
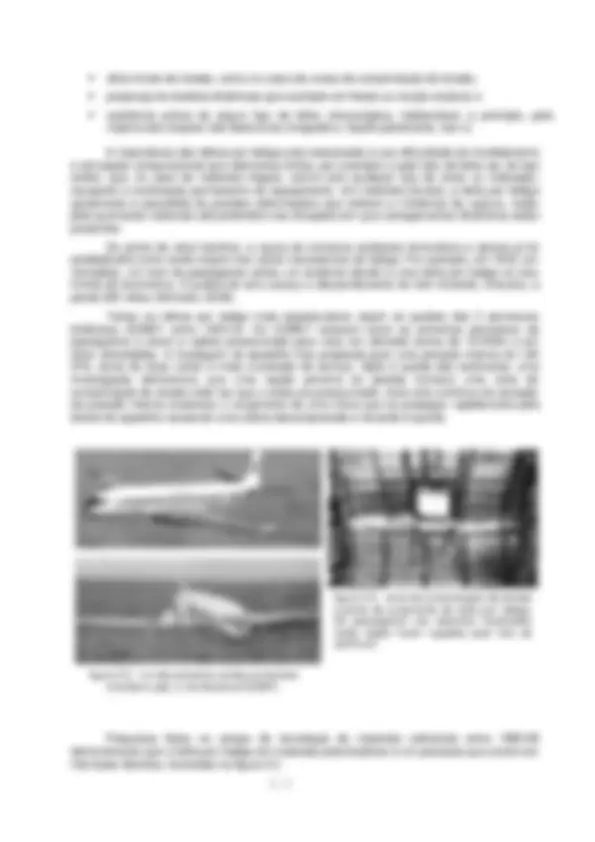
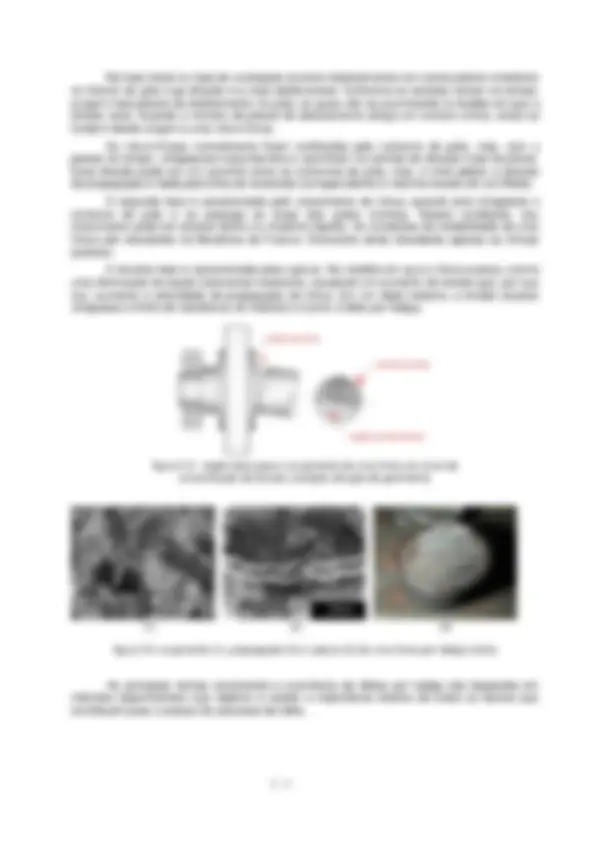
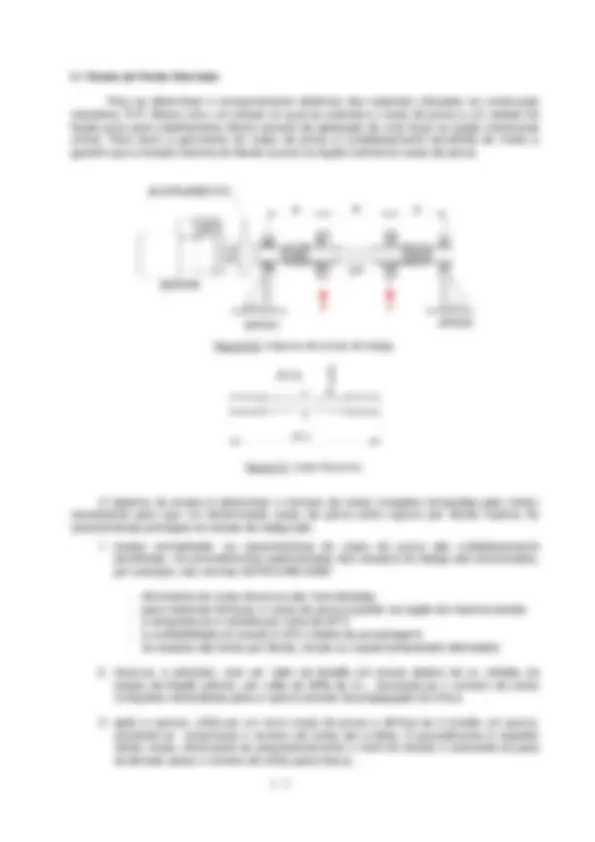
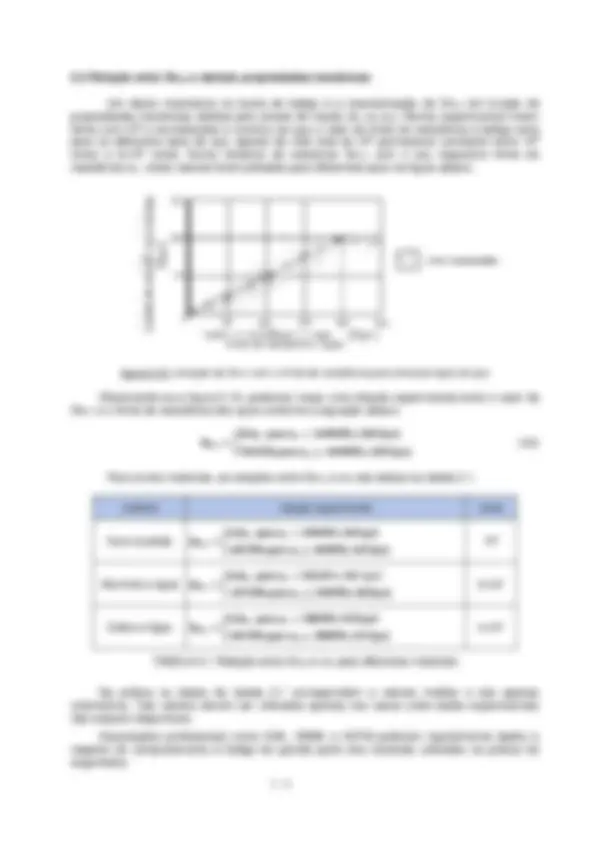
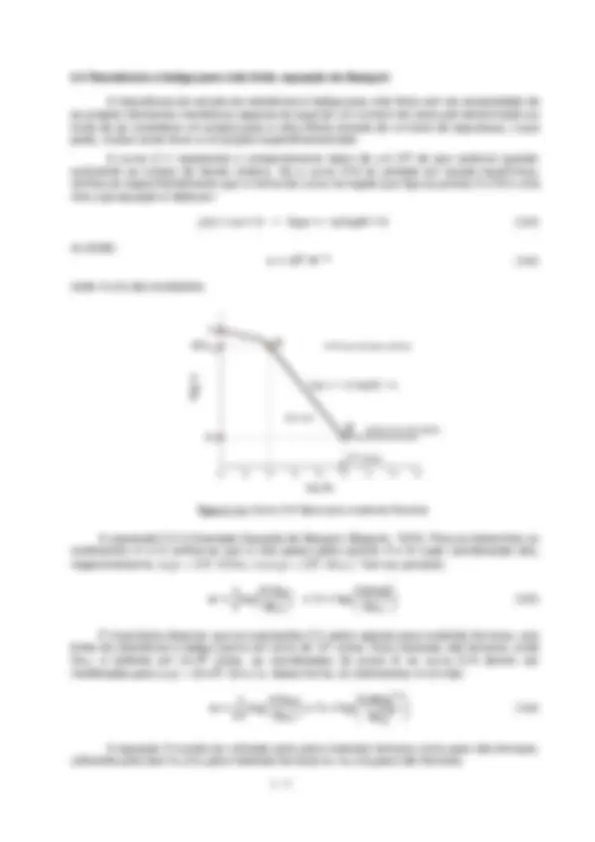
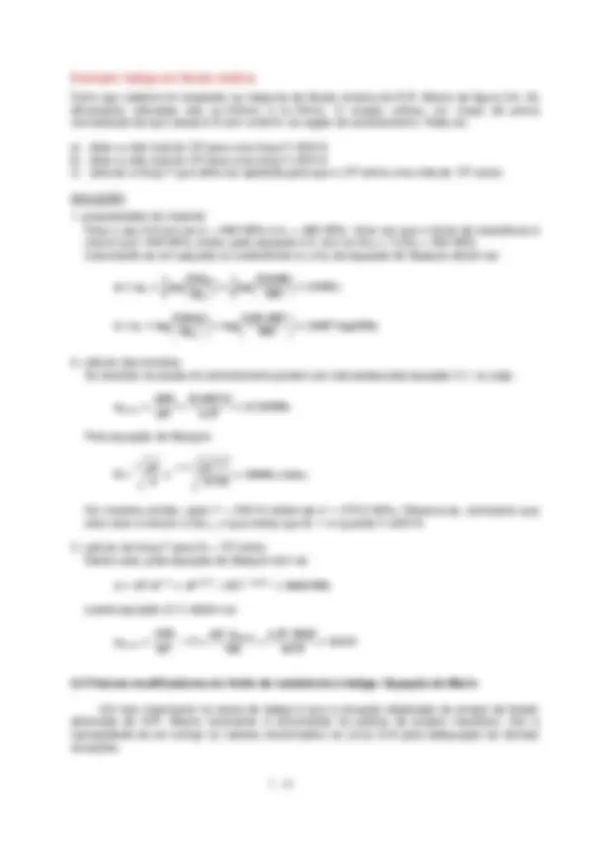
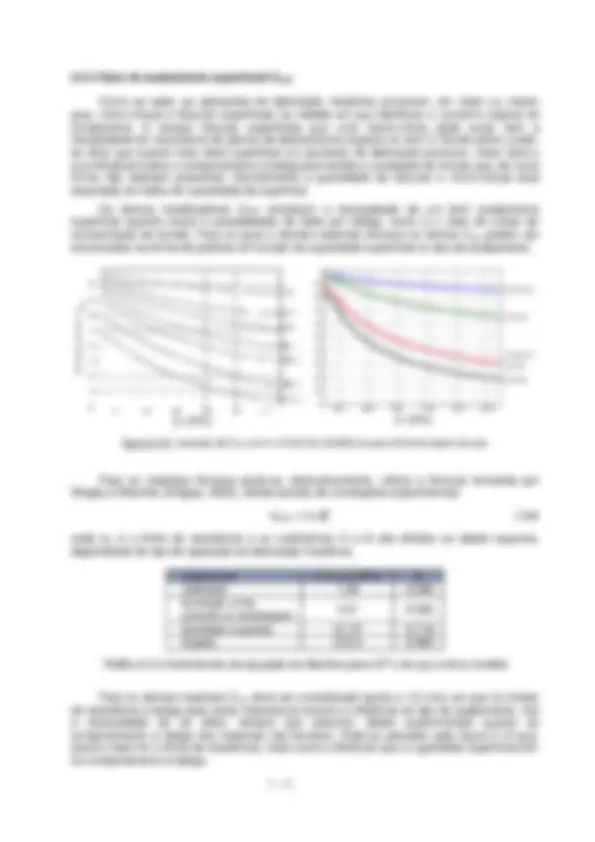
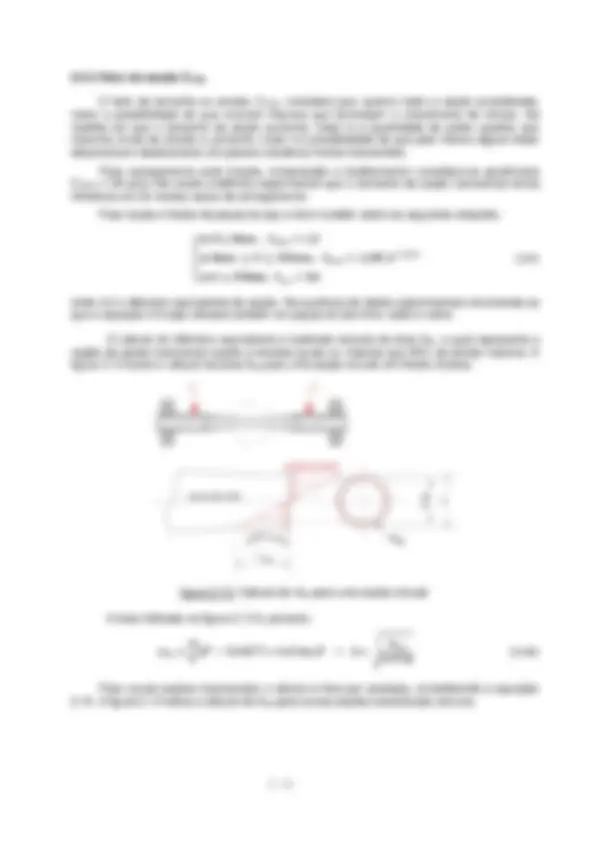
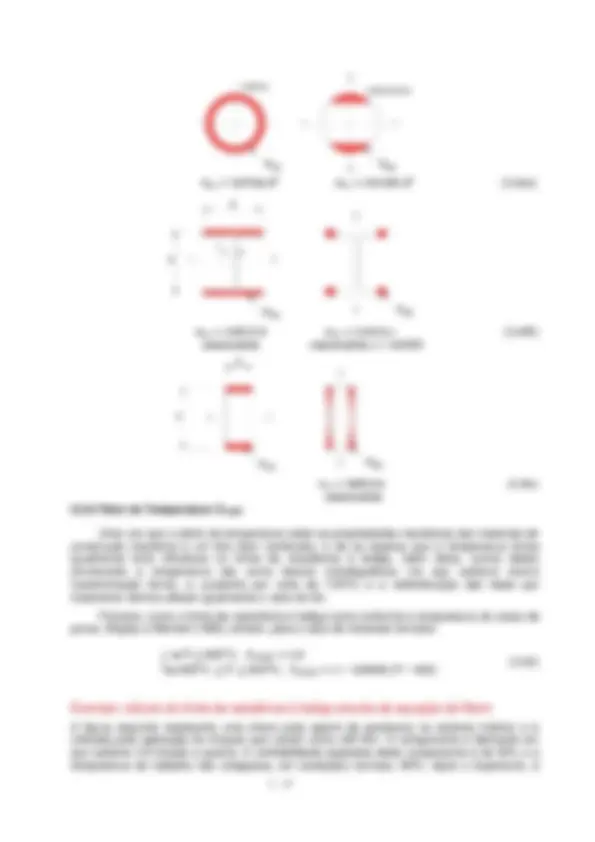
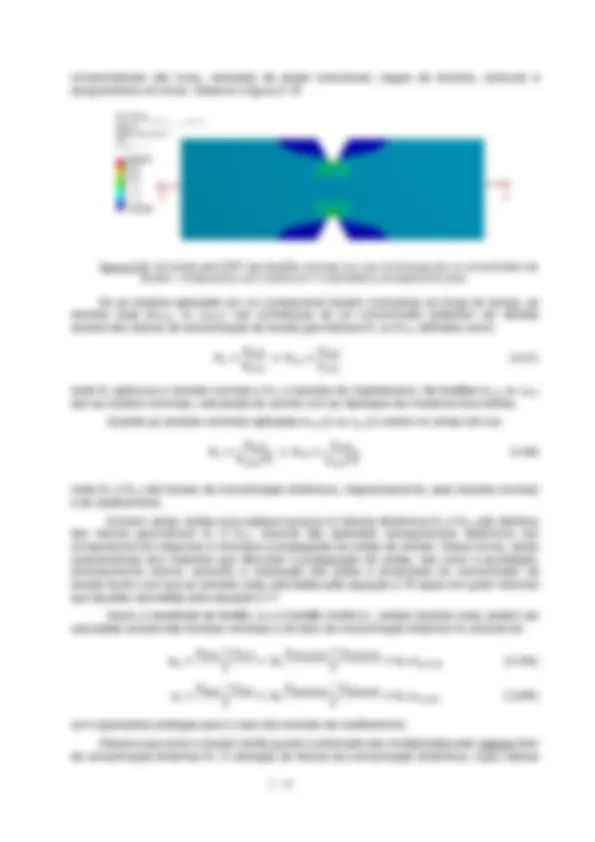
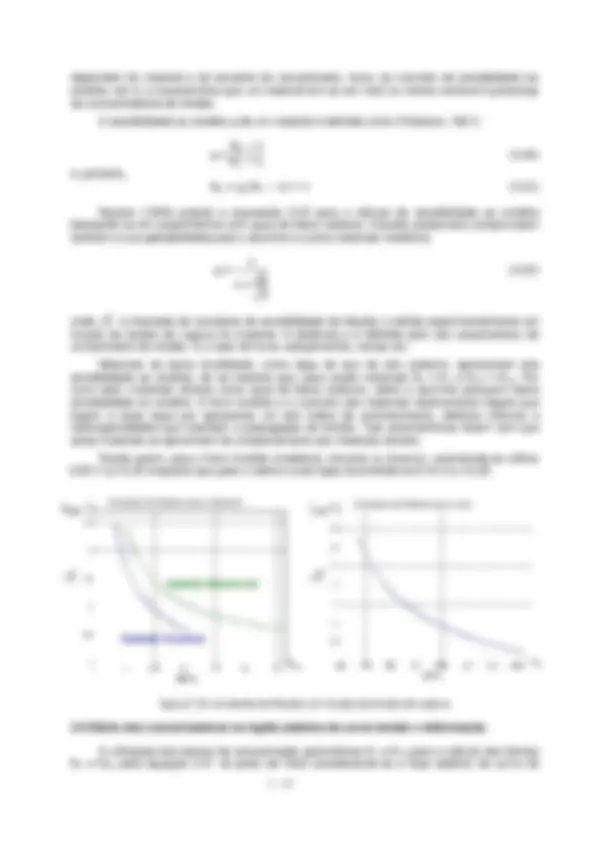

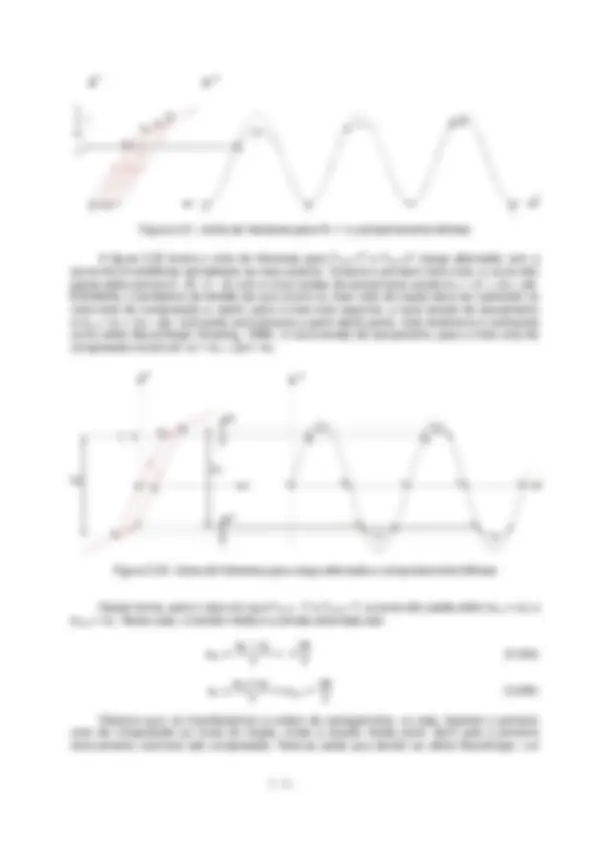
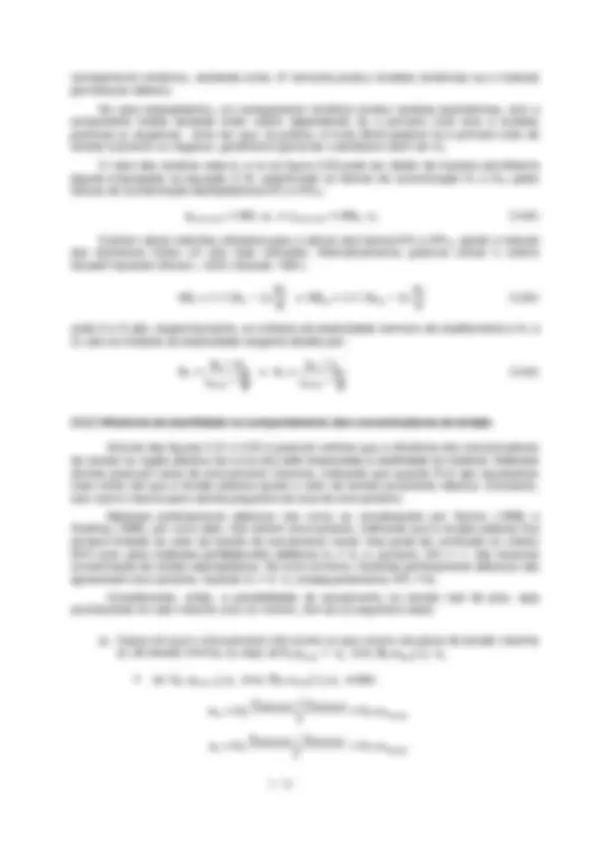
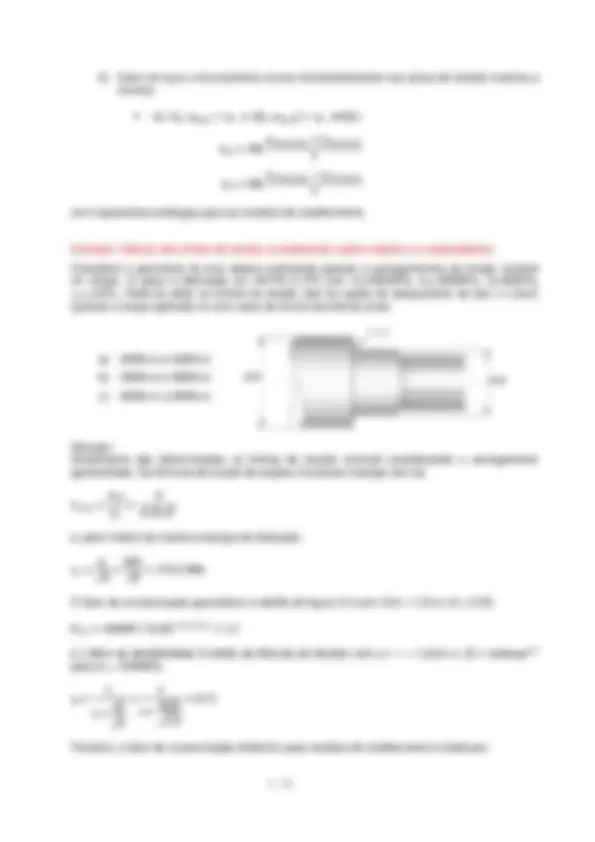
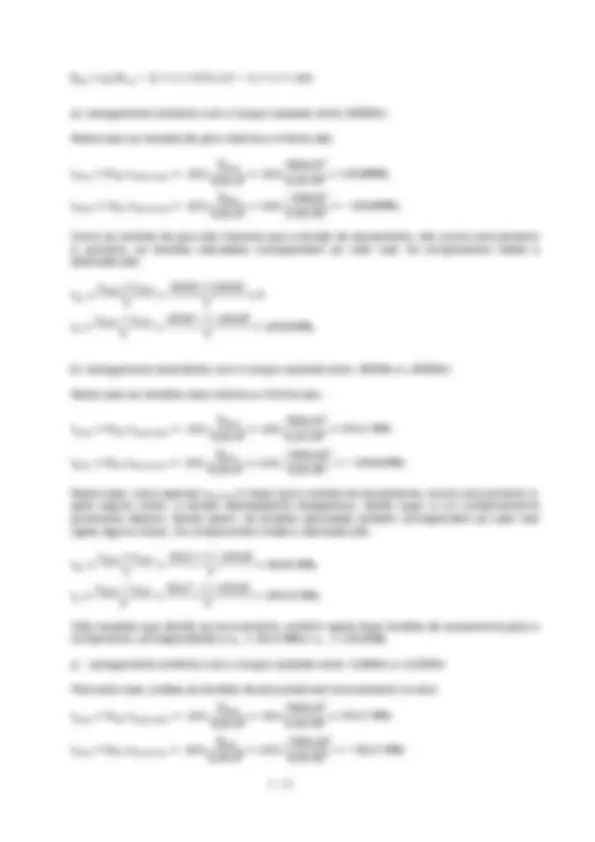
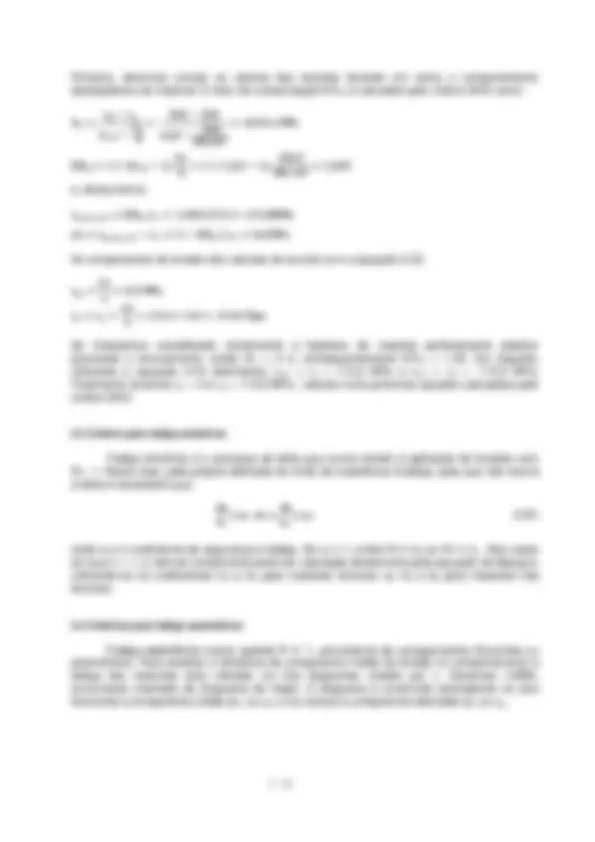
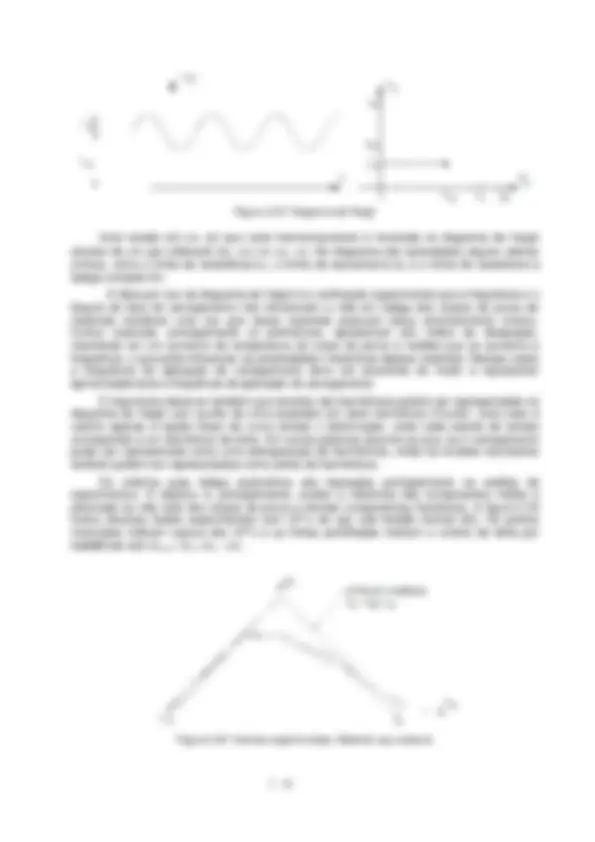
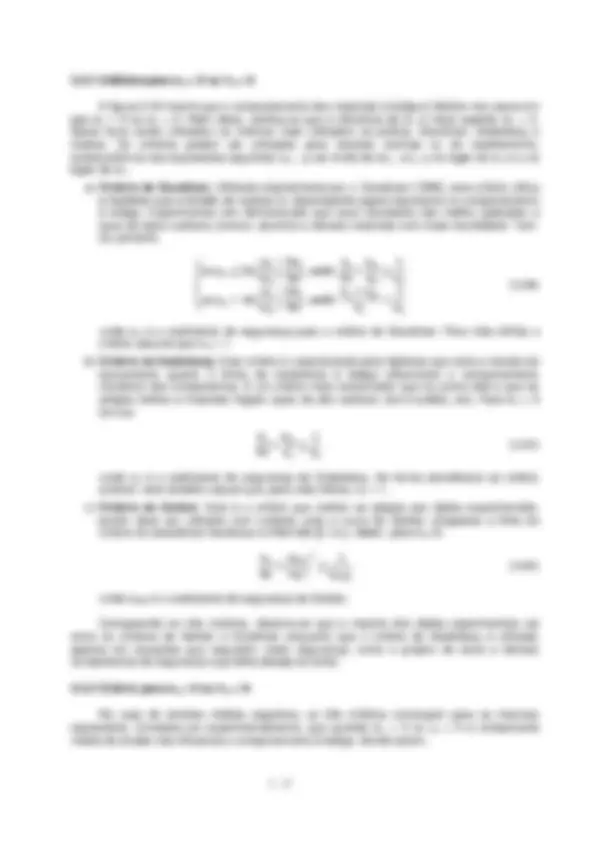
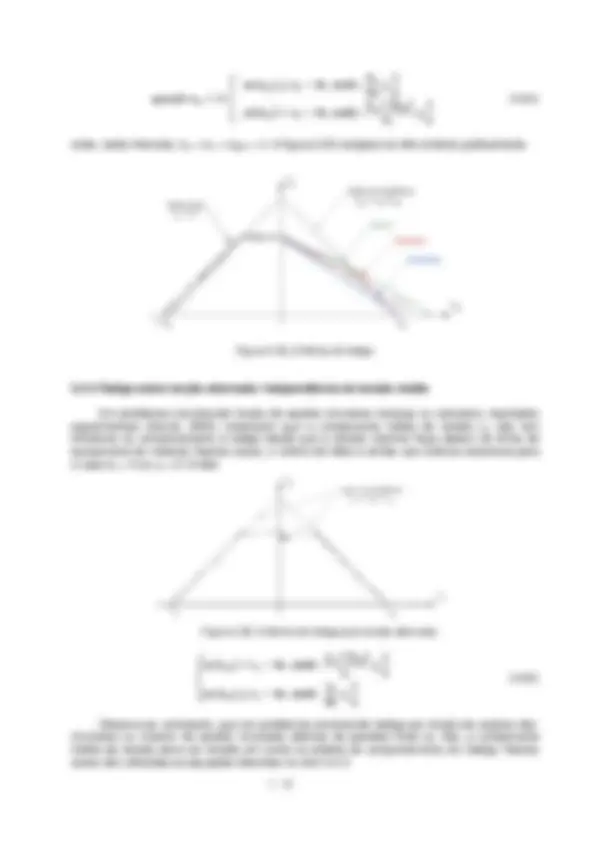
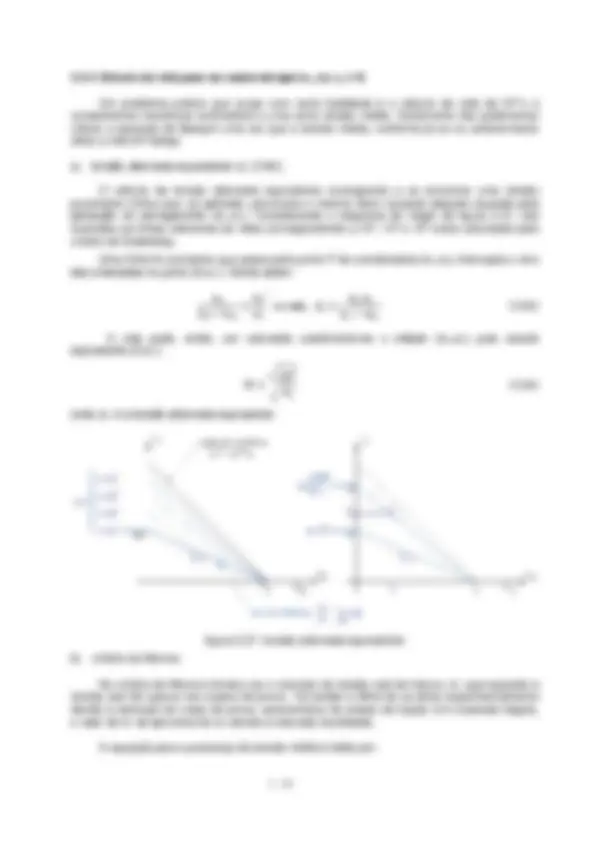
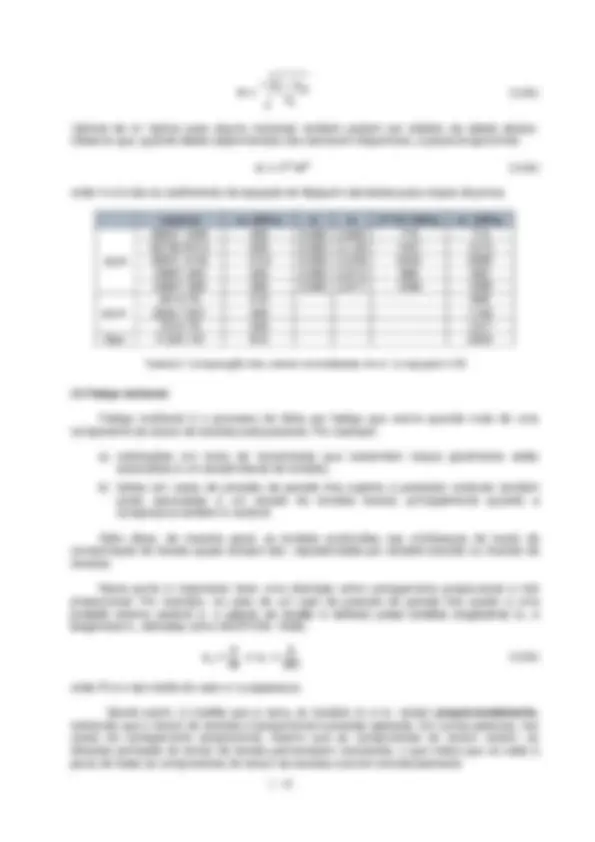
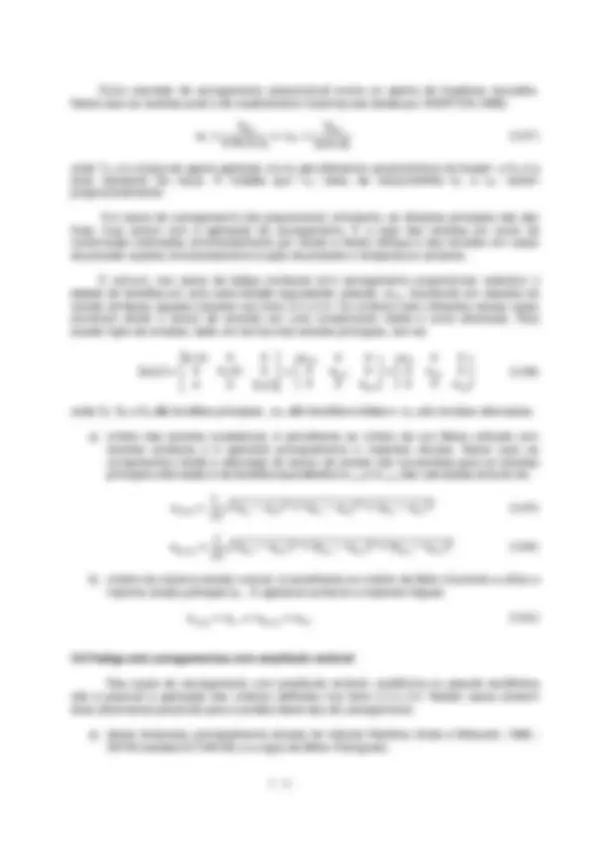
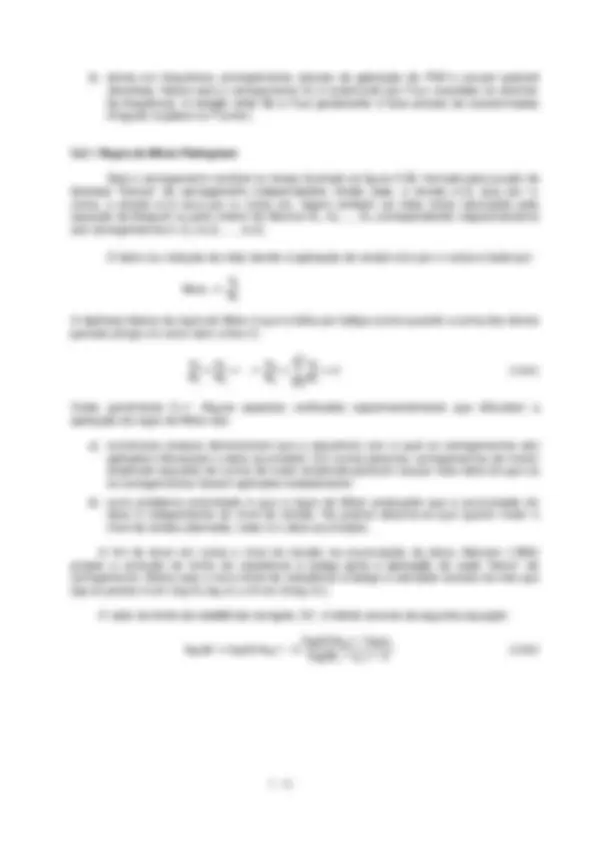
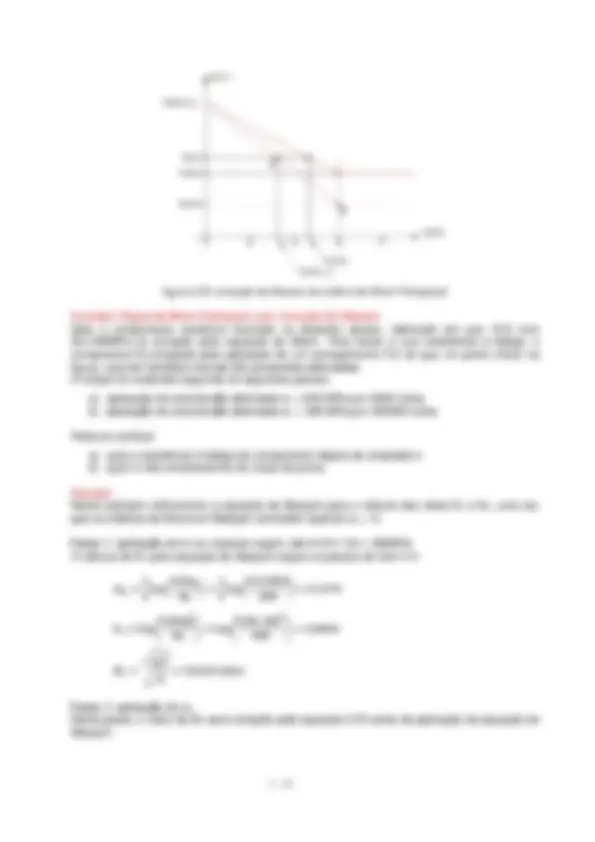
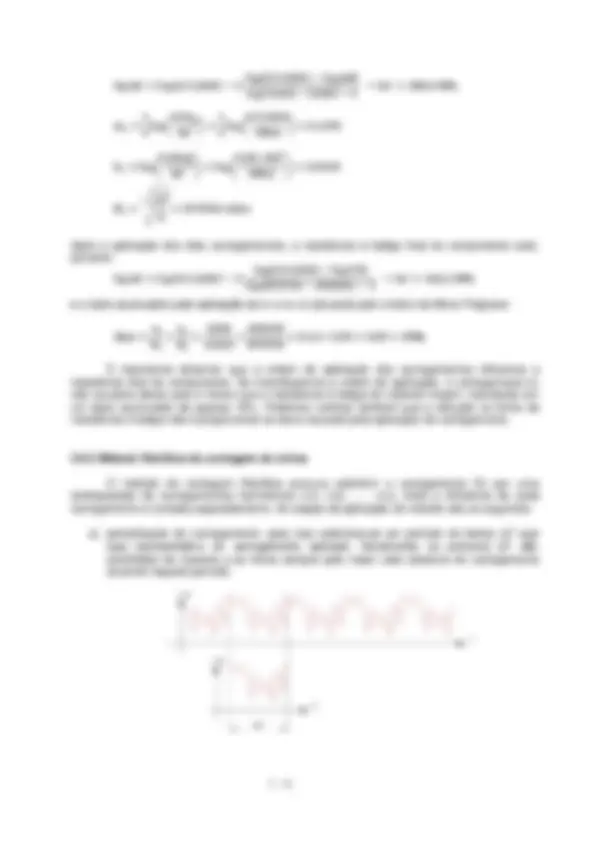
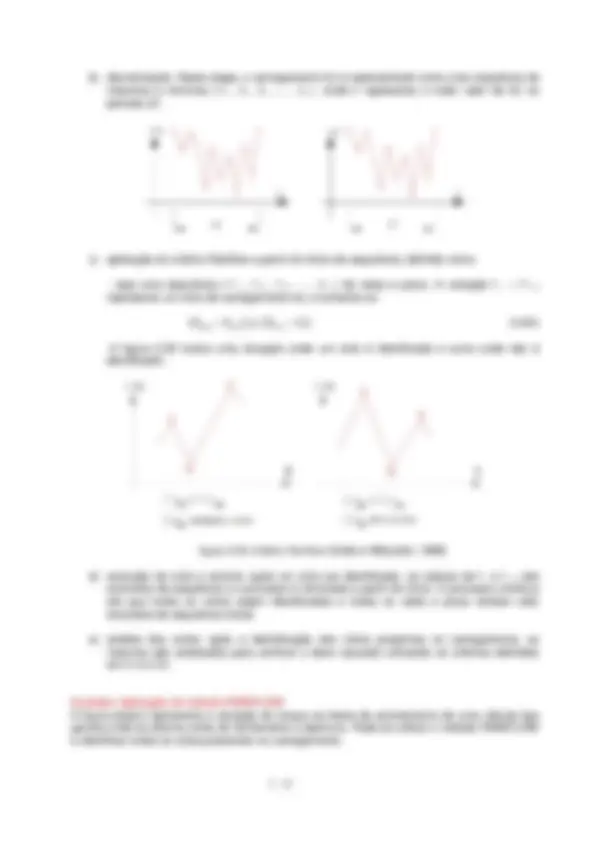
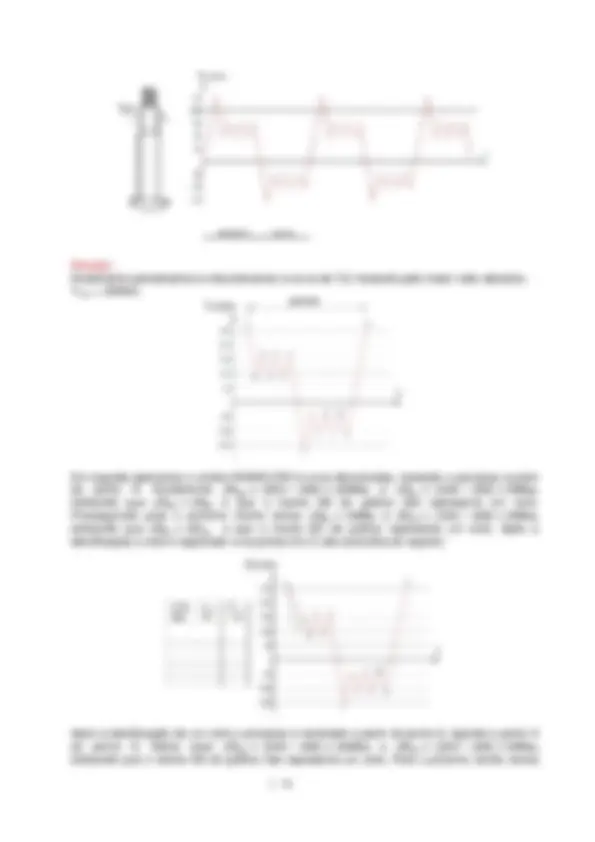
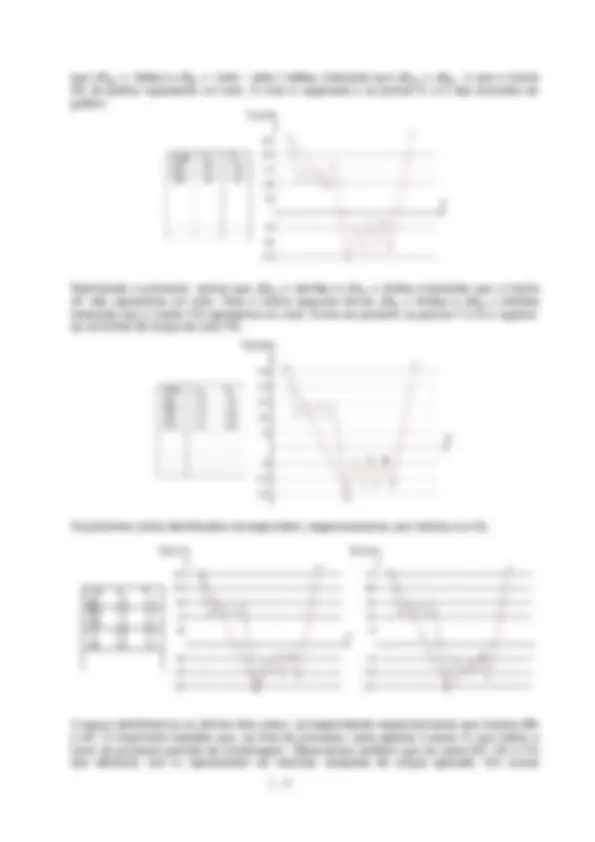
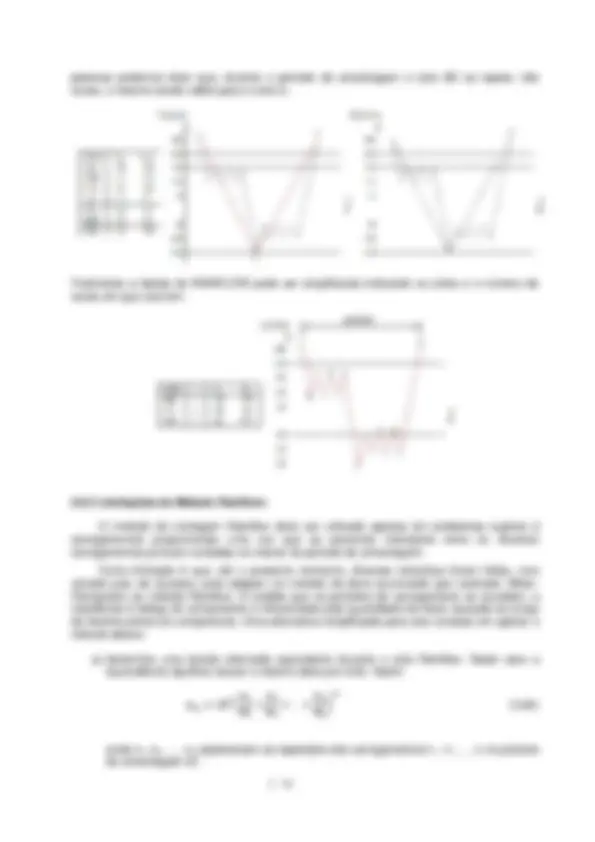
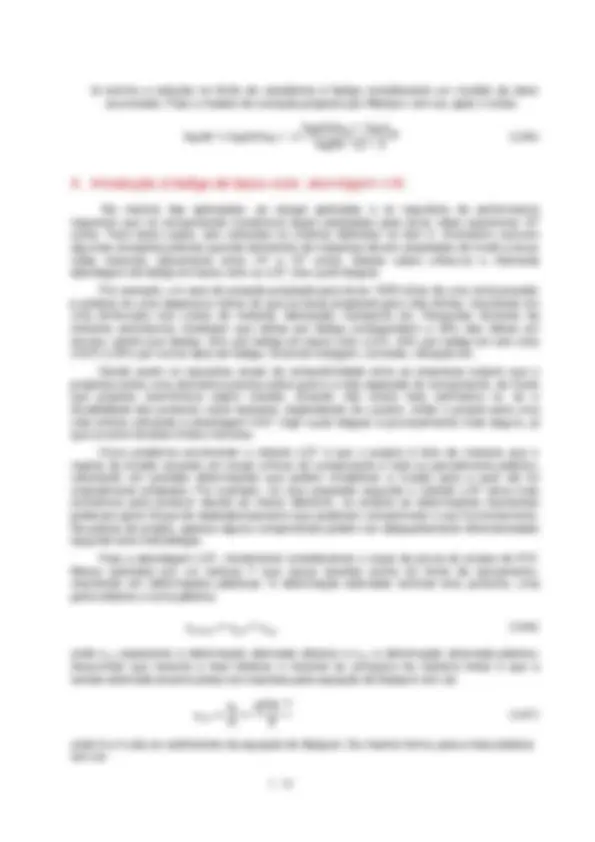
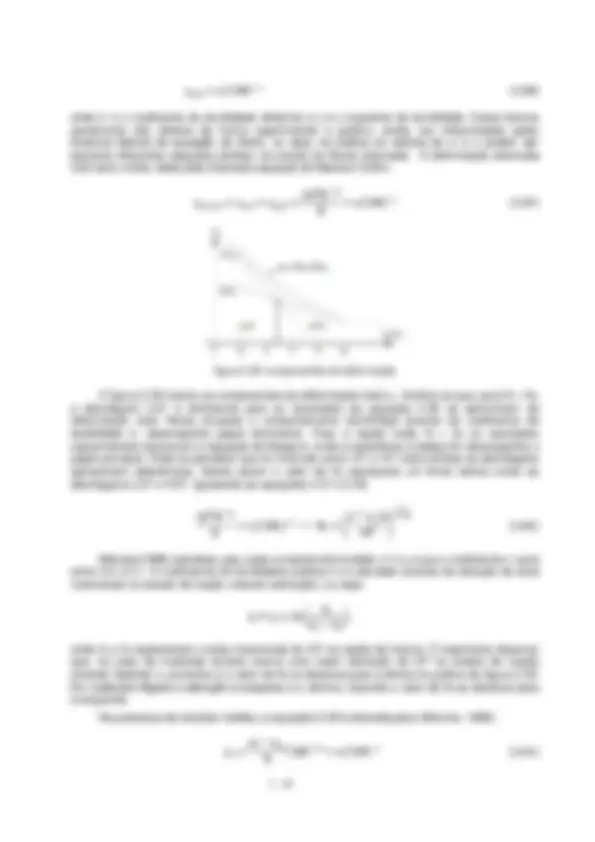
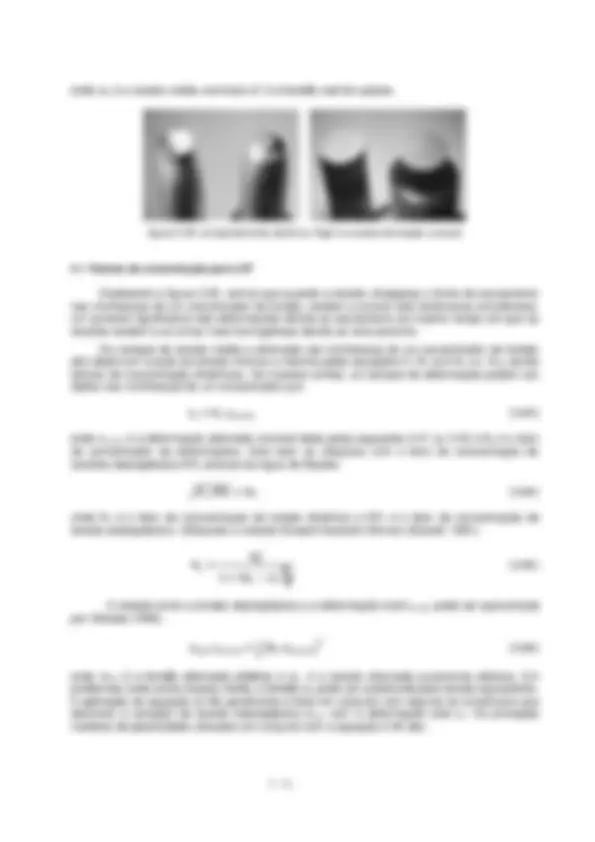
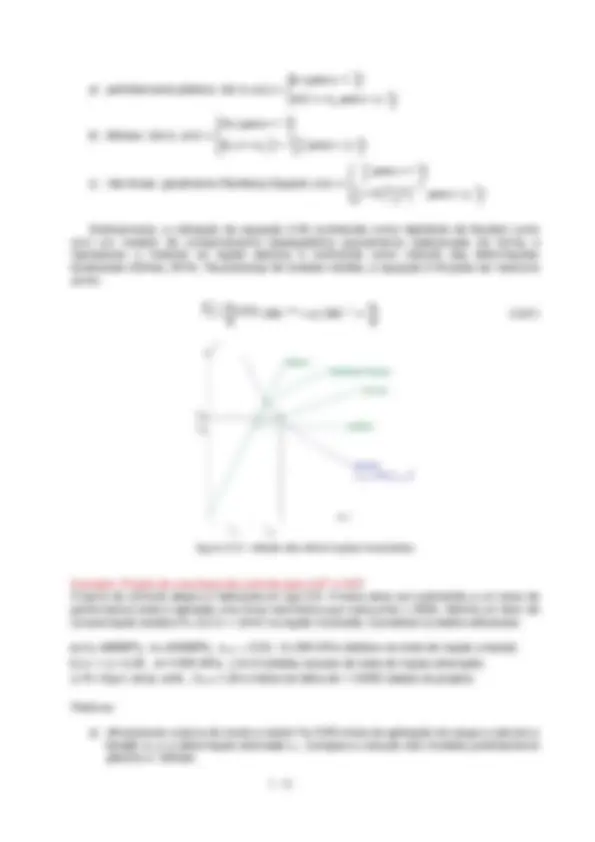

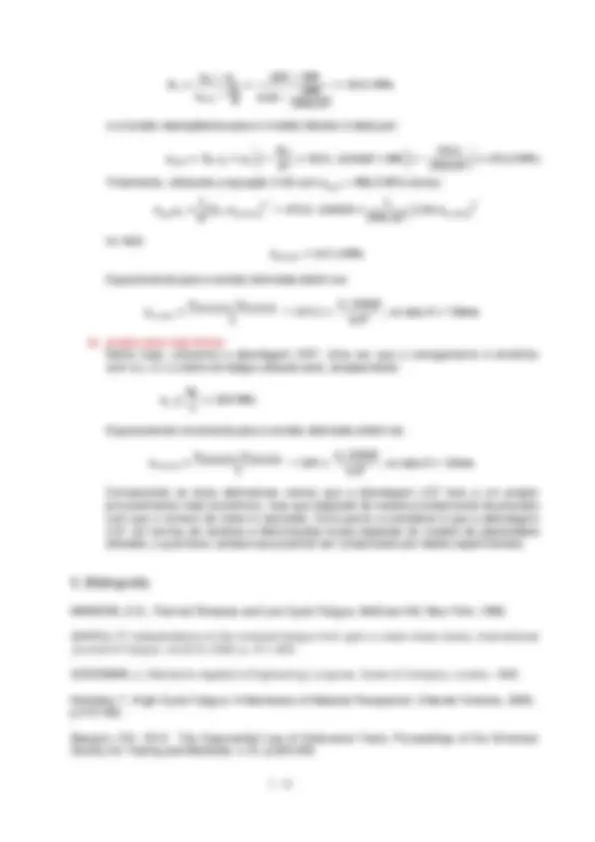
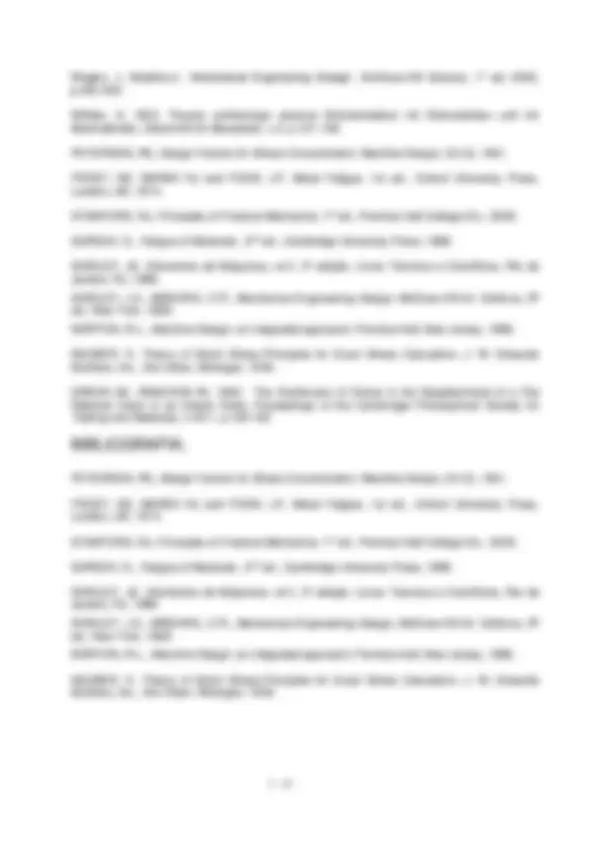
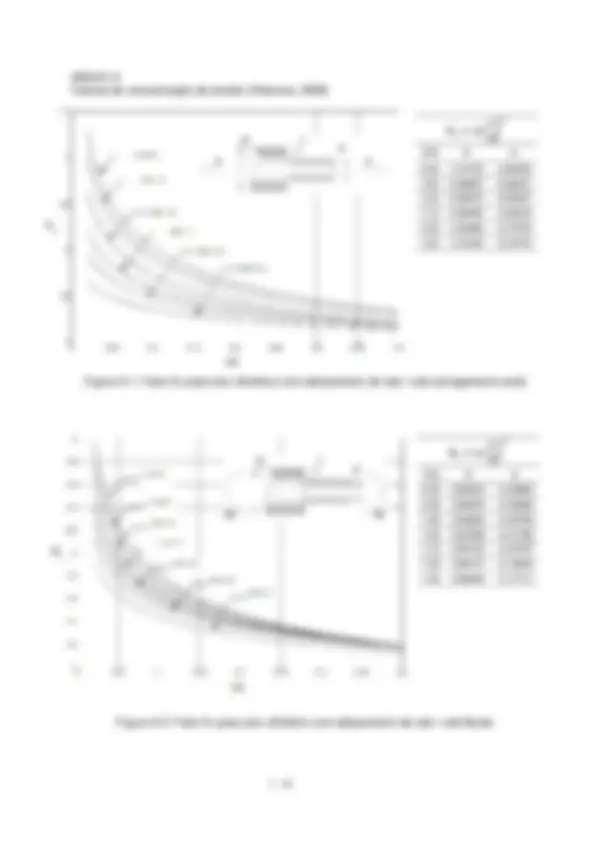
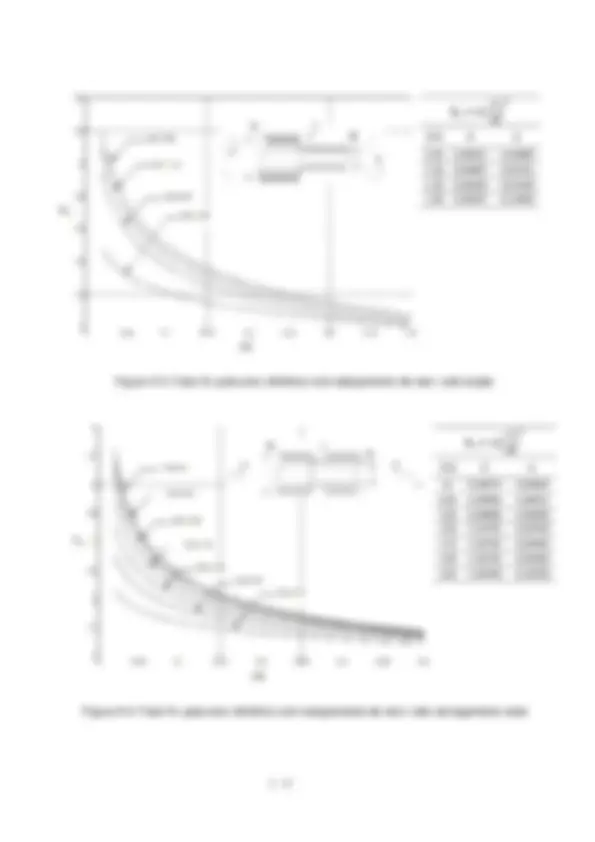
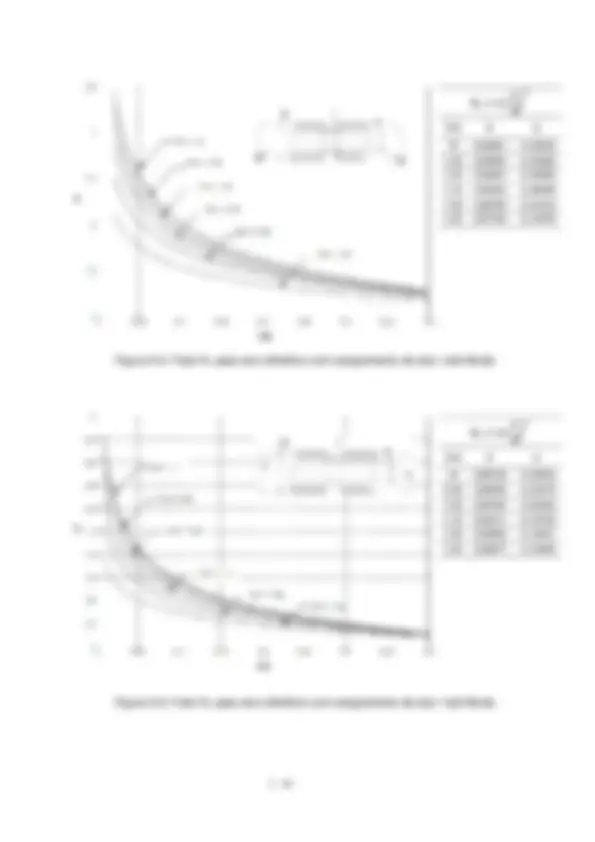
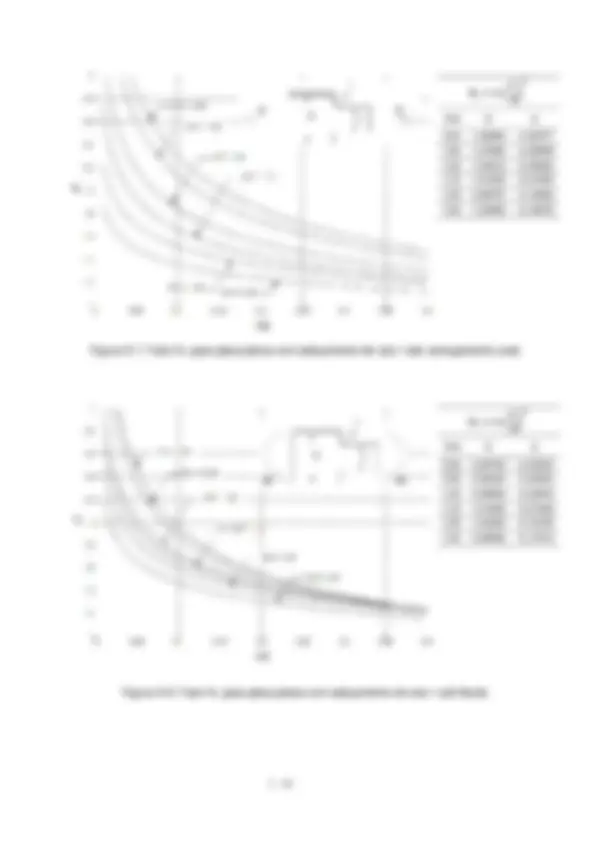
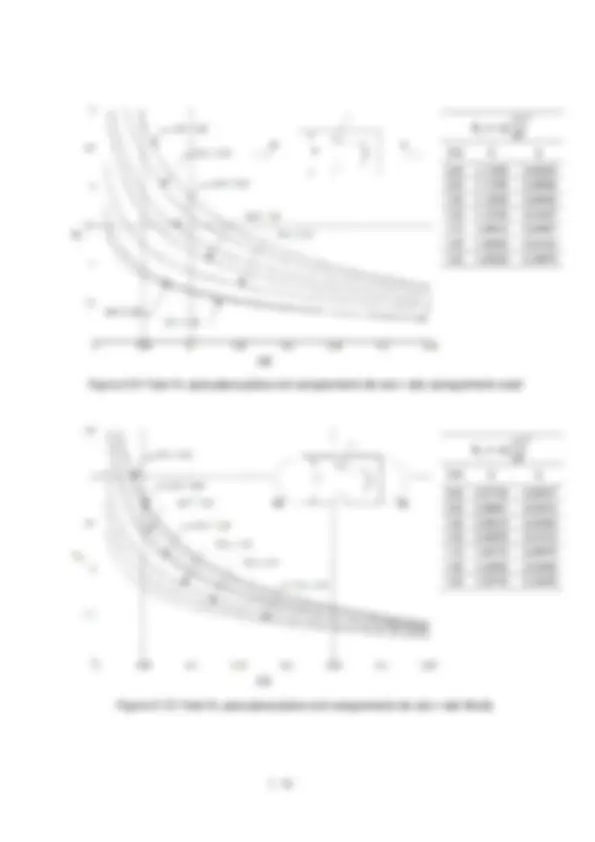
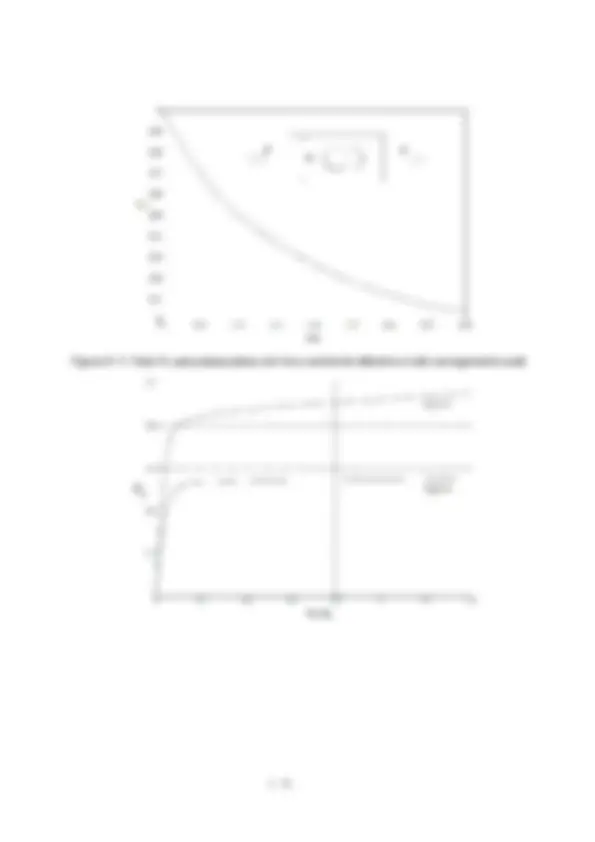
Estude fácil! Tem muito documento disponível na Docsity
Ganhe pontos ajudando outros esrudantes ou compre um plano Premium
Prepare-se para as provas
Estude fácil! Tem muito documento disponível na Docsity
Prepare-se para as provas com trabalhos de outros alunos como você, aqui na Docsity
Os melhores documentos à venda: Trabalhos de alunos formados
Prepare-se com as videoaulas e exercícios resolvidos criados a partir da grade da sua Universidade
Responda perguntas de provas passadas e avalie sua preparação.
Ganhe pontos para baixar
Ganhe pontos ajudando outros esrudantes ou compre um plano Premium
Comunidade
Peça ajuda à comunidade e tire suas dúvidas relacionadas ao estudo
Descubra as melhores universidades em seu país de acordo com os usuários da Docsity
Guias grátis
Baixe gratuitamente nossos guias de estudo, métodos para diminuir a ansiedade, dicas de TCC preparadas pelos professores da Docsity
Falha é definida como qualquer mudança em um elemento de máquina que o torna impróprio ou inapto para a função ao qual foi projetado. Na teoria de máquinas, as falhas são geralmente classificadas segundo o tipo de agente causador, modo de ocorrência e consequências da falha. A melhor forma de prever a resistência de um componente de máquina é através de um ensaio experimental ou computacional no qual são simuladas condições próximas das esperadas daquelas encontradas em serviço.
Tipologia: Notas de aula
1 / 51
Esta página não é visível na pré-visualização
Não perca as partes importantes!
Falha é definida como qualquer mudança em um elemento de máquina que o torna
impróprio ou inapto para a função ao qual foi projetado. Na teoria de máquinas, as falhas são
geralmente classificadas segundo o tipo de agente causador, modo de ocorrência e
consequências da falha.
do material.
progressiva. A falha é causada por uma falha localizada devido à propagação de
trinca na região de estricção do corpo de prova.
constante causando falha localizada por propagação de trinca em regiões
normalmente de alta concentração de tensão.
altas dependendo do ensaio, causando falha volumétrica e generalizada.
A melhor forma de prever a resistência de um componente de máquina é através de um
ensaio experimental ou computacional no qual são simuladas condições próximas das
esperadas daquelas encontradas em serviço. Dessa forma, são responsabilidades da equipe
de projeto:
A escolha quanto ao tipo e modo de falha geralmente recai sobre qual o modelo de
escoamento que deve ser adotado. Podem ser utilizados critérios estáticos, geralmente
originados no ensaio de tração uniaxial – critérios de Rankine, Tresca ou von Mises – ou
critérios dinâmicos oriundos da ocorrência de fadiga em baixo ou alto ciclo. Algumas vezes
também podem ser utilizados critérios que envolvam desgaste ou corrosão.
A grande maioria dos critérios envolvendo o projeto e dimensionamento de elementos
de máquinas tem como base teorias que utilizam tanto o ensaio de tração unidimensional
quanto o ensaio de fadiga em flexão rotativa. Os materiais utilizados como matéria prima para
os componentes das máquinas (eixos, parafusos, engrenagens, etc) são classificados pelos
projetistas em dúcteis ou frágeis.
Como esta classificação é mais ou menos arbitrária, ela permite a comparação entre o
comportamento de dois materiais mas não permite avaliar em termos absolutos qual é dúctil e
qual é frágil. Neste texto é adotado o seguinte critério de classificação:
escoamento. Os materiais dúcteis tem a vantagem de absorver maior energia mecânica até
a ruptura do que um material frágil com aproximadamente o mesmo limite de escoamento.
Neste texto, são considerados materiais dúcteis aqueles que apresentam uma deformação
específica máxima observada no ensaio de tração uniaxial ε max
for maior ou igual a 0,015.
escoamento no ensaio de tração uniaxial. Tipicamente, materiais como o ferro fundido (com
exceção do maleável), aços de alto carbono e alguns aços ligados são considerados
materiais de construção mecânica frágeis. Um material é dito frágil quando a deformações
específica máxima observada no ensaio de tração uniaxial εmax for menor que 0,015.
Na determinação das propriedades mecânicas dos materiais através do diagrama
tensão-deformação a aplicação da carga é gradual. Os valores obtidos através deste ensaio se
aplicam aos critérios conhecidos como estáticos.
Por outro lado, as condições que frequentemente ocorrem em estruturas mecânicas são
solicitações dinâmicas, onde a tensão e a deformação variam de forma mais ou menos
arbitrária em pequenos intervalos de tempo, como no caso de um eixo em uma máquina
rotativa. Esta variação temporal das solicitações leva a estrutura à um estado diferente daquele
utilizado no ensaio de tração, ocasionando algumas vezes a falha por fadiga.
A falha por fadiga é um processo gradual, iniciado geralmente com pequenas trincas
invisíveis a olho nu, que se desenvolvem de forma progressiva e cumulativa, levando a peça a
falhar bruscamente após um determinado número de solicitações ou ciclos.
A grande maioria das falhas por fadiga estão relacionadas à propagação de trincas
através do componente. Geralmente devem estar presentes as seguintes condições:
figura 2.1: comparação entre o comportamento de
um material dúctil (ABNT 1020 com max
=0,053) e
um material frágil (aço ligado com max=0,012)
Na fase inicial ou fase de nucleação ocorrem deslizamentos em certos planos cristalinos
no interior do grão cuja direção é a mais desfavorável. Conforme as tensões variam no tempo,
surgem mais planos de deslizamento no grão, os quais vão se acumulando à medida em que a
tensão varia. Quando o número de planos de deslizamento atinge um número crítico, estas se
fundem dando origem a uma micro-trinca.
As micro-trincas normalmente ficam confinadas pelo contorno de grão, mas, com o
passar do tempo, ultrapassam essa barreira e caminham no sentido da direção mais favorável.
Essa direção pode ser um caminho entre os contornos de grão, mas, a nível global, a direção
de propagação é dada pela linha de isotensão correspondente à máxima tensão de von Mises.
A segunda fase é caracterizada pelo crescimento da trinca, quando esta ultrapassa o
contorno de grão e se propaga ao longo dos grãos vizinhos. Nestas condições, seu
crescimento pode ser estável (lento) ou instável (rápido). As condições de instabilidade de uma
trinca são estudadas na Mecânica da Fratura. Doravante serão estudadas apenas as trincas
estáveis.
A terceira fase é caracterizada pela ruptura. Na medida em que a trinca avança, ocorre
uma diminuição da seção transversal resistente, causando um aumento de tensão que, por sua
vez, aumenta a velocidade de propagação da trinca. Em um dado instante, a tensão atuante
ultrapassa o limite de resistência do material e ocorre a falha por fadiga.
figura 2.4: região típica para o surgimento de uma trinca em zona de
concentração de tensão (variação abrupta de geometria)
(1) (2) (3)
figura 2.5: surgimento (1), propagação (2) e ruptura (3) de uma trinca por fadiga cíclica
As principais teorias envolvendo a ocorrência de falhas por fadiga são baseadas em
métodos experimentais cujo objetivo é avaliar a importância relativa de todos os fatores que
contribuem para o avanço do processo de falha.
2.1 Ensaio de Flexão Alternada
Para se determinar o comportamento dinâmico dos materiais utilizados na construção
mecânica, R.R. Moore criou um ensaio no qual se submete o corpo de prova a um estado de
flexão pura (sem cisalhamento direto) através da aplicação de uma força na seção transversal
crítica. Para tanto a geometria do corpo de prova é cuidadosamente escolhida de modo a
garantir que a tensão máxima de flexão ocorra na região central do corpo de prova.
Figura 2.6: máquina de ensaio de fadiga.
figura 2.7: corpo de prova.
O objetivo do ensaio é determinar o número de ciclos (rotações fornecidas pelo motor)
necessários para que um determinado corpo de prova sofra ruptura por flexão rotativa As
características principais do ensaio de fadiga são:
escolhidas. Os procedimentos padronizados dos ensaios de fadiga são encontrados,
por exemplo, nas normas ASTM E466-E468:
o
(obtida via
ensaio de tração prévio), por volta de 90% de σ R
, anotando-se o número de ciclos
/(rotações) necessárias para a ruptura através de propagação de trinca.
anotando-se novamente o número de ciclos até a falha. O procedimento é repetido
várias vezes, diminuindo-se progressivamente o nível de tensão e anotando-se para
os demais casos o número de ciclos para fratura.
A curva S-N da figura 2.8 ilustra o comportamento de um corpo de prova de aço ABNT
1040 quando submetido ao ensaio de fadiga em flexão rotativa. Pode-se perceber que, abaixo
de certo valor de tensão (no caso, aproximadamente 300 MPa), não ocorre ruptura do corpo de
prova por fadiga. Uma consequência disso é que, se quisermos impedir a ocorrência de fadiga,
devemos manter a tensão em qualquer ponto do corpo de prova abaixo deste valor.
O valor de tensão abaixo da qual não ocorre a ruptura do corpo de prova é chamado
limite de resistência à fadiga e indicado por Sn CP
. O limite de resistência à fadiga para corpos
de prova de aço ocorre normalmente entre 10
6
ciclos e 10
7
ciclos.
Analisando o gráfico da figura 2.8 pode-se dizer ainda que o comportamento da curva
S-N para o aço e suas ligas varia dependendo da região considerada:
3
ciclos temos a chamada fadiga de baixo ciclo. Nesta
região o crescimento das trincas é melhor explicado em termos da deformação
ao invés da tensão pois o material é solicitado por tensões alternadas maiores
que a tensão limite de escoamento. Recomenda-se que qualquer previsão de
vida que ocorra entre 0 e 10
3
ciclos seja encarada com o devido cuidado.
3
e 10
6
ciclos ocorre a chamada fadiga de alto ciclo. A
maioria dos problemas de fadiga em componentes mecânicos ocorre nessa
região.
6
ciclos para materiais ferrosos temos a região de vida
infinita. Neste caso não ocorre falha por fadiga e diz-se que N → .
Outros materiais de construção mecânica importantes como alumínio, cobre e ligas de
magnésio não apresentam o patamar característico da figura 2. 8 e são sujeitos à fadiga mesmo
para pequenos valores da tensão atuante. A figura 2. 9 ilustra o comportamento à fadiga de dois
corpos de prova de materiais com aproximadamente as mesmas características de resistência
mecânica (σ R
e σ E
). Pode-se perceber que o comportamento dos dois é distinto uma vez que o
material não ferroso (liga de alumínio) não apresenta o patamar de vida infinita. Além disso,
para um valor de tensão acima de 400 MPa, o CP de alumínio tem uma vida maior que o
correspondente CP de aço carbono.
Para materiais não-ferrosos (alumínio, cobre, magnésio, etc) e suas ligas, a resistência à
fadiga, para propósitos de cálculo, é escolhida como o valor de tensão que resulta em uma vida
de 5x
8
ciclos para o corpo de prova no ensaio de flexão alternada.
figura 2.9: Comparação entre as
curvas S-N materiais ferrosos e não-
ferrosos.
2.3 Relação entre Sn CP
e demais propriedades mecânicas
Um tópico importante na teoria de fadiga é a caracterização de SnCP em função de
propriedades mecânicas obtidas pelo ensaio de tração ( R
ou E
). Muitos experimentos foram
feitos com CP´s normalizados e concluiu-se que o valor do limite de resistência à fadiga varia
para os diferentes tipos de aço, apesar da vida total do CP permanecer constante entre 10
6
ciclos e 5x
6
ciclos. Numa tentativa de relacionar Sn CP
com o seu respectivo limite de
resistência R
, estes valores foram plotados para diferentes aços na figura abaixo:
figura 2.10: variação de SnCP com o limite de resistência para diversos tipos de aço
Observando-se a figura 2.10, podemos traçar uma relação experimental entre o valor de
SnCP e o limite de resistência dos aços conforme a equação abaixo:
Sn
CP
= {
0 , 5 σ
R
para σ
R
< 1400MPa ( 200 Kpsi)
700 MPa para σ
R
≥ 1400MPa ( 200 Kpsi)
( 2. 2 )
Para outros materiais, as relações entre Sn CP
e R
são dadas na tabela 2.1.
material relação experimental ciclos
Ferro fundido Sn
CP
= {
0 , 4 σ
R
para σ
R
< 400MPa
( 60 Kpsi
)
160 MPa para σ
R
≥ 400MPa ( 60 Kpsi)
10
6
Alumínio e ligas Sn
CP
= {
0 , 4 σ
R
para σ
R
< 330MPa
( 48 Kpsi
)
130 MPa para σ
R
≥ 330MPa ( 48 Kpsi)
5x
8
Cobre e ligas Sn
CP
= {
0 , 4 σ
R
para σ
R
< 280MPa
( 40 Kpsi
)
100 MPa para σ
R
≥ 280MPa ( 40 Kpsi)
5x
8
TABELA 2.1 Relação entre Sn CP
e σ R
para diferentes materiais
Na prática os dados da tabela 2.1 correspondem a valores médios e são apenas
orientativos. Tais valores devem ser utilizados apenas nos casos onde dados experimentais
não estarem disponíveis.
Associações profissionais como SAE, ASME e ASTM publicam regularmente dados a
respeito do comportamento à fadiga de grande parte dos materiais utilizados na prática de
engenharia.
limite de resistência (Kpsi)
0 50 100 150 200 250
150
100
50
experimentos
aproximação
Certo aço carbono foi ensaiado na máquina de flexão rotativa de R.R. Moore da figura 2.6. As
dimensões utilizadas são a=150mm e b=70mm. O ensaio utilizou um corpo de prova
normalizado de aço classe 6.8 com d=8mm na região do estreitamento. Pede-se:
a) obter a vida total do CP para uma força F= 300 N
b) obter a vida total do CP para uma força F= 200 N
c) calcular a força F que deve ser aplicada para que o CP tenha uma vida de 10
5
ciclos
Para o aço 6.8 tem-se r
= 600 MPa e e
= 480 MPa. Uma vez que o limite de resistência é
menor que 1400 MPa, então, pela equação 2. 2 , tem-se Sn CP
= 0,5σ R
= 300 MPa.
Calculando-se em seguida os coeficientes m 6
e b 6
da equação de Basquin obtém-se:
m = m
6
=
1
3
log (
0 , 9 σ
R
Sn
CP
1
3
log (
0 , 9. 600
300
b = b
6
= log (
0 , 81 σ
R
2
Sn
CP
) = log (
0 , 81. 600
2
300
) = 2 , 9877 log(MPa)
As tensões na seção do estreitamento podem ser calculadas pela equação 2.1, ou seja:
σ
flexão
=
16Fb
πd
3
=
π. 8
3
= 417 , 8 MPa
Pela equação de Basquin:
N =
√
10
b
σ
m
10
2 , 9877
417 , 8
0 , 0851
= 20390 , 1 ciclos
De maneira similar, para F = 200 N obtém-se σ = 278,5 MPa. Observa-se, entretanto que
este valor é inferior a Sn CP
, o que indica que N → ∞ quando F=200 N.
5
ciclos:
Neste caso, pela equação de Basquin tem-se
σ = 10
b
. N
−m
= 10
2 , 9877
.
( 10
5
)
− 0 , 0851
= 364 , 9 MPa
e pela equação (2.1) obtém-se:
σ
flexão
=
12Fb
πd
3
→ F =
πd
3
. σ
flexão
16b
=
π. 8
3
. 364 , 9
= 524 N
2.5 Fatores modificadores do limite de resistência à fadiga: Equação de Marin
Um fato importante na teoria de fadiga é que a situação idealizada do ensaio de flexão
alternada de R.R. Moore raramente é encontrada na prática de projeto mecânico. Daí a
necessidade de se corrigir os valores encontrados na curva S-N para adequação às demais
situações.
Por exemplo, se um engenheiro deseja analisar o comportamento à fadiga de uma peça
forjada, os dados do ensaio de flexão alternada com corpos de prova polidos não seriam de
grande ajuda, uma vez que existe influência do acabamento superficial no comportamento à
fadiga dos materiais metálicos.
Os fatores que diferenciam os dados dos ensaios de fadiga daqueles encontrados em
situações reais podem ser agrupados em seis categorias distintas: carregamento, fatores
estatísticos, acabamento superficial, fator de escala (tamanho), temperatura e fatores diversos,
tais como presença de tensões residuais, corrosão, tratamentos superficiais (ex. nitretação),
tamanho de grão e severidade de choques.
O limite de resistência à fadiga corrigido, indicado simplesmente por Sn é obtido em
função de Sn CP
através da equação de Marin:
Sn = C
CARGA
CONF
DIV
SUP
TAM
TEMP
. Sn
CP
onde:
CARGA
: carregamento, sensibilidade da peça ao tipo de solicitação.
CONF
: confiabilidade, considera que fadiga é um processo estatístico
SUP
: superfície, leva em conta diferentes acabamentos superficiais
TAM
: tamanho, considera diferenças entre o tamanho do CP e da peça
TEMP
: variação das propriedades mecânicas com a temperatura
Os coeficientes na equação 2.7 são chamados de corretores de Marin. Tais fatores são
obtidos através de ensaios de laboratório, com o objetivo de identificar a influência que um
determinado parâmetro tem no comportamento à fadiga de um certo material.
Por exemplo, suponha que você deseja saber qual a influência que o processo
termoquímico de anodização tem no limite de resistência à fadiga no aço AISI 1040.
Inicialmente prepara-se um conjunto A contendo CP´s idênticos, os quais são testados na
máquina de ensaio de flexão alternada, obtendo o valor de Sn A
por volta de 10
6
ciclos. Em
seguida, outro conjunto B contendo também CP´s idênticos aos do tipo A é preparado. O
conjunto B é anodizado testado na máquina de flexão alternada obtendo também o valor de
Sn B
por volta de 10
6
ciclos. No final da experiência os valores de Sn A
e Sn B
são comparados,
chegando-se à conclusão que Sn B
é, na média, 30% menor que Sn A
. Dessa forma, quando se
deseja obter o limite de resistência à fadiga de peças de aço AISI 1040 nitretadas, utiliza-se
Div
Os dados a seguir ilustram o trabalho de muitos pesquisadores e foram coletados
pacientemente ao longo de mais de 80 anos de experiências e são, ainda hoje, objeto de
estudo na área de tecnologia e ciência dos materiais.
2 .5.1 Fator de Carregamento C CARGA
Este fator depende basicamente da sensibilidade do material frente ao tipo de
solicitação externa. Leva em conta diferenças entre o ensaio de flexão alternada, tomado como
referência, e outro tipo de solicitação. Para a determinação do fator de correção devido ao
cisalhamento puro e torção alternada foi utilizado o critério da máxima energia de distorção.
Tem-se, assim:
2 .5.4 Fator de acabamento superficial C SUP
Como se sabe, as operações de fabricação mecânica provocam, em maior ou menor
grau, micro-trincas e fissuras superficiais na medida em que danificam o contorno original do
componente. É nessas fissuras superficiais que uma macro-trinca pode surgir sem a
necessidade do mecanismo de planos de deslizamento exposto no item 2. Sendo assim, pode-
se dizer que quanto mais dano superficial um processo de fabricação provocar, maior será a
sua influência sobre o comportamento à fadiga pois facilita a nucleação de trincas que, de outra
forma não estariam presentes. Normalmente a quantidade de fissuras e micro-trincas está
associada ao índice de rugosidade da superfície
Os fatores modificadores C SUP
enfatizam a necessidade de um bom acabamento
superficial quando existe a possibilidade de falha por fadiga, como é o caso de zonas de
concentração de tensão. Para os aços e demais materiais ferrosos os fatores C sup
podem ser
encontrados na forma de gráficos em função da rugosidade superficial ou tipo de acabamento.
figura 2. 1 2: variação de Csup com o limite de resistência para diversos tipos de aço
Para os materiais ferrosos pode-se, alternativamente, utilizar a fórmula fornecida por
Shigley e Mischke (Shigley, 2003), obtida através de correlações experimentais:
SUP
= A. σ
R
B
onde R
é o limite de resistência e os coeficientes A e B são obtidos na tabela seguinte,
dependendo do tipo de operação de fabricação mecânica.
acabamento A ( R
em MPa) B
retificado 1.58 - 0.
laminado a frio,
usinado ou estampado
laminado a quente 57.70 - 0.
forjado 272.0 - 0.
TABELA 2. 4 Coeficientes da equação de Mischke para CP´s de aço e ferro fundido
Para os demais materiais C sup
deve ser considerado iguais a 1, 0 uma vez que os limites
de resistência à fadiga para estes materiais já incluem a influência do tipo de acabamento. Daí
a necessidade de se obter, sempre que possível, dados experimentais quanto ao
comportamento à fadiga dos materiais não ferrosos. Pode-se perceber pela figura 2.12 que,
quanto maior for o limite de resistência, maior será a influência que a rugosidade superficial tem
no comportamento à fadiga.
400 600 800 1.000 1.200 1.
0
1
USINADO
LAMINADO A
QUENTE
FORJADO
RETIFICADO
sR (MPa) s R
(MPa)
2.5.5 Fator de escala C TAM
O fator de tamanho ou escala, C TAM
, considera que, quanto maior a seção considerada,
maior a possibilidade de que ocorram fissuras que favoreçam o crescimento de trincas. Na
medida em que o tamanho da seção aumenta, maior é a quantidade de grãos sujeitos aos
mesmos níveis de tensão e, portanto, maior é a possibilidade de que pelo menos alguns deles
desenvolvam deslizamento em planos cristalinos menos favorecidos.
Para carregamento axial (tração, compressão e cisalhamento) considera-se geralmente
TAM
=1.00 pois não existe evidência experimental que o tamanho da seção transversal tenha
influência em Sn nestes casos de carregamento.
Para torção e flexão de peças de aço e ferro fundido valem as seguintes relações:
se d ≤ 8mm , C
tam
se 8mm ≤ d ≤ 250mm, C
tam
= 1 , 189. d
− 0 , 097
se d ≥ 250mm, C
tam
= 0 , 6
onde d é o diâmetro equivalente da seção. Na ausência de dados experimentais recomenda-se
que a equação 2.9 seja utilizada também em peças de alumínio, latão e cobre.
O cálculo do diâmetro equivalente é realizado através da área A 95
, a qual representa a
região da seção transversal sujeita a tensões iguais ou maiores que 95% da tensão máxima. A
figura 2.13 ilustra o cálculo da área A 95
para uma seção circular em flexão rotativa.
figura 2.13: Cálculo de A 95
para uma seção circular
A área indicada na figura 2.13 é, portanto:
95
π
d
2
0 ,9d
2
= 0 , 0766. d
2
→ d =
95
Para outras seções transversais o cálculo é feito por analogia, considerando a equação
2.10. A figura 2.14 indica o cálculo de A 95
para outras seções transversais comuns.
aplicado jateamento com limalha de ferro, o que aumenta a resistência à fadiga em 20%.
Determine o limite de resistência à fadiga para a seção transversal AA indicada no desenho.
Solução:
Inicialmente pode-se perceber que o esforço F aplicado pela mão do operador causa na seção
AA tensões de flexão devidas ao momento da força e tensões de cisalhamento devidas à força
cortante. Desprezando-se o efeito da cortante, o único esforço atuante na seção AA é,
portanto, devido ao carregamento de flexão variável no tempo. Tem-se, dessa forma:
material: aço classe 4.8 com σ R
= 400 MPa e σ e
= 320 MPa.
Pela equação 2.2, o limite Sn do aço 4.8 é obtido aproximando-se Sn = 0,5.σ R
= 200MPa. Os
coeficientes da equação de Marin são:
CARGA
= 1,0 (a seção A-A é submetida a tensões de flexão alternada)
CONF
= 1,0 (para uma confiabilidade de 50%)
DIV
= 1,2 (jateamento aumenta Sn em 20%)
SUP
= 0,7 (para aço forjado, eq. 2.8)
TEMP
= 1,0 (temperatura abaixo de 450ºC)
Como a seção AA não é circular, é necessário obter um diâmetro equivalente através do
cálculo de A 95
. Para a seção transversal em I com flexão no eixo 1- 1 na figura 2.14b tem-se:
95
= 0,05.b.h = 5,67mm
2
e, portanto:
d = √
A 95
0 , 0766
= 8 ,60mm → C
TAM
− 0 , 097
Finalmente, utilizando-se a equação de Marin obtém-se:
Sn = C
CARGA
CONF
DIV
SUP
TAM
TEMP
. Sn
CP
= 162 , 1 MPa
Na grande maioria das aplicações, as cargas aplicadas em elementos mecânicos podem
dar origem a variações da tensão no tempo bastante complicadas. Considere a figura 2.16 que
ilustra a variação no tempo da força aplicada no ponto de uma suspensão tipo McPhearson.
figura 2.16: força típicas no encaixe superior de uma suspensão tipo McPhearson
É comum, através da análise de Fourier, expressar uma grande variedade de
carregamentos periódicos ou transientes através da soma de funções harmônicas (Sneddon,
2010). Sendo assim, para a análise de carregamentos complexos no tempo, deve-se começar
pelo estudo de uma única força harmônica. Observe o exemplo a seguir.
figura 2.17: decomposição de uma tensão harmônica (1) em componentes alternada (2) e média (3)
Da figura 2.17, podemos extrair, a partir do gráfico de (t) a componente média ( m
) e a
componente alternada ( a
). Tem-se, portanto:
σ
m
σ
max
min
e σ
a
σ
max
− σ
min
e define-se ainda a razão de tensão, R, como:
σ
max
σ
min
No entanto, uma vez que as tensões mostradas no gráfico não correspondem à tensão
real devido à presença de entalhes e concentradores de tensão, estas devem ainda ser
multiplicadas pelos respectivos fatores de concentração de tensão.
Entalhes ou concentradores de tensão representam qualquer descontinuidade
geométrica que interrompa o “fluxo natural” de esforços através da peça. Exemplos de
F(t)
dependem do material e do tamanho do concentrador, levou ao conceito de sensibilidade ao
entalhe, isto é, a característica que um material tem ao ser mais ou menos sensível à presença
de concentradores de tensão.
A sensibilidade ao entalhe q de um material é definida como (Peterson, 1951):
q =
F
T
e, portanto,
F
= q. (K
T
Neuber (1946) propôs a expressão 2.22 para o cálculo da sensibilidade ao entalhe
baseando-se em experimentos com aços de baixo carbono. Estudos posteriores comprovaram
também a sua aplicabilidade para o alumínio e outros materiais metálicos:
q =
a
ρ
onde √
𝑎 é chamada de constante de sensibilidade de Neuber e obtida experimentalmente em
função da tensão de ruptura do material. A distância ρ é definida pelo raio característico do
concentrador de tensão. É o caso de furos, adoçamentos, roscas etc.
Materiais de baixa ductilidade, como ligas de aço de alto carbono, apresentam alta
sensibilidade ao entalhe, de tal maneira que, para esses materiais K F
T
e K FS
TS
. Por
outro lado, materiais dúcteis como aços de baixo carbono, cobre e alumínio possuem baixa
sensibilidade ao entalhe. O ferro fundido e o concreto são materiais relativamente frágeis que
fogem a essa regra por apresentar um alto índice de amortecimento, defeitos internos e
heterogeneidades que retardam a propagação de tensão. Tais características fazem com que
estes materiais se aproximem do comportamento aos materiais dúcteis.
Sendo assim, para o ferro fundido (maleável, cinzento ou branco), recomenda-se utilizar
0,05 ≤ q ≤ 0,20 enquanto que para o cobre e suas ligas recomenda-se 0,10 ≤ q ≤ 0,20.
figura 2.1 9 : constante de Neuber em função da tensão de ruptura
3.2 Efeito dos concentradores na região plástica da curva tensão x deformação
A utilização dos fatores de concentração geométricos K T
e K TS
para o cálculo dos fatores
F
e K FS
pela equação 2.21 só pode ser feita considerando-se a fase elástica da curva de
Constante de Neuber para o Alumínio
Constante de Neuber para o Aço
tensão monotônica do material uma vez que a obtenção dos fatores geométricos pressupõe
que o material se comporte linearmente.
Dessa forma alguns autores (NORTON, 1998 e Dowling, 19 98 ) argumentam que, após o
escoamento, a influência do concentrador de tensão diminui, pois, as tensões reais ficam
limitadas à tensão de escoamento, resultando em uma região plástica” onde não existe
concentração de tensão. O tamanho desta região plástica e o valor da tensão dependem da
ductilidade do material, de maneira que materiais perfeitamente plásticos (onde não ocorre
encruamento) tem regiões plásticas maiores. Para o caso elástico, isso pode ser observado na
simulação abaixo, onde a força F atuando na figura 2.18 foi aumentada fazendo o material
escoar na região do concentrador de tensão. Podemos perceber o surgimento de uma região
onde a tensão não se apresenta concentrada como é caso em que σ X
< σ e
figura 2.20: comparação da região do concentrador para σ X
σ e
(a esquerda) e σ X
< σ e
(a direita)
Entretanto, embora o fenômeno da atenuação da concentração de tensão ocorra para o
caso estático, no caso de tensões dinâmicas o encruamento do material, que ocorre a cada
novo ciclo de aplicação da carga, aumenta gradativamente a tensão de escoamento.
Para ilustrar isso, admite-se incialmente que o comportamento elastoplástico do material
obedeça a um modelo não-linear, com a curva σ(ε) ilustrada na figura 2.21 e que a força
aplicada na chapa da figura 2. 18 varie no tempo de maneira harmônica com R=0, ou seja
min
=0 e F max
=F (carga pulsante). Durante o primeiro ciclo de aplicação da força, representado
por A→B→C→D, ocorre encruamento com a nova tensão de escoamento localizada em σ C
. No
segundo ciclo, representado por D→C→E→F ocorreria novo encruamento com o escoamento
ocorrendo a partir de σ=σ c
e a tensão de escoamento aumentaria novamente para σ esc
= σ E
Percebemos que, à medida que os ciclos de carregamento se sucedem, a curva elasto-
plástica de σ(t) se aproxima gradativamente da curva puramente elástica, de modo que a partir
de um certo número de ciclos, o fenômeno de concentração de tensão reaparece com a nova
tensão de escoamento localizada em σe= σmax = kF.σmax,nom.
escoamento
concentração de tensão