
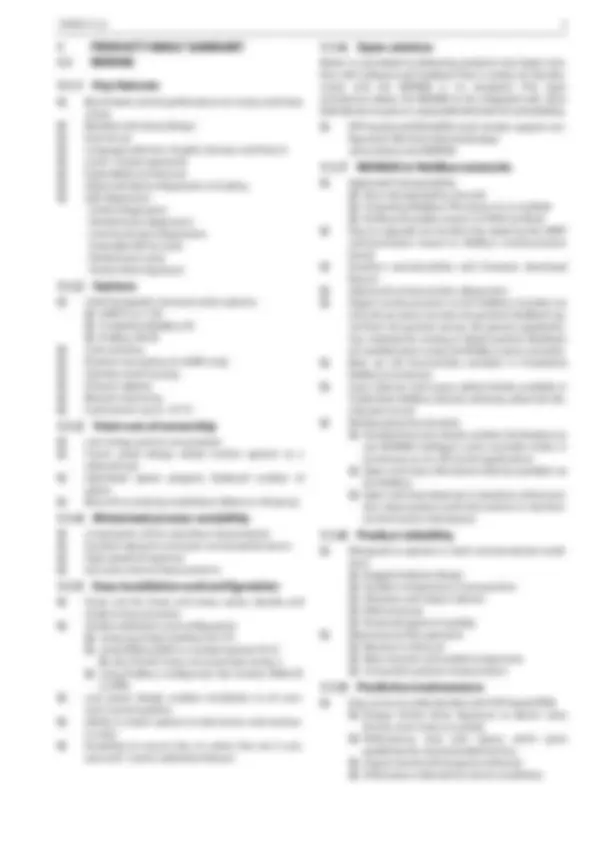
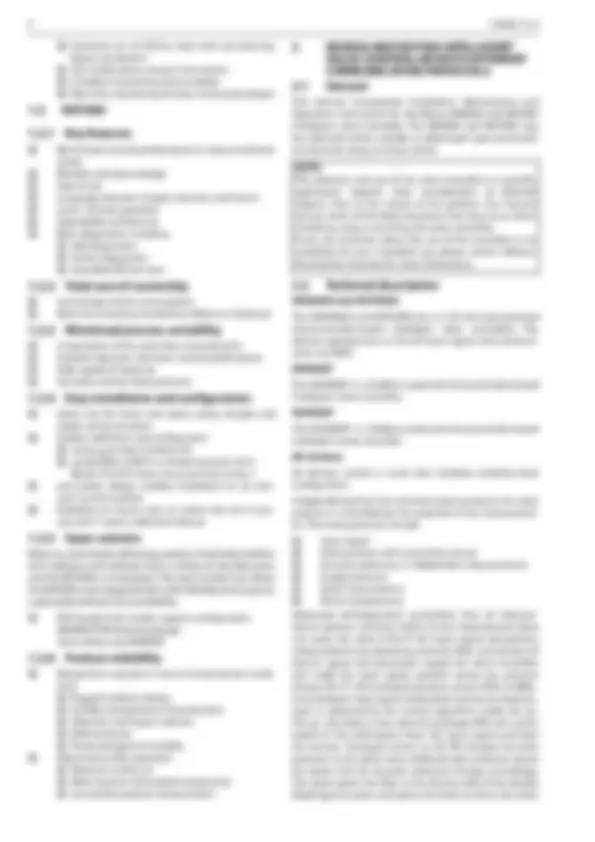
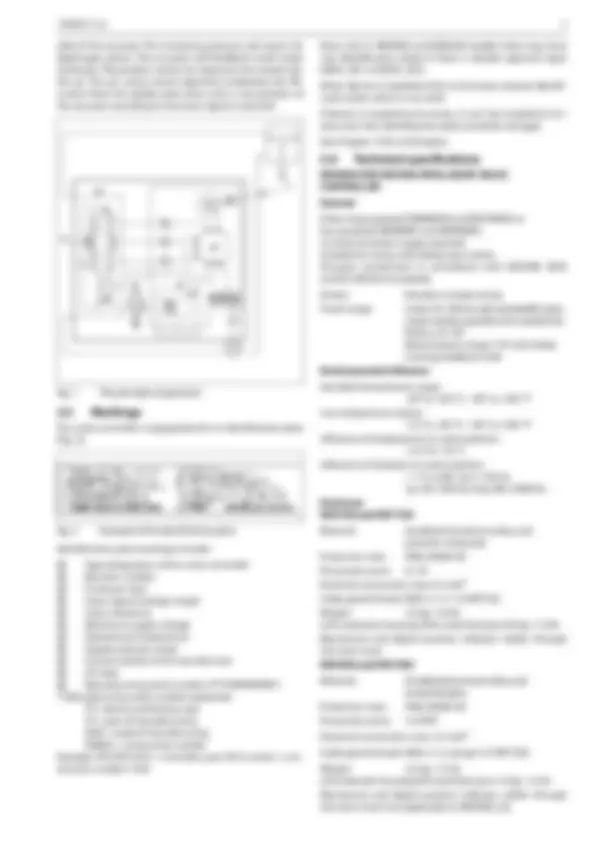
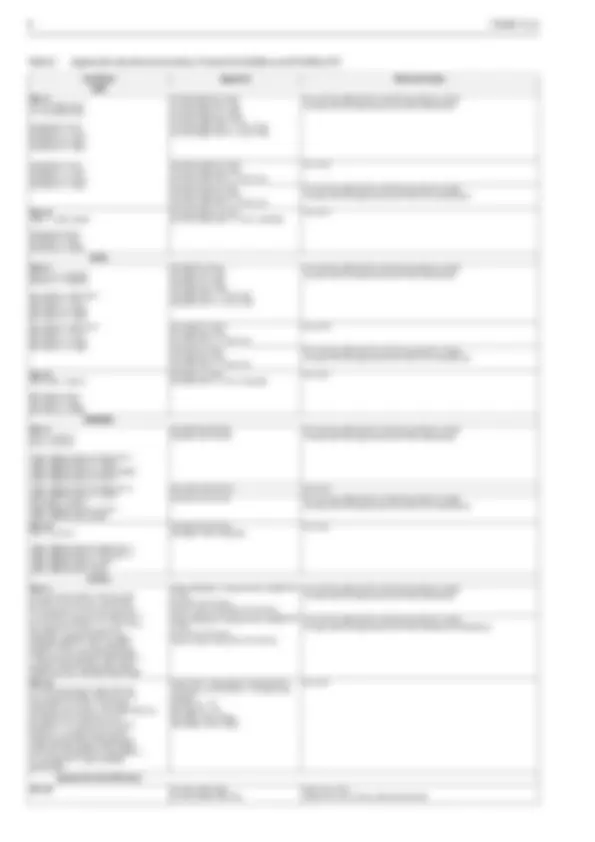
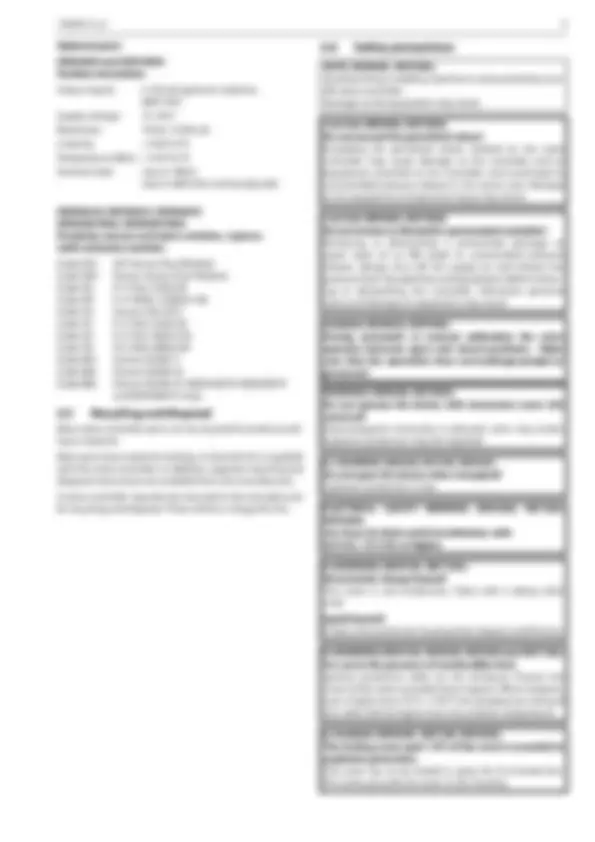
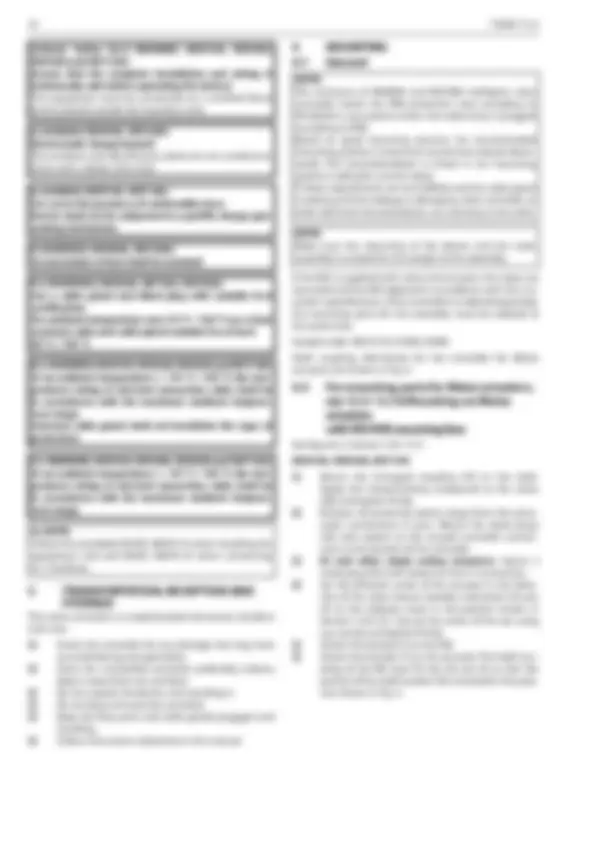
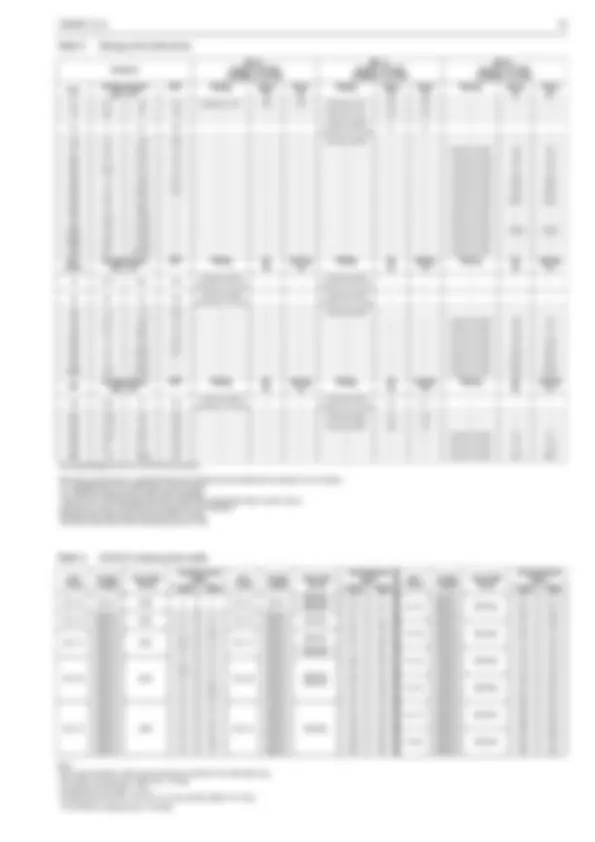
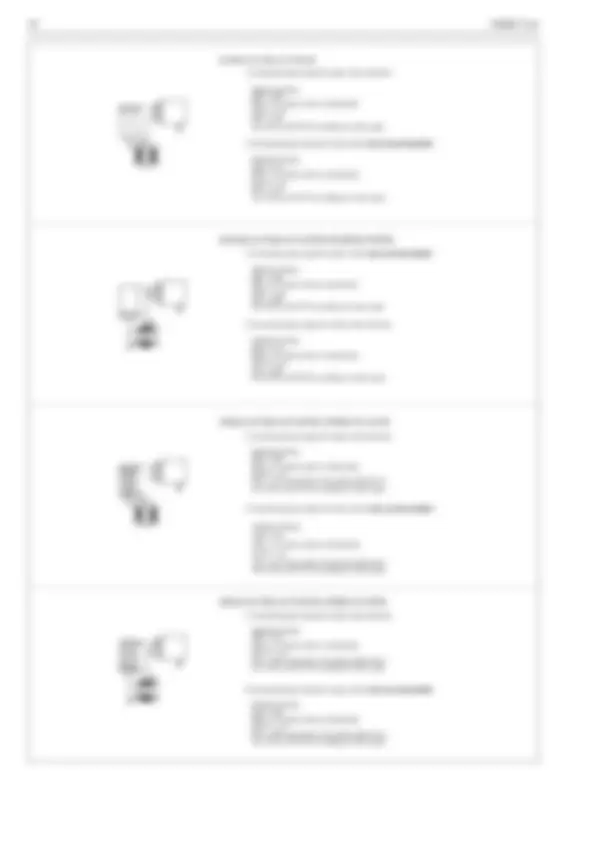
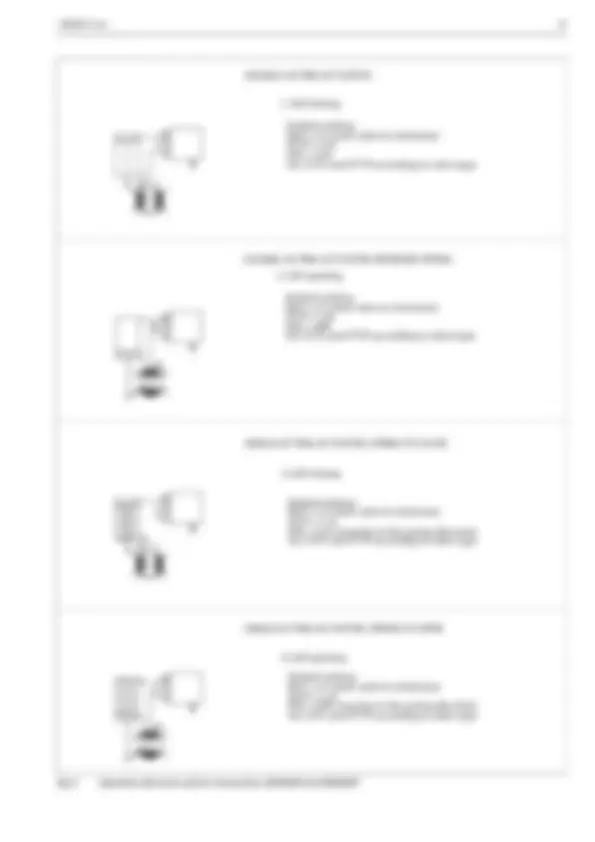
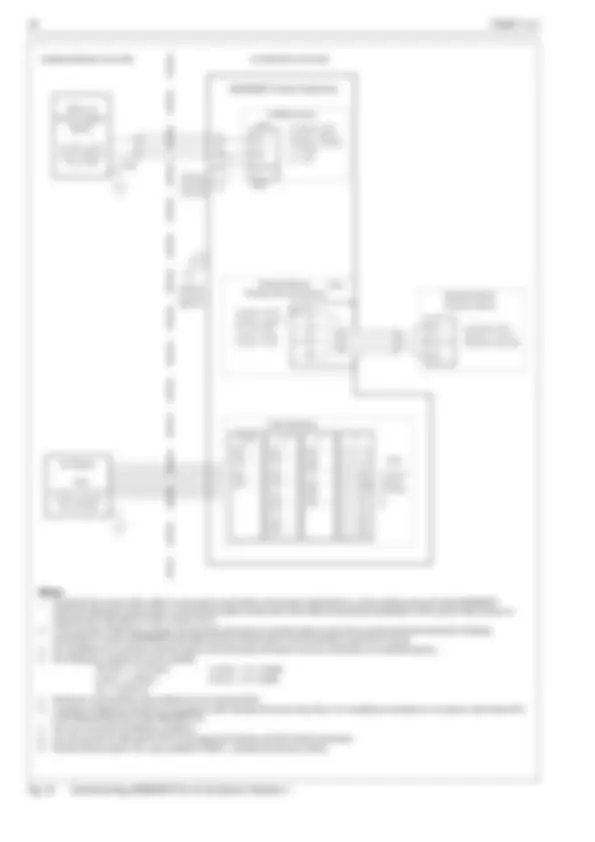
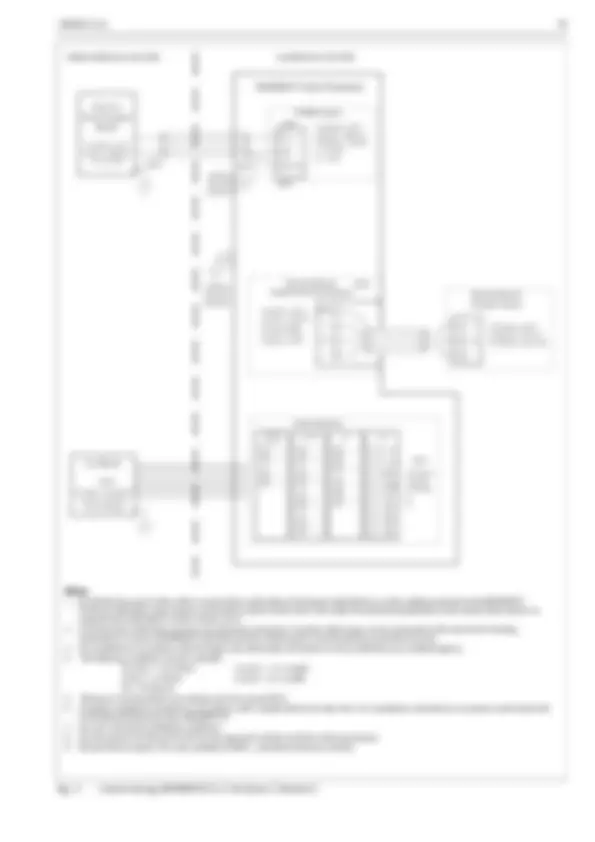
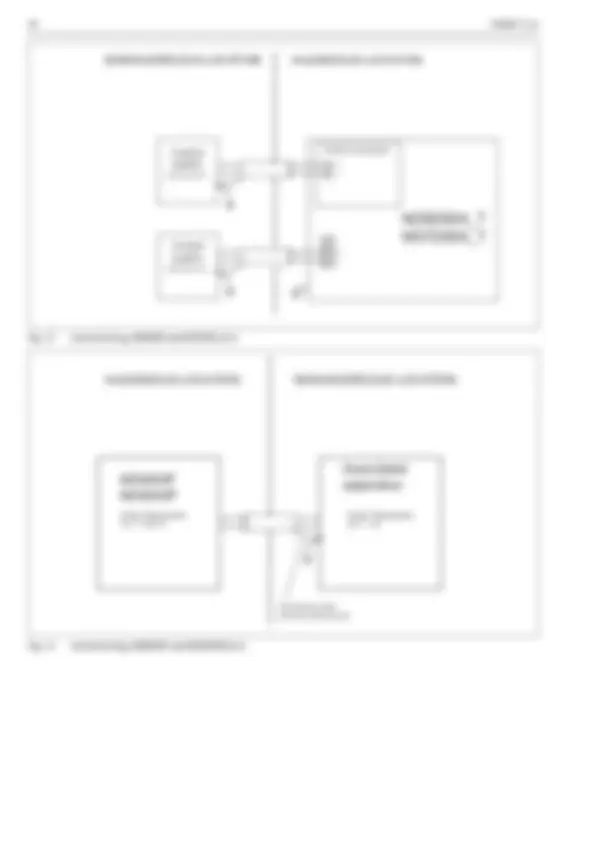
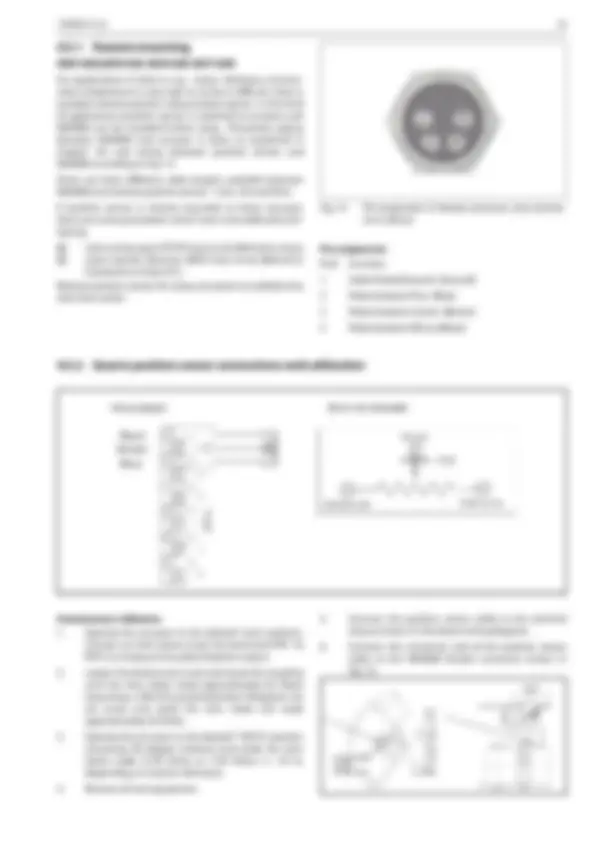
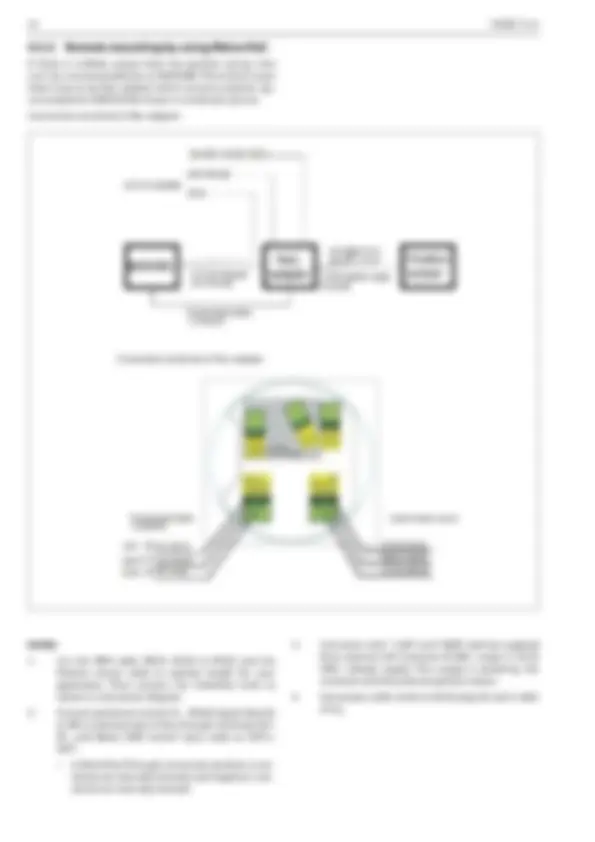
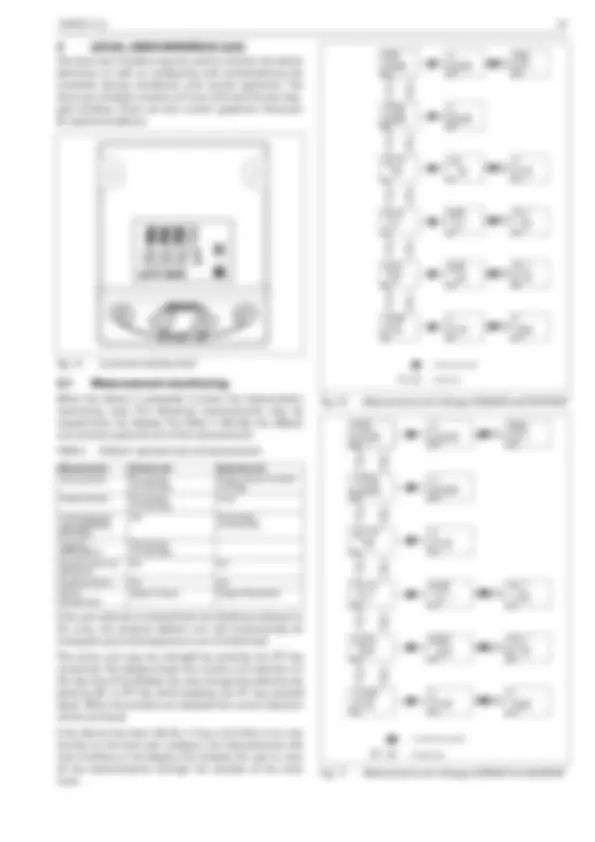
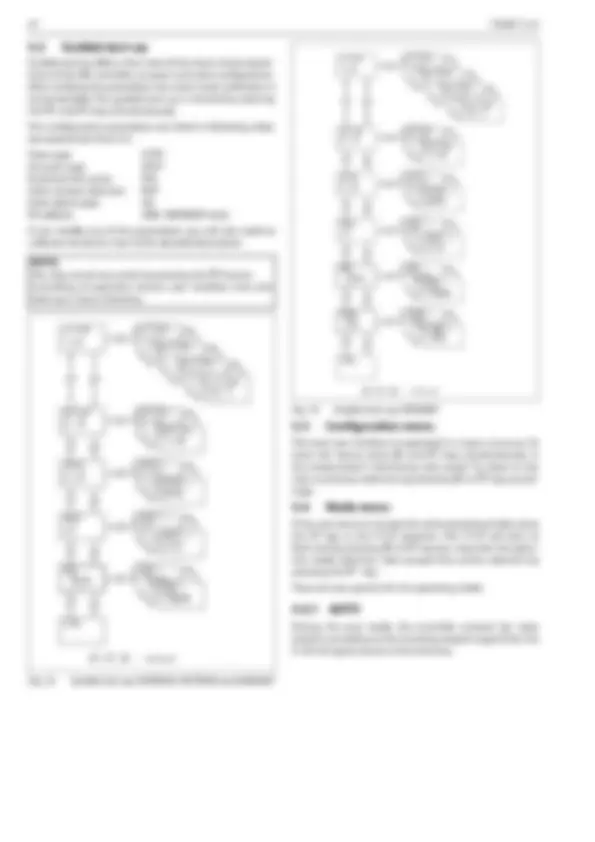
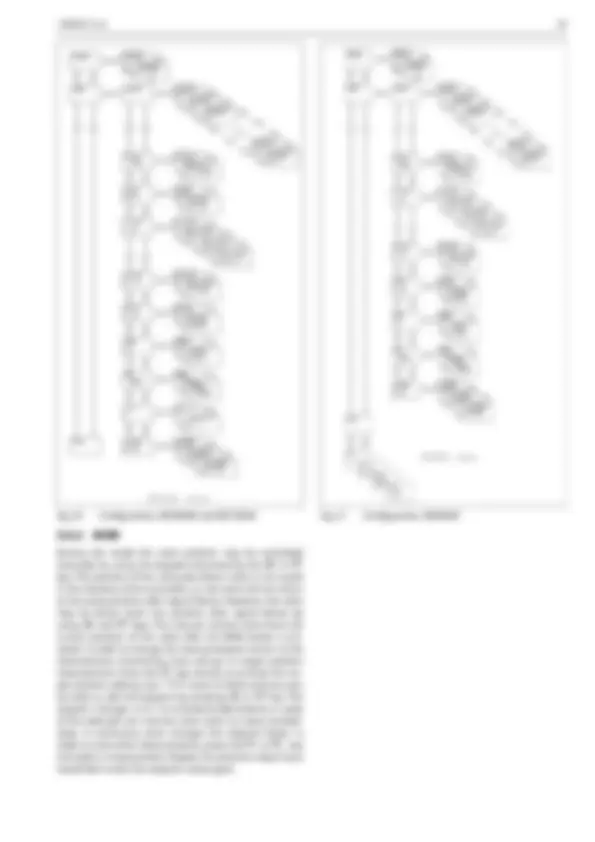
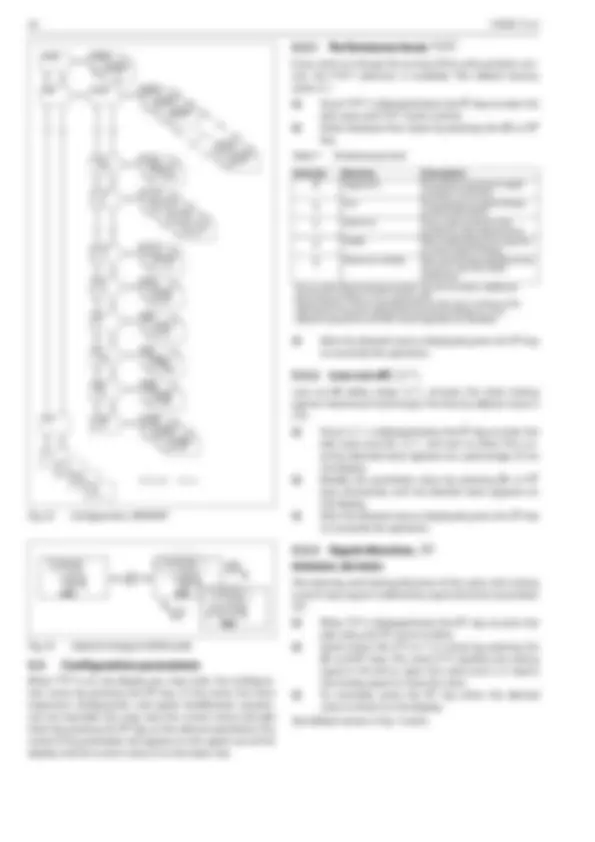
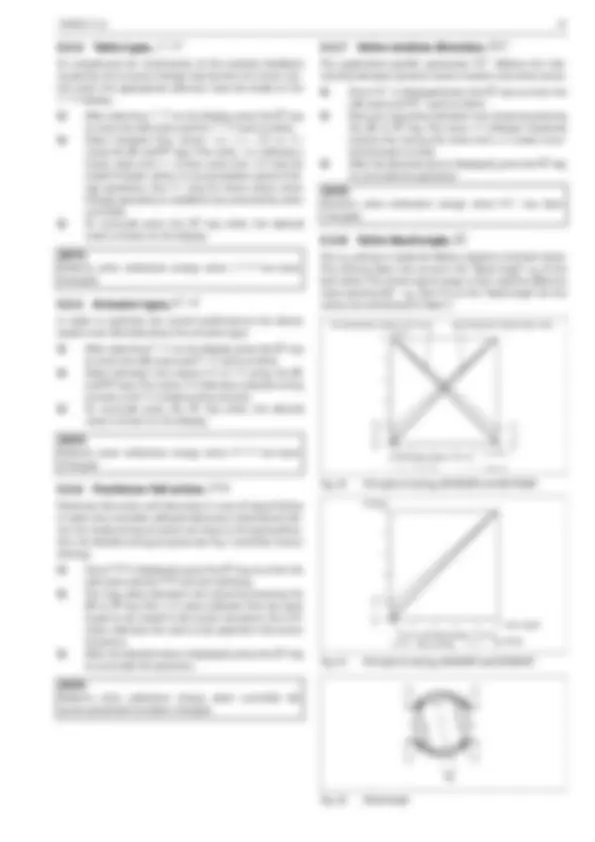
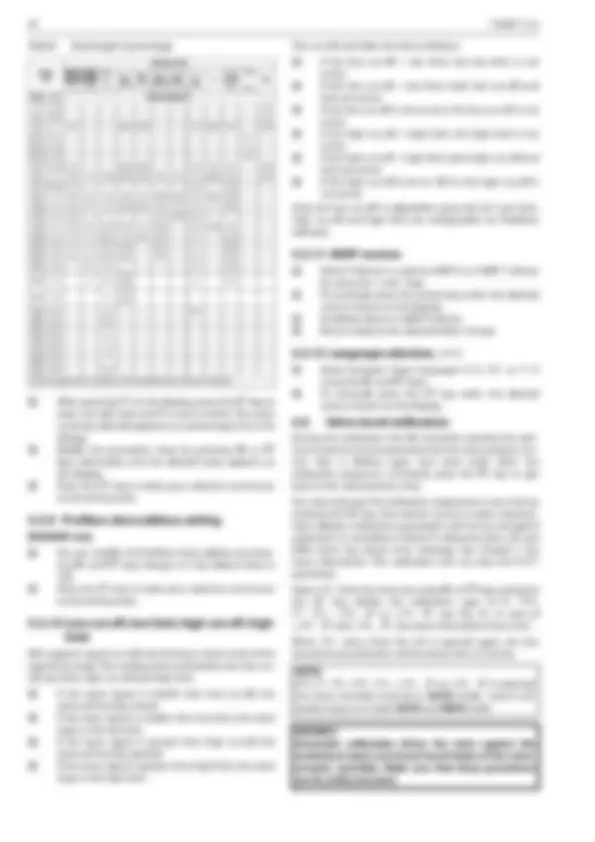
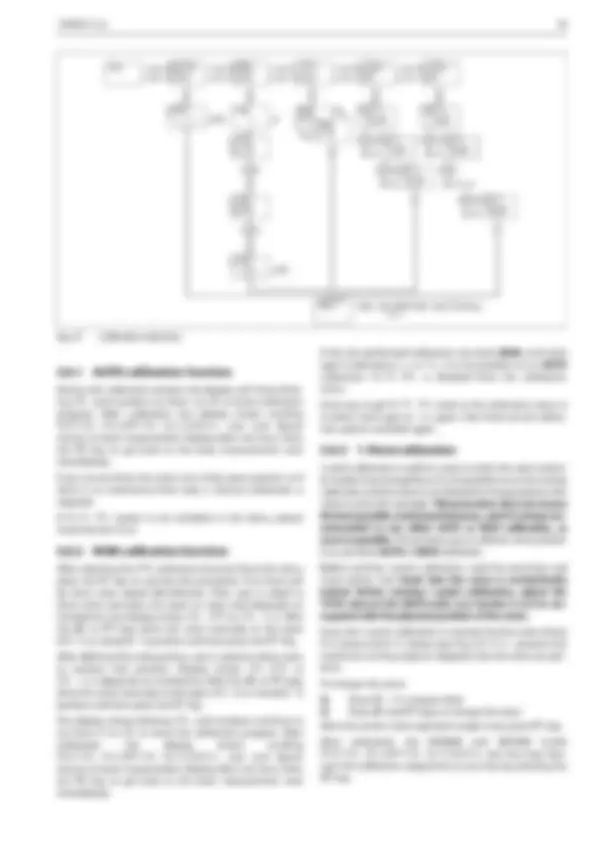
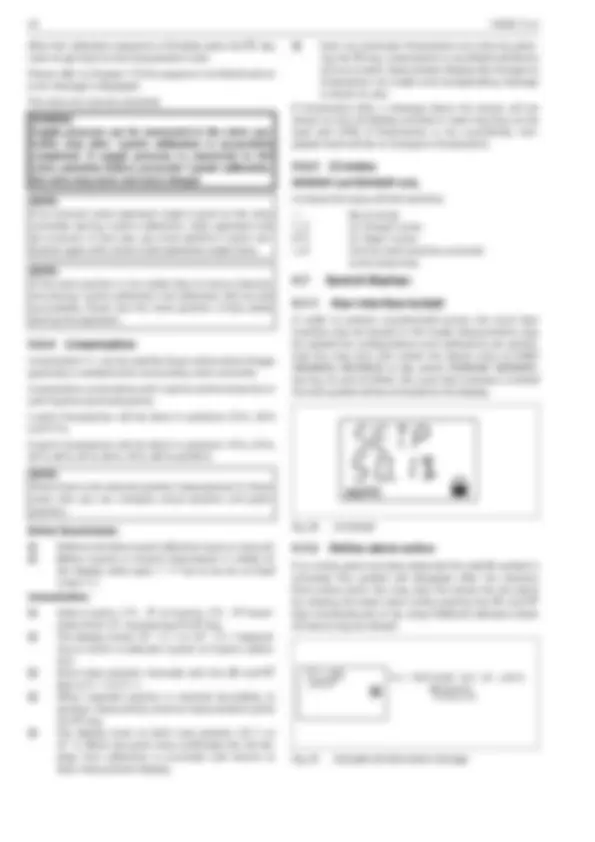
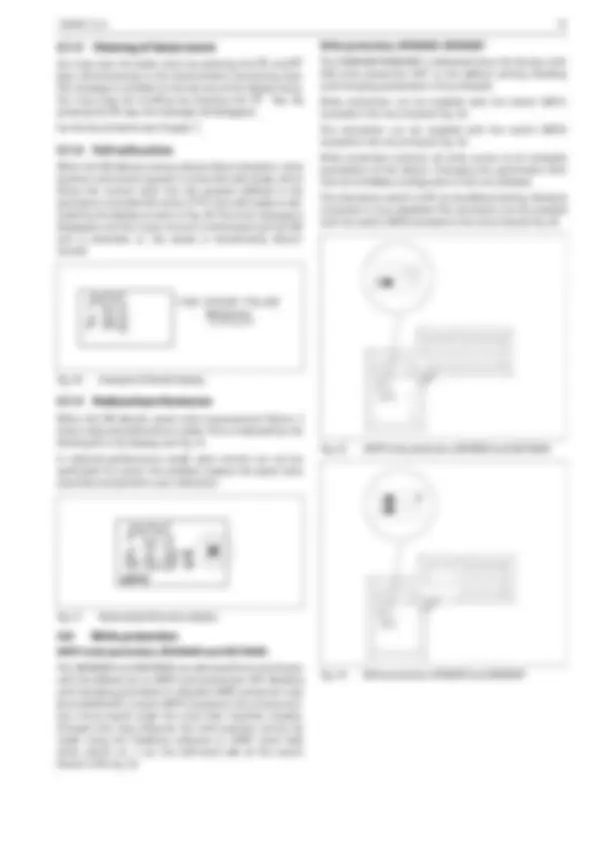
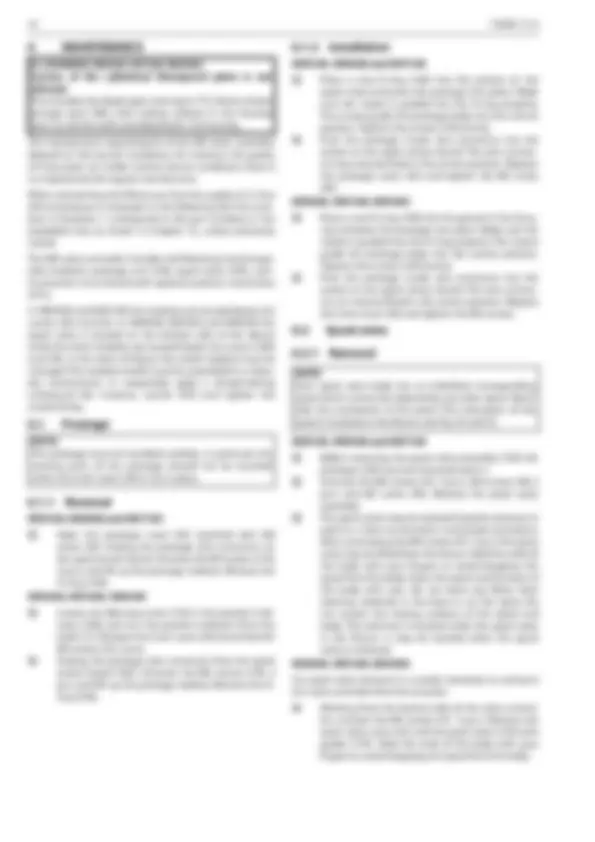
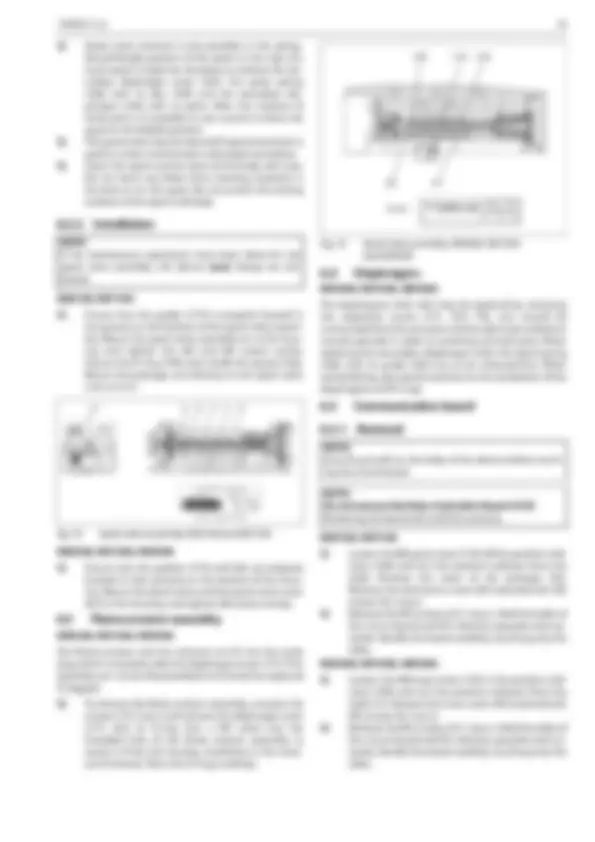
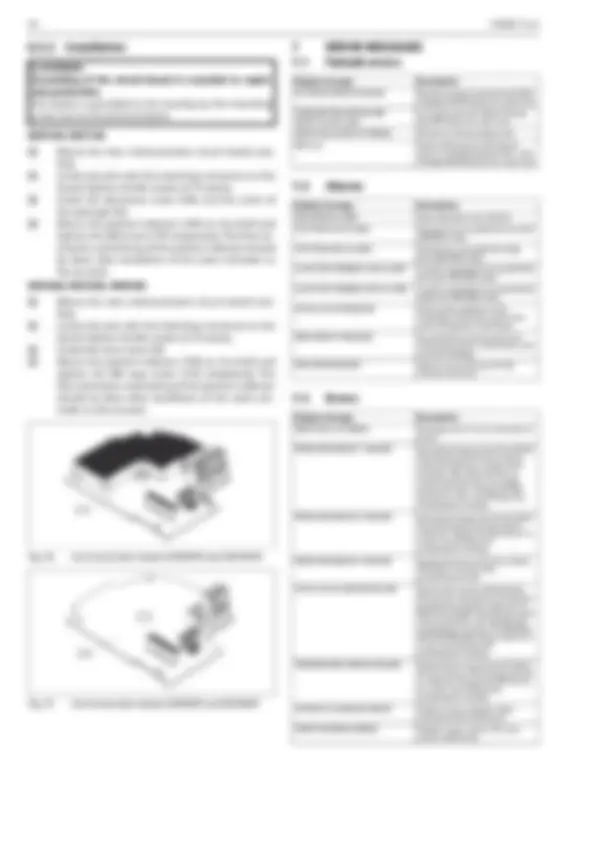
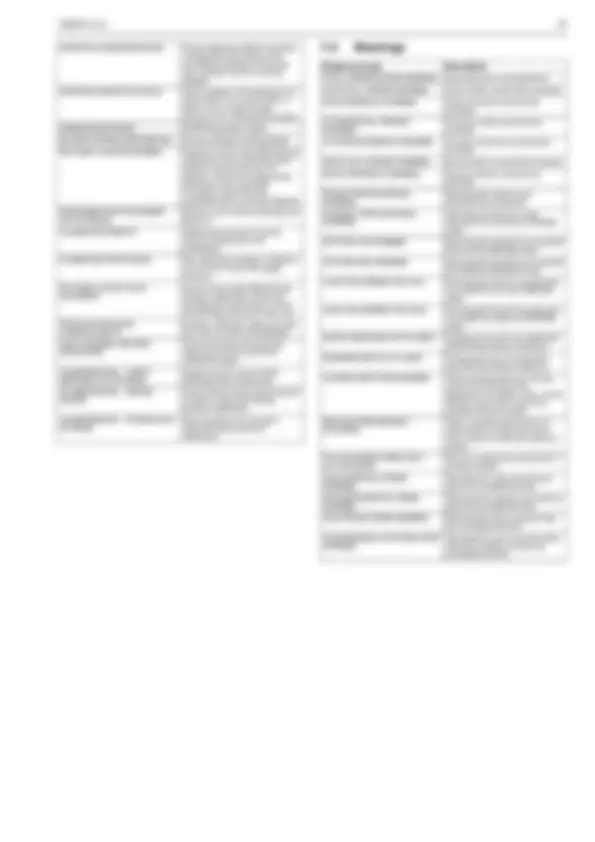
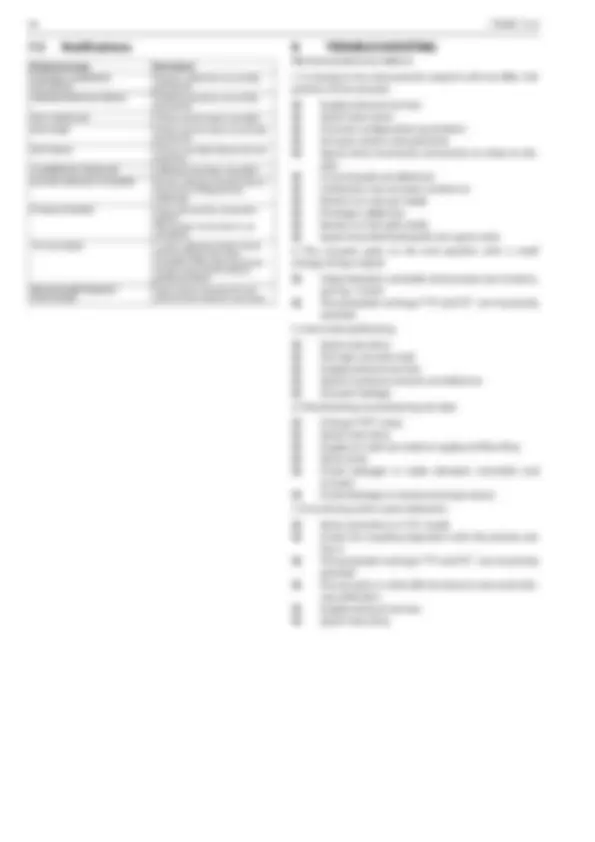
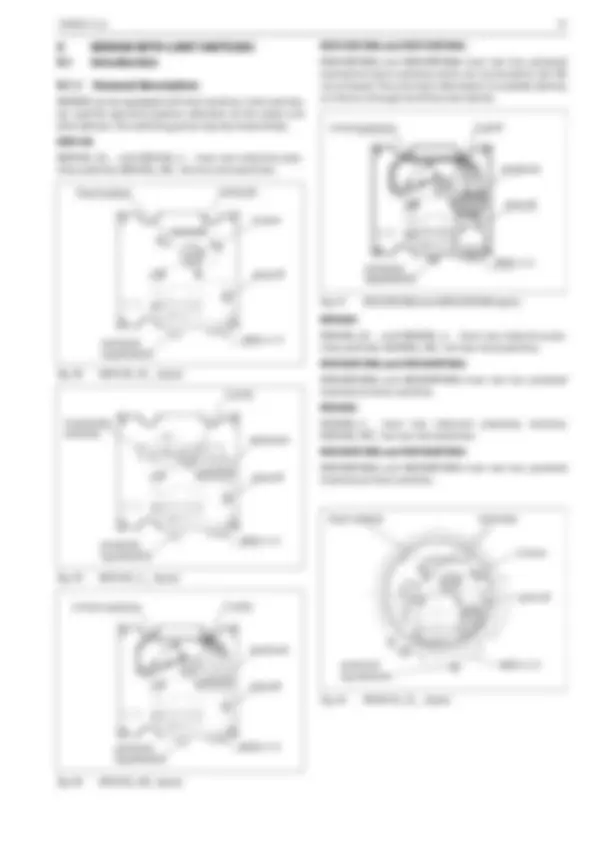
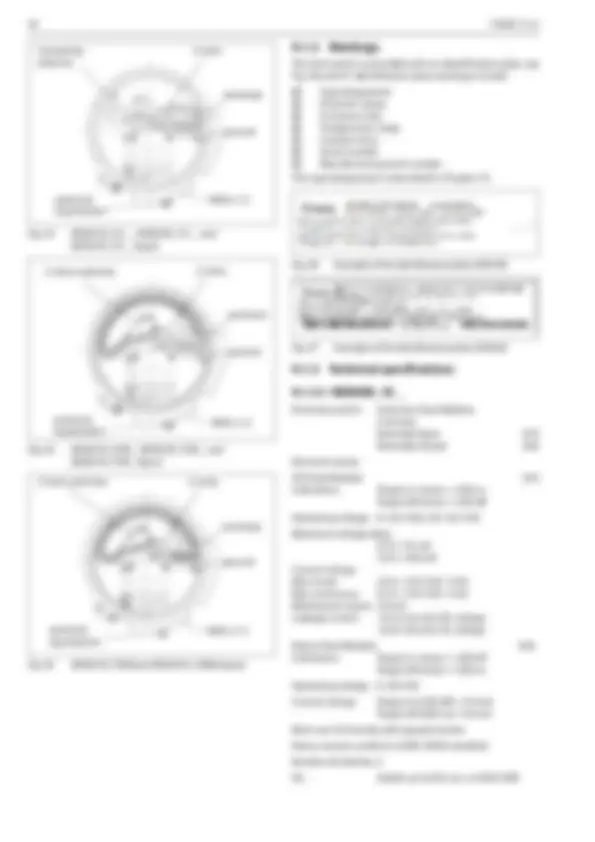
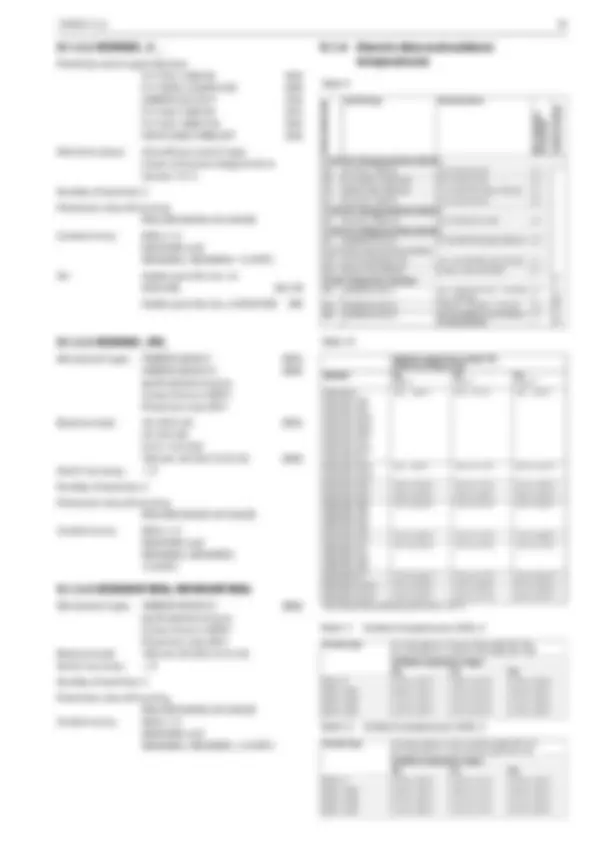
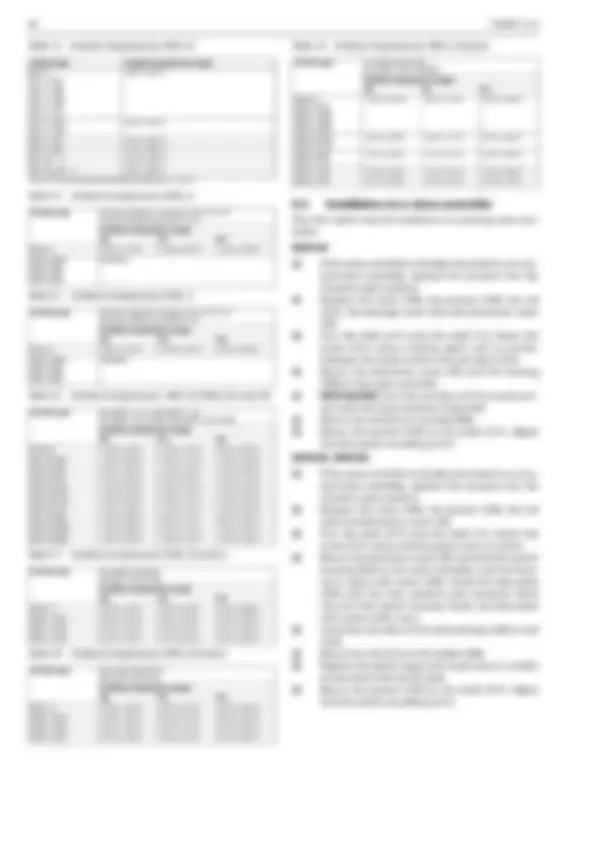
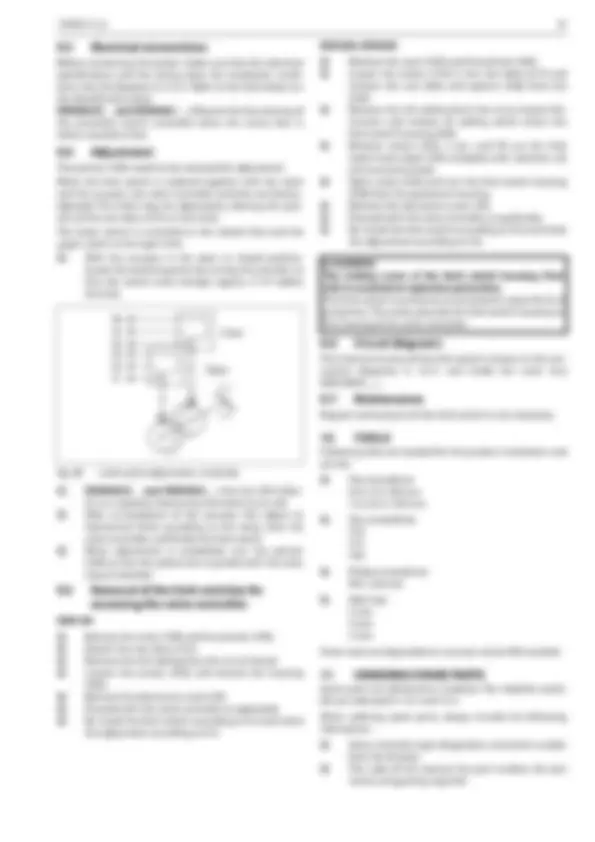
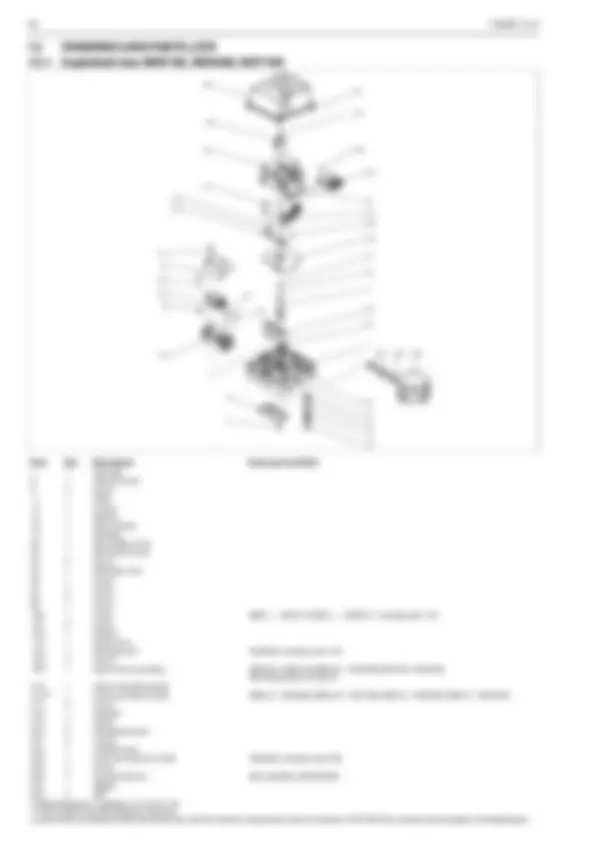
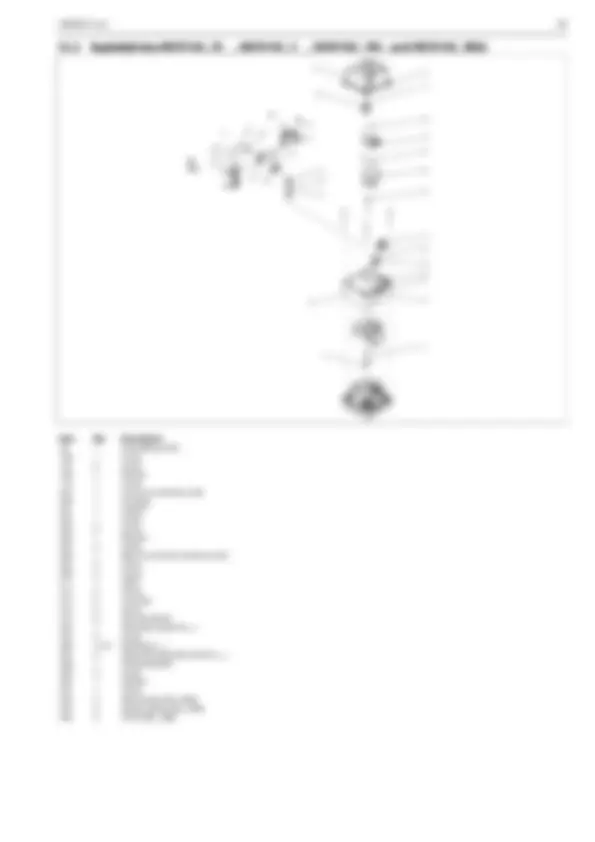
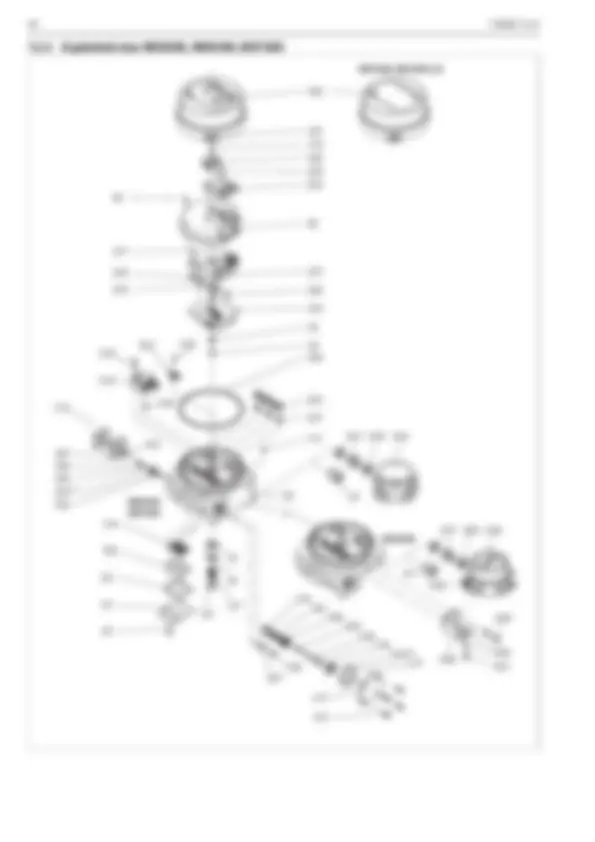
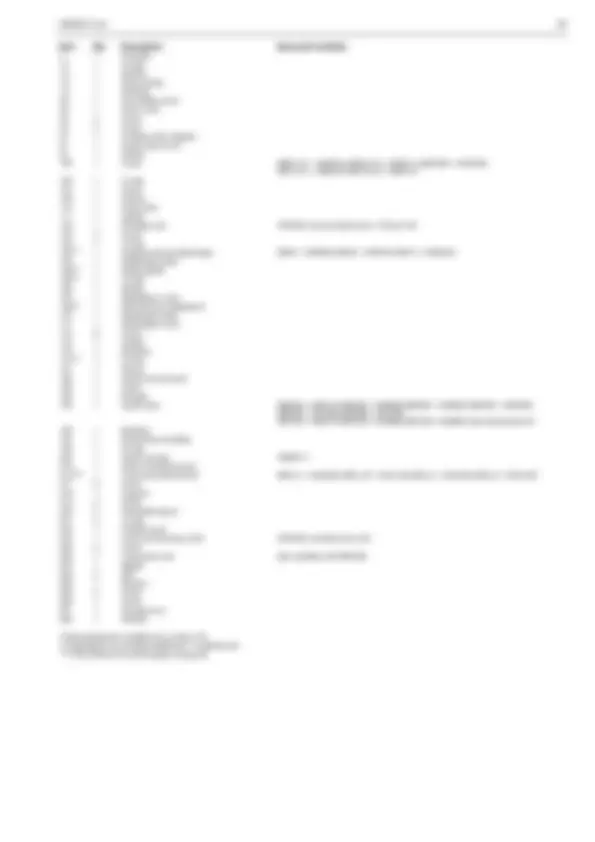
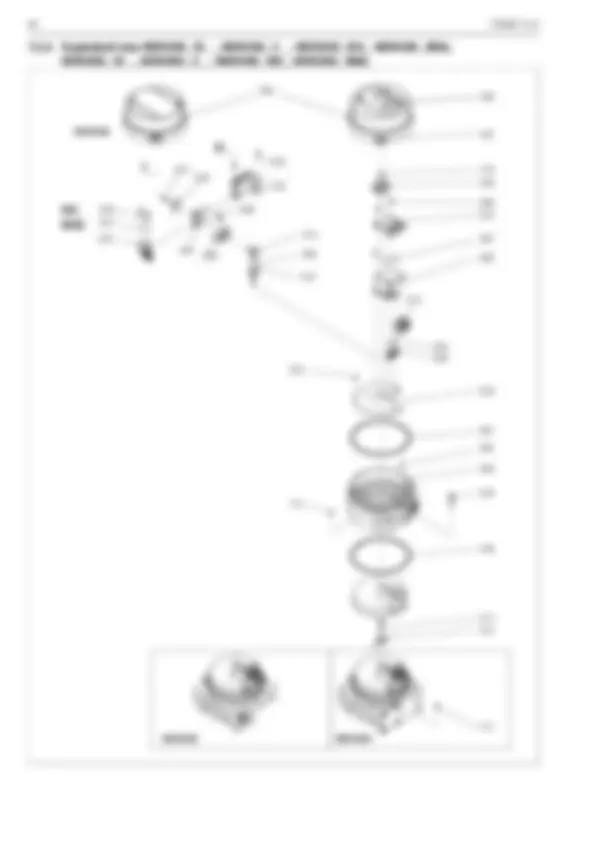
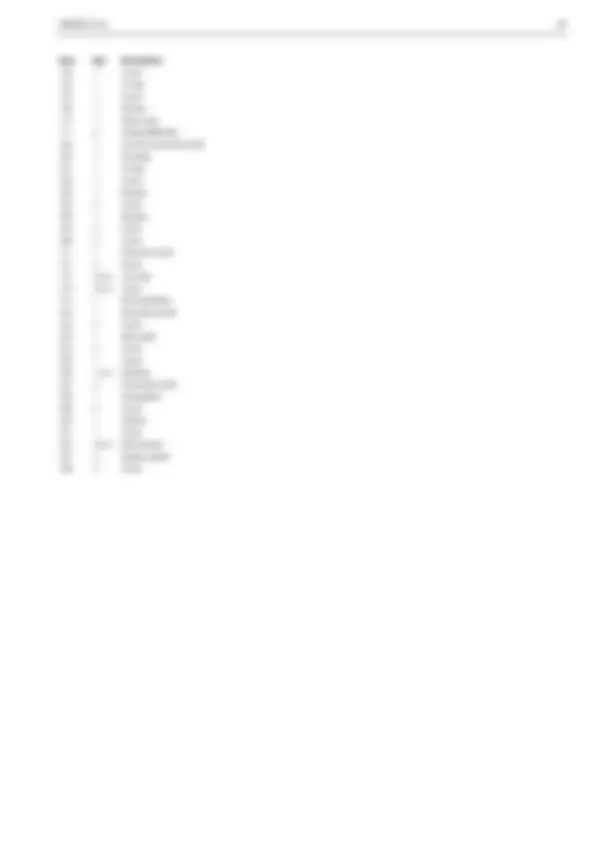
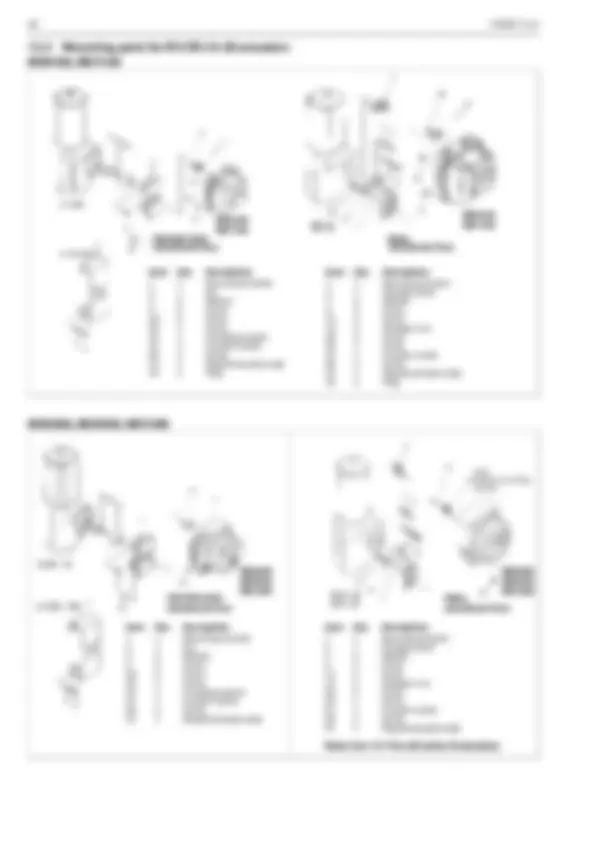
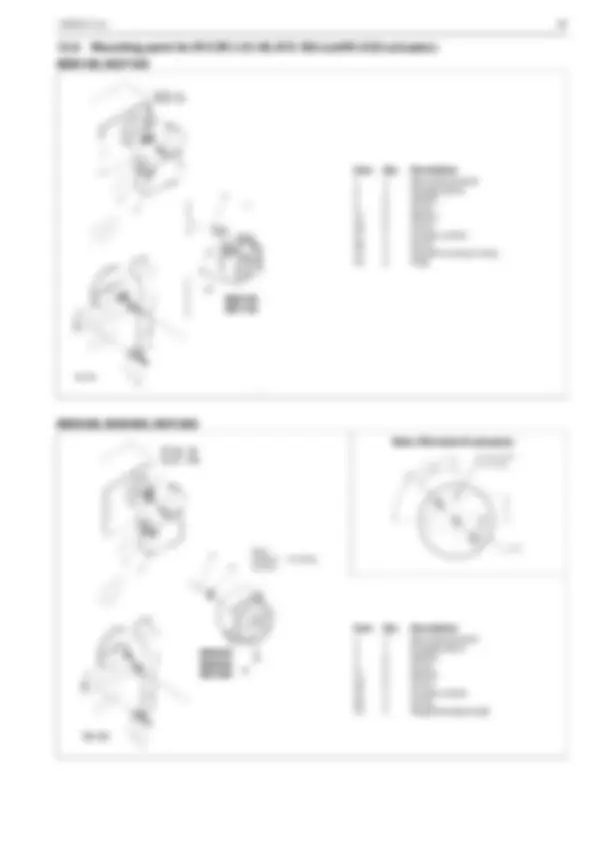
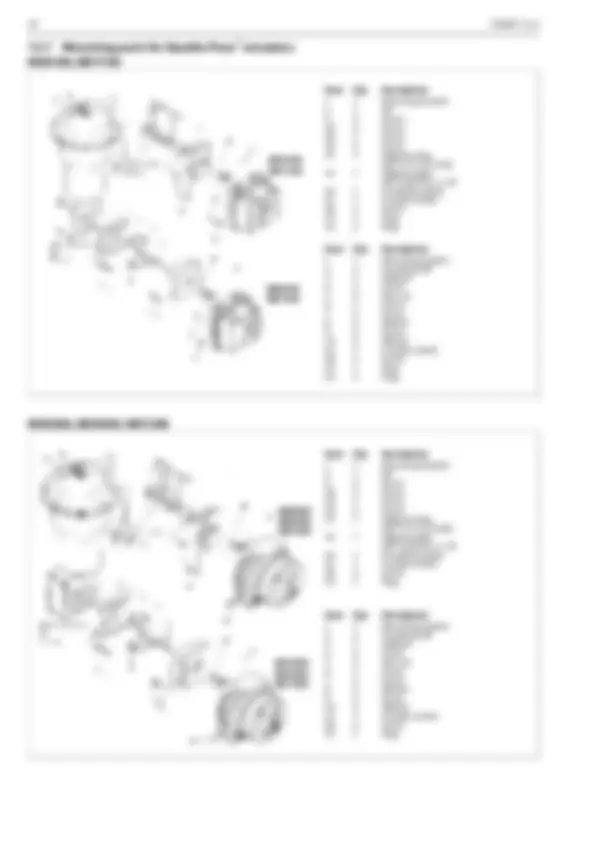
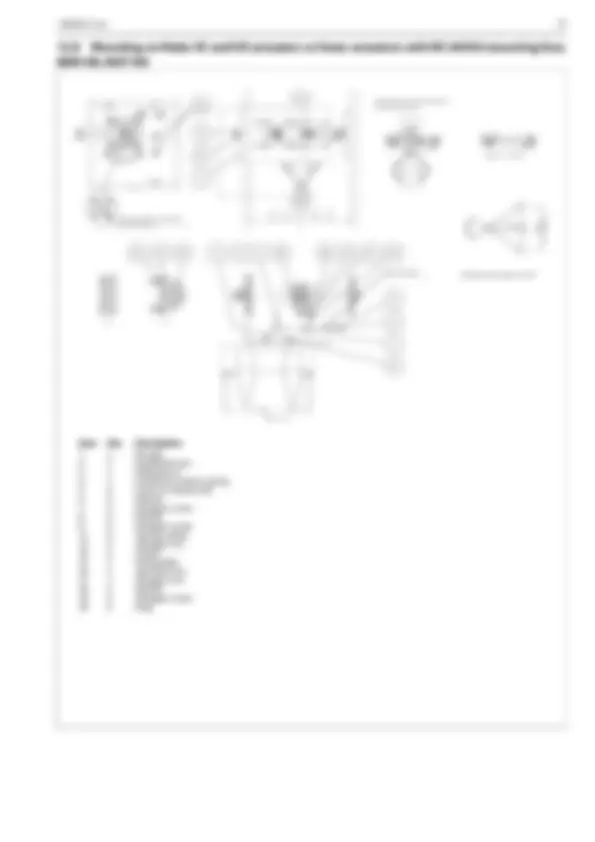
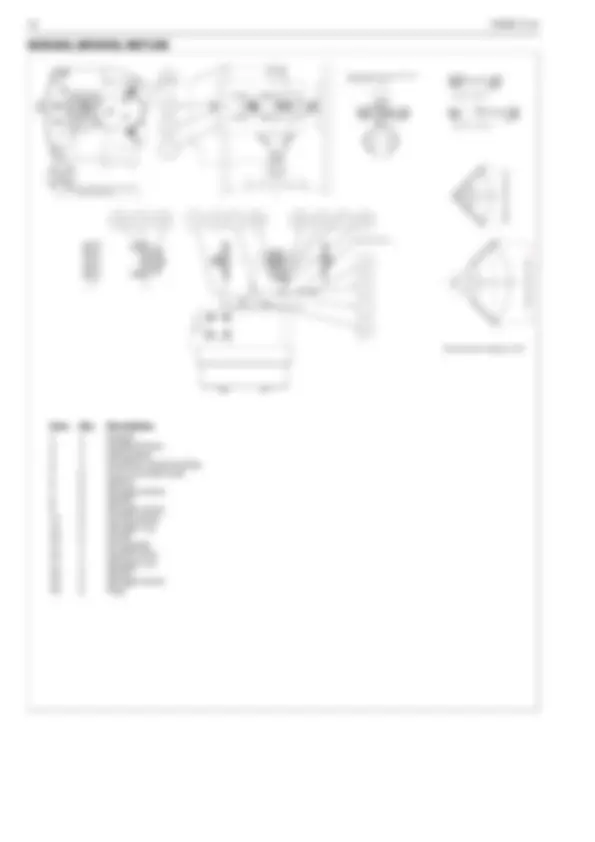
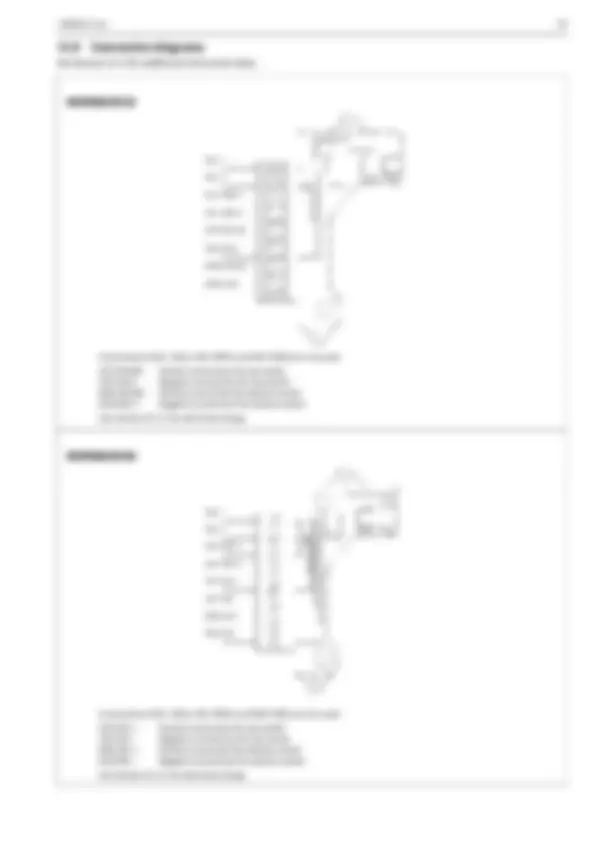
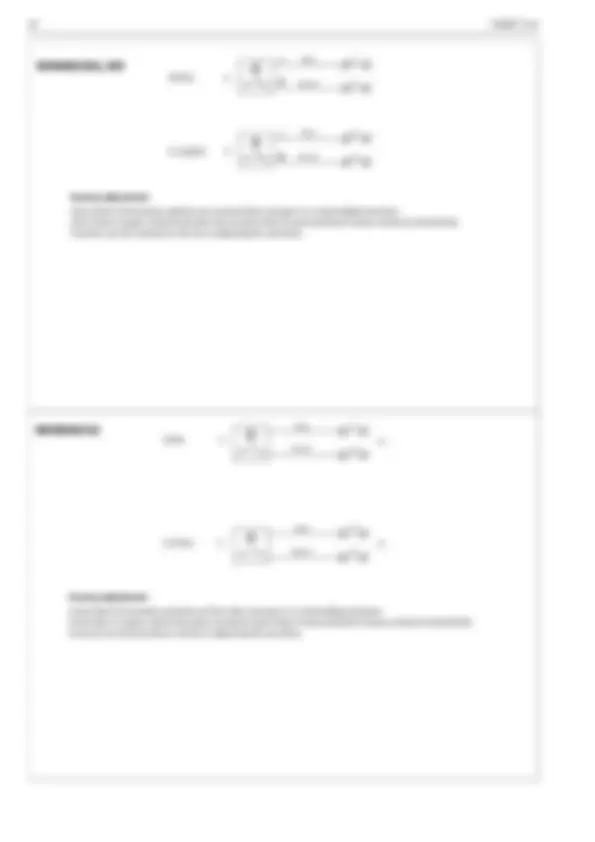
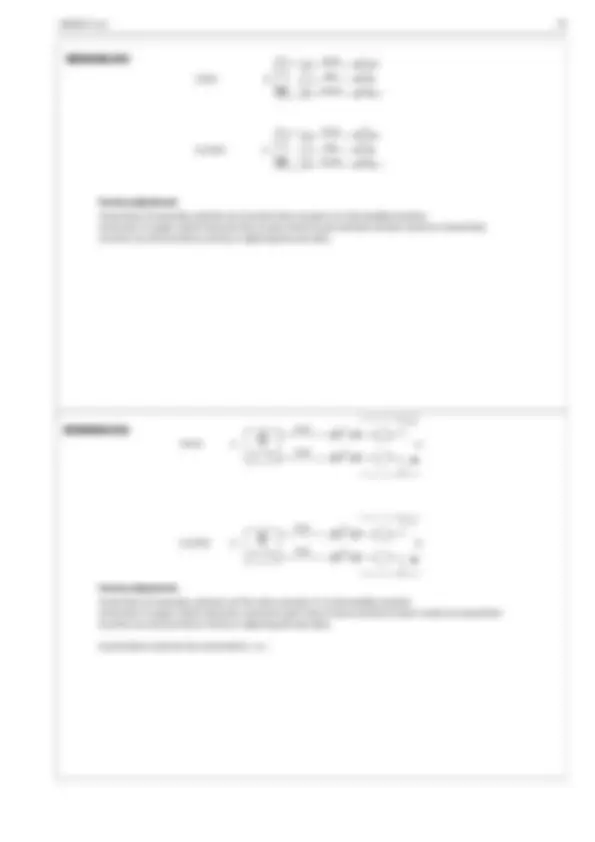
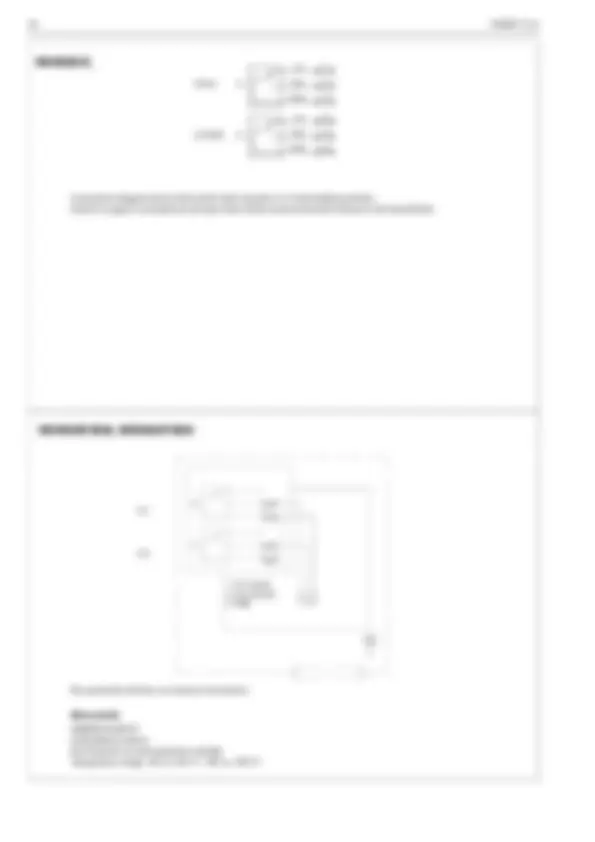
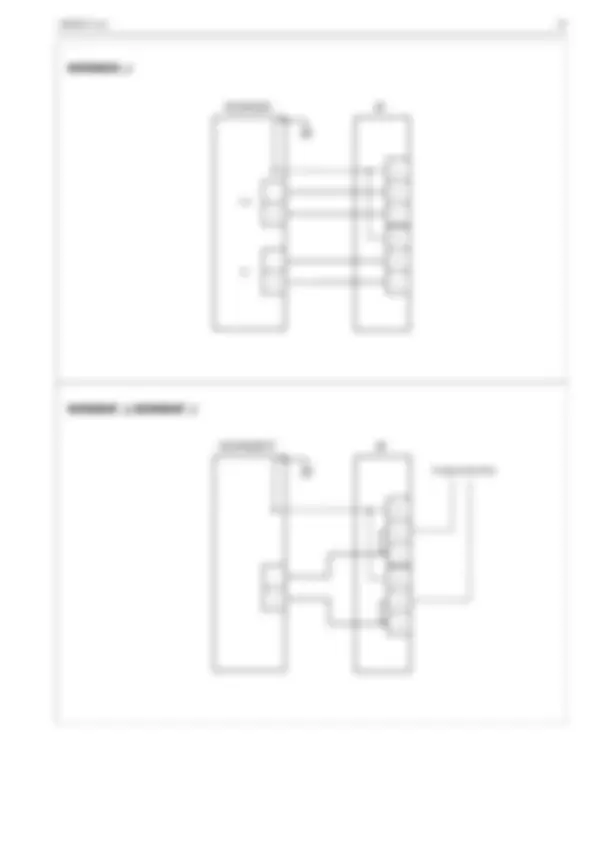
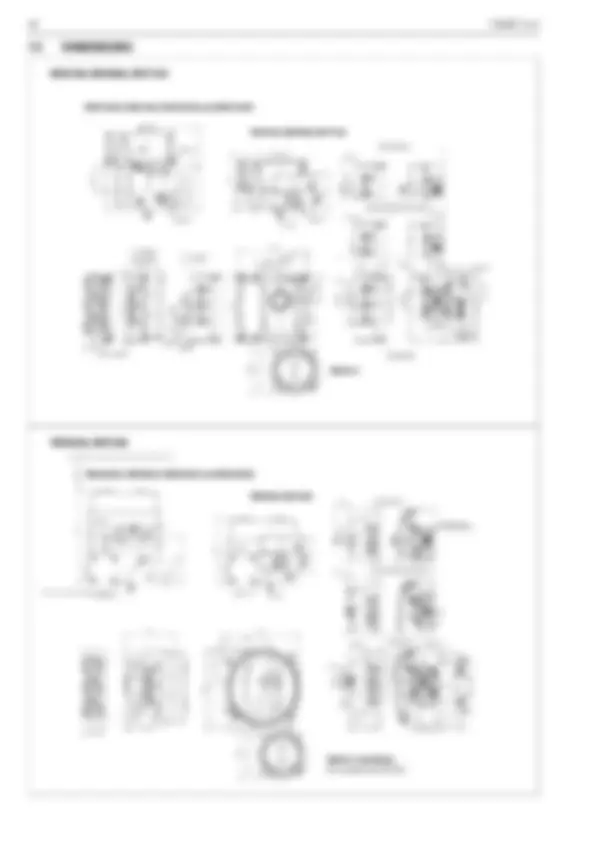
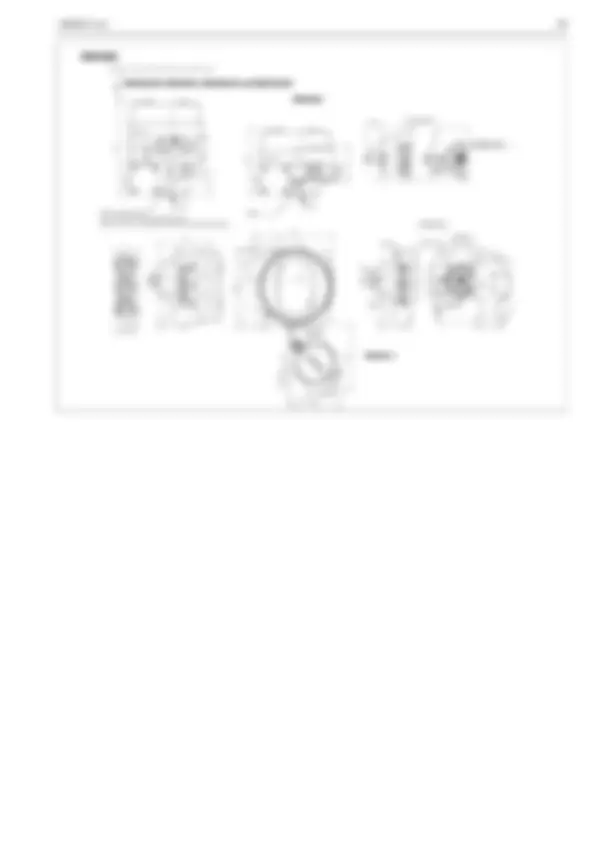
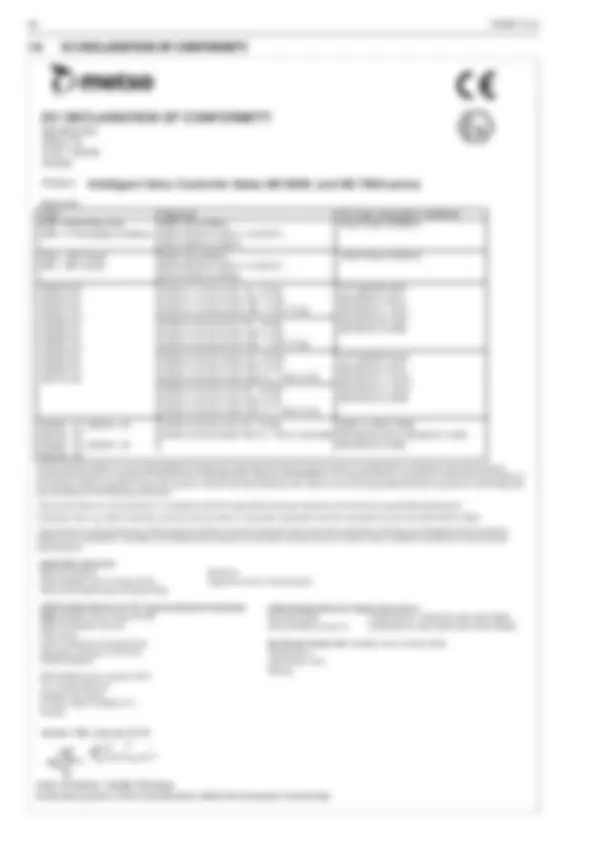
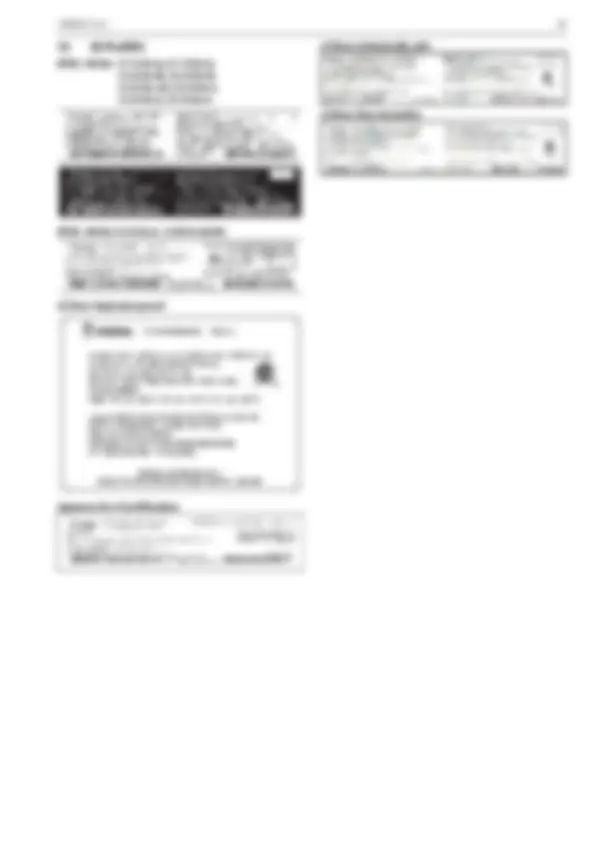
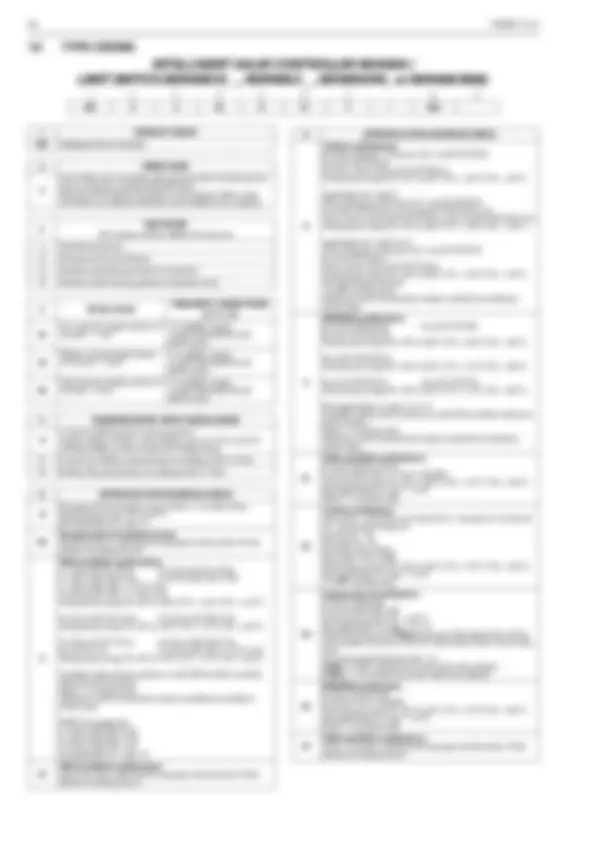
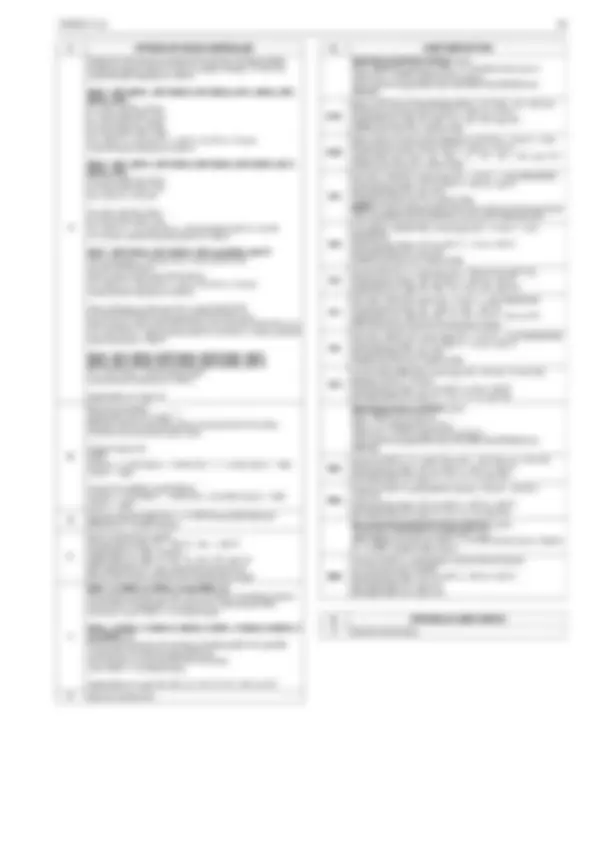
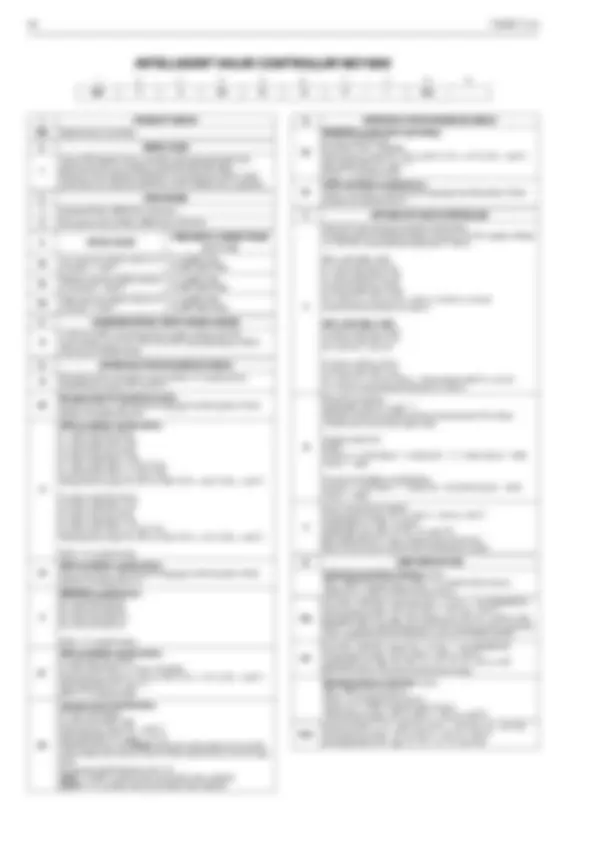
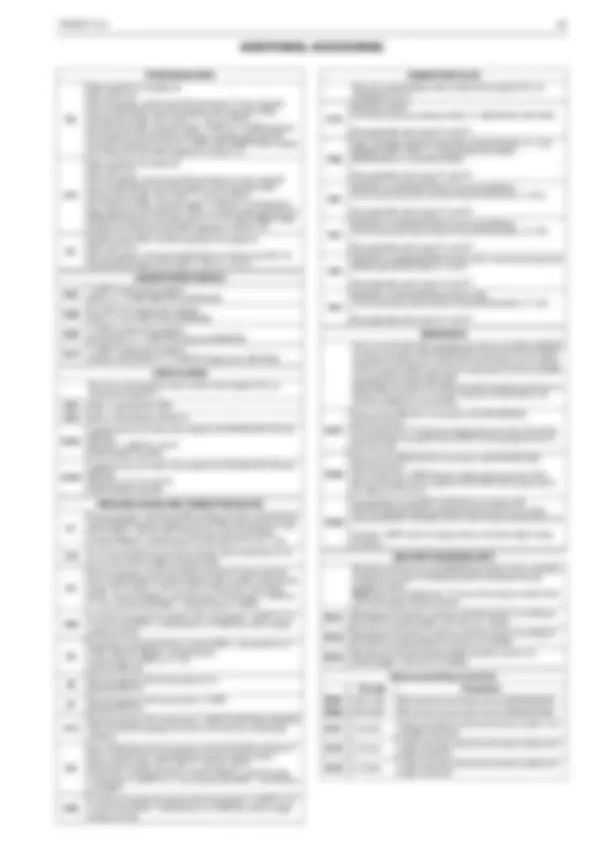
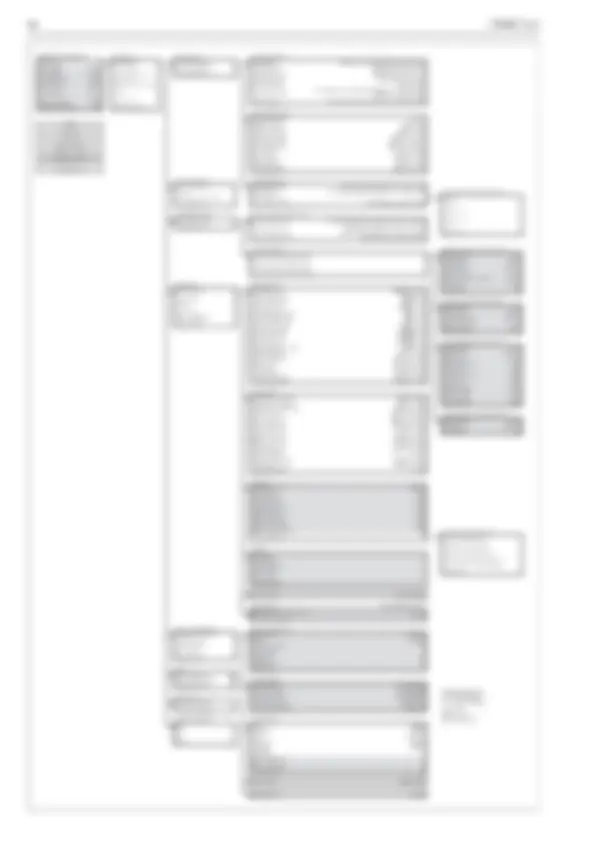
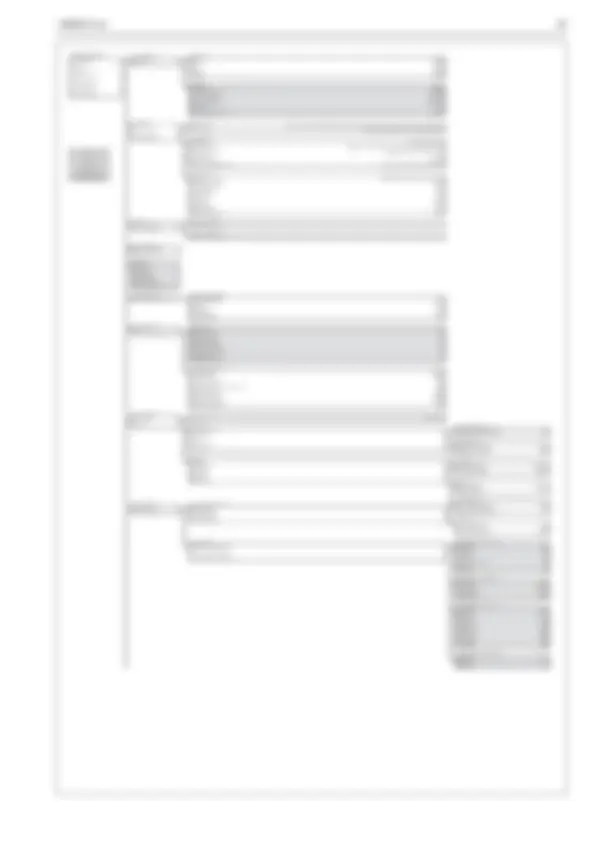
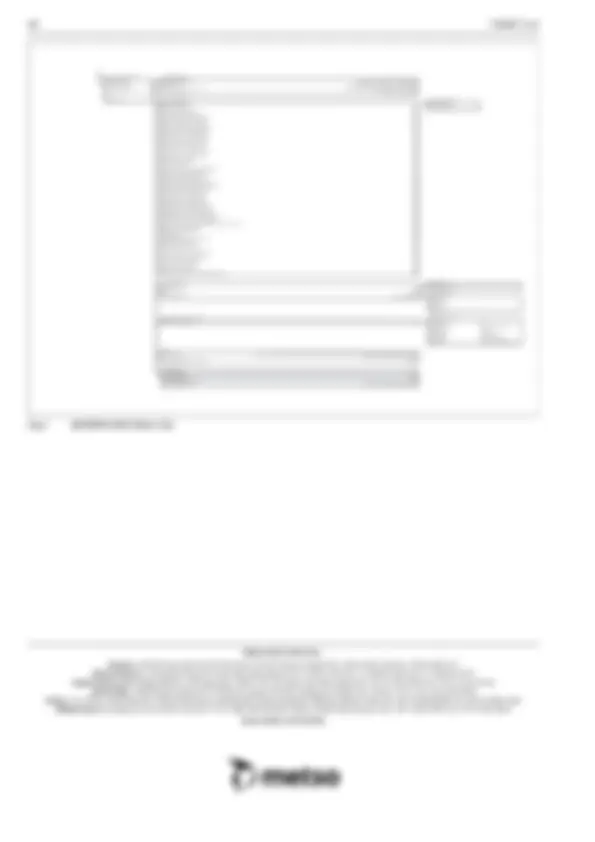
Estude fácil! Tem muito documento disponível na Docsity
Ganhe pontos ajudando outros esrudantes ou compre um plano Premium
Prepare-se para as provas
Estude fácil! Tem muito documento disponível na Docsity
Prepare-se para as provas com trabalhos de outros alunos como você, aqui na Docsity
Os melhores documentos à venda: Trabalhos de alunos formados
Prepare-se com as videoaulas e exercícios resolvidos criados a partir da grade da sua Universidade
Responda perguntas de provas passadas e avalie sua preparação.
Ganhe pontos para baixar
Ganhe pontos ajudando outros esrudantes ou compre um plano Premium
Comunidade
Peça ajuda à comunidade e tire suas dúvidas relacionadas ao estudo
Descubra as melhores universidades em seu país de acordo com os usuários da Docsity
Guias grátis
Baixe gratuitamente nossos guias de estudo, métodos para diminuir a ansiedade, dicas de TCC preparadas pelos professores da Docsity
Manual do nd900 na qual mostra o seu funcionamento
Tipologia: Manuais, Projetos, Pesquisas
1 / 68
Esta página não é visível na pré-visualização
Não perca as partes importantes!
7 ND90 71 en • 5/
READ THESE INSTRUCTIONS FIRST! These instructions provide information about the safe handling and operation of the intelligent valve controller. If you require additional assistance, please contact the manufacturer or manufacturer's representative. Addresses and phone numbers are printed on the back cover. See also www.metso.com/valves for the latest documentation. SAVE THESE INSTRUCTIONS!
Subject to change without notice. All trademarks are property of their respective owners.
2.1 General....................................................................... 4 2.2 Technical description............................................ 4 2.3 Markings .................................................................... 5 2.4 Technical specifications ....................................... 5 2.5 Recycling and disposal ......................................... 9 2.6 Safety precautions ................................................. 9 3 TRANSPORTATION, RECEPTION AND STORAGE.............................................................. 4 MOUNTING .......................................................... 4.1 General ................................................................... 4.2 For mounting parts for Metso actuators, see 12.5–12.10.Mounting on Metso actuators with VDI/VDE mounting face ........................... 4.3 Mounting on Neles VC and VD actuators or linear actuators with IEC 60534 mounting face ............................................................................ 4.4 Piping........................................................................ 4.5 Electrical connections......................................... 5 LOCAL USER INTERFACE (LUI) ............................ 5.1 Measurement monitoring................................. 5.2 Guided start-up..................................................... 5.3 Configuration menu............................................ 5.4 Mode menu ............................................................ 5.5 Configuration parameters................................. 5.6 Valve travel calibration....................................... 5.7 Special displays ..................................................... 5.8 Write protection.................................................... 6 MAINTENANCE .................................................... 6.1 Prestage ................................................................... 6.2 Spool valve ............................................................. 6.3 Flame arrestor assembly.................................... 6.4 Diaphragms............................................................ 6.5 Communication board ....................................... 7 ERROR MESSAGES............................................... 7.1 Failsafe errors......................................................... 7.2 Alarms....................................................................... 7.3 Errors......................................................................... 7.4 Warnings ................................................................. 7.5 Notifications ...........................................................
9.1 Introduction ........................................................... 9.2 Installation on a valve controller .................... 9.3 Electrical connections......................................... 9.4 Adjustment............................................................. 9.5 Removal of the limit switches for accessing the valve controller.............................................. 9.6 Circuit diagrams.................................................... 9.7 Maintenance .......................................................... 10 TOOLS .................................................................. 41 11 ORDERING SPARE PARTS ................................... 41 12 DRAWINGS AND PARTS LISTS............................ 42 12.1 Exploded view ND9100, ND9400, ND7100 .................................................................... 12.2 Exploded view ND9100_/D__, ND9100_/I__, ND9100_/K0_ and ND9100_/B06 ................... 12.3 Exploded view ND9200, ND9300, ND7200 44 12.4 Exploded view ND9200_/D__, ND9200_/I__, ND9200_/K0_, ND9200_/B06, ND9300_/D__, ND9300_/I__, ND9300_/K0_, ND9300_/B06_ ...................................................... 12.5 Mounting parts for B1C/B1J 6- actuators.................................................................. 12.6 Mounting parts for B1C/B1J 25-50, B1C 502 and B1J322 actuators.......................................... 12.7 Mounting parts for Quadra-Powr ® actuators.................................................................. 12.8 Mounting on Neles VC and VD actuators or linear actuators with IEC 60534 mounting face. ........................................................................... 12.9 Connection diagrams.......................................... 13 DIMENSIONS ................................................... 58 14 EC DECLARATION OF CONFORMITY.................. 60 15 ID PLATES ............................................................ 61 16 TYPE CODING ...................................................... 62
Extensive set of off-line tests with accurate key figure calculations Fast notifications using on-line alarms Condition monitoring tool available Real time monitoring of valve control parameters
Benchmark control performance on rotary and linear valves Reliable and robust design Ease of use Language selection: English, German and French Local / remote operation Expandable architecture Basic diagnostics including Self-diagnostics Online diagnostics Extended off-line tests
Low energy and air consumption Retro-fit to existing installations (Neles or 3rd party)
Linearisation of the valve flow characteristics Excellent dynamic and static control performance High-speed of response Accurate internal measurements
Same unit for linear and rotary valves, double and single-acting actuators Simple calibration and configuration using Local User Interface (H) using DTM or EDD in a remote location (H, F) see 375/475 menu structure from annex 1 Low power design enables installation to all com- mon control systems Possibility to mount also on valves that are in pro- cess with 1-point calibration feature
Metso is committed to delivering products that freely interface with software and hardware from a variety of manufacturers; and the ND7000 is no exception. This open architecture allows the ND7000 to be integrated with other field devices to give an unprecedented level of controllability.
FDT based multi-vendor support configuration ND9000 DTM download page: www.metso.com/ND
Designed to operate in harsh environmental condi- tions Rugged modular design Excellent temperature characteristics Vibration and impact tolerant IP66 enclosure Protected against humidity Maintenance free operation Resistant to dirty air Wear resistant and sealed components Contactless position measurement
This manual incorporates Installation, Maintenance and Operation Instructions for the Metso ND9000 and ND intelligent valve controller. The ND9000 and ND7000 may be used with either cylinder or diaphragm type pneumatic actuators for rotary or linear valves.
ND9000H and ND7000H The ND9000H and ND7000H are a 4–20 mA loop-powered microcontroller-based intelligent valve controllers. The devices operate even at 3.6 mA input signal and communi- cates via HART. ND9000F The ND9000F is a fieldbus powered microcontroller-based intelligent valve controller. ND9000P The ND9000P is a fieldbus powered microcontroller-based intelligent valve controller. All versions All devices contain a Local User Interface enabling local configuration. Independently from the communication protocol, the valve position is controlled by the powerful 32-bit microcontrol- ler. The measurements include: Input signal Valve position with contactless sensor Actuator pressures, 2 independent measurements Supply pressure Spool valve position Device temperature Advanced self-diagnostics guarantees that all measure- ments operate correctly. Failure of one measurement does not cause the valve to fail if the input signal and position measurements are operating correctly. After connections of electric signal and pneumatic supply the micro controller (μC) reads the input signal, position sensor (α), pressure sensors (Ps, P1, P2) and spool position sensor (SPS). A differ- ence between input signal and position sensor (α) measure- ment is detected by the control algorithm inside the μC. The μC calculates a new value for prestage (PR) coil current based on the information from the input signal and from the sensors. Changed current to the PR changes the pilot pressure to the spool valve. Reduced pilot pressure moves the spool and the actuator pressures change accordingly. The spool opens the flow to the driving side of the double diaphragm actuator and opens the flow out from the other
The selection and use of the valve controller in a specific application requires close consideration of detailed aspects. Due to the nature of the product, this manual cannot cover all the likely situations that may occur when installing, using or servicing the valve controller. If you are uncertain about the use of the controller or its suitability for your intended use, please contact Metso’s Automation business for more information.
side of the actuator. The increasing pressure will move the diaphragm piston. The actuator and feedback shaft rotate clockwise. The position sensor (α) measures the rotation for the μC. The μC using control algorithm modulates the PR- current from the steady state value until a new position of the actuator according to the input signal is reached.
The valve controller is equipped with an identification plate (Fig. 2).
Identification plate markings include:
Type designation of the valve controller Revision number Enclosure class Input signal (voltage range) Input resistance Maximum supply voltage Operational temperature Supply pressure range Contact details of the manufacturer CE mark Manufacturing serial number TTYYWWNNNN*) *) Manufacturing serial number explained: TT= device and factory sign YY= year of manufacturing WW = week of manufacturing NNNN = consecutive number Example: PH13011234 = controller, year 2013, week 1, con- secutive number 1234.
Note, that in ND9200 and ND9300 models there may have two identification plates if there is double approval (type ND92_XE1 or ND93_XE1). When device is installed to Ed i or Ex d area, remove identifi- cation plate which is not valid. If device is installed to Ex d area, it can't be installed to Ex i area even that identification plate would be changed. See Chapter 15 for all ID plates.
General Either loop powered (ND9000H and ND7000H) or bus powered (ND9000F and ND9000P), no external power supply required. Suitable for rotary and sliding-stem valves. Actuator connections in accordance with VDI/VDE 3845 and IEC 60534-6 standards. Action: Double or single acting Travel range: Linear; 10–120 mm with standard IEC parts. Larger strokes possible with suitable kits Rotary; 45–95°. Measurement range 110° with freely rotating feedback shaft. Environmental Influence Standard temperature range: -40° to +85 °C / -40° to +185 °F Low temperature option: -53° to +85 °C / -64° to +185 °F Influence of temperature on valve position: < 0.5 % / 10 °C Influence of vibration on valve position: < 1 % under 2g 5–150 Hz, 1g 150–300 Hz, 0.5g 300–2000 Hz Enclosure ND9100 and ND Material: Anodised aluminium alloy and polymer composite Protection class: IP66, NEMA 4X Pneumatic ports: G 1/ Electrical connection: max 2.5 mm 2 Cable gland thread: M20 x 1.5 / 1/2 NPT (U) Weight: 1.8 kg / 4.0 lb with extension housing (limit switches) plus 0.8 kg / 1.8 lb Mechanical and digital position indicator visible through the main cover ND9200 and ND Material: Anodised aluminium alloy and tempered glass Protection class: IP66, NEMA 4X Pneumatic ports: 1/4 NPT Electrical connection: max. 2.5 mm 2 Cable gland thread: M20 x 1.5, except 1/2 NPT (E2) Weight: 3.4 kg / 7.5 lb with extension housing (limit switches) plus 1.0 kg / 2.2 lb Mechanical and digital position indicator visible through the main cover (not applicable to ND9200_E2)
Fig. 1 The principle of operation
Fig. 2 Example of the identification plate
Approvals
Table 1 Approvals and electrical values, HART
Certificate Approval Electrical values ATEX ND_X VTT 09 ATEX 033X VTT 09 ATEX 034X EN 60079-0: 2012 EN 60079-11: 2012 EN 60079-26: 2007 EN 60079-31: 2009
II 1G Ex ia IIC T6...T4 Ga II 1D Ex ta IIIC T90 °C Da II 2 G Ex ib IIC T6...T4 Gb II 2 D Ex tb IIIC T90 °C Db
Input: Ui ≤ 28 V, Ii ≤ 120 mA, Pi ≤ 1 W, Ci ≤ 22 nF, Li ≤ 53 μH. Output: Ui ≤ 28 V, Ii ≤ 120 mA, Pi ≤ 1 W, Ci ≤ 22 nF, Li ≤ 53 μH.
EN 60079-0: 2012 EN 60079-11: 2012 EN 60079-15: 2010 EN 60079-31: 2009
II 3 G Ex nA IIC T6...T4 Gc II 3 D Ex tc IIIC T90 °C Dc
Input: Ui ≤ 30 V, Ii ≤ 152 mA Output: Ui ≤ 30 V, Ii ≤ 152 mA II 3 G Ex ic IIC T6...T4 Gc II 3 D Ex tc IIIC T90 °C Dc
Input: Ui ≤ 30 V, Ii ≤ 152 mA, Pmax = device limits itself, Ci ≤ 22 nF, Li ≤ 53 μH. Output: Ui ≤ 30 V, Ii ≤ 152 mA, Pmax = device limits itself, Ci ≤ 22 nF, Li ≤ 53 μH. ND_E SIRA 11 ATEX 1006X EN 60079-0: EN 60079-1: EN 60079-31:
II 2 G Ex d IIC T6...T4 Gb II 2 D Ex tb IIIC T80 °C...T105 °C Db IP
Input: Ui ≤ 30 V Output: Ui ≤ 30 V, Pmax = device limits itself.
IECEx ND_X IECEx VTT 10.0004X IECEx VTT 10.0005X IEC 60079-0: 2007/ IEC 60079-11: 2011 IEC 60079-26: 2006 IEC 60079-31: 2008
Ex ia IIC T6...T4 Ga Ex ta IIIC T90 °C Da Ex ib IIC T6...T4 Gb Ex tb IIIC T90 °C Db
Input: Ui ≤ 28 V, Ii ≤ 120 mA, Pi ≤ 1 W, Ci ≤ 22 nF, Li ≤ 53 μH Output: Ui ≤ 28 V, Ii ≤ 120 mA, Pi ≤ 1 W, Ci ≤ 22 nF, Li ≤ 53 μH.
IEC 60079-0: 2007/ IEC 60079-11: 2011 IEC 60079-15: 2010, IEC 60079-31: 2008
Ex nA IIC T6...T4 Gc Ex tc IIIC T90 °C Dc
Input: Ui ≤ 30 V, Ii ≤ 152 mA Output: Ui ≤ 30 V, Ii ≤ 152 mA Ex ic IIC T6...T4 Gc Ex tc IIIC T90 °C Dc
Input: Ui ≤ 30 V, Ii ≤ 152 mA, Pmax = device limits itself, Ci ≤ 22 nF, Li ≤ 53 μH Output: Ui ≤ 30 V, Ii ≤ 152 mA, Pmax = device limits itself, Ci ≤ 22 nF, Li ≤ 53 μH. ND_E IECEx SIR 11.0001X IEC 60079-0: IEC 60079-1: IEC 60079-31:
Ex d IIC T6...T4 Gb Ex tb IIIC T80 °C...T105 °C Db IP
Input: Ui ≤ 30 V Output: Ui ≤ 30 V, Pmax = device limits itself.
INMETRO ND_Z NCC 12.0793 X NCC 12.0794 X ABNT NBR IEC 60079-0: ABNT NBR IEC 60079-11: ABNT NBR IEC 60079-26:2008 (2009) ABNT NBR IEC 60079-27:
Ex ia IIC T4/T5/T6 Ga Ex ia IIC T4/T5/T6 Gb
Input: Ui ≤ 28 V, Ii ≤ 120 mA, Pi ≤ 1 W, Ci ≤ 22 nF, Li ≤ 53 μH Output: Ui ≤ 28 V, Ii ≤ 120 mA, Pi ≤ 1 W, Ci ≤ 22 nF, Li ≤ 53 μH.
ABNT NBR IEC 60079-0: ABNT NBR IEC 60079-11: IEC 60079-15: ABNT NBR IEC 60079-27: ABNT NBR IEC 60529:
Ex nA IIC T4/T5/T6 Gc Input: Ui ≤ 30 V, Ii ≤ 152 mA Output: Ui ≤ 30 V, Ii ≤ 152 mA Ex ic IIC T4/T5/T6 Gc Input: Ui ≤ 30 V, Ii ≤ 152 mA, Pmax = device limits itself, Ci ≤ 22 nF, Li ≤ 53 μH. Output: Ui ≤ 30 V, Ii ≤ 152 mA, Pmax = device limits itself, Ci ≤ 22 nF, Li ≤ 53 μH. ND_E NCC 12.0795 X ABNT NBR IEC 60079-0: ABNT NBR IEC 60079-1:2009 (2011) ABNT NBR IEC 60079-31: ABNT NBR IEC 60529:
Ex d IIC T4/T5/T6 Gb Ex tb IIIC T100 °C Db IP
Input: Ui ≤ 30 V Output: Ui ≤ 30 V, Pmax = device limits itself.
cCSAus ND_U CSA Std C22.2 No.25-1966, CSA Std C22.2 No.30-M1986, CAN/CSA-C22. No.94-M91, C22.2 No. 142-M1987, CAN/CSA C22.2 61010-1-04, CAN/CSAC22. No 60079-0-07, CAN/CSA-C22. No 60079-1-07, CAN/ CSA C22.2 No 60079-31-12, CAN/CSA-C22.2 No. 60529-05, FM 3600 (1998), FM 3615 (2006), FM 3810 (2005), ANSI/ NEMA 250-1991, ISA 60079-0-07, ISA 60079-1- 07, ISA 60079-31-2009, ANSI/IEC 60529:
IS Class I, Division 1, Groups A, B, C, and D; T4/T5/T Ex ia IIC T4/T5/T6 Ga IS Class I, Zone 0 AEx ia IIC T4/T5/T6 Ga
Input: Ui ≤ 28 V, Ii ≤ 120 mA, Pi ≤ 1 W, Ci ≤ 22 nF, Li ≤ 53 μH Output: Ui ≤ 28 V, Ii ≤ 120 mA, Pi ≤ 1 W, Ci ≤ 22 nF, Li ≤ 53 μH.
Class I, Division 2, Groups A, B, C, and D; T4/ T5/T Ex nA IIC T4/T5/T6 Gc or Ex nA ia IIC T4/T5/T Gc Ga Class I, Zone 2 AEx nA IIC T4/T5/T6 Gc or Ex nA ia IIC T4/T5/T6 Gc Ga
Input: Ui ≤ 30 V. Output: Ui ≤ 30 V.
ND_E CSA Std C22.2 No.25-1966, CSA Std C22.2 No.30-M1986, CAN/CSA-C22. No.94-M91, C22.2 No. 142-M1987, CAN/CSA C22.2 61010-1-04, CAN/CSAC22. No 60079-0-07, CAN/CSA-C22. No 60079-1-07, CAN/ CSA C22.2 No 60079-31-12, CAN/CSA-C22.2 No. 60529-05, FM 3600 (1998), FM 3615 (2006), FM 3810 (2005), ANSI/ NEMA 250-1991, ISA 60079-0-07, ISA 60079-1- 07, ISA 60079-31-2009, ANSI/IEC 60529:
Class I, Div 1, Groups B, C, D; Class II, Div 1, Groups E,F,G; Class III; T4…T6, Enclosure type 4X Ex d IIC T4…T AEx d IIC T4…T Ex tb IIIC T100 °C IP AEx tb IIIC T100 °C IP
Input: Ui ≤ 30 V Output: Ui ≤ 30 V, Pmax = device limits itself.
Japanese Ex-d Certification: ND_E4 II 2 G Ex d IIC T6 Gb II 2 D Ex tb IIIC T80°C Db
Input: Ui ≤ 30 V Output: Ui ≤ 30 V, Pmax = device limits itself.
Table 2 Approvals and electrical values, FOUNDATION fieldbus and Profibus PA
Certificate Approval Electrical values ATEX ND_X VTT 09 ATEX 033X VTT 09 ATEX 034X EN 60079-0: 2012 EN 60079-11: 2012 EN 60079-26: 2007 EN 60079-31: 2009
II 1G Ex ia IIC T6...T4 Ga II 1D Ex ta IIIC T90 °C Da II 2 G Ex ib IIC T6...T4 Gb II 2 D Ex tb IIIC T90 °C Db II 1 D Ex ia IIIC T90 °C...T120 °C Da II 2 D Ex ib IIIC T90 °C...T120 °C Db
Ui ≤ 24 V, Ii ≤ 380 mA, Pi ≤ 5.32 W, Ci ≤ 5 nF, Li ≤ 10 μH. Comply with the requirements for FISCO field device
EN 60079-0: 2012 EN 60079-11: 2012 EN 60079-15: 2010 EN 60079-31: 2009
II 3 G Ex nA IIC T6...T4 Gc II 3 D Ex tc IIIC T90 °C Dc II 3 D Ex ic IIIC T90 °C...T120 °C Dc
Ui ≤ 24 V
II 3 G Ex ic IIC T6...T4 Gc II 3 D Ex tc IIIC T90 °C Dc II 3 D Ex ic IIIC T90 °C...T120 °C Dc
Ui ≤ 32 V, Ii ≤ 380 mA, Pi ≤ 5.32 W, Ci ≤ 5 nF, Li ≤ 10 μH. Comply with the requirements for FISCO Ex ic field device ND_E SIRA 11 ATEX 1006X EN 60079-0: EN 60079-1: EN 60079-31:
II 2 G Ex d IIC T6...T4 Gb II 2 D Ex tb IIIC T80 °C...T105 °C Db IP
Ui ≤ 32 V
IECEx ND_X IECEx VTT 10.0004X IECEx VTT 10.0005X IEC 60079-0: 2007/ IEC 60079-11: 2011 IEC 60079-26: 2006 IEC 60079-31: 2008
Ex ia IIC T6...T4 Ga Ex ta IIIC T90 °C Da Ex ib IIC T6...T4 Gb Ex tb IIIC T90 °C Db Ex ia IIIC T90 °C...T120 °C Da Ex ib IIIC T90 °C...T120 °C Db
Ui ≤ 24 V, Ii ≤ 380 mA, Pi ≤ 5.32 W, Ci ≤ 5 nF, Li ≤ 10 μH. Comply with the requirements for FISCO field device
IEC 60079-0: 2007/ IEC 60079-11: 2011 IEC 60079-15: 2010, IEC 60079-31: 2008
Ex nA IIC T6...T4 Gc Ex tc IIIC T90 °C Dc Ex ic IIIC T90 °C...T120 °C Dc
Ui ≤ 24 V
Ex ic IIC T6...T4 Gc Ex tc IIIC T90 °C Dc Ex ic IIIC T90 °C...T120 °C Dc
Ui ≤ 32 V, Ii ≤ 380 mA, Pi ≤ 5.32 W, Ci ≤ 5 nF, Li ≤ 10 μH. Comply with the requirements for FISCO Ex ic field device ND_E IECEx SIR 11.0001X IEC 60079-0: IEC 60079-1: IEC 60079-31:
Ex d IIC T6...T4 Gb Ex tb IIIC T80 °C...T105 °C Db IP
Ui ≤ 32 V
INMETRO ND_Z NCC 12.0793 X NCC 12.0794 X ABNT NBR IEC 60079-0:2008 (2011) ABNT NBR IEC 60079-11: ABNT NBR IEC 60079-26:2008 (2009) ABNT NBR IEC 60079-27:
Ex ia IIC T4/T5/T6 Ga Ex ia IIC T4/T5/T6 Gb
Ui ≤ 24 V, Ii ≤ 380 mA, Pi ≤ 5.32 W, Ci ≤ 5 nF, Li ≤ 10 μH. Comply with the requirements for FISCO field device
ABNT NBR IEC 60079-0:2008 (2011) ABNT NBR IEC 60079-11: IEC 60079-15: ABNT NBR IEC 60079-27: ABNT NBR IEC 60529:
Ex nA IIC T4/T5/T6 Gc Ui ≤ 24 V Ex ic IIC T4/T5/T6 Gc Ui ≤ 32 V, Ii ≤ 380 mA, Pi ≤ 5.32 W, Ci ≤ 5 nF, Li ≤ 10 μH. Comply with the requirements for FISCO Ex ic field device
ND_E NCC 12.0795 X ABNT NBR IEC 60079-0:2008 (2011) ABNT NBR IEC 60079-1:2009 (2011) ABNT NBR IEC 60079-31: ABNT NBR IEC 60529:
Ex d IIC T4/T5/T6 Gb Ex tb IIIC T100 °C Db IP
Ui ≤ 32 V
cCSAus ND_U CSA C22.2 No. 0-M91, CSA C22.2 No. 94-M91, CSA C22.2 No. 142-M1987, CSA C22.2 No. 157-92, CSA C22.2 No. 213-M1987, CSA C22.2 No. 60079-0:11, CSA C22.2 No. 60079-11:11, CSA C22. No. 60079-15:12, CSA C22.2 No. 60529:05, ANSI/ISA 60079-0: 2009, ANSI/ISA 60079-11: 2012, ANSI/ISA 60079-15: 2012, FM 3600 November 1998, FM 3610 October 1999, FM 3611 October 1999, FM 3810-2005, ANSI/ NEMA 250:1991, ANSI/IEC 60529:
Class I, Division 1, Groups A, B, C, and D; T4/ T5/T Ex ia IIC T4/T5/T6 Ga Class I, Zone 0 AEx ia IIC T4/T5/T6 Ga
Ui ≤ 24 V, Ii ≤ 380 mA, Pi ≤ 5.32 W, Ci ≤ 5 nF, Li ≤ 10 μH. Comply with the requirements for FISCO field device
Class I, Division 2, Groups A, B, C, and D; T4/ T5/T Ex ic IIC T4/T5/T6 Gc Class I, Zone 2 AEx ic IIC T4/T5/T6 Gc
Ui ≤ 32 V, Ii ≤ 380 mA, Pi ≤ 5.32 W, Ci ≤ 5 nF, Li ≤ 10 μH. Comply with the requirements for FISCO Model Ex ic field device
ND_E CSA Std C22.2 No.25-1966, CSA Std C22.2 No.30-M1986, CAN/CSA-C22. No.94-M91, C22.2 No. 142-M1987, CAN/CSA C22.2 61010-1-04, CAN/CSAC22. No 60079-0-07, CAN/CSA-C22. No 60079-1-07, CAN/ CSA C22.2 No 60079-31-12, CAN/CSA-C22.2 No. 60529-05, FM 3600 (1998), FM 3615 (2006), FM 3810 (2005), ANSI/ NEMA 250-1991, ISA 60079-0-07, ISA 60079-1- 07, ISA 60079-31-2009, ANSI/IEC 60529:
Class I, Div 1, Groups B, C, D; Class II, Div 1, Groups E, F, G; Class III; T4…T6, Enclosure type 4X Ex d IIC T4…T AEx d IIC T4…T Ex tb IIIC T100 °C IP AEx tb IIIC T100 °C IP
Ui ≤ 32 V
Japanese Ex-d Certification: ND_E4 II 2 G Ex d IIC T6 Gb II 2 D Ex tb IIIC T80°C Db
Input: Ui ≤ 30 V Output: Ui ≤ 30 V, Pmax = device limits itself.
The valve controller is a sophisticated instrument, handle it with care.
Check the controller for any damage that may have occurred during transportation. Store the uninstalled controller preferably indoors, keep it away from rain and dust. Do not unpack the device until installing it. Do not drop or knock the controller. Keep the flow ports and cable glands plugged until installing. Follow instructions elsewhere in this manual.
If the ND is supplied with valve and actuator, the tubes are mounted and the ND adjusted in accordance with the cus- tomer’s specifications. If the controller is ordered separately, the mounting parts for the assembly must be ordered at the same time. Sample order: (B1CU13)-Z-ND9_06HN Shaft coupling alternatives for the controller for Metso actuators are shown in Fig. 6.
See figures in Section 12.6–12.7. ND9100, ND9400, ND Mount the H-shaped coupling (47) to the shaft. Apply the thread-locking compound to the screw (48) and tighten firmly. Remove all protective plastic plugs from the pneu- matic connections (5 pcs.). Mount the metal plugs (54) with sealant to the unused controller connec- tions at the bottom of the controller. BJ and other single acting actuators: mount a metal plug (53) with sealant to the C1 connection. Set the direction arrow of the actuator in the direc- tion of the valve closure member and attach the ear (2) to the indicator cover in the position shown in Section 12.6-12.7. Secure the screw of the ear using e.g. Loctite and tighten firmly. Attach the bracket (1) to the ND. Attach the bracket (1) to the actuator. The shaft cou- pling of the ND must fit into the ear (2) so that the pointer of the shaft washer (16) is located in the posi- tion shown in Fig. 5.
Intrinsic Safety (Ex i) WARNING (ND9100, ND9200, ND9300 and ND7100): Ensure that the complete installation and wiring is intrinsically safe before operating the device! The equipment must be connected via a certified Zener barrier placed outside the hazardous area.
Ex WARNING (ND9200, ND7200) : Electrostatic charge hazard! The windows and identification plate are non-conductive. Clean with a damp cloth only!
Ex WARNING (ND9100, ND7100) : For use in the presence of combustible dust. Device shall not be subjected to a prolific charge gen- erating mechanism.
Ex WARNING (ND9000, ND7000): Accumulation of dust shall be avoided!
Ex d WARNING (ND9200, ND7200, ND9300): Use a cable gland and blind plug with suitable Ex d certification. For ambient temperature over 70 °C / 158 °F use a heat resistant cable and cable gland suitable for at least 90 °C / 194 °F.
Ex n WARNING (ND9100, ND9200, ND9300 and ND7100): At an ambient temperature ≥ +70 °C / 158 °F, the tem- perature rating of selected connection cable shall be in accordance with the maximum ambient tempera- ture range. Selected cable gland shall not invalidate the type of protection.
Ex i WARNING (ND9100, ND9200, ND9300 and ND7100): At an ambient temperature ≥ +70 °C / 158 °F, the tem- perature rating of selected connection cable shall be in accordance with the maximum ambient tempera- ture range.
Ex NOTE: Follow the standards EN/IEC 60079-14 when installing the equipment and and EN/IEC 60079-25 when connecting Ex i interfaces.
The enclosure of ND9000 and ND7000 intelligent valve controller meets the IP66 protection class according to EN 60529 in any position when the cable entry is plugged according to IP66. Based on good mounting practice, the recommended mounting position is electrical connections placed down- wards. This recommendation is shown in our mounting position coding for control valves. If these requirements are not fulfilled, and the cable gland is leaking and the leakage is damaging valve controller or other electrical instrumentation, our warranty is not valid.
NOTE: Make sure the mounting of the device and the valve assembly is suitable for the weight of the assembly.
Make sure the mounting bracket is suitable for the weight of the controller. See detailed weight infor- mation in Section 2.4. ND9300: Extra mounting holes exist in the housing for additional support. See dimension drawings for ND9300 in Chapter 13. The use of this extra support is mandatory in addition to the standard face. ND9300: Due to the extra weight of stainless steel version and/or possible heavy vibration, make sure there are proper supports in the pipeline to hold the weight of the valve assembly. Mount the H-shaped coupling (47) to the shaft. Apply the thread-locking compound to the screw (48) and tighten firmly. Remove the protective plastic plugs from pneumatic connections C2, S and C1. Leave the metal plugs (54) in the unused connections at the bottom of the con- troller. BJ and other single acting actuators: install a metal plug (53) with sealant to the C1 connection. Set the direction arrow of the actuator in the direc- tion of the valve closure member and attach the ear (2) to the indicator cover in the position shown in Section 12.6-12.7. Secure the screw of the ear using e.g. Loctite and tighten firmly. Attach the bracket (1) to the controller. Attach the bracket (1) to the actuator. The shaft cou- pling of the controller must fit into the ear (2) so that the pointer is located in the position shown in Fig. 5.
See figure in Section 12. ND9100, ND9400, ND Attach the feedback arm with spacer to the valve controller shaft. Note the position of the mark on the shaft as in 12.10. Apply thread locking compound to the screws and tighten firmly. Attach the spring to the feedback arm as shown in Section 12.10. Mount the valve controller mounting bracket loosely to the yoke of the actuator. Remove all plastic plugs from all actuator connec- tions. Mount the metal plugs (54) with sealant to the unused controller connections at the bottom of the controller. Mount the valve controller loosely to the mounting bracket guiding the pin on the actuator stem to the slot of the feedback arm. Align the bracket and the valve controller with the actuator stem and adjust their position so that the feedback arm is approximately at a 90° angle to the actuator stem (in the mid-stroke position). Tighten the valve controller mounting bracket screws. Adjust the distance of the valve controller to the pin on the actuator stem so that the pin stays in the lever slot at full stroke. Ensure also that the maximum angle of the lever does not exceed 45° in either direction. Maximum allowed travel of the lever is shown in Section 12.10. Best control performance is achieved when the feedback lever utilises the maxi- mum allowed angle (±45° from horizontal position). The whole range should be at least 45°. Make sure that the valve controller is in right angle and tighten all the mounting bolts. Ensure that the valve controller complies with previ- ous steps. Check that the actuator pin does not touch the valve controller case throughout the entire stroke of the actuator. If the actuator pin is too long it may be cut to size. Apply grease (Molykote or equivalent) to the contact surfaces of the actuator pin and the feedback arm to reduce wear. ND9200, ND7200, ND Make sure the mounting bracket is suitable for the weight of the controller. See detailed weight infor- mation in Section 2.4. ND9300: Extra mounting holes exist in the housing for additional support. See dimension drawings for ND9300 in Chapter 13. The use of this extra support is mandatory in addition to the standard face. ND9300: Due to the extra weight of stainless steel version and/or possible heavy vibration, make sure there are proper supports in the pipeline to hold the weight of the valve assembly.
Fig. 3 Mounting on Metso actuator with VDI/VDE mounting face
C1 (^) The pointer on the coupling must stay in this sector
Table 5. VD & VC stroking time table
Note:
Table 4 Piping and stroke times
Actuator
ND_2_ Supply 1/4" NPT Actuator 1/4" NPT
ND_3_ Supply 1/4" NPT Actuator 1/4" NPT
ND_6_ Supply 1/2" NPT Actuator 1/2" NPT B1C Stroke volumedm (^3) / in 3 NPT^ Piping^ Open(s) Close(s) Piping^ Open(s) Close(s) Piping^ Open(s) Close(s) 6 0.3 18 1/4 6 mm or 1/4" 1.6* 1.6* 6 mm or 1/4" 1.0* 1.0* – – – 9 0.6 37 1/4 – – – 6 mm or 1/4" 2.0 2.0 – – – 11 1.1 67 3/8 – – – (^) [6 mm or 1/4" (x)]10 mm or 3/8" 4.1 4.1 – – – 13 2.3 140 3/8 – – – 10 mm or 3/8" – – – – – 17 4.3 262 1/2 – – – – – – 10 mm or 3/8" 3.6 3. 20 5.4 330 1/2 – – – – – – 10 mm or 3/8" 5.0 5. 25 10.5 610 1/2 – – – – – – 10 mm or 3/8" 9.5 9. 32 21 1282 3/4 – – – – – – 10 mm or 3/8" 18.0 18. 40 43 2624 3/4 – – – – – – 10 mm or 3/8" 35.0 35. 50 84 5126 1 – – – – – – 10 mm or 3/8" 67.0 67. 60 121 7380 1 – – – – – – 10 mm or 3/8" – – 75 189 11500 1 – – – – – – 10 mm or 3/8" – – 502 195 11900 1 – – – – – – 10 mm or 3/8" 130.0 130. 602 282 17200 1 – – – – – – 10 mm or 3/8" – – 752 441 26900 1 – – – – – – 10 mm or 3/8" – – B1J B1JA
Stroke volume dm^3 / in^3
NPT Piping Air (s)
Spring (s)
Piping Air (s)
Spring (s)
Piping Air (s)
Spring (s) 6 0.47 28.7 3/8 (^) [6 mm or 1/4" (x)]10 mm or 3/8" – – (^) [6 mm or 1/4" (x)]10 mm or 3/8" – – – – – 8 0.9 55 3/8 (^) [6 mm or 1/4" (x)]10 mm or 3/8" – – (^) [6 mm or 1/4" (x)]10 mm or 3/8" – – – – – 10 1.8 110 3/8 – – – 10 mm or 3/8" – – – 12 3.6 220 1/2 – – – – – – 10 mm or 3/8" 3.0 5. 16 6.7 409 1/2 – – – – – – 10 mm or 3/8" 5.8 7. 20 13 793 3/4 – – – – – – 10 mm or 3/8" 9.0 14. 25 27 2048 3/4 – – – – – – 10 mm or 3/8" 19.0 25. 32 53 3234 1 – – – – – – 10 mm or 3/8" 36.0 50. 322 106 6468 1 – – – – – – 10 mm or 3/8" 70.0 100. QP Stroke volumedm (^3) / in 3 NPT^ Piping^ Air(s) Spring(s) Piping^ Air(s) Spring(s) Piping^ Air(s) Spring(s) 1C 0.62 37 3/8 (^) [6 mm or 1/4" (x)]10 mm or 3/8" –* –* (^) [6 mm or 1/4" (x)]10 mm or 3/8" 1.2* 2.1* – – – 2C 1.08 66 3/8 – – – 10 mm or 3/8" 2.4 3.0 – – – 3C 2.18 133 3/8 – – – 10 mm or 3/8" 4.8 5.2 – – – 4C 4.34 265 3/8 – – – – – – 10 mm or 3/8" 3.2 3. 5C 8.7 531 3/8 – – – – – – 10 mm or 3/8" 7.5 11. 6C 17.5 1068 3/4 – – – – – – 10 mm or 3/8" 12.0 20. Air supply piping 10 mm or 3/8" for all actuators. Pipe sizes are nominal, i.e. approximately outer diameter. Inner diameter is typically 2 mm smaller. x = Standard pipe size used in Neles control valves. (x) = Minimum pipe size (if smaller than standard). *) Spool size 2 is preferred for accurate control and standard for Neles control valves. Spool size 3 can be used if fast full stroke times are required. Stroking times have been measured without valve. Tests have been done with supply pressure of 5 bar.
Act'r Series
Stroke length
Controller Series
Stroking time (Sec.) (^) SeriesAct'r Strokelength ControllerSeries
Stroking time (Sec.) (^) SeriesAct'r Strokelength ControllerSeries
Stroking time (Sec.) Load Vent Load Vent Load Vent VD_25 20mm NDX 3 3 VD_25 20mm ND9202ND9203^54 75 VC_30 60mm80mm ND9206^68
VD_29 20mm40mm^ NDX 33 34 VD_29 20mm40mm^ ND9203 58 107 100mm^10 VC_
80mm ND
8 10 VD_
20mm NDX
3 3. VD_
20mm (^) ND9203 9 11 100mm 10 11 40mm 3.5 4 40mm 11 16 120mm 11 12 50mm 4 5 50mm ND9206 7 8 VC_
100mm ND
13 13
VD_
20mm NDX
3 4 VD_
20mm ND ND
16 19 120mm 15 14 40mm 3.5 5 40mm 9 11 140mm 17 16 50mm 4 6 50mm 10 12 VC_
120mm ND
18 16 60mm 5 6.5 60mm 11 13 140mm 21 19 70mm 6 7.5 70mm 12 14 180mm 25 21
VD_
20mm
NDX
3 6
VD_
20mm
ND
9 11 VC_
140mm ND
20 19 40mm 4 7 40mm 12 15 180mm 24 22 50mm 5 8 50mm 14 17 240mm 28 27 60mm 6 9 60mm 16 19 VC_
180mm ND
31 30 70mm 7 10 70mm 18 21 240mm 35 31 80mm 8 11 80mm 20 23 280mm 39 34
SINGLE-ACTING ACTUATOR, SPRING TO OPEN
SINGLE-ACTING ACTUATOR, SPRING TO CLOSE
DOUBLE-ACTING ACTUATOR, REVERSED PIPING Increasing input signal to open valve (not recommended) Default setting: DIR = OPE ROT = cC (close valve to clockwise) ATYP = 2-A PFA = OPE A0, CUTL and VTYP according to valve type
.
Increasing input signal to open valve (not recommended) Default setting: DIR = OPE ROT = cC (close valve to clockwise) ATYP = 1-A PFA = OPE (must be in the spring direction) A0, CUTL and VTYP according to valve type
DOUBLE-ACTING ACTUATOR Increasing input signal to open valve (shown) Default setting: DIR = OPE ROT = cC (close valve to clockwise) ATYP = 2-A PFA = CLO A0, CUTL and VTYP according to valve type
.
The ND9000H and ND7000H is powered by a standard 4– mA current loop that also functions as a carrier to the HART communication.
The input signal cable is led through a
M20 x 1.5 cable gland, or 1/2 NPT cable gland (U, E2)
Connect the conductors to the terminal strip as shown in Fig. 9. It is recommended that the earthing of the input cable shield be carried out from the DCS end only.
The position transmitter is connected to 2-pole terminal PT as shown in Fig. 9. The position transmitter needs an exter- nal power supply. The ND9000H / ND7000H and the posi- tion transmitter circuits are galvanically isolated and withstand a 600 V AC voltage.
The ND9000F is powered by F OUNDATION fieldbus (IEC 61158-2). The ND9000P is powered by Profibus PA (IEC 61158-2). The same bus cable is used also for the fieldbus communi- cation. The bus cable is led through a M20 x 1.5 cable gland, or 1/2 NPT cable gland (U, E2) Connect the conductors to the terminal strip as shown in Fig. 10. Reverse polarity protection permits connection of the bus cables in any order. The cable shield can be grounded by connecting the shield to the earth connection screw. The shield can be left uncon- nected by using the empty terminal.
Please note following before mounting the cover of the valve controller: Attach the LUI (223) cabling to the sticker on the reverse side of the LUI. Check that the cabling does not get squeezed by the electronics cover (39) or the device cover (100). Check using a feeler gauge that the clearance between the position indicator (109) and the elec- tronics cover is 1 mm.
The ND9000H and ND700H equal a load of 485 Ω in the current loop.
Fig. 7 Terminals, ND9000H and ND7000H
HART connection
position transmitter connection (optional)
Fig. 8 Terminals, ND9000F and ND9000P
Fig. 9 Control wiring, ND9000H and ND7000H, Ex i
NONHAZARDOUSLOCATION HAZARDOUSLOCATIO N
Ex i Barrier Uo (Voc) ≤ 28 V Io (Isc) ≤ 120 mA Po ≤ 1 W
Ex i Barrier Uo (Voc) ≤ 28 V Io (Isc) ≤ 120 mA Po ≤ 1 W
ND9000H Valve Positioner
Position Transmitter X300 (^) Ui (Vmax) = 28 V Ii (Imax) = 120 mA Pi (Pmax) = 1 W Li = 53 uH Ci = 22 nF
1 2
‐
Analog mA Input X Ui (Vmax) = 28 V Ii (Imax) = 120 mA Pi (Pmax) = 1 W Li = 53 uH Ci = 22 nF
2 3
‐
Earthing terminal (internal)
Earthing terminal (external)
NOTE 1NOTE 1 (^) NOTE 1
NOTE 1
NOTE 1
Limit Switches
Ui (Vmax) Ii (Imax) Pi (Pmax) Li Ci
Ex i Barrier
Uo (Voc) ≤ Ui (Vmax) Io (Isc) ≤ Ii (Imax) Po ≤ Pi (Pmax)
11 13 14 16
L‐ L+ L‐ L+
12
11 L‐
13 L+
15
14 L‐
16 L+
I02, I09, I57, I60 I
NOTE 8
NOTE 8
1 SHD
NOTE 2
Remote Mount Position Sensor Interface Uo (Voc) = 3.53 V Io (Isc) = 12.6 mA Po = 11.1 mW Lo (La) = 10 uH Co (Ca) = 10 nF
SHD
CNT ‐
1 2 3 4
Remote Mount Position Sensor
Ui (Vmax) ≥ 3.53 V Ii (Imax) ≥ 12.6 mA (^2) Pi (Pmax) ≥ 11.1 mW 3
CNT ‐
1 +
NOTE 9
(SOL1) (SOL2) PWR1)(SOL PWR2)(SOL TOPSW+ TOPSW‐ BTMSW+ BTMSW‐
D 11 12 13 14 15 16 17 18
L‐ L+ L‐ L+ L‐ L+ L‐ L+
I41, I
Notes
Fig. 11 Control wiring, ND9000F/P, Ex ’ic’ for Zone 2 / Division 2
NONHAZARDOUSLOCATION HAZARDOUSLOCATIO N
FISCO ’ic’ Power Supply / Barrier Uo (Voc) ≤ 32 V Io (Isc) ≤ 380 mA Po ≤ 5.32 W
ND9000F/P Valve Positioner
Fieldbus Input X102 (^) Ui (Vmax) = 32 V Ii (Imax) = 380 mA Pi (Pmax) = 5.32 W Li = 10 uH Ci = 5 nF
1 2
‐ 3 SHD Earthing terminal (internal)
Earthing terminal (external)
NOTE 1NOTE 1 (^) NOTE 1
Limit Switches
Ui (Vmax) Ii (Imax) Pi (Pmax) Li Ci
Ex i Barrier
Uo (Voc) ≤ Ui (Vmax) Io (Isc) ≤ Ii (Imax) Po ≤ Pi (Pmax)
11 13 14 16
L‐ L+ L‐ L+
12
11 L‐ 13 L+
15
14 L‐
16 L+
I02, I09, I57, I60 I
NOTE 8
NOTE 8
NOTE 2
(SOL1) (SOL2) PWR1)(SOL PWR2)(SOL SW+TOP TOPSW‐ BTMSW+ BTMSW‐
D 11 12 13 14 15 16 17 18
L‐ L+ L‐ L+ L‐ L+ L‐ L+
I41, I
Remote Mount Position Sensor Interface Uo (Voc) = 5.0 V Io (Isc) = 17.8 mA Po = 22.2 mW Lo (La) = 10 uH Co (Ca) = 10 nF
SHD
CNT ‐
1 2 3 4
Remote Mount Position Sensor
Ui (Vmax) ≥ 5.0 V Ii (Imax) ≥ 17.8 mA (^2) Pi (Pmax) ≥ 22.2 mW 3
CNT ‐
1 +
NOTE 9
Notes
Fig. 12 Control wiring, ND9000 and ND7000, Ex d
Fig. 13 Control wiring, ND9000F and ND9000P, Ex d
Control system Uout max 30 V
Control system Uout max 30 V
ND9200H_T ND7200H_T
P osition T ransmitter
ND9200F ND9200P
Entity Parameters: Ui ≤ 32.0 V
Entity Parameters: Uo ≤ Ui
connect the cable shield to earth ground
Associated apparatus