
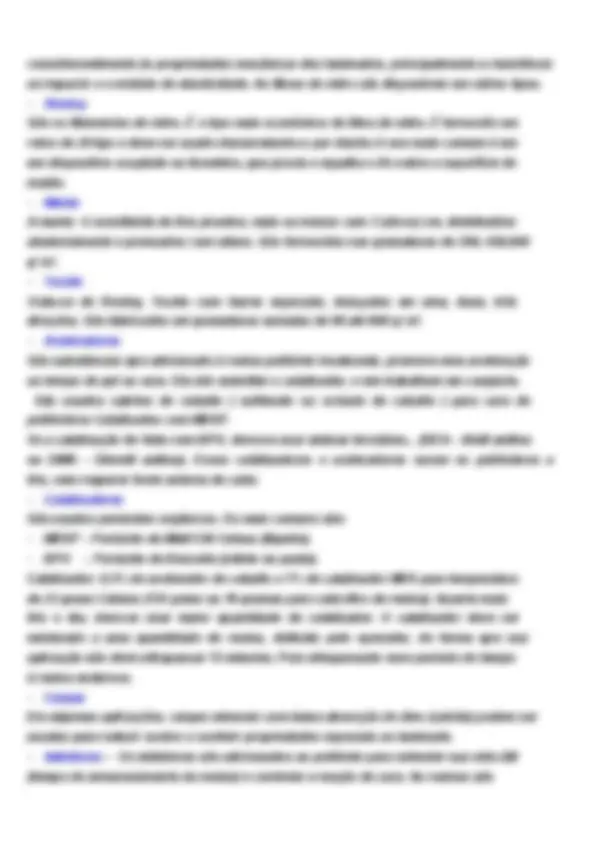
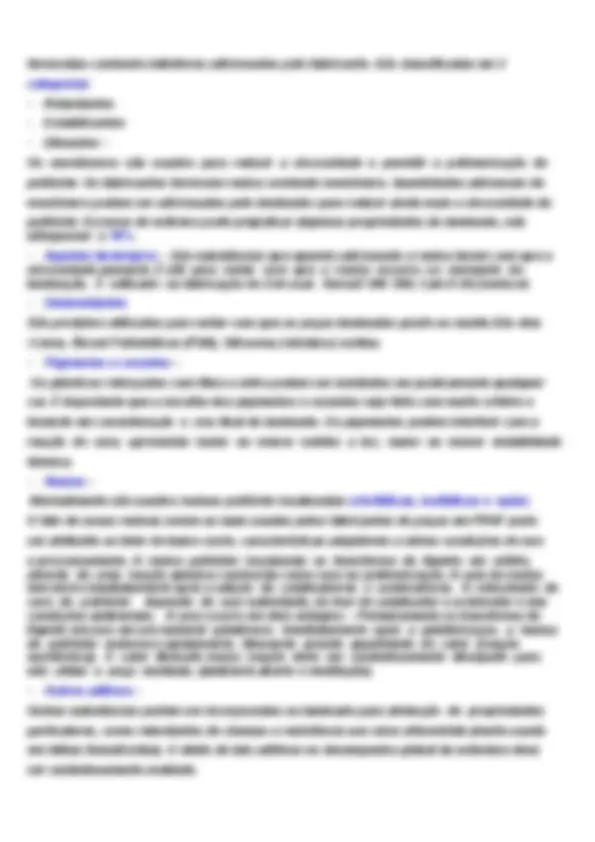
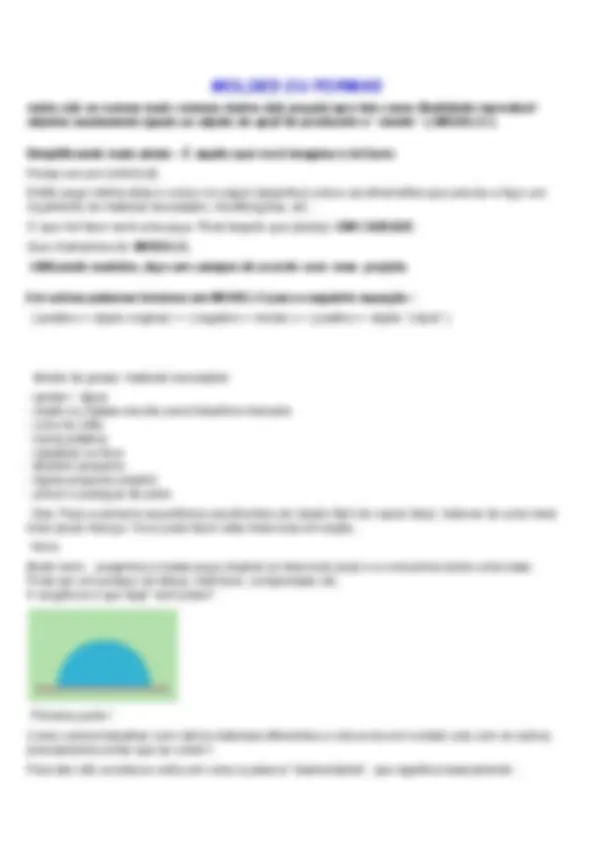
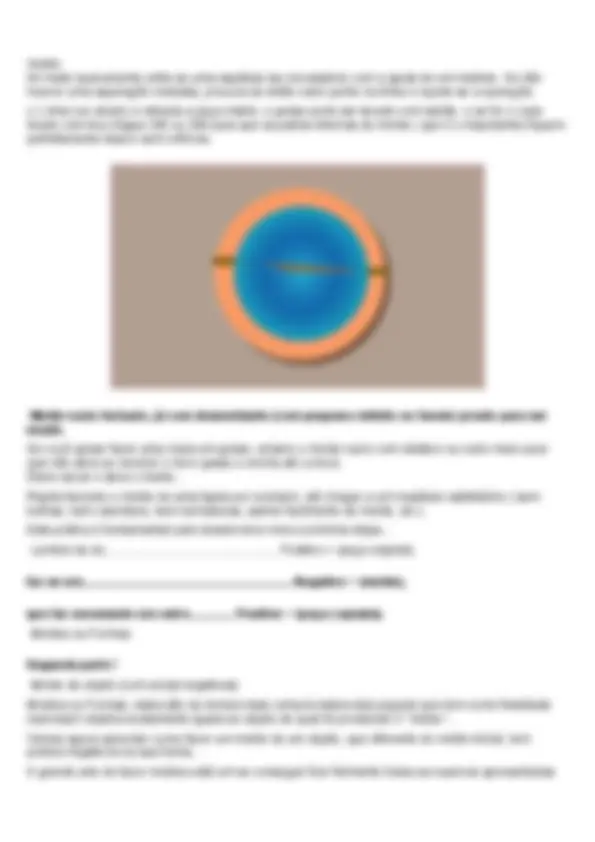
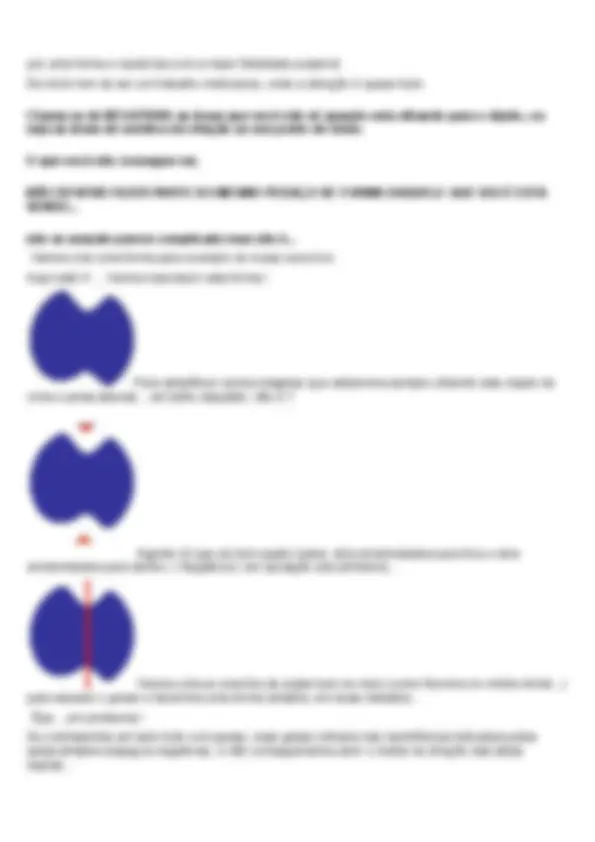
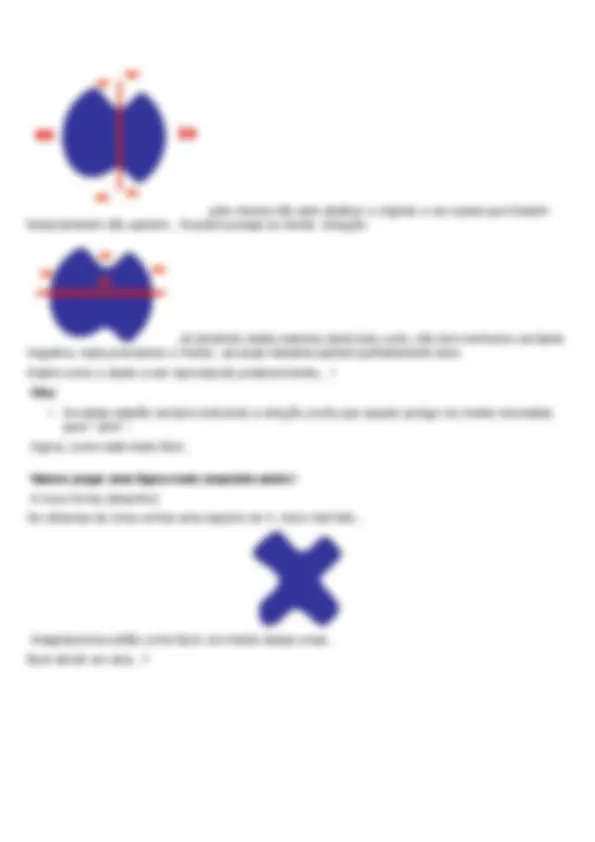
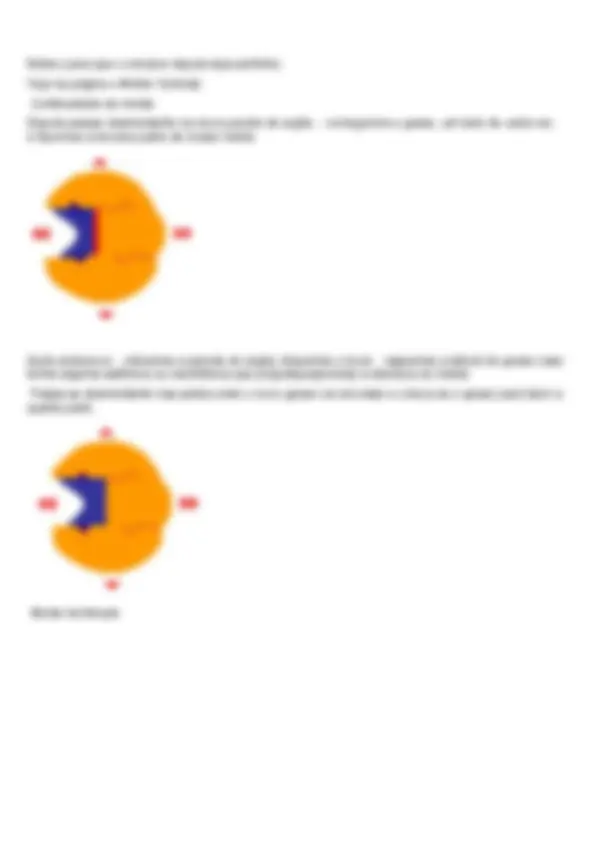
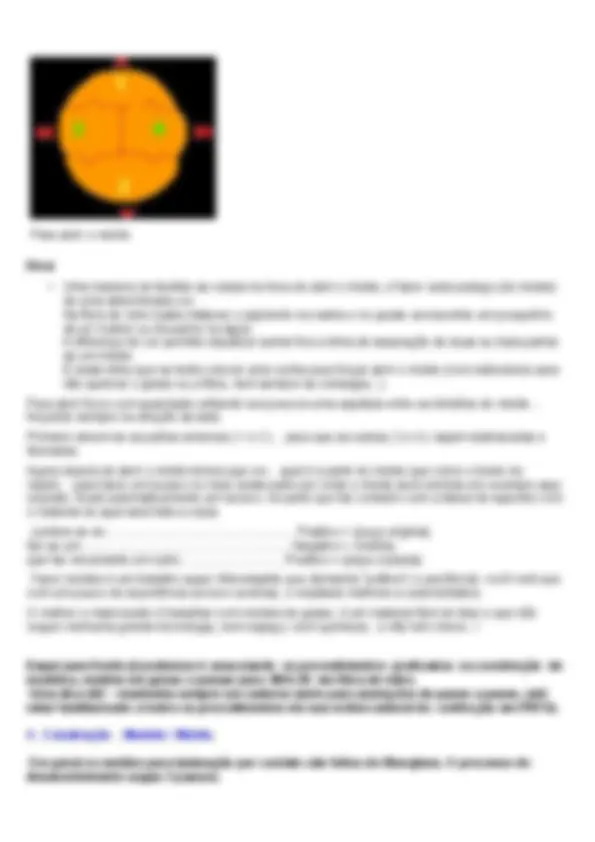

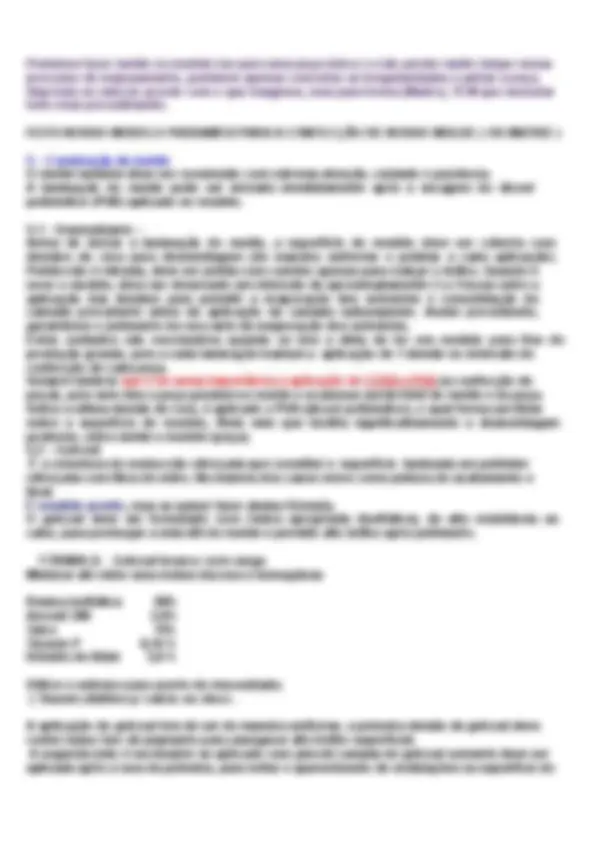
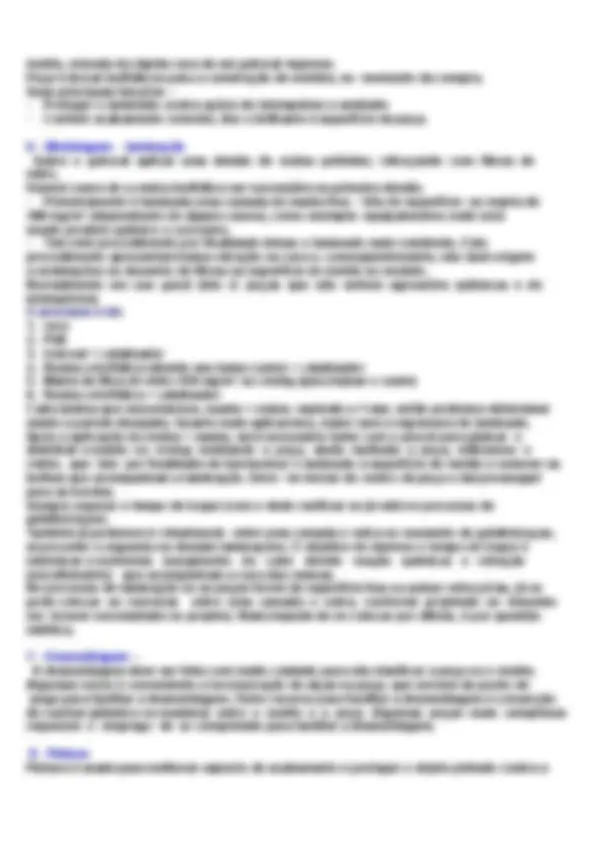
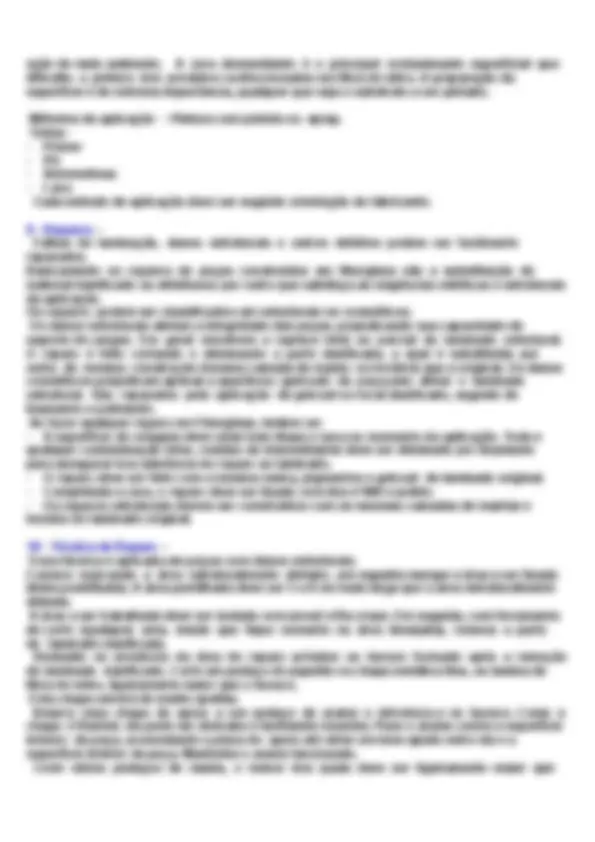
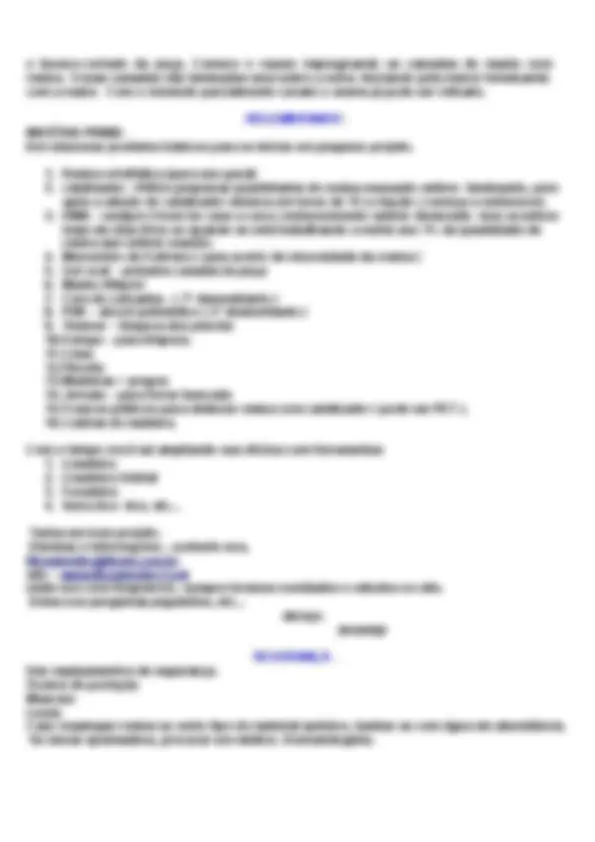
Estude fácil! Tem muito documento disponível na Docsity
Ganhe pontos ajudando outros esrudantes ou compre um plano Premium
Prepare-se para as provas
Estude fácil! Tem muito documento disponível na Docsity
Prepare-se para as provas com trabalhos de outros alunos como você, aqui na Docsity
Os melhores documentos à venda: Trabalhos de alunos formados
Prepare-se com as videoaulas e exercícios resolvidos criados a partir da grade da sua Universidade
Responda perguntas de provas passadas e avalie sua preparação.
Ganhe pontos para baixar
Ganhe pontos ajudando outros esrudantes ou compre um plano Premium
Comunidade
Peça ajuda à comunidade e tire suas dúvidas relacionadas ao estudo
Descubra as melhores universidades em seu país de acordo com os usuários da Docsity
Guias grátis
Baixe gratuitamente nossos guias de estudo, métodos para diminuir a ansiedade, dicas de TCC preparadas pelos professores da Docsity
MODELADOR EM FIBRA DE VIDRO
Tipologia: Notas de estudo
1 / 21
Esta página não é visível na pré-visualização
Não perca as partes importantes!
Compósitos são sistemas constituídos de dois ou mais materiais componentes. No que se refere aos compósitos de fibra de vidro, os principais ingredientes normalmente,são as fibras de vidro e uma resina plástica. Adicionam-se reforços de fibra de vidro à resina, tanto numa moldagem quanto num processo de fabricação, os quais dão forma ao componente final. Quando a resina cura, solidifcando-se, é reforçada pela fibra de vidro. A forma da parte final depende do molde, da ferramenta ou ferramental que se controla a geometria do compósito durante o processo. A resistência do compósito depende, primeiramente da quantidade, da disposição e do tipo de reforço na resina.Tipicamente, quanto maior a quantidade de reforço, maior será a resistência. Em alguns casos, as fibras de vidro são combinadas com outras fibras, como as de carbono e aramidas, criando um compósito Híbrido que combina as propriedades de mais de um material de reforço. Além disso, freqüentemente os compósitos são formulados com cargas (pó de mámore, cimento, minérios diversos, etc.) e aditivos que mudam os seus parâmetros de processo e desempenho. Seria impraticável relacionar os inúmeros polímeros que podem ser melhorados com as fibras de vidro; no entanto, todos os polímeros acabam caindo em um dos dois grupos básicos: RESINA - Liquido viscoso, após adição de alguns ingredientes (catalisadores e aceleradores) esse liquido se transforma em sólido rígido, infusível e insolúvel. A cura ou solidificação dessas resinas se processa a temperatura ambiente e sem requerer pressão externa, o que permite a fabricação de peças grandes e complexas em moldes simples e baratos. TIPOS DE RESINAS - TERMOFIXAS E TERMOPLÁSTICAS. Termofixos ou resinas termorrígidas curam em estado irreversível. Compara-se a resina termofixa a um ovo, uma vez cozido, essencialmente, permanece no mesmo estado (não voltado ao seu estado liquido). Uma vez prontos, não mais se fundem. São rígidos e frágeis, sendo muito estáveis a variações de temperatura. Uma das características de se confeccionar com resinas termofixas é seu custo benefício, podendo ser laminados em moldes simples e baratos, viabilizando a comercialização de peças grandes e complexas, com baixos volumes de produção (não há necessidade de investimos caros e instalações volumosas de equipamentos para se fazer peças em fibra
de vidro em baixa escala). Mudanças de projeto – São facilmente realizadas nos moldes de produção, dispensando a construção de novos moldes. Baixo custo de acabamento – Geralmente as peças de Fiberglass são moldadas na cor desejada, com Gelcoat, dispensando pintura de acabamento. Baixo custo de manutenção – Com Fiberglass, os custos de manutenção são baixos devido a alta inércia química e resistência às intempéries, inerente ao material. Como exemplo de resinas termofixas para compósitos, temos as resinas poliéster, insaturadas, éster-vinílicas, epóxi, uretânicas e fenólicas. Termoplásticos ou resinas termoplásticas, tem estrutura molecular linear, que amolece repetidamente quando aquecida em direção ao seu ponto de fusão e endurece quando resfriada. Em termos simples, pode-se comparar um termoplástico à parafina, a qual flui quando aquecida e endurece tomando sua forma quando resfriada. A principal característica desses polímeros é poder ser fundidas diversas vezes. Para se trabalhar com esse tipo de resina é necessário investimento em equipamentos como: Injetora, compressor, estufa de secagem... e outros. Como exemplo de resina termoplástica para compósitos, temos, polipropileno, polietileno, poliestireno, ABS, Nylon, PEEK, etc... 3 - SOBRE A LAMINAÇÃO E MATÉRIAS PRIMAS A laminação feita em molde aberto vem sendo largamente empregada pela industria dos plásticos reforçados para produzir uma grande variedade de peças, especialmente estruturas de grandes dimensões e exigindo altas propriedades mecânicas. As fibras de vidro contribuem estabilidade dimensional, resistência ao calor, e altas propriedades mecânicas aos laminados. As demais propriedades – resistência química ou elétrica, acabamento, cor, etc...,são determinadas pela Resina de poliéster. As fibras de vidro são especialmente desenvolvidas para ter desempenho tanto na laminação como no produto acabado. A escolha das matérias primas mais adequadas depende das necessidades ditadas pelo uso final a que a peça se destina, como por exemplo, resistência a intempéries, ao fogo, ao impacto, e outras. Uma vez familiarizado com as matérias primas que compõem o laminado, o transformador (laminador) pode escolher a melhor combinação para as suas necessidades. MATÉRIAS PRIMAS MAIS COMUNS E BÁSICAS. Faremos uma leitura dos produtos utilizados para se laminar em fibra de vidro, e logo abaixo uma relação de produtos que comumente são incorporados aos produtos devido a necessidade de cada trabalho a ser desenvolvido. 2.1 Fibras de vidro – As fibras de vidro atuam como reforço das resinas poliéster ou viniléster, aumentado
fornecidas contendo inibidores adicionados pelo fabricante. São classificadas em 2 categorias: · Retardantes · Estabilizantes · Diluentes – Os monômeros são usados para reduzir a viscosidade e permitir a polimerização do poliéster. Os fabricantes fornecem resina contendo monômero. Quantidades adicionais de monômero podem ser adicionadas pelo laminador para reduzir ainda mais a viscosidade do poliéster. Excesso de estireno pode prejudicar algumas propriedades do laminado, não ultrapassar a 10%. · Agentes tixotrópico – São substâncias que quando adicionado a resina fazem com que a viscosidade aumente. É útil para evitar com que a resina escorra no momento da laminação. È utilizado na fabricação do Gel-coat. Aerosil 200 /300, Cab-O-Sil,Santocel. · Desmoldantes São produtos utilizados para evitar com que as peças laminadas grude no molde.São eles :Ceras, Álcool Polivinílicos (PVA), Silicones,Celofane,Lecitina. · Pigmentos e corantes – Os plásticos reforçados com fibra e vidro podem ser moldados em praticamente qualquer cor. È importante que a escolha dos pigmentos e corantes seja feito com muito critério e levando em consideração o uso final do laminado. Os pigmentos podem interferir com a reação de cura, apresentar maior ou menor solidez a luz, maior ou menor estabilidade térmica. · Resina – Normalmente são usados resinas poliéster insaturadas ortoftálicas, isoftálicas e epóxi. O fato de essas resinas serem as mais usadas pelos fabricantes de peças em PRVF pode ser atribuído ao fator de baixo custo, características adaptáveis a várias condições de uso e processamento. A resina poliéster insaturada se transforma de líquido em sólido, através de uma reação química conhecida como cura ou polimerização. A cura da resina tem início imediatamente após a adição de catalisadores e aceleradores. A velocidade de cura do poliéster depende de sua reatividade, do teor de catalisador e acelerador e das condições ambientais. A cura ocorre em dois estágios – Primeiramente se transforma de líquido viscoso em um material gelatinoso. Imediatamente após a gelatinizaçao, a massa de poliéster endurece rapidamente, liberando grande quantidade de calor (reação exotérmica). O calor liberado nessa reação deve ser cuidadosamente dissipado para não afetar a peça moldada. (ambiente aberto e ventilação). · Outros aditivos - Outras substâncias podem ser incorporadas ao laminado para obtenção de propriedades particulares, como retardantes de chamas e resistência aos raios ultravioleta (muito usado em telhas translúcidas). O efeito de tais aditivos no desempenho global da estrutura deve ser cuidadosamente avaliado.
estes são os nomes mais comuns dados à(s) peça(s) que tem como finalidade reproduzir objetos exatamente iguais ao objeto do qual foi produzido o" molde ".( MODELO ). Simplificando mais ainda – É aquilo que você imagina e irá fazer. Pense em um CAIAQUE. Então pego minha idéia e coloco no papel (desenho),coloco as dimensões que preciso e faço um orçamento de material necessário, modificações, etc... O que irei fazer será uma peça Real daquilo que planejo. UM CAIAQUE. Que chamamos de MODELO. Utilizando madeira ,faço um caiaque de acordo com meu projeto. Em outras palavras teremos um MODELO para a seguinte equação : ( positivo = objeto original ) + ( negativo = molde ) = ( positivo = objeto "cópia" ) Molde de gesso: material necessário
Primeira parte do molde terminada, espera-se endurecer o gesso... Retira-se a parede de argila. Para que as duas partes se encaixem perfeitamente deve-se fazer pequenas cavidades ( dentes em forma de V ), nesta primeira parte do molde. Agora temos que passar novamente desmoldante na parte da fôrma de gesso que estava colada na argila e nas novas cavidades. A seguir aplicaremos o gesso como na primeira parte... Gesso terminado, esperar (aquecer e) endurecer... Terceira parte! Abrir o molde e retirar o objeto é uma tarefa feita com muito cuidado para não danificar nem o objeto que está no interior e nem o molde. a )Depois do gesso já frio, solta-se da base com a ajuda de uma espátula, forçando a passagem entre a base e o gesso. b ) Uma vez solto da base, mas sobre ela procura-se a linha de junção entre a duas metades do
molde. Ali muito suavemente enfia-se uma espátula (se necessário) com a ajuda de um martelo. Se não houver uma separação imediata, procura-se então outro ponto na linha e repete-se a operação. c ) Uma vez aberto e retirada a peça matriz, o gesso pode ser lavado com sabão, e se for o caso lixado com lixa d'água 200 ou 300 para que as partes internas do molde ( que é o importante) fiquem perfeitamente lisas e sem orifícios. Molde vazio fechado, já com desmoldante (com pequeno defeito no fundo) pronto para ser usado. Se você quiser fazer uma cópia em gesso, amarre o molde vazio com elástico ou outro meio para que não abra ao receber o novo gesso e encha até a boca. Deixe secar e abra o molde... Repita fazendo o molde de uma tigela por exemplo, até chegar a um resultado satisfatório ( sem bolhas, nem calombos, nem rachaduras, saindo facilmente do molde, etc.). Esta prática é fundamental para desenvolver-mos a próxima etapa... Lembre-se do.................................................... Positivo = (peça original), faz-se um............................................................... Negativo = (molde), que faz novamente um outro............. Positivo = (peça copiada). Moldes ou Formas Segunda parte! Molde de objeto (com areas negativas) Moldes ou Formas, estes são os nomes mais comuns dados à(s) peça(s) que tem como finalidade reproduzir objetos exatamente iguais ao objeto do qual foi produzido o" molde ". Vamos agora aprender como fazer um molde de um objeto, que diferente do molde inicial, tem pontos negativos na sua forma... A grande arte de fazer moldes está em se conseguir tirar fielmente todas as nuances apresentadas
pelo menos não sem destruir o original, e as copias que fossem feitas também não sairiam... ficariam presas no molde. Solução: Já dividindo desta maneira daria tudo certo, não tem nenhuma cavidade negativa, nada prendendo o molde...as duas metades sairiam perfeitamente bem. Assim como o objeto a ser reproduzido posteriormente...! Obs:
Não vai dar, porque ele vai se prender e não vai abrir... as setas externas perto da linha vermelha mostram, aonde ele vai prender... Que temos de fazer? Evitar os pontos que agarrem nosso molde.. .estudamos bem... pensamos com muita calma... e resolvemos que uma boa saída seria faze- lo em quatro partes... assim cada uma pode sair numa direção sem estar presa a outra...lembre-se :
feitas.( para que o encaixe depois seja perfeito). Veja na página o Molde 1(inicial). Continuidade do molde Depois passar desmoldante na nova parede de argila... começamos o gesso, um lado de cada vez.. e fazemos a terceira parte de nosso molde. Após endurecer... retiramos a parede de argila, limpamos o local... raspamos a lateral do gesso caso tenha alguma saliência ou reentrância que prejudique(prenda) a abertura do molde. Passa-se desmoldante nas partes onde o novo gesso vai encostar e coloca-se o gesso para fazer a quarta parte. Molde terminado
Para abrir o molde Dica:
4.3 - Masseamento – Todas as frestas da madeira devem ser preenchidas com a massa plástica e em seguida lixadas com lixa nº 120. A madeira do lado não-acabado (lado oposto a superfície acabada) deve ser coberta com uma demão de resina poliéster, para que não absorva umidade e mantenha inalteradas as dimensões do modelo. 4.4 - Cobrimento do modelo – O lado acabado deve ser coberto com uma demão de massa plástica, seguida de uma camada de resina. A massa plástica é usada para nivelar as irregularidades do modelo Este exemplo é de um modelo para confecção de molde ou matriz.
Cada peça, devido ao seu formato, tem sua técnica de produção,. Dado os princípios básicos, o resultado dependerá da análise global de cada caso específico e a habilidade particular de como proceder na execução do molde e laminado. O transformador deve determinar por si próprio a melhor combinação de materiais e técnicas de produção mais adequada às suas necessidades. A superfície deve ser lixada, se necessário, o masseamento deve ser repetido até ser obtida superfície lisa e regular. O pó da lixamento é removido com estopa embebida em thinner. Em seguida a superfície do modelo é coberta por uma camada de manta ou tecido, impregnada com resina poliéster, Todo cuidado deve ser tomado para evitar falhas na laminação dessa camada. Após a cura da resina, eventuais irregularidades são eliminadas com lixamento. 4.5 – Acabamento – O acabamento é feito masseando detalhes que ainda existirão e cobrindo a superfície do modelo com uma demão de resina de fácil lixamento (parafinada).Essa cobertura deve preencher todas irregularidades superficiais grosseiras e a aplicação deve ser feita com resina de baixa viscosidade. Após a cura, ou endurecimento, a cobertura é lixada com lixa dágua nº 300 e depois lixa nº 600. Para melhor acabamento, a superfície pode ser pintada com tinta de auto brilho. O modelo pode agora ser preparado para a laminação do molde. Esse preparo inclui: 1- Polimento com massa de polir automotiva 2- Aplicação de 5 demãos de cera desmoldante, com polimento de cada demão logo após cada aplicação. (dar brilho na cera, não retira-la). 3- Aplicação PVA – álcool polivinilico. Notas:
molde, oriunda da rápida cura de um gelcoat espesso. Peça Gelcoat Isoftálicos para a construção de moldes, no momento da compra. Suas principais funções – · Proteger o laminado contra ações de intempéries e umidade · Conferir acabamento colorido, liso e brilhante à superfície da peça. 6 – Modelagem - laminação Sobre o gelcoat aplicar uma demão de resina poliéster, reforçando com fibras de vidro. Haverá casos de a resina Isoftálica ser necessária na primeira demão. · Primeiramente é laminada uma camada de manta fina – Véu de superfície ou manta de 300 mg/m² (dependendo de alguns casos), como exemplo: equipamentos onde será usado produto químico e corrosivo. · Tem este procedimento por finalidade deixar o laminado mais resistente. Este procedimento apresentará baixa retração na cura e, conseqüentemente, não dará origem a ondulações ou desenho de fibras na superfície do molde ou modelo. Normalmente em uso geral (isto é: peças que não sofrem agressões químicas e de intempéries) O processo é de:
ação do meio ambiente. A cera desmoldante é o principal contaminante superficial que dificulta a pintura dos produtos confeccionados em fibra de vidro. A preparação da superfície é de extrema importância, qualquer que seja o substrato a ser pintado. Métodos de aplicação – Pintura com pistola ou spray. Tintas - · Primer · PU · Automotivas · Laca Cada método de aplicação deve ser seguido orientação do fabricante. 9 - Reparos – Falhas de laminação, danos estruturais e outros defeitos podem ser facilmente reparados. Basicamente os reparos de peças construídos em fiberglass são a substituição do material danificado ou defeituoso por outro que satisfaça as exigências estéticas e estruturais da aplicação. Os reparos podem ser classificados em estruturais ou cosméticos. Os danos estruturais afetam a integridade das peças, prejudicando sua capacidade de suporte de cargas. Em geral envolvem a ruptura total ou parcial do laminado estrutural. O reparo é feito cortando e eliminando a parte danificada, a qual é substituída por outra de mesma construção (mesma camada de manta ou tecidos) que a original. Os danos cosméticos prejudicam apenas a aparência (gelcoat) da peça,sem afetar o laminado estrutural. São reparados pela aplicação de gelcoat no local danificado, seguido de lixamento e polimento. Ao fazer qualquer reparo em Fiberglass, lembre-se: · A superfície de colagem deve estar bem limpa e seca no momento da aplicação. Toda e qualquer contaminação (óleo, resíduo de desmoldante) deve ser eliminado por lixamento para assegurar boa aderência do reparo ao laminado. · O reparo deve ser feito com a mesma resina, pigmentos e gelcoat de laminado original. · Completada a cura, o reparo deve ser lixado com lixa nº600 e polido. · Os reparos estruturais devem ser construídos com as mesmas camadas de mantas e tecidos do laminado original. 10 - Técnica de Reparo – Essa técnica é aplicada em peças com danos estruturais. Comece marcando a área estruturalmente afetada ,em seguida marque a área a ser lixada (linha pontilhada). A área pontilhada deve ser 5 a 8 cm mais larga que a área estruturalmente afetada. A área a ser trabalhada deve ser isolada com jornal e fita crepe. Em seguida, com ferramenta de corte (qualquer uma, desde que fique somente na área desejada), remova a parte do laminado danificada. Desbaste os arredores da área de reparo próximo ao buraco formado após a remoção do laminado danificado. Corte um pedaço de papelão ou chapa metálica fina, ou lamina de fibra de vidro, ligeiramente maior que o buraco. Esta chapa servirá de molde auxiliar. Amarre essa chapa de apoio a um pedaço de arame e introduza-a no buraco. Como a chapa é flexível, ela pode ser dobrada e facilmente inserida. Puxe o arame contra a superfície interior da peça, acomodando a placa de apoio até obter um bom ajuste entre ela e a superfície interior da peça. Mantenha o arame tencionado. Corte vários pedaços de manta, o menor dos quais deve ser ligeiramente maior que