
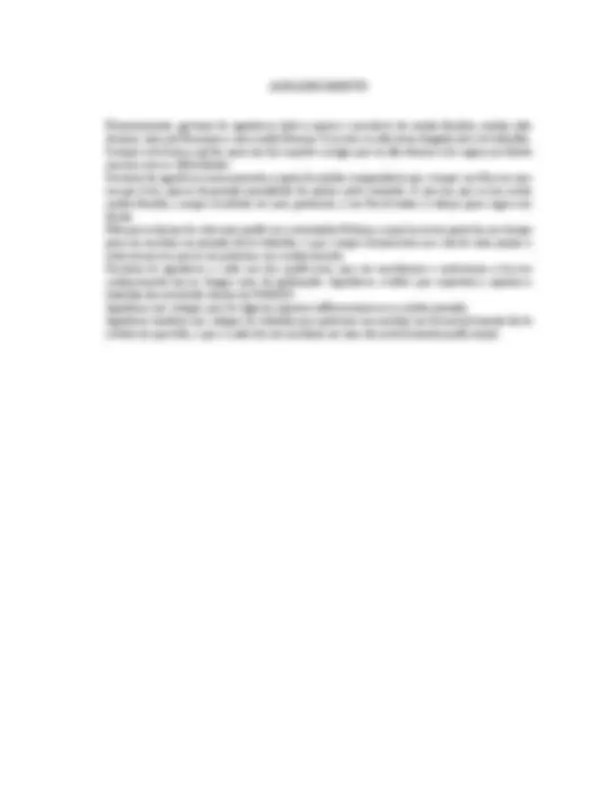
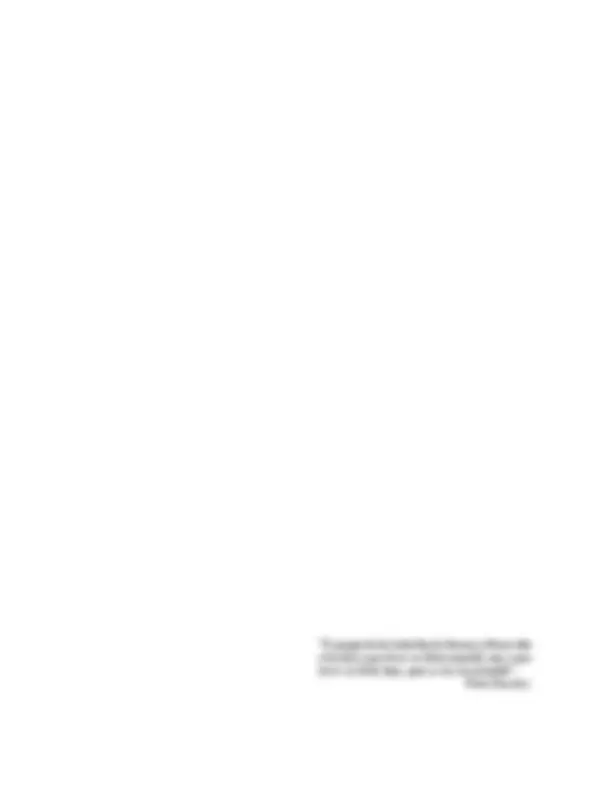
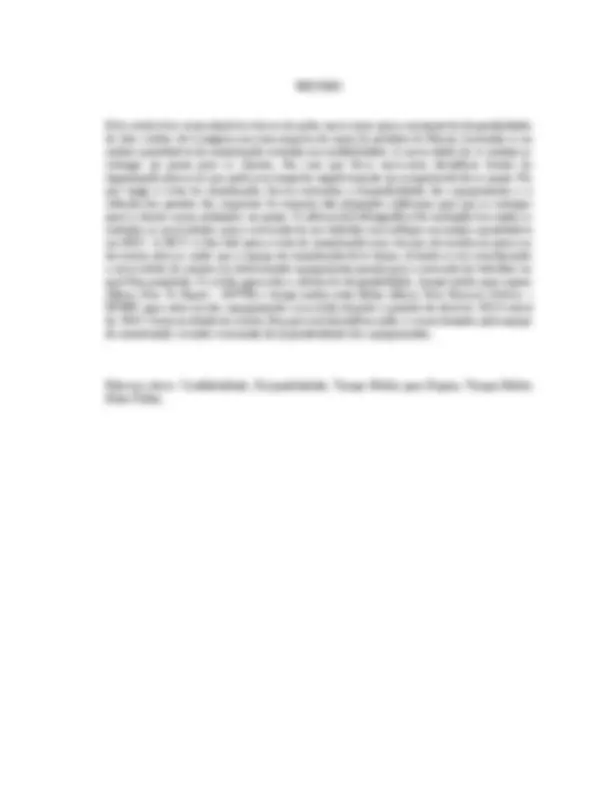
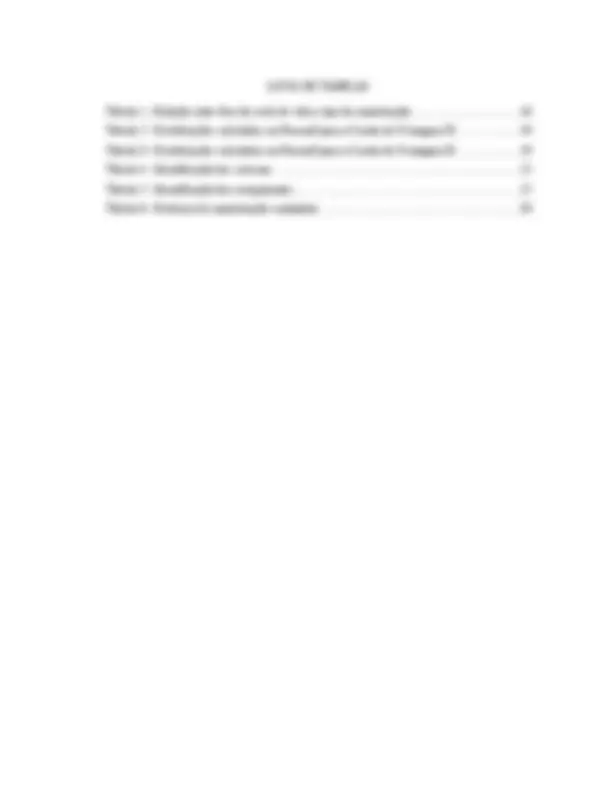
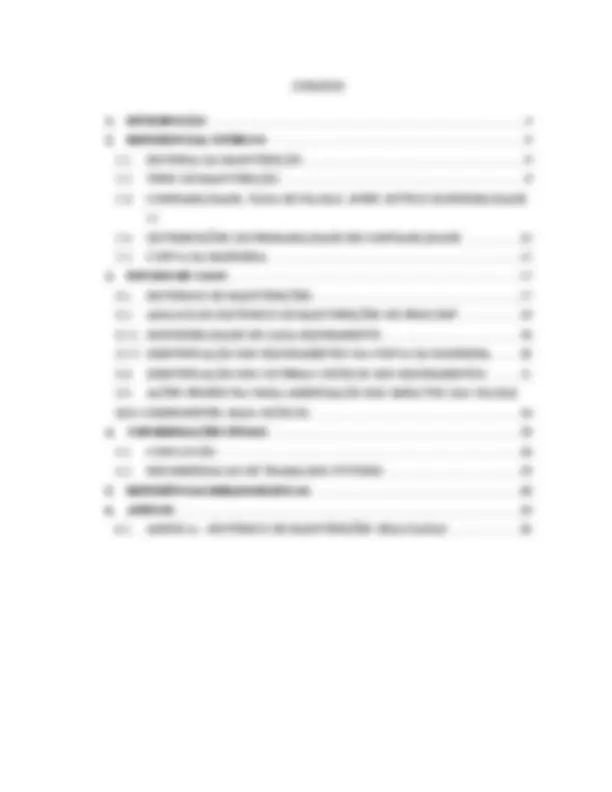
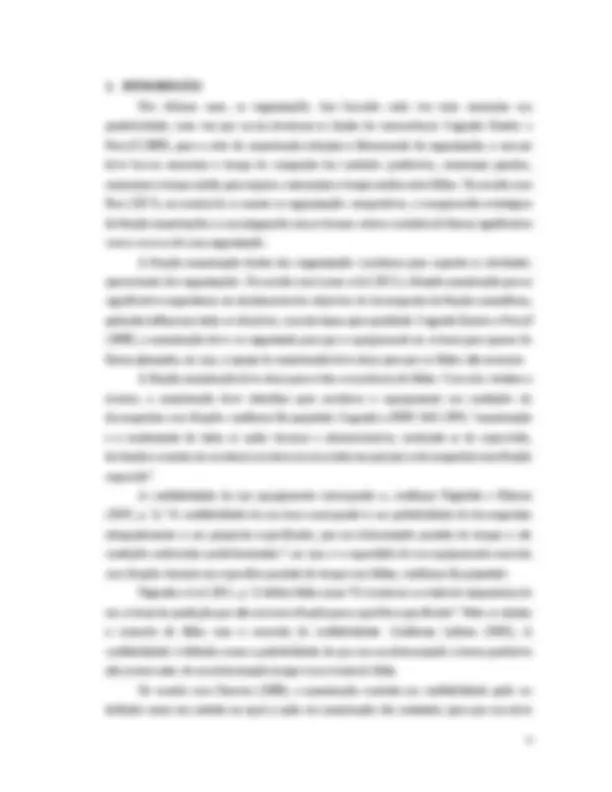
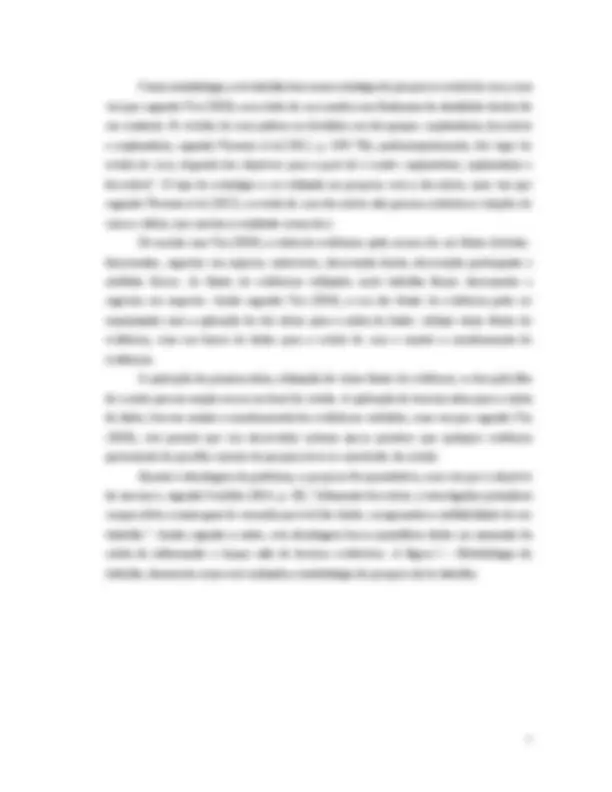
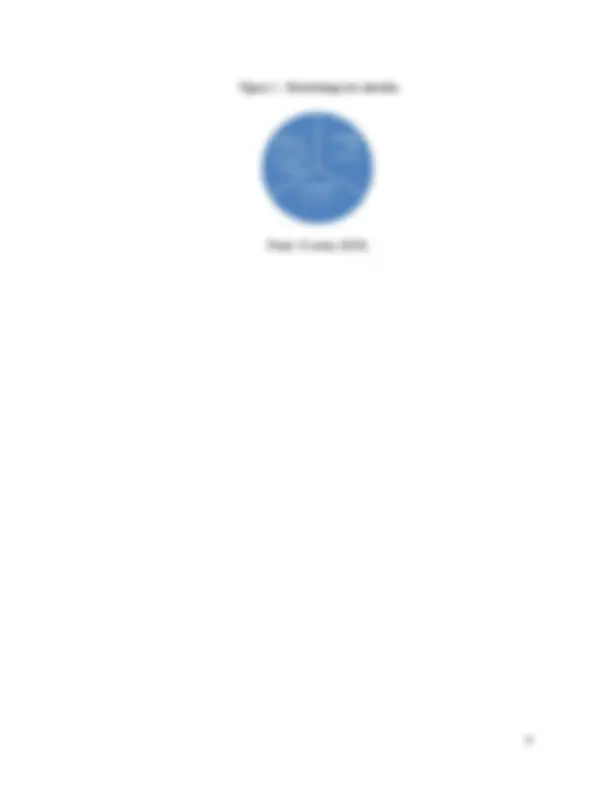

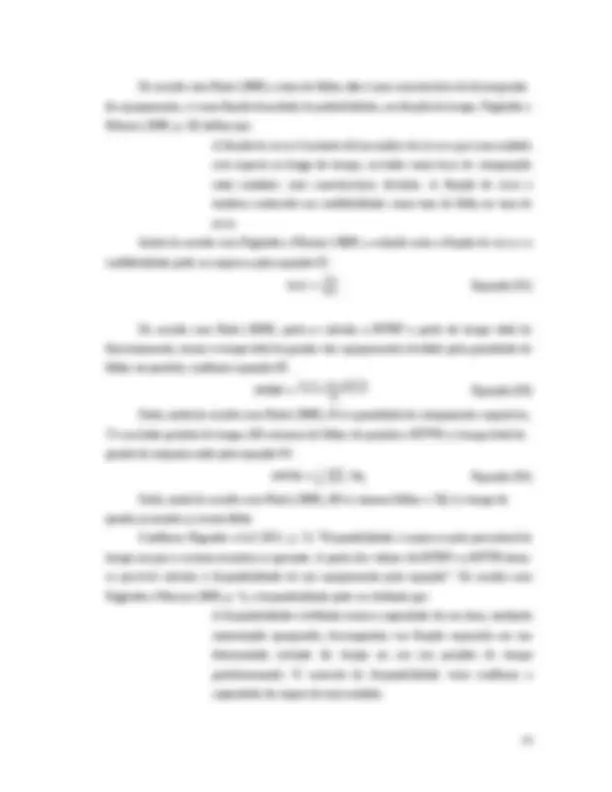
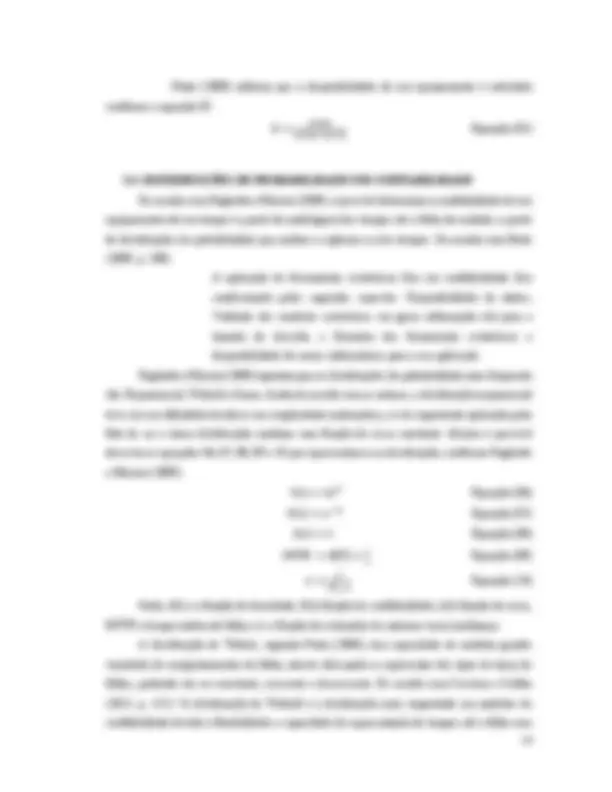
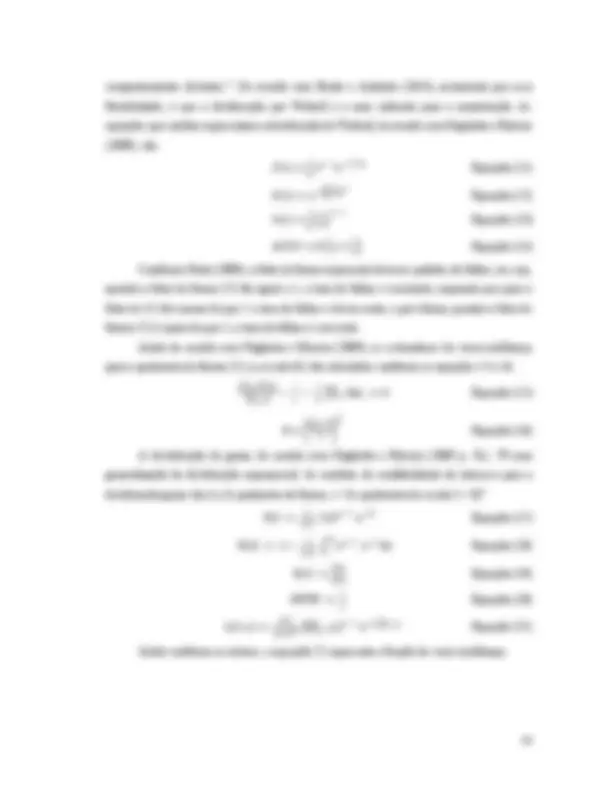
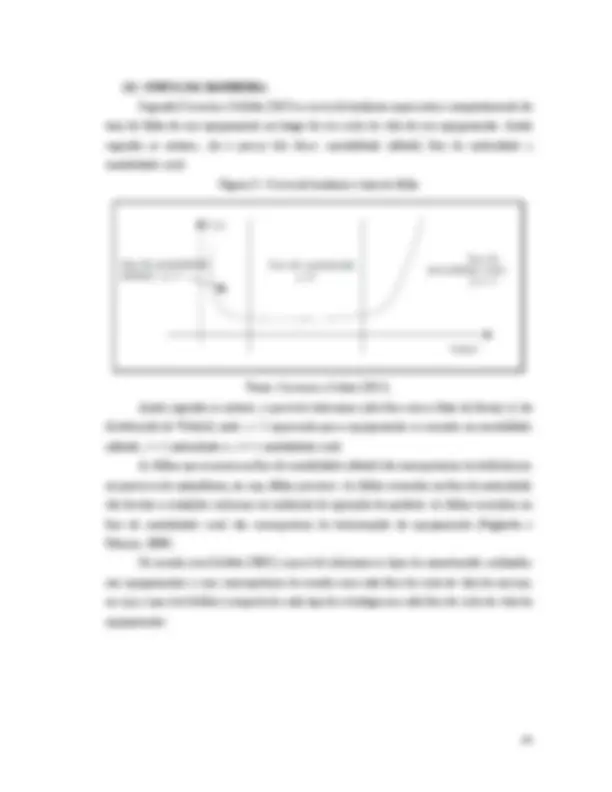
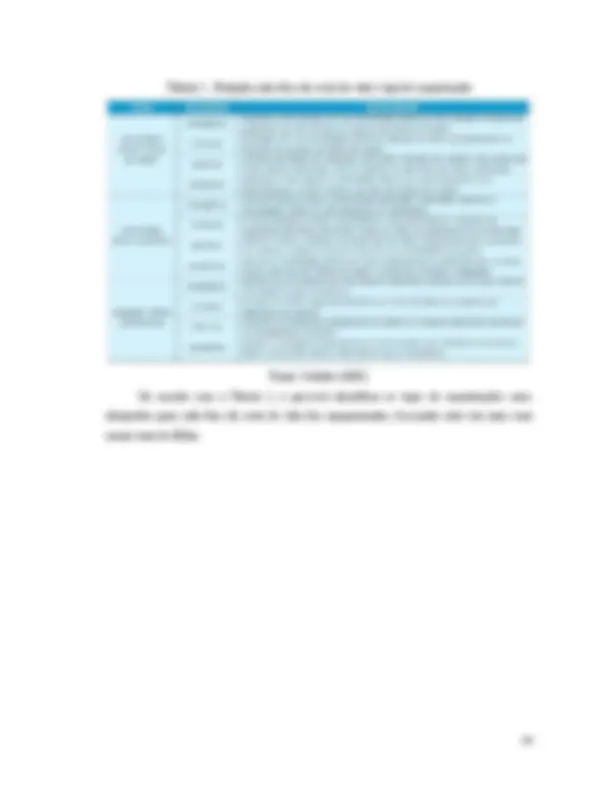
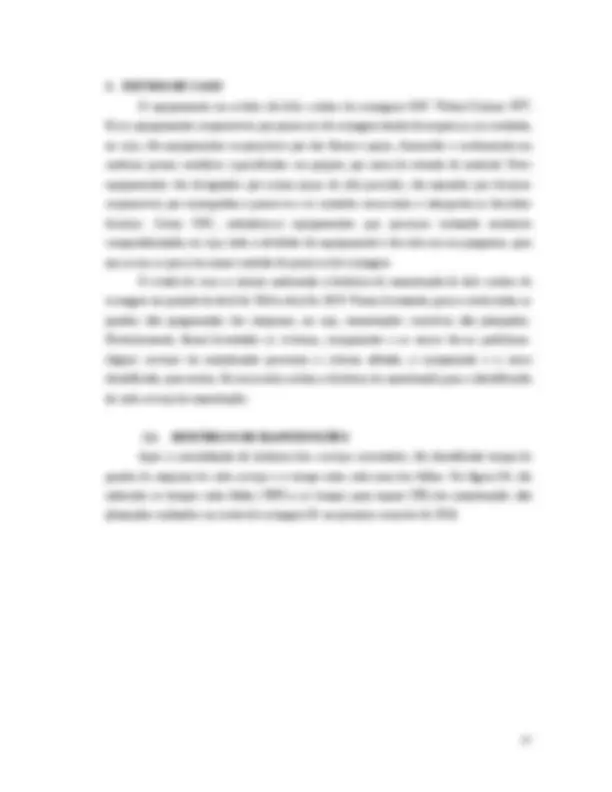
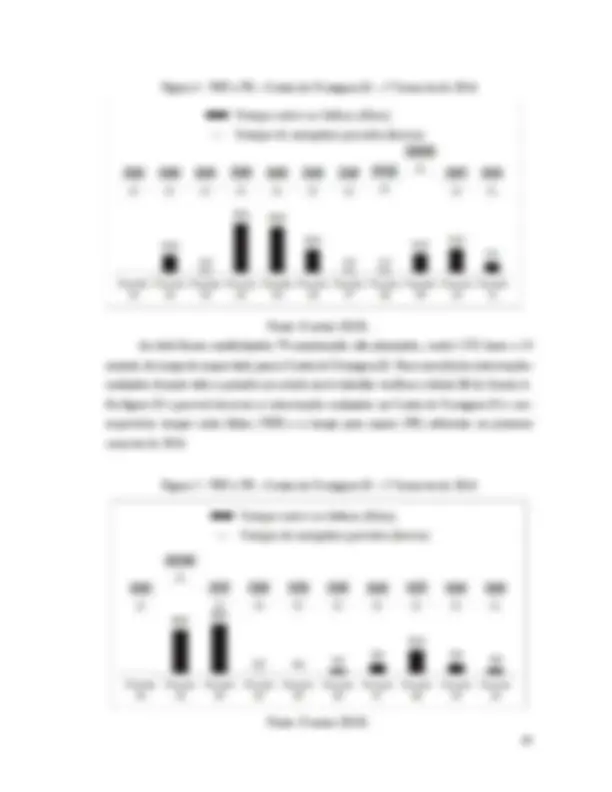
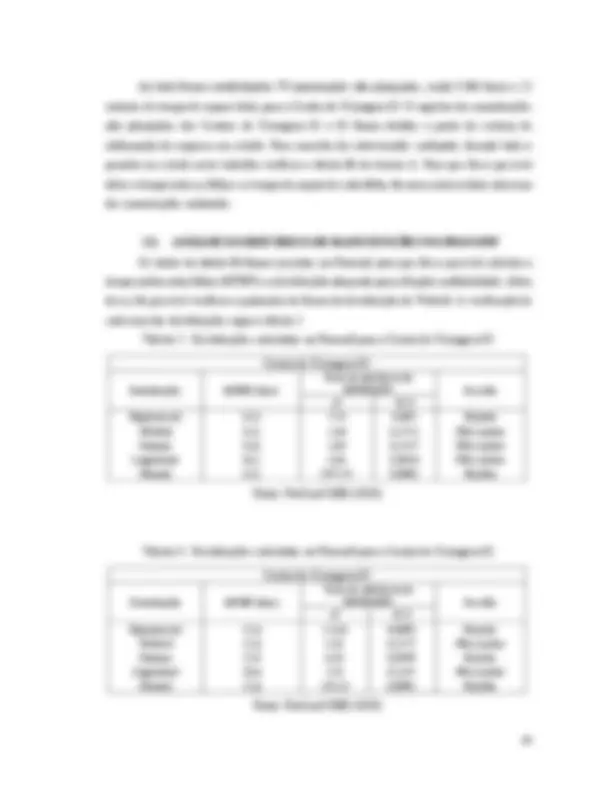
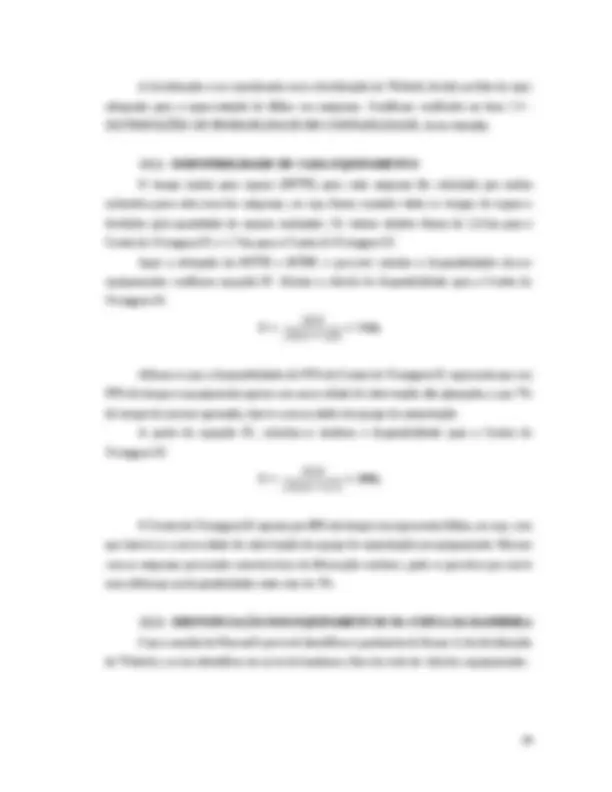
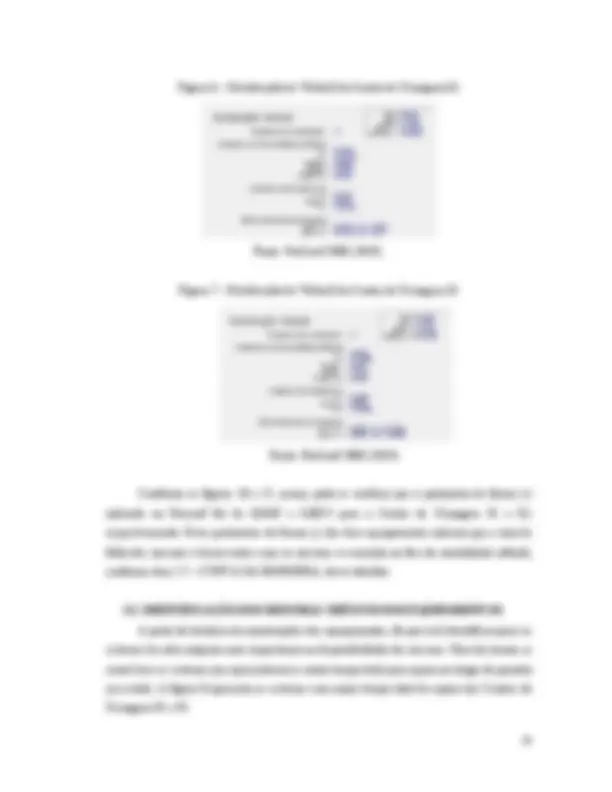
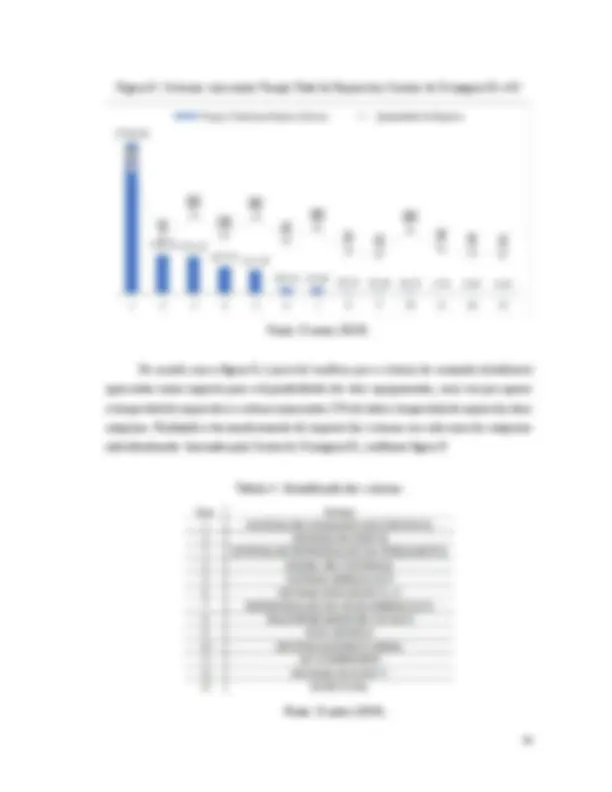
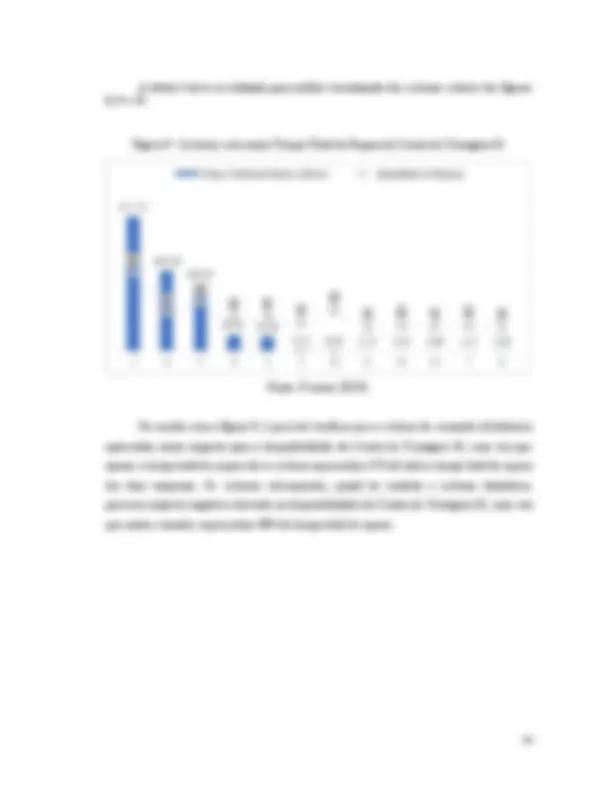
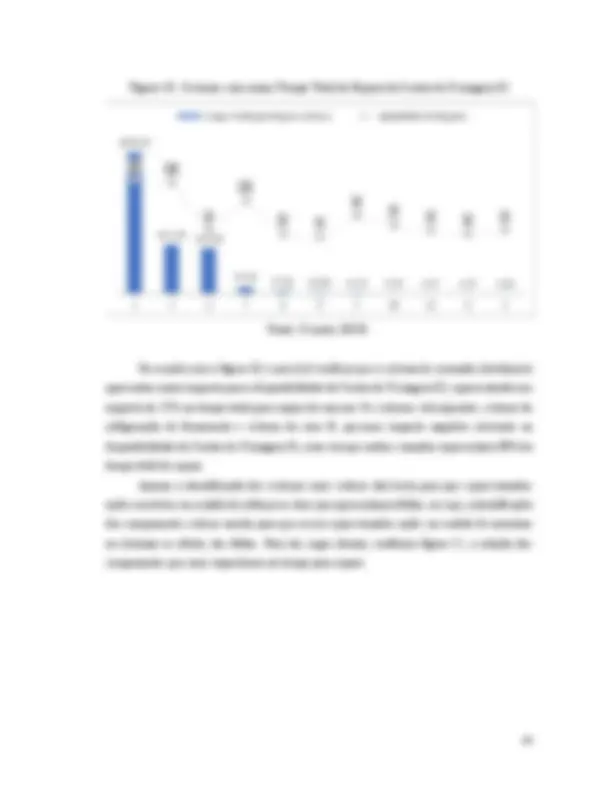
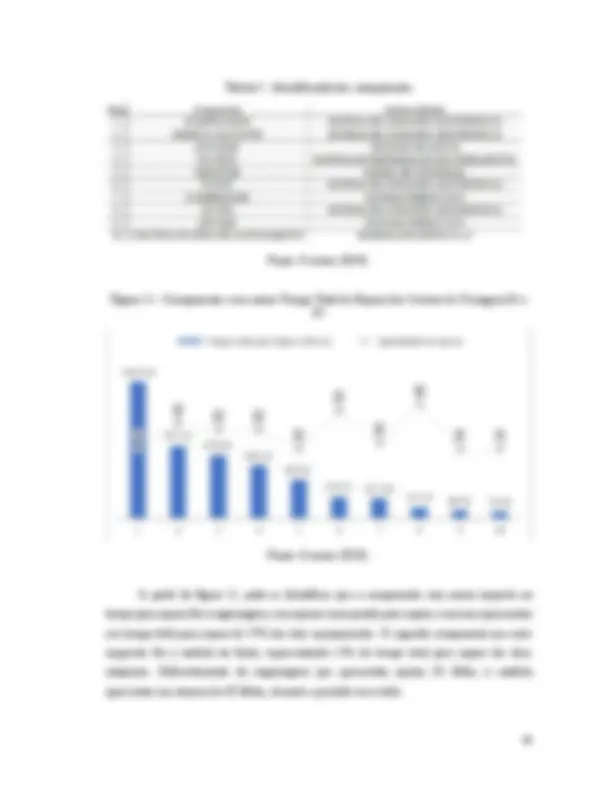
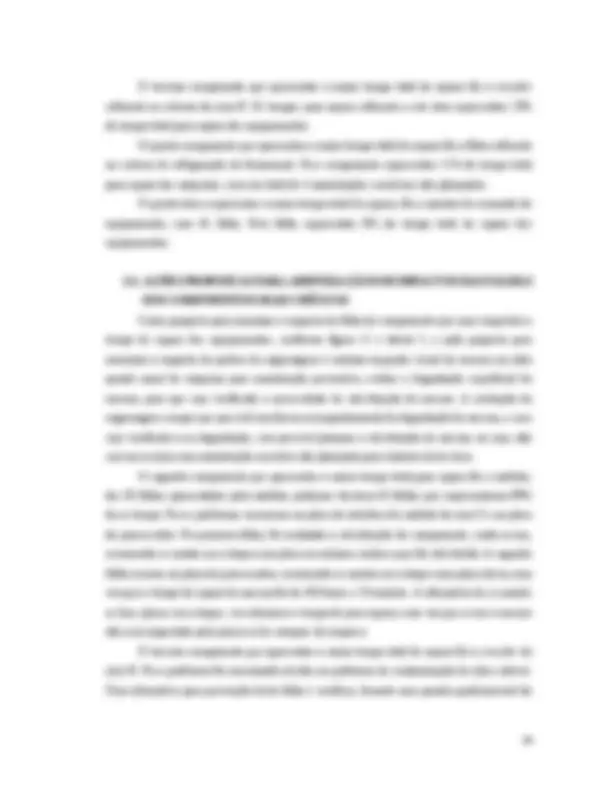
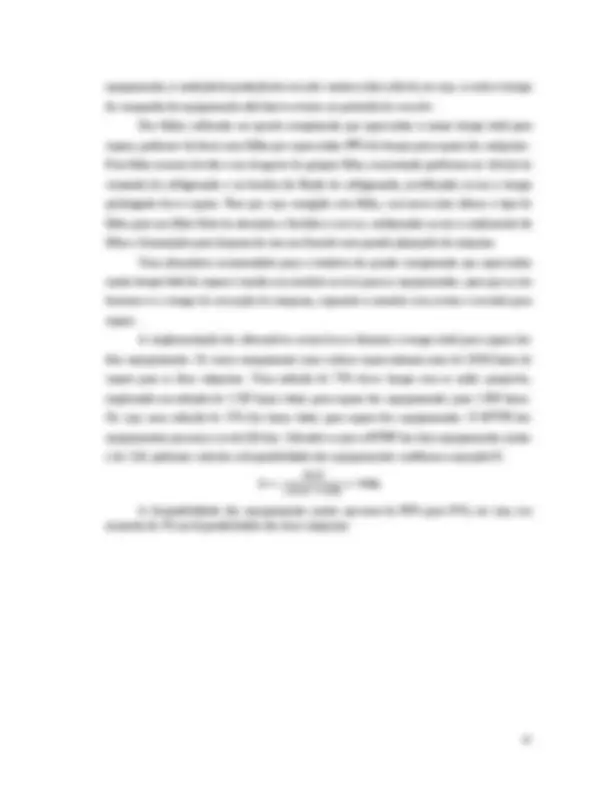
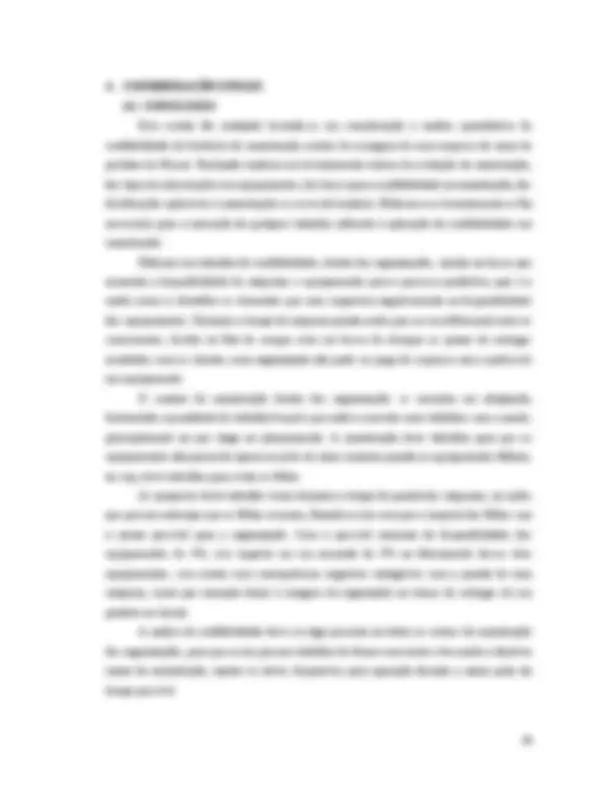
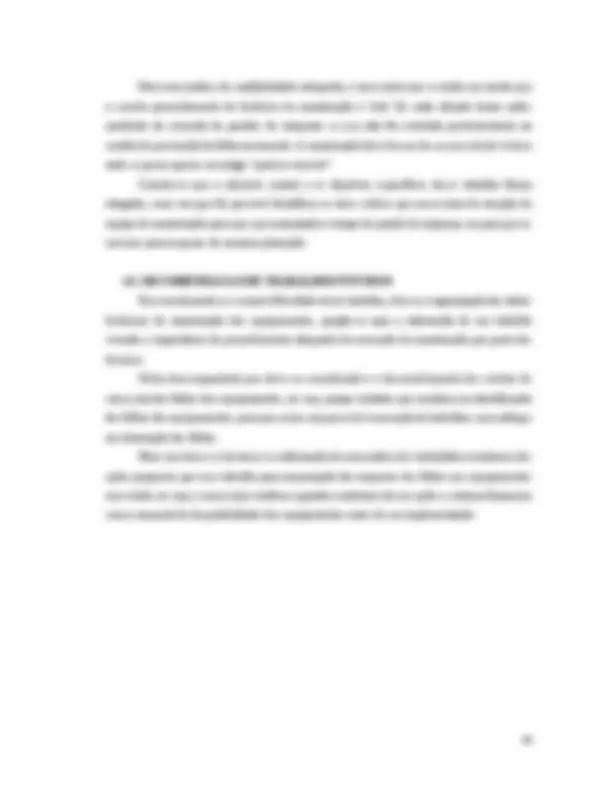
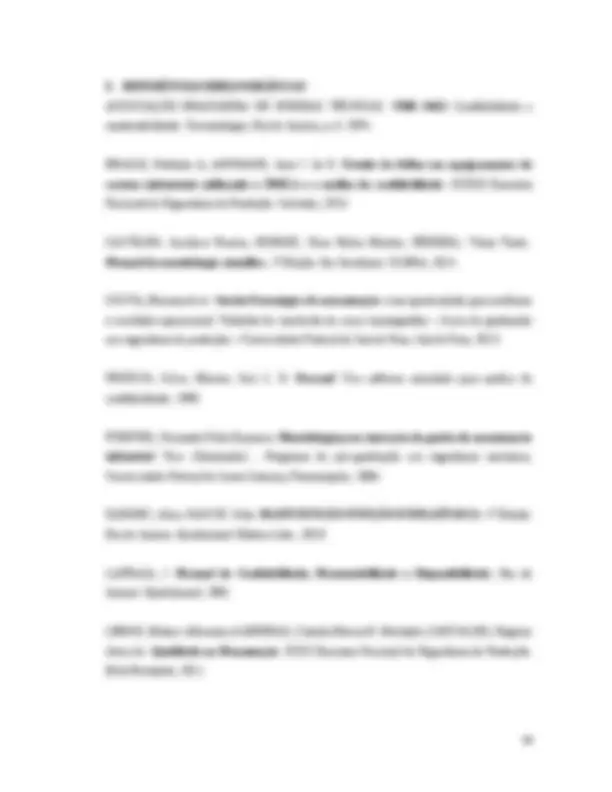
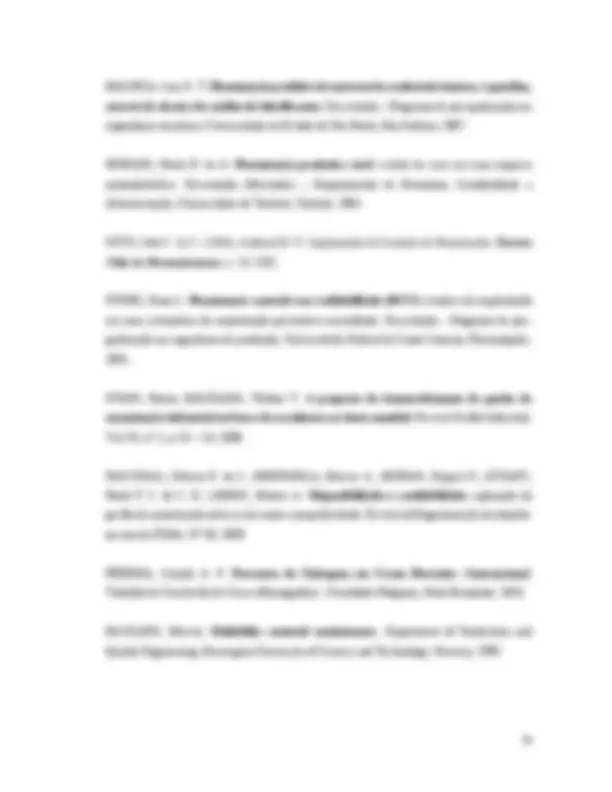
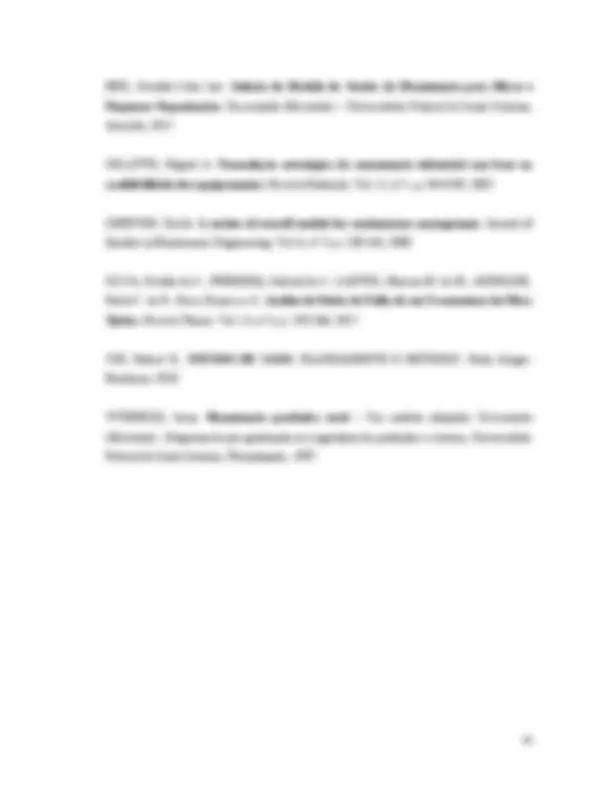
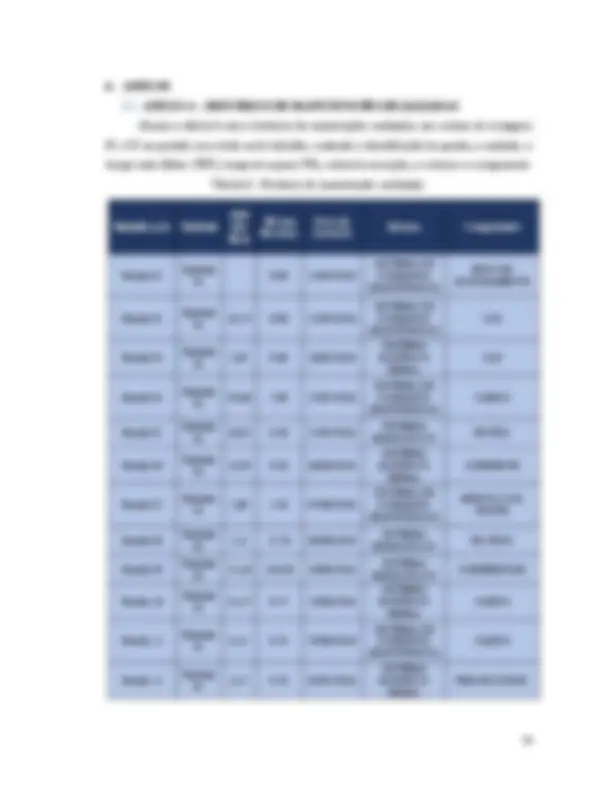
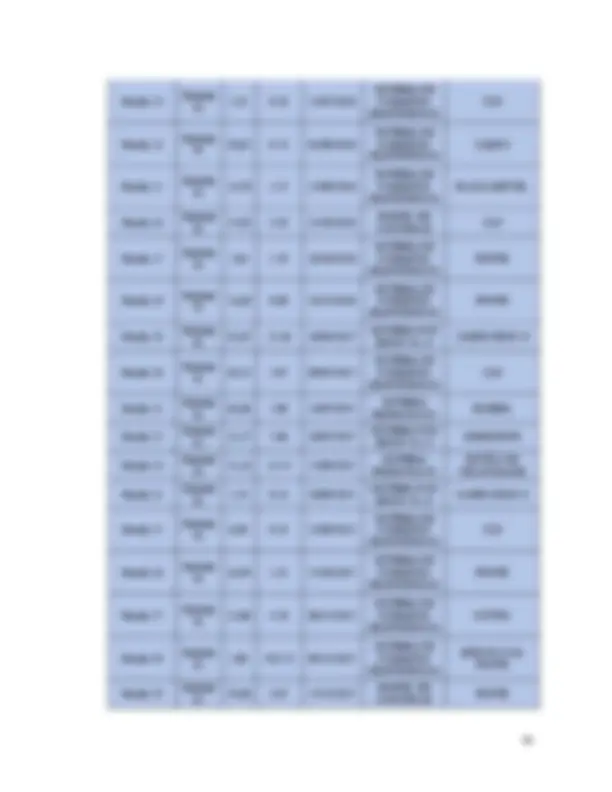
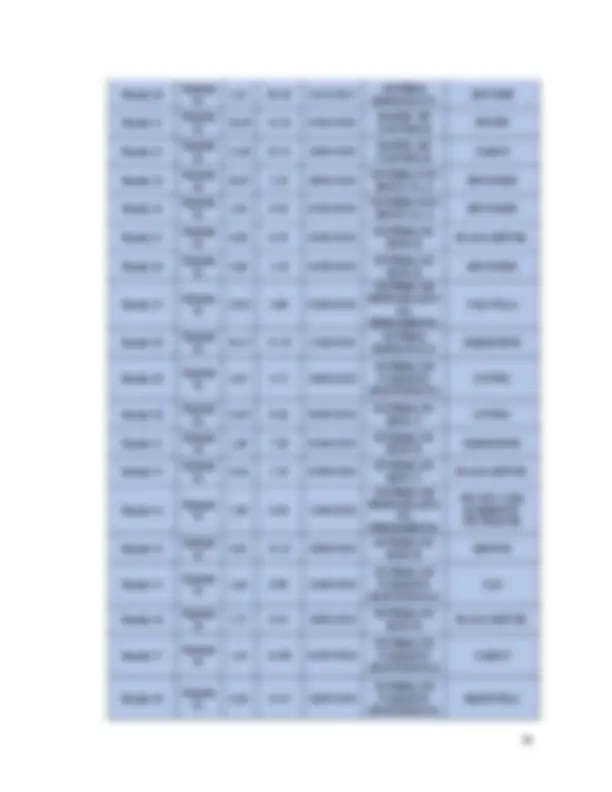
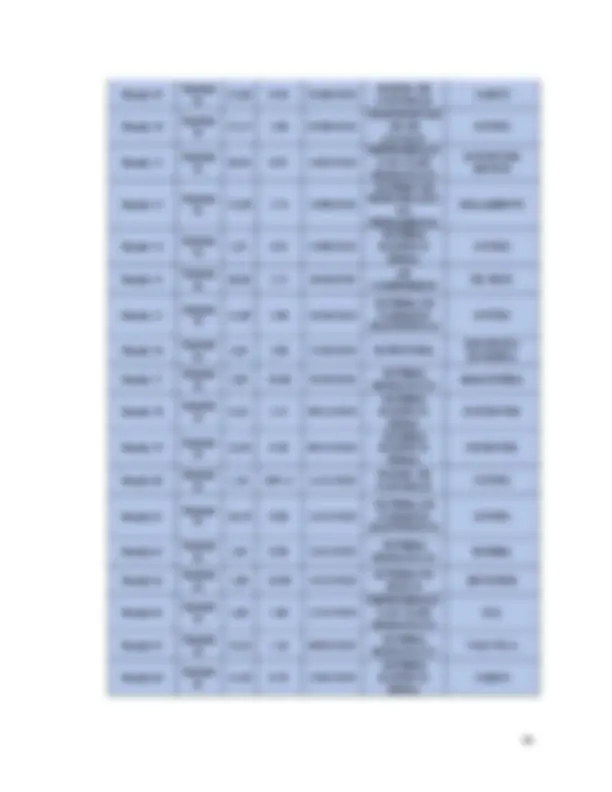
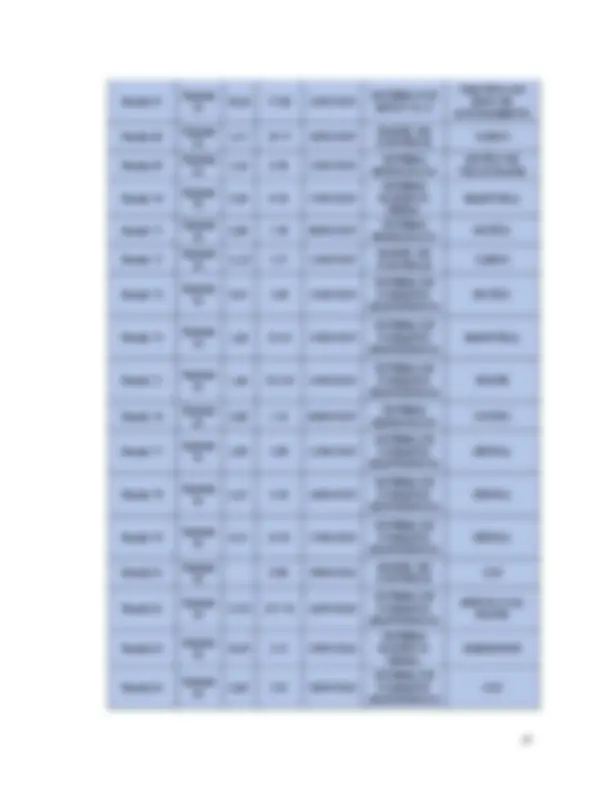
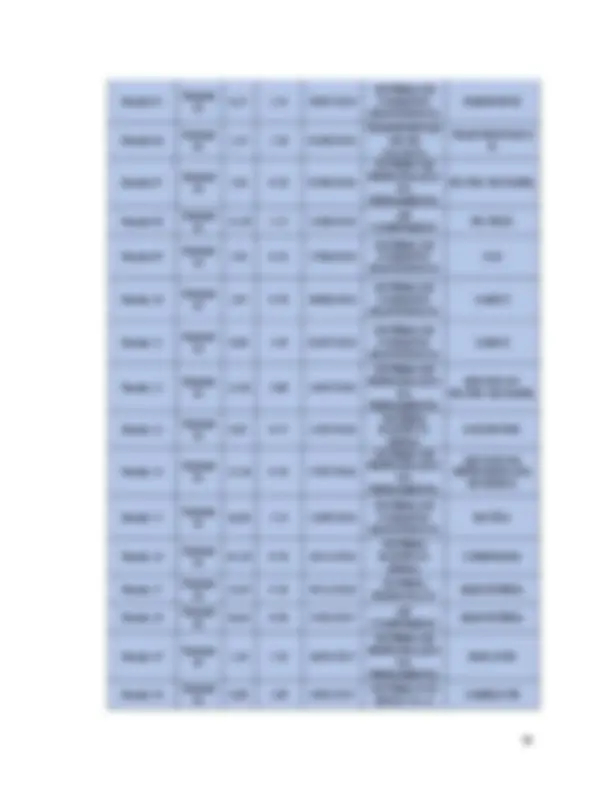
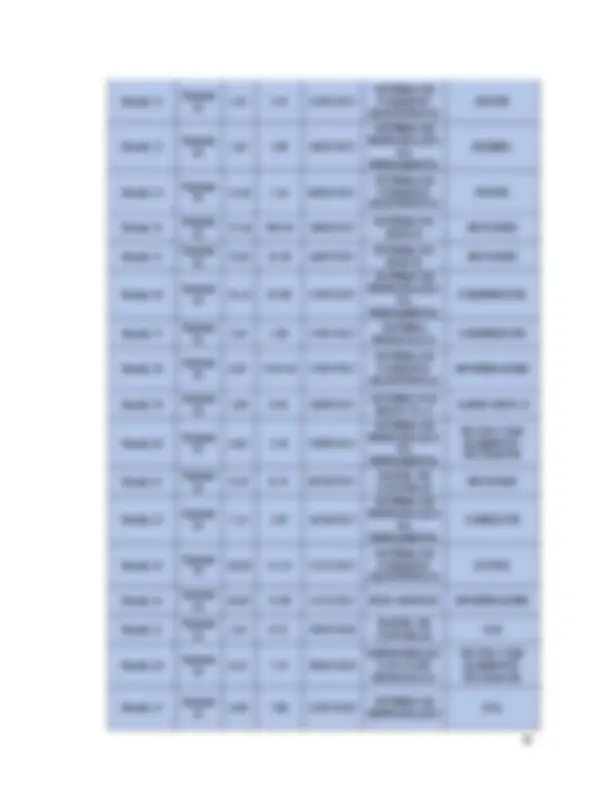
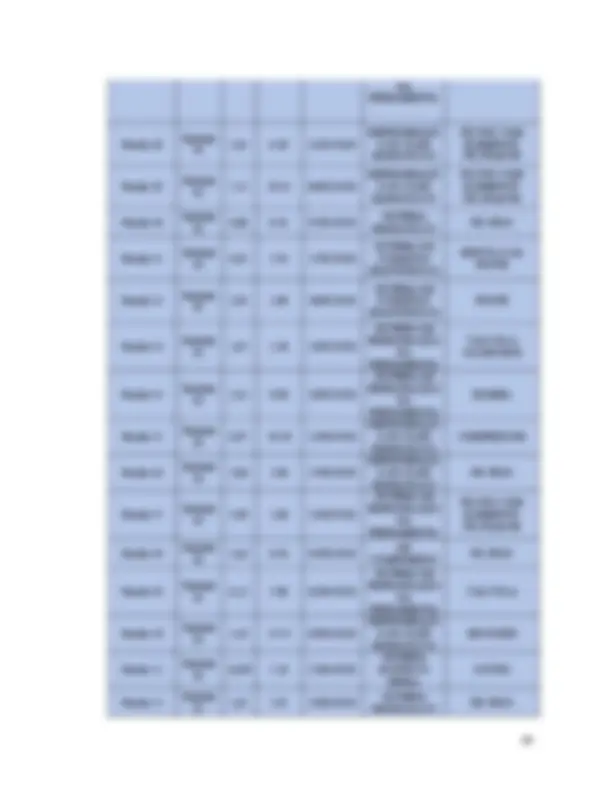
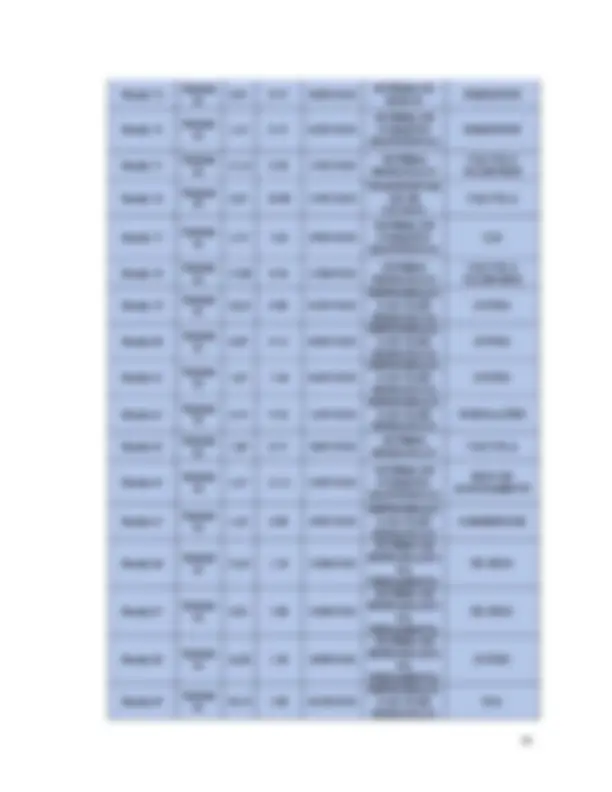
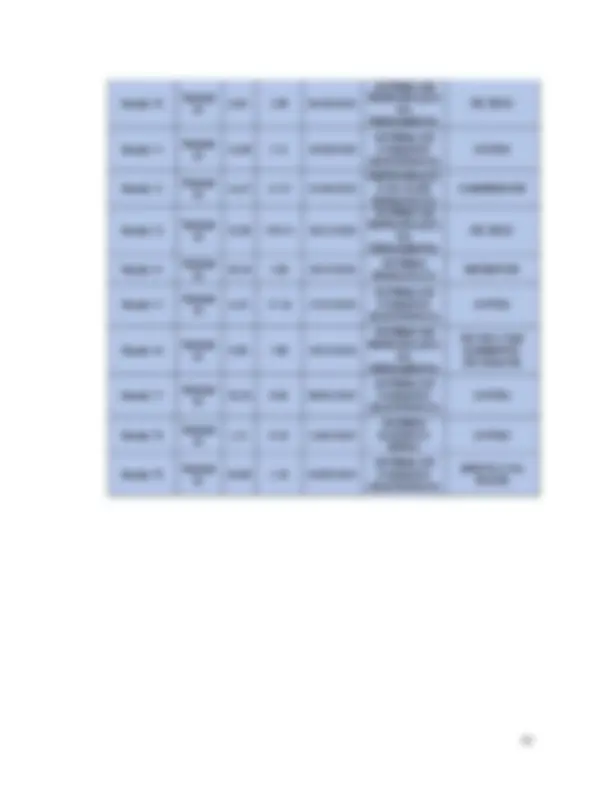
Estude fácil! Tem muito documento disponível na Docsity
Ganhe pontos ajudando outros esrudantes ou compre um plano Premium
Prepare-se para as provas
Estude fácil! Tem muito documento disponível na Docsity
Prepare-se para as provas com trabalhos de outros alunos como você, aqui na Docsity
Os melhores documentos à venda: Trabalhos de alunos formados
Prepare-se com as videoaulas e exercícios resolvidos criados a partir da grade da sua Universidade
Responda perguntas de provas passadas e avalie sua preparação.
Ganhe pontos para baixar
Ganhe pontos ajudando outros esrudantes ou compre um plano Premium
Comunidade
Peça ajuda à comunidade e tire suas dúvidas relacionadas ao estudo
Descubra as melhores universidades em seu país de acordo com os usuários da Docsity
Guias grátis
Baixe gratuitamente nossos guias de estudo, métodos para diminuir a ansiedade, dicas de TCC preparadas pelos professores da Docsity
Trabaho de conclusão de curso sobre análise quantitativa de manutenção centrada em confiabilidade de centros de usinagem
Tipologia: Teses (TCC)
1 / 48
Esta página não é visível na pré-visualização
Não perca as partes importantes!
FACULDADE PROFESSOR MIGUEL ÂNGELO DA SILVA SANTOS – FeMASS
Nome do aluno
Christian de Sousa Lima
Trabalho Final do curso de graduação em Engenharia
de Produção, da Faculdade Professor Miguel Ângelo
da Silva Santos (FeMASS), para obtenção do grau de
BACHAREL em Engenharia de Produção.
Professor Orientador de TCC: Hilário Mendes de Carvalho, MSc
“O propósito do trabalho de formar o futuro não
é decidir o que deve ser feito amanhã, mas o que
deve ser feito hoje, para se ter um amanhã”.
Peter Drucker.
Este estudo teve como objetivo a busca de ações necessárias para o aumento da disponibilidade
de dois centros de usinagem em uma empresa do ramo de petróleo de Macaé, baseando-se na
análise quantitativa da manutenção centrada em confiabilidade. A necessidade de se realizar as
entregas no prazo para os clientes, fez com que fosse necessário identificar dentro da
organização processos que pudessem impactar negativamente no cumprimento desse prazo. No
que tange o setor de manutenção, buscar aumentar a disponibilidade dos equipamentos e a
redução das paradas das maquinas de maneira não planejada colaboram para que as entregas
para o cliente sejam realizadas no prazo. O referencial bibliográfico foi realizado buscando-se
entender as necessidades para a execução de um trabalha com enfoque em análise quantitativa
em MCC. A MCC se faz vital para o setor de manutenção uma vez que ela auxilia no processo
decisório sobre as ações que a equipe de manutenção deve tomar, levando-se em consideração
a necessidade de manter um determinado equipamento pronto para a execução de trabalhos ao
qual fora projetado. O estudo apresenta o cálculo de disponibilidade, tempo médio para reparo
(Mean Time To Repair – MTTR) e tempo médio entre falhas (Mean Time Between Failure –
MTBF) para cada um dos equipamentos em estudo durante o período de abril de 2013 à abril
de 2016. Como resultado do estudo, fora possível identificar ações a serem tomadas pela equipe
de manutenção visando o aumento da disponibilidade dos equipamentos.
Palavras-chave: Confiabilidade, Disponibilidade, Tempo Médio para Reparo, Tempo Médio
Entre Falhas.
Figura 11 - Componentes com maior Tempo Total de Reparo dos Centros de Usinagem 01 e
4
Nos últimos anos, as organizações tem buscado cada vez mais aumentar sua
produtividade, uma vez que assim destacam-se diante da concorrência. Segundo Kardec e
Nascif (2009), para o setor de manutenção otimizar o faturamento da organização, o mesmo
deve buscar aumentar o tempo de campanha das unidades produtivas, minimizar paradas,
minimizar o tempo médio para reparo e maximizar o tempo médio entre falhas. De acordo com
Reis (2017), no cenário de se manter as organizações competitivas, a compreensão estratégica
da função manutenção e a sua integração com os demais setores contribui de forma significativa
com o sucesso de uma organização.
A função manutenção dentro das organizações corrobora para suportar as atividades
operacionais das organizações. De acordo com Lemos et al (2011), a função manutenção possui
significativa importância no atendimento dos objetivos de desempenho da função manufatura,
podendo influenciar todos os objetivos, com destaque para qualidade. Segundo Kardec e Nascif
(2009), a manutenção deve ser organizada para que o equipamento ou sistema pare apenas de
forma planejada, ou seja, a equipe de manutenção deve atuar para que as falhas não ocorram.
A função manutenção deve atuar para evitar a ocorrência de falhas. Caso elas venham a
ocorrer, a manutenção deve trabalhar para recolocar o equipamento em condições de
desempenhar suas funções conforme foi projetado. Segundo a NBR 5462-1994, “manutenção
é a combinação de todas as ações técnicas e administrativas, incluindo as de supervisão,
destinadas a manter ou recolocar um item em um estado no qual possa desempenhar uma função
requerida”.
A confiabilidade de um equipamento corresponde a, conforme Fogliatto e Ribeiro
(2019, p. 2), “A confiabilidade de um item corresponde à sua probabilidade de desempenhar
adequadamente o seu propósito especificado, por um determinado período de tempo e sob
condições ambientais predeterminadas”, ou seja, é a capacidade de um equipamento executar
suas funções durante um específico período de tempo sem falhar, conforme foi projetado.
Fagundes et al (2011, p. 2) define falha como “O evento ou o estado de inoperância de
um sistema de produção que não executa a função para a qual foi especificado”. Pode-se alinhar
o conceito de falha com o conceito de confiabilidade. Conforme Lafraia (2002), A
confiabilidade é definida como a probabilidade de que em um determinado sistema produtivo
não ocorra antes de um determinado tempo t um evento de falha.
De acordo com Sherwin (2000), a manutenção centrada em confiabilidade pode ser
definida como um método no qual a ações da manutenção são realizadas para que um ativo
5
continue a desempenhar suas funções conforme fora projetado. Ou seja, o foco das ações da
manutenção é na confiabilidade. De acordo com Fuentes (2006), A MCC pode, entre outros
fatores, melhorar a disponibilidade, confiabilidade e segurança do sistema.
De acordo com Nunes (2001), a manutenção centrada em confiabilidade tem como
origem o final dos anos 50, na indústria de aviação comercial dos Estados Unidos, em um
momento em que se buscava maneiras de se otimizar a manutenção preventiva. Conforme
Rausand (1998), o objetivo principal da manutenção centrada em confiabilidade é a redução do
custo de manutenção, focando apenas nas funções mais importantes do sistema, e evitando ou
removendo ações da manutenção que não são estritamente necessárias.
Este trabalho fez uso do software Proconf 98. O Proconf, conforme Fritsch e Ribeiro
(1998) “É um programa computacional projetado para o ajuste de distribuições de tempos de
para dados de confiabilidade, através do uso de métodos analíticos e métodos gráficos”. Ainda
segundo os autores, o software fornece a taxa de falha e confiabilidade de um equipamento para
um específico tempo, estimativas de parâmetros de distribuição e seus respectivos intervalos de
confiança. De acordo com Silva et al (2017), o software elabora o teste de aderência de cada
uma das distribuições e aponta quais distribuições podem ou não ser rejeitadas, através dos
testes de qui-quadrado (χ²) e Kolmogorov-Smirnov (K-S).
Fogliatto e Ribeiro (2009) definem que o teste do qui-quadrado (χ²) é realizado somando
o quadrado das diferenças entre os dados projetados e os dados reais em diferentes intervalos,
caso a soma ultrapasse determinado valor de confiança, diz-se que para esse intervalo, análise
probabilística deve ser rejeitada. Ainda segundo os autores, o teste Kolmogorov-Smirnov (K-
S) é realizado de maneira parecida com o teste do qui-quadrado (χ²), com a diferença de que
considera frequências acumuladas ou invés de frequências absolutas.
Os centros de usinagem em estudo são equipamentos essenciais para o processo de
usinagem na empresa em estudo, uma vez que possuem capacidades de trabalho que não são
possíveis de serem realizadas em outros equipamentos da empresa. O processo de usinagem,
de acordo com Pereira (2018), é pela produção de materiais metálicos ou compósitos com
tamanhos, formas e acabamentos diversos. Ainda segundo o autor, o processo de usinagem é
ligado ao desbaste de uma determinada matéria prima, ou seja, a retirada de material para a
fabricação de produtos com determinadas especificações requeridas.
Como objetivo geral, este trabalho buscou propor ações para aumentar a disponibilidade
de dois centros de usinagem de uma empresa do ramo offshore localizada em Macaé, com base
7
Como metodologia, este trabalho tem como estratégia de pesquisa o estudo de caso, uma
vez que segundo Yin (2010), um estudo de caso analisa um fenômeno da atualidade dentro do
seu contexto. Os estudos de caso podem ser divididos em três grupos: exploratório, descritivo
e explanatório, segundo Turrioni et al (2012, p. 149) “Há, predominantemente, três tipos de
estudo de caso, dependo dos objetivos para o qual ele é usado: exploratório, explanatório e
descritivo”. O tipo de estratégia a ser utilizada na pesquisa será a descritiva, uma vez que
segundo Turrioni et al (2012), o estudo de caso descritivo não procura estabelecer relações de
causa e efeito, mas mostrar a realidade como ela é.
De acordo com Yin (2010), a coleta de evidências pode ocorrer de seis fontes distintas:
documentos, registros em arquivo, entrevistas, observação direta, observação participante e
artefatos físicos. As fontes de evidências utilizadas neste trabalho foram: documentos e
registros em arquivos. Ainda segundo Yin (2010), o uso das fontes de evidência pode ser
maximizado com a aplicação de três ideias para a coleta de dados: utilizar várias fontes de
evidência, criar um banco de dados para o estudo de caso e manter o encadeamento de
evidências.
A aplicação da primeira ideia, utilização de várias fontes de evidência, se deu pelo fato
de o autor possuir amplo acesso ao local de estudo. A aplicação da terceira ideia para a coleta
de dados, buscou manter o encadeamento das evidências coletadas, uma vez que segundo Yin
(2010), isto permiti que um observador externo possa perceber que qualquer evidência
proveniente de questões iniciais da pesquisa leve às conclusões do estudo.
Quanto à abordagem do problema, a pesquisa foi quantitativa, uma vez que o objetivo
da mesma é, segundo Castilho (2014, p. 18), “Altamente descritivo, o investigador pretenderá
sempre obter o maior grau de correção possível dos dados, assegurando a confiabilidade de seu
trabalho.”. Ainda segundo o autor, esta abordagem busca quantificar dados no momento da
coleta de informações e lançar mão de técnicas estatísticas. A figura 1 – Metodologia do
trabalho, demonstra como será realizada a metodologia de pesquisa deste trabalho.
8
Figura 1 - Metodologia do trabalho
Fonte: O autor (2019).
10
Figura 2 - Tipos de manutenção
Fonte: Adaptado de Otani e Machado (2008)
Na figura 2, pode-se observar os tipos de manutenção, que classificam as atividades da
equipe de manutenção.
Segundo a NBR 5462/1994 (p. 7), a manutenção corretiva é a “Manutenção efetuada
após a ocorrência de uma pane destinada a recolocar um item em condições de executar uma
função requerida”. A diferença entre a manutenção corretiva não planejada e a manutenção
corretiva planejada, é que, segundo Otani e Machado (2008), a manutenção corretiva não
planejada é a correção da falha de maneira aleatória, é a correção da falha, este tipo de falha
implica em altos custos. Ainda segundo os autores, a manutenção corretiva planejada é uma
correção de uma falha identificada a partir de um acompanhamento preditivo ou detectivo, pelo
fato de ser planejada, tende a ficar mais barata, segura e rápida.
A manutenção preventiva, segundo Nirabedini e Iranmanesh (2013, p. 1), “A
manutenção preventiva é a programação do plano de manutenção que previne a ocorrência de
paradas de produção e falhas. Pode-se dividir a manutenção preventiva em dois grupos centrais
de manutenção, planejada ou baseada na condição. A diferença entre estes dois subgrupos é a
determinação do tempo de manutenção”. De acordo com Xenos (1998), a manutenção
preventiva, sem que seja levado em consideração o tempo de parada de máquina, é mais custosa
do que a manutenção corretiva, devido ao fato de as peças serem substituídas antes do término
de sua vida útil. Ainda segundo o autor, a grande vantagem dessa estratégia é a diminuição das
ocorrências de falha, aumento na disponibilidade dos equipamentos e diminuição das paradas
de máquina.
A manutenção preditiva, segundo Malpica (2007, p.18), “Consiste no monitoramento
regular das condições mecânicas reais das máquinas, e do rendimento operativo dos sistemas
de processo, assegurando assim intervalos máximos entre os reparos.”. O monitoramento das
condições de um equipamento pode ocorrer de diversas maneiras, de acordo com Neto e Lima
11
(2002, p. 11) “As principais características dos aparelhos que permitem isto são que eles
registram a variação das vibrações e também medem diversos outros parâmetros, tais como:
pressão, temperatura desempenho, aceleração, entre outros.”. Conforme Xenos (1998), esse
tipo de manutenção permite melhorar o rendimento dos materiais a serem substituídos em um
equipamento, devido ao fato de essa substituição ocorrer somente no momento próximo do fim
da vida útil desses materiais.
A manutenção detectiva ocorre quando, segundo Paschoal et al (2009), um equipamento
durante o seu funcionamento ele realiza uma auto verificação em busca de alguma falha oculta
ou que seja difícil ser percebida pelo operador ou pela equipe de manutenção. O conceito de
manutenção detectiva e manutenção preditiva se confundem, uma vez que, ainda segundo
Paschoal et al (2009, p. 6) “Na manutenção preditiva, faz-se necessário o diagnóstico a partir
da medição de parâmetros. Na manutenção detectiva, o diagnóstico é obtido de forma direta a
partir do processamento das informações colhidas junto à planta.”. Ou seja, na manutenção
preditiva existe a necessidade de interpretação dos dados, enquanto que na manutenção
detectiva, a informação da falha é fornecida pelo sistema.
Para o entendimento de confiabilidade, é necessário verificar o estudo das funções de
confiabilidade, taxa de falhas, tempo médio entre falhas (Mean Time Between Failure –
MTBF), tempo médio para reparo (Mean Time To Repair - MTTR) e a disponibilidade.
Para o cálculo da função confiabilidade de uma unidade apresentar sucesso em um
determinado tempo de operação, tomando como base o tempo inicial sendo 0, Fogliatto e
Ribeiro (2009, p. 10) definem que:
Suponha n0 unidades idênticas submetidas a teste em condições
predefinidas. Transcorrido o intervalo (t – Δt, t), nf (t) unidades
falharam e ns(t) unidades sobreviveram, tal que nf (t) + ns (t) = n0. A
confiabilidade da unidade é definida como a sua probabilidade
acumulada de sucesso; assim, em um tempo t, a função de
confiabilidade R(t) é:
t
୬ୱ(୲)
୬ୱ (୲)ା୬ (୲)
୬ୱ(୲)
୬
Equação (01)
13
Pinto (2009) informa que a disponibilidade de um equipamento é calculada
conforme a equação 05:
ାୖ
Equação (05)
De acordo com Fogliatto e Ribeiro (2009), é possível determinar a confiabilidade de um
equipamento até um tempo t a partir da modelagem dos tempos até a falha da unidade, a partir
de distribuições de probabilidade que melhor se aplicam a estes tempos. De acordo com Pinto
(2009, p. 188):
A aplicação de ferramentas estatísticas fica em confiabilidade fica
condicionada pelos seguintes aspectos: Disponibilidade de dados;
Validade dos modelos estatísticos em gerar informação útil para a
tomada de decisão; e Domínio das ferramentas estatísticas e
disponibilidade de meios informáticos para a sua aplicação.
Fogliatto e Ribeiro (2009) apontam que as distribuições de probabilidade mais frequente
são: Exponencial, Weibull e Gama. Ainda de acordo com os autores, a distribuição exponencial
teve seu uso difundido devido à sua simplicidade matemática, e é de importante aplicação pelo
fato de ser a única distribuição contínua com função de risco constante. Abaixo é possível
observar as equações 06, 07, 08, 09 e 10 que representam essa distribuição, conforme Fogliatto
e Ribeiro (2009):
f(t) = λe
୲
Equação (06)
R(t) = e
ି ୲
Equação (07)
h(t) = λ Equação (08)
ଵ
ఒ
Equação (09)
୬
∑ ୲୧
సభ
Equação (10)
Onde, f(t) é a função de densidade, R(t) função de confiabilidade, h(t) função de risco,
MTTF o tempo médio até falha e Ʌ a função do estimador de máxima verossimilhança.
A distribuição de Weibul, segundo Pinto (2009), tem capacidade de modelar grande
variedade de comportamentos de falha, através dela pode-se representar três tipos de taxas de
falhas, podendo ela ser constante, crescente e decrescente. De acordo com Cerveira e Sellito
(2015, p. 412) “A distribuição de Weibull é a distribuição mais importante em modelos de
confiabilidade devido à flexibilidade e capacidade de representação de tempos até a falha com
14
comportamentos distintos.”. De acordo com Braile e Andrade (2013), justamente por essa
flexibilidade, é que a distribuição por Weibull é a mais indicada para a manutenção. As
equações que melhor representam a distribuição de Weibull, de acordo com Fogliatto e Ribeiro
(2009), são:
ఊ
ఏ
ఊିଵ
ି ௧
ϒ
/ఏ
Equação (11)
ି ቀ
ഇ
ቁ(
ഇ
)
ϒ
Equação (12)
ϒ
ఏ
௧
ఏ
ϒି ଵ
Equação (13)
ଵ
ϒ
ቁ Equação (14)
Conforme Pinto (2009), o fator de forma representa diversos padrões de falhas, ou seja,
quando o fator de forma (ϒ) for igual a 1, a taxa de falhas é constante, enquanto que para o
fator de (ϒ) for menor do que 1 a taxa de falhas é decrescente, e por último, quando o fator de
forma (ϒ) é maior do que 1, a taxa de falhas é crescente.
Ainda de acordo com Fogliatto e Ribeiro (2009), os estimadores de verossimilhança
para o parâmetro de forma (ϒ) e a escala (θ) são calculados conforme as equações 15 e 16.
∑ ୲
ɼ
୪୬୲
సభ
∑ ୲
ɼ
సభ
ଵ
ɼ
ଵ
୬
lnt
୧
୬
୧ୀଵ
= 0 Equação (15)
θ =
∑ ୲
ɼ
సభ
୬
భ
ɼ
Equação (16)
A distribuição de gama, de acordo com Fogliatto e Ribeiro (2009 p. 31), “É uma
generalização da distribuição exponencial. As medidas de confiabilidade de interesse para a
distribuição gama são (t ≥ 0, parâmetro de forma γ > 0 e parâmetro de escala λ > 0)”
f
t
ɼ(୷)
λt
୷ିଵ
e
ି ୲
Equação (17)
t
ଵ
ɼ
( ୷
)
∫ x
୷ିଵ
୲
e
ି ୶
dx Equação (18)
h
t
(୲)
ୖ (୲)
Equação (19)
ஓ
Equação (20)
L(λ, γ) =
ಋ
[ ɼ
( ஓ
)]
[∏ t
୧
୬
୧ୀଵ
ஓିଵ
e
ି ∑ ୲
సభ
Equação (21)
Ainda conforme os autores, a equação 21 representa a função de verossimilhança.