
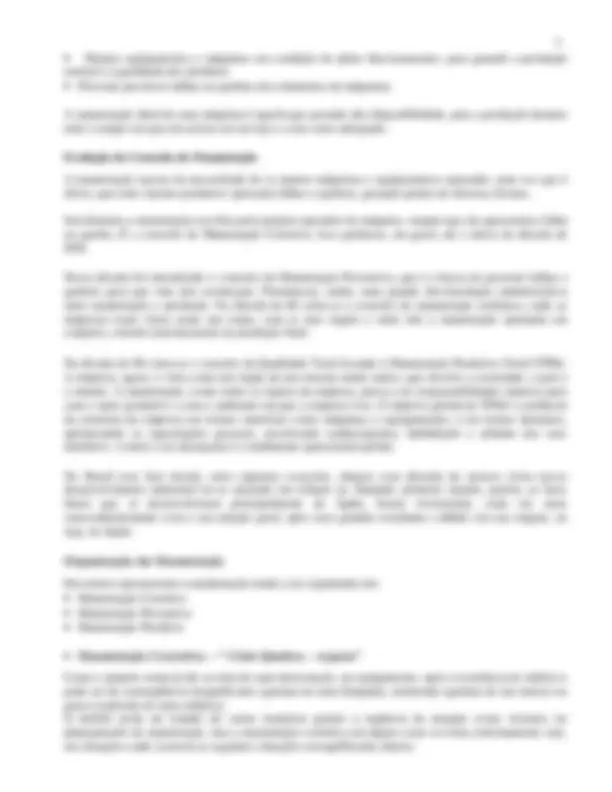
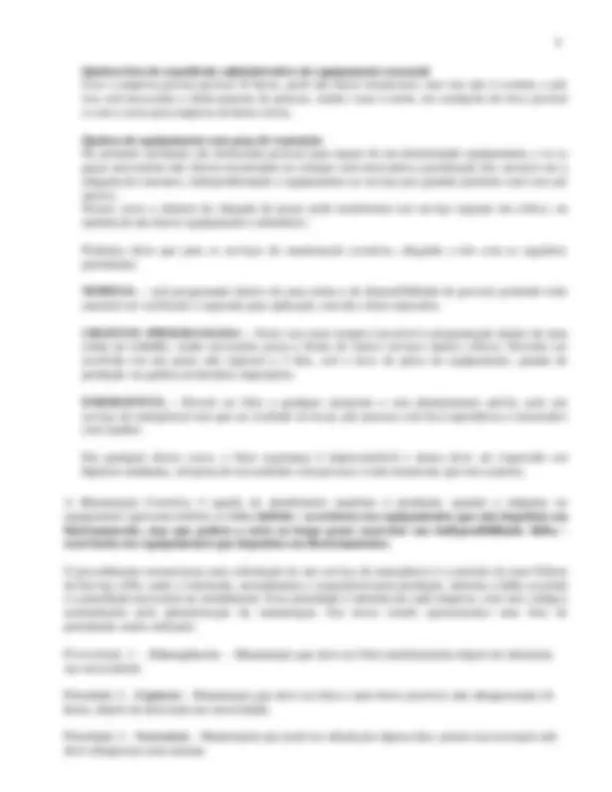
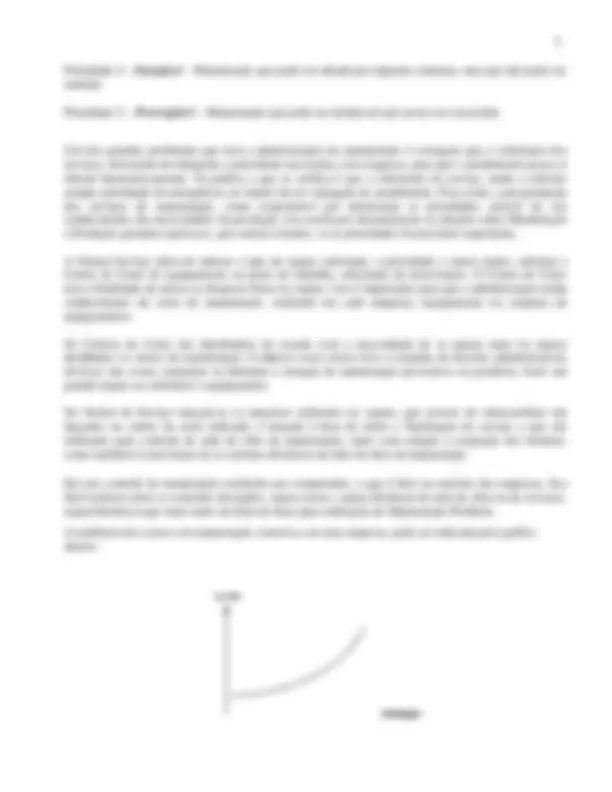

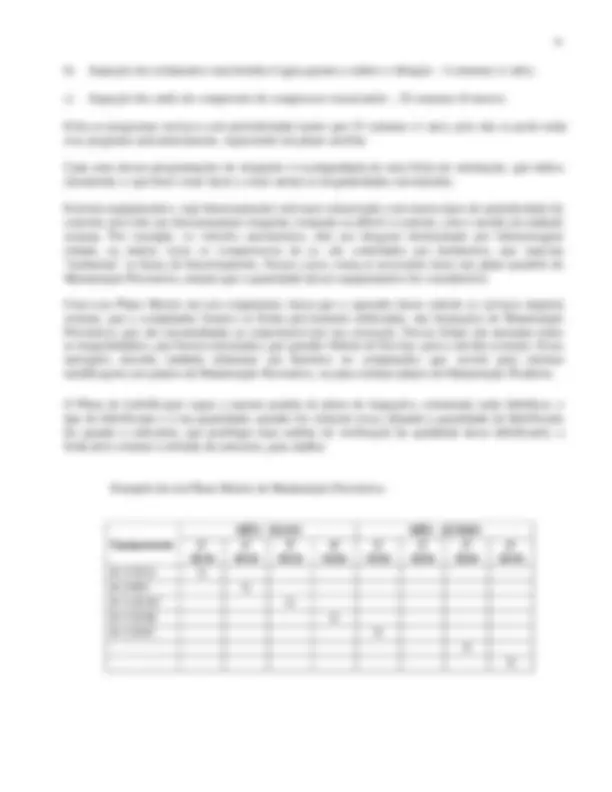
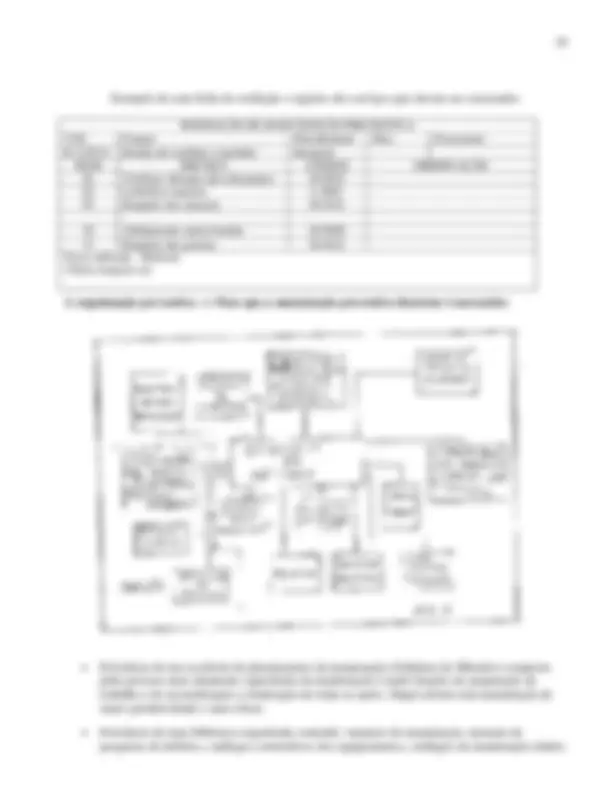


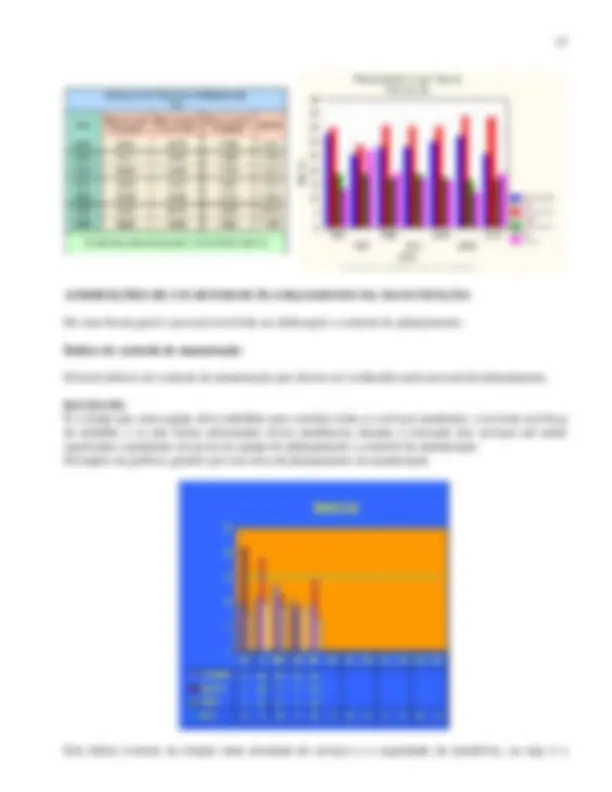
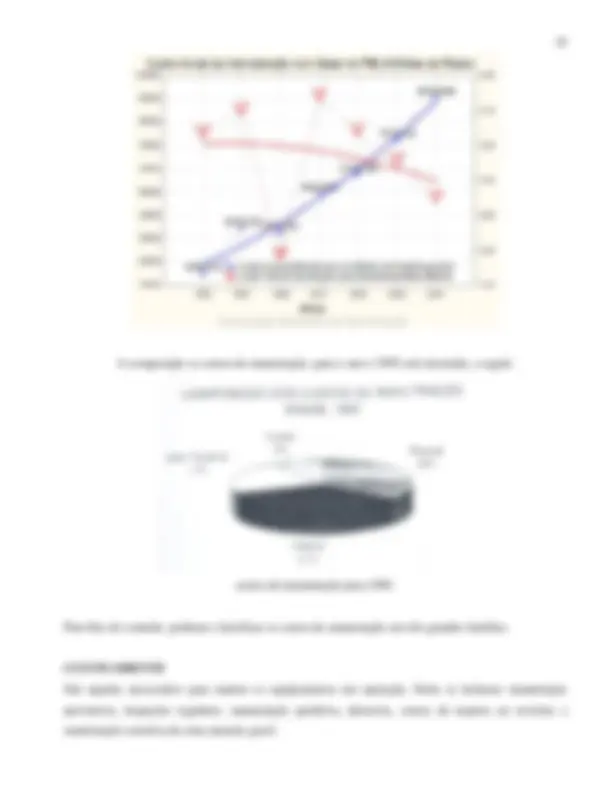
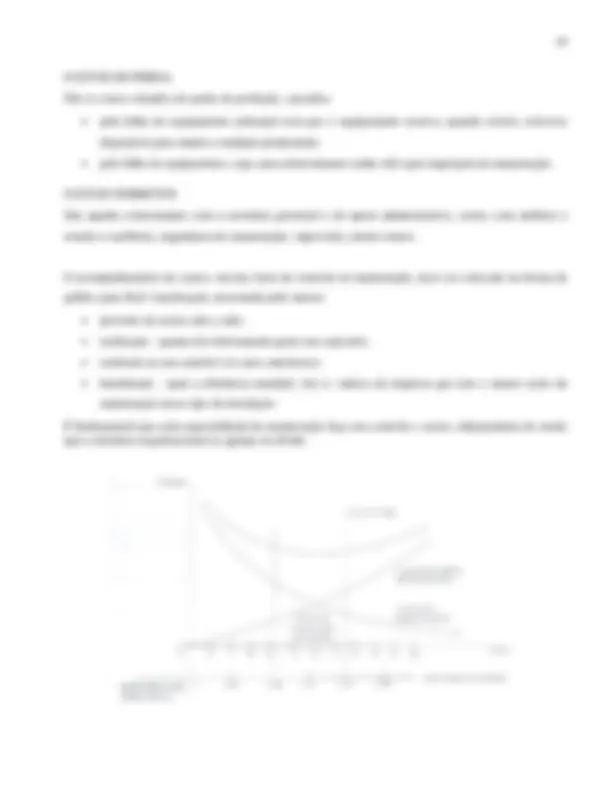
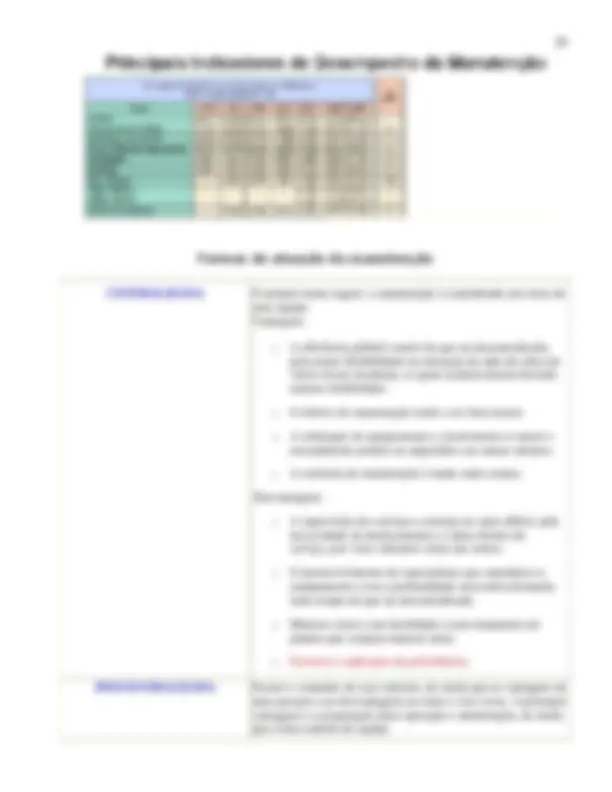
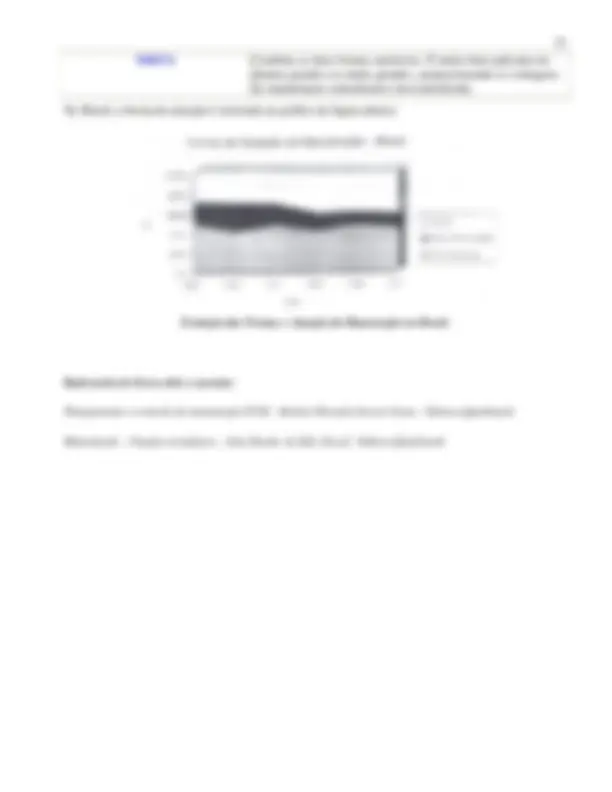
Estude fácil! Tem muito documento disponível na Docsity
Ganhe pontos ajudando outros esrudantes ou compre um plano Premium
Prepare-se para as provas
Estude fácil! Tem muito documento disponível na Docsity
Prepare-se para as provas com trabalhos de outros alunos como você, aqui na Docsity
Os melhores documentos à venda: Trabalhos de alunos formados
Prepare-se com as videoaulas e exercícios resolvidos criados a partir da grade da sua Universidade
Responda perguntas de provas passadas e avalie sua preparação.
Ganhe pontos para baixar
Ganhe pontos ajudando outros esrudantes ou compre um plano Premium
Comunidade
Peça ajuda à comunidade e tire suas dúvidas relacionadas ao estudo
Descubra as melhores universidades em seu país de acordo com os usuários da Docsity
Guias grátis
Baixe gratuitamente nossos guias de estudo, métodos para diminuir a ansiedade, dicas de TCC preparadas pelos professores da Docsity
Técnicas de planejamento de manutenção
Tipologia: Notas de estudo
1 / 21
Esta página não é visível na pré-visualização
Não perca as partes importantes!
Introdução.
Tudo começou com os primeiros passos da Revolução Industrial, iniciada no Inglaterra no século passado. No início as linhas de produção têxteis eram artesanais e feitas nas casas de cada artesão, onde a operação e as eventuais quebras nos teares eram reparadas pelo próprio “operador”, ou seja, o dono da máquina. Com a invenção da máquina a vapor, começaram a surgir teares de produção dada vezes maiores, com trabalhadores se revezando em turno de trabalhos desumanos, que faziam com que uma quebra de equipamento parasse uma linha de produção. Nesse momento de início de complexidade das máquinas apareceram as primeiras pessoas especializadas em reparo dos equipamentos com a rapidez necessária, e, portanto “especialistas em manutenção”. O conceito da palavra manutenção é: “ Toda atividade que se realiza através de processos diretos ou indiretos nos equipamentos , obras ou instalações , com a finalidade de assegurar-lhes condições de cumprir com segurança e eficiência as funções para as quais foram fabricadas , levando em consideração as condições operativas e econômicas .” Desde os tempos de James Watt e George Stephenson até hoje a complexidade do maquinário vem crescendo de modo acelerado. Com o advento do computador e a avançada engenharia de controle , a tecnologia de processo de produção expandiu-se. Como conseqüência de custo da fábrica e do maquinário Ter crescido enormemente, fez-se necessário assegurar a máxima utilização efetiva desta fábrica. O padrão de desenvolvimento nas indústrias de capital intensivo tem sido, portanto, crescente no uso de dois ou três turnos de trabalho, e isso deixa pouco ou nenhum tempo para reparos essenciais do maquinário, lubrificação e manutenção regular. Muito trabalho desse tipo teria sido previamente executado durante a noite ou em fins de semana, enquanto o maquinário estivesse parado. Com as operações contínuas tornaram-se umas necessidades. Alguma estratégia definitiva precisa ser desenvolvida para obter a máxima eficiência. Mesmo com um único turno de trabalho, a complexidade do maquinário demanda um programa cuidadosamente planejado de manutenção.
Com a globalização da economia, a busca da qualidade total em serviços, produtos e gerenciamento ambiental passaram a ser a meta de todas as empresas. A manutenção, como todos os órgãos das empresas, assumiu cada vez mais o seu papel de manter cada vez mais o estado de máquinas e equipamentos e prevenir falhas e quebras evitando:
Os programas de manutenção devem estar estruturados, para que a empresa obtenha os maiores resultados, com o mínimo de despesas e cumpra as políticas administrativas ditadas pela direção.
Conceitos e Objetivos
Podemos entender manutenção como o conjunto de cuidados técnicos indispensáveis ao funcionamento regular e permanente de máquinas, equipamentos, ferramentas e instalações. Esses cuidados envolvem a conservação, a adequação, a substituição, a restauração e a prevenção. De um modo geral a manutenção em uma empresa tem como objetivo:
Quebra fora do expediente administrativo de equipamento essencial Caso a empresa possua pessoal 24 horas, pode não haver transtornos, mas isto não é comum, e pôr isso será necessário o deslocamento de pessoas, muitas vezes à noite, em condições de risco pessoal e com o custo para empresa de horas extras.
Quebra de equipamento sem peça de reposição. No primeiro momento são deslocadas pessoas para reparo de um determinado equipamento, e se as peças necessárias não forem encontradas no estoque será necessária a paralisação dos serviços ate a chegada dos mesmos, indisponibizando o equipamento ao serviço por grandes períodos (em caso até meses). Nesses casos a demora da chegada de peças pode transformar um serviço urgente em crítico, na medida de não haver equipamentos substitutos.
Podemos dizer que para os serviços de manutenção corretiva, chegarão a nós com as seguintes prioridades.
NORMAL – será programado dentro de uma rotina e de disponibilidade de pessoal, podendo todo material ser verificado e separado para aplicação com dia e hora marcados.
URGENTE (PROGRAMADA) – Neste caso nem sempre é possível a programação dentro de uma rotina de trabalho, sendo necessário passa a frente de outros serviços menos críticos. Deverão ser resolvida em um prazo não superior a 3 dias, sob o risco de perca do equipamento, parada de produção ou quebra em horários impróprios.
EMERGENCIA - Deverá ser feito a qualquer momento e sem planejamento prévio, pois um serviço de emergência tem que ser avaliado no local, pôr pessoas com boa experiência e executados com rapidez.
Em qualquer destes casos, o fator segurança é imprescindível e nunca deve ser esquecido em hipótese nenhuma, sob pena de um acidente com pessoas e todo transtorno que isto acarreta.
A Manutenção Corretiva é aquela de atendimento imediato á produção, quando a máquina ou equipamento apresenta defeito ou falha (defeito - ocorrência nos equipamentos que não impedem seu funcionamento, mas que podem a curto ou longo prazo acarretar sua indisponibilidade. falha – ocorrência nos equipamentos que impedem seu funcionamento).
O procedimento normal para uma solicitação de um serviço de emergência é a emissão de uma Ordem de Serviço (OS), onde o solicitante, normalmente o responsável pela produção, informa a falha ocorrida e a prioridade necessária no atendimento. Essa prioridade é adotada em cada empresa, com seus códigos normalizados pela administração da manutenção. Em nosso estudo apresentamos uma lista de prioridades muito utilizada:
Pr ior idade 1 – Emergên cia – Manutenção que deve ser feita imediatamente depois de detectada sua necessidade.
Prioridade 2 – Urgência – Manutenção que deve ser feita o mais breve possível, não ultrapassando 24 horas, depois de detectada sua necessidade.
Prioridade 3 – Necessária – Manutenção que pode ser adiada por alguns dias, porem sua execução não deve ultrapassar uma semana.
Prioridade 4 – Desejável – Manutenção que pode ser adiada por algumas semanas, mas que não pode ser omitida.
Prioridade 5 – Prorrogável – Manutenção que pode ser adiada até que possa ser executada.
Um dos grandes problemas que tem a administração da manutenção é conseguir que o solicitante dos serviços, determine devidamente a prioridade necessária, sem exageros, para que o atendimento possa se efetuar harmoniosamente. Na prática o que se verifica é que o solicitante do serviço, tende a solicitar sempre prioridade de emergência, no intuito de ter vantagem no atendimento. Fica assim, a programação dos serviços de manutenção, como responsável por determinar as prioridades através do seu conhecimento das necessidades da produção. Isso acaba por desarmonizar as relações entre Manutenção e Produção gerando equívocos, que seriam evitados, se as prioridades fossem bem respeitadas.
A Ordem Serviço além de indicar o tipo de reparo solicitado, a prioridade e outros dados, informa o Centro de Custo do equipamento ou posto de trabalho, solicitante da intervenção. O Centro de Custo tem a finalidade de alocar as despesas feitas no reparo. Isso é importante para que a administração tenha conhecimento do custo de manutenção, realizado em cada máquina, equipamento ou conjunto de equipamentos.
Os Centros de Custo são distribuídos de acordo com a necessidade de se apurar mais ou menos detalhados os custos de manutenção. Conhecer esses custos leva a tomadas de decisão administrativas diversas tais como; aumentar ou diminuir a atuação da manutenção preventiva ou preditiva, fazer um grande reparo ou substituir o equipamento.
Na Ordem de Serviço lançam-se os materiais utilizados no reparo, que através do almoxarifado são lançados no centro de custo indicado, é lançada à hora de início e finalização do serviço e que são utilizadas para controle de mão de obra de manutenção, tanto com relação à ocupação dos homens, como também é uma forma de se calcular eficiência de mão de obra da manutenção.
Em um controle de manutenção realizado por computador, o que é feito na maioria das empresas, fica fácil realizar todos os controles desejados, sejam custos, sejam eficiência de mão de obra ou de serviços, sejam históricos que mais tarde servirão de base para realização de Manutenção Preditiva.
A tendência dos custos em manutenção corretiva, em uma empresa, pode ser indicada pelo gráfico abaixo:
tempo
É todo serviço programado de controle, conservação e restauração dos equipamentos, obras ou instalações executadas com a finalidade de mante-las em condições satisfatórias de operação e de prevenir contra possíveis ocorrências que acarretem sua indisponibilidade. A manutenção preventiva se caracteriza pelos seguintes aspectos abaixo:
Ë programada.
Ë periódica
Força paradas parciais e/ou completas de uma unidade ou equipamento.
Requer pesquisa a catálogos e manuais de fabricantes de equipamentos para estabelecer o momento da intervenção no mesmo, os pontos a serem verificados e os materiais que deverão ser substituídos. Deverá ser estudada sempre que possível as interdisciplinaridades de funções, pois não faz sentido parar uma bomba para manutenção preventiva sem aproveitar para efetuar o mesmo serviço no motor, e instrumentos de indicação e controle, ou serviços de caldeiraria ou pintura no mesmo equipamento.
A Manutenção Preventiva tem como finalidade, a realização de tarefas que prolonguem a vida de máquinas e equipamentos, prevenindo quebras e procurando observar o equipamento com diversos métodos de medições e análise, que levem a programação de manutenção corretiva, antes que o equipamento falhe. A manutenção preventiva trabalha com inspeções periódicas, de maneira a prevenir falhas e mesmo prolongando a vida de componentes que muitas vezes, por recomendações de históricos anteriores, deveriam ser trocadas, mas que através análises diversas, constatam-se a sua integridade, ganhando uma sobrevida. Na manutenção preventiva, normalmente, se inclui a lubrificação que, a priore, teria caráter de manutenção preditiva, mas que, através de acompanhamentos normalizados pela manutenção preventiva, pode-se prolongar a vida do lubrificante, diminuindo custos.
Objetivos
Os principais objetivos das empresas são normalmente redução de custos, melhorarem a qualidade dos produtos, aumento de produção, preservação do meio ambiente, aumento da vida útil das máquinas e equipamentos e redução dos acidentes de trabalho. Um Programa de Manutenção Preventiva bem elaborada embora, inicialmente, agregue custos, contribui imensamente para alcançar esses objetivos.
Programa de Manutenção Preventiva
Para se montar um Programa de Manutenção Preventiva deve-se inicialmente:
a) Decidir qual o tipo de máquina ou equipamento que deverá ser incluído no programa, de acordo com a sua importância, do ponto de vista da Manutenção e da Operação.
b) Efetuar o levantamento e posterior cadastramento, de todos os equipamentos que serão incluídos no Programa.
c) Levantar o histórico desses equipamentos.
d) Elaborar manuais de procedimentos para manutenção preventiva, indicando as periodicidades das inspeções e/ou intervenções.
e) Prever materiais e recursos humanos, envolvidos no programa.
f) Preparar um Plano Mestre de inspeções. O plano mestre mais usual é aquele que tem como unidade de controle a semana, uma vez que o ano tem exatamente 52 semanas. Uma vez preparado, ele tem vida infinita, não importando o dia mês ou ano em que se esteja. Como o computador é hoje um equipamento relativamente barato, torna-se inviável um plano manual, que tem grandes dificuldades de execução.
g) Treinar o pessoal da equipe de manutenção.
Plano Mestre de Manutenção Preventiva
Como foi dito anteriormente, o ano tem exatamente 52 semanas. Procura-se, enquadrar as inspeções ou outras atividades de manutenção preventiva, em número de semanas, exemplos:
a) Inspeção do funcionamento das válvulas de um compressor estacionário – periodicidade – Semanal
Exemplo de uma ficha de avaliação e registro dos serviços que devem ser executados
INSTRUÇÃO DE MANUTENÇÃO PREVENTIVA TAG Função Periodicidade Data Executante B 11203A Bomba de combate a incêndio bimestral ITEM SERVIÇO CÓDIGO OBSERVAÇÃO 01 Verificar vibração dos rolamentos M 0032 02 Lubrificar mancais L 0001 03 Reaperto dos mancais M 0341
10 Alinhamento motor-bomba M 0400 11 Reaperto das gaxetas M 0422 Graxa utilizada - Molicote Ultima inspeção em
A organização preventiva --> Para que a manutenção preventiva funcione é necessário:
pelos fabricantes) e desenhos de projeto atualizados (as-built).
o Fichas históricas dos equipamentos contendo registro das manutenções efetuadas e defeitos encontrados;
o Fichas de tempos de reparo, com cálculo atualizado de valores médios;
o Fichas de planejamento prévio normatizando os trabalhos repetitivos de manutenção. Nestas fichas contém-se: composição das equipes de manutenção, materiais, peças de reposição e ferramentas, PRRT, com a seqüência lógica das várias atividades implicadas;
o Existência de plannings nos quais se mostram os trabalhos em curso e a realizar no próximo futuro. Devem existir plannings locais nas oficinas;
o Existência de um serviço de emissão de requisições ou pedidos de trabalho, contendo a descrição do trabalho, os tempos previstos, a lista de itens a requisitar e a composição da equipe especializada;
o Emissão de mapas de rotinas diárias;
o Existência de um serviço de controle, habilitado a calcular dados estatísticos destinados à confiabilidade e à produção;
o Existência de um serviço de emissão de relatórios resumidos das grandes manutenções periódicas;
o Existência de interações organizadas com o almoxarifado e os serviços de produção.
É caracterizada pela assistência técnica ao equipamento, mediante o acompanhamento, medição, análise e comparação de itens e parâmetros indicativos do estado e condição do sistema, comparado com o padrão.
Podemos exemplificar este tipo de manutenção, pôr um procedimento de análise periódica do líquido isolante de um transformador, no qual parâmetros físicos e químicos do óleo e pelos componentes em suspensão no mesmo, permitem que se possam se avaliados com precisão o estado de conservação e possíveis anomalias, avaliando se o mesmo deve ser desligado para reparos ou se deve continuara operar até uma próxima análise do óleo.
Salientamos que uma análise individual pode levar a erros de interpretação e portanto, para uma análise segura dos resultados obtidos é necessário um conjunto de dados que nos indique uma “tendência” , dos dados obtidos.
Isto fica bem claro quando temos o exemplo de análise de vibração de equipamentos, pois em um determinado momento pode apresentar índices altos e a tendência ao longo do período ser de estabilização dos resultados, evitando assim uma intervenção indevida.
Condições básicas: O equipamento, o sistema ou a instalação devem permitir algum tipo de monitoramento/medição;
O equipamento, o sistema ou a instalação devem merecer esse tipo de ação, em função dos custos envolvidos;
As falhas devem ser oriundas de causas que possam ser monitoradas e ter sua progressão acompanhada;
Deve ser estabelecido um programa de acompanhamento, análise e diagnóstico, sistematizado;
É fundamental que a mão-de-obra da manutenção responsável pela análise e diagnóstico seja bem treinada. Não basta medir; é preciso analisar os resultados e formular diagnósticos.
Manutenção detectiva é a atuação efetuada em sistemas de proteção buscando detectar FALHAS OCULTAS ou não-perceptíveis ao pessoal de operação e manutenção.
Ex.: o botão de lâmpadas de sinalização e alarme em painéis.
A identificação de falhas ocultas é primordial para garantir a confiabilidade. Em sistemas complexos, essas ações só devem ser levadas a efeito por pessoal da área de manutenção, com treinamento e habilitação para tal, assessorado pelo pessoal de operação.
É cada vez maior a utilização de computadores digitais em instrumentação e controle de processo nos mais diversos tipos de plantas industriais.
São sistemas de aquisição de dados, controladores lógicos programáveis, sistemas digitais de controle distribuídos - SDCD, multi-loops com computador supervisório e outra infinidade de arquiteturas de controle somente possíveis com o advento de computadores de processo.
A principal diferença, é o nível de automatização. Na manutenção preditiva, faz-se necessário o diagnóstico a partir da medição de parâmetros; na manutenção detectiva, o diagnóstico é obtido de forma direta a partir do processamento das informações colhidas junto à planta.
Há apenas que se considerar, a possibilidade de falha nos próprios sistemas de detecção de falhas, sendo esta possibilidade muito remota. De uma forma ou de outra, a redução dos níveis de paradas indesejadas por manutenções não programadas, fica extremamente reduzida.
É uma nova concepção que constitui a segunda quebra de paradigma na manutenção. Praticar engenharia de manutenção é deixar de ficar consertando continuadamente, para procurar as causas básicas, modificar situações permanentes de mau desempenho, deixar de conviver com problemas crônicos, melhorar padrões e sistemáticas, desenvolver a manutenibilidade e dar feedback ao projeto, interferir tecnicamente nas compras. Ainda mais: aplicar técnicas modernas, estar nivelado com a manutenção de primeiro mundo.
O gráfico acima mostra a melhoria de resultados, à medida que se evolui dentre os tipos de manutenção. As duas mudanças de inclinação representam as quebras de paradigma. Observe o salto significativo quando se adota engenharia de manutenção.
Em seguida temos alguns gráficos comparativos com relação aos diversos tipos de manutenção:
Comparação de custos (1998)
Evolução dos tipos de manutenção
soma de todas as horas previstas em HH em carteira divididas pela capacidade instalada da equipe de executantes. Esse HH instalado deve levar em consideração certa perda, pois nenhum profissional estará a todo tempo a frente do serviço.
Backlog = ( ΣΣΣΣ HH em carteira / ΣΣΣΣ HH total da equipe disponível)
INDICE DE RETRABALHO
Percentual de horas trabalhadas de serviços terminados , reabertos por qualquer motivo, em relação ao total de horas trabalhadas no período.
Indice de retrabalho = ( ΣΣΣΣ HH em OM reaberta / ΣΣΣΣ HH total no período ) x 100%
Fornece a real situação situação ,da ação planejamento e programação, indicando o percentual de horas de manutenção foram dedicadas em correntiva.
Indice de corretiva = ( ΣΣΣΣ HMC / ΣΣΣΣ HMC + ΣΣΣΣ HMP ) x 100%
HMC – Horas de manutenção correteiva HMP – Horas de manutenção preventiva
INDICE DE PREVENTIVA (Ip)
Fornece a real situação situação ,da ação planejamento e programação, indicando o percentual de horas de manutenção foram dedicadas em preventiva.
Indice de corretiva = ( ΣΣΣΣ HMP / ΣΣΣΣ HMC + ΣΣΣΣ HMP ) x 100%
HMC – Horas de manutenção correteiva HMP – Horas de manutenção preventiva
MTBF – Mean Time Between Failures ( Tempo médio entre falhas)
Tempo definido como a divisão das horas disponíveis do equipamento para operação (HD) e o número de
intervenções corretivas neste equipamento no período (NC).
MTBF=(HD/NC)
MTTR – Mean Time to Repair ( Tempo médio de Reparo)
Tempo definido como a divisão das horas indisponíveis do equipamento para operação devido a manutenção
(HIM) e o número de intervenções corretivas neste equipamento no período (NC).
MTTR=(HIM/NC)
MTPF – Tempo médio para falha
Existem determinados componentes que não sofrerão reparos, ou seja, após falharem são descartados e substituidos por novos, tendo então um MTTR igual a zero.O tempo médio para falha tem como enfoque este tipo de componente , consistindo na relação entre o total de horas disponíveis do equipamento para operação (HD) dividido pelo número de falhas detectadas em componentes não reparáveis.
MTPF=(HD/Número de falhas)
Este índice se aplica bem para estivatisvas como troca de lâmpadas ou mesmo espectativa de queima de fusíveis.
Antigamente, quando se falava em custos de manutenção a maioria dos gerentes achava que:
No Brasil, o custo da manutenção em relação ao faturamento das empresas vem apresentando uma
tendência de queda, situando-se em 1997 em 4,39%. O gráfico a seguir mostra essa evolução (Fonte:
ABRAMAN - Associação Brasileira de Manutenção):
Custos da Manutenção no Brasil.
São os custos oriundos de perda de produção, causados:
São aqueles relacionados com a estrutura gerencial e de apoio administrativo, custos com análises e
estudos e melhoria, engenharia de manutenção, supervisão, dentre outros.
O acompanhamento de custos, um dos itens de controle na manutenção, deve ser colocado na forma de
gráfico para fácil visualização, mostrando pelo menos:
É fundamental que cada especialidade da manutenção faça um controle e custos, independente do modo que a estrutura organizacional as agrupa ou divide.
Formas de atuação da manutenção
CENTRALIZADA O próprio nome sugere: a manutenção é centralizada em torno de uma equipe. Vantagens:
o A eficiência global é maior do que na descentralizada, pela maior flexibilidade na alocação da mão-de-obra em vários locais da planta, os quais acabam desenvolvendo maiores habilidades.
o O efetivo de manutenção tende a ser bem menor.
o A utilização de equipamentos e instrumentos é maior e normalmente podem ser adquiridos em menor número.
o A estrutura de manutenção é muito mais enxuta.
Desvantagens:
o A supervisão dos serviços costuma ser mais difícil, pela necessidade de deslocamentos a várias frentes de serviço, por vezes distantes umas das outras.
o O desenvolvimento de especialistas que entendam os equipamentos com a profundidade necessária demanda mais tempo do que na descentralizada.
o Maiores custos com facilidades como transporte em plantas que ocupam maiores áreas.
o Favorece a aplicação da polivalência.
DESCENTRALIZADA Ocorre o contrário do caso anterior, de modo que as vantagens de uma passam a ser desvantagens na outra e vice-versa. A principal vantagem é a cooperação entre operação e manutenção, de modo que exista espírito de equipe.