
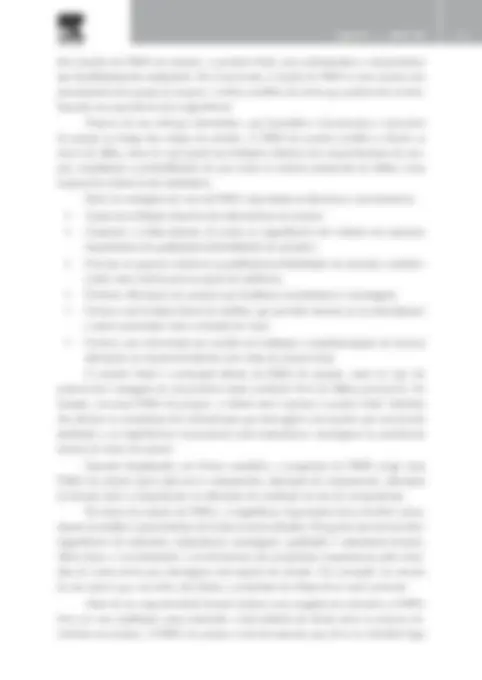
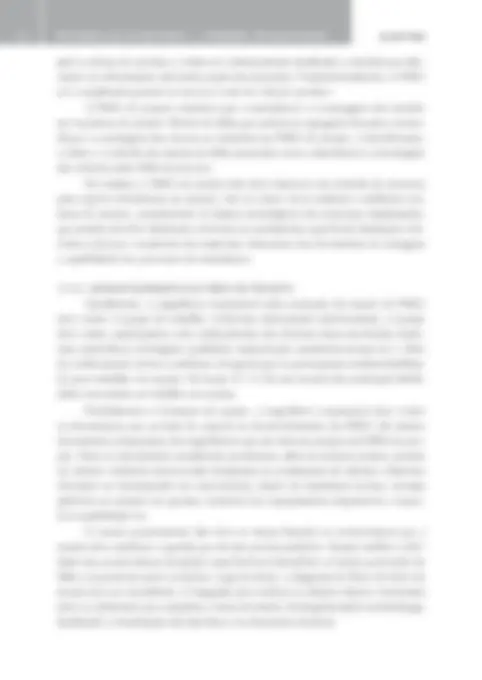
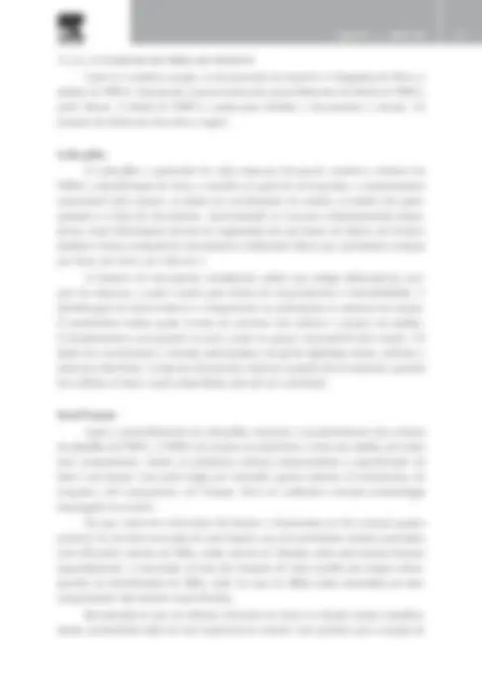
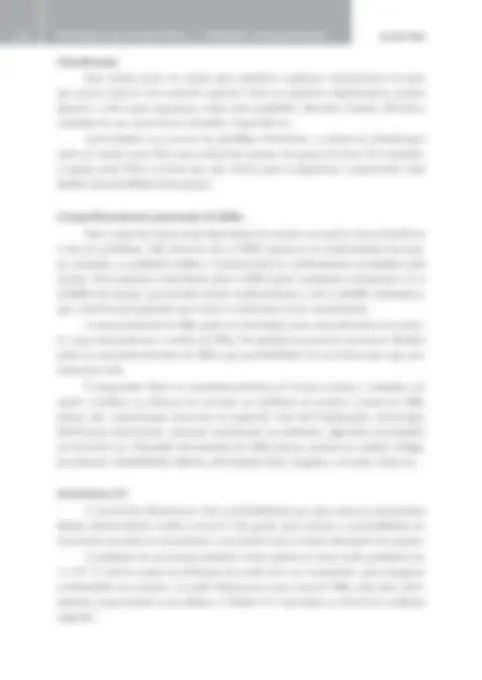
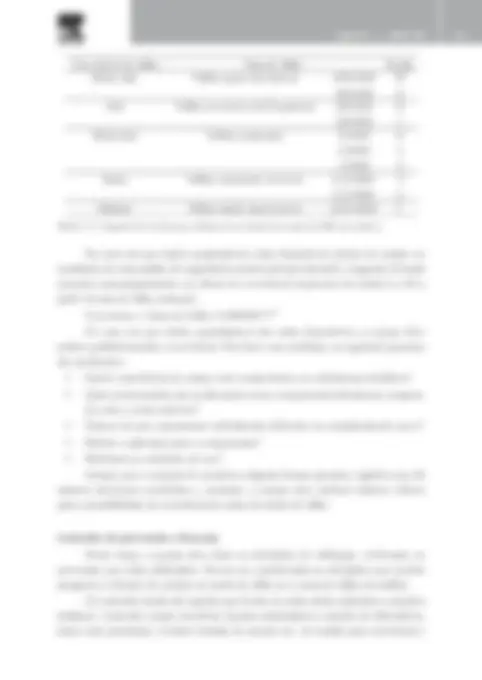
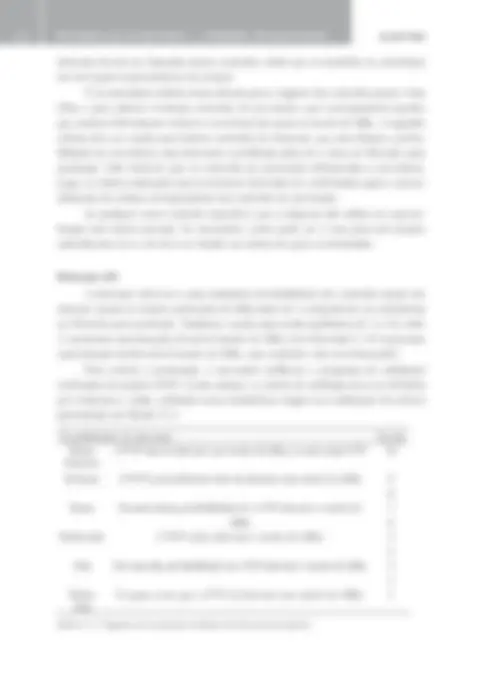
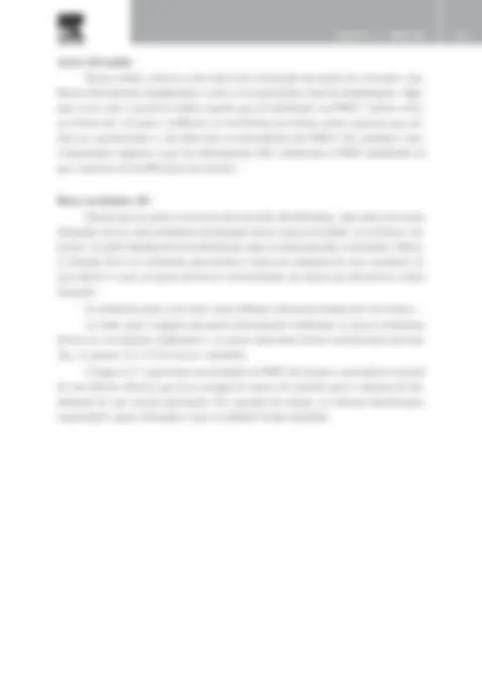
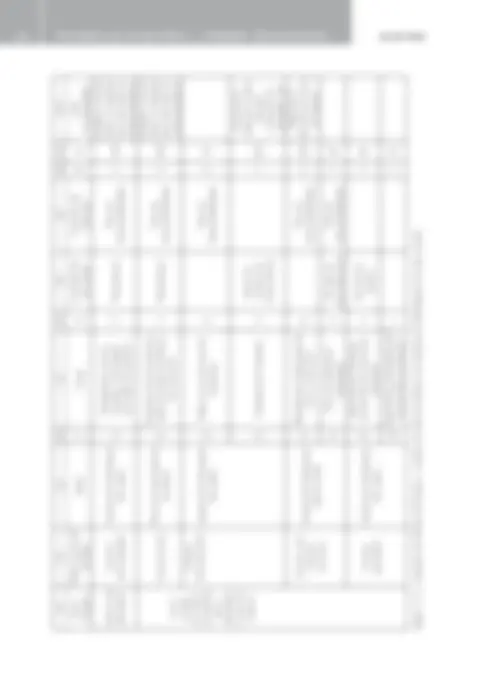
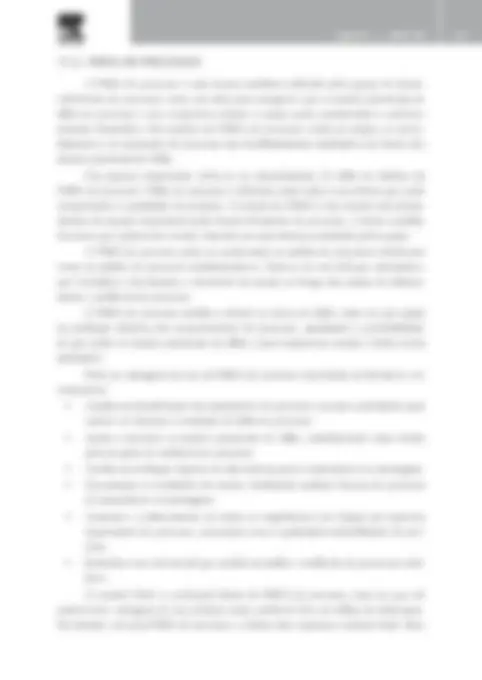
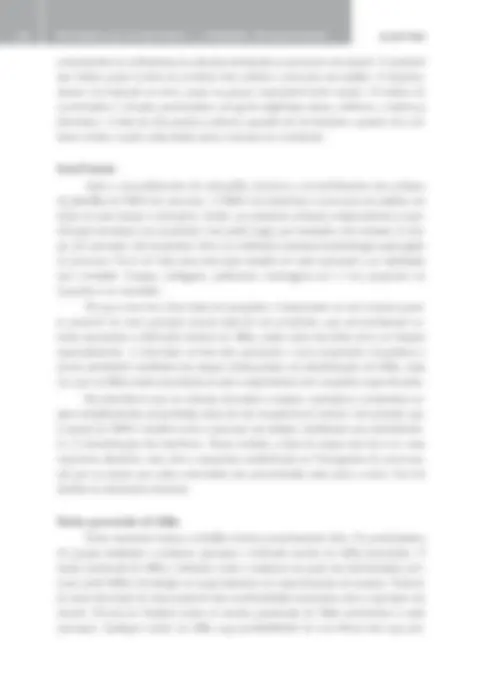
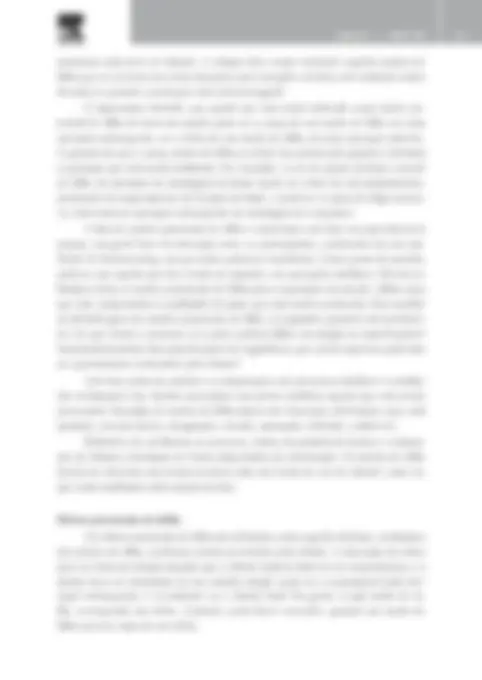
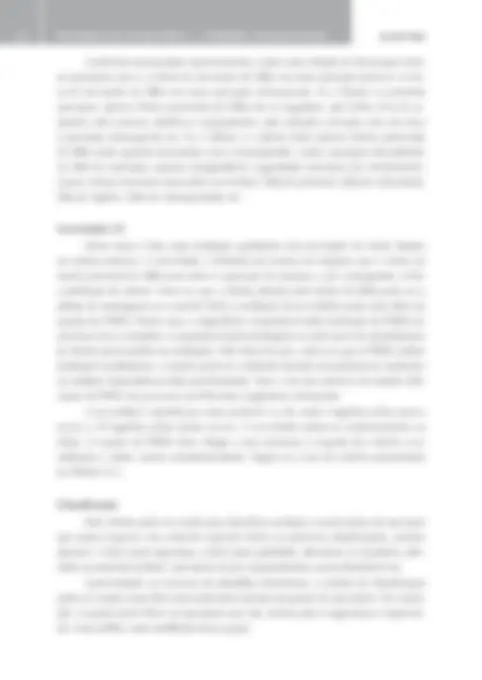
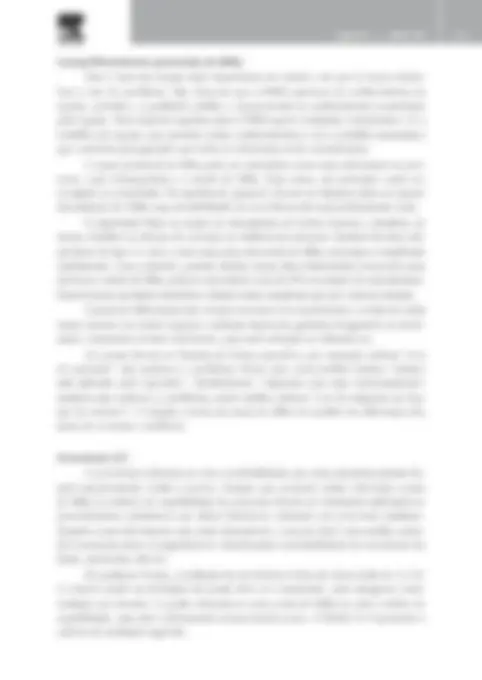
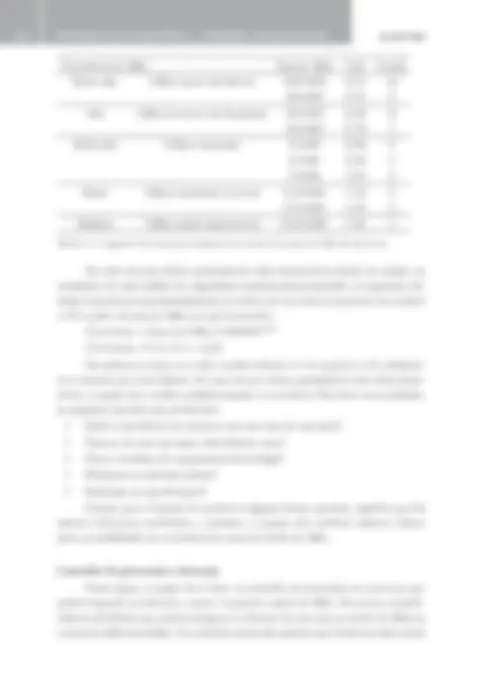
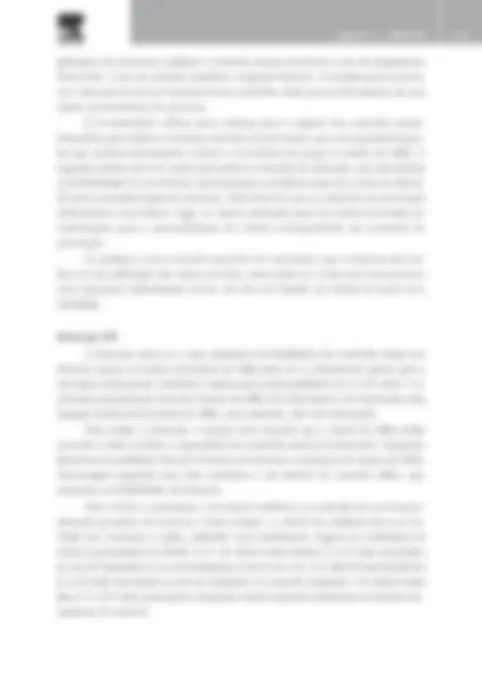
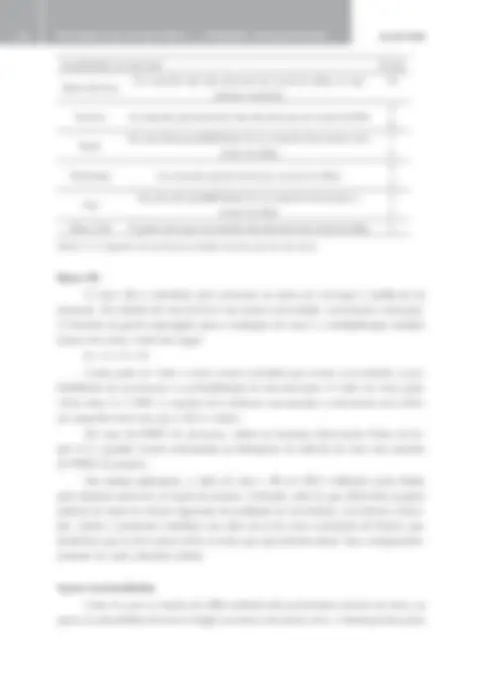
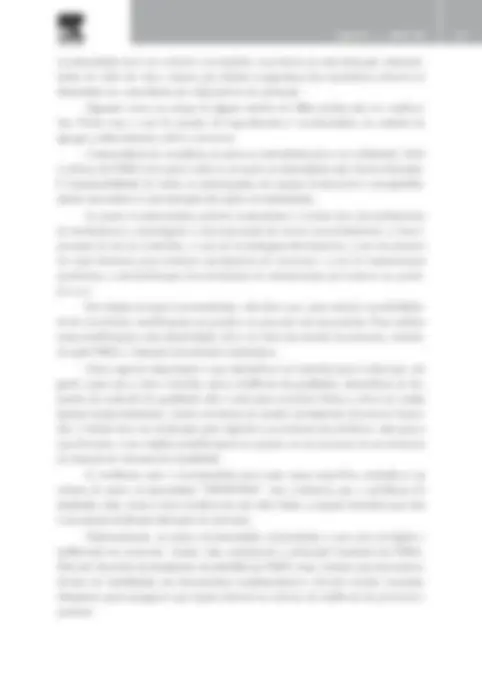
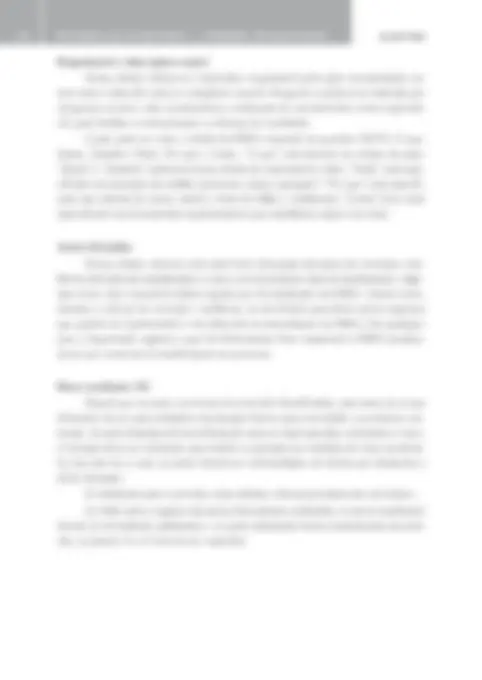
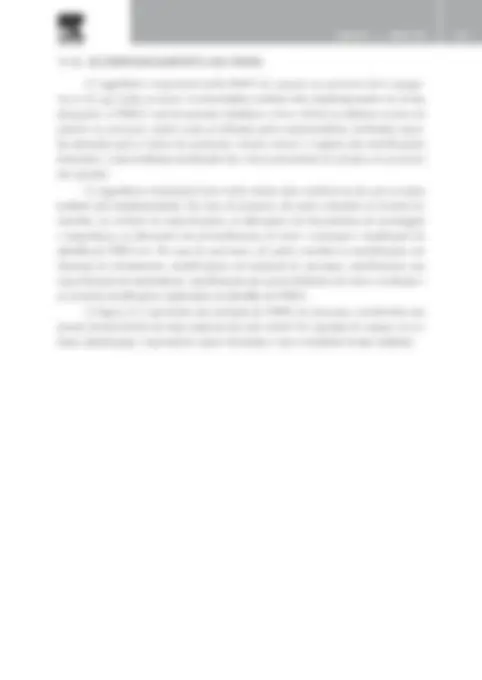
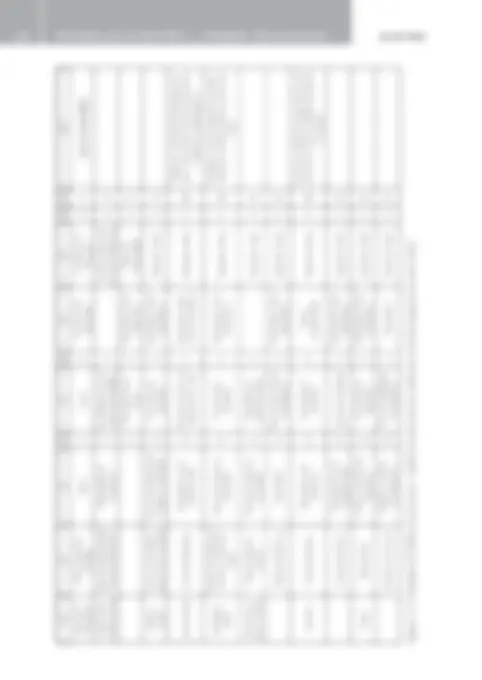
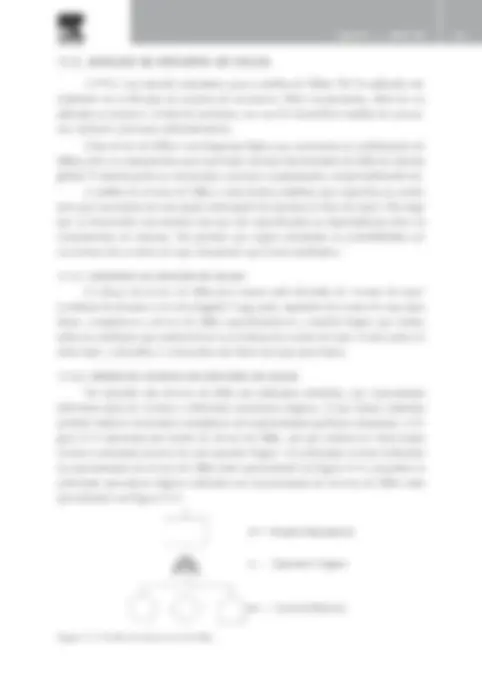
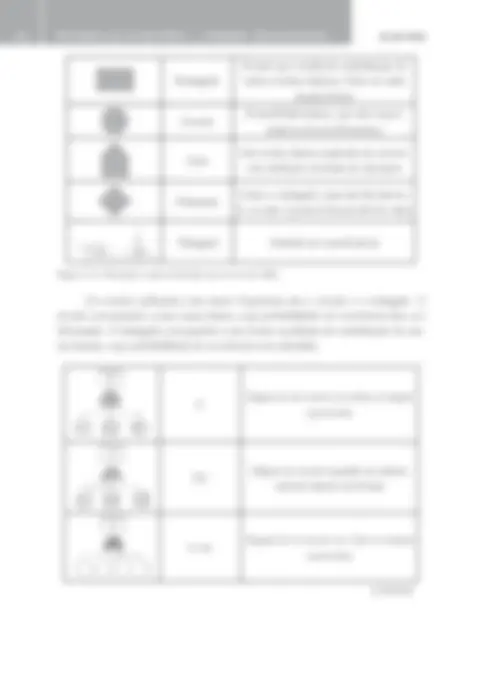
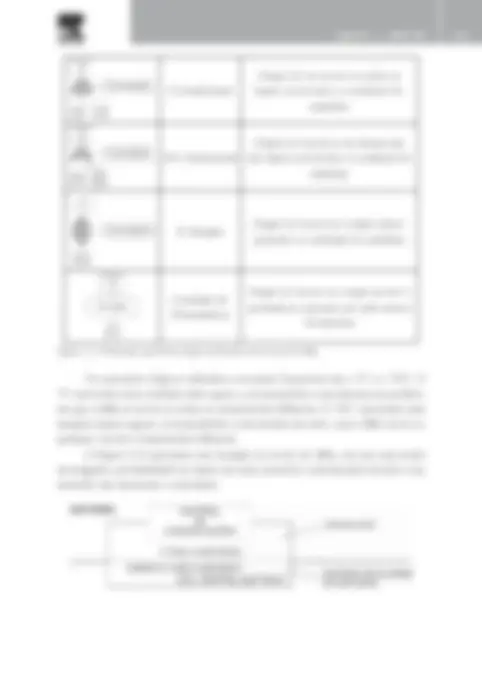
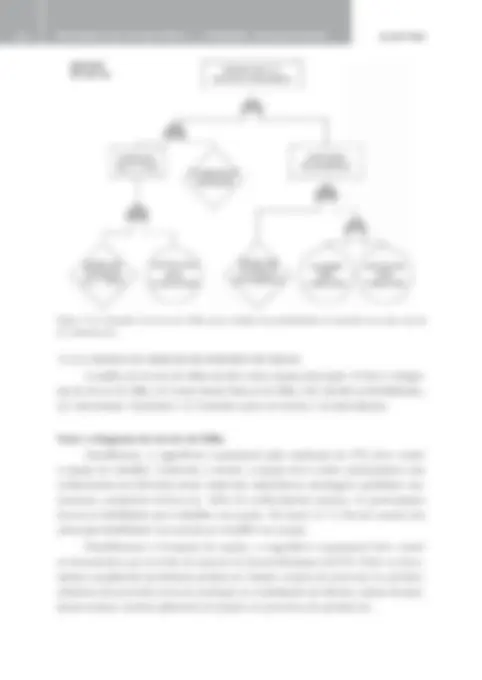

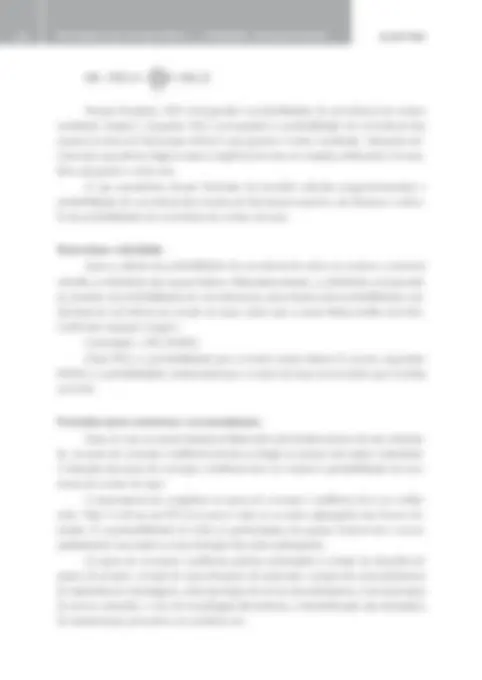
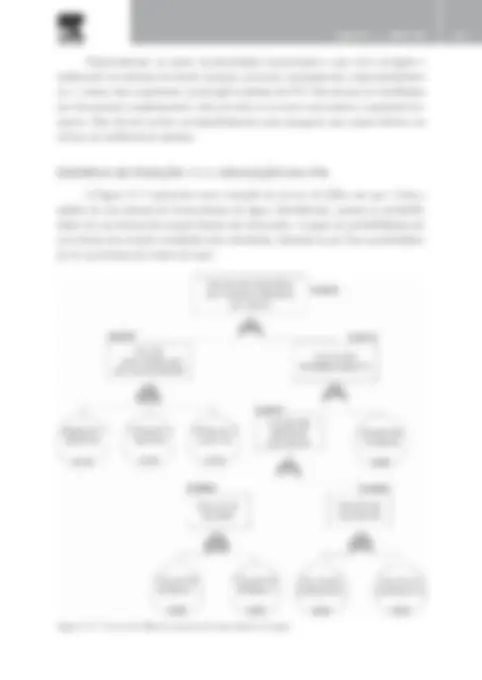
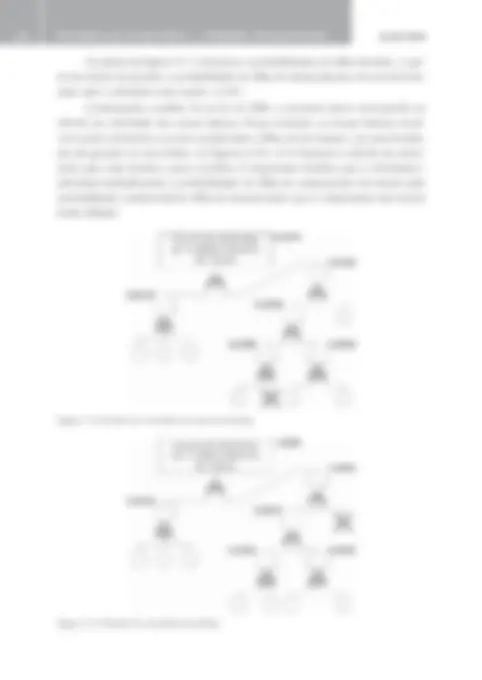
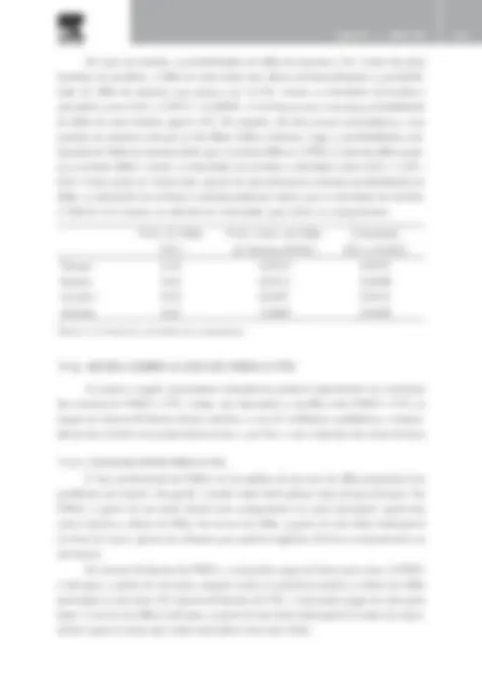
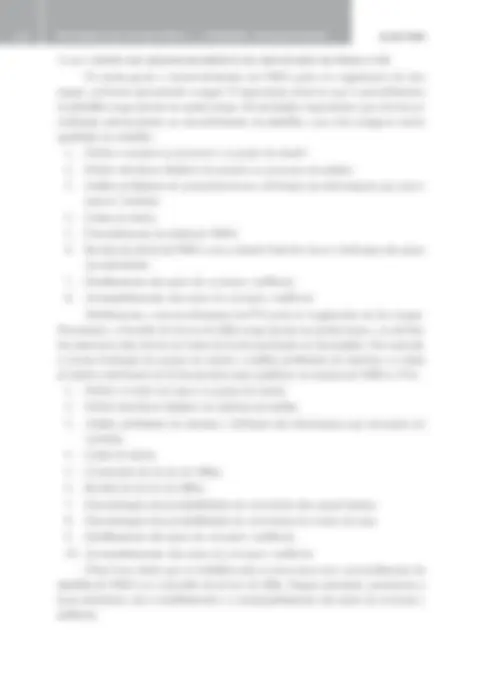
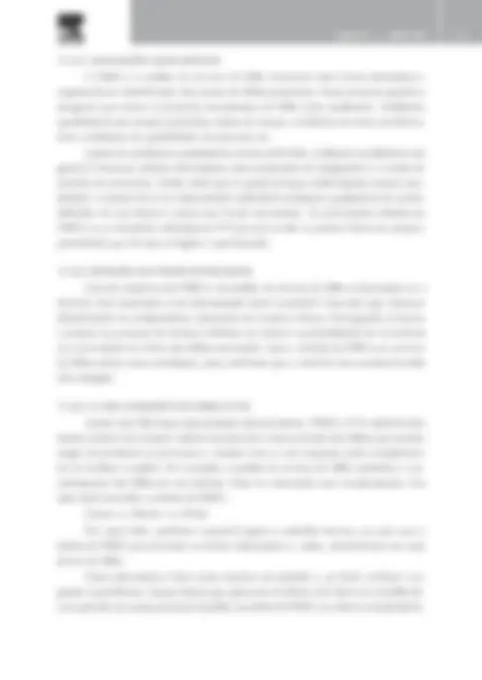
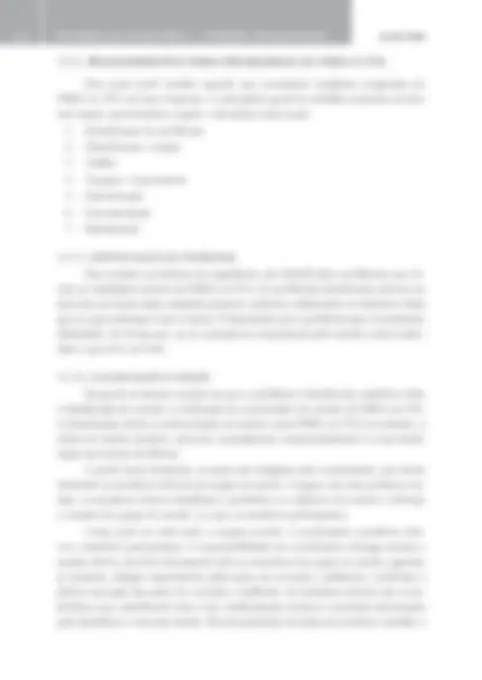
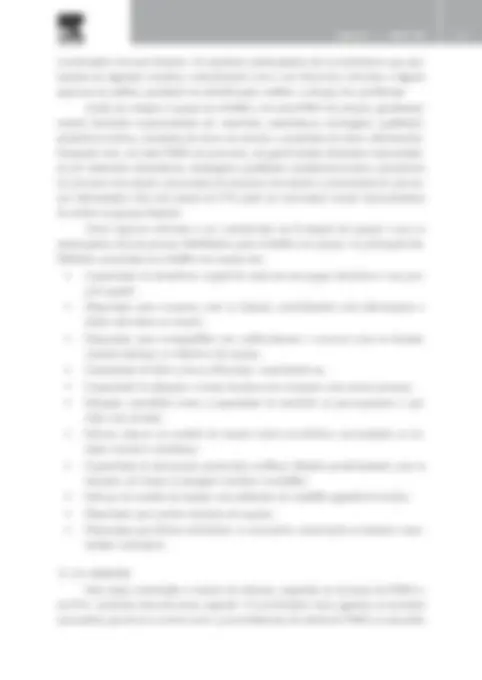
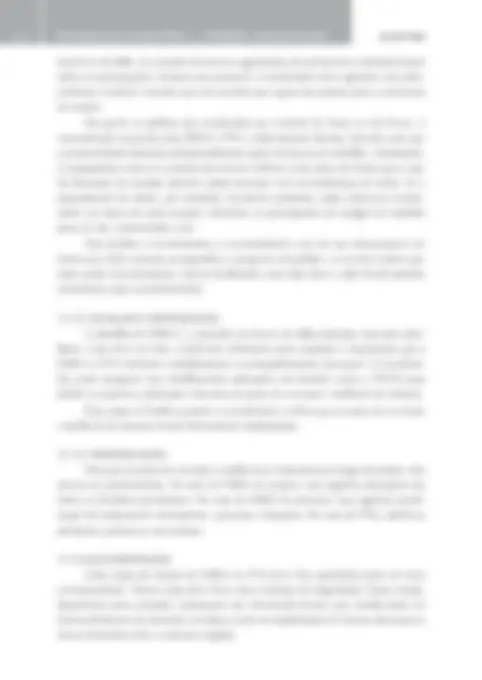
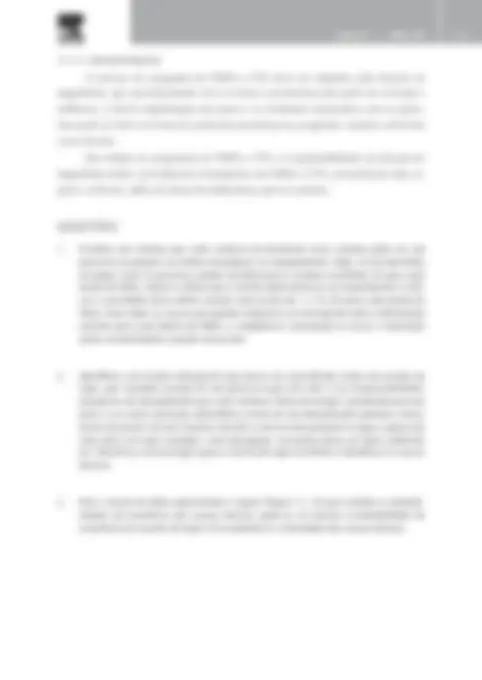

Estude fácil! Tem muito documento disponível na Docsity
Ganhe pontos ajudando outros esrudantes ou compre um plano Premium
Prepare-se para as provas
Estude fácil! Tem muito documento disponível na Docsity
Prepare-se para as provas com trabalhos de outros alunos como você, aqui na Docsity
Os melhores documentos à venda: Trabalhos de alunos formados
Prepare-se com as videoaulas e exercícios resolvidos criados a partir da grade da sua Universidade
Responda perguntas de provas passadas e avalie sua preparação.
Ganhe pontos para baixar
Ganhe pontos ajudando outros esrudantes ou compre um plano Premium
Comunidade
Peça ajuda à comunidade e tire suas dúvidas relacionadas ao estudo
Descubra as melhores universidades em seu país de acordo com os usuários da Docsity
Guias grátis
Baixe gratuitamente nossos guias de estudo, métodos para diminuir a ansiedade, dicas de TCC preparadas pelos professores da Docsity
Exemplos de como fazer e aplicar o FMA e FTA
Tipologia: Manuais, Projetos, Pesquisas
Oferta por tempo limitado
Compartilhado em 28/10/2019
5
(3)1 documento
1 / 44
Esta página não é visível na pré-visualização
Não perca as partes importantes!
Em oferta
Este capítulo apresenta as técnicas de FMEA e FTA. Após uma breve introdu- ção, a FMEA de projeto e a FMEA de processo são apresentadas. O material referente a FMEA baseia-se na QS-9000 (2005) e é enriquecido com comentários e observa- ções oriundas da experiência prática dos autores no uso dessas técnicas. Em seguida, é feita a apresentação da FTA, indicando seus passos e formulário de cálculo. O capítulo é finalizado discutindo-se o uso conjunto dessas técnicas e estabelecendo procedimentos para a implantação de programas de FMEA e FTA.
A garantia da qualidade exige excelência em projeto e excelência em proces- sos. A excelência em projeto implica potencial para a qualidade. A excelência em processo transforma esse potencial em qualidade real. Como será visto neste capí- tulo, FMEA e FTA são técnicas que auxiliam na busca por excelência em projeto e processo.
A FMEA ( Failure Mode and Effects Analysis ou Análise dos Modos e Efeitos de Falha) é uma técnica de confiabilidade que tem como objetivos: (i) reconhecer e ava- liar as falhas potenciais que podem surgir em um produto ou processo, (ii) identificar ações que possam eliminar ou reduzir a chance de ocorrência dessas falhas, e (iii) documentar o estudo, criando um referencial técnico que possa auxiliar em revisões e desenvolvimentos futuros do projeto ou processo. A FTA ( Failure Tree Analysis ou Análise de Árvores de Falha) é uma técnica de confiabilidade que tem como objetivos: (i) partindo de um evento de topo, indese-
174 Flavio Fogliatto e José Luis Duarte Ribeiro^ |^ Confiabilidade e Manutenção Industrial^ ELSEVIER
jável, identifi car todas as combinações de causas que podem originá-lo; (ii) estudar a probabilidade de ocorrência dessas causas, e em função disso, do evento de topo; (iii) priorizar ações que visam bloquear essas causas. É importante entender que os engenheiros sempre analisaram os seus produtos e processos usando um raciocínio similar àquele da FMEA e FTA. Contudo, essas for- mas de raciocínio consolidaram-se como técnica a partir da década de 1960, quando ocorreram as primeiras aplicações na indústria aeronáutica. Atualmente, o comprome- timento das empresas dos diversos segmentos com a melhoria contínua de seus produ- tos e processos torna fundamental a aplicação regular de técnicas como FMEA e FTA. Essas técnicas revelam os pontos fracos do sistema e, assim, fornecem subsí- dios para as atividades de melhoria contínua. FMEA e FTA têm a vantagem de siste- matizarem o diagnóstico de produtos e processos. Essas técnicas auxiliam a detectar e eliminar possíveis ocorrências de falha e fornecem uma hierarquia de prioridades para as ações. A aplicação da FMEA e FTA ocorre em equipes multifuncionais. A responsa- bilidade pela condução de um estudo de FMEA e FTA deve ser delegada a um indi- víduo, mas o estudo em si deve ser feito por uma equipe. Em geral, a equipe deve conter engenheiros com conhecimento de projeto, desenvolvimento de fornecedo- res, manufatura, qualidade, confiabilidade, vendas e assistência técnica. Um fator importante para o sucesso dos programas de FMEA e FTA é a lo- calização temporal dos estudos. Sempre que possível, os estudos devem ser feitos antes do evento , e não após a ocorrência da falha. Os estudos de FMEA e FTA têm muito maior valor agregado quando são executados antes que um modo potencial de falha tenha sido inadvertidamente incorporado ao projeto ou processo. A aplica- ção de FMEA ou FTA nas fases iniciais do projeto permite que eventuais mudanças sejam implementadas com maior facilidade, bloqueando crises futuras. Além disso, os estudos de FMEA e FTA reduzem a possibilidade de implementar alterações que venham a criar problemas no futuro. Idealmente, os estudos de FMEA e FTA têm uma natureza cíclica, acompa- nhando as atividades de melhoria contínua de produtos e processos. O mundo atual é caracterizado por inovações que acontecem com frequência crescente. Novas espe- cificações, novos materiais, novas tecnologias surgem dia a dia. Num ambiente como esse, em que mudança e evolução passam a ser regras, técnicas como FMEA e FTA tornam-se ainda mais importantes.
A FMEA de projeto é uma técnica analítica utilizada pela equipe ou enge- nheiro de projeto como um meio para assegurar que os modos potenciais de falha e seus respectivos efeitos e causas serão considerados e suficientemente discutidos.
176 Flavio Fogliatto e José Luis Duarte Ribeiro^ |^ Confiabilidade e Manutenção Industrial^ ELSEVIER
após o esboço do produto, e então ser continuamente atualizado, à medida que alte- rações ou informações adicionais sejam incorporadas. Fundamentalmente, a FMEA só é completada quando se encerra o ciclo de vida do produto. A FMEA de projeto considera que a manufatura e a montagem irão atender aos requisitos do projeto. Modos de falha que podem ser agregados durante a manu- fatura e a montagem não devem ser incluídos na FMEA de projeto. A identificação, o efeito e o controle dos modos de falha associados com a manufatura e a montagem são cobertos pela FMEA de processo. No entanto, a FMEA de projeto não deve basear-se em controle do processo para superar deficiências no projeto. Em vez disso, deve enfatizar a melhoria con- tínua do projeto, considerando os limites tecnológicos dos processos implantados, que podem envolver limitações referentes ao acabamento superficial, limitações refe- rentes à dureza e resistência dos materiais, dimensões das ferramentas de usinagem e capabilidade dos processos de manufatura.
11.2.1. DESENVOLVIMENTO DA FMEA DE PROJETO Inicialmente, o engenheiro responsável pela condução do estudo de FMEA deve reunir a equipe de trabalho. Conforme mencionado anteriormente, a equipe deve conter participantes com conhecimento das diversas áreas envolvidas (mate- riais, manufatura, montagem, qualidade, manutenção, assistência técnica etc.). Além do conhecimento técnico, também é desejável que os participantes tenham habilida- de para trabalhar em equipe. Na Seção 11.7.2, há um resumo das principais habili- dades necessárias ao trabalho em equipe. Paralelamente à formação da equipe, o engenheiro responsável deve reunir os documentos que servirão de suporte ao desenvolvimento da FMEA. Há muitos documentos à disposição dos engenheiros que são úteis no preparo da FMEA de pro- jeto. Entre os documentos usualmente pertinentes, além do próprio projeto, podem ser citados: relatórios descrevendo demandas ou reclamações de clientes, relatórios referentes ao desempenho da concorrência, dados da assistência técnica, normas aplicáveis ao projeto em questão, sumários dos equipamentos disponíveis e respec- tiva capabilidade etc. O estudo propriamente dito deve se iniciar listando as características que o projeto deve satisfazer e aquelas que ele não precisa satisfazer. Quanto melhor a defi- nição das características desejadas, mais fácil será identificar os modos potenciais de falha e as possíveis ações corretivas. Logo de início, o diagrama de bloco do item em estudo deve ser desenhado. O diagrama deve indicar as relações físicas e funcionais entre os elementos que compõem o item em estudo, homogeneizando terminologia, facilitando a visualização das interfaces e as discussões técnicas.
Capítulo 11 | FMEA e FTA (^) 177
11.2.2. A PLANILHA DE FMEA DE PROJETO Uma vez reunida a equipe, os documentos de suporte e o diagrama de bloco, a análise de FMEA, fisicamente caracterizada pelo preenchimento da tabela de FMEA, pode iniciar. A tabela de FMEA é usada para facilitar e documentar o estudo. Os campos da tabela são descritos a seguir.
Cabeçalho O cabeçalho é particular de cada empresa. Em geral, contém o número da FMEA, a identificação do item, o modelo ao qual ele corresponde, o departamento responsável pelo estudo, os dados do coordenador do estudo, os dados dos parti- cipantes e a data do documento. Aproveitando os recursos computacionais dispo- níveis, essas informações devem ser registradas em um banco de dados, de forma a facilitar a busca avançada de documentos (utilizando filtros que permitam a seleção por item, por setor, por data etc.).
O número do documento usualmente utiliza um código alfanumérico pró- prio da empresa, o qual é usado para efeitos de arquivamento e rastreabilidade. A identificação do item esclarece o componente ou subsistema ou sistema em estudo. O modelo/ano indica quais versões do produto irão utilizar o projeto em análise. O departamento corresponde ao setor, seção ou grupo responsável pelo estudo. Os dados do coordenador e demais participantes em geral englobam nome, telefone e endereço eletrônico. A data do documento esclarece quando ele foi iniciado, quando foi a última revisão e qual a data limite para ele ser concluído.
Item/Função
Após o preenchimento do cabeçalho, inicia-se o preenchimento das colunas da planilha de FMEA. A FMEA de projeto irá desdobrar o item em análise em todos seus componentes. Assim, as primeiras colunas compreendem a especificação do item e sua função. Isso pode exigir, por exemplo, quatro colunas: (i) subsistema, (ii) conjunto, (iii) componente, (iv) função. Deve ser utilizada a mesma terminologia empregada no projeto. No que concerne à descrição da função, é importante ser tão concisa quanto possível. Se um item tem mais de uma função, que provavelmente estarão associadas com diferentes modos de falha, então devem ser listadas cada uma dessas funções separadamente. A descrição correta das funções do item auxilia nas etapas subse- quentes de identificação de falha, uma vez que as falhas estão associadas ao não- cumprimento das funções especificadas.
Recomenda-se que as colunas referentes ao item ou função sejam completa- mente preenchidas antes de dar sequência ao estudo. Isso permite que a equipe de
Capítulo 11 | FMEA e FTA (^) 179
o cliente pode observar ou experimentar, lembrando que o cliente pode ser interno ou externo. Os efeitos devem ser estabelecidos em termos do item específico que está sen- do analisado. Conforme mencionado, existe uma relação de hierarquia entre os com- ponentes. Por exemplo, o componente 1 pode quebrar por fratura, o que vai causar afrouxamento no componente 2, resultando em operação intermitente do sistema. A operação intermitente significa uma queda de desempenho e leva à insatisfação do cliente. Se o foco do estudo é o componente 2, então afrouxamento é o modo de falha, e operação intermitente (percebida pelo usuário) é o efeito do modo de falha. Típicos efeitos potenciais de falha são: ruído, aspecto desagradável, vibração, folga, operação intermitente, falta de operação, odor desagradável etc.
Severidade (S)
Neste item é feita uma avaliação qualitativa da severidade do efeito listado na coluna anterior. Vale observar que, uma vez que a FMEA utiliza avaliações qualitati- vas, o estudo pode ser realizado mesmo na ausência de medições ou análises mate- máticas mais aprofundadas. Esse é um dos motivos da ampla utilização da FMEA em diferentes segmentos industriais. A severidade é medida por uma escala de 1 a 10, onde 1 significa efeito pouco severo e 10 significa efeito muito severo. A severidade aplica-se exclusivamente ao efeito. A equipe de FMEA deve chegar a um consenso a respeito do critério a ser utilizado e, então, usá-lo consistentemente. Sugere-se o uso do critério apresentado na Tabela 11.1.
Severidade do efeito Escala Muito alta Quando compromete a segurança da operação ou envolve infração a regulamentos governamentais
10 9 Alta Quando provoca alta insatisfação do cliente, por exemplo, um veículo ou aparelho que não opera, sem comprometer a segurança ou implicar infração
8 7
Moderada Quando provoca alguma insatisfação, devido à queda do desem- penho ou mau funcionamento de partes do sistema
6 5 Baixa Quando provoca uma leve insatisfação, o cliente observa apenas uma leve deterioração ou queda no desempenho
4 3 Mínima Falha que afeta minimamente o desempenho do sistema, e a maioria dos clientes talvez nem mesmo note sua ocorrência
2 1
Tabela 11.1: Sugestão de escala para avaliação dos efeitos dos modos de falha.
180 Flavio Fogliatto e José Luis Duarte Ribeiro^ |^ Confiabilidade e Manutenção Industrial^ ELSEVIER
Classificação Esta coluna pode ser usada para classificar qualquer característica do item que possa requerer um controle especial. Entre as possíveis classificações, podem aparecer: crítico para segurança, crítico para qualidade, alterada a função, alterada a condição de uso, itens novos (desenho / material) etc. Aproveitando os recursos de planilhas eletrônicas, a coluna de classificação pode ser usada como filtro para selecionar apenas um grupo de itens. Por exemplo, a equipe pode filtrar os itens que são críticos para a segurança e empreender uma análise mais detalhada desse grupo.
Causas/Mecanismos potenciais de falha Esta é uma das etapas mais importantes do estudo, na qual se busca identificar a raiz do problema. Vale observar que a FMEA apoia-se no conhecimento da equi- pe, portanto, a qualidade análise é proporcional ao conhecimento acumulado pela equipe. Dois aspectos contribuem para a FMEA gerar resultados consistentes: (i) o trabalho em equipe, que permite somar conhecimentos, e (ii) o trabalho sistemático, que contribui para garantir que todos os elementos serão considerados. A causa potencial de falha pode ser entendida como uma deficiência no proje- to, cuja consequência é o modo de falha. Na medida do possível, devem ser listadas todas as causas/mecanismos de falha cuja probabilidade de ocorrência não seja pra- ticamente nula. É importante listar as causas/mecanismos de forma concisa e completa, de modo a facilitar os esforços de correção ou melhoria do projeto. Causas de falha típicas são: especificação incorreta de material, vida útil inadequada, sobrecarga, lubrificação insuficiente, proteção insuficiente ao ambiente, algoritmo incompleto ou incorreto etc. Enquanto mecanismos de falha típicos, podem ser citados: fadiga, escoamento, instabilidade elástica, deformação lenta, desgaste, corrosão, fusão etc.
Ocorrência (O) A ocorrência relaciona-se com a probabilidade que uma causa ou mecanismo listado anteriormente venha a ocorrer. Em geral, para reduzir a probabilidade de ocorrência da causa ou mecanismo, é necessário que se façam alterações no projeto. A avaliação da ocorrência também é feita usando-se uma escala qualitativa de 1 a 10. O critério usado na definição da escala deve ser consistente, para assegurar continuidade nos estudos. A escala relaciona-se com a taxa de falha, mas não é dire- tamente proporcional a esta última. A Tabela 11.2 apresenta o critério de avaliação sugerido.
182 Flavio Fogliatto e José Luis Duarte Ribeiro^ |^ Confiabilidade e Manutenção Industrial^ ELSEVIER
detecção devem ser baseadas nesses controles, dado que os modelos ou protótipos em uso sejam representativos do projeto. É recomendado utilizar duas colunas para o registro dos controles atuais. Uma delas é para indicar eventuais controles de prevenção, que correspondem àqueles que podem efetivamente reduzir a ocorrência da causa ou modo de falha. A segunda coluna deve ser usada para indicar controles de detecção, que não afetam a proba- bilidade de ocorrência, mas detectam o problema antes de o item ser liberado para produção. Vale observar que os controles de prevenção influenciam a ocorrência. Logo, os valores indicados para ocorrência deveriam ser confirmados após o preen- chimento da coluna correspondente aos controles de prevenção. Se qualquer outro controle específico, que a empresa não utiliza ou cuja uti- lização não estava prevista, for necessário, como pode ser o caso para um projeto radicalmente novo, ele deve ser listado na coluna de ações recomendadas.
Detecção (D) A detecção refere-se a uma estimativa da habilidade dos controles atuais em detectar causas ou modos potenciais de falha antes de o componente ou subsistema ser liberado para produção. Também é usada uma escala qualitativa de 1 a 10, onde 1 representa uma situação favorável (modo de falha será detectado) e 10 representa uma situação desfavorável (modo de falha, caso existente, não será detectado). Para reduzir a pontuação, é necessário melhorar o programa de validação/ verificação do projeto (PVP). Como sempre, o critério de avaliação deve ser definido por consenso e, então, utilizado com consistência. Sugere-se a utilização do critério apresentado na Tabela 11.3. Possibilidade de detecção Escala Muito Remota
O PVP não irá detectar esse modo de falha, ou não existe PVP 10
Remota O PVP provavelmente não irá detectar esse modo de falha 9 8 Baixa Há uma baixa probabilidade de o PVP detectar o modo de falha
Moderada O PVP pode detectar o modo de falha 5 4 Alta Há uma alta probabilidade de o PVP detectar o modo de falha 3 2 Muito Alta
É quase certo que o PVP irá detectar esse modo de falha 1
Tabela 11.3: Sugestão de escala para avaliação da detecção em projetos.
Capítulo 11 | FMEA e FTA (^) 183
Risco (R) O risco (R) é calculado para priorizar as ações de correção e melhoria do projeto. No cálculo do risco leva-se em conta a severidade, ocorrência e detecção. A fórmula em geral empregada para a avaliação do risco é a multiplicação simples desses três itens, conforme segue: R = S × O × D Como pode ser visto, o risco cresce à medida que cresce a severidade, a pro- babilidade de ocorrência e a probabilidade de não detecção. O valor do risco pode variar entre 1 e 1.000, e a equipe deve deslocar sua atenção e concentrar seus esfor- ços naqueles itens em que o risco é maior. É importante entender que o valor de risco não segue um comportamento linear. Isso acontece por dois motivos: primeiro, trata-se de um produto (o resultado cresce geometricamente à medida que crescem os valores das parcelas) e, segundo, a escala utilizada para avaliar ocorrência é claramente não linear. Assim, o valor médio de Risco, correspondente a uma situação intermediária de severidade, ocorrência e detecção, não é 500, mas 5 × 5 × 5 = 125. Isso faz com que, em muitas aplicações, o valor de Risco = 80 ou 100 seja utilizado como limite para disparar ações de corre- ção do projeto. Contudo, sabendo que diferentes equipes podem ser mais ou menos rigorosas na avaliação de severidade, ocorrência e detecção, pode ser mais prudente utilizar o princípio de Pareto, atuando nos itens que apresentam maior risco, inde- pendentemente do valor absoluto obtido.
Outro ponto a ser considerado é que se pode obter o mesmo valor de risco para diferentes combinações das parcelas. Existe um consenso na literatura que, para um mesmo valor de risco, é mais grave a situação em que a severidade é maior, segui- da da situação em que a probabilidade de não detecção é maior. Também é consenso na literatura que a avaliação de risco pode ser aprimorada se existirem informações quantitativas mais precisas. Uma abordagem mais consistente envolveria o cálculo do risco financeiro, calculado como: Risco Financeiro = Perda Financeira × Probabilidade de Ocorrência × Proba- bilidade de não Detecção
Nesse caso, a perda financeira corresponde ao prejuízo associado à ocorrência do modo de falha, que pode implicar substituição de um pequeno componente ou grandes indenizações oriundas de prejuízos materiais, ambientais ou humanos. Já a probabilidade de ocorrência e a probabilidade de não-detecção devem ser expressas percentualmente, enquanto probabilidades concretas. Entretanto, na maioria das aplicações, essas informações mais precisas refe- rentes a perdas financeiras e probabilidades não estão disponíveis ou demandariam muito tempo para serem reunidas. Então, a avaliação qualitativa obtida a partir do
Capítulo 11 | FMEA e FTA (^) 185
Ações efetuadas Nessa coluna, entra-se com uma breve descrição das ações de correção e me- lhoria efetivamente implantadas e com a correspondente data da implantação. Algu- mas vezes, não é possível realizar aquilo que foi idealizado na FMEA. Outras vezes, no esforço de correção e melhoria, os envolvidos percebem outros aspectos que po- dem ser aprimorados e vão além das recomendações da FMEA. Em qualquer caso, é importante registrar o que foi efetivamente feito, mantendo a FMEA atualizada no que concerne às modificações de projeto.
Risco resultante (R) Depois que as ações corretivas tiverem sido identificadas, mas antes de serem efetuadas, faz-se uma estimativa da situação futura para severidade, ocorrência e de- tecção. As ações listadas devem influenciar uma ou mais parcelas, reduzindo o Risco. A redução deve ser suficiente para incluir o item na condição de risco aceitável. Se esse não for o caso, as ações devem ser reformuladas, de modo que alcancem o efeito desejado.
Se nenhuma ação é prevista, essas últimas colunas permanecem em branco. Ao fi nal, após o registro das ações efetivamente realizadas, os riscos resultantes devem ser novamente analisados e, se ações adicionais forem consideradas necessá- rias, os passos 12 a 15 devem ser repetidos.
A Figura 11.1 apresenta um exemplo de FMEA de projeto, associada ao estudo de um chicote elétrico que leva energia do motor de partida para o sistema de ilu- minação de um veículo automotor. Por questão de espaço, as colunas classificação, responsável, ações efetuadas e risco resultante foram omitidas.
186 Flavio Fogliatto e José Luis Duarte Ribeiro^ |^ Confiabilidade e Manutenção Industrial^ ELSEVIER
(2)
(3)
(4)
(5)
(7)
(8)
(9)
(9)
10
(11)
(12)
Item /Função
Modo potencial
de falha
Efeito
S^
Causa
O^
Controles deprevenção
Controles dedetecção
D^
R^
Ação recomendada
Chicote doalternador
Circuito interrompido
Sistema de iluminação
não opera
8
Rompimento de fiosdurante a montagem(por falha de projeto)
5
Treinamento
Teste de funcionabilidade
3
120
Ampliar o uso detubos corrugadospara proteção decantos metálicos
Levarenergiado motorde partidapara oalternadore caixa defusíveis
Curto-circuito
Pane nos instrumentos
do painel
8
Exposição de fios desenca-pados às partes metálicas
da carroceria
5
Treinamento
Teste de funcionabilidade
4
160
Ampliar o uso detubos corrugadospara proteção decantos metálicos
Circuito desconectado
Sistema de iluminação
não opera
8
Falha no uso da trava de
segurança
2
Teste de funcionabilidade
2
32
8
Oxidação de terminais
4
Desenvol-vimento defornecedores
7
224
Desenvolverdispositivo paraprotegerterminais deumidade e pó
Circuito com
conexãoincorreta
Sistema de iluminação
opera errado
8
Identificação inadequada de
fios e conectores
6
Teste de funcionabilidade
5
240
Aprimorar a bancada de testes
de chicote
8
Erro no manual de
montagem
2
Revisão deprocedimentos
Teste de funcionabilidade
3
48
Circuitoqueimado
Sistema de iluminação
não opera
10
Aquecimento demasia-do dos fios por percurso
incorreto
3
Revisão deprojeto
3
90
10
Aquecimento demasiado dosfios por falta de proteção
1
7
70
Figura 11.1: exemplo de FMEA de Projeto – estudo do chicote elétrico do sistema de iluminação de um veículo.
188 Flavio Fogliatto e José Luis Duarte Ribeiro^ |^ Confiabilidade e Manutenção Industrial^ ELSEVIER
bém são clientes os projetistas dos itens que estão sendo processados e os engenhei- ros responsáveis pelo processo subsequente. Quando implantado de forma completa, o programa de FMEA exige um FMEA de processo para cada novo processo, alteração de etapas do processo ou al- teração nas condições de contorno (matérias-primas, mão-de-obra, meio ambiente, métodos, equipamentos). No início do estudo de FMEA, o engenheiro responsável deve envolver ati- vamente na análise representantes de todas as áreas afetadas. Usualmente, isso irá envolver engenheiros de materiais, manufatura, montagem, qualidade e assistência técnica. Além disso, é recomendado o envolvimento dos projetistas responsáveis pelo desenho do item que será processado e dos engenheiros responsáveis pelos pro- cessos que interagem com aquele em estudo (fornecedores e clientes). Por exemplo, no estudo do processo de polimento, o responsável pela usinagem da peça (fornece- dor) e o responsável pela pintura (cliente) deveriam estar presentes. Além de ser uma atividade formal, muitas vezes exigida em contratos, a FMEA deve fomentar o intercâmbio de ideias entre os setores de projeto, manufatura e montagem. A FMEA de processo é um documento que deve ser iniciado logo após o esboço do processo, considerando todas as operações de manufatura, desde a produ- ção dos componentes básicos até a montagem final. Ela auxilia a antecipar, resolver e monitorar preocupações potenciais associadas com a confiabilidade do processo e deve ser continuamente atualizada, acompanhando o ciclo de melhoria contínua (alterações) no processo. A FMEA de processo considera que a produção do item de acordo com o projeto irá atender aos requisitos do cliente. Falhas associadas com deficiências de projeto não devem ser incluídas na FMEA de processo. A identificação, o efeito e o controle dos modos de falha associados com o projeto são cobertos pela FMEA de projeto. No entanto, a FMEA de processo não deve basear-se em mudanças no pro- jeto para superar deficiências no processo. Vale mencionar que a FMEA também pode auxiliar no desenvolvimento de novos equipamentos ou dispositivos para o processo. Nesse caso, o equipamento ou dispositivo é considerado um produto e usa-se a FMEA de projeto para analisar e desenvolver o mesmo.
11.3.1. DESENVOLVIMENTO DA FMEA DE PROCESSO Inicialmente, o engenheiro responsável pela condução do estudo de FMEA deve reunir a equipe de trabalho. Conforme mencionado anteriormente, a equipe deve conter participantes com conhecimento das diversas áreas envolvidas (mate- riais, manufatura, montagem, qualidade, manutenção, assistência técnica etc.). Além do conhecimento técnico, também é desejável que os participantes tenham habilida-
Capítulo 11 | FMEA e FTA (^) 189
de para trabalhar em equipe. Na Seção 11.7.2 há um resumo das principais habilida- des necessárias ao trabalho em equipe. Paralelamente à formação da equipe, o engenheiro responsável deve reunir os documentos que servirão de suporte ao desenvolvimento da FMEA de processo. Há muitos documentos à disposição dos engenheiros que são úteis no preparo da FMEA de processo. Entre os documentos usualmente pertinentes, além do próprio projeto do processo, podem ser citados: descrição das etapas do processo, manuais de treina- mento e operação, manuais de segurança, resumo da capacidade e capabilidade dos equipamentos, especificações a serem atendidas, normas aplicáveis. Quanto melhor a defi nição das especificações a serem atendidas, mais fácil será identificar os modos potenciais de falha e as ações corretivas. O estudo propriamente dito deve iniciar listando as características que o pro- cesso deve satisfazer e aquelas que ele não precisa satisfazer. Quanto melhor a de- finição das características desejadas, mais fácil será identificar os modos potenciais de falha e as possíveis ações corretivas. Logo de início, deve ser feito o desenho do fluxograma do processo, indicando o encadeamento geral das etapas do processo. Esse desenho deve esclarecer a sequência de etapas que compõem o processo, ho- mogeneizando terminologia, facilitando a visualização das interfaces e as discussões técnicas.
11.3.2. A PLANILHA DE FMEA DE PROCESSO Uma vez reunida a equipe, os documentos de suporte e o fluxograma das eta- pas do processo, a análise de FMEA de processo, fisicamente caracterizada pelo pre- enchimento da tabela de FMEA, pode iniciar. A tabela de FMEA é usada para facilitar e documentar o estudo. Os campos da tabela são descritos a seguir.
Cabeçalho O cabeçalho é particular de cada empresa. Em geral, contém o número da FMEA, a identificação do processo, a identifi cação do(s) item(ns) associado(s) ao processo, o modelo ao qual ele corresponde, o departamento responsável pelo estu- do, os dados do coordenador do estudo, os dados dos participantes e a data do do- cumento. Aproveitando os recursos computacionais disponíveis, essas informações devem ser registradas em um banco de dados, de forma a facilitar a busca avançada de documentos (utilizando filtros que permitam a seleção por item, por setor, por data etc.). O número do documento usualmente utiliza um código alfanumérico próprio da empresa, o qual é usado para efeitos de arquivamento e rastreabilidade. A identi- ficação do processo esclarece as etapas em estudo. A identificação do item esclarece o
Capítulo 11 | FMEA e FTA (^) 191
ticamente nula deve ser listado. A relação deve conter inclusive aqueles modos de falha que só ocorrem em certas situações (por exemplo, em dias com umidade muito elevada ou quando a produção está sobrecarregada). É importante entender que aquilo que está sendo indicado como modo po- tencial de falha do item em estudo pode ser a causa de um modo de falha em uma operação subsequente, ou o efeito de um modo de falha em uma operação anterior. A questão do que é causa, modo de falha ou efeito fi ca esclarecida quando é definida a operação que está sendo analisada. Por exemplo, o erro no ajuste da haste é modo de falha da operação de montagem da haste (pode ser efeito de um amassamento, produzido na etapa anterior de furação da haste, e pode ser a causa de folga excessi- va, observada na operação subsequente de montagem do conjunto). A lista de modos potenciais de falha é construída com base na experiência da equipe, em geral fruto da interação entre os participantes, conduzida em um am- biente de brainstorming , em que todos podem se manifestar. Como ponto de partida, pode-se usar aquilo que deu errado no passado, em operações similares. Devem ser listados todos os modos potenciais de falha para a operação em estudo, falhas estas que irão comprometer a qualidade da parte que está sendo produzida. Para auxiliar na identificação dos modos potenciais de falha, as seguintes questões são pertinen- tes: de que forma o processo ou a parte podem falhar em atingir as especificações? Independentemente das especificações de engenharia, que outros aspectos poderiam ser questionados (criticados) pelo cliente?
Um bom ponto de partida é a comparação com processos similares e a análise das reclamações dos clientes associadas com partes similares àquela que está sendo processada. Exemplos de modos de falha típicos são: fissurado, deformado, sujo, mal ajustado, circuito aberto, desgastado, riscado, amassado, dobrado, colado etc. Relatórios de problemas no processo, dados da assistência técnica e reclama- ção de clientes costumam ser fontes importantes de informação. Os modos de falha devem ser descritos em termos técnicos (não em forma de voz do cliente), uma vez que serão analisados pela equipe técnica.
Efeitos potenciais de falha
Os efeitos potenciais de falha são definidos como aqueles defeitos, resultantes dos modos de falha, conforme seriam percebidos pelo cliente. A descrição do efeito deve ser feita em função daquilo que o cliente poderá observar ou experimentar, e o cliente deve ser entendido no seu sentido amplo: pode ser o responsável pela ope- ração subsequente, o revendedor ou o cliente final. Em geral, a cada modo de fa- lha corresponde um efeito. Contudo, pode haver exceções, quando um modo de falha provoca mais de um efeito.
192 Flavio Fogliatto e José Luis Duarte Ribeiro^ |^ Confiabilidade e Manutenção Industrial^ ELSEVIER
Conforme mencionado anteriormente, existe uma relação de hierarquia entre as operações, isto é, o efeito de um modo de falha em uma operação pode ser a cau- sa de um modo de falha em outra operação subsequente. Se o cliente é a próxima operação, típicos efeitos potenciais de falha são os seguintes: não fecha, fora de es- quadro, não conecta, danifica o equipamento, não coincide a furação, põe em risco a operação subsequente etc. Se o cliente é o cliente final, típicos efeitos potenciais de falha serão aqueles associados com o desempenho: ruído, operação intermitente ou falta de operação, aspecto desagradável, rugosidade excessiva (ou insuficiente), requer esforço excessivo para abrir (ou fechar), falta de potência, falta de velocidade, falta de rigidez, falta de estanqueidade etc.
Severidade (S) Neste item é feita uma avaliação qualitativa da severidade do efeito listado na coluna anterior. A severidade é definida em termos do impacto que o efeito do modo potencial de falha tem sobre a operação do sistema e, por conseguinte, sobre a satisfação do cliente. Uma vez que o cliente afetado pelo modo de falha pode ser a planta de montagem ou o usuário final, a avaliação da severidade pode estar além da equipe de FMEA. Nesse caso, o engenheiro responsável pela condução da FMEA de processo deve consultar o responsável pela montagem ou pelo setor de atendimento ao cliente para auxiliar na avaliação. Vale observar que, uma vez que a FMEA utiliza avaliações qualitativas, o estudo pode ser realizado mesmo na ausência de medições ou análises matemáticas mais aprofundadas. Esse é um dos motivos da ampla utili- zação da FMEA de processo em diferentes segmentos industriais. A severidade é medida por uma escala de 1 a 10, onde 1 significa efeito pouco severo e 10 significa efeito muito severo. A severidade aplica-se exclusivamente ao efeito. A equipe de FMEA deve chegar a um consenso a respeito do critério a ser utilizado e, então, usá-lo consistentemente. Sugere-se o uso do critério apresentado na Tabela 11.1.
Classificação Esta coluna pode ser usada para classificar qualquer característica da operação que possa requerer um controle especial. Entre as possíveis classificações, podem aparecer: crítico para segurança, crítico para qualidade, alterados os requisitos, alte- radas as matérias-primas, operações novas (equipamentos, procedimentos) etc. Aproveitando os recursos de planilhas eletrônicas, a coluna de classificação pode ser usada como filtro para selecionar apenas um grupo de operações. Por exem- plo, a equipe pode filtrar as operações que são críticas para a segurança e empreen- der uma análise mais detalhada desse grupo.