
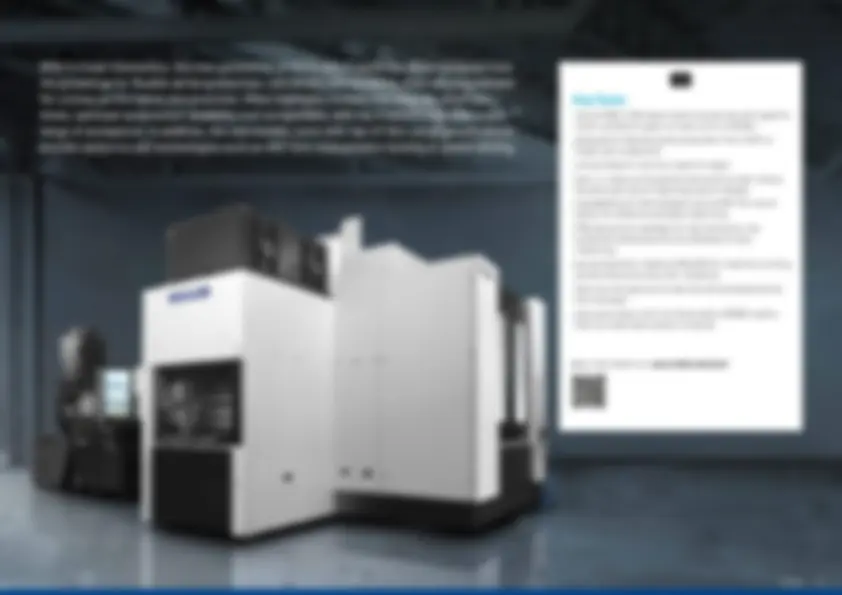
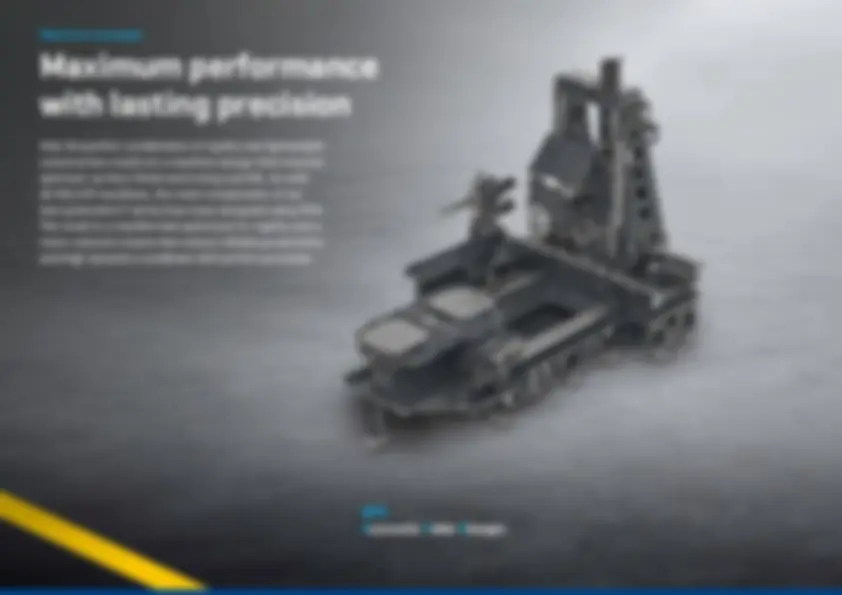
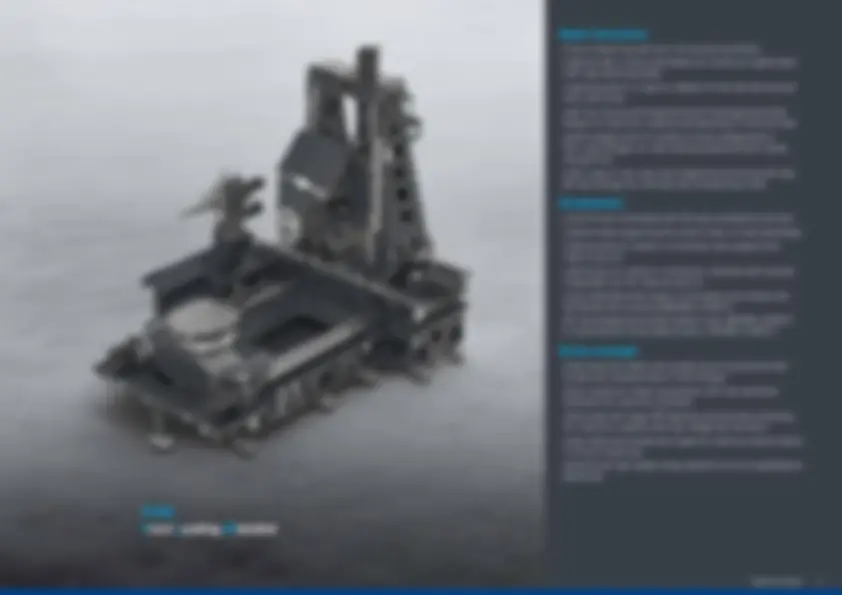
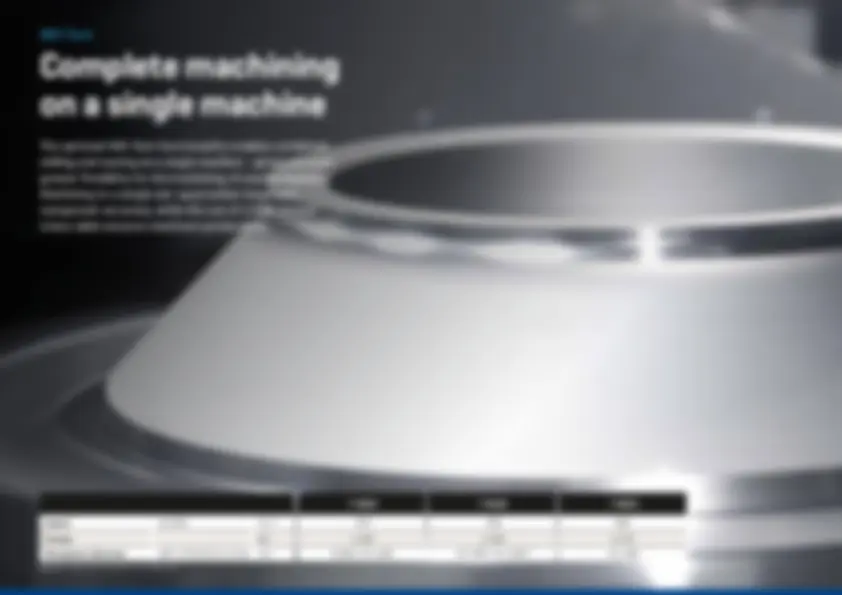
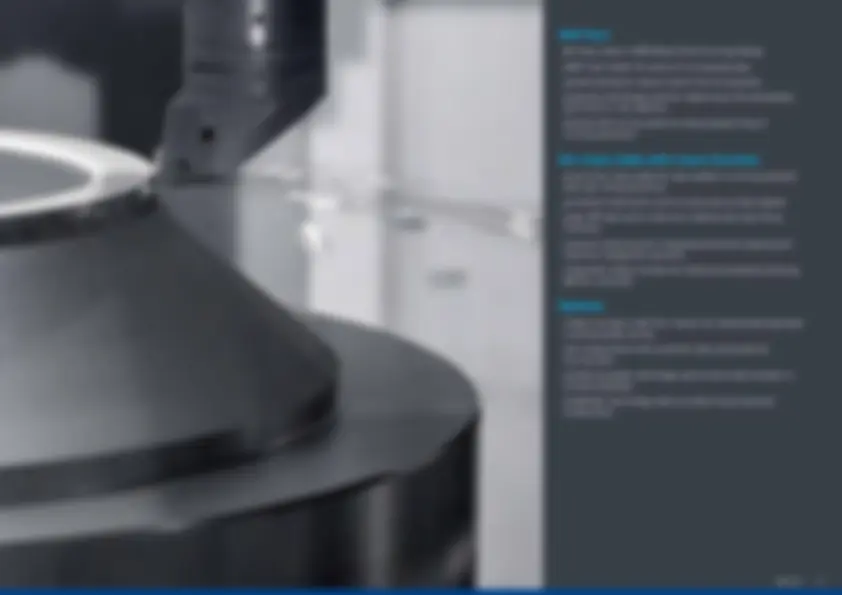
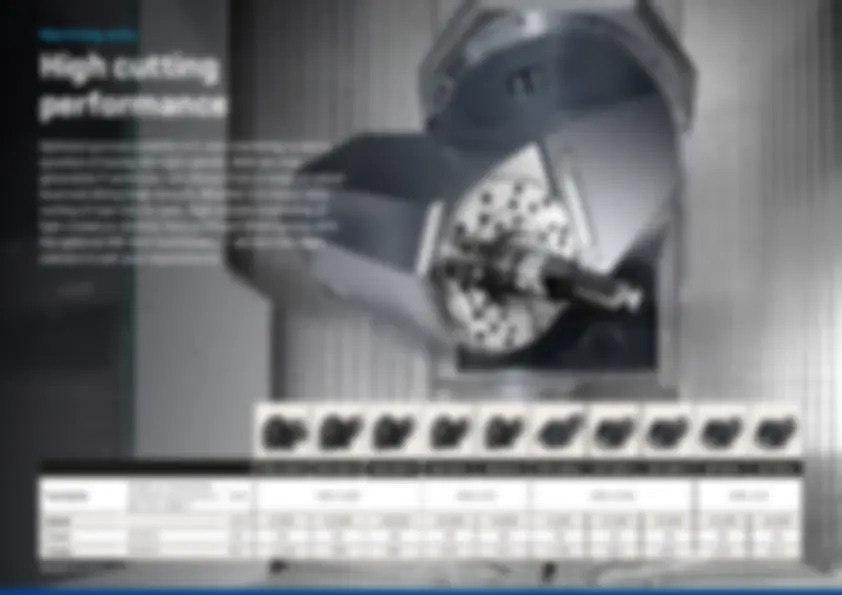
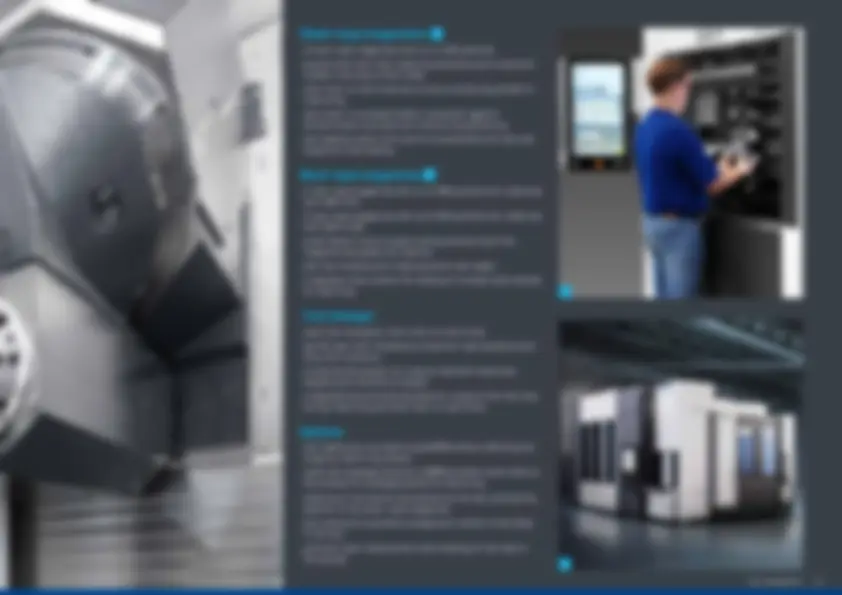
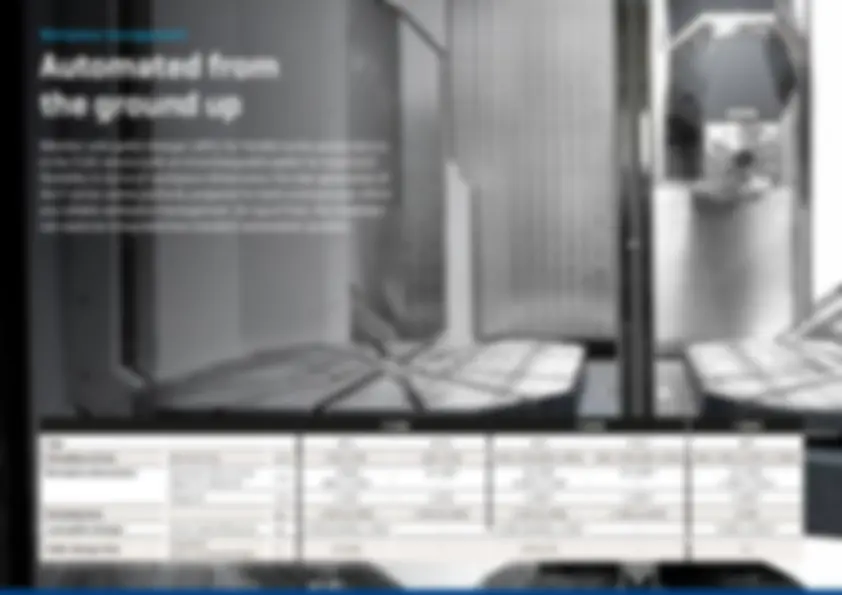
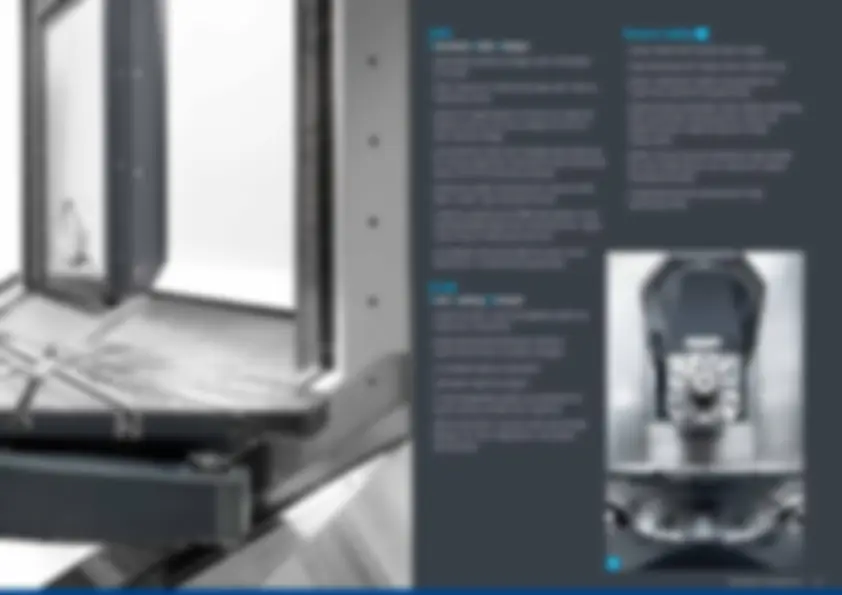
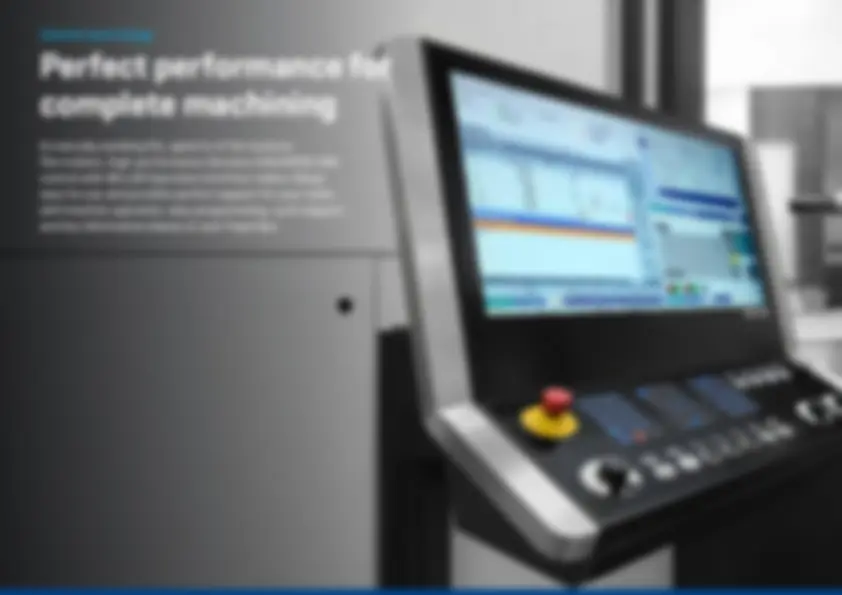
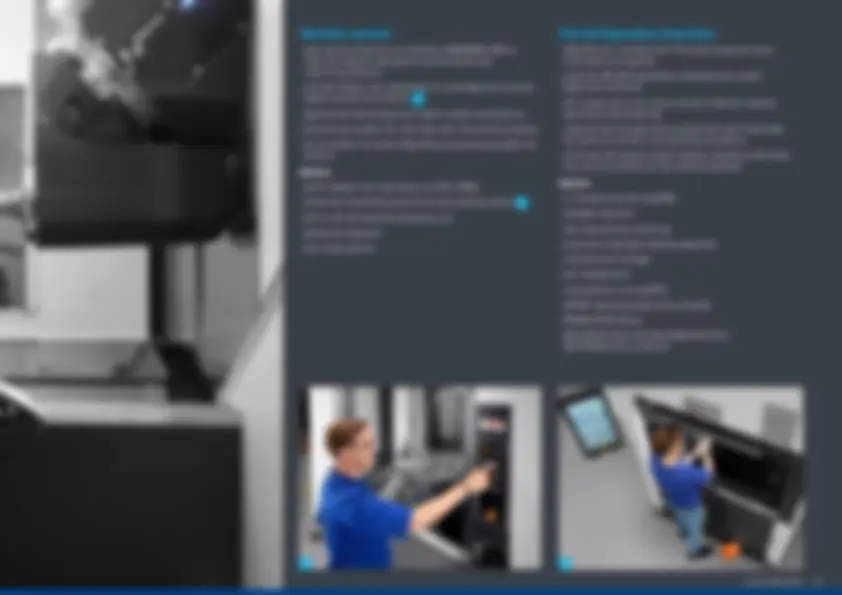
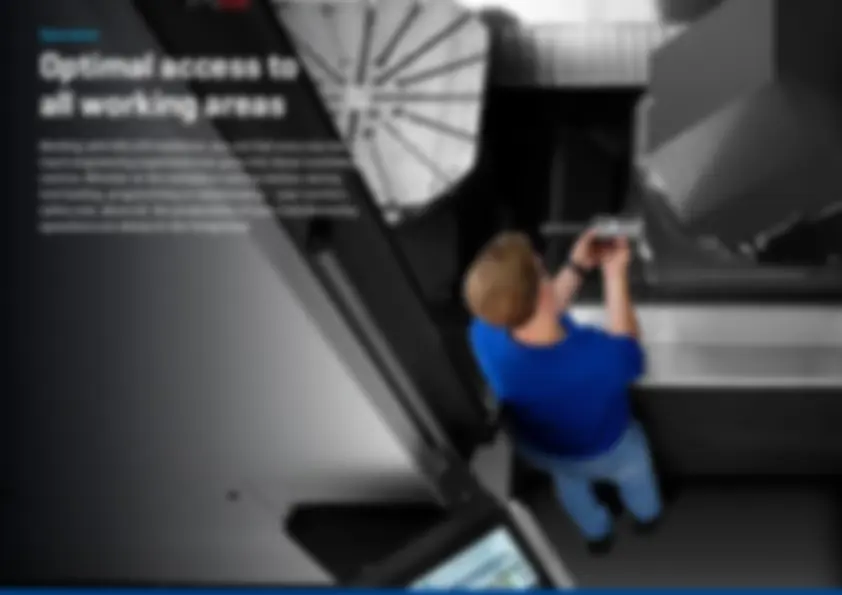
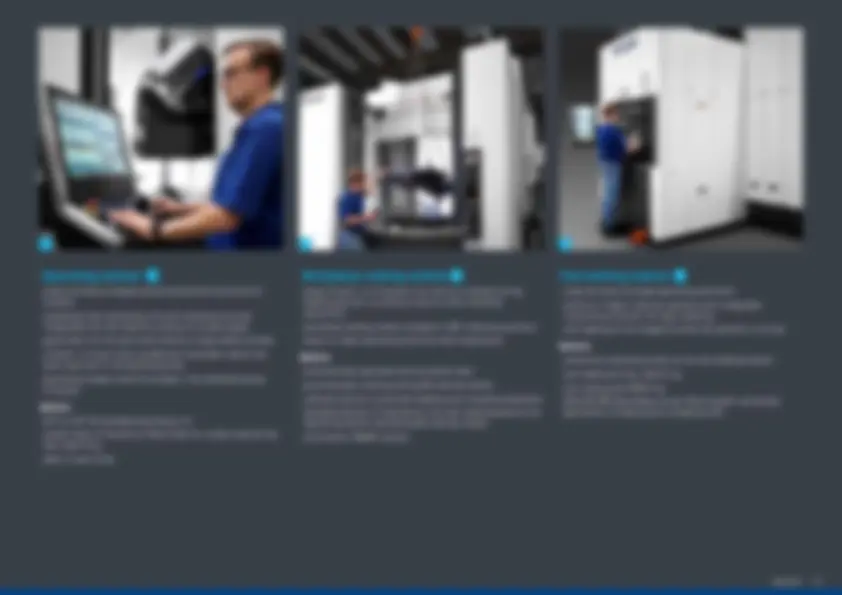
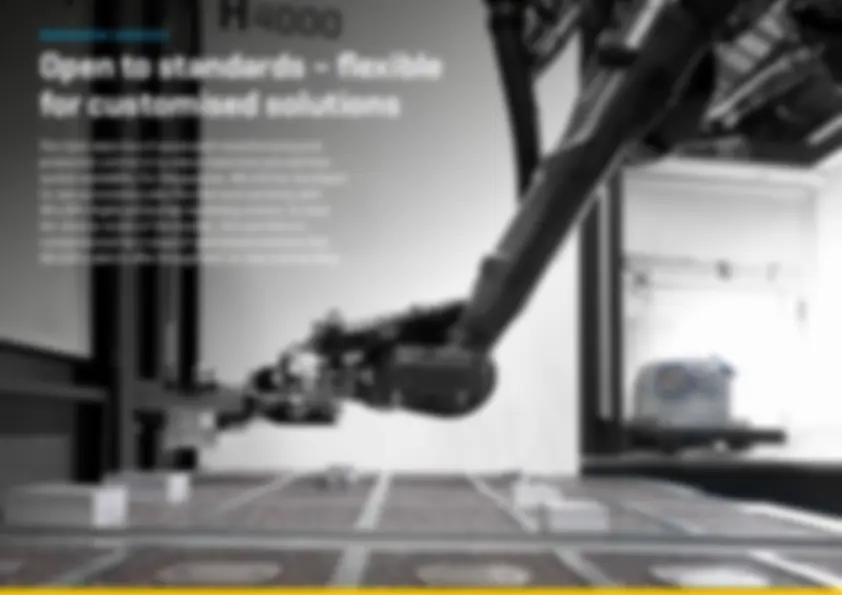
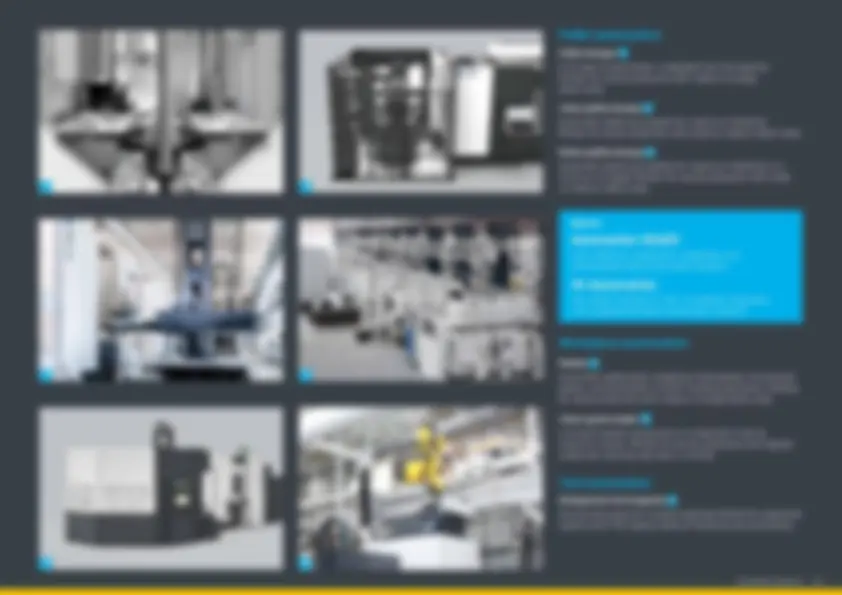
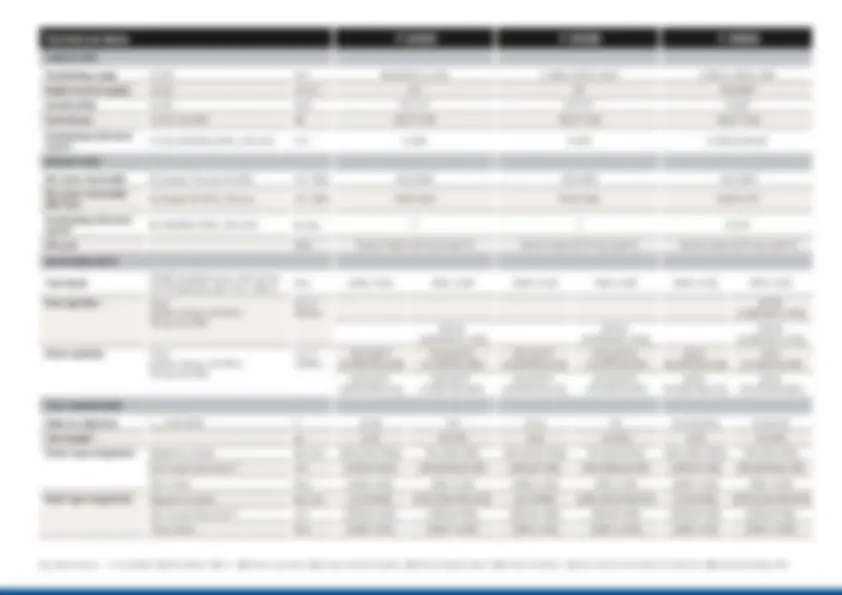
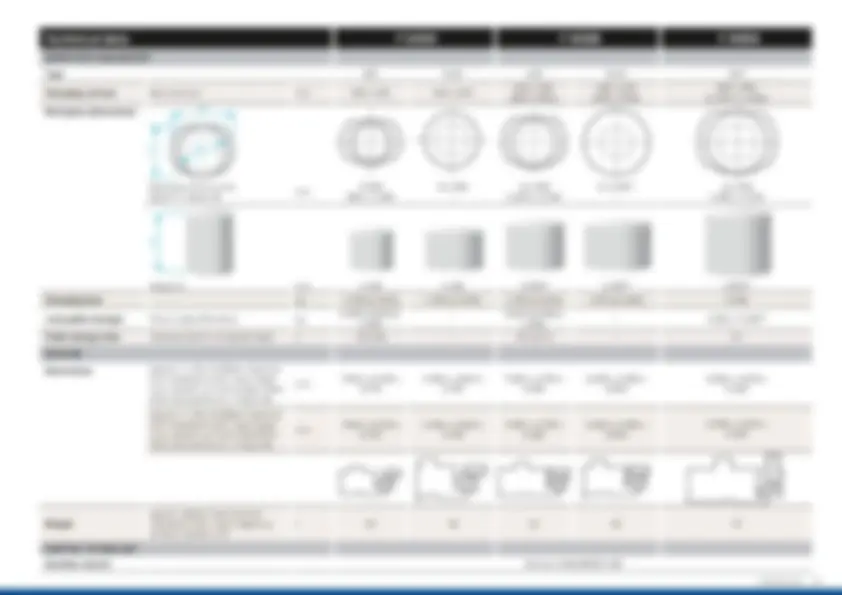
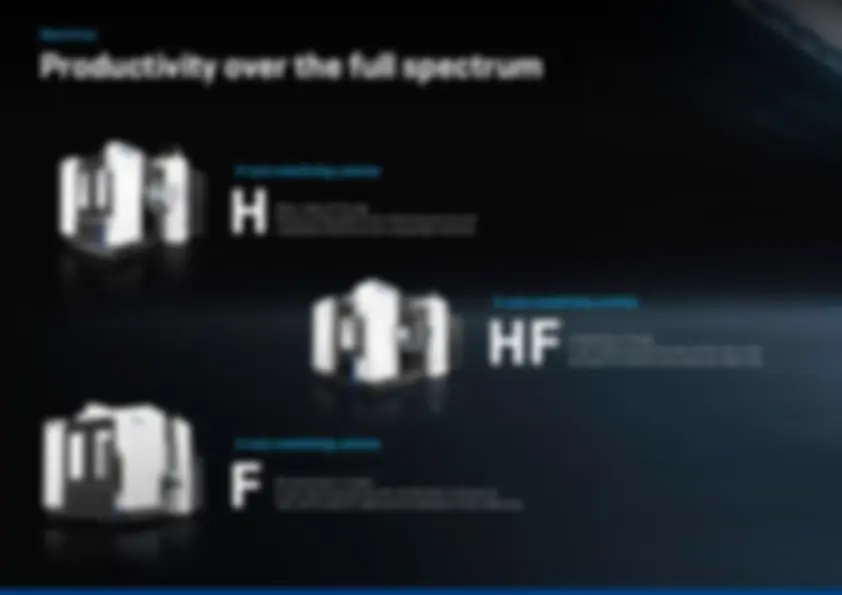
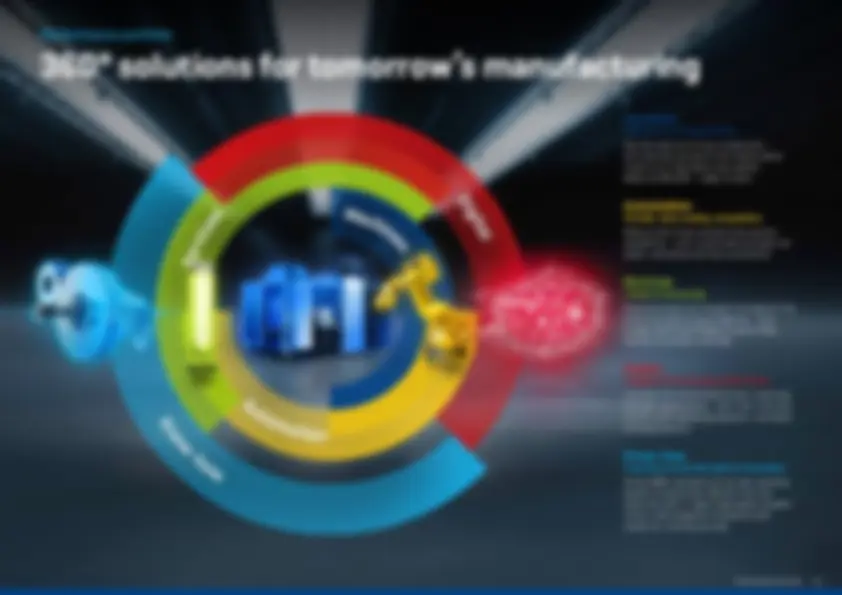
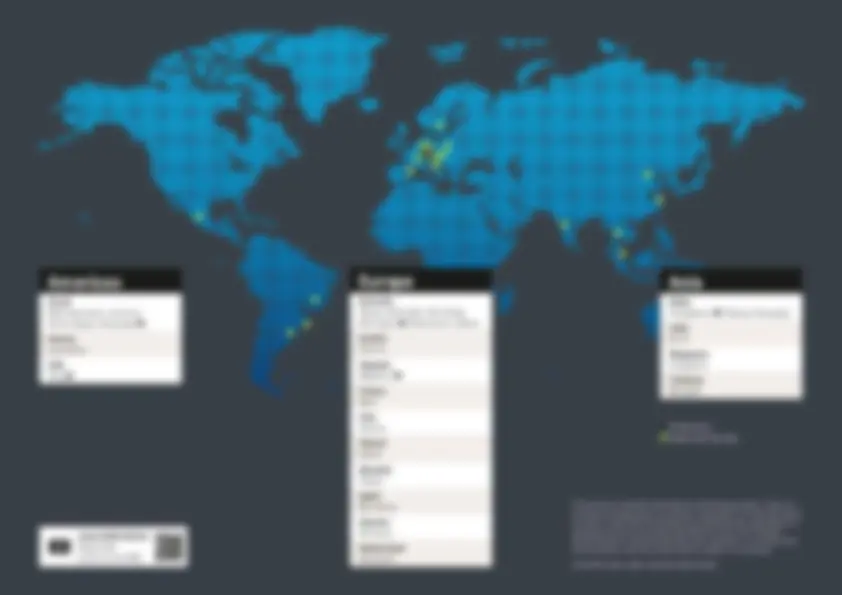
Estude fácil! Tem muito documento disponível na Docsity
Ganhe pontos ajudando outros esrudantes ou compre um plano Premium
Prepare-se para as provas
Estude fácil! Tem muito documento disponível na Docsity
Prepare-se para as provas com trabalhos de outros alunos como você, aqui na Docsity
Os melhores documentos à venda: Trabalhos de alunos formados
Prepare-se com as videoaulas e exercícios resolvidos criados a partir da grade da sua Universidade
Responda perguntas de provas passadas e avalie sua preparação.
Ganhe pontos para baixar
Ganhe pontos ajudando outros esrudantes ou compre um plano Premium
Comunidade
Peça ajuda à comunidade e tire suas dúvidas relacionadas ao estudo
Descubra as melhores universidades em seu país de acordo com os usuários da Docsity
Guias grátis
Baixe gratuitamente nossos guias de estudo, métodos para diminuir a ansiedade, dicas de TCC preparadas pelos professores da Docsity
Documentos de instrução técnica
Tipologia: Resumos
1 / 28
Esta página não é visível na pré-visualização
Não perca as partes importantes!
Contents
Designed for
Production
Machine concept
Maximum performance
with lasting precision
APC
_5-axis machining centres in horizontal orientation _machine bed in cross-bed design for maximum rigidity even with high clamping loads _traversing column in gantry-design for fast positioning and short idle times _cast iron structural components with topology optimised design for maximum stability and damping in the force flow _pallet changer with lift-swivel principle, designed as a fork-type changer for high clamping load and short pallet change time _chain-type or rack-type tool magazines combined with fast NC tool changer for shortest tool provisioning times
_robust 5-axis kinematics with 5th axis provided by the tool _machine bed supporting the X and Z axes in cross bed design _machine column moves in X-direction and supports the machining unit _machining unit moves in Y-direction, compact and robustly integrated into the machine column _rotary table (B-axis) moves in Z-direction and rotates the workpiece continuously (360,000 x 0.001°) _5th axis designed as swivel head (C-axis, 350,000 x 0.001°) or optionally as tilting head (A-axis, 175,000 x 0.001°)
_linear axes with wide roller guides driven by precision ball screws with cooled drives or drive flanges _direct, absolute measuring systems with low positional tolerance for maximum precision _rotary axes with large YRT bearing and automatic clamping for maximum stability and high tangential moments _rotary table with duplex worm gear for maximum performance in 5-axis machining _direct driven high-speed rotary table for mill-turn applications (optional)
FLEX
Machine concept 5
PRO equipment package
_two ball screws in the Z-axis
_increased feed force in the Z-axis
_reduced positional tolerances in all axes
_milling technology package (ONE Dynamics) for optimum path guidance and perfect surface finish
_highest dynamics in the linear axes
_fast, backlash-free swivel drive in the 5-axis head
_optimum set-up of all components
_AutoSet function for optimum drive parameters to suit the current clamping load
_AutoCal function for optimum accuracy of 5-axis kinematics
Equipment 7
Mill-Turn
Complete machining
on a single machine
Speed S3 40% min -1^700 700 Torque Nm 2,600 2,600 4, Workpiece diameter APC / FLEX (Full circle) mm Ø 900 / Ø 1,300 Ø 1,000 / Ø 1,540 1)^ Ø 1,
Machining units
High cutting
performance
PCUe 100 G DCU 100 M SCU 100 M DCU 63 M SCU 63 M PCTe 100 G DCT 100 M SCT 100 M DCT 63 M SCT 63 M
Tool shank
SK/BT for PCUe/PCTe available as an option | Mill-Turn: HSK-T
Size HSK-A 100 HSK-A 63 HSK-A 100 HSK-A 63
Speed min -1^ 8,000 12,000 15,000 16,000 18,000 6,000 12,000 15,000 16,000 18, Power S6 40 % kW 60 52 45 50 45 60 52 45 50 45 Torque S6 40 % Nm 1,146 400 282 228 121 1,146 100 282 228 121
Standard: DCU 100 M
1
2
_machining units with 5th axis provided by the tool with robust swivel head or tilting head kinematics
_8 machining units with high-speed motor spindles for universal use
_2 machining units with gear-driven spindles, perfect for cutting difficult-to-machine materials
_HSK-A 100 tool shank as standard for machining units with motor and gear-driven spindles (HSK-A 63 optional)
_automatic clamping of the 5th axis, optional hydraulic clamping for maximum stability in heavy-duty machining with tilted rotary axes
_sturdy cast iron guide slide with high dynamic rigidity and damping
_high projection length in vertical position for precise machining behind the rotary centre of the rotary table
_compact design and high rigidity thanks to the robust 45° swivel head kinematics and short distance between bearing and tool shank
_dynamic, backlash-free swivel drive with electrically pre-loaded motors
_large C swivelling range of 350° for high flexibility in 5-sided machining
_integrated LED light (WorkLIGHT) as standard and remaining path display as part of the optional SETUP-Assist function
_large swivel range enables machining of negative angles and undercuts
_bearings on both sides provide maximum rigidity during roughing and finishing operations
_HSK-A 100 spindle with a gearbox unit and a maximum torque of 1,146 Nm
_175° swivel range for maximum flexibility in 5-sided machining
SETUP-Assist _assistance system that actively supports the operator when running in processes _remaining path display integrated into the machining units 1 _collision monitoring between machine components and tools 2 _utilisation display for linear axes, rotary table and spindle
HELLER attachment head support (MSK) _precondition for the use of attachment heads, (e.g. angular heads) _enlarged support basis with three-point rest _integrated torque input and media transfer
Machining units 11
1
2
_3 chain-type magazines with up to 150 positions
_double chain with high traversing dynamics and sturdy tool holders mounted on both sides
_short tool-to-tool times due to tool provisioning parallel to machining
_tool shank in enclosed holders: protection against contamination and optimum hold during positioning
_tool loading station with optimum accessibility for fast and ergonomic tool loading
_2 rack-type magazines with up to 489 positions for machines with HSK-A 63
_4 rack-type magazines with up to 425 positions for machines with HSK-A 100
_small footprint due to space-saving positioning of the magazine alongside the machine
_fast tool handling with highly dynamic tool loader
_integrated rotary station for loading of multiple tools parallel to machining
_rapid tool change for short chip-to-chip times
_two NC axes with lift/swivel principle for high dynamics and long-term precision
_sturdy double gripper for a secure hold with heavy tool weights and moments of weight
_integrated tool provisioning place for supply of the next tool during machining and short tool-to-tool times
_tool loading during machining (HZPR) without affecting the ongoing machining process
_rapid tool breakage detection (SBBK) enables shank tools to be checked for breakage parallel to machining
_cleaning of tool shanks and pockets at the tool provisioning position of the chain-type magazines
_tool coding for automatic storage and transfer of tool data in the tool
_precision laser measurement and checking of the tools in the spindle
Tool management 13
Workpiece management
Automated from
the ground up
Type APC FLEX APC FLEX APC Clamping surface Nominal size mm 630 x 630 630 x 630 630 x 630 (800 x 800) 630 x 630 (800 x 800) 800 x 800 (1,000 x 1,000) Workpiece dimensions Diameter D Full circle Depth T x Width W mm^
900 x 1,
1,000 x 1,
1,400 x 1, Height H mm 1,100 1,100 1,300 1)^ 1,300 1)^ 1,500 1) Clamping load kg 1,500 (2,000) 1,500 (2,000) 1,500 (2,000) 1,500 (2,000) 2, Load pallet changer Total / load difference kg 2,000 (3,000) / 1,500 – 2,000 (3,000) / 1,500 – 4,000 / 2,000 1)
Pallet change time Standard(with increased load) s 15 (18) – 14.5 (17) – 21
( ) = Optional values - = Not available 1) Consider limitations 2) Stand-Alone (IN-Automation: Ø 1,400 mm)
_coolant units: paper band filter or backflush filter with high tank volumes available as options
_internal coolant supply (IKZ) through the tool with high pressure 50 bar (optional: 70 bar)
_internal coolant supply with up to 7 pressure steps freely programmable via NC program
_external tool cooling (AKZ) with flushing nozzles (optional) integrated into the spindle
_integrated work area shower with adjustable nozzles for optimum flushing of the work area and cooling of the workpiece
Options
_coolant cooler
_coolant temperature control unit for high thermal stability and precision
_automatic filling of the coolant unit
_oil skimmer for separation of foreign oil from the cooling lubricant tank
_automatic setting station flushing
Supply and disposal
For maximum
chip removal rates
1
2
2
_F 5000/6000: free chip fall below the spindle and quick removal from the work area
_F 8000: chip removal from the work area to the rear of the machine via spiral conveyors
_chip conveyor either as scraper belt or hinged conveyor, depending on the application (optional)
_steep stainless steel side panels and slat coverings with self-cleaning effect to prevent chip deposits 1
_integrated work area shower to support rapid chip removal
_extraction unit for the removal of coolant mist from the work area (operating principle: mechanical air filter) (optional)
_easy maintenance with optimum accessibility, all supply units at a glance
_central oil-air lubrication for key components
_sealing air and selective blow-off of interfaces for continuous, smooth machine operation
_media interface for hydraulic workpiece clamping with up to 250 bar (optional)
_compressed air and water guns integrated into the machine housing at the workpiece loading station and operating station 2
Supply and disposal 17
1 2
_high-performance control Siemens SINUMERIK ONE to meet the highest standards of performance and machining precision
_console-design main operating unit and ergonomic control panels around the machine (^1)
_digital drive technology and modern system architecture
_Profinet bus system for ultra-fast real-time communication
_IO link system for direct diagnostics and parametrisation of sensors
Options
_panel-design main operating unit (ITC 2400)
_convenient operating panel at the tool loading station (^2)
_HT 2 or HT 10 handheld operating unit
_additional keyboard
_work area camera
_HELLER user interface with 4 function areas for more information at a glance _practical HELLER applications (Xtends) with useful additional functions _24” screen and multi-touch function, ideal for viewing documents and drawings _machine control panel with pushbuttons and 3 overrides for optimum control in all operating situations _third override reduces rapid traverse, helping to eliminate the risk of a collision during manual operation
Options _in-process monitoring (IPM) _damage reduction _tool requirements planning _automatic loading/unloading sequence _maintenance manager _job management _interpolation turning (IPT) _SETUP-Assist (process setup wizard) _PRODUCTION-Assist _HELLER Services Interface (HSI) and other HELLER4Industry products
Control technology 19
Operation
Optimal access to
all working areas