
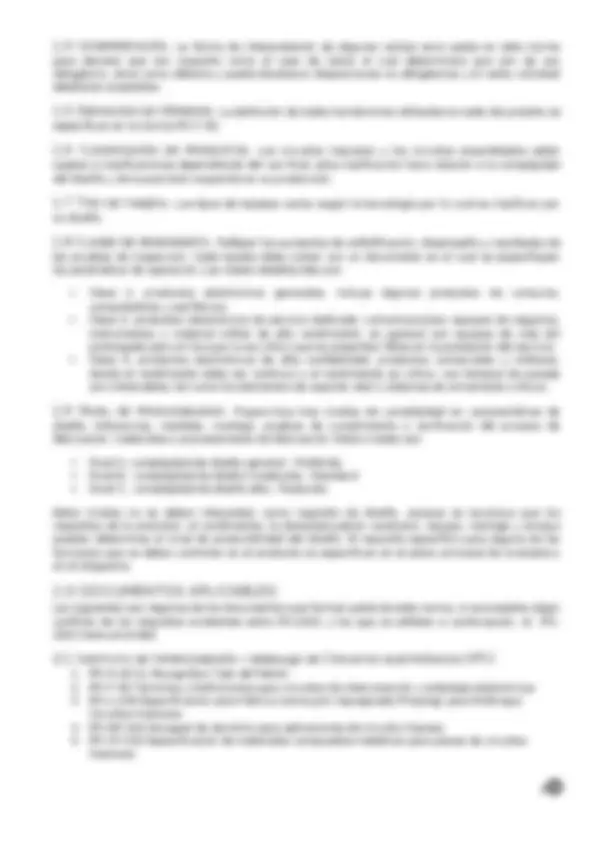
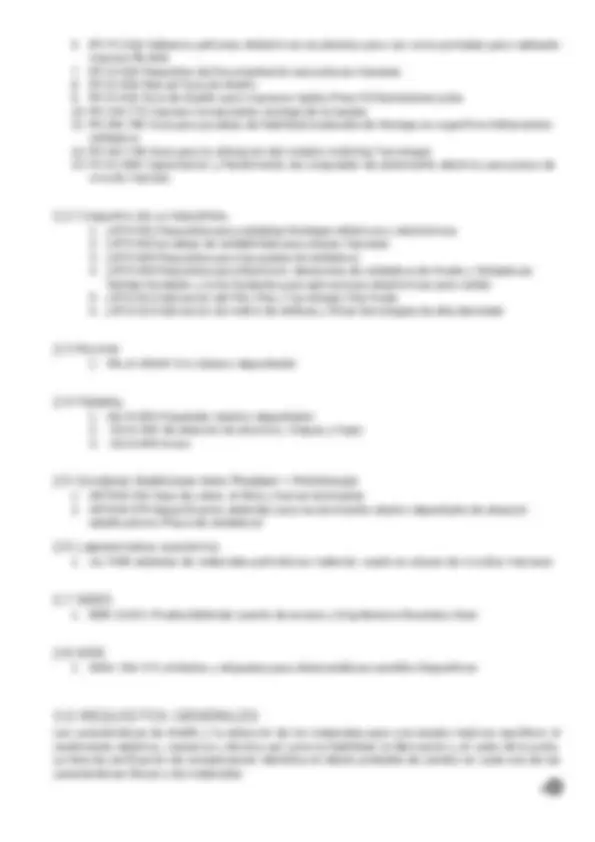
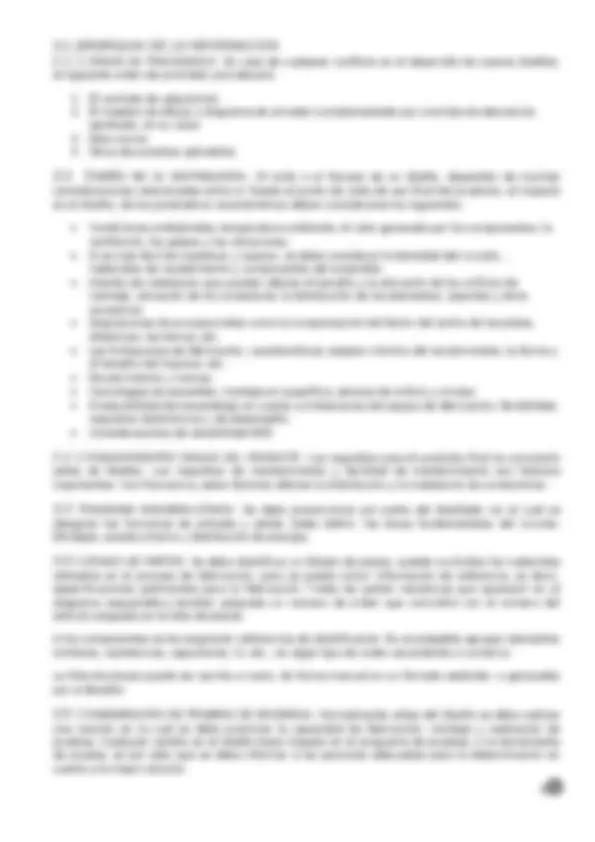
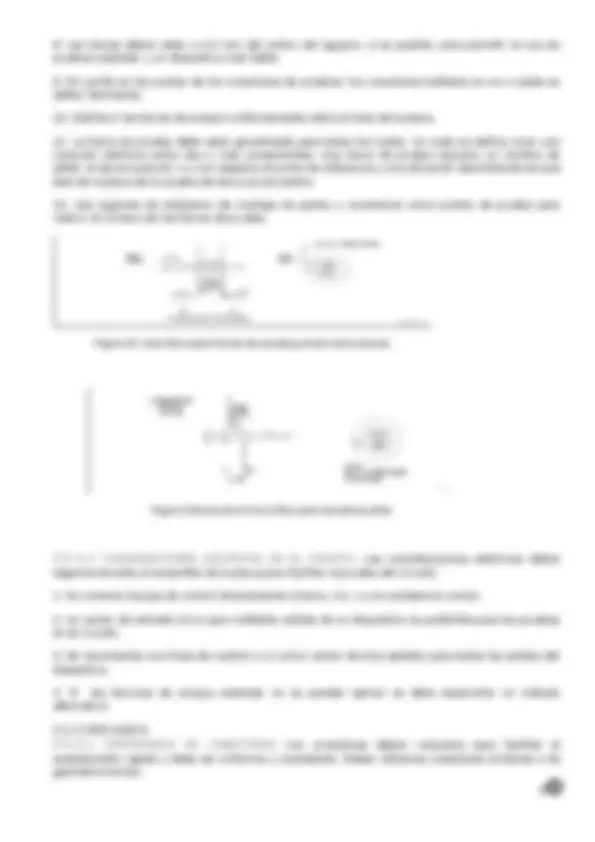
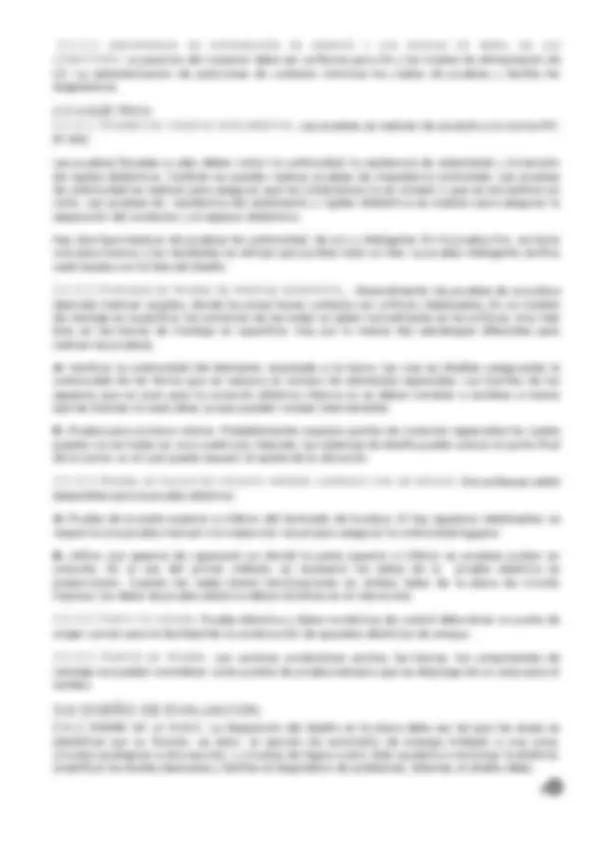
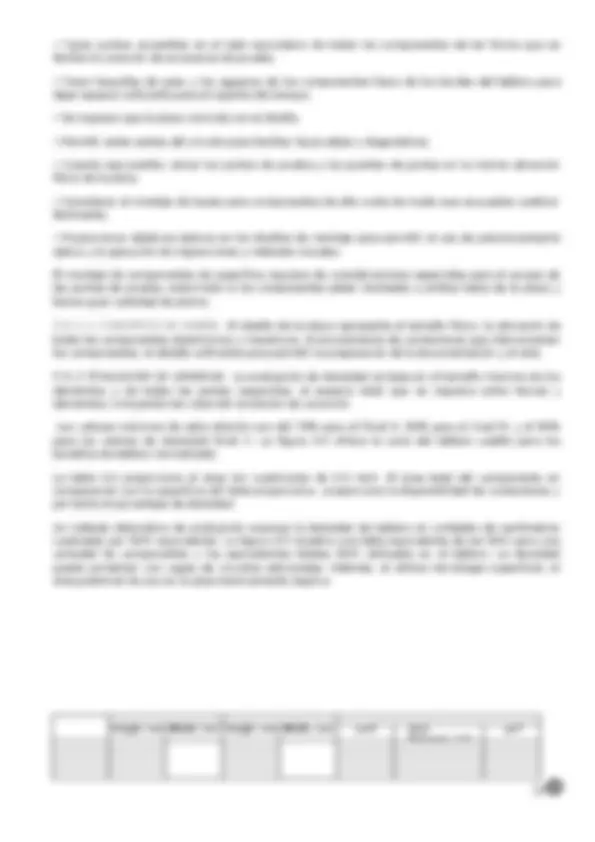
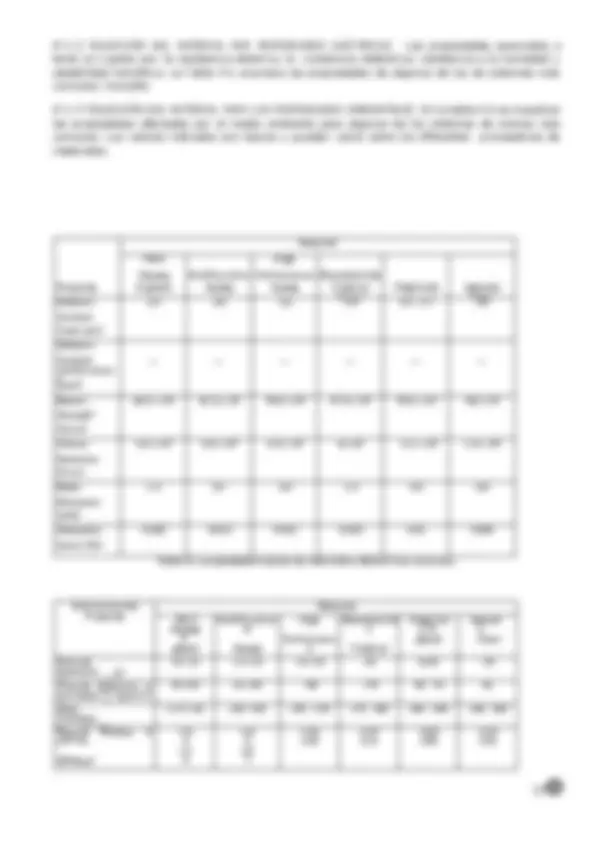
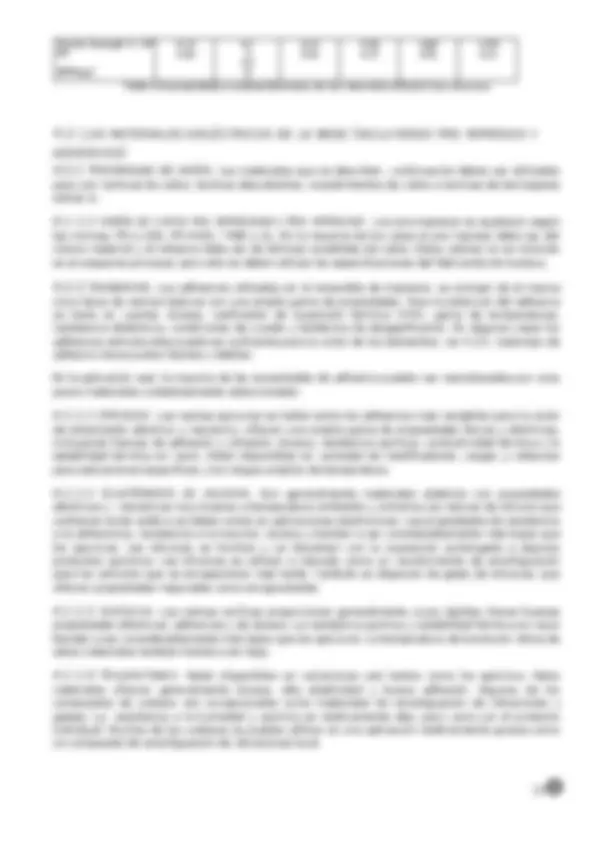
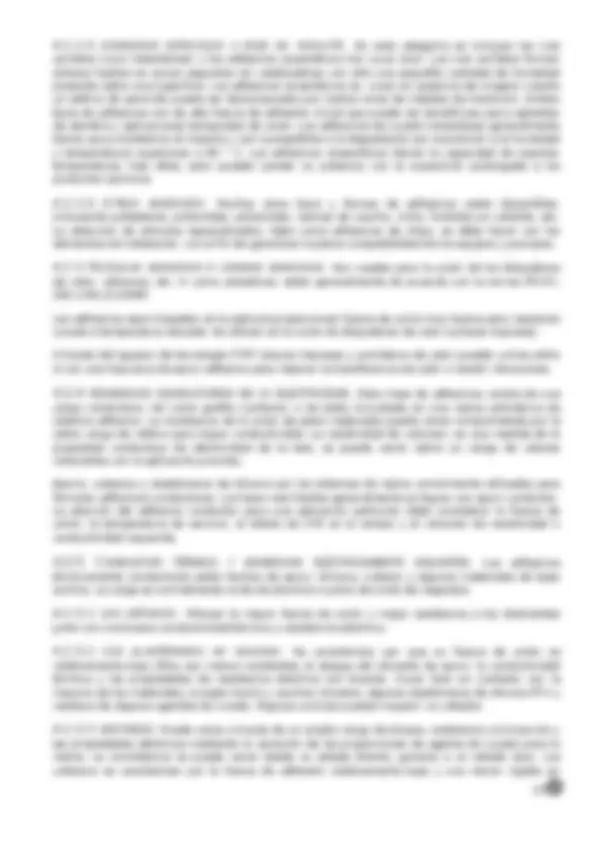
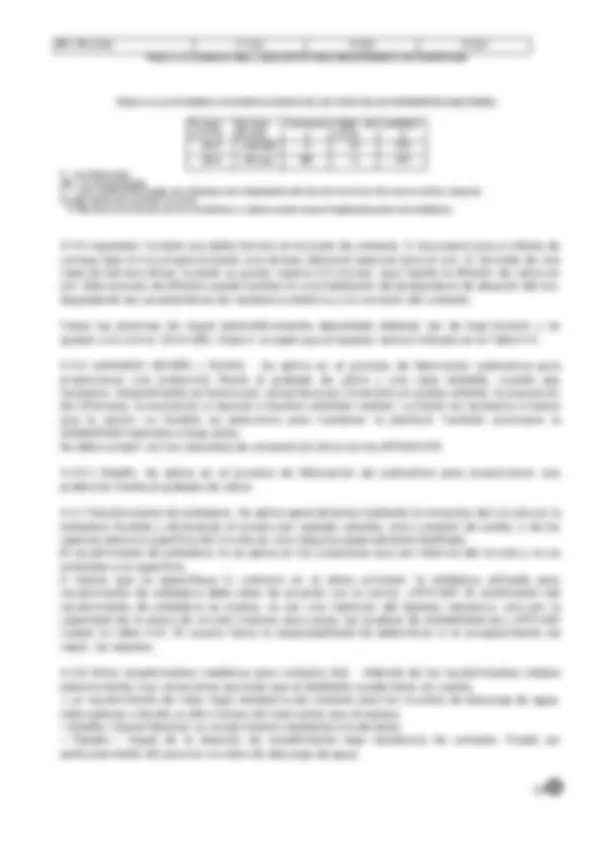
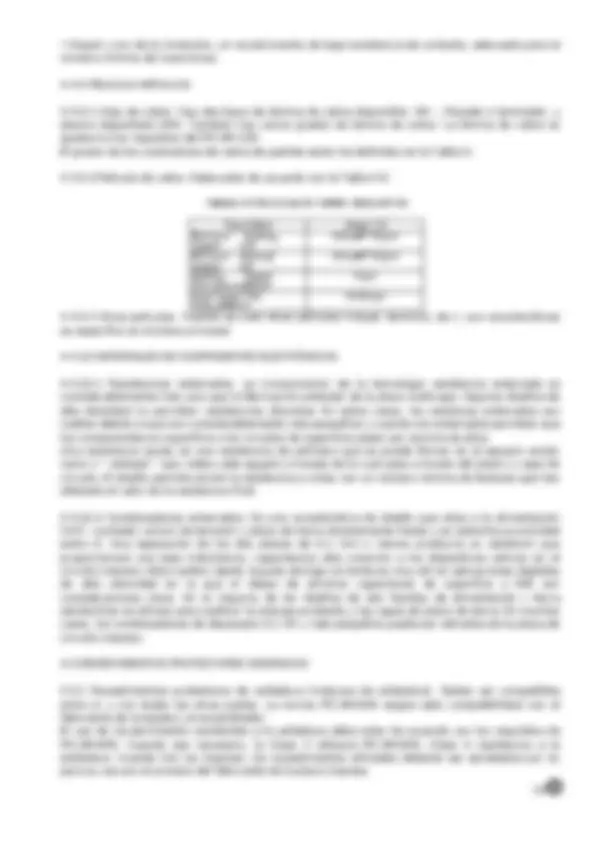
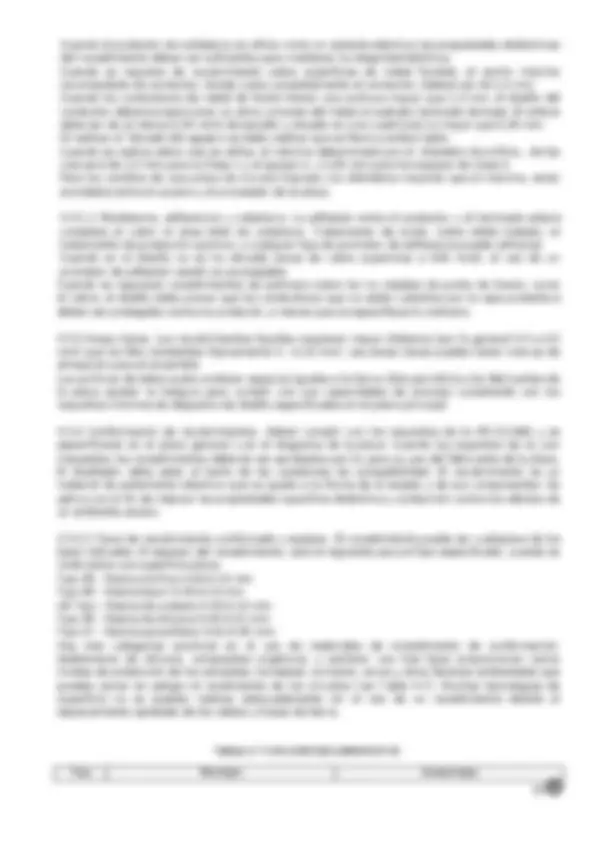
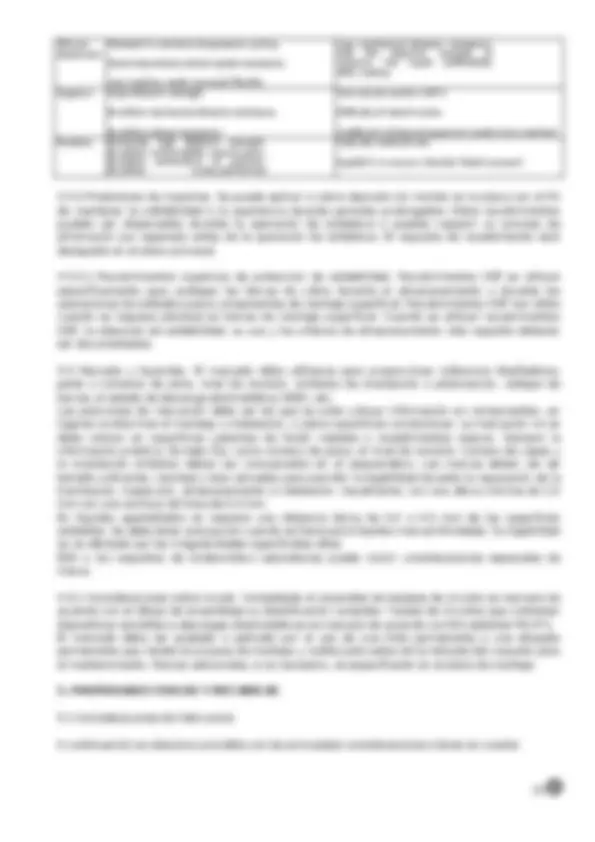
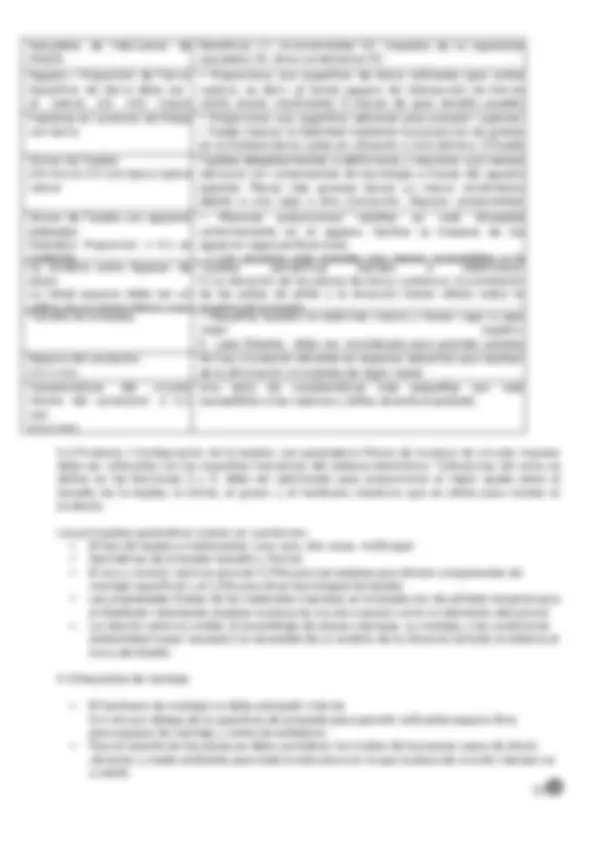
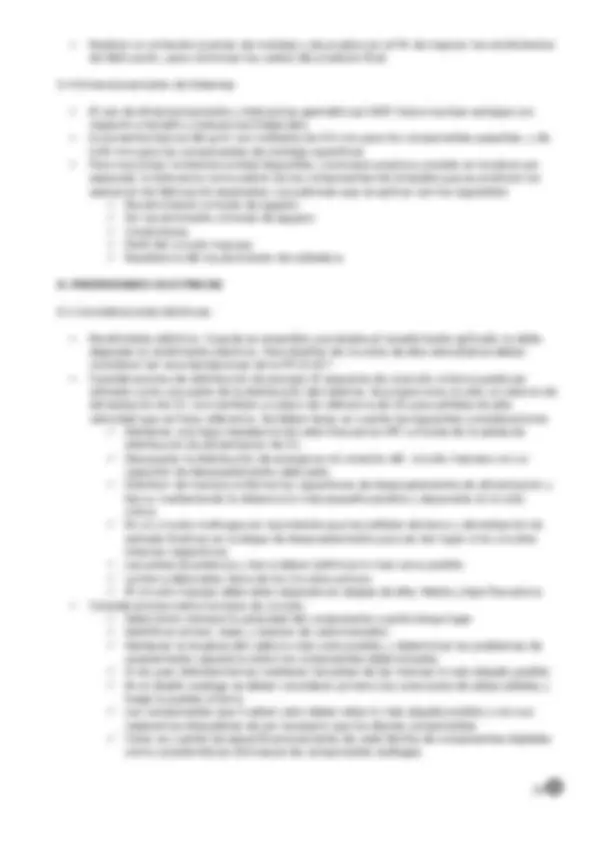
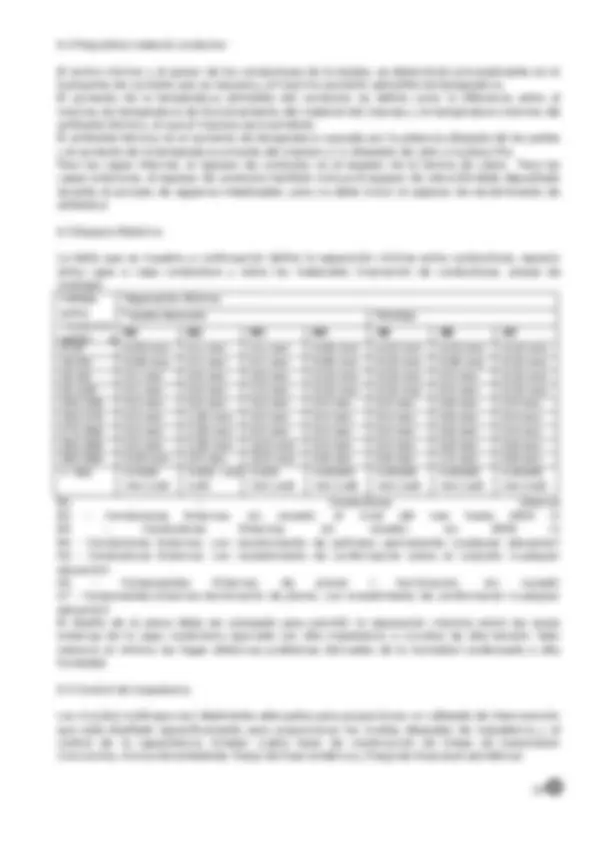
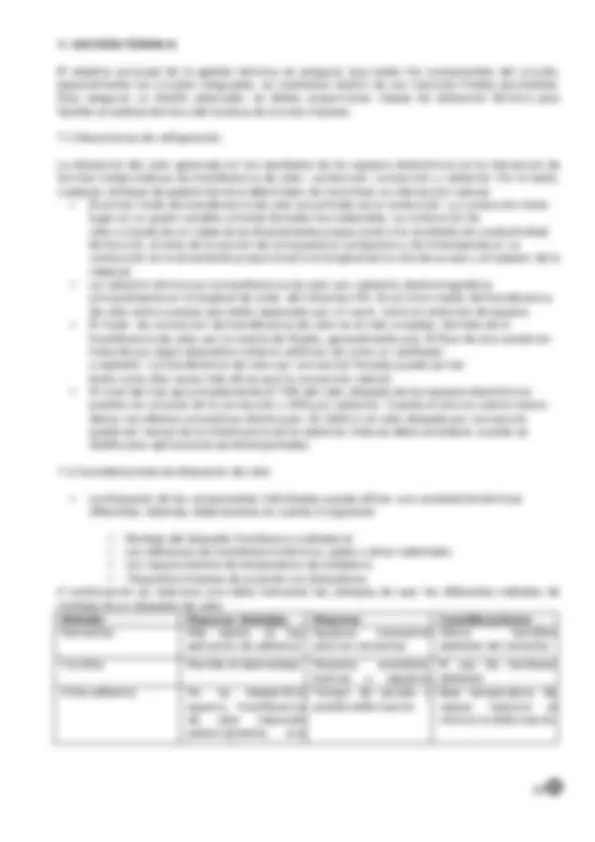
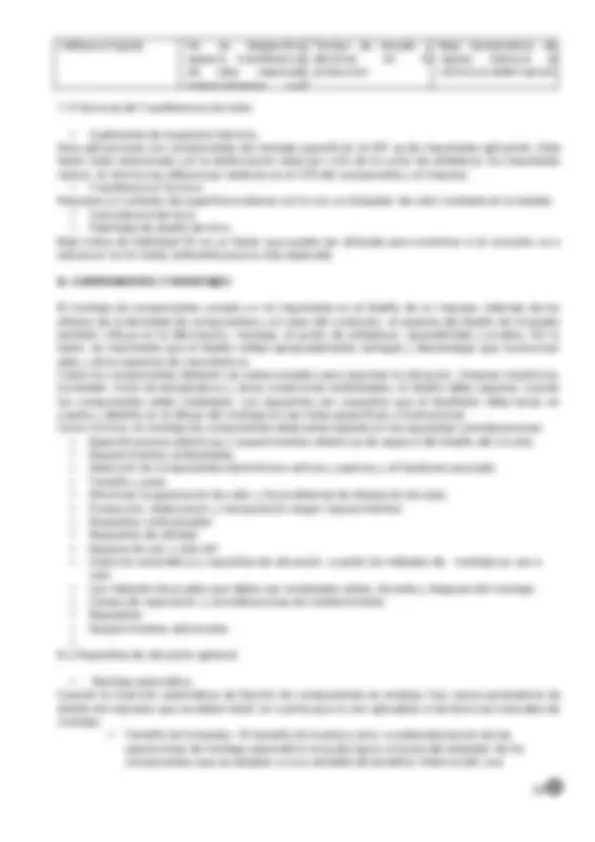
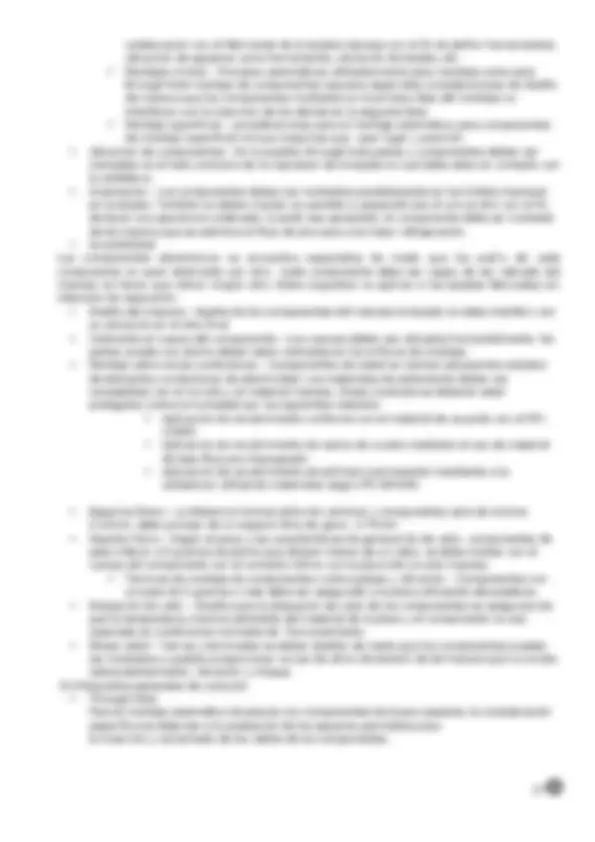
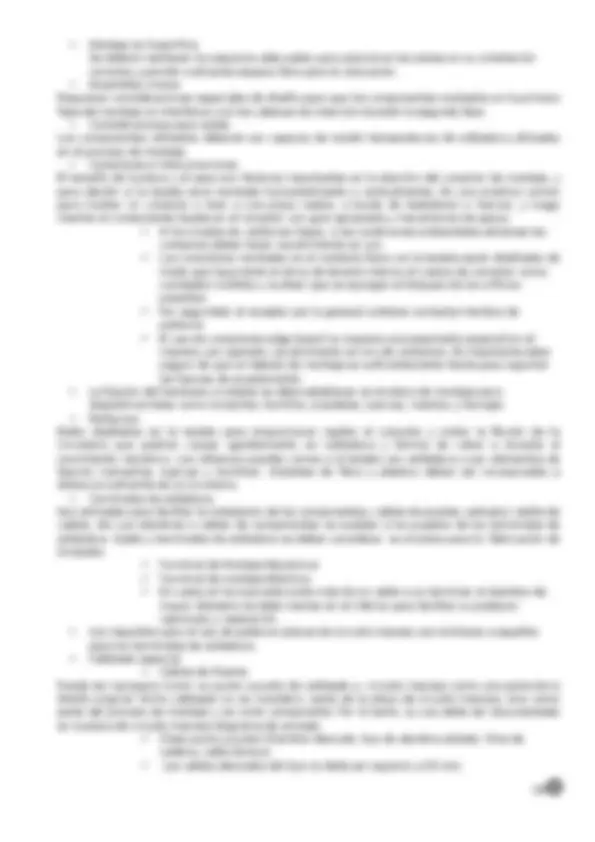
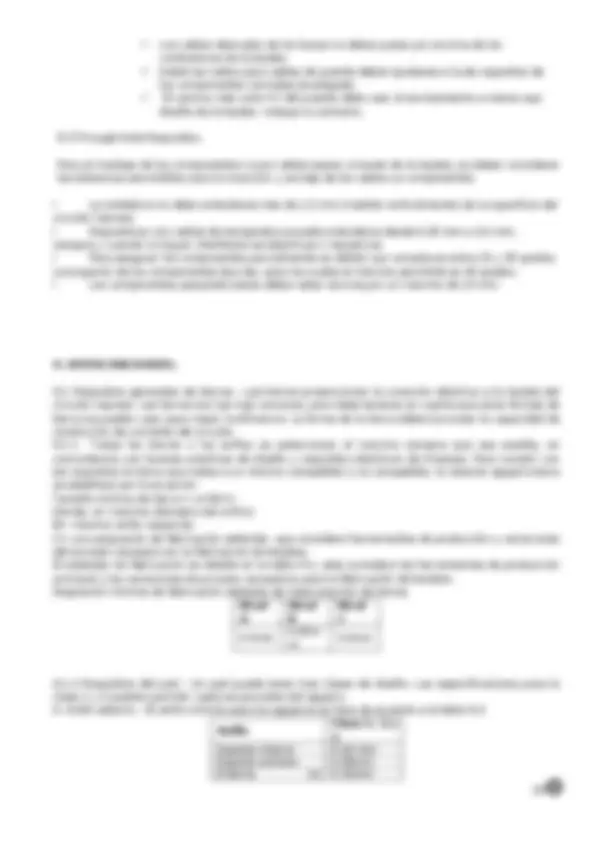
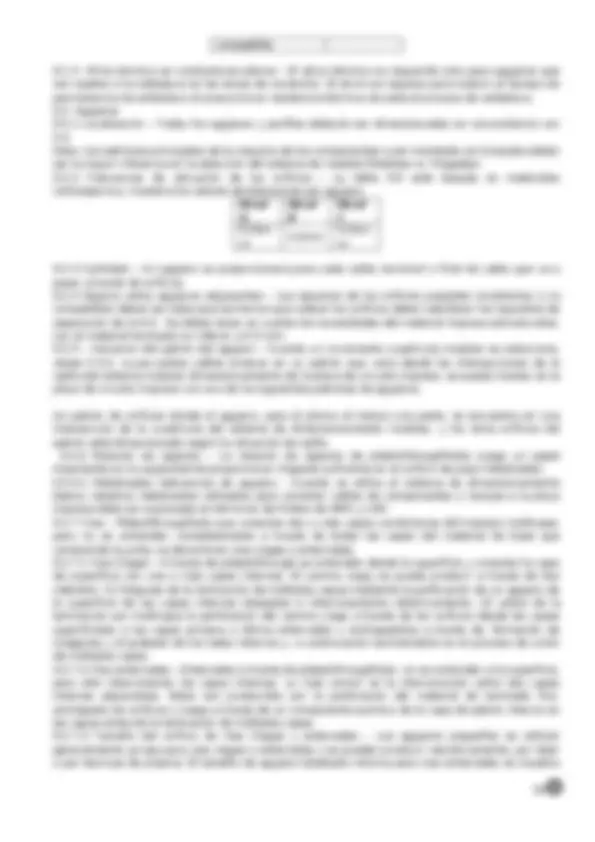
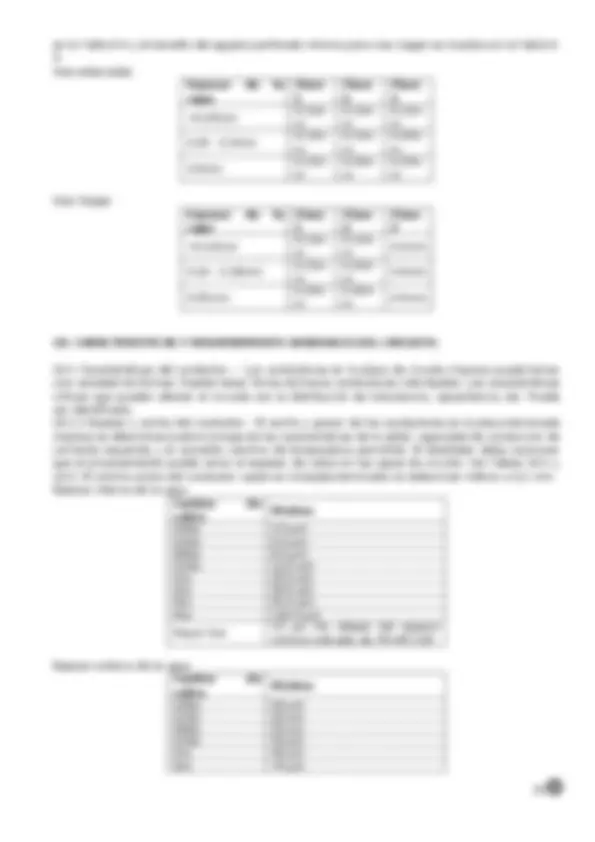
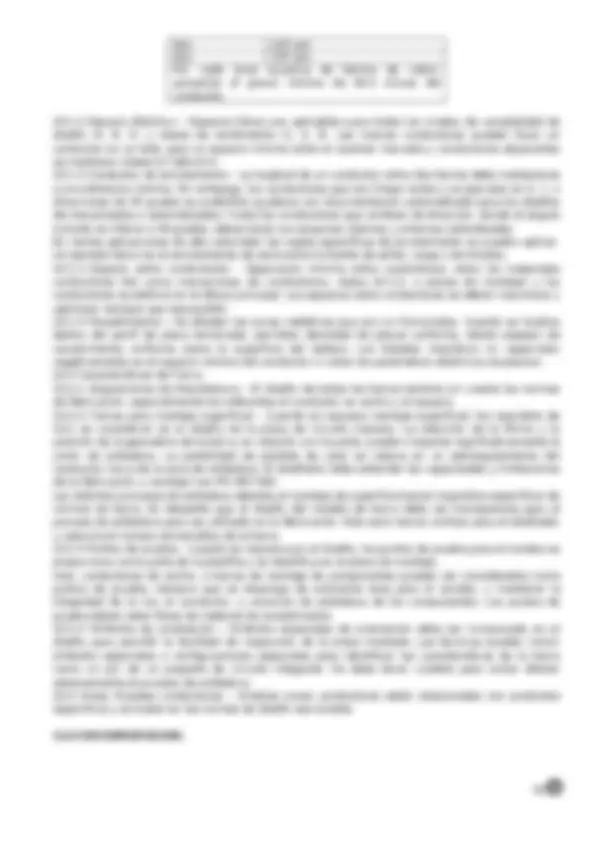
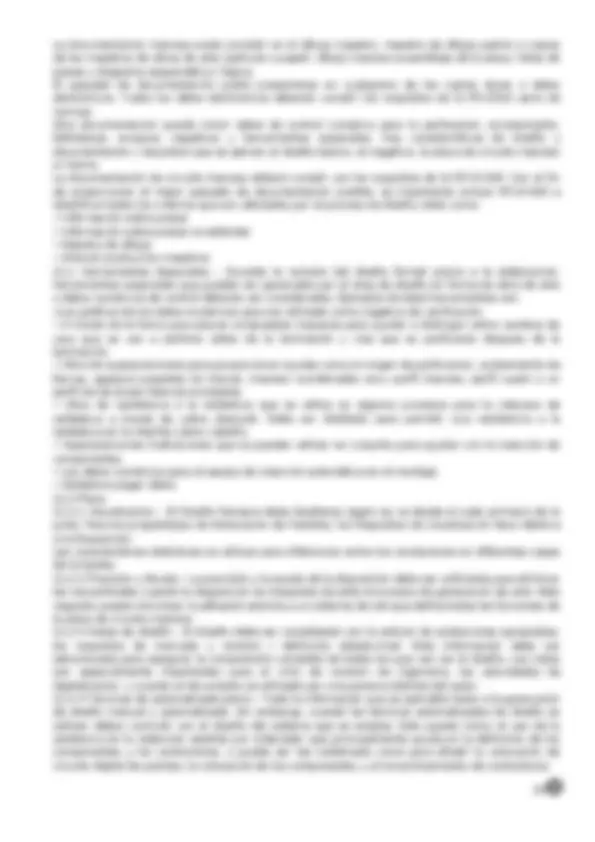
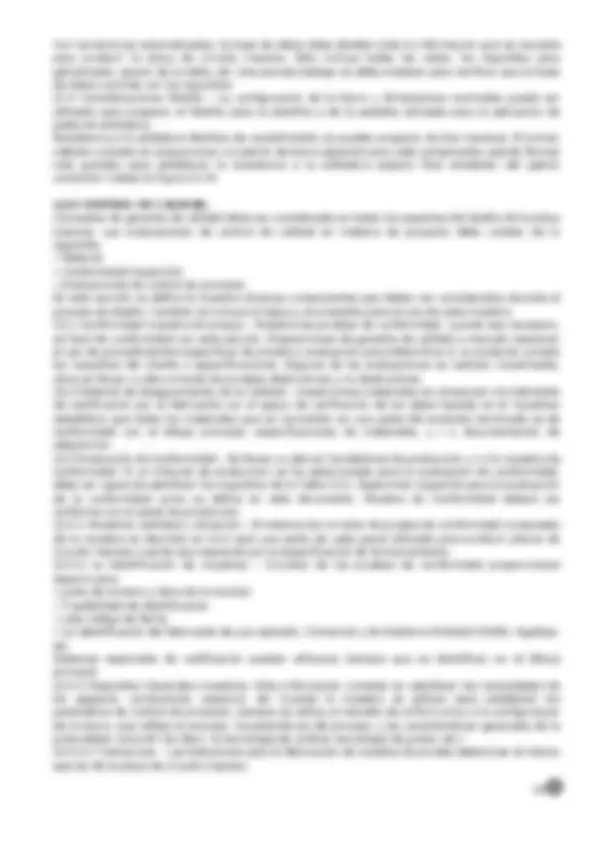
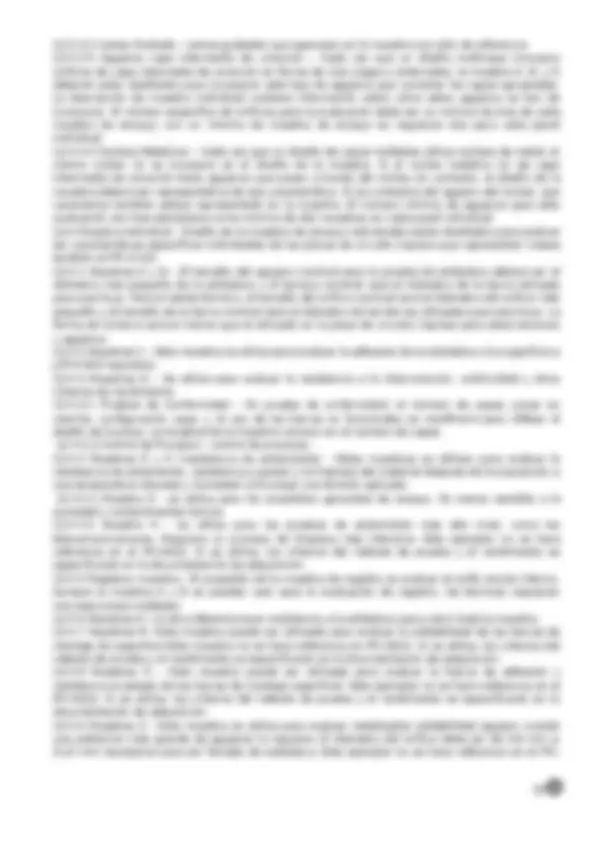
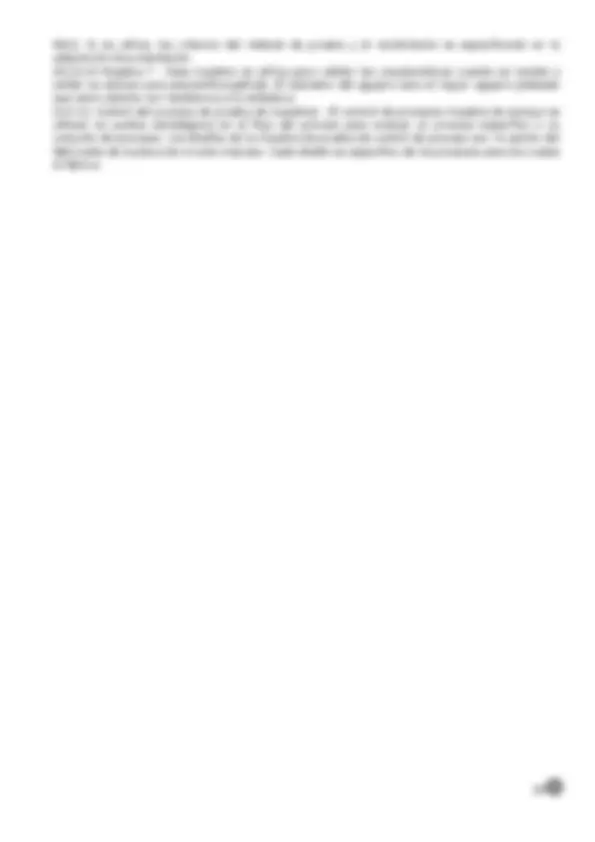
Prepara tus exámenes y mejora tus resultados gracias a la gran cantidad de recursos disponibles en Docsity
Gana puntos ayudando a otros estudiantes o consíguelos activando un Plan Premium
Prepara tus exámenes
Prepara tus exámenes y mejora tus resultados gracias a la gran cantidad de recursos disponibles en Docsity
Prepara tus exámenes con los documentos que comparten otros estudiantes como tú en Docsity
Los mejores documentos en venta realizados por estudiantes que han terminado sus estudios
Estudia con lecciones y exámenes resueltos basados en los programas académicos de las mejores universidades
Responde a preguntas de exámenes reales y pon a prueba tu preparación
Consigue puntos base para descargar
Gana puntos ayudando a otros estudiantes o consíguelos activando un Plan Premium
Comunidad
Pide ayuda a la comunidad y resuelve tus dudas de estudio
Descubre las mejores universidades de tu país según los usuarios de Docsity
Ebooks gratuitos
Descarga nuestras guías gratuitas sobre técnicas de estudio, métodos para controlar la ansiedad y consejos para la tesis preparadas por los tutores de Docsity
Resumen del estándar IPC 2221, donde se explican las reglas que se deben cumplir para poder hacer el diseño de una placa correctamente
Tipo: Resúmenes
1 / 36
Esta página no es visible en la vista previa
¡No te pierdas las partes importantes!
En oferta
Las normas y Publicaciones del IPC están diseñadas para facilitar la interacción entre fabricantes y compradores, facilitando el intercambio y la mejora de los productos además pretende ayudar al comprador a seleccionar y obtener el menor plazo posible el producto adecuado para su necesidad particular, la aplicación de estas normas y demás publicaciones son de uso voluntario por todos aquellos que no sean miembros de la IPC, de modo tal que la norma puede ser aplicada a nivel nacional o internacional. Esta norma tiene por objeto proporcionar información sobre los requisitos en el diseño de circuitos impresos orgánico. Todos los aspectos y detalles de los requisitos de diseño se tratan en la medida en que se aplican a un amplio espectro de diseños que utilizan materiales orgánicos o materiales orgánicos en combinación con materiales inorgánicos (metal, vidrio, cerámica, etc.) para proporcionar una estructura para el montaje y la interconexión de los componentes electrónicos, electromecánicos y mecánicos. Una vez que el montaje de componentes y elementos de interconexión se ha seleccionado el podrá solicitar un documento en el cual se especifique la tecnología elegida. El IPC proporcionar documentos distintos que se centran en aspectos específicos de problemas de embalaje electrónicos. Como la tecnología cambia las normas específicas de enfoque se actualizarán, en nuevas normas de enfoque agregado al conjunto de documentos. El IPC invita a todo usuario a plantear sugerencias para la mejora de cada uno de los documentos elaborados.
Esta norma establece los requisitos generales para el diseño y ensamble de tarjetas electrónicas.
construcción de estructuras de interconexión. El montaje de los componentes se puede realizar por medio de hoyos pasantes, de superficie o fine pitch. Los materiales pueden ser de cualquier combinación capaz de realizar la función física, térmica, ambiental y electrónica dentro del diseño.
físico, y se complementa por varios documentos sectoriales que proporcionan información y mayor atención a los aspectos específicos del impreso. Ejemplo de ello son: IPC-2222 Diseño de impresos orgánicos de estructura rígida. IPC-2223 Diseño de impresos orgánicos de estructura Flexible. IPC-2224 Diseño de impreso, formato de tarjeta de PC, IPC-2225 Diseño para módulos orgánicos multichip (MCM). IPC-2226 Interconexión de alta densidad (IDH) estructura diseño de la tarjeta. IPC-2227 Diseño de placa orgánica con cableado discreto. La lista es un resumen parcial. Los documentos son parte del conjunto de documentos del PWB que se identifica como IPC-
métricas del SI.
Las características de diseño y la selección de los materiales para una tarjeta implican equilibrar el rendimiento eléctrico, mecánico y térmico así como la fiabilidad, la fabricación y el costo de la junta. La lista de verificación de compensación identifica el efecto probable de cambio en cada una de las características físicas o de materiales
el siguiente orden de prioridad, prevalecerá:
consideraciones relacionadas entre sí. Desde el punto de vista de uso final del producto, el impacto en el diseño, de los parámetros característicos deben considerarse los siguientes.
antes de diseñar. Los requisitos de mantenimiento y facilidad de mantenimiento son factores importantes. Con frecuencia, estos factores afectan la distribución y la instalación de conductores.
designen las funciones de entrada y salida. Debe definir, las áreas fundamentales del circuito, blindajes, puesta a tierra y distribución de energía.
utilizados en el proceso de fabricación, pero se puede incluir información de referencia, es decir, especificaciones pertinentes para la fabricación. Todas las partes mecánicas que aparecen en el diagrama esquemático tendrán asignado un número de orden que coincidirá con el número del artículo asignado en la lista de piezas. A los componentes se les asignarán referencias de identificación. Es aconsejable agrupar elementos similares, resistencias, capacitores, IC, etc., en algún tipo de orden ascendente o numérico. La lista de piezas puede ser escrita a mano, de forma manual en un formato estándar, o generadas por ordenador.
una reunión en la cual se debe examinar la capacidad de fabricación, montaje y realización de pruebas. Cualquier cambio en el diseño tiene impacto en el programa de pruebas, o la herramienta de prueba, es por esto que se debe informar a las personas adecuadas para la determinación en cuanto a la mejor solución.
se sabe si la tarjeta pasa o no las prueba. Hay muchas variaciones en este esquema. Algunos ejemplos son:
calificado en especial si la operación del ensamble es de baja calidad, para reducir los costos y el tiempo se tienen algunas consideraciones generales. Los elementos polarizados deben estar orientados 180 ° en desfase con otros elementos de la tarjeta, los elementos no polarizados deben tener identificado en primer pin o se debe identificar un pin específico. Es preferible el uso de conectores de prueba en vez de puntos de prueba. Las tierras utilizadas para la conexión en pruebas debe ser la misma que se encuentra en la red y el circuito, se deben identificar puntos estratégicos para el sondeo de las señales. Durante el diseño se deben tener en cuenta elementos adyacentes o conductores externos con poco aislamiento, esto con el fin de evitar cortocircuitos. La separación de los circuitos análogos de los digitales y la agrupación de los conectores de prueba pueden ayudar a mejorar las pruebas.
elementos en corto, abiertos, invertidos, mal ensamblados y otros defectos. En la verificación de circuitos digitales se puede aplicar un proceso conocido como retroceso (norma IPC-T-50).
uñas, son dispositivos con sondas flexibles que conectan cada nodo con la junta a prueba. Se deben seguir unas pautas en el ensamble:
seguirse durante el ensamble de la placa para facilitar la prueba del circuito:
acoplamiento rápido y debe ser uniforme y consistente. Deben utilizarse conectores similares o de geometría similar. Figura 3.1 área libre para tierras de prueba y otras instrucciones. Figura 3.2 área de la tierra libre para las partes altas
todos los componentes electrónicos y mecánicos, el enrutamiento de conductores que interconectan los componentes, el detalle suficiente para permitir la preparación de la documentación y el arte.
elementos y de todas las partes requeridas, el especio total que se requiera entre tierras y elementos, incluyendo las rutas del conductor de conexión. Los valores máximos de esta relación son del 70% para el Nivel A, 80% para el nivel B, y el 90% para los valores de densidad Nivel C. La figura 3-4 ofrece la zona del tablero usable para los tamaños de tablero normalizado. La tabla 3-2 proporciona el área (en cuadriculas de 0,5 mm). El área total del componente en comparación con la superficie útil total proporciona, proporciona la disponibilidad de conductores y por tanto el porcentaje de densidad. Un método alternativo de evaluación expresa la densidad de tablero en unidades de centímetros cuadrados por SOIC equivalente. La figura 3-5 muestra una tabla equivalente de las SOIC para una variedad de componentes y los equivalentes totales SOIC utilizados en el tablero. La densidad puede aumentar con capas de circuitos adicionales. Además, al utilizar tecnología superficial, el área potencial de uso en la placa teóricamente duplica. Height, mm Width, mm Height, mm Width, mm mm^2 Grid Elements 0. cm^2
C4 260 245 56300 225200 563 Figura 3-4 ejemplo de cálculo de superficie útil, mm Tabla 3-2 Área de cuadriculas de componentes Component Description Type^1 Number of Grid Elements^2 0.5 mm Grid Date of issue No. DENSITY EVALUATION Revlsed DESCRIPTION: SOICs per square centimeter Comp. ñame # of comp. or IC equiv Comments 8 SOIC. 14 SOIC 1. 16 SOIC 1. 16L SOIC 1. 20 SOIC 1. 24 SOIC 1. 28 SOIC 1. 18 PLCC 1. 18L PLCC 1. 20 PLCC 1. 28 PLCC 1. 44 PLCC 2.
tener en cuenta son, la resistencia eléctrica, la constancia dieléctrica, resistencia a la humedad y estabilidad hidrolítica. La Tabla 4-1 enumera las propiedades de algunos de los de sistemas más comunes. Consulte
las propiedades afectadas por el medio ambiente para algunos de los sistemas de resinas más comunes. Los valores indicados son típicos y pueden variar entre los diferentes proveedores de materiales. Material FR-4 High (Epoxy Multifunction al Performance Bismalaimide Property E-glass) Epoxy Epoxy Triazine/ Epoxy Polyimide Cyanate Dielectric 3.9 3.5 3.4 2.9 3.5 - 3.7^ Ester 2. Constant (neat resin) Dielectric Constant (reinforcemen t/ — — — — — — resin)^1 Electric 39.4 x 10^3 51.2 x 10^3 70.9 x 10^3 47.2 x 10^3 70.9 x 10^3 65 x 10^3 Strength^2 (V/mm) Volume 4.0 x 10^6 3.8 x 10^6 4.9 x 10^6 4x 10^6 2.1 x 10^6 1.0 x 10^6 Resistivity (D-cm) Water 1.3 0.1 0.3 1.3 0.5 0. Absorption (wt%) Dissipation 0.022 0.019 0.012 0.015 0.01 0. Factor (DX) Tabla 4.1 propiedades típicas de materiales dieléctricos comunes. Environmental Property Material FR- (Epoxy E- glass) Multifunction al Epoxy High Performanc e Bismalaimid e Triazine/ Polyimid e (E- glass) Cyanat e Ester Thermal Expansión xy- plane (ppm/°C) 16- 19 1 4 - 1 8 1 4 - 1 8 -15 8-18 - Thermal Expansión z- axis below Tg^3 (ppm/°C) 5 0 - 8 5 4 4 - 8 0 -44 ~70 35 - 70 81 Glass Transition Temp. Tg (°C) 110-140 130 -160 165 - 190 175 - 200 220 - 280 180 - 260 Flexural Modulus (x 1010 Pa) Fill^1 Warp^2
6
0
6
7
Tensile Strength (x 10^8 Pa) Fill^1 Warp^2
3
8
Tabla 4.2 propiedades medioambientales de los materiales dieléctricos comunes
para unir laminas de cobre, laminas descubiertas, revestimientos de cobre o laminas de termopares entres sí.
las normas; IPC-L-109, IPC-4101, 746E o UL. En la mayoría de los casos el pre impreso debe ser del mismo material y el refuerzo debe ser de láminas revestidas de cobre. Estos valores no se incluirán en el esquema principal, pero sólo se deben utilizar las especificaciones del fabricante de la placa.
cinco tipos de resinas básicas con una amplia gama de propiedades. Para la selección del adhesivo se tiene en cuenta; dureza, coeficiente de expansión térmica (CTE), gama de temperaturas, resistencia dieléctrica, condiciones de curado y tendencia de desgasificación. En algunos casos los adhesivos estructurales puede ser suficiente para la unión de los elementos, ver 4.2.5. Cada tipo de adhesivo tiene puntos fuertes y débiles. En la aplicación real, la mayoría de las necesidades de adhesivo pueden ser reemplazadas por unos pocos materiales cuidadosamente seleccionados.
de aislamiento eléctrico y mecánico, ofrecen una amplia gama de propiedades físicas y eléctricas, incluyendo fuerzas de adhesión y cohesión, dureza, resistencia química, conductividad térmica y la estabilidad térmica en vacío. Están disponibles en variedad de modificadores, cargas y refuerzos para aplicaciones específicas y los rangos amplios de temperatura.
eléctricas y mecánicas muy buenas a temperatura ambiente y extrema Las resinas de silicona que contienen ácido acético se deben evitar en aplicaciones electrónicas. Las propiedades de resistencia a la adherencia, resistencia a la tracción, dureza y tienden a ser considerablemente más bajos que los epoxicas. Las siliconas se hinchan y se disuelven con la exposición prolongada a algunos productos químicos. Las siliconas se utilizan a menudo como un recubrimiento de amortiguación para los artículos que se encapsularan más tarde. También se disponen de geles de siliconas, que ofrecen propiedades mejoradas como encapsulantés.
propiedades eléctricas, adhesivas y de dureza. La resistencia química y estabilidad térmica en vacío tienden a ser considerablemente más bajos que los epóxicos. La temperatura de transición vítrea de estos materiales también tiende a ser baja
materiales ofrecen generalmente dureza, alta elasticidad y buena adhesión. Algunos de los compuestos de uretano son excepcionales como materiales de amortiguación de vibraciones y golpes. La resistencia a la humedad y química es relativamente alta, pero varía con el producto individual. Muchos de los uretanos se pueden utilizar en una aplicación relativamente gruesa como un compuesto de amortiguación de vibraciones local.
relación a los epóxicos. Son menos resistentes al ataque del solvente, su conductividad térmica y propiedades de resistencia eléctrica son buenas.
diseño donde las propiedades de conducción térmica no son críticas, el uso de adhesivos estructurales (ver 4.2.2) en lugar de los adhesivos térmicos pueden ser aceptables según lo determinado por análisis térmico y puede ser una alternativa más rentable.
materiales enumerados en el IPC-4101 y IPC-231-FC. Cuando la norma (UL) se impone, el material utilizado debe ser aprobado por UL para su uso por el fabricante de la placa impresa. Las temperaturas de punto caliente no deberán exceder las temperaturas especificadas para el material laminado seleccionado. Ver IPC-2222 para la temperatura máxima de funcionamiento especificado para materiales laminados. Los materiales utilizados (con revestimiento de cobre, pre impregnado, hoja de cobre, radiador, etc.) deberán ser especificados en el patrón de dibujo.
añade un pigmento cambia a un color, existe la posibilidad de retardar el pigmento de la capacidad de la resina de impregnación para humedecer completamente todos y cada uno de las fibras de vidrio. Sin humectación completa, la humedad puede ser atrapada. El papel de color no debe utilizarse porque el material por lo general cuesta más. Retrasos de producción también pueden ser ocasionados por la falta de disponibilidad de las existencias de color. Si el stock de color se requiere, deberá ser especificado en la documentación de adquisición.
el plano principal.
es el de contribuir a la formación de la estructura conductora. Más allá de esta función principal, ofrecen ventajas adicionales tales como la prevención de la corrosión, soldabilidad mejorada a largo plazo, resistencia al desgaste, y otros. Los requisitos de espesor y la integridad de chapados de recubrimientos metálicos y en los tablones se harán de conformidad con los requisitos de la Tabla 4- 3 para la clase apropiada de los equipos. A menos que se especifique lo contrario en plano principal, los chapados de recubrimientos metálicos deberán cumplir los requisitos especificados en 4.4.1 a través de 4.4.8.
superficie y a través de los agujeros de la placa de circuito impreso como un resultado de procesar el panel perforado a través de una serie de soluciones químicas. Normalmente, este es el primer paso en el proceso de recubrimiento y es generalmente 0,6 a 2,5 m de espesor, también se puede utilizar cobre electrolítico, esto es conocido como forro aditivo. 4.4.2 Recubrimientos semiconductor. Los recubrimientos de metalización se utilizan como un recubrimiento conductivo de arranque antes de la deposición de cobre electrolítico y se aplican a la pared del agujero. El recubrimiento debe ser de calidad suficiente para la deposición metálica posterior y deberá ser no migratorio. Este proceso es típicamente dependiente fabricante y no se especifica en el plan principal. 4.4.3 Revestimiento de cobre electrolítico. El cobre electrolítico puede ser depositado a partir de varios electrolitos diferentes, incluyendo fluoroborato de cobre, cianuro de cobre, sulfato de cobre, y pirofosfato de cobre. El sulfato de cobre y pirofosfato de cobre son los electrolitos más comúnmente utilizados para la construcción de la deposición de cobre sobre la superficie y a través de los agujeros hasta el espesor requerido. Este tipo de recubrimiento por lo general produce el requisito de cobre de espesor final.
4.4.4 Capa de oro. Una variedad de laminados de oro están disponibles. Estos pueden ser electrolíticos, no electrolíticos o depósitos de inmersión. Puede venir en oro 24k suave, 23 + k de oro duro (endurecimiento, utiliza cantidades pequeñas de cobalto, níquel o hierro que son mescladas con el oro), o el recubrimiento puede ser una aleación de quilates inferior (14k-20k) para algunas aplicaciones. El laminado en oro sirve para varios propósitos:
Cuando el protector de soldadura se utiliza como un aislante eléctrico las propiedades dieléctricas del revestimiento deben ser suficientes para mantener la integridad eléctrica. Cuando se requiere de recubrimiento sobre superficies de metal fundido, el ancho máximo recomendado de conductor, donde cubre completamente el conductor, deberá ser de 1,3 mm. Cuando los conductores de metal de fusión tienen una anchura mayor que 1,3 mm, el diseño del conductor deberá proporcionar un alivio a través del metal al sustrato laminado de base. El relieve debe ser de al menos 6,45 mm2 de tamaño y situado en una cuadrícula no mayor que 6,35 mm. Al realizar el llenado del agujero se debe realizar que se llene a ambos lados. Cuando se realiza sobre vías se utiliza, el máximo determinado por el diámetro de orificio, de las vías será de 1,0 mm para la Clase 1 y el equipo 2, y 0,65 mm para los equipos de clase 3. Para los cambios de cara placa de circuito impreso con diámetros mayores que el máximo, serán acordados entre el usuario y el proveedor de la placa. 4.5.1.1 Resistencia, adherencia y cobertura. La adhesión entre el protector y el laminado estará completa al cubrir el área total de cobertura. Tratamiento de óxido, cobre doble tratado, el tratamiento de protección química, o cualquier tipo de promotor de adherencia puede utilizarse. Cuando en el diseño no se ha aliviado áreas de cobre superiores a 625 mm2, el uso de un promotor de adhesión resistir es aconsejable. Cuando se requieren revestimientos de polímero sobre los no metales de punto de fusión, como el cobre, el diseño debe prever que los conductores que no están cubiertos por la capa protectora deben ser protegidos contra la oxidación, a menos que se especifique lo contrario. 4.5.2 Areas claras. Los recubrimientos líquidos requieren mayor distancia (por lo general 0,4 a 0, mm) que los foto resistentes (típicamente 0 - 0,13 mm). Las áreas claras pueden tener marcas de alineación para el ensamble. Los archivos de datos suele contener espacios iguales a la tierra. Esto permitirá a los fabricantes de la placa ajustar la holgura para cumplir con sus capacidades de proceso cumpliendo con los requisitos mínimos de despacho de diseño especificados en el plano principal. 4.5.2 Conformación de recubrimientos. Deben cumplir con los requisitos de la IPC-CC-830 y se especificarán en el plano general o en el diagrama de la placa. Cuando los requisitos de UL son impuestas, los revestimientos deberán ser aprobados por UL para su uso del fabricante de la placa. El diseñador debe estar al tanto de las cuestiones de compatibilidad. El recubrimiento es un material de aislamiento eléctrico que se ajusta a la forma de la tarjeta y de sus componentes. Se aplica con el fin de mejorar las propiedades superficie dieléctrica y protección contra los efectos de un ambiente severo. 4.5.2.1 Tipos de recubrimiento conformado y espesor. El revestimiento puede ser cualquiera de los tipos indicados. El espesor del revestimiento, será el siguiente para el tipo especificado, cuando se mide sobre una superficie plana: Tipo AR - Resina Acrílica 0.03-0.13 mm Tipo ER - Resina Epoxi 0.03-0.13 mm UR Tipo - Resina de uretano 0.03-0.13 mm Tipo SR - Resina de silicona 0.05-0.21 mm Tipo XY - Resina paraxilileno 0.01-0.05 mm Hay tres categorías químicas en el uso de materiales de revestimiento de conformación: elastómeros de silicona, compuestos orgánicos, y parileno. Los tres tipos proporcionan varios niveles de protección de los solventes, humedad, corrosión, arcos y otros factores ambientales que pueden poner en peligro el rendimiento de los circuitos (ver Tabla 4-7). Muchas tecnologías de superficie no se pueden realizar adecuadamente sin el uso de un revestimiento debido al espaciamiento apretado de los cables y trazas de tierra. TABLA 4-7 FUNCIONES RECUBRIMIENTOS Tipo Ventajas Desventajas