
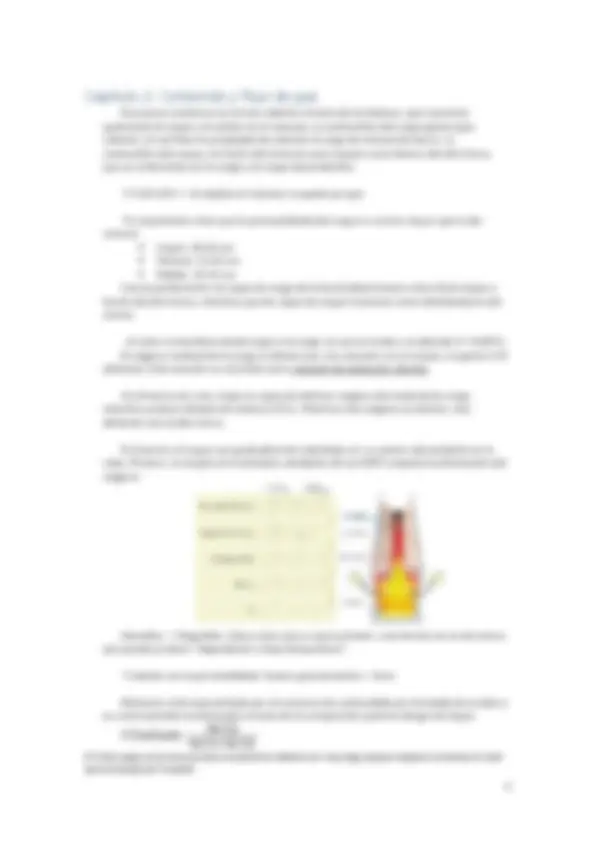
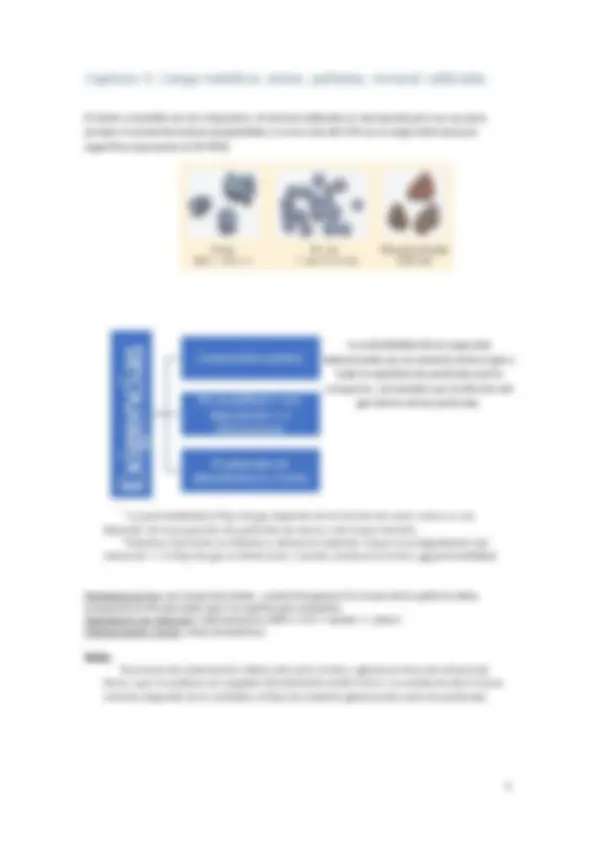
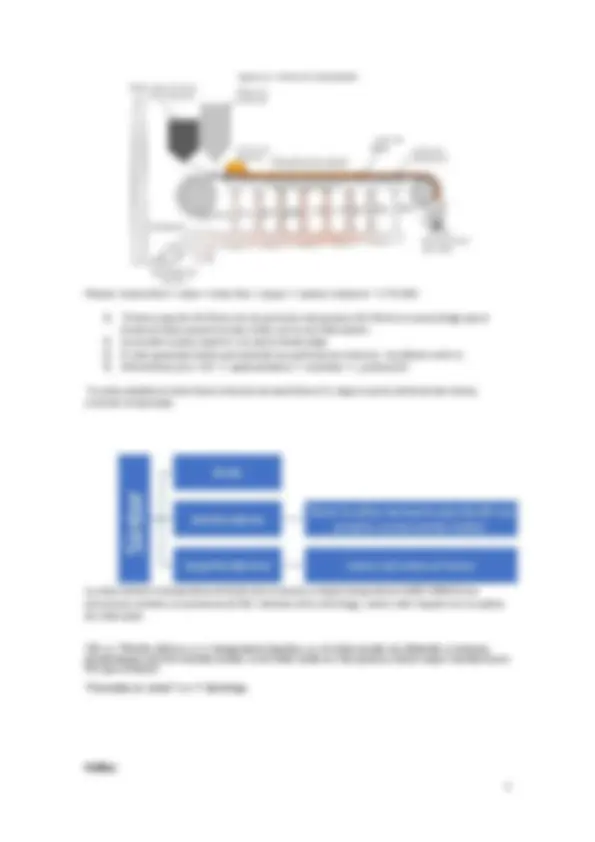
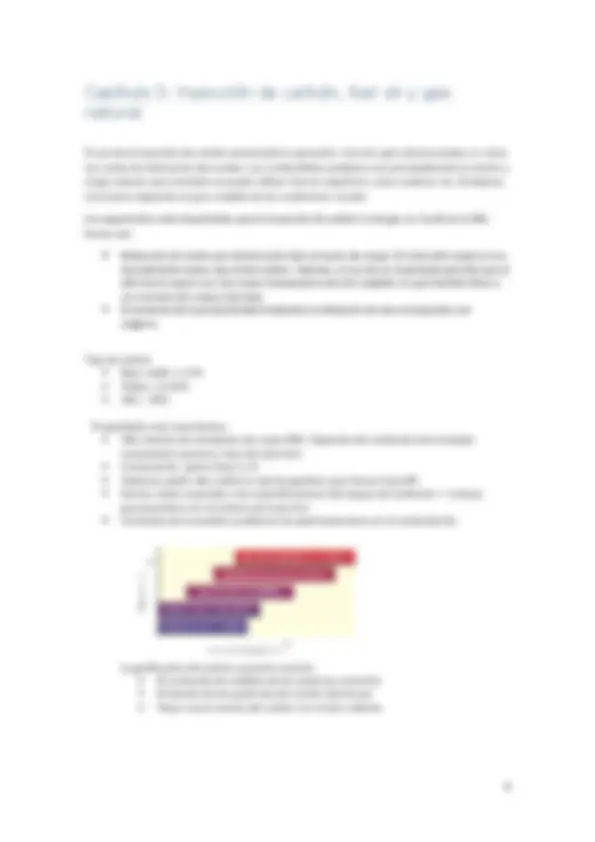
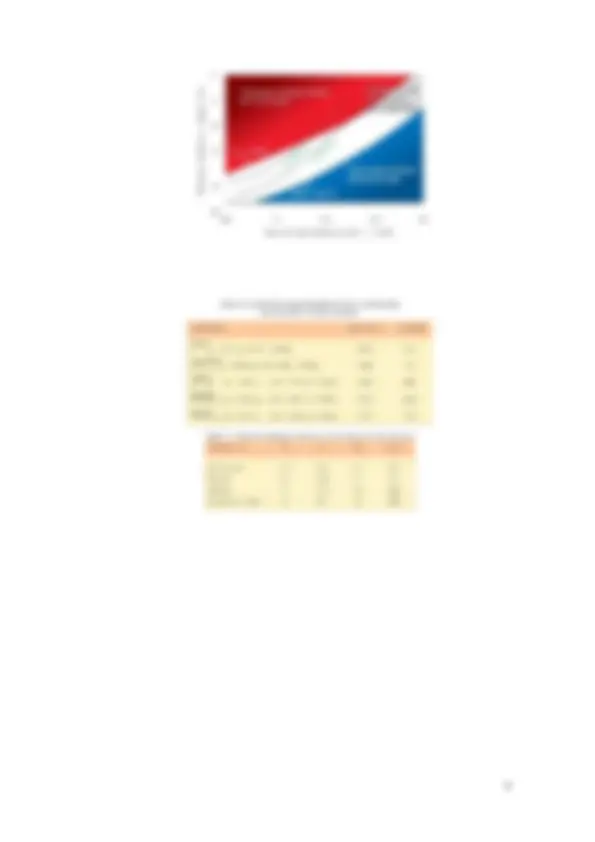
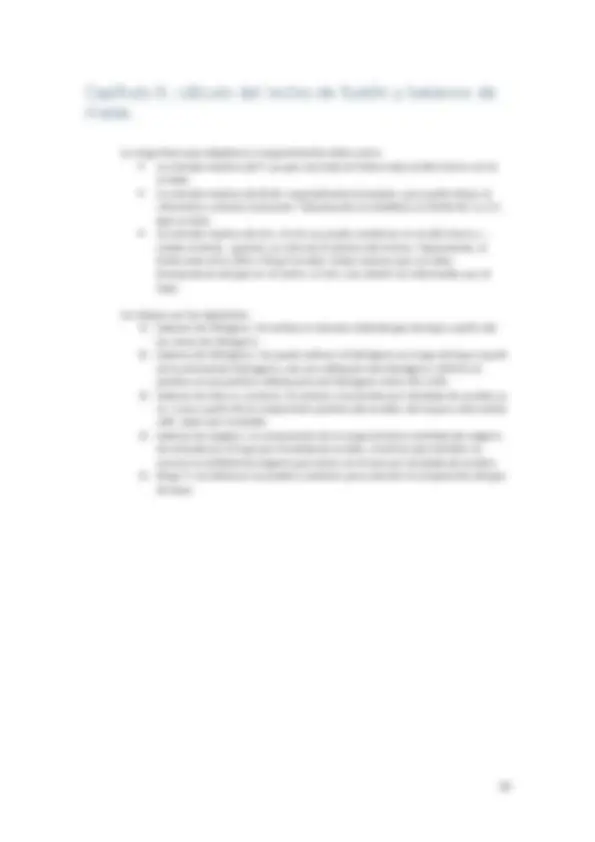
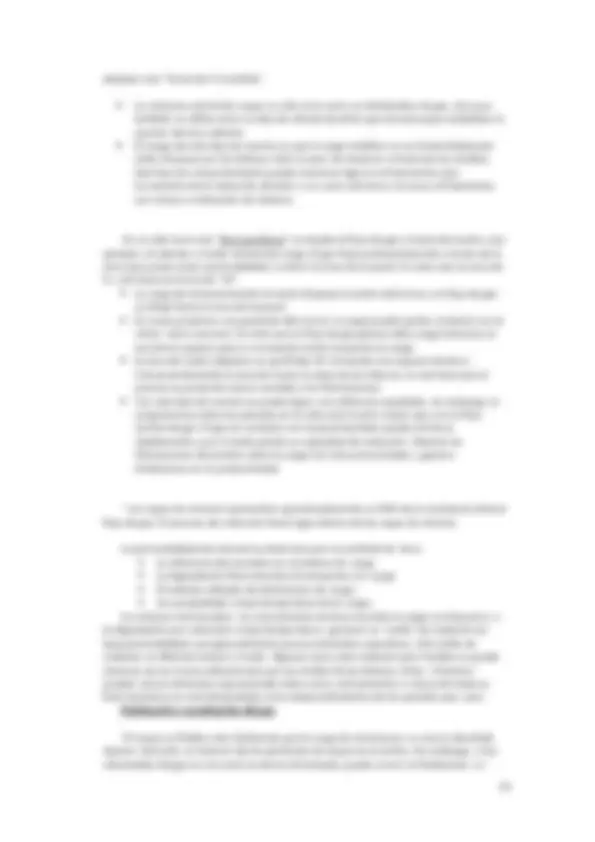
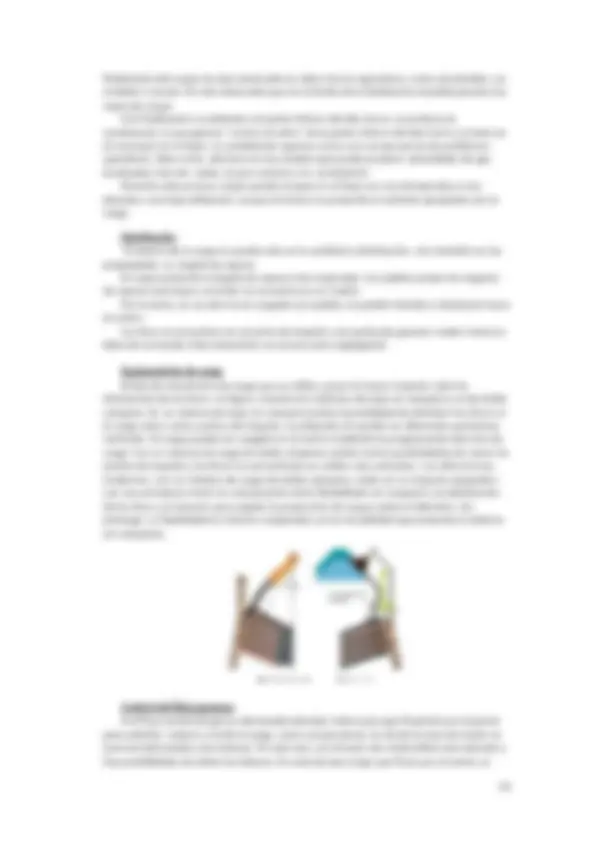
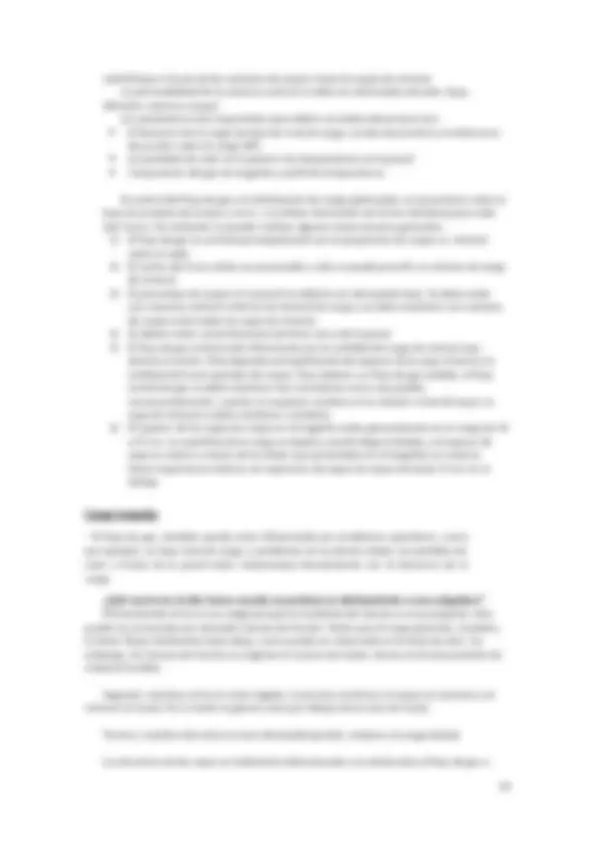
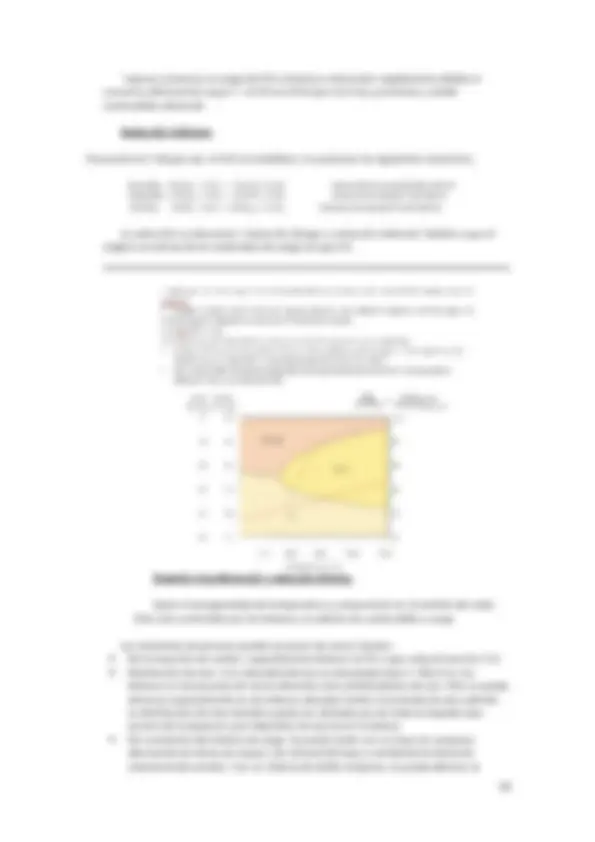
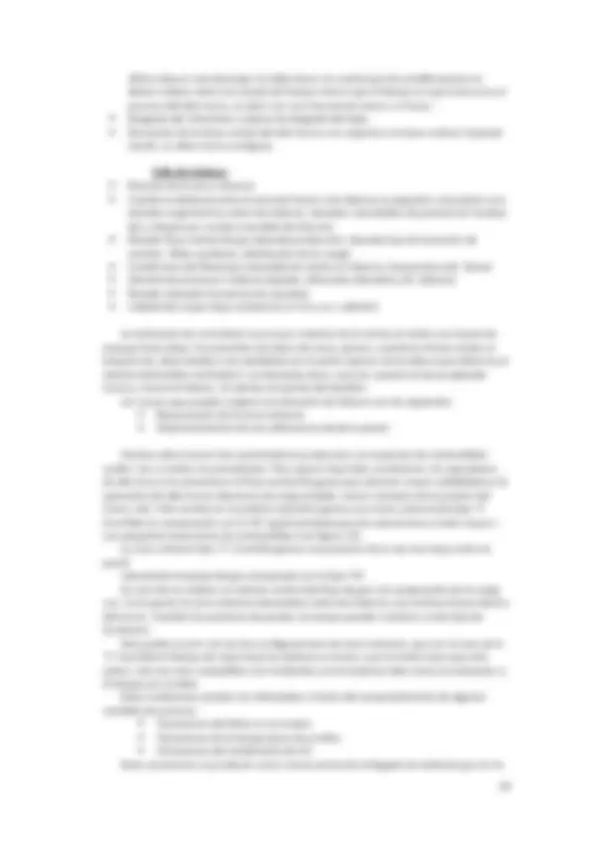
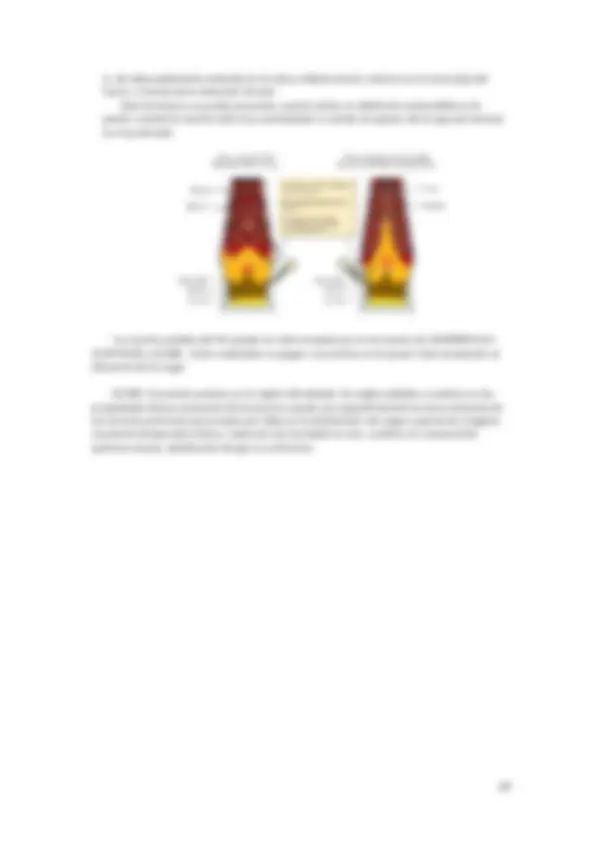
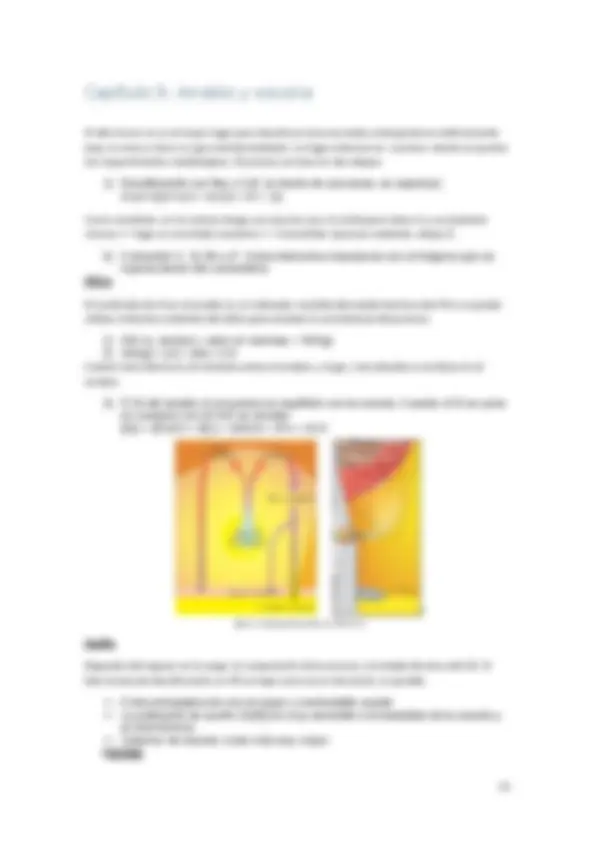
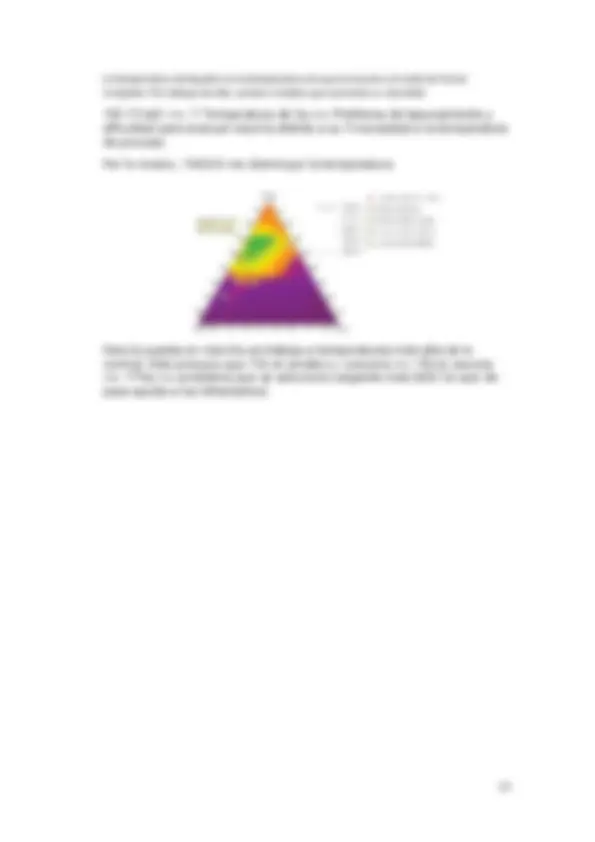
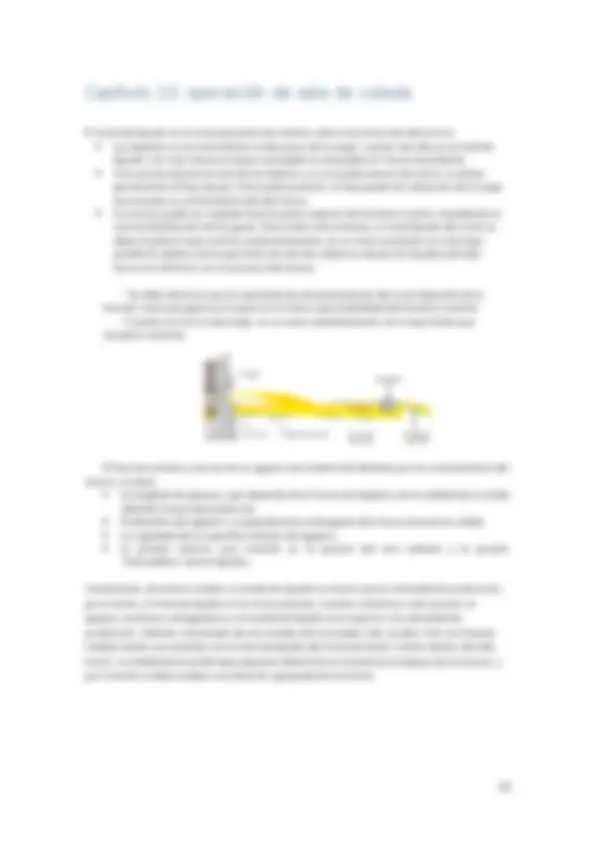
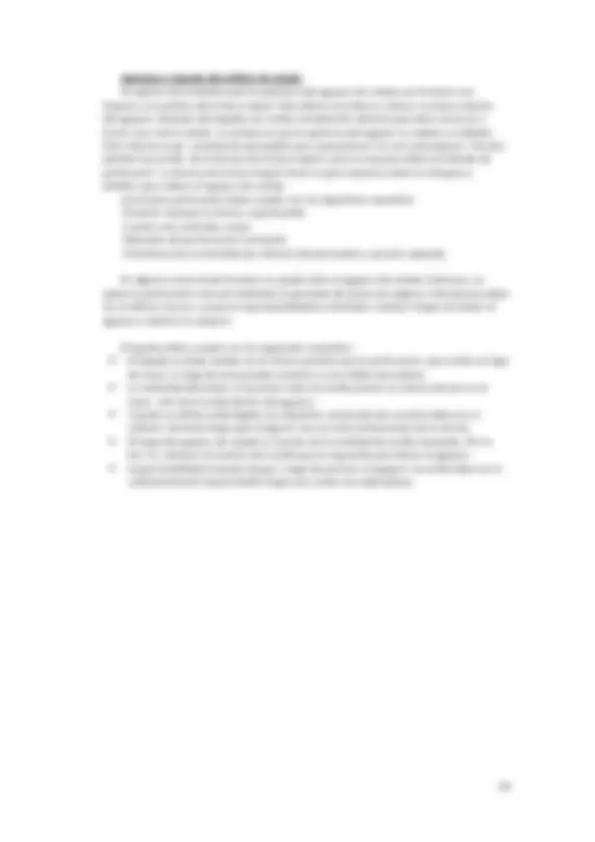
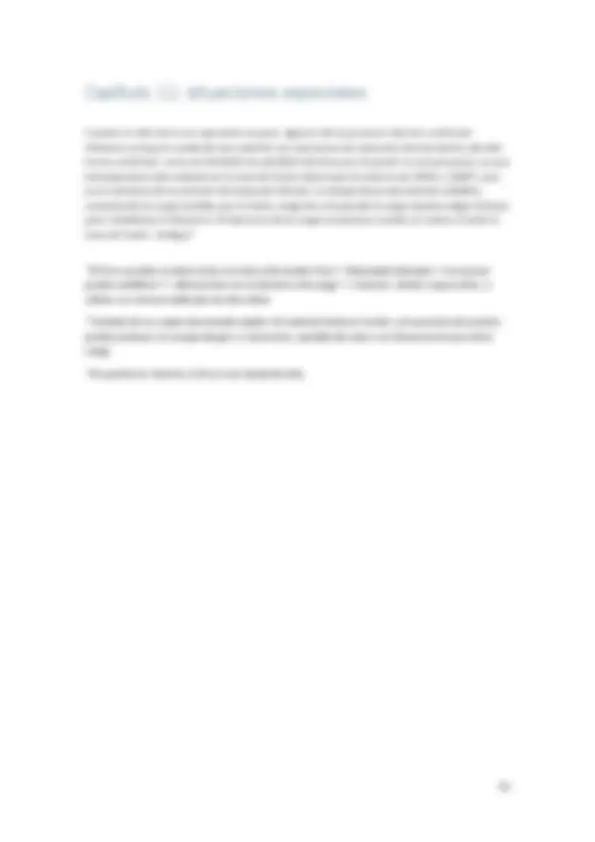
Prepara tus exámenes y mejora tus resultados gracias a la gran cantidad de recursos disponibles en Docsity
Gana puntos ayudando a otros estudiantes o consíguelos activando un Plan Premium
Prepara tus exámenes
Prepara tus exámenes y mejora tus resultados gracias a la gran cantidad de recursos disponibles en Docsity
Prepara tus exámenes con los documentos que comparten otros estudiantes como tú en Docsity
Los mejores documentos en venta realizados por estudiantes que han terminado sus estudios
Estudia con lecciones y exámenes resueltos basados en los programas académicos de las mejores universidades
Responde a preguntas de exámenes reales y pon a prueba tu preparación
Consigue puntos base para descargar
Gana puntos ayudando a otros estudiantes o consíguelos activando un Plan Premium
Comunidad
Pide ayuda a la comunidad y resuelve tus dudas de estudio
Descubre las mejores universidades de tu país según los usuarios de Docsity
Ebooks gratuitos
Descarga nuestras guías gratuitas sobre técnicas de estudio, métodos para controlar la ansiedad y consejos para la tesis preparadas por los tutores de Docsity
Caracteriticas y variables intrinsecas del proceso de fusión del hierro por vía de alto horno.
Tipo: Resúmenes
1 / 25
Esta página no es visible en la vista previa
¡No te pierdas las partes importantes!
*El tamaño de la cuba define la PRODUCTIVIDAD *Mineral + coque + carbon + caliza => arrabio + escoria (caliza + ceniza + impurezas) *El reductor principal es el CO *Todo AH muere por el crisol por eso quiero ESTABILIDAD OPERACIONAL Partes: Descripción del proceso: Un alto horno se carga con capas alternadas de coque y materiales que contienen hierro. Se insufla aire caliente (1200°C) dentro del alto horno por medio de toberas. El aire caliente gasifica los combustibles: coque y combustibles auxiliares inyectados a través de las toberas. En este proceso, el oxígeno del aire se transforma en monóxido de carbono (CO gas). El gas resultante tiene alta temperatura de llama, entre 2100 y 2300°C. El coque se consume frente a las toberas, creando vacío. Este gas caliente asciende a través del horno, realizando un número de funciones vitales. Calentamiento del coque en el área del etalaje/vientre. Fusión de la carga de mineral de hierro, creando vacío. Calentamiento del material en la cuba del alto horno. Eliminación de parte del oxígeno de la carga a través de reacciones químicas. Al fundirse, el mineral de hierro genera arrabio y escoria, que gotean hacia el crisol, desde donde se evacuan a través del orificio de colada (piquera). En la zona de goteo, el arrabio y la escoria consumen coque, creando vacío.
*Fuerza impulsora en el proceso del alto horno: el proceso en contracorriente general vacio en las zonas indiciadas, provocando el descenso de la carga. La parte superior del alto horno está cerrada a la atmósfera, debido a que los altos hornos modernos operan con una alta presión en el tope. Hay dos sistemas de tope diferentes: El sistema de doble campana, equipado además con una armadura móvil con el propó- sito de distribuir la carga. El tope sin campanas, que realiza la distribución de la carga mediante un canalón giratorio.
El sinter y el pellet son los mejorcitos; el mineral calibrado es más barato pero se usa poco porque no presenta buenas propiedades y nunca más del 15% en la carga total (aunq en argentina representa el 30-40%).
Mezcla: mineral fino + caliza + sinter fino + coque => tambor rotatorio + 5-7% H2O
Las funciones más importantes del coque son: Genera el calor necesario para fundir la carga. Por su estructura, otorga pemeabilidad. Soporte para la carga del horno Provee el carbono necesario para la carburación del arrabio. La calidad del coque se caracteriza por: El tamaño medio y la distribución granulométrica del mismo. El tamaño medio del coque metalúrgico está generalmente dentro del rango de 45 a 55 mm. La distribución de ta- maños debe ser ajustada para permitir la buena permeabilidad. La fracción mayor a 80 mm indica un deficiente control sobre el proceso de coquización. La resistencia física a la degradación causada por el transporte y otras tensiones me- cánicas. Los parámetros utilizados para esta propiedad son: I40, M40 y la estabilidad. Estos parámetros definen la distribución granulométrica después de la estabilización del coque. La resistencia a la abrasión se determina a través de los ensayos I10, M40 y dureza. La reactividad del coque. El coque puede reaccionar con CO2, que ataca la matriz del coque y conlleva a un consumo mayor en el alto horno. El coque de reactividad baja (IR, índice de reactividad del coque) y de resistencia más alta después de la reacción (CSR, resistencia del coque después de la reacción), tiene una resistencia mecánica mayor en la parte inferior del alto horno. La regularidad de la calidad del coque. La constancia diaria de la calidad del coque – en especial, del tamaño y de la distribución granulométrica del mismo– es un área fre- cuentemente descuidada en la operación del alto horno. La irregularidad de la calidad del coque lleva a la aparición de diferencias en la distribución de la carga, y puede in- fluir en la distribución del flujo del gas dentro del alto horno. Composición química (ley carbono, % ceniza, %volatil, humedad, contenido de S, + contenido de Na y P que actual como catalizador para reacción C+CO2 y no C+O2) El coque se produce a partir de una mezcla de carbones que se calienta a altas temperatu- ras (1200°C) en un ambiente libre de aire. A medida que la temperatura aumen- ta, la materia volátil del carbón escapa y se forma una matriz sólida de carbono: esta es la coquización del carbón
El uso de la inyección de carbón pulverizado (o granular), fuel oil y gas natural pueden re- ducir los costos de fabricación de arrabio. Los combustibles auxiliares son principalmente el carbón y el gas natural, pero también se puede utilizar fuel oil, alquitrán y otros materia- les. El balance económico depende en gran medida de las condiciones locales Los argumentos más importantes para la inyección de carbón (o de gas na- tural) en el alto horno son: Reducción de costos por disminución del consumo de coque. El costo del coque es sus- tancialmente mayor que el del carbón. Además, el uso de un inyectante permite que el alto horno opere con una mayor temperatura de aire soplado, lo que también lleva a un consumo de coque más bajo. El aumento de la productividad mediante la utilización de aire enriquecido con oxígeno. Tipo de carbón Bajo volátil: 6-12% Medio: 12-30% Alto: >30% Propiedades más importantes: Alta relación de reemplazo de coque (RR). Depende del contenido de humedad, composición química y tasa de inyección. Composición: quiero bajo S y P Material volátil: alto volátil es fácil de gasificar pero tienen bajo RR. Dureza: debe responder a las especificaciones del equipo de molienda => manejo granulométrico en el sistema de inyección. Contenido de humedad: problemas de apelmazamiento en la manipulación. La gasificación del carbón aumenta cuando: El contenido de volátiles de los carbones aumenta. El tamaño de las partículas de carbón disminuye. Mejor sea la mezcla del carbón con el aire caliente.
La carga tiene que adaptarse a requerimientos tales como: La entrada máxima de P, ya que casi todo el fósforo deja el alto horno con el arrabio. La entrada máxima de álcali, especialmente el potasio, que puede atacar al refractario y afectar el proceso. Típicamente se establece un límite de 1 a 1, kg/t arrabio. La entrada máxima de zinc: el zinc se puede condensar en el alto horno y – similar al álcali – generar un ciclo de Zn dentro del mismo. Típicamente, el límite está entre 100 y 150 g/t arrabio. Debe notarse que con altas temperaturas del gas en el centro, el zinc y los álcalis son eliminados por el tope Las etapas son las siguientes:
Para que la carga pueda descender por gravedad tiene que crearse vacío en alguna parte del alto horno. ¿Dónde se genera vacío? Primero: el coque se quema frente a las toberas, creando así vacío en esa zona. Segundo: el gas caliente asciende a través del alto horno y funde el material de carga. El liquido ocupa menos volumen y se genera un vacio. Tercero: el arrabio que gotea consume carbono. Este elemento es usado para la carbu- ración del hierro así como también para las reacciones de reducción directa En ocasiones el descenso de carga de un alto horno puede tornarse errático. ¿Cómo es es- te mecanismo? Los materiales de la carga y el coque fluyen con bastante facilidad a través de las tolvas, como puede observarse en el sistema de carga de un alto horno. Como consecuencia, en el área del alto horno donde el material es granular, la carga me-tálica y el coque fluyen con una facilidad similar a la de las áreas donde se produce vacío. Aún así, los operarios del alto horno están familiarizados con descensos irregulares de carga. Tales fenómenos son: “colgaduras” (no hay descenso de carga) y “deslizamientos” (descenso rápido y descontrolado de la carga). Del análisis en esta sección se desprende que, en general, la causa del descenso irregular de la carga se encuentra en la configuración de la zona de fusión. La fuerza descendente más importante es el peso de la carga, la fuerza ascendente más importante es la diferencia de presión entre el aire y la presión de tope. La zona cohesiva es la zona que ofrece mayor resistencia al flujo gaseoso, lo que conduce a la mayor caída de presión en la columna de carga y también a la fuerza ascendente más importante. Si esta diferencia de presión es muy grande, puede alterar el descenso de la carga En la práctica operativa, el descenso lento de la carga es a menudo un indicador de un pro- ceso irregular del alto horno. Las razones pueden ser: La fuerza ascendente es muy elevada. Los operarios experimentados tienen conoci- miento de la diferencia de presión máxima entre los niveles de carga que permite un funcionamiento sin problemas. Si el máximo diferencial de presión es excedido
adoptan una “forma de V invertida”. La columna central de coque no sólo sirve como un distribuidor de gas, sino que también se utiliza como un tipo de válvula de alivio que funciona para estabilizar la presión del aire caliente. El riesgo de este tipo de marcha es que la carga metálica no se funda totalmente antes de pasar por las toberas (esto se pue- de observar a través de las mirillas). Este tipo de comportamiento puede ocasionar ligeros enfriamientos (por incremento de la reducción directa), o en casos extremos, bruscos enfriamientos con rotura o inclinación de toberas. -En un alto horno de “flujo periférico” se impide el flujo de gas a través del centro, por ejemplo, al calentar y fundir mineral de carga. El gas fluye preferentemente a través de la zona que posee mejor permeabilidad, es decir la zona de la pared. En este caso la zona de fu- sión toma la forma de “W”. La carga de mineral durante la fusión bloquea el centro del horno y el flujo de gas se dirige hacia la zona de la pared. En zonas próximas a la pared del alto horno, la carga puede perder contacto con el refrac- tario (ranuras). En este caso el flujo de gas genera altas cargas térmicas al encontrar espacio para su circulación (entre la pared y la carga la zona de fusión adquiere un perfil tipo W, formando una especie de disco. Consecuentemente la zona de fusión se aleja de las toberas, lo cual hace que el proceso se presente menos sensible a las fluctuaciones. Con este tipo de marcha se puede lograr una eficiencia aceptable, sin embargo, la carga térmica sobre las paredes en la cuba será mucho mayor que con el flujo central de gas. El gas en contacto con la pared también puede enfriarse rápidamente y por lo tanto pierde su capacidad de reducción. Además las fluctuaciones de presión sobre la carga son más pronunciadas, y genera limitaciones en la productividad.
fluidización del coque ha sido observada en altos hornos operativos, como así también, en modelos a escala. Ha sido observado que en el limite de la fluidización el pellet penetra las capas de coque. Si la fluidización se extiende a la parte inferior del alto horno, se produce la canalización, lo que genera “cortos circuitos” de la parte inferior del alto horno (y hasta en el raceway) con el tope. La canalización aparece como una consecuencia de problemas operativos, tales como, demoras en las coladas que puede producir velocidades de gas localizadas más ele- vadas, lo que conduce a la canalización. Durante este proceso, el gas puede escapar en el tope con una temperatura muy elevada y una baja utilización, ya que el mismo no presentó el contacto apropiado con la carga. Distribución *El diseño de la carga no queda solo en la cantidad y distribución, sino también en las propiedades: ej: ángulo de reposo El coque presenta el ángulo de reposo más empinado. Los pellets poseen los ángulos de reposo más bajos y el sinter se encuentra en el medio. Por lo tanto, en un alto horno cargado con pellets, los pellets tienden a deslizarse hacia el centro. Los finos se concentran en el punto de impacto y las partículas gruesas ruedan hacia los lados de la meseta. Este mecanismo se conoce como segregación Equipamiento de carga El tipo de mecanismo de carga que se utiliza, posee el mayor impacto sobre la distribución de los finos. La Figura muestra los sistemas de tope sin campana y el de doble campana. En un sistema de tope sin campana existe la posibilidad de distribuir los finos en la carga sobre varios puntos de impacto, movilizando el canalón en diferentes posiciones verticales. El coque puede ser cargado en el centro mediante la programación del ciclo de carga. Con un sistema de carga de doble campana existen menos posibilidades de variar los puntos de impacto y los finos se concentrarán en anillos más estrechos. Los altos hornos modernos, con un sistema de carga de doble campana, están en su mayoría equipados con una armadura móvil, la cual presenta cierta flexibilidad con respecto a la distribución de los finos y al mineral, para regular la proporción de coque sobre el diámetro. Sin embargo, su flexibilidad es inferior comparada con la versatilidad que presenta el sistema sin campanas. Control del flujo gaseoso Si el flujo central de gas es demasiado elevado, habrá poco gas fluyendo por la pared para calentar, reducir y fundir la carga, como consecuencia, la raíz de la zona de fusión se acercará demasiado a las toberas. En este caso, el consumo de combustible será elevado y hay posibilidades de dañar las toberas. Es esencial que el gas que fluye por el centro se
través de ellas. Esto conduce nuevamente a la generación de áreas donde la carga no se reduce adecuadamente y permanecen en un estado cohesivo demasiado tiempo. Estás áreas formarán puentes que volverán a colgar el horno. El problema solo puede ser resuelto, restableciendo la estructura de capas dentro del alto horno, lo cual significa, que el contenido total del horno debe ser renovado; el horno tiene que ser operado a viento reducido durante 5 a 10 horas
La producción de un alto horno se relaciona directamente con la cantidad de coque que se quema frente a las toberas en régimen estacionario. Esto es debido a que, en el tope del alto horno cada carga de coque ingresa con una cantidad determinada de mineral. En régimen estacionario, el arrabio se produce tan pronto como se quema el coque. La productividad de un alto horno aumenta cuanto menos combustible se utilice por tonelada de arrabio. El calor del aire caliente y el calor que se genera por la combustión de coque en el raceway, se utilizan para fundir la carga. El calor que se encuentra disponible para fundir la
carga depende de la cantidad de gas que se produce y de la temperatura de llama, la "temperatura adiabática de llama del raceway" (RAFT). 2C+O2=2CO H2O+C=CO+H La temperatura de llama se encuentran normalmente en el rango de 2000°C a 2300°C y es- tá influenciada por las condiciones del raceway. Cualitativamente: la temperatura de llama aumenta si: La temperatura del aire caliente se eleva El porcentaje de oxígeno en el aire caliente aumenta. La temperatura de llama disminuye si: La humedad se eleva en el aire caliente Aumenta la inyección de combustible, ya que ingresan a la zona de combustión los com- bustibles fríos en lugar del coque que ingresa caliente. El efecto final también depende de la composición del combustible auxiliar. En la Figura 62, se presenta el equilibrio entre CO C+ CO 2 en función de la temperatura. La línea graficada indica el equilibrio de las reacciones llamadas "Boudouard". A temperaturas por encima de los 1100°C, todo el CO 2 se transforma en CO, si está en con- tacto con coque. Por lo tanto, a las temperaturas elevadas del etalaje y de la zona de fusión del alto horno, sólo se presenta monóxido de carbono A temperaturas por debajo de los 500°C, todo el CO tiende a descomponerse en C+CO 2. El carbono que se genera de esta forma es muy fino y se denomina carbono "Boudouard". En la práctica operativa se puede observar la descomposición del monóxido de carbono por deposición de C sobre el material refractario. Este es generalmente un proceso muy lento. Reducción directa: FeO+CO=Fe+CO CO2+C=CO
Feo+C=Fe+CO => Reducción directa xq el C se consume directamente Se deben tener en cuenta observaciones importantes: La reducción directa utiliza carbono (coque) y genera gas CO extra. La reducción directa demanda mucha energía. Solo toma 1/3 del óxigeno en la carga (el 2/3 lo hace la indirecta)
último skip en una descarga. Se debe tener en cuenta que las modificaciones se deben realizar sobre una escala de tiempo menor que el tiempo en que transcurre el proceso del alto horno, es decir con una frecuencia menor a 6 horas. Desgaste del refractario o placas de desgaste del tope. Desviación de la línea central del alto horno con respecto a la línea vertical. Especial- mente, en altos hornos antiguos. Falla de toberas: Posición de la zona cohesiva Cuando la distancia entre la zona de fusión y las toberas es pequeña, se produce una elevada carga térmica sobre las toberas; elevadas velocidades de producción localiza- das y ataque por arrabio (mordida de tiburón). Elevado flujo central de gas (elevada producción, elevada tasa de inyección de combus- tibles auxiliares, distribución de la carga) Condiciones del Raceway (velocidad de viento en toberas, temperatura de llama) Simetría de procesos ( toberas tapadas, diferentes diámetros de toberas) Paradas (elevada frecuencia de paradas) Calidad del coque (baja resistencia en frío y en caliente) La inclinación de una tobera ocurre por rotación de la misma al recibir una fuerza de empuje hacia abajo. Se presentan dos tipos de casos, graves: cuando la misma recibe un impacto tal, observándose una abolladura en la parte superior de la tobera que deforma el asiento del bastidor (enfriador). Los llamados leves, ocurren cuando la fuerza aplicada marca y mueve la tobera, sin afectar el asiento del bastidor. Las causas que pueden originar la inclinación de toberas son las siguientes: Baja posición de la zona cohesiva Desprendimiento de una adherencia desde la pared Muchos altos hornos han aumentado la producción y la inyección de combustibles sustitu- tos a niveles sin precedentes. Para operar bajo tales condiciones, los operadores de alto horno incrementaron el flujo central de gases para alcanzar mayor estabilidad en la operación del alto horno (descenso de carga estable, menor variación de la presión del horno, etc). Este cambio en la práctica operativa genera una zona cohesiva del tipo ‘V’ invertida en comparación con la ‘W’ experimentada para las operaciones a todo coque o con pequeñas inyecciones de combustibles (ver figura 72). La zona cohesiva tipo ‘V’ invertida genera una posición de la raíz mas baja contra la pared reduciendo el pasaje de gas comparado con la tipo ‘W’. En caso de no realizar un estricto control del flujo de gas y la composición de la carga con- tra la pared, la zona cohesiva descenderá sobre las toberas y las inclinará hacia dentro del horno. También las practicas de parada /arranque pueden conducir a este tipo de fenómeno. Esto puede ocurrir con las dos configuraciones de zona cohesiva, pero en el caso de la ‘V’ invertida el tiempo de viaje hacia las toberas es menor y por lo tanto hace que esta opera- ción sea más susceptible a los incidentes con las toberas tales como la inclinación o el ataque por arrabio. Estas condiciones pueden ser detectadas a través del comportamiento de algunas variables de proceso: Variaciones del Silicio en el arrabio Variaciones de la temperatura de arrabio Variaciones del rendimiento de CO Estas variaciones se producen como consecuencia de la llegada de material que no ha
si- do adecuadamente reducido en la cuba y deberá tomar carbono en la zona baja del horno, a través de la reducción directa Este fenómeno se puede presentar cuando existe un déficit de combustible en la pared, cuando la marcha está muy centralizada o cuando el espesor de la capa de mineral es muy elevado *La marcha estable del AH puede ser interrumpida por la formación de ADHERENCIAS - SCAFFOLDS o SCABS-. Estos materiales se pegan y acumulan en la pared, interrumpiendo el descenso de la carga -SCABS: formación pastosa en la región del etalake. Se origina debido a cambios en las propiedades físicas (aumento de la escoria cuando cae repentinamente la zona cohesiva) de las escorias primarias provocadas por fallas en la distribución de carga y operación irregular (aumento temperatura llama, reducción de humedad en aire, cambios en composición quimica escoria, distribución de gas no uniforme).