
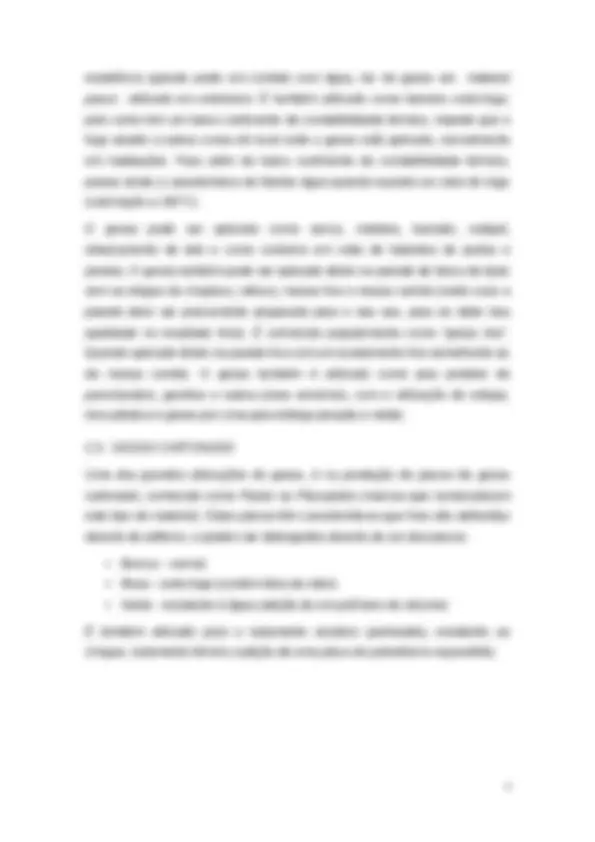
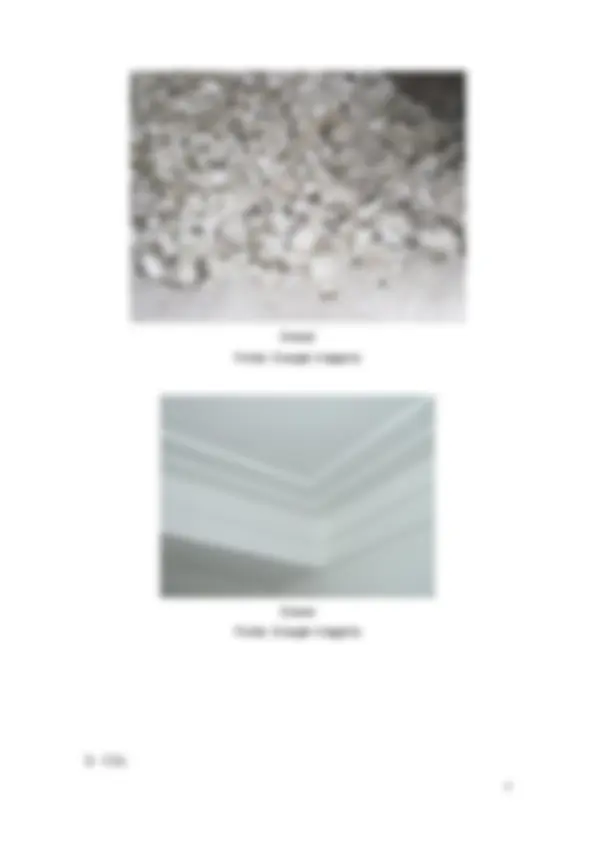
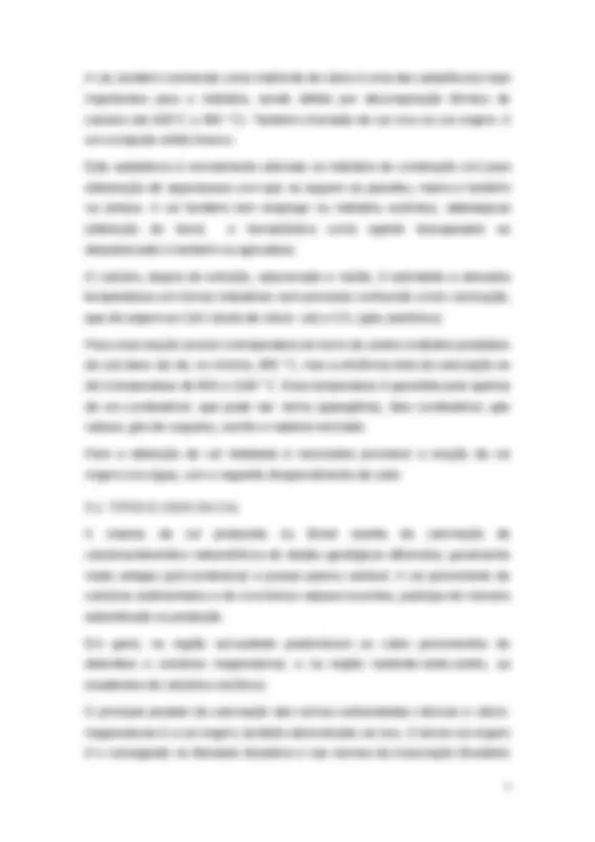
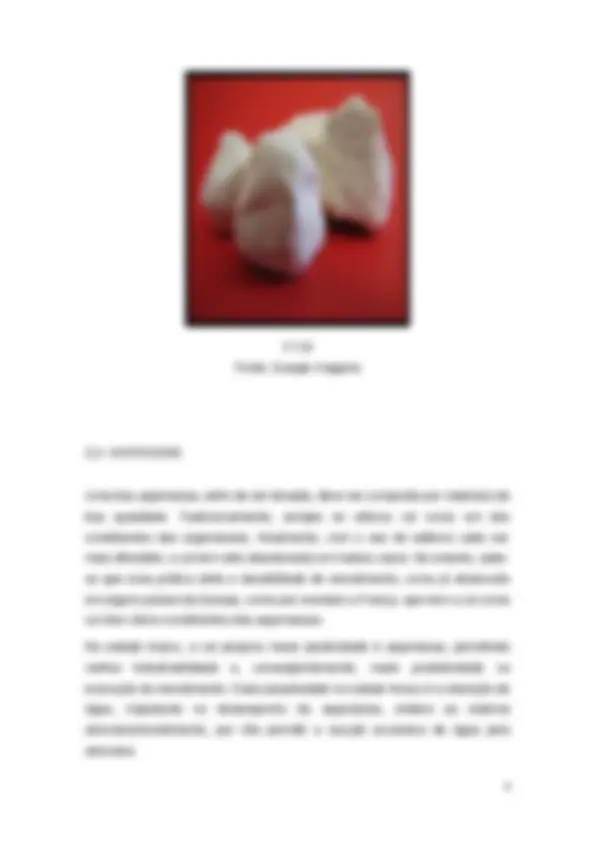
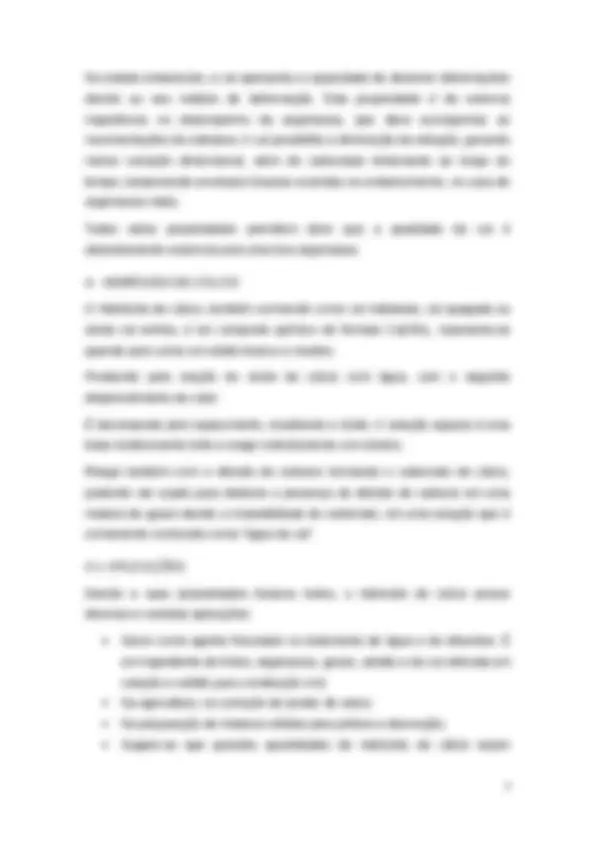
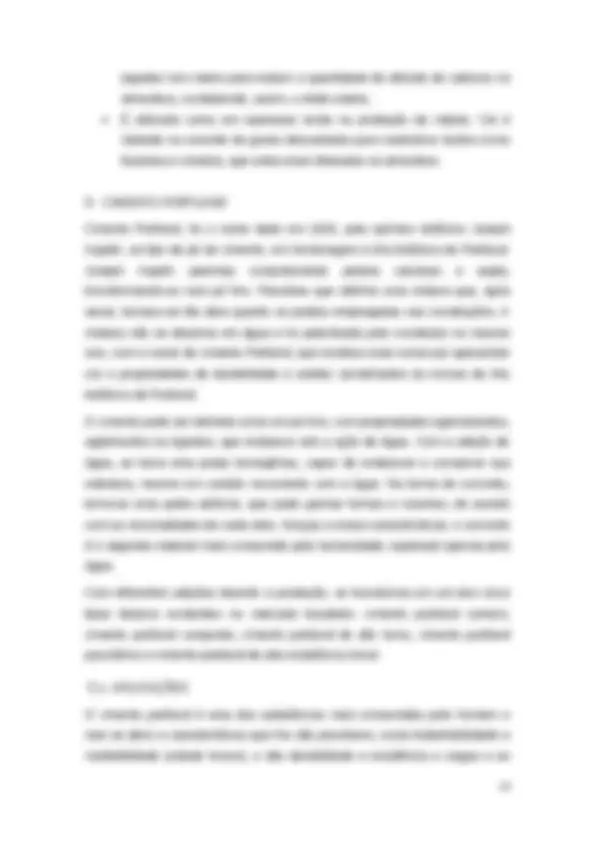
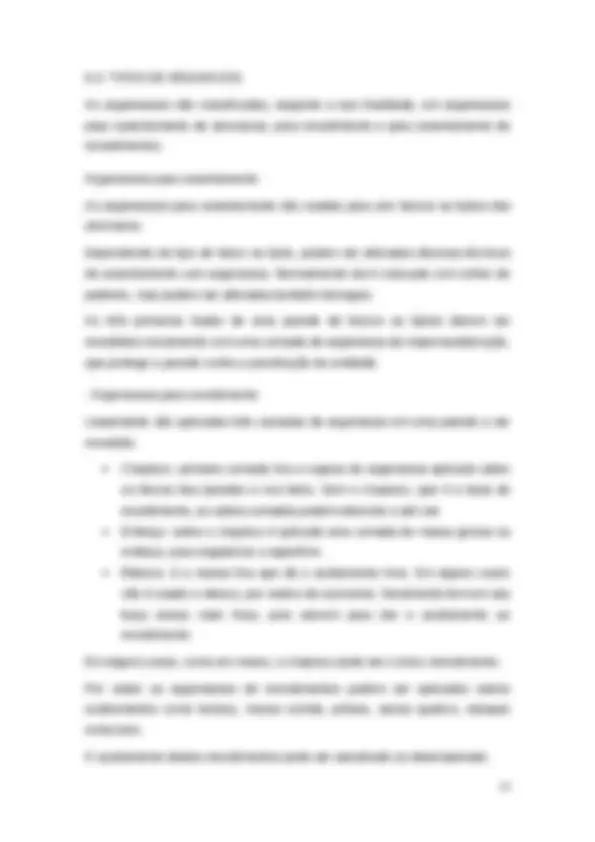
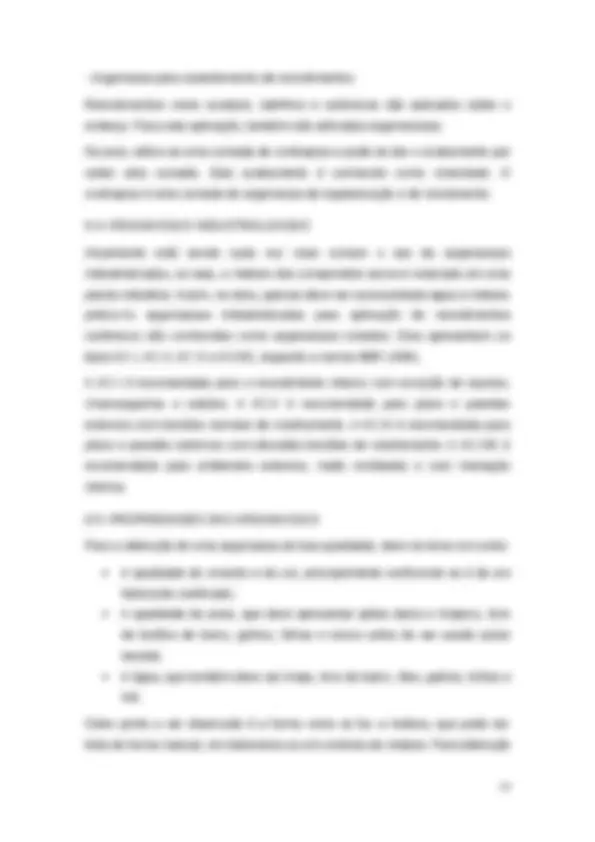
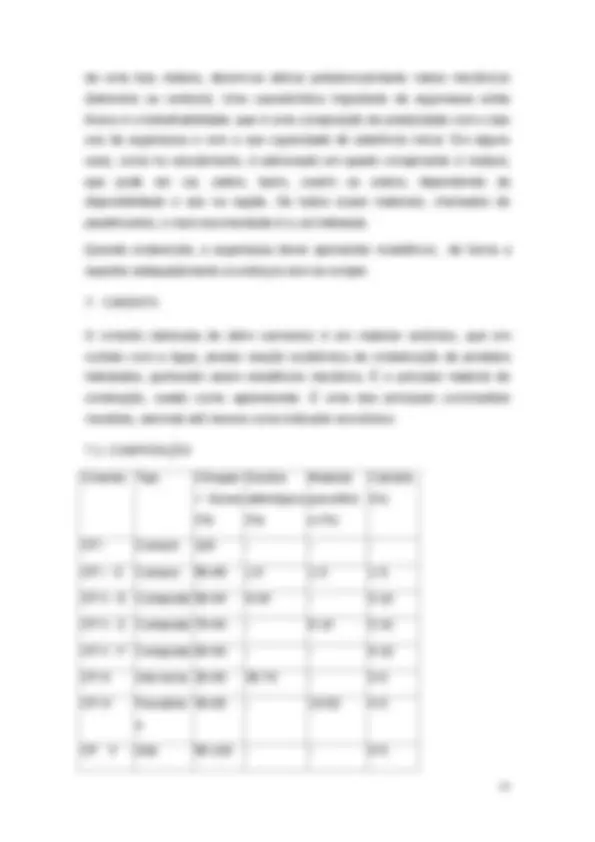
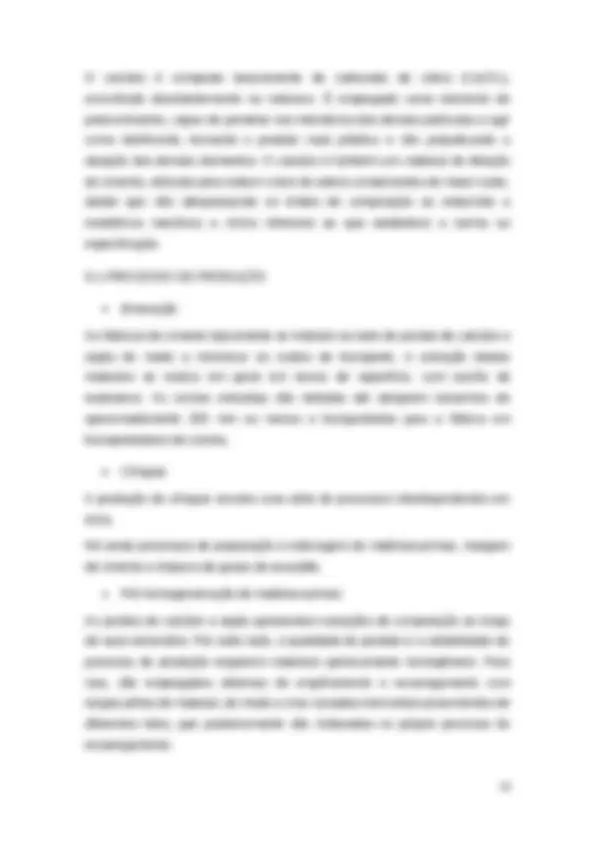
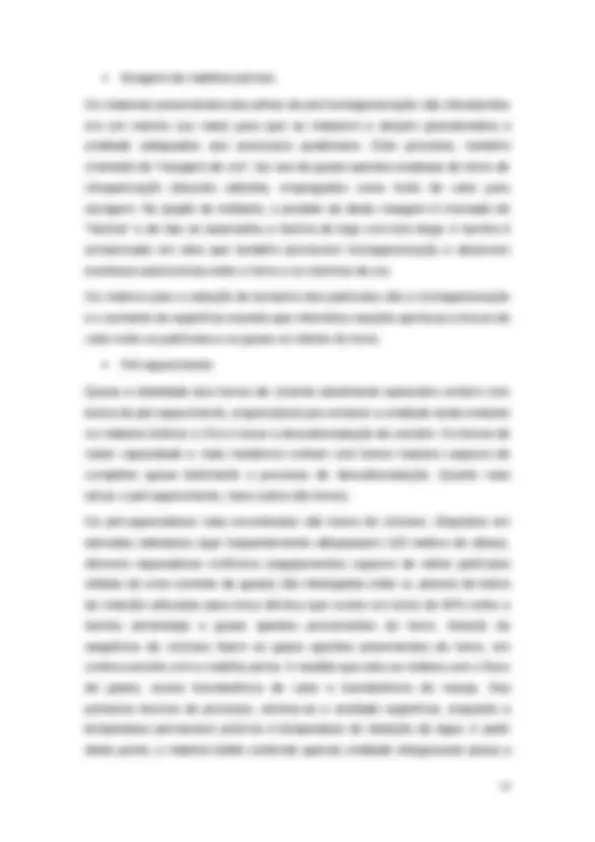
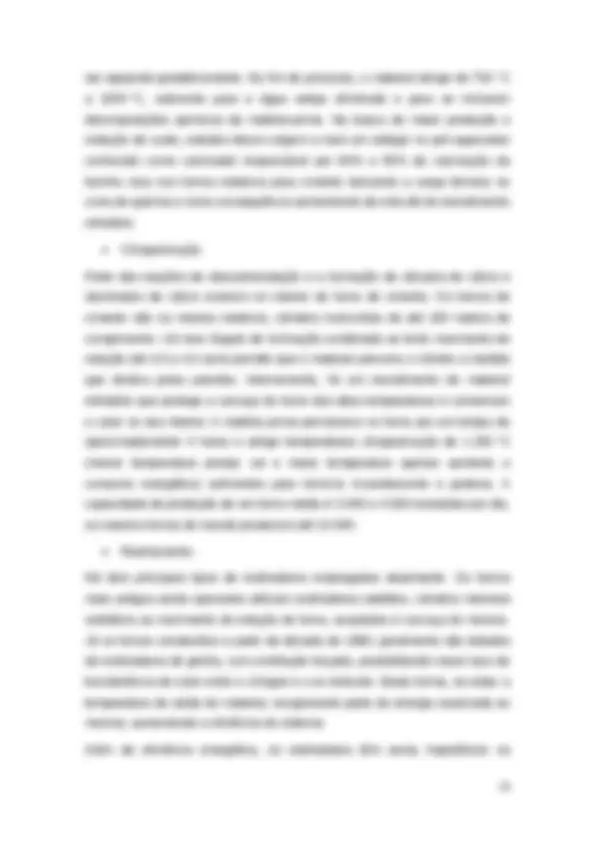
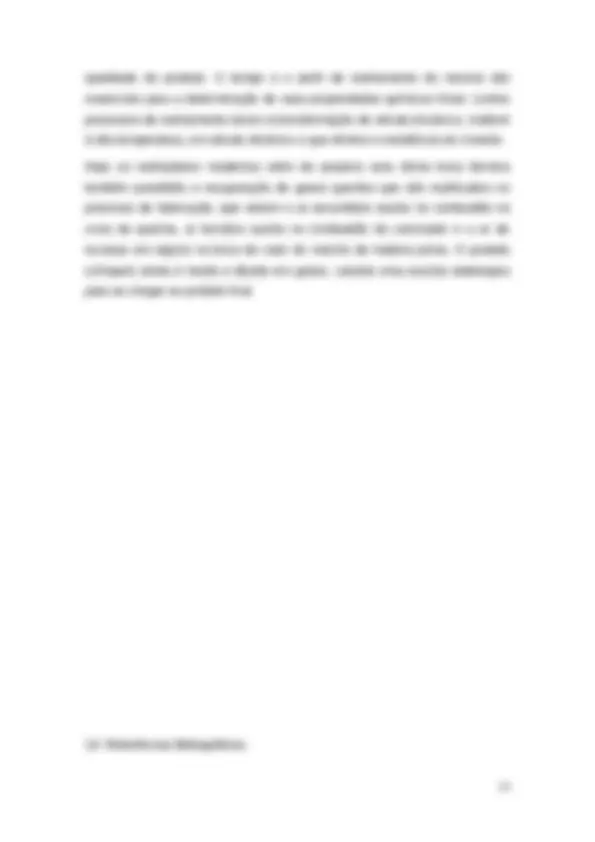
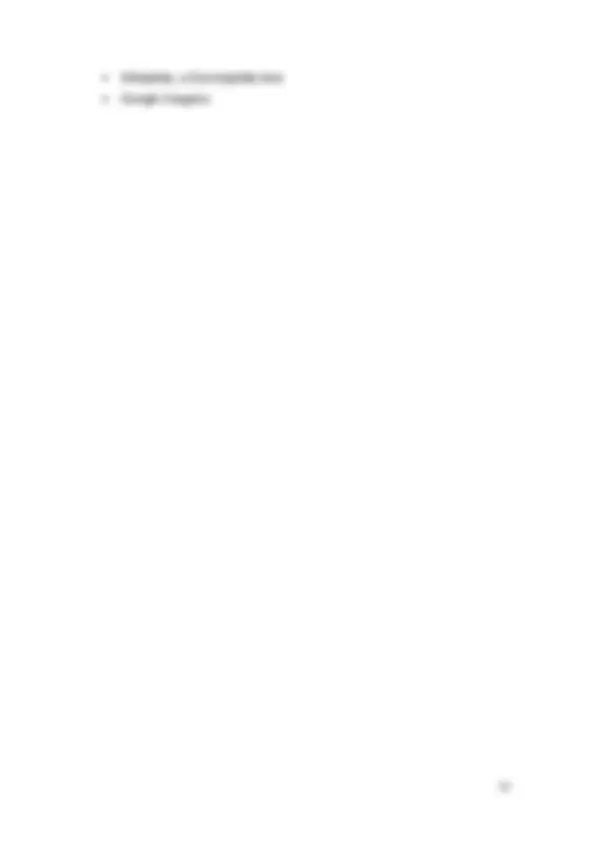
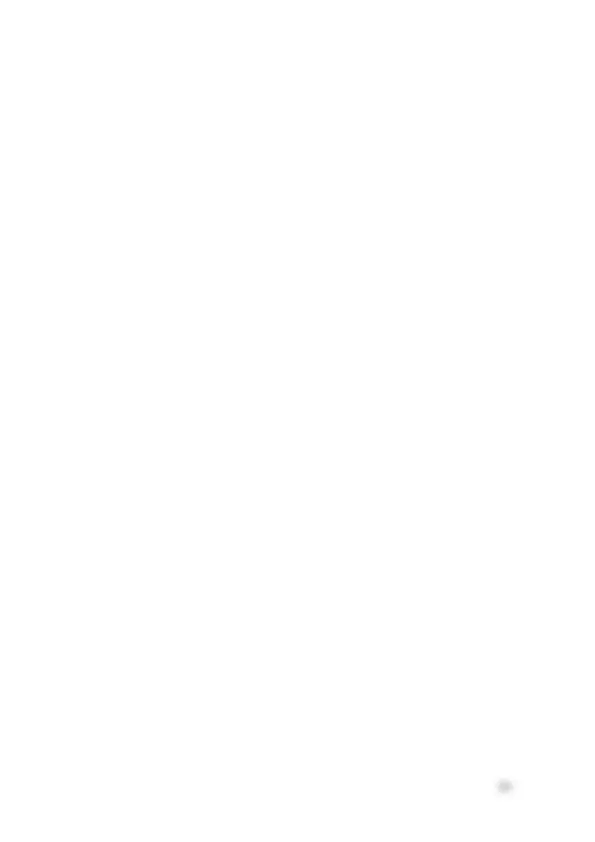
Estude fácil! Tem muito documento disponível na Docsity
Ganhe pontos ajudando outros esrudantes ou compre um plano Premium
Prepare-se para as provas
Estude fácil! Tem muito documento disponível na Docsity
Prepare-se para as provas com trabalhos de outros alunos como você, aqui na Docsity
Os melhores documentos à venda: Trabalhos de alunos formados
Prepare-se com as videoaulas e exercícios resolvidos criados a partir da grade da sua Universidade
Responda perguntas de provas passadas e avalie sua preparação.
Ganhe pontos para baixar
Ganhe pontos ajudando outros esrudantes ou compre um plano Premium
Comunidade
Peça ajuda à comunidade e tire suas dúvidas relacionadas ao estudo
Descubra as melhores universidades em seu país de acordo com os usuários da Docsity
Guias grátis
Baixe gratuitamente nossos guias de estudo, métodos para diminuir a ansiedade, dicas de TCC preparadas pelos professores da Docsity
Uma visão geral de aglomerantes orgânicos e inorgânicos, incluindo resina acrílica, cola, mástique, betuminosos, gesso e cimento portland. Descrevemos as propriedades, processos de fabricação e aplicativos de cada tipo de aglomerante. O texto também aborda a importância da cal hidratada na indústria da construção civil.
Tipologia: Trabalhos
1 / 23
Esta página não é visível na pré-visualização
Não perca as partes importantes!
Aglomerante é o material ativo, ligante, com a principal finalidade de formar uma pasta que promove a união entre grãos de agregrados, que é utilizado na obtenção de argamassas e concretos. Um aglomerante em contato com água forma uma pasta, a qual é moldável e maleável, que permite a formação de natas. Os aglomerantes são classificados como: Poliméricos: são os aglomerantes que tem reação devido a polimerização de uma matriz. Aéreos: são os aglomerantes que endurecem pela ação química do CO 2 no ar, como por exemplo, a cal aérea. Hidráulicos: são aglomerantes que endurecem pela ação exclusiva de água como por exemplo, a cal hidráulico e o cimento Potland entre outos. 1.1 - TIPOS DE AGLOMERANTES Aglomerantes orgânicos poliméricos resina epoxídica resina acrílica cola mástique betuminosos alcatrão asfalto derivados da destilação do petróleo Aglomerante inorgânicos
Aglomerantes aéreos (que fazem presa em contato com o ar) gesso cal aérea Aglomerantes hidráulicos (não necessitam de estar expostos ao ar para fazer presa) cal hidráulica ou hidratada cimento Portland 2- GESSO O gesso é um aglomerante produzido a partir da gipsita (também denominada por pedra de gesso ), composto basicamente de sulfato de cálcio di-hidratado. Historicamente foi utilizado como ligante em povos da Antiguidade que ocupavam zonas com climas secos, tais como Egito ou Fenícia. 2.1- PROCESSO DE FABRICAÇÃO Após a extração da pedra de gesso, este material é britado, ou seja, é fragmentado mecanicamente formando pequenos pedaços de pedra. É feita em seguida a calcinação desses mesmos fragmentos num forno rotativo a cerca de 160°C. Neste processo o material perde água, formando assim sulfato de cálcio semi-hidratado (CaSO 4 ½ H 2 O). Uma vez calcinado, o material é moído formando o característico pó branco que é comercializado. No Brasil é amplamente extraído no município de Grajaú, no Maranhão, considerado um dos maiores produtores de gesso e derivados do mundo. O pólo gesseiro do Araripe Pernambucano tem uma reserva estimada de 22 bilhões de toneladas de gipsita, uma das reservas mais expressivas do mundo e a maior já medida no Brasil. 2.2- UTILIZAÇÃO EM CONSTRUÇÃO CIVIL O gesso é um material muito utilizado em construção devido às suas propriedades de aderência. A sua maleabilidade fazem da argamassa deste ligante um bom material para a execução de pormenores decorativos em paredes e tetos, assim como fazer o estuque que reveste as paredes. É um bom isolante térmico e acústico devido ao fato de ter uma baixa condutibilidade térmica e um elevado coeficiente de absorção acústica. Contudo, a sua fraca
Gesso Fonte: Google Imagens Gesso Fonte: Google Imagens 3- CAL
A cal, também conhecida como hidróxido de cálcio é uma das substâncias mais importantes para a indústria, sendo obtida por decomposição térmica de calcário (de 825°C a 900 °C). Também chamada de cal viva ou cal virgem, é um composto sólido branco. Esta substância é normalmente utilizada na indústria da construção civil para elaboração de argamassas com que se erguem as paredes, muros e também na pintura. A cal também tem emprego na indústria cerâmica, siderúrgicas (obtenção do ferro) e farmacêutica como agente branqueador ou desodorizador e também na agricultura. O calcário, depois de extraído, selecionado e moído, é submetido a elevadas temperaturas em fornos industriais num processo conhecido como calcinação, que dá origem ao CaO (óxido de cálcio: cal) e CO 2 (gás carbônico). Para essa reação ocorrer à temperatura do forno da caieira (indústria produtora de cal) deve ser de, no mínimo, 850 °C, mas a eficiência total da calcinação se dá à temperatura de 900 a 1000 °C. Essa temperatura é garantida pela queima de um combustível, que pode ser: lenha (gasogênio), óleo combustível, gás natural, gás de coqueira, carvão e material reciclado. Para a obtenção da cal hidratada é necessário promover a reação da cal virgem com água, com o seguinte desprendimento de calor. 3.1- TIPOS E USOS DA CAL A maioria da cal produzida no Brasil resulta da calcinação de calcários/dolomitos metamórficos de idades geológicas diferentes; geralmente muito antigas (pré-cambriana) e possui pureza variável. A cal proveniente de calcários sedimentares e de concheiros naturais recentes, participa de maneira subordinada na produção. Em geral, na região sul-sudeste predominam as cales provenientes de dolomitos e calcários magnesianos, e na região nordeste-norte-centro, as resultantes de calcários calcíticos. O principal produto da calcinação das rochas carbonatadas cálcicas e cálcio- magnesianas é a cal virgem, também denominada cal viva. O termo cal virgem é o consagrado na literatura brasileira e nas normas da Associação Brasileira
quase todo o território nacional, a facilidade e abundância da sua oferta – ainda que para cales especiais o suprimento, às vezes implique em transporte mais longo e ao seu baixo custo – o menor entre os reagentes químicos alcalinos e os aglomerantes cimentantes. A Cal Fonte: Google Imagens
A Cal Fonte: Google Imagens 3.2- VANTAGENS Uma boa argamassa, além de ser dosada, deve ser composta por materiais de boa qualidade. Tradicionalmente, sempre se utilizou cal como um dos constituintes das argamassas. Atualmente, com o uso de aditivos cada vez mais difundido, a cal tem sido abandonada em muitos casos. No entanto, sabe- se que essa prática afeta a durabilidade de revestimento, como já observado em alguns países da Europa, como por exemplo a França, que tem a cal como um dos vários constituintes das argamassas. No estado fresco, a cal propicia maior plasticidade à argamassa, permitindo melhor trabalhabilidade e, conseqüentemente, maior produtividade na execução do revestimento. Outra propriedade no estado fresco é a retenção de água, importante no desempenho da argamassa, relativo ao sistema alvenaria/revestimento, por não permitir a sucção excessiva de água pela alvenaria.
jogadas nos mares para reduzir a quantidade de dióxido de carbono na atmosfera, combatendo, assim, o efeito estufa; É utilizado como um supressor ácido na produção de metais. Cal é injetada na corrente de gases descartados para neutralizar ácidos como fluoretos e cloretos, que antes eram liberados na atmosfera. 5- CIMENTO PORTLAND Cimento Portland, foi o nome dado em 1824 , pelo químico britânico Joseph Aspdin, ao tipo de pó de cimento, em homenagem à ilha britânica de Portland. Joseph Aspdin queimou conjuntamente pedras calcárias e argila, transformando-as num pó fino. Percebeu que obtinha uma mistura que, após secar, tornava-se tão dura quanto as pedras empregadas nas construções. A mistura não se dissolvia em água e foi patenteada pelo construtor no mesmo ano, com o nome de cimento Portland, que recebeu esse nome por apresentar cor e propriedades de durabilidade e solidez semelhantes às rochas da ilha britânica de Portland. O cimento pode ser definido como um pó fino, com propriedades aglomerantes, aglutinantes ou ligantes, que endurece sob a ação de água. Com a adição de água, se torna uma pasta homogênea, capaz de endurecer e conservar sua estrutura, mesmo em contato novamente com a água. Na forma de concreto, torna-se uma pedra artificial, que pode ganhar formas e volumes, de acordo com as necessidades de cada obra. Graças a essas características, o concreto é o segundo material mais consumido pela humanidade, superado apenas pela água. Com diferentes adições durante a produção, se transforma em um dos cinco tipos básicos existentes no mercado brasileiro: cimento portland comum, cimento portland composto, cimento portland de alto forno, cimento portland pozolânico e cimento portland de alta resistência inicial. 5.1- APLICAÇÕES O cimento portland é uma das substâncias mais consumidas pelo homem e isso se deve a características que lhe são peculiares, como trabalhabilidade e moldabilidade (estado fresco), e alta durabilidade e resistência a cargas e ao
fogo (estado duro). Insubstituível em obras civis, o cimento pode ser empregado tanto em peças de mobiliário urbano como em grandes barragens, em estradas ou edificações, em pontes, tubos de concreto ou telhados. Pode até ser matéria-prima para a arte. 5.2- PROCESSO DE FABRICAÇÃO A fabricação do cimento Portland basea-se em três etapas fundamentais: Mistura e moagem da matéria-prima (calcários, margas e brita de rochas); Produção do clínquer (forno rotativo a 1400ºC + arrefecimento rápido); Moagem do clínquer e mistura com gesso.
As argamassas são classificadas, segundo a sua finalidade, em argamassas para assentamento de alvenarias, para revestimento e para assentamento de revestimentos. Argamassas para assentamento As argamassas para assentamento são usadas para unir blocos ou tijolos das alvenarias. Dependendo do tipo de bloco ou tijolo, podem ser utilizadas diversas técnicas de assentamento com argamassa. Normalmente ela é colocada com colher de pedreiro, mas podem ser utilizadas também bisnagas. As três primeiras fiadas de uma parede de blocos ou tijolos devem ser revestidas inicialmente com uma camada de argamassa de impermeabilização, que protege a parede contra a penetração da umidade.
ARI resistênci a inicial Cimento Fonte: Google Imagens 8- ARGILA POZOLÂNICA As pozolanas ativadas reagem espontaneamente com CaO em fase aquosa, por conterem elevado teor de sílica ativa SiO 2. Esta característica levou ao uso de pozolanas como ligante hidráulico complementar ao clínquer, com a característica de tornar os concretos mais impermeáveis o que é útil na construção de barragens, por exemplo. As pozolanas são originalmente argilas contendo cinzas vulcânicas, encontradas na região de Pozzuoli, Italia. Atualmente, materiais com origens diferentes, mas com composições semelhantes também são considerados pozolânicos, tais como as pozolanas ativadas artificialmente e alguns sub-produtos industriais como cinzas volantes provenientes da queima de carvão mineral. O processo de ativação de argilas é amplamente praticado pela própria indústria de cimentos, é geralmente realizado em fornos rotativos semelhantes aqueles utilizados na fabricação de clínquer ou mesmo em antigos fornos de clínquer adaptados, trabalhando a temperaturas mais baixas (até 900 °C) e menor tempo de residência.
Assim como a escória siderúrgica, as pozolanas frequentemente têm menor custo comparadas ao clínquer e só podem substituí-lo até um determinado grau. Argila Fonte: Google Imagens Argila Fonte: Google Imagens 9- CALCÁRIO
Moagem de matérias-primas Os materiais provenientes das pilhas de pré-homogeneização são introduzidos em um moinho (ou mais) para que se misturem e atinjam granulometria e umidade adequadas aos processos posteriores. Este processo, também chamado de "moagem de cru", faz uso de gases quentes residuais do forno de clinquerização (descrito adiante), empregados como fonte de calor para secagem. No jargão da indústria, o produto da desta moagem é chamado de "farinha" e de fato se assemelha a farinha de trigo com tom bege. A farinha é armazenada em silos que também promovem homogeneização e absorvem eventuais assincronias entre o forno e os moinhos de cru. Os motivos para a redução de tamanho das partículas são a homogeneização e o aumento da superfície exposta que intensifica reações químicas e trocas de calor entre as partículas e os gases no interior do forno. Pré-aquecimento Quase a totalidade dos fornos de cimento atualmente operantes contam com torres de pré-aquecimento, responsáveis por remover a umidade ainda restante no material (inferior a 1%) e iniciar a descarbonatação do calcário. Os fornos de maior capacidade e mais modernos contam com torres maiores capazes de completar quase totalmente o processo de descarbonatação. Quanto mais eficaz o pré-aquecimento, mais curtos são fornos. Os pré-aquecedores mais encontrados são torres de ciclones. Dispostos em elevadas estruturas (que frequentemente ultrapassam 100 metros de altura), diversos separadores ciclônicos (equipamentos capazes de retirar partículas sólidas de uma corrente de gases) são interligados entre si, através de tubos de imersão utilizados para troca térmica que ocorre em torno de 80% entre a farinha alimentada e gases quentes provenientes do forno. Através da sequência de ciclones fluem os gases quentes provenientes do forno, em contra-corrente com a matéria prima. A medida que esta se mistura com o fluxo de gases, ocorre transferência de calor e transferência de massa. Nos primeiros trechos do processo, elimina-se a umidade superficial, enquanto a temperatura permanece próxima à temperatura de ebulição da água. A partir deste ponto, o material sólido contendo apenas umidade intergranular passa a
ser aquecido gradativamente. No fim do processo, o material atinge de 700 °C a 1000 °C, suficiente para a água esteja eliminada e para se iniciarem decomposições químicas da matéria-prima. Na busca de maior produção e redução de custo, estudos deram origem a mais um estágio no pré-aquecedor conhecido como calcinador responsável por 60% a 95% da calcinação da farinha crua nos fornos rotativos para cimento baixando a carga térmica na zona de queima e como consequência aumentando da vida útil do revestimento refratário. Clinquerização Parte das reações de descarbonatação e a formação de silicatos de cálcio e aluminatos de cálcio ocorrem no interior do forno de cimento. Os fornos de cimento são na maioria rotativos, cilindros horizontais de até 160 metros de comprimento. Um leve ângulo de inclinação combinado ao lento movimento de rotação (de 0,5 a 4,0 rpm) permite que o material percorra o cilindro a medida que desliza pelas paredes. Internamente, há um revestimento de material refratário que protege a carcaça do forno das altas temperaturas e conservam o calor no seu interior. A matéria prima permanece no forno por um tempo de aproximadamente 4 horas e atinge temperaturas clinquerização de 1.230 °C (menor temperatura produz cal e maior temperatura apenas aumenta o consumo energético) suficientes para torná-la incandescente e pastosa. A capacidade de produção de um forno médio é 3.000 a 4.000 toneladas por dia, os maiores fornos do mundo produzem até 10.000. Resfriamento Há dois principais tipos de resfriadores empregados atualmente. Os fornos mais antigos ainda operantes utilizam resfriadores satélites, cilindros menores solidários ao movimento de rotação do forno, acoplados à carcaça do mesmo. Já os fornos construídos a partir da década de 1980 , geralmente são dotados de resfriadores de grelha, com ventilação forçada, possibilitando maior taxa de transferência de calor entre o clínquer e o ar entrante. Desta forma, se reduz a temperatura de saída do material, recuperando parte da energia associada ao mesmo, aumentando a eficiência do sistema. Além da eficiência energética, os resfriadores têm suma importância na