
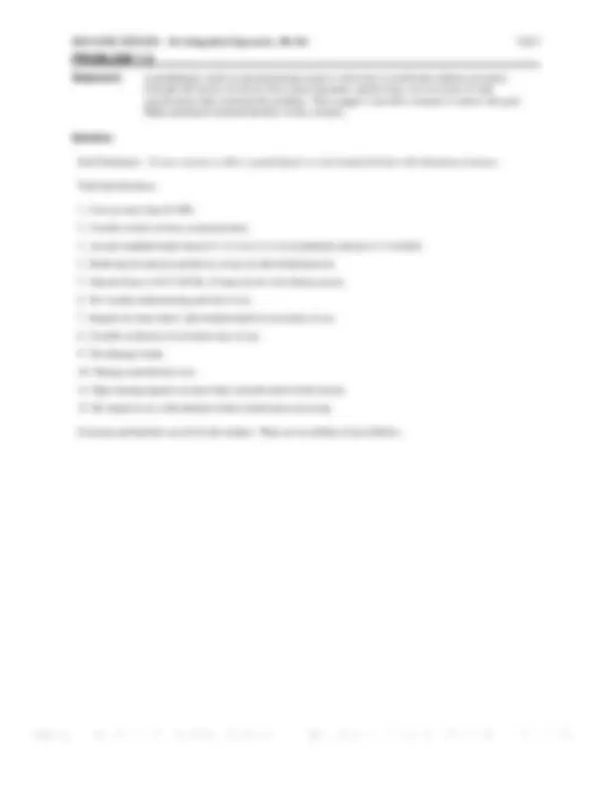
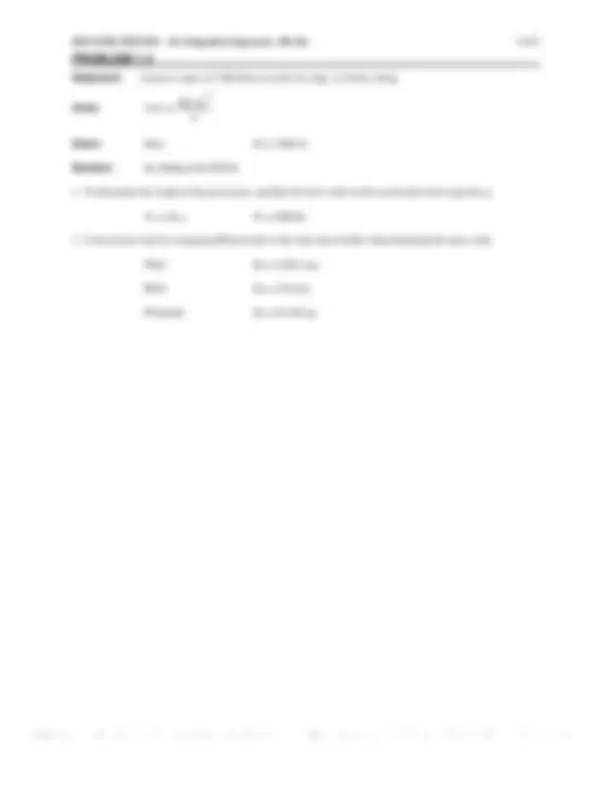
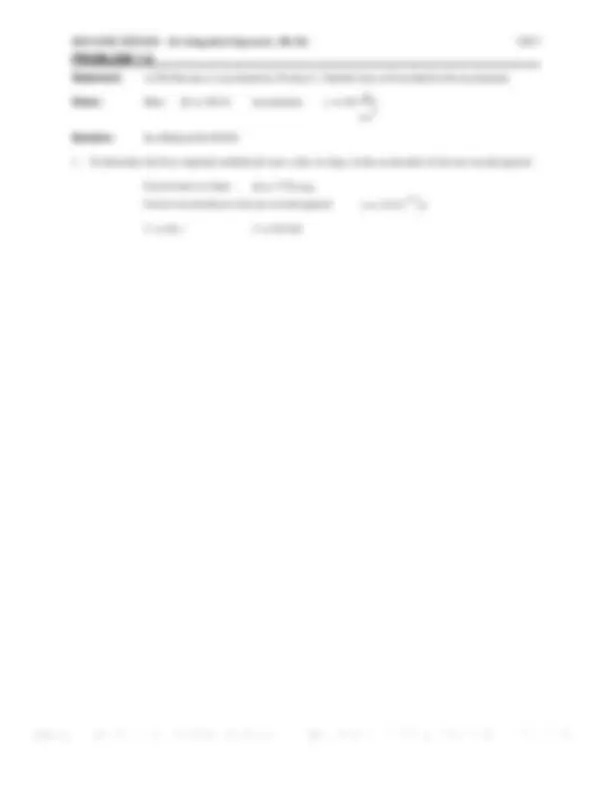
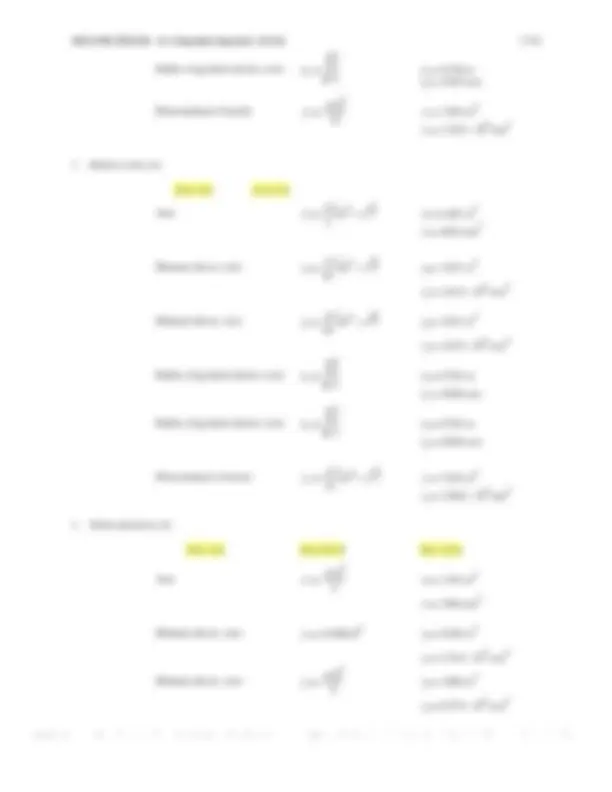
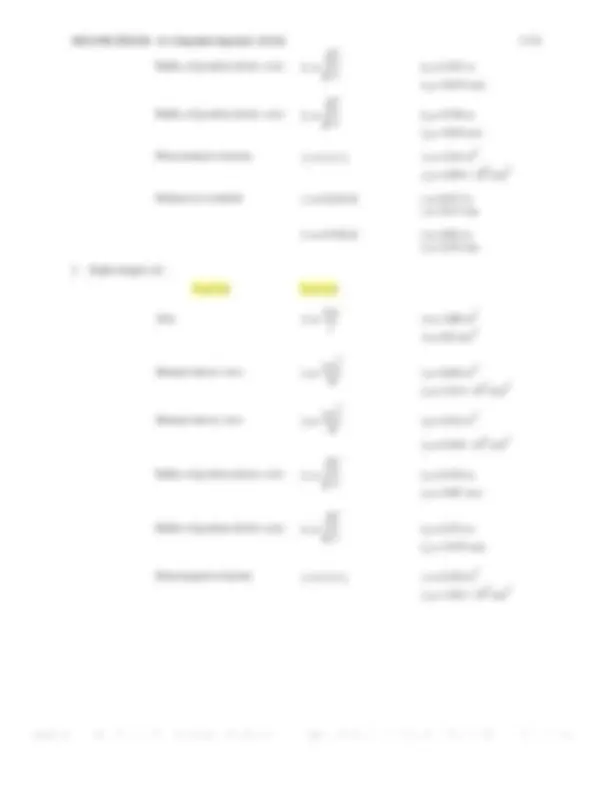
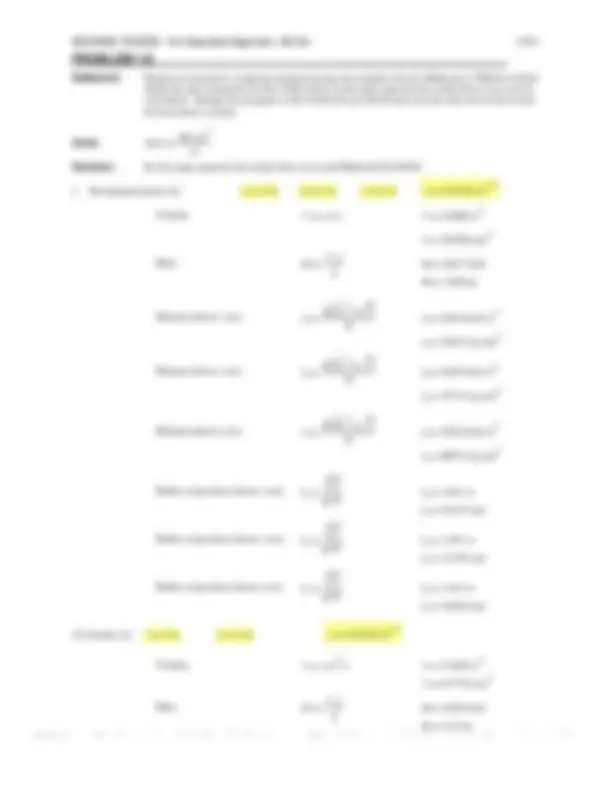
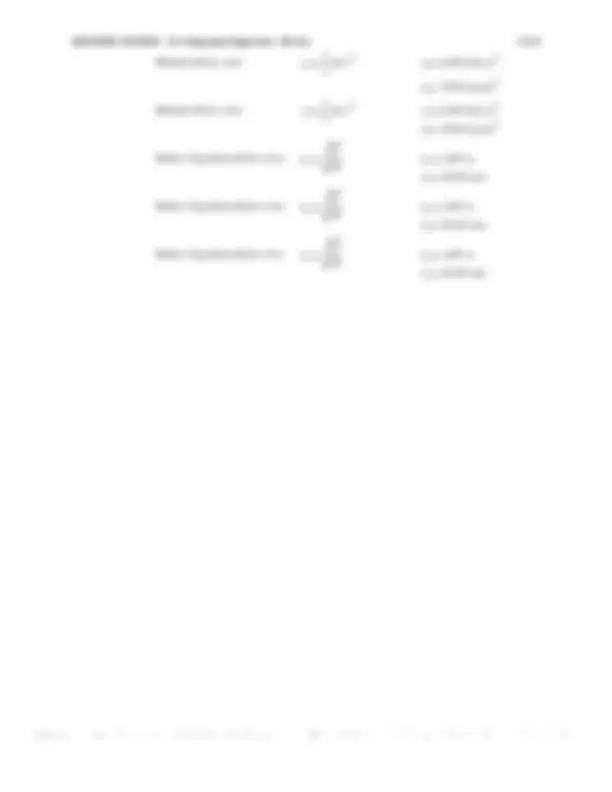
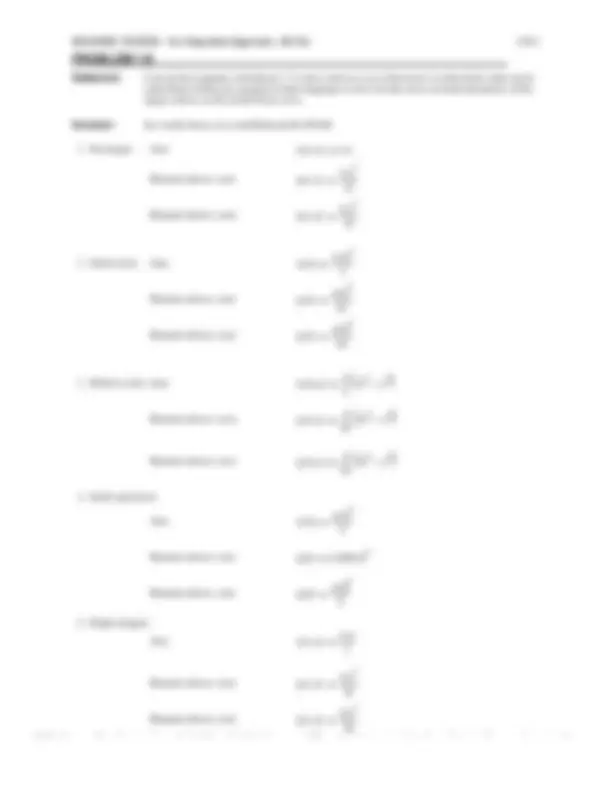
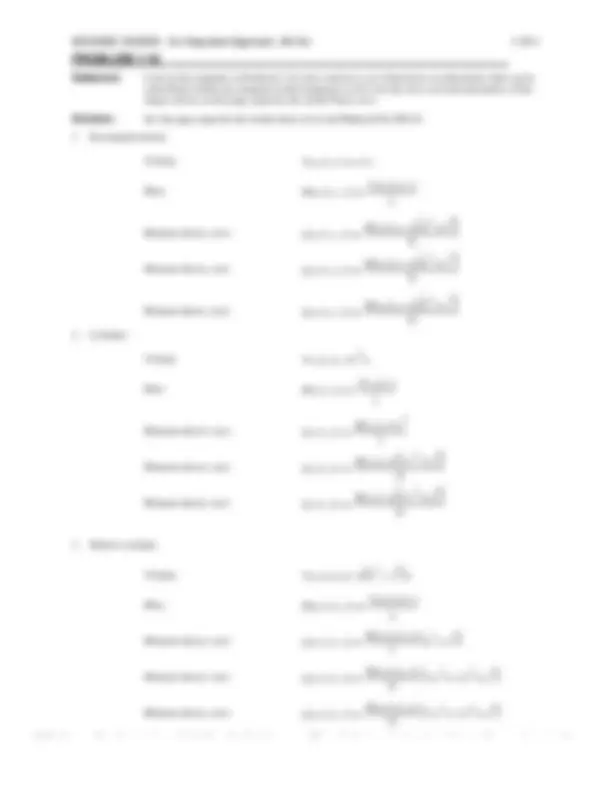
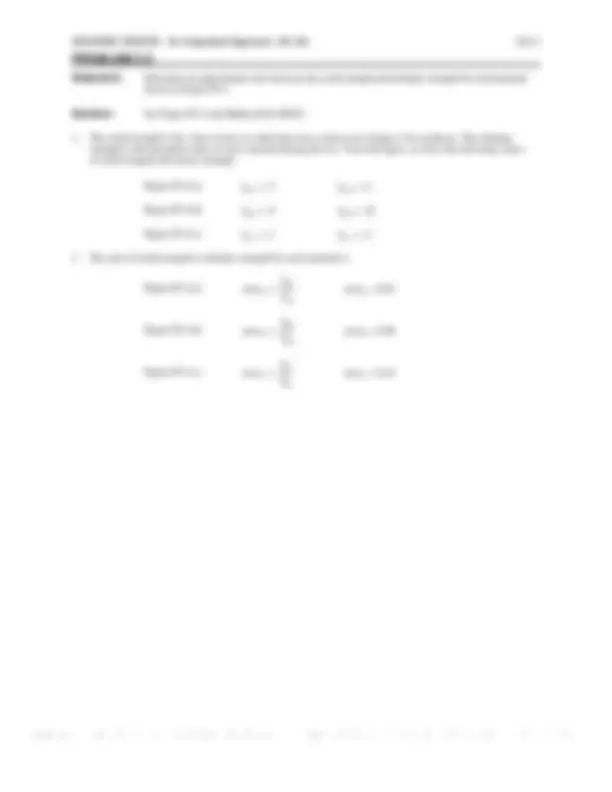
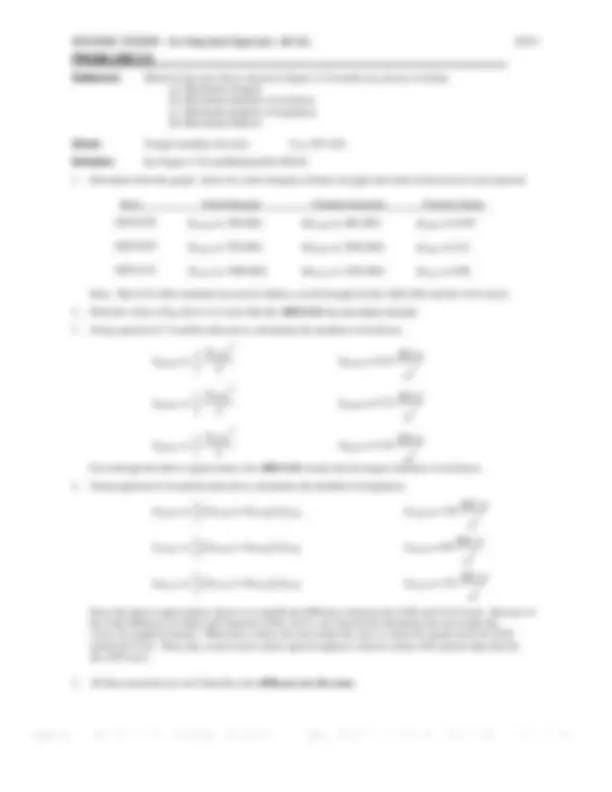
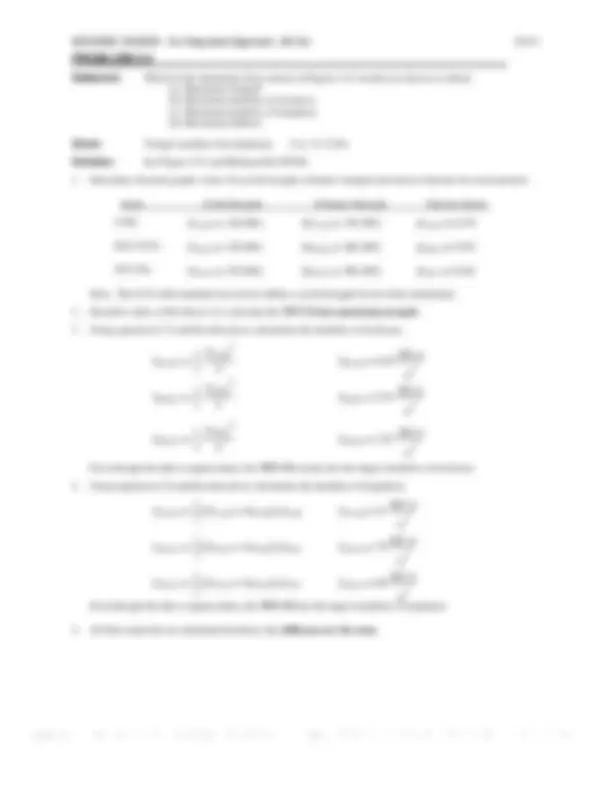
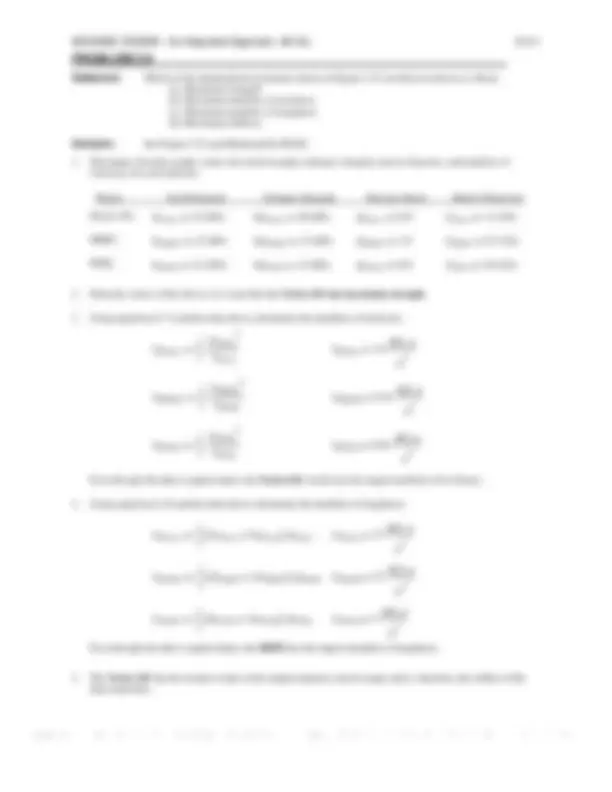
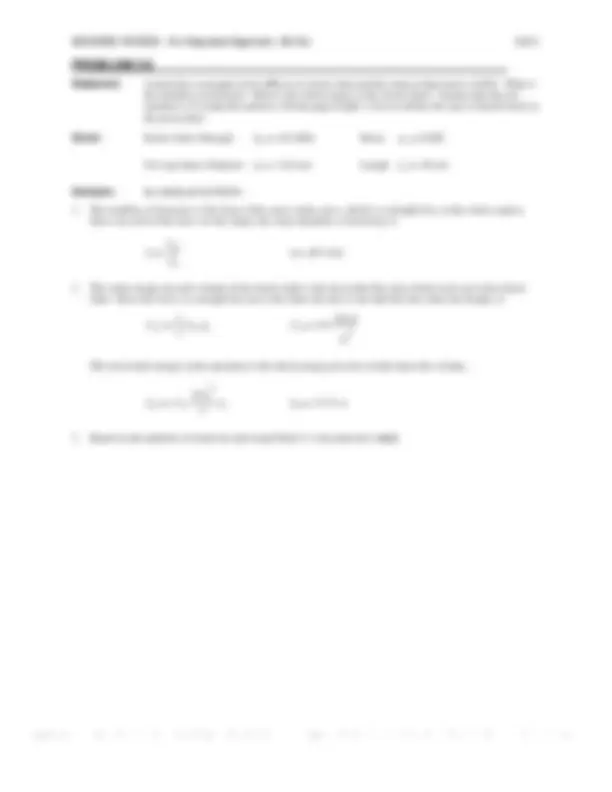
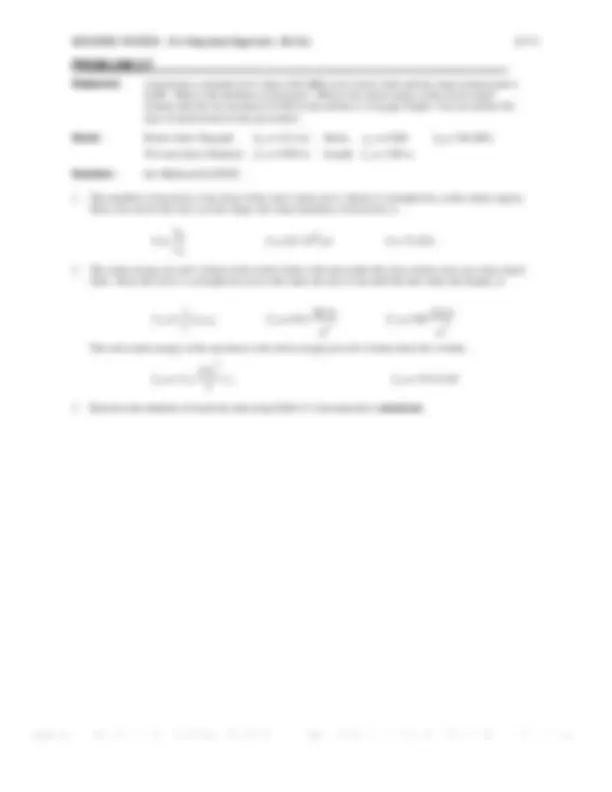
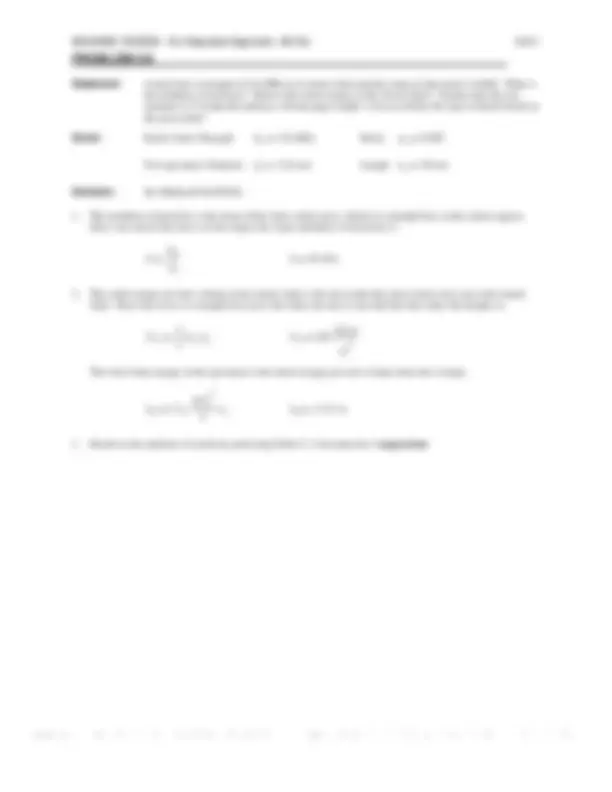
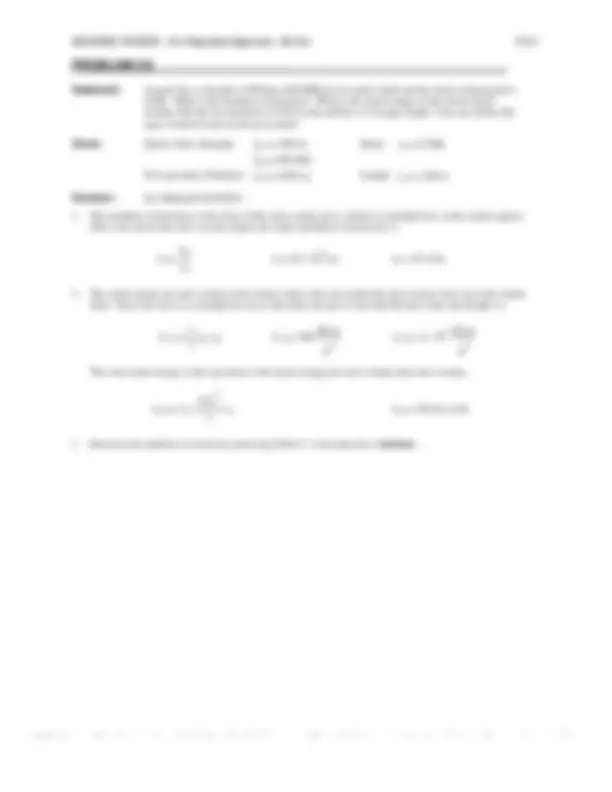
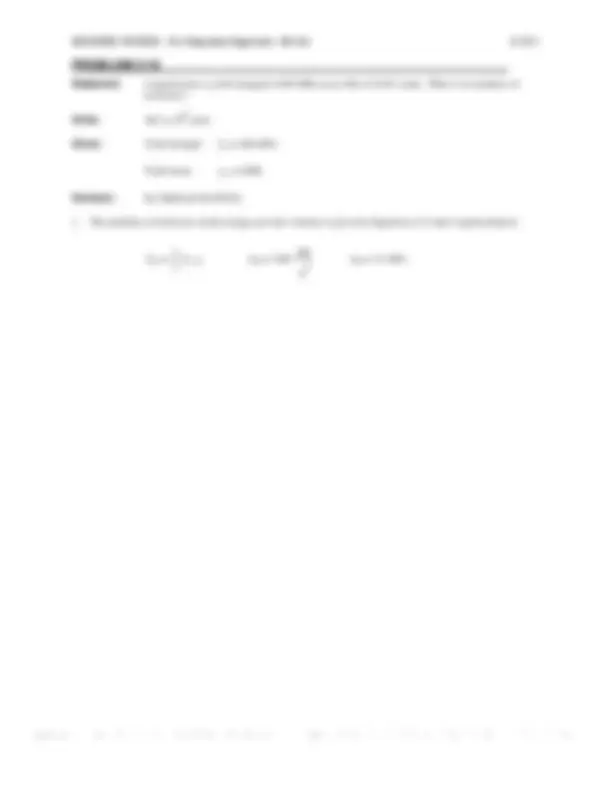
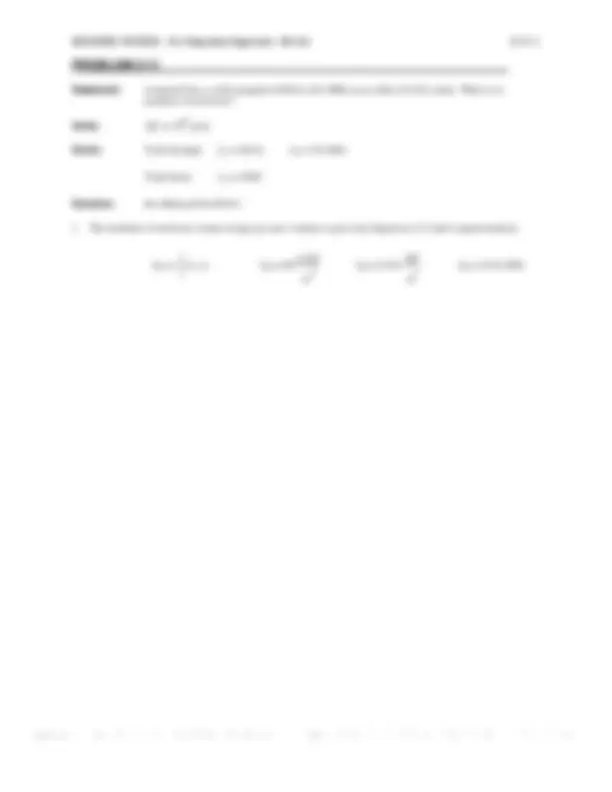
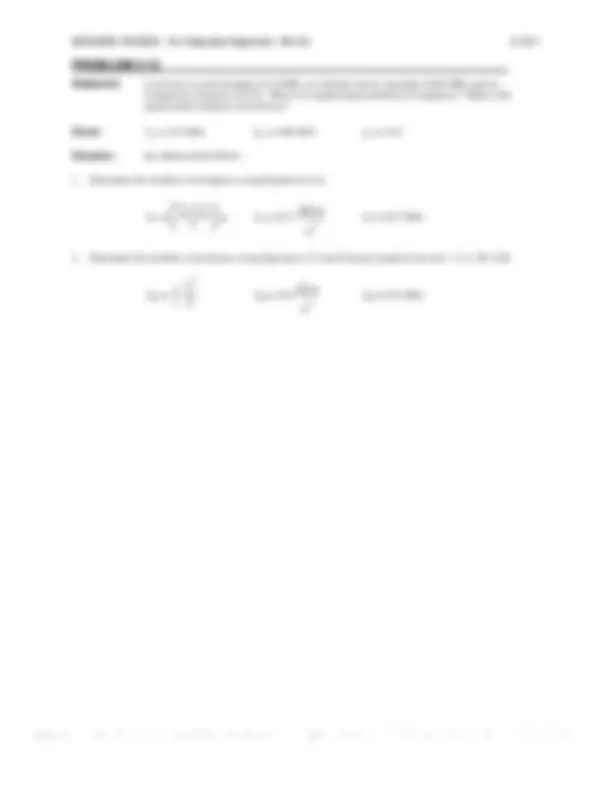
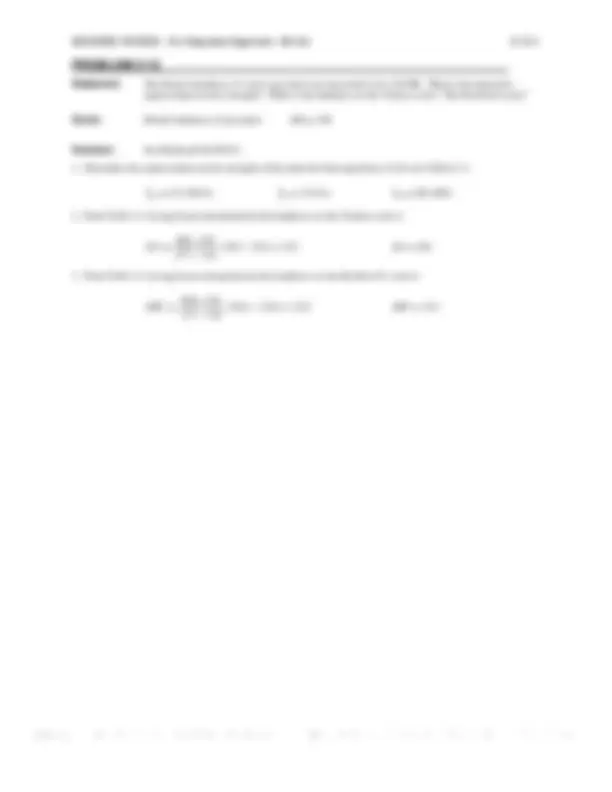
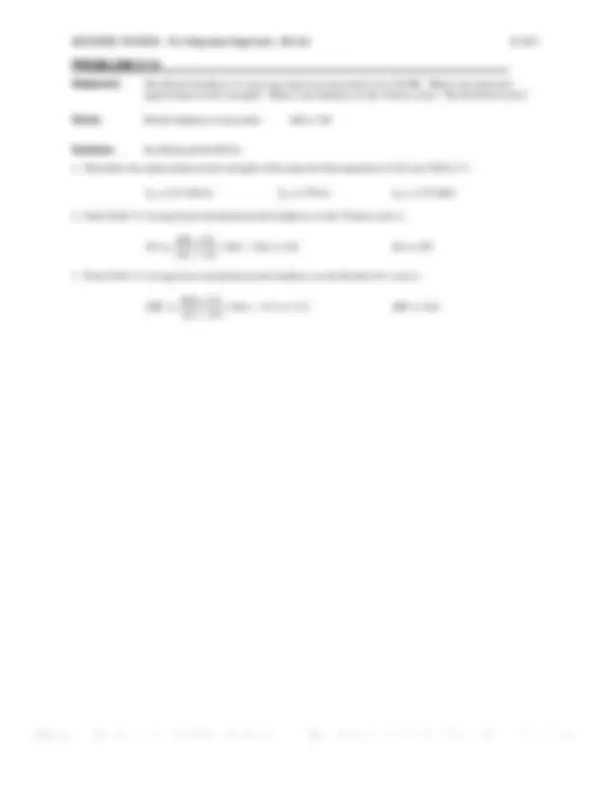
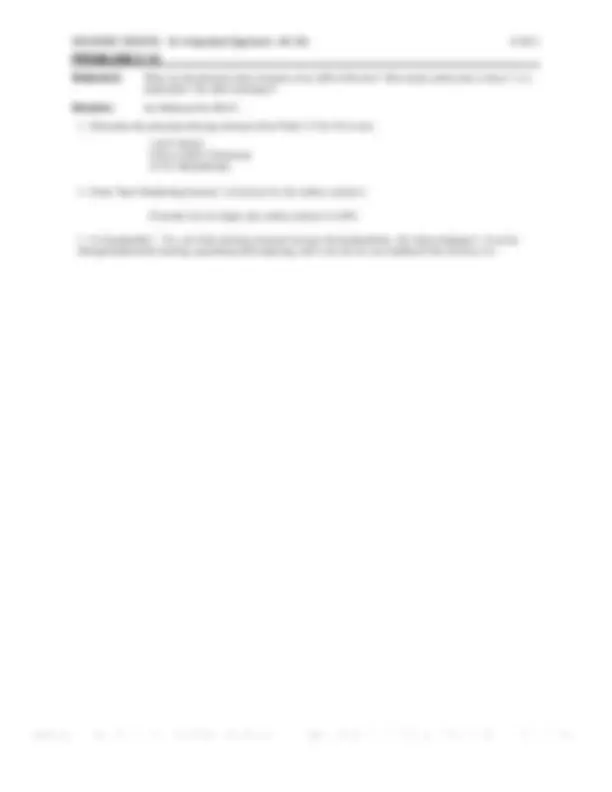
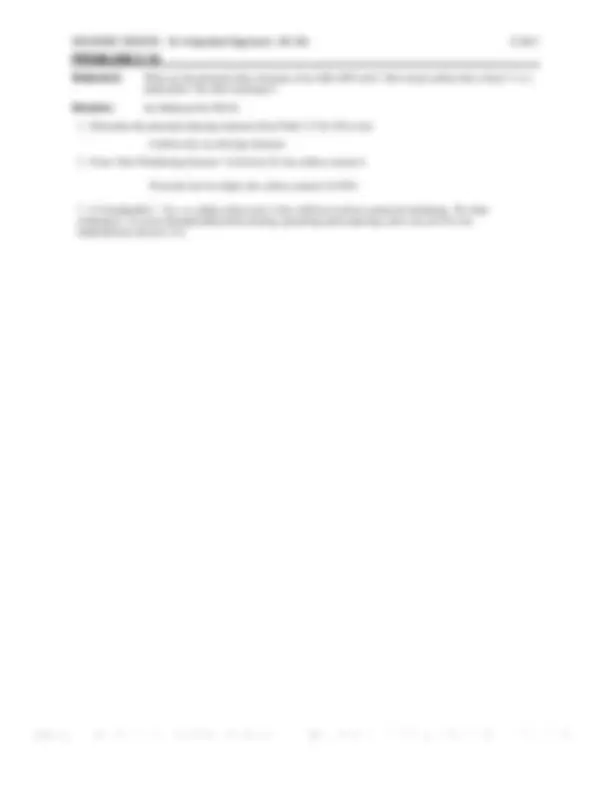
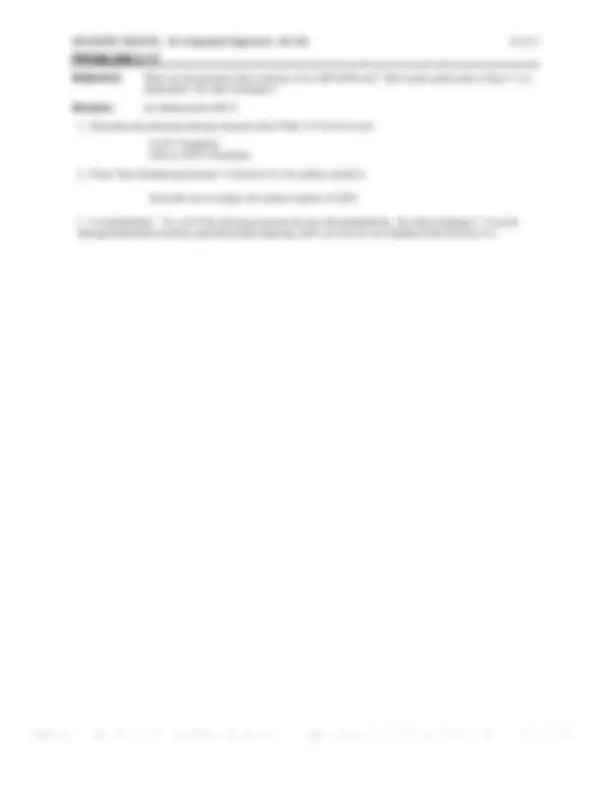
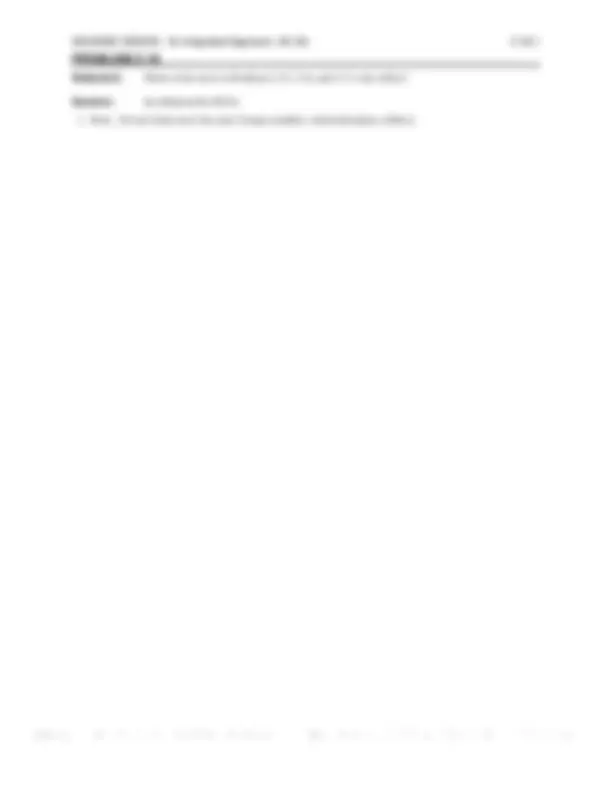
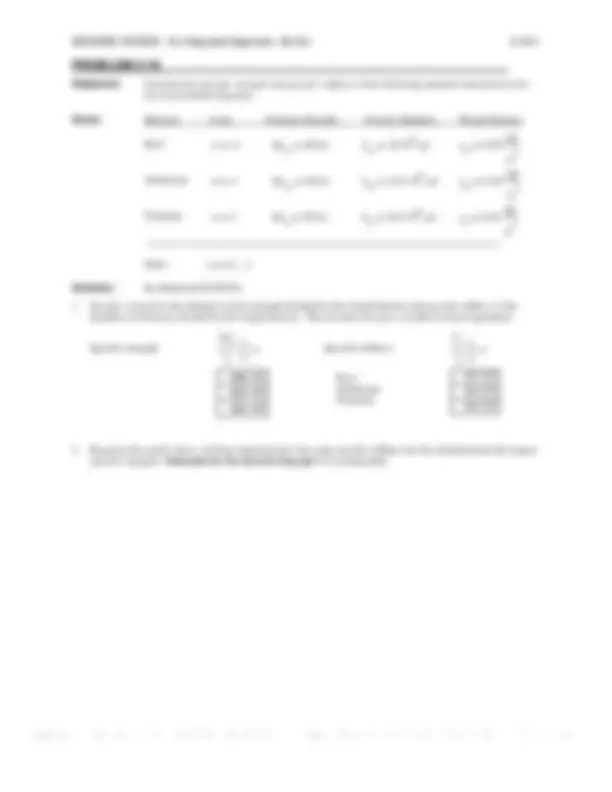
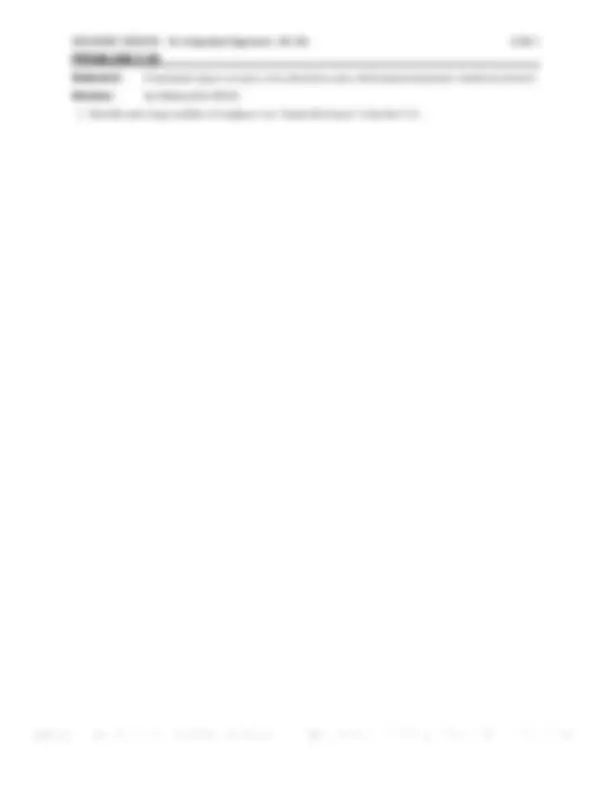
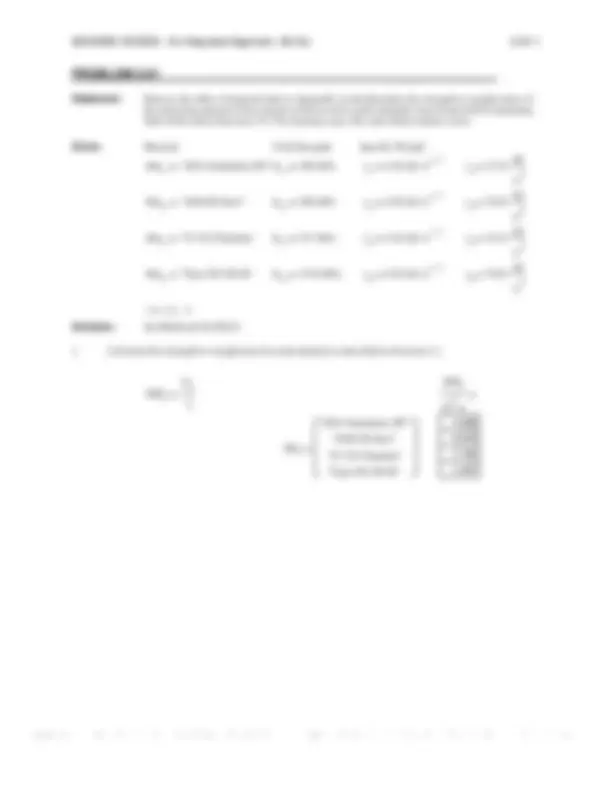
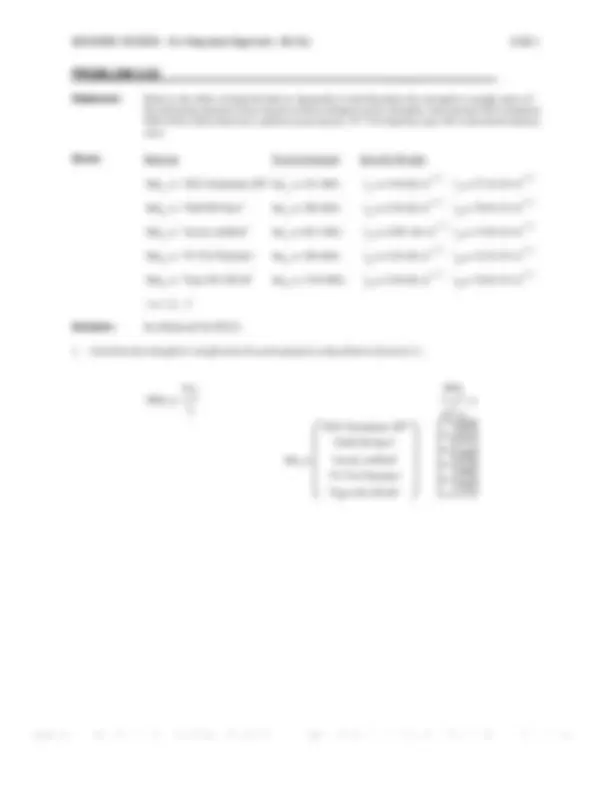
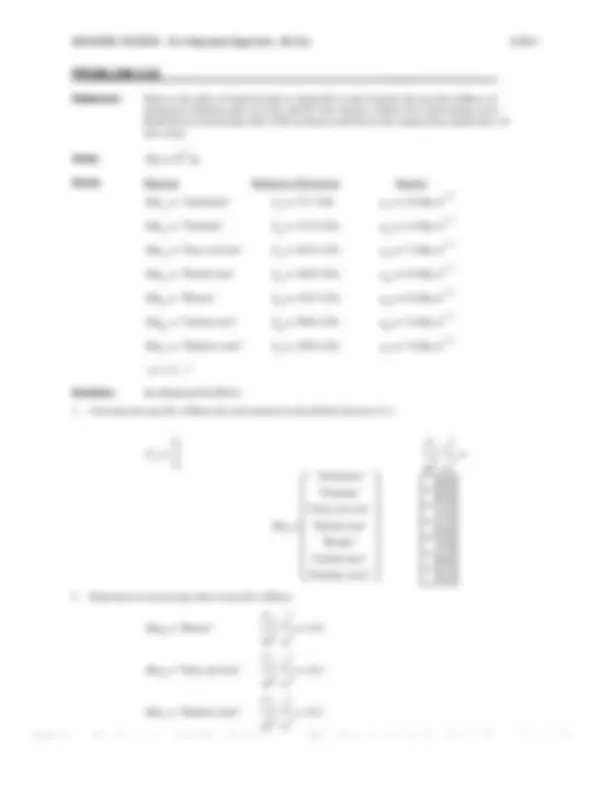
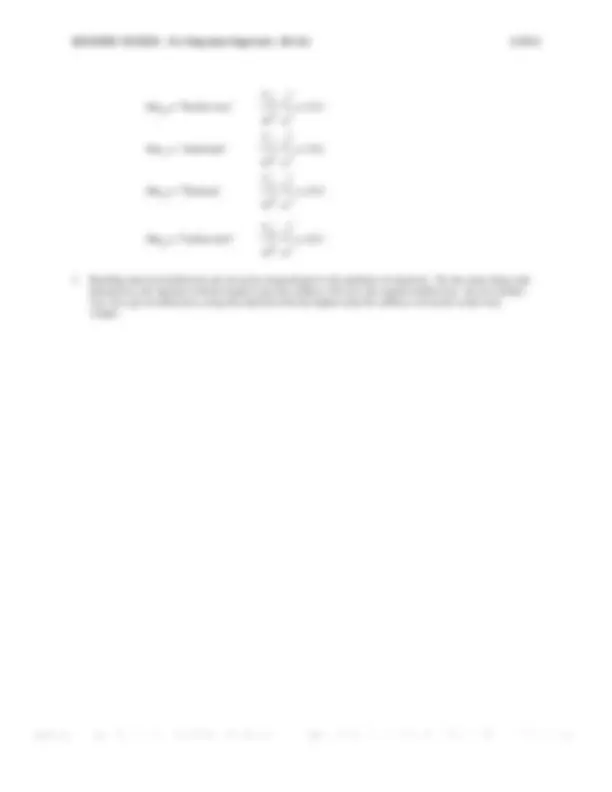
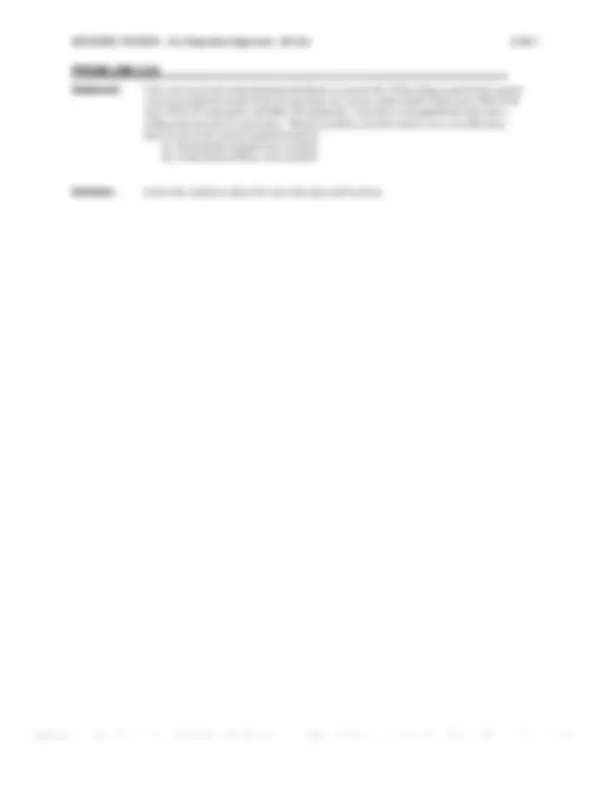
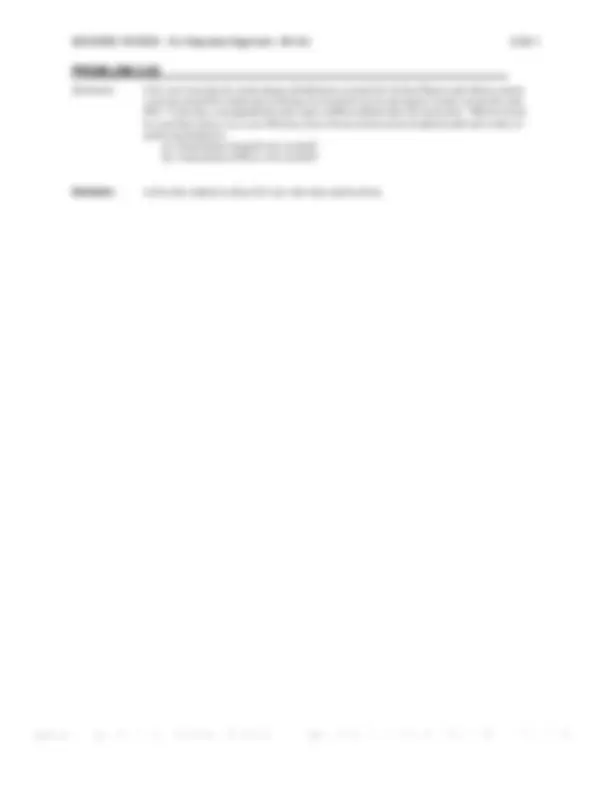
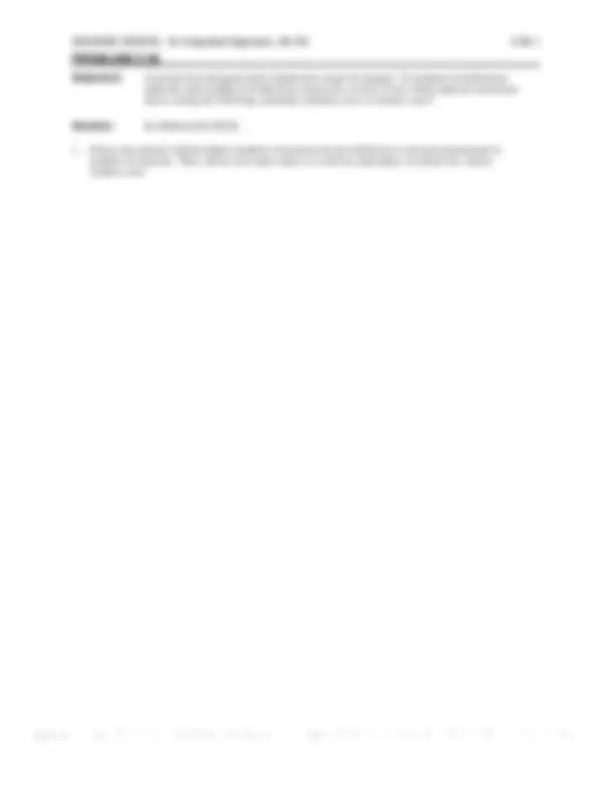
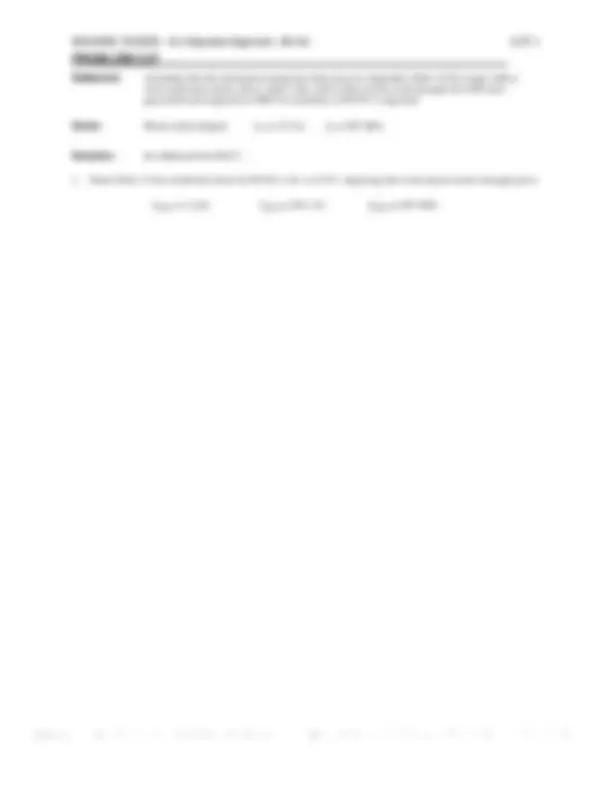
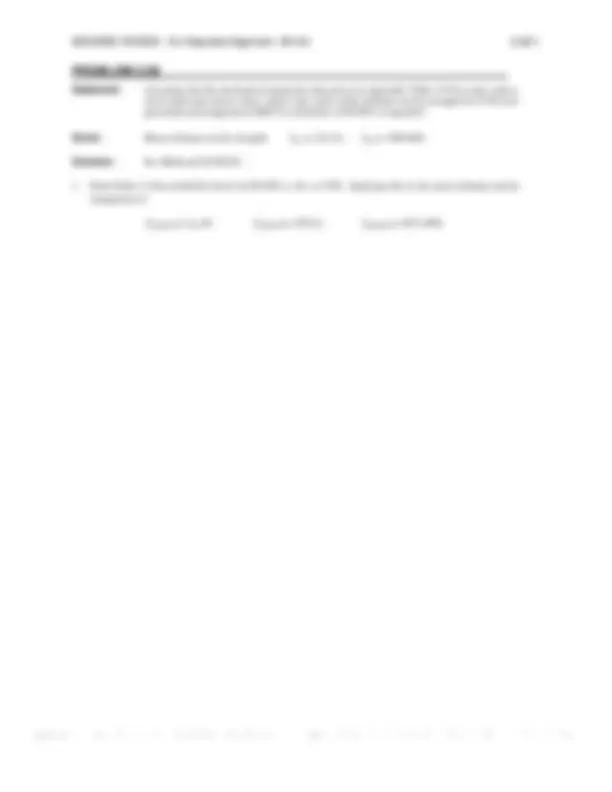
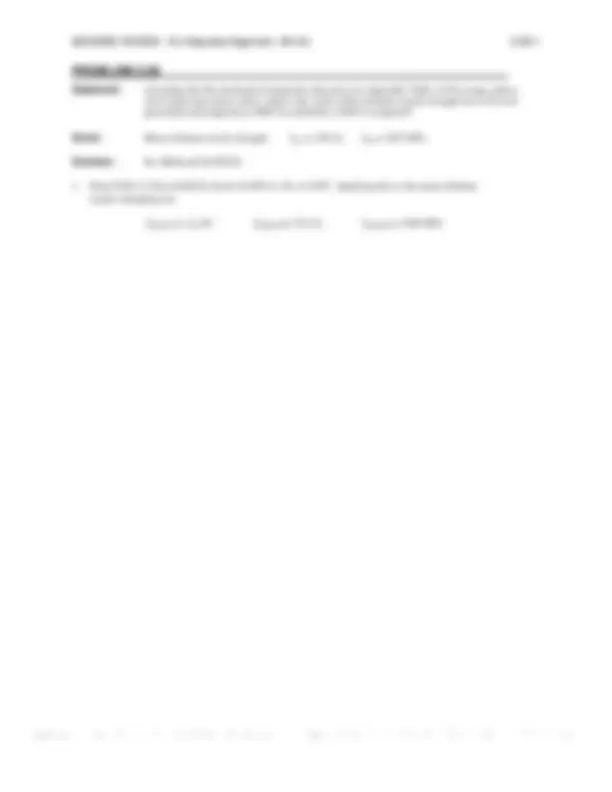
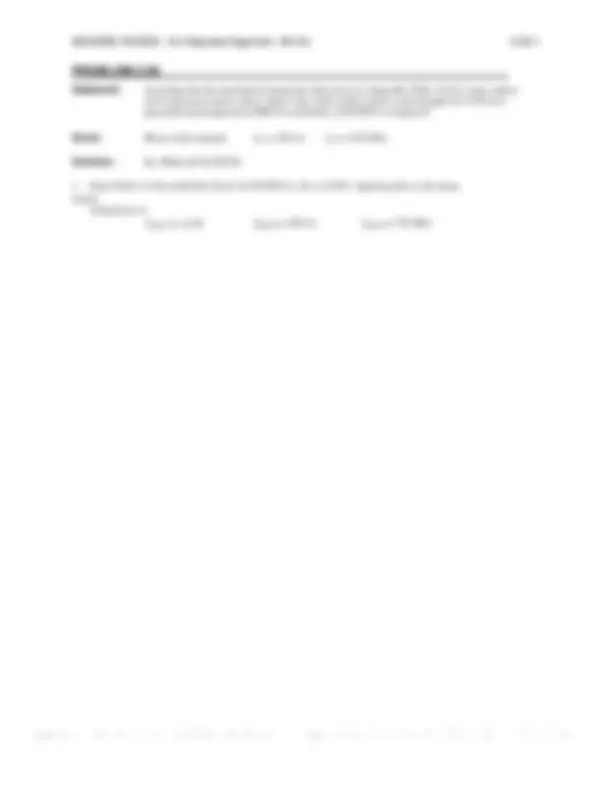
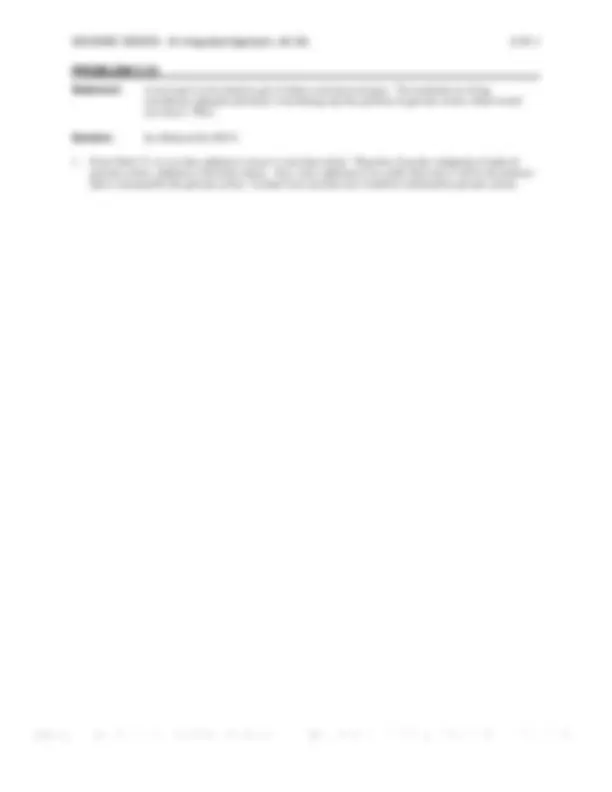
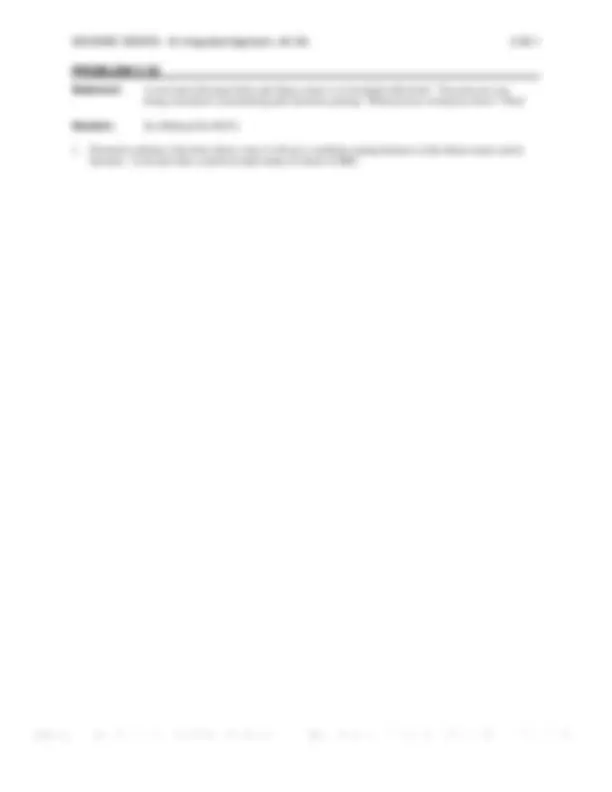
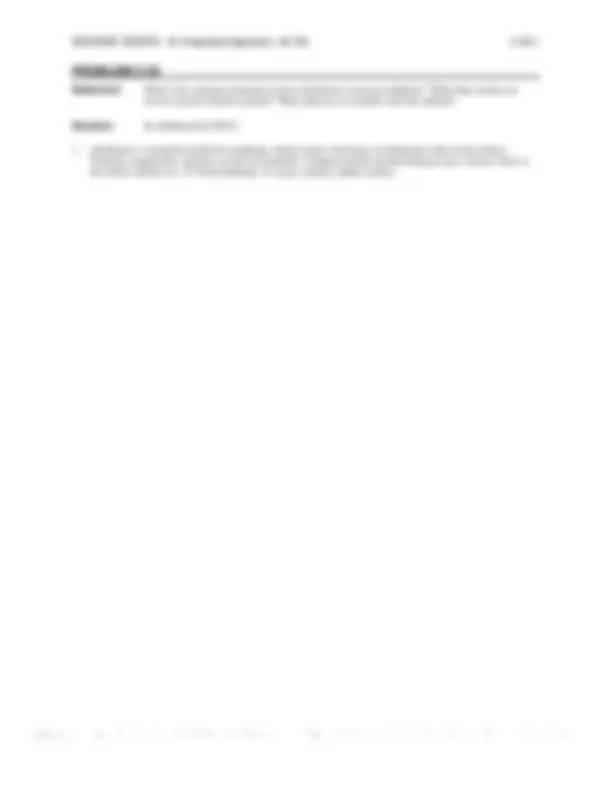
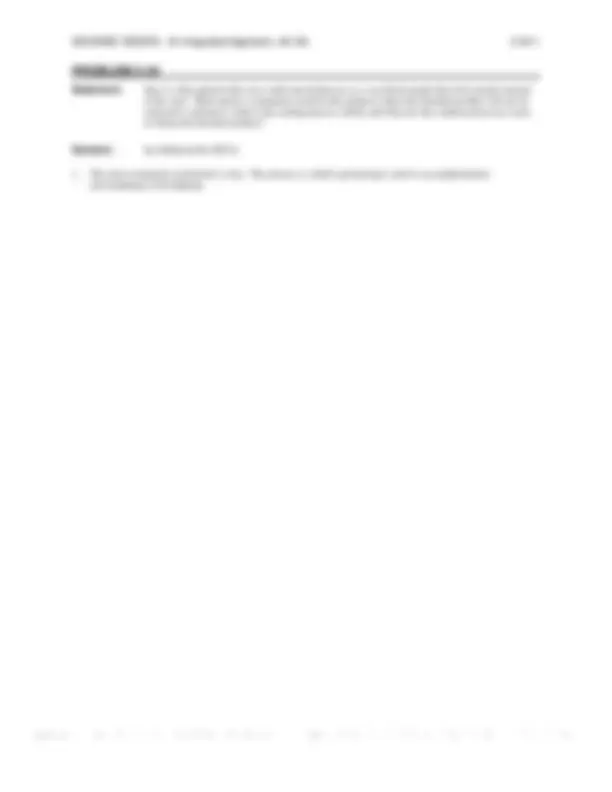
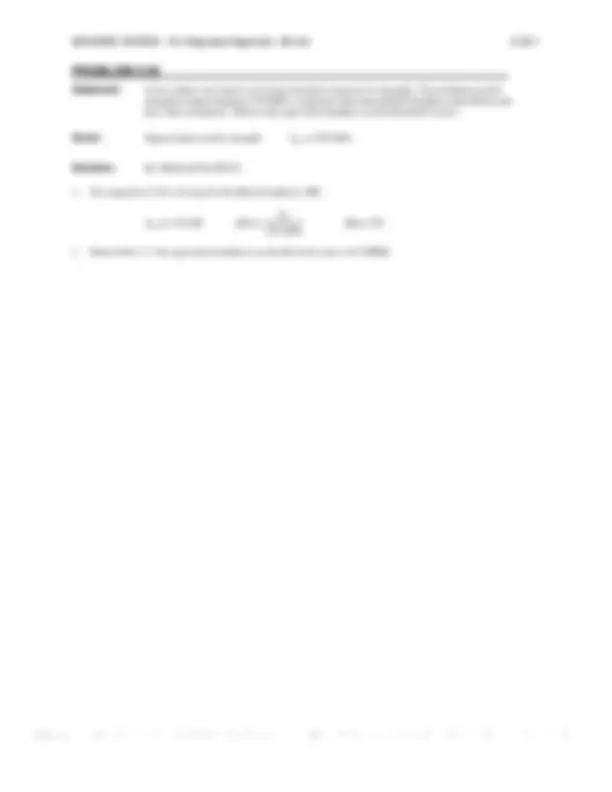
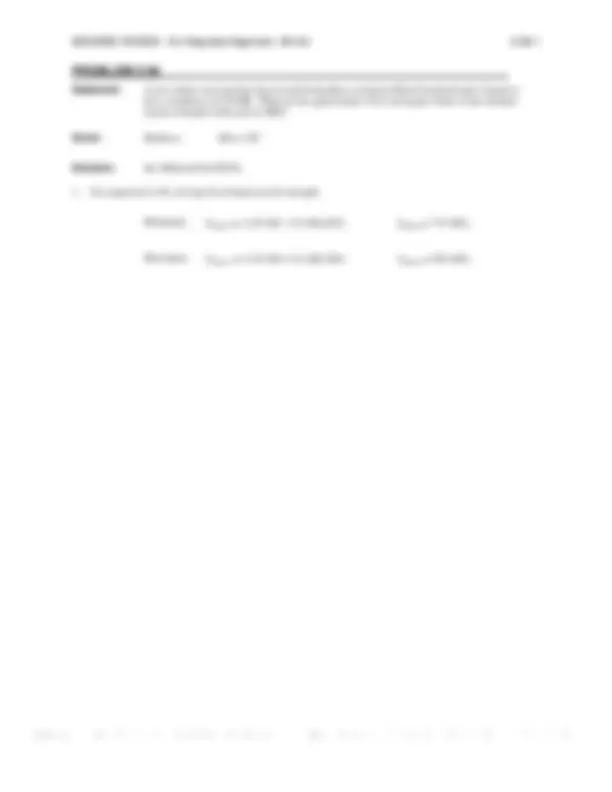
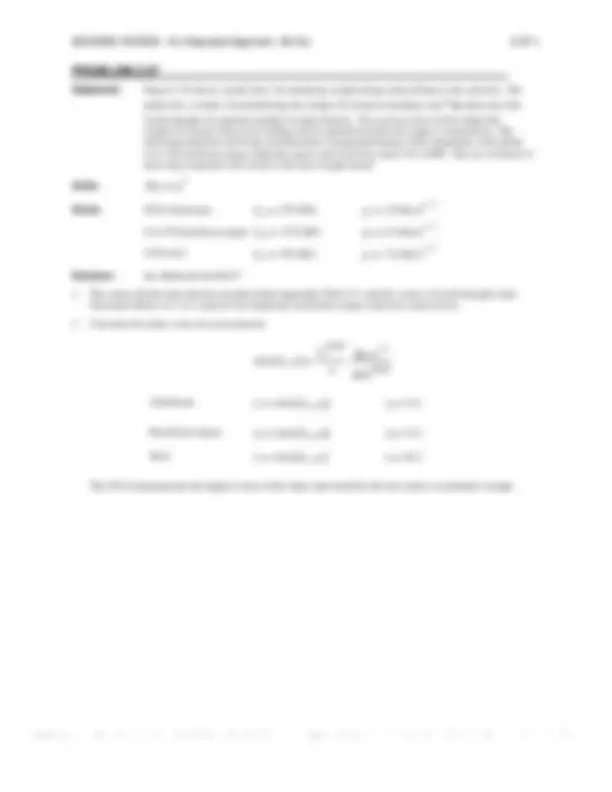
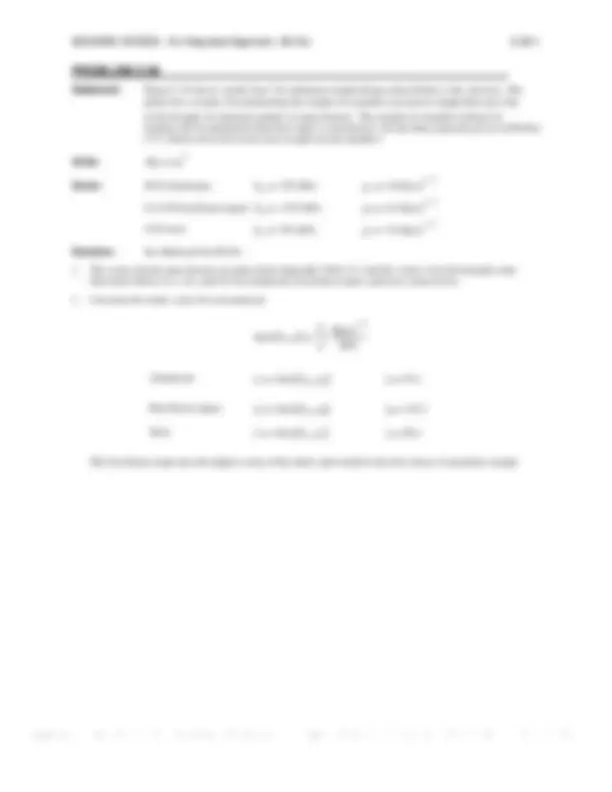
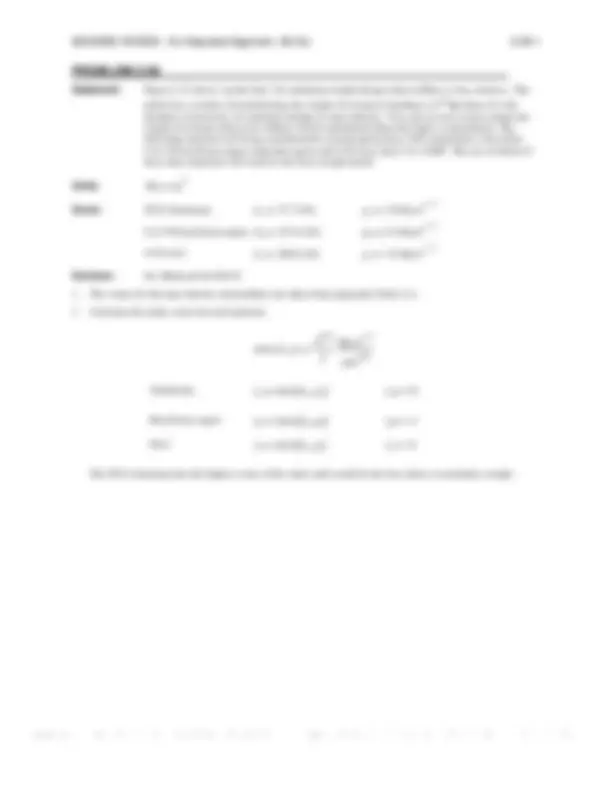
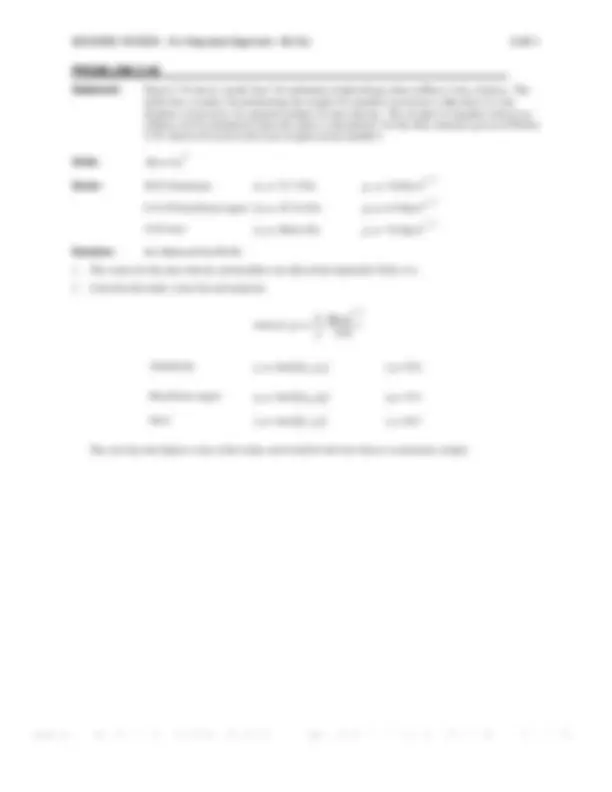
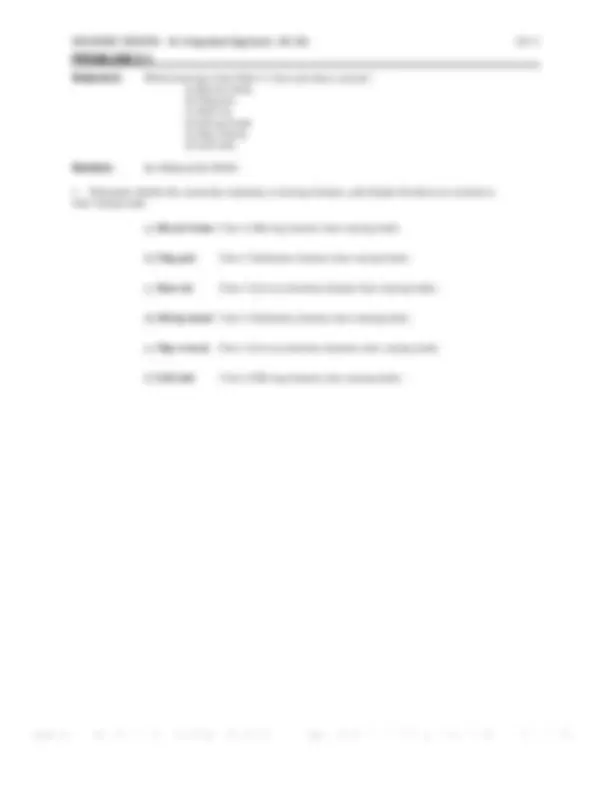
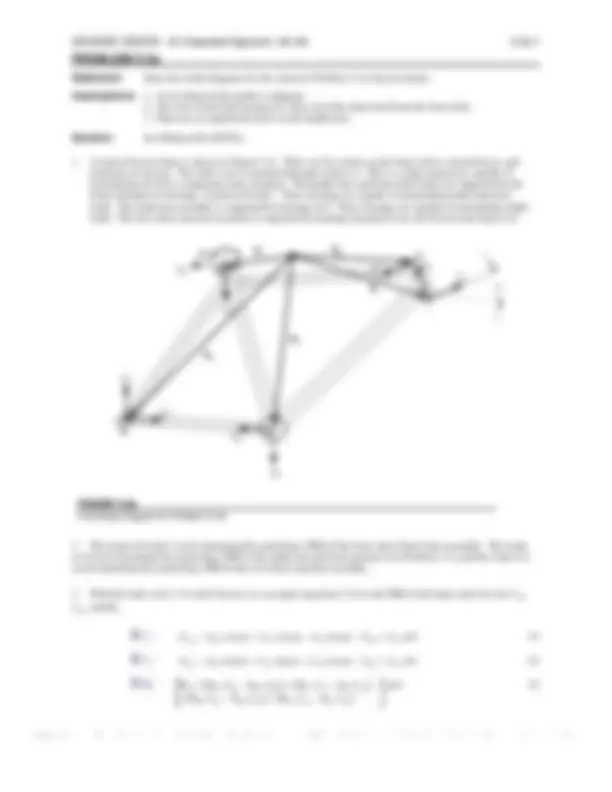
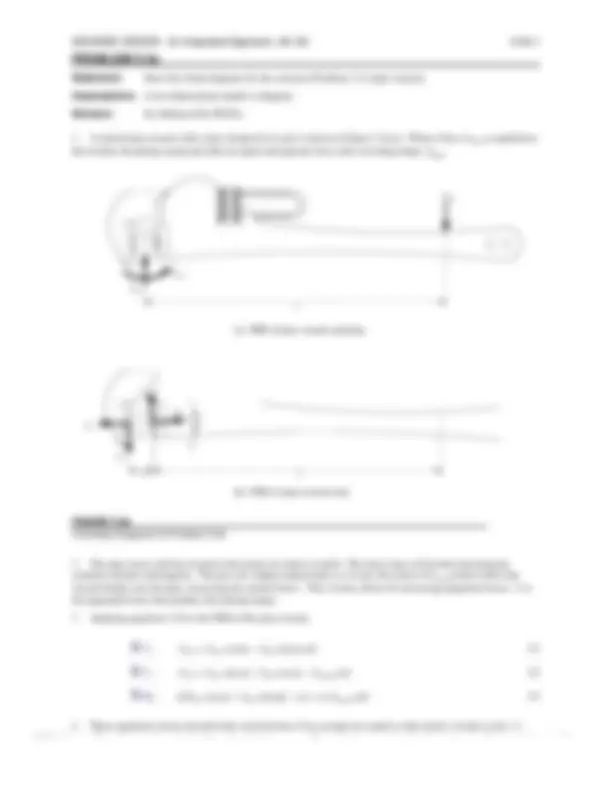
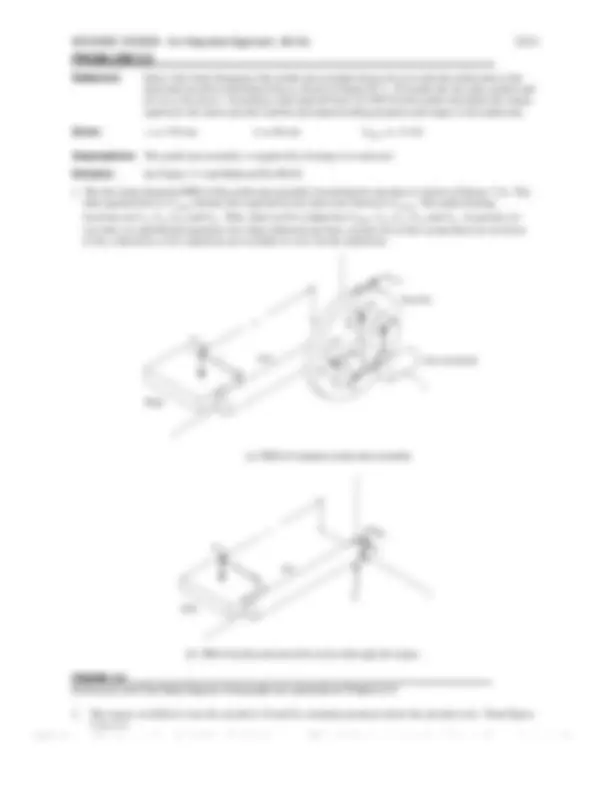
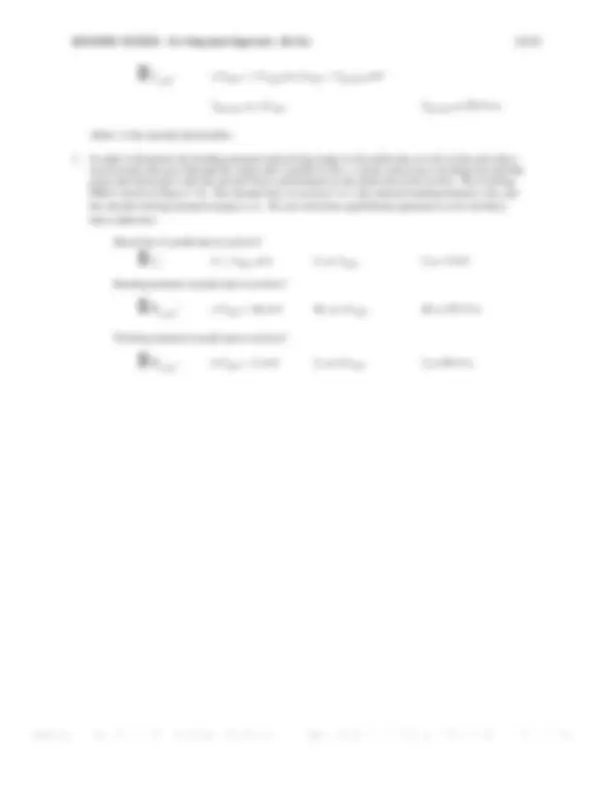
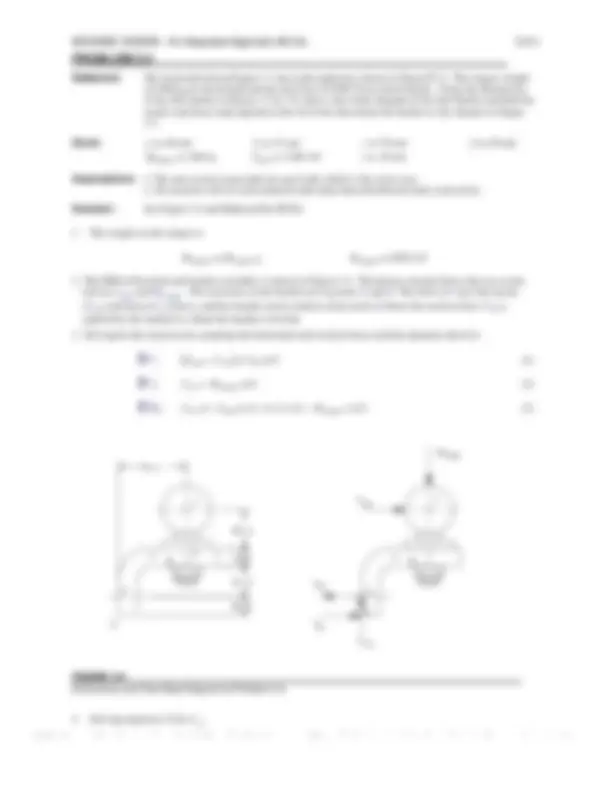
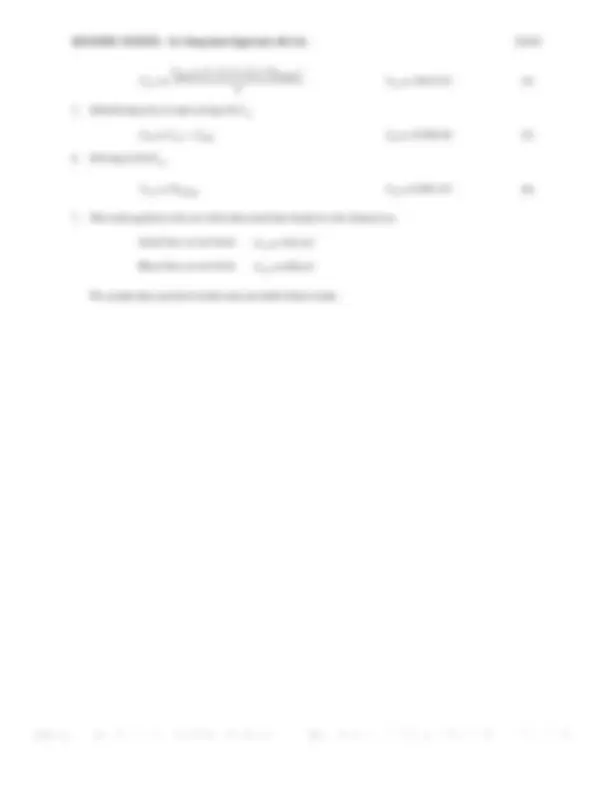
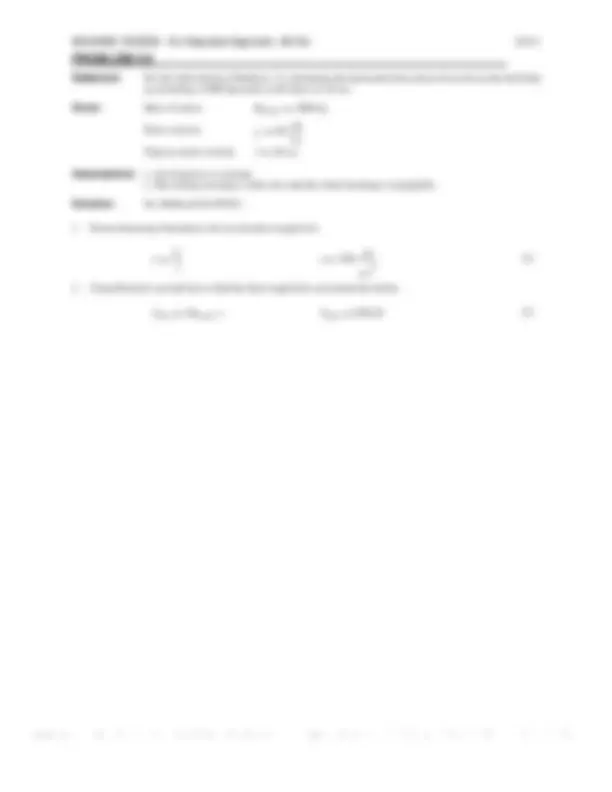
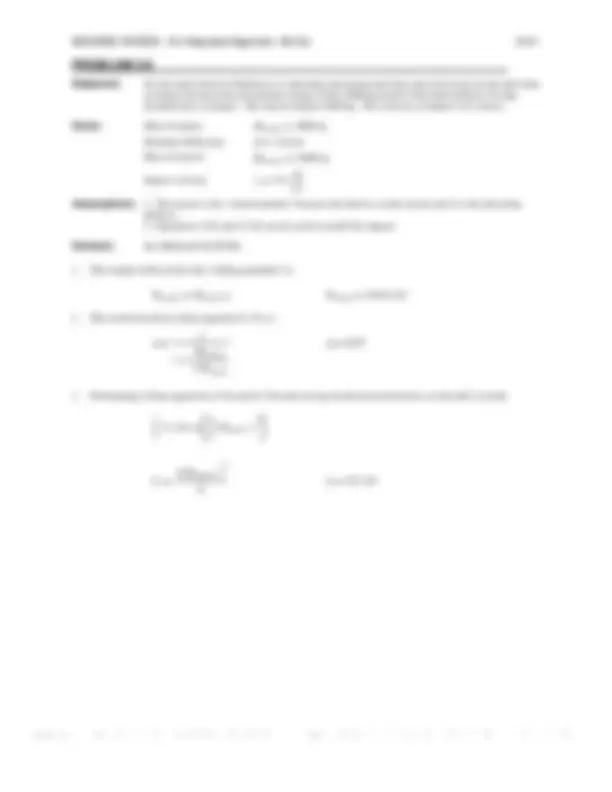
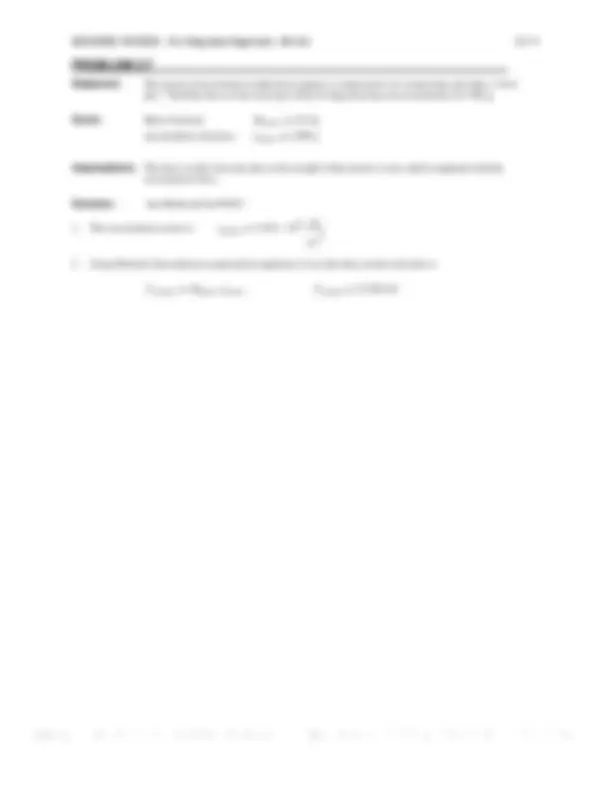
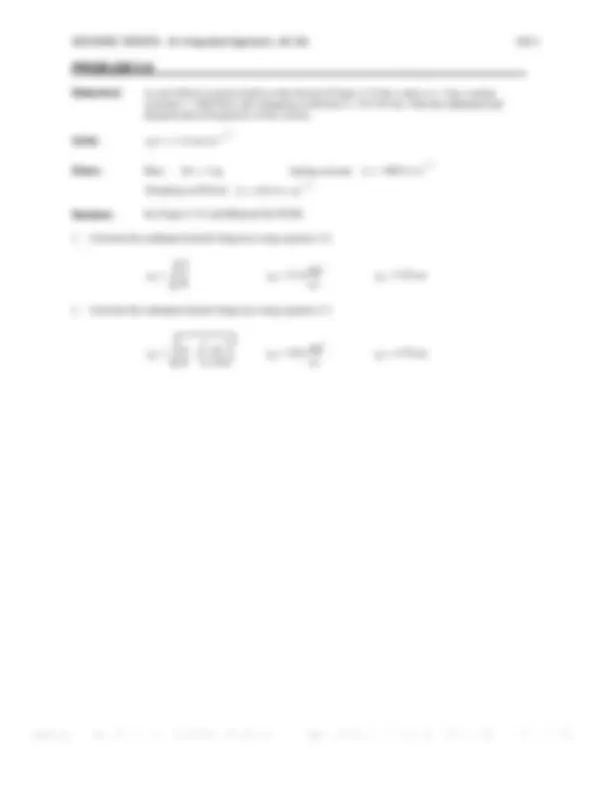
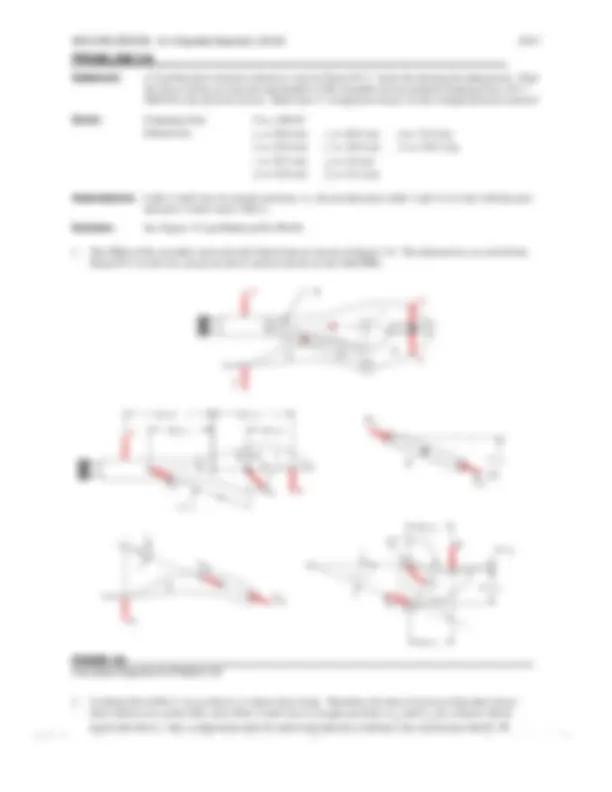
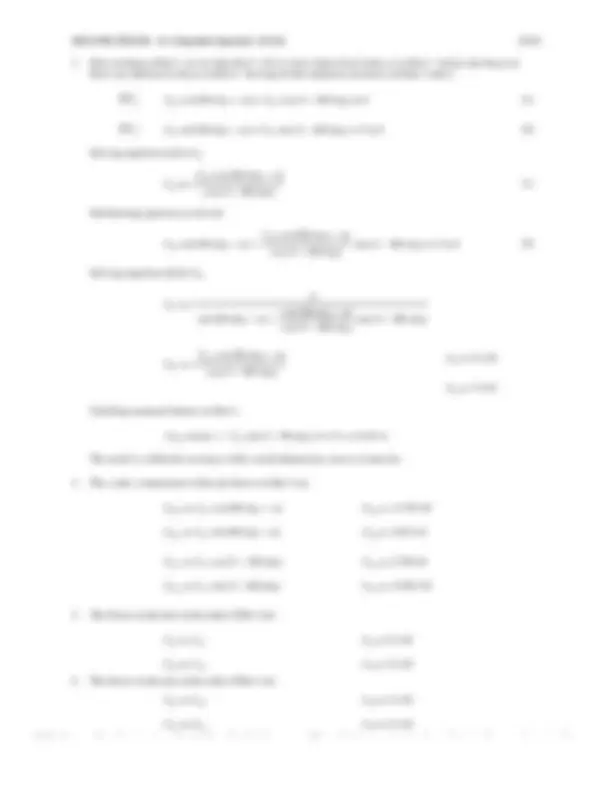
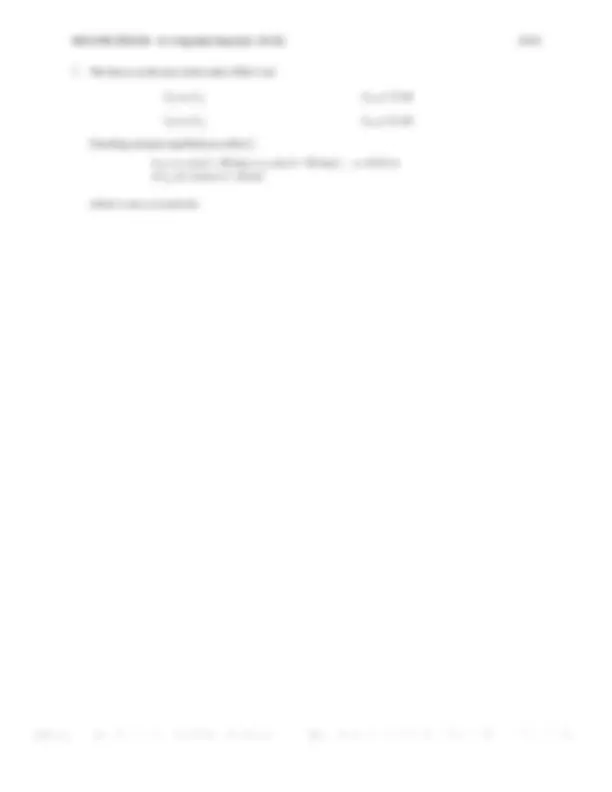
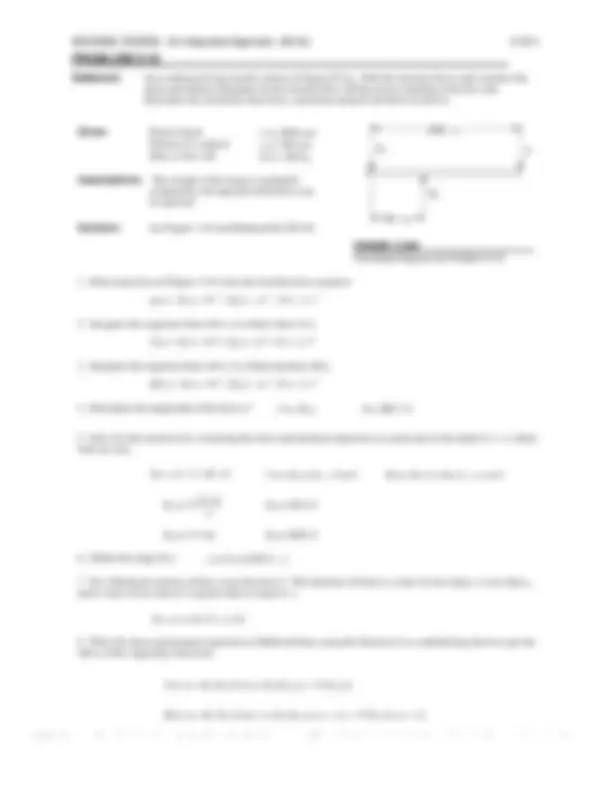
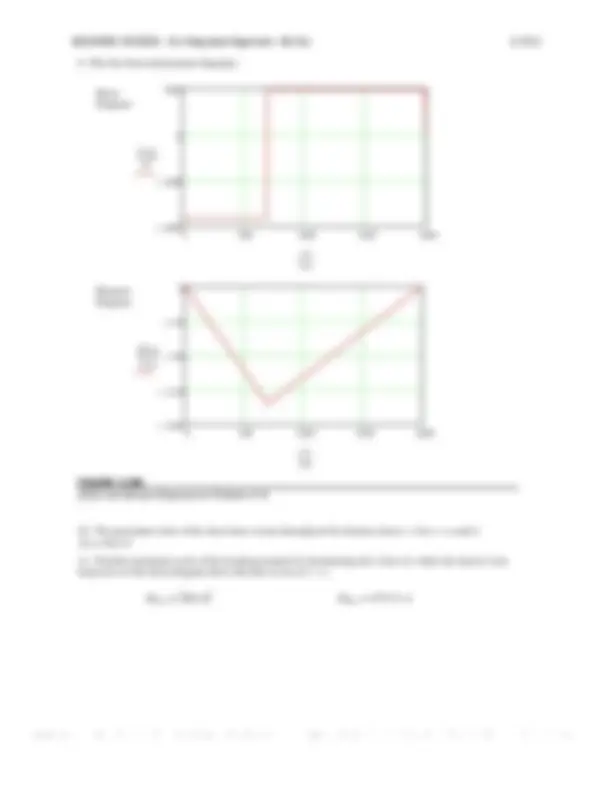
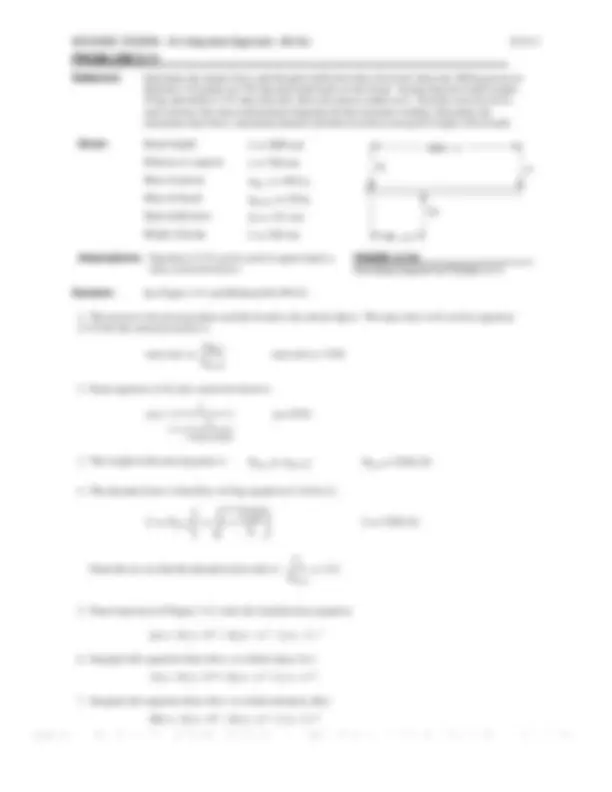
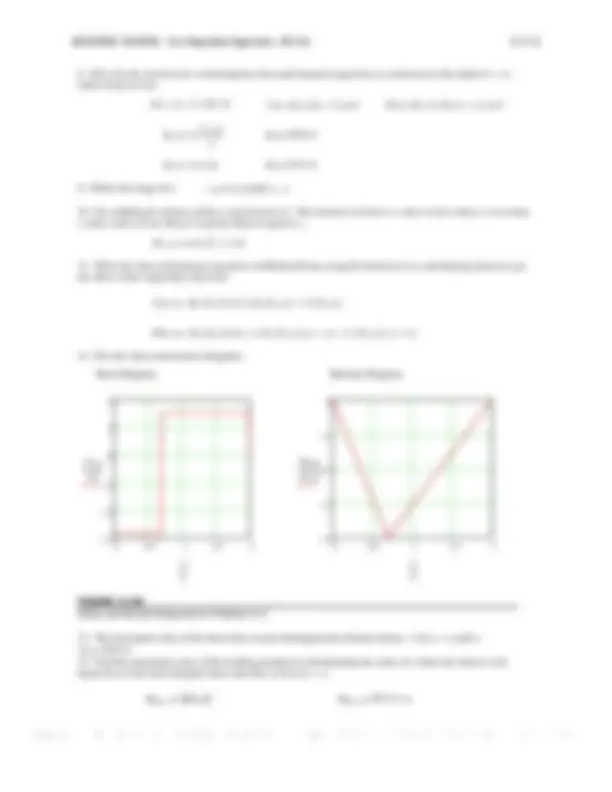
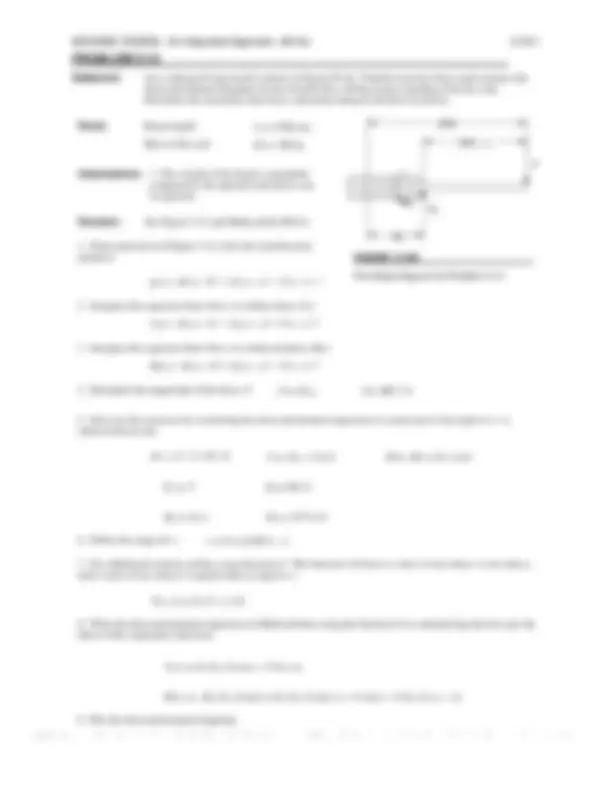
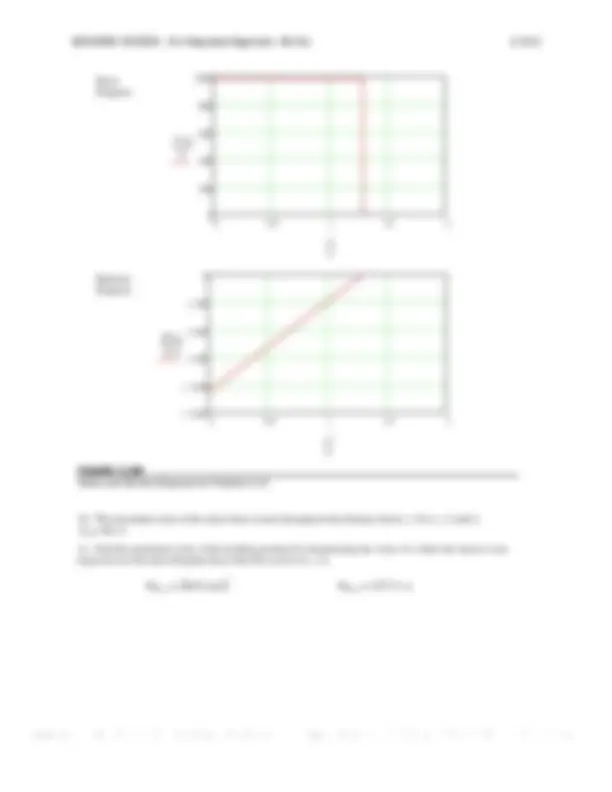
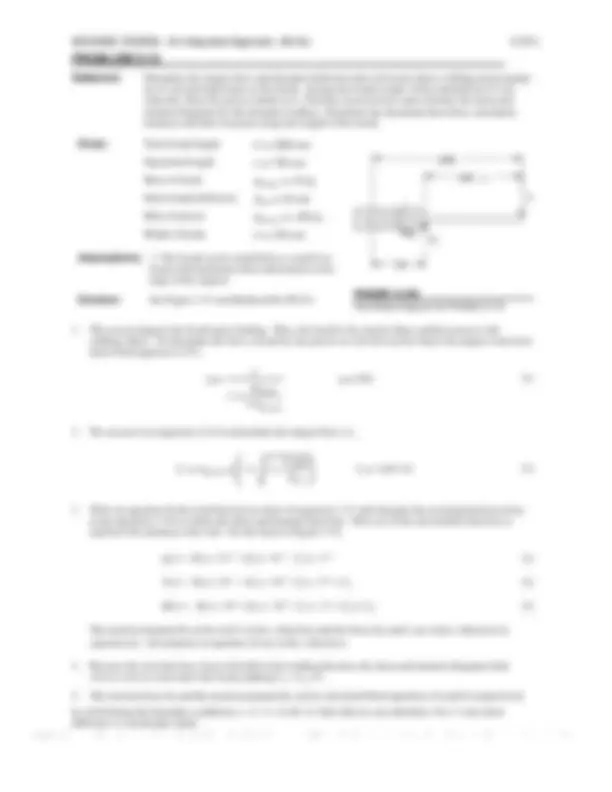

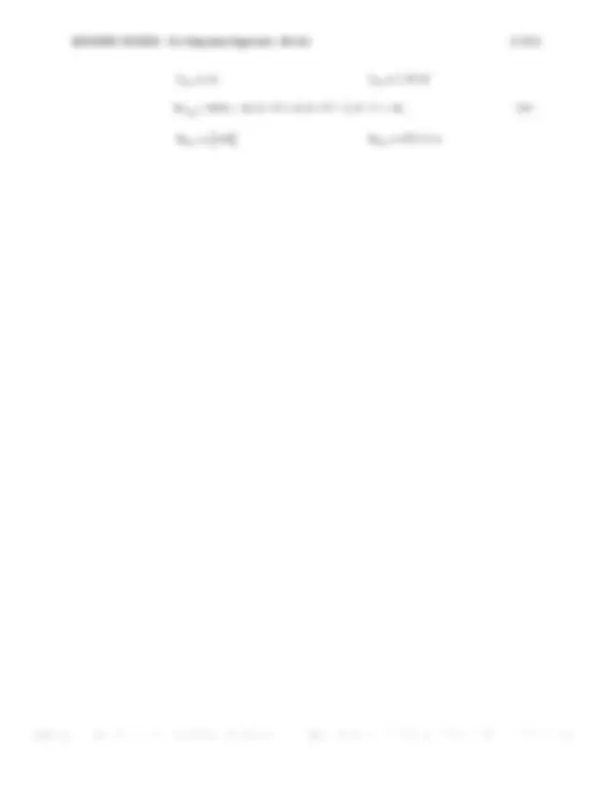
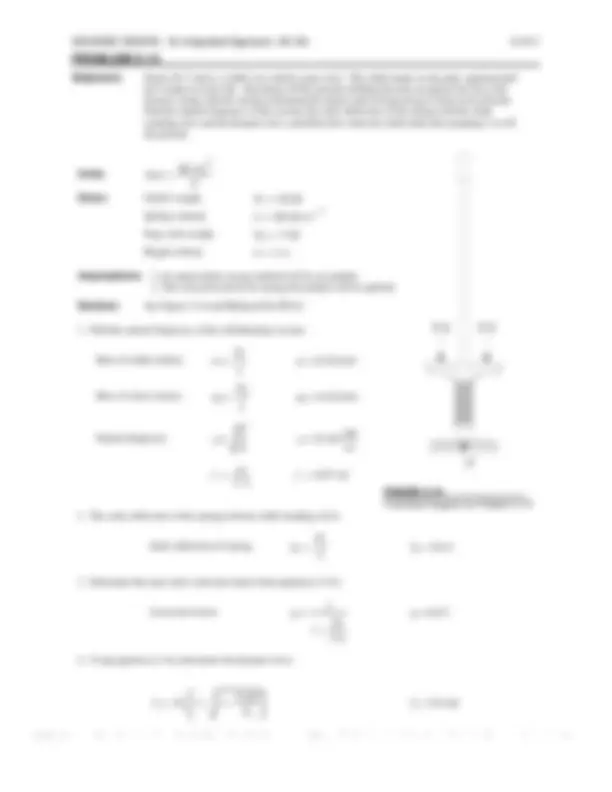
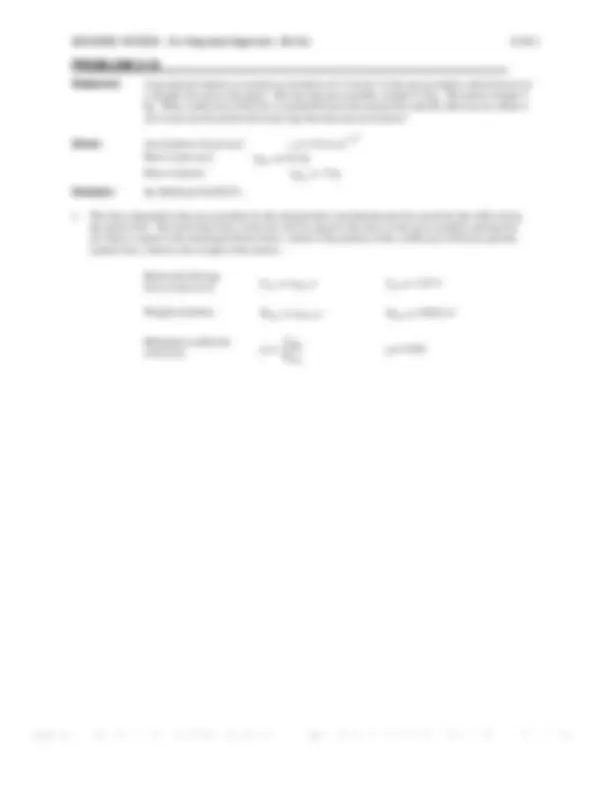
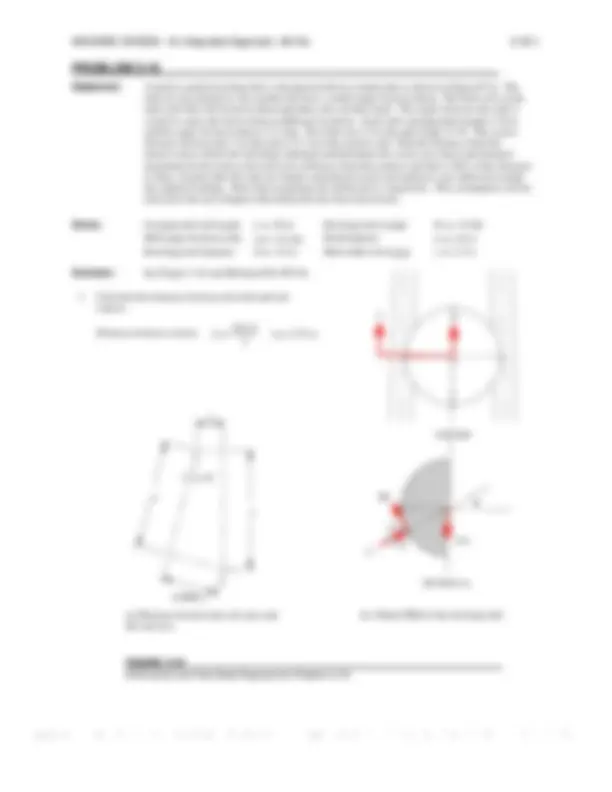
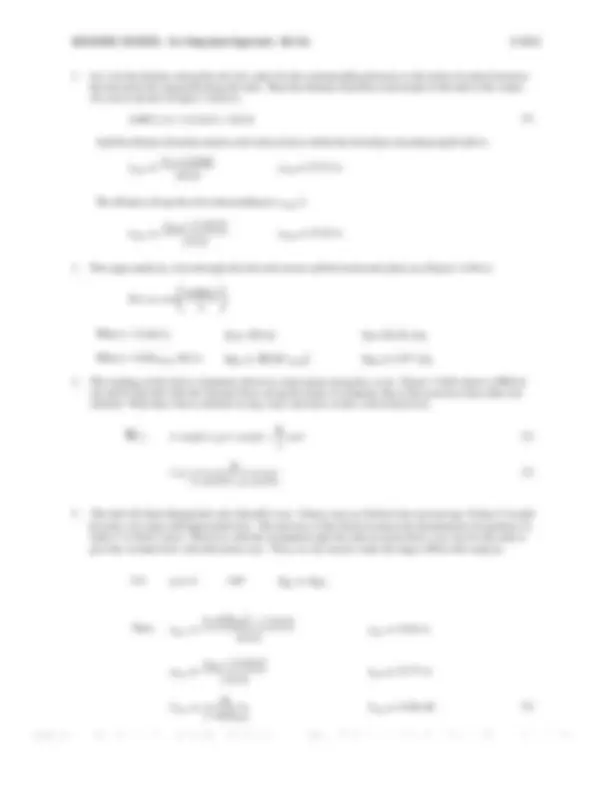
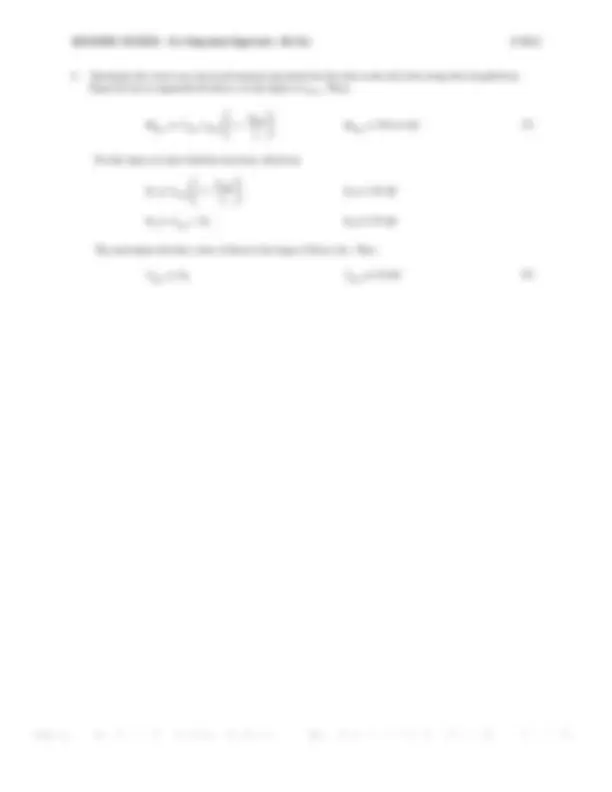
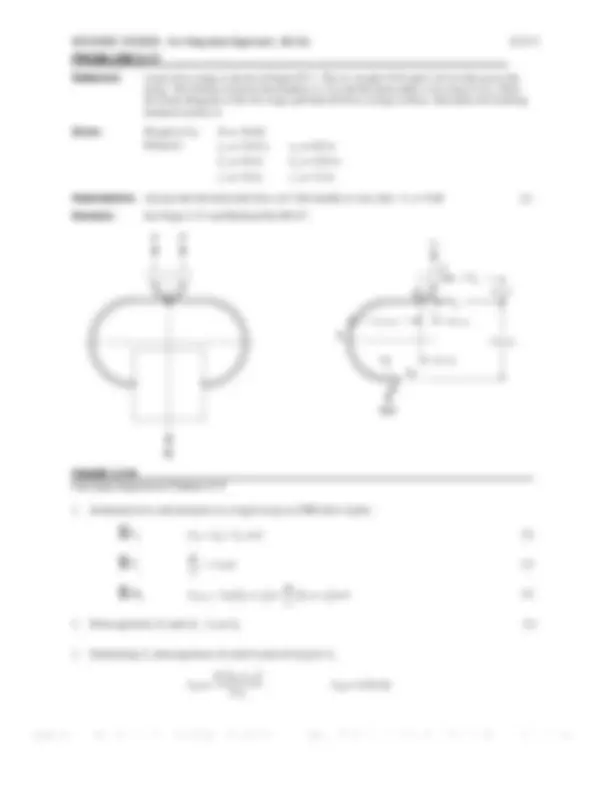
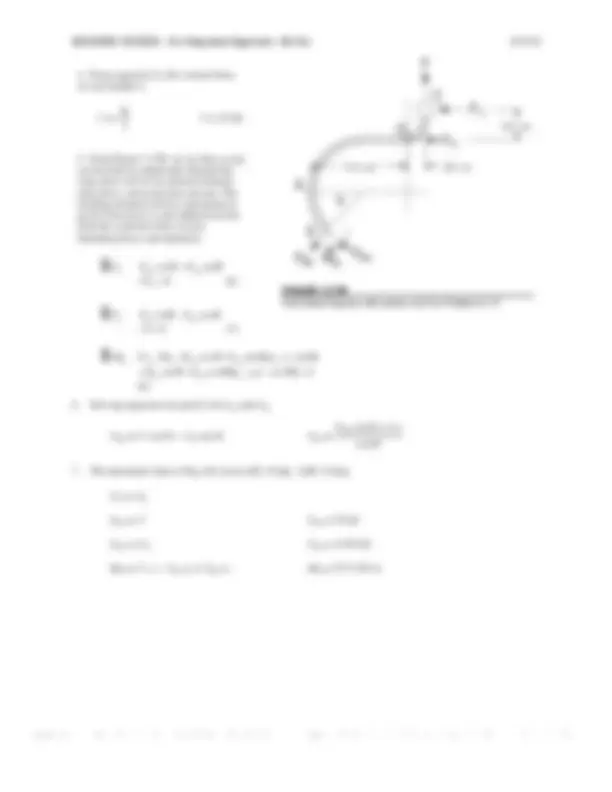
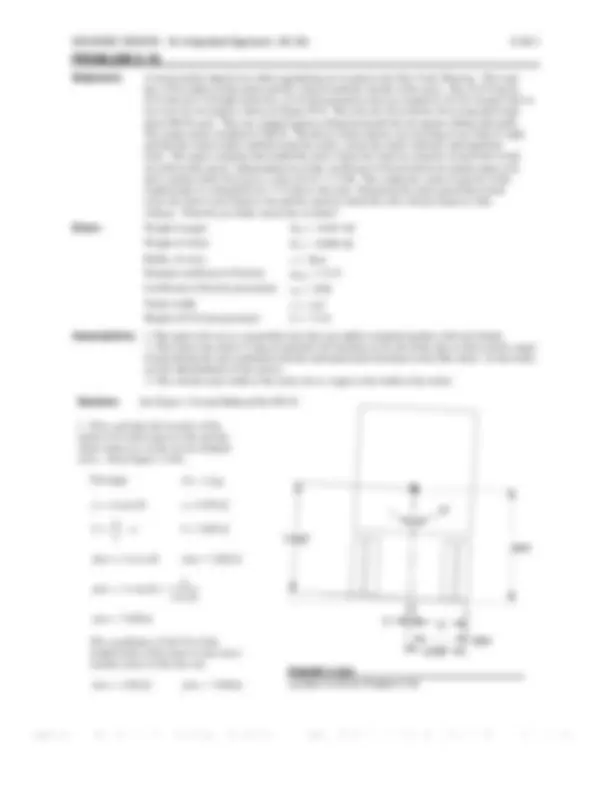
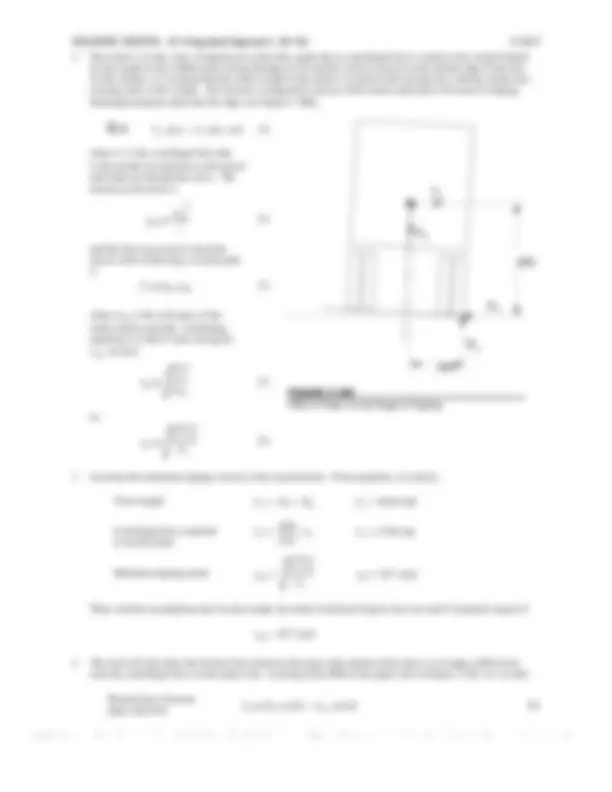
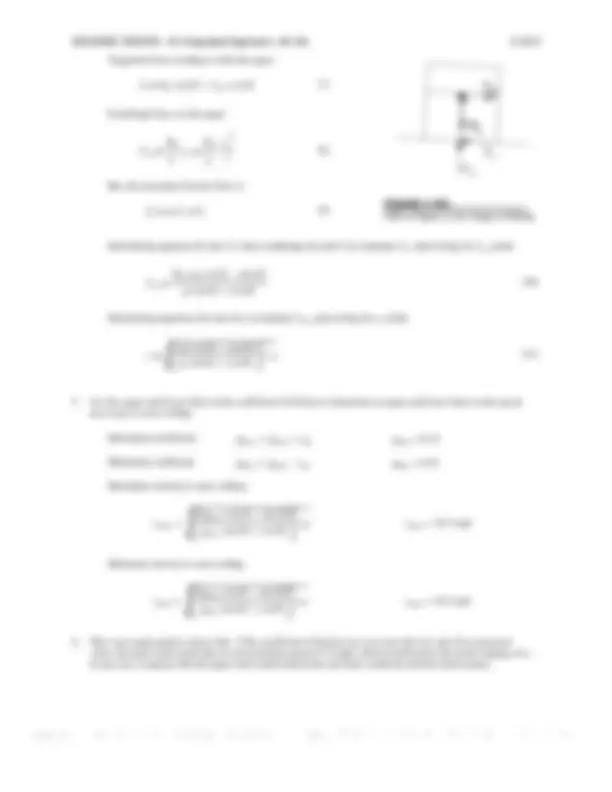
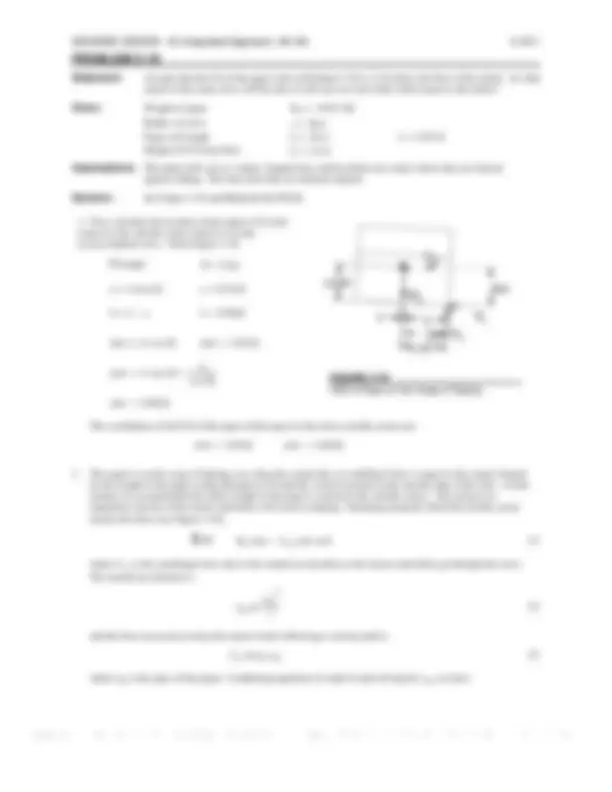
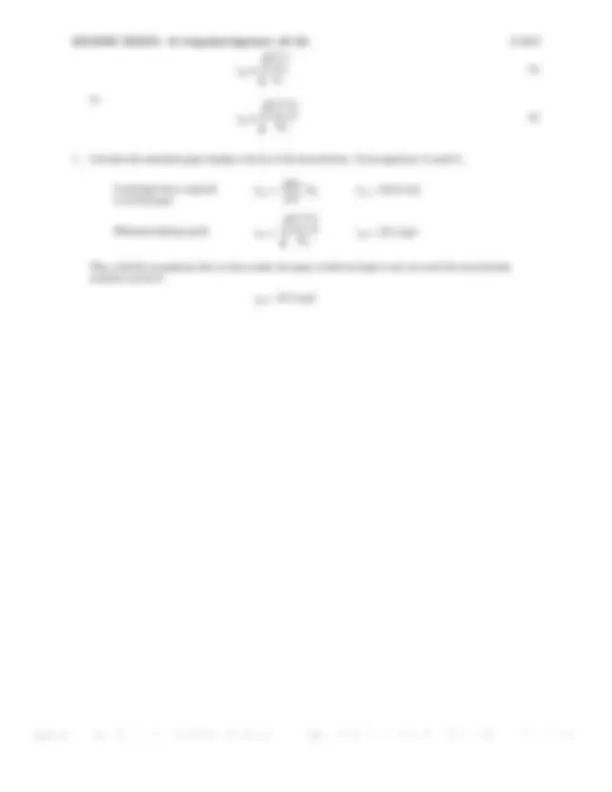
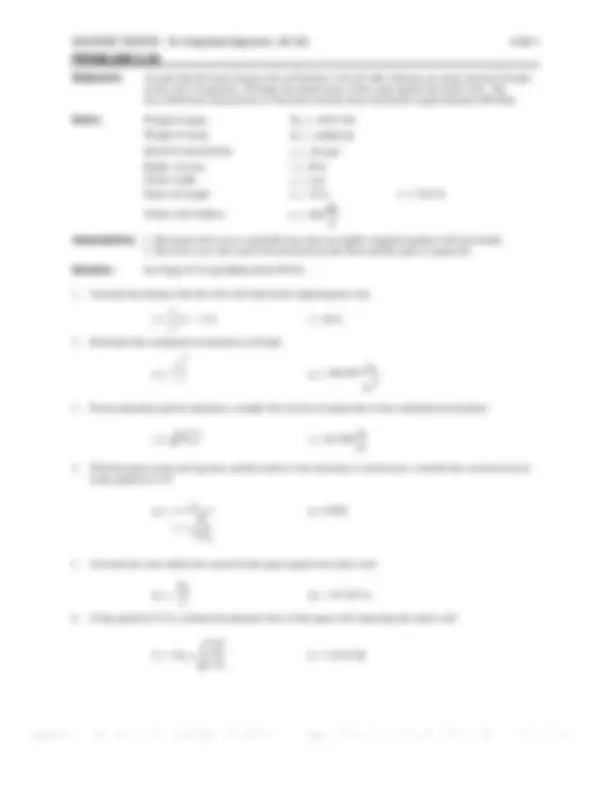
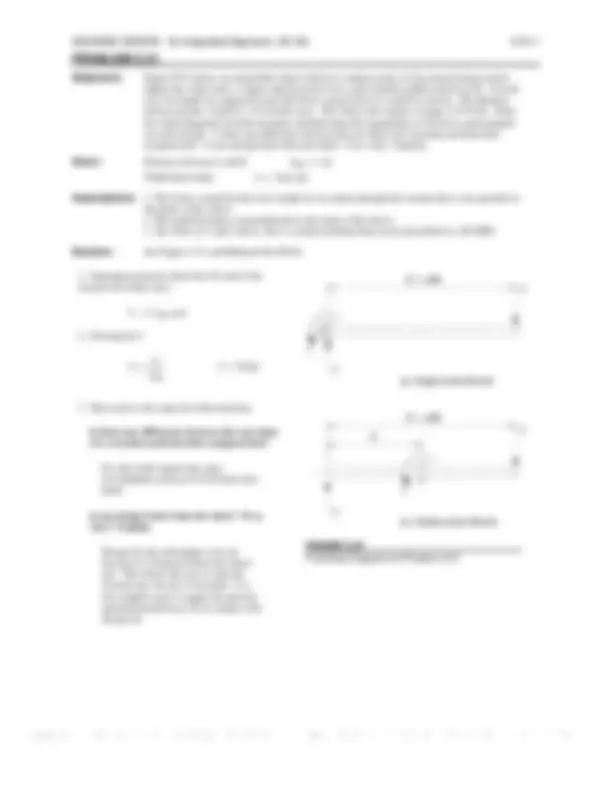
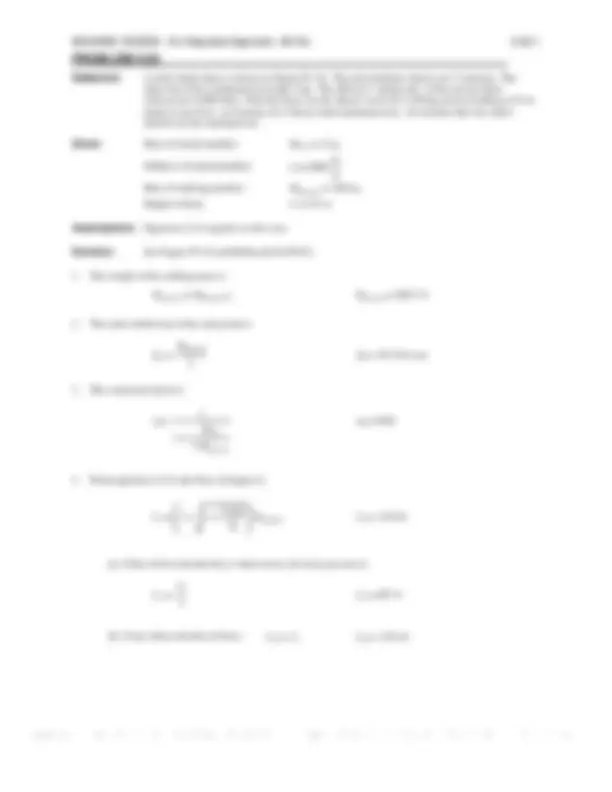
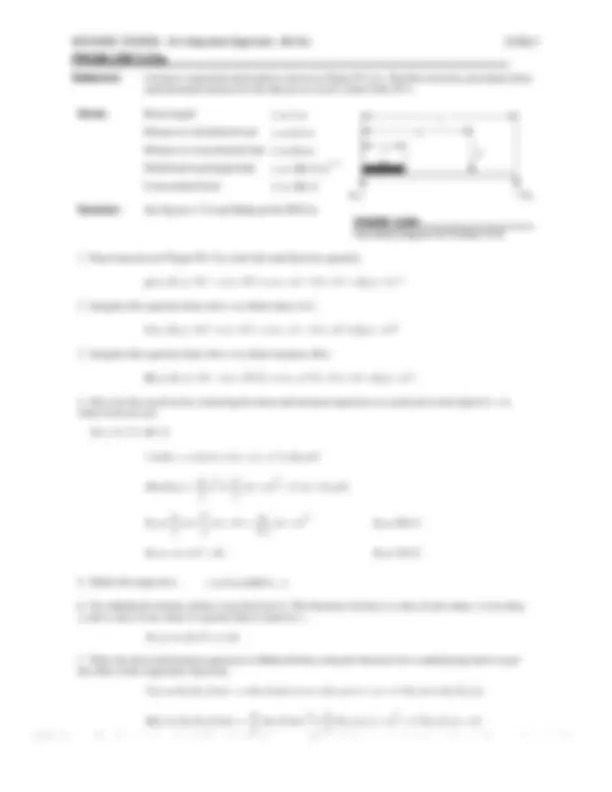
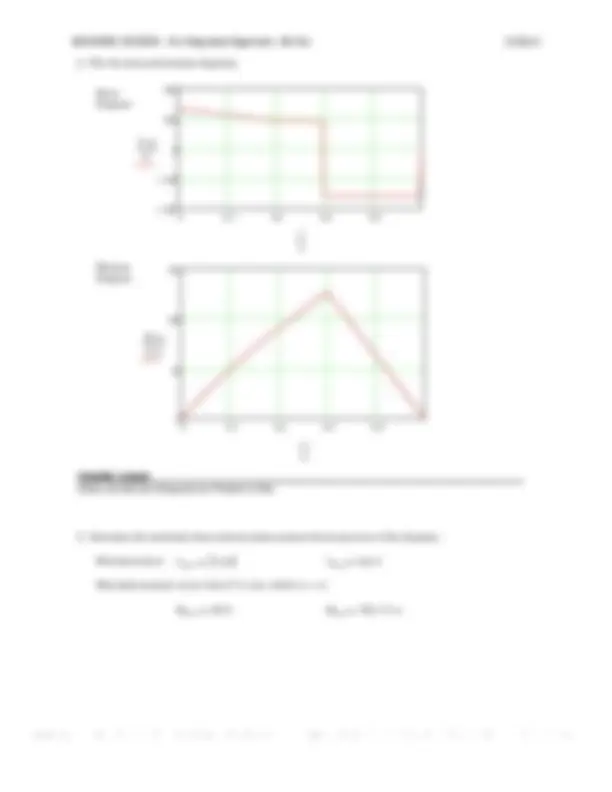
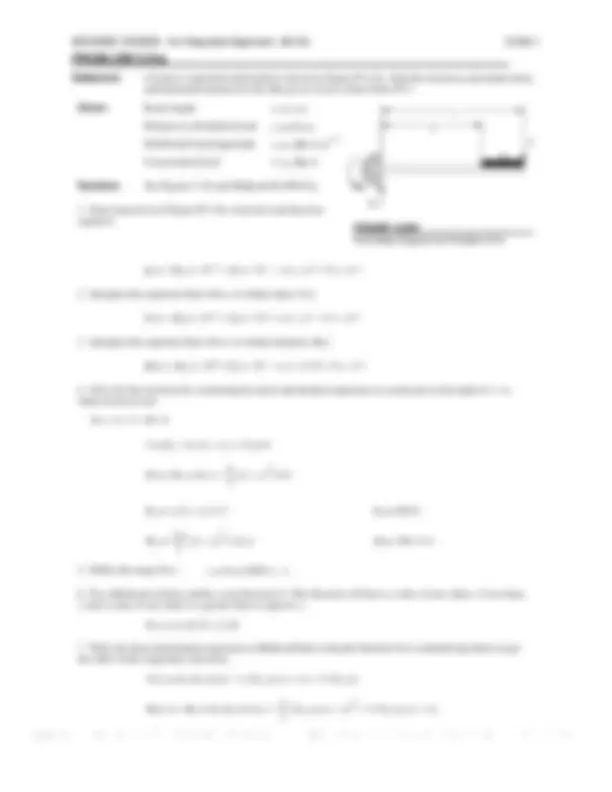
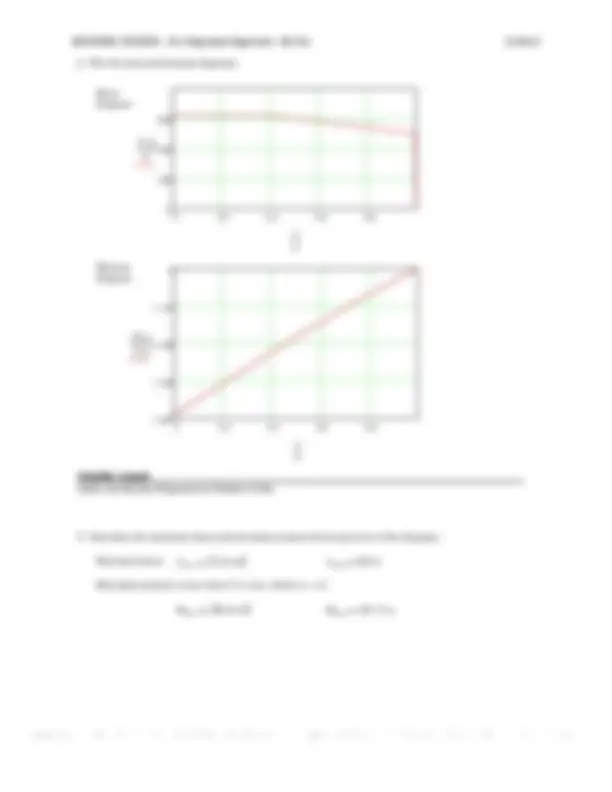
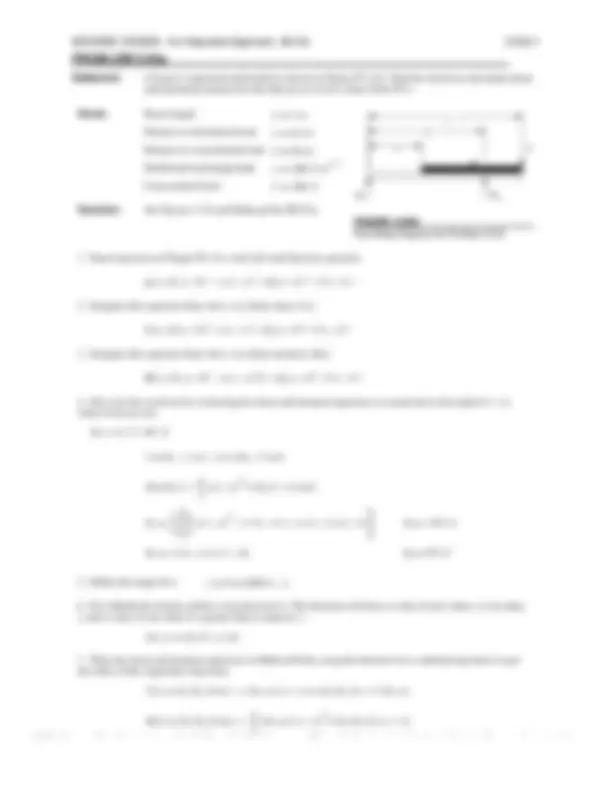
Estude fácil! Tem muito documento disponível na Docsity
Ganhe pontos ajudando outros esrudantes ou compre um plano Premium
Prepare-se para as provas
Estude fácil! Tem muito documento disponível na Docsity
Prepare-se para as provas com trabalhos de outros alunos como você, aqui na Docsity
Os melhores documentos à venda: Trabalhos de alunos formados
Prepare-se com as videoaulas e exercícios resolvidos criados a partir da grade da sua Universidade
Responda perguntas de provas passadas e avalie sua preparação.
Ganhe pontos para baixar
Ganhe pontos ajudando outros esrudantes ou compre um plano Premium
Comunidade
Peça ajuda à comunidade e tire suas dúvidas relacionadas ao estudo
Descubra as melhores universidades em seu país de acordo com os usuários da Docsity
Guias grátis
Baixe gratuitamente nossos guias de estudo, métodos para diminuir a ansiedade, dicas de TCC preparadas pelos professores da Docsity
Livro solucionário Projeto de Maquinas (Norton).
Tipologia: Exercícios
1 / 1269
Esta página não é visível na pré-visualização
Não perca as partes importantes!
Statement: It is often said, "Build a better mousetrap and the world will beat a path to your door." Consider this problem and write a goal statement and a set of at least 12 task specifications that you would apply to its solution. Then suggest 3 possible concepts to achieve the goal. Make annotated, freehand sketches of the concepts.
Solution:
Goal Statement: Create a mouse-free environment. Task Specifications:
Statement: A bowling machine is desired to allow quadriplegic youths, who can only move a joystick, to engage in the sport of bowling at a conventional bowling alley. Consider the factors involved, write a goal statement, and develop a set of at least 12 task specifications that constrain this problem. Then suggest 3 possible concepts to achieve the goal. Make annotated, freehand sketches of the concepts.
Solution:
Goal Statement: Create a means to allow a quadriplegic to bowl. Task Specifications:
Statement: Convert a mass of 1 000 lbm to (a) lbf, (b) slugs, (c) blobs, (d) kg.
Units: blob lbf sec
in
Given: Mass M := 1000 lb
Solution: See Mathcad file P0104.
W := M g W = 1000 lbf
Slugs (^) M =31.081 slug Blobs (^) M =2.59 blob Kilograms (^) M =453.592 kg
Statement: A 250-lbm mass is accelerated at 40 in/sec2. Find the force in lb needed for this acceleration.
Given: Mass M := 250 lb Acceleration a 40 in sec^2
Solution: See Mathcad file P0105.
Convert mass to slugs: (^) M =7.770 slug Convert acceleration to feet per second squared: (^) a =3.333 s -^2 ft F := M a F =25.9 lbf
Statement: Prepare an interactive computer program (using, for example, Excell, Mathcad, or TKSolver) from which the cross-sectional properties for the shapes shown in the inside front cover can be calculated. Arrange the program to deal with both ips and SI unit systems and convert the results between those systems.
Solution: See the inside front cover and Mathcad file P0107.
Moment about x -axis (^) Ix b h
12 Ix 16.000 in ^4 Ix 6.660 106 mm^4
Moment about y -axis (^) Iy h b
12 Iy 9.000 in ^4 Iy 3.746 106 mm^4
Radius of gyration about x -axis (^) k (^) x Ix (^) A k (^) x 1.155 in k (^) x 29.329 mm
Radius of gyration about y -axis (^) k (^) y Iy (^) A k (^) y 0.866 in k (^) y 21.997 mm
Polar moment of inertia (^) J (^) z Ix Iy J (^) z 25.000 in^4 J (^) z 1.041 107 mm^4
4 A 7.069 in ^2 A 4560 mm^2
Moment about x -axis (^) Ix^ π^ D
64 Ix 3.976 in ^4 Ix 1.655 106 mm^4
Moment about y -axis (^) Iy^ π^ D
64 Iy 3.976 in ^4 Iy 1.655 106 mm^4
Radius of gyration about x -axis (^) k (^) x Ix (^) A k (^) x 0.750 in k (^) x 19.05 mm
Radius of gyration about y -axis (^) k (^) y Iy (^) A k k (^) y (^) y 0.75019.05 inmm
Polar moment of inertia (^) J (^) z^ π^ D
32 J (^) z 7.952 in ^4 J (^) z 3.310 106 mm^4
D 3 in d 1 in Area (^) A^ π 4 D
A 4054 mm^2
Moment about x -axis (^) Ix^ π 64 D
Ix 1.635 106 mm^4
Moment about y -axis (^) Iy^ π 64 D
Iy 1.635 106 mm^4
Radius of gyration about x -axis (^) k (^) x Ix (^) A k (^) x 0.791 in k (^) x 20.08 mm
Radius of gyration about y -axis (^) k (^) y Iy (^) A k (^) y 0.791 in k (^) y 20.08 mm
Polar moment of inertia (^) J (^) z^ π 32 D
J (^) z 3.269 106 mm^4
D 3 in R 0.5 D R 1.5 in
Area (^) A^ π^ D
8 A 3.534 in ^2 A 2280 mm^2
Moment about x -axis (^) Ix 0.1098 R^4 Ix 0.556 in^4 Ix 2.314 105 mm^4 Moment about y -axis (^) Iy^ π^ R
8 Iy 1.988 in ^4 Iy 8.275 105 mm^4
Statement: Prepare an interactive computer program (using, for example, Excell, Mathcad, or TKSolver) from which the mass properties for the solids shown in the page opposite the inside front cover can be calculated. Arrange the program to deal with both ips and SI unit systems and convert the results between those systems.
Units: blob lbf sec
in
Solution: See the page opposite the inside front cover and Mathcad file P0108.
Volume (^) V a b c V 24.000 in^3 V 393290 mm^3 Mass (^) M V ^ γ (^) g M 0.017 blob M 3.048 kg
Moment about x -axis (^) Ix M^ a
12 Ix 0.019 blob in ^2 Ix 2130.4 kg mm ^2
Moment about y -axis (^) Iy M^ a
12 Iy 0.029 blob in ^2 Iy 3277.6 kg mm ^2
Moment about z -axis (^) Iz M^ b
12 Iz 0.036 blob in ^2 Iz 4097.0 kg mm ^2
Radius of gyration about x -axis (^) k (^) x Ix (^) M k (^) x 1.041 in k (^) x 26.437 mm
Radius of gyration about y -axis (^) k (^) y Iy (^) M k (^) y 1.291 in k (^) y 32.791 mm
Radius of gyration about z -axis (^) k (^) z Iz (^) M k (^) z 1.443 in k (^) z 36.662 mm
2.Cylinder, let: r 2 in L 3 in γ 0.30 lbf in ^3
Volume (^) V π r 2 L V 37.699 in^3 V 617778 mm^3 Mass (^) M V ^ γ (^) g M 0.029 blob M 5.13 kg
Moment about x -axis (^) Ix M r
2 Ix 0.059 blob in ^2 Ix 6619.4 kg mm ^2 Moment about y -axis (^) Iy M^^3 r
12 Iy 0.051 blob in ^2 Iy 5791.9 kg mm ^2 Moment about z -axis (^) Iz M^^3 r
12 Iz 0.051 blob in ^2 Iz 5791.9 kg mm ^2
Radius of gyration about x -axis (^) k (^) x Ix (^) M k (^) x 1.414 in k (^) x 35.921 mm
Radius of gyration about y -axis (^) k (^) y Iy (^) M k (^) y 1.323 in k (^) y 33.601 mm
Radius of gyration about z -axis (^) k (^) z Iz (^) M k (^) z 1.323 in k (^) z 33.601 mm
a 2 in b 3 in L 4 in γ 0.28 lbf in ^3
V 1029630 mm^3
Mass (^) M V ^ γ (^) g M 0.046 blob M 7.98 kg
Moment about x -axis (^) Ix M 2 a
Ix 3.3 104 kg mm ^2
Moment about y -axis (^) Iy M 12 3 a
Iy 2.4 104 kg mm ^2
Moment about z -axis (^) Iz M 12 3 a
Iz 2.4 104 kg mm ^2
Radius of gyration about x -axis (^) k (^) x Ix (^) M k (^) x 2.550 in k (^) x 64.758 mm
Radius of gyration about y -axis (^) k (^) y Iy (^) M k (^) y 2.141 in k (^) y 54.378 mm
Moment about y -axis (^) Iy^2 5 ^ Mr ^2 Iy 0.295 blob in ^2 Iy 33362 kg mm ^2
Moment about z -axis (^) Iz^2 5 ^ Mr ^2 Iz 0.295 blob in ^2 Iz 33362 kg mm ^2
Radius of gyration about x -axis (^) k (^) x Ix (^) M k (^) x 1.897 in k (^) x 48.193 mm
Radius of gyration about y -axis (^) k (^) y Iy (^) M k (^) y 1.897 in k (^) y 48.193 mm
Radius of gyration about z -axis (^) k (^) z Iz (^) M k (^) z 1.897 in k (^) z 48.193 mm
Statement: Convert the template in Problem 1-7 to have and use a set of functions or subroutines that can be called from within any program in that language to solve for the cross-sectional properties of the shapes shown on the inside front cover.
Solution: See inside front cover and Mathcad file P0109.
Moment about x -axis (^) Ix ( b h ) b h
Moment about y -axis (^) Iy ( b h ) h b
Moment about x -axis (^) Ix ( D )^ π^ D
Moment about y -axis (^) Iy ( D )^ π^ D
Moment about x -axis (^) Ix ( D d )^ π 64 D
Moment about y -axis (^) Iy ( D d )^ π 64 D
Moment about x -axis (^) Ix ( R ) 0.1098 R^4
Moment about y -axis (^) Iy ( R )^ π^ R
Moment about x -axis (^) Ix ( b h ) b h
Moment about y -axis (^) Iy ( b h ) h b
Volume (^) V r h ( )^ π^ r 2 h 3
Mass (^) M r h ( γ) V r h (^ )^ γ g
Moment about x -axis (^) Ix ( r h γ) 3 10 ^ M r h (^ ^ γ) r
Moment about y -axis (^) Iy ( r h γ) M r h ( γ) 12 r
Moment about z -axis (^) Iz ( r h γ) M r h ( γ) 12 r
Volume (^) V r ( ) 4 3 ^ π r
Mass (^) M r ( γ) V r ( )^ γ g
Moment about x -axis (^) Ix ( r γ) 2 5 ^ M r (^ ^ γ) r
Moment about y -axis (^) Iy ( r γ) 2 5 ^ M r (^ ^ γ) r
Moment about z -axis (^) Iz ( r γ) 2 5 ^ M r (^ ^ γ) r
Statement: Figure P2-1 shows stress-strain curves for three failed tensile-test specimens. All are plotted on the same scale. (a) Characterize each material as brittle or ductile. (b) Which is the stiffest? (c) Which has the highest ultimate strength? (d) Which has the largest modulus of resilience? (e) Which has the largest modulus of toughness?
Solution: See Figure P2-1 and Mathcad file P0201.
P21a := 12 ⋅ σ ya ⋅ ε ya P21a =12.
P21b := 12 ⋅ σ yb ⋅ ε yb P21b = 9
P21c := 12 ⋅ σ yc ⋅ ε yc P21c =2.
P2-1 (a) has the largest modulus of resilience
Statement: Which of the steel alloys shown in Figure 2-19 would you choose to obtain (a) Maximum strength (b) Maximum modulus of resilience (c) Maximum modulus of toughness (d) Maximum stiffness
Given: Young's modulus for steel E 207 GPa Solution: See Figure 2-19 and Mathcad file P0203.
Steel Yield Strength Ultimate Strength Fracture Strain AISI 1020: (^) Sy 1020 300 MPa Sut 1020 400 MPa ε f 1020 0. AISI 1095: (^) Sy 1095 550 MPa Sut 1095 1050 MPa ε f 1095 0. AISI 4142: (^) Sy 4142 1600 MPa Sut 4142 2430 MPa ε f 4142 0. Note: The 0.2% offset method was used to define a yield strength for the AISI 1095 and the 4142 steels.
UR1020^12 Sy 1020^2 E UR1020 0. MN m m^3
Sy 1095^2 E UR1095 0. MN m m^3
Sy 4142^2 E UR4142 6. MN m m^3
Even though the data is approximate, the AISI 4142 clearly has the largest modulus of resilience.
UT1020 12 Sy (^) 1020 Sut 1020 ε f 1020 UT1020 128 MN m m^3
UT1095 12 Sy (^) 1095 Sut 1095 ε f 1095 UT1095 88 MN m m^3
UT4142 12 Sy (^) 4142 Sut 4142 ε f 4142 UT4142 121 MN m m^3
Since the data is approximate, there is no significant difference between the 1020 and 4142 steels. Because of the wide difference in shape and character of the curves, one should also determine the area under the curves by graphical means. When this is done, the area under the curve is about 62 square units for 1020 and 66 for 4142. Thus, they seem to have about equal toughness, which is about 50% greater than that for the 1095 steel.
Statement: Which of the aluminum alloys shown in Figure 2-21 would you choose to obtain (a) Maximum strength (b) Maximum modulus of resilience (c) Maximum modulus of toughness (d) Maximum stiffness
Given: Young's modulus for aluminum E 71.7 GPa Solution: See Figure 2-21 and Mathcad file P0204.
Alum Yield Strength Ultimate Strength Fracture Strain 1100: (^) Sy 1100 120 MPa Sut 1100 130 MPa ε f 1100 0. 2024-T351: (^) Sy 2024 330 MPa Sut 2024 480 MPa ε f 2024 0. 7075-T6: (^) Sy 7075 510 MPa Sut 7075 560 MPa ε f 7075 0. Note: The 0.2% offset method was used to define a yield strength for all of the aluminums.
UR1100^12 Sy 1100^2 E UR1100 0. MN m m^3
Sy 2024^2 E UR2024 0. MN m m^3
Sy 7075^2 E UR7075 1. MN m m^3
Even though the data is approximate, the 7075-T6 clearly has the largest modulus of resilience.
UT1100 12 Sy (^) 1100 Sut 1100 ε f 1100 UT1100 21 MN m m^3
UT2024 12 Sy (^) 2024 Sut 2024 ε f 2024 UT2024 79 MN m m^3
UT7075 12 Sy (^) 7075 Sut 7075 ε f 7075 UT7075 88 MN m m^3
Even though the data is approximate, the 7075-T6 has the largest modulus of toughness.