
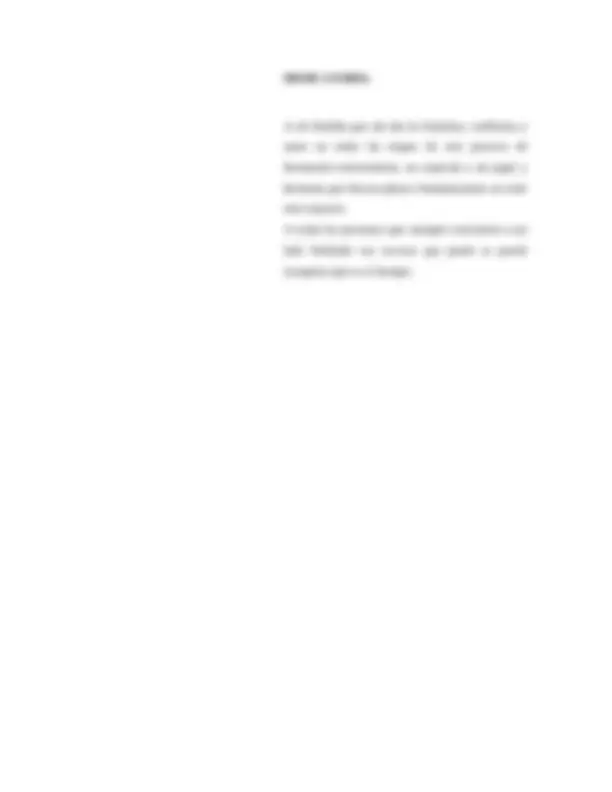
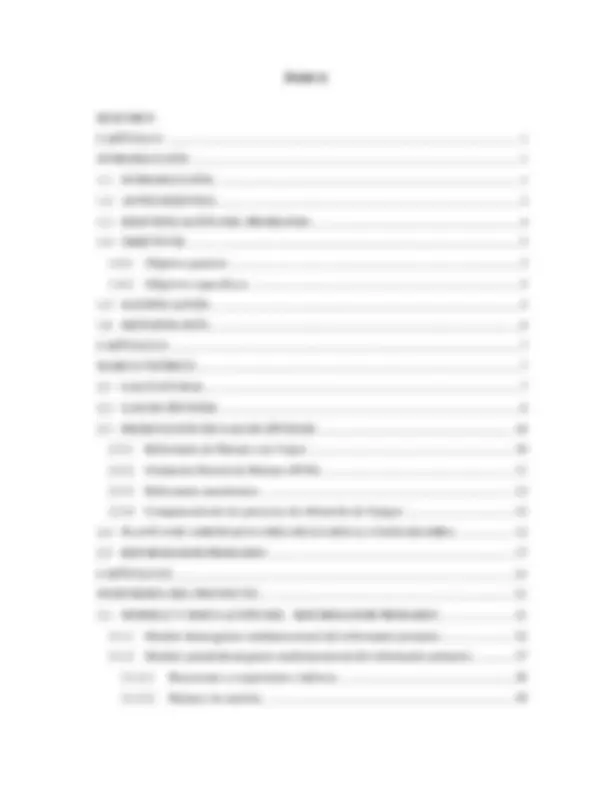
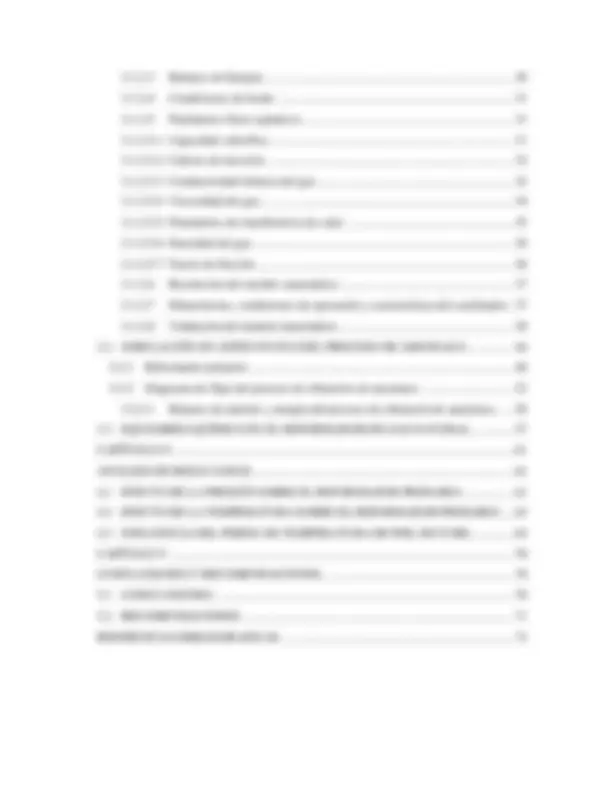
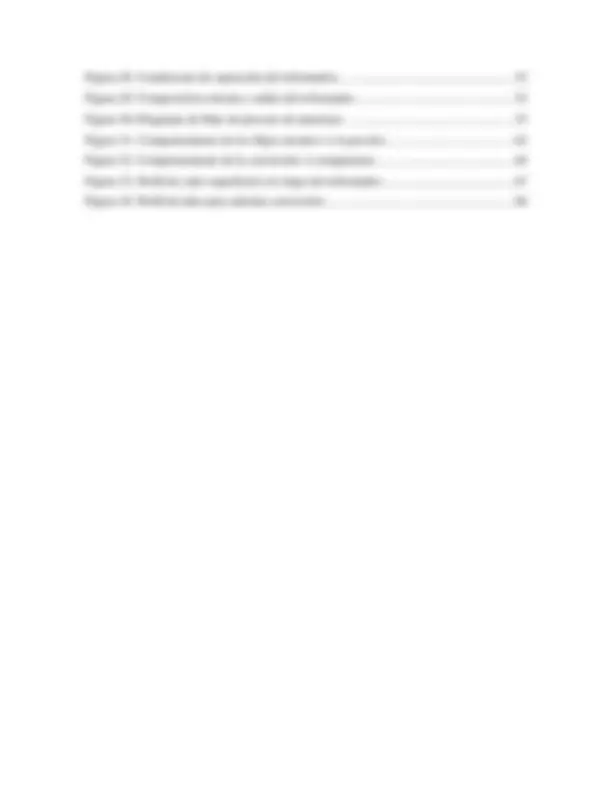
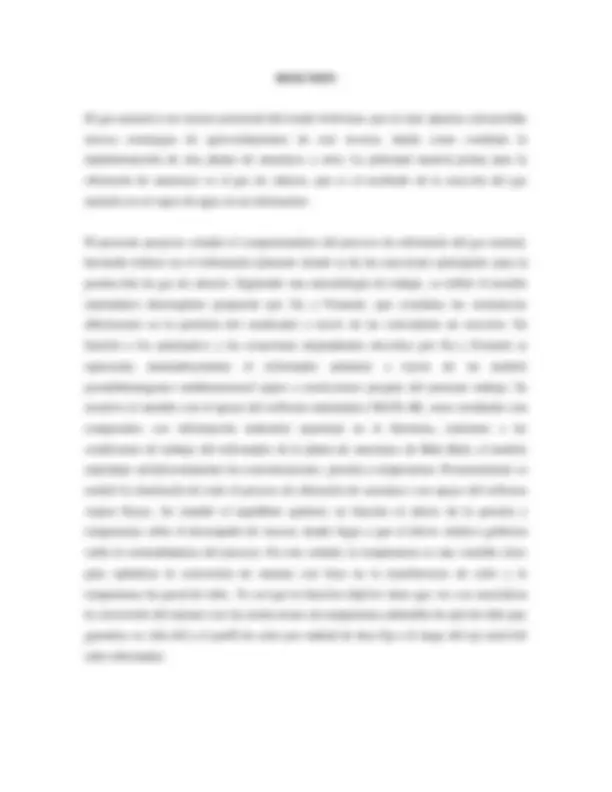
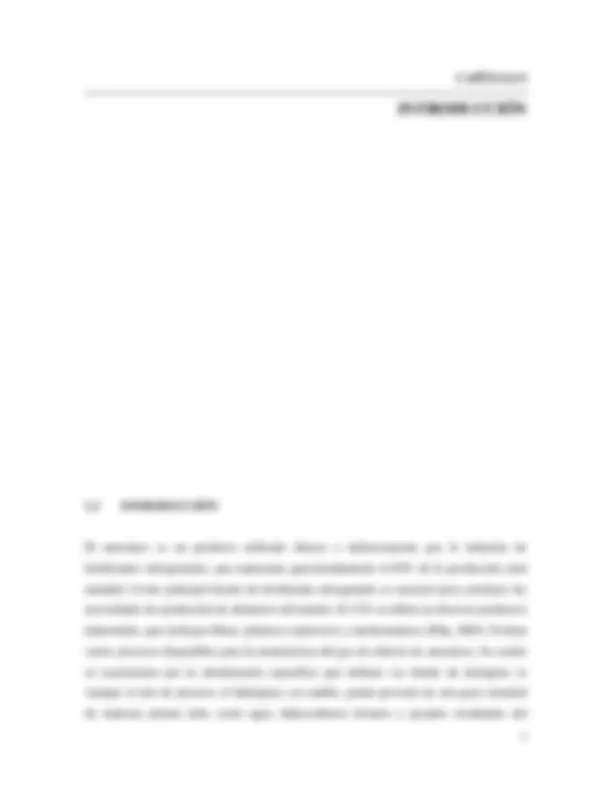
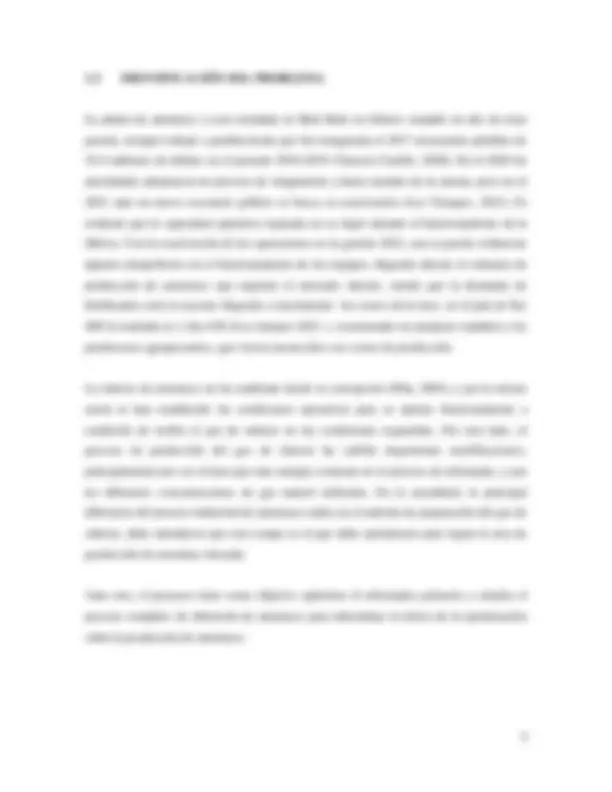
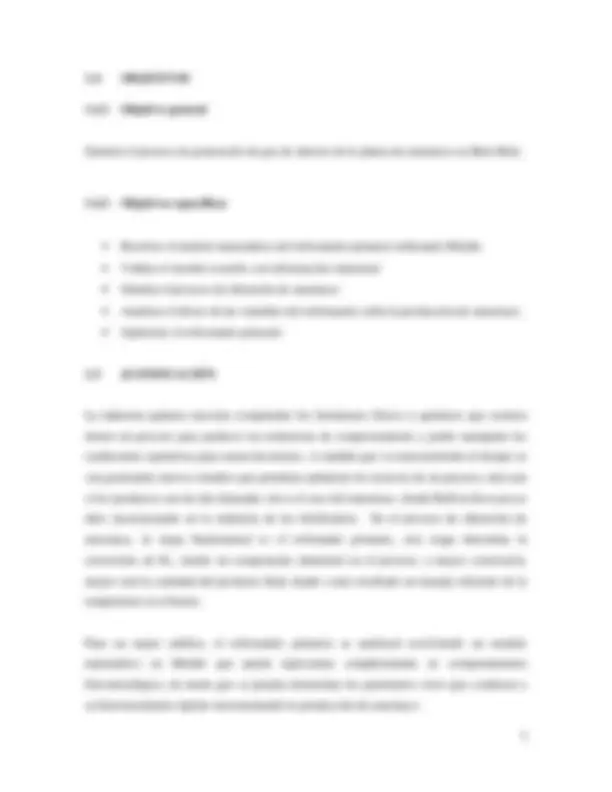
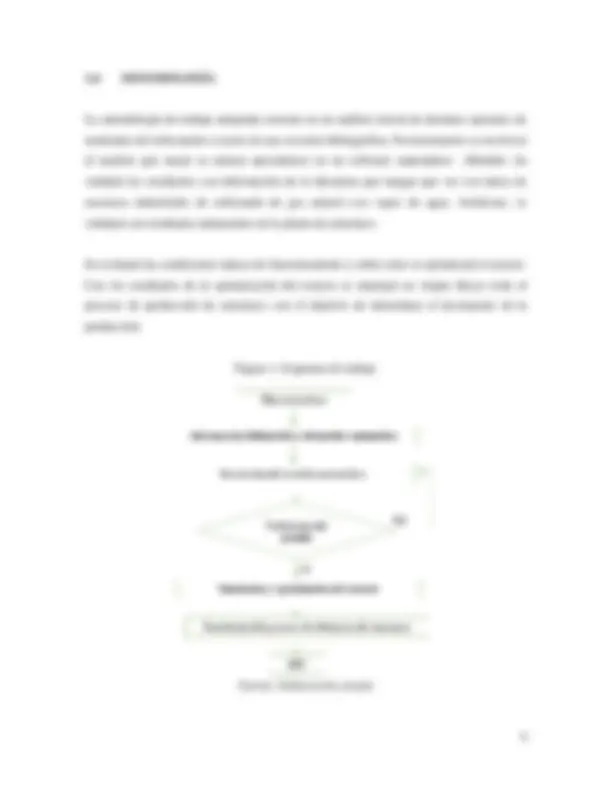
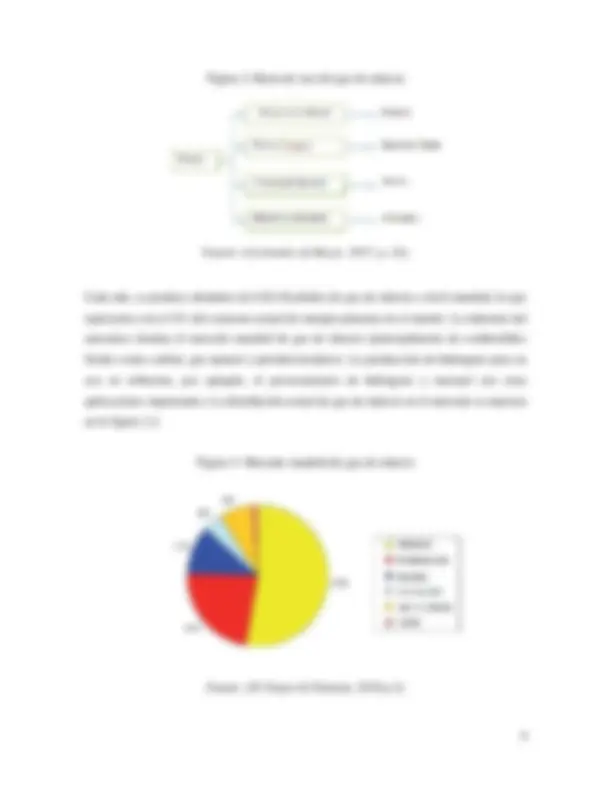
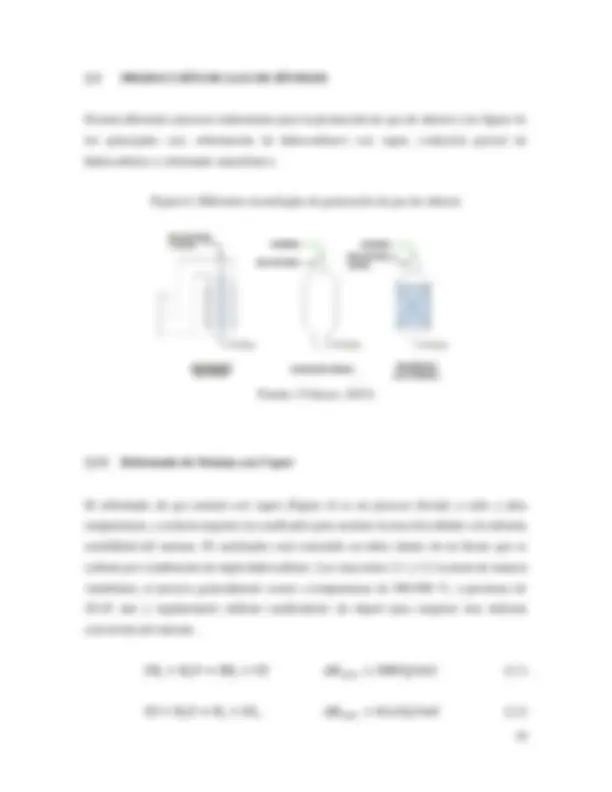
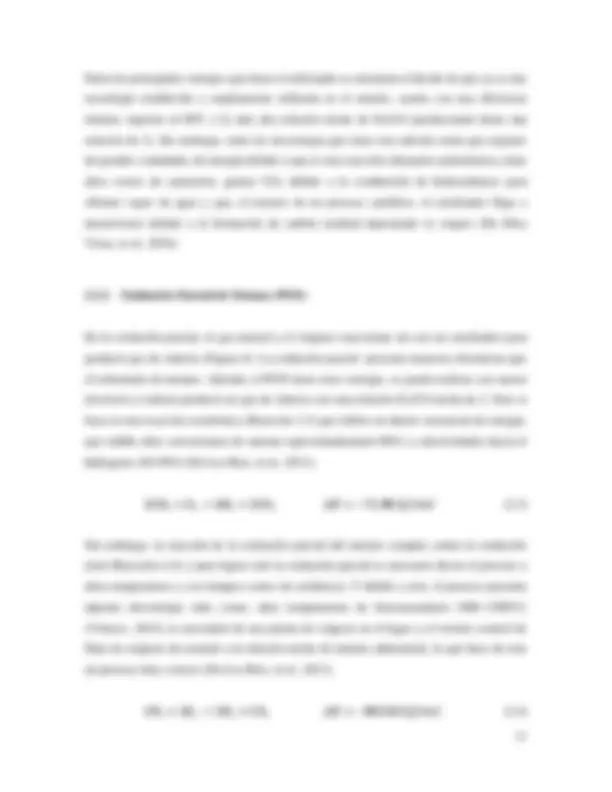
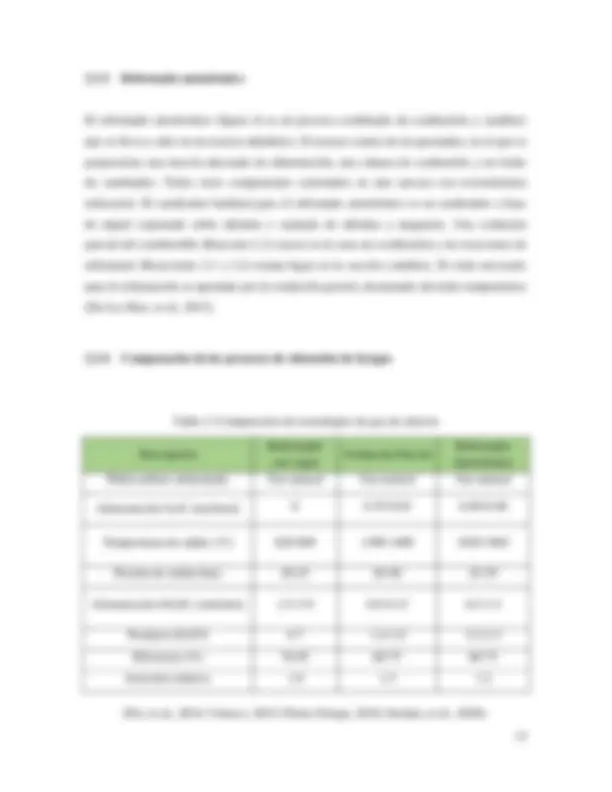
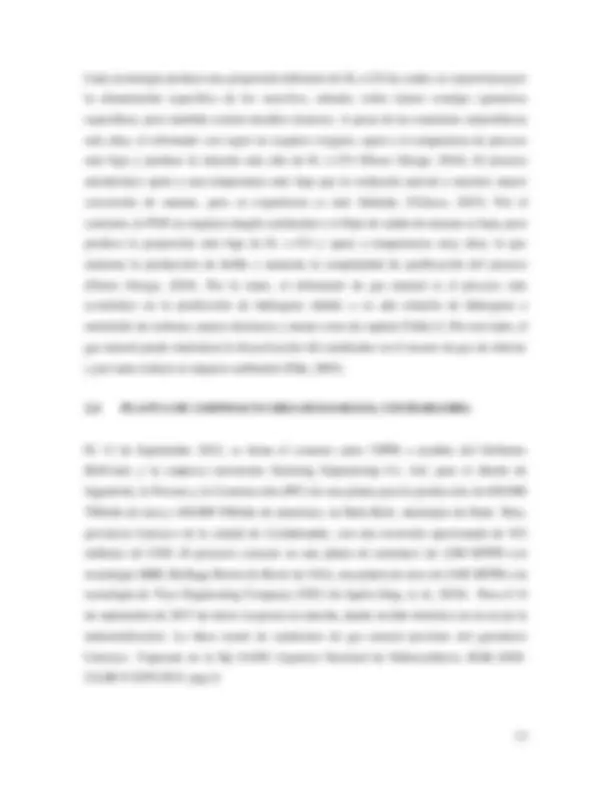
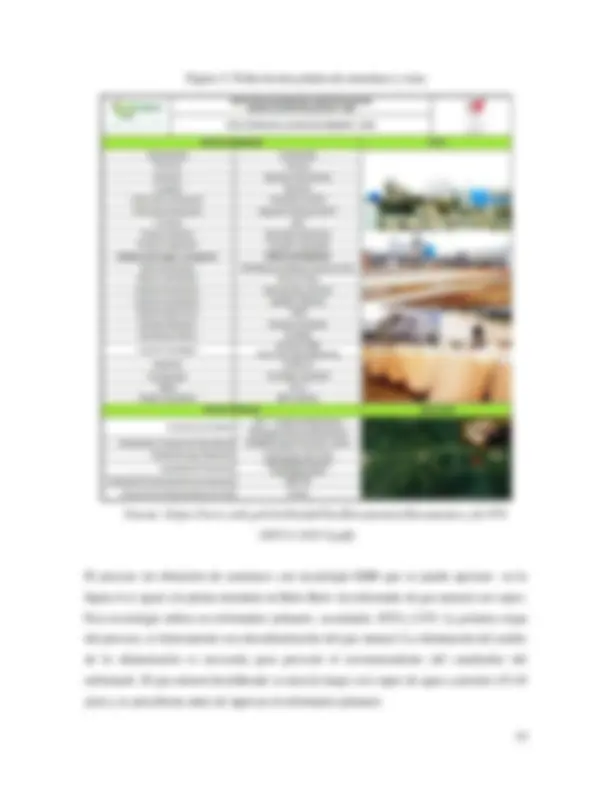
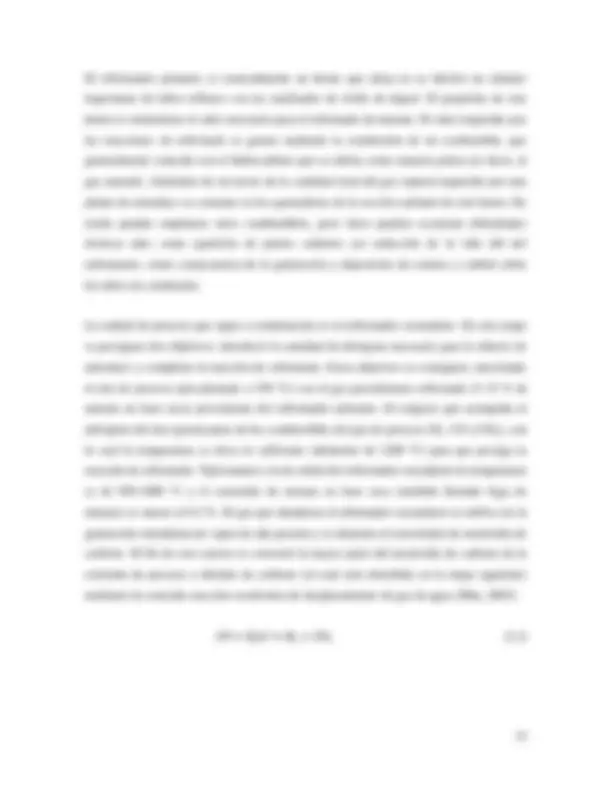
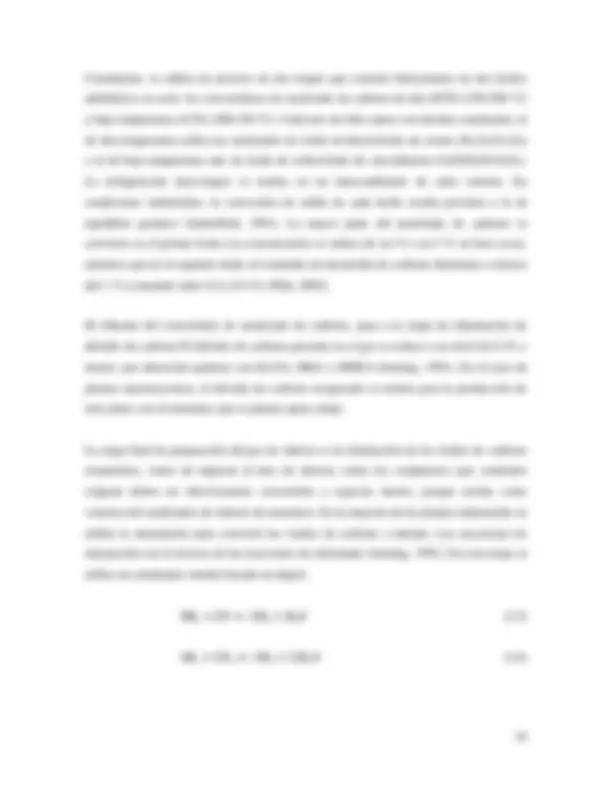
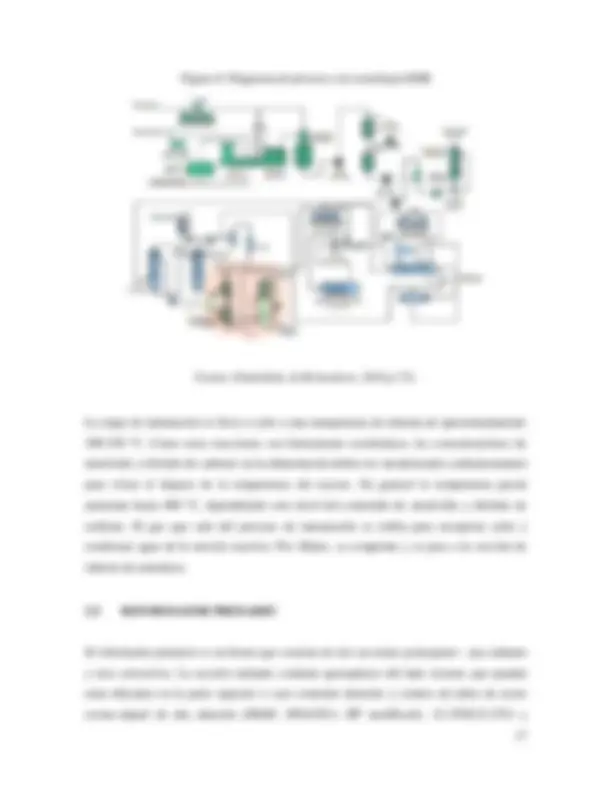
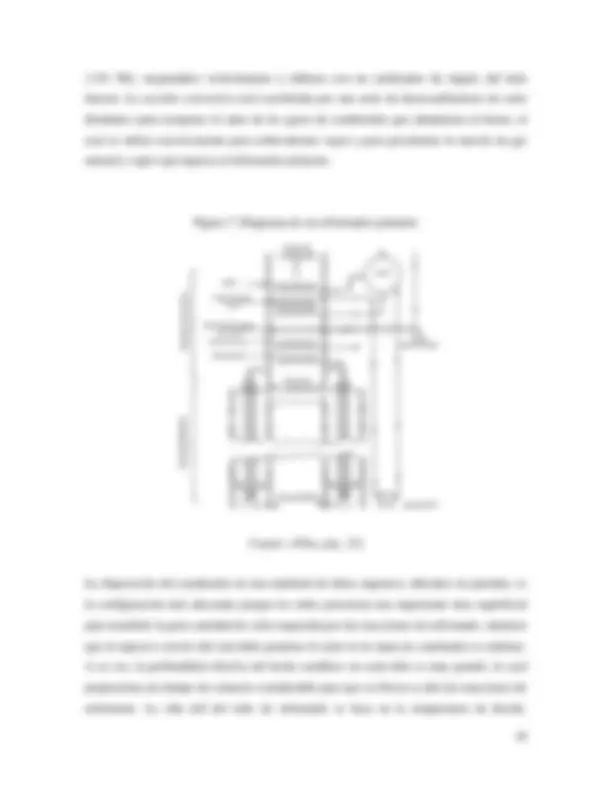
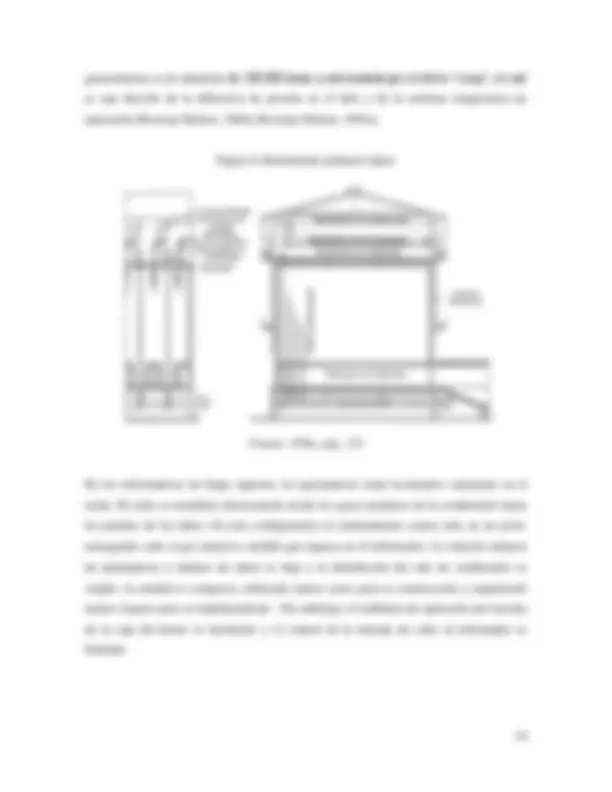
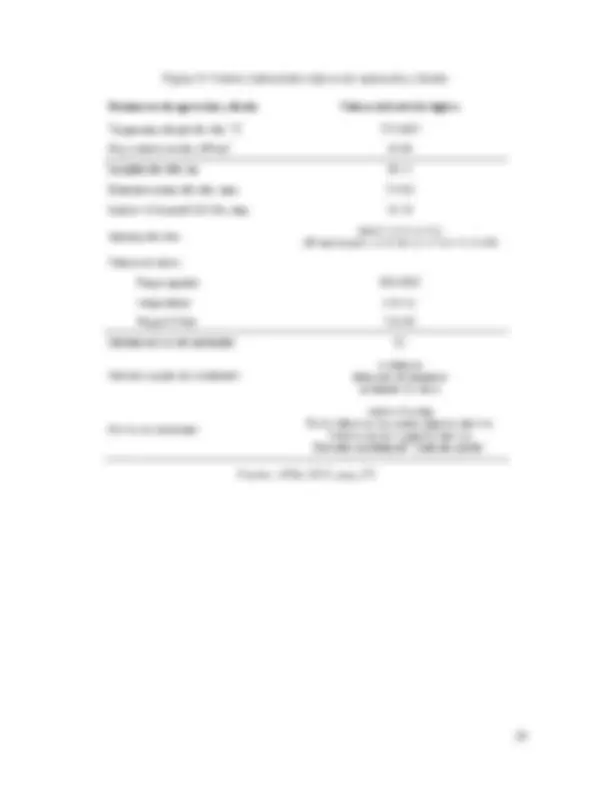
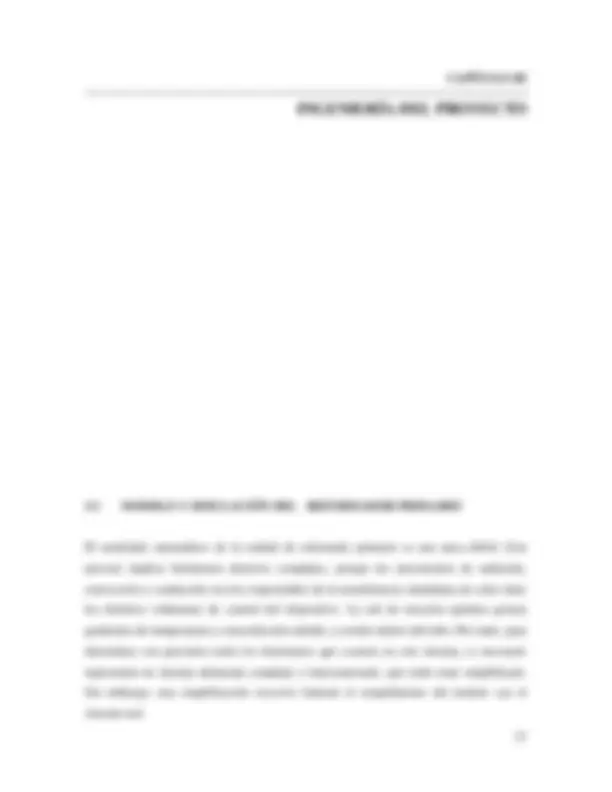
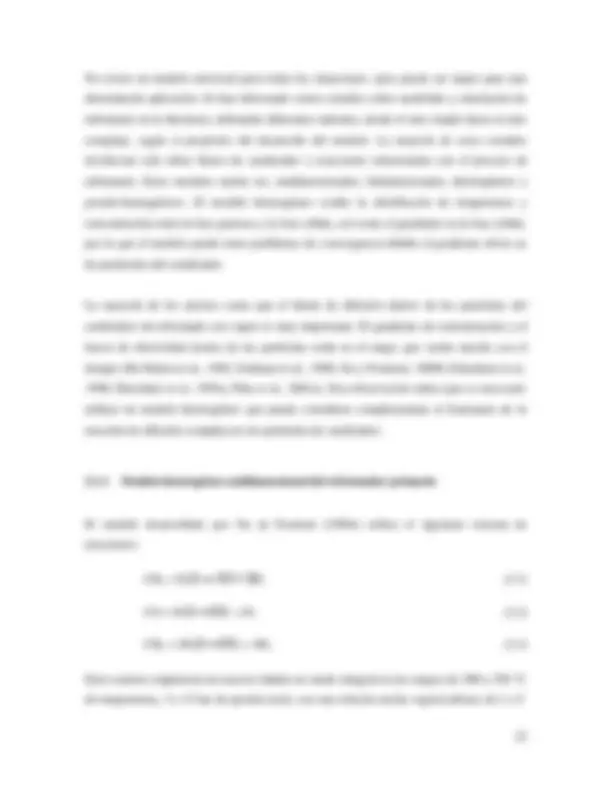
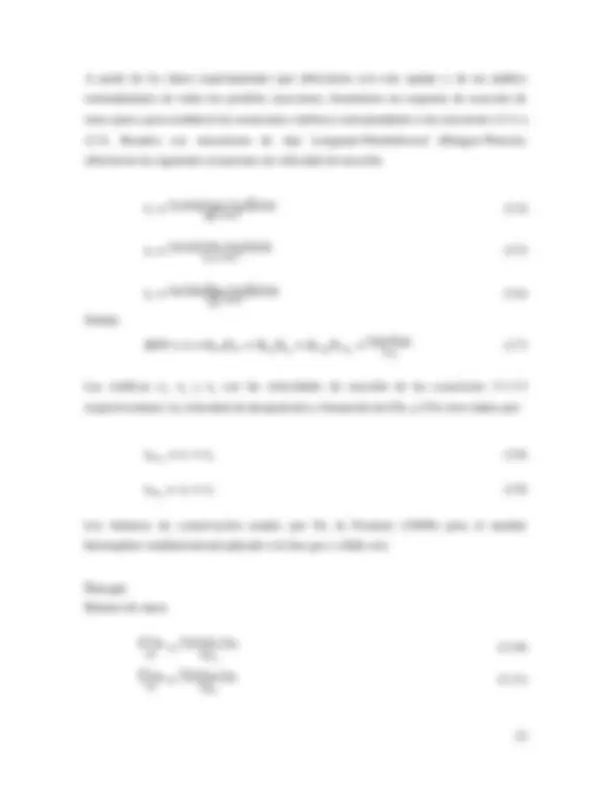
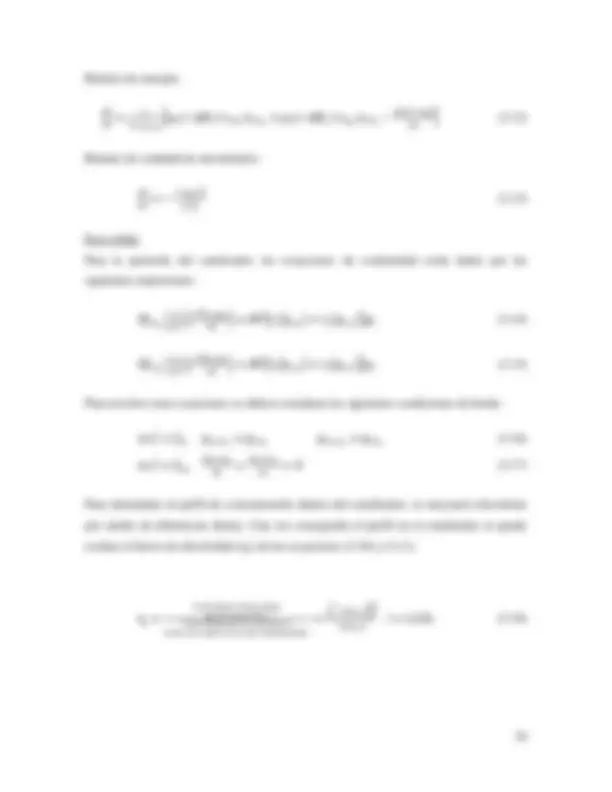
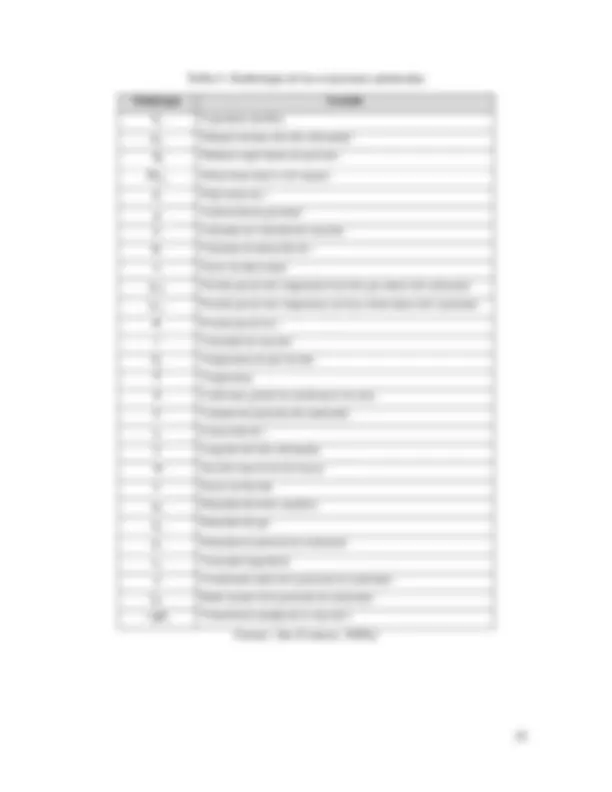
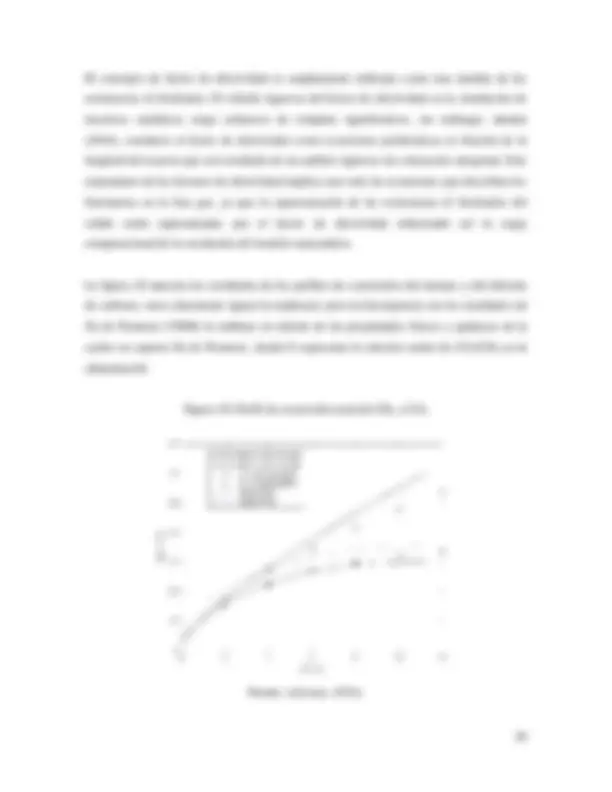
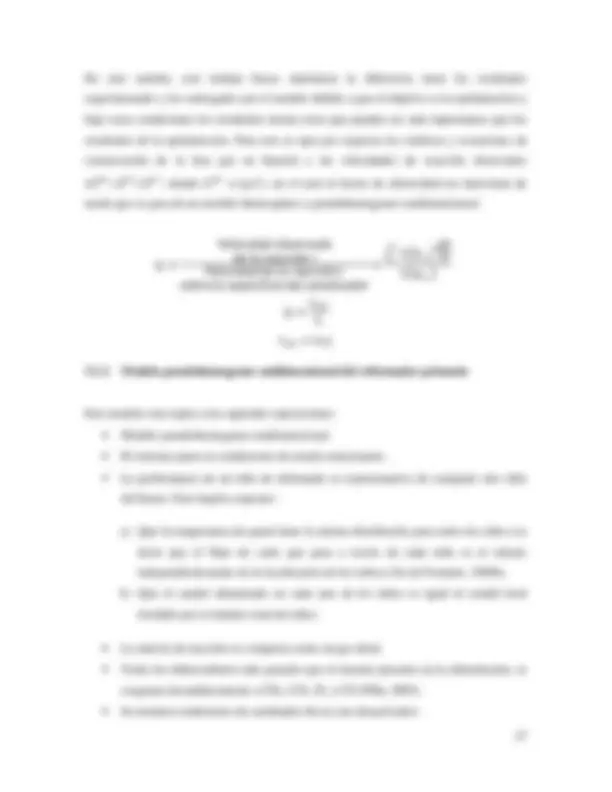
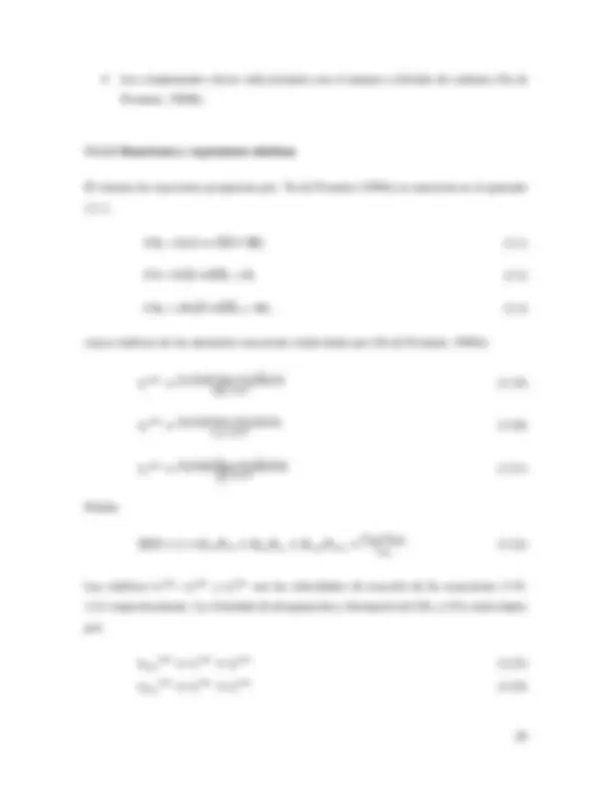

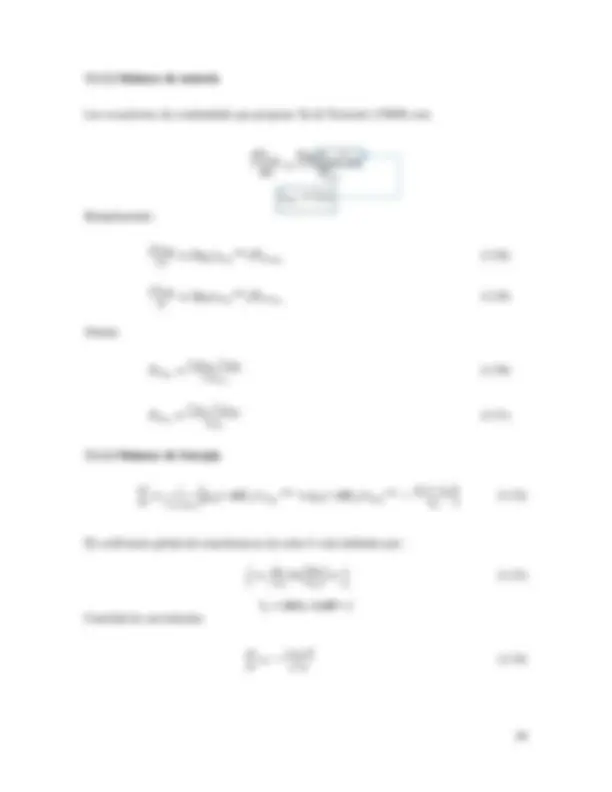
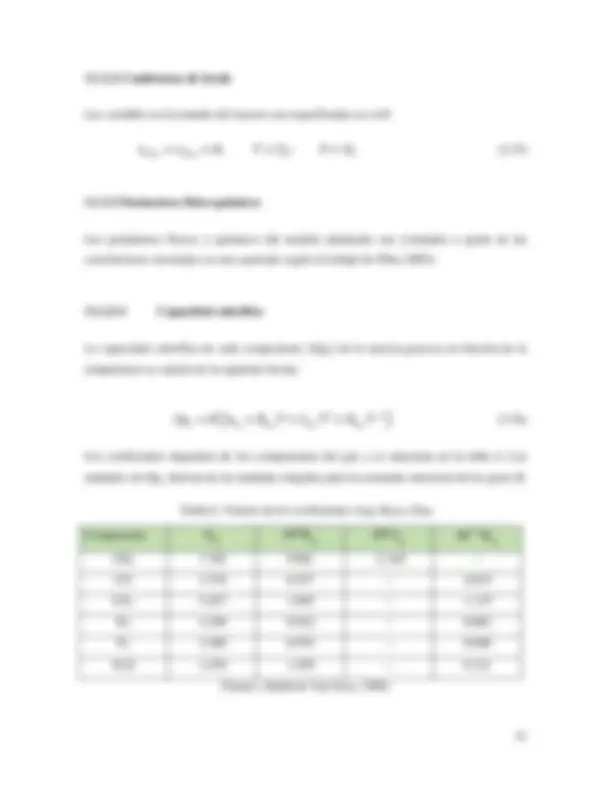
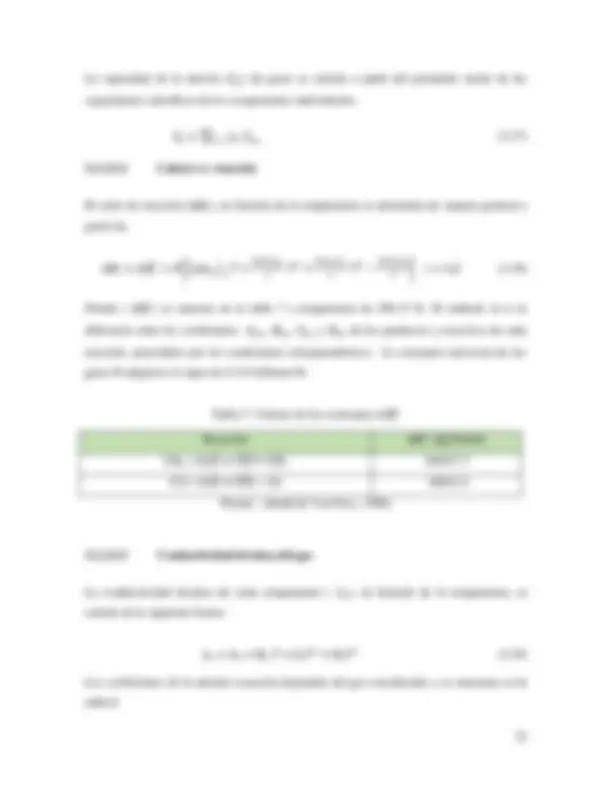
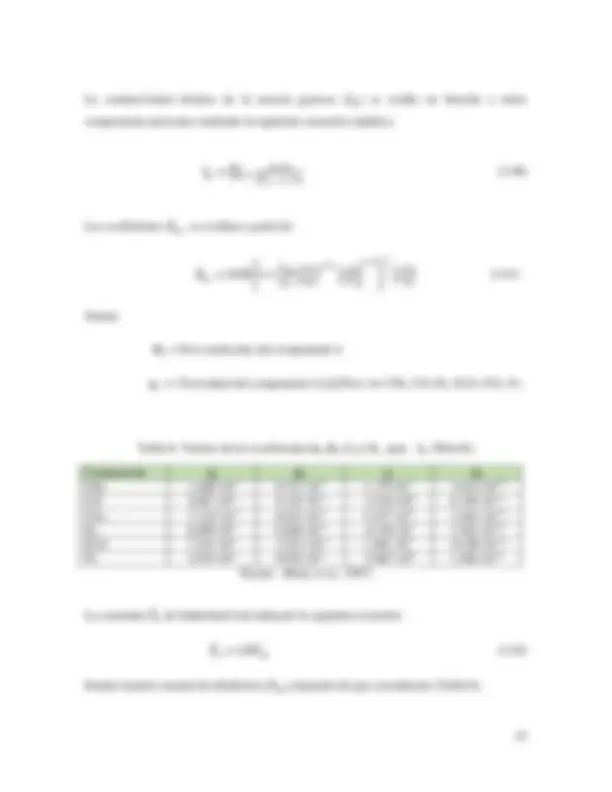
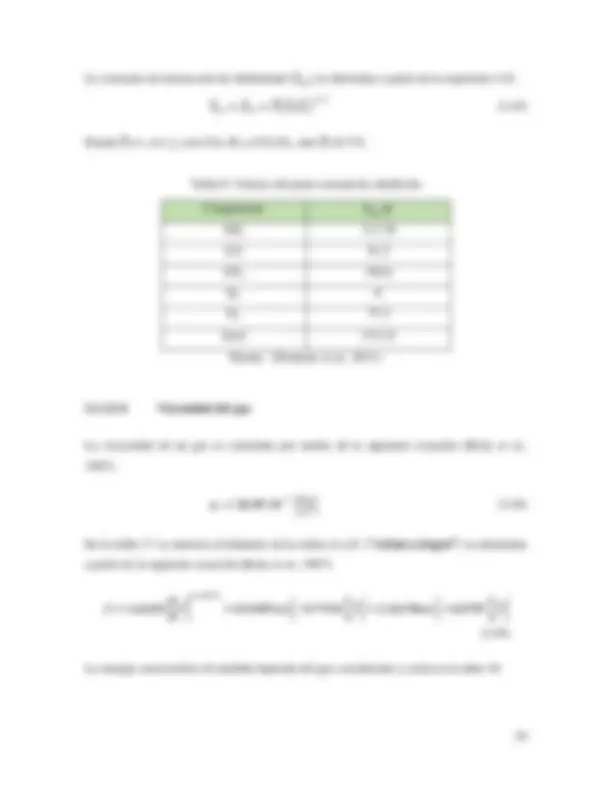
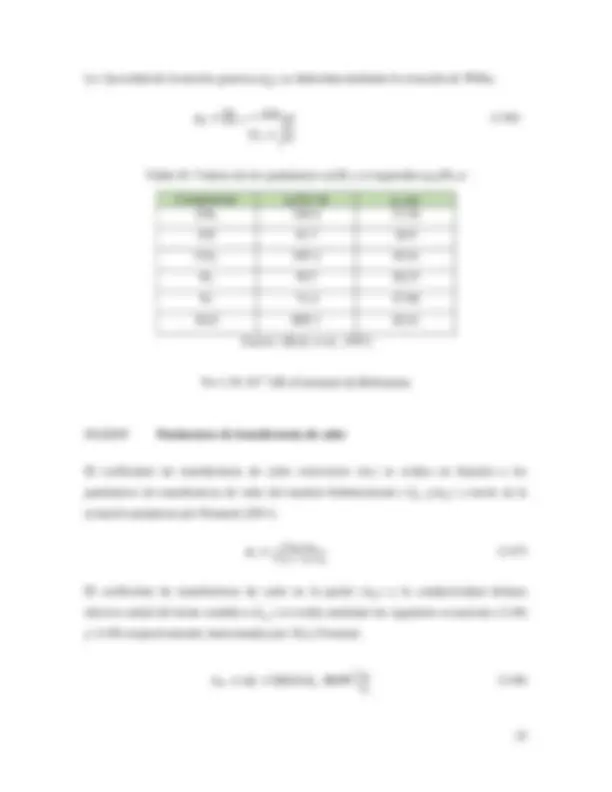
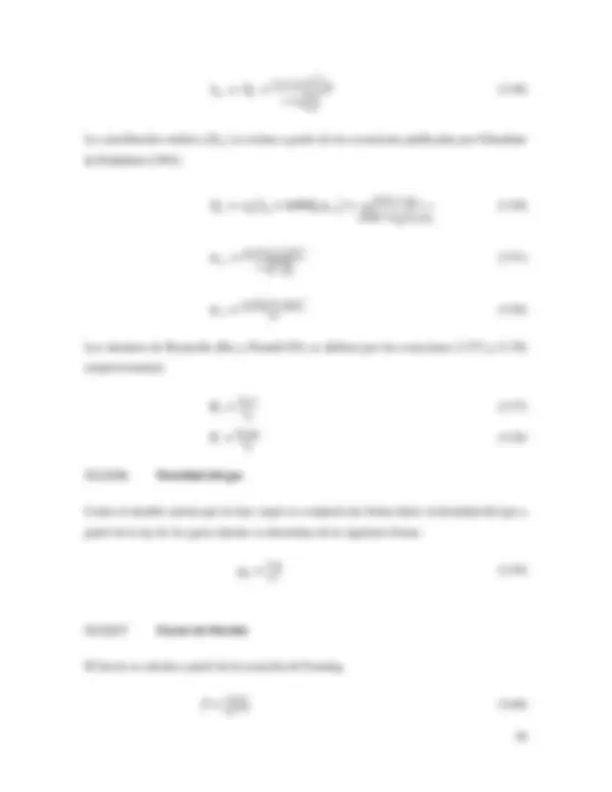
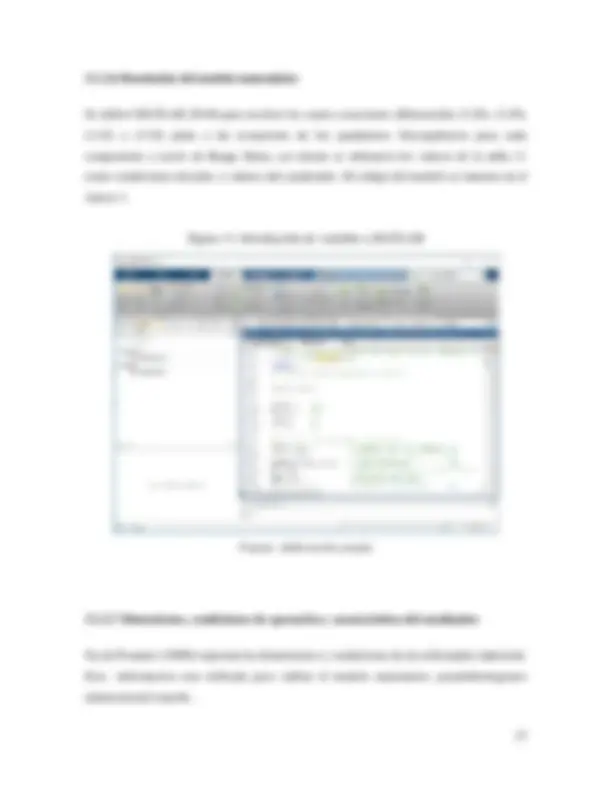
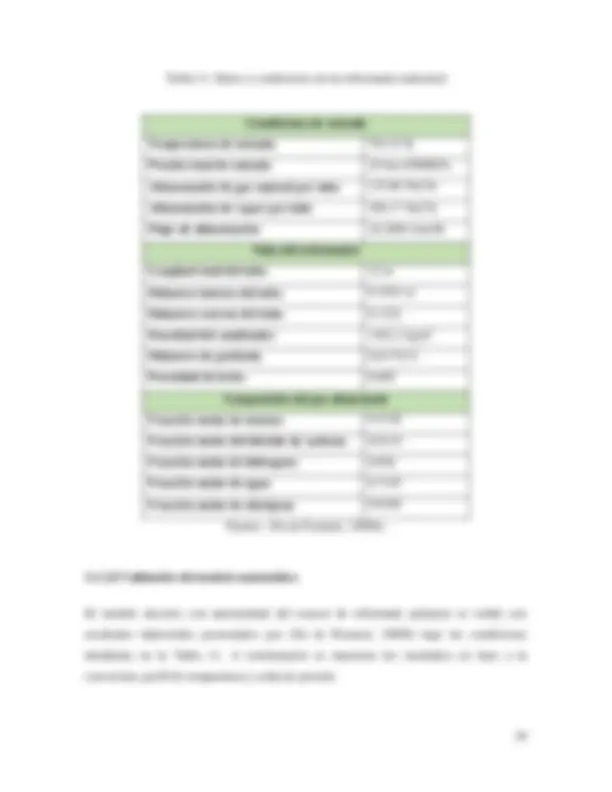
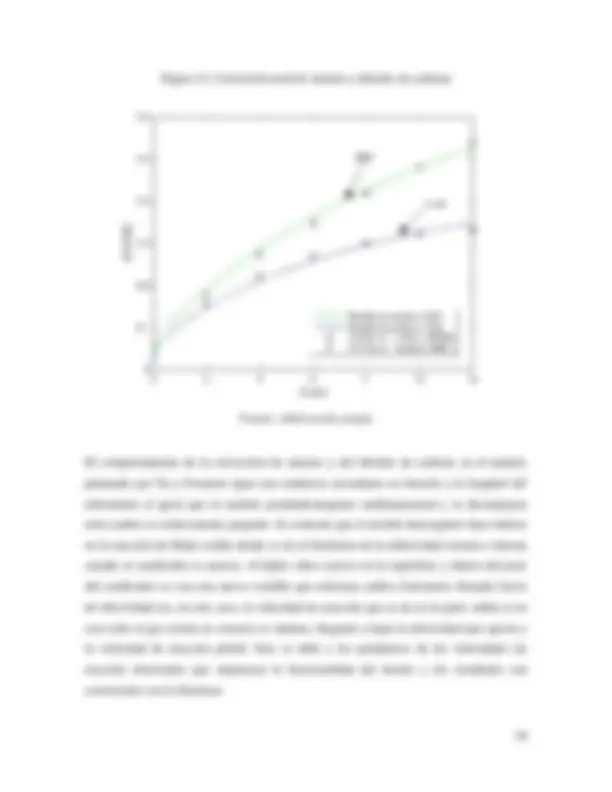
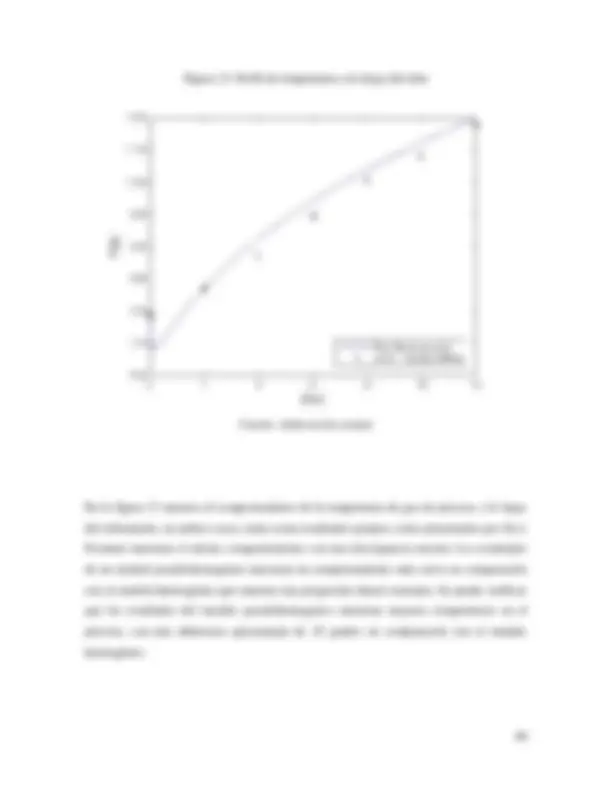
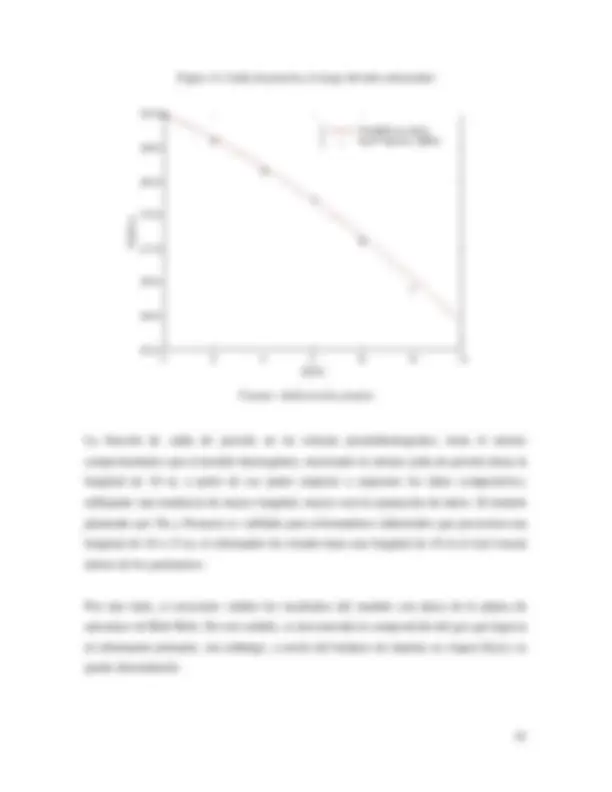
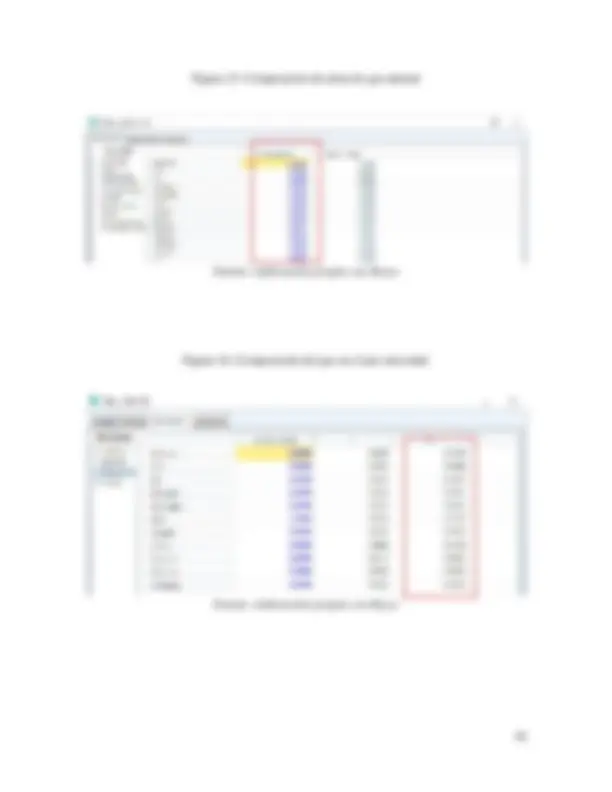
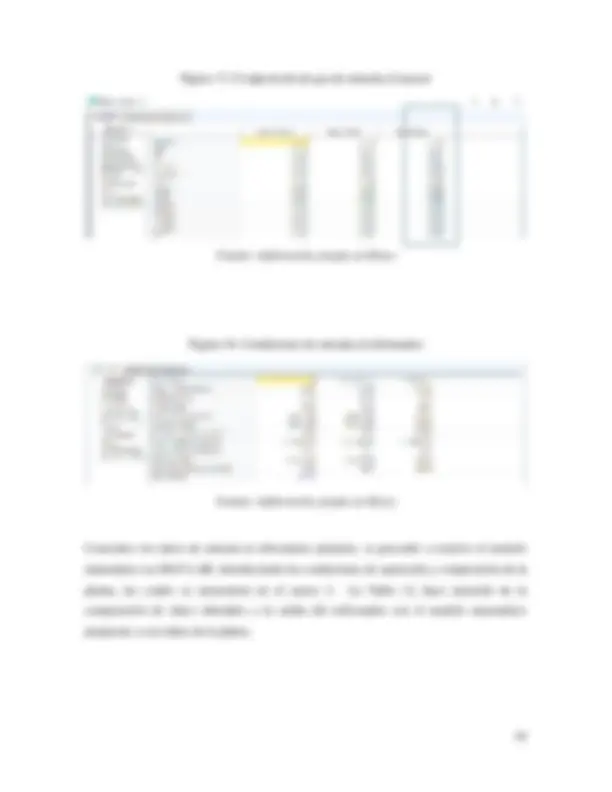
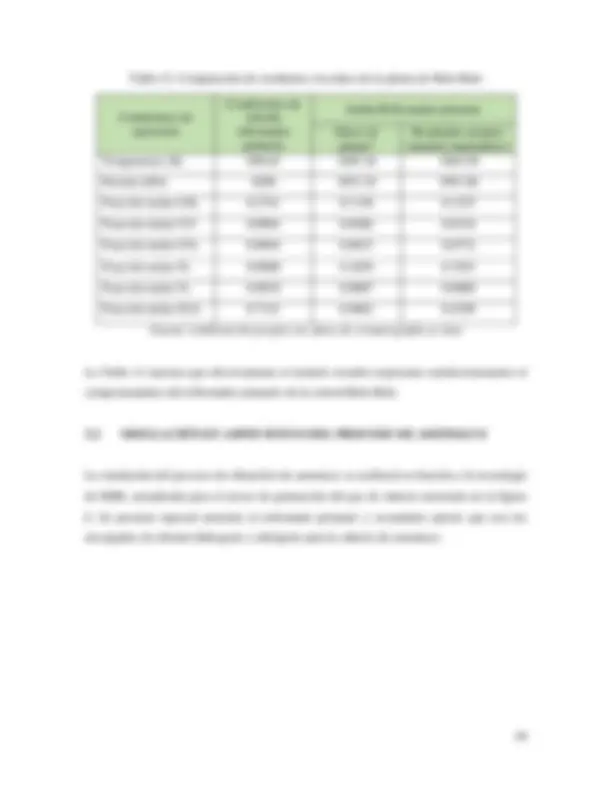
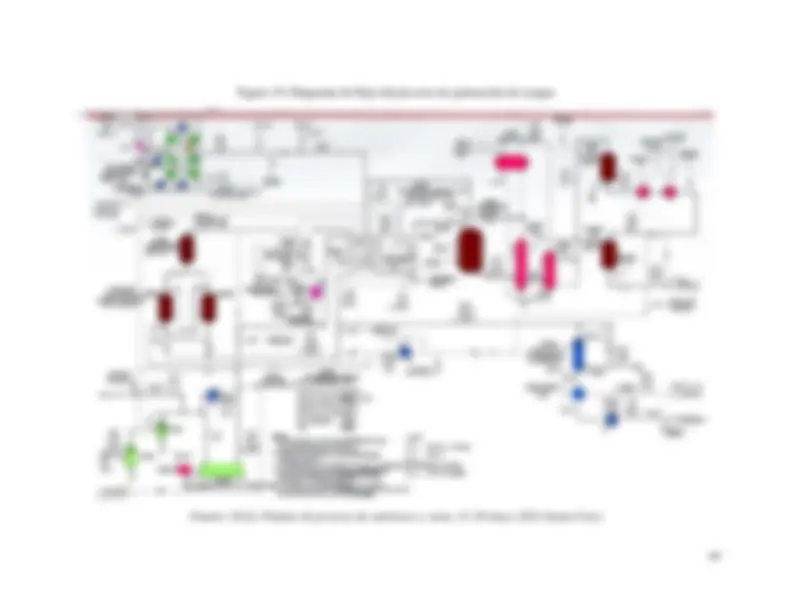
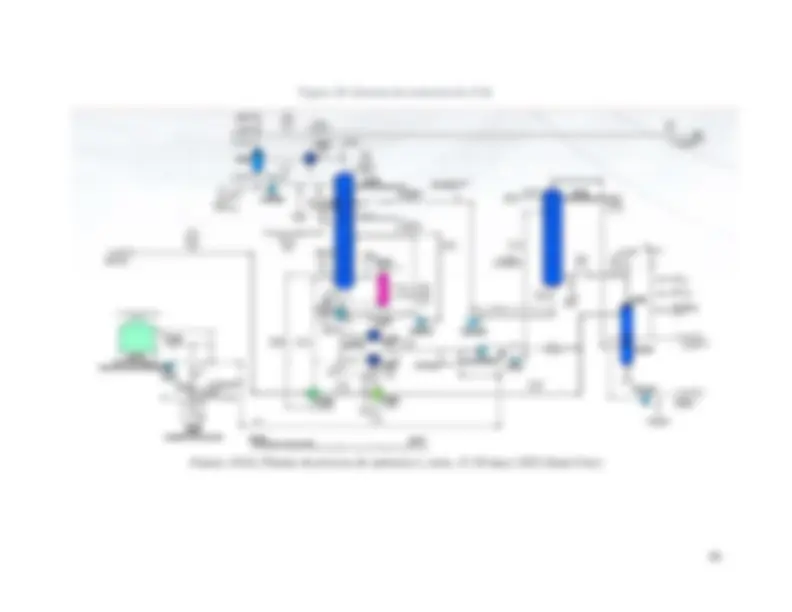
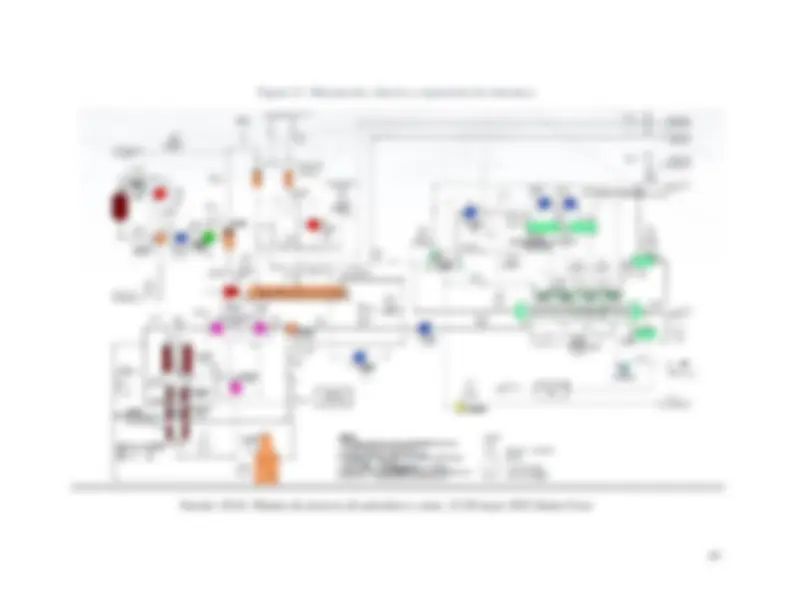
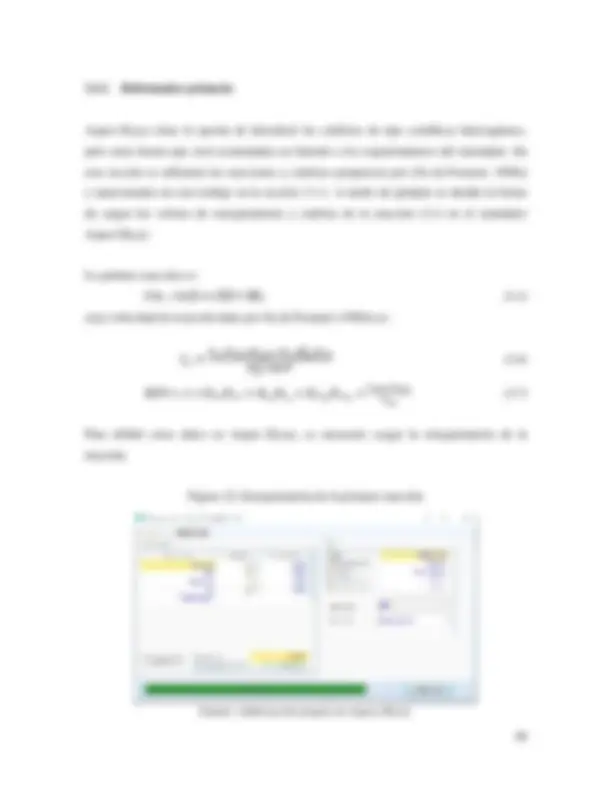
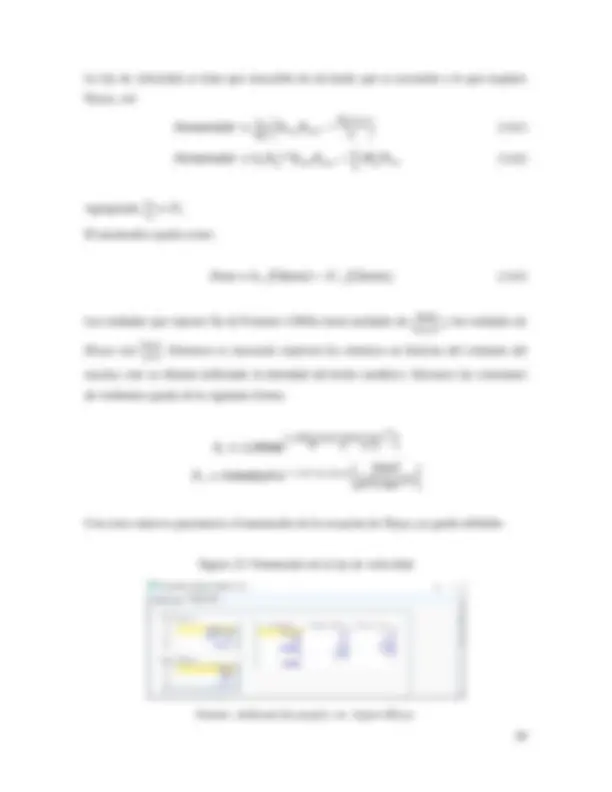
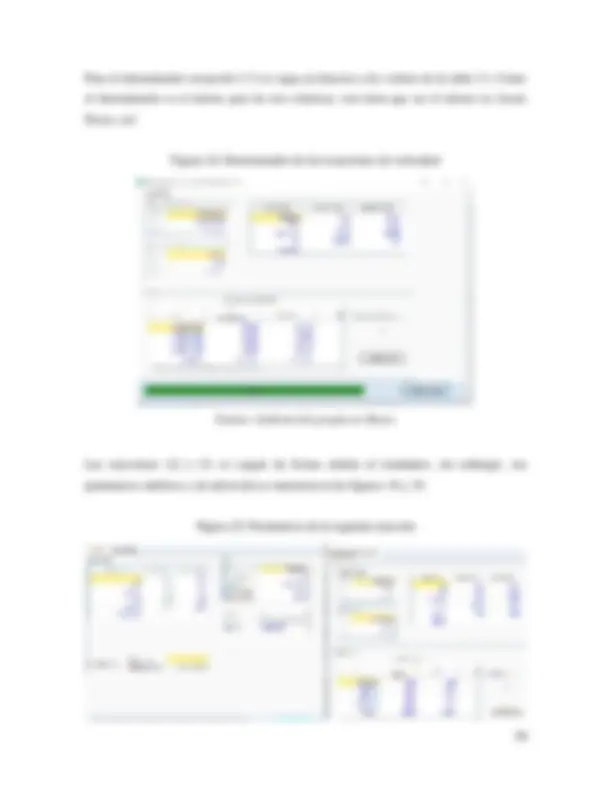
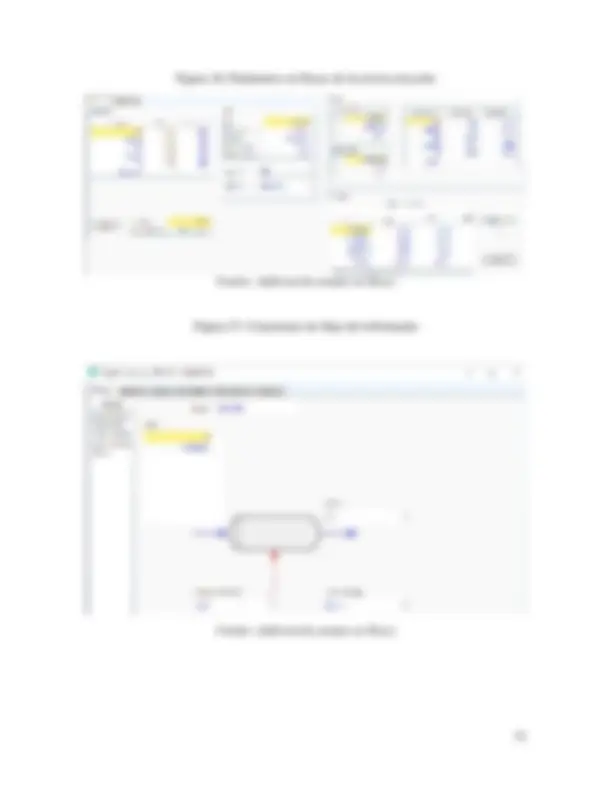
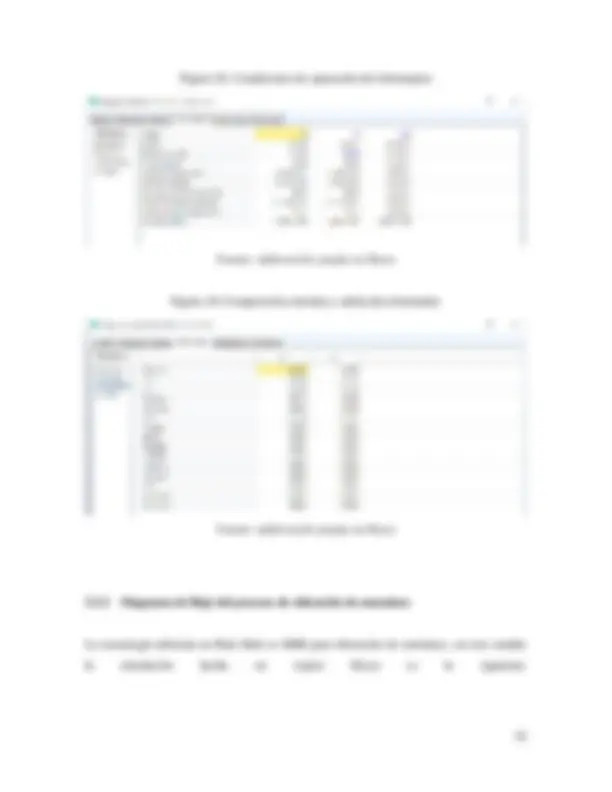
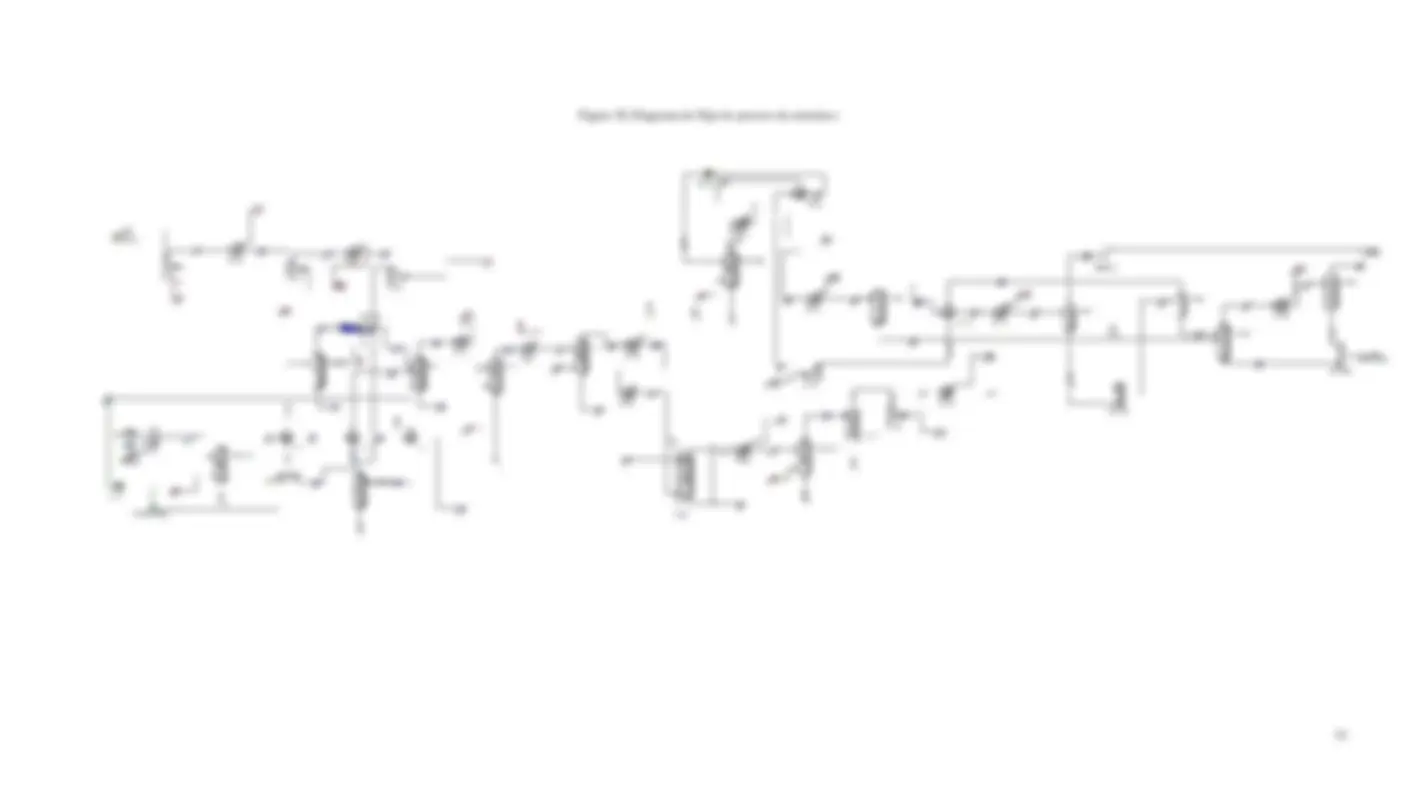
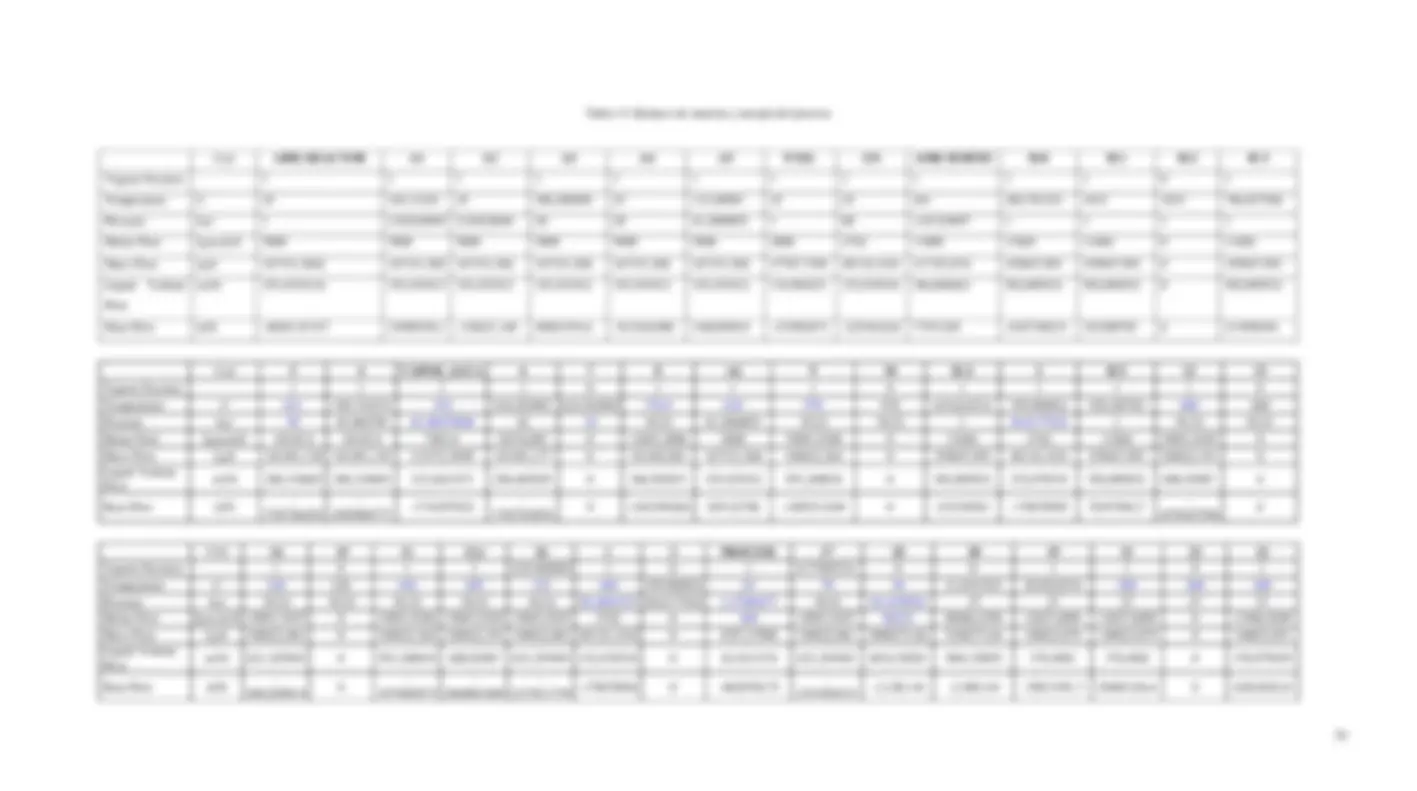

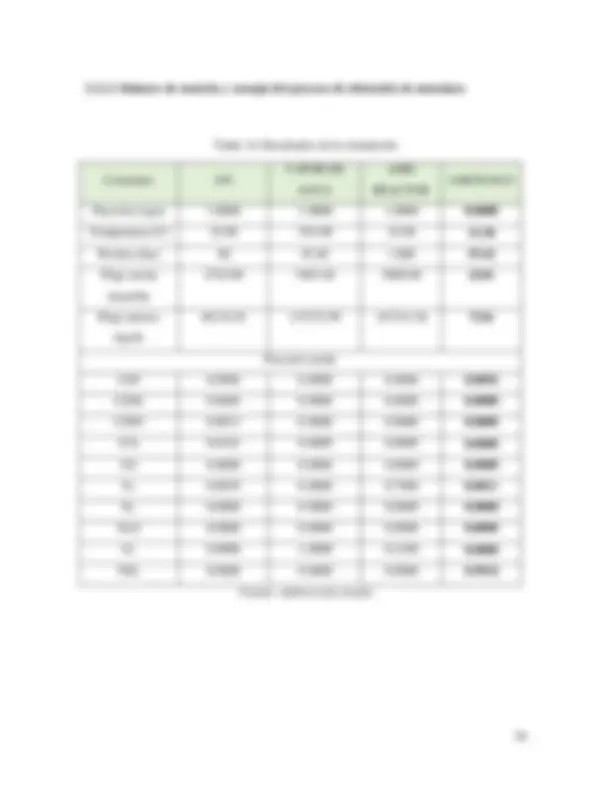
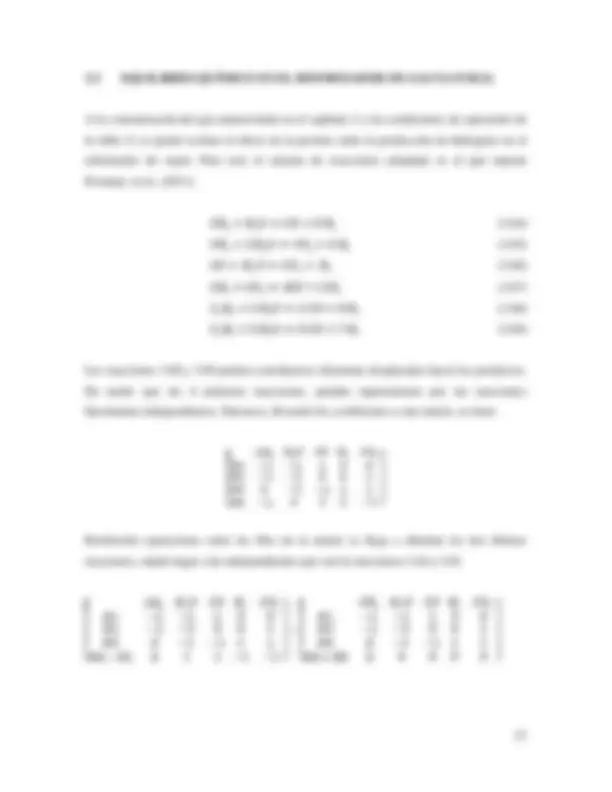
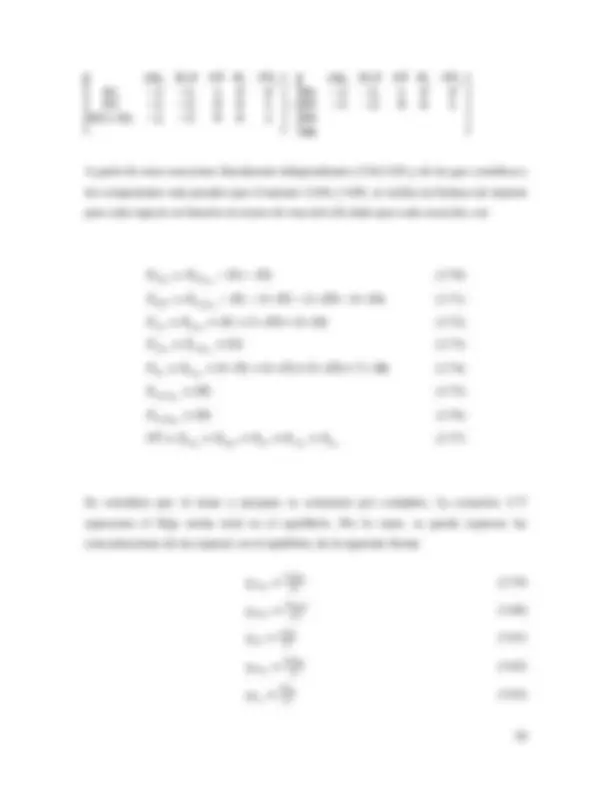
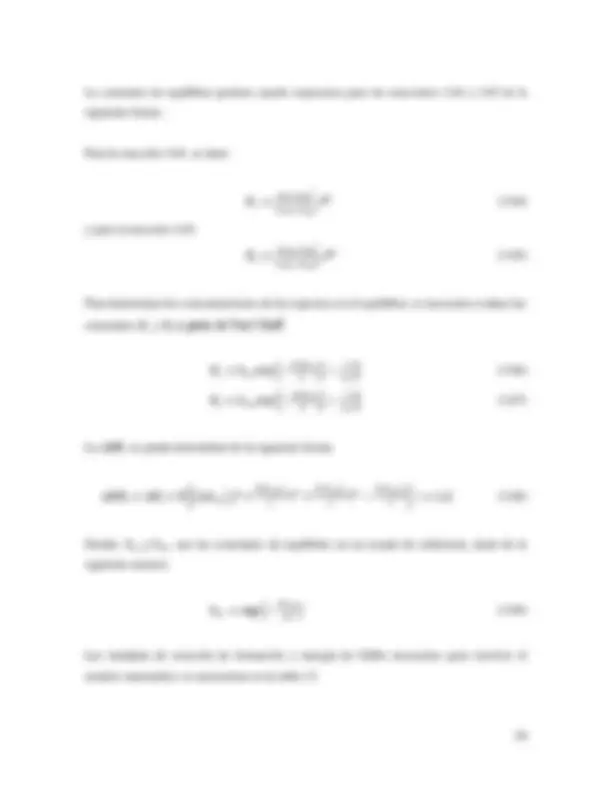
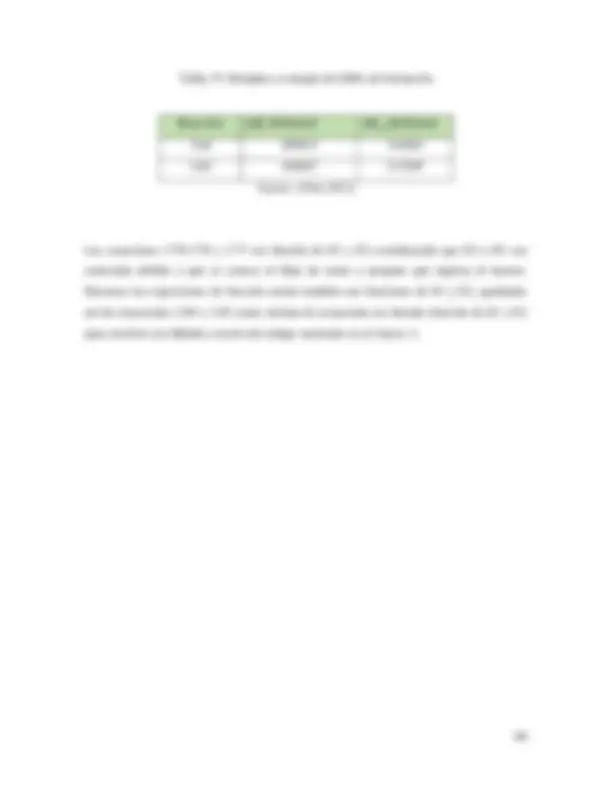
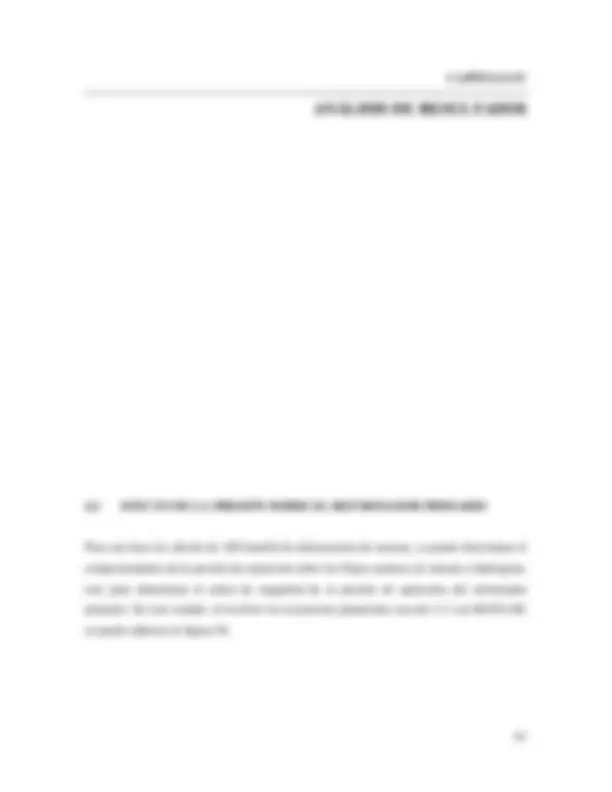
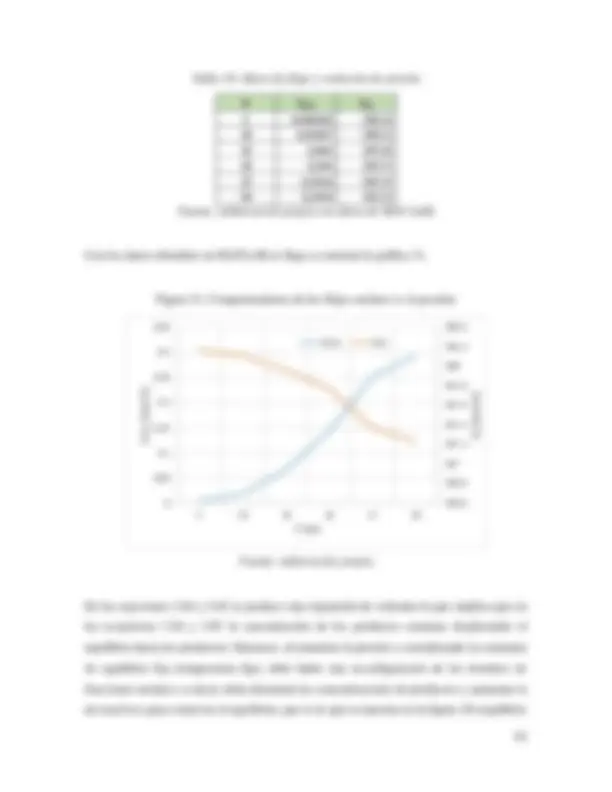
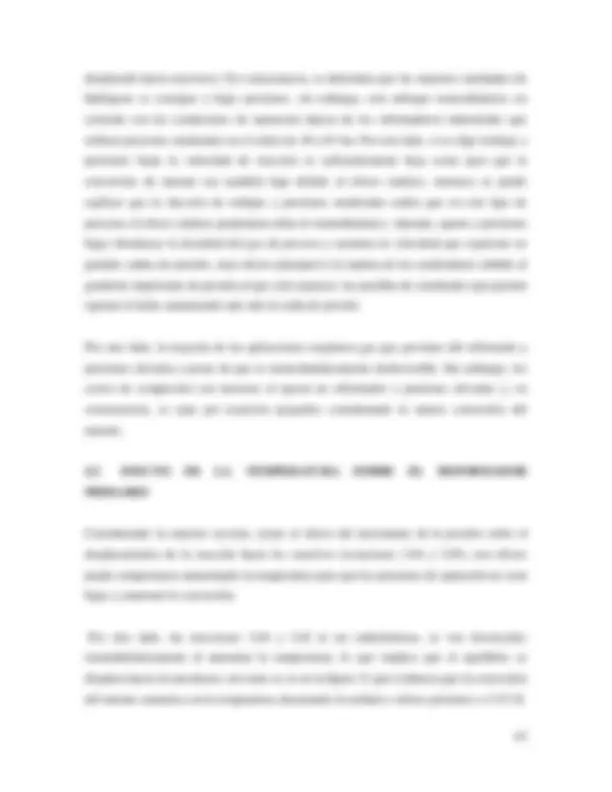
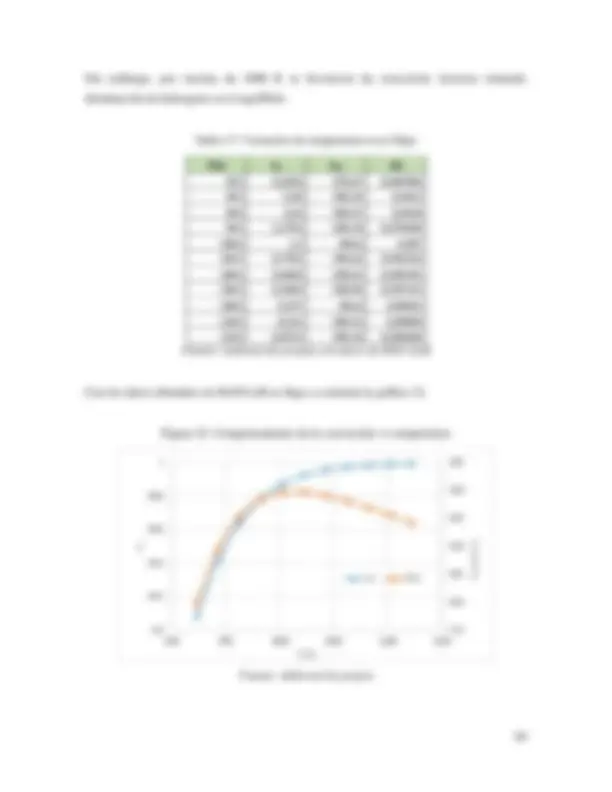
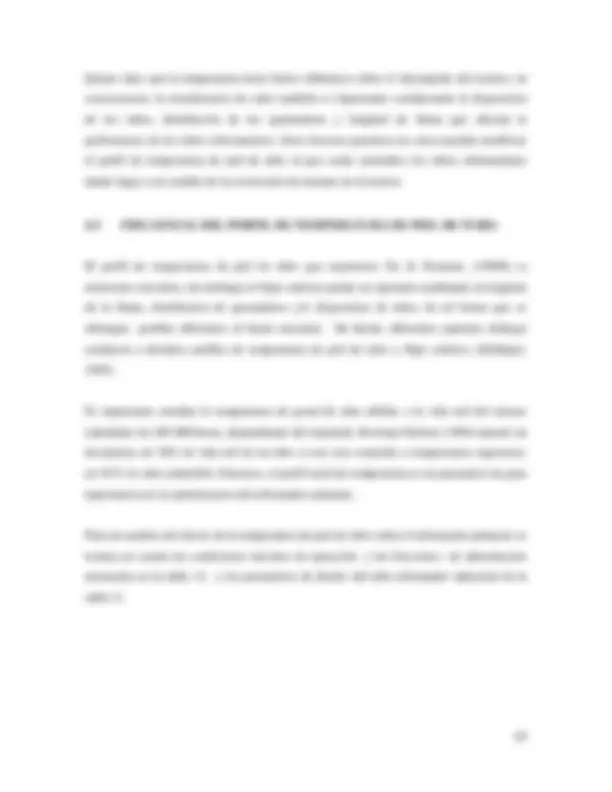
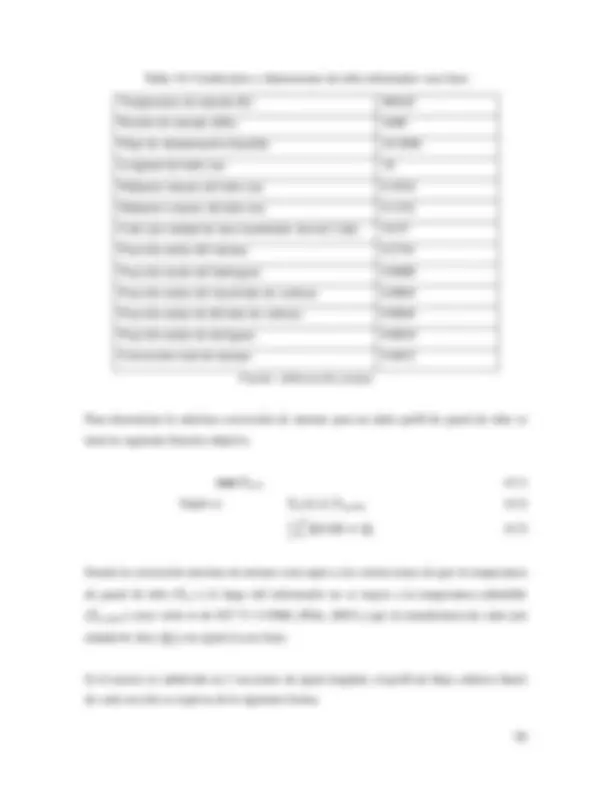
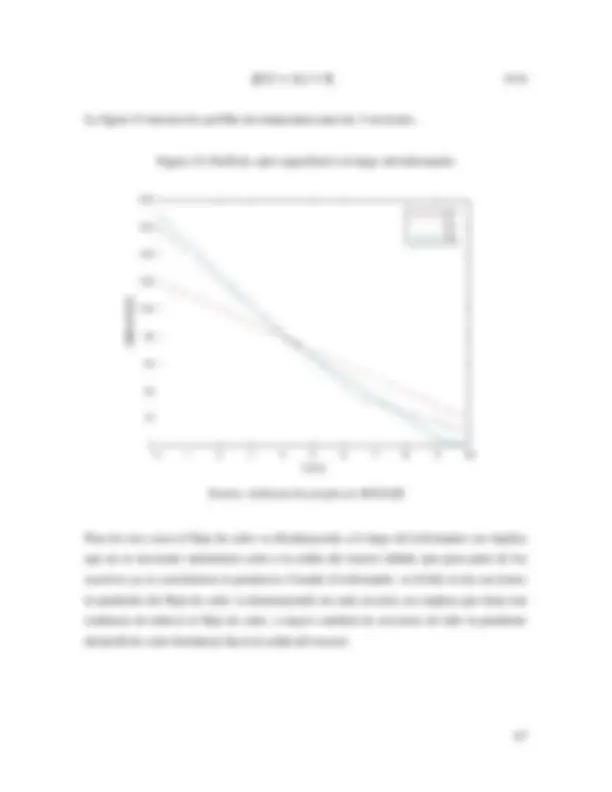
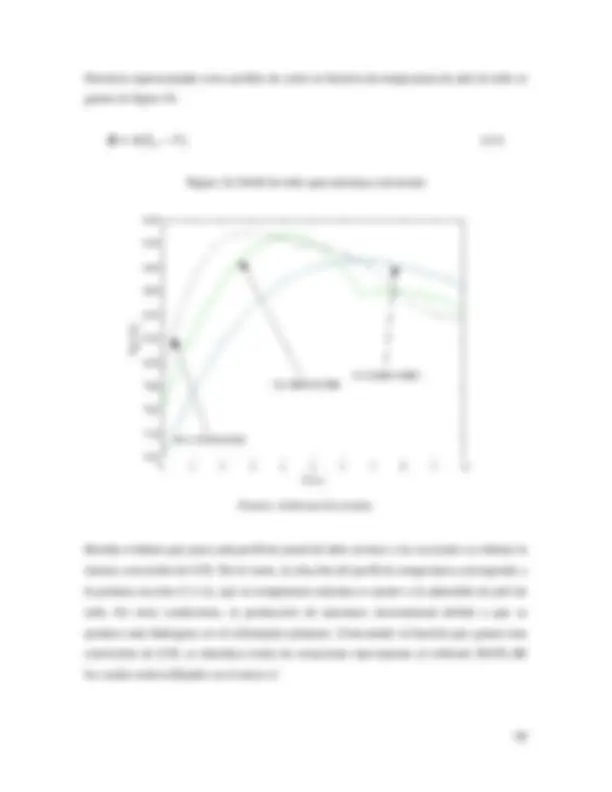
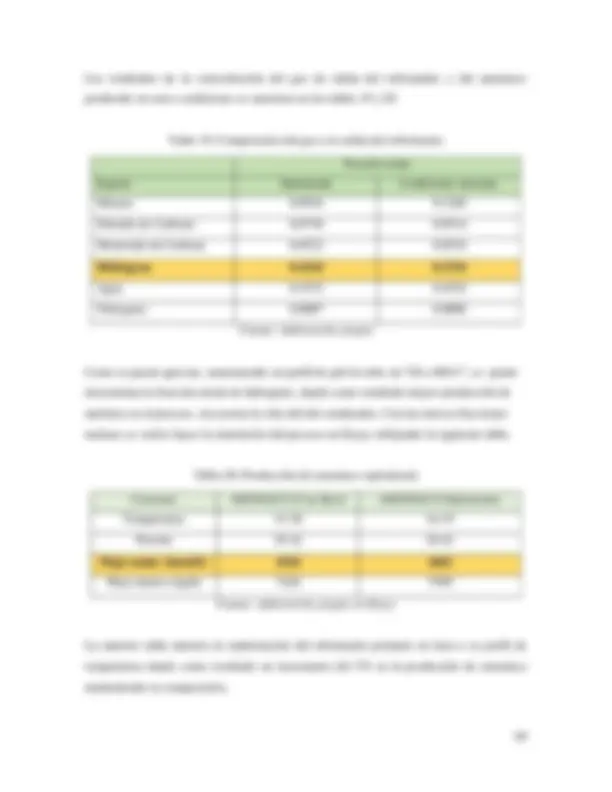


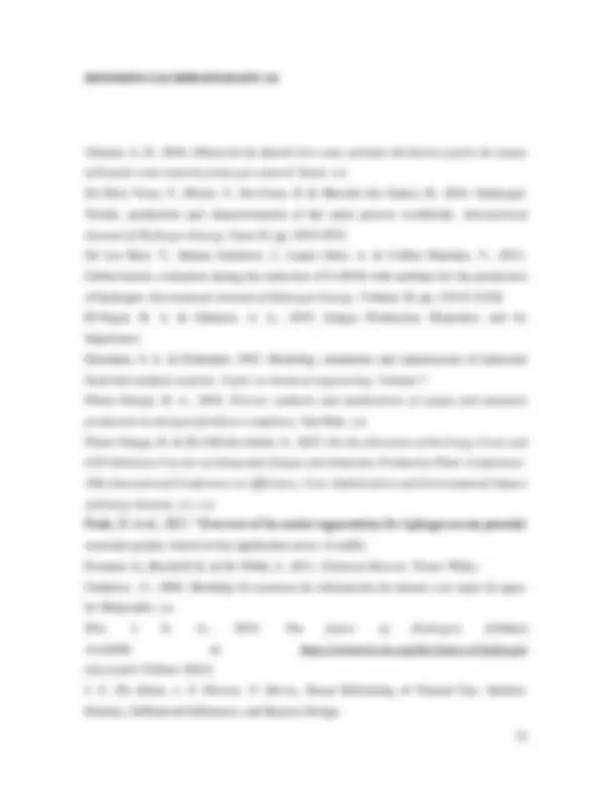
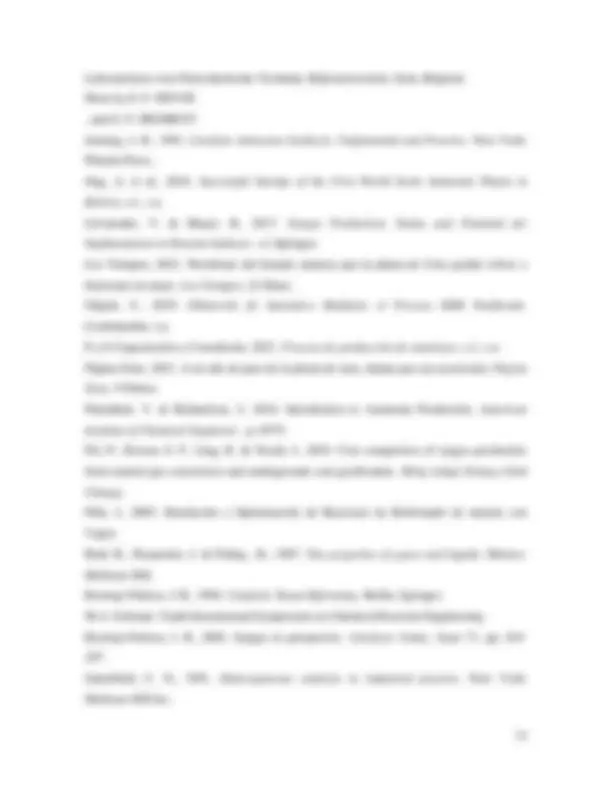
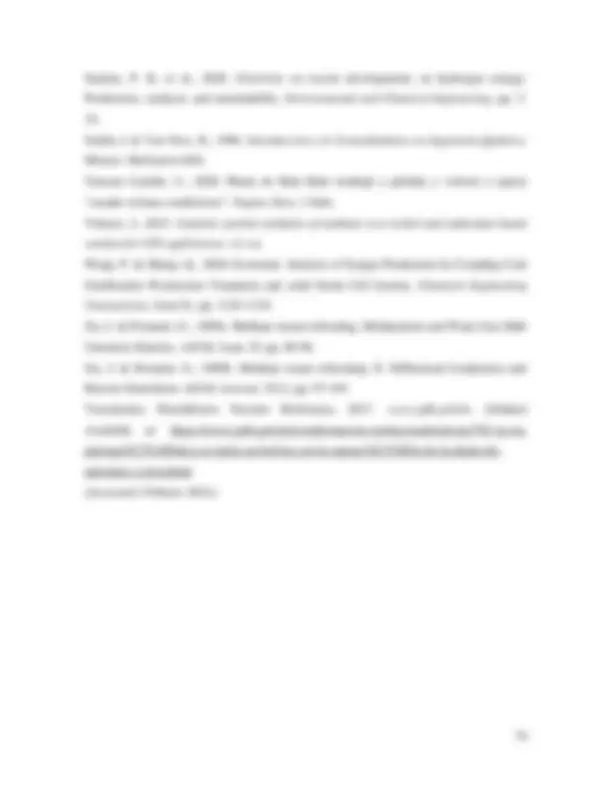
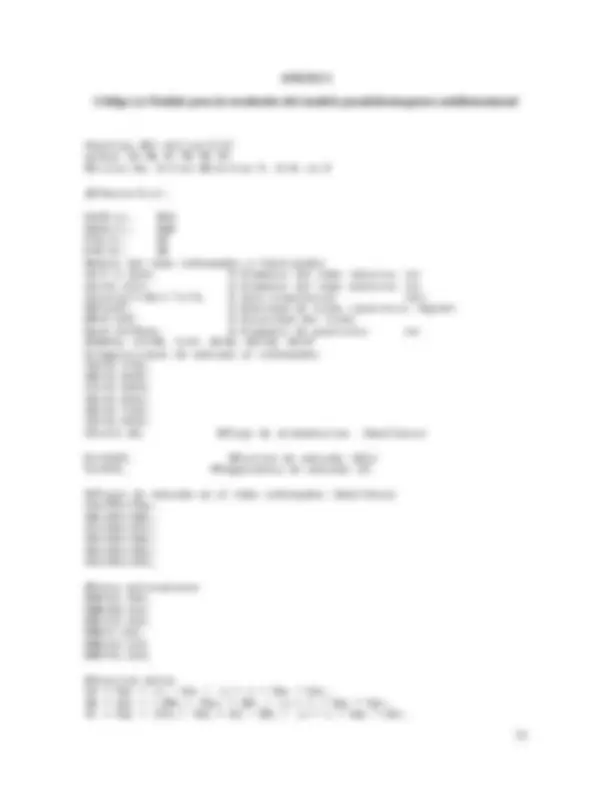
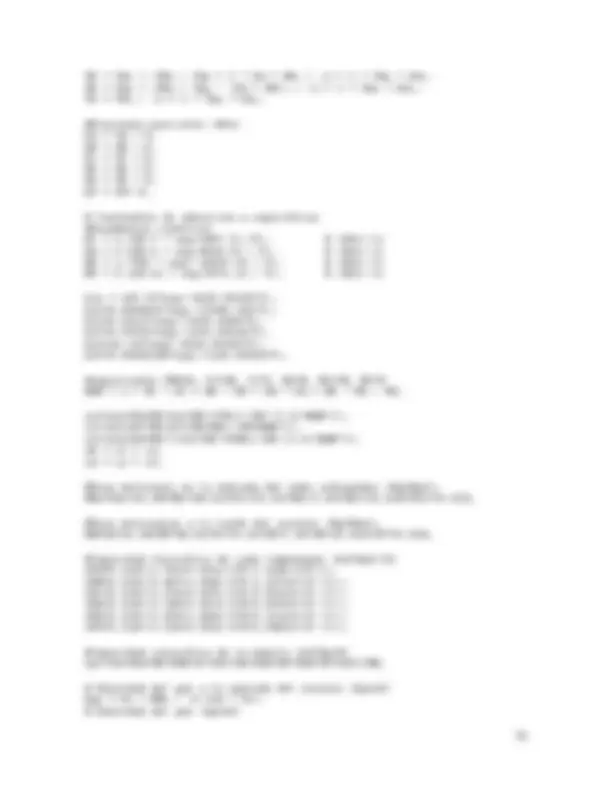
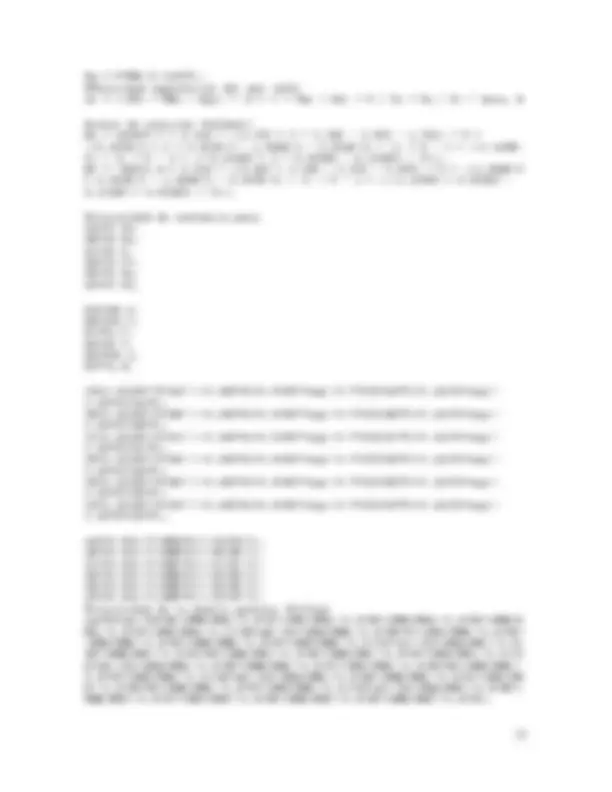
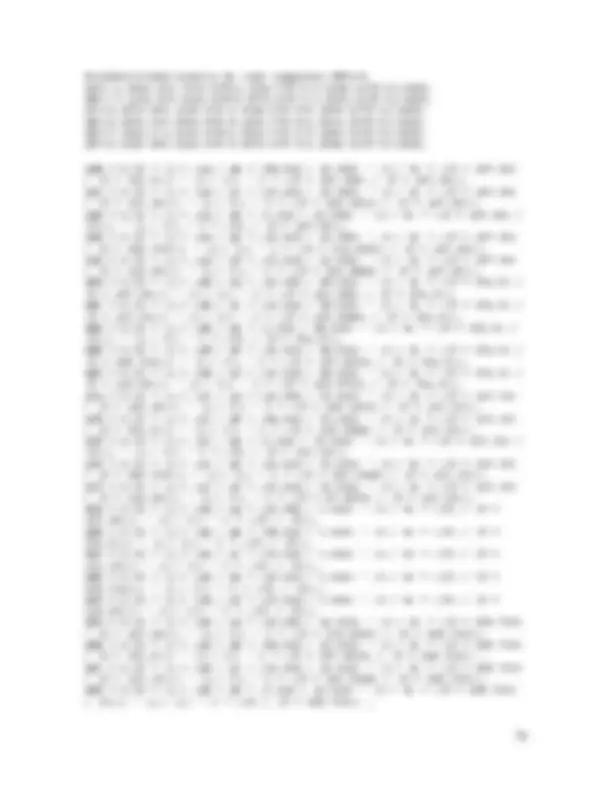
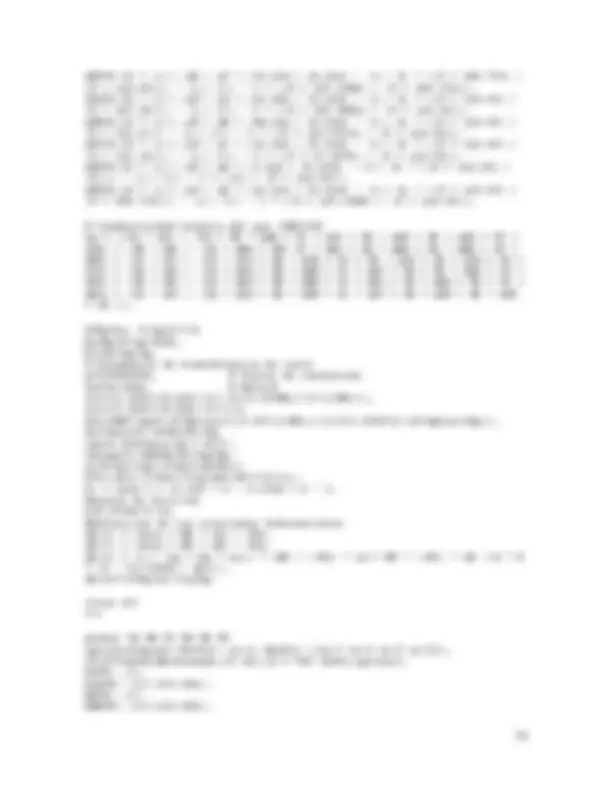
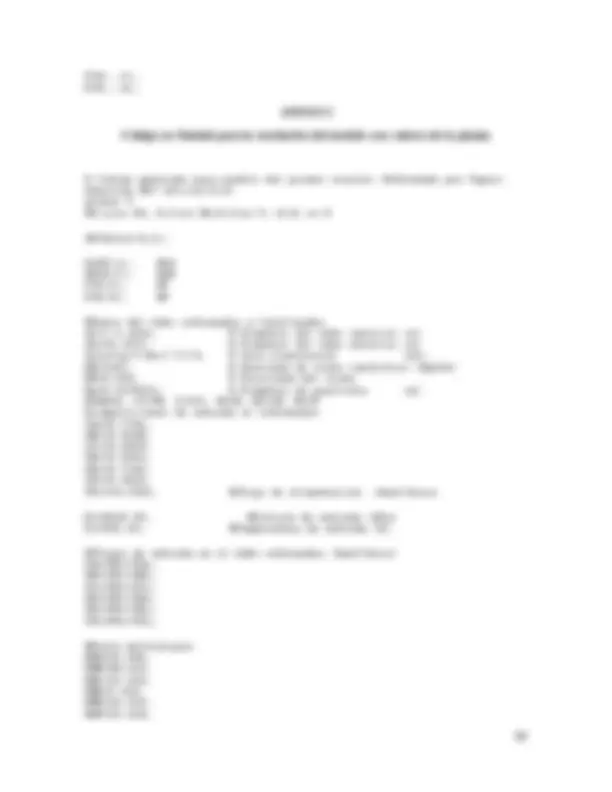
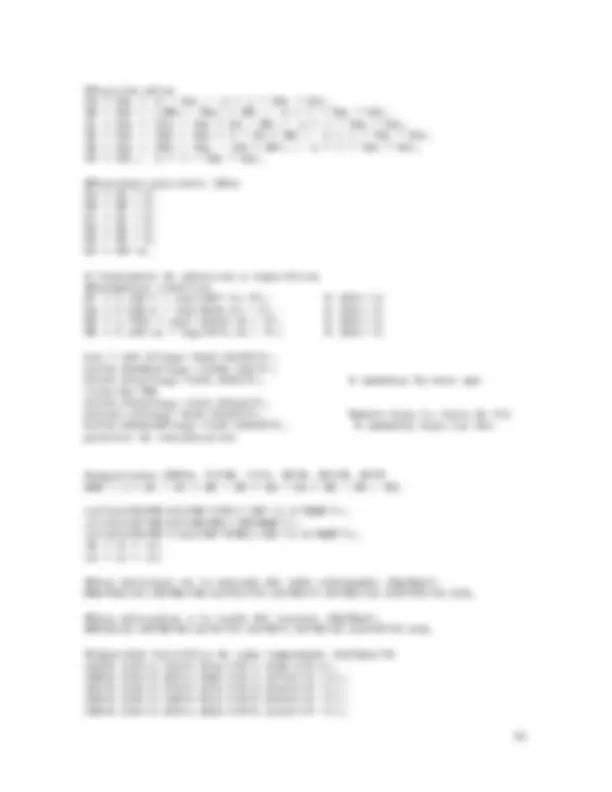
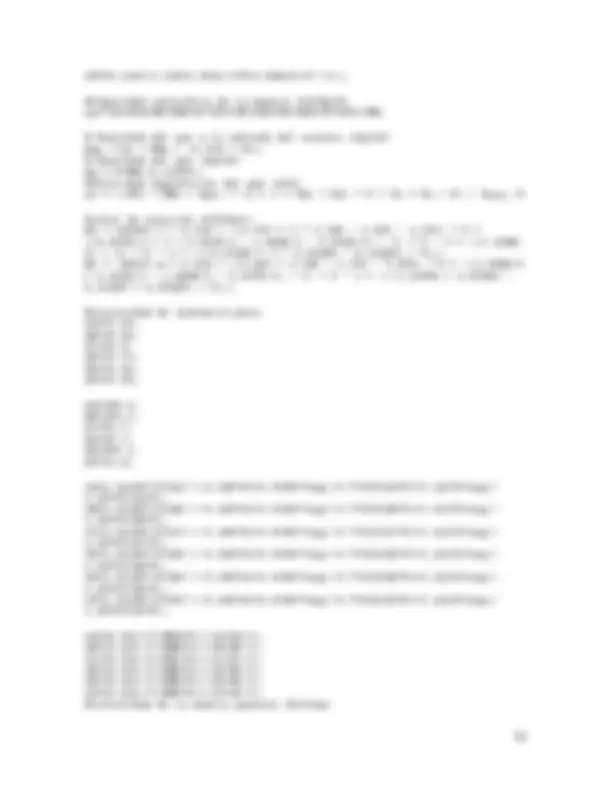
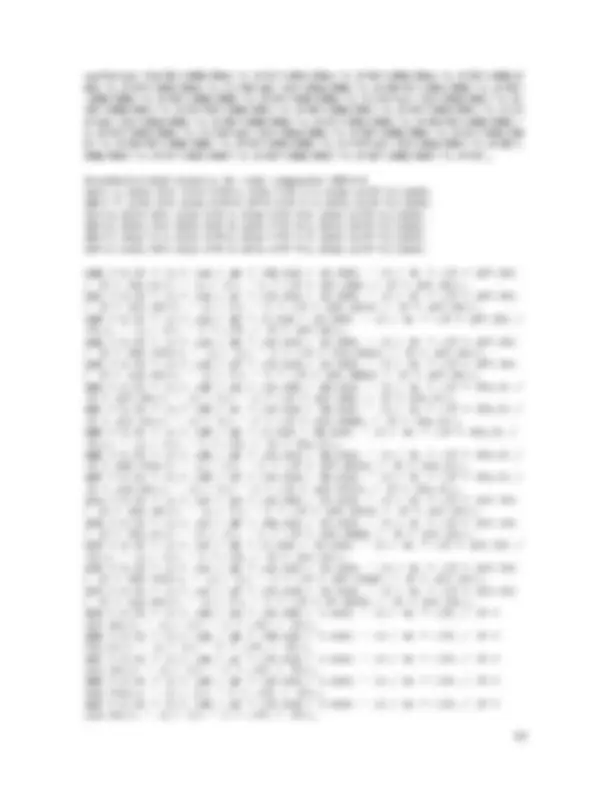
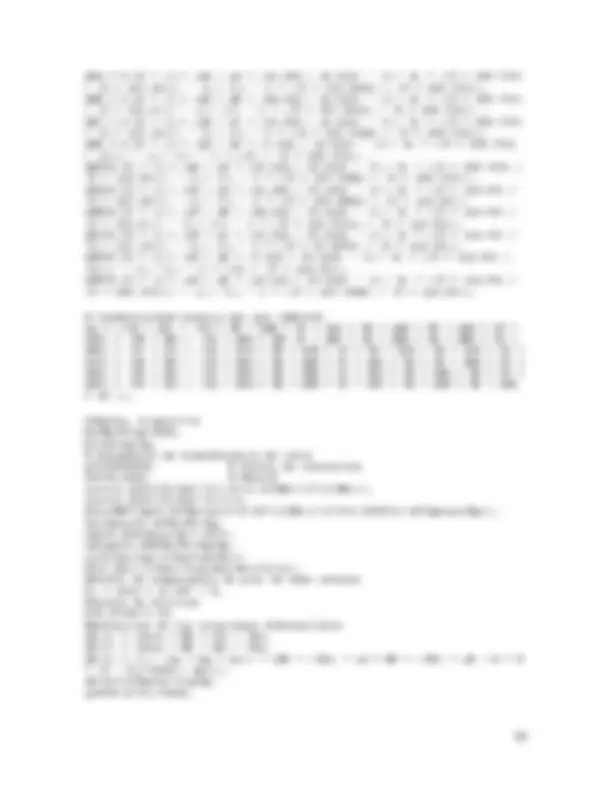
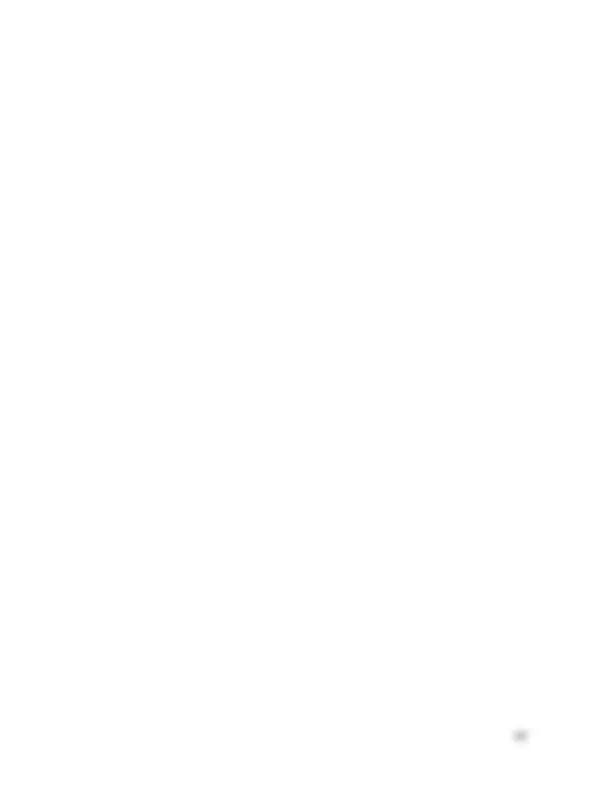
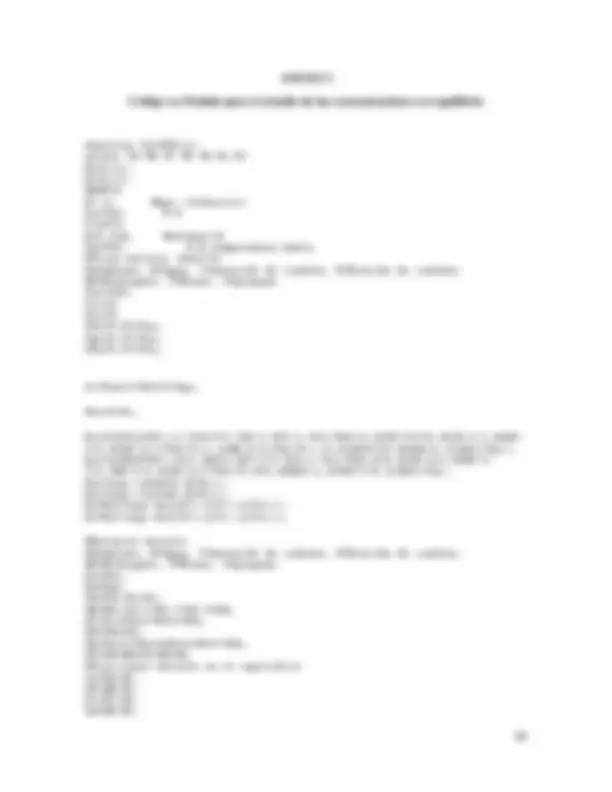
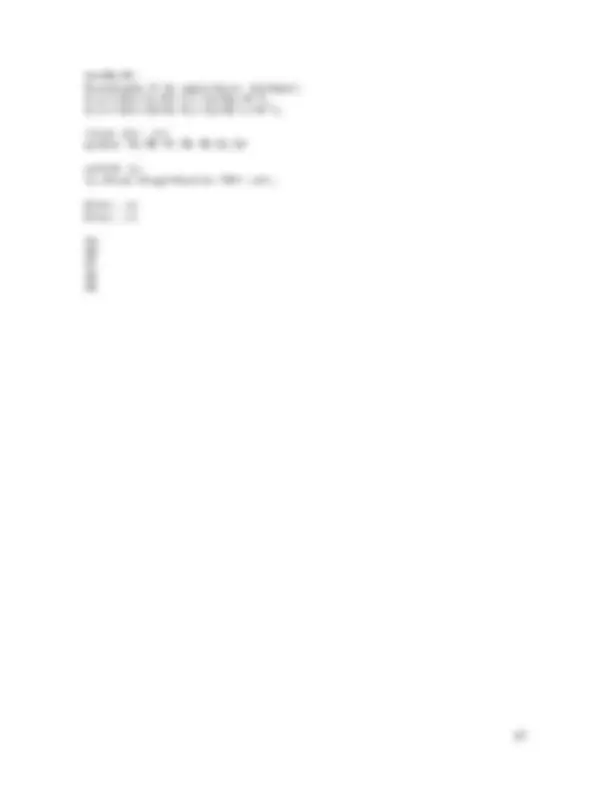
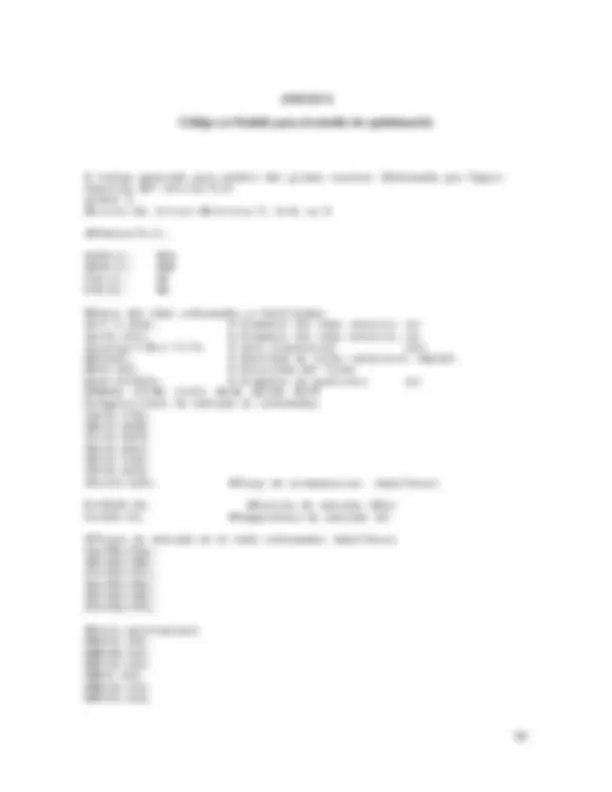
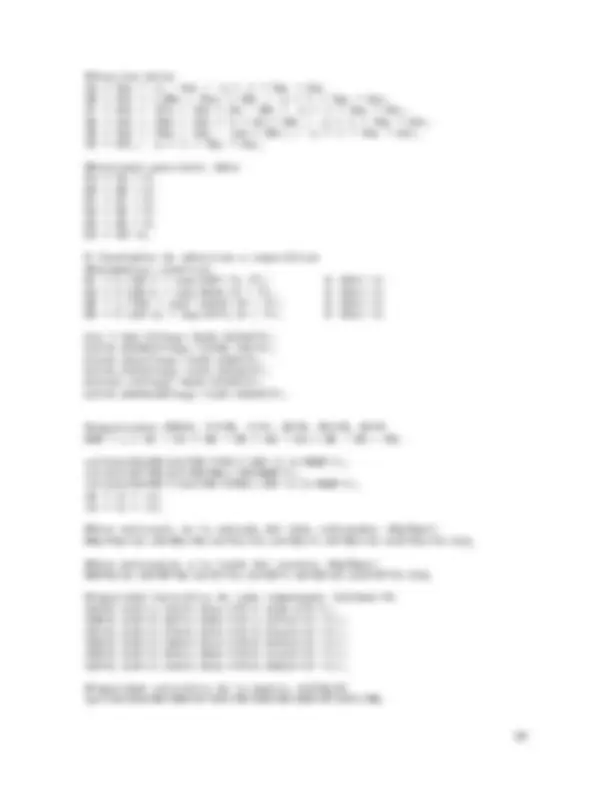
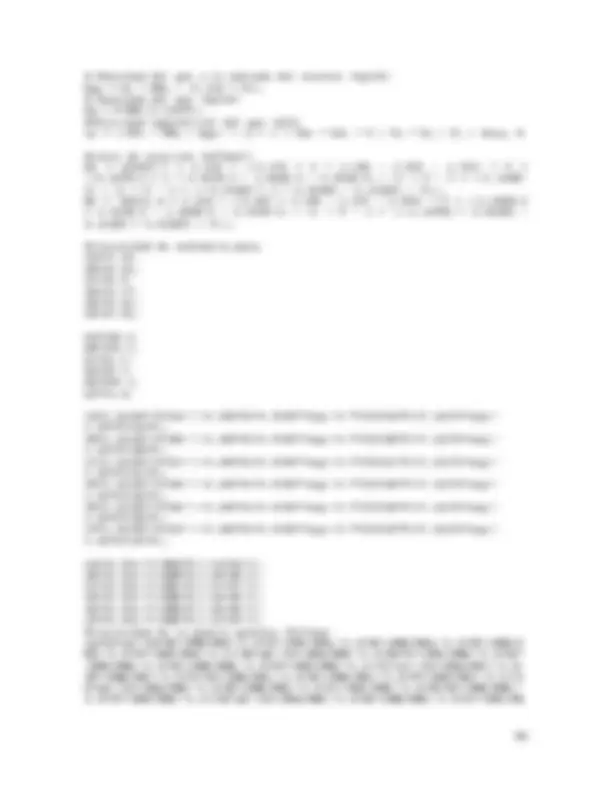
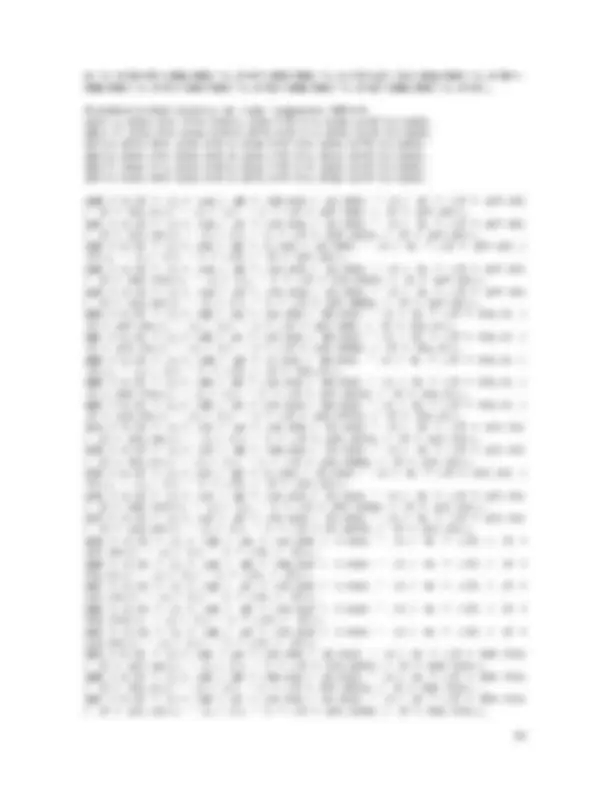
Prepara tus exámenes y mejora tus resultados gracias a la gran cantidad de recursos disponibles en Docsity
Gana puntos ayudando a otros estudiantes o consíguelos activando un Plan Premium
Prepara tus exámenes
Prepara tus exámenes y mejora tus resultados gracias a la gran cantidad de recursos disponibles en Docsity
Prepara tus exámenes con los documentos que comparten otros estudiantes como tú en Docsity
Los mejores documentos en venta realizados por estudiantes que han terminado sus estudios
Estudia con lecciones y exámenes resueltos basados en los programas académicos de las mejores universidades
Responde a preguntas de exámenes reales y pon a prueba tu preparación
Consigue puntos base para descargar
Gana puntos ayudando a otros estudiantes o consíguelos activando un Plan Premium
Comunidad
Pide ayuda a la comunidad y resuelve tus dudas de estudio
Descubre las mejores universidades de tu país según los usuarios de Docsity
Ebooks gratuitos
Descarga nuestras guías gratuitas sobre técnicas de estudio, métodos para controlar la ansiedad y consejos para la tesis preparadas por los tutores de Docsity
Simulacion de procesos industriales
Tipo: Tesis
1 / 102
Esta página no es visible en la vista previa
¡No te pierdas las partes importantes!
En primer lugar a Dios por guiarme en el camino y fortalecerme para empezar un camino lleno de éxitos. A mi familia y a la familia de mi esposa por su apoyo incondicional en todo este tiempo, mostrando un cariño eterno. A mis docentes por haber compartido sus conocimientos a lo largo de todo este tiempo de formación académica, impartiendo sabiduría que será muy valioso para mí desempeño laboral. A todos mis amigos por estar presentes en todo este recorrido lleno de aventuras y experiencias inolvidables.
INTRODUCCIÓN 1.1 INTRODUCCIÓN El amoníaco es un producto utilizado directa o indirectamente por la industria de fertilizantes nitrogenados, que representa aproximadamente el 85% de la producción total mundial. Como principal fuente de fertilizante nitrogenado es esencial para satisfacer las necesidades de producción de alimentos del mundo. El 15% se utiliza en diversos productos industriales, que incluyen fibras, plásticos explosivos y medicamentos (Piña, 2003). Existen varios procesos disponibles para la manufactura del gas de síntesis de amoníaco, los cuales se caracterizan por la alimentación específica que utilizan. La fuente de nitrógeno es siempre el aire de proceso, el hidrógeno, en cambio, puede provenir de una gran variedad de materias primas tales como agua, hidrocarburos livianos y pesados resultantes del
refinado de crudo, carbón, gas natural o a veces de una combinación de estas materias primas. Uno de los recursos con mayor abundancia en el mercado global son los hidrocarburos por el cual la mayoría de las plantas de amónico se basan el uso de gas natural como materia prima, en ese sentido se viene desarrollando diferentes tecnologías de las cuales tres son las principales: reformado con vapor (SMR), oxidación parcial catalítica (POX) y reformado auto térmico (ATR). El reformado con vapor es la tecnología preferida para la producción de gas de síntesis de la industria del gas natural para producir amoníaco debido a su madurez industrial (Rostrup-Nielsen, 2002). En la etapa de reformado con vapor, el gas de síntesis se produce en un horno, donde se hace reaccionar una mezcla de metano y agua en un tubo equipado con un catalizador (generalmente níquel) para obtener una mezcla de hidrógeno y algo de gas de carbono. Esta etapa es altamente sensible debido a las condiciones de operación como ser la temperatura, presión y la temperatura de piel de tubo que afectan la cinética y las velocidades de reacciones endotérmicas, el propósito de este horno es suministrar el calor necesario para el reformado de metano. El calor requerido por las reacciones de reformado se genera mediante la combustión de un combustible. El proceso de obtención de amónico conlleva numerosas etapas de las cuales los principales son: purificación de la alimentación, reformado primario y secundario, conversión de monóxido de carbono, remoción de dióxido de carbono, purificación del gas de síntesis, síntesis y recuperación del amoníaco. Como la industria de fertilizantes representa el mayor mercado de consumo mundial de nitrógeno y con una política de estado de industrializar el gas natural dándole un valor agregado, en este sentido, el 24 de octubre de 2011, Yacimientos Petrolíferos Fiscales Bolivianos (YPFB) anunció la construcción de una planta de amoniaco y urea en Bulo Bulo, ubicada en la ciudad de Cochabamba y el 14 de septiembre de 2017, la planta da inició la producción, utilizando una tecnología KBR en el proceso de amoniaco y Toyo Engineering para el proceso de urea.
La planta de amoniaco y urea instalada en Bulo Bulo en febrero cumplió un año de estar parada, siempre trabajó a perdida desde que fue inaugurada el 2017 alcanzando pérdidas de 34.4 millones de dólares en el periodo 2018- 2019 (Tancara Castillo, 2020). En el 2020 las autoridades plantearon un proceso de reingeniería y hasta traslado de la misma, pero en el 2021 ante un nuevo escenario político se busca su reactivación (Los Tiempos, 2021). Es evidente que la capacidad operativa esperada no se logró durante el funcionamiento de la fábrica. Con la reactivación de las operaciones en la gestión 2021, aun se puede evidenciar algunos desperfectos en el funcionamiento de los equipos, llegando afectar el volumen de producción de amoniaco que requiere el mercado interno, siendo que la demanda de fertilizantes está en ascenso llegando a incrementar los costos de la urea en el país de $us 400 la tonelada (t) a $us 830 (Los tiempos 2021 ), ocasionando un perjuicio también a los productores agropecuarios, que vieron encarecidos sus costos de producción La síntesis de amoniaco no ha cambiado desde su concepción (Piña, 2003), y por la misma razón se han establecido las condiciones operativas para su óptimo funcionamiento a condición de recibir el gas de síntesis en las condiciones requeridas. Por otro lado, el proceso de producción del gas de síntesis ha sufrido importantes modificaciones, principalmente por ser el área que más energía consume en el proceso de reformado, y por las diferentes concentraciones de gas natural utilizadas. En la actualidad, la principal diferencia del proceso industrial de amoniaco radica en el método de preparación del gas de síntesis, debe entenderse que este campo es el que debe optimizarse para lograr la tasa de producción de amoniaco deseada. Ante esto, el proyecto tiene como objetivo optimizar el reformador primario y simular el proceso completo de obtención de amoniaco para determinar el efecto de la optimización sobre la producción de amoniaco.
1.4.1 Objetivo general Simular el proceso de generación de gas de síntesis de la planta de amoniaco en Bulo Bulo. 1.4.2 Objetivos específicos Resolver el modelo matemático del reformador primario utilizando Matlab. Validar el modelo resuelto con información industrial. Simular el proceso de obtención de amoniaco Analizar el efecto de las variables del reformador sobre la producción de amoniaco. Optimizar el reformador primario 1.5 JUSTIFICACIÓN La industria química necesita comprender los fenómenos físicos y químicos que ocurren dentro un proceso para predecir sus tendencias de comportamiento y poder manipular las condiciones operativas para tomar decisiones. A medida que va transcurriendo el tiempo se van generando nuevos estudios que permitan optimizar los recursos de un proceso, más aun si los productos son de alta demanda, tal es el caso del amoniaco, donde Bolivia lleva pocos años incursionando en la industria de los fertilizantes. En el proceso de obtención de amoniaco, la etapa fundamental es el reformado primario, esta etapa determina la conversión de H 2 , siendo un componente elemental en el proceso, a mayor conversión, mayor será la cantidad del producto final, dando como resultado un manejo eficiente de la temperatura en el horno. Para un mejor análisis, el reformador primario se analizará resolviendo un modelo matemático en Matlab que pueda representar completamente su comportamiento fenomenológico, de modo que se puedan determinar los parámetros clave que conducen a su funcionamiento óptimo incrementando la producción de amoniaco.
CAPÍTULO II MARCO TEÓRICO 2.1 GAS NATURAL El gas natural es una mezcla de hidrocarburos livianos en estado gaseoso, donde el principal componente es el metano aproximadamente en una proporción de 80 a 95 % que se encuentran en pozos gasíferos a grandes profundidades. Una vez extraído del suelo es transportado a plantas de tratamiento para extraer los contaminantes y residuos. Bolivia cuenta con grandes reservas de gas natural, así mismo se considera un energético limpio debido a que no contiene azufre en su composición. El gas alimentado a la planta de amoniaco y urea proviene de la planta de procesamiento de gas natural “Carrasco”.
Tabla 1 : Cromatografía del gas alimentado a la planta VARIABLE VALOR TEMPERATURA (F) 74, PRESION (Psi) 1301. C1 90.9577 % C2 6.8085 % C3 0.1287 % iC4 0.0013 % nC4 0.0013 % iC5 0.0000 % nC5 0.0000 % C6+ 0.0000 % CO 2 1.6256 % N 2 0.3867 % G.E. 0. P.C. (BTU/SCF) 1030. Fuente: (elaboración propia con datos de cromatografía en situ)
2. 2 GAS DE SÍNTESIS El termino Gas de Síntesis (Syngas) es usado para describir una mezcla gaseosa que contiene H 2 y CO, junto con cantidades pequeñas de CO 2 y CH 4. Puede producirse a partir del Gas Natural, gases de refinería, hidrocarburos pesados y carbón. Este combustible es usado como producto intermedio para producir numerosos productos químicos como se muestra en la figura 2.
Existen diferentes procesos industriales para la producción de gas de síntesis (ver figura 4), los principales son: reformación de hidrocarburos con vapor, oxidación parcial de hidrocarburos y reformado autotérmico. Figura 4 : Diferentes tecnologías de generación de gas de síntesis
2. 3 .1 Reformado de Metano con Vapor El reformado de gas natural con vapor (Figura 4) es un proceso llevado a cabo a altas temperaturas, y todavía requiere un catalizador para acelerar la reacción debido a la altísima estabilidad del metano. El catalizador está contenido en tubos dentro de un horno que se calienta por combustión de algún hidrocarburo. Las reacciones 2.1 y 2.2 ocurren de manera simultánea, el proceso generalmente ocurre a temperaturas de 500 - 900 °C, a presiones de 20 - 4 5 atm y regularmente utilizan catalizadores de níquel para asegurar una máxima conversión del metano. 𝐶𝐻 4 + 𝐻 2 𝑂 ↔ 3 𝐻 2 + 𝐶𝑂 ∆𝐻 298 𝐾 = 208 𝑘𝐽/𝑚𝑜𝑙 (2. 1 ) 𝐶𝑂 + 𝐻 2 𝑂 ↔ 𝐻 2 + 𝐶𝑂 2 ∆𝐻 298 𝐾 = 41. 2 𝑘𝐽/𝑚𝑜𝑙 ( 2 .2) Fuente: (Velasco, 2015)
Entre las principales ventajas que tiene el reformado se encuentra el hecho de que ya es una tecnología establecida y ampliamente utilizada en el mundo, cuenta con una eficiencia térmica superior al 80% y la más alta relación molar de H 2 /CO (produciendo hasta una relación de 3). Sin embargo, entre las desventajas que tiene este método están que requiere de grandes cantidades de energía debido a que es una reacción altamente endotérmica, tiene altos costos de operación, genera CO 2 debido a la combustión de hidrocarburos para obtener vapor de agua y que, al tratarse de un proceso catalítico, el catalizador llega a desactivarse debido a la formación de carbón residual depositado (o coque) (Da Silva Veras, et al., 2016).
2. 3 .2 Oxidación Parcial de Metano (POX) En la oxidación parcial, el gas natural y el oxígeno reaccionan sin con un catalizador para producir gas de síntesis (Figura 4). La oxidación parcial presenta mayores eficiencias que el reformado de metano. Además, el POX tiene otras ventajas, se puede realizar con menor inversión y todavía producir un gas de síntesis con una relación H 2 /CO molar de 2. Este se basa en una reacción exotérmica (Reacción 2. 3 ) que infiere un ahorro sustancial de energía, que exhibe altas conversiones de metano (aproximadamente 90%) y selectividades hacia el hidrogeno (94-99%) (De Los Rios, et al., 2013). 2 𝐶𝐻 4 + 𝑂 2 → 4 𝐻 2 + 2 𝐶𝑂 2 ∆𝐻 = − 71. 88 𝑘𝐽/𝑚𝑜𝑙 (2.3) Sin embargo, la reacción de la oxidación parcial del metano compite contra la oxidación total (Reacción 2.4) y para lograr solo la oxidación parcial es necesario llevar el proceso a altas temperaturas y con tiempos cortos de residencia. Y debido a esto, el proceso presenta algunas desventajas tales como: altas temperaturas de funcionamiento (900~1500°C) (Velasco, 2015), la necesidad de una planta de oxígeno en el lugar y el estricto control de flujo de oxígeno de acuerdo a la relación molar de metano alimentado, lo que hace de este un proceso muy costoso (De Los Rios, et al., 2013). 𝐶𝐻 4 + 2 𝑂 2 → 2 𝐻 2 + 𝐶𝑂 2 ∆𝐻 = − 802. 55 𝑘𝐽/𝑚𝑜𝑙 ( 2 .4)