
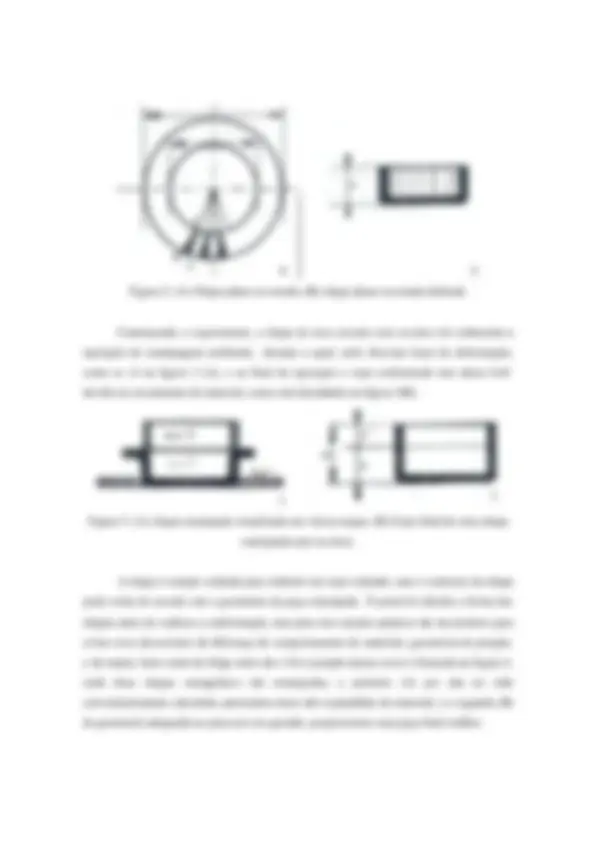
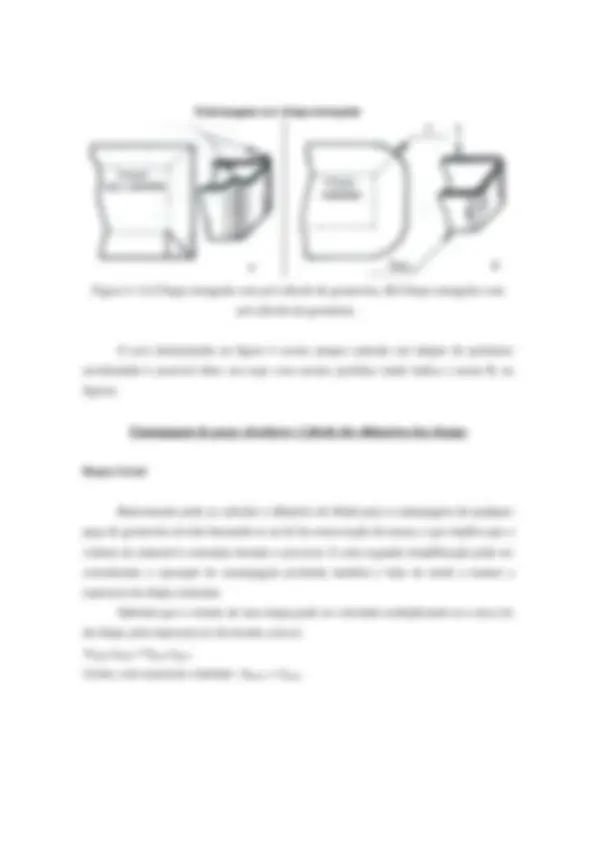
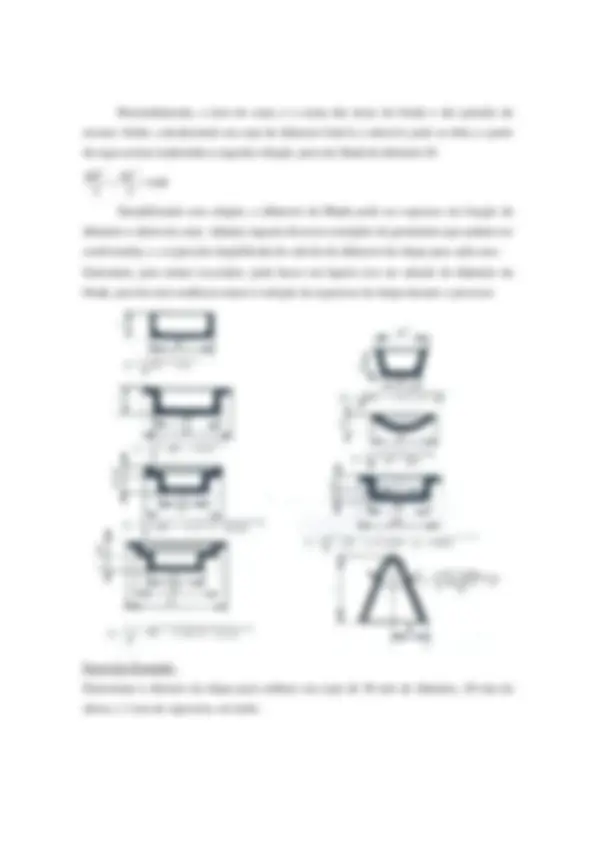
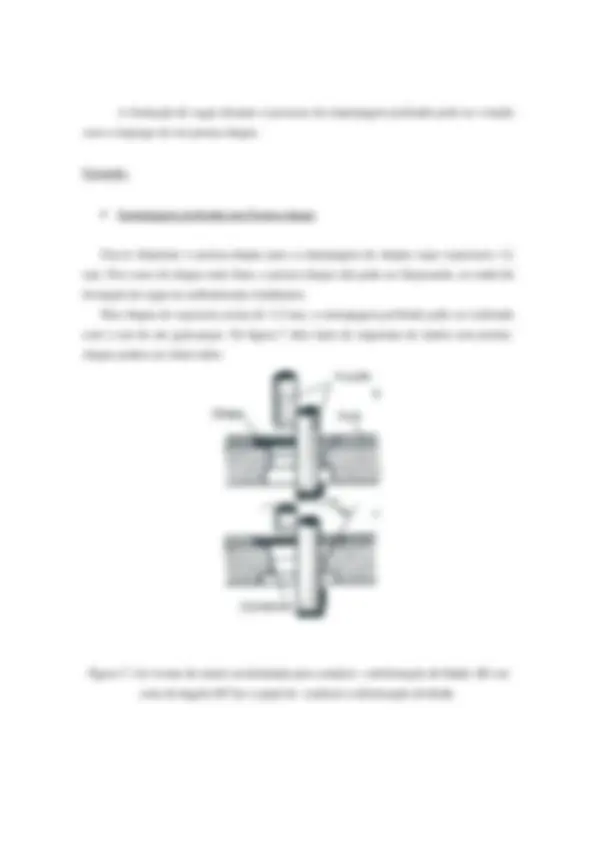
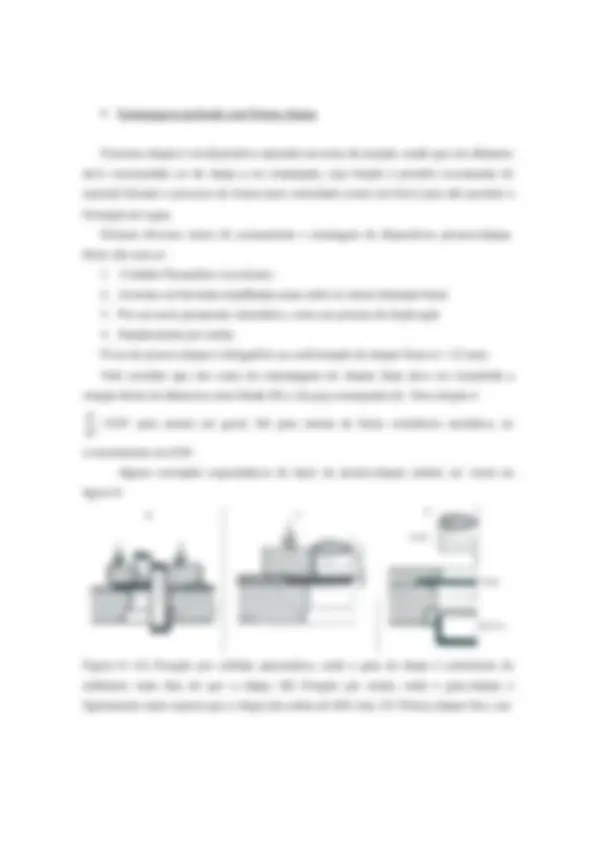
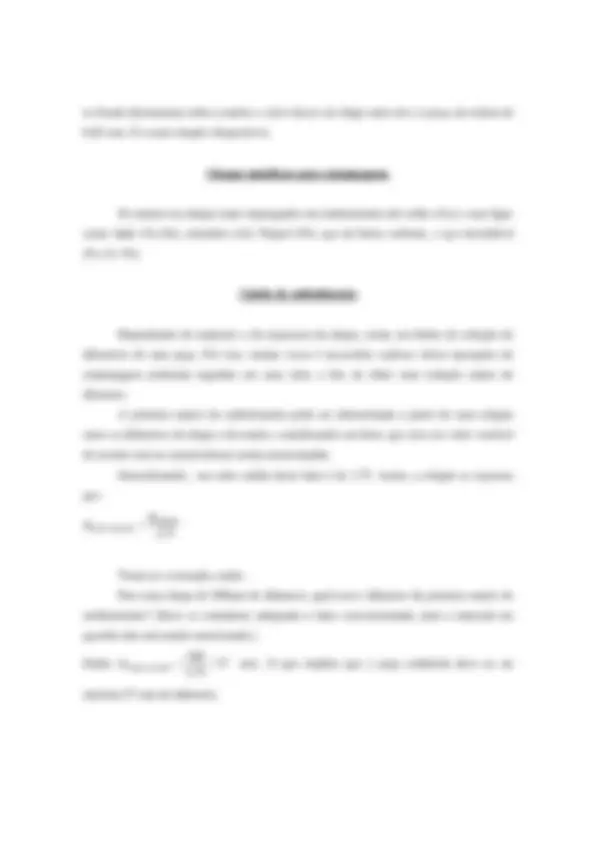
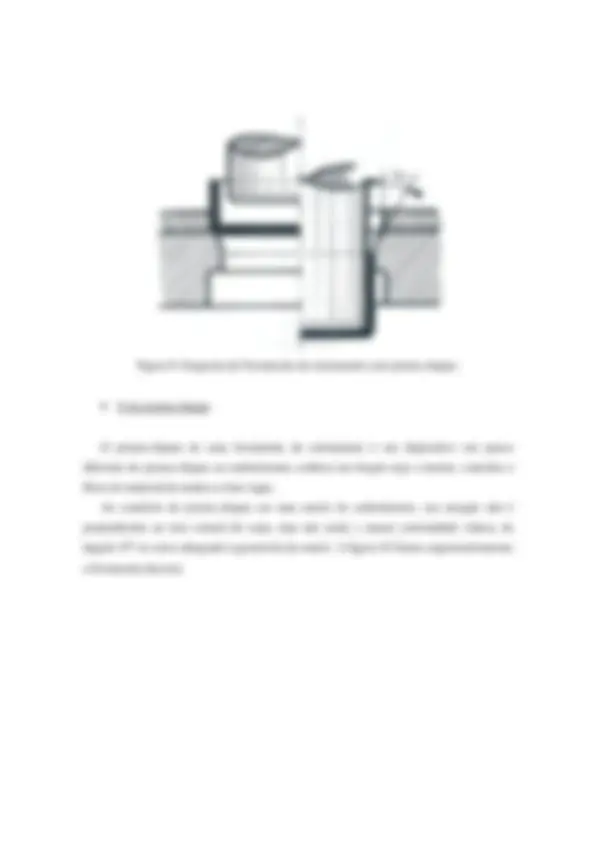
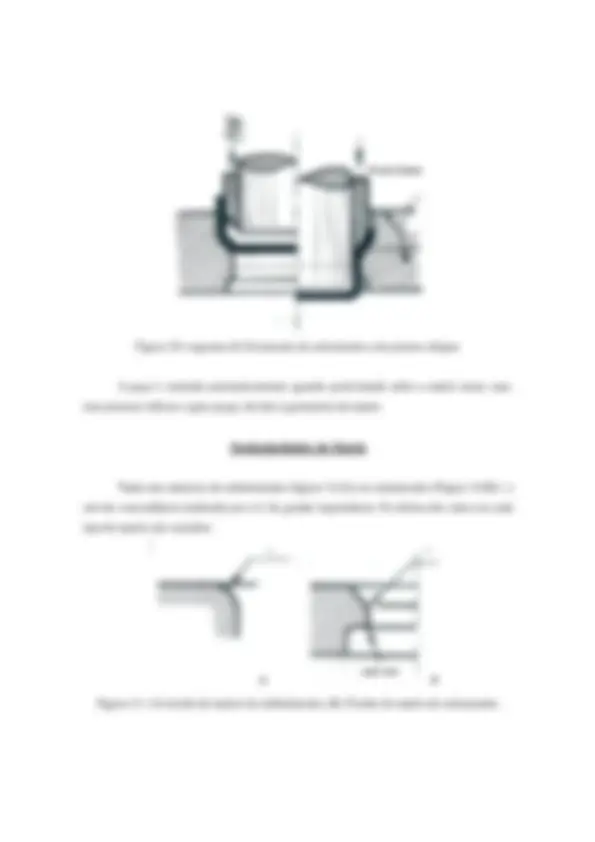
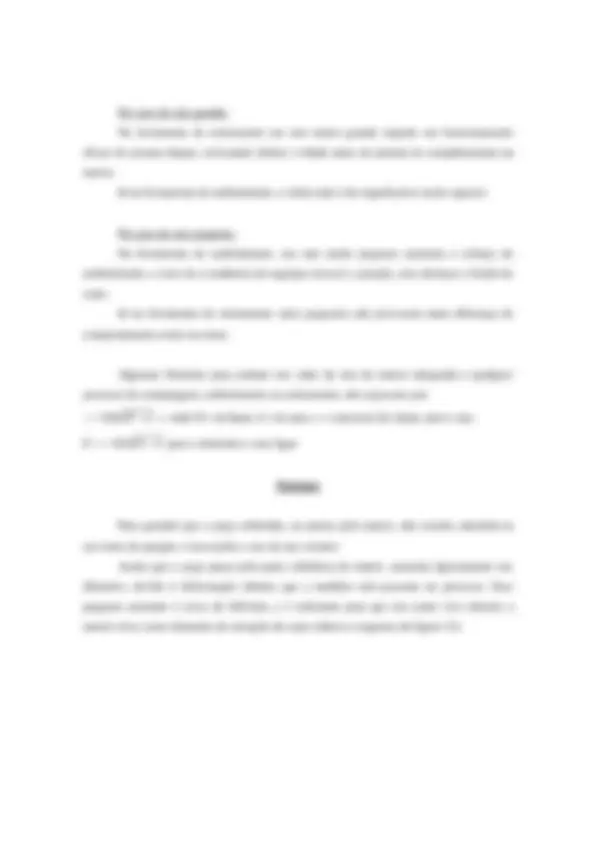
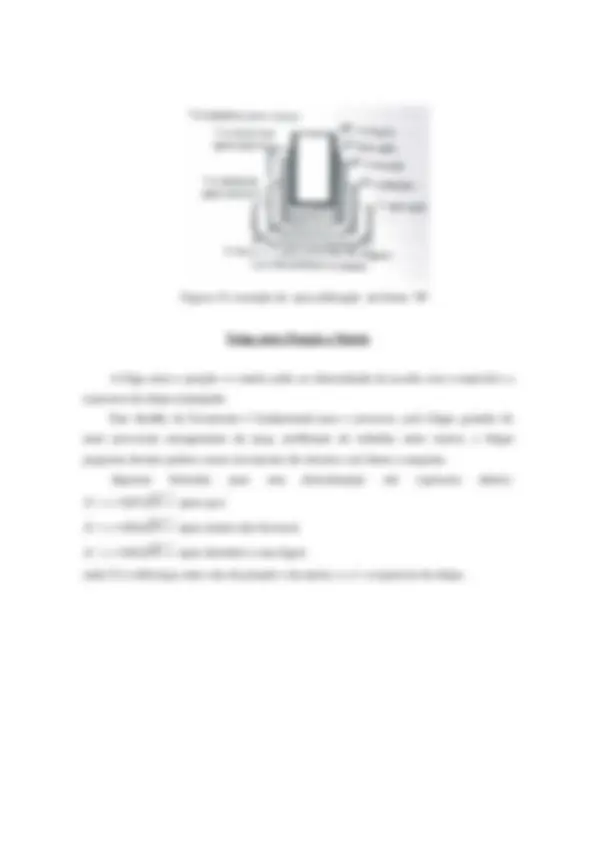
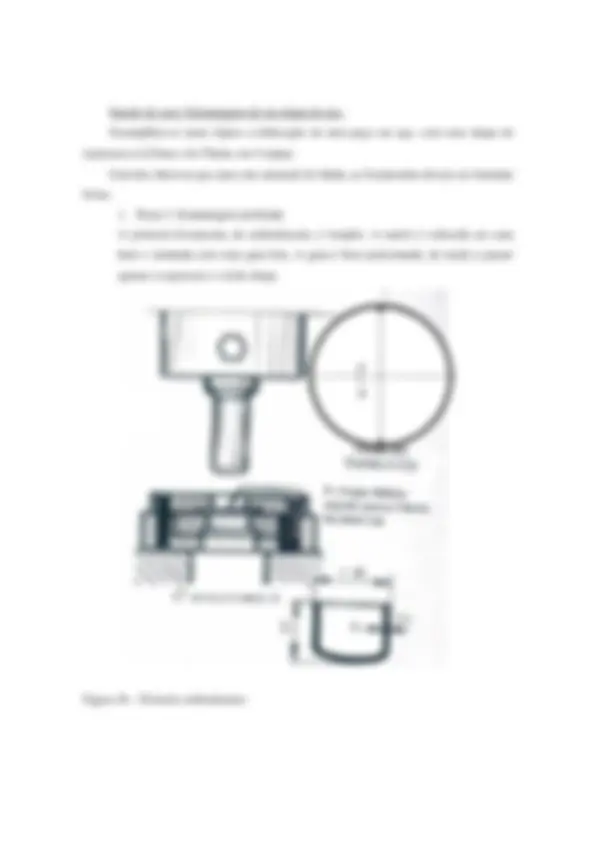
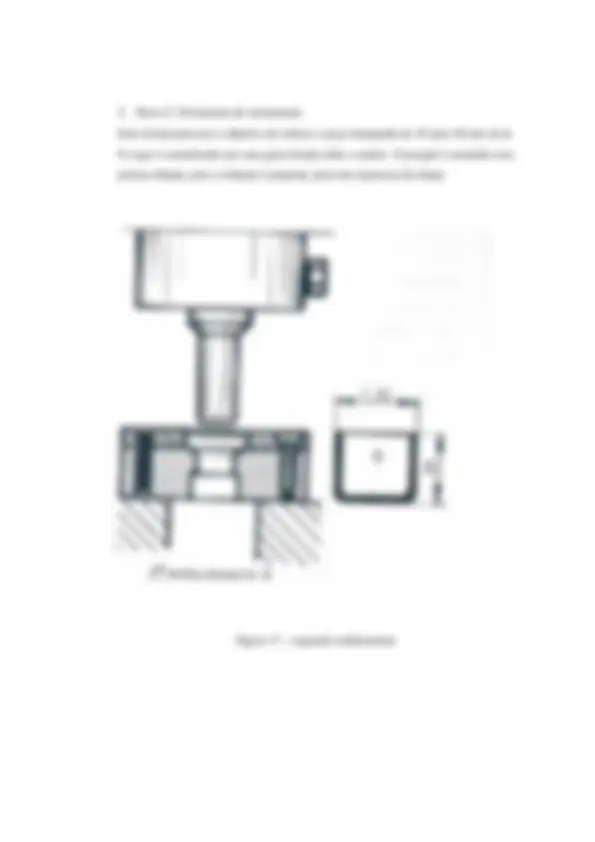
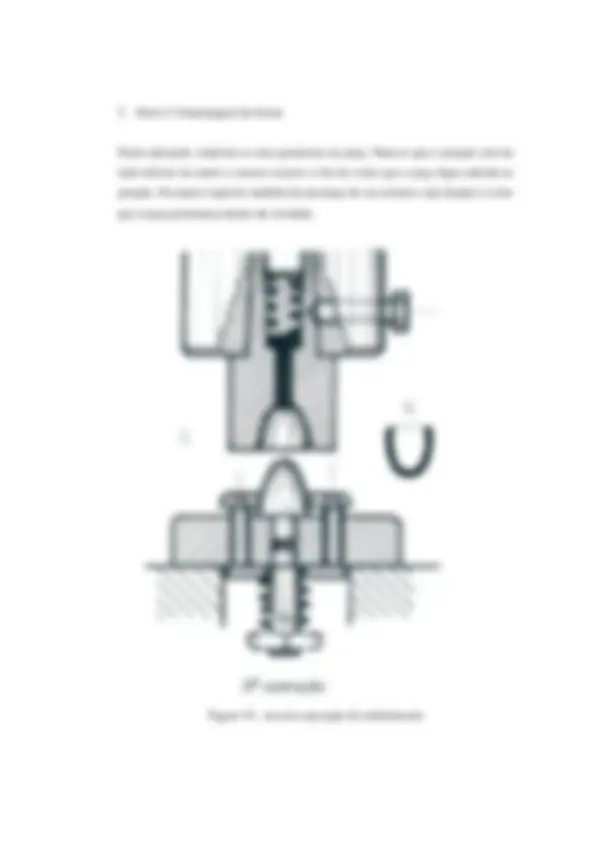
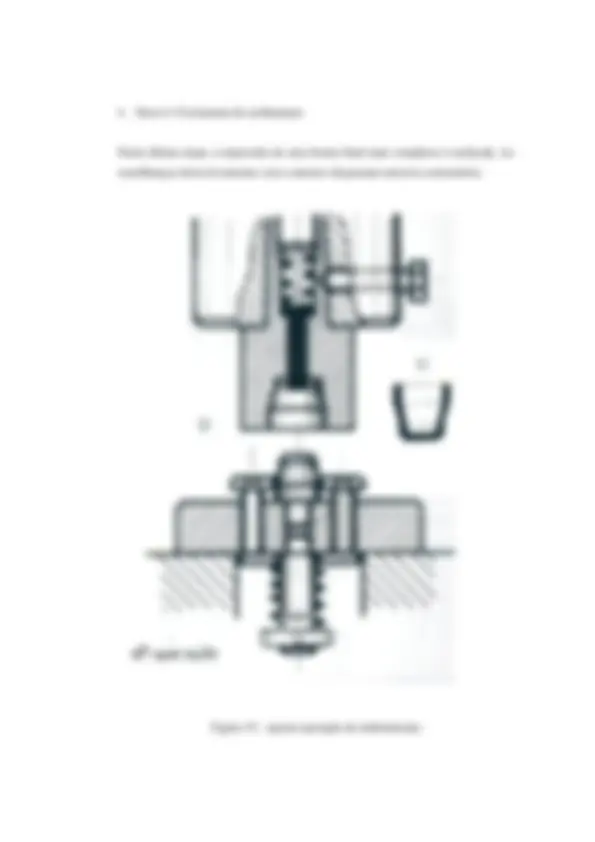
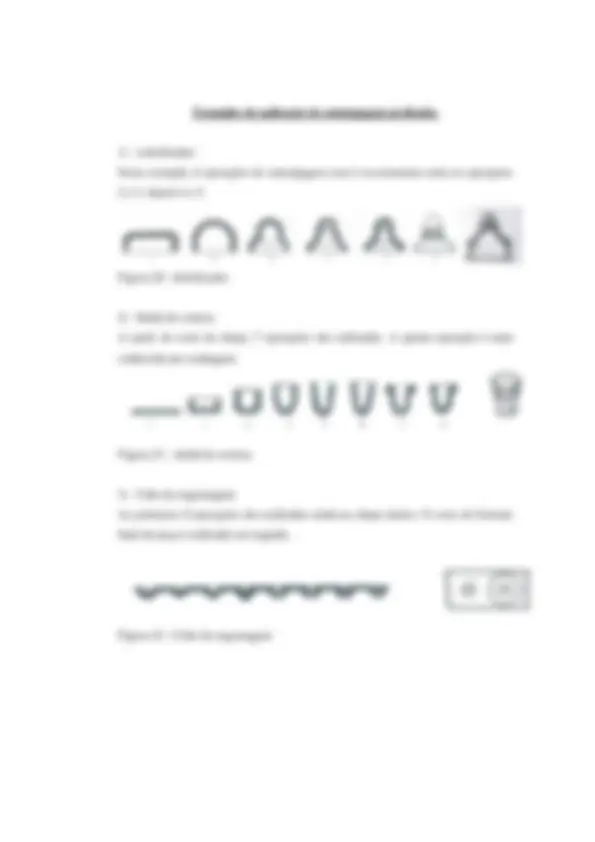
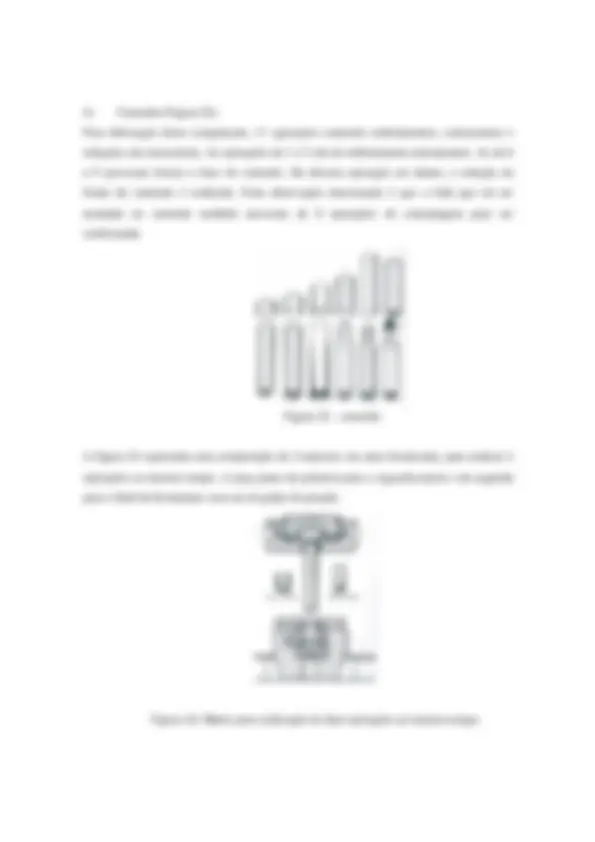
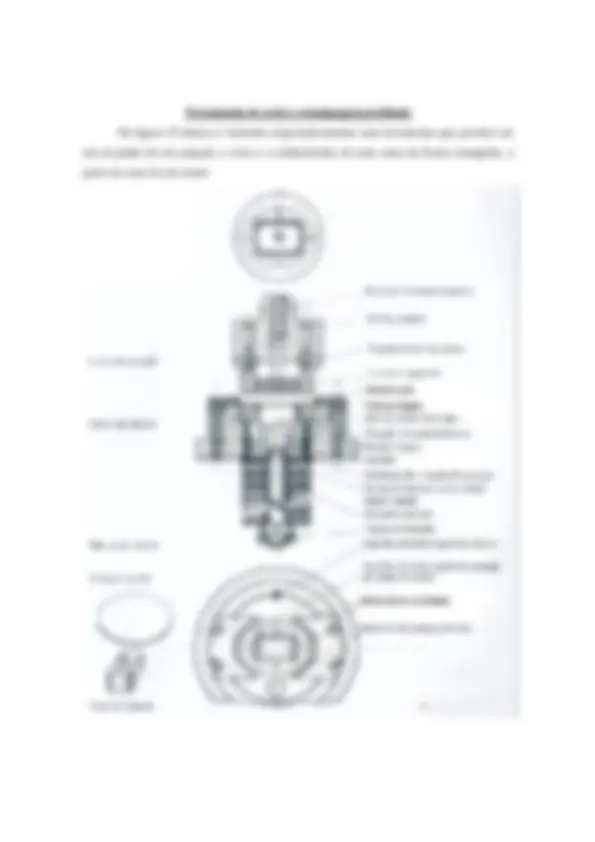
Estude fácil! Tem muito documento disponível na Docsity
Ganhe pontos ajudando outros esrudantes ou compre um plano Premium
Prepare-se para as provas
Estude fácil! Tem muito documento disponível na Docsity
Prepare-se para as provas com trabalhos de outros alunos como você, aqui na Docsity
Os melhores documentos à venda: Trabalhos de alunos formados
Prepare-se com as videoaulas e exercícios resolvidos criados a partir da grade da sua Universidade
Responda perguntas de provas passadas e avalie sua preparação.
Ganhe pontos para baixar
Ganhe pontos ajudando outros esrudantes ou compre um plano Premium
Comunidade
Peça ajuda à comunidade e tire suas dúvidas relacionadas ao estudo
Descubra as melhores universidades em seu país de acordo com os usuários da Docsity
Guias grátis
Baixe gratuitamente nossos guias de estudo, métodos para diminuir a ansiedade, dicas de TCC preparadas pelos professores da Docsity
Apostilas de Engenharia Mecânica sobre o estudo da Conformação de Chapas, Estampagem de peças circulares: Cálculo dos diâmetros das chapas, Estampagem de peças retangulares: determinação do Blank.
Tipologia: Notas de estudo
1 / 25
Esta página não é visível na pré-visualização
Não perca as partes importantes!
Princípio
A conformação de chapas é uma operação que consiste em transformar uma chapa plana em um copo de forma côncava sem mudar a espessura da chapa.Constitui um trabalho de deformação plástica.
Escoamento de material
Na operação de estampagem profunda, sofre deformação plástica somente o trecho da chapa plana que ocupa a área compreendida entre o diâmetro final do copo “d”, e o inicial da chapa “D”, conforme se observa na figura 1.
Figura 1: Esquema da área submetida à deformação na operação de estampagem profunda.
De acordo com a figura 1, a área correspondente a pequenos triângulos (indicados por ABC) é que sofrem deslocamento da região plana em direção ao topo da peça estampada. Em um experimento, foram retirados da chapa plana vários setores circulares, representados por BÂC na ilustração da figura 2(A). Em seguida, com a chapa recortada a operação de estampagem foi realizada, resultando em um copo de altura h como se observa na figura 2(B), onde por causa da ausência de material nas áreas triangulares citadas, ocorre nesta peça apenas dobramento da chapa.
Figura 4: (A) Chapa retangular sem pré-cálculo de geometria, (B) Chapa retangular com pré-cálculo de geometria.
O erro demonstrado na figura 4 ocorre porque somente em chapas de perímetro arredondado é possível obter um copo com arestas perfeitas (onde indica a aresta B, na figura).
Estampagem de peças circulares: Cálculo dos diâmetros das chapas
Regra Geral
Basicamente pode se calcular o diâmetro do blank para a estampagem de qualquer peça de geometria circular baseando-se na lei da conservação da massa, o que implica que o volume de material é constante durante o processo. E uma segunda simplificação pode ser considerada: a operação de estampagem profunda também é feita de modo a manter a espessura da chapa constante. Sabendo que o volume de uma chapa pode ser calculado multiplicando-se a área (A) da chapa, pela espessura (e) da mesma, tem-se: Ablank.eblank =Apeça.epeça. Assim, com espessura constante: Ablank = Apeça.
Resumidamente, a área do copo, é a soma das áreas do fundo e das paredes do mesmo. Então, considerando um copo de diâmetro final d, e altura h, pode se obter, a partir da regra acima explicitada a seguinte relação, para um blank de diâmetro D:
πD (^) 4 (^) = πd 4 + π dh 2 2
Simplificando esta relação, o diâmetro do Blank pode ser expresso em função do diâmetro e altura do copo. Adiante seguem diversos exemplos de geometrias que podem ser conformadas, e a expressão simplificada do calculo do diâmetro da chapa para cada caso. Entretanto, para metais recozidos, pode haver um ligeiro erro no calculo do diâmetro do blank, pois há uma tendência maior à redução da espessura da chapa durante o processo.
Exercício Exemplo: Determinar o dímetro da chapa para embutir um copo de 30 mm de diâmetro, 20 mm de altura, e 1 mm de espessura, em latão.
Figura 6: esquema de estudo do recorte inicial de uma peça estampada retangular.
A formação de rugas durante o processo de estampagem profunda pode ser evitada com o emprego de um prensa-chapas.
Exemplo:
Usa-se dispensar o prensa-chapas para a estampagem de chapas cujas espessuras 1, mm. Nos casos de chapas mais finas, o prensa-chapas não pode ser dispensado, ou então há formação de rugas no embutimento, fatalmente. Para chapas de espessura acima de 1,2 mm, a estampagem profunda pode ser realizada com o uso de um guia-peças. Na figura 7 dois tipos de esquemas de matriz sem prensa- chapas podem ser observados.
Figura 7: (A) Aresta da matriz arredondada para conduzir a deformação do blank; (B) um cone de ângulo 60º faz o papel de conduzir a deformação do blank.
se fixado diretamente sobre a matriz, e deve haver um folga entre ele e a peça, da ordem de 0,02 mm. É o mais simples dispositivo).
Chapas metálicas para estampagem:
Os metais em chapas mais empregados em embutimento são cobre (Cu) e suas ligas como latão (Cu-Zn), alumínio (Al), Níquel (Ni), aço de baixo carbono, e aço inoxidável (Fe, Cr, Ni).
Limite de embutimento
Dependendo do material, e da espessura da chapa, existe um limite de redução de diâmetros de uma peça. Por isso, muitas vezes é necessário realizar várias operações de estampagem profunda seguidas em uma série a fim de obter uma redução maior de diâmetro. A primeira matriz de embutimento pode ser determinada a partir de uma relação entre os diâmetros da chapa e da matriz, considerando um fator, que tem seu valor variável de acordo com as características acima mencionadas. Generalizando, um valor médio deste fator é de 1,75. Assim, a relação se expressa por:
. 1 , 75 φ (^) PRIMMATRIZ =^ φ^ CHAPA
Toma-se o exemplo, então: Para uma chapa de 100mm de diâmetro, qual será o diâmetro da primeira matriz de embutimento? (Deve se considerar adequado o fator convencionado, pois o material em questão não está sendo mencionado.)
Então: φ (^) PRIM. MATRIZ = 1100 , 75 = 57 mm. O que implica que a peça embutida deve ter no
máximo 57 mm de diâmetro.
Estiramento
Para que o copo embutido tenha uma parede mais alta, ou seja mais fundo, ele precisa passar por várias operações conhecidas como estiramento. Ao projetar uma peça que necessite destas operações, deve-se procurar reduzir ao mínimo número de operações intermediárias, visto que muitas operações intermediárias aumentam o tempo de processamento, e o custo ferramental, que precisará de muitas ferramentas intermediárias.
O número de operações de estiramento, varia de acordo com alguns fatores, dentre eles o uso do prensa-chapas, ou não, espessura do material e a ductilidade do mesmo. As reduções de diâmetro das operações de estiramento, dependentes então dos fatores agora citados, variam de 10 a 20%, para a maioria dos materiais. Assim, usam-se coeficientes baseados nesta percentagem de redução para chegar ao número final de operações. Um exemplo interessante seria estudar o caso de uma chapa circular de diâmetro de 100mm, que resultou em um copo embutido de 57 mm de diâmetro. Supondo que o diâmetro final desejado de se alcançar seja de 30 mm, com uma redução média de 15% (isso significa: usar coeficiente de 0,85 (1 - 0,15)). Assim, o diâmetro da primeira matriz de estiramento é calculado: 57mm x 0,85 = 48,5 mm. Sucessivamente, o segundo será: 48,5 x 0,85 = 41 mm, O terceiro diâmetro vem a ser: 41 x 0,85 = 35 mm, E o quarto diâmetro pode ser: 35 x 0,85 = 29,7mm, mas como 30 mm é a medida desejada, usa-se 30 mm de diâmetro final, após 4 operações. Isso implica que são necessárias quatro matrizes de estiramento e uma matriz de embutimento para conformar esta peça. Um segundo Exemplo é necessário: Na prática, deve-se fazer um copo em cobre, espessura 1 mm, φ35mm, altura 40mm. Para resolver este problema é necessário seguir o procedimento abaixo:
Figura 9: Esquema de Ferramenta de estiramento sem prensa-chapas.
O prensa-chapas de uma ferramenta de estiramento é um dispositivo um pouco diferente do prensa-chapas no embutimento, embora sua função seja a mesma: controlar o fluxo de material de modo a evitar rugas. Ao contrário do prensa-chapas em uma matriz de embutimento, sua atuação não é perpendicular ao eixo central do copo, mas sim axial, e possui extremidade cônica, de ângulo 45º ou outro adequado à geometria da matriz. A figura 10 ilustra esquematicamente a ferramenta descrita.
Figura 10: esquema de ferramenta de estiramento com prensa-chapas.
A peça é centrada automaticamente quando posicionada sobre a matriz neste caso, sem precisar utilizar o guia peças, devido à geometria da matriz.
Particularidades da Matriz
Tanto nas matrizes de embutimento (figura 11(A)) ou estiramento (Figura 11(B)) o raio de concordância (indicado por r) é de grande importância. Os efeitos dos raios em cada tipo de matriz são variados:
Figura 11: (A) trecho de matriz de embutimento, (B) Trecho de matriz de estiramento.
Figura 12: Canto vivo que retém a peça em uma matriz de embutimento.
Um exemplo interessante de extrator pode ser observado na figura 13 e consiste em um anel dividido em 2 ou mais partes, apoiadas na base da matriz, fixadas por uma mola circular. Durante o processo, a própria peça embutida é responsável pelo seu afastamento. Assim que a peça passa pelo anel extrator, a mola o faz contrair-se, impedindo o retrocesso da peça.
Figura 13: esquema de extrator de anéis em uma matriz de embutimento.
Punção
O punção é o componente responsável pela formação da geometria da peça estampada, por isso sua forma é de grande importância. As formas mais comuns em processos de embutimento estão ilustradas na figura 14, e são:
Figura 14: formas mais comuns de punções em processos de embutimento.
Estudo de caso: Estampagem de um chapa de aço. Exemplifica-se neste tópico a fabricação de uma peça em aço, com uma chapa de espessura e=2,5mm e φ =76mm, em 4 etapas. Convém observar que para este material de blank, as ferramentas devem ser bastante fortes.
Figura 16 – Primeiro embutimento
φ = 7 6φ = 7 6
Figura 17 – segundo embutimento