
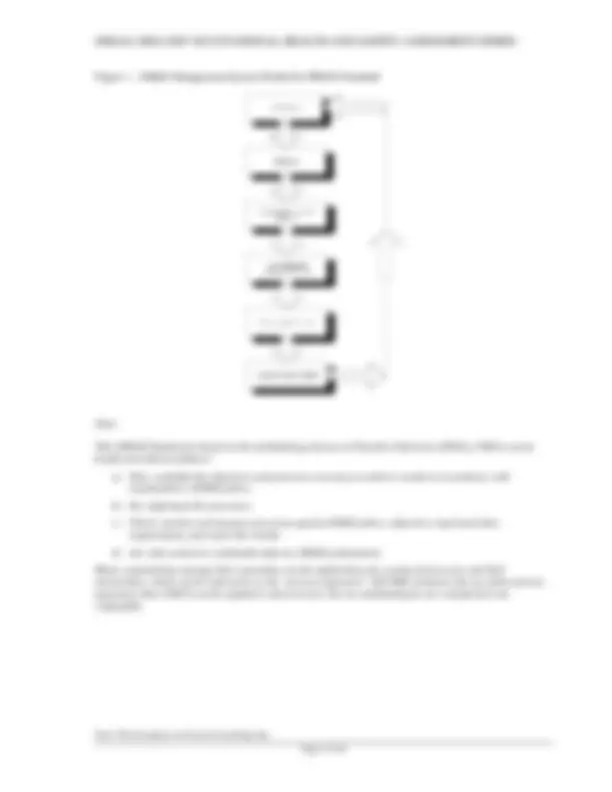
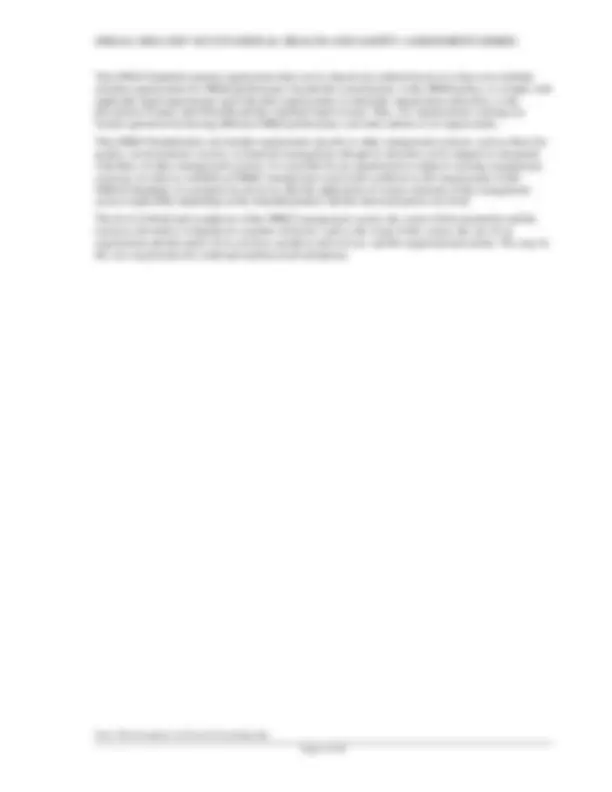
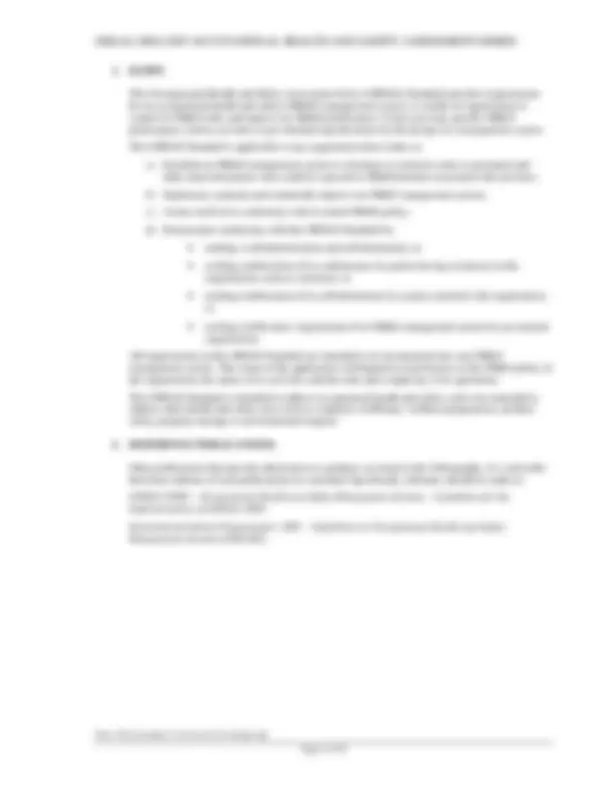

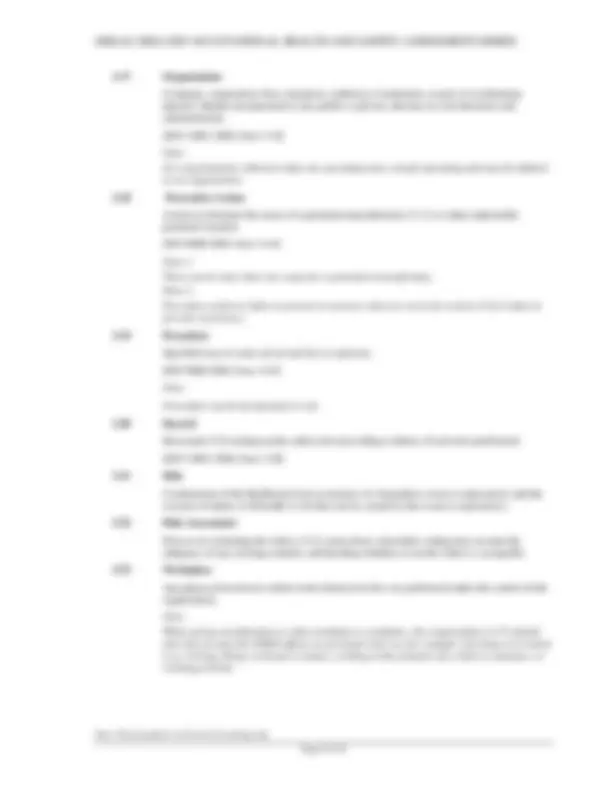

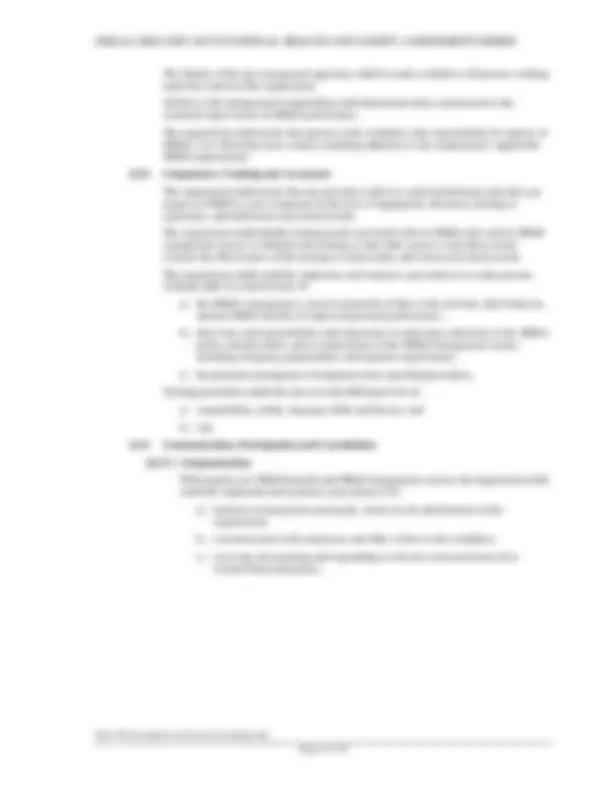
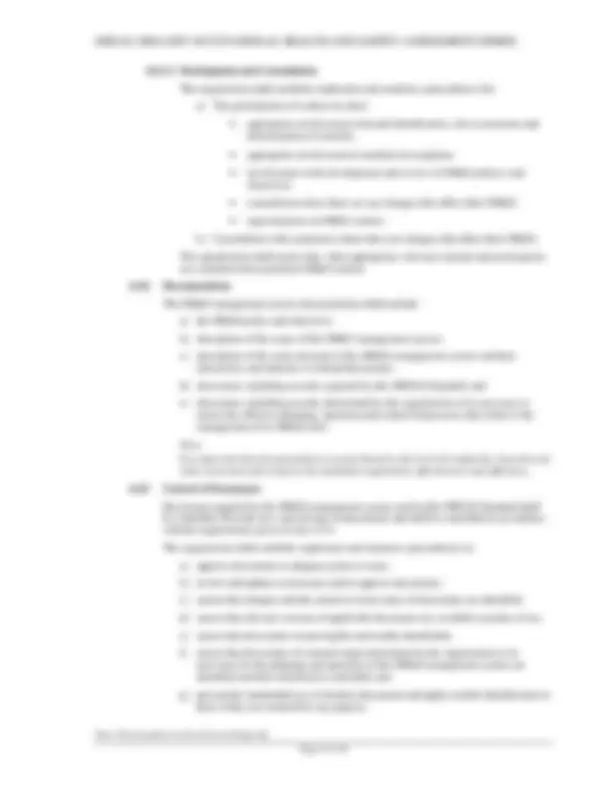
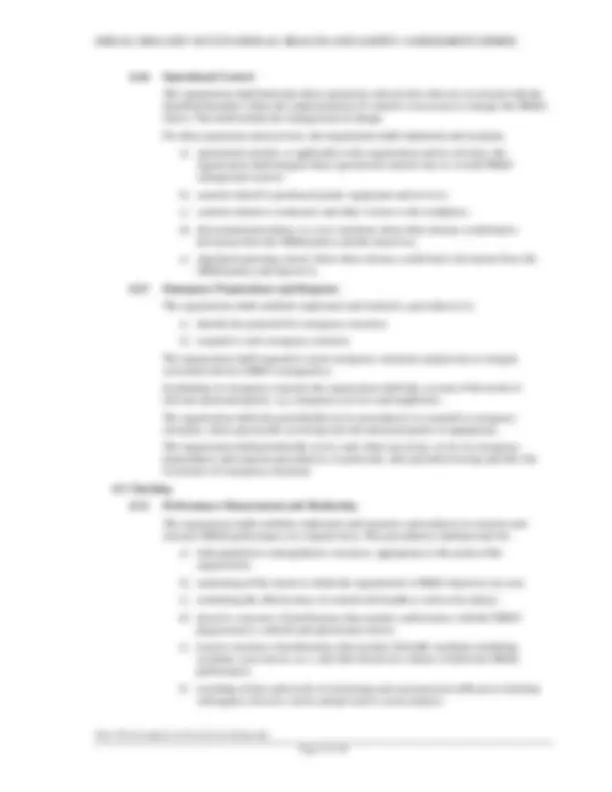


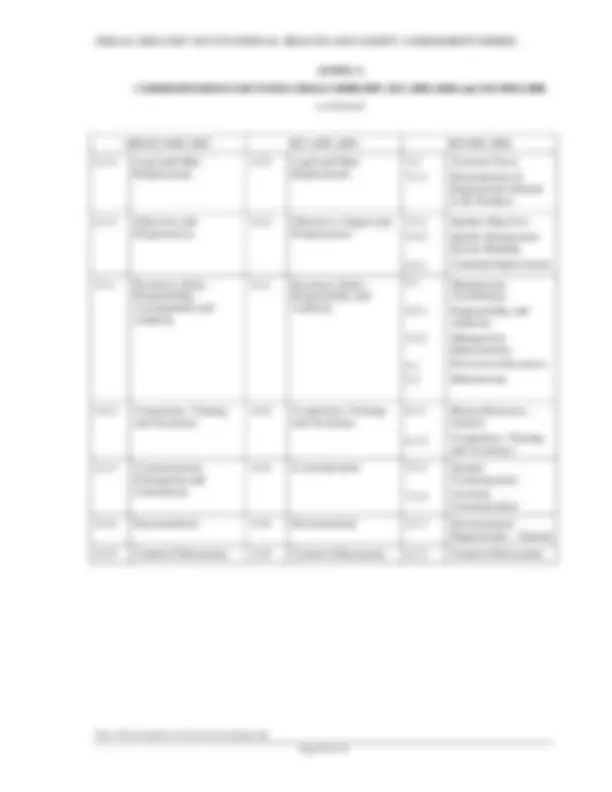
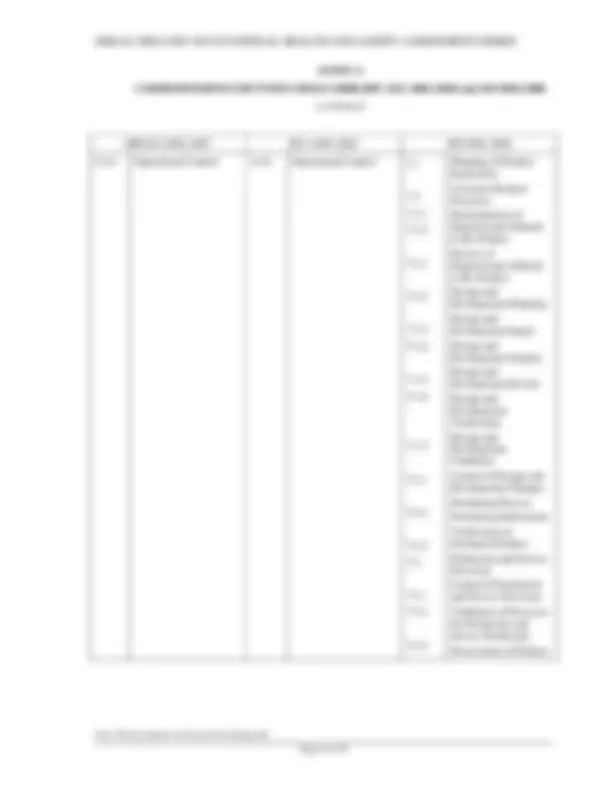

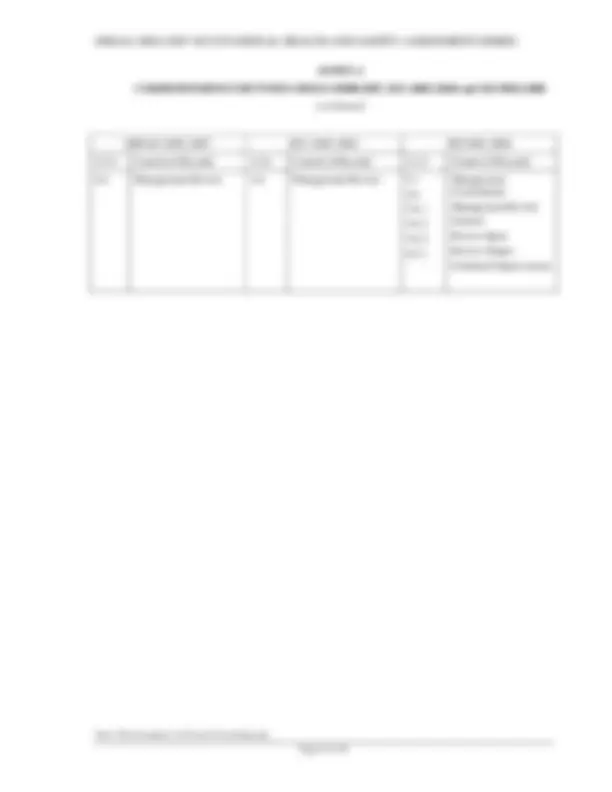


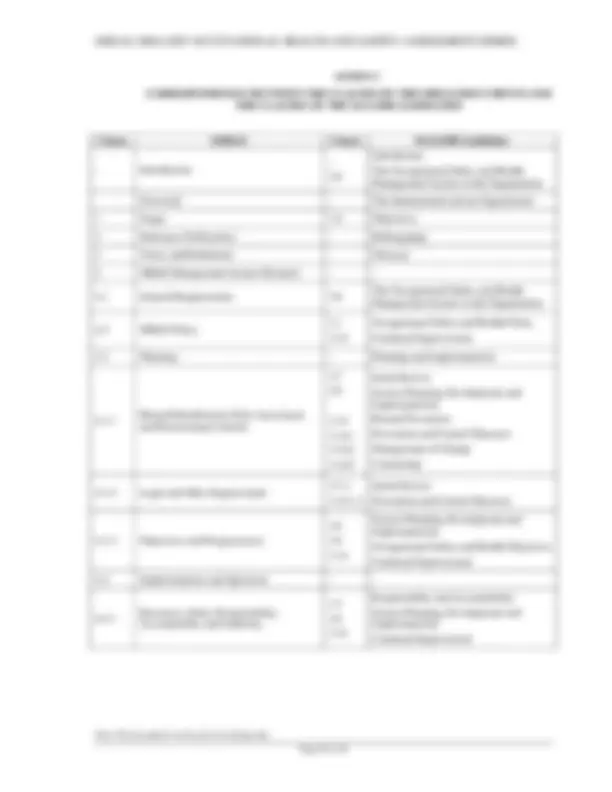
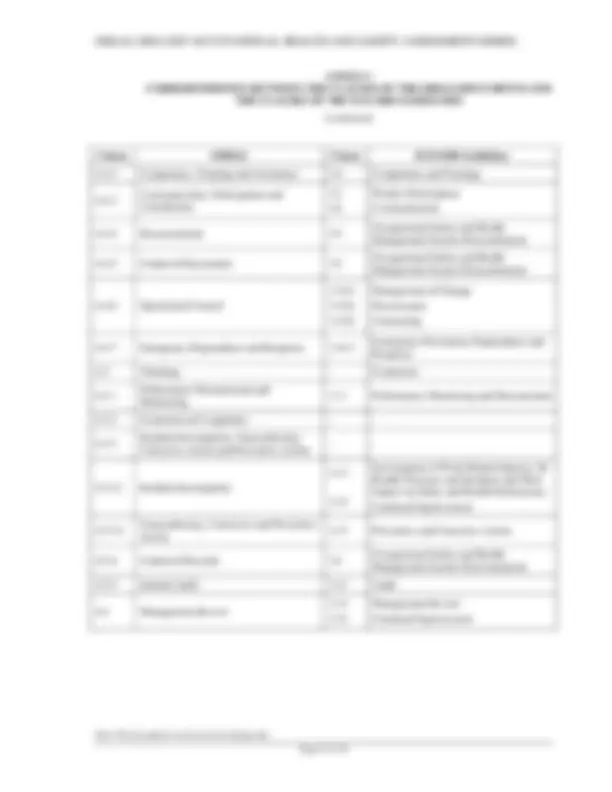

Estude fácil! Tem muito documento disponível na Docsity
Ganhe pontos ajudando outros esrudantes ou compre um plano Premium
Prepare-se para as provas
Estude fácil! Tem muito documento disponível na Docsity
Prepare-se para as provas com trabalhos de outros alunos como você, aqui na Docsity
Os melhores documentos à venda: Trabalhos de alunos formados
Prepare-se com as videoaulas e exercícios resolvidos criados a partir da grade da sua Universidade
Responda perguntas de provas passadas e avalie sua preparação.
Ganhe pontos para baixar
Ganhe pontos ajudando outros esrudantes ou compre um plano Premium
Comunidade
Peça ajuda à comunidade e tire suas dúvidas relacionadas ao estudo
Descubra as melhores universidades em seu país de acordo com os usuários da Docsity
Guias grátis
Baixe gratuitamente nossos guias de estudo, métodos para diminuir a ansiedade, dicas de TCC preparadas pelos professores da Docsity
The ohsas standards for occupational health and safety (oh&s) management systems. It covers the elements of an effective oh&s management system, including planning, implementation, monitoring, and continual improvement. The document also discusses the pdca cycle and the role of top management in establishing and maintaining an oh&s management system.
Tipologia: Notas de estudo
1 / 28
Esta página não é visível na pré-visualização
Não perca as partes importantes!
Note: This document is to be used for training only.
Note: This document is to be used for training only.
Organizations of all kinds are increasingly concerned with achieving and demonstrating sound occupational health and safety (OH&S) performance by controlling their OH&S risks, consistent with their OH&S policy and objectives. They do so in the context of increasingly stringent legislation, the development of economic policies and other measures that foster good OH&S practices, and increased concern expressed by interested parties about OH&S issues.
Many organizations have undertaken OH&S “reviews” or “audits” to assess their OH&S performance. On their own, however, these “reviews” and “audits” may not be sufficient to provide an organization with the assurance that its performance not only meets, but will continue meet, its legal and policy requirements. To be effective, they need to be conducted within a structured management system that is integrated within the organization.
The OHSAS Standards covering OH&S management are intended to provide organizations with the elements of an effective OH&S management system that can be integrated with other management requirements and help organizations achieve OH&S and economic objectives. These standards, like other International Standards, are not intended to be used to create non-tariff trade barriers or to increase or change organization’s legal obligations.
This OHSAS Standards specifies requirements for an OH&S management system to enable an organization to develop and implement a policy and objectives which take into account legal requirements and information about OH&S risks. It is intended to apply to all types and sizes of organizations and to accommodate diverse geographical, cultural and social conditions. The basis of the approach is shown in Figure 1. The success of the system depends on commitment from all levels and functions of the organization, and especially from top management. A system of this kind enables an organization to develop an OH&S policy, establish objectives and processes to achieve the policy commitments, take action as needed to improve its performance and demonstrate the conformity of the system to the requirements of this OHSAS Standard. The overall aim of this OHSAS Standard is to support and promote good OH&S practices, in balance with socio-economic needs. It should be noted that many of the requirements can be addressed concurrently or revisited at any time.
The second edition of this OHSAS Standard is focused on clarification of the first edition, and has taken due consideration of the provisions of ISO 9001, ISO 14001, ILO-OSH, and other management system standards or publications to enhance the compatibility of these standards for the benefit of the user community.
There is an important distinction between this OHAS Standard, which describes the requirements for an organization’s OH&S management system and can be used for certification / registration and / or self- declaration of an organization’s OH&S management system, and a non-certifiable guideline intended to provide generic assistance to an organization for establishing, implementing or improving an OH&S management system. OH&S management encompasses a full range of issues, including those with strategic and competitive implications. Demonstration of successful implementation of this OHSAS Standard can be used by an organization to assure interested parties that an appropriate OH&S management system is in place.
Those organizations requiring more general guidance on a broad range of OH&S management system issues are referred to OHSAS 18002. Any reference to other International Standards is for information only.
Note: This document is to be used for training only.
This OHAS Standard contains requirements that can be objectively audited; however it does not establish absolute requirements for OH&S performance beyond the commitments, in the OH&S policy, to comply with applicable legal requirements and with other requirements to which the organization subscribes, to the prevention of injury and ill health and the continual improvement. Thus, two organizations carrying out similar operations but having different OH&S performance can both conform to its requirements.
This OH&S Standard does not include requirements specific to other management systems, such as those for quality, environmental, security, or financial management, though its elements can be aligned or integrated with those of other management systems. It is possible for an organization to adapt its existing management system(s) in order to establish an OH&S management system that conforms to the requirements of this OHSAS Standard. It is pointed out, however, that the application of various elements of the management system might differ depending on the intended purpose and the interested parties involved.
The level of detail and complexity of the OH&S management system, the extent of documentation and the resources devoted to it depend on a number of factors, such as the scope of the system, the size of an organization and the nature of its activities, products and services, and the organizational culture. The may be the case in particular for small and medium-sized enterprises.
Note: This document is to be used for training only.
This Occupational Health and Safety Assessment Series (OHSAS) Standard specifies requirements for an occupational health and safety (OH&S) management system, to enable an organization to control its OH&S risks and improve its OH&S performance. It does not state specific OH&S performance criteria, nor does it give detailed specifications for the design of a management system. This OHSAS Standard is applicable to any organization that wishes to: a) Establish an OH&S management system to eliminate or minimize risks to personnel and other interested parties who could be exposed to OH&S hazards associated with activities; b) Implement, maintain and continually improve an OH&S management system; c) Assure itself of its conformity with its stated OH&S policy; d) Demonstrate conformity with this OHSAS Standard by:
Other publications that provide information or guidance are listed in the bibliography. It is advisable that latest editions of such publications be consulted. Specifically, reference should be made to: OHSAS 18002 – Occupational Health and Safety Management Systems – Guidelines for the Implementation of OHSAS 18001 International Labour Organization: 2001 – Guidelines on Occupational Health and Safety Management Systems (OSH-MS)
Note: This document is to be used for training only.
3.7 Hazard Identification Process of recognizing that a hazard (3.6) exists and defining its characteristics 3.8 Ill Health Identifiable, adverse physical or mental condition arising from and / or made worse by a work activity and / or work-related situation. 3.9 Incident Work-related event(s) in which an injury or ill health (3.8) (regardless of severity) or fatality occurred, or could have occurred. Note 1: An accident is an incident which has given rise to injury, ill health or fatality. Note 2: An incident where no injury, ill health, or fatality occurs may also be referred to as a “near-miss”, “near-hit”, “close call” or “dangerous occurrence”. Note 3: An emergency situation (see 4.4.7) is a particular type of incident. 3.10 Interested Party Person or group, inside or outside the workplace (3.23), concerned with or affected by the OH&S performance (3.15) of an organization (3.17). 3.11 Nonconformity Non-fulfillment of a requirement. [ISO 9000:2005, Item 3.6.2; ISO 14001, Item 3.15] Note: A nonconformity can be any deviation from:
Note: This document is to be used for training only.
3.13 OH&S Management System Part of an organization’s (3.17) management system used to develop and implement its OH&S policy (3.16) and manage its OH&S risks (3.21). Note 1: A management system is a set of interrelated elements used to establish policy and objectives and to achieve those objectives. Note 2: A management system includes organizational structure, planning activities (including, for example, risk assessment and the setting of objectives), responsibilities, practices, procedures (3.19), processes and resources. Note 3: Adapted from ISO 14001:2004, Item 3.8. 3.14 OH&S Objective OH&S goal, in term of OH&S performance (3.15), that an organization’s (3.17) sets itself to achieve. Note 1: Objectives should be qualified wherever practicable. Note 2: The item 4.3.3 requires that OH&S objectives are consistent with the OH&S policy (3.16). 3.15 OH&S Performance Measurable results of an organization’s (3.17) management of its OH&S risks (3.21). Note 1: OH&S performance measurement includes measuring the effectiveness of the organization’s controls. Note 2: In the context of OH&S management systems (3.13) OH&S policy (3.16), OH&S objectives (3.14), and OH&S performance requirements. 3.16 OH&S Policy Overall intentions and direction of an organization’s (3.17) related to its OH&S performance (3.15) as formally expressed by top management. Note 1: The OH&S policy provides a framework for action and for the setting of OH&S objectives. (3.14). Note 2: Adapted from ISO 14001:2004, Item 3.11.
Note: This document is to be used for training only.
4.1 General Requirements The organization shall establish, document, implement, maintain and continually improve an OH&S management system in accordance with the requirements of this OHSAS Standard and determine how it will fulfill these requirements. The organization shall define and document the scope of its OH&S management system. 4.2 OH&S Policy Top management shall define and authorize the organization’s OH&S policy and ensure that within the defined scope of its OH&S management system it: a) Is appropriate to the nature and scale of the organization’s OH&S risks; b) Includes a commitment to prevention of injury and ill health and continual improvement in OH&S management and OH&S performance; c) Includes a commitment to at least comply with applicable legal requirements and with other requirements to which the organization subscribes that relate to its OH&S hazards; d) Provides the framework for setting and reviewing OH&S objectives; e) Is documented, implemented and maintained; f) Is communicated to all persons working under the control of the organization with the intent that they are made of their individual OH&S obligations; g) Is available to interested parties; and h) Is reviewed periodically to ensure that it remains relevant and appropriate to the organization. 4.3 Planning 4.3.1 Hazard Identification, Risk Assessment and Determining Controls The organization shall establish, implement and maintain a procedure(s) for the ongoing hazard identification, risk assessment, and determination of necessary controls. The procedure(s) for hazard identification and risk assessment shall take into account: a) routine and non-routine activities; b) activities of all persons having access to workplace (including contractors and visitors) ; c) human behavior, capabilities and other human factors; d) identified hazards originating outside the workplace capable of adversely affecting the health and safety of persons under the control of the organization within the workplace; e) hazards created in the vicinity of the workplace by work-related activities under the control of the organization; Note: It may be more appropriate for such hazards to be assessed as an environmental aspect.
Note: This document is to be used for training only.
f) infrastructure, equipment and materials at the workplace, whether provided by the organization or others; g) changes or proposed changes in the organization, its activities, or materials; h) modifications to the OH&S management system, including temporary changes, and their impacts on operations, processes, and activities; i) any applicable legal obligations relating to risk assessment and implementation of necessary controls; j) the design of work area processes. Installations, machinery / equipment, operating procedures and work organization, including their adaptation to human capabilities. The organization’s methodology for hazard identification and risk assessment shall: a) be defined with respect to its scope, nature and timing to ensure it is proactive rather than reactive; and b) provide for the identification, priorization and documentation of risks, and the application of controls, as appropriate. For the management of change, the organization shall identify the OH&S hazards and OH&S risks associated with changes in the organization, the OH&S management system, or its activities, prior to the introduction of such changes. The organization shall ensure that results of these assessments are considered when determining controls. When determining controls, or considering changes to existing controls, consideration shall be given to reducing the risks according to the following hierarchy: a) elimination; b) substitution; c) engineering controls; d) signage / warnings and / or administrative controls; e) personal protective equipment. The organization shall document and keep the results of identification of hazards, risk assessment and determined control up-to-date. The organization shall ensure that OH&S risks and determined controls are taken into account when establishing, implementing and maintaining its OH&S management system. 4.3.2 Legal and Other Requirements The organization shall establish, implement and maintain a procedure(s) for identifying and accessing the legal and other OH&S requirements that are applicable to it. The organization shall ensure that these applicable legal requirements and other requirements to which the organization subscribes are taken into account in establishing, implementing and maintaining its OH&S management system. The organization shall keep this information up-to-date. The organization shall communicate relevant information on legal and other requirements to persons working under the control of the organization, and other relevant interested parties.
Note: This document is to be used for training only.
The identity of the top management appointee shall be made available to all persons working under the control of the organization. All those with management responsibility shall demonstrate their commitment to the continual improvement of OH&S performance. The organization shall ensure that persons in the workplace take responsibility for aspects of OH&S, over which they have control, including adherence to the organization’s applicable OH&S requirements. 4.4.2 Competence, Training and Awareness The organization shall ensure that any person(s) under its control performing tasks that can impact on OH&S is (are) competent on the basis of appropriate education, training or experience, and shall retain associated records. The organization shall identify training needs associated with its OH&S risks and its OH&S management system. It shall provide training or take other action to meet these needs, evaluate the effectiveness of the training or action taken, and retain associated records. The organization shall establish, implement and maintain a procedure(s) to make persons working under its control aware of: a) the OH&S consequences, actual or potential, of their work activities, their behavior, and the OH&S benefits of improved personal performance; b) their roles and responsibilities and importance in achieving conformity to the OH&S policy and procedures and to requirements of the OH&S management system, including emergency preparedness and response requirements; c) the potential consequences of departure from specified procedures. Training procedures shall take into account differing levels of: a) responsibility, ability, language skills and literacy; and b) risk. 4.4.3 Communication, Participation and Consultation 4.4.3.1 Communication With regard to its OH&S hazards and OH&S management system, the organization shall establish, implement and maintain a procedure(s) for: a) internal communication among the various levels and functions of the organization; b) communication with contractors and other visitors to the workplace; c) receiving, documenting and responding to relevant communications from external interested parties.
Note: This document is to be used for training only.
4.4.3.2 Participation and Consultation The organization shall establish, implement and maintain a procedure(s) for: a) The participation of workers by their:
Note: This document is to be used for training only.
If equipment is required to monitor or measure performance, the organization shall establish and maintain procedures for the calibration and maintenance of such equipment, as appropriate. Records of calibration and maintenance activities and results shall be retained. 4.5.2 Evaluation of Compliance 4.5.2.1 Consistent with its commitment to compliance the organization shall establish, implement and maintain a procedure(s) for periodically evaluating compliance with applicable legal requirements. The organization shall keep records of the results of the periodic evaluations. Note: The frequency of periodic evaluation may vary for differing legal requirements. 4.5.2.2 The organization shall evaluate compliance with other requirements to which it subscribes. The organization may wish to combine this evaluation with the evaluation of legal compliance referred to item 4.5.2.1 or to establish a separate procedure(s). The organization shall keep records of the results of the periodic evaluations. Note: The frequency of periodic evaluation may vary for differing other requirements to which the organization subscribes. 4.5.3 Incident Investigation, Nonconformity, Corrective Action and Preventive Action 4.5.3.1 Incident Investigation The organization shall establish, implement and maintain a procedure(s) to record, investigate and analyse incidents in order to: a) determine underlying OH&S deficiencies and other factors that might be causing or contributing to the occurrence of incidents; b) identify the need for corrective action; c) identify opportunities for preventive action; d) identify opportunities for continual improvement; e) communicate the results of such investigations. The investigations shall be performed in a timely manner. Any identified need for corrective action or opportunities for preventive action shall be dealt with the relevant parts of 4.5.3.2. The results of incident investigations shall be documented and maintained. 4.5.3.2 Nonconformity, Corrective Action and Preventive Action The organization shall establish, implement and maintain a procedure(s) for dealing with actual and potential nonconformity(ies) and for taking corrective action and preventive action. The procedure(s) shall define requirements for: a) identifying and correcting nonconformity(ies) and taking action(s) to mitigate their OH&S consequences; b) investigating nonconformity(ies), determining their cause(s) and taking actions in order to avoid their recurrence; c) evaluating the need for action(s) to prevent nonconformity(ies) and implementing appropriate actions designed to avoid their occurrence;
Note: This document is to be used for training only.
d) recording and communicating the results of corrective action(s) and preventive action(s) taken; and, e) reviewing the effectiveness of corrective action(s) and preventive action(s) taken. Where the corrective action and preventive action identifies new or changed hazards or the need for new or changed controls, the procedure shall require that the proposed actions shall be taken through a risk assessment prior to implementation. Any corrective action or preventive action taken to eliminate the causes of actual and potential nonconformity(ies) shall be appropriate to the magnitude of problems and commensurate with the OH&S risk(s) encountered. The organization shall ensure that any necessary changes arising from corrective action and preventive action are made to the OH&S management system documentation. 4.5.4 Control of Records The organization shall establish and maintain records as necessary to demonstrate conformity to the requirements of its OH&S management system and of this OHSAS Standard, and the results achieved. The organization shall establish, implement and maintain a procedure(s) for the identification, storage, protection, retrieval, retention and disposal of records. Records shall be and remain legible, identifiable and traceable. 4.5.5 Internal Audit The organization shall ensure that internal audits of OH&S management system are conducted at planned intervals to: a) determine whether the OH&S management system:
Note: This document is to be used for training only.
CORRESPONDENCE BETWEEN OHSAS 18000:2007, ISO 14001:2004 and ISO 9001:
Introduction General Process Approach Relationship with ISO 9004 Compatibility with Other Management Systems
1 Scope 1 Scope 1
Scope General Application
2 Normative References 2 Normative References 2 Normative References
3 Terms and Definitions 3 Terms and Definitions 3 Terms and Definitions
4 OH&S Management System Elements
4 Environmental Management System Requirements
4 Quality Management System
4.1 General Requirements 4.1 General Requirements 4.
5.5.
General Requirements Responsibility, Authority and communication Responsibility and Authority
4.2 OH&S Policy 4.2 Environmental Policy 5.
8.5.
Management Commitment Quality Policy Continual Improvement
4.3 Planning 4.3 Planning 5.4 Planning
4.3.1 Hazard Identification, Risk Assessment and Determining Controls
4.3.1 Environmental Aspects 5. 7.2. 7.2.
Customer Focus Determination of Requirements Related to the product Review of Requirements Related to the Product
Note: This document is to be used for training only.
CORRESPONDENCE BETWEEN OHSAS 18000:2007, ISO 14001:2004 and ISO 9001: (continued)
4.3.2 Legal and Other Requirements
4.3.2 Legal and Other Requirements
Customer Focus Determination of Requirements Related to the Products
4.3.3 Objectives and Programme(s)
4.3.3 Objectives, Targets and Programme(s)
Quality Objectives Quality Management System Planning Continual Improvement
4.4.1 Resources, Roles, Responsibility, Accountability and Authority
4.4.1 Resources, Roles, Responsibility and Authority
Management Commitment Responsibility and Authority Management Representative Provision of Resources Infrastructure
4.4.2 Competence, Training and Awareness
4.4.2 Competence, Training and Awareness
Human Resources _ General Competence, Training and Awareness
4.4.3 Communication, Participation and Consultation
4.4.3 Communication 5.5.
Internal Communication Customer Communication
4.4.4 Documentation 4.4.4 Documentation 4.2.1 Documentation Requirements _ General
4.4.5 Control of Documents 4.4.5 Control of Documents 4.2.3 Control of Documents