
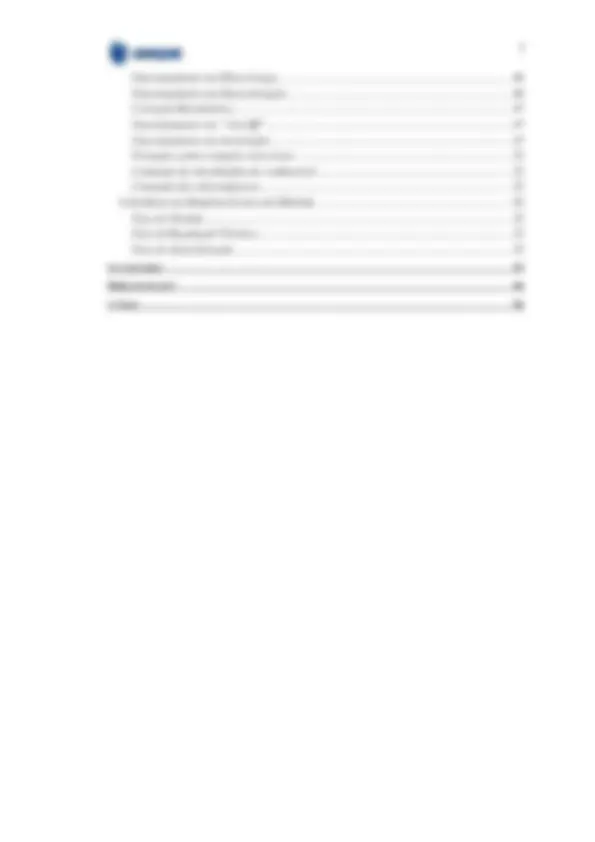
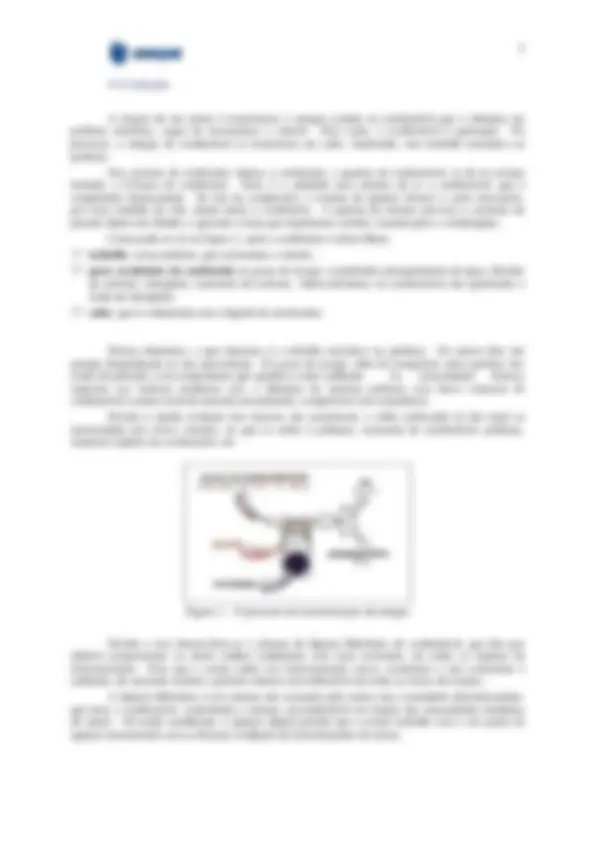
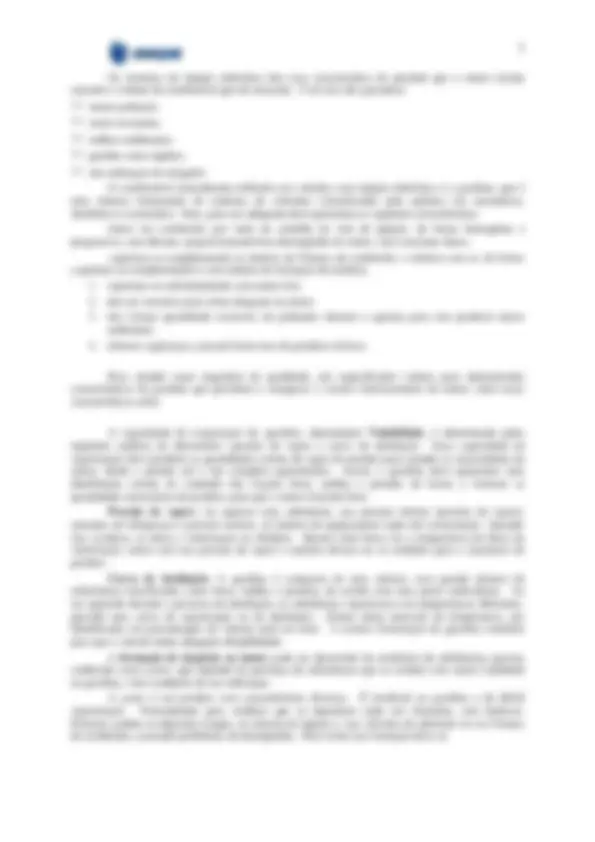
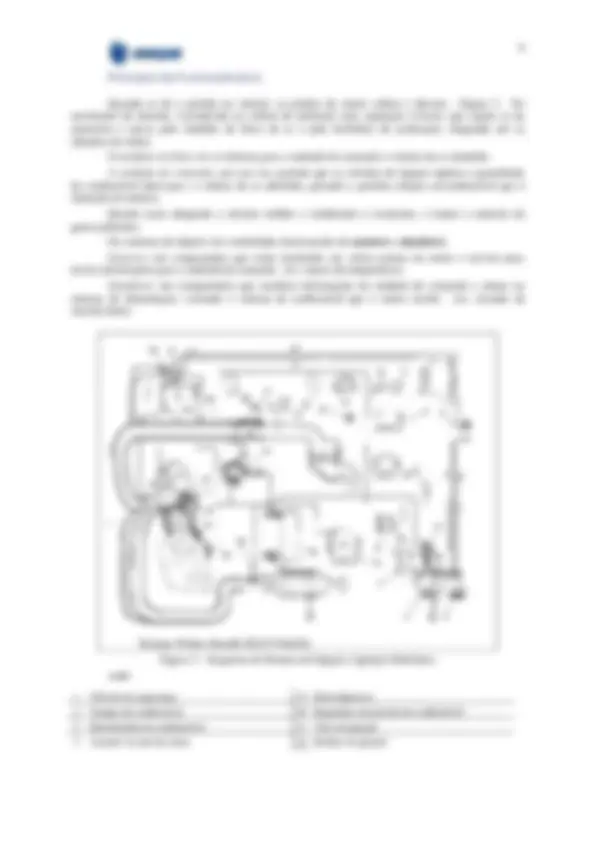
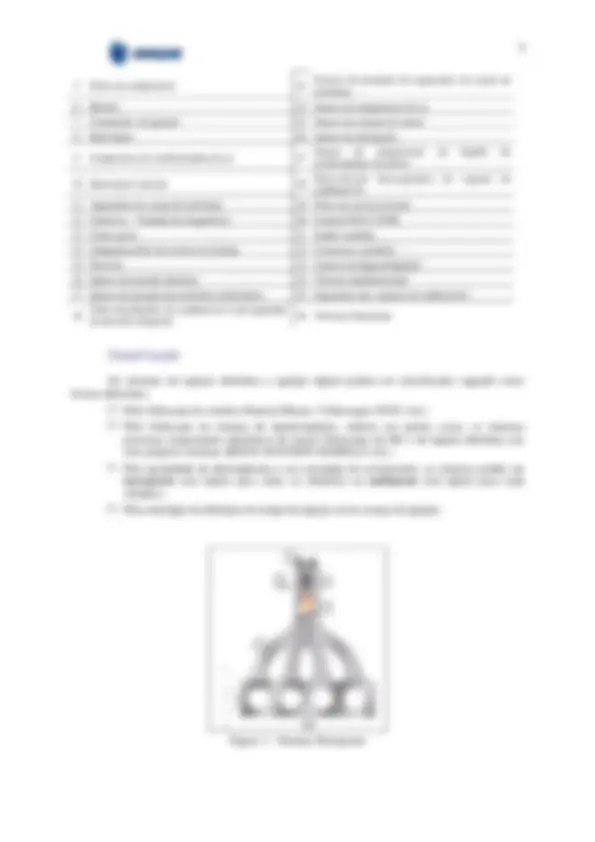
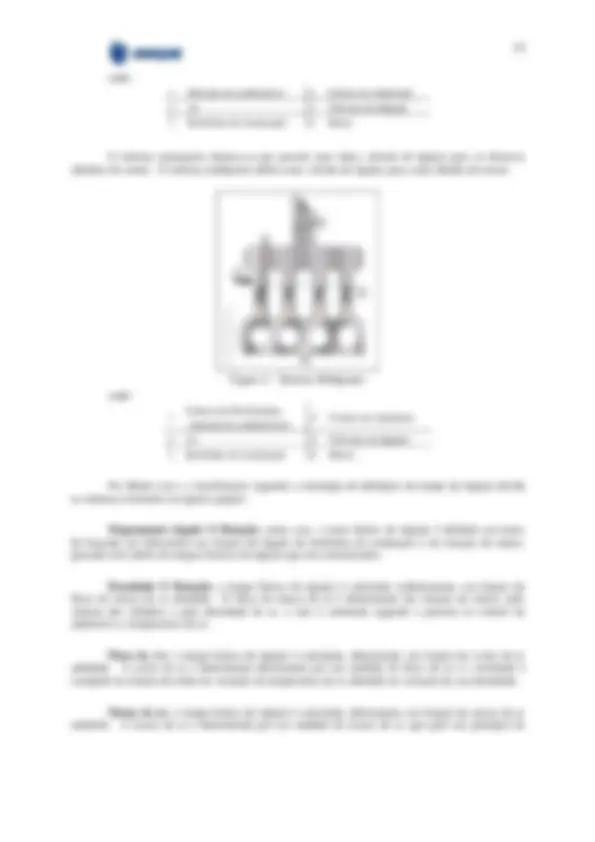
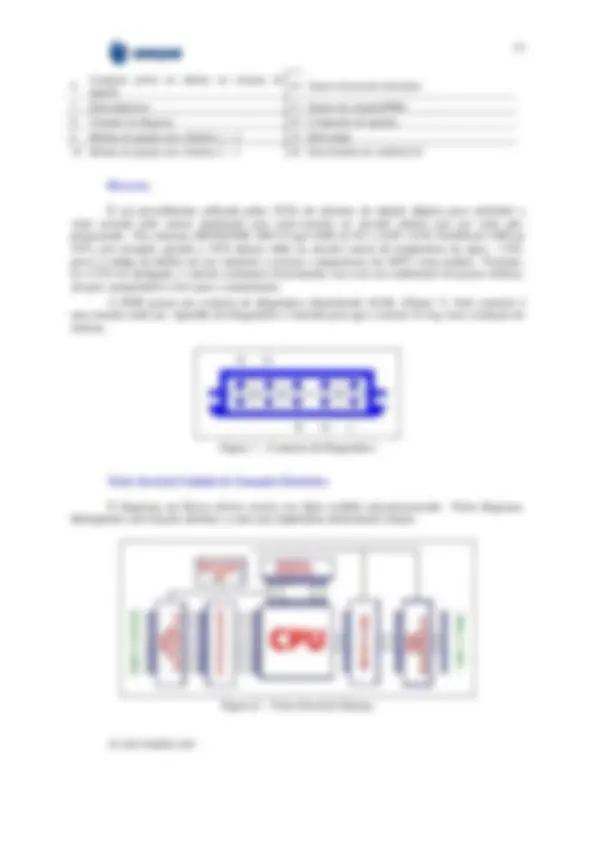
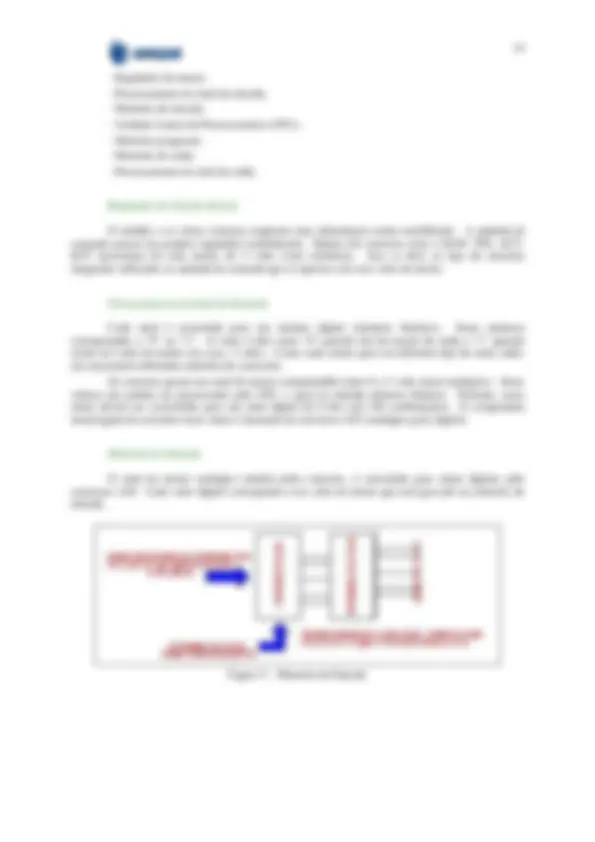
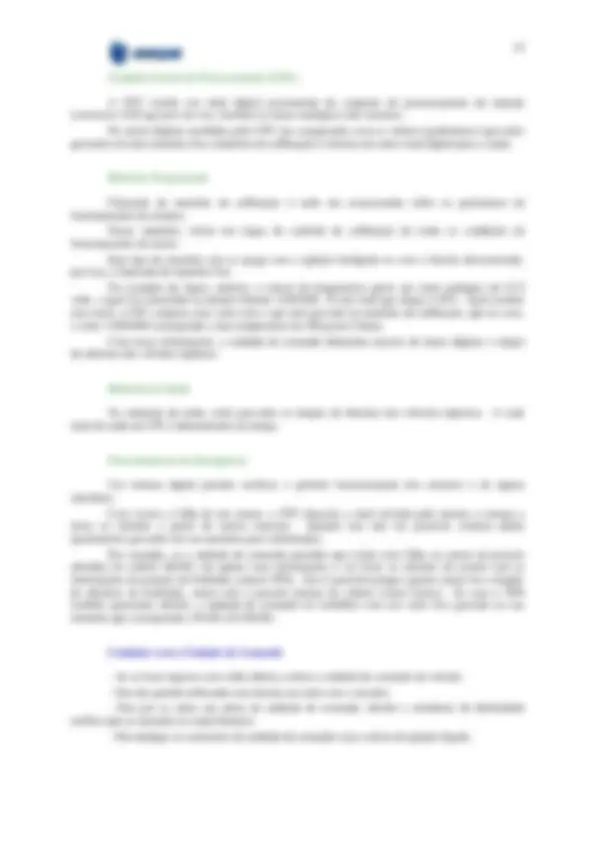
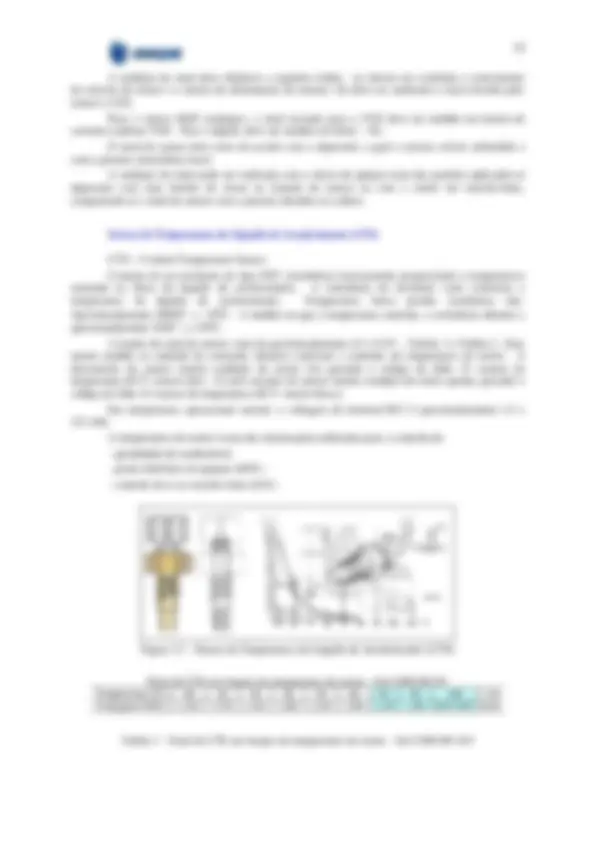
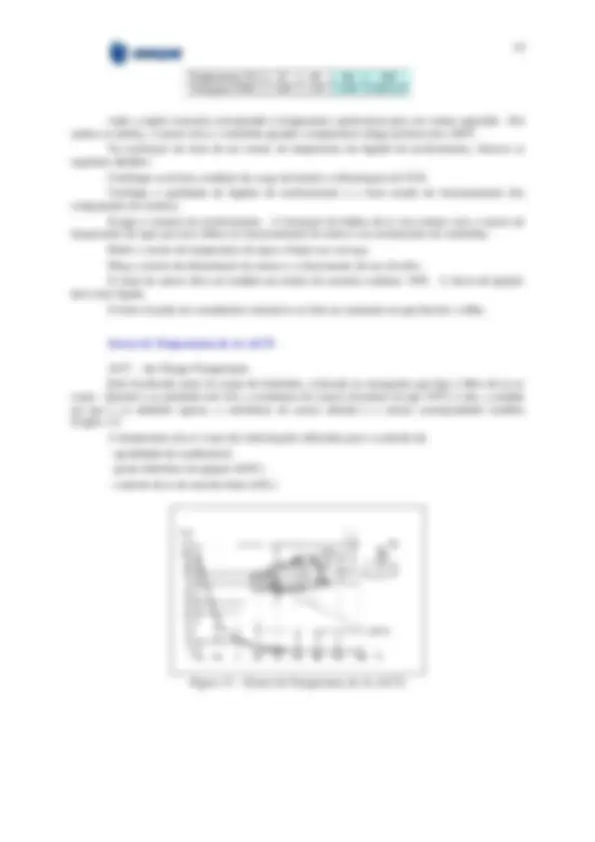
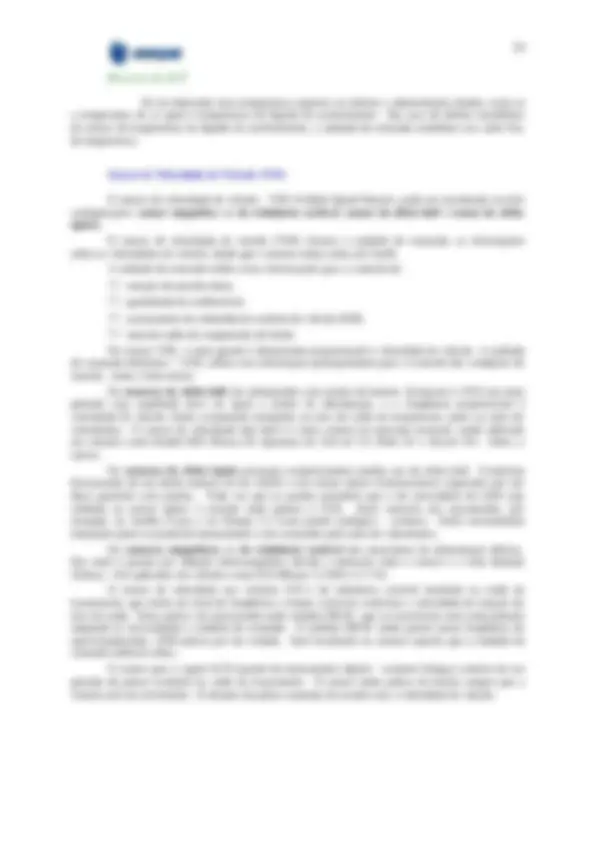
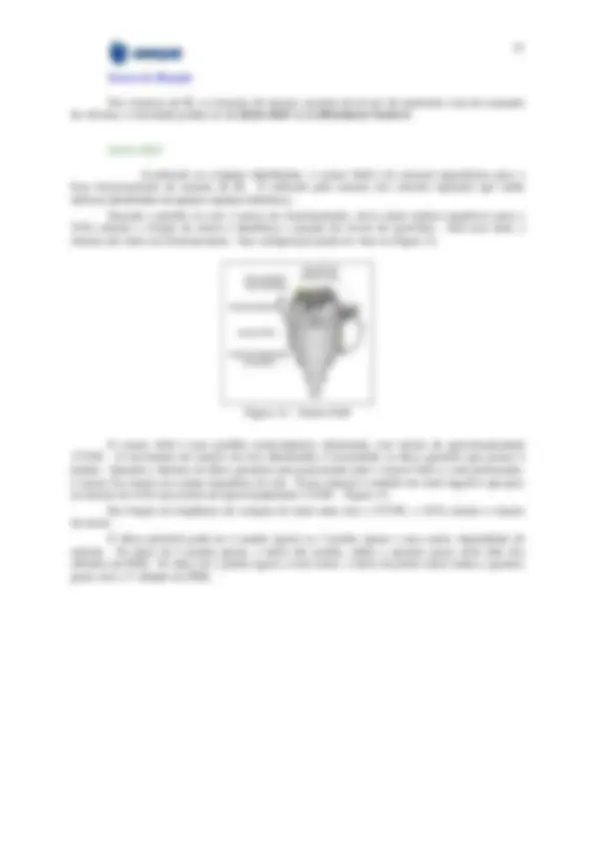
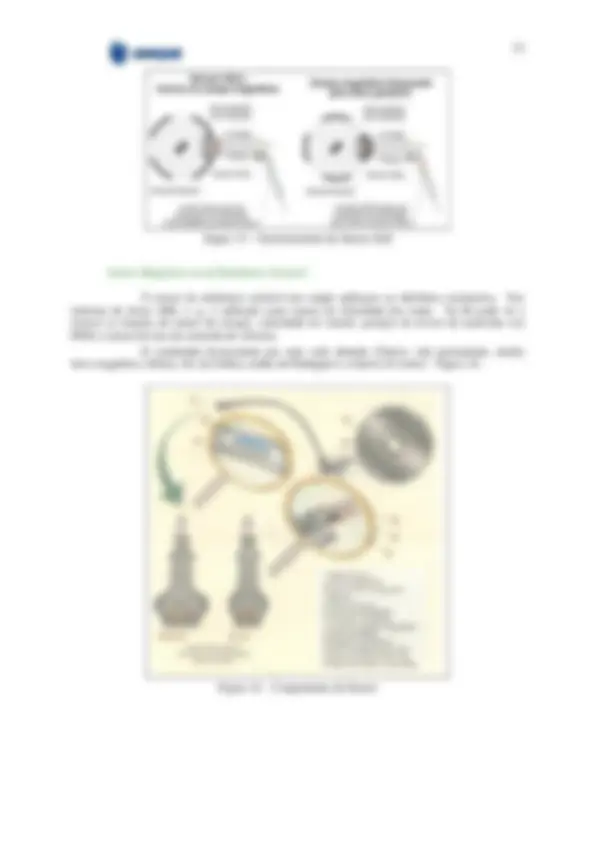
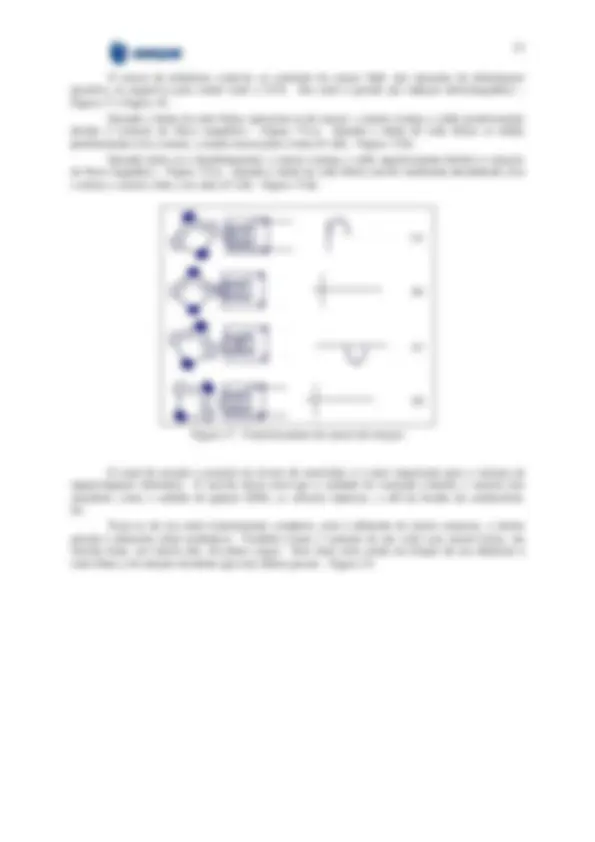
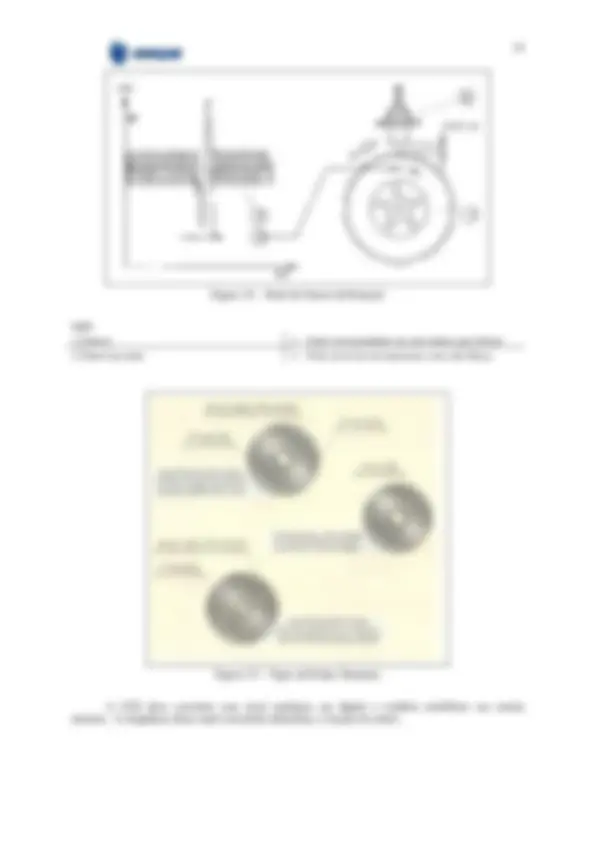
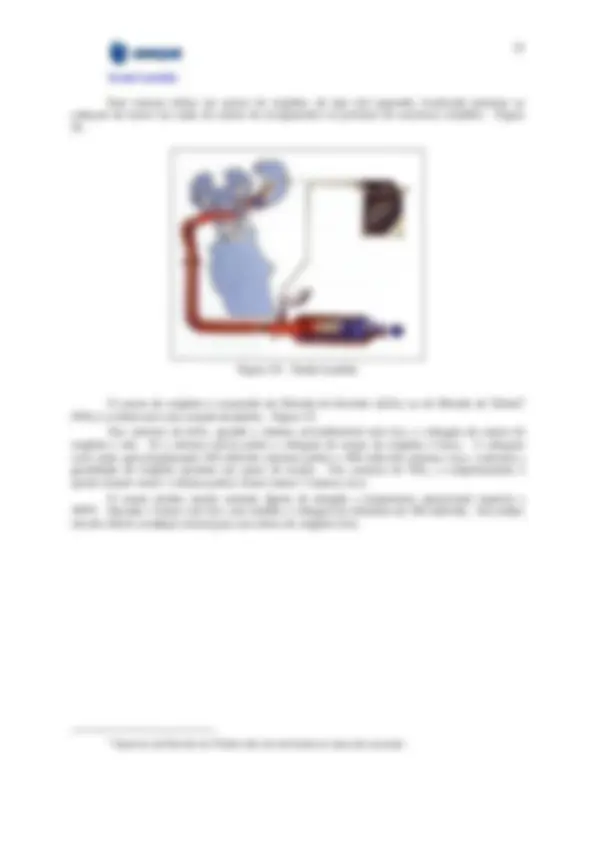
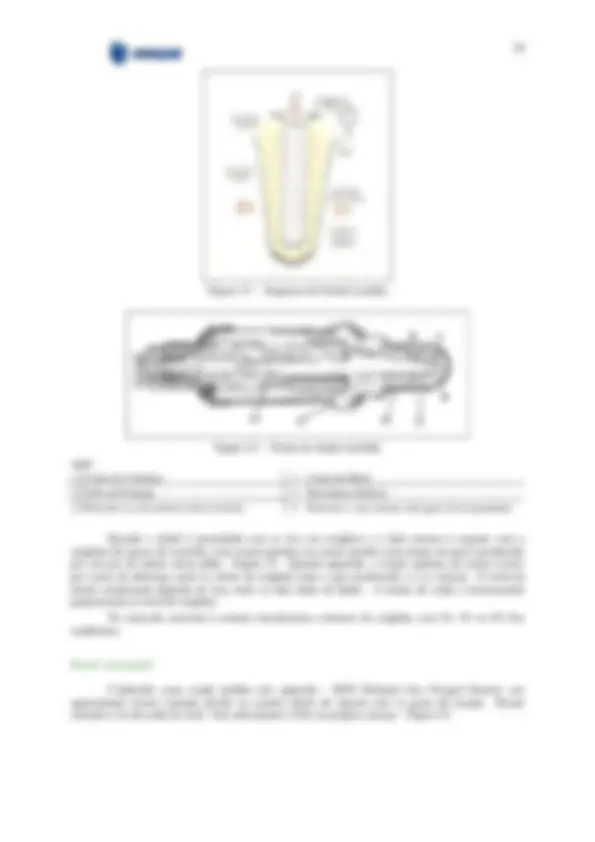
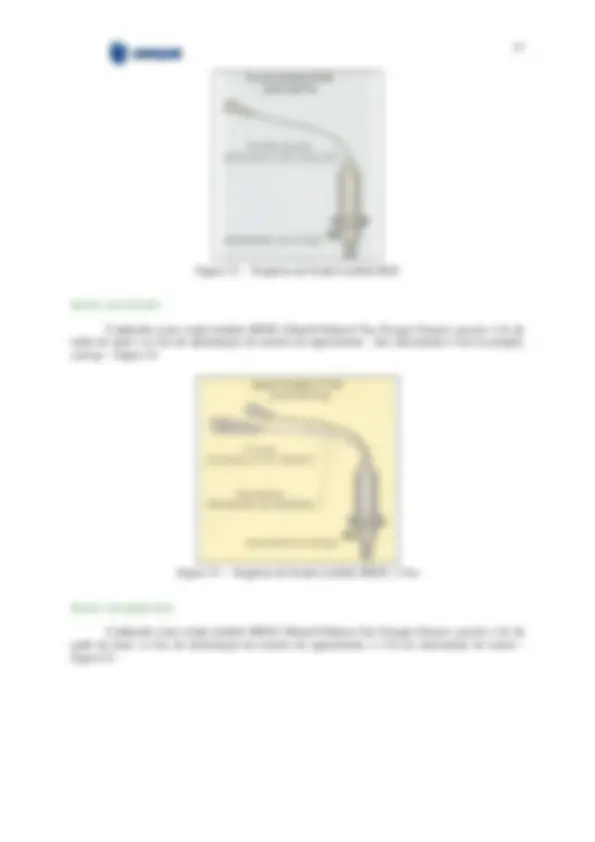
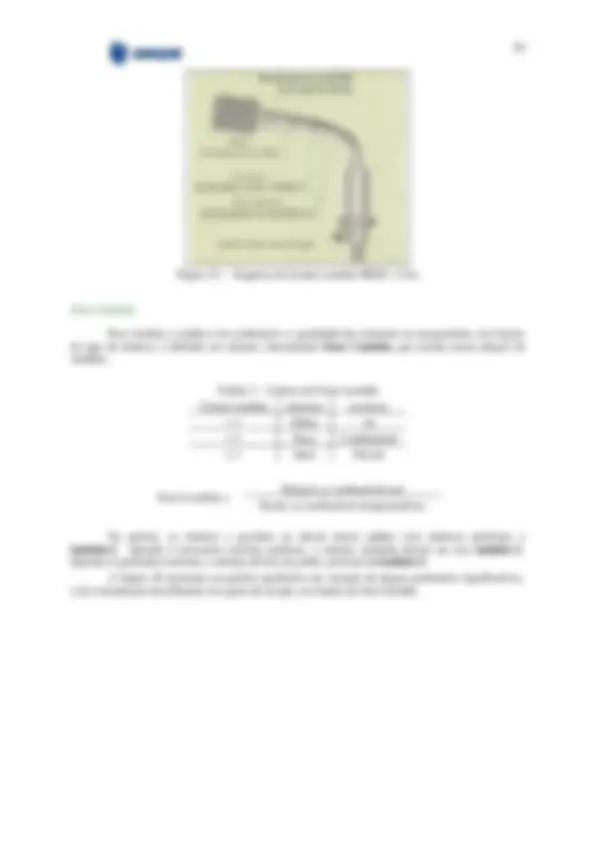
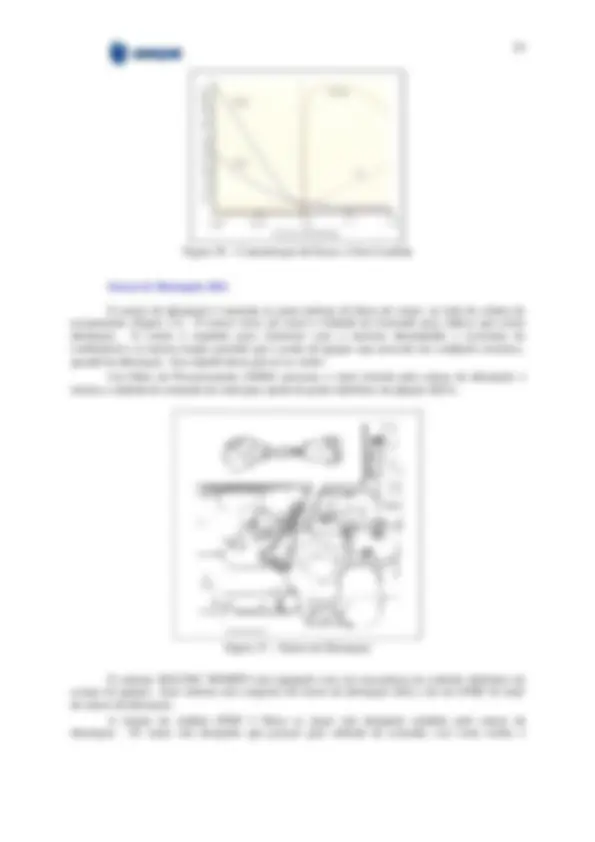
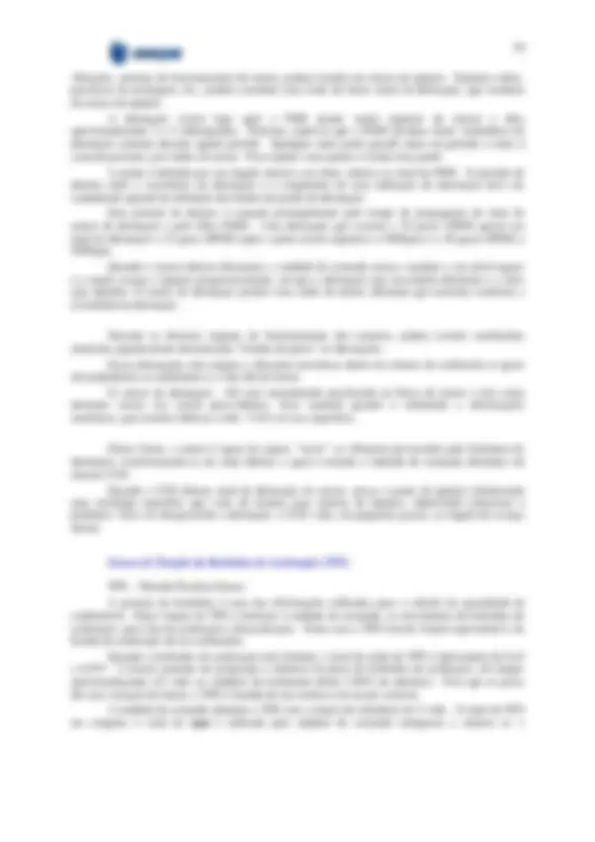
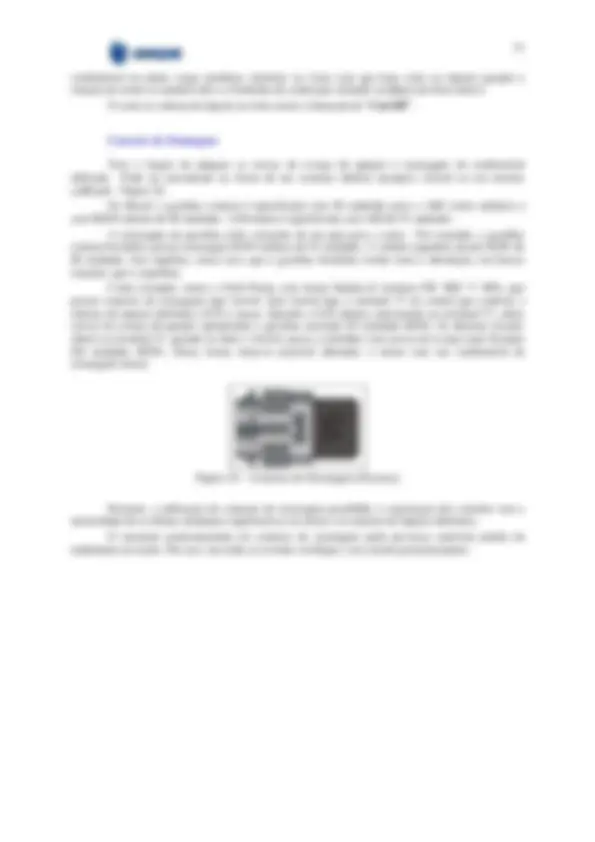
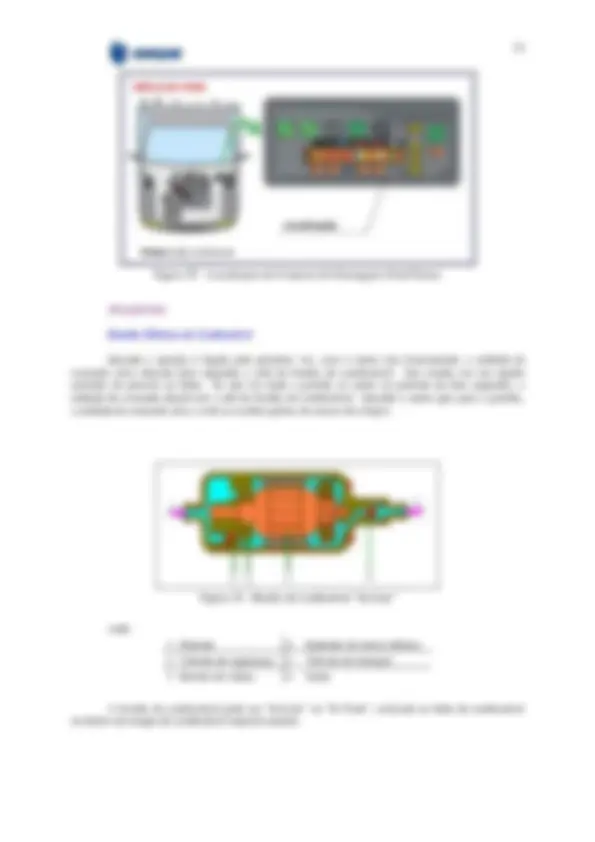
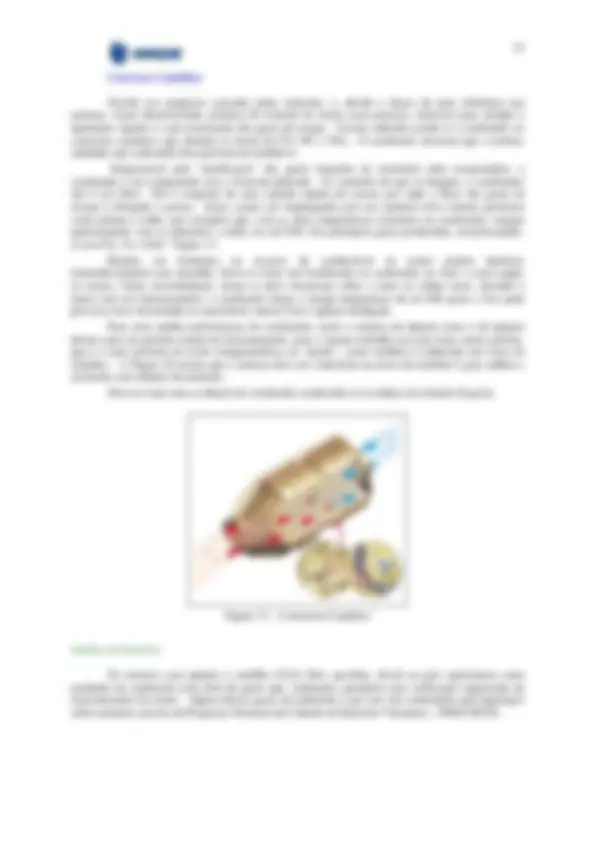
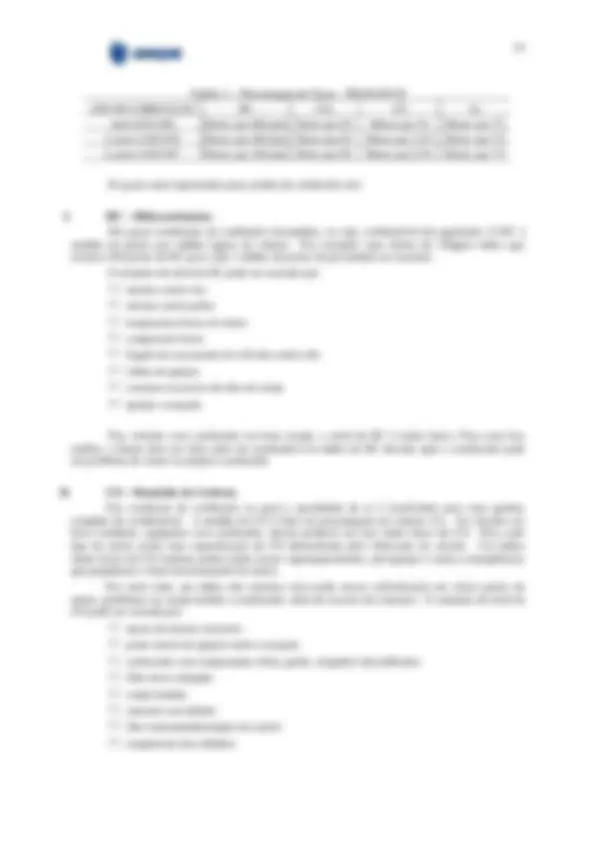
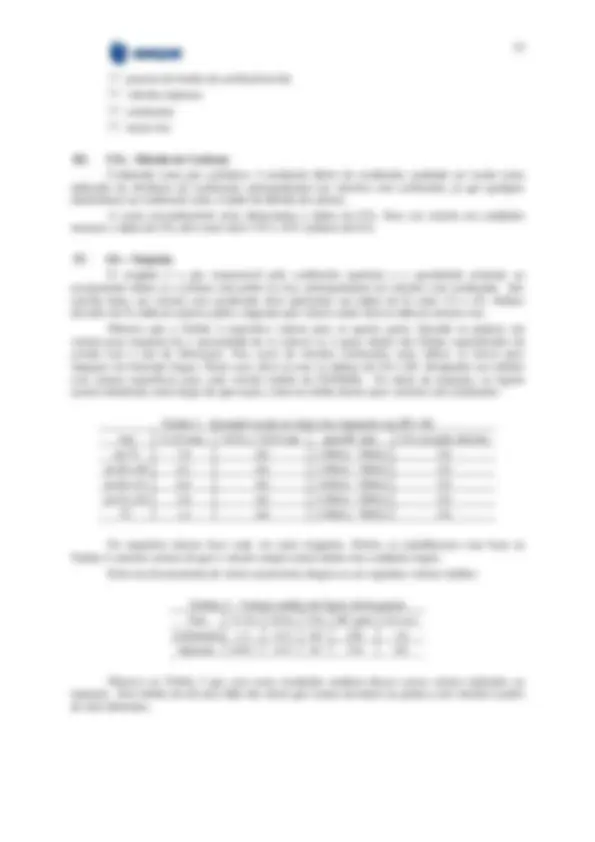
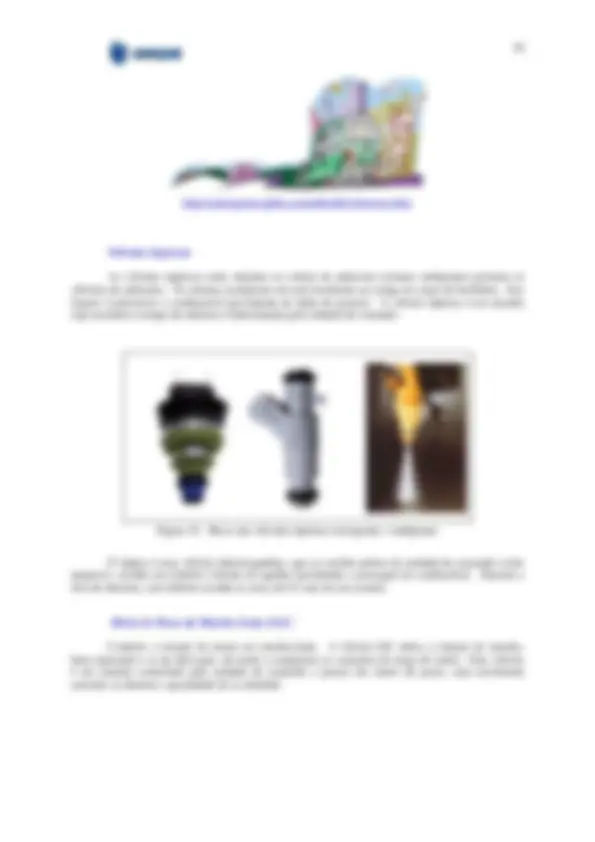
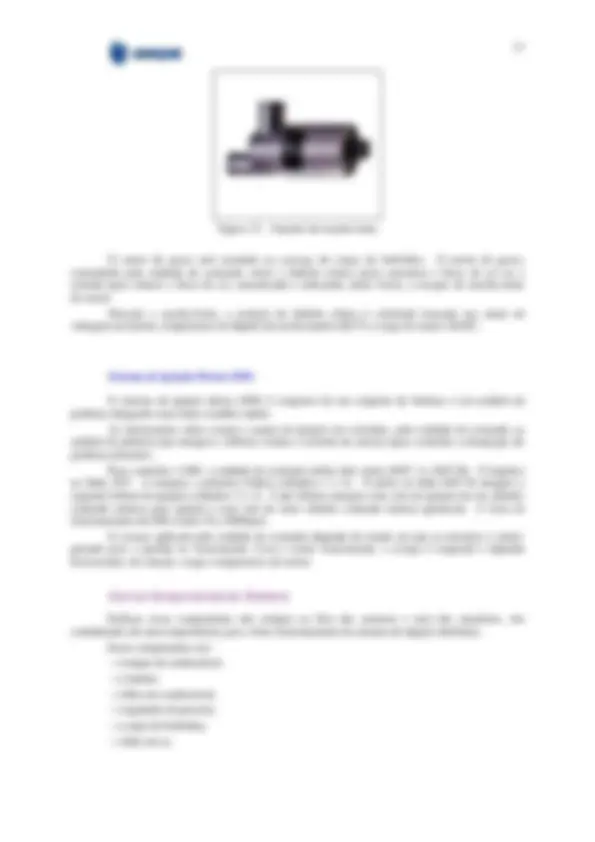
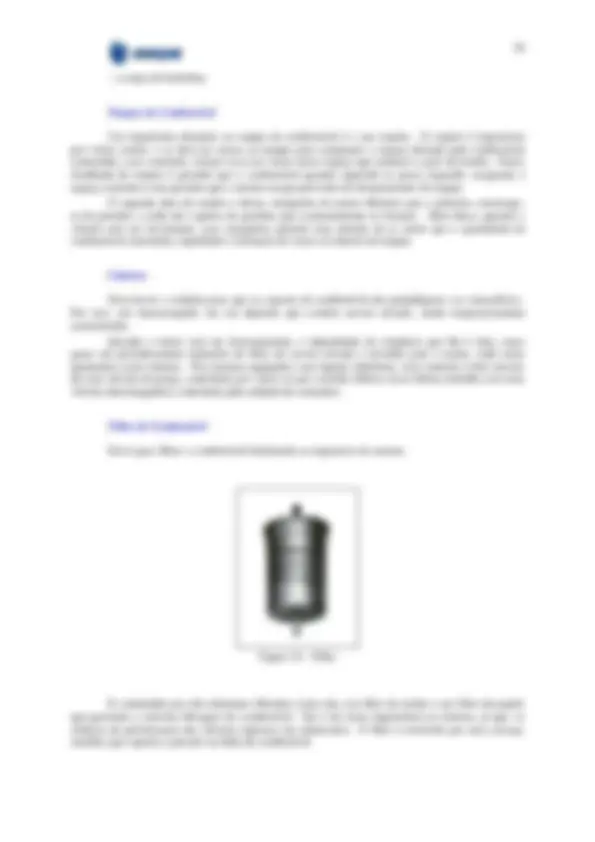
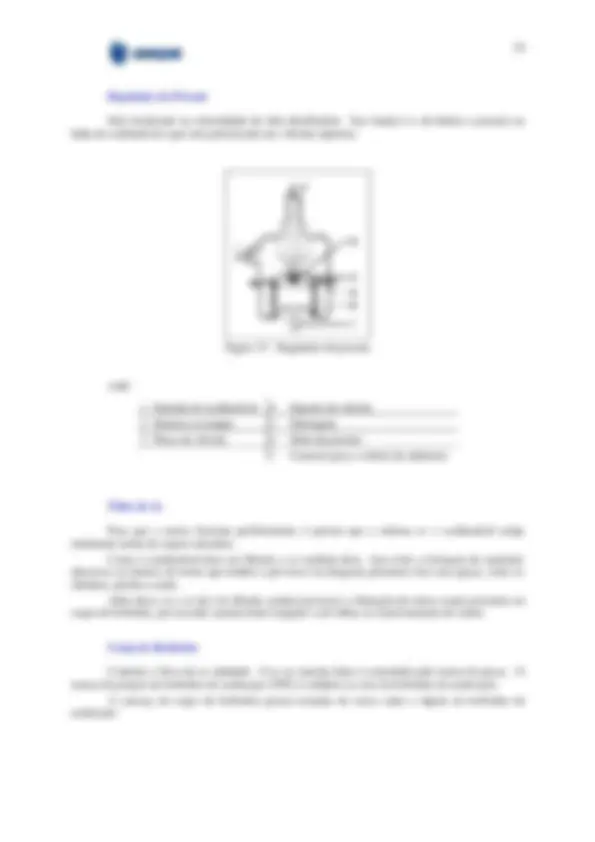
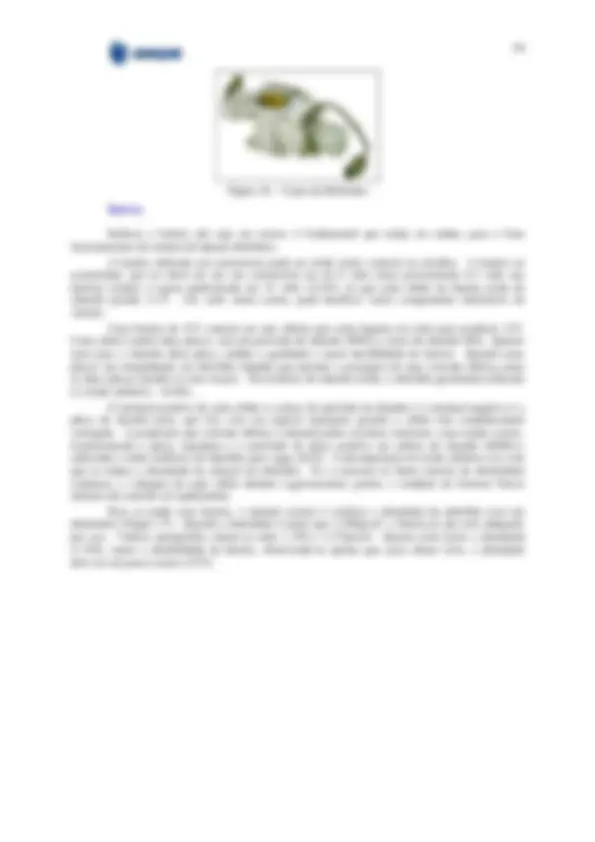
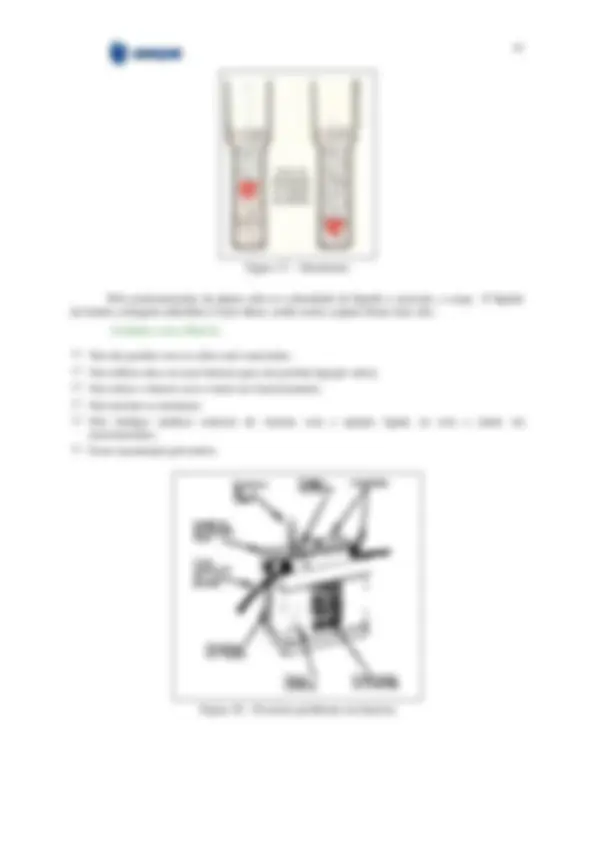
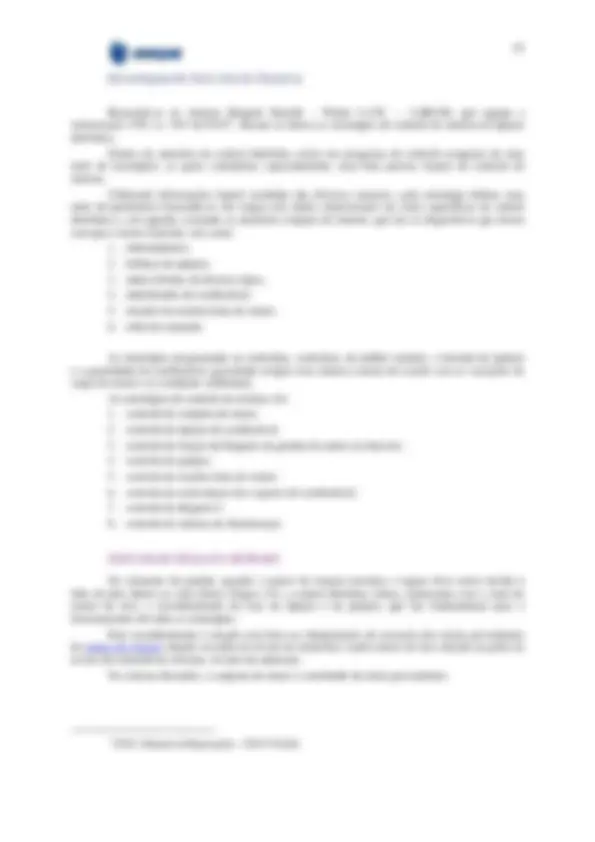
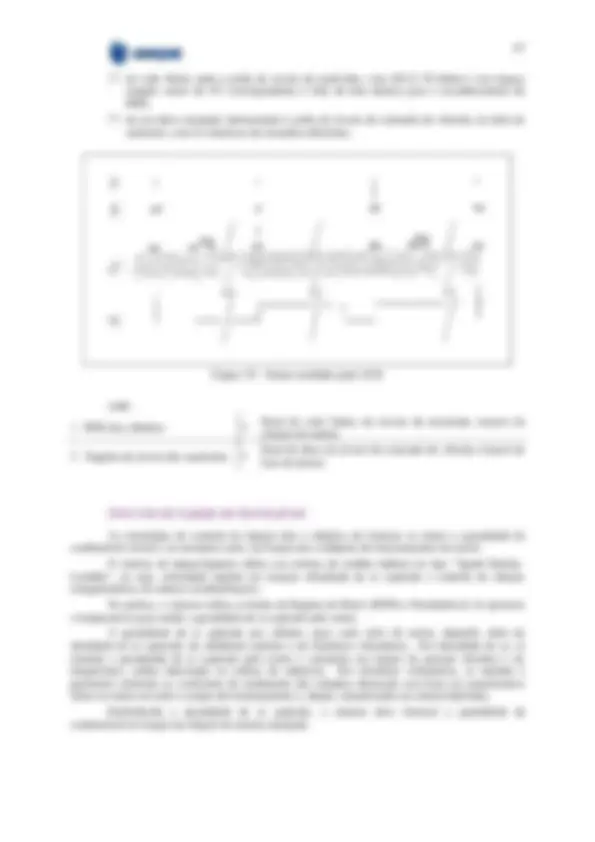
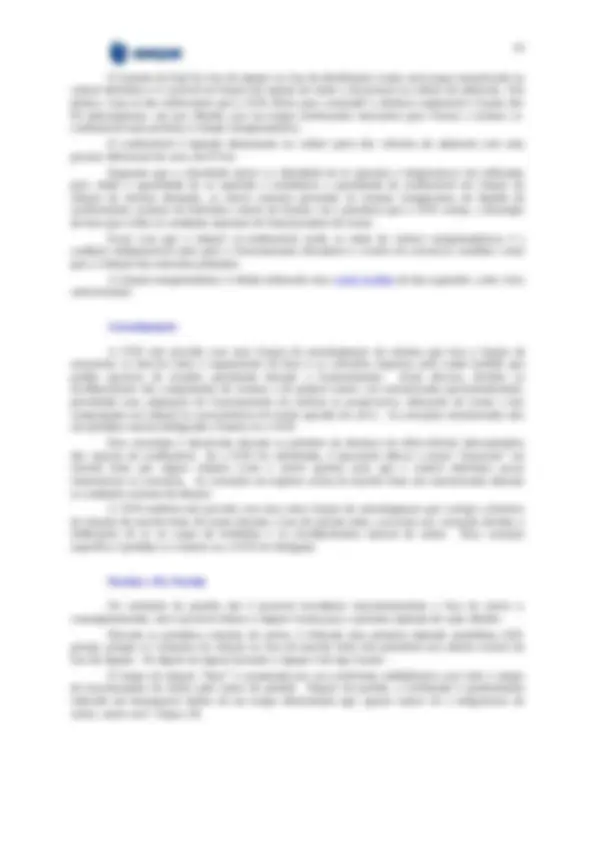
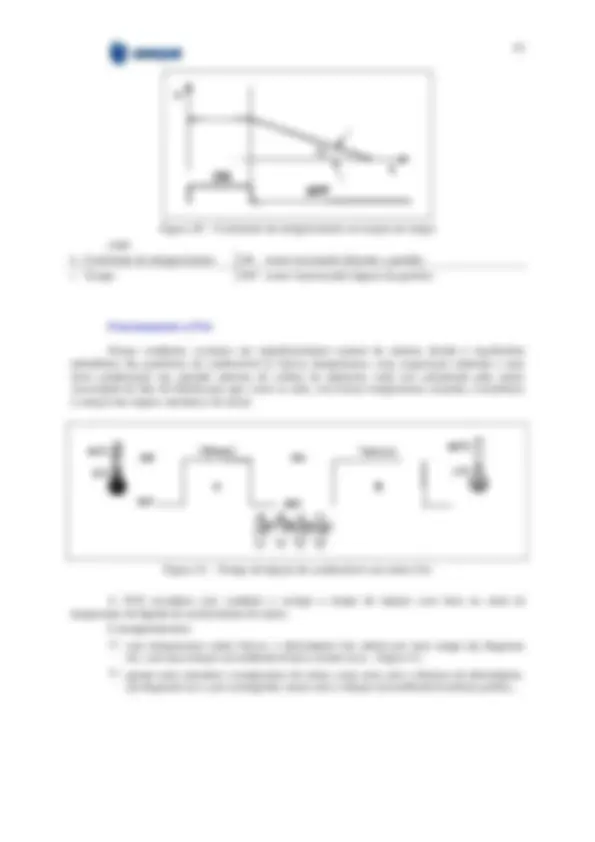

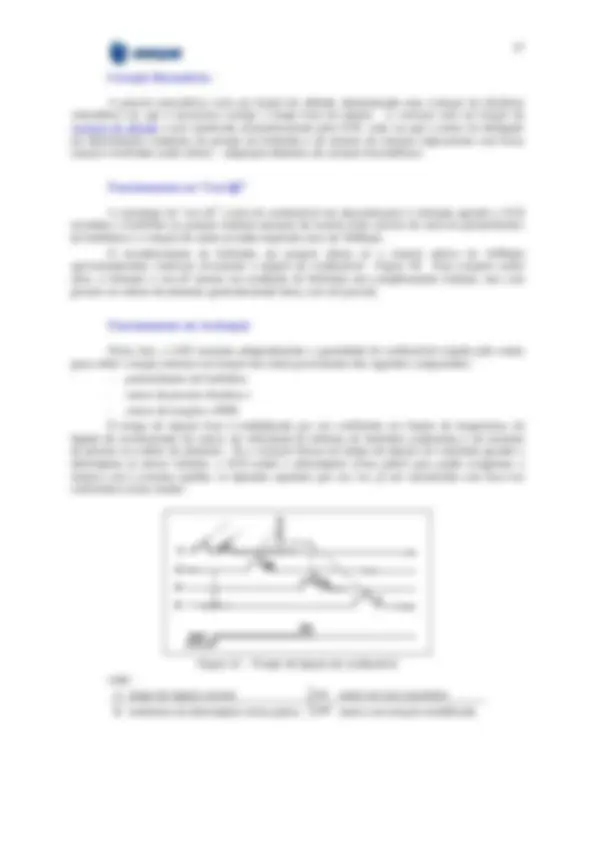
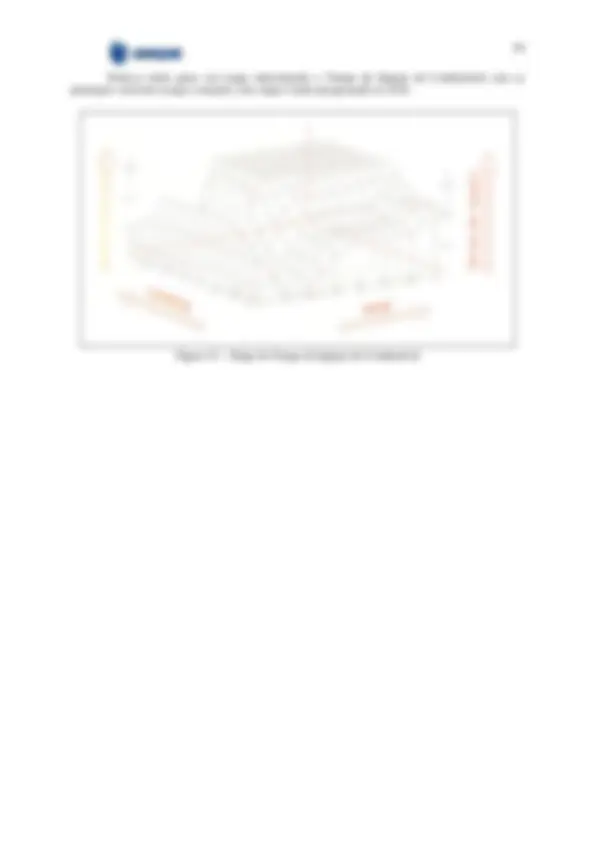
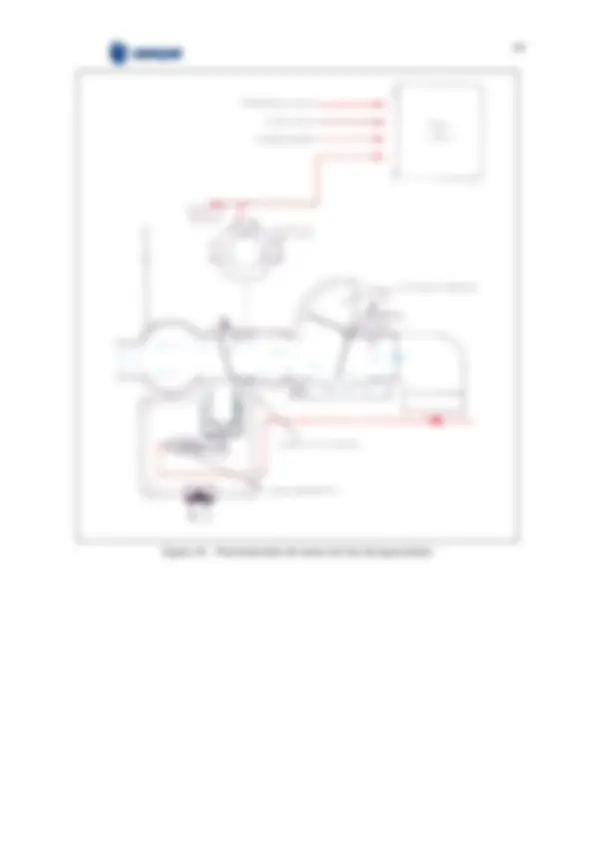
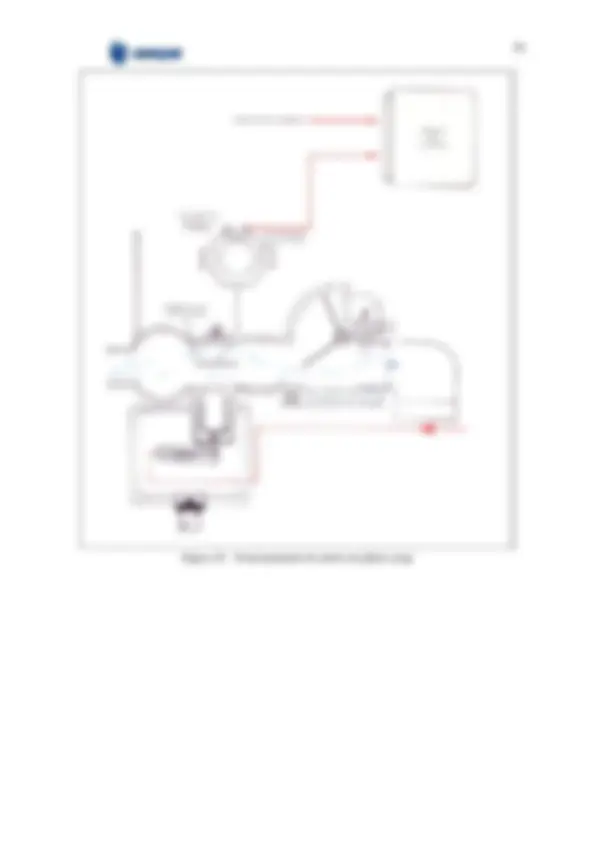
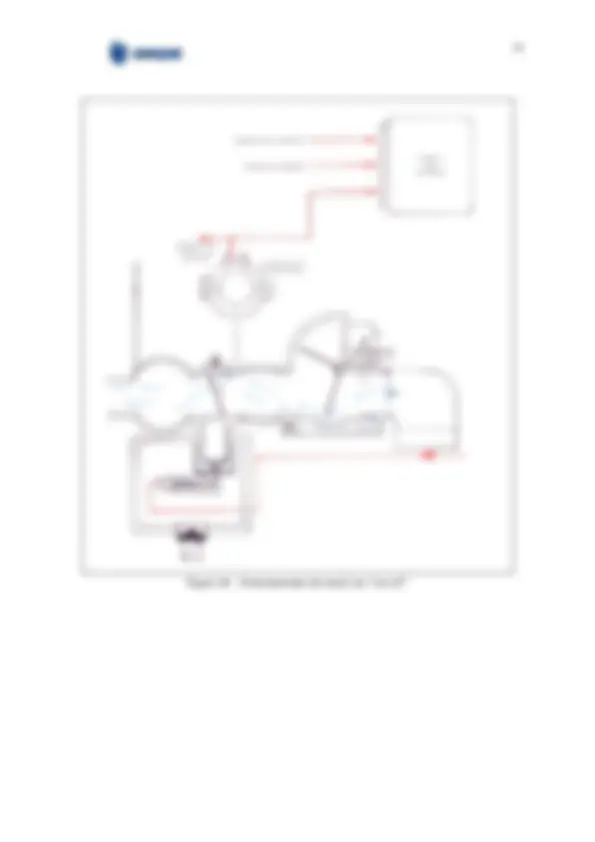
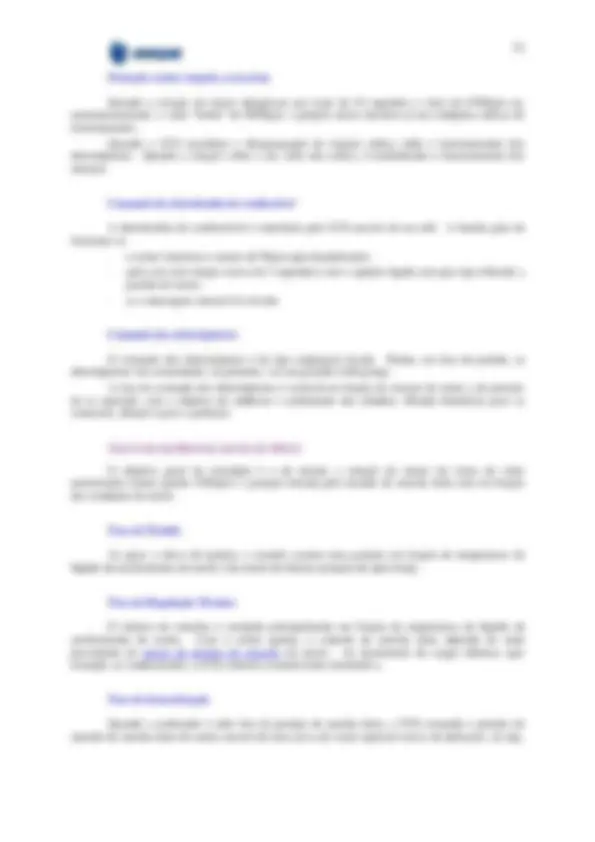
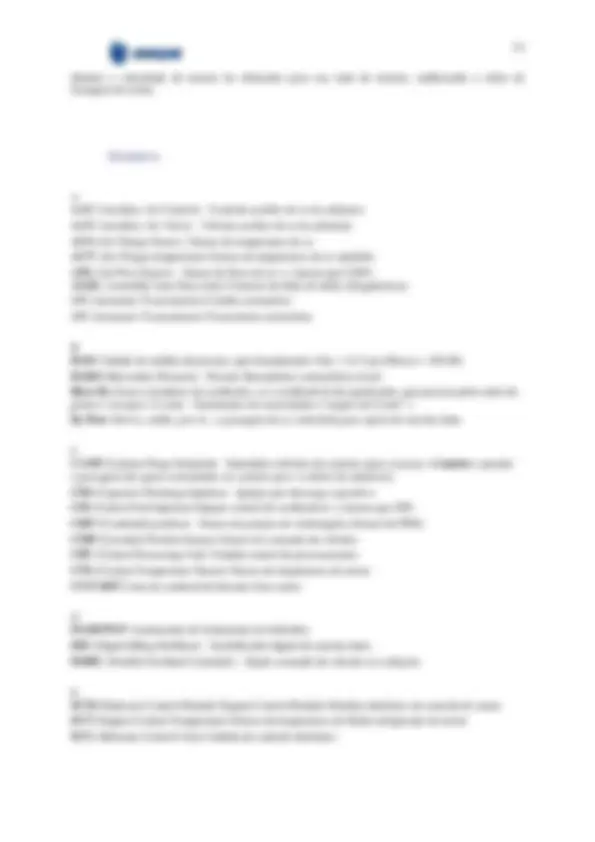
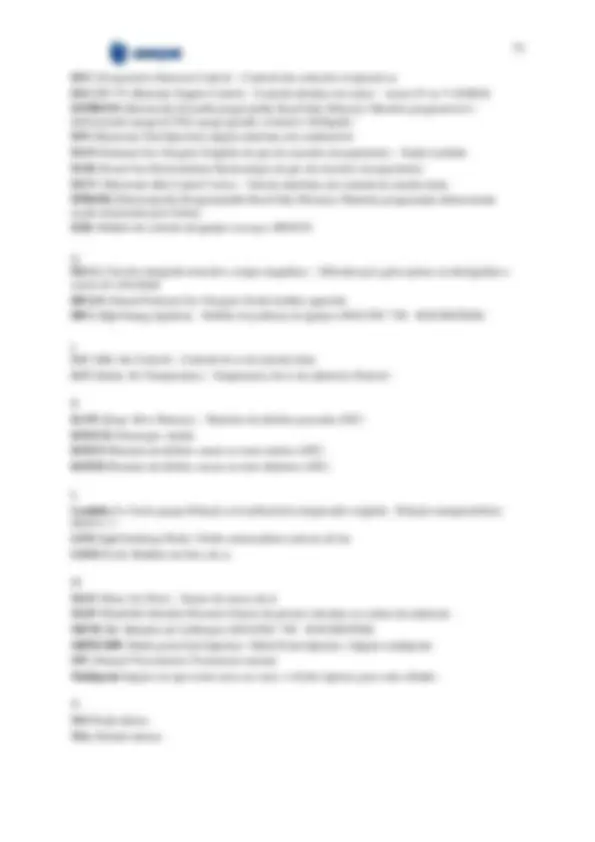
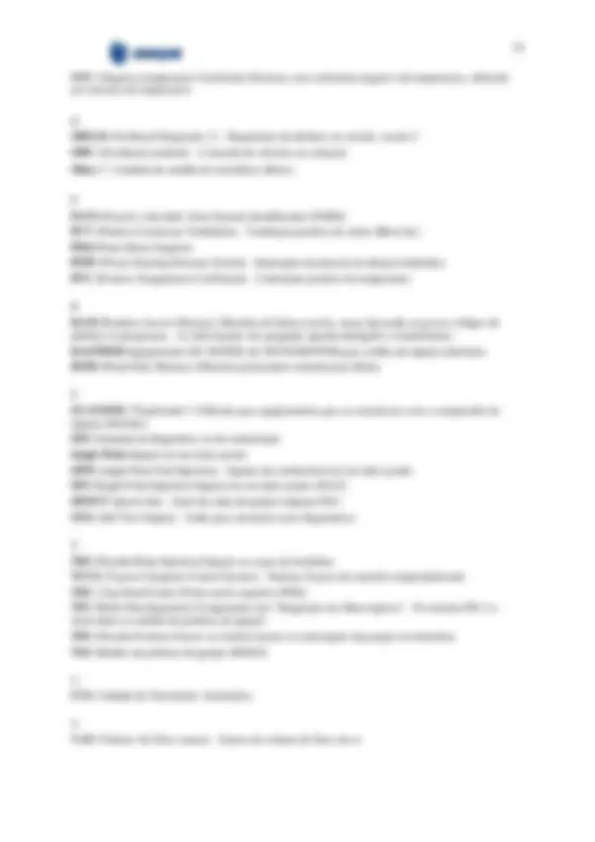
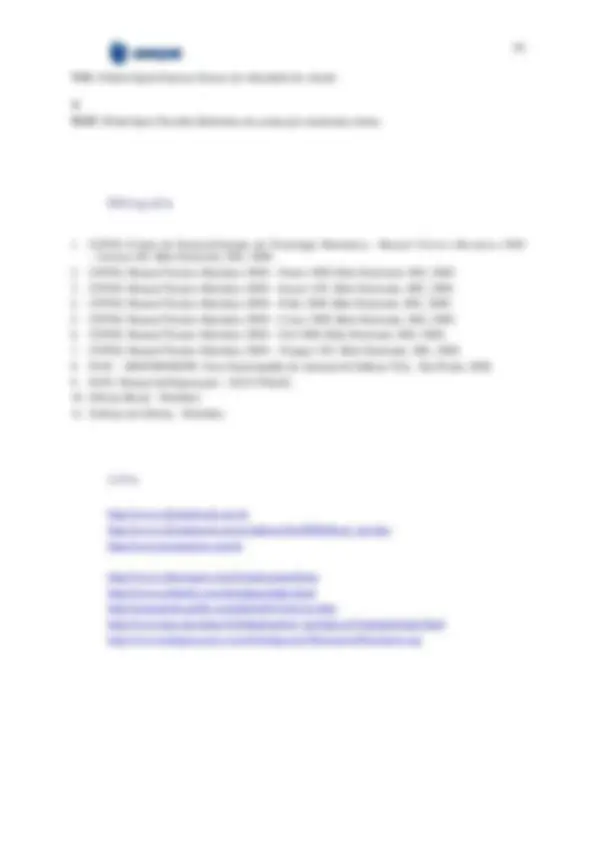
Estude fácil! Tem muito documento disponível na Docsity
Ganhe pontos ajudando outros esrudantes ou compre um plano Premium
Prepare-se para as provas
Estude fácil! Tem muito documento disponível na Docsity
Prepare-se para as provas com trabalhos de outros alunos como você, aqui na Docsity
Os melhores documentos à venda: Trabalhos de alunos formados
Prepare-se com as videoaulas e exercícios resolvidos criados a partir da grade da sua Universidade
Responda perguntas de provas passadas e avalie sua preparação.
Ganhe pontos para baixar
Ganhe pontos ajudando outros esrudantes ou compre um plano Premium
Comunidade
Peça ajuda à comunidade e tire suas dúvidas relacionadas ao estudo
Descubra as melhores universidades em seu país de acordo com os usuários da Docsity
Guias grátis
Baixe gratuitamente nossos guias de estudo, métodos para diminuir a ansiedade, dicas de TCC preparadas pelos professores da Docsity
Básico sobre injeção eletrônica
Tipologia: Notas de estudo
Oferta por tempo limitado
Compartilhado em 30/12/2010
4.5
(2)1 documento
1 / 56
Esta página não é visível na pré-visualização
Não perca as partes importantes!
Em oferta
Panambi, abril de 2002
Introdução
A função de um motor é transformar a energia contida no combustível que o alimenta em potência mecânica, capaz de movimentar o veículo. Para tanto, o combustível é queimado. No processo, a energia do combustível se transforma em calor, finalmente, tem trabalho mecânico ou potência.
Nos motores de combustão interna a combustão, a queima de combustível, se dá no recinto fechado: a Câmara de combustão. Nela, é a admitida uma mistura de ar e combustível, que é comprimida intensamente. No fim da compressão, o sistema de ignição fornece o calor necessário, por uma centelha da vela, dando início a combustão. A queima da mistura provoca o aumento da pressão dentro do cilindro, e gerando a força que impulsiona o pistão, fazendo girar o virabrequim.
Como pode-se ver na Figura 1, após a combustão o motor libera:
?? trabalho , como potência, que movimenta o veículo;
?? gases resultantes da combustão ou gases de escape, constituídos principalmente de água, dióxido de carbono, nitrogênio, monóxido de carbono, hidrocarbonetos ou combustíveis não queimados e óxido de nitrogênio;
?? calor , que é e eliminado com o líquido do arrefecedor.
Desses elementos, o que interessa é o trabalho mecânico ou potência. Os outros dois são energia desperdiçada ou não aproveitada. Os gases de escape, além de transportar calor (perdas) são fontes de poluição, com componentes que agridem o meio ambiente. As necessidades básicas impostas aos motores modernos são: a obtenção da máxima potência com baixo consumo de combustível e menor nível de emissões de poluentes, compatíveis com tal potência.
Devido à rápida evolução dos motores dos automóveis o velho carburador já não supri as necessidades dos novos veículos, no que se refere à poluição, economia de combustível, potência, respostas rápidas nas acelerações, etc.
Figura 1 – O processo de transformação de energia
Devido a isso desenvolveu-se o sistema de Injeção Eletrônica de combustível, que têm por objetivo proporcionar ao motor melhor rendimento com mais economia, em todos os regimes de funcionamento. Para que o motor tenha um funcionamento suave, econômico e não contamine o ambiente, ele necessita receber a perfeita mistura ar/combustível em todas as faixas de rotação.
A Injeção Eletrônica é um sistema não acionado pelo motor mas comandado eletronicamente, que dosa o combustível, controlando a mistura ar/combustível em função das necessidades imediatas do motor. De modo semelhante, a ignição digital permite que o motor trabalhe com o seu ponto de ignição sincronizado com as diversas condições de funcionamento do motor.
Os sistemas de injeção eletrônica têm essa característica de permitir que o motor receba somente o volume de combustível que ele necessita. Com isso eles garantem:
?? menor poluição;
?? maior economia;
?? melhor rendimento;
?? partidas mais rápidas;
?? não utilização do afogador.
O combustível normalmente utilizado em veículos com injeção eletrônica é a gasolina, que é uma mistura balanceada de centenas de solventes (classificados pela química em aromáticos, oleofínicos e saturados). Esta, para ser adequada deve apresentar as seguintes características:
entrar em combustão por meio da centelha da vela de ignição, de forma homogênea e progressiva, sem detonar, proporcionando bom desempenho do motor, sem ocasionar danos.
vaporizar-se completamente no interior da Câmara de combustão, e mistura com ar, de forma a queimar-se completamente e com mínimo de formação de resíduos.
Para atender esses requisitos da qualidade, são especificados valores para determinadas características da gasolina que permitem a assegurar o correto funcionamento do motor, entre essas características estão:
A capacidade de evaporação da gasolina, denominada Volatilidade , é determinada pelas seguintes análises de laboratório: pressão de vapor e curva de destilação. Essa capacidade de vaporização deve produzir as quantidades correta de vapor do produto para atender as necessidades do motor, desde a partida até o seu completo aquecimento. Assim, a gasolina deve apresentar uma distribuição correta do conteúdo das frações leves, médias e pesadas de forma a fornecer as quantidades necessárias do produto, para que o motor funcione bem.
Pressão de vapor: Ao aquecer uma substância, sua pressão interna (pressão de vapor), aumenta até ultrapassar a pressão externa, no interior do equipamento onde está armazenada. Quando isso acontece, se inicia a valorização ou ebulição. Quanto mais baixa for a temperatura de início da valorização, maior será sua pressão de vapor e maiores devem ser os cuidados para o manuseio do produto.
Curva de destilação: A gasolina é composta de uma mistura com grande número de substâncias classificadas como leves, médias e pesadas, de acordo com seus pesos moleculares. Ao ser aquecida durante o processo de destilação, as substâncias vaporizam e em temperaturas diferentes, gerando uma curva de vaporização ou de destilação. Dentro desse intervalo de temperatura, são identificadas em porcentagem do volume total em teste. A correta formulação da gasolina contribui para que o veículo tenha adequada dirigibilidade.
A formação de depósito no motor pode ser decorrente da existência de substâncias pastosa conhecida como goma , que depende da presença de substâncias que se oxidam com maior facilidade na gasolina, e das condições de sua utilização.
A goma é um produto com características diversas. É insolúvel na gasolina e de difícil vaporização. Normalmente gera resíduos que se depositam onde são formadas, sem deslocar. Portanto, podem se depositar tanque, no sistema de injeção e, nas válvulas de admissão ou na Câmara de combustão, causando problemas de desempenho. Para evitar sua formação deve se:
A mistura ideal ou estequiométrica, quando queimada, produz no escapamento somente dióxido de carbono, água e nitrogênio mas, devido às imperfeições da combustão na câmara de combustão, sempre existirão poluentes nos gases de escapamento. A relação estequiométrica varia de acordo com o tipo de combustível e pode ser calculada pela seguinte equação:
onde y e z são as quantidades de hidrogênio e oxigênio dos combustíveis (CHyOz = fórmula bruta média).^1
Assim têm-se, aproximadamente as seguintes relações:
Produto
ar/comb kg/kg
densidade ml/kgar
Metanol CH 4 O 6,46 0,796 194, Etanol CH 3 O0,5 8,989 0,794 140, MTBE CH2,4O0,2 11,75 0,744 114, Gasolina Pura CH1,86 14,569 0,7426 92,
gasolina: 14,7: gasolina com 20% de álcool: 12,5: álcool: 8,5: No caso do motor a gasolina, são necessárias 14,7 partes de ar para a cada parte de combustível, para obter nos uma mistura estequiométrica.
A combustão incompleta produz, além do dióxido de carbono e do vapor de água, os seguintes poluentes:
?? monóxido de carbono: um ambiente com 0,3% de CO provoca a morte em cerca de 30 minutos; ?? hidrocarbonetos: combustível não queimado; ?? óxidos de nitrogênio: o nitrogênio, que deverá passar inalterado pela combustão, se associa ao oxigênio formando os óxidos de nitrogênio.
No Brasil, os veículos não são feitos para gasolina pura e sim para gasolina “ C ” (com 22% de etanol), fazendo com que a dosagem seja (para o estequiométrico) da ordem de 100ml por quilograma de ar.
Verifica-se que os motores brasileiros consomem cerca de 8,2% mais de combustível (em volume) por conta deste fato (100? 92,4 = 1,082). Portanto não é possível comparar com a autonomia do mesmo modelo em um outro país.
(^1) Fonte: Petrobrás: www.petrobras.com.br
Princípio de Funcionamento
Quando se dá a partida no veículo, os pistões do motor sobem e descem - Figura 2. No movimento de descida, é produzida no coletor de admissão uma aspiração (vácuo), que aspira ar da atmosfera e passa pelo medidor de fluxo de ar e pela borboleta de aceleração, chegando até os cilindros do motor.
O medidor do fluxo de ar informa para a unidade de comando o volume de ar admitido. A unidade de comando , por sua vez, permite que as válvulas de injeção injetem a quantidade de combustível ideal para o volume de ar admitido, gerando a perfeita relação ar/combustível que é chamada de mistura.
Quanto mais adequada a mistura melhor o rendimento e economia, e menor a emissão de gases poluentes.
Os sistemas de injeção são constituídos basicamente de sensores e atuadores. Sensores são componentes que estão instalados em vários pontos do motor e servem para enviar informações para a unidade de comando. (ex: sensor de temperatura)
Atuadores são componentes que recebem informações da unidade de comando e atuam no sistema de alimentação, variando o volume de combustível que o motor recebe. (ex: atuador de marcha lenta)
Sistema Weber-Marelli (FIAT PALIO) Figura 2 – Esquema do Sistema de Injeção e Ignição Eletrônica onde:
1 Válvula de segurança 19 Eletroinjetores 2 Tanque de combustível 20 Regulador de pressão do combustível 3 Eletrobomba de combustível 21 Vela de ignição 4 Atuador de marcha lenta 22 Bobina de ignição
onde: 1 Entrada de combustível 4 Coletor de Admissão 2 Ar 5 Válvulas de Injeção 3 Borboleta de Aceleração 6 Motor
O sistema monoponto destaca-se por possuir uma única válvula de injeção para os diversos cilindros do motor. O sistema multiponto utiliza uma válvula de injeção para cada cilindro do motor.
Figura 4 – Sistema Multiponto onde:
1
Galeria de Distribuição (entrada de combustível)
4 Coletor de Admissão
2 Ar 5 Válvulas de Injeção 3 Borboleta de Aceleração 6 Motor
No último caso, a classificação segundo a estratégia de definição do tempo de injeção divide os sistemas existentes em quatro grupos:
Mapeamento ângulo X Rotação: neste caso, o temo básico de injeção é definido em testes de bancada em laboratório em função de ângulo da borboleta de aceleração e da rotação do motor, gerando uma tabela de tempos básicos de injeção que são memorizados.
Densidade X Rotação: o tempo básico de injeção é calculado, indiretamente, em função do fluxo de massa de ar admitido. O fluxo de massa de ar é determinado ela rotação do motor, pelo volume dos cilindros e pela densidade do ar, e este é calculado segundo a pressão no coletor de admissão e a temperatura do ar.
Fluxo de Ar: o tempo básico de injeção é calculado, diretamente, em função da vazão de ar admitido. A vazão de ar é determinada diretamente por um medidor de fluxo de ar e o resultado é corrigido em função do efeito da variação da temperatura do ar admitido na variação da sua densidade.
Massa de ar: o tempo básico de injeção é calculado, diretamente, em função da massa de ar admitido. A massa de ar é determinada por um medidor de massa de ar, que pelo seu princípio de
funcionamento já corrige automaticamente, as variações da pressão atmosférica, da temperatura ambiente e até da umidade relativa do ar.
Componentes
Unidade de Comando Eletrônico
A também chamada de Centralina ou Central Eletrônica, a Unidade de Comando Eletrônico ( UCE) é o cérebro do sistema - Figura 5. É uma unidade de tipo digital com microprocessador, caracterizada pela elevada velocidade de cálculo, precisão, confiabilidade, versatilidade, baixo consumo de energia e sem necessidade de manutenção. É ela que determina, pela ação dos atuadores, para obter o melhor funcionamento possível do motor - Figura 6. Deste modo a quantidade de combustível injetada é dosada pela unidade de comando através do tempo de abertura das válvulas de injeção, também conhecido como tempo de injeção.
Figura 5 – Unidade de Comando Eletrônico da BOSH
Ao ser ligada a chave de ignição (sem dar partida), a UCE é alimentada. A mesma acende uma lâmpada de diagnóstico^2 e aciona, por alguns segundos, a Bomba Elétrica de Combustível, objetivando pressurizar o sistema de alimentação^3. Junto a isso, envia uma tensão de 5V VDC para a maioria dos sensores do sistema e passa a receber o sinal característico de cada um deles (temperatura da água, pressão no coletor de admissão, temperatura do ar, posição da borboleta de aceleração, etc...). Durante a partida e com o motor funcionando, recebe sinal do Sensor de Rotação. Enquanto captar esse sinal a UCE irá manter a bomba elétrica de combustível acionada e controlará a(s) válvula(s) injetora(s), bobina de ignição e a rotação da marcha lenta.
Com base no sinal dos sensores, a UCE pode ainda controlar o sistema de partida a frio, no caso de veículos a álcool, o eletro-ventilador de arrefecimento^4 , o desligamento da embreagem do compressor do condicionador de ar, etc.
(^2) A lâmpada de diagnóstico não é encontrada em todos os veículos injetados. A maioria dos veículos
FORD e VW não a possuem. (^3) Em alguns veículos como Corsa MPFI, Omega 2.0, Santana Executive, Escort XR3 2.0i, o
acionamento da bomba só acontece quando é dada a partida. (^4) Na maioria dos veículos, o eletro-ventilador é controlado por um interruptor térmico (“Cebolão”).
Porém em veículos como o Kadett EFI, Monza EFI, Ipanema EFI, S10 EFI, Blazer EFI, Corsa MPFI, Ford KA 1.0 e 1.3, Fiesta 1.0 e 1.3, o controle é feito pela UCE.
6 Lâmpadainjeção piloto^ de^ defeito^ no^ sistema^ de 16 Sensor de pressão absolunta
7 Eletroinjetores 17 Sensor de rotações/PMS
8 Tomada de diagnose 18 Comutador de ignição
9 Bobina de ignição dos cilindros 1 – 4 19 Relé duplo
10 Bobina de ignição dos cilindros 2 - 3 20 Eletrobomba de combustível
Recovery
É um procedimento utilizado pelas UCEs de sistemas de injeção digitais para substituir o valor enviado pelo sensor danificado (em curto-circuito ou circuito aberto) por um valor pré- programado. Nos sistemas MOTRONIC MP 9.0 (gol 1000 mi 8V) e IAW 1AVS (Gol/Parati 1000 mi 16V), por exemplo, quando a UCE detecta falha no circuito sensor de temperatura da água – CTS, grava o código de defeito em sua memória e assume a temperatura de 100ºC como padrão. Portanto, se o CTS for desligado, o veículo continuará funcionando, mas com um rendimento um pouco inferior, até que o proprietário o leve para a manutenção.
A UCE possui um conector de diagnóstico denominado ALDL (Figura 7). Este conector é uma tomada onde um, Aparelho de Diagnóstico é inserido para que o mesmo se faça uma avaliação do sistema.
Figura 7 – Conector de Diagnóstico
Visão Geral da Unidade de Comando Eletrônico
O diagrama em blocos abaixo mostra um típico módulo microprocessado. Neste diagrama, distinguimos sete funções distintas e cada uma implementa determinada função.
Figura 8 – Visão Geral do Sistema
As sete funções são:
Regulador de Tensão Interno
O módulo e os vários sensores requerem uma alimentação muito estabilizada. A unidade de comando possui seu próprio regulador/ estabilizador. Muitos dos sensores como o MAP, TPS, ACT, ECT necessitam de uma tensão de 5 volts como referência. Isso se deve ao tipo de circuitos integrados utilizados na unidade de comando que só operam com esse valor de tensão.
Processamento do Sinal de Entrada
Cada sinal é convertido para um número digital (números binários). Esses números correspondem a “0” ou “1”. O valor é tido como “0” quando não há tensão de saída e “1” quando existe um valor de tensão (no caso, 5 volts). Como cada sensor gera um diferente tipo de sinal, então são necessários diferentes métodos de conversão.
Os sensores geram um sinal de tensão compreendido entre 0 a 5 volts (sinal analógico). Estes valores não podem ser processados pela CPU, a qual só entende números binários. Portanto, esses sinais devem ser convertidos para um sinal digital de 8 bits (até 256 combinações). O componente encarregado de converter esses sinais é chamado de conversor A/D (analógico para digital).
Memória de Entrada
O sinal de tensão analógico emitido pelos sensores, é convertido para sinais digitais pelo conversor A/D. Cada valor digital corresponde a um valor de tensão que está gravado na memória de entrada.
Figura 9 – Memória de Entrada
Sensores
Servem para informar a unidade de comando sobre as diversas condições de funcionamento do motor, como a temperatura do líquido de arrefecimento e do ar admitido, a pressão interna do coletor de admissão, a posição em que se encontra a borboleta de aceleração e outros.
A maioria dos sensores trabalha com uma tensão de referência de 5VCC (devido ao tipo de circuito integrado utilizado na UC - família MOS e CMOS) e está ligado em série com um resistor fixo (no interior da unidade de comando) formando um divisor de tensão.
Na Figura 10, podemos observar que R1 (resistor fixo) está ligado em série com o sensor (resistor variável) formando um divisor de tensão.
Figura 10 - Sensores
Quanto maior for a resistência do sensor, menor será a queda de tensão em R1 que é monitorado pelo integrado IC1. Esse integrado é como se fosse um voltímetro e envia o sinal de tensão para o processador principal (CPU) onde é decodificado.
Um sensor pode variar sua resistência de diversas maneiras:
Sensor de Pressão Absoluta do Coletor (MAP)
MAP – Manifold Absolute Pressure Este sensor mede a alteração da pressão no coletor de admissão, que resulta da variação de carga do motor. O sensor é capaz de medir a pressão de 0,2 até 1,05 bar (de 20 a 105 kPa).
A unidade de comando recebe as informações em forma de sinais de tensão, que variam entre 0,5 a 1,0 volt em marcha-lenta (baixa pressão no coletor; vácuo alto). A tensão pode passar dos 4, volts com a borboleta totalmente aberta (alta pressão no coletor; vácuo baixo).
Assim que a chave de ignição é ligada, o sensor MAP informa a unidade de comando o valor da pressão atmosférica, para que se possa dar o cálculo perfeito da densidade do ar. A pressão atmosférica varia conforme a altitude (quanto mais alto, menor será a pressão atmosférica).
O elemento sensível contido na peça de plástico - Figura 11(a) - é composto de uma ponte de resistências (ponte de Wheatstone) serigrafadas numa placa de cerâmica muito fina (diafragma) de forma circular, montada na parte inferior de um suporte de forma anular - Figura 11(b). O diafragma separa duas câmaras: na câmara inferior lacrada, foi criado o vácuo, enquanto que a câmara superior está em comunicação direta com o coletor de admissão.
Normalmente, o sensor MAP é ligado à tomada de pressão no coletor através de uma mangueira de borracha. Em sistemas mais modernos como os utilizados nos veículos Volkswagen MI, Novo Vectra, Família Palio 8V (após 99), o sensor vem parafusado diretamente sobre o coletor de admissão (não utiliza mangueira de tomada de pressão).
Este sensor trabalha com uma pequena membrana de cristal do tipo "piezo-resistivo" que varia sua resistência de acordo com o grau de deformação desta membrana. Quanto maior for o grau de deformação, maior será a sua resistência e menor será a tensão recebida pela Unidade de Comando (maior no sensor), que mantém a alimentação rigorosamente constante (5V).
As informações do sensor de pressão absolutas (MAP) são utilizadas para os cálculos da quantidade de ar admitido (massa de ar) e para o avanço da ignição (de acordo com a carga do motor).
Para se calcular o volume de combustível a ser injetado, a unidade de comando se baseia na temperatura do ar admitido e pressão do coletor (para se saber a densidade) e mais as informações de rotação e taxa de cilindrada do motor. Com essas informações, é possível definir a quantidade de combustível a ser injetado, mantendo-se a proporção ideal de mistura ar/combustível.
Recovery do MAP
No caso de falha do sensor MAP, a unidade de comando controlará a quantidade de combustível e o ponto de centelhamento, baseado num valor de substituição Este valor leva em consideração, principalmente, o sinal do sensor de posição da borboleta (TPS).
(a) (b) Figura 11 – (a) Sensor MAP e (b) Ponte de Wheatstone
Na realização do teste de um sensor de pressão absoluta no coletor de admissão – MAP observe os seguintes detalhes:
Certifique-se da boa condição da carga da bateria e alimentação da UCE; Verifique se a mangueira de tomada de pressão do sensor (caso exista) não está furada ou entupida. Mantenha a tomada de pressão desobstruída.
O teste do sensor deve ser realizado com os conectores do sensor e da UCE ligados (circuito do sensor em carga), somente dessa forma pode-se simular a verdadeira condição de funcionamento do sensor;
Temperatura (ºC) 25 40 80 100 Voltagem (VDC) 3,00 2,20 0,80 0,60-0,
onde a região marcada corresponde à temperatura operacional para um motor aquecido. Em ambas as tabelas, o sensor ativa a ventoinha quando a temperatura chega próxima dos 100ºC.
Na realização do teste de um sensor de temperatura do líquido de arrefecimento, observe os seguintes detalhes:
Certifique-se da boa condição da carga da bateria e alimentação da UCE; Verifique a qualidade do líquido de arrefecimento e o bom estado de funcionamento dos componentes do sistema;
Sangre o sistema de arrefecimento. A formação de bolhas de ar em contato com o sensor de temperatura da água provoca falhas no funcionamento do motor e no acionamento da ventoinha;
Retire o sensor de temperatura da água e limpe sua carcaça; Meça a tensão de alimentação do sensor e o aterramento de seu circuito; O sinal do sensor deve ser medido em tensão de corrente contínua VDC. A chave de ignição deve estar ligada.
O teste só pode ser considerado conclusivo se feito no momento em que houver a falha.
Sensor de Temperatura do Ar (ACT)
ACT – Air Charge Temperature Está localizado antes do corpo de borboleta, colocado na mangueira que liga o filtro de ar ao corpo. Quando o ar admitido está frio, a resistência do sensor (termistor do tipo NTC) é alta, a medida em que o ar admitido aquece, a resistência do sensor diminui e a tensão correspondente também (Figura 13)
A temperatura do ar é uma das informações utilizadas para o controle de:
Figura 13 – Sensor de Temperatura do Ar (ACT)
Recovery do ACT
Se for detectada uma temperatura superior ou inferior a determinados limites, toma-se a temperatura do ar igual à temperatura do líquido de arrefecimento. Em caso de defeito simultâneo do sensor de temperatura do líquido de arrefecimento, a unidade de comando estabelece um valor fixo de temperatura.
Sensor de Velocidade do Veículo (VSS)
O sensor de velocidade do veículo - VSS (Vehicle Speed Sensor), pode ser encontrado em três configurações: sensor magnético ou de relutância variável , sensor de efeito hall e sensor de efeito óptico.
O sensor de velocidade do veículo (VSS) fornece a unidade de comando, as informações sobre as velocidades do veículo, desde que o mesmo esteja acima de 1km/h.
A unidade de comando utiliza essas informações para o controle de: ?? rotação de marcha-lenta; ?? quantidade de combustível; ?? acionamento do solenóide de controle da válvula EGR; ?? sinal de saída do computador de bordo. No sensor VSS, o sinal gerado é diretamente proporcional à velocidade do veículo. A unidade de comando eletrônico - UCE, utiliza esta informação principalmente para o controle das condições de marcha - lenta e freio-motor.
Os sensores de efeito hall são alimentados com tensão de bateria. Fornecem à UCE um sinal pulsado cuja amplitude deve ser igual a tensão de alimentação, e a freqüência proporcional à velocidade do veículo. Estão comumente instalados no eixo de saída da transmissão, junto ao cabo do velocímetro. O sensor de velocidade tipo hall é o mais comum no mercado nacional, sendo utilizado em veículos como Kadett EFI, Monza efi, Ipanema efi, Gol mi 1.0, Palio 16 v, Escort 16v - Zetec, e outros.
Os sensores de efeito óptico possuem comportamento similar aos de efeito hall. Consistem basicamente de um diodo emissor de luz (LED) e um sensor óptico (fototransistor) separados por um disco giratório com janelas. Toda vez que as janelas permitem que a luz procedente do LED seja refletida no sensor óptico é enviado sinal (pulso) à UCE. Estes sensores são encontrados, por exemplo, na família Corsa e no Omega 2.2 (com painel analógico - comum). Estão normalmente instalados junto ao painel de instrumentos e são acionados pelo cabo do velocímetro.
Os sensores magnéticos ou de relutância variável não necessitam de alimentação elétrica. Seu sinal é gerado por indução eletromagnética devido a interação entre o sensor e a roda dentada (fônica). São aplicados em veículos como S10 /Blazer 2.2 EFI e 4.3 V6.
O sensor de velocidade nos veículos S10 é de relutância variável instalado na saída da transmissão, que emite um sinal de freqüência e tensão variáveis conforme a velocidade de rotação do eixo de saída. Estes pulsos são processados pelo módulo DRAC, que os transforma num sinal pulsado adaptado às necessidades a unidade de comando. O módulo DRAC emite pulsos numa freqüência de aproximadamente, 2500 pulsos por km rodado. Está localizado no mesmo suporte que a unidade de comando (debaixo dela).
O sensor para a opção LCD (painel de instrumentos digital - somente Omega) consiste de um gerador de pulsos montado na saída da transmissão. O sensor emite pulsos de tensão sempre que o veículo está em movimento. O número de pulsos aumenta de acordo com a velocidade do veículo.