
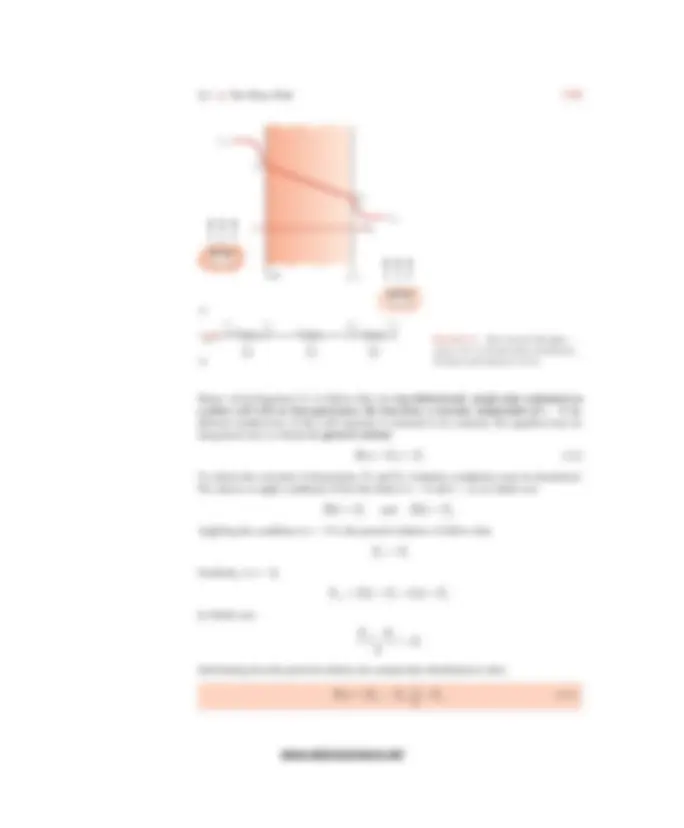
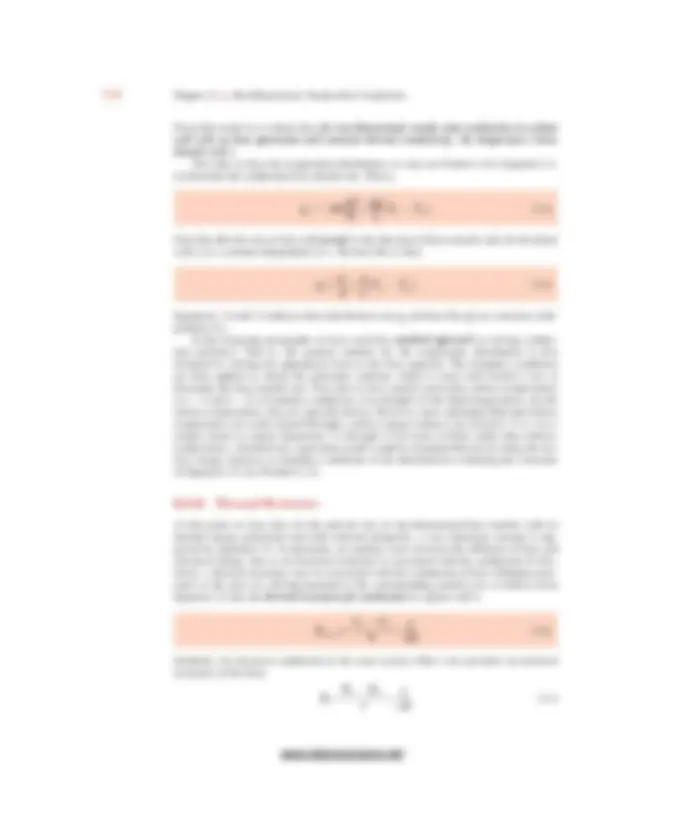
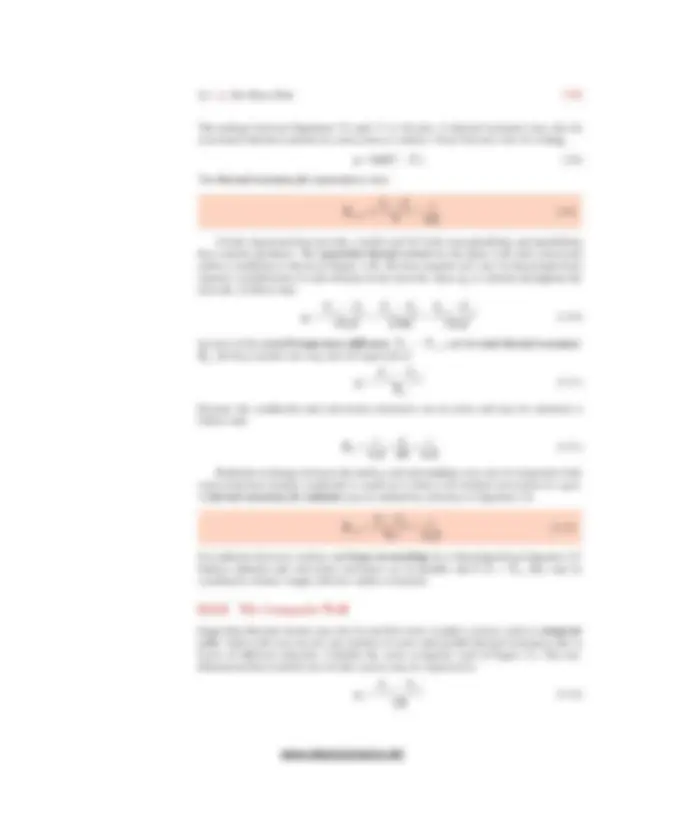
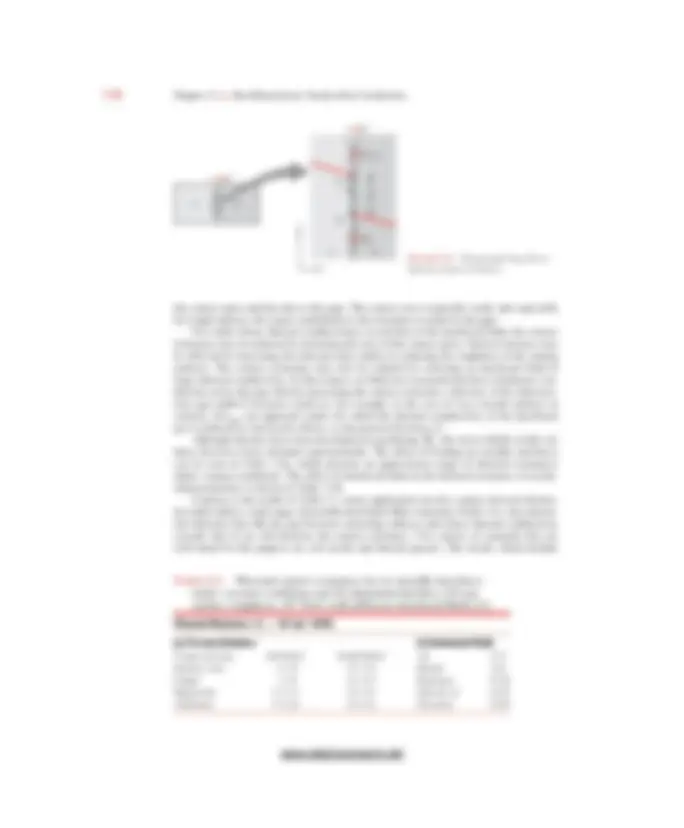
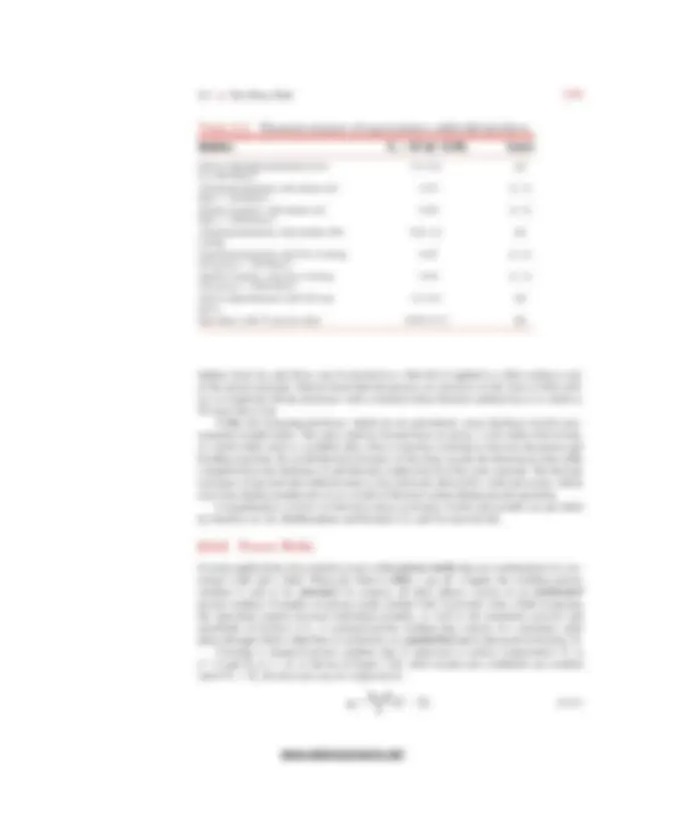
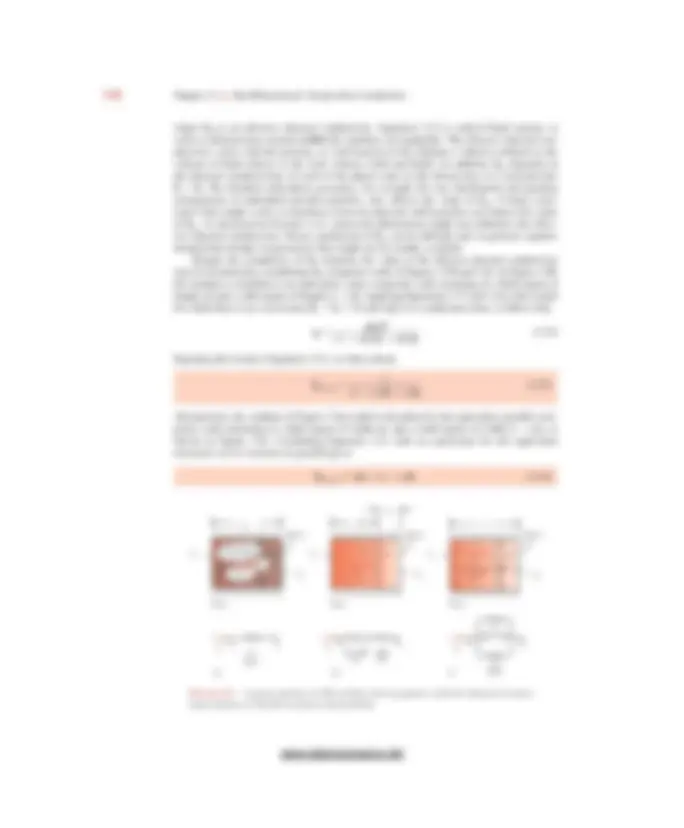
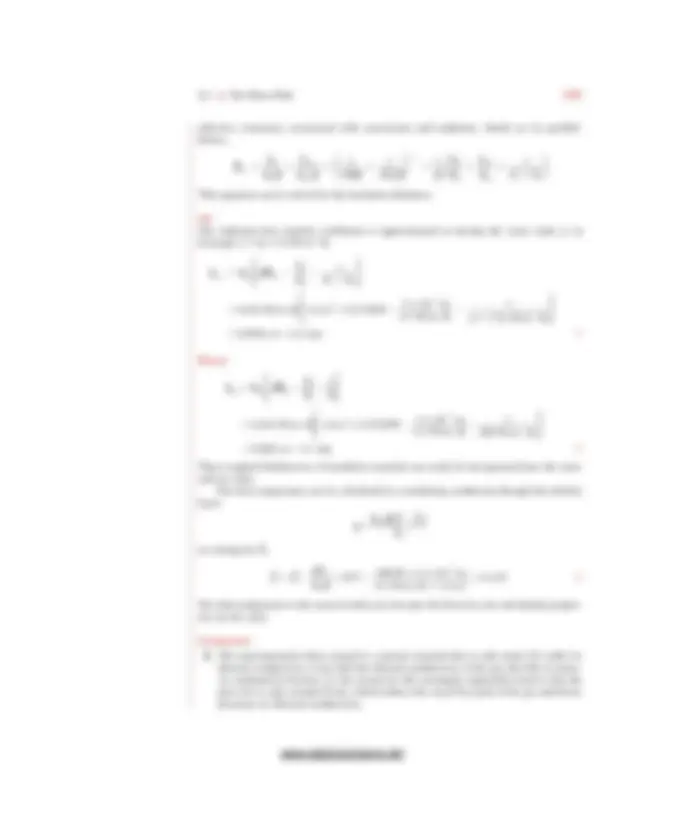
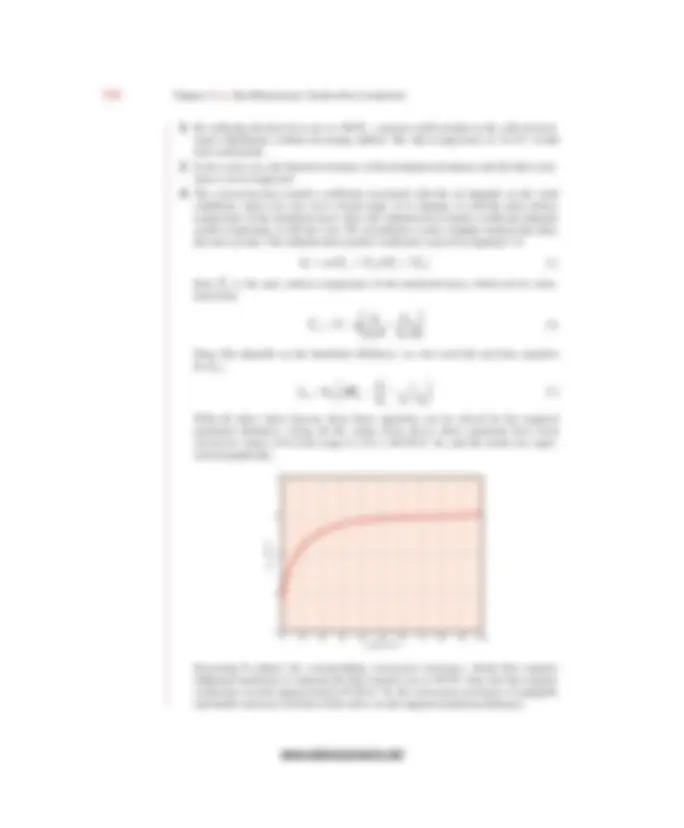
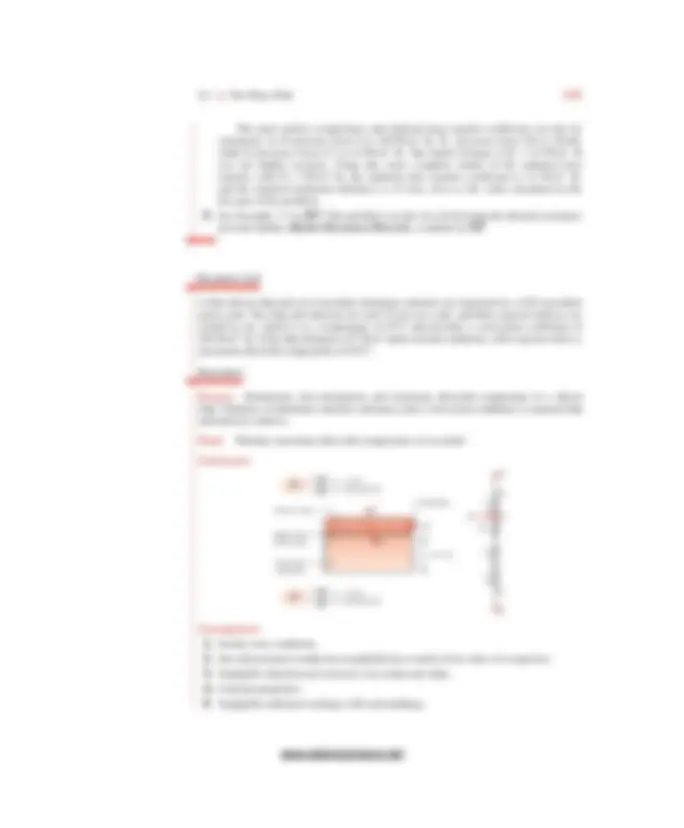
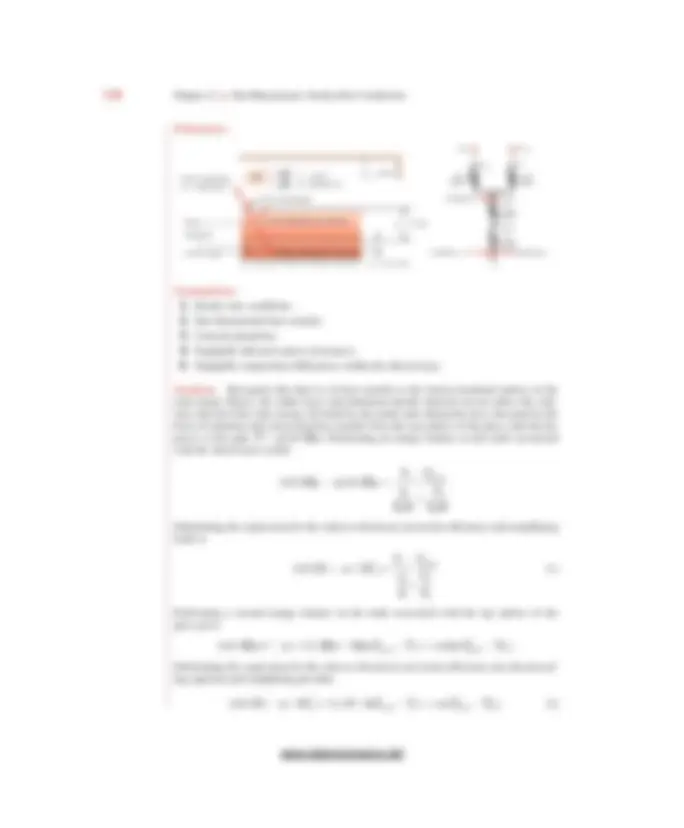
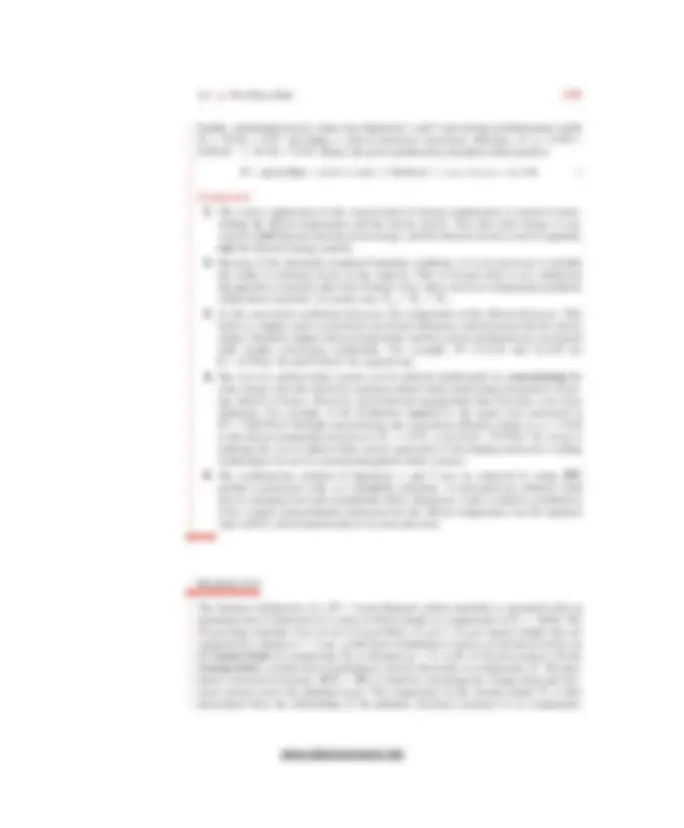
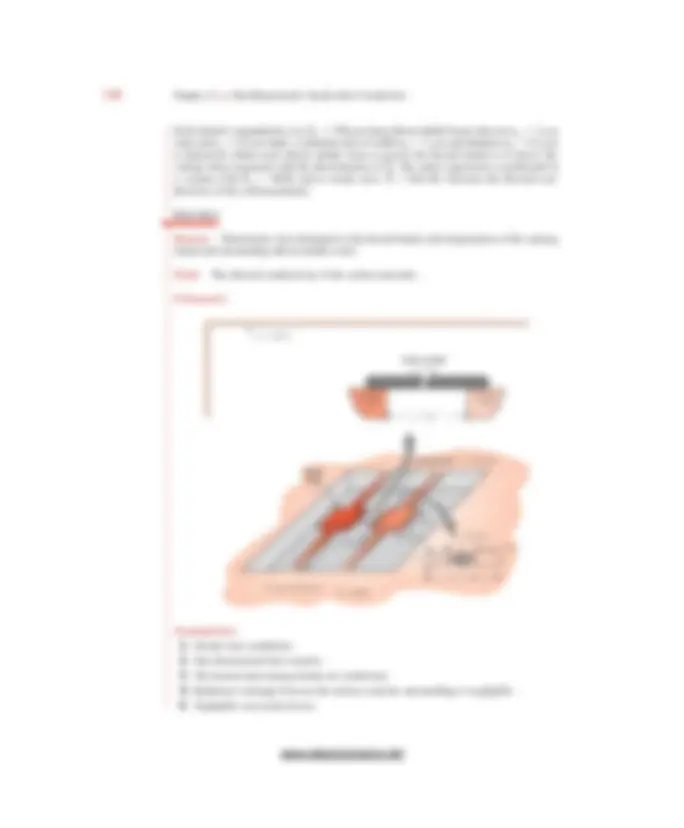
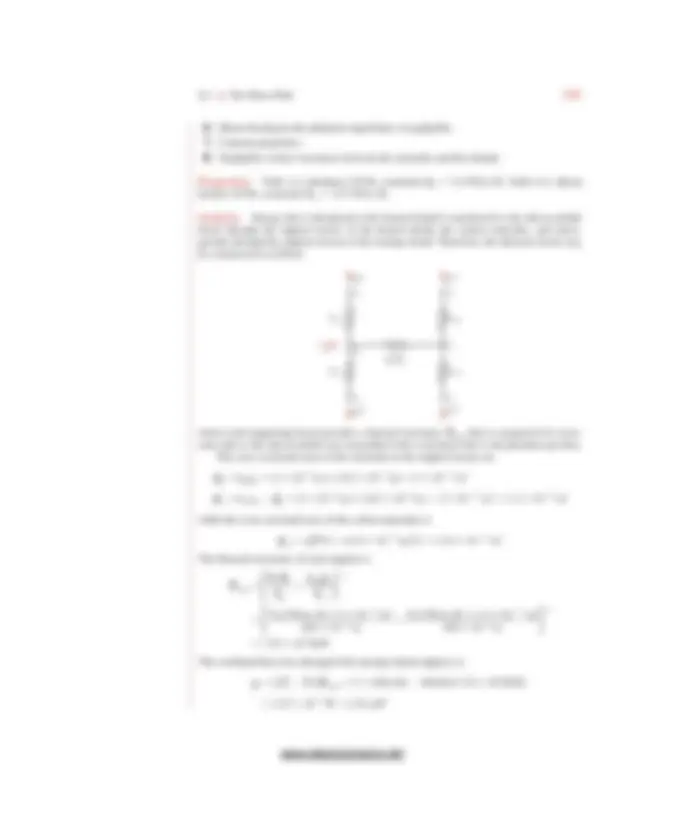
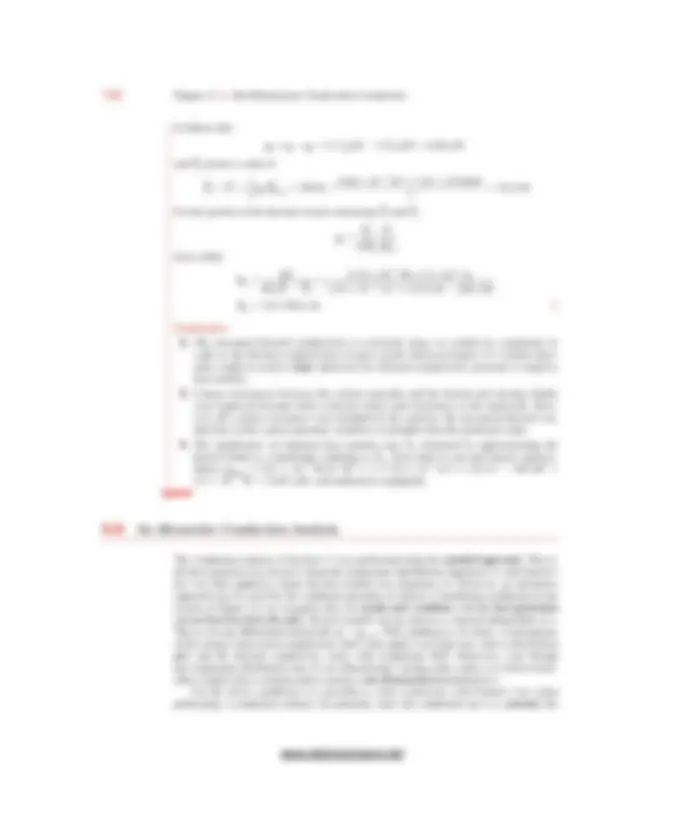
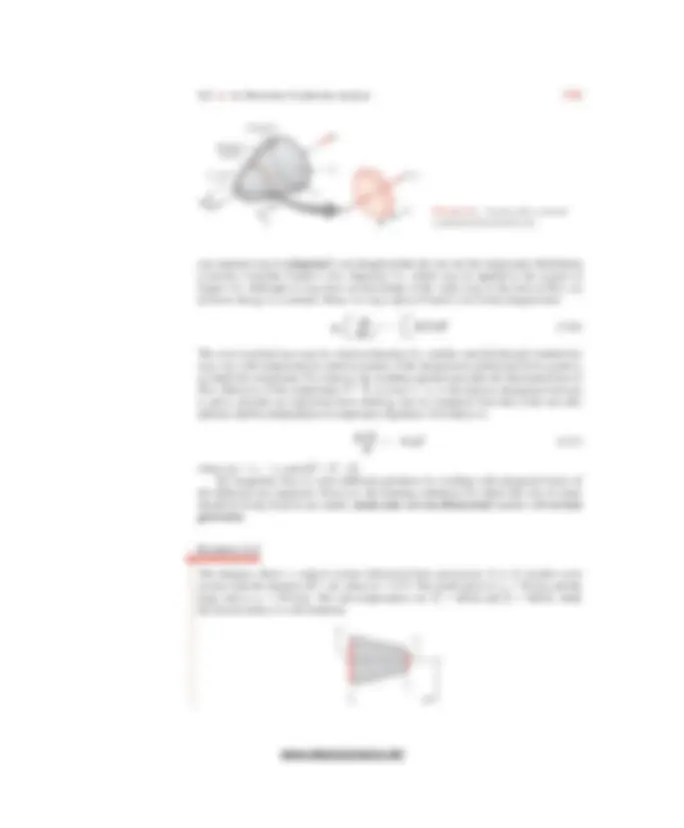
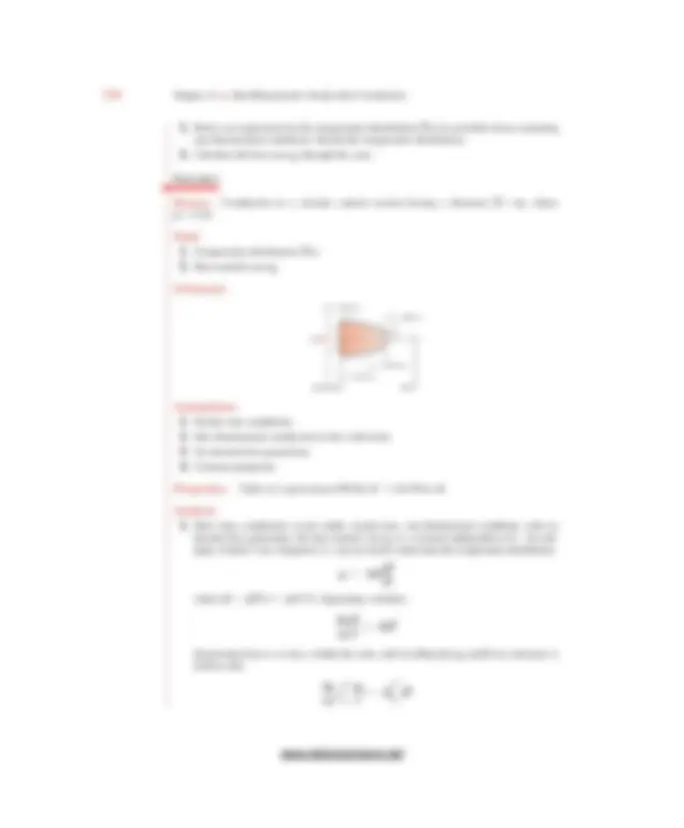
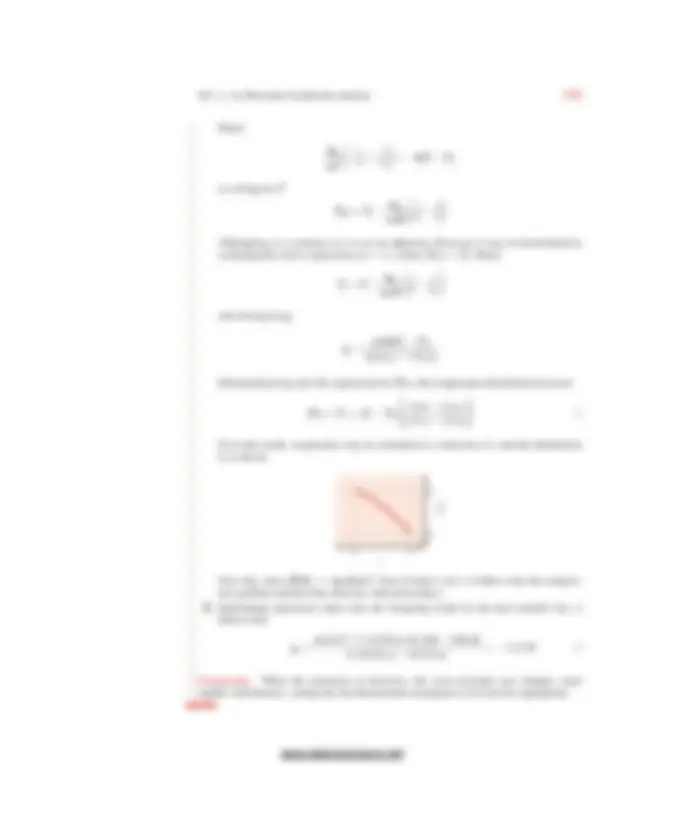

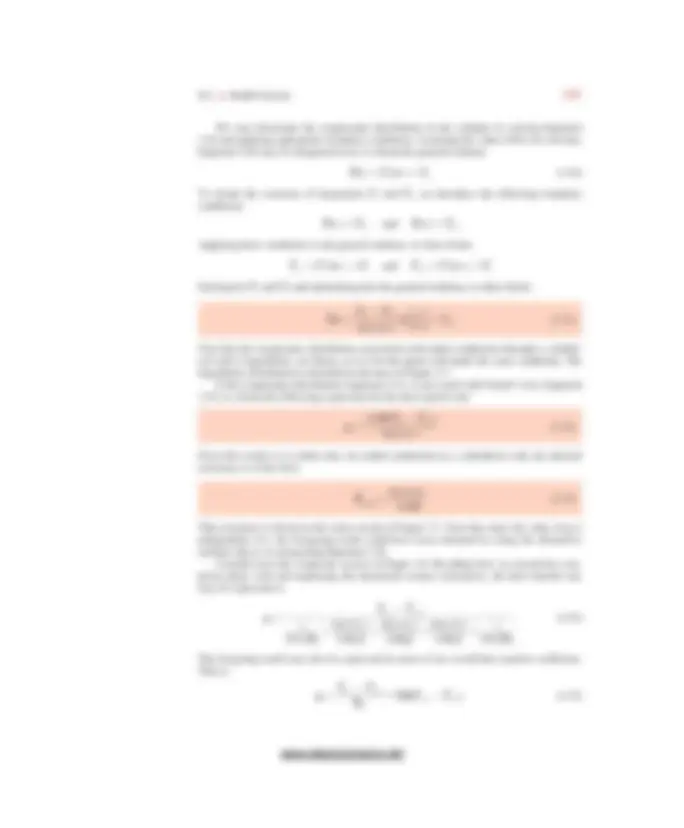
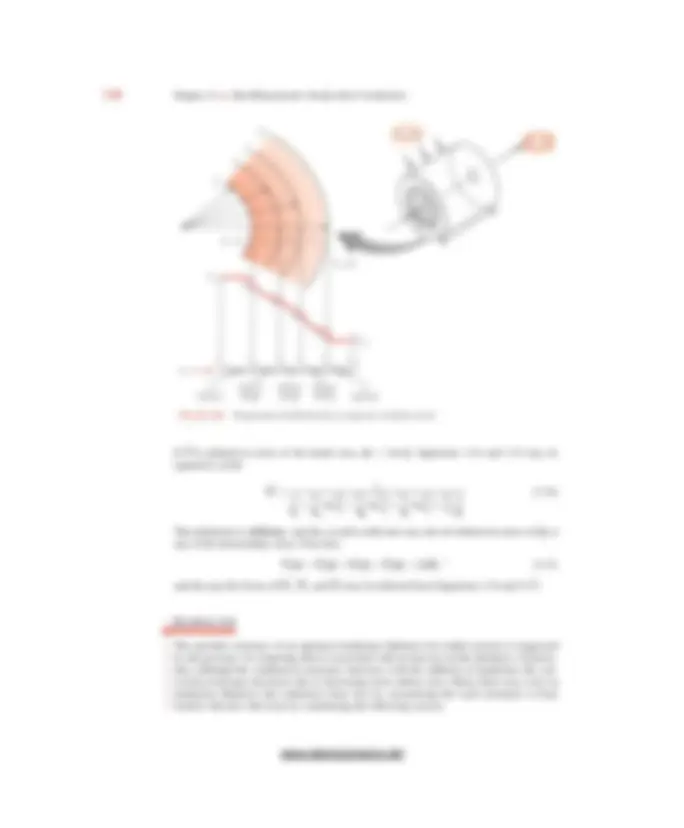
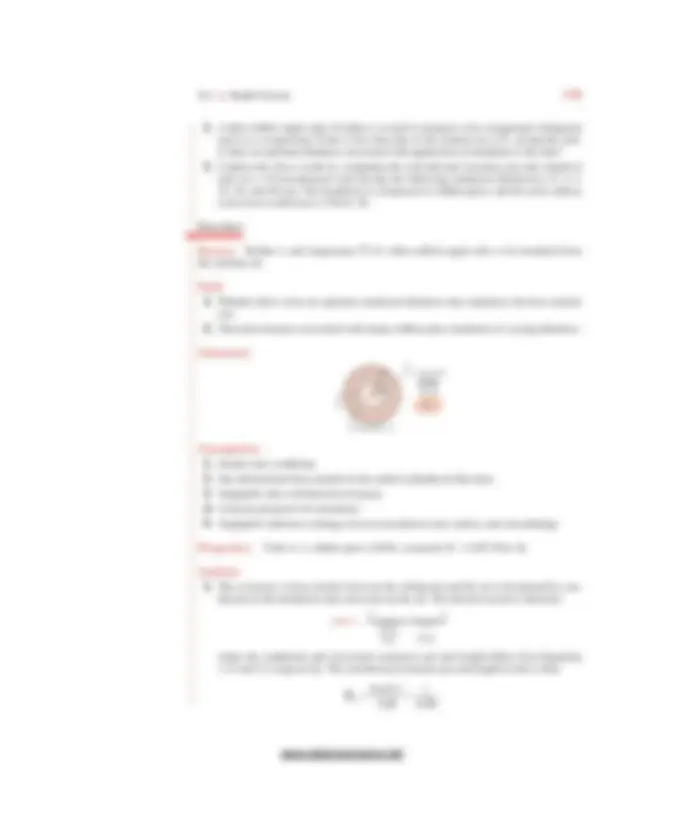

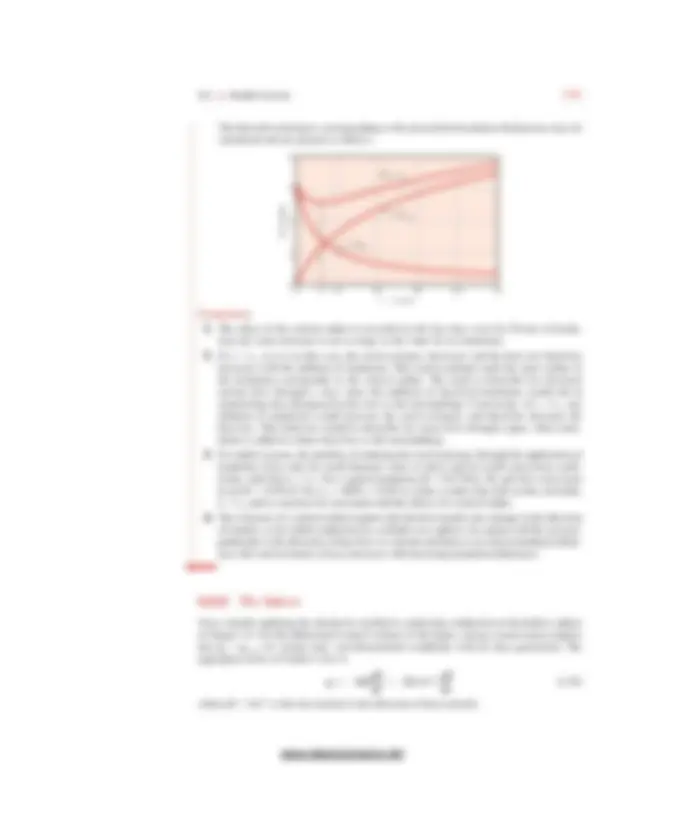
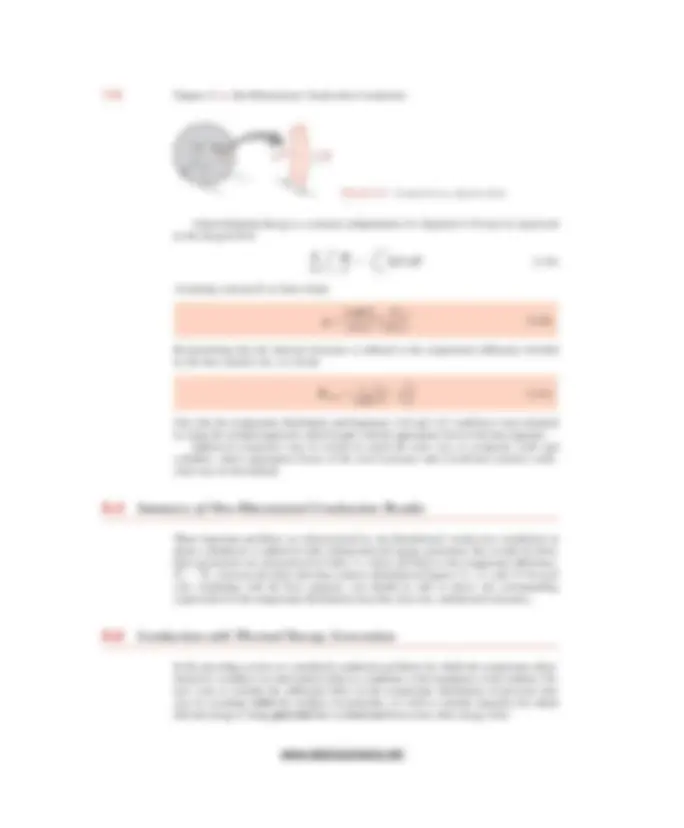
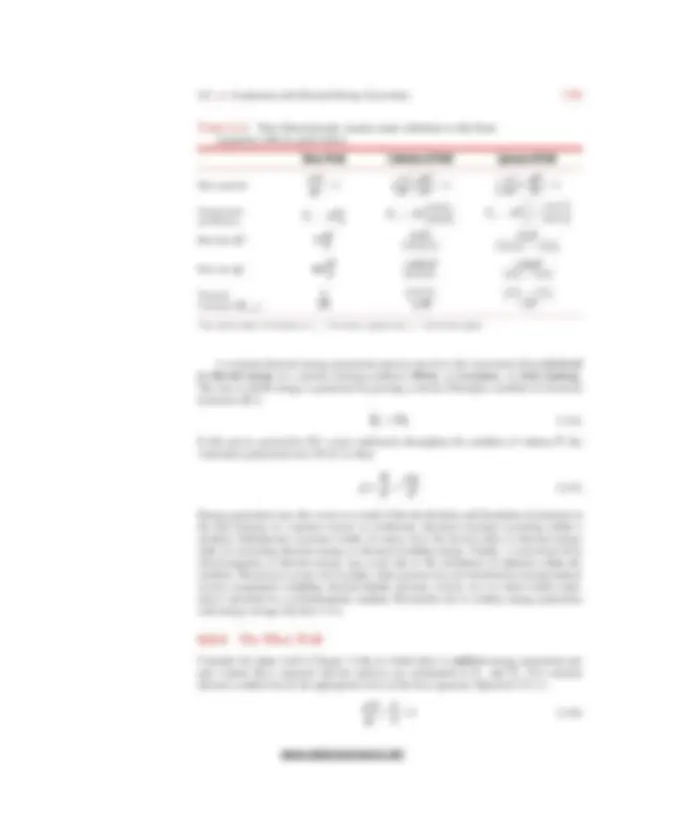
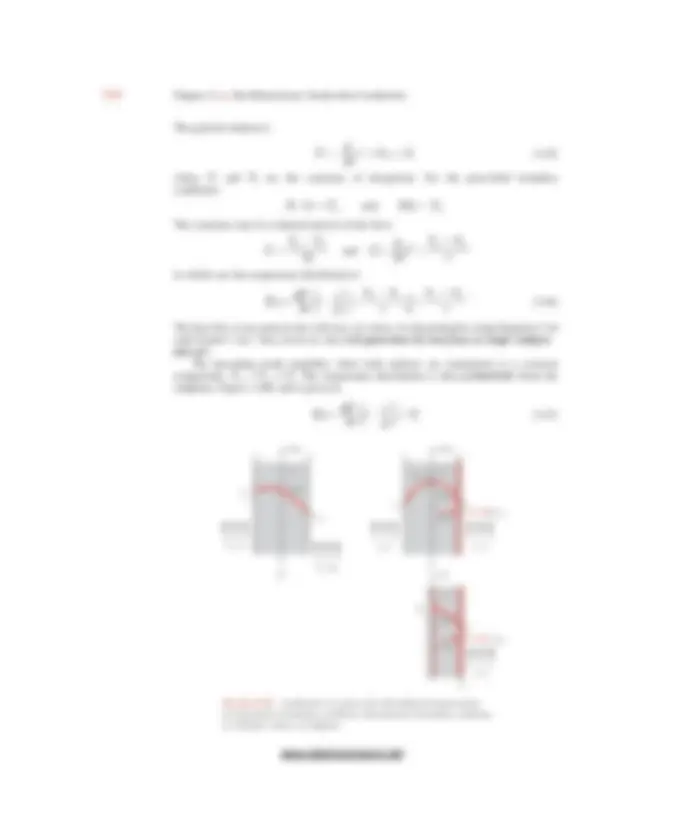
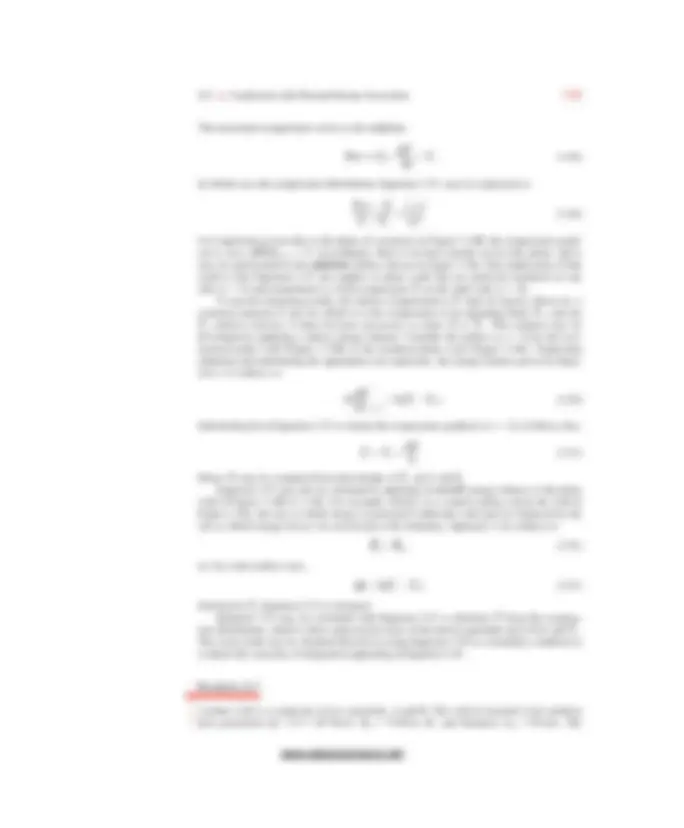
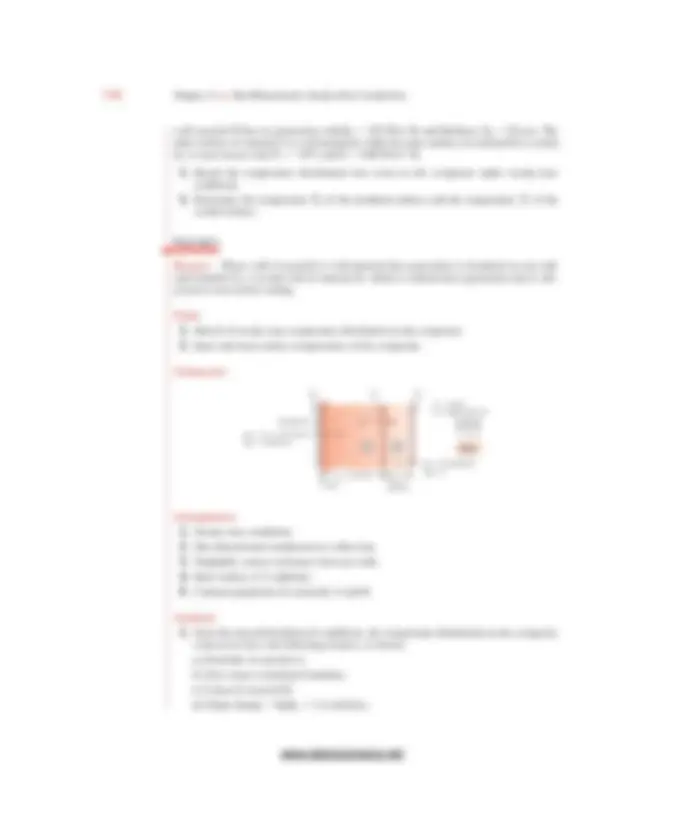
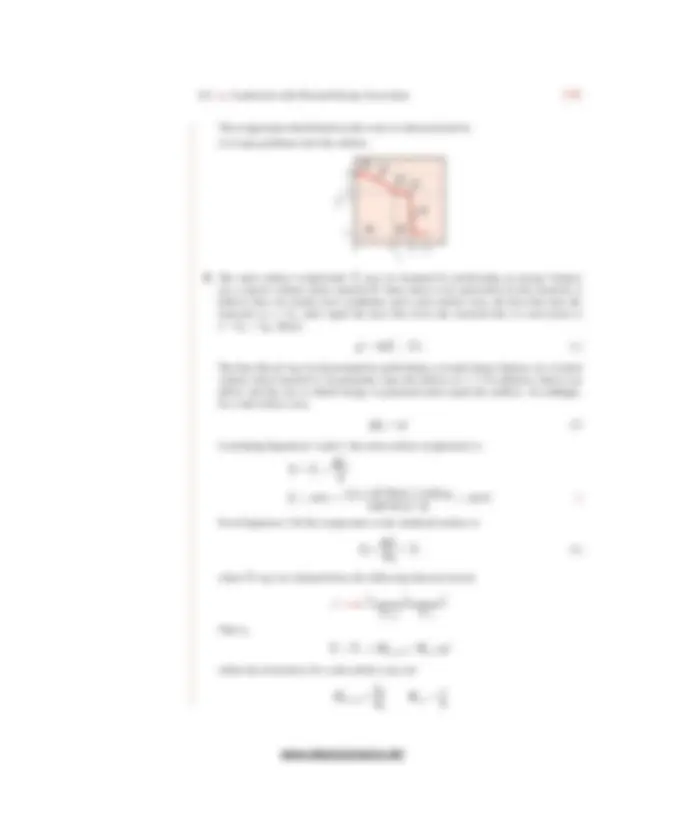
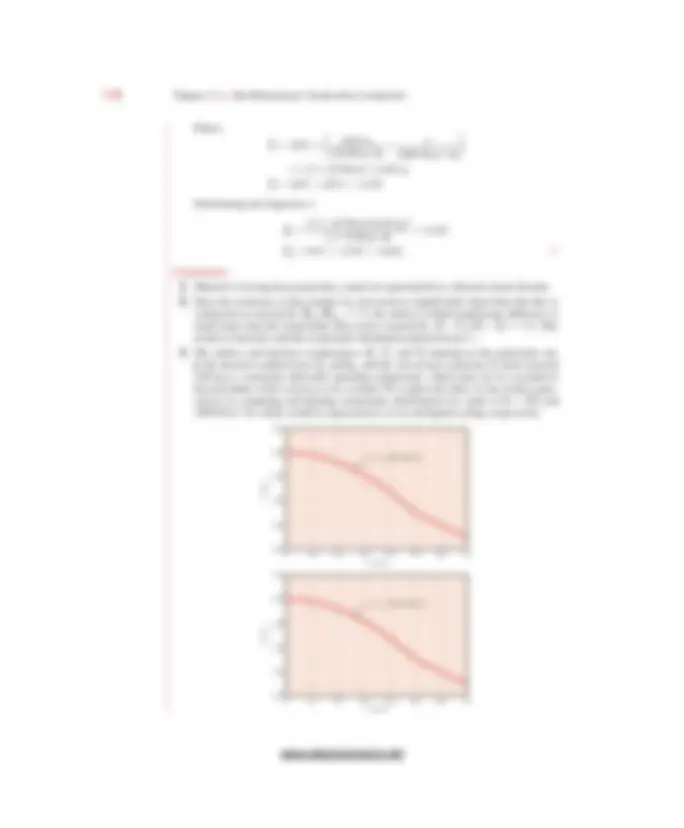
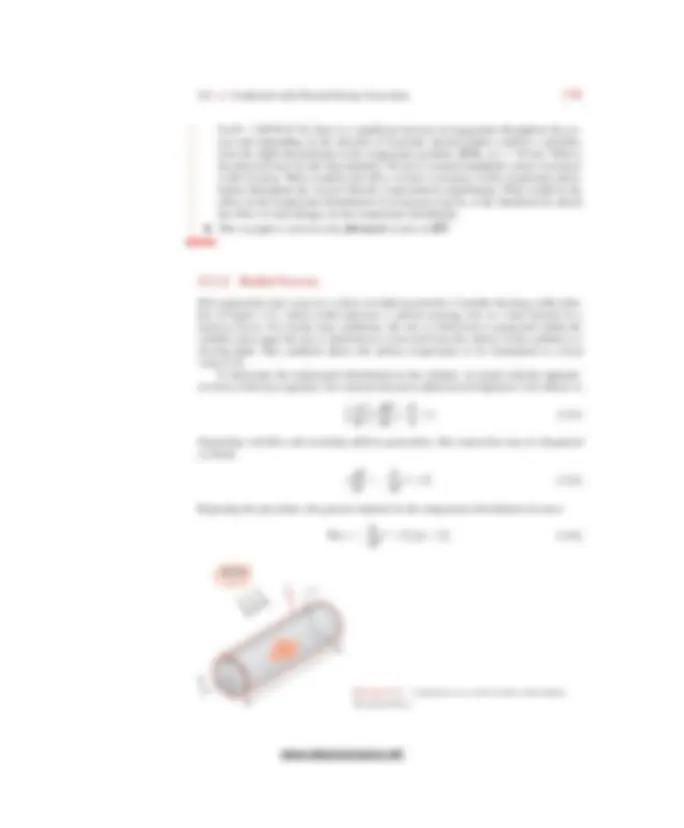
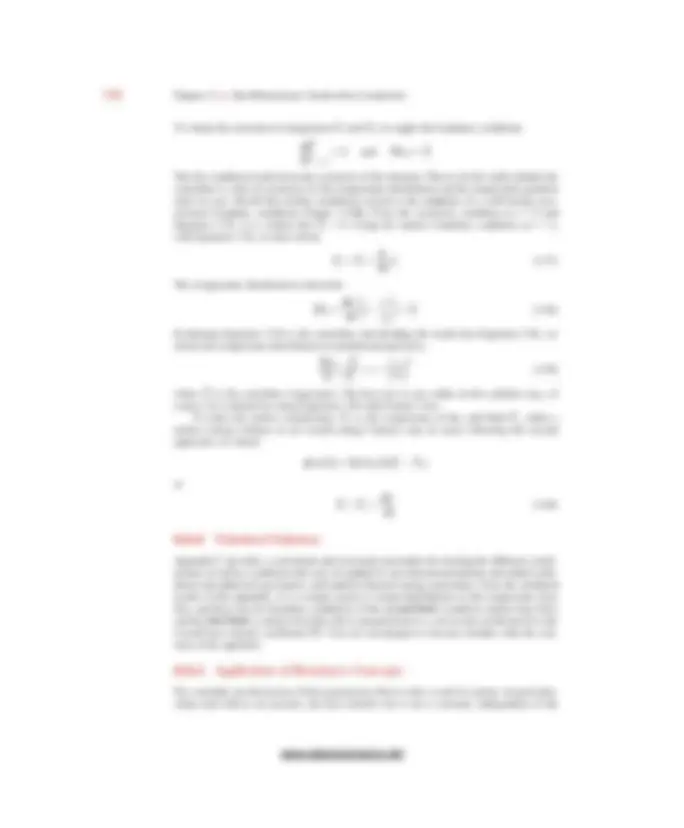
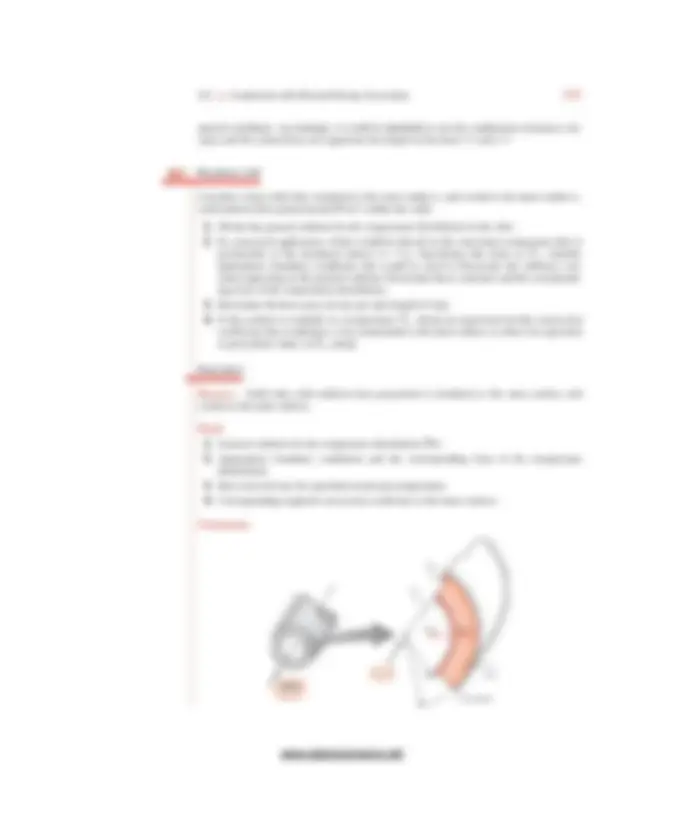
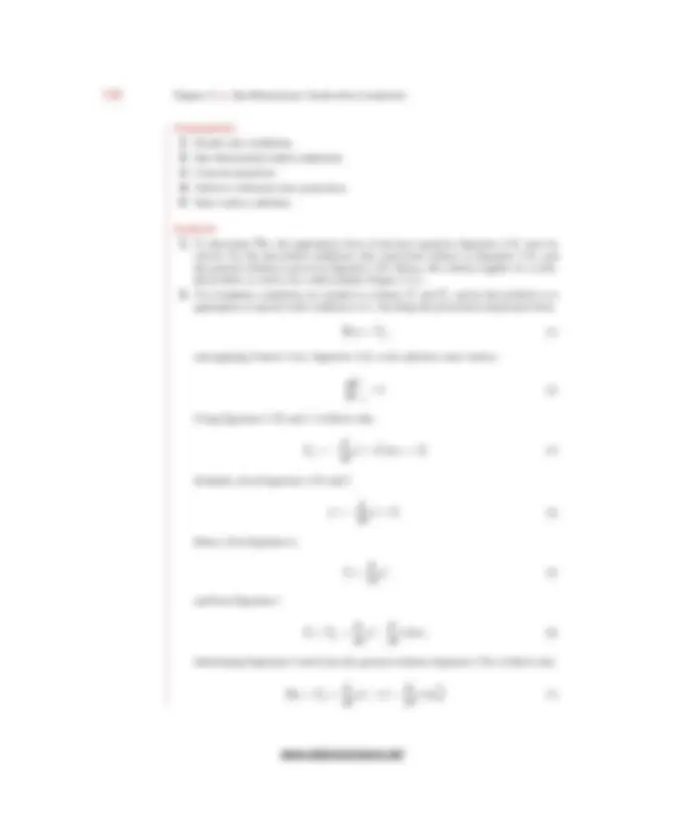
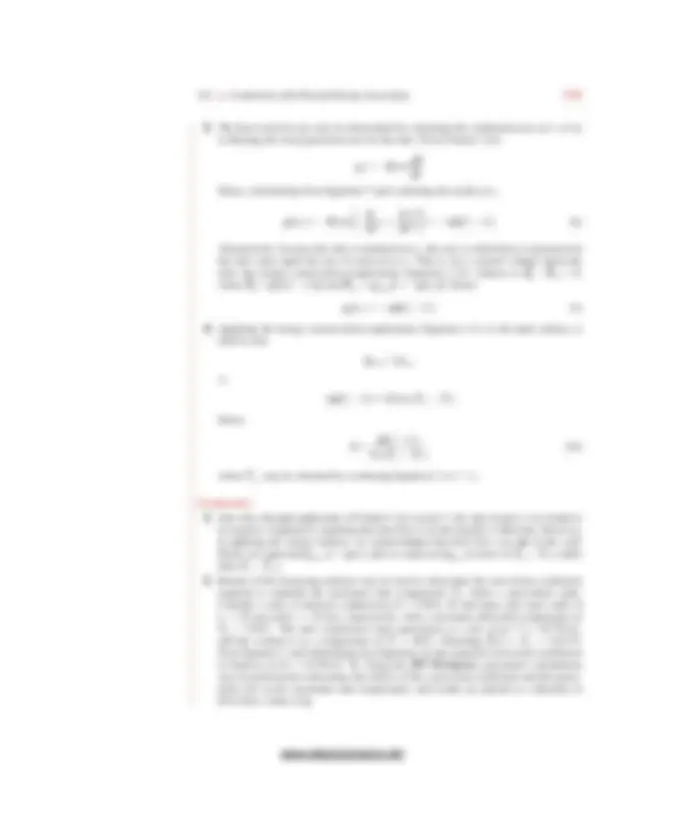
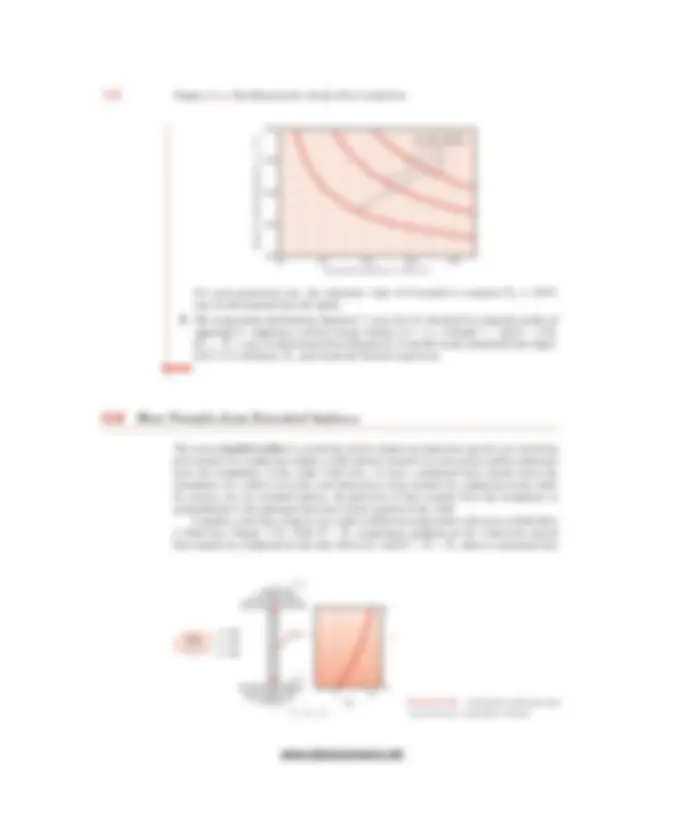
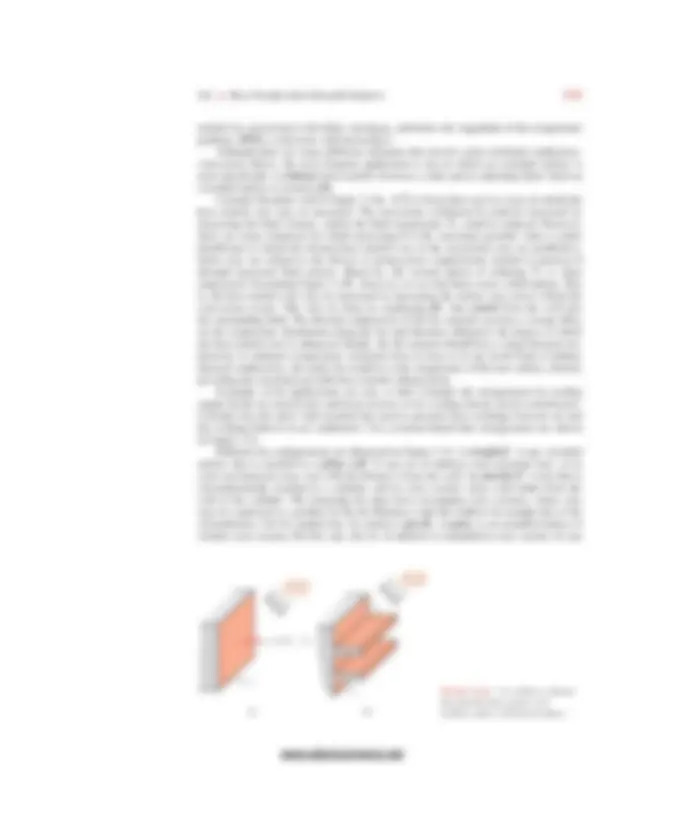
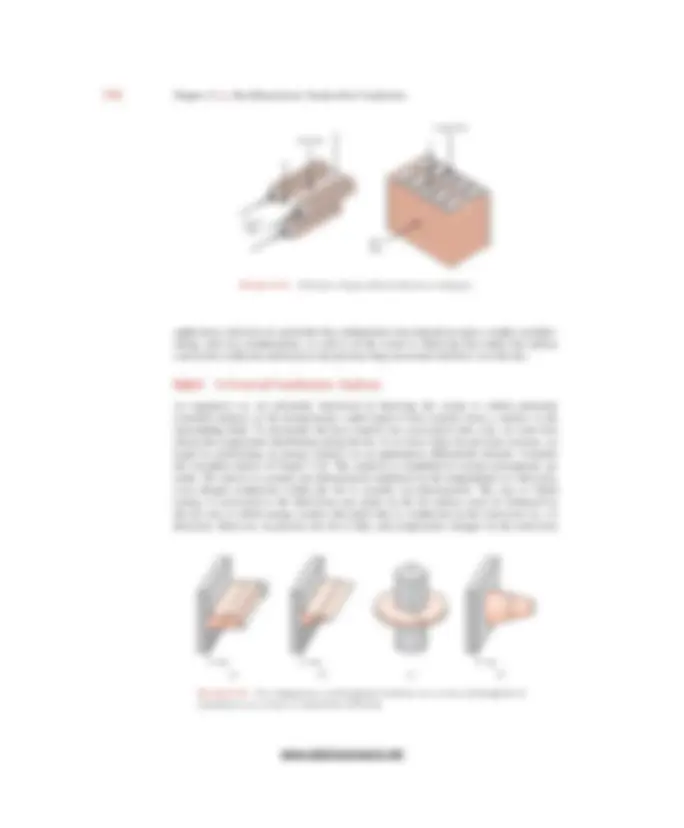
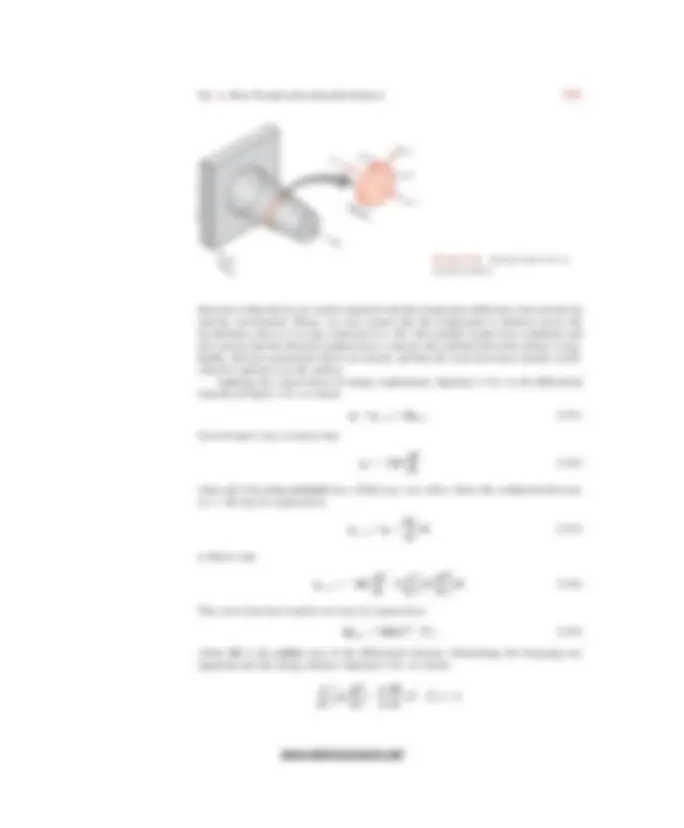
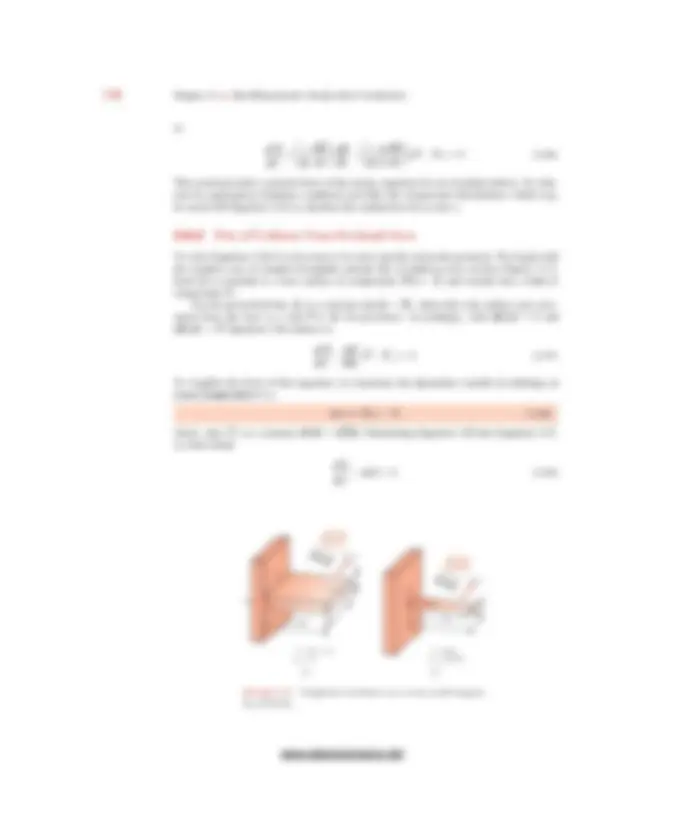
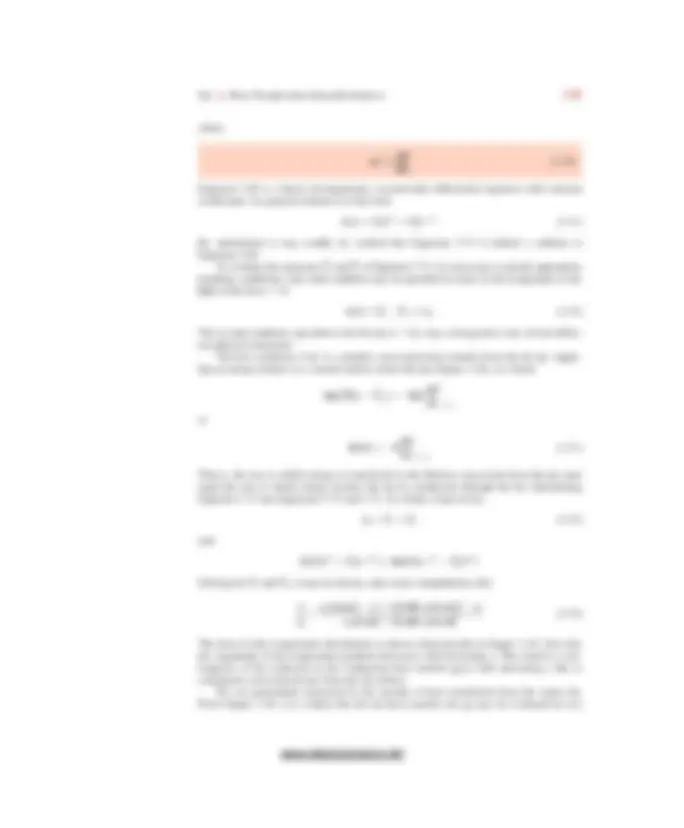
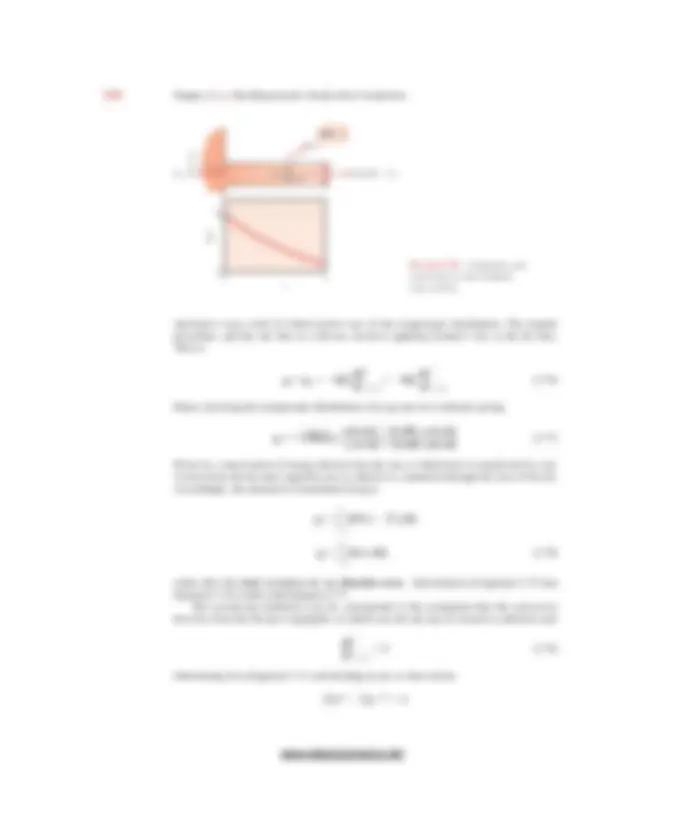
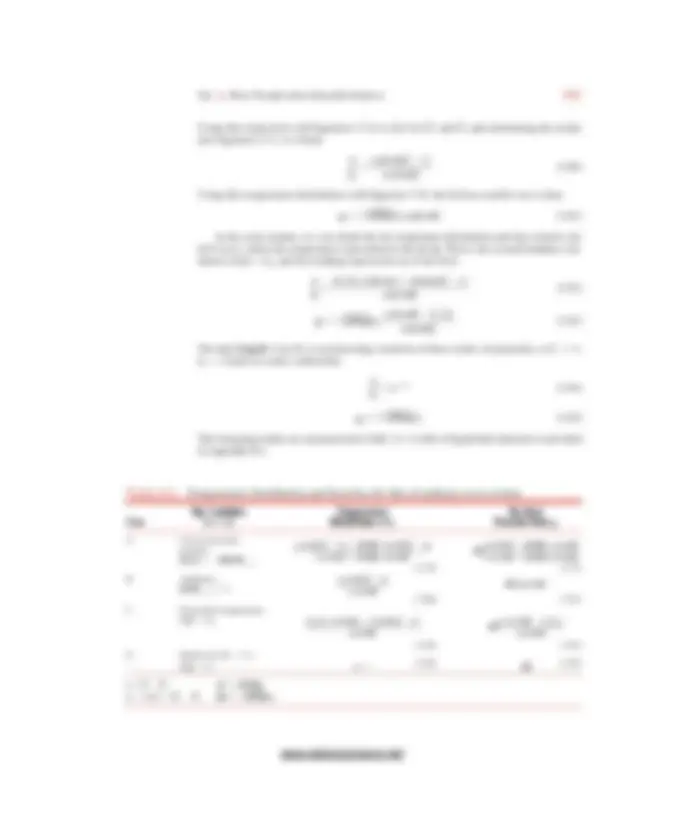
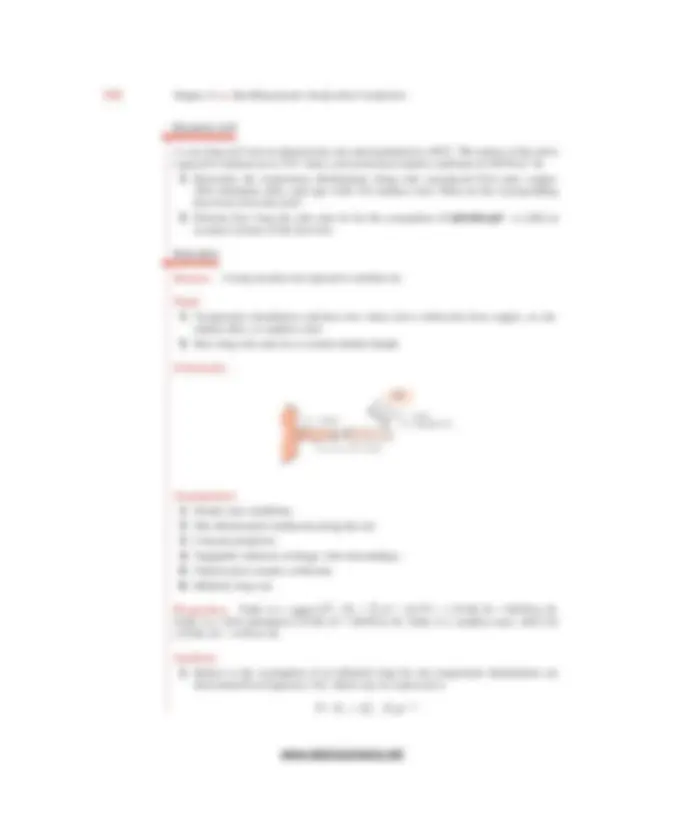
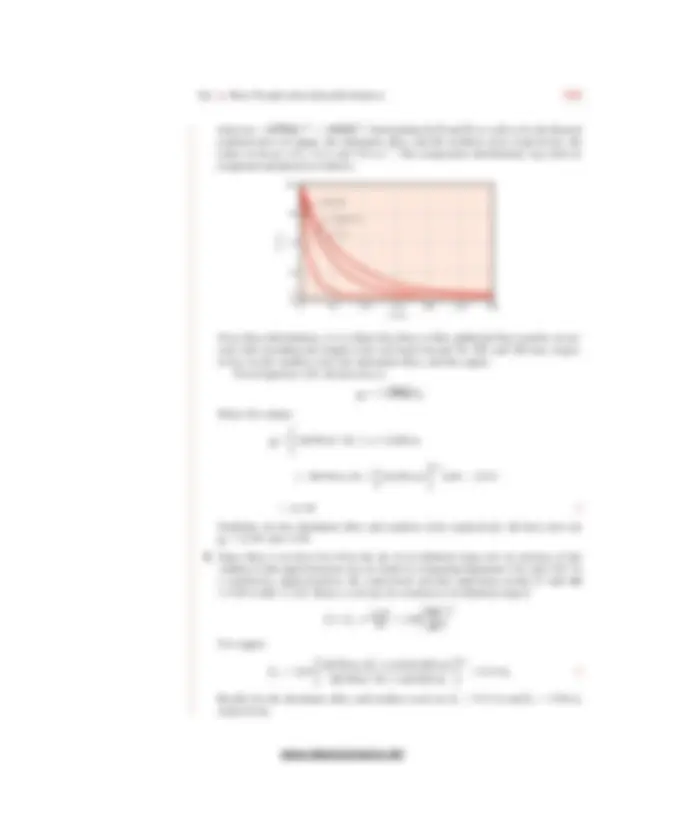
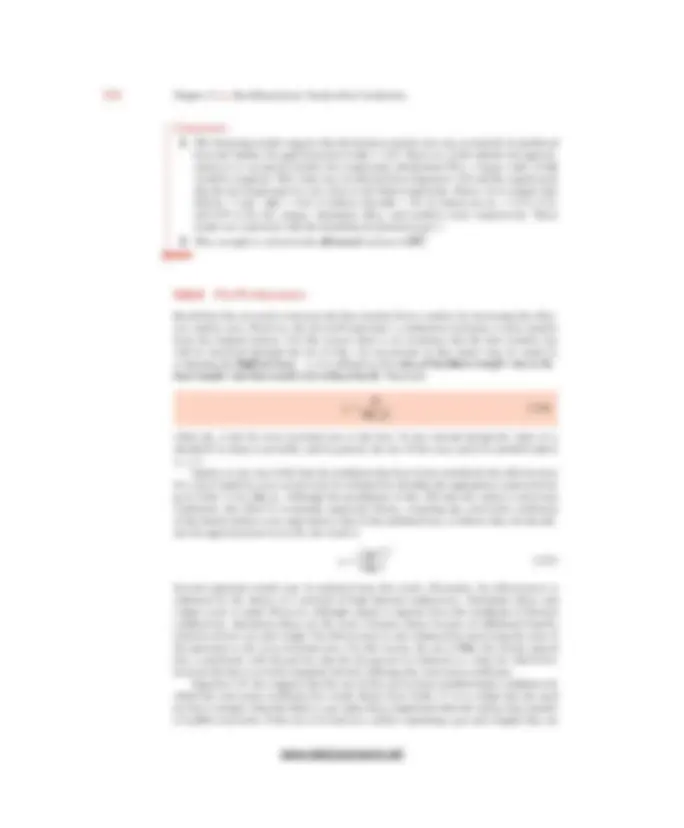
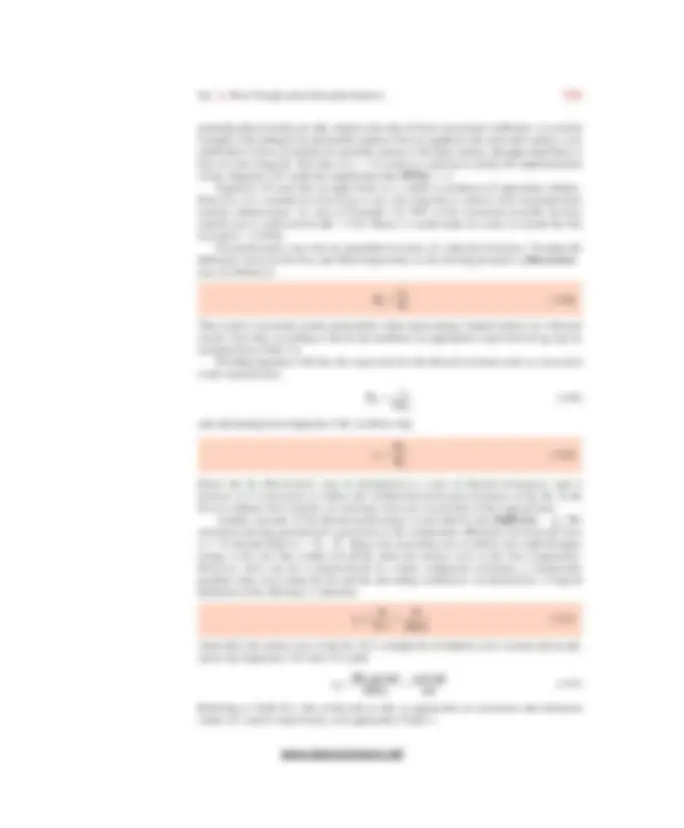
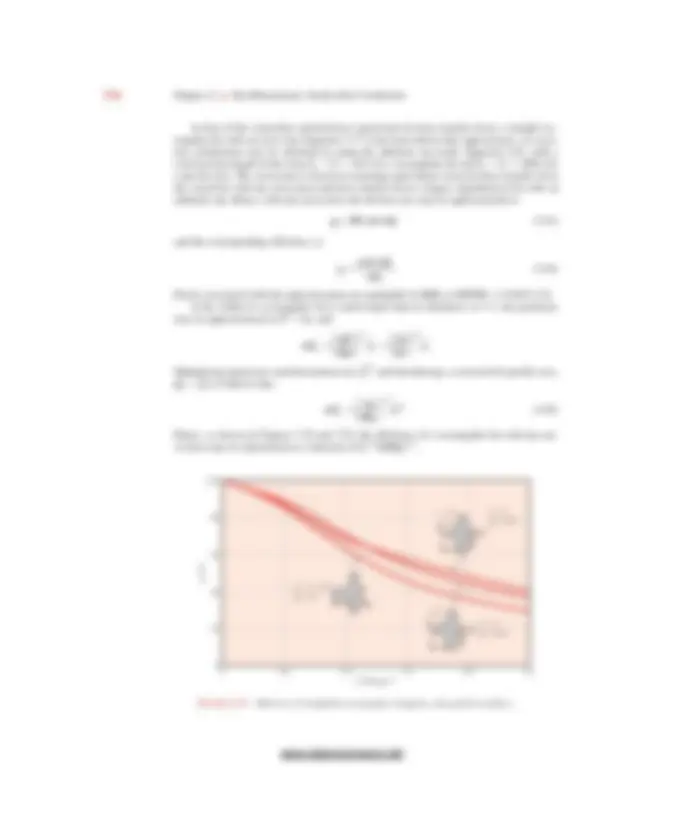
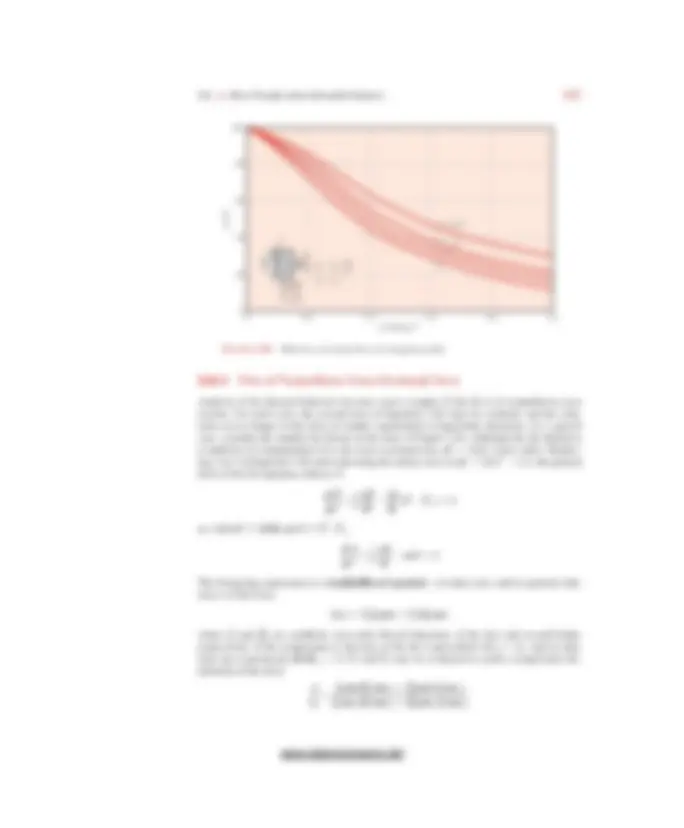
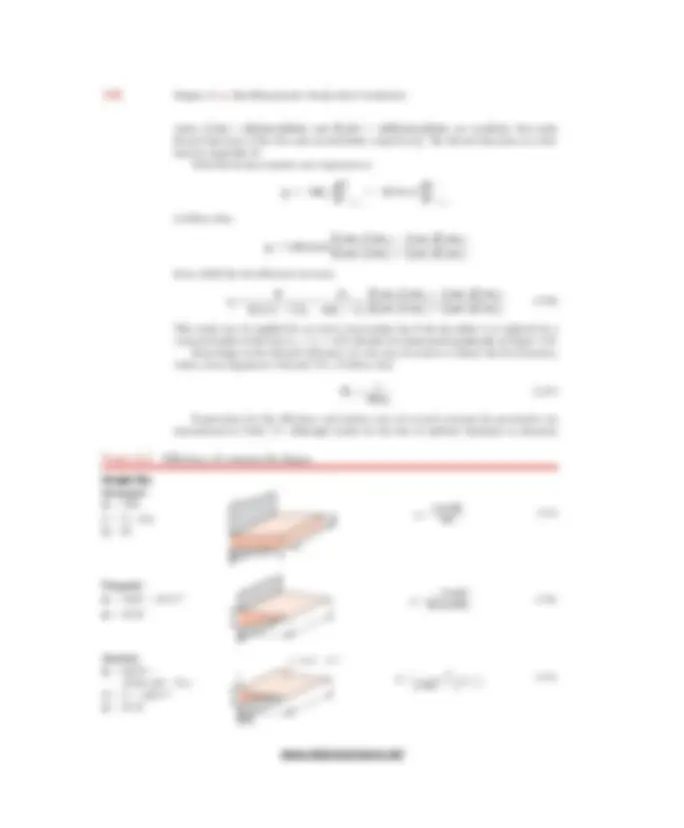
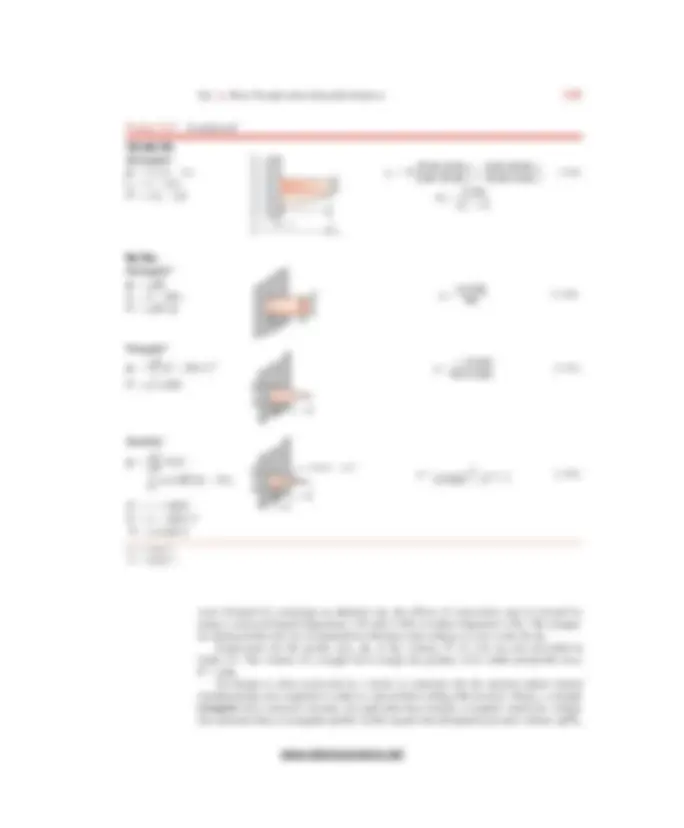

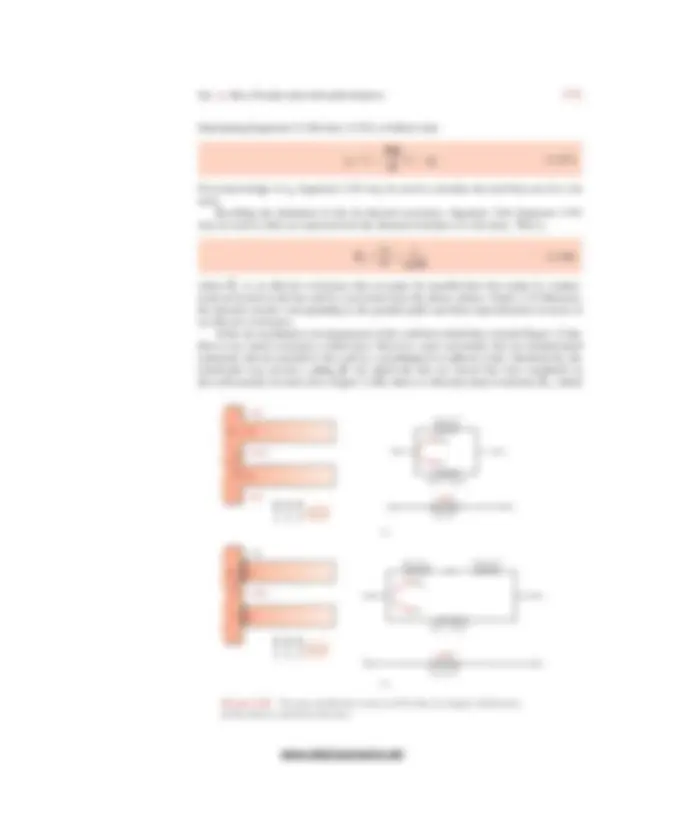
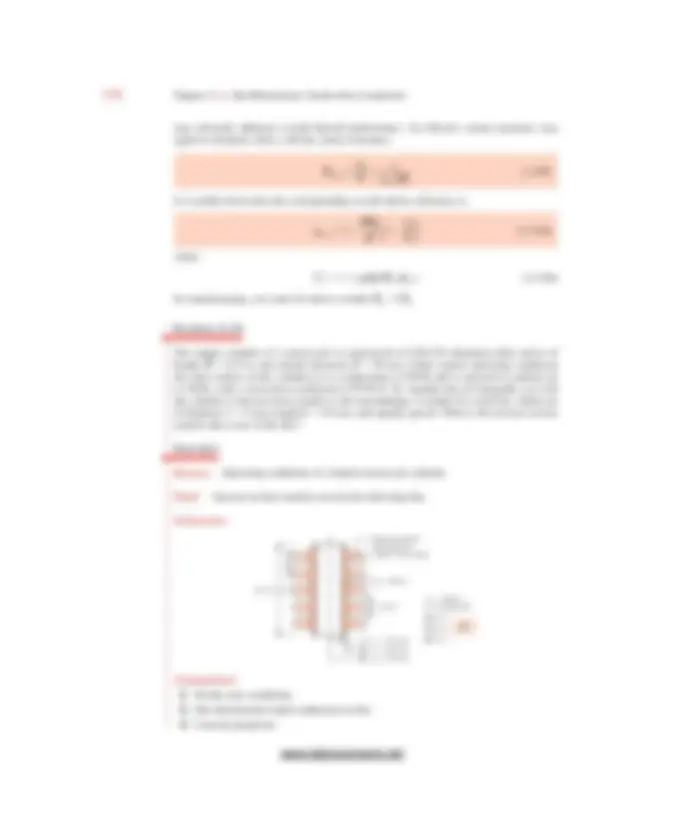
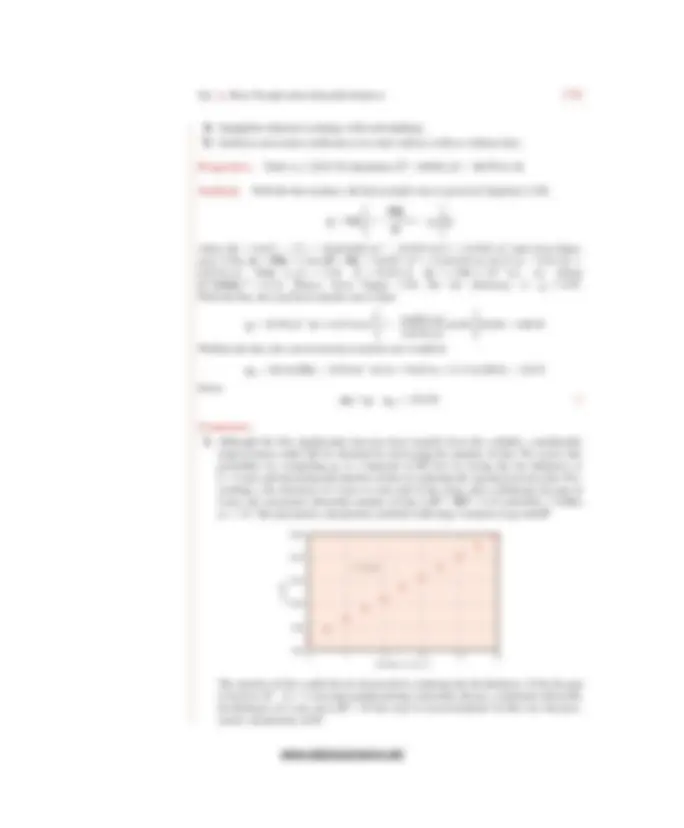
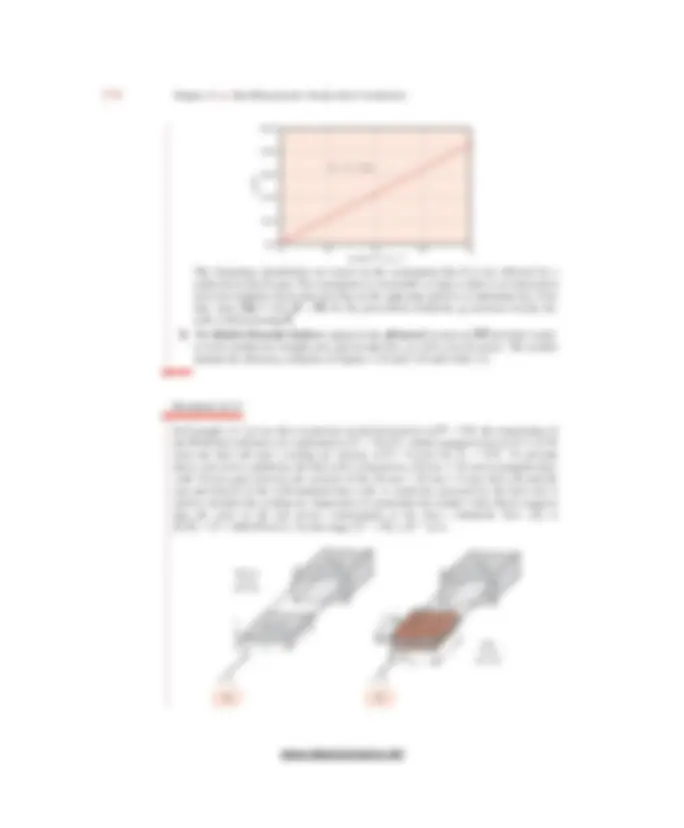
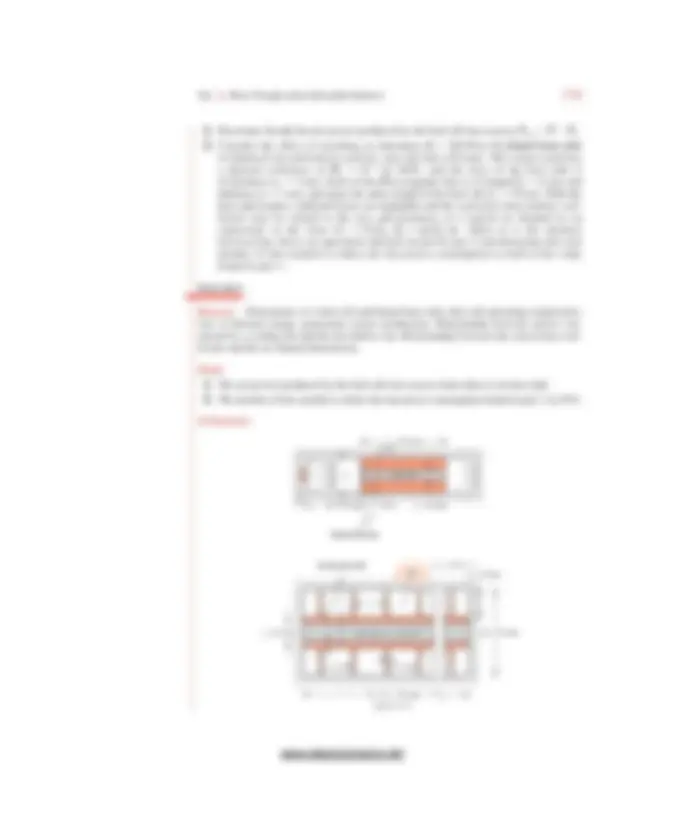
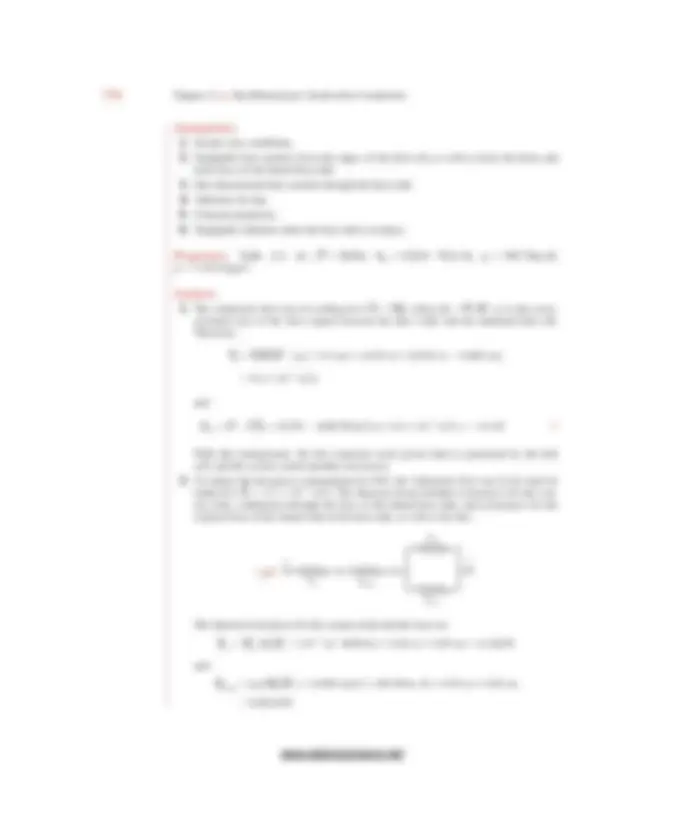
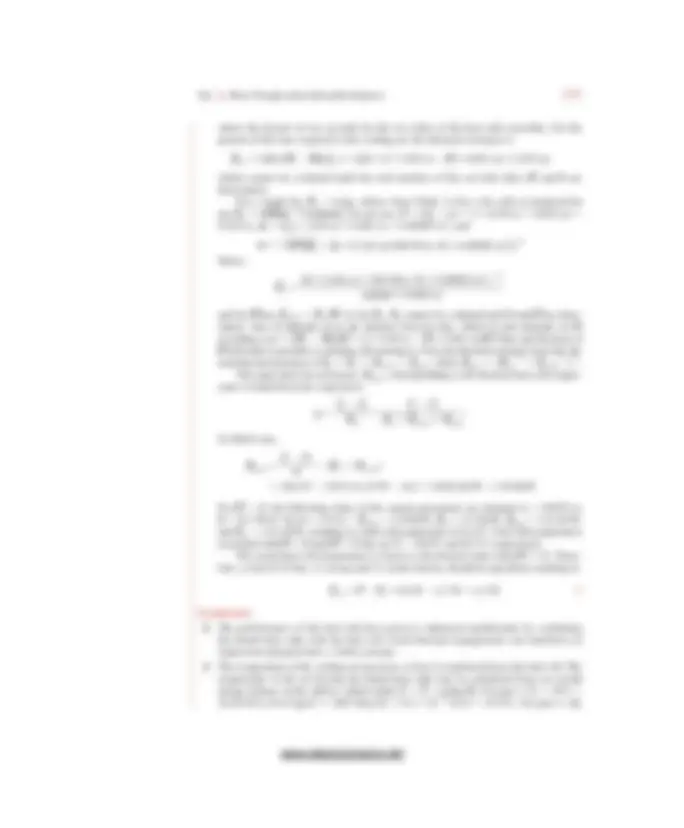
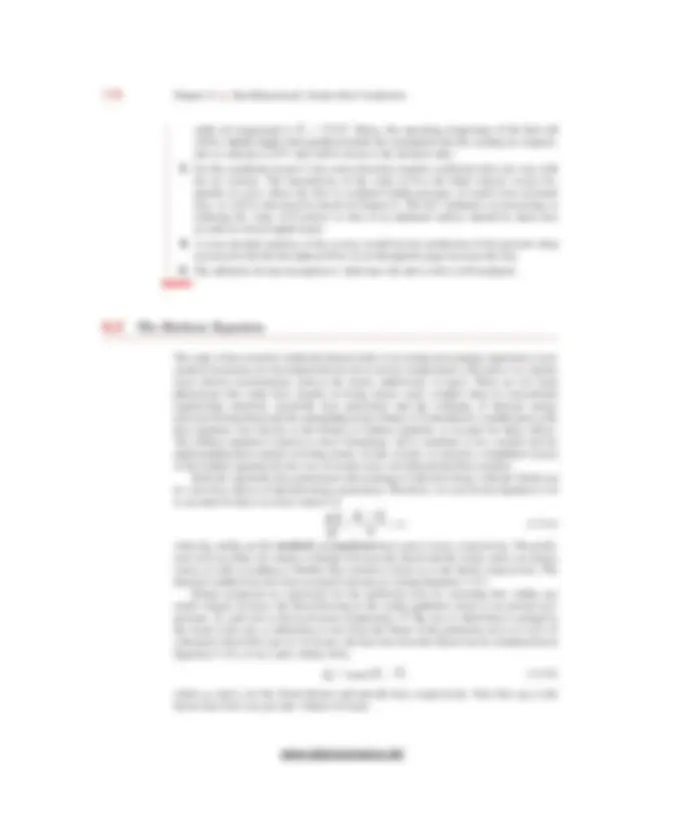
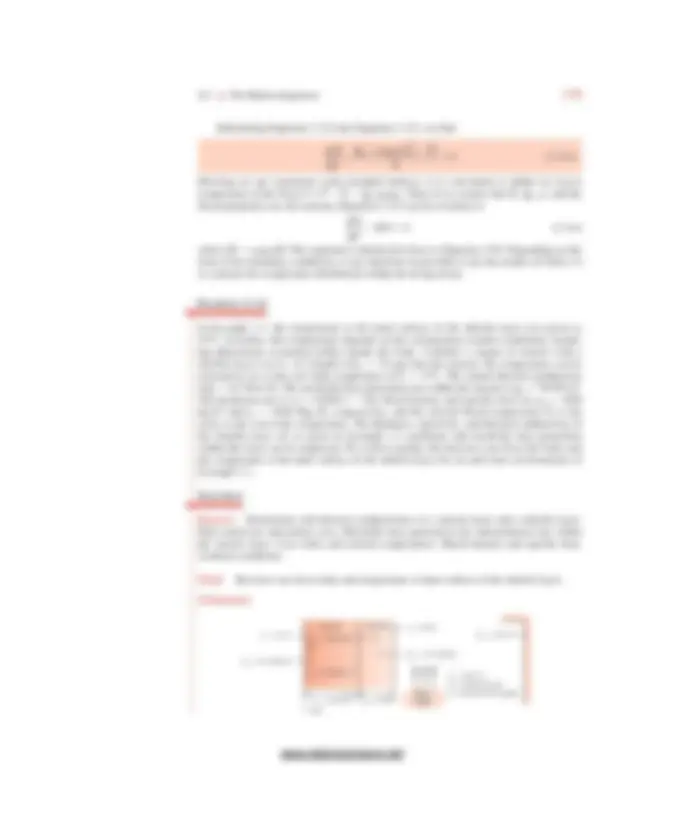
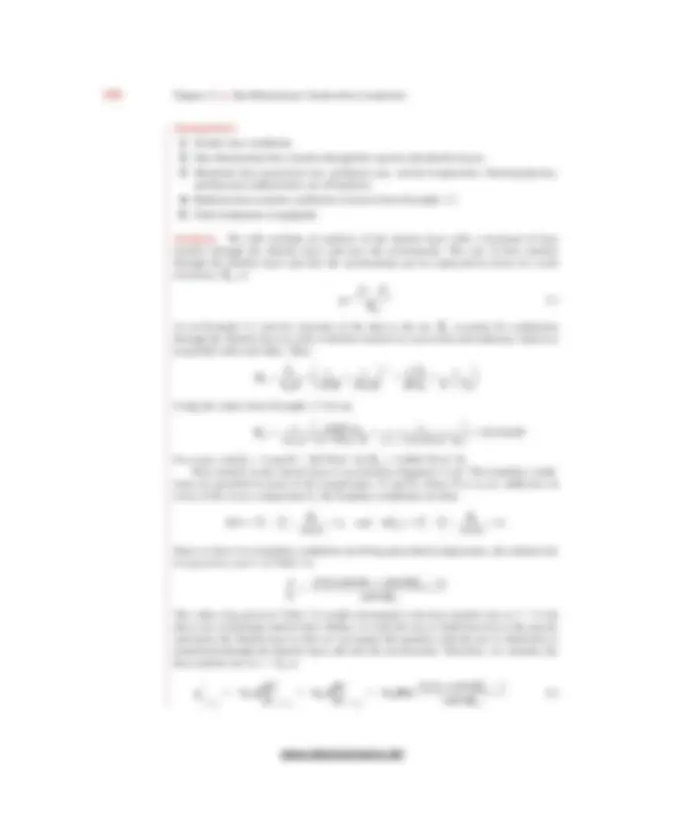
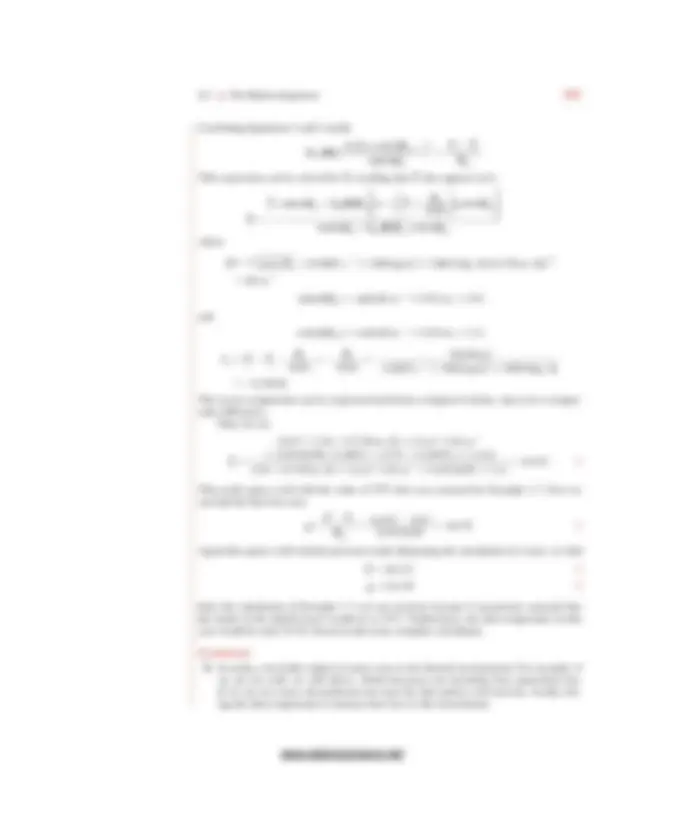
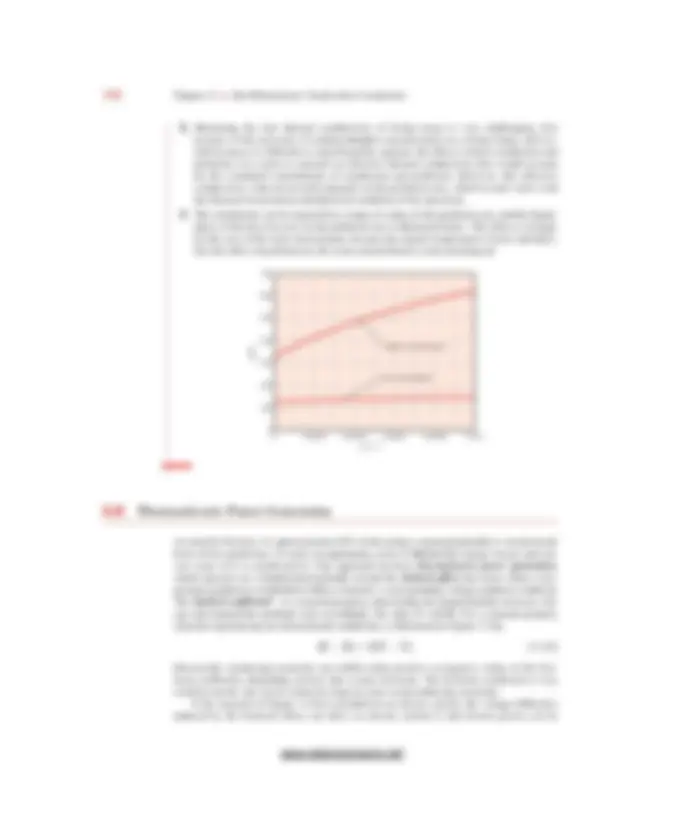
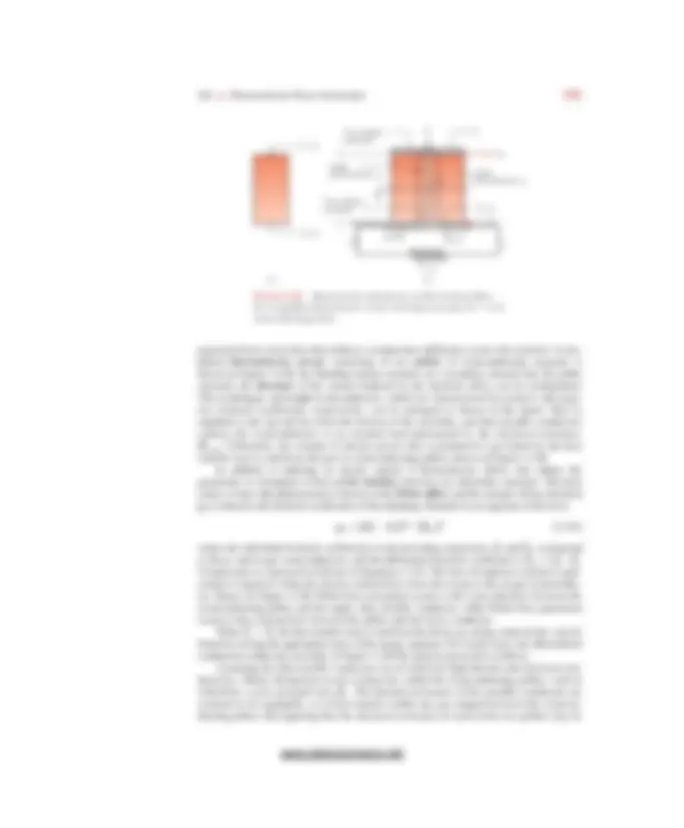
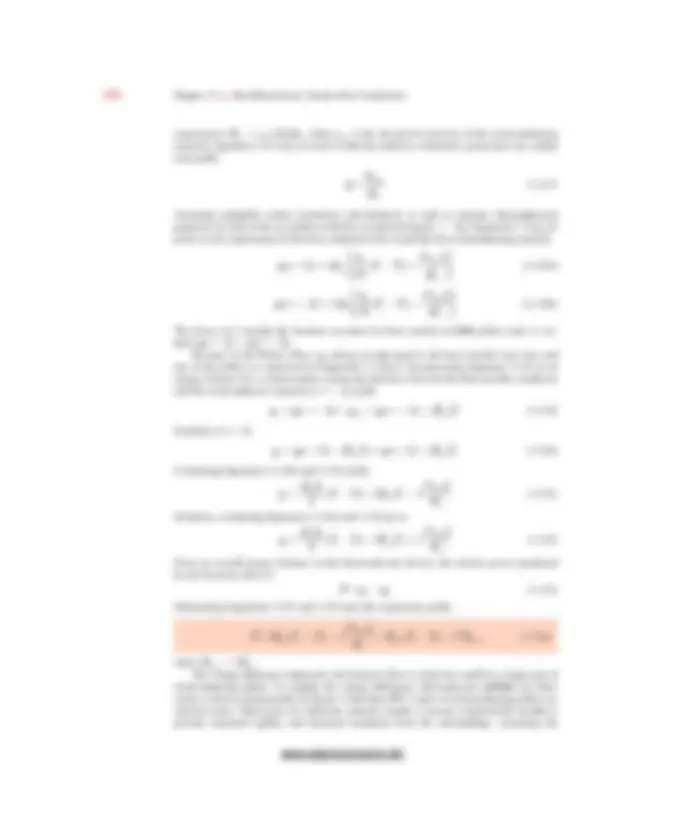
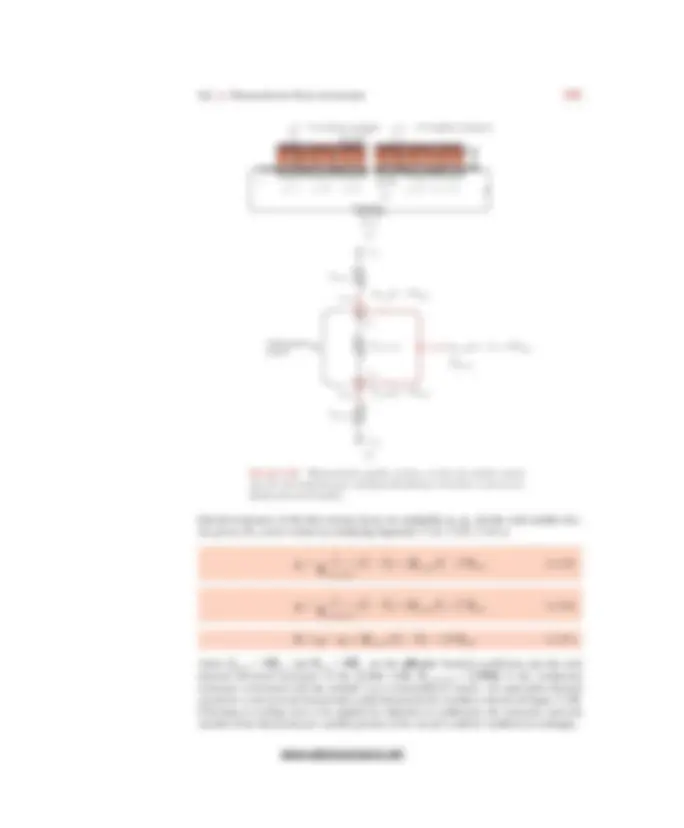
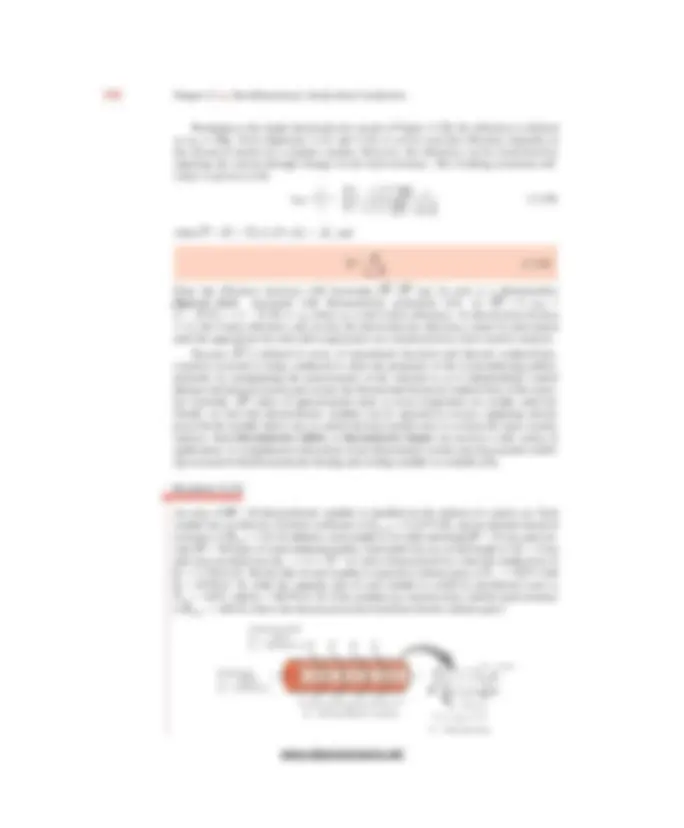
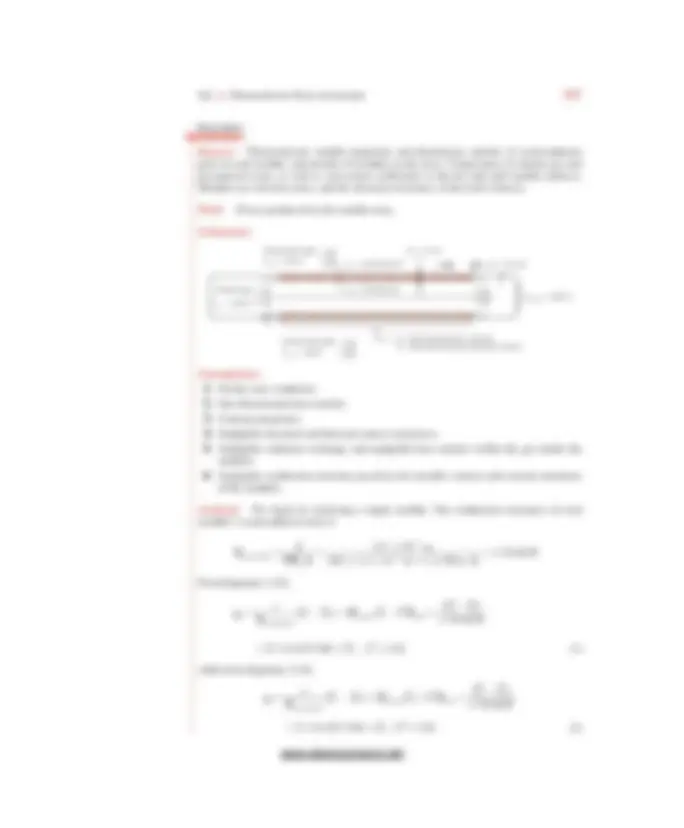
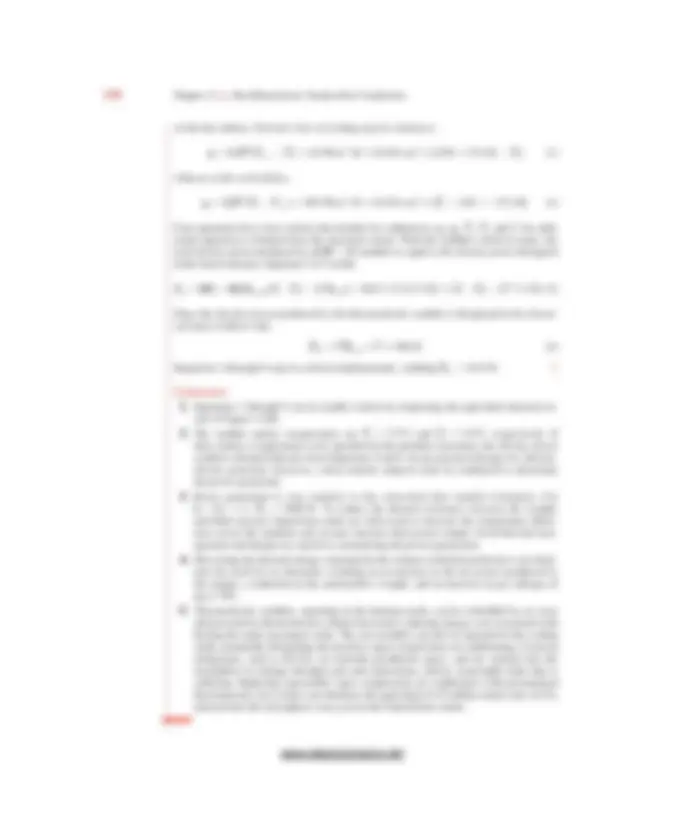
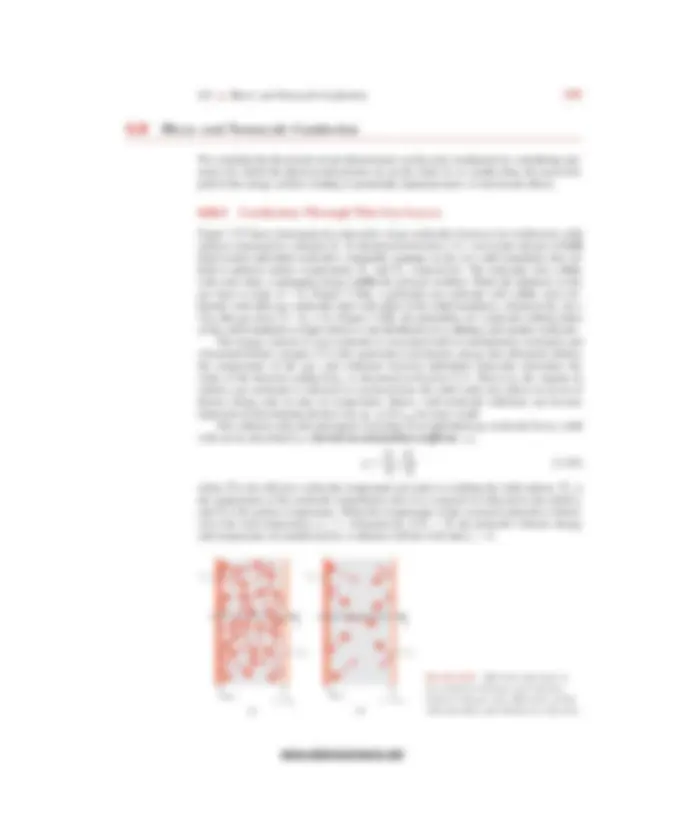
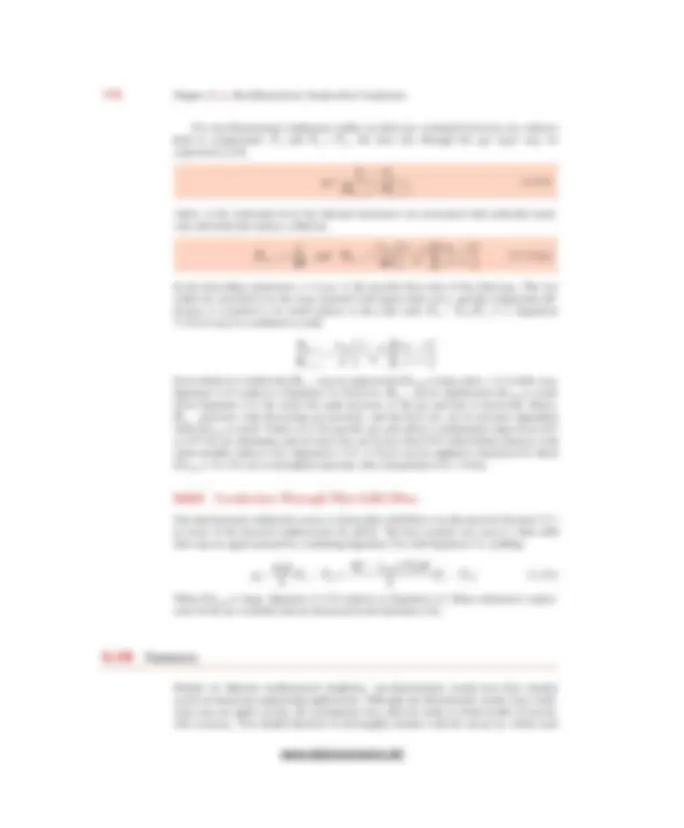
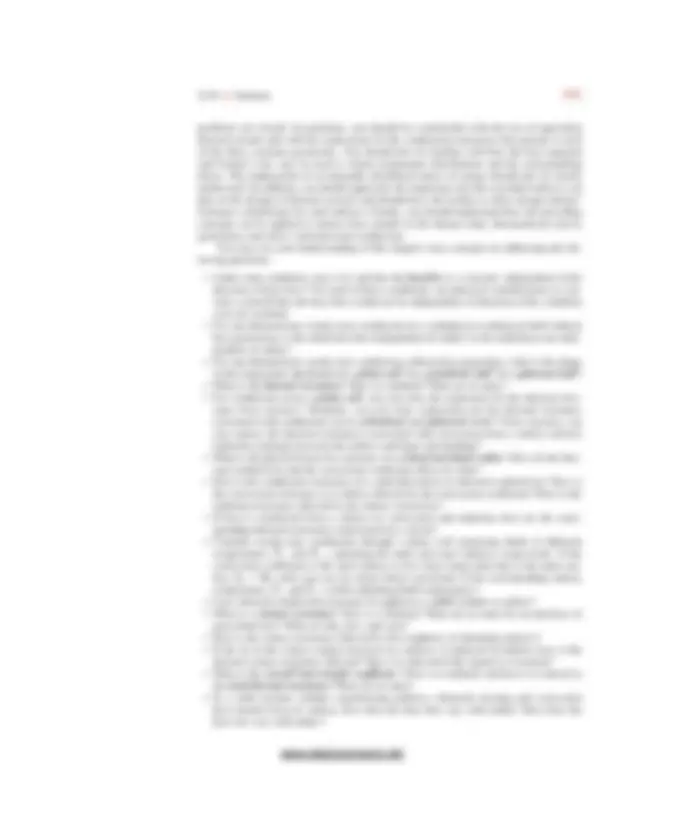
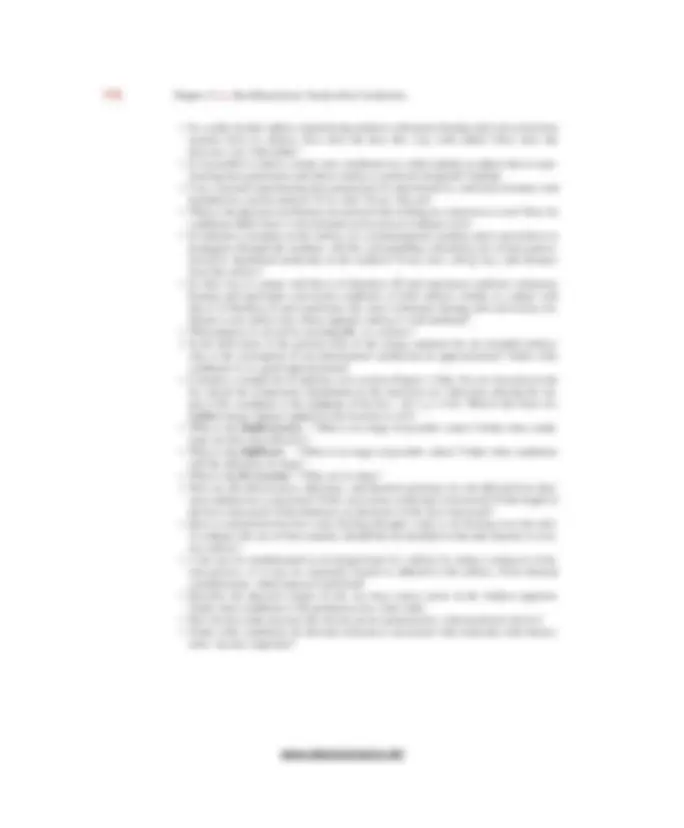
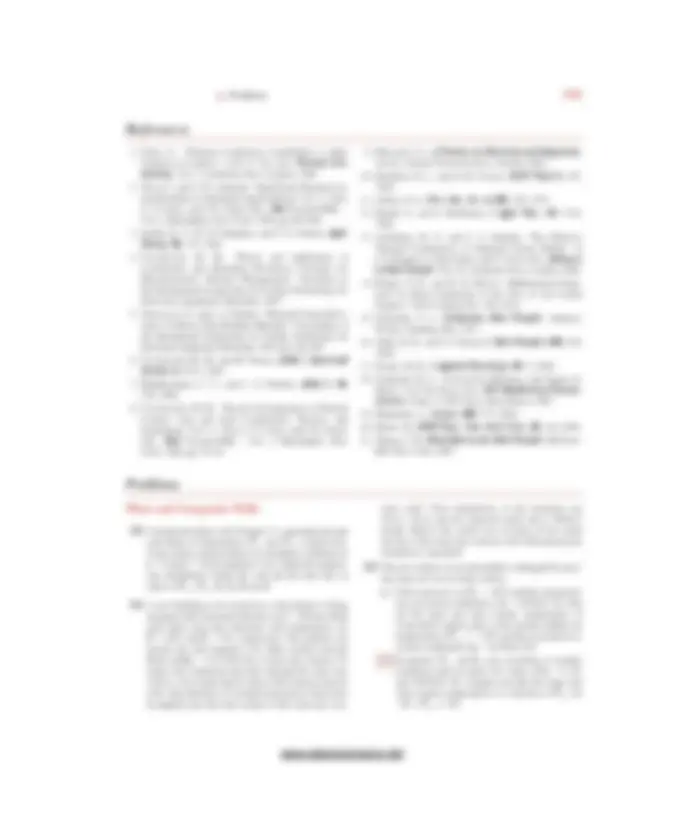
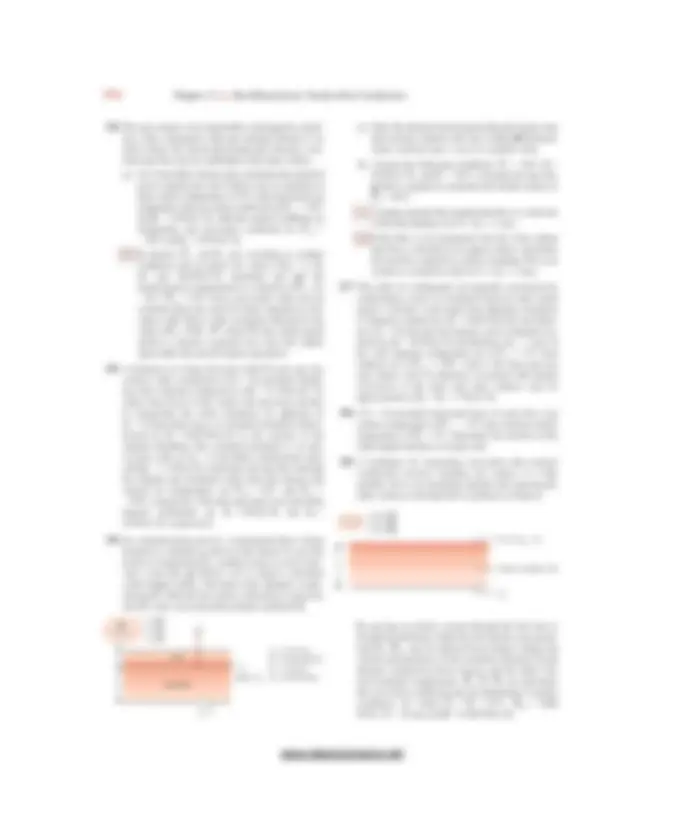
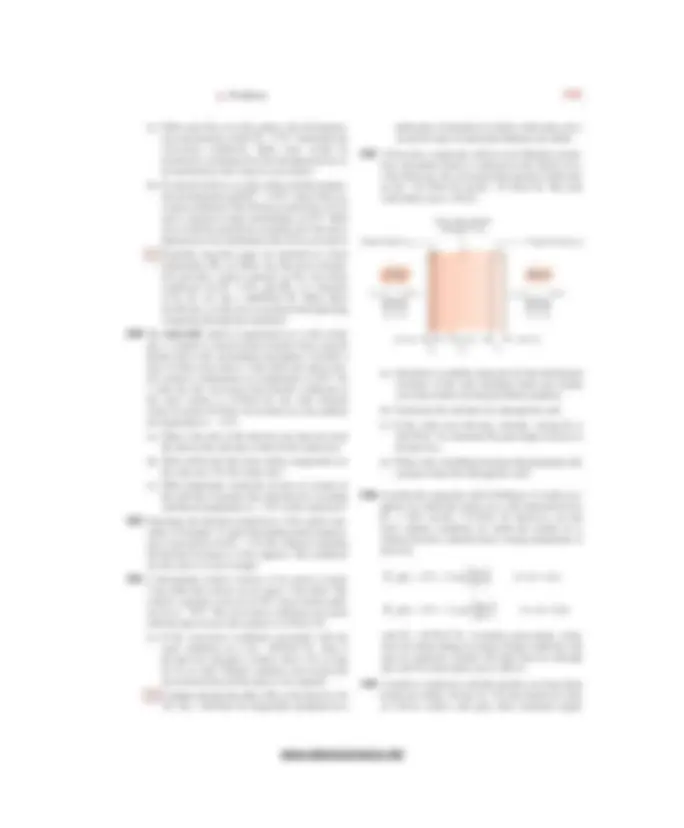
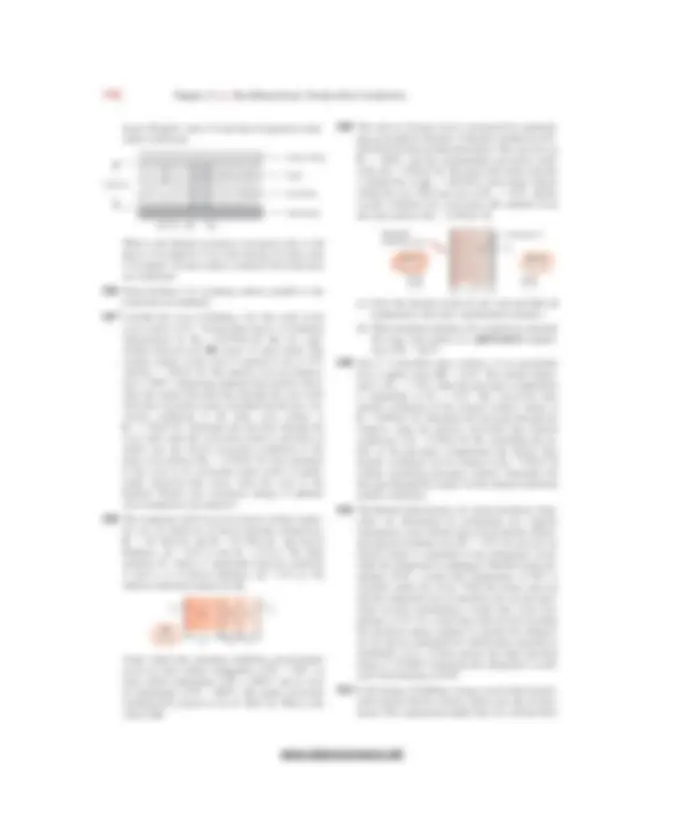
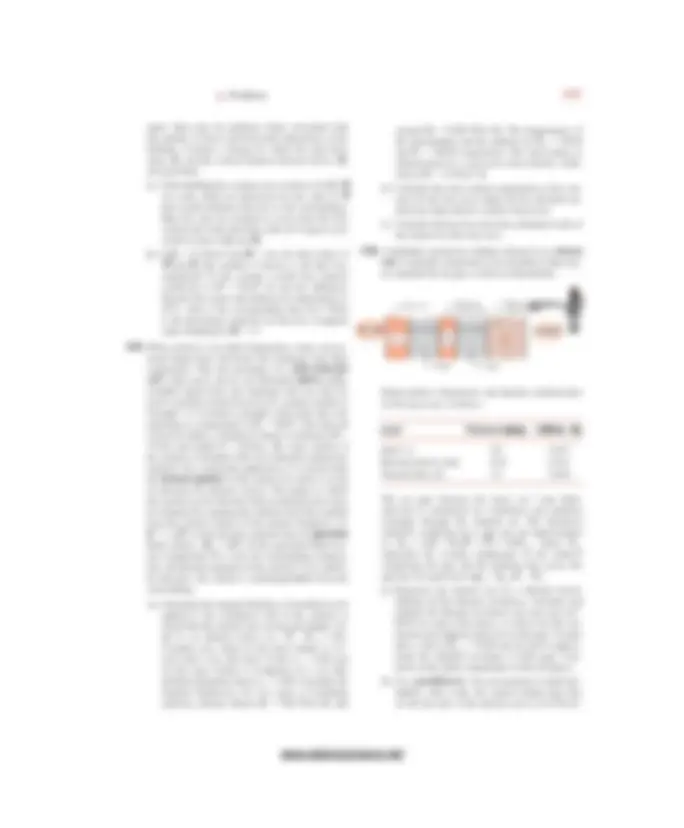
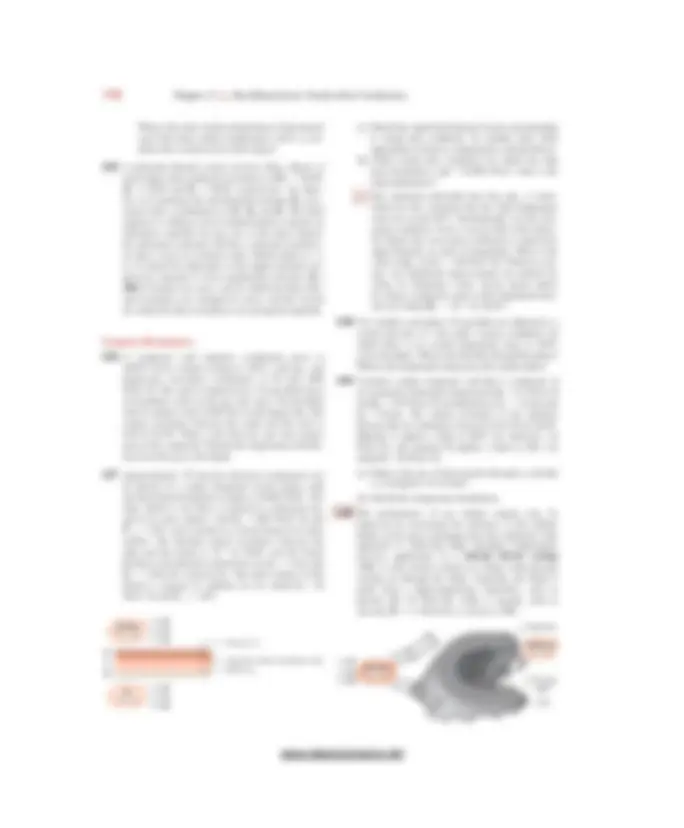
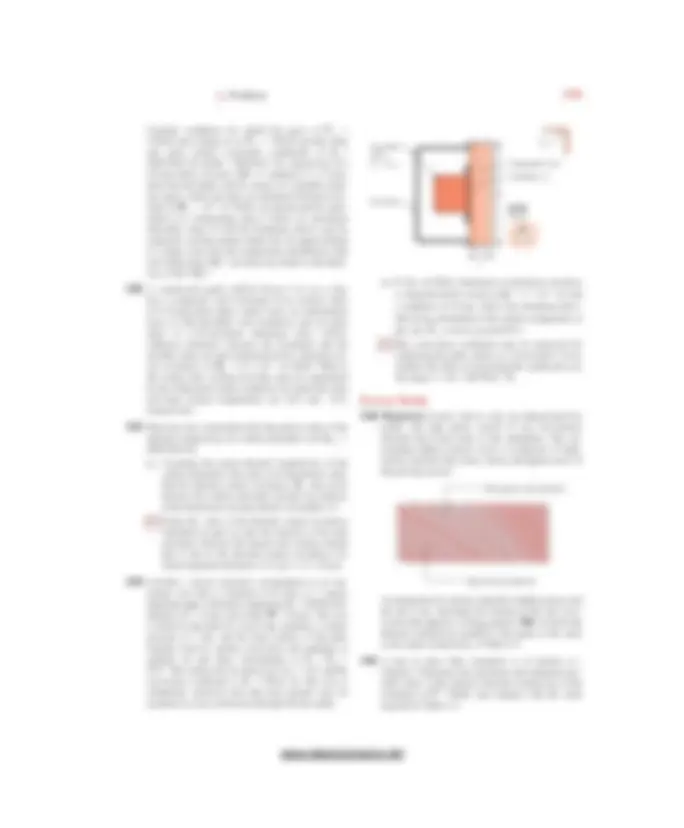
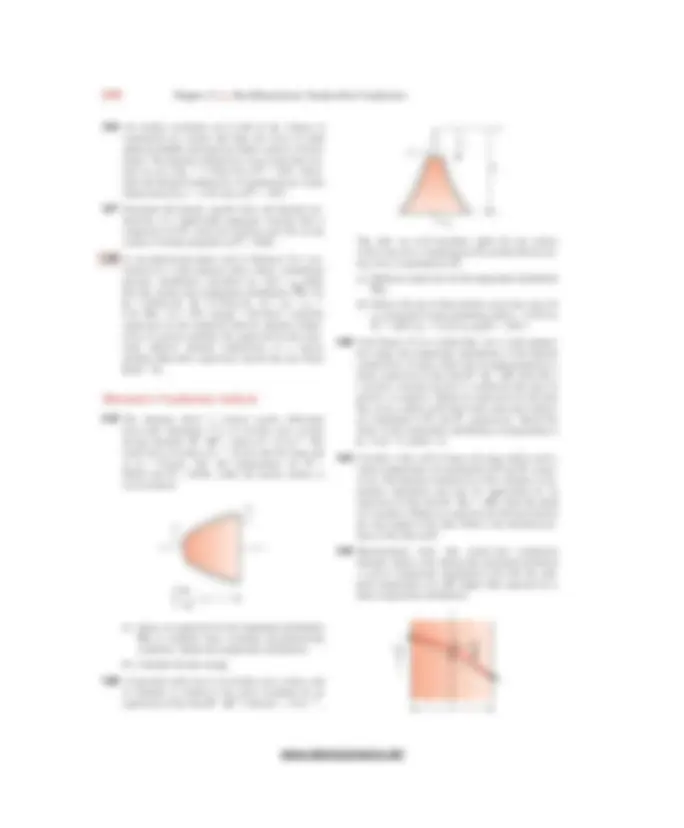
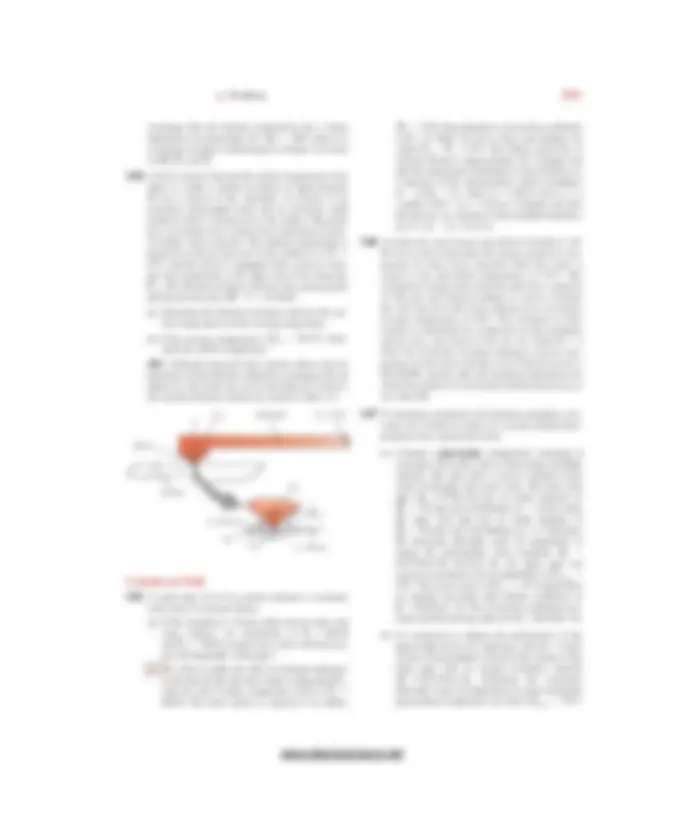
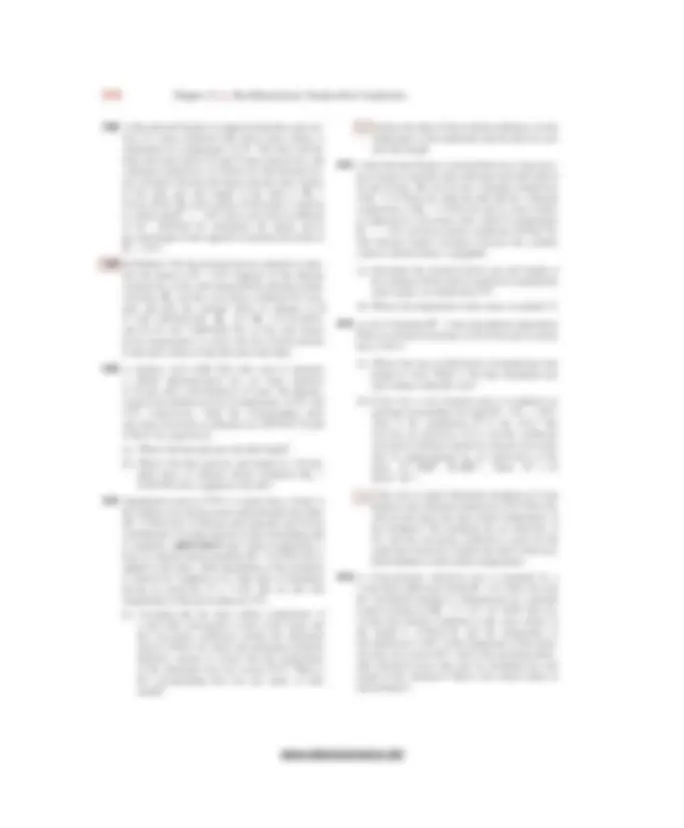
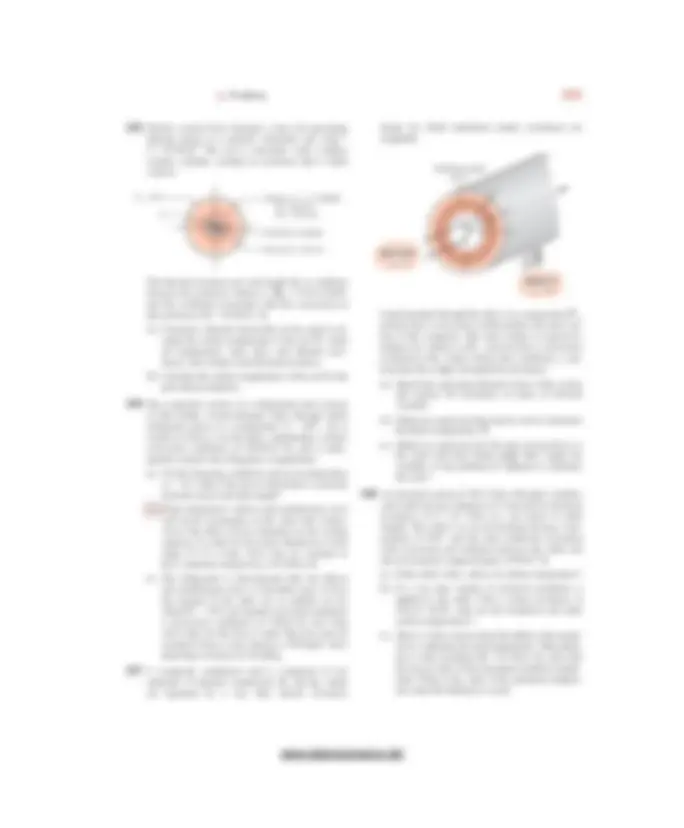
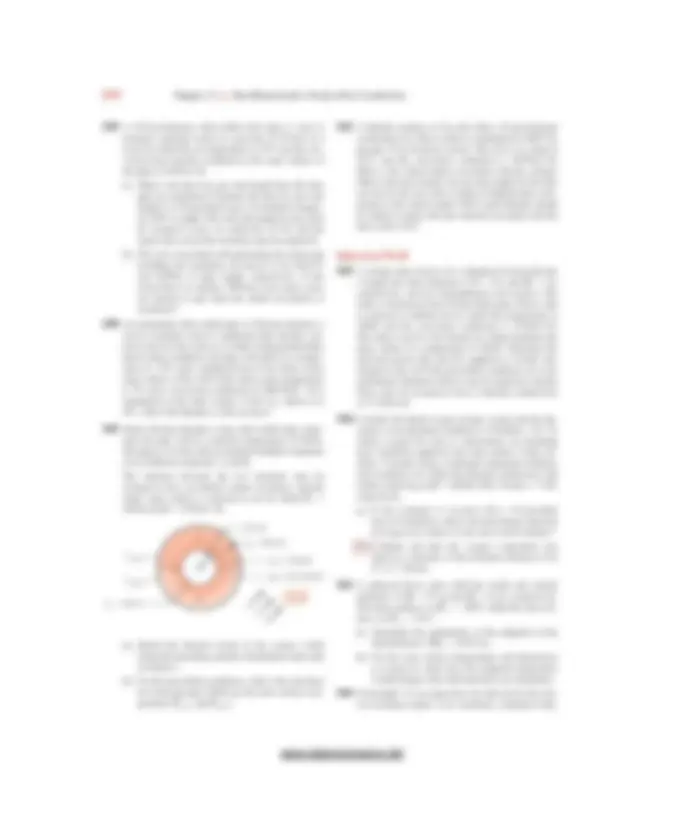
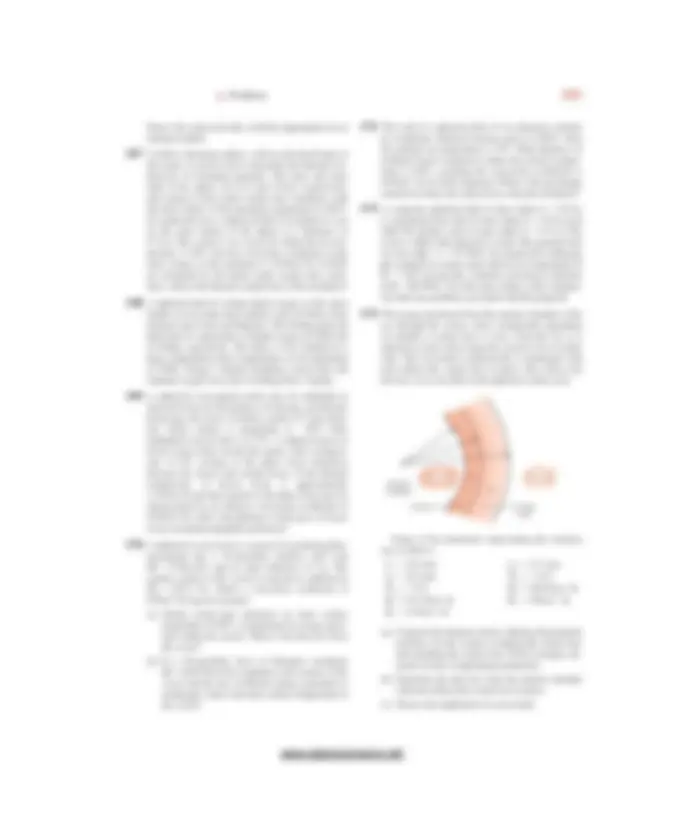
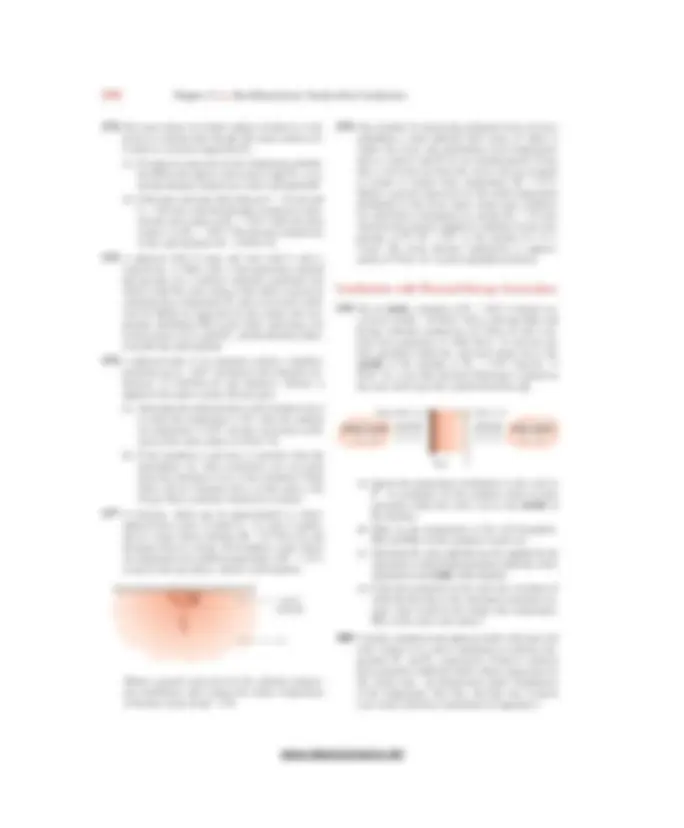
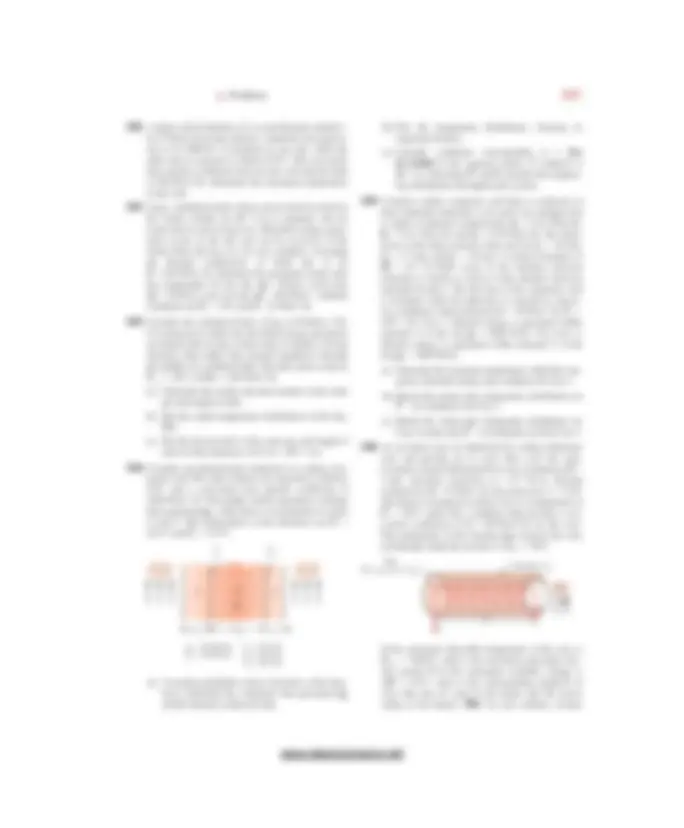
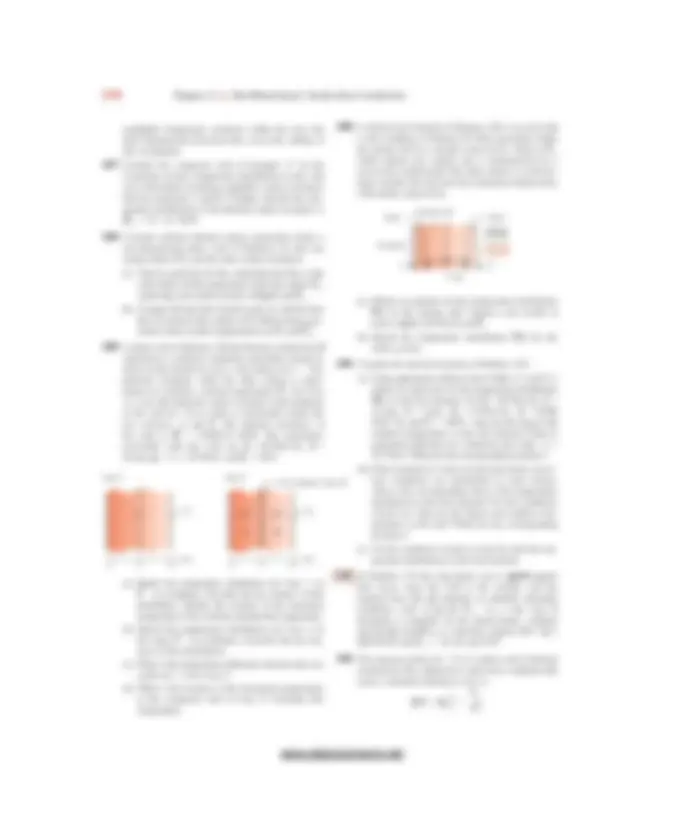
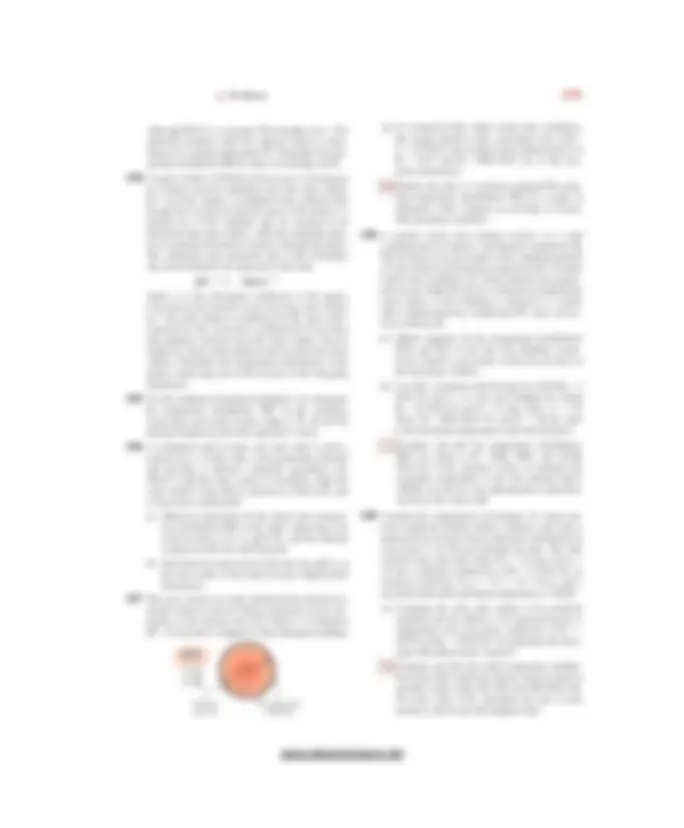
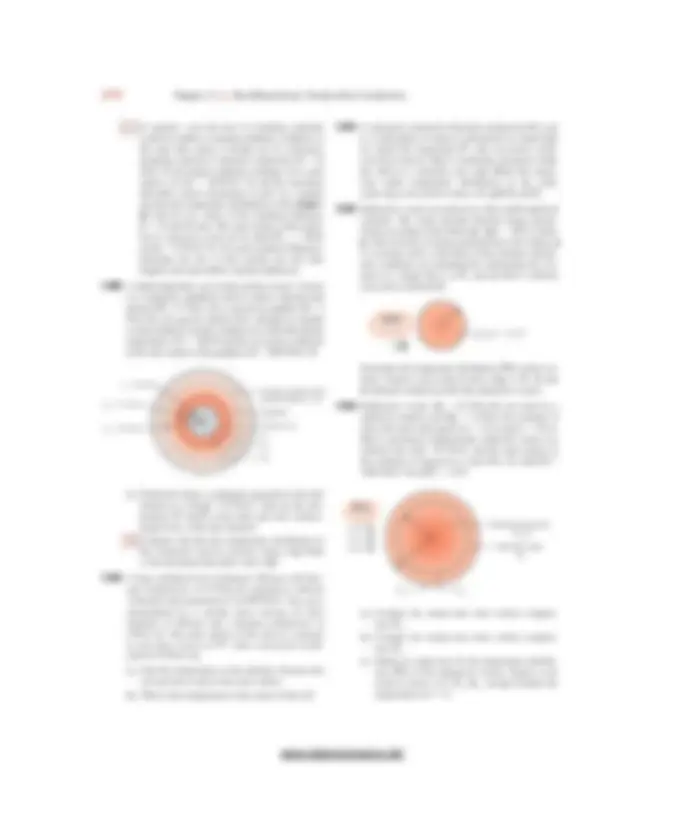
Prepara tus exámenes y mejora tus resultados gracias a la gran cantidad de recursos disponibles en Docsity
Gana puntos ayudando a otros estudiantes o consíguelos activando un Plan Premium
Prepara tus exámenes
Prepara tus exámenes y mejora tus resultados gracias a la gran cantidad de recursos disponibles en Docsity
Prepara tus exámenes con los documentos que comparten otros estudiantes como tú en Docsity
Los mejores documentos en venta realizados por estudiantes que han terminado sus estudios
Estudia con lecciones y exámenes resueltos basados en los programas académicos de las mejores universidades
Responde a preguntas de exámenes reales y pon a prueba tu preparación
Consigue puntos base para descargar
Gana puntos ayudando a otros estudiantes o consíguelos activando un Plan Premium
Comunidad
Pide ayuda a la comunidad y resuelve tus dudas de estudio
Descubre las mejores universidades de tu país según los usuarios de Docsity
Ebooks gratuitos
Descarga nuestras guías gratuitas sobre técnicas de estudio, métodos para controlar la ansiedad y consejos para la tesis preparadas por los tutores de Docsity
traducción capitulo 3 libro transferencia
Tipo: Resúmenes
1 / 121
Esta página no es visible en la vista previa
¡No te pierdas las partes importantes!
Steady-State
Conduction
112 Chapter 3 One-Dimensional, Steady-State Conduction
I n this chapter we treat situations for which heat is transferred by diffusion under one- dimensional, steady-state conditions. The term one-dimensional refers to the fact that only one coordinate is needed to describe the spatial variation of the dependent variables. Hence, in a one-dimensional system, temperature gradients exist along only a single coordinate direction, and heat transfer occurs exclusively in that direction. The system is characterized by steady-state conditions if the temperature at each point is independent of time. Despite their inherent simplicity, one-dimensional, steady-state models may be used to accurately represent numerous engineering systems. We begin our consideration of one-dimensional, steady-state conduction by discussing heat transfer with no internal generation of thermal energy (Sections 3.1 through 3.4). The objective is to determine expressions for the temperature distribution and heat transfer rate in common (planar, cylindrical, and spherical) geometries. For such geometries, an addi- tional objective is to introduce the concept of thermal resistance and to show how thermal circuits may be used to model heat flow, much as electrical circuits are used for current flow. The effect of internal heat generation is treated in Section 3.5, and again our objective is to obtain expressions for determining temperature distributions and heat transfer rates. In Section 3.6, we consider the special case of one-dimensional, steady-state conduction for extended surfaces. In their most common form, these surfaces are termed fin and are used to enhance heat transfer by convection to an adjoining fluid. In addition to determining related temperature distributions and heat rates, our objective is to introduce performance parameters that may be used to determine their efficacy. Finally, in Sections 3.7 through 3.9 we apply heat transfer and thermal resistance concepts to the human body, including the effects of metabolic heat generation and perfusion ; to thermoelectric power generation driven by the Seebeck effect ; and to micro- and nanoscale conduction in thin gas layers and thin solid film.
For one-dimensional conduction in a plane wall, temperature is a function of the x -coordinate only and heat is transferred exclusively in this direction. In Figure 3.1 a , a plane wall sepa- rates two fluids of different temperatures. Heat transfer occurs by convection from the hot fluid at T ,1 to one surface of the wall at T (^) s ,1, by conduction through the wall, and by con- vection from the other surface of the wall at Ts ,2 to the cold fluid at T ,2. We begin by considering conditions within the wall. We first determine the temperature distribution, from which we can then obtain the conduction heat transfer rate.
The temperature distribution in the wall can be determined by solving the heat equation with the proper boundary conditions. For steady-state conditions with no distributed source or sink of energy within the wall, the appropriate form of the heat equation is Equation 2.
d (3.1) dx
k dT dx
From this result it is evident that, for one-dimensional, steady-state conduction in a plane wall with no heat generation and constant thermal conductivity, the temperature varies linearly with x. Now that we have the temperature distribution, we may use Fourier’s law, Equation 2.1, to determine the conduction heat transfer rate. That is,
Note that A is the area of the wall normal to the direction of heat transfer and, for the plane wall, it is a constant independent of x. The heat flux is then
Equations 3.4 and 3.5 indicate that both the heat rate q (^) x and heat flux q x are constants, inde- pendent of x. In the foregoing paragraphs we have used the standard approach to solving conduc- tion problems. That is, the general solution for the temperature distribution is first obtained by solving the appropriate form of the heat equation. The boundary conditions are then applied to obtain the particular solution, which is used with Fourier’s law to determine the heat transfer rate. Note that we have opted to prescribe surface temperatures at x 0 and x L as boundary conditions, even though it is the fluid temperatures, not the surface temperatures, that are typically known. However, since adjoining fluid and surface temperatures are easily related through a surface energy balance (see Section 1.3.1), it is a simple matter to express Equations 3.3 through 3.5 in terms of fluid, rather than surface, temperatures. Alternatively, equivalent results could be obtained directly by using the sur- face energy balances as boundary conditions of the third kind in evaluating the constants of Equation 3.2 (see Problem 3.1).
At this point we note that, for the special case of one-dimensional heat transfer with no internal energy generation and with constant properties, a very important concept is sug- gested by Equation 3.4. In particular, an analogy exists between the diffusion of heat and electrical charge. Just as an electrical resistance is associated with the conduction of elec- tricity, a thermal resistance may be associated with the conduction of heat. Defining resis- tance as the ratio of a driving potential to the corresponding transfer rate, it follows from Equation 3.4 that the thermal resistance for conduction in a plane wall is
Similarly, for electrical conduction in the same system, Ohm’s law provides an electrical resistance of the form
R (^) e (3.7)
Es ,1 Es , I
Rt ,cond
Ts ,1 Ts , qx ^
kA
q x
qx A
k L
( Ts ,1 Ts ,2)
q (^) x kA dT dx
kA L
( T (^) s ,1 Ts ,2)
114 Chapter 3 One-Dimensional, Steady-State Conduction
The analogy between Equations 3.6 and 3.7 is obvious. A thermal resistance may also be associated with heat transfer by convection at a surface. From Newton’s law of cooling,
(3.8)
The thermal resistance for convection is then
Circuit representations provide a useful tool for both conceptualizing and quantifying heat transfer problems. The equivalent thermal circuit for the plane wall with convection surface conditions is shown in Figure 3.1 b. The heat transfer rate may be determined from separate consideration of each element in the network. Since qx is constant throughout the network, it follows that
In terms of the overall temperature difference , T ,1 T ,2, and the total thermal resistance , R tot , the heat transfer rate may also be expressed as
Because the conduction and convection resistances are in series and may be summed, it follows that
Radiation exchange between the surface and surroundings may also be important if the convection heat transfer coefficient is small (as it often is for natural convection in a gas). A thermal resistance for radiation may be defined by reference to Equation 1.8:
For radiation between a surface and large surroundings , hr is determined from Equation 1.9. Surface radiation and convection resistances act in parallel, and if T T sur, they may be combined to obtain a single, effective surface resistance.
Equivalent thermal circuits may also be used for more complex systems, such as composite walls. Such walls may involve any number of series and parallel thermal resistances due to layers of different materials. Consider the series composite wall of Figure 3.2. The one- dimensional heat transfer rate for this system may be expressed as
qx (3.14)
Rt
Rt ,rad
Ts T sur q rad ^
hr A
R tot 1 h 1 A
kA
h 2 A
q (^) x
R tot
qx
T ,1 Ts , 1/ h 1 A
T (^) s ,1 Ts , L / kA
T (^) s ,2 T , 1/ h 2 A
Rt ,conv
Ts T q ^
hA
q hA ( Ts T )
3.1 The Plane Wall 115
Composite walls may also be characterized by series–parallel configurations, such as that shown in Figure 3.3. Although the heat flow is now multidimensional, it is often reason- able to assume one-dimensional conditions. Subject to this assumption, two different thermal circuits may be used. For case ( a ) it is presumed that surfaces normal to the x -direction are isothermal, whereas for case ( b ) it is assumed that surfaces parallel to the x -direction are adiabatic. Different results are obtained for R tot , and the corresponding values of q bracket the actual heat transfer rate. These differences increase with increasing k F k G, as multidimensional effects become more significant.
Although neglected until now, it is important to recognize that, in composite systems, the temperature drop across the interface between materials may be appreciable. This tempera- ture change is attributed to what is known as the thermal contact resistance , R (^) t,c. The effect is shown in Figure 3.4, and for a unit area of the interface, the resistance is defined as
The existence of a finite contact resistance is due principally to surface roughness effects. Contact spots are interspersed with gaps that are, in most instances, air filled. Heat transfer is therefore due to conduction across the actual contact area and to conduction and/or radiation across the gaps. The contact resistance may be viewed as two parallel resistances: that due to
R t , c
q x
FIGURE 3.3 Equivalent thermal circuits for a series–parallel composite wall.
____^ L E k E A
____ L H k H A
L E L F = L G L H
k E k H E H
k G G
k F T 1
x
T 2
Area, A
qx (^) ________ L G k G( A /2)
________^ L F k F( A /2)
T 1 T 2
________^ L E k E( A /2)
________^ L H k H( A /2)
qx (^) ________ L G k G( A /2)
________^ L F k F( A /2)
T 1 T 2
( a )
________^ L E k E( A /2)
________^ L H k H( A /2)
( b )
F
3.1 The Plane Wall 117
the contact spots and that due to the gaps. The contact area is typically small, and, especially for rough surfaces, the major contribution to the resistance is made by the gaps. For solids whose thermal conductivities exceed that of the interfacial fluid, the contact resistance may be reduced by increasing the area of the contact spots. Such an increase may be effected by increasing the joint pressure and/or by reducing the roughness of the mating surfaces. The contact resistance may also be reduced by selecting an interfacial fluid of large thermal conductivity. In this respect, no fluid (an evacuated interface) eliminates con- duction across the gap, thereby increasing the contact resistance. Likewise, if the character- istic gap width L becomes small (as, for example, in the case of very smooth surfaces in contact), L / mfp can approach values for which the thermal conductivity of the interfacial gas is reduced by microscale effects, as discussed in Section 2.2. Although theories have been developed for predicting Rt,c , the most reliable results are those that have been obtained experimentally. The effect of loading on metallic interfaces can be seen in Table 3.1 a , which presents an approximate range of thermal resistances under vacuum conditions. The effect of interfacial fluid on the thermal resistance of an alu- minum interface is shown in Table 3.1 b. Contrary to the results of Table 3.1, many applications involve contact between dissimi- lar solids and/or a wide range of possible interstitial (filler) materials (Table 3.2). Any intersti- tial substance that fills the gap between contacting surfaces and whose thermal conductivity exceeds that of air will decrease the contact resistance. Two classes of materials that are well suited for this purpose are soft metals and thermal greases. The metals, which include
118 Chapter 3 One-Dimensional, Steady-State Conduction
FIGURE 3.4 Temperature drop due to thermal contact resistance.
q g " ap
q c " ontact
qx"
A B
qx" (^) T A
T B
A B
∆ T
T
x
TABLE 3.1 Thermal contact resistance for ( a ) metallic interfaces under vacuum conditions and ( b ) aluminum interface (10- m surface roughness, 10^5 N/m^2 ) with different interfacial fluids [1]
Thermal Resistance, R t , c 104 (m^2 K/W)
( a ) Vacuum Interface ( b ) Interfacial Fluid Contact pressure 100 kN/m 2 10,000 kN/m^2 Air 2. Stainless steel 6–25 0.7–4.0 Helium 1. Copper 1–10 0.1–0.5 Hydrogen 0. Magnesium 1.5–3.5 0.2–0.4 Silicone oil 0. Aluminum 1.5–5.0 0.2–0.4 Glycerine 0.
where k eff is an effective thermal conductivity. Equation 3.21 is valid if fluid motion, as well as radiation heat transfer within the medium, are negligible. The effective thermal con- ductivity varies with the porosity or void fraction of the medium which is defined as the volume of fluid relative to the total volume (solid and fluid). In addition, k eff depends on the thermal conductivities of each of the phases and, in this discussion, it is assumed that ks kf. The detailed solid phase geometry, for example the size distribution and packing arrangement of individual powder particles, also affects the value of k eff. Contact resis- tances that might evolve at interfaces between adjacent solid particles can impact the value of k eff. As discussed in Section 2.2.1, nanoscale phenomena might also influence the effec- tive thermal conductivity. Hence, prediction of k eff can be difficult and, in general, requires detailed knowledge of parameters that might not be readily available. Despite the complexity of the situation, the value of the effective thermal conductivity may be bracketed by considering the composite walls of Figures 3.5 b and 3.5 c. In Figure 3.5 b , the medium is modeled as an equivalent, series composite wall consisting of a fluid region of length L and a solid region of length (1 – ) L. Applying Equations 3.17 and 3.18 to this model for which there is no convection ( h 1 h 2 0) and only two conduction terms, it follows that
(3.22)
Equating this result to Equation 3.21, we then obtain
Alternatively, the medium of Figure 3.5 a could be described by the equivalent, parallel com- posite wall consisting of a fluid region of width w and a solid region of width (1 – ) w , as shown in Figure 3.5 c. Combining Equation 3.21 with an expression for the equivalent resistance of two resistors in parallel gives
k eff,max kf (1 ) ks (3.24)
k eff,min 1 (1 )/ ks / kf
qx A^ T (1 ) L / ks L / kf
120 Chapter 3 One-Dimensional, Steady-State Conduction
FIGURE 3.5 A porous medium. ( a ) The medium and its properties. ( b ) Series thermal resistance representation. ( c ) Parallel resistance representation.
L
A
L
T 2
T 1
x x x
( a )
ks
(1 − ) L
T 2
T 1
qx
( b )
kf ks
L
T 2
T 1 qx.s
( c )
kf
L
(1 − ) w
q (^) x.f
, ks , kf , k eff
qx
w
qx T^1 T^2 T 2 (1 − ) L ks A
L k (^) f A
qx T 1 T 2 L k eff A
qx T^1
L k (^) s (1 − ) A
L kf A
w
Area A Area A Area A
While Equations 3.23 and 3.24 provide the minimum and maximum possible values of k eff, more accurate expressions have been derived for specific composite systems within which nanoscale effects are negligible. Maxwell [9] derived an expression for the effective electrical conductivity of a solid matrix interspersed with uniformly distributed, noncon- tacting spherical inclusions. Noting the analogy between Equations 3.6 and 3.7, Maxwell’s result may be used to determine the effective thermal conductivity of a saturated porous medium consisting of an interconnected solid phase within which a dilute distribution of spherical fluid regions exists, resulting in an expression of the form [10]
Equation 3.25 is valid for relatively small porosities ( 0.25) as shown schematically in Figure 3.5 a [11]. It is equivalent to the expression introduced in Example 2.2 for a fluid that contains a dilute mixture of solid particles, but with reversal of the fluid and solid. When analyzing conduction within porous media, it is important to consider the poten- tial directional dependence of the effective thermal conductivity. For example, the media represented in Figure 3.5 b or Figure 3.5 c would not be characterized by isotropic proper- ties, since the effective thermal conductivity in the x -direction is clearly different from val- ues of k eff in the vertical direction. Hence, although Equations 3.23 and 3.24 can be used to bracket the actual value of the effective thermal conductivity, they will generally overpre- dict the possible range of k eff for isotropic media. For isotropic media, expressions have been developed to determine the minimum and maximum possible effective thermal con- ductivities based solely on knowledge of the porosity and the thermal conductivities of the solid and fluid. Specifically, the maximum possible value of k eff in an isotropic porous medium is given by Equation 3.25, which corresponds to an interconnected, high thermal conductivity solid phase. The minimum possible value of k eff for an isotropic medium corre- sponds to the case where the fluid phase forms long, randomly oriented fingers within the medium [12]. Additional information regarding conduction in saturated porous media is available [13].
In Example 1.7, we calculated the heat loss rate from a human body in air and water envi- ronments. Now we consider the same conditions except that the surroundings (air or water) are at 10 C. To reduce the heat loss rate, the person wears special sporting gear (snow suit and wet suit) made from a nanostructured silica aerogel insulation with an extremely low thermal conductivity of 0.014 W/m K. The emissivity of the outer surface of the snow and wet suits is 0.95. What thickness of aerogel insulation is needed to reduce the heat loss rate to 100 W (a typical metabolic heat generation rate) in air and water? What are the resulting skin temperatures?
SOLUTION
Known: Inner surface temperature of a skin/fat layer of known thickness, thermal con- ductivity, and surface area. Thermal conductivity and emissivity of snow and wet suits. Ambient conditions.
k eff (^)
kf 2 ks 2 ( ks kf ) kf 2 ks ( ks kf )
ks
3.1 The Plane Wall 121
effective resistance associated with convection and radiation, which act in parallel. Hence,
This equation can be solved for the insulation thickness.
Air The radiation heat transfer coefficient is approximated as having the same value as in Example 1.7: h (^) r = 5.9 W/m 2 K.
Water
These required thicknesses of insulation material can easily be incorporated into the snow and wet suits. The skin temperature can be calculated by considering conduction through the skin/fat layer:
or solving for T (^) s ,
The skin temperature is the same in both cases because the heat loss rate and skin/fat proper- ties are the same.
Comments:
1. The nanostructured silica aerogel is a porous material that is only about 5% solid. Its thermal conductivity is less than the thermal conductivity of the gas that fills its pores. As explained in Section 2.2, the reason for this seemingly impossible result is that the pore size is only around 20 nm, which reduces the mean free path of the gas and hence decreases its thermal conductivity.
Ts Ti
qL sf k sf A
(^3) m 0.3 W/m K 1.8 m^2
q
k sf A ( Ti Ts ) L sf
0.0061 m 6.1 mm
0.014 W/m K1.8 m 2 0.25 K/W 3 10
(^3) m 0.3 W/m K
200 W/m^2 K
L ins k ins AR tot
L sf k sf
h
0.0044 m 4.4 mm
0.014 W/m K1.8 m^2 0.25 K/W 3 10 ^3 m 0.3 W/m K
(2 5.9) W/m^2 K
L ins k ins AR tot
L sf k sf
h hr
R tot
L sf k sf A
L ins k ins A
(^) 1 1/ hA
1/ hr A
1 1 A
L sf k sf
L ins k ins
h hr
3.1 The Plane Wall 123
2. By reducing the heat loss rate to 100 W, a person could remain in the cold environ- ments indefinitely without becoming chilled. The skin temperature of 34.4 C would feel comfortable. 3. In the water case, the thermal resistance of the insulation dominates and all other resis- tances can be neglected. 4. The convection heat transfer coefficient associated with the air depends on the wind conditions, and it can vary over a broad range. As it changes, so will the outer surface temperature of the insulation layer. Since the radiation heat transfer coefficient depends on this temperature, it will also vary. We can perform a more complete analysis that takes this into account. The radiation heat transfer coefficient is given by Equation 1.9:
(1)
Here Ts,o is the outer surface temperature of the insulation layer, which can be calcu- lated from
Since this depends on the insulation thickness, we also need the previous equation for L ins:
With all other values known, these three equations can be solved for the required insulation thickness. Using all the values from above, these equations have been solved for values of h in the range 0 h 100 W/m 2 K, and the results are repre- sented graphically.
Increasing h reduces the corresponding convection resistance, which then requires additional insulation to maintain the heat transfer rate at 100 W. Once the heat transfer coefficient exceeds approximately 60 W/m^2 K, the convection resistance is negligible and further increases in h have little effect on the required insulation thickness.
7 6 5 4 3 0
h (W/m^2 •K)
L ins
(mm)
10 20 30 40 50 60 70 80 90 100
L ins k ins AR tot
L sf k sf
h hr
Ts , o Ti q
L sf k sf A
L ins k ins A
hr ( Ts , o T sur)( Ts^2 , o^ T sur^2 )
124 Chapter 3 One-Dimensional, Steady-State Conduction
Properties: Table A.1, pure aluminum ( T 350 K): k 239 W/m K.
Analysis: Heat dissipated in the chip is transferred to the air directly from the exposed surface and indirectly through the joint and substrate. Performing an energy balance on a control surface about the chip, it follows that, on the basis of a unit surface area,
or
To conservatively estimate T (^) c , the maximum possible value of 0.9 10 ^4 m^2 K/W is obtained from Table 3.2. Hence
or
Hence the chip will operate below its maximum allowable temperature.
Comments:
1. The joint and substrate thermal resistances are much less than the convection resistance. The joint resistance would have to increase to the unrealistically large value of 50 10 ^4 m^2 K/W, before the maximum allowable chip temperature would be exceeded. 2. The allowable power dissipation may be increased by increasing the convection coeffi- cients, either by increasing the air velocity and/or by replacing the air with a more effective heat transfer fluid. Exploring this option for 100 h 2000 W/m^2 K with Tc 85 C, the following results are obtained.
As h l , q 2 l 0 and virtually all of the chip power is transferred directly to the fluid stream.
q"c
× 10
(W/m
2 )
0 500 1000 1500 2000
0 h (W/m^2 • K)
Tc = 85°C
Tc 25 C 50.3 C 75.3 C
^100 ^
(0.9 0.33 100) 10 ^4
1 m^2 K/W
Tc 25 C 10 4 W/m^2
Tc T qc (^) h 1 R t , c ( L / k ) (1/ h )
1
R t , c
q c
Tc T (1/ h )
T (^) c T R t , c ( L / k ) (1/ h )
q c q 1 q 2
126 Chapter 3 One-Dimensional, Steady-State Conduction
3. As calculated, the difference between the air temperature ( T 25 C) and the chip temperature ( Tc 75.3 C) is 50.3 K. Keep in mind that this is a temperature difference and therefore is the same as 50.3 C. 4. Consider conditions for which airflow over the chip (upper) or substrate (lower) surface ceases due to a blockage in the air supply channel. If heat transfer from either surface is negligible, what are the resulting chip temperatures for? [Answer, 126 C or 125 C]
A photovoltaic panel consists of (top to bottom) a 3-mm-thick ceria-doped glass ( kg 1. W/m K), a 0.1-mm-thick optical grade adhesive ( ka 145 W/m K), a very thin layer of sili- con within which solar energy is converted to electrical energy, a 0.1-mm-thick solder layer ( k sdr 50 W/m K), and a 2-mm-thick aluminum nitride substrate ( k an 120 W/m K). The solar-to-electrical conversion efficiency within the silicon layer decreases with increasing silicon temperature, T si, and is described by the expression a – bT si, where a 0.553 and b 0.001 K^1. The temperature T is expressed in kelvins over the range 300 K T si 525 K. Of the incident solar irradiation, G 700 W/m^2 , 7% is reflected from the top surface of the glass, 10% is absorbed at the top surface of the glass, and 83% is transmitted to and absorbed within the silicon layer. Part of the solar irradiation absorbed in the silicon is con- verted to thermal energy, and the remainder is converted to electrical energy. The glass has an emissivity of 0.90, and the bottom as well as the sides of the panel are insulated. Determine the electric power P produced by an L 1-m-long, w 0.1-m-wide solar panel for conditions characterized by h 35 W/m^2 K and T T sur 20 C.
Known: Dimensions and materials of a photovoltaic solar panel. Material properties, solar irradiation, convection coefficient and ambient temperature, emissivity of top panel surface and surroundings temperature. Partitioning of the solar irradiation, and expression for the solar-to-electrical conversion efficiency.
Find: Electric power produced by the photovoltaic panel.
T ∞ = 20°C h = 35 W/m 2 •^ K
G = 700 W/m 2
Glass Adhesive
Solder
Electric power to grid, P
Substrate
Silicon layer Lg^ = 3 mm
L = 1 m
La = 0.1 mm
L an = 2 mm L sdr = 0.1 mm
Air T sur = 20 °C
q c 10 4 W/m 2
3.1 The Plane Wall 127
Finally, substituting known values into Equations 1 and 2 and solving simultaneously yields T si 307 K 34 C, providing a solar-to-electrical conversion efficiency of 0.553 – 0.001 K^1 307 K 0.247. Hence, the power produced by the photovoltaic panel is
Comments:
1. The correct application of the conservation of energy requirement is crucial to deter- mining the silicon temperature and the electric power. Note that solar energy is con- verted to both thermal and electrical energy, and the thermal circuit is used to quantify only the thermal energy transfer. 2. Because of the thermally insulated boundary condition, it is not necessary to include the solder or substrate layers in the analysis. This is because there is no conduction through these materials and, from Fourier’s law, there can be no temperature gradients within these materials. At steady state, T sdr T an T si. 3. As the convection coefficient increases, the temperature of the silicon decreases. This leads to a higher solar-to-electrical conversion efficiency and increased electric power output. Similarly, higher silicon temperatures and less power production are associated with smaller convection coefficients. For example, P 13.6 W and 14.6 W for h 15 W/m^2 K and 55 W/m 2 K, respectively. 4. The cost of a photovoltaic system can be reduced significantly by concentrating the solar energy onto the relatively expensive photovoltaic panel using inexpensive focus- ing mirrors or lenses. However, good thermal management then becomes even more important. For example, if the irradiation supplied to the panel were increased to G 7,000 W/m^2 through concentration, the conversion efficiency drops to 0. as the silicon temperature increases to T si 119 C, even for h 55 W/m^2 K. A key to reducing the cost of photovoltaic power generation is developing innovative cooling technologies for use in concentrating photovoltaic systems. 5. The simultaneous solution of Equations 1 and 2 may be achieved by using IHT , another commercial code, or a handheld calculator. A trial-and-error solution could also be obtained, but with considerable effort. Equations 1 and 2 could be combined to write a single transcendental expression for the silicon temperature, but the equation must still be solved numerically or by trial-and-error.
The thermal conductivity of a D 14-nm-diameter carbon nanotube is measured with an instrument that is fabricated of a wafer of silicon nitride at a temperature of T 300 K. The 20- m-long nanotube rests on two 0.5- m-thick, 10 m 10 m square islands that are separated by a distance s 5 m. A thin layer of platinum is used as an electrical resistor on the heated island (at temperature Th ) to dissipate q 11.3 W of electrical power. On the sensing island , a similar layer of platinum is used to determine its temperature, T (^) s. The plat- inum’s electrical resistance, R ( Ts ) E / I , is found by measuring the voltage drop and elec- trical current across the platinum layer. The temperature of the sensing island, Ts , is then determined from the relationship of the platinum electrical resistance to its temperature.
P 0.83 GLw 0.247 0.83 700 W/m 2 1 m 0.1 m 14.3 W
3.1 The Plane Wall 129
Each island is suspended by two L sn 250- m-long silicon nitride beams that are w sn 3 m wide and t sn 0.5 m thick. A platinum line of width w pt 1 m and thickness t pt 0.2 m is deposited within each silicon nitride beam to power the heated island or to detect the voltage drop associated with the determination of Ts. The entire experiment is performed in a vacuum with T sur 300 K and at steady state, Ts 308.4 K. Estimate the thermal con- ductivity of the carbon nanotube.
SOLUTION
Known: Dimensions, heat dissipated at the heated island, and temperatures of the sensing island and surrounding silicon nitride wafer.
Find: The thermal conductivity of the carbon nanotube.
Schematic:
Assumptions:
1. Steady-state conditions. 2. One-dimensional heat transfer. 3. The heated and sensing islands are isothermal. 4. Radiation exchange between the surfaces and the surroundings is negligible. 5. Negligible convection losses.
w sn = 3 μ m
D = 14 nm
Ts = 308.4 K
w pt = 1 μ m
s = 5 μ m
Sensing island
Carbon nanotube
Heated island
Heated island Th
Sensing island
T sur = 300 K
Silicon nitride block (^) T ∞ = 300 K
L sn = 250 μ m
t pt = 0.2 μ m
10 μ m 10 μ m
s = 5 μ m
t sn = 0.5 μ m
130 Chapter 3 One-Dimensional, Steady-State Conduction