
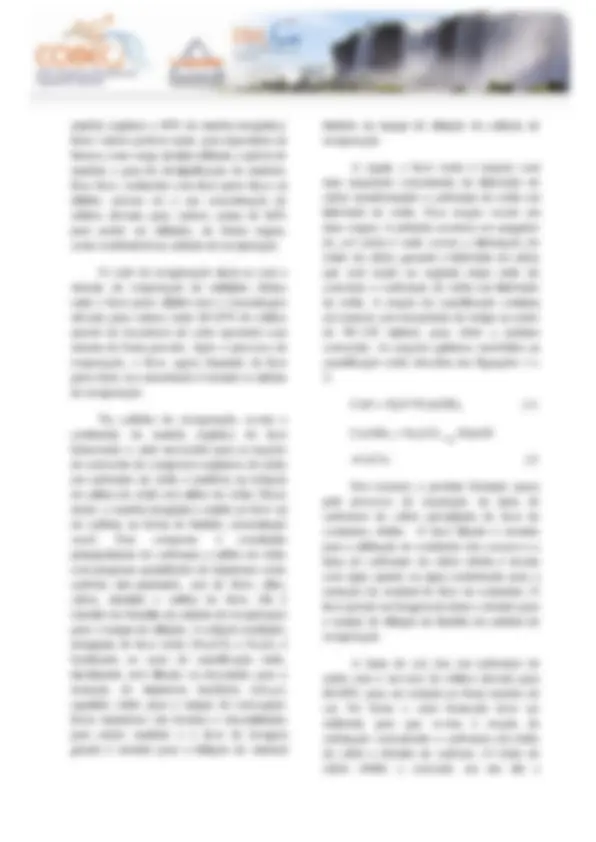
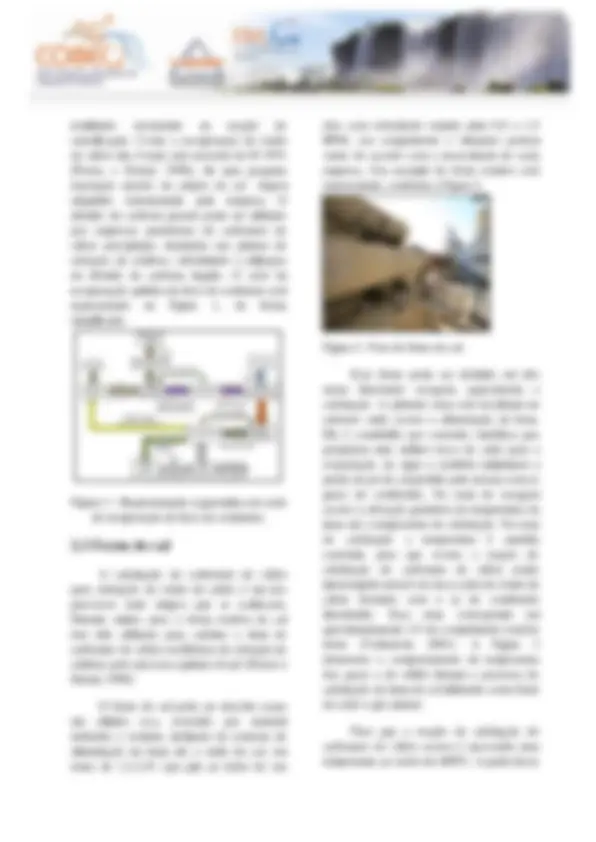
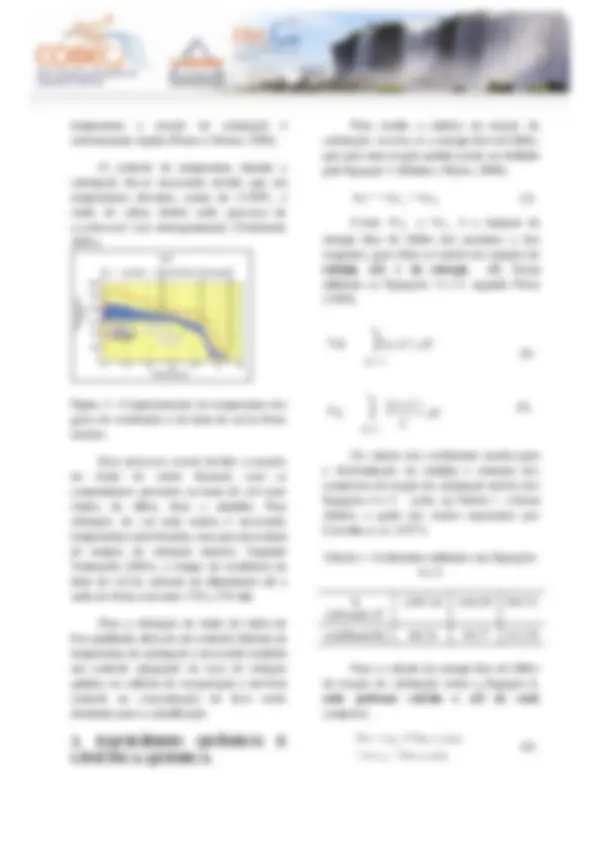
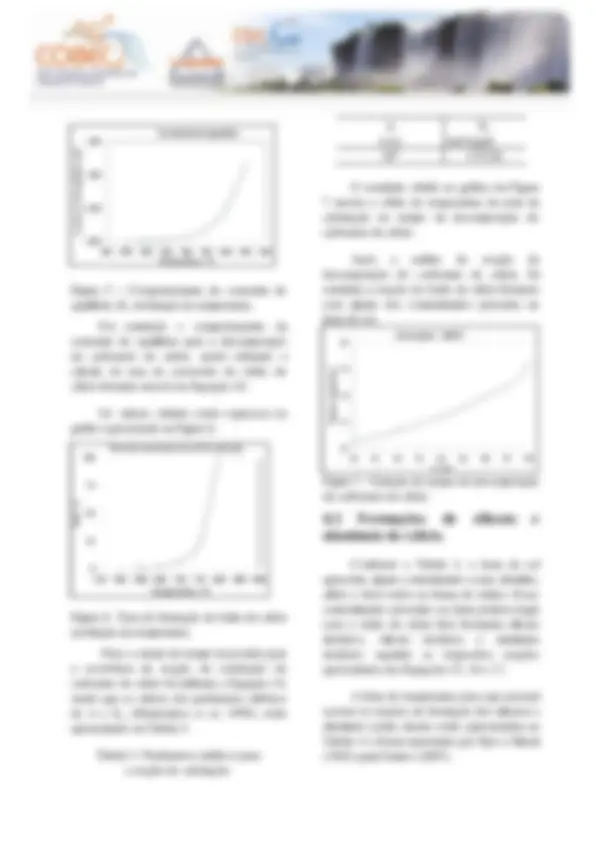
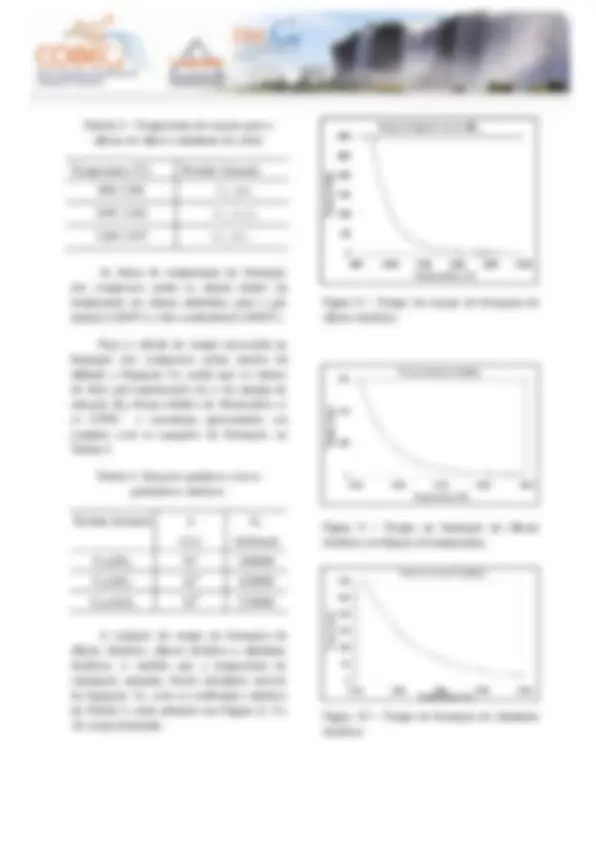
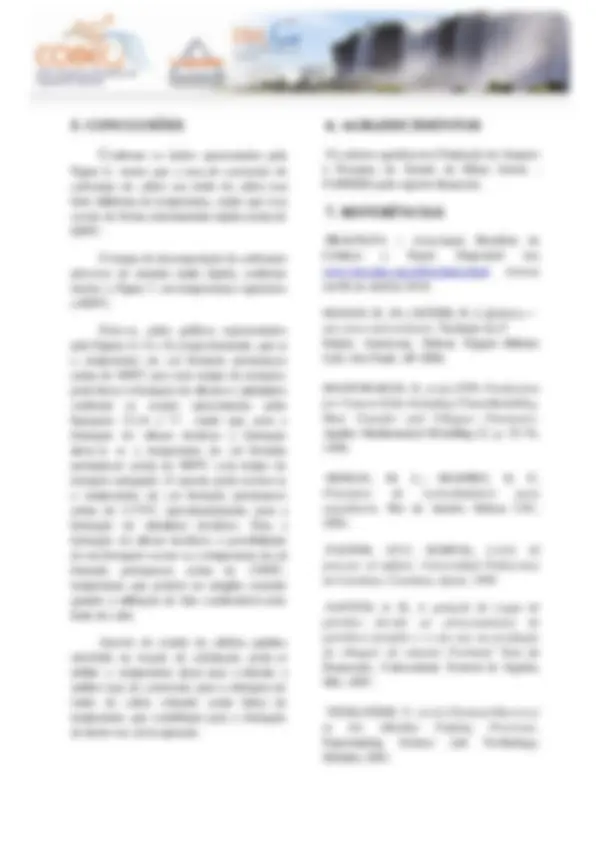
Estude fácil! Tem muito documento disponível na Docsity
Ganhe pontos ajudando outros esrudantes ou compre um plano Premium
Prepare-se para as provas
Estude fácil! Tem muito documento disponível na Docsity
Prepare-se para as provas com trabalhos de outros alunos como você, aqui na Docsity
Os melhores documentos à venda: Trabalhos de alunos formados
Prepare-se com as videoaulas e exercícios resolvidos criados a partir da grade da sua Universidade
Responda perguntas de provas passadas e avalie sua preparação.
Ganhe pontos para baixar
Ganhe pontos ajudando outros esrudantes ou compre um plano Premium
Comunidade
Peça ajuda à comunidade e tire suas dúvidas relacionadas ao estudo
Descubra as melhores universidades em seu país de acordo com os usuários da Docsity
Guias grátis
Baixe gratuitamente nossos guias de estudo, métodos para diminuir a ansiedade, dicas de TCC preparadas pelos professores da Docsity
Cinética quimica da reação de calcinação da lama de cal gerada no ciclo de recuperação quimica da industria de extração de celulose
Tipologia: Notas de estudo
1 / 10
Esta página não é visível na pré-visualização
Não perca as partes importantes!
H.M. dos REIS 1 , J.C. F. MACEDO^2 e R.J. da SILVA^3 (^1) Escola SENAI “Theobaldo De Nigris”, Departamento de Celulose e Papel
2 e-mail:^ celulosepapel114@sp.senai.br Universidade Nove de Julho, Diretoria de Ciências Exatas- São Paulo, Sp e-mail: julio.macedo@uninove.com.br (^3) Universidade Federal de Itajubá, IEM, Instituto de Engenharia Mecânica e-mail: rogeriojs@unifei.edu.br
RESUMO – Durante o ciclo da recuperação dos produtos químicos utilizados na indústria para a extração de celulose pelo processo kraft, tem-se a reação de calcinação do carbonato de sódio no forno rotativo de cal. O carbonato de cálcio utilizado, chamado de lama de cal, é proveniente da reação de caustificação, reação esta que consiste na adição de óxido de cálcio na solução de licor verde (hidróxido de sódio e carbonato de cálcio), obtendo-se assim o licor necessário para o cozimento dos cavacos de madeira. O forno de cal fecha o ciclo da recuperação química destinada para a preparação do licor de cozimento dos cavacos tornando esse processo economicamente atrativo. Este trabalho tem como finalidade principal estudar a cinética química das reações ocorridas na zona de calcinação do forno a fim de avaliar a eficiência na obtenção do óxido de cálcio. PALAVRAS-CHAVE: recuperação química; calcinação; cinética química, extração de celulose, processo Kraft.
Ao longo do tempo, a indústria brasileira de extração de celulose vem crescendo e em 2008 ocupava a quarta posição mundial com quase 13 milhões de toneladas de celulose extraída e o 11º lugar entre os principais fabricantes de papel do mundo, com mais de nove milhões de toneladas (BRACELPA, 2009). A principal matéria-prima utilizada na extração de celulose vem da madeira do eucalipto e cerca de 80% dos processos químicos utilizados na extração são executados pelo processo Kraft, também conhecido como
processo sulfato, que tem como uma de suas vantagens o ciclo de recuperação, relativamente fácil, dos seus reagentes químicos. A reação de calcinação, ocorrida no forno rotativo de cal, durante o processo de recuperação dos reagentes químicos, corresponde a etapa final do ciclo de recuperação do processo de polpação química Kraft.
No forno rotativo a obtenção do óxido de cálcio é processada pela calcinação do carbonato de cálcio, composto predominante na lama de cal gerada pela reação de
caustificação da solução aquosa de licor verde (Na 2 CO 3 e Na 2 S).
O principal objetivo deste trabalho foi estudar a influência da temperatura e do tempo de retenção da lama de cal na zona de calcinação através da cinética química da reação de calcinação.
O processo Kraft , desenvolvido por Dahl em 1884, é o método químico mais empregado, atualmente, para a extração da celulose da madeira. Nesse tipo de processo, a solução utilizada para o cozimento dos cavacos é composta, principalmente, por hidróxido de sódio e sulfeto de sódio. As características principais do processo Kraft prima pela extração de pasta celulósica de qualidade, avaliada pela resistência físico-mecânica, pelo alto grau de “alvura” alcançada na polpa branqueada, o eficiente sistema de recuperação dos produtos químicos e a redução do tempo de deslignificação em relação a outros processos porém, o processo tem como desvantagens o baixo rendimento na extração da celulose de aproximadamente 50%, e também, devido a problemas ambientais causados por emissões atmosféricas de poluentes, que incluem o odor característico do enxofre e de material particulado. Esses problemas estão sendo minimizados através de melhoria no processo e investimentos em sistemas mais eficientes para o tratamento desses poluentes.
O processo de extração da celulose inicia-se introduzindo os cavacos de madeira, sem casca, para serem cozidos em um vaso pressurizado chamado de digestor, que na presença de um licor denominado licor de cozimento, solução composta por hidróxido de sódio e sulfeto de sódio. A temperatura é controlada para manter-se entre 160-170ºC e
durante um determinado tempo de retenção, que permita a reação de degradação da lignina, um polímero amorfo que atua como ligante entre as fibras e que confere firmeza e rigidez a estrutura lenhosa. A relação tempo/temperatura está relacionada com algumas variáveis como, espécie da madeira, grau de deslignificação requerida, carga de álcali aplicada entre outros. Ao fim do cozimento, descarregam-se os cavacos em um tanque despressurizado, conhecido como blow tank, promovendo a separação das fibras através de diferença de pressão entre o digestor e o tanque de descarga, desprendendo gases e efetuando o desfibramento, obtendo-se, assim a pasta celulósica, denominada pasta marrom. A pasta obtida é então enviada do tanque de descarga para o setor de lavagem e depuração, sendo lavada exaustivamente com condensado para que seja efetuado o processo de remoção dos produtos químicos solubilizados pelo cozimento e depurada para remoção de contaminantes sólidos como cavacos mal cozidos, materiais abrasivos, plásticos entre outros.
Durante o cozimento da madeira, tem-se a formação do licor preto, uma solução aquosa complexa constituída por compostos orgânicos solubilizados (frações de lignina, extrativos e fibras) e, também, compostos inorgânicos residuais de sais de sódio (carbonato de sódio, sulfato de sódio entre outros). Esse licor é extraído durante o processo de lavagem da pasta marrom e tem fundamental importância para a empresa, que através da sua reutilização no ciclo da recuperação torna o processo economicamente viável além de diminuir impactos ambientais, de forma direta e indireta com o seu uso.
O licor preto extraído na lavagem da pasta possui concentração de sólidos entre 10- 20%, composto, em média, por 60% de
reutilizado novamente na reação de caustificação. Como a recuperação do óxido de cálcio não é total, está em torno de 85-95% (Pastor e Hortal, 1990), há uma pequena reposição através da adição de cal virgem adquirido externamente pela empresa. O dióxido de carbono gerado pode ser utilizado por empresas produtoras de carbonato de cálcio precipitado, instaladas nas plantas de extração de celulose, substituindo a utilização do dióxido de carbono liquido. O ciclo da recuperação química do licor de cozimento está representado na Figura 1, de forma simplificada.
Figura 1 – Representação esquemática do ciclo de recuperação do licor de cozimento.
A calcinação do carbonato de cálcio para obtenção do óxido de cálcio é um dos processos mais antigos que se conhecem. Durante muitos anos, o forno rotativo de cal tem sido utilizado para calcinar a lama de carbonato de cálcio em fábricas de extração de celulose pelo processo químico Kraft (Pastor e Hortal, 1990).
O forno de cal pode ser descrito como um cilindro oco, revestido por material refratário e isolante, inclinado do extremo de alimentação da lama até a saída da cal, em torno de 1,2-2,4º, que gira ao redor do seu
eixo com velocidade variada entre 0,5 a 1, RPM, seu comprimento e diâmetro podem variar de acordo com a necessidade de cada empresa. Um exemplo de forno rotativo está representado, conforme a Figura 2.
Figura 2- Foto do forno de cal.
Esse forno pode ser dividido em três zonas funcionais: secagem, aquecimento e calcinação. A primeira zona está localizada no extremo onde ocorre a alimentação da lama. Ela é constituída por correntes metálicas que propiciam uma melhor troca de calor para a evaporação da água e também minimizam a perda de pó de cal perdida pelo arraste com os gases de combustão. Na zona de secagem ocorre a elevação gradativa da temperatura da lama até a temperatura de calcinação. Na zona de calcinação a temperatura é mantida constante para que ocorra a reação de calcinação do carbonato de cálcio sendo interrompida através da troca calor do óxido de cálcio formado com o ar de combustão introduzido. Essa zona corresponde em aproximadamente 1/3 do comprimento total do forno (Venkatesh, 2001). A Figura 3 demonstra o comportamento da temperatura dos gases e do sólido durante o processo da calcinação da lama de cal utilizando como fonte de calor o gás natural.
Para que a reação de calcinação do carbonato de cálcio ocorra é necessário uma temperatura ao redor de 800ºC. A partir dessa
temperatura a reação de calcinação é extremamente rápida (Pastor e Hortal, 1990).
O controle de temperatura durante a calcinação faz-se necessário devido que em temperaturas elevadas, acima de 1150ºC, o óxido de cálcio obtido sofre processo de overburned (cal sobrequeimada) (Venkatesh, 2001).
Figura 3- Comportamento da temperatura dos gases de combustão e da lama de cal no forno rotativo.
Esse processo ocorre devido a reações do óxido de cálcio formado com os contaminantes presentes na lama de cal como óxidos de silício, ferro e alumínio. Para obtenção de cal mais reativa é necessário temperaturas mais brandas, mas que necessitam de tempos de retenção maiores. Segundo Venkatesh (2001), o tempo de residência da lama de cal do extremo de alimentação até a saída do forno está entre 170 a 270 min.
Para a obtenção de óxido de cálcio de boa qualidade além de um controle eficiente da temperatura de calcinação e necessário também um controle adequado da taxa de redução química na caldeira de recuperação e um bom controle na concentração do licor verde destinado para a caustificação.
Para avaliar a cinética da reação de calcinação, recorre-se a energia livre de Gibbs, que para uma reação química pode ser definida pela Equação 3 (Mahan e Myers, 2000).
G GP GR
Como GP e GR é a variação da energia livre de Gibbs dos produtos e dos reagentes, para obter os valores da variação de entalpia, ∆H, e da entropia, ∆S, foram utilizadas as Equações 4 e 5, segundo Perry (1999).
Os valores dos coeficientes usados para a determinação da entalpia e entropia dos compostos da reação de calcinação através das Equações 4 e 5 estão na Tabela 1 e foram obtidos a partir dos dados reportados por Carvalho et al. (1977).
Tabela 1- Coeficientes utilizados nas Equações 4 e 5.
hf (kJ/kmol).10^3
sf (kJ/kmol.K) 88,74 39,77 213,
Para o cálculo da energia livre de Gibbs da reação de calcinação temos a Equação 6, onde podemos calcular o ∆G de cada composto.
f f
G [( h H ).4,1 8 6 ] [T .(s S).4,1 6 8]
H Cp T dT
Te ( ) 298 , 15
dT T
Cp T S
Te
298,
O presente trabalho teve como objetivos estudar a influência da temperatura na transformação carbonato/óxido de cálcio e na formação de silicatos e aluminatos.
A composição típica da lama de cal utilizada (Pastor e Hortal, 1990) está descrita na Tabela 2.
Tabela 2- Composição típica da lama de cal nas indústrias de extração de celulose.
Composto Composição (%) CaCO 3 90- SiO 2 1- Al 2 O 3 0,
A reação principal que ocorre no forno, a calcinação, é descrita pela Equação 9. Além da reação de calcinação foi estudado também o comportamento do tempo de formação de reações paralelas do óxido de cálcio com contaminantes presentes na lama de cal na possível formação de silicato dicálcico, Ca 2 SiO 4 e tricálcico, Ca 3 SiO 5 , conforme Equações 15 e 16 e formação de aluminato tricálcico, Ca 3 Al 2 O 6 , Equação 17.
2 CaO SiO 2 Ca 2 SiO 4 (15)
CaO Ca 2 SiO 4 Ca 3 SiO 5 (16)
3 CaO Al 2 O 3 Ca 3 Al 2 O 6 (17)
Como primeira parte do estudo foi avaliado o comportamento da decomposição do carbonato de sódio em função da elevação de temperatura.
Para isso, verificamos o comportamento da reação de calcinação através do cálculo da energia Livre de Gibbs, pela Equação 3, com o auxilio das Equações 4 e 5.
Os coeficientes necessários para a realização dos cálculos estão relacionados na Tabela 2. O gráfico exposto na Figura 4 mostra o comportamento da energia livre de Gibbs para a reação representada pela Equação 9.
A faixa de temperatura analisada foi de 500-850ºC, que compreende a faixa onde a reação de calcinação começa a formar óxido de cálcio e a temperatura onde a calcinação é máxima.
Figura 4 – Comportamento da energia livre de Gibbs em função da temperatura.
Calculado a energia livre de Gibbs, foi determinado o valor da constante de equilíbrio para a reação de calcinação (KCO2) pela Equação 8 em função da temperatura utilizando-se da Equação 9.
Os valores obtidos para a constante de equilíbrio para a reação de decomposição do carbonato de cálcio estão apresentados na Figura 5.
Figura 5 – Comportamento da constante de equilíbrio, K, em função da temperatura.
Foi estudado o comportamento da constante de equilíbrio para a decomposição do carbonato de cálcio, sendo efetuado o cálculo da taxa de conversão do óxido de cálcio formado através da Equação 10.
Os valores obtidos estão expressos no gráfico apresentado na Figura 6.
Figura 6- Taxa de formação de óxido de cálcio em função da temperatura.
Para o estudo do tempo necessário para a ocorrência da reação de calcinação do carbonato de cálcio foi utilizada a Equação 14, sendo que os valores dos parâmetros cinéticos de A e EA (Mastorakos et al, 1999), estão apresentados na Tabela 3.
Tabela 3- Parâmetros cinéticos para a reação de calcinação.
(1/s)
Ea (kJ/ kmol) 108 175728
O resultado obtido no gráfico da Figura 7 mostra o efeito da temperatura da zona de calcinação no tempo de decomposição do carbonato de cálcio.
Após a análise da reação de decomposição do carbonato de cálcio, foi estudada a reação do óxido de cálcio formado com alguns dos contaminantes presentes na lama de cal.
Figura 7- Variação do tempo de decomposição do carbonato de cálcio.
Conforme a Tabela 2, a lama de cal apresenta alguns contaminantes como alumínio, silício e ferro todos na forma de óxidos. Esses contaminantes presentes na lama podem reagir com o óxido de cálcio livre formando silicato dicálcico, silicato tricálcico e aluminato tricálcico segundo as respectivas reações apresentadas nas Equações 15, 16 e 17.
A faixa de temperatura para que possam ocorrer às reações de formação dos silicatos e aluminato acima citadas estão apresentadas na Tabela 4 e foram reportadas por Bye e Ghosh (1983) apud Santos (2007).
Figura 6, vemos que a taxa de conversão de carbonato de cálcio em óxido de cálcio tem forte influência da temperatura, sendo que essa ocorre de forma extremamente rápida acima de 800ºC.
O tempo de decomposição do carbonato processa de maneira muita rápida, conforme mostra a Figura 7, em temperaturas superiores a 800ºC.
Nota-se, pelos gráficos representados pela Figuras 8, 9 e 10, respectivamente, que se a temperatura da cal formada permanecer acima de 900ºC por certo tempo de retenção, pode haver a formação de silicatos e aluminatos conforme as reação apresentadas pelas Equações 15,16 e 17 sendo que, para a formação do silicato dicálcico a formação inicia-se se a temperatura da cal formada permanecer acima de 900ºC com tempo de retenção adequado. O mesmo pode ocorrer se a temperatura da cal formada permanecer acima de 1175ºC, aproximadamente, para a formação do aluminato tricálcico. Para a formação do silicato tricálcico, a possibilidade de sua formação ocorre se a temperatura da cal formada permanecer acima de 1500ºC, temperatura que poderá ser atingida somente quando a utilização de óleo combustível como fonte de calor.
Através do estudo da cinética química envolvida na reação de calcinação, pode-se definir a temperatura ideal para controlar a melhor taxa de conversão para a obtenção do óxido de cálcio evitando assim faixas de temperatura que contribuam para a formação de inertes na cal recuperada.
Os autores agradecem à Fundação de Amparo à Pesquisa do Estado de Minas Gerais - FAPEMIG pelo suporte financeiro.
BRACELPA – Associação Brasileira de Celulose e Papel. Disponível em: www.bracelpa.org.br/bra/index.html. Acesso em 06 de abril de 2010.
MAHAN, B., M. e MYERS, R. J. Química – um curso universitário. Tradução da 4ª Edição Americana. Editora Edgard Blücher Ltda. São Paulo. SP 2000.
MASTORAKOS, E., et al. , CFD. Predictions for Cement Kilns Including FlameModelling, Heat Transfer and Clínquer Chemestry. Applies Mathematical Modelling 23, p. 55 - 76,
MORAN, M. L.; SHAPIRO, H. N. Princípios de termodinâmica para engenharia. Rio de Janeiro: Editora LTC,
PASTOR, J.F.C; HORTAL, J.A.G. El proceso al sulfato. Universidad Politecnica de Cataluna, Cataluna, Spain, 1990
SANTOS, A. R., A geração de coque de petróleo devido ao processamento de petróleos pesados e o seu uso na produção de clínquer de cimento Portland. Tese de Doutorado. Universidade Federal de Itajubá, MG, 2007.
VENKATESH, V.; et al. Chemical Recovery in the Alkaline Pulping Processes. Papermaking Science and Technology, Helsinki, 2001.