
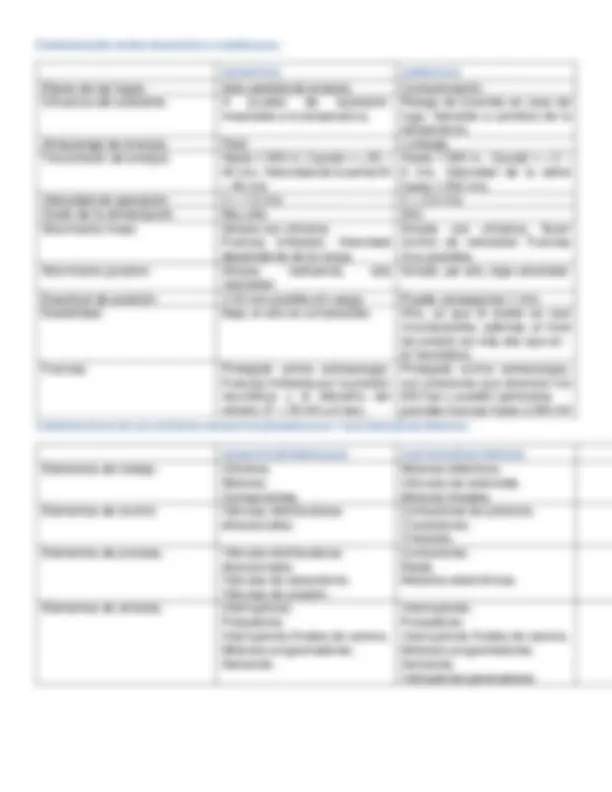
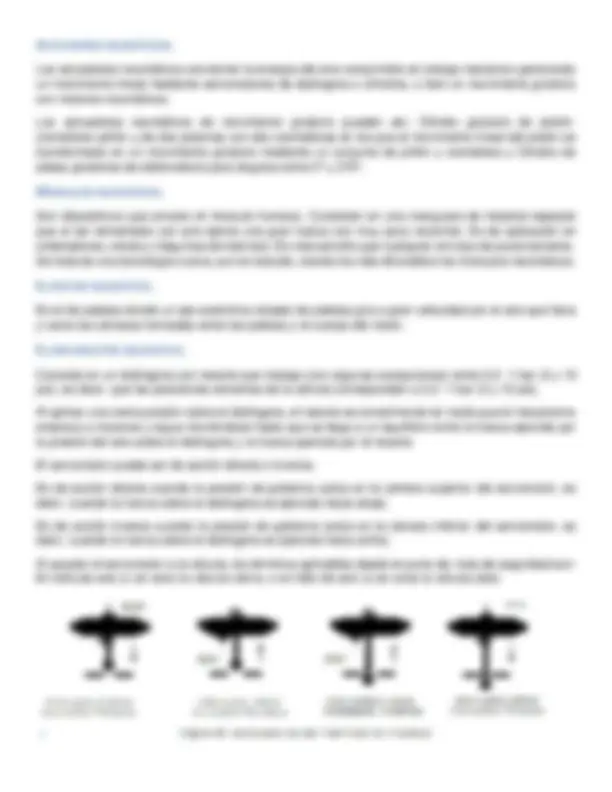

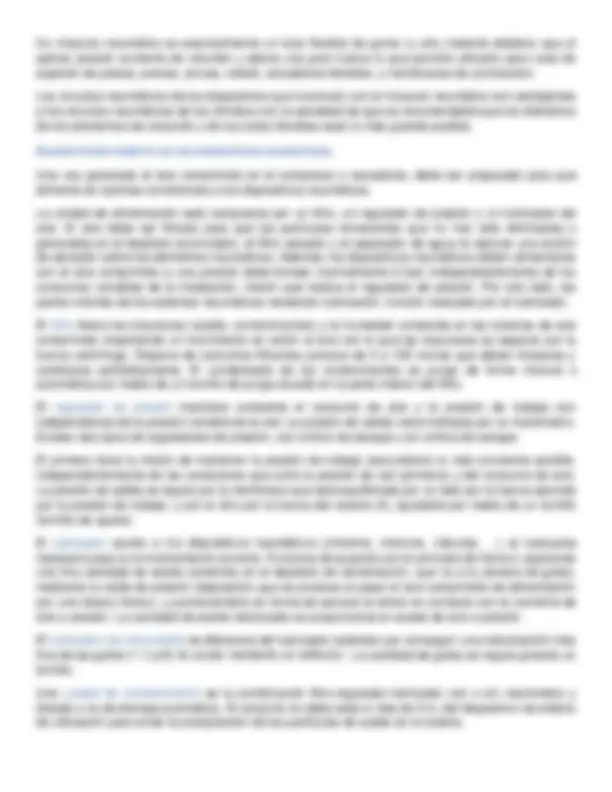
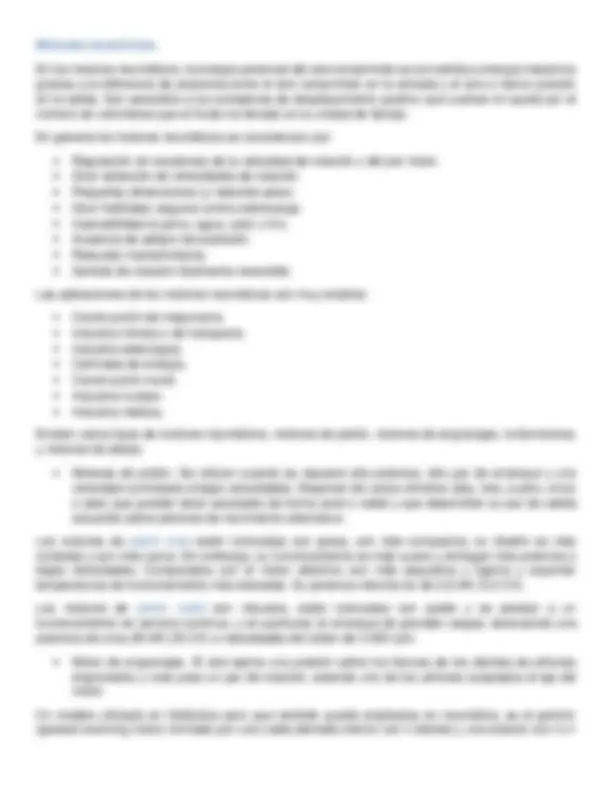
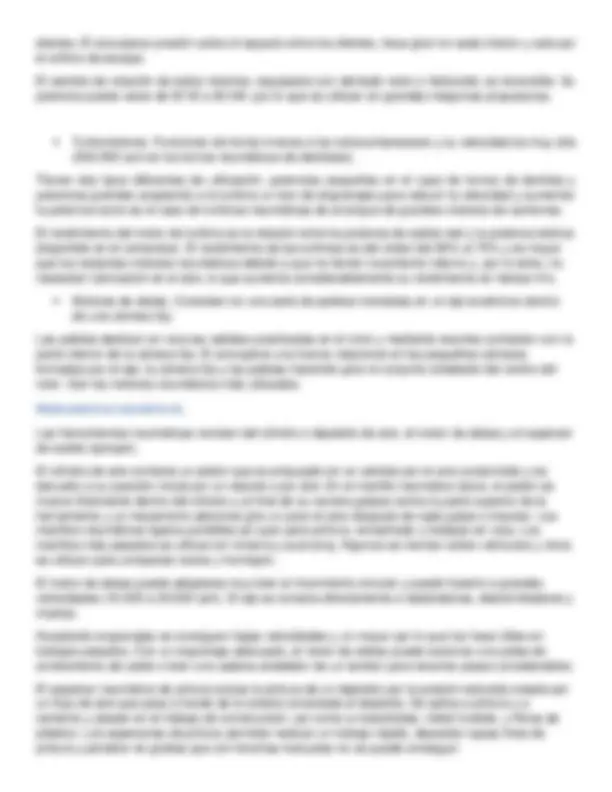
Prepara tus exámenes y mejora tus resultados gracias a la gran cantidad de recursos disponibles en Docsity
Gana puntos ayudando a otros estudiantes o consíguelos activando un Plan Premium
Prepara tus exámenes
Prepara tus exámenes y mejora tus resultados gracias a la gran cantidad de recursos disponibles en Docsity
Prepara tus exámenes con los documentos que comparten otros estudiantes como tú en Docsity
Los mejores documentos en venta realizados por estudiantes que han terminado sus estudios
Estudia con lecciones y exámenes resueltos basados en los programas académicos de las mejores universidades
Responde a preguntas de exámenes reales y pon a prueba tu preparación
Consigue puntos base para descargar
Gana puntos ayudando a otros estudiantes o consíguelos activando un Plan Premium
Comunidad
Pide ayuda a la comunidad y resuelve tus dudas de estudio
Descubre las mejores universidades de tu país según los usuarios de Docsity
Ebooks gratuitos
Descarga nuestras guías gratuitas sobre técnicas de estudio, métodos para controlar la ansiedad y consejos para la tesis preparadas por los tutores de Docsity
Resumen de algunos trabajos relacionados a la Neumática
Tipo: Resúmenes
1 / 11
Esta página no es visible en la vista previa
¡No te pierdas las partes importantes!
Ricardo Huerta Carrera
TSU MECATRÓNICA ÁREA AUTOMATIZACIÓN 3 - C T/V
La palabra neumática se refiere al estudio del movimiento del aire y así en sus comienzos el hombre utilizó el viento en la navegación y en el uso de los molinos para moler grano y bombear agua. En 1868 George Westinghouse fabricó un freno de aire que revolucionó la seguridad en el transporte ferroviario. Es a partir de 1950 que la neumática se desarrolla ampliamente en la industria con el desarrollo paralelo de los sensores
Proporcionan un movimiento controlado con el empleo de cilindros y motores neumáticos y se aplican en herramientas, válvulas de control y posicionadotes, martillos neumáticos, pistolas para pintar, motores neumáticos, sistemas de empaquetado, elevadores, herramientas de impacto, prensas neumáticas, robots industriales, vibradores, frenos neumáticos, etc.
El bajo coste de sus componentes, su facilidad de diseño e implementación y el bajo par o la fuerza escasa que puede desarrollar a las bajas presiones con que trabaja (típico 6 bar) lo que constituye un factor de seguridad. Otras características favorables son el riesgo nulo de explosión, su conversión fácil al movimiento giratorio, así como al lineal, la posibilidad de transmitir energía a grandes distancias, una construcción y mantenimiento fáciles y la economía en las aplicaciones.
Imposibilidad de obtener velocidades estables debido a la compresibilidad del aire, los altos costes de la energía neumática y las posibles fugas que reducen el rendimiento.
una estación de generación y preparación del aire comprimido formada por un compresor de aire, un depósito, un sistema de preparación del aire (filtro, lubricador y regulador de presión), una red de tuberías para llegar al utilizador y un conjunto de preparación del aire para cada dispositivo neumático individual.
Los sistemas neumáticos se complementan con los eléctricos y electrónicos lo que les permite obtener un alto grado de sofisticación y flexibilidad. Utilizan válvulas solenoide, señales de realimentación de interruptores magnéticos, sensores e interruptores eléctricos de final de carrera. El PLC ( programmable logic controller ) les permite programar la lógica de funcionamiento de un cilindro o de un conjunto de cilindros realizando una tarea específica. En determinadas aplicaciones, tales como en movimientos de aproximación rápido y avance lento, típicos de las fresadoras y rectificadoras, en la sujeción de piezas utilizada en los cortes a alta velocidad sobre materiales duros y en la automatización de procesos de producción, se combinan la neumática y la hidráulica en un circuito-oleoneumático , utilizando la parte neumática para el accionamiento y control y la parte hidráulica para el actuador.
Los actuadores neumáticos convierten la energía del aire comprimido en trabajo mecánico generando un movimiento lineal mediante servomotores de diafragma o cilindros, o bien un movimiento giratorio con motores neumáticos. Los actuadores neumáticos de movimiento giratorio pueden ser: Cilindro giratorio de pistón- cremallera–piñón y de dos pistones con dos cremalleras en los que el movimiento lineal del pistón es transformado en un movimiento giratorio mediante un conjunto de piñón y cremallera y Cilindro de aletas giratorias de doble efecto para ángulos entre 0° y 270°.
Son dispositivos que emulan el músculo humano. Consisten en una manguera de material especial que al ser alimentado con aire ejerce una gran fuerza con muy poco recorrido. Es de aplicación en ordenadores, robots y máquinas de todo tipo. Es más sencillo que cualquier otro tipo de accionamiento. Se trata de una tecnología nueva, aun en estudio, siendo los más difundidos los músculos neumáticos.
Es el de paletas donde un eje excéntrico dotado de paletas gira a gran velocidad por el aire que llena y vacía las cámaras formadas entre las paletas y el cuerpo del motor.
Consiste en un diafragma con resorte que trabaja (con algunas excepciones) entre 0,2- 1 bar (3 y 15 psi), es decir, que las posiciones extremas de la válvula corresponden a 0,2- 1 bar (3 y 15 psi). Al aplicar una cierta presión sobre el diafragma, el resorte se comprime de tal modo que el mecanismo empieza a moverse y sigue moviéndose hasta que se llega a un equilibrio entre la fuerza ejercida por la presión del aire sobre el diafragma y la fuerza ejercida por el resorte. El servomotor puede ser de acción directa o inversa. Es de acción directa cuando la presión de gobierno actúa en la cámara superior del servomotor, es decir, cuando la fuerza sobre el diafragma es ejercida hacia abajo. Es de acción inversa cuando la presión de gobierno actúa en la cámara inferior del servomotor, es decir, cuando la fuerza sobre el diafragma es ejercida hacia arriba. Al acoplar el servomotor a la válvula, los términos aplicables desde el punto de vista de seguridad son: En fallo de aire (o sin aire) la válvula cierra, o en fallo de aire (o sin aire) la válvula abre.
Idealmente, con una señal de 0,2 bar (3 psi) la válvula debe estar en la posición 0% de su carrera y para una señal de 1 bar (15 psi) en la posición 100%. Asimismo, debe existir una proporcionalidad entre las señales intermedias y sus correspondientes posiciones. En la práctica las válvulas de control se desvían de este comportamiento debido a las causas siguientes:
El cilindro neumático consiste en un cilindro cerrado con un pistón en su interior que desliza y que transmite su movimiento al exterior mediante un vástago. Se compone de las tapas trasera y delantera, de la camisa donde se mueve el pistón, del propio pistón, de las juntas estáticas y dinámicas del pistón y del anillo rascador que limpia el vástago de suciedad. En el cilindro neumático de doble efecto , el aire a presión entra por el orificio de la cámara trasera y, al llenarla, hace avanzar el vástago, que en su carrera comprime el aire de la cámara delantera que se escapa al exterior a través del correspondiente orificio. En la carrera inversa del vástago se invierte el proceso, penetrando ahora el aire por la cámara delantera y siendo evacuado al exterior por el orificio de la cámara trasera. El cilindro neumático de simple efecto funciona de forma similar exceptuando que la carrera inversa se efectúa gracias a la acción del muelle.
El expulsor neumático , se utiliza para soplar y expulsar piezas elaboradas de dispositivos, herramientas de troquelado, cintas de transporte, y de equipos envasadores, mediante un chorro de aire comprimido. Se compone de un depósito dimensionado para la cantidad de aire que se precisa y de una válvula de lanzadera. La mordaza neumática permite conseguir fuerzas elevadas de sujeción en las pinzas (tipo DIN 6343), con muy poco consumo de aire comprimido. Sus aplicaciones típicas son la sujeción de piezas de trabajo en taladradoras y fresadoras, los trabajos de montaje con atornilladores neumáticos o eléctricos y las máquinas de avance circular y trenes transfer. La mesa de deslizamiento sobre colchón de aire (figura 2.75) permite desplazar con comodidad y precisión, piezas o mecanismos pesados sobre mesas de máquinas o trenes de montaje. El colchón de aire así obtenido permite desplazar la mesa con la carga sin ninguna dificultad. A título de ejemplo, un mecanismo de 1500 N de peso que precisa una fuerza de desplazamiento de 320 N, ésta baja a 3 N con el deslizamiento sobre colchón de aire. El carro deslizante es otro tipo de mesa que permite mover y posicionar piezas de forma rápida y precisa mediante cilindros neumáticos con control de caudal, sensores de posición y amortiguadores de choque y acústicos. Se emplea como unidad de avance para la alimentación de piezas en unidades de mecanizado. El equipo neumático de tres ejes se utiliza en operaciones con robots cuando es necesario posicionar la pieza que se mecaniza o bien las herramientas de mecanización en puntos determinados del espacio, es decir, las mordazas, pinzas o los dispositivos de sujeción deben poder moverse en las tres dimensiones.
consiste en un pistón cuyo vástago tiene una cremallera que engrana con una rueda dentada o piñón. De esta manera, el movimiento del pistón es transmitido por el vástago a la rueda dentada con una rotación que puede variar de 45, 90, 180 y 360º Puede ser de simple cremallera o de doble cremallera. Se utiliza en aplicaciones de transferencia, descarga, desplazamiento de levas, fijación de mecanismos, unión, rotación, apriete, apertura y cierre y agitación. El cilindro de aleta giratoria contiene varios cilindros de doble efecto con aletas pivotantes y el ángulo máximo del movimiento es de unos 270º que puede ajustarse y detectarse mediante sensores detectores de posiciones finales.
Los músculos artificiales intentan emular el músculo biológico del hombre y se aplican a ordenadores, robots y máquinas de todo tipo. Los músculos biológicos poseen una relación excelente masa/rendimiento, y son capaces de ejecutar movimientos ágiles y suaves. La fuerza desarrollada por el músculo es: Fuerza F * Brazo de la fuerza f = Carga P * Brazo de la carga p Luego se ve que ejerce una gran fuerza con una carrera corta.
Un músculo neumático es esencialmente un tubo flexible de goma (u otro material elástico) que al aplicar presión aumenta de volumen y ejerce una gran fuerza lo que permite utilizarlo para usos de sujeción de piezas, prensa, pinzas, robots, actuadores flexibles, y membranas de contracción. Los circuitos neumáticos de los dispositivos que funcionan con el músculo neumático son semejantes a los circuitos neumáticos de los cilindros con la salvedad de que es recomendable que los diámetros de los elementos de conexión y de los tubos flexibles sean lo más grande posible.
Una vez generado el aire comprimido en el compresor y secadores, debe ser preparado para que alimente en óptimas condiciones a los dispositivos neumáticos. La unidad de alimentación está compuesta por un filtro, un regulador de presión y un lubricador del aire. El aire debe ser filtrado para que las partículas remanentes que no han sido eliminadas o generadas en el depósito acumulador, el filtro secador y el separador de agua no ejerzan una acción de abrasión sobre los elementos neumáticos. Además, los dispositivos neumáticos deben alimentarse con el aire comprimido a una presión determinada (normalmente 6 bar) independientemente de los consumos variables de la instalación, misión que realiza el regulador de presión. Por otro lado, las partes móviles de los sistemas neumáticos necesitan lubricación, función realizada por el lubricador. El filtro libera las impurezas (aceite, contaminantes) y la humedad contenida en las tuberías de aire comprimido impartiendo un movimiento en ciclón al aire con lo que las impurezas se separan por la fuerza centrífuga. Dispone de cartuchos filtrantes porosos de 5 a 100 micras que deben limpiarse y cambiarse periódicamente. El condensado de los contaminantes se purga de forma manual o automática por medio de un tornillo de purga situado en la parte inferior del filtro. El regulador de presión mantiene constante el consumo de aire y la presión de trabajo con independencia de la presión variable de la red. La presión de salida viene indicada por un manómetro. Existen dos tipos de reguladores de presión, con orificio de escape y sin orificio de escape. El primero tiene la misión de mantener la presión de trabajo (secundaria) lo más constante posible, independientemente de las variaciones que sufra la presión de red (primaria) y del consumo de aire. La presión de salida se regula por la membrana que está equilibrada por un lado por la fuerza ejercida por la presión de trabajo, y por el otro por la fuerza del resorte (2), ajustable por medio de un tornillo (tornillo de ajuste). El lubricador aporta a los dispositivos neumáticos (cilindros, motores, válvulas, …) el lubricante necesario para su funcionamiento correcto. Funciona de acuerdo con el principio de Venturi, aspirando una fina cantidad de aceite contenido en el depósito de alimentación, que va a la cámara de goteo, mediante la caída de presión (depresión) que se produce al pasar el aire comprimido de alimentación por una tobera Venturi, y pulverizándolo en forma de aerosol al entrar en contacto con la corriente de aire a presión. La cantidad de aceite nebulizado es proporcional al caudal de aire a presión. El lubricador de microniebla se diferencia del lubricador estándar por conseguir una nebulización más fina de las gotas (> 2 μm) de aceite mediante un deflector. La cantidad de gotas se regula girando un tornillo. Una unidad de mantenimiento es la combinación filtro-regulador-lubricador con o sin manómetro y dotado o no de drenaje automático. El conjunto no debe estar a más de 5 m. del dispositivo neumático de utilización para evitar la precipitación de las partículas de aceite en la tubería.
dientes. El aire ejerce presión sobre el espacio entre los dientes, hace girar la rueda interior y sale por el orificio de escape. El sentido de rotación de estos motores, equipados con dentado recto o helicoidal, es reversible. Su potencia puede variar de 50 W a 50 kW, por lo que se utilizan en grandes máquinas propulsoras. Turbomotores. Funcionan de forma inversa a los turbocompresores y su velocidad es muy alta (500.000 rpm en los tornos neumáticos de dentistas). Tienen dos tipos diferentes de utilización, potencias pequeñas en el caso de tornos de dentista y potencias grandes acoplando a la turbina un tren de engranajes para reducir la velocidad y aumentar la potencia como es el caso de turbinas neumáticas de arranque de grandes motores de camiones. El rendimiento del motor de turbina es la relación entre la potencia de salida real y la potencia teórica disponible en el compresor. El rendimiento de las turbinas es del orden del 65% al 75% y es mayor que los restantes motores neumáticos debido a que no tienen rozamiento interno y, por lo tanto, no necesitan lubricación en el aire, lo que aumenta considerablemente su rendimiento en tiempo frío. Motores de aletas. Consisten en una serie de paletas montadas en un eje excéntrico dentro de una cámara fija. Las paletas deslizan en ranuras radiales practicadas en el rotor y mediante resortes contactan con la parte interior de la cámara fija. El aire ejerce una fuerza rotacional en las pequeñas cámaras formadas por el eje, la cámara fija y las paletas haciendo girar el conjunto alrededor del centro del rotor. Son los motores neumáticos más utilizados.
Las herramientas neumáticas constan del cilindro o depósito de aire, el motor de aletas y el aspersor de aceite (sprayer). El cilindro de aire contiene un pistón que es empujado en un sentido por el aire comprimido y es devuelto a su posición inicial por un resorte o por aire. En el martillo neumático típico, el pistón se mueve libremente dentro del cilindro y al final de su carrera golpea contra la parte superior de la herramienta y un mecanismo adicional gira un poco el pico después de cada golpe o impulso. Los martillos neumáticos ligeros portátiles se usan para pintura, remachado y trabajos en roca. Los martillos más pesados se utilizan en minería y quarrying. Algunos se montan sobre vehículos y otros se utilizan para compactar arena u hormigón. El motor de aletas puede adaptarse muy bien al movimiento circular y puede hacerlo a grandes velocidades (10.000 a 20.000 rpm). El eje se conecta directamente a taladradoras, destornilladores y muelas. Acoplando engranajes se consiguen bajas velocidades y un mayor par lo que los hace útiles en trabajos pesados. Con un engranaje adecuado, el motor de aletas puede accionar una polea de arrollamiento de cable o bien una cadena alrededor de un tambor para levantar pesos considerables. El aspersor neumático de pintura extrae la pintura de un depósito por la presión reducida creada por un flujo de aire que pasa a través de la tubería conectada al depósito. Se aplica a pintura y a cemento y plaster en el trabajo de construcción, así como a insecticidas, metal fundido, y fibras de plástico. Los aspersores de pintura permiten realizar un trabajo rápido, depositar capas finas de pintura y penetrar en grietas que con brochas manuales no se puede conseguir.