
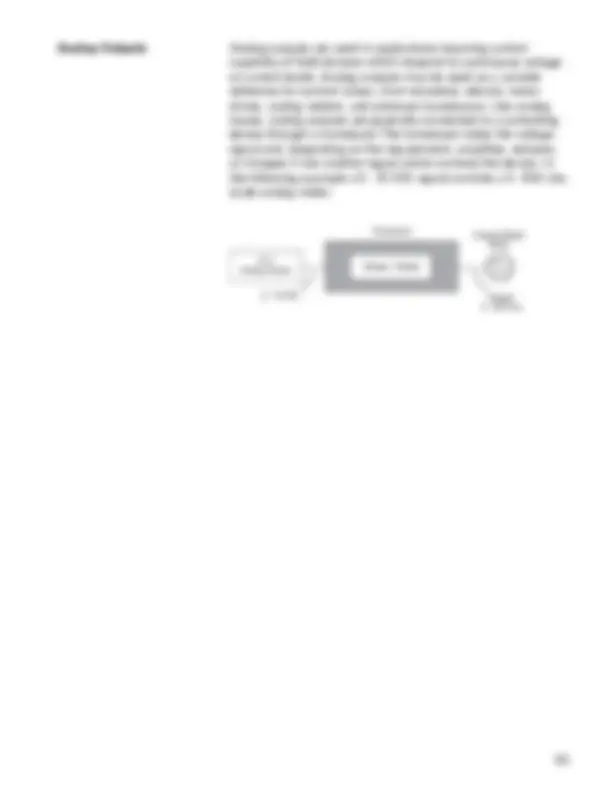
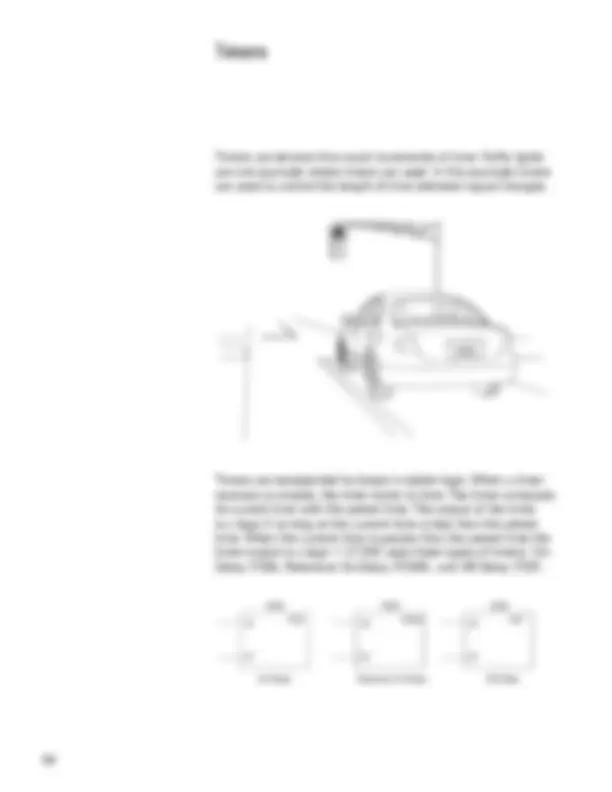
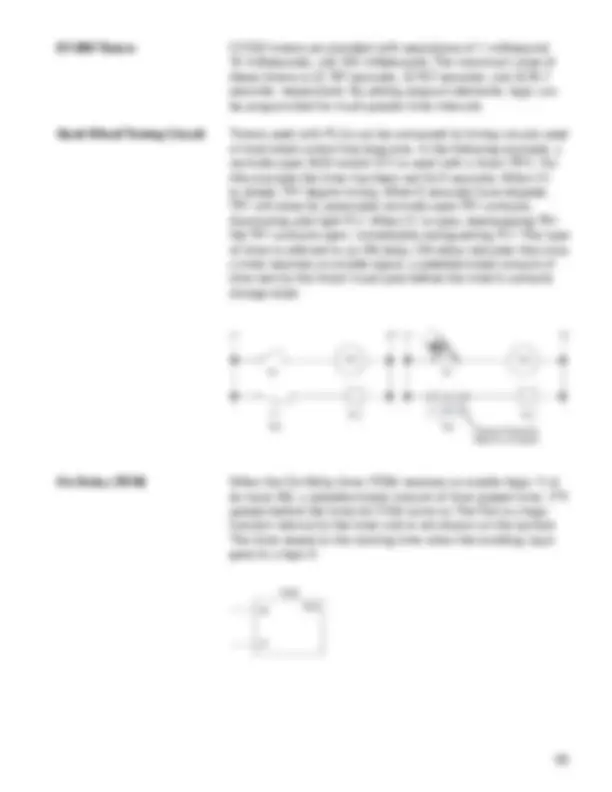
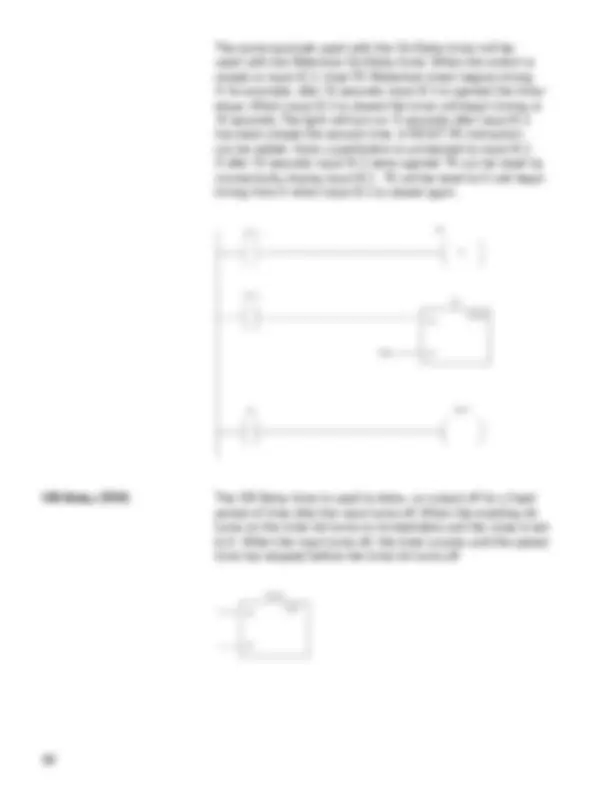
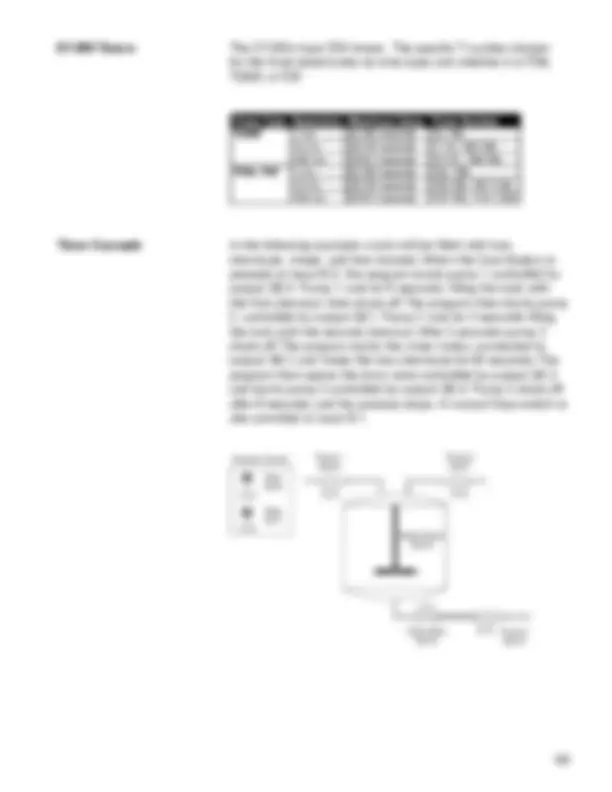
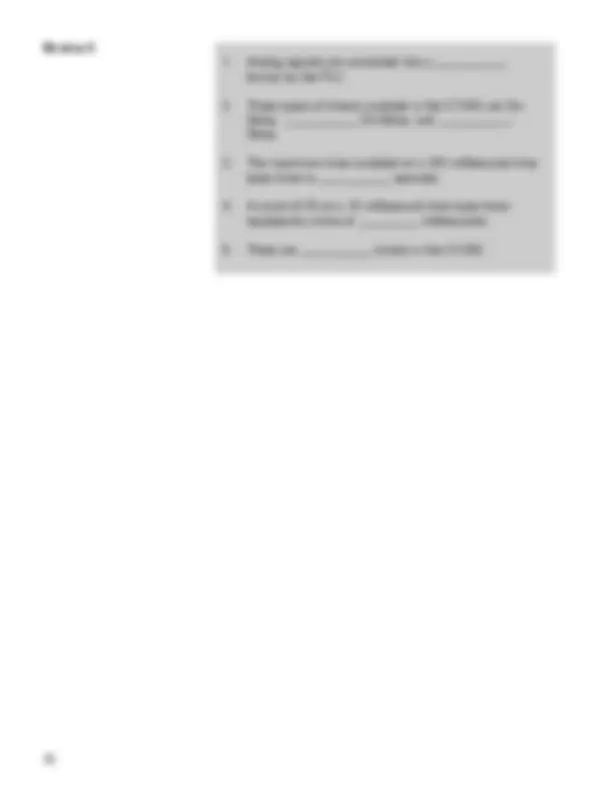
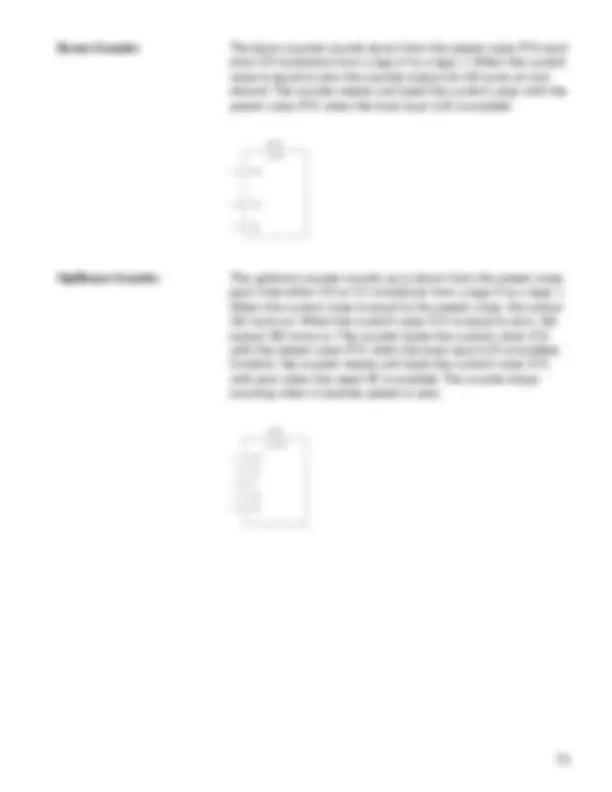
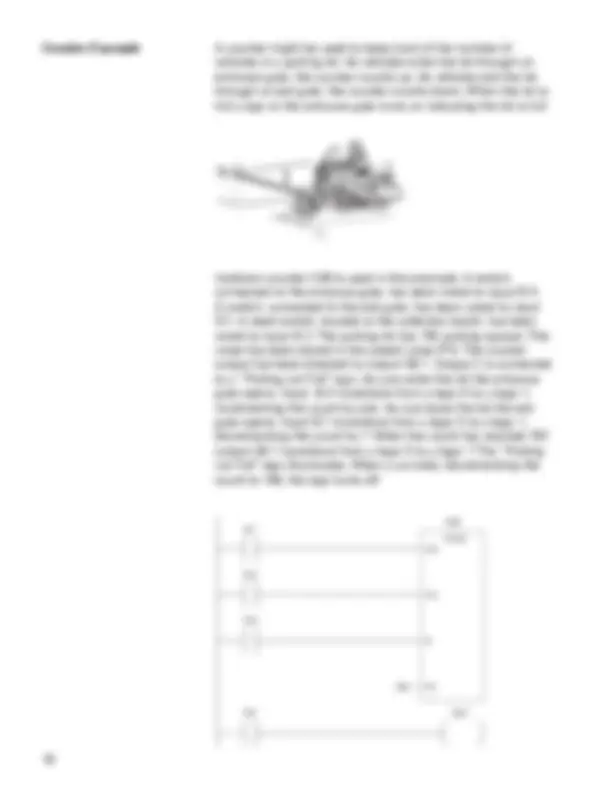
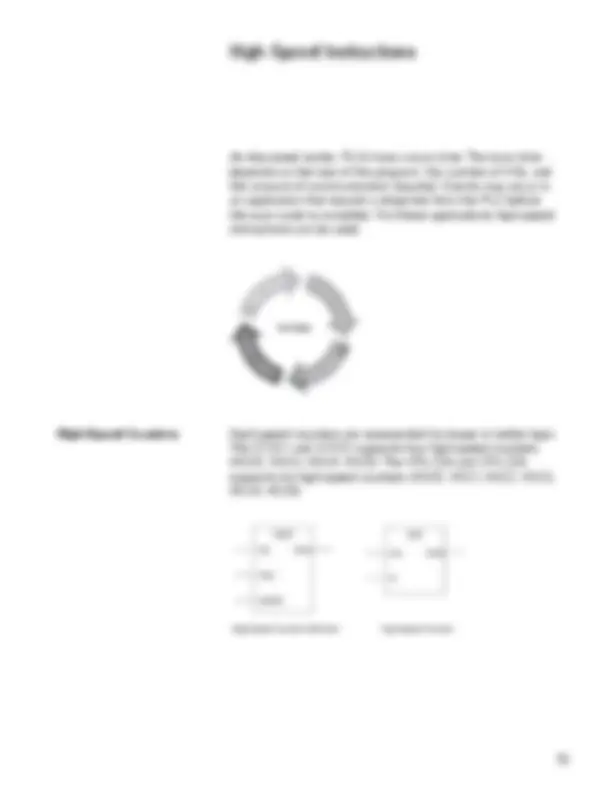
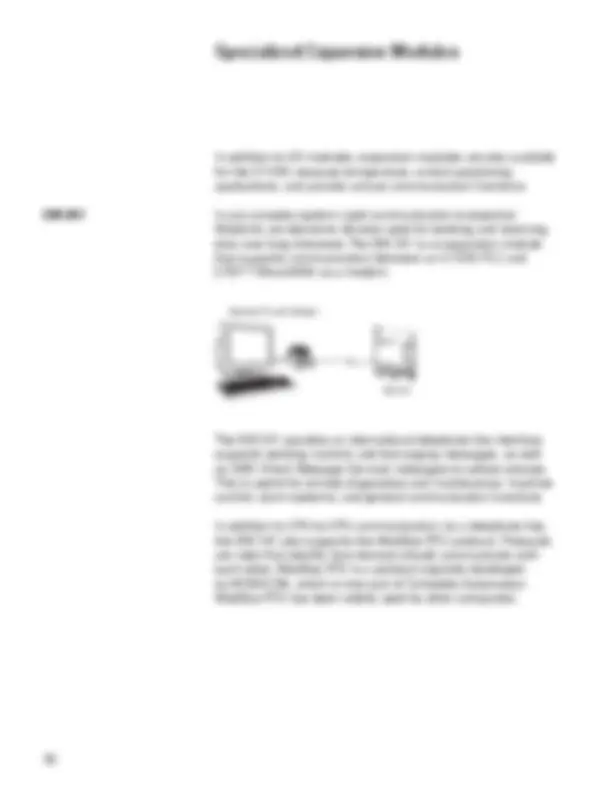
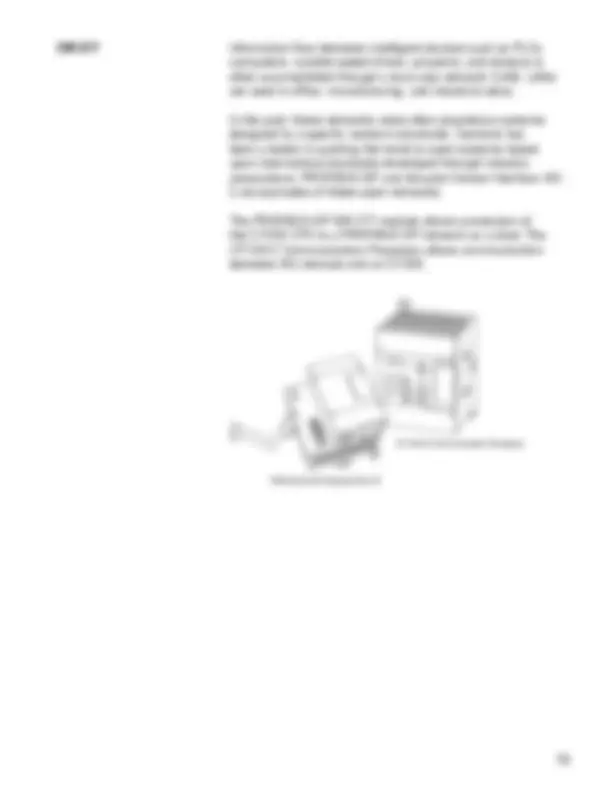
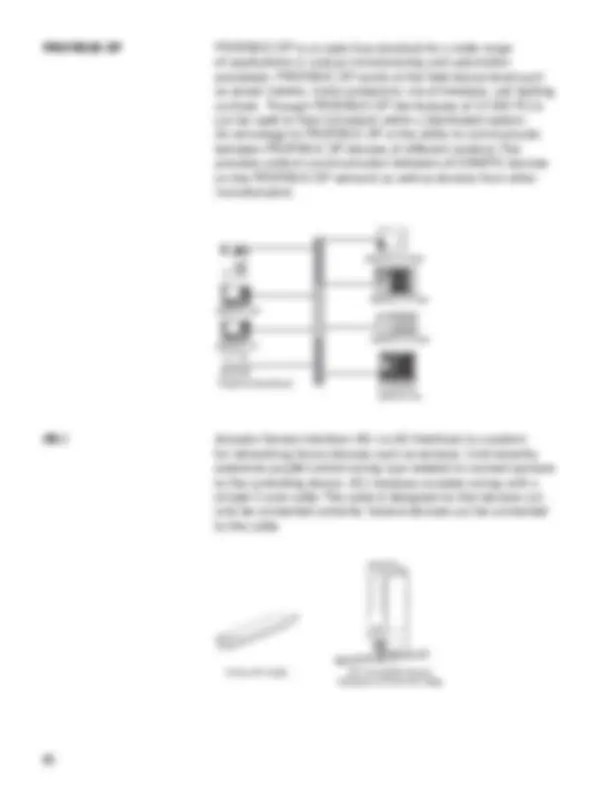
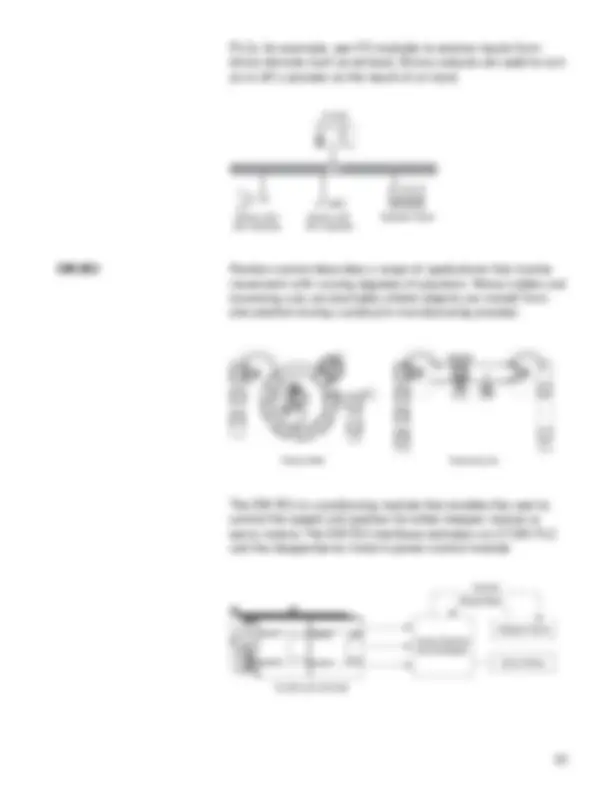
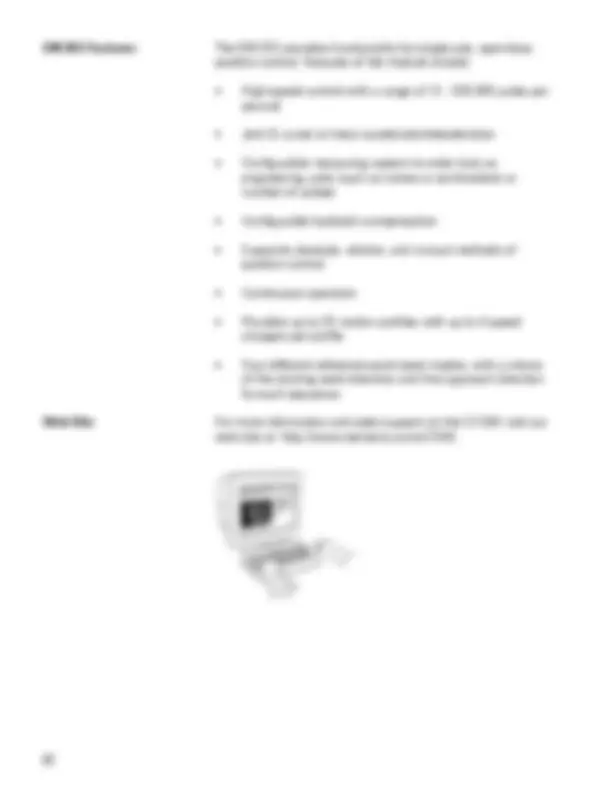
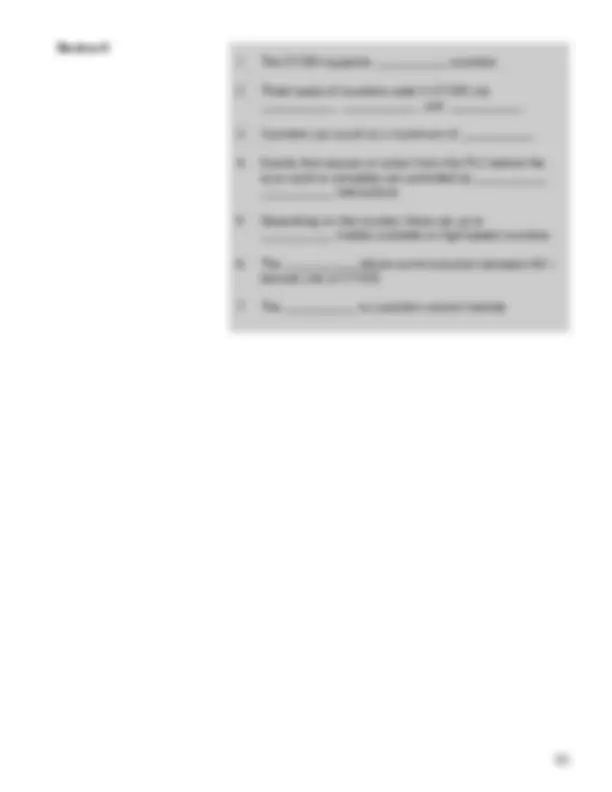

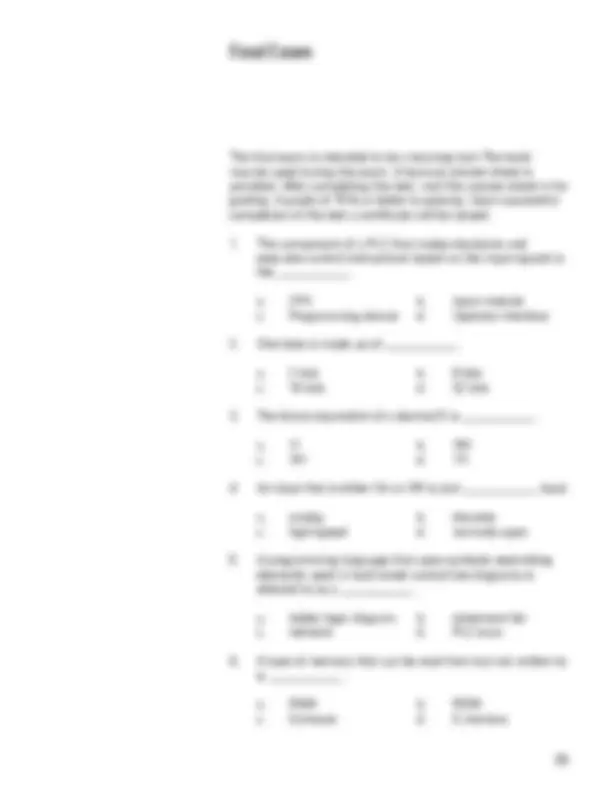
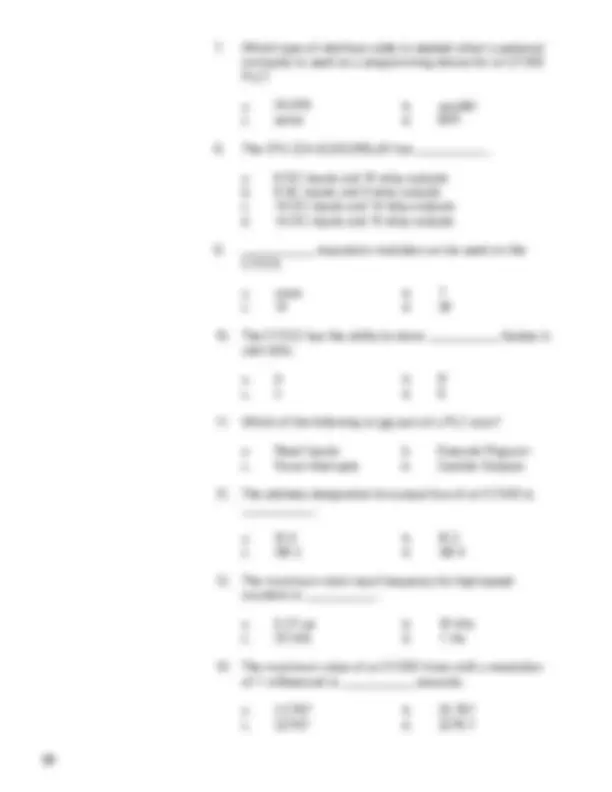
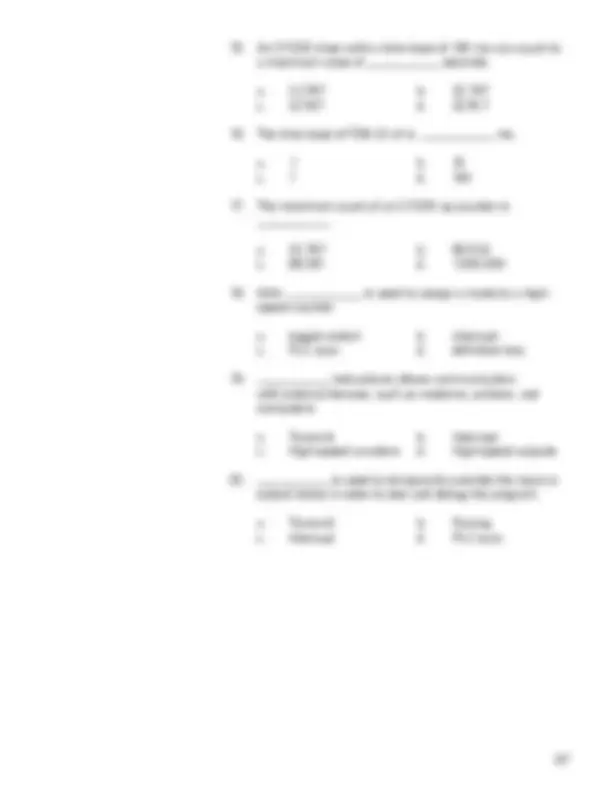
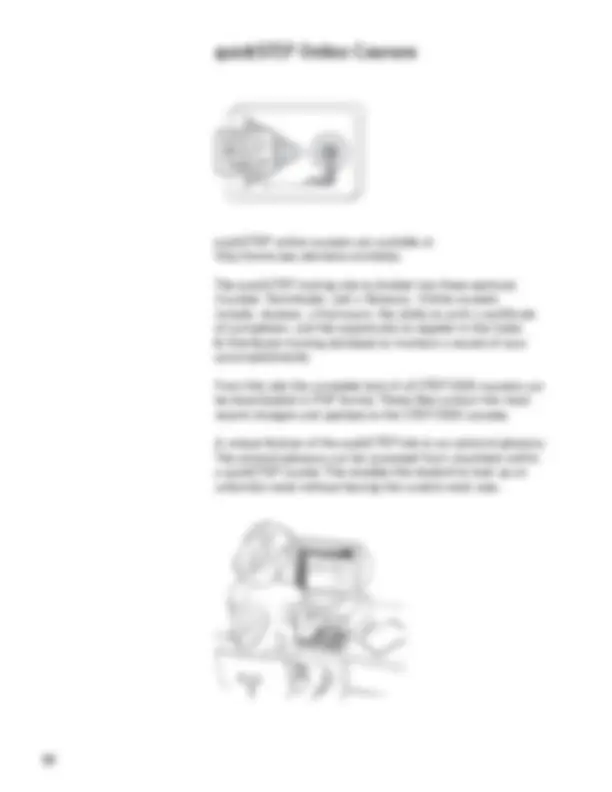
Estude fácil! Tem muito documento disponível na Docsity
Ganhe pontos ajudando outros esrudantes ou compre um plano Premium
Prepare-se para as provas
Estude fácil! Tem muito documento disponível na Docsity
Prepare-se para as provas com trabalhos de outros alunos como você, aqui na Docsity
Os melhores documentos à venda: Trabalhos de alunos formados
Prepare-se com as videoaulas e exercícios resolvidos criados a partir da grade da sua Universidade
Responda perguntas de provas passadas e avalie sua preparação.
Ganhe pontos para baixar
Ganhe pontos ajudando outros esrudantes ou compre um plano Premium
Comunidade
Peça ajuda à comunidade e tire suas dúvidas relacionadas ao estudo
Descubra as melhores universidades em seu país de acordo com os usuários da Docsity
Guias grátis
Baixe gratuitamente nossos guias de estudo, métodos para diminuir a ansiedade, dicas de TCC preparadas pelos professores da Docsity
PLCs também deve trabalhar com sinais contínuos ou analógicos. Típico sinais analógicos são 0-10 VDC ou 4-20 mA. Os sinais analógicos são usado para representar mudança de valores como velocidade, temperatura, peso e nível. A PLC não podem processar esses sinais em uma forma analógica. O PLC tem de converter o sinal analógico em uma representação digital. Um módulo de expansão, capaz de converter o sinal analógico, deve ser usado. O S7-200 módulos analógicos converter voltagem padr
Tipologia: Notas de estudo
1 / 28
Esta página não é visível na pré-visualização
Não perca as partes importantes!
PLCs must also work with continuous or analog signals. Typical analog signals are 0 - 10 VDC or 4 - 20 mA. Analog signals are used to represent changing values such as speed, temperature, weight, and level. A PLC cannot process these signals in an analog form. The PLC must convert the analog signal into a digital representation. An expansion module, capable of converting the analog signal, must be used. The S7- analog modules convert standard voltage and current analog values into a 12-bit digital representation. The digital values are transferred to the PLC for use in register or word locations.
In addition, analog modules are available for use with thermocouple and RTD type sensors used in to achieve a high level of accuracy in temperature measurement.
Application Example A field device that measures a varying value is typically connected to a transducer. In the following example a scale is connected to a load cell. A load cell is a device that takes a varying value and converts it to a variable voltage or current output. In this example the load cell is converting a value of weight into a 0 - 10 VDC output. The output value depends entirely on the manufactured specifications for the device. This load cell outputs 0 - 10 VDC for a 0 - 500 Lbs input. The 0 - 10 VDC load cell output is connected to the input of an analog expansion module.
The example application can be expanded to include a conveyor system with a gate to direct packages of varying weight. As packages move along the conveyor they are weighed. A package that weighs at or greater than a specified value is routed along one conveyor path. A package that weighs less than a specified value is routed along another conveyor path, where it will later be inspected for missing contents.
Timers are devices that count increments of time. Traffic lights are one example where timers are used. In this example timers are used to control the length of time between signal changes.
Timers are represented by boxes in ladder logic. When a timer receives an enable, the timer starts to time. The timer compares its current time with the preset time. The output of the timer is a logic 0 as long as the current time is less than the preset time. When the current time is greater than the preset time the timer output is a logic 1. S7-200 uses three types of timers: On- Delay (TON), Retentive On-Delay (TONR), and Off-Delay (TOF).
S7-200 Timers S7-200 timers are provided with resolutions of 1 millisecond, 10 milliseconds, and 100 milliseconds. The maximum value of these timers is 32.767 seconds, 327.67 seconds, and 3276. seconds, respectively. By adding program elements, logic can be programmed for much greater time intervals.
Hard-Wired Timing Circuit Timers used with PLCs can be compared to timing circuits used in hard-wired control line diagrams. In the following example, a normally open (NO) switch (S1) is used with a timer (TR1). For this example the timer has been set for 5 seconds. When S is closed, TR1 begins timing. When 5 seconds have elapsed, TR1 will close its associated normally open TR1 contacts, illuminating pilot light PL1. When S1 is open, deenergizing TR1, the TR1 contacts open, immediately extinguishing PL1. This type of timer is referred to as ON delay. ON delay indicates that once a timer receives an enable signal, a predetermined amount of time (set by the timer) must pass before the timer’s contacts change state.
On-Delay (TON) When the On-Delay timer (TON) receives an enable (logic 1) at its input (IN), a predetermined amount of time (preset time - PT) passes before the timer bit (T-bit) turns on. The T-bit is a logic function internal to the timer and is not shown on the symbol. The timer resets to the starting time when the enabling input goes to a logic 0.
A small sample of the flexibility of PLCs is shown in the following program logic. By reprogramming the T37 contact as a normally closed contact, the function of the circuit is changed to cause the indicator light to turn off only when the timer times out. This function change was accomplished without changing or rewiring I/O devices.
T
150
I0.
Q0.
TON
T IN
PT
Retentive On-Delay (TONR) The Retentive On-Delay timer (TONR) functions in a similar manner to the On-Delay timer (TON). There is one difference. The Retentive On-Delay timer times as long as the enabling input is on, but does not reset when the input goes off. The timer must be reset with a RESET (R) instruction.
The same example used with the On-Delay timer will be used with the Retentive On-Delay timer. When the switch is closed at input I0.3, timer T5 (Retentive timer) begins timing. If, for example, after 10 seconds input I0.3 is opened the timer stops. When input I0.3 is closed the timer will begin timing at 10 seconds. The light will turn on 5 seconds after input I0. has been closed the second time. A RESET (R) instruction can be added. Here a pushbutton is connected to input I0.2. If after 10 seconds input I0.3 were opened, T5 can be reset by momentarily closing input I0.2. T5 will be reset to 0 and begin timing from 0 when input I0.3 is closed again.
T
T
150
I0.
I0.
Q0.
R
TONR
T IN
PT
Off-Delay (TOF) The Off-Delay timer is used to delay an output off for a fixed period of time after the input turns off. When the enabling bit turns on the timer bit turns on immediately and the value is set to 0. When the input turns off, the timer counts until the preset time has elapsed before the timer bit turns off.
TOF
TXXX IN
PT
Review 5
Counters used in PLCs serve the same function as mechanical counters. Counters compare an accumulated value to a preset value to control circuit functions. Control applications that commonly use counters include the following:
A bottling machine, for example, may use a counter to count bottles into groups of six for packaging.
Down Counter The down counter counts down from the preset value (PV) each time CD transitions from a logic 0 to a logic 1. When the current value is equal to zero the counter output bit (Q) turns on (not shown). The counter resets and loads the current value with the preset value (PV) when the load input (LD) is enabled.
PV
LD
CD
CTD
XXX
Up/Down Counter The up/down counter counts up or down from the preset value each time either CD or CU transitions from a logic 0 to a logic 1. When the current value is equal to the preset value, the output QU turns on. When the current value (CV) is equal to zero, the output QD turns on. The counter loads the current value (CV) with the preset value (PV) when the load input (LD) is enabled. Similarly, the counter resets and loads the current value (CV) with zero when the reset (R) is enabled. The counter stops counting when it reaches preset or zero.
PV
LD
CD CU R
CTUD
XXX
Counter Example A counter might be used to keep track of the number of vehicles in a parking lot. As vehicles enter the lot through an entrance gate, the counter counts up. As vehicles exit the lot through an exit gate, the counter counts down. When the lot is full a sign at the entrance gate turns on indicating the lot is full.
Up/down counter C48 is used in this example. A switch, connected to the entrance gate, has been wired to input I0.0. A switch, connected to the exit gate, has been wired to input I0.1. A reset switch, located at the collection booth, has been wired to input I0.2. The parking lot has 150 parking spaces. This value has been stored in the preset value (PV). The counter output has been directed to output Q0.1. Output 2 is connected to a “Parking Lot Full” sign. As cars enter the lot the entrance gate opens. Input I0.0 transitions from a logic 0 to a logic 1, incrementing the count by one. As cars leave the lot the exit gate opens. Input I0.1 transitions from a logic 0 to a logic 1, decrementing the count by 1. When the count has reached 150 output Q0.1 transitions from a logic 0 to a logic 1. The “Parking Lot Full” sign illuminates. When a car exits, decrementing the count to 149, the sign turns off.
Definition Boxes and The high-speed counter definition boxes are used to assign High-Speed Counters a mode to the counter. High-speed counters can be defined by the definition box to operate in any of the twelve available modes. It should be noted that not all counters can operate in all of the available modes. Refer to the S7-Programmable Controller System Manual for definitions available for each counter. Each counter has dedicated inputs for clocks, direction control, reset, and start where these functions are supported. The maximum clock input frequency is 20 kHz. For the two-phase counters, both clocks may be run at 20 kHz. In quadrature mode, 1x or 4x counting rates can be selected. At 1x rate the maximum counting frequency is 20 kHz. At 4x rate the maximum counting frequency is 80 kHz.
Positioning Positioning is one example of an application that can use high-speed counters. In the following illustration a motor is connected through a starter to a PLC output. The motor shaft is connected to an encoder and a positioning actuator. The encoder emits a series of pulses as the motor turns. In this example the program will move an object from position 1 to position 6. Assume the encoder generates 600 pulses per revolution, and it takes 1000 motor revolutions to move the object from one position to another. To move the object from position 1 to position 6 (5 positions) would take 5000 motor revolutions. The counter would count up 30,000 counts ( revolutions x 600 pulses per revolution) and stop the motor.
Interrupts Interrupts are another example of an instruction that must be executed before the PLC has completed the scan cycle. Interrupts in the S7-200 are prioritized in the following order:
PTO Pulse train output (PTO) is used to provide a series of pulses to an output device, such as a stepper motor driver. The PTO provides a square wave output for a specified number of pulses and a specified cycle time. The number of pulses can be from 1 to 4,294,967,295 pulses. PTOs have a 50% duty cycle. This means the pulse is off for the same amount of time it is on. The number of pulses and the cycle time can be changed with an interrupt. In the following example each pulse is on for 500 ms, and off for 500 ms. After four pulses an interrupt occurs which changes the cycle time to 1000 ms.
Q0. 4 Pulses 500 milliseconds Each
4 Pulses 1000 milliseconds Each Interrupt Occurs
PWM The Pulse Width Modulation (PWM) function provides a fixed cycle time with a variable duty cycle time. When the pulse width is equal to the cycle time, the duty cycle is 100% and the output is turned on continuously. In the following example the output has a 10% duty cycle (on 10% off 90%). After an interrupt the cycle switches to a 50% duty cycle (on 50%, off 50%).
Q0.
On Off On Off
10% Duty Cycle
50% Duty Cycle
The PWM function can be used to provide a programmable or adjustable control of machine timing. This allows machine operation to be varied to compensate for product variations or mechanical wear.
Transmit Transmit allows communication with external devices, such as modems, printers, computers, via the serial interface. See the section titled “Connecting External Devices” for examples.
EM 277 Information flow between intelligent devices such as PLCs, computers, variable speed drives, actuators, and sensors is often accomplished through a local area network (LAN). LANs are used in office, manufacturing, and industrial areas.
In the past, these networks were often proprietary systems designed to a specific vendor’s standards. Siemens has been a leader in pushing the trend to open systems based upon international standards developed through industry associations. PROFIBUS-DP and Actuator Sensor Interface (AS- i) are examples of these open networks.
The PROFIBUS-DP EM 277 module allows connection of the S7-200 CPU to a PROFIBUS-DP network as a slave. The CP 243-2 Communication Processor allows communication between AS-i devices and an S7-200.
PROFIBUS DP PROFIBUS DP is an open bus standard for a wide range of applications in various manufacturing and automation processes. PROFIBUS DP works at the field device level such as power meters, motor protectors, circuit breakers, and lighting controls. Through PROFIBUS DP the features of S7-200 PLCs can be used to their full extent within a distributed system. An advantage to PROFIBUS DP is the ability to communicate between PROFIBUS DP devices of different vendors. This provides uniform communication between all SIMATIC devices on the PROFIBUS DP network as well as devices from other manufacturers.
AS-i Actuator Sensor Interface (AS-i or AS-Interface) is a system for networking binary devices such as sensors. Until recently, extensive parallel control wiring was needed to connect sensors to the controlling device. AS-i replaces complex wiring with a simple 2-core cable. The cable is designed so that devices can only be connected correctly. Several devices can be connected to the cable.