

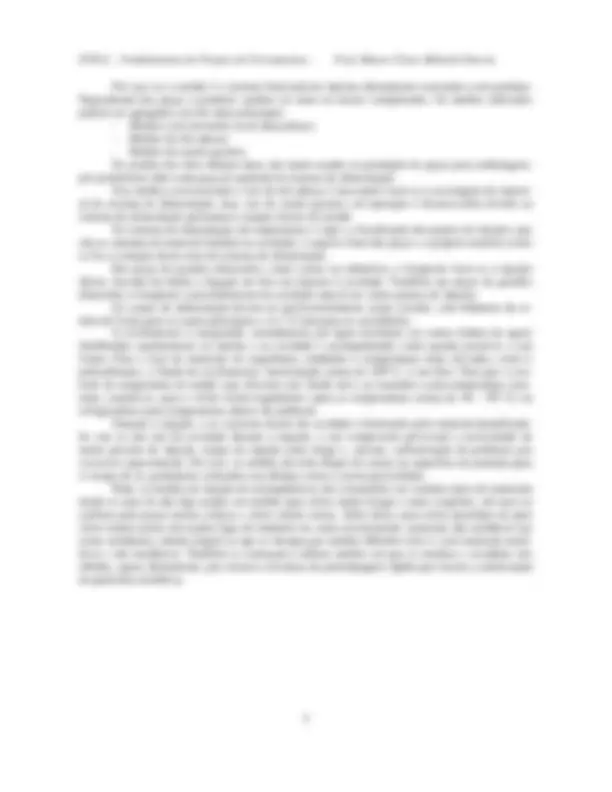
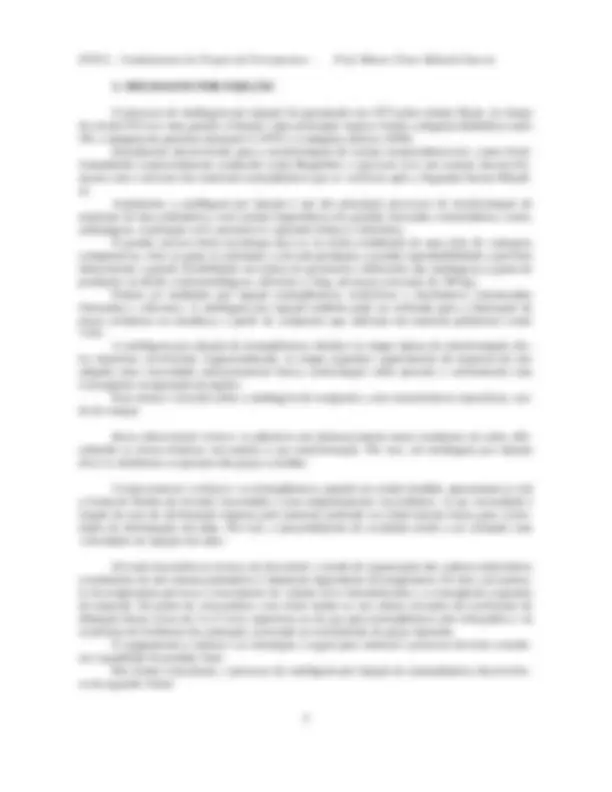
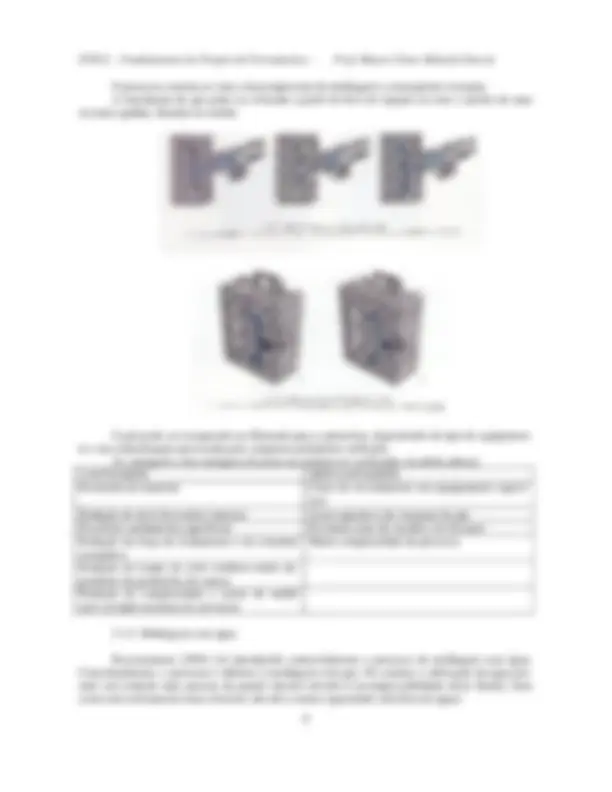
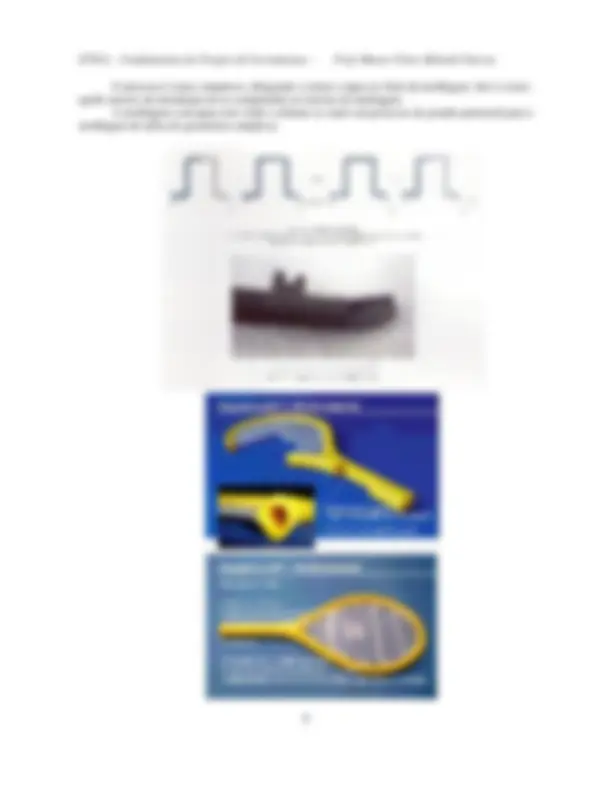
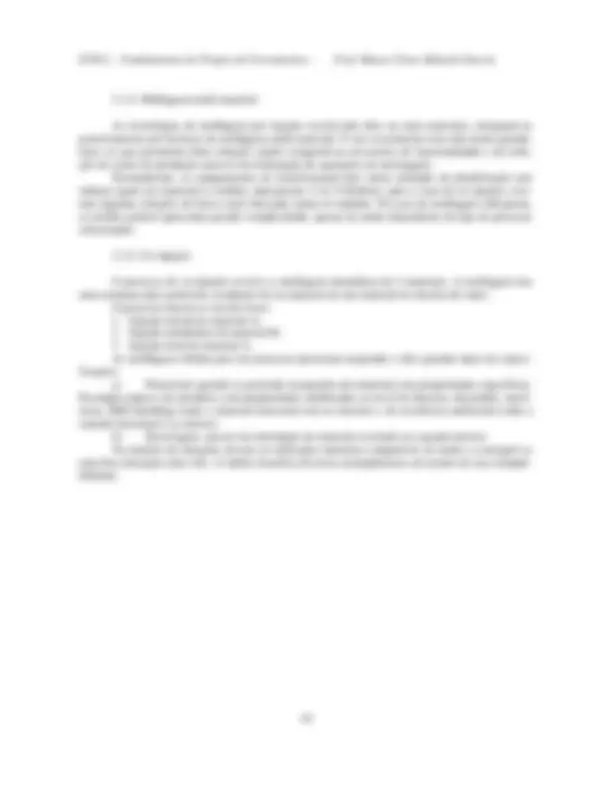
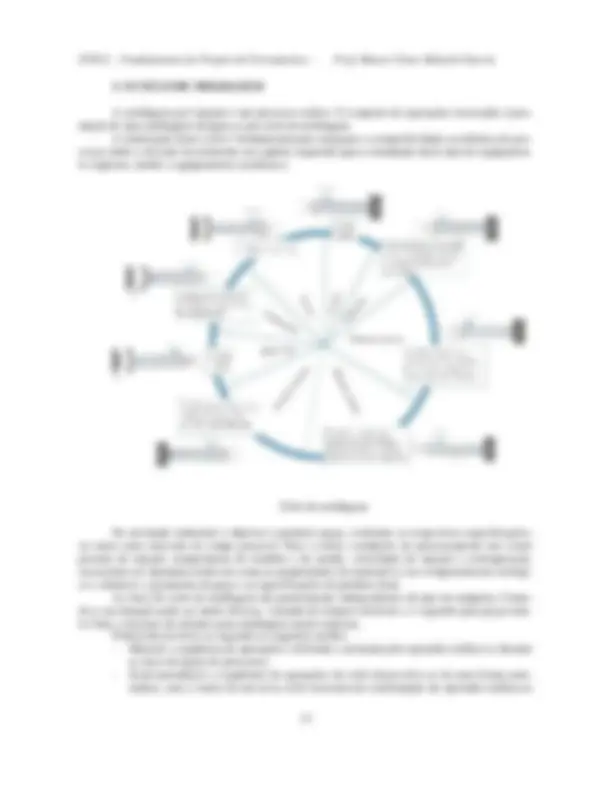
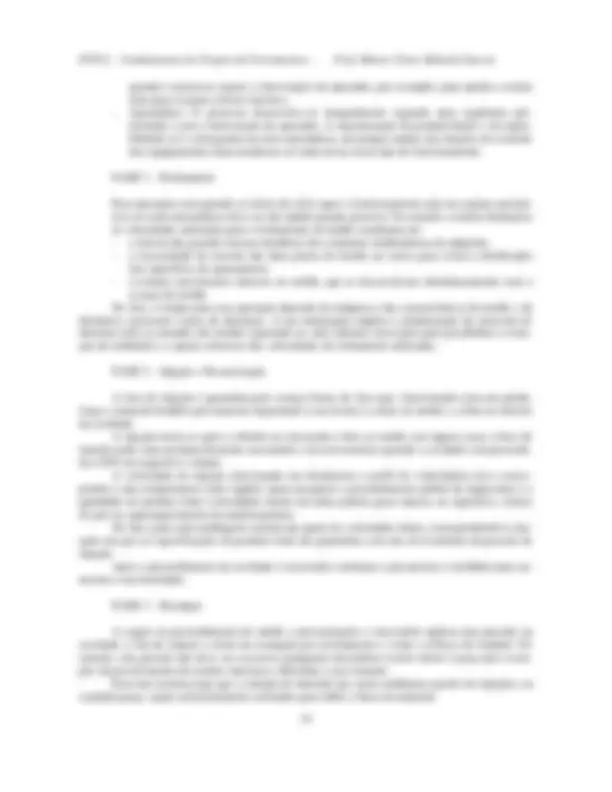
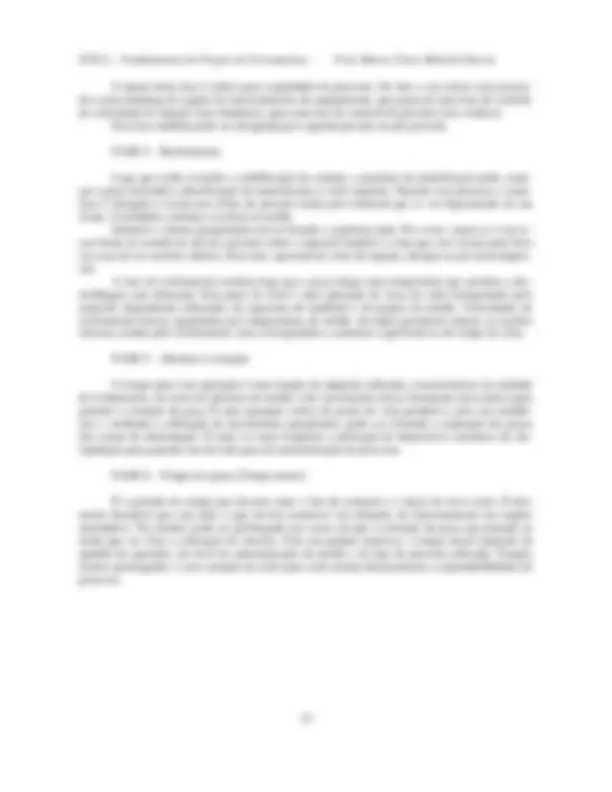
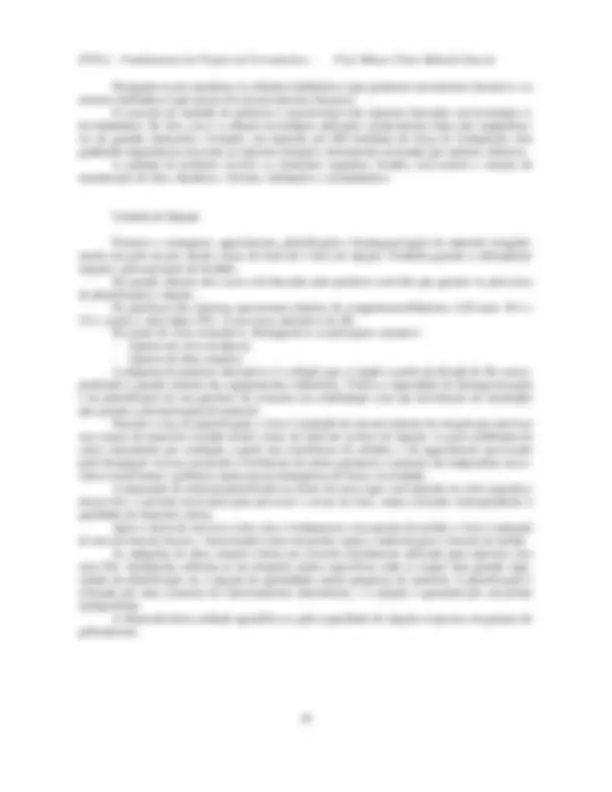
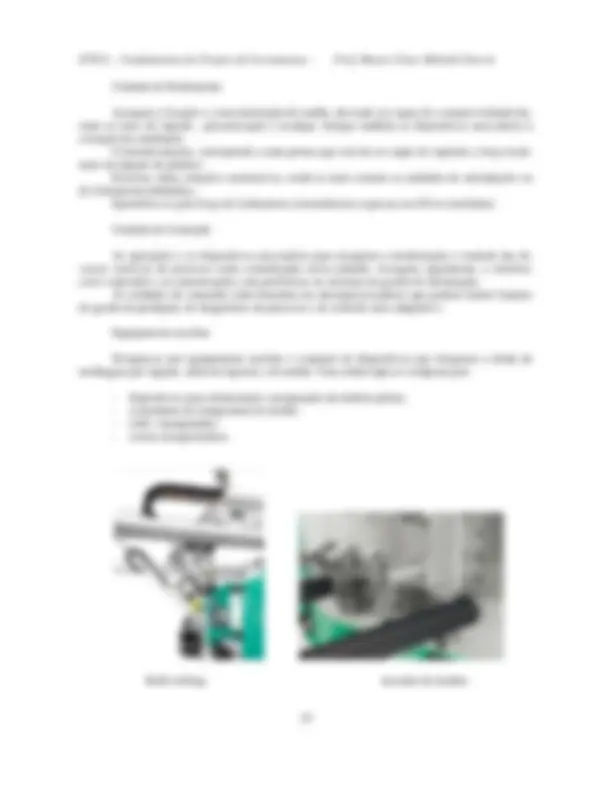
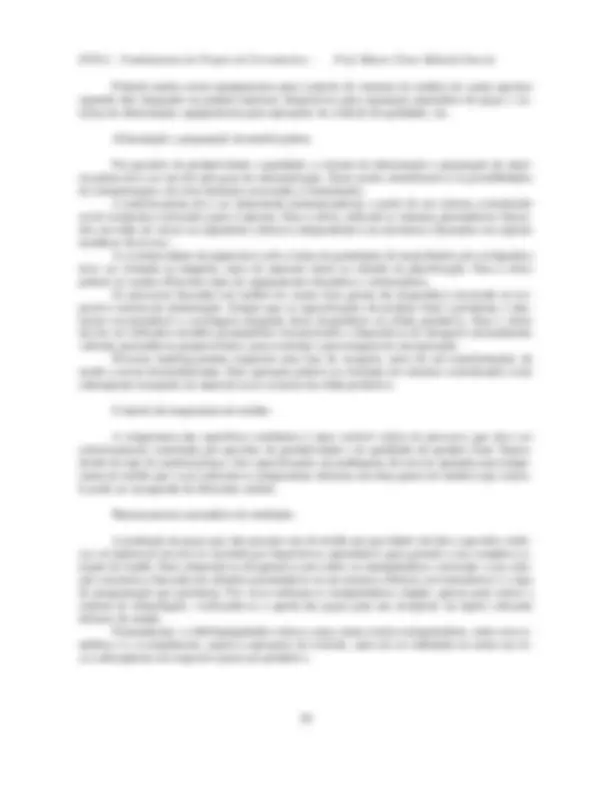
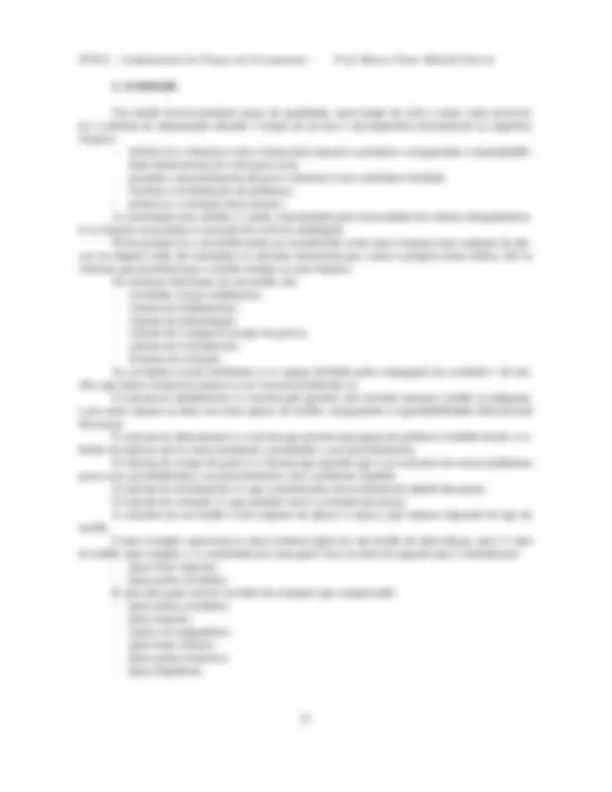
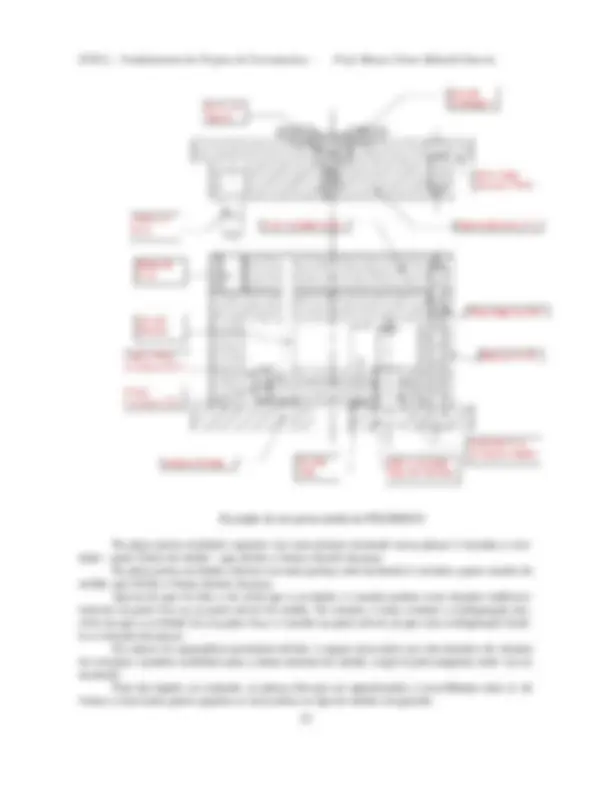
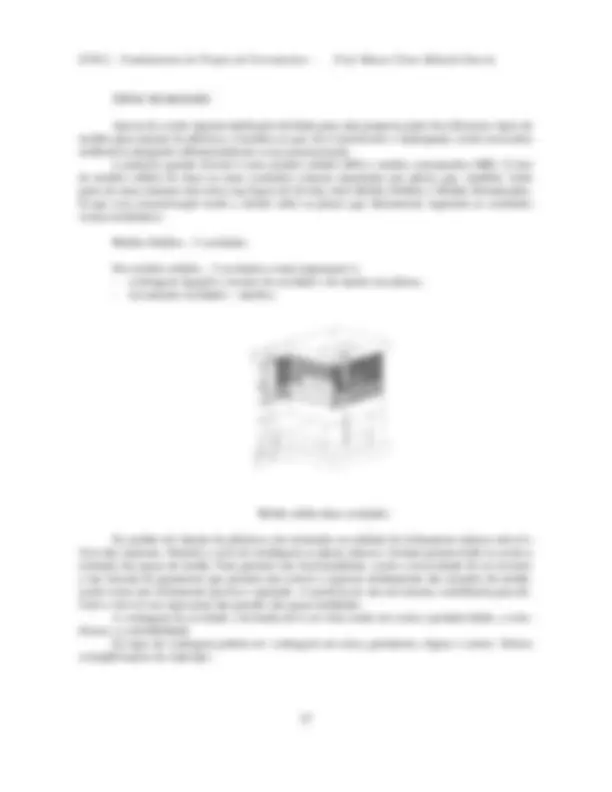
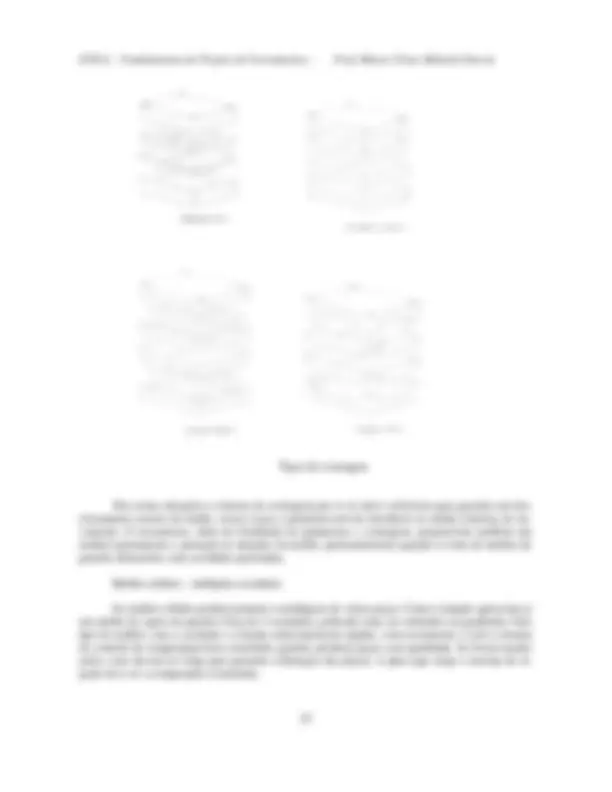
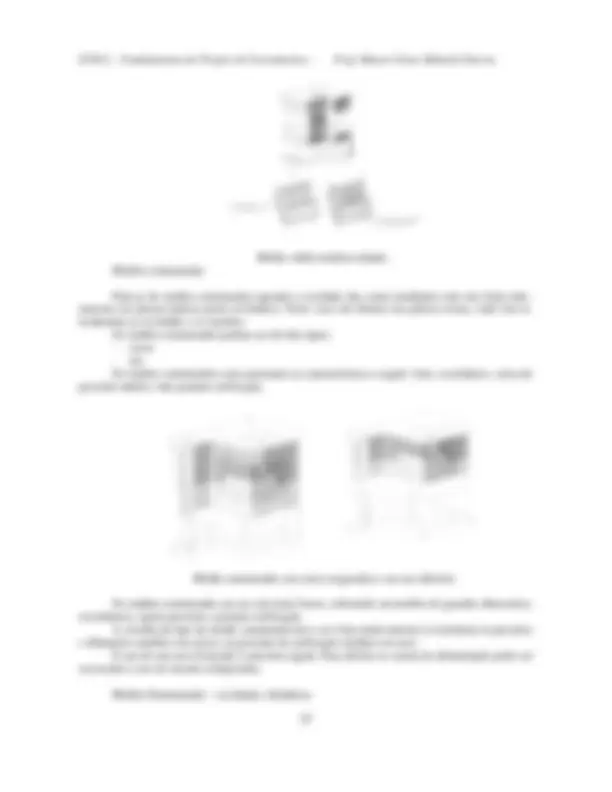
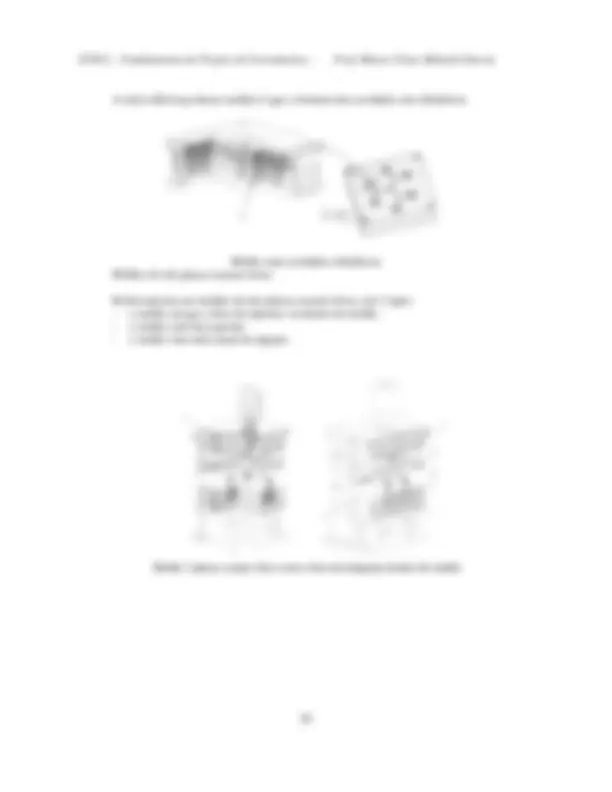
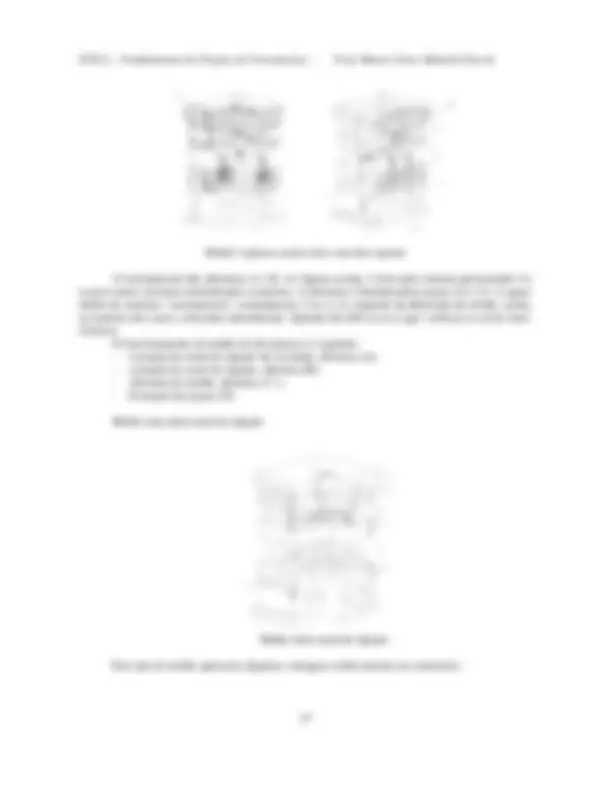
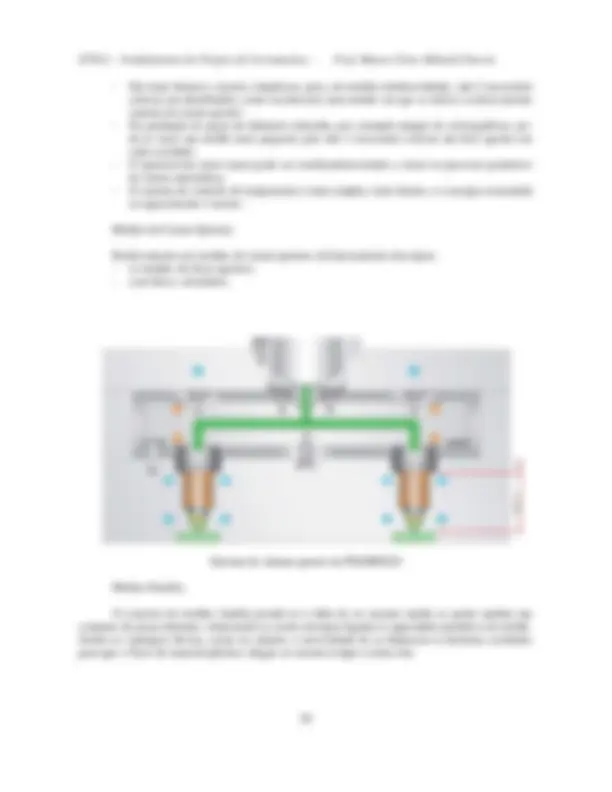
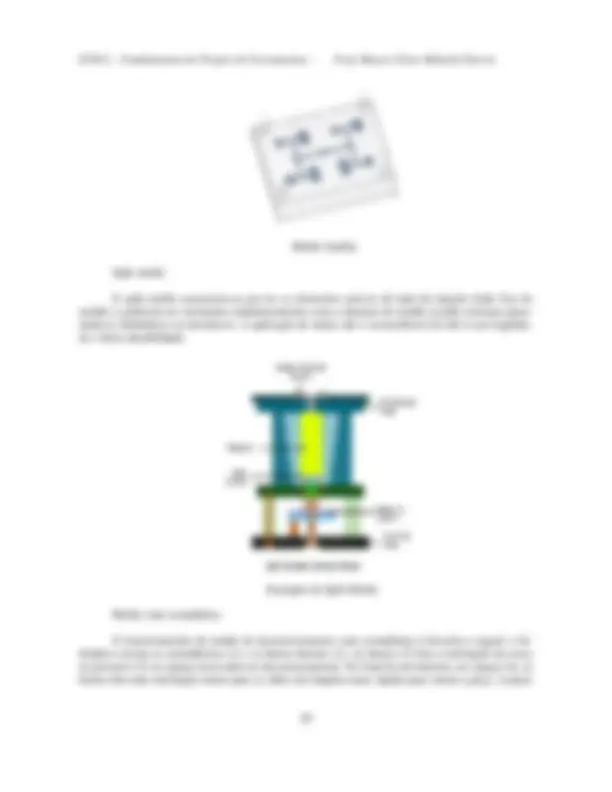
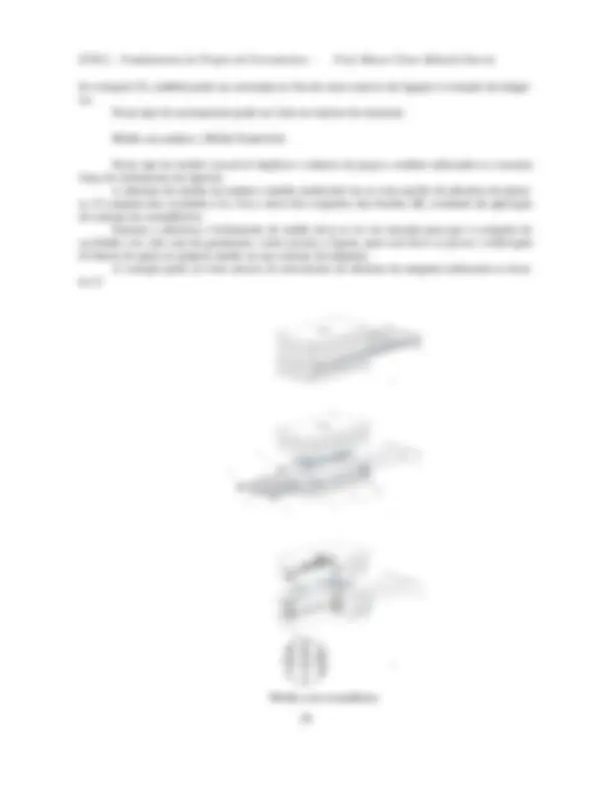
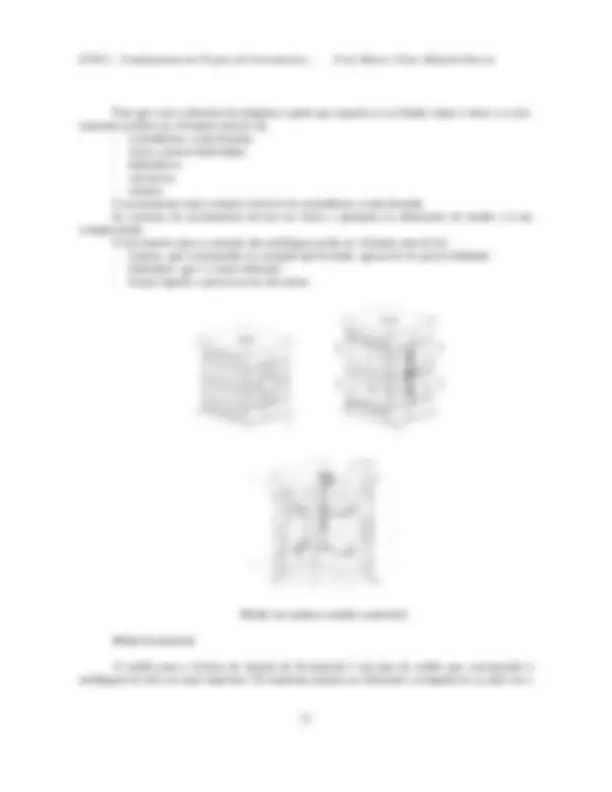
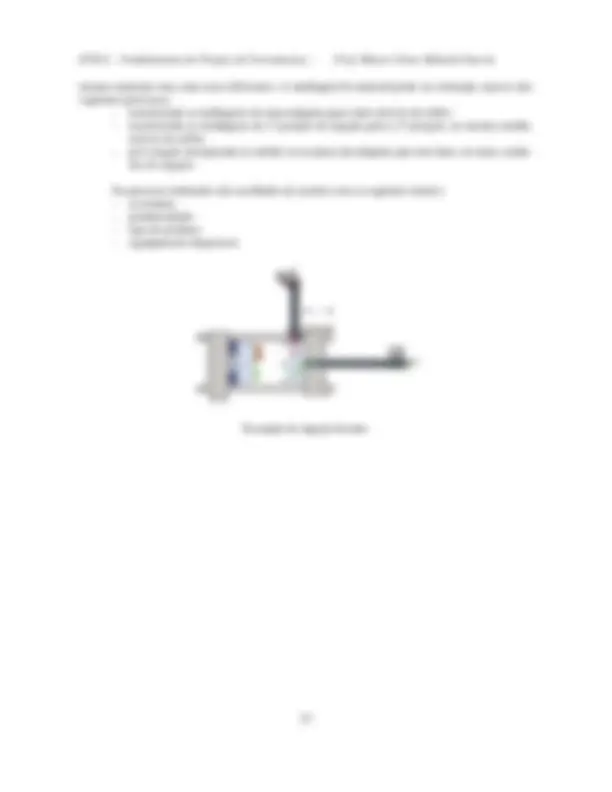
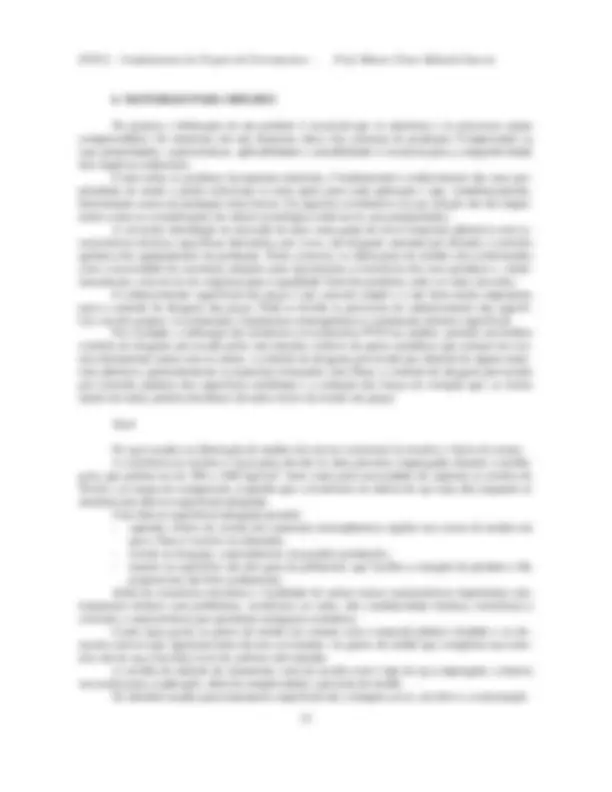

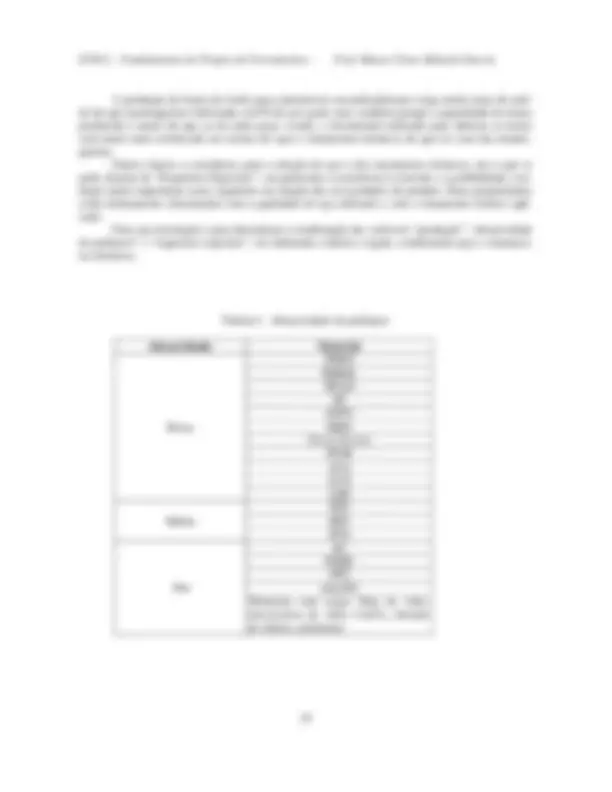
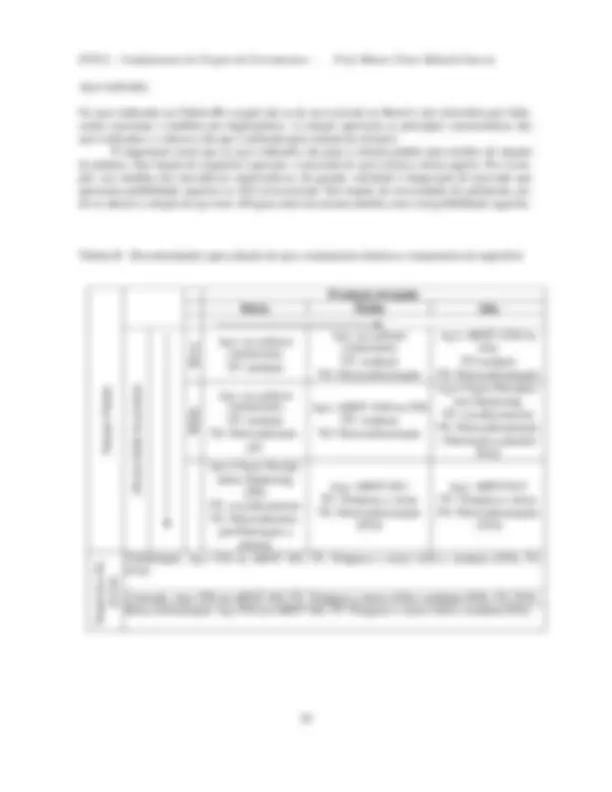
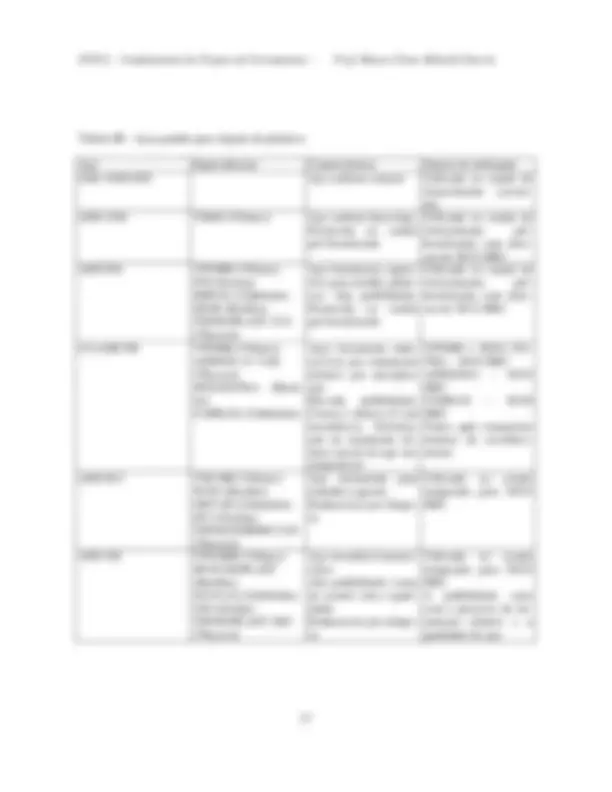
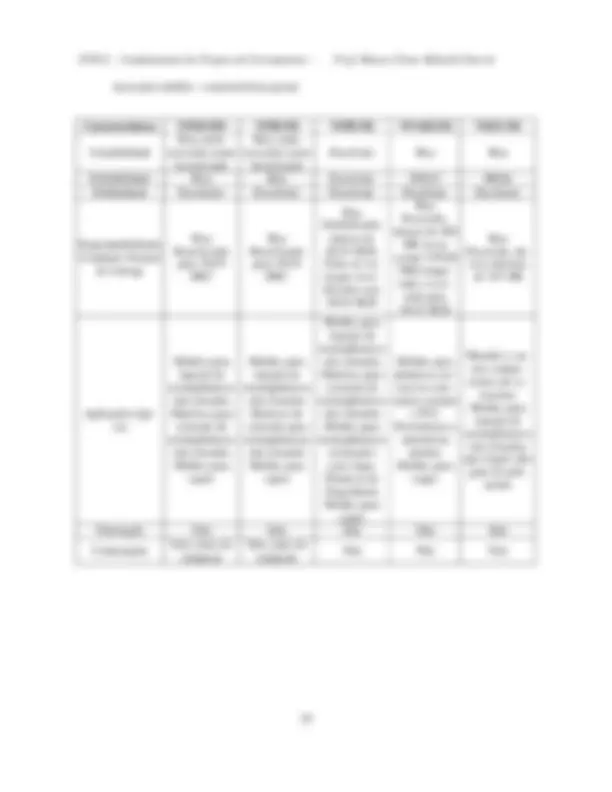
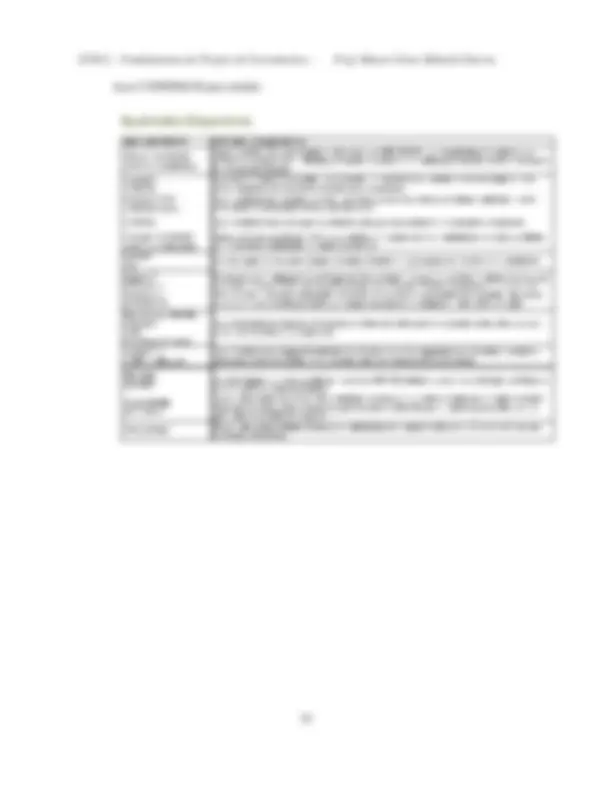
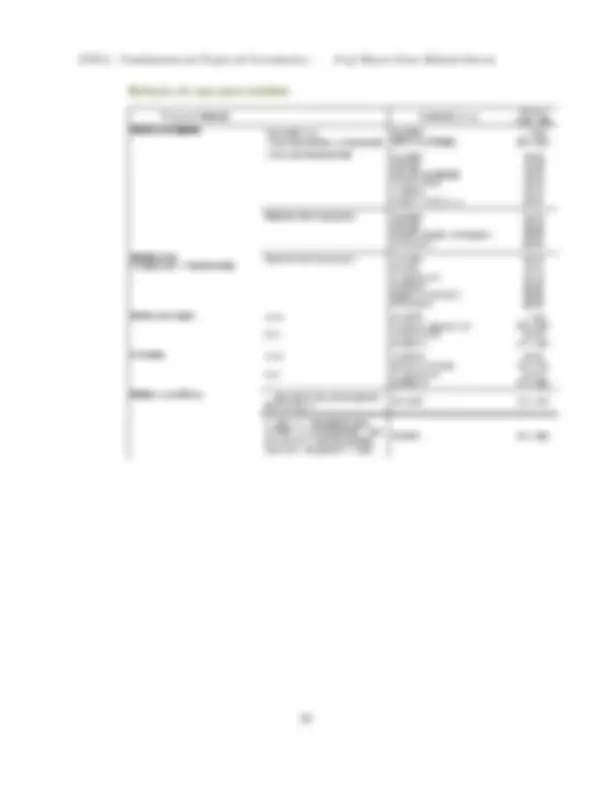
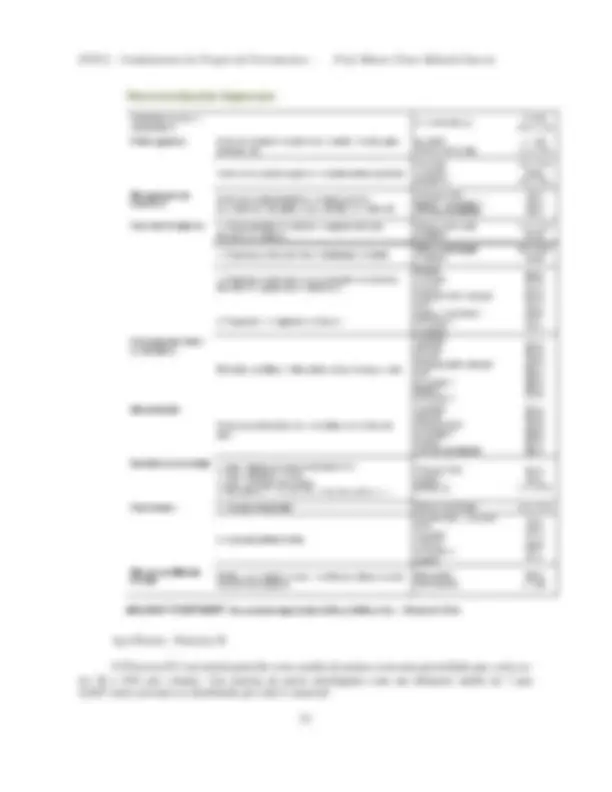
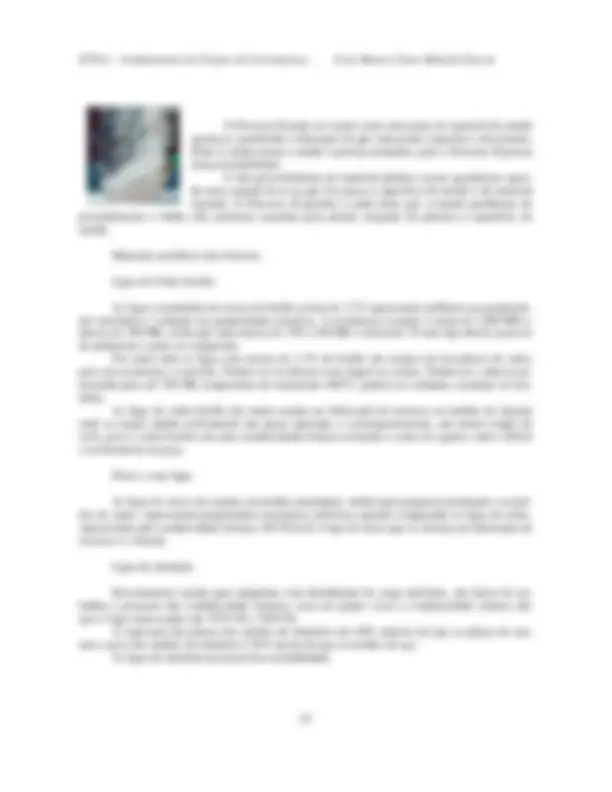
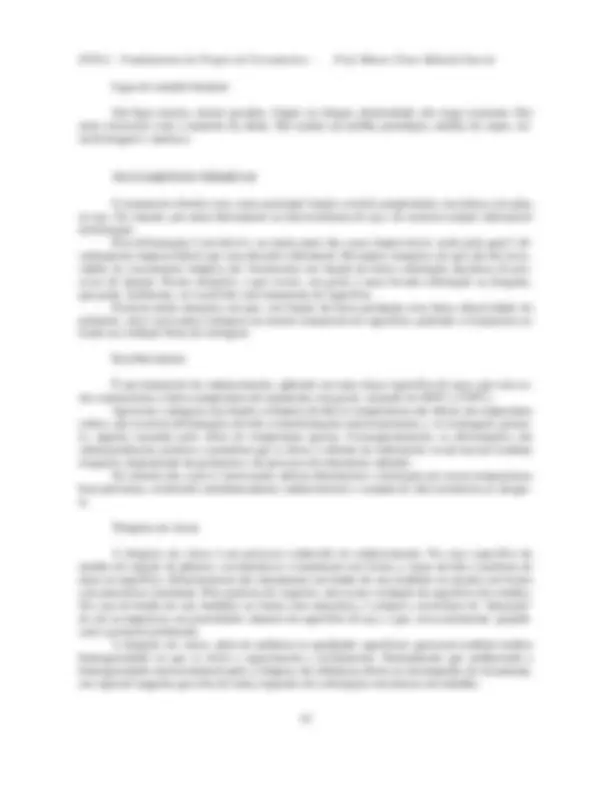
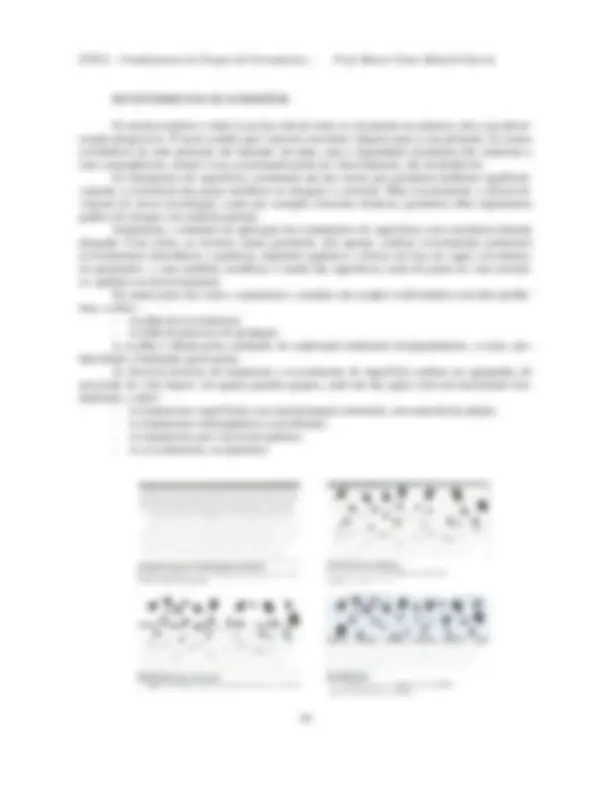
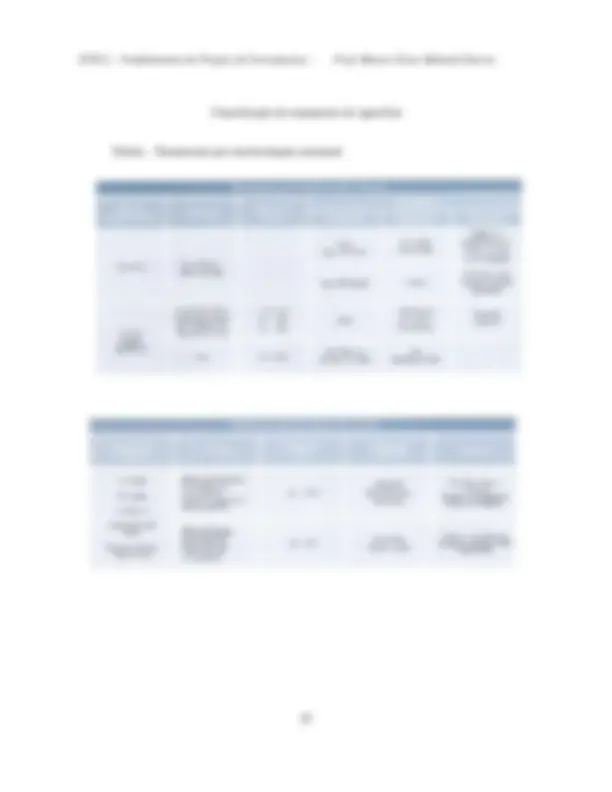
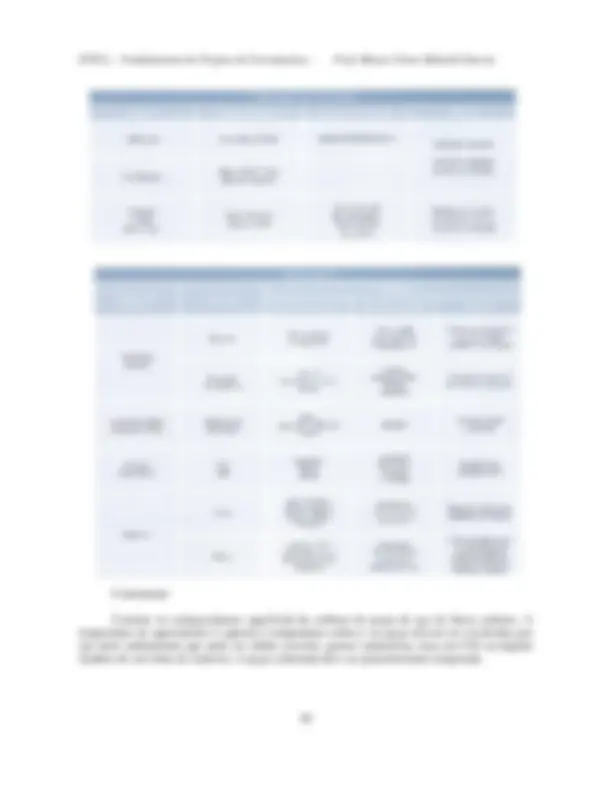
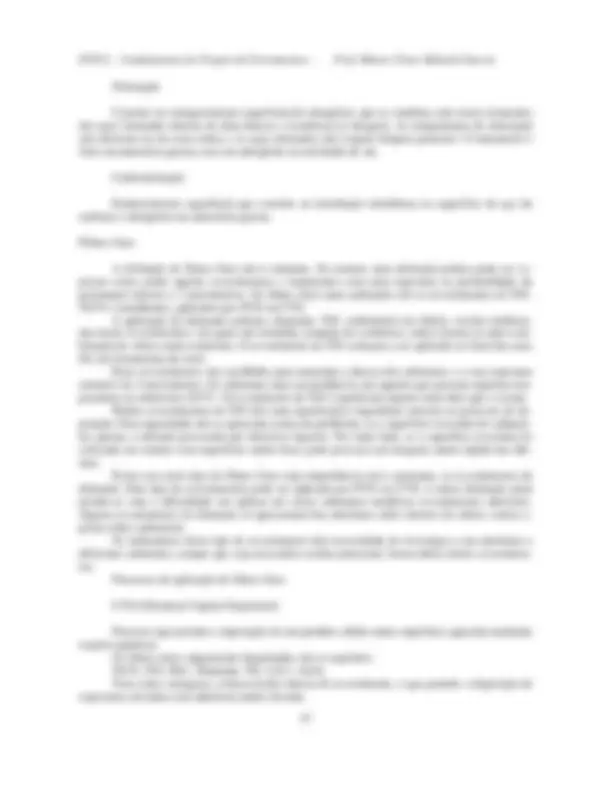
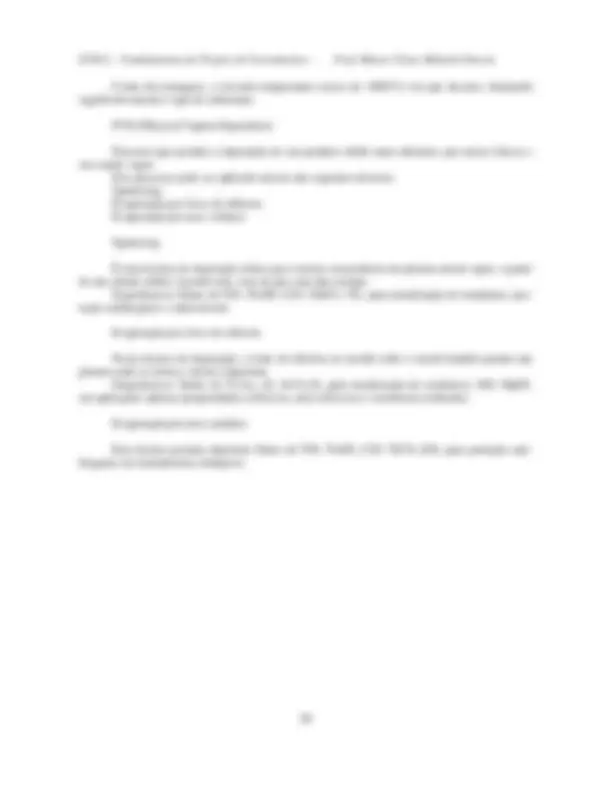
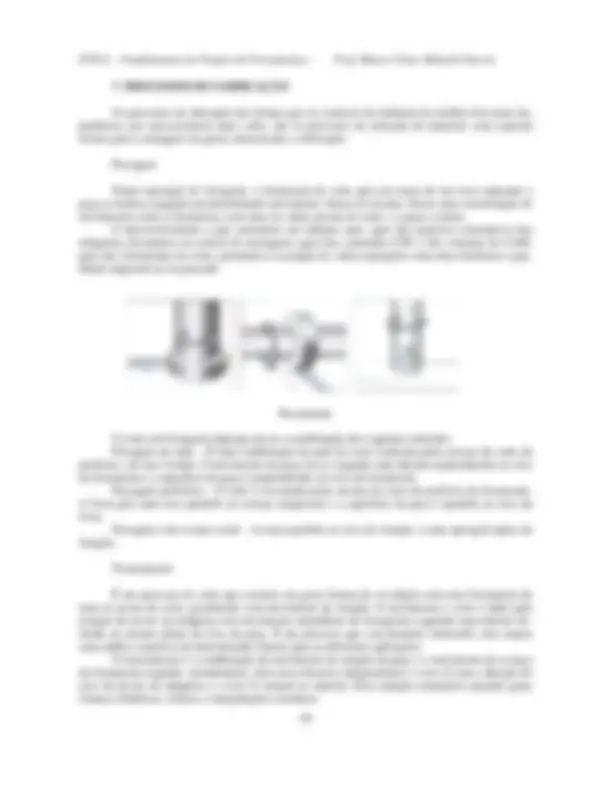
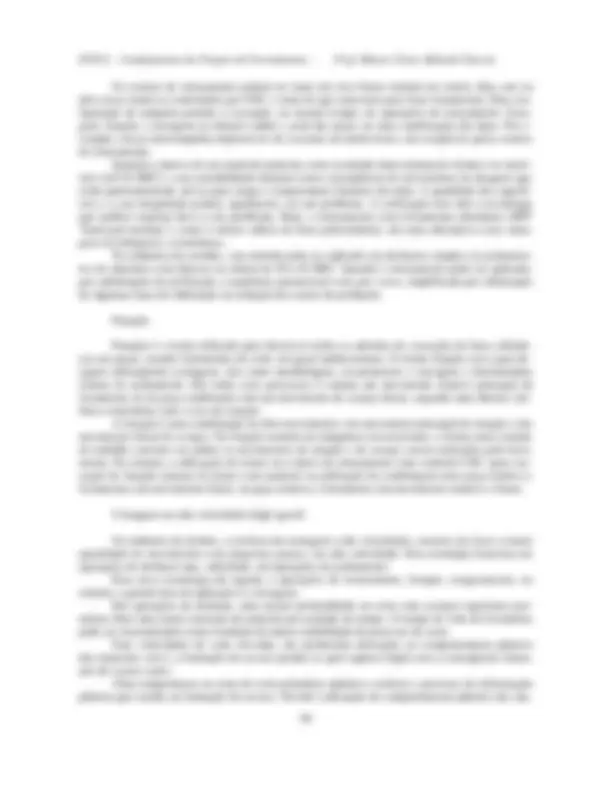
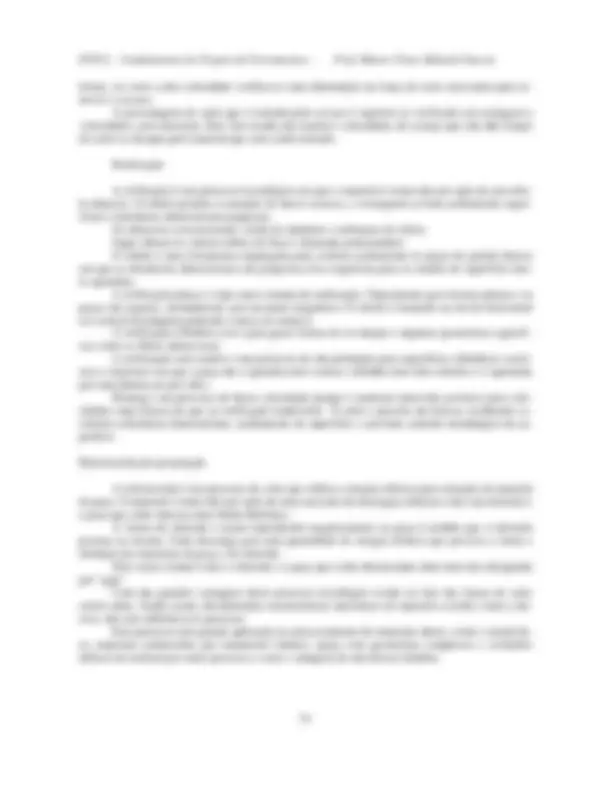
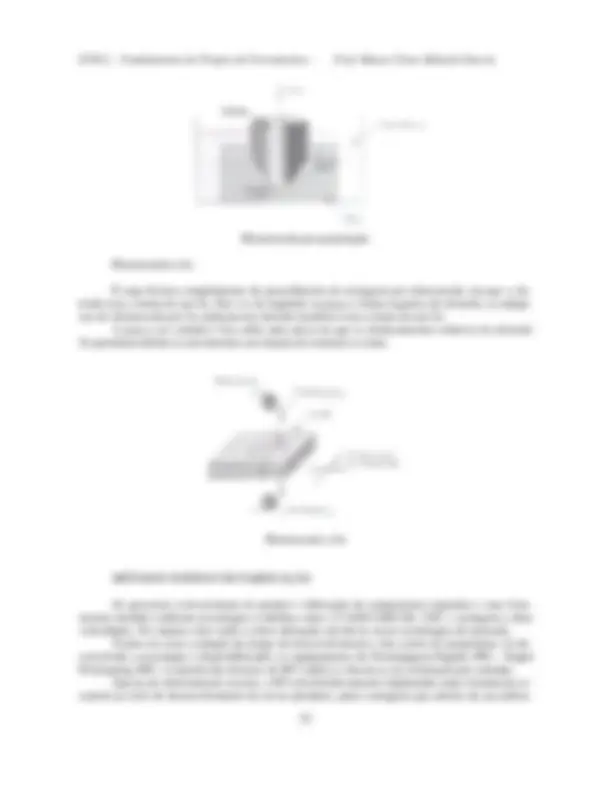
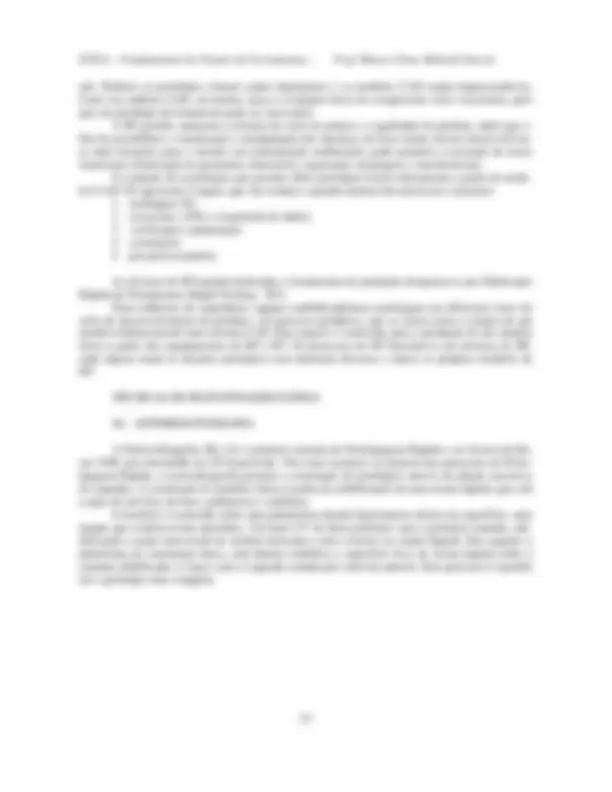
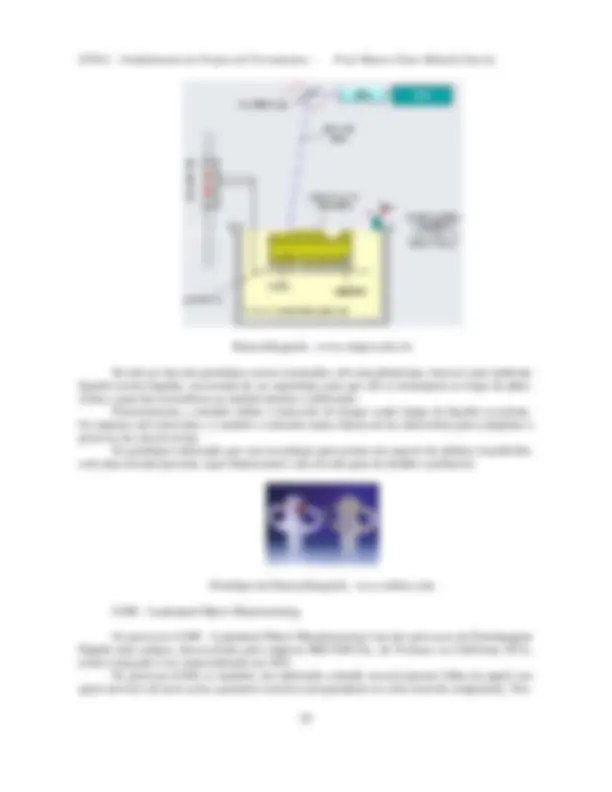
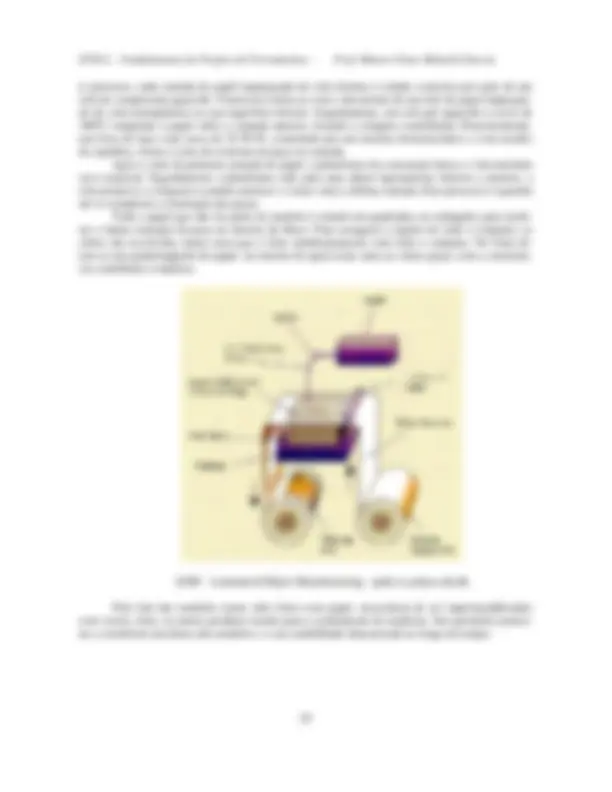
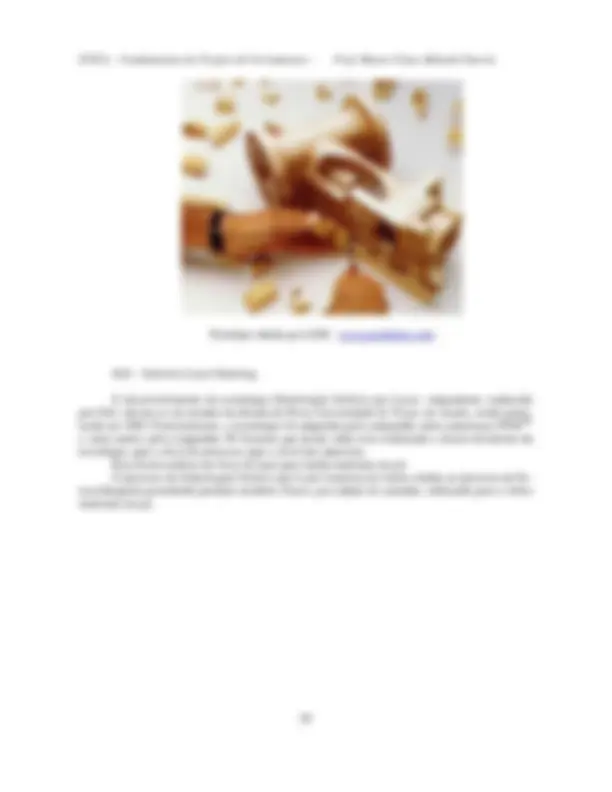
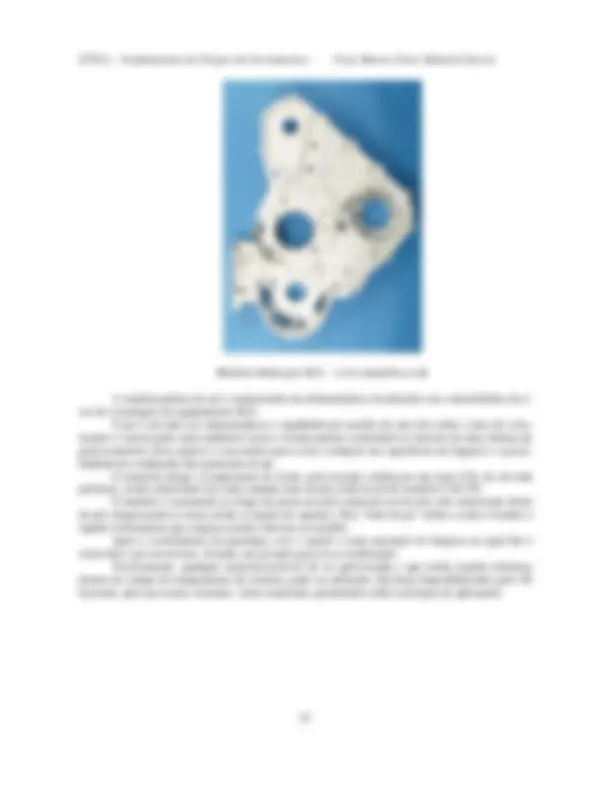
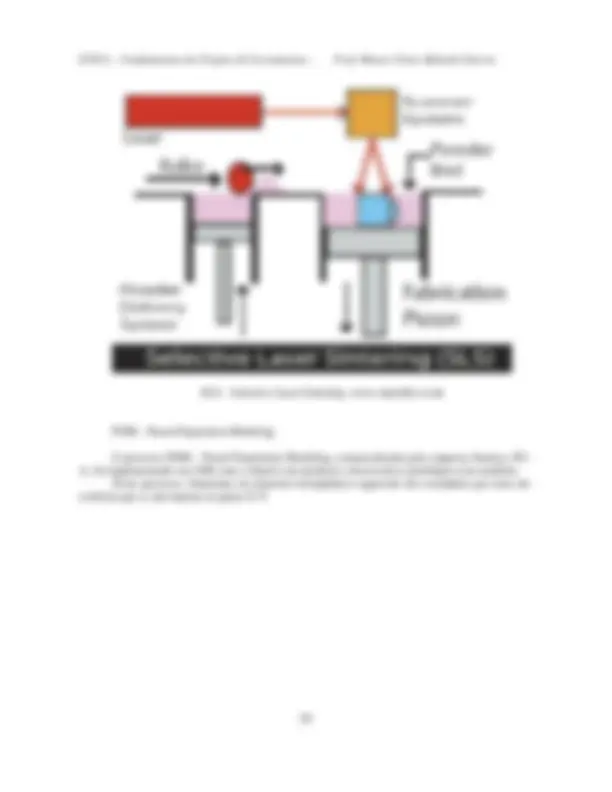
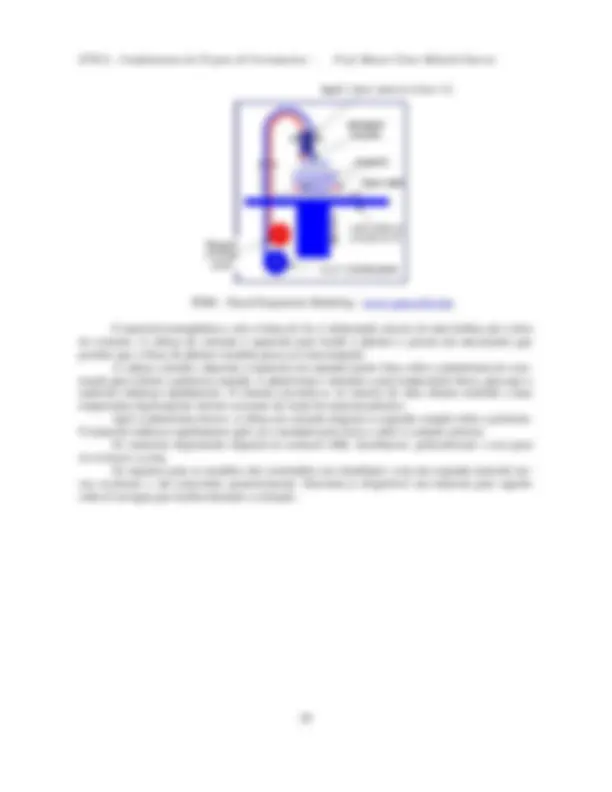
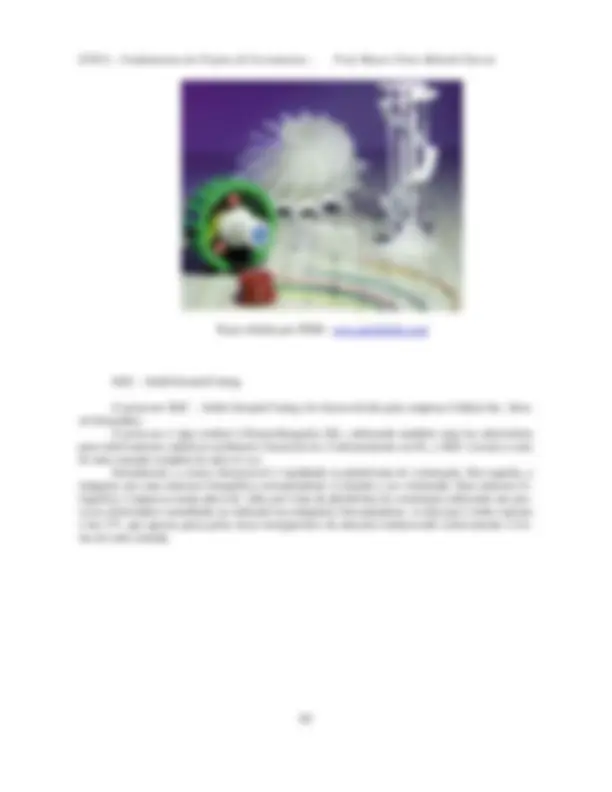
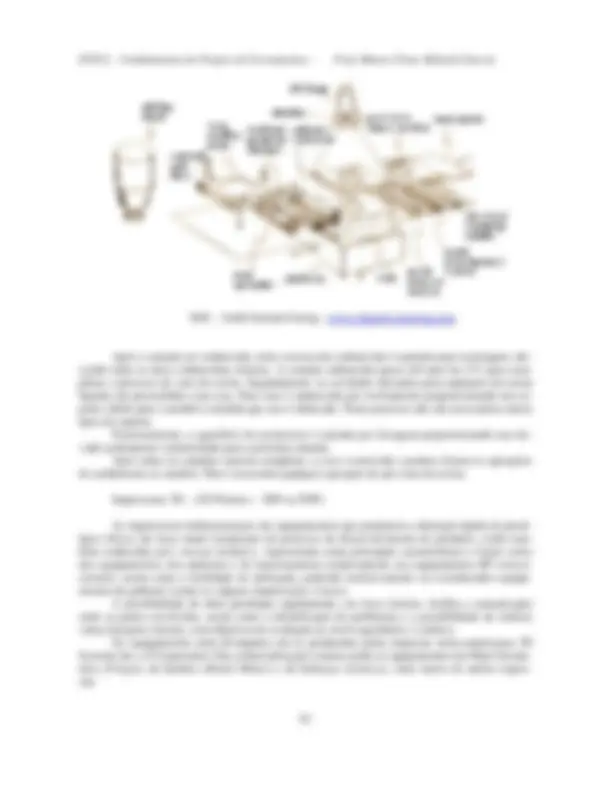
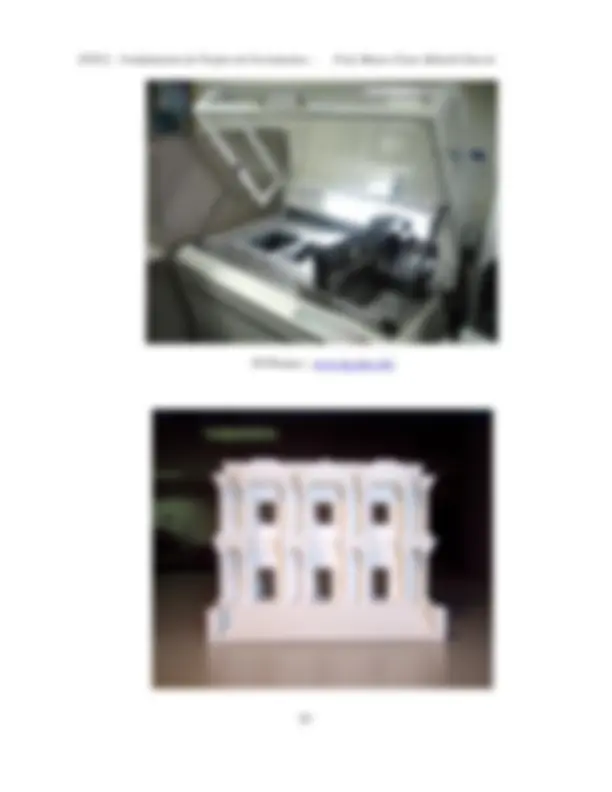
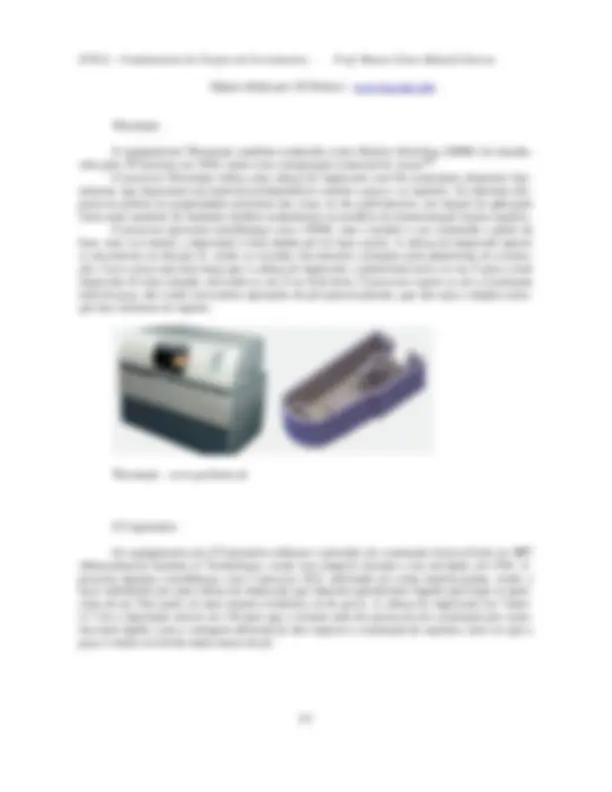
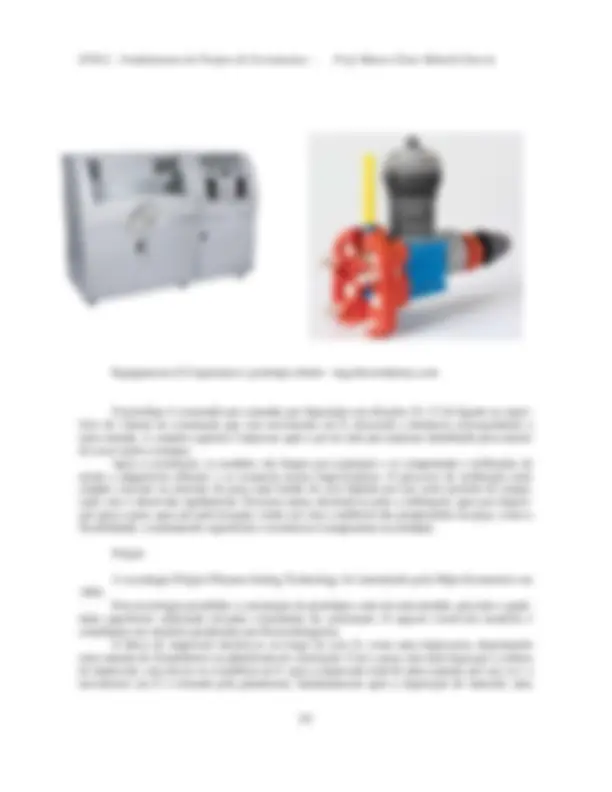
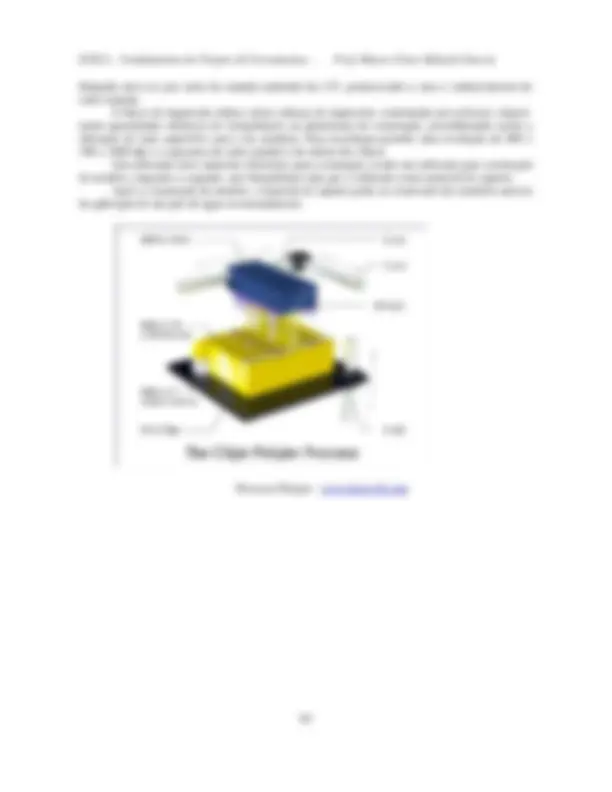
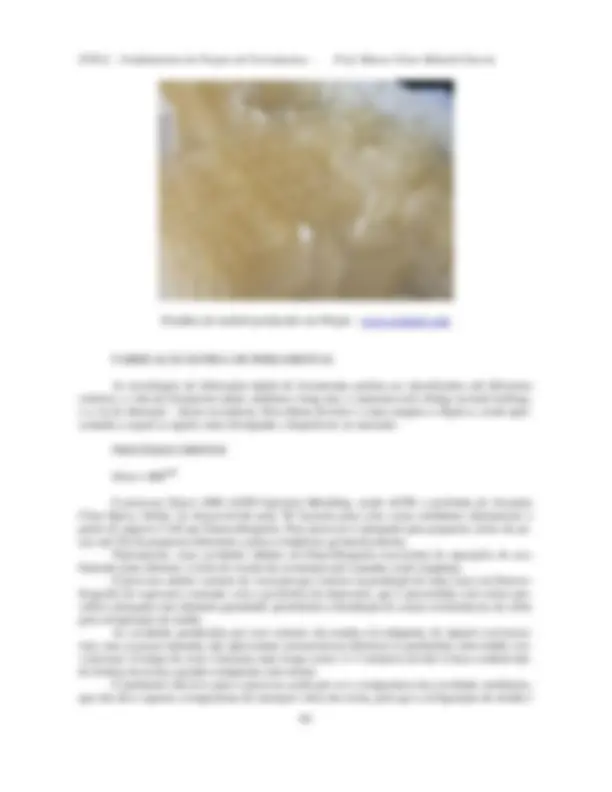

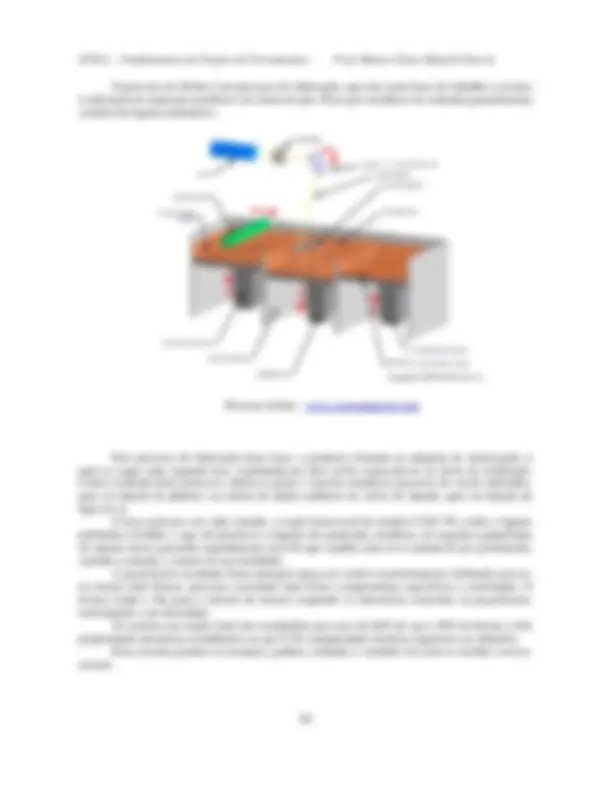
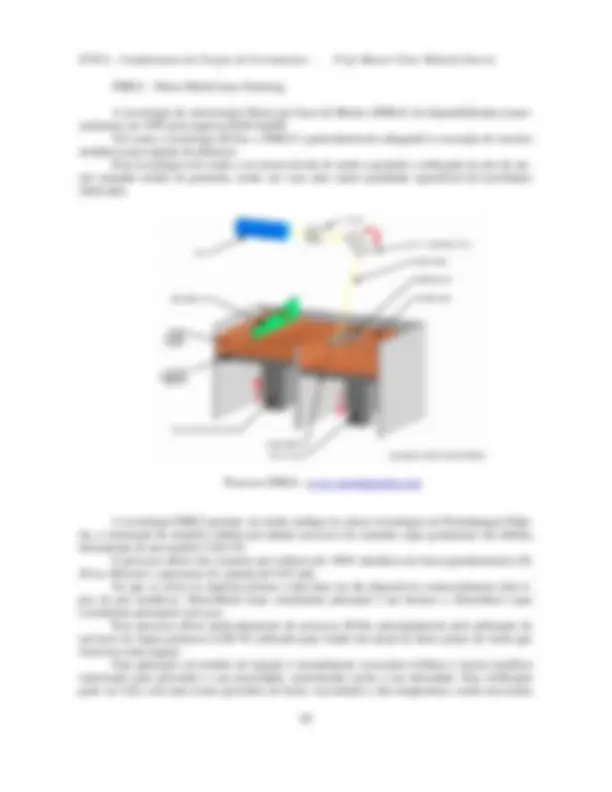
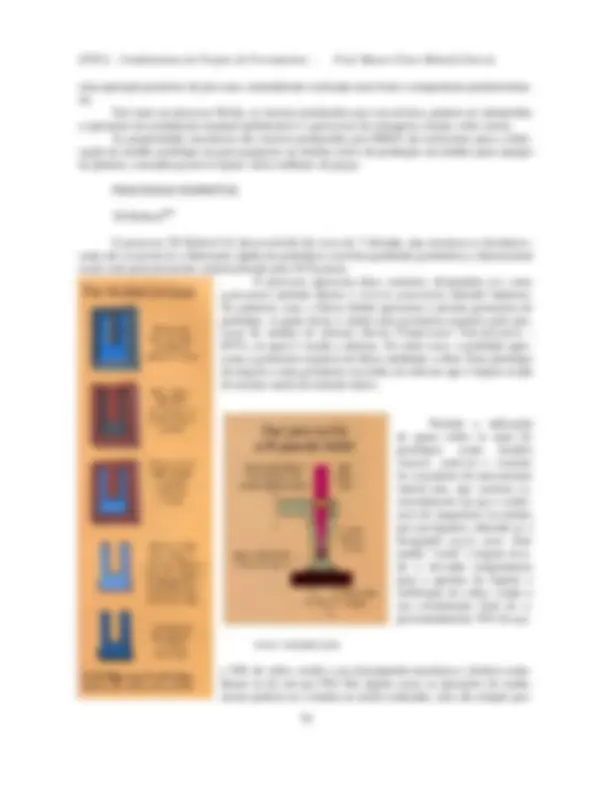
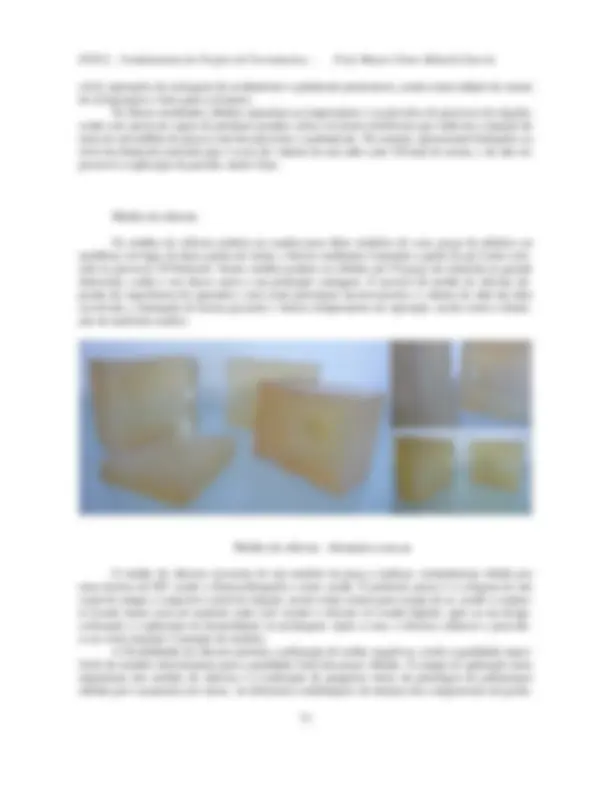
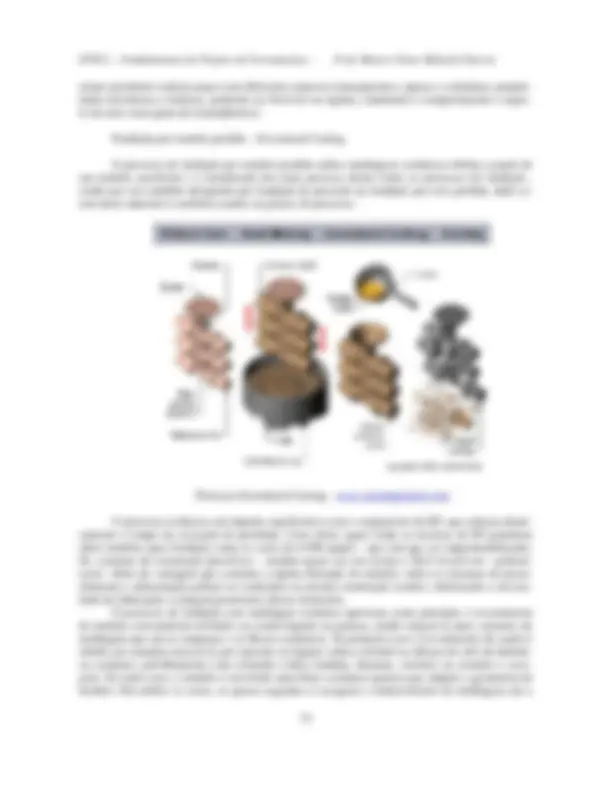
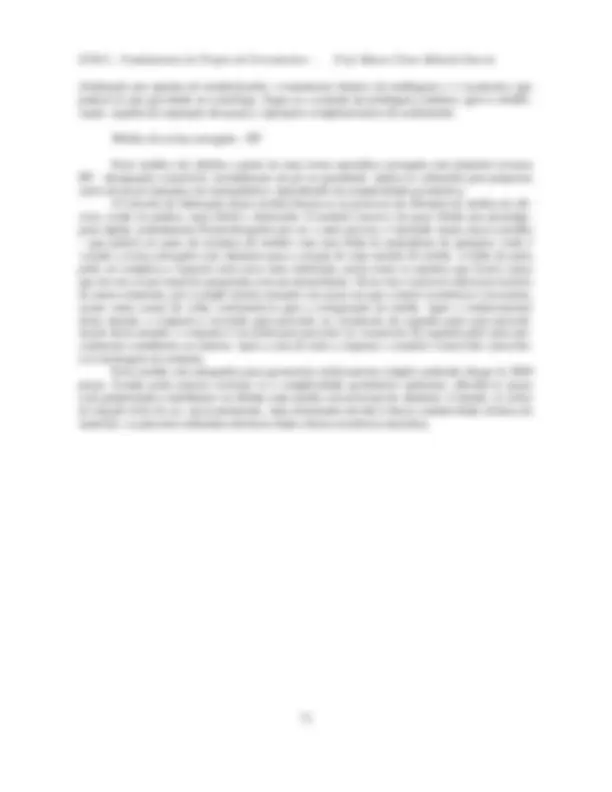
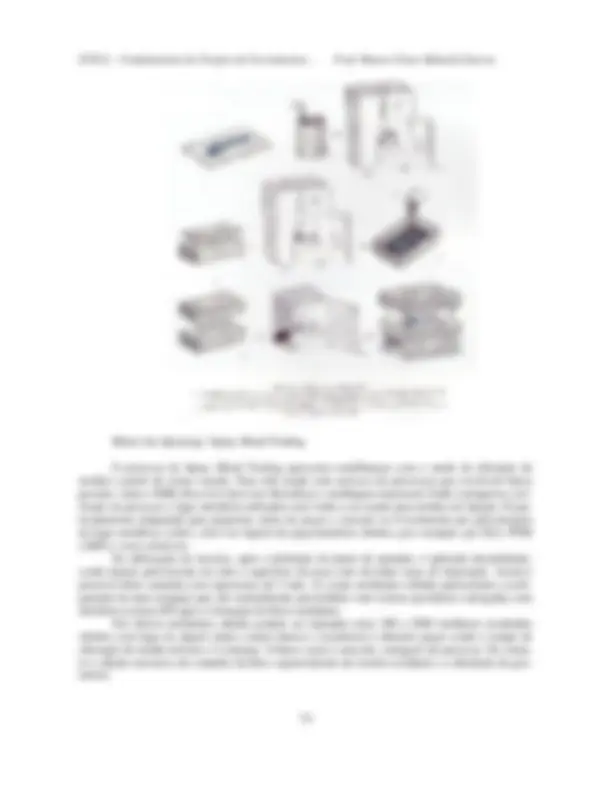
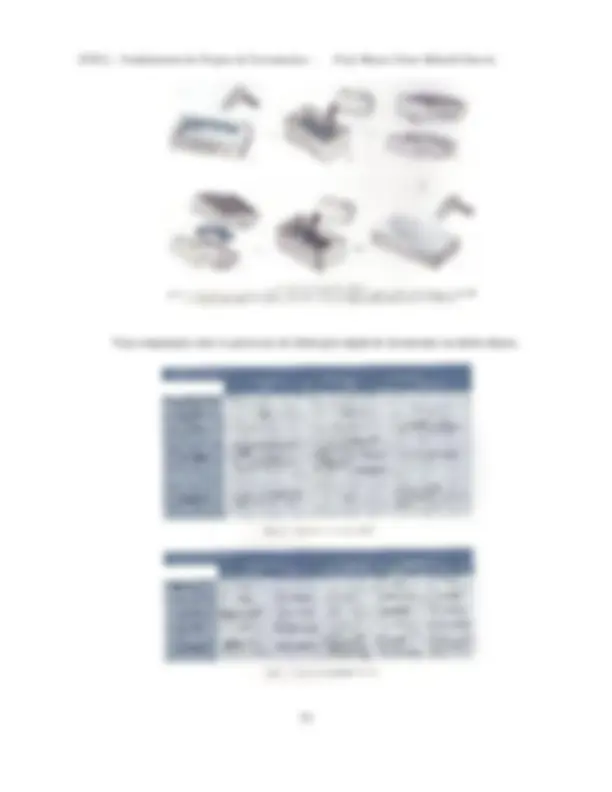
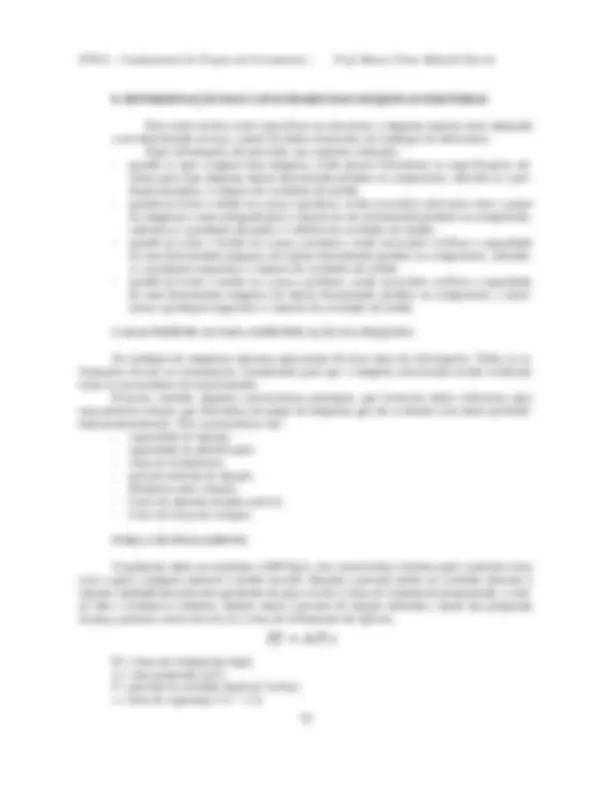
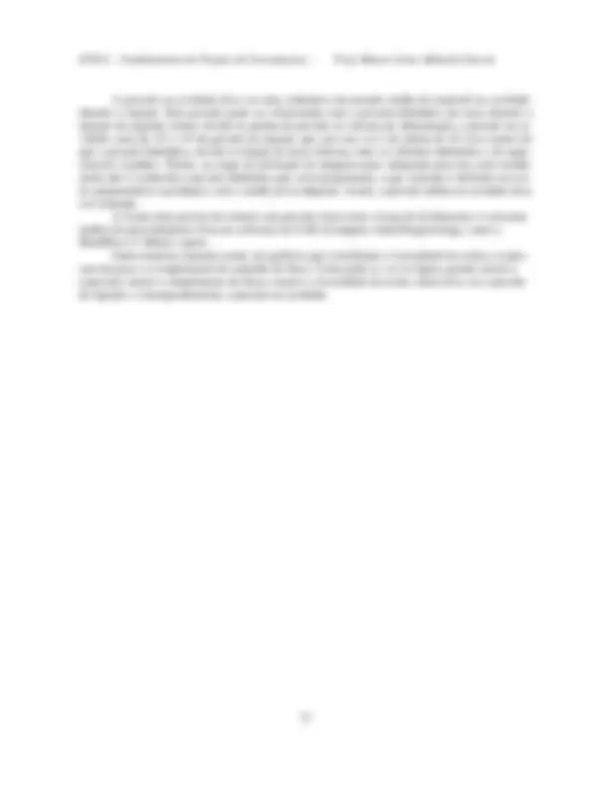
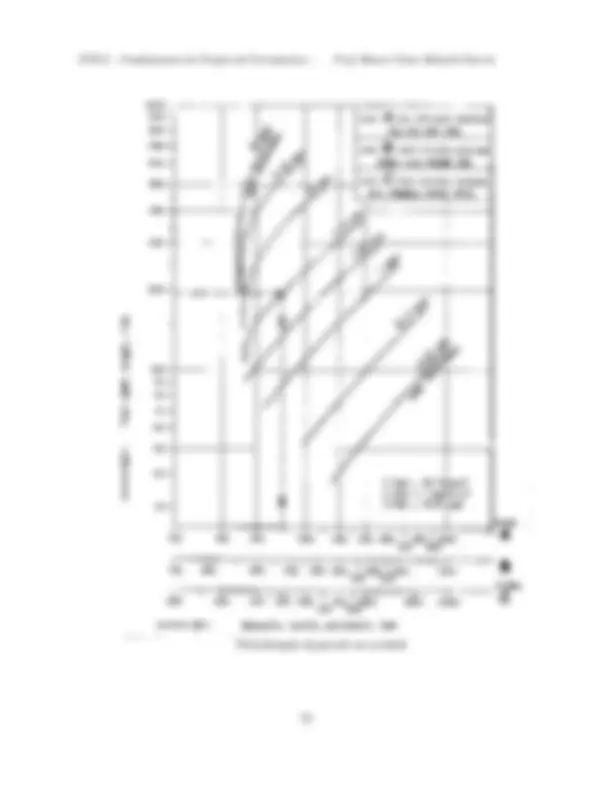
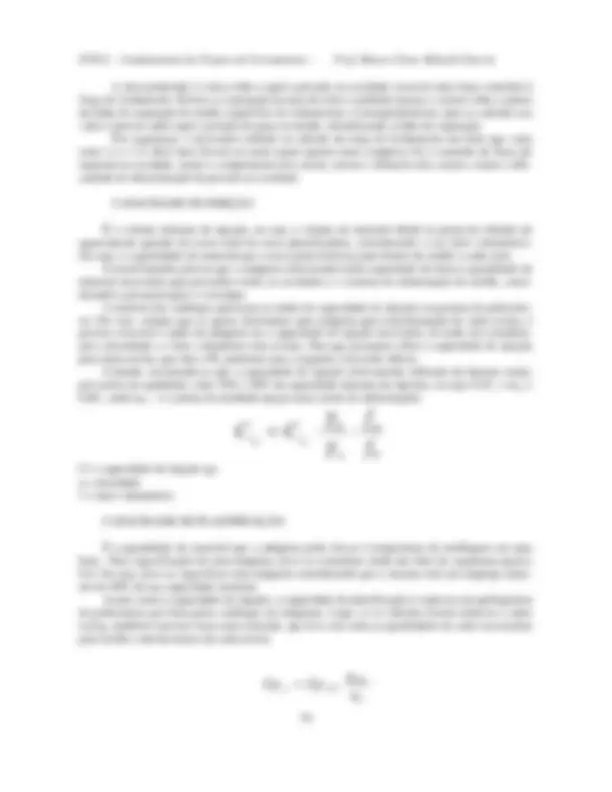
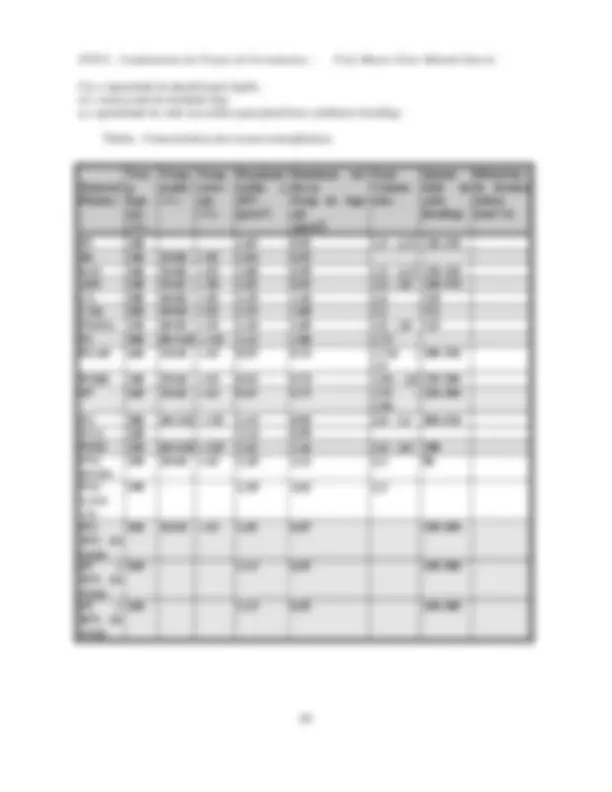
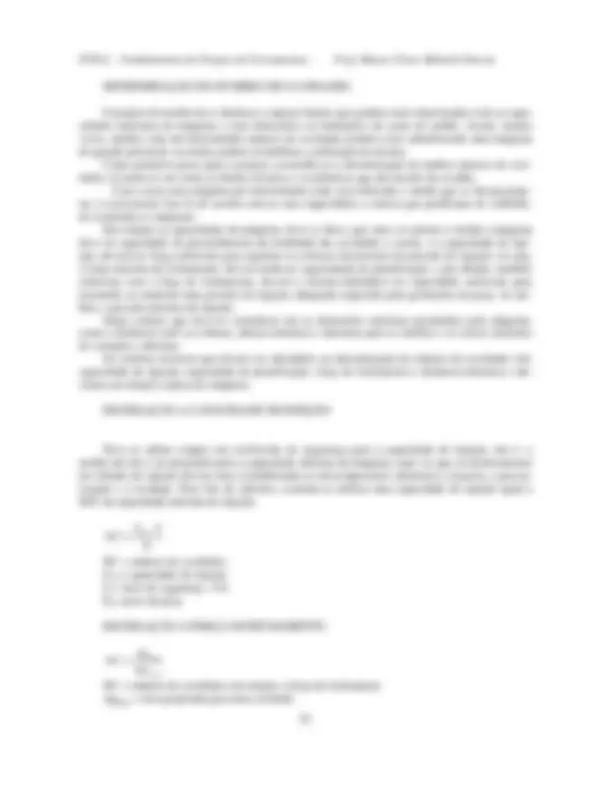
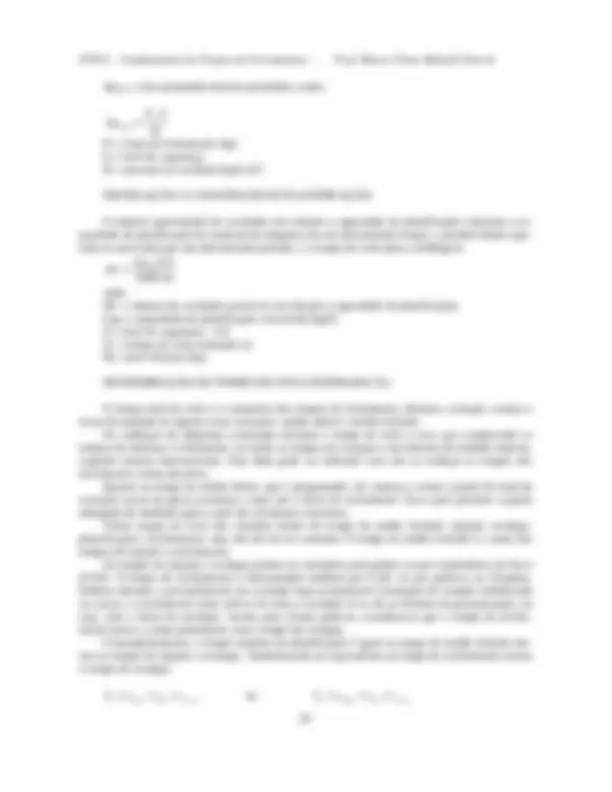
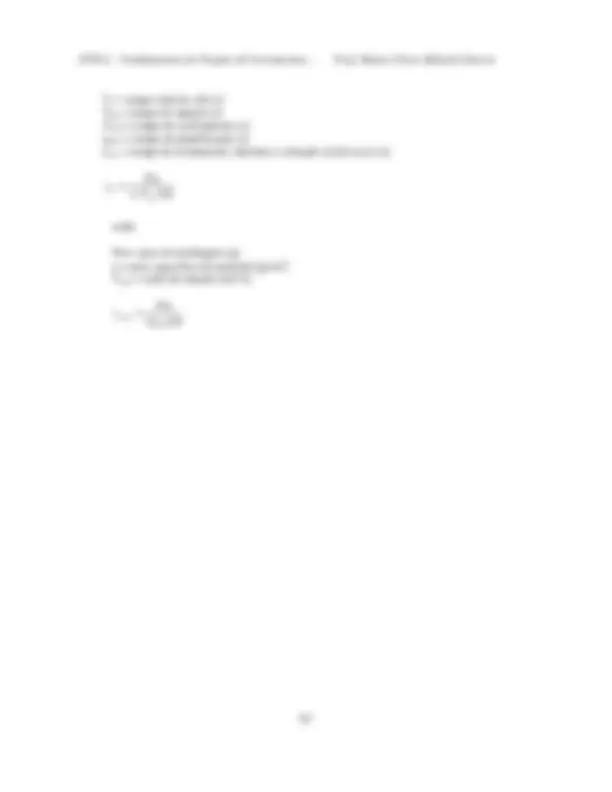
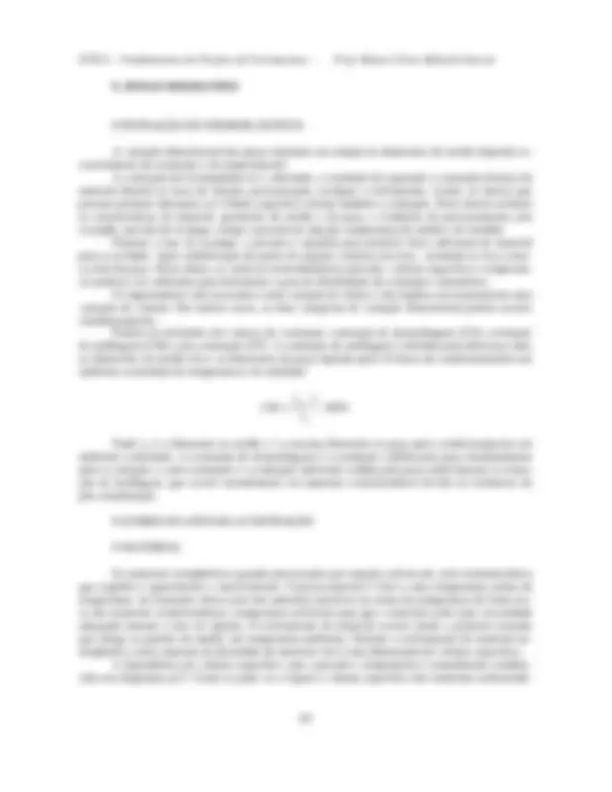
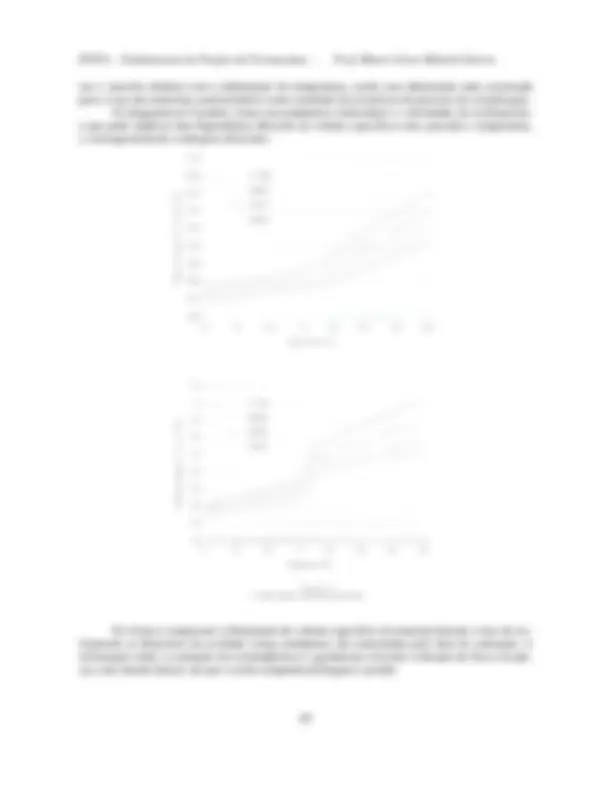
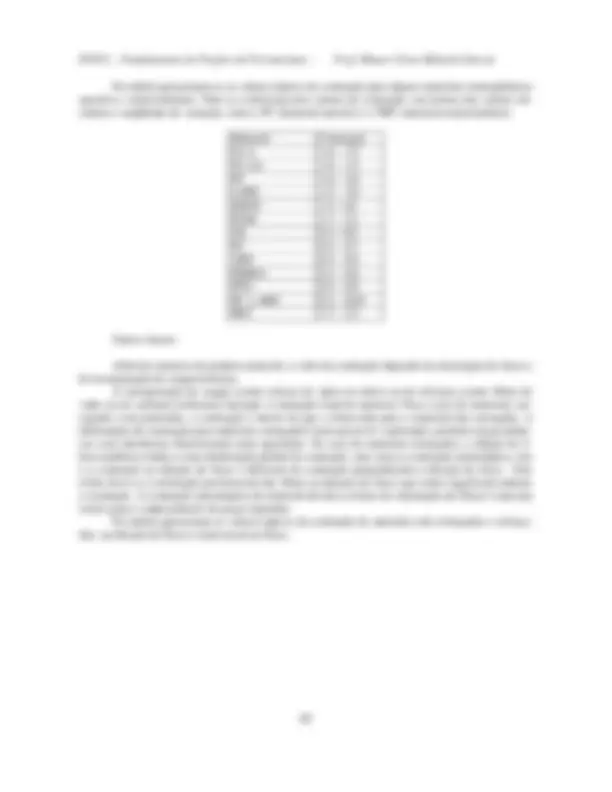
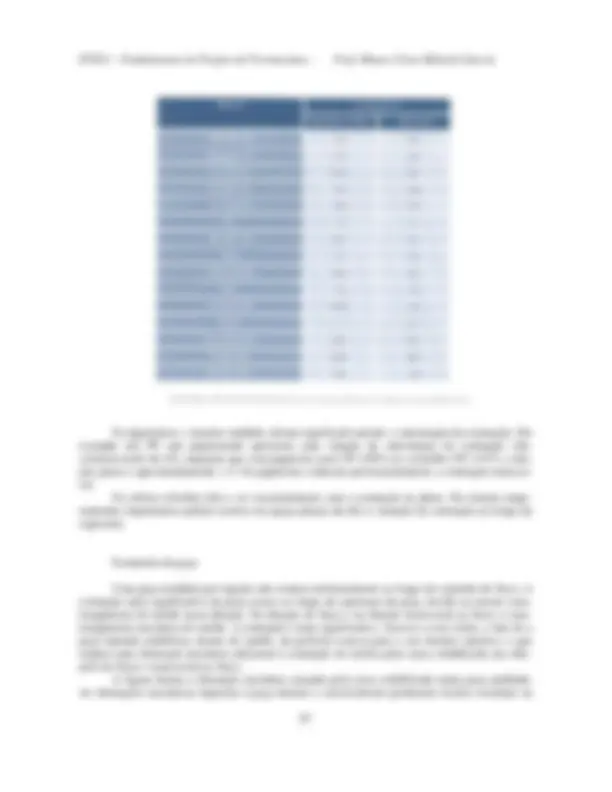
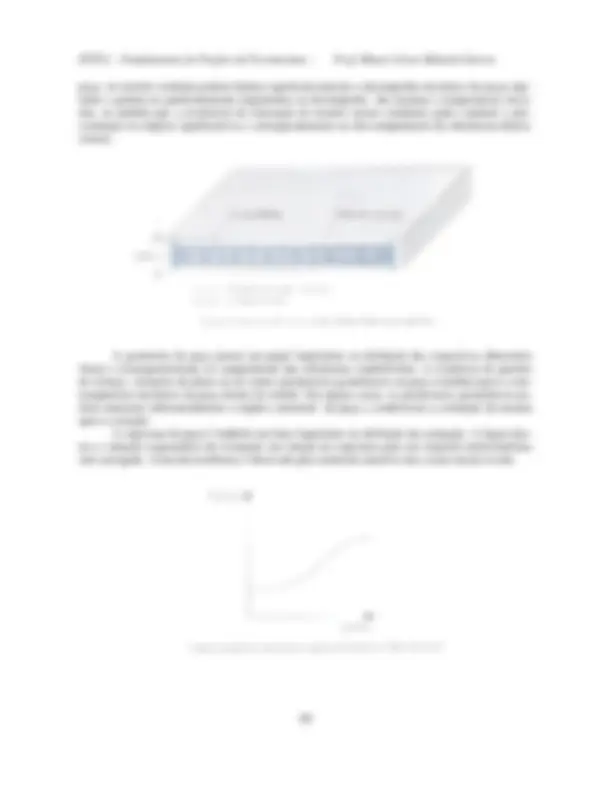
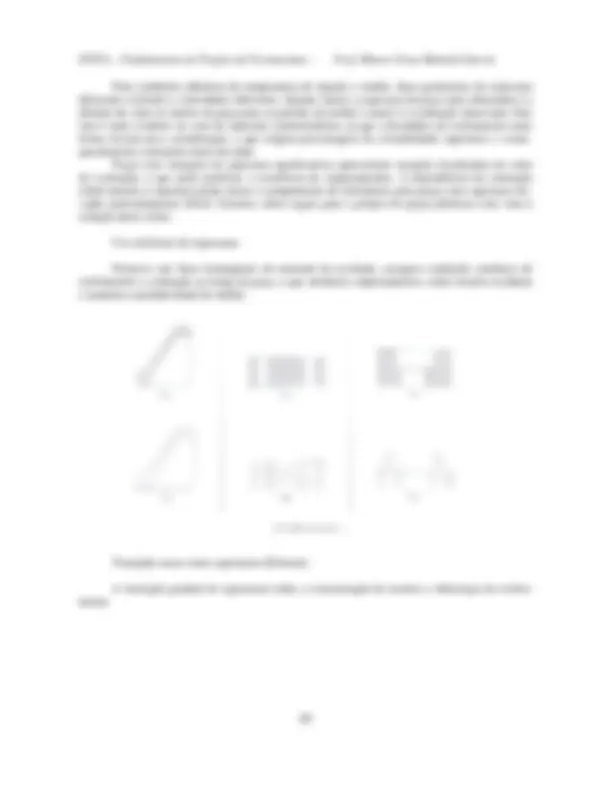
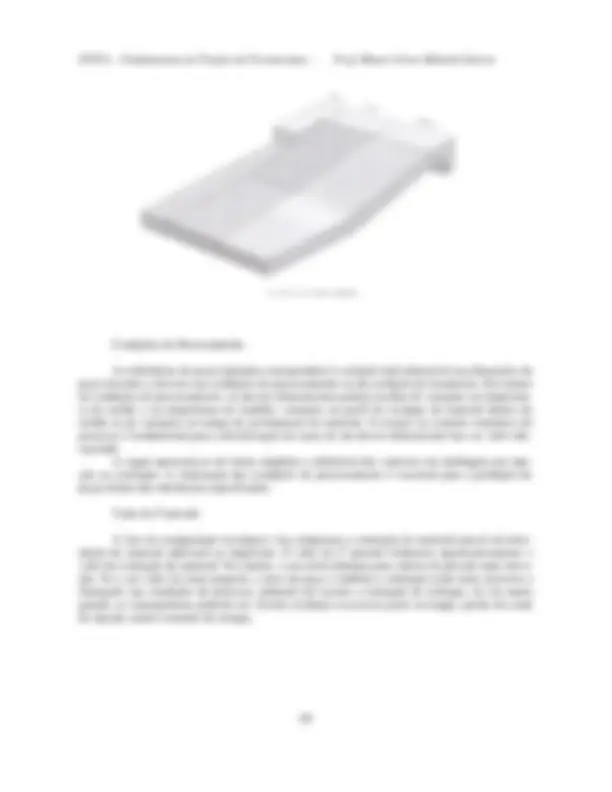
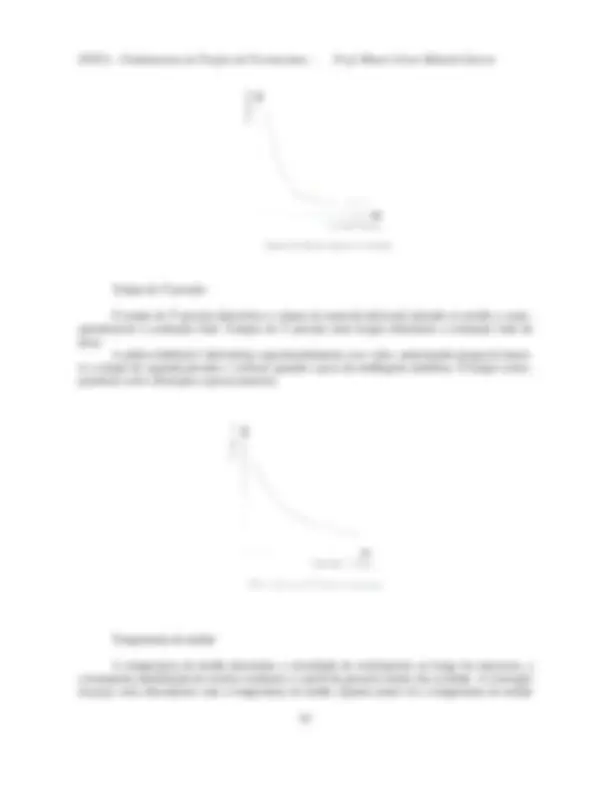
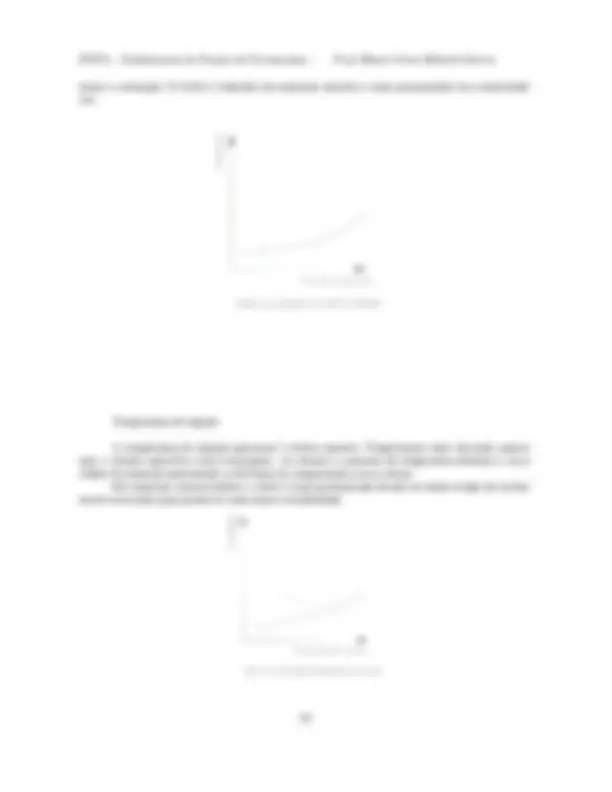
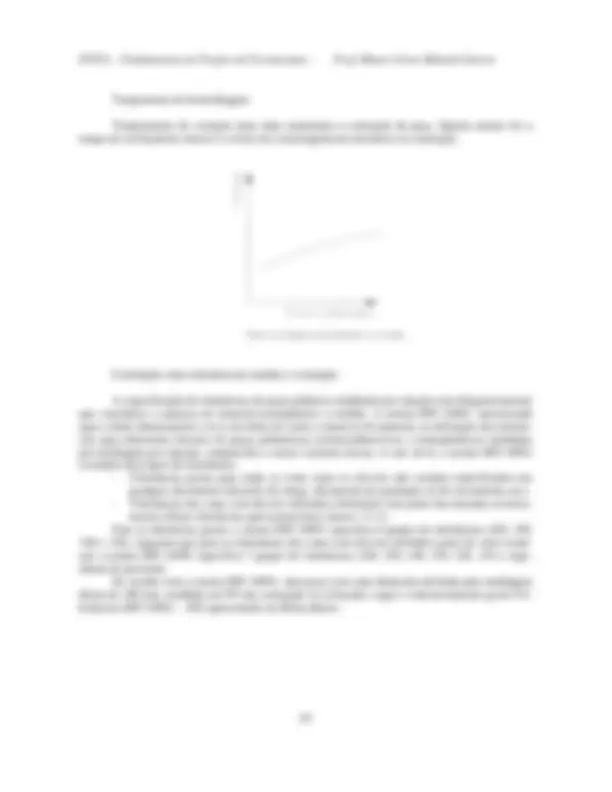
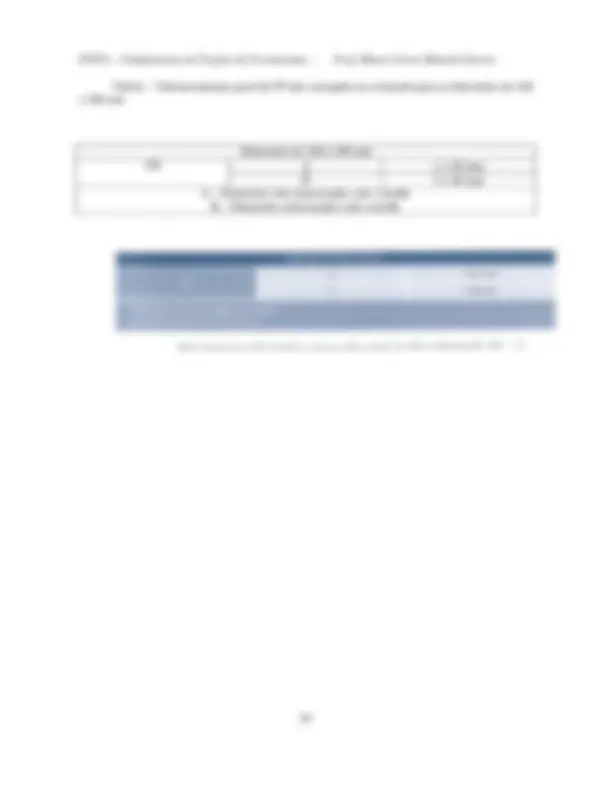
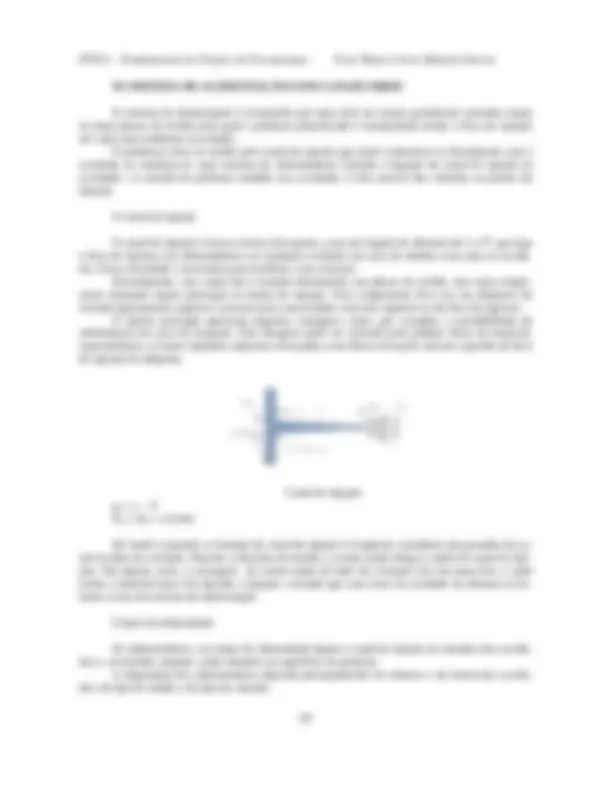
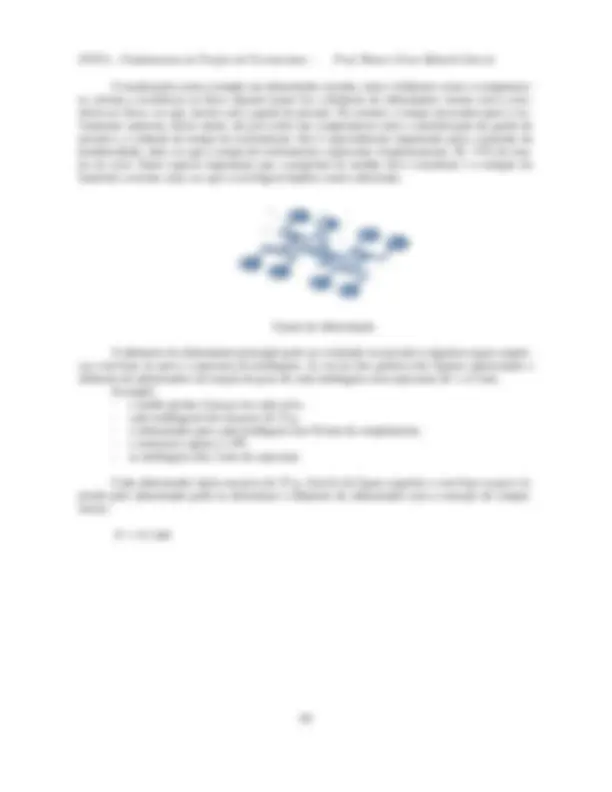
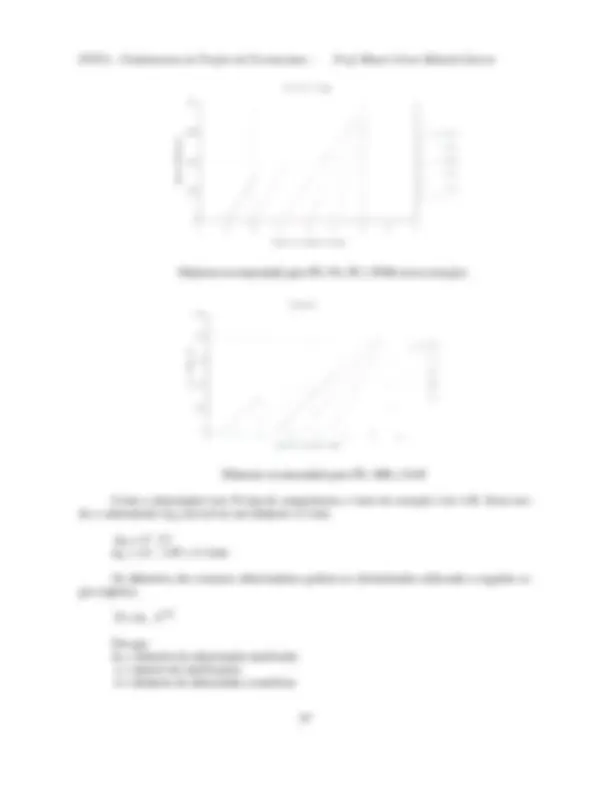
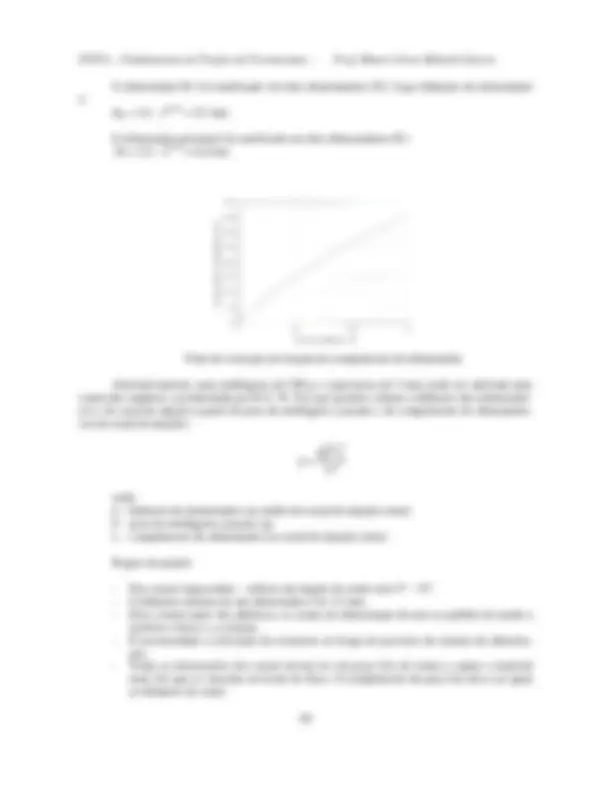
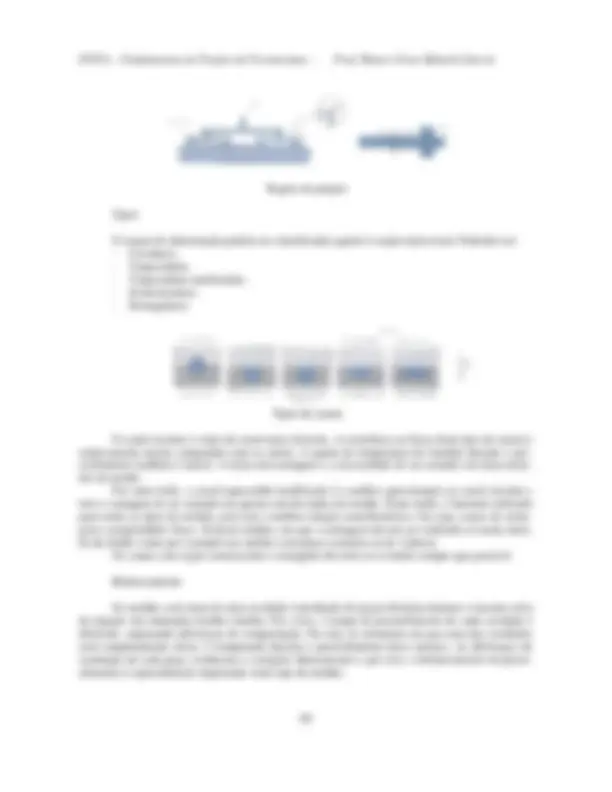
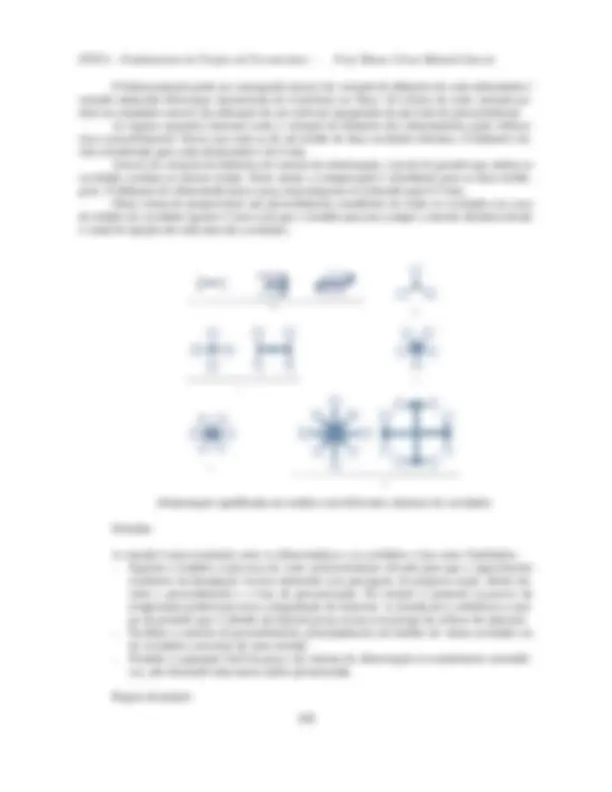
Estude fácil! Tem muito documento disponível na Docsity
Ganhe pontos ajudando outros esrudantes ou compre um plano Premium
Prepare-se para as provas
Estude fácil! Tem muito documento disponível na Docsity
Prepare-se para as provas com trabalhos de outros alunos como você, aqui na Docsity
Os melhores documentos à venda: Trabalhos de alunos formados
Prepare-se com as videoaulas e exercícios resolvidos criados a partir da grade da sua Universidade
Responda perguntas de provas passadas e avalie sua preparação.
Ganhe pontos para baixar
Ganhe pontos ajudando outros esrudantes ou compre um plano Premium
Comunidade
Peça ajuda à comunidade e tire suas dúvidas relacionadas ao estudo
Descubra as melhores universidades em seu país de acordo com os usuários da Docsity
Guias grátis
Baixe gratuitamente nossos guias de estudo, métodos para diminuir a ansiedade, dicas de TCC preparadas pelos professores da Docsity
Os moldes de injeção são, atualmente, as ferramentas mais usadas no processamento de polímeros. Os primeiros moldes foram concebidos, ainda no século XIX, quando os irmãos Hyatt, nos Estados Unidos, patentearam a primeira máquina de injeção para um material celulósico. Um molde de injeção pode ser entendido como um conjunto de sistemas funcionais, que permitem que o espaço em que a peça vai ser moldada, definido pela cavidade, seja preenchido com o plástico fundido em condições controladas pelos
Tipologia: Esquemas
1 / 232
Esta página não é visível na pré-visualização
Não perca as partes importantes!
Por sua vez o molde é o sistema funcional da injetora diretamente associado a um produto. Dependendo das peças a produzir, podem ser mais ou menos complicados. Os moldes utilizados podem ser agrupados em três tipos principais:
O processo de moldagem por injeção foi patenteado em 1872 pelos irmãos Hyatt. Ao longo do século XX teve uma grande evolução, cujos principais marcos foram a máquina hidráulica (anos 40), a máquina de parafuso alternativo (1951) e a máquina elétrica (1988). Inicialmente desenvolvido para a transformação de resinas termoendurecíveis, como fenol- formaldeído (comercialmente conhecido como Baquelite), o processo teve um enorme desenvolvi- mento com o advento dos materiais termoplásticos que se verificou após a Segunda Guerra Mundi- al. Atualmente, a moldagem por injeção é um dos principais processos de transformação de materiais de base polimérica, com enorme importância nos grandes mercados consumidores, como, embalagens, construção civil, automóvel e material elétrico e eletrônico. O grande sucesso desta tecnologia deve-se ao efeito combinado de uma série de vantagens comparativas, entre as quais se salientam: a elevada produção, a grande reprodutibilidade e precisão dimensional, a grande flexibilidade em termos de geometria e dimensões das moldagens (a gama de produção vai desde a micromoldagens, inferiores a 1mg, até peças com mais de 100 kg). Podem ser moldados por injeção termoplásticos, termofixos e elastômeros vulcanizados (borrachas e silicones). A moldagem por injeção também pode ser utilizada para a fabricação de peças cerâmicas ou metálicas, a partir de compostos que utilizam um material polimérico como vetor. A moldagem por injeção de termoplásticos obedece às etapas típicas de transformação des- tes materiais, envolvendo, sequencialmente, as etapas seguintes: aquecimento do material até este adquirir uma viscosidade suficientemente baixa; conformação sobre pressão; e resfriamento com conseqüente recuperação da rigidez. Esta rotina é exercida sobre a moldagem de compostos, com características específicas, sen- do de realçar:
Baixa difusividade térmica : os plásticos são intrinsecamente maus condutores de calor, difi- cultando as trocas térmicas necessárias à sua transformação. Por isso, em moldagem por injeção deve-se minimizar a espessura das peças a moldar.
Comportamento reológico : os termoplásticos, quando no estado fundido, apresentam-se sob a forma de fluidos de elevada viscosidade e com comportamento viscoelástico. A sua viscosidade é função da taxa de deformação imposta pelo material, podendo ser relativamente baixa para veloci- dades de deformação elevadas. Por isso, o preenchimento de cavidades tende a ser efetuado com velocidades de injeção elevadas.
Elevada dependência térmica da densidade : o modo de organização das cadeias moleculares constituintes de um sistema polimérico é altamente dependente da temperatura. De fato, um aumen- to da temperatura provoca o crescimento do volume livre intermolecular e a conseqüente expansão do material. Do ponto de vista prático, este efeito traduz-se em valores elevados do coeficiente de dilatação linear (cerca de 5 a 6 vezes superiores ao do aço para termoplásticos não reforçados) e na existência do fenômeno da contração, associado ao resfriamento de peças injetadas O equipamento a utilizar e as estratégias a seguir para otimizar o processo deverão conside- rar a qualidade do produto final. Em termos conceituais, o processo de moldagem por injeção de termoplásticos desenvolve- se da seguinte forma:
A solução da espuma estrutural é especialmente vantajosa em moldagens espessas. No en- tanto, como a condutividade térmica do material é inferior, os tempos de ciclo são longos. Logo, alguns dos equipamentos industriais incluem várias unidade de fechamento, servidas por uma única unidade de plastificação. O sucesso do processo implica a utilização de um agente expansor, capaz de se decompor na gama de temperaturas de processamento do polímero a usar e a sua correta dispersão na massa fun- dida.
Fig. – Moldagem por espuma estrutural
As principais potencialidades e vantagens do processo são:
No entanto, existem também diversas desvantagens, como:
2.1.2. Moldagem com gás
A moldagem com gás é um dos processo em grande expansão, que veio revolucionar a tec- nologia da moldagem por injeção a partir dos inícios da década de noventa. Em 1991 entrou na in- dústria automóvel (General Motors) e, desde então, tornou-se standard em várias aplicações. O processo se beneficia da característica típica da injeção, a formação da camada de material solidificado (provocada pelo resfriamento junto às paredes moldantes) no interior da qual flui o ma- terial subseqüente. Esta camada é utilizada para conduzir um fluido que pressuriza uniformemente a moldagem pelo interior e acelera o processo de resfriamento. O gás (tipicamente hidrogênio) é injetado no interior da massa fundida durante o imediata- mente a seguir a fase de preechimento. Seguem-se as etapas de recalque e resfriamento que se desenvolvem sob uma pressão unio- forme em toda a moldagem como resultado da pressão hidrostática gerada pelo fluido.
O processo conclui-se com a descompressão da moldagem e conseqüente extração. A introdução do gás pode ser efetuada a partir do bico de injeção ou com o auxílio de uma ou mais agulhas situadas no molde.
O gás pode ser recuperado ou libertado para a atmosfera, dependendo do tipo de equipamen- to e da contaminação provocada pelo composto polimérico utilizado. As vantagens e desvantagens do processo podem ser verificadas na tabela abaixo: VANTAGENS DESVANTAGENS Economia de material Custo de investimento em equipamento especí- fico Redução do nível de tensões internas Custo operativo do consumo de gás Excelente acabamento superficial Eventual custo de royalties ou licenças Redução da força de fechamento e do consumo energético
Maior complexidade do processo
Redução do tempo de ciclo (embora muito de- pendente da geometria em causa) Redução de complexidade e custos do molde (por exemplo ausência de nervuras)
2.1.3. Moldagem com água
Recentemente (2001) foi introduzido comercialmente o processo de moldagem com água. Conceitualmente, o processo é idêntico à moldagem com gás. No entanto, a utilização da água per- mite um controle mais preciso da parede interior (devido à incompressibilidade deste fluido), bem como um resfriamento mais eficiente (devido a maior capacidade calorífica da água).
2.1.4. Moldagem multi-material
As tecnologias de moldagem por injeção envolvendo dois ou mais materiais, designam-se genericamente por técnicas de moldagem multi-material. O seu crescimento tem sido muito grande, uma vez que permitem obter soluções muito competitivas em termos de funcionalidade e de redu- ção de custos de produção (através da eliminação de operações de montagem). Normalmente, os equipamentos de transformação têm várias unidades de plastificação (em número igual aos materiais a moldar, tipicamente 2 ou 3) Embora, para o caso de co-injeção, exis- tam algumas soluções de baixo custo baseadas numa só unidade. No caso de moldagem sobreposta, os moldes podem apresentar grande complexidade, apesar de muito dependente do tipo de processo selecionado.
2.1.5. Co-injeção
O processo de co-injeção envolve a moldagem simultânea de 2 materiais. A moldagem tem uma estrutura tipo sandwich, resultante do escoamento de um material no interior do outro. O processo baseia-se em três fases:
Os principais fabricantes de equipamento têm diversos modelos de máquinas multi-material. Existem no mercado várias configurações relativamente às unidades de injeção. São conhecidos casos de sobremoldagens com 6 materiais (ou cores) diferentes.
A moldagem por injeção é um processo cíclico. O conjunto de operações necessário à pro- dução de uma moldagem designa-se por ciclo de moldagem. A otimização deste ciclo é fundamental para assegurar a competitividade econômica do pro- cesso, dado o elevado investimento em capital, requerido para a instalação deste tipo de equipamen- to (injetora, molde e equipamentos auxiliares).
Ciclo de moldagem
Na atividade industrial o objetivo é produzir peças, conforme as respectivas especificações, no mais curto intervalo de tempo possível. Para o efeito, condições de processamento tais como pressão de injeção, temperaturas do fundido e do molde, velocidade de injeção e contrapressão, necessitam ser ajustadas tendo em conta as propriedades do material (o seu comportamento reológi- co e térmico), a geometria da peça e as especificações do produto final. As fases do ciclo de moldagem são praticamente independentes do tipo de máquina. Contu- do a sua duração pode ser muito diversa, variando de tempos inferiores a 1 segundo para peças mui- to finas, a dezenas de minutos para moldagens muito espessas. Poderá desenvolver-se segundo os seguintes modos:
quando o processo requer a intervenção do operador, por exemplo, para ajudar a retirar uma peça ou para colocar insertos).
FASE 1 – Fechamento
Esta operação corresponde ao início do ciclo (quer o funcionamento seja em regime automá- tico ou semi-automático) deve ser tão rápido quanto possível. No entanto, existem limitações às velocidades utilizadas para o fechamento do molde resultantes de:
FASE 2 – Injeção e Pressurização
A fase de injeção é garantida pelo avanço linear do fuso que, funcionando com um pistão, força o material fundido (previamente depositado à sua frente) a entrar no molde e a fluir no interior da cavidade. A injeção inicia-se após o cilindro ter encostado o bico ao molde (em alguns casos o bico de injeção pode estar permanentemente encostado) e deverá terminar quando a cavidade está preenchi- da a 95% do respectivo volume. A velocidade de injeção selecionada (ou idealmente o perfil de velocidades) deve corres- ponder a um compromisso entre rapidez (para assegurar o preenchimento global da impressão) e a qualidade do produto final (velocidades muito elevadas podem gerar marcas na superfície, efeitos de jato ou superaquecimento da matéria-prima). De fato, para cada moldagem existirá um ajuste de velocidade ótimo, correspondendo à situ- ação em que as especificações do produto final são garantidas com um nível mínimo da pressão de injeção. Após o preenchimento da cavidade é necessário continuar a pressurizar o moldado para au- mentar a sua densidade.
FASE 3 – Recalque
A seguir ao preenchimento do molde e pressurização, é necessário aplicar uma pressão na cavidade, a fim de reduzir o efeito da contração por resfriamento e evitar o refluxo do fundido. No entanto, esta pressão não deve ser excessiva porquanto daí podem ocorrer danos à peça (por exem- plo, desenvolvimento de tensões internas) e dificultar a sua extração. Esta fase termina logo que a entrada do material nas zonas moldantes (ponto de injeção), ou a própria peça, sejam suficientemente resfriados para inibir o fluxo de material.
O sucesso da tecnologia de moldagem por injeção é o resultado do efeito combinado de di- versos fatores, como:
Injetora Arburg
As injetoras podem ser classificadas de diferentes maneiras, como:
Quanto à natureza dos materiais processados Injetoras para termoplásticos, termoendurecíveis ou borrachas As injetoras são na grande maioria máquinas de processamento de termoplásticos. A molda- gem de termoendurecíveis ou de borrachas baseia-se na utilização de temperaturas relativamente baixas no cilindro de plastificação e de moldes muito quentes (cerca de 150 a 180ºC) para garanti- rem o processo de cura/vulcanização. Estas máquinas têm parafusos de comprimento reduzido, para minimizar o tempo de residência a evitar a cura prematura do composto moldado.
Quanto ao tipo de acionamento Injetoras hidráulicas, elétricas, pneumáticas e mistas. A grande maioria das injetoras atuais é baseada em potência óleo-hidráulica. Esta tecnologia garante o ajuste de pressões e de deslocamentos (com velocidades controladas). No entanto, é uma tecnologia de baixo rendimento energético e com dificuldades em garantir ambientes de trabalho de elevada limpeza.
As máquinas elétricas têm vindo a ganhar importância comercial desde os finais da década de 80, com máquinas de pequena e média dimensão (até 4000 kN de força de fechamento). Aliam um baixo consumo energético, ambiente de trabalho limpo e resposta muito rápida. Alguns equipamentos de pequena dimensão são baseados em dispositivos pneumáticos. Recentemente, têm vindo a ganhar importância as soluções mistas que combinam aciona- mento hidráulico e elétrico.
Quanto à dimensão Injetoras micro, pequenas, médias e grandes. As dimensões das injetoras são normalmente quantificada pela força de fechamento, respec- tivamente, assim:
Injetoras pequenas Menos de 1000 kN Injetoras médias 1000 a 5000 kN Injetoras grandes Superiores a 5000 kN
As máquinas de maiores dimensões atingem 50 000 a 90 000 kN de força de fechamento. Existem igualmente injetoras capazes de injetar micropeças (moldagens com massa inferior a 0, g). Estas máquinas requerem uma unidade de injeção especial capaz de dosar e injetar quantidade de materiais tão reduzidos.
A constituição típica de uma injetora é baseada em quatro unidades:
Representação esquemática de uma injetora
Unidade de potência
O conceito de unidade de potência está indissociavelmente ligado à máquina de acionamento hidráulico. Os diversos atuadores são alimentados por óleo a pressão e vazão controlados, desen- volvendo os movimentos e as pressões necessárias às diferentes funções do processo. Fornece a energia adequada aos diversos atuadores da máquina. Está baseada num sistema de pressão óleo-hidráulico, cuja bomba respectiva é acionada por um motor elétrico.
Unidade de Fechamento
Assegura a fixação e a movimentação do molde, devendo ser capaz de a manter fechado du- rante as fases de injeção, pressurização e recalque. Integra também os dispositivos necessários à extração dos moldados. Construtivamente, corresponde a uma prensa que terá de ser capaz de suportar a força resul- tante da injeção do plástico. Existem várias soluções construtivas, sendo as mais comuns as unidades de articulações ou de fechamento hidráulico. Quantifica-se pela força de fechamento (normalmente expressa em kN ou toneladas).
Unidade de Comando
As operações e os dispositivos necessários para assegurar a monitoração e controle das di- versas variáveis do processo estão centralizadas nesta unidade. Assegura, igualmente, a interface com o operador e as comunicações com periféricos ou sistemas de gestão de informação. As unidades de comando estão baseadas em microprocessadores que podem incluir funções de gestão da produção, de diagnóstico de processo e de controle auto-adaptativo.
Equipamento auxiliar
Designa-se por equipamento auxiliar o conjunto de dispositivos que integram a célula de moldagem por injeção, além da injetora e do molde. Uma célula típica é composta por:
Robô Arburg trocador de moldes
Poderão ainda existir equipamentos para controle de sistemas de moldes de canais quentes (quando não integrados na própria injetora), dispositivos para separação automática de peças e sis- temas de alimentação, equipamentos para operações de controle de qualidade, etc.
Alimentação e preparação da matéria-prima
Por questões de produtividade e qualidade, o circuito de alimentação e preparação de maté- ria-prima deve ter um elevado grau de automatização. Deste modo, minimizam-se as possibilidades de contaminação e de erros humanos associados a formulações. A matéria-prima deve ser alimentada automaticamente a partir de um sistema centralizado ou de recipientes colocados junto à injetora. Para o efeito, utilizam-se sistemas pneumáticos (basea- dos em redes de vácuo ou aspiradores elétricos independentes) ou mecânicos (baseados em espirais metálicas flexíveis). A eventual adição de pigmentos (sob a forma de granulados de masterbatch, pós ou líquidos) deve ser efetuada na máquina, antes do material entrar no cilindro de plastificação. Para o efeito podem ser usados diferentes tipos de equipamentos dosadores e misturadores. Os processos baseados em moldes de canais frios geram um desperdício associado ao res- pectivo sistema de alimentação. Sempre que as especificações do produto final o permitam, é alta- mente recomendável a reciclagem integrada deste desperdício na célula produtiva. Para o efeito devem ser utilizados moinhos granuladores insonorizados e dispositivos de dosagem (normalmente válvulas pneumáticas proporcionais), para controlar a percentagem de incorporação. Diversas matérias-primas requerem uma fase de secagem, antes da sua transformação, de modo a serem desumidificadas. Esta operação poderá ser efetuada em sistemas centralizados (com subseqüente transporte de material seco) ou junto da célula produtiva.
Controle da temperatura de moldes
A temperatura das superfícies moldantes é uma variável crítica do processo, que deve ser criteriosamente controlada por questões de produtividade e de qualidade do produto final. Depen- dendo do tipo de matéria-prima e das especificações da moldagem, deverá ser ajustada uma tempe- ratura de molde (por vezes utilizam-se temperaturas distintas nas duas partes do molde) cujo contro- le pode ser assegurado de diferentes modos.
Manuseamento automático de moldados
A produção de peças que não possam cair do molde por gravidade (devido a questões estéti- cas ou logísticas) deverá ser assistida por dispositivos automáticos para garantir a sua completa ex- tração do molde. Estes dispositivos designam-se por robôs ou manipuladores consoante a sua solu- ção construtiva (baseada em cilindros pneumáticos ou em motores elétricos servoatuadores) e o tipo de programação que permitem. Por vezes utilizam-se manipuladores simples apenas para retirar o sistema de alimentação, verificando-se a queda das peças para um recipiente ou tapete colocado debaixo do molde. Normalmente, o robô/manipulador coloca a peça numa esteira transportadora, onde esta es- tabiliza e é, eventualmente, sujeita a operações de controle, antes de ser embalada ou entrar nas fa- ses subseqüentes do respectivo processo produtivo.