
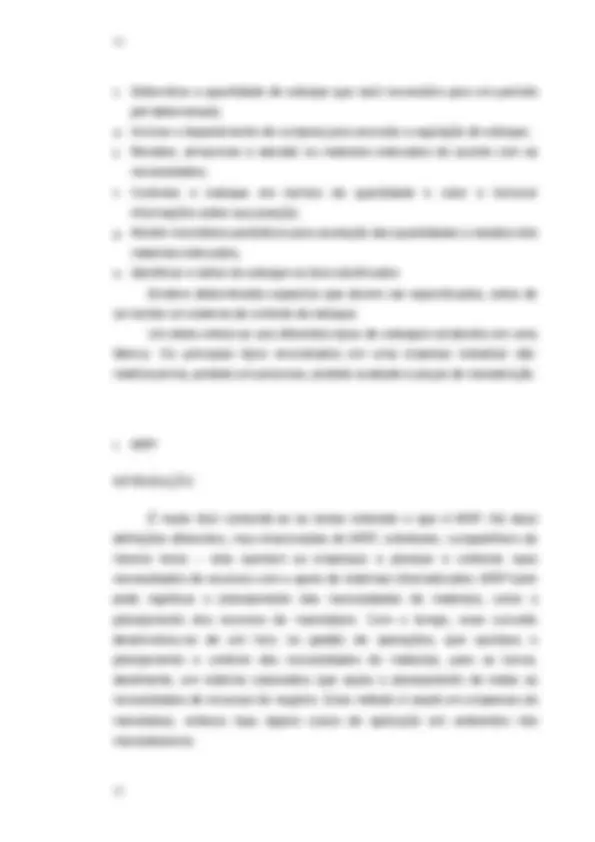
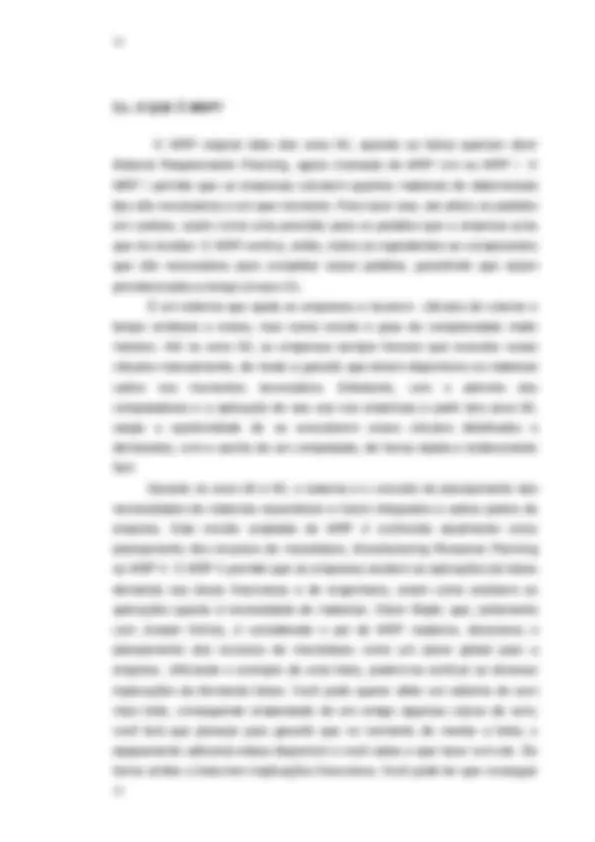
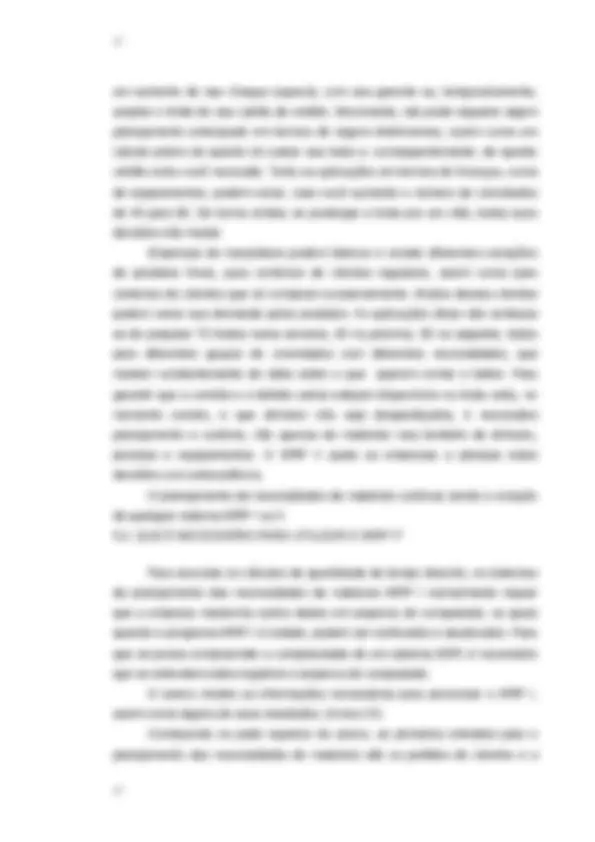
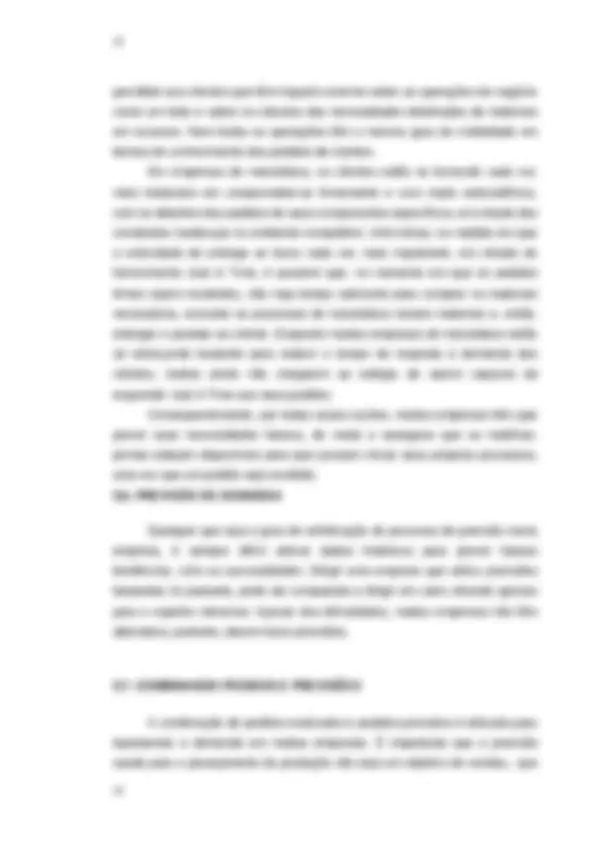
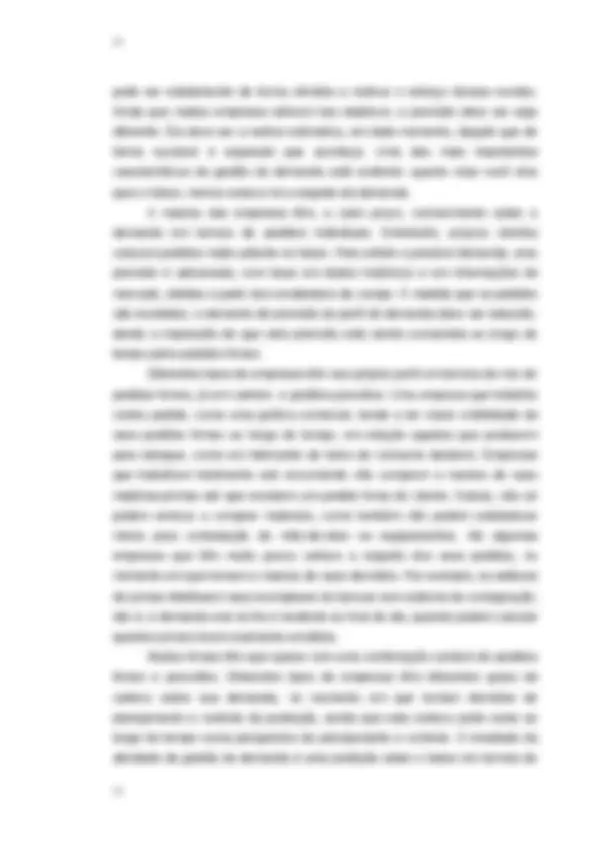
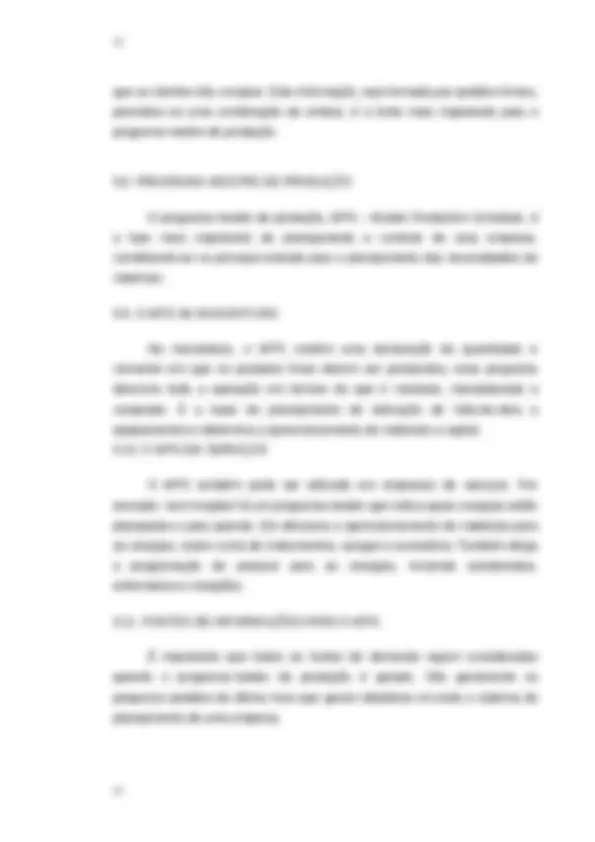
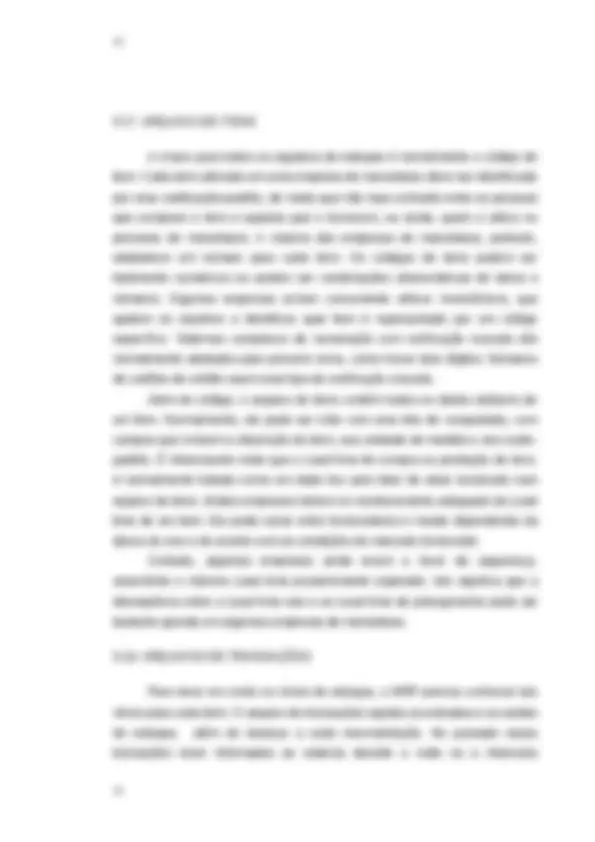
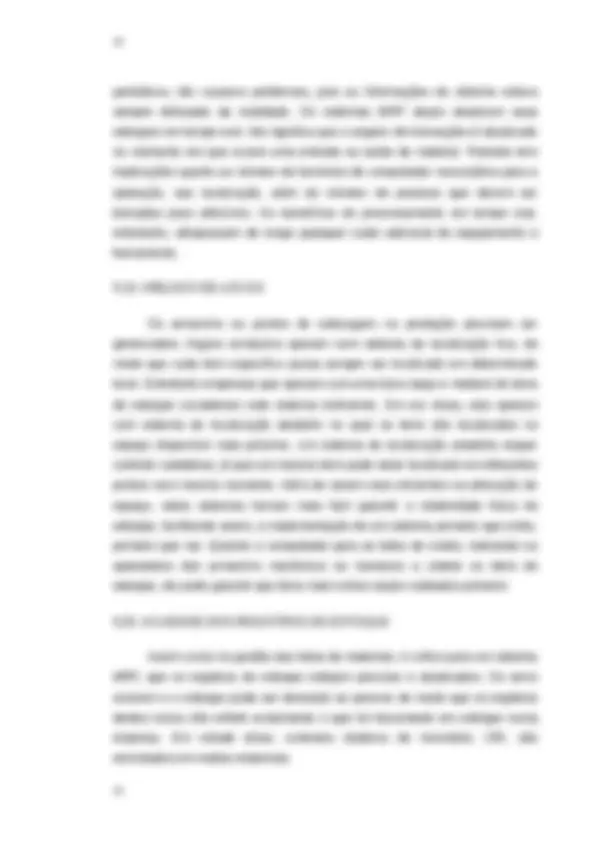
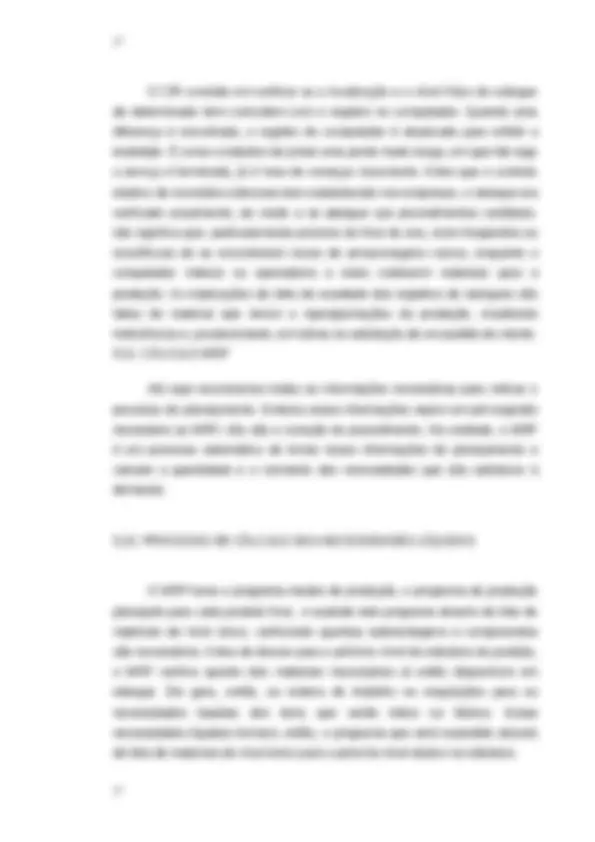
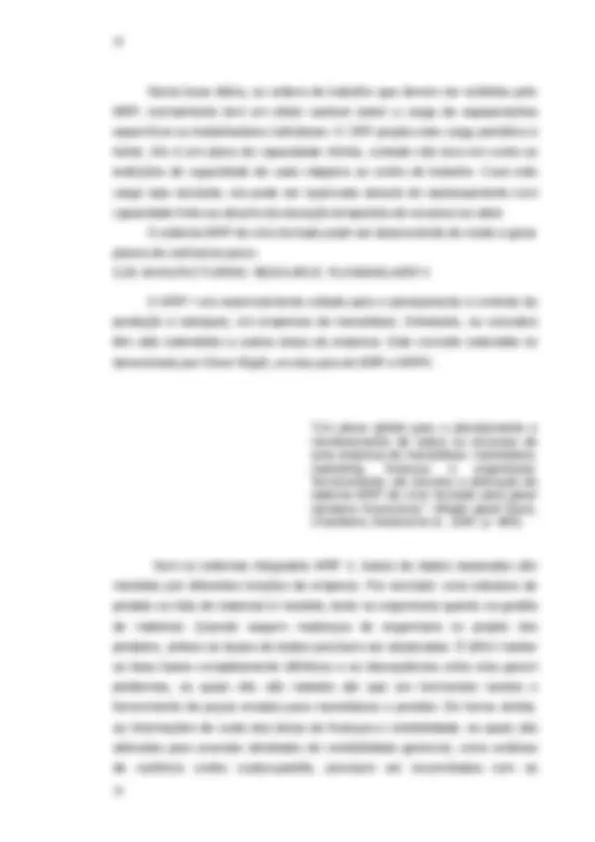
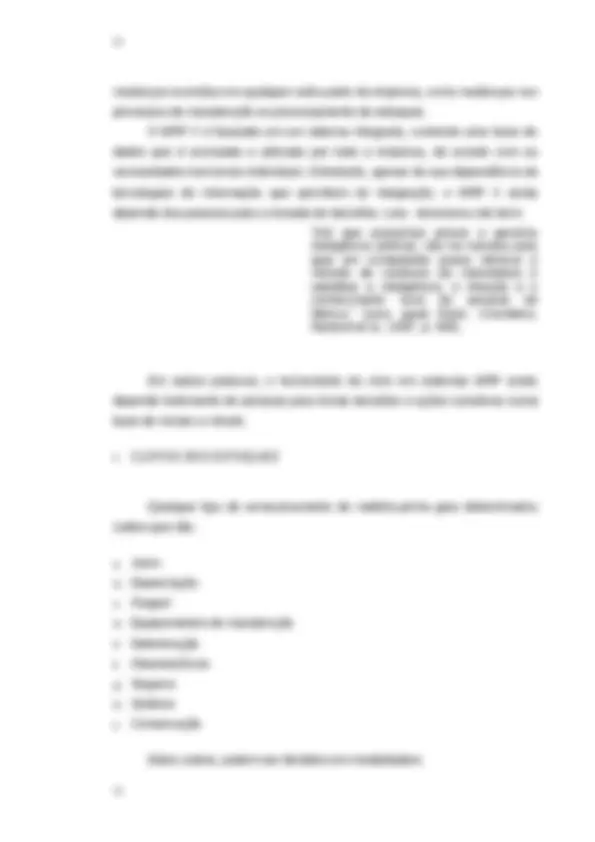
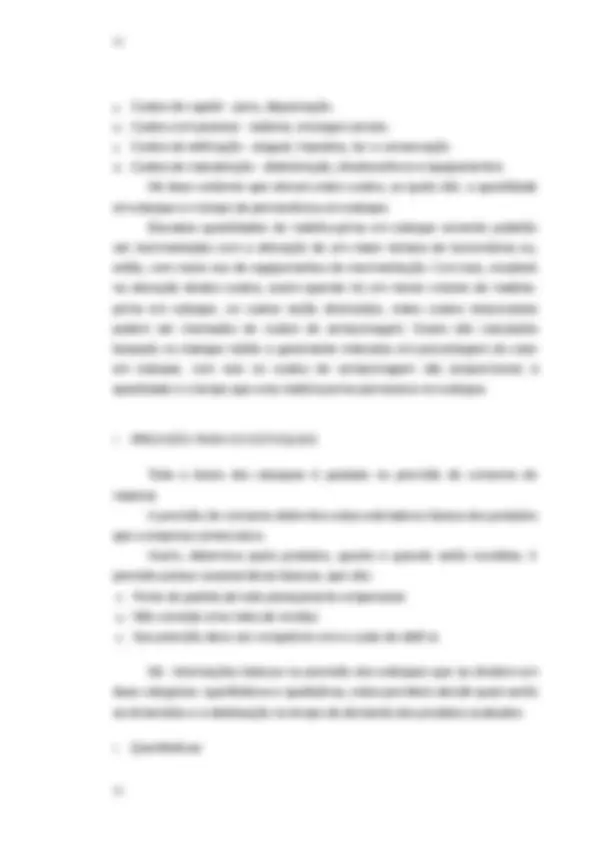
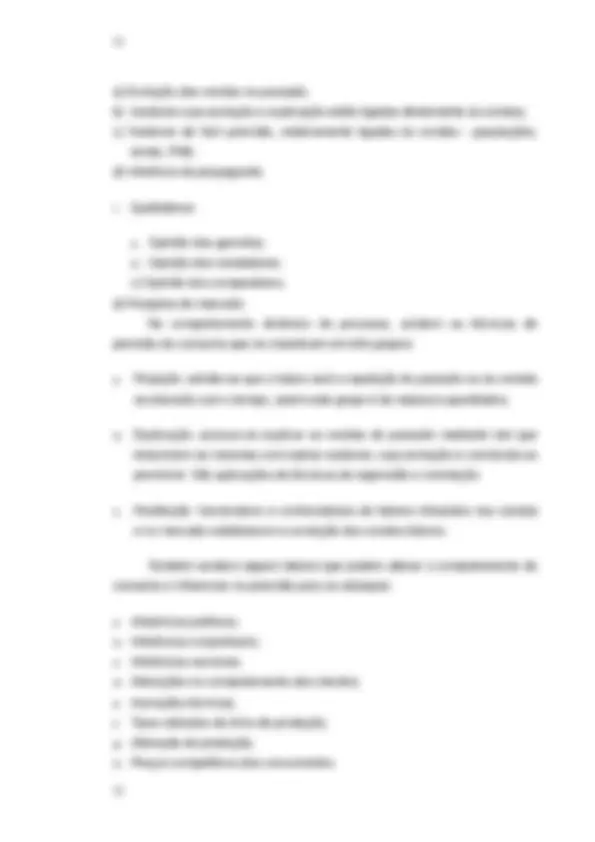
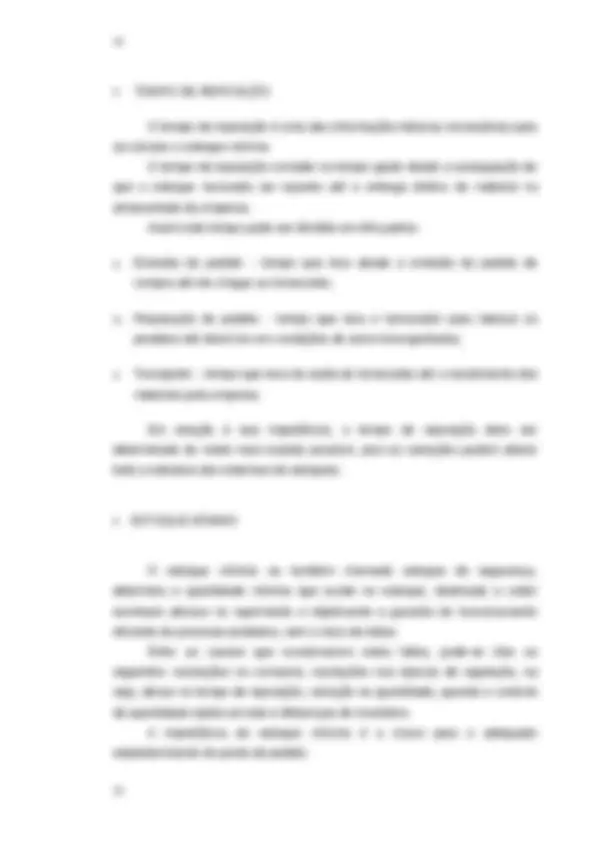
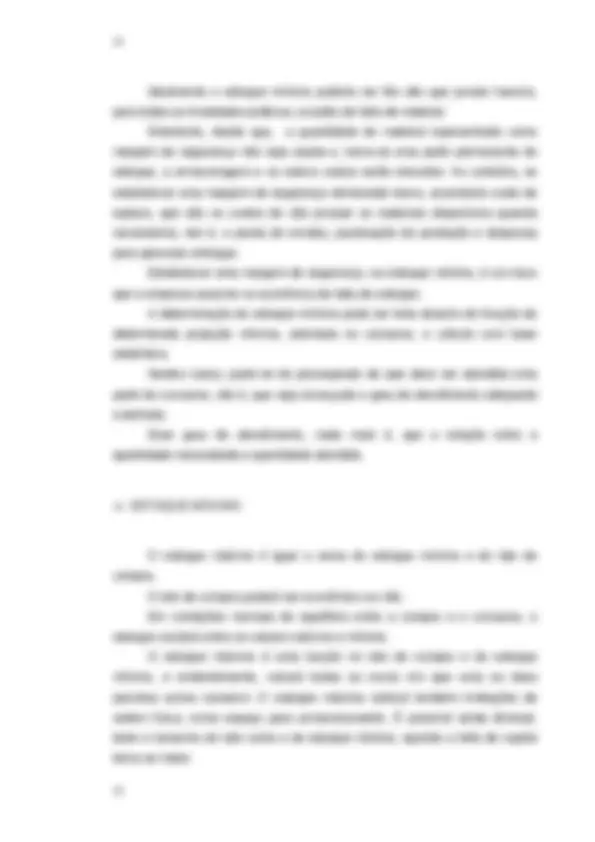
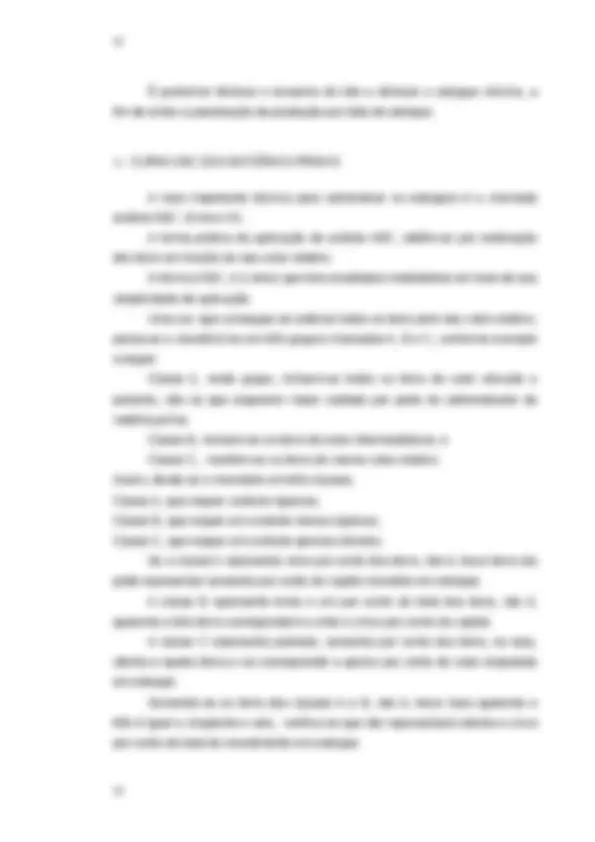
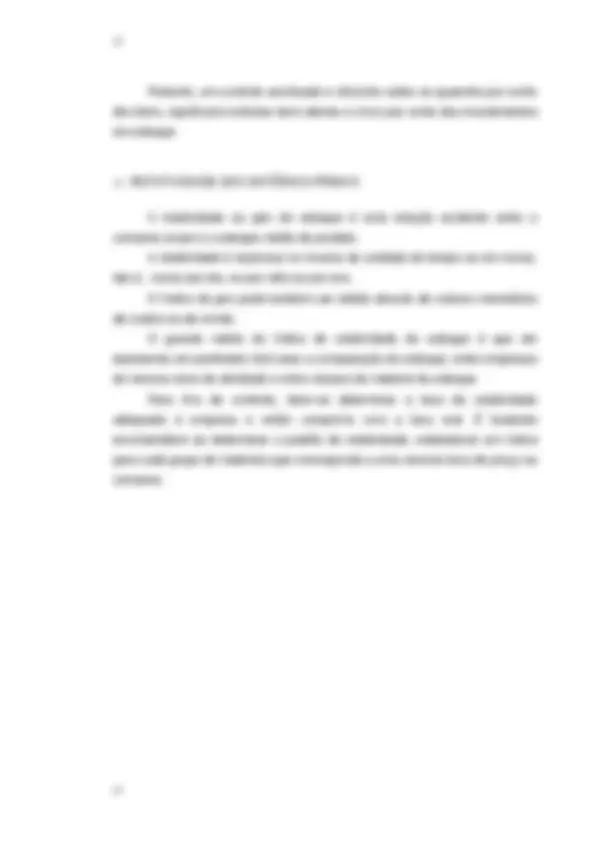
Estude fácil! Tem muito documento disponível na Docsity
Ganhe pontos ajudando outros esrudantes ou compre um plano Premium
Prepare-se para as provas
Estude fácil! Tem muito documento disponível na Docsity
Prepare-se para as provas com trabalhos de outros alunos como você, aqui na Docsity
Os melhores documentos à venda: Trabalhos de alunos formados
Prepare-se com as videoaulas e exercícios resolvidos criados a partir da grade da sua Universidade
Responda perguntas de provas passadas e avalie sua preparação.
Ganhe pontos para baixar
Ganhe pontos ajudando outros esrudantes ou compre um plano Premium
Comunidade
Peça ajuda à comunidade e tire suas dúvidas relacionadas ao estudo
Descubra as melhores universidades em seu país de acordo com os usuários da Docsity
Guias grátis
Baixe gratuitamente nossos guias de estudo, métodos para diminuir a ansiedade, dicas de TCC preparadas pelos professores da Docsity
Este documento aborda o controle de estoque em empresas, seus objetivos, políticas e o sistema mrp ii (manufacturing resource planning) para planejamento de recursos. O texto explica as principais funções do controle de estoque, como manter inventários periódicos, identificar itens danificados, e o papel do mrp na gestão de necessidades de materiais.
Tipologia: Notas de estudo
1 / 25
Esta página não é visível na pré-visualização
Não perca as partes importantes!
A função do Controle de Estoque é maximizar o efeito lubrificante no feedback de vendas não realizadas, ajudando no ajuste do planejamento de produção. A administração do controle de estoque deve minimizar o capital total investido em estoques, pois ele é caro e aumenta continuamente, uma vez que, o custo financeiro também se eleva. Uma empresa não poderá trabalhar sem estoque, pois, sua função amortecedora entre vários estágios de produção vai até a venda final do produto. Somente algumas matérias-primas têm a vantagem de estocar, em razão da influência da entrega do fornecedor. Outras matérias-primas especiais, o fornecedor precisa de vários dias para produzi-la. O controle de estoque é de suma importância para a empresa, sendo que controla-se os desperdícios, desvios, apura-se valores para fins de análise, bem como, apura o demasiado investimento, o qual prejudica o capital de giro. Quanto maior é o investimento, também maior é a capacidade e a responsabilidade de cada setor da empresa. Os objetivos dos departamentos de compras, de produção, de vendas e financeiro, deverá ser conciliado pela administração de controle de estoques, sem prejudicar a operacionalidade da empresa. A responsabilidade da divisão de estoques já é antiga; os materiais caem sobre o almoxarife, que zela pelas reposições necessárias. Na administração moderna, a responsabilidade dos estoques fica sob uma única pessoa. Os departamentos tradicionais ficam livres desta responsabilidade e podem dedicar-se à sua função primária.
O objetivo do controle de estoque é otimizar o investimento em estoque, aumentando o uso dos meios internos da empresa, diminuindo as necessidades de capital investido. O estoque do produto acabado, matéria-prima e material em processo não serão vistos como independentes. Todas as decisões tomadas sobre um dos tipos de estoque, influenciarão os outros tipos. Às vezes acabam se esquecendo dessa regra nas estruturas de organização mais tradicionais e conservadoras. O controle de estoque tem também o objetivo de planejar, controlar e replanejar o material armazenado na empresa.
A administração geral da empresa deverá determinar ao departamento de controle de estoque, o programa de objetivos a serem atingidos, isto é, estabelece certos padrões que sirvam de guias aos programadores e controladores e também de critérios para medir o desenvolvimento do departamento. Estas políticas são diretrizes que, de maneira geral, são as seguintes: a) Metas de empresas quando há tempo de entrega dos produtos ao cliente; b) Definição do número de depósitos de almoxarifados e da lista de materiais a serem estocados nele; c) Até que nível deverão flutuar os estoques para atender uma alta ou baixa demanda ou uma alteração de consumo; d) As definições das políticas são muito importantes ao bom funcionamento da administração de estoques.8G
Para se organizar um setor de controle de estoque, inicialmente deveremos descrever suas principais funções: a) Determinar o que deve permanecer em estoque. Número de itens; b) Determinar quando se deve reabastecer o estoque. Prioridade;
O MRP original data dos anos 60, quando as letras queriam dizer Material Requirements Planning, agora chamado de MRP Um ou MRP I. O MRP I permite que as empresas calculem quantos materiais de determinado tipo são necessários e em que momento. Para fazer isso, ele utiliza os pedidos em carteira, assim como uma previsão para os pedidos que a empresa acha que irá receber. O MRP verifica, então, todos os ingredientes ou componentes que são necessários para completar esses pedidos, garantindo que sejam providenciados a tempo.(Anexo IX). É um sistema que ajuda as empresas a fazerem cálculos de volume e tempo similares a esses, mas numa escala e grau de complexidade muito maiores. Até os anos 60, as empresas sempre tiveram que executar esses cálculos manualmente, de modo a garantir que teriam disponíveis os materiais certos nos momentos necessários. Entretanto, com o advento dos computadores e a aplicação de seu uso nas empresas a partir dos anos 60, surgiu a oportunidade de se executarem esses cálculos detalhados e demorados, com o auxílio de um computador, de forma rápida e relativamente fácil. Durante os anos 80 e 90, o sistema e o conceito do planejamento das necessidades de materiais expandiram e foram integrados a outras partes da empresa. Esta versão ampliada do MRP é conhecida atualmente como planejamento dos recursos de manufatura, Manufacturing Resourse Planning ou MRP II. O MRP II permite que as empresas avaliem as aplicações da futura demanda nas áreas financeiras e de engenharia, assim como analisem as aplicações quanto à necessidade de materiais. Oliver Wight, que, juntamente com Joseph Orlicky, é considerado o pai do MRP moderno, descreveu o planejamento dos recursos de manufatura como um plano global para a empresa. Utilizando o exemplo de uma festa, podem-se verificar as diversas implicações da demanda futura. Você pode querer obter um sistema de som mais forte, conseguindo emprestado de um amigo algumas caixas de som; você terá que planejar para garantir que no momento de montar a festa, o equipamento adicional esteja disponível e você sabia o que fazer com ele. De forma similar a festa tem implicações financeiras. Você pode ter que conseguir
um aumento de seu cheque especial, com seu gerente ou, temporariamente, ampliar o limite do seu cartão de crédito. Novamente, isto pode requerer algum planejamento antecipado em termos de alguns telefonemas, assim como um cálculo prévio do quanto irá custar sua festa e, consequentemente, de quanto crédito extra você necessita. Tanto as aplicações em termos de finanças, como de equipamentos, podem variar, caso você aumente o número de convidados de 40 para 80. De forma similar, se postergar a festa por um mês, todas suas decisões irão mudar. Empresas de manufatura podem fabricar e vender diferentes variações de produtos finais, para centenas de clientes regulares, assim como para centenas de clientes que só compram ocasionalmente. Muitos desses clientes podem variar sua demanda pelos produtos. As aplicações disso são similares as de preparar 75 festas numa semana, 40 na próxima, 50 na seguinte, todas para diferentes grupos de convidados com diferentes necessidades, que mudam constantemente de idéia sobre o que querem comer e beber. Para garantir que a comida e a bebida certas estejam disponíveis na festa certa, no momento correto, e que dinheiro não seja desperdiçados, é necessário planejamento e controle, não apenas de materiais mas também de dinheiro, pessoas e equipamentos. O MRP II ajuda as empresas a planejar estas decisões com antecedência. O planejamento de necessidades de materiais continua sendo o coração de qualquer sistema MRP I ou II. 5.2. QUE É NECESSÁRIO PARA UTILIZAR O MRP I?
Para executar os cálculos de quantidade de tempo descrito, os sistemas de planejamento das necessidades de materiais MRP I normalmente requer que a empresa mantenha certos dados em arquivos de computador, os quais quando o programa MRP I é rodado, podem ser verificados e atualizados. Para que se possa compreender a complexidade de um sistema MRP, é necessário que se entendam estes registros e arquivos de computador. O anexo mostra as informações necessárias para processar o MRP I, assim como alguns de seus resultados. (Anexo IX). Começando na parte superior do anexo, as primeiras entradas para o planejamento das necessidades de materiais são os pedidos de clientes e a
A função de vendas, na maioria das empresas, normalmente gerencia uma carteira de pedidos dinâmica e mutante, composta por pedidos confirmados de clientes. Essa carteira de pedidos pode ser um registro em papel numa empresa pequena, mas tende a consistir em um arquivo de computador em empresas médias e grandes. Normalmente, essa carteira de pedidos conterá informações sobre cada pedido de um cliente. Para o processo de cálculo das necessidades de materiais do MRP I, são de particular interesse os registros do que exatamente cada cliente pediu, em que quantidade e em que momento.
Os pedidos de venda, normalmente, representam um comprometimento contratual por parte do cliente. Entretanto, dependendo do negócio em que uma empresa esteja, este comprometimento pode não ser tão firme como possa parecer. Os clientes podem mudar de idéia sobre o que necessitam, mesmo depois de ter feito seus pedidos. Eles podem requerer uma quantidade maior ou menor de um item específico ou mudar a data necessária para a entrega do material. Em virtude da flexibilidade e o serviço ao cliente estarem tornando-se fatores competitivos cada vez mais importantes, alterações das necessidades estão se tornando características cada vez mais comuns na maioria das empresas. Se os clientes estão comprando bens industriais como componentes, pode ser que seus próprios clientes sejam a causa da mudança de necessidades. Considerando que, alguns dos clientes possam solicitar mudanças em seus pedidos, não uma vez, mas várias, mesmo depois que o pedido foi solicitado, fica evidente que a gestão da carteira de pedidos é um processo dinâmico e complexo. As organizações devem decidir quanto à flexibilidade que irão permitir aos clientes e em que grau seus clientes deverão arcar com as conseqüências das mudanças que solicitarem. As decisões sobre a forma de flexibilidade, é
permitido aos clientes que têm impacto enorme sobre as operações do negócio como um todo e sobre os cálculos das necessidades detalhadas de materiais em recursos. Nem todas as operações têm o mesmo grau de visibilidade em termos do conhecimento dos pedidos de clientes. Em empresas de manufatura, os clientes estão se tornando cada vez mais relutantes em comprometer-se firmemente e com muita antecedência, com os detalhes dos pedidos de seus componentes específicos, em virtude das constantes mudanças no ambiente competitivo. Além disso, na medida em que a velocidade de entrega se torna cada vez mais importante, em virtude do fornecimento Just in Time, é possível que, no momento em que os pedidos firmes sejam recebidos, não haja tempo suficiente para comprar os materiais necessários, executar os processos de manufatura nesses materiais e, então, entregar o produto ao cliente. Enquanto muitas empresas de manufatura estão se esforçando bastante para reduzir o tempo de resposta à demanda dos clientes, muitas ainda não chegaram ao estágio de serem capazes de responder Just in Time aos seus pedidos. Consequentemente, por todas essas razões, muitas empresas têm que prever suas necessidades futuras, de modo a assegurar que as matérias- primas estejam disponíveis para que possam iniciar seus próprios processos, uma vez que um pedido seja recebido. 5.6. PREVISÃO DE DEMANDA
Qualquer que seja o grau de sofisticação do processo de previsão numa empresa, é sempre difícil utilizar dados históricos para prever futuras tendências, ciclo ou sazonalidades. Dirigir uma empresa que utiliza previsões baseadas no passado, pode ser comparado a dirigir um carro olhando apenas para o espelho retrovisor. Apesar das dificuldades, muitas empresas não têm alternativa, portanto, devem fazer previsões.
A combinação de pedidos realizados e pedidos previstos é utilizada para representar a demanda em muitas empresas. É importante que a previsão usada para o planejamento da produção não seja um objetivo de vendas, que
que os clientes irão comprar. Esta informação, seja formada por pedidos firmes, previsões ou uma combinação de ambos, é a fonte mais importante para o programa-mestre de produção.
O programa-mestre de produção, MPS – Master Production Schedule, é a fase mais importante do planejamento e controle de uma empresa, constituindo-se na principal entrada para o planejamento das necessidades de materiais.
5.9. O MPS NA MANUFATURA
Na manufatura, o MPS contém uma declaração da quantidade e momento em que os produtos finais devem ser produzidos; esse programa direciona toda a operação em termos do que é montado, manufaturado e comprado. É a base do planejamento de utilização de mão-de-obra e equipamentos e determina o aprovisionamento de materiais e capital. 5.10. O MPS EM SERVIÇOS
O MPS também pode ser utilizado em empresas de serviços. Por exemplo: num hospital há um programa-mestre que indica quais cirurgias estão planejadas e para quando. Ele direciona o aprovisionamento de materiais para as cirurgias, assim como de instrumentos, sangue e acessórios. Também dirige a programação de pessoal para as cirurgias, incluindo anestesistas, enfermeiras e cirurgiões.
5.11. FONTES DE INFORMAÇÕES PARA O MPS
É importante que todas as fontes de demanda sejam consideradas quando o programa-mestre de produção é gerado. São geralmente os pequenos pedidos de última hora que geram distúrbios em todo o sistema de planejamento de uma empresa.
Exemplo: empresas irmãs podem tomar emprestado alguns componentes sem prévio-aviso. Se tais práticas são permitidas, os sistemas de planejamento e controle precisa considerá-las.
5.12. REGISTRO DO PROGRAMA-MESTRE DE PRODUÇÃO
O programa-mestre de produção é constituído de registros com escala de tempo que contém, para cada produto final, as informações de demanda e estoque disponível atual. Usando esta informação, o estoque disponível é projetado à frente no tempo. Quando não há estoque suficiente para satisfazer à demanda futura, quantidades de pedidos são inseridas na linha do programa- mestre.
5.13. EXEMPLO DE PRÁTICA RUIM NA PROGRAMAÇÃO-MESTRE
Infelizmente muitas empresas aceitam todos os pedidos de clientes e tentam atendê-los. Há duas possibilidades aqui. A primeira, é que a produção falha em atender, não consegue manufaturar os produtos, frustrando seu cliente. A segunda é que, de alguma forma, a empresa sempre consegue dar uma solução. Isto indica que seu sistema de planejamento está carregando capacidade em excesso, ou folgas, que não são percebidas no processo MRP. Ambos os cenários representam práticas ruins na gestão de sistema MRP. Algumas empresas que usam esse sistema, ainda tratam erradamente o programa-mestre de produção como um objetivo em vez de um plano. Há exemplos de programadores mestres de produção que programam dez por cento a mais, na esperança de que seu programa seja atendido. As implicações de um programa-mestre não realístico são enormes. Se este é superestimado em dez por cento, dez por cento a mais de material é aprovisionado e dez por cento a mais de mão-de-obra são programados.
5.14. A LISTA DE MATERIAIS
O programa mestre dirige o restante do processo MRP. Tendo estabelecido este nível de programação, o MRP executa os cálculos para determinar a quantidade e o momento das necessidades de montagens, submontagens e materiais de modo a atender o programa.
A chave para todos os registros de estoque é normalmente o código do item. Cada item utilizado em uma empresa de manufatura deve ser identificado por uma codificação-padrão, de modo que não haja confusão entre as pessoas que compram o item e aquelas que o fornecem, ou ainda, quem o utiliza no processo de manufatura. A maioria das empresas de manufatura, portanto, estabelece um número para cada item. Os códigos de itens podem ser totalmente numéricos ou podem ser combinações alfanuméricas de letras e números. Algumas empresas acham conveniente utilizar mnemônicos, que ajudam os usuários a identificar qual item é representado por um código específico. Sistemas complexos de numeração com verificação cruzada são normalmente adotados para prevenir erros, como trocar dois dígitos. Números de cartões de crédito usam esse tipo de verificação cruzada. Além do código, o arquivo de itens contém todos os dados estáveis de um item. Normalmente, ele pode ser visto com uma tela de computador, com campos que incluem a descrição do item, sua unidade de medida e seu custo- padrão. É interessante notar que o Lead time de compra ou produção do item, é normalmente tratado como um dado fixo pelo fator de estar localizado num arquivo de itens. Muitas empresas falham no monitoramento adequado do Lead time de um item. Ele pode variar entre fornecedores e mudar dependendo da época do ano e de acordo com as condições do mercado fornecedor. Contudo, algumas empresas ainda erram a favor da segurança, assumindo o máximo Lead time possivelmente esperado. Isto significa que a discrepância entre a Lead time real e ao Lead time de planejamento pode ser bastante grande em algumas empresas de manufatura.
5.18. ARQUIVOS DE TRANSAÇÕES
Para levar em conta os níveis de estoque, o MRP precisa conhecer tais níveis para cada item. O arquivo de transações registra as entradas e as saídas do estoque, além do balanço a cada movimentação. No passado essas transações eram informadas ao sistema durante a noite ou a intervalos
periódicos; isto causava problemas, pois as informações do sistema estava sempre defasada da realidade. Os sistemas MRP atuais atualizam seus estoques em tempo real. Isto significa que o arquivo de transações é atualizado no momento em que ocorre uma entrada ou saída de material. Portanto tem implicações quanto ao número de terminais de computador necessários para a operação, sua localização, além do número de pessoas que devem ser treinadas para utilizá-los. Os benefícios do processamento em tempo real, entretanto, ultrapassam de longe qualquer custo adicional de equipamento e treinamento.
5.19. ARQUIVO DE LOCAIS
Os armazéns ou pontos de estocagem na produção precisam ser gerenciados. Alguns armazéns operam num sistema de localização fixa, de modo que cada item específico possa sempre ser localizado em determinado local. Entretanto empresas que operam com uma faixa larga e mutável de itens de estoque consideram este sistema ineficiente. Em vez disso, elas operam com sistema de localização aleatório no qual os itens são localizados no espaço disponível mais próximo. Um sistema de localização aleatória requer controle cuidadoso, já que um mesmo item pode estar localizado em diferentes pontos num mesmo momento. Além de serem mais eficientes na utilização do espaço, estes sistemas tornam mais fácil garantir a rotatividade física do estoque, facilitando assim, a implementação de um sistema primeiro que entra, primeiro que sai. Quando o computador gera as listas de coleta, instruindo os operadores dos armazéns mecânicos ou humanos a coletar os itens do estoque, ele pode garantir que itens mais velhos sejam coletados primeiro.
5.20. ACUIDADE DOS REGISTROS DE ESTOQUE
Assim como na gestão das listas de materiais, é crítico para um sistema MRP, que os registros de estoque estejam precisos e atualizados. Os erros ocorrem e o estoque pode ser desviado ou perecer de modo que os registros destes nunca irão refletir exatamente o que há fisicamente em estoque numa empresa. Em virtude disso, controles rotativos de inventário, CRI, são executados em muitas empresas.
Novamente o estoque disponível desses itens é verificado; ordens de trabalho são geradas para as necessidades líquidas dos itens que serão feitos na fábrica, sendo também geradas as ordens de compra para as necessidades líquidas dos itens que serão adquiridos de fornecedores. Este processo continua até que se segue ao nível mais baixo da estrutura do produto.
Além de calcular a quantidade de materiais necessários, o MRP também considera quando cada um desses componentes é necessário, isto é, os momentos da programação de materiais. Ele faz isto através de um processo denominado programação para trás, que leva em conta os Lead time de cada nível de montagem. Mas também existe alguns itens que só podem ser adquiridos em tamanhos de lotes mínimos. Em virtude do tempo e do custo envolvido em preparar uma máquina, pode ser que se considere eficiente utilizá-la apenas se for para um tamanho de lote razoável. De forma similar, alguns itens comprados são adquiridos em embalagens fechadas, em quantidades tais, que permita que se consiga um desconto, mesmo que dessa forma se esteja comprando mais que o necessário. Outra razão para que algumas empresas produzam ou comprem mais do que eles necessitam no momento, é obter uma margem de segurança para o caso de variações não planejadas, tanto na demanda como no fornecimento.
Quando o MRP foi originalmente utilizado na manufatura, os planos de materiais eram emitidos no início da semana, sendo o planejamento completamente refeito na próxima semana, quando então era emitido novo conjunto de planos. Este processo era repetido semanalmente, mas não havia um ciclo de realimentação para dizer se o plano era atingível e se tinha realmente sido atingido. Os sistemas MRP que inicialmente incluíram ciclos de realimentação, ficaram conhecidos como MRP de ciclo fechado.
O fechamento do ciclo de planejamento em sistemas de MRP envolve a confrontação dos planos de produção contra os recursos disponíveis. Portanto, a capacidade é verificada ao longo de todo o processo e, caso os planos propostos não sejam variáveis em qualquer nível, eles são revisados. Todos os sistemas MRP, mesmos os mais simples, são sistemas de ciclo fechado. Eles utilizam três rotinas de planejamento para confrontar os planos de produção contra os recursos produtivos:
a) Planos de necessidades de recursos; b) Planos de capacidade grosso modo; c) Planos de necessidades de capacidade. 5.25. PLANO DE NECESSIDADES DE RECURSOS
Os planos de necessidades de recursos são planos estáticos que envolvem a análise do futuro de longo prazo, de forma a prever as necessidades de grandes partes estruturais da unidade produtiva, como o número, a localização e o tamanho de novas unidades. Como eles constituem tentativas de viabilizar a produção no longo prazo, através da obtenção dos recursos necessários, são algumas vezes chamados de planos de capacidade infinita, dado que assumem uma habilidade quase infinita de estabelecer dados sobre os níveis de produção, caso a demanda garanta sua necessidade.
5.26. PLANOS DE CAPACIDADE A GROSSO MODO RCCP – ROUGH-CUT CAPACITY PLANS
No médio e curto prazo, os programas mestres de produção devem utilizar a capacidade disponível. O ciclo de realimentação neste nível confronta o MPS somente contra os gargalos e recursos-chaves; se o MPS não é viável, ele deve ser ajustado. Logo, diferentemente do plano de necessidades de recursos, os planos de capacidade grosso modo são planos de capacidade finita, porque devem operar com certas restrições.
mudanças ocorridas em qualquer outra parte da empresa, como mudanças nos processos de manutenção ou processamento de estoques. O MRP II é baseado em um sistema integrado, contendo uma base de dados que é acessada e utilizada por toda a empresa, de acordo com as necessidades funcionais individuais. Entretanto, apesar de sua dependência de tecnologias de informação que permitam tal integração, o MRP II ainda depende das pessoas para a tomada de decisões. Levy descreveu isto bem: “Até que possamos prover a genuína inteligência artificial, não há maneira pela qual um computador possa otimizar a miríade de variáveis da manufatura e substituir a inteligência, a intuição e o conhecimento local do pessoal de fábrica.” (Levy apud Slack, Chambers, Harland et al., 1997, p. 465).
Em outras palavras, o fechamento do ciclo em sistemas MRP ainda depende fortemente de pessoas para tomar decisões e ações corretivas numa base de minuto a minuto.
Qualquer tipo de armazenamento de matéria-prima gera determinados custos que são:
a) Juros b) Depreciação c) Aluguel d) Equipamentos de manutenção e) (^) Deterioração f) Obsolescência g) Seguros h) Salários i) Conservação
Estes custos, podem ser divididos em modalidades:
a) Custos de capital - juros, depreciação. b) Custos com pessoal - salários, encargos sociais. c) Custos de edificação - aluguel, impostos, luz e conservação. d) Custos de manutenção - deterioração, obsolescência e equipamentos. Há duas variáveis que elevam estes custos, as quais são: a quantidade em estoque e o tempo de permanência em estoque. Elevadas quantidades de matéria-prima em estoque somente poderão ser movimentadas com a utilização de um maior número de funcionários ou, então, com maior uso de equipamentos de movimentação. Com isso, resultará na elevação destes custos, assim quando há um menor volume de matéria- prima em estoque, os custos serão diminuídos, estes custos relacionados podem ser chamados de custos de armazenagem. Esses são calculados baseado no estoque médio e geralmente indicados em porcentagem do valor em estoque, com isso os custos de armazenagem são proporcionais à quantidade e o tempo que uma matéria-prima permanece em estoque.
Toda a teoria dos estoques é pautada na previsão do consumo de material. A previsão de consumo determina estas estimativas futuras dos produtos que a empresa comercializa. Assim, determina quais produtos, quanto e quando serão vendidos. A previsão possui características básicas, que são: a) (^) Ponto de partida de todo planejamento empresarial b) Não consiste uma meta de vendas c) Sua previsão deve ser compatível com o custo de obtê-la
Há informações básicas na previsão dos estoques que se dividem em duas categorias: quantitativas e qualitativas, estas permitem decidir quais serão as dimensões e a distribuição no tempo da demanda dos produtos acabados.