
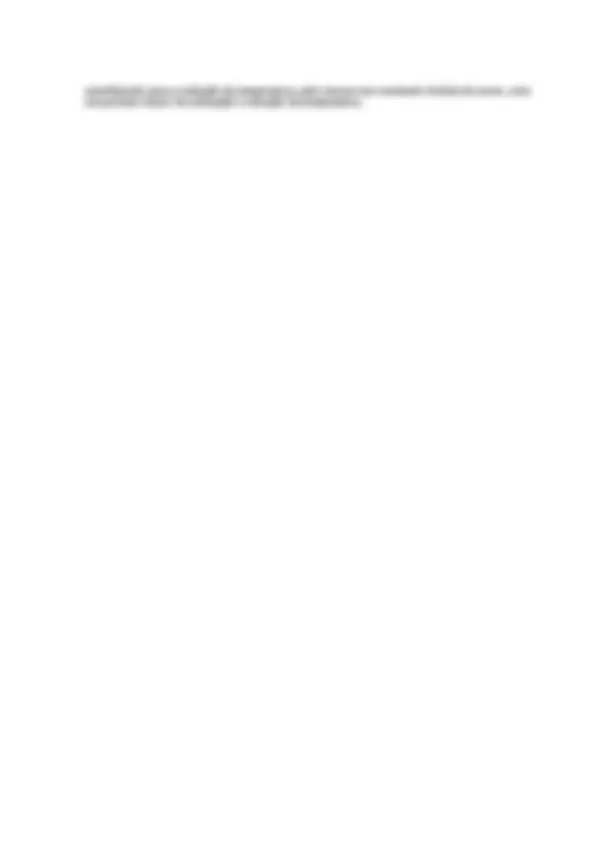
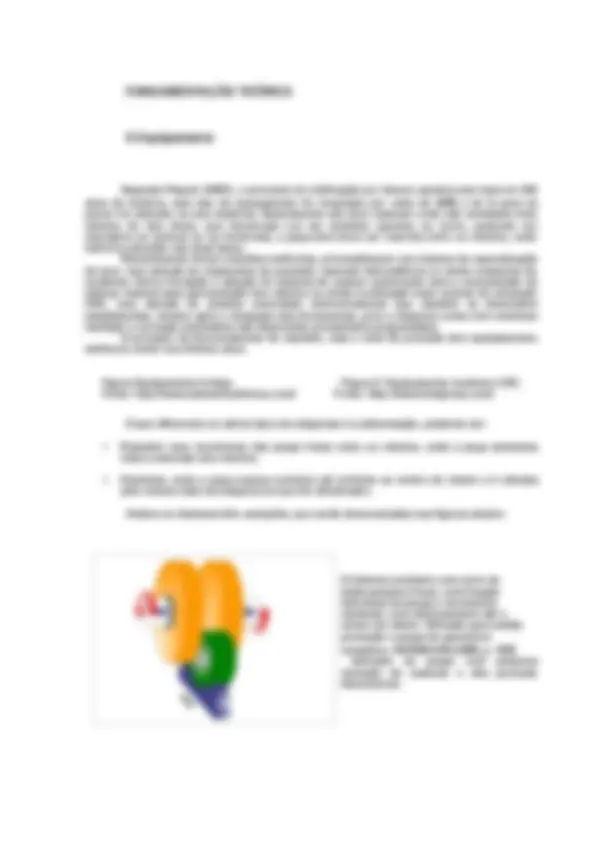
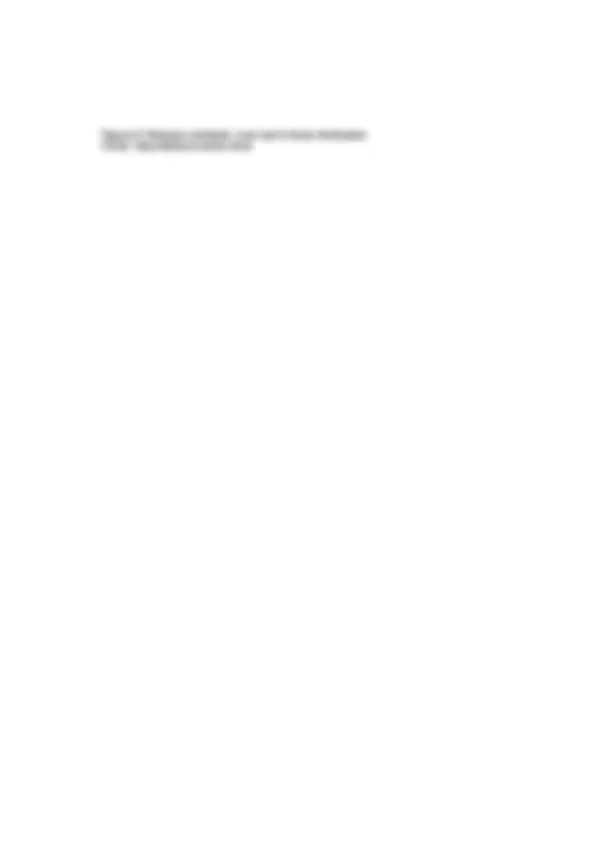
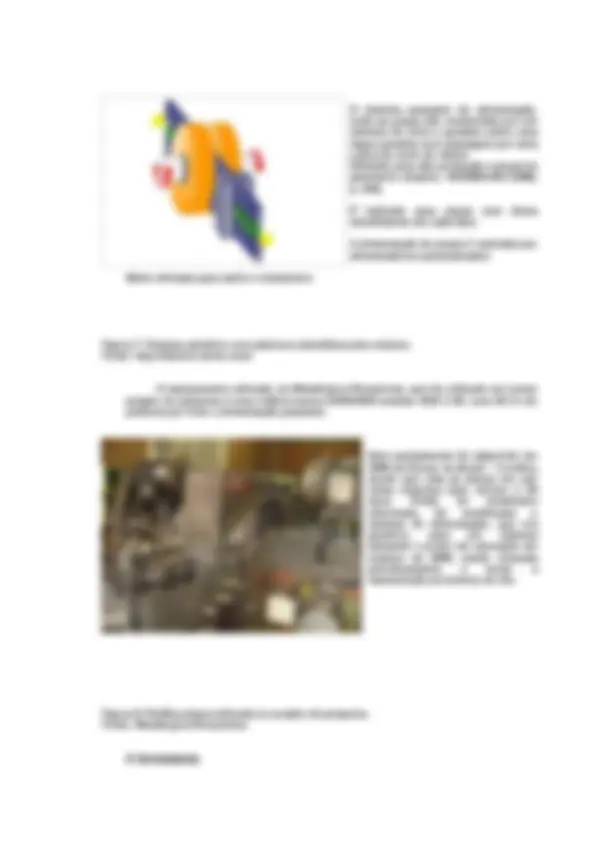
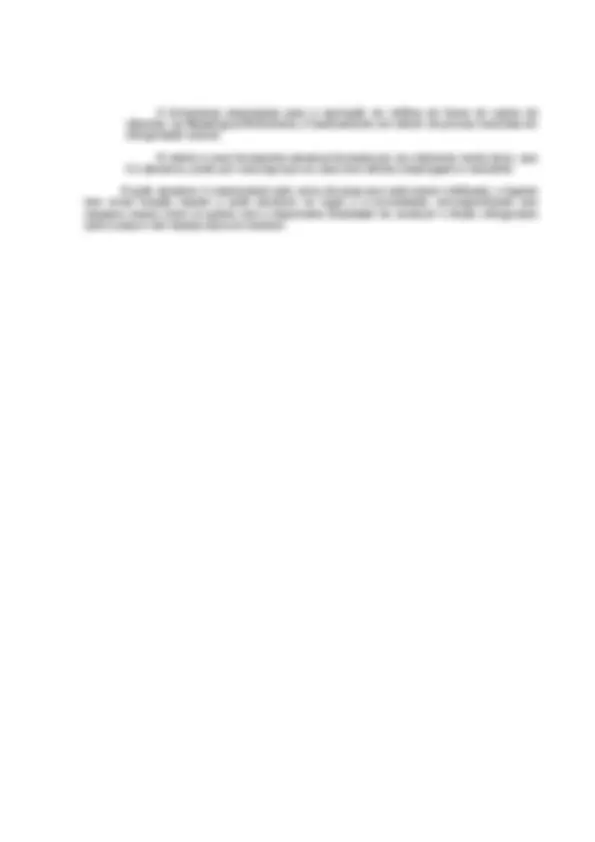
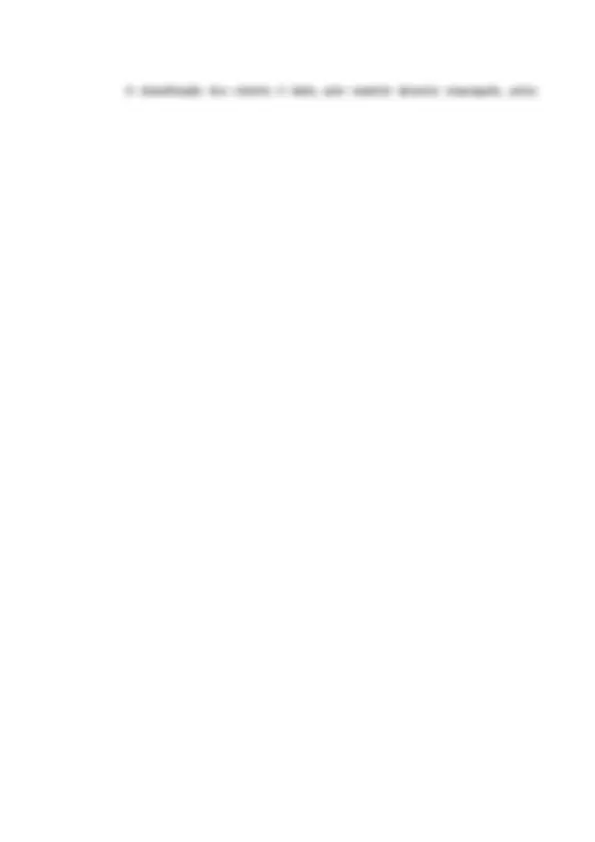
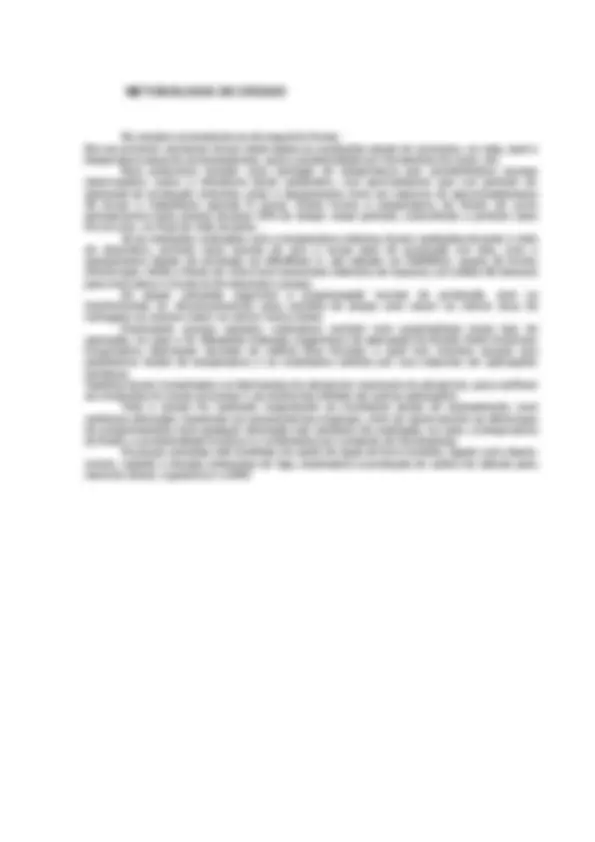
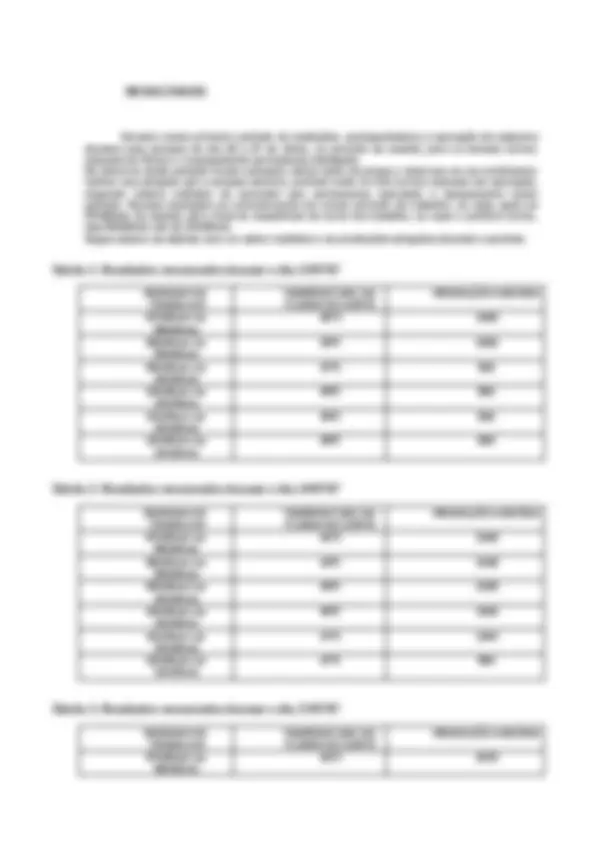
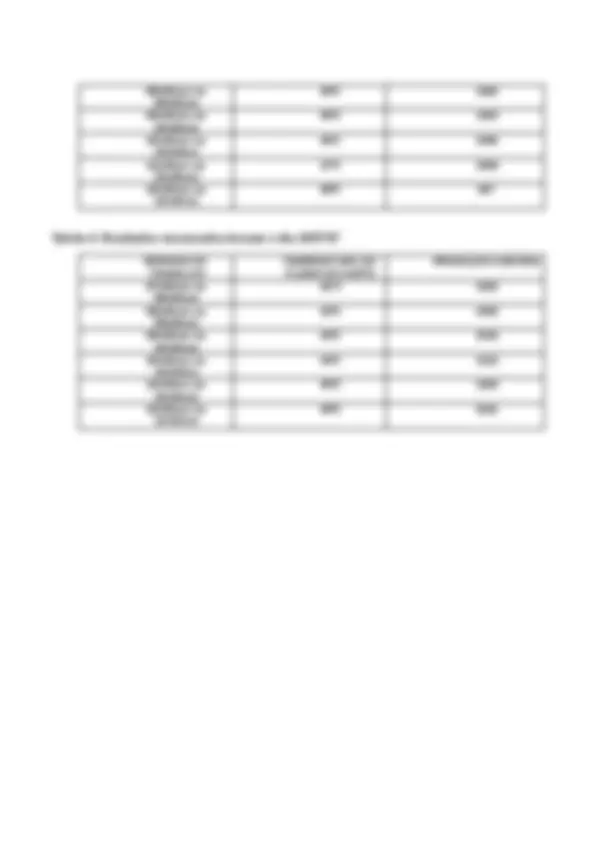
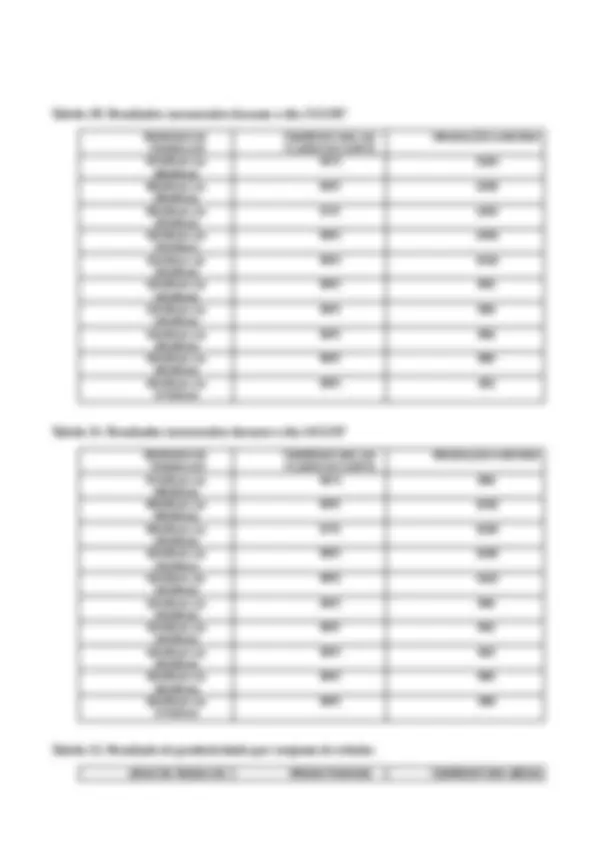
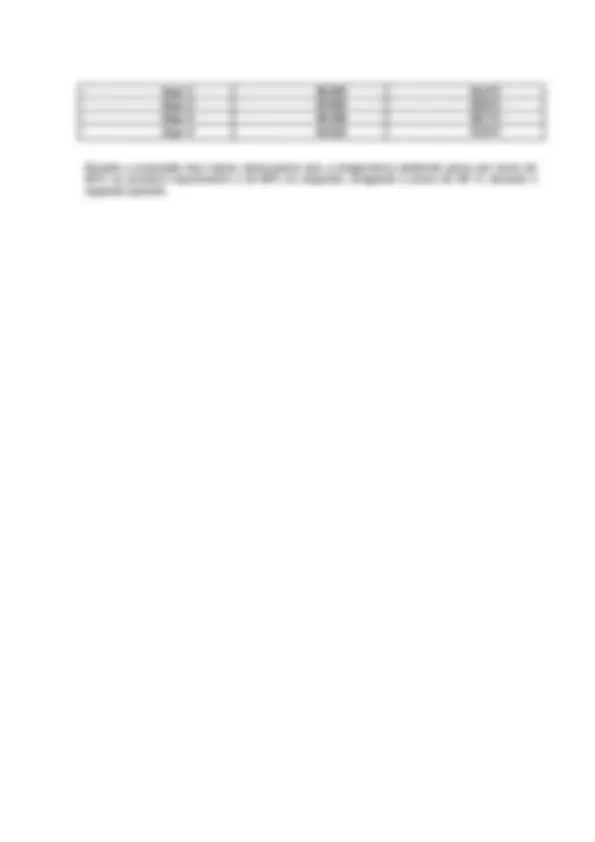
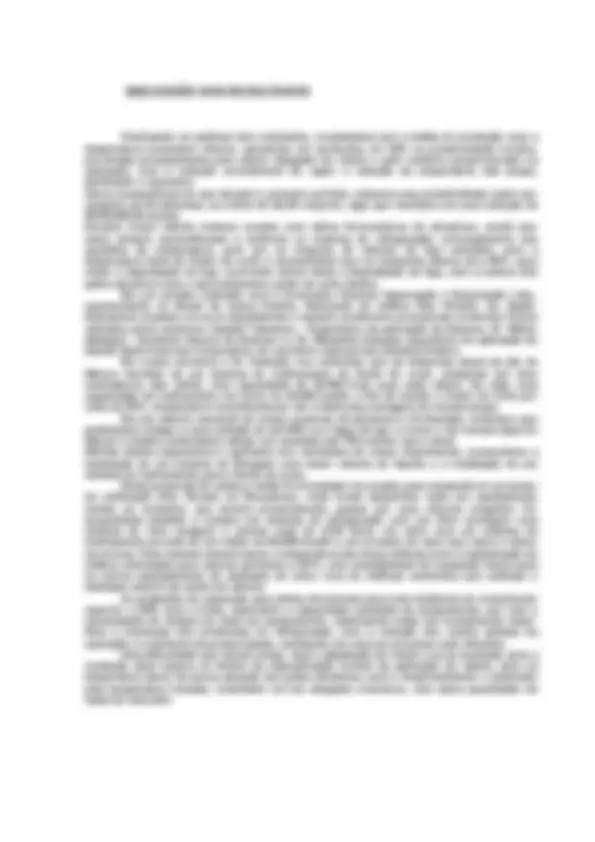
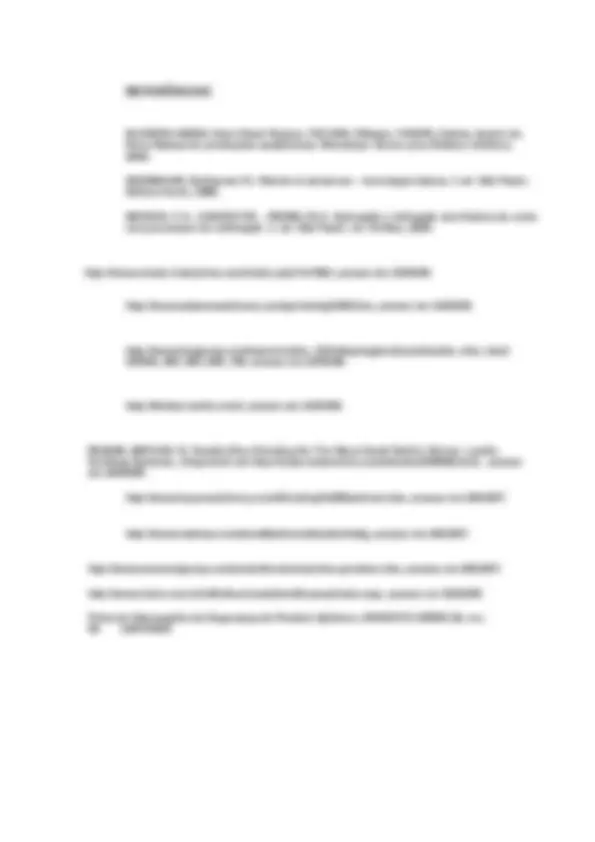
Estude fácil! Tem muito documento disponível na Docsity
Ganhe pontos ajudando outros esrudantes ou compre um plano Premium
Prepare-se para as provas
Estude fácil! Tem muito documento disponível na Docsity
Prepare-se para as provas com trabalhos de outros alunos como você, aqui na Docsity
Os melhores documentos à venda: Trabalhos de alunos formados
Prepare-se com as videoaulas e exercícios resolvidos criados a partir da grade da sua Universidade
Responda perguntas de provas passadas e avalie sua preparação.
Ganhe pontos para baixar
Ganhe pontos ajudando outros esrudantes ou compre um plano Premium
Comunidade
Peça ajuda à comunidade e tire suas dúvidas relacionadas ao estudo
Descubra as melhores universidades em seu país de acordo com os usuários da Docsity
Guias grátis
Baixe gratuitamente nossos guias de estudo, métodos para diminuir a ansiedade, dicas de TCC preparadas pelos professores da Docsity
Abrasivos - Abrasivos
Tipologia: Notas de estudo
1 / 21
Esta página não é visível na pré-visualização
Não perca as partes importantes!
O projeto proposto tem como principais finalidades a verificação prática das influências da temperatura do fluido de corte na operação de retificação plana tipo, Disc Grinder (discos opostos), nesse tipo de usinagem a principal fonte geradora de calor é a fricção entre as ferramentas abrasivas e a superfície do material a ser usinado. Por sua vez a função principal do fluido de corte é refrigerar esta operação, trocando com as peças, parte do calor gerado na operação e contribuindo para redução dos choques térmicos, causadores de trincas e imperfeições superficiais. Nosso estudo é baseado em observação de um processo já implantado com algumas simulações em pequena escala das condições idéias de refrigeração, as quais foram obtidas junto as fornecedores de abrasivos e fornecedores de equipamentos. Segundo estes as condições ideais de trabalho são com temperaturas de fluidos na faixa de 25°C a 35°C, sendo que acima destes valores, observaremos uma perda considerável no rendimento da ferramenta abrasiva e principalmente efeitos indesejáveis nas peças produzidas, tipo variações dimensionais, de acabamento superficial, marcas ocasionadas por queimas e principalmente trincas geradas pela pressão de corte e pela elevada temperatura na operação. O projeto proposto avaliará nas diversas condições de temperatura, o rendimento atingido em produtividade e os resultados obtidos, seja dimensional ou acabamento superficial. Todos os experimentos serão executados no mesmo equipamento, alterando-se somente a ferramenta abrasiva e a peça-obra, nosso nível de experimentação será relacionado às condições atuais para a realização destes experimentos.
The proposed project has as main purpose of the verification practice influences the temperature of the fluid cutting in the operation of adjustment flat type, Disc Grinder (opposing discs), this type of
(^1) Projeto de Pesquisa do PGP; (^2) Acadêmico do Curso de Engenharia de Produção, e-mail: cesar@riosulense.com.br ;
(^3) Acadêmico do Curso de Engenharia de Produção, e-mail: maycon@riosulense.com.br ; (^4) Acadêmico do Curso de Engenharia de Produção, e-mail: rcalheiro@yahoo.com.br ;
(^5) Orientadora do projeto de pesquisa, professora da Universidade para o Desenvolvimento do
Alto Vale do Itajaí (UNIDAVI), mestre em Engenharia de Produção – Qualidade e Produtividade, e-mail: apasqualini@unidavi.edu.br; (^6) Orientador do projeto de pesquisa, professor da Universidade para o Desenvolvimento do
Alto Vale do Itajaí (UNIDAVI), especialista em Engenharia de Produção, e-mail: leandros@unidavi.edu.br ; (^7) Orientador do projeto de pesquisa, professor da Universidade para o Desenvolvimento do
Alto Vale do Itajaí (UNIDAVI), especialista em Administração - Gestão Estratégica de Negócios, e-mail: giva@unidavi.edu.br ;
machining the main source for generating heat is the friction between the tool and abrasive surface of the material to be machined. In turn the main function of cutting fluid is cool this operation, replacing the pieces, the heat generated in the operation and contributing to reduction of thermal shock, resulting in cracks and imperfections surface. Our study is based on observation of a process already deployed with some simulations on a small scale the conditions of cooling ideas, which were obtained from the suppliers of abrasive and suppliers of equipment. According to the ideal conditions of work are of fluids with temperatures in the range 25 ° C to 35 ° C, above which these values, observe a loss considerable income in the tool and abrasive effects mainly in the parts produced, type dimensional variations, of the surface, marks caused by burns and broken generated mainly by the pressure of cut and the high temperature in the operation. The proposed project will evaluate the various conditions of temperature, the yield reached in productivity and results, whether or dimensional surface finishing. All experiments will be performed in the same equipment, changing it is only a tool and abrasive piece-work, our level of testing will be related to current conditions for the achievement of these experiments.
O processo de retificação plana com retíficas Disc Grind, de duplo disco oposto, são bastante difundo nas empresas de peças automotivas e de componentes de linha branca, principalmente fabricantes de compressores para refrigeração e ar condicionado. Sua principal vantagem em relação aos processos convencionais com a usinagem de uma face por ciclo, é a produtividade. Por trata-se de um processo contínuo, não necessitando da acomodação de peças sobre um gabarito ou sobre uma mesa magnética, como ocorre em outros processos de retificação plana, onde apenas um cabeçote se desloca e as peças ficam dispostas sobre uma mesa de apoio. O processo de discos opostos tem como uma das maiores vantagens, além da produtividade, a possibilidade de usinagem simultâneas de ambas as faces de uma peça, o que confere maior precisão dimensional, principalmente nas características de dimensão lineares, batimento e paralelismo. Uma desvantagem é o alto custo do equipamento, que atualmente oscila em torno de R$ 1.200.000,00 por um equipamento novo, podendo ultrapassar o US$ 1500.000,00, para uma máquina CNC, Top de Linha. Nosso projeto de pesquisa abordará uma das principais variáveis do processo e que mais comprometem o custo desta operação. A temperatura dos fluído de corte, por se tratar de um processo com remoção de até 1,5mm de material por passada, há a geração muito calor, fator que compromete o desempenho da ferramenta abrasiva, que necessita de uma temperatura adequada, que possibilite a abrasão do material sem o desprendimento da liga que dá sustentação aos grãos abrasivos. Nosso projeto será baseado em experimentações realizadas em períodos diferenciados do ano onde a temperatura ambiente contribui de forma espontânea para a redução da temperatura, bem como em momento onde o equipamento sofreu menor utilização,
Segundo Paquin (1997), o processo de retificação por discos opostos tem mais de 100
anos de história, este tipo de equipamento foi inventado por volta de 1890 e de lá para cá pouco foi alterado na sua essência. Basicamente são dois mancais onde são montados dois rebolos do tipo disco, que funcionam um em sentidos opostos ao outro, podendo ser montados na vertical ou na horizontal, a peça-obra deve ser inserida entre os rebolos, onde sofrerá a abrasão nas duas faces. Recentemente foram incluídas melhorias, principalmente nos sistema de mancalização do eixo, com adoção de rolamentos de precisão, mancais hidrostáticos ou ainda rolamento de cerâmica. Outra inovação é adoção de sistema de avanço motorizado sem a necessidade de esforço manual para aproximação dos rebolos ou ainda a utilização mais recente de comando CNC, com adoção de sistema controlado eletronicamente que mantêm as dimensões estabelecidas, mesmo após o desgaste das ferramentas, pois a máquina conta com sistemas medição e correção automática das dimensões previamente programadas. O principio de funcionamento foi mantido, mas o nível de precisão dos equipamentos melhorou muito nos últimos anos.
Figura Equipamento Antigo. Figura 2: Equipamento moderno CNC. Fonte: http://www.adamsmachinery.com/ Fonte: http://www.kmtgroup.com/
O que diferencia os vários tipos de máquinas é a alimentação, podendo ser:
Ambos os sistemas têm variações, que serão demonstradas nas figuras abaixo:
O sistema oscilante com carro de deslocamento linear, com fixação individual de peças e movimento oscilante, com deslocamento até o centro do rebolo. Utilizado para média produção e peças de geometria complexa. NUSSBAUM (1988, p. 342) Aplicado às peças com pequena remoção de material e alta precisão dimensional.
Figura 3: Sistema oscilante, com carro linear deslizante. Fonte: http://diskus-werke.com/
Figura 6: Sistema giratório com abertura simultânea dos rebolos. Fonte: http://diskus-werke.com/
O sistema passante de alimentação, onde as peças são conduzidas por um sistema de rolos e guiadas sobre uma régua paralela com passagem por toda a área de corte do rebolo. Utilizado para alta produção e peças de geometria simples. NUSSBAUM (1988, p. 343)
É indicado para peças com áreas semelhantes em cada face.
A alimentação de peças é realizada por alimentadores automatizados
Muito utilizada para anéis e rolamentos
Figura 7: Sistema giratório com abertura simultânea dos rebolos. Fonte: http://diskus-werke.com/
O equipamento utilizado na Metalúrgica Riosulense, que foi utilizado em nosso projeto de pesquisa é uma retífica marca GARDNER modelo SDG 3 30, com 30 Cv de potência por fuso e alimentação passante.
Este equipamento foi adquirido em 1995 da Denso do Brasil – Curitiba, sendo que esta já estava em uso nesta empresa pelo menos a 20 anos. Então foi totalmente reformada, foi modificado o sistema de alimentação, que era giratório, para um sistema passante e posto em operação em outubro de 1995, sendo revisada periodicamente e tenso a manutenção preventiva em dia.
Figura 8: Retífica plana utilizada no projeto de pesquisa. Fonte: Metalúrgica Riosulense.
A classificação dos rebolos é dada, pelo material abrasivo empregado, pelos
tamanhos dos grãos de que é composto, pela dureza do rebolo, pelo tipo de liga empregado, pela estrutura adotada e pelo tipo de aplicação, como segue a figura abaixo:
Figura 9: Tabela de referência Icder. Fonte: http://www.icder.com.br.
Na Tabela acima está destacada a especificação A46.3 - P6 – V, ou seja um rebolo vitrificado, representado pela letra “V”, de óxido de alumínio cinza, representado pela letra “A”, duro, representado pela letra “P”, estrutura média, representada pelo número “6” e grão predominante 46, com adição de um percentual de outro tamanho de grão.
O rebolo adotado em nosso experimento tem a seguinte especificação “DA46. O10B”:
Um rebolo de liga resinóide (“B”) de grão predominante 46, com adição de 40% de grão 80, com dureza média (“O”), estrutura aberto (“10”) e abrasivo misto, óxido de alumínio branco e óxido de alumínio cinza (“DA”).
O rebolo de porca inserida é o modelo de rebolo utilizado nas máquinas Disc Grinder, sendo provavelmente estes rebolos os mais difíceis de formular, os conhecidos fatores como: tipo de material a ser retificado, dimensão da peça, quantidade de material a remover, potência da máquina, tipo de alimentação, velocidade do rebolo, dimensões do rebolo (diâmetro e furo) e refrigerante, devem ser claramente discriminados para que o fabricante possa especificar as primeiras características dos rebolos. É importante considerar que a parte central nestes rebolos trabalha com velocidade periférica quase nula. Para compensar esta variação de velocidade periférica, alguns rebolos são fabricados com diversas zonas concêntricas de diferentes durezas ou especificações diferentes. NUSSBAUM (1988, p. 345)
Em nosso equipamento é utilizado um óleo solúvel sintético Grind 22, com concentração média de 4%, da marca Houghton, de longa duração, com inibidores de corrosão, específico para operações de retificação.
Este fluido de corte está em uso neste equipamento há três anos e este tem bom poder de troca térmicos e aditivos que propiciam uma boa lubricidade a operação com o mínimo de evaporação.
Para avaliação das alterações de temperatura optamos pelo controle da concentração, na proporção máxima recomendada pelo fabricante, ou seja, 5% durante todas as medições realizadas.
O volume do tanque de fluido de corte é de 800 litros, sendo que todo o fluido em aplicação circula por um separador magnético, para eliminar os resíduos metálicos e limalhas provenientes da operação e posteriormente por um filtro de tecido não tecido a gravidade com malha de 30 micras, ou seja, retenção de partículas com dimensão superior a 0,03mm.
Os ensaios procederam-se da seguinte forma: Em um primeiro momento foram observadas as condições atuais do processo, ou seja, qual a temperatura atual de processamento, qual a produtividade por ferramenta de corte, etc. Para podermos simular uma variação de temperatura que possibilitasse nossas observações, sobre a influência deste parâmetro, nos aproveitamos que um período de demanda de produção reduzida, onde o equipamento teria um repouso de aproximadamente 15 horas e trabalharia apenas 9 horas. Desta forma a temperatura do fluido de corte permaneceria mais amena durante 70% do tempo neste período, coincidindo o período mais frio do ano, no final do mês de julho. Já as medições realizadas com a temperatura máxima, foram realizadas durante o mês de dezembro, período mais quente do ano e numa fase de produção em alta, com o equipamento ligado de domingo às 22h30min h, até sábado as 13h00min, quase de forma ininterrupta. Onde o fluido de corte teve momentos mínimos de repouso, em média 30 minutos para intervalos e trocas de ferramentas e peças. As peças usinadas seguiram a programação normal de produção, sem os interferências ou direcionamentos para escolha de peças com maior ou menor área de usinagem ou mesmo maior ou menor sobre metal. Finalizando nossos estudos, realizamos contato com especialistas neste tipo de operação, no caso o Sr. Masahiko Hamada, engenheiro de aplicação da Daisho Seiki American Corporation, fabricante mundial de retífica Disc Grinder, o qual nos orientou quanto aos parâmetros ideais de temperatura e os resultados obtidos por sua empresa em aplicações similares. Também foram consultados os fabricantes de abrasivos nacionais de abrasivos, para verificar as condições de nosso processo e as melhorias obtidas em outras aplicações. Todo o ensaio foi realizado respeitando as condições atuais do equipamento, sem nenhuma alteração, mantendo as características originais, a fim de observarmos as diferenças de comportamento sem qualquer alteração nas variáveis em avaliação, no caso, a temperatura do fluido, a produtividade horária e o rendimento por conjunto de ferramentas. As peças usinadas são fundidas em anéis de ligas de ferro fundido, ligado com níquel, cromo, cobalto e demais elementos de liga, destinados à produção de sedes de válvula para motores diesel, a gasolina e a GNV.
Durante nosso primeiro período de medições, acompanhamos a operação da máquina durante uma semana do dia 23 a 27 de Julho, no período da manhã, pois os demais turnos estavam de férias e o equipamento permanecia desligado. No decorrer deste período foram usinados vários tipos de peças e observou-se um rendimento melhor aos atingido até a semana anterior, período onde os três turnos estavam em operação, segundo relatos colhidos do operador que permaneceu operando o equipamento neste período. Nossas medições se concentraram em nosso período de trabalho, ou seja, após as 07h00min da manhã, até o final do expediente do turno em trabalho, no caso o primeiro turno, das 05h00min até às 13h30min. Segue abaixo as tabelas com os valore medidos e as produções atingidas durante o período.
07h00min às 08h00min
08h00min às 09h00min
09h30min às 10h30min
10h30min às 11h30min
11h30min às 12h30min
12h30min às 13h30min
07h00min às 08h00min
08h00min às 09h00min
09h30min às 10h30min
10h30min às 11h30min
11h30min às 12h30min
12h30min às 13h30min
07h00min às 08h00min
07h00min às 08h00min
08h00min às 09h00min
09h30min às 10h30min
10h30min às 11h30min
11h30min às 12h30min
12h30min às 13h30min
Produção por ferramenta:
Jogo 1 56.518 46,23°C Jogo 2 54.152 44,75°C
A segunda etapa da coleta de dados foi realizada entre os dias 10 a dia 14 de Dezembro de 2007, nos mesmos horários que no experimento anterior. Porém neste horário a produção estava à plena carga, com os três turnos ativos e com a temperatura ambiente mais elevada. No caso da condição anterior, o período das 05h00min até as 07h00min era suficiente para elevar a temperatura do fluido de corte da temperatura ambiente para próximo dos 45°C. Neste novo momento a temperatura não tendia a baixar pela ação da temperatura ambiente, pois a temperatura do fluido, não chegava a baixar, pois o equipamento permanecia em ciclo durante todo o período. Sendo então a temperatura inicial, muito superior a ambiente, condição oposta as anteriores, onde a temperatura de partida era a temperatura ambiente.
07h00min às 08h00min
08h00min às 09h00min
09h30min às 10h30min
10h30min às 11h30min
11h30min às 12h30min
12h30min às 13h30min
13h30min às 14h30min
14h30min às 15h30min
15h30min às 16h30min
16h30min às 17h03min
07h00min às 08h00min
08h00min às 09h00min
09h30min às 10h30min
10h30min às 11h30min
11h30min às 12h30min
12h30min às 13h30min
13h30min às 14h30min
14h30min às 15h30min
15h30min às 16h30min
16h30min às 17h03min
07h00min às 08h00min
08h00min às 09h00min
09h30min às 10h30min
10h30min às 11h30min
11h30min às 12h30min
12h30min às 13h30min
13h30min às 14h30min
14h30min às 15h30min
15h30min às 16h30min
16h30min às 17h03min
Jogo 1 46.253 51,4°C Jogo 2 44.924 53,9°C Jogo 3 46.168 52,7°C Jogo 4 42.623 57,8°C
Durante a execução dos testes observamos que a temperatura ambiente girou um torno de 16°C no primeiro experimento e de 28°c no segundo, chegando a picos de 34° C, durante o segundo período.
Finalizando as análises dos resultados, constatamos que a média de produção com a temperatura levemente inferior, apresenta um acréscimo de 10% na produtividade horária, provocada principalmente pelo menor desgaste do rebolo e pelo conforto proporcionado na operação, com a redução considerável do vapor e redução da temperatura das peças, facilitando o manuseio. Outra conseqüência foi que durante o primeiro período, notamos uma produtividade maior por conjunto de ferramentas, na ordem de 22,3% superior, algo que resultaria em uma redução de R$ 65.000,00 anuais. Durante nosso estudo tivemos contato com vários fornecedores de abrasivos, sendo que estes sempre aconselhavam a melhoria no sistema de refrigeração, principalmente nas questões de temperatura, pois por se tratarem de rebolos de liga resinóide, pois a temperatura ideal do fluido de corte é aconselhável que se mantenha abaixo dos 45°C, para evitar a degradação da liga, ocorrendo acima desta a degradação da liga, com a soltura dos grãos abrasivos sem o aproveitamento poder de corte destes. Em um contato realizado com o fornecedor Scanner Importação e Exportação Ltda., representante no Brasil da marca Daisho, fabricante de retífica Disc Grinder, do Japão. Estávamos orçando um novo equipamento e quando recebemos as proposta comercial, fomos visitados pelos senhores Tadashi Takemoto – Engenheiro da aplicação da Scanner, Sr. Milton Sakaguti – Vendedor técnico da Scanner e o Sr. Masahiko Hamada, engenheiro de aplicação da Daisho Seiki American Corporation, do escritório regional dos Estados Unidos. Em nossa conversa o Sr. Hamada, nos comentou que as máquinas atuais já são de fábrica munidas de um sistema de resfriamento de fluido de corte, composto por dois resfriadores, tipo chiller, com capacidade de 15.000 Kcal, para cada rebolo. Ou seja, uma capacidade de resfriamento em torno de 30.000 kcal/h, a fim de manter o fluido de corte por volta de 25°C, temperatura considerada por ele a ideal para usinagem de nossas peças. Em um cálculo resumido de nosso consumo de abrasivos o Sr.Hamada, comentou que poderíamos chegar a uma redução de até 50% na s ligas de aço e cromo e em nossas ligas de Níquel e cobalto, poderíamos atingir um resultado até 70% melhor que o atual. Munido destes argumentos e apoiados nos resultados de nosso experimento, propusemos a instalação de um sistema de filtragem com maior volume de liquido e a instalação de um sistema de resfriamento para o fluido de corte. Nossa proposta foi aceita e então foi formulado um projeto para expansão do processo de retificação Disc Grinder da Riosulense, onde foram adquiridos mais um equipamento similar ao existente, que deverá primeiramente, passar por uma reforma completa. Foi programada também a compra um sistema de refrigeração com um filtro ecológico com sistema de retro lavagem e volume total de 1700 litros, em série com um sistema de resfriamento provido de um chiller de 90.000 Kcal/h e um trocador de calor tipo casco e tubos em bronze. Este sistema deverá baixar a temperatura das duas retificas (com a implantação da retífica reformada) para valores próximos a 25°C, com possibilidade de expansão futura para os outros equipamentos de desbaste do setor, com as retíficas centerless que realizam o desbaste externo da sedes de válvula. As projeções de expansão para alinha direcionam para uma tendência de crescimento superior a 30%, para a linha, superando a capacidade instalada do equipamento, por isso a necessidade de compra de mais um equipamento, viabilizando então um investimento maior. Para a resolução dos problemas de refrigeração, com a redução dos custos globais da operação e a melhoria da produtividade, resultando em uma um processo mais eficiente. Uma dificuldade que deverá surgir, será a adaptação do rebolo a nova condição, pois a condição atual supera os limites da especificação normal da aplicação do rebolo, pois na temperatura atual, há pouca atuação dos grãos abrasivos, pois o desprendimento e acelerado pela temperatura elevada, resultando em um desgaste excessivo, com baixa quantidade de material removido.