
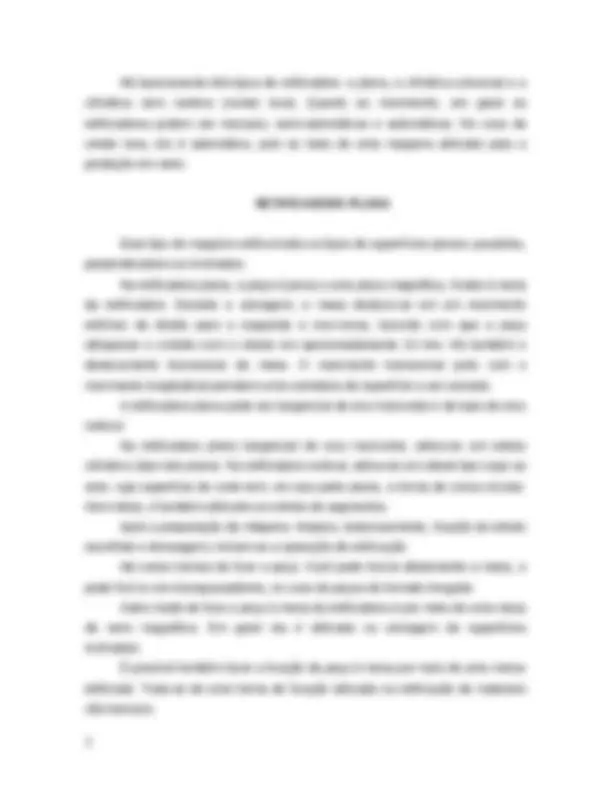
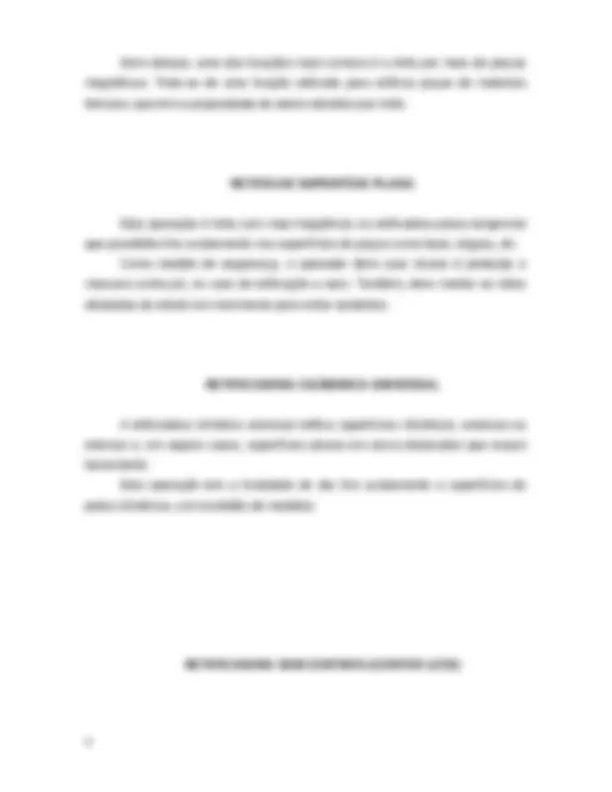
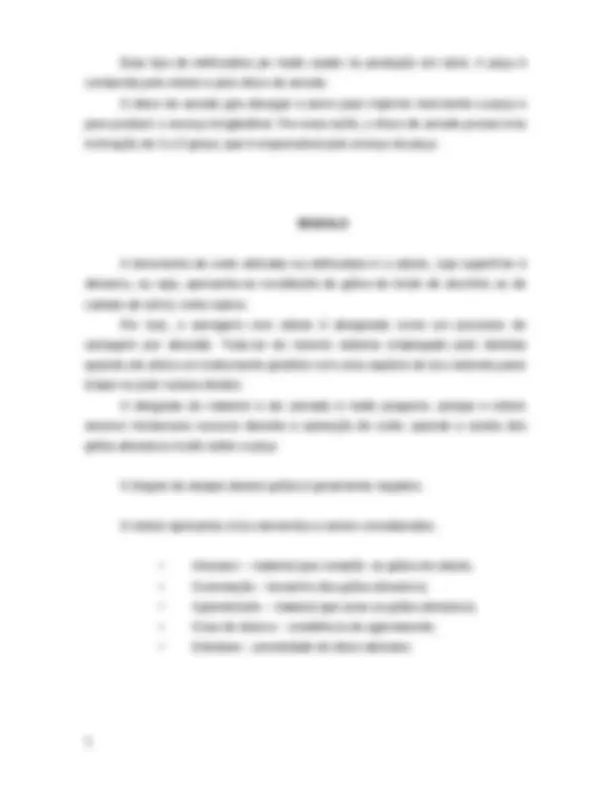
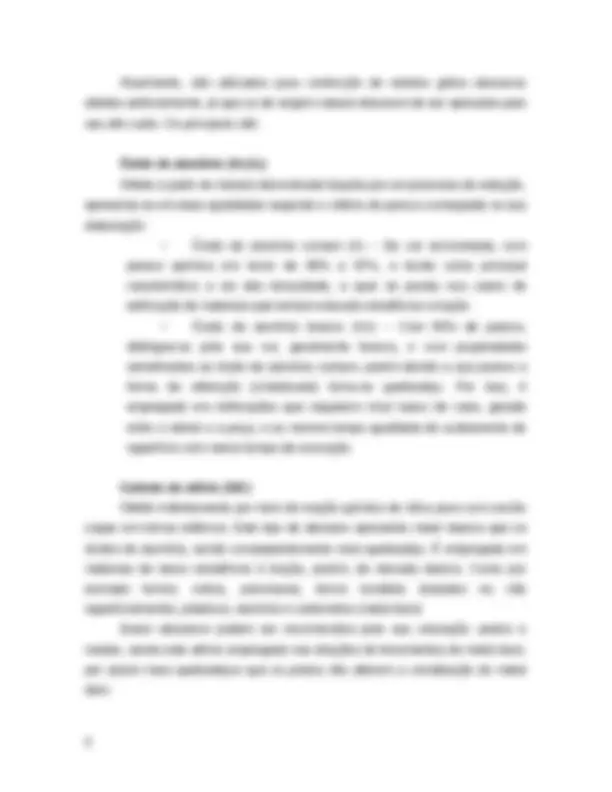
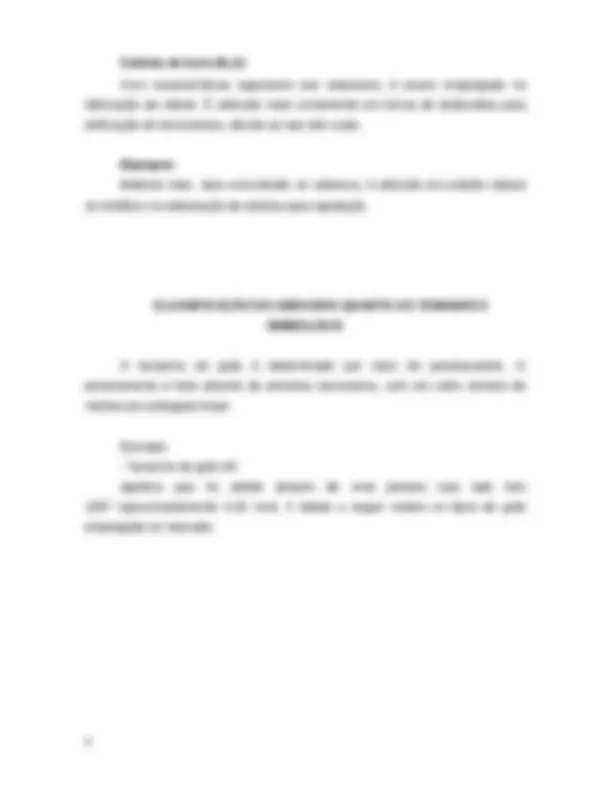
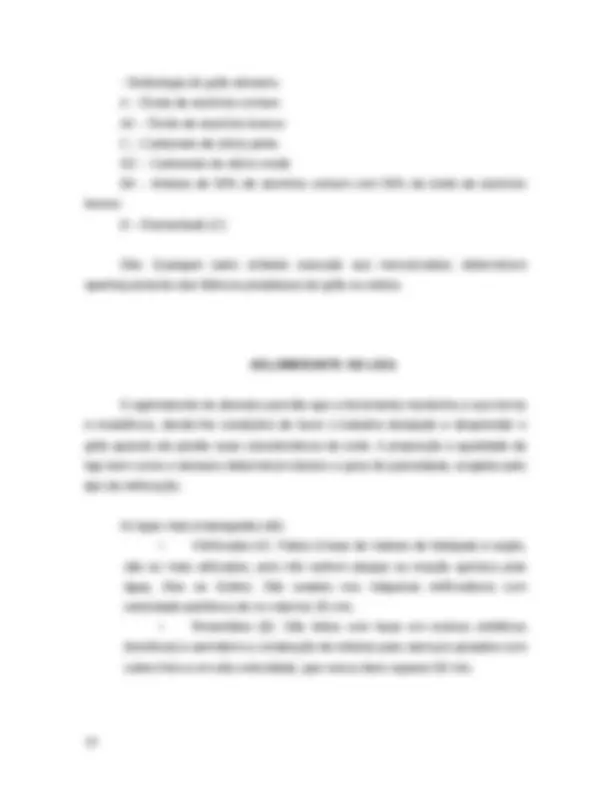
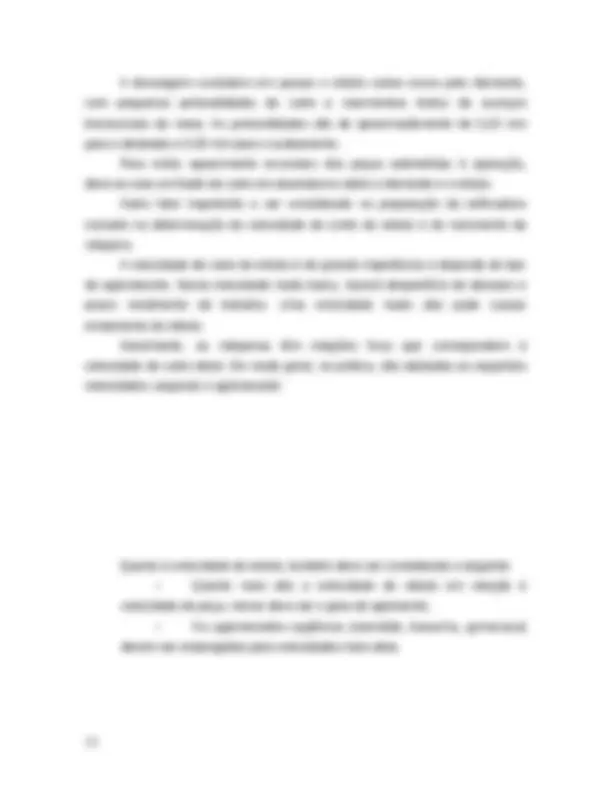
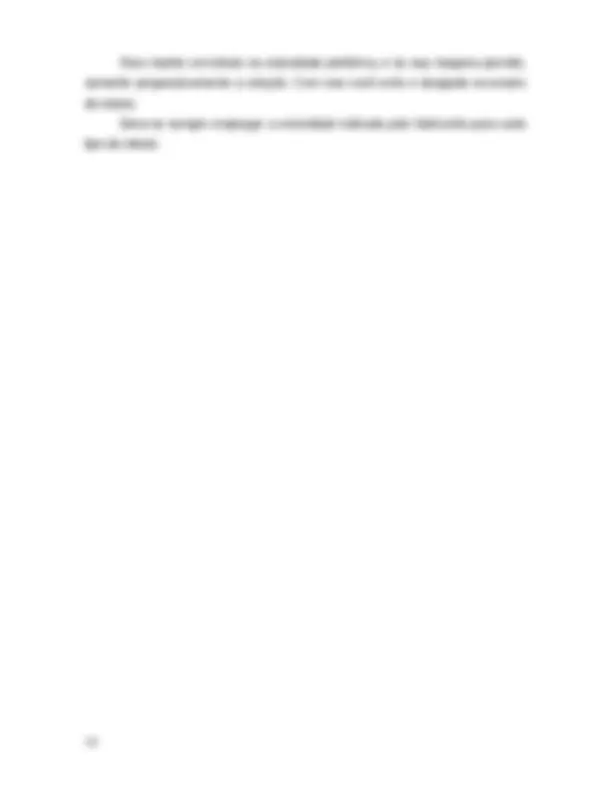
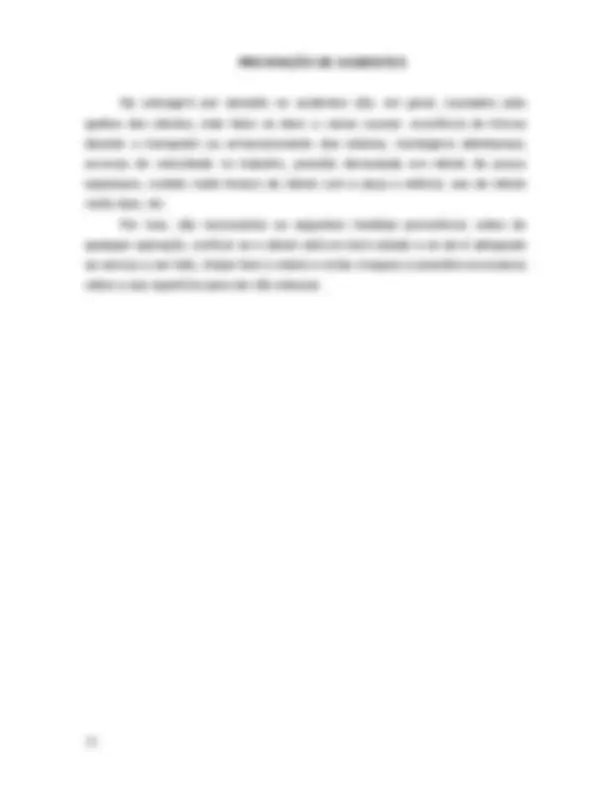
Estude fácil! Tem muito documento disponível na Docsity
Ganhe pontos ajudando outros esrudantes ou compre um plano Premium
Prepare-se para as provas
Estude fácil! Tem muito documento disponível na Docsity
Prepare-se para as provas com trabalhos de outros alunos como você, aqui na Docsity
Os melhores documentos à venda: Trabalhos de alunos formados
Prepare-se com as videoaulas e exercícios resolvidos criados a partir da grade da sua Universidade
Responda perguntas de provas passadas e avalie sua preparação.
Ganhe pontos para baixar
Ganhe pontos ajudando outros esrudantes ou compre um plano Premium
Comunidade
Peça ajuda à comunidade e tire suas dúvidas relacionadas ao estudo
Descubra as melhores universidades em seu país de acordo com os usuários da Docsity
Guias grátis
Baixe gratuitamente nossos guias de estudo, métodos para diminuir a ansiedade, dicas de TCC preparadas pelos professores da Docsity
O trabalho não está dos melhores, mas já serve para uma grande ajuda
Tipologia: Trabalhos
1 / 15
Esta página não é visível na pré-visualização
Não perca as partes importantes!
Retificadoras são^ máquinas^ operatrizes^ derivadas^ dos^ tornos^ mecânicos. São altamente especializadas na atividade de retificar, ou seja, de tornar reto ou exato, dispor em linha reta, corrigir e polir peças e componentes cilíndricos ou planos.
Os virabrequins^ de^ motor^ a^ explosão,^ por^ exemplo,^ depois^ de confeccionados, têm suas medidas de acabamento terminadas numa retificadora.
Outro exemplo seriam os corpos como barramentos e prismas^ de precisão das próprias máquinas operatrizes, que são acabados em suas medidas finais por retíficas planas e cilíndricas. O processo de retificação é executado por ferramentas^ chamadas^ de esmeratrizes, que são pedras fabricadas com materiais abrasivos cujos formatos podem ser cilíndricos, ovalizados, esféricos, etc. Em geral, as pedras são presas a eixos (pontas montadas) e giram em altíssima rotação. Dessa forma, o componente a ser retificado é montado num suporte, numa mesa coordenada ou num eixo, e recebe o atrito da esmeratriz, que vai retirando o material em quantidades muito pequenas, até chegar ao ponto ou dimensão determinados pelo projeto.
A retificação é um processo de usinagem por abrasão que retifica a superfície de uma peça. Retificar significa corrigir irregularidades de superfícies de peças.
Assim, a retificação tem por objetivo:
a) reduzir rugosidades ou saliências e rebaixos de superfícies usinadas com maquinas-ferramenta, como furadeira, torno, plaina, fresadora; b) (^) Dar à superfície da peça a exatidão de medidas que permita obter peças semelhantes que possam ser substituídas umas pelas outras; c) Retificar peças que tenham sudi deformadas ligeiramente durante um pricesso de tratamento térmico; d) Remover camadas finas de material endurecidos por têmpera, cementação ou nitretação.
A retificadora é uma maquina empregada na usinagem de peças para dar as suas superfícies uma exatidão maior e um melhor acabamento do que os conseguidos em maquinas convencionais. Os matérias ou peças geralmente precisam ser submetidos a tratamento térmico de têmpera para serem retificados.
Alem dessas, uma das fixações mais comuns é a feita por meio de placas magnéticas. Trata-se de uma fixação utilizada para retificar peças de materiais ferrosos, que tem a propriedade de serem atraídos por imãs.
Esta operação é feita com mais freqüência na retificadora plana tangencial que possibilita fino acabamento nas superfícies de peças como base, réguas, etc. Como medida de segurança, o operador deve usar óculos d proteção e mascara contra pó, no caso de retificação a seco. Também, deve manter as mãos afastadas do rebolo em movimento para evitar acidentes.
A retificadora cilíndrica universal retifica superfícies cilíndricas, externas ou internas e, em alguns casos, superfícies planas em eixos rebaixados que exijam faceamento. Esta operação tem a finalidade de dar fino acabamento a superfícies de pelas cilíndricas, com exatidão de medidas.
Esse tipo de retificadora pe muito usado na produção em série. A peça é conduzida pelo rebolo e pelo disco de arraste. O disco de arraste gira devagar e serve para imprimir movimento a peça e para produzir o avanço longitudinal. Por essa razão, o disco de arraste possui uma inclinação de 3 a 5 graus, que é responsável pelo avanço da peça.
A ferramenta de corte utilizada na retificadora é o rebolo, cuja superfície é abrasiva, ou seja, apresenta-se constituída de grãos de óxido de alumínio ou de carbeto de silício, entre outros. Por isso, a usinagem com rebolo é designada como um processo de usinagem por abrasão. Trata-se do mesmo sistema empregado pelo dentista quando ele utiliza um instrumento giratório com uma espécie de lixa redonda parar limpar ou polir nossos dentes. O desgaste do material a ser usinado é muito pequeno, porque o rebolo arranca minúsculos cavacos durante a operação de corte, quando a aresta dos grãos abrasivos incide sobre a peça.
O ângulo de ataque desses grãos é geralmente negativo.
O rebolo apresenta cinco elementos a serem considerados.
Rugosidades são irregularidades microscópicas que se formam na superfície da peça, durante o processo de usinagem. Na retificação, elas podem ser causadas por folgas nos eixos, irregularidades no movimento da meã, desbastamento do rebolo e granulação do abrasivo, entre outras causas. No quadro abaixo, podemos observar a relação entre rugosidade, granulação do abrasivo e a profundidade de corte do rebolo.
Esses procedimentos referem-se à escolha e balanceamento do rebolo, sua montagem na máquina retificadora, à dressagem e medidas de segurança, que devem ser tomadas pelo operador. Os fabricantes de rebolos adotam um código internacional, constituído de letras e números para indicar as especificações do rebolo. Para a escolha do rebolo são levados em conta: abrasivos, grãos, dureza, estrutura e aglomerantes.
Atualmente, são utilizados para confecção de rebolos grãos abrasivos obtidos artificialmente, já que os de origem natural deixaram de ser aplicados pelo seu alto custo. Os principais são:
Óxido de alumínio (Al 2 O 3 ) Obtido a partir do mineral denominado bauxita por um processo de redução, apresenta-se em duas qualidades segundo o critério de pureza conseguida na sua elaboração:
Carbeto de silício (SIC) Obtido indiretamente por meio de reação química de sílica pura com carvão coque em fornos elétricos. Este tipo de abrasivo apresenta maior dureza que os óxidos de alumínio, sendo conseqüentemente mais quebradiço. É empregado em materiais de baixa resistência à tração, porém, de elevada dureza. Como por exemplo temos: vidros, porcelanas, ferros fundidos (tratados ou não superficialmente), plásticos, alumínio e carbonetos (metal duro). Esses abrasivos podem ser reconhecidos pela sua coloração: pretos e verdes, sendo este ultimo empregado nas afiações de ferramentas de metal duro; por serem mais quebradiços que os pretos não alteram a constituição do metal duro.
Obs: Qualquer outro símbolo anexado aos mencionados, determinam aperfeiçoamento das fábricas produtoras de grão ou rebolo.
O aglomerante do abrasivo permite que a ferramenta mantenha a sua forma e resistência, dando-lhe condições de fazer o trabalho desejado e desprender o grão quando ele perder suas características de corte. A proporção e qualidade da liga bem como o abrasivo determinam dureza e grau de porosidade, exigidos pelo tipo de retificação.
As ligas mais empregadas são:
O grau de dureza de um rebolo é a medida do poder de retenção dos grãos abrasivos pelo aglomerante. Um rebolo muito duro retém sues grãos até depois de estes terem perdido a capacidade de corte. Um rebolo muito mole perde seus grãos antes de estes terem executado inteiramente o trabalho. No caso de usinagem de materiais que tendem a empastar o rebolo, deve-se usar um rebolo mole, que solte os grãos com mais facilidade.
Depois de escolher o rebolo, é preciso balanceá-lo e dressá-lo. Assim, ele fica bem equilibrado, evita vibrações na retificadora e permite a obtenção de superfícies de acabamento fino. Como podemos estar balanceando um rebolo: Primeiramente, verifica-se o rebolo em relação a trincas, para isso, é necessário suspender o rebolo pelo furo e submetê-lo a pequenos e suaves golpes, dados com um macete ou cabo de chave de fenda. Se o rebolo não estiver trincado, ele produzirá um leve som metálico, mas se estiver trincando o som será “apagado”. Neste caso, o rebolo deve ser substituído. Os rebolos possuem um rotulo de papel em suas laterais. Esses rótulos não devem ser retirados, pois servem para melhorar o assentamento dos flanges, visto
A dressagem consistem em passar o rebolo varias vezes pelo diamante, com pequenas profundidades de corte e movimentos lentos de avanços transversais da mesa. As profundidades são de aproximadamente de 0,02 mm para o desbaste e 0,05 mm para o acabamento. Para evitar aquecimento excessivo das peças submetidas à operação, deve-se usar um fluido de corte em abundancia sobre o diamante e o rebolo. Outro fator importante a ser considerado na preparação da retificadora consiste na determinação da velocidade de conte do rebolo e do movimento da máquina. A velocidade de corte do rebolo é de grande importância e depende do tipo do aglomerante. Numa velocidade muito baixa, haverá desperdício de abrasivo e pouco rendimento de trabalho. Uma velocidade muito alta pode causar rompimento do rebolo. Geralmente, as máquinas têm rotações fixas que correspondem à velocidade de corte ideial. De modo geral, na prática, são adotadas as seguintes velocidades, segundo o aglomerante:
Quanto à velocidade do rebolo, também deve ser considerado o seguinte:
Para manter um rebolo na velocidade periférica, e se sua maquina permitir, aumente progressivamente a rotação. Com isso você evita o desgaste excessivo do rebolo. Deve-se sempre empregar a velocidade indicada pelo fabricante para cada tipo de rebolo.