
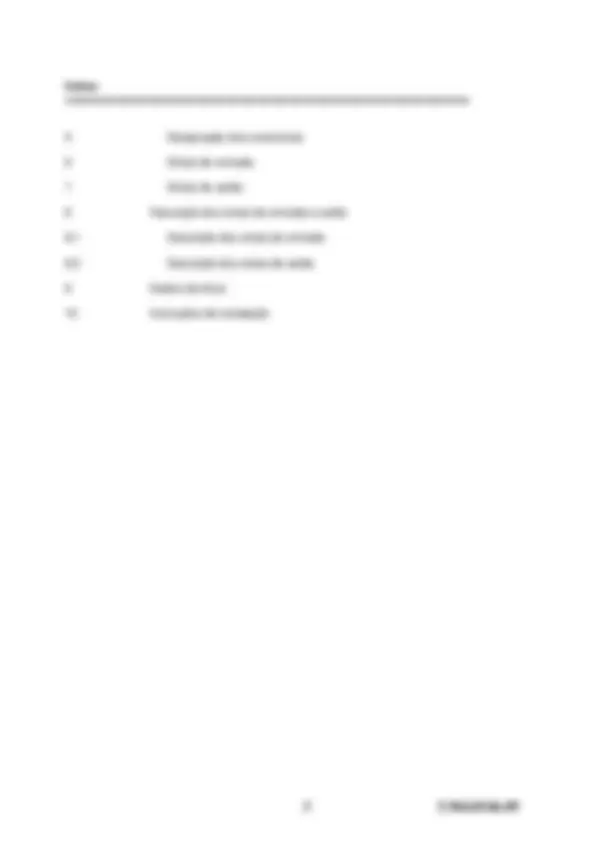
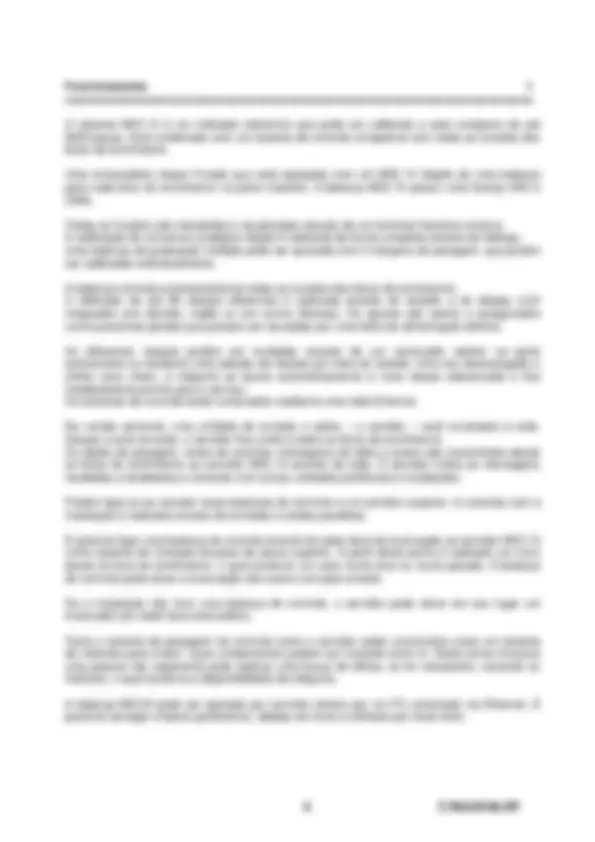
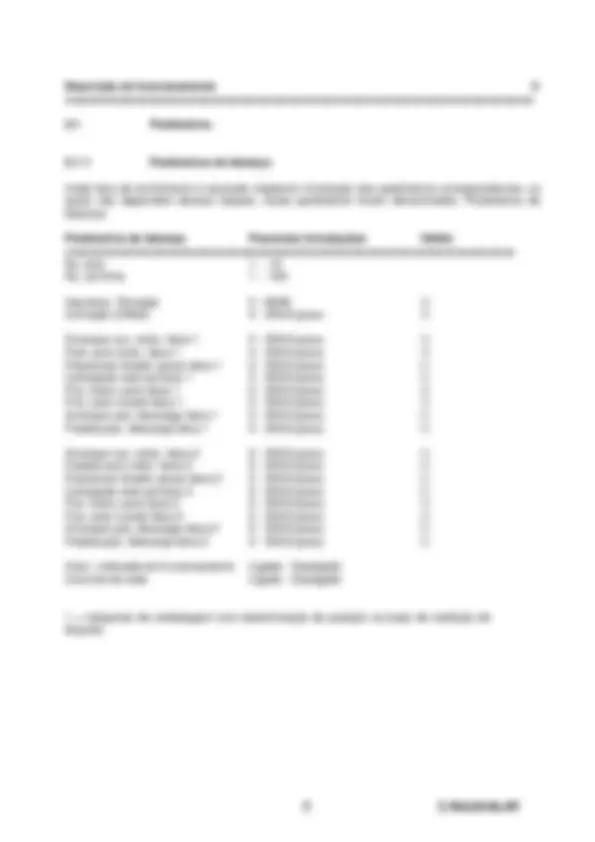
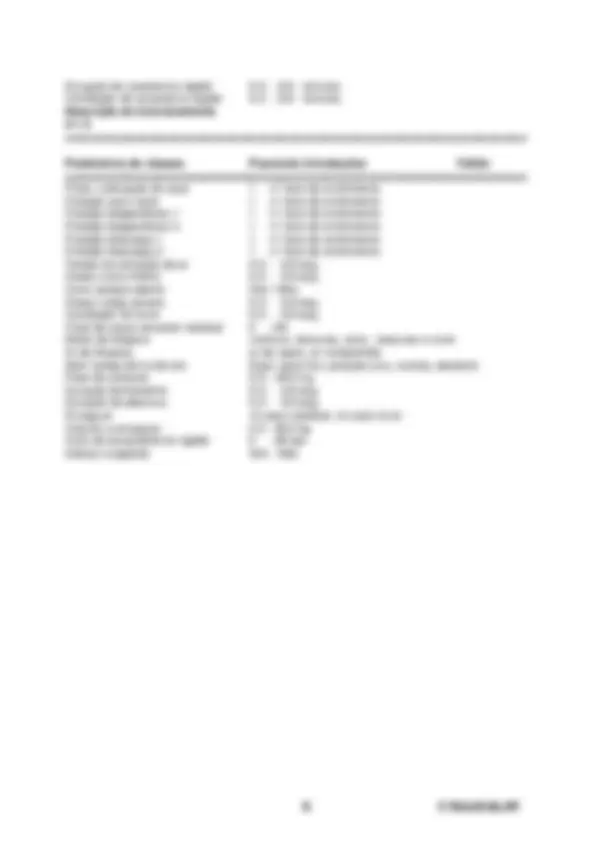
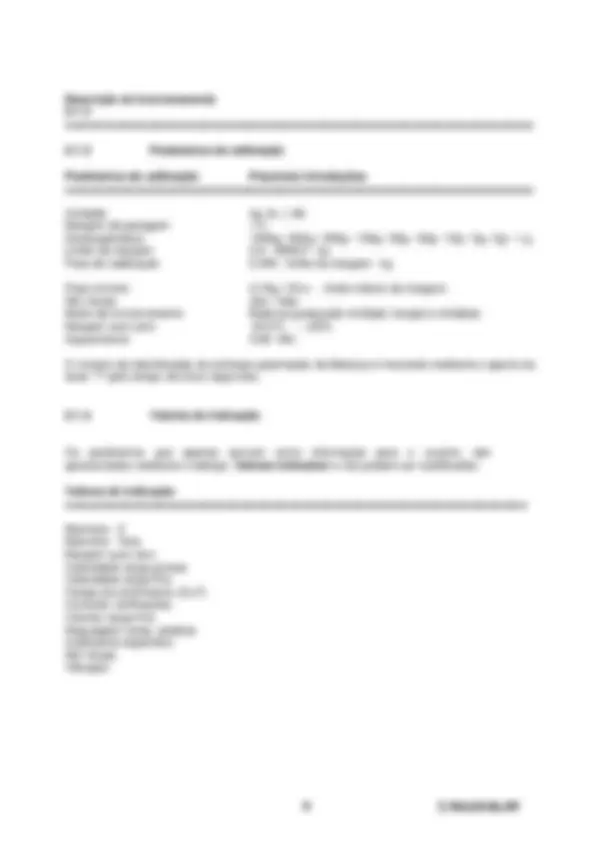
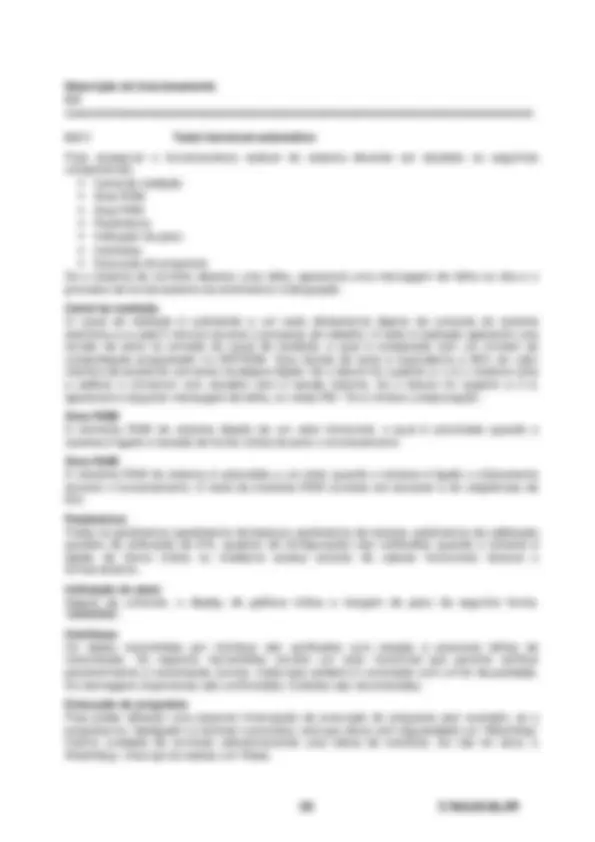
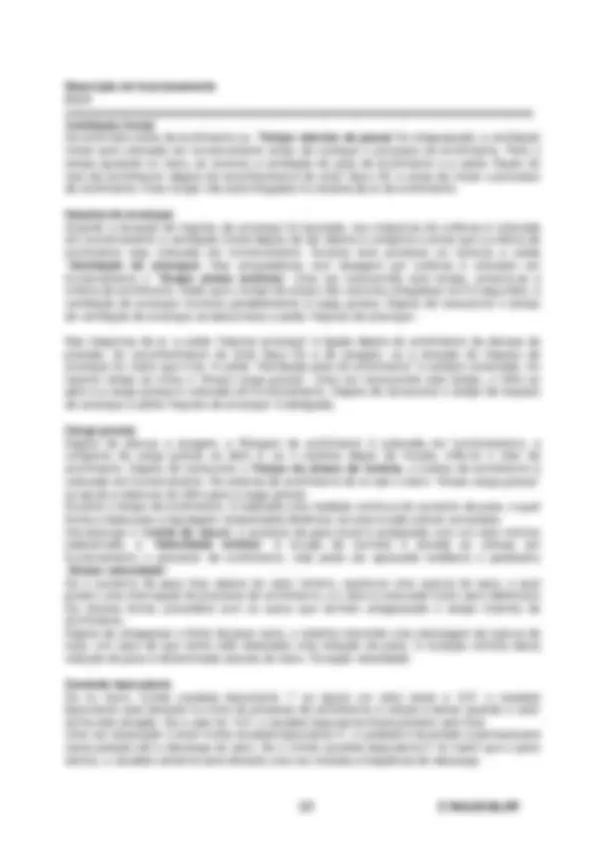
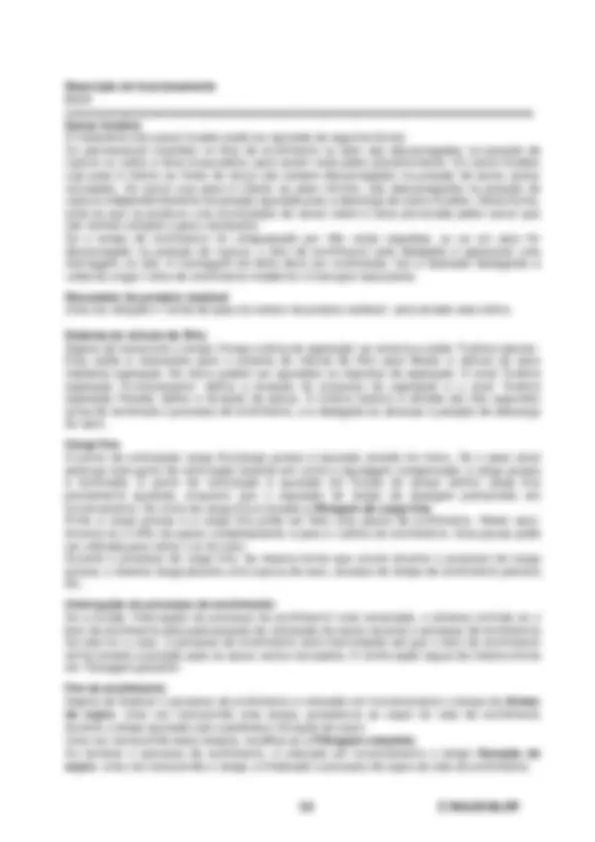
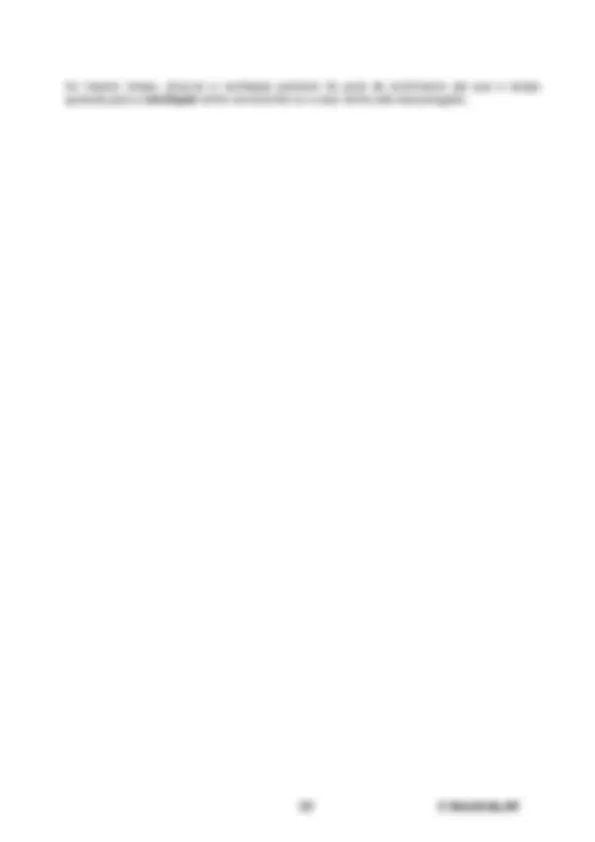
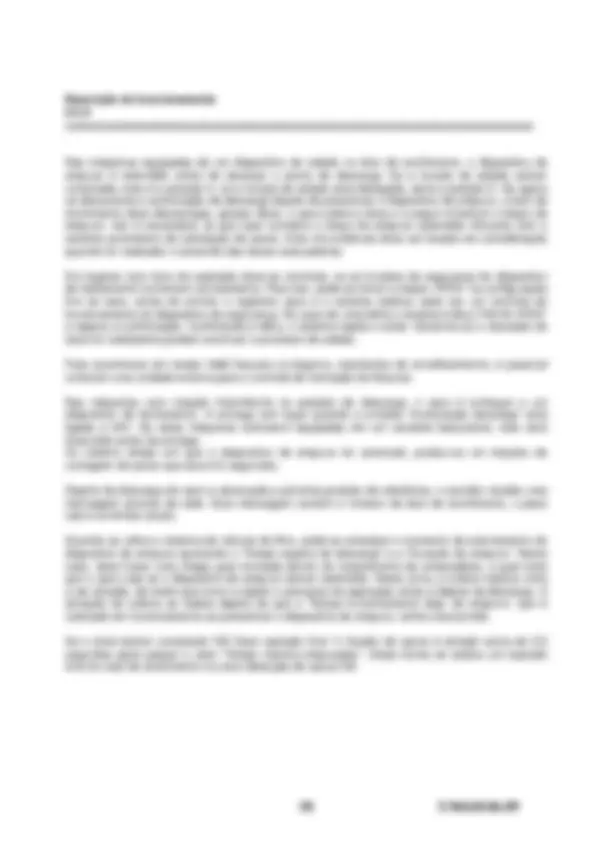

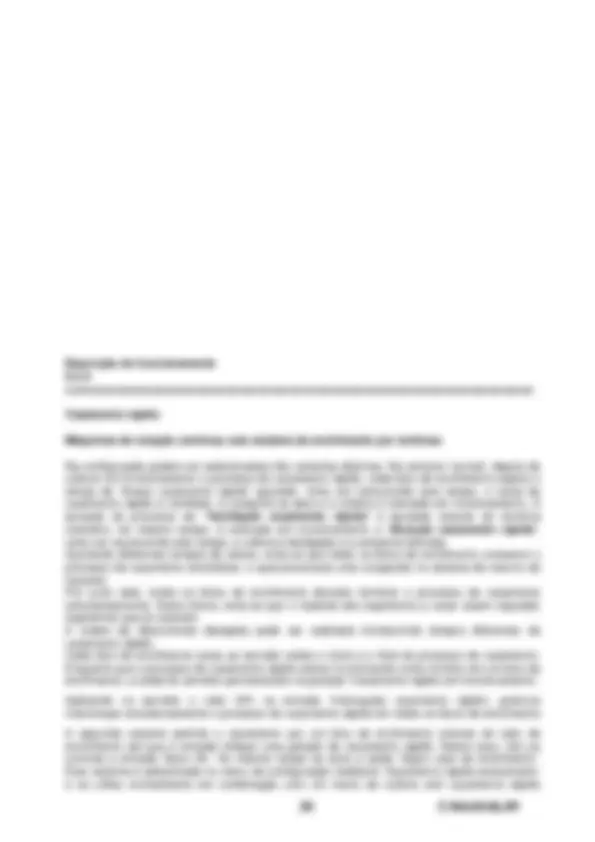
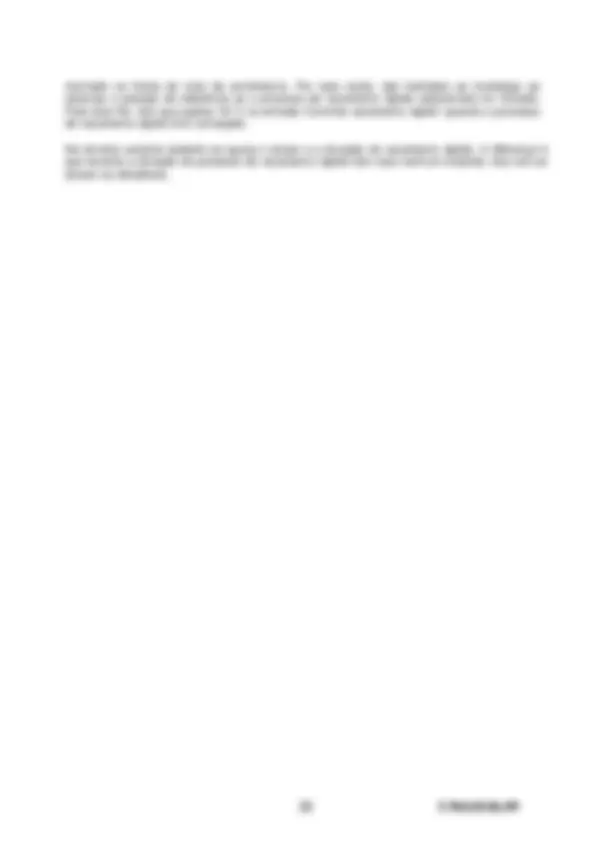
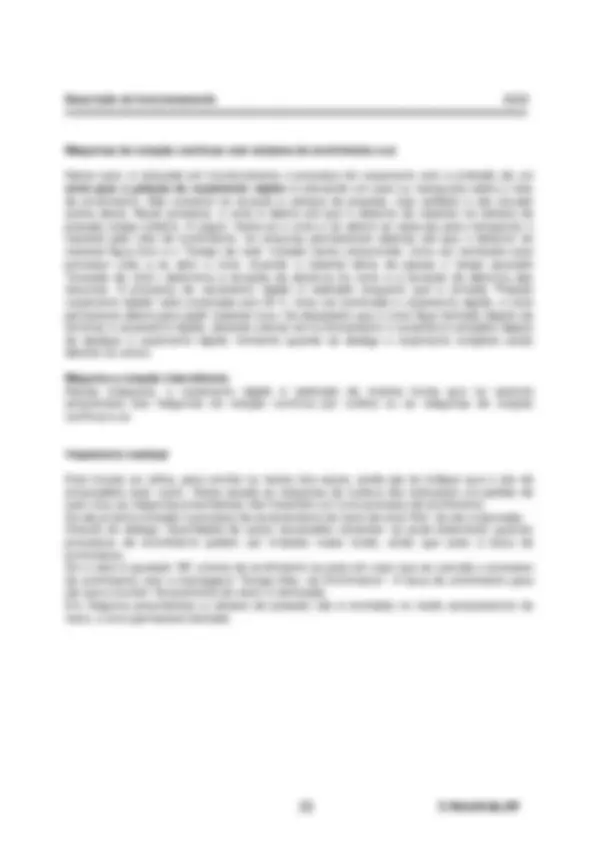
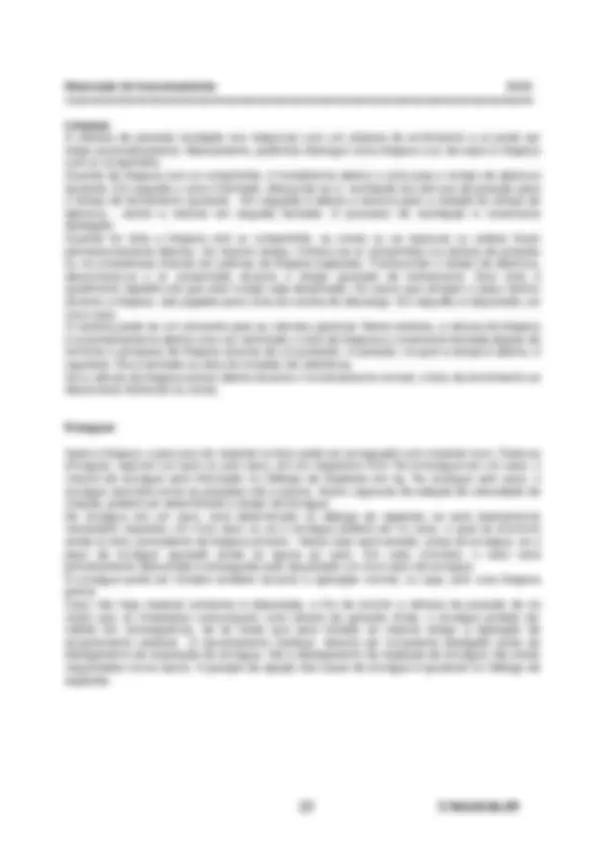
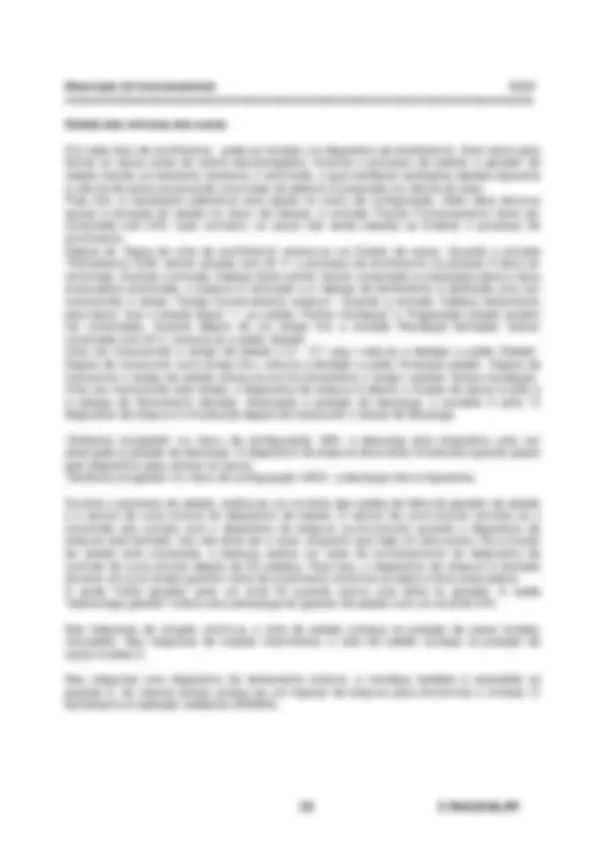
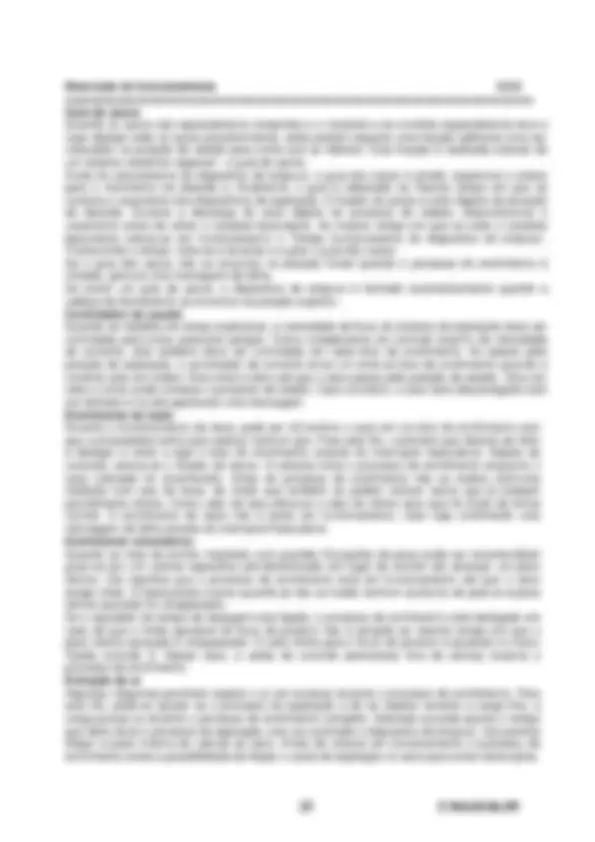
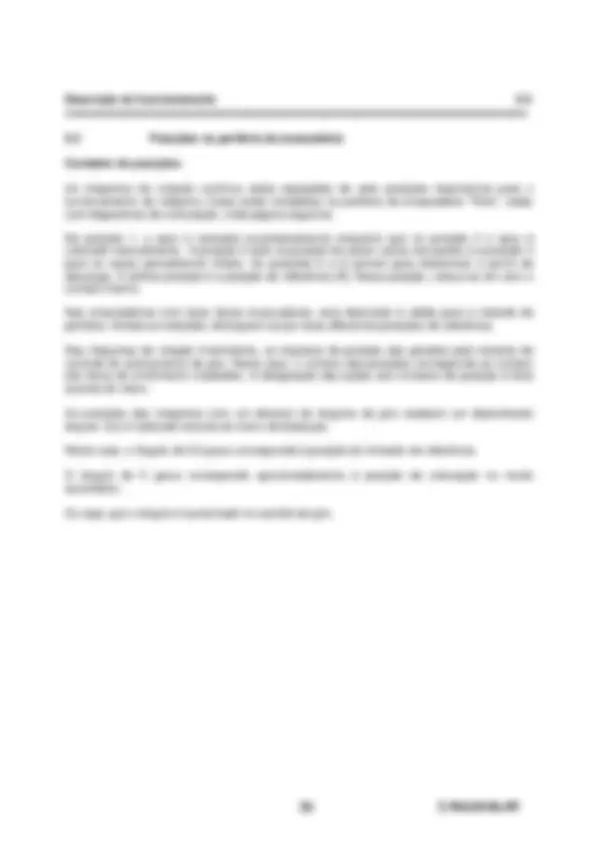
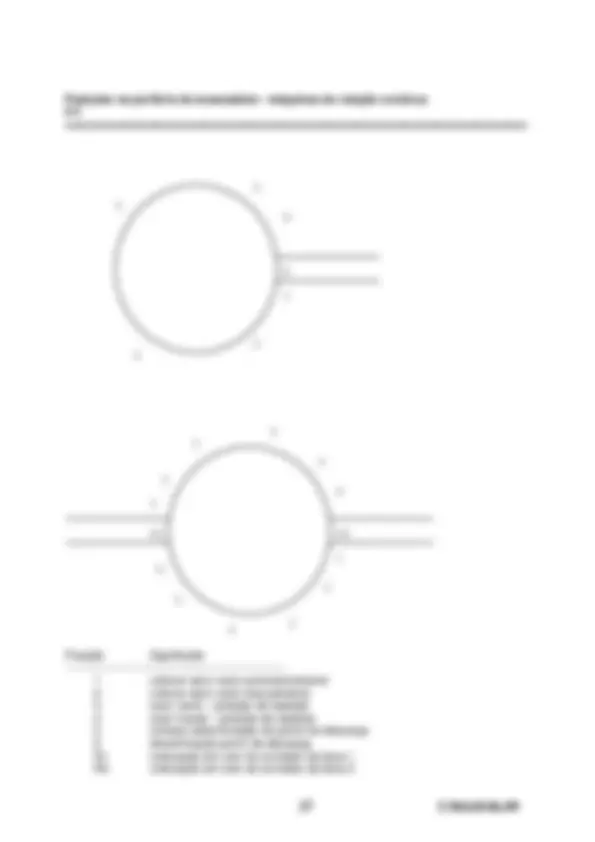
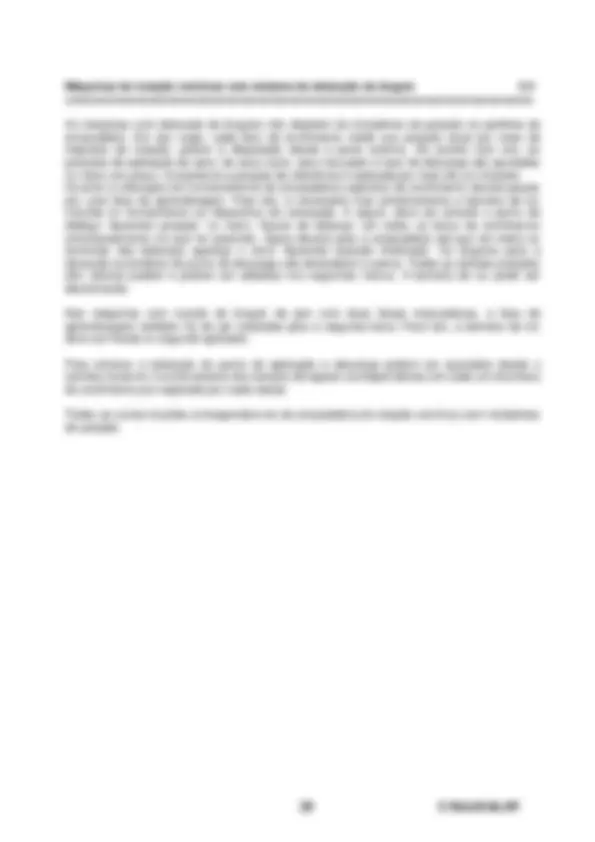
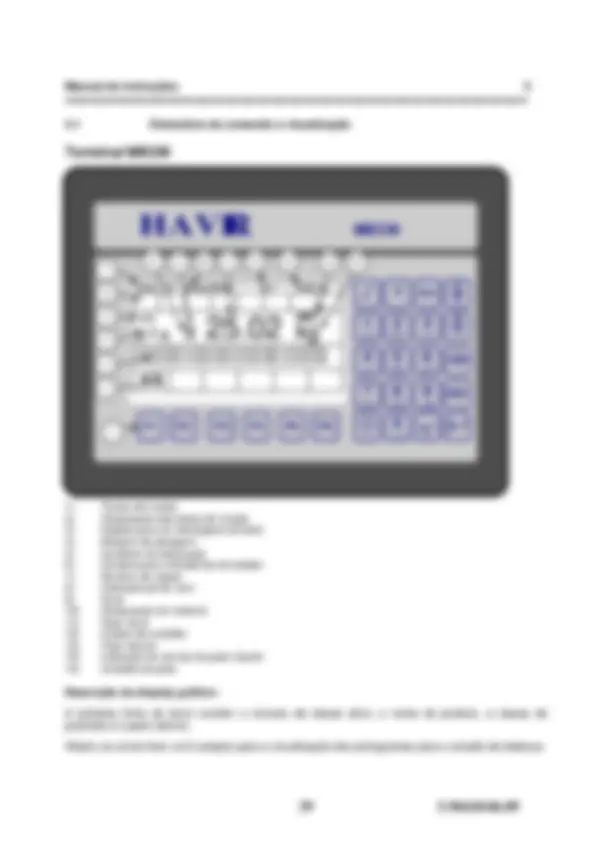

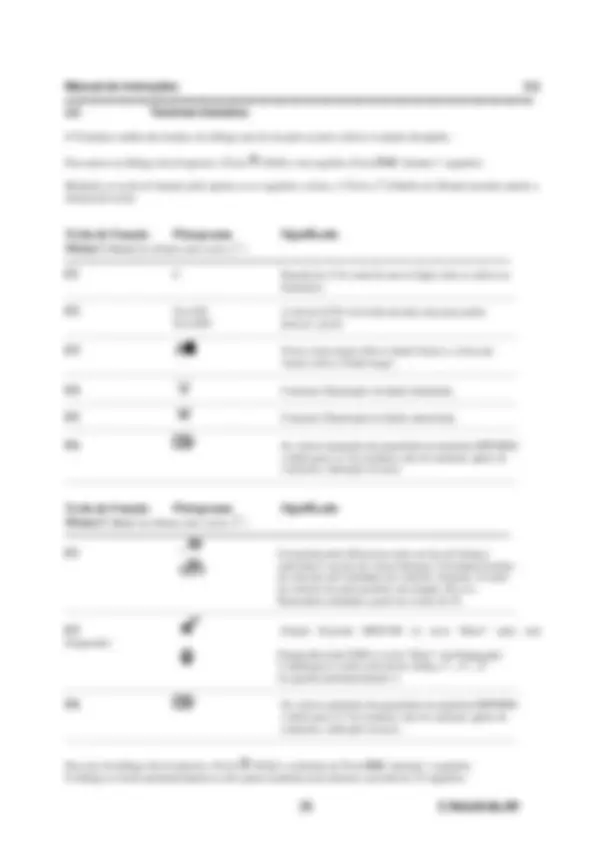
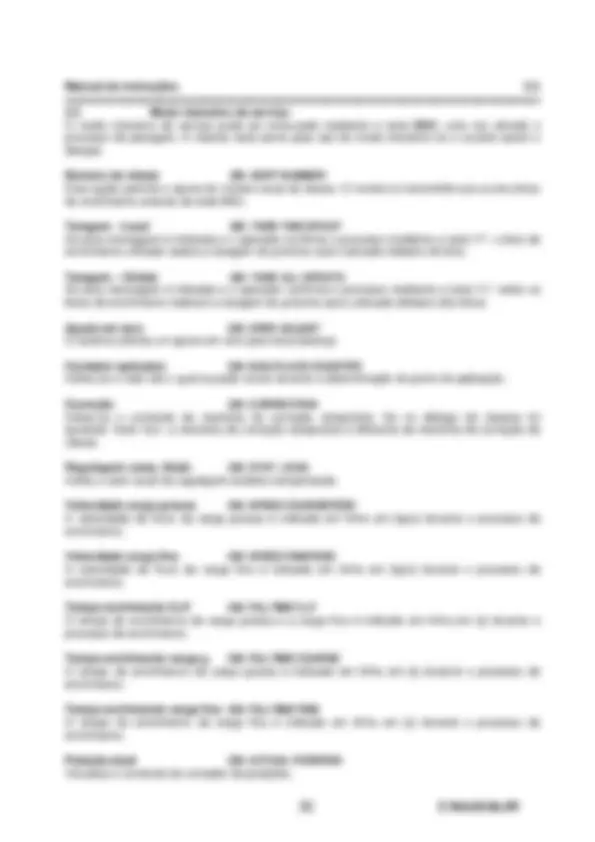
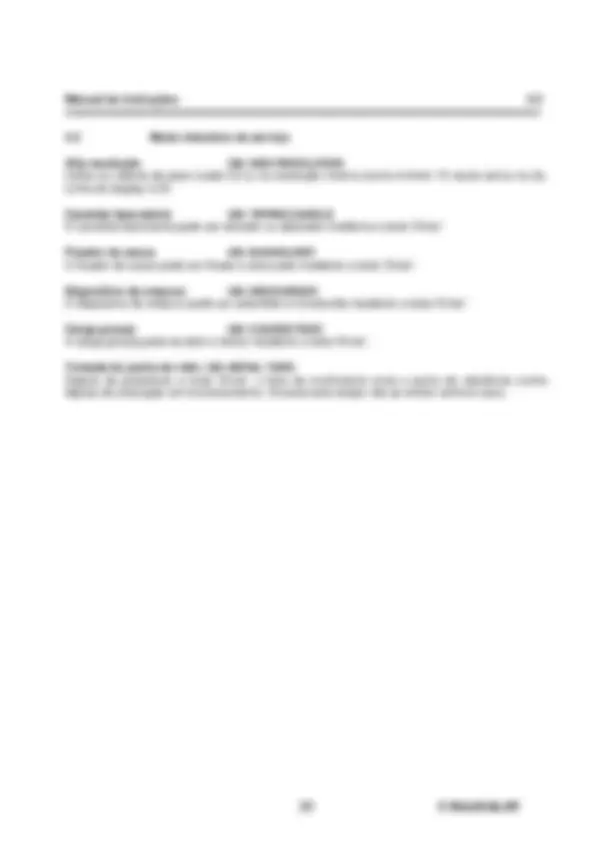
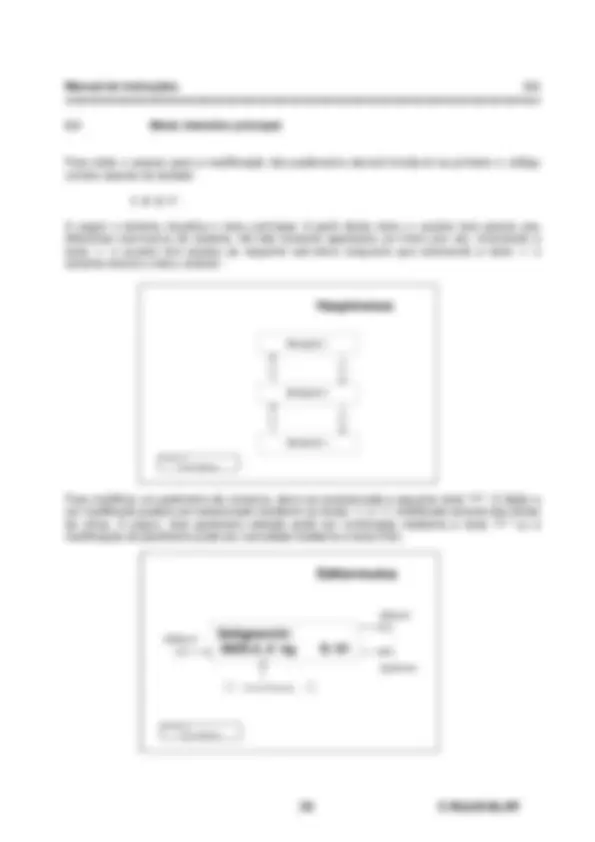
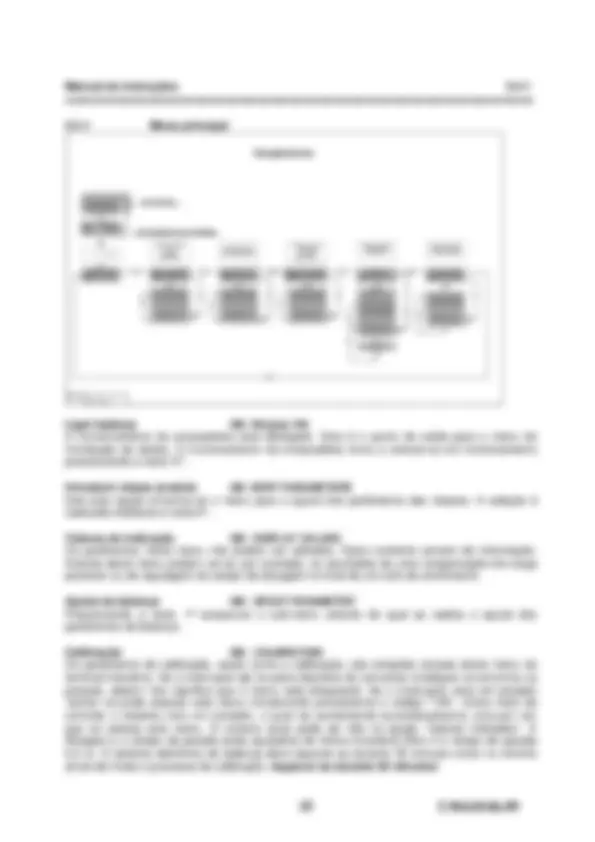
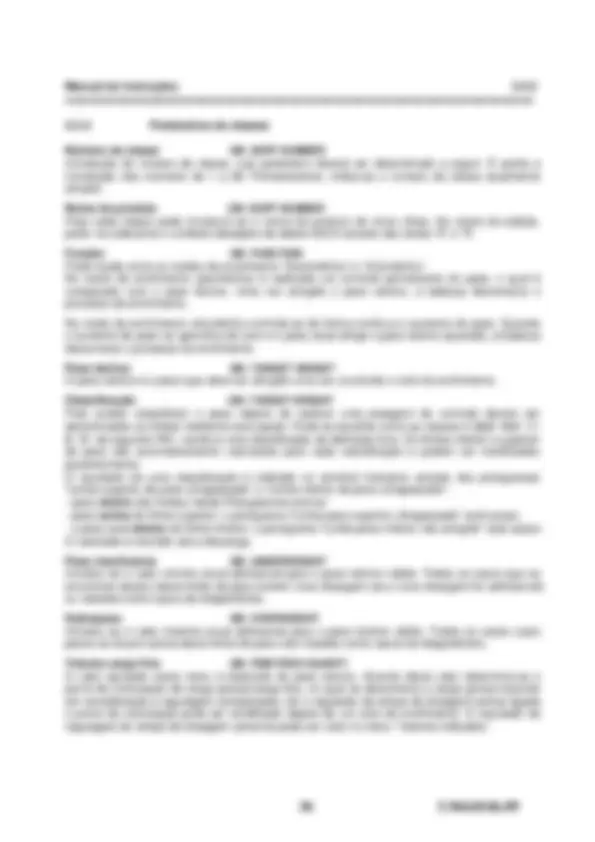
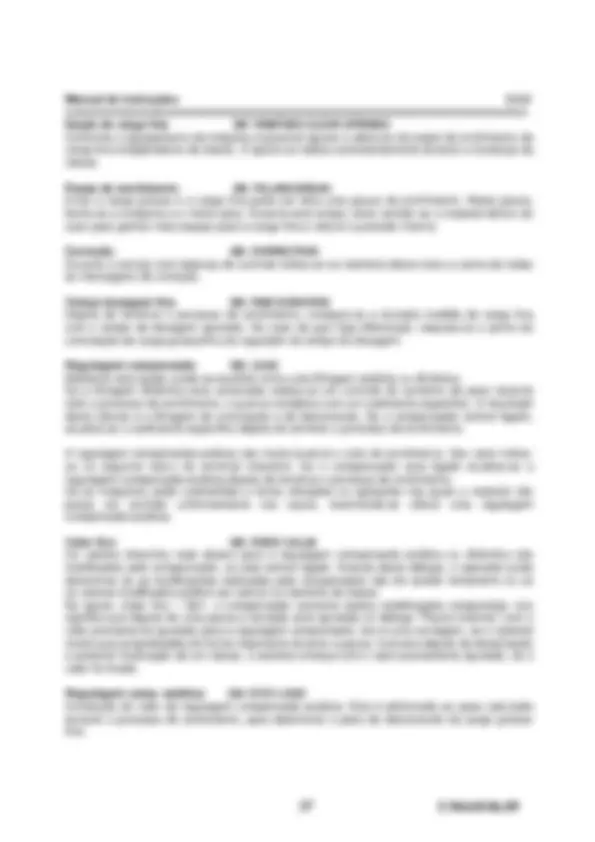
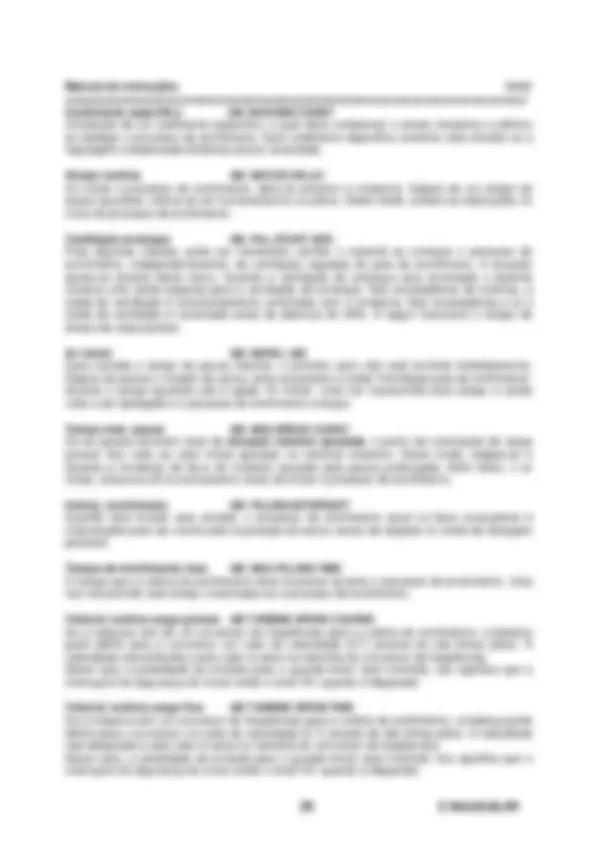
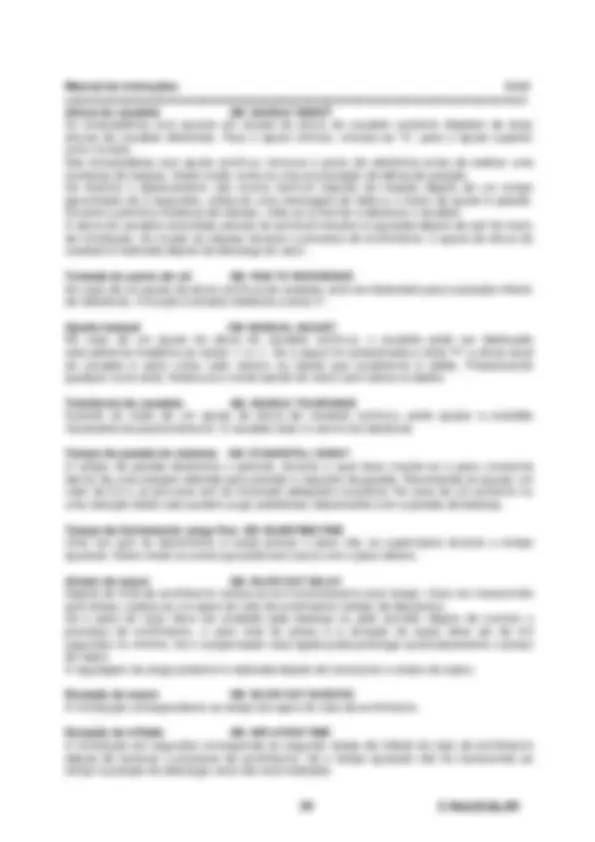
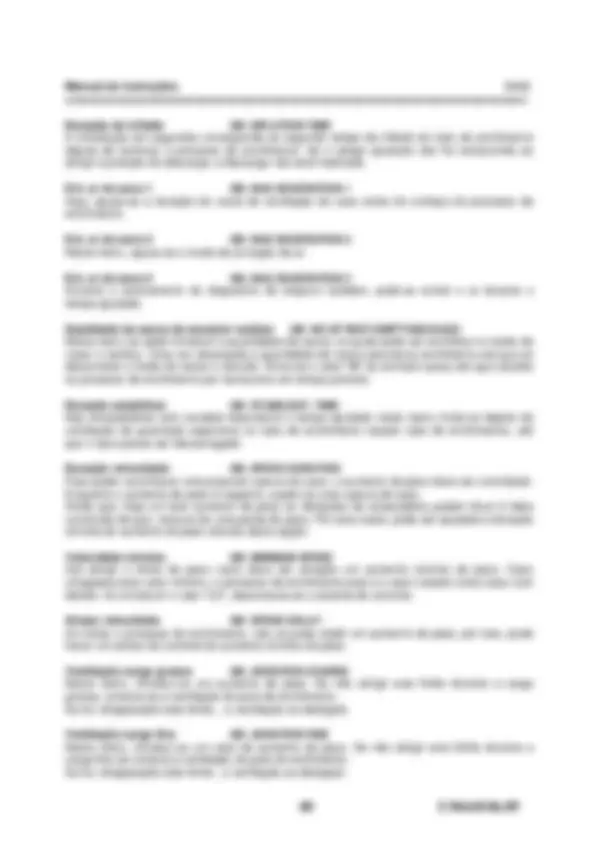
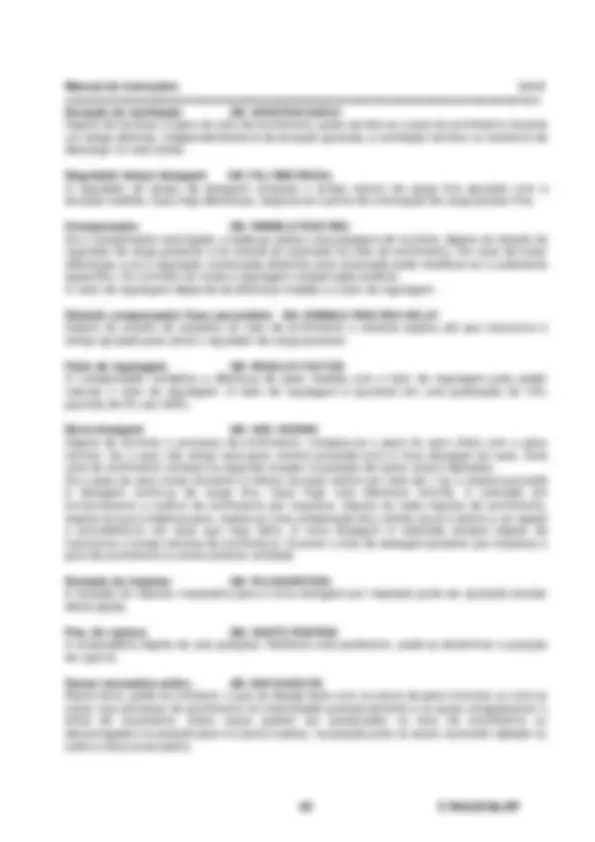
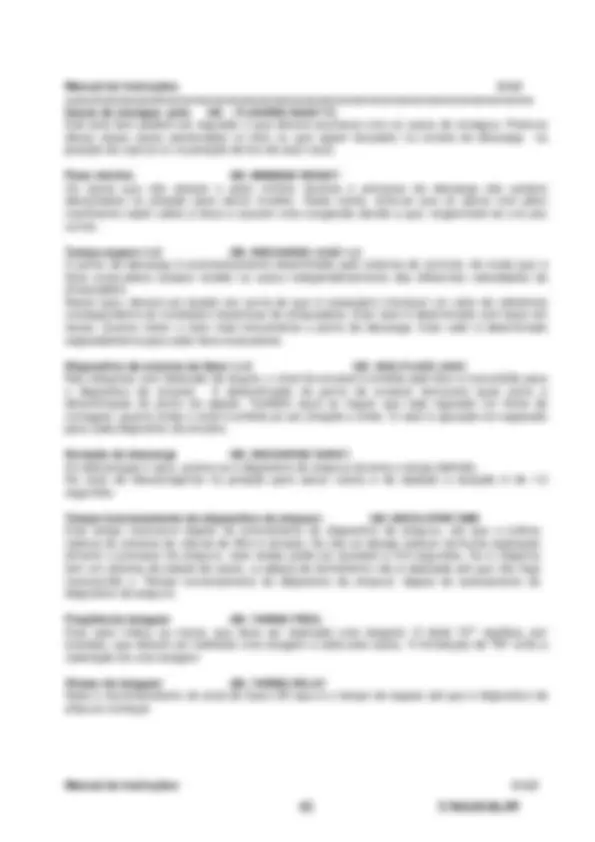
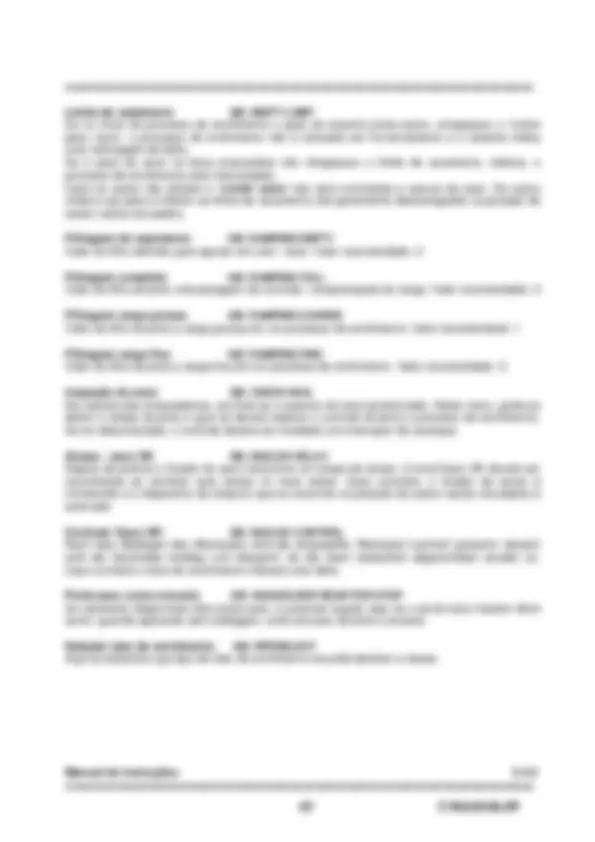
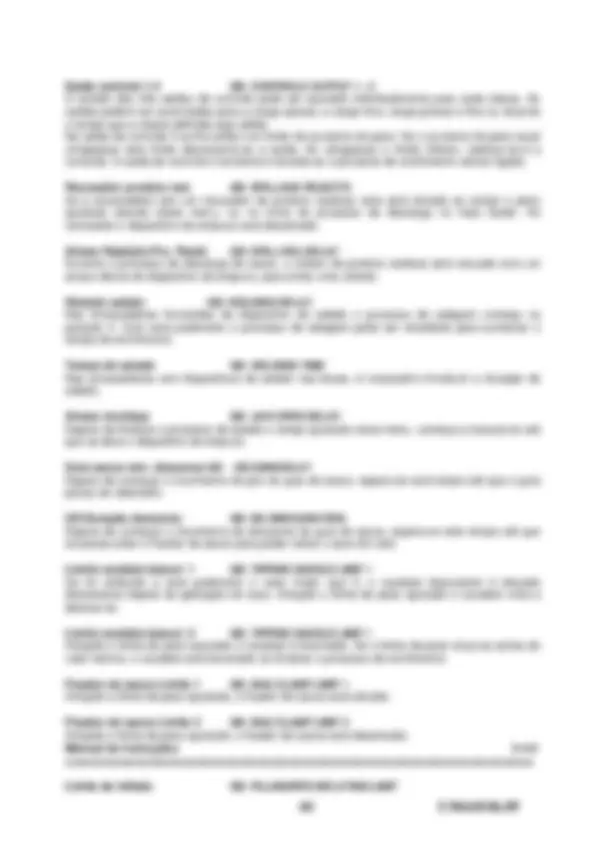
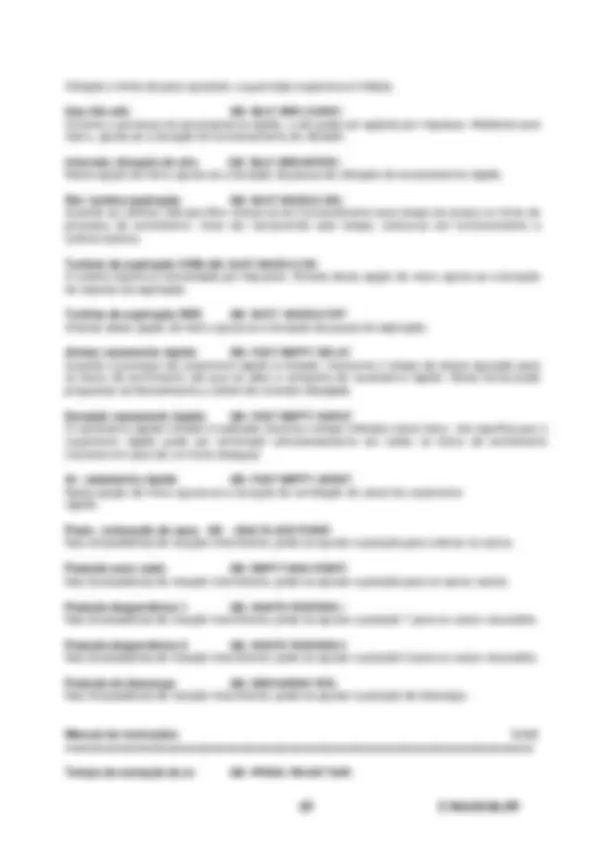
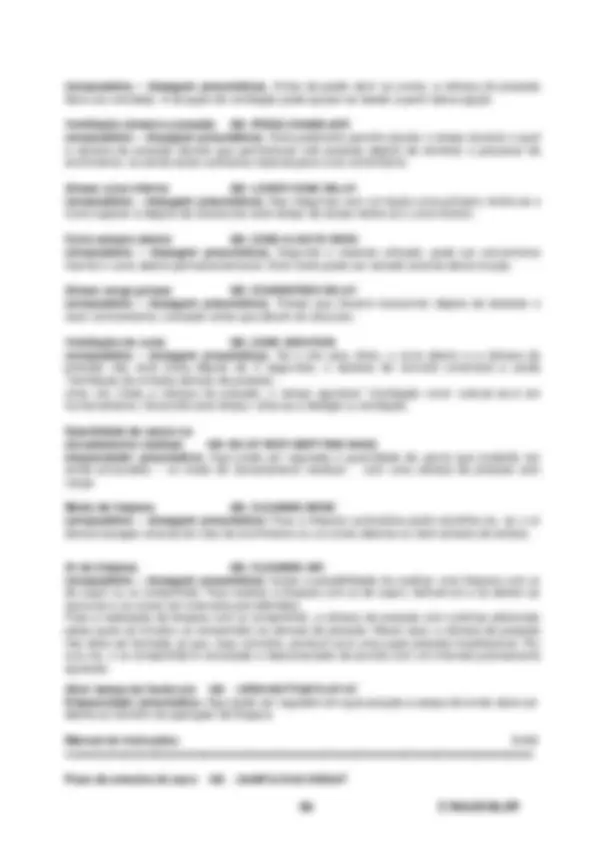
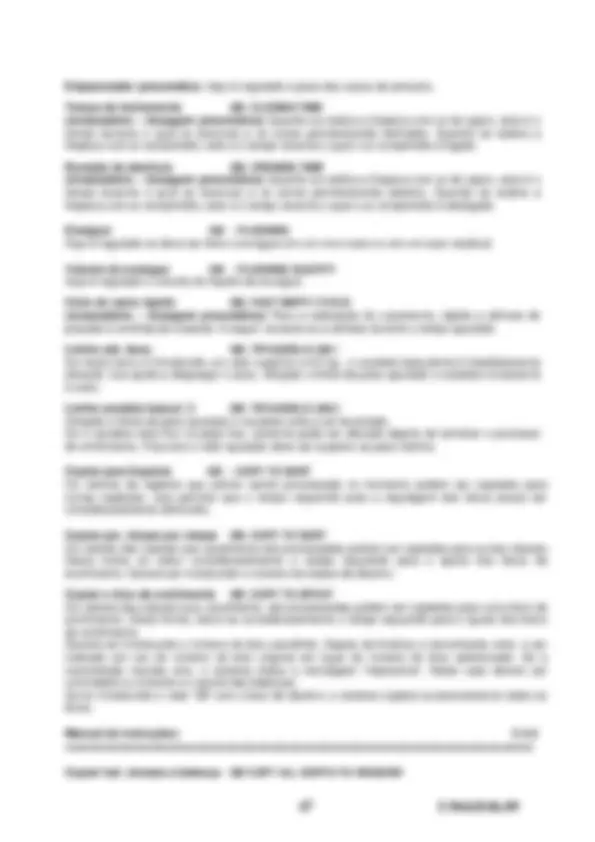
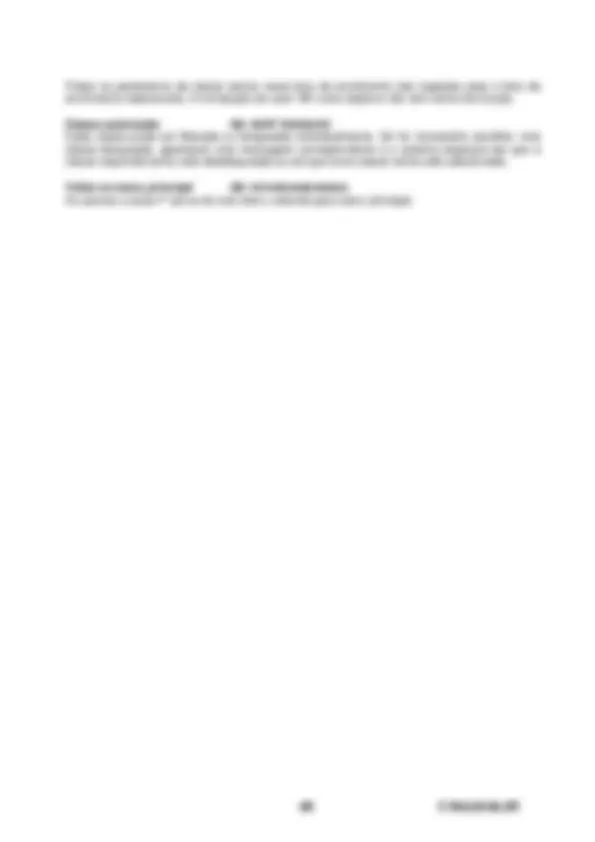
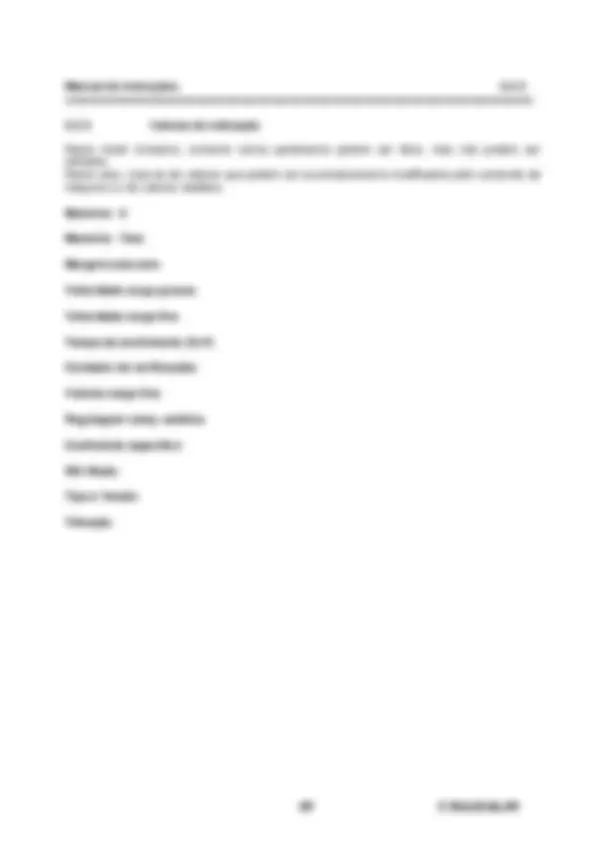
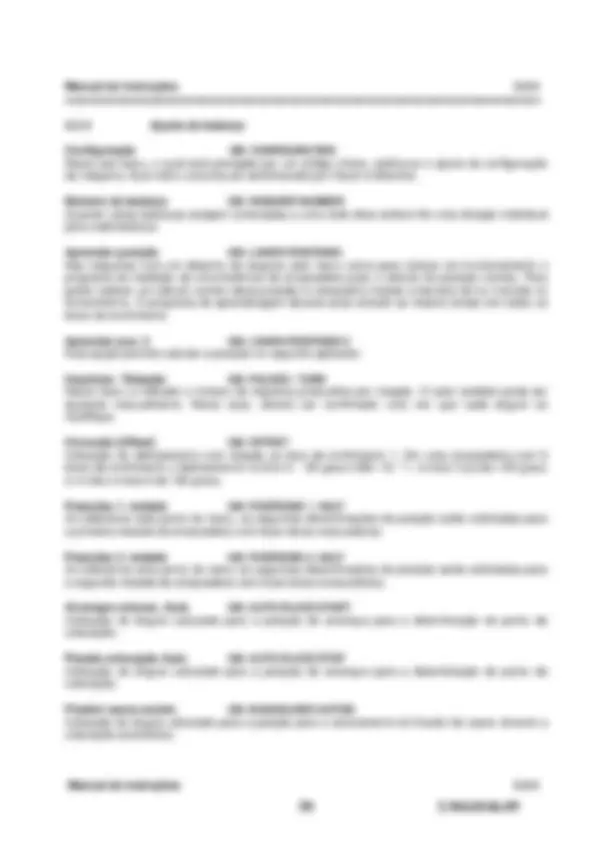
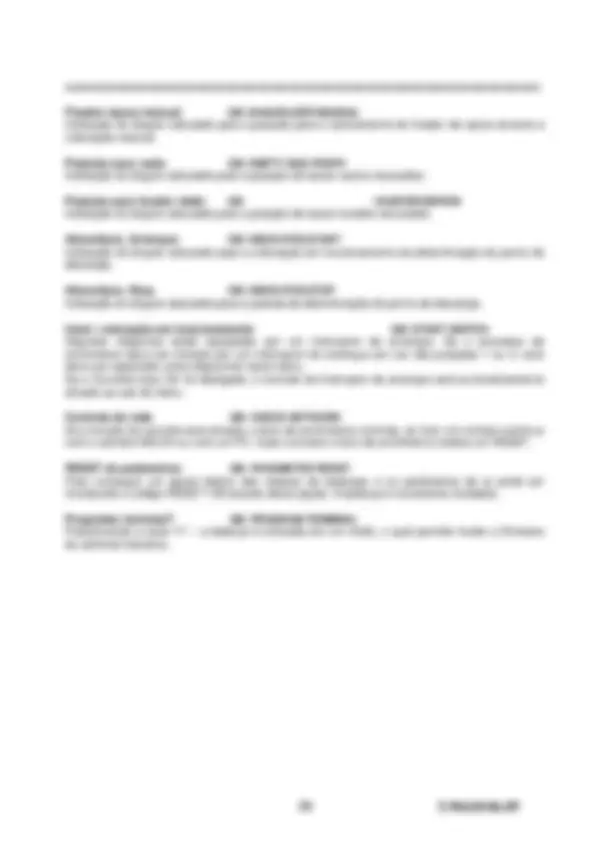
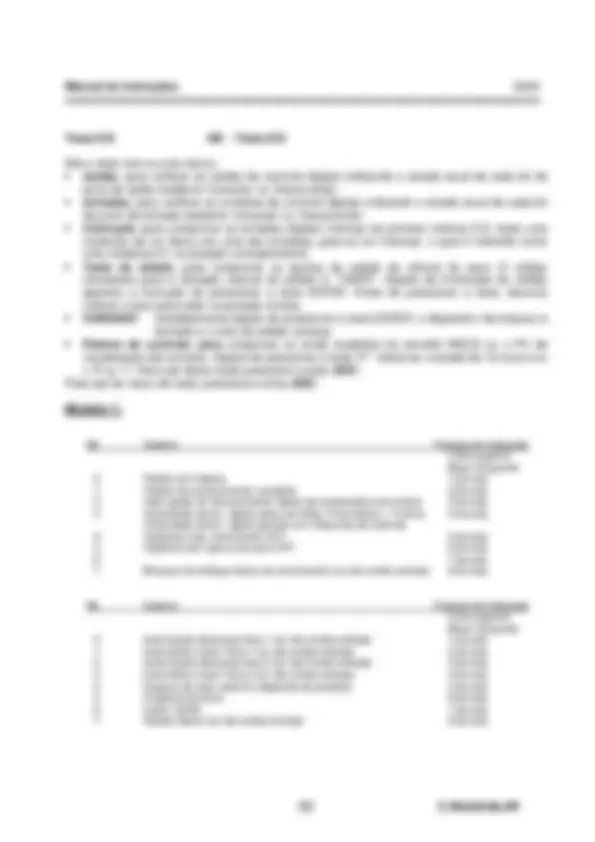
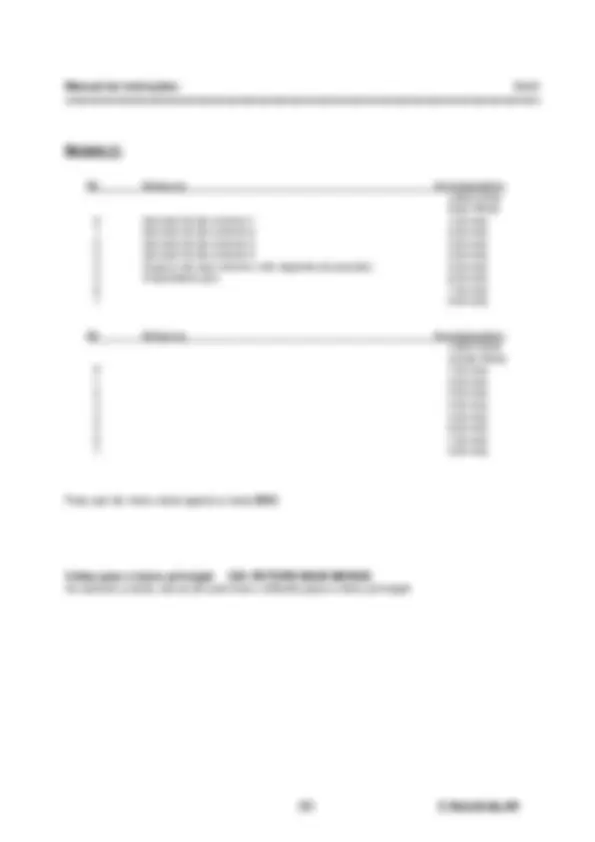
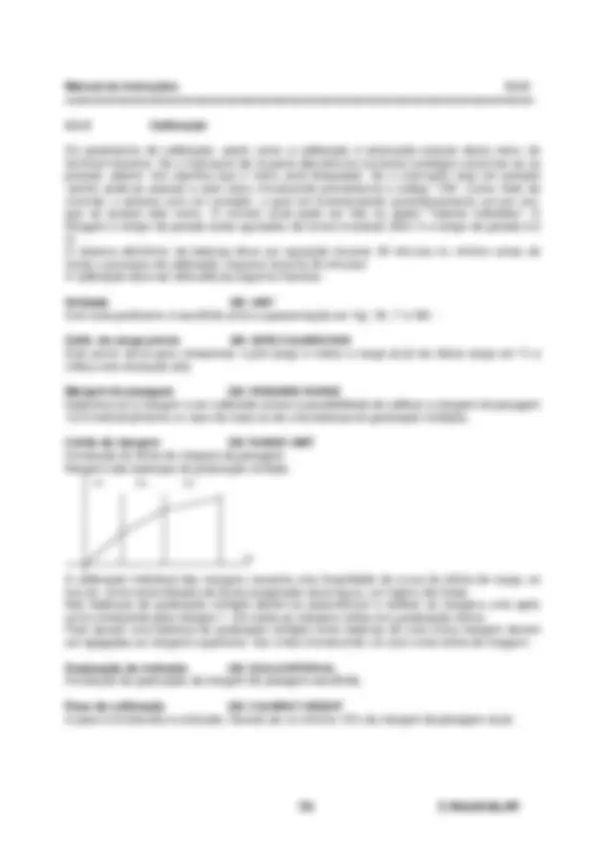
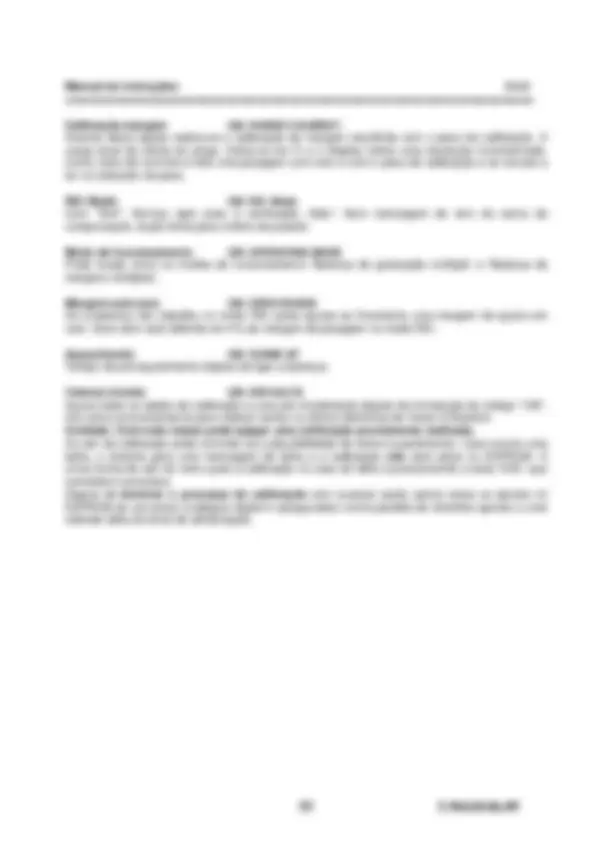
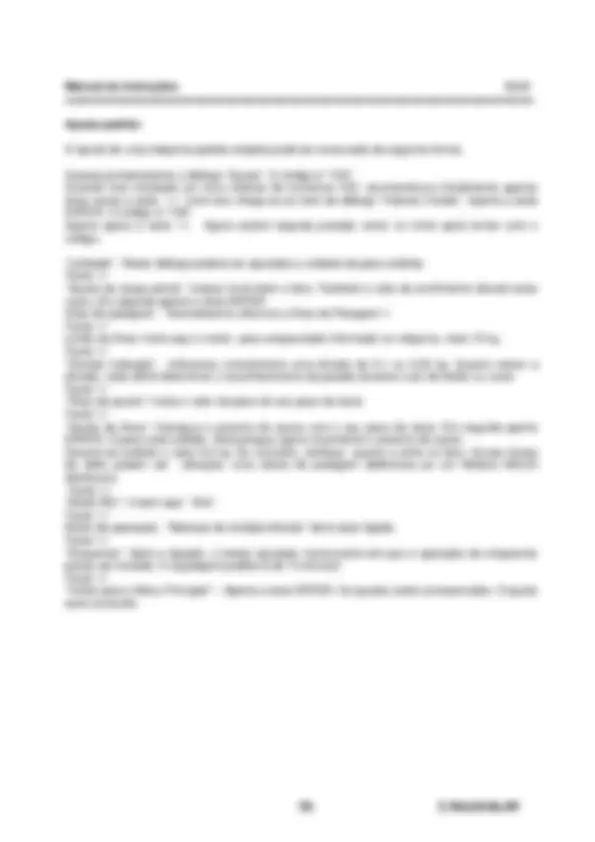
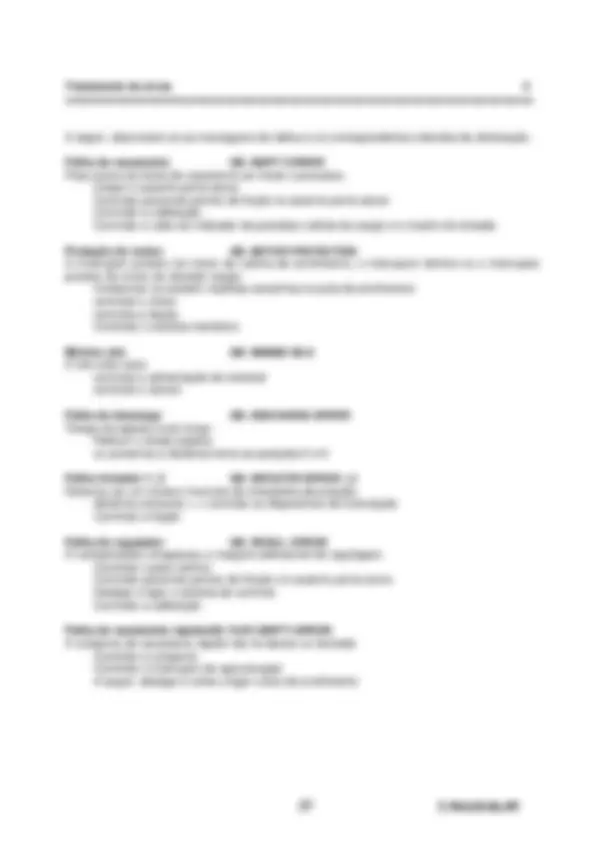
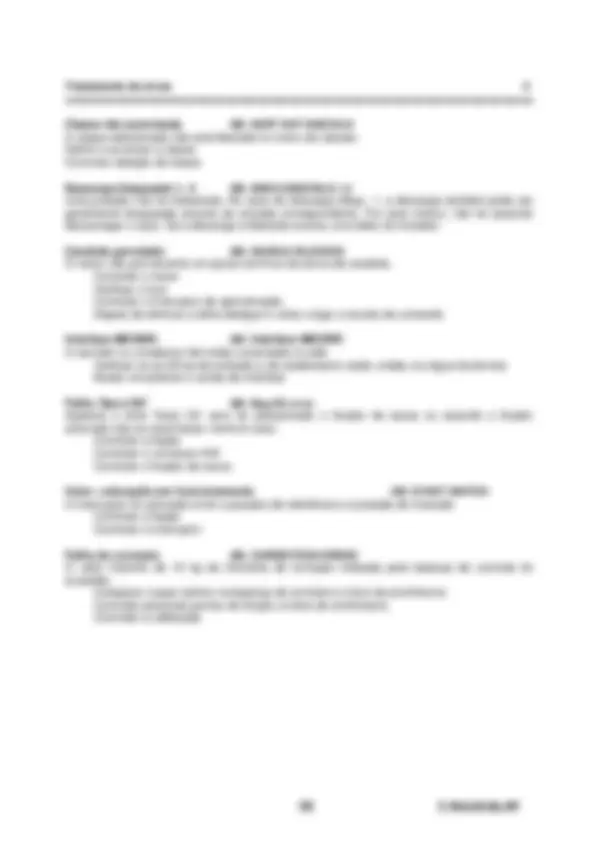
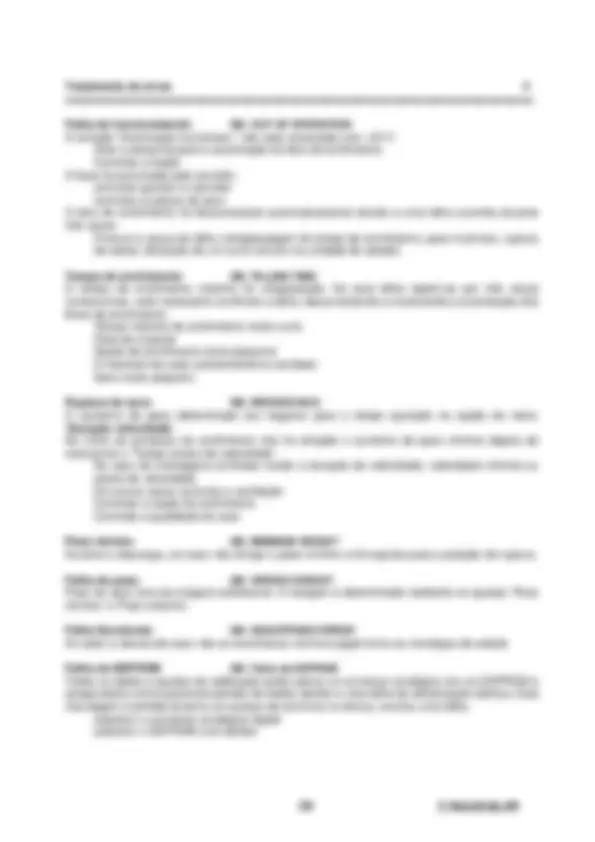
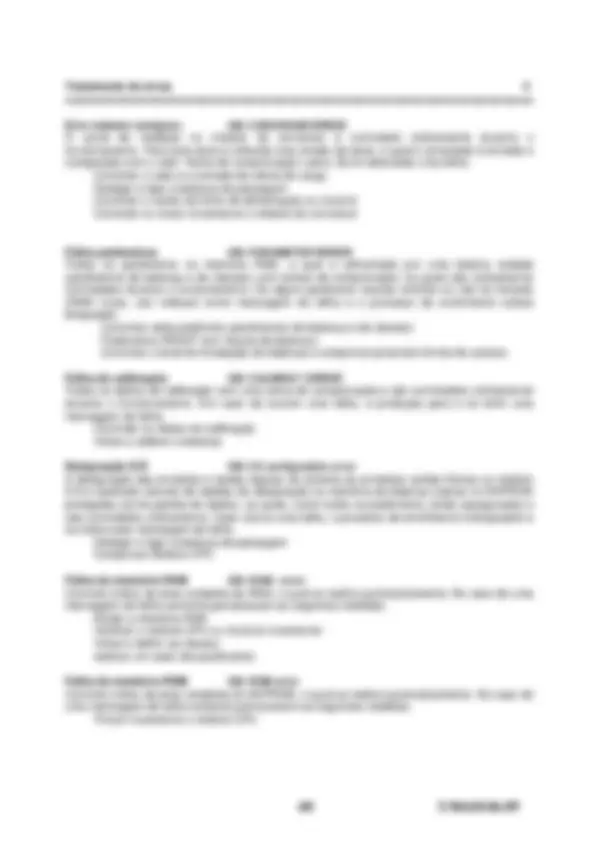
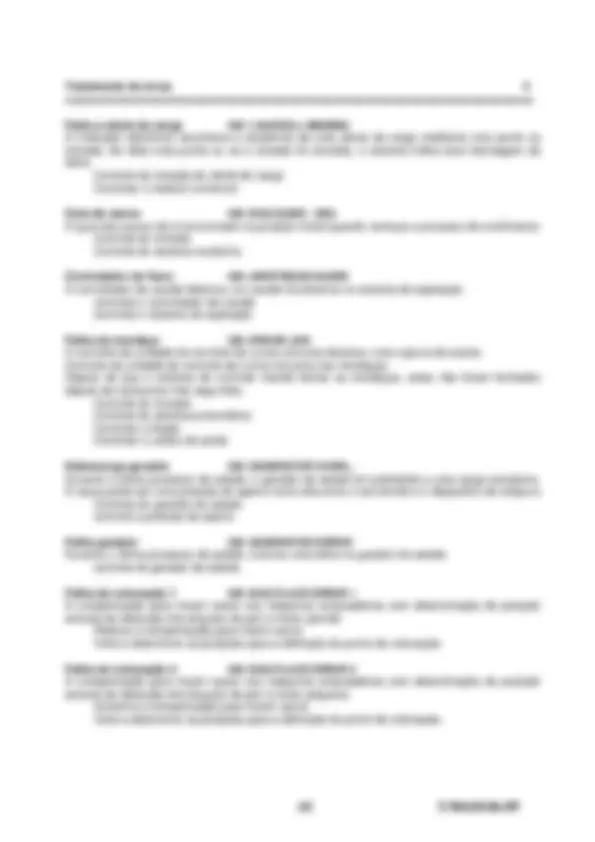
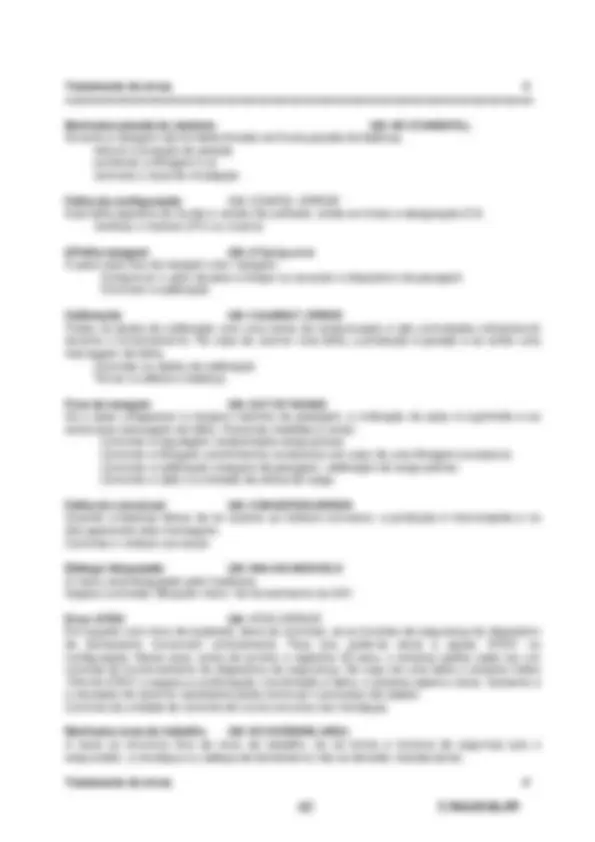
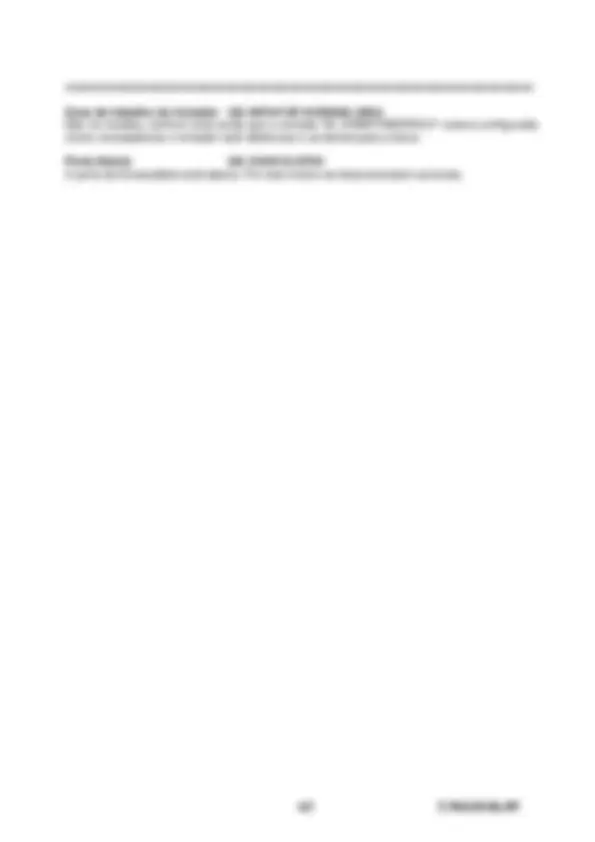
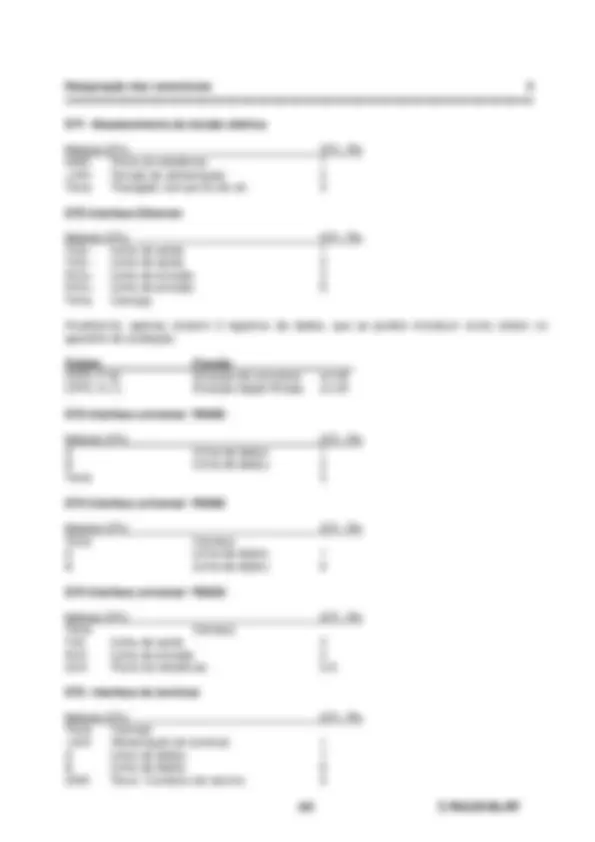
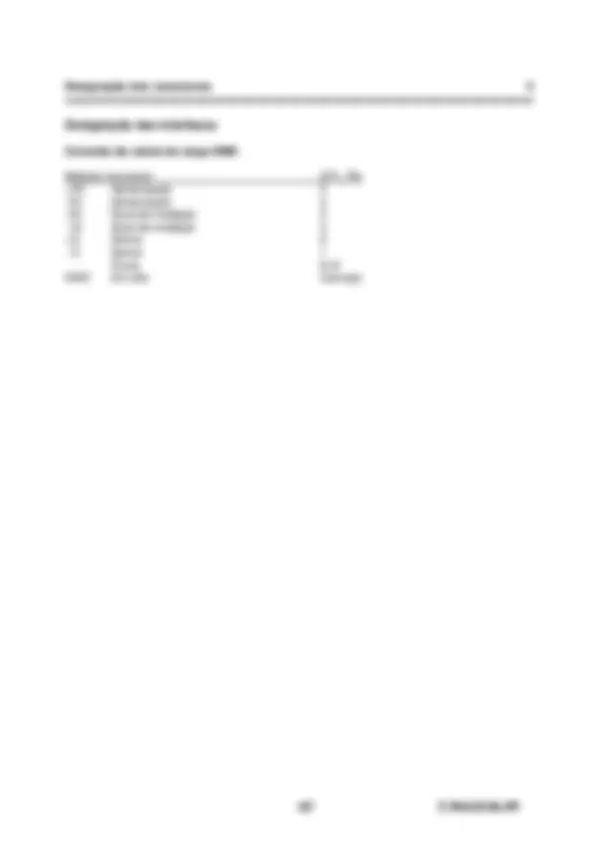
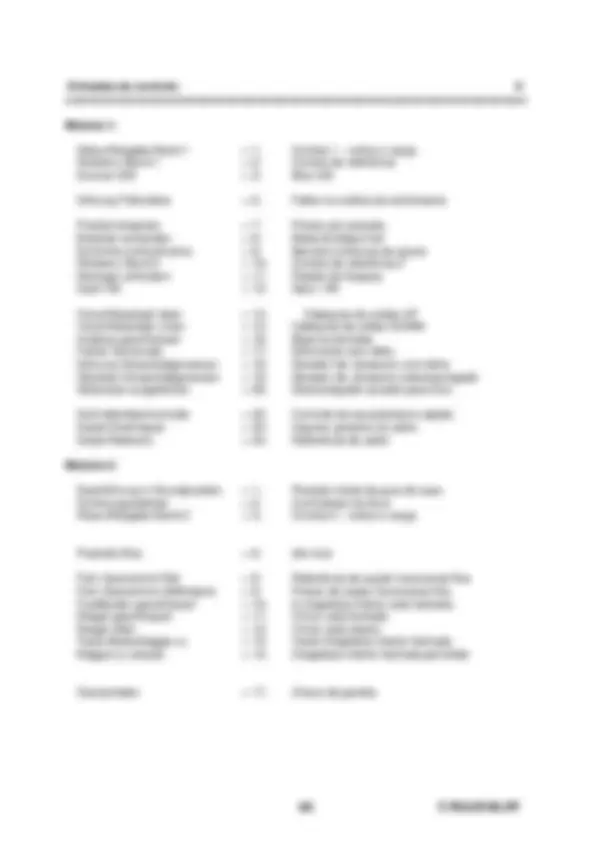
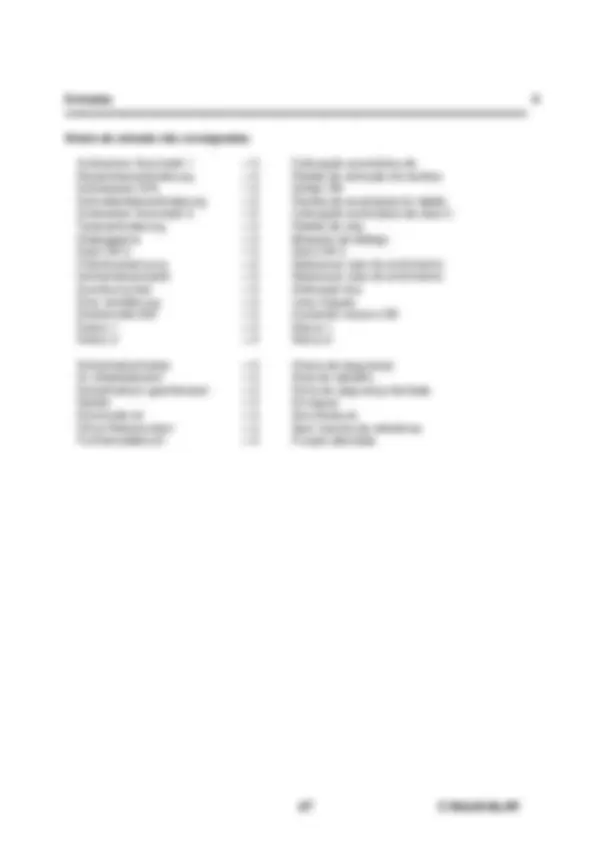
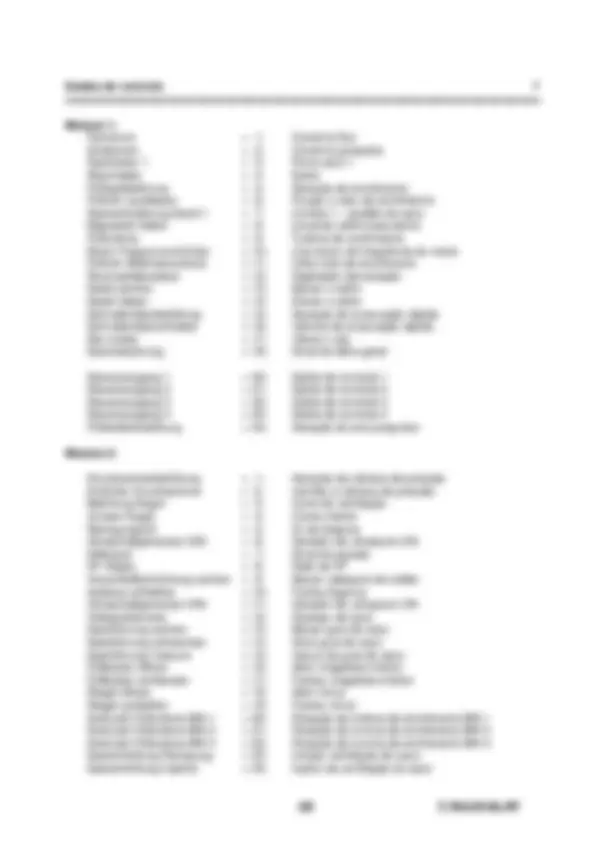
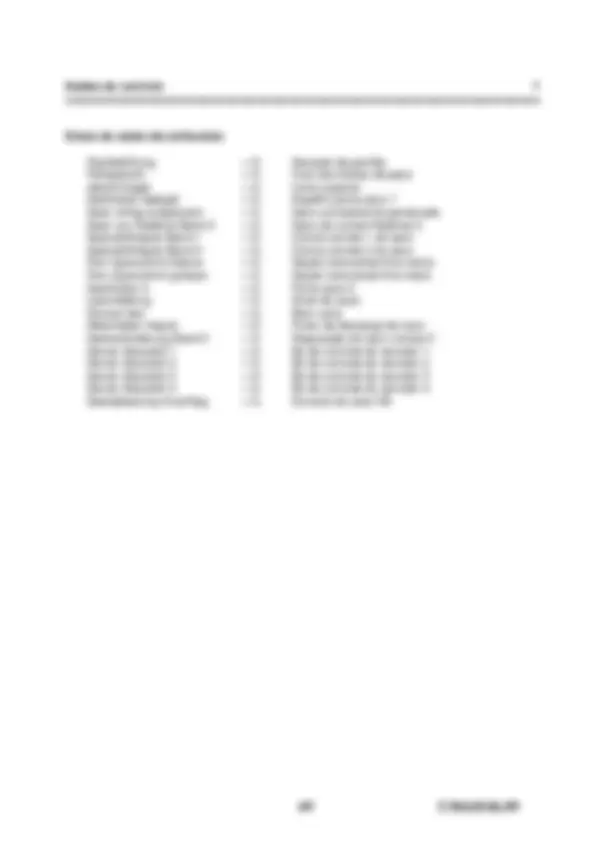
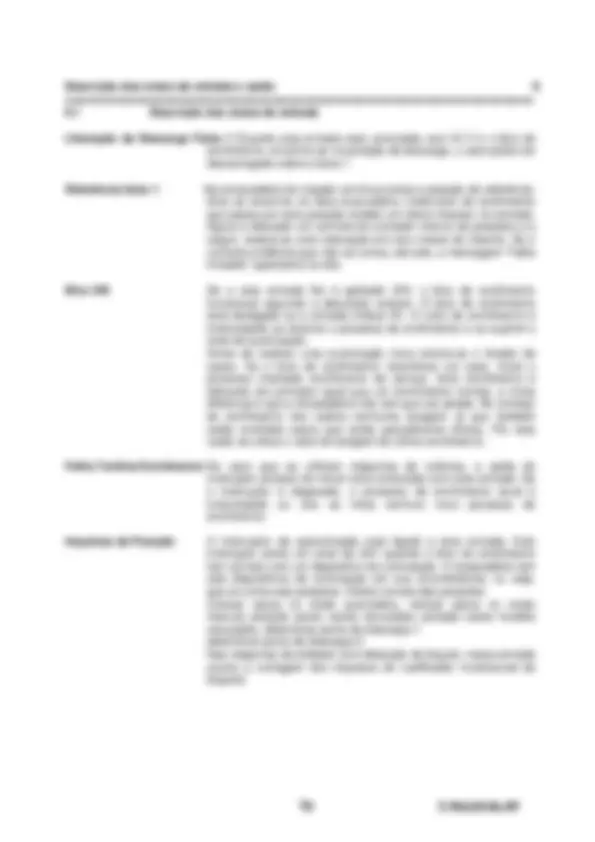
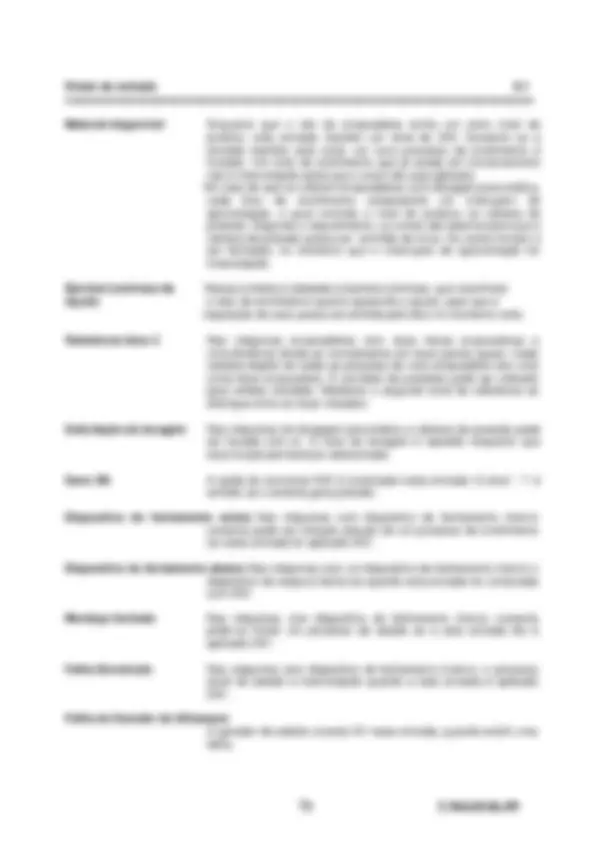
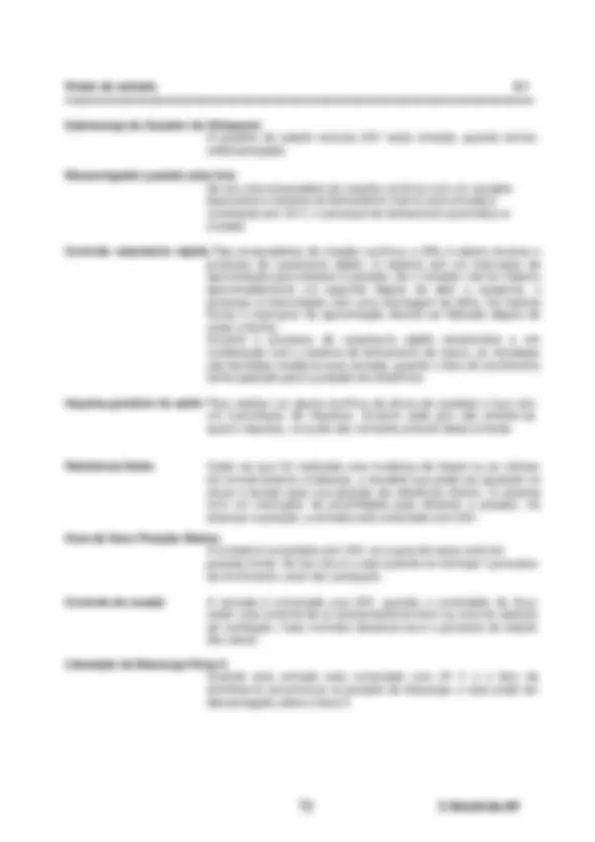
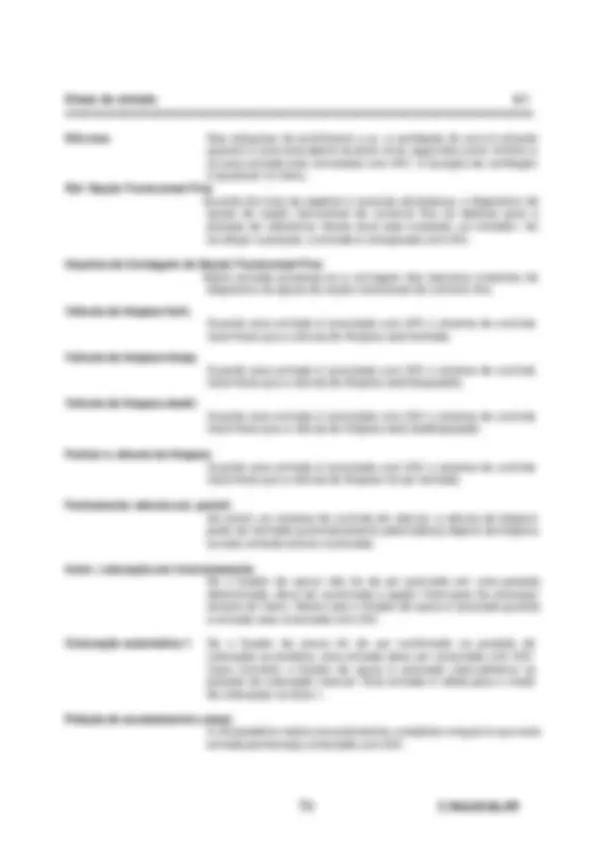
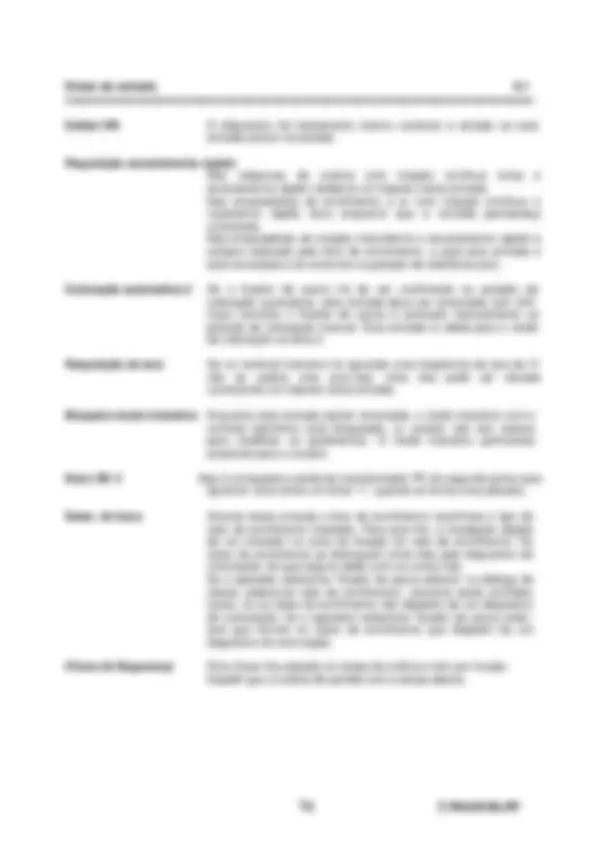
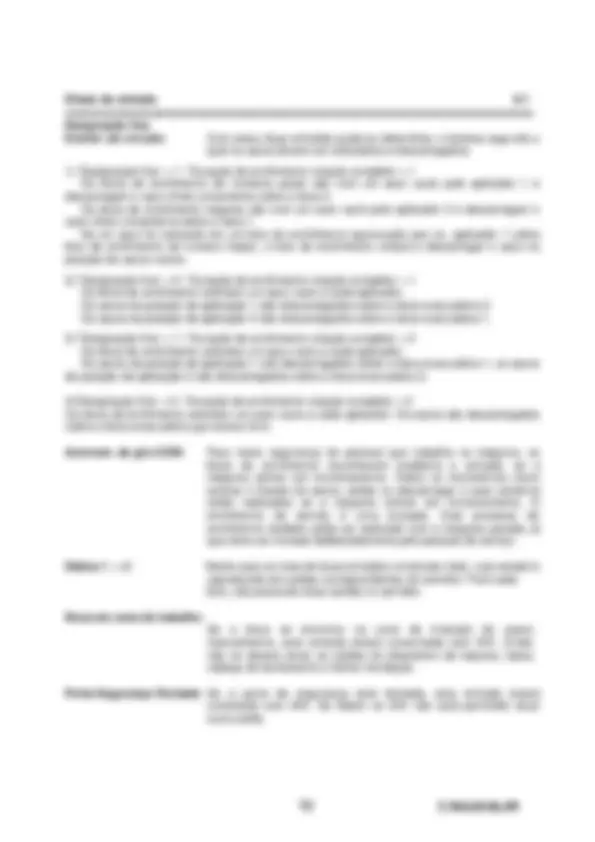
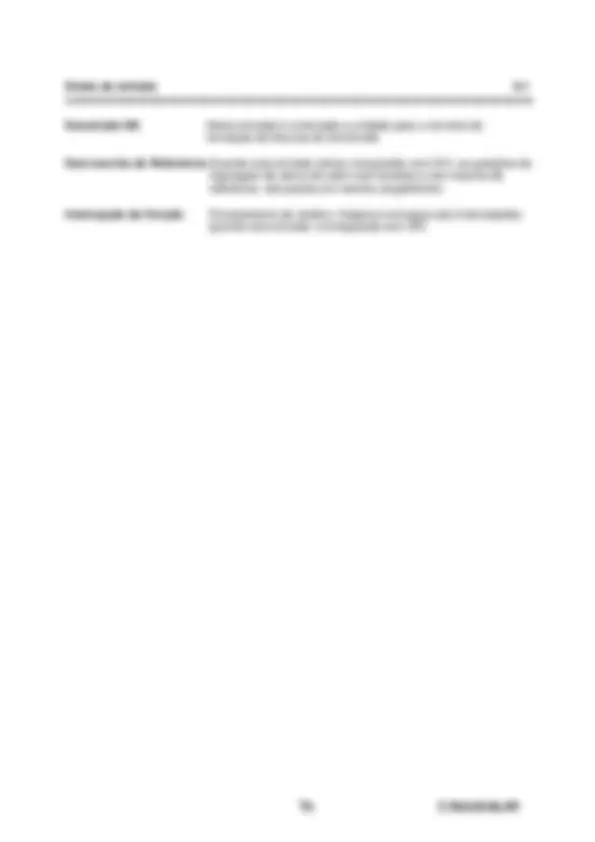
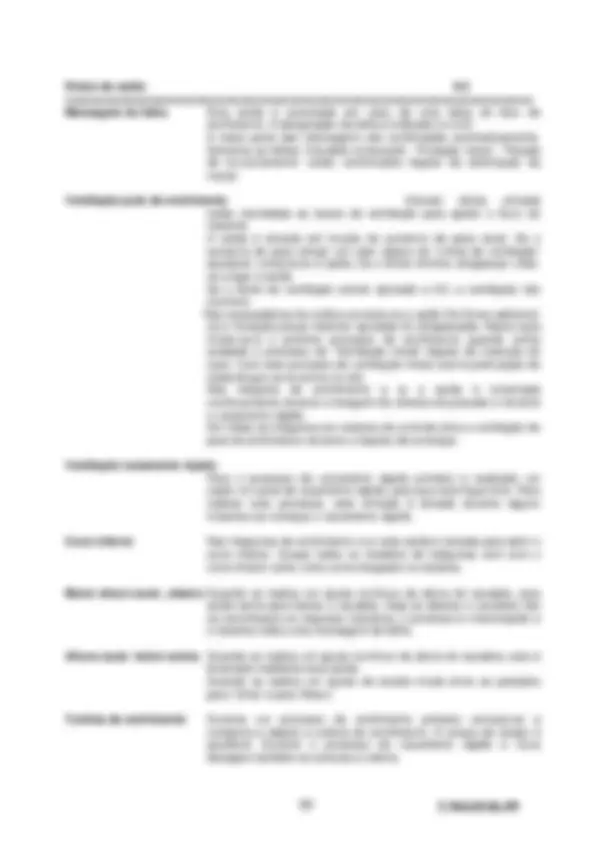
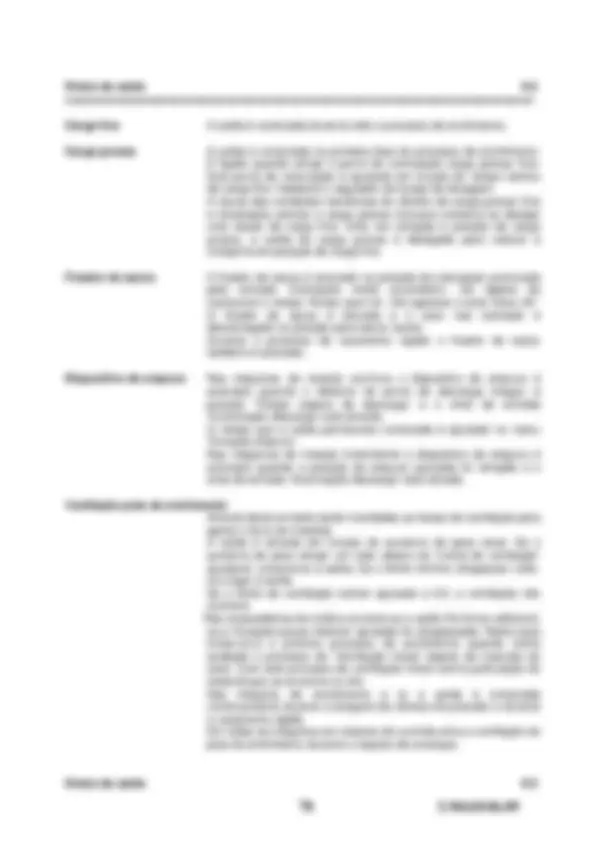
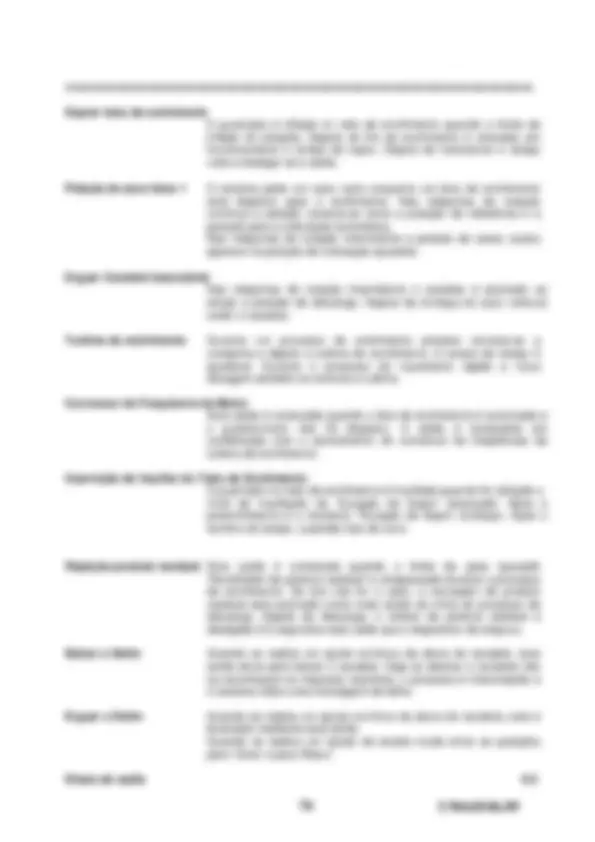
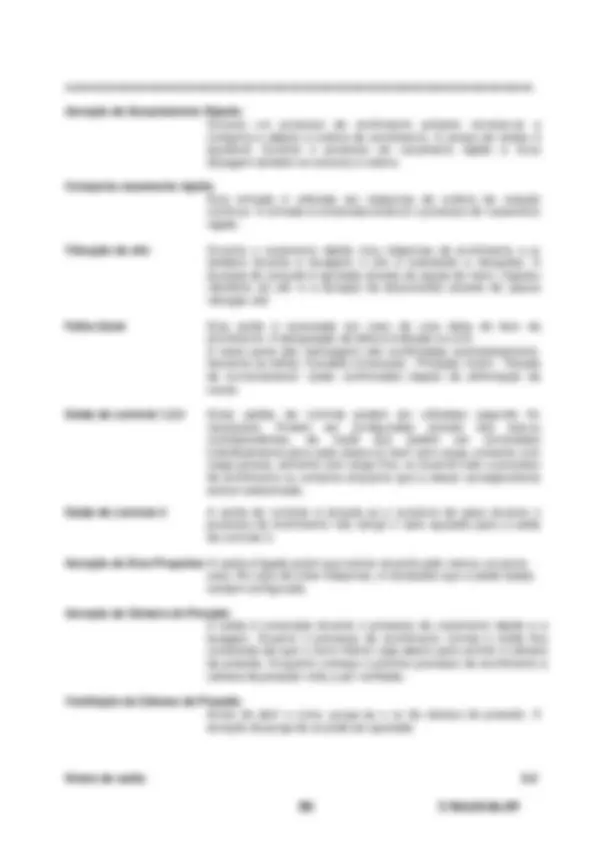
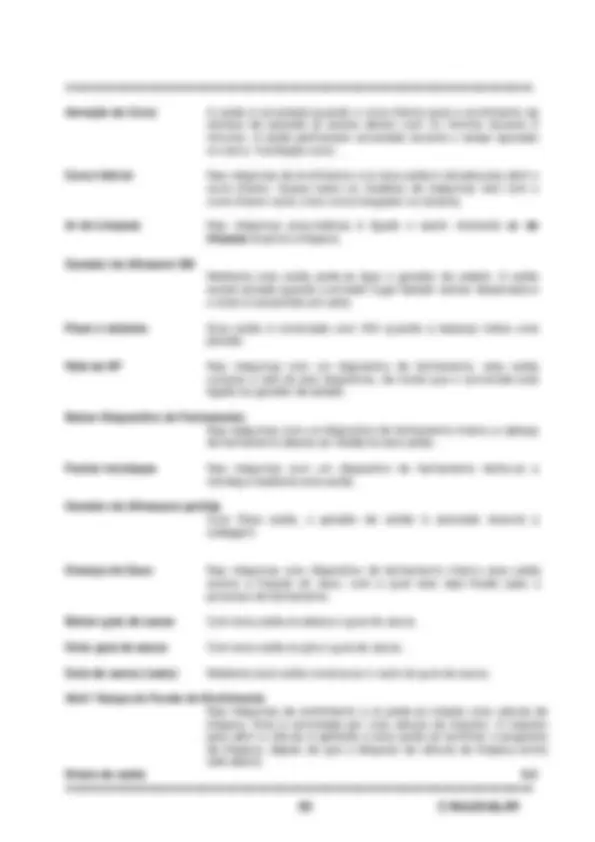
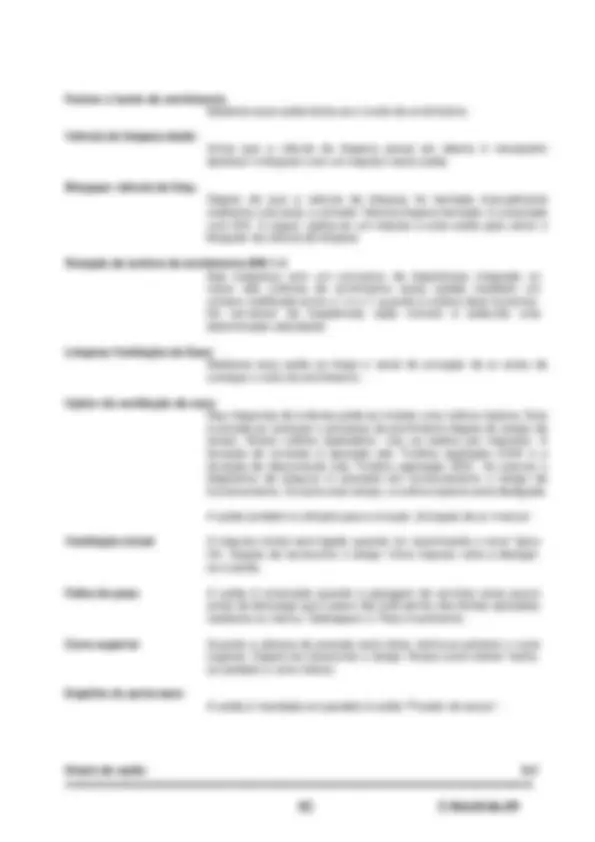
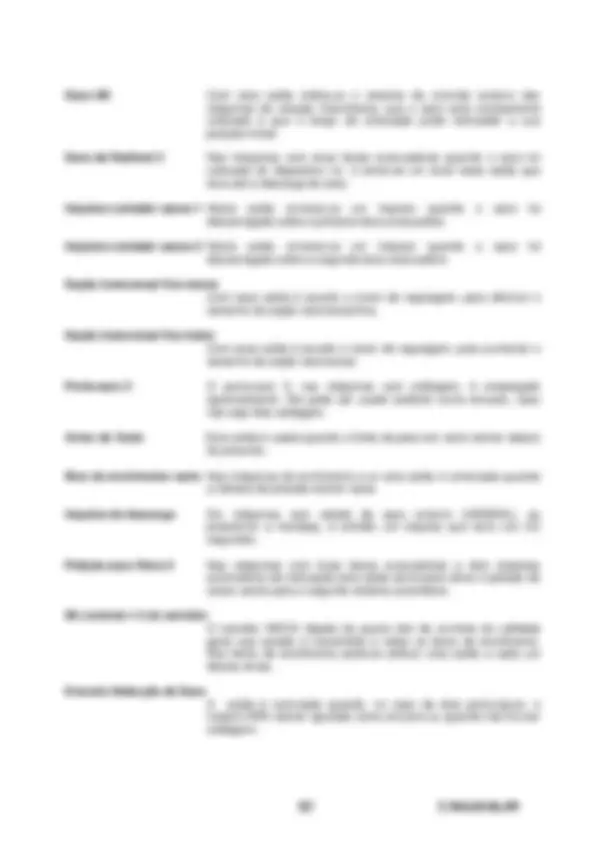
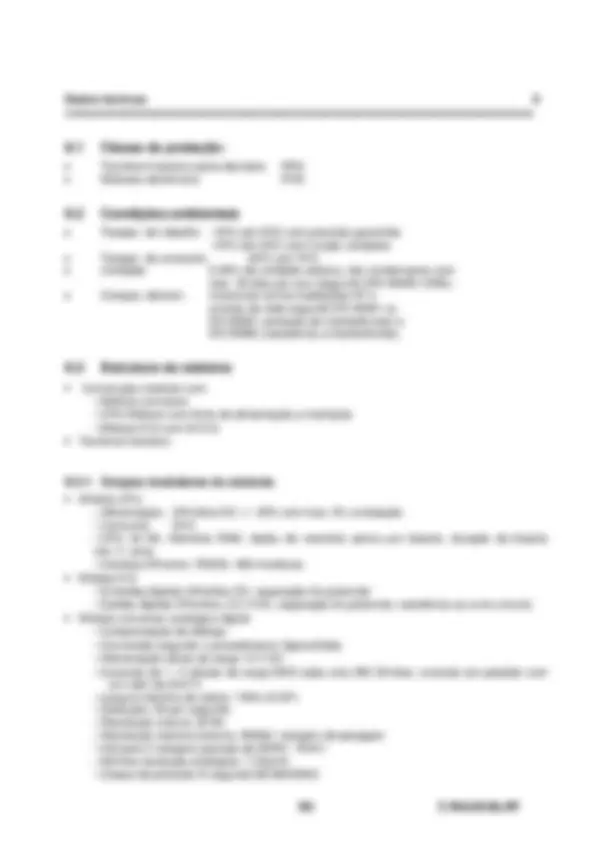
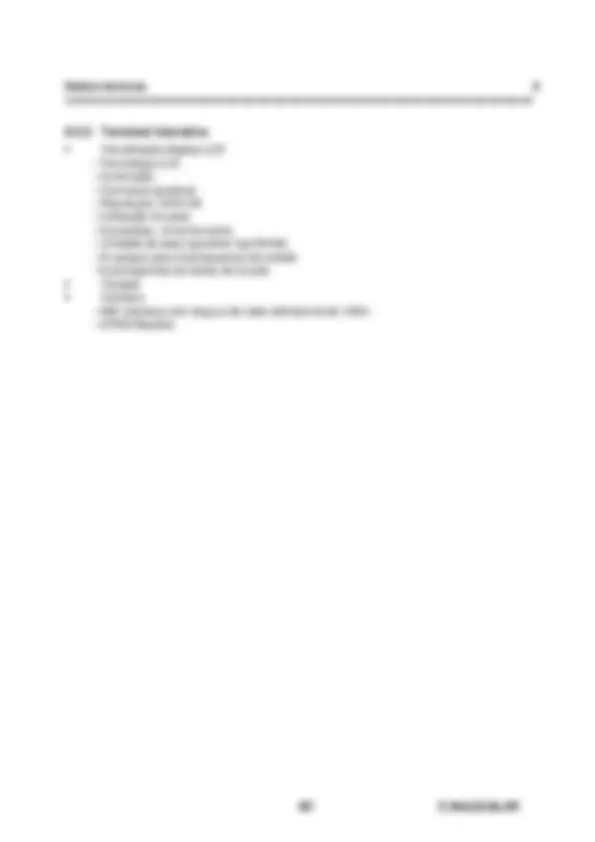
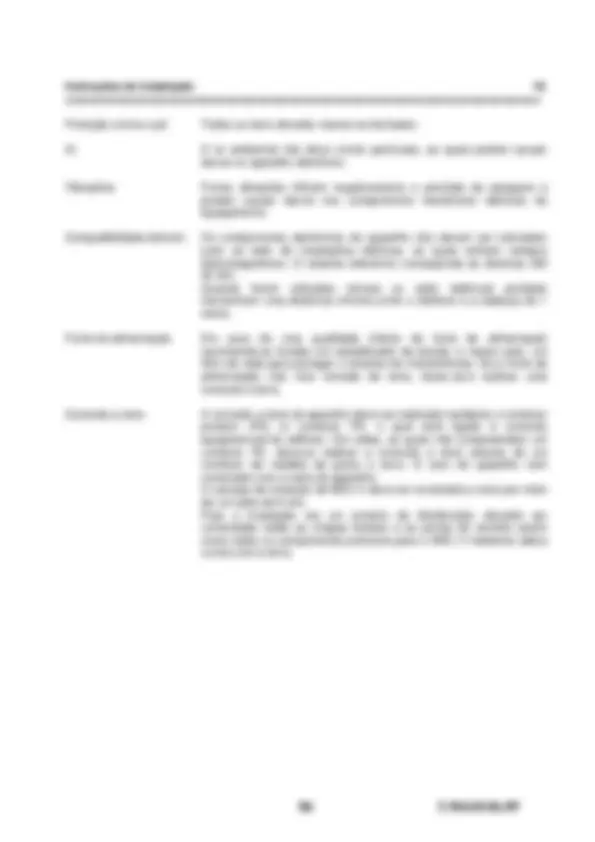
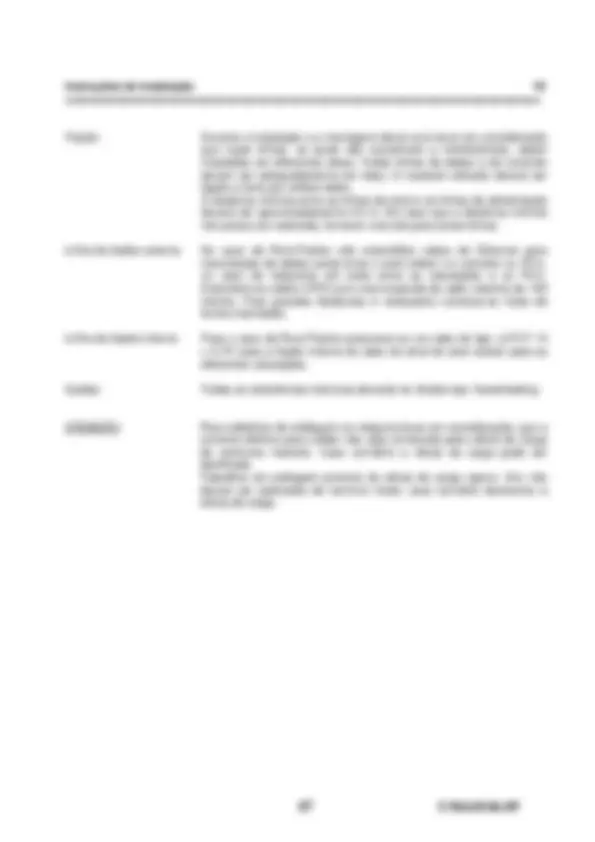
Estude fácil! Tem muito documento disponível na Docsity
Ganhe pontos ajudando outros esrudantes ou compre um plano Premium
Prepare-se para as provas
Estude fácil! Tem muito documento disponível na Docsity
Prepare-se para as provas com trabalhos de outros alunos como você, aqui na Docsity
Os melhores documentos à venda: Trabalhos de alunos formados
Prepare-se com as videoaulas e exercícios resolvidos criados a partir da grade da sua Universidade
Responda perguntas de provas passadas e avalie sua preparação.
Ganhe pontos para baixar
Ganhe pontos ajudando outros esrudantes ou compre um plano Premium
Comunidade
Peça ajuda à comunidade e tire suas dúvidas relacionadas ao estudo
Descubra as melhores universidades em seu país de acordo com os usuários da Docsity
Guias grátis
Baixe gratuitamente nossos guias de estudo, métodos para diminuir a ansiedade, dicas de TCC preparadas pelos professores da Docsity
manual para ensacadeira rotativa haver mc 2
Tipologia: Manuais, Projetos, Pesquisas
1 / 87
Esta página não é visível na pré-visualização
Não perca as partes importantes!
Índice ===============================================================
1 Funcionamento
2 Descrição do funcionamento
2.1 Parâmetros
2.1.1 Parâmetros bicos de enchimento
2.1.2 Parâmetros de classes
2.1.3 Parâmetros de calibração
2.2 Descrição do funcionamento
2.2.1 Teste funcional automático
2.2.2 Funcionamento
2.3 Posições na periferia da ensacadeira
2.4 Detecção do ângulo
3 Manual de instruções
3.1 Elementos de comando e visualização
3.1.1 Mensagens de serviço
3.2 Terminal interativo
3.3 Modo interativo de serviço
3.4 Modo interativo principal
3.4.1 Menu principal
3.4.2 Parâmetros de classes
3.4.3 Valores de indicação
3.4.4 Ajuste da balança
3.4.5 Calibração
4 Tratamento de erros
Funcionamento 1 =========================================================================
O sistema MEC III é um indicador eletrônico que pode ser calibrado e está composto de até 6000 peças. Está combinado com um sistema de controle compatível com todas as funções dos bicos de enchimento.
Uma ensacadeira classe Furado que está equipada com um MEC III dispõe de uma balança para cada bico de enchimento na parte rotatória. A balança MEC III possui uma licença MID e OIML.
Todas as funções são mandadas e visualizadas através de um terminal interativo externo. A calibração do conversor analógico-digital é realizada de forma completa através do diálogo. Uma balança de graduação múltipla pode ser ajustada com 3 margens de pesagem, que podem ser calibradas individualmente.
A balança controla automaticamente todas as funções dos bicos de enchimento. A definição de até 99 classes diferentes é realizada através do teclado e do display LCD integrados (em alemão, inglês ou em outros idiomas). Os ajustes são salvos e assegurados contra possíveis perdas que possam ser causadas por uma falha da alimentação elétrica.
As diferentes classes podem ser mudadas através de um comutador seletor na parte estacionária ou mediante uma seleção de classes por meio do teclado. Uma vez descarregado o último saco cheio, a máquina se ajusta automaticamente à nova classe selecionada e fica imediatamente pronta para o serviço. Os sistemas de controle estão conectados mediante uma rede Ethernet.
Na versão opcional, uma unidade de entrada e saída – o servidor – está conectada à rede. Graças a esta conexão, o servidor fica unido a todos os bicos de enchimento. Os dados de pesagem, sinais de controle, mensagens de falha e avisos são transmitidos desde os bicos de enchimento ao servidor MEC III através da rede. O servidor indica as mensagens recebidas e estabelece a conexão com outras unidades periféricas e instalações.
Podem ligar-se ao servidor duas balanças de controle e um servidor superior. A conexão com a instalação é realizada através de entradas e saídas paralelas.
É possível ligar uma balança de controle através de cada faixa de evacuação ao servidor MEC III como sistema de correção de peso de sacos superior. A partir deste ponto é realizado um novo ajuste do bico de enchimento, o qual produziu um saco muito leve ou muito pesado. A balança de controle pode ativar a evacuação dos sacos com peso errado.
Se a instalação não tiver uma balança de controle, o servidor pode ativar em seu lugar um evacuador por cada faixa evacuadora.
Tanto o sistema de pesagem/ de controle como o servidor estão construídos como um sistema de módulos para inserir, cujos componentes podem ser trocados entre si. Desta forma inclusive uma pessoa não experiente pode realizar uma busca de falhas, se for necessário, trocando os módulos, o qual aumenta a disponibilidade da máquina.
A balança MECIII pode ser operada por controle remoto por um PC conectado via Ethernet. É possível carregar e baixar parâmetros, tabelas em texto e software por esse meio.
Descrição do funcionamento 2 =========================================================================
2.1 Parâmetros
2.1.1 Parâmetros de balança
Cada bico de enchimento é ajustado mediante introdução dos parâmetros correspondentes, os quais não dependem dessas classes. Estes parâmetros foram denominados ‘Parâmetros de balança’.
Parâmetros de balança Possíveis introduções Válido ====================================================================== No. bico 1 - 16 No. de linha 1 - 199
Impulsos / Rotação 0 - 9999 1) Correção (Offset) 0 - 359,9 graus 1)
Arranque aut. coloc. faixa 1 0 - 359,9 graus 1) Paro auto coloc. faixa 1 0 - 359,9 graus 1) Pressionar fixador sacos faixa 1 0 - 359,9 graus 1) Colocação manual faixa 1 0 - 359,9 graus 1) Pos. Saco vazio faixa 1 0 - 359,9 graus 1) Pos. saco furado faixa 1 0 - 359,9 graus 1) Arranque pos. descarga faixa 1 0 - 359,9 graus 1) Parada pos. descarga faixa 1 0 - 359,9 graus 1)
Arranque aut. coloc. faixa 2 0 - 359,9 graus 1) Parada auto coloc. faixa 2 0 - 359,9 graus 1) Pressionar fixador sacos faixa 2 0 - 359,9 graus 1) Colocação manual faixa 2 0 - 359,9 graus 1) Pos. Saco vazio faixa 2 0 - 359,9 graus 1) Pos. saco furado faixa 2 0 - 359,9 graus 1) Arranque pos. descarga faixa 2 0 - 359,9 graus 1) Parada pos. descarga faixa 2 0 - 359,9 graus 1)
Interr. colocada em funcionamento Ligado - Desligado Controle de rede Ligado - Desligado
1 = máquinas de embalagem com determinação da posição na base de medição de ângulos
Descrição do funcionamento 2.1. ========================================================================
Parâmetros de classes Possíveis introduções Válido ======================================================================== Fator de regulagem 0 - 150% Nova dosagem Não, carga fina, carga grossa Duração do impulso 0,1 - 9,9 seg. Pos. de ruptura 2 - 5 Posição saco furado/ def. Pos. ruptura, faixa, bico descarga, saco vazio rej. Posição enxague. Pos. ruptura, faixa, bico descarga, saco vazio rej. Peso mínimo 0,0 - 80,0 Kg Tempo espera descarga Faixa 1 0 - 999 Tempo espera descarga Faixa 2 0 - 999 Dispositivo de encaixe de saco 1 0 - 999 Dispositivo de encaixe de saco 2 0 - 999 Duração de descarga 0,0 - 9,9 seg. Tempo de funcionamento dispositivo de empuxo 0,0 - 9,9 segundos Freqüência de tara /0 0 - 99 Retardo de tara 0,00 – 9,9 seg. Limite vazio 0,0 - 9,9 Kg Filtragem vazia 0- Filtragem completa 0- Filtragem carga grossa 0- Filtragem carga fina 0- Controlar Saco OK até arranque, limite vazio, não, sempre Atraso - saco OK 0,0 - 9,9 seg. Controle ‘Saco OK’ Sim / Não Soprar Saco Ok Sim / Não Porta-saco como encosto Sim - Não Saída de controle 1 Não, carga fina, carga grossa Grossa + fina, sempre Saída de controle 2 Não, carga fina, carga grossa Grossa + fina, sempre Saída de controle 3 0,0 - 45,0 Kg/seg. Saída de controle 4 Não, carga fina, carga grossa Grossa + fina, sempre Atraso selado 0,0 - 5,0 seg. Tempo de selado 0,0 - 0,7 seg. Atraso mordaça 0,0 - 9,9 seg. Limite cavalete basculante 1 0,0 - 80,0 Kg Limite cavalete basculante 2 0,0 - 80,0 Kg Fixador de sacos Limite 1 0,0 - 80,0 Kg Fixador de sacos Limite 2 0,0 - 80,0 Kg Limite de enchimento 0,0 - 80,0 Kg Recusador de produto residual 0,0 - 80,0 Kg Atraso recusador de produto resid. 0,0 - 9,9 seg. Impulso vibratório do silo 0,0 - 9,9 seg. Pausa vibração do silo 0,0 - 9,9 seg. Atraso turbina de aspiração 0,0 - 9,9 seg. Ligar turbina de aspiração 0,0 - 9,9 seg. Desligar turbina de aspiração 0,0 - 9,9 seg. Atraso vazamento rápido 0,0 - 9,9 minutos
Duração de vazamento rápido 0,0 - 9,9 minutos Ventilação de vazamento rápido 0,0 - 9,9 minutos Descrição do funcionamento 2.1. ========================================================================
Parâmetros de classes Possíveis introduções Válido ======================================================================== Posic. colocação do saco 1 -n° bico de enchimento Posição saco vazio 1 -n° bico de enchimento Posição desperdícios 1 1 -n° bico de enchimento Posição desperdícios 2 1 -n° bico de enchimento Posição descarga 1 1 -n° bico de enchimento Posição descarga 2 1 -n° bico de enchimento Tempo de extração de ar 0,0 - 9,9 seg. Atraso cone inferior 0,0 - 9,9 seg. Cone sempre aberto Sim / Não Atraso carga grossa 0,0 - 9,9 seg. Ventilação do cone 0,0 - 9,9 seg. Total de sacos esvaziar residual 0 - 99 Modo de limpeza nenhum, tesouras, cone , tesouras e cone Ar de limpeza ar de sopro, ar comprimido Abrir tampa de fundo em Saco vazio lixo, posição Lixo, correia, aleatório Peso da amostra 0,0 – 80,0 kg Duração fechamento 0,0 - 9,9 seg. Duração de abertura 0,0 - 9,9 seg. Enxaguar no saco residual, no saco novo Volume a enxaguar 0,0 - 80,0 kg Ciclo de esvaziamento rápido 0 - 99 sec Liberar a espécie Sim - Não
**Descrição do funcionamento
=========================================================================**
2.2.1 Teste funcional automático
Para assegurar o funcionamento estável do sistema deverão ser testados os seguintes componentes:
Canal de medição O canal de medição é submetido a um teste diretamente depois da conexão do sistema eletrônico e a cada 5 minutos durante o processo de trabalho. O teste é realizado aplicando uma tensão de teste na entrada do canal de medição, a qual é comparada com um número de comprobação programado no EEPROM. Esta tensão de teste é equivalente a 90% do valor máximo da escala do conversor analógico-digital. Se o desvio for superior a ½ d, o sistema volta a calibrar o conversor com escalem zero e escala máxima. Se o desvio for superior a 2 d, aparecerá a seguinte mensagem de falha, no modo R61 ”Erro número comprovação”.
Área ROM A memória ROM do sistema dispõe de um valor horizontal, o qual é controlado quando o sistema é ligado e testado de forma cíclica durante o funcionamento.
Área RAM A memória RAM do sistema é submetida a um teste quando o sistema é ligado e ciclicamente durante o funcionamento. O teste da memória RAM consiste em escrever e ler seqüências de bits.
Parâmetros Todos os parâmetros (parâmetros de balança, parâmetros de classes, parâmetros de calibração, quadros de atribuição de E/S, quadros de configuração) são verificados quando o sistema é ligado de forma cíclica ou mediante acesso através de valores horizontais durante o funcionamento.
Indicação do peso Depois da conexão, o display de gráficos indica a margem de peso da seguinte forma: ‘88888888’.
Interfaces Os dados transmitidos por interface são verificados com relação a possíveis falhas de transmissão. Os registros transmitidos contêm um valor horizontal que permite verificar posteriormente a transmissão correta. Cada byte também é controlado com um bit de paridade. As mensagens importantes são confirmadas. Colisões são reconhecidas.
Execução do programa Para poder detectar uma possível interrupção da execução do programa (por exemplo, se o programa for ‘desligado’) e reiniciar o processo, terá que ativar com regularidade um ”Watchdog” interno (unidade de controle) sobrescrevendo uma célula de memória. Se não for ativa, o Watchdog– Interrupt irá realizar um Reset.
Descrição do funcionamento 2.2. ========================================================================
2.2.2 Funcionamento
Colocação em funcionamento: Depois da colocação em funcionamento, o sistema eletrônico realiza um processo de iniciação e verifica todos os parâmetros salvos por uma bateria seladora. Depois de realizado este controle visual inicia-se a contagem do tempo ” Warm up ” ( aquecimento ) se este for ajustado. A seguir a balança seleciona automaticamente a classe que foi previamente ajustada. Se for um servidor ligado, a balança se conecta a este para realizar o número de classe atual a partir do servidor.
Introdução de um saco vazio: A respeito da introdução de sacos deverão distinguir-se diferentes configurações:
Ensacadeira de rotação contínua, sem sistema de colocação de sacos automático: Os sacos são colocados manualmente. O fixador de sacos é acionado na posição 1 ou 2. Ele depende da entrada ‘Colocação Manual/ Automática’. Se a entrada está conectada com 24 V, o fixador de sacos é acionado na posição 2. Também poderá ser instalado um interruptor de arranque. Neste caso o fixador de sacos será acionado quando o interruptor for disparado pelo saco vazio.
Ensacadeira de rotação contínua, com sistema de colocação de sacos automático instalado, mas fora de serviço: A entrada ‘Manual/ Automática’ está conectada com 24 V, de modo que o fixador de sacos é acionado na posição 2, para que o operário possa colocar o saco manualmente.
Ensacadeira de rotação contínua, o sistema de colocação de sacos automático está em serviço: A entrada ‘Manual/Automática’ está conectada com 0 V, de modo que o fixador de sacos é acionado na posição 1, para que o saco possa ser colocado pelo sistema automático.
Ensacadeira com rotação intermitente: Nestas máquinas, o saco é colocado enquanto que a ensacadeira está parada. A barreira de luz instalada reage quando o saco se encontra em sua posição correta. Neste momento é acionado o fixador de sacos. A barreira de luz está conectada à saída ‘Interruptor de arranque’.
Uma vez acionado, o fixador de sacos comprova-se se o saco estiver corretamente inserido no tubo de enchimento. Se depois de transcorrer o tempo ajustado no menu ‘Atraso Saco Ok’ não aparece o sinal Saco Ok, o saco vazio será transportado a uma posição especial para sacos vazios (de desperdícios). Se o sinal “Saco Ok ” aparecer antes que o tempo tenha transcorrido, será iniciado imediatamente o processo de enchimento.
Descrição do funcionamento 2.2. ========================================================================= Ventilação inicial Se entre dois ciclos de enchimento ou ‘Tempo máximo de pausa’ foi ultrapassado, a ventilação inicial será colocada em funcionamento antes de começar o processo de enchimento. Para o tempo ajustado no menu se conecta a ventilação do pote de enchimento e a saída ‘ Sopro do tubo de enchimento ’ depois do reconhecimento do sinal ‘Saco Ok’ e antes de iniciar o processo de enchimento. Esta função não está integrada no sistema de ar de enchimento.
Impulso de arranque Quando a duração de impulso de arranque foi ajustada, nas máquinas de turbinas é colocada em funcionamento a ventilação inicial depois de ser aberta a comporta e antes que a turbina de enchimento seja colocada em funcionamento. Durante este processo se conecta a saída ‘ Ventilação de arranque’. Nas ensacadeiras com dosagem por turbinas é colocado em funcionamento o ‘ Tempo atraso turbinas’. Uma vez transcorrido este tempo, conecta-se a turbina de enchimento. Dado que o tempo de atraso não costuma ultrapassar os 0,5 segundos, a ventilação de arranque funciona paralelamente à carga grossa. Depois de transcorrer o tempo de ventilação de arranque se desconecta a saída ‘Impulso de arranque’.
Nas máquinas de ar, a saída ”Impulso arranque” é ligada depois do enchimento da câmara de pressão, do reconhecimento do sinal Saco Ok e da taragem, se a duração do impulso de arranque for maior que 0,0s. A saída ”Ventilação pote de enchimento” é sempre conectada. Ao mesmo tempo se inicia o ”Atraso carga grossa”. Uma vez transcorrido este tempo, o trilho se abre e a carga grossa é colocada em funcionamento. Depois de transcorrer o tempo de impulso de arranque a saída ‘Impulso de arranque’ é desligada.
Carga grossa Depois de efetuar a taragem, a filtragem de enchimento é colocada em funcionamento, a comporta da carga grossa se abre e, se o sistema dispor da função, infla-se o tubo de enchimento. Depois de transcorrer o Tempo de atraso da turbina, a turbina de enchimento é colocada em funcionamento. No sistema de enchimento de ar sob o menu “Atraso carga grossa” se ajusta a abertura do trilho para a carga grossa. Durante o tempo de enchimento, é realizada uma medição contínua do aumento de peso, a qual forma a base para a regulagem compensada dinâmica, se esta função estiver conectada. Até alcançar o ‘Limite de vácuo’, o aumento de peso atual é comparado com um valor mínimo selecionado, a ‘Velocidade mínima’. A função de controle é ativada ao colocar em funcionamento o processo de enchimento, mas pode ser aprazada mediante o parâmetro ‘Atraso velocidade’. Se o aumento de peso ficar abaixo do valor mínimo, supõe-se uma ruptura de saco, o qual produz uma interrupção do processo de enchimento, e o saco é evacuado como saco defeituoso. Da mesma forma, procederá com os sacos que tenham ultrapassado o tempo máximo de enchimento. Depois de ultrapassar o limite de peso vazio, o sistema transmite uma mensagem de ruptura de saco, em caso de que tenha sido detectada uma redução de peso. A duração mínima desta redução de peso é determinada através do menu ‘Duração velocidade’.
Cavalete basculante Se no menu “Limite cavalete basculante 1” se ajusta um valor maior a ‘0,0’, o cavalete basculante será elevado no início do processo de enchimento e voltará a baixar quando o valor tenha sido atingido. Se o valor for ‘0,0’, o cavalete basculante ficará primeiro sem fixar. Uma vez alcançado o sinal ‘Limite cavalete basculante 2’, o cavalete é levantado e permanecerá nesta posição até a descarga do saco. Se o ‘Limite cavalete basculante 2’ for maior que o peso teórico, o cavalete somente será elevado uma vez iniciada a freqüência de descarga.
Descrição do funcionamento 2.2. ========================================================================= Sacos furados O tratamento dos sacos furados pode ser ajustado da seguinte forma: Ou permanecem inseridos no bico de enchimento ou bem são descarregados na posição de ruptura ou sobre a faixa evacuadora, para serem evacuados posteriormente. Os sacos furados cujo peso é inferior ao limite de vácuo são sempre descarregados na posição de sacos vazios recusados. Os sacos cujo peso é inferior ao peso mínimo, são descarregados na posição de ruptura independentemente da posição ajustada para a descarga de sacos furados. Desta forma, evita-se que se produza uma acumulação de sacos sobre a faixa provocada pelos sacos que não tenham atingido o peso necessário. Se o tempo de enchimento for ultrapassado por três vezes seguidas, ou se um saco for descarregado na posição de ruptura, o bico de enchimento será desligado e aparecerá uma mensagem na tela. A mensagem de falha deve ser confirmada. Isto é realizado desligando e voltando a ligar o bico de enchimento mediante o interruptor basculante.
Recusador de produto residual Uma vez atingido o ‘Limite de peso do coletor de produto residual’, será ativado este último.
Sistema de válvula de filtro Depois de transcorrer o tempo ‘Atraso turbina de aspiração’ se conecta a saída ‘Turbina injetora’. Esta saída é necessária para o sistema de válvula de filtro para liberar a válvula do saco mediante aspiração. No menu podem ser ajustados os impulsos de aspiração. O sinal ‘Turbina aspiração Funcionamento’ define a duração do processo de aspiração e o sinal ‘Turbina aspiração Parada’ define a duração da pausa. A turbina injetora é ativada até três segundos antes de terminado o processo de enchimento, e é desligada ao alcançar a posição de descarga do saco.
Carga fina O ponto de comutação carga fina/carga grossa é ajustado através do menu. Se o peso atual alcançar este ponto de comutação levando em conta a regulagem compensada, a carga grossa é terminada. O ponto de comutação é ajustado em função do tempo teórico carga fina previamente ajustado, enquanto que o regulador do tempo de dosagem permanece em funcionamento. No início da carga fina é ativada a filtragem de carga fina. Entre a carga grossa e a carga fina pode ser feita uma pausa de enchimento. Neste caso, encerra-se o trilho de passo completamente e para a turbina de enchimento. Esta pausa pode ser utilizada para retirar o ar do saco. Durante o processo de carga fina, da mesma forma que ocorre durante o processo de carga grossa, o sistema reage perante uma ruptura de saco, excesso de tempo de enchimento previsto, etc.
Interrupção do processo de enchimento Se a função ‘Interrupção do processo de enchimento’ está conectada, o sistema controla se o bico de enchimento pára pela posição de colocação de sacos durante o processo de enchimento. Se este for o caso, o processo de enchimento será interrompido até que o bico de enchimento tenha tomado a posição para os sacos vazios recusados. A continuação segue da mesma forma em ‘Dosagem posterior’.
Fim de enchimento Depois de finalizar o processo de enchimento é colocado em funcionamento o tempo de Atraso de sopro. Uma vez transcorrido este tempo, procede-se ao sopro do tubo de enchimento durante o tempo ajustado sob o parâmetro Duração de sopro. Uma vez transcorrido estes tempos, modifica-se a Filtragem completa. Ao terminar o processo de enchimento, é colocado em funcionamento o tempo Duração de sopro. Uma vez transcorrido o tempo, é finalizado o processo de sopro do tubo de enchimento.
Descrição do funcionamento 2.2. =========================================================================
Regulador tempo de dosagem Durante o ciclo de enchimento, a balança controla o tempo de duração da carga fina. Depois de finalizar o processo de enchimento, o regulador do tempo de dosagem corrige o ponto de comutação de carga grossa/ fina para cumprir com o tempo pré-selecionado de dosagem fina. Se as pausas durarem mais que a duração máxima ajustada , o ponto de comutação de carga grossa/ fina volta ao valor inicial ajustado no terminal interativo. Deste modo, adapta-se o sistema à mudança de fluxo do material causado pela pausa prolongada. Portanto, é recomendável partir de um ponto de comutação relativamente baixo.
Compensador Se o compensador estiver ligado, realiza-se uma pesagem de controle diretamente depois de transcorrer o atraso de sopro.
Se o resultado da pesagem de controle diferir do peso teórico, realiza-se uma modificação do ajuste do coeficiente específico (se a regulagem compensada dinâmica estiver conectada) ou da regulagem compensada estática. O valor de regulagem depende da diferença medida e do fator de regulagem. Este é ajustado através do menu de parâmetros de balança mediante a classe ‘ fator de regulagem ’.
Classificação Se o processo de classificação estiver ligado, o sistema realiza um registro do peso atual após realizar uma pesagem de controle, a qual é posteriormente comparada com os limites ajustados X (x) segundo R61. Estes limites não devem ser inferiores à classe da balança Ref(x) e se orientam pelos seguintes valores:
Valor da massa de carga Classe X(1) 500g < M ≤ 1.000g 15g 1000g < M ≤ 10000g 1,5% 10.000g < M ≤ 15.000g 150g 15000g < M 1%
Os valores limites das classificações (x) ajustadas no parâmetro Classificação terão que se multiplicar pelos valores X(1) indicados na tabela, por exemplo: X(2) => 2 X(1). X(2) => 2 X(1). Em cada ajuste de limites de classificação, os valores se adaptam automaticamente aos parâmetros ‘Limite superior de peso’ e ‘ Limite inferior de peso ’. Estes podem ser editados (por exemplo, reduzidos) posteriormente modificando os limites ajustados. O parâmetro X(x) permite o ajuste livre de limites. A classificação aciona o símbolo " ", se o peso controlado atualmente for insuficiente. Da mesma maneira aparece o símbolo " " no caso de um excesso de peso. Se o peso se encontrar dentro dos limites, ambos símbolos se incidem. Se os limites forem ultrapassados tanto para cima como para baixo, o saco será tratado como saco defeituoso tal como foi introduzido no menu do terminal interativo. Se os sacos furados forem descarregados sobre a faixa evacuadora o sistema emite o sinal ‘Peso incorreto’. Em conseqüência disto, o sistema de controle pode iniciar a evacuação do saco.
Descrição do funcionamento 2.2. ========================================================================
Nova dosagem No modo de funcionamento ‘Nova dosagem’, o saco não é imediatamente descarregado se não alcançar o ‘ Limite inferior de peso’. No lugar de descarregar o saco, este torna a ser cheio. A nova dosagem termina como mais tarde, depois de ter transcorrido o tempo de enchimento máximo. Se a diferença do peso teórico for inferior a 1 kg se procederá à nova dosagem do saco por impulsos. A duração dos impulsos pode ajustar-se através da classe ‘ Duração de impulsos ’. Depois de cada impulso, espera-se o tempo ajustado na classe ‘ Duração de parada’, a seguir é modificada a classe filtragem em parada e volta a esperar. Uma vez realizada esta operação, é efetuada uma pesagem de controle. Durante o ciclo de nova dosagem por impulsos, o sistema de ventilação do pote de enchimento permanece continuamente em funcionamento. Em caso de as diferenças ultrapassarem 1 kg, será dosado novamente de forma contínua. A seção transversal de enchimento para a nova dosagem se ajusta através do menu ‘Nova dosagem’ a carga grossa ou carga fina. A seção transversal permanece constante até alcançar o peso teórico. Depois da descarga do saco dosado posteriormente, os sinais de correção da balança de controle serão ignorados durante dois ciclos da ensacadeira.
Filtro digital O filtro digital é uma conexão sucessiva de dois níveis de filtro, cada um com uma formação de valor intermediário dos valores do conversor A/D. A seguinte tabela contém o número dos valores calculados por cada nível de filtro, os resultantes tempos de produção, bem como os coeficientes específicos MK no simulador em função dos possíveis valores de filtragem (0-6):
Filtrage Valor p. nível de Tempo MK [s] 0 1 ca. 0,5 ca. 0, 1 4 ca. 0,6 ca. 0, 2 8 ca. 0,8 ca. 0, 3 16 ca. 1,0 ca. 0, 4 32 ca. 1,6 ca. 0, 5 64 ca. 2,5 ca. 1, 6 100 ca. 4,0 ca. 1,
O tempo de produção indica o tempo requerido até que o valor na saída do filtro tenha atingido 100% do valor de entrada. Os valores para a indicação do peso no terminal interativo são filtrados por um 3 o^ nível de filtros, o qual não vem indicado.
Descarga do saco Nas máquinas de rotação contínua, o ponto de descarga é determinado automaticamente pelo sistema de controle em função da velocidade de rotação da ensacadeira. O saco somente deve ser descarregado se a faixa evacuadora estiver conectada. A descarga pode impedir conectando a entrada ‘Autorização descarga’ em posição lógica ”0” através do controle externo mediante o anel coletor. Nas ensacadeiras com duas faixas evacuadoras na saída ‘Saco de Radimat 2’ é ativada quando o saco atual for colocado na segunda metade da ensacadeira. Com esta informação, o sistema de controle externo pode determinar a faixa evacuadora, sobre a qual irão cair os sacos descarregados. A descarga pode ser impedida procedendo da forma descrita mais acima.
Descrição do funcionamento 2.2. =========================================================================
Ajuste da altura do cavalete A cada uma das 99 classes possíveis, pode atribuir-se o parâmetro ‘Altura de cavalete’. A programação é realizada através do menu de classes.
A altura do cavalete pode ser introduzida diretamente. Existe a possibilidade do procedimento ”Teach-in”. Neste caso, seleciona-se inicialmente a classe ‘Tomar pos. de referência’. O cavalete abaixa até alcançar o ponto de referência. A seguir, mediante a classe ‘ Deslocamento manual’ através das teclas ' > ' e ' < ', pode-se deslocar o cavalete até que a altura ajustada corresponda aos requisitos. A altura ajustada é salva na memória de classes acionando a tecla ' '. Pressionando uma tecla que não seja uma das três mencionadas, torna a sair deste modo sem ter salvo a altura do cavalete.
Durante uma mudança de classes posteriores depois da descarga do saco, toma-se primeiro a posição de referência e depois a nova altura do cavalete.
Quando a entrada “Marcha sem referência” estiver ligada com 24V, tem lugar o arranque direto sem marcha de referência das posições da regulagem de altura do selim sem escalas.
No caso de realizar um ajuste em escala com cilindro, verificará, uma vez ativado o cilindro, se o sistema tiver previsto um ajuste em escala. Este processo demorará alguns segundos. Caso tenha ajustado erroneamente uma altura de cavalete em escala, o sistema indicará automaticamente. Se houver um ajuste contínuo do respectivo motor e este não reagir, o sistema emitirá uma mensagem de falha. Ao mesmo tempo, desconecta-se o ajuste contínuo internamente para evitar danos mecânicos. A autorização do ajuste contínuo será realizada depois da desconexão e conexão da fonte de alimentação.
Regulagem por balança de controle
Existem dois processos possíveis de como uma balança de controle pode regular os bicos. Ou a balanço de controle está conectada ao servidor por meio de uma linha de sinalização ou então a balança de controle troca diretamente as suas informações com os bicos. Se a máquina contiver uma balança de controle e um servidor MEC III, a balança pode iniciar a remessa de um sinal de regulagem a um bico de enchimento através do servidor. O tamanho da passagem de regulagem é introduzida no servidor. A regulagem provoca uma mudança da memória de correção na balança. Se a balança de controle detectar um saco com peso excessivo e se o bico de enchimento receber o sinal de regulagem, o valor da passagem de regulagem será deduzido da memória de ‘Correção’. De forma análoga, adiciona-se o valor correspondente ao valor salvo na memória. O peso teórico interno, os limites de peso e o peso de comutação são aumentados pelo valor da memória de correção. O valor de correção não pode ser negativo. Se uma regulagem causar um valor negativo, o sistema indicaria a mensagem de falha ‘Falha correção’. No segundo caso, a balança de controle transmite o peso de saco medido ao bico causador. O bico executa uma regulamentação de corrente saliente com base nesse peso. No Diálogo de Espécies, o fator de regulagem para a corrente saliente pode ser ajustado com o peso da b alança de controle. Também neste caso, a memória de correção será afetada. O peso teórico interno, os limites de peso e o peso de comutação serão elevados correspondentemente ao valor da memória de correção.
Descrição do funcionamento 2.2. =========================================================================
Vazamento rápido
Máquinas de rotação contínua com sistema de enchimento por turbinas
Na configuração podem ser selecionadas três variantes distintas. Na variante ‘normal’, depois de colocar em funcionamento o processo de vazamento rápido, cada bico de enchimento espera o tempo de ‘Atraso vazamento rápido’ ajustado. Uma vez transcorrido este tempo, o canal de vazamento rápido é ventilado, a comporta se abre e a turbina é colocada em funcionamento. A duração do processo de ‘ Ventilação vazamento rápido’ é ajustada através do terminal interativo. Ao mesmo tempo, é colocado em funcionamento a ‘ Duração vazamento rápido’. Uma vez transcorrido este tempo, a turbina é desligada e a comporta fechada. Ajustando diferentes tempos de atraso, evita-se que todos os bicos de enchimento comecem o processo de vazamento simultâneo, o qual provocaria uma congestão no sistema de retorno de material. Por outro lado, todos os bicos de enchimento deverão terminar o processo de vazamento simultaneamente. Desta forma, evita-se que o material dos segmentos a vazar caiam naqueles segmentos que já vazaram. A ordem de desconexão desejada pode ser realizada introduzindo tempos diferentes de vazamento rápido. Cada bico de enchimento avisa ao servidor sobre o início e o final do processo de vazamento. Enquanto que o processo de vazamento rápido estiver funcionando como mínimo em um bico de enchimento, a saída do servidor permanecerá na posição ‘Vazamento rápido em funcionamento’.
Aplicando no servidor o valor 24V na entrada ‘Interrupção vazamento rápido’, pode-se interromper simultaneamente o processo de vazamento rápido em todos os bicos de enchimento.
A segunda variante permite o vazamento por um bico de enchimento através do tubo de enchimento até que a entrada indique uma petição de vazamento rápido. Neste caso, não se controla a entrada ‘Saco Ok.’ Ao mesmo tempo se ativa a saída ‘Sopro tubo de enchimento’. Esta variante é selecionada no menu de configuração mediante ‘Vazamento rápido estacionário’ e se utiliza normalmente em combinação com um morro de turbina com vazamento rápido