
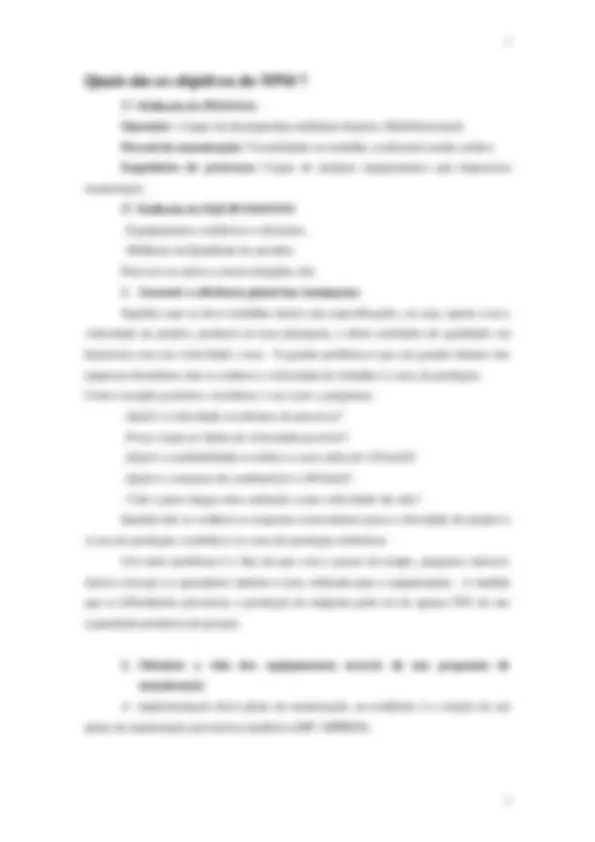
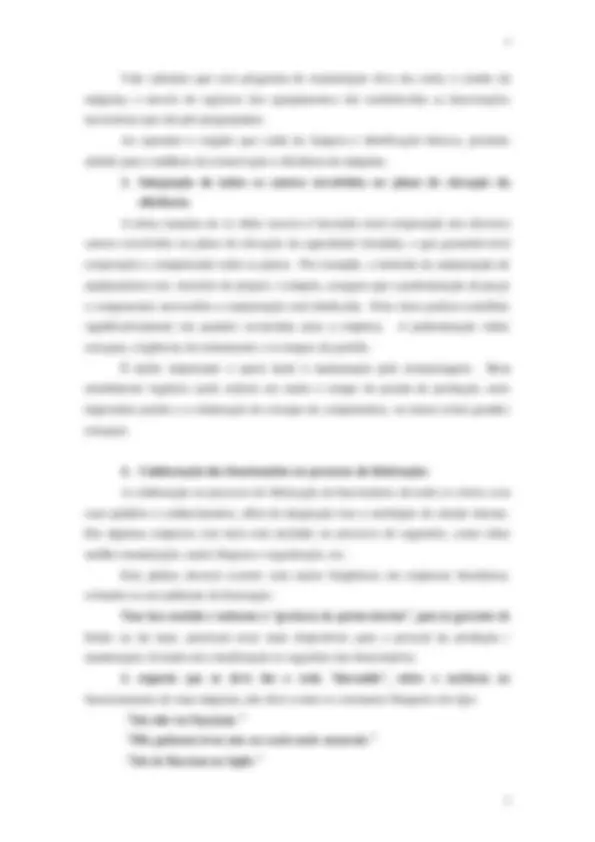
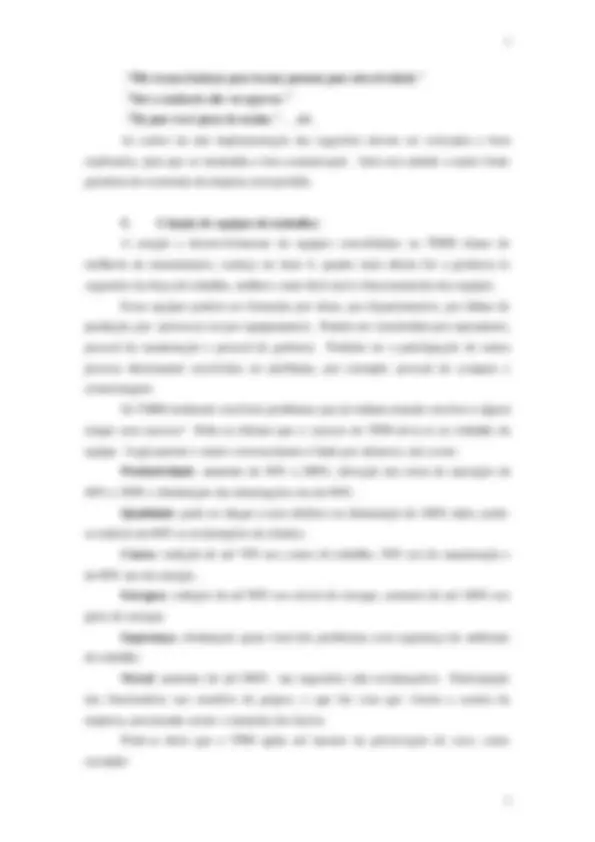
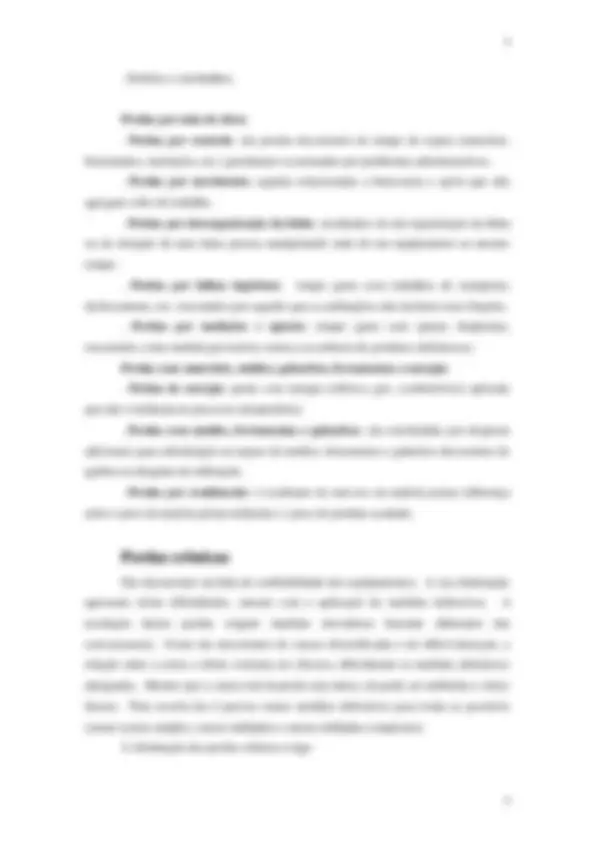
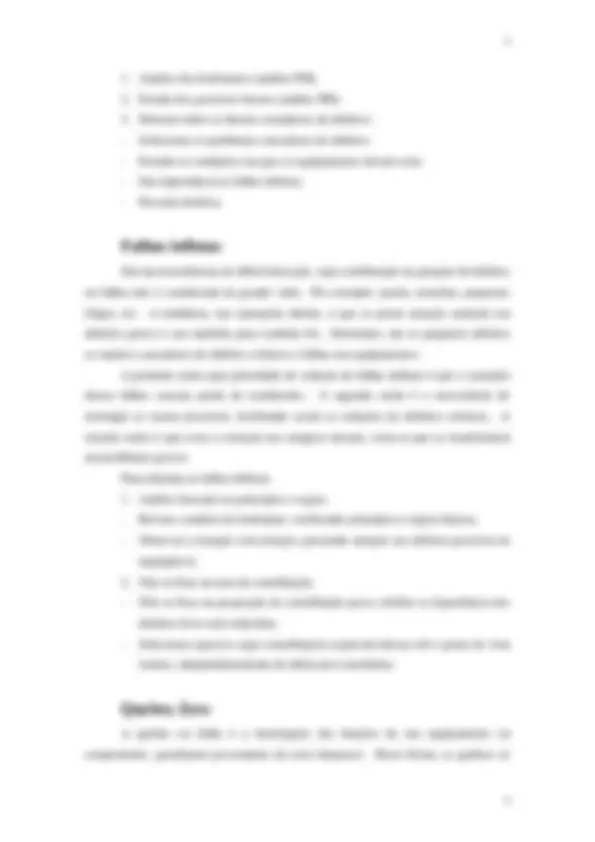
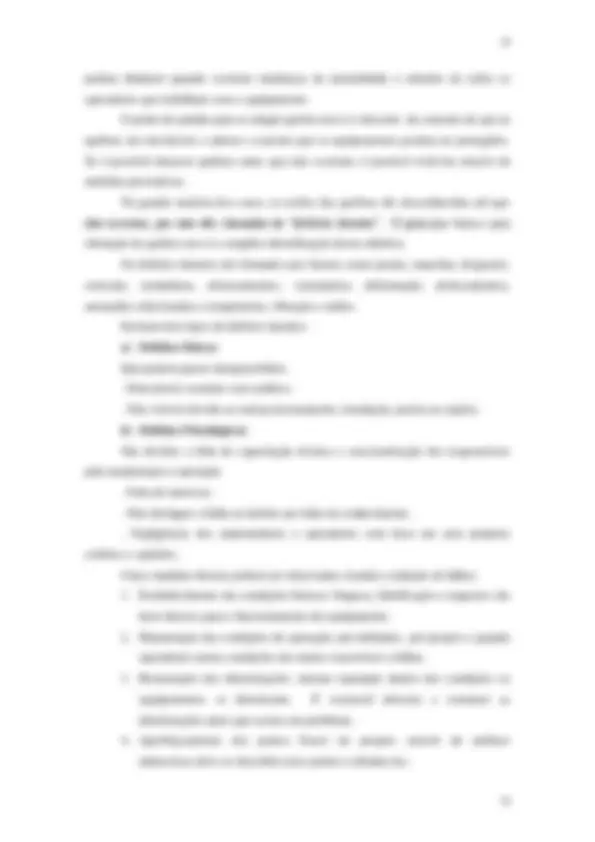
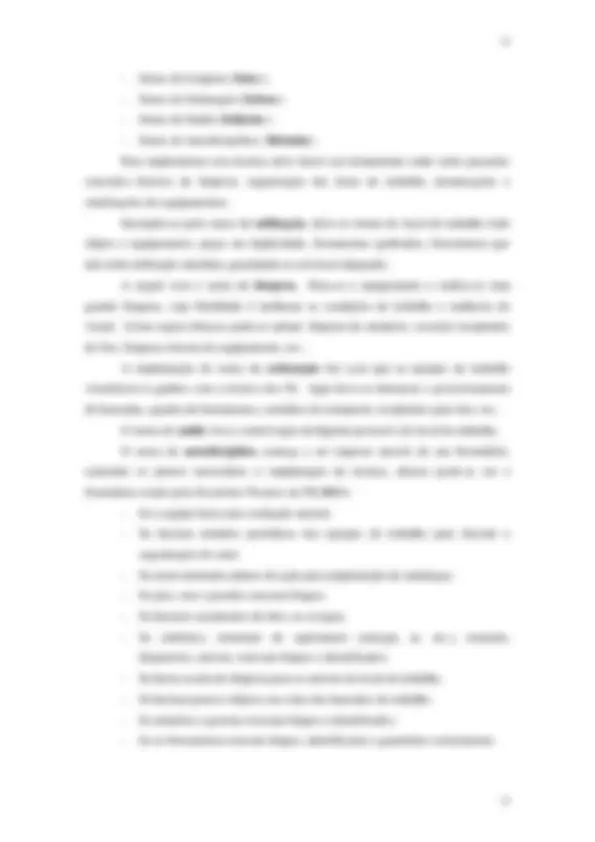
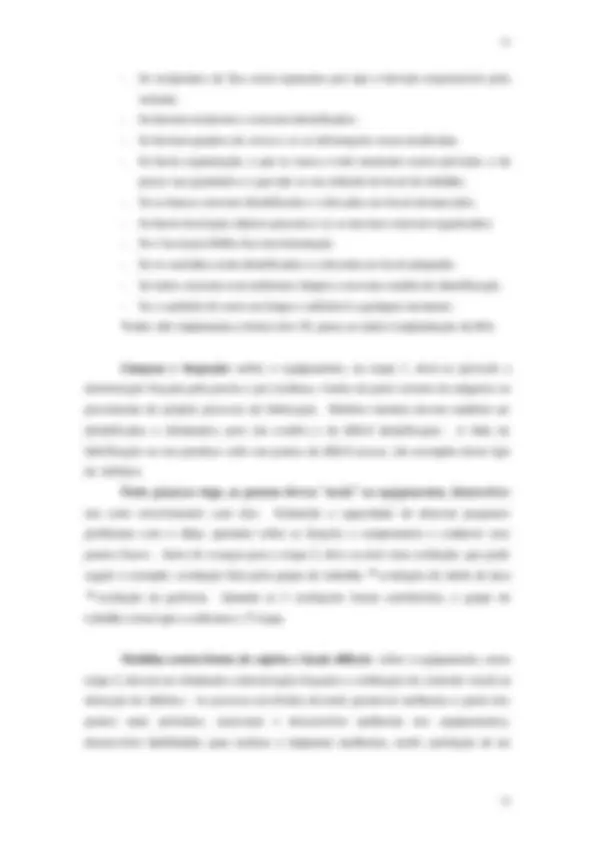
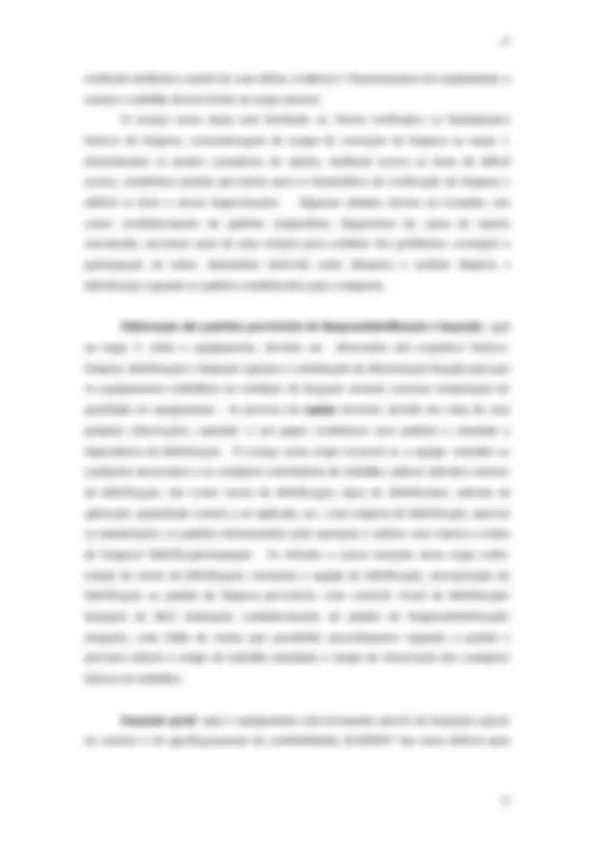
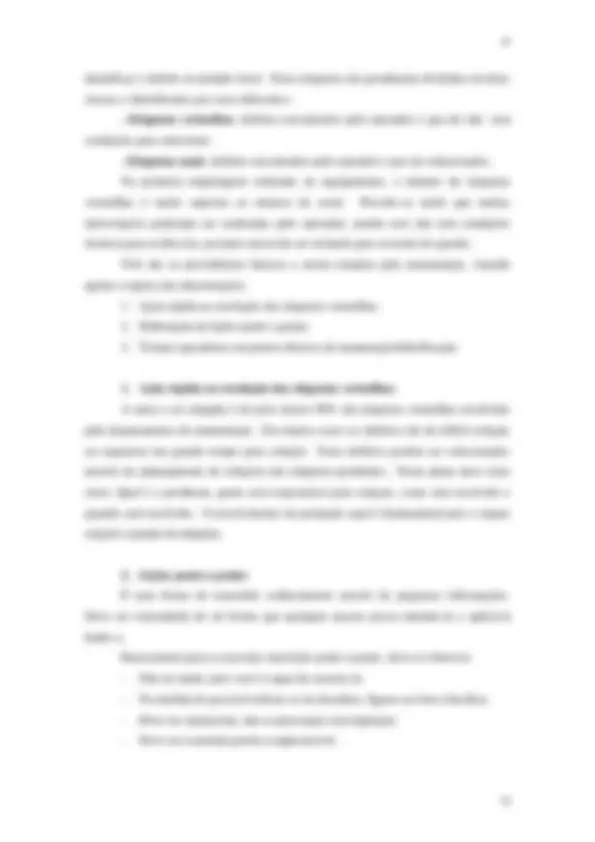
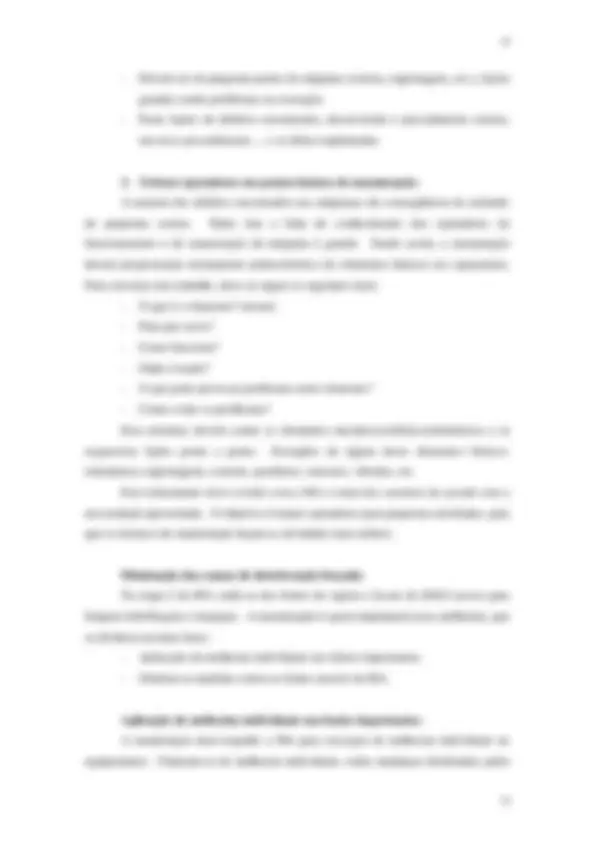
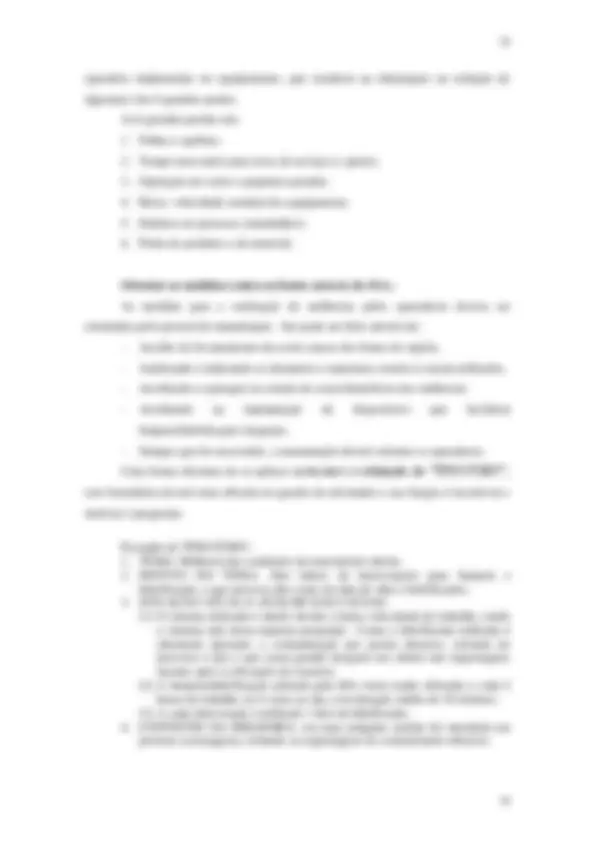
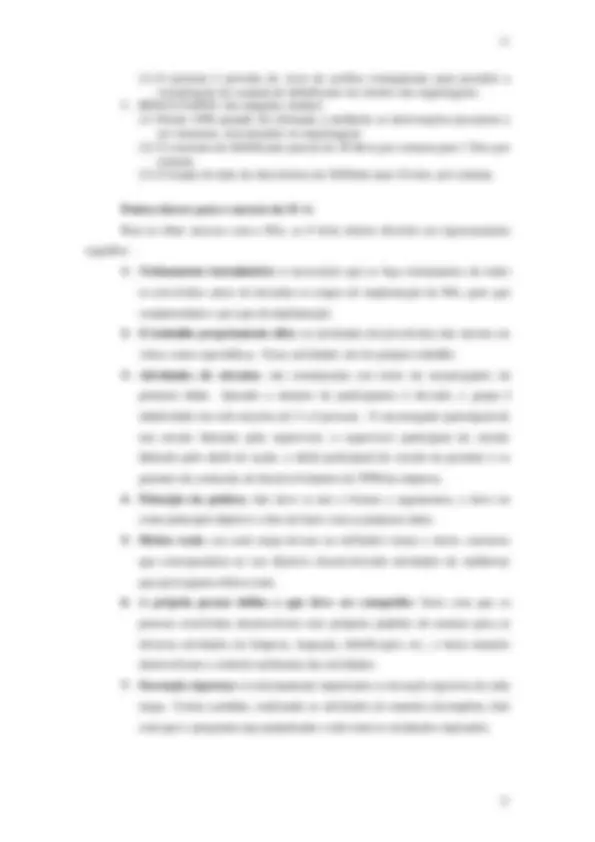
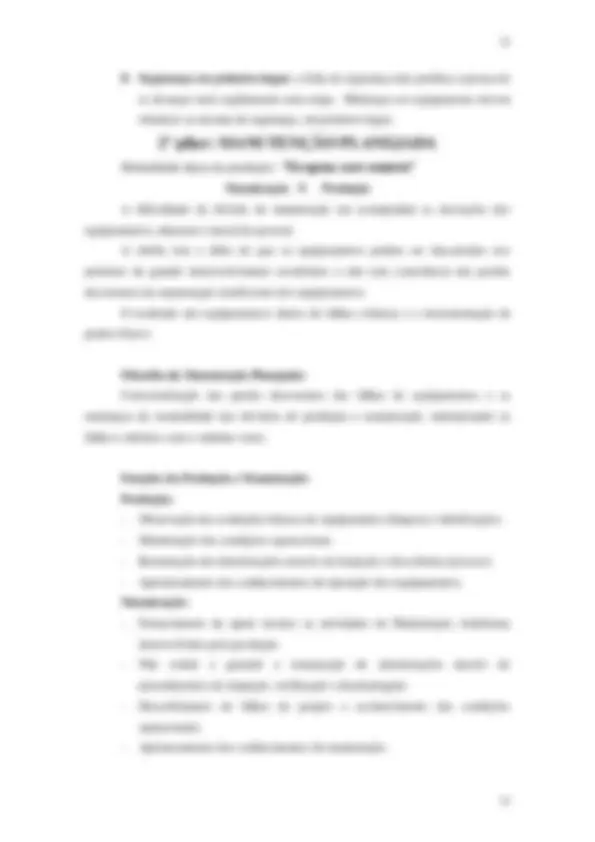
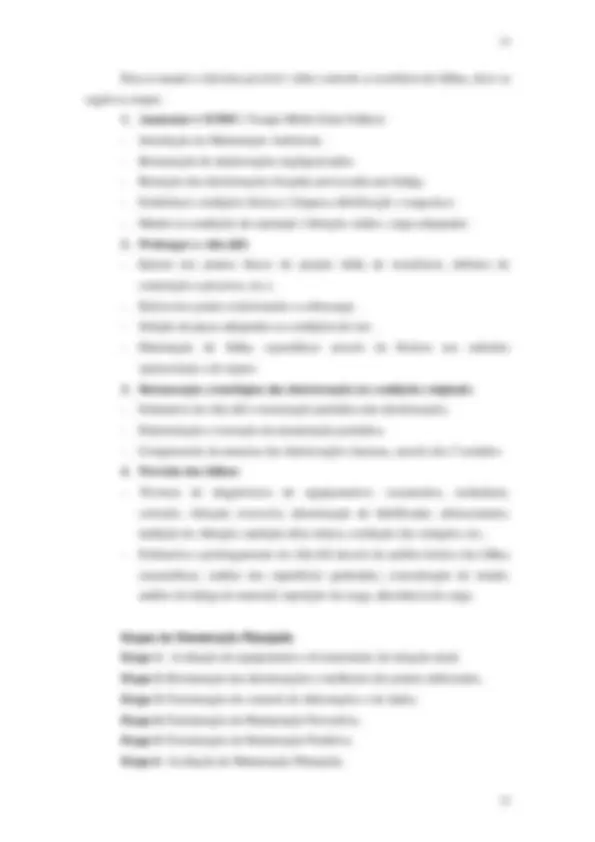
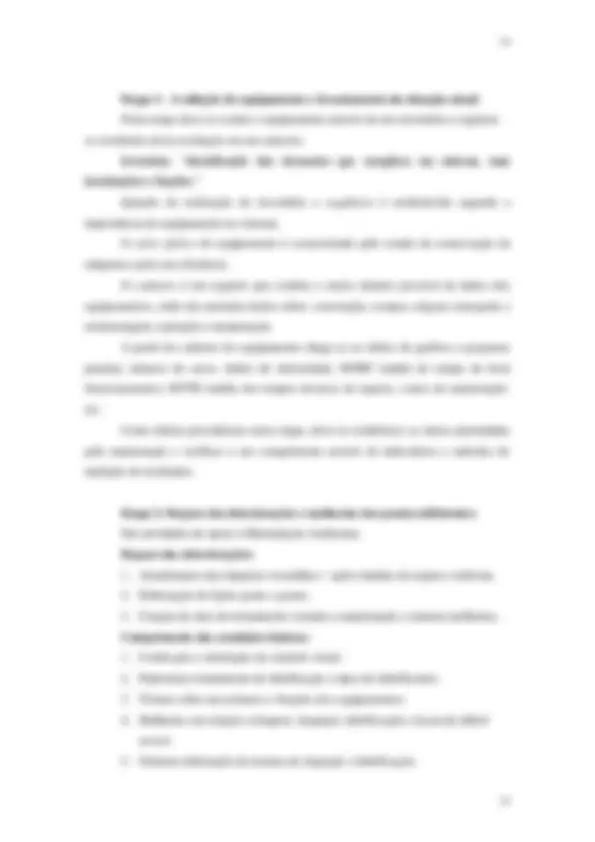
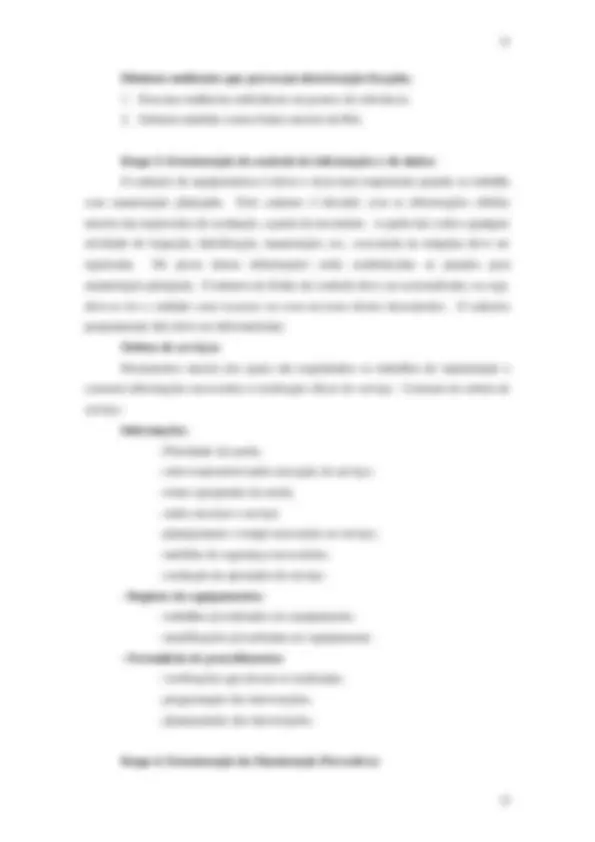
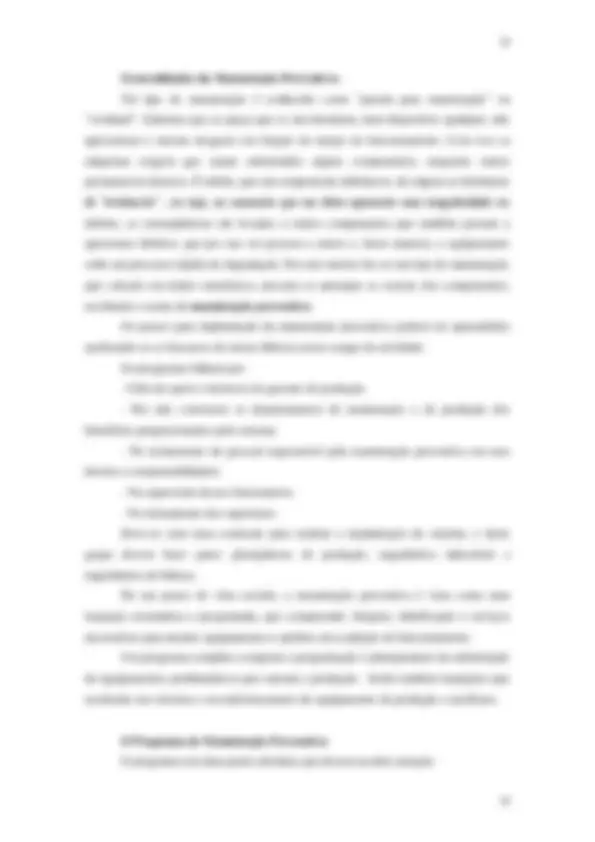
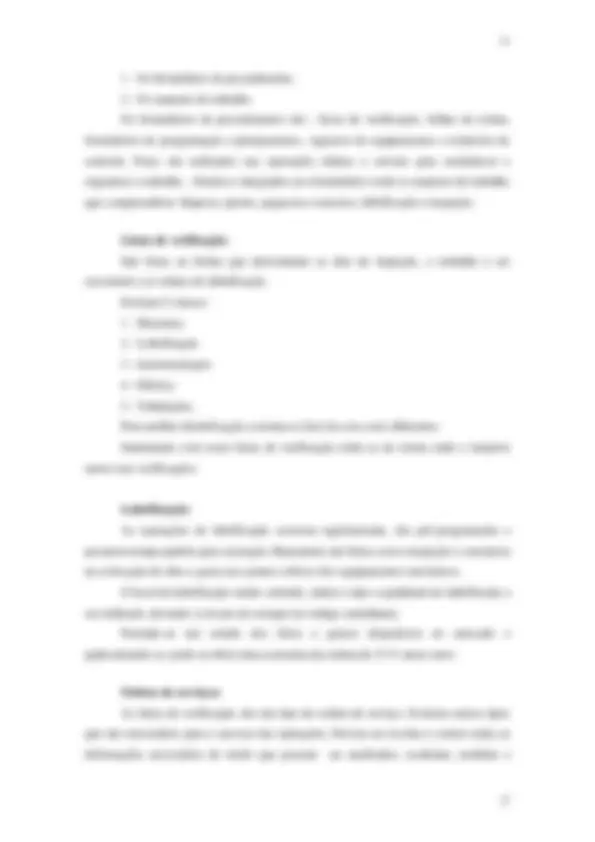
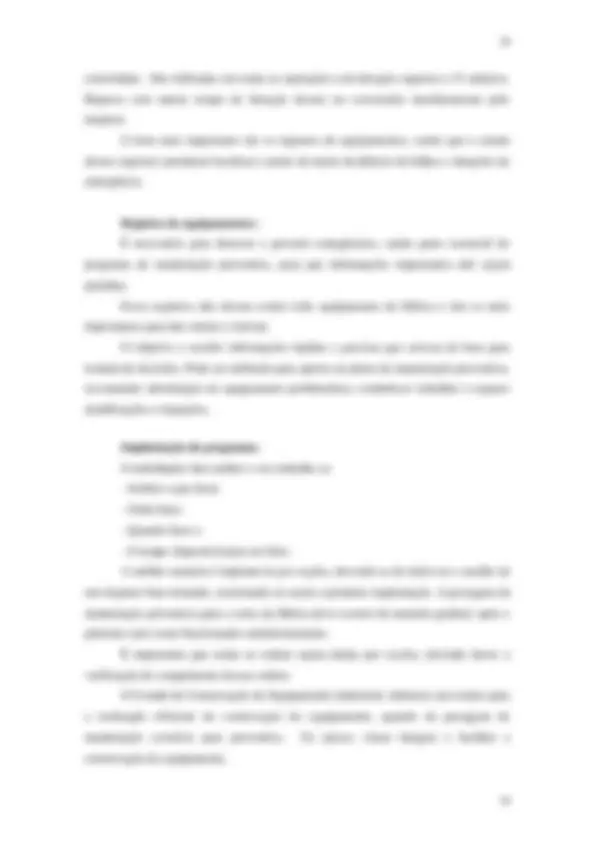
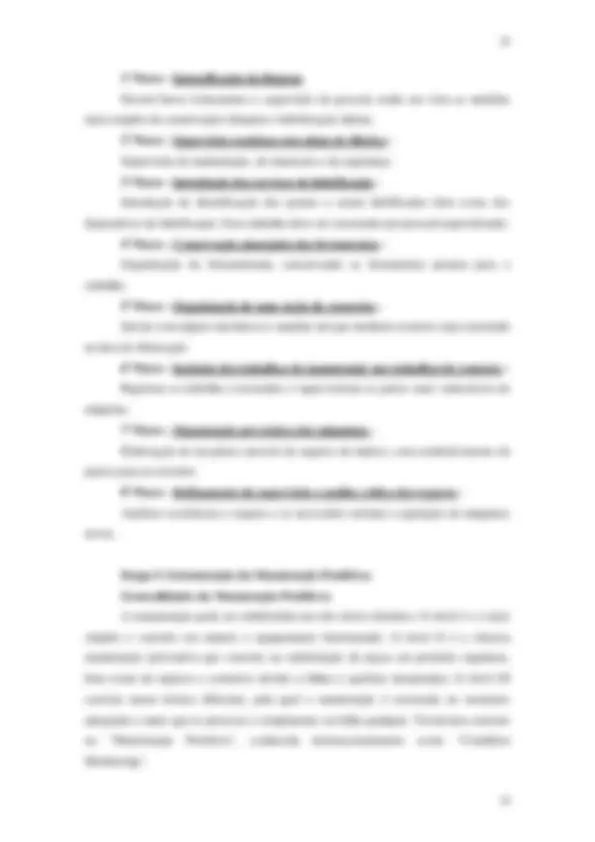
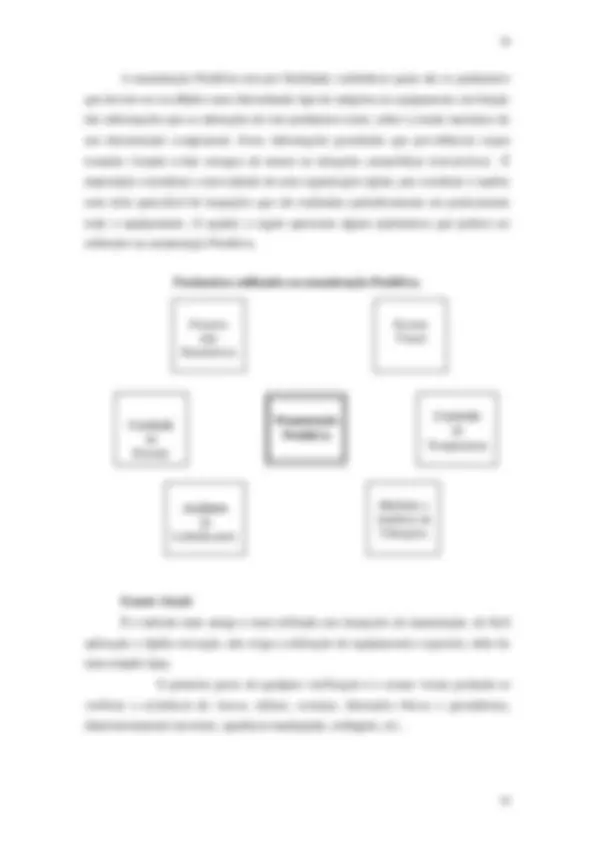
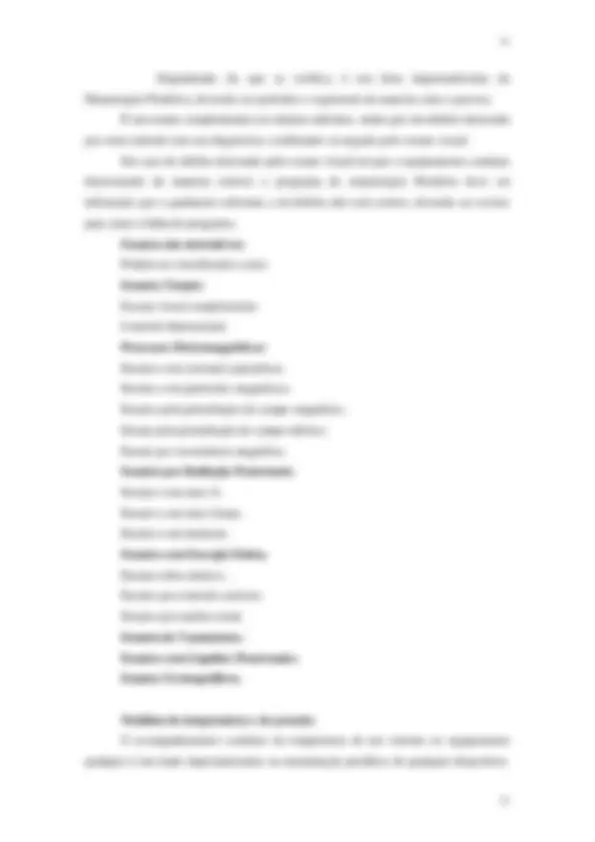
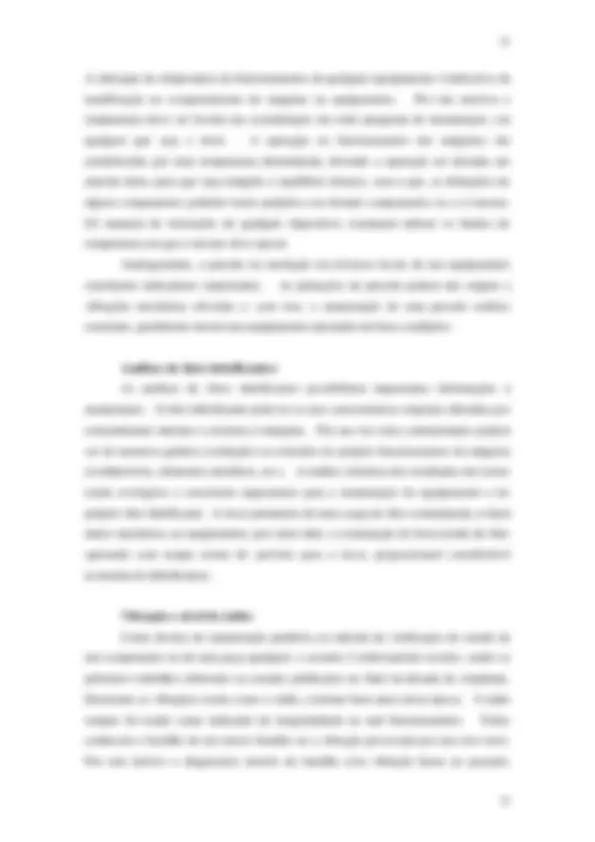
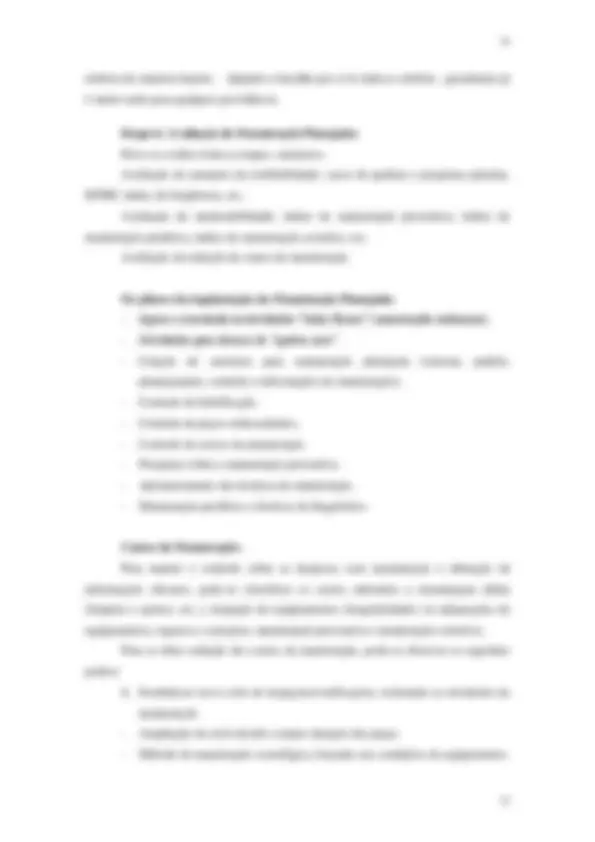
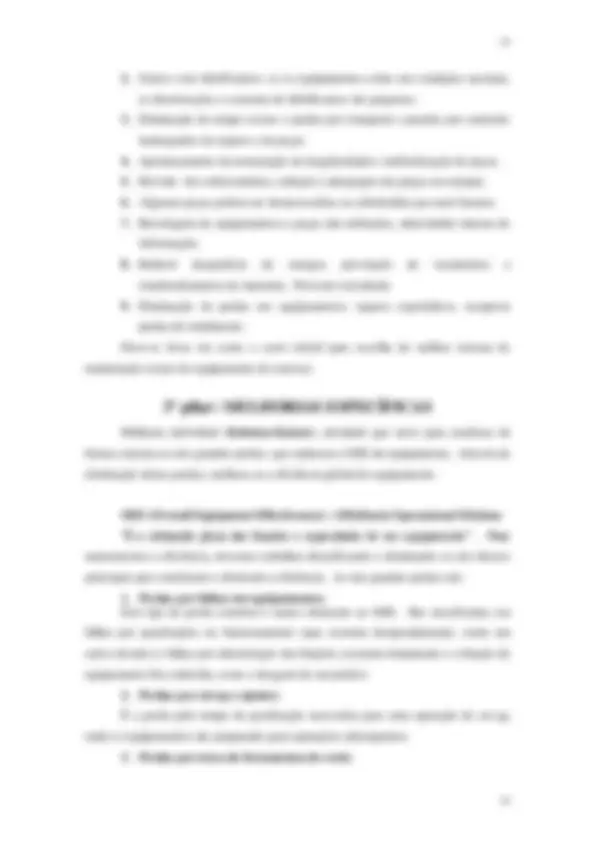
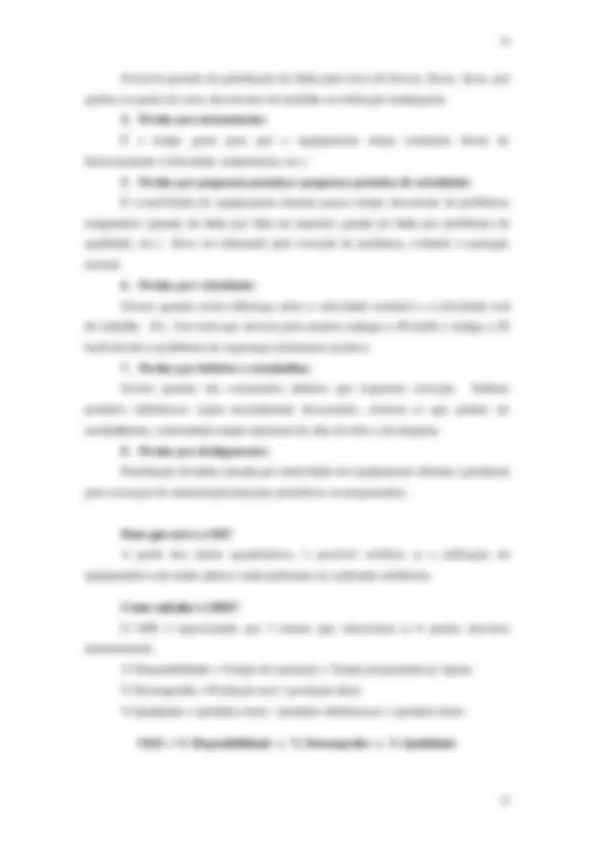
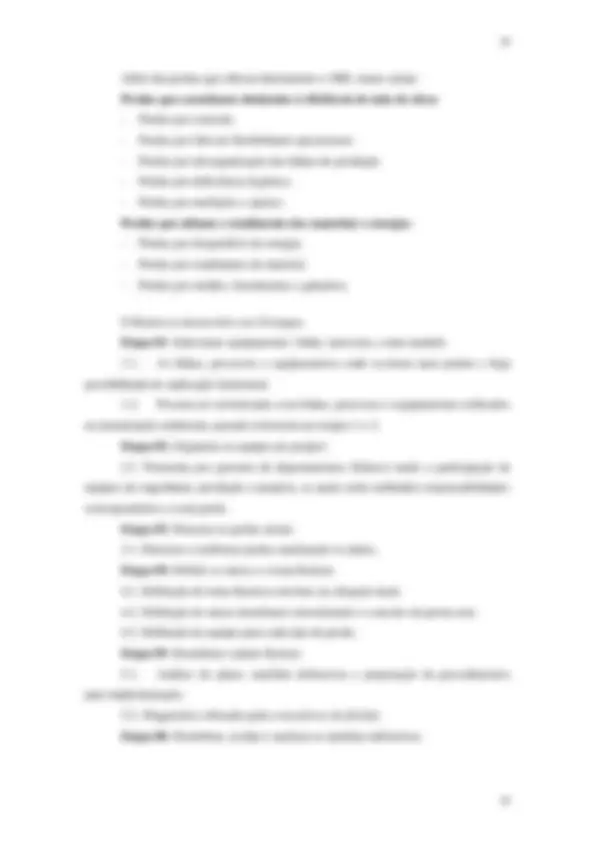
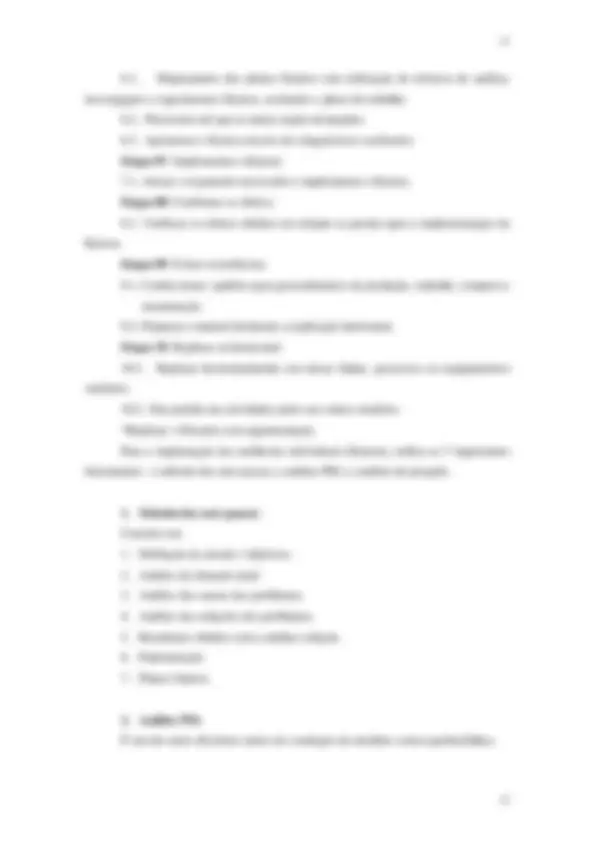
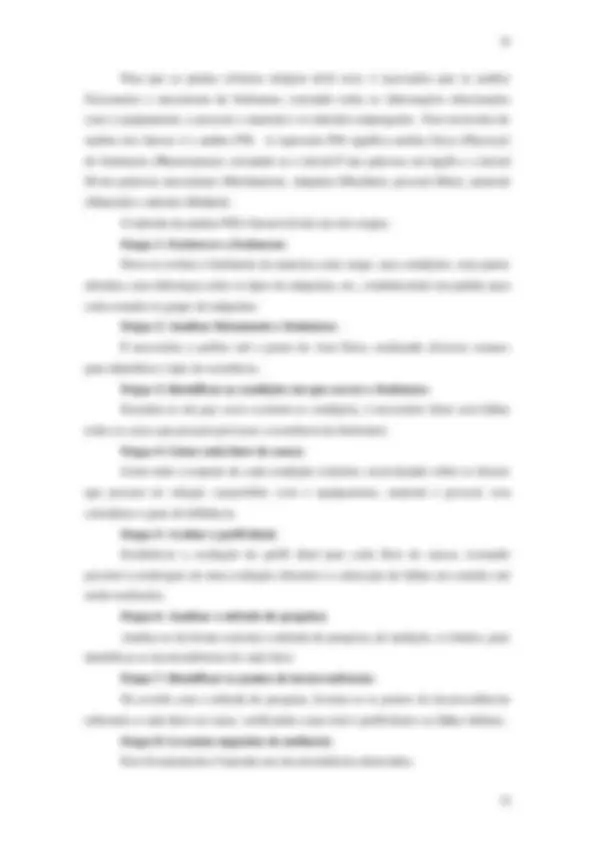
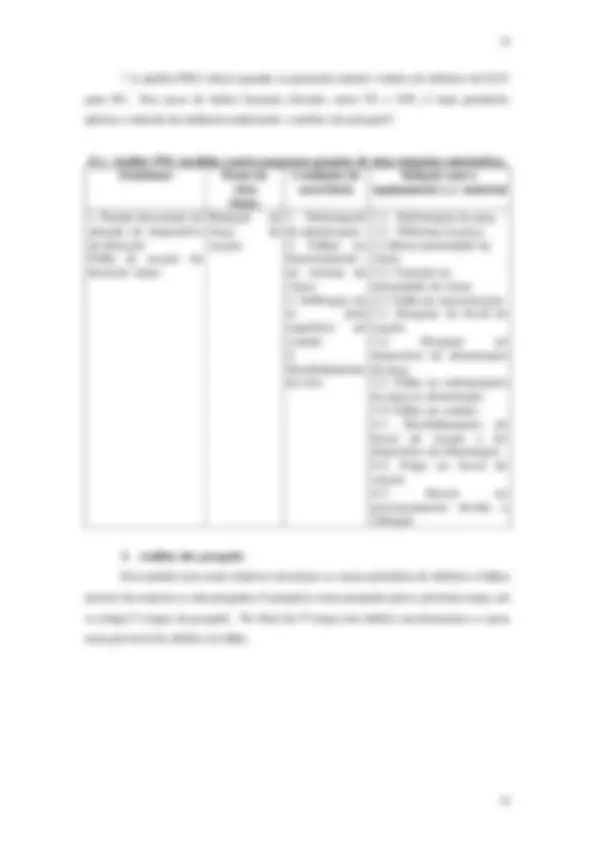
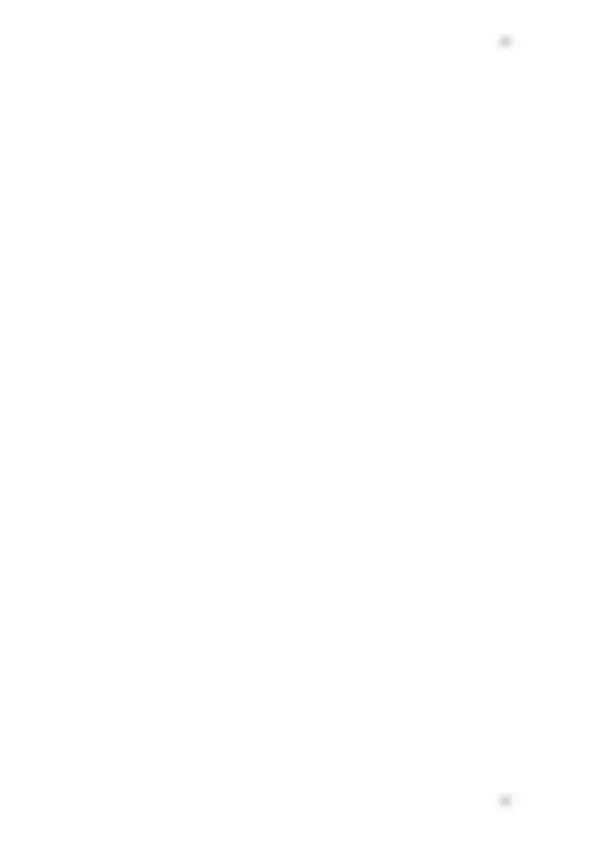
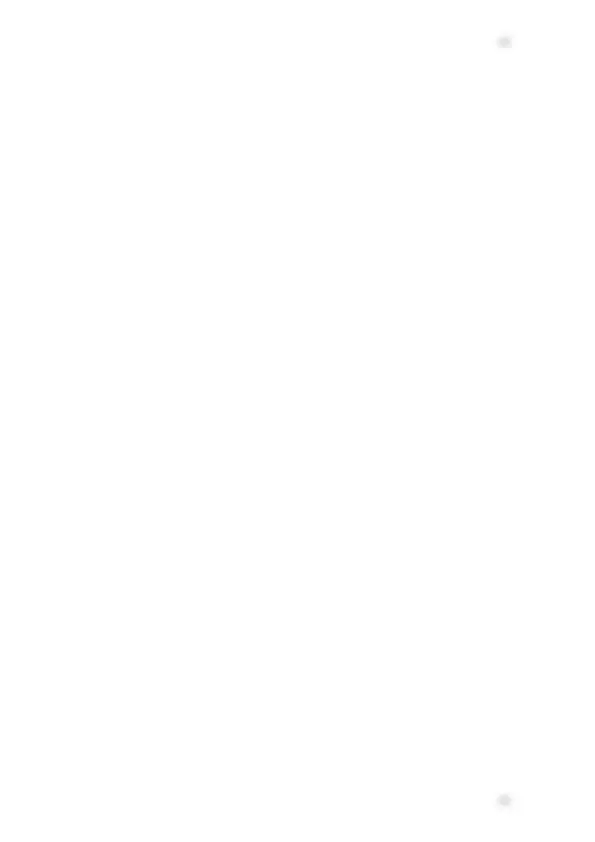
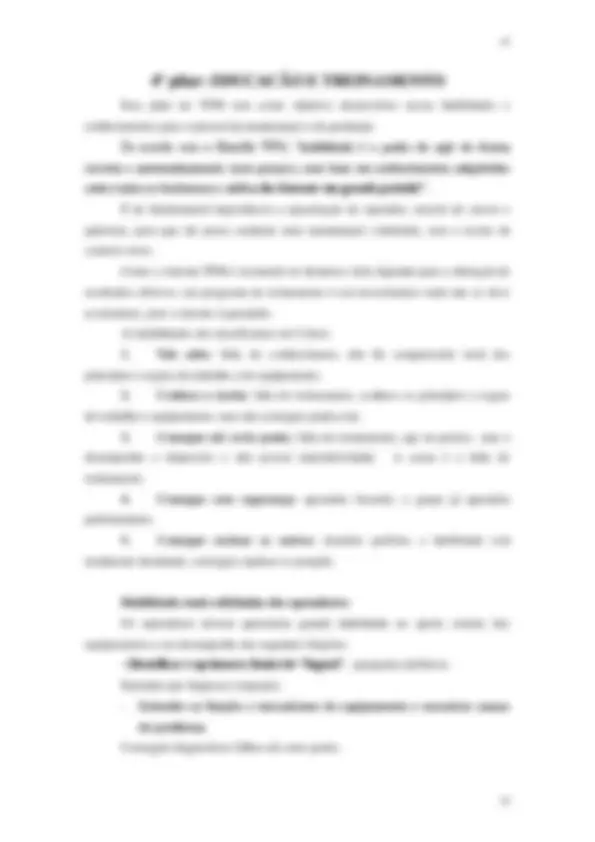
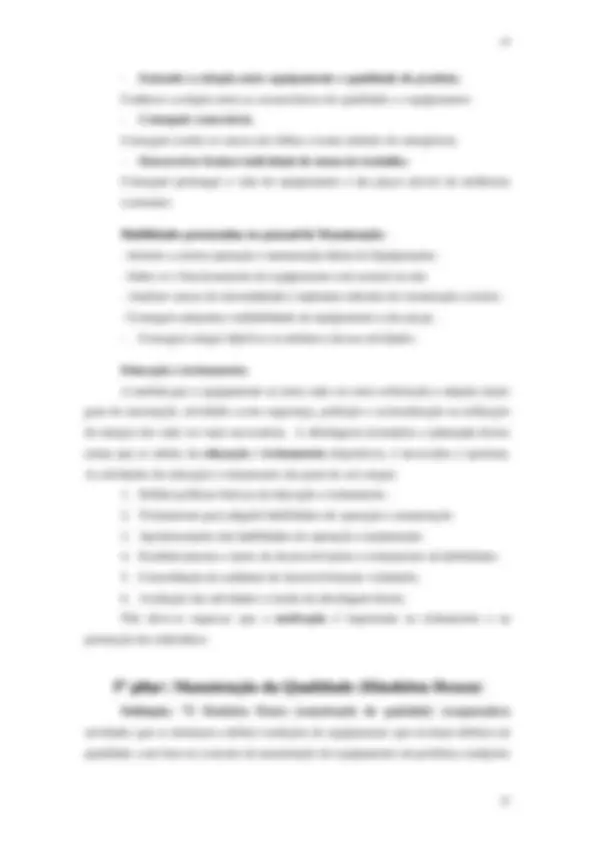
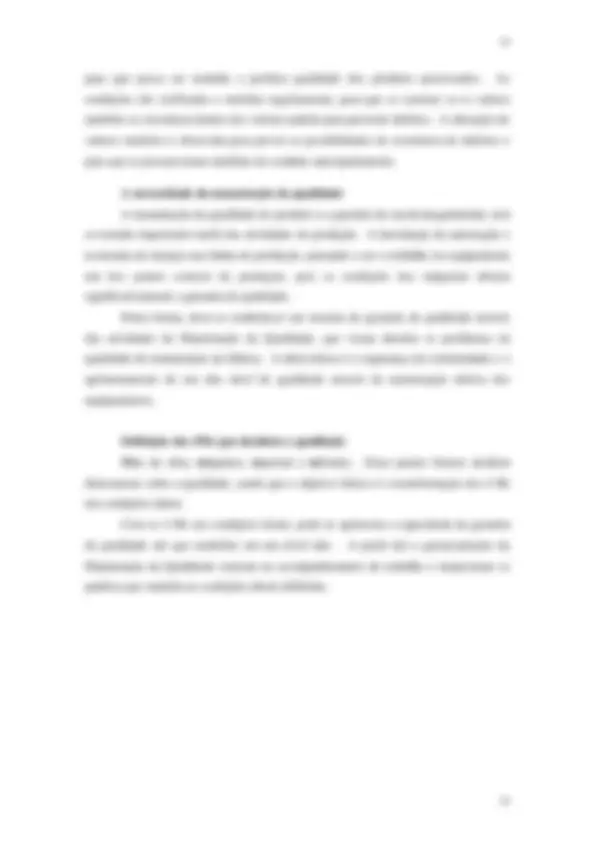
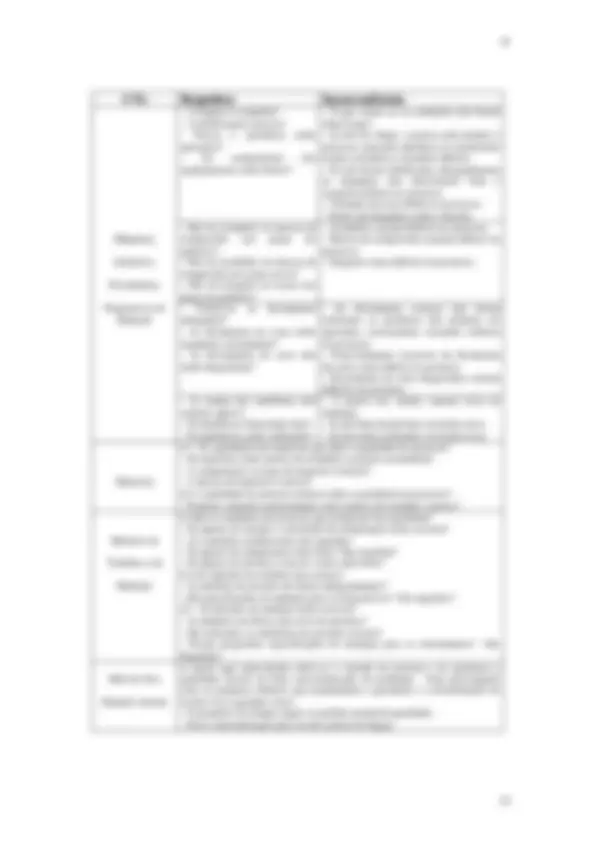
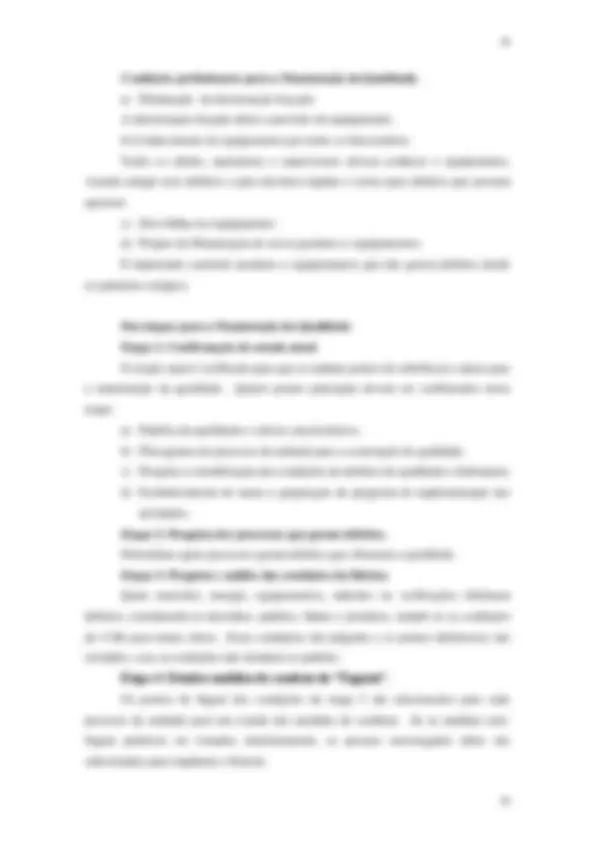
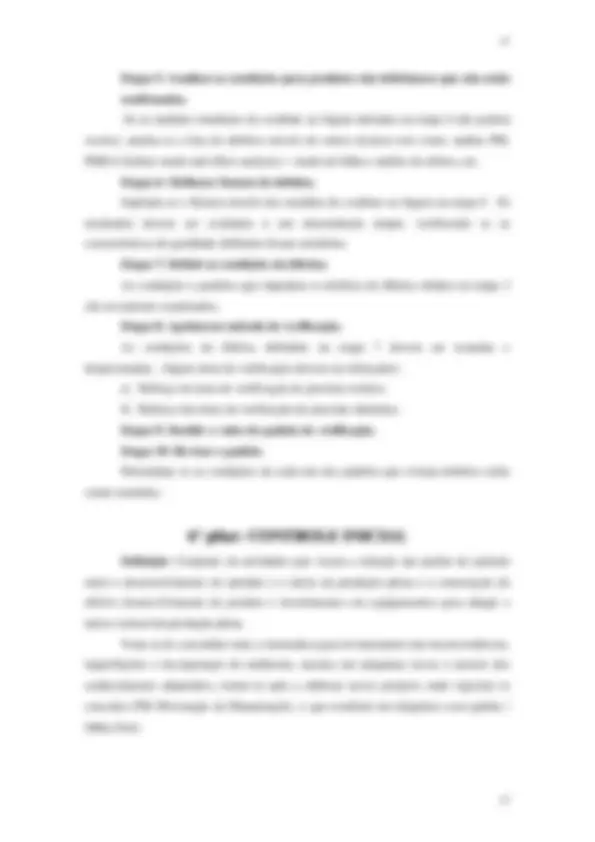
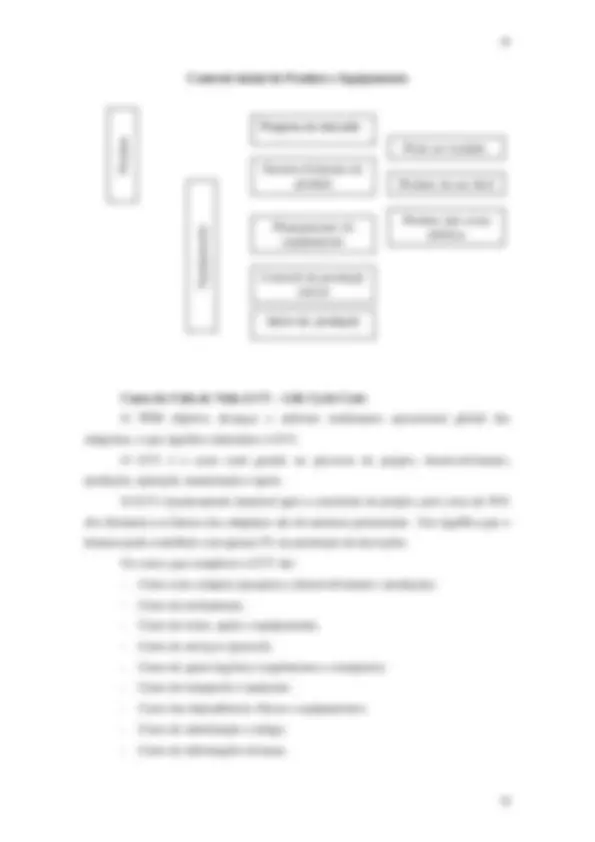
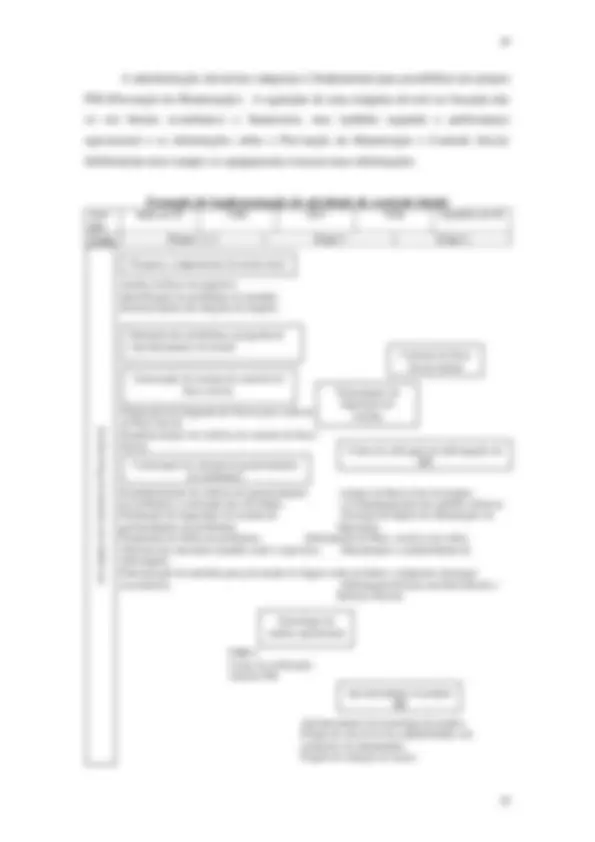

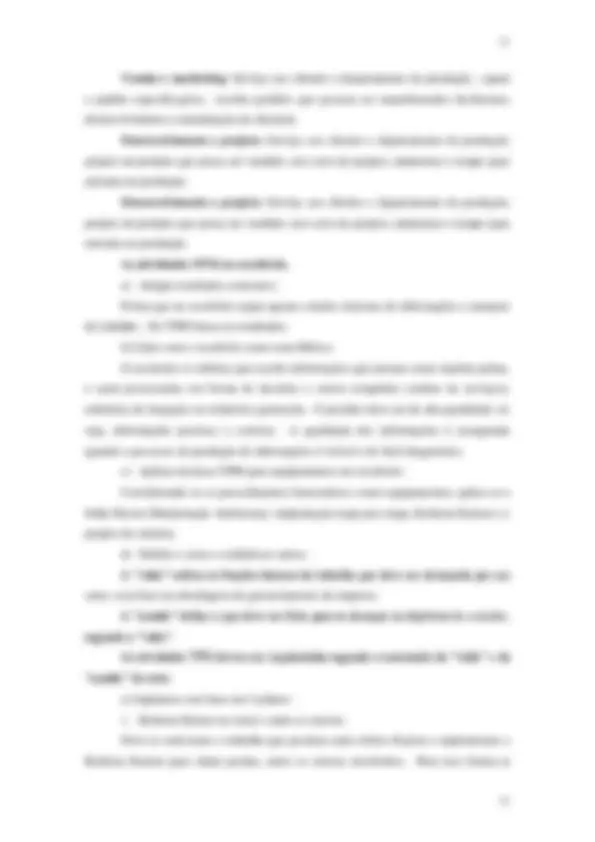
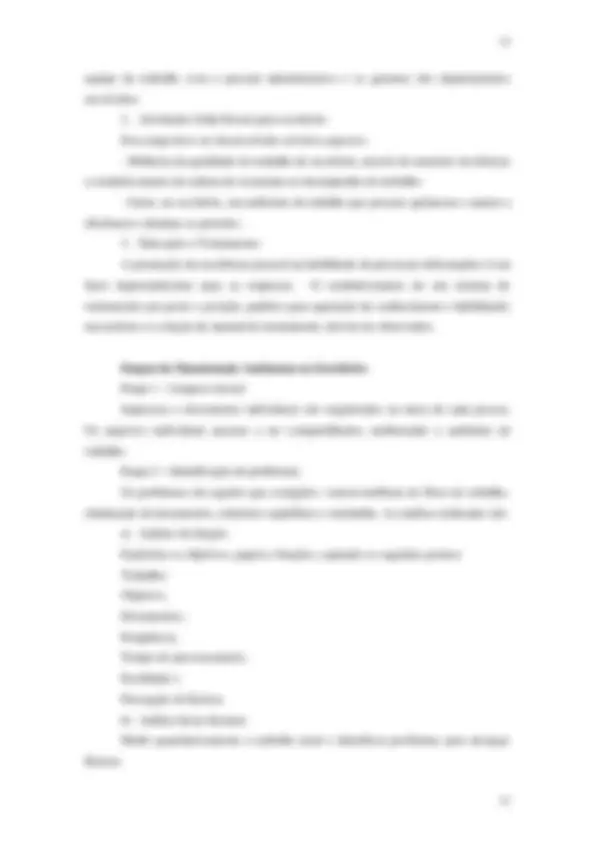
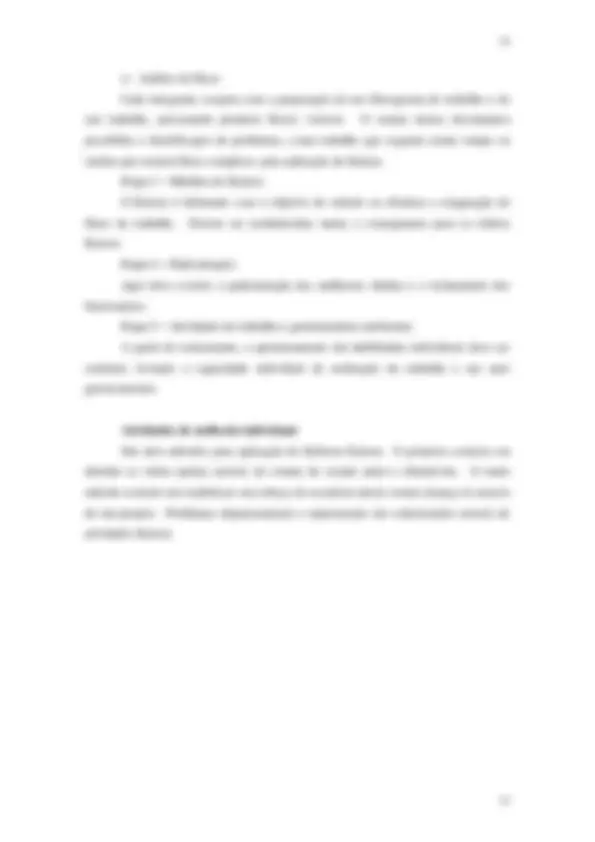
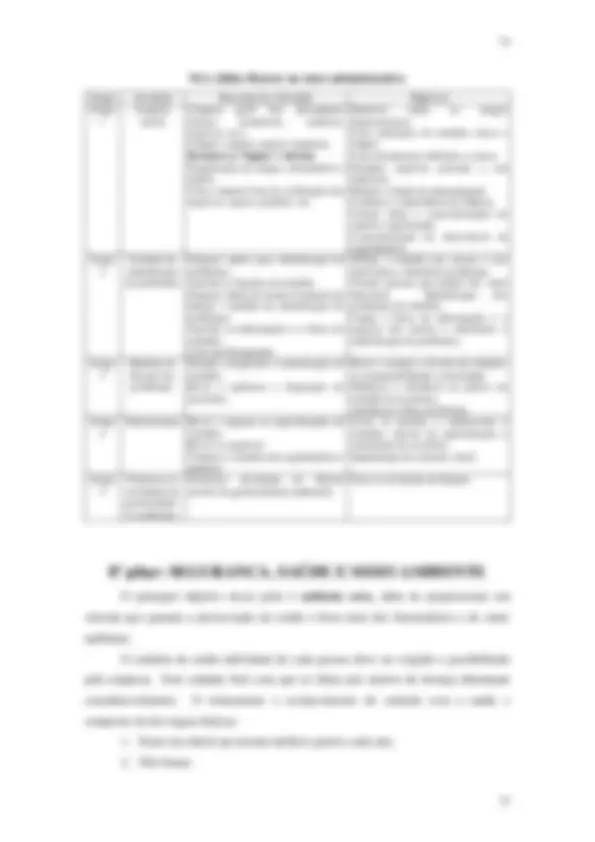
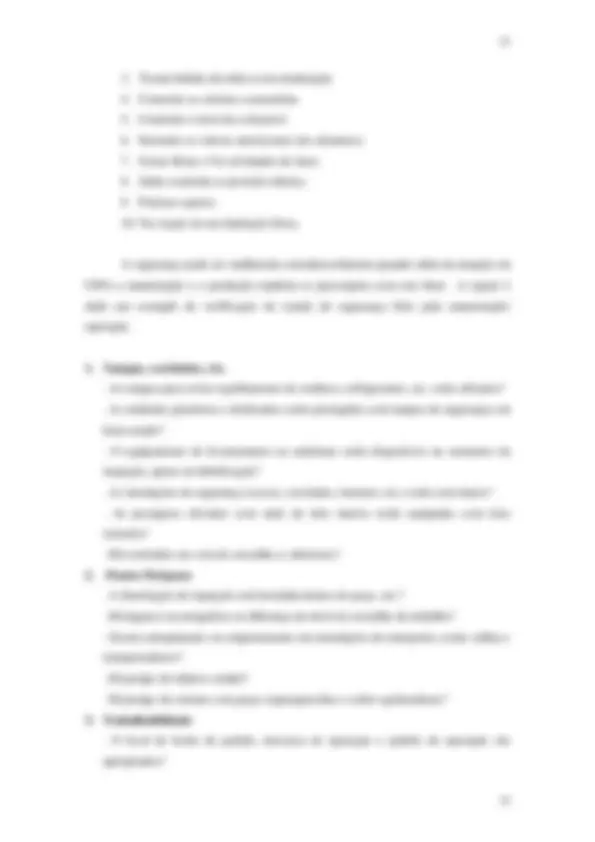
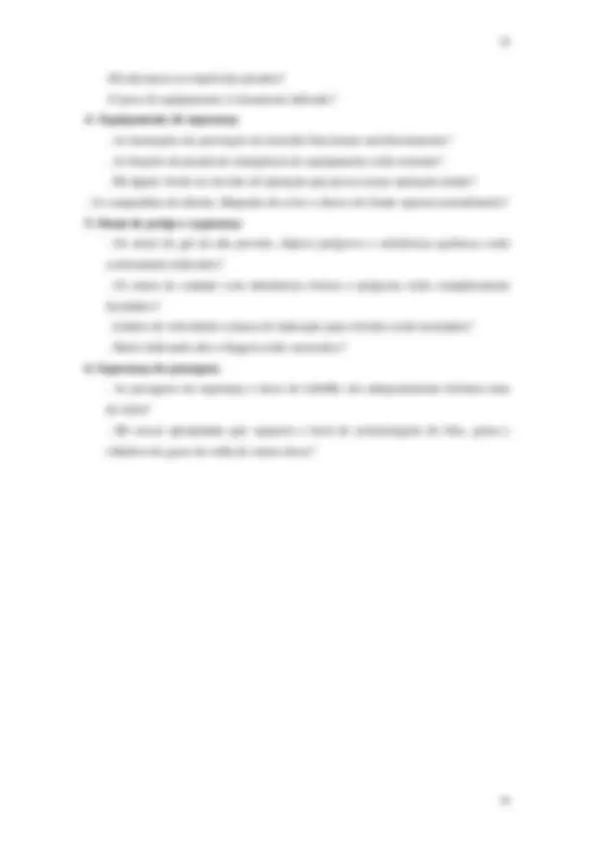
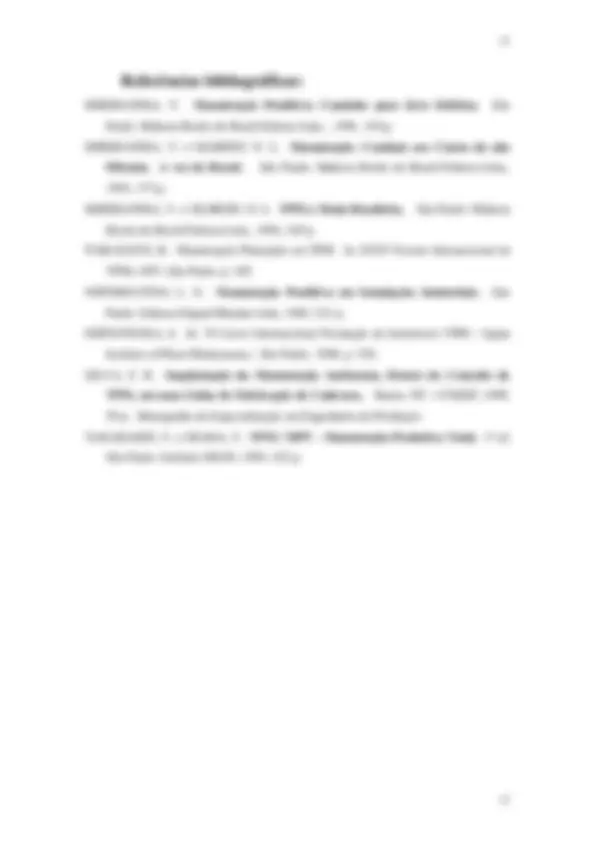
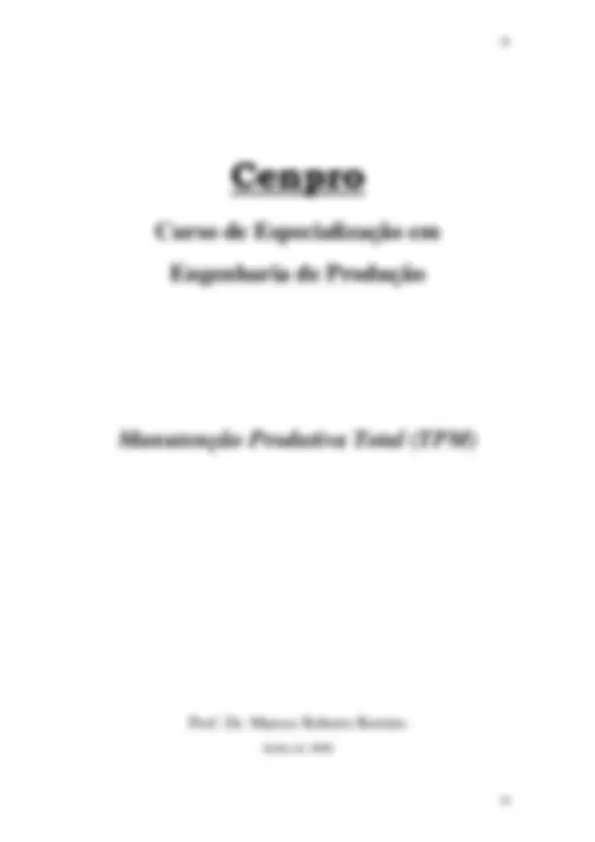
Estude fácil! Tem muito documento disponível na Docsity
Ganhe pontos ajudando outros esrudantes ou compre um plano Premium
Prepare-se para as provas
Estude fácil! Tem muito documento disponível na Docsity
Prepare-se para as provas com trabalhos de outros alunos como você, aqui na Docsity
Os melhores documentos à venda: Trabalhos de alunos formados
Prepare-se com as videoaulas e exercícios resolvidos criados a partir da grade da sua Universidade
Responda perguntas de provas passadas e avalie sua preparação.
Ganhe pontos para baixar
Ganhe pontos ajudando outros esrudantes ou compre um plano Premium
Comunidade
Peça ajuda à comunidade e tire suas dúvidas relacionadas ao estudo
Descubra as melhores universidades em seu país de acordo com os usuários da Docsity
Guias grátis
Baixe gratuitamente nossos guias de estudo, métodos para diminuir a ansiedade, dicas de TCC preparadas pelos professores da Docsity
TPM - apostila utilizada para estudo de mecânica
Tipologia: Manuais, Projetos, Pesquisas
1 / 58
Esta página não é visível na pré-visualização
Não perca as partes importantes!
MANUTENÇÃO: “Ato ou efeito de manter” “ Medidas necessárias para conservação” DEFEITO: Ocorrências no equipamento que não impedem o funcionamento, todavia pode, a curto ou a longo prazo acarretar a sua indisponibilidade. FALHA: Ocorrências no equipamento que impedem o seu funcionamento. COMPONENTE: Engenho essencial ao funcionamento de uma atividade mecânica, elétrica, etc., que conjugado a outro(s) cria(m) o potencial de realizar trabalho. Ex.: Um motor, uma bomba, um compressor, etc. EQUIPAMENTO: Conjunto de componentes interligados com que se realiza as atividades de uma instalação. Ex.: um trator, uma máquina operatriz, etc. SISTEMA: Conjunto de equipamentos necessários para realizar uma função de uma instalação. Ex.: uma frota de tratores, um conjunto de tornos mecânicos, etc.
PRIORIDADES: A prioridade é definida como: “intervalo de tempo que deve decorrer entre a constatação da necessidade da manutenção e o início desta atividade”. As prioridades são estabelecidas de acordo com a importância e a natureza do sistema com que se trabalha. A seguir é dado um exemplo. Prioridade 1 ou Emergência: manutenção realizada tão logo seja constatada a sua necessidade. Ex.: falha em equipamento prioritário. Prioridade 2 ou Urgência: manutenção a ser realizada o mais breve possível, não sendo passadas 24 horas após a constatação da necessidade. Ex.: defeito próximo a falha em equipamento prioritário ou falha em equipamento secundário. Prioridade 3 ou Necessária: manutenção que pode aguardar alguns dias, não ultrapassando uma semana. Ex.: manutenção preventiva em equipamento prioritário devido a programação preestabelecida ou reparos de defeitos em equipamentos secundários. Prioridade 4 ou Desejável: manutenção que pode aguardar algumas semanas, mas não omitida. Ex.: manutenção preventiva programada em equipamento secundário ou falha de equipamento que não interfira na produção.
Prioridade 5 ou Prorrogável: manutenção que pode deixar de ser realizada. Ex.: defeito em equipamento que não interfira na produção ou melhorias estéticas.
O TPM significa “Total Productive Management” e busca a eficiência máxima do Sistema de Produção com a participação de todos os funcionários. Surgiu, há décadas, no Japão, e chegou aos Estados Unidos em 1987, tendo logo em seguida sido introduzido no Brasil, através de visitas do Dr. Seiichi Nakajima. Segundo o Dr. Nakajima , a melhor prevenção contra quebras deve partir de um agente bem particular, o operador , daí a frase “Da minha máquina cuido eu”. O TPMº – Total Productive Management (Gerência Produtiva Total), só é alcançada quando se tiver: TPMº = TPM ¹ + TPM^2 + TPM^3 + TPM^4 , onde: TPM¹ - Total Productive Maintenance (Manutenção Produtiva Total): onde a preocupação maior é com a relação entre a manutenção e a operação, buscando a melhoria da disponibilidade do equipamento, a sua confiabilidade, etc. TPM^2 – Total Productive Manufacturing (Fabricação Produtiva Total): onde se cria uma grande parceria entre os empregados da produção. TPM^3 – Total Process Management (Gerência de Processo Total): é a administração das interfaces do processo total da linha do negócio. TPM^4 – Total Personnel Motivation (Motivação Total do Pessoal): quando os empregados terão: conhecimento, aptidões, ferramentas, o desejo e a vontade de influenciar a lucratividade global do processo. Todos os empregados são “gerentes” dos seus próprios serviços e recebem autorização para melhorar quaisquer conexões que façam parte do seu trabalho.
Construir no próprio local de trabalho mecanismos para prevenir as diversas perdas (genba-genbutsu), tendo como objetivo o ciclo de vida útil do sistema de produção. Abrange-se todos os departamentos: manutenção, operação, transportes e outras facilidades, engenharia de projetos, engenharia de planejamento, estoques e armazenagem, compras, finanças e contabilidade.
Vale salientar que este programa de manutenção leva em conta o estado da máquina, e através de registros dos equipamentos são estabelecidas as intervenções necessárias que são pré-programadas. Ao operador é exigido que cuide da limpeza e lubrificação básicas, primeira atitude para a melhora da conservação e eficiência da máquina.
3. Integração de todos os setores envolvidos no plano de elevação da eficiência: A única maneira de se obter sucesso é havendo total cooperação dos diversos setores envolvidos no plano de elevação da capacidade instalada, o que garantirá total cooperação e compreensão entre as partes. Por exemplo, a inclusão da manutenção de equipamentos nas decisões de projeto / compras, assegura que a padronização de peças e componentes necessários a manutenção será obedecida. Estes itens podem contribuir significativamente em grandes economias para a empresa. A padronização reduz estoques, exigências de treinamento e os tempos de partida. É muito importante o apoio dado à manutenção pela armazenagem. Bom atendimento logístico pode reduzir em muito o tempo de parada de produção, mais importante porém e a otimização do estoque de componentes, ou tentar evitar grandes estoques. 4. Colaboração dos funcionários no processo de fabricação: A colaboração no processo de fabricação de funcionários de todos os níveis com suas aptidões e conhecimentos, além da integração traz a satisfação do cliente interno. Em algumas empresas este item está incluído no processo de sugestões, como obter melhor manutenção, maior limpeza e organização, etc. Esta prática deveria ocorrer com maior freqüência em empresas brasileiras, evitando-se um ambiente de frustração. Uma boa medida é instaurar a “gerência de portas abertas”, pois os gerentes de frente ou de topo, precisam estar mais disponíveis para o pessoal da produção / manutenção, levando em consideração as sugestões dos funcionários. A resposta que se deve dar a cada “discussão”, sobre a melhoria no funcionamento de uma máquina, não deve conter os constantes bloqueios do tipo: . “Isto não vai funcionar.” . “Não podemos levar isto em conta neste momento.” . “Isto só funciona no Japão.”
. “Não temos dinheiro para treinar pessoas para esta atividade.” . “Isto o sindicato não vai aprovar.” . “Dá para você parar de sonhar.”......etc. As razões da não implementação das sugestões devem ser colocadas e bem explicadas, para que se mantenha a boa comunicação. Sem esta atitude a maior fonte geradora de economia da empresa será perdida. 5. Criação de equipes de trabalho: A criação e desenvolvimento de equipes consolidadas ou TMM (times de melhoria da manutenção), começa no item 4, quanto mais aberta for a gerência às sugestões da força de trabalho, melhor e mais fácil será o funcionamento das equipes. Essas equipes podem ser formadas por áreas, por departamentos, por linhas de produção, por processos ou por equipamentos. Podem ser constituídas por operadores, pessoal da manutenção e pessoal da gerência. Poderão ter a participação de outras pessoas diretamente envolvidas no problema, por exemplo: pessoal de compras e armazenagem. Os TMM realmente resolvem problemas que já tenham tentado resolver a algum tempo sem sucesso? Pode-se afirmar que o sucesso do TPM deve-se ao trabalho de equipe. Logicamente o maior convencimento é dado por números, tais como: Produtividade : aumento de 50% a 200%, elevação das taxas de operação de 40% a 100% e diminuição das interrupções em até 80%. Qualidade : pode-se chegar a zero defeitos ou diminuição de 100% deles, pode- se reduzir em 80% as reclamações de clientes. Custos : redução de até 70% nos custos de trabalho, 50% nos de manutenção e de 80% nos de energia. Estoques : redução de até 90% nos níveis de estoque, aumento de até 100% nos giros de estoque. Segurança : eliminação quase total dos problemas com segurança do ambiente de trabalho. Moral : aumento de até 500% nas sugestões (não reclamações). Participação dos funcionários nas reuniões de grupos, o que faz com que vistam a camisa da empresa, procurando assim o aumento dos lucros. Pode-se dizer que o TPM ajuda até mesmo na preservação do sexo, como exemplo:
Promoção do TPM como parte de uma política e de uma organização objetiva.
A filosofia TPM está calcada na identificação e eliminação de perdas, que são: As 7 principais perdas em equipamentos são:
. Falhas em equipamentos. . Set-up e ajustes. . Troca de ferramentas de corte. . Perdas por acionamento. . Perdas por pequenas paradas. . Perdas por velocidade.
. Defeitos e retrabalhos.
Perdas por mão de obra:
. Perdas por controle : são perdas decorrentes do tempo de espera (materiais, ferramentas, instruções, etc.) geralmente ocasionadas por problemas administrativos. . Perdas por movimento : aquelas relacionadas a burocracia e ações que não agregam valor de trabalho. . Perdas por desorganização da linha : resultantes da má organização da linha ou da situação de uma única pessoa manipulando mais de um equipamento ao mesmo tempo. . Perdas por falhas logísticas : tempo gasto com trabalhos de transporte, deslocamento, etc. executados por aqueles que as atribuições não incluem estas funções. . Perdas por medições e ajustes : tempo gasto com ajustes freqüentes, executados como medida preventiva contra a ocorrência de produtos defeituosos. Perdas com materiais, moldes, gabaritos, ferramentas e energia: . Perdas de energia : perda com energia (elétrica, gás, combustíveis) aplicada que não é utilizada no processo (desperdício). . Perdas com moldes, ferramentas e gabaritos : são constituídas por despesas adicionais para substituição ou reparo de moldes, ferramentas e gabaritos decorrentes de quebra ou desgaste de utilização. . Perdas por rendimento : é resultante do mal uso da matéria prima (diferença entre o peso da matéria prima utilizada e o peso do produto acabado.
São decorrentes da falta de confiabilidade dos equipamentos. A sua eliminação apresenta sérias dificuldades, mesmo com a aplicação de medidas defensivas. A resolução destas perdas exigem medidas inovadoras bastante diferentes das convencionais. Como são decorrentes de causas diversificadas e de difícil detecção, a relação entre a causa e efeito costuma ser obscura, dificultando as medidas defensivas adequadas. Mesmo que a causa real da perda seja única, ela pode ser atribuída a vários fatores. Para resolve-las é preciso tomar medidas defensivas para todas as possíveis causas (causa simples, causas múltiplas e causas múltiplas compostas). A eliminação das perdas crônicas exige:
podem diminuir quando ocorrem mudanças de mentalidade e atitudes de todos os operadores que trabalham com o equipamento. O ponto de partida para se atingir quebra zero é o descarte do conceito de que as quebras são inevitáveis e adotar o conceito que os equipamentos podem ser protegidos. Se é possível detectar quebras antes que elas ocorram, é possível evitá-las através de medidas preventivas. Na grande maioria dos casos, as razões das quebras são desconhecidas até que elas ocorram, por isso são chamadas de “defeitos latentes”. O princípio básico para obtenção da quebra zero é a completa identificação destes defeitos. Os defeitos latentes são formados por fatores como poeira, manchas, desgastes, corrosão, rachaduras, afrouxamentos, vazamentos, deformação, deslocamentos, anomalias relacionadas a temperatura, vibração e ruídos. Existem dois tipos de defeitos latentes: a) Defeitos físicos: Que podem passar desapercebidos.
. Detectáveis somente com análises. . Não visíveis devido ao mal posicionamento, instalação, poeira ou sujeira. b) Defeitos Psicológicos: São devidos a falta de capacitação técnica e conscientização dos responsáveis pela manutenção e operação. . Falta de interesse. . Não distingue a falha ou defeito por falta de conhecimento. . Negligência dos mantenedores e operadores com base em seus próprios critérios e opiniões. Cinco medidas básicas podem ser observadas visando a redução de falhas:
O Programa TPM é composto de oito pilares de sustentação, como se vê a seguir:
Limpeza e Inspeção: s obre o equipamento, na etapa 1, deve-se prevenir a deterioração forçada pela poeira e por resíduos, vindos da parte externa da máquina ou proveniente do próprio processo de fabricação. Defeitos latentes devem também ser identificados e eliminados, pois são ocultos e de difícil identificação. A falta de lubrificação ou um parafuso solto em pontos de difícil acesso, são exemplos deste tipo de defeitos. Nesta primeira etapa, as pessoas devem “sentir” os equipamentos, desenvolver um certo envolvimento com eles. Estimular a capacidade de detectar pequenos problemas com o olhar, aprender sobre as funções e componentes e conhecer seus pontos fracos. Antes de avançar para a etapa 2, deve ocorrer uma avaliação, que pode seguir o exemplo: avaliação feita pelo grupo de trabalho avaliação do chefe de área avaliação da gerência. Quando as 3 avaliações forem satisfatórias, o grupo de trabalho estará apto a enfrentar a 3ª etapa.
Medidas contra fontes de sujeira e locais difíceis : sobre o equipamento, nesta etapa 2, deverá ser eliminada a deterioração forçada e a utilização do controle visual na detecção de defeitos. As pessoas envolvidas deverão promover melhorias a partir dos pontos mais próximos, raciocinar e desenvolver melhorias nos equipamentos, desenvolver habilidades para realizar e implantar melhorias, sentir satisfação de ter
inspeções e providenciar correções; fazer com que as inspeções sejam rotineiras e eficientes. *KAIZEN: prática de melhorias contínuas, obtidas por pequenas mudanças nos processos existentes, através da criatividade das pessoas que trabalham com o equipamento. Normalmente tornam o ambiente de trabalho melhor e não requerem investimentos ou apenas pequenos dispêndios.
As pessoas devem: familiarizar-se com os métodos de inspeção; compreender funções e mecanismos dos equipamentos; utilizar-se dos dados coletados e ser participativas nas reuniões; utilizar-se das atividades Kaizen e entender a importância da educação para a comunicação. Para avançar nesta etapa 4, devem: adquirir conhecimentos e capacitação através dos manuais de verificações; diagnosticar e reparar pequenos defeitos através da inspeção geral e preparar padrão experimental para inspeção autônoma. Para tanto as atitudes a serem tomadas são: compreensão das estruturas e das funções dos produtos; compreender regras de garantia de qualidade; definir ferramentas (gabaritos, medidores, etc.) para garantir a qualidade imposta ao produto; preparação de material didático para qualificação em inspeção geral; implementação de qualificação de lideres; acompanhamento de cursos de qualificação; preparação dos manuais de verificação. Inspeção autônoma : na inspeção autônoma o operador é capacitado para detectar os problemas antes que ocorram. O alvo desta etapa é a implementação da inspeção através do manual de padrões de inspeção. Devem ser bem definidas as atribuições de inspeções da manutenção e da operação. As inspeções devem ser realizadas diariamente e dez pontos importantes devem ser observados:
Padronização : essa etapa visa a organização, a ordem e a efetivação do controle de manutenção através de padronização. As principais atividades desta etapa são: a revisão dos itens a serem controlados no local de trabalho e a revisão do controle feito visualmente. O ponto importante nesta etapa é a realização e a ordem em termos gerais, tanto no aspecto físico como no administrativo.
Controle autônomo : Até aqui nesta última etapa, foram atribuídas as qualificações necessárias ao operador. Desta maneira o operador deverá ter a capacidade de trabalhar com espirito de autonomia. O principal item desta etapa é a utilização das habilidades adquiridas nas etapas anteriores, para analisar-se os dados sobre quebra/falha, técnicas de melhorias e aumento de eficiência do equipamento e capacitação técnica para pequenos ajustes.
Funções da Manutenção na Manutenção Autônoma: Basicamente a área de manutenção terá como função dar suporte à operação para a implementação da MA. Os pontos básicos a serem considerados são:
Reparo das deteriorações: Quando inicia-se as atividades de TPM em um equipamento, os operadores encontrarão diversos defeitos que deverão ser identificados por etiquetas, uma forma de
Eliminação das causas de deterioração forçada: Na etapa 2 da MA cuida-se das fontes de sujeira e locais de difícil acesso para limpeza lubrificação e inspeção. A manutenção é quem implantará estas melhorias, que se dividem em duas fases:
Aplicação de melhorias individuais nas fontes importantes: A manutenção dará respaldo a MA para execução de melhorias individuais no equipamento. Chamam-se de melhorias individuais, todas mudanças idealizadas pelos
operários implantadas no equipamento, que resultem na eliminação ou redução de alguma(s) das 6 grandes perdas. As 6 grandes perdas são:
Orientar as medidas contra as fontes através da MA.: As medidas para a realização de melhorias pelos operadores devem ser orientadas pelo pessoal da manutenção. Isto pode ser feito através de:
Exemplo de TPM STORY: