
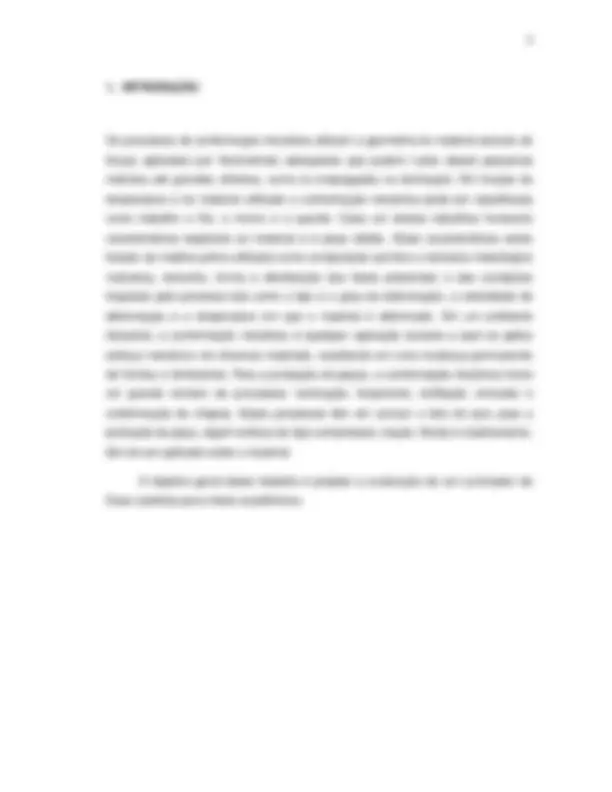
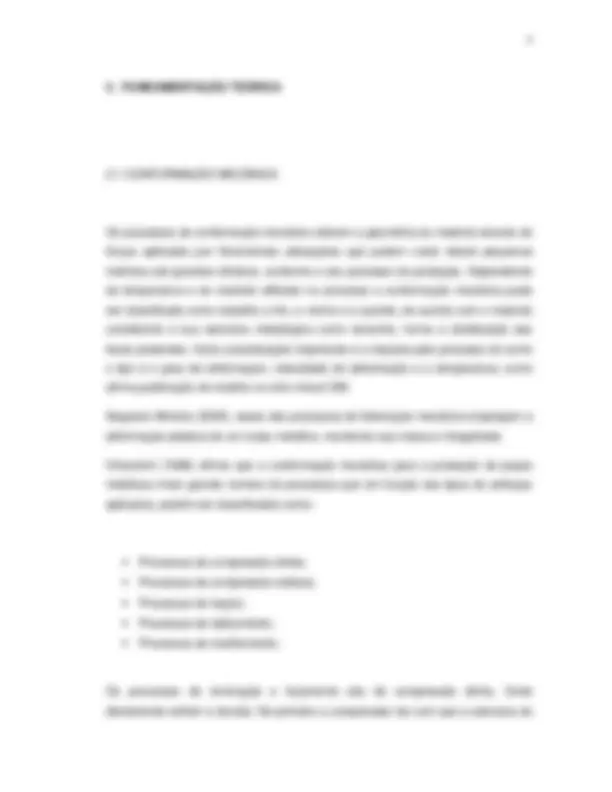
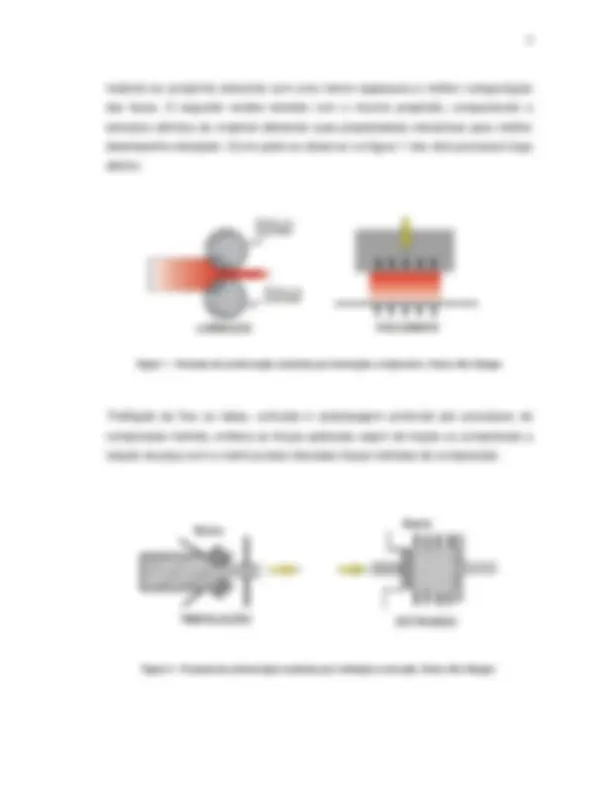
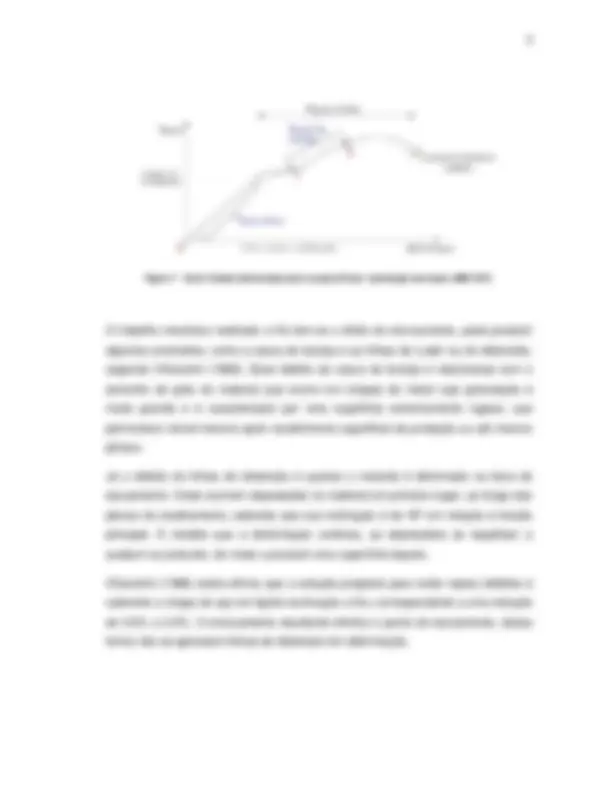
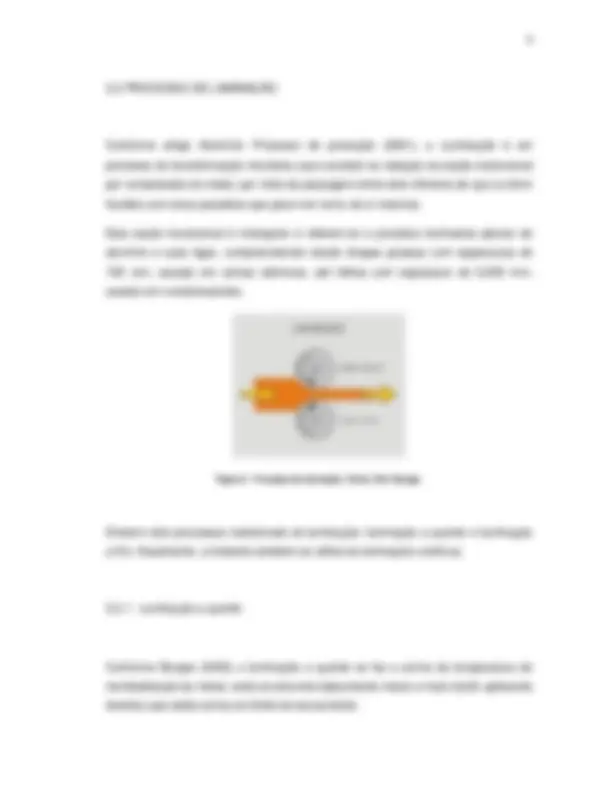
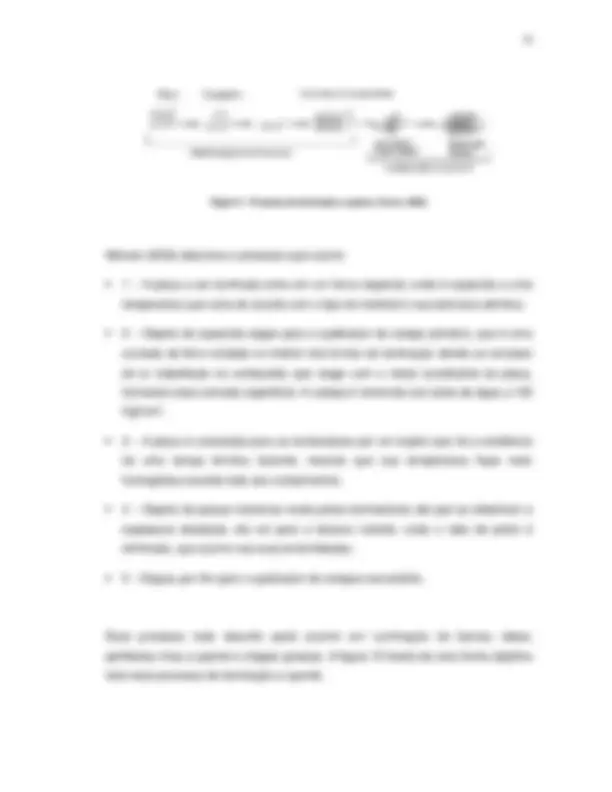
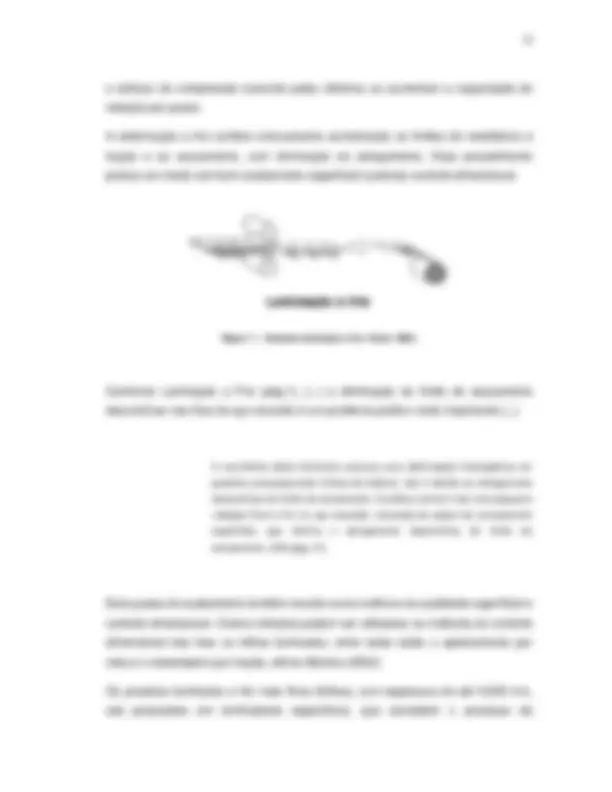
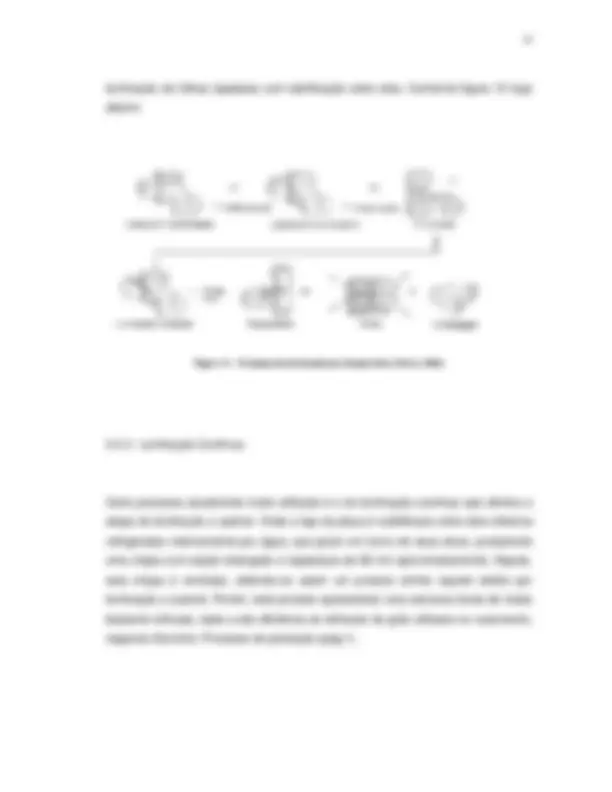
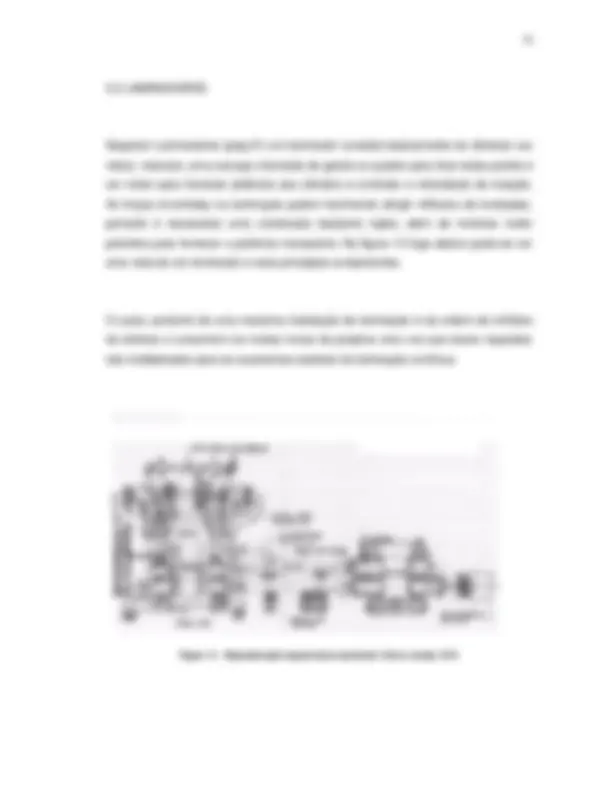
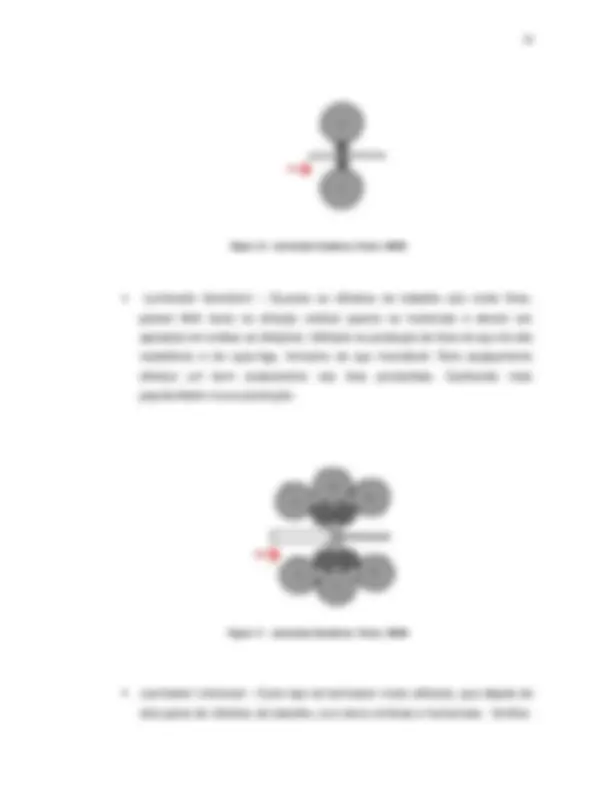
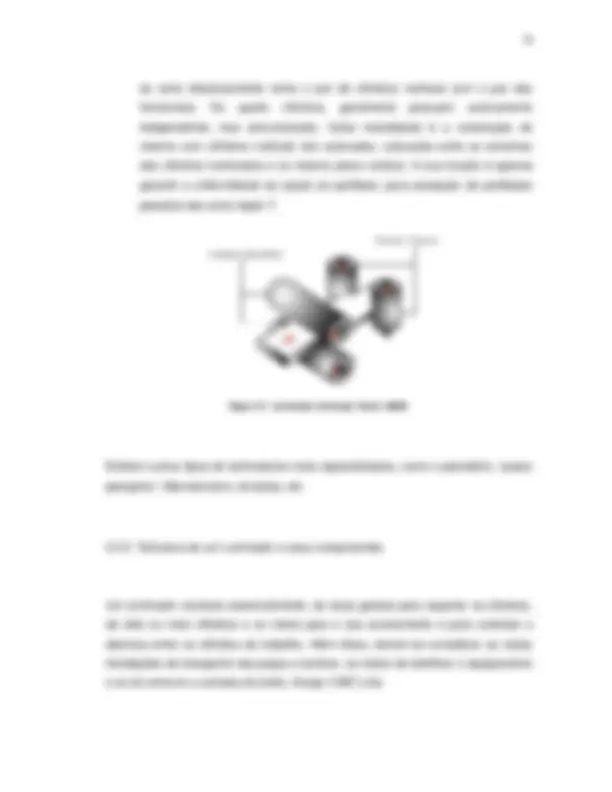
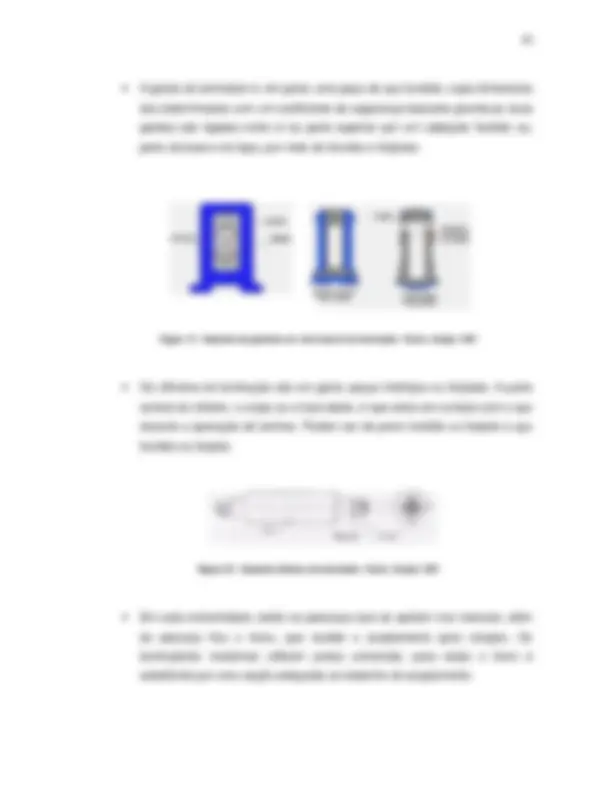
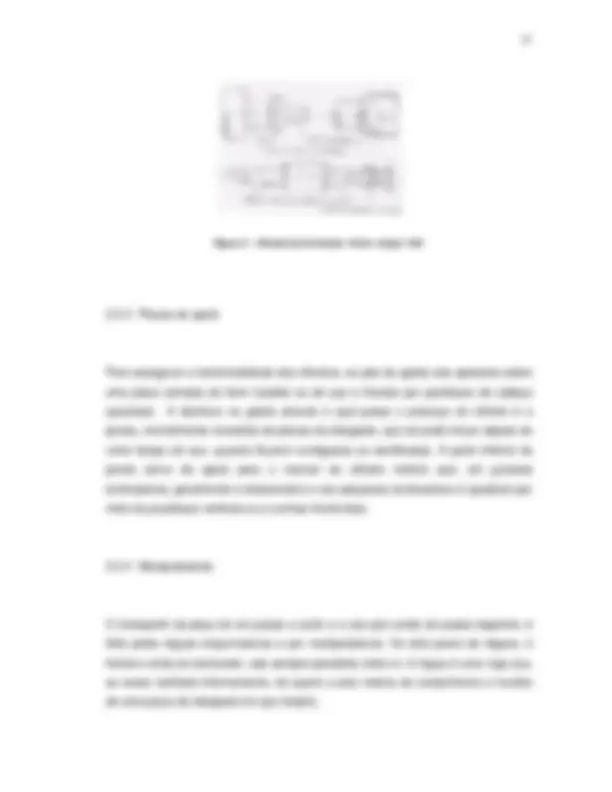
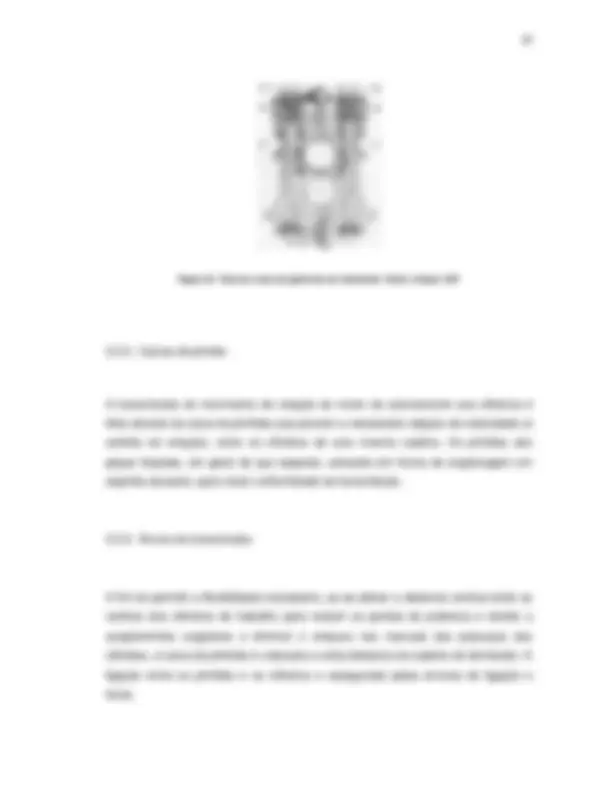
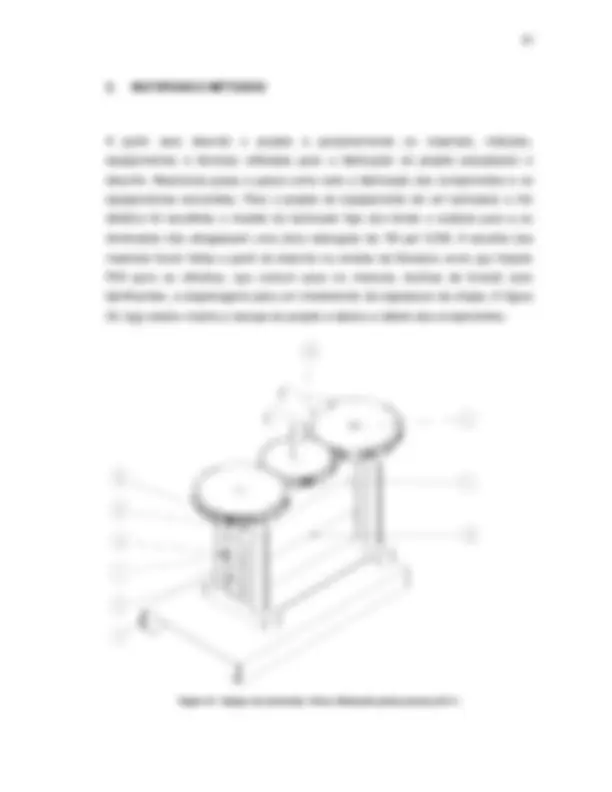
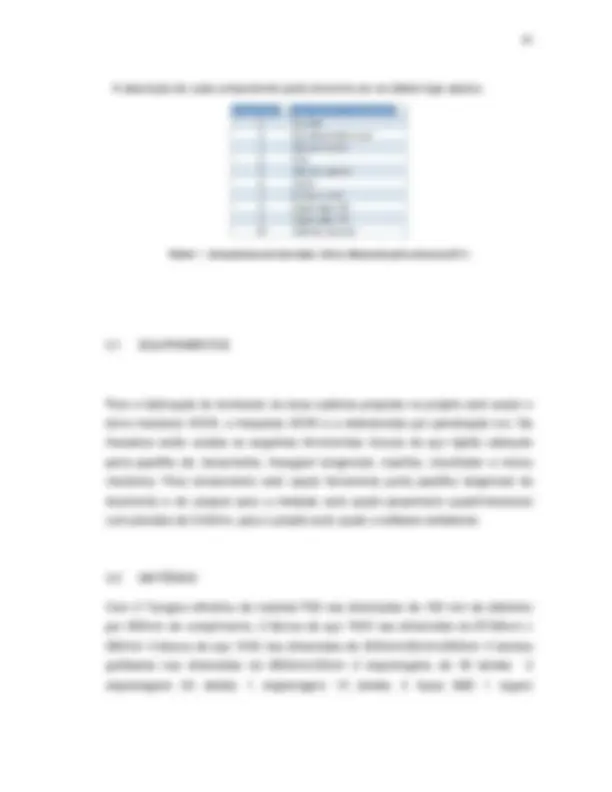
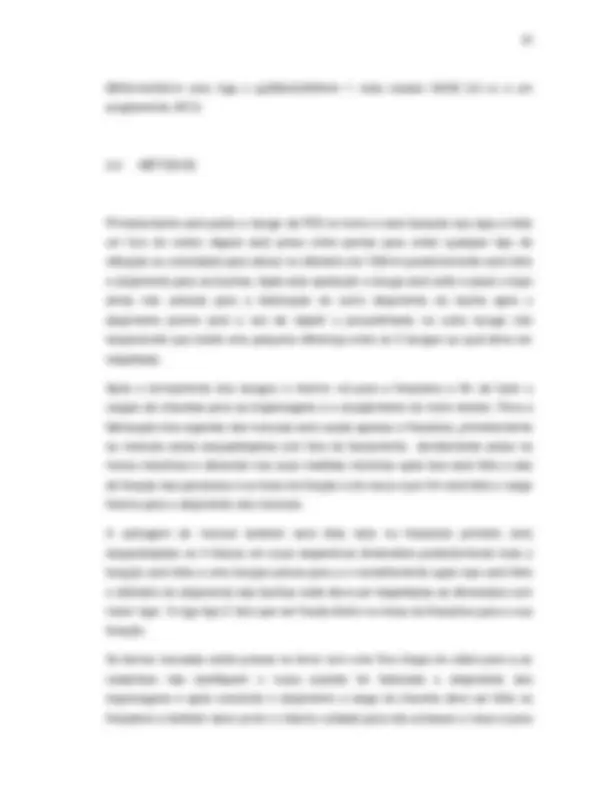
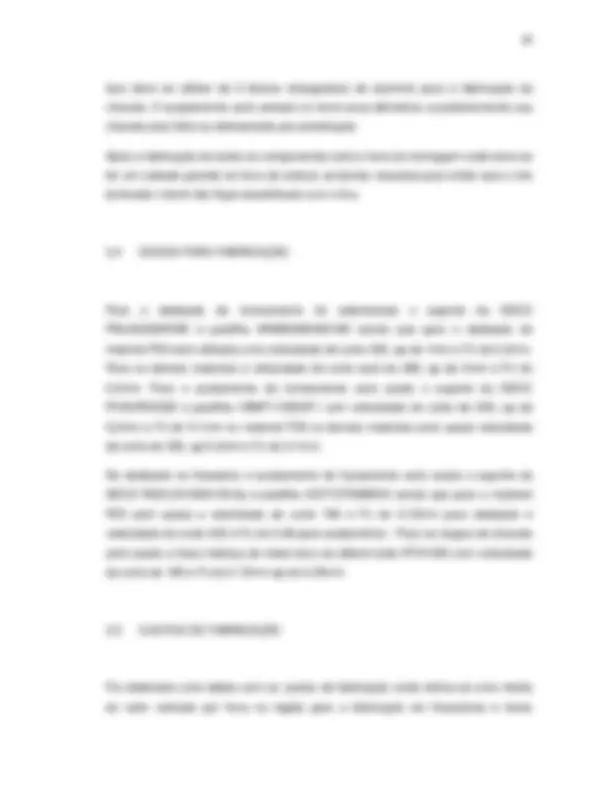
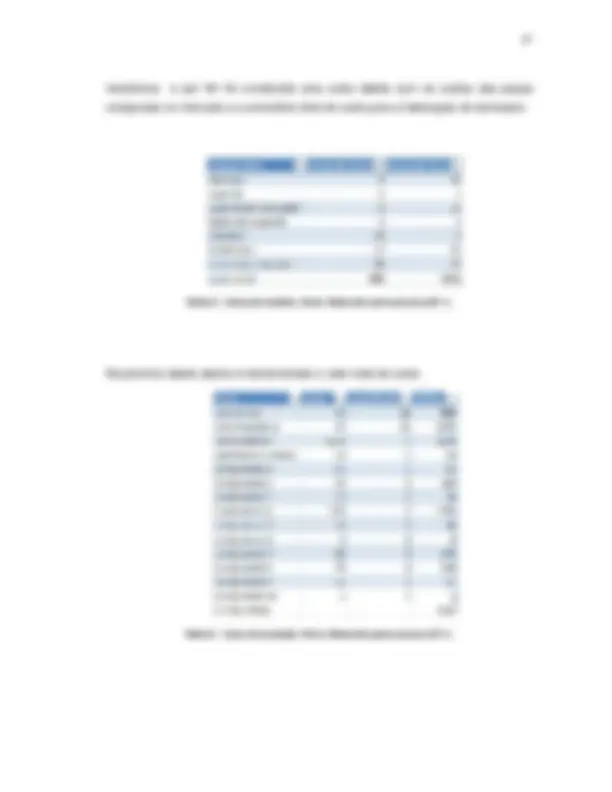
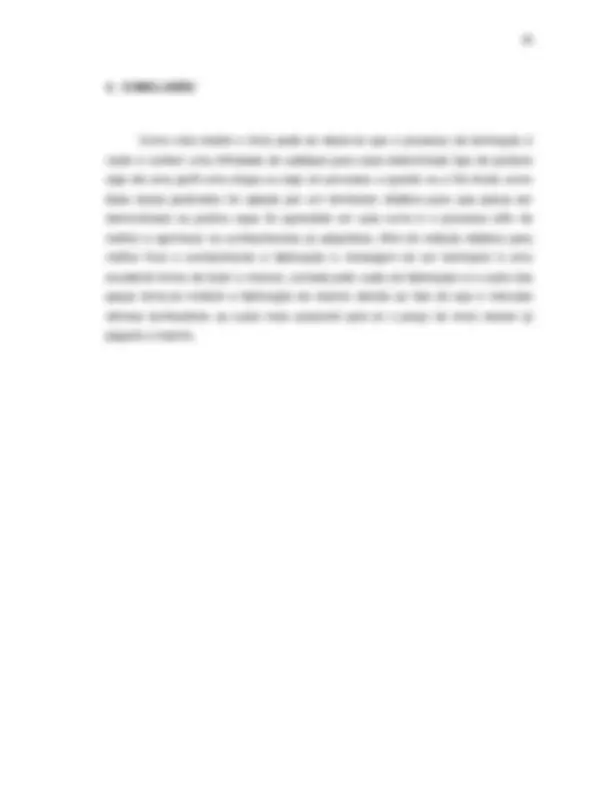
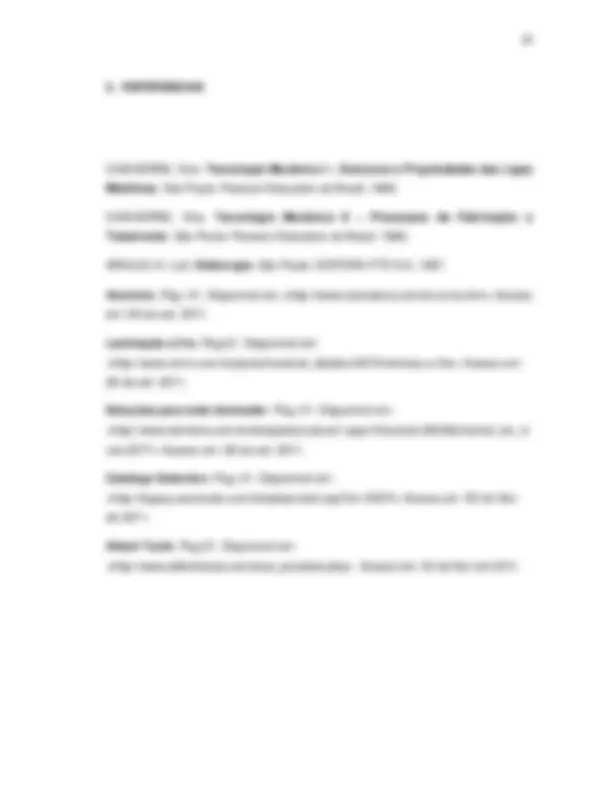
Estude fácil! Tem muito documento disponível na Docsity
Ganhe pontos ajudando outros esrudantes ou compre um plano Premium
Prepare-se para as provas
Estude fácil! Tem muito documento disponível na Docsity
Prepare-se para as provas com trabalhos de outros alunos como você, aqui na Docsity
Os melhores documentos à venda: Trabalhos de alunos formados
Prepare-se com as videoaulas e exercícios resolvidos criados a partir da grade da sua Universidade
Responda perguntas de provas passadas e avalie sua preparação.
Ganhe pontos para baixar
Ganhe pontos ajudando outros esrudantes ou compre um plano Premium
Comunidade
Peça ajuda à comunidade e tire suas dúvidas relacionadas ao estudo
Descubra as melhores universidades em seu país de acordo com os usuários da Docsity
Guias grátis
Baixe gratuitamente nossos guias de estudo, métodos para diminuir a ansiedade, dicas de TCC preparadas pelos professores da Docsity
Os processos de conformação mecânica alteram a geometria do material através de forças aplicadas por ferramentas adequadas que podem variar desde pequenas matrizes até grandes cilindros, como os empregados na laminação. Em função da temperatura e do material utilizado a conformação mecânica pode ser classificada como trabalho a frio, a morno e a quente. Cada um destes trabalhos fornecerá características especiais ao material e à peça obtida. Estas características serão função da matéria prima ut
Tipologia: Trabalhos
Oferta por tempo limitado
Compartilhado em 29/06/2012
4.8
(5)15 documentos
1 / 29
Esta página não é visível na pré-visualização
Não perca as partes importantes!
Em oferta
DEPARTAMENTO DE ENGENHARIA MECÃNICA UNIVERSIDADE DA REGIÃO DE JOINVILLE – UNIVILLE
Disciplina: Processo de Fabricação I Professo: Renato Cristofoline Alunos: Diego José Legart Deovani Kenpner Ricardo Spezzia Cleiton Vanzuita Jovino Hlenka Rafael Eger Joinville 2011
Os processos de conformação mecânica alteram a geometria do material através de forças aplicadas por ferramentas adequadas que podem variar desde pequenas matrizes até grandes cilindros, conforme o seu processo de produção. Dependendo da temperatura e do material utilizado no processo a conformação mecânica pode ser classificada como trabalho a frio, a morno e a quente, de acordo com o material constituinte e sua estrutura metalúrgica como tamanho, forma e distribuição das faces presentes. Outra consideração importante é a imposta pelo processo tal como o tipo e o grau de deformação, velocidade de deformação e a temperatura, como afirma publicação de matéria no sítio virtual CIM. Segundo Moreira (2000), esses são processos de fabricação mecânica empregam a deformação plástica de um corpo metálico, mantendo sua massa e integridade. Chiaverini (1986) afirma que a conformação mecânica para a produção de peças metálicas inclui grande número de processos que em função dos tipos de esforços aplicados, podem ser classificados como: Processos de compressão direta; Processos de compressão indireta; Processos de tração; Processos de dobramento; Processos de cisalhamento; Os processos de laminação e forjamento são de compressão direta. Onde diretamente sofrem a tensão. No primeiro a compressão faz com que a estrutura do
material se comprima deixando com uma menor espessura e melhor compactação das faces. O segundo recebe tensões com o mesmo propósito, compactando a estrutura atômica do material alterando suas propriedades mecânicas para melhor desempenho desejado. Como pode se observar na figura 1 dos dois processos logo abaixo. Figura 1 - Processo de conformação mecânica por laminação e forjamento. Fonte: Mm Borges Trefilação de fios ou tubos, extrusão e estampagem profunda são processos de compressão indireta, embora as forças aplicadas sejam de tração ou compressão a reação da peça com a matriz produz elevadas forças indiretas de compressão. Figura 2 - Processo de conformação mecânica por trefilação e extrusão. Fonte: Mm Borges.
Figura 5 - Processo de conformação mecânica por dobramento. Fonte: Mm Borges. Figura 6 - Processo de conformação mecânica por corte ocorrendo o cisalhamento. Fonte: Mm Borges. Conforme (Chiaverini 1986) as operações de conformação mecânica são processos de trabalho dentro da fase plástica do metal, como pode ser observado na figura 6. Sendo que existe a classificação de trabalho mecânico primário e secundário. O primário é onde se conforma um lingote para se produzir uma peça simples, como placas, tarugos, barras, chapas, etc. Já o secundário é responsável por refinar a estrutura presentes nos metais e ligas, onde se procura melhorar suas propriedades mecânicas. E sabe-se que para esses processos citados a temperatura é de grande influencia, tanto que se classificam como trabalho a quente e trabalho a frio.
Figura 7 - Curva Tensão deformação para os aços (Fonte- Laminação dos Aços- ABM1997) O trabalho mecânico realizado a frio tem-se o efeito do encruamento, pode produzir algumas anomalias, como a casca de laranja e as linhas de Luder ou de distensão, segundo Chiaverini (1986). Esse defeito da casca de laranja é relacionado com o tamanho de grão do material que ocorre em chapas de metal cuja granulação é muito grande e é caracterizado por uma superfície extremamente rugosa, que permanece visível mesmo após recobrimento superficial de proteção ou até mesmo pintura. Já o defeito de linhas de distensão é quando o material é deformado na faixa de escoamento. Onde ocorrem depressões no material em primeiro lugar, ao longo dos planos de cisalhamento, sabendo que sua inclinação é de 45° em relação à tensão principal. À medida que a deformação continua, as depressões se espalham a acabam se juntando, de modo a produzir uma superfície áspera. Chiaverini (1986) ainda afirma que a solução proposta para evitar esses defeitos é submeter a chapa de aço em ligeira laminação a frio, correspondente a uma redução de 0,5% a 2,0%. O encruamento resultante elimina o ponto de escoamento, dessa forma não se aparecem linhas de distensão em deformação.
Figura 9 - Processo de laminação a quente. Fonte: ABAL Monezi (2002) descreve o processo que ocorre: 1 – A placa a ser laminada entra em um forno especial, onde é aquecida a uma temperatura que varia de acordo com o tipo de material e sua estrutura atômica; 2 – Depois de aquecida segue para o quebrador de carepa primário, que é uma camada de ferro oxidada no interior dos fornos de laminação devido ao excesso de ar trabalhado na combustão que reage com o metal constituinte da placa, formando essa camada superficial. A carepa é removida com jatos de água a 120 Kgf/cm²; 3 – A placa é conduzida para os laminadores por um trajeto que há a existência de uma tampa térmica isolante, visando que sua temperatura fique mais homogênea durante todo seu comprimento; 4 – Depois de passar inúmeras vezes pelos laminadores até que se obtenham a espessura desejada, ela vai para a tesoura volante, onde o rabo de peixe é eliminado, que ocorre nas suas extremidades; 5 – Segue, por fim para o quebrador de carepas secundário. Esse processo todo descrito pode ocorrer em Laminação de barras; tubos; perfilados; tiras a quente e chapas grossas. A figura 10 ilustra de uma forma objetiva todo esse processo de laminação a quente.
Figura 10 - Processo de laminação a quente. Fonte: Monezi Borges (2003) afirma que os cilindros utilizados no processo possuem geratriz retilínea ou canais entalhados de forma mais ou menos complicada. Os produtos são arrastados pelo cilindro sob o efeito de forças de atrito, que se tem origem na superfície de contato dos cilindros e do metal laminado. Na ausência dessas forças de atrito não haveria possibilidade de laminação, sendo o atrito no processo um fator extremamente importante. Durante a passagem pelos cilindros do laminador o material é estendido no sentido longitudinal que produz um forte alongamento no produto laminado. Produzindo um deslocamento de material em suas laterais, provocando certo alargamento. As vantagens e desvantagens da laminação a quente são listadas por Monezi (2002): O trabalho a quente permite o emprego de menor esforço mecânico; A estrutura do metal é refinada pelo trabalho a quente, de modo que sua tenacidade melhora; Elimina a porosidade e segrega as impurezas a altas temperaturas; Deformação mais profundidade devido a continuada recristalização que ocorre durante o processo;
o esforço de compressão exercido pelos cilindros ou aumentam a capacidade de redução por passe. A deformação a frio confere encruamento aumentando os limites de resistência à tração e ao escoamento, com diminuição do alongamento. Esse procedimento produz um metal com bom acabamento superficial e preciso controle dimensional. Figura 11 - Desenho laminação a frio. Fonte: ABAL Conforme Laminação a Frio (pág.1), [...] a eliminação do limite de escoamento descontínuo nas tiras de aço recozido é um problema prático muito importante [...]. A ocorrência deste fenômeno provoca uma deformação heterogênea em posterior processamento (linhas de Lüders). Isto é devido ao alongamento descontínuo do limite de escoamento. A prática normal é dar uma pequena redução final a frio no aço recozido, chamada de passe de encruamento superficial, que elimina o alongamento descontínuo do limite de escoamento, CIM (pág. 01). Esse passe de acabamento também resulta numa melhora da qualidade superficial e controle dimensional. Outros métodos podem ser utilizados na melhoria do controle dimensional das tiras ou folhas laminadas, entre estes estão o aplainamento por rolos e o desempeno por tração, afirma Moreira (2002). Os produtos laminados a frio mais finos (folhas), com espessura de até 0,005 mm, são produzidos em laminadores específicos, que concebem o processo de
laminação de folhas dupladas com lubrificação entre elas. Conforme figura 1 2 logo abaixo: Figura 12 - Processo de laminação pra chapas finas. Fonte: ABAL 2.2.3 Laminação Contínua Outro processo atualmente muito utilizado é o de laminação contínua que elimina a etapa de laminação a quente. Onde a liga da placa é solidificada entre dois cilindros refrigerados internamente por água, que giram em torno de seus eixos, produzindo uma chapa com seção retangular e espessura de 0 6 mm aproximadamente. Depois, esta chapa é enrolada, obtendo-se assim um produto similar àquele obtido por laminação a quente. Porém, este produto apresentará uma estrutura bruta de fusão bastante refinada, dada a alta eficiência do refinador de grão utilizado no vazamento, segundo Alumínio: Processo de produção (pág.1).
2.3.1 Tipos de laminadores Conforme o tipo de chapa e sua espessura a ser desejada pelo fabricante, diversos tipos de laminadores existem para melhor auxiliar na produção, diminuindo o tempo e facilitando o processamento do produto final. Araújo (1967) afirma que a classificação dos laminadores é de conformidade com a disposição das cadeiras. Sabendo que um conjunto com cilindros e seus mancais e seus suportes, são chamados de uma “cadeira” de laminação. Laminador Duo – O mais simples dentre os outros, é constituído por dois cilindros de eixo horizontais, colocados verticalmente um sobre o outro. Podendo ser reversível ou não. Nos duos não reversíveis, o sentido do giro dos cilindros não pode ser invertido e o material só pode ser laminado em um sentido. Nos reversíveis, a inversão da rotação dos cilindros permite que a laminação ocorra nos dois sentidos de passagem entre os rolos. Este tipo de laminador é o mais antigo e mais simples, sendo usados no passado na laminação de chapas e, ainda hoje, para tarugos, trens contínuos de perfis pequenos e trens de fio- máquina. Figura 14 – Laminador Duo. Fonte: CIMM
Laminador trio – Onde os cilindros sempre giram no mesmo sentido. Porém, o material pode ser laminado nos dois sentidos, passando-o alternadamente entre o cilindro superior e o intermediário e entre o intermediário e o inferior, como se percebe na figura abaixo. Nunca são reversíveis. Inicialmente o material a laminar era manuseado por meio de ganchos ou barras manuais para colocar o material na parte superior, porém atualmente utilizam-se mesas elevatórias ou basculantes. São usados em trens desbastadores para lingotes pequenos, trens de perfis grandes, médios e pequenos, cadeiras acabadoras de trens de fio-máquina abertos. Figura 15 - Laminador Trio. Fonte:CIMM Laminador Quádruo – Conforme se laminam materiais cada vez mais finos, há interesse em utilizar cilindros de trabalho de pequeno diâmetro, que tem a desvantagem de fletir, e devem ser apoiados por cilindros de encosto. Pode ser reversível ou não também. Para evitar o defeito de fletir, existem quatro cilindros, montados um sobre o outro na horizontal, sendo que os que estão no meio são chamados cilindros de trabalho com menor diâmetro e os inferiores e superiores, chamados de cilindros de encosto ou apoio, possuem maior diâmetro. São utilizados para chapas grossas com espessura uniforme, utilizados a quente e a frio para chapas e tiras.
se certo distanciamento entre o par de cilindros verticais com o par dos horizontais. Os quatro cilindros, geralmente possuem acionamento independente, mas sincronizados. Outra modalidade é a construção do mesmo com cilindros verticais não acionados, colocados entre os extremos dos cilindros horizontais e no mesmo plano vertical. A sua função é apenas garantir a uniformidade da seção do perfilado, para produção de perfilados pesados tais como duplo T. Figura 18 - Laminador Universal. Fonte: CIMM Existem outros tipos de laminadores mais especializados, como o planetário, “passo peregrino”, Mannesmann, de bolas, etc. 2.3.2 Estrutura de um Laminador e seus componentes Um laminador consiste essencialmente, de duas gaiolas para suportar os cilindros, de dois ou mais cilindros e os meios para o seu acionamento e para controlar a abertura entre os cilindros de trabalho. Além disso, devem-se considerar as várias instalações de transporte das peças a laminar, os meios de lubrificar o equipamento e os de remover a camada de óxido. Araújo (1967) cita:
A gaiola do laminador é, em geral, uma peça de aço fundido, cujas dimensões são determinadas com um coeficiente de segurança bastante grande,as duas gaiolas são ligadas entre si na parte superior por um cabeçote fundido ou, perto da base e do topo, por meio de tirantes e forjados. Figura 19 - Desenho de ganhola em vista lateral do laminador. Fonte: Araújo 1967 Os cilindros de laminação são em geral, peças inteiriças ou forjadas. A parte central do cilindro, o corpo ou a face deste, é que entra em contato com o aço durante a operação de laminar. Podem ser de perro fundido ou forjado e aço fundido ou forjado Figura 20 - Desenho cilindro do laminador. Fonte: Araújo 1967 Em cada extremidade, estão os pescoços que se apóiam nos mancais, além do pescoço fica o trevo, que recebe o acoplamento para rotação. Os laminadores modernos utilizam juntas universais, para estas o trevo é substituído por uma seção adequada ao desenho do acoplamento.