
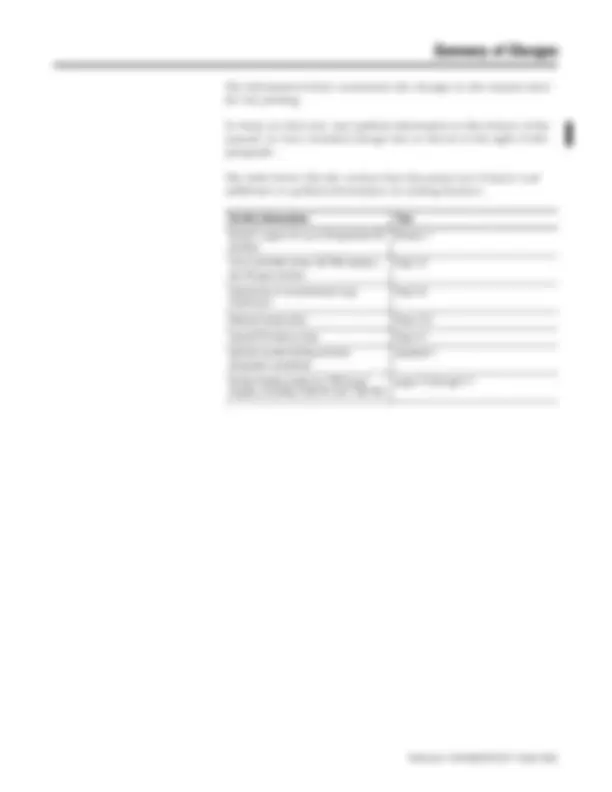
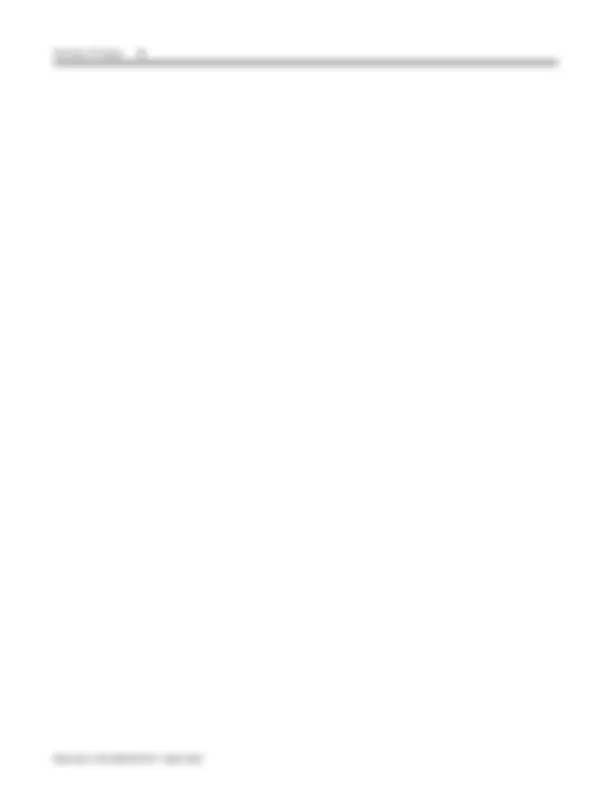
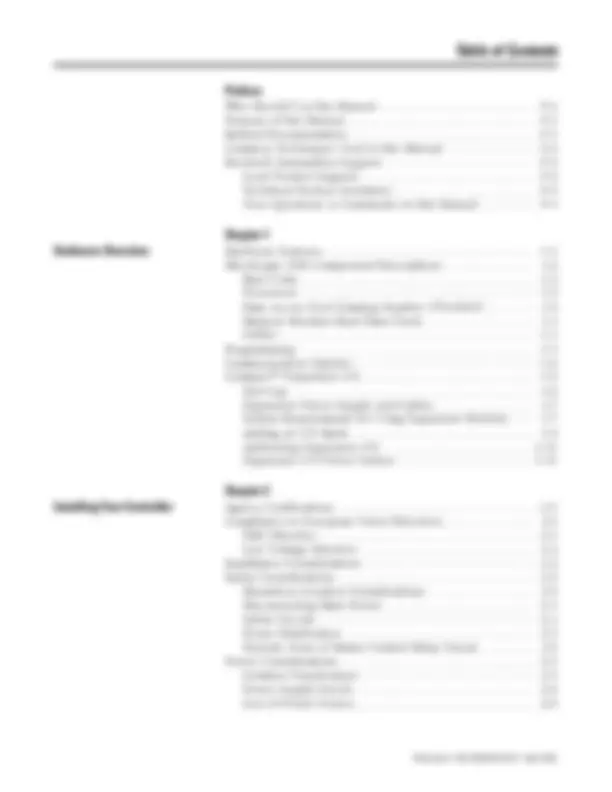
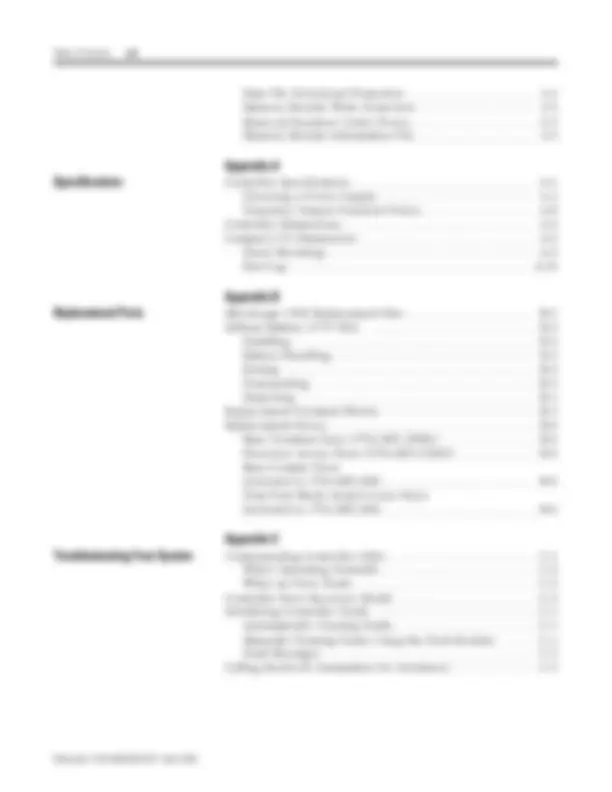
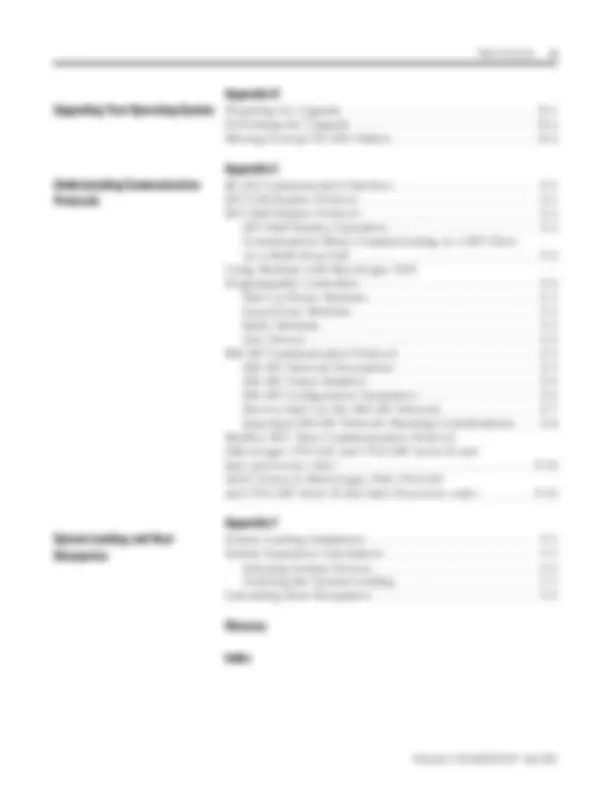
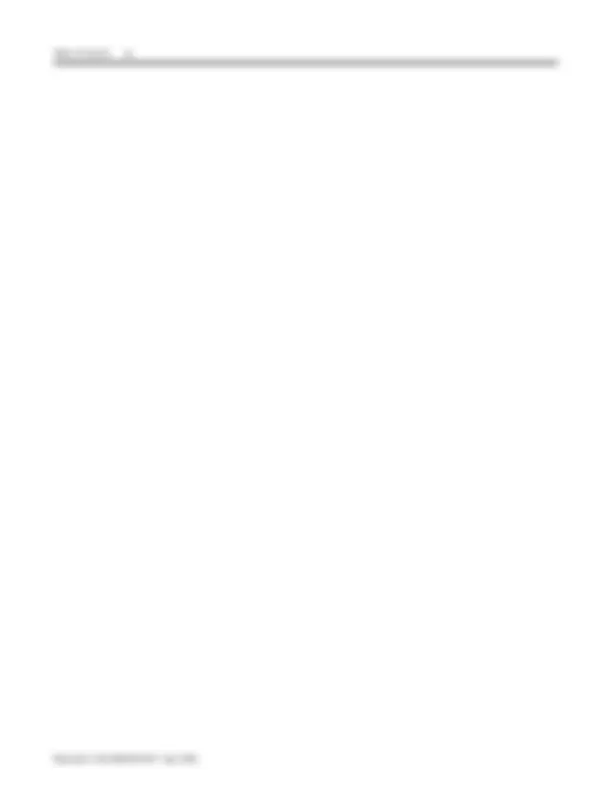
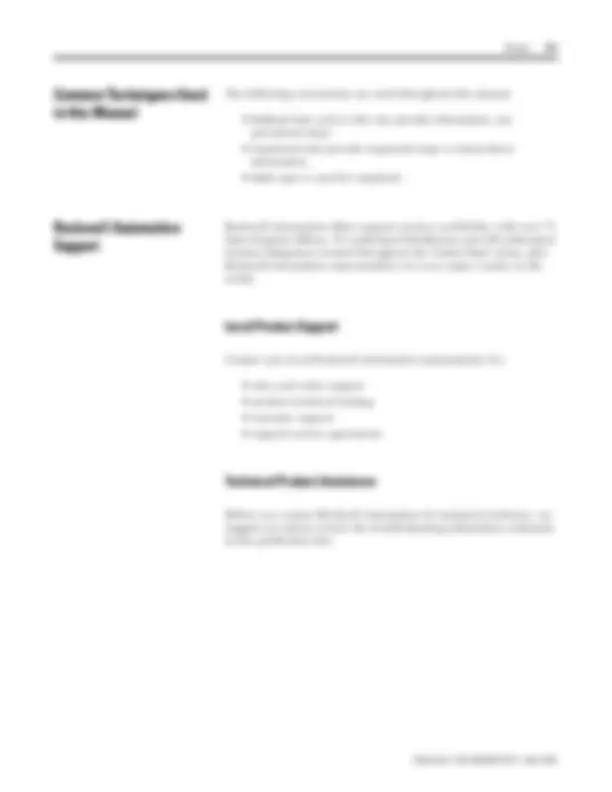
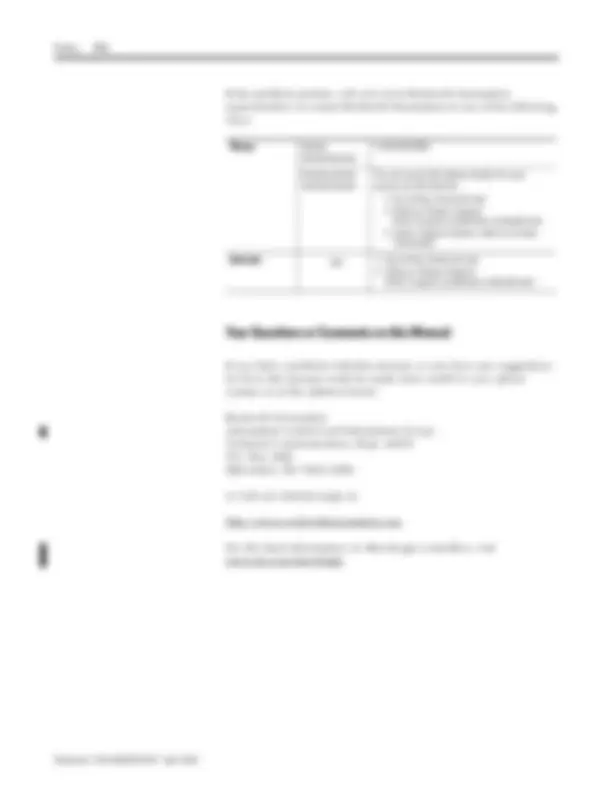
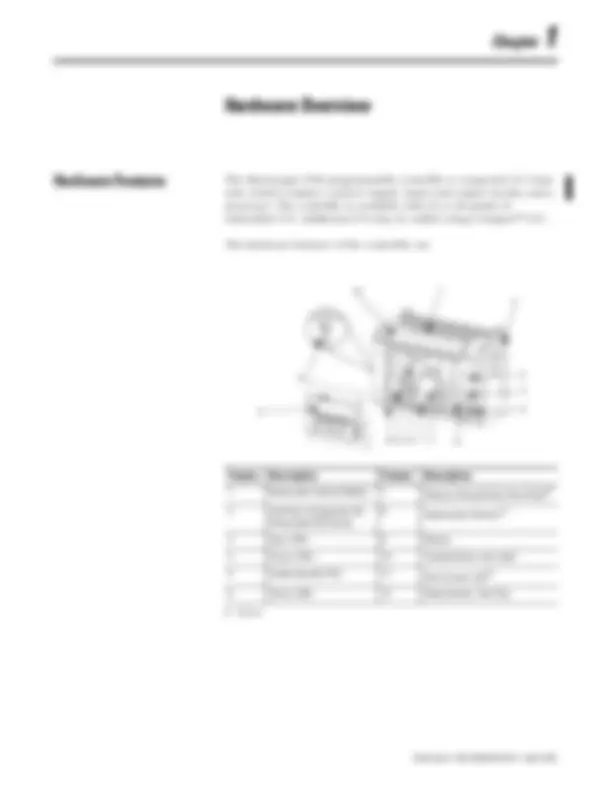
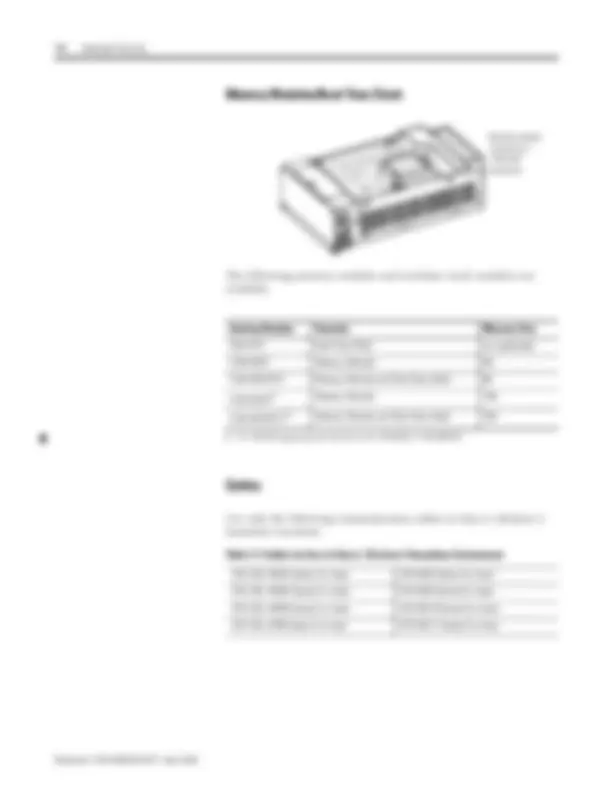
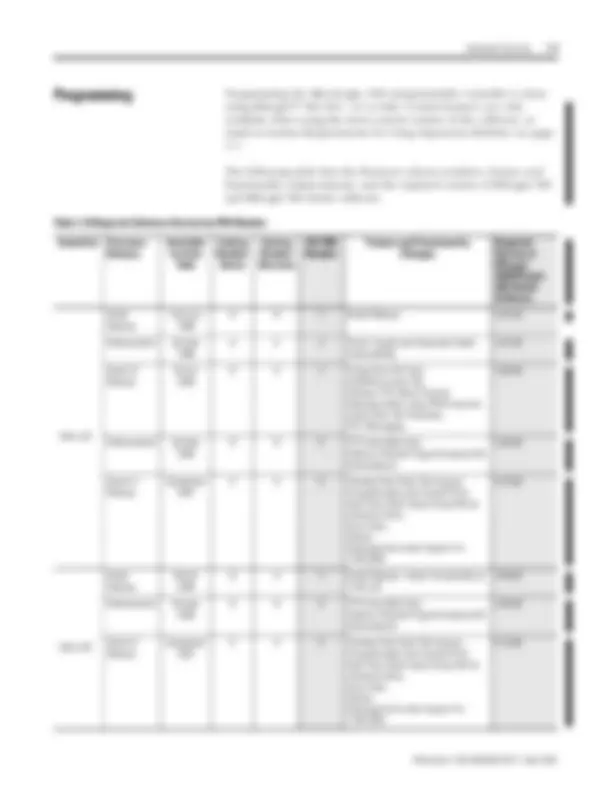
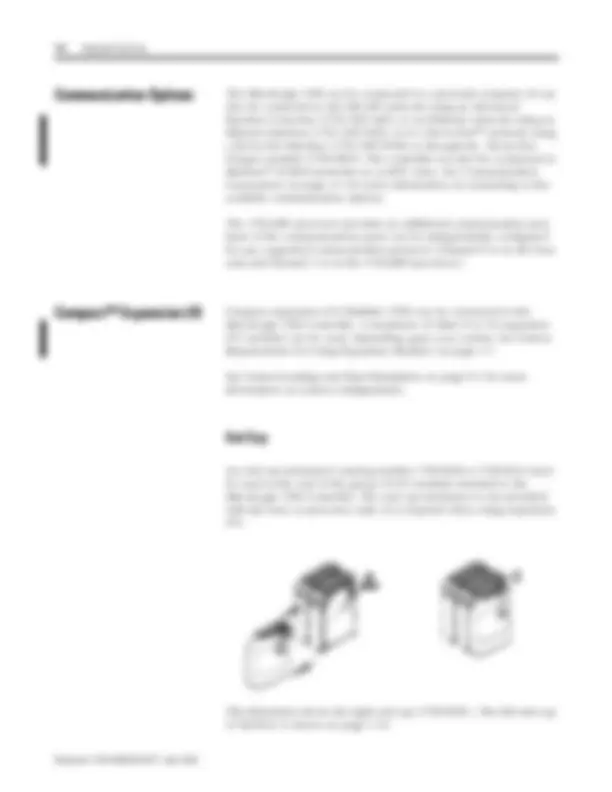
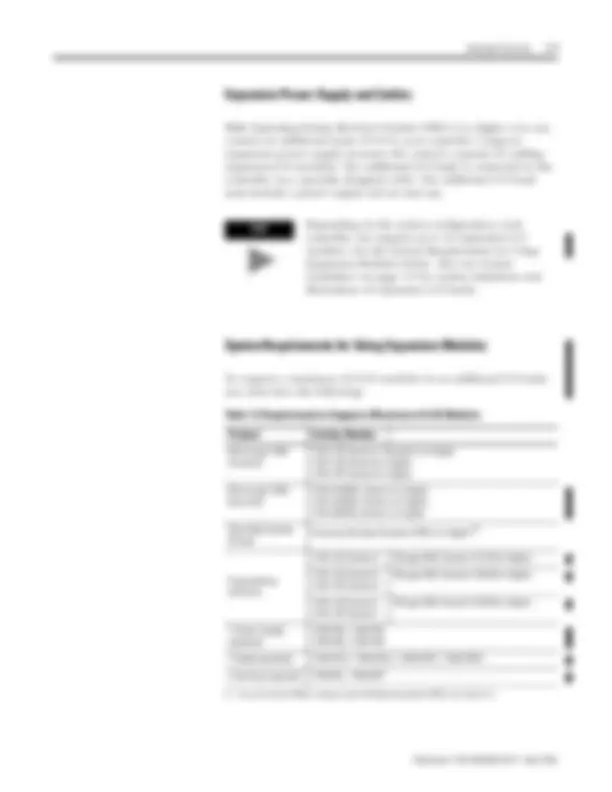
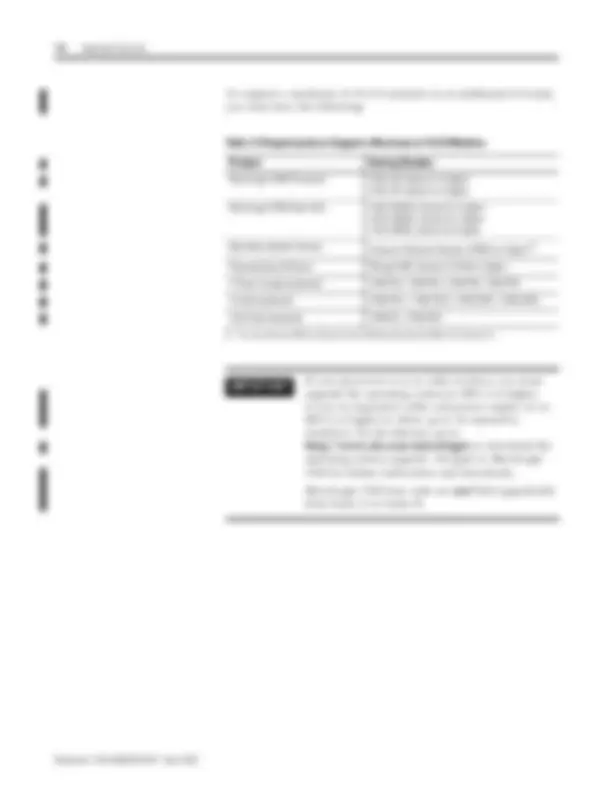
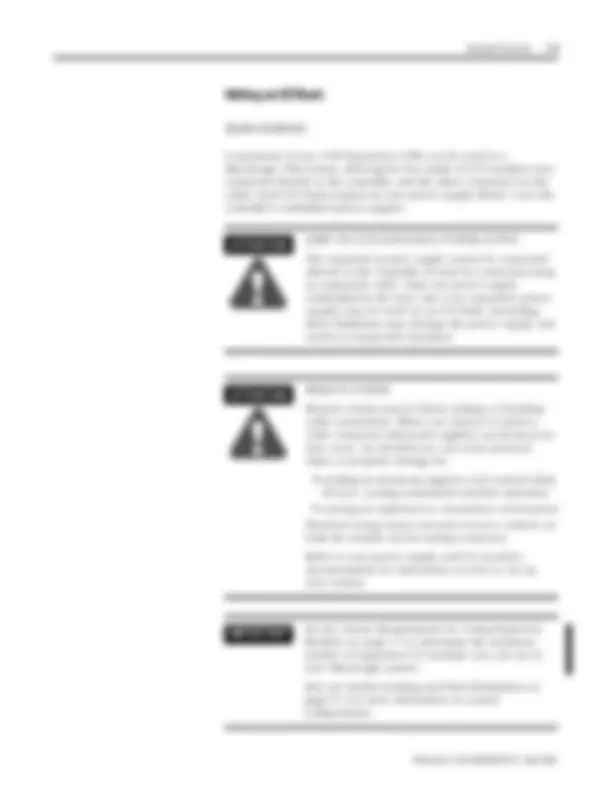
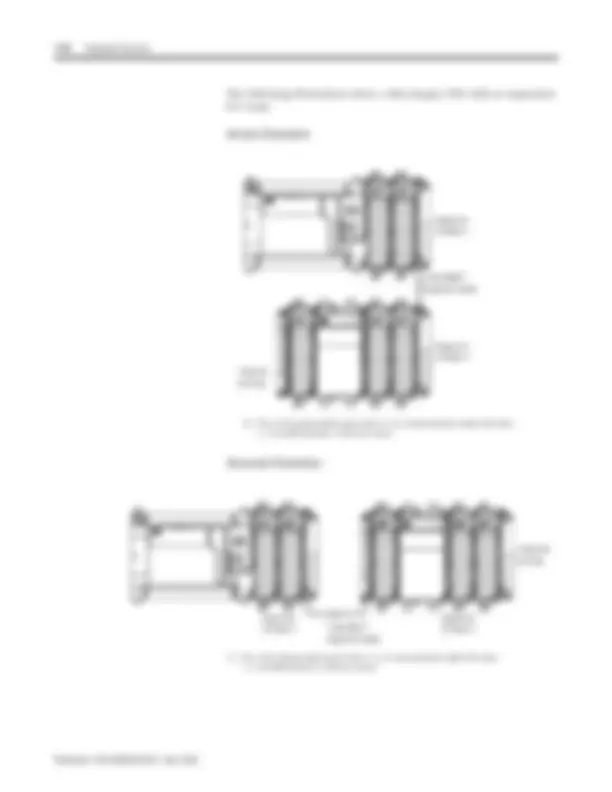
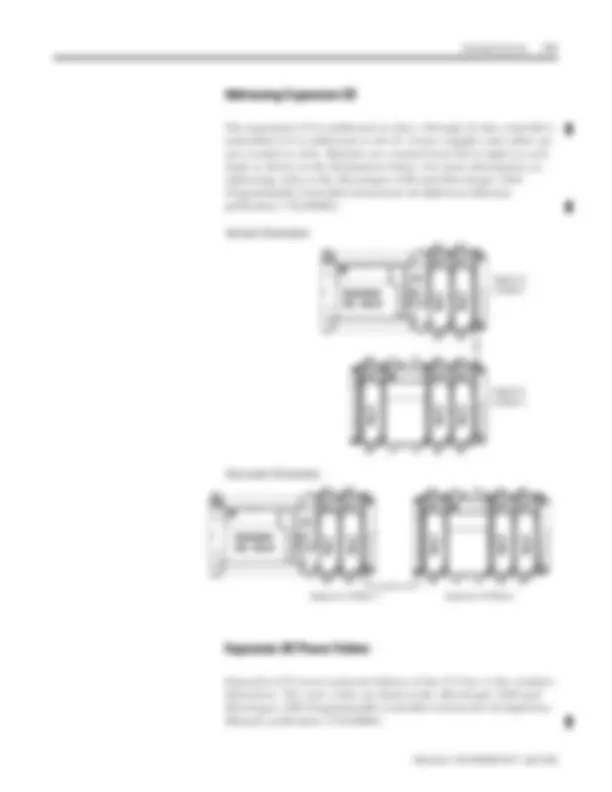
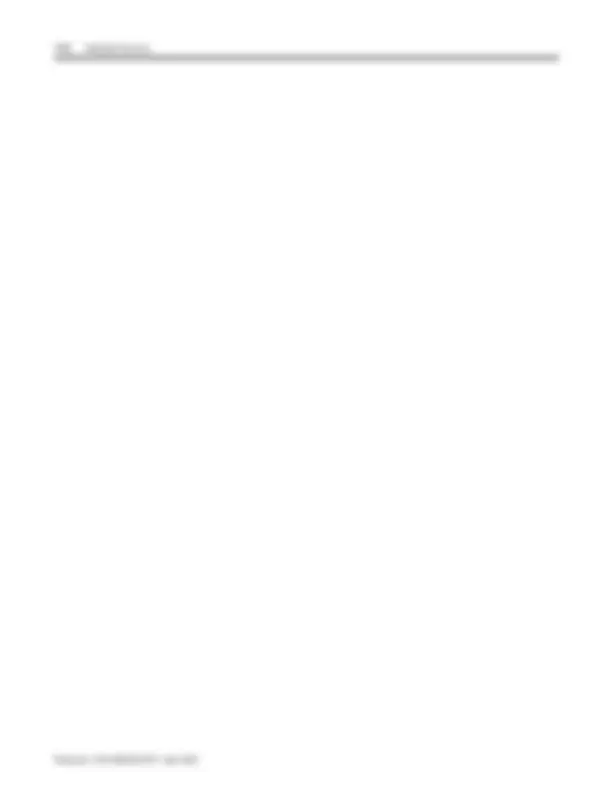
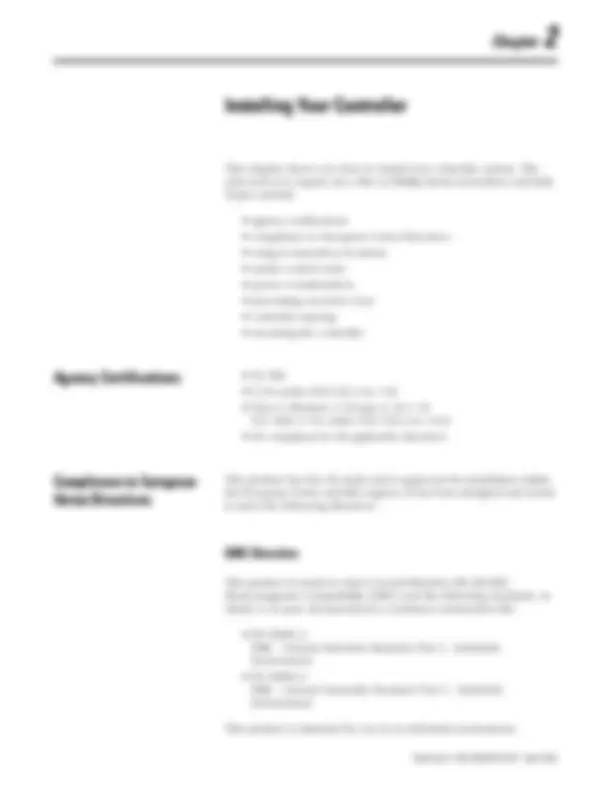
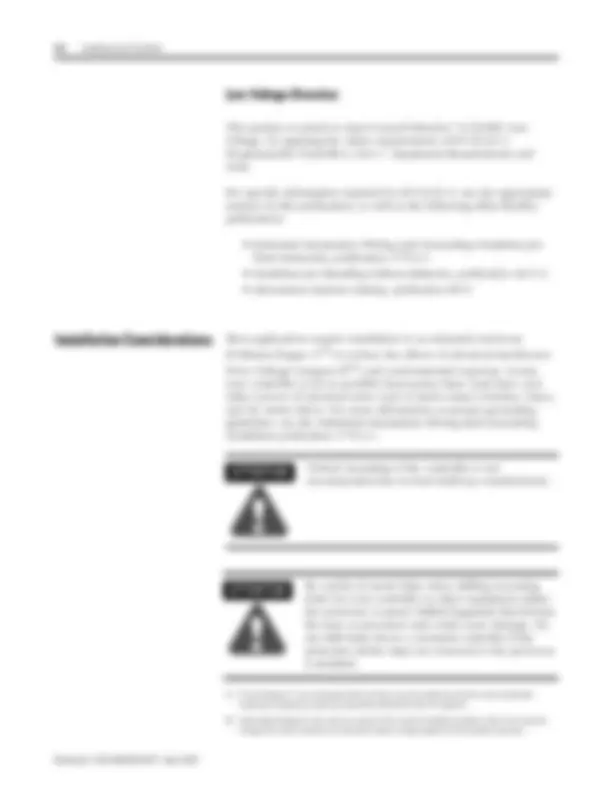
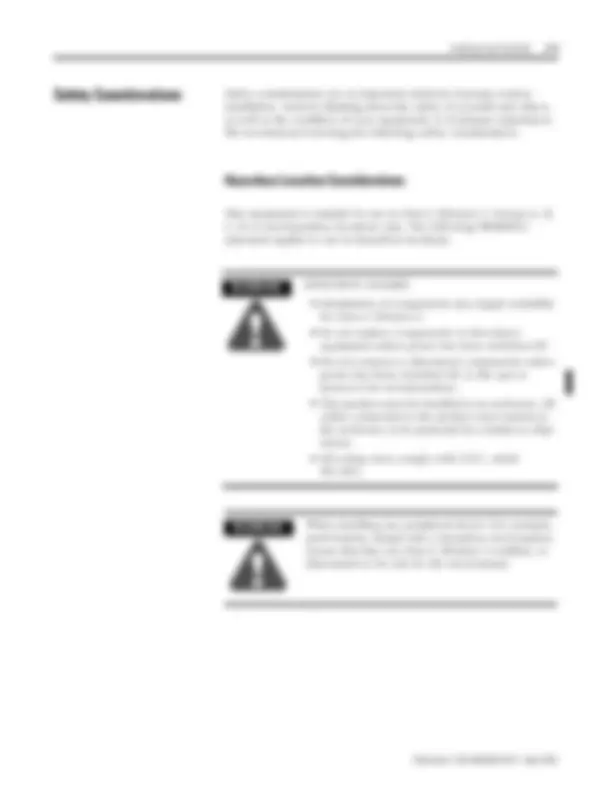
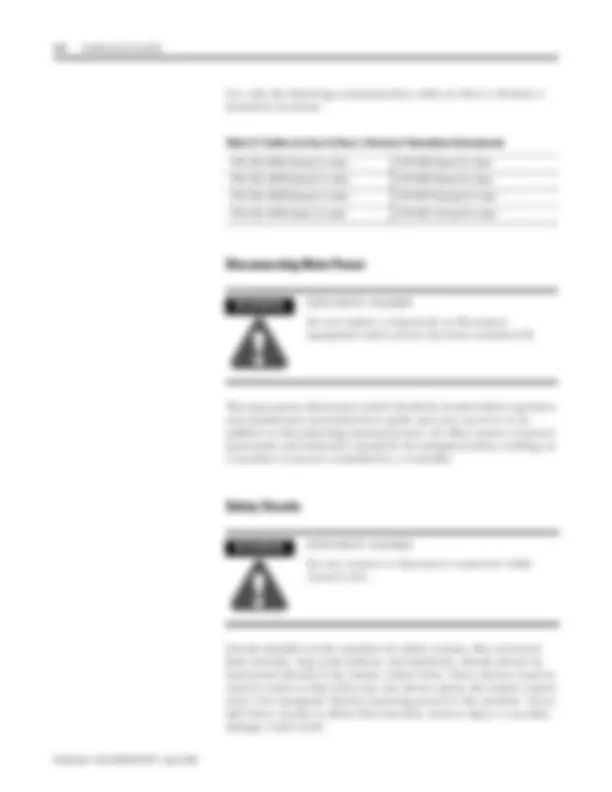
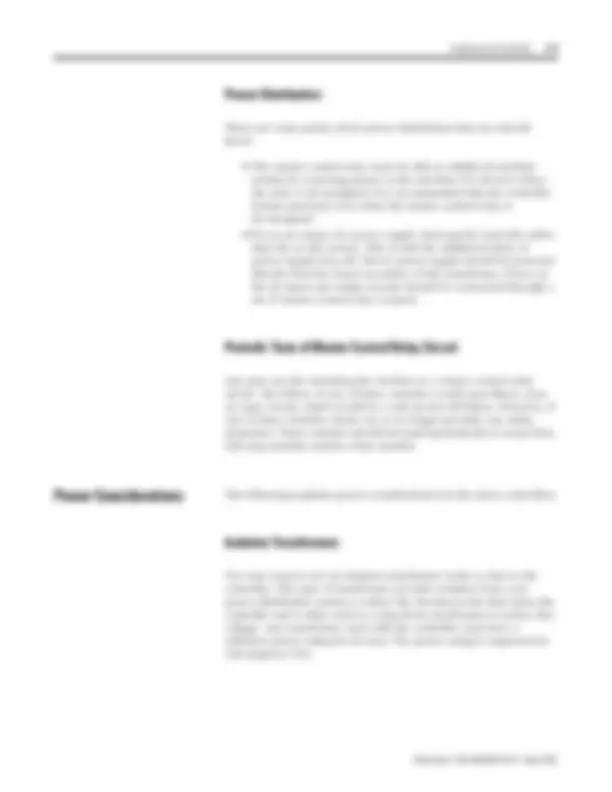
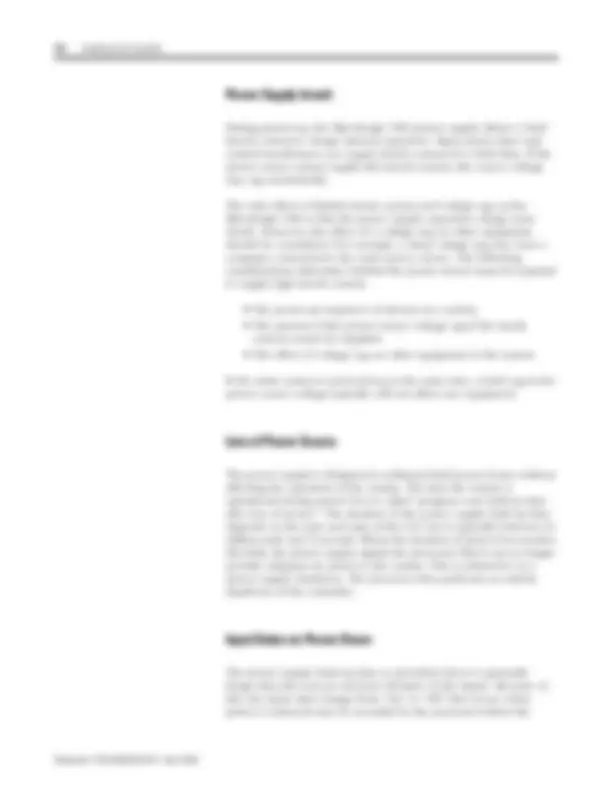
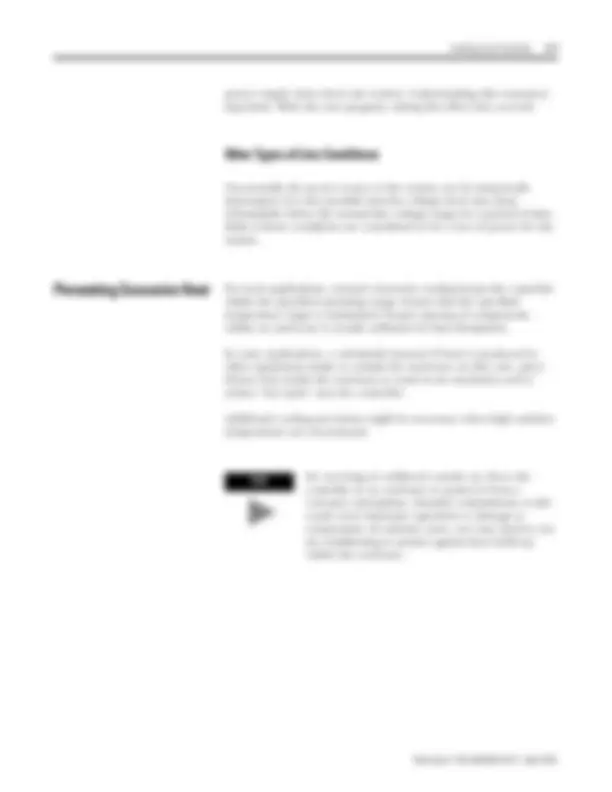
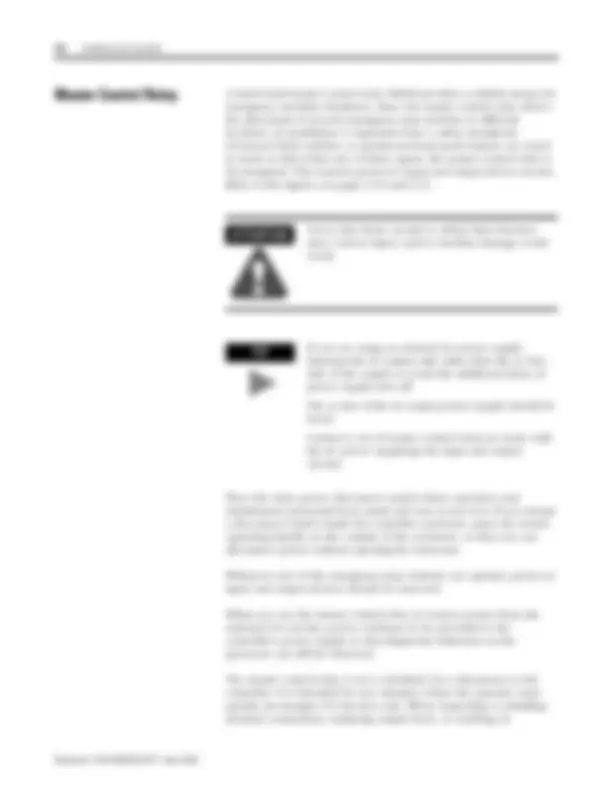
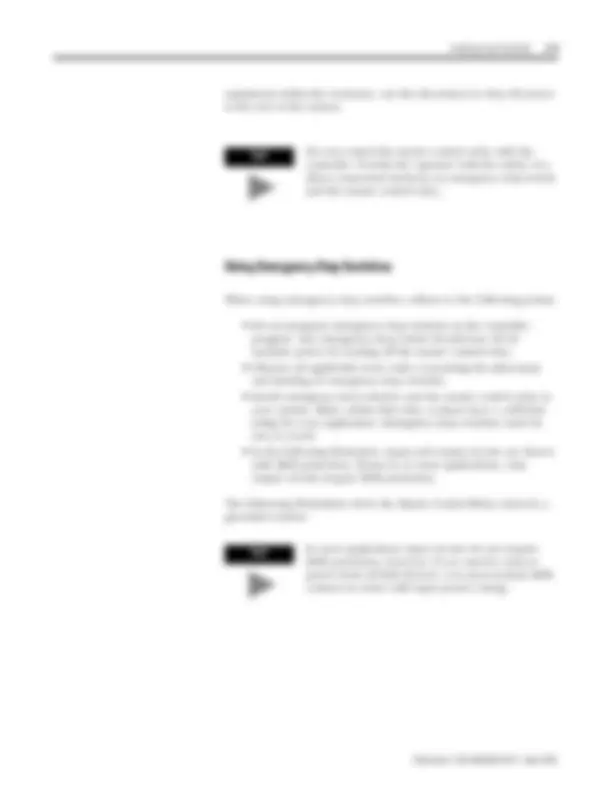
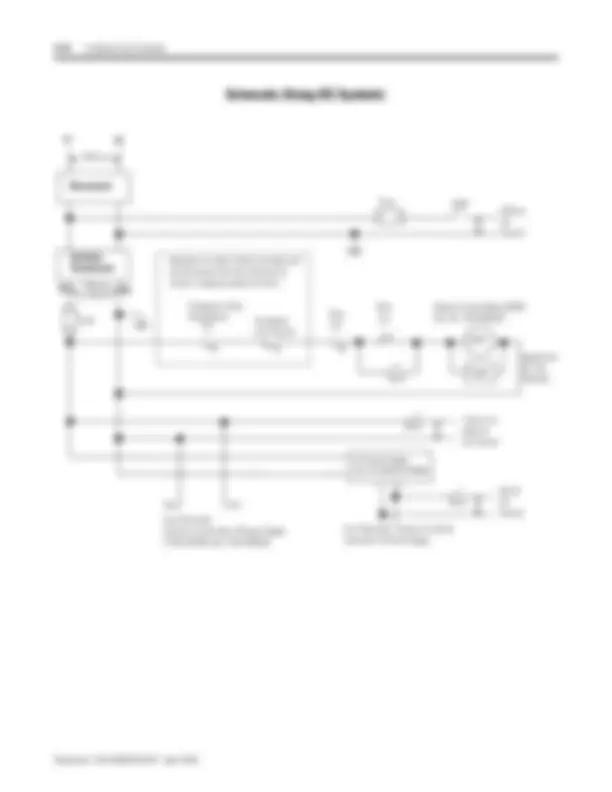
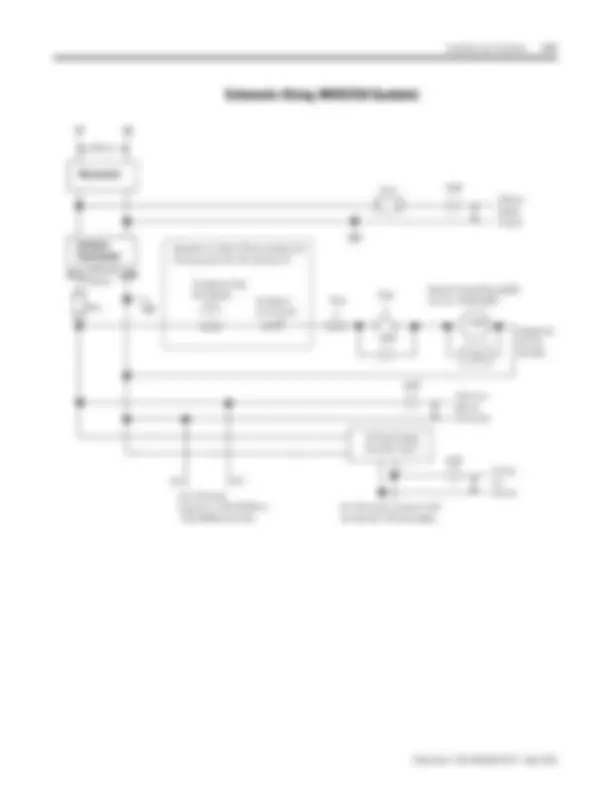
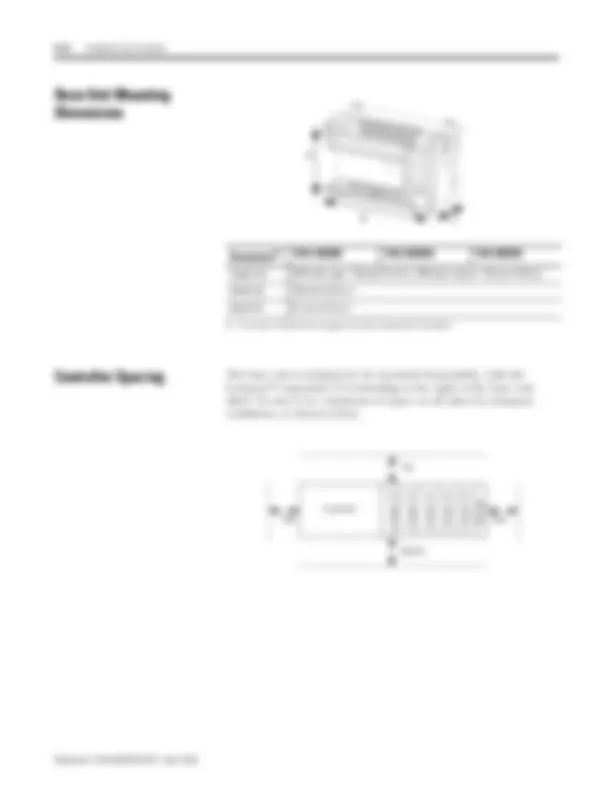
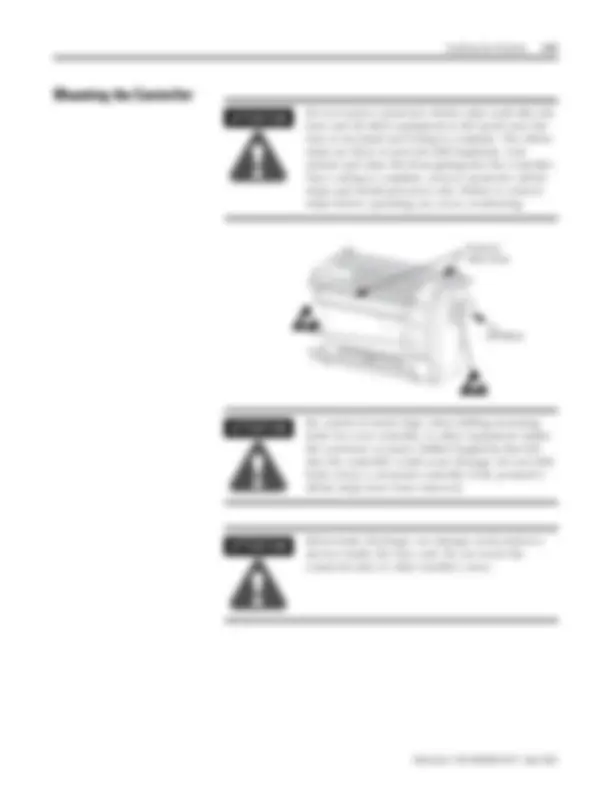
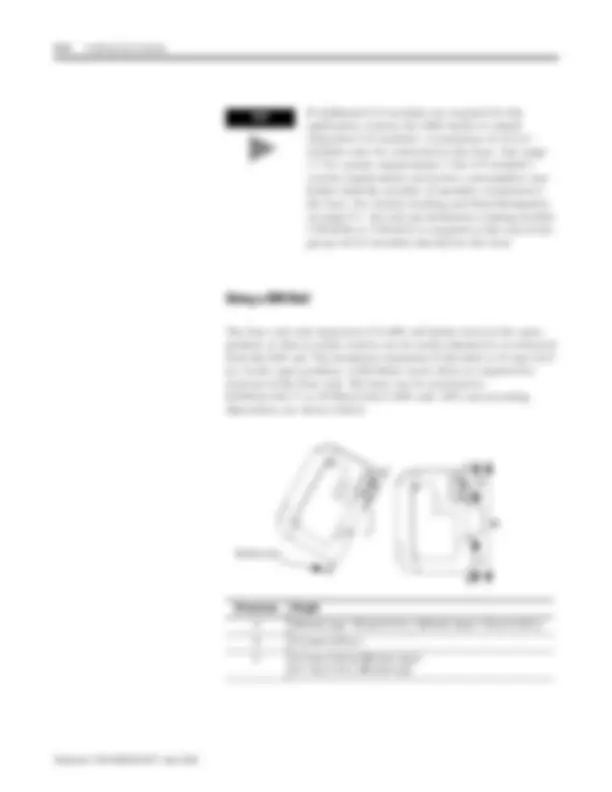
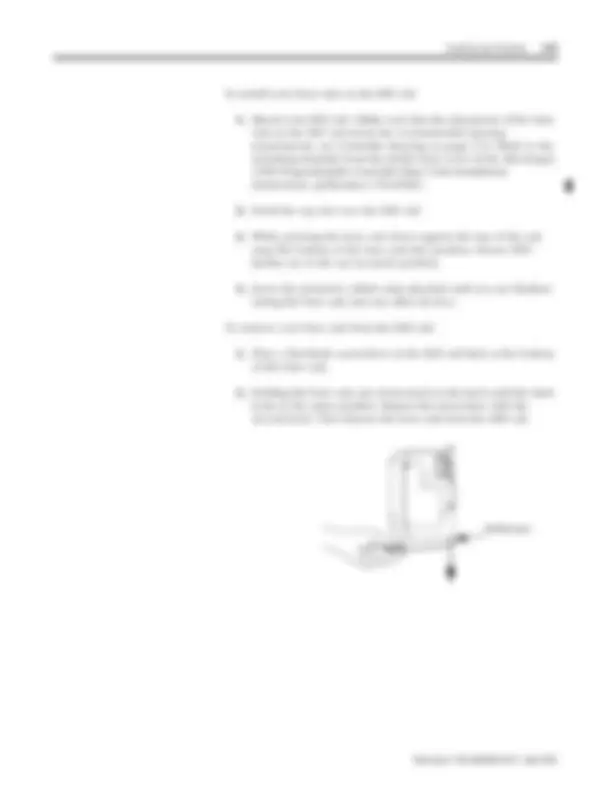
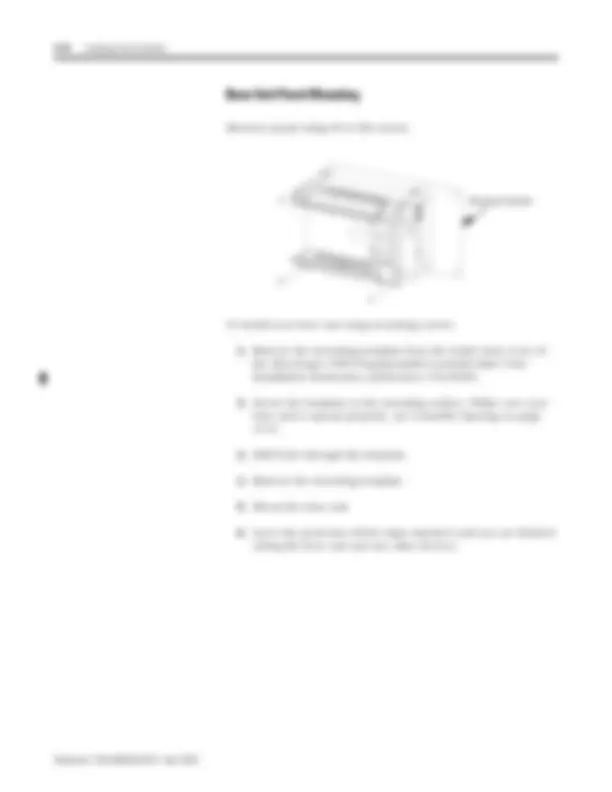
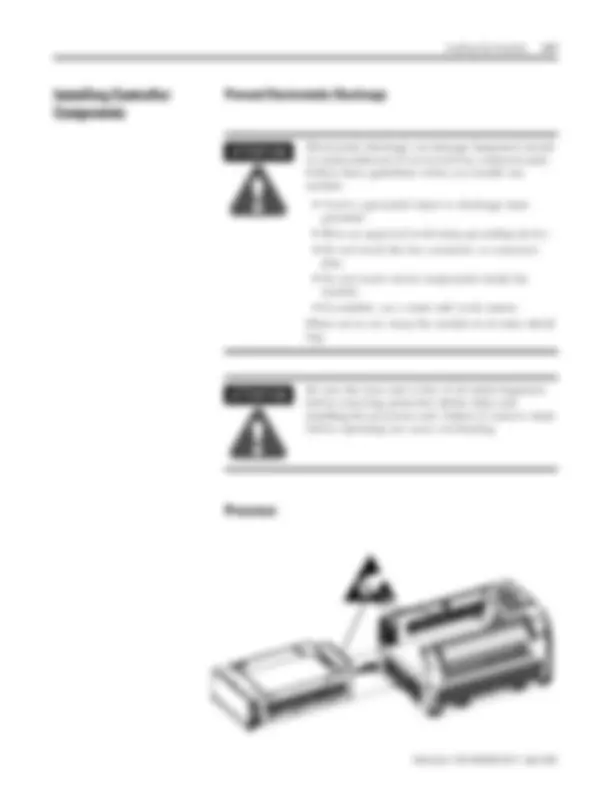
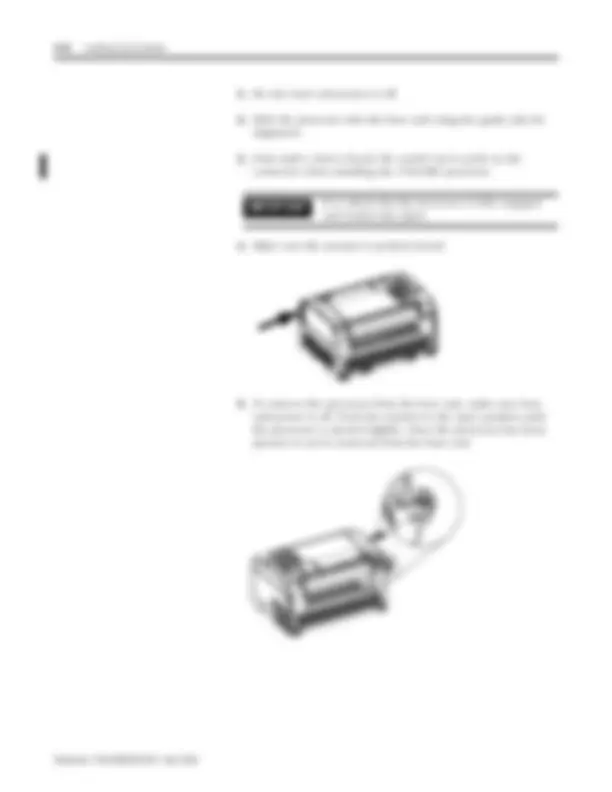
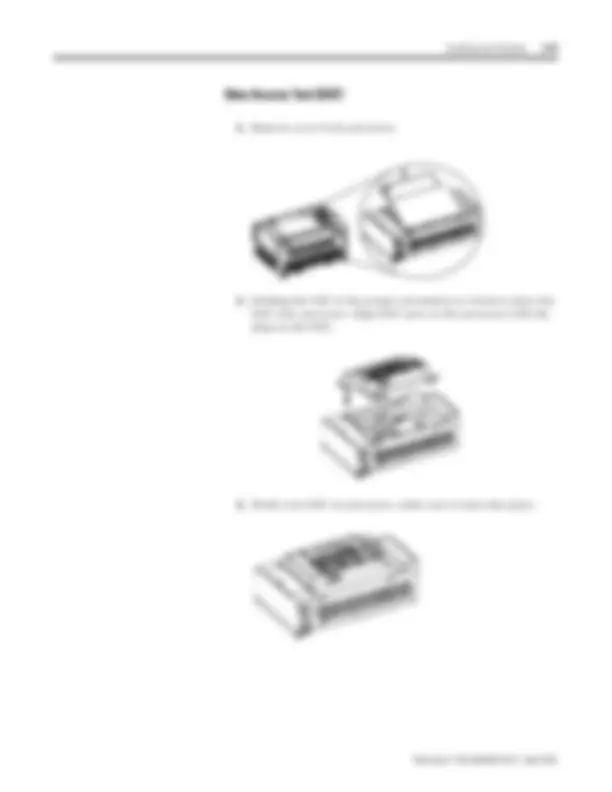
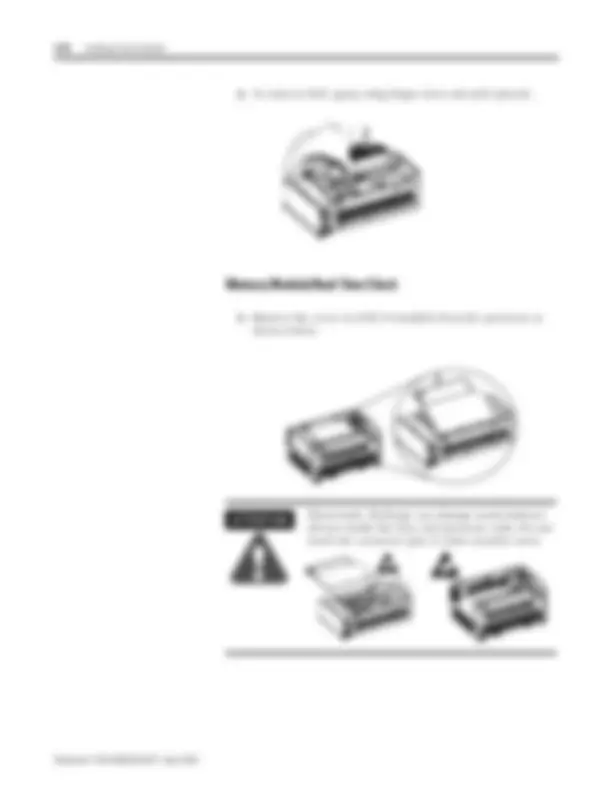
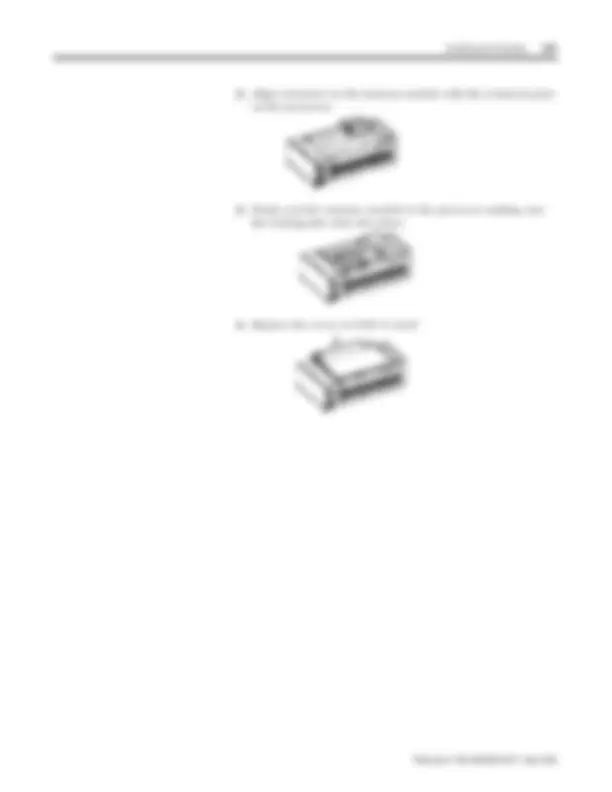
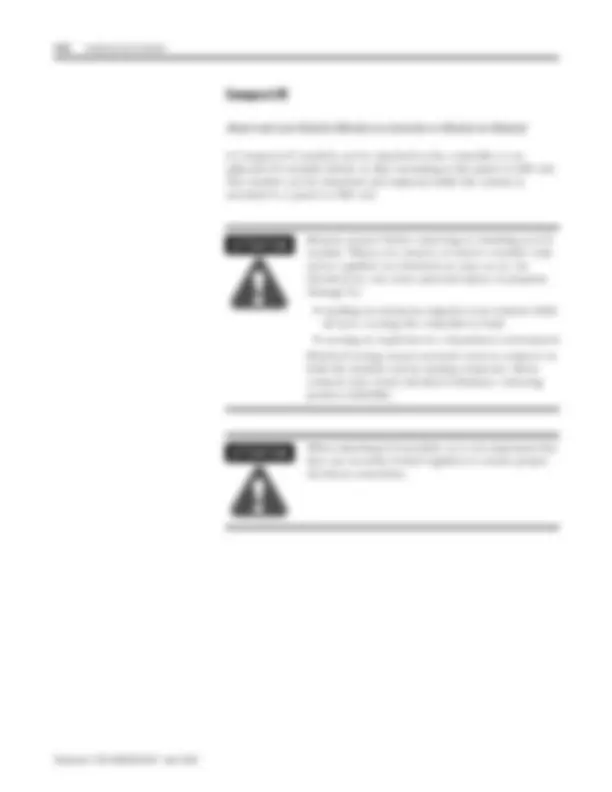
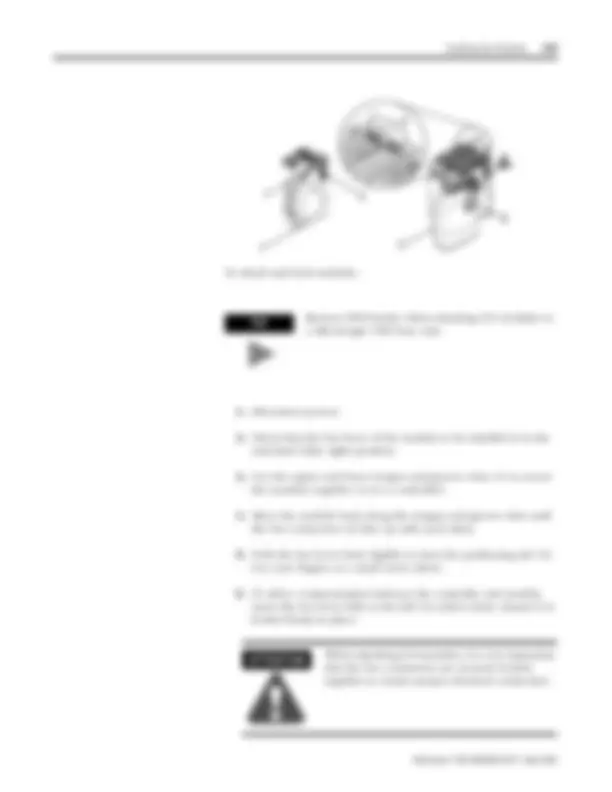
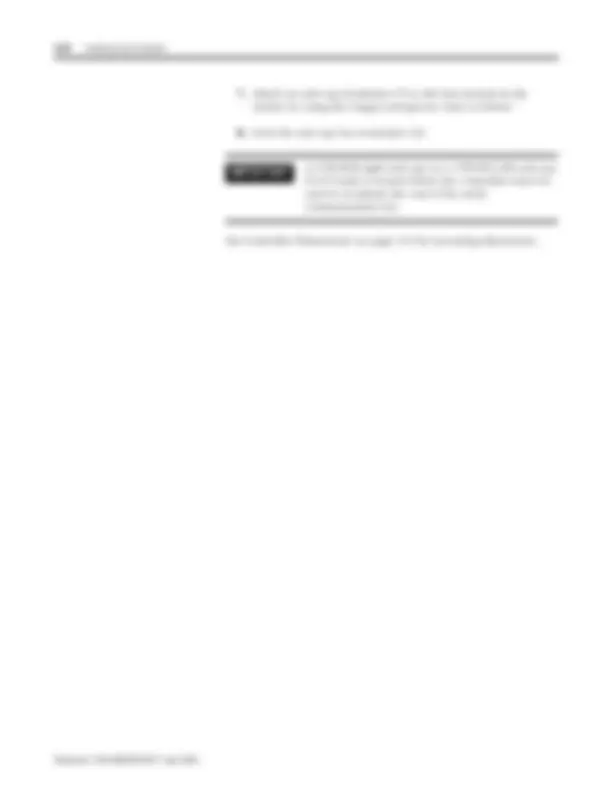
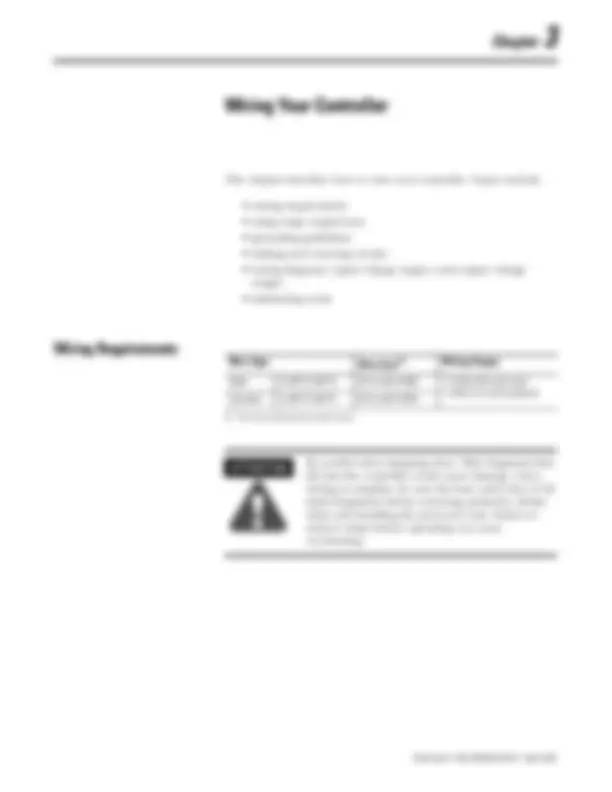
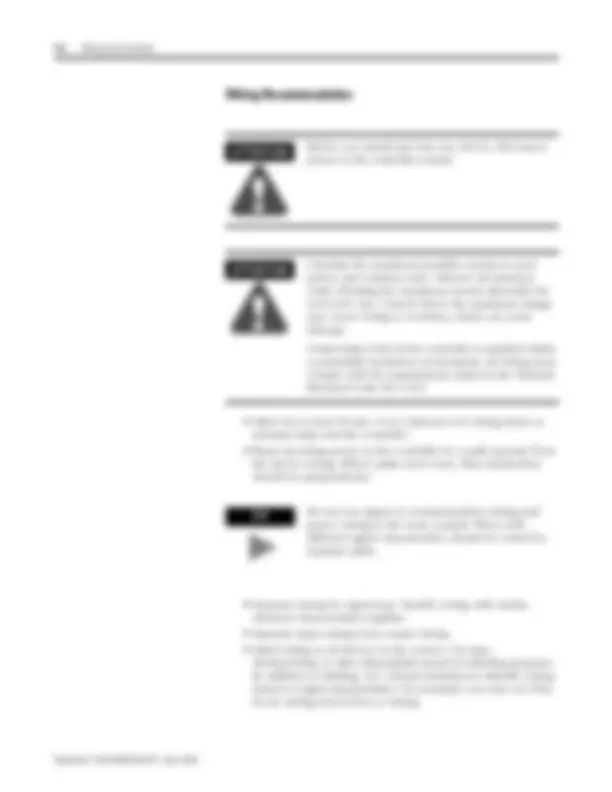
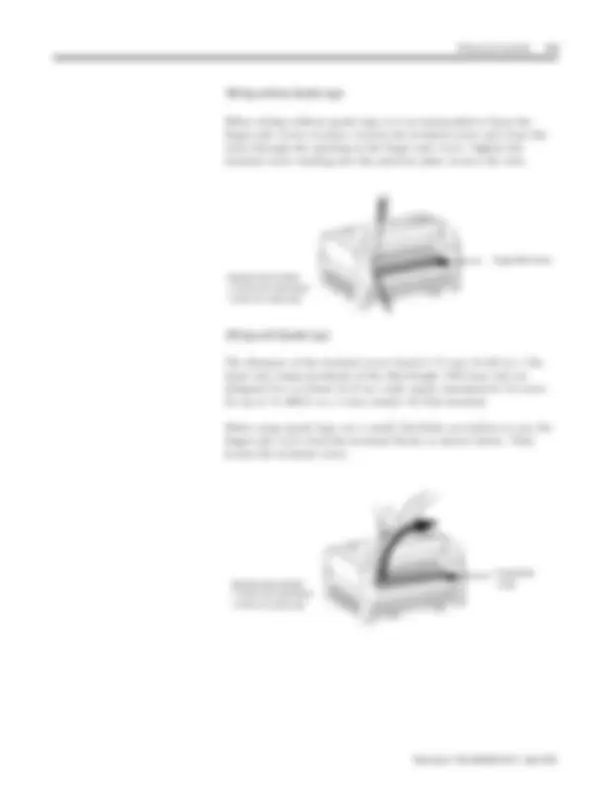
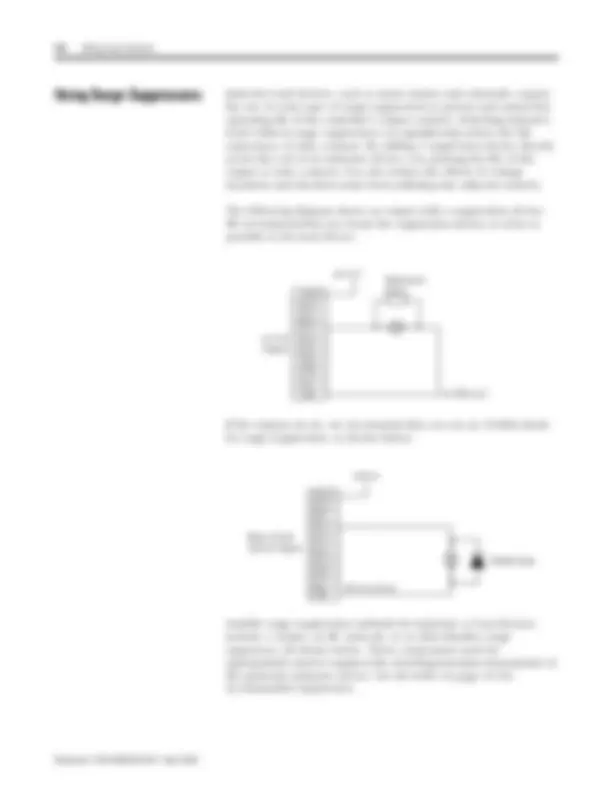
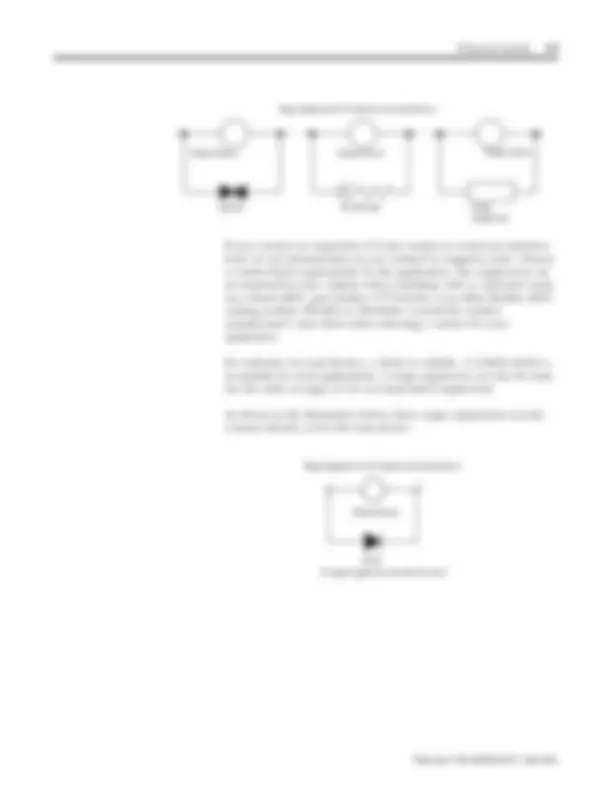
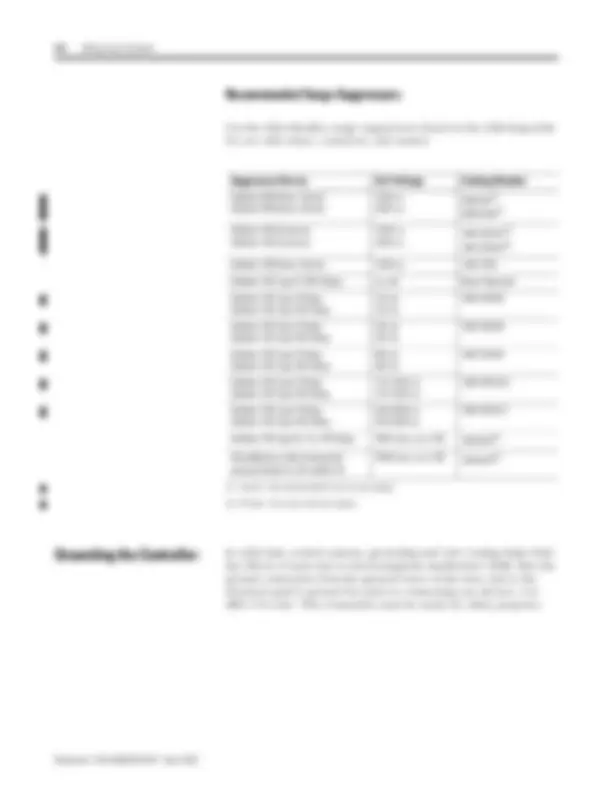
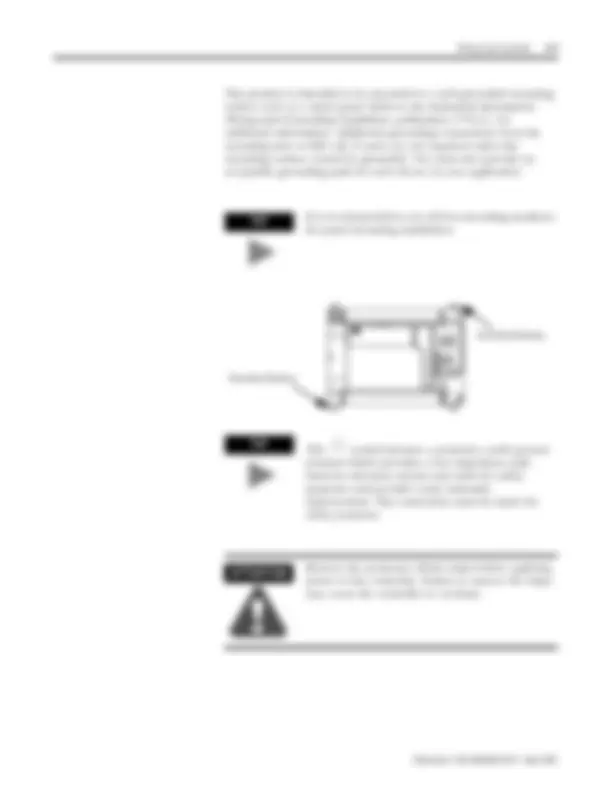
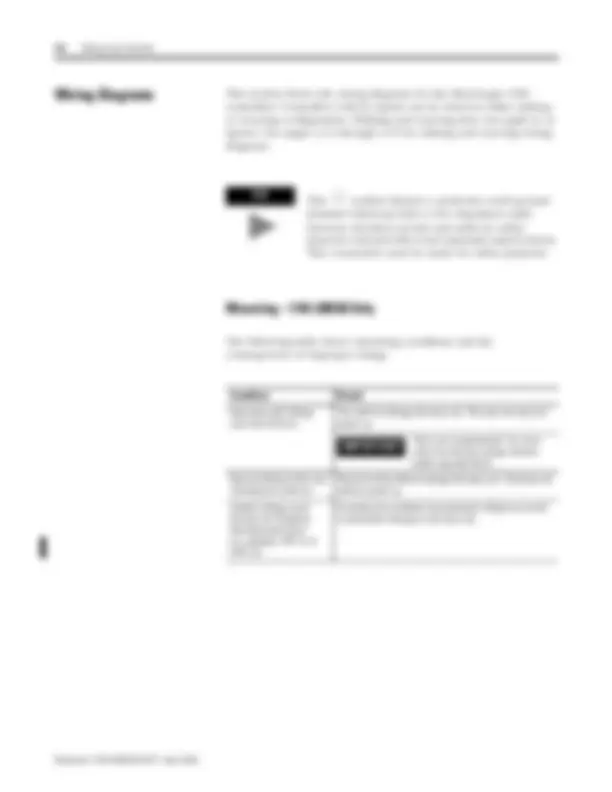
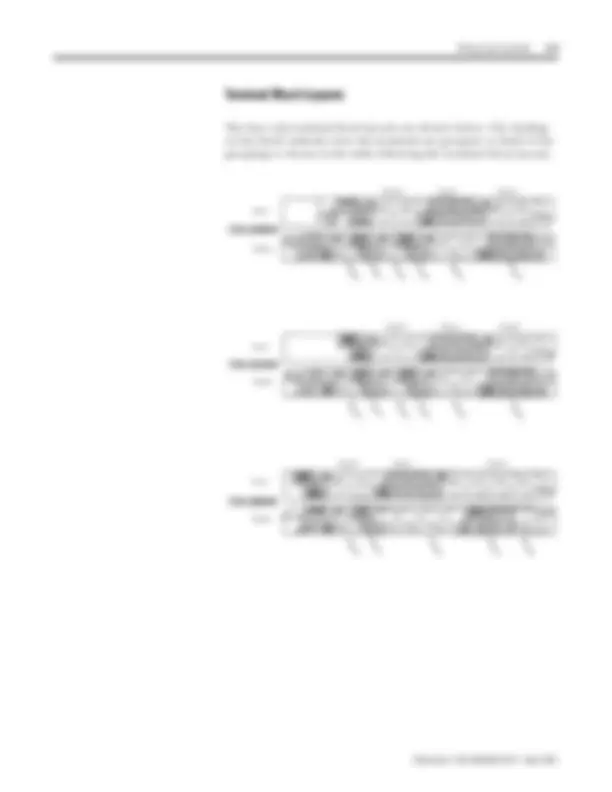
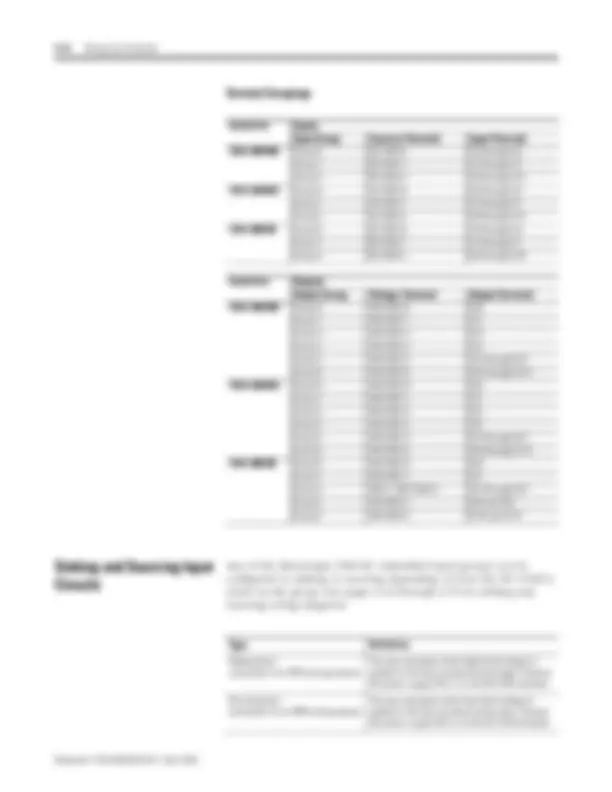
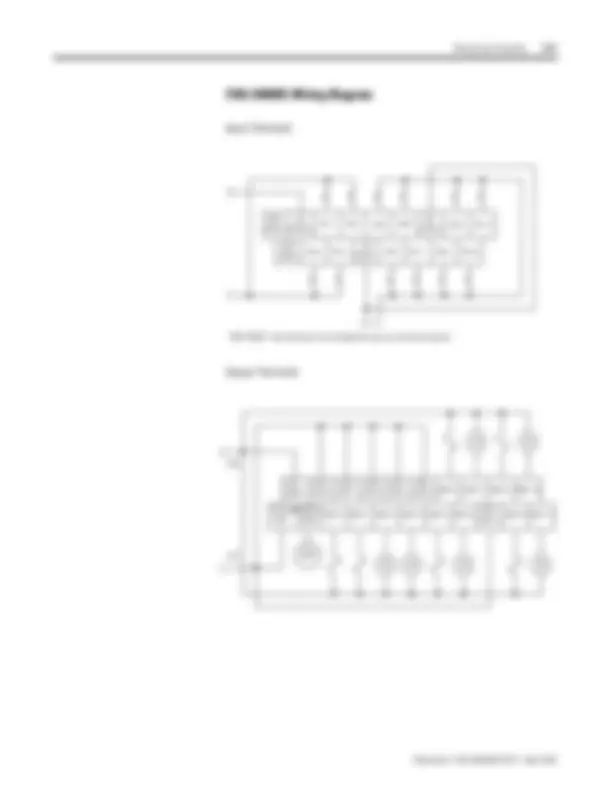
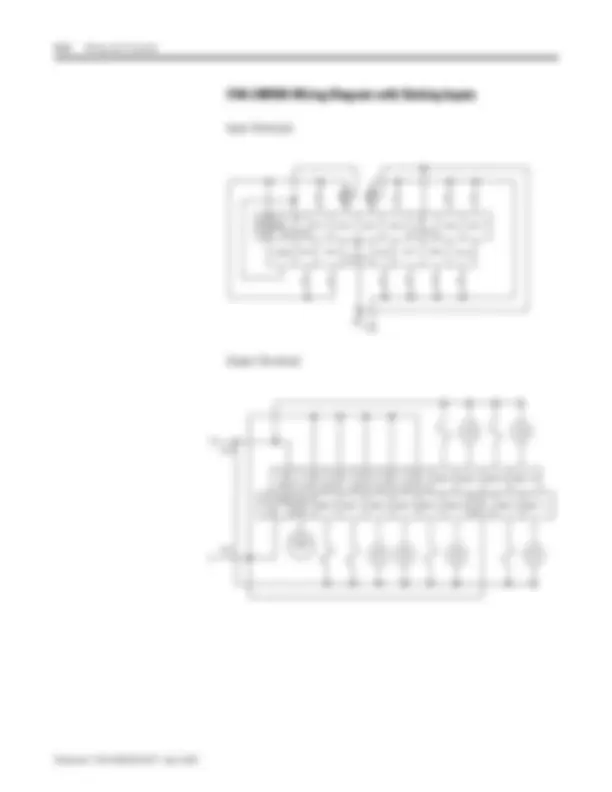
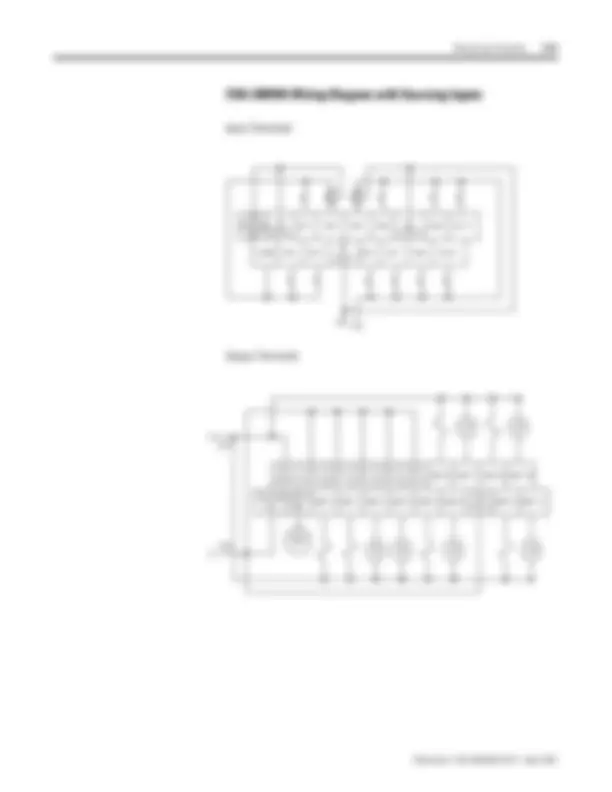
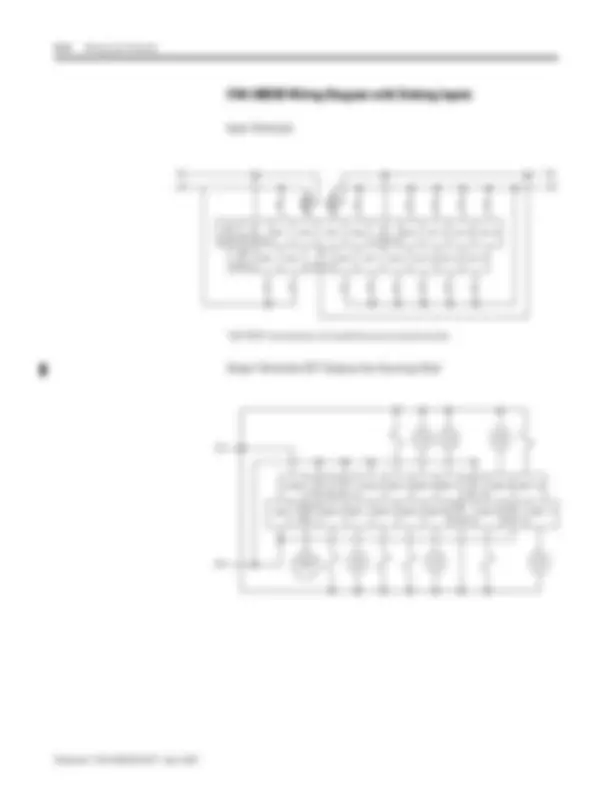
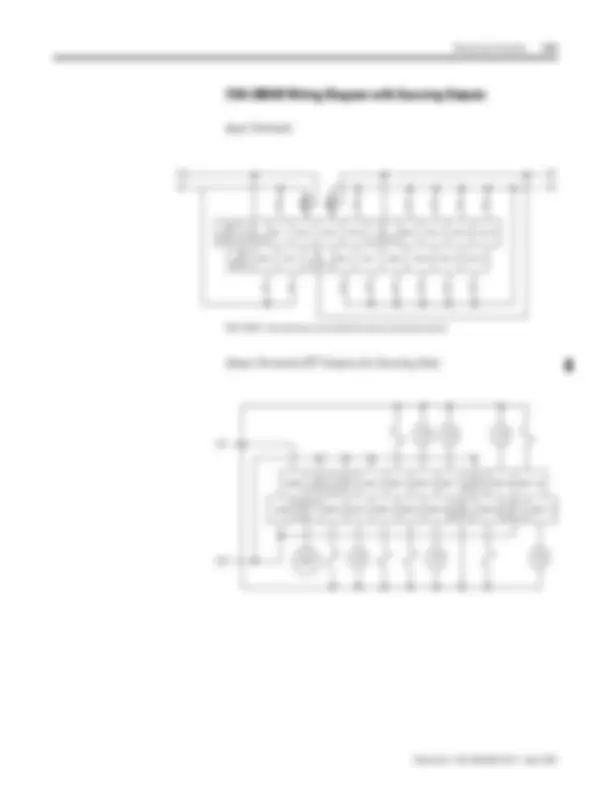
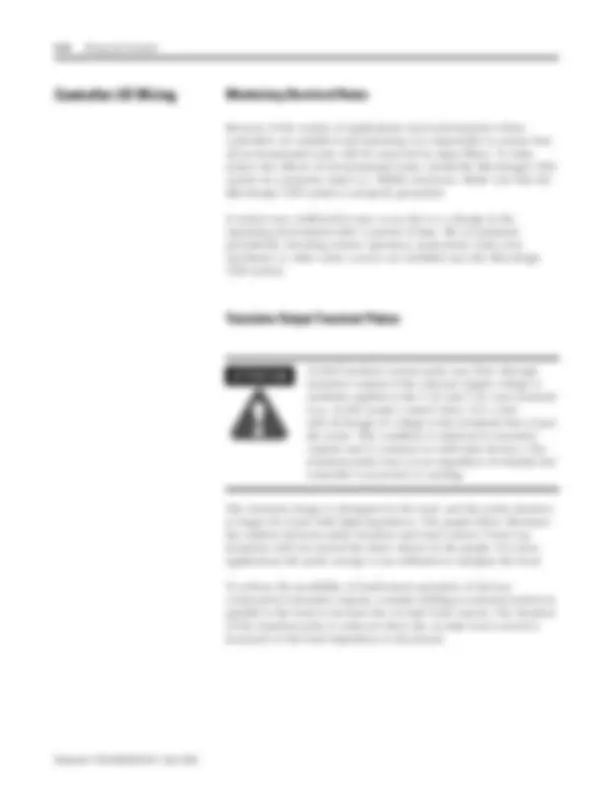
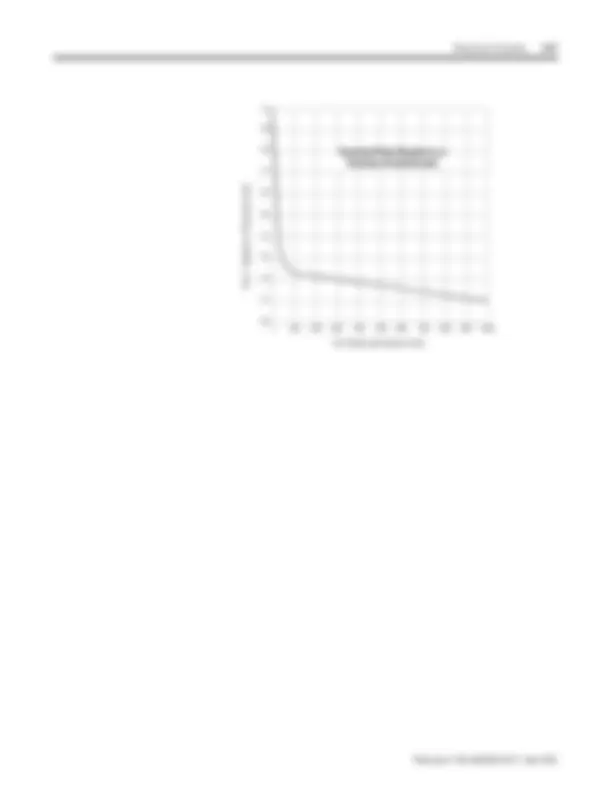
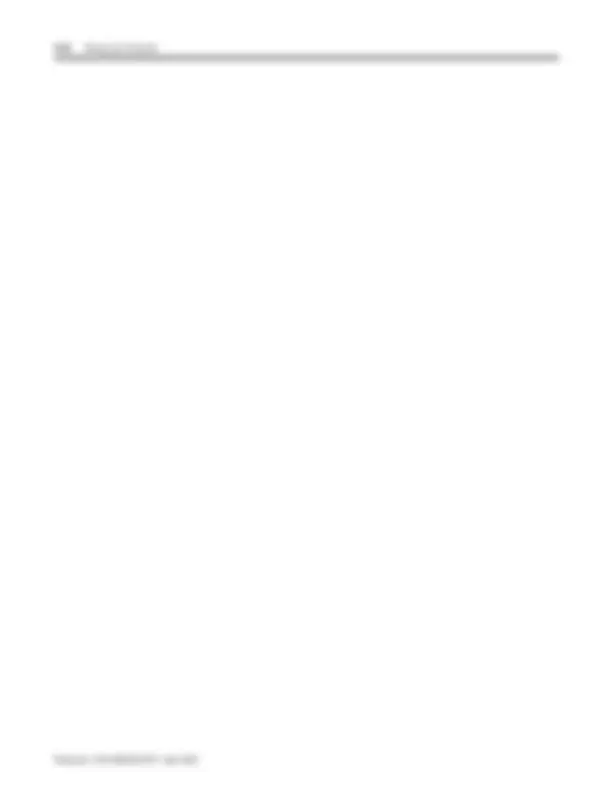
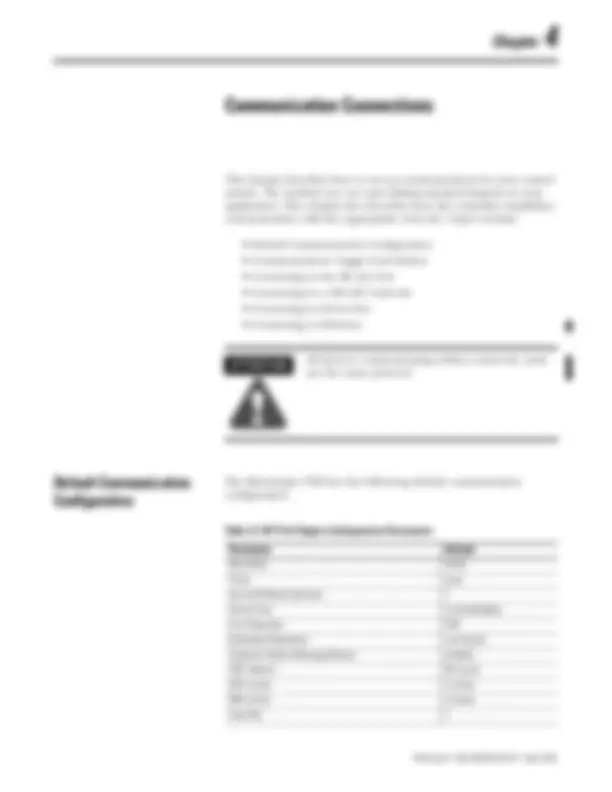
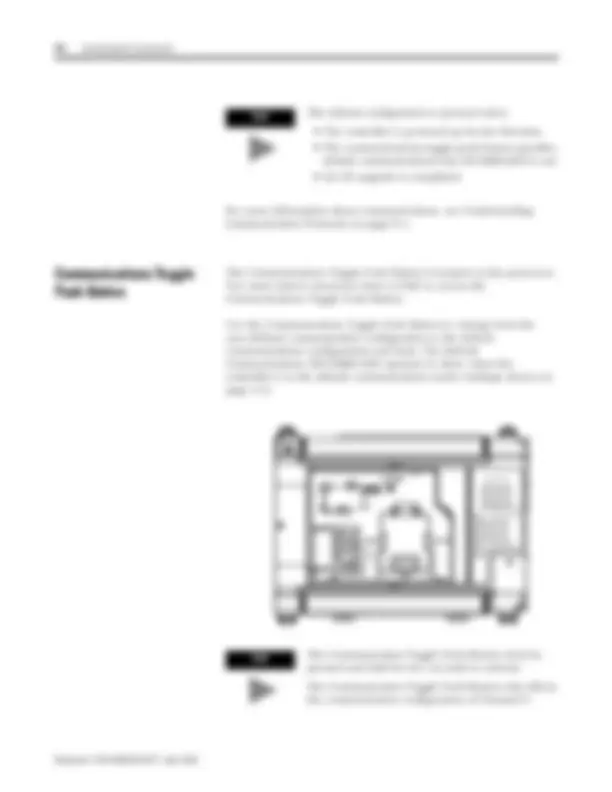
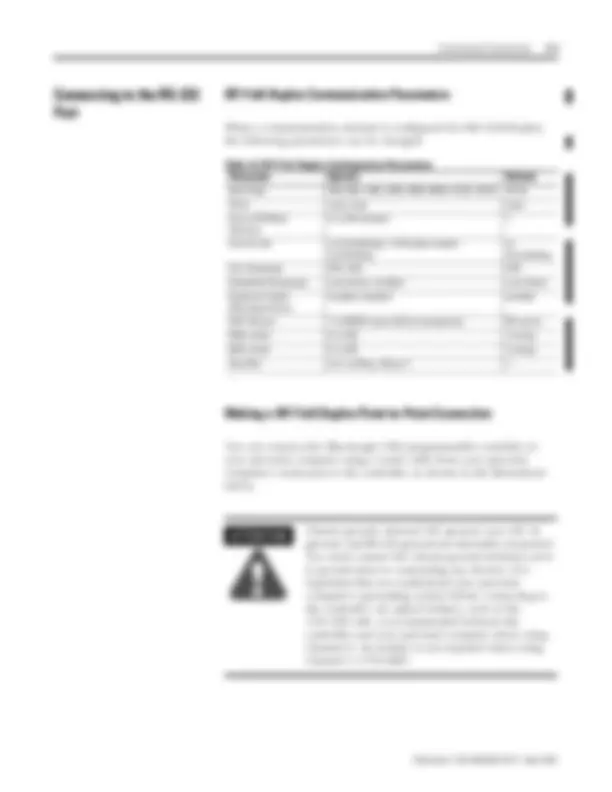
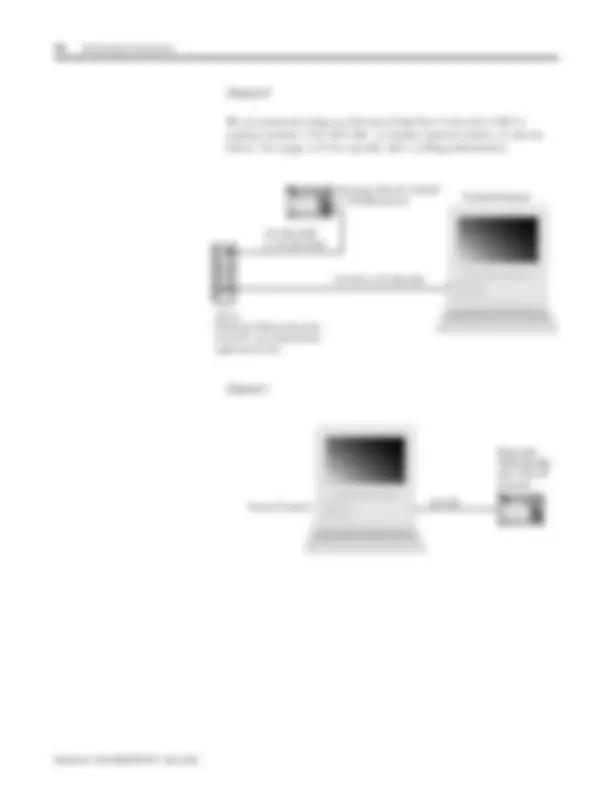
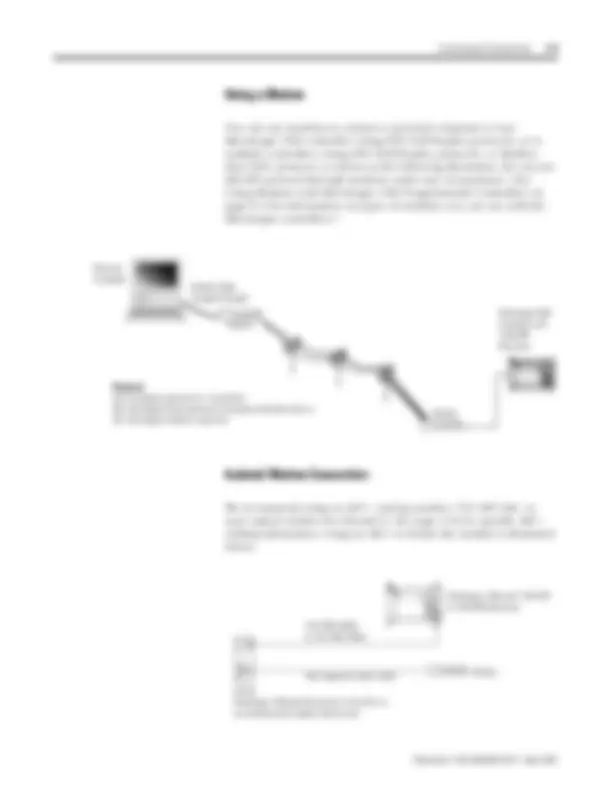
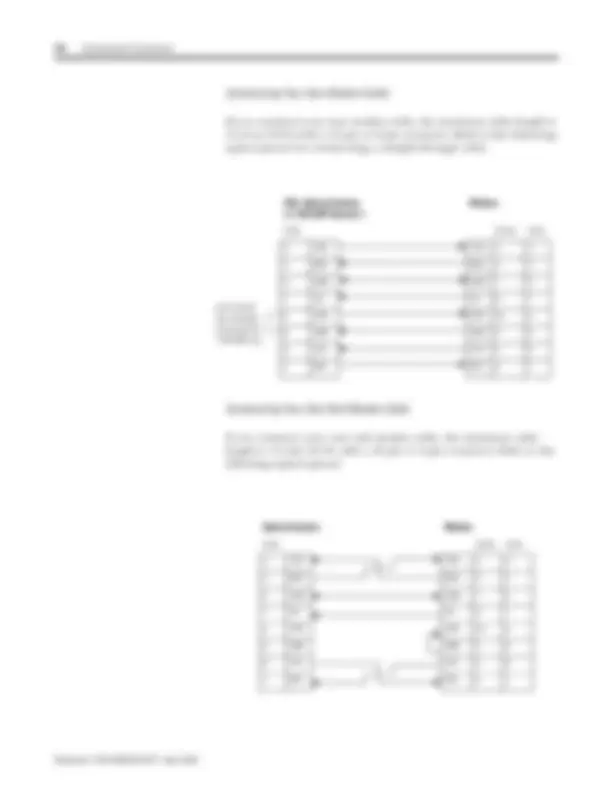
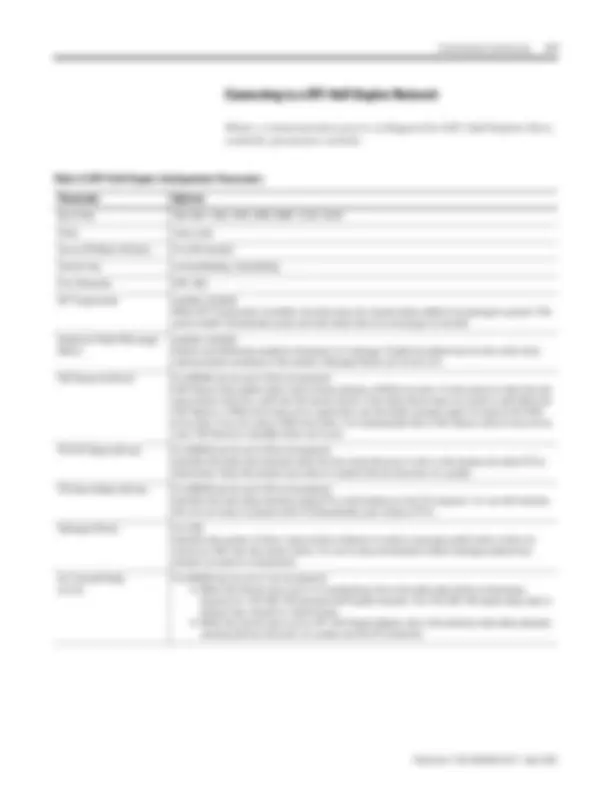
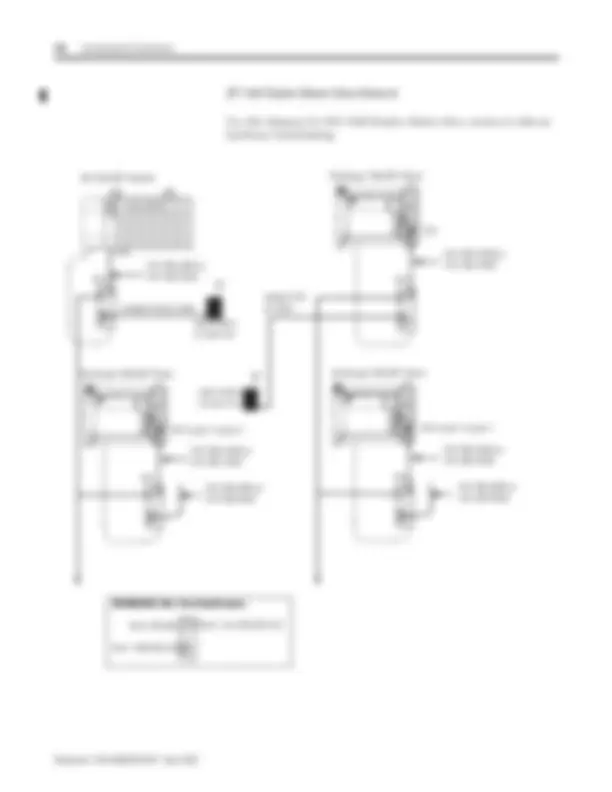
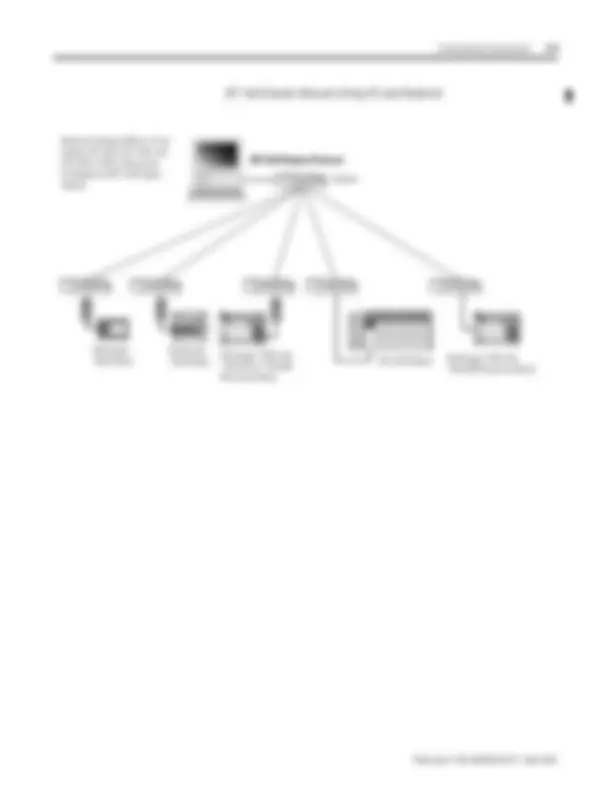
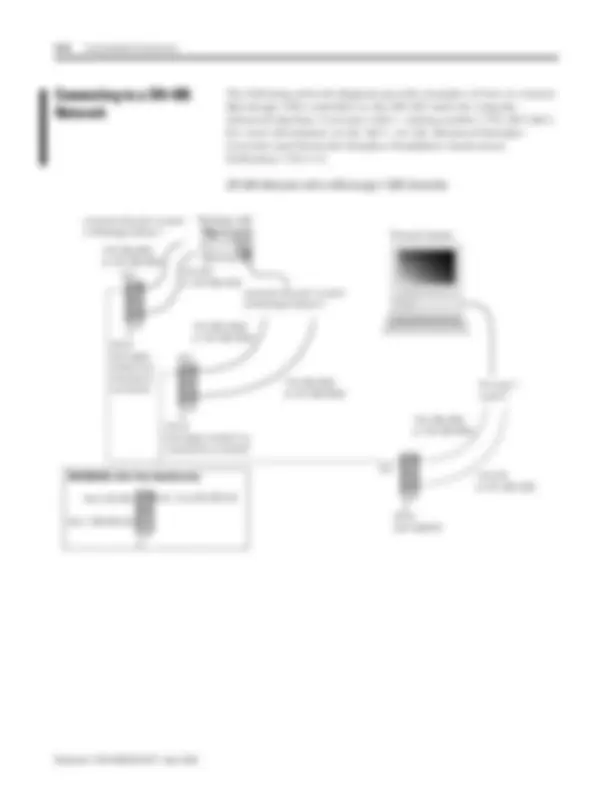
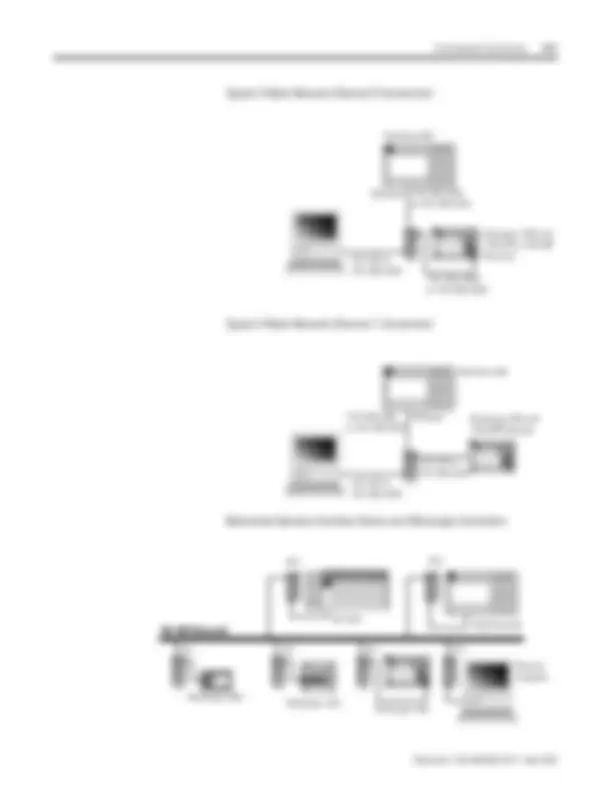
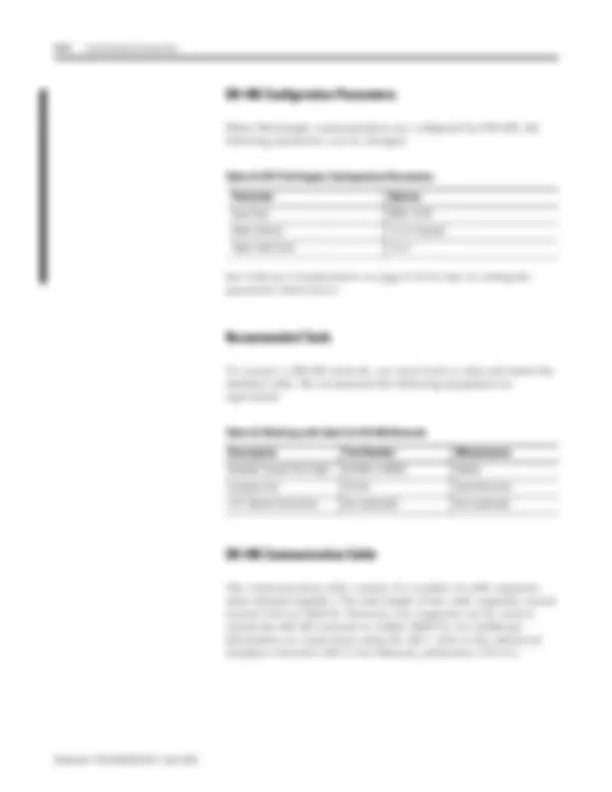
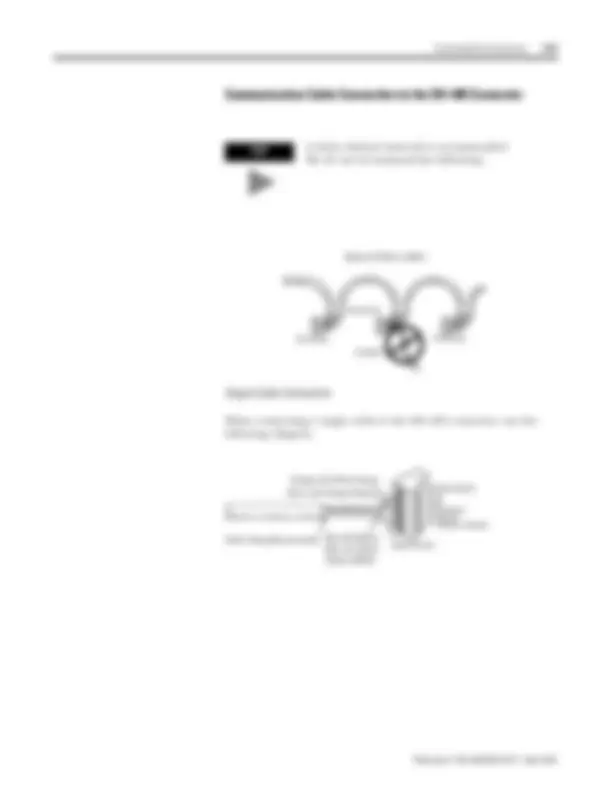
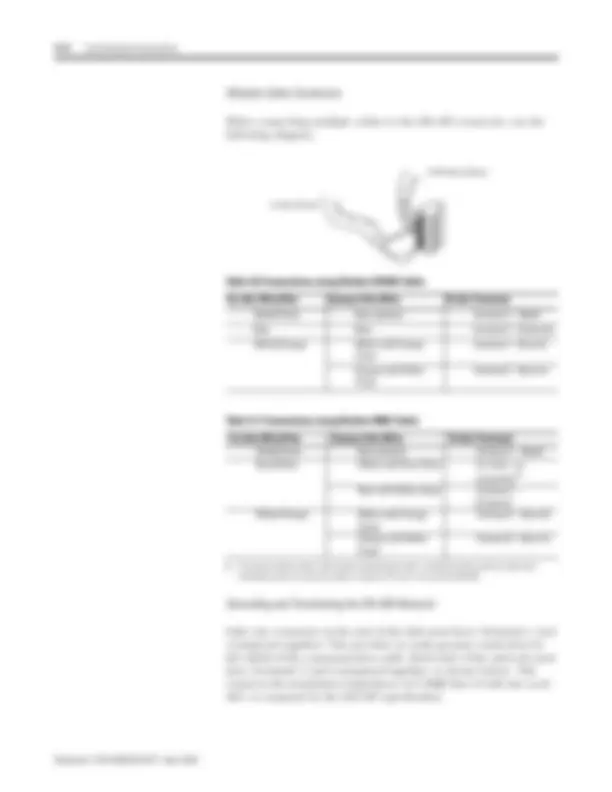
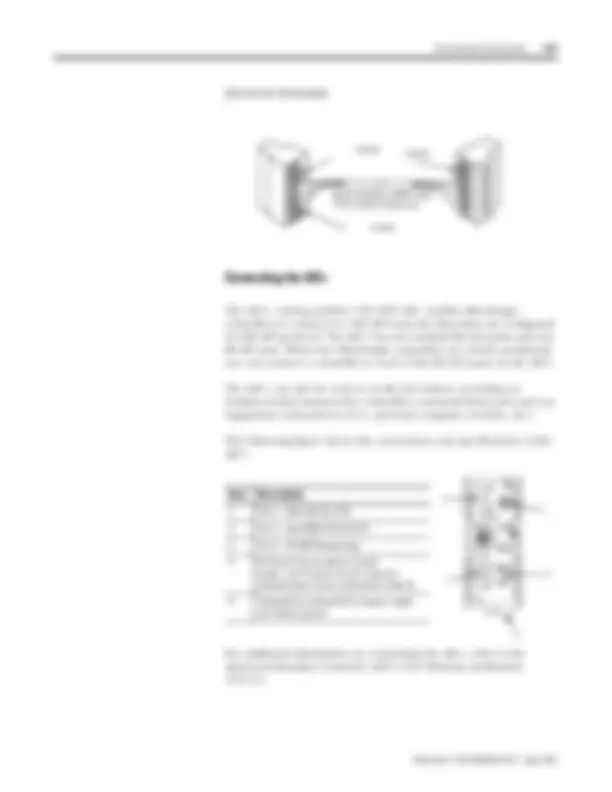
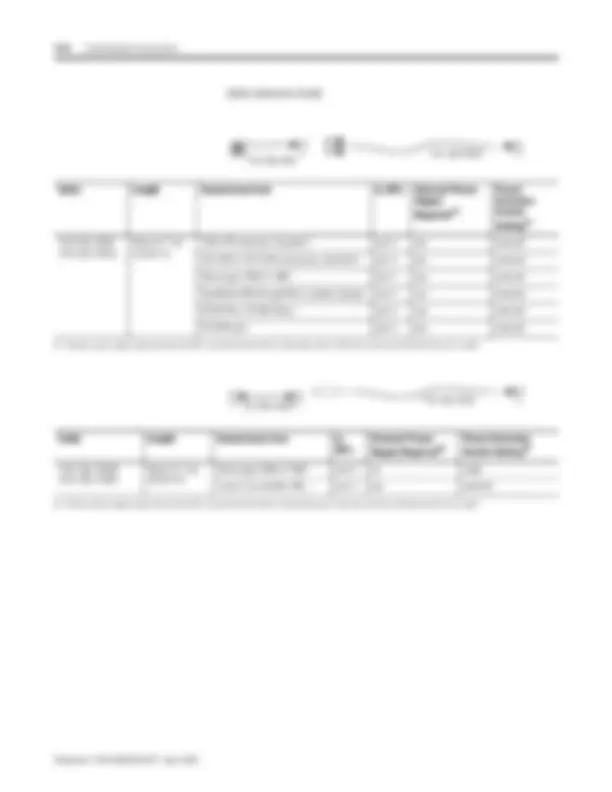
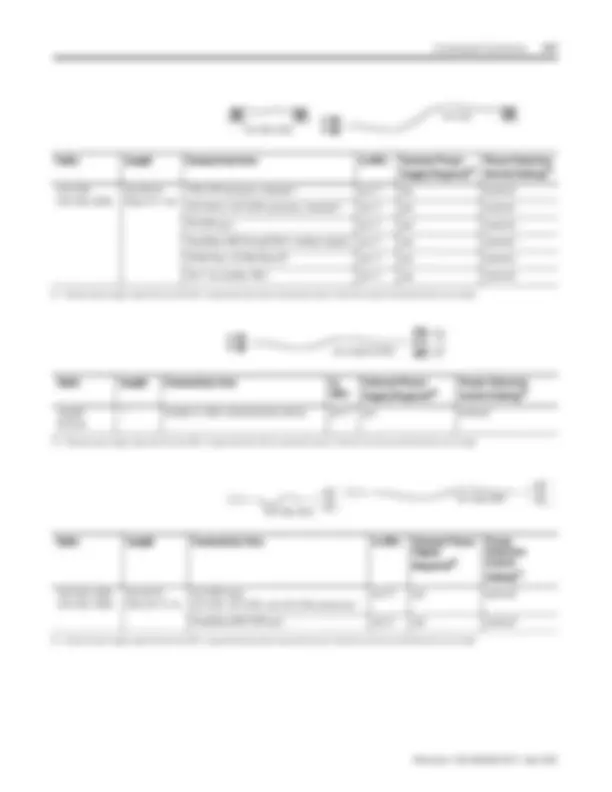
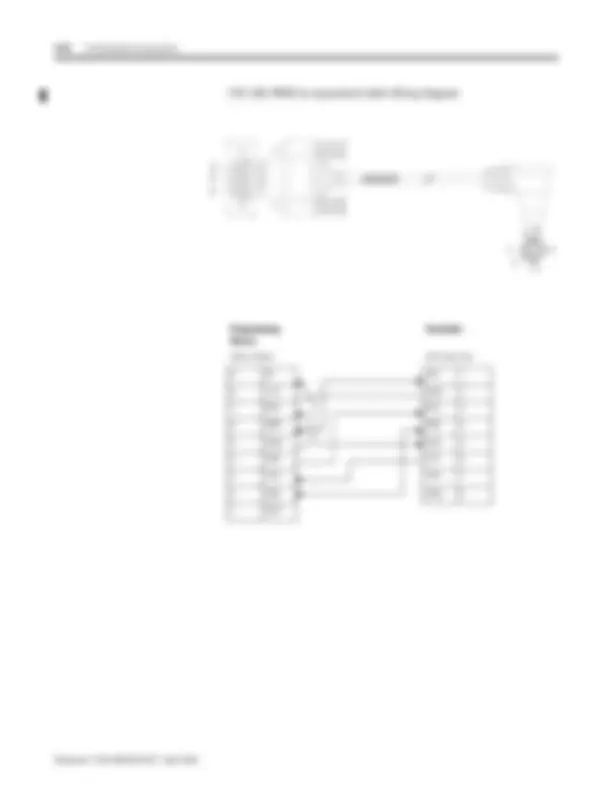
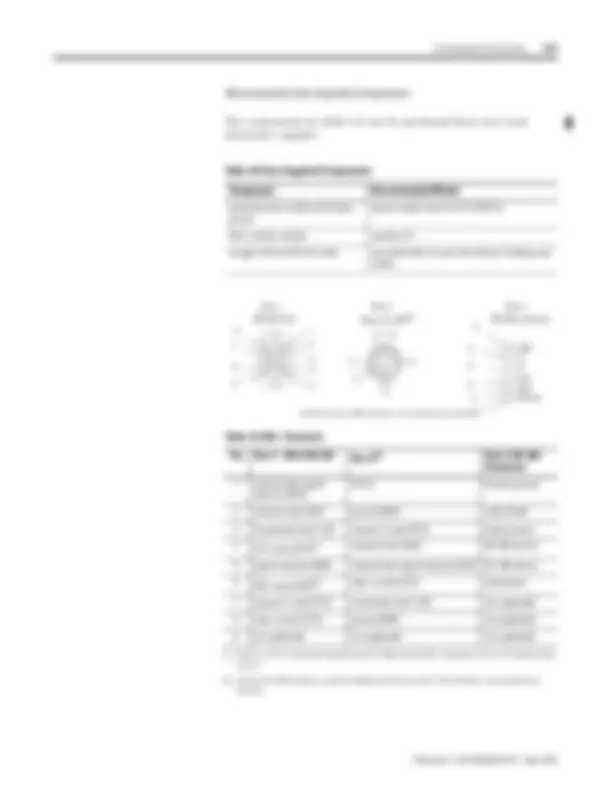
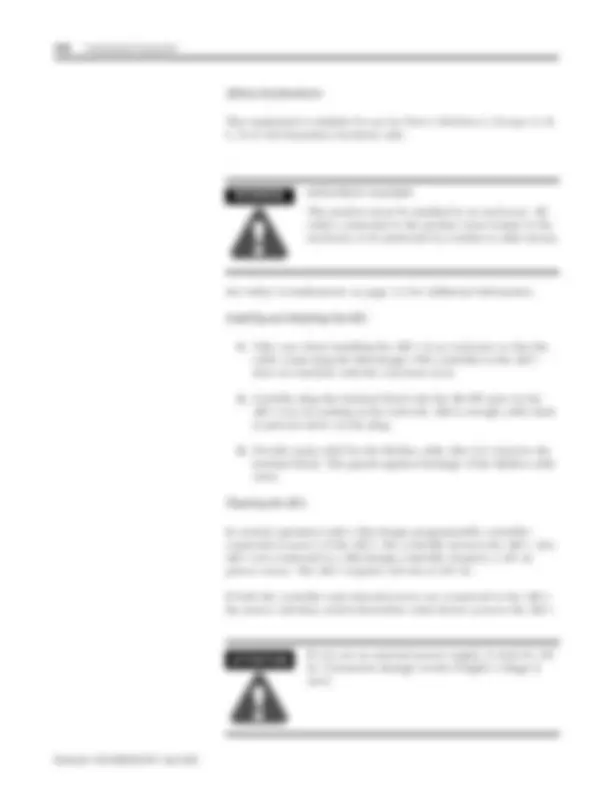
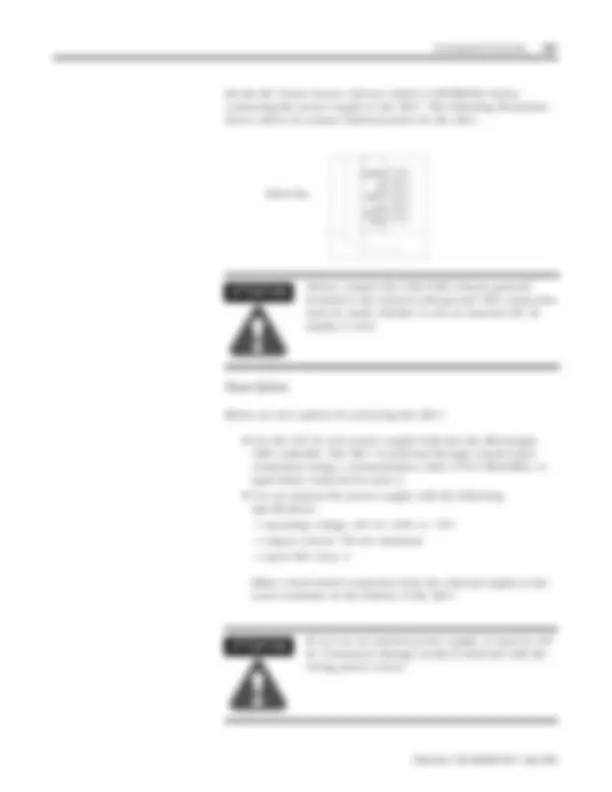
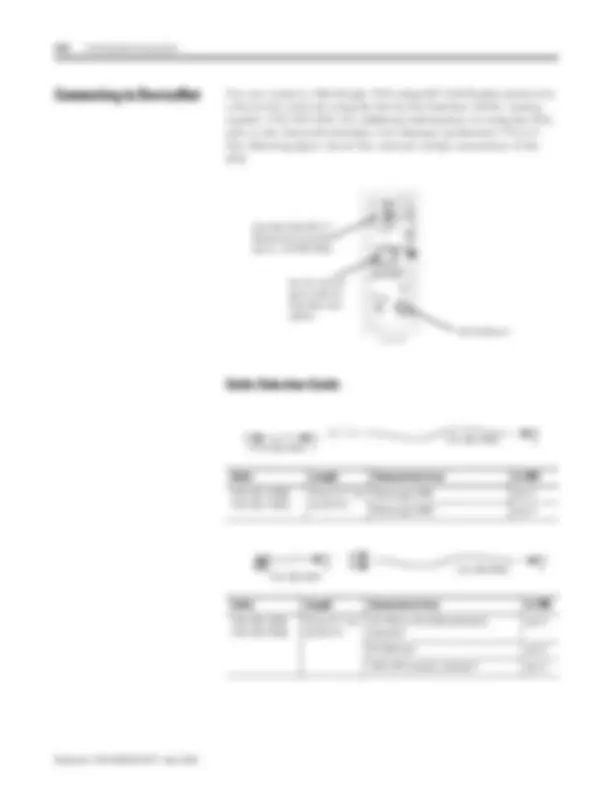
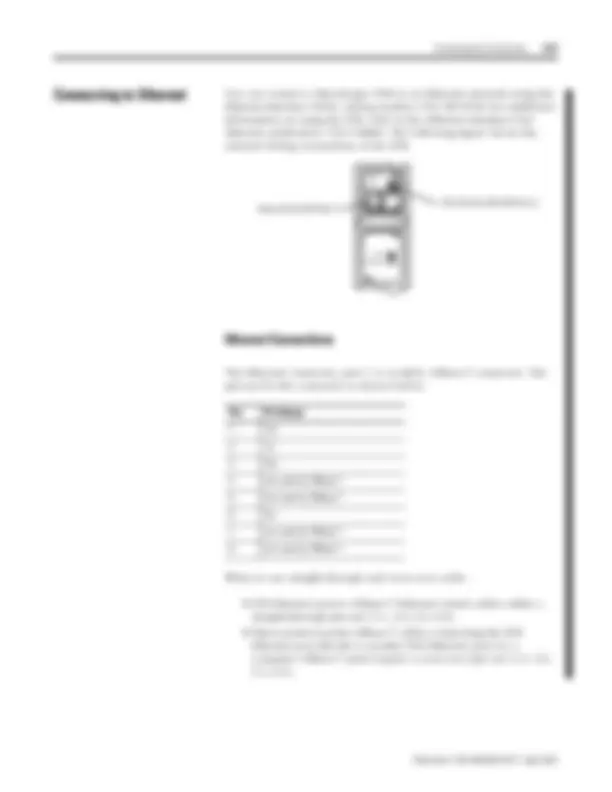
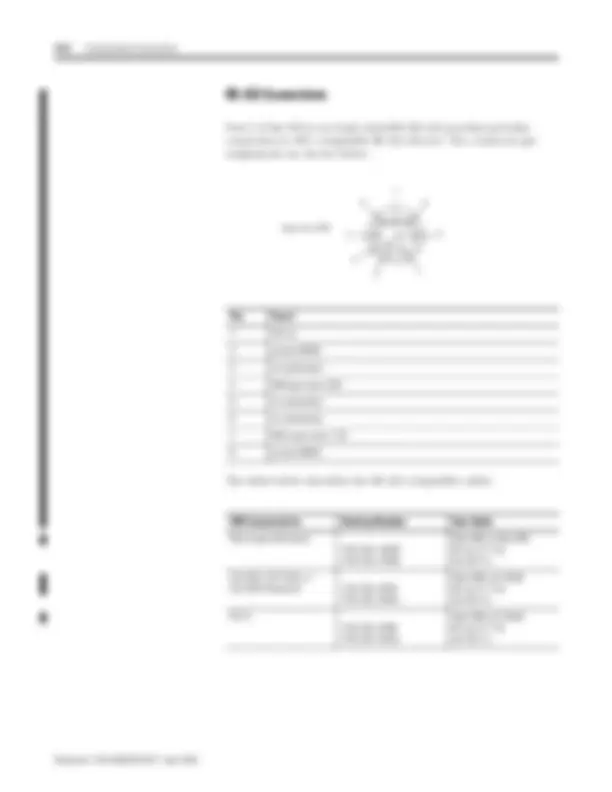
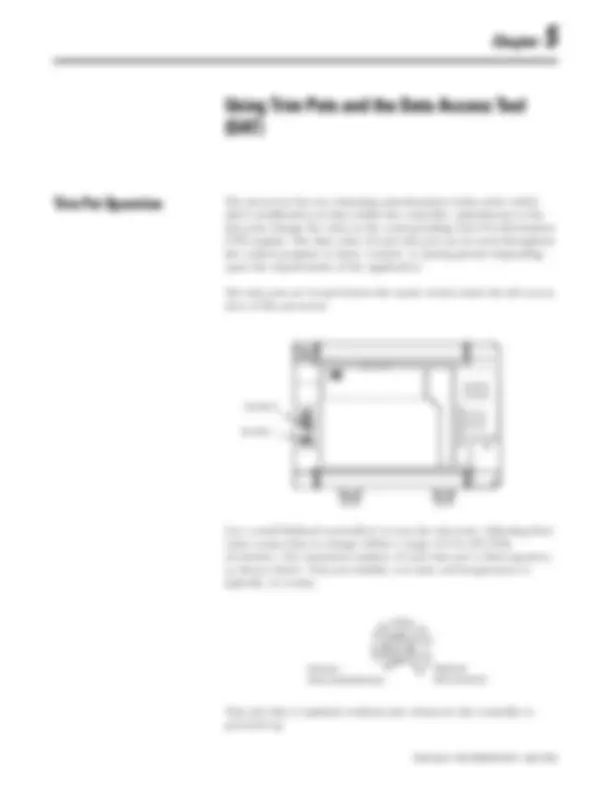
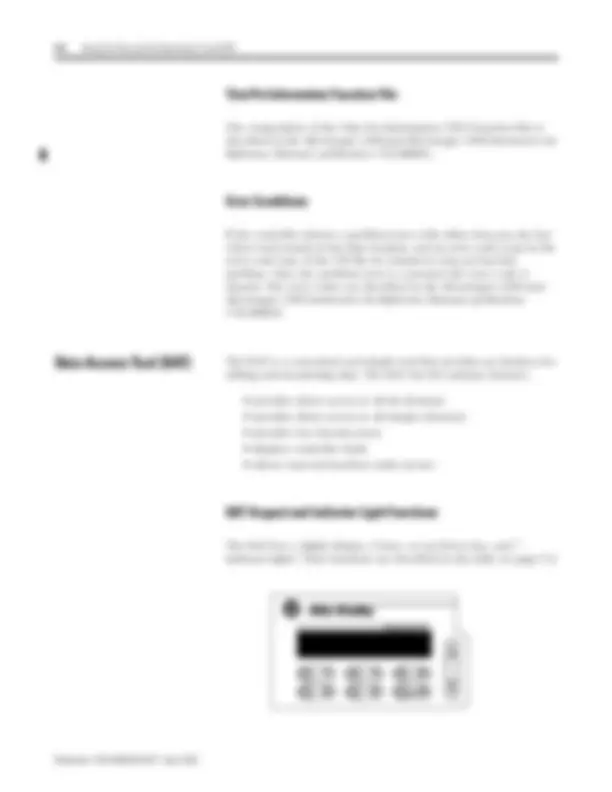
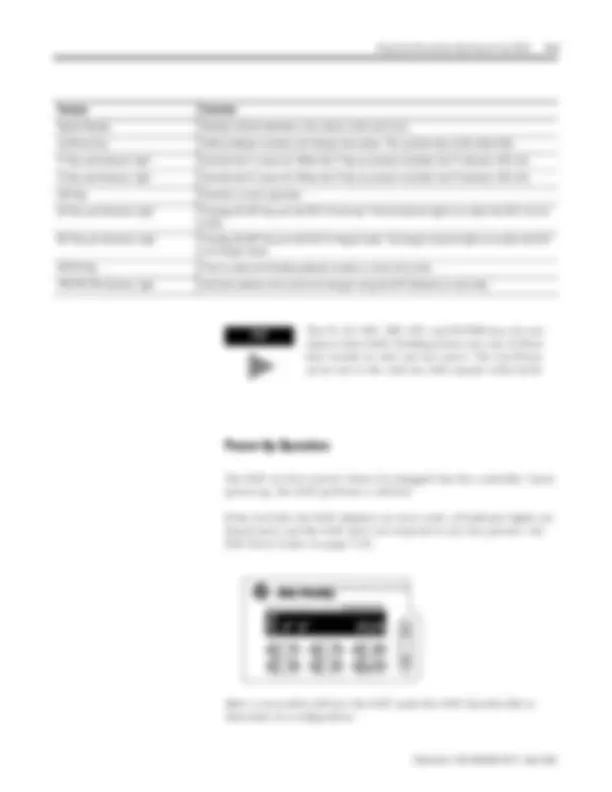
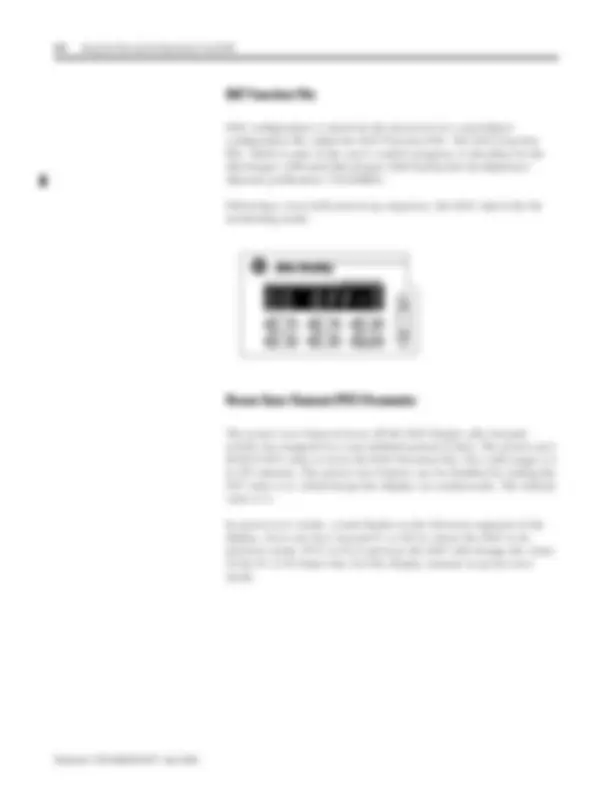
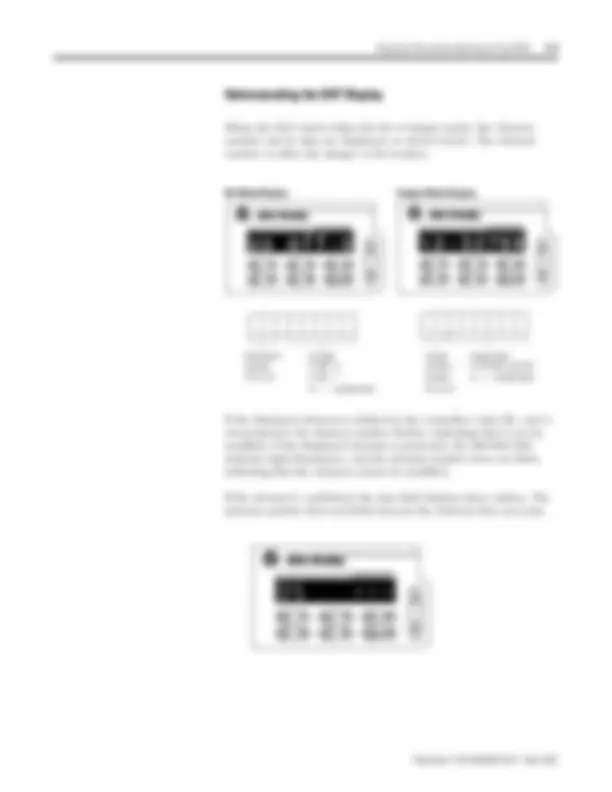
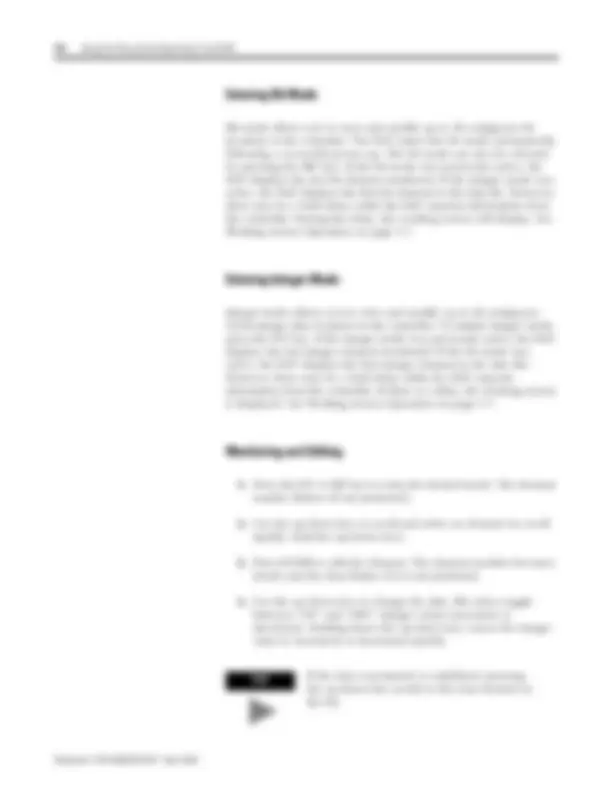
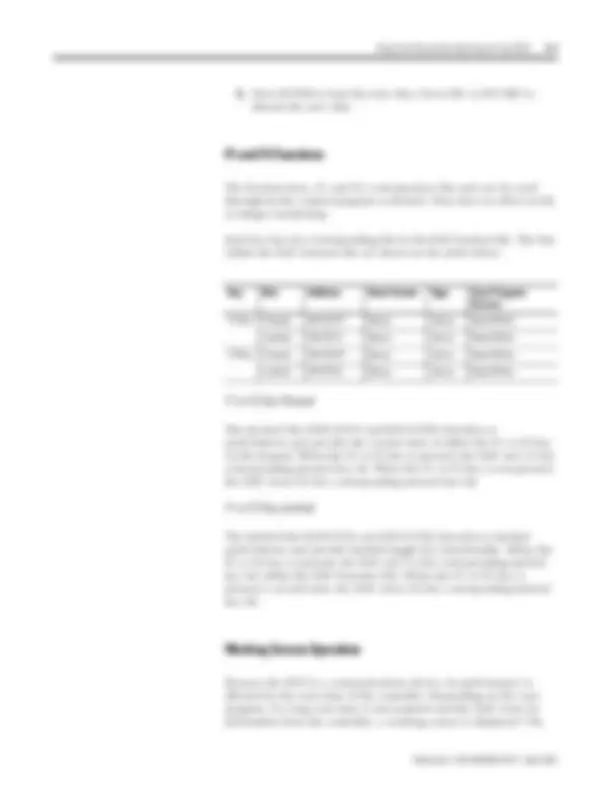
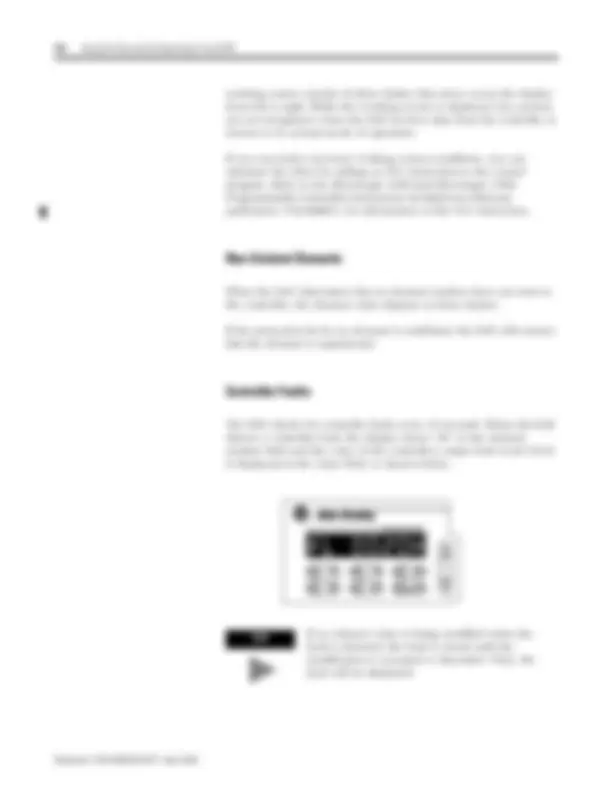
Estude fácil! Tem muito documento disponível na Docsity
Ganhe pontos ajudando outros esrudantes ou compre um plano Premium
Prepare-se para as provas
Estude fácil! Tem muito documento disponível na Docsity
Prepare-se para as provas com trabalhos de outros alunos como você, aqui na Docsity
Os melhores documentos à venda: Trabalhos de alunos formados
Prepare-se com as videoaulas e exercícios resolvidos criados a partir da grade da sua Universidade
Responda perguntas de provas passadas e avalie sua preparação.
Ganhe pontos para baixar
Ganhe pontos ajudando outros esrudantes ou compre um plano Premium
Comunidade
Peça ajuda à comunidade e tire suas dúvidas relacionadas ao estudo
Descubra as melhores universidades em seu país de acordo com os usuários da Docsity
Guias grátis
Baixe gratuitamente nossos guias de estudo, métodos para diminuir a ansiedade, dicas de TCC preparadas pelos professores da Docsity
Mocrologix 1500 - User Manual
Tipologia: Manuais, Projetos, Pesquisas
1 / 174
Esta página não é visível na pré-visualização
Não perca as partes importantes!
User Manual
Important User Information Because of the variety of uses for the products described in this publication, those responsible for the application and use of this control equipment must satisfy themselves that all necessary steps have been taken to assure that each application and use meets all performance and safety requirements, including any applicable laws, regulations, codes and standards.
The illustrations, charts, sample programs and layout examples shown in this guide are intended solely for purposes of example. Since there are many variables and requirements associated with any particular installation, Allen-Bradley does not assume responsibility or liability (to include intellectual property liability) for actual use based upon the examples shown in this publication.
Allen-Bradley publication SGI-1.1, Safety Guidelines for the Application, Installation and Maintenance of Solid-State Control (available from your local Allen-Bradley office), describes some important differences between solid-state equipment and electromechanical devices that should be taken into consideration when applying products such as those described in this publication.
Reproduction of the contents of this copyrighted publication, in whole or part, without written permission of Rockwell Automation, is prohibited.
Throughout this publication, notes may be used to make you aware of safety considerations. The following annotations and their accompanying statements help you to identify a potential hazard, avoid a potential hazard, and recognize the consequences of a potential hazard:
MicroLogix, Compact I/O, and RSLogix are trademarks of Rockwell Automation.
WARNING
Identifies information about practices or circumstances that can cause an explosion in a hazardous environment, which may lead to personal injury or death, property damage, or economic loss.
ATTENTION
Identifies information about practices or circumstances that can lead to personal injury or death, property damage, or economic loss.
IMPORTANT Identifies information that is critical for successful application and understanding of the product.
Publication 1764-UM001B-EN-P - March 2002
Summary of Changes iv
Table of Contents x
P-1 Publication 1764-UM001B-EN-P - April 2002
Preface
Read this preface to familiarize yourself with the rest of the manual. It provides information concerning:
Who Should Use this
Manual
Use this manual if you are responsible for designing, installing, programming, or troubleshooting control systems that use MicroLogix 1500 controllers.
You should have a basic understanding of electrical circuitry and familiarity with relay logic. If you do not, obtain the proper training before using this product.
Purpose of this Manual This manual is a reference guide for MicroLogix 1500 controllers. It describes the procedures you use to install, wire, and troubleshoot your controller. This manual:
Refer to publication 1762-RM001, MicroLogix 1200 and MicroLogix 1500 Programmable Controllers Instruction Set Reference Manual for the MicroLogix 1200 and 1500 instruction set and for application examples to show the instruction set in use. Refer to your programming software user documentation for more information on programming your MicroLogix 1500 controller.
Related Documentation The documents listed on page P-2 contain additional information concerning Rockwell Automation products. If you would like a copy, you can:
Preface P-
Common Techniques Used
in this Manual
The following conventions are used throughout this manual:
Rockwell Automation
Support
Rockwell Automation offers support services worldwide, with over 75 Sales/Support Offices, 512 authorized Distributors and 260 authorized Systems Integrators located throughout the United States alone, plus Rockwell Automation representatives in every major country in the world.
Contact your local Rockwell Automation representative for:
Before you contact Rockwell Automation for technical assistance, we suggest you please review the troubleshooting information contained in this publication first.
Preface P-
If the problem persists, call your local Rockwell Automation representative or contact Rockwell Automation in one of the following ways:
If you find a problem with this manual, or you have any suggestions for how this manual could be made more useful to you, please contact us at the address below:
Rockwell Automation Automation Control and Information Group Technical Communication, Dept. A602V P.O. Box 2086 Milwaukee, WI 53201-
or visit our internet page at:
http://www.rockwellautomation.com
For the latest information on MicroLogix controllers, visit www.ab.com/micrologix
Phone United States/Canada
1.440.646.
Outside United States/Canada
You can access the phone number for your country via the Internet:
1-2 Hardware Overview
MicroLogix 1500
Component Descriptions
A controller is composed of a processor (1764-LSP or enhanced 1764-LRP with RS-232 port) and one of the base units listed below. The FET transistor outputs are available on the 1764-28BXB base only.
Catalog Number
Line Power Inputs Outputs High Speed I/O
1764-24AWA 120/240V ac (12) 120V ac (12) Relay, 2 isolated relays per unit
n/a
1764-24BWA 120/240V ac (8) Standard 24V dc (4) Fast 24V dc
(12) Relay, 2 isolated relays per unit
(4) 20 kHz input
1764-28BXB 24V dc (8) Standard 24V dc (8) Fast 24V dc
(6) Relay, 2 isolated relays per unit (4) Standard 24V dc FET (2) Fast 24V dc FET
(8) 20 kHz input (2) 20 kHz output
Hardware Overview 1-
Processor (Catalog Number 1764-LSP)
Processor (Catalog Number 1764-LRP)
Communications Port
1764-DAT mounted on 1764-LSP processor.
Hardware Overview 1-
Programming Programming the MicroLogix 1500 programmable controller is done using RSLogix™ 500, Rev. 4.0 or later. Certain features are only available when using the most current version of the software, as noted in System Requirements for Using Expansion Modules on page 1-7.
The following table lists the firmware release numbers, feature and functionality enhancements, and the required version of RSLogix 500 and RSLogix 500 Starter software.
Table 1.B Required Software Version by FRN Number
Controller Firmware Release
Available for Sale Date
Catalog Number Series
Catalog Number Revision
OS FRN Number
Feature and Functionality Changes
Required Version of RSLogix 500/RSLogix 500 Starter Software
1764-LSP
Initial Release
February 1999
A B 2 Initial Release 3.01.
Enhancement October 1999
A C 3 Power Supply and Expansion Cable Compatibility
3.01.
Series B Release
March 2000
B A 4 String Data File Type, ASCII Instruction Set, Modbus RTU Slave Protocol, Ramping (when using PWM outputs), Static Data File Protection, RTC Messaging
4.00.
Enhancement October 2000
B B 5 PTO Controlled Stop, Memory Module Program Compare Bit Enhancement
4.50.
Series C Release
September 2001
C A 6 Floating Point Data File Support, Programmable Limit Switch (PLS), Real Time Clock Adjust (Copy Word), Absolute Value, Gray Code, Recipe, Message Instruction Support for 1769-SDN
5.10.
1764-LRP
Initial Release
March 2000
B A 4 Initial Release - Same Functionality as 1764-LSP
4.00.
Enhancement October 2000
B B 5 PTO Controlled Stop, Memory Module Program Compare Bit Enhancement
4.50.
Series C Release
September 2001
C A 6 Floating Point Data File Support, Programmable Limit Switch (PLS), Real Time Clock Adjust (Copy Word), Absolute Value, Gray Code, Recipe, Message Instruction Support for 1769-SDN
5.10.
1-6 Hardware Overview
Communication Options The MicroLogix 1500 can be connected to a personal computer. It can also be connected to the DH-485 network using an Advanced Interface Converter (1761-NET-AIC), to an Ethernet network using an Ethernet Interface (1761-NET-ENI), or to a DeviceNet™ network using a DeviceNet Interface (1761-NET-DNI) or through the DeviceNet Scanner module (1769-SDN). The controller can also be connected to Modbus™ SCADA networks as an RTU slave. See Communication Connections on page 4-1 for more information on connecting to the available communication options.
The 1764-LRP processor provides an additional communication port. Each of the communications ports can be independently configured for any supported communication protocol. (Channel 0 is on the base unit and Channel 1 is on the 1764-LRP processor.)
Compact™ Expansion I/O Compact expansion I/O (Bulletin 1769) can be connected to the MicroLogix 1500 Controller. A maximum of either 8 or 16 expansion I/O modules can be used, depending upon your system. See System Requirements for Using Expansion Modules on page 1-7.
See System Loading and Heat Dissipation on page F-1 for more information on system configurations.
An end cap terminator (catalog number 1769-ECR or 1769-ECL) must be used at the end of the group of I/O modules attached to the MicroLogix 1500 Controller. The end cap terminator is not provided with the base or processor units. It is required when using expansion I/O.
This illustration shows the right end cap (1769-ECR ). The left end cap (1769-ECL) is shown on page 1-10.