
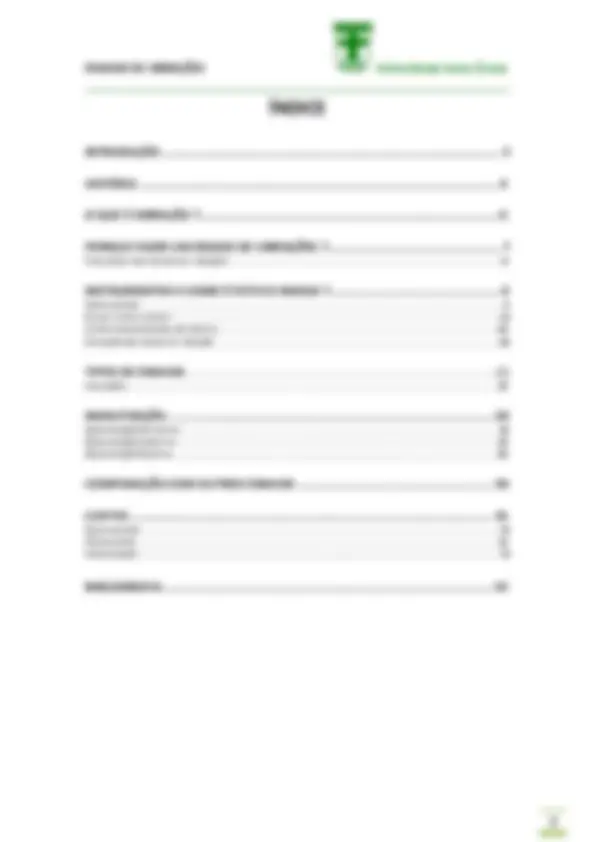
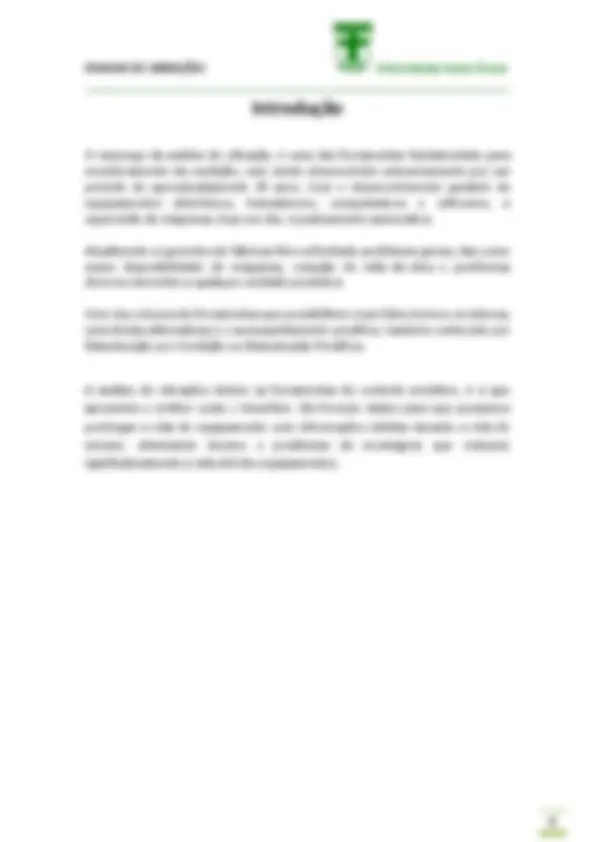
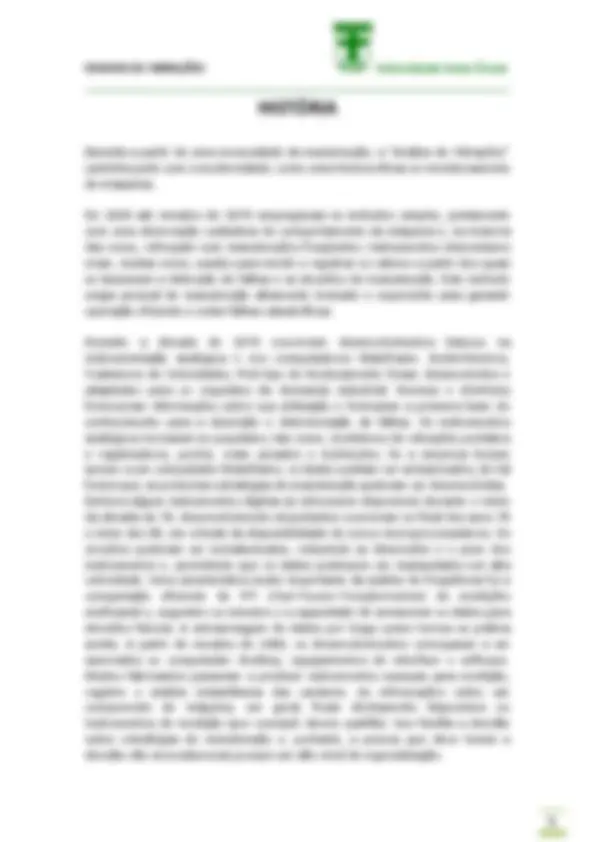
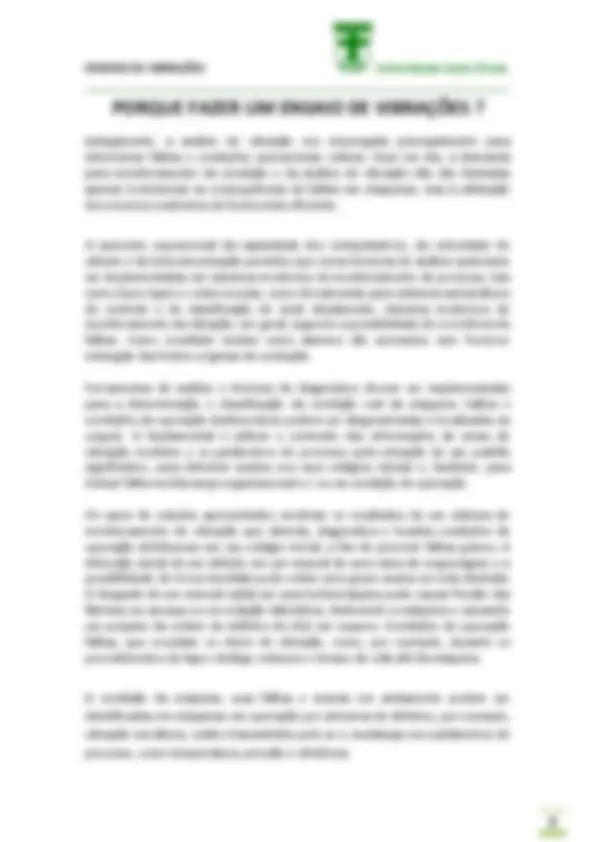
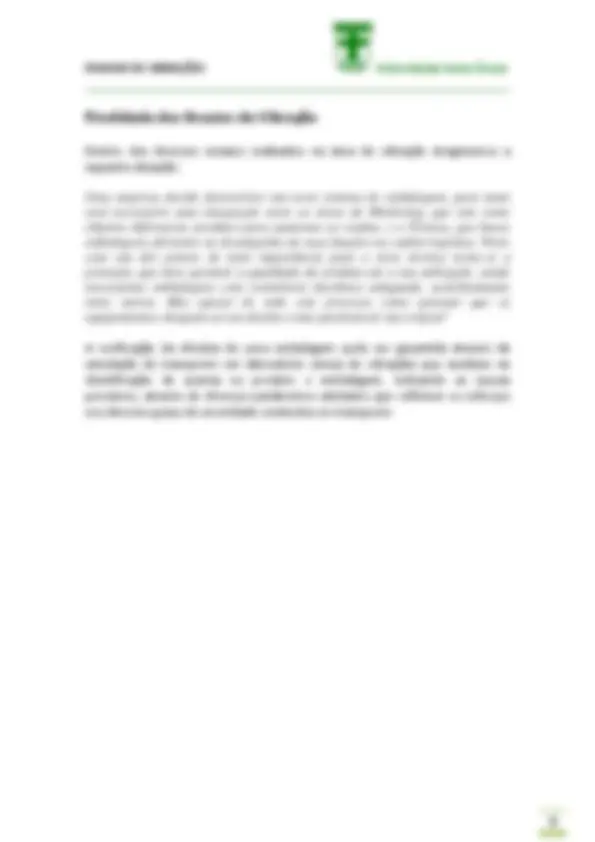
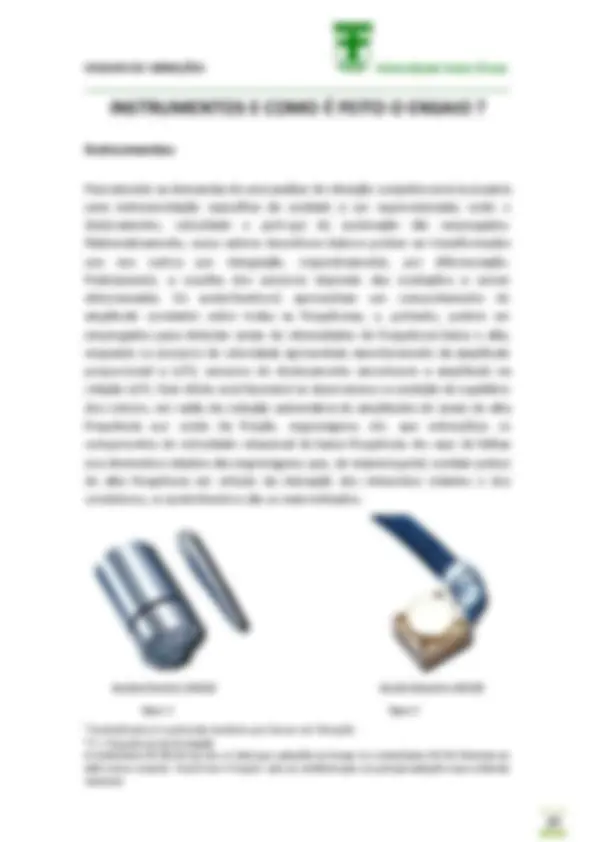
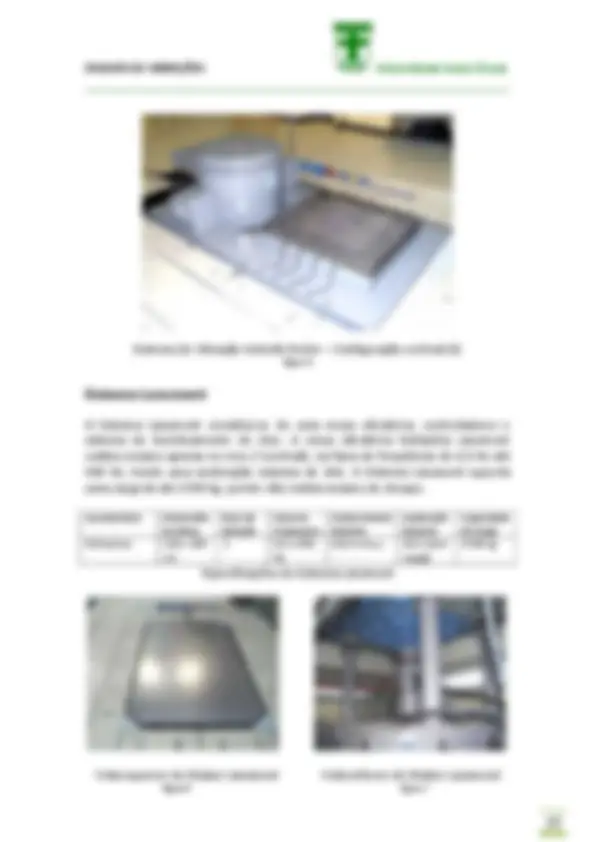
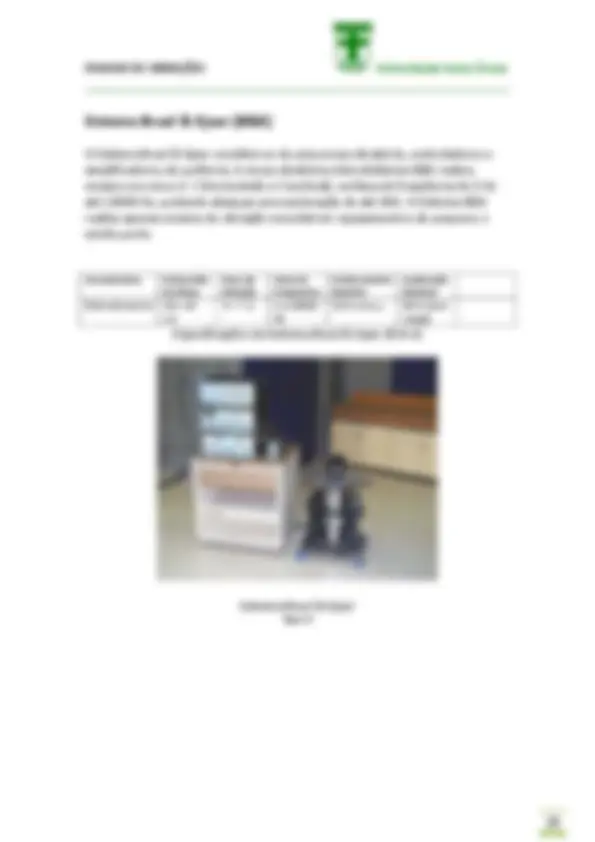
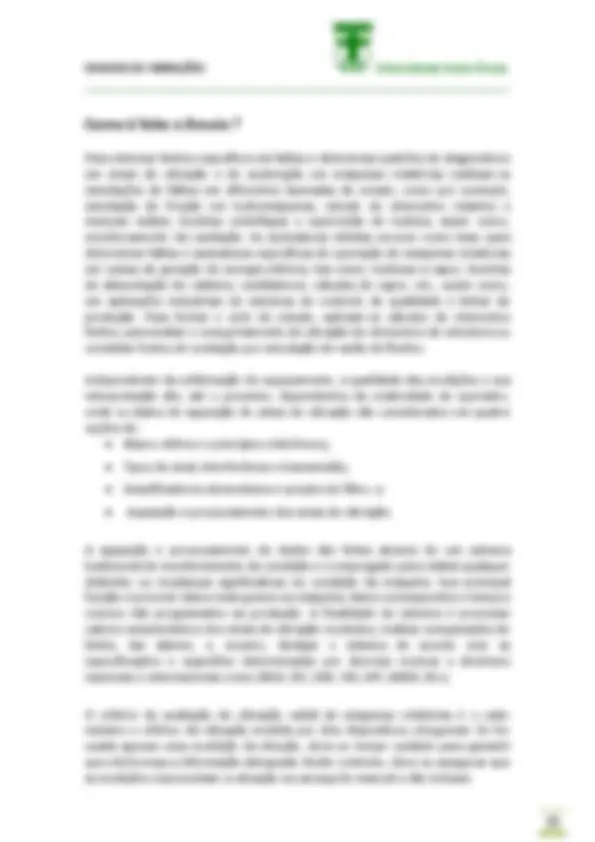
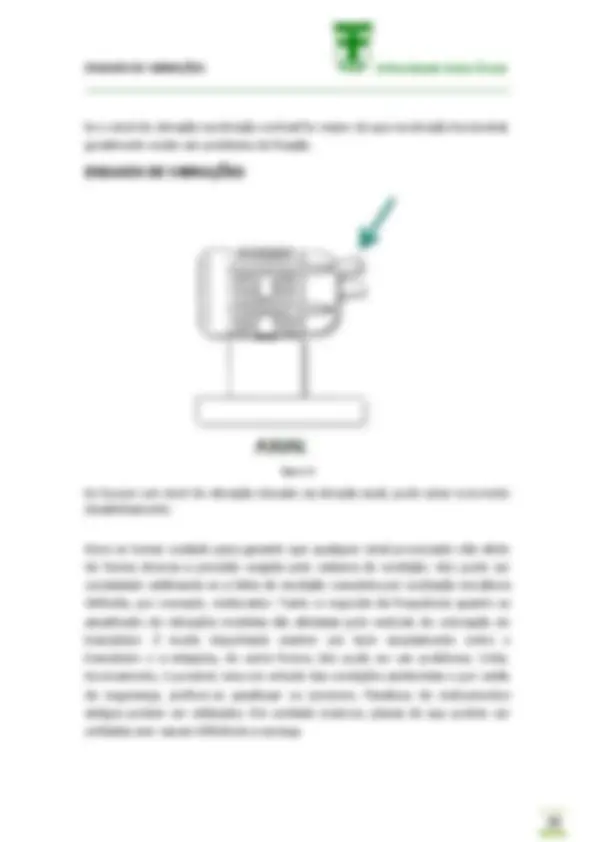
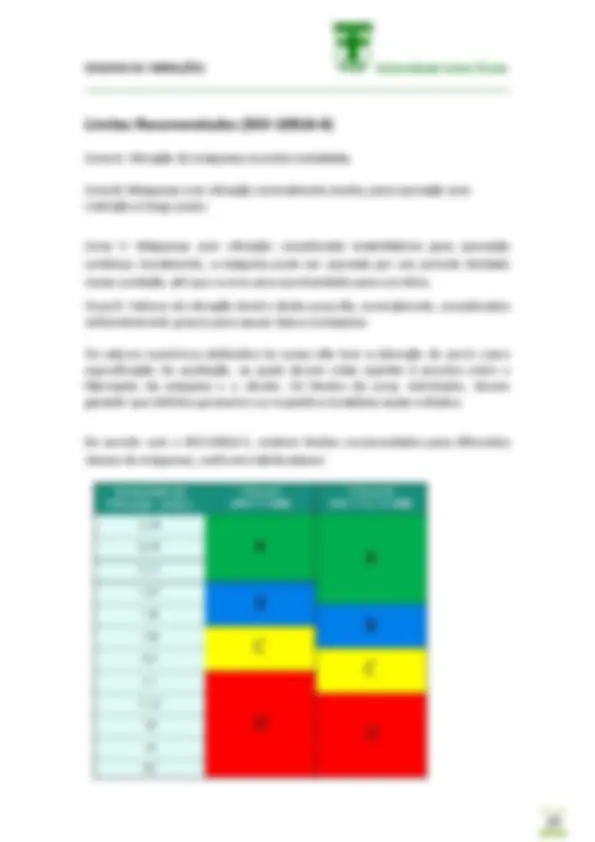
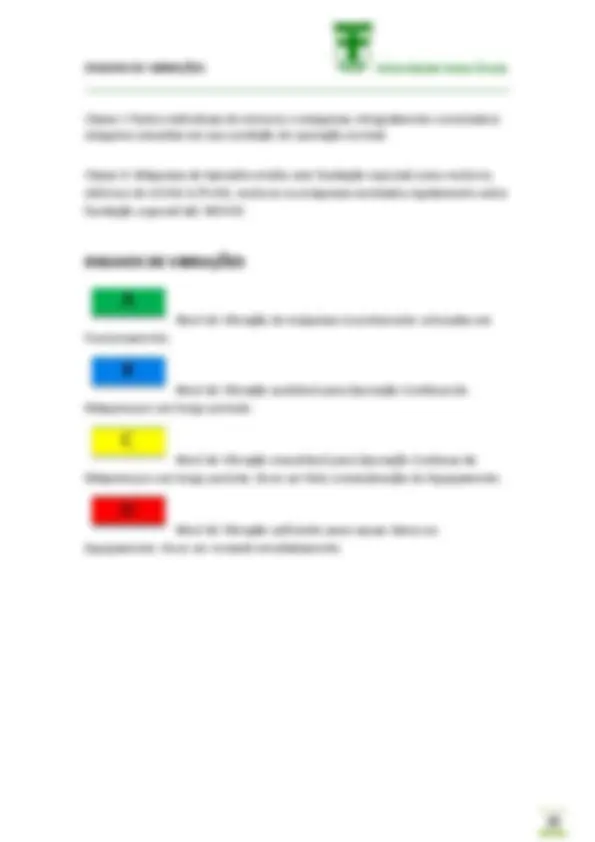
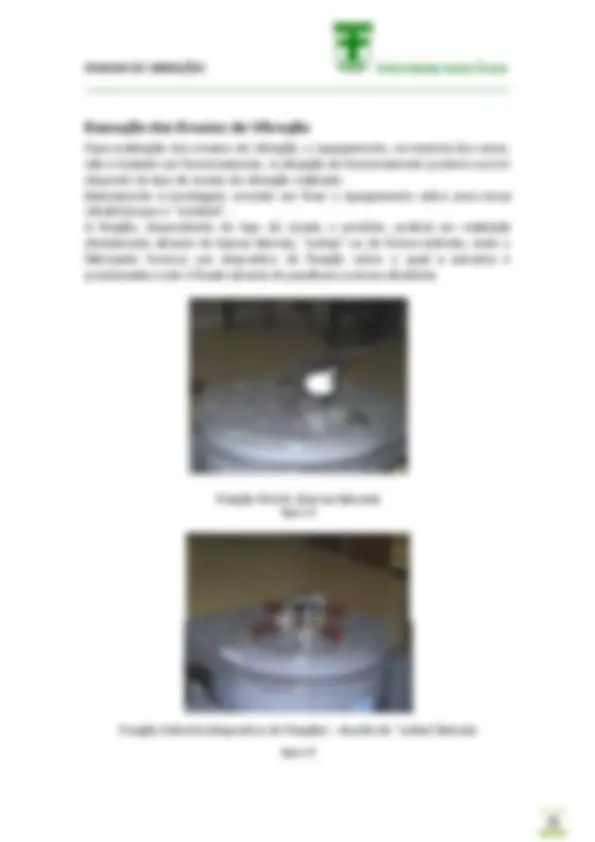
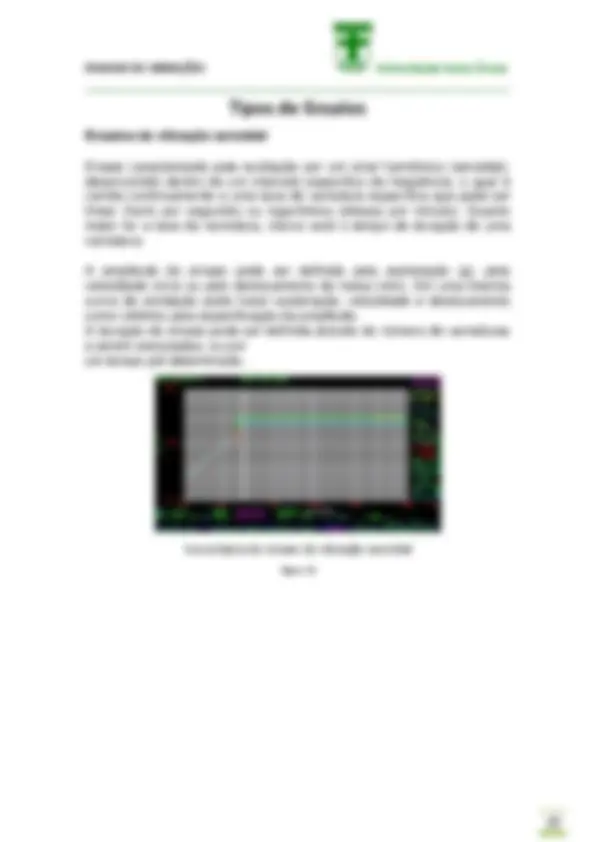
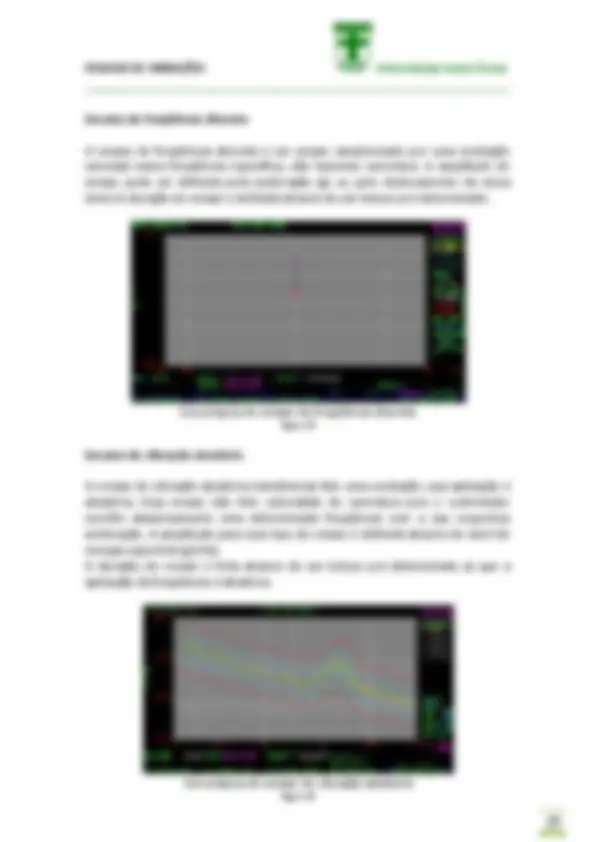
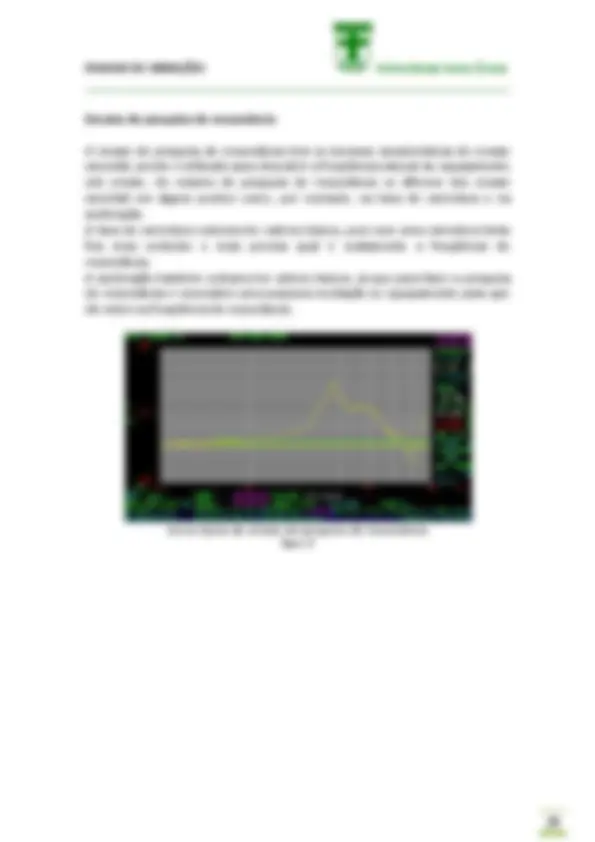
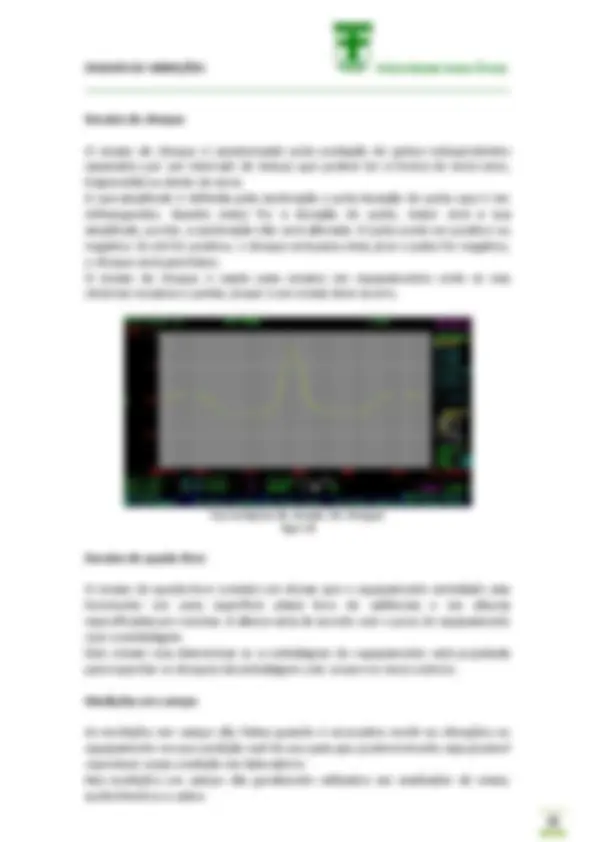
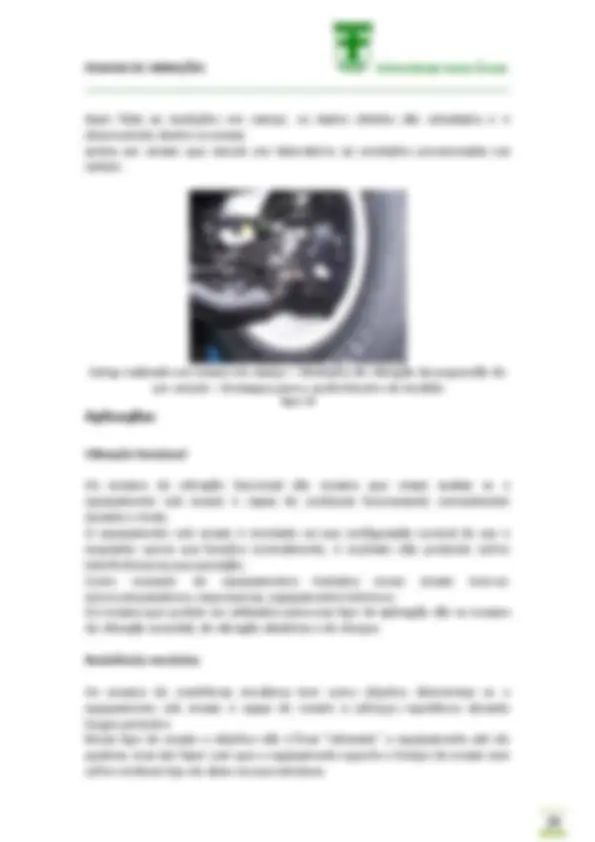
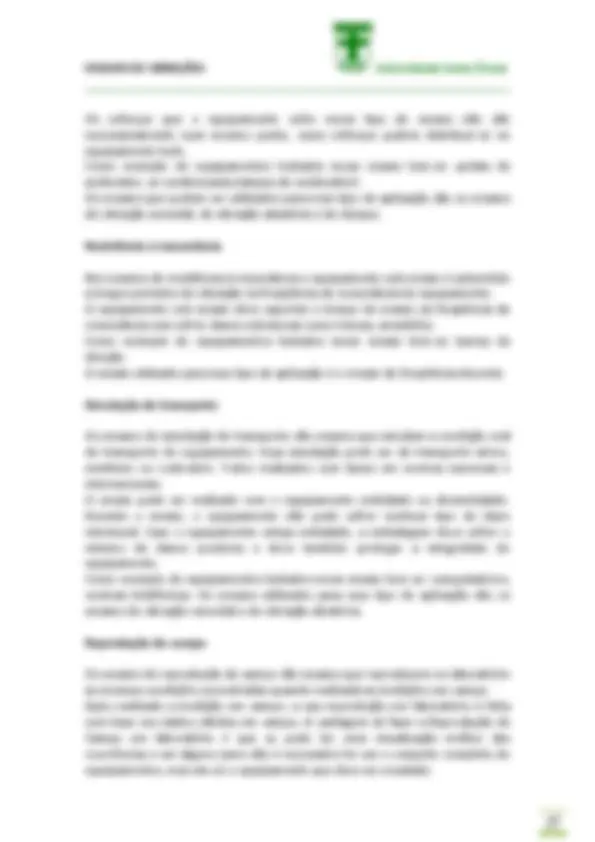
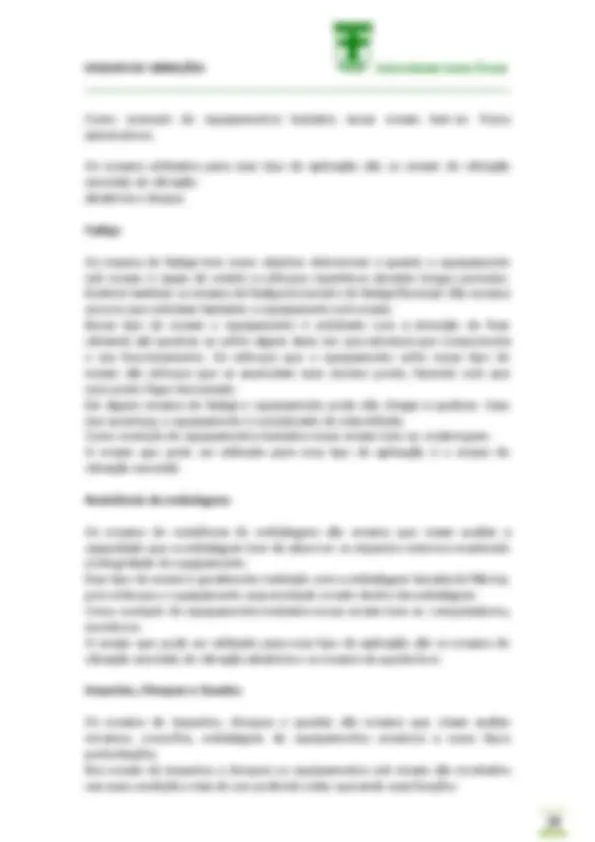
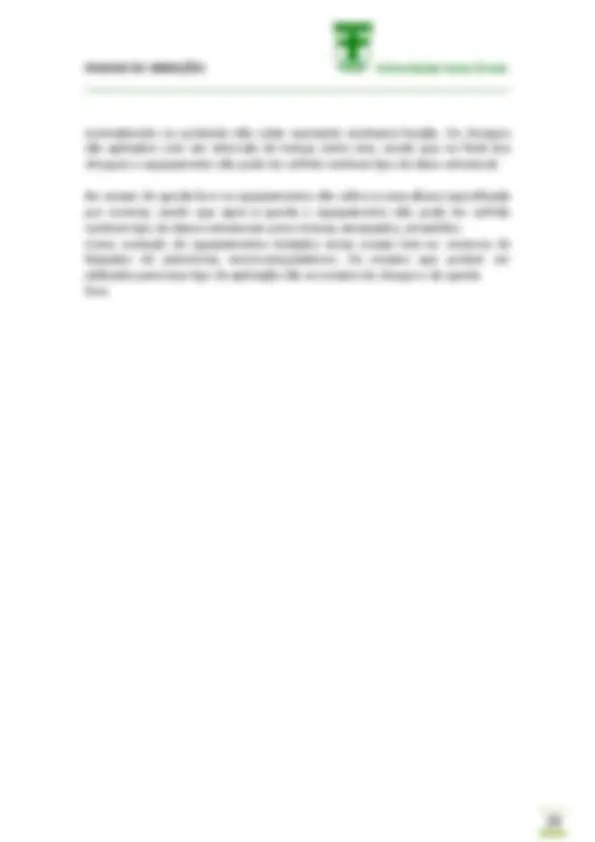
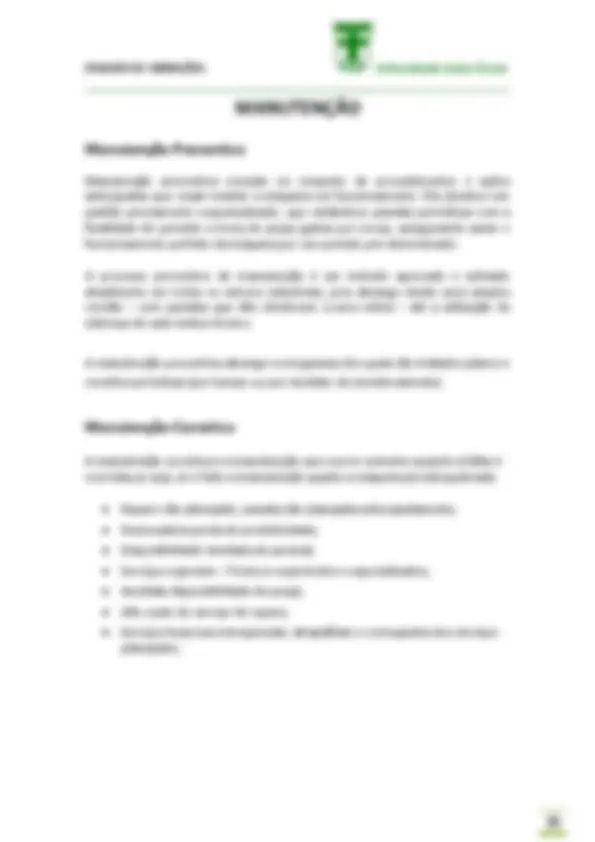
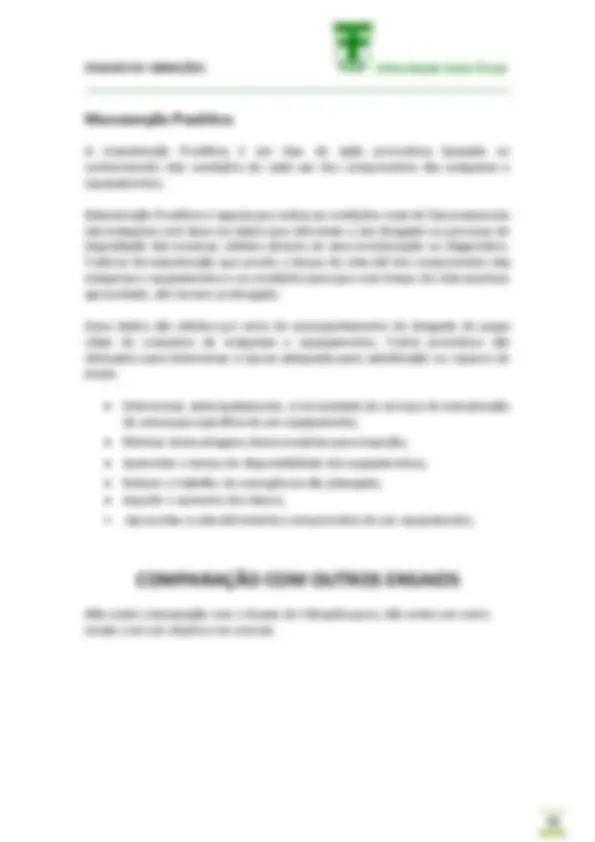
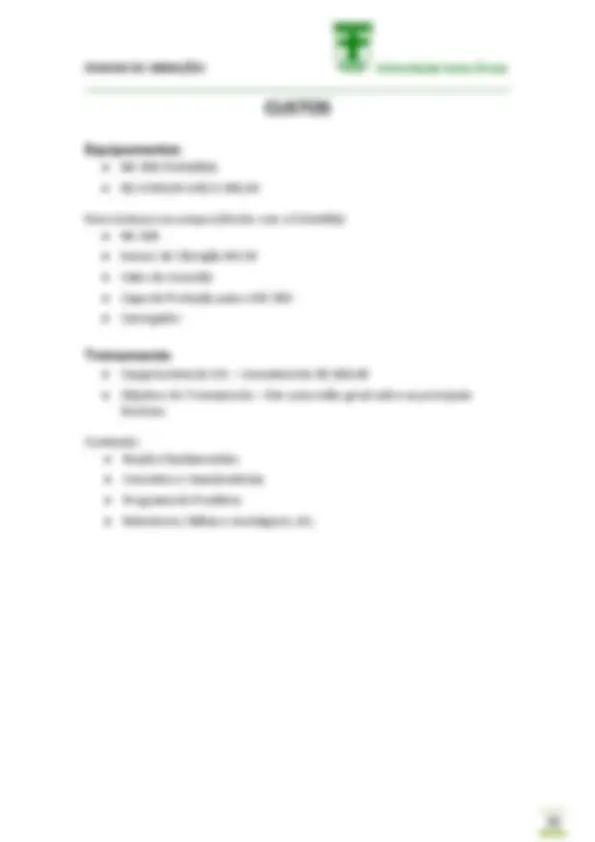
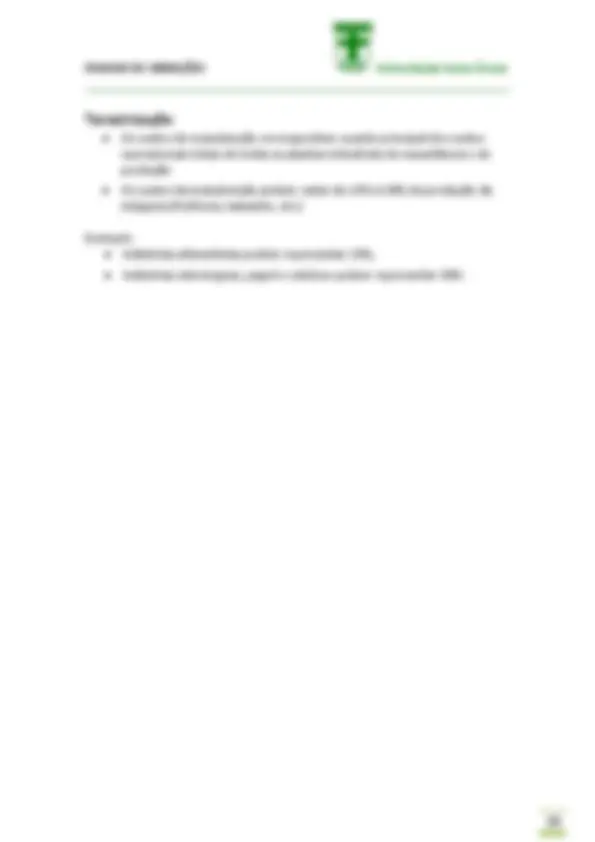
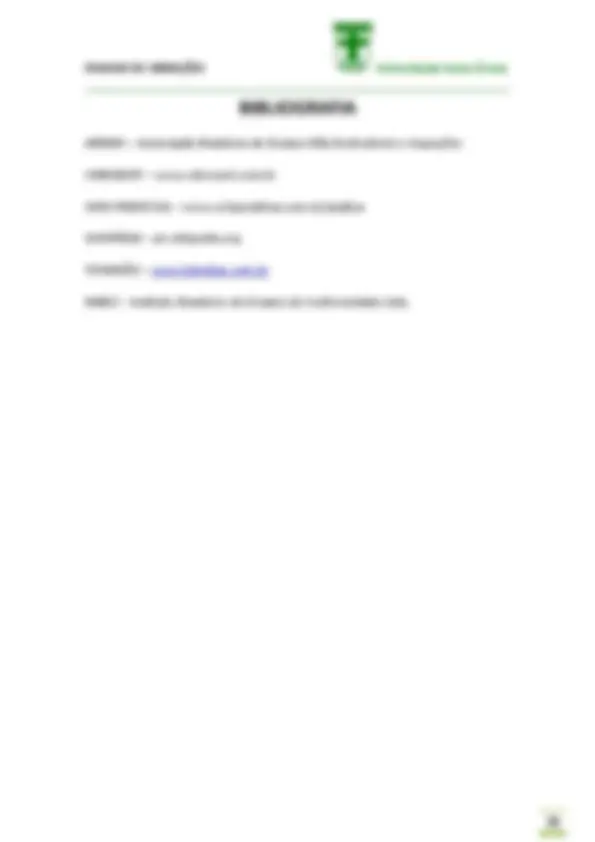
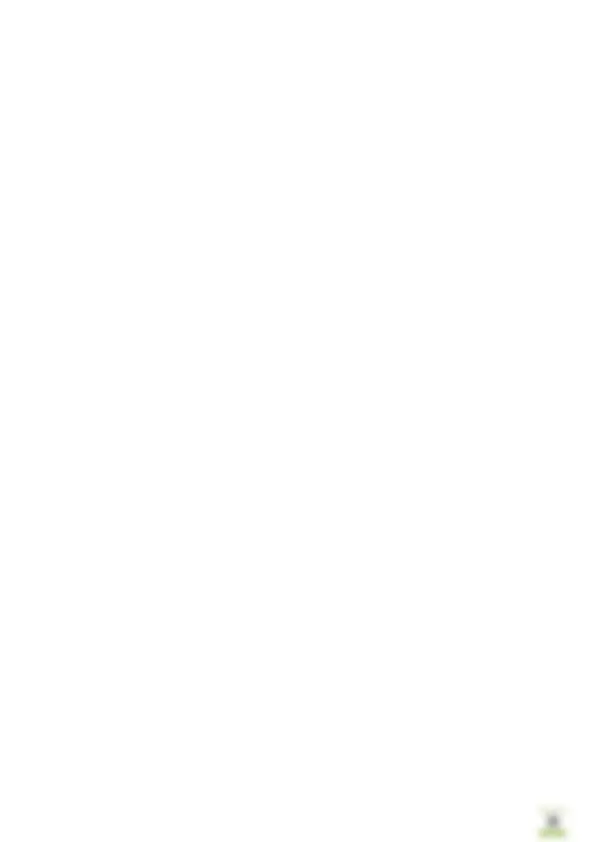
Estude fácil! Tem muito documento disponível na Docsity
Ganhe pontos ajudando outros esrudantes ou compre um plano Premium
Prepare-se para as provas
Estude fácil! Tem muito documento disponível na Docsity
Prepare-se para as provas com trabalhos de outros alunos como você, aqui na Docsity
Os melhores documentos à venda: Trabalhos de alunos formados
Prepare-se com as videoaulas e exercícios resolvidos criados a partir da grade da sua Universidade
Responda perguntas de provas passadas e avalie sua preparação.
Ganhe pontos para baixar
Ganhe pontos ajudando outros esrudantes ou compre um plano Premium
Comunidade
Peça ajuda à comunidade e tire suas dúvidas relacionadas ao estudo
Descubra as melhores universidades em seu país de acordo com os usuários da Docsity
Guias grátis
Baixe gratuitamente nossos guias de estudo, métodos para diminuir a ansiedade, dicas de TCC preparadas pelos professores da Docsity
Trabalho (tutoria) completo sobre Mecânica Aplicada.
Tipologia: Notas de estudo
1 / 35
Esta página não é visível na pré-visualização
Não perca as partes importantes!
_______________________________________________________________________
Universidade Santa Úrsula _______________________________________________________________________
MECÂNICA APLICADA
_______________________________________________________________________
Introdução
O emprego da análise de vibração, é uma das ferramentas fundamentais para monitoramento da condição, vem sendo desenvolvido extensivamente por um período de aproximadamente 35 anos. Com o desenvolvimento paralelo de equipamentos eletrônicos, transdutores, computadores e softwares, a supervisão de máquinas, hoje em dia, é praticamente automática.
Atualmente os gerentes de fábricas têm enfrentado problemas gerais, tais como maior disponibilidade de máquinas, redução de mão-de-obra e problemas diversos inerentes a qualquer unidade produtiva.
Com isso a busca de ferramentas que possibilitem esses fatos tornou-se intensa, uma destas alternativas é o acompanhamento preditivo, também conhecido por Manutenção por Condição ou Manutenção Preditiva.
A análise de vibrações dentre as ferramentas do controle preditivo, é a que
apresenta o melhor custo / benefício. Ela fornece dados para que possamos
prolongar a vida do equipamento com informações obtidas durante a vida do
mesmo, eliminando desvios e problemas de montagens que reduzem
significativamente a vida útil dos equipamentos.
_______________________________________________________________________
HISTÓRIA
Nascida a partir de uma necessidade da manutenção, a “Análise de Vibrações” caminha junto com a modernidade, como uma técnica eficaz no monitoramento de máquinas.
De 1969 até meados de 1970 empregavam-se métodos simples, juntamente com uma observação cuidadosa do comportamento da máquina e, na maioria das vezes, reforçado com manutenções freqüentes. Instrumentos elementares eram, muitas vezes, usados para medir e registrar os valores a partir dos quais se baseavam a detecção de falhas e as decisões de manutenção. Este método exigia pessoal de manutenção altamente treinado e experiente para garantir operação eficiente e evitar falhas catastróficas.
Durante a década de 1970 ocorreram desenvolvimentos básicos na instrumentação analógica e nos computadores Mainframe. Acelerômetros, Tradutores de Velocidades, Pick-Ups de Deslocamento foram desenvolvidos e adaptados para os requisitos da demanda industrial. Normas e diretrizes forneceram informações sobre sua utilização e formaram a primeira base do conhecimento para a descrição e determinação de falhas. Os instrumentos analógicos tornaram-se populares, tais como, medidores de vibrações portáteis e registradores, porém, eram pesados e incômodos. Se a empresa tivesse acesso a um computador Mainframe, os dados podiam ser armazenados, de tal forma que, as primeiras estratégias de manutenção puderam ser desenvolvidas. Embora alguns instrumentos digitais já estivessem disponíveis durante o início da década de 70, desenvolvimento importantes ocorreram no final dos anos 70 e início dos 80, em virtude da disponibilidade de novos microprocessadores. Os circuitos puderam ser miniaturizados, reduzindo as dimensões e o peso dos instrumentos e, permitindo que os dados pudessem ser manipulados em alta velocidade. Uma característica muito importante da análise de freqüência foi a computação eficiente do FFT ( Fast-Fourier-Transformation ) de medições multicanal e, segundos ou minutos e a capacidade de armazenar os dados para decisões futuras. A armazenagem de dados por longo prazo tornou-se prática aceita. A partir de meados de 1980, os desenvolvimentos começaram a ser associados so computador desktop, equipamentos de interface e software. Muitos fabricantes passaram a produzir instrumentos manuais para medição, registro e análise instantâneas das variáveis. As informações sobre um componente de máquina, em geral, ficam diretamente disponíveis no instrumentos de medição (por exemplo desvio padrão). Isso facilita a decisão sobre estratégias de manutenção e, portanto, a pessoa que deve tomar a decisão não necessitas mais possuir um alto nível de especialização.
_______________________________________________________________________
O QUE É VIBRAÇÃO?
Definição: “ É qualquer movimento que se repete, regular ou irregularmente, depois de um intervalo de tempo. ”
Vibração é o efeito oscilatório de corpos materiais. Sendo movimento, é chamada vibração mecânica. Quando através do tato, sentimos a oscilação de uma corda de violão, por exemplo, sabemos intuitivamente o que é uma vibração mecânica e podemos, inclusive, ver o seu movimento. Todos os materiais podem vibrar e a maneira com que irão vibrar, depende das características do próprio material e da excitação externa. Considere-se como modelo vibratório, uma mola presa ao teto que tenha um
peso na sua extremidade livre. Inicialmente a mola se encontra em posição de
equilíbrio, mas, se o peso for deslocado a uma certa distância e solto em
seguida, a mola iniciará um movimento oscilatório em torno da sua posição de
equilíbrio. A maior distância que a mola atinge em relação a seu ponto de
equilíbrio é chamada amplitude de movimento, e o tempo que a mesma leva
pra completar um ciclo chama-se Período. O número de vezes que ela oscila em
um segundo é chamado freqüência do movimento e sua unidade é o Hertz [Hz].
Um Hertz corresponde a um ciclo por segundo.
Figura 1
Além da freqüência e da amplitude das vibrações mecânicas, são também
geralmente consideradas as velocidades e acelerações do corpo vibrante.
_______________________________________________________________________
PORQUE FAZER UM ENSAIO DE VIBRAÇÕES?
Antigamente, a análise de vibração era empregada principalmente para determinar falhas e condições operacionais críticas. Hoje em dia, a demanda para monitoramento da condição e da análise de vibração não são limitadas apenas à minimizar as consequências de falhas em máquinas, mas à utilização dos recursos existentes de forma mais eficiente.
O aumento exponencial da capacidade dos computadores, da velocidade de cálculo e da telecomunicação permitiu que novas técnicas de análise pudessem ser implementadas em sistemas modernos de monitoramento de processo, tais como fuzzy logics e redes neurais, como ferramentas para sistemas automáticos de controle e de classificação de sinal. Atualmente, sistemas modernos de monitoramento da vibração, em geral, sugerem a possibilidade de ocorrência de falhas. Como resultado muitas vezes alarmes são acionados sem fornecer indicação das fontes originais de excitação.
Ferramentas de análise e técnicas de diagnóstico devem ser implementadas para a determinação e classificação da condição real da máquina. Falhas e condições de operação desfavoráveis podem ser diagnosticadas e localizadas na origem. O fundamental é utilizar o conteúdo das informações de sinais de vibração medidos e os parâmetros do processo pela extração de um padrão significativo, para detectar avarias nos seus estágios iniciais e, também, para indicar falha na liderança organizacional e / ou na condição de operação.
Os casos de estudos apresentados mostram os resultados de um sistema de monitoramento de vibração que detecta, diagnostica e localiza condições de operação defeituosas em seu estágio inicial, a fim de prevenir falhas graves. A detecção inicial de um defeito em um mancal de uma caixa de engrenagem e a possibilidade de troca imediata pode evitar uma grave avaria na roda dentada. O desgaste de um mancal radial em uma turbomáquina pode causar fricção das lâminas na carcaça ou na vedação labiríntica, destruindo a máquina e causando um prejuízo da ordem de milhões de US$ em reparos. Condições de operação falhas, que excedam os níveis de vibração, como, por exemplo, durante os procedimentos de liga e desliga, reduzem o tempo de vida útil da máquina.
A condição da máquina, suas falhas e avarias em andamento podem ser
identificadas em máquinas em operação por sintomas de defeitos, por exemplo,
vibração mecânica, ruídos transmitidos pelo ar e mudanças nos parâmetros de
processo, como temperatura, pressão e eficiência.
_______________________________________________________________________
INSTRUMENTOS E COMO É FEITO O ENSAIO?
Para atender as demandas de uma análise de vibração completa será necessária
uma instrumentação específica da unidade a ser supervisionada, onde o
deslocamento, velocidade e pick-ups de aceleração são empregados.
Matematicamente, esses valores descritivos básicos podem ser transformados
uns nos outros por integração, respectivamente, por diferenciação.
Praticamente, a escolha dos sensores depende das excitações a serem
determinadas. Os acelerômetros1 apresentam um comportamento de
amplitude constante sobre todas as frequências, e, portanto, podem ser
empregados para detectar sinais de intensidades de frequência baixa e alta,
enquanto os sensores de velocidade apresentam amortecimento da amplitude
proporcional a 1/F2, sensores de deslocamento amortecem a amplitude na
relação 1/F2. Esse efeito será favorável se observarmos a condição de equilíbrio
dos rotores, em razão da redução automática de amplitudes de sinais de alta
frequência por conta da fricção, engrenagens, etc. que sobrepõem os
componentes de velocidade rotacional de baixa frequência. No caso de falhas
nos elementos rolantes das engrenagens, que, de maneira geral, excitam pulsos
de alta frequência em virtude da interação dos elementos rolantes e dos
condutores, os acelerômetros são os mais indicados.
Acelerômetro NK20 Acelerômetro NK Figura 2 Figura 3
¹ Acelerômetro é conhecido também por Sensor de Vibração ² F = Frequência de Excitação O Acelerômetro NK 20 é de Aço Inox e é ideal para aplicações em Campo. Já o Acelerômetro NK 25 é fabricado em latão e tem o nome de “ Acelerômetro Protegido ” pela sua resistência;pois, sua principal aplicação é para ambientes industriais.
_______________________________________________________________________
A escolha do sensor depende, em grande parte, das frequências a serem analisadas, onde a aceleração, em geral, cobre frequências de 0 a 20 KHz, velocidades de 2 Hz a 2 KHz e deslocamento de 0 a 300 Hz. Existem diversas técnicas que podem ser utilizadas sozinhas ou combinadas para identificar padrões de vibração.
Finalmente, a resposta de um sistema de monitoramento da vibração, no início das falhas e condições de operação inadequadas, depende, basicamente, da instrumentação utilizada. Quanto mais rápida for necessária uma resposta, mais indicado será o uso de um sistema hard-wired3 do que coletores de dados portáteis. Onde a ocorrência de falhas for maior, será mais fácil justificar os custo, por exemplo, grandes turbinas a vapor, normalmente, são monitoradas permanentemente, enquanto equipamentos auxiliares, como bombas a vácuo podem ser inspecionadas por unidades portáteis.
Sistemas de monitoramento da condição, baseados em medições da vibração,
provaram sua superioridade, no passado, em razão da reflexão de avarias
significativas no comportamento da vibração, determinada por medição da
aceleração, velocidade e deslocamento. Para atingir essas metas, nos últimos 30
anos, máquinas de grande porte são equipadas com sistemas de
monitoramento da condição, os quais identificam “distúrbios” na operação
rotineira da máquina, principalmente, os níveis de vibração.
Sensores de Vibração em Turbina a Vapor Figura 4
_______________________________________________________________________
Sistema de Vibração Unholtz Dickie – Configuração vertical (Z) Figura 5
O Sistema Lansmont constitui-se de uma mesa vibratória, controladores e sistema de bombeamento de óleo. A mesa vibratória hidráulica Lansmont realiza ensaios apenas no eixo Z (vertical), na faixa de freqüência de 0,5 Hz até 500 Hz, tendo uma aceleração máxima de 10G. O Sistema Lansmont suporta uma carga de até 2700 kg, porém não realiza ensaios de choque.
Caracteristica Dimensões da Mesa
Eixos de Exitação
Faixa de Frequencia
Deslocamento Maximo
Aceleração Maxima
Capacidade de Carga Hidraulica 110 x 200 cm
Z 0,5 a 500 Hz
60,0 mmp-p 10 G (sem carga)
2700 kg
Especificações do Sistema Lansmont
Vista superior do Shaker Lansmont Vista inferior do Shaker Lansmont Figura 6 Figura 7
_______________________________________________________________________
O Sistema Bruel & Kjaer constitui-se de uma mesa vibratória, controladores e amplificadores de potência. A mesa vibratória eletrodinâmica B&K realiza ensaios nos eixos X , Y (horizontal) e Z (vertical), na faixa de freqüência de 5 Hz até 10000 Hz, podendo alcançar uma aceleração de até 80G. O Sistema B&K realiza apenas ensaios de vibração senoidal em equipamentos de pequeno e médio porte.
Caracteristica Dimensões da Mesa
Eixos de Exitação
Faixa de Frequencia
Deslocamento Maximo
Aceleração Maxima Eletrodinamica 30 x 30 cm
X - Y - Z 2 a 10000 Hz
25,4 mmp-p 80 G (sem carga) Especificações do Sistema Bruel & Kjaer (B & K)
Sistema Bruel & Kjaer Figura 8
_______________________________________________________________________
ressonâncias ou amplificações locais. As localizações e direções para medição da vibração devem ser aquelas que forneçam sensibilidade adequada às forças
hidráulicas da máquina, sob diversas condições de operação. Tipicamente, em geral, serão necessárias duas medições radiais ortogonais em cada tampa de mancal.
A vibração medida na guia inferior do mancal de máquinas verticais pode, algumas vezes, ser mal interpretada; níveis de vibração medidos em tais mancais e seus suportes auxiliares, os quais estão rigidamente incorporados na construção, são produzidos por forças hidráulicas, transmitidas diretamente da máquina hidráulica através da fundação. Tal vibração não, necessariamente, fornece a imagem correta da vibração de sistemas de eixos rotatórios.
Para a finalidade de monitoramento, apenas em alguns casos as posições de medições podem ser reduzidas para as mais importantes, principalmente, em conjuntos de máquinas com quatro ou mais mancais. A seleção deve ser baseada na análise de desempenho da vibração. As localizações preferenciais para medições devem, quando possível, ser aquelas que produzem eventos perturbadores mais significativos nas amplitudes da carcaça do mancal. Tais posições podem ser determinadas por medições de ensaio.
A instalação de um único transdutor no pedestal ou carcaça do mancal, em posição ligeiramente inclinada, é, em geral, considerada adequada para monitoramento contínuo de bombas. Para monitoramento da vibração axial de uma máquina, como regra geral, é suficiente um transdutor montado no mancal de empuxo.
Medições absolutas de vibração em carcaça de mancal são geralmente feitas em conjuntos de máquinas usando transdutores sísmicos (ISSO 10816-5).
O trabalho de medição requer que as medições sejam feitas nas partes expostas, que são normalmente acessíveis e representativas do suporte da estrutura.
_______________________________________________________________________
Conforme instruções do próprio manual do instrumento NK 300, fabricado pela
Teknikão, veremos as principais posições nas figuras abaixo:
Figura 9
O nível de vibração na direção horizontal em geral é o mais alto, pois é o sentido
em que as máquinas tem maior liberdade de movimento.
Figura 10
_______________________________________________________________________
Zona A: Vibração de máquinas recentes instaladas.
Zona B: Máquinas com vibração normalmente aceita, para operação sem restrição a longo prazo.
Zona C: Máquinas com vibração considerada insatisfatória para operação
contínua. Geralmente, a máquina pode ser operada por um período limitado
nessa condição, até que ocorra uma oportunidade para corretiva.
Zona D: Valores de vibração dentro desta zona são, normalmente, considerados suficientemente graves para causar danos à máquina.
Os valores numéricos atribuídos às zonas não tem a intenção de servir como especificação de aceitação, as quais devem estar sujeitas à acordos entre o fabricante da máquina e o cliente. Os limites da zona, entretanto, devem garantir que defeitos grosseiros ou requisitos irrealistas sejam evitados.
De acordo com o ISO-10816-1, existem limites recomendados para diferentes
classes de máquinas, conforme tabela abaixo:
_______________________________________________________________________
Classe I: Partes individuais de motores e máquinas, integralmente conectada à máquina completa em sua condição de operação normal.
Classe II: Máquinas de tamanho médio sem fundação especial como motores
elétricos de 15 KW à 75 KW, motores ou máquinas montados rigidamente sobre
fundação especial até 300 KW.
Nível de Vibração de máquinas recentemente colocadas em
Funcionamento.
Nível de Vibração aceitável para Operação Contínua da
Máquina por um longo período.
Nível de Vibração inaceitável para Operação Contínua da
Máquina por um longo período. Deve ser feito a manutenção do Equipamento.
Nível de Vibração suficiente para causar danos ao
Equipamento. Deve ser revisado imediatamente.