
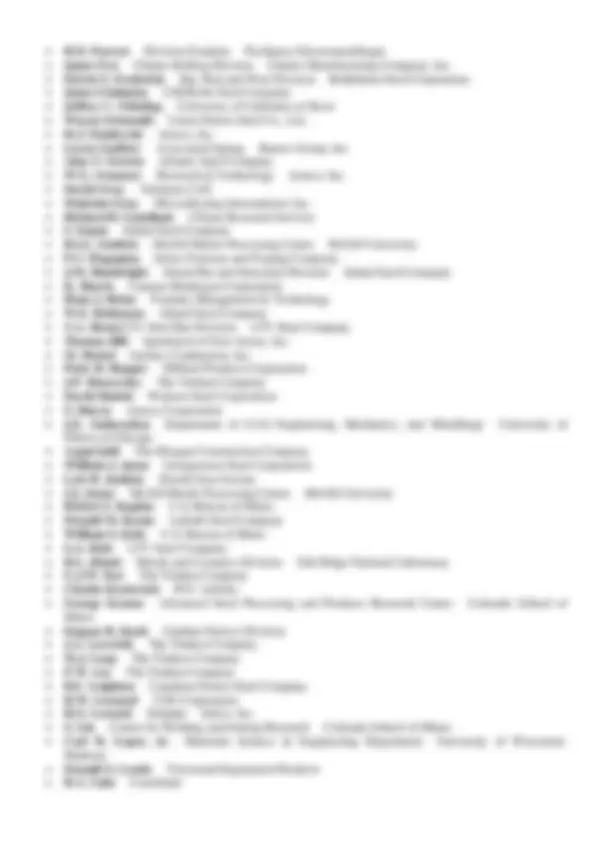
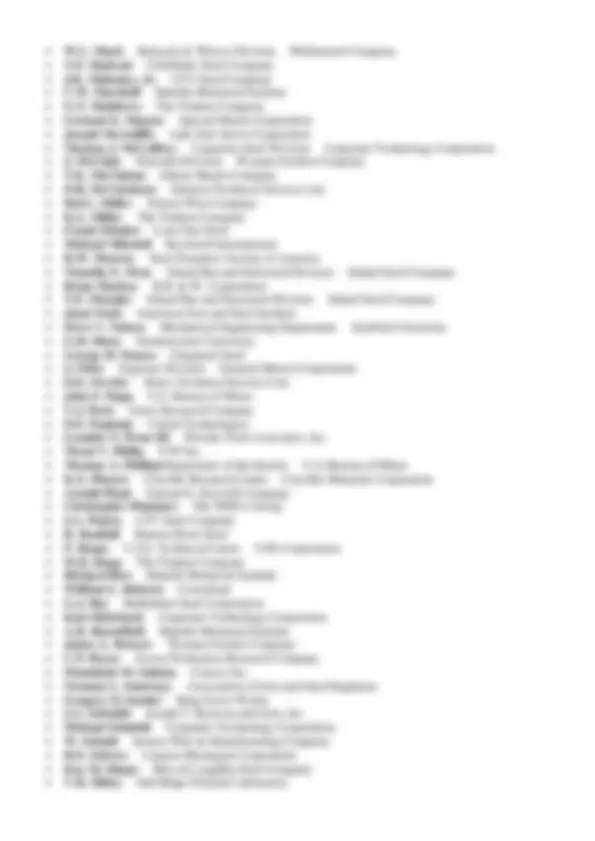

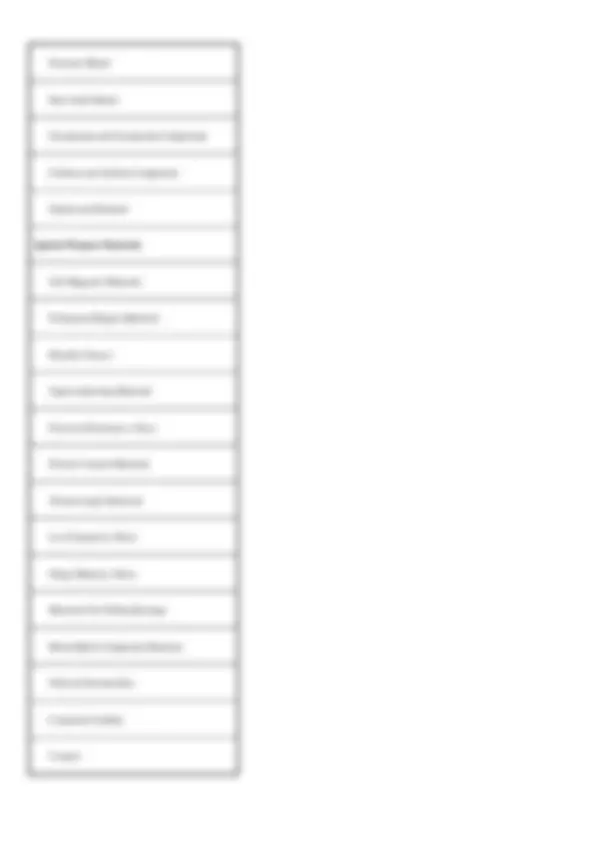
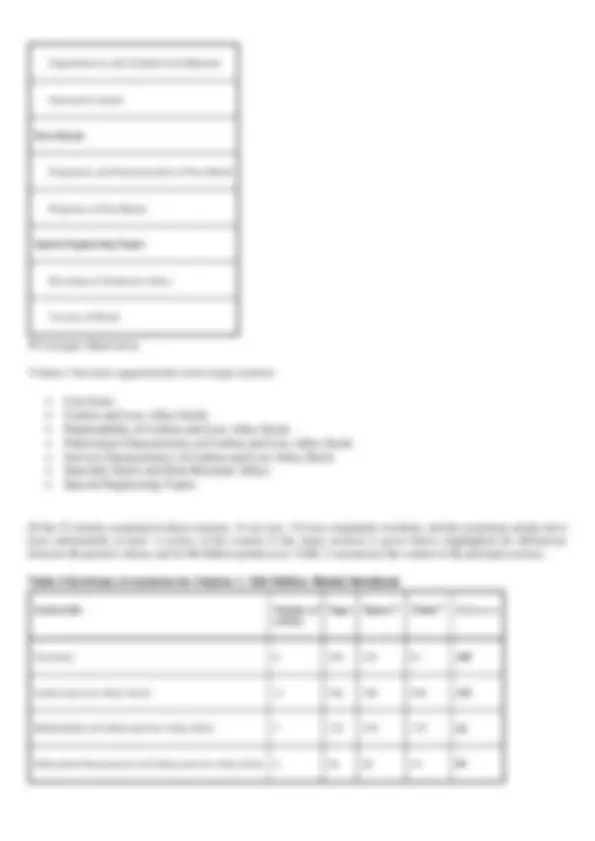
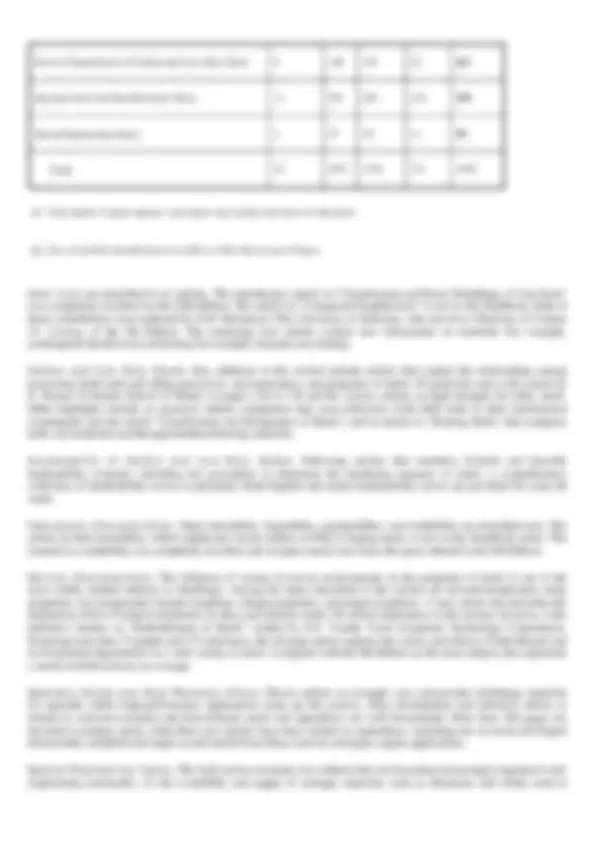
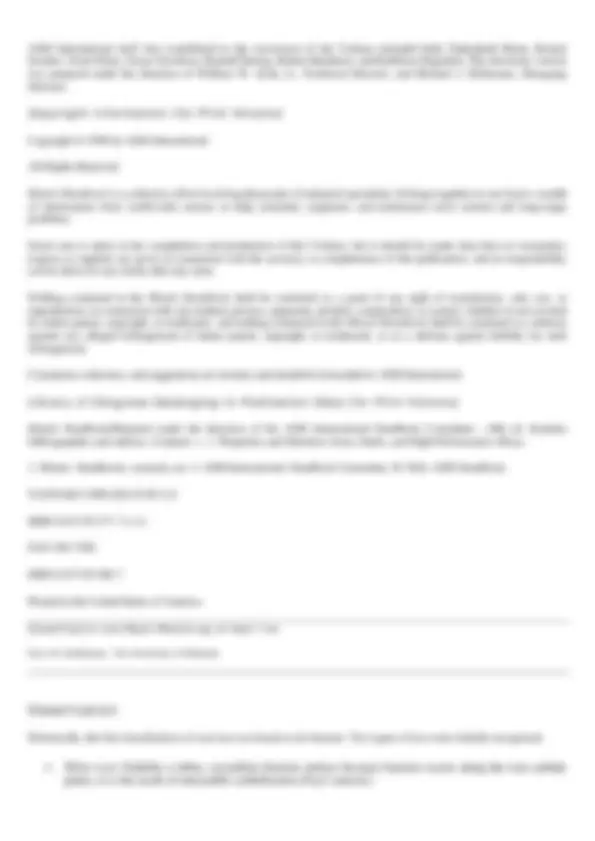
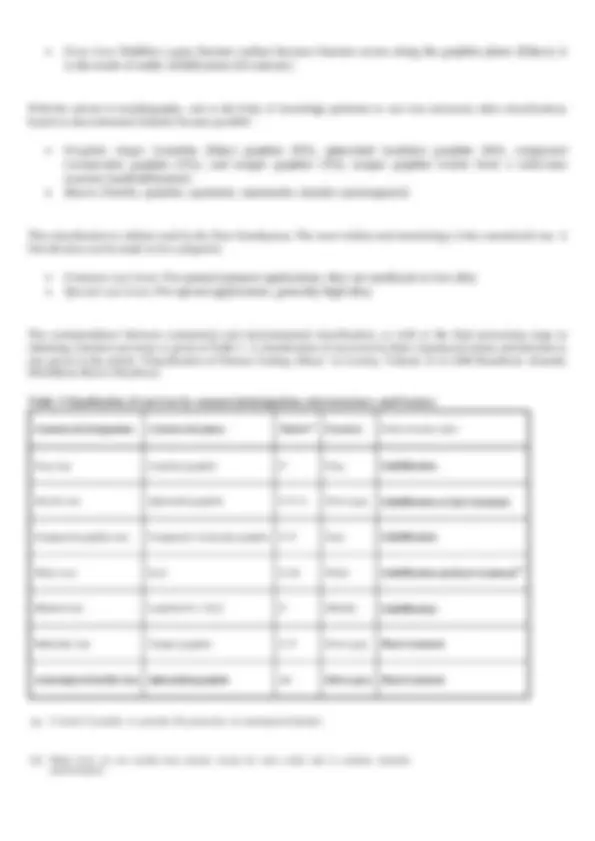
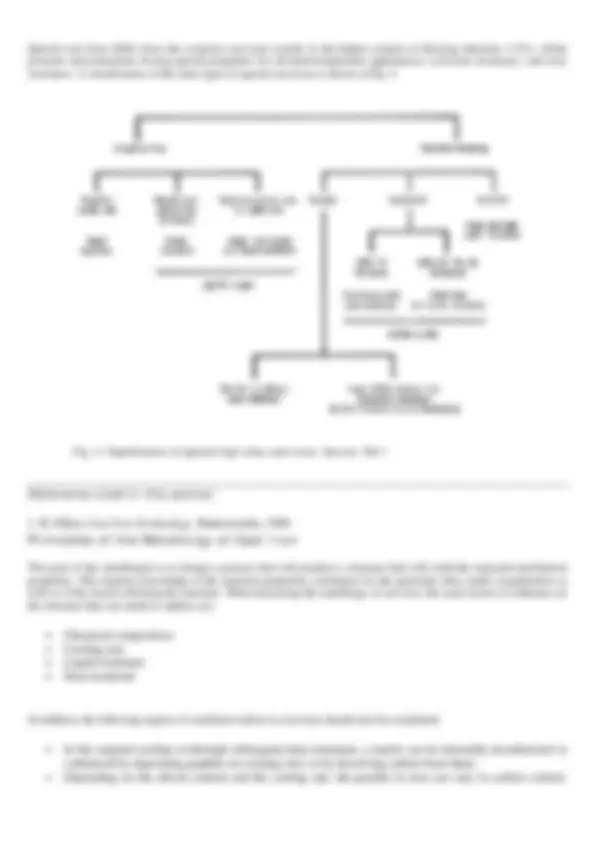
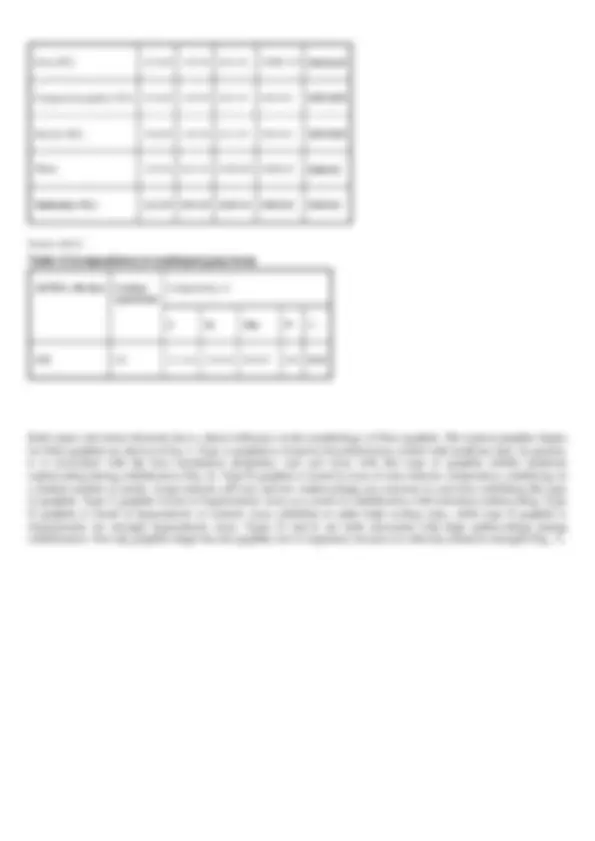
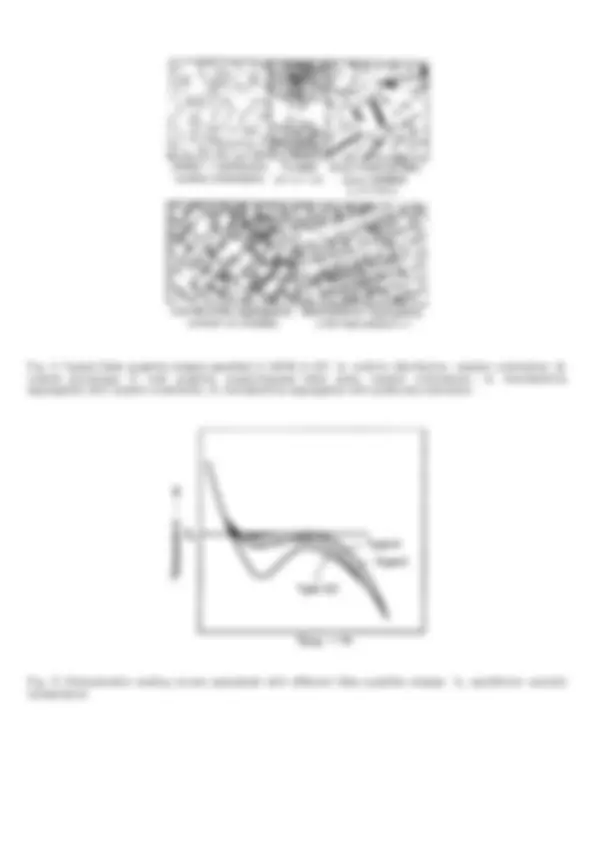
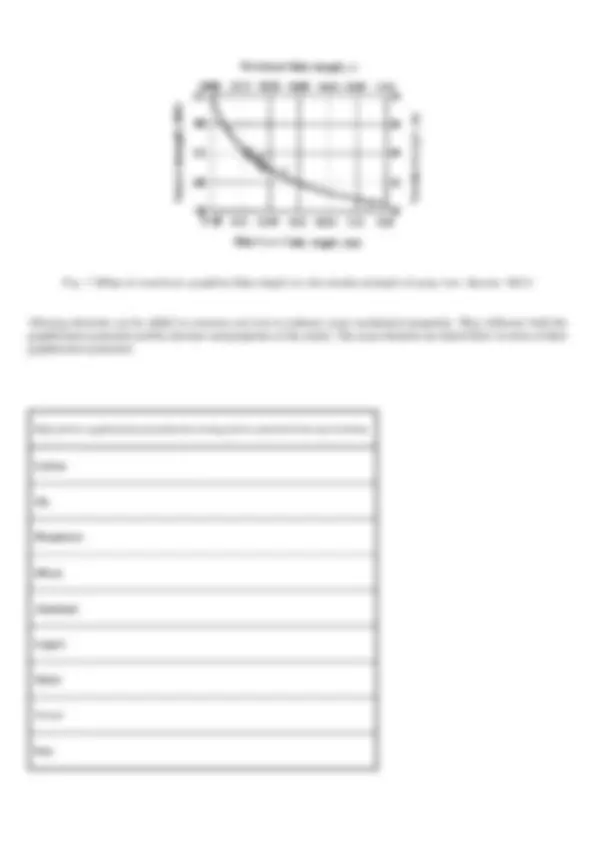
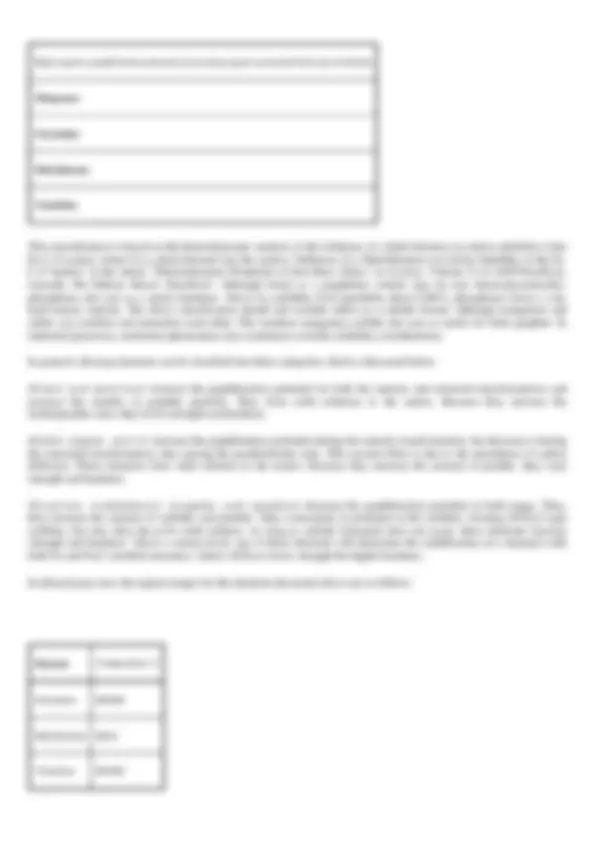
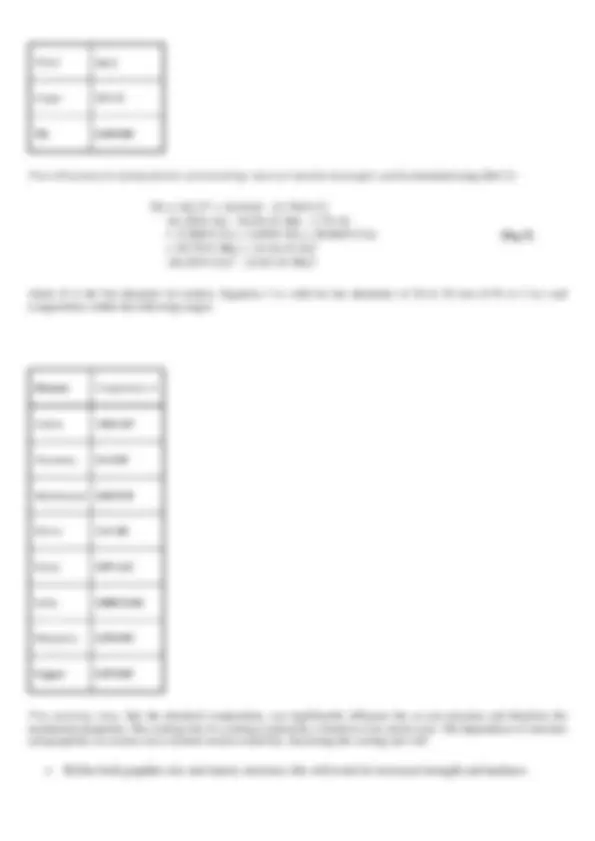
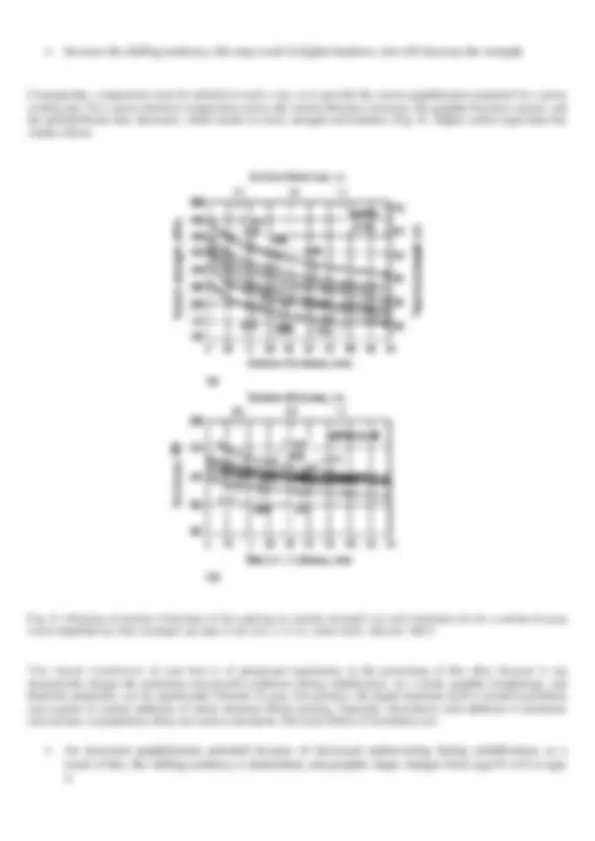
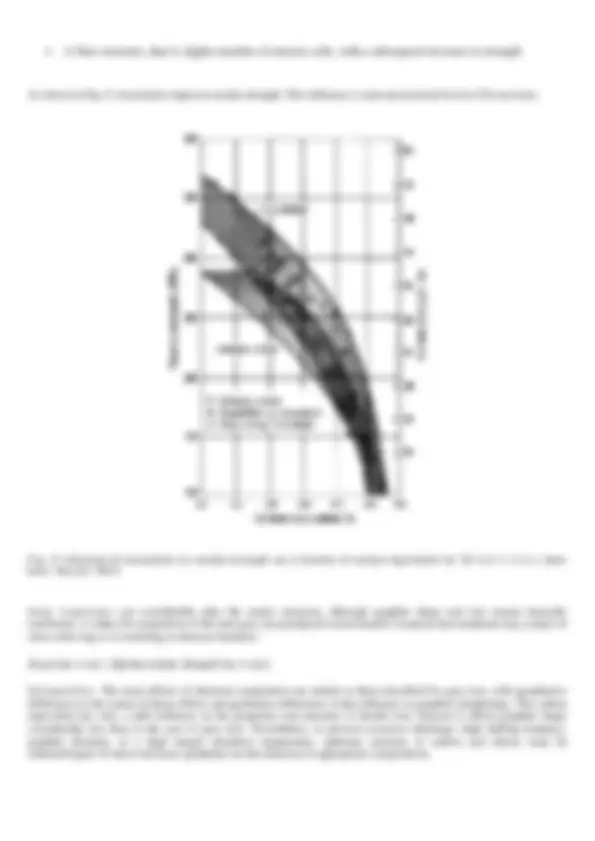
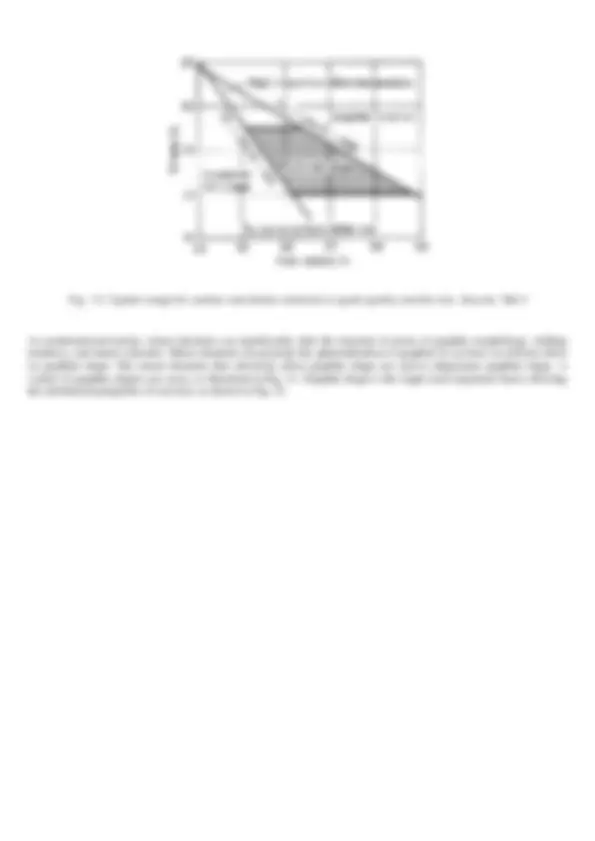


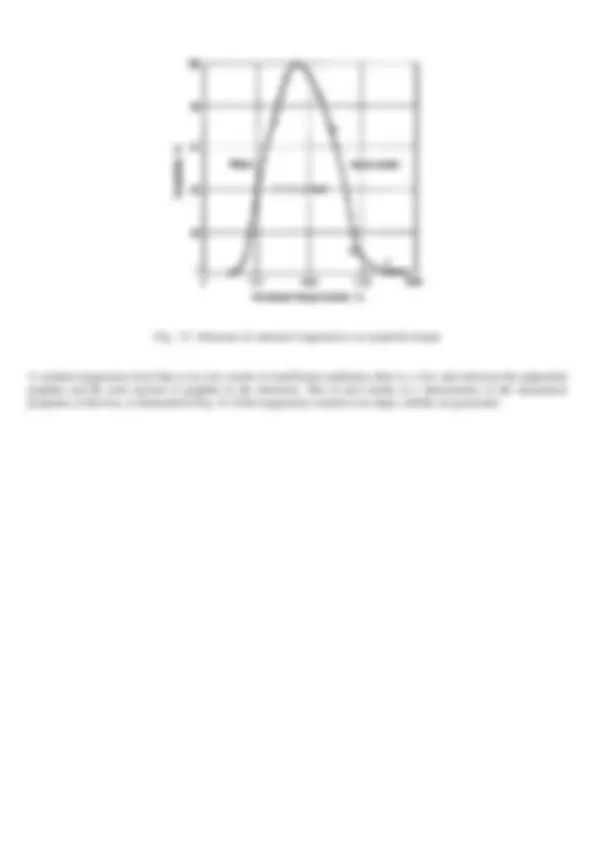
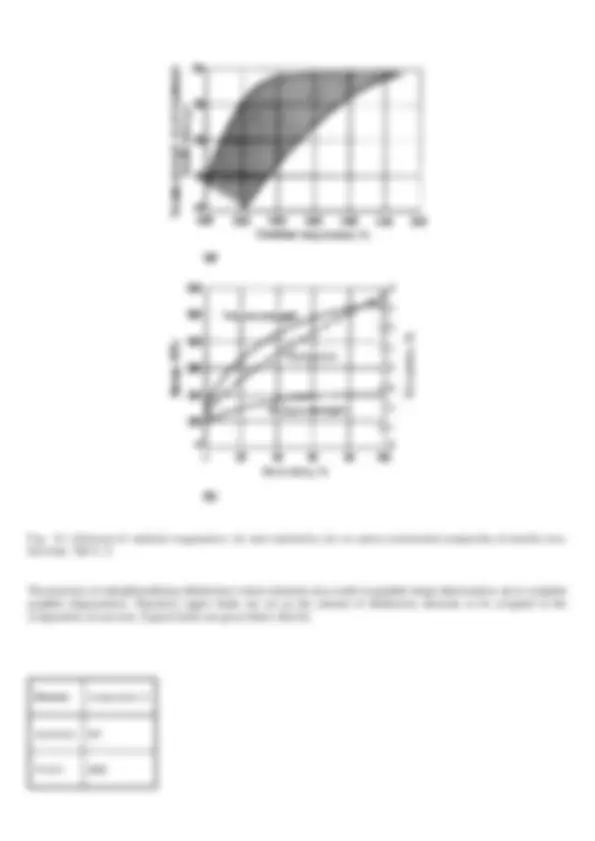
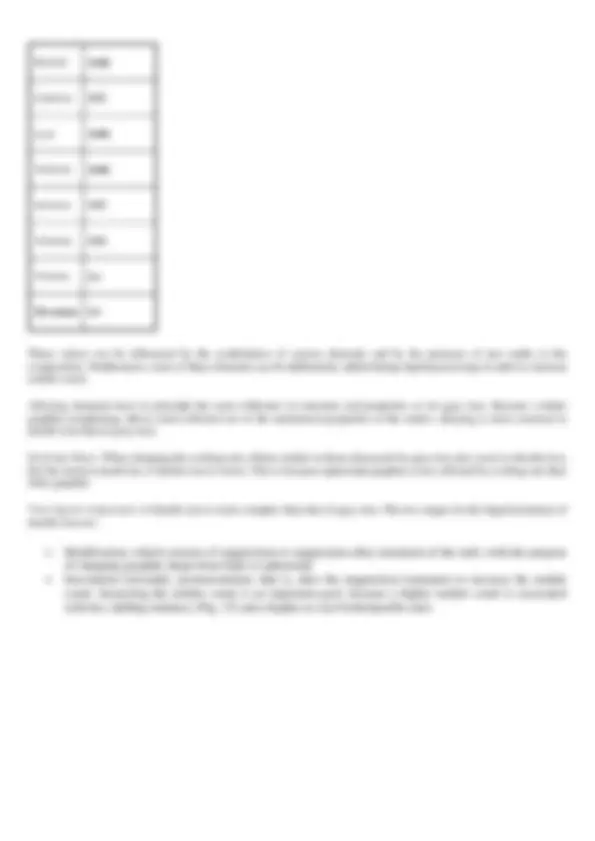
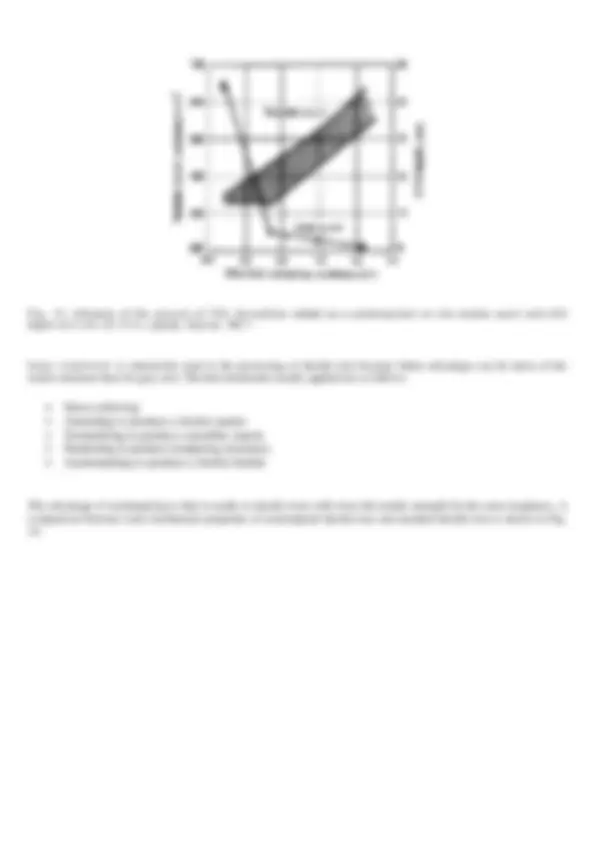
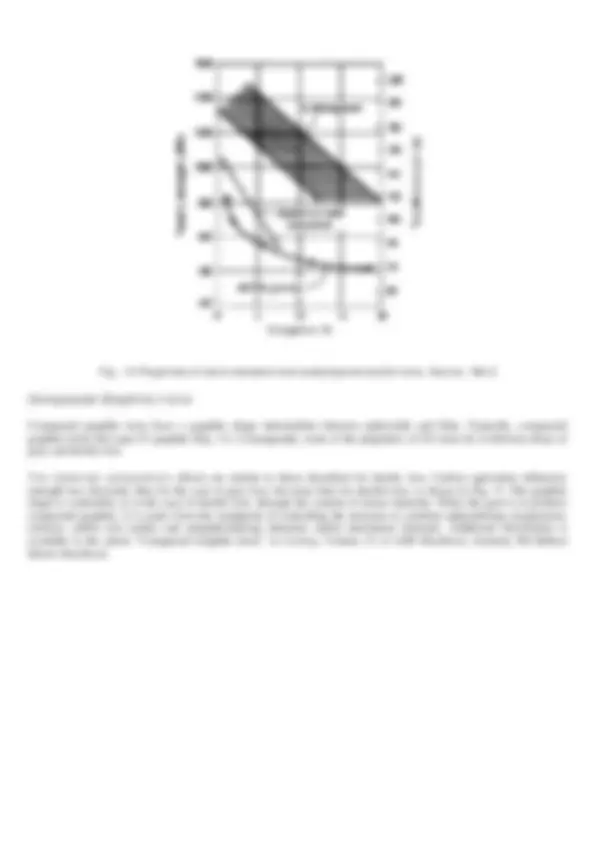

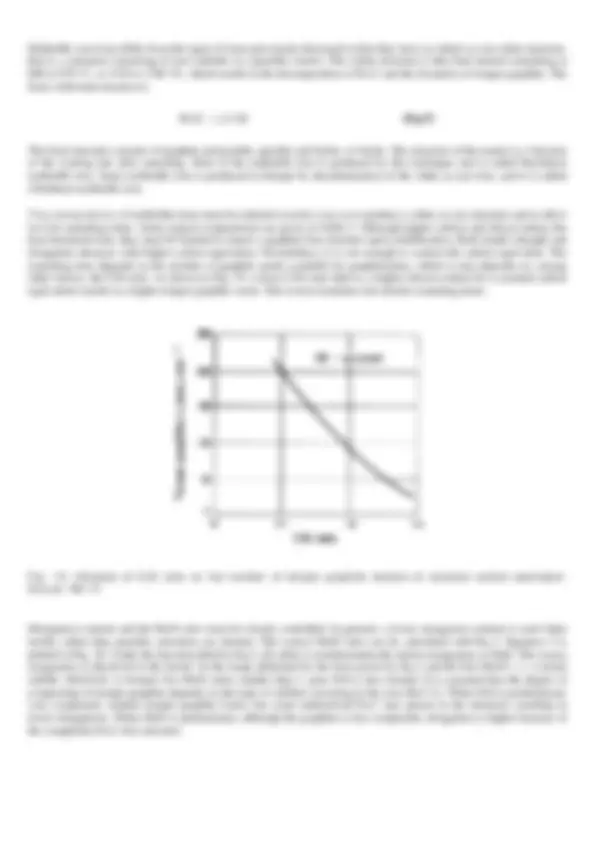
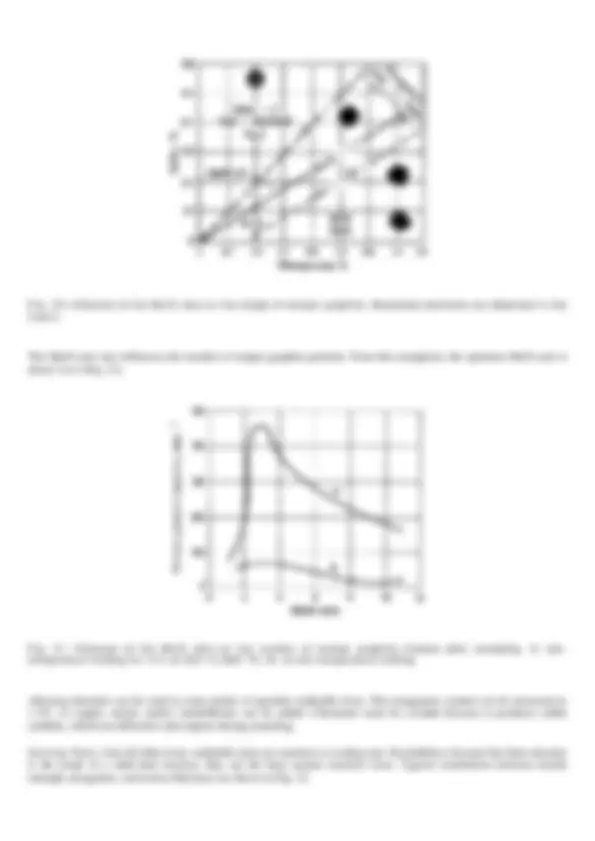
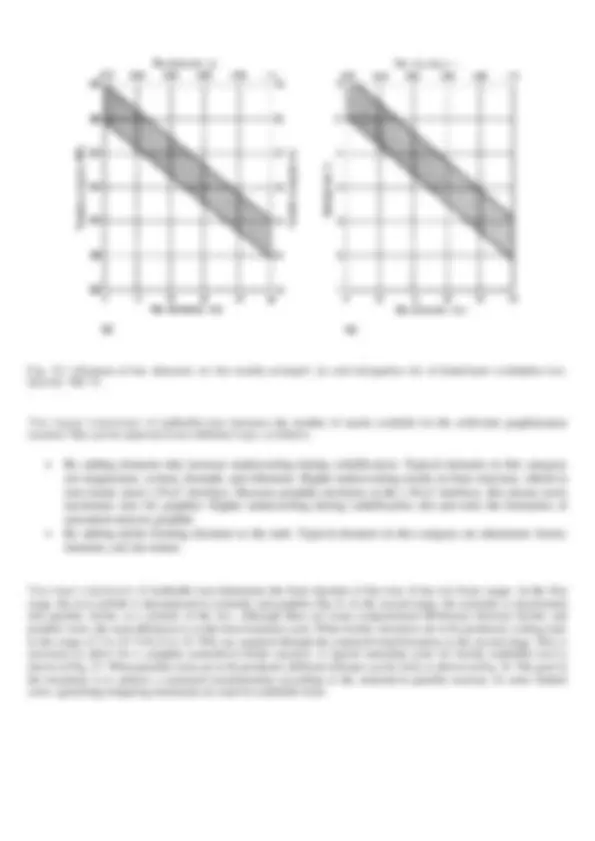
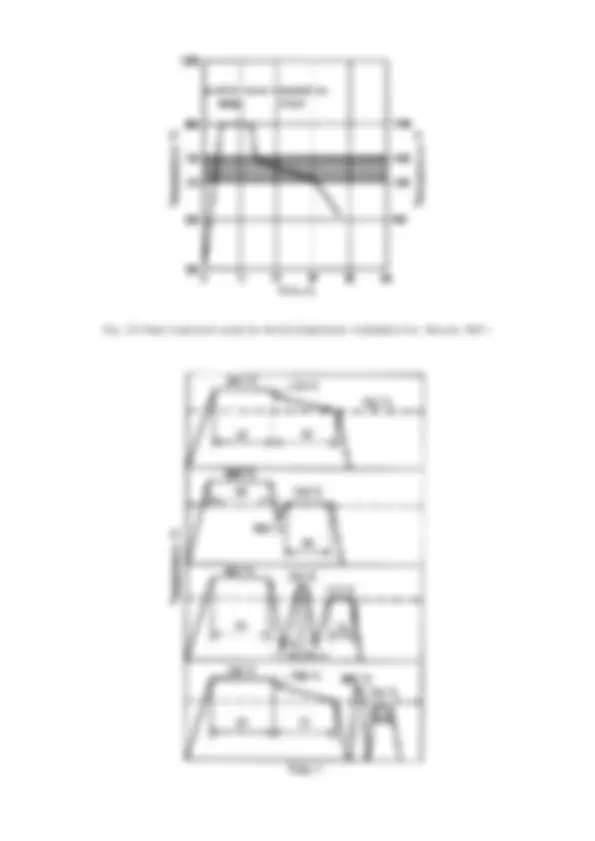
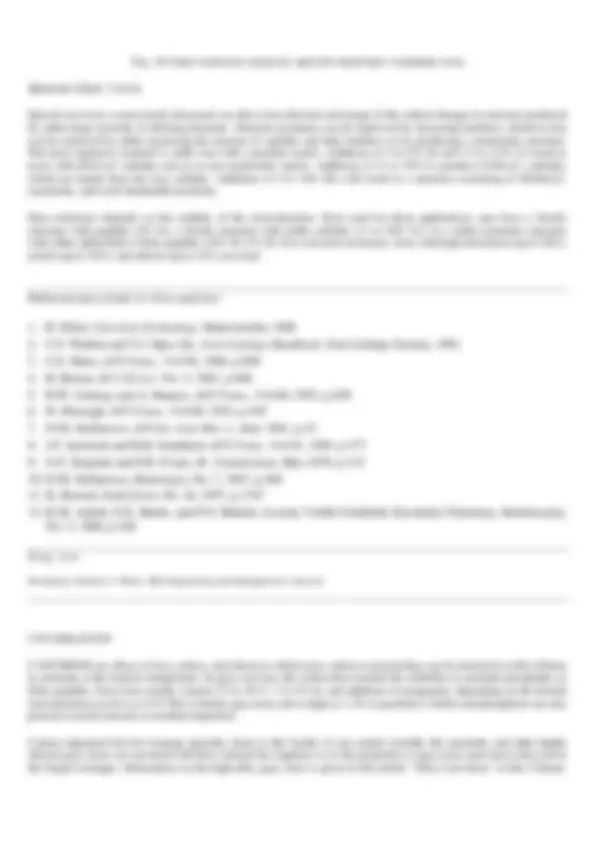
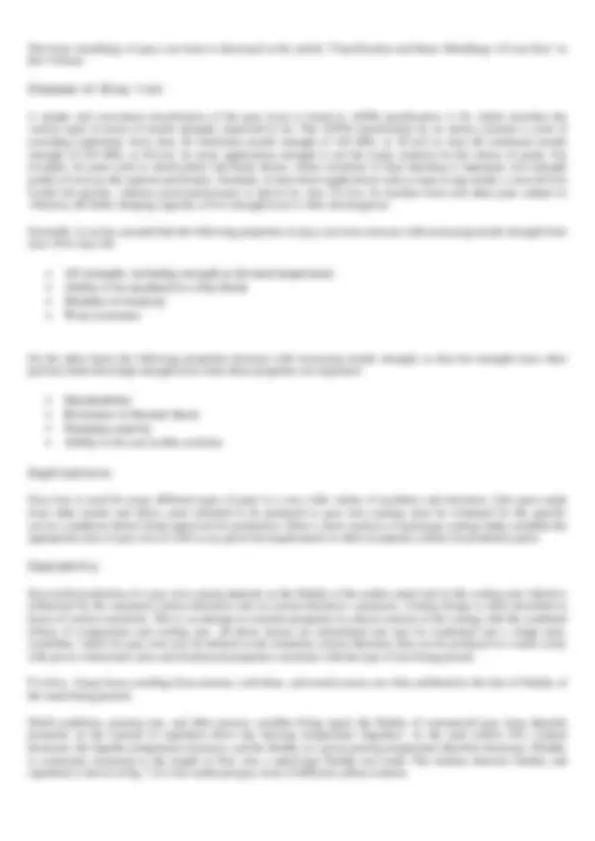
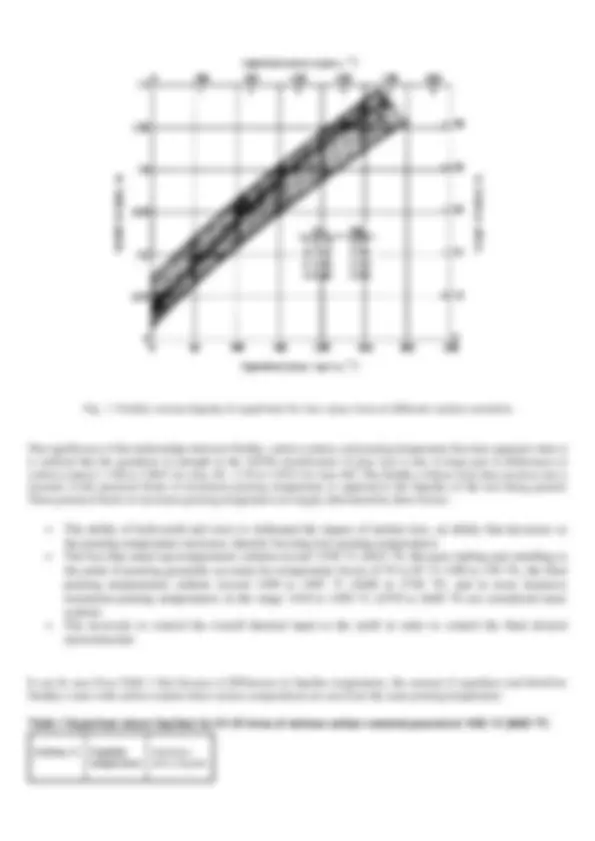
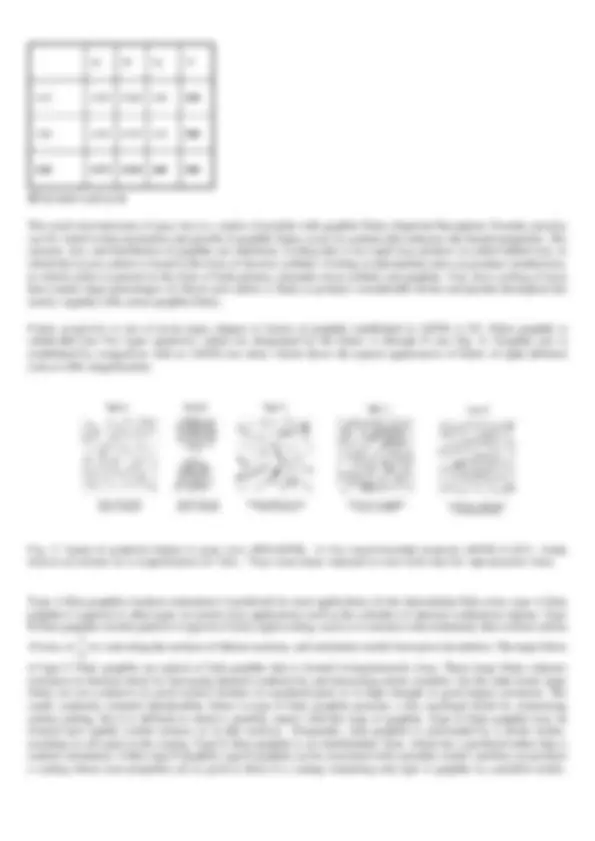
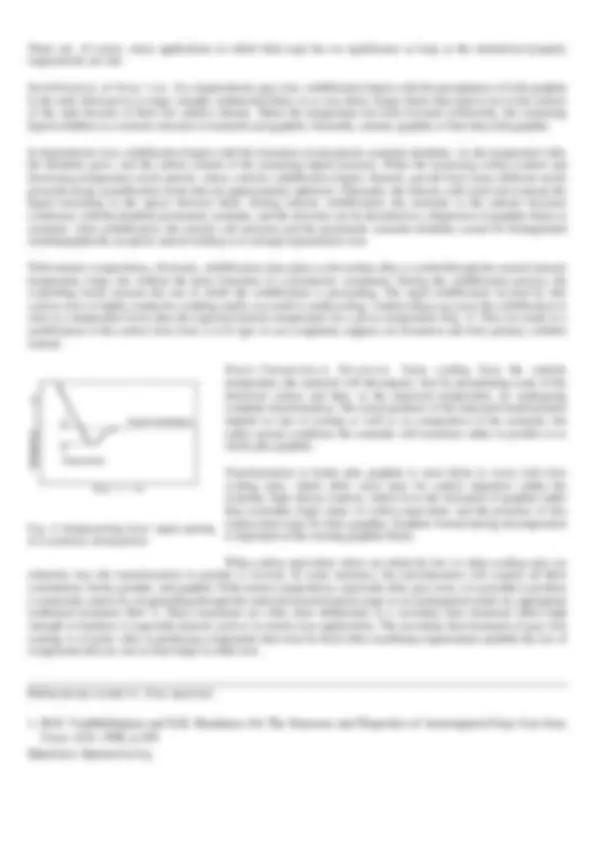
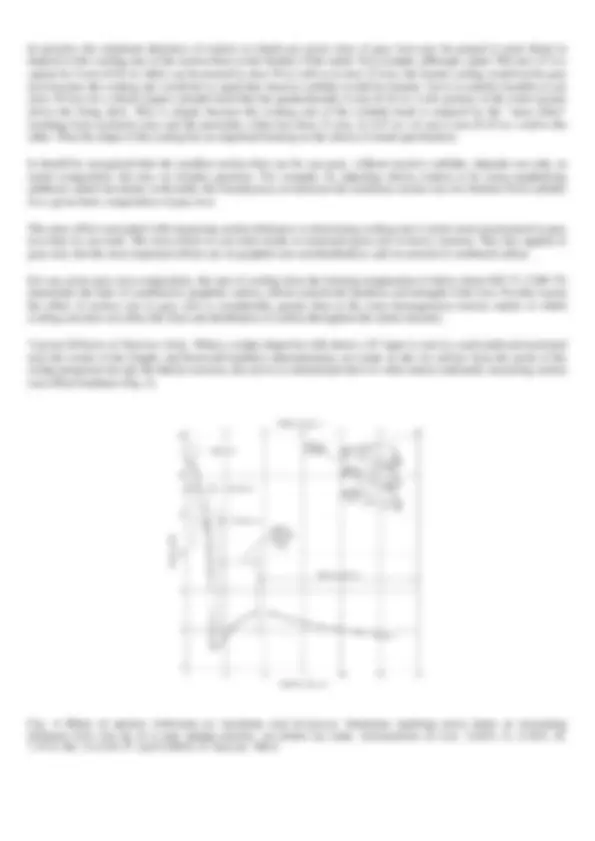
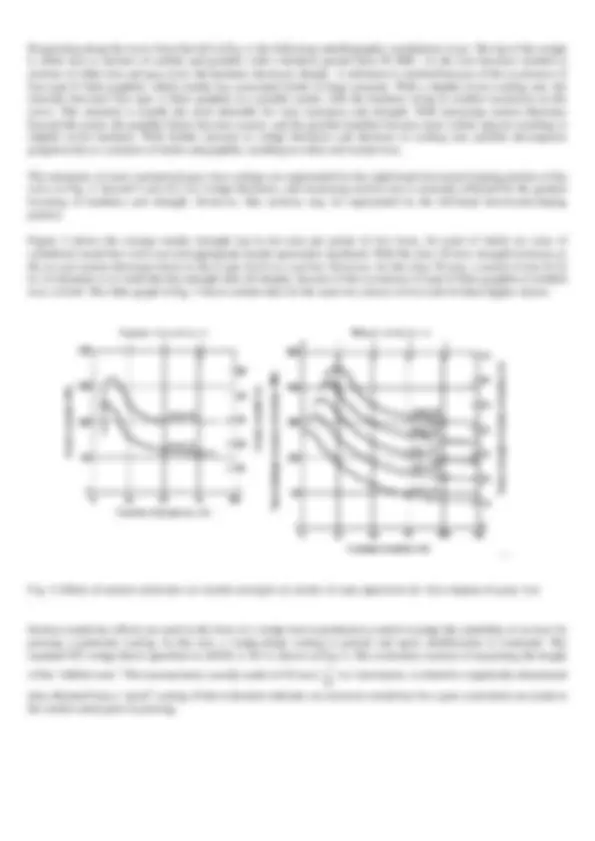
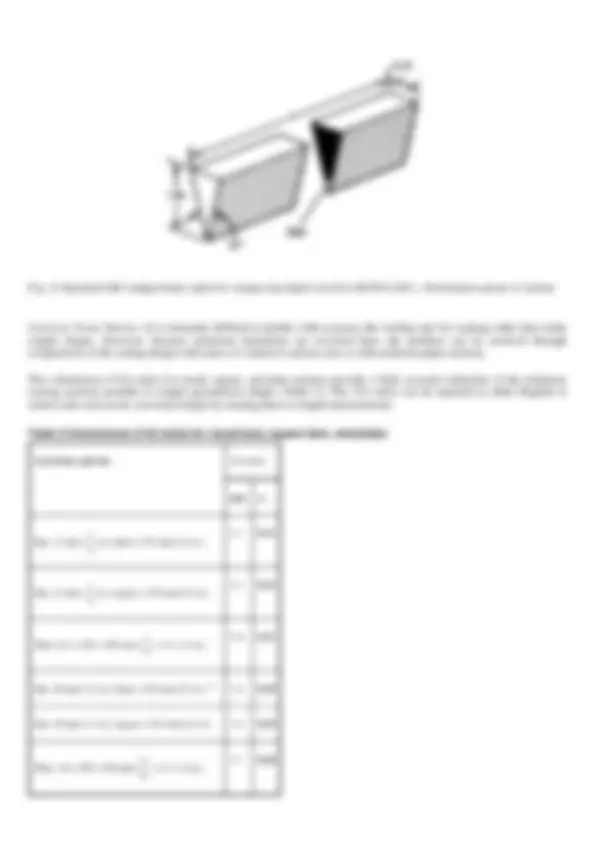
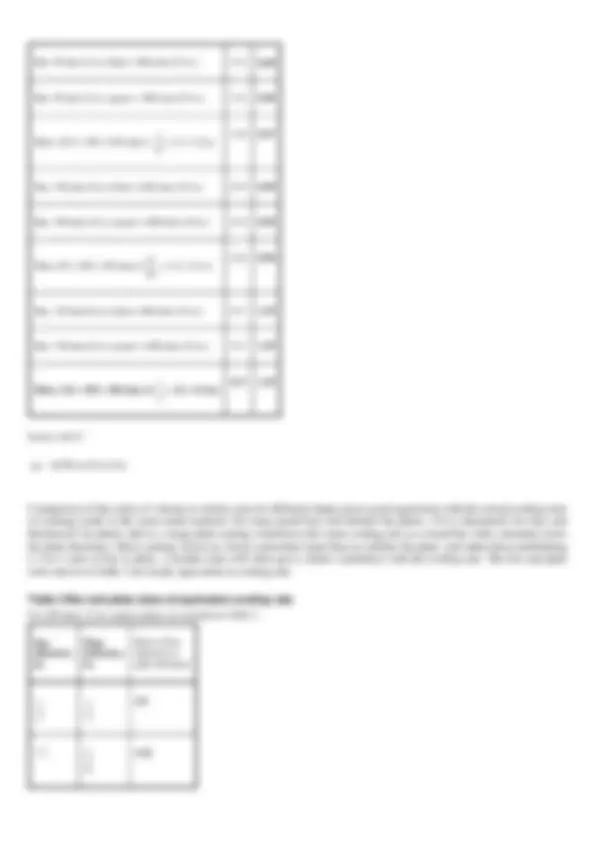
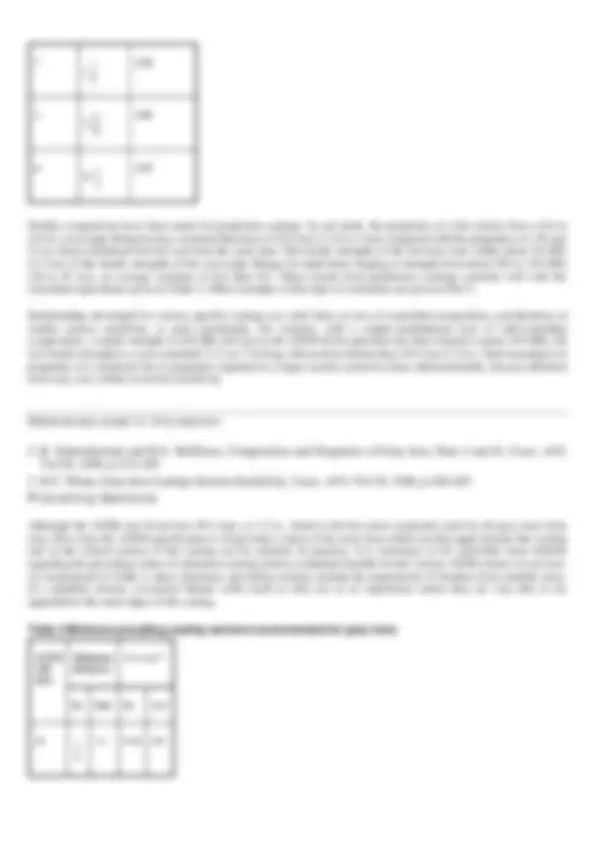
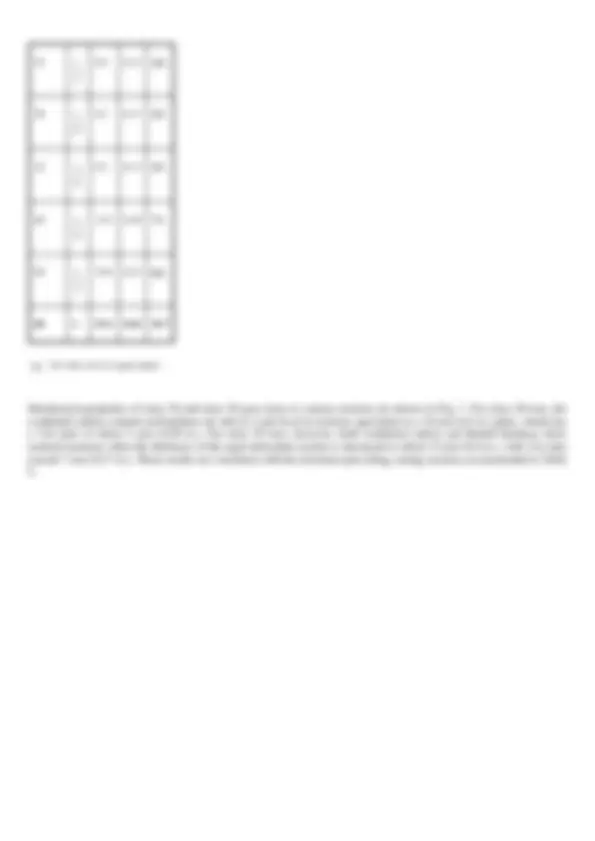
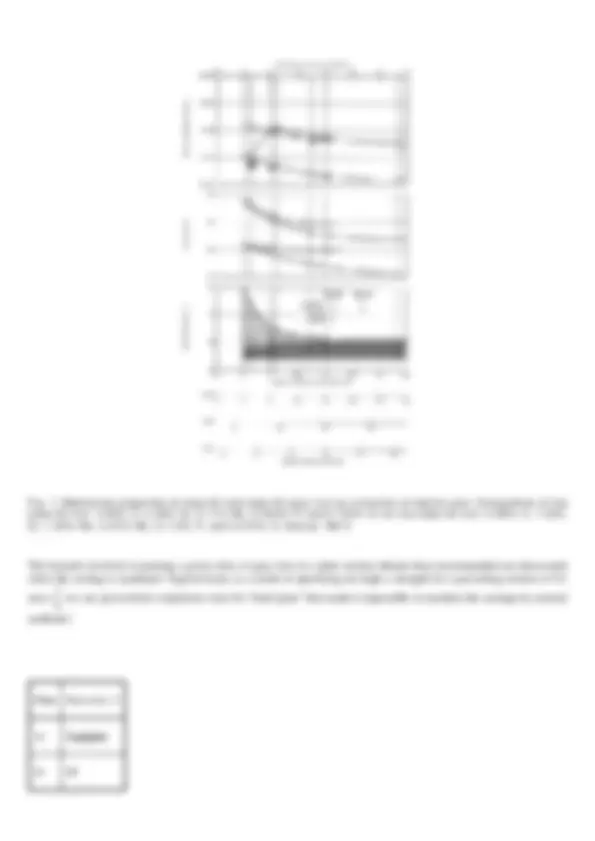
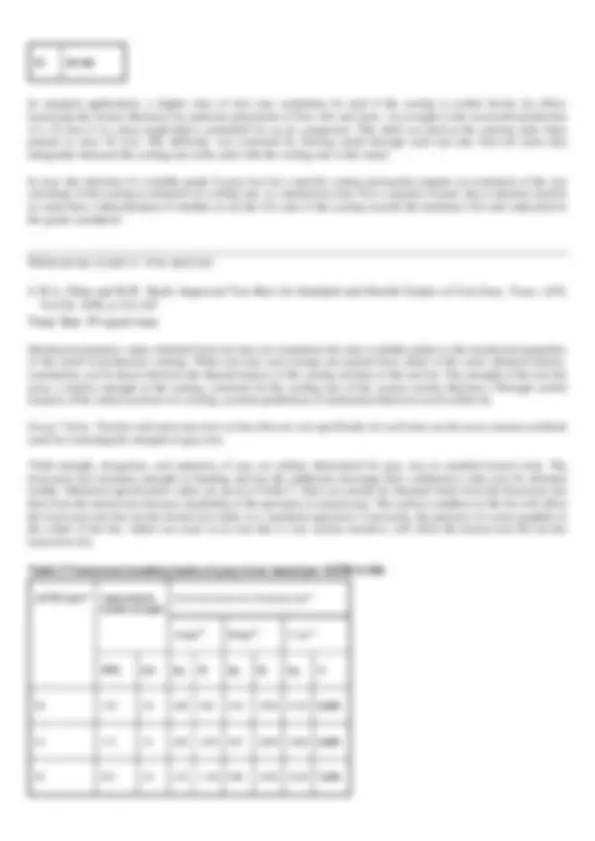
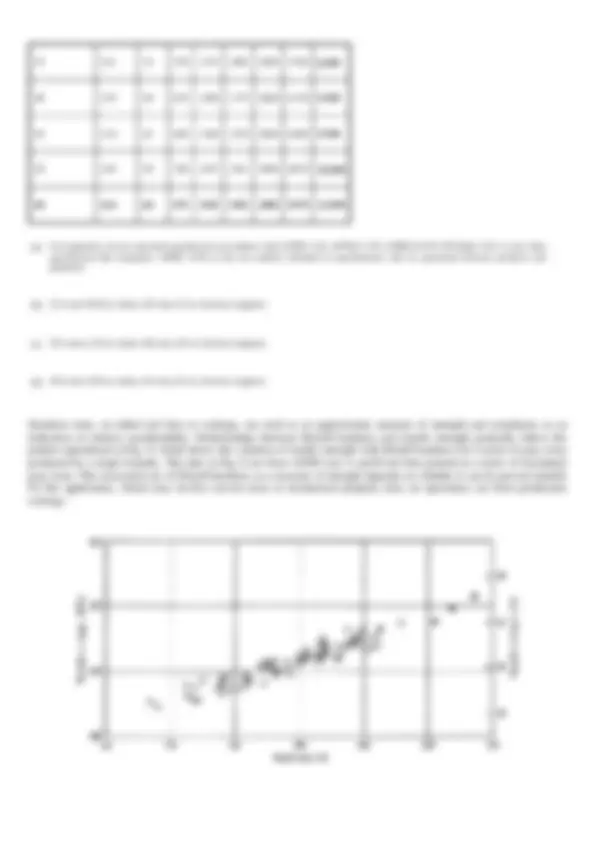
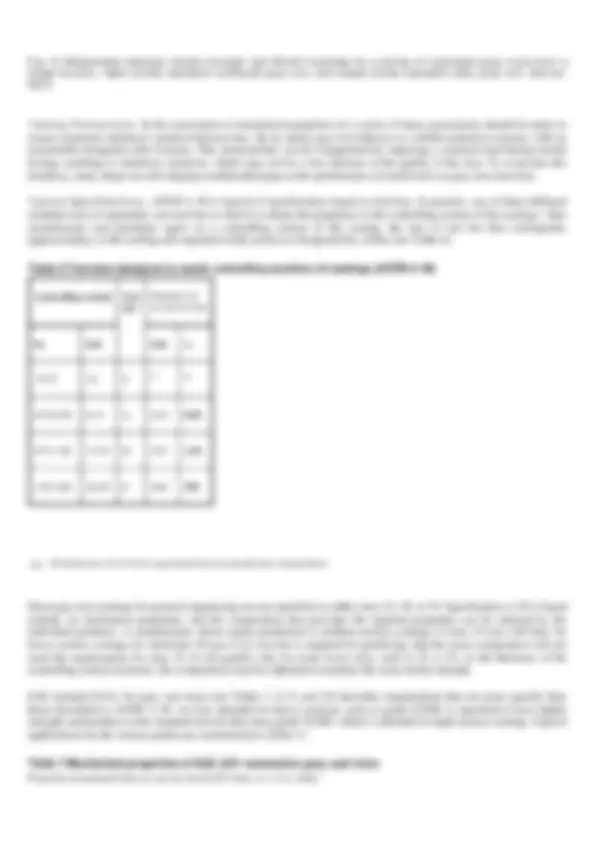
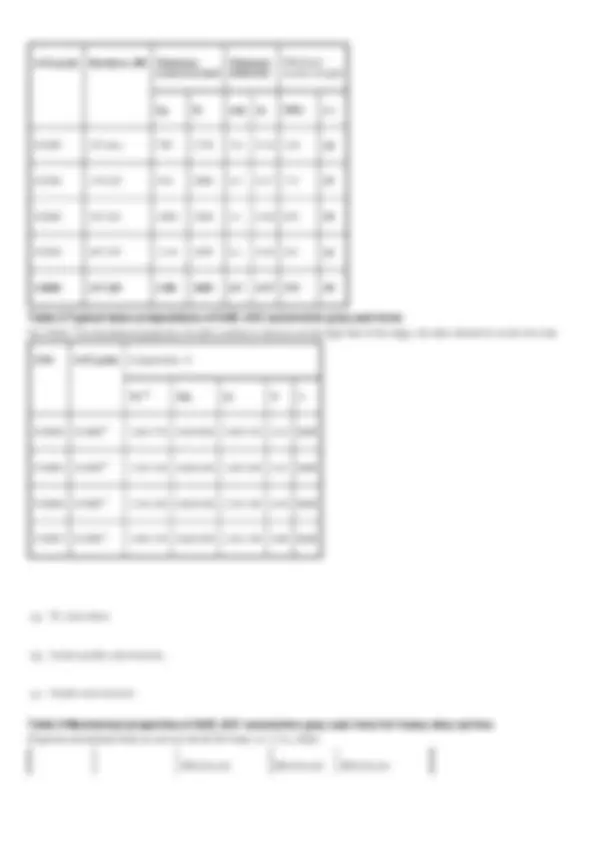
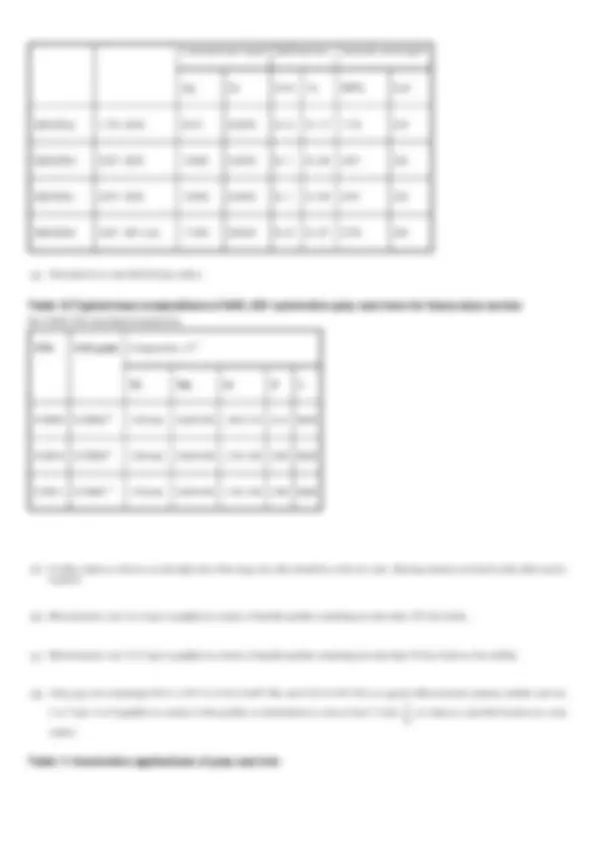
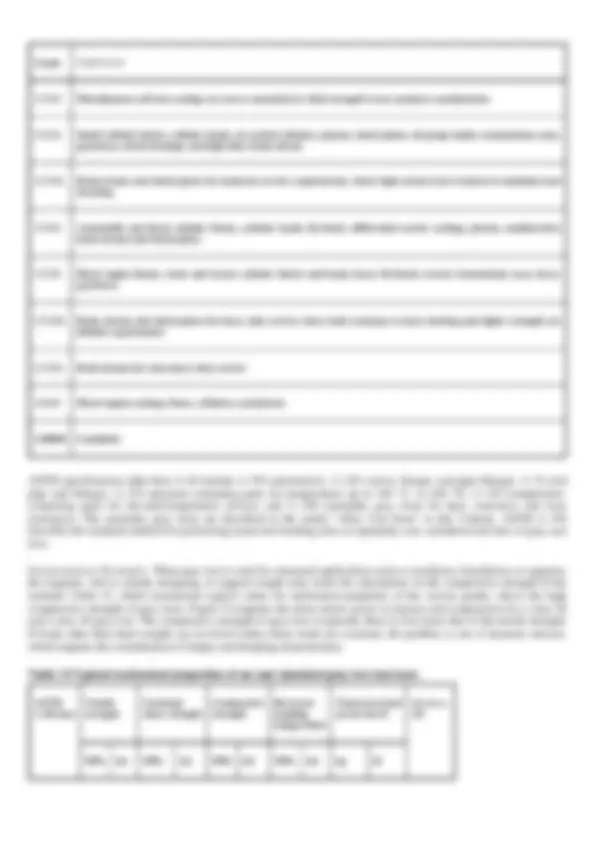
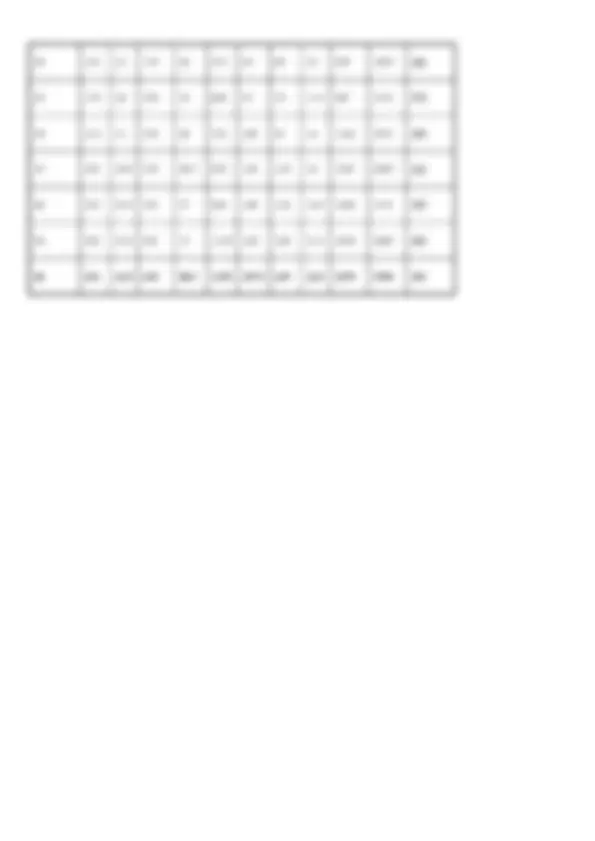
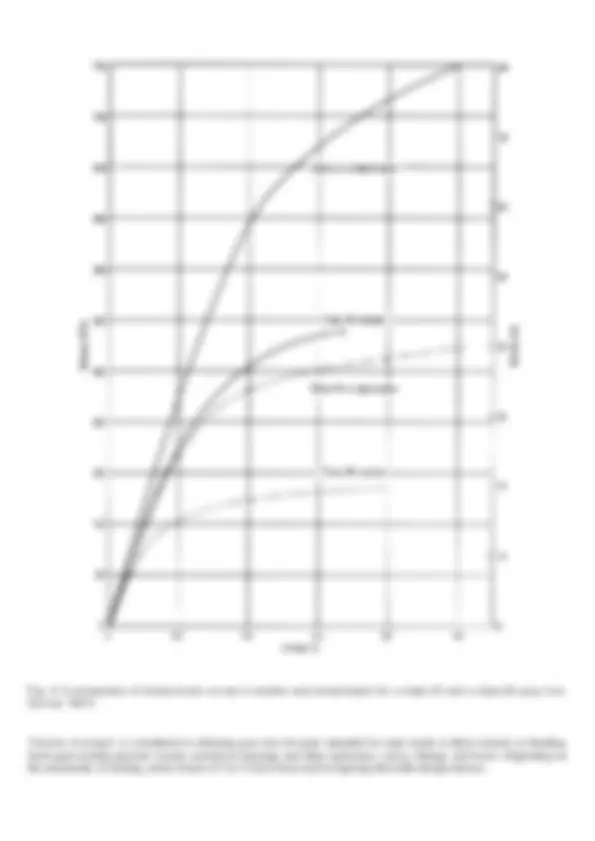
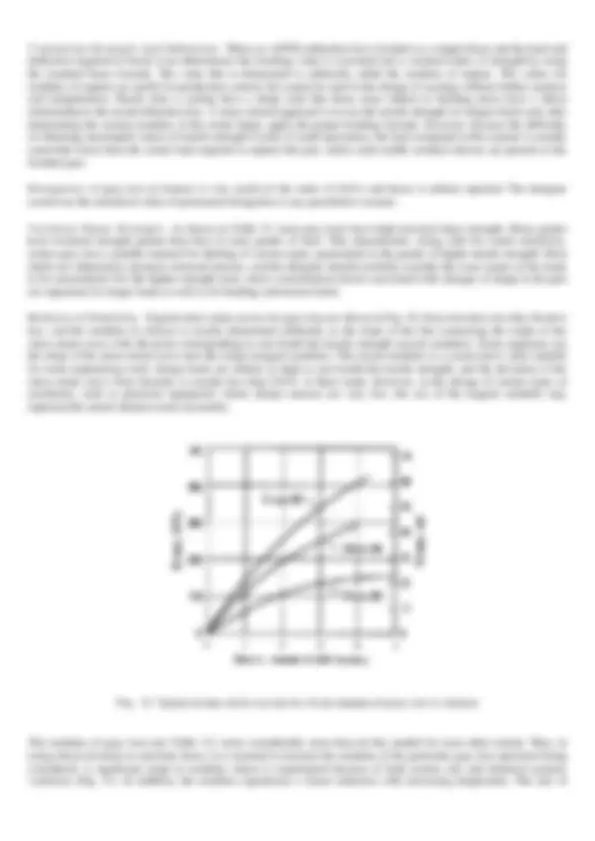
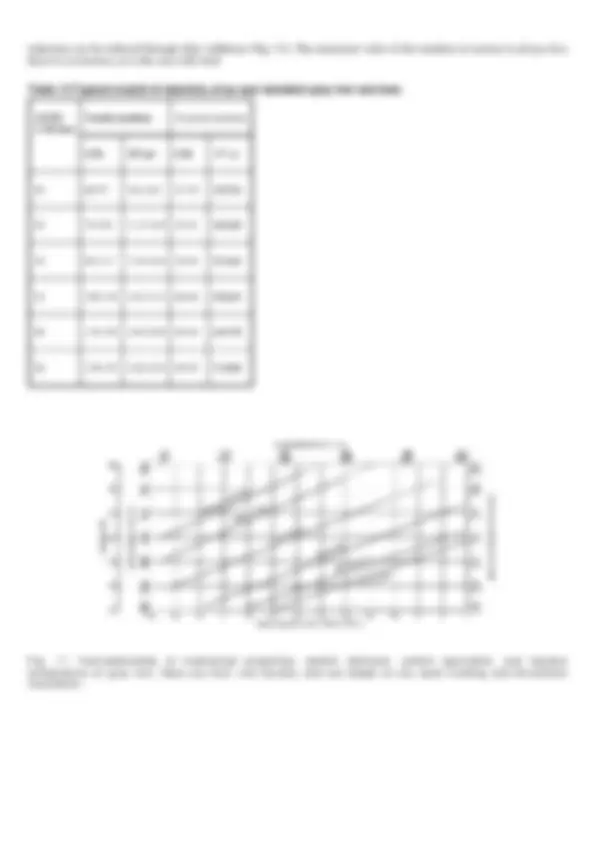
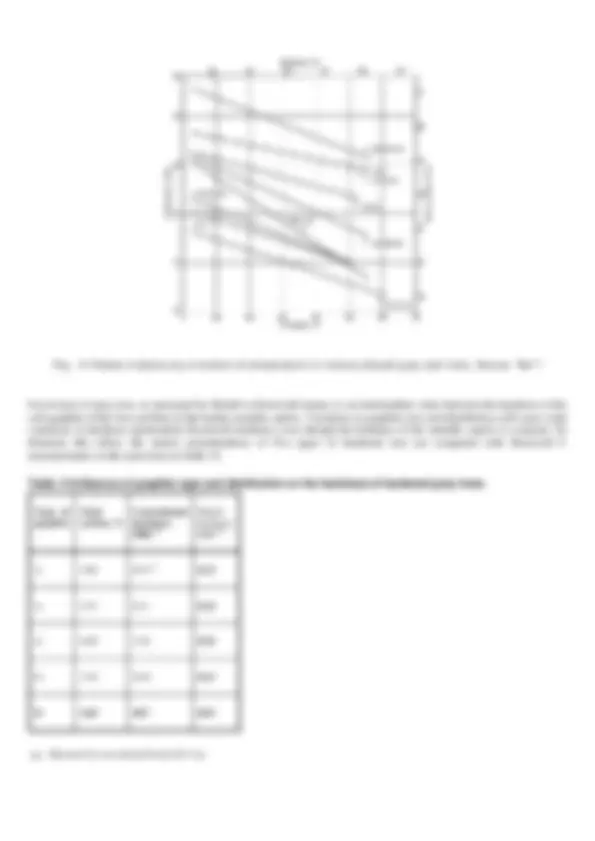
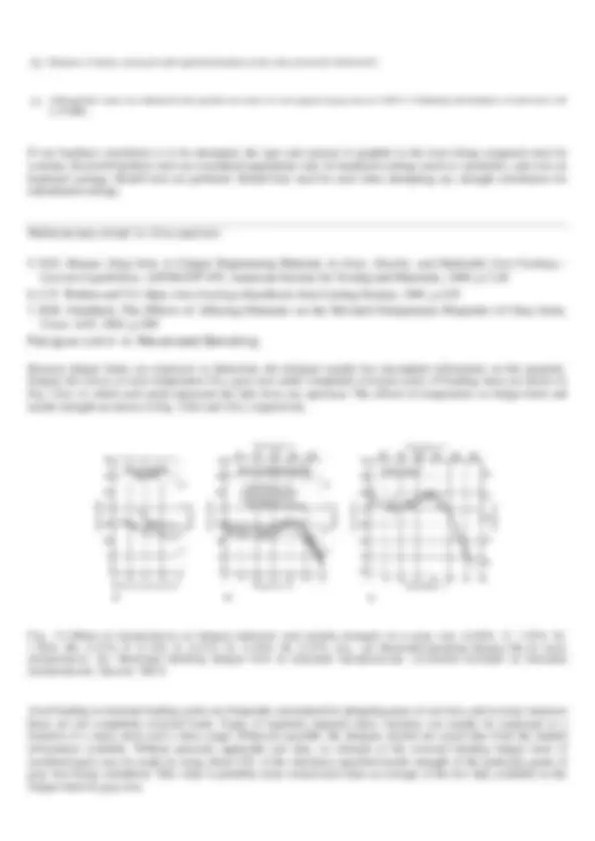
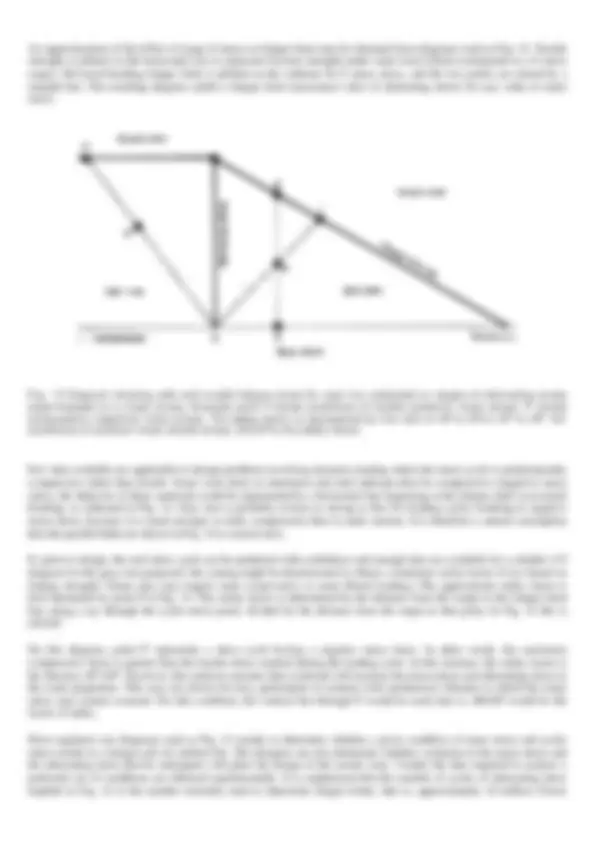
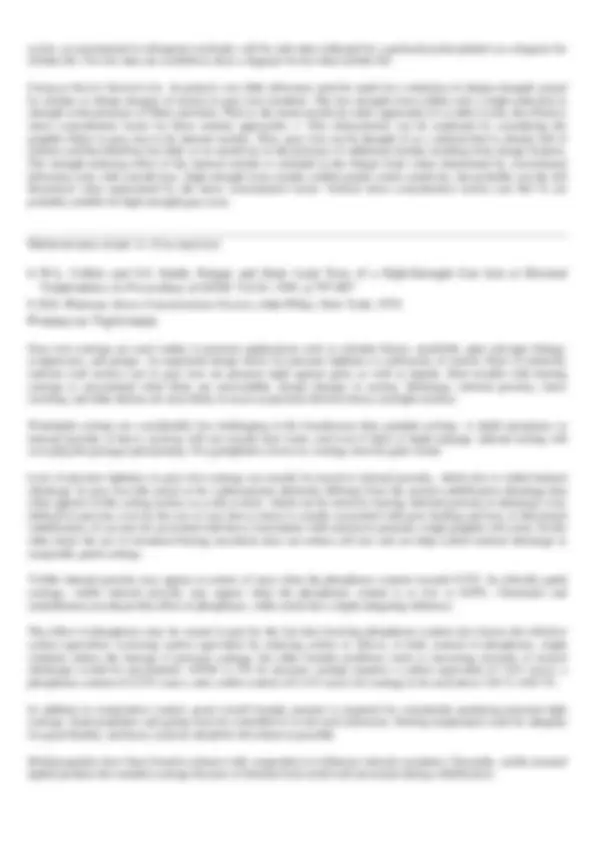
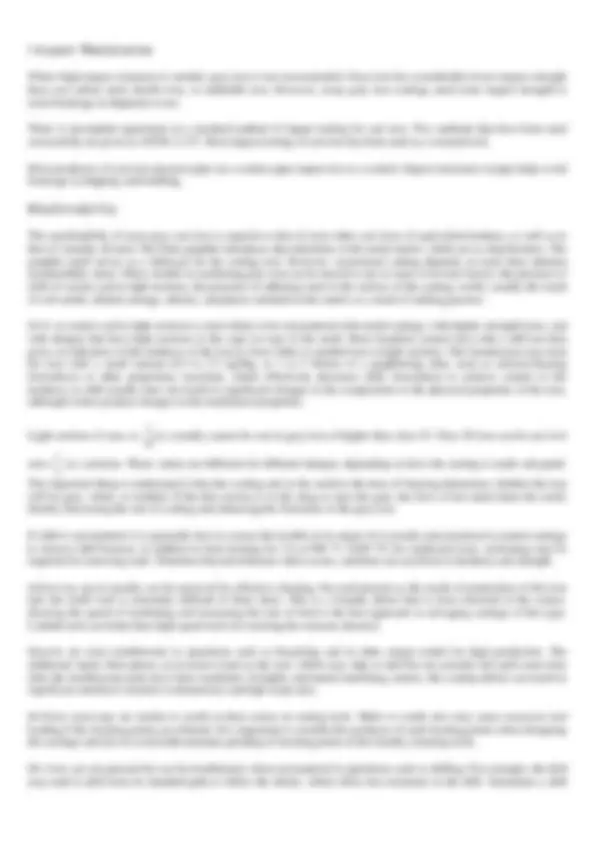
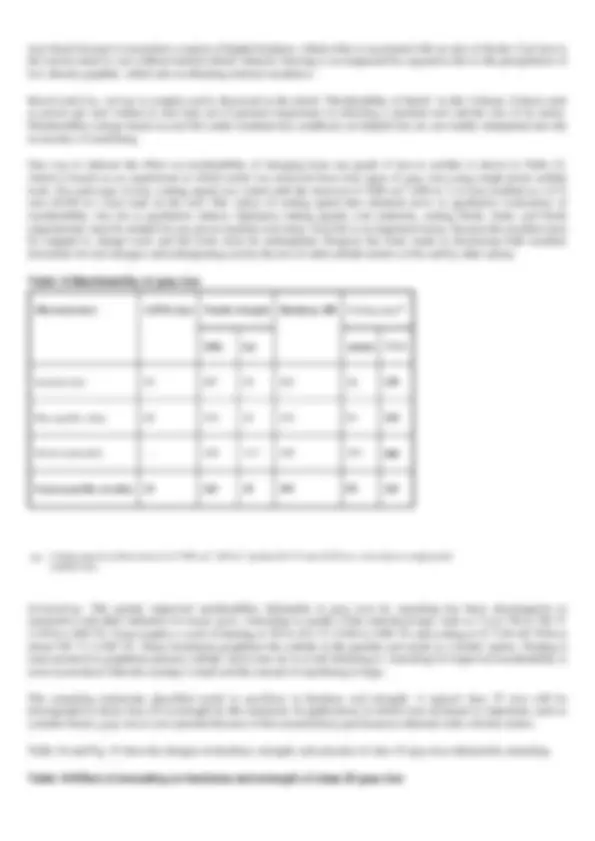
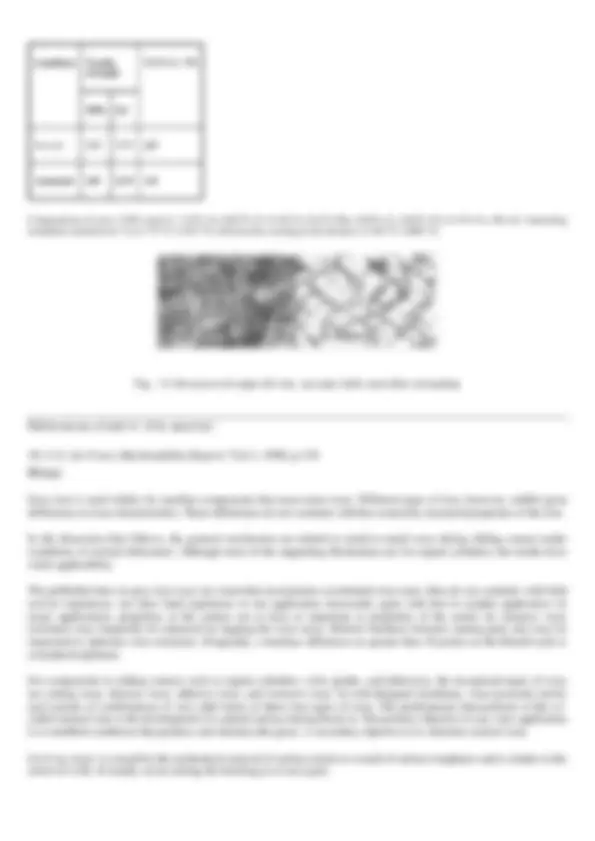
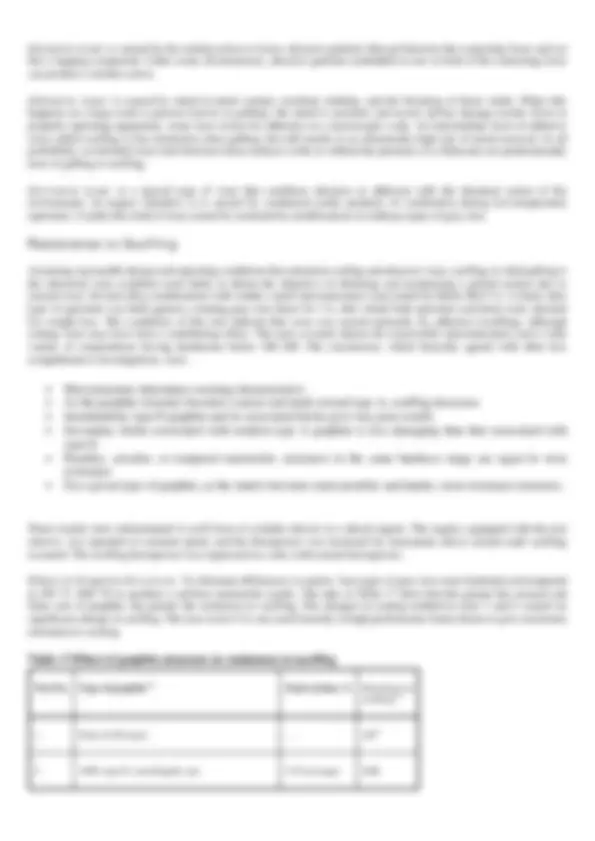
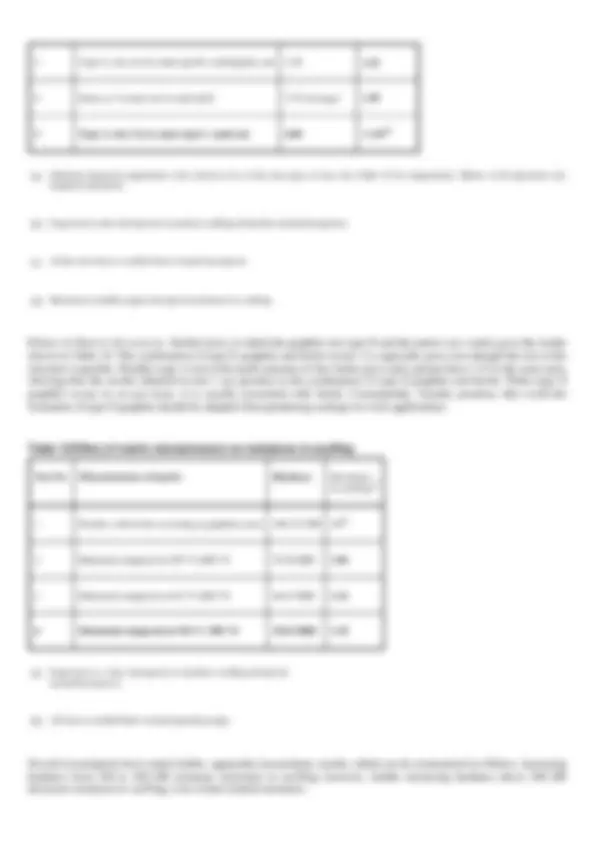
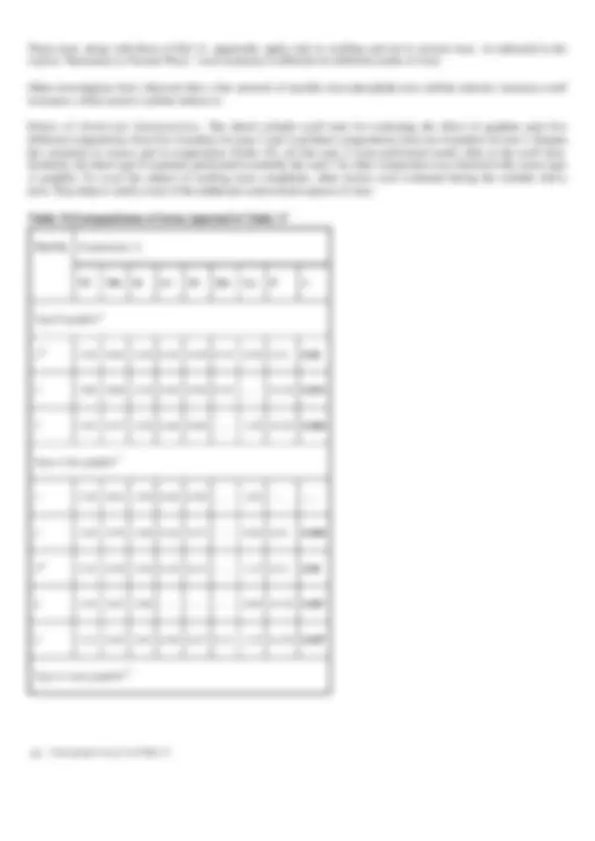
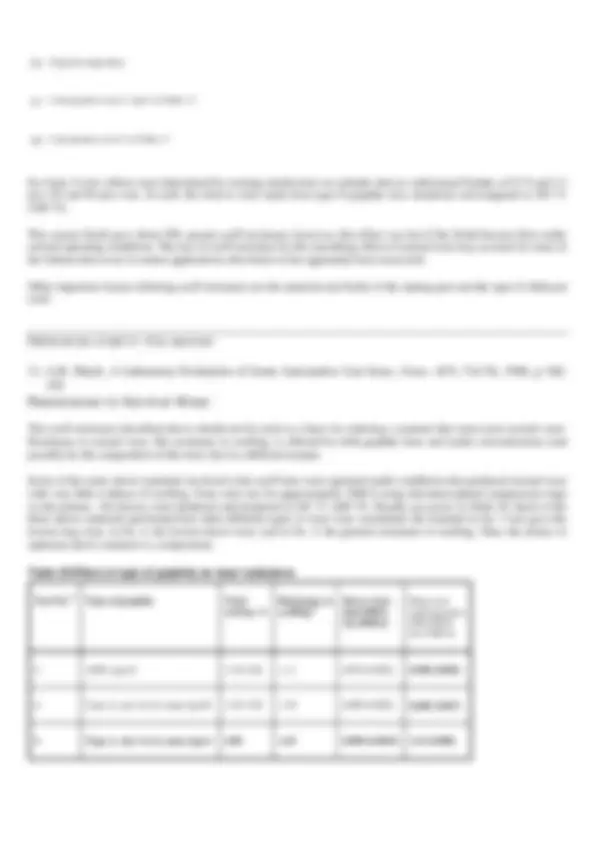
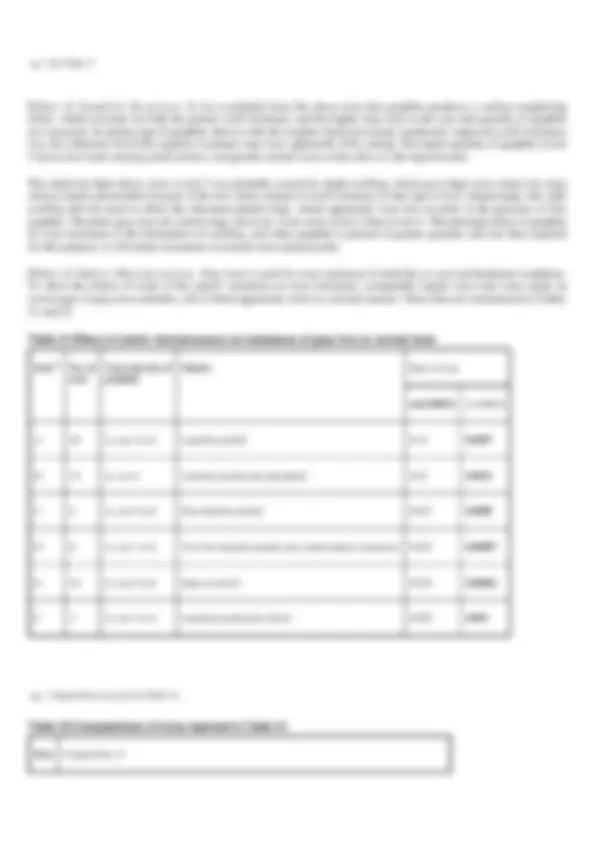
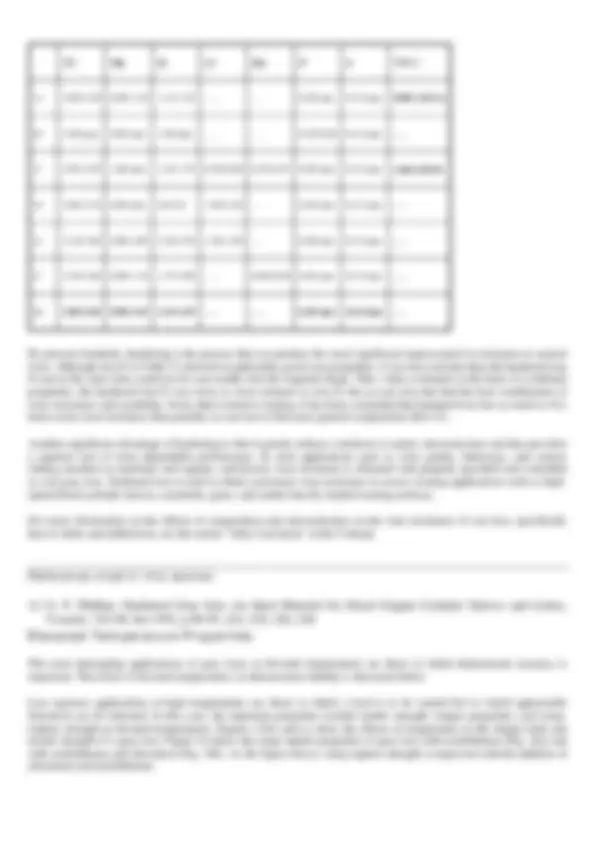
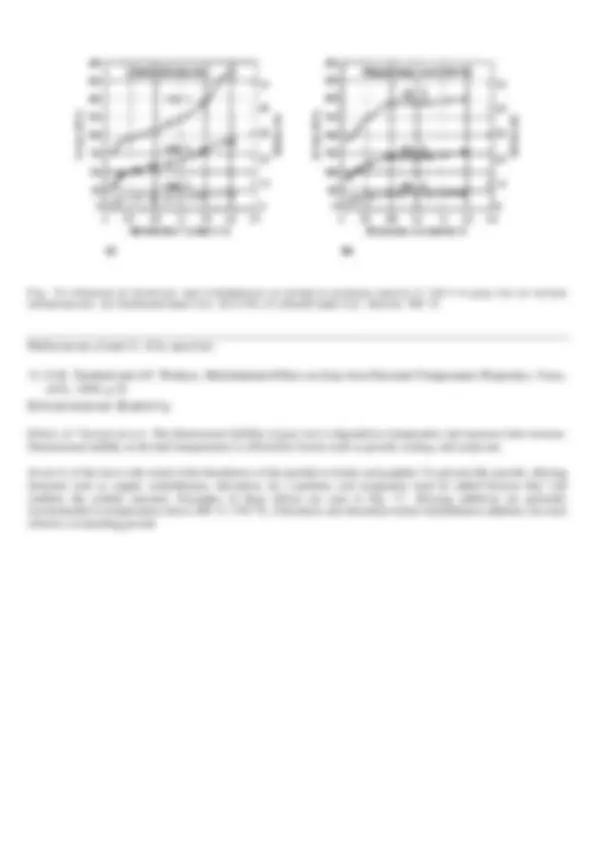
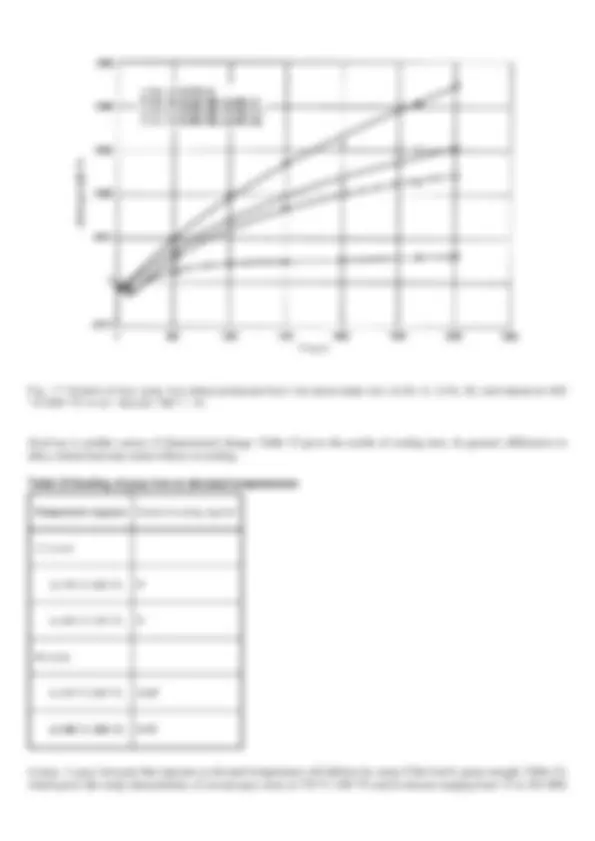
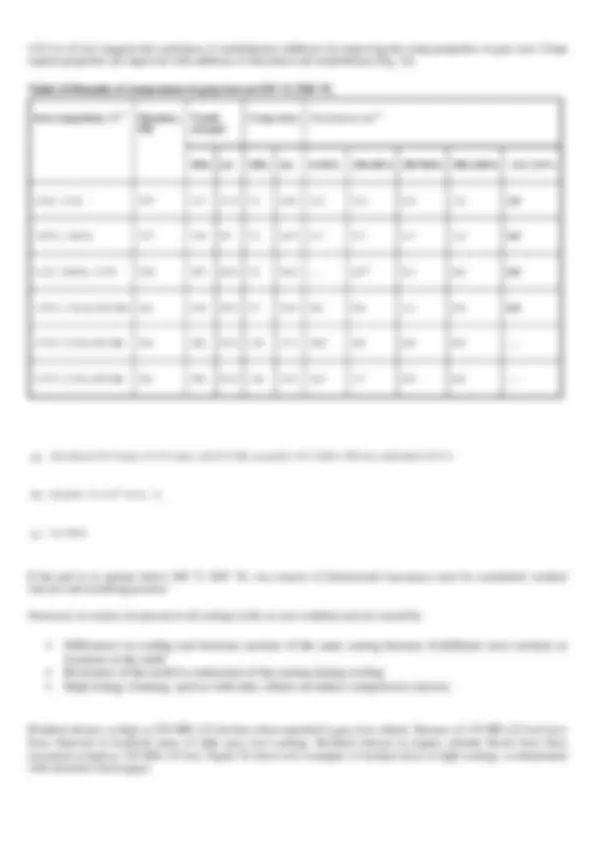
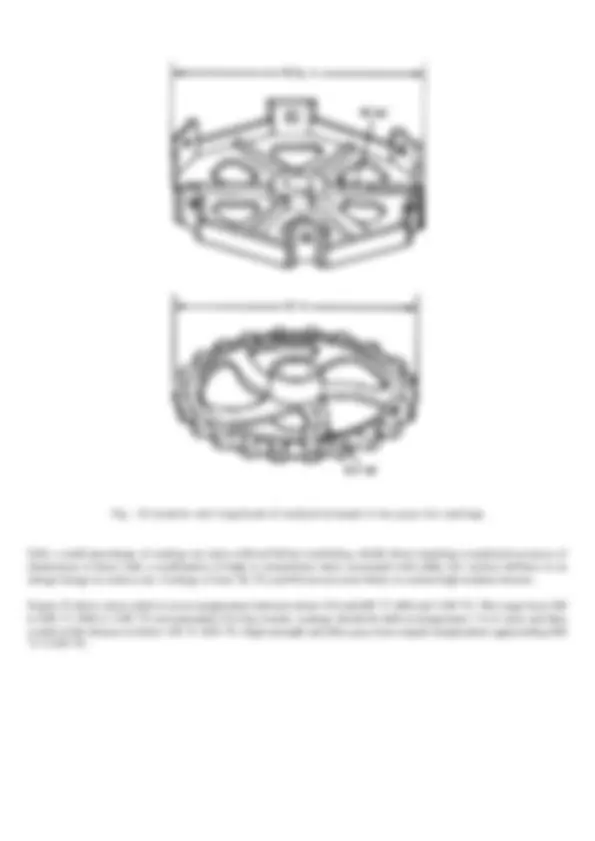
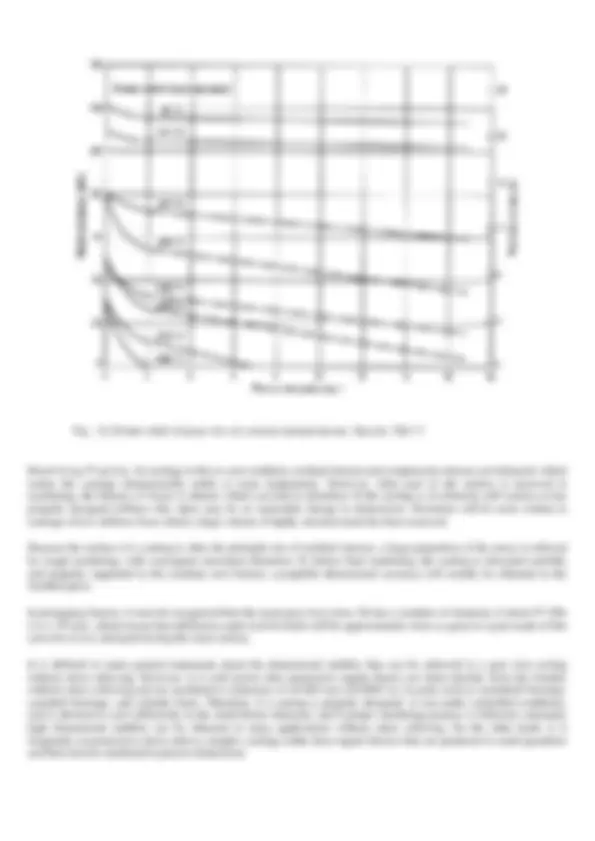
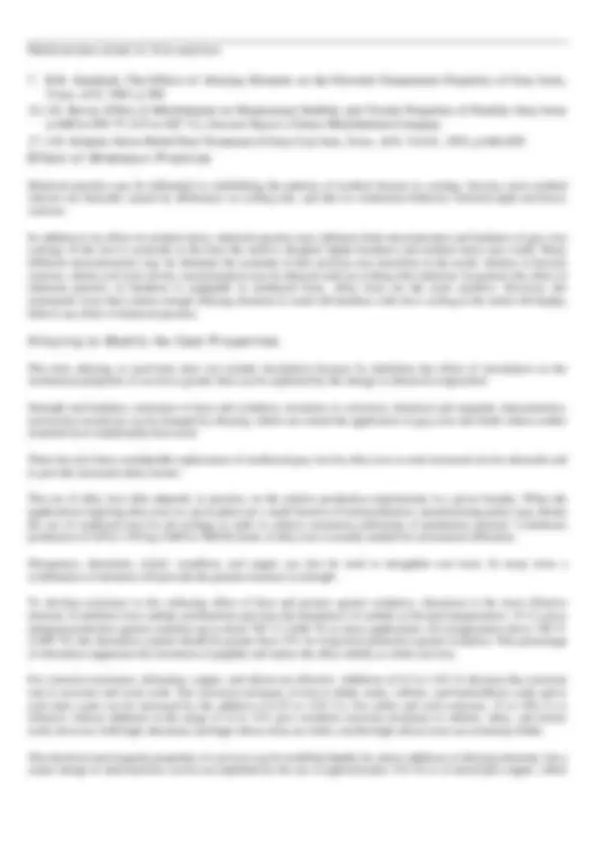
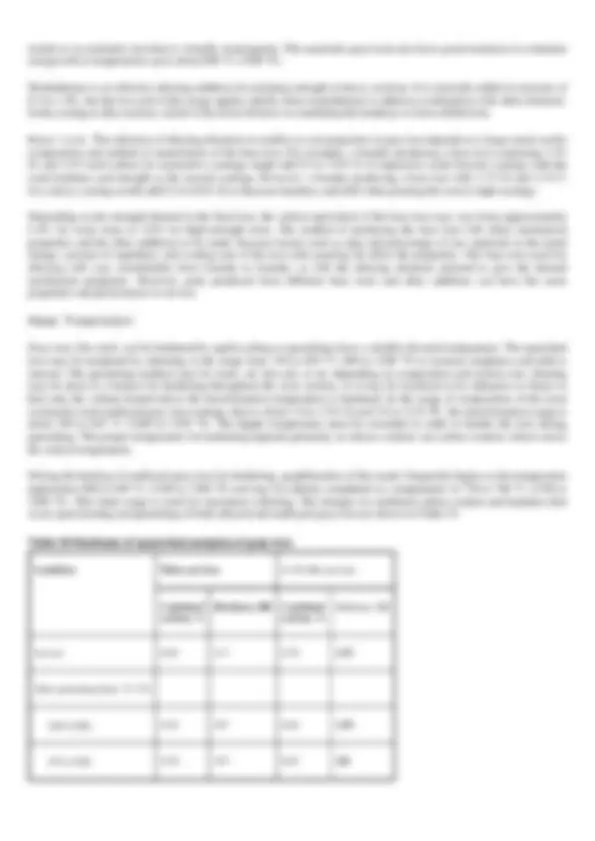
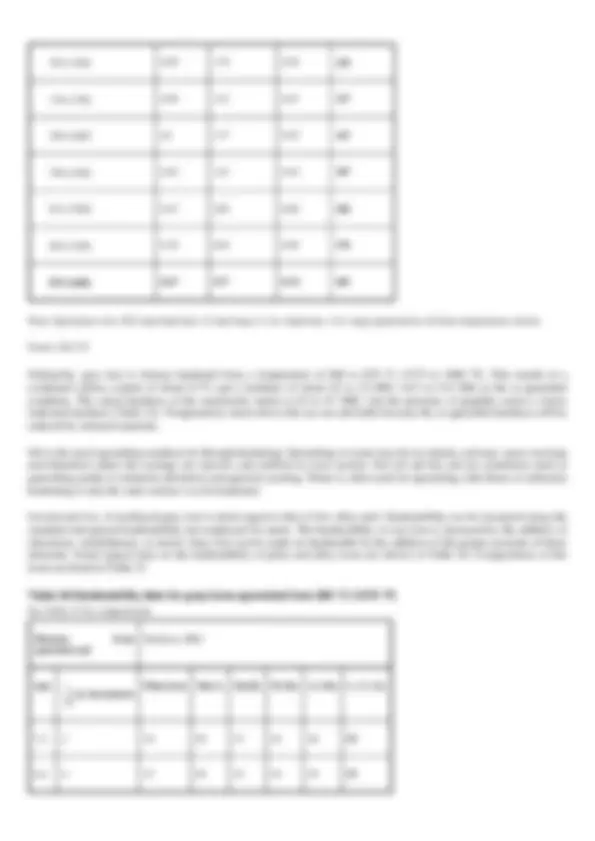
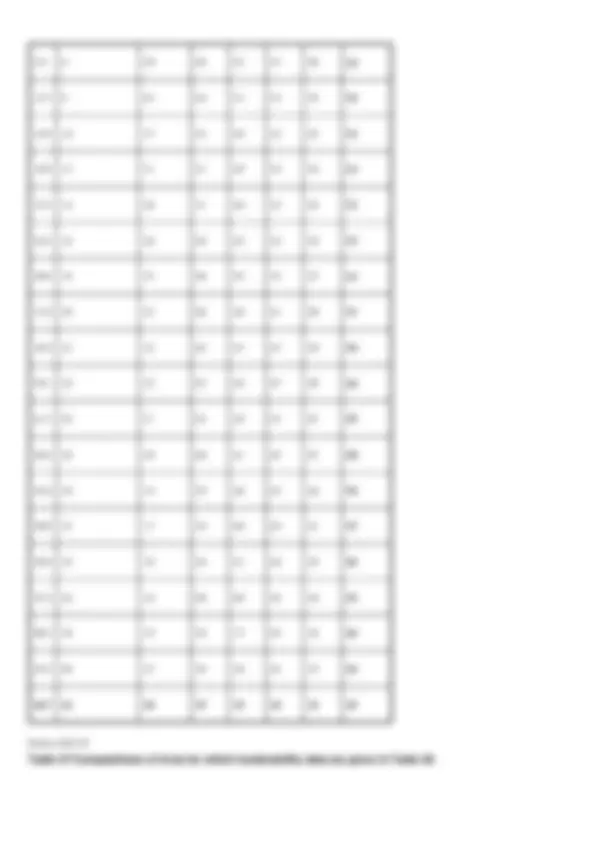
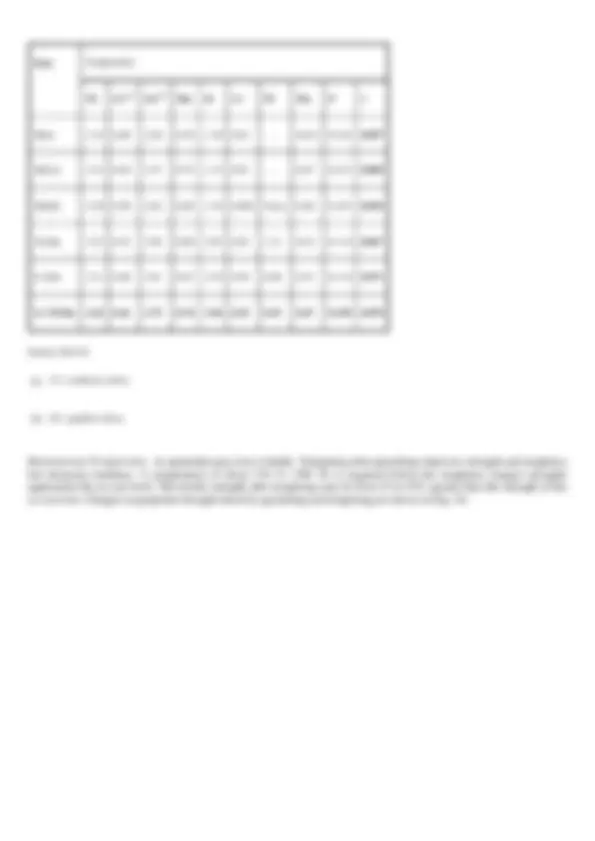
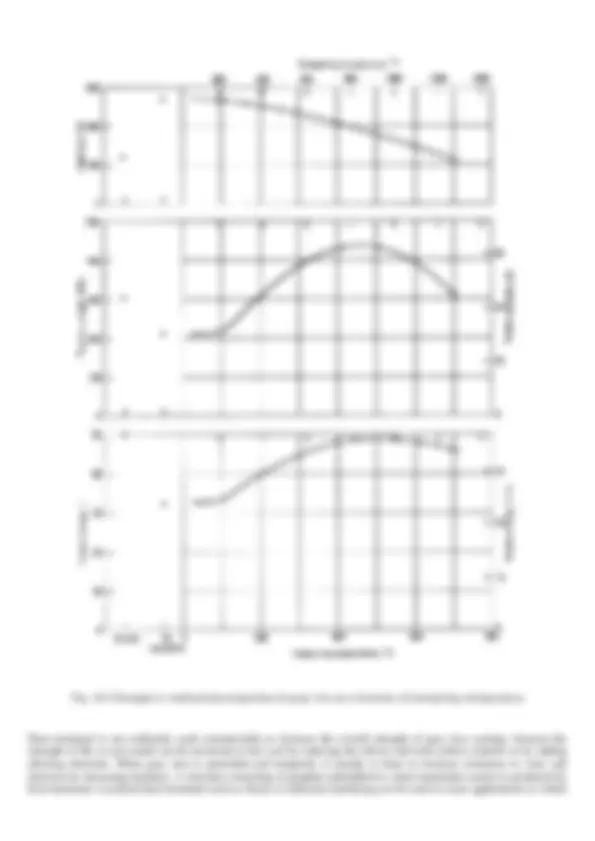
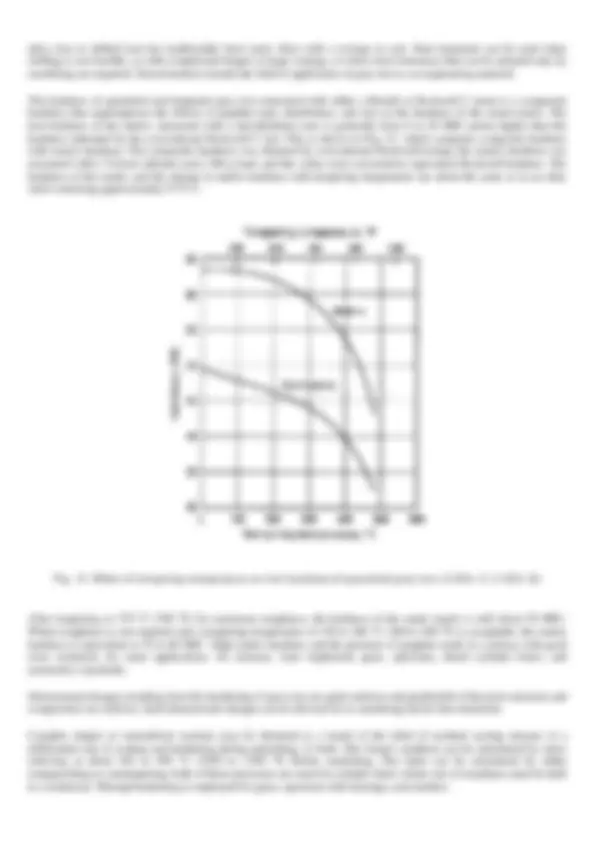
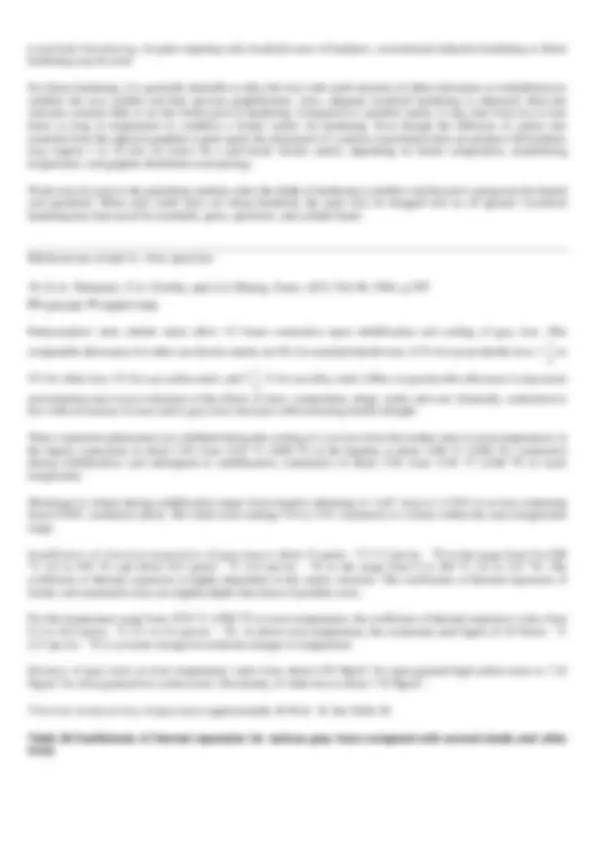
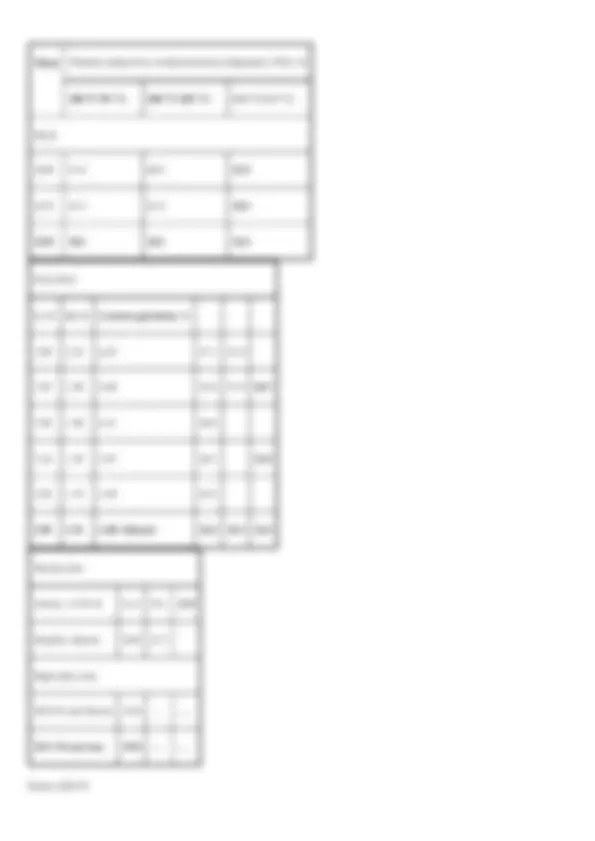
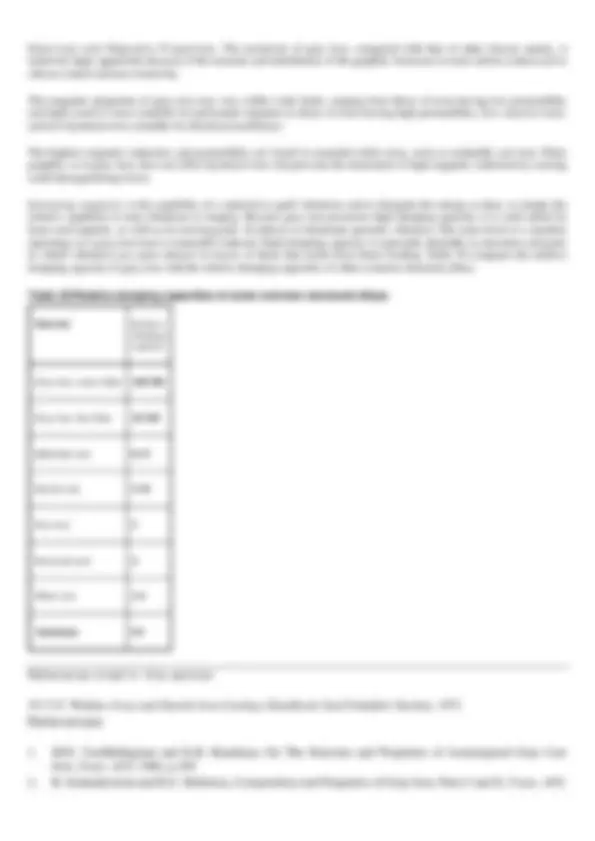
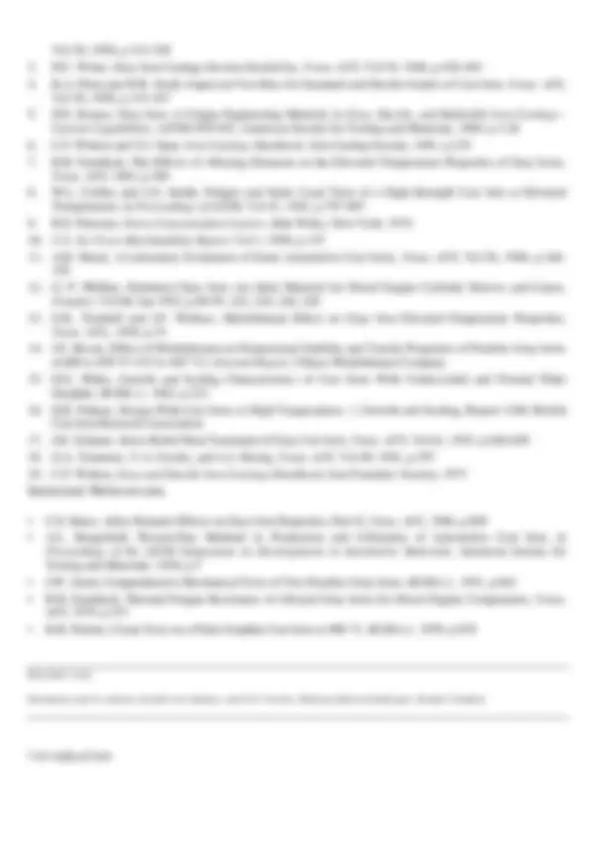
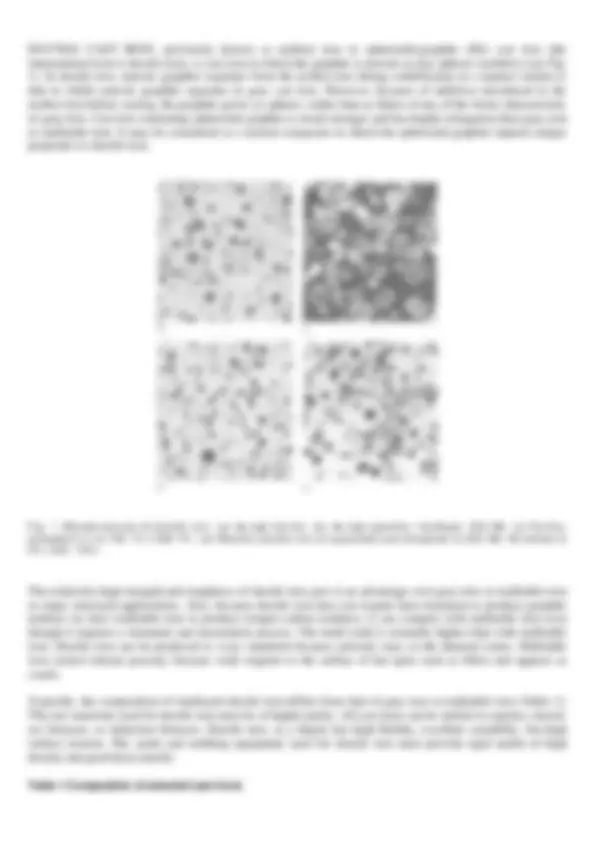
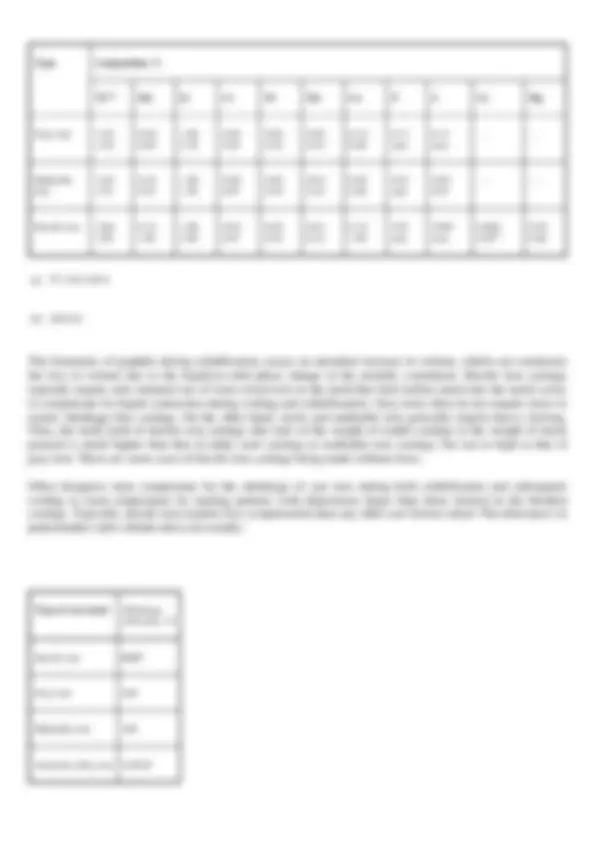
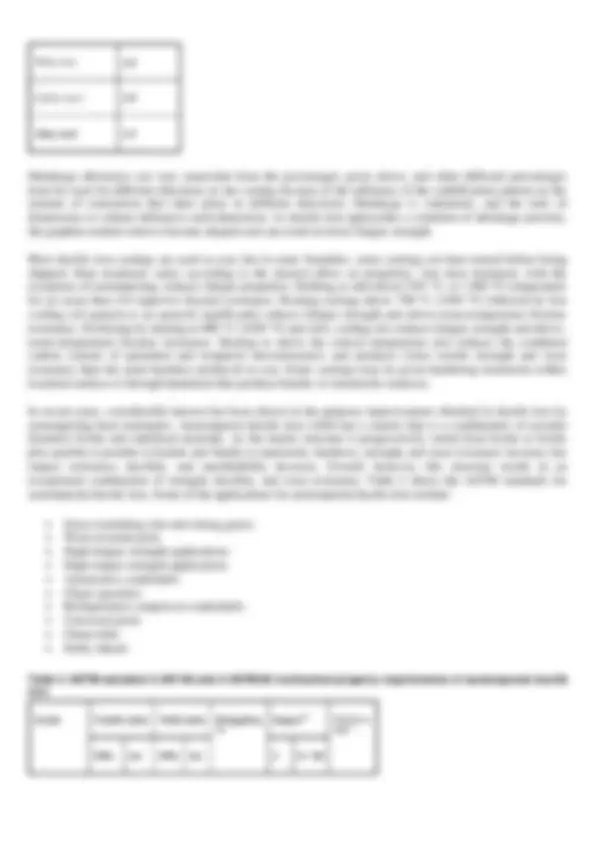
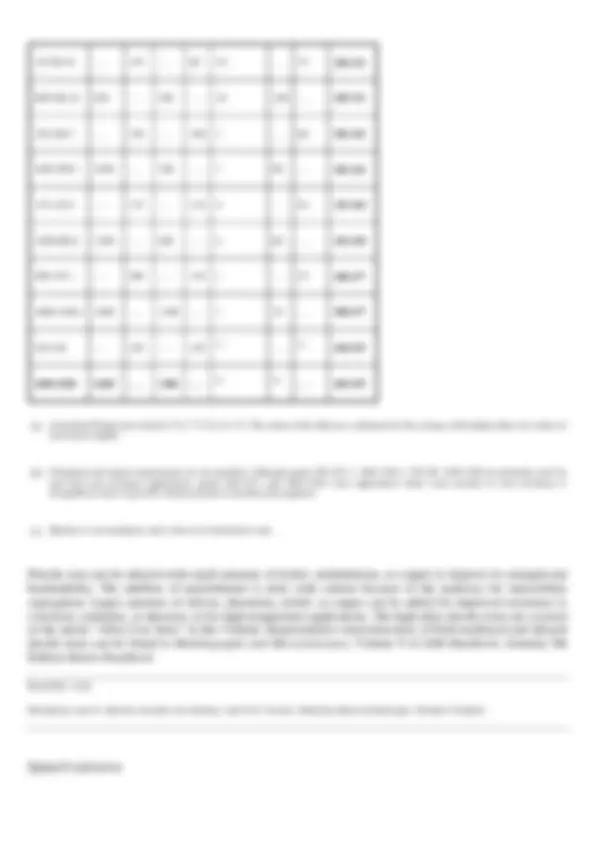
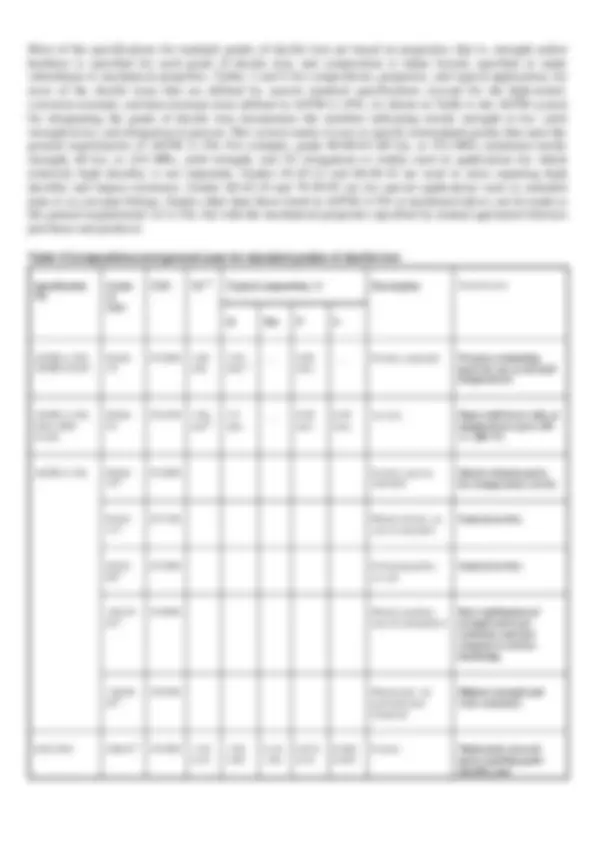
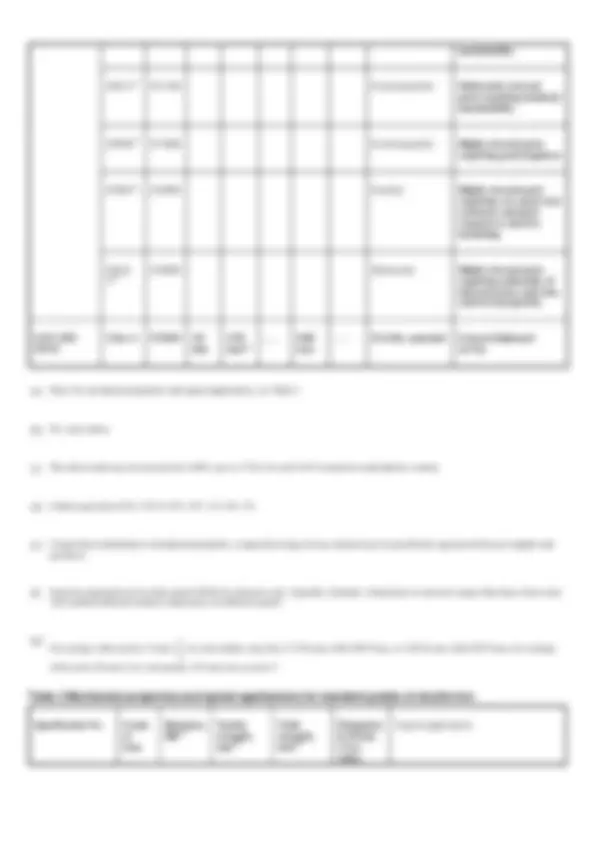
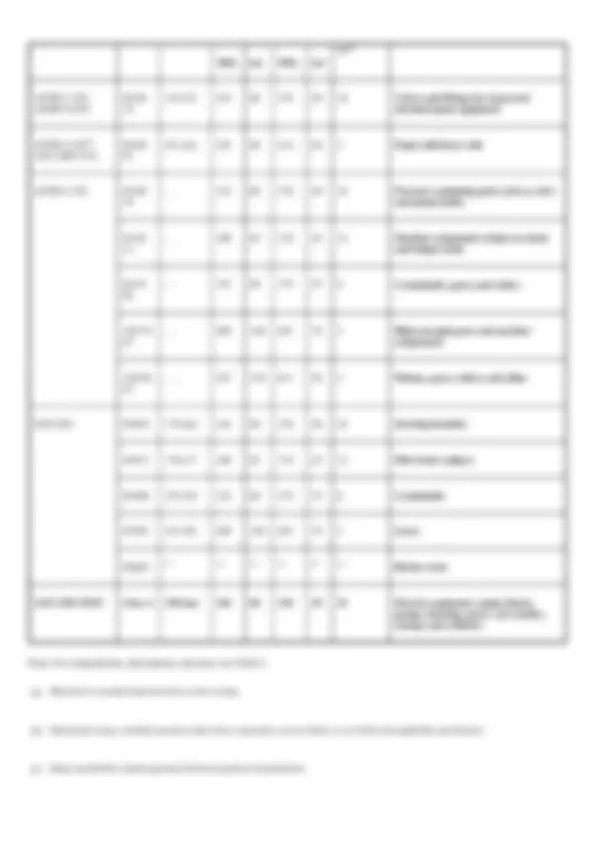
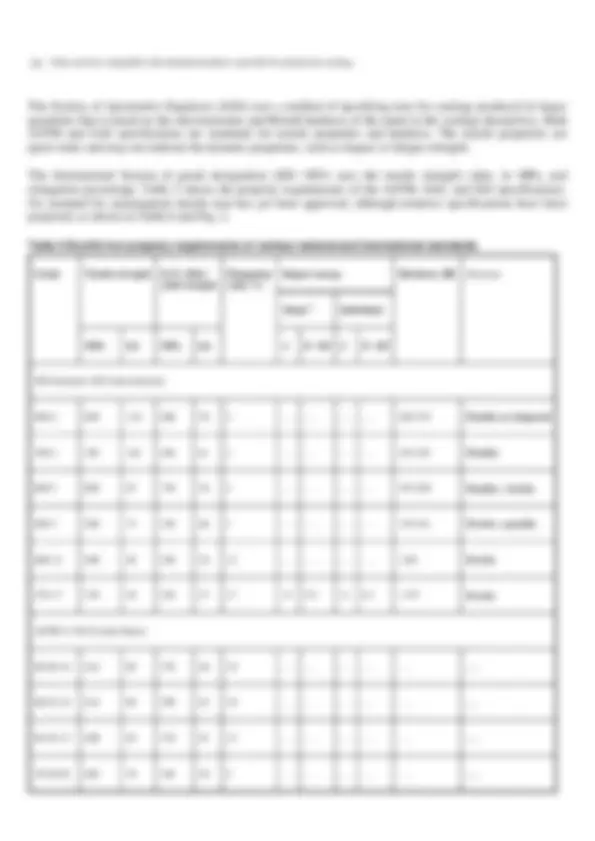
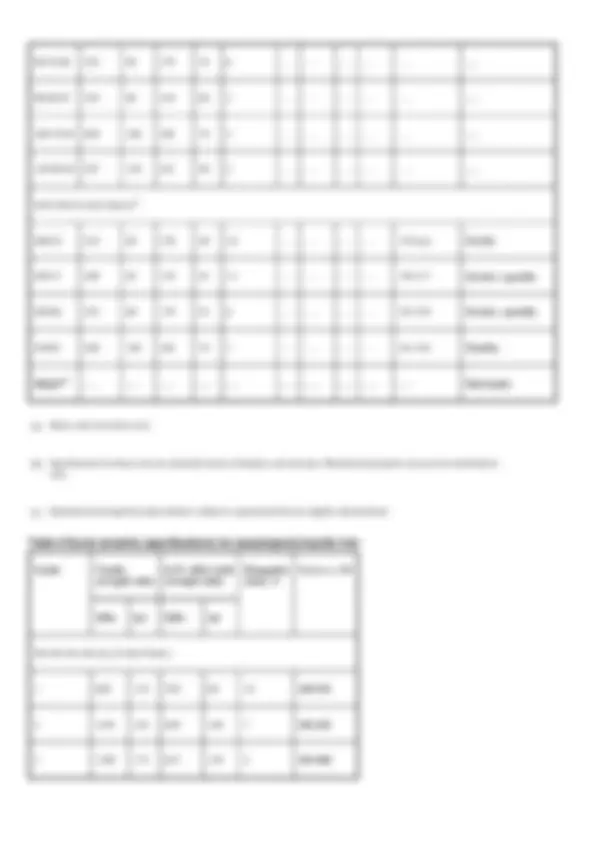
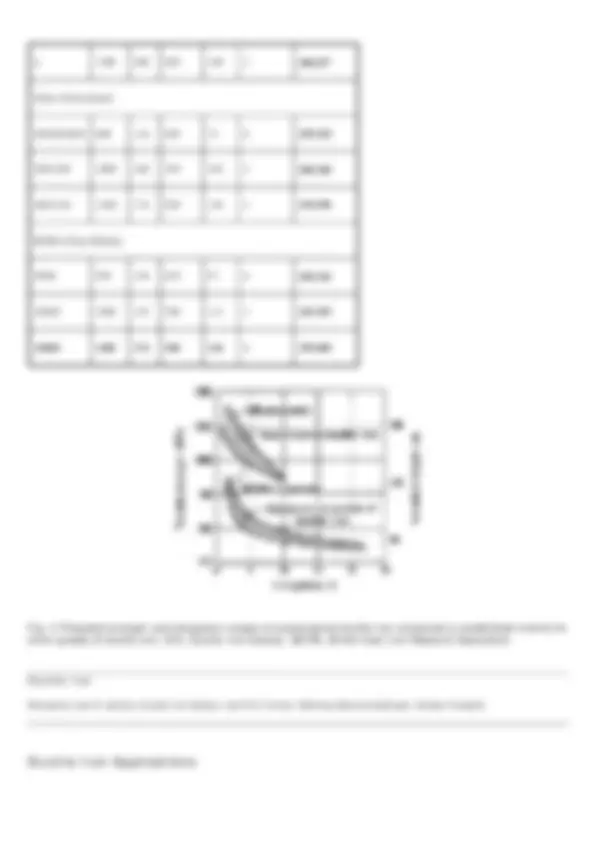
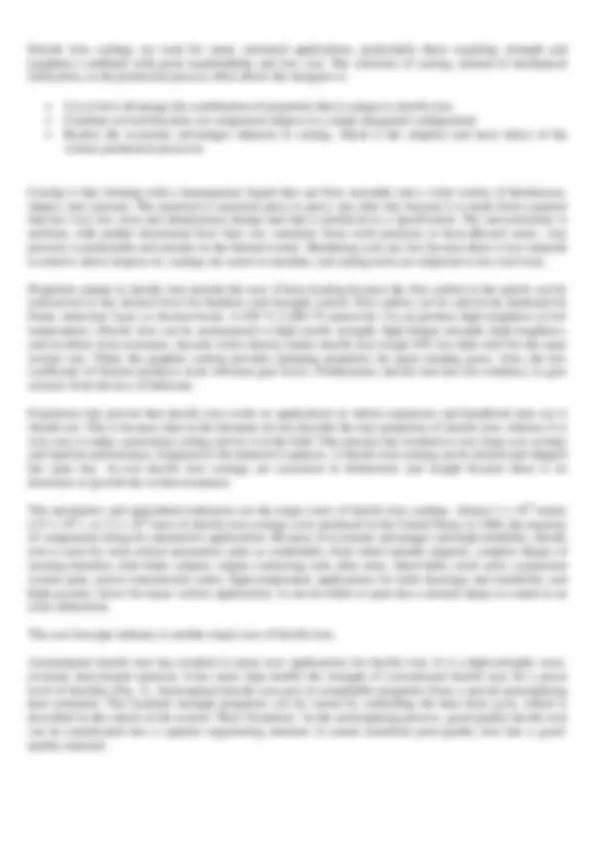
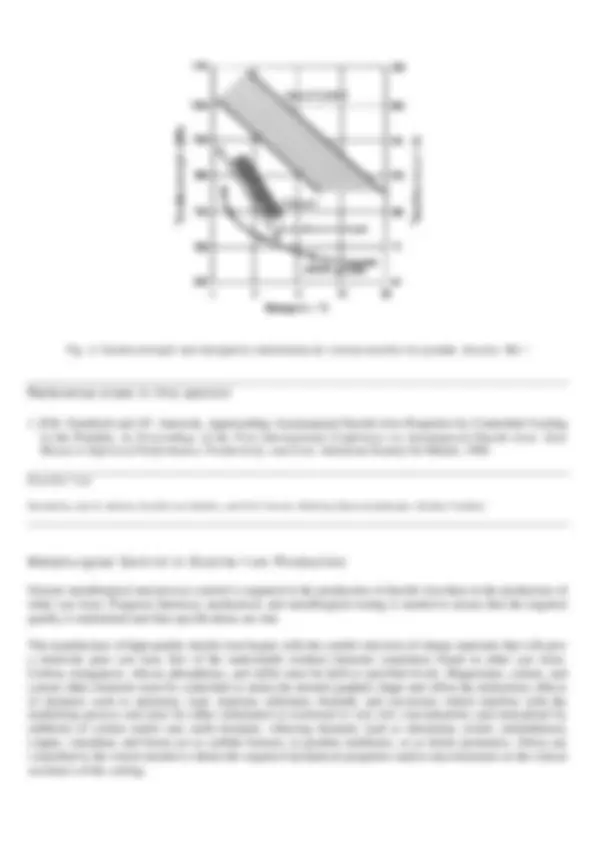
Estude fácil! Tem muito documento disponível na Docsity
Ganhe pontos ajudando outros esrudantes ou compre um plano Premium
Prepare-se para as provas
Estude fácil! Tem muito documento disponível na Docsity
Prepare-se para as provas com trabalhos de outros alunos como você, aqui na Docsity
Os melhores documentos à venda: Trabalhos de alunos formados
Prepare-se com as videoaulas e exercícios resolvidos criados a partir da grade da sua Universidade
Responda perguntas de provas passadas e avalie sua preparação.
Ganhe pontos para baixar
Ganhe pontos ajudando outros esrudantes ou compre um plano Premium
Comunidade
Peça ajuda à comunidade e tire suas dúvidas relacionadas ao estudo
Descubra as melhores universidades em seu país de acordo com os usuários da Docsity
Guias grátis
Baixe gratuitamente nossos guias de estudo, métodos para diminuir a ansiedade, dicas de TCC preparadas pelos professores da Docsity
Materiais - Materiais
Tipologia: Notas de estudo
1 / 2521
Esta página não é visível na pré-visualização
Não perca as partes importantes!
The Materials Information Company
Volume 1 Publication Information and Contributors
Properties and Selection: Irons, Steels, and High-Performance Alloys was published in 1990 as Volume 1 of the 10th Edition Metals Handbook. With the second printing (1993), the series title was changed to ASM Handbook. The Volume was prepared under the direction of the ASM International Handbook Committee.
Authors and Reviewers
Foreword
For nearly 70 years the Metals Handbook has been one of the most widely read and respected sources of information on the subject of metals. Launched in 1923 as a single volume, it has remained a durable reference work, with each succeeding edition demonstrating a continuing upward trend in growth, in subject coverage, and in reader acceptance. As we enter the final decade of the 20th century, the ever-quickening pace of modern life has forced an increasing demand for timely and accurate technical information. Such a demand was the impetus for this, the 10th Edition of Metals Handbook.
Since the publication of Volume 1 of the 9th Edition in 1978, there have been significant technological advances in the field of metallurgy. The goal of the present volume is to document these advances as they pertain to the properties and selection of cast irons, steels, and superalloys. A companion volume on properties and selection of nonferrous alloys, special-purpose materials, and pure metals will be published this autumn. Projected volumes in the 10th Edition will present expanded coverage on processing and fabrication of metals; testing, inspection, and failure analysis; microstructural analysis and materials characterization; and corrosion and wear phenomena (the latter a subject area new to the Handbook series).
During the 12 years it took to complete the 17 volumes of the 9th Edition, the high standards for technical reliability and comprehensiveness for which Metals Handbook is internationally known were retained. Through the collective efforts of the ASM Handbook Committee, the editorial staff of the Handbook, and nearly 200 contributors from industry, research
Cast Aluminum Alloys
Aluminum-Lithium Alloys
Aluminum P/M Alloys
Wrought Copper and Copper Alloys
Cast Copper Alloys
Copper P/M Products
Nickel and Nickel Alloys
Beryllium-Copper and Beryllium-Nickel Alloys
Cobalt and Cobalt Alloys
Magnesium and Magnesium Alloys
Tin and Tin Alloys
Zinc and Zinc Alloys
Lead and Lead Alloys
Refractory Metals and Alloys
Wrought Titanium and Titanium Alloys
Cast Titanium Alloys
Titanium P/M Alloys
Zirconium and Hafnium
Uranium and Uranium Alloys
Beryllium
Precious Metals
Rare Earth Metals
Germanium and Germanium Compounds
Gallium and Gallium Compounds
Indium and Bismuth
Special-Purpose Materials
Soft Magnetic Materials
Permanent Magnet Materials
Metallic Glasses
Superconducting Materials
Electrical Resistance Alloys
Electric Contact Materials
Thermocouple Materials
Low Expansion Alloys
Shape-Memory Alloys
Materials For Sliding Bearings
Metal-Matrix Composite Materials
Ordered Intermetallics
Cemented Carbides
Cermets
Service Characteristics of Carbon and Low-Alloy Steels 6 140 219 22 567
Specialty Steels and Heat-Resistant Alloys 11 252 249 163 358
Special Engineering Topics 2 27 29 11 50
Totals 53 1033 1216 731 1426
(a) Total number of figure captions; some figures may include more than one illustration.
(b) Does not include unnumbered in-text tables or tables that are part of figures
Cast irons are described in six articles. The introductory article on "Classification and Basic Metallurgy of Cast Irons" was completely rewritten for the 10th Edition. The article on "Compacted Graphite Iron" is new to the Handbook. Both of these contributions were authored by D.M. Stefanescu (The University of Alabama), who served as Chairman of Volume 15, Casting , of the 9th Edition. The remaining four articles contain new information on materials (for example, austempered ductile iron) and testing (for example, dynamic tear testing).
Carbon and Low-Alloy Steels. Key additions to this section include articles that explain the relationships among processing (both melt and rolling processes), microstructures, and properties of steels. Of particular note is the article by G. Krauss (Colorado School of Mines) on pages 126 to 139 and the various articles on high-strength low-alloy steels. Other highlights include an extensive tabular compilation that cross-references SAE-AISI steels to their international counterparts (see the article "Classification and Designation of Steels") and an article on "Bearing Steels" that compares both case-hardened and through-hardened bearing materials.
Hardenability of Carbon and Low-Alloy Steels. Following articles that introduce H-steels and describe hardenability concepts, including test procedures to determine the hardening response of steels, a comprehensive collection of hardenability curves is presented. Both English and metric hardenability curves are provided for some 86 steels.
Fabrication Characteristics. Sheet formability, forgeability, machinability, and weldability are described next. The article on bulk formability, which emphasizes recent studies on HSLA forging steels, is new to the Handbook series. The material on weldability was completely rewritten and occupies nearly four times the space allotted in the 9th Edition.
Service Characteristics. The influence of various in-service environments on the properties of steels is one of the most widely studied subjects in metallurgy. Among the topics described in this section are elevated-temperature creep properties, low-temperature fracture toughness, fatigue properties, and impact toughness. A new article also describes the deleterious effect of neutron irradiation on alloy and stainless steels. Of critical importance to this section, however, is the definitive treatise on "Embrittlement of Steels" written by G.F. Vander Voort (Carpenter Technology Corporation). Featuring more than 75 graphs and 372 references, this 48-page article explores the causes and effects of both thermal and environmental degradation on a wide variety of steels. Compared with the 9th Edition on the same subject, this represents a nearly tenfold increase in coverage.
Specialty Steels and Heat-Resistant Alloys. Eleven articles on wrought, cast, and powder metallurgy materials for specialty and/or high-performance applications make up this section. Alloy development and selection criteria as related to corrosion-resistant and heat-resistant steels and superalloys are well documented. More than 100 pages are devoted to stainless steels, while three new articles have been written on superalloys--including one on newly developed directionally solidified and single-crystal nickel-base alloys used for aerospace engine applications.
Special Engineering Topics. The final section examines two subjects that are becoming increasingly important to the engineering community: (1) the availability and supply of strategic materials, such as chromium and cobalt, used in
stainless steel and superalloy production, and (2) the current efforts to recycle highly alloyed materials. Both of these subjects are new to the Handbook series. A second article on recycling of nonferrous alloys will be published in Volume 2 of the 10th Edition.
Acknowledgments
Successful completion of this Handbook required the cooperation and talents of literally hundreds of professional men and women. In terms of the book's technical content, we are indebted to the authors, reviewers, and miscellaneous contributors-some 200 strong-upon whose collective experience and knowledge rests the accuracy and authority of the volume. Thanks are also due to the ASM Handbook Committee and its capable Chairman, Dennis D. Huffman (The Timken Company). The ideas and suggestions provided by members of the committee proved invaluable during the two years of planning required for the 10th edition. Lastly, we would like to acknowledge the efforts of those companies who have worked closely with ASM's editorial and production staff on this and many other Handbook volumes. Our thanks go to Byrd Data Imaging for their tireless efforts in maintaining a demanding typesetting schedule, to Rand McNally & company for the care and quality brought to printing the Handbook, and to Precision Graphics, Don O. Tech, Accurate Art, and HaDel Studio for their attention to detail during preparation of Handbook artwork. Their combined efforts have resulted in a significant and lasting contribution to the metals industry.
The Editors
General Information
Officers and Trustees of ASM INTERNATIONAL (1990-1991)
Trustees
Members of the ASM Handbook Committee (1990-1991)
ASM International staff who contributed to the conversion of the Volume included Sally Fahrenholz-Mann, Bonnie Sanders, Scott Henry, Grace Davidson, Randall Boring, Robert Braddock, and Kathleen Dragolich. The electronic version was prepared under the direction of William W. Scott, Jr., Technical Director, and Michael J. DeHaemer, Managing Director.
Copyright Information (for Print Volume)
Copyright © 1990 by ASM International
All Rights Reserved.
Metals Handbook is a collective effort involving thousands of technical specialists. It brings together in one book a wealth of information from world-wide sources to help scientists, engineers, and technicians solve current and long-range problems.
Great care is taken in the compilation and production of this Volume, but it should be made clear that no warranties, express or implied, are given in connection with the accuracy or completeness of this publication, and no responsibility can be taken for any claims that may arise.
Nothing contained in the Metals Handbook shall be construed as a grant of any right of manufacture, sale, use, or reproduction, in connection with any method, process, apparatus, product, composition, or system, whether or not covered by letters patent, copyright, or trademark, and nothing contained in the Metals Handbook shall be construed as a defense against any alleged infringement of letters patent, copyright, or trademark, or as a defense against liability for such infringement.
Comments, criticisms, and suggestions are invited, and should be forwarded to ASM International.
Library of Congress Cataloging-in-Publication Data (for Print Volume)
Metals Handbook/Prepared under the direction of the ASM International Handbook Committee _10th ed. Includes bibliographies and indexes. Contents: v. 1. Properties and Selection: Irons, Steels, and High-Performance Alloys.
TA459.M43 1990 620.1'6 90-
ISBN 0-87170-377-7 (v.1)
SAN 204-
ISBN 0-87170-380-
Printed in the United States of America
Classification and Basic Metallurgy of Cast Iron
Doru M. Stefanescu, The University of Alabama
Classification
Historically, the first classification of cast iron was based on its fracture. Two types of iron were initially recognized:
With the advent of metallography, and as the body of knowledge pertinent to cast iron increased, other classifications based on microstructural features became possible:
This classification is seldom used by the floor foundryman. The most widely used terminology is the commercial one. A first division can be made in two categories:
The correspondence between commercial and microstructural classification, as well as the final processing stage in obtaining common cast irons, is given in Table 1. A classification of cast irons by their commercial names and structure is also given in the article "Classification of Ferrous Casting Alloys" in Casting, Volume 15 of ASM Handbook, formerly 9th Edition Metals Handbook.
Table 1 Classification of cast iron by commercial designation, microstructure, and fracture
Commercial designation Carbon-rich phase Matrix(a)^ Fracture Final structure after
Gray iron Lamellar graphite P Gray Solidification
Ductile iron Spheroidal graphite F, P, A Silver-gray Solidification or heat treatment
Compacted graphite iron Compacted vermicular graphite F, P Gray Solidification
White iron Fe 3 C P, M White Solidification and heat treatment(b)
Mottled iron Lamellar Gr + Fe 3 C P Mottled (^) Solidification
Malleable iron Temper graphite F, P Silver-gray Heat treatment
Austempered ductile iron Spheroidal graphite At Silver-gray Heat treatment
(a) F, ferrite; P, pearlite; A, austenite; M, martensite; At, austempered (bainite).
(b) White irons are not usually^ heat treated, except for stress relief and to continue austenite transformation.
This is a ternary system, and the carbon content of pearlite can be as low as 0.50% with 2.5% Si
The following sections in this article discuss some of the basic principles of cast iron metallurgy. More detailed descriptions of the metallurgy of cast irons are available in separate articles in this Volume describing certain types of cast irons. The Section "Ferrous Casting Alloys" in Casting, Volume 15 of ASM Handbook, formerly 9th Edition Metals Handbook, also contains more detailed descriptions on the metallurgy of cast irons.
Gray Iron (Flake Graphite Iron)
The composition of gray iron must be selected in such a way as to satisfy three basic structural requirements:
For common cast iron, the main elements of the chemical composition are carbon and silicon. Figure 3 shows the range of carbon and silicon for common cast irons as compared with steel. It is apparent that irons have carbon in excess of the maximum solubility of carbon in austenite, which is shown by the lower dashed line. A high carbon content increases the amount of graphite or Fe 3 C. High carbon and silicon contents increase the graphitization potential of the iron as well as its castability.
Fig. 3 Carbon and silicon composition ranges of common cast irons and steel. Source: Ref 2
The combined influence of carbon and silicon on the structure is usually taken into account by the carbon equivalent (CE):
CE = % C + 0.3(% Si)
Additional information on carbon equivalent is available in the article "Thermodynamic Properties of Iron-Base Alloys" in Casting, Volume 15 of ASM Handbook, formerly 9th Edition Metals Handbook. Although increasing the carbon and silicon contents improves the graphitization potential and therefore decreases the chilling tendency, the strength is adversely affected (Fig. 4). This is due to ferrite promotion and the coarsening of pearlite.
Fig. 4 General influence of carbon equivalent on the tensile strength of gray iron. Source: Ref 2
The manganese content varies as a function of the desired matrix. Typically, it can be as low as 0.1% for ferritic irons and as high as 1.2% for pearlitic irons, because manganese is a strong pearlite promoter.
From the minor elements, phosphorus and sulfur are the most common and are always present in the composition. They can be as high as 0.15% for low-quality iron and are considerably less for high-quality iron, such as ductile iron or compacted graphite iron. The effect of sulfur must be balanced by the effect of manganese. Without manganese in the iron, undesired iron sulfide (FeS) will form at grain boundaries. If the sulfur content is balanced by manganese, manganese sulfide (MnS) will form, which is harmless because it is distributed within the grains. The optimum ratio between manganese and sulfur for an FeS-free structure and maximum amount of ferrite is:
% Mn = 1.7(% S) + 0.15 (Eq 2)
Other minor elements, such as aluminum, antimony, arsenic, bismuth, lead, magnesium, cerium, and calcium, can significantly alter both the graphite morphology and the microstructure of the matrix.
The range of composition for typical unalloyed common cast irons is given in Table 2. The typical composition range for low- and high-grade unalloyed gray iron (flake graphite iron) cast in sand molds is given in Table 3.
Table 2 Range of compositions for typical unalloyed common cast irons
Type of iron Composition, %
C Si Mn P S
Fig. 5 Typical flake graphite shapes specified in ASTM A 247. A, uniform distribution, random orientation; B, rosette groupings; C, kish graphite (superimposed flake sizes, random orientation); D, interdendritic segregation with random orientation; E, interdendritic segregation with preferred orientation
Fig. 6 Characteristic cooling curves associated with different flake graphite shapes. T E, equilibrium eutectic temperature
Fig. 7 Effect of maximum graphite flake length on the tensile strength of gray iron. Source: Ref 3
Alloying elements can be added in common cast iron to enhance some mechanical properties. They influence both the graphitization potential and the structure and properties of the matrix. The main elements are listed below in terms of their graphitization potential:
High positive graphitization potential (decreasing positive potential from top to bottom)
Carbon
Tin
Phosphorus
Silicon
Aluminum
Copper
Nickel
Neutral
Iron