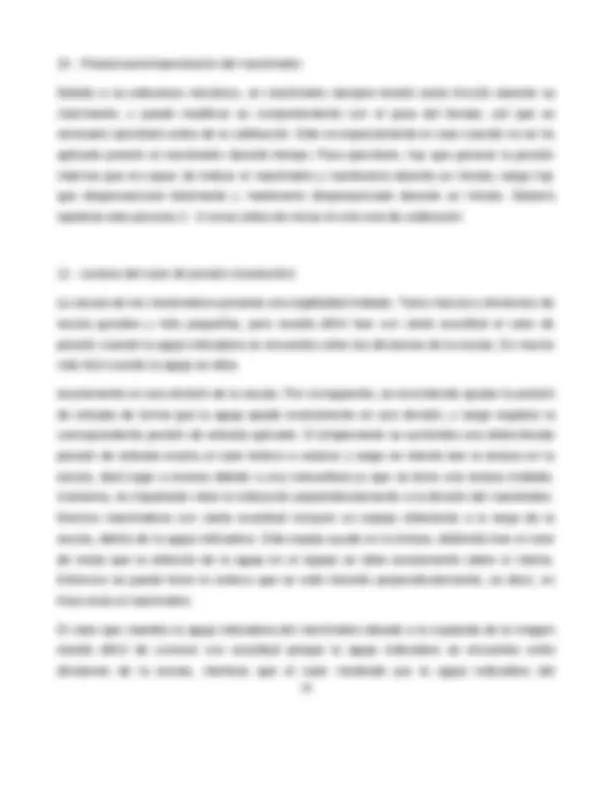
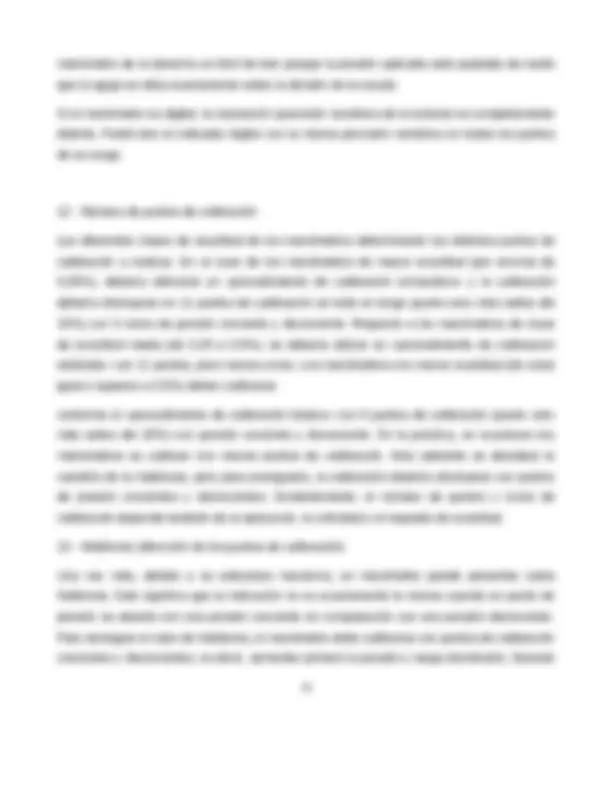
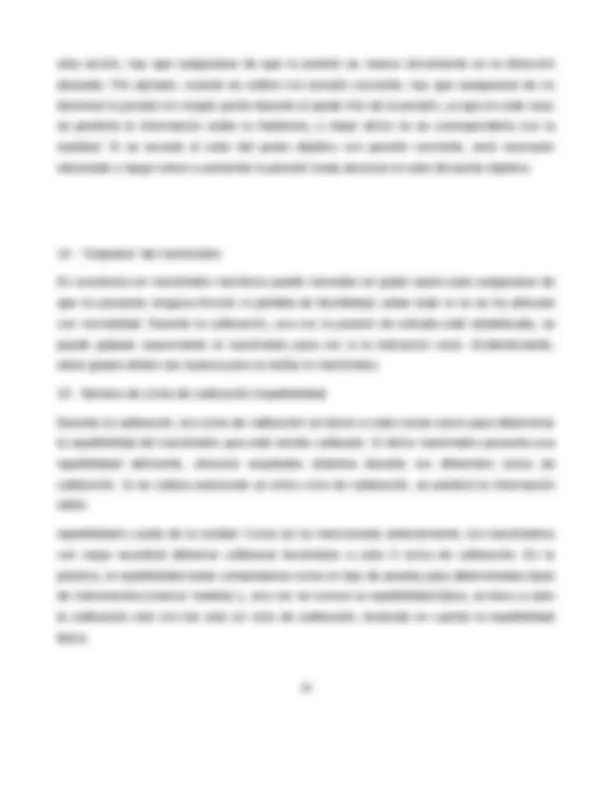
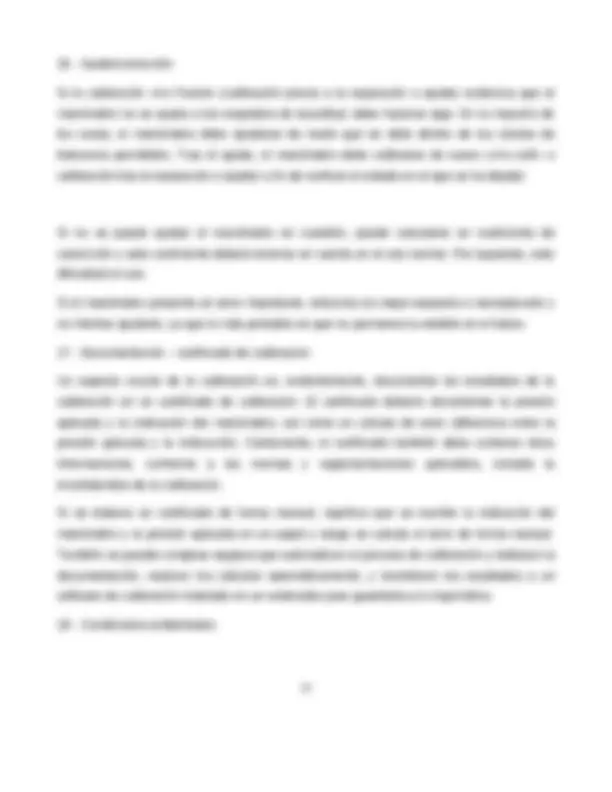
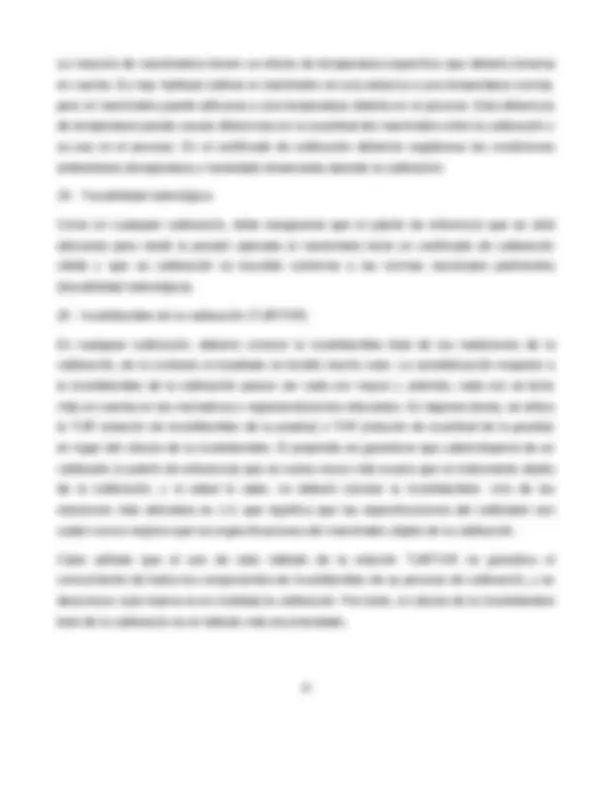
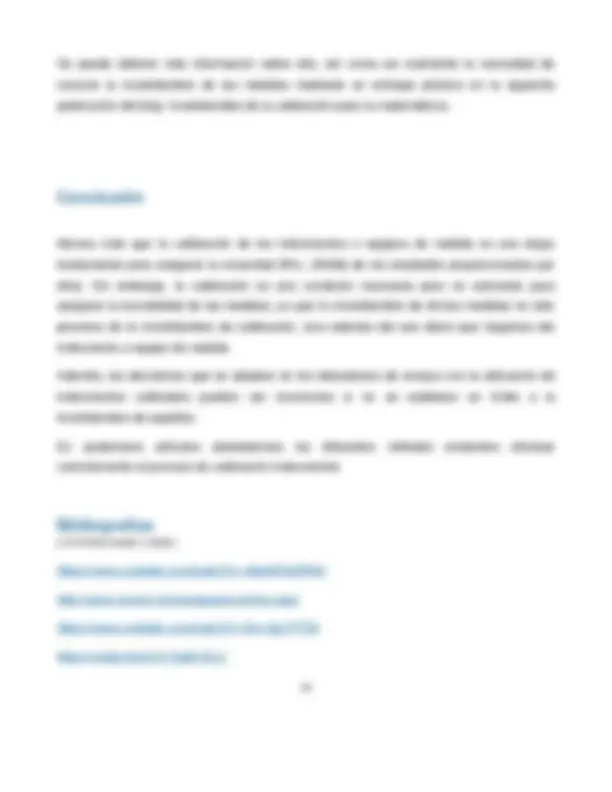
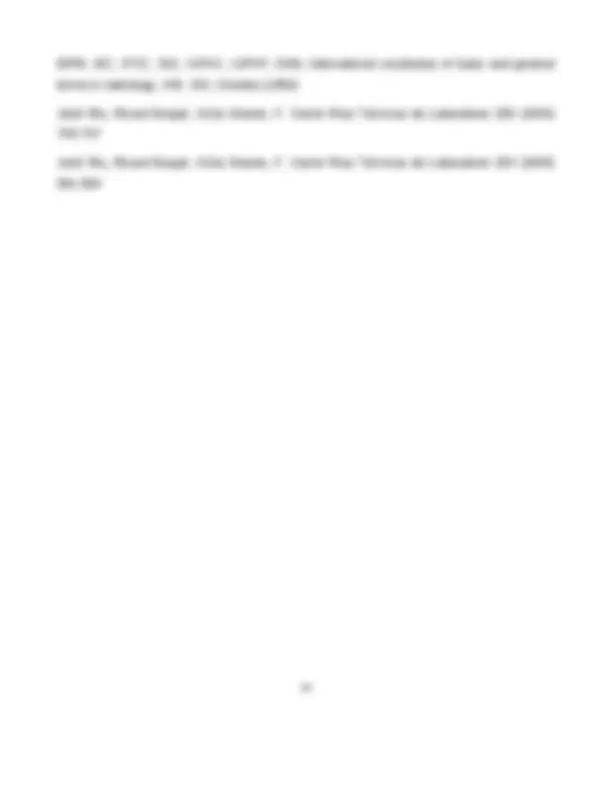
Prepara tus exámenes y mejora tus resultados gracias a la gran cantidad de recursos disponibles en Docsity
Gana puntos ayudando a otros estudiantes o consíguelos activando un Plan Premium
Prepara tus exámenes
Prepara tus exámenes y mejora tus resultados gracias a la gran cantidad de recursos disponibles en Docsity
Prepara tus exámenes con los documentos que comparten otros estudiantes como tú en Docsity
Los mejores documentos en venta realizados por estudiantes que han terminado sus estudios
Estudia con lecciones y exámenes resueltos basados en los programas académicos de las mejores universidades
Responde a preguntas de exámenes reales y pon a prueba tu preparación
Consigue puntos base para descargar
Gana puntos ayudando a otros estudiantes o consíguelos activando un Plan Premium
Comunidad
Pide ayuda a la comunidad y resuelve tus dudas de estudio
Descubre las mejores universidades de tu país según los usuarios de Docsity
Ebooks gratuitos
Descarga nuestras guías gratuitas sobre técnicas de estudio, métodos para controlar la ansiedad y consejos para la tesis preparadas por los tutores de Docsity
El proceso de calibración de diferentes tipos de instrumentos de medición, como transmisores de nivel y de flujo, y los métodos comparativa y de punto fijo en calibración de temperatura. Además, se abordan los desafíos que pueden encontrarse durante la calibración, como contaminación, diferencia de altura y par, y el número de puntos y ciclos de calibración necesarios según la clase de exactitud del instrumento.
Tipo: Apuntes
1 / 24
Esta página no es visible en la vista previa
¡No te pierdas las partes importantes!
Asignatura
Nombre del alumno
Docente
Carrera
Reporte
Introducción........................................................................................................................................................... 4 Proceso De Calibración Transmisor de presión....................................................................................................... 5 Proceso De Calibración De Transmisor De Nivel..................................................................................................... 7 Proceso de calibración Transmisor de Flujo........................................................................................................... 8
La calibración de un instrumento involucra la comparación de la lectura del instrumento que se está calibrando con la lectura generada por un instrumento de referencia (o patrón), bajo determinadas condiciones. Otro aspecto de la calibración incluye la documentación de los desvíos registrados entre el instrumento bajo investigación y el patrón de referencia; el cálculo de la incertidumbre resultante y la creación del certificado de calibración conteniendo los datos obtenidos y la trazabilidad. Para contar con medidas confiables y con trazabilidad a patrones nacionales con reconocimiento internacional, el CENAM desarrolla los patrones de medición con el más alto nivel de exactitud en el país y disemina su exactitud a los sectores productivo, comercial y social, a través de los servicios de calibración y medición que se proporcionan al Sistema Nacional de Calibración (SNC). El SNC está conformado por laboratorios secundarios, que son empresas especializadas que ofrecen servicios de calibración a terceros, y por laboratorios industriales, que están dedicados a satisfacer sus necesidades internas de calibración. Estos laboratorios fungen como agentes multiplicadores para llevar la exactitud y confiabilidad de la medición desde los patrones nacionales hasta los instrumentos de trabajo, que son millones en el país y que sería imposible calibrar en un solo laboratorio nacional. Contar con mediciones confiables contribuye a la calidad de los productos nacionales, a la productividad en los procesos de producción, y a la equidad de las transacciones comerciales al asegurar la cantidad de productos y servicios que se venden por unidad de medida. Una calibración de fábrica sólo considera la histéresis y determina la desviación. La calibración de fábrica se documenta en un certificado de aceptación según DIN EN 10 204.
Los instrumentos de medición se pueden comprobar en los laboratorios de calibración. Esta comprobación se realiza según los procedimientos de una calibración de fábrica o de una calibración trazable según la norma ISO 17025. En ambos casos, los resultados de la calibración se documentan en un certificado de calibración, y para el instrumento a calibrar, es decir, su instrumento de medición, se emite una etiqueta de calibración. La diferencia: únicamente una calibración según ISO 17025 garantiza la trazabilidad al patrón nacional. Se crea una jerarquía de calibración, de acuerdo con la clasificación de los patrones, desde los patrones de la empresa de servicios públicos o de fábrica, pasando por los patrones de referencia, hasta los estándares nacionales. También se miden las fuentes de error como la histéresis y la repetibilidad. Estos se documentan junto con el error de medición y con la incertidumbre de la referencia que se resume en la incertidumbre de medición ampliada. En comparación con la calibración de fábrica, la calibración según ISO 17025 es, por lo tanto, más exacta, más completa y, sobre todo, reconocida internacionalmente.
Los fabricantes de transmisores de presión han mejorado la precisión y el diseño tecnológico en estos dispositivos inteligentes de medición de presión. Muchas herramientas de calibración convencionales se han vuelto insuficientes o los transmisores de presión de alta precisión simplemente no se pueden probar y calibrar. Por lo que se requieren mejores soluciones de prueba. Verificar y documentar el rendimiento y ajuste de un transmisor de presión inteligente HART puede requerir muchas herramientas. Realizar esta tarea con un calibrador compatible con HART, como el Fluke 754, simplifica la tarea y reduce la cantidad de instrumentos necesarios. Antes de ponerlo en práctica, instale el módulo adaptador de presión en la bomba de mano con el sello a rosca. Una vez que el adaptador esté correctamente instalado en la bomba,
Los sensores funcionan mediante flotadores con transmisión magnética. El sistema magnético del flotador actúa sobre una cadena de resistencias, que corresponde a un conexionado de interrupción potenciométrico. La resistencia es proporcional con la altura de nivel. La cadena de resistencias va montada en un circuito formado por un conjunto de Reed/ resistencia. La señal varía en intervalos pequeños desde 5 a 18 mm. Flotador magnético Un flotador con imán incorporado se traslada con el nivel, montado en un tubo con uno o varios contactos Reed incorporados. El imán actúa sobre los contactos en las posiciones de interrupción previamente configuradas permitiendo la monitorización de distintos niveles. El sencillo y probado principio de funcionamiento permite un amplio espectro de aplicaciones. Además, realiza su función sin efectos de burbujas, conductividad, di electricidad, presión, vacío, temperatura, vapor, condensación, burbujas, ebullición y vibraciones. Si las demandas de precisión no son demasiado altas y un tanque es relativamente poco profundo, una simple varilla medidora insertada en el tanque será suficiente para verificar la lectura de salida de cualquier otra forma de sensor de nivel que se use para monitorear el nivel del líquido en el tanque. Sin embargo, esto sólo proporciona un punto de calibración, y sólo se podrán obtener otros puntos de calibración al poner más líquido en el tanque o al vaciar un poco de líquido del tanque.
Esto aumenta el nivel de líquido en pasos, y cada uno crea un punto de calibración único. Finalmente, la cantidad de líquido agregado se puede medir en términos de su volumen o en términos de su masa. Sin embargo, se puede obtener una mayor precisión al efectuar una calibración de medidores de nivel, si el líquido añadido se mide en términos de su masa. El líquido utilizado en el tanque con frecuencia tiene que ser el mismo que el que mide normalmente el sensor que se está calibrando, pues la gravedad específica del líquido medido es crucial para el funcionamiento de los sistemas hidrostáticos y los sensores de nivel capacitivos.
Un medidor de flujo o flujómetro (También se pueden encontrar con el nombre de medidores de caudal o caudalímetros) es un instrumento que se usa para medir el flujo másico o en su defecto volumétrico de un gas o líquido. Ventajas de los transmisores de flujo en las calderas
El medidor de flujo electromagnético no se recomienda por la baja conductividad del agua utilizada en calderas. El medidor por dispersión térmica es ideal para gases secos (no funciona para vapor) y es más costoso. El transmisor de ultrasonido funciona bien para líquidos pero es más costoso. Ventajas de los transmisores de flujo en las calderas Combinando dos medidores de flujo (Vapor y agua) con una sonda capacitiva, se puede desarrollar un control de 3 elementos de nivel de agua, además de un control de demanda. Lo cual permite que la caldera gane entre un 0.1 y 4% de eficiencia. Permite detectar fallas en el sistema con mayor facilidad. Mejora considerablemente la seguridad (Medición en tiempo real de todas las variables que están involucradas en el proceso). Permite realizar un control o registro, sobre el vapor generado para cada proceso. Permite encontrar puntos a mejorar en los procesos donde se utiliza el vapor (Acciones estratégicas). Ahorro energético (Como un Iceberg) Requiere mediciones por áreas y seguimiento a las mismas. Medidor recomendado para Calderas: Colmaquinas recomienda el medidor de flujo Vortex por las siguientes razones: Resiste altas temperaturas y altas presiones. Puede ser usado en los 3 fluidos principales de la caldera Agua, Gas y Vapor. Fácil configuración e instalación. Vortex es ideal en gases y vapores
En la tecnología de calibración de temperatura, existen dos métodos de calibración: la calibración comparativa y la calibración de punto fijo. El método de calibración que se utilizará se definirá a través de las demandas sobre la precisión y el tipo de instrumento de prueba. El método comparativo representa el método de calibración más utilizado. Entonces, ¿en qué se diferencian los métodos de calibración comparativa y de calibración de punto fijo? Usando el ejemplo de calibrar un termómetro de resistencia, este artículo de blog explica ambos métodos y, por lo tanto, intenta transmitir al lector una mejor comprensión. La calibración comparativa Como su nombre ya lo indica, este tipo de calibración se lleva a cabo comparando el termómetro de resistencia que se está probando con un termómetro de referencia de mayor calidad. Por tanto, la referencia de mayor calidad debe presentar una precisión de tres o cuatro veces mayor que la del termómetro que se está probando. Ambos termómetros se colocan en una única fuente de temperatura homogénea. Al colocar los termómetros, se debe tener cuidado de asegurar una pequeña distancia entre ellos y que los puntos sensibles (es decir, los puntos de medición) estén a la misma altura. Como fuente de temperatura, generalmente se utilizan baños líquidos o calibradores de pozo seco. La calibración de punto fijo La calibración de punto fijo, a diferencia de la calibración comparativa, se realiza contra los puntos de fusión, congelación y triple definidos de la Escala Internacional de Temperatura de 1990 (ITS-90). Los puntos fijos definen las temperaturas a las que se altera el estado físico
Los manómetros se dividen en diferentes clases de exactitud que determinan la exactitud del manómetro, además de otras características. Normalmente, los rangos de presión disponibles se dividen en pasos con coeficientes de 1, 1.6, 2.5, 4 y 6 que continúan hasta la década siguiente (10, 16, 25, 40, 60), y así sucesivamente. Los diferentes diámetros de las escalas de los manómetros suelen ser de 40, 50, 63, 80, 100, 115, 160 y 250 mm (1 ½, 2, 2 ½, 4, 4 ½, y 6 pulgadas). Los manómetros de mayor exactitud suelen tener un diámetro mayor. Los conectores de presión suelen ser machos de rosca paralela (G) según la norma ISO 228-1, o bien de rosca cónica (NPT) según la norma ANSI/ASME B1.20.1. Son también manómetros, pero digitales, aquellos que incluyen una indicación numérica de la presión en lugar de un indicador analógico. Este artículo se centra en los manómetros analógicos, aunque la mayoría de los principios son válidos para ambos. Los manómetros se utilizan con frecuencia en todas las industrias y son instrumentos muy habituales que requieren calibración. Como con cualquier dispositivo de medición de procesos, deberían calibrarse periódicamente a fin de garantizar que sus mediciones sean correctas. El hecho de que los manómetros sean instrumentos mecánicos añade el riesgo de desviación debido al estrés mecánico. Principio básico de la calibración Si simplificamos al mínimo el principio de calibración de un manómetro, podemos afirmar que cuando calibramos un manómetro, facilitamos una entrada de presión conocida con gran exactitud y leemos la indicación en la escala del manómetro, y luego lo documentamos y comparamos. La diferencia entre los valores es el error y este debería ser menor que la exactitud requerida aplicable al manómetro. 20 ASPECTOS QUE SE DEBEN TENER EN CUENTA 1 - Clases de exactitud Los manómetros están disponibles en distintas clases de exactitud. Las clases de exactitud se especifican en las normas ASME B40.100 (clases de exactitud del 0,1 al 5% del rango de
escala) y EN 837 (clases de exactitud del 0,1 al 4% del rango de escala). La especificación de la clase de exactitud suele expresarse como «% del rango de escala», lo que significa que si la clase de exactitud es del 1 % y el rango de escala va de 0 a 100 psi, la exactitud es de ±1 psi. Se debe conocer la clase de exactitud del manómetro que se va a calibrar, ya que evidentemente ello determinará el nivel aceptable de exactitud, pero también tendrá otros efectos sobre el procedimiento de calibración. 2 - Medio o fluido transmisor de la presión Al calibrar manómetros, el medio transmisor de la presión más frecuente es un gas o líquido. El gas más habitual es el aire normal, pero en algunas aplicaciones también pueden utilizarse otros gases como el nitrógeno. Los líquidos más frecuentes son el agua o el aceite. El medio transmisor de la presión durante la calibración depende del medio utilizado en el proceso al cual está conectado el manómetro. El medio también depende del rango de presión. La calibración de los manómetros de baja presión resulta más práctica realizarla con aire/gas, pero a medida que aumenta el rango de presión, es más práctico y también más seguro utilizar un líquido como medio transmisor. 3 - Contaminación El manómetro, mientras permanece instalado en un proceso, utiliza un tipo determinado de medio o fluido de presión, lo que debería tenerse en cuenta a la hora de seleccionar el medio transmisor de la presión en la calibración. Durante la calibración, no se debería utilizar ningún medio transmisor de la presión que pueda causar problemas cuando el manómetro se instale de nuevo en el proceso. De la misma forma, puede ocurrir a la inversa, es decir, que el medio transmisor del proceso puede resultar perjudicial para el equipo de calibración. Puede existir suciedad dentro del manómetro que puede penetrar en el equipo de calibración y causar daños. En la calibración de aquellos manómetros que operan con gas, es posible emplear una trampa para la suciedad/humedad, pero en el caso de manómetros que operan con líquido, debería limpiarse el manómetro antes de llevar a cabo la calibración. Una de las situaciones más extremas se da cuando un manómetro es utilizado para medir presión de oxígeno. Si durante la calibración entra aceite o grasa en el manómetro, éste se
A modo de ejemplo, si el agua es el medio (densidad: 997,56 kg/m³), la gravedad local es de 9,8 m/s² y existe una diferencia de 1 metro entre el DUT y el equipo de referencia, esto dará lugar a un error de 9,8 kPa (98 mbar ó 1,42 psi). Es importante recordar que, en función de la presión a medir, el error causado por la diferencia de altura puede ser significativo. 5 - Prueba de fugas en los tubos de conexión Si durante la calibración existe alguna fuga en alguno de los tubos, pueden producirse errores imprevisibles. Por tanto, antes de la calibración se debe realizar una prueba de fugas. La prueba de fugas más sencilla consiste en presurizar el sistema y dejar que la presión se estabilice durante un tiempo, y controlar que la presión no disminuya en exceso. Algunos sistemas de calibración (controladores de presión) pueden mantener la presión incluso en caso de fuga, si se dispone de un controlador que ajuste de manera dinámica la presión. En este caso, es difícil detectar cualquier fuga, por lo que el controlador debe tener cerradas totalmente sus válvulas para poder realizar una prueba de fugas en un sistema cerrado. El efecto adiabático también debe tenerse en cuenta en sistemas cerrados, en especial cuando se utiliza un gas como medio transmisor de la presión, tal como se explica en el siguiente apartado. 6 - Efecto adiabático En un sistema cerrado con un gas como medio transmisor de la presión, la temperatura del gas afecta al volumen del gas, lo que a su vez tiene un efecto en la presión. Cuando la presión aumenta rápidamente, la temperatura del gas también aumenta, y esta temperatura más elevada hace que el gas se expanda, adquiera un volumen mayor y también una presión mayor. Cuando la temperatura empieza a enfriarse, el volumen del gas es cada vez menor y esto causará una pérdida de presión. Esta pérdida de presión puede parecer una fuga en el sistema, pero en realidad se debe al efecto adiabático causado por el cambio en la
temperatura del gas. Cuanto más rápido cambia la presión, mayor es el efecto. El cambio de presión causado por este efecto se verá reflejado gradualmente a medida que se estabilice la temperatura. Por tanto, si se modifica la presión rápidamente, hay que dejar que se estabilice la lectura de presión durante un tiempo antes de determinar que hay una fuga en el sistema. 7 – Par En especial en el caso de manómetros sensibles al par, no hay que ejercer una fuerza excesiva cuando se conecten los adaptadores de presión al manómetro, ya que este podría resultar dañado. Se recomienda seguir las instrucciones del fabricante en relación con el par de apriete permitido, así como emplear las herramientas y los adaptadores correctos y los sellos apropiados. 8 - Posición de calibración/montaje Dado que los manómetros analógicos son instrumentos mecánicos, su posición afectará a la lectura. Por tanto, se recomienda calibrarlos en la misma posición en la que se utilizan en el proceso. También se deberían tener en cuenta las especificaciones del fabricante en cuanto a la posición de funcionamiento/montaje. Una especificación típica acerca de la posición/montaje es que un cambio de 5 grados en la posición no debería modificar la indicación del manómetro en más de la mitad (0,5 veces) de su clase de exactitud. 9 - Generación de presión Para calibrar un manómetro, se deben tener los medios para poder aplicarle presión. Se puede hacer de distintas formas: se puede emplear una bomba manual generadora de presión, una botella con un regulador de presión o incluso una balanza de pesos muertos. Este último proporcionará una presión con gran exactitud y no se necesitará un calibrador o referencia para medir la presión, pero una balanza de pesos muertos es cara, no está diseñada para ser un dispositivo móvil, requiere mucha atención durante el uso y requiere de un mayor mantenimiento y limpieza que otros dispositivos. Es más habitual y práctico utilizar una bomba manual de generación de presión y un dispositivo con una buena exactitud de medición (calibrador) para medir la presión. Para generar la presión al manómetro a calibrar, también se puede utilizar un controlador de presión.
manómetro de la derecha es fácil de leer porque la presión aplicada está ajustada de modo que la aguja se sitúa exactamente sobre la división de la escala: Si el manómetro es digital, la resolución (precisión numérica de la lectura) es completamente distinta. Podrá leer el indicador digital con la misma precisión numérica en todos los puntos de su rango. 12 - Número de puntos de calibración Las diferentes clases de exactitud de los manómetros determinarán los distintos puntos de calibración a realizar. En el caso de los manómetros de mayor exactitud (por encima de 0,05%), debería utilizarse un «procedimiento de calibración exhaustivo» y la calibración debería efectuarse en 11 puntos de calibración en todo el rango (punto cero más saltos del 10%) con 3 ciclos de presión creciente y decreciente. Respecto a los manómetros de clase de exactitud media (de 0,05 a 0,5%), se debería utilizar un «procedimiento de calibración estándar» con 11 puntos, pero menos ciclos. Los manómetros con menor exactitud (de clase igual o superior a 0,5%) deben calibrarse conforme al «procedimiento de calibración básico» con 6 puntos de calibración (punto cero más saltos del 20%) con presión creciente y decreciente. En la práctica, en ocasiones los manómetros se calibran con menos puntos de calibración. Más adelante se abordará la cuestión de la histéresis, pero para averiguarla, la calibración debería efectuarse con puntos de presión crecientes y decrecientes. Evidentemente, el número de puntos y ciclos de calibración depende también de la aplicación, la criticidad y el requisito de exactitud. 13 - Histéresis (dirección de los puntos de calibración) Una vez más, debido a su estructura mecánica, un manómetro puede presentar cierta histéresis. Esto significa que la indicación no es exactamente la misma cuando un punto de presión se aborda con una presión creciente en comparación con una presión decreciente. Para averiguar el valor de histéresis, el manómetro debe calibrarse con puntos de calibración crecientes y decrecientes, es decir, aumentar primero la presión y luego disminuirla. Durante
esta acción, hay que asegurarse de que la presión se mueve únicamente en la dirección deseada. Por ejemplo, cuando se calibre con presión creciente, hay que asegurarse de no disminuir la presión en ningún punto durante el ajuste fino de la presión, ya que en este caso se perdería la información sobre la histéresis, o mejor dicho no se correspondería con la realidad. Si se excede el valor del punto objetivo con presión creciente, será necesario retroceder y luego volver a aumentar la presión hasta alcanzar el valor del punto objetivo. 14 - “Golpeteo” del manómetro En ocasiones un manómetro mecánico puede necesitar un golpe suave para asegurarse de que no presenta ninguna fricción ni pérdida de flexibilidad, sobre todo si no se ha utilizado con normalidad. Durante la calibración, una vez la presión de entrada esté estabilizada, se puede golpear suavemente el manómetro para ver si la indicación varía. Evidentemente, estos golpes deben ser suaves para no dañar el manómetro. 15 - Número de ciclos de calibración (repetibilidad) Durante la calibración, los ciclos de calibración se llevan a cabo varias veces para determinar la repetibilidad del manómetro que está siendo calibrado. Si dicho manómetro presenta una repetibilidad deficiente, ofrecerá resultados distintos durante los diferentes ciclos de calibración. Si se calibra realizando un único ciclo de calibración, se perderá la información sobre repetibilidad y parte de la verdad. Como se ha mencionado anteriormente, los manómetros con mejor exactitud deberían calibrarse llevándose a cabo 3 ciclos de calibración. En la práctica, la repetibilidad suele comprobarse como un tipo de prueba para determinados tipos de instrumentos (marca/ modelo) y, una vez se conoce la repetibilidad típica, se lleva a cabo la calibración real con tan solo un ciclo de calibración, teniendo en cuenta la repetibilidad típica.