
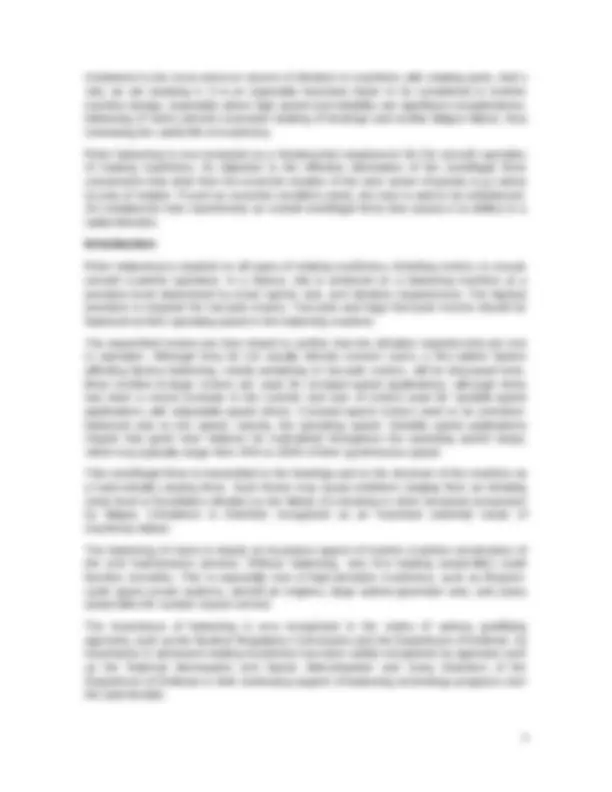
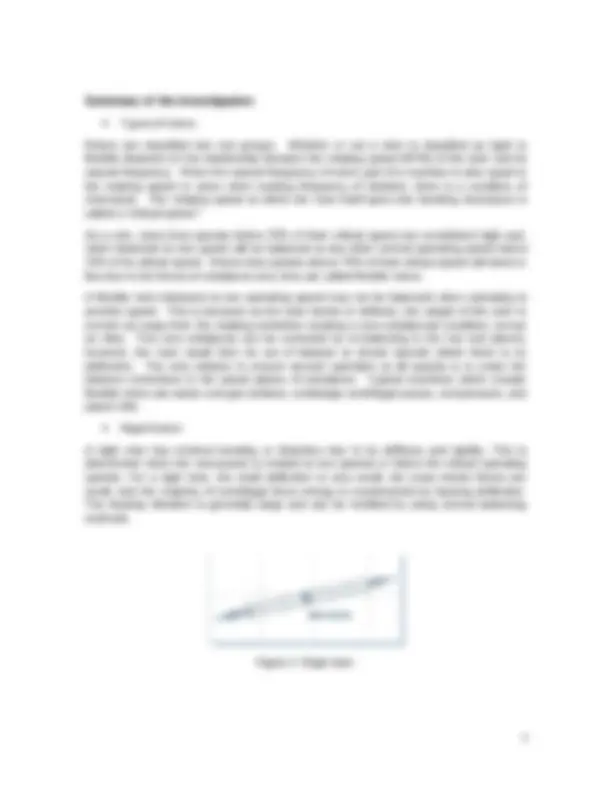
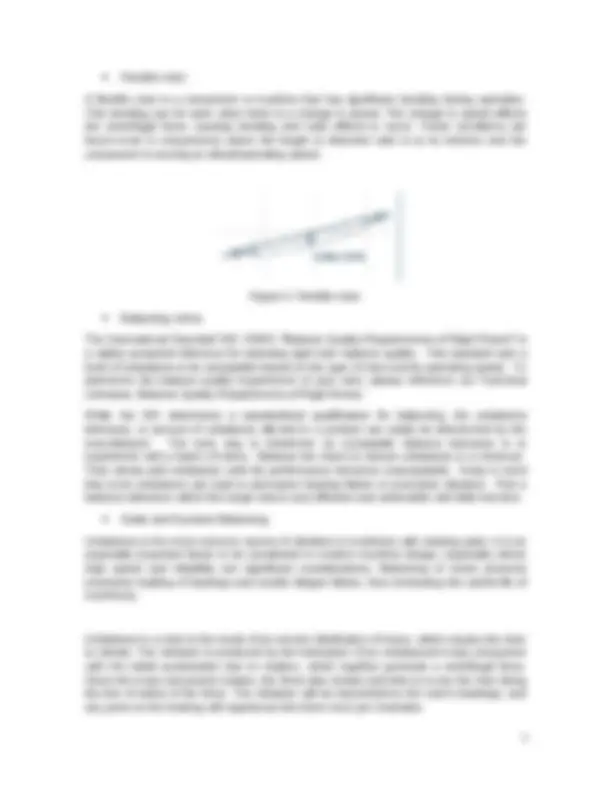
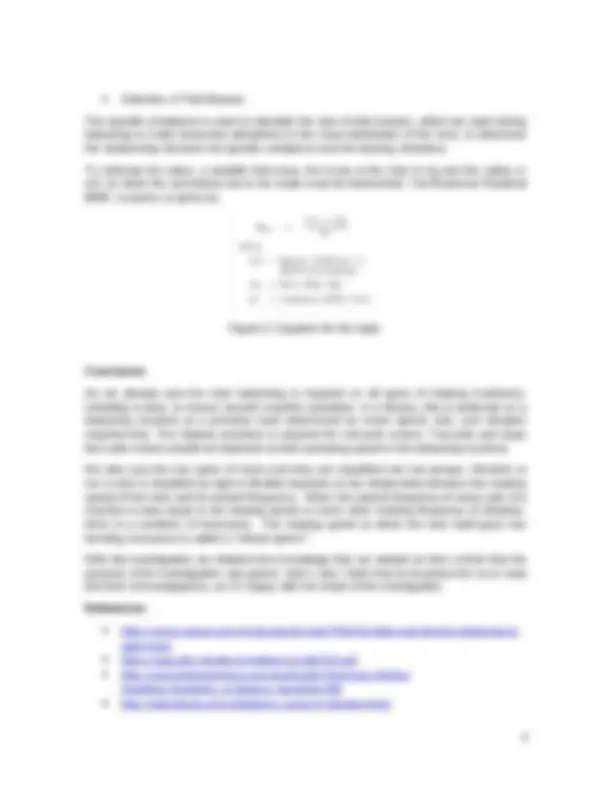
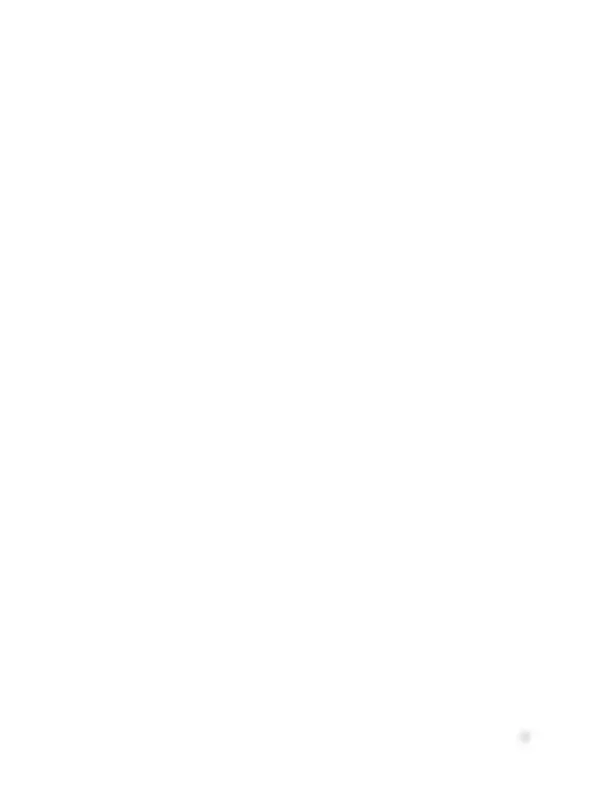
Prepara tus exámenes y mejora tus resultados gracias a la gran cantidad de recursos disponibles en Docsity
Gana puntos ayudando a otros estudiantes o consíguelos activando un Plan Premium
Prepara tus exámenes
Prepara tus exámenes y mejora tus resultados gracias a la gran cantidad de recursos disponibles en Docsity
Prepara tus exámenes con los documentos que comparten otros estudiantes como tú en Docsity
Los mejores documentos en venta realizados por estudiantes que han terminado sus estudios
Estudia con lecciones y exámenes resueltos basados en los programas académicos de las mejores universidades
Responde a preguntas de exámenes reales y pon a prueba tu preparación
Consigue puntos base para descargar
Gana puntos ayudando a otros estudiantes o consíguelos activando un Plan Premium
Comunidad
Pide ayuda a la comunidad y resuelve tus dudas de estudio
Descubre las mejores universidades de tu país según los usuarios de Docsity
Ebooks gratuitos
Descarga nuestras guías gratuitas sobre técnicas de estudio, métodos para controlar la ansiedad y consejos para la tesis preparadas por los tutores de Docsity
The importance of rotor balancing in mechanical vibrations, focusing on rigid and flexible rotors. Unbalance is the primary cause of vibration in rotating machinery, leading to issues such as excessive noise, foundation vibration, and even component failure. Balancing ensures smooth operation and extends machinery life. the concept of critical speed, balancing limits, static and dynamic balancing, and the selection of trial masses.
Tipo: Guías, Proyectos, Investigaciones
1 / 9
Esta página no es visible en la vista previa
¡No te pierdas las partes importantes!
Types of rotors: Rotors are classified into two groups. Whether or not a rotor is classified as rigid or flexible depends on the relationship between the rotating speed (RPM) of the rotor and its natural frequency. When the natural frequency of some part of a machine is also equal to the rotating speed or some other exciting frequency of vibration, there is a condition of resonance. The rotating speed at which the rotor itself goes into bending resonance is called a "critical speed." As a rule, rotors that operate below 70% of their critical speed are considered rigid and, when balanced at one speed will be balanced at any other normal operating speed below 70% of its critical speed. Rotors that operate above 70% of their critical speed will bend or flex due to the forces of unbalance and, thus are called flexible rotors. A flexible rotor balanced at one operating speed may not be balanced when operating at another speed. This is because as the rotor bends or deflects, the weight of the rotor is moved out away from the rotating centerline creating a new unbalanced condition, known as whip. This new unbalance can be corrected by re-balancing in the two end planes; however, the rotor would then be out of balance at slower speeds where there is no deflection. The only solution to ensure smooth operation at all speeds is to make the balance corrections in the actual planes of unbalance. Typical machines which contain flexible rotors are steam and gas turbines, multistage centrifugal pumps, compressors, and paper rolls. Rigid Rotors A rigid rotor has minimal bending or distortion due to its stiffness and rigidity. This is determined when the component is rotated at low speeds or below the critical operating speeds. For a rigid rotor, the shaft deflection is very small, the mass inertia forces are small, and the majority of centrifugal force energy is counteracted by bearing deflection. The bearing vibration is generally large and can be rectified by using normal balancing methods. Figure 1: Rigid rotor.
Flexible rotor: A flexible rotor is a component or machine that has significant bending during operation. This bending can be seen when there is a change in speed. The change in speed affects the centrifugal force, causing bending and twist effects to occur. These conditions are found more in components where the length to diameter ratio is at its extreme and the component is running at critical/operating speed. Figure 2. Flexible rotor. Balancing Limits The International Standard ISO 1940/1 "Balance Quality Requirements of Rigid Rotors" is a widely accepted reference for selecting rigid rotor balance quality. This standard sets a level of unbalance to be acceptable based on the type of rotor and its operating speed. To determine the balance quality requirement of your rotor, please reference our Technical Literature, Balance Quality Requirements of Rigid Rotors. While the ISO determines a standardized qualification for balancing, the unbalance tolerance, or amount of unbalance allowed in a product can easily be determined by the manufacturer. The best way to determine an acceptable balance tolerance is to experiment with a batch of rotors. Balance the rotors to reduce unbalance to a minimum. Then slowly add unbalance until the performance becomes unacceptable. Keep in mind that more unbalance can lead to premature bearing failure or excessive vibration. Pick a balance tolerance within this range that is cost effective and achievable with little lost time. Static and Dynamic Balancing: Unbalance is the most common source of vibration in machines with rotating parts. It is an especially important factor to be considered in modern machine design, especially where high speed and reliability are significant considerations. Balancing of rotors prevents excessive loading of bearings and avoids fatigue failure, thus increasing the useful life of machinery. Unbalance in a rotor is the result of an uneven distribution of mass, which causes the rotor to vibrate. The vibration is produced by the interaction of an unbalanced mass component with the radial acceleration due to rotation, which together generate a centrifugal force. Since the mass component rotates, the force also rotates and tries to move the rotor along the line of action of the force. The vibration will be transmitted to the rotor's bearings, and any point on the bearing will experience this force once per revolution.
a statically balanced rotor; however, during faster rotations, there is an increased chance of bending moments. Scenario C shows an unacceptable attempt of balancing a rotor. The correction weight was added in a different plane than the one containing the rotor center of gravity. The rotor may be considered statically balanced, due to the fact that no heavy spot would swing to the bottom if the rotor were suspended and allowed to spin freely; however, when the rotor is rotated, the original heavy spot and correction weight, being located in different planes, produce moments of inertia which cause the central principal axis to intersect the rotating centerline, thus creating another type of unbalance. Figure 4. Acceptable static unbalance fixes. Dynamic rotor: Dynamic unbalance is the most common type of unbalance and is defined simply as unbalance where the central principal axis and the rotating centerline do no coincide or touch. This type of unbalance exists whenever static and couple unbalance are present, but where the static unbalance is not in direct line with either couple component. As a result, the central principal axis is both tilted and displaced from the rotating centerline. Generally, a condition of dynamic unbalance will reveal comparative phase readings which are neither the same nor directly opposite one another. This type of unbalance can only be solved by making weight corrections in a minimum of two planes. Figure 5. Dynamic rotor.
Selection of Trial Masses The specific unbalance is used to calculate the size of trial masses, which are used during balancing to make temporary alterations to the mass distribution of the rotor, to determine the relationship between the specific unbalance and the bearing vibrations. To estimate the value, a suitable trial mass, the mass oi the rotor in kg and the radius m mm at which the corrections are to be made must be determined. The Maximum Residual MMR, in grams, is given by: Figure 6. Equation for the topic. Conclusion : As we already saw the rotor balancing is required on all types of rotating machinery, including motors, to ensure smooth machine operation. In a factory, this is achieved on a balancing machine at a precision level determined by motor speed, size, and vibration requirements. The highest precision is required for two-pole motors. Two-pole and large four-pole motors should be balanced at their operating speed in the balancing machine. We also saw the two types of rotors and they are classified into two groups. Whether or not a rotor is classified as rigid or flexible depends on the relationship between the rotating speed of the rotor and its natural frequency. When the natural frequency of some part of a machine is also equal to the rotating speed or some other exciting frequency of vibration, there is a condition of resonance. The rotating speed at which the rotor itself goes into bending resonance is called a "critical speed." With this investigation we obtained the knowledge that we wanted so then a think that the purpose of the investigation was gotten, that´s why I think that its important for us to read this kind of investigations, so I’m happy with the result of the investigation. References : https://www.yumpu.com/en/document/read/7936761/static-and-dynamic-balancing-of- rigid-rotors https://apps.dtic.mil/dtic/tr/fulltext/u2/a181731.pdf http://www.betamachinery.com/assets/pdfs/Technical_Articles/ Simplified_Prediction_of_Balance_Sensitivity.PDF http://irdproducts.com/unbalance---cause-of-vibration.html