
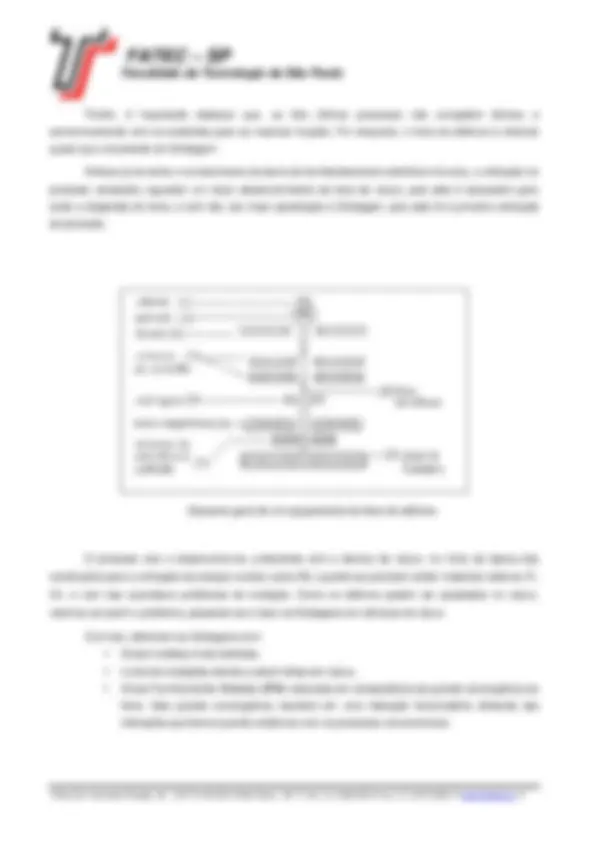
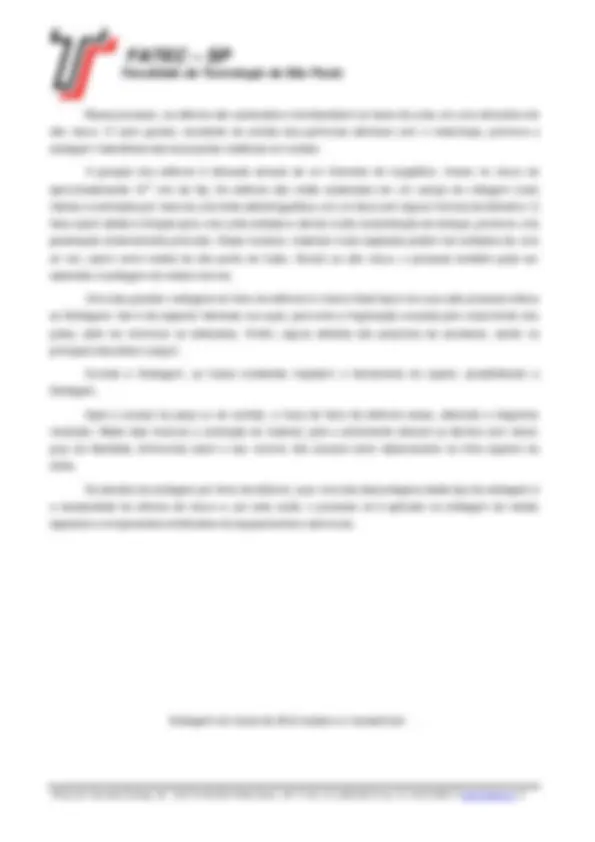
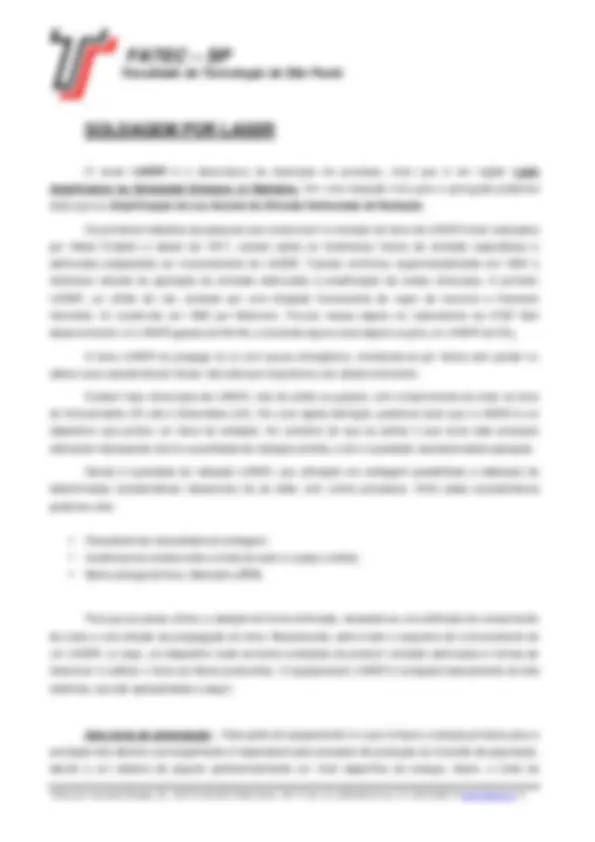
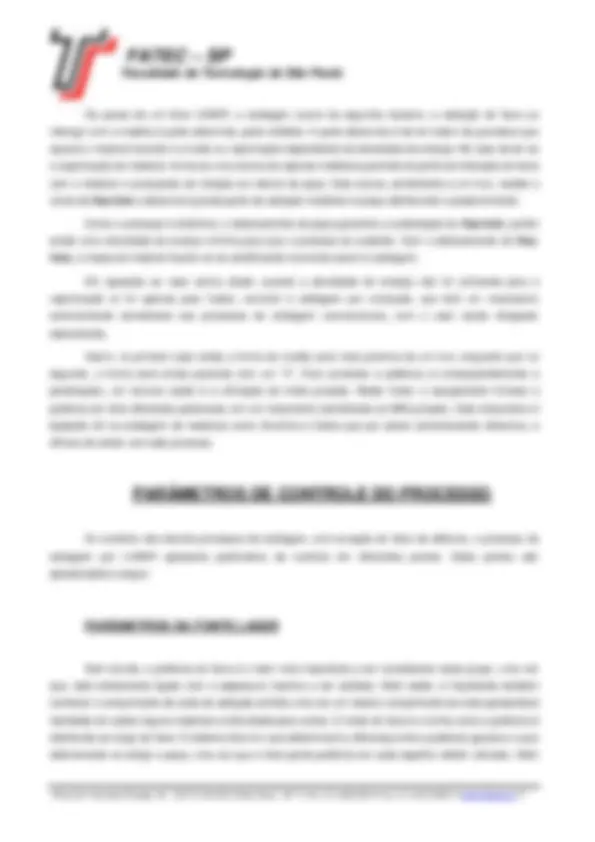
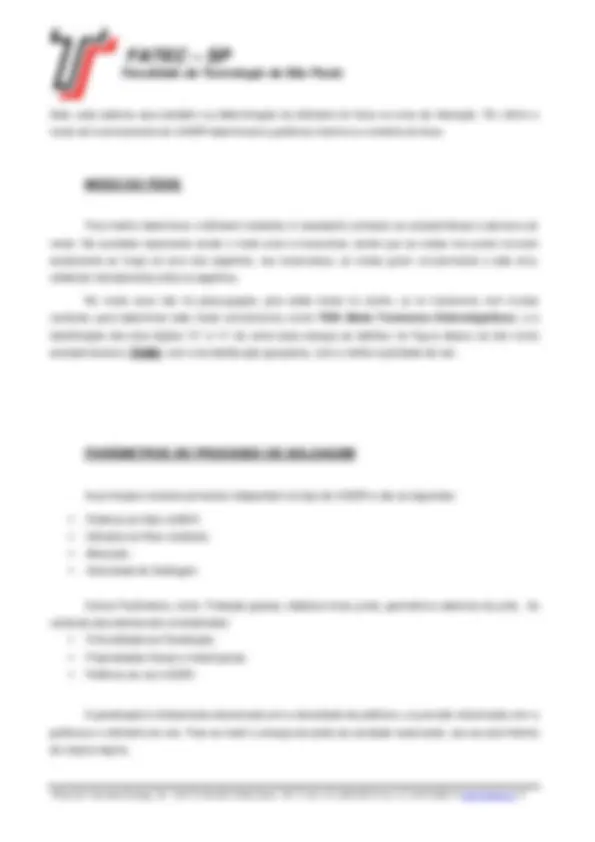
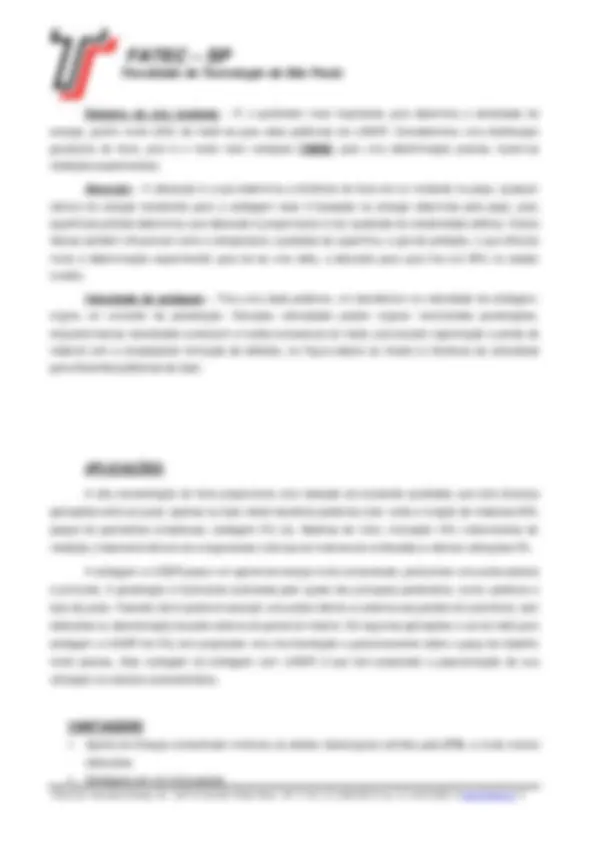
Estude fácil! Tem muito documento disponível na Docsity
Ganhe pontos ajudando outros esrudantes ou compre um plano Premium
Prepare-se para as provas
Estude fácil! Tem muito documento disponível na Docsity
Prepare-se para as provas com trabalhos de outros alunos como você, aqui na Docsity
Os melhores documentos à venda: Trabalhos de alunos formados
Prepare-se com as videoaulas e exercícios resolvidos criados a partir da grade da sua Universidade
Responda perguntas de provas passadas e avalie sua preparação.
Ganhe pontos para baixar
Ganhe pontos ajudando outros esrudantes ou compre um plano Premium
Comunidade
Peça ajuda à comunidade e tire suas dúvidas relacionadas ao estudo
Descubra as melhores universidades em seu país de acordo com os usuários da Docsity
Guias grátis
Baixe gratuitamente nossos guias de estudo, métodos para diminuir a ansiedade, dicas de TCC preparadas pelos professores da Docsity
Trabalho que é realizado para ser utilizado como fonte de estudos para a Prova de PP-II Métodos de Soldagem. Apresenta algumas informações sobre os procedimentos das Soldagens por Resistência: Pontos e Costura; Feixe de Elétrons; e Parâmetros para a Soldagem por LASER e suas influências na peça.
Tipologia: Trabalhos
1 / 11
Esta página não é visível na pré-visualização
Não perca as partes importantes!
SOLDAGEM POR RESISTÊNCIA A soldagem por resistência é um processo no quais as peças a serem unidas são coalescidas pelo calor gerado por efeito de resistência elétrica, quando se passa uma corrente através de um circuito elétrico do qual fazem parte às peças em referência. As partes a serem unidas são mantidas em contato sobre pressão. O processo é dividido em dois grandes grupos: 1 – Soldagem por Superposição e 2 – Soldagem de Topo. O primeiro grupo é bastante utilizado em chapas finas e folhas sendo ainda subdividido em dois métodos: a soldagem por pontos e a soldagem por costura. O principio de funcionamento da soldagem por pontos verifica-se que as chapas são mantidas em contato por meio de dois eletrodos de cobre, e uma corrente elétrica bastante intensa percorre o circuito durante um curto período de tempo. A passagem dessa corrente provoca a liberação de calor na interface de contato das duas chapas, por efeito de resistência elétrica. As superfícies são então fundidas e a pressão mantida entre as chapas é suficiente para formar o ponto de solda. A liberação de calor também ocorre no ponto de contato entre a chapa e o eletrodo, mas este é resfriado internamente, razão pela qual não provoca a sua própria fusão nem a da chapa com a qual está em contato. A soldagem por pontos é largamente utilizada na união de chapas de espessura de 1/4″ entretanto, espessuras com até 1 ″ ou mais podem ser utilizadas nesse processo, porém, utilizam-se equipamentos especiais. A grande vantagem da soldagem por pontos são as altas velocidades e facilidade de automação com uma alta taxa de produção, más o processo apresenta algumas limitações como: Desmontagem do equipamento para manutenção é difícil; Soldagem por pontos tem menor resistência à tração e a fadigas; Limitações das espessuras. O método de soldagem por costura é verificado que a união do material é efetuada de maneira semelhante à soldagem por pontos. Neste caso, porém, utiliza-se um par de discos que rolam sobre as chapas e, mediante as descargas elétricas intermitentes, executa-se a costura desejada. Neste método, também a pressão é aplicada para manter o contato entre as chapas. Normalmente, as costuras são executadas de modo contínuo, embora possam ser interrompidas e equiespaçadas. Este método é muito empregado, quando se deseja uma estanqueidade efetiva da união. Já a corrente elétrica da soldagem é cerca de 1,5 a 2,0 vezes maior, e a força aplicada é de 1,2 a 1,6 vezes mais intensa que a utilizada na soldagem por pontos.
Para se ter uma idéia, para se unir duas chapa de 0,8 mm de espessura, trabalha-se com uma corrente elétrica de aproximadamente 1500 ampéres e uma força de 300 kg. A soldagem por resistência de topo é um método através do qual é possível soldar barras, tubos, ou mesmo chapas, igualmente por efeito de resistência elétrica, após alinhá-los na direção de seu eixo longitudinal e mantê-los sob pressão durante a passagem da corrente elétrica. Este grupo também é subdividido em dois outros métodos: a soldagem a topo por descarga elétrica (Flesh Butt Welding) e a soldagem a topo por fluência (Upset Welding). No primeiro método, é gerado um arco elétrico entre as extremidades das peças a serem soldadas e, quando elas estiverem suficientemente aquecidas, é aplicada uma força intensa e momentânea para concluir a operação de soldagem. O processo aquecimento da junta é progressivo e deve-se à formação de pequenas descargas elétricas entre as partes metálicas em contato, quando as extremidades são justapostas. Esta operação é repetida até que se atinja a temperatura de soldagem, ocasião em que a pressão mais intensa é aplicada. No método de soldagem a topo por influência , os materiais a serem unidos são inicialmente aquecidos por resistência, pela passagem de uma corrente elétrica muito intensa. Após isso, há a aplicação de força na direção axial. A preparação da soldagem exige que as extremidades das peças em contato sejam usinadas e desengraxadas, pois a presença de substancias como óxidos podem prejudicar a soldagem. A velocidade de aquecimento, neste caso, é muito lenta e, portanto, a soldagem é mais demorada, o que pode levar à criação de uma larga zona termicamente afetada, prejudicando a qualidade da soldagem. SOLDAGEM POR FEIXE DE ELÉTRONS O feixe de elétrons é uma tecnologia utilizada para processamento de materiais, utilizando o calor gerado pelo impacto dos elétrons com o material a trabalhar. Devido às diferentes possibilidades de aplicar-se este calor sobre a peça (convergindo-o ou espalhando-o por mecanismos óticos) têm-se diferentes formas de utilizar o feixe eletrônico; como por exemplo: Soldagem Corte Tratamento superficial Micro-usinagem
Nesse processo, os elétrons são acelerados e bombardeiam as faces da junta, em uma atmosfera de alto vácuo. O calor gerado, resultante da colisão das partículas atômicas com o metal-base, promove a soldagem instantânea das duas partes metálicas em contato. A geração dos elétrons é efetuada através de um filamento de tungstênio, imerso no vácuo de aproximadamente 10-^5 mm de Hg. Os elétrons são então acelerados em um campo de voltagem muito intenso e colimados por meio de uma lente eletromagnética, em um feixe com alguns mícrons de diâmetro. O feixe assim obtido é dirigido para uma junta soldada e devido à alta concentração de energia, promove uma penetração extremamente profunda. Dessa maneira, materiais muito espessos podem ser soldados de uma só vez, assim como metais de alto ponto de fusão. Devido ao alto vácuo, o processo também pode ser estendido à soldagem de metais nocivos. Uma das grandes vantagens do feixe de elétrons é o baixo Heat-Input com que este processo efetua as Soldagens. Isto é de especial interesse nos aços, pois evita a fragilização causada pelo crescimento dos grãos, além de minimizar as distorções. Porém, alguns defeitos são possíveis de acontecer, sendo os principais discutidos a seguir: Durante a Soldagem, as forças existentes impedem o fechamento do capilar, possibilitando a Soldagem. Após o avanço da peça ou do canhão, a força do feixe de elétrons cessa, alterando o diagrama mostrado. Nesta fase inicia-se a contração do material, pois o esfriamento deixará os átomos com menor grau de liberdade, diminuindo assim o seu volume. Isto causará certo rebaixamento na linha superior da solda. Da decisão da soldagem por feixe de elétrons, quer uma das desvantagens deste tipo de soldagem é a necessidade da câmara de vácuo e, por esta razão, o processo só é aplicado na soldagem de metais especiais e componentes sofisticados de equipamentos e estruturas. Soldagem em locais de difícil acesso ou inacessíveis_._
SOLDAGEM POR LASER O nome LASER é a abreviatura da descrição do processo, claro que é em inglês: Light Amplification by Stimulated Emission of Radiation. Em uma tradução livre para o português podemos dizer que é a Amplificação da Luz Através da Emissão Estimulada de Radiação. Os primeiros trabalhos de pesquisa que conduziram à invenção do feixe de LASER foram realizados por Albert Einstein e datam de 1917, versam sobre os fenômenos físicos de emissão espontânea e estimulada subjacentes ao funcionamento do LASER. Townes confirmou experimentalmente em 1954 o fenômeno através da aplicação da emissão estimulada à amplificação de ondas ultracurtas. O primeiro LASER, um sólido de rubi, excitado por uma lâmpada fluorescente de vapor de mercúrio e filamento helicoidal, foi construído em 1960 por Maimann. Poucos meses depois os Laboratórios da AT&T Bell desenvolveram um LASER gasoso de He-Ne, e somente alguns anos depois surgiria um LASER de CO 2. O feixe LASER se propaga no ar com pouca divergência, orientando-se por óticas sem perder ou alterar suas características físicas, fato este que impulsionou seu desenvolvimento. Existem hoje vários tipos de LASER, indo do sólido ao gasoso, com comprimentos de onda na faixa do Infravermelho (IF) até o Ultravioleta (UV). Em uma rápida definição, podemos dizer que o LASER é um dispositivo que produz um feixe de radiação. Ao contrário do que se pensa o que torna este processo altamente interessante não é a quantidade de radiação emitida, e sim a qualidade resultante desta operação. Devido à qualidade da radiação LASER, sua utilização em soldagem possibilitará a obtenção de determinadas características impossíveis de se obter com outros processos. Entre estas características podemos citar: Elevadíssimas velocidades de soldagem; Ausências de contato entre a fonte de calor e a peça a soldar; Baixa entrega térmica, distorção e ZTA. Para que se possa utilizar a radiação de forma otimizada, necessita-se uma definição do comprimento de onda e uma direção de propagação do feixe. Basicamente, este é todo o esquema de funcionamento de um LASER, ou seja, um dispositivo onde se tenha condições de produzir emissão estimulada e formas de direcionar e calibrar o feixe de fótons produzidos. O equipamento LASER é composto basicamente de três sistemas, que são apresentados a seguir. Uma fonte de alimentação – Esta parte do equipamento é a que fornece a energia primária para a excitação dos átomos e principalmente é responsável pelo processo de produção da inversão de população, devido a um sistema de popular preferencialmente um nível específico de energia. Assim, a fonte de
CONSTRUÇÃO DE LASER GASOSO (LASER DE CO 2 ) O LASER CO 2 , chamados de LASERs de alta potência, largamente empregados para solda e corte. O ressonador ótico, neste caso, consiste de um tubo de descarga de gás pelo qual passa o gás de LASER, aqui uma mistura de CO 2 , N 2 , He. Neste é aplicada uma tensão contínua da ordem de dezenas de Kilo Volts (KV). O meio LASER tem uma pressão de operação de aproximadamente 100 Mbar. O calor de perda que surge na descarga elétrica deve ser eliminado, pois o laser só trabalha de modo eficiente com uma temperatura abaixo de 200º C. Por meio de descarga luminosa elétrica o CO 2 é estimulado. Neste arranjo o raio laser tem uma potência de até 700 W/m de comprimento de ressonador. De forma a se obter altas potências em uma construção compacta o tubo ressonador é "dobrado" em várias partes. O LASER de CO 2 trabalha em operação contínua ou pulsada. Devido à sua alta potência e do bom grau de rendimento, pode ser usado para soldar chapas mais espessas, no caso de aço, chega-se hoje até 38,0 mm com um LASER de 45 KW, na Tabela abaixo se descreve alguns tipos. TABELA - CARACTERÍSTICAS DE DIFERENTES TIPOS DE LASERS DE CO 2 PRINCÍPIO DE FUNCIONAMENTO DO PROCESSO FLUXO DE GÁS
Descarga (V) DC DC AC DC AC Potência (KW) 0,4-1,5 0,5-6,0 0,5-6,0 1,5-45,0 1,0-10, Modulação Muito boa boa muito boa regular boa Flutuações de Potência não rápidas não lentas não Pulsável sim sim sim não sim Estabilidade de Pulso muito boa regular boa - boa
De posse de um feixe LASER, a soldagem ocorre da seguinte maneira: a radiação do feixe ao interagir com a matéria é parte absorvida, parte refletida. A parte absorvida é de tal ordem de grandeza que aquece o material levando-o a fusão ou vaporização dependendo da densidade de energia. No caso de ter-se a vaporização do material, forma-se uma coluna de vapores metálicos partindo do ponto de interação do feixe com o material e avançando em direção ao interior da peça. Esta coluna, semelhante a um furo, recebe o nome de Key-hole e absorverá grande parte da radiação incidente na peça distribuindo-o posteriormente. Como o processo é dinâmico, o deslocamento da peça garantirá a sustentação do Key-hole , porém existe uma velocidade de avanço mínima para que o processo se sustente. Com o deslocamento do Key- hole, a massa de material líquido vai se solidificando ocorrendo assim à soldagem. Em oposição ao caso acima citado, quando a densidade de energia não for suficiente para a vaporização (e for apenas para fusão), ocorrerá à soldagem por condução, que terá um mecanismo extremamente semelhante aos processos de soldagem convencionais, com o calor sendo dissipado lateralmente. Assim, no primeiro caso então a forma do cordão será mais próxima de um furo, enquanto que no segundo, a forma será amais parecida com um "V". Para aumentar a potência (e conseqüentemente a penetração), um recurso usado é a utilização de modo pulsado. Neste modo, o equipamento fornece a potência em dois diferentes patamares, em um mecanismo semelhante ao MIG pulsado. Este mecanismo é bastante útil na soldagem de materiais como Alumínio e Cobre que por serem extremamente reflexivos, e difíceis de soldar com este processo. PARÂMETROS DE CONTROLE DO PROCESSO Ao contrário dos demais processos de soldagem, com exceção do feixe de elétrons, o processo de soldagem por LASER apresenta parâmetros de controle em diferentes pontos. Estes pontos são apresentados a seguir.
Sem dúvida, a potência do feixe é o fator mais importante a ser considerado neste grupo, uma vez que, está diretamente ligado com a espessura máxima a ser soldada. Além deste, é importante também conhecer o comprimento de onda da radiação emitida uma vez um mesmo comprimento de onda apresentará facilidade em soldar alguns materiais e dificuldade para outros. O modo do feixe é a forma como a potência é distribuída ao longo do feixe. O sistema ótico é o que determinará a diferença entre a potência gerada e a que efetivamente vai atingir a peça, uma vez que o feixe perde potência em cada espelho refletor utilizado. Além
Diâmetro do raio incidente – É o parâmetro mais importante, pois determina a densidade de energia, porém muito difícil de medir-se para altas potências de LASER. Consideremos uma distribuição gaussiana do feixe, pois é o modo mais vantajoso TEM00 , para uma determinação precisa, fazem-se medições experimentais. Absorção – A absorção é a que determina a eficiência do feixe de luz incidente na peça, qualquer cálculo da energia transferida para a soldagem laser é baseada na energia absorvida pela peça, para superfícies polidas determinou que absorção é proporcional à raiz quadrada da resistividade elétrica. Outros fatores também influenciam como a temperatura, qualidade da superfície, o gás de proteção, o que dificulta muito à determinação experimental, para ter-se uma idéia, a absorção para aços fica em 90% no estado fundido. Velocidade de soldagem – Para uma dada potência, um decréscimo na velocidade de soldagem, origina um aumento da penetração. Elevadas velocidades podem originar insuficientes penetrações, enquanto baixas velocidades conduzem a fusões excessivas do metal, provocando vaporização e perda de material com a conseqüente formação de defeitos, na Figura abaixo se mostra à influência da velocidade para diferentes potências de laser.
A alta concentração do feixe proporciona uma radiação de excelente qualidade, que terá diversas aplicações entre as quais, apenas na área metal-mecânica podemos citar: corte e furação de materiais 60% (peças de geometrias complexas), soldagem 5% (ex. Baterias de Lítio), marcação 10% (instrumentos de medição), tratamento térmico de componentes (válvulas de motores de combustão) e demais utilizações 5%. A soldagem a LASER possui um aporte de energia muito concentrado, produzindo uma solda estreita e profunda. A penetração é facilmente controlada pelo ajuste dos principais parâmetros, como: potência e taxa de pulso. Fazendo isto é possível executar uma solda interna ou externa aos painéis do automóvel, sem distorções ou descoloração da parte externa do painel do mesmo. Em algumas aplicações o uso do robô para soldagem a LASER de CO 2 tem propiciado uma movimentação e posicionamento sobre a peça de trabalho muito precisa. Esta vantagem da soldagem com LASER é que tem propiciado a popularização de sua utilização na indústria automobilística.
Aporte de Energia concentrado minimiza os efeitos metalúrgicos sofridos pela ZTA , e muito menos distorções; Soldagens em um único passe;
Não requer metal de adição, sendo livre de eventuais contaminações por este; Como é um processo que não há contato com a peça, favorece a soldagem em locais de difícil acesso; Permite soldar peças muito fina, e em pequenas distâncias, entre cortes; O LASER pode ser automatizado.
Baixa eficiência aproximadamente menos que 10%; Oferece dificuldade para mudar o ponto focal; O equipamento é de baixa potência; Limitação de espessura pela potência do equipamento; Problemas com refletividade em alguns materiais; As juntas têm estreitas tolerâncias de ajuste. BIBLIOGRAFIA: OKUMURA, TOSHIE e TANIGUCHI, CÉLIO. – Engenharia de Soldagem e Aplicações. Editora LTC - Rio de Janeiro 1982; Manual de Tecnologia em Fabricação e Soldagem, (CD-ROM) Versão 3.0 – São Paulo 2002;
http://www.infosolda.com.br/soldagem_laser.htm http://www.CIMM.com.br