
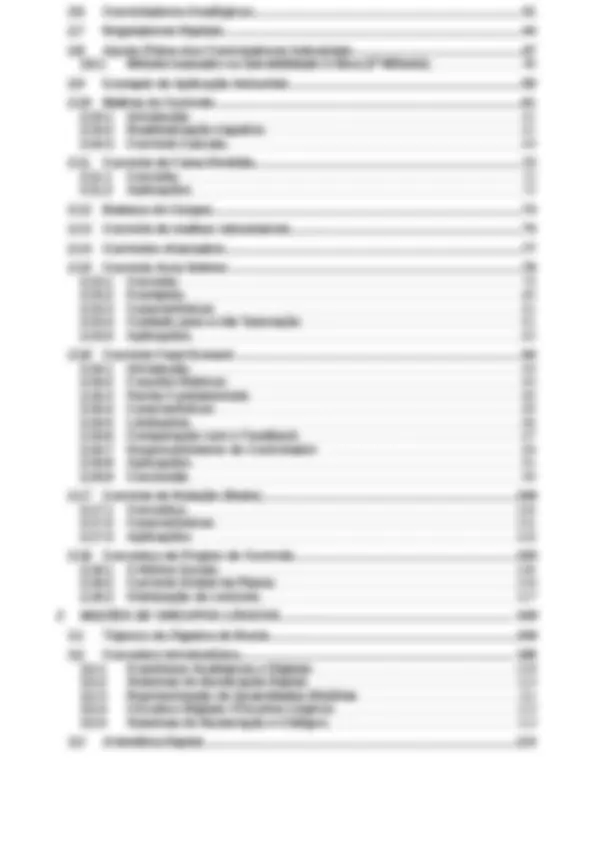
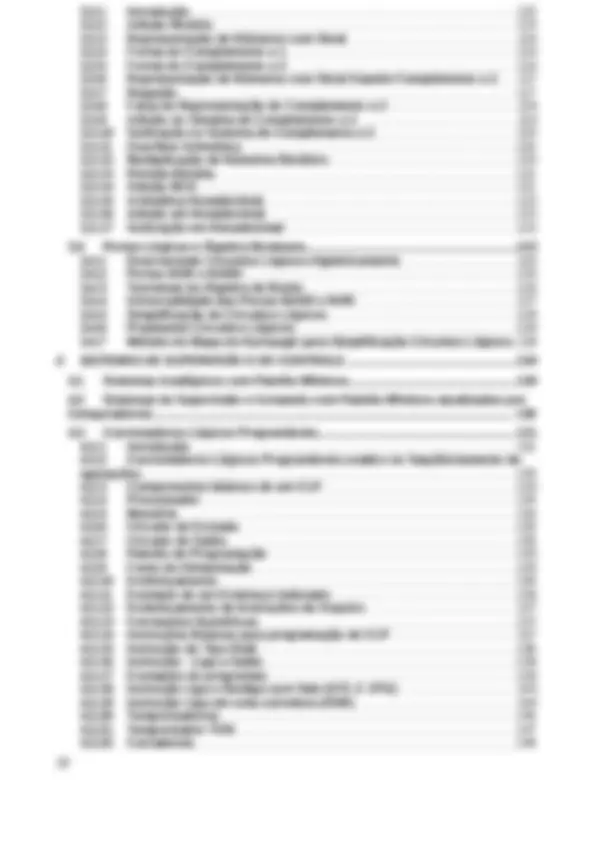
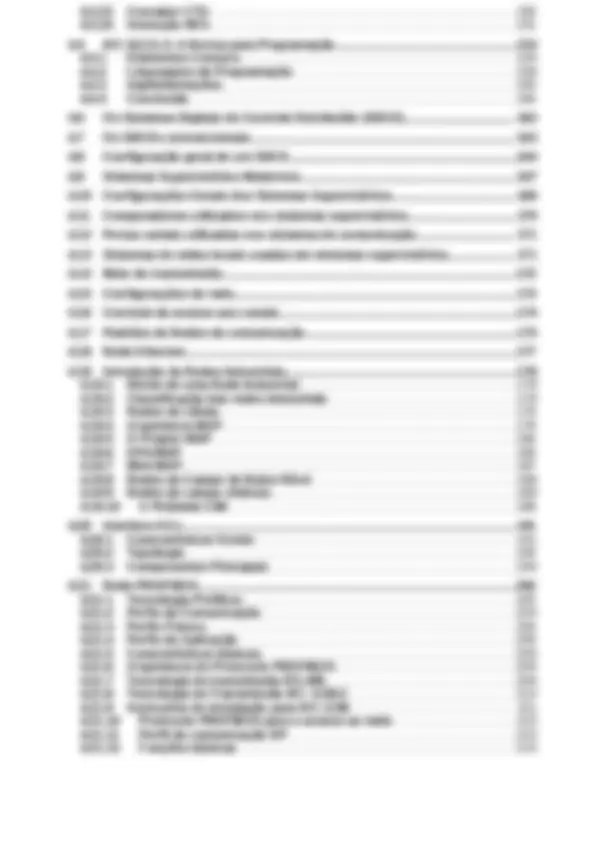
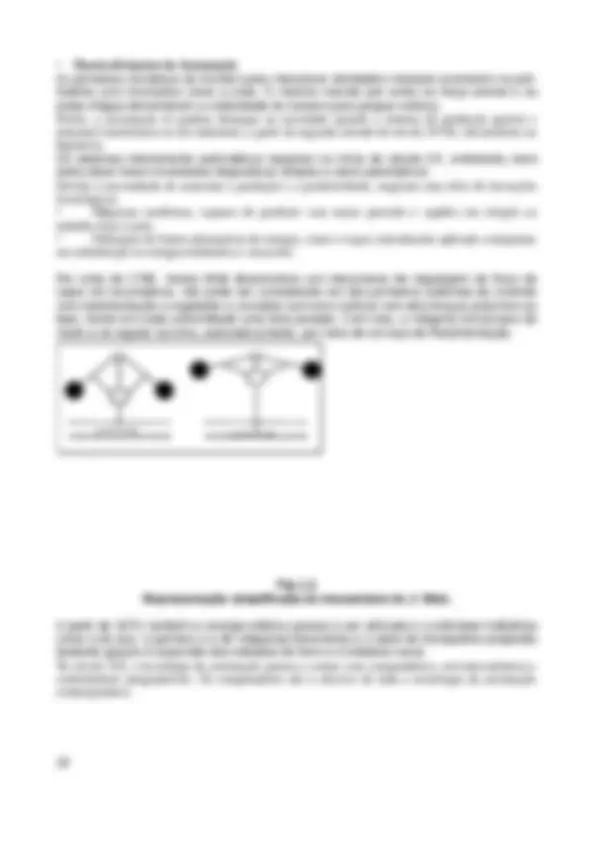
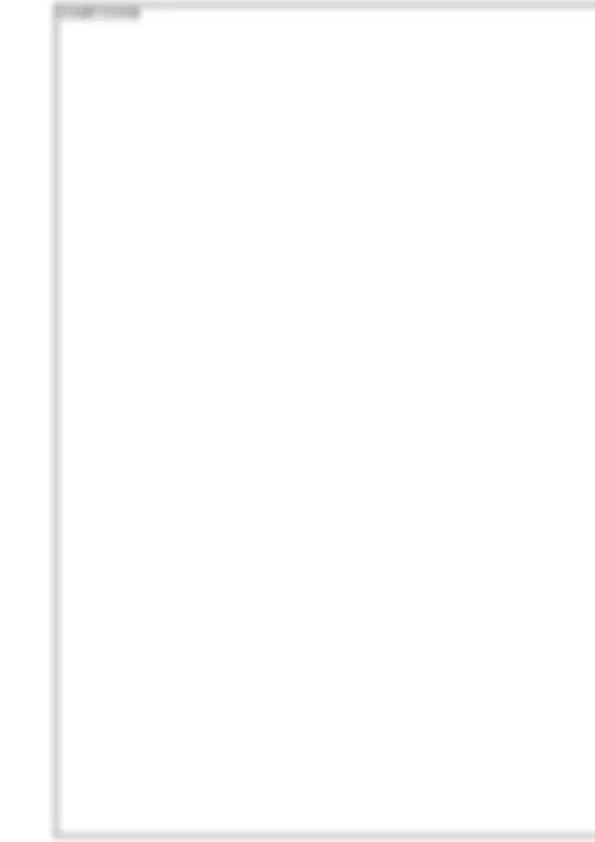
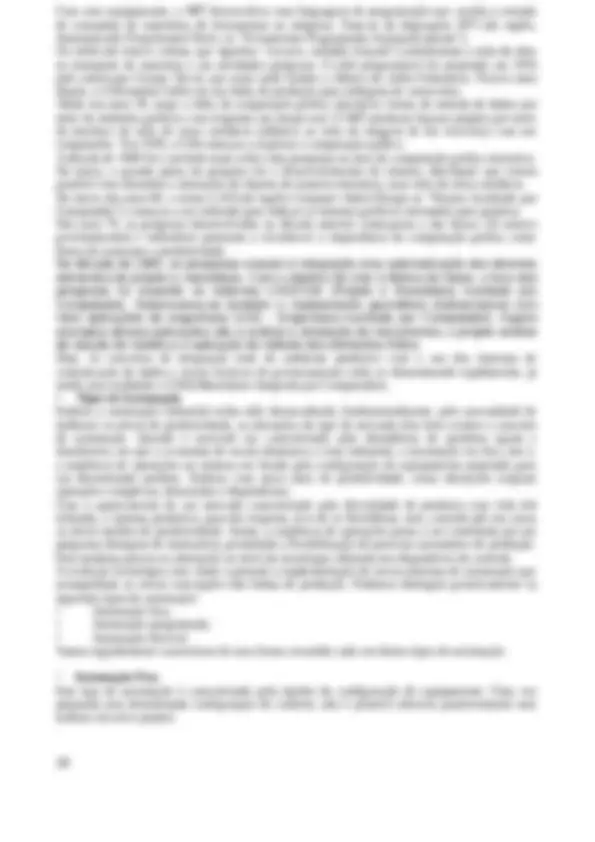
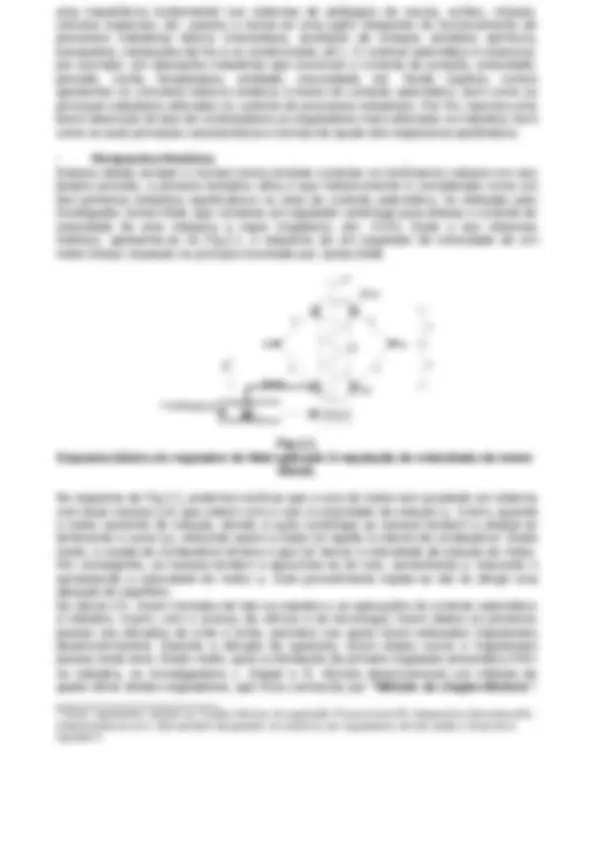
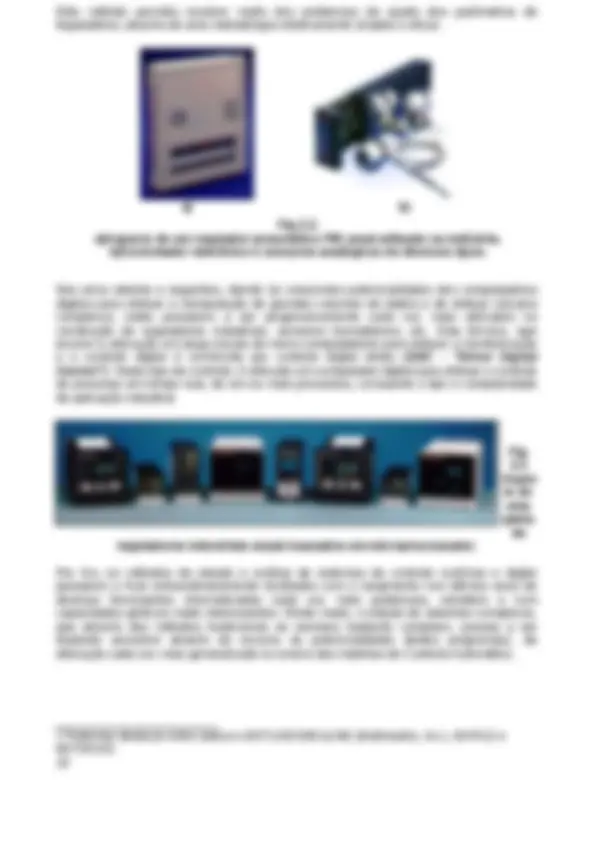
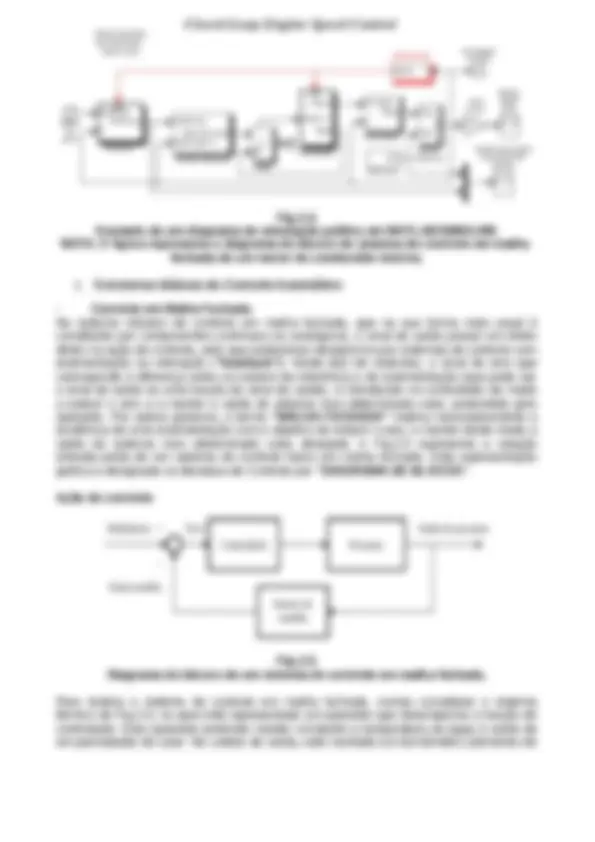
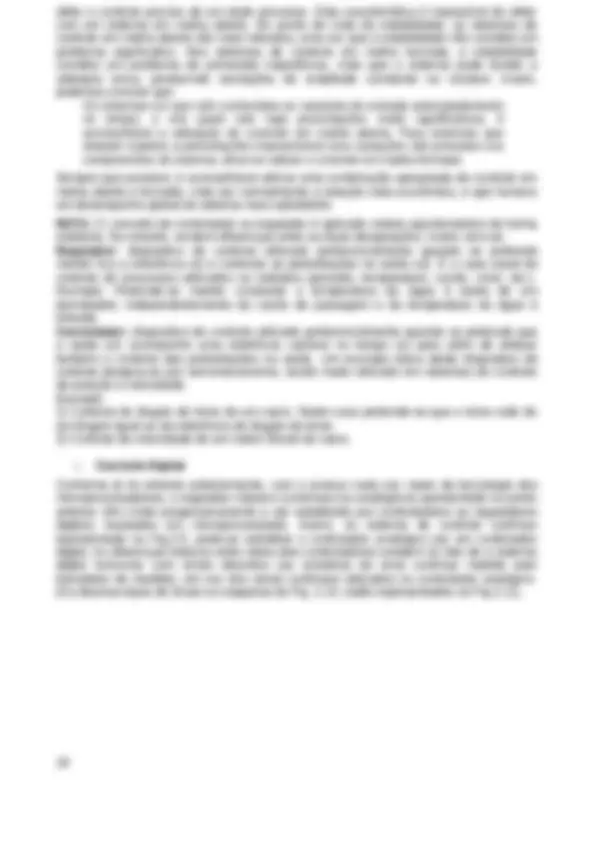
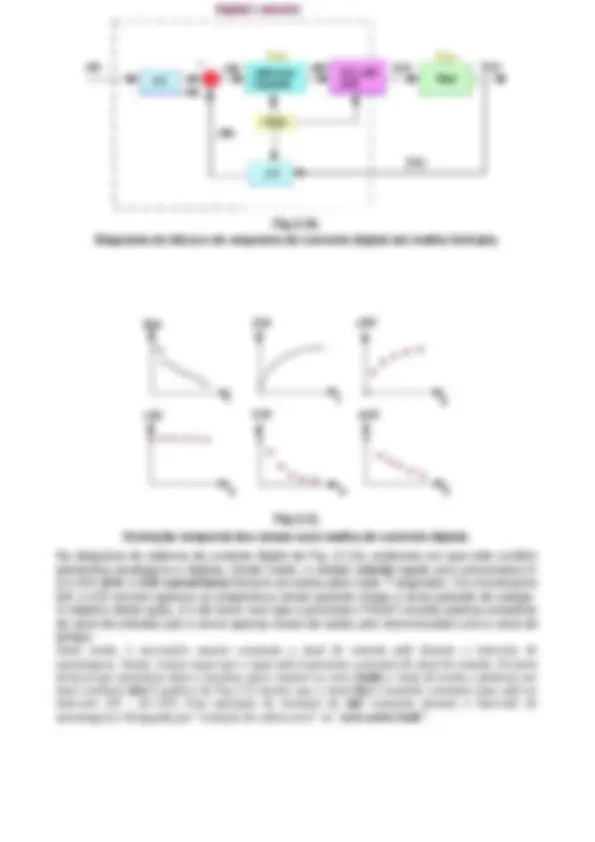
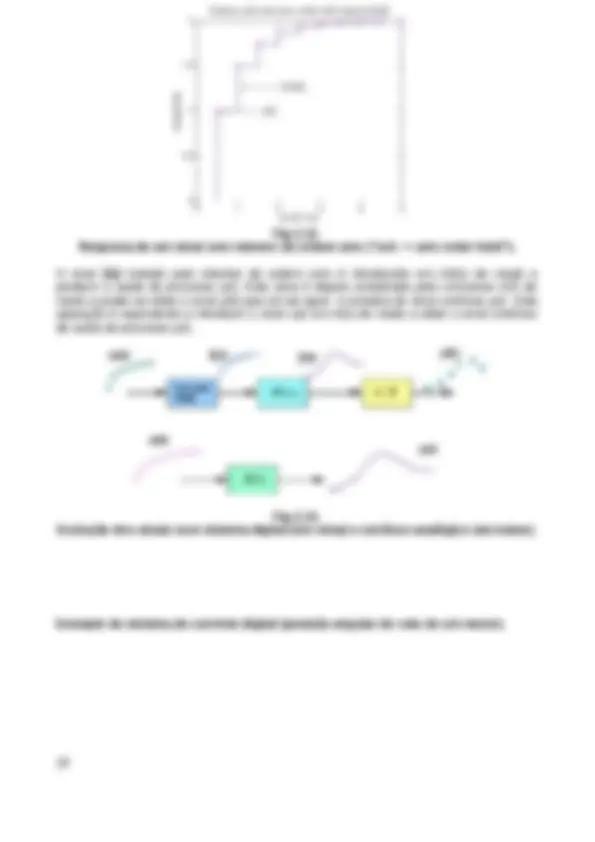
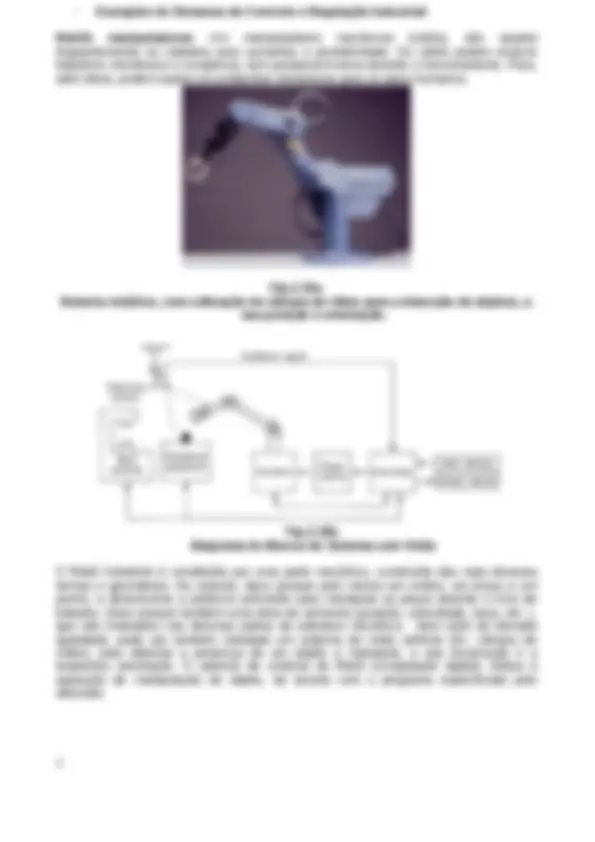
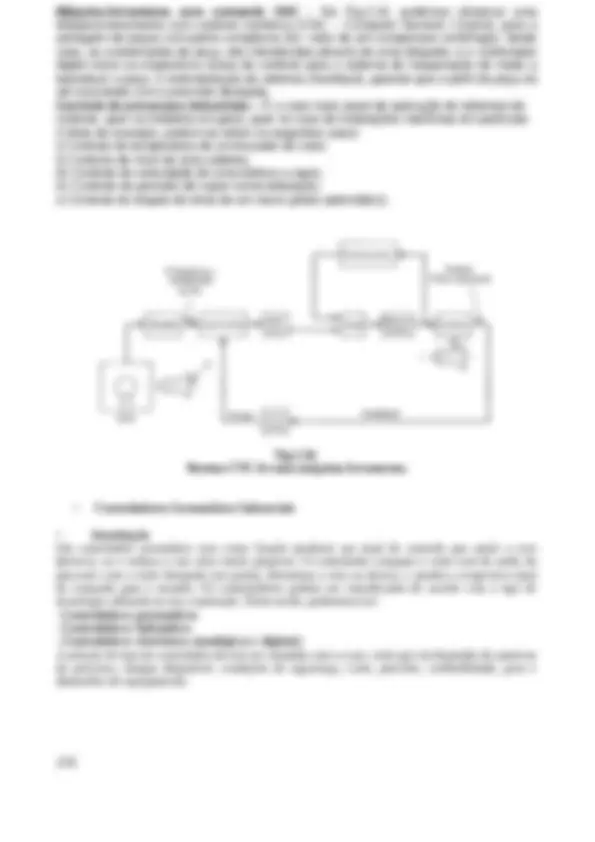
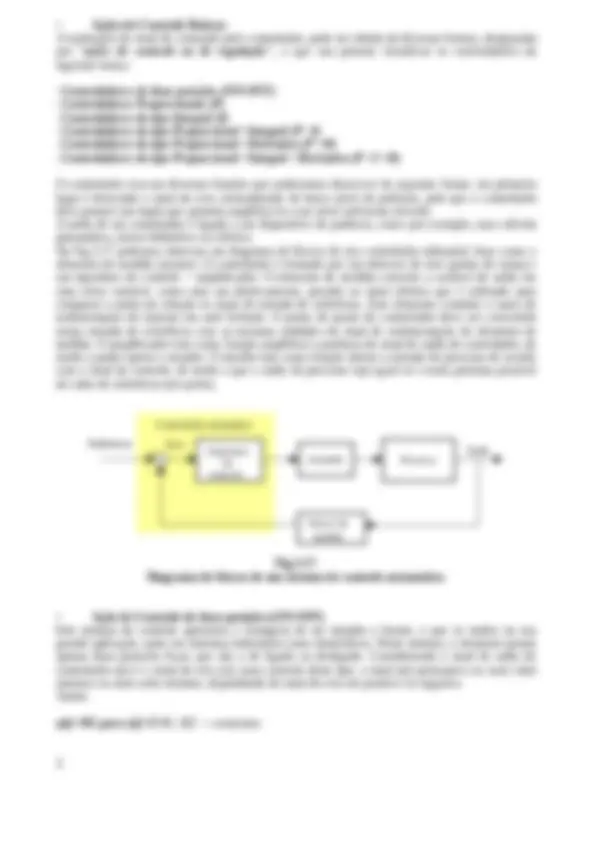
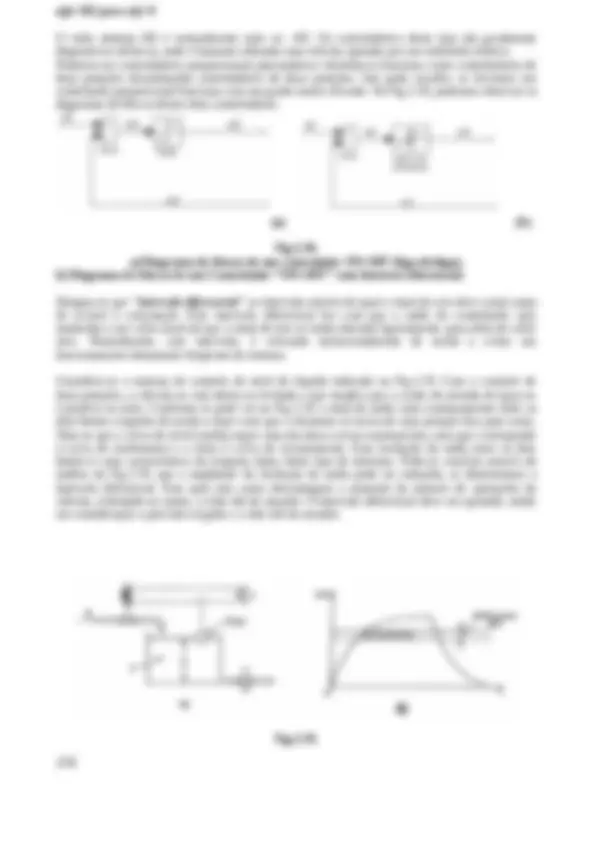
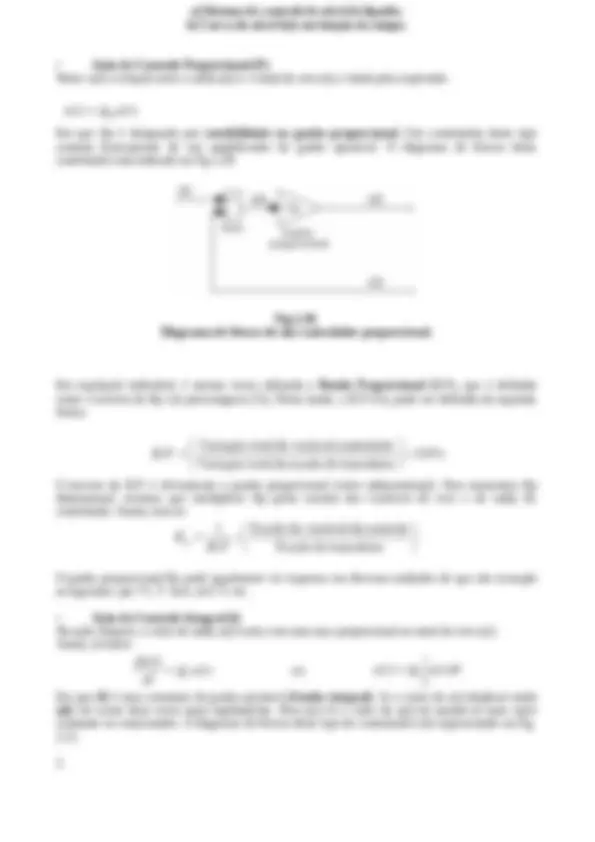
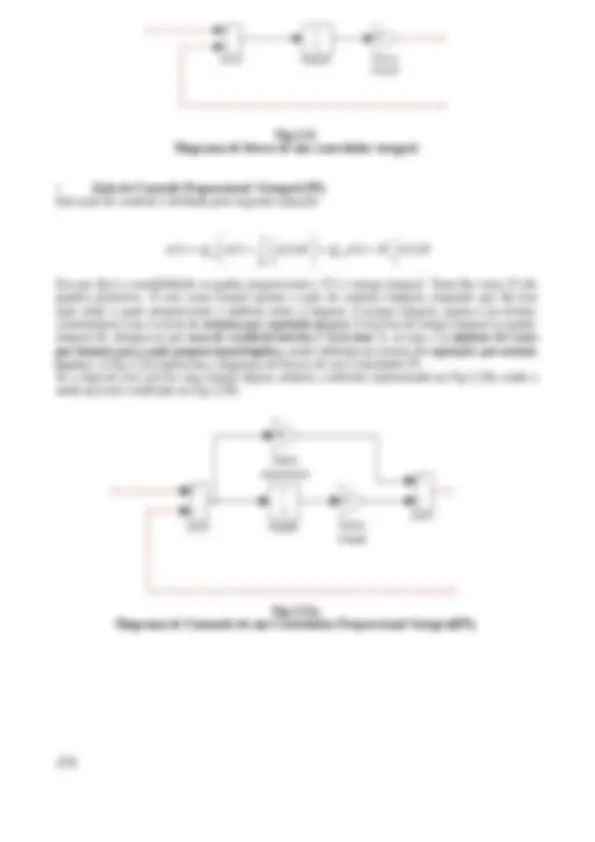
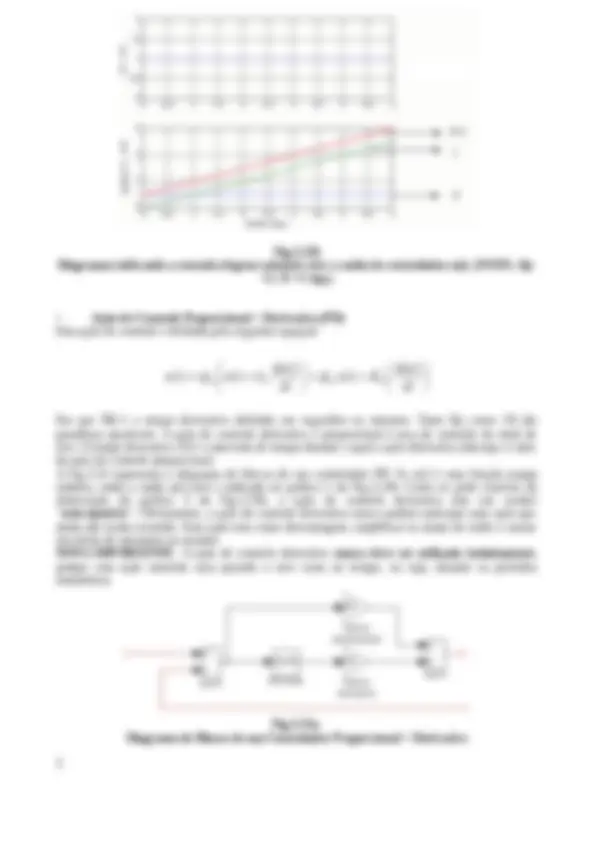
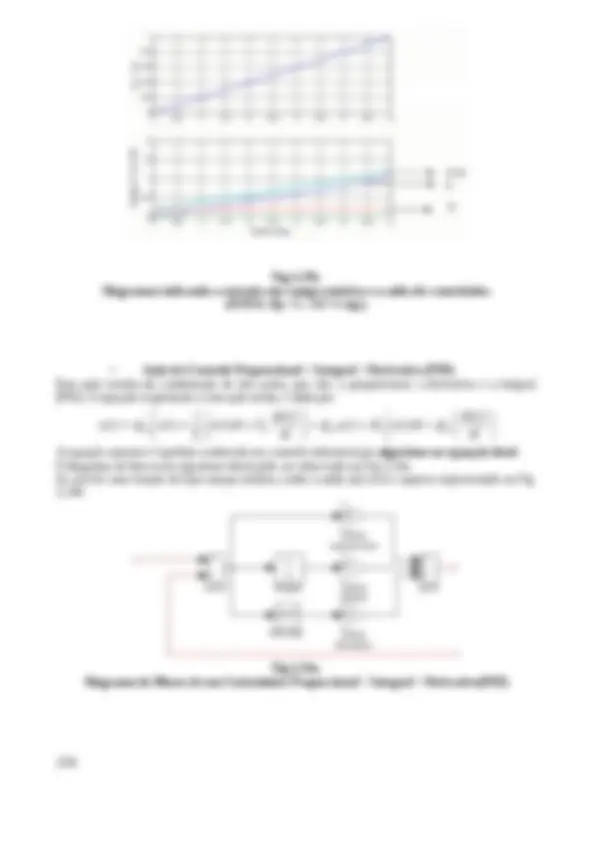
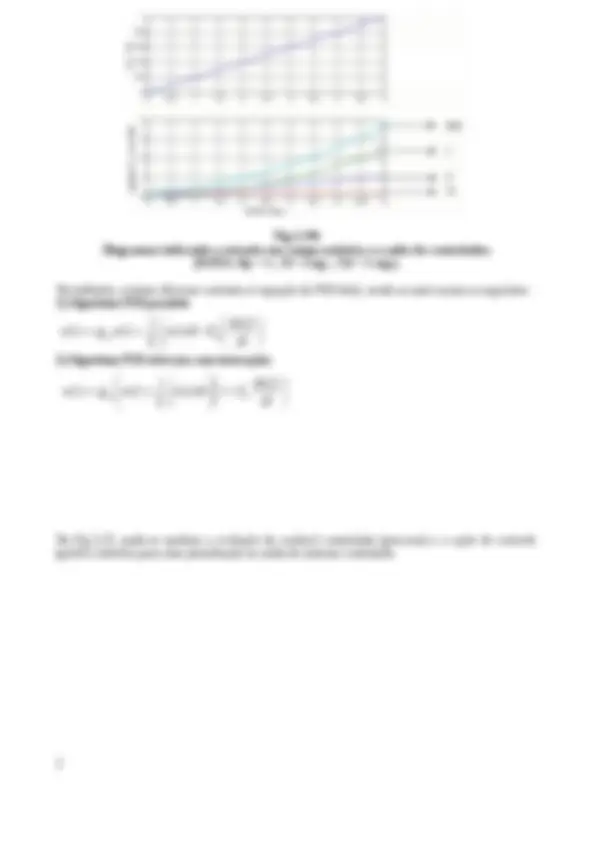
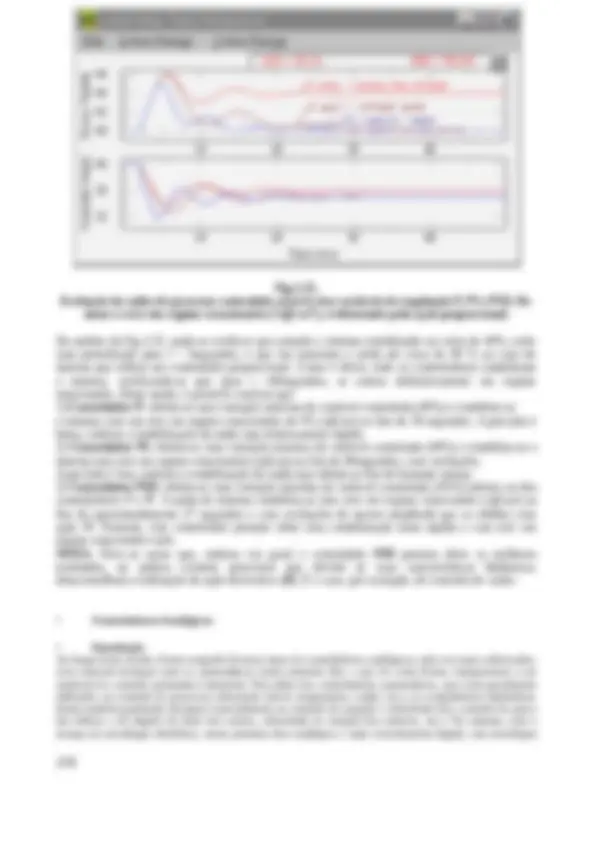
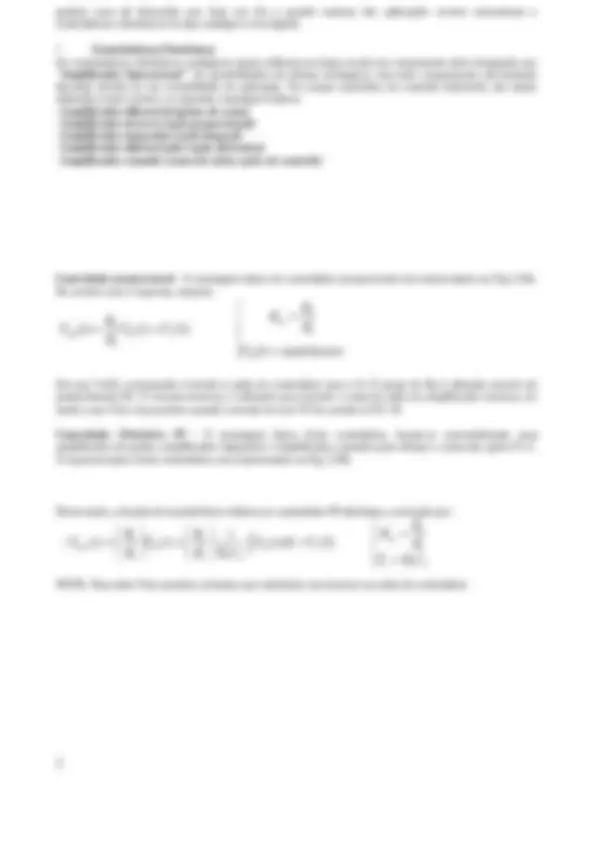
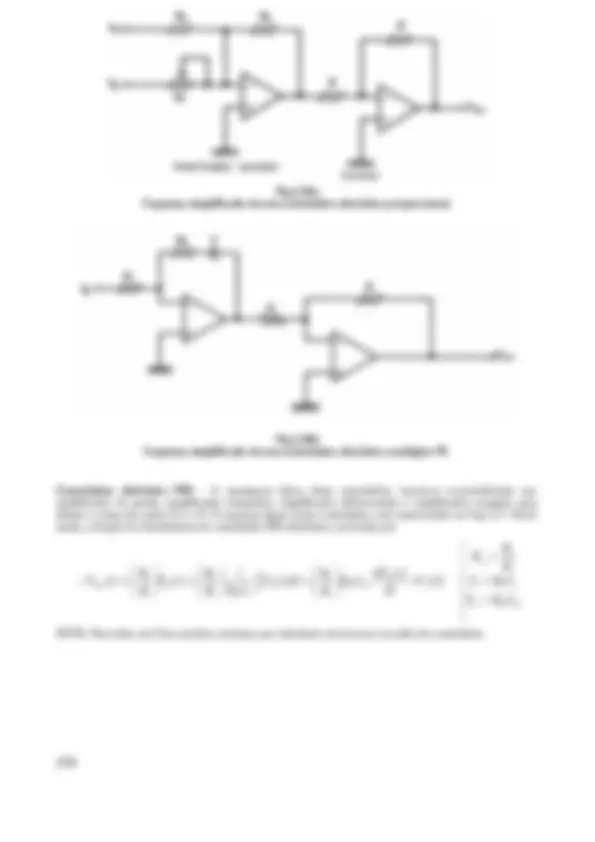
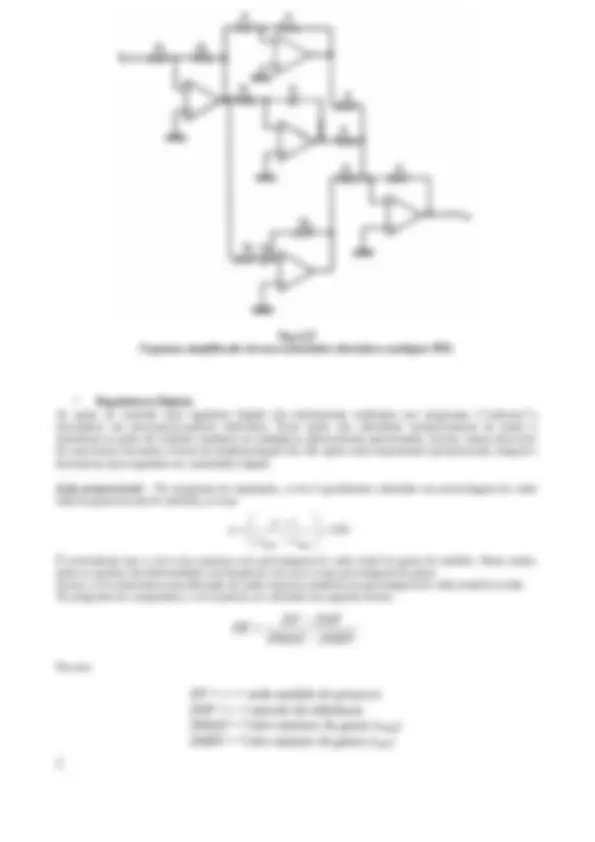
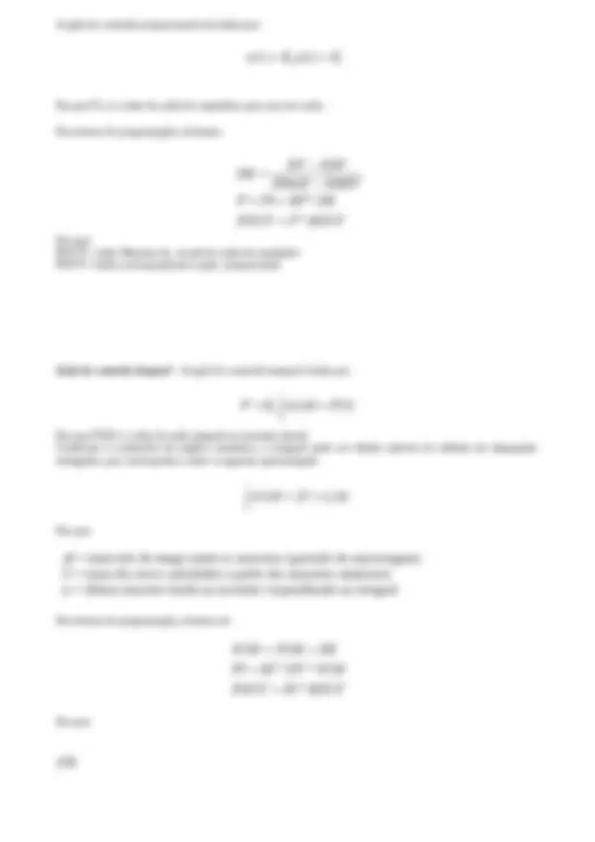
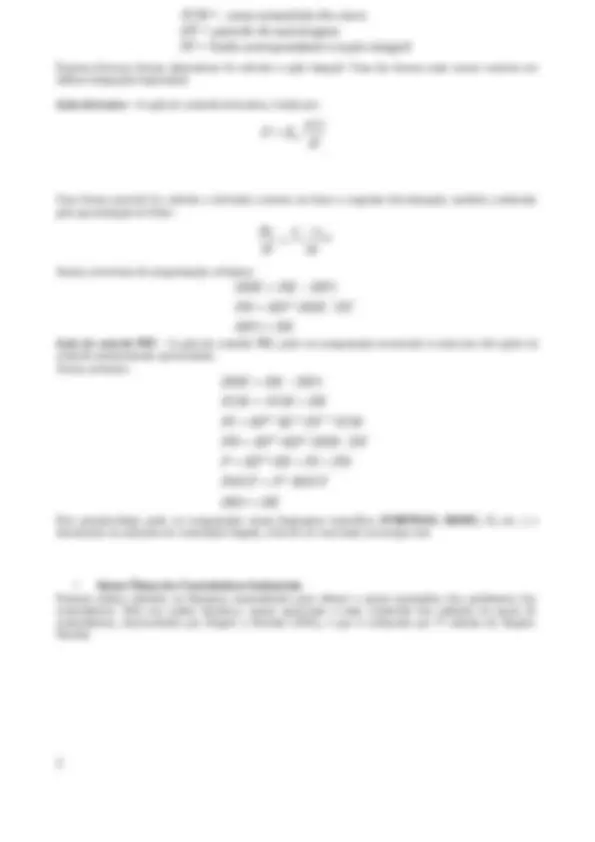
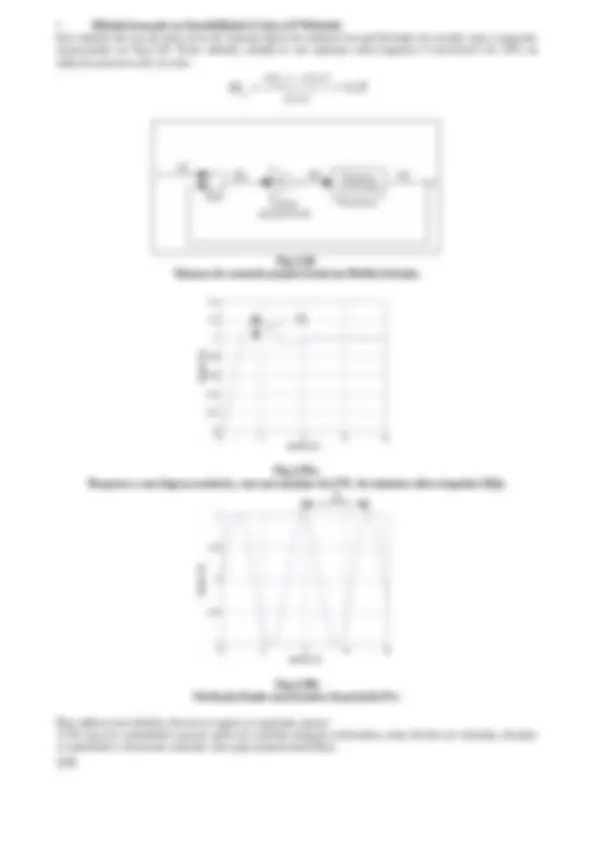
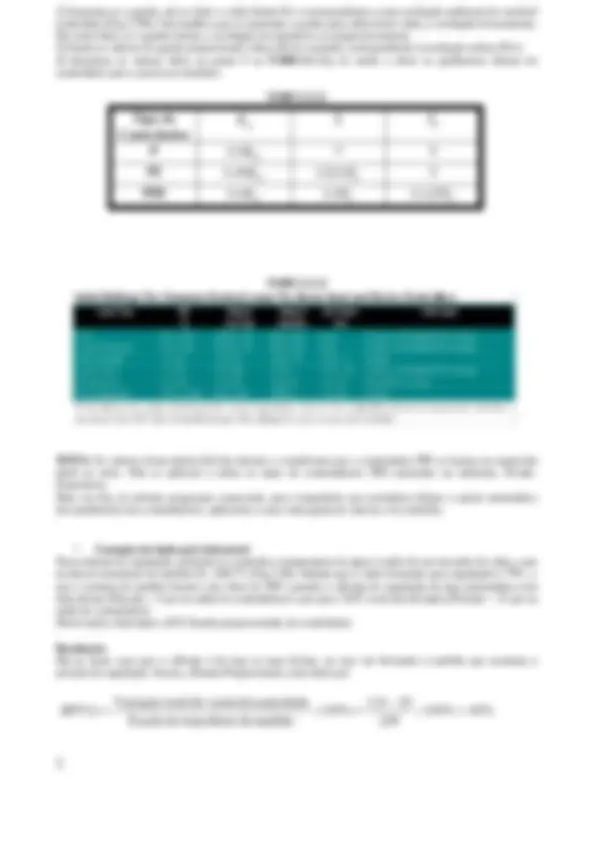
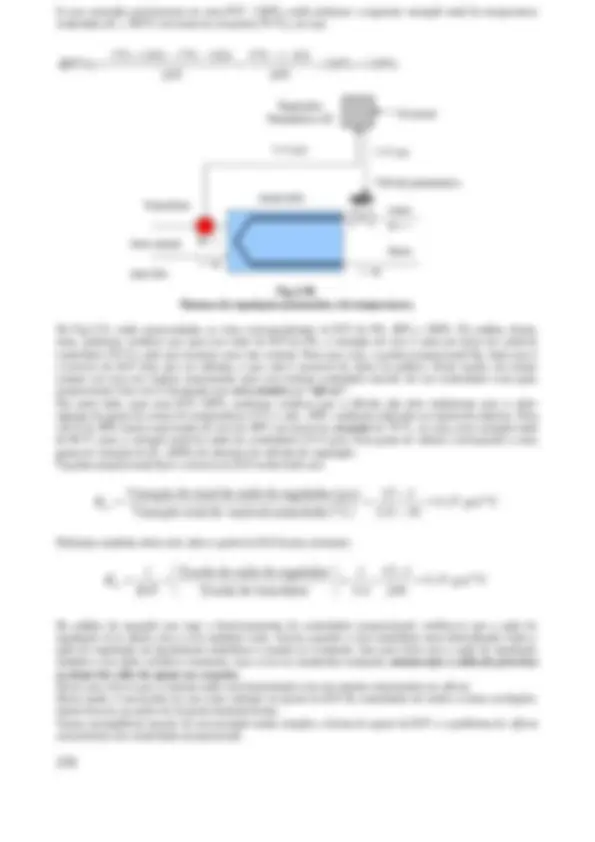
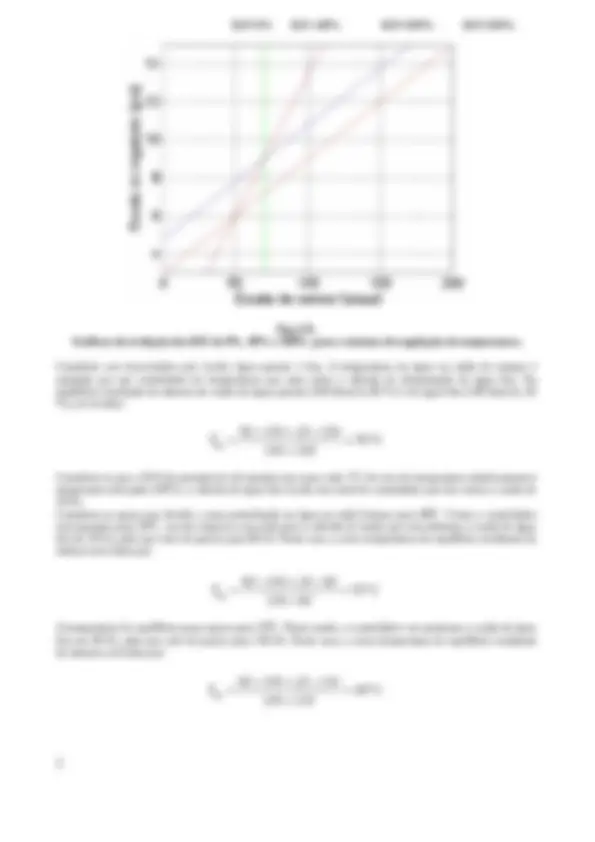
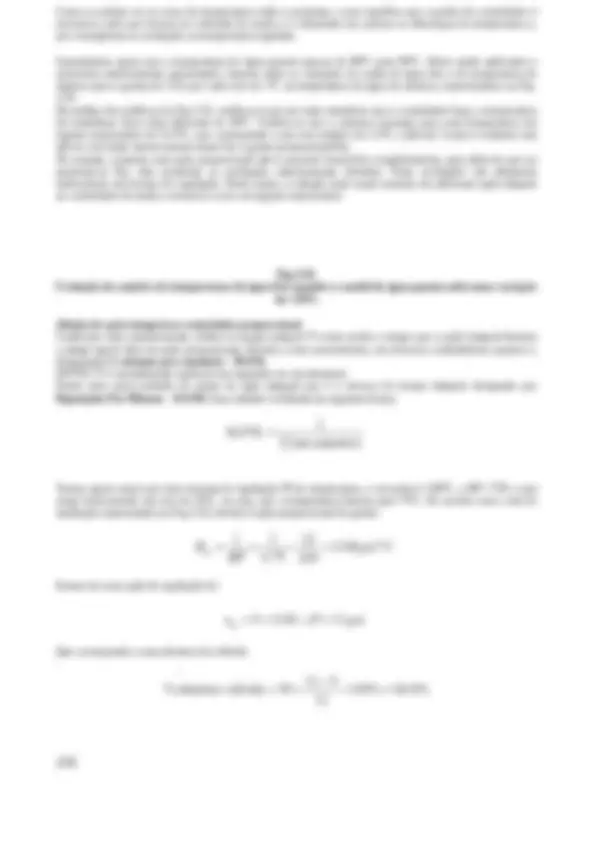
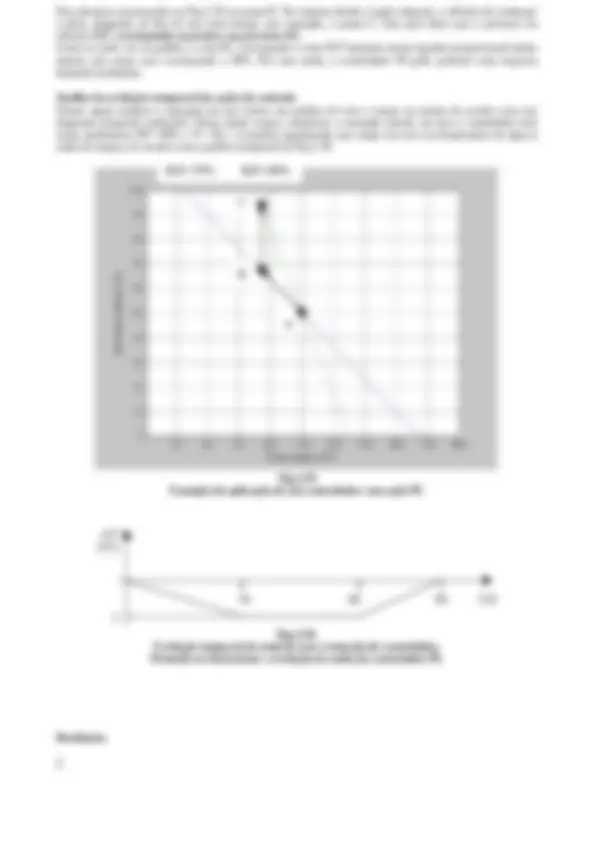
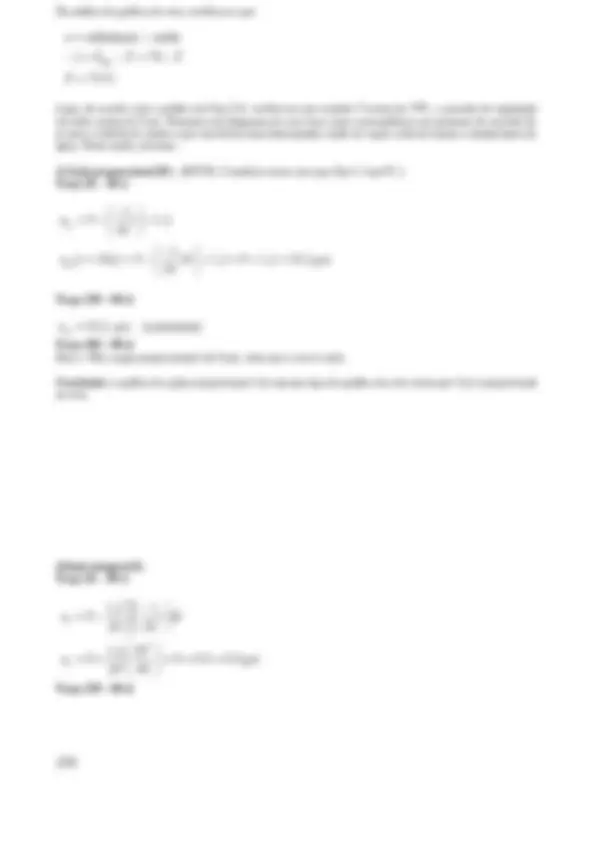
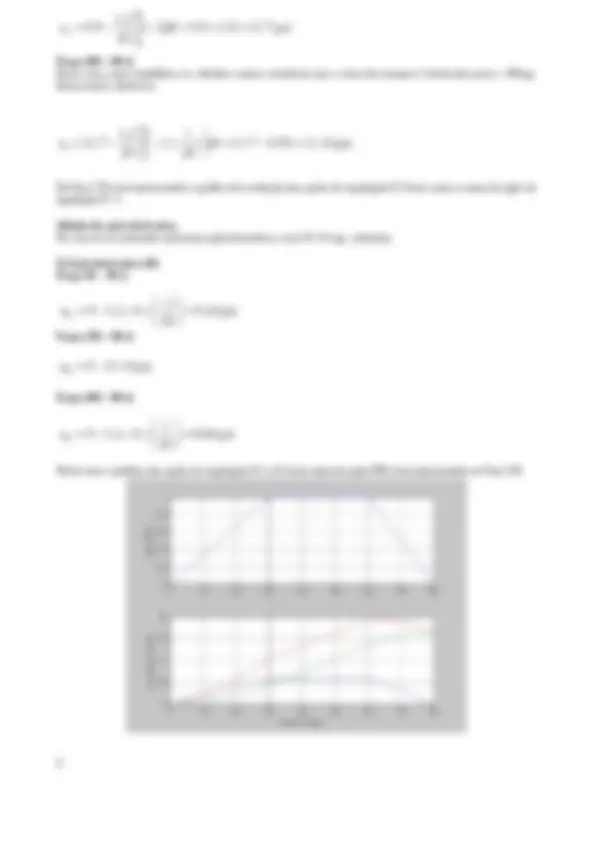
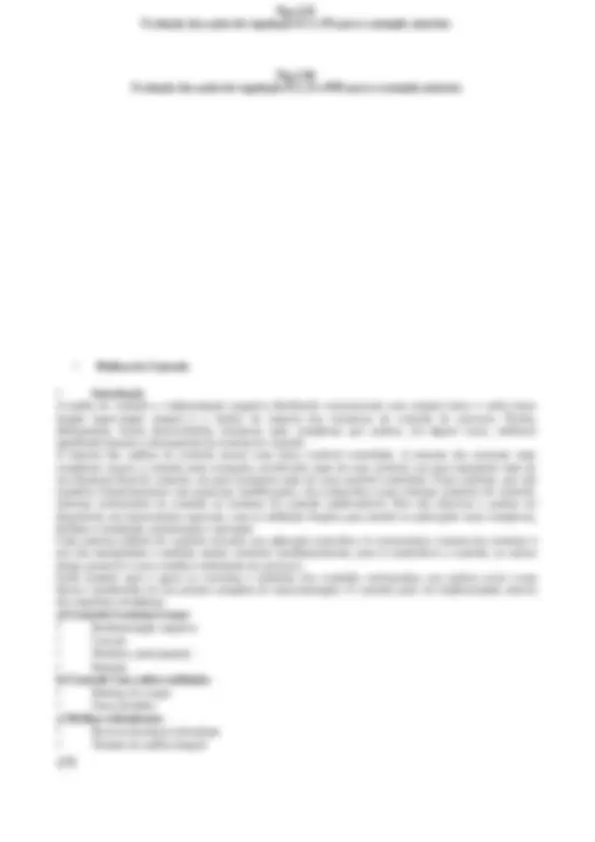
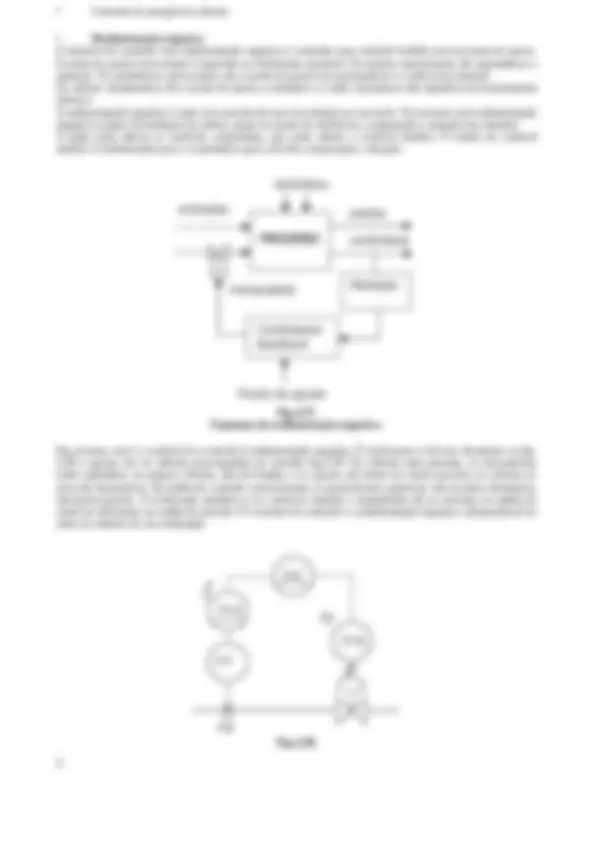
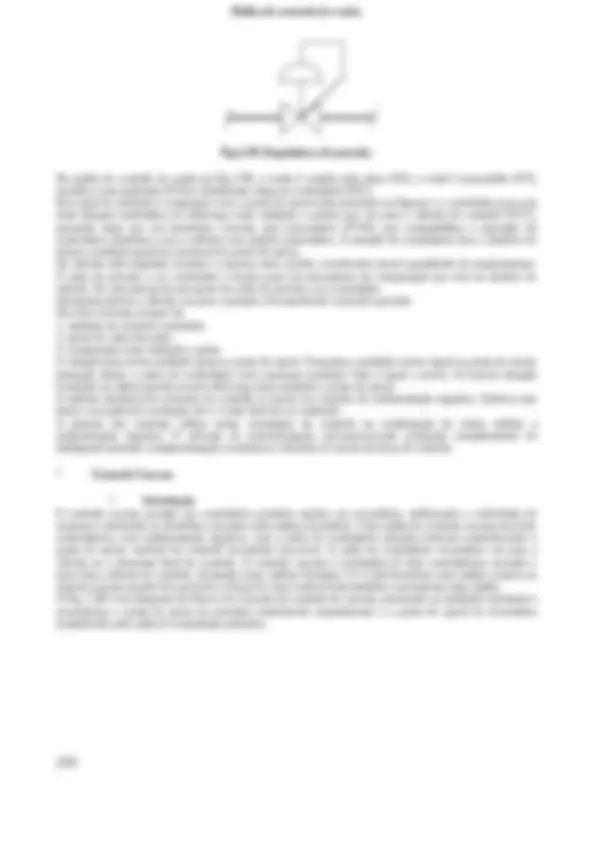
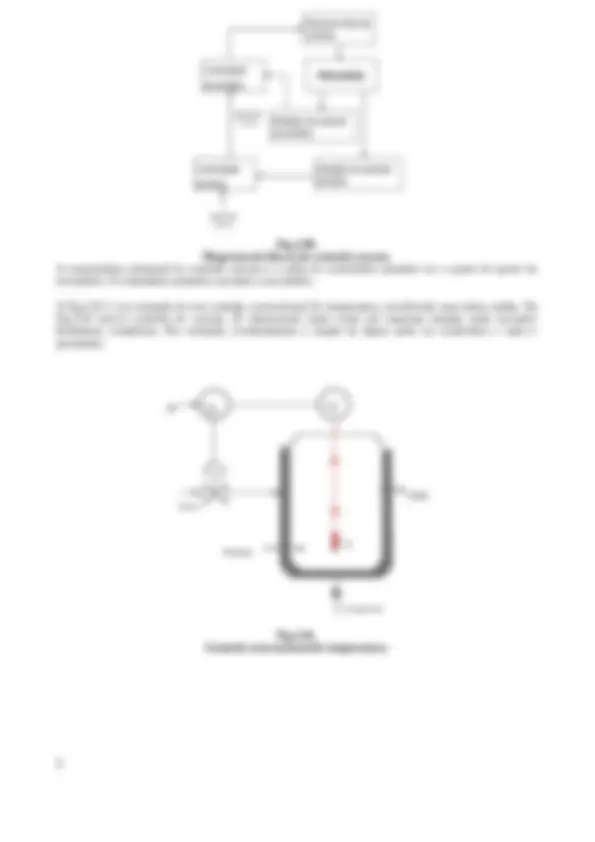
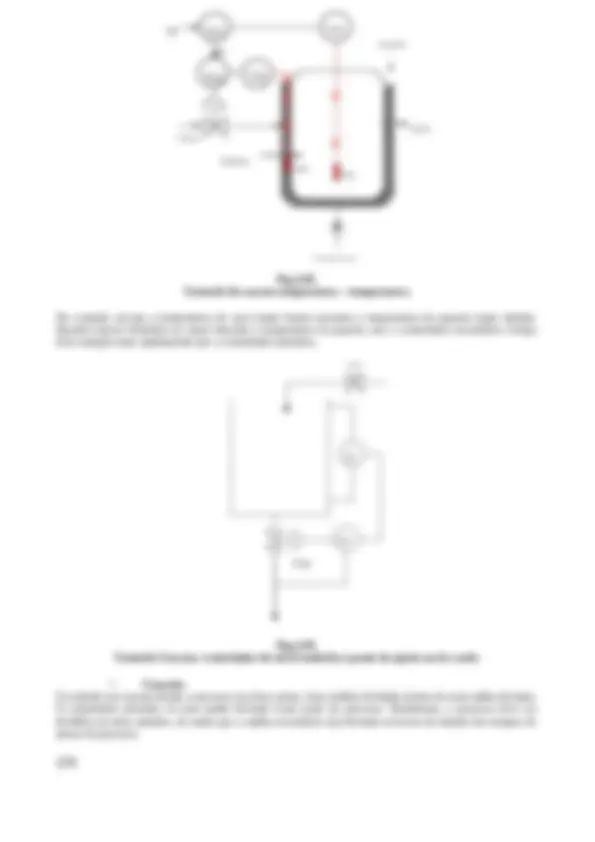
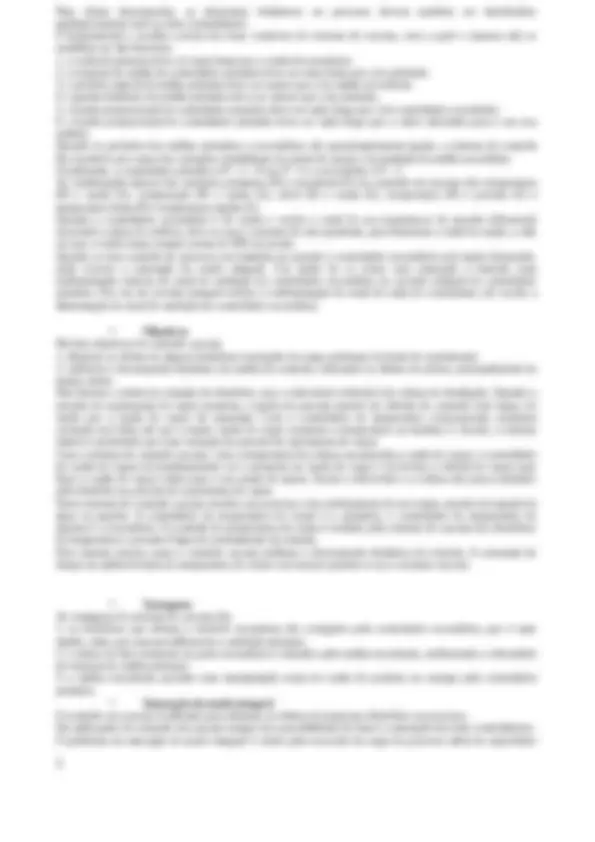
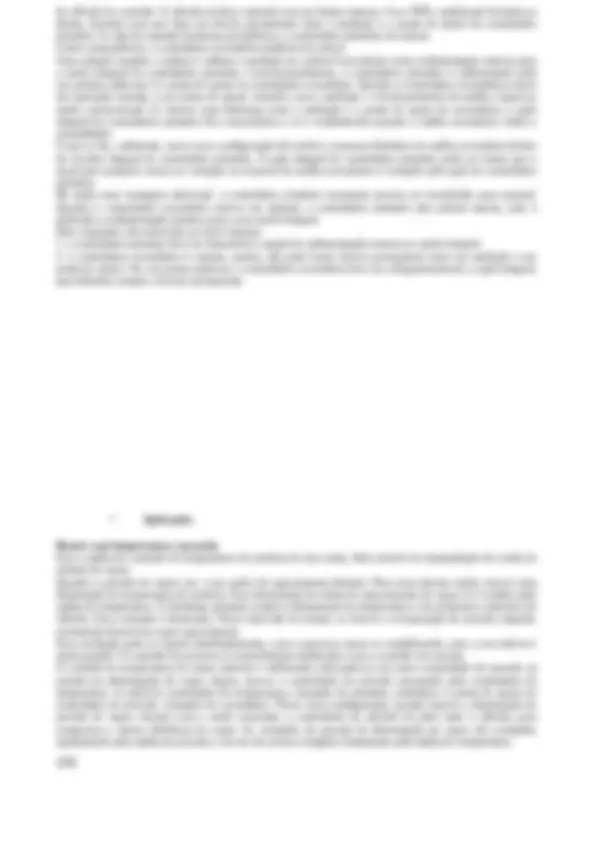
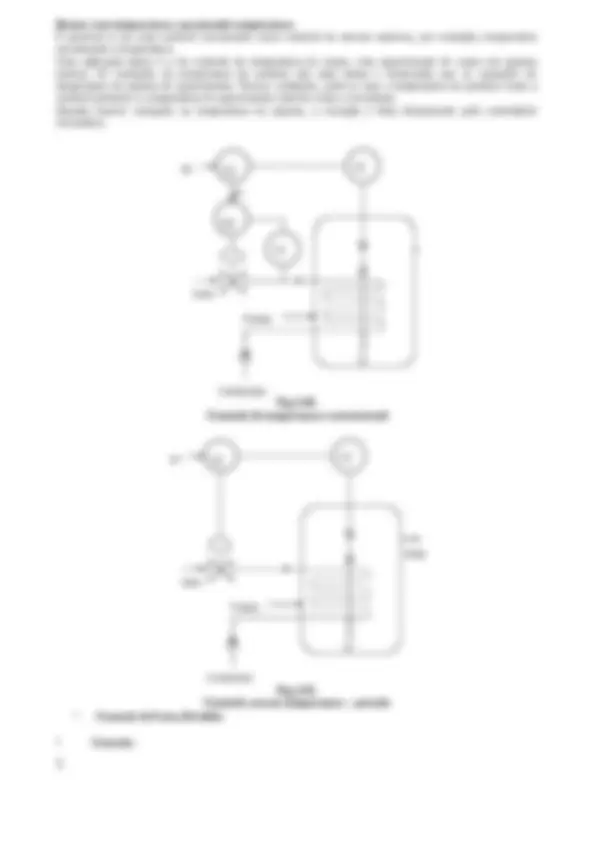
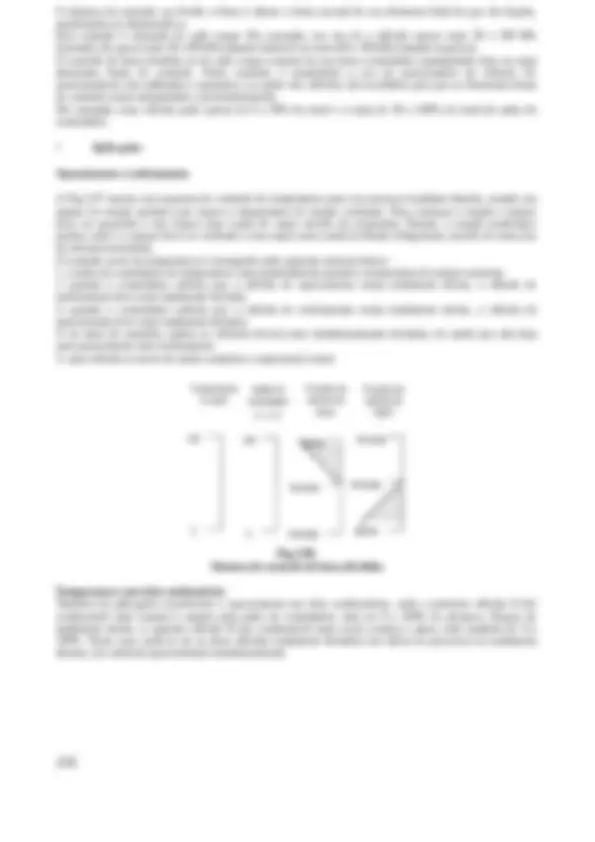
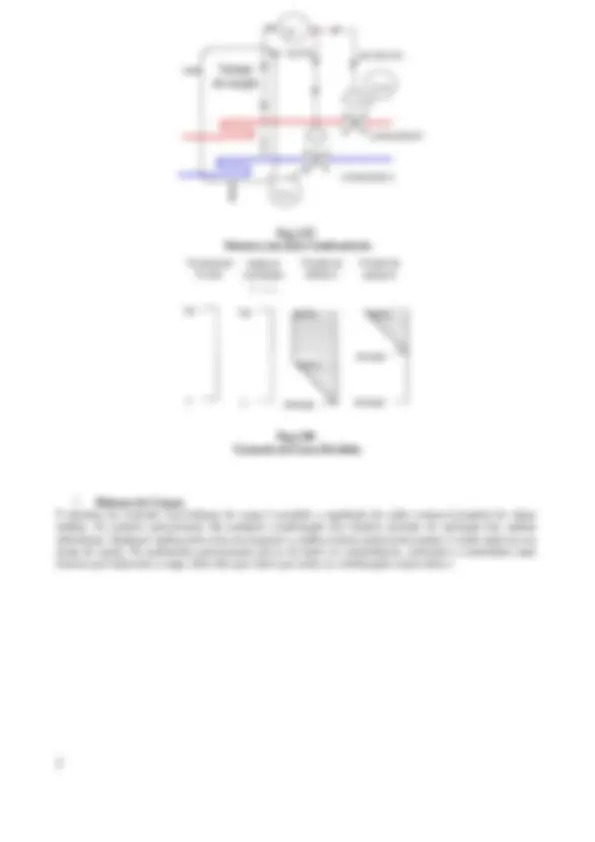
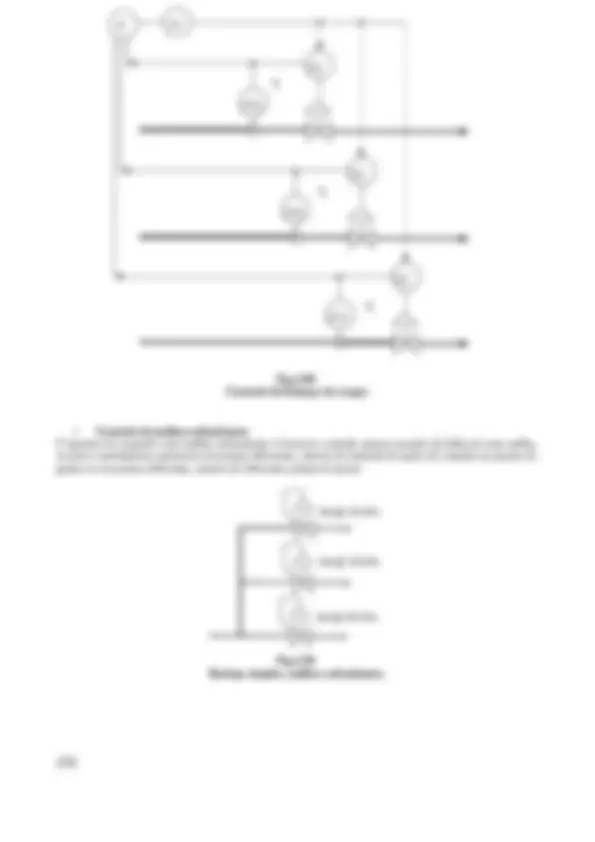
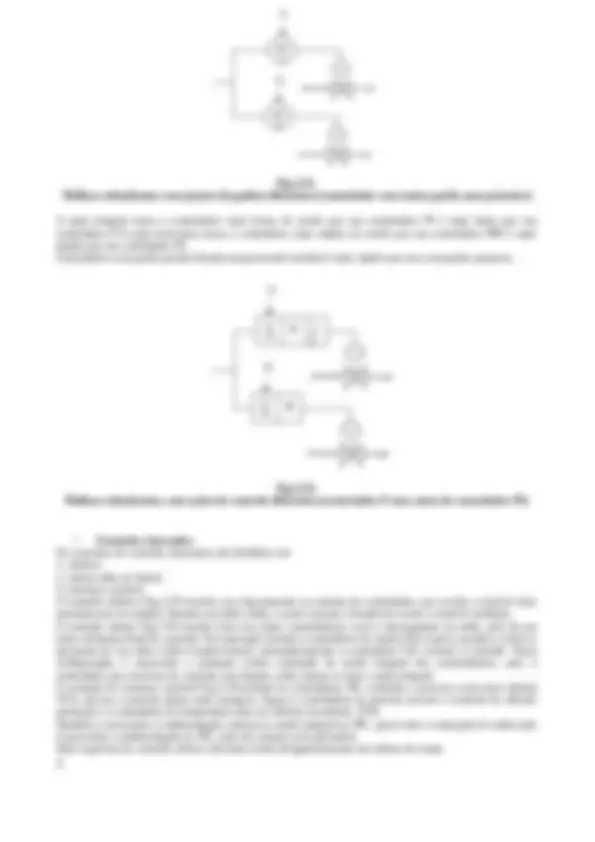
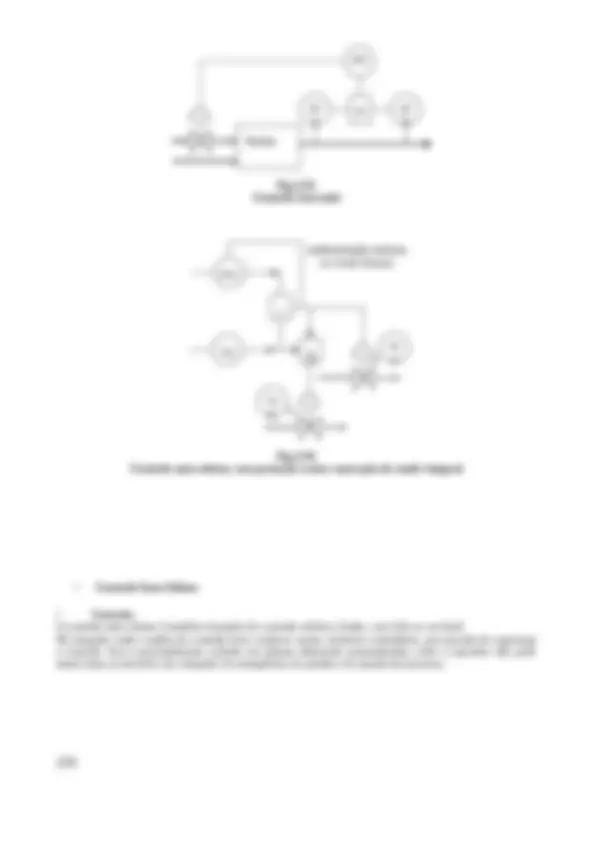
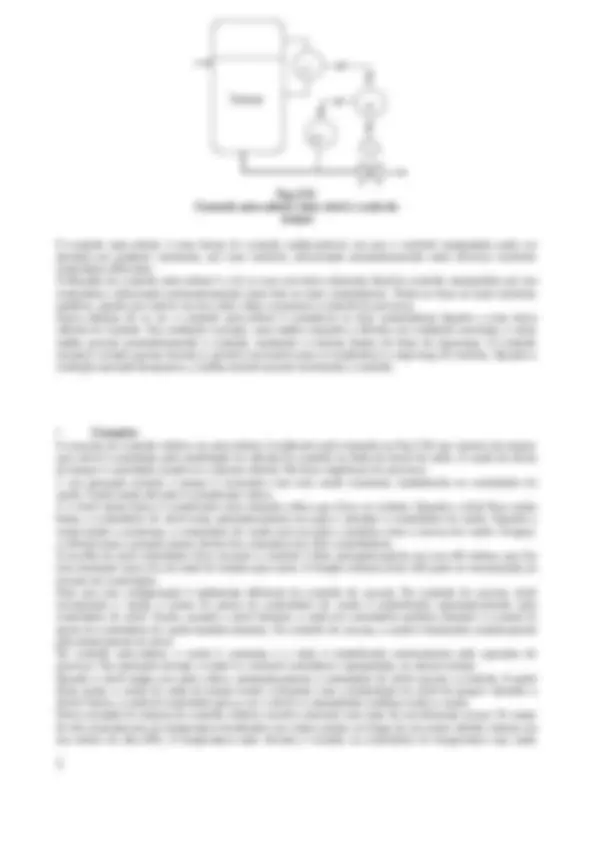
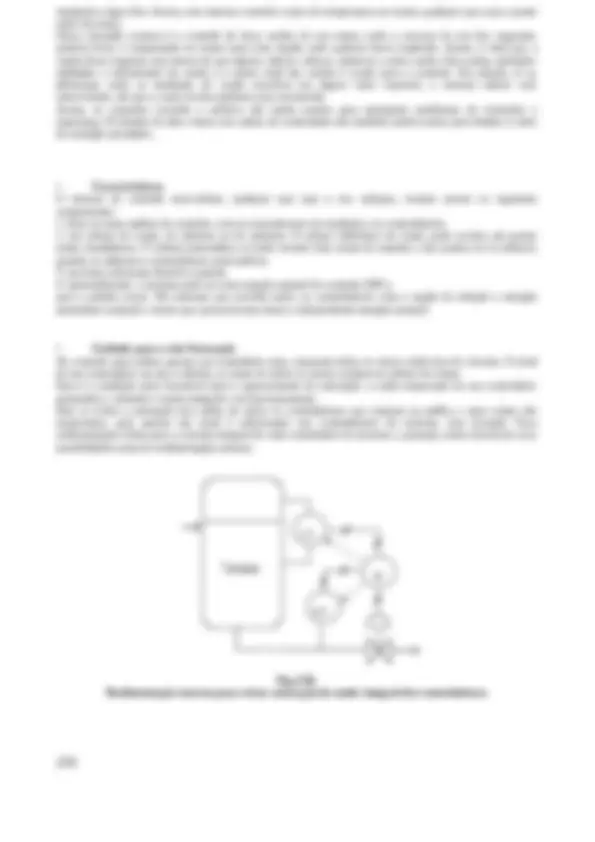
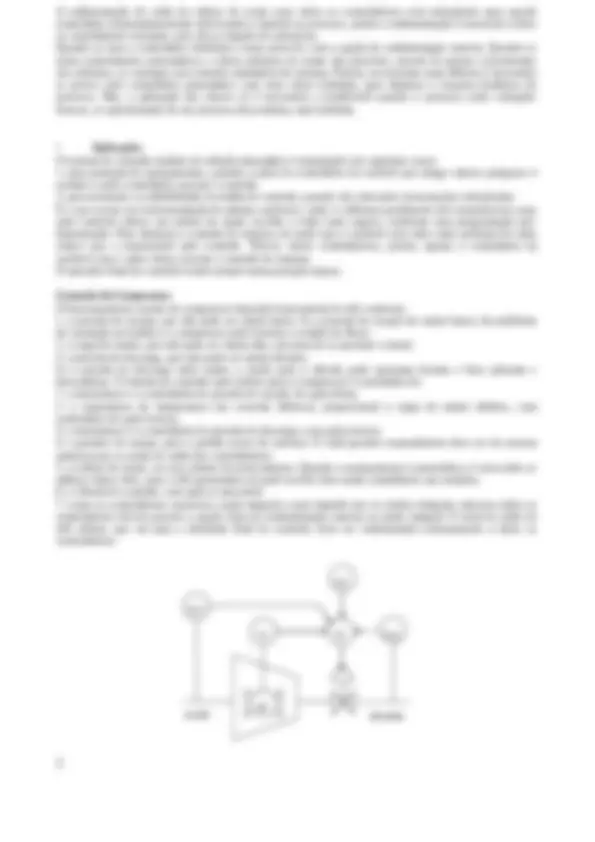
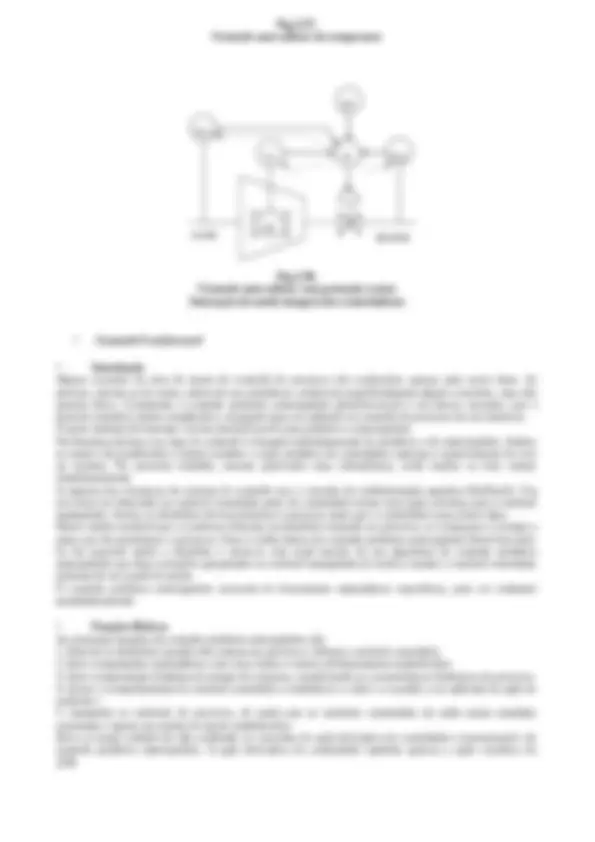
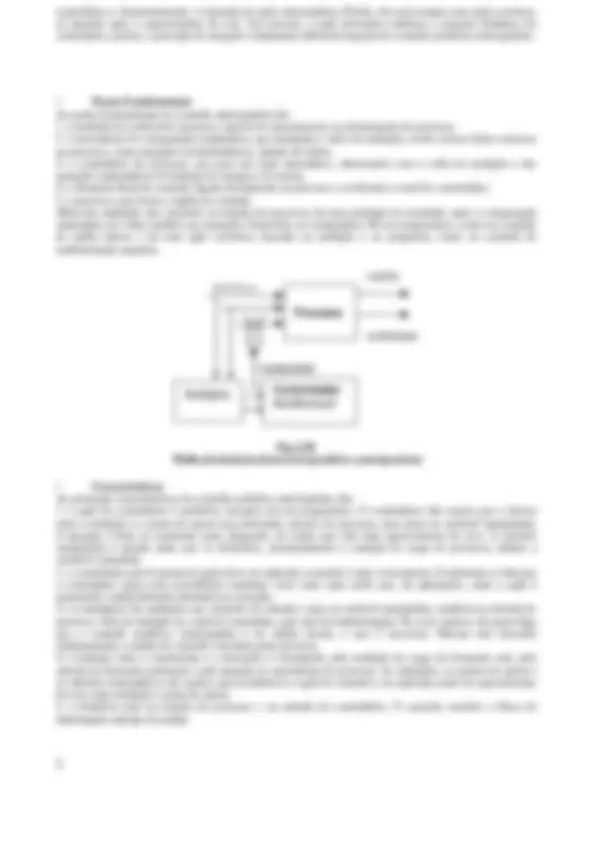
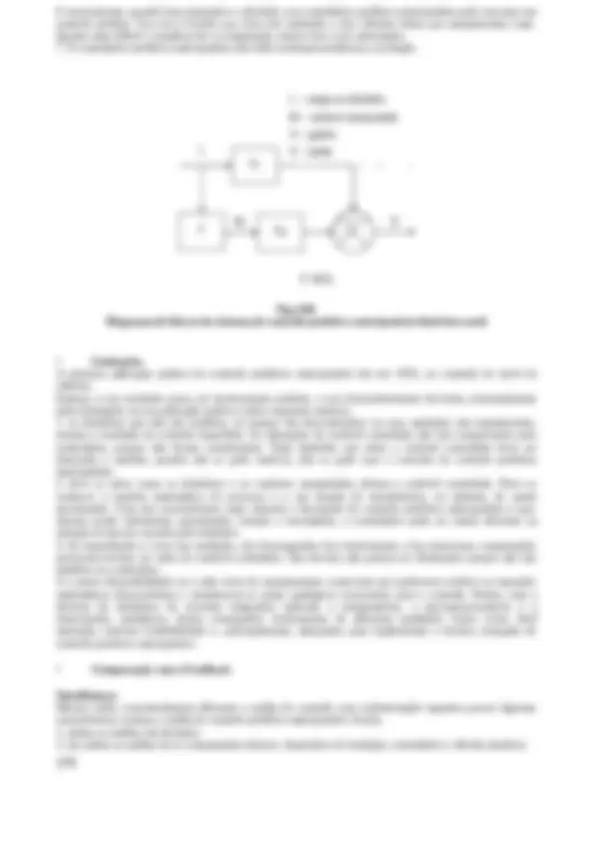
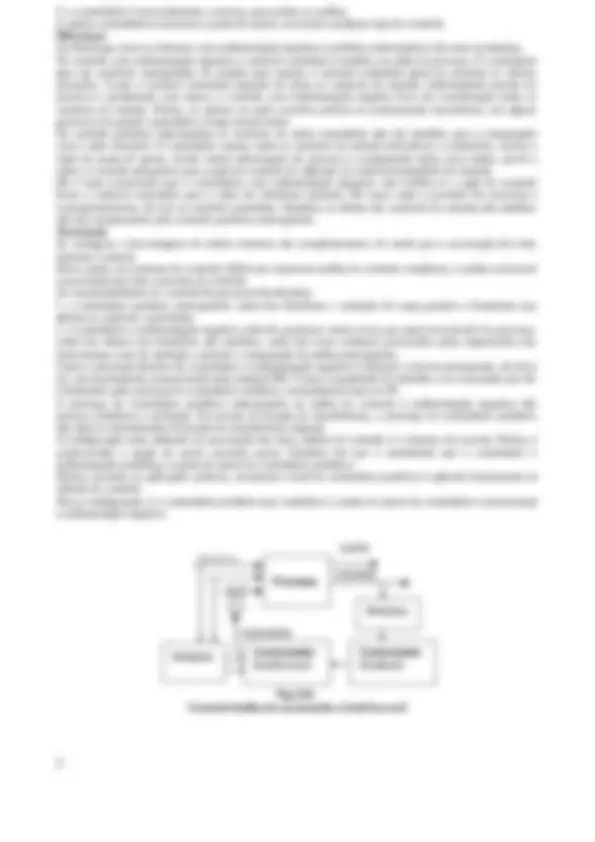
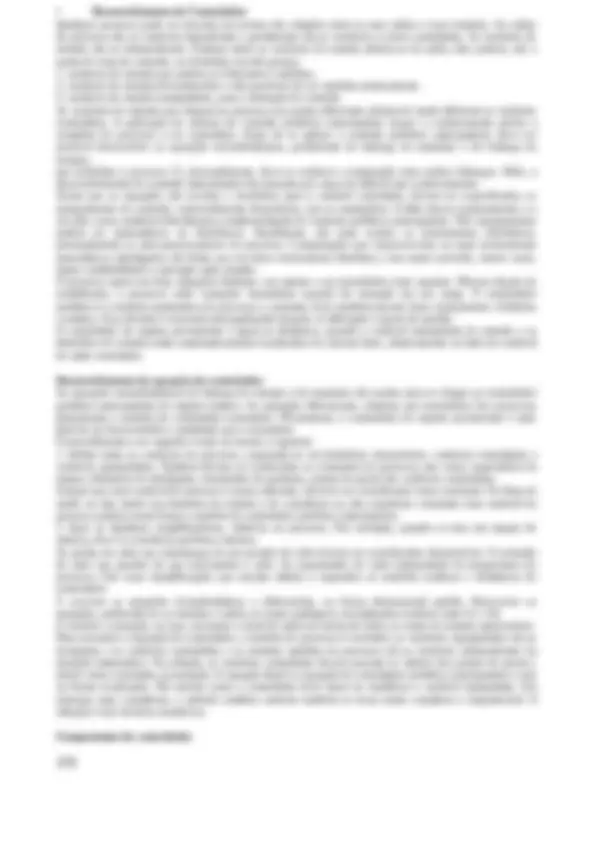
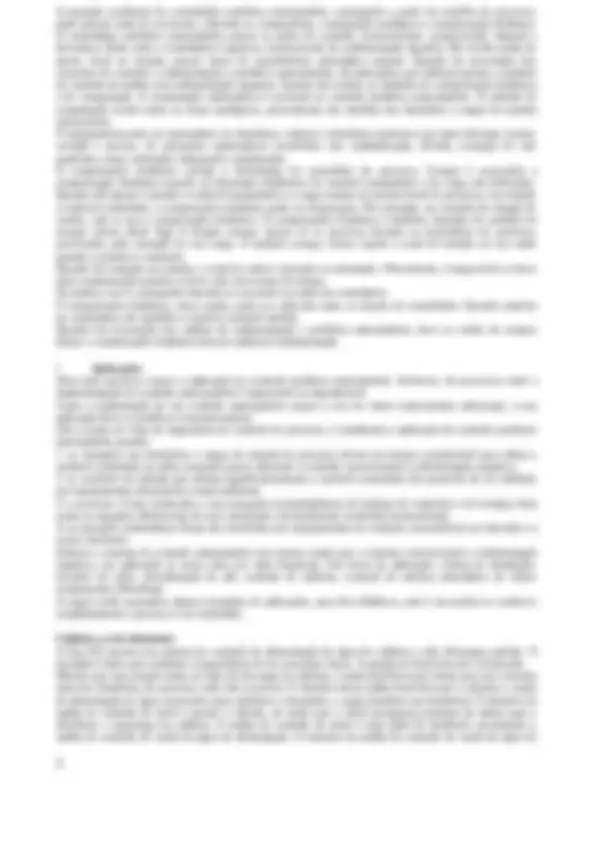
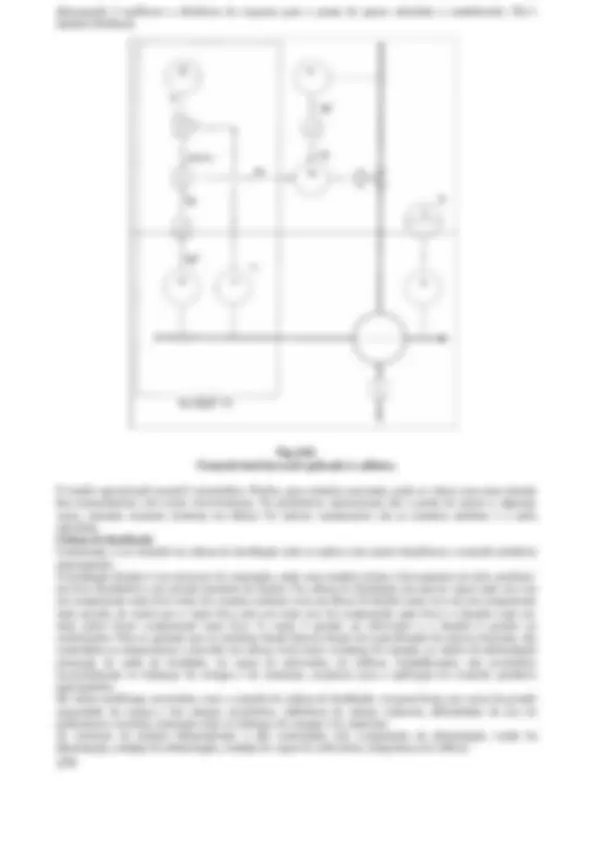
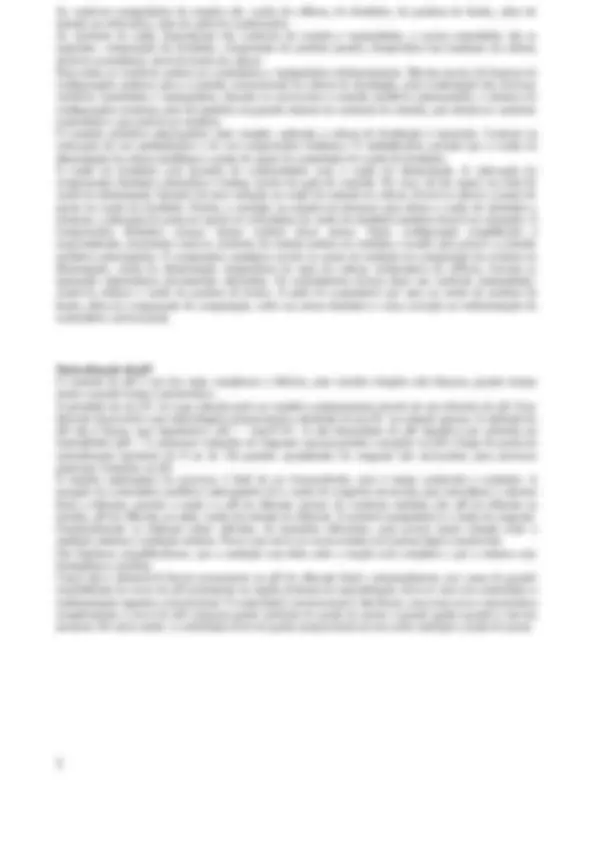
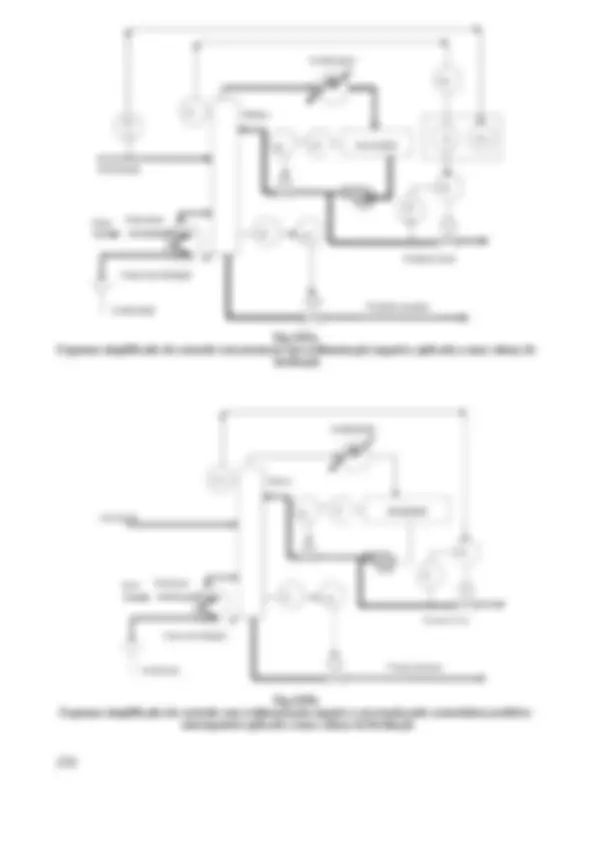
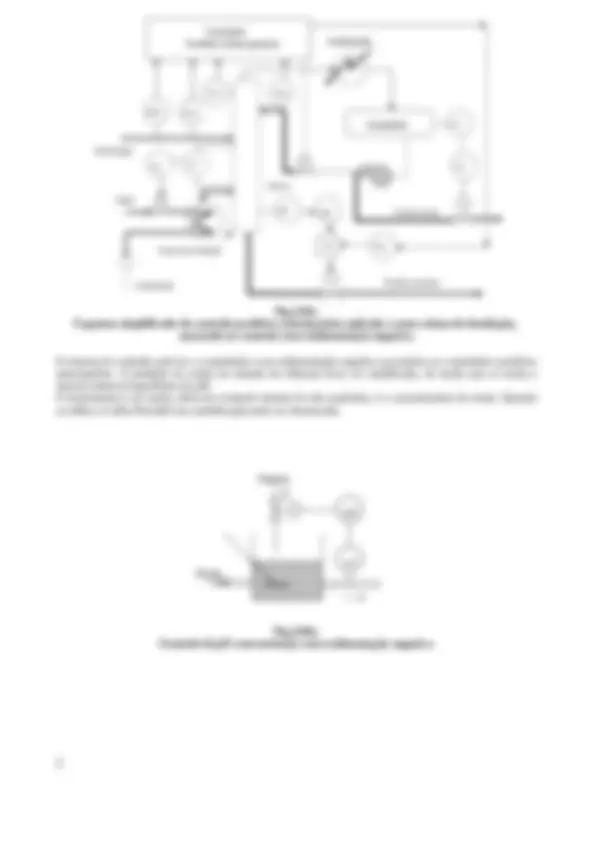
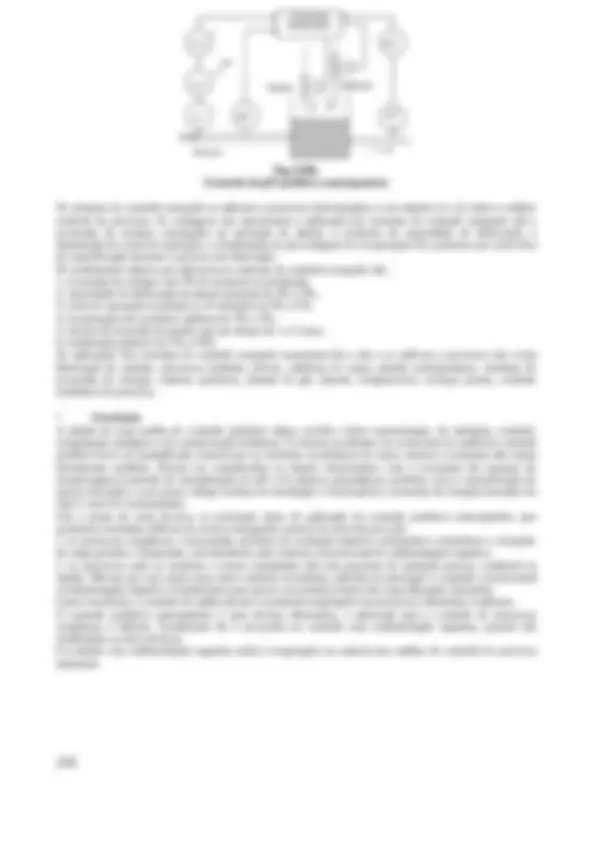
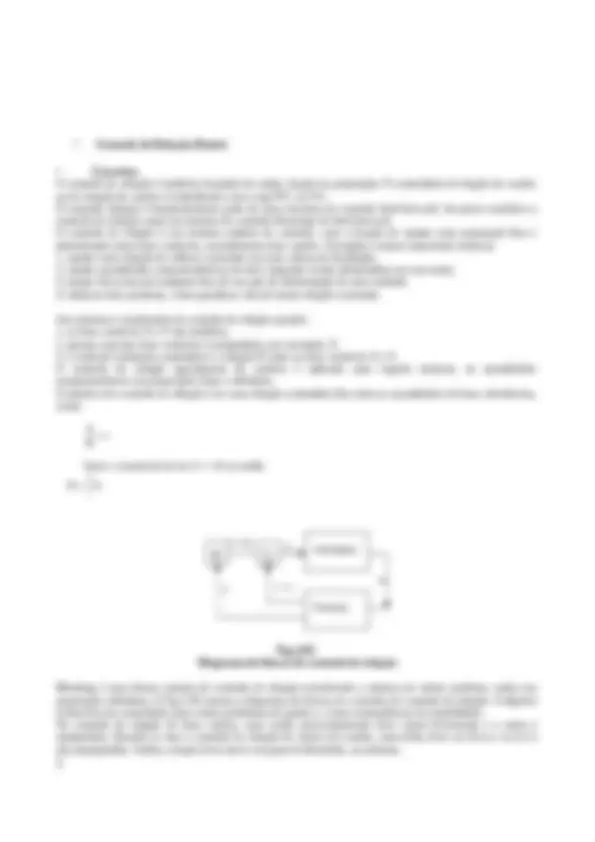
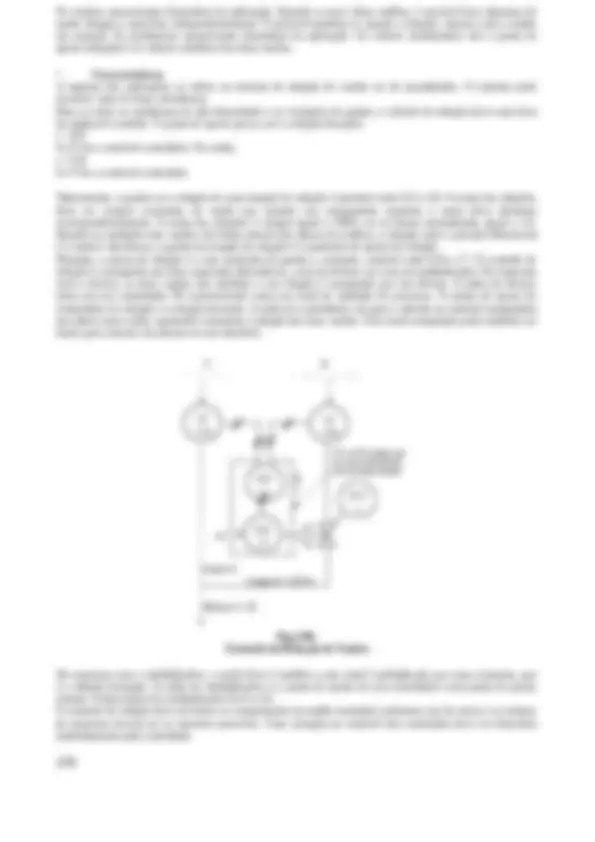
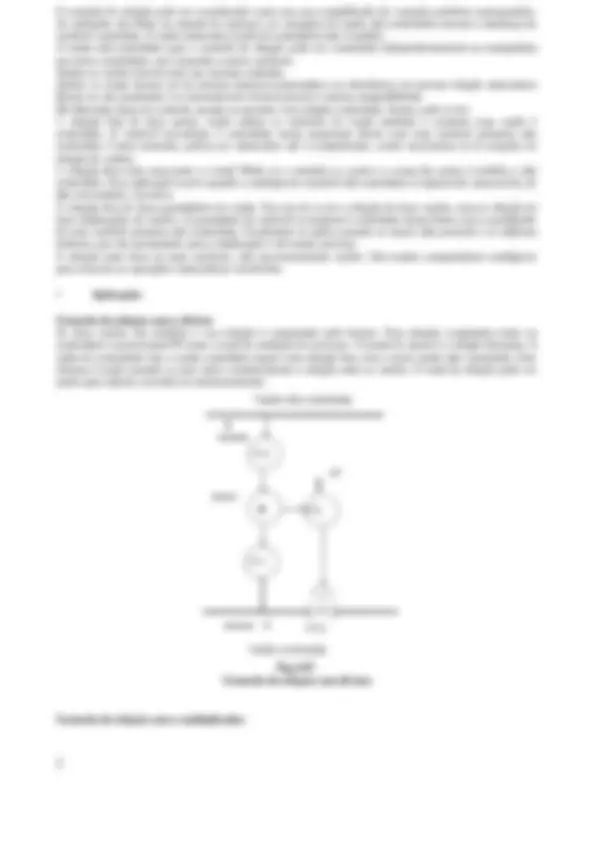
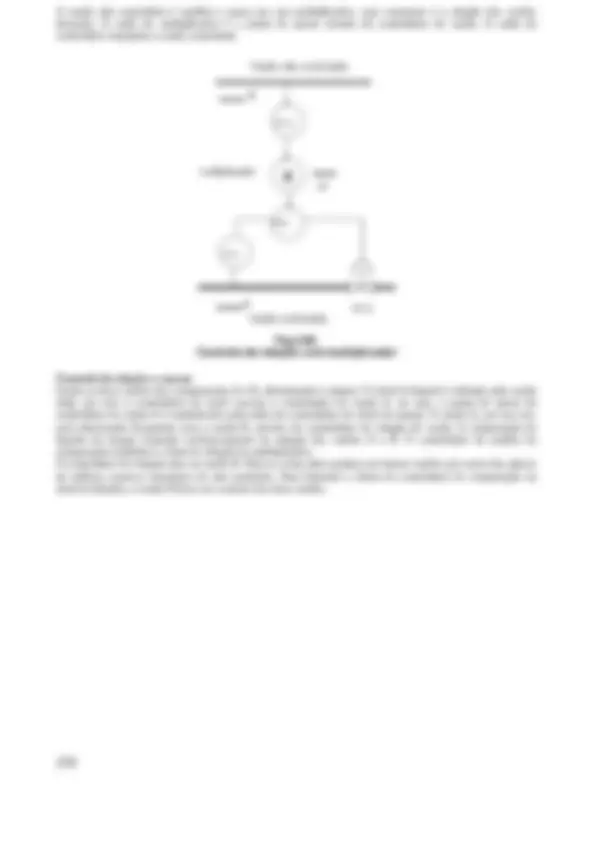
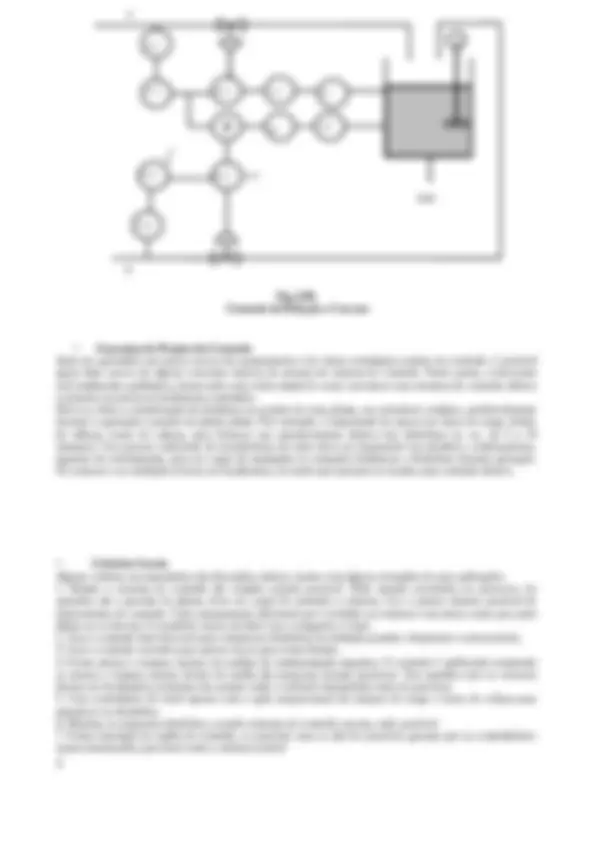
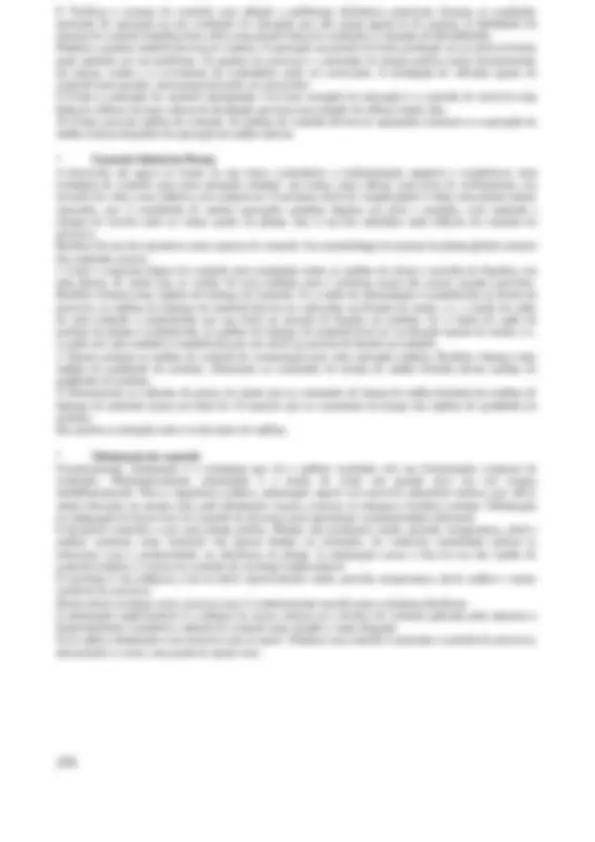
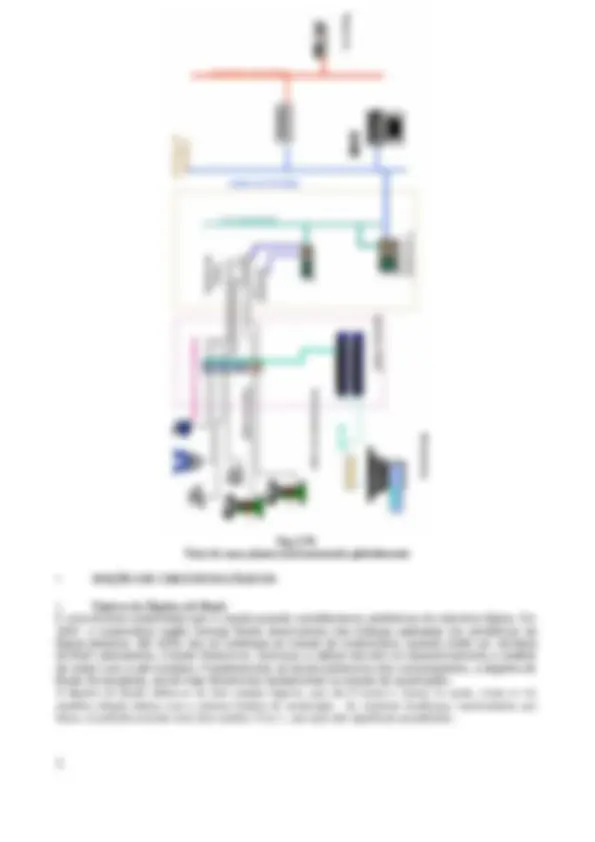
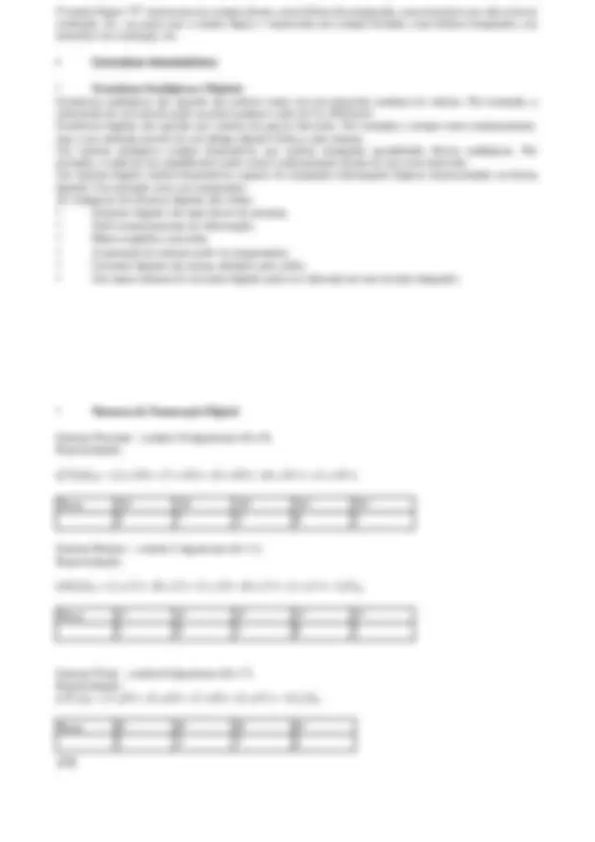
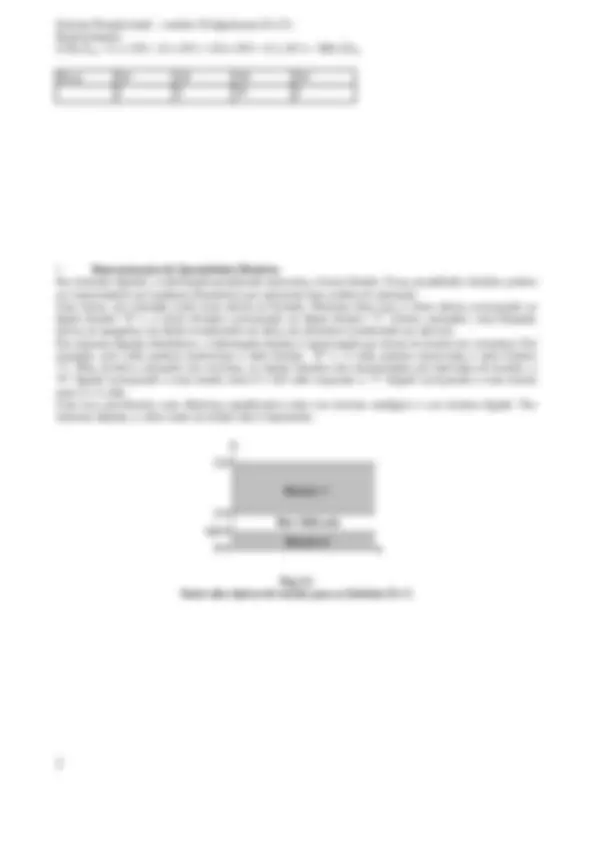
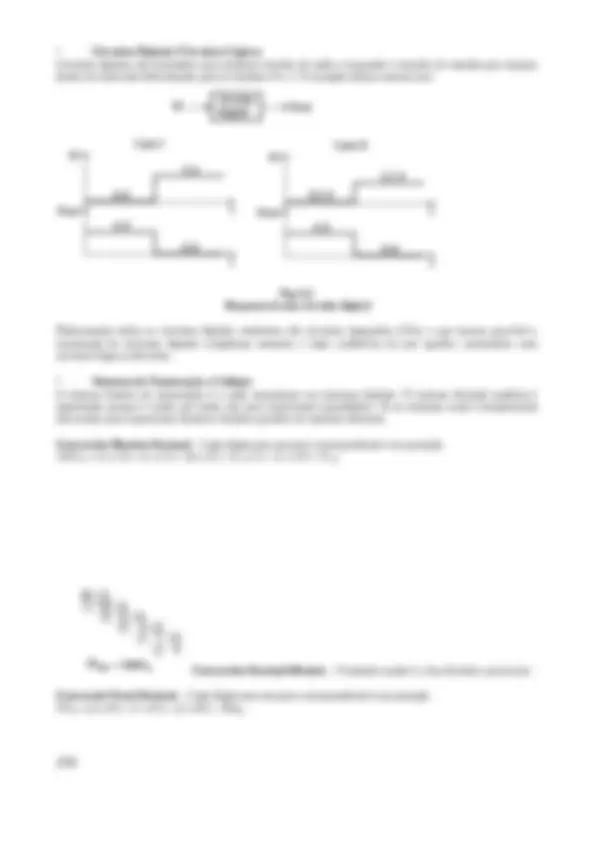
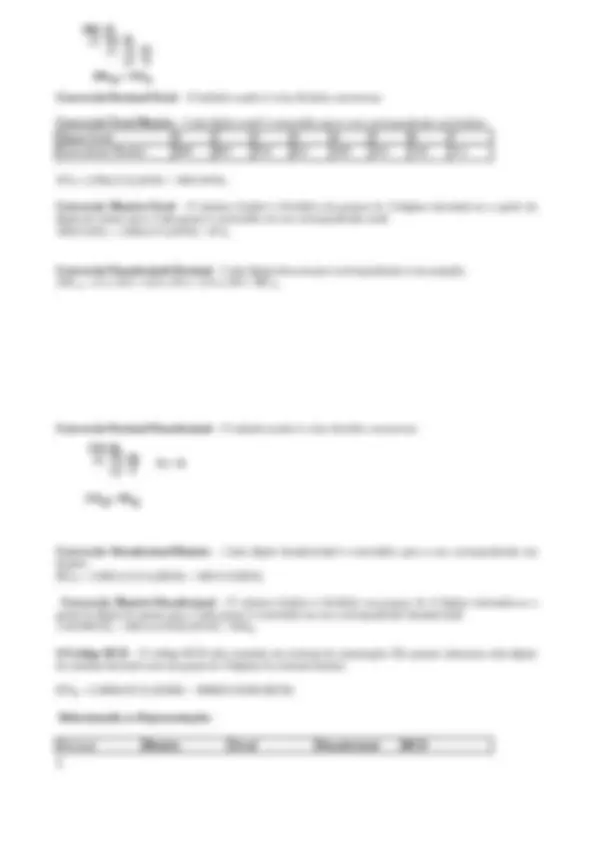
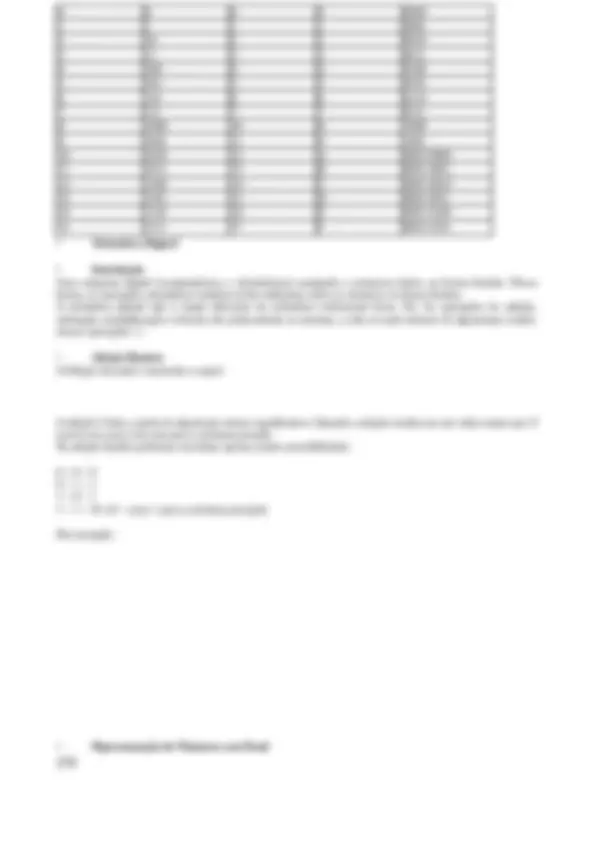
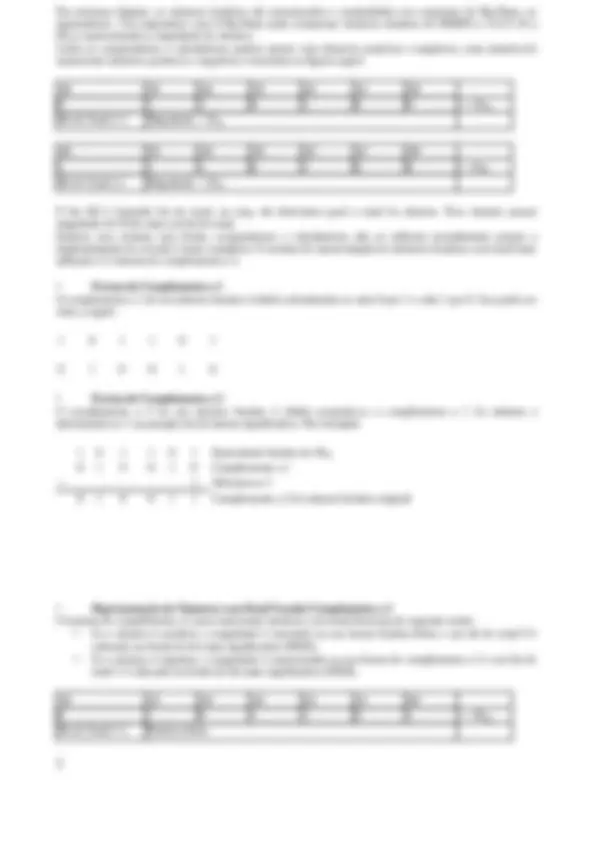
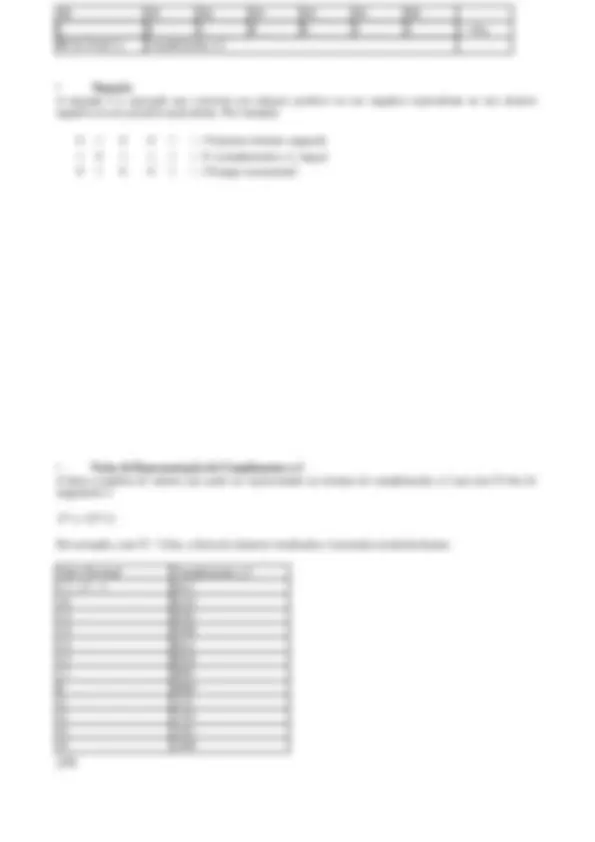
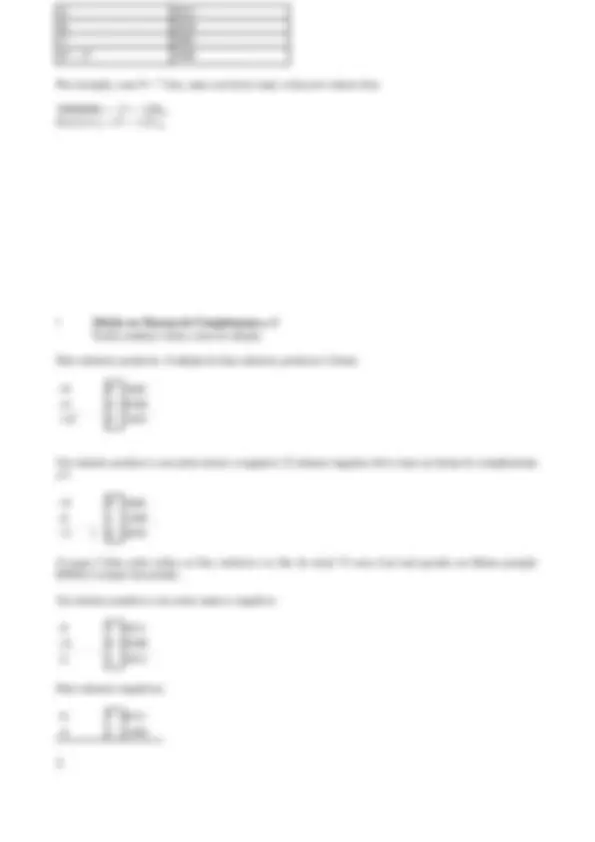
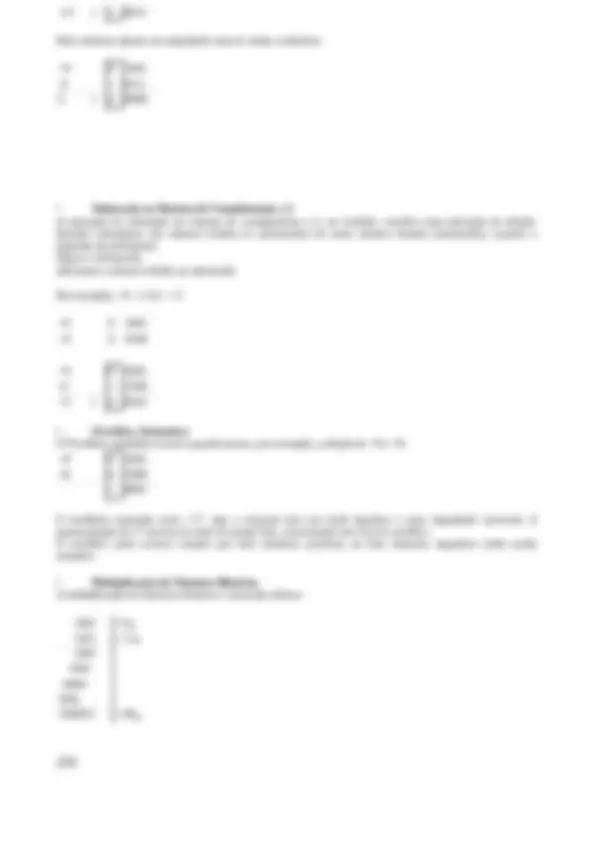
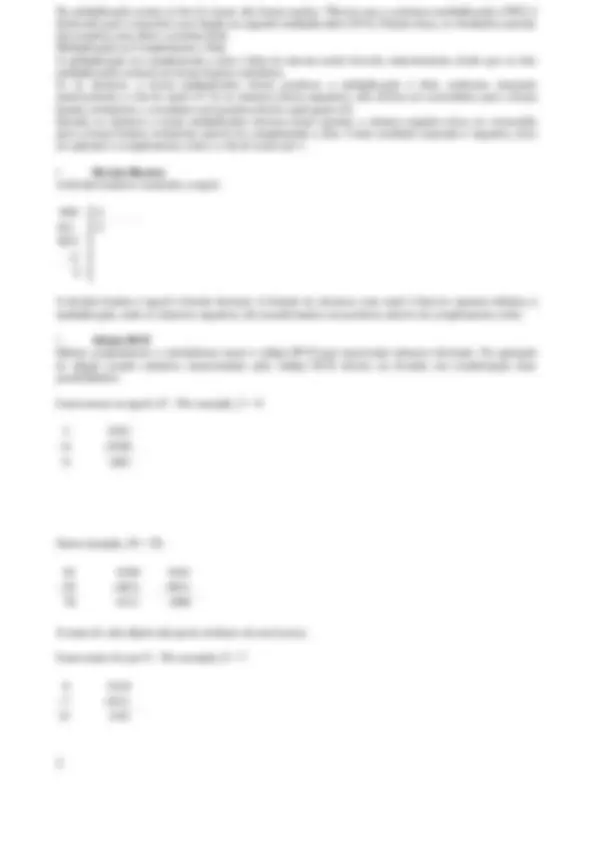
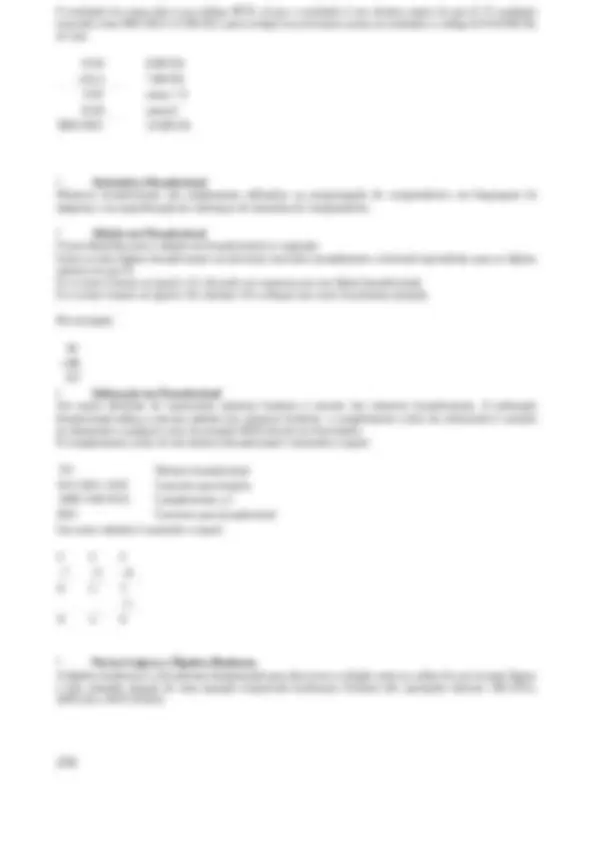
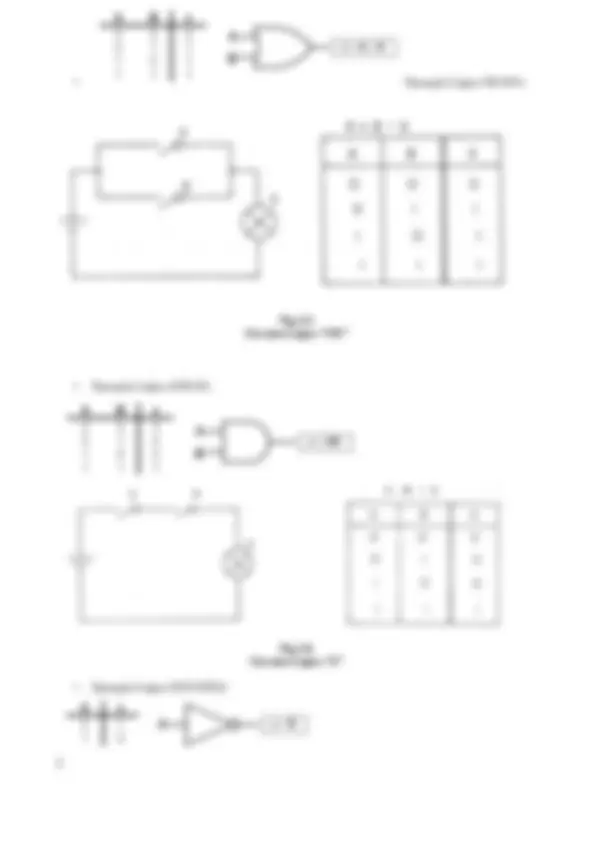
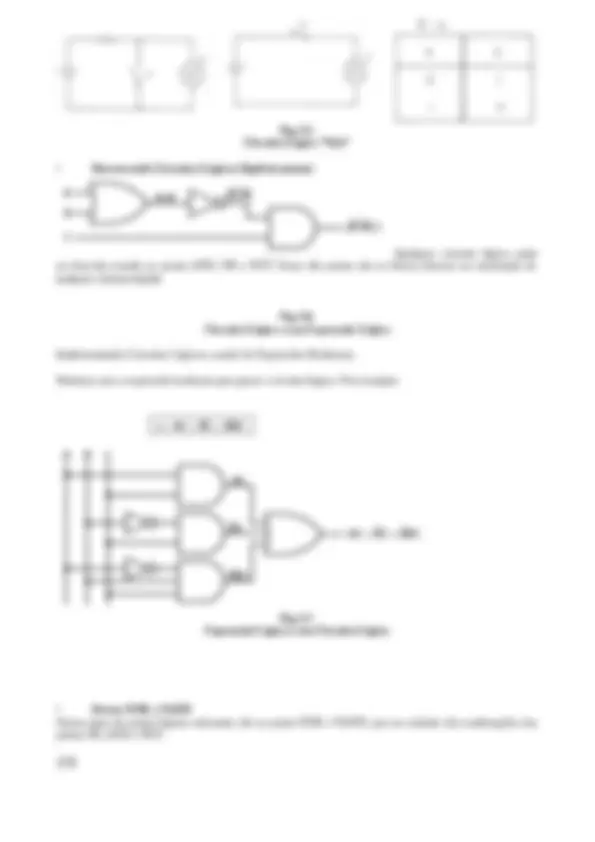
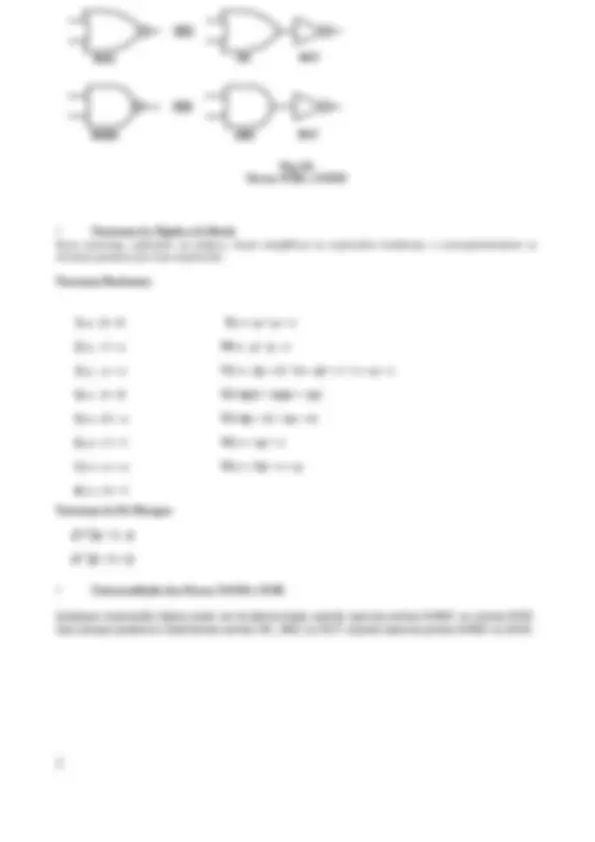
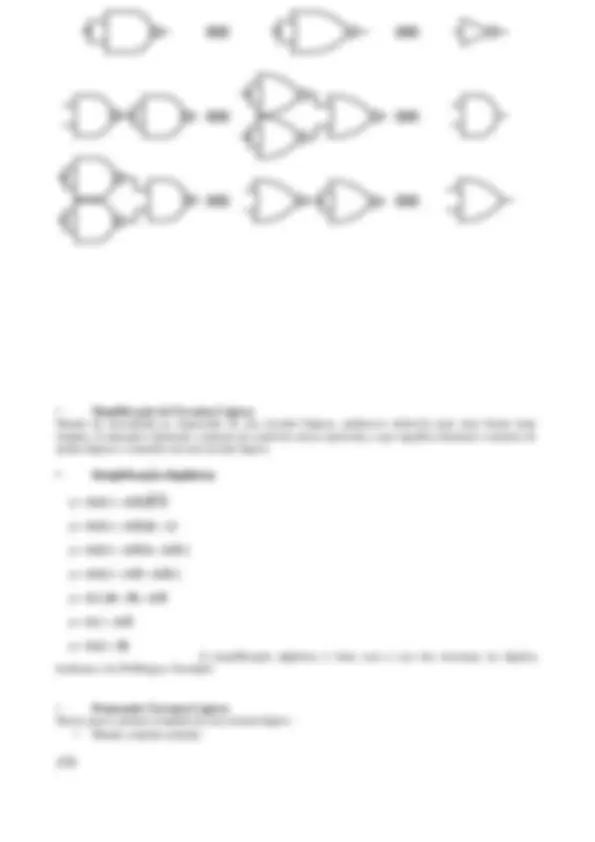
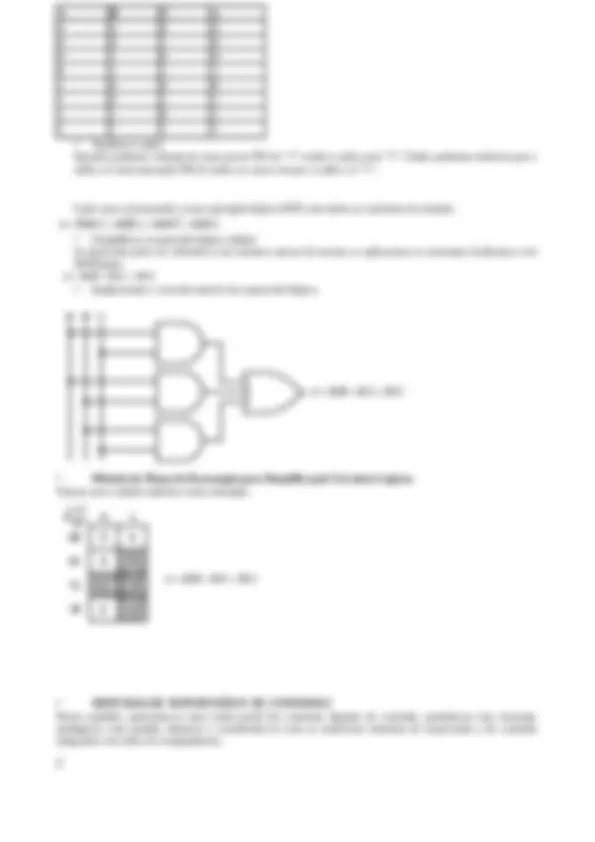
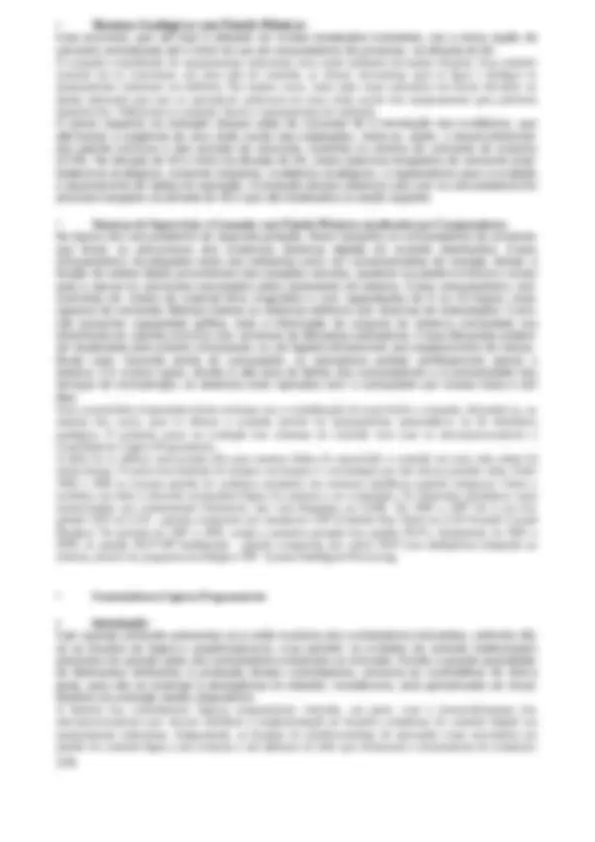
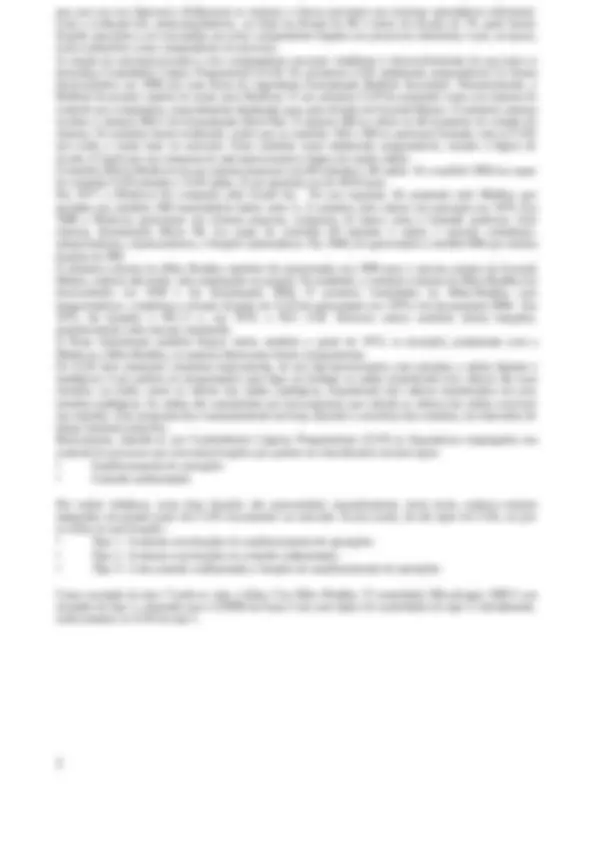
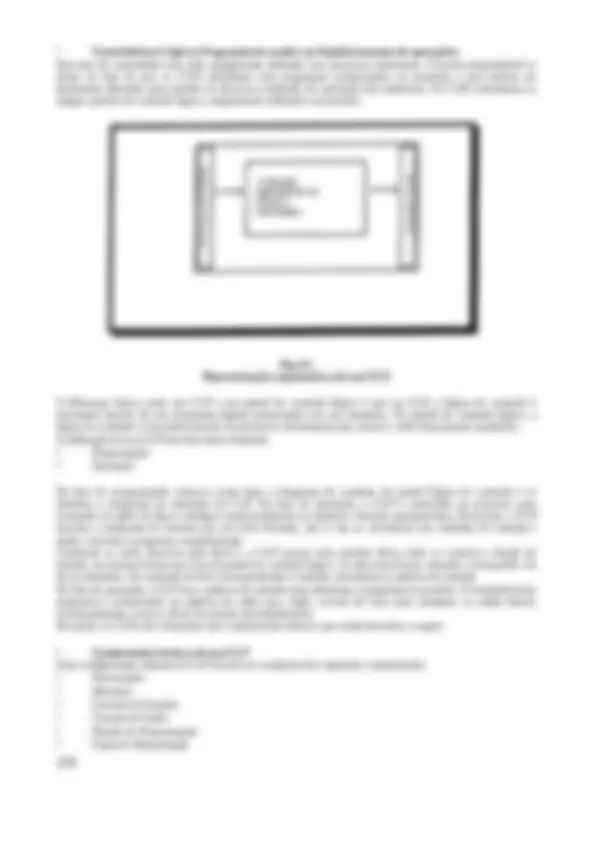
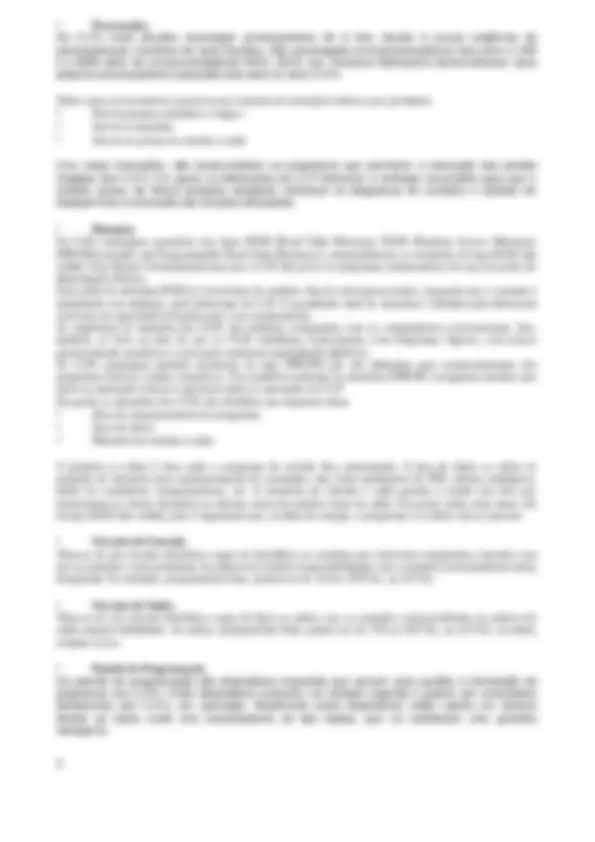
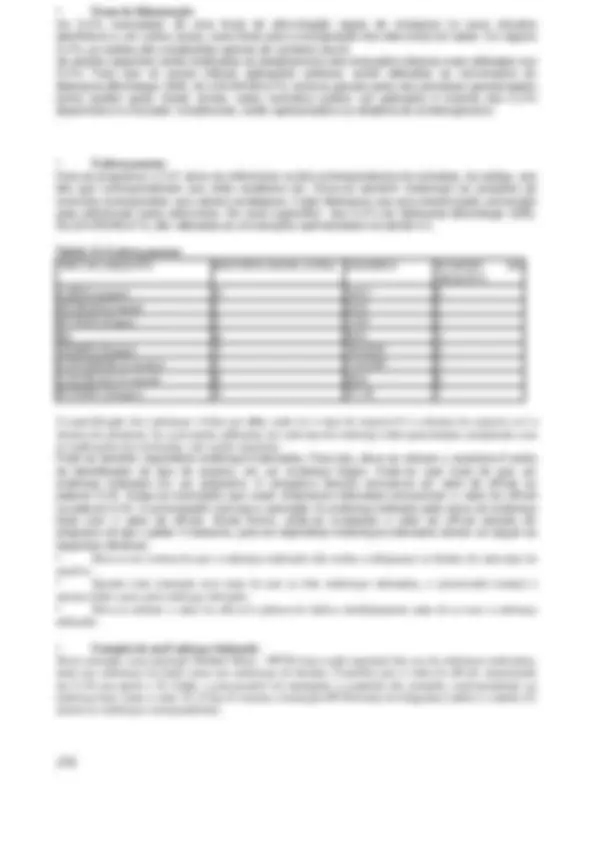
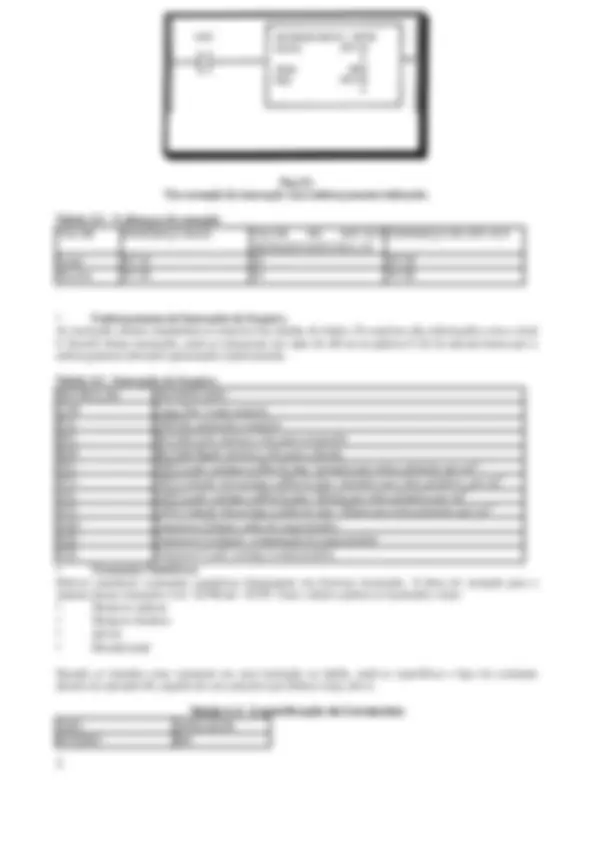
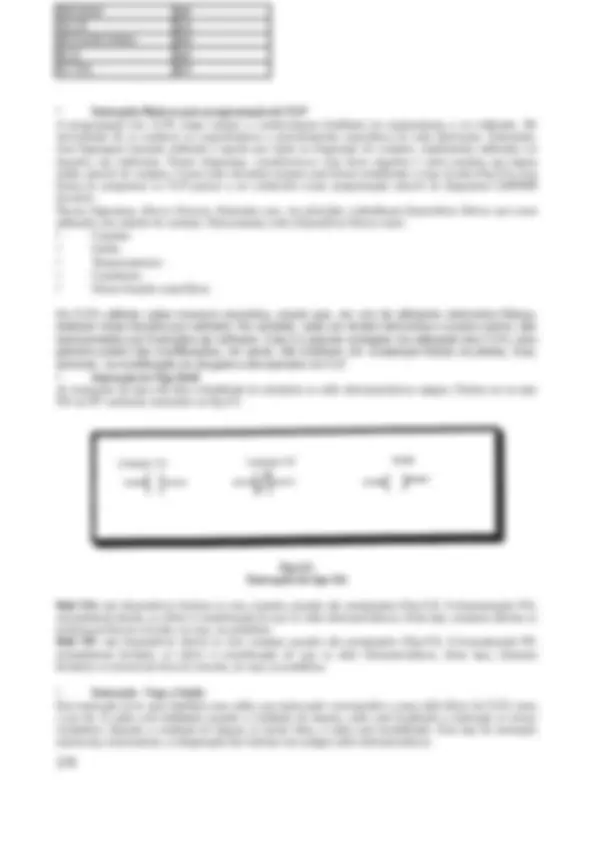
Estude fácil! Tem muito documento disponível na Docsity
Ganhe pontos ajudando outros esrudantes ou compre um plano Premium
Prepare-se para as provas
Estude fácil! Tem muito documento disponível na Docsity
Prepare-se para as provas com trabalhos de outros alunos como você, aqui na Docsity
Os melhores documentos à venda: Trabalhos de alunos formados
Prepare-se com as videoaulas e exercícios resolvidos criados a partir da grade da sua Universidade
Responda perguntas de provas passadas e avalie sua preparação.
Ganhe pontos para baixar
Ganhe pontos ajudando outros esrudantes ou compre um plano Premium
Comunidade
Peça ajuda à comunidade e tire suas dúvidas relacionadas ao estudo
Descubra as melhores universidades em seu país de acordo com os usuários da Docsity
Guias grátis
Baixe gratuitamente nossos guias de estudo, métodos para diminuir a ansiedade, dicas de TCC preparadas pelos professores da Docsity
Apostila Sistemas de Automação e Controle - SENAI
Tipologia: Notas de estudo
Oferta por tempo limitado
Compartilhado em 02/10/2012
4.9
(17)22 documentos
1 / 254
Esta página não é visível na pré-visualização
Não perca as partes importantes!
Em oferta
Sistemas de Automação e Controle SENAI – ES, 2005. Direitos de Reprodução para a CST
Apostila elaborada pelo Professor de Instrumentação/Automação Industrial: Fábio da Costa Pinto.
Departamento Regional do Espírito Santo CETEC – Centro de Educação e Tecnologia Arivaldo Fontes
6.2 Meios de Comunicação da IHM...................................................................... 334
7 SISTEMA PIMS.........................................................................................................
7.1 Apresentação................................................................................................... 343 7.2 Comunicação com Sistemas Externos.......................................................... 343
7.3 Modelo de Gerenciamento de Dados CST..................................................... 344
8 BIBLIOGRAFIA........................................................................................................ 346
Automação é um sistema de equipamentos eletrônicos e/ou mecânicos que controlam seu próprio funcionamento, quase sem a intervenção do homem. Automação é diferente de mecanização. A mecanização consiste simplesmente no uso de máquinas para realizar um trabalho, substituindo assim o esforço físico do homem. Já a automação possibilita fazer um trabalho por meio de máquinas controladas automaticamente, capazes de se regularem sozinhas.
Fig.1.1. Evolução da automatização ao longo dos tempos.
Por volta de 1788, James Watt desenvolveu um mecanismo de regulagem do fluxo do vapor em locomotivas. Isto pode ser considerado um dos primeiros sistemas de controle com realimentação e regulador e consistia num eixo vertical com dois braços próximos ao topo, tendo em cada extremidade uma bola pesada. Com isso, a máquina funcionava de modo a se regular sozinha, automaticamente, por meio de um laço de Realimentação.
Fig.1.2. Representação simplificada do mecanismo de J. Watt.
A partir de 1870, também a energia elétrica passou a ser utilizada e a estimular indústrias como a do aço, a química e a de máquinas-ferramenta e o setor de transportes progrediu bastante graças à expansão das estradas de ferro e à indústria naval. No século XX, a tecnologia da automação passou a contar com computadores, servomecanismos e controladores programáveis. Os computadores são o alicerce de toda a tecnologia da automação contemporânea.
Com esse equipamento, o MIT desenvolveu uma linguagem de programação que auxilia a entrada de comandos de trajetórias de ferramentas na máquina. Trata-se da linguagem APT (do inglês, Automatically Programmed Tools, ou “Ferramentas Programadas Automaticamente”). Os robôs (do tcheco robota, que significa "escravo, trabalho forçado") substituíram a mão-de-obra no transporte de materiais e em atividades perigosas. O robô programável foi projetado em 1954 pelo americano George Devol, que mais tarde fundou a fábrica de robôs Unimation. Poucos anos depois, a GM instalou robôs em sua linha de produção para soldagem de carrocerias. Ainda nos anos 50, surge a idéia da computação gráfica interativa : forma de entrada de dados por meio de símbolos gráficos com respostas em tempo real. O MIT produziu figuras simples por meio da interface de tubo de raios catódicos (idêntico ao tubo de imagem de um televisor) com um computador. Em 1959, a GM começou a explorar a computação gráfica. A década de 1960 foi o período mais crítico das pesquisas na área de computação gráfica interativa. Na época, o grande passo da pesquisa foi o desenvolvimento do sistema sketchpad, que tornou possível criar desenhos e alterações de objetos de maneira interativa, num tubo de raios catódicos. No inicio dos anos 60, o termo CAD (do inglês Computer Aided Design ou "Projeto Auxiliado por Computador") começou a ser utilizado para indicar os sistemas gráficos orientados para projetos. Nos anos 70, as pesquisas desenvolvidas na década anterior começaram a dar frutos. Os setores governamentais e industriais passaram a reconhecer a importância da computação gráfica como forma de aumentar a produtividade. Na década de 1980, as pesquisas visaram à integração e/ou automatização dos diversos elementos de projeto e manufatura. Com o objetivo de criar a fábrica do futuro, o foco das pesquisas foi expandir os sistemas CAD/CAM (Projeto e Manufatura Auxiliado por Computador). Desenvolveu-se também o modelamento geométrico tridimensional com mais aplicações de engenharia (CAE - Engenharia Auxiliada por Computador). Alguns exemplos dessas aplicações são a análise e simulação de mecanismos, o projeto análise de injeção de moldes e a aplicação do método dos elementos finitos. Hoje, os conceitos de integração total do ambiente produtivo com o uso dos sistemas de comunicação de dados e novas técnicas de gerenciamento estão se disseminando rapidamente, já sendo uma realidade o CIM (Manufatura Integrada por Computador).
As operações a realizar são em geral simples e a complexidade do sistema tem, sobretudo a ver com a integração de um elevado número de operações a realizar. Os aspectos típicos da automação fixa são:
Podem-se referir como exemplos de sistemas de automação programável as máquinas de Comando Numérico (“CNC – Computer Numeric Control”) com início de atividade em 1952 e as primeiras aplicações de robôs industriais em 1961. (Ver Fig.1.4).
Fig.1. Exemplo de aplicação industrial de um robô: alimentação de peças de uma máquina-ferramenta. (Fonte: Eshed Robotec).
uma importância fundamental nos sistemas de pilotagem de navios, aviões, mísseis, veículos espaciais, etc. passou a tornar-se uma parte integrante do funcionamento de processos industriais típicos (manufatura, produção de energia, produtos químicos, transportes, instalações de frio e ar condicionado, etc.). O controle automático é essencial, por exemplo, em operações industriais que envolvam o controle de posição, velocidade, pressão, vazão, temperatura, umidade, viscosidade, etc. Neste capítulo, vamos apresentar os conceitos básicos relativos à teoria do controle automático, bem como as principais estruturas utilizadas no controle de processos industriais. Por fim, faremos uma breve descrição do tipo de controladores ou reguladores mais utilizados na indústria, bem como as suas principais características e formas de ajuste dos respectivos parâmetros.
Fig.2.1. Esquema básico do regulador de Watt aplicado à regulação de velocidade de motor Diesel.
No esquema da Fig.2.1, podemos verificar que o veio do motor tem acoplado um sistema com duas massas ( m ) que rodam com o veio à velocidade de rotação ω. Assim, quando o motor aumenta de rotação, devido à ação centrífuga as massas tendem a afastar-se diminuindo o curso ( y ), elevando assim a haste ( h ) ligada à válvula de combustível. Deste modo, o caudal de combustível diminui o que faz baixar a velocidade de rotação do motor. Por conseguinte, as massas tendem a aproximar-se do veio, aumentando y , baixando h aumentando a velocidade do motor ω. Este procedimento repete-se até se atingir uma situação de equilíbrio. No século XX, foram iniciados de fato os estudos e as aplicações do controle automático à indústria. Assim, com o avanço da ciência e da tecnologia, foram dados os primeiros passos nas décadas de vinte e trinta, períodos nos quais foram efetuados importantes desenvolvimentos. Durante a década de quarenta, foram dados novos e importantes passos nesta área. Deste modo, após a introdução do primeiro regulador pneumático PID 1
na indústria, os investigadores J. Ziegler e N. Nichols desenvolveram um método de ajuste ótimo destes reguladores, que ficou conhecido por "Método de Ziegler-Nichols".
1 Estes reguladores utilizam as 3 ações básicas de regulação: Proporcional (P), Integral (I) e Derivativa (D), relativamente ao erro. São também designados na indústria, por reguladores de três ações (“three-term- regulator”).
Este método permitiu resolver muito dos problemas de ajuste dos parâmetros de reguladores, através de uma metodologia relativamente simples e eficaz.
a) b) Fig.2.2. a)Aspecto de um regulador pneumático PID atual utilizado na indústria. b)Controlador eletrônico e sensores analógicos de diversos tipos.
Nos anos setenta e seguintes, devido ás crescentes potencialidades dos computadores digitais para efetuar a manipulação de grandes volumes de dados e de efetuar cálculos complexos, estes passaram a ser progressivamente cada vez mais utilizados na construção de reguladores industriais, sensores transdutores, etc. Esta técnica, que recorre à utilização em larga escala de micro-computadores para efetuar a monitorização e o controle digital é conhecida por controle digital direto ( DDC - "Direct Digital Control"). Neste tipo de controle, é utilizado um computador digital para efetuar o controle do processo em tempo real, de um ou mais processos, consoante o tipo e complexidade da aplicação industrial.
Fig. 2.3. Aspec to de uma gama de reguladores industriais atuais baseados em microprocessador.
Por fim, os métodos de estudo e análise de sistemas de controle contínuo e digital passaram a ficar extraordinariamente facilitados com o surgimento nos últimos anos de diversas ferramentas informatizadas cada vez mais poderosas, versáteis e com capacidades gráficas muito interessantes. Deste modo, o estudo de sistemas complexos, que através dos métodos tradicionais se revelava bastante complexo, passou a ser bastante acessível através do recurso às potencialidades destes programas 2 , de utilização cada vez mais generalizada no ensino das matérias de Controle Automático.
(^2) Podemos destacar entre outros o MATLAB/SIMULINK (Mathworks, Inc.), MAPLE e MATHCAD.
medida) que mede a temperatura real da água quente (variável de saída do sistema). Deste modo, em função das indicações fornecidas pelo elemento de medida, o operador irá manipular a válvula de controle de vazão de vapor de aquecimento, de modo a manter a temperatura da água o mais próxima possível do valor desejado.
Fig.2.6. Esquema de Controle Manual de um Sistema Térmico.
Se em vez do operador, for utilizado um controlador automático, conforme apresentado na Fig.2.7, o sistema de controle passa a designar-se por automático. Neste caso, o operador seleciona a temperatura de referência ( "set-point" ) no controlador. A saída do processo (temperatura real da água quente à saída do permutador de calor), é medida pelo transdutor de temperatura, e comparada no controlador com a temperatura de referência de modo a gerar um sinal de erro. Tomando como base este sinal de erro, o controlador gera um sinal de comando3 para a válvula de regulação de vapor (atuador). Este sinal de comando permite variar gradualmente a abertura da válvula, e, por conseguinte a vazão de vapor a admitir no permutador. Deste modo, é possível controlar automaticamente a temperatura da água à saída do permutador, sem que seja necessária a intervenção do operador.
Fig.2.7.
3 Sinal de controle -> o sinal de saída do regulador, é normalmente do tipo elétrico, pneumático ou hidráulico. É enviado para o atuador através de uma interface de potência (amplificador, conversor, corrente-pressão (I/P), etc.).
Esquema do sistema de regulação automática de um sistema térmico.
a) b) c) d) Fig.2.8. Dispositivo de regulação de temperatura com componentes atuais. a) Transdutor de temperatura. b) Controlador digital PID. c) Conversor corrente-pressão (Conversor I-P), que converte o sinal de controle de 4-20 mA para pressão (3-15 psi). d) Válvula de regulação com comando por ar comprimido (3-15 psi = 0.21-1.05 bar).
Como podemos verificar através das figuras anteriores, os dois sistemas funcionam de uma forma muito semelhante. Deste modo, os olhos do operador e o termômetro, constituem o dispositivo análogo ao sistema de medida de temperatura; o seu cérebro é análogo ao controlador automático, realiza a comparação entre os valores de temperatura desejada e medida, e gera o respectivo sinal de comando. Este sinal é veiculado pelos seus músculos que realizam a abertura ou fecho da válvula, os quais têm um papel análogo ao motor da válvula de regulação de vapor.
Fig.2.9. Diagrama de blocos de um sistema de controle em malha aberto.
Como se pode observar na figura, neste tipo de controle, a saída não é comparada com a entrada de referência. Deste modo, para cada valor da saída irá corresponder uma condição de funcionamento fixa. No entanto, na presença de perturbações, o sistema não irá atingir os objetivos desejados. Na prática, o controle em malha ou malha aberto, somente deve ser utilizado em sistemas para os quais a relação entre a entrada e a saída seja bem conhecida, e que não tenham perturbações internas ou externas significativas.
Fig.2.10. Diagrama de blocos do esquema de controle digital em malha fechada.
Fig.2.11. Evolução temporal dos sinais num malha de controle digital.
No diagrama do sistema de controle digital da Fig. (2.10), podemos ver que este contém elementos analógicos e digitais. Deste modo, o relógio (clock) ligado aos conversores A/ D e D/A (D/A e A/D converters) fornece um pulso para cada T segundos. Os conversores D/A e A/D enviam apenas os respectivos sinais quando chega o sinal pulsado de relógio. O objetivo desta ação, é o de fazer com que o processo (“Plant”) receba apenas amostras do sinal de entrada u(k) e envie apenas sinais de saída y(k ) sincronizados com o sinal de relógio. Deste modo, é necessário manter constante o sinal de entrada u(k) durante o intervalo de amostragem. Assim, vamos supor que o sinal u(k) representa a amostra do sinal de entrada. Existem técnicas que permitem obter a amostra u(k) e manter ou reter ( hold ) o sinal de modo a produzir um sinal contínuo û( t) .O gráfico da Fig.2.12 mostra que o sinal û( t) é mantido constante para u(k) no intervalo [kT ; (k+1)T]. Esta operação de retenção de û( t) constante durante o intervalo de amostragem é designada por "retenção de ordem zero" ou " zero-order hold".
Fig.2.12. Resposta de um sinal com retentor de ordem zero ("zoh -> zero order hold").
O sinal û( t) tratado pelo retentor de ordem zero é introduzido em H2(s) de modo a produzir a saída do processo y(t). Este sinal é depois amostrado pelo conversor A/D de modo a poder-se obter o sinal y(k) que irá ser igual à amostra do sinal contínuo y(t). Esta operação é equivalente a introduzir o sinal u(t) em H(s) de modo a obter o sinal contínuo de saída do processo y(t).
Fig.2.13. Evolução dos sinais num sistema digital (em cima) e contínuo analógico (em baixo).
Exemplo de sistema de controle digital (posição angular do veio de um motor).