
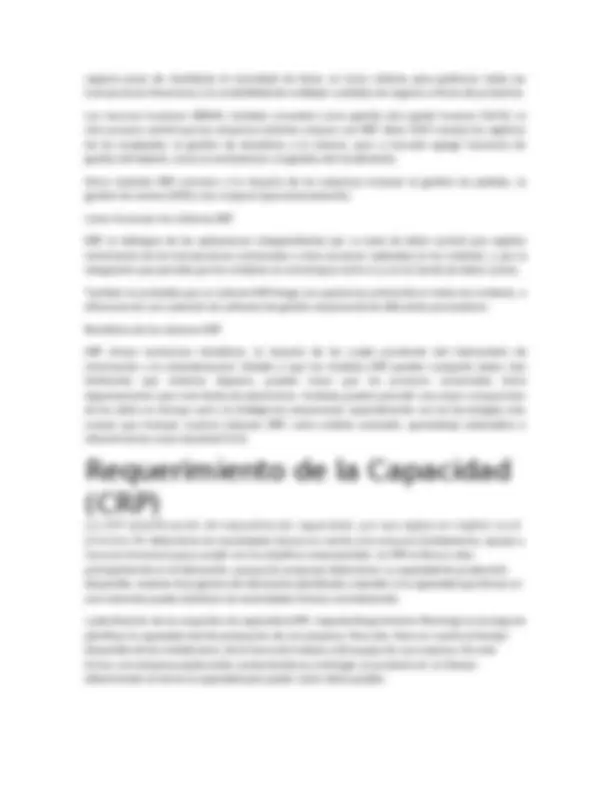
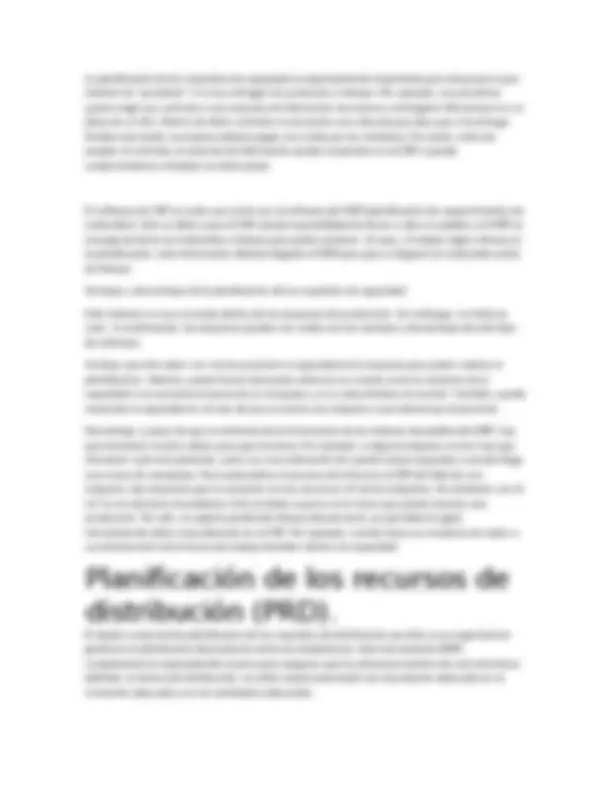
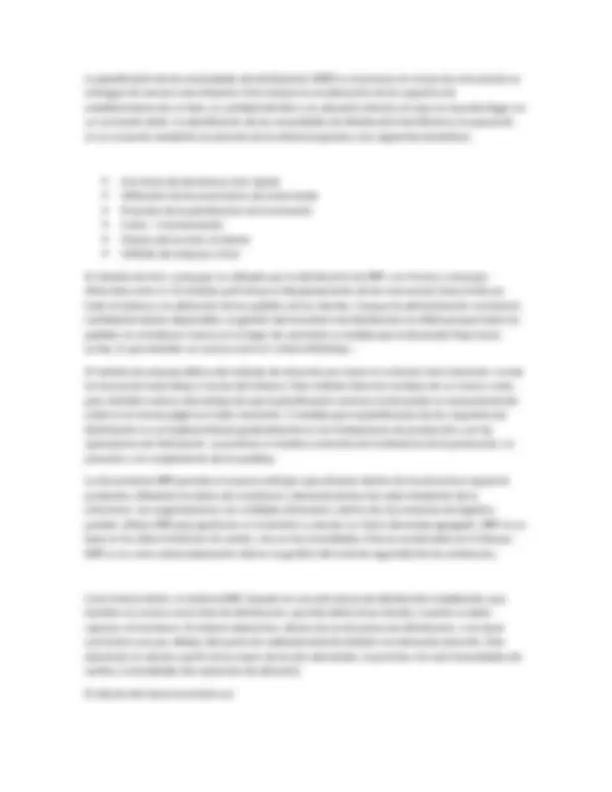
Prepara tus exámenes y mejora tus resultados gracias a la gran cantidad de recursos disponibles en Docsity
Gana puntos ayudando a otros estudiantes o consíguelos activando un Plan Premium
Prepara tus exámenes
Prepara tus exámenes y mejora tus resultados gracias a la gran cantidad de recursos disponibles en Docsity
Prepara tus exámenes con los documentos que comparten otros estudiantes como tú en Docsity
Los mejores documentos en venta realizados por estudiantes que han terminado sus estudios
Estudia con lecciones y exámenes resueltos basados en los programas académicos de las mejores universidades
Responde a preguntas de exámenes reales y pon a prueba tu preparación
Consigue puntos base para descargar
Gana puntos ayudando a otros estudiantes o consíguelos activando un Plan Premium
Comunidad
Pide ayuda a la comunidad y resuelve tus dudas de estudio
Descubre las mejores universidades de tu país según los usuarios de Docsity
Ebooks gratuitos
Descarga nuestras guías gratuitas sobre técnicas de estudio, métodos para controlar la ansiedad y consejos para la tesis preparadas por los tutores de Docsity
Planificacion de laproduccion del procesos
Tipo: Resúmenes
1 / 7
Esta página no es visible en la vista previa
¡No te pierdas las partes importantes!
La planificación de requerimientos de materiales (MRP) es un sistema utilizado para identificar y calcular los componentes y las acciones necesarias para la fabricación de un producto. El MRP puede dividirse en tres pasos principales: gestionar el inventario disponible, identificar las necesidades adicionales y planificar y programar su producción o adquisición. Los sistemas de planificación de requerimientos de materiales suelen incluir estas funcionalidades básicas: El Programa Maestro de Producción (MPS) vincula la demanda con la capacidad de fabricación. Define qué hay que producir, cuándo y en qué cantidades. La lista de materiales (BOM) enumera los pasos y elementos necesarios para crear un producto. Se utiliza para cuantificar los requisitos y organizar la fabricación. La gestión de inventarios mantiene y hace un seguimiento de los niveles de existencias necesarios de los componentes requeridos e informa de las adquisiciones. La estimación del plazo de entrega calcula el tiempo en el que se reciben las materias primas (plazo de entrega del material) y se producen y envían los productos terminados (plazo de producción). Aunque teóricamente es posible manejarlo en papel, los sistemas MRP modernos están basados en el ordenador y se ofrecen como software dedicado o como módulos integrados en suites de gestión de la producción más amplias, como los ERP de fabricación. En cualquier caso, un sistema MRP suele incluir tanto la gestión de inventarios como la planificación y programación de la producción. La abreviatura MRP suele referirse también a la Planificación de Recursos de Manufactura, conocida también como MRP II. MRP II es esencialmente un sistema MRP más avanzado que incluye la previsión de la demanda, la planificación empresarial y las funcionalidades de back-office además de lo que ofrece MRP I. Procesos El proceso de planificación de requerimientos de materiales puede dividirse en cuatro pasos básicos: Estimar la demanda y los materiales necesarios para satisfacerla. El paso inicial del proceso de Planificación de Requerimientos de Materiales es determinar la demanda del cliente y los requisitos para satisfacerla. Utilizando la lista de materiales (BOM) una lista de materias primas, conjuntos y componentes necesarios para fabricar el producto final MRP desglosa la demanda en materias primas y componentes específicos. Comprobar la demanda con el inventario y asignar los recursos. Este paso consiste en comprobar la demanda con los materiales ya disponibles en el inventario. A continuación, la planificación de
requerimientos de materiales distribuye los recursos consecuentemente. En otras palabras, el proceso de MRP asigna el inventario precisamente donde se necesita. Programación de la producción. El siguiente paso en el proceso es simplemente calcular la cantidad de tiempo y mano de obra necesaria para completar la fabricación. También se proporciona una fecha límite. Seguimiento. El último paso del proceso es la supervisión de cualquier problema. La planificación de requerimientos de materiales puede alertar automáticamente a los responsables de cualquier retraso e incluso sugerir planes de contingencia para cumplir los plazos de construcción.
La evolución de los sistemas de planificación de requerimientos de materiales condujo al desarrollo del ERP en la década de 1990. ERP son las siglas de Enterprise Resource Planning (Planificación de Recursos Empresariales) y se considera una de las categorías más comunes de software empresarial en la actualidad. Aunque el ERP solía ser el campo por excelencia de las grandes empresas, hoy en día su uso está muy extendido tanto en las pequeñas como en las grandes empresas. Al igual que la MRP, este modelo también puede ayudarle a planificar su producción, programar listas y gestionar el inventario. Sin embargo, el alcance del ERP va mucho más allá del segmento de la fabricación. El ERP es un método que permite centralizar la información y los procesos de flujo de trabajo. Hace un uso inteligente de las prácticas de gestión de datos al almacenar todos los datos relacionados con el flujo de trabajo en un único punto, lo que permite que los diferentes procesos empresariales extraigan datos de esa ubicación específica con el fin de obtener información y tomar decisiones empresariales productivas. ERP, término correspondiente a la planificación de recursos empresariales (Enterprise Resource Planning), es un software diseñado para administrar e integrar las funciones de los procesos comerciales centrales como finanzas, recursos humanos, cadena de suministro y administración de inventario en un solo sistema. Ampliamente utilizado en empresas de todos los tamaños, ERP se considera imprescindible para las grandes empresas y se está implementando cada vez más en pequeñas empresas en crecimiento. La complejidad de la economía global y las demandas de los consumidores modernos han hecho que agilizar los procesos comerciales y administrar y optimizar los datos sea fundamental. El ERP suele ser la base de estas capacidades. Un sistema ERP consta de componentes o módulos de software, cada uno de los cuales se centra en un proceso empresarial distinto. Ciertos módulos se consideran "básicos" para casi todos los tipos de negocios y son los primeros en implementarse: El módulo de finanzas ERP automatiza la contabilidad básica, la facturación, el análisis financiero, la previsión y la generación de informes. A menudo, es la razón principal por la que una empresa pasa a un ERP desde un software de contabilidad independiente. La creciente complejidad del
La planificación de los requisitos de capacidad es especialmente importante para empresas cuyos clientes les “penalizan” si no les entregan los productos a tiempo. Por ejemplo, una aerolínea quiere exigir por contrato a una empresa de fabricación de aviones a entregarle 100 aviones en un plazo de un año. Dentro de dicho contrato se encuentra una cláusula que dice que si la entrega finaliza más tarde, la empresa deberá pagar una multa por las molestias. Por tanto, antes de aceptar el contrato, la empresa de fabricación puede comprobar en el CRP si puede comprometerse a finalizar en dicho plazo. El software de CRP se suele usar junto con el software de MRP (planificación de requerimientos de materiales). Esto se debe a que el CRP calcula la posibilidad de llevar a cabo un pedido y el MRP se encarga de tener los materiales a tiempo para poder producir. Así que, si hubiera algún retraso en la planificación, esta información debería llegarle al MRP para que no lleguen los materiales antes de tiempo. Ventajas y desventajas de la planificación de los requisitos de capacidad Este sistema es muy conocido dentro de las empresas de producción. Sin embargo, no todas lo usan. A continuación, las empresas pueden ver cuáles son las ventajas y desventajas de este tipo de software: Ventaja: permite saber con mucha precisión la capacidad de la empresa para poder realizar la planificación. Además, puede tomar elementos externos en cuenta como la variación de la capacidad si se aumenta el personal y/o el equipo y si se subcontratara el servicio. También, puede recalcular la capacidad en el caso de que se averíe una máquina o que disminuya el personal. Desventaja: a pesar de que se alimenta de la información de las órdenes de pedido del MRP, hay que introducir muchos datos para que funcione. Por ejemplo, si alguna máquina va mal, hay que introducir cuál manualmente, junto con una estimación de cuándo estará reparada o cuando llega una nueva de reemplazo. Para automatizar el proceso de informar al CRP del fallo de una máquina, hay empresas que lo conectan con los sensores IoT de las máquinas. No obstante, con el IoT no se soluciona el problema. Esto se debe a que no es lo único que puede retrasar una producción. Por ello, se seguirá perdiendo tiempo del personal, ya que deberá seguir introduciendo datos manualmente en el CRP. Por ejemplo, cuando haya una mudanza de sedes o una disminución de la fuerza de trabajo también afecta a la capacidad.
El objeto comercial de planificación de los requisitos de distribución permite a una organización gestionar la distribución del producto entre las instalaciones. Esta herramienta (DRP) complementa la capacidad del usuario para asegurar que los almacenes dentro de una estructura definida, la factura de distribución, se están reaprovisionando con el producto adecuado en el momento adecuado y en las cantidades adecuadas.
La planificación de las necesidades de distribución (DRP) es el proceso en el que las mercancías se entregan de manera más eficiente. Esto incluye la consideración de los aspectos de establecimiento de un bien, la cantidad del bien y la ubicación directa a la que se necesita llegar en un momento dado. La planificación de las necesidades de distribución beneficiará a la operación en su conjunto mediante el aumento de la eficiencia gracias a los siguientes beneficios: Una toma de decisiones más rápida Utilización de las previsiones de la demanda Precisión de la planificación de la iniciación Costo – Concienciación Mejora del servicio al cliente Método de empujar o tirar El método de tirar o empujar es utilizado por la distribución de DRP, con tirones y empujes diferentes entre sí. El método pull incluye el desplazamiento de las mercancías hacia arriba en todo el sistema y la obtención de los pedidos de los clientes. Aunque la administración controla la cantidad de bienes disponibles, la gestión del inventario de distribución es difícil porque todos los pedidos se consideran nuevos en el lugar de suministro a medida que la demanda fluye hacia arriba, lo que también se conoce como el «efecto Bullwhip». El método de empuje difiere del método de atracción por hacer lo contrario de la atracción: enviar la mercancía hacia abajo a través del sistema. Este método tiene las ventajas de un menor costo, pero también está en desventaja de que la planificación central y la demanda no necesariamente están en la misma página en todo momento. A medida que la planificación de los requisitos de distribución se va implementando gradualmente en las instalaciones de producción y en las operaciones de fabricación, se produce un drástico aumento de la eficiencia de la producción, la precisión y el cumplimiento de los pedidos. La herramienta DRP permite al usuario anticipar qué almacén dentro de la estructura requerirá productos utilizando los datos de inventario y demanda dentro de cada instalación de la estructura. Las organizaciones con múltiples almacenes, dentro de una empresa de logística pueden utilizar DRP para gestionar su inventario y calcular su futura demanda agregada. DRP no se basa en los datos históricos de ventas, sino en las necesidades futuras escalonadas en el tiempo. DRP es un socio extremadamente vital en la gestión del nivel de seguridad de las existencias. Como hemos dicho, el sistema DRP, basado en una estructura de distribución establecida, que también se conoce como lista de distribución, permite determinar dónde y cuándo se debe reponer el inventario. El sistema determina, dentro de la estructura de distribución, si el stock económico cae por debajo del punto de reabastecimiento debido a la demanda entrante. Esta demanda se calcula a partir de la mayor de las dos demandas, la prevista o la real (necesidades de ventas o necesidades de reposición de almacén). El cálculo del stock económico es: