
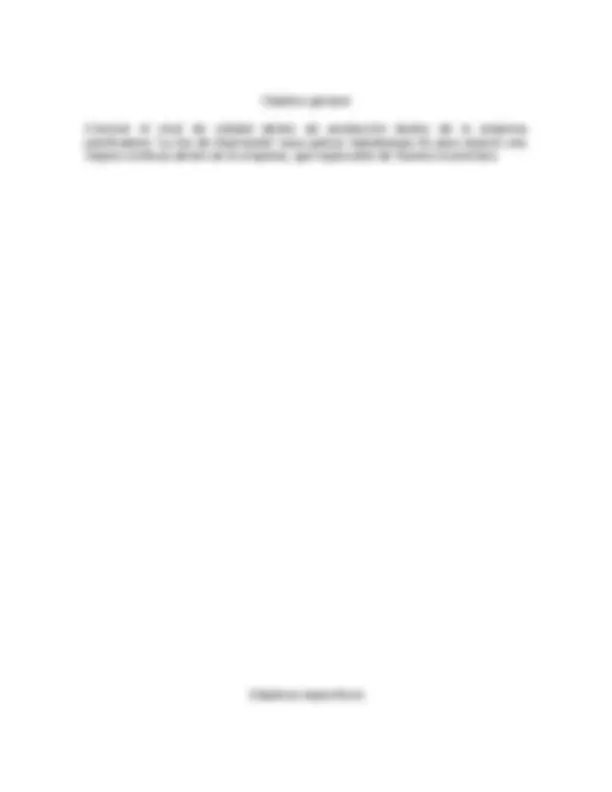
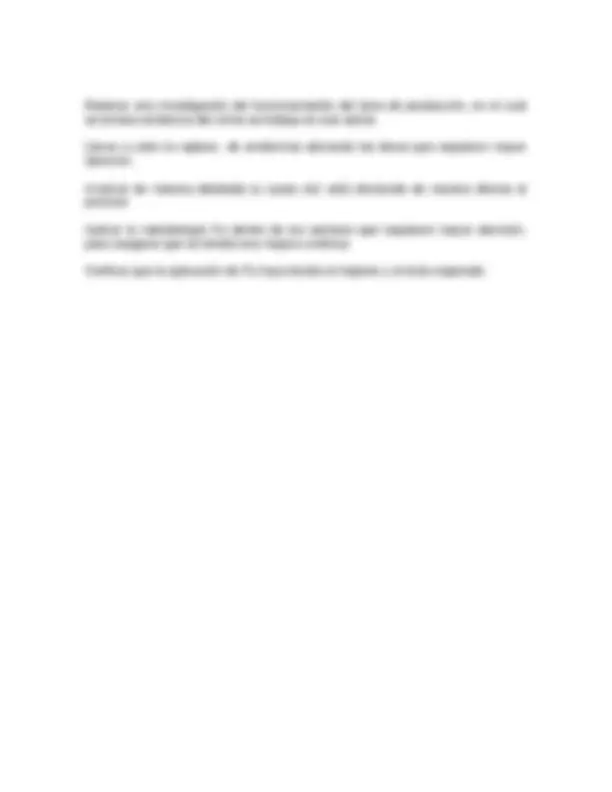
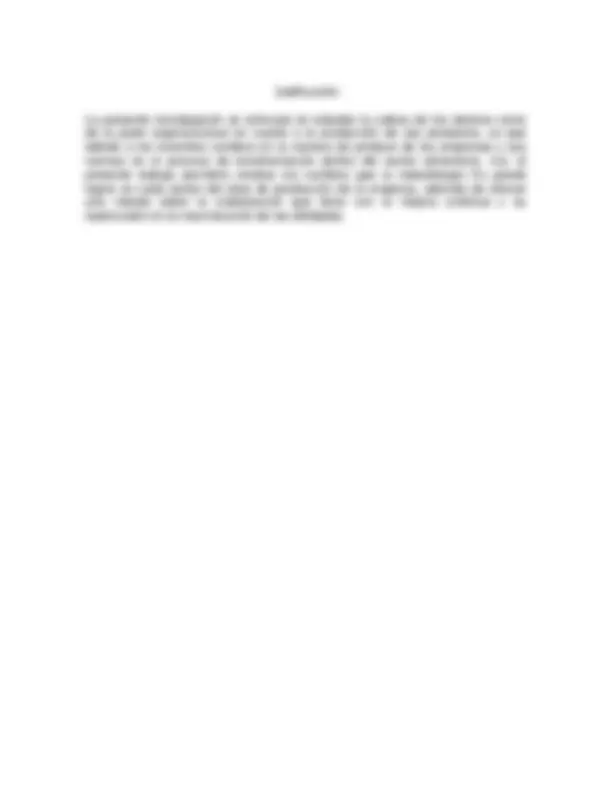
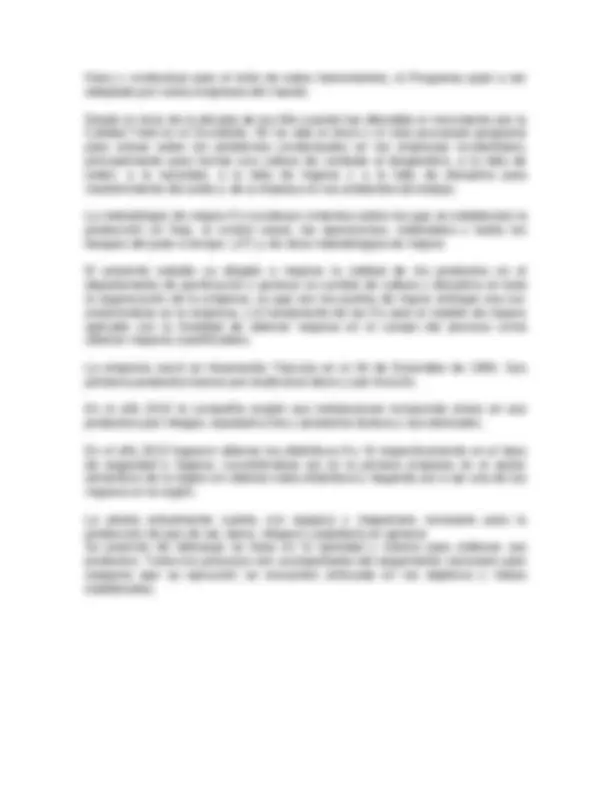
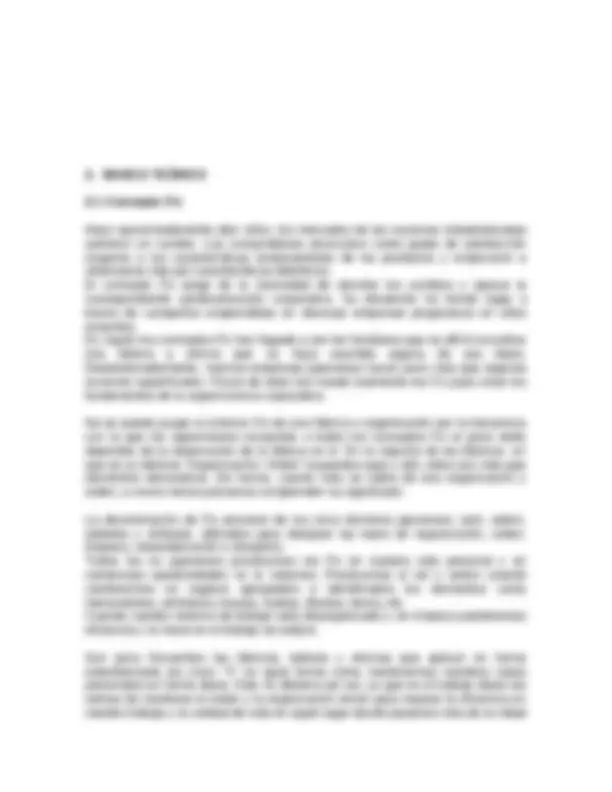
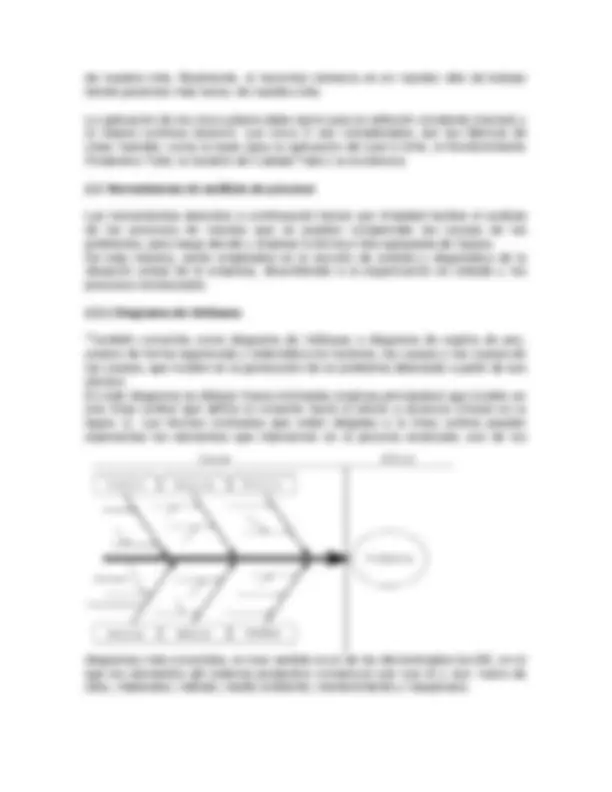
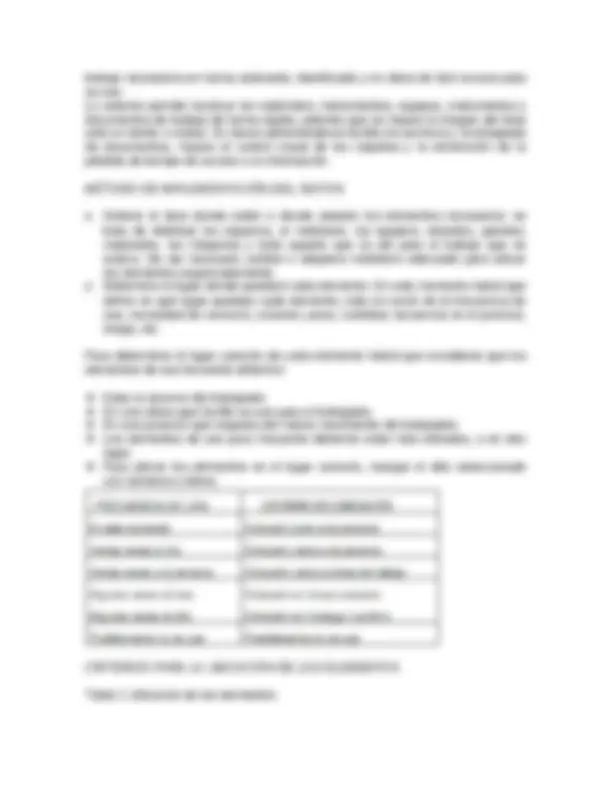
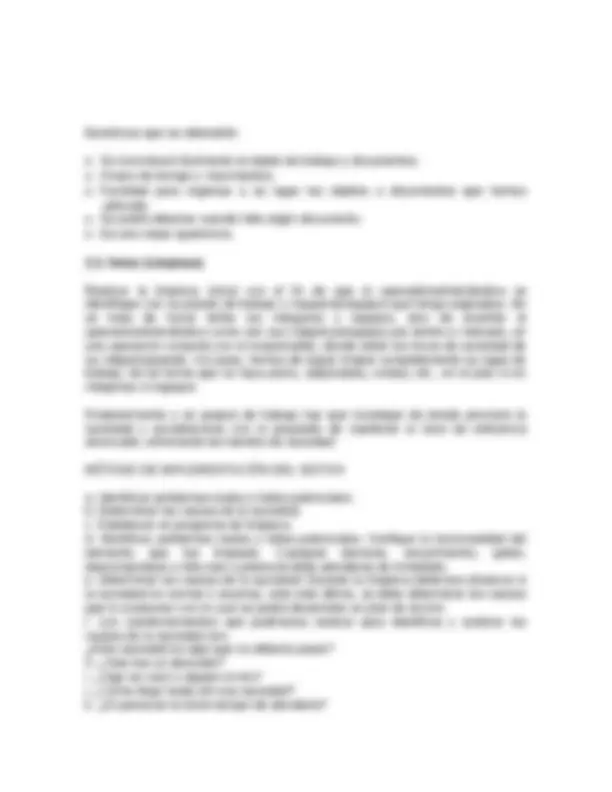
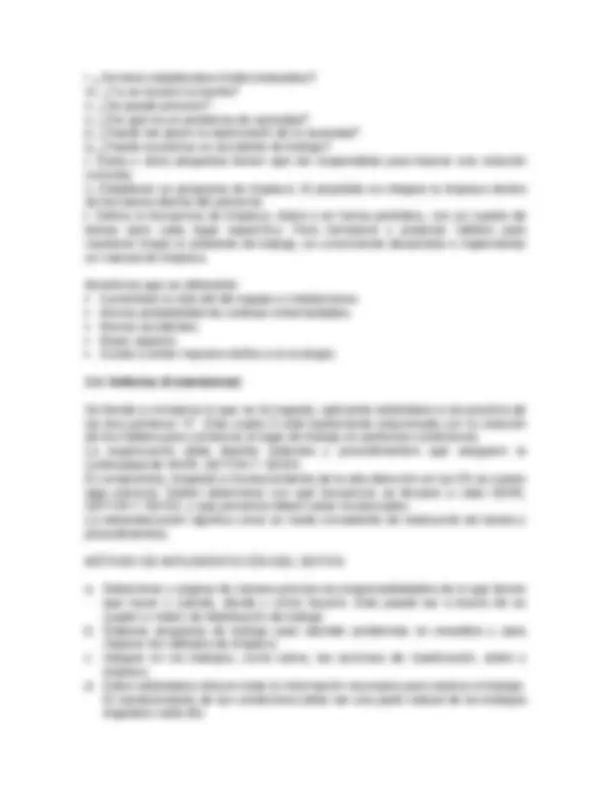
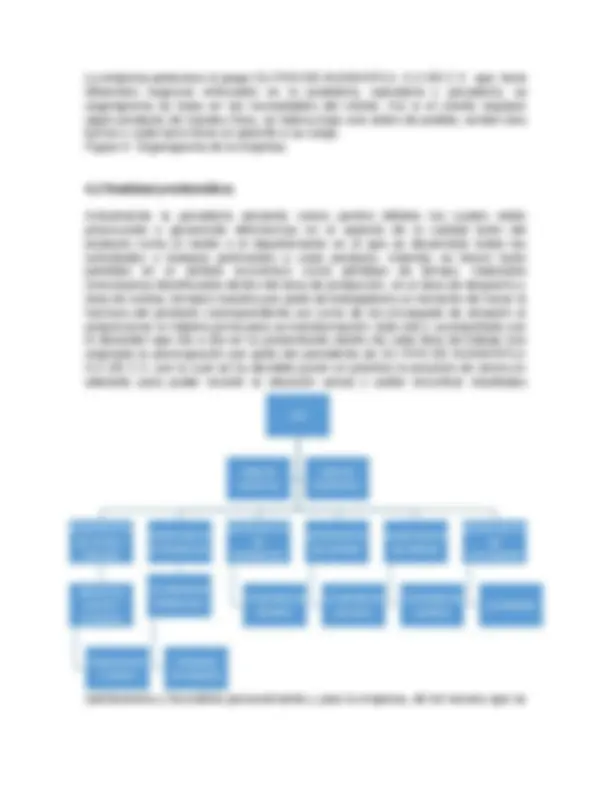
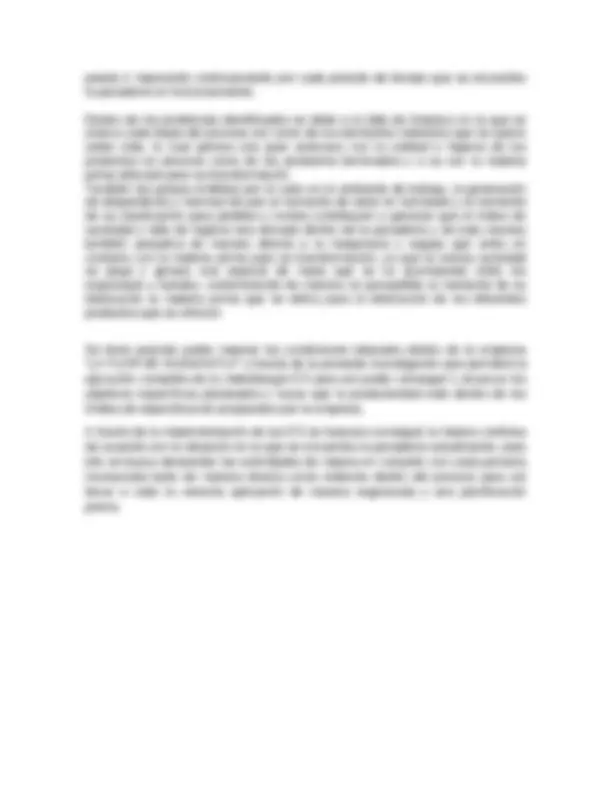
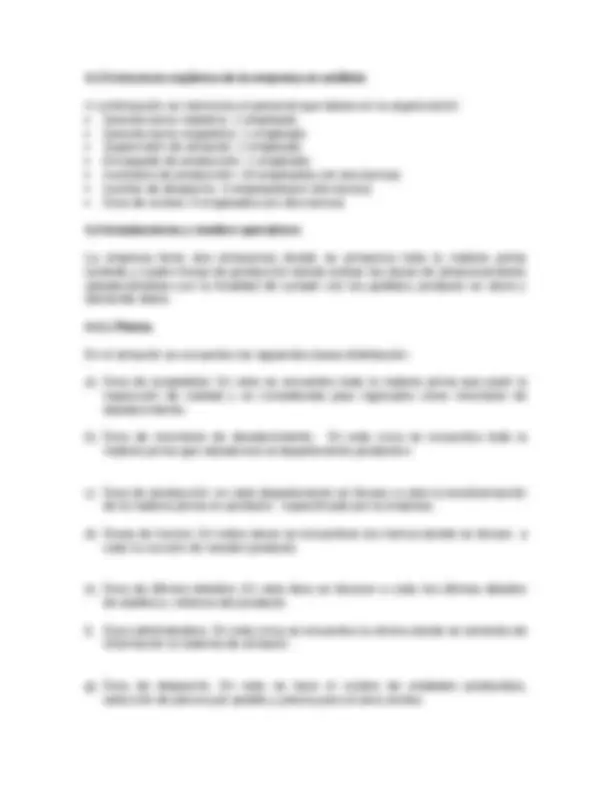
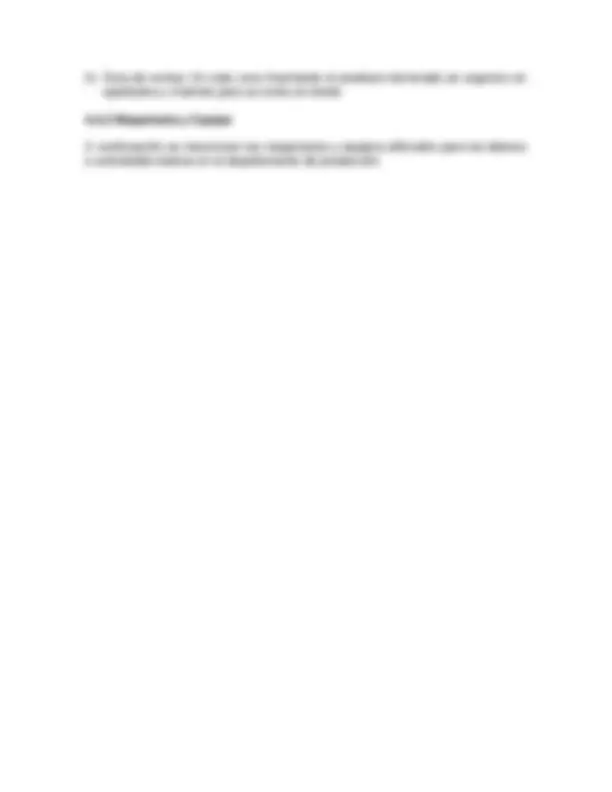
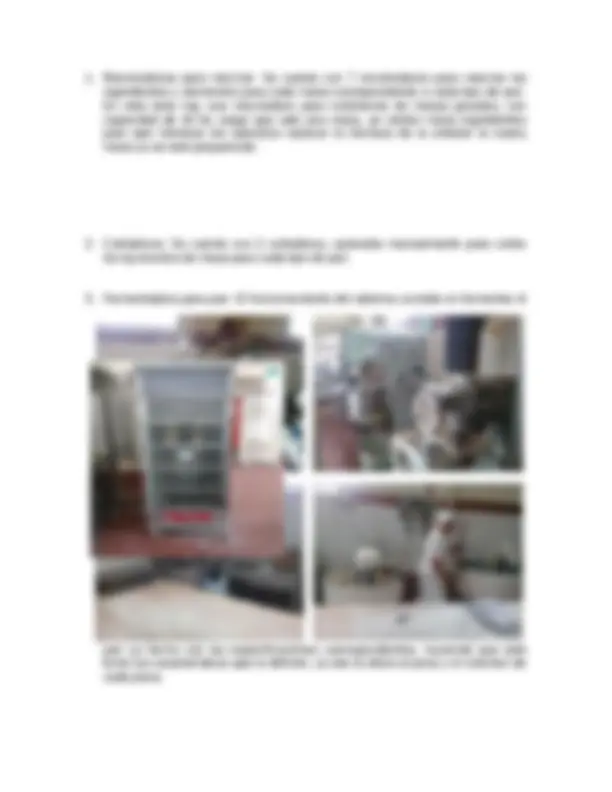
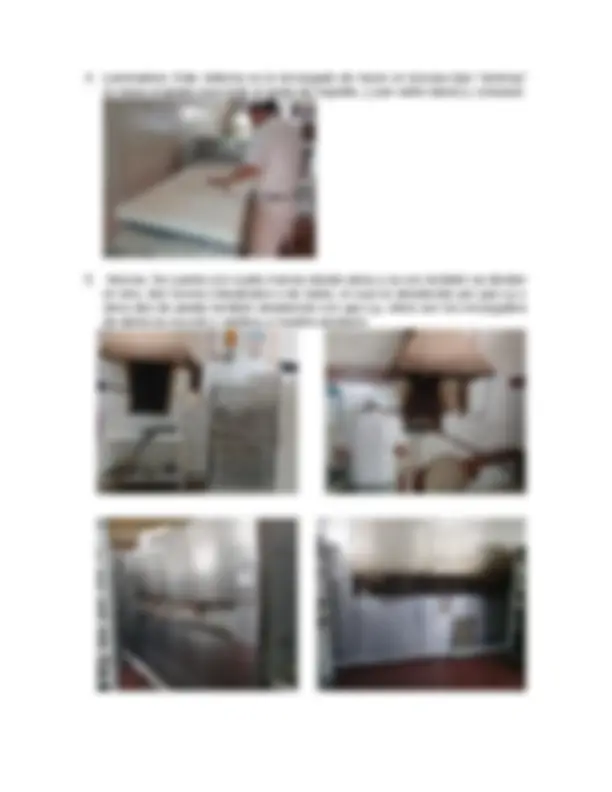
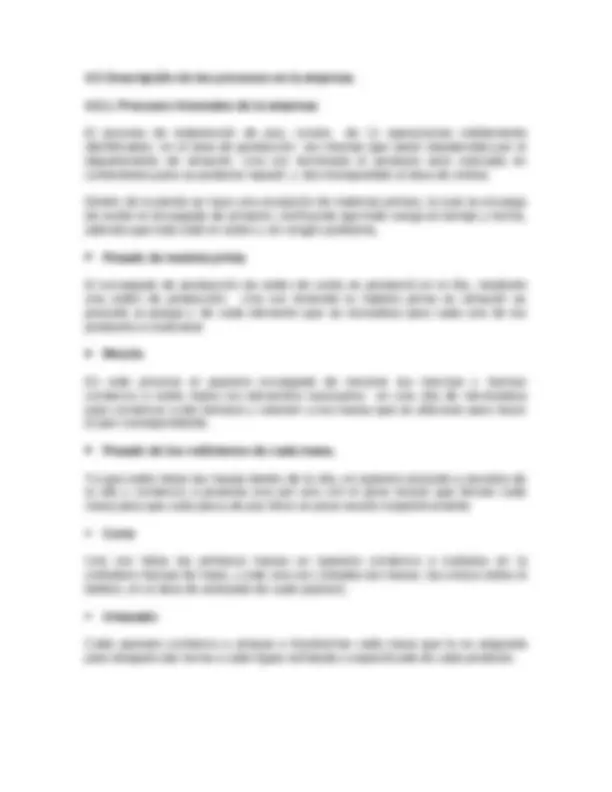
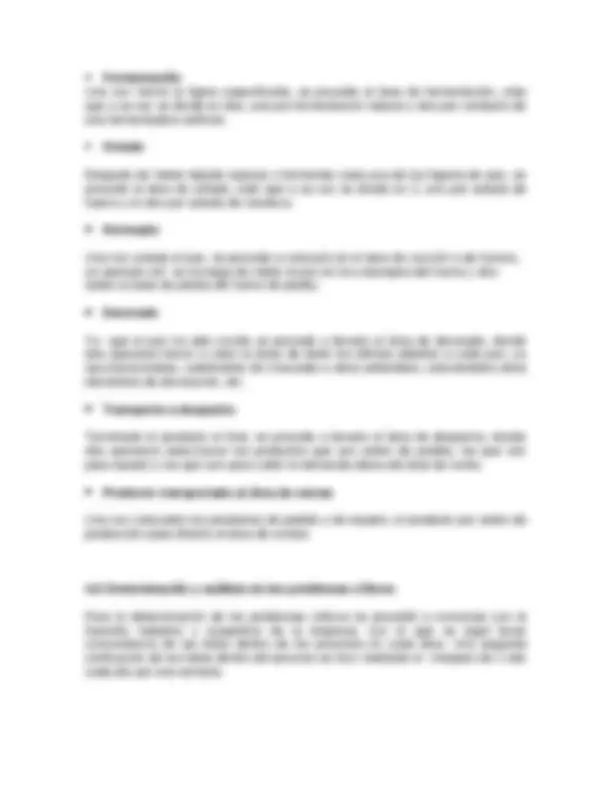
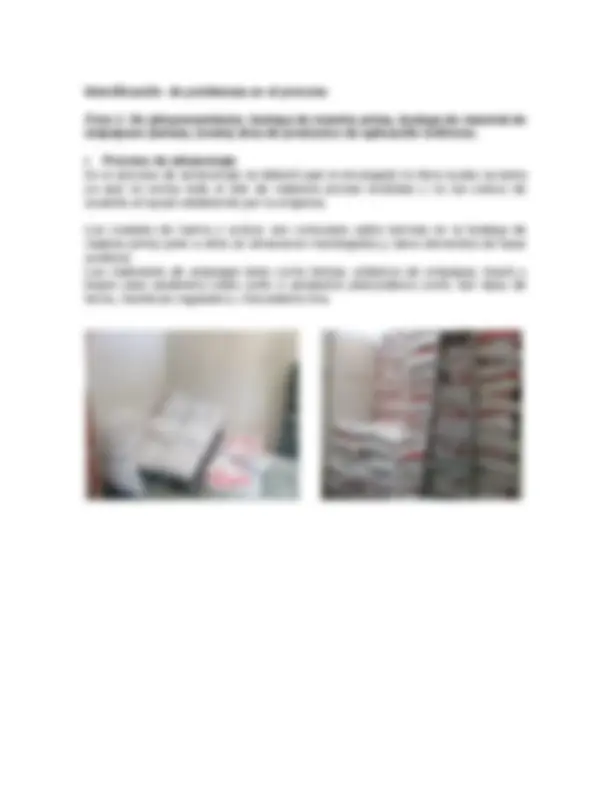
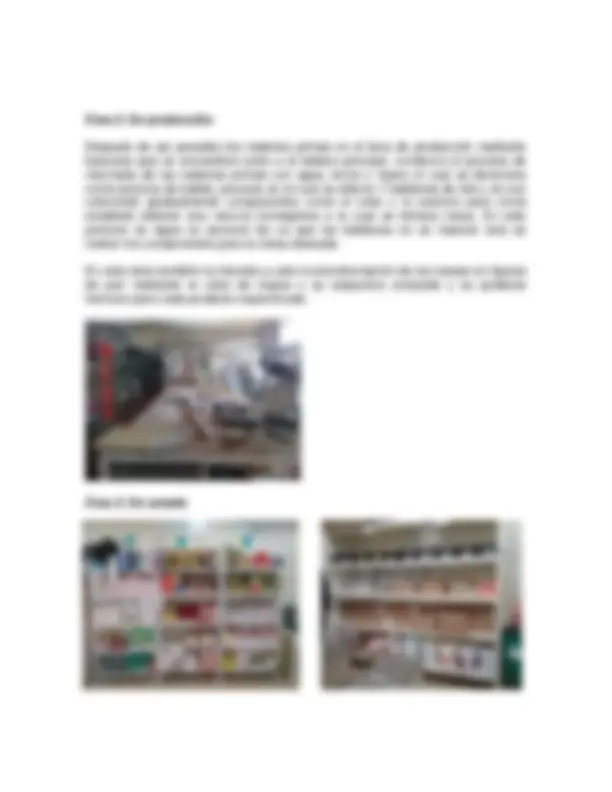
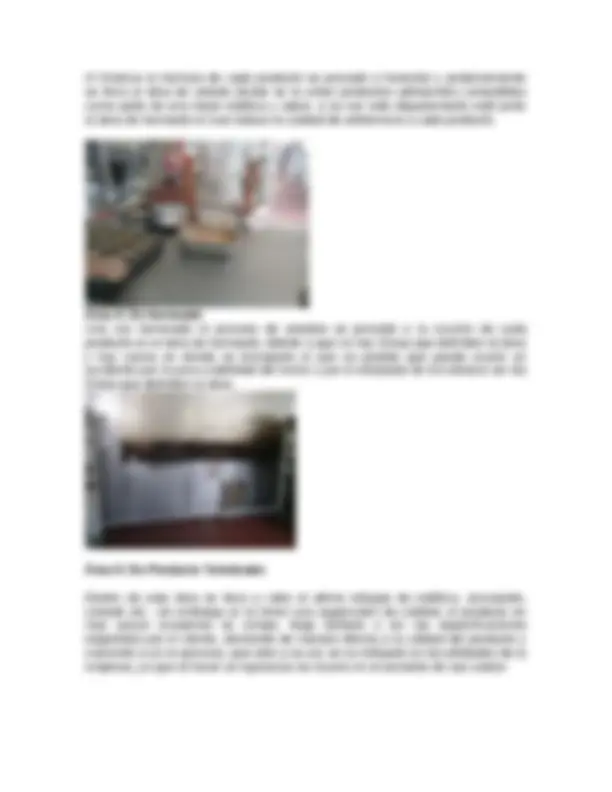
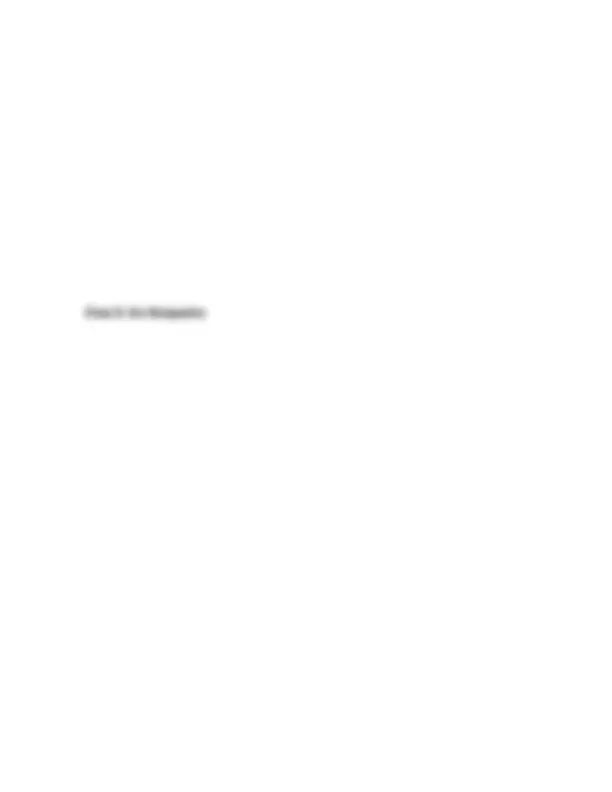
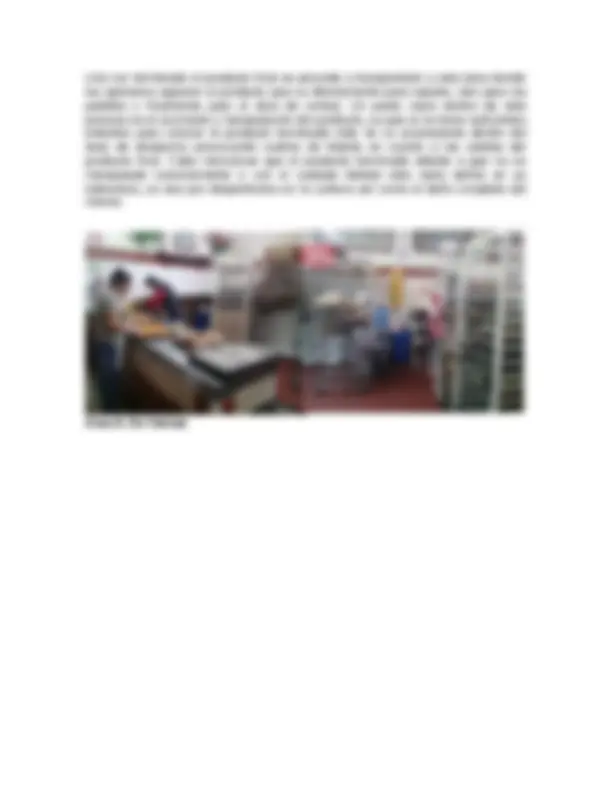
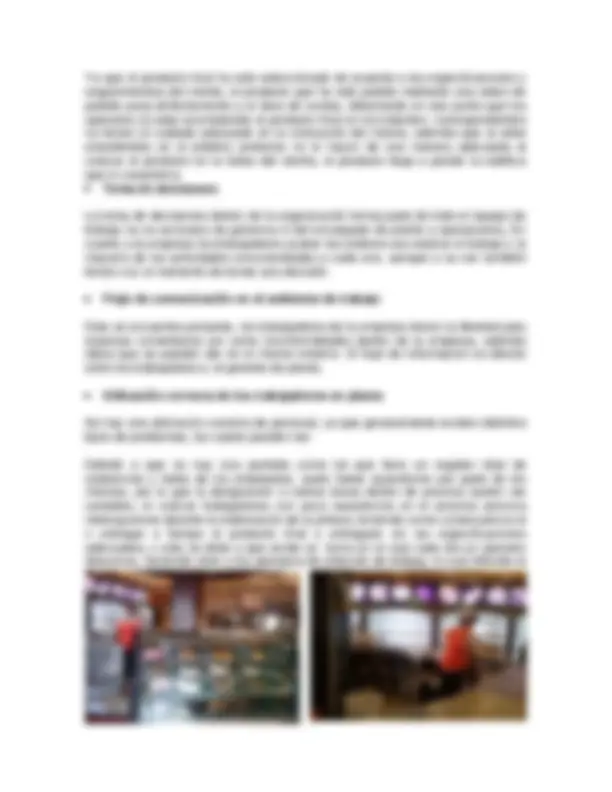
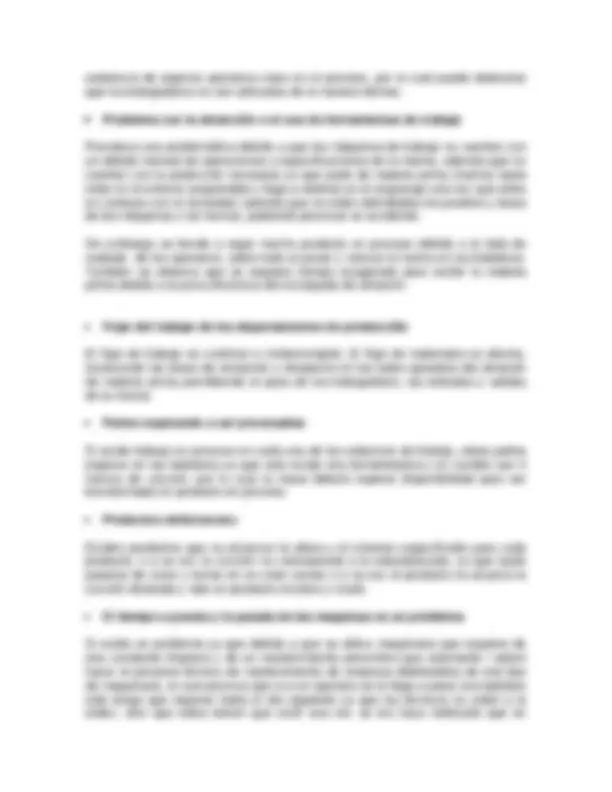
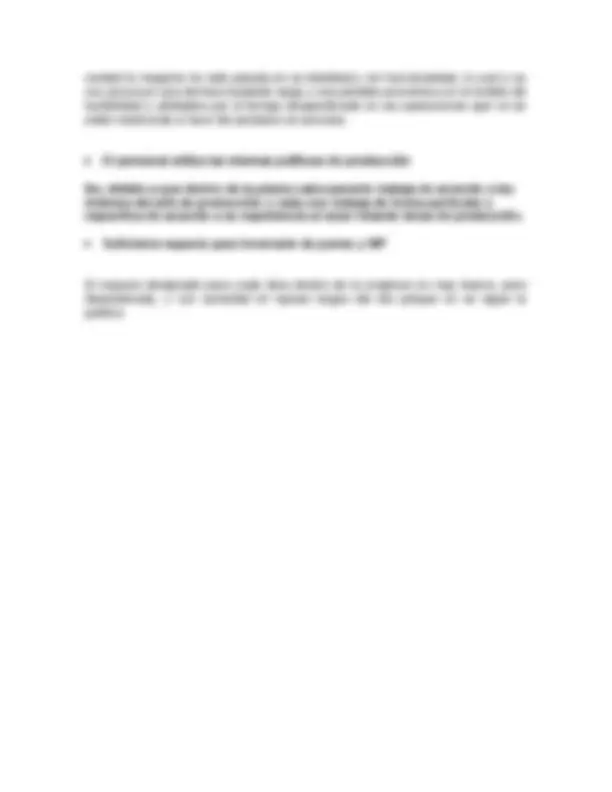
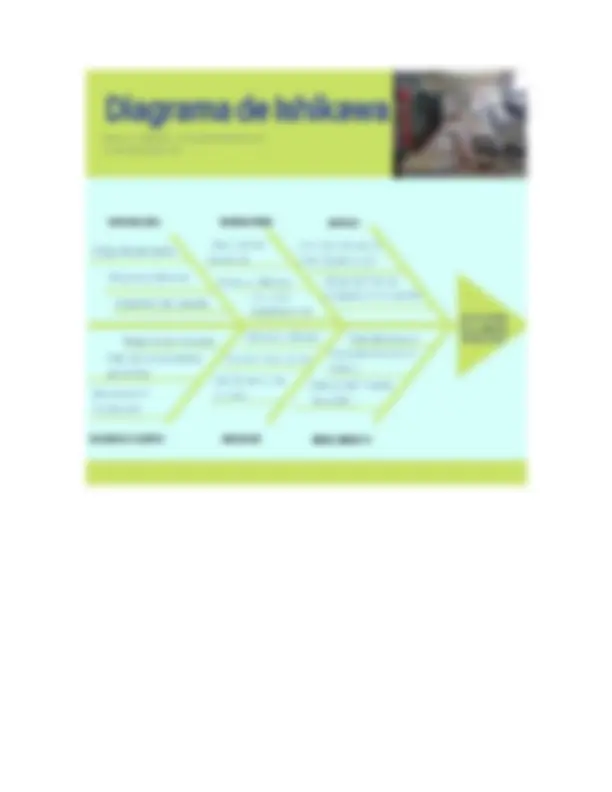
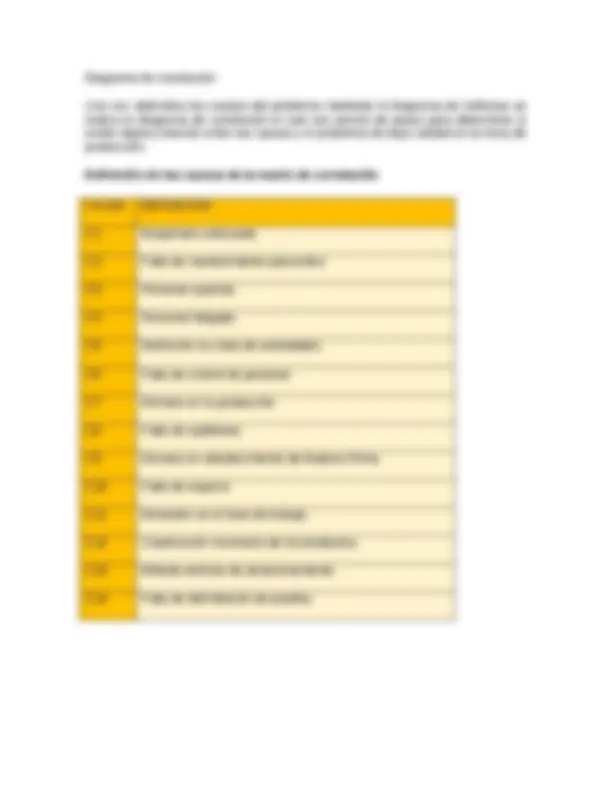
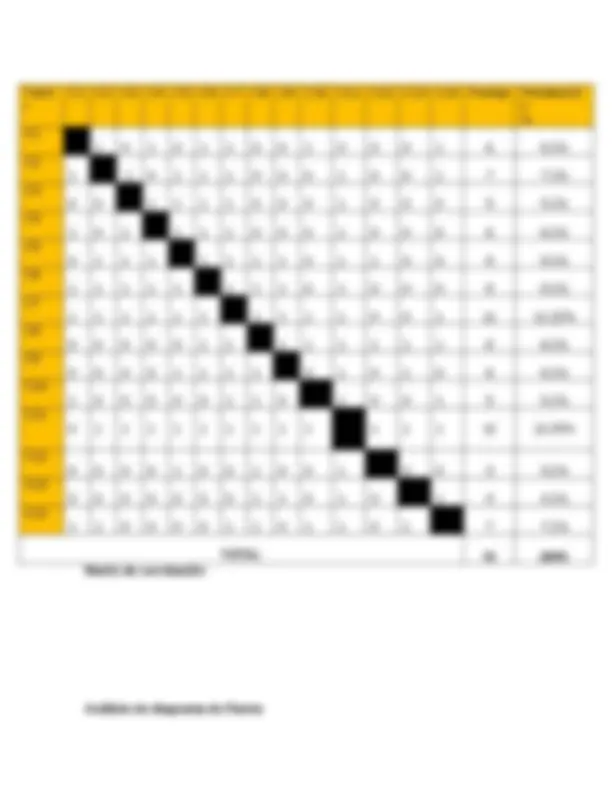
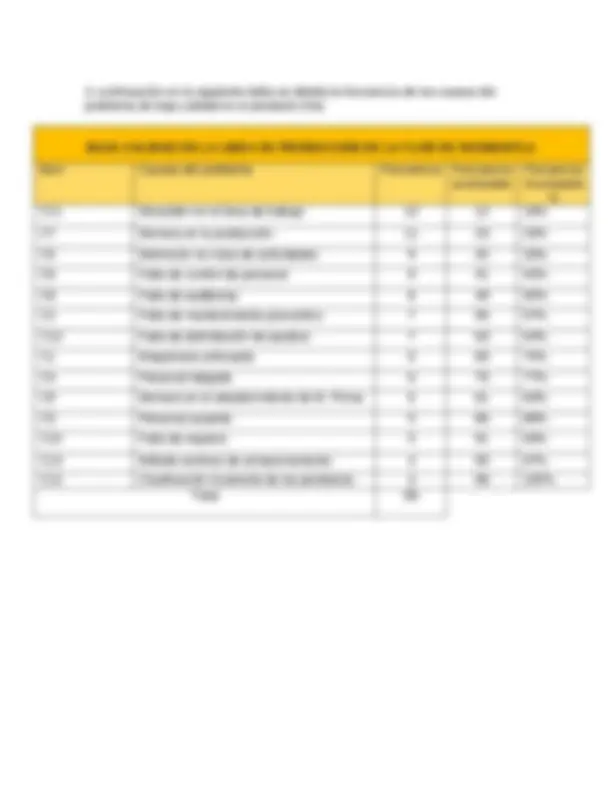

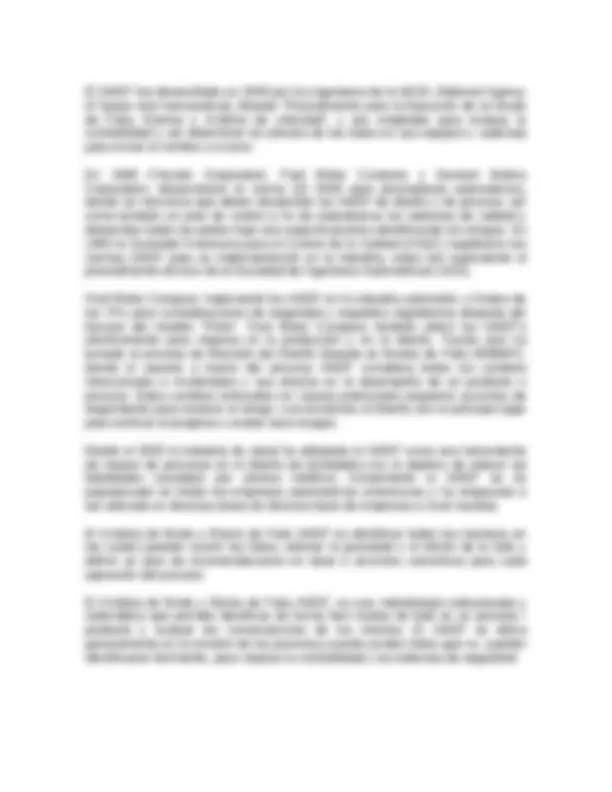
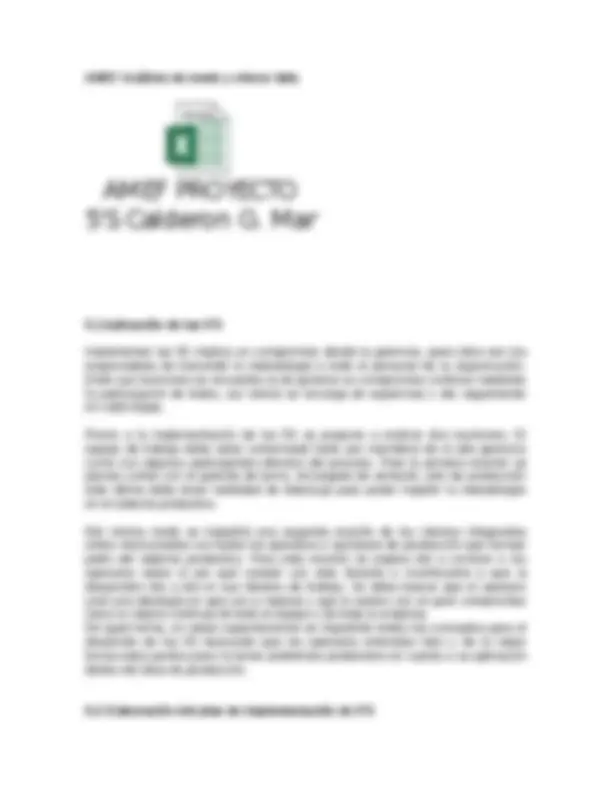
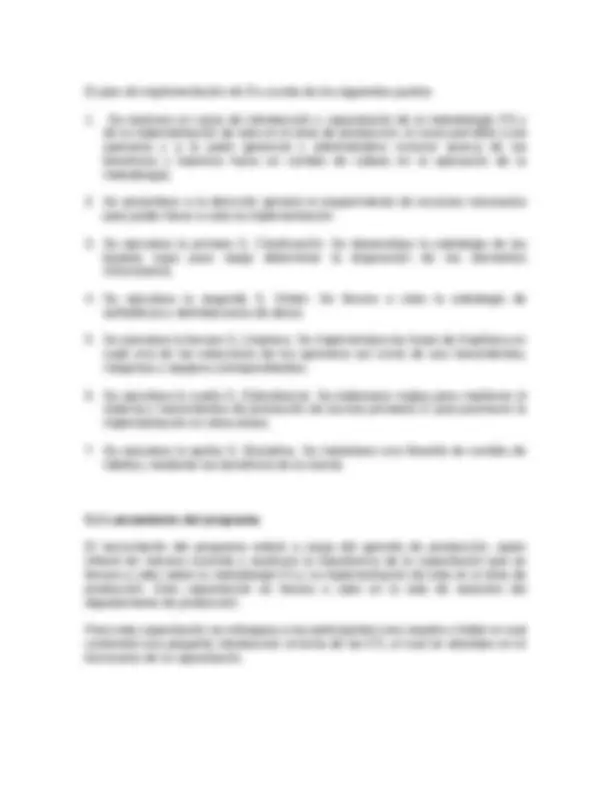
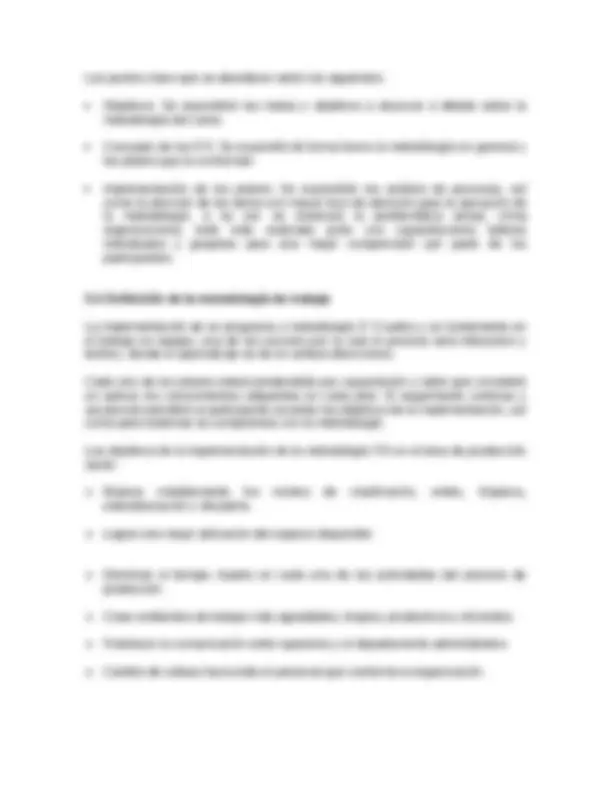
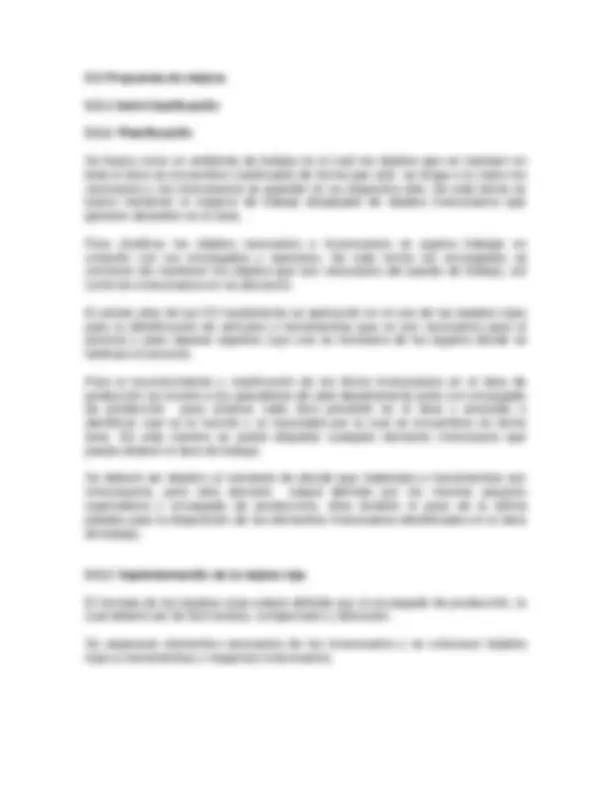
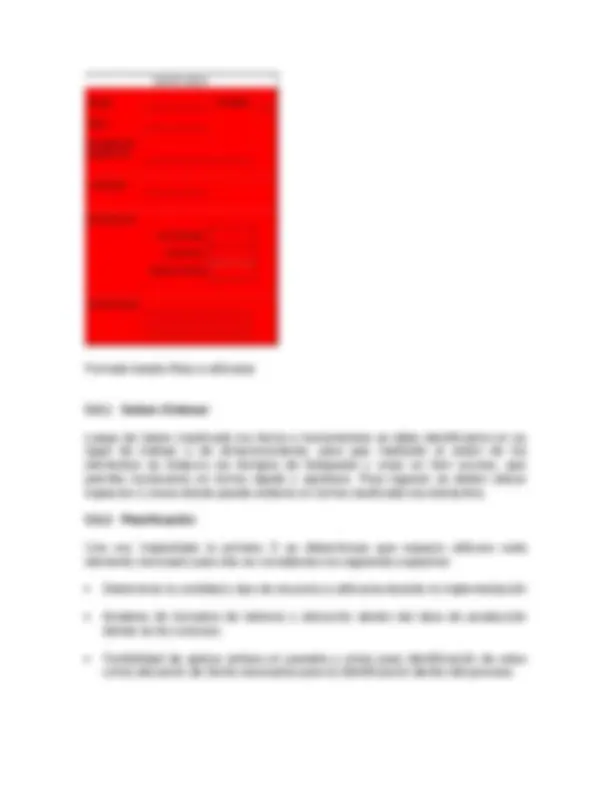
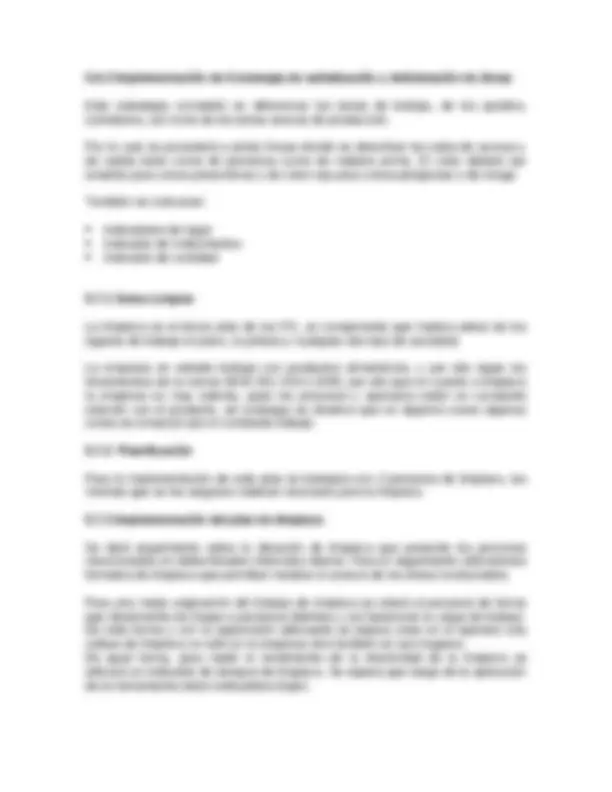
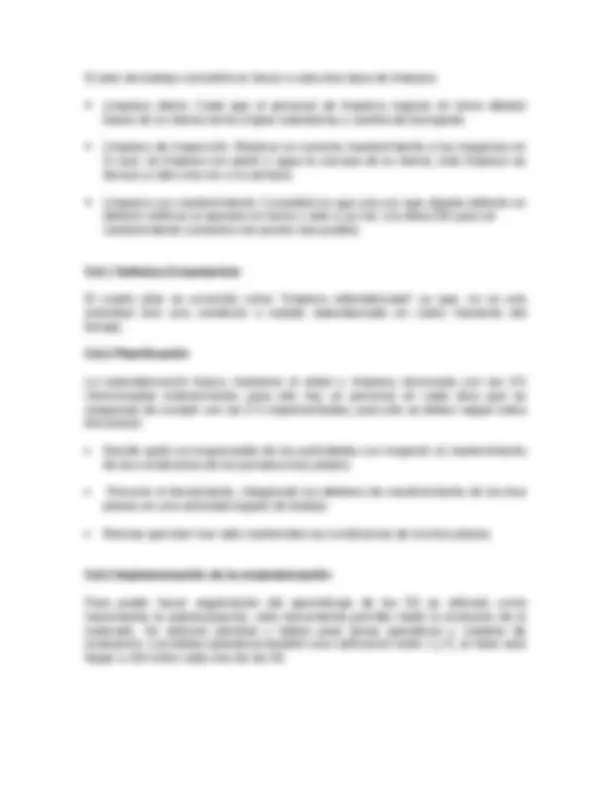
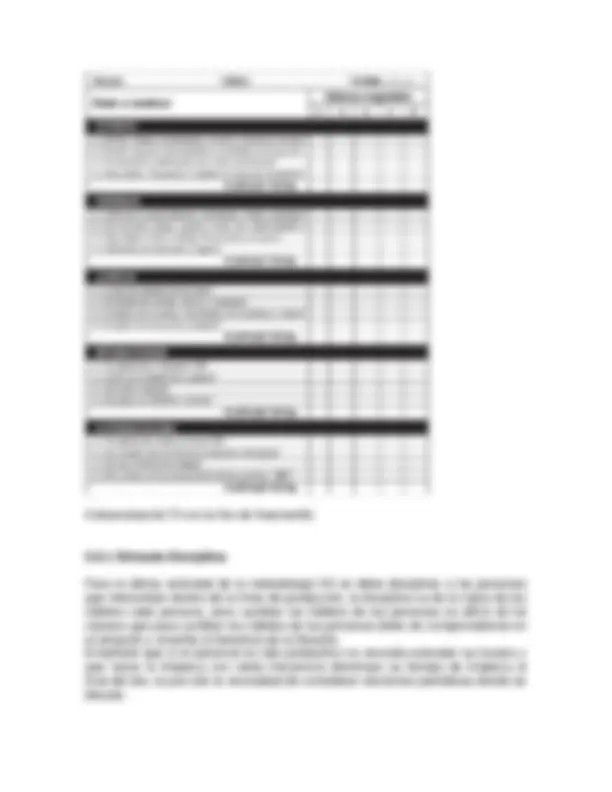
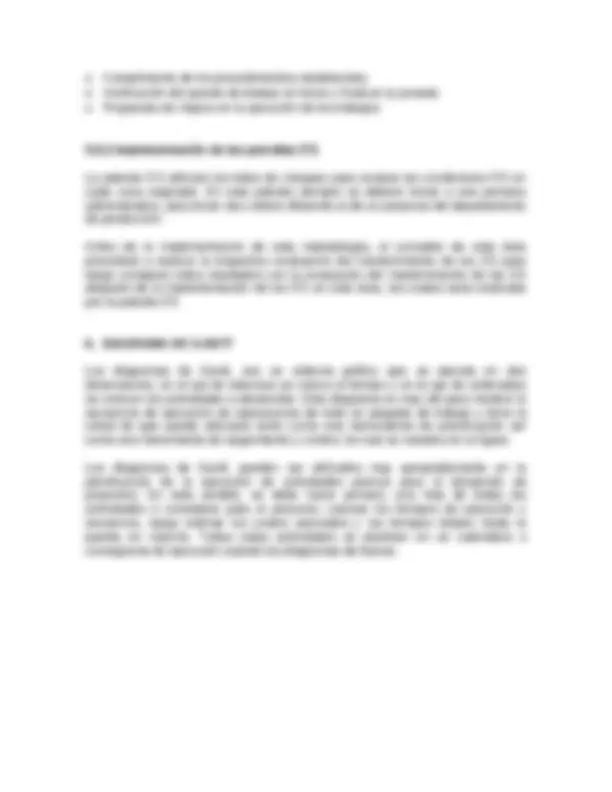
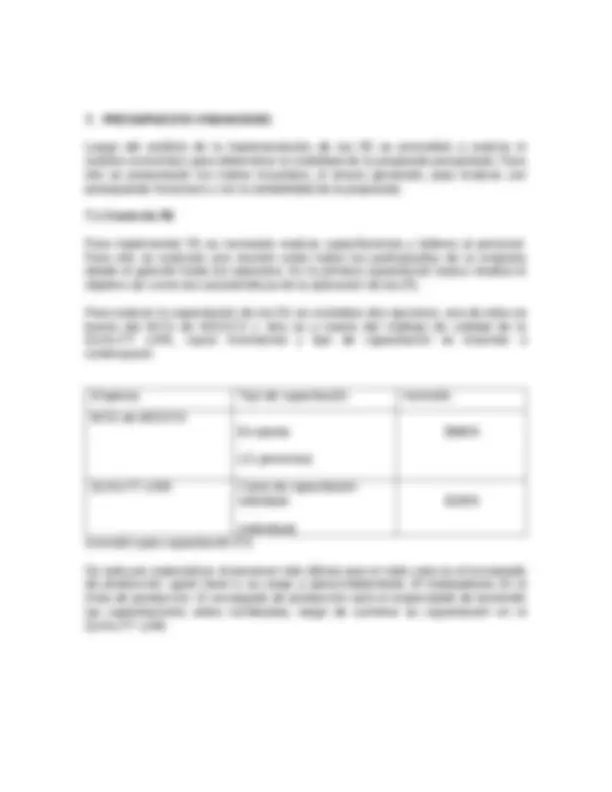
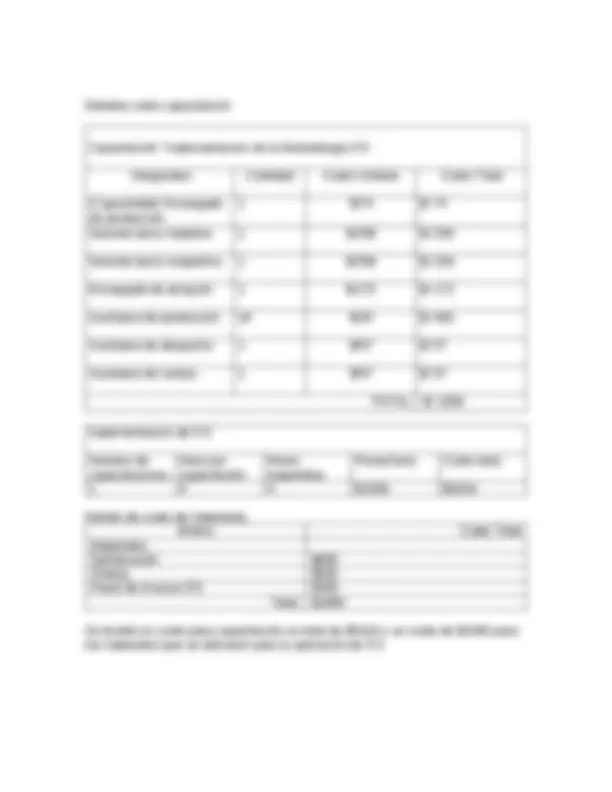
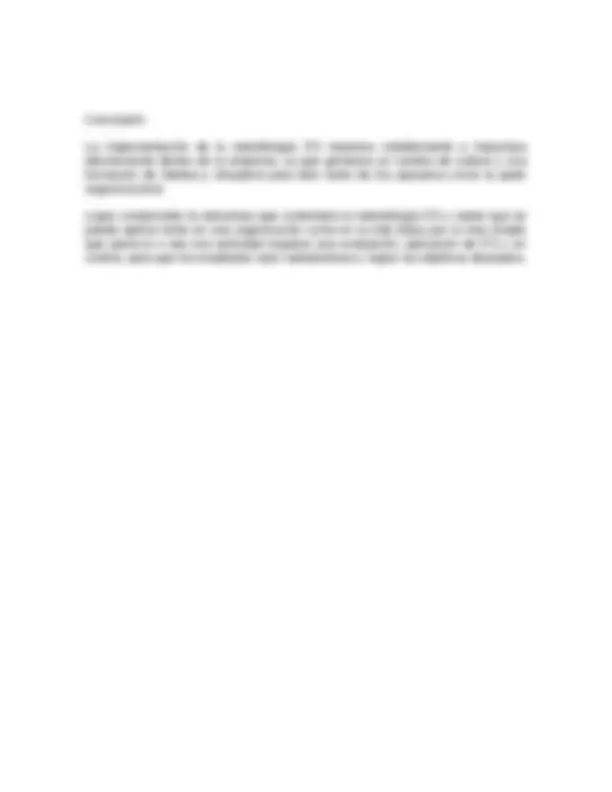
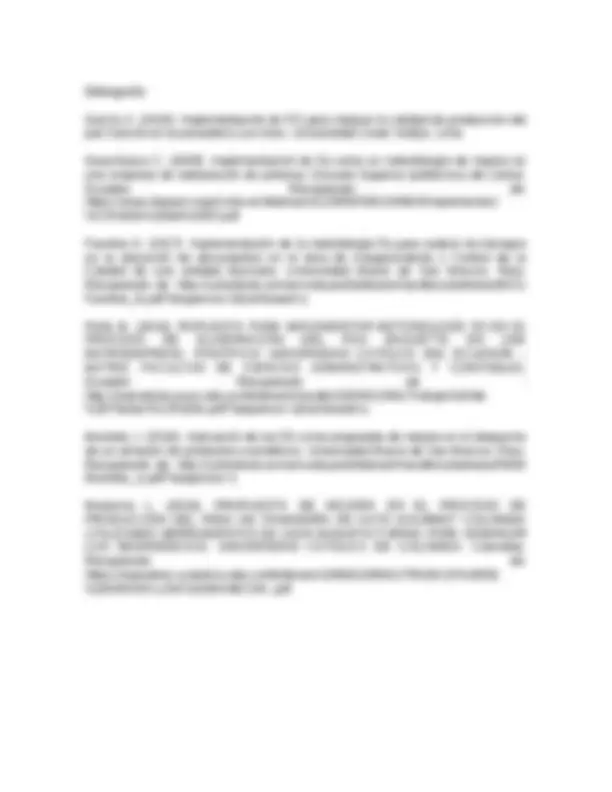
Prepara tus exámenes y mejora tus resultados gracias a la gran cantidad de recursos disponibles en Docsity
Gana puntos ayudando a otros estudiantes o consíguelos activando un Plan Premium
Prepara tus exámenes
Prepara tus exámenes y mejora tus resultados gracias a la gran cantidad de recursos disponibles en Docsity
Prepara tus exámenes con los documentos que comparten otros estudiantes como tú en Docsity
Los mejores documentos en venta realizados por estudiantes que han terminado sus estudios
Estudia con lecciones y exámenes resueltos basados en los programas académicos de las mejores universidades
Responde a preguntas de exámenes reales y pon a prueba tu preparación
Consigue puntos base para descargar
Gana puntos ayudando a otros estudiantes o consíguelos activando un Plan Premium
Comunidad
Pide ayuda a la comunidad y resuelve tus dudas de estudio
Descubre las mejores universidades de tu país según los usuarios de Docsity
Ebooks gratuitos
Descarga nuestras guías gratuitas sobre técnicas de estudio, métodos para controlar la ansiedad y consejos para la tesis preparadas por los tutores de Docsity
Aplicacion de la metologia 5s en una panaderia
Tipo: Guías, Proyectos, Investigaciones
1 / 52
Esta página no es visible en la vista previa
¡No te pierdas las partes importantes!
“2019, Año del Caudillo del Sur, Emiliano Zapata”
Planteamiento del problema Aplicar la metodología 5’s en el área de producción de una empresa, debido a que la misma requiere un cambio de cultura, ya que sus productos son de calidad, sin embargo en cuestión de organización necesitan ideas que colaboren para llevar a una mejora continua, y ser líder en la región. Se llevara a cabo en el periodo Octubre-Noviembre del año 2019, en una panificadora establecida en la ciudad de Huamantla Tlaxcala. Lo realizara el alumno Manuel Calderón Guzmán alumno de la carrera de Ingeniería Industrial en el Instituto tecnológico de Apizaco. Se realizara un análisis a detalle de la situación en la que se encuentra la empresa, para así poder definir qué sector del área de producción necesita más atención y poder aplicar 5’s. Cubrirá el 100% de la empresa y este tendrá un costo de acuerdo al presupuesto de la misma.
Realizar una investigación del funcionamiento del área de producción, en el cual se tomara evidencia del cómo se trabaja en ese sector. Llevar a cabo la captura de evidencias ubicando las áreas que requieren mayor atención. Analizar de manera detallada la causa raíz está afectando de manera directa al proceso Aplicar la metodología 5’s dentro de los sectores que requieren mayor atención, para asegurar que se tendrá una mejora continua Verificar que la aplicación de 5’s haya tenido el impacto y el éxito esperado
Justificación La presente investigación se enfocará en estudiar la cultura de los obreros como de la parte organizacional en cuanto a la producción de sus productos, ya que debido a los recientes cambios en la manera de producir de las empresas y sus normas en el proceso de transformación dentro del sector alimenticio. Así, el presente trabajo permitirá mostrar los cambios que la metodología 5’s puede lograr en cada sector del área de producción de la empresa, además de ofrecer una mirada sobre la colaboración que tiene con la mejora continua y su repercusión en la maximización de las utilidades.
Después la derrota sufrida en la II Guerra Mundial, el Japón buscó en su industria la principal fuente de recuperación económica. Como hasta ese momento la gran mayoría de los productos japoneses no tenía una buena imagen en los mercados europeos y norte-americano, la industria necesitaba producir productos de alta calidad y con precios competitivos, lo que exigía alta productividad. En el intento de implantación de algunos sistemas de calidad y productividad utilizados en las empresas del Occidente en el momento, la industria japonesa enfrentó varias limitaciones, principalmente de orden cultural. Desperdicio, desorganización, suciedad, falta de higiene, falta de procedimientos y falta de autodisciplina eran características comunes en los ambientes de trabajo japoneses. Por cuenta de eso, fue desarrollado un programa para actuar en estos tipos de problemas, con las siguientes características: el programa tenía que ser de simple entendimiento por cualquier persona, independiente de su nivel académico, jerárquico o social; tenía que ser practicado por toda la empresa; que fuese capaz de mejorar las condiciones de trabajo en día a día, sin demasiadas inversiones; y que fuese autosustentable, o sea, había que ser practicado como un hábito. Eso se pasó en el final de la década de los 50s, inicialmente para combatir al desperdicio, el desorden y la suciedad. Posteriormente para combatir la falta de higiene y la indisciplina. No hay una convergencia de informaciones sobre quien creó el Programa 5S. Algunos autores citan que fue el Dr. Kaoru Ishikawa, Ingeniero Químico japonés, principal diseminador de los conceptos de calidad total en aquel país. Esa referencia es debido ser el Profesor Ishikawa el responsable por la creación de los Círculo de Control de la Calidad, que tenía como principio popularizar los conceptos de estadística aplicada a la calidad. Pero, no hay ninguna citación en sus propios libros sobre esta supuesta referencia. Después de transformarse en una gran potencia económica, en la década de los 80s, Japón pasó a ser motivo de investigaciones por empresas de otros países, deseando conocer las herramientas de gestión utilizadas para justificar sus grandes aumentos de productividad (Calidad Total, Sistema Toyota de Producción, Just-In-Time o Lean Manufacturing; Mantenimiento Productivo Total – TPM; Círculos de Control de Calidad; el principio de mejora continua – KAIZEN). Como la mayoría de las empresas japonesas trata el Programa 5S como una base
física y conductual para el éxito de estas herramientas, el Programa pasó a ser adoptado por varias empresas del mundo. Desde el inicio de la década de los 90s cuando fue difundido el movimiento por la Calidad Total en el Occidente, 5S ha sido el único y el más procurado programa para actuar sobre los problemas conductuales en las empresas occidentales, principalmente para formar una cultura de combate al desperdicio, a la falta de orden, a la suciedad, a la falta de higiene y a la falta de disciplina para mantenimiento del orden y de la limpieza en los ambientes de trabajo. La metodología de mejora 5’s construye cimientos sobre los que se establecerá la producción en flujo, el control visual, las operaciones, estándares y todos los bloques del justo a tiempo. (JIT) y de otras metodologías de mejora. El presente estudio va dirigido a mejorar la calidad de los productos en el departamento de panificación y generar un cambio de cultura y disciplina en toda la organización de la empresa, ya que son los puntos de mayor enfoque una vez analizándose en la empresa, y el fundamento de las 5’s será el modelo de mejora aplicado con la finalidad de obtener mejoras en el campo del proceso como obtener mejoras cuantificables. La empresa nació en Huamantla Tlaxcala en el 06 de Diciembre de 1994. Sus primeros productos fueron pan tradicional dulce y pan francés. En el año 2010 la compañía amplio sus instalaciones incluyendo ahora en sus productos pan integral, repostería fina y productos lácteos y sus derivados. En el año 2015 lograron obtener los distintivos H y M respectivamente en el área de seguridad e higiene, convirtiéndose así en la primera empresa en el sector alimenticio de la región en obtener estos distintivos y llegando así a ser una de las mejores en la región. La planta actualmente cuenta con equipos y maquinaria necesaria para la producción de pan de sal, dulce, integral y pastelería en general. Su posición de liderazgo se basa en la seriedad y valores para elaborar sus productos. Todos los procesos son acompañados del seguimiento necesario para asegurar que su ejecución se encuentre enfocada en los objetivos y metas establecidas.
de nuestra vida. Realmente, si hacemos números es en nuestro sitio de trabajo donde pasamos más horas de nuestra vida. La aplicación de los cinco pilares debe servir para la reflexión constante (hensei) y la mejora continua (keizen). Las cinco S son consideradas, por las fábricas de clase mundial, como la base para la aplicación del just in time, el Mantenimiento Productivo Total, la Gestión de Calidad Total y la excelencia. 2.2 Herramientas de análisis de proceso Las herramientas descritas a continuación tienen por finalidad facilitar el análisis de los procesos de manera que se puedan comprender las causas de los problemas, para luego decidir y emplear la técnica más apropiada de mejora. De esta manera, serán empleadas en la sección de análisis y diagnóstico de la situación actual de la empresa, describiendo a la organización en estudio y los procesos involucrados. 2.2.1 Diagrama de Ishikawa “También conocida como diagrama de Ishikawa o diagrama de espina de pez, analiza de forma organizada y sistemática los factores, las causas y las causas de las causas, que inciden en la generación de un problema detectado a partir de sus efectos. En este diagrama se dibujan líneas inclinadas (espinas principales) que inciden en una línea central que define el conjunto hacia el efecto a alcanzar (Véase en la figura 1). Las flechas inclinadas que están dirigidas a la línea central pueden representar los elementos que intervienen en el proceso analizado; uno de los diagramas más conocidos, en ese sentido es el de las denominadas las 6M, en el que los elementos del sistema productivo comienzan por una M y son: mano de obra, materiales, método, medio ambiente, mantenimiento y maquinaria.
Figura 1. Diagrama de Ishikawa. Por tanto, el diagrama de Ishikawa ayuda a la identificación de las causas del problema, lo que permite determinar su origen y llevar a cabo las acciones adecuadas para resolverlo de raíz. El hecho de ser una herramienta creada por un grupo de trabajo fomenta el pensamiento creativo, prolífico y divergente, con un nivel común de comprensión del problema y una versión más contrastada de las causas. Las flechas principales de las causas (espinas principales), puede representar en otras ocasiones, los elementos del que se compone el producto y también los puestos del trabajo del proceso.” 2.2.2. Diagrama de Pareto Esta herramienta ayuda en la toma de decisiones sobre que causas hay que resolver prioritariamente para lograr mayor efectividad en la resolución de problemas. Así, en el caso de haber identificado la causa de defectos por medio del diagrama de Ishikawa, pueden haber aparecido muchas posibles causas y ahora interesa concentrarse en las más relevantes. La regla consiste en considerar que aproximadamente el 80% de las consecuencias de un fenómeno (por ejemplo, los defectos de calidad), son debidas a unas pocas e importantes causas (alrededor del 20% de ellas). Con objeto de seleccionar las causas más relevantes, se ordenan las mismas situándolas de mayor a menor incidencia (frecuencia o coste) a partir de la izquierda, tal como indica la figura 1. También se representa una curva que establece, para cada causa, el porcentaje total de fallos sobre el total, donde se aprecia en mayor o menor medida la regla anterior de Pareto. El diagrama de Pareto pone de manifiesto la importancia relativa de las diferentes causas y ayuda a decidir la línea de actuación frente a un problema. El uso continuo de estos diagramas permitirá supervisar y verificar la eficacia de las soluciones para la resolución de los problemas.
trabajo necesarios en forma ordenada, identificada y en sitios de fácil acceso para su uso. Lo anterior permite localizar los materiales, herramientas, equipos, instrumentos y documentos de trabajo de forma rápida, además que se mejore la imagen del área ante el cliente o visitas. En áreas administrativas facilita los archivos y la búsqueda de documentos, mejora el control visual de las carpetas y la eliminación de la pérdida de tiempo de acceso a la información. MÉTODO DE IMPLEMENTACIÓN DEL SEITON o Ordene el área donde están o donde estarán los elementos necesarios: se trata de distribuir los espacios, el mobiliario, los equipos, estantes, gavetas, materiales, las máquinas y todo aquello que es útil para el trabajo que se realiza. De ser necesario cambie o adquiera mobiliario adecuado para ubicar los elementos organizadamente. o Determine el lugar donde quedará cada elemento: En este momento habrá que definir en qué lugar quedara cada elemento, esto en razón de la frecuencia de uso, necesidad de cercanía, volumen, peso, cantidad, secuencia en el proceso, riesgo, etc. Para determinar el lugar correcto de cada elemento habrá que considerar que los elementos de uso frecuente deberían: Estar al alcance del trabajador. En una altura que facilite su uso para el trabajador. En una posición que requiera del menor movimiento del trabajador. Los elementos de uso poco frecuente deberían estar más retirados, o en otro lugar. Para ubicar los elementos en el lugar correcto, marque el sitio seleccionado con números o letras. CRITERIOS PARA LA UBICACIÓN DE LOS ELEMENTOS Tabla 1 Ubicacion de los elementos.
Beneficios que se obtendrán: o Se encontrará fácilmente el objeto de trabajo y documentos. o Ahorro de tiempo y movimientos. o Facilidad para regresar a su lugar los objetos o documentos que hemos utilizado. o Se podrá detectar cuando falta algún documento. o Da una mejor apariencia. 3.3. Seiso (Limpieza) Realizar la limpieza inicial con el fin de que el operador/administrativo se identifique con su puesto de trabajo y maquinas/equipos que tenga asignados. No se trata de hacer brillar las máquinas y equipos, sino de enseñar al operario/administrativo como son sus máquinas/equipos por dentro e indicarle, en una operación conjunta con el responsable, donde están los focos de suciedad de su máquina/puesto. Así pues, hemos de lograr limpiar completamente su lugar de trabajo, de tal forma que no haya polvo, salpicadura, virutas, etc., en el piso ni en máquinas ni equipos. Posteriormente y en grupos de trabajo hay que investigar de donde proviene la suciedad y sensibilizarse con el propósito de mantener el nivel de referencia alcanzado, eliminando las fuentes de suciedad. MÉTODO DE IMPLEMENTACIÓN DEL SEITON a. Identificar problemas reales o fallas potenciales. b. Determinar las causas de la suciedad. c. Establecer un programa de limpieza. d. Identificar problemas reales o fallas potenciales: Verifique la funcionalidad del elemento que fue limpiado. Cualquier derrame, escurrimiento, goteo, descompostura o falla real o potencial debe atenderse de inmediato. e. Determinar las causas de la suciedad: Durante la limpieza debemos observar si la suciedad es normal o anormal, ante esto último, se debe determinar las causas que lo ocasionan con lo cual se podrá desarrollar un plan de acción. f. Los cuestionamientos que podríamos realizar para identificar y analizar las causas de la suciedad son: ¿Esta suciedad es algo que no debería pasar? h. ¿Solo fue un descuido? i. ¿Algo se cayó o alguien lo tiro? j. ¿Cómo llego hasta allí esa suciedad? k. ¿El personal no tiene tiempo de atenderlo?
Beneficios que se obtendrán: Se guarda le conocimiento producido durante años. Se mejora el bienestar del personal al crear un hábito de conservar impecable el sitio de trabajo de forma permanente. El personal aprende a conocer con profundidad el equipo y elementos de trabajo. Se evitan errores de limpieza que puedan conducir a riesgos laborales. Se dan las condiciones para que el personal tenga un mejor desempeño en su trabajo, lo que impacta en su productividad. 3.5. Shitsuke (Disciplina) La disciplina es el apego a una serie de reglas que norman la vida de una comunidad, de la organización o de nuestra propia vida; la disciplina es orden y control personal que se logra a través de un entrenamiento de las facultades mentales, físicas o morales. El éxito va acompañado de la disciplina, las casualidades son temporales. Practicando y practicando es como lograremos cambiar nuestros hábitos. Cuando se practica continuamente SEIRI, SEITON, SEISO Y SEIKETSU se ha adquirido el hábito adquirido, por lo que se ha logrado la disciplina. ACCIONES PARA PROMOVER LA DISCIPLINA La disciplina se puede lograr si los trabajadores de la organización se vuelven conscientes y asumen un compromiso real para cambiar sus hábitos y mantener una disciplina de orden y limpieza. La organización debería comprometerse a: o Cumplir y vigilar que se cumplan de manera sistemática con los estándares de trabajo establecidos. o Asegurarse de que estén claramente definidas las responsabilidades y que estas las conoce y comprende el personal. o Crear conciencia de la importancia del orden y la limpieza y de cómo contribuye cada trabajador, o bien de los efectos del desorden y la suciedad. o Educar al personal sobre los principios y técnicas de las 5S. o Hacer partícipe al personal en la búsqueda de soluciones y acciones de mejora. o Asegurarse de la eficacia del entrenamiento en las actividades que implica el programa. o Reconocer el desempeño sobresaliente y estimular a los que aún no lo logran. o Retroalimentar de inmediato cuando no se logran los resultados. o Establecer un proceso y herramientas de seguimiento eficaz para verificar y evaluar el cumplimiento sistemático y el progreso de cada área. o Propiciar respeto por la preservación del orden y la limpieza de las áreas comunes.
o Establecer ayudas visuales que orienten o recuerden al personal para que mantengan el orden y la limpieza. o Ser congruentes como jefes, demostrando como jefes y con hechos. o Asumir con entusiasmo la implantación de las 5S. o Crear un equipo promotor o líder para la implementación de las 5S en toda la entidad. o Suministrar los recursos para la implantación de las 5S. o Publicar fotos del antes y el después. o Establecer rutinas diarias de aplicación, por ejemplo, los 5 minutos de 5S, eventos mensuales y semestrales.”
4. DIAGNÓSTICO Y ANÁLISIS DE LA SITUACIÓN ACTUAL. La empresa objeto de estudio, es una empresa cuyo giro de negocio es el de la panificación, con el complemento de repostería fina y productos lácteos y sus derivados. El caso en particular sobre el cual se realiza el estudio pertenece al negocio de panadería cuyas operaciones tanto de almacenaje, recepción, transformación, venta y distribución se realiza de forma particular dependiendo de las necesidades del cliente. 4.1 Estructura Orgánica
pueda ir mejorando continuamente por cada periodo de tiempo que se encuentre la panadería en funcionamiento. Dentro de los problemas identificados se debe a la falta de limpieza en la que se realiza cada etapa del proceso así como de los elementos indirectos que se ejerce sobre este, lo cual genera una gran amenaza con la calidad e higiene de los productos en proceso como de los productos terminados y a su vez la materia prima utilizada para su transformación. También las grasas emitidas por el calor en el ambiente de trabajo, la generación de desperdicios y mermas de pan al momento de estar en horneado y al momento de su clasificación para pedidos y ventas contribuyen o generan que el índice de suciedad y falta de higiene sea elevado dentro de la panadería y de esta manera también perjudica de manera directa a la maquinaria y equipo que entra en contacto con la materia prima para su transformación, ya que la misma suciedad se pega y genera una especie de masa que se va acumulando entre los engranajes y bandas, contaminando de manera no perceptible al momento de su fabricación la materia prima que se utiliza para la fabricación de los diferentes productos que se ofrecen. Se tiene previsto poder mejorar las condiciones laborales dentro de la empresa “LA FLOR DE HUAMANTLA” a través de la presente investigación que permitirá la ejecución completa de la metodología 5’S para así poder conseguir y alcanzar los objetivos específicos planteados y hacer que la productividad este dentro de los límites de especificación propuestos por la empresa. A través de la implementación de las 5’S se buscara conseguir la mejora continua de acuerdo con la situación en la que se encuentra la panadería actualmente, para ello se busca desarrollar las actividades de mejora en conjunto con cada persona involucrada tanto de manera directa como indirecta dentro del proceso para así llevar a cabo la correcta aplicación de manera organizada y una planificación previa.
4.3 Estructura orgánica de la empresa en análisis A continuación se menciona al personal que labora en la organización: Gerente turno matutino- 1 empleado Gerente turno vespertino- 1 empleado Supervisión de almacén- 1 empleado Encargado de producción- 1 empleado Auxiliares de producción- 24 empleados (en dos turnos) Auxiliar de despacho- 4 empleados(en dos turnos) Área de ventas- 6 empleados (en dos turnos) 4.4 Instalaciones y medios operativos La empresa tiene dos almacenes donde se almacena toda la materia prima recibida y cuatro líneas de producción donde actúan las áreas de almacenamiento abasteciéndolas con la finalidad de cumplir con los pedidos, producto en stock y demanda diaria. 4.4.1 Planta. En el almacén se encuentra las siguientes áreas distribución: a) Área de aceptables: En esta se encuentra toda la materia prima que pasó la inspección de calidad y es considerada para ingresarla como inventario de abastecimiento. b) Área de inventario de abastecimiento: En esta zona se encuentra toda la materia prima que abastecerá al departamento productivo c) Área de producción: en este departamento se llevara a cabo la transformación de la materia prima en producto especificado por la empresa. d) Áreas de hornos: En estas áreas se encuentran los hornos donde se llevara a cabo la cocción de nuestro producto e) Área de últimos detalles: En esta área se llevaran a cabo los últimos detalles de estética y rellenos del producto. f) Área administrativa: En esta zona se encuentra la oficina donde se alimenta de información al sistema de almacén. g) Área de despacho: En esta se hace el conteo de unidades producidas, selección de piezas por pedido y piezas para el área ventas.